Unit 4 Cutting 2 s Cutting Processes and
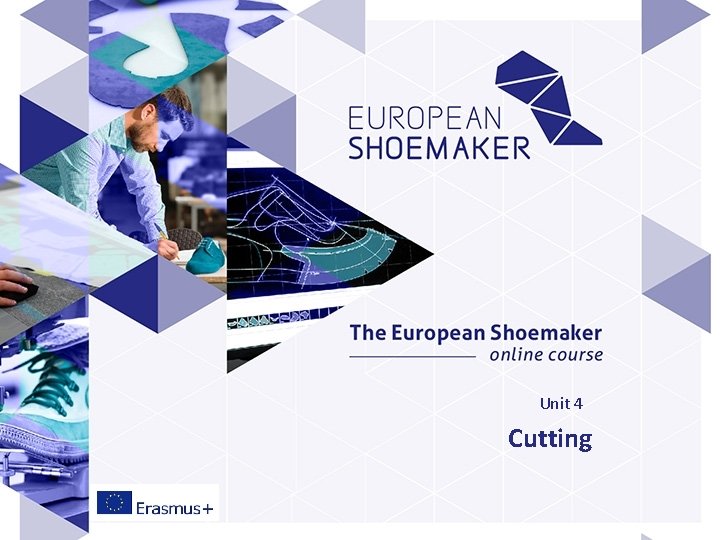
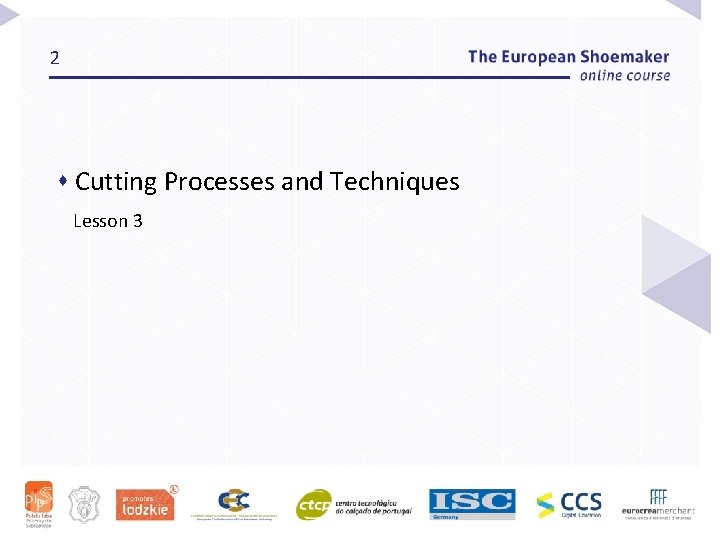
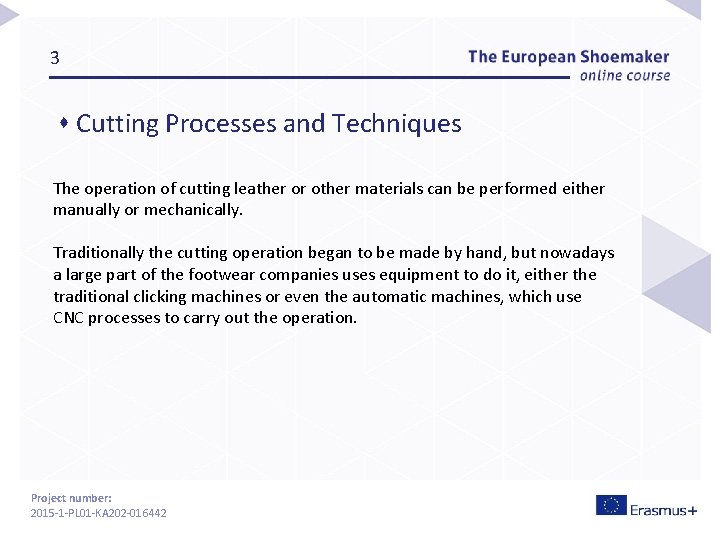
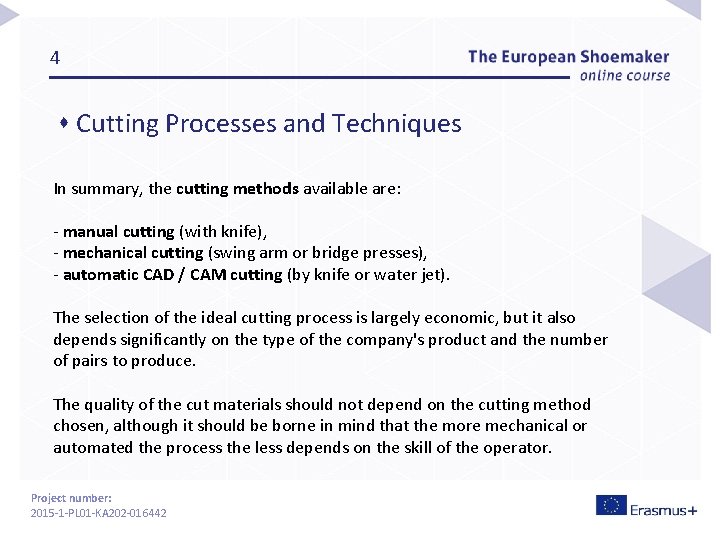
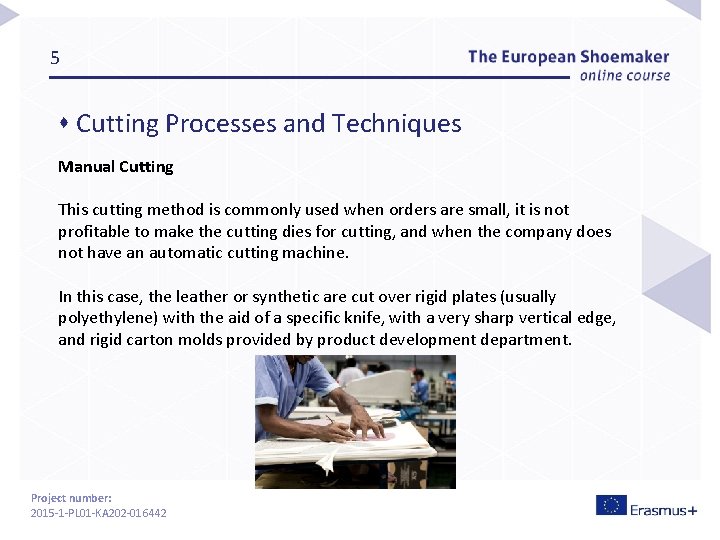
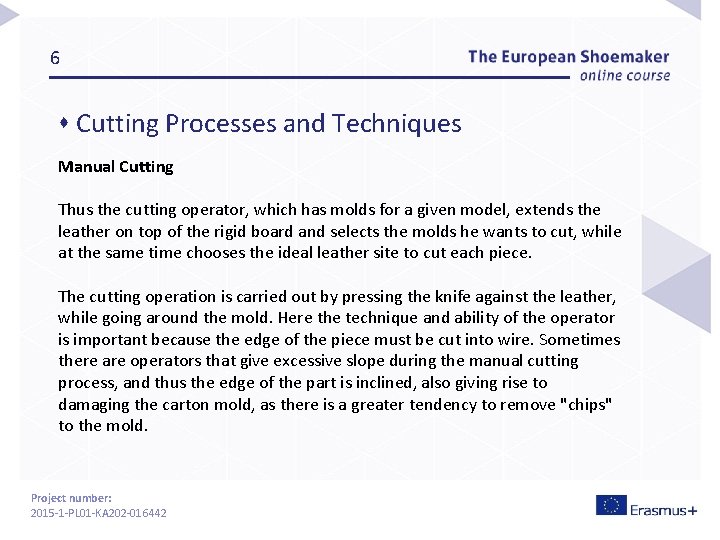
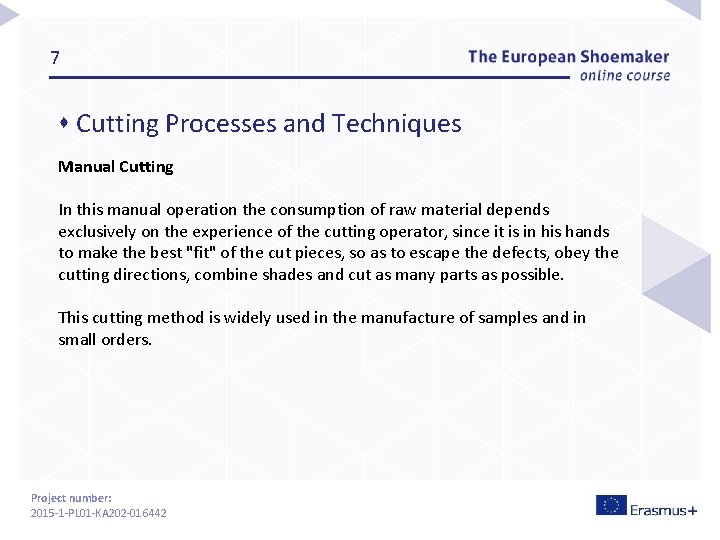
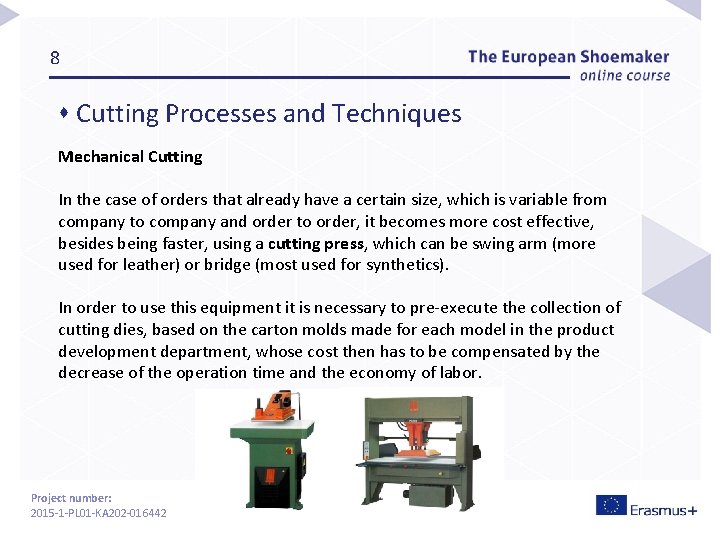
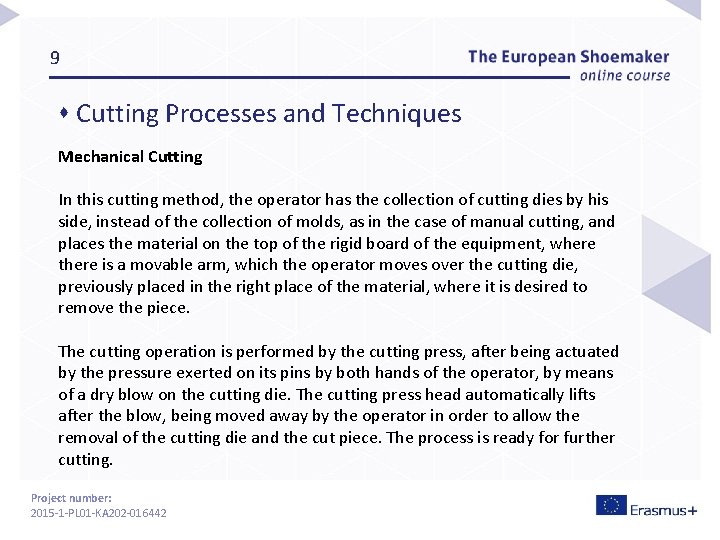
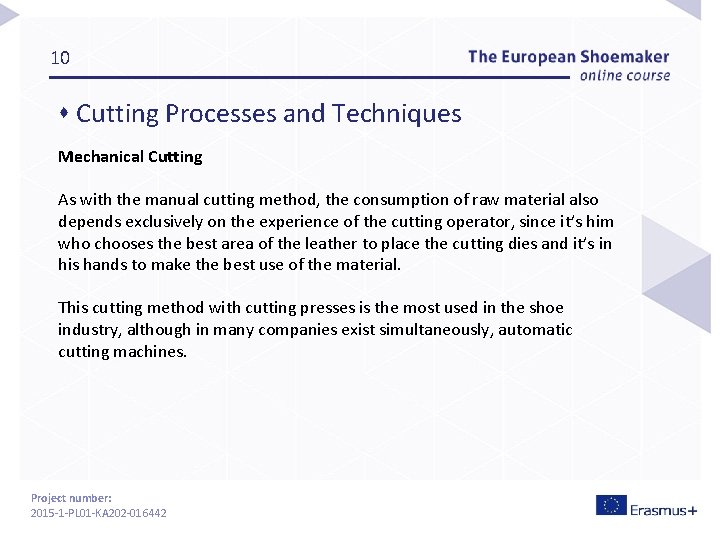
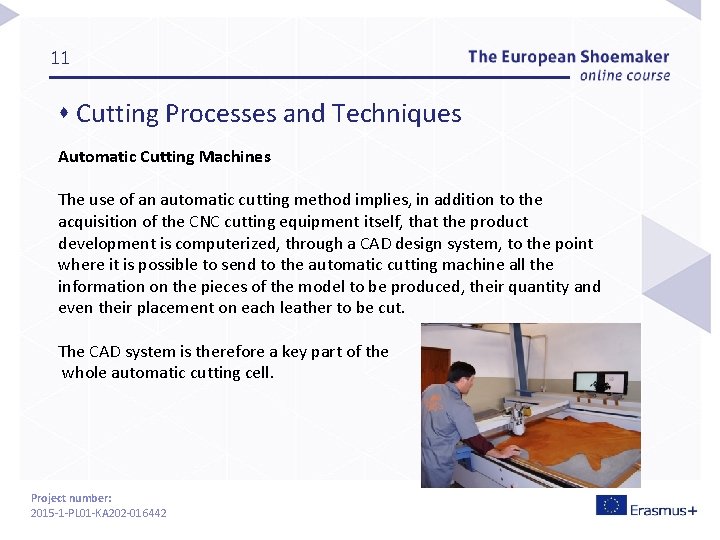
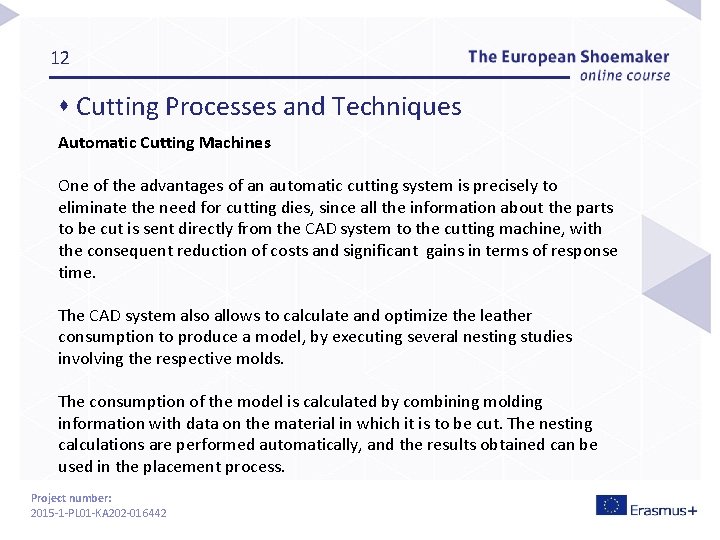
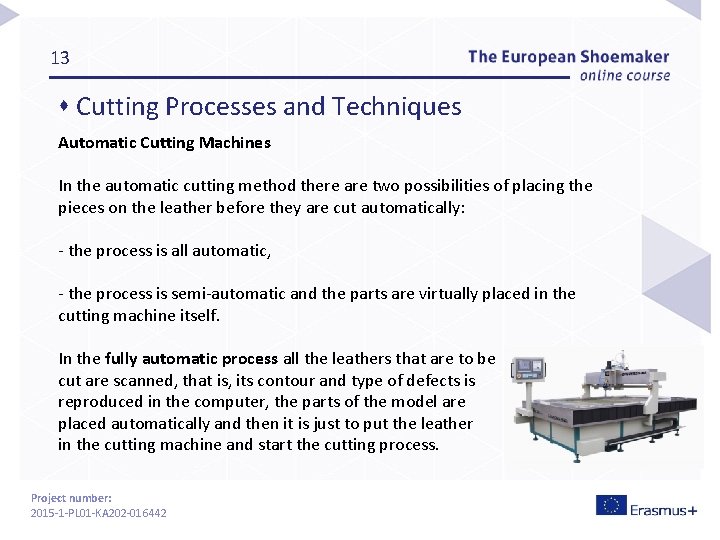
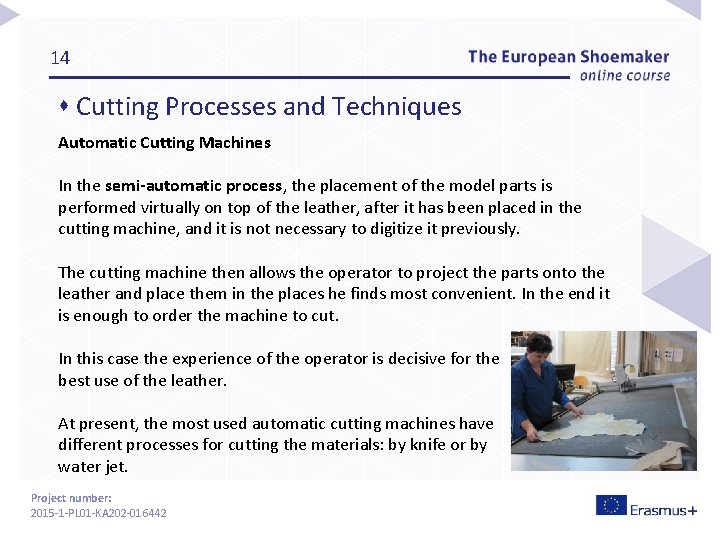
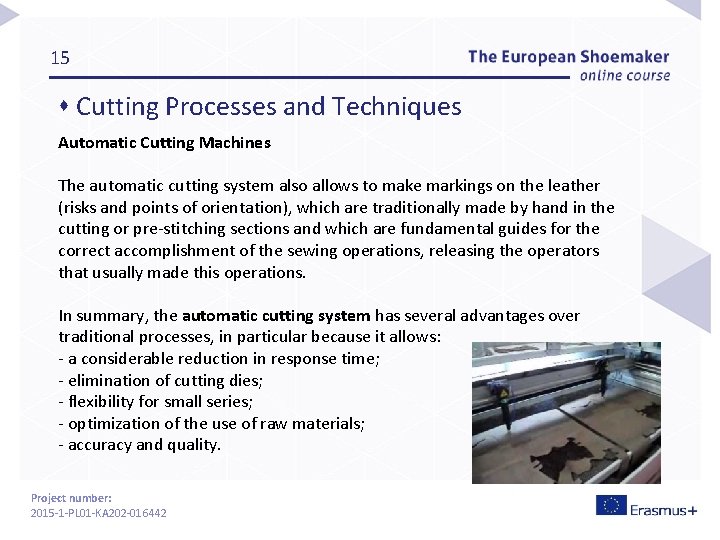
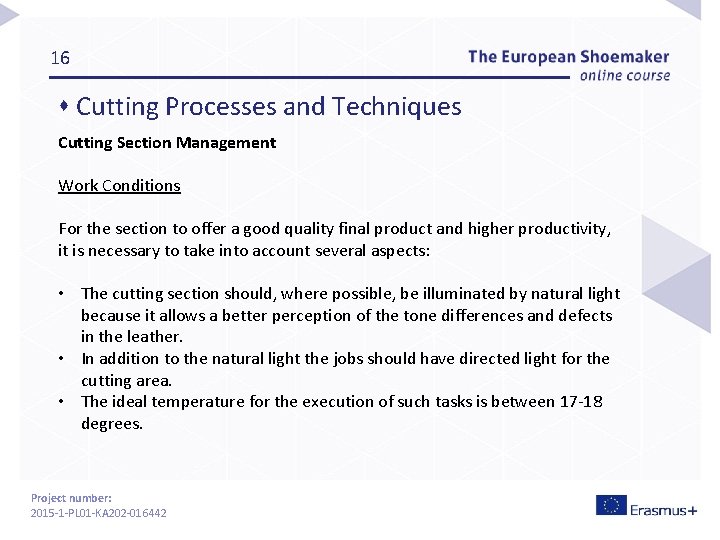
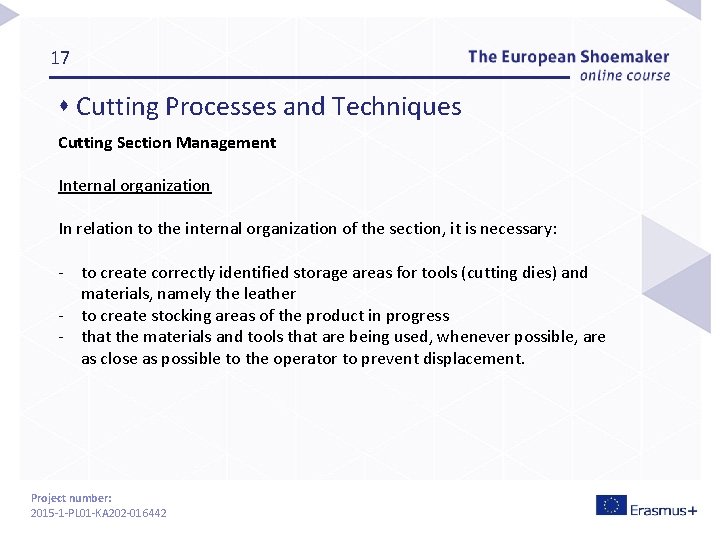
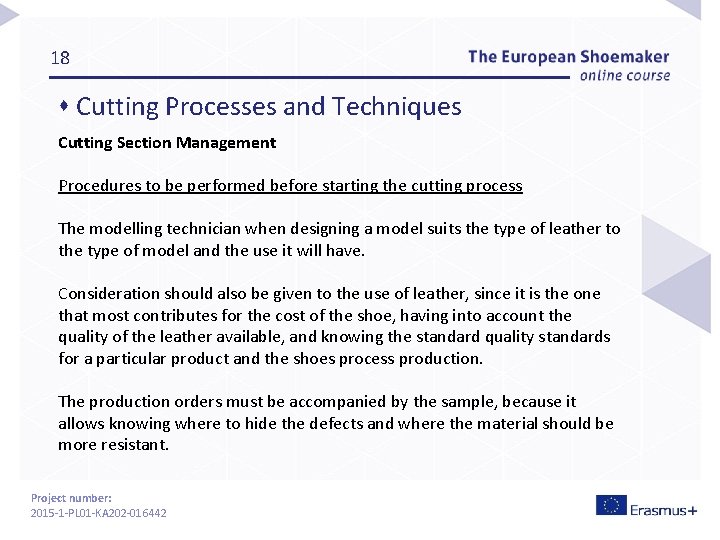
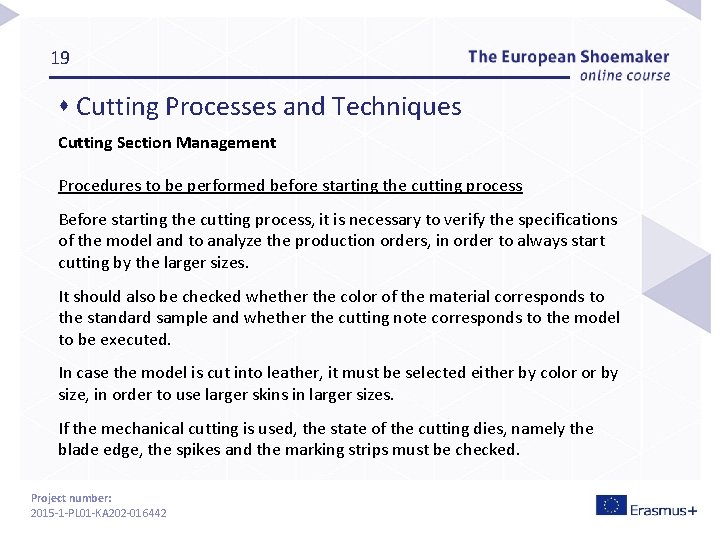
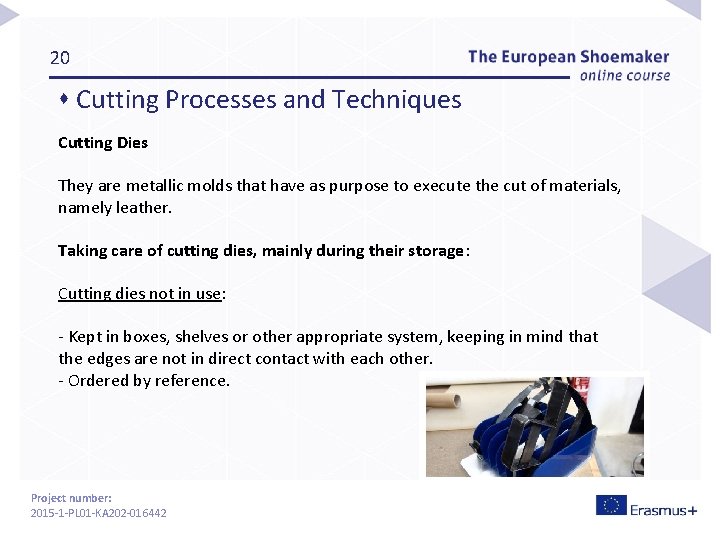
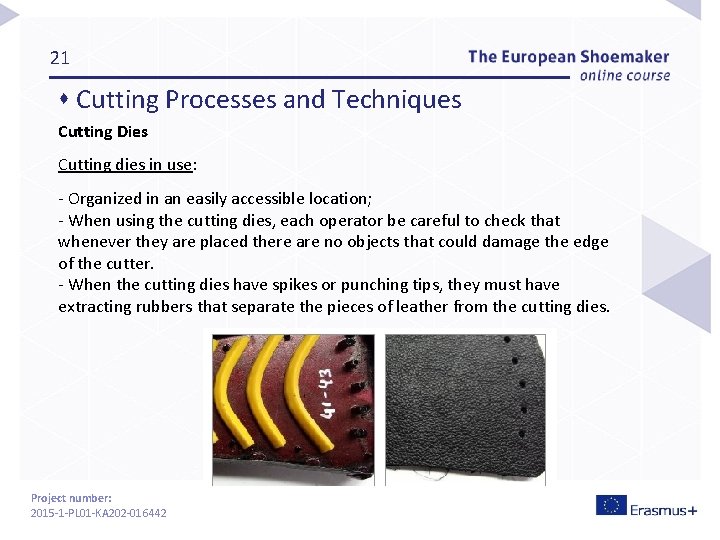
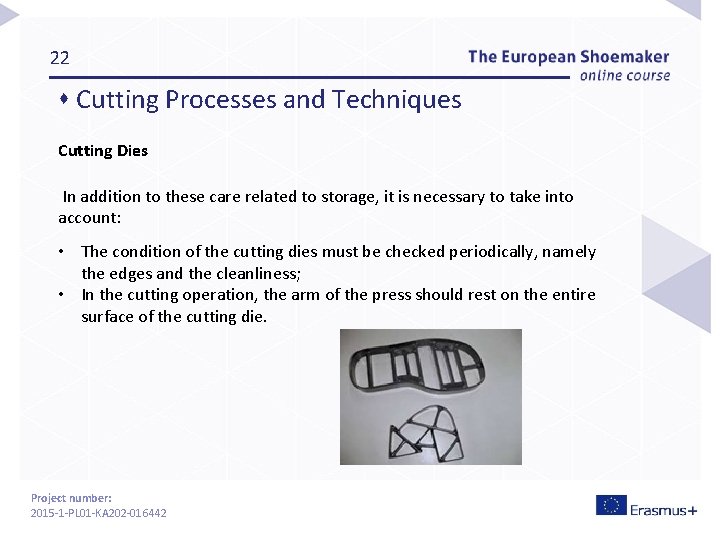
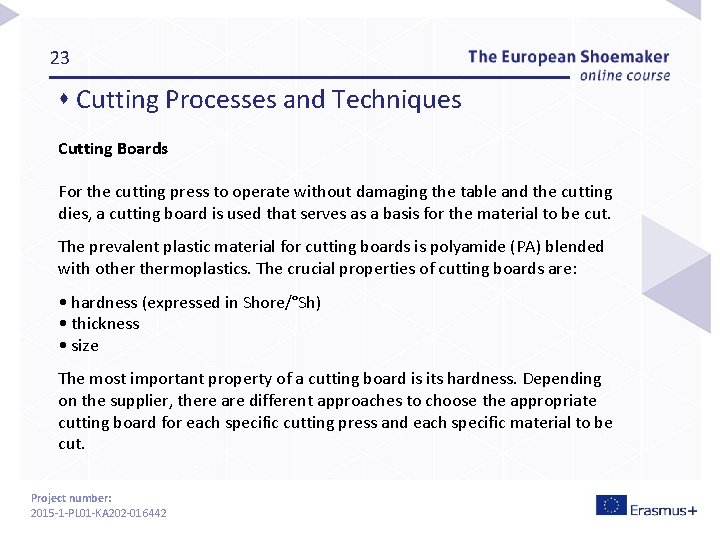
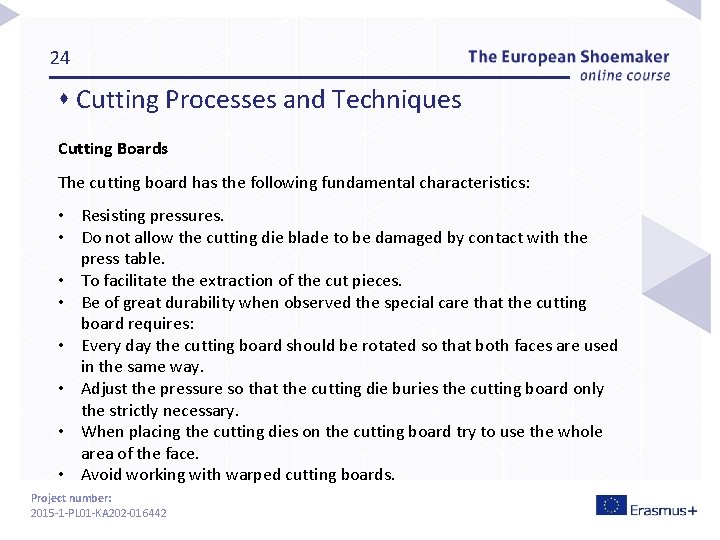
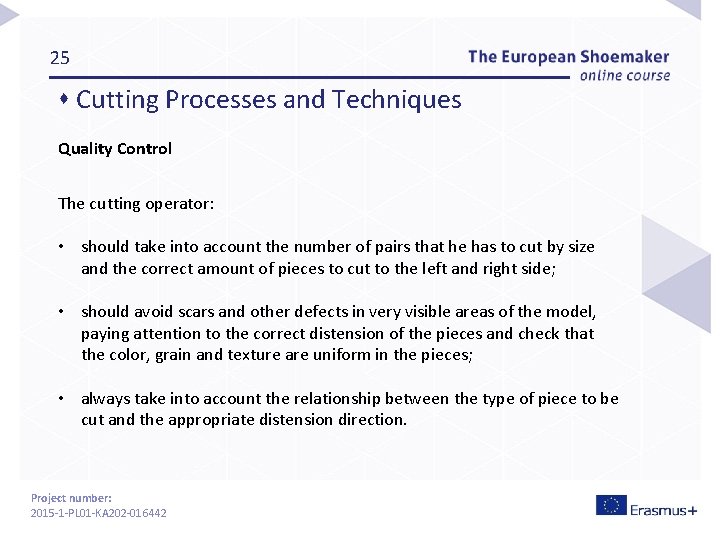
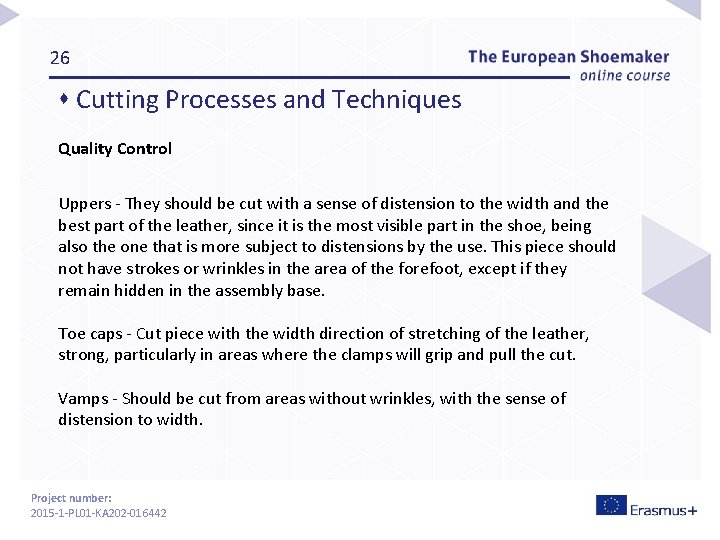

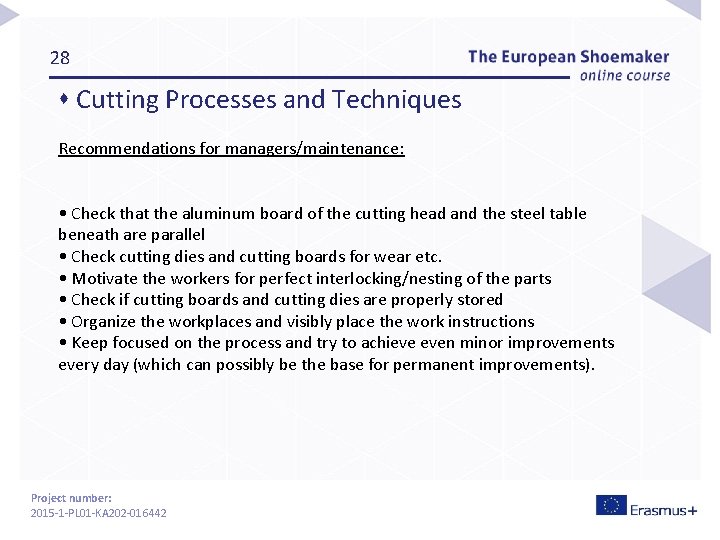
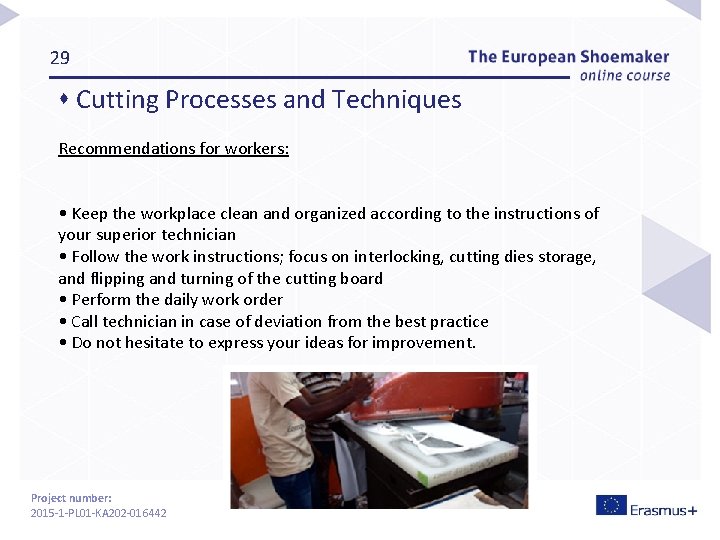
- Slides: 29
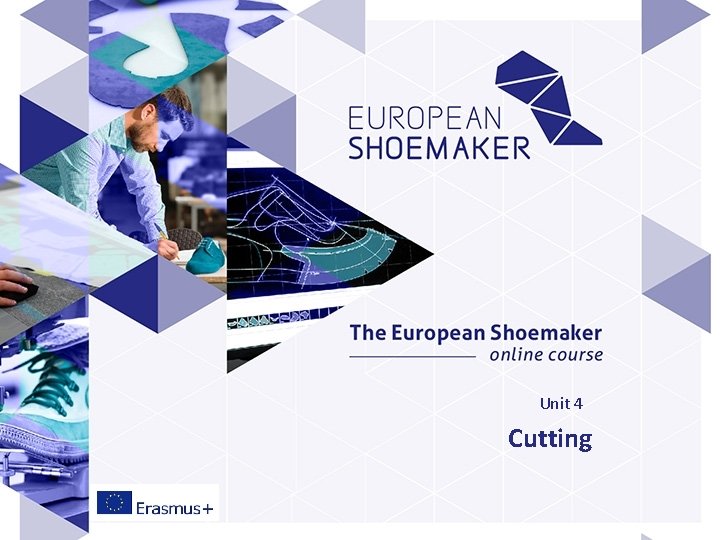
Unit 4 Cutting
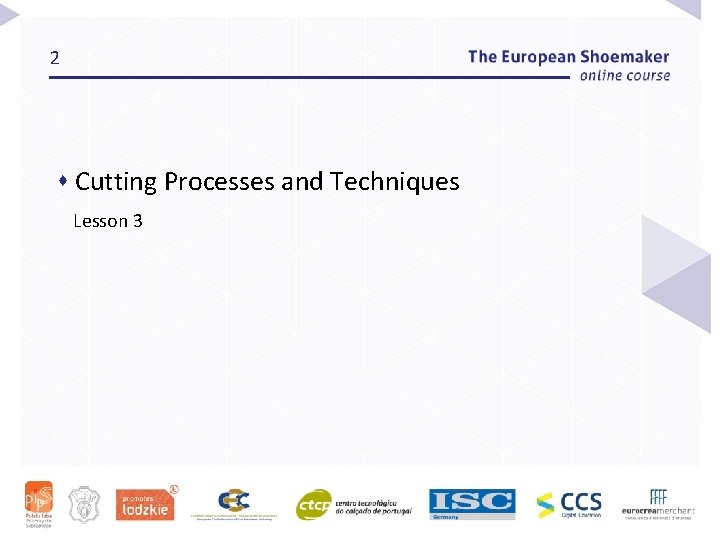
2 s Cutting Processes and Techniques Lesson 3
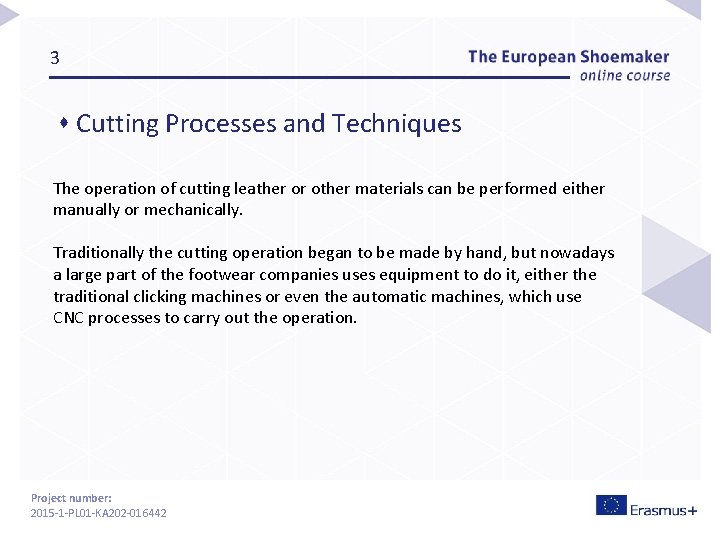
3 s Cutting Processes and Techniques The operation of cutting leather or other materials can be performed either manually or mechanically. Traditionally the cutting operation began to be made by hand, but nowadays a large part of the footwear companies uses equipment to do it, either the traditional clicking machines or even the automatic machines, which use CNC processes to carry out the operation. Project number: 2015 -1 -PL 01 -KA 202 -016442
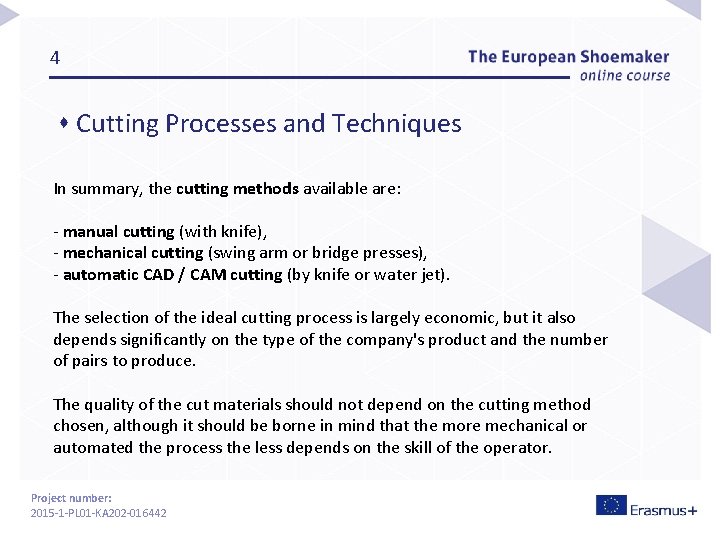
4 s Cutting Processes and Techniques In summary, the cutting methods available are: - manual cutting (with knife), - mechanical cutting (swing arm or bridge presses), - automatic CAD / CAM cutting (by knife or water jet). The selection of the ideal cutting process is largely economic, but it also depends significantly on the type of the company's product and the number of pairs to produce. The quality of the cut materials should not depend on the cutting method chosen, although it should be borne in mind that the more mechanical or automated the process the less depends on the skill of the operator. Project number: 2015 -1 -PL 01 -KA 202 -016442
