Types of Concrete Need of a concrete Concrete
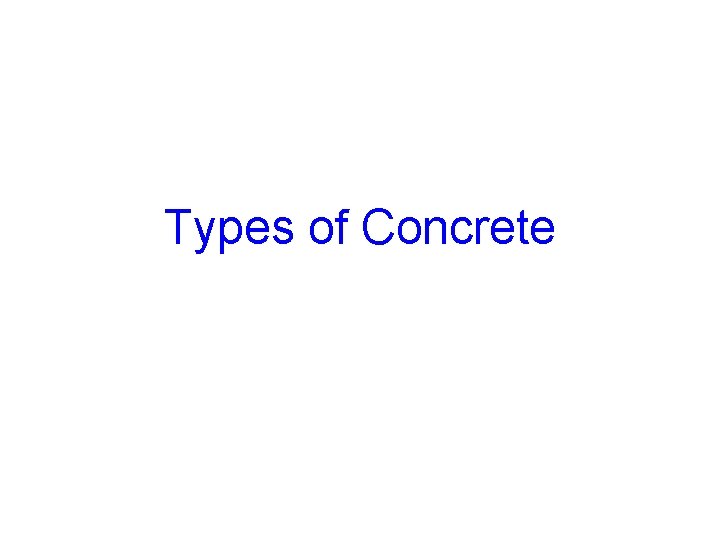
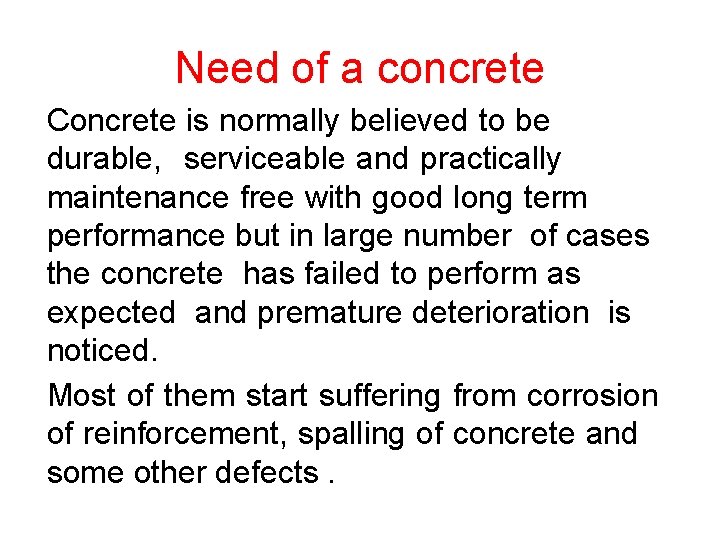
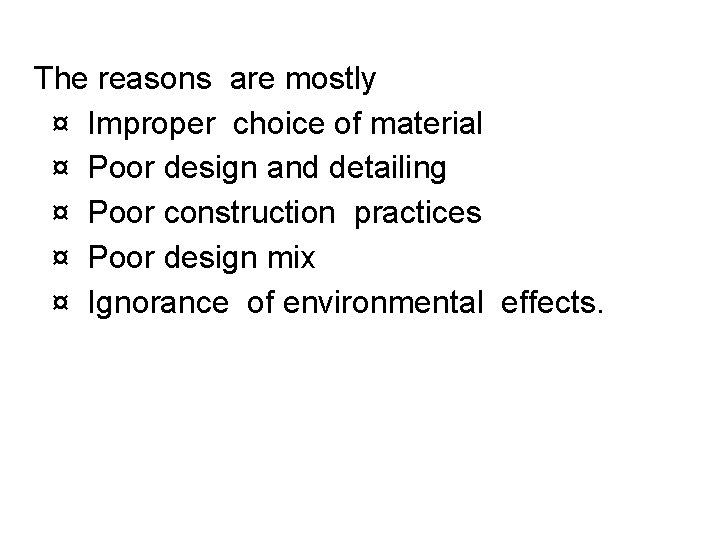
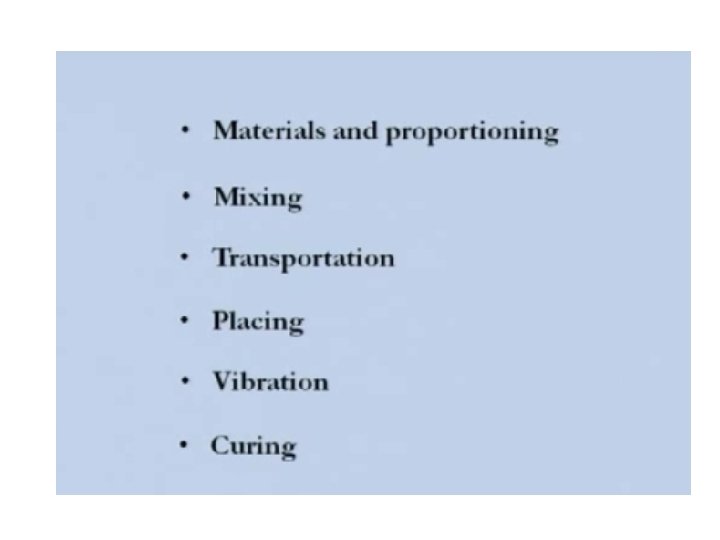
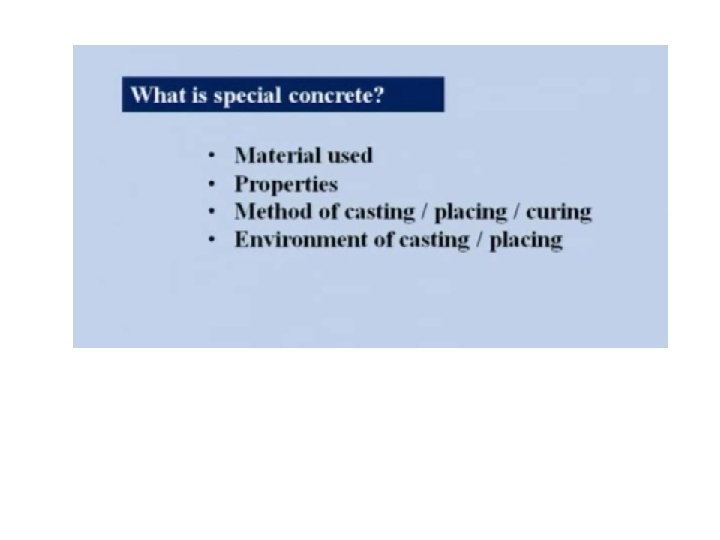
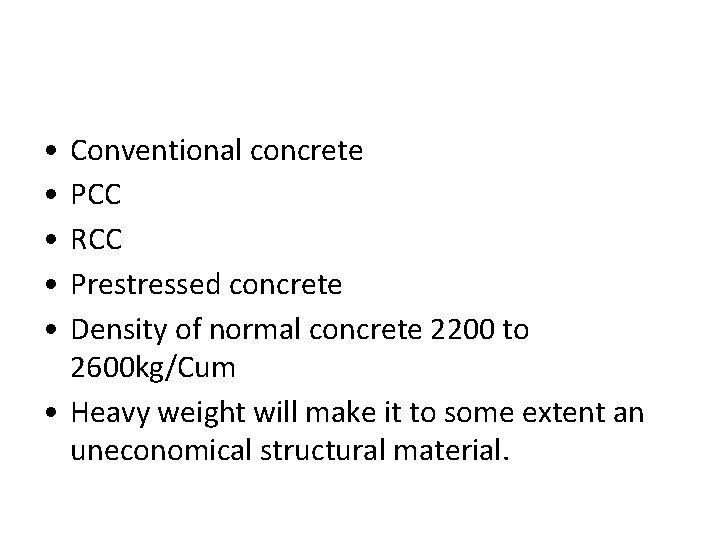
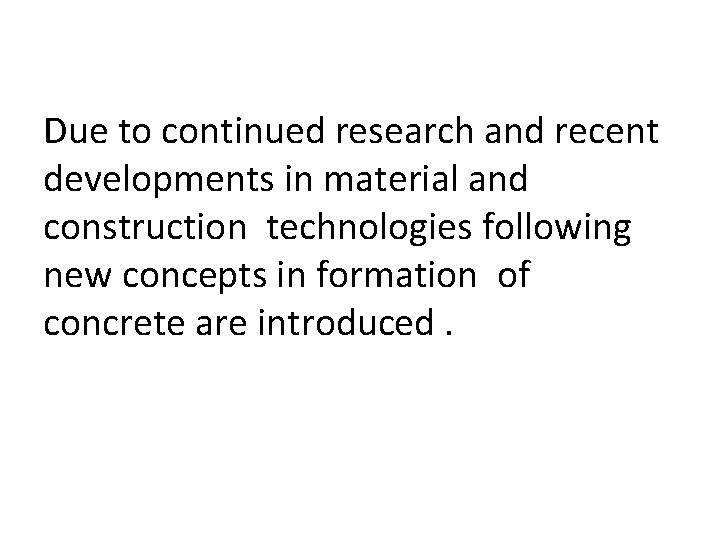
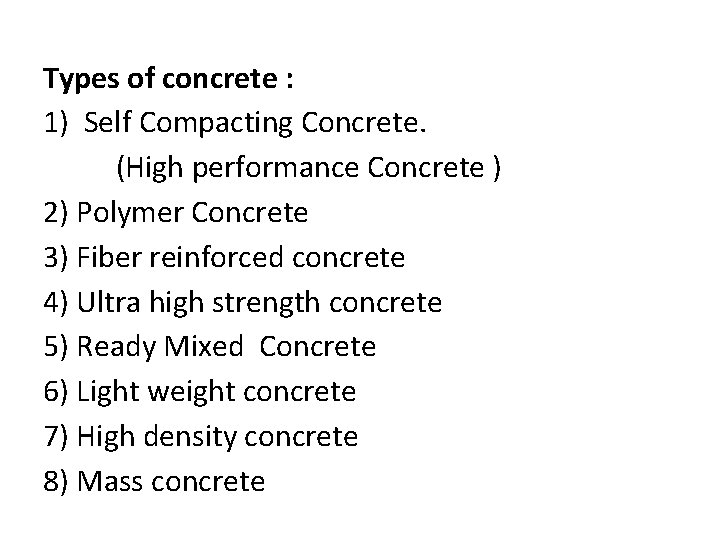
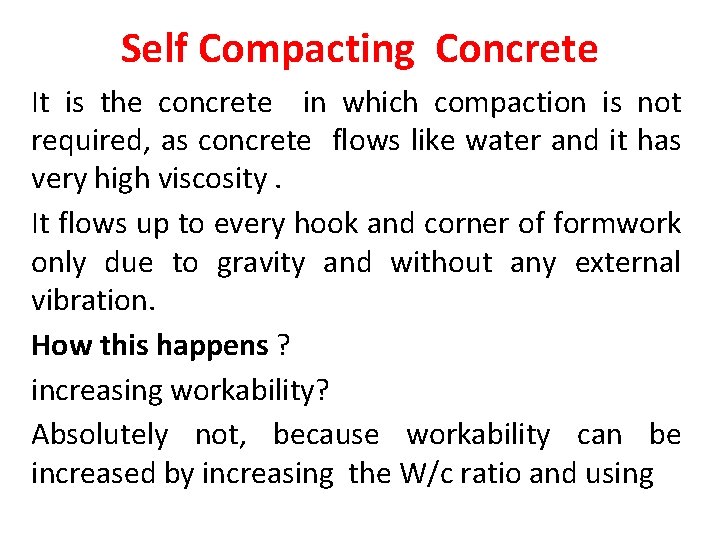
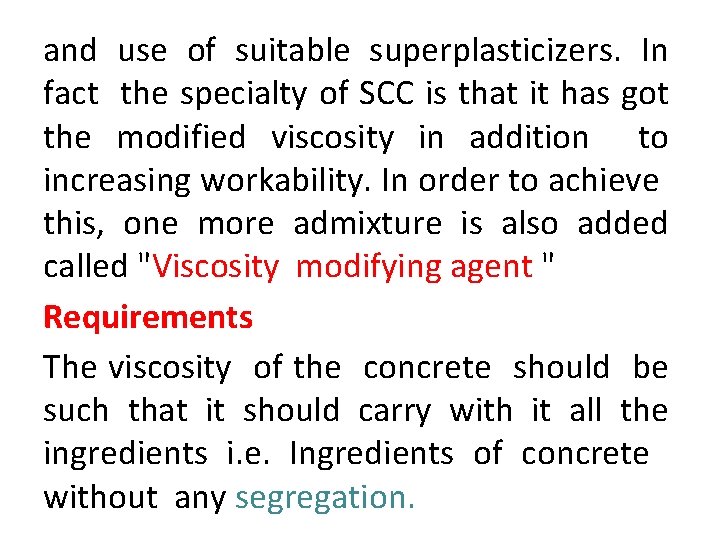
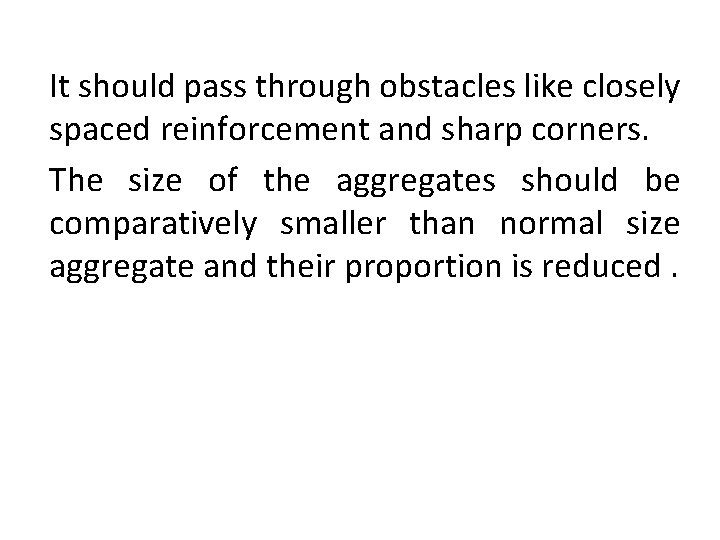
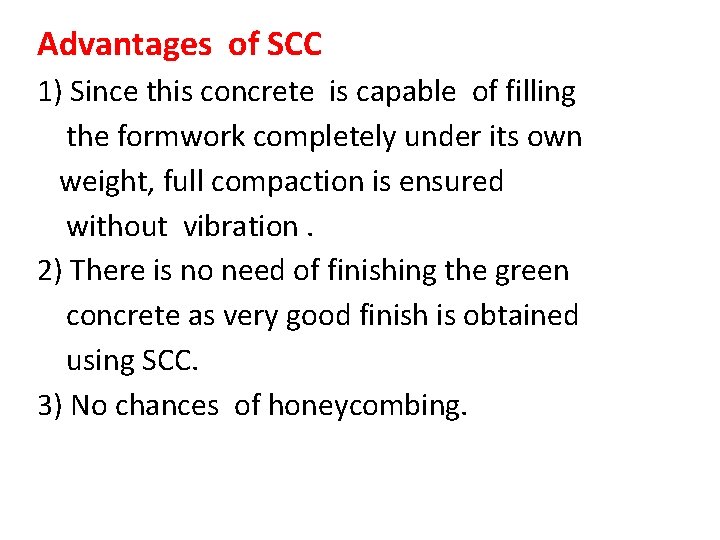
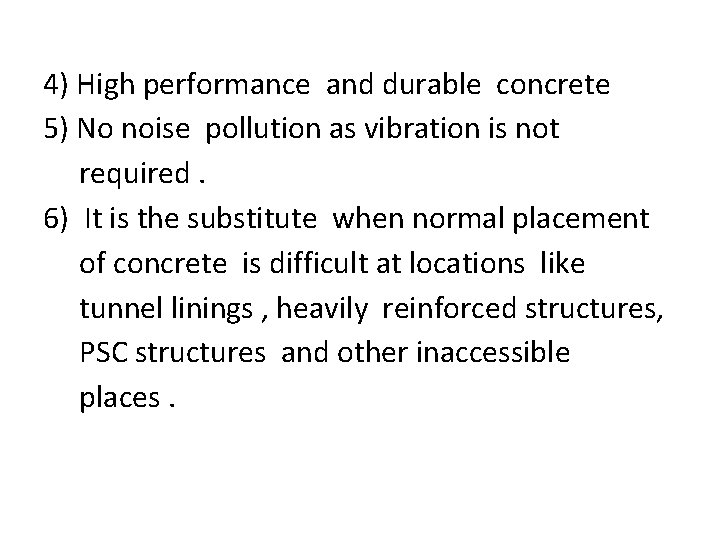
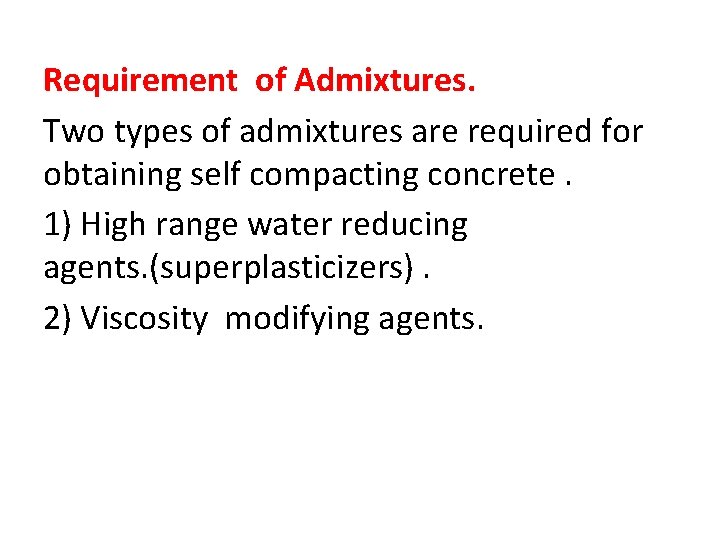
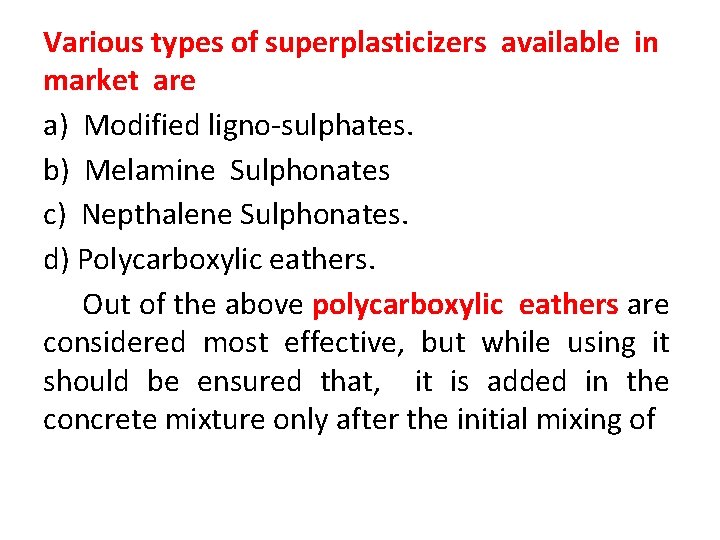
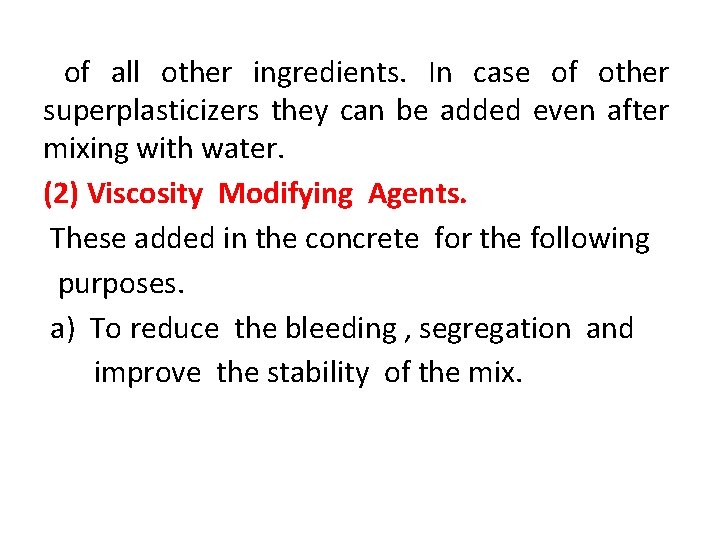
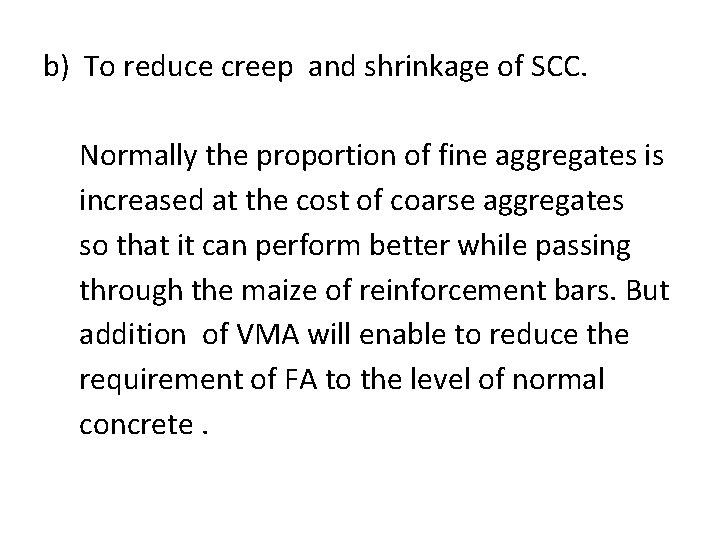
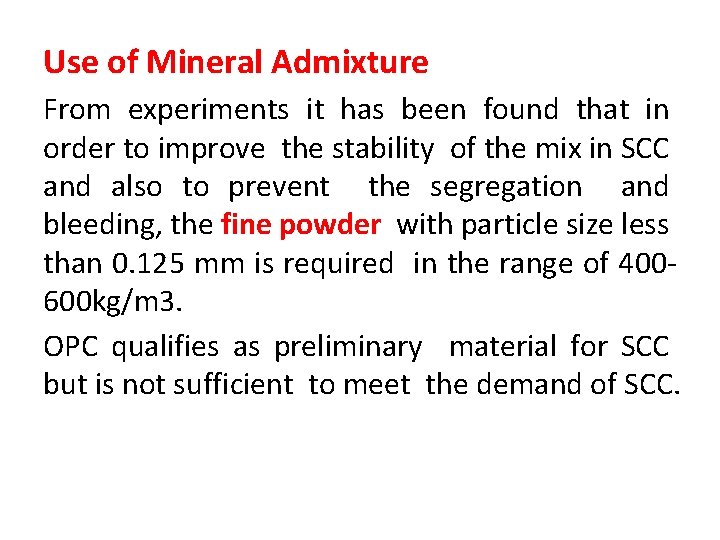
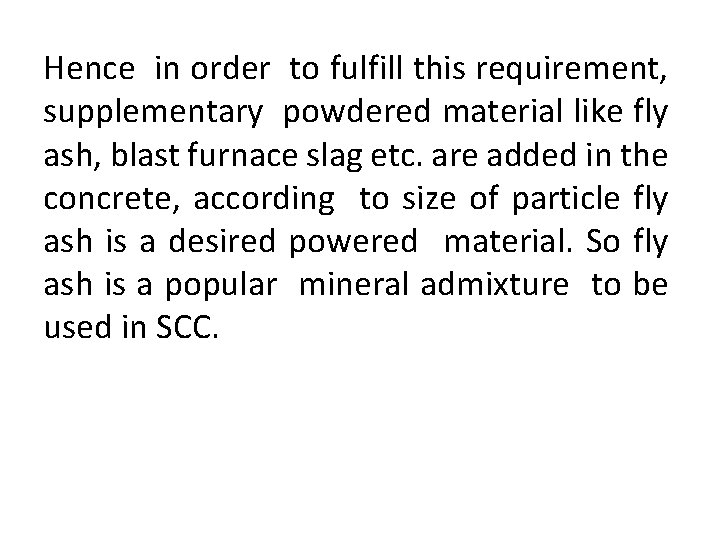
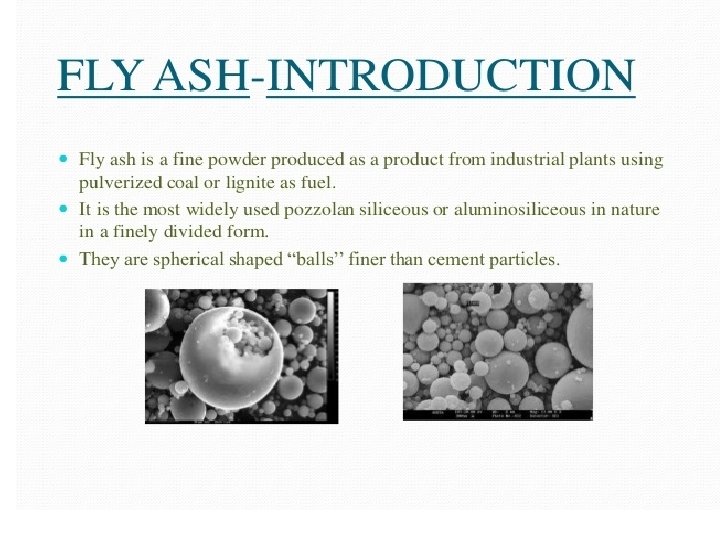
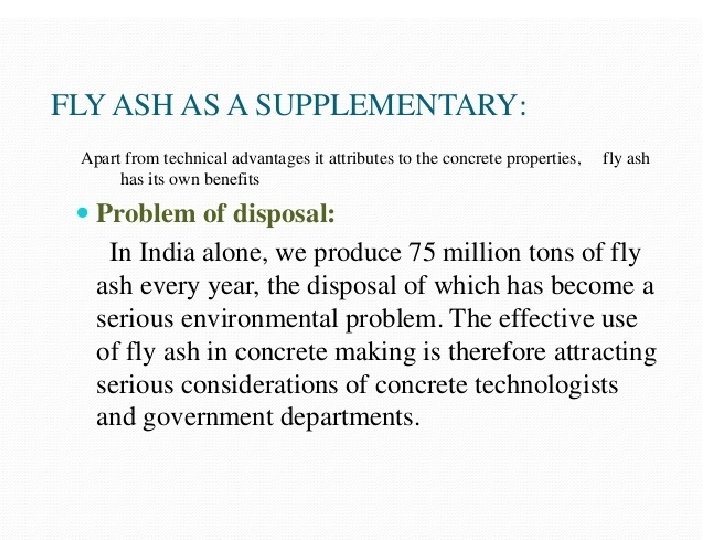
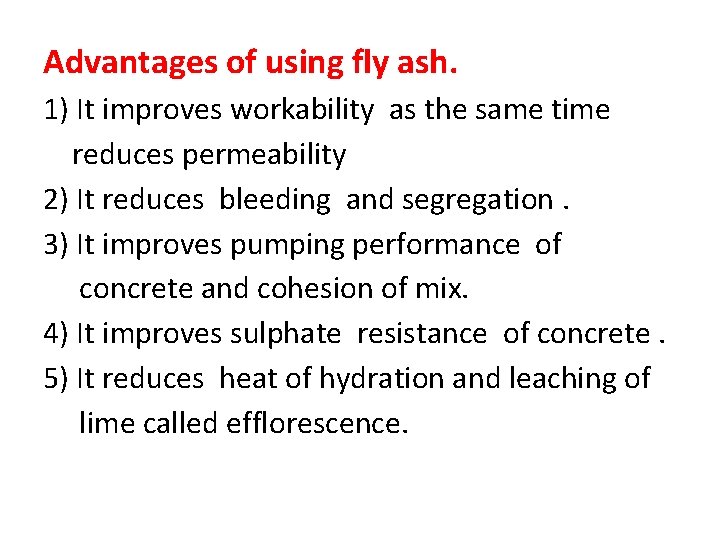
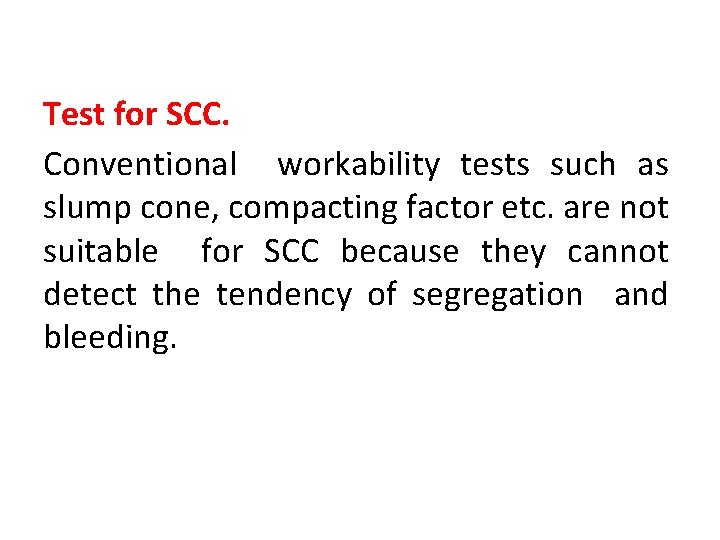
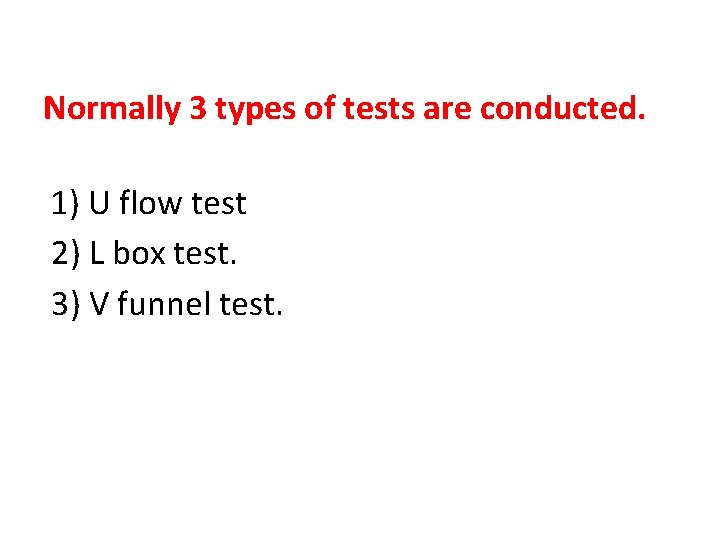
