STRUCTURAL LIGHTWEIGHT CONCRETE Structural lightweight concrete is similar
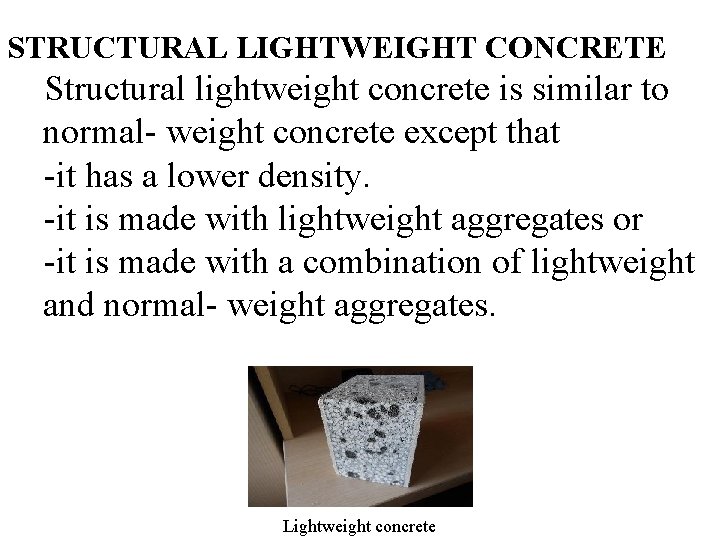
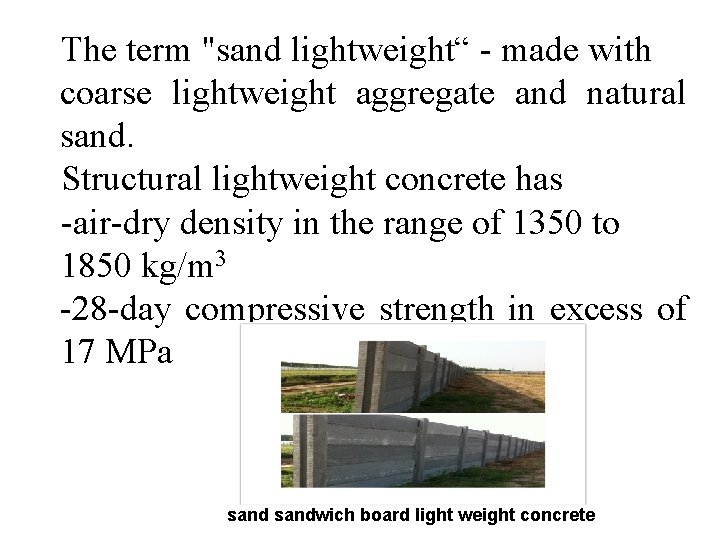
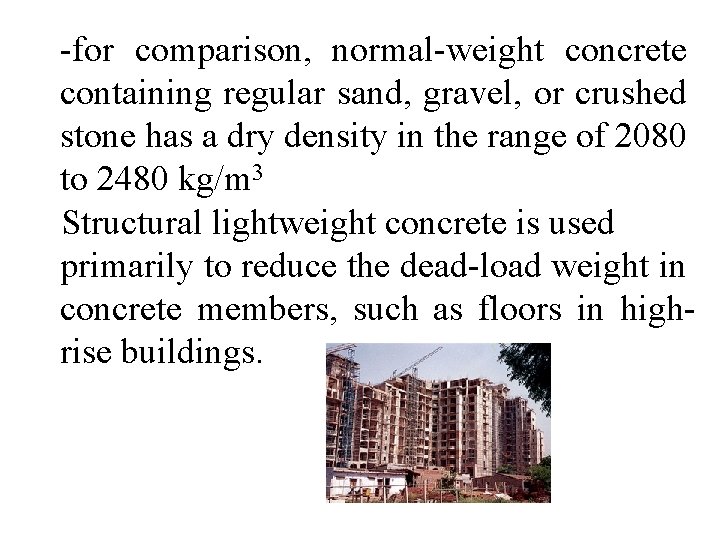
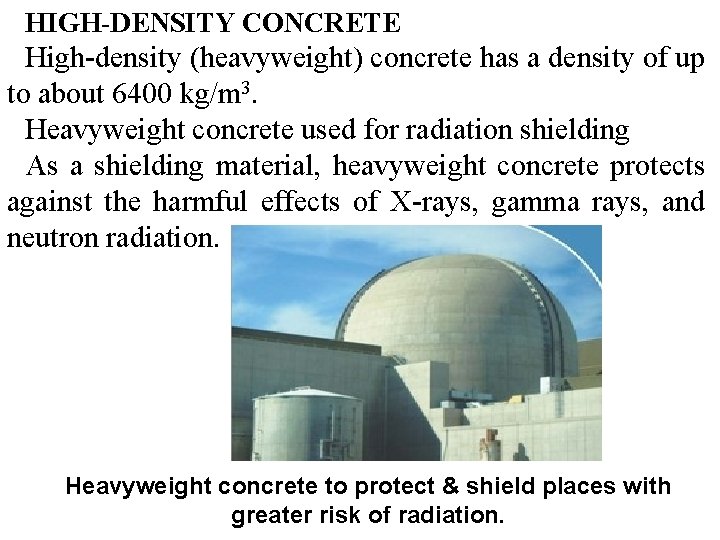
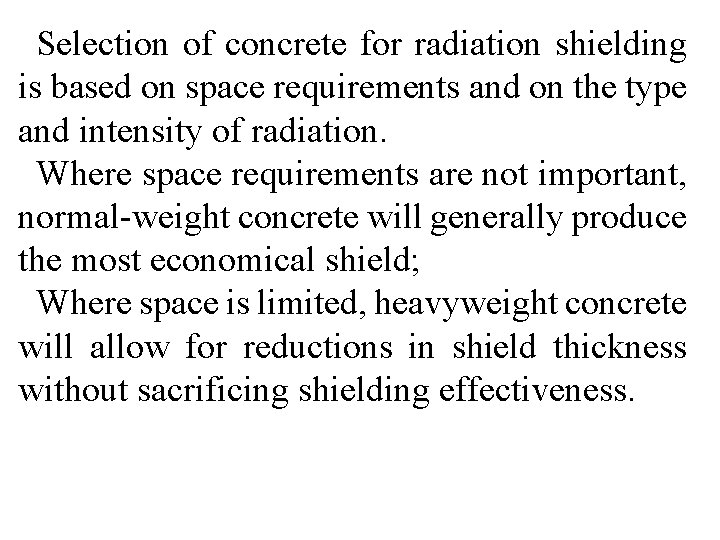
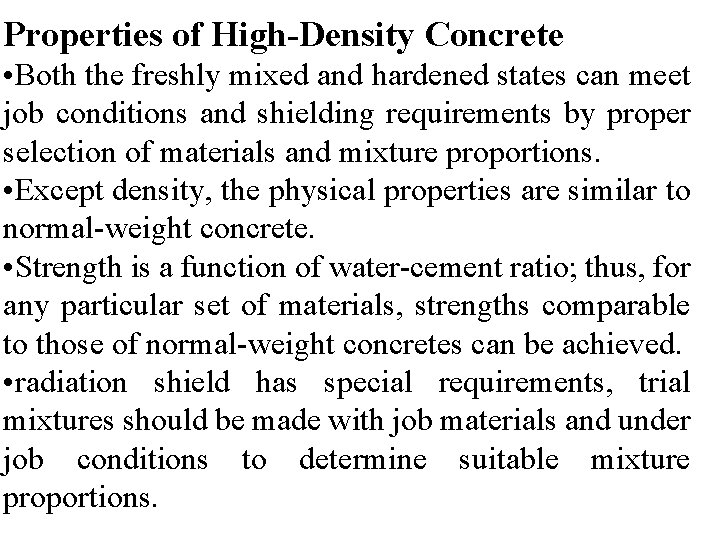
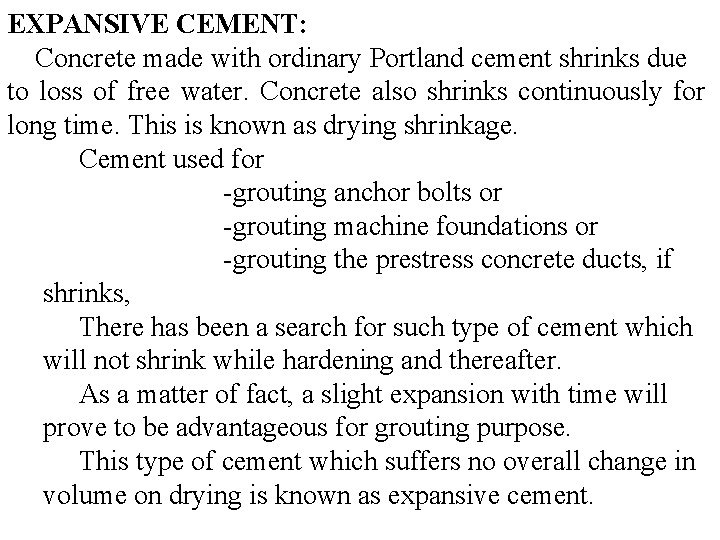
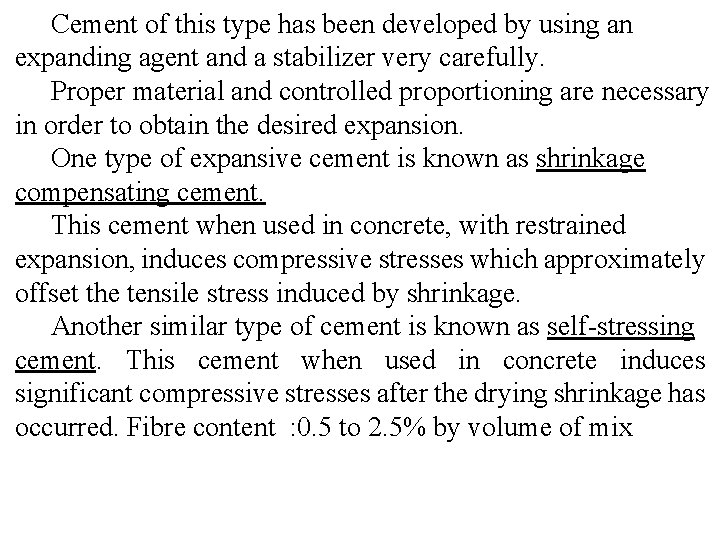
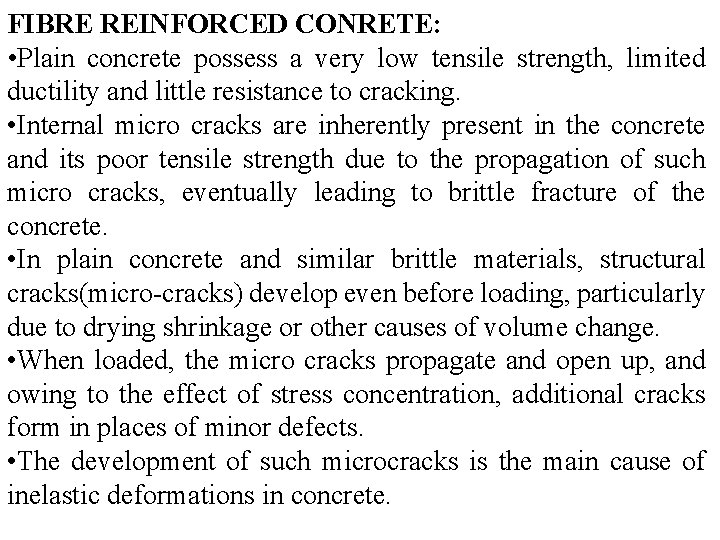
