UNDERSTANDING ISO 9001 2008 DISCUSSION TOPICS Definition and
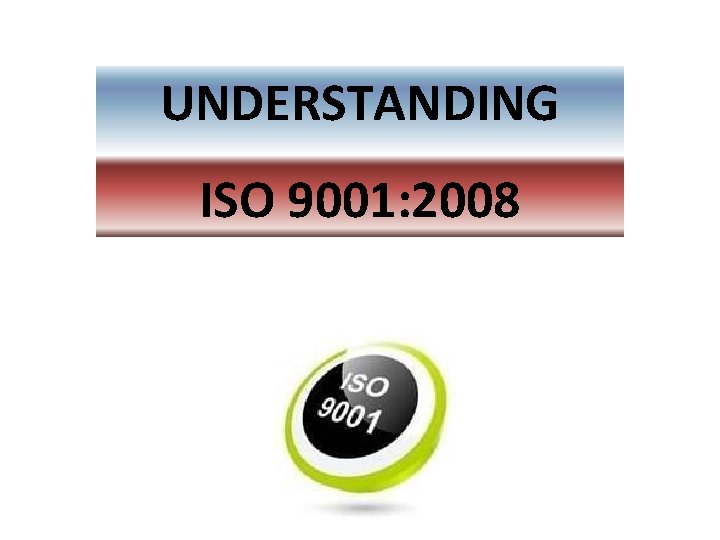
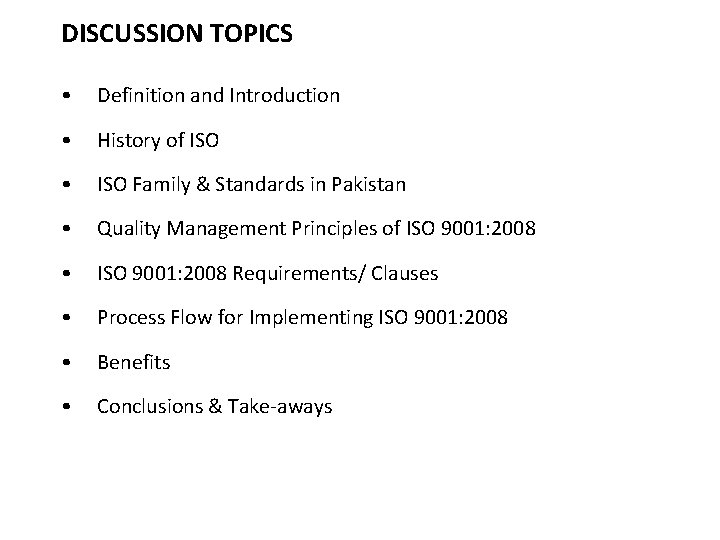
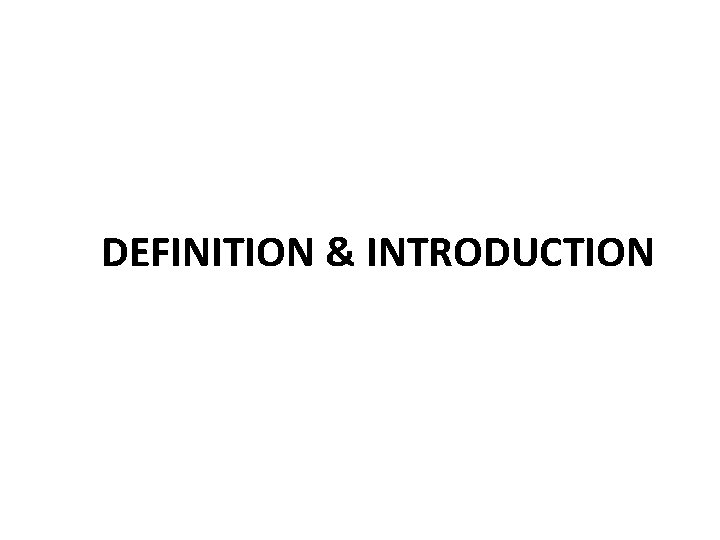
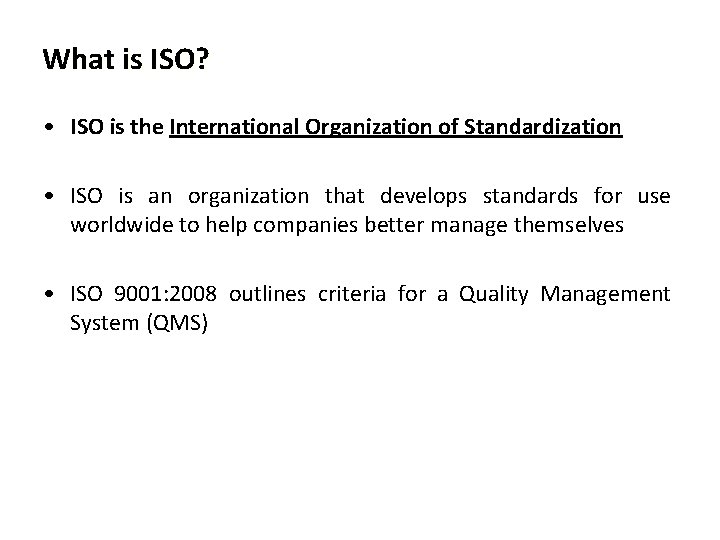
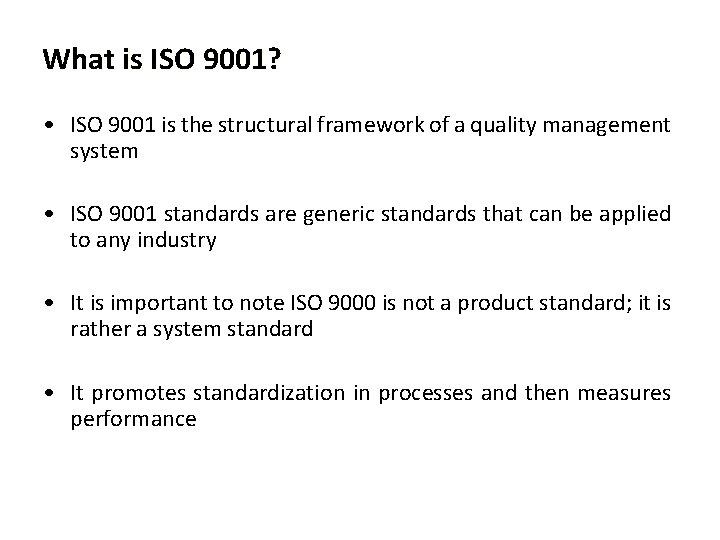
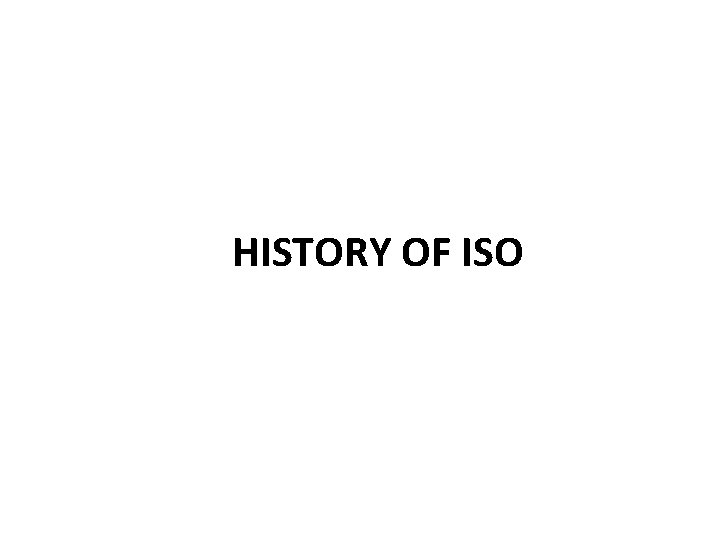
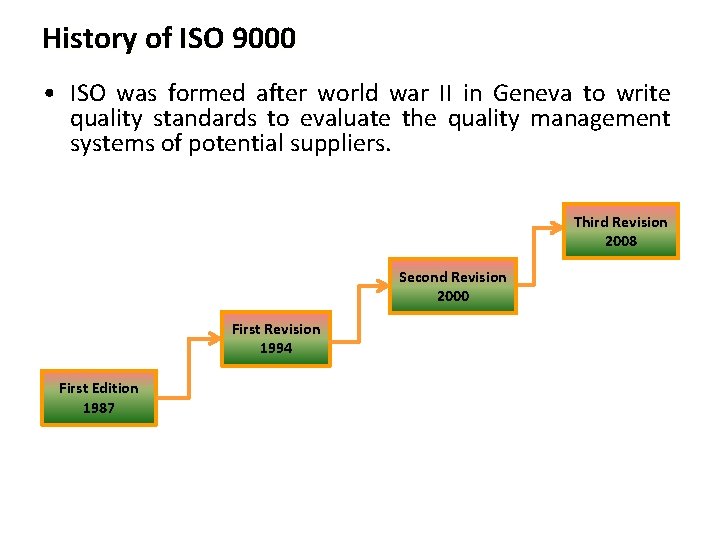
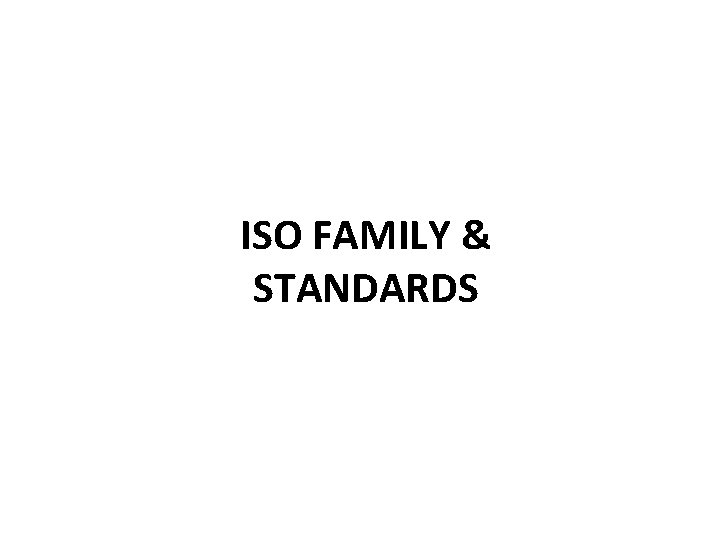
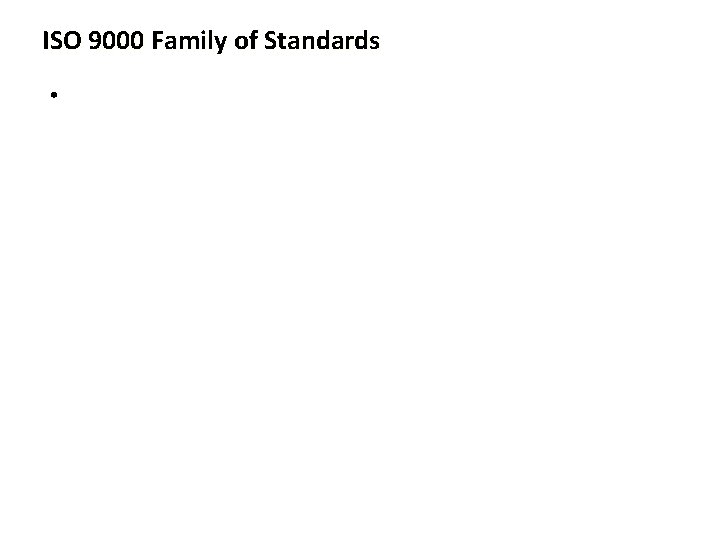
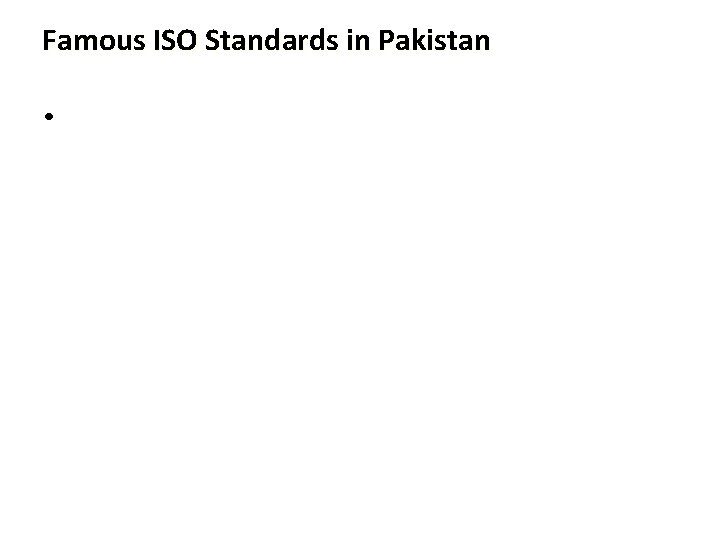
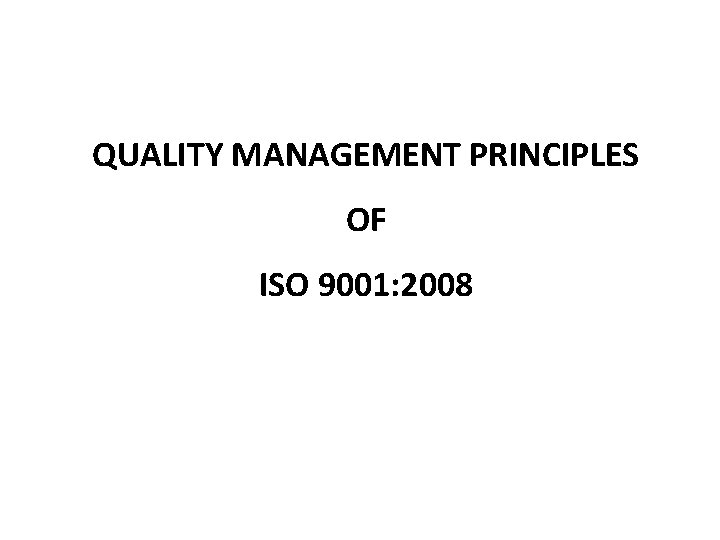
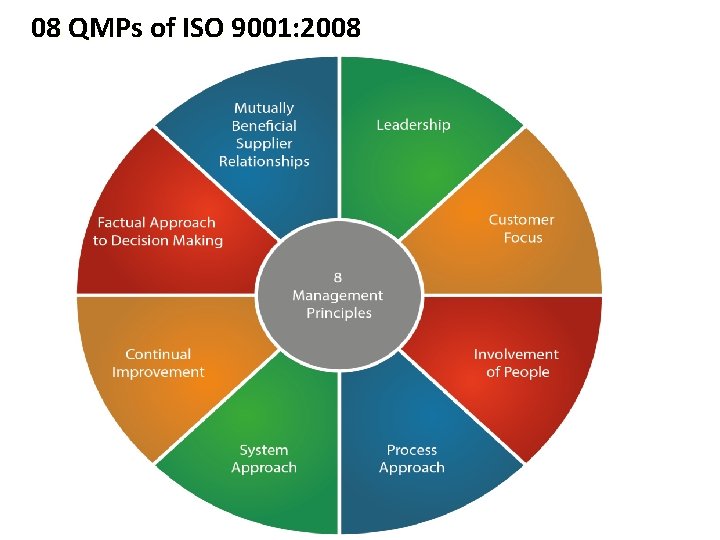
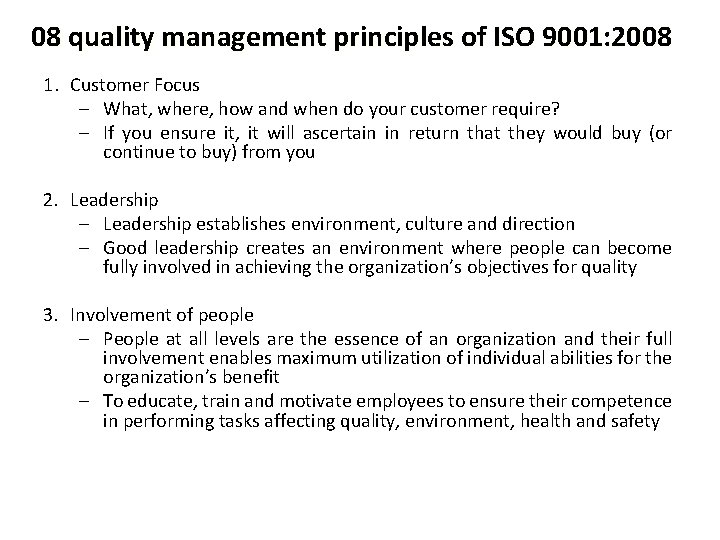
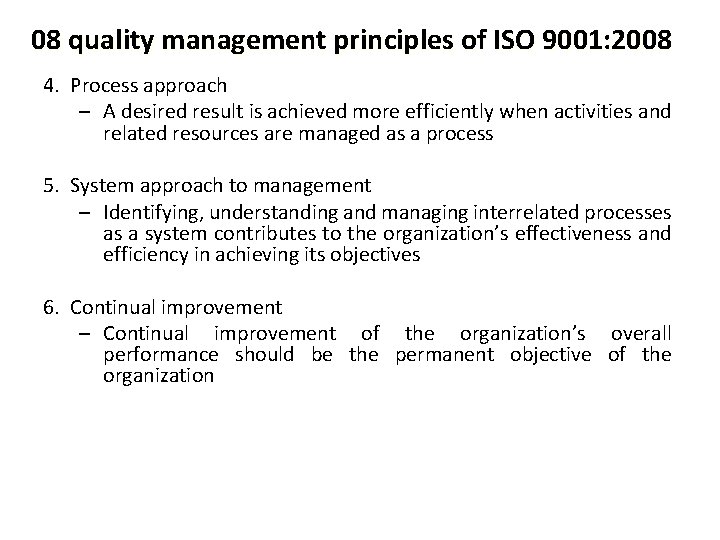
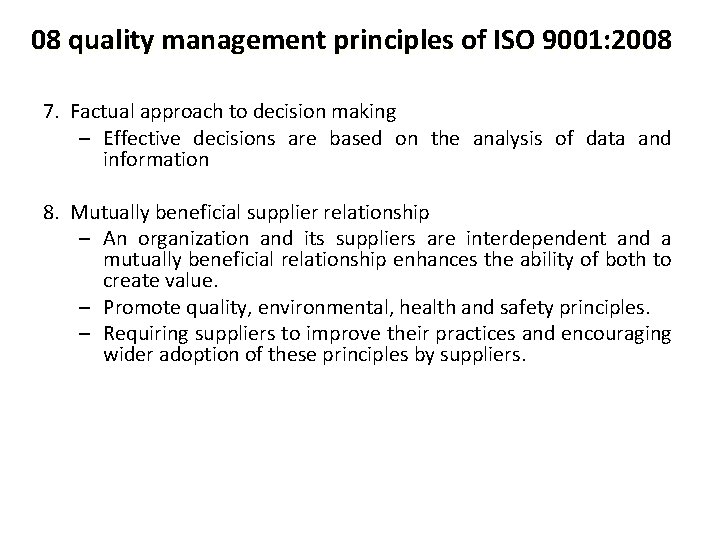
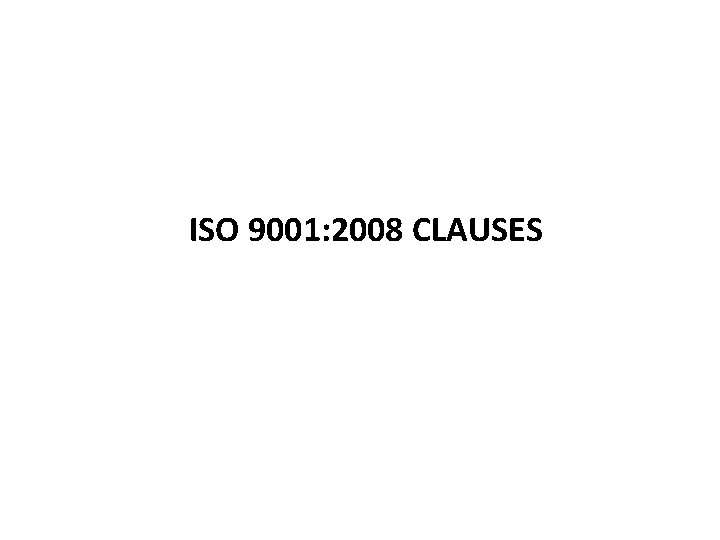
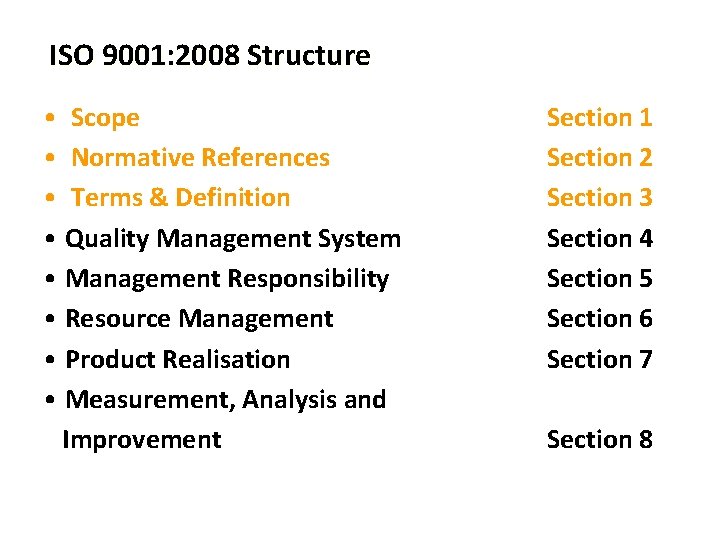
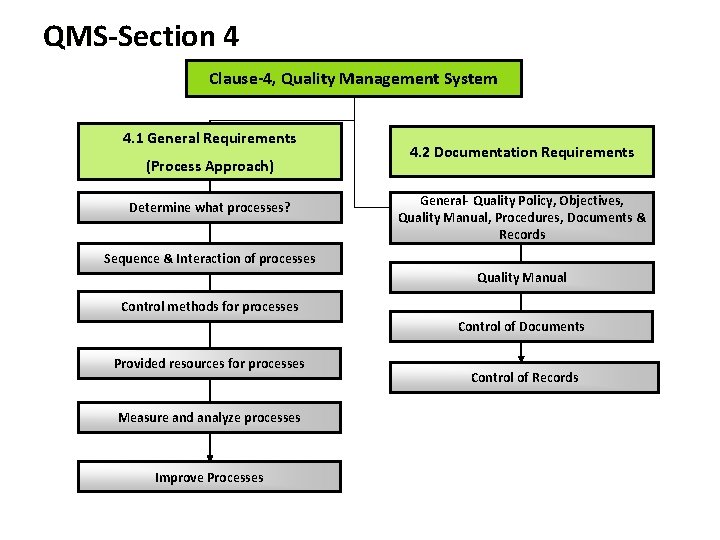
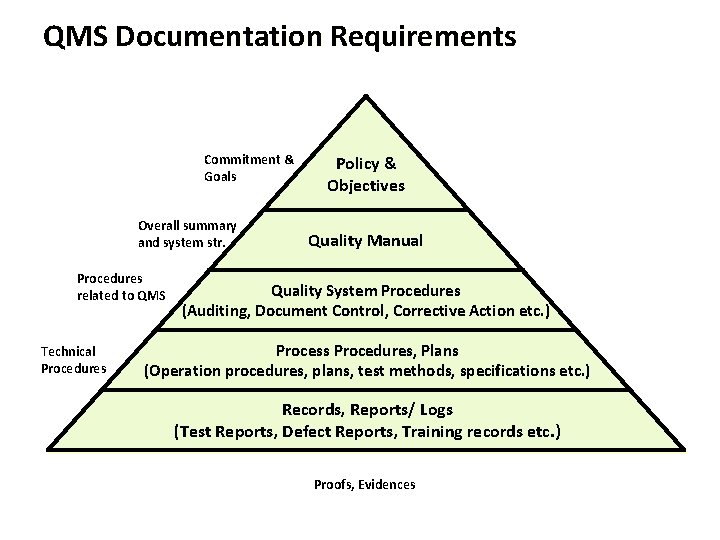
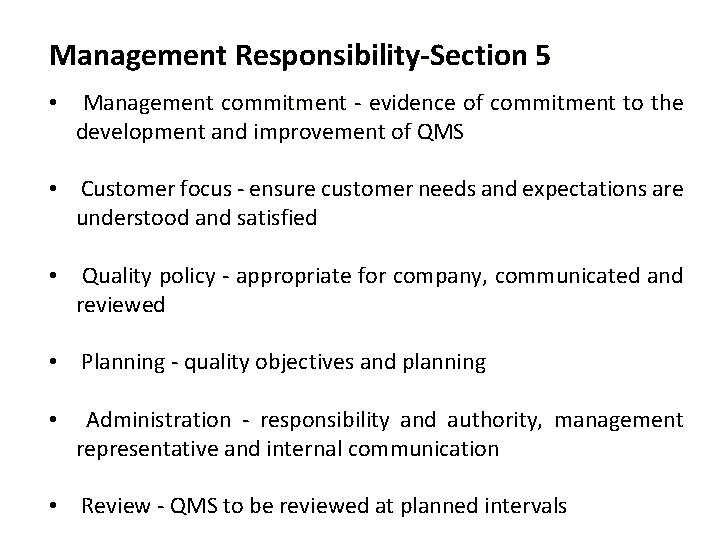
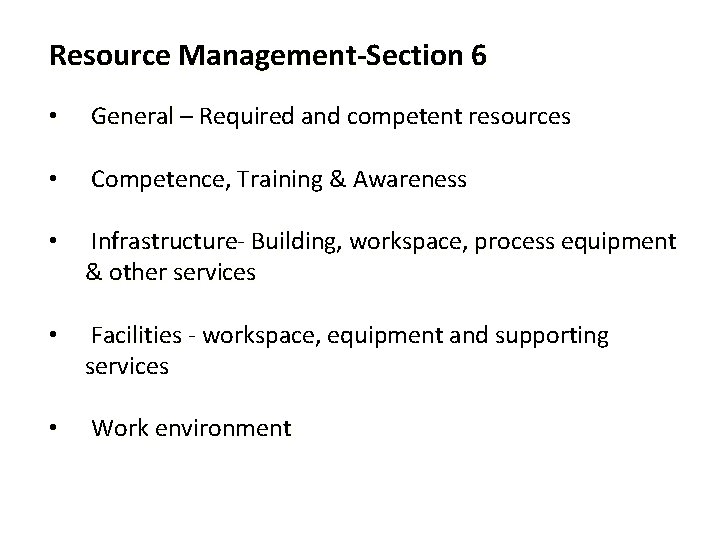
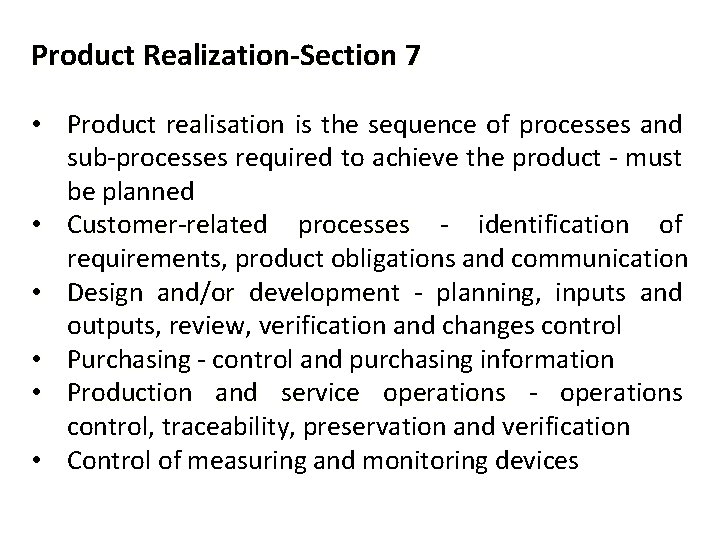
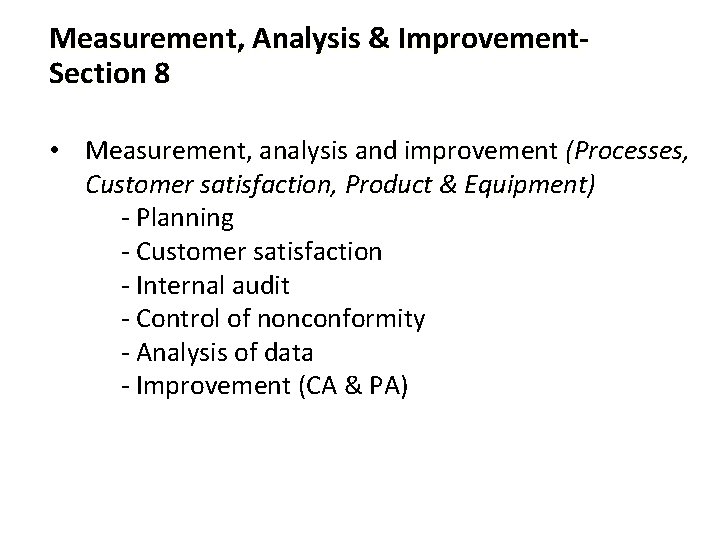
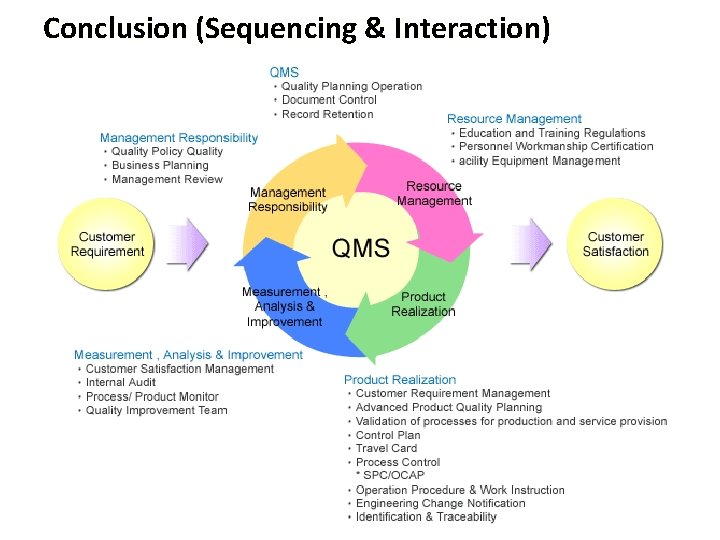
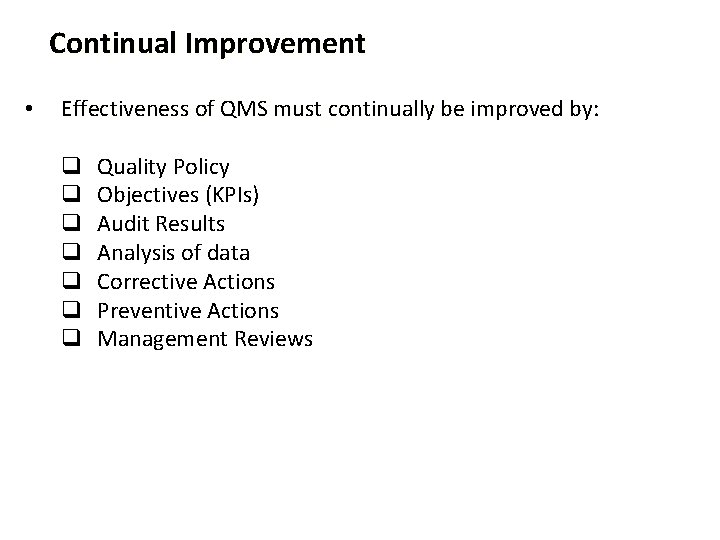
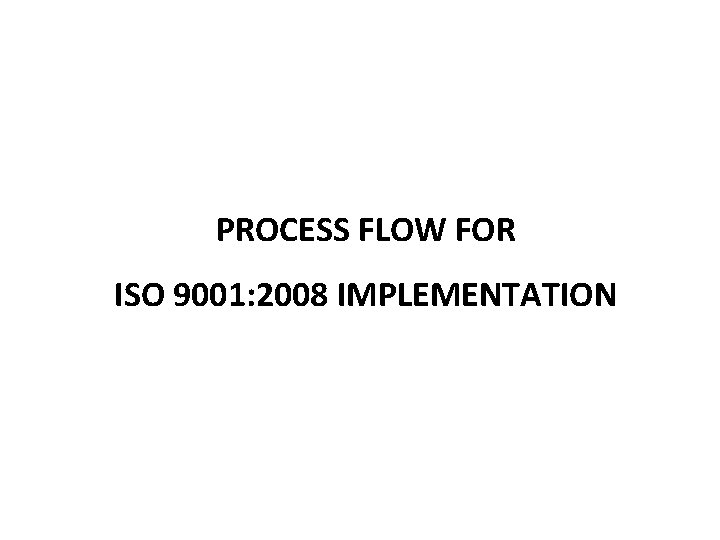
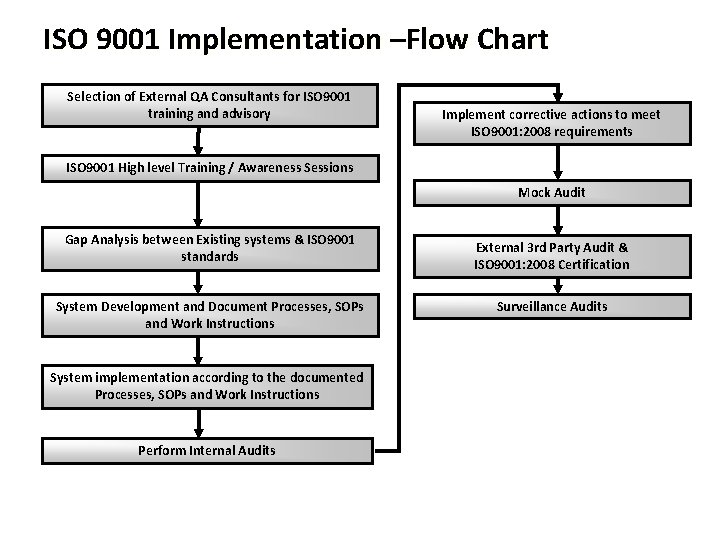
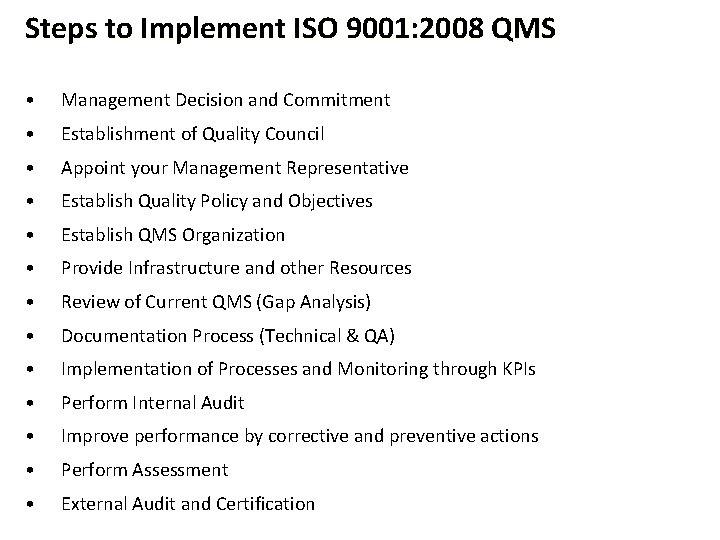
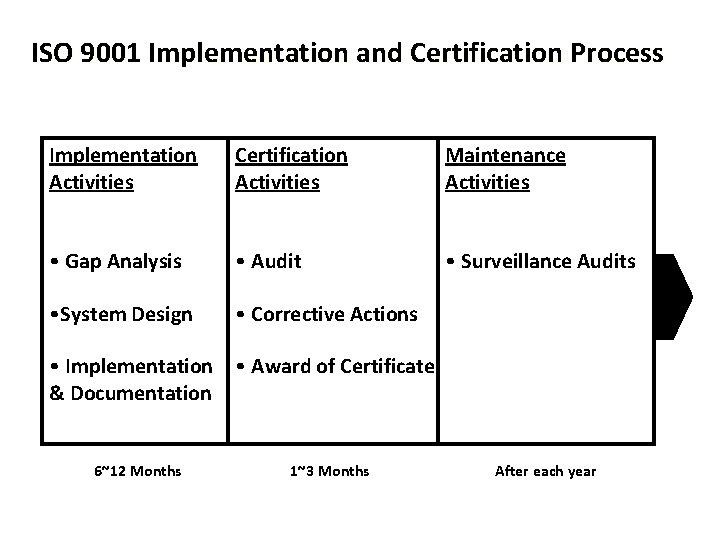
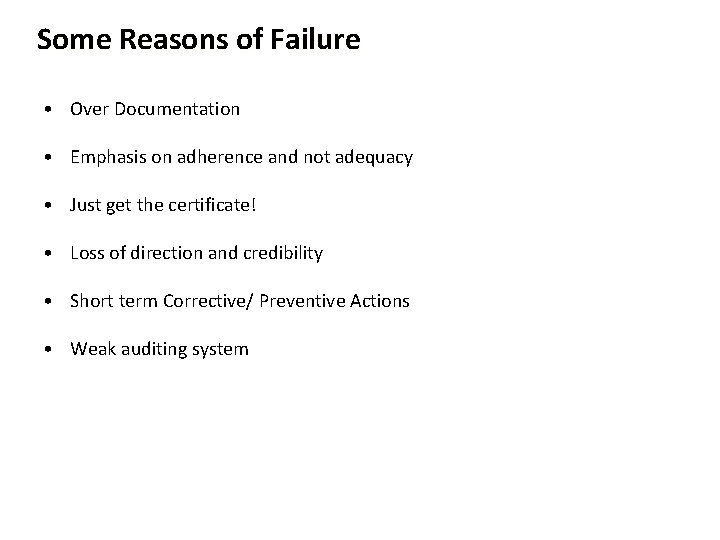
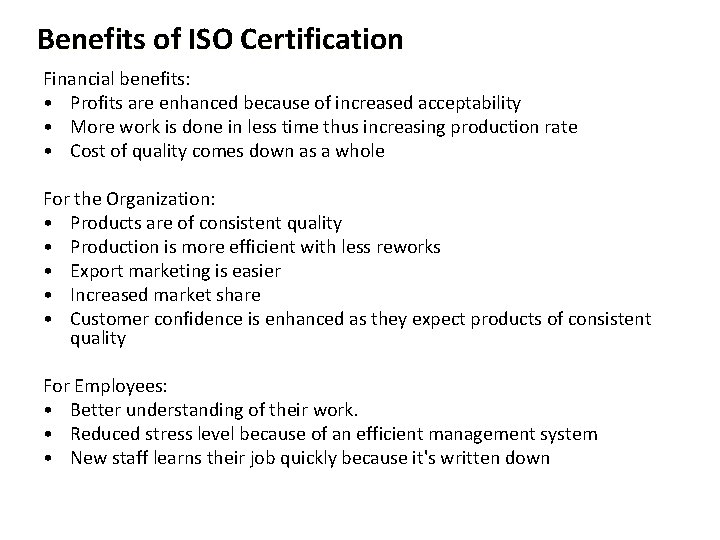
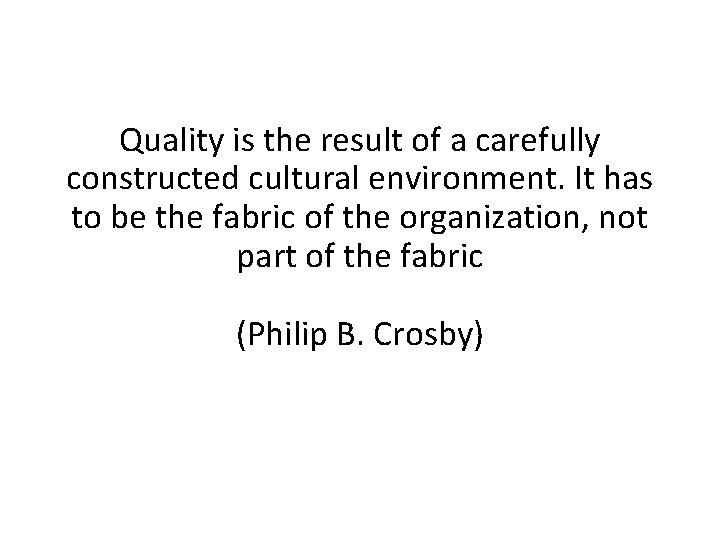
- Slides: 32
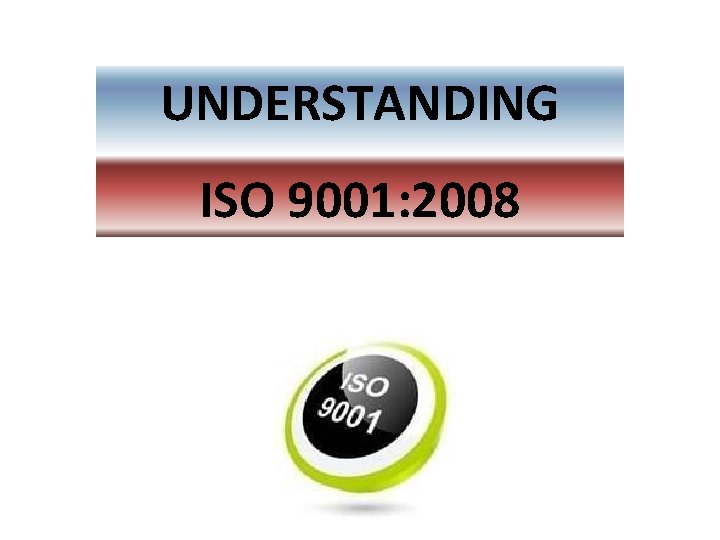
UNDERSTANDING ISO 9001: 2008
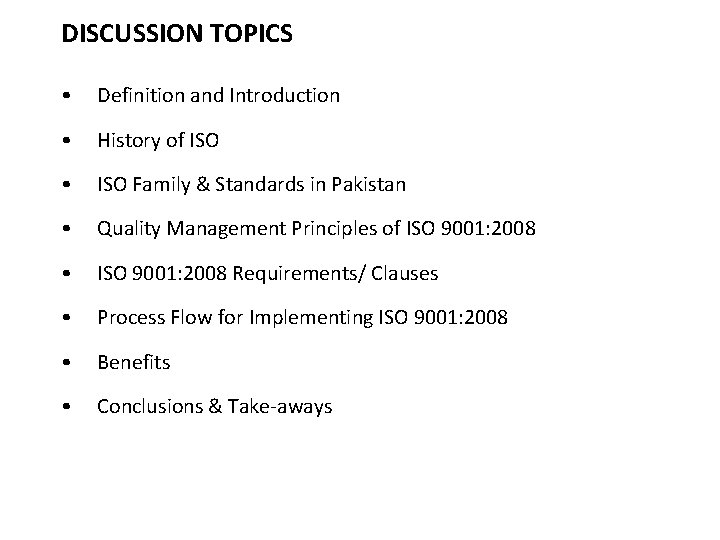
