TFAWS Active Thermal Paper Session Porescale approach to
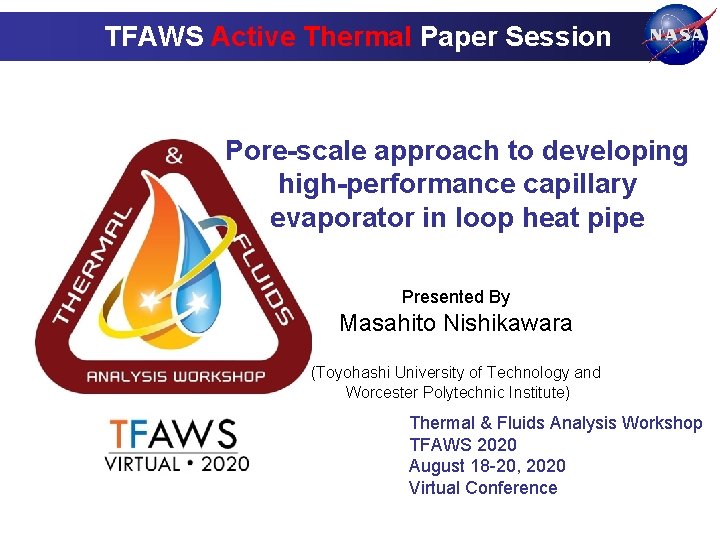
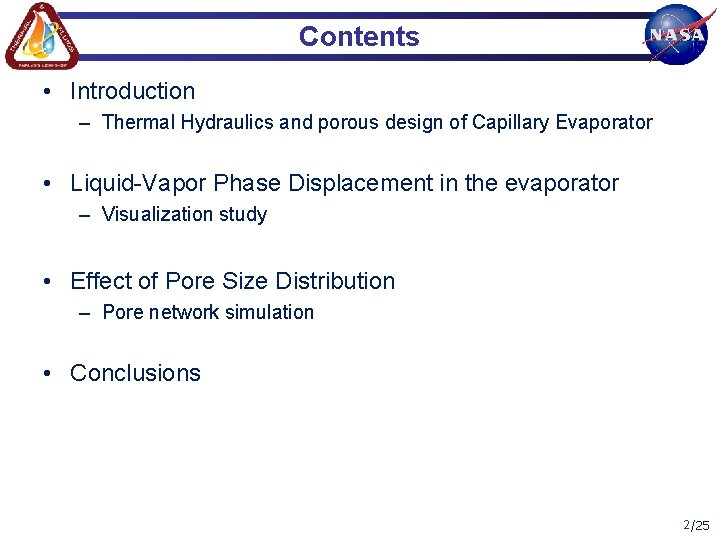
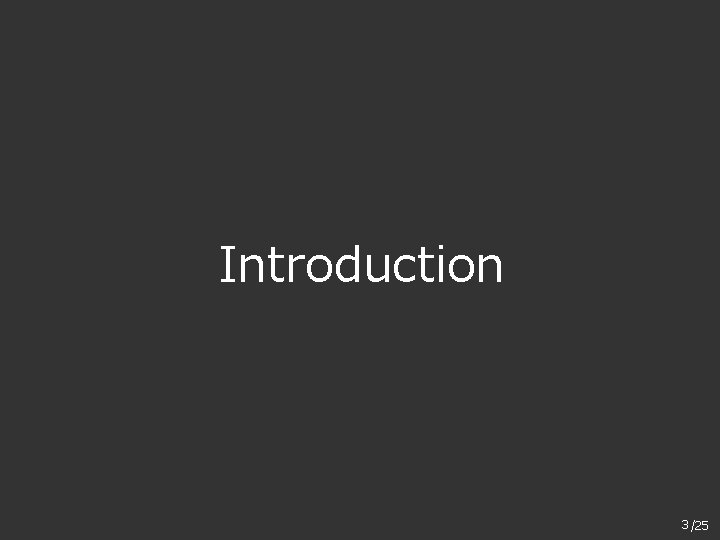
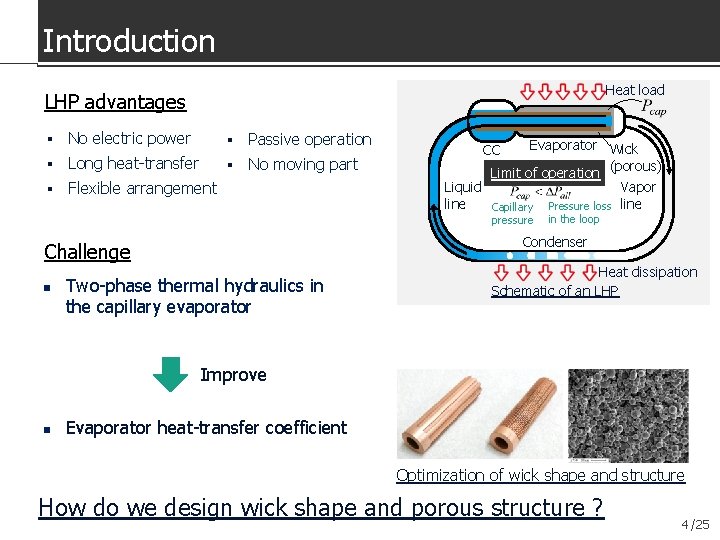
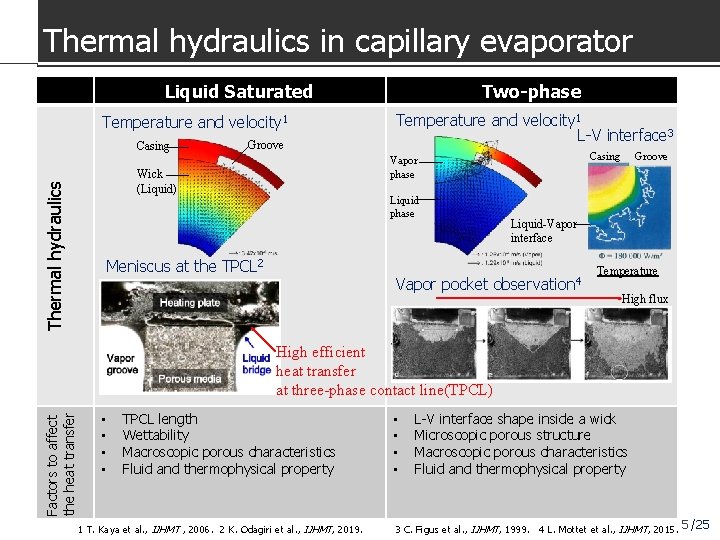
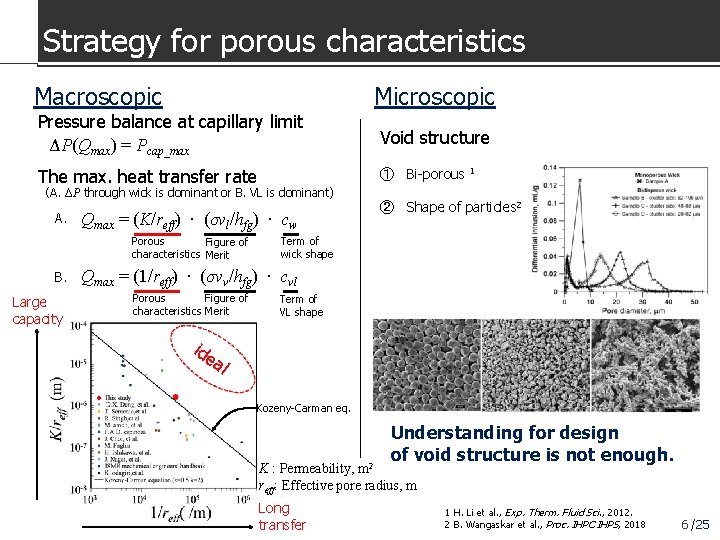
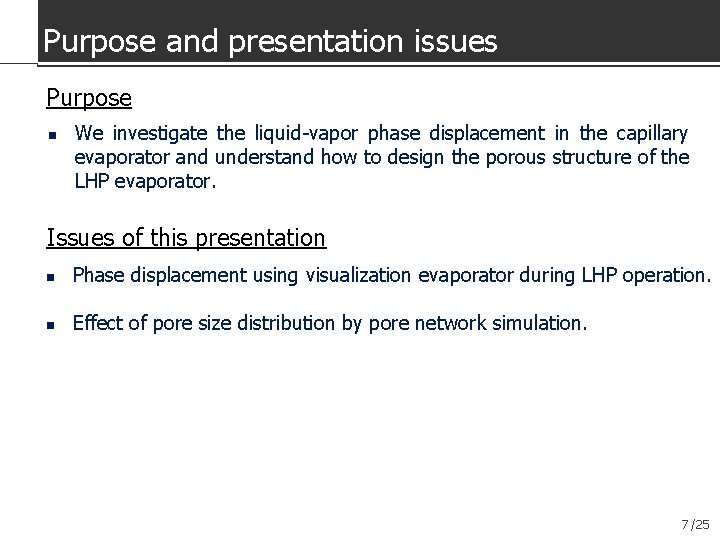
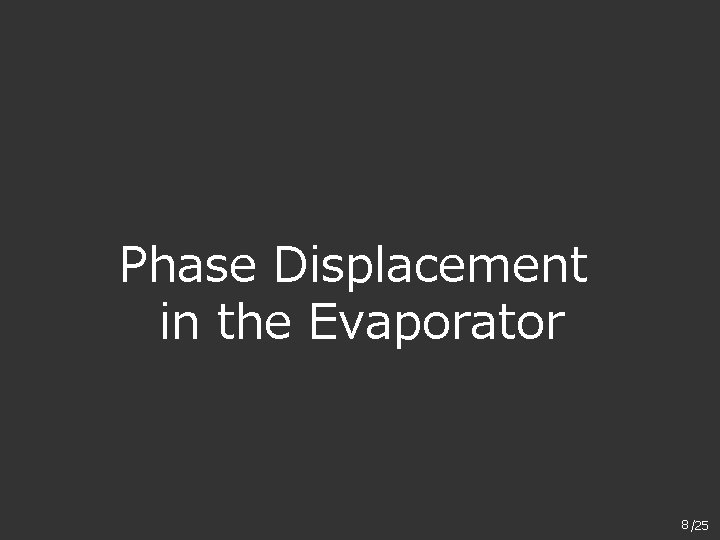
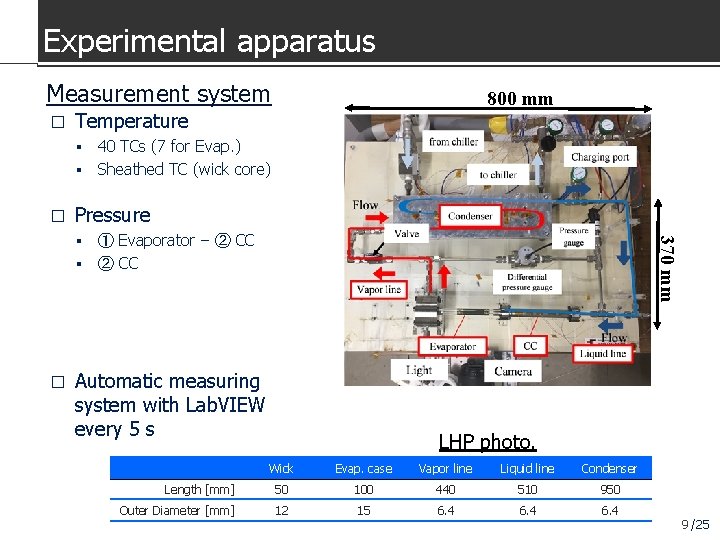
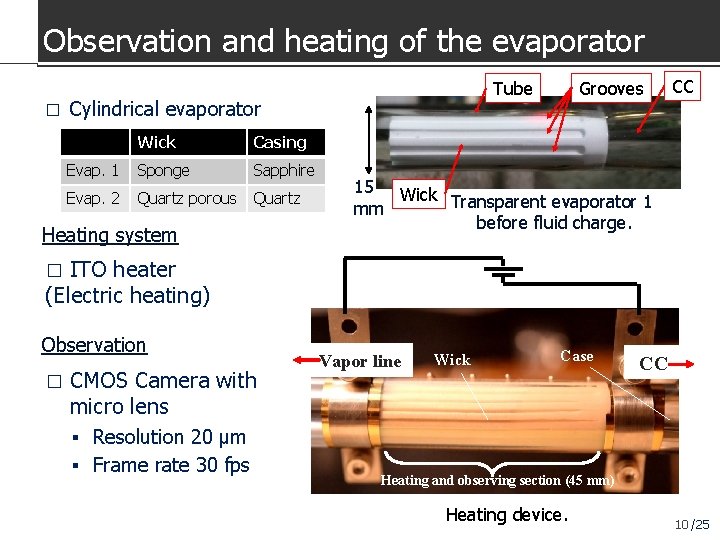
![Results with sponge wick 5. 6 5. 1 Heat load [W] 3. 9 3. Results with sponge wick 5. 6 5. 1 Heat load [W] 3. 9 3.](https://slidetodoc.com/presentation_image_h/099ab8c98666a0cc51f1494776bbeada/image-11.jpg)
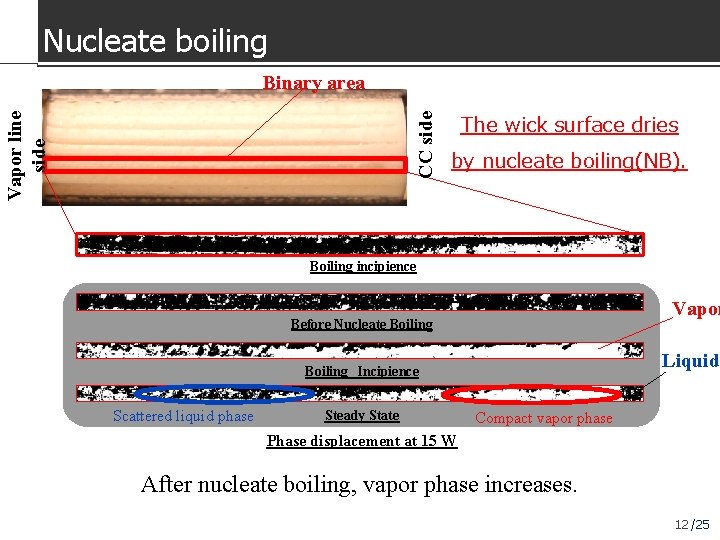
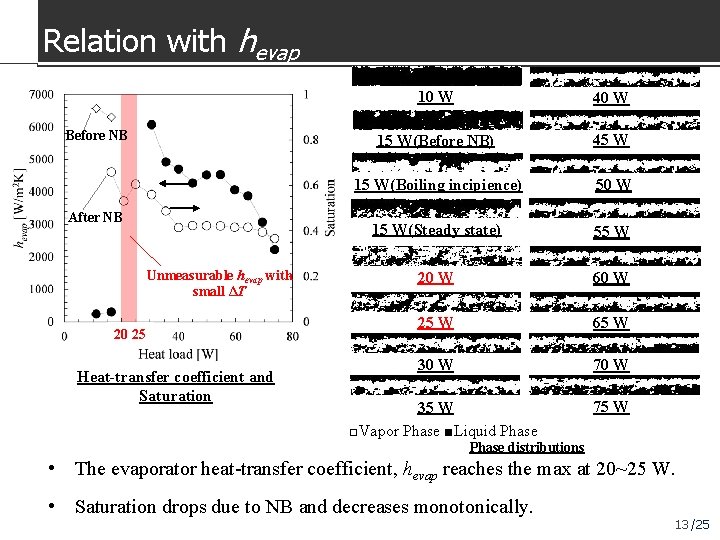
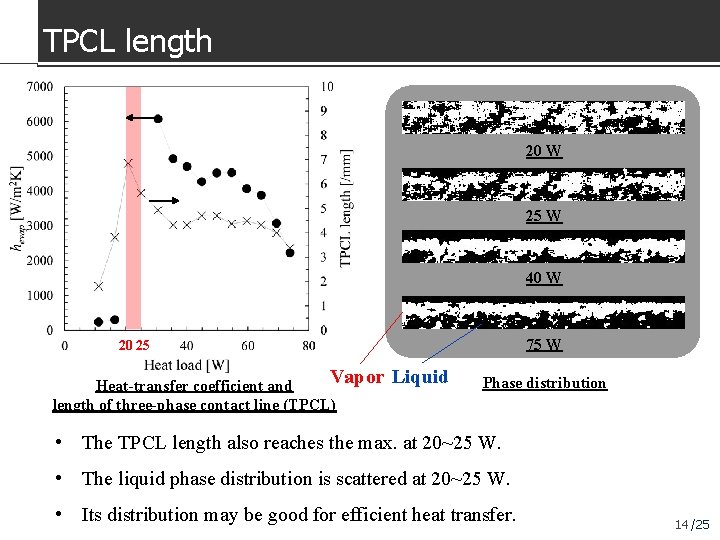
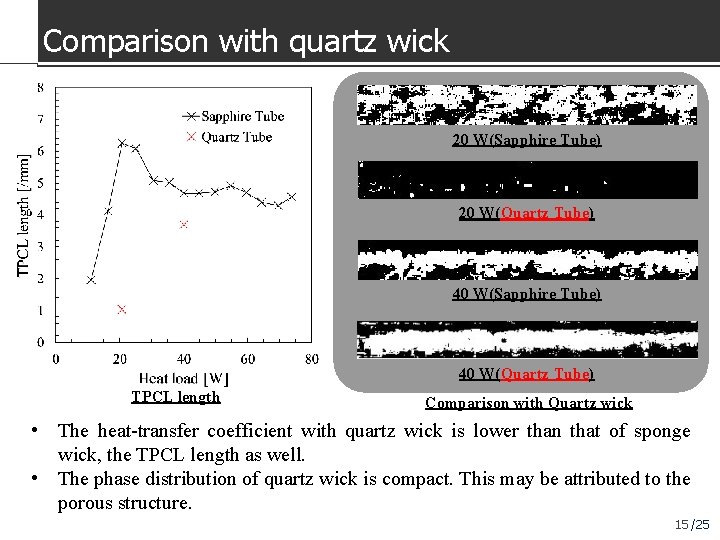
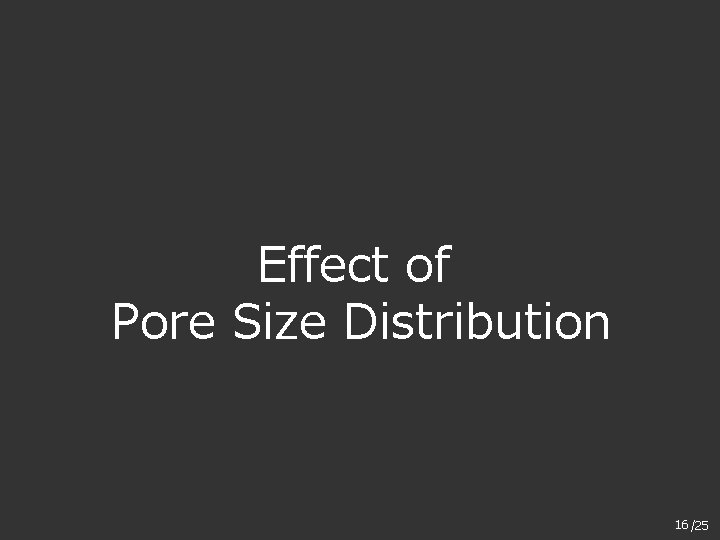
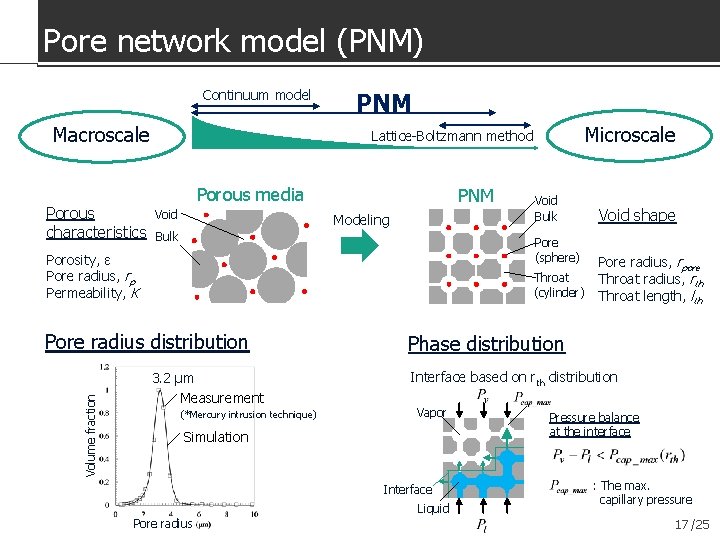
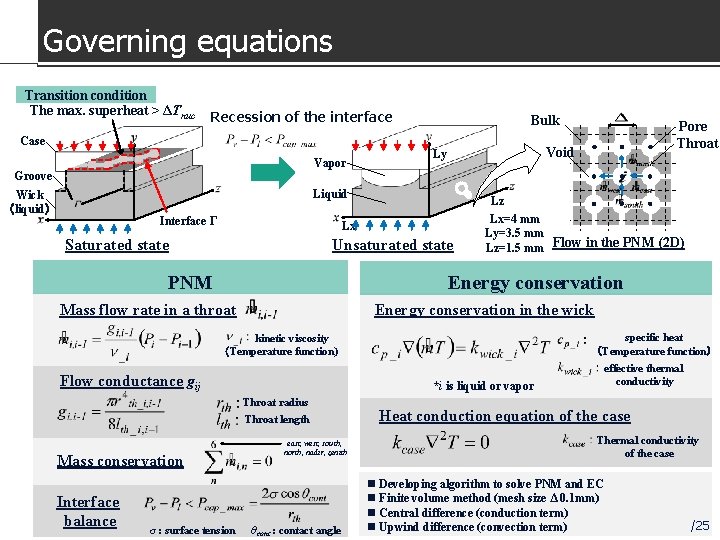
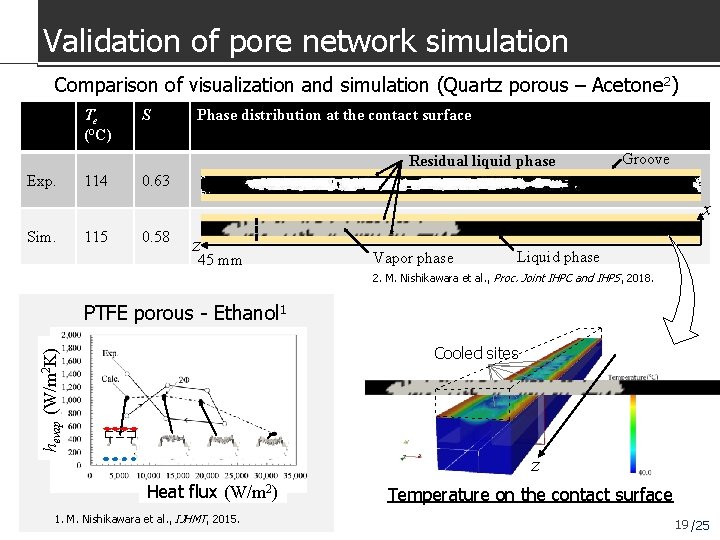
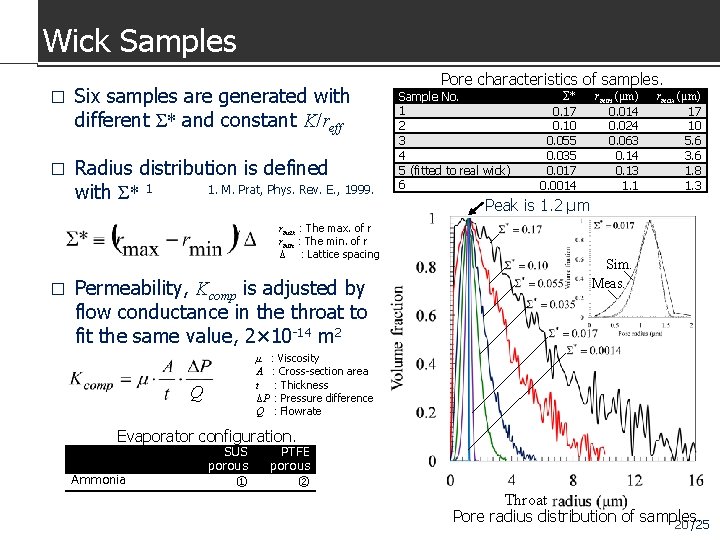
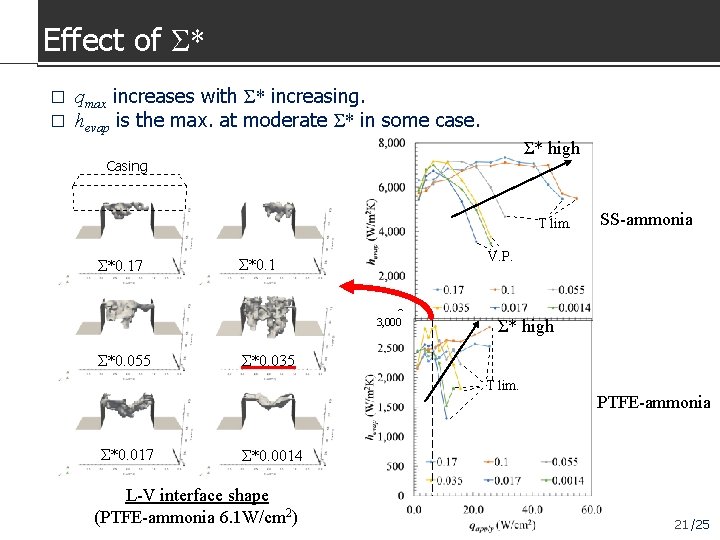
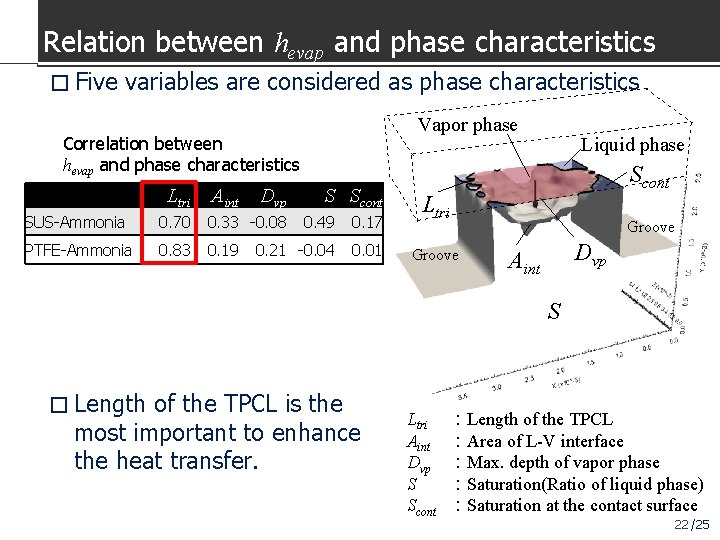
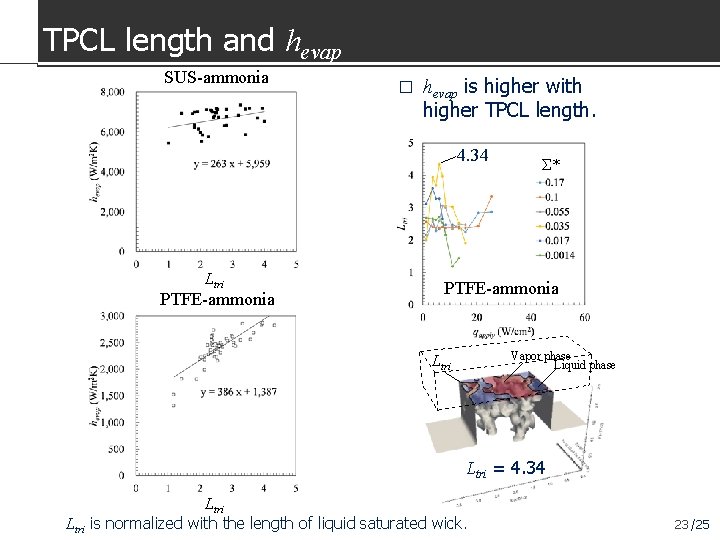
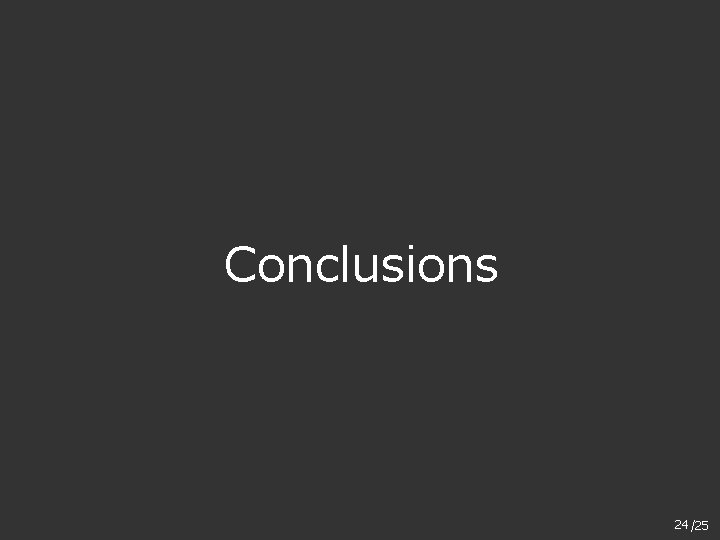
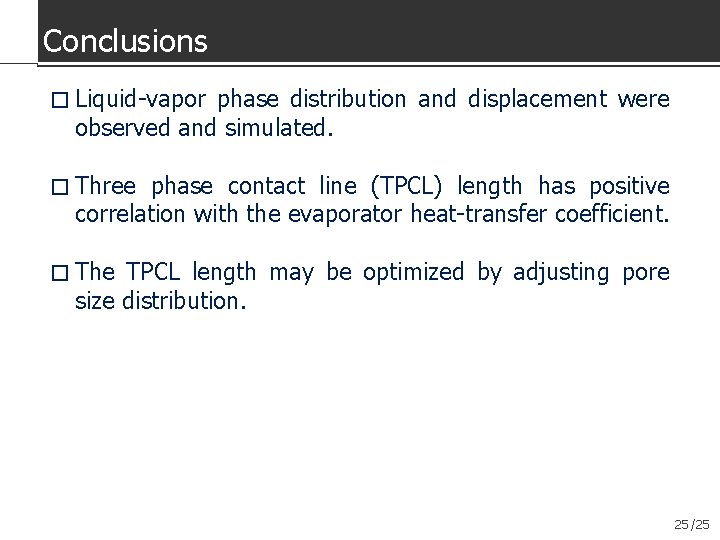
- Slides: 25
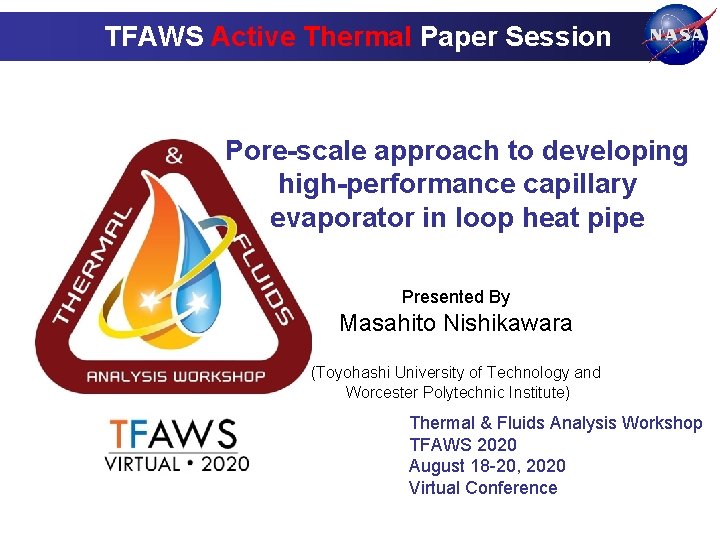
TFAWS Active Thermal Paper Session Pore-scale approach to developing high-performance capillary evaporator in loop heat pipe Presented By Masahito Nishikawara (Toyohashi University of Technology and Worcester Polytechnic Institute) Thermal & Fluids Analysis Workshop TFAWS 2020 August 18 -20, 2020 Virtual Conference