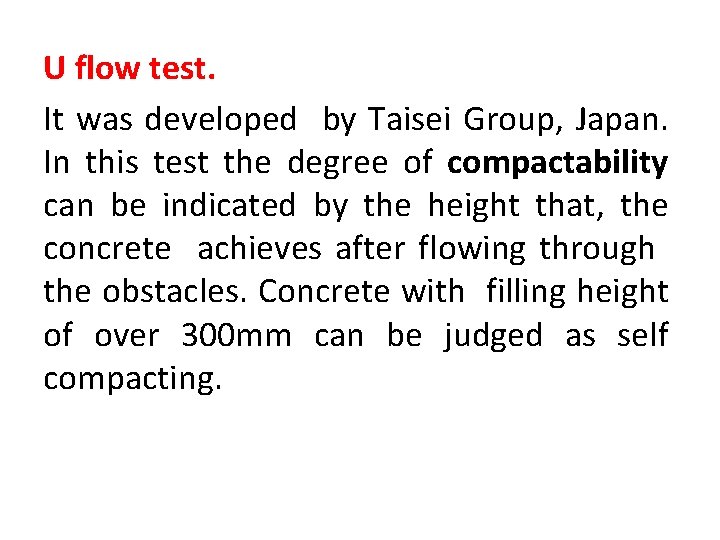
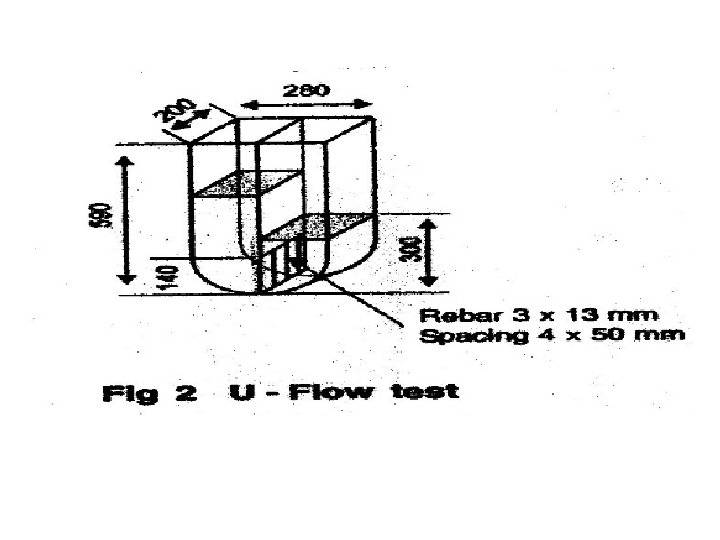
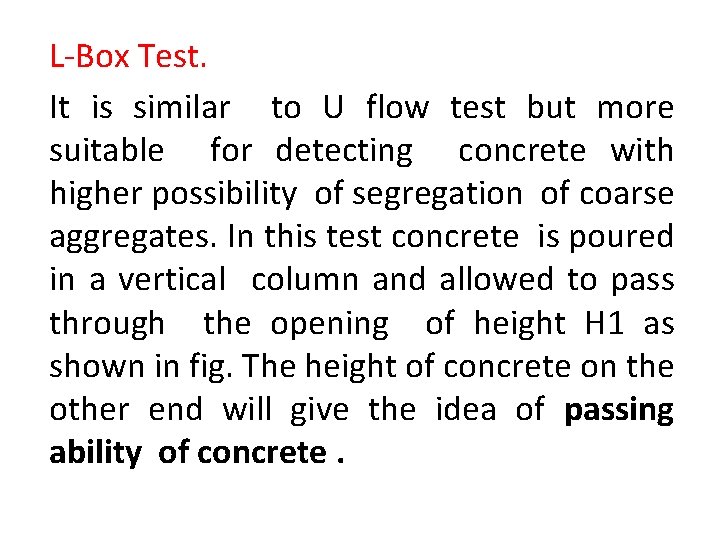
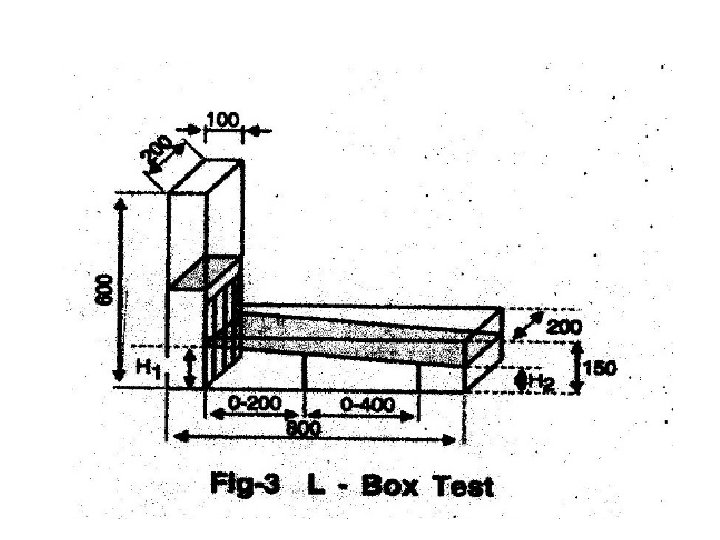
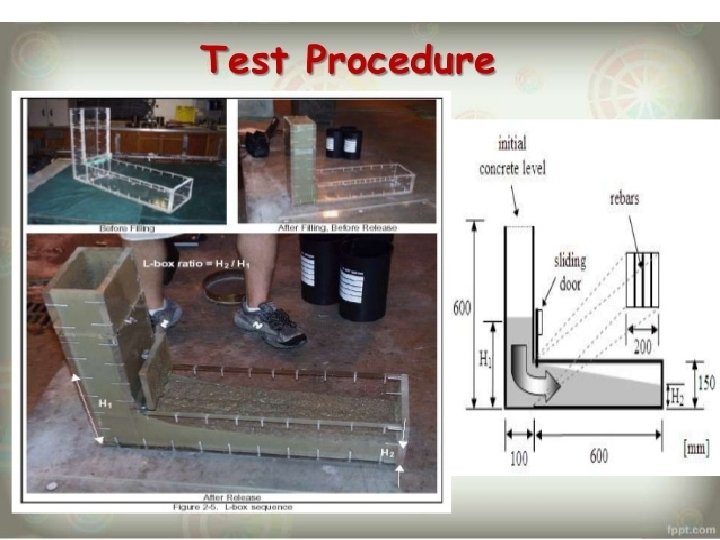
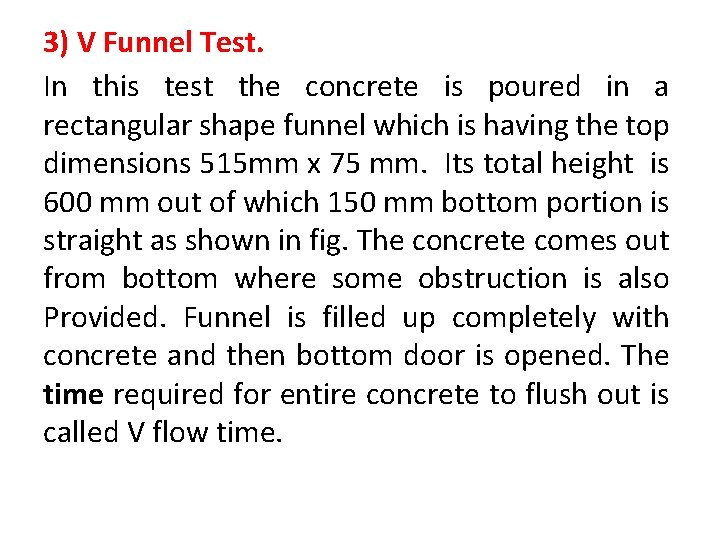
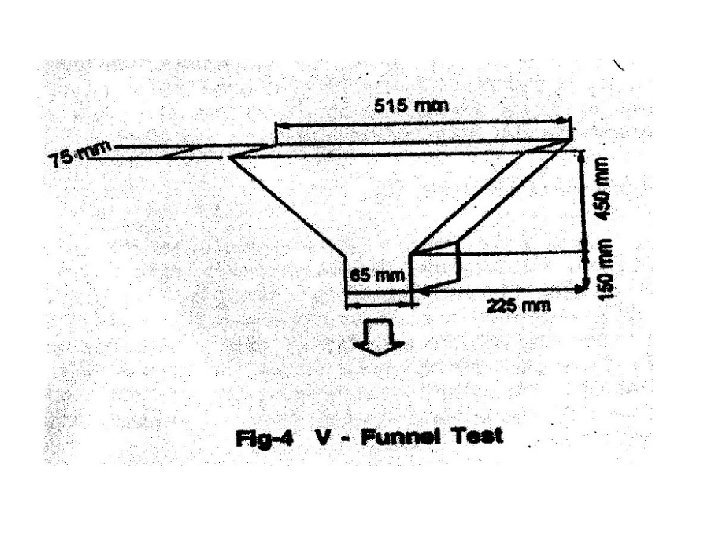
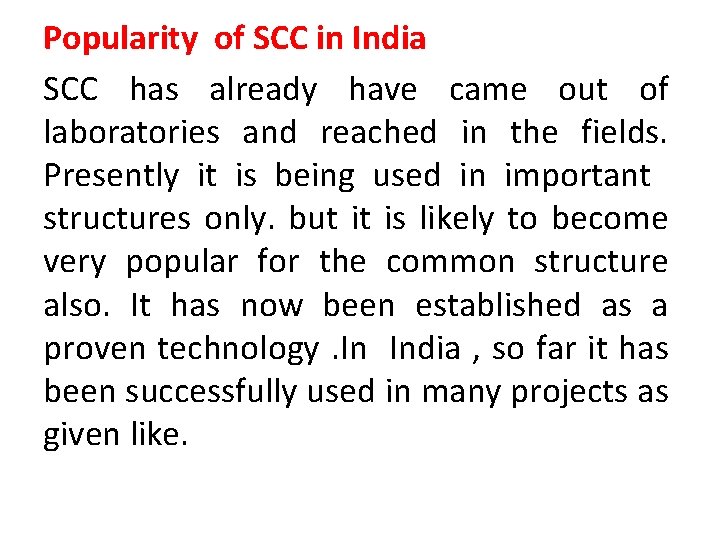
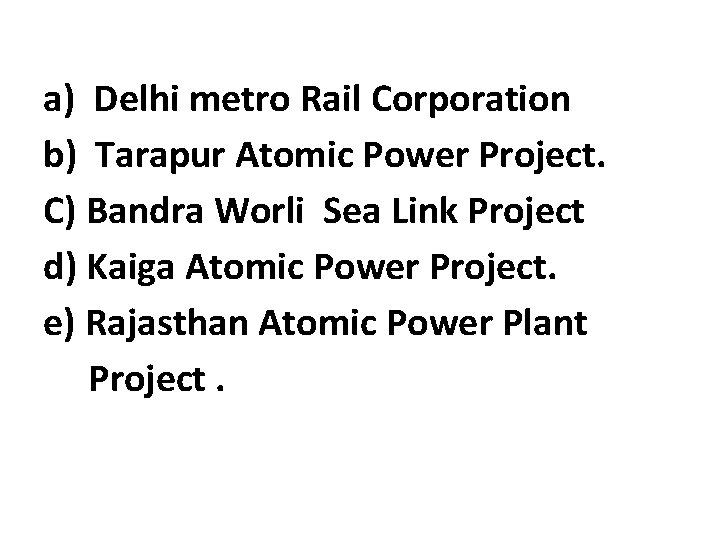
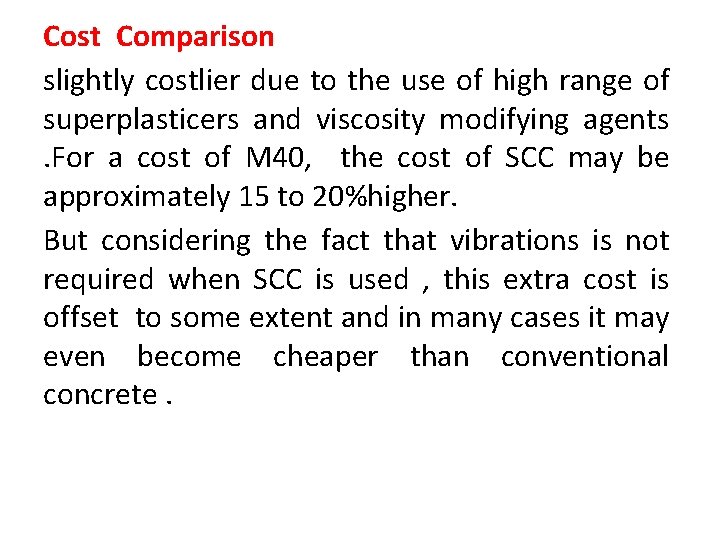
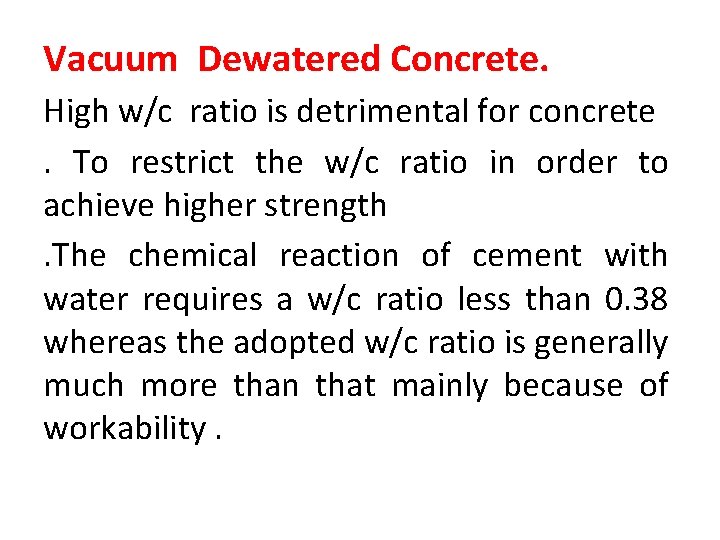

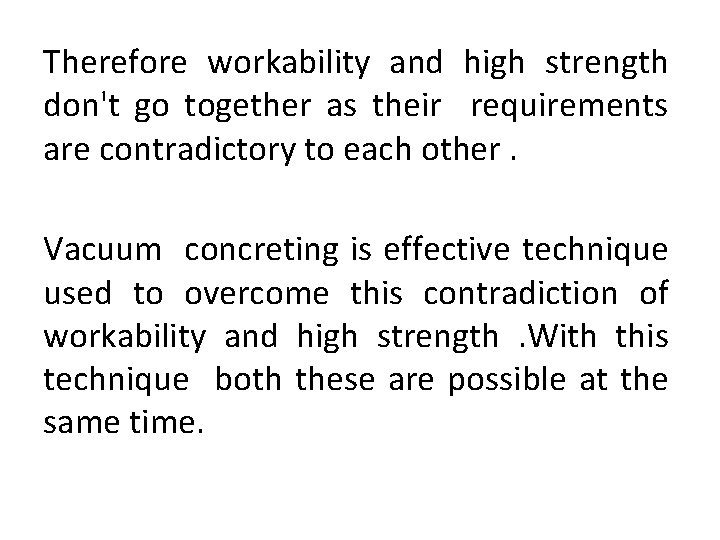
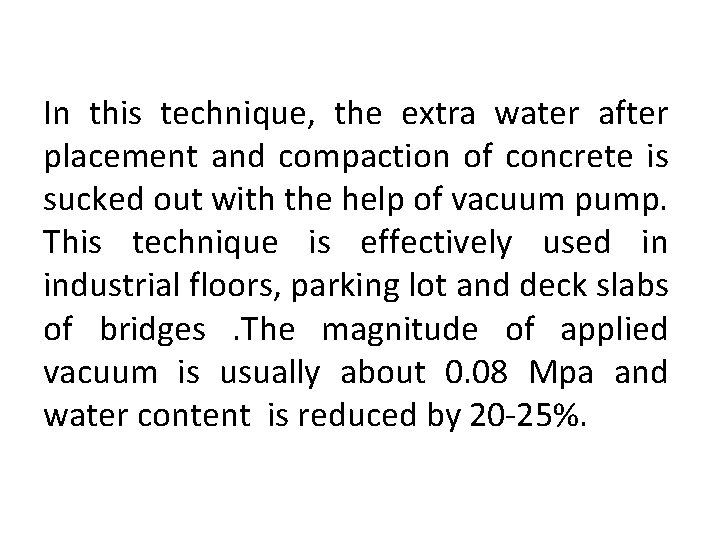
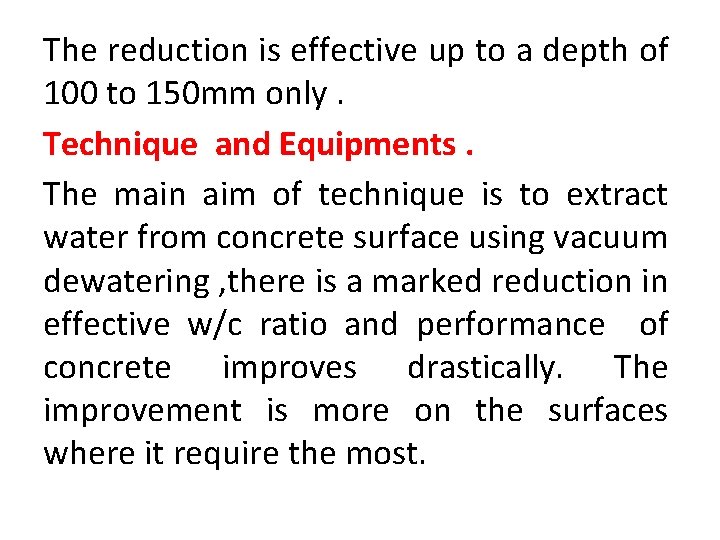
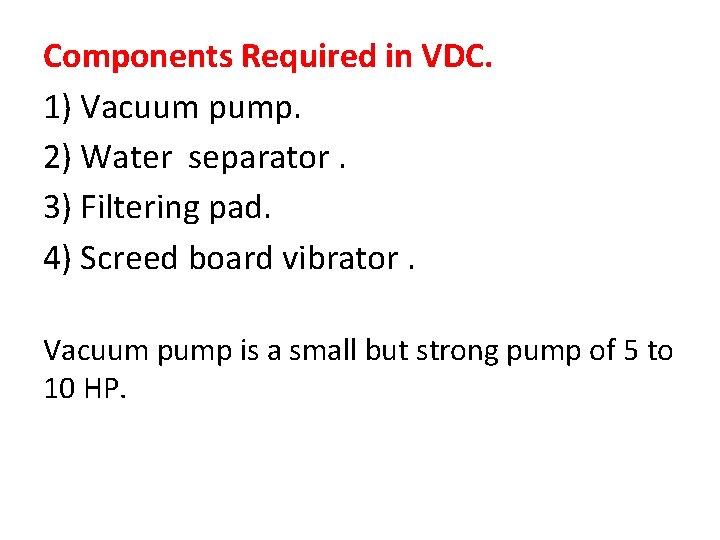
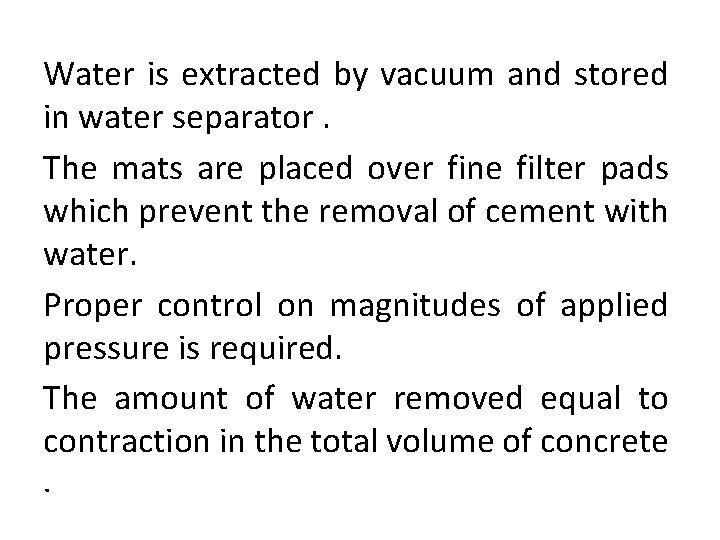
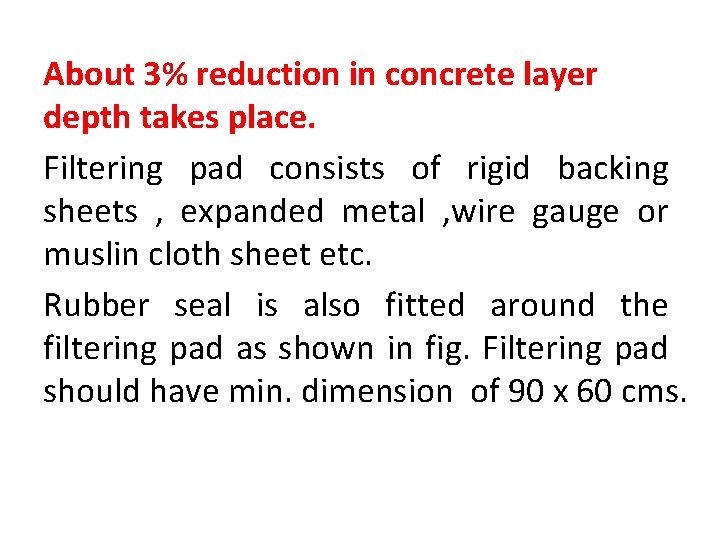
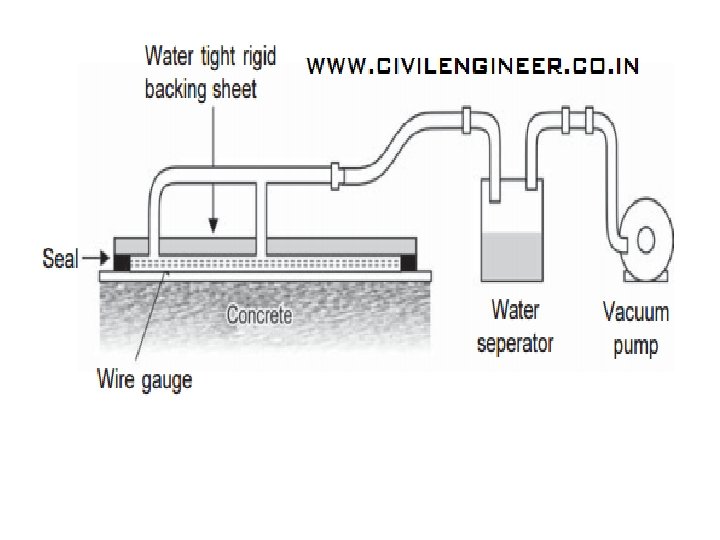
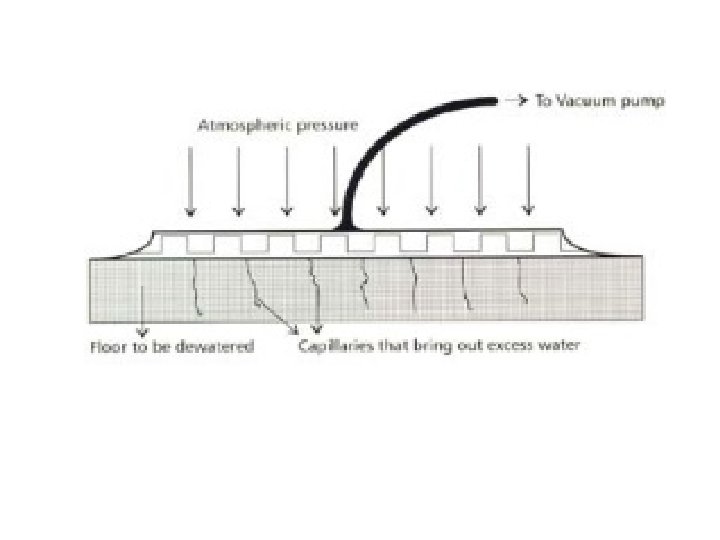
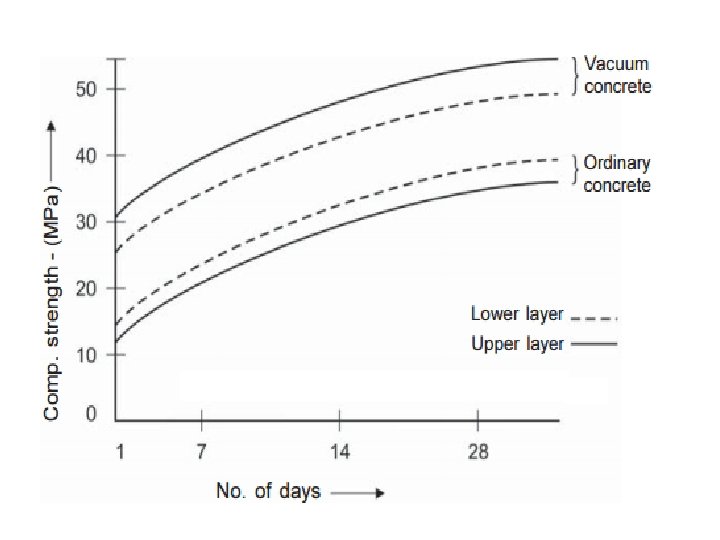
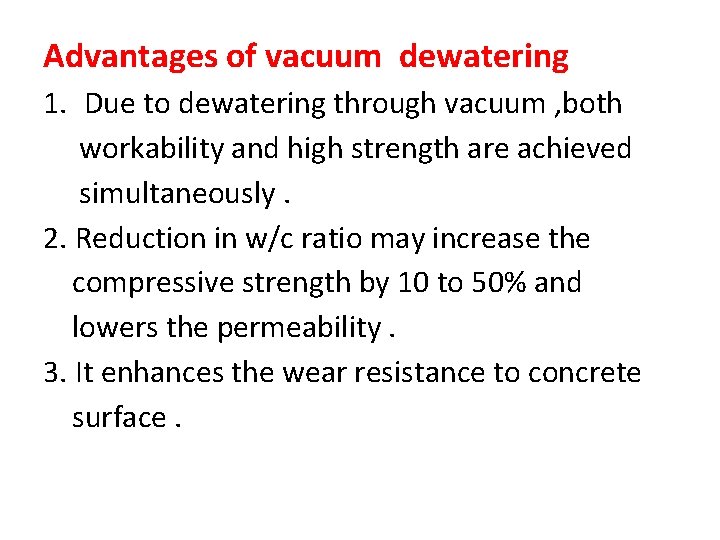
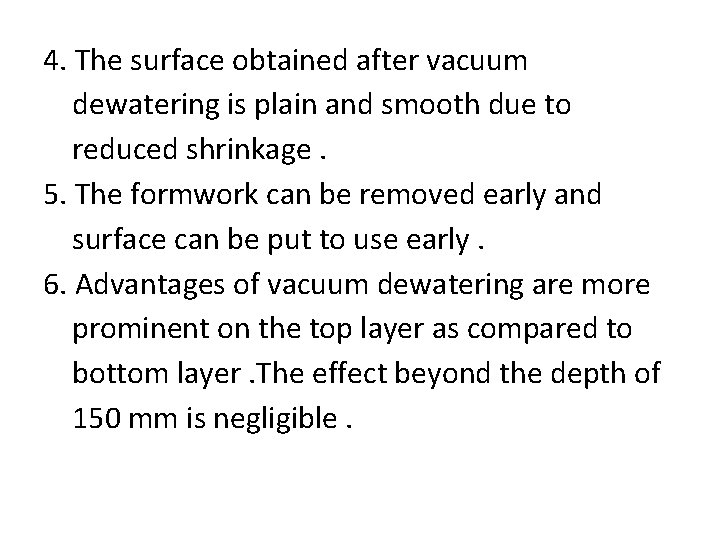
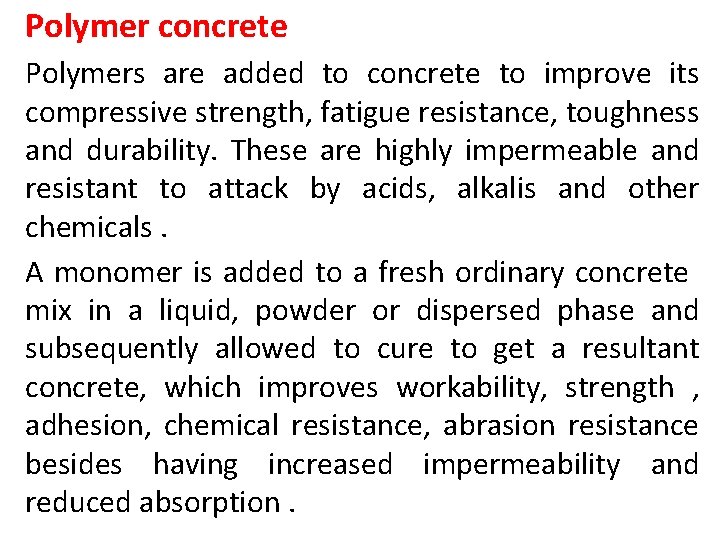

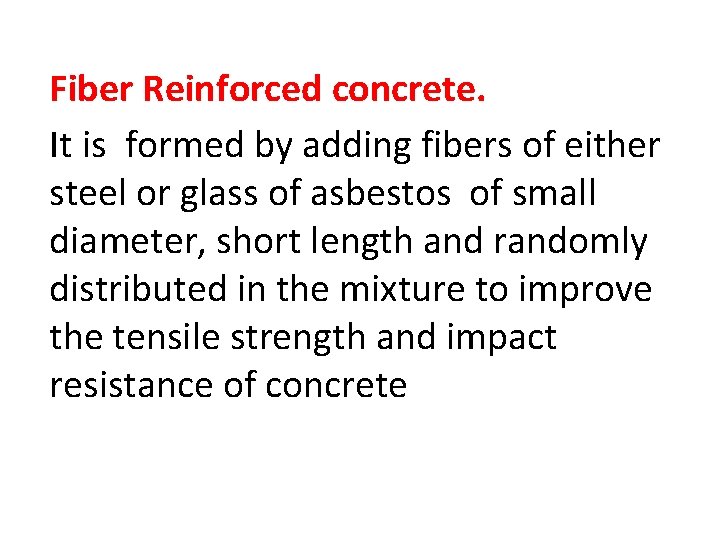
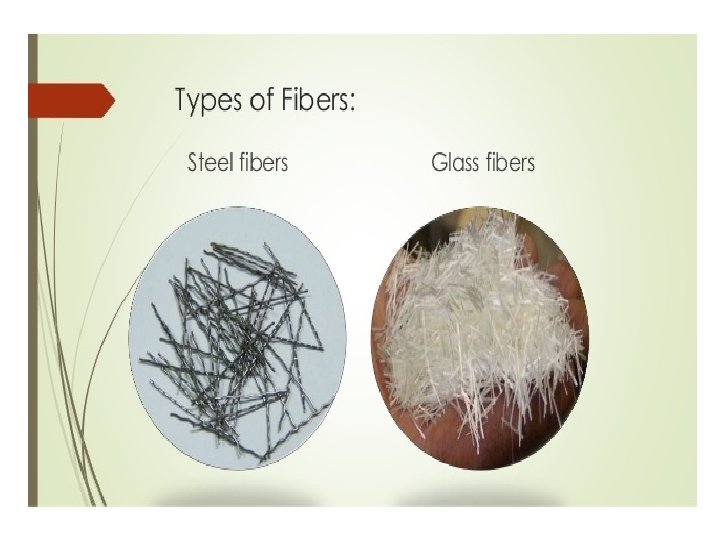