DISCUSSION TOPICS • Definition and Introduction • History of ISO • ISO Family & Standards in Pakistan • Quality Management Principles of ISO 9001: 2008 • ISO 9001: 2008 Requirements/ Clauses • Process Flow for Implementing ISO 9001: 2008 • Benefits • Conclusions & Take-aways
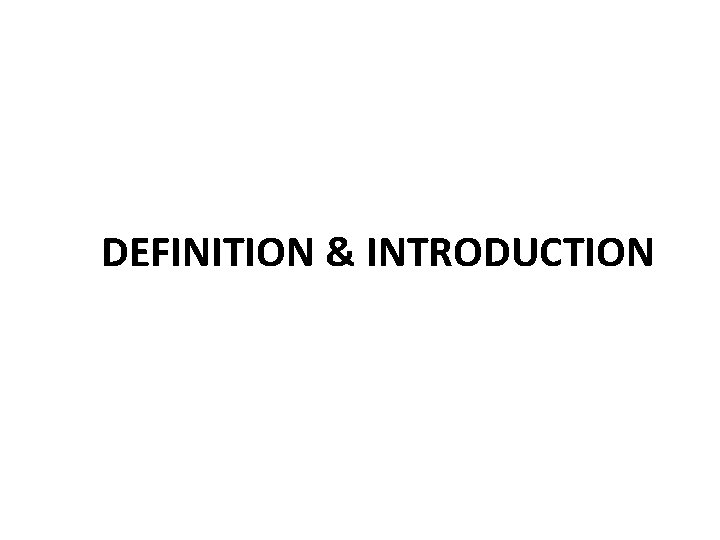
DEFINITION & INTRODUCTION
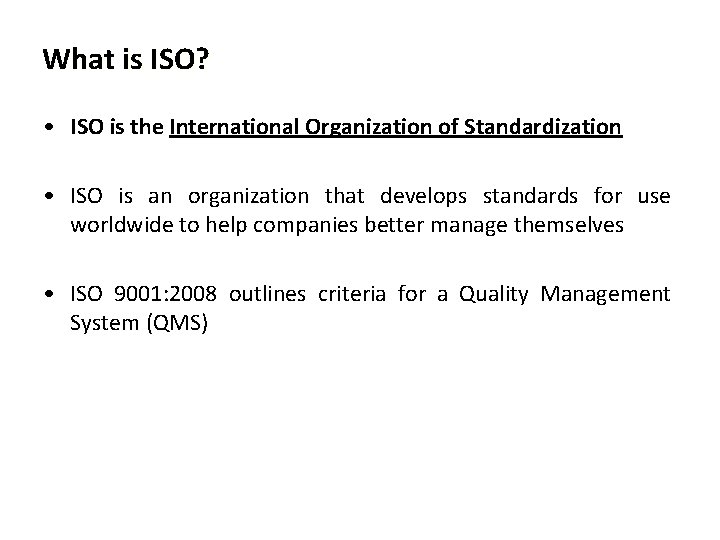
What is ISO? • ISO is the International Organization of Standardization • ISO is an organization that develops standards for use worldwide to help companies better manage themselves • ISO 9001: 2008 outlines criteria for a Quality Management System (QMS)
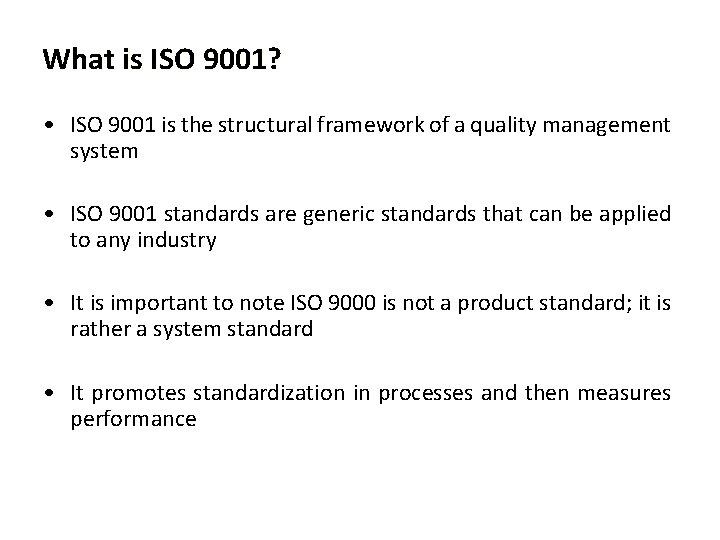
What is ISO 9001? • ISO 9001 is the structural framework of a quality management system • ISO 9001 standards are generic standards that can be applied to any industry • It is important to note ISO 9000 is not a product standard; it is rather a system standard • It promotes standardization in processes and then measures performance
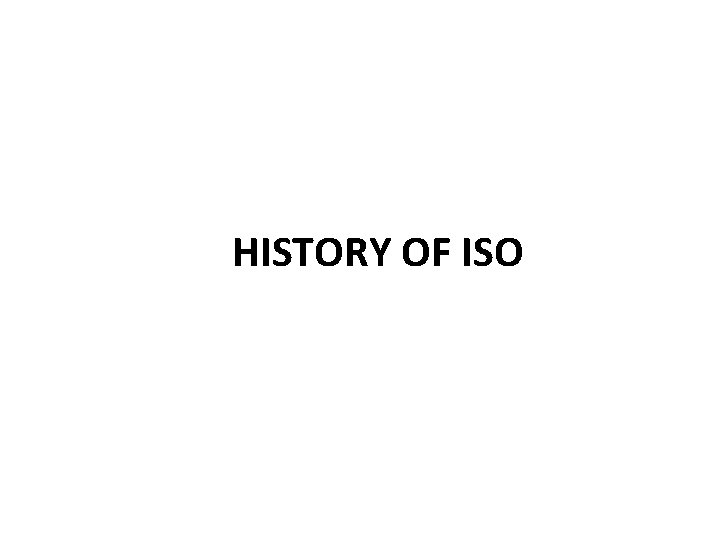
HISTORY OF ISO
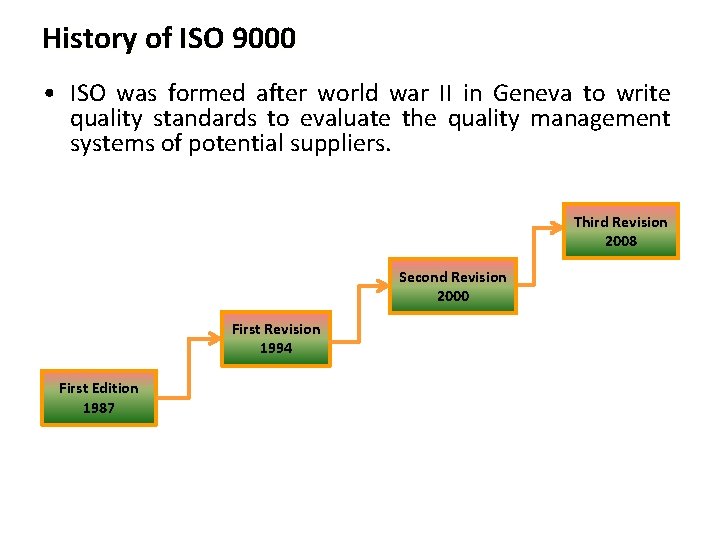
History of ISO 9000 • ISO was formed after world war II in Geneva to write quality standards to evaluate the quality management systems of potential suppliers. Third Revision 2008 Second Revision 2000 First Revision 1994 First Edition 1987
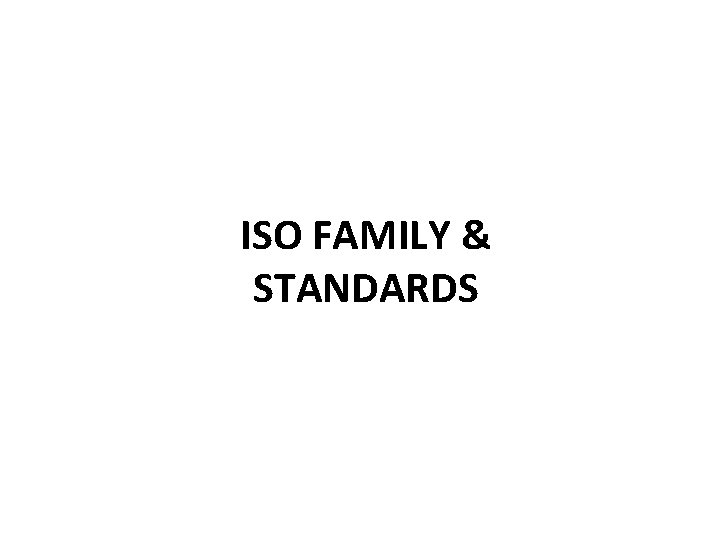
ISO FAMILY & STANDARDS
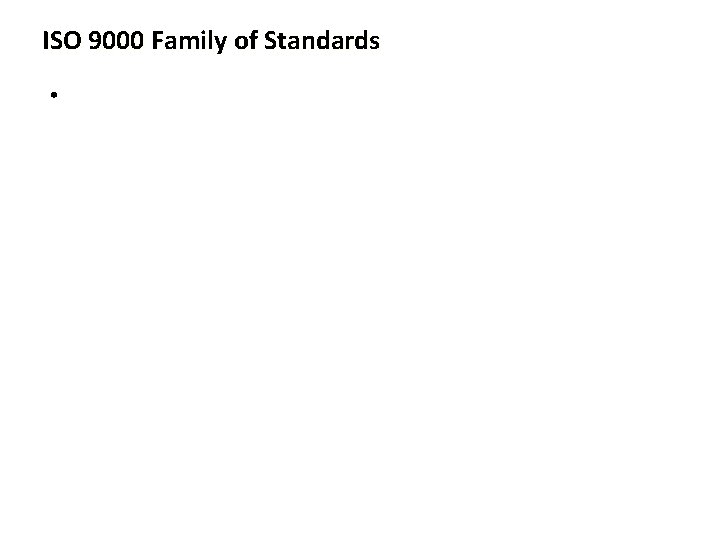
ISO 9000 Family of Standards • •
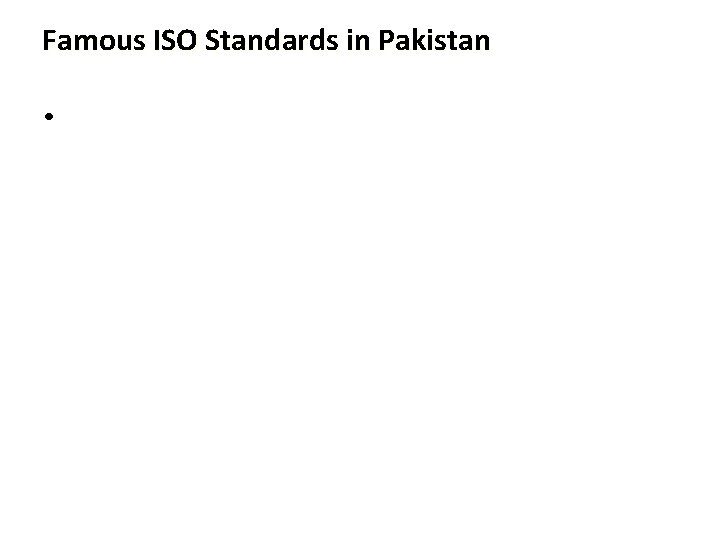
