Technology Integration Integrating new technologies into facilities maintenance
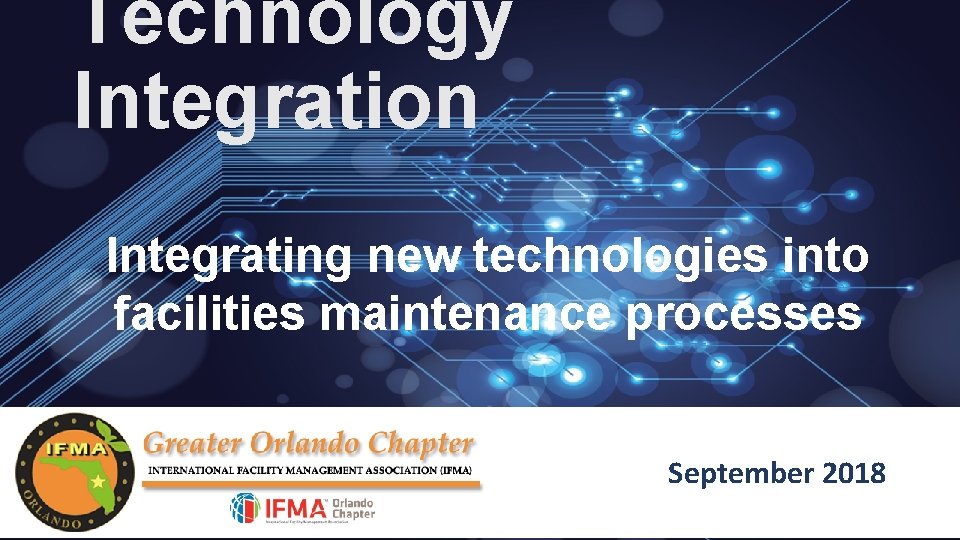
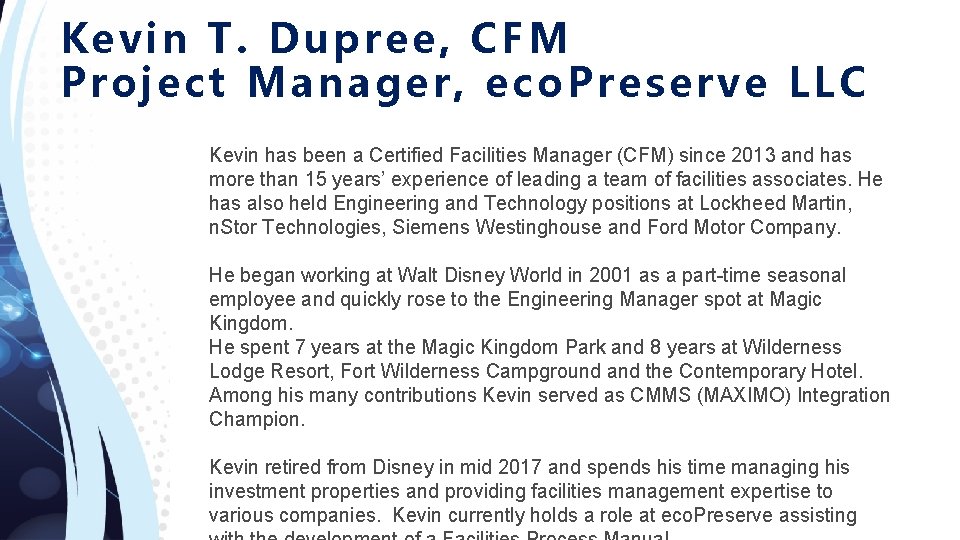
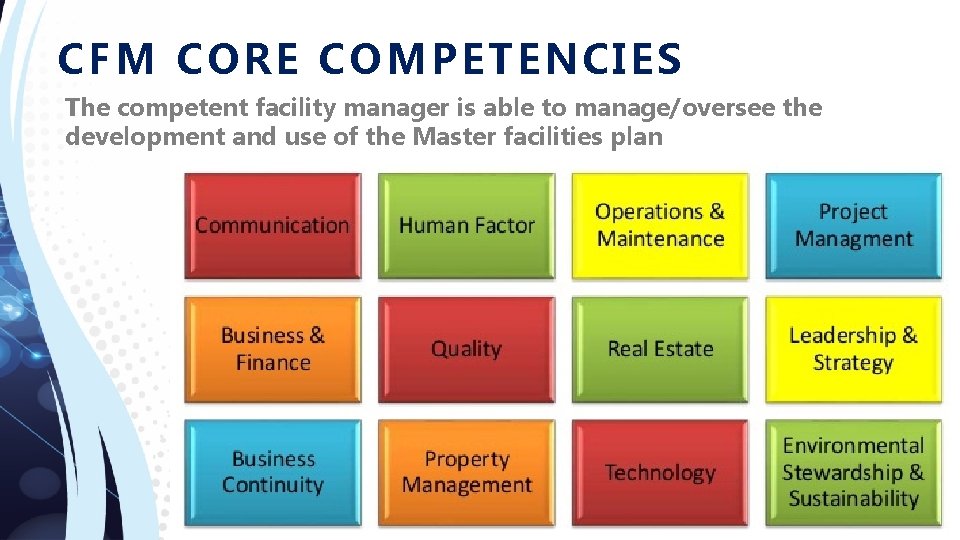
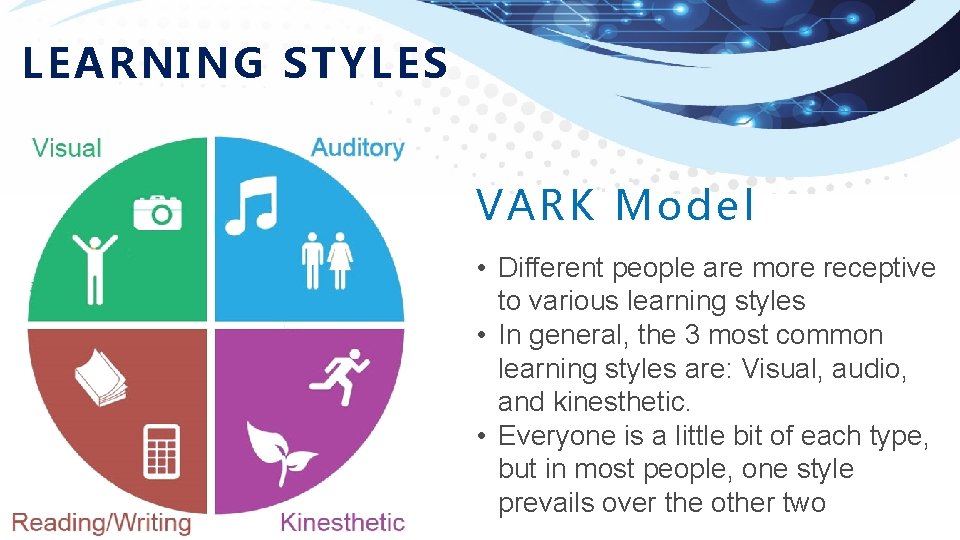
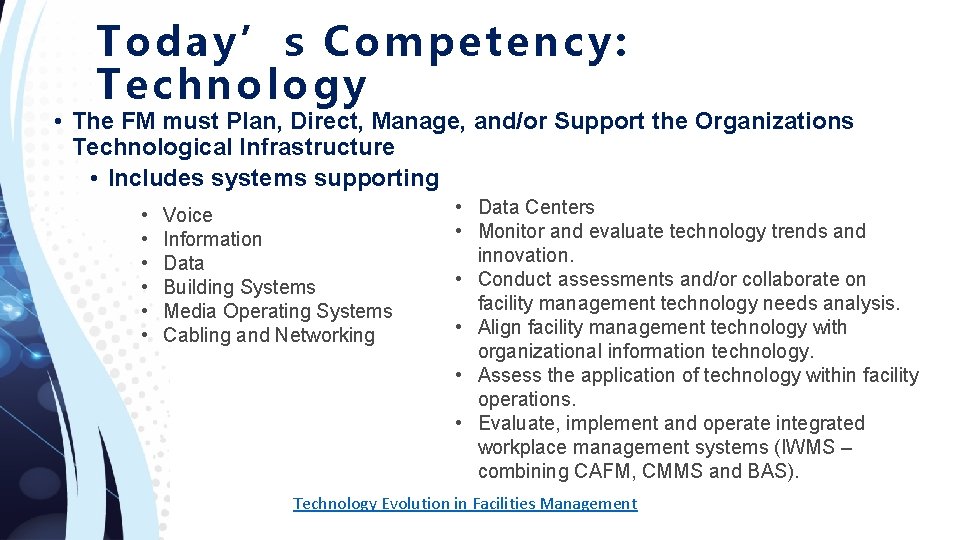
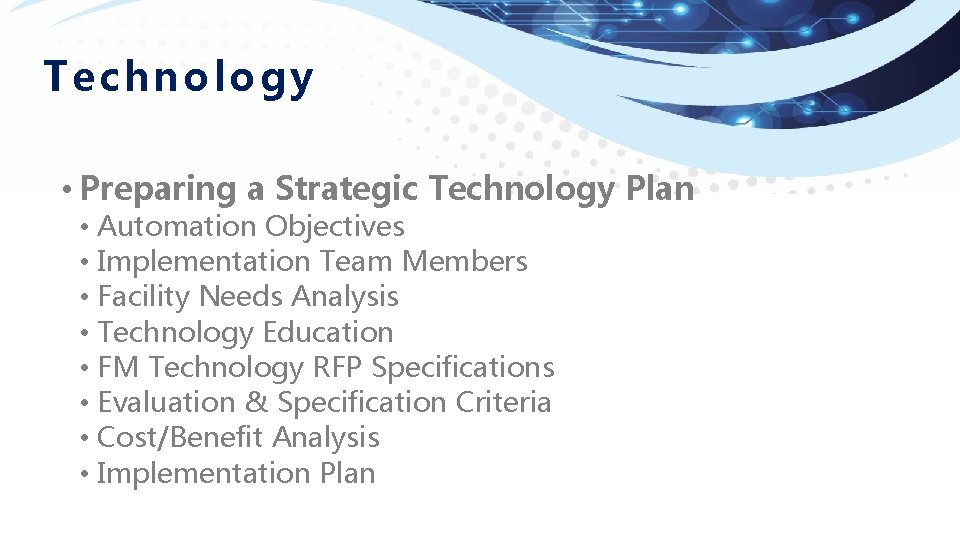
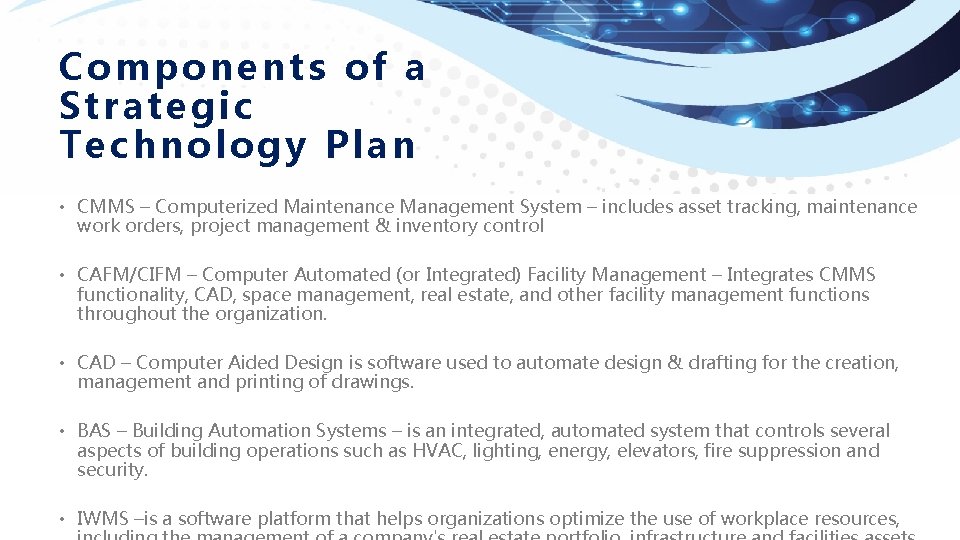
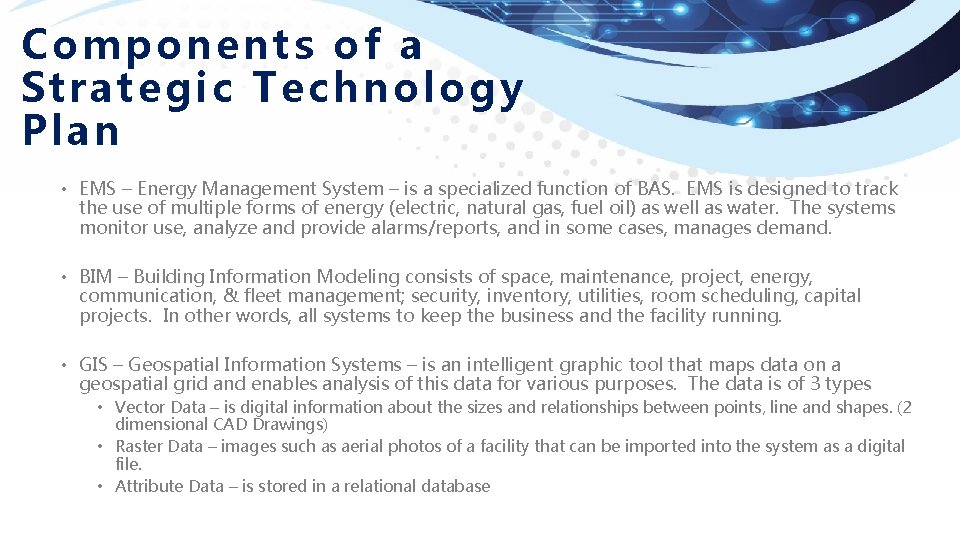
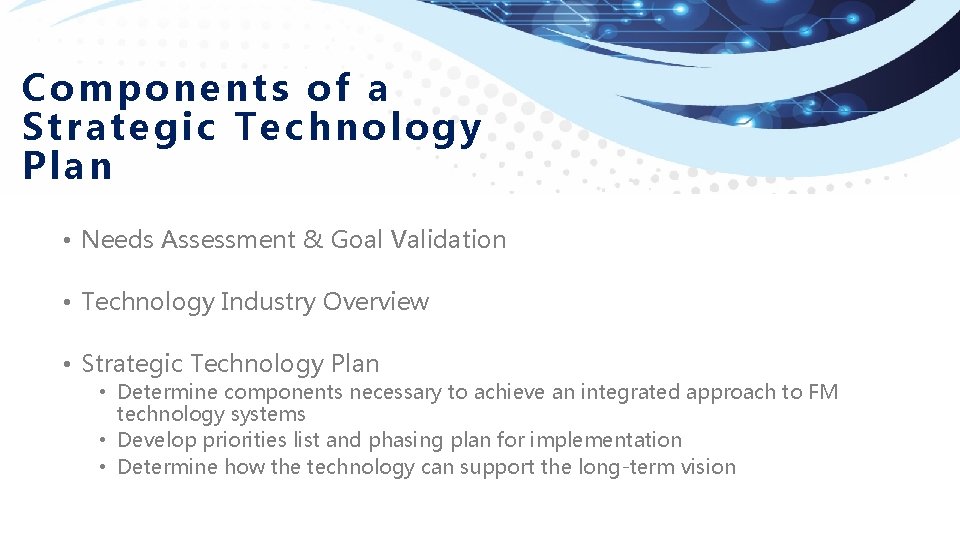
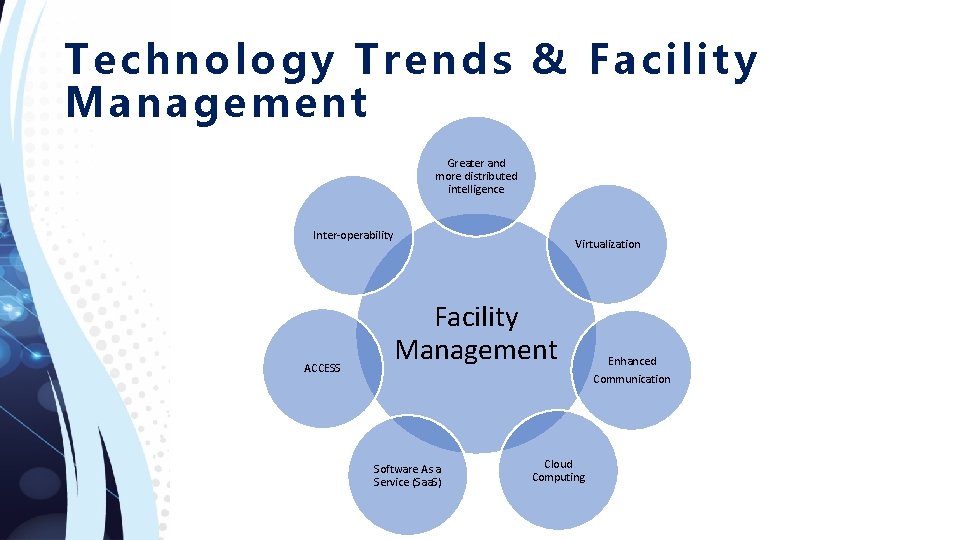
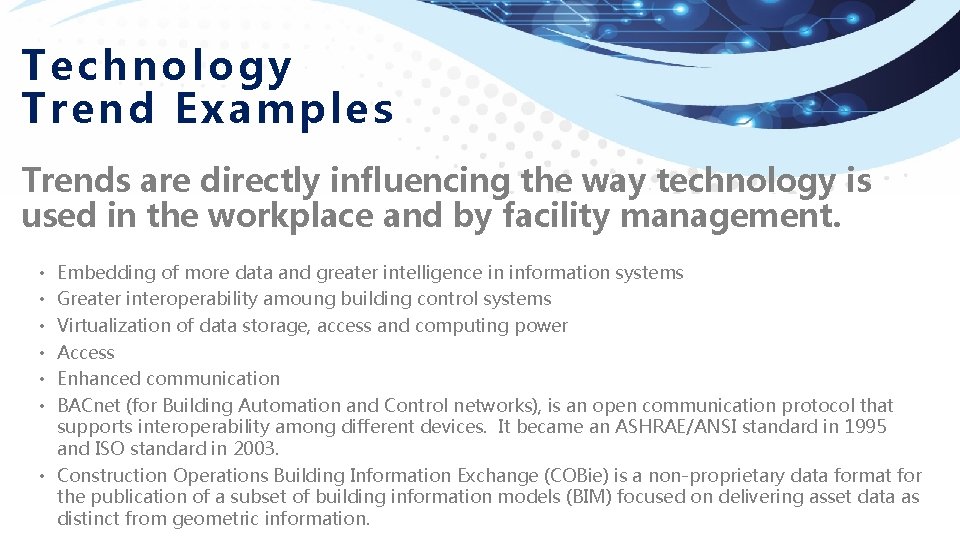
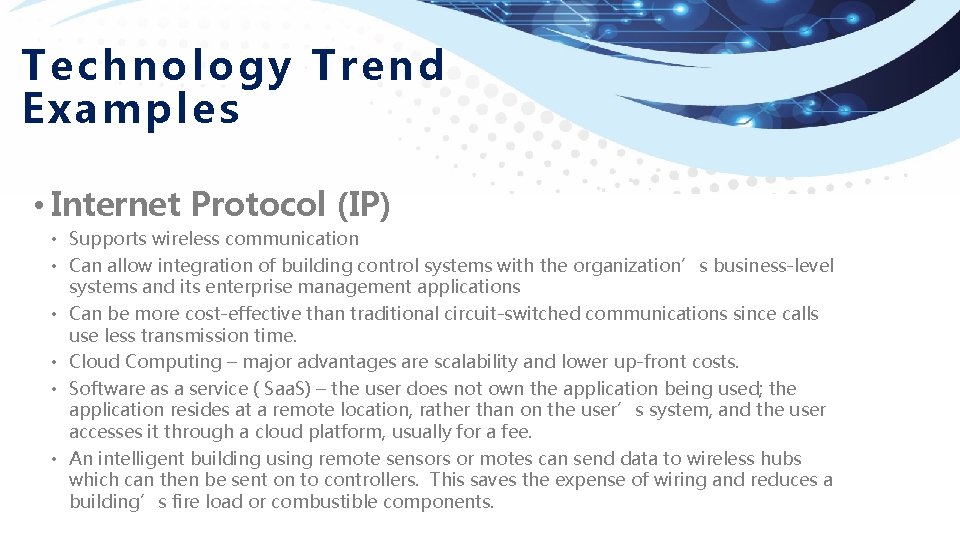
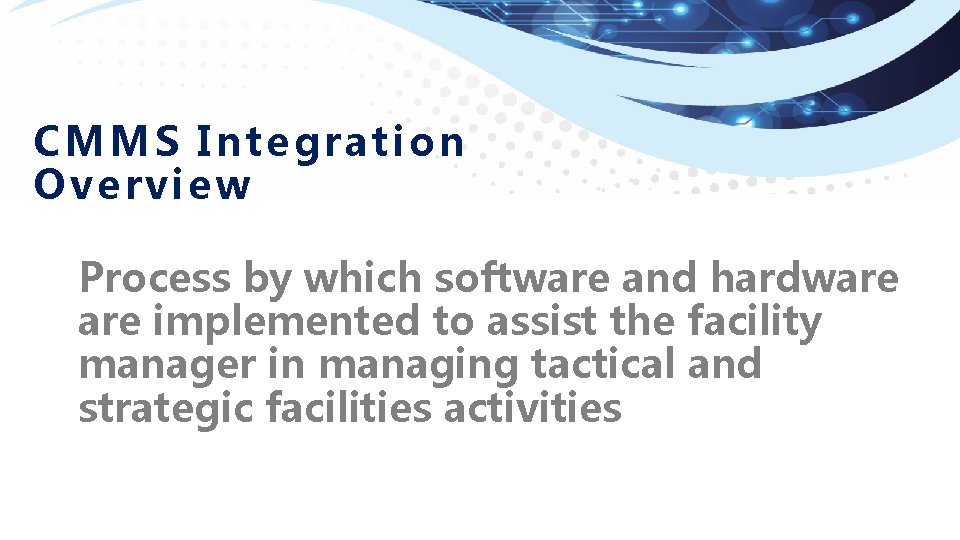
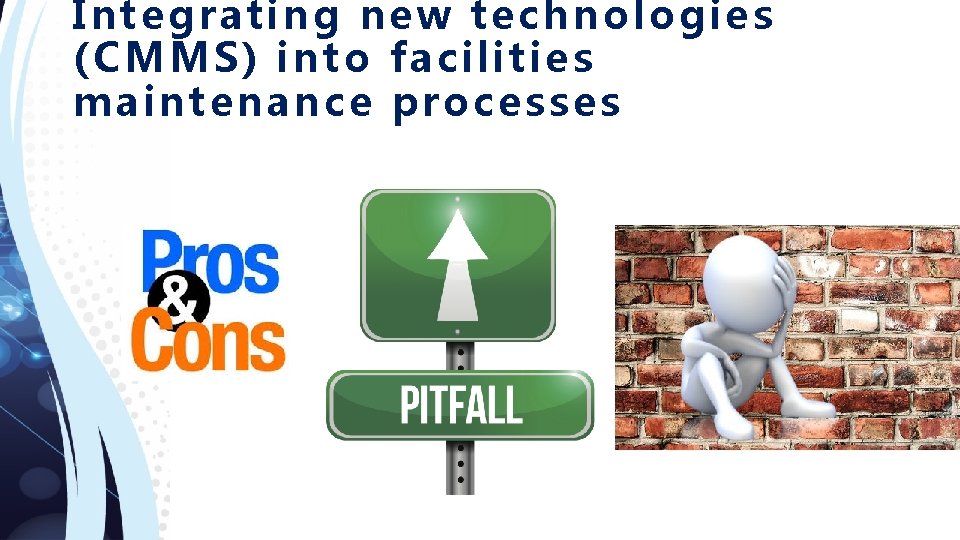
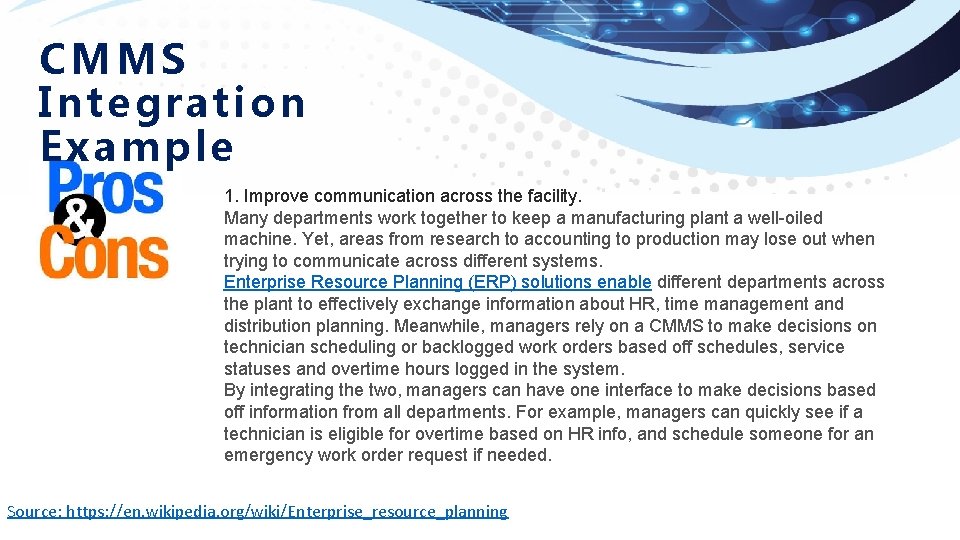
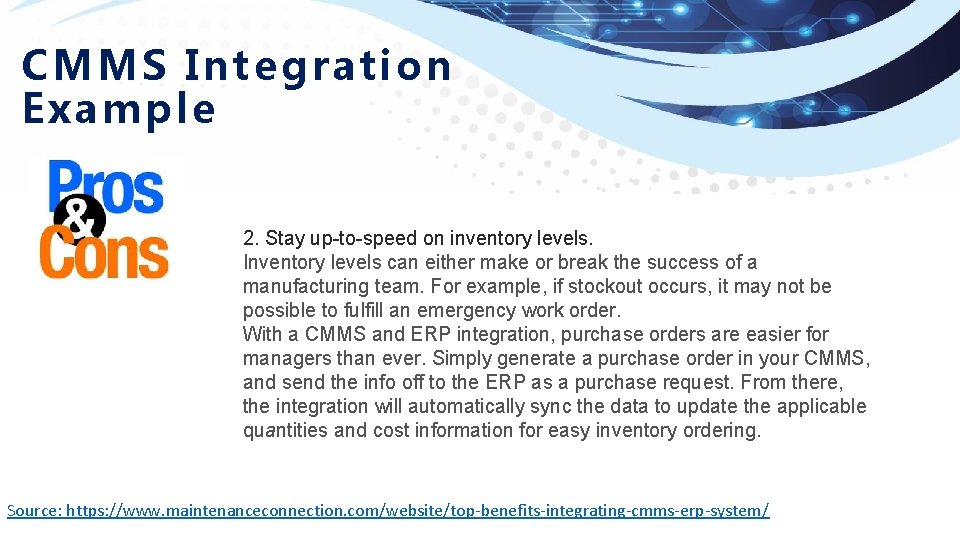
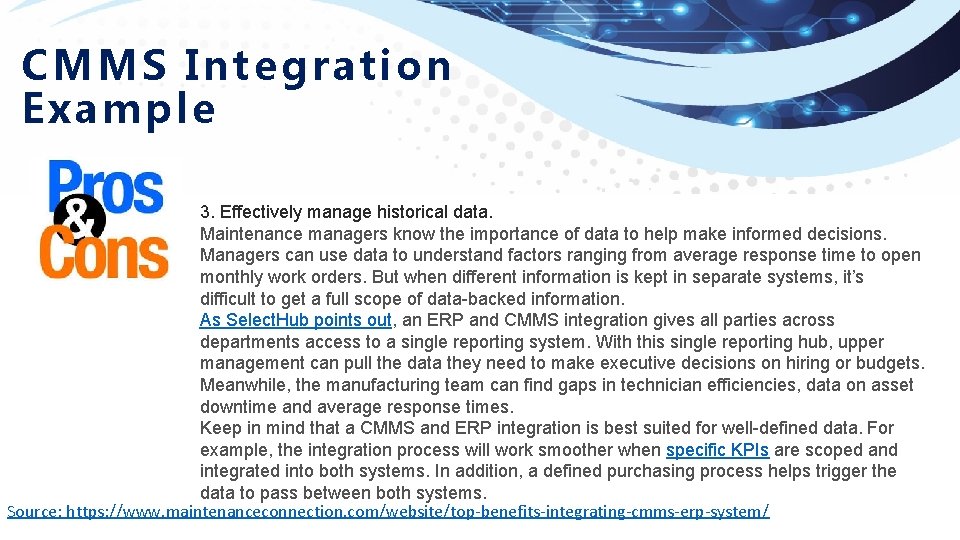
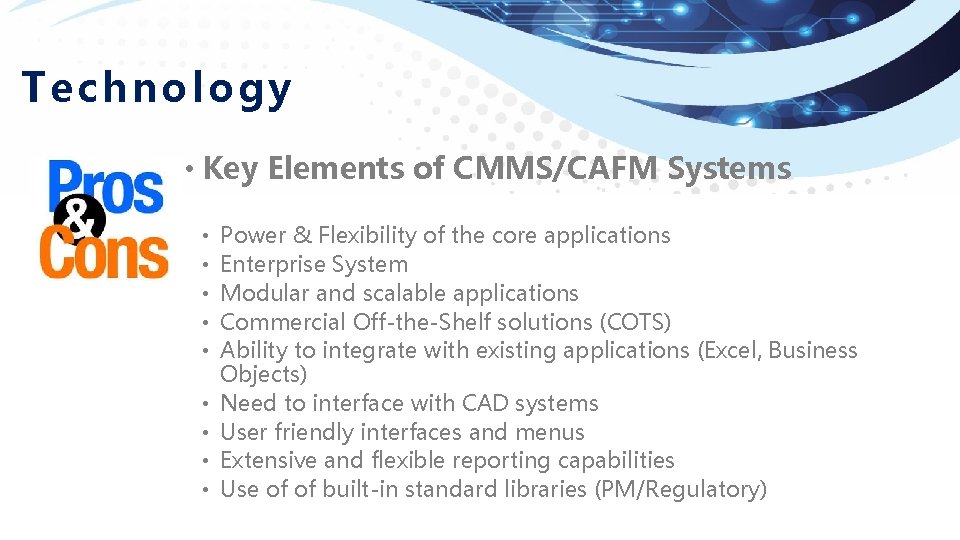
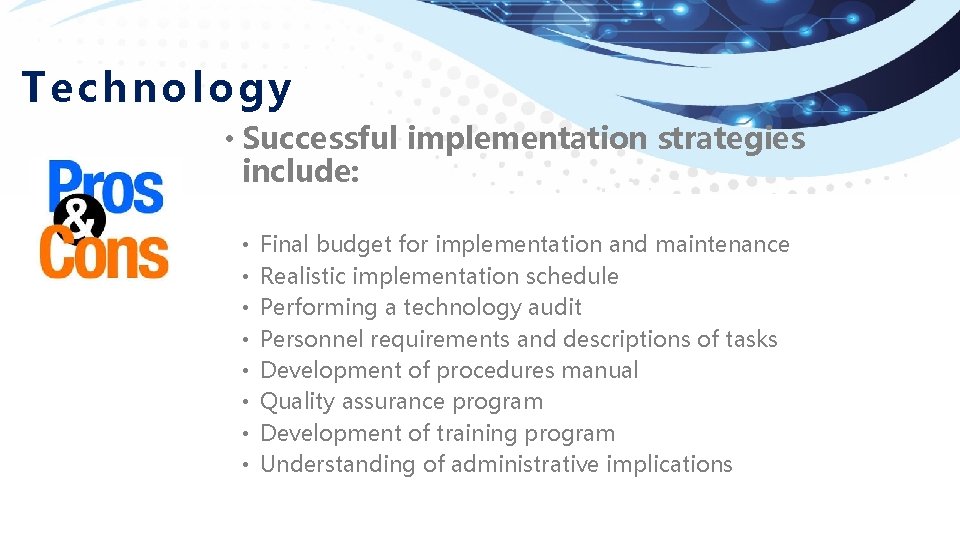
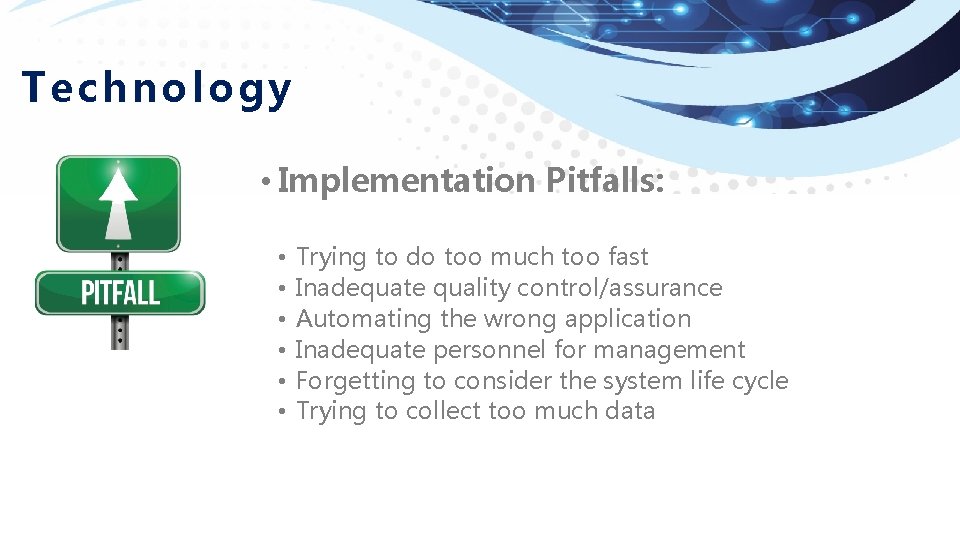
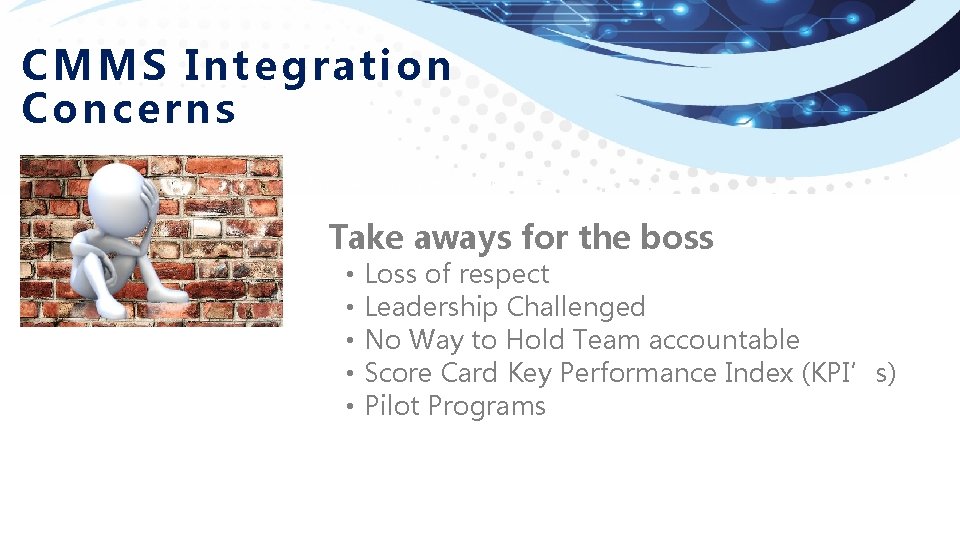
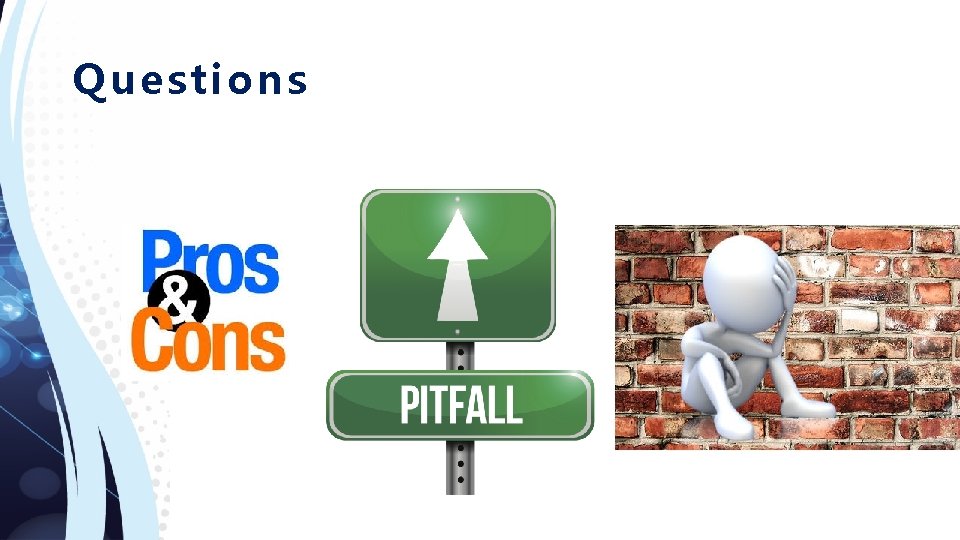
- Slides: 22
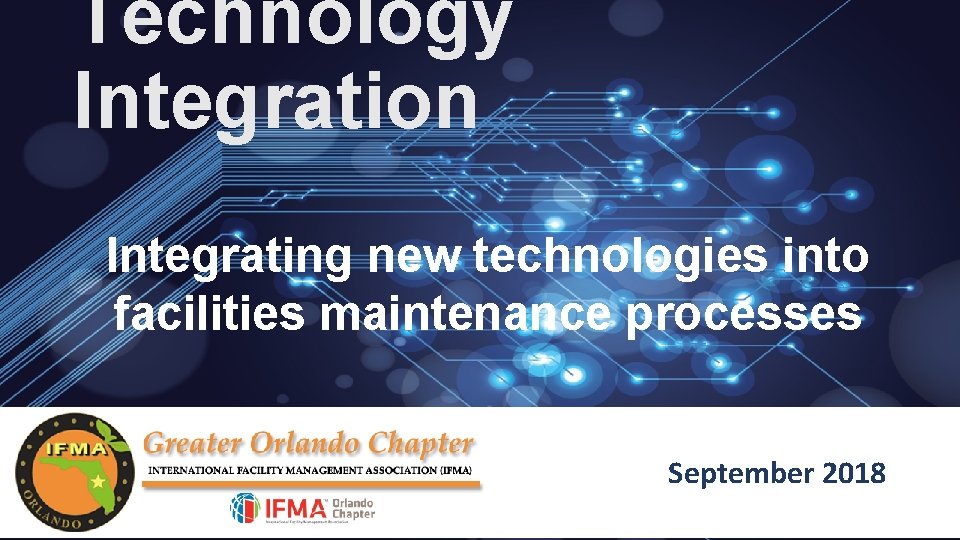
Technology Integration Integrating new technologies into facilities maintenance processes September 2018
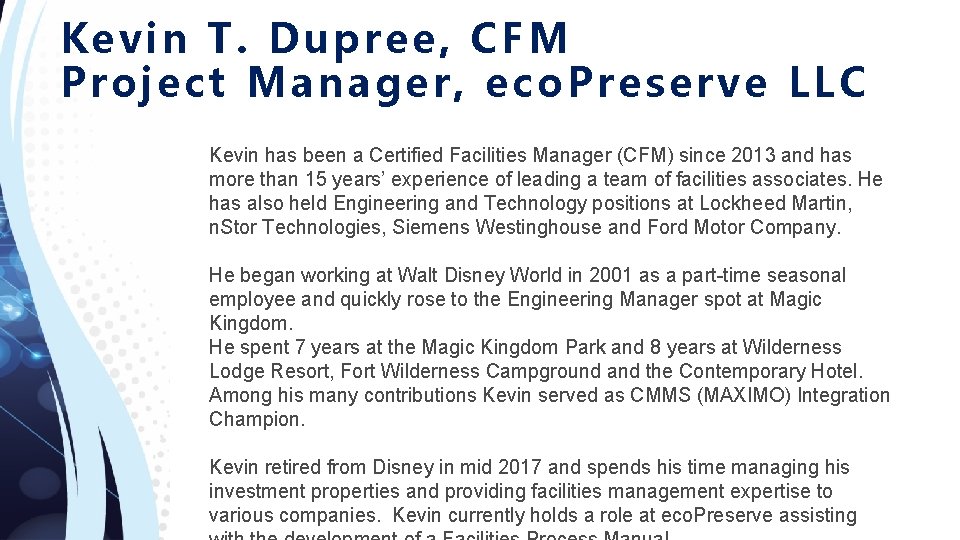