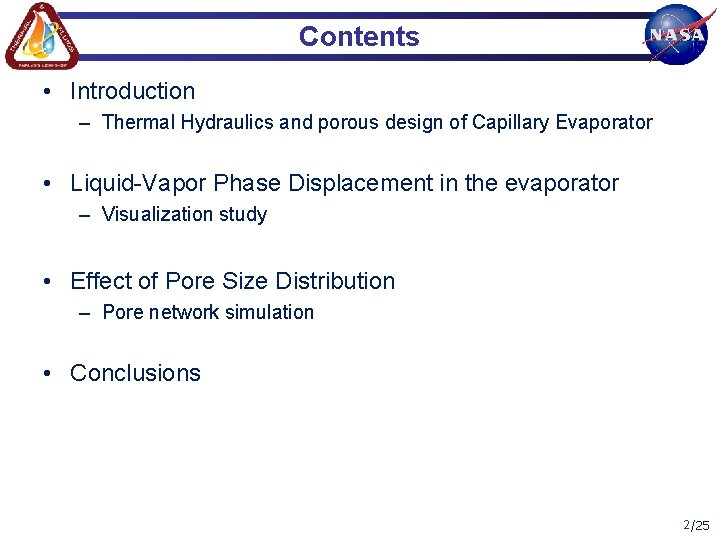
Contents • Introduction – Thermal Hydraulics and porous design of Capillary Evaporator • Liquid-Vapor Phase Displacement in the evaporator – Visualization study • Effect of Pore Size Distribution – Pore network simulation • Conclusions 2 /25
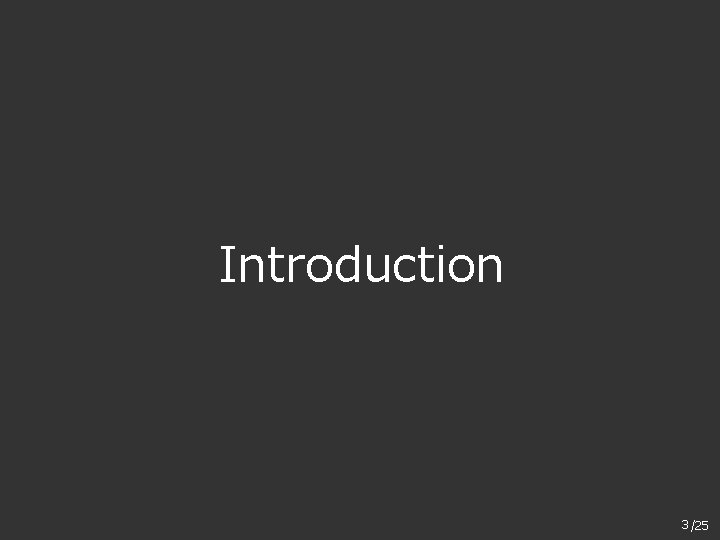
Introduction 3 /25
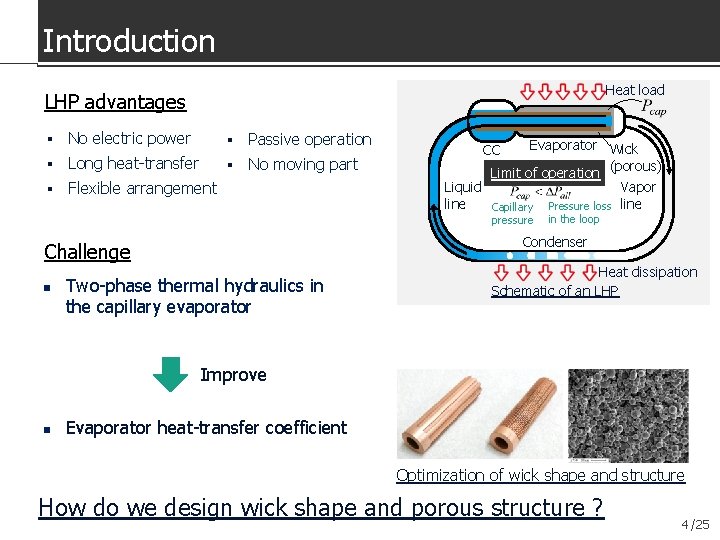
Introduction Heat load LHP advantages No electric power Passive operation Long heat-transfer No moving part Flexible arrangement Evaporator Wick (porous) Limit of operation Liquid Vapor line Capillary Pressure loss line CC pressure Condenser Challenge n in the loop Two-phase thermal hydraulics in the capillary evaporator Heat dissipation Schematic of an LHP Improve n Evaporator heat-transfer coefficient Optimization of wick shape and structure How do we design wick shape and porous structure ? 4 /25
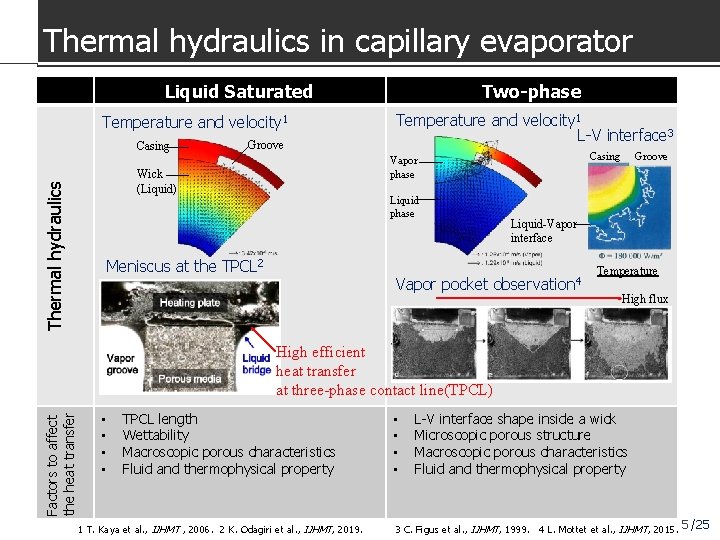
Thermal hydraulics in capillary evaporator Liquid Saturated Temperature and velocity 1 Casing Groove Temperature and velocity 1 L-V interface 3 Casing Vapor phase Wick (Liquid) Thermal hydraulics Two-phase Liquid phase Meniscus at the TPCL 2 Groove Liquid-Vapor interface Vapor pocket observation 4 Temperature High flux Factors to affect the heat transfer High efficient heat transfer at three-phase contact line(TPCL) • • TPCL length Wettability Macroscopic porous characteristics Fluid and thermophysical property 1 T. Kaya et al. , IJHMT , 2006. 2 K. Odagiri et al. , IJHMT, 2019. • • L-V interface shape inside a wick Microscopic porous structure Macroscopic porous characteristics Fluid and thermophysical property 3 C. Figus et al. , IJHMT, 1999. 4 L. Mottet et al. , IJHMT, 2015. 5 /25