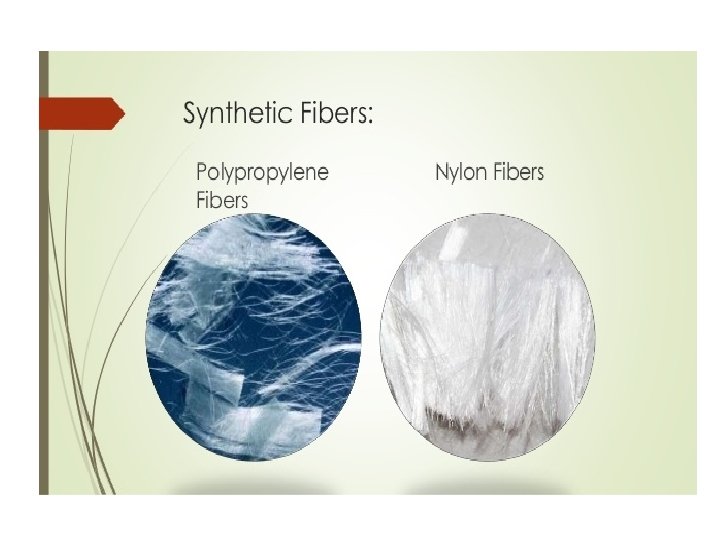
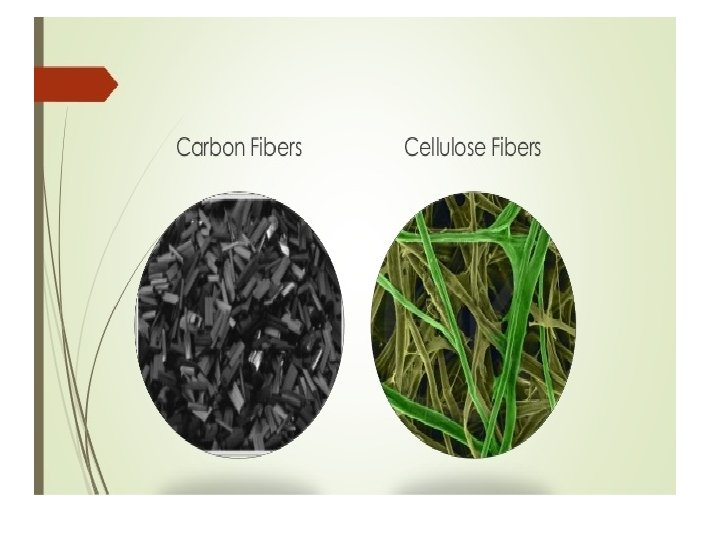
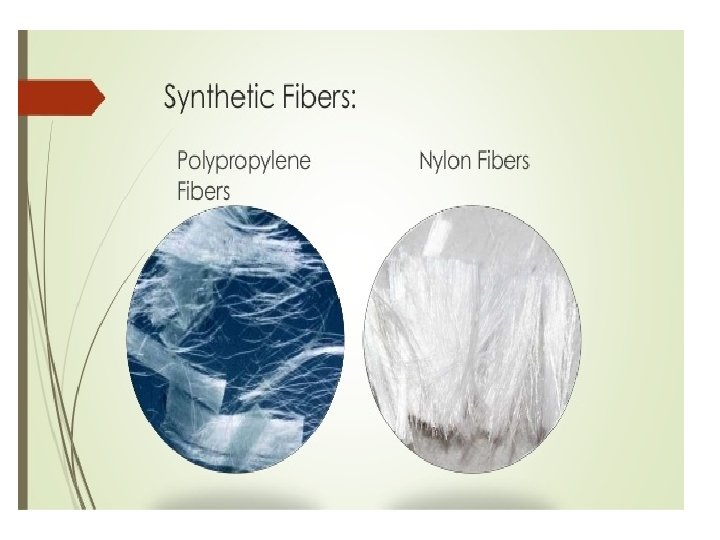
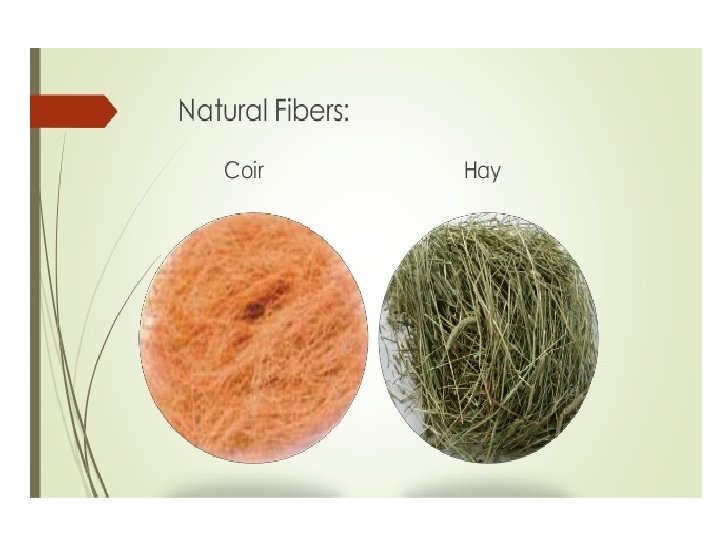
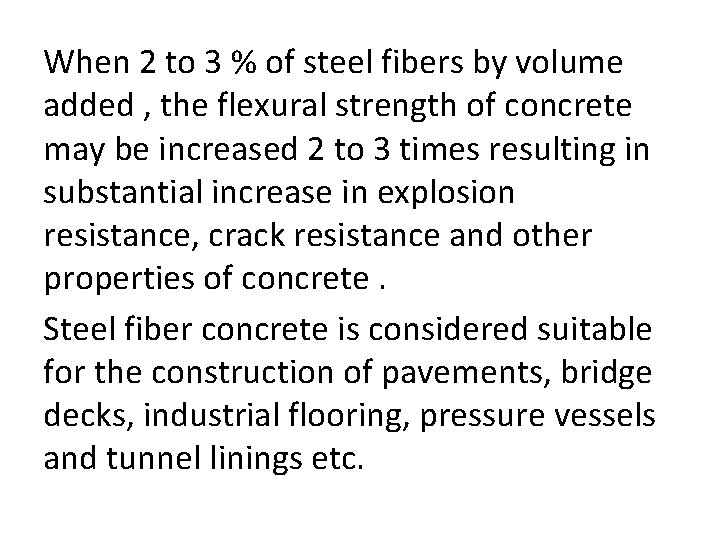
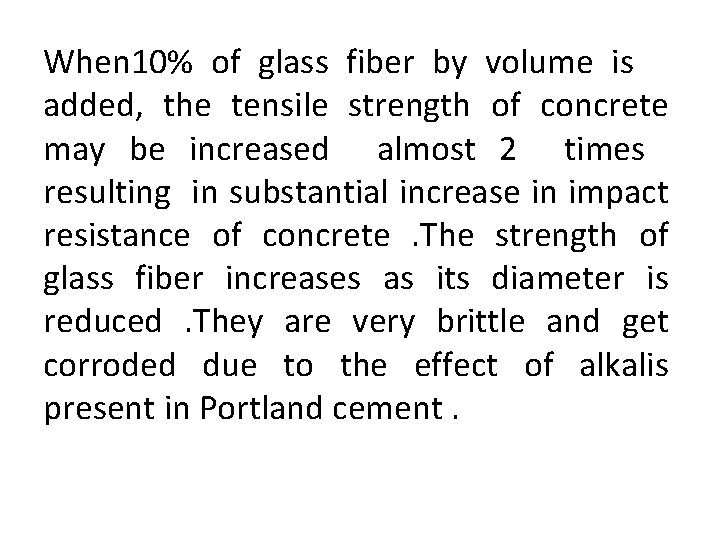
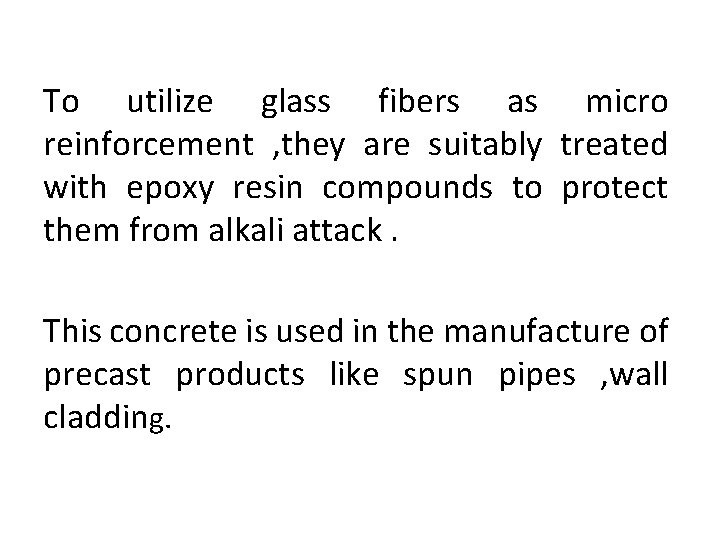
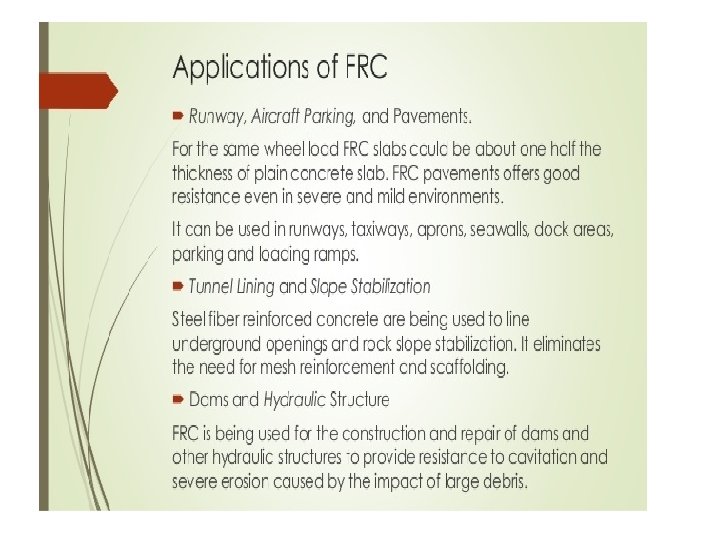
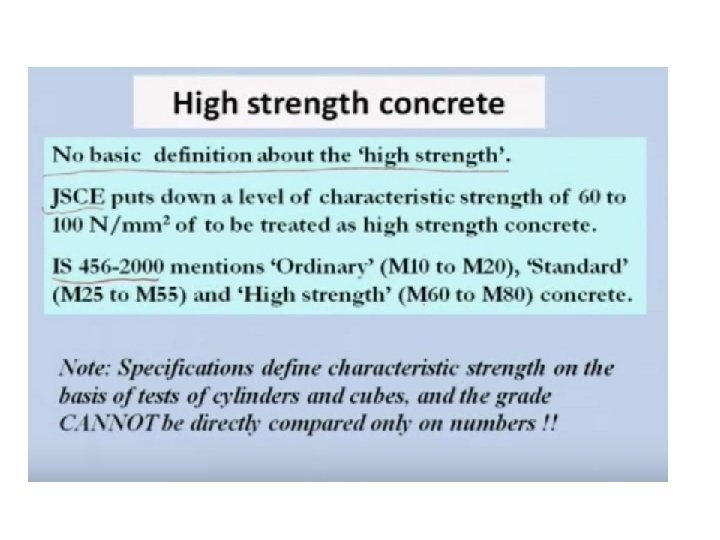
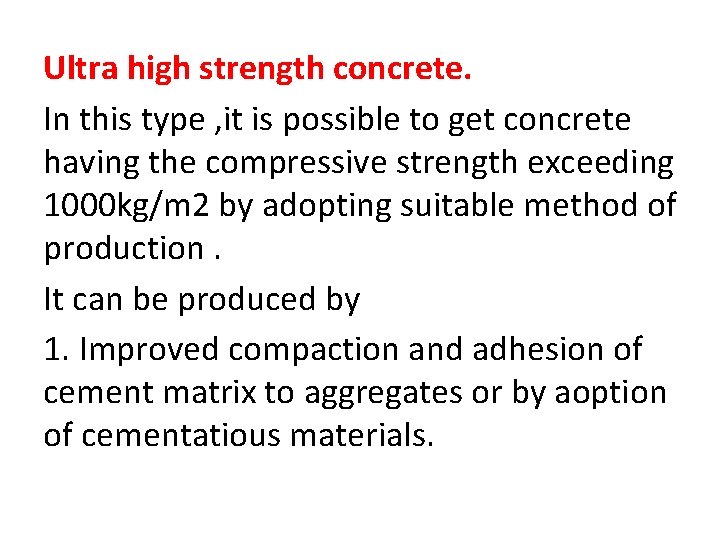
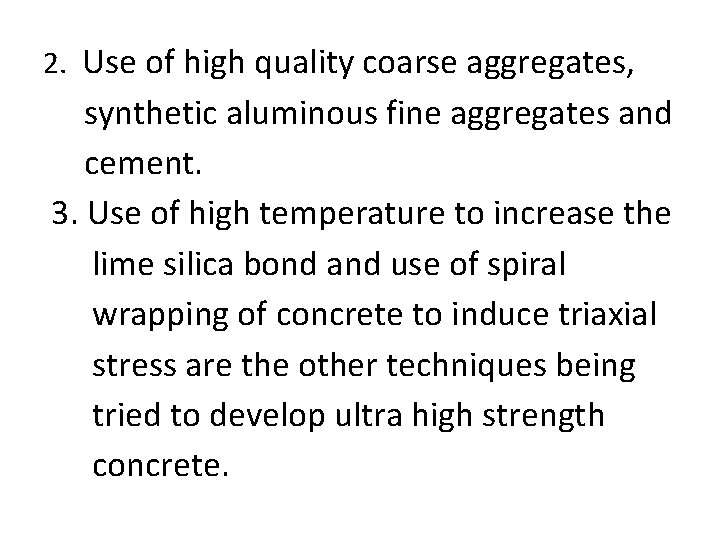
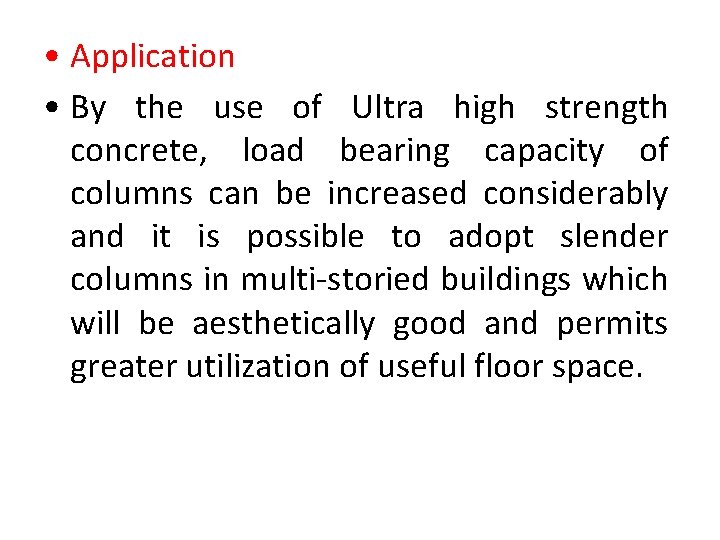
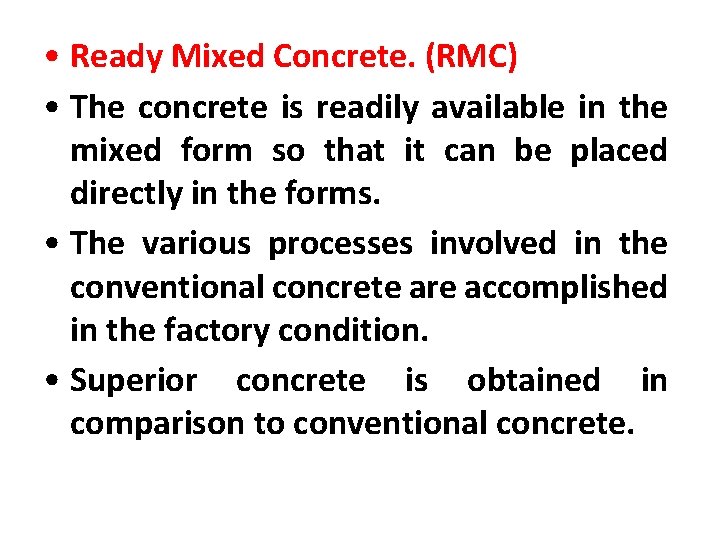
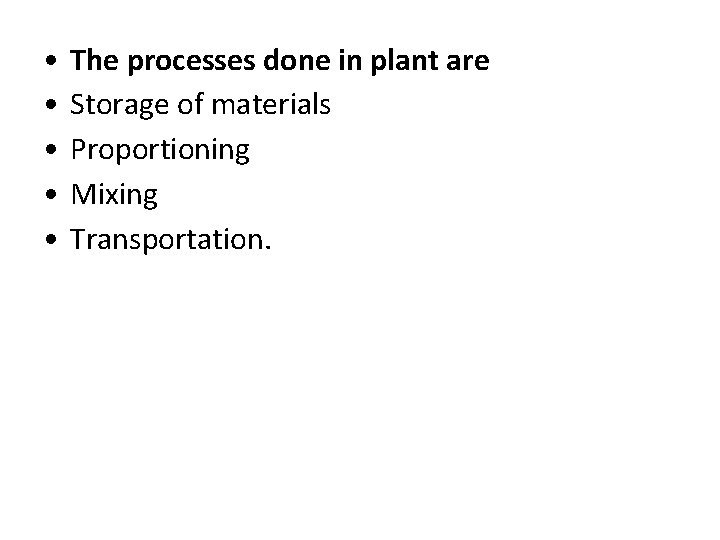
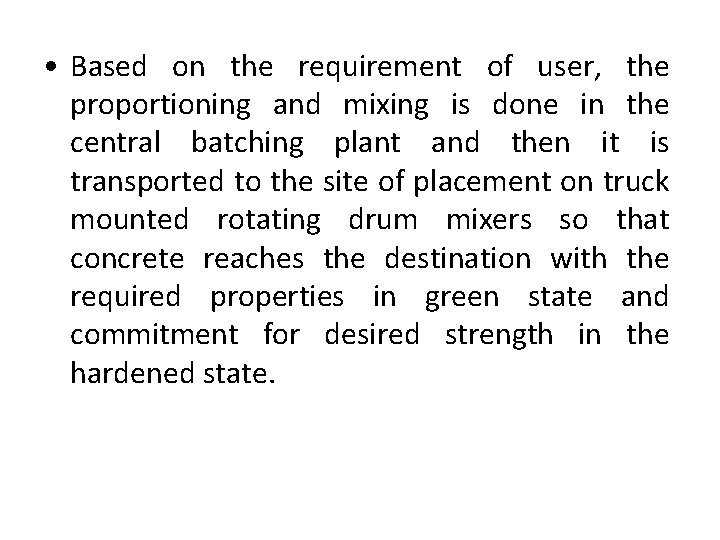
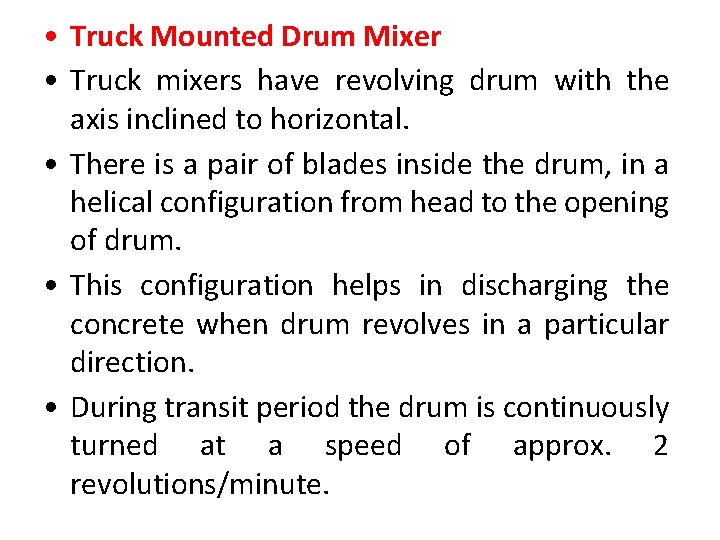
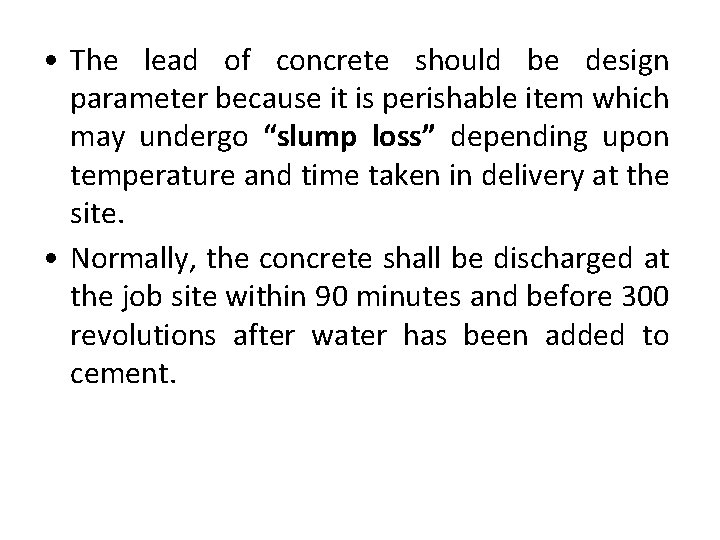
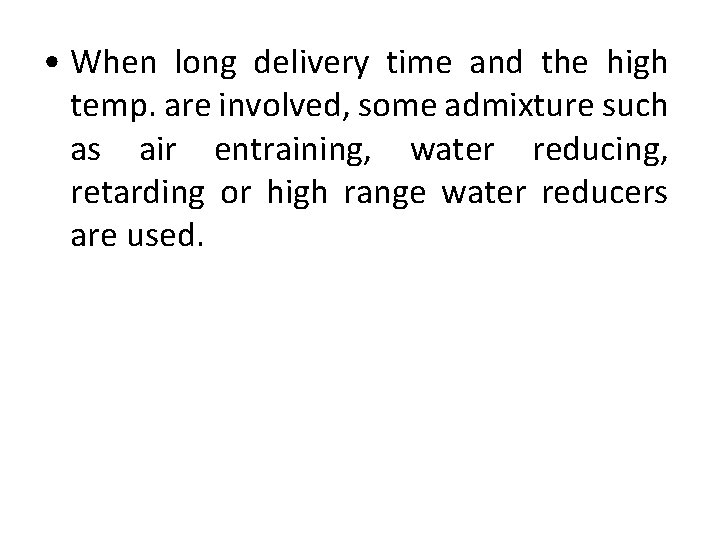
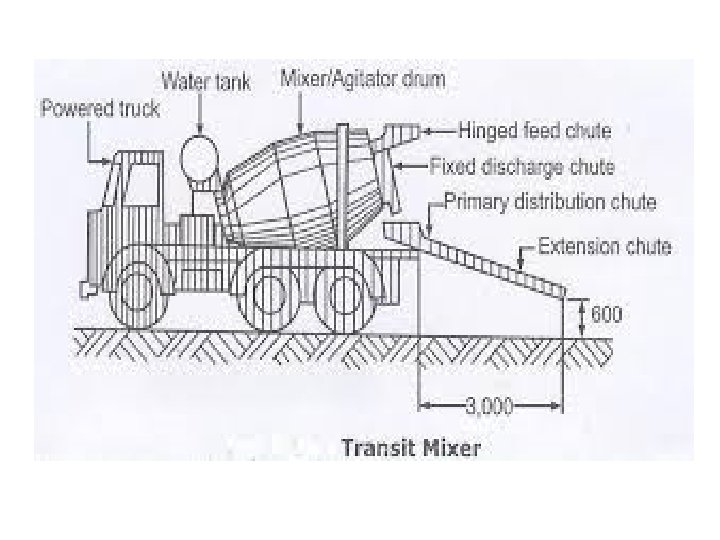
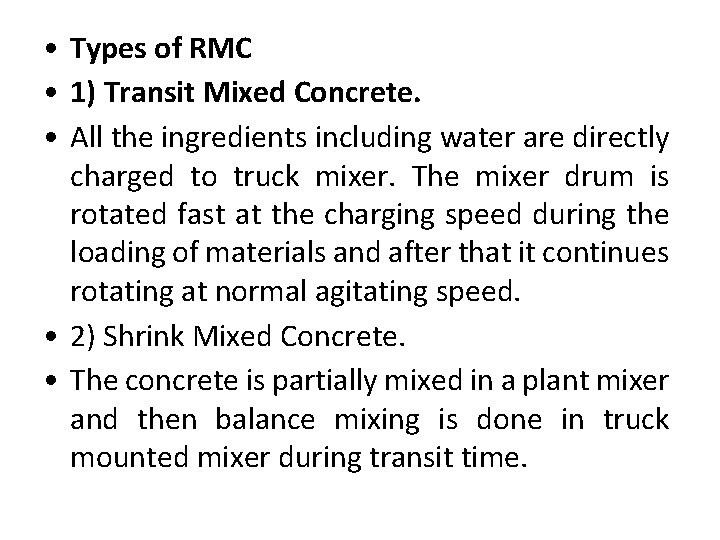
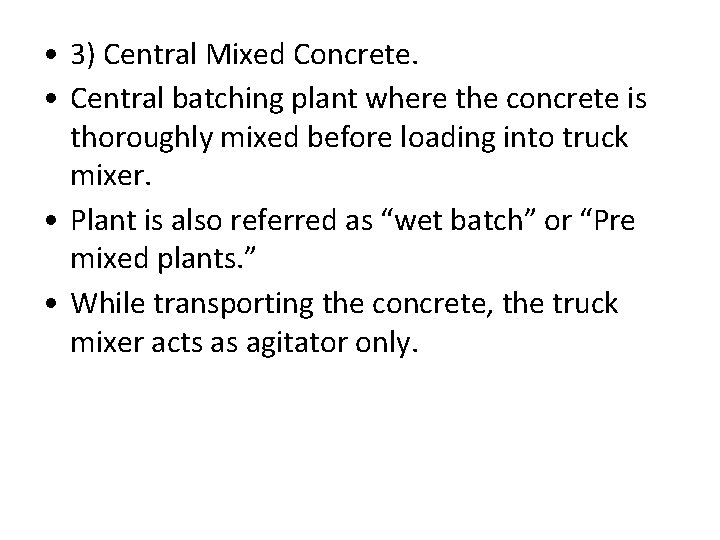
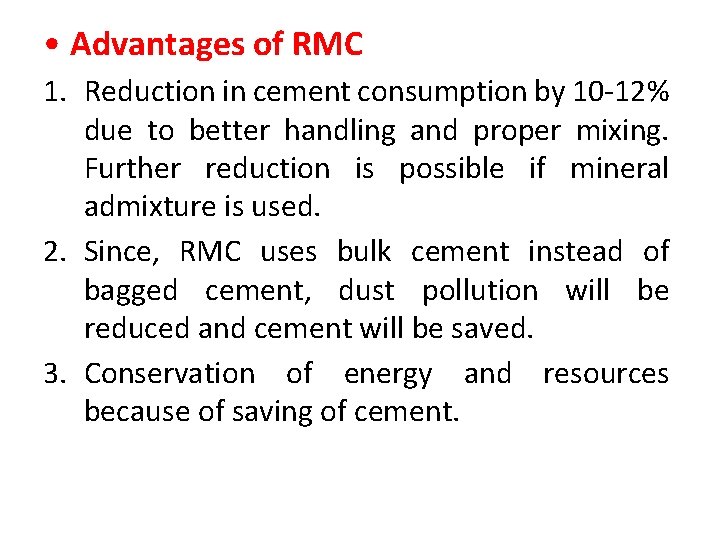
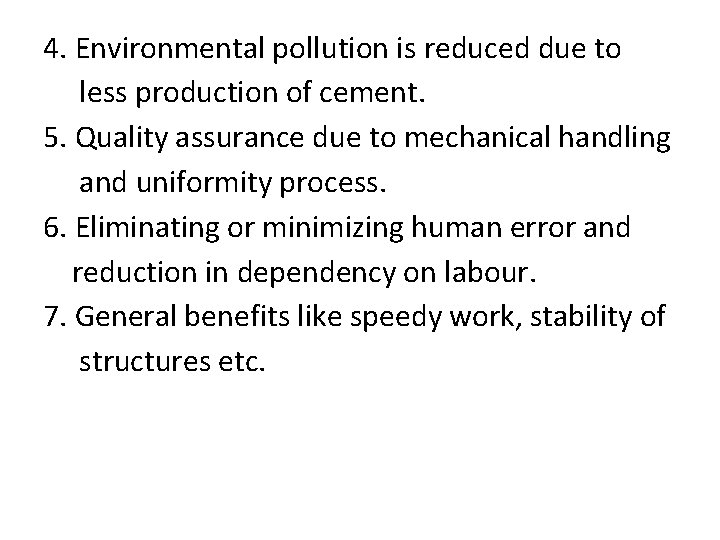
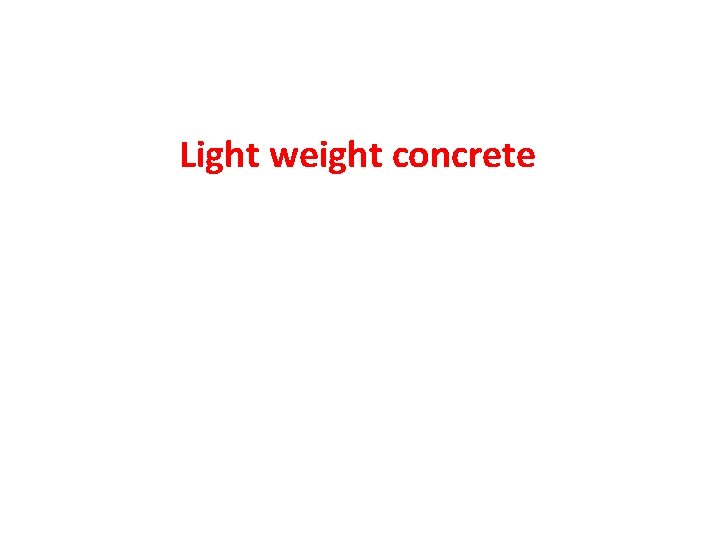
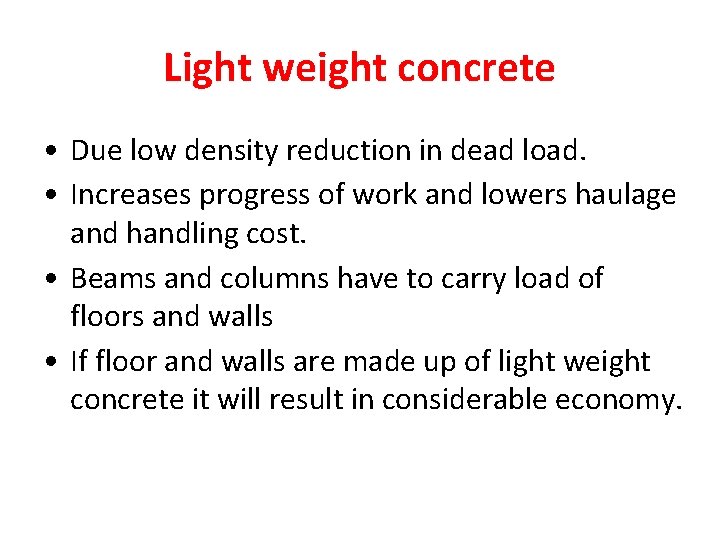