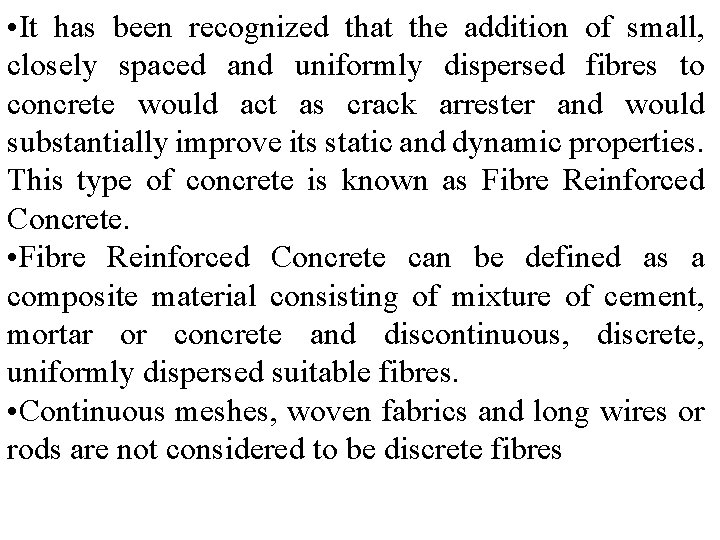
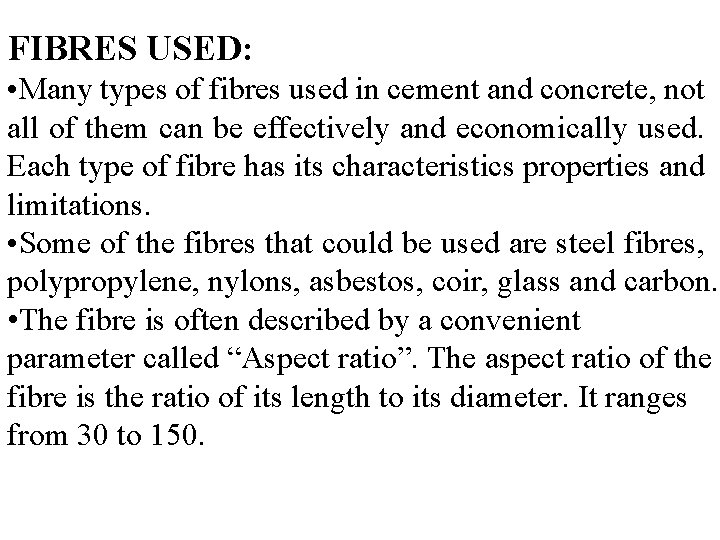
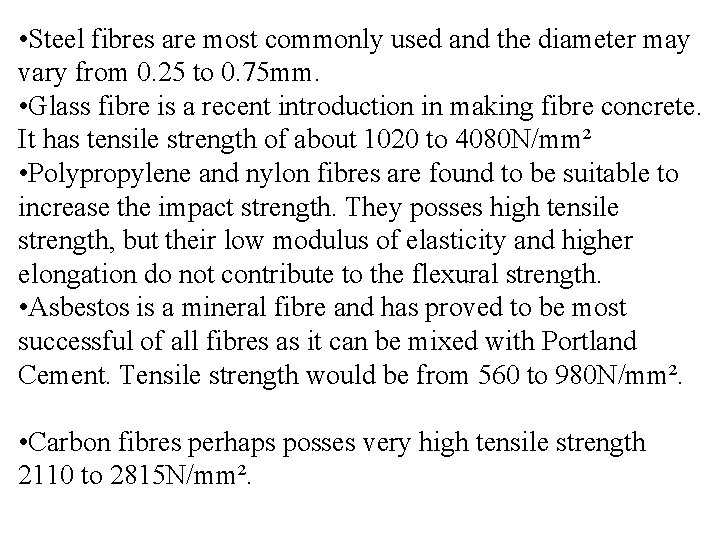
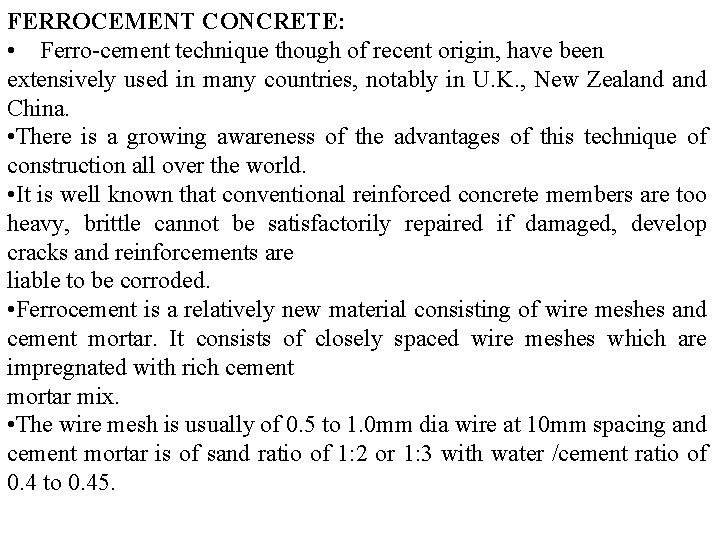
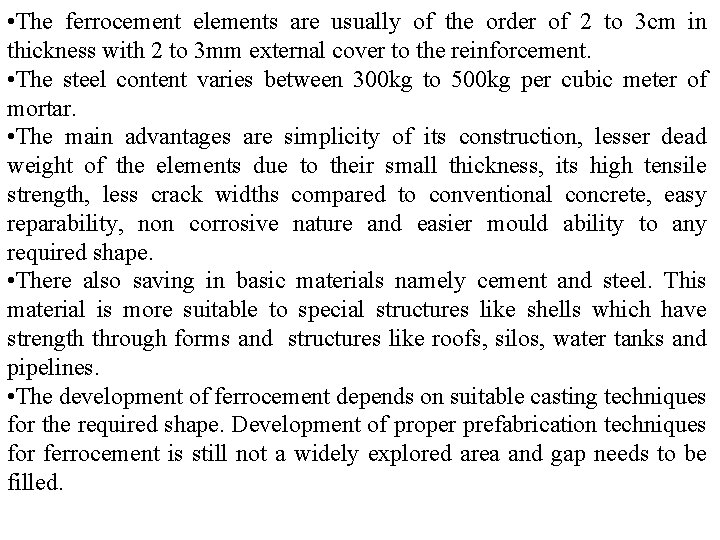
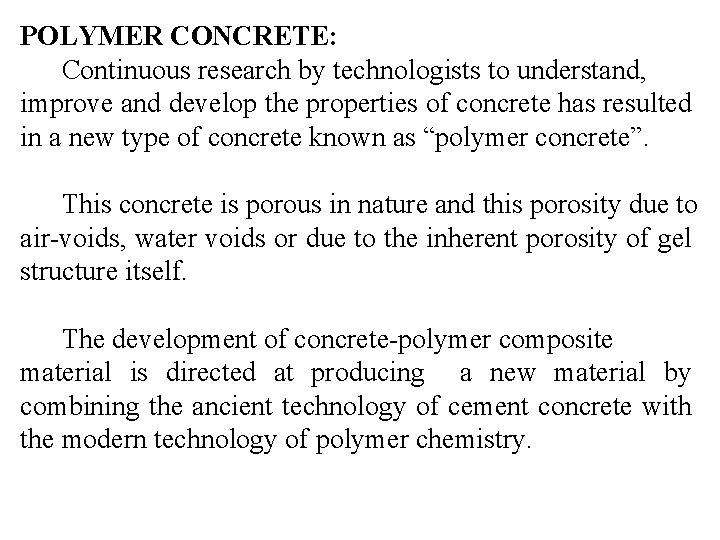
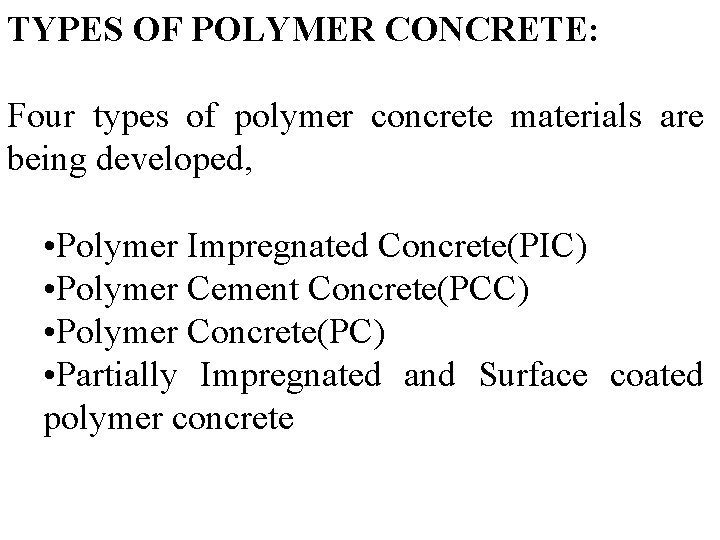
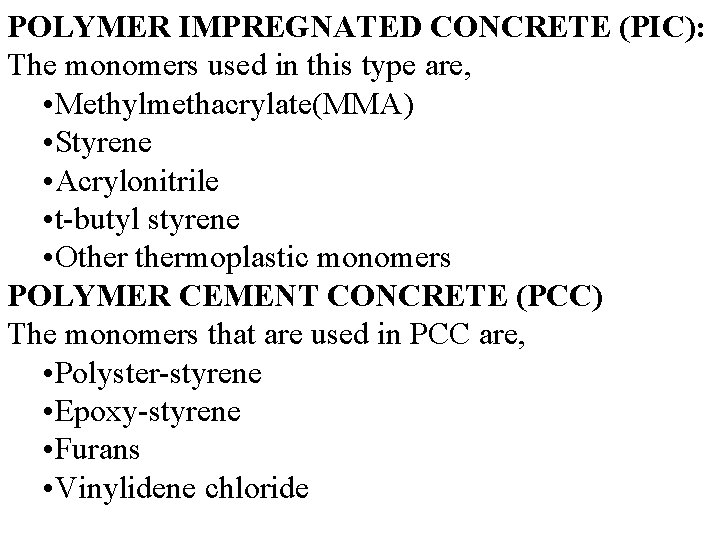
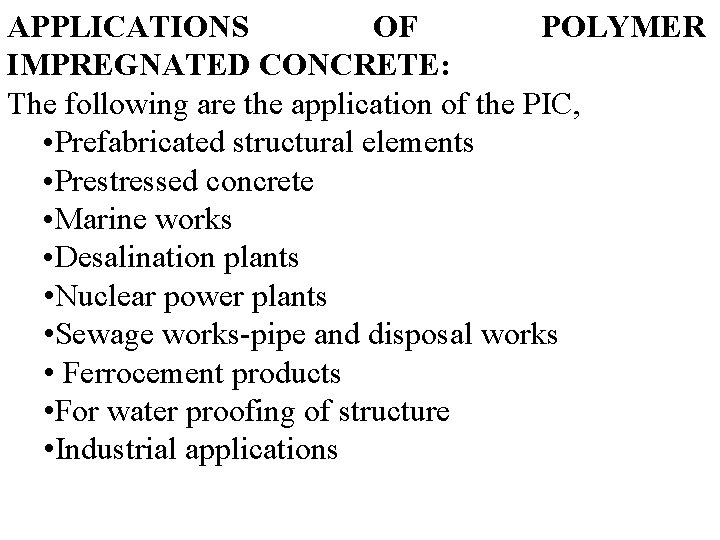
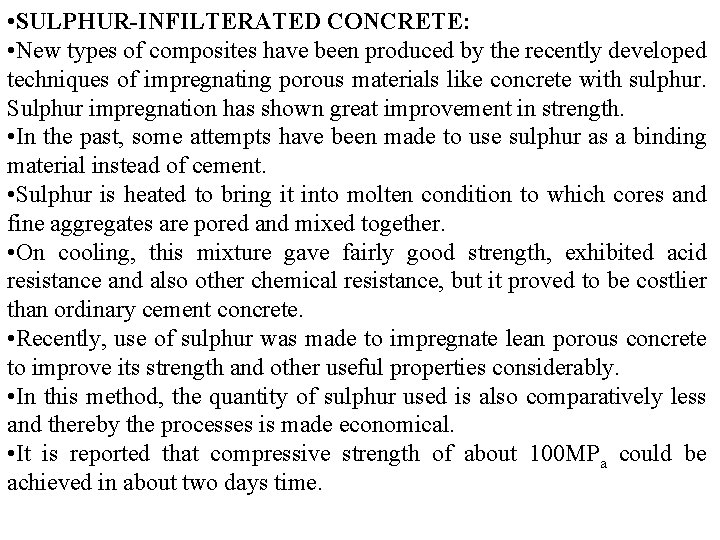
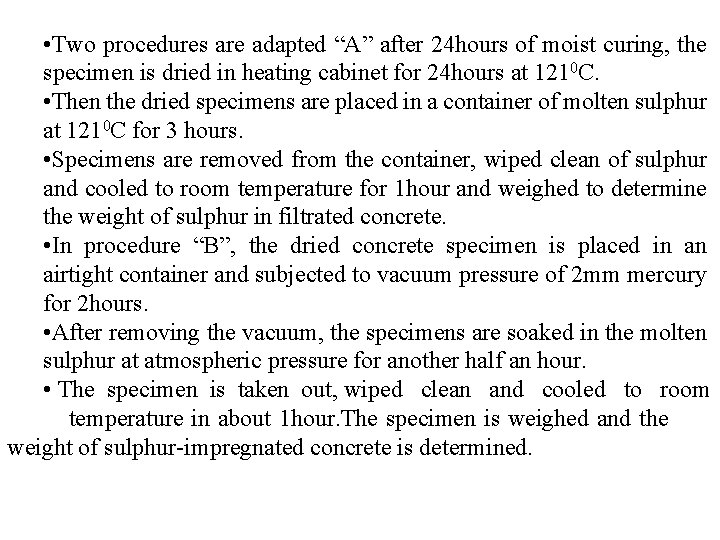
- Slides: 20
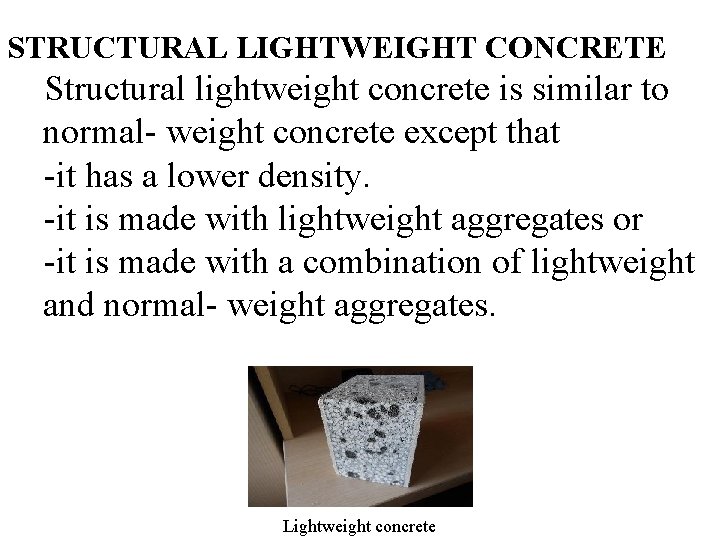