Kevin T. Dupree, CFM Pr oject Manager, eco. Preserve LLC Kevin has been a Certified Facilities Manager (CFM) since 2013 and has more than 15 years’ experience of leading a team of facilities associates. He has also held Engineering and Technology positions at Lockheed Martin, n. Stor Technologies, Siemens Westinghouse and Ford Motor Company. He began working at Walt Disney World in 2001 as a part-time seasonal employee and quickly rose to the Engineering Manager spot at Magic Kingdom. He spent 7 years at the Magic Kingdom Park and 8 years at Wilderness Lodge Resort, Fort Wilderness Campground and the Contemporary Hotel. Among his many contributions Kevin served as CMMS (MAXIMO) Integration Champion. Kevin retired from Disney in mid 2017 and spends his time managing his investment properties and providing facilities management expertise to various companies. Kevin currently holds a role at eco. Preserve assisting
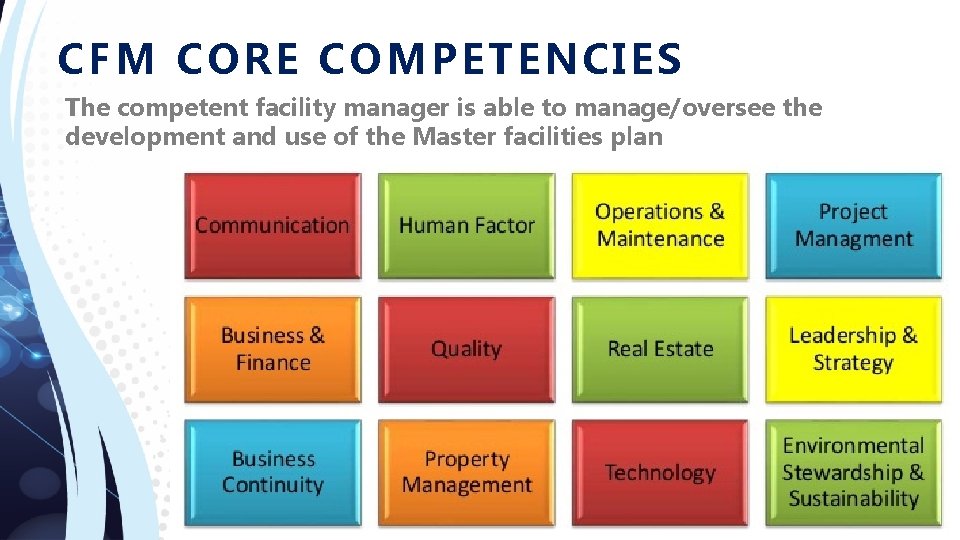
CF M C ORE CO MPE T ENCIES The competent facility manager is able to manage/oversee the development and use of the Master facilities plan
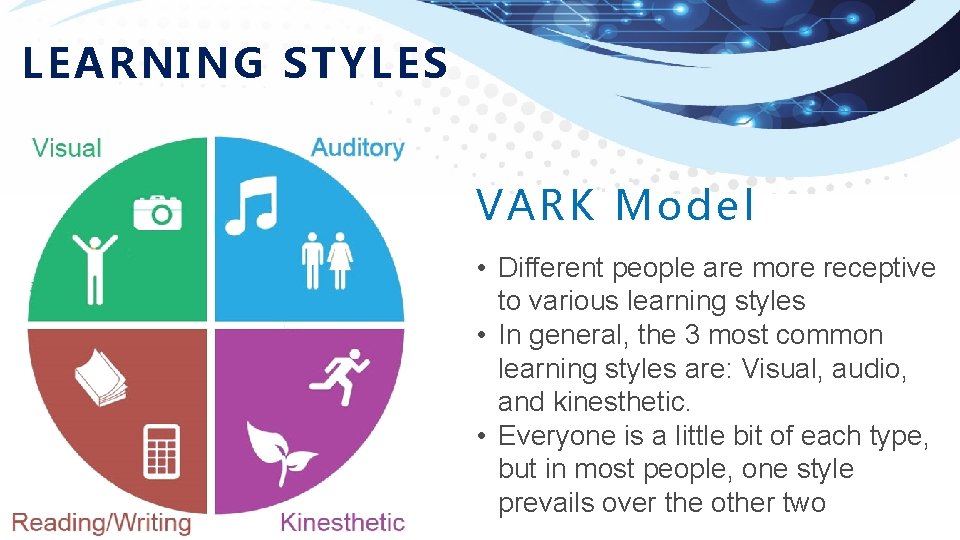
LEARNING STYLES VARK Mod el • Different people are more receptive to various learning styles • In general, the 3 most common learning styles are: Visual, audio, and kinesthetic. • Everyone is a little bit of each type, but in most people, one style prevails over the other two
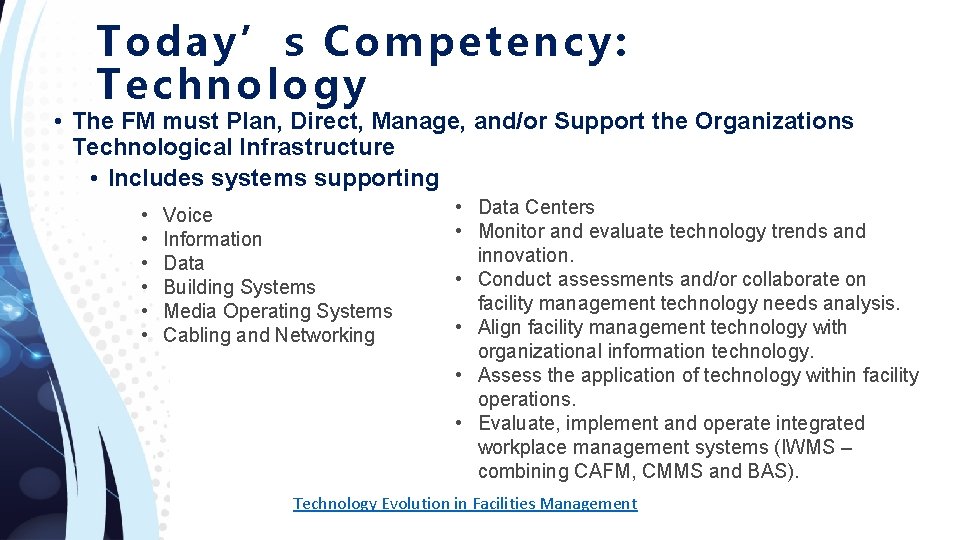