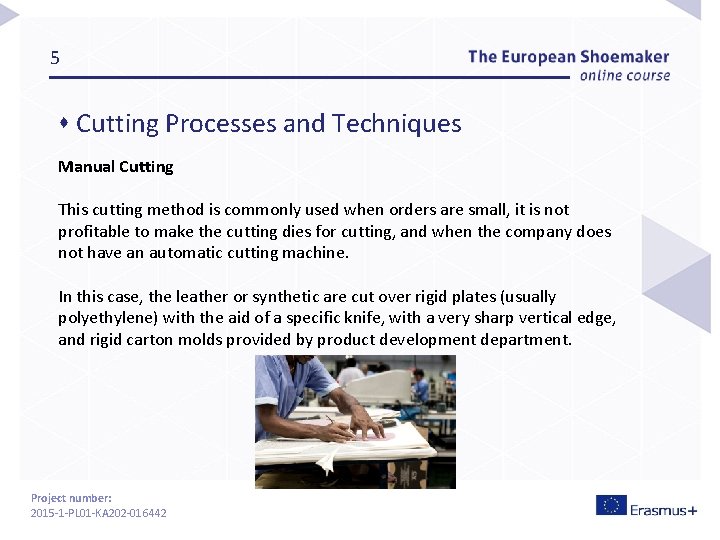
5 s Cutting Processes and Techniques Manual Cutting This cutting method is commonly used when orders are small, it is not profitable to make the cutting dies for cutting, and when the company does not have an automatic cutting machine. In this case, the leather or synthetic are cut over rigid plates (usually polyethylene) with the aid of a specific knife, with a very sharp vertical edge, and rigid carton molds provided by product development department. Project number: 2015 -1 -PL 01 -KA 202 -016442
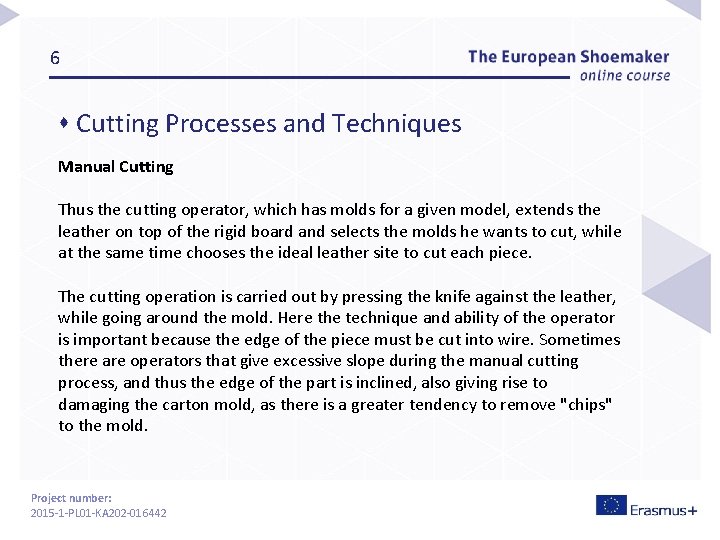
6 s Cutting Processes and Techniques Manual Cutting Thus the cutting operator, which has molds for a given model, extends the leather on top of the rigid board and selects the molds he wants to cut, while at the same time chooses the ideal leather site to cut each piece. The cutting operation is carried out by pressing the knife against the leather, while going around the mold. Here the technique and ability of the operator is important because the edge of the piece must be cut into wire. Sometimes there are operators that give excessive slope during the manual cutting process, and thus the edge of the part is inclined, also giving rise to damaging the carton mold, as there is a greater tendency to remove "chips" to the mold. Project number: 2015 -1 -PL 01 -KA 202 -016442
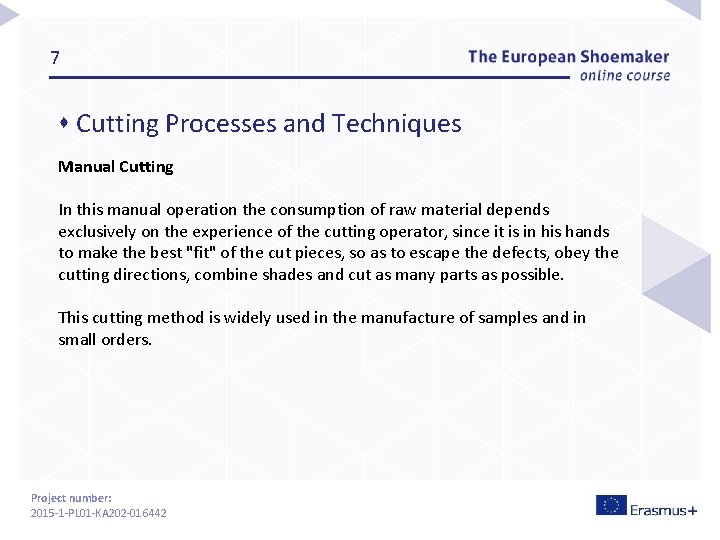
7 s Cutting Processes and Techniques Manual Cutting In this manual operation the consumption of raw material depends exclusively on the experience of the cutting operator, since it is in his hands to make the best "fit" of the cut pieces, so as to escape the defects, obey the cutting directions, combine shades and cut as many parts as possible. This cutting method is widely used in the manufacture of samples and in small orders. Project number: 2015 -1 -PL 01 -KA 202 -016442
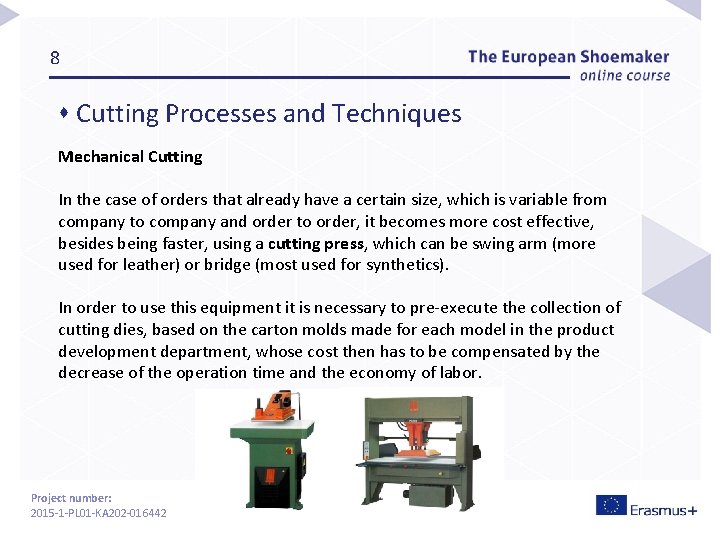
8 s Cutting Processes and Techniques Mechanical Cutting In the case of orders that already have a certain size, which is variable from company to company and order to order, it becomes more cost effective, besides being faster, using a cutting press, which can be swing arm (more used for leather) or bridge (most used for synthetics). In order to use this equipment it is necessary to pre-execute the collection of cutting dies, based on the carton molds made for each model in the product development department, whose cost then has to be compensated by the decrease of the operation time and the economy of labor. Project number: 2015 -1 -PL 01 -KA 202 -016442