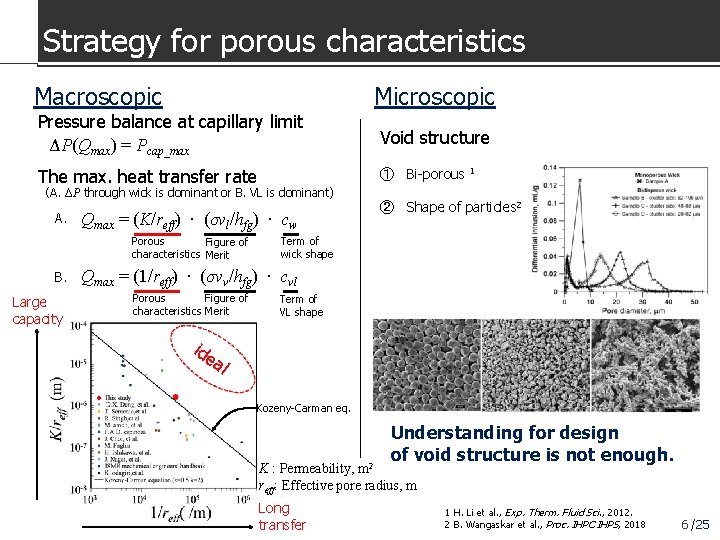
Strategy for porous characteristics Macroscopic Microscopic Pressure balance at capillary limit ΔP(Qmax) = Pcap_max Void structure The max. heat transfer rate ① Bi-porous 1 (A. ΔP through wick is dominant or B. VL is dominant) A. Qmax = (K/reff) ∙ (σνl/hfg) ∙ cw Porous Figure of characteristics Merit B. Large capacity ② Shape of particles 2 Term of wick shape Qmax = (1/reff) ∙ (σνv/hfg) ∙ cvl Porous Figure of characteristics Merit Term of VL shape ide al Kozeny-Carman eq. Understanding for design of void structure is not enough. K : Permeability, m 2 reff: Effective pore radius, m Long transfer 1 H. Li et al. , Exp. Therm. Fluid Sci. , 2012. 2 B. Wangaskar et al. , Proc. IHPC IHPS, 2018 6 /25
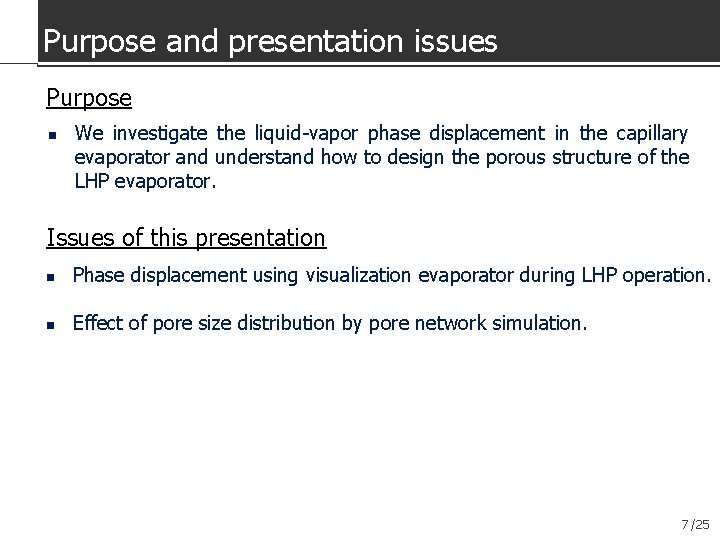
Purpose and presentation issues Purpose n We investigate the liquid-vapor phase displacement in the capillary evaporator and understand how to design the porous structure of the LHP evaporator. Issues of this presentation n Phase displacement using visualization evaporator during LHP operation. n Effect of pore size distribution by pore network simulation. 7 /25
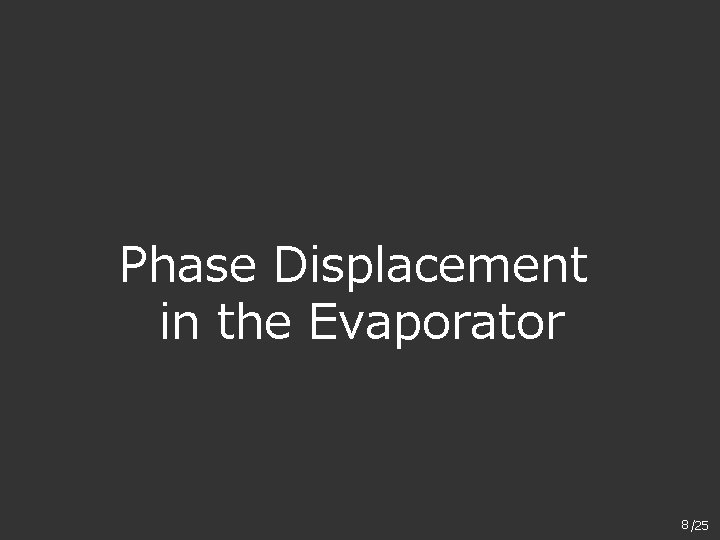
Phase Displacement in the Evaporator 8 /25
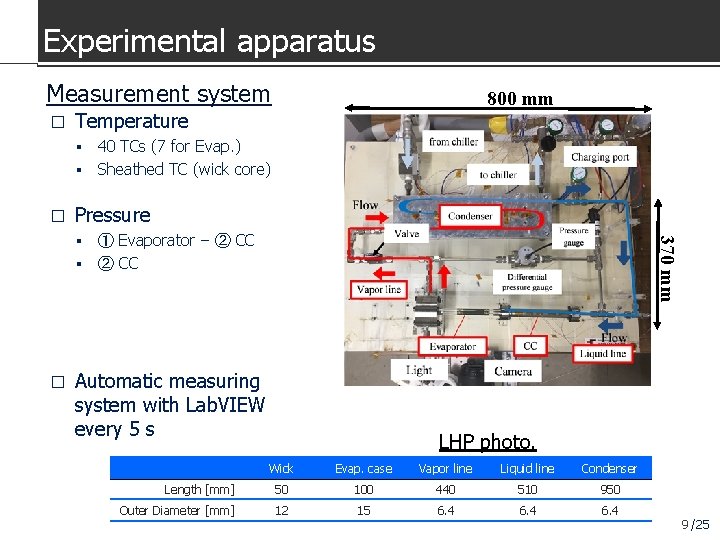
Experimental apparatus Measurement system � 800 mm Temperature 40 TCs (7 for Evap. ) Sheathed TC (wick core) � Pressure 370 mm ① Evaporator − ② CC � Automatic measuring system with Lab. VIEW every 5 s LHP photo. Wick Evap. case Vapor line Liquid line Condenser Length [mm] 50 100 440 510 950 Outer Diameter [mm] 12 15 6. 4 9 /25