Today’s Compet ency: Technol ogy • The FM must Plan, Direct, Manage, and/or Support the Organizations Technological Infrastructure • Includes systems supporting • • • Voice Information Data Building Systems Media Operating Systems Cabling and Networking • Data Centers • Monitor and evaluate technology trends and innovation. • Conduct assessments and/or collaborate on facility management technology needs analysis. • Align facility management technology with organizational information technology. • Assess the application of technology within facility operations. • Evaluate, implement and operate integrated workplace management systems (IWMS – combining CAFM, CMMS and BAS). Technology Evolution in Facilities Management
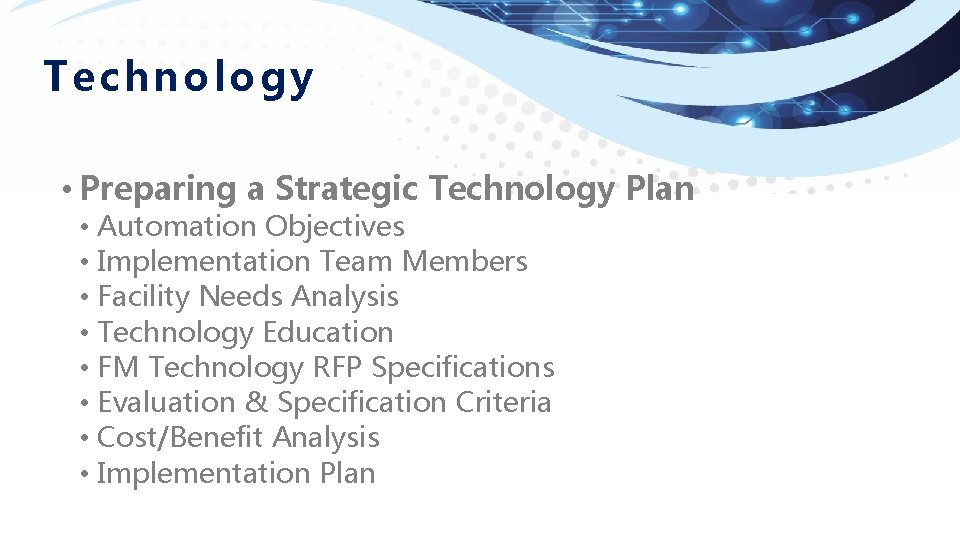
Tec hnolo gy • Preparing a Strategic Technology Plan • Automation Objectives • Implementation Team Members • Facility Needs Analysis • Technology Education • FM Technology RFP Specifications • Evaluation & Specification Criteria • Cost/Benefit Analysis • Implementation Plan
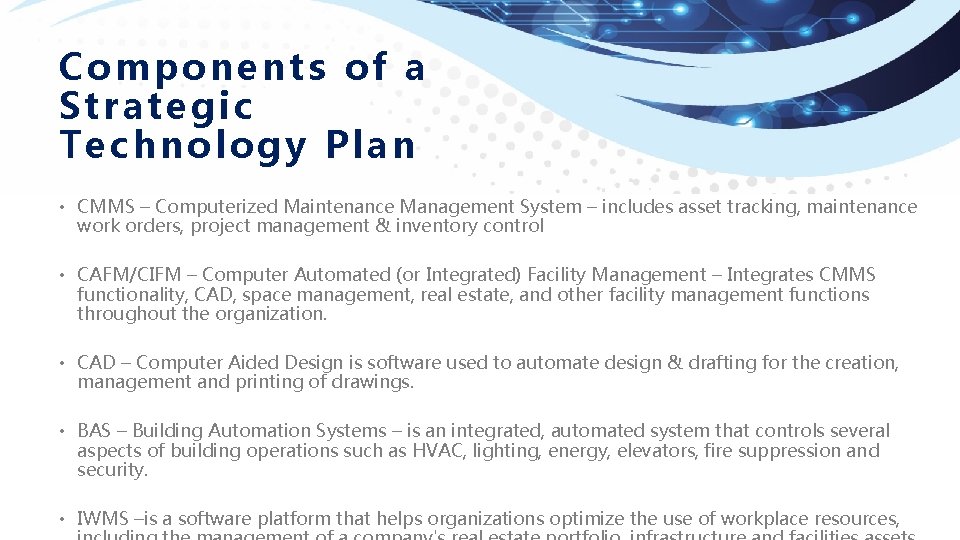
Components of a Strategic Technology Plan • CMMS – Computerized Maintenance Management System – includes asset tracking, maintenance work orders, project management & inventory control • CAFM/CIFM – Computer Automated (or Integrated) Facility Management – Integrates CMMS functionality, CAD, space management, real