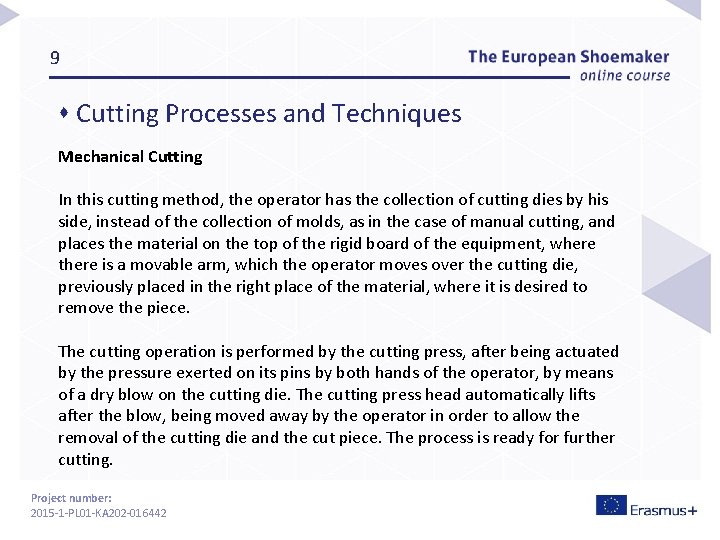
9 s Cutting Processes and Techniques Mechanical Cutting In this cutting method, the operator has the collection of cutting dies by his side, instead of the collection of molds, as in the case of manual cutting, and places the material on the top of the rigid board of the equipment, where there is a movable arm, which the operator moves over the cutting die, previously placed in the right place of the material, where it is desired to remove the piece. The cutting operation is performed by the cutting press, after being actuated by the pressure exerted on its pins by both hands of the operator, by means of a dry blow on the cutting die. The cutting press head automatically lifts after the blow, being moved away by the operator in order to allow the removal of the cutting die and the cut piece. The process is ready for further cutting. Project number: 2015 -1 -PL 01 -KA 202 -016442
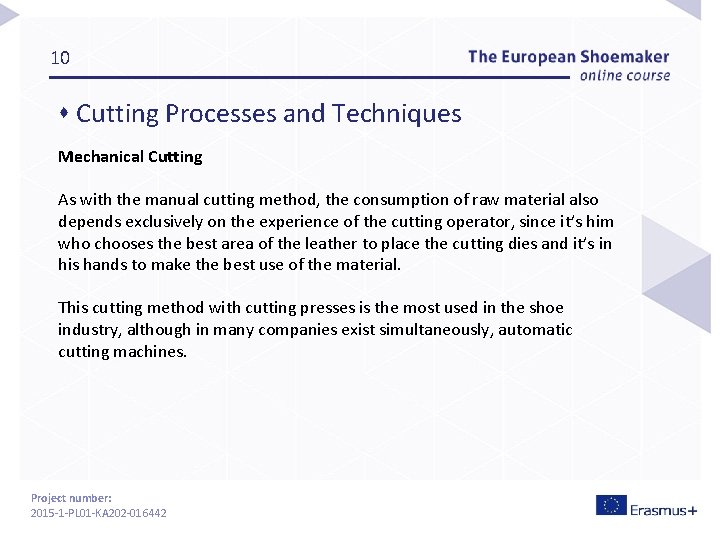
10 s Cutting Processes and Techniques Mechanical Cutting As with the manual cutting method, the consumption of raw material also depends exclusively on the experience of the cutting operator, since it’s him who chooses the best area of the leather to place the cutting dies and it’s in his hands to make the best use of the material. This cutting method with cutting presses is the most used in the shoe industry, although in many companies exist simultaneously, automatic cutting machines. Project number: 2015 -1 -PL 01 -KA 202 -016442
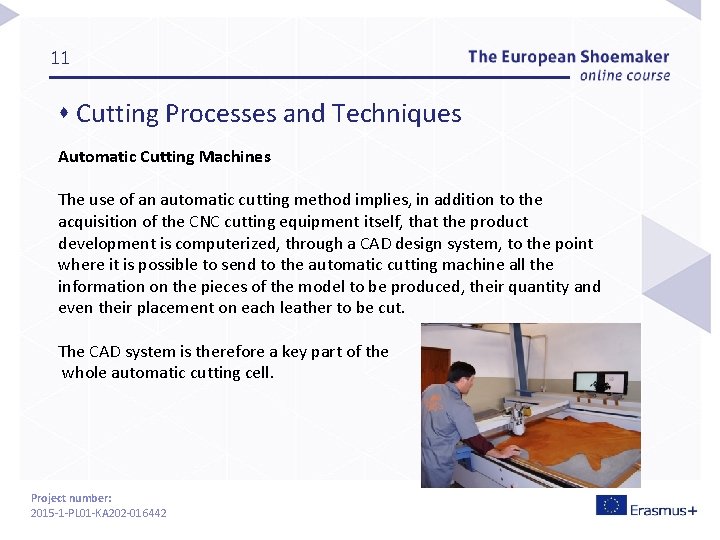
11 s Cutting Processes and Techniques Automatic Cutting Machines The use of an automatic cutting method implies, in addition to the acquisition of the CNC cutting equipment itself, that the product development is computerized, through a CAD design system, to the point where it is possible to send to the automatic cutting machine all the information on the pieces of the model to be produced, their quantity and even their placement on each leather to be cut. The CAD system is therefore a key part of the whole automatic cutting cell. Project number: 2015 -1 -PL 01 -KA 202 -016442
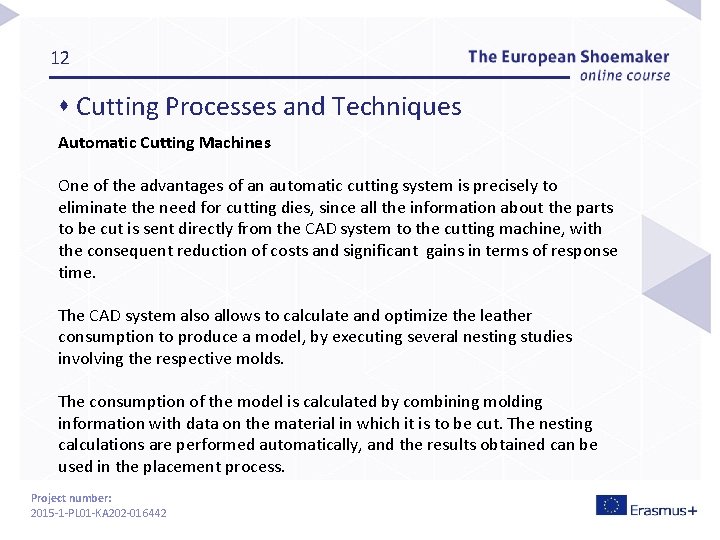