STRUCTURAL LIGHTWEIGHT CONCRETE Structural lightweight concrete is similar to normal- weight concrete except that -it has a lower density. -it is made with lightweight aggregates or -it is made with a combination of lightweight and normal- weight aggregates. Lightweight concrete
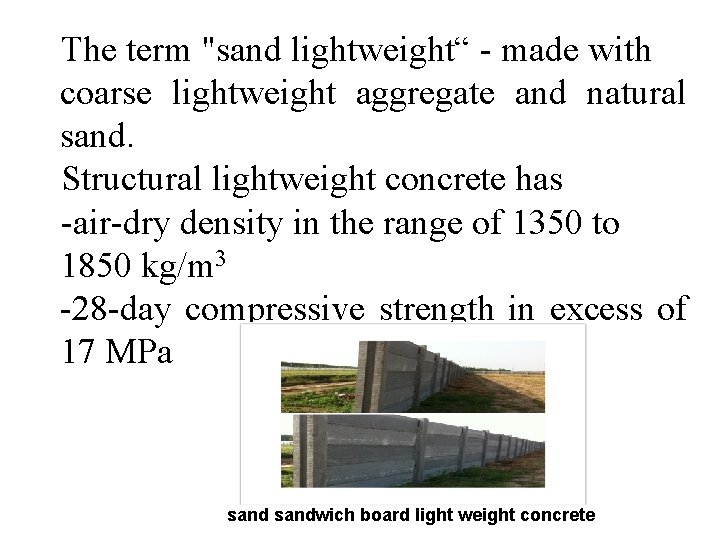
The term "sand lightweight“ - made with coarse lightweight aggregate and natural sand. Structural lightweight concrete has -air-dry density in the range of 1350 to 1850 kg/m 3 -28 -day compressive strength in excess of 17 MPa sandwich board light weight concrete
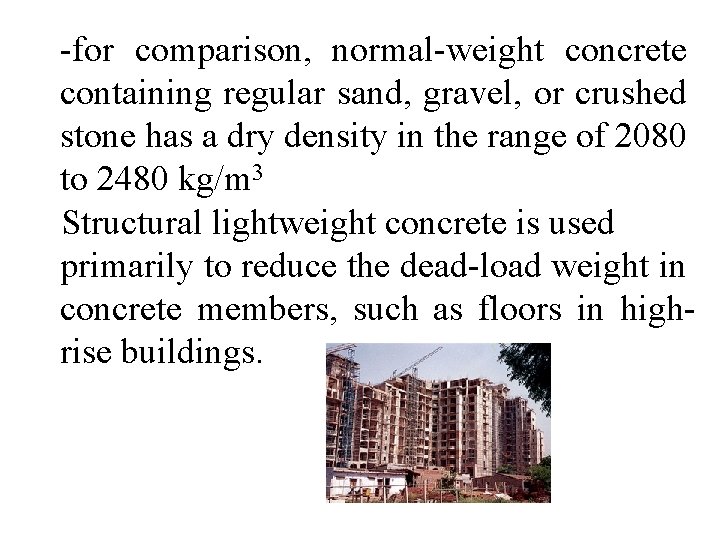
-for comparison, normal-weight concrete containing regular sand, gravel, or crushed stone has a dry density in the range of 2080 to 2480 kg/m 3 Structural lightweight concrete is used primarily to reduce the dead-load weight in concrete members, such as floors in highrise buildings.