estate, and other facility management functions throughout the organization. • CAD – Computer Aided Design is software used to automate design & drafting for the creation, management and printing of drawings. • BAS – Building Automation Systems – is an integrated, automated system that controls several aspects of building operations such as HVAC, lighting, energy, elevators, fire suppression and security. • IWMS –is a software platform that helps organizations optimize the use of workplace resources,
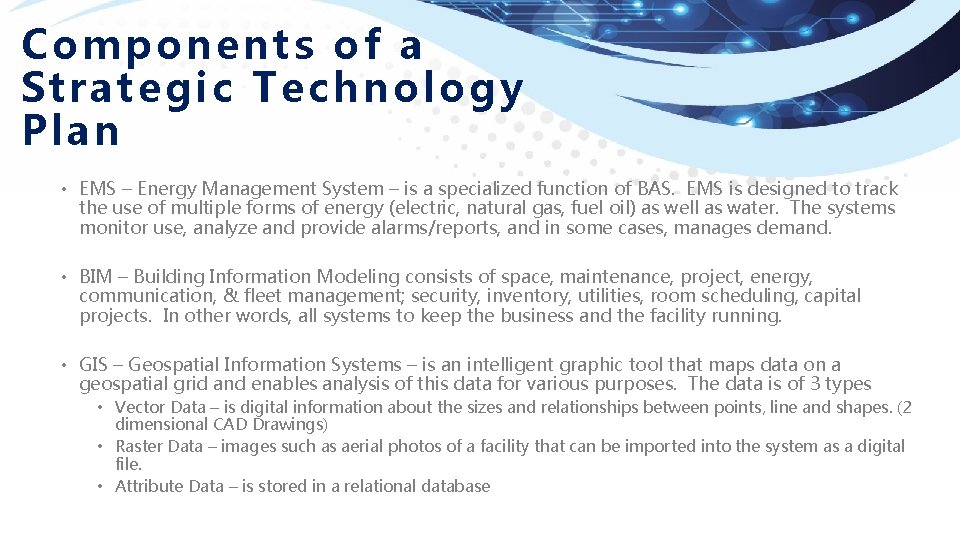
Components of a Strategic Technology Plan • EMS – Energy Management System – is a specialized function of BAS. EMS is designed to track the use of multiple forms of energy (electric, natural gas, fuel oil) as well as water. The systems monitor use, analyze and provide alarms/reports, and in some cases, manages demand. • BIM – Building Information Modeling consists of space, maintenance, project, energy, communication, & fleet management; security, inventory, utilities, room scheduling, capital projects. In other words, all systems to keep the business and the facility running. • GIS – Geospatial Information Systems – is an intelligent graphic tool that maps data on a geospatial grid and enables analysis of this data for various purposes. The data is of 3 types • Vector Data – is digital