12 s Cutting Processes and Techniques Automatic Cutting Machines One of the advantages of an automatic cutting system is precisely to eliminate the need for cutting dies, since all the information about the parts to be cut is sent directly from the CAD system to the cutting machine, with the consequent reduction of costs and significant gains in terms of response time. The CAD system also allows to calculate and optimize the leather consumption to produce a model, by executing several nesting studies involving the respective molds. The consumption of the model is calculated by combining molding information with data on the material in which it is to be cut. The nesting calculations are performed automatically, and the results obtained can be used in the placement process. Project number: 2015 -1 -PL 01 -KA 202 -016442
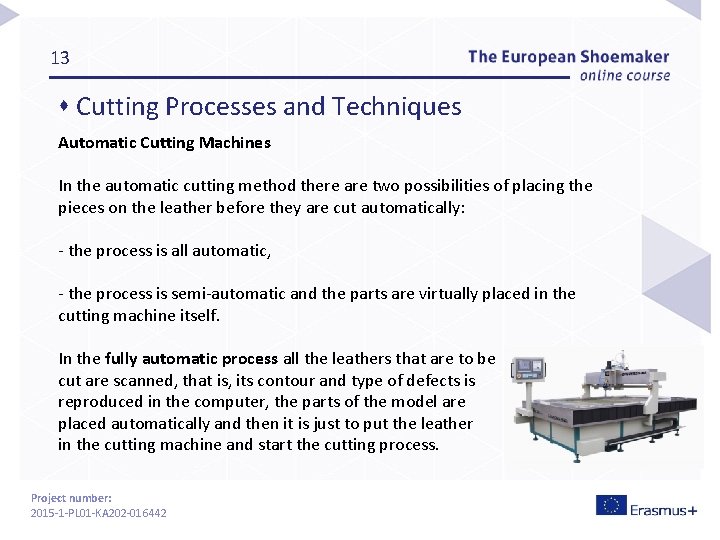
13 s Cutting Processes and Techniques Automatic Cutting Machines In the automatic cutting method there are two possibilities of placing the pieces on the leather before they are cut automatically: - the process is all automatic, - the process is semi-automatic and the parts are virtually placed in the cutting machine itself. In the fully automatic process all the leathers that are to be cut are scanned, that is, its contour and type of defects is reproduced in the computer, the parts of the model are placed automatically and then it is just to put the leather in the cutting machine and start the cutting process. Project number: 2015 -1 -PL 01 -KA 202 -016442
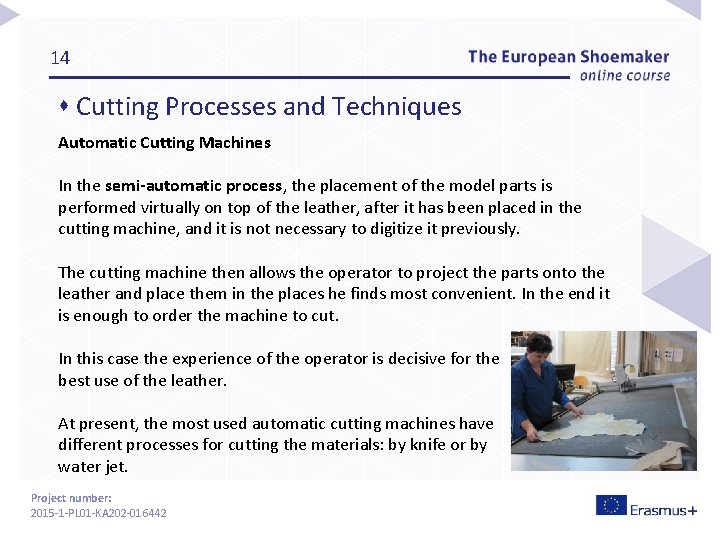
14 s Cutting Processes and Techniques Automatic Cutting Machines In the semi-automatic process, the placement of the model parts is performed virtually on top of the leather, after it has been placed in the cutting machine, and it is not necessary to digitize it previously. The cutting machine then allows the operator to project the parts onto the leather and place them in the places he finds most convenient. In the end it is enough to order the machine to cut. In this case the experience of the operator is decisive for the best use of the leather. At present, the most used automatic cutting machines have different processes for cutting the materials: by knife or by water jet. Project number: 2015 -1 -PL 01 -KA 202 -016442
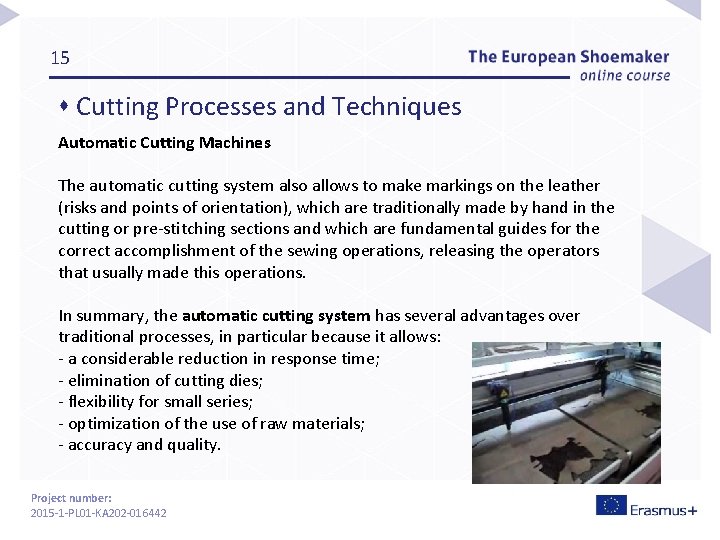
15 s Cutting Processes and Techniques Automatic Cutting Machines The automatic cutting system also allows to make markings on the leather (risks and points of orientation), which are traditionally made by hand in the cutting or pre-stitching sections and which are fundamental guides for the correct accomplishment of the sewing operations, releasing the operators that usually made this operations. In summary, the automatic cutting system has several advantages over traditional processes, in particular because it allows: - a considerable reduction in response time; - elimination of cutting dies; - flexibility for small series; - optimization of the use of raw materials; - accuracy and quality. Project number: 2015 -1 -PL 01 -KA 202 -016442