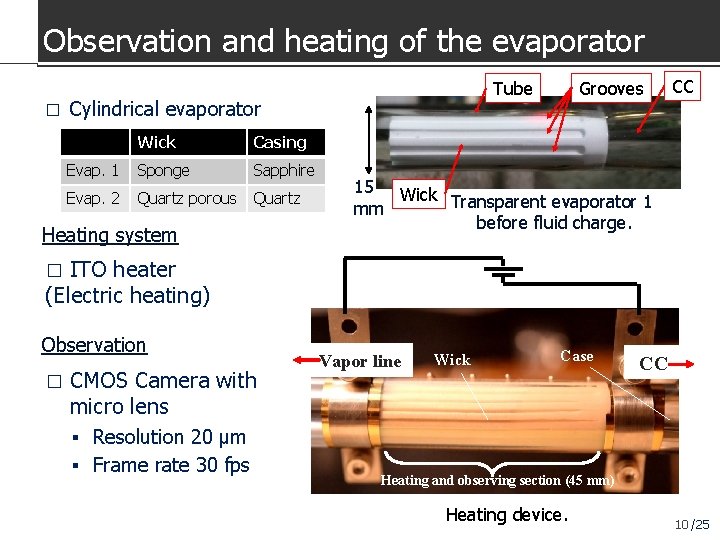
Observation and heating of the evaporator � Cylindrical evaporator Wick Casing Evap. 1 Sponge Sapphire Evap. 2 Quartz porous Quartz Heating system Grooves Tube CC 15 Wick Transparent evaporator 1 mm before fluid charge. ITO heater (Electric heating) � Observation � CMOS Camera with micro lens Vapor line Wick Case CC Resolution 20 μm Frame rate 30 fps Heating and observing section (45 mm) Heating device. 10 /25
![Results with sponge wick 5 6 5 1 Heat load W 3 9 3 Results with sponge wick 5. 6 5. 1 Heat load [W] 3. 9 3.](https://slidetodoc.com/presentation_image_h/099ab8c98666a0cc51f1494776bbeada/image-11.jpg)
Results with sponge wick 5. 6 5. 1 Heat load [W] 3. 9 3. 4 2. 8 2. 2 1. 7 Heat flux [W/cm 2] 4. 5 1. 1 0. 6 0 Time history of temperature and heat load (10 -80 -10 W) Core state at 15 W Core state at 20 W • The max. heat load was 80 W (4. 5 W/cm 2). • Depending on the phase state in the wick core, behavior of the evaporator temperature changes between 15 W and 20 W. 11 /25
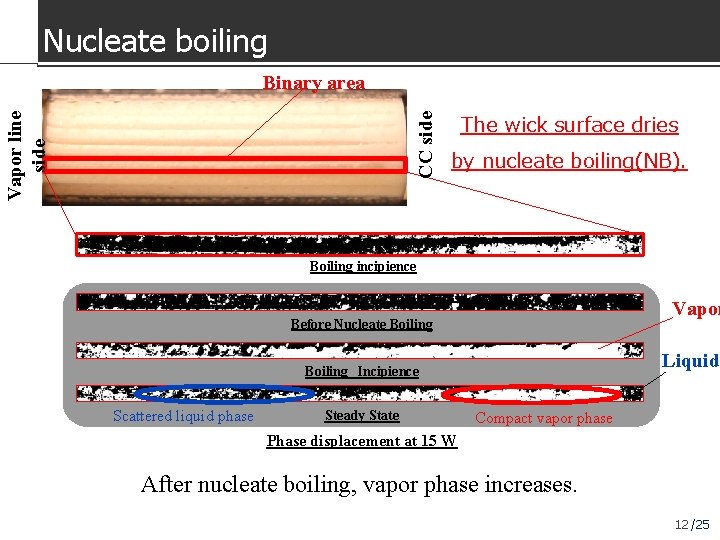
Nucleate boiling CC side Vapor line side Binary area The wick surface dries by nucleate boiling(NB). Boiling incipience Vapor Before Nucleate Boiling Liquid Boiling Incipience Scattered liquid phase Steady State Compact vapor phase Phase displacement at 15 W After nucleate boiling, vapor phase increases. 12 /25
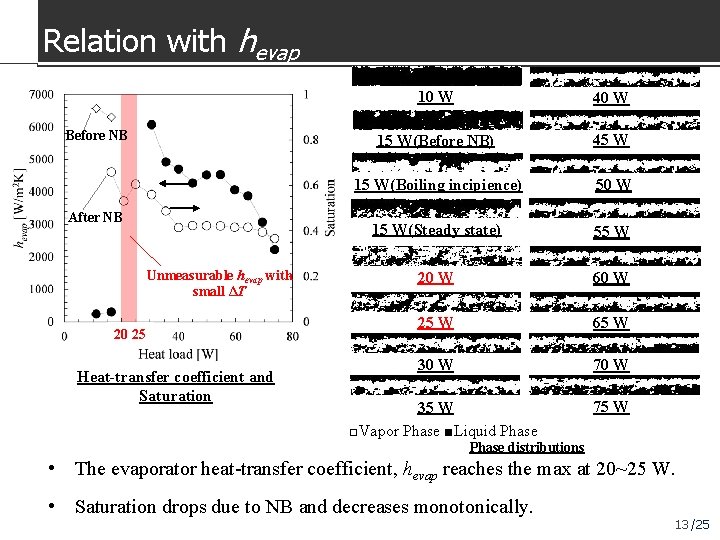