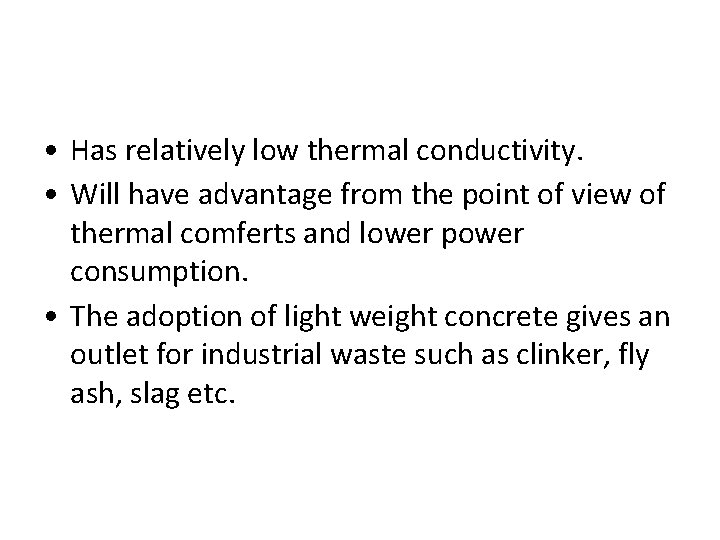
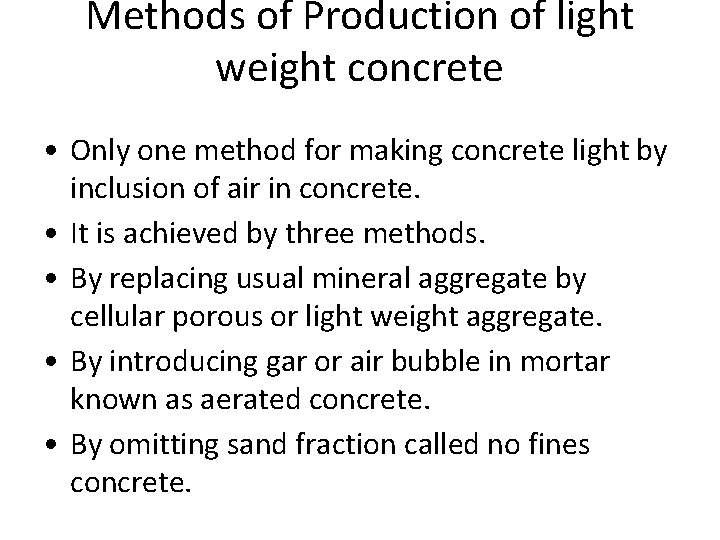
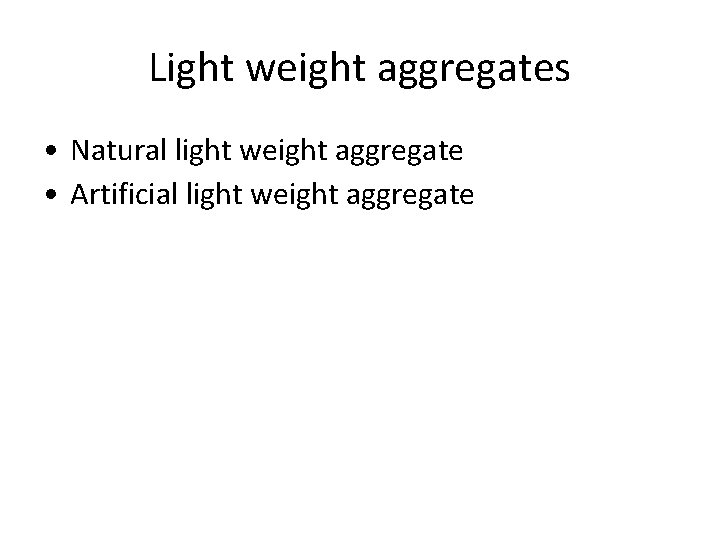
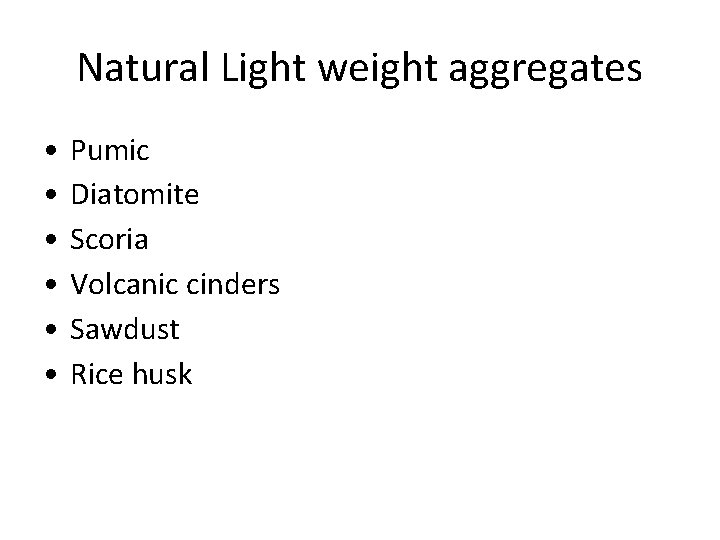
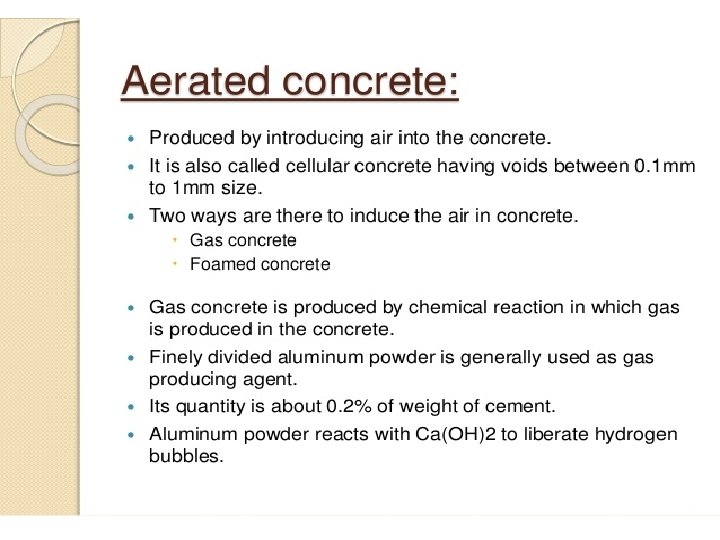
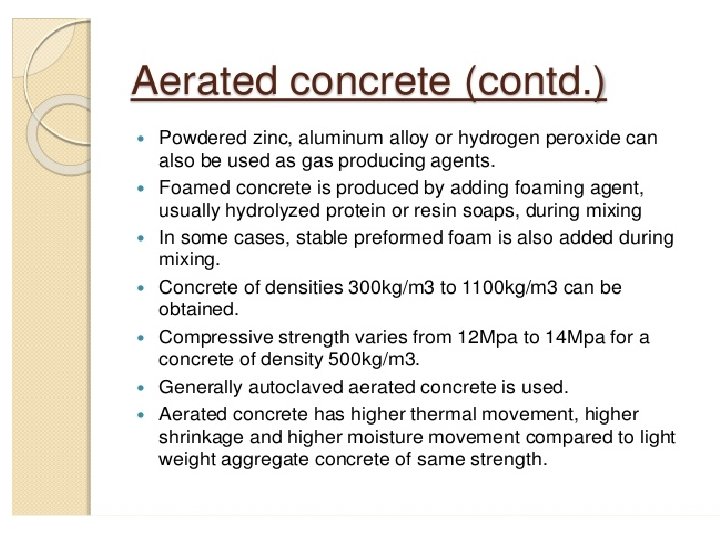
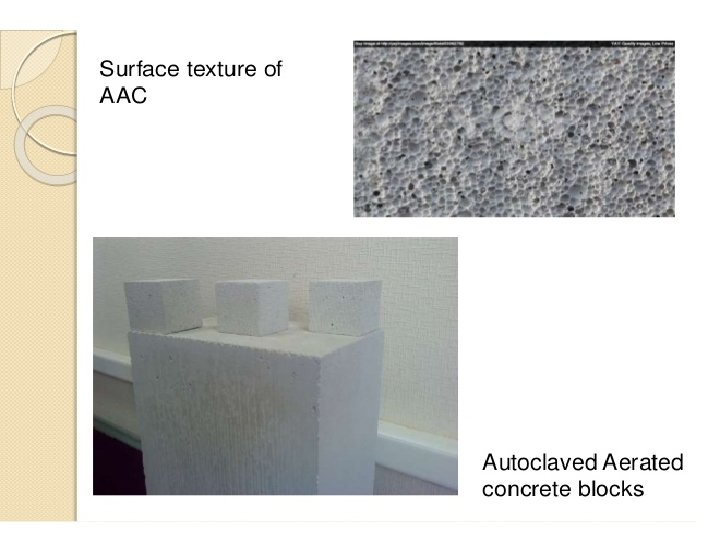

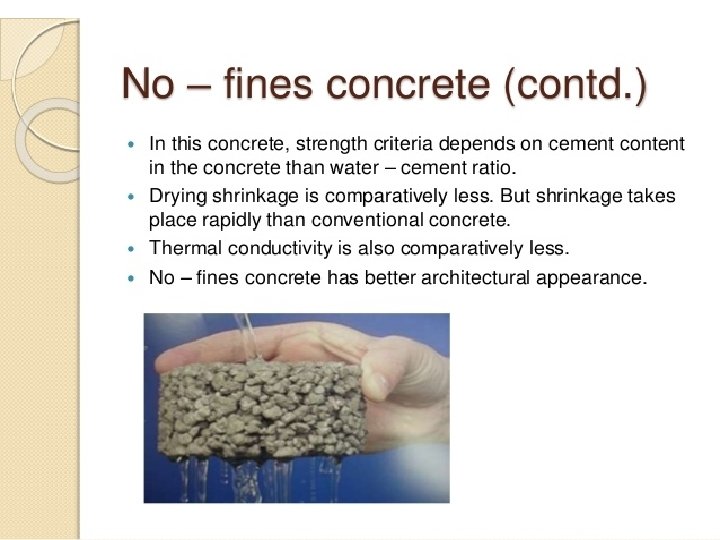
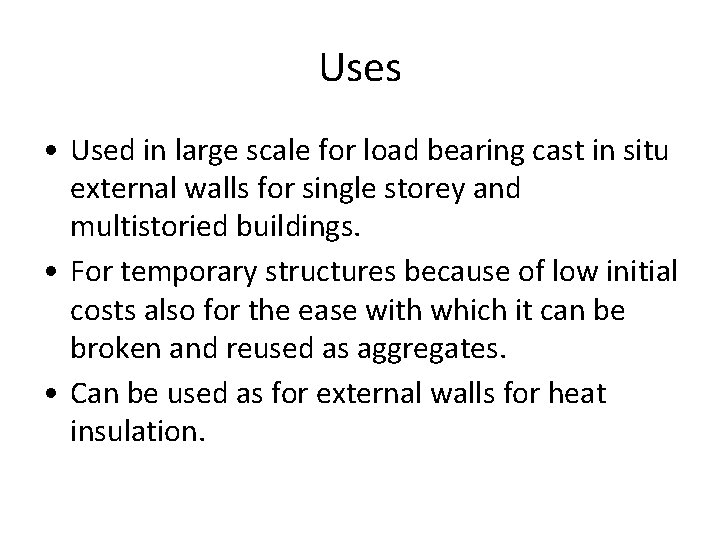
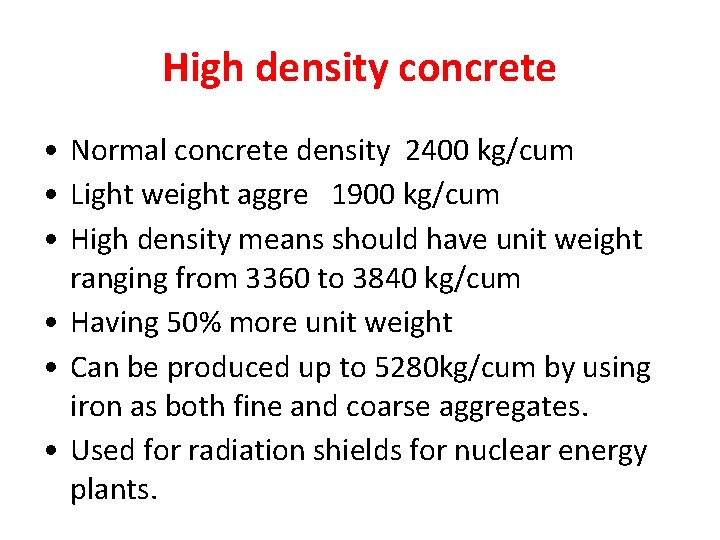
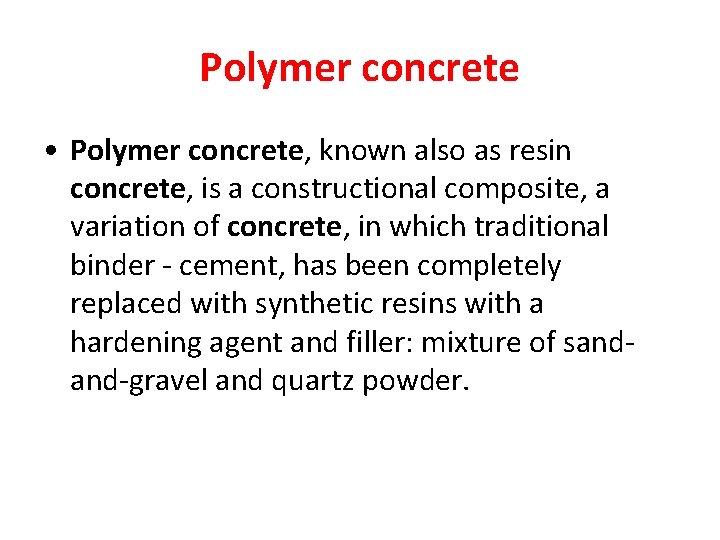
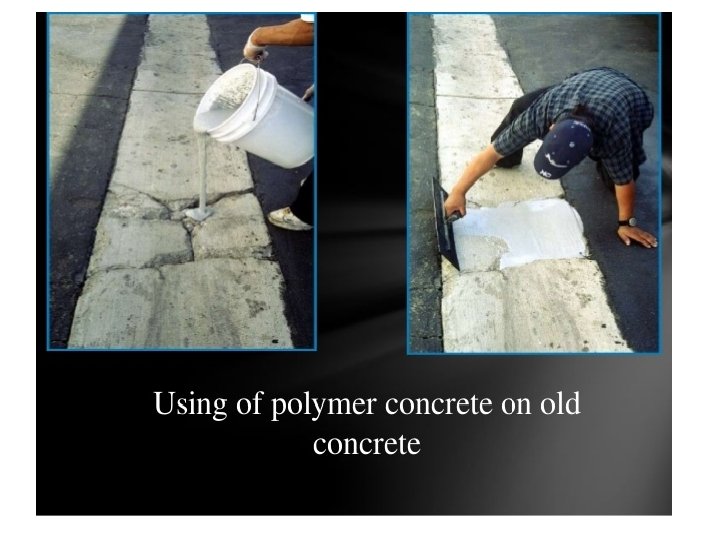
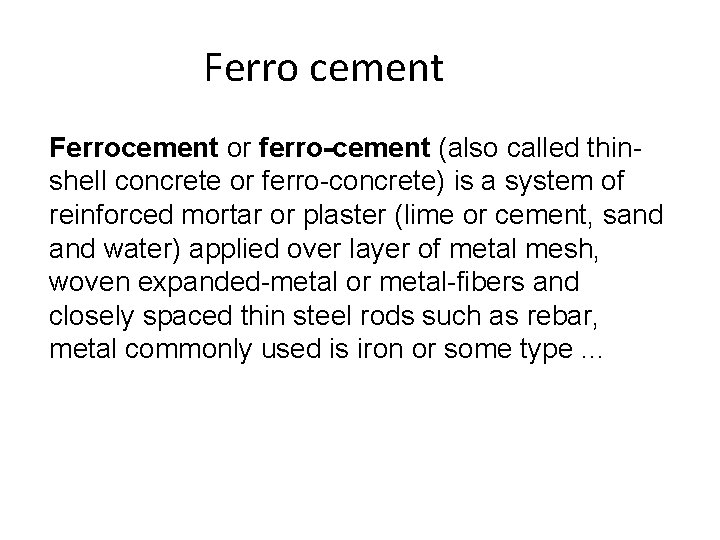
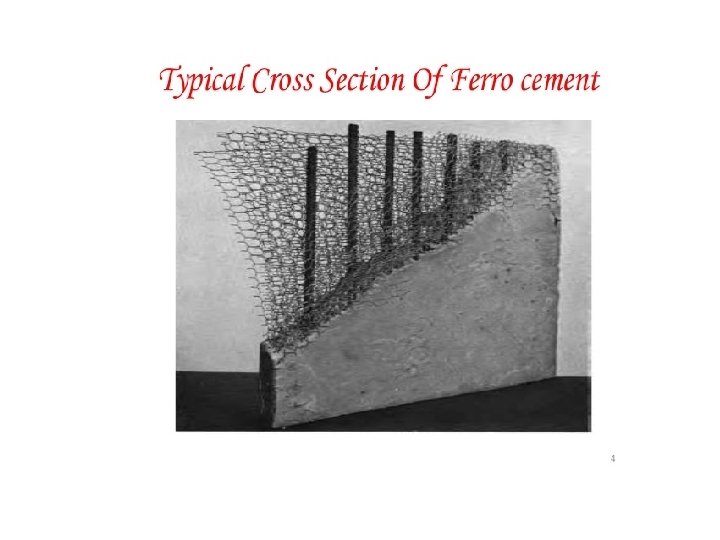
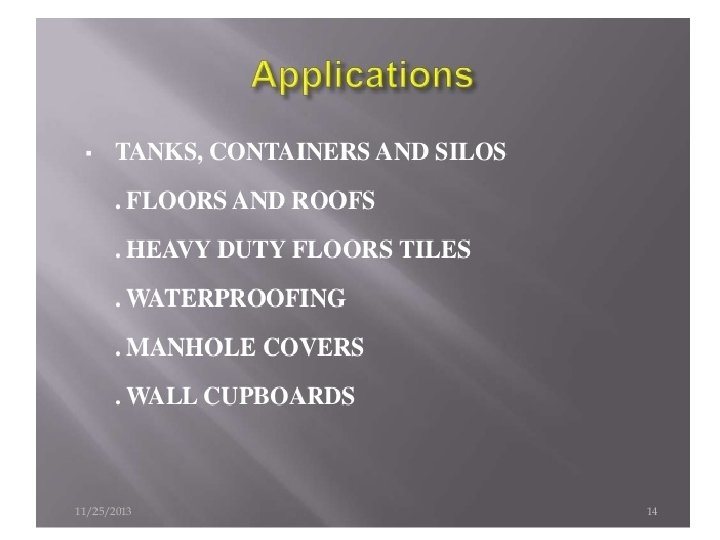
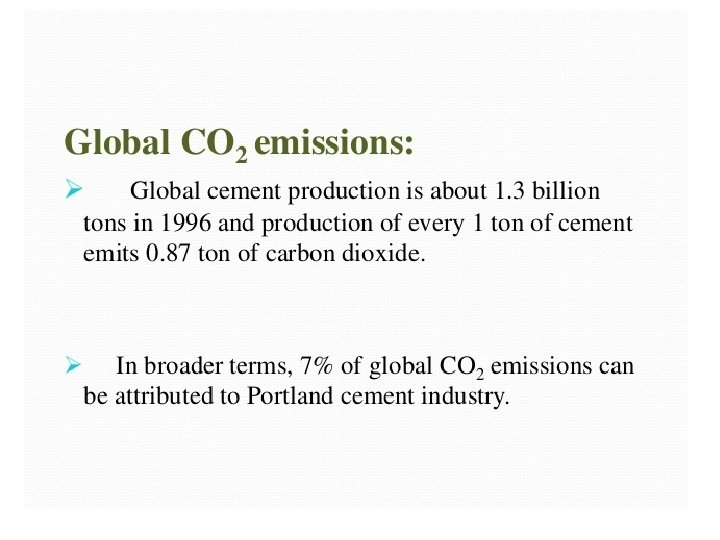
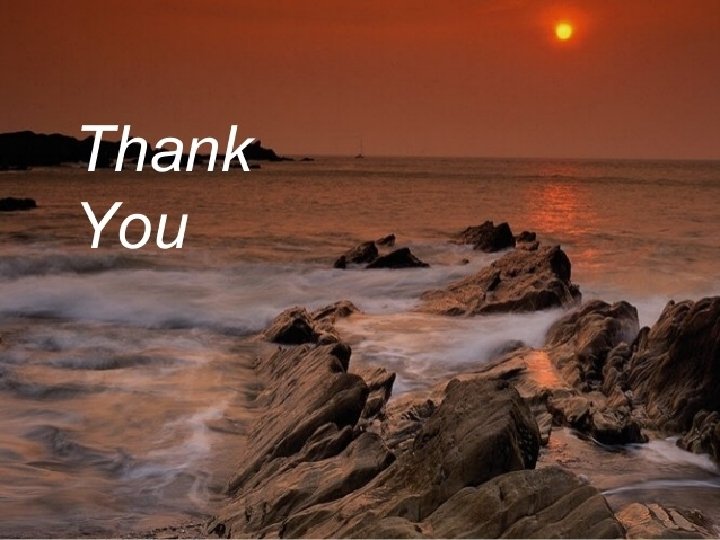
- Slides: 94
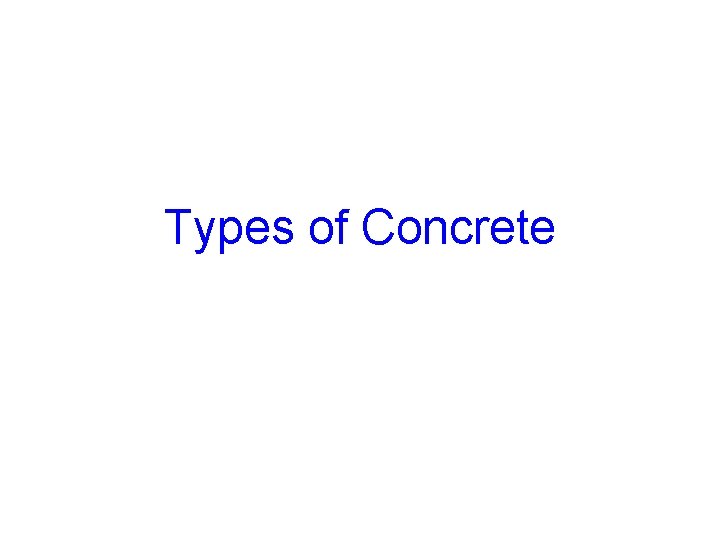
Types of Concrete
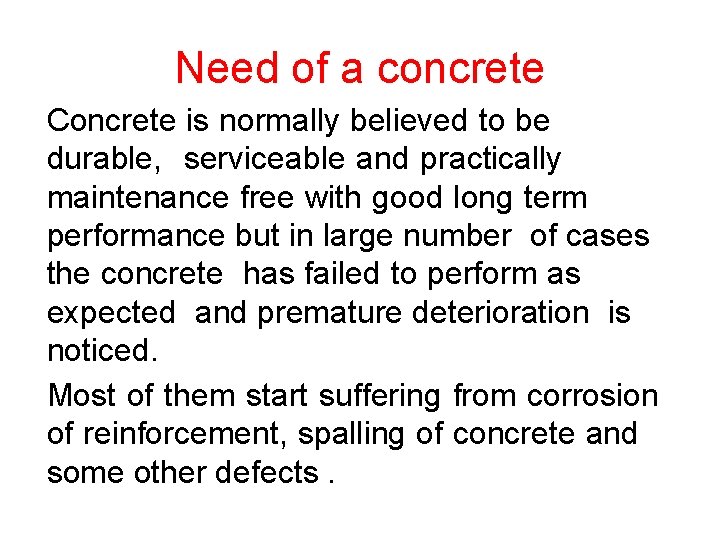
Need of a concrete Concrete is normally believed to be durable, serviceable and practically maintenance free with good long term performance but in large number of cases the concrete has failed