Famous ISO Standards in Pakistan •
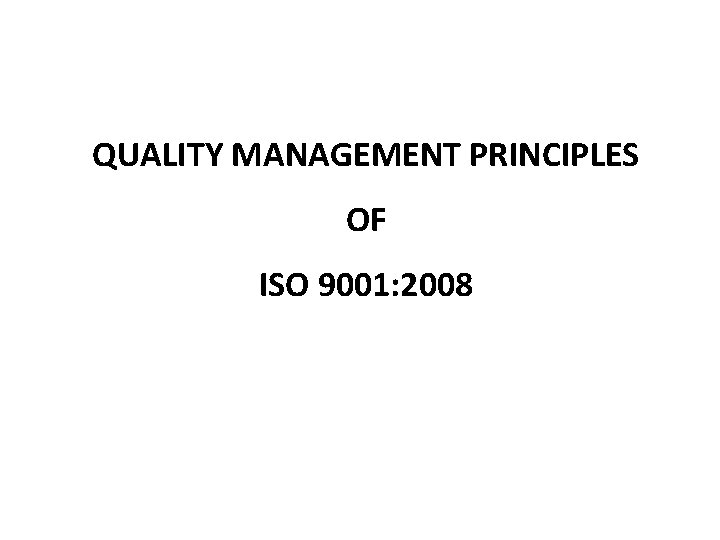
QUALITY MANAGEMENT PRINCIPLES OF ISO 9001: 2008
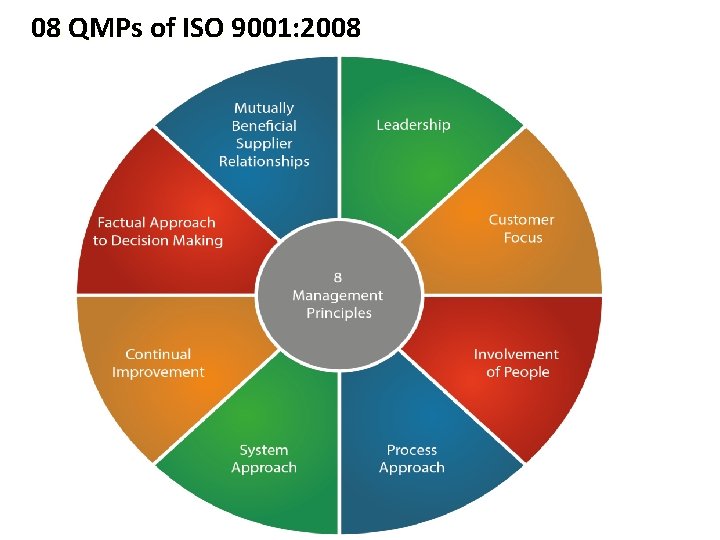
08 QMPs of ISO 9001: 2008
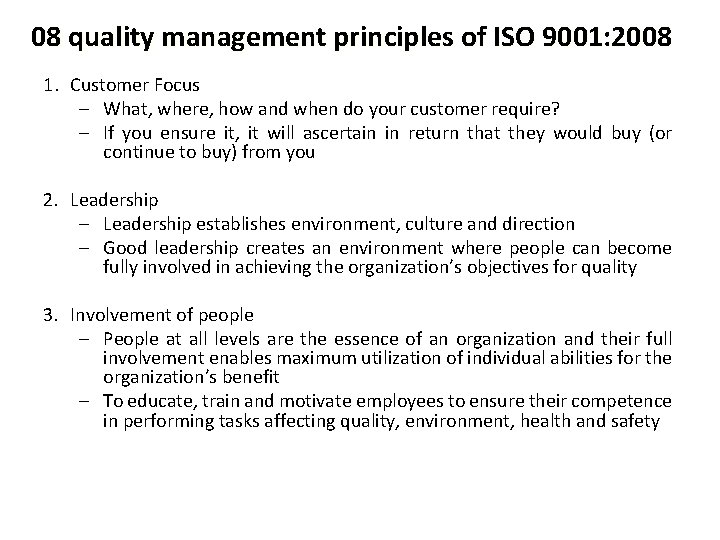
08 quality management principles of ISO 9001: 2008 1. Customer Focus – What, where, how and when do your customer require? – If you ensure it, it will ascertain in return that they would buy (or continue to buy) from you 2. Leadership – Leadership establishes environment, culture and direction – Good leadership creates an environment where people can become fully involved in achieving the organization’s objectives for quality 3. Involvement of people – People at all levels are the essence of an organization and their full involvement enables maximum utilization of individual abilities for the organization’s benefit – To educate, train and motivate employees to ensure their competence in performing tasks affecting quality, environment, health and safety
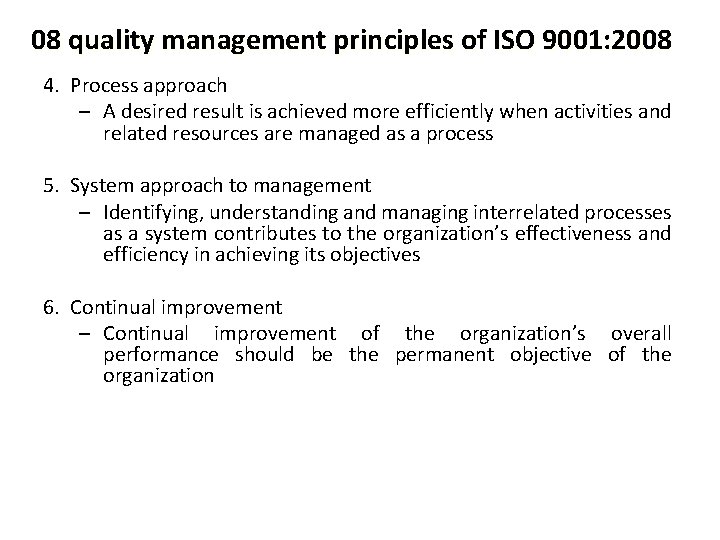
08 quality management principles of ISO 9001: 2008 4. Process approach – A desired result is achieved more efficiently when activities and related resources are managed as a process 5. System approach to management – Identifying, understanding and managing interrelated processes as a system contributes to the organization’s effectiveness and efficiency in achieving its objectives 6. Continual improvement – Continual improvement of the organization’s overall performance should be the permanent objective of the organization