Relation with hevap Before NB After NB Unmeasurable hevap with small ΔT 20 25 Heat-transfer coefficient and Saturation 10 W 40 W 15 W(Before NB) 45 W 15 W(Boiling incipience) 50 W 15 W(Steady state) 55 W 20 W 60 W 25 W 65 W 30 W 70 W 35 W □Vapor Phase ■Liquid Phase 75 W Phase distributions • The evaporator heat-transfer coefficient, hevap reaches the max at 20~25 W. • Saturation drops due to NB and decreases monotonically. 13 /25
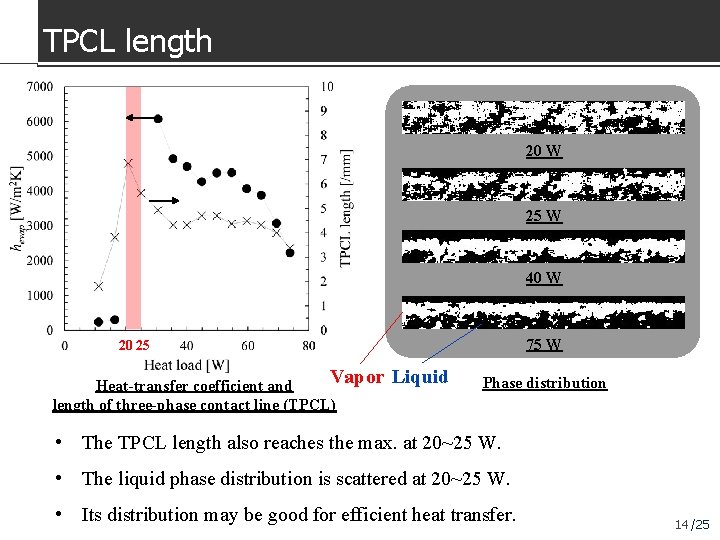
TPCL length 20 W 25 W 40 W 75 W 20 25 Vapor Heat-transfer coefficient and length of three-phase contact line (TPCL) Liquid Phase distribution • The TPCL length also reaches the max. at 20~25 W. • The liquid phase distribution is scattered at 20~25 W. • Its distribution may be good for efficient heat transfer. 14 /25
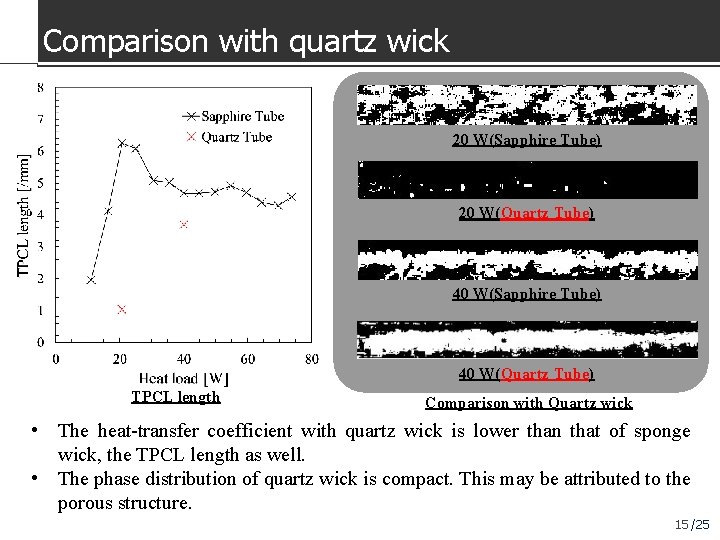
Comparison with quartz wick 20 W(Sapphire Tube) 20 W(Quartz Tube) 40 W(Sapphire Tube) 40 W(Quartz Tube) TPCL length Comparison with Quartz wick • The heat-transfer coefficient with quartz wick is lower than that of sponge wick, the TPCL length as well. • The phase distribution of quartz wick is compact. This may be attributed to the porous structure. 15 /25
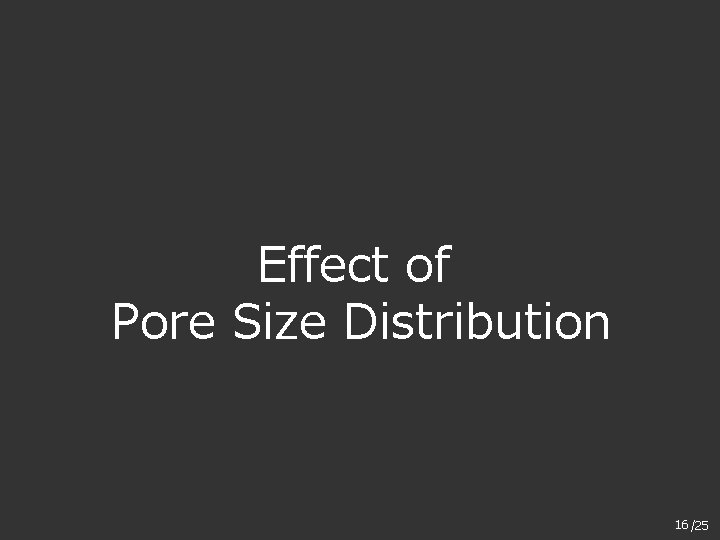
Effect of Pore Size Distribution 16 16 /25
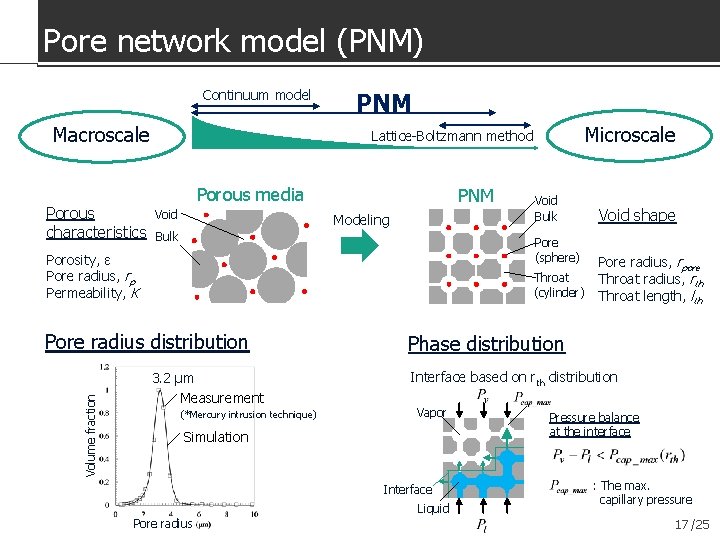
Pore network model (PNM) Continuum model Macroscale Porous characteristics PNM Porous media Void PNM Modeling Bulk Void Bulk Pore (sphere) Porosity, ε Pore radius, rp Permeability, K Throat (cylinder) Pore radius distribution Volume fraction Microscale Lattice-Boltzmann method 3. 2 μm Measurement (*Mercury intrusion technique) Pore radius, rpore Throat radius, rth Throat length, lth Phase distribution Interface based on rth distribution Vapor Simulation Interface Liquid Pore radius Void shape Pressure balance at the interface : The max. capillary pressure 17 /25