to perform as expected and premature deterioration is noticed. Most of them start suffering from corrosion of reinforcement, spalling of concrete and some other defects.
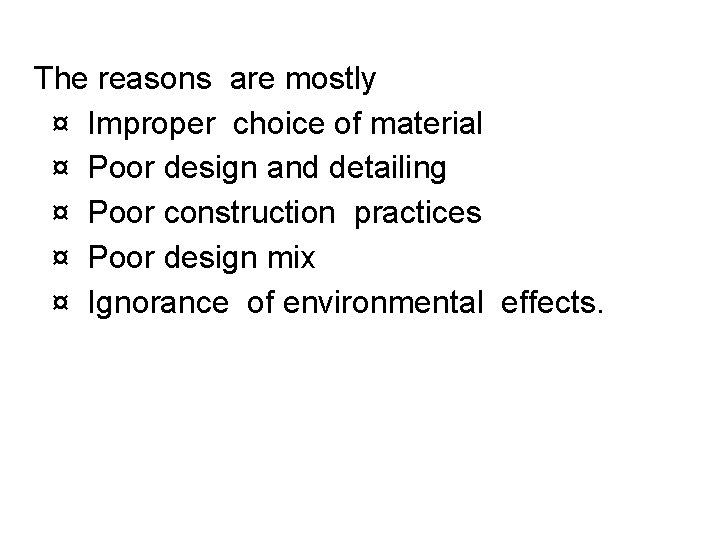
The reasons are mostly ¤ Improper choice of material ¤ Poor design and detailing ¤ Poor construction practices ¤ Poor design mix ¤ Ignorance of environmental effects.
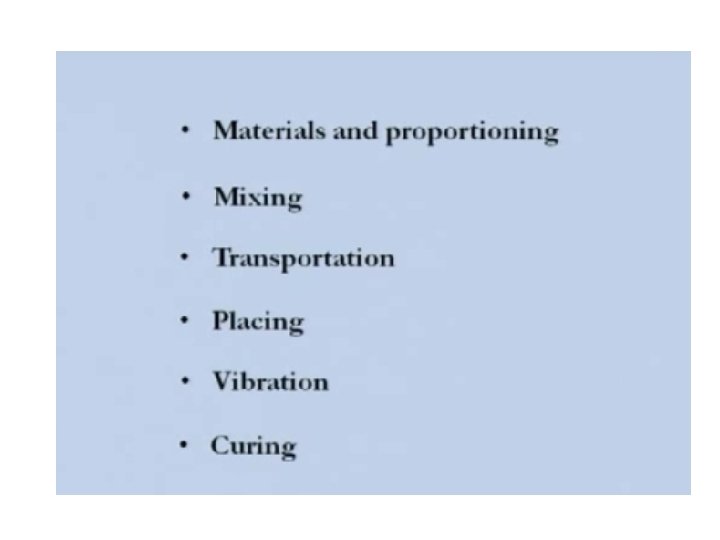
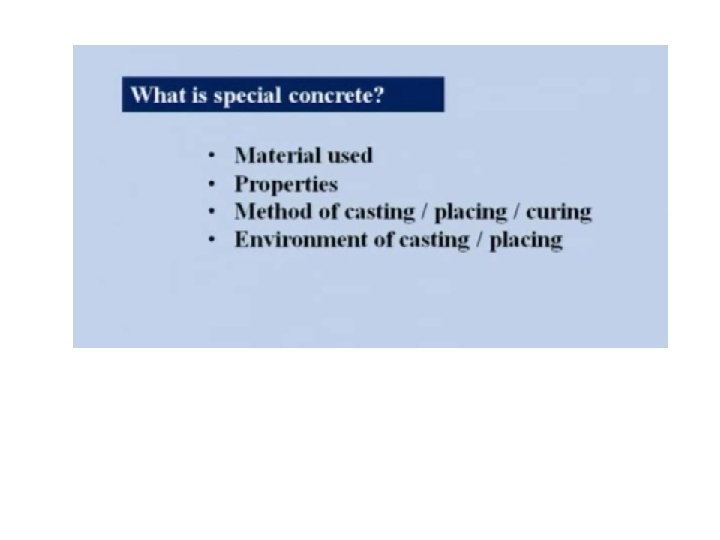
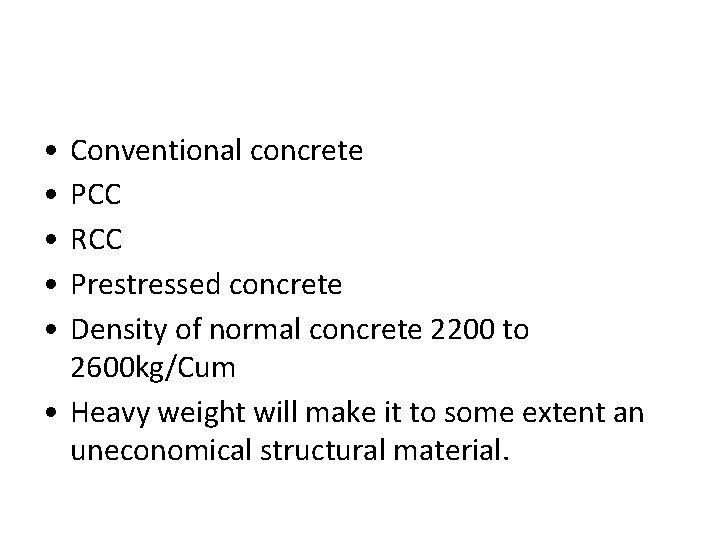
• • • Conventional concrete PCC RCC Prestressed concrete Density of normal concrete 2200 to 2600 kg/Cum • Heavy weight will make it to some extent an uneconomical structural material.
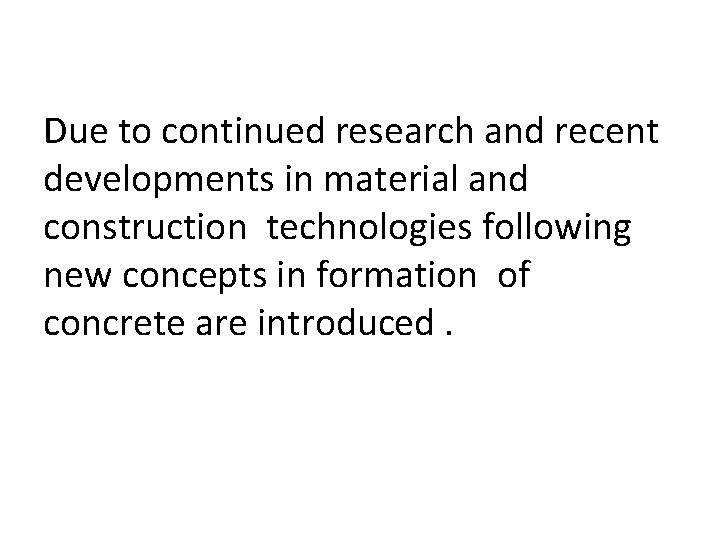
Due to continued research and recent developments in material and construction technologies following new concepts in formation of concrete are introduced.
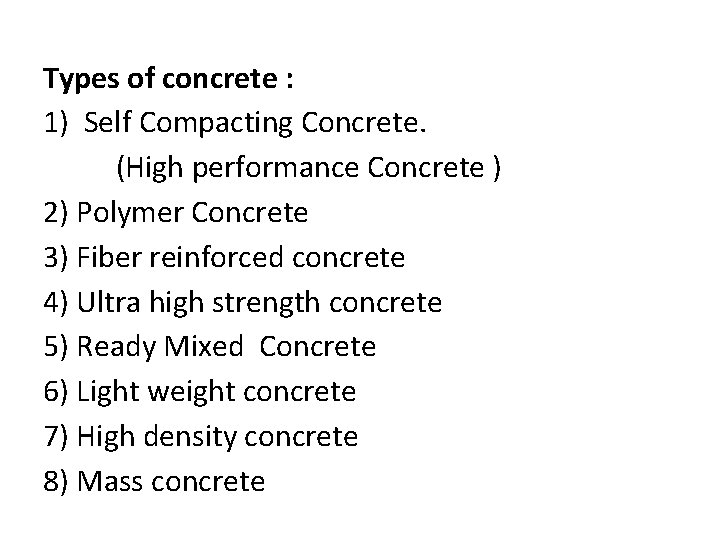