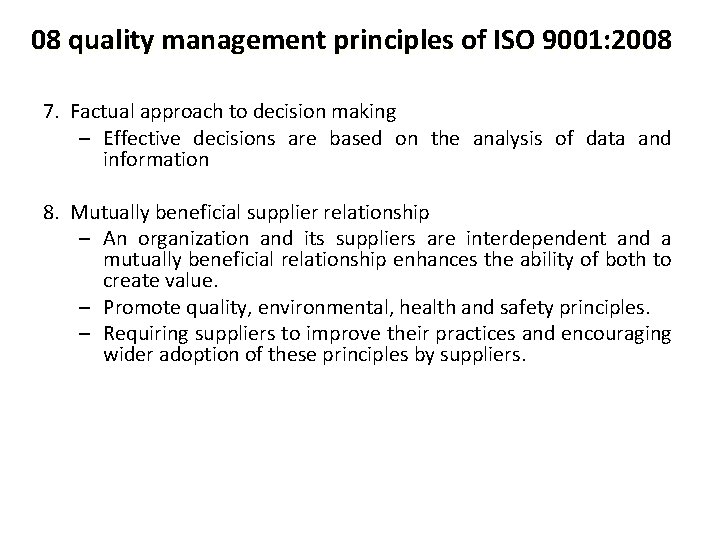
08 quality management principles of ISO 9001: 2008 7. Factual approach to decision making – Effective decisions are based on the analysis of data and information 8. Mutually beneficial supplier relationship – An organization and its suppliers are interdependent and a mutually beneficial relationship enhances the ability of both to create value. – Promote quality, environmental, health and safety principles. – Requiring suppliers to improve their practices and encouraging wider adoption of these principles by suppliers.
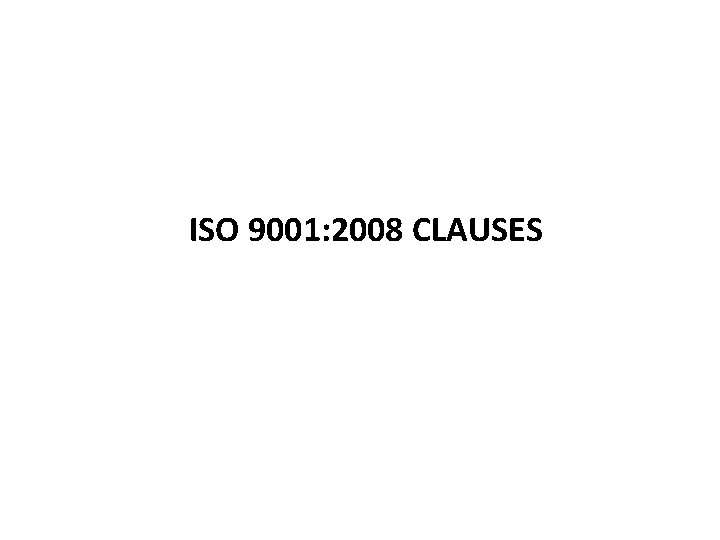
ISO 9001: 2008 CLAUSES
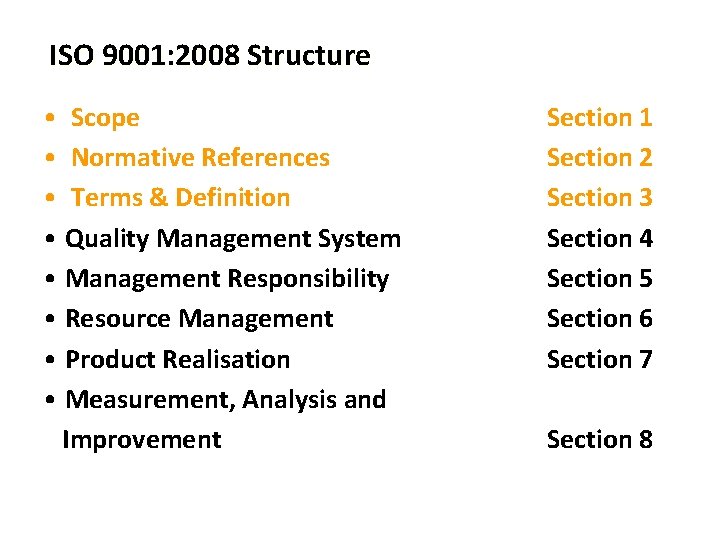
ISO 9001: 2008 Structure • Scope • Normative References • Terms & Definition • Quality Management System • Management Responsibility • Resource Management • Product Realisation • Measurement, Analysis and Improvement Section 1 Section 2 Section 3 Section 4 Section 5 Section 6 Section 7 Section 8
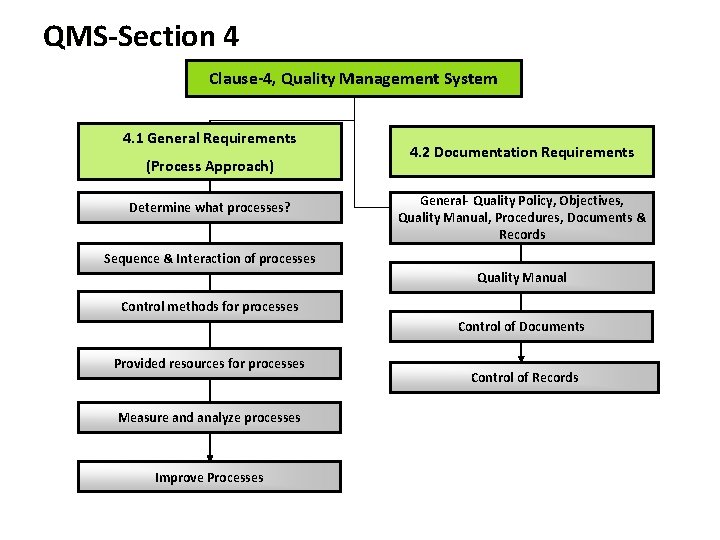
QMS-Section 4 Clause-4, Quality Management System 4. 1 General Requirements (Process Approach) Determine what processes? 4. 2 Documentation Requirements General- Quality Policy, Objectives, Quality Manual, Procedures, Documents & Records Sequence & Interaction of processes Quality Manual Control methods for processes Control of Documents Provided resources for processes Measure and analyze processes Improve Processes Control of Records