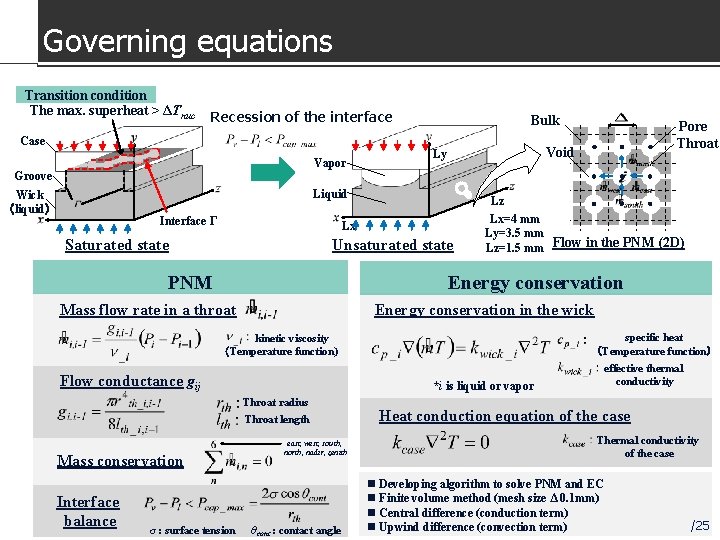
Governing equations Transition condition The max. superheat > ΔTnuc Recession of the interface Bulk Case pressure The max. Vapor difference capillary at the interface pressure Groove Void Ly Liquid Wick (liquid) Interface Γ Lz Lx Saturated state Unsaturated state PNM Lx=4 mm Ly=3. 5 mm Lz=1. 5 mm Flow in the PNM (2 D) Energy conservation Mass flow rate in a throat Energy conservation in the wick specific heat (Temperature function) kinetic viscosity (Temperature function) Flow conductance gij Throat length Mass conservation σ : surface tension effective thermal conductivity *i is liquid or vapor Throat radius Interface balance Pore Throat east, west, south, north, nadir, zenith θcont : contact angle Heat conduction equation of the case Thermal conductivity of the case n Developing algorithm to solve PNM and EC n Finite volume method (mesh size Δ 0. 1 mm) n Central difference (conduction term) n Upwind difference (convection term) 18 /25
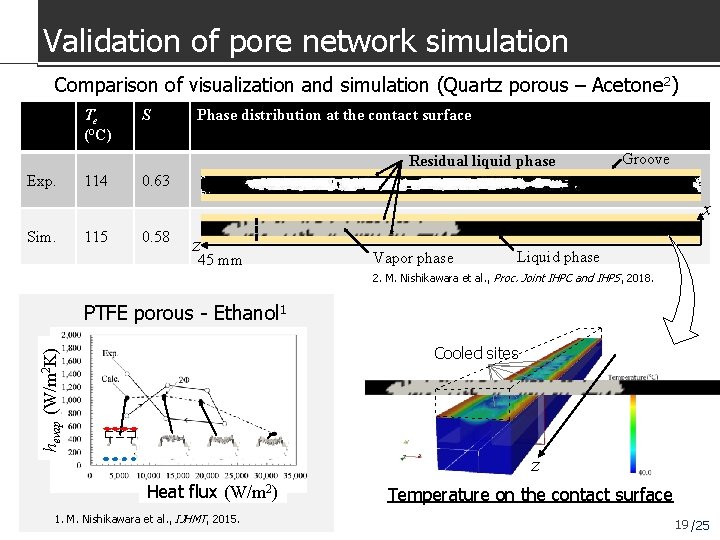
Validation of pore network simulation Comparison of visualization and simulation (Quartz porous – Acetone 2) Te (°C) S Phase distribution at the contact surface Residual liquid phase Exp. 114 Groove 0. 63 x Sim. 115 0. 58 z 45 mm Vapor phase Liquid phase 2. M. Nishikawara et al. , Proc. Joint IHPC and IHPS, 2018. PTFE porous - Ethanol 1 hevap (W/m 2 K) Cooled sites z Heat flux (W/m 2) 1. M. Nishikawara et al. , IJHMT, 2015. Temperature on the contact surface 19 /25