Types of concrete : 1) Self Compacting Concrete. (High performance Concrete ) 2) Polymer Concrete 3) Fiber reinforced concrete 4) Ultra high strength concrete 5) Ready Mixed Concrete 6) Light weight concrete 7) High density concrete 8) Mass concrete
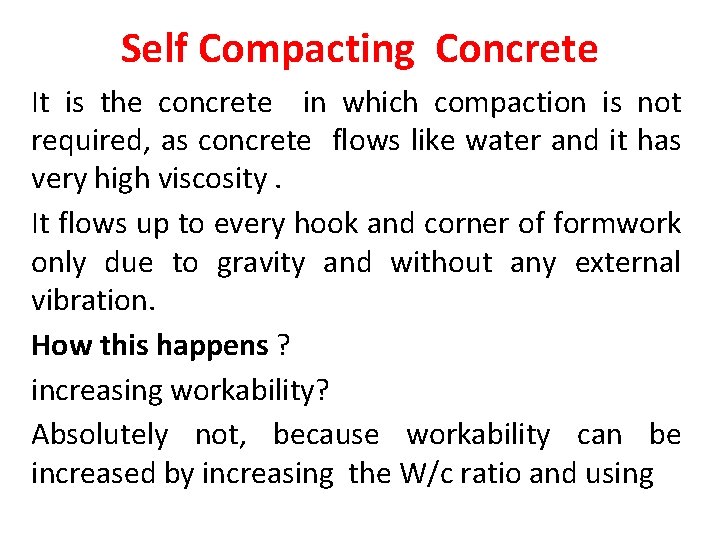
Self Compacting Concrete It is the concrete in which compaction is not required, as concrete flows like water and it has very high viscosity. It flows up to every hook and corner of formwork only due to gravity and without any external vibration. How this happens ? increasing workability? Absolutely not, because workability can be increased by increasing the W/c ratio and using
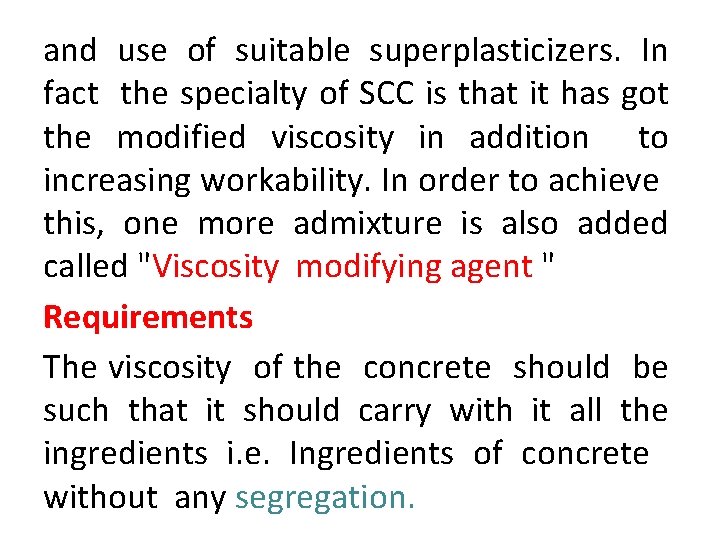
and use of suitable superplasticizers. In fact the specialty of SCC is that it has got the modified viscosity in addition to increasing workability. In order to achieve this, one more admixture is also added called "Viscosity modifying agent " Requirements The viscosity of the concrete should be such that it should carry with it all the ingredients i. e. Ingredients of concrete without any segregation.