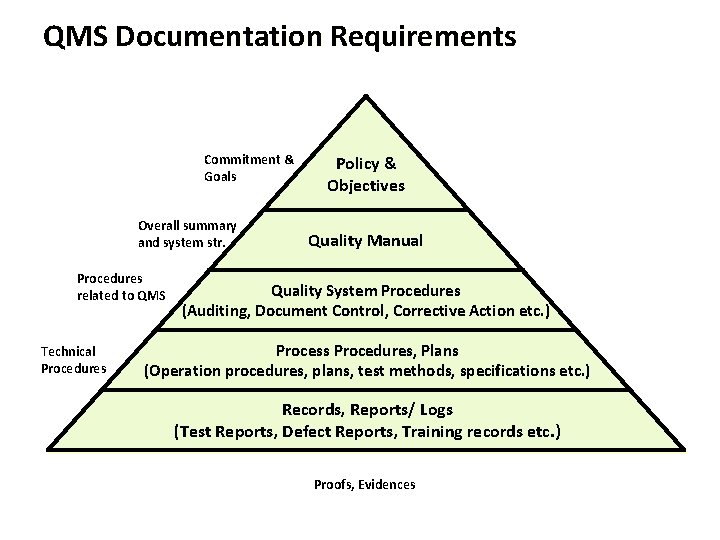
QMS Documentation Requirements Commitment & Goals Overall summary and system str. Procedures related to QMS Technical Procedures Policy & Objectives Quality Manual Quality System Procedures (Auditing, Document Control, Corrective Action etc. ) Process Procedures, Plans (Operation procedures, plans, test methods, specifications etc. ) Records, Reports/ Logs (Test Reports, Defect Reports, Training records etc. ) Proofs, Evidences
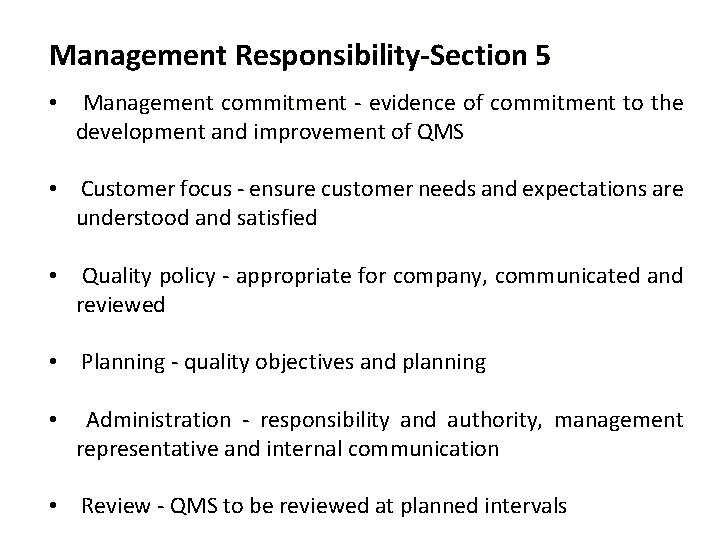
Management Responsibility-Section 5 • Management commitment - evidence of commitment to the development and improvement of QMS • Customer focus - ensure customer needs and expectations are understood and satisfied • Quality policy - appropriate for company, communicated and reviewed • Planning - quality objectives and planning • Administration - responsibility and authority, management representative and internal communication • Review - QMS to be reviewed at planned intervals
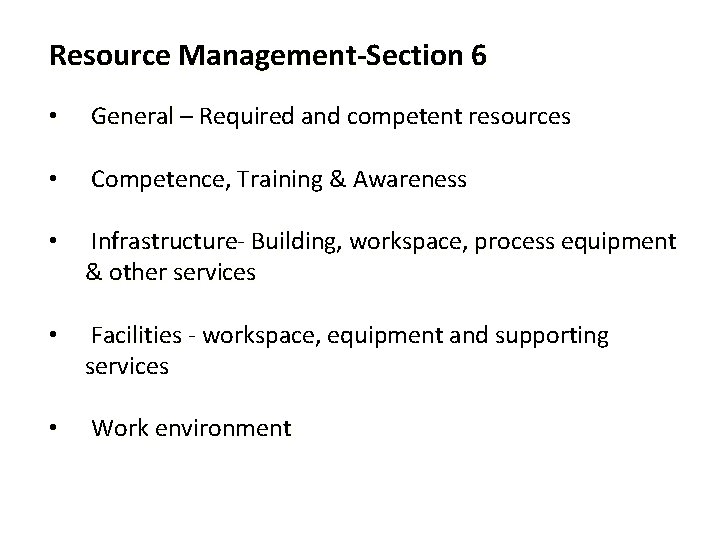
Resource Management-Section 6 • General – Required and competent resources • Competence, Training & Awareness • Infrastructure- Building, workspace, process equipment & other services • Facilities - workspace, equipment and supporting services • Work environment
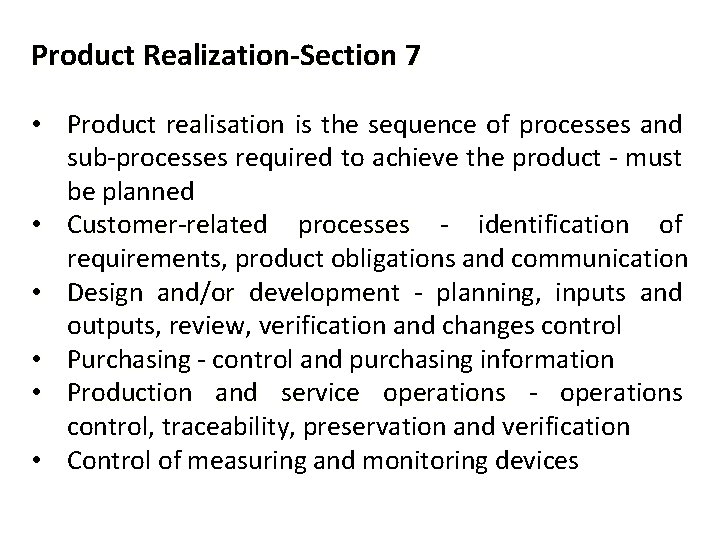