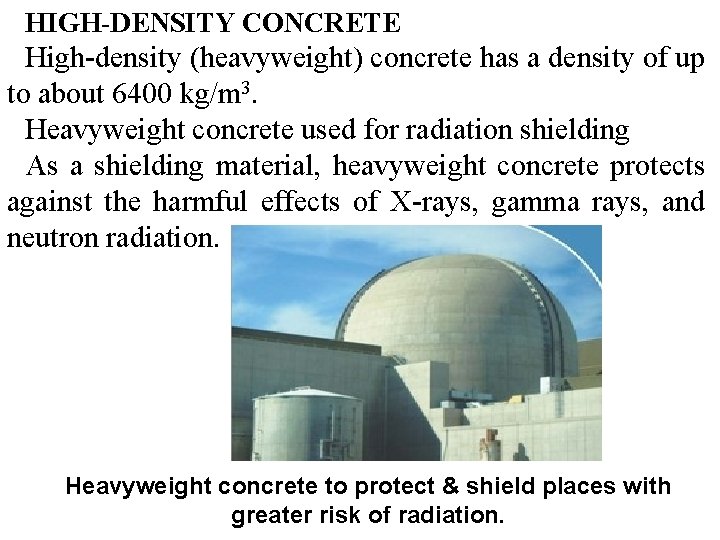
HIGH-DENSITY CONCRETE High-density (heavyweight) concrete has a density of up to about 6400 kg/m 3. Heavyweight concrete used for radiation shielding As a shielding material, heavyweight concrete protects against the harmful effects of X-rays, gamma rays, and neutron radiation. Heavyweight concrete to protect & shield places with greater risk of radiation.
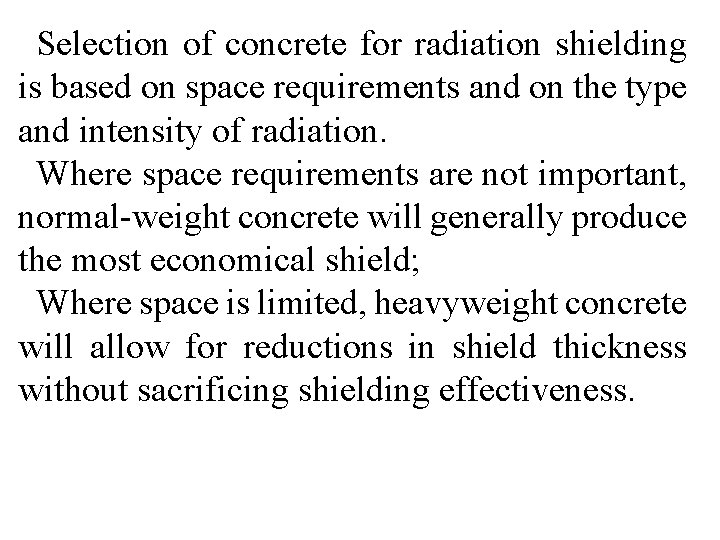
Selection of concrete for radiation shielding is based on space requirements and on the type and intensity of radiation. Where space requirements are not important, normal-weight concrete will generally produce the most economical shield; Where space is limited, heavyweight concrete will allow for reductions in shield thickness without sacrificing shielding effectiveness.
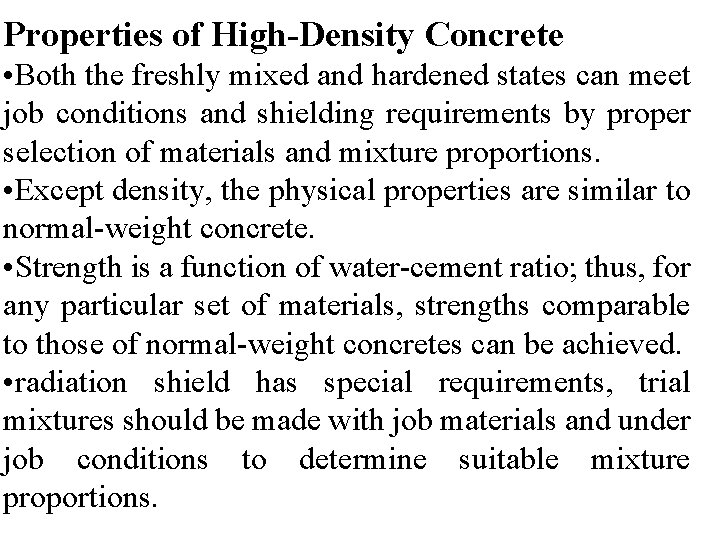
Properties of High-Density Concrete • Both the freshly mixed and hardened states can meet job conditions and shielding requirements by proper selection of materials and mixture proportions. • Except density, the physical properties are similar to normal-weight concrete. • Strength is a function of water-cement ratio; thus, for any particular set of materials, strengths comparable to those of normal-weight concretes can be achieved. • radiation shield has special requirements, trial mixtures should be made with job materials and under job conditions to determine suitable mixture proportions.
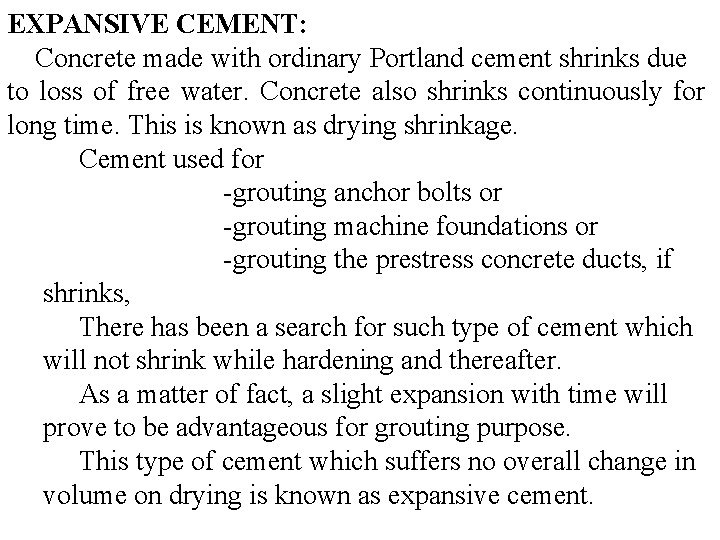
EXPANSIVE CEMENT: Concrete made with ordinary Portland cement shrinks due to loss of free water. Concrete also shrinks continuously for long time. This is known as drying shrinkage. Cement used for -grouting anchor bolts or -grouting machine foundations or -grouting the prestress concrete ducts, if shrinks, There has been a search for such type of cement which will not shrink while hardening and thereafter. As a matter of fact, a slight expansion with time will prove to be advantageous for grouting purpose. This type of cement which suffers no overall change in volume on drying is known as expansive cement.