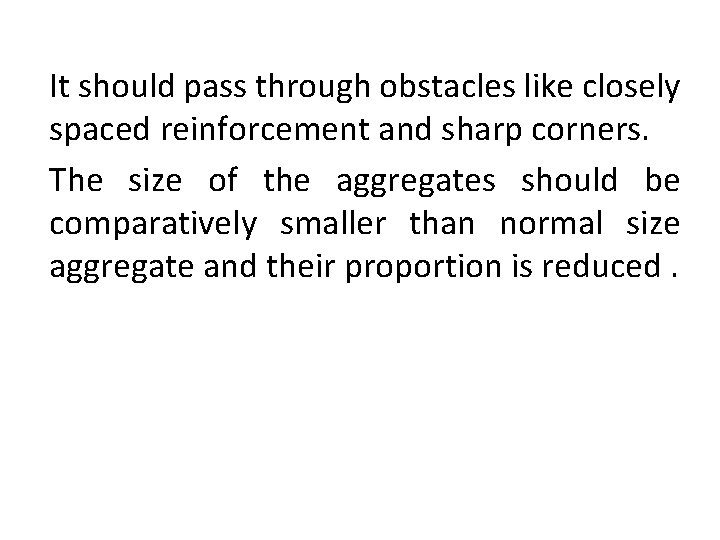
It should pass through obstacles like closely spaced reinforcement and sharp corners. The size of the aggregates should be comparatively smaller than normal size aggregate and their proportion is reduced.
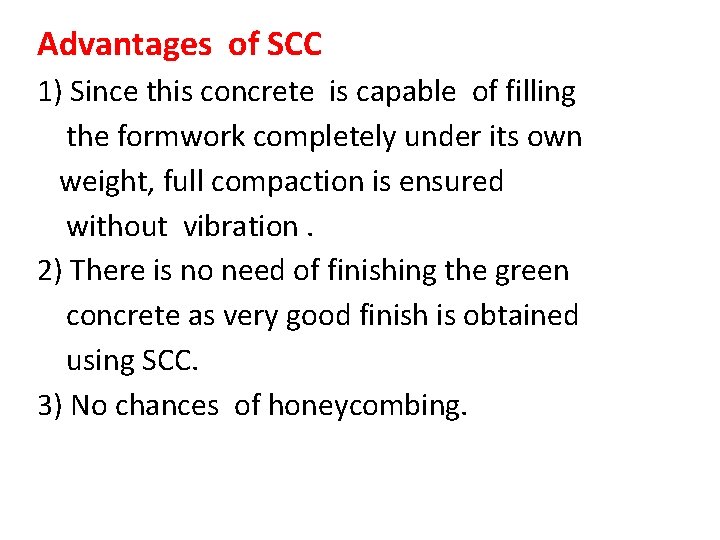
Advantages of SCC 1) Since this concrete is capable of filling the formwork completely under its own weight, full compaction is ensured without vibration. 2) There is no need of finishing the green concrete as very good finish is obtained using SCC. 3) No chances of honeycombing.
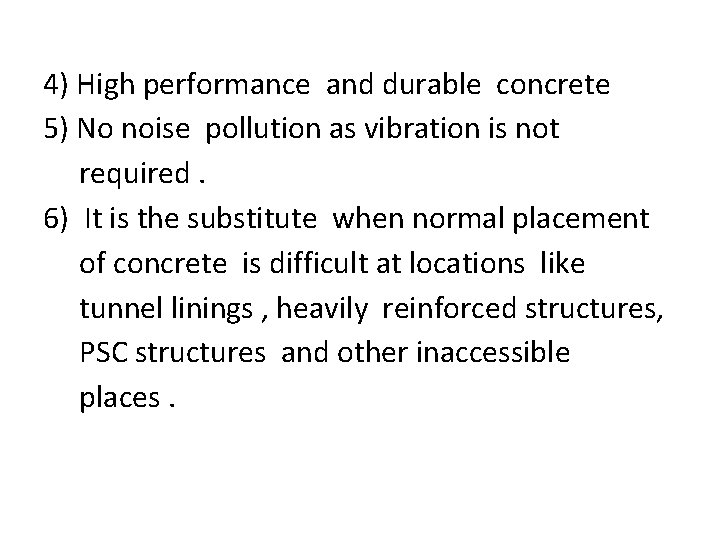
4) High performance and durable concrete 5) No noise pollution as vibration is not required. 6) It is the substitute when normal placement of concrete is difficult at locations like tunnel linings , heavily reinforced structures, PSC structures and other inaccessible places.
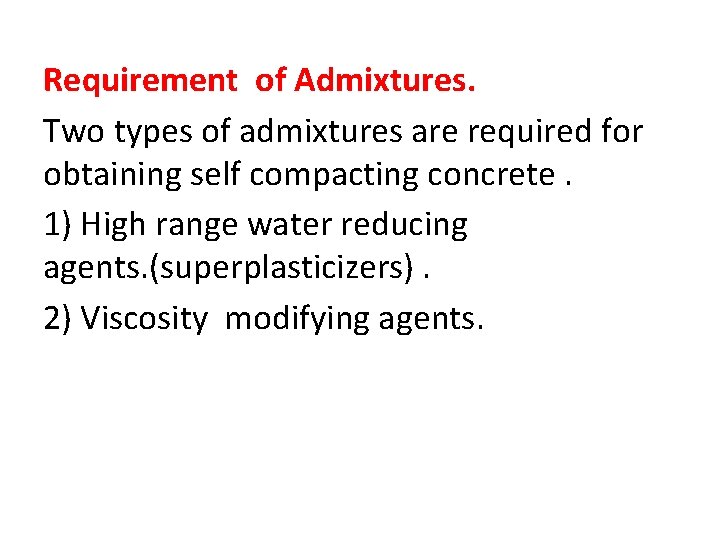
Requirement of Admixtures. Two types of admixtures are required for obtaining self compacting concrete. 1) High range water reducing agents. (superplasticizers). 2) Viscosity modifying agents.
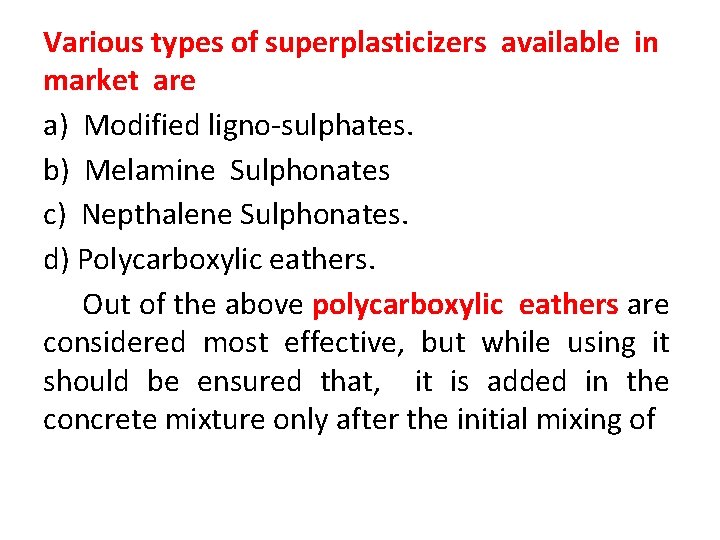
Various types of superplasticizers available in market are a) Modified ligno-sulphates. b) Melamine Sulphonates c) Nepthalene Sulphonates. d) Polycarboxylic eathers. Out of the above polycarboxylic eathers are considered most effective, but while using it should be ensured that, it is added in the concrete mixture only after the initial mixing of
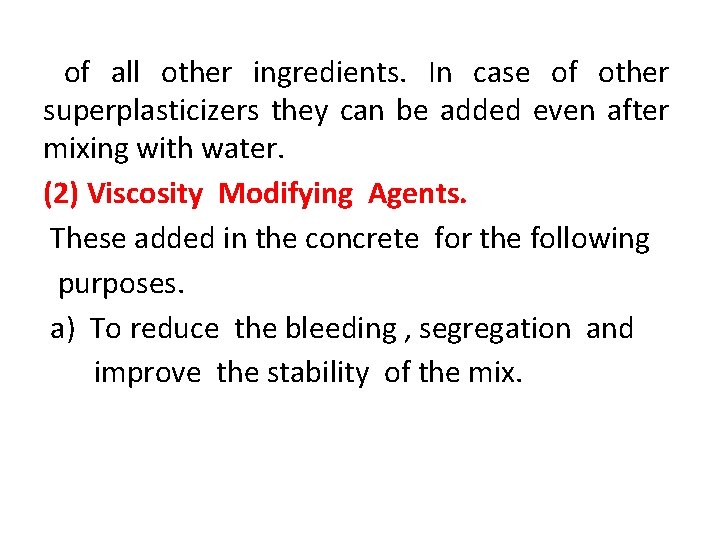
of all other ingredients. In case of other superplasticizers they can be added even after mixing with water. (2) Viscosity Modifying Agents. These added in the concrete for the following purposes. a) To reduce the bleeding , segregation and improve the stability of the mix.
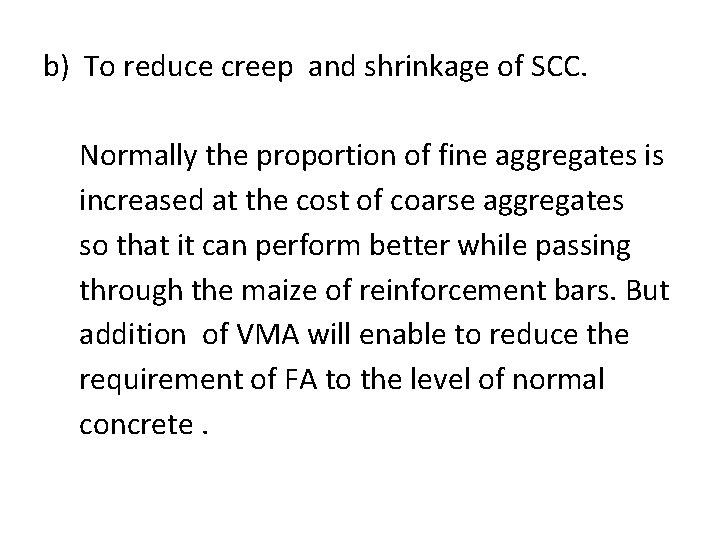
b) To reduce creep and shrinkage of SCC. Normally the proportion of fine aggregates is increased at the cost of coarse aggregates so that it can perform better while passing through the maize of reinforcement bars. But addition of VMA will enable to reduce the requirement of FA to the level of normal concrete.
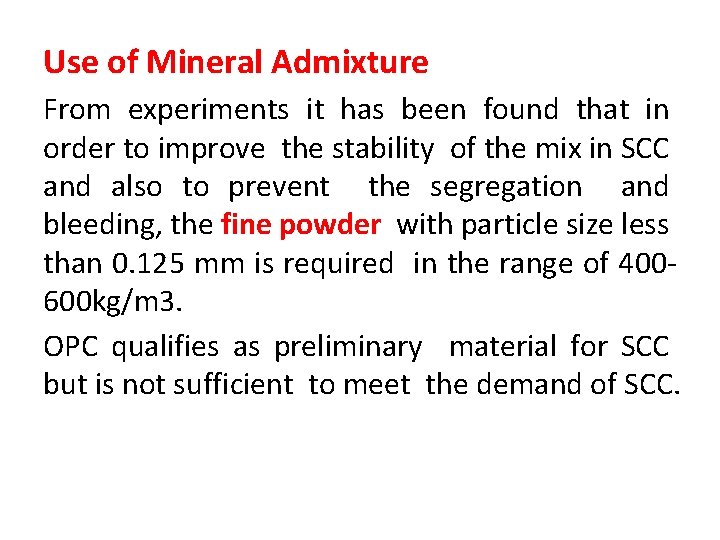
Use of Mineral Admixture From experiments it has been found that in order to improve the stability of the mix in SCC and also to prevent the segregation and bleeding, the fine powder with particle size less than 0. 125 mm is required in the range of 400600 kg/m 3. OPC qualifies as preliminary material for SCC but is not sufficient to meet the demand of SCC.
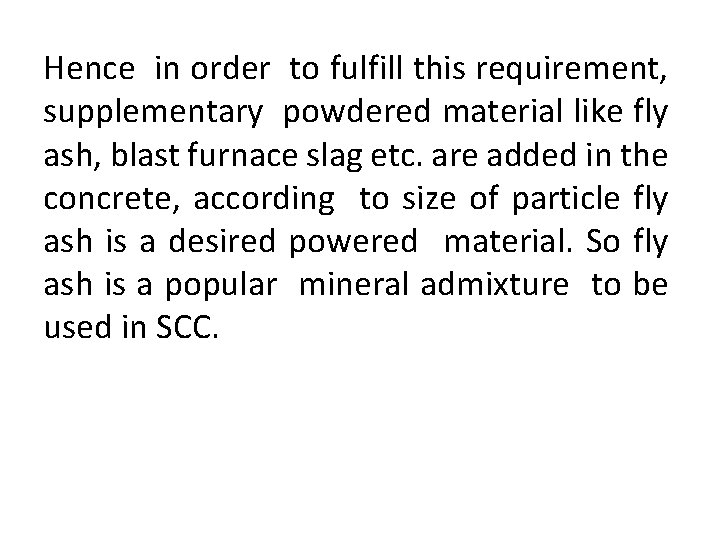
Hence in order to fulfill this requirement, supplementary powdered material like fly ash, blast furnace slag etc. are added in the concrete, according to size of particle fly ash is a desired powered material. So fly ash is a popular mineral admixture to be used in SCC.
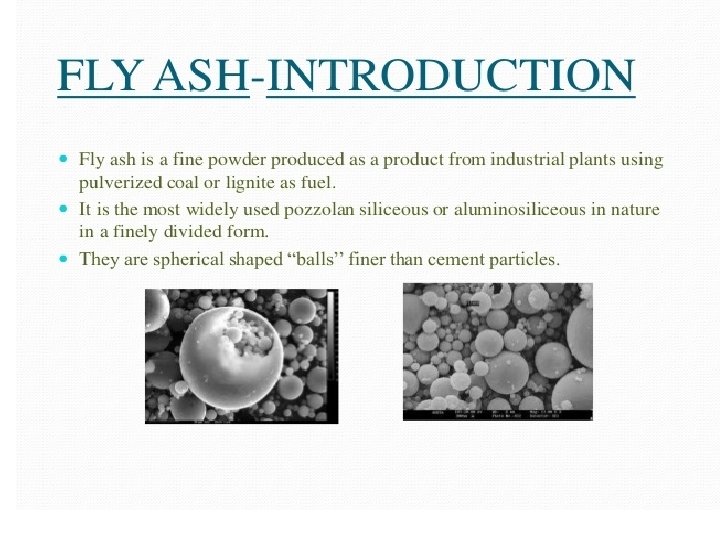
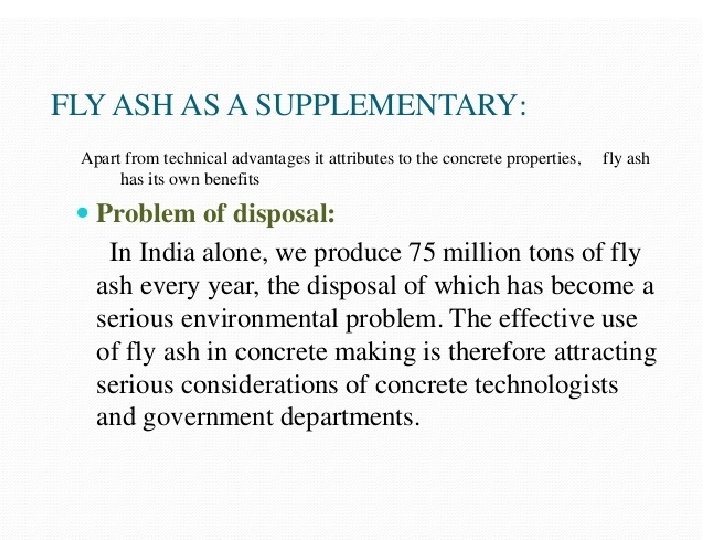
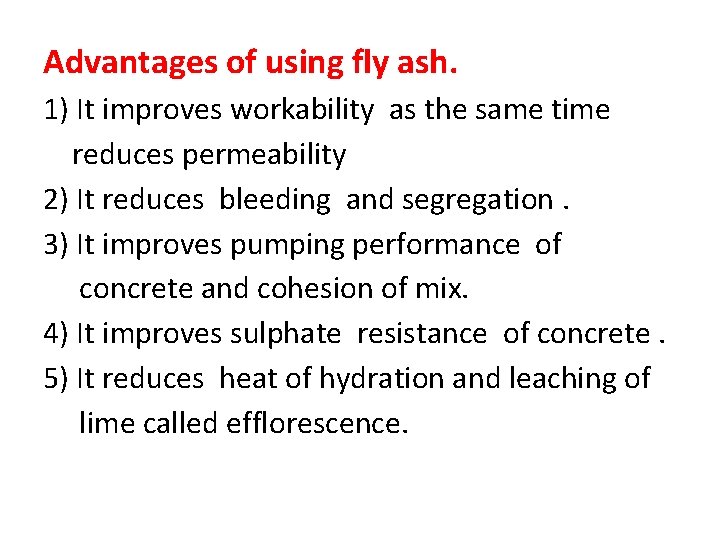
Advantages of using fly ash. 1) It improves workability as the same time reduces permeability 2) It reduces bleeding and segregation. 3) It improves pumping performance of concrete and cohesion of mix. 4) It improves sulphate resistance of concrete. 5) It reduces heat of hydration and leaching of lime called efflorescence.
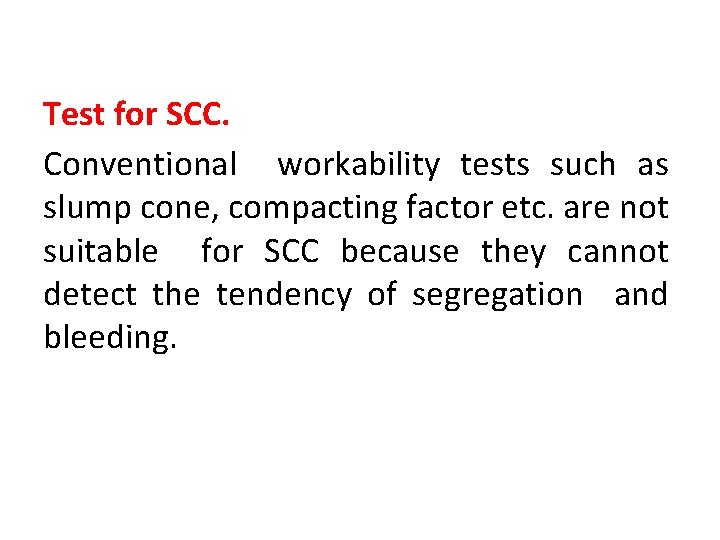
Test for SCC. Conventional workability tests such as slump cone, compacting factor etc. are not suitable for SCC because they cannot detect the tendency of segregation and bleeding.
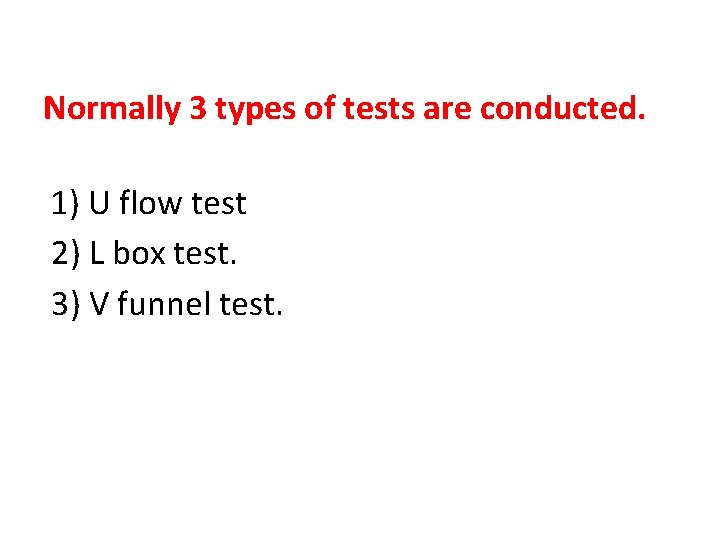
Normally 3 types of tests are conducted. 1) U flow test 2) L box test. 3) V funnel test.