Product Realization-Section 7 • Product realisation is the sequence of processes and sub-processes required to achieve the product - must be planned • Customer-related processes - identification of requirements, product obligations and communication • Design and/or development - planning, inputs and outputs, review, verification and changes control • Purchasing - control and purchasing information • Production and service operations - operations control, traceability, preservation and verification • Control of measuring and monitoring devices
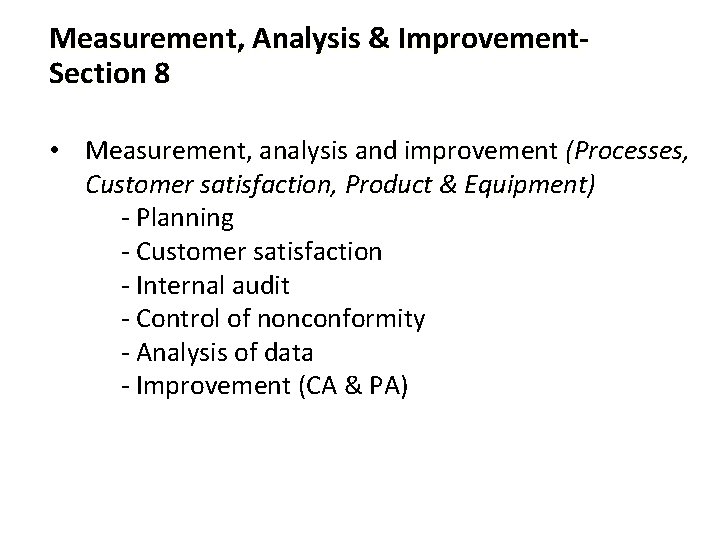
Measurement, Analysis & Improvement. Section 8 • Measurement, analysis and improvement (Processes, Customer satisfaction, Product & Equipment) - Planning - Customer satisfaction - Internal audit - Control of nonconformity - Analysis of data - Improvement (CA & PA)
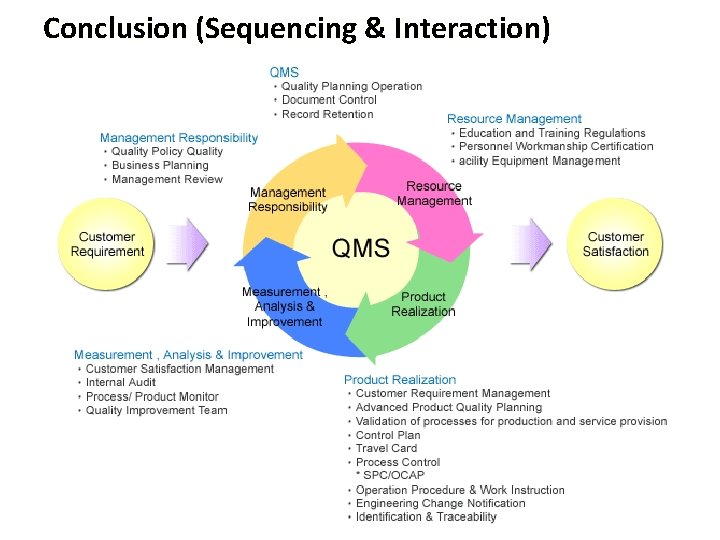
Conclusion (Sequencing & Interaction)
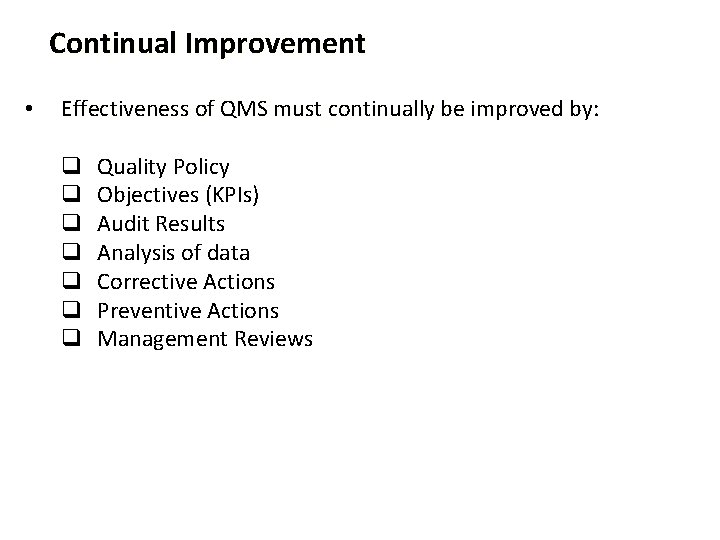
Continual Improvement • Effectiveness of QMS must continually be improved by: q q q q Quality Policy Objectives (KPIs) Audit Results Analysis of data Corrective Actions Preventive Actions Management Reviews
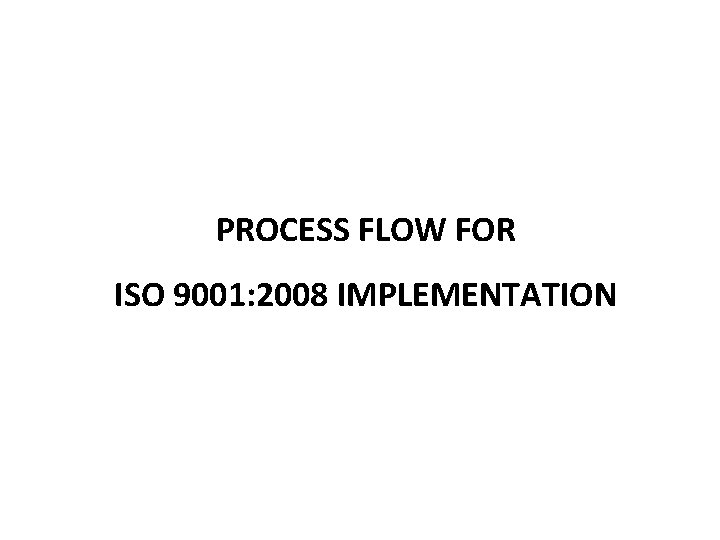
PROCESS FLOW FOR ISO 9001: 2008 IMPLEMENTATION
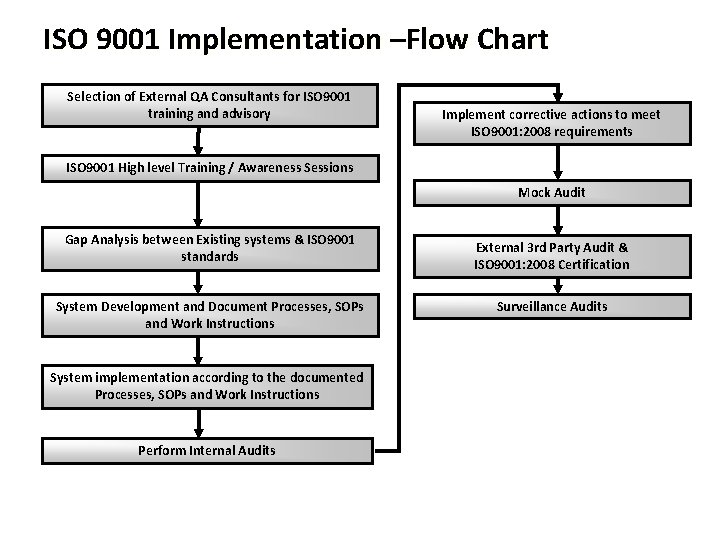
ISO 9001 Implementation –Flow Chart Selection of External QA Consultants for ISO 9001 training and advisory Implement corrective actions to meet ISO 9001: 2008 requirements ISO 9001 High level Training / Awareness Sessions Mock Audit Gap Analysis between Existing systems & ISO 9001 standards System Development and Document Processes, SOPs and Work Instructions System implementation according to the documented Processes, SOPs and Work Instructions Perform Internal Audits External 3 rd Party Audit & ISO 9001: 2008 Certification Surveillance Audits