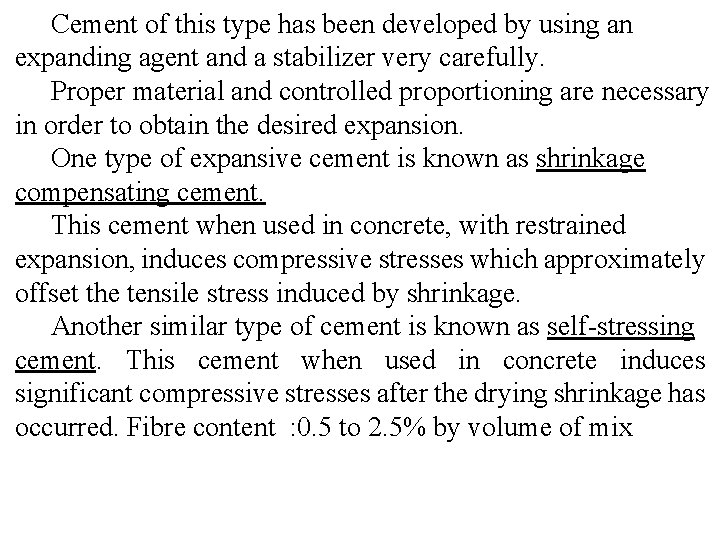
Cement of this type has been developed by using an expanding agent and a stabilizer very carefully. Proper material and controlled proportioning are necessary in order to obtain the desired expansion. One type of expansive cement is known as shrinkage compensating cement. This cement when used in concrete, with restrained expansion, induces compressive stresses which approximately offset the tensile stress induced by shrinkage. Another similar type of cement is known as self-stressing cement. This cement when used in concrete induces significant compressive stresses after the drying shrinkage has occurred. Fibre content : 0. 5 to 2. 5% by volume of mix
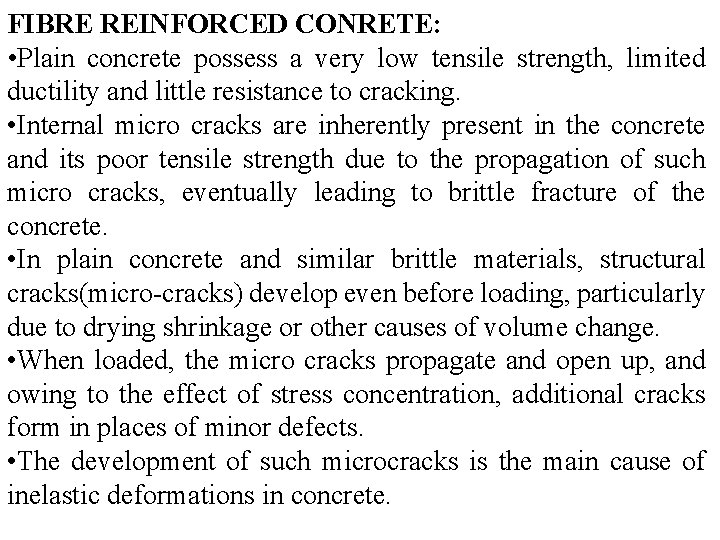
FIBRE REINFORCED CONRETE: • Plain concrete possess a very low tensile strength, limited ductility and little resistance to cracking. • Internal micro cracks are inherently present in the concrete and its poor tensile strength due to the propagation of such micro cracks, eventually leading to brittle fracture of the concrete. • In plain concrete and similar brittle materials, structural cracks(micro-cracks) develop even before loading, particularly due to drying shrinkage or other causes of volume change. • When loaded, the micro cracks propagate and open up, and owing to the effect of stress concentration, additional cracks form in places of minor defects. • The development of such microcracks is the main cause of inelastic deformations in concrete.
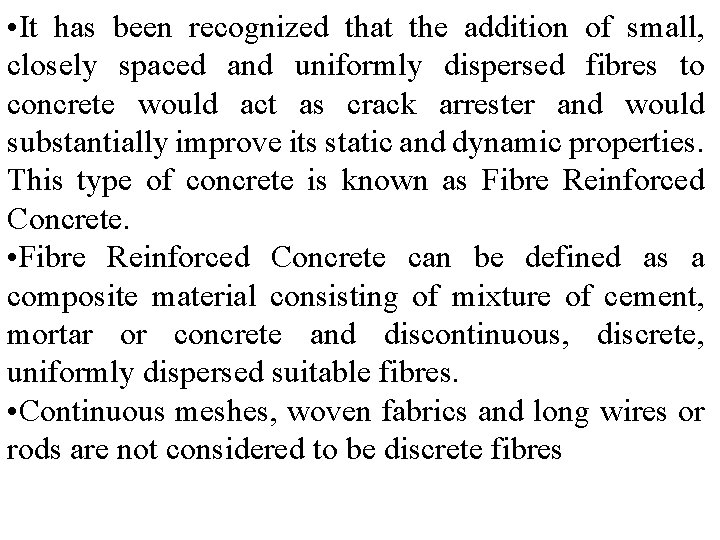
• It has been recognized that the addition of small, closely spaced and uniformly dispersed fibres to concrete would act as crack arrester and would substantially improve its static and dynamic properties. This type of concrete is known as Fibre Reinforced Concrete. • Fibre Reinforced Concrete can be defined as a composite material consisting of mixture of cement, mortar or concrete and discontinuous, discrete, uniformly dispersed suitable fibres. • Continuous meshes, woven fabrics and long wires or rods are not considered to be discrete fibres
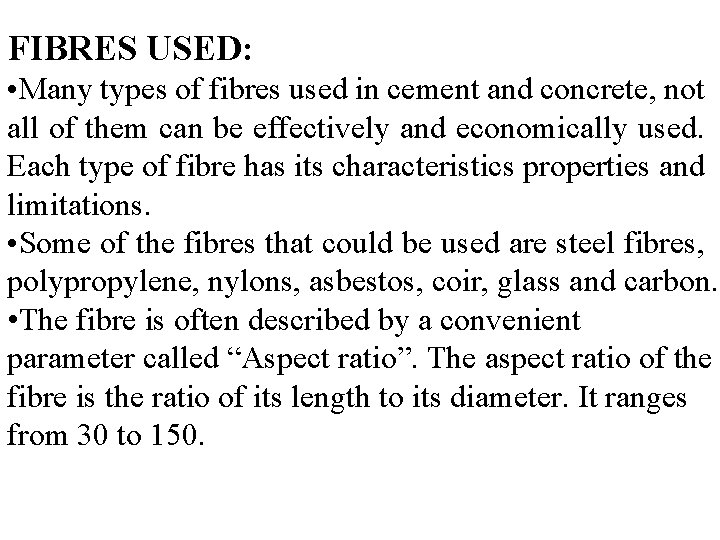
FIBRES USED: • Many types of fibres used in cement and concrete, not all of them can be effectively and economically used. Each type of fibre has its characteristics properties and limitations. • Some of the fibres that could be used are steel fibres, polypropylene, nylons, asbestos, coir, glass and carbon. • The fibre is often described by a convenient parameter called “Aspect ratio”. The aspect ratio of the fibre is the ratio of its length to its diameter. It ranges from 30 to 150.
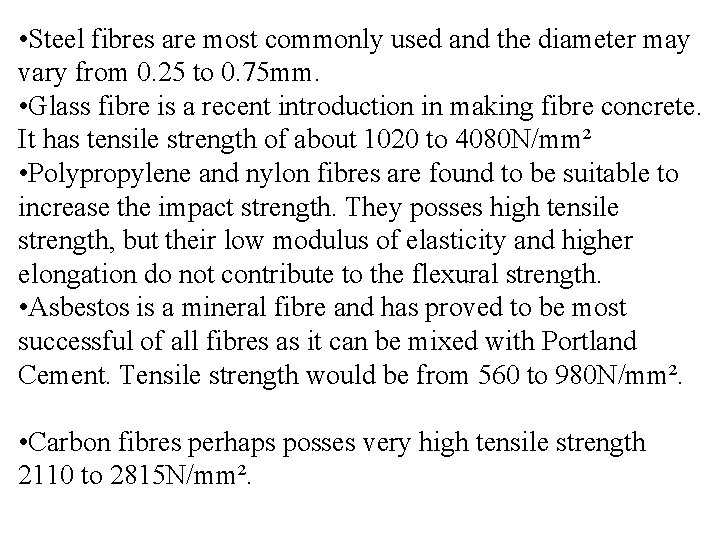
• Steel fibres are most commonly used and the diameter may vary from 0. 25 to 0. 75 mm. • Glass fibre is a recent introduction in making fibre concrete. It has tensile strength of about 1020 to 4080 N/mm² • Polypropylene and nylon fibres are found to be suitable to increase the impact strength. They posses high tensile strength, but their low modulus of elasticity and higher elongation do not contribute to the flexural strength. • Asbestos is a mineral fibre and has proved to be most successful of all fibres as it can be mixed with Portland Cement. Tensile strength would be from 560 to 980 N/mm². • Carbon fibres perhaps posses very high tensile strength 2110 to 2815 N/mm².