information about the sizes and relationships between points, line and shapes. (2 dimensional CAD Drawings) • Raster Data – images such as aerial photos of a facility that can be imported into the system as a digital file. • Attribute Data – is stored in a relational database
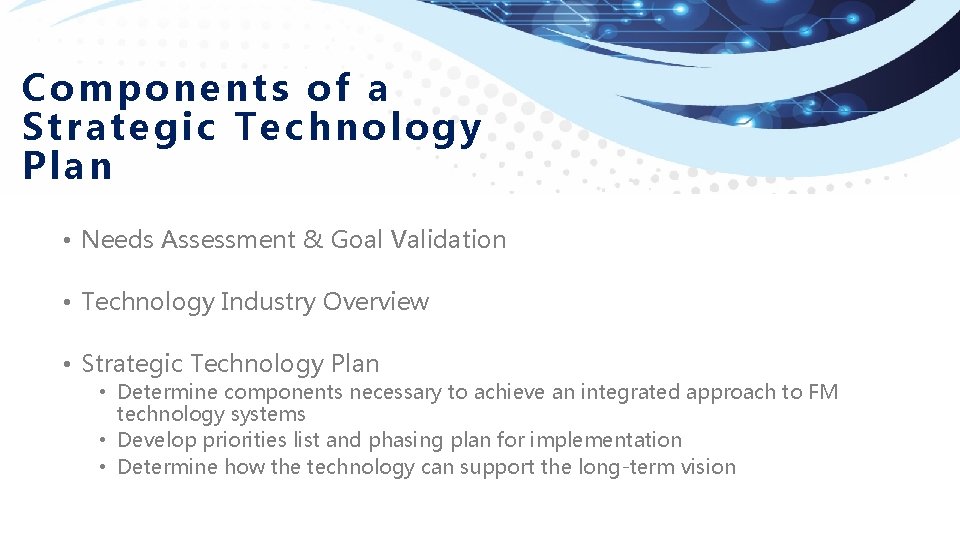
Components of a Strategic Technology Plan • Needs Assessment & Goal Validation • Technology Industry Overview • Strategic Technology Plan • Determine components necessary to achieve an integrated approach to FM technology systems • Develop priorities list and phasing plan for implementation • Determine how the technology can support the long-term vision
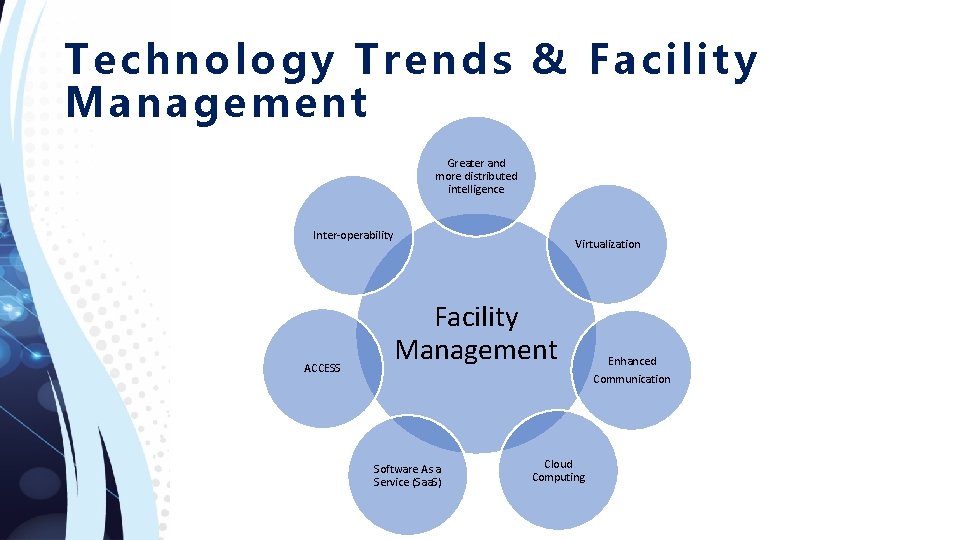
Technology Trends & Facilit y Man ageme nt Greater and more distributed intelligence Inter-operability ACCESS Virtualization Facility Management Software As a Service (Saa. S) Cloud Computing Enhanced Communication
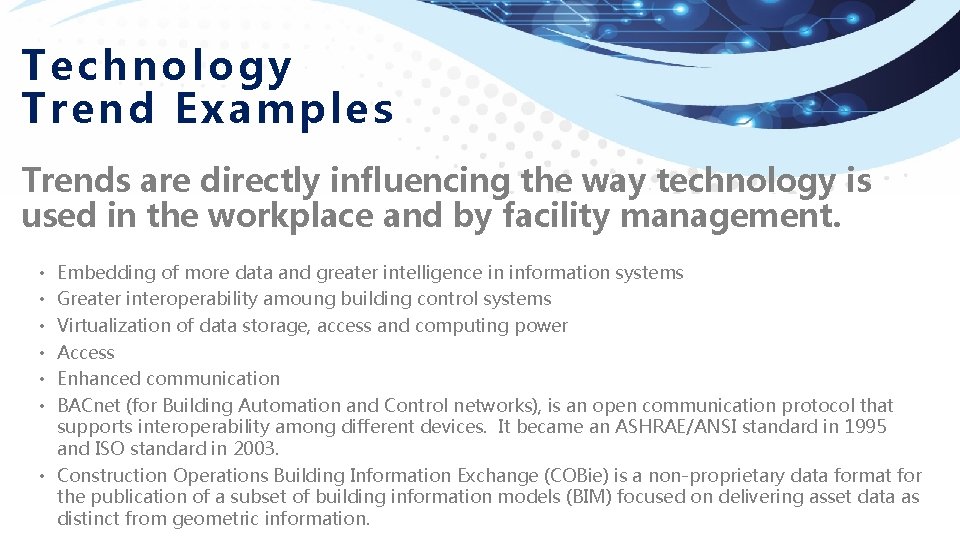
Technology Trend Examples Trends are directly influencing the way technology is used in the workplace and by facility management. Embedding of more data and greater intelligence in information systems Greater interoperability amoung building control systems Virtualization of data storage, access and computing power Access Enhanced communication BACnet (for Building Automation and