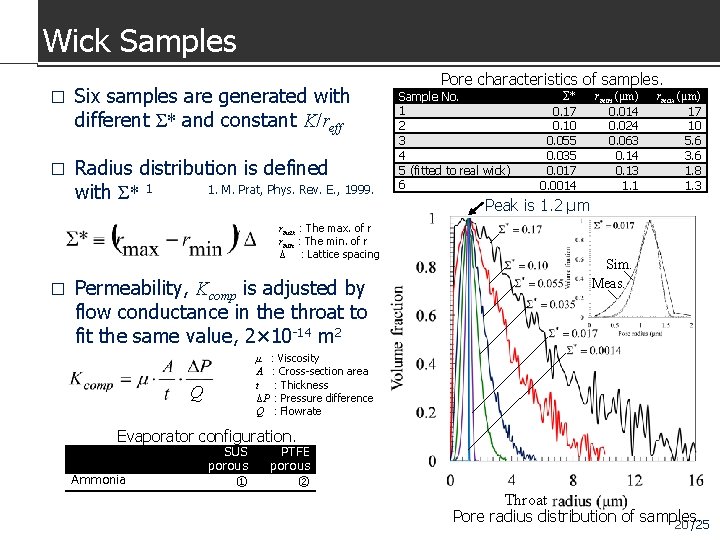
Wick Samples � Six samples are generated with different Σ* and constant K/reff � Radius distribution is defined 1. M. Prat, Phys. Rev. E. , 1999. with Σ* 1 rmax:The max. of r rmin:The min. of r Δ :Lattice spacing � Permeability, Kcomp is adjusted by flow conductance in the throat to fit the same value, 2× 10 -14 m 2 Pore characteristics of samples. Sample No. 1 2 3 4 5 (fitted to real wick) 6 Σ* 0. 17 0. 10 0. 055 0. 035 0. 017 0. 0014 rmin (μm) 0. 014 0. 024 0. 063 0. 14 0. 13 1. 1 rmax (μm) 17 10 5. 6 3. 6 1. 8 1. 3 Peak is 1. 2 μm Sim. Meas. μ :Viscosity A :Cross-section area t :Thickness ΔP:Pressure difference Q :Flowrate Q Evaporator configuration. Ammonia SUS porous ① PTFE porous ② Throat Pore radius distribution of samples. 20 /25
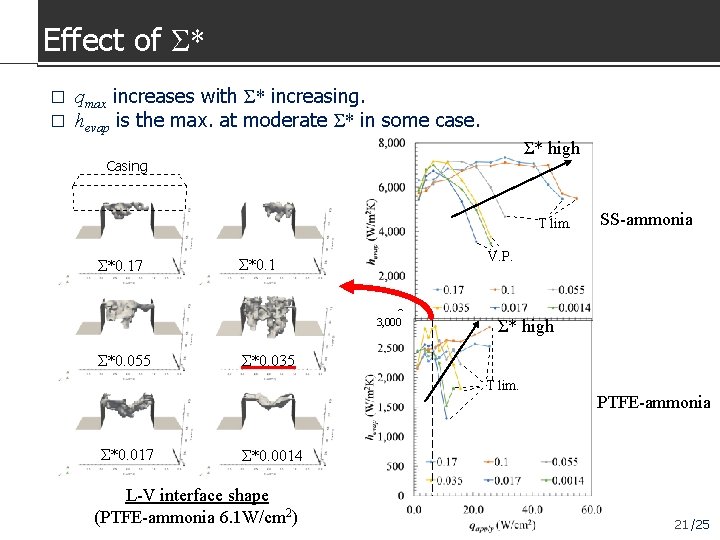
Effect of Σ* � � qmax increases with Σ* increasing. hevap is the max. at moderate Σ* in some case. Σ* high Casing T lim. Σ*0. 17 V. P. Σ*0. 1 0 3, 000 Σ*0. 055 Σ* high Σ*0. 035 T lim. Σ*0. 017 SS-ammonia PTFE-ammonia Σ*0. 0014 L-V interface shape (PTFE-ammonia 6. 1 W/cm 2) 21 /25
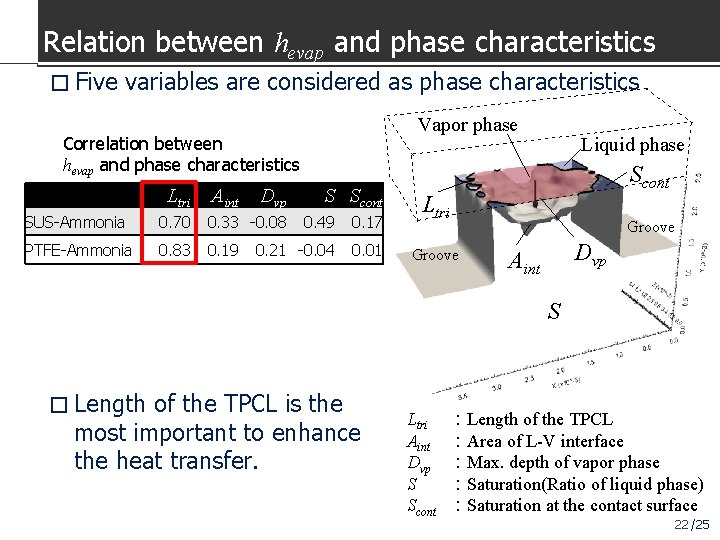
Relation between hevap and phase characteristics � Five variables are considered as phase characteristics Vapor phase Correlation between hevap and phase characteristics Ltri Aint Dvp SUS-Ammonia 0. 70 0. 33 -0. 08 PTFE-Ammonia 0. 83 0. 19 S Scont 0. 49 0. 17 0. 21 -0. 04 0. 01 Liquid phase Scont Ltri Groove Dvp Aint S � Length of the TPCL is the most important to enhance the heat transfer. Ltri Aint Dvp S Scont :Length of the TPCL :Area of L-V interface :Max. depth of vapor phase :Saturation(Ratio of liquid phase) :Saturation at the contact surface 22 /25