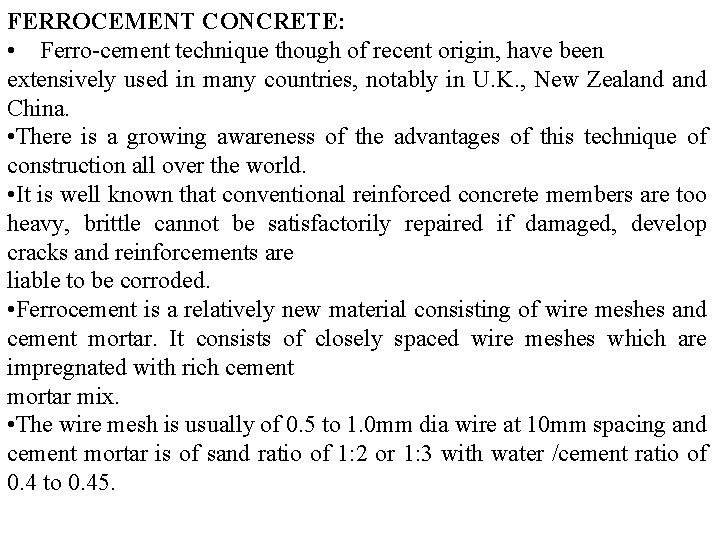
FERROCEMENT CONCRETE: • Ferro-cement technique though of recent origin, have been extensively used in many countries, notably in U. K. , New Zealand China. • There is a growing awareness of the advantages of this technique of construction all over the world. • It is well known that conventional reinforced concrete members are too heavy, brittle cannot be satisfactorily repaired if damaged, develop cracks and reinforcements are liable to be corroded. • Ferrocement is a relatively new material consisting of wire meshes and cement mortar. It consists of closely spaced wire meshes which are impregnated with rich cement mortar mix. • The wire mesh is usually of 0. 5 to 1. 0 mm dia wire at 10 mm spacing and cement mortar is of sand ratio of 1: 2 or 1: 3 with water /cement ratio of 0. 4 to 0. 45.
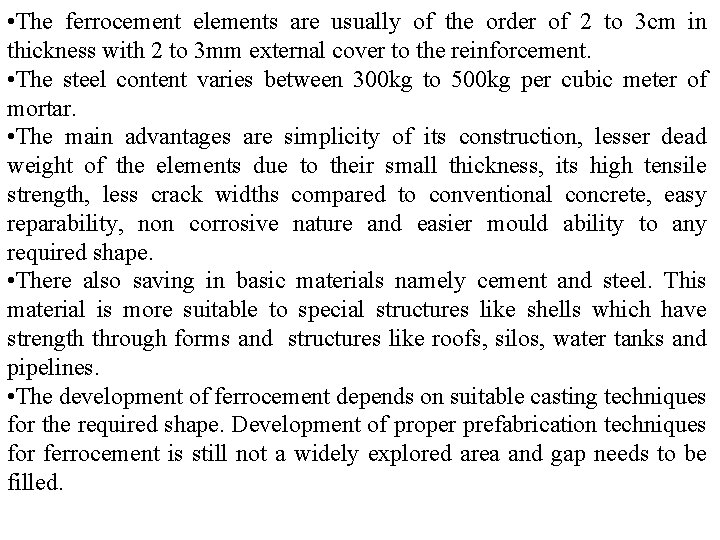
• The ferrocement elements are usually of the order of 2 to 3 cm in thickness with 2 to 3 mm external cover to the reinforcement. • The steel content varies between 300 kg to 500 kg per cubic meter of mortar. • The main advantages are simplicity of its construction, lesser dead weight of the elements due to their small thickness, its high tensile strength, less crack widths compared to conventional concrete, easy reparability, non corrosive nature and easier mould ability to any required shape. • There also saving in basic materials namely cement and steel. This material is more suitable to special structures like shells which have strength through forms and structures like roofs, silos, water tanks and pipelines. • The development of ferrocement depends on suitable casting techniques for the required shape. Development of proper prefabrication techniques for ferrocement is still not a widely explored area and gap needs to be filled.
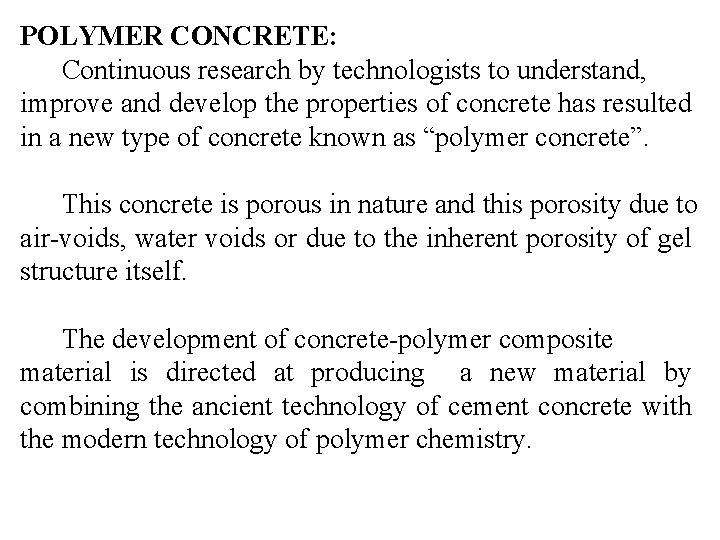
POLYMER CONCRETE: Continuous research by technologists to understand, improve and develop the properties of concrete has resulted in a new type of concrete known as “polymer concrete”. This concrete is porous in nature and this porosity due to air-voids, water voids or due to the inherent porosity of gel structure itself. The development of concrete-polymer composite material is directed at producing a new material by combining the ancient technology of cement concrete with the modern technology of polymer chemistry.