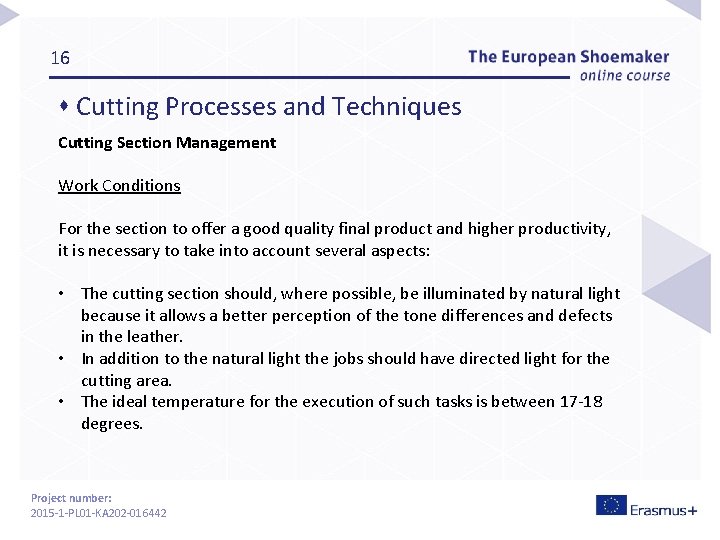
16 s Cutting Processes and Techniques Cutting Section Management Work Conditions For the section to offer a good quality final product and higher productivity, it is necessary to take into account several aspects: • The cutting section should, where possible, be illuminated by natural light because it allows a better perception of the tone differences and defects in the leather. • In addition to the natural light the jobs should have directed light for the cutting area. • The ideal temperature for the execution of such tasks is between 17 -18 degrees. Project number: 2015 -1 -PL 01 -KA 202 -016442
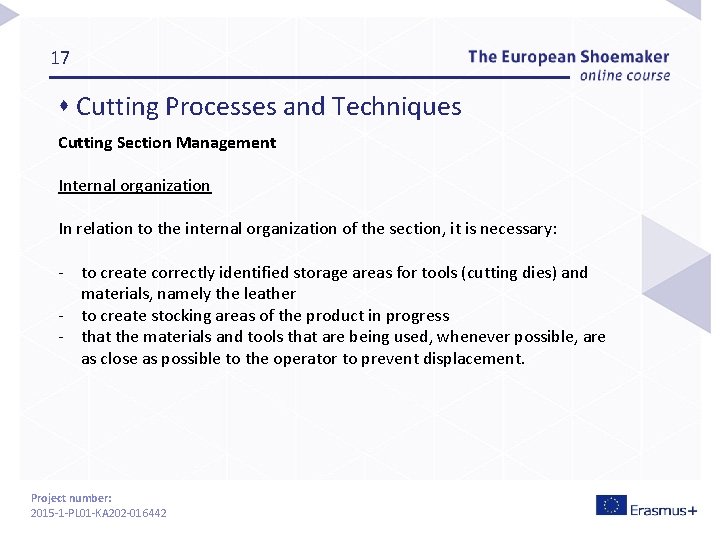
17 s Cutting Processes and Techniques Cutting Section Management Internal organization In relation to the internal organization of the section, it is necessary: - to create correctly identified storage areas for tools (cutting dies) and materials, namely the leather - to create stocking areas of the product in progress - that the materials and tools that are being used, whenever possible, are as close as possible to the operator to prevent displacement. Project number: 2015 -1 -PL 01 -KA 202 -016442
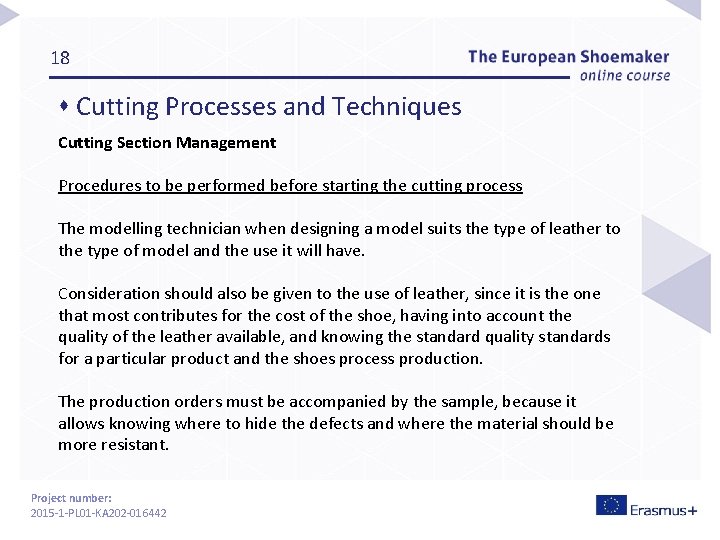
18 s Cutting Processes and Techniques Cutting Section Management Procedures to be performed before starting the cutting process The modelling technician when designing a model suits the type of leather to the type of model and the use it will have. Consideration should also be given to the use of leather, since it is the one that most contributes for the cost of the shoe, having into account the quality of the leather available, and knowing the standard quality standards for a particular product and the shoes process production. The production orders must be accompanied by the sample, because it allows knowing where to hide the defects and where the material should be more resistant. Project number: 2015 -1 -PL 01 -KA 202 -016442
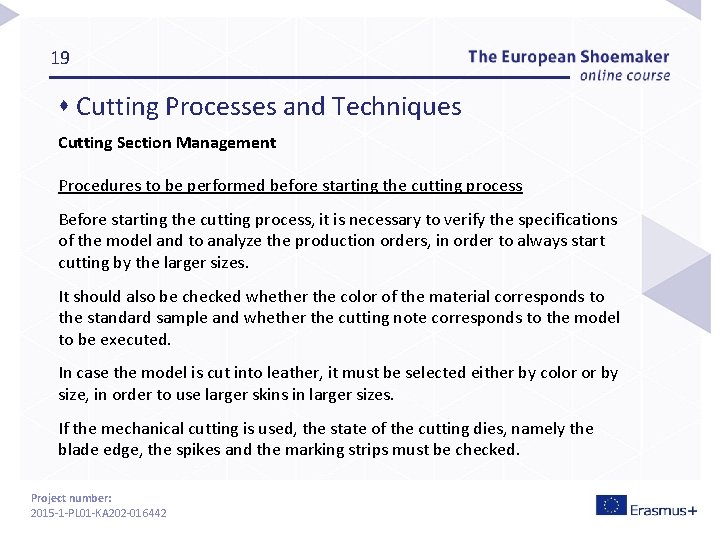