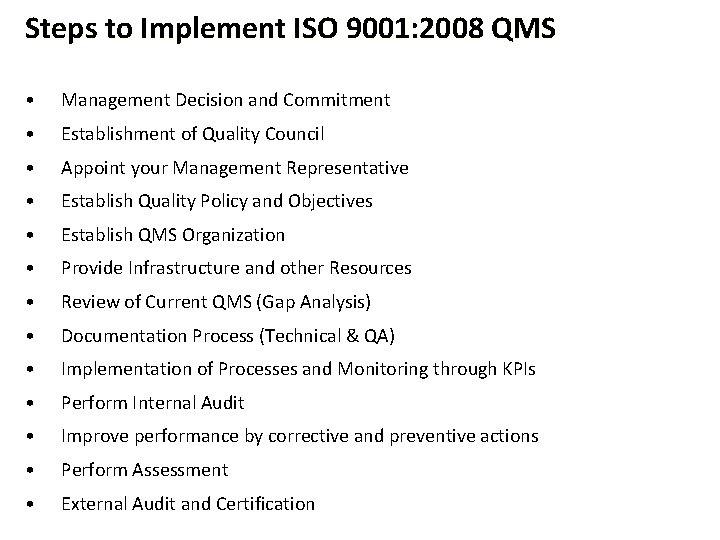
Steps to Implement ISO 9001: 2008 QMS • Management Decision and Commitment • Establishment of Quality Council • Appoint your Management Representative • Establish Quality Policy and Objectives • Establish QMS Organization • Provide Infrastructure and other Resources • Review of Current QMS (Gap Analysis) • Documentation Process (Technical & QA) • Implementation of Processes and Monitoring through KPIs • Perform Internal Audit • Improve performance by corrective and preventive actions • Perform Assessment • External Audit and Certification
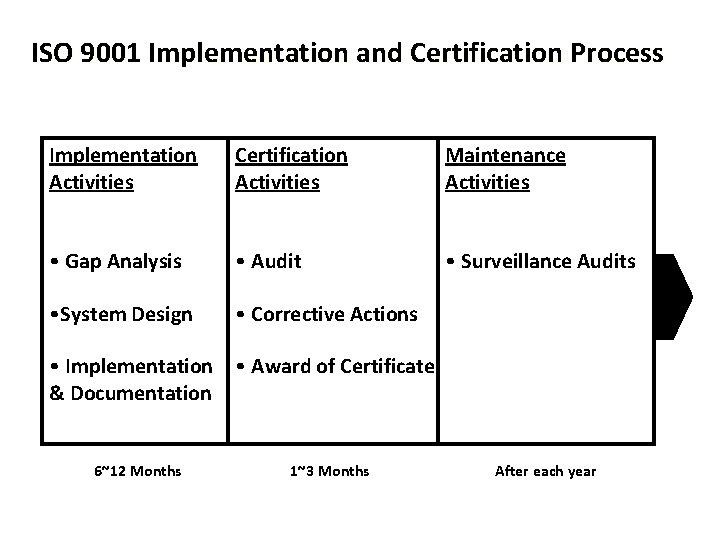
ISO 9001 Implementation and Certification Process Implementation Activities Certification Activities Maintenance Activities • Gap Analysis • Audit • Surveillance Audits • System Design • Corrective Actions • Implementation • Award of Certificate & Documentation 6~12 Months 1~3 Months After each year
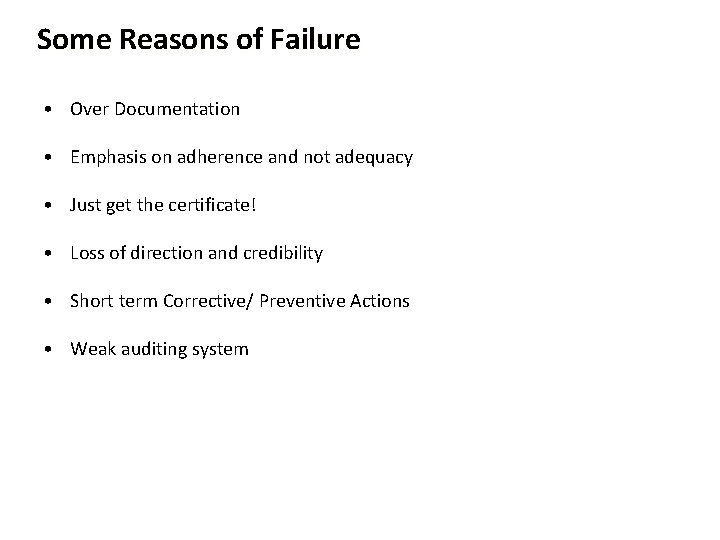
Some Reasons of Failure • Over Documentation • Emphasis on adherence and not adequacy • Just get the certificate! • Loss of direction and credibility • Short term Corrective/ Preventive Actions • Weak auditing system
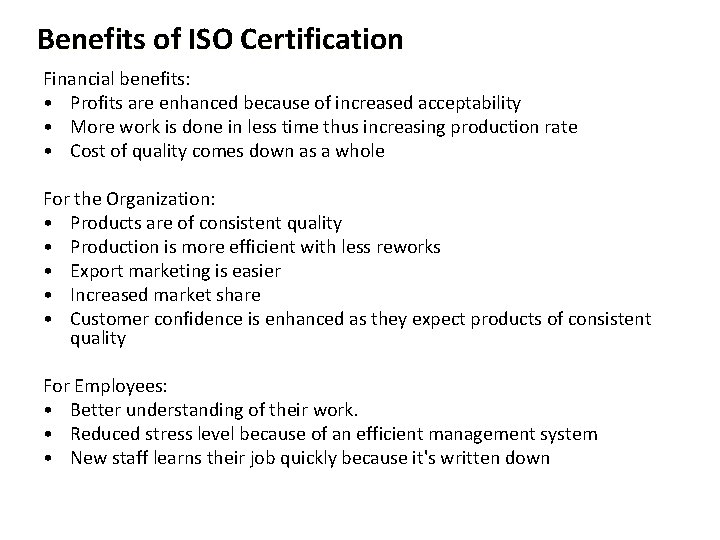