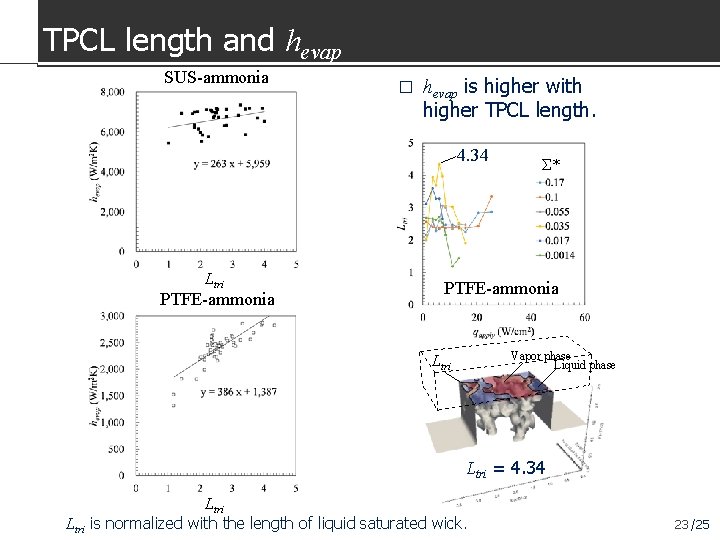
TPCL length and hevap SUS-ammonia � hevap is higher with higher TPCL length. 4. 34 Ltri PTFE-ammonia Σ* PTFE-ammonia Vapor phase Liquid phase Ltri = 4. 34 Ltri is normalized with the length of liquid saturated wick. 23 /25
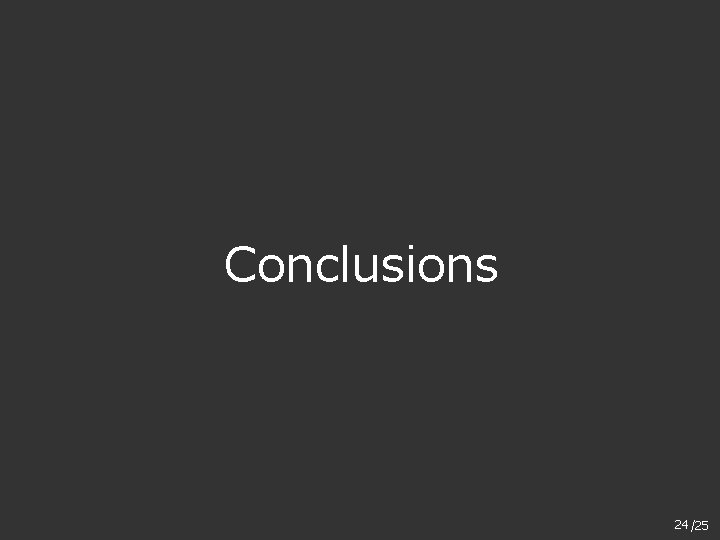
Conclusions 24 24 /25
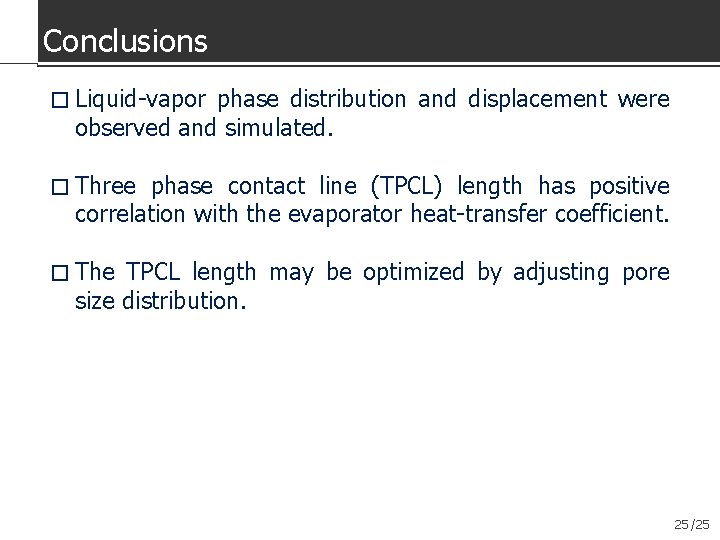
Conclusions � Liquid-vapor phase distribution and displacement were observed and simulated. � Three phase contact line (TPCL) length has positive correlation with the evaporator heat-transfer coefficient. � The TPCL length may be optimized by adjusting pore size distribution. 25 /25
Nasa tfaws
Replexen
Section 3 using thermal energy answers
Thermal transfer vs direct thermal printing
Active session history
Active session history
Brown paper method
3 to 8 decoder truth table
Membrane structures that function in active transport
Primary active transport vs secondary active transport
Paper 2 aice general paper
General paper essay questions
Child development: an active learning approach 4th edition
Americans continue to value an active approach to life.
Thinking like an engineer an active learning approach
Aice general paper hand approach
Aice general paper hand approach
The hand approach general paper
Vc vs datagram
Theoretical models of counseling
Waterfall and shower approach
Multiple approach-avoidance
Cognitive approach vs behavioral approach
Research approaches definition
Approach to system development
Deep learning approach and surface learning approach