19 s Cutting Processes and Techniques Cutting Section Management Procedures to be performed before starting the cutting process Before starting the cutting process, it is necessary to verify the specifications of the model and to analyze the production orders, in order to always start cutting by the larger sizes. It should also be checked whether the color of the material corresponds to the standard sample and whether the cutting note corresponds to the model to be executed. In case the model is cut into leather, it must be selected either by color or by size, in order to use larger skins in larger sizes. If the mechanical cutting is used, the state of the cutting dies, namely the blade edge, the spikes and the marking strips must be checked. Project number: 2015 -1 -PL 01 -KA 202 -016442
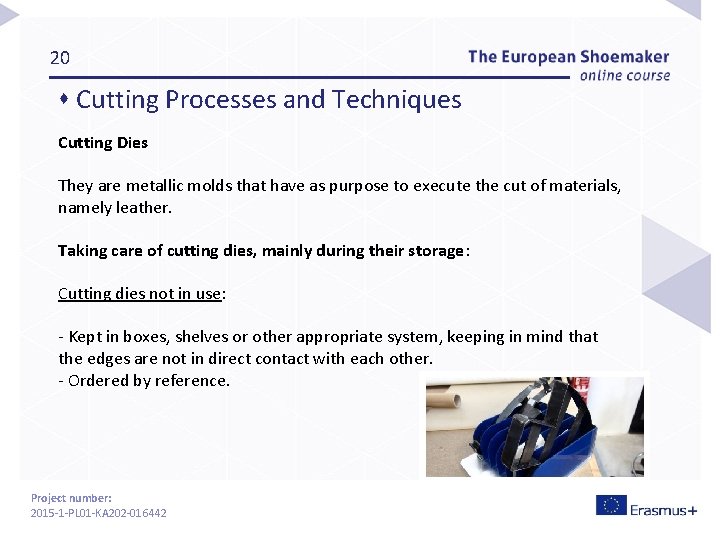
20 s Cutting Processes and Techniques Cutting Dies They are metallic molds that have as purpose to execute the cut of materials, namely leather. Taking care of cutting dies, mainly during their storage: Cutting dies not in use: - Kept in boxes, shelves or other appropriate system, keeping in mind that the edges are not in direct contact with each other. - Ordered by reference. Project number: 2015 -1 -PL 01 -KA 202 -016442
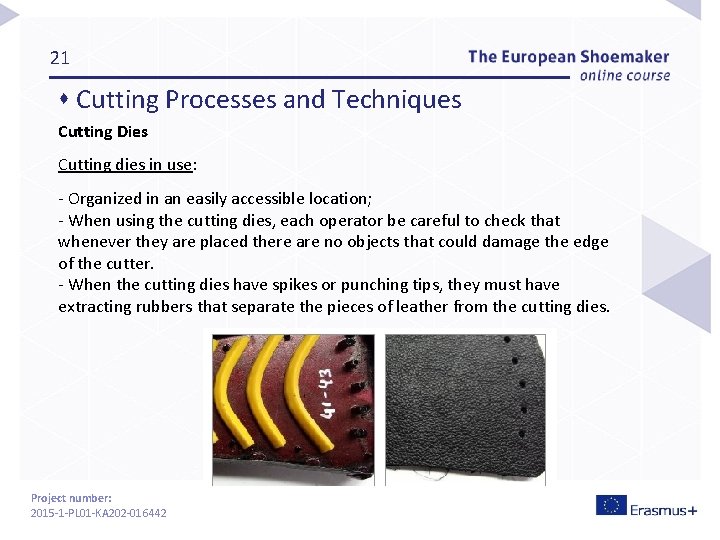
21 s Cutting Processes and Techniques Cutting Dies Cutting dies in use: - Organized in an easily accessible location; - When using the cutting dies, each operator be careful to check that whenever they are placed there are no objects that could damage the edge of the cutter. - When the cutting dies have spikes or punching tips, they must have extracting rubbers that separate the pieces of leather from the cutting dies. Project number: 2015 -1 -PL 01 -KA 202 -016442
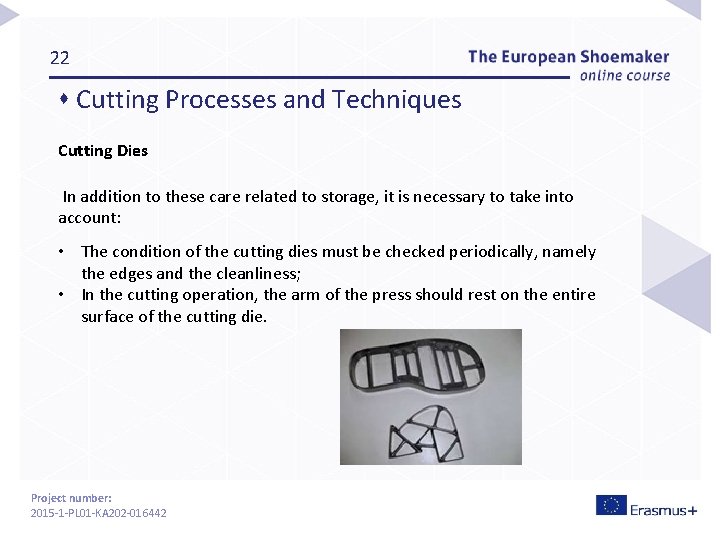
22 s Cutting Processes and Techniques Cutting Dies In addition to these care related to storage, it is necessary to take into account: • The condition of the cutting dies must be checked periodically, namely the edges and the cleanliness; • In the cutting operation, the arm of the press should rest on the entire surface of the cutting die. Project number: 2015 -1 -PL 01 -KA 202 -016442
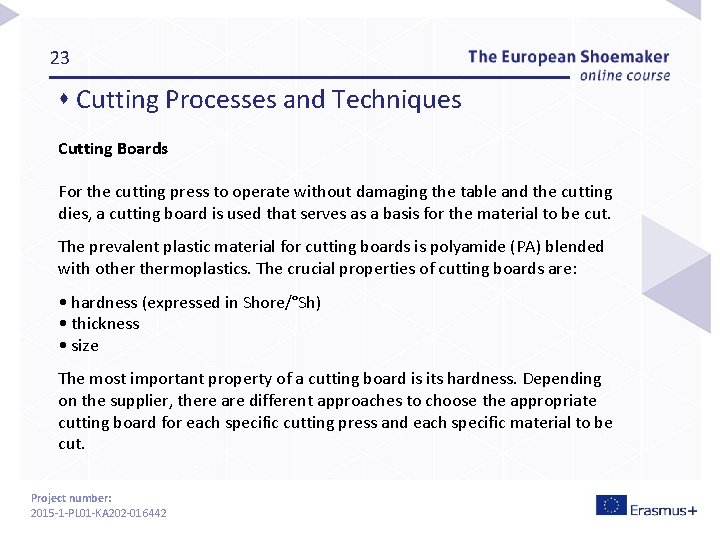
23 s Cutting Processes and Techniques Cutting Boards For the cutting press to operate without damaging the table and the cutting dies, a cutting board is used that serves as a basis for the material to be cut. The prevalent plastic material for cutting boards is polyamide (PA) blended with othermoplastics. The crucial properties of cutting boards are: • hardness (expressed in Shore/°Sh) • thickness • size The most important property of a cutting board is its hardness. Depending on the supplier, there are different approaches to choose the appropriate cutting board for each specific cutting press and each specific material to be cut. Project number: 2015 -1 -PL 01 -KA 202 -016442