Control networks), is an open communication protocol that supports interoperability among different devices. It became an ASHRAE/ANSI standard in 1995 and ISO standard in 2003. • Construction Operations Building Information Exchange (COBie) is a non-proprietary data format for the publication of a subset of building information models (BIM) focused on delivering asset data as distinct from geometric information. • • •
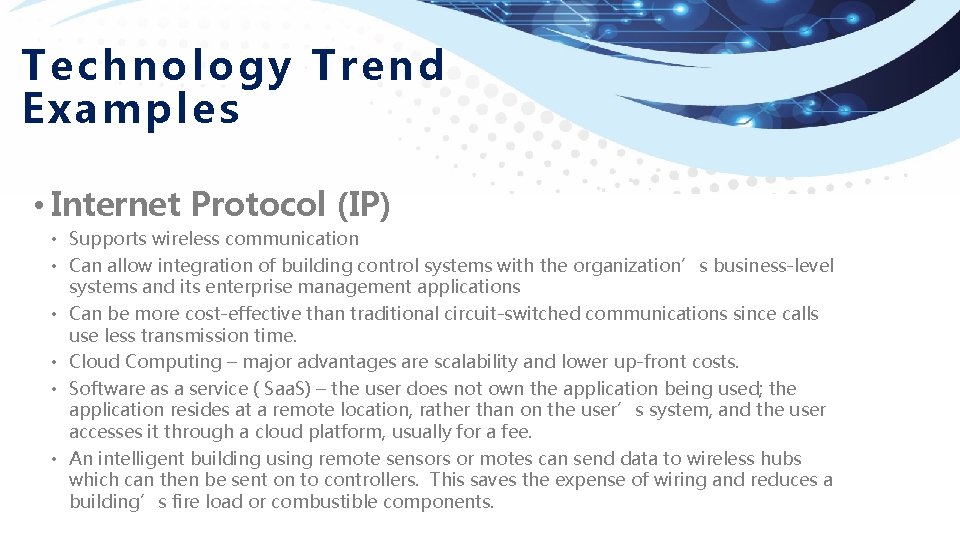
Technology Trend Examples • Internet Protocol (IP) • Supports wireless communication • Can allow integration of building control systems with the organization’s business-level systems and its enterprise management applications • Can be more cost-effective than traditional circuit-switched communications since calls use less transmission time. • Cloud Computing – major advantages are scalability and lower up-front costs. • Software as a service ( Saa. S) – the user does not own the application being used; the application resides at a remote location, rather than on the user’s system, and the user accesses it through a cloud platform, usually for a fee. • An intelligent building using remote sensors or motes can send data to wireless hubs which can then be sent on to controllers. This saves the expense of wiring and reduces a building’s fire load or combustible components.