Benefits of ISO Certification Financial benefits: • Profits are enhanced because of increased acceptability • More work is done in less time thus increasing production rate • Cost of quality comes down as a whole For the Organization: • Products are of consistent quality • Production is more efficient with less reworks • Export marketing is easier • Increased market share • Customer confidence is enhanced as they expect products of consistent quality For Employees: • Better understanding of their work. • Reduced stress level because of an efficient management system • New staff learns their job quickly because it's written down
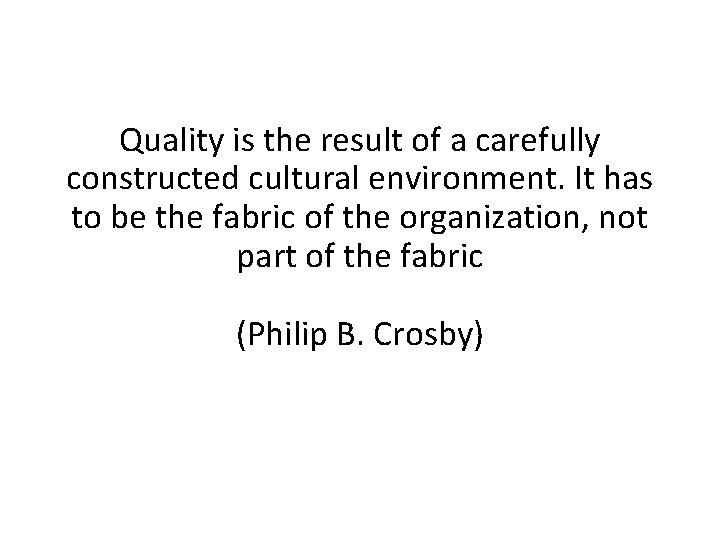
Quality is the result of a carefully constructed cultural environment. It has to be the fabric of the organization, not part of the fabric (Philip B. Crosby)
Used il acl 9000
Norme iso 9001 2008
Norma iso 9001: 2008
Iso 9001:2008 certification in mumbai
Ohsas 18001 iso 14001 comparison
Iso 9001:2015 process interaction matrix
2008 2008
Iso 9001:2015 presentation
Iso 9001 clauses
Time representation format
Iso 9001 software development
Iso 9001 software quality assurance
Major changes in iso 9001 for 2015
Norma tecnica colombiana iso 9001
Iso 9001:2000
Tqm of kfc
20000/12/2
Iso 9001 awareness training
Iso 9001 environmental management system
Iso tc 176 sc 2
Objective of quality
Iso 9001 summary
Iso 9001 2000 training
Iso 37001 checklist
Iso 10110 optics drawing standards
Klausul 5 iso 9001
Mario boada
Iso stands for
Conclusion iso 9001
Synonym for extremely important
Alba cutting machine
änderungsmanagement iso 9001
Iso 9001 customer satisfaction