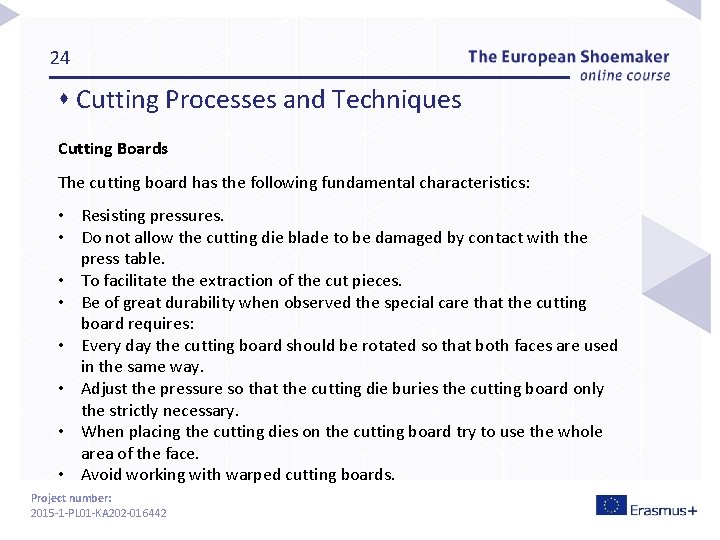
24 s Cutting Processes and Techniques Cutting Boards The cutting board has the following fundamental characteristics: • Resisting pressures. • Do not allow the cutting die blade to be damaged by contact with the press table. • To facilitate the extraction of the cut pieces. • Be of great durability when observed the special care that the cutting board requires: • Every day the cutting board should be rotated so that both faces are used in the same way. • Adjust the pressure so that the cutting die buries the cutting board only the strictly necessary. • When placing the cutting dies on the cutting board try to use the whole area of the face. • Avoid working with warped cutting boards. Project number: 2015 -1 -PL 01 -KA 202 -016442
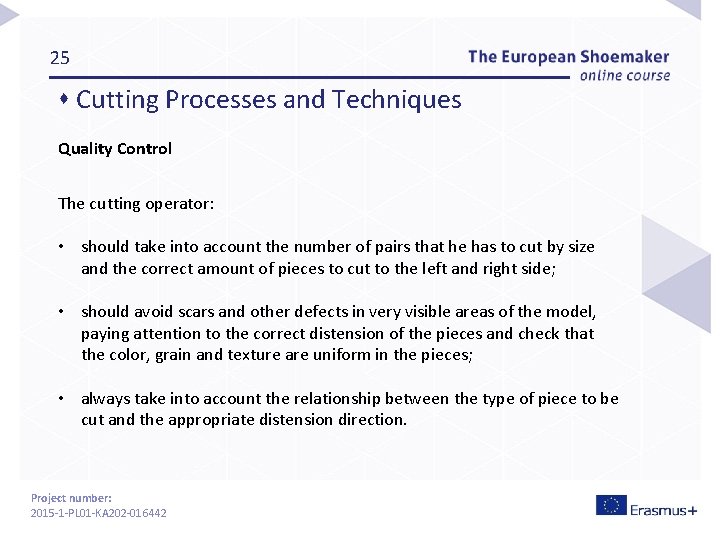
25 s Cutting Processes and Techniques Quality Control The cutting operator: • should take into account the number of pairs that he has to cut by size and the correct amount of pieces to cut to the left and right side; • should avoid scars and other defects in very visible areas of the model, paying attention to the correct distension of the pieces and check that the color, grain and texture are uniform in the pieces; • always take into account the relationship between the type of piece to be cut and the appropriate distension direction. Project number: 2015 -1 -PL 01 -KA 202 -016442
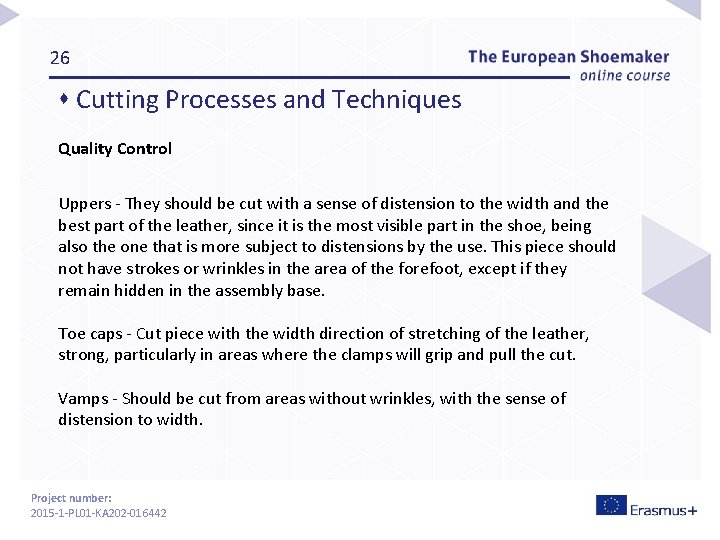
26 s Cutting Processes and Techniques Quality Control Uppers - They should be cut with a sense of distension to the width and the best part of the leather, since it is the most visible part in the shoe, being also the one that is more subject to distensions by the use. This piece should not have strokes or wrinkles in the area of the forefoot, except if they remain hidden in the assembly base. Toe caps - Cut piece with the width direction of stretching of the leather, strong, particularly in areas where the clamps will grip and pull the cut. Vamps - Should be cut from areas without wrinkles, with the sense of distension to width. Project number: 2015 -1 -PL 01 -KA 202 -016442