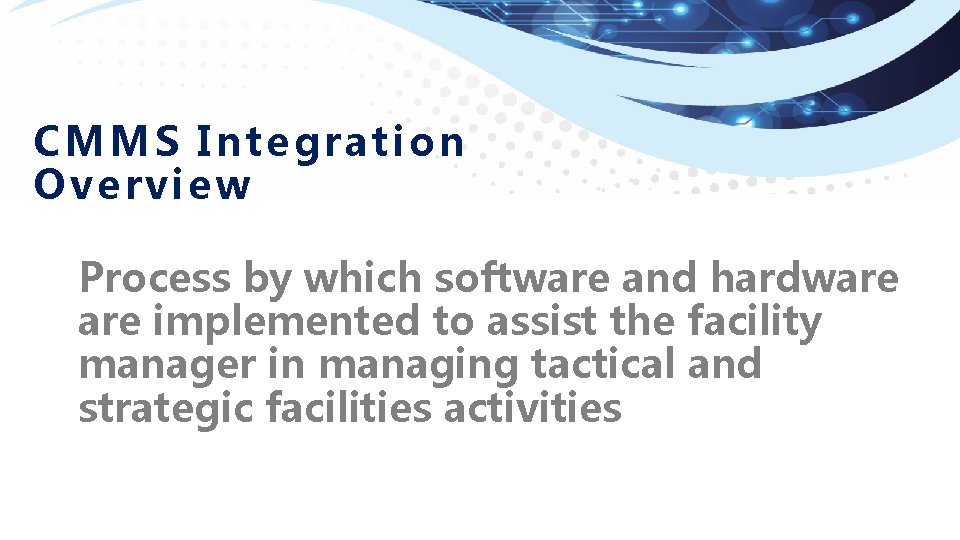
C MMS Integration Ov erview Process by which software and hardware implemented to assist the facility manager in managing tactical and strategic facilities activities
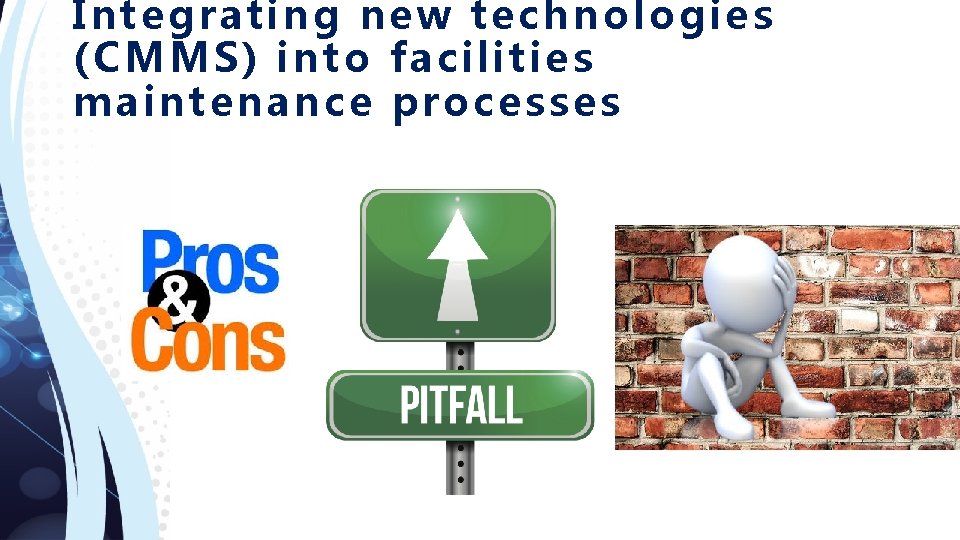
In te gra ting new tech nolog ies (CMM S) int o faciliti es main tena nce processes
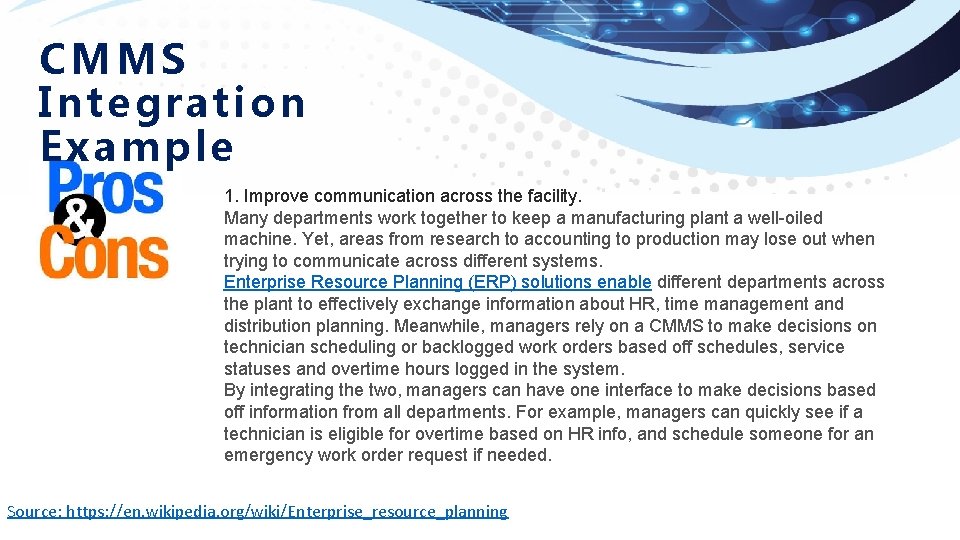
CMMS Integration E xa mple 1. Improve communication across the facility. Many departments work together to keep a manufacturing plant a well-oiled machine. Yet, areas from research to accounting to production may lose out when trying to communicate across different systems. Enterprise Resource Planning (ERP) solutions enable different departments across the plant to effectively exchange information about HR, time management and distribution planning. Meanwhile, managers rely on a CMMS to make decisions on technician scheduling or backlogged work orders based off schedules, service statuses and overtime hours logged in the system. By integrating the two, managers can have one interface to make decisions based off information from all departments. For example, managers can quickly see if a technician is eligible for overtime based on HR info, and schedule someone for an emergency work order request if needed. Source: https: //en. wikipedia. org/wiki/Enterprise_resource_planning
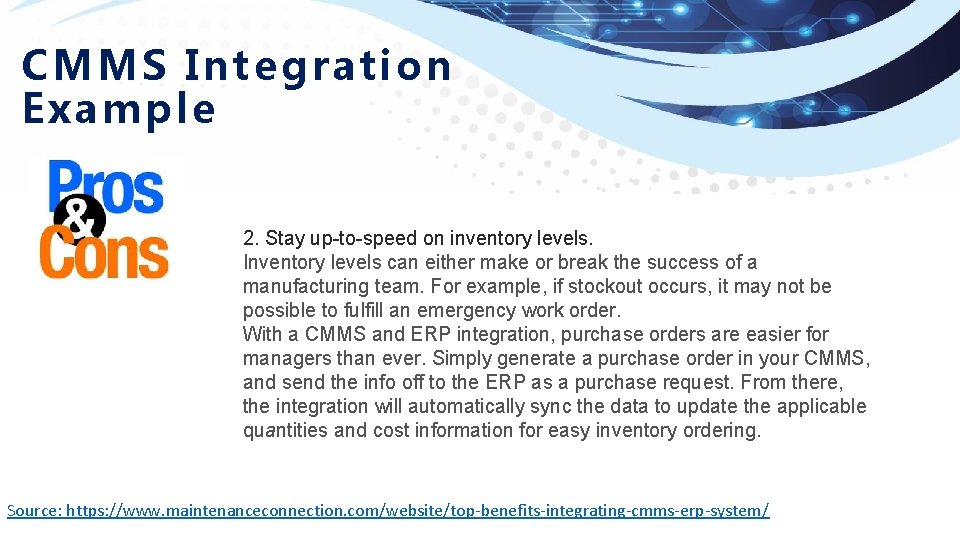
CMMS Integration Example 2. Stay up-to-speed on inventory levels. Inventory levels can either make or break the success of a manufacturing team. For example, if stockout occurs, it may not be possible to fulfill an emergency work order. With a CMMS and ERP integration, purchase orders are easier for managers than ever. Simply generate a purchase order in your CMMS, and send the info off to the ERP as a purchase request. From there, the integration will automatically sync the data to update the applicable quantities and cost information for easy inventory ordering. Source: https: //www. maintenanceconnection. com/website/top-benefits-integrating-cmms-erp-system/
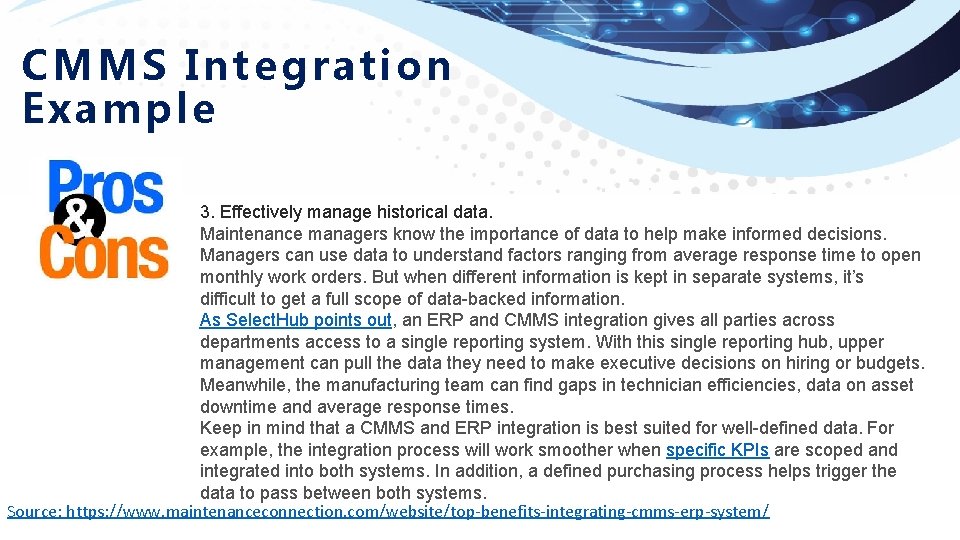
CMMS Integration Example 3. Effectively manage historical data. Maintenance managers know the importance of data to help make informed decisions. Managers can use data to understand factors ranging from average response time to open monthly work orders. But when different information is kept in separate systems, it’s difficult to get a full scope of data-backed information. As Select. Hub points out, an ERP and CMMS integration gives all parties across departments access to a single reporting system. With this single reporting hub, upper management can pull the data they need to make executive decisions on hiring or budgets. Meanwhile, the manufacturing team can find gaps in technician efficiencies, data on asset downtime and average response times. Keep in mind that a CMMS and ERP integration is best suited for well-defined data. For example, the integration process will work smoother when specific KPIs are scoped and integrated into both systems. In addition, a defined purchasing process helps trigger the data to pass between both systems. Source: https: //www. maintenanceconnection. com/website/top-benefits-integrating-cmms-erp-system/