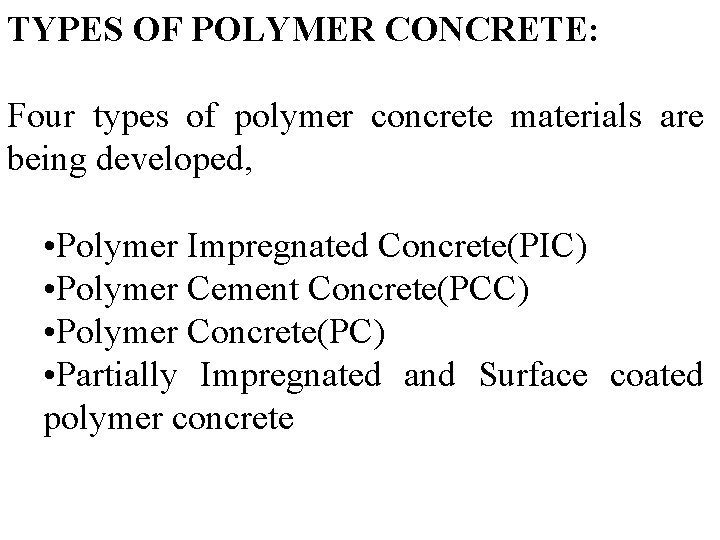
TYPES OF POLYMER CONCRETE: Four types of polymer concrete materials are being developed, • Polymer Impregnated Concrete(PIC) • Polymer Cement Concrete(PCC) • Polymer Concrete(PC) • Partially Impregnated and Surface coated polymer concrete
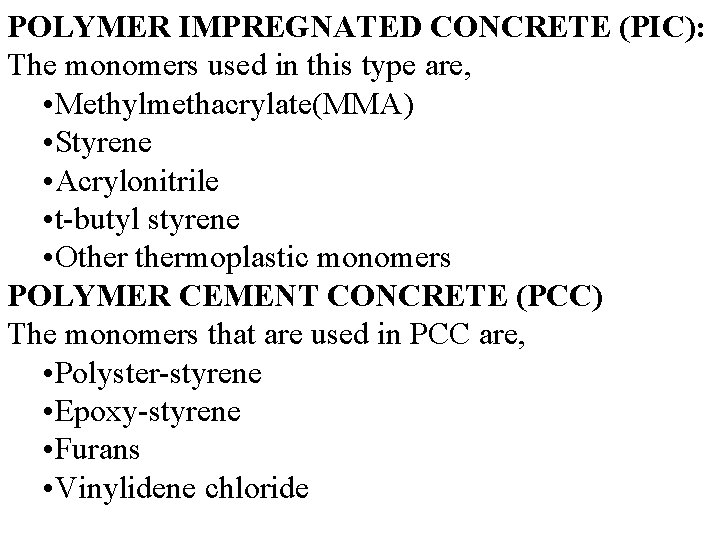
POLYMER IMPREGNATED CONCRETE (PIC): The monomers used in this type are, • Methylmethacrylate(MMA) • Styrene • Acrylonitrile • t-butyl styrene • Othermoplastic monomers POLYMER CEMENT CONCRETE (PCC) The monomers that are used in PCC are, • Polyster-styrene • Epoxy-styrene • Furans • Vinylidene chloride
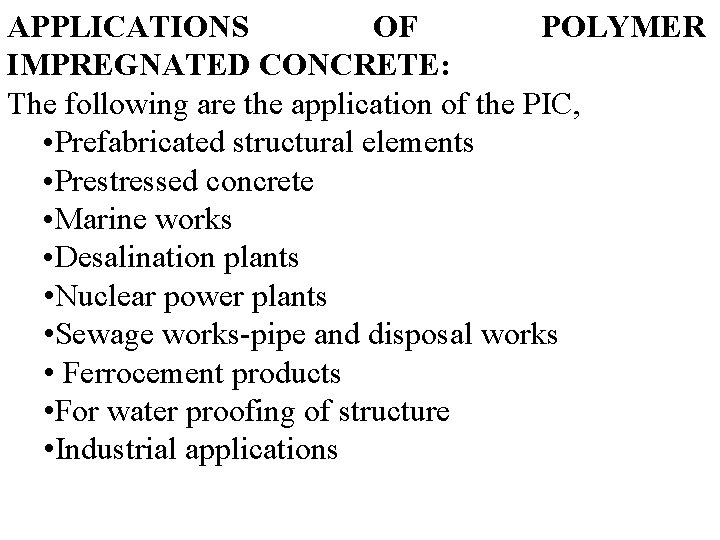
APPLICATIONS OF POLYMER IMPREGNATED CONCRETE: The following are the application of the PIC, • Prefabricated structural elements • Prestressed concrete • Marine works • Desalination plants • Nuclear power plants • Sewage works-pipe and disposal works • Ferrocement products • For water proofing of structure • Industrial applications
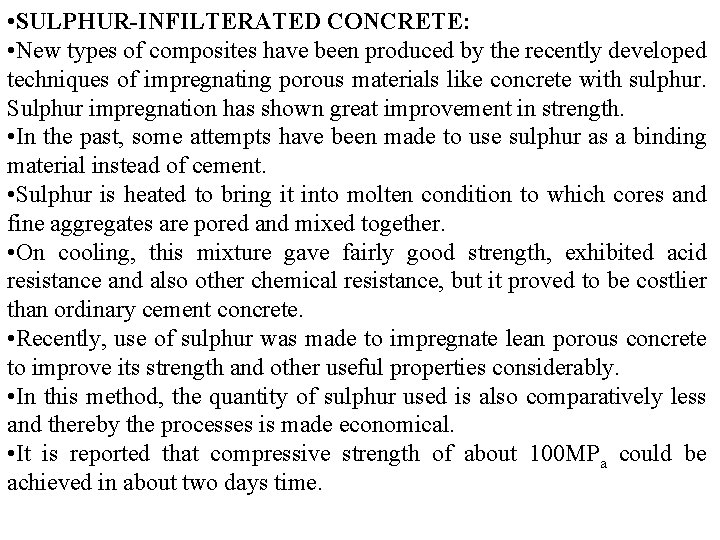
• SULPHUR-INFILTERATED CONCRETE: • New types of composites have been produced by the recently developed techniques of impregnating porous materials like concrete with sulphur. Sulphur impregnation has shown great improvement in strength. • In the past, some attempts have been made to use sulphur as a binding material instead of cement. • Sulphur is heated to bring it into molten condition to which cores and fine aggregates are pored and mixed together. • On cooling, this mixture gave fairly good strength, exhibited acid resistance and also other chemical resistance, but it proved to be costlier than ordinary cement concrete. • Recently, use of sulphur was made to impregnate lean porous concrete to improve its strength and other useful properties considerably. • In this method, the quantity of sulphur used is also comparatively less and thereby the processes is made economical. • It is reported that compressive strength of about 100 MPa could be achieved in about two days time.
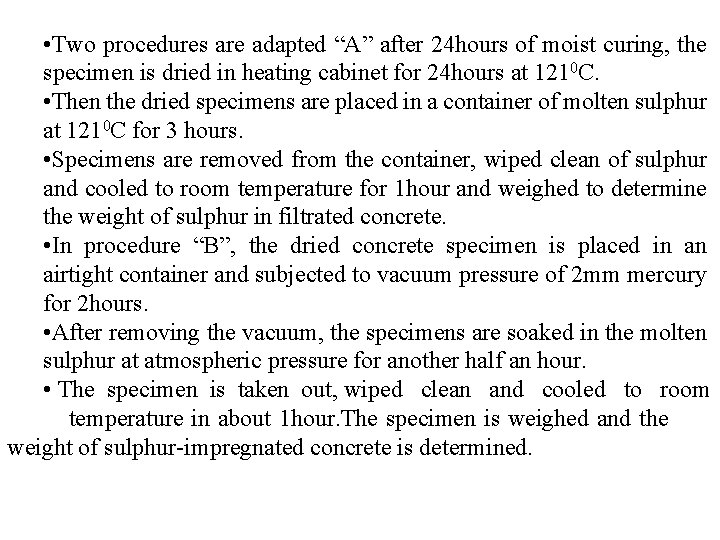
• Two procedures are adapted “A” after 24 hours of moist curing, the specimen is dried in heating cabinet for 24 hours at 1210 C. • Then the dried specimens are placed in a container of molten sulphur at 1210 C for 3 hours. • Specimens are removed from the container, wiped clean of sulphur and cooled to room temperature for 1 hour and weighed to determine the weight of sulphur in filtrated concrete. • In procedure “B”, the dried concrete specimen is placed in an airtight container and subjected to vacuum pressure of 2 mm mercury for 2 hours. • After removing the vacuum, the specimens are soaked in the molten sulphur at atmospheric pressure for another half an hour. • The specimen is taken out, wiped clean and cooled to room temperature in about 1 hour. The specimen is weighed and the weight of sulphur-impregnated concrete is determined.
Design and control of concrete mixtures
Eabassoc
Propiedades fisicoquímicas del agua
Lo similar disuelve lo similar
Members of an avian species of identical plumage congregate
Similar disuelve a similar
Scip panel construction
Informal inventory
Concrete semi concrete abstract
Lightweight rpc
Dartmouth russian
Literal and figurative examples
Honeytoken accounts ata
Lightweight alloys
Lwapp to autonomous
Almmii
Lightweight
Roof truss gusset plates
Slab vs splint
Json xml alternatives
Lightweight vs heavyweight framework