27 s Cutting Processes and Techniques Quality Control Quarters - They should be cut with a sense of distension to the width, of the best part after the cutting of the uppers/toe caps/vamps. The quarter on the inside allows to hide small wrinkles or folds of the leather. Tongue - This piece can be cut from lower quality areas, may contain small defects and its sense of distension is length. Trims/Strips of buckles - The distension direction of these pieces should be to length and can be cut of flexible skin, but never of parts not usable. Project number: 2015 -1 -PL 01 -KA 202 -016442
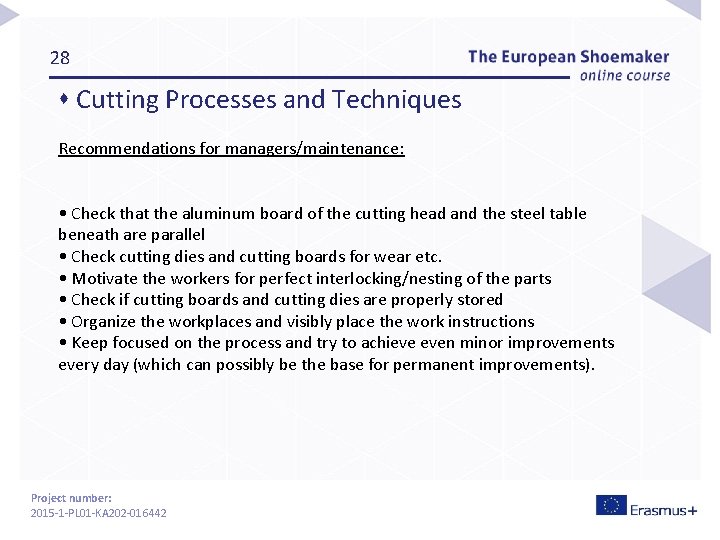
28 s Cutting Processes and Techniques Recommendations for managers/maintenance: • Check that the aluminum board of the cutting head and the steel table beneath are parallel • Check cutting dies and cutting boards for wear etc. • Motivate the workers for perfect interlocking/nesting of the parts • Check if cutting boards and cutting dies are properly stored • Organize the workplaces and visibly place the work instructions • Keep focused on the process and try to achieve even minor improvements every day (which can possibly be the base for permanent improvements). Project number: 2015 -1 -PL 01 -KA 202 -016442
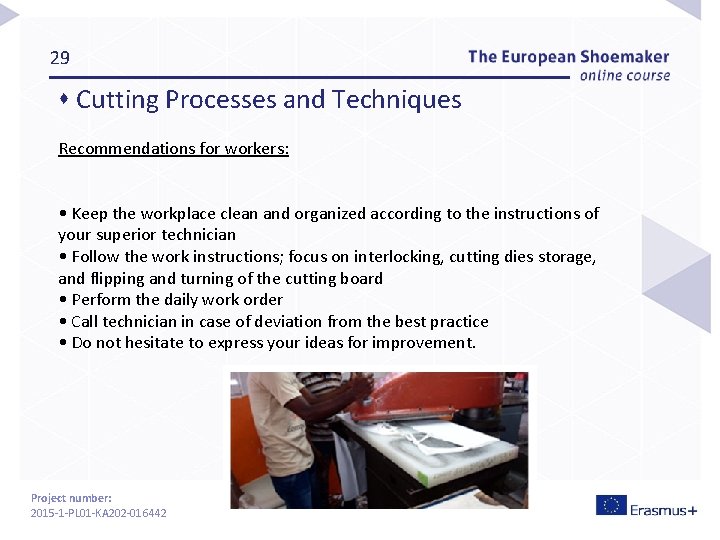
29 s Cutting Processes and Techniques Recommendations for workers: • Keep the workplace clean and organized according to the instructions of your superior technician • Follow the work instructions; focus on interlocking, cutting dies storage, and flipping and turning of the cutting board • Perform the daily work order • Call technician in case of deviation from the best practice • Do not hesitate to express your ideas for improvement. Project number: 2015 -1 -PL 01 -KA 202 -016442
Concurrent in os
Gingival margin trimmer uses
Non cutting dental instruments
Dental bur
Marking tools in sewing
Orthogonal cutting is dimensional metal cutting
Unit 24 cutting with oxyfuels and other gases
Unit 6 review questions
Hyp opp adj triangle
Unit process and unit operation
What is unit operation and unit process
Study of behavior and mental processes
Wharton risk management
Algo and amal
Dynamics of a community
It is used to process materials by hand.
Irreversible process in thermodynamics
Data dictionary ipt
Marzano element 19
Designing and managing service product
Word formation processes
Marketing processes and consumer behavior
Participants processes and circumstances
7 types of jaycustomers
The scientific study of behavior and mental processes
Inputs outputs transformation processes and feedback
Glacial processes and landforms
Cultural patterns and processes
Cookery skills techniques and processes
Marketing processes and consumer behavior