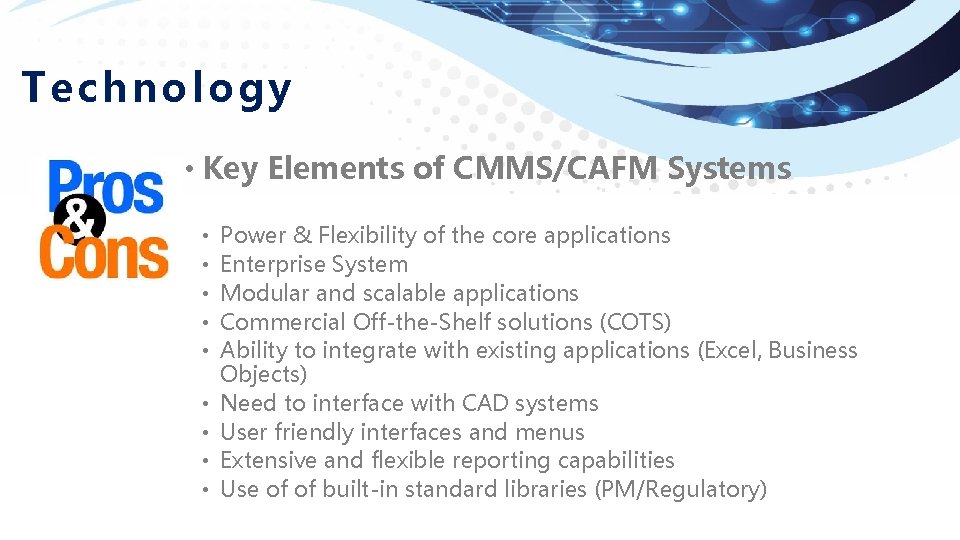
Technology • Key Elements of CMMS/CAFM Systems • • • Power & Flexibility of the core applications Enterprise System Modular and scalable applications Commercial Off-the-Shelf solutions (COTS) Ability to integrate with existing applications (Excel, Business Objects) Need to interface with CAD systems User friendly interfaces and menus Extensive and flexible reporting capabilities Use of of built-in standard libraries (PM/Regulatory)
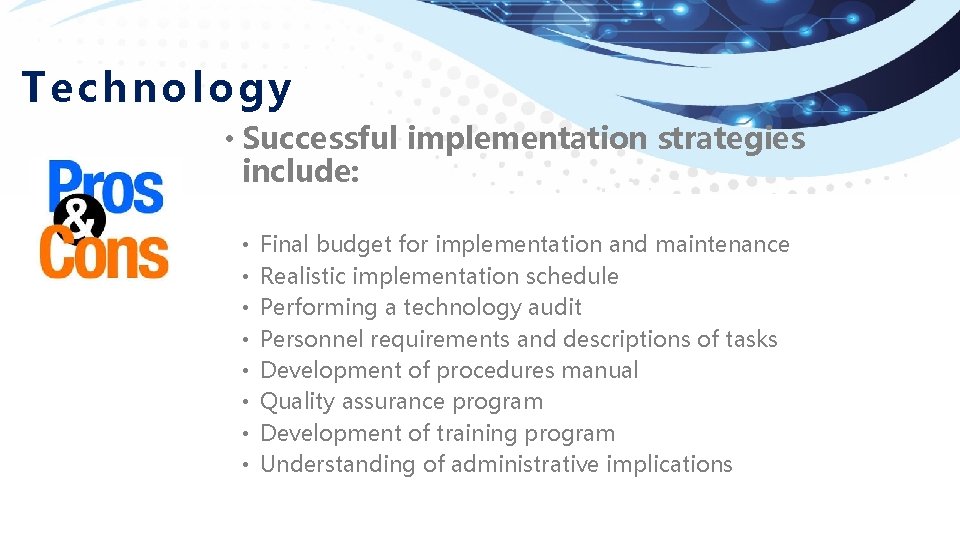
Technology • Successful implementation strategies include: • • Final budget for implementation and maintenance Realistic implementation schedule Performing a technology audit Personnel requirements and descriptions of tasks Development of procedures manual Quality assurance program Development of training program Understanding of administrative implications
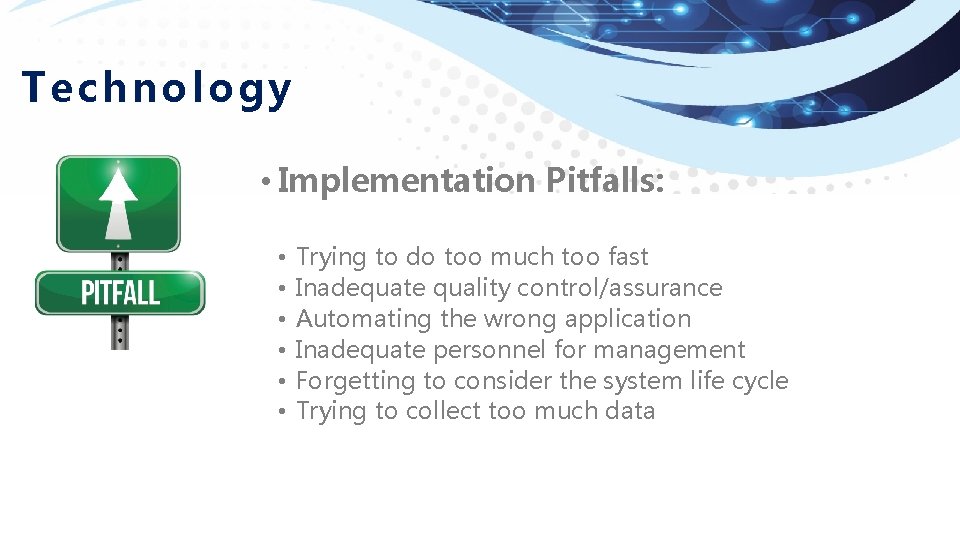
Technology • Implementation Pitfalls: • • • Trying to do too much too fast Inadequate quality control/assurance Automating the wrong application Inadequate personnel for management Forgetting to consider the system life cycle Trying to collect too much data
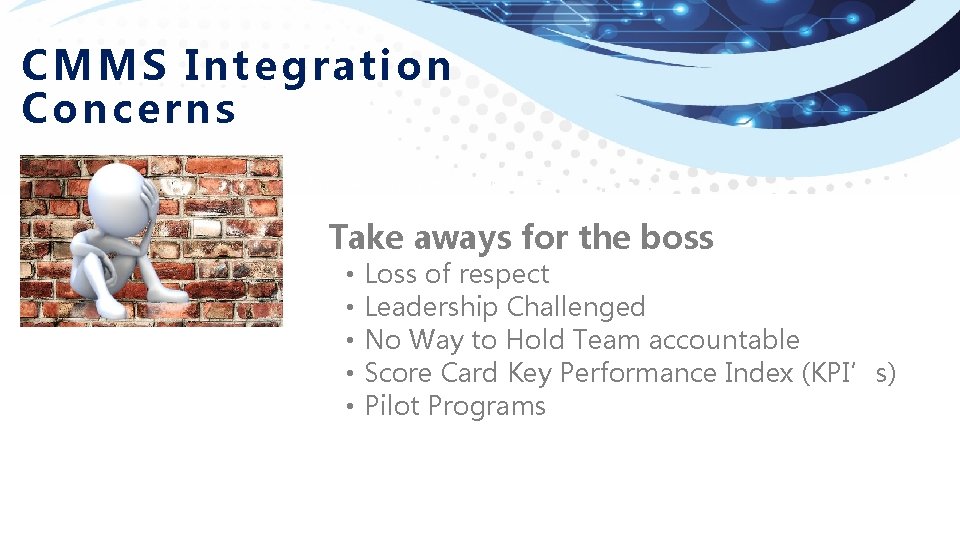
CMMS Integration Concerns RFID Security Systems integration Facilities management - end user Storage Scalability - IT Bandwidth Scalability - IT Training Super User - IT - end user • Loss of respect Tech support - IT - end user • Leadership Challenged Pilot program - All Mobile integration - IT • No Way to Hold Team accountable Example Passive RFID (Magic band ) Take aways for the boss • Score Card Key Performance Index (KPI’s) • Pilot Programs
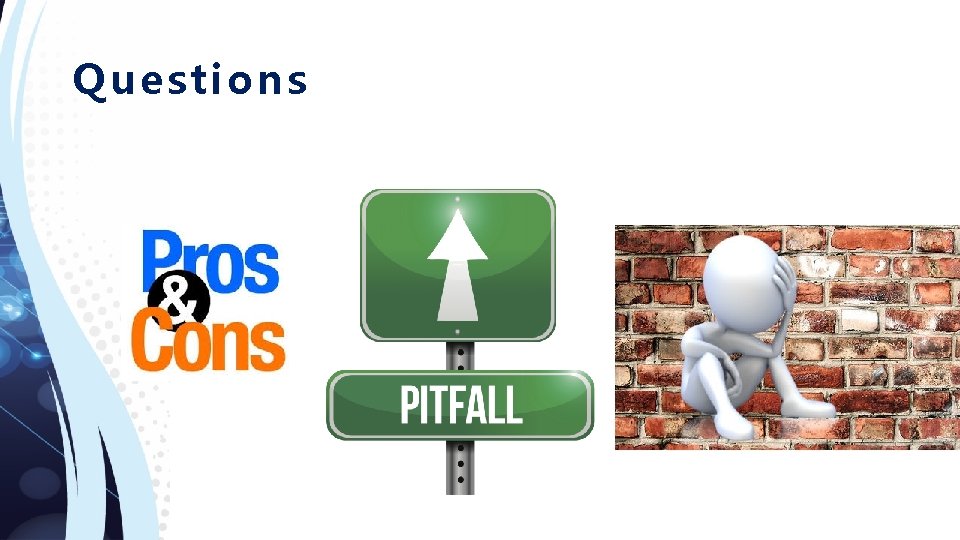
Que stio ns
Middle level integration
Quote integration methods
Paragraph writing
Gigp-28
Data integration with xml and semantic web technologies
Mashups meaning
Data mashups and gis are data integration technologies.
E commerce architecture and technologies in web technology
Three dimensions of corporate strategy
Horizontal integration
Simultaneous integration
Technology and maintenance council
Transcontinent
New disruptive technologies 2021
New disruptive technologies
Tip model educational technology
Technology integration planning model diagram
Phases of technology integration planning model
Technology integration planning
Wildfire technology integration
Florida technology integration matrix
Integrating quotes mla
Sensory input, integration motor output example