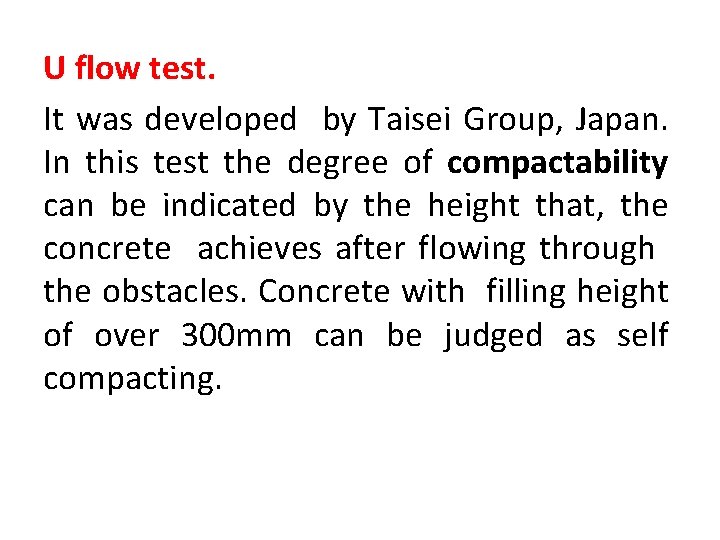
U flow test. It was developed by Taisei Group, Japan. In this test the degree of compactability can be indicated by the height that, the concrete achieves after flowing through the obstacles. Concrete with filling height of over 300 mm can be judged as self compacting.
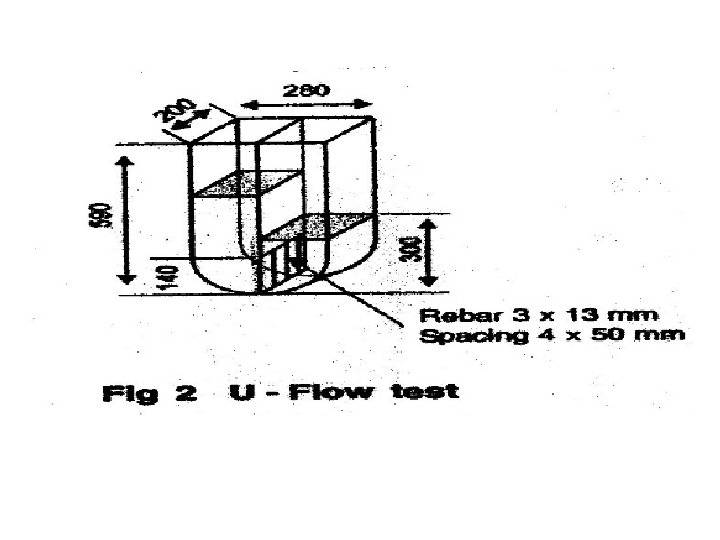
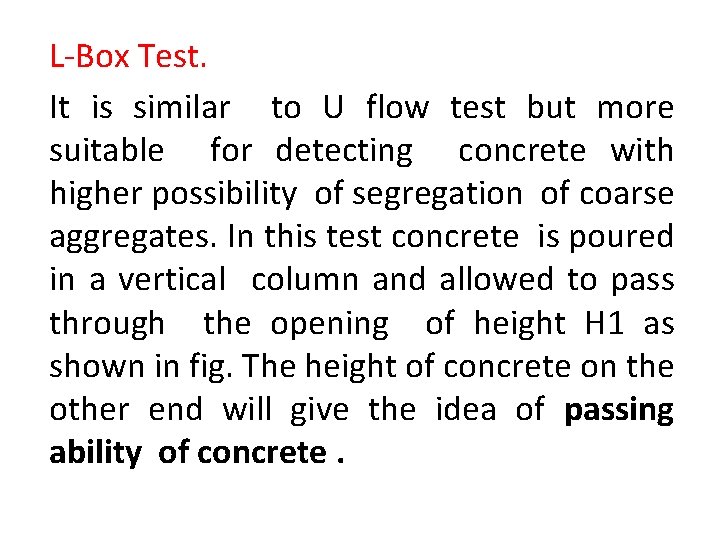
L-Box Test. It is similar to U flow test but more suitable for detecting concrete with higher possibility of segregation of coarse aggregates. In this test concrete is poured in a vertical column and allowed to pass through the opening of height H 1 as shown in fig. The height of concrete on the other end will give the idea of passing ability of concrete.
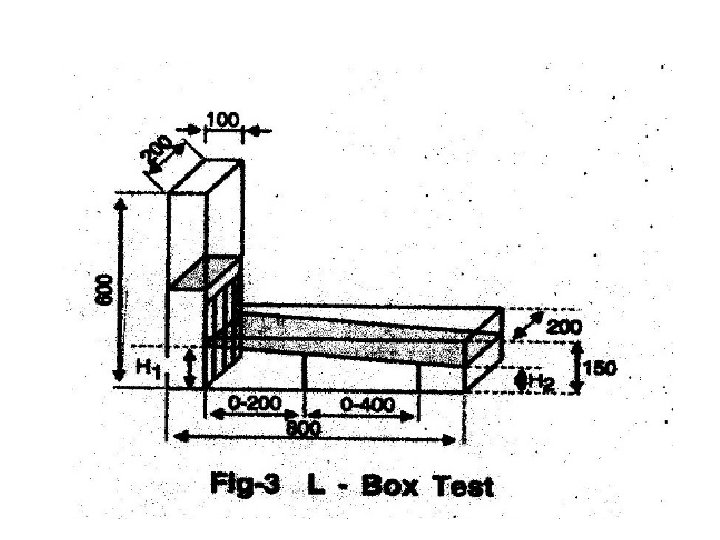
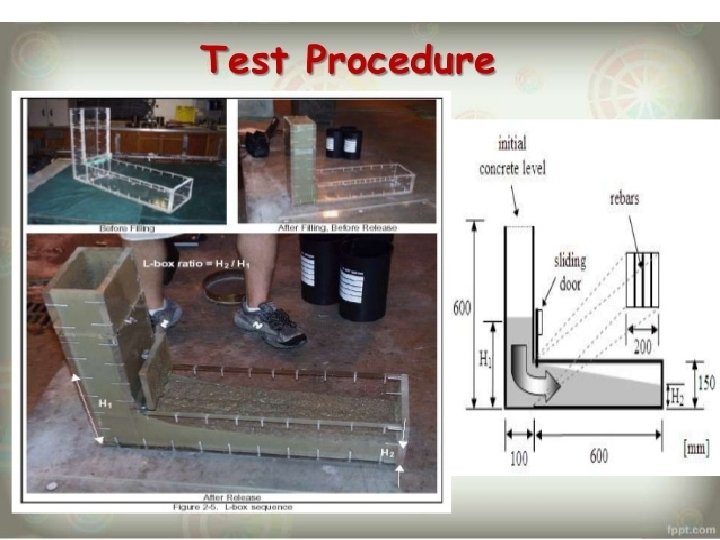
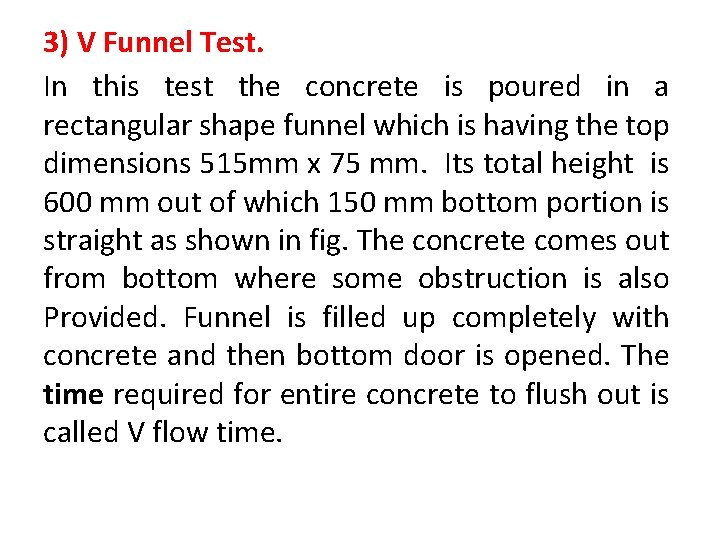
3) V Funnel Test. In this test the concrete is poured in a rectangular shape funnel which is having the top dimensions 515 mm x 75 mm. Its total height is 600 mm out of which 150 mm bottom portion is straight as shown in fig. The concrete comes out from bottom where some obstruction is also Provided. Funnel is filled up completely with concrete and then bottom door is opened. The time required for entire concrete to flush out is called V flow time.
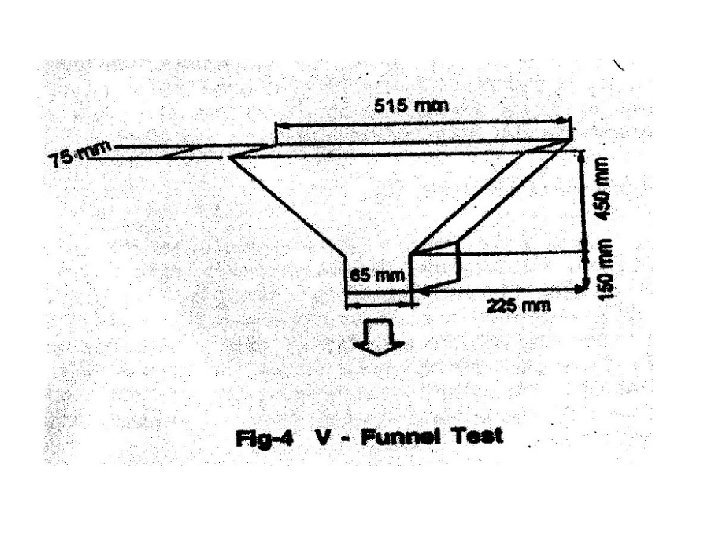
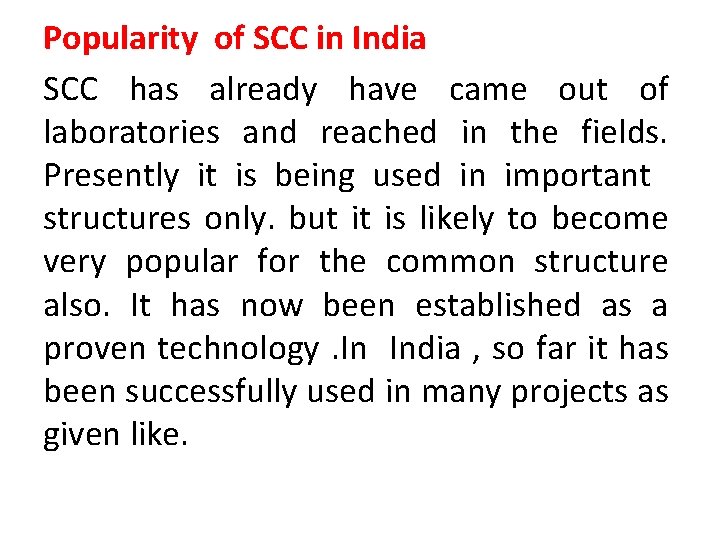
Popularity of SCC in India SCC has already have came out of laboratories and reached in the fields. Presently it is being used in important structures only. but it is likely to become very popular for the common structure also. It has now been established as a proven technology. In India , so far it has been successfully used in many projects as given like.
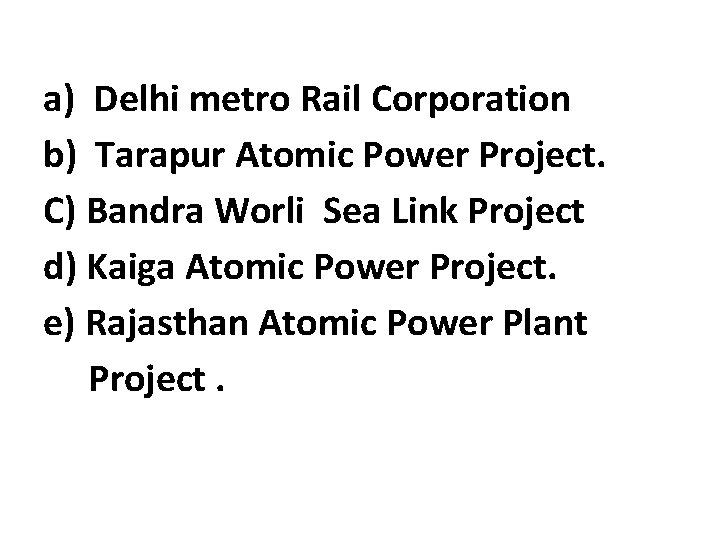
a) Delhi metro Rail Corporation b) Tarapur Atomic Power Project. C) Bandra Worli Sea Link Project d) Kaiga Atomic Power Project. e) Rajasthan Atomic Power Plant Project.
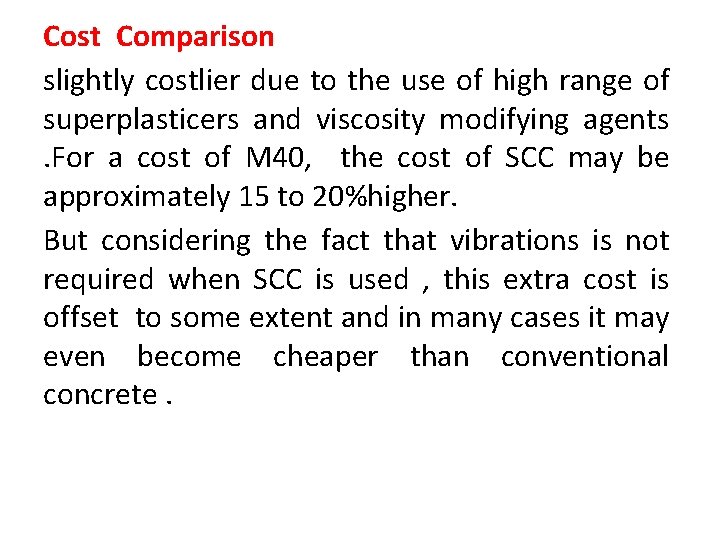
Cost Comparison slightly costlier due to the use of high range of superplasticers and viscosity modifying agents. For a cost of M 40, the cost of SCC may be approximately 15 to 20%higher. But considering the fact that vibrations is not required when SCC is used , this extra cost is offset to some extent and in many cases it may even become cheaper than conventional concrete.
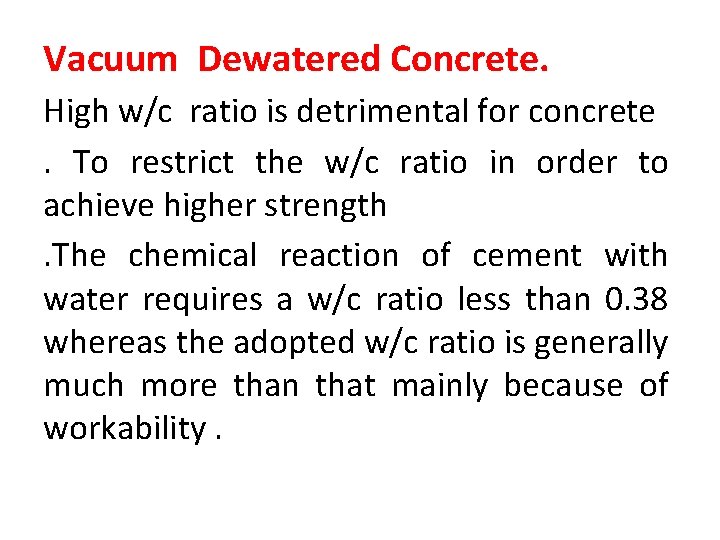
Vacuum Dewatered Concrete. High w/c ratio is detrimental for concrete. To restrict the w/c ratio in order to achieve higher strength. The chemical reaction of cement with water requires a w/c ratio less than 0. 38 whereas the adopted w/c ratio is generally much more than that mainly because of workability.

Workability is also important for concrete , so it can be placed in formwork easily without honeycombing. After the requirement of workability is over , this excess water will eventually evaporate leaving capillary pores in the concrete. These pores result into high permeability and less strength of concrete
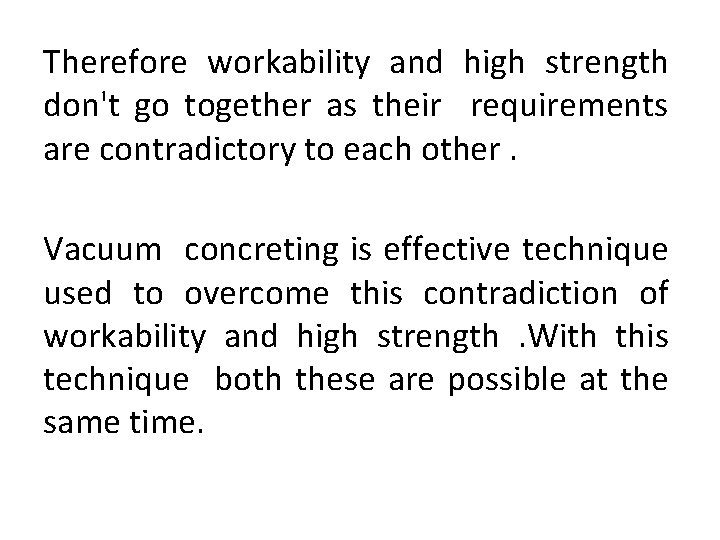
Therefore workability and high strength don't go together as their requirements are contradictory to each other. Vacuum concreting is effective technique used to overcome this contradiction of workability and high strength. With this technique both these are possible at the same time.
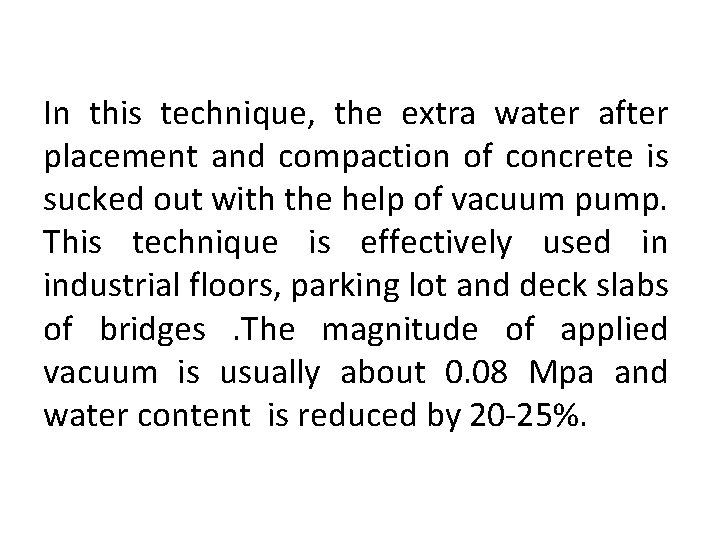
In this technique, the extra water after placement and compaction of concrete is sucked out with the help of vacuum pump. This technique is effectively used in industrial floors, parking lot and deck slabs of bridges. The magnitude of applied vacuum is usually about 0. 08 Mpa and water content is reduced by 20 -25%.
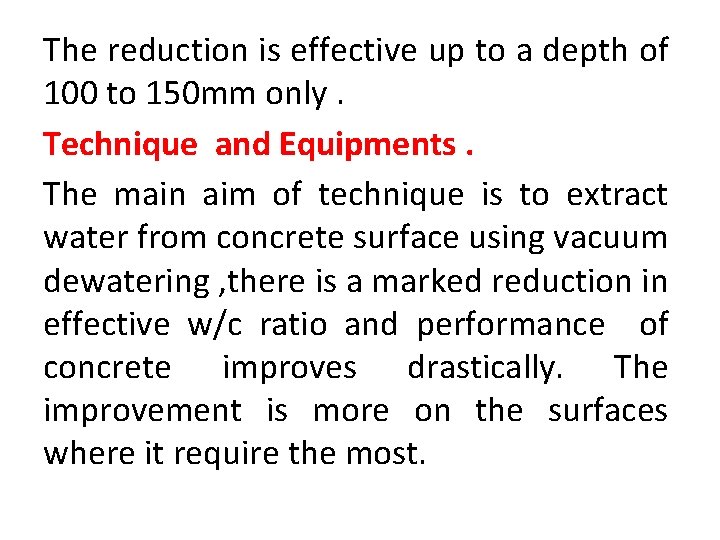
The reduction is effective up to a depth of 100 to 150 mm only. Technique and Equipments. The main aim of technique is to extract water from concrete surface using vacuum dewatering , there is a marked reduction in effective w/c ratio and performance of concrete improves drastically. The improvement is more on the surfaces where it require the most.
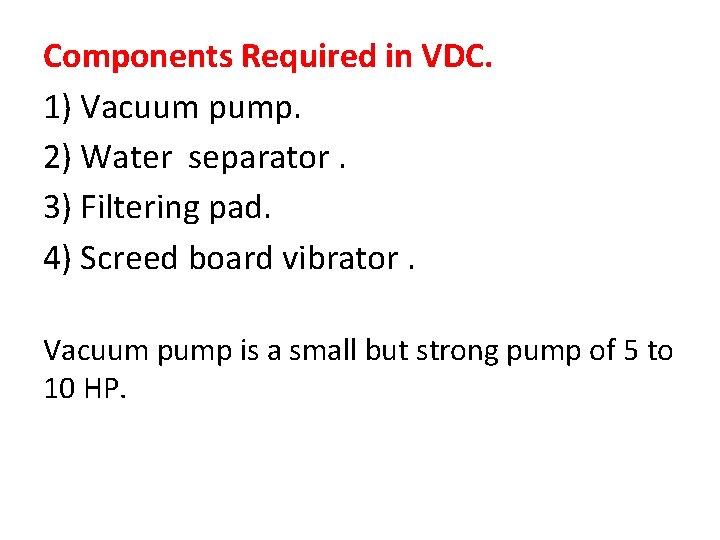
Components Required in VDC. 1) Vacuum pump. 2) Water separator. 3) Filtering pad. 4) Screed board vibrator. Vacuum pump is a small but strong pump of 5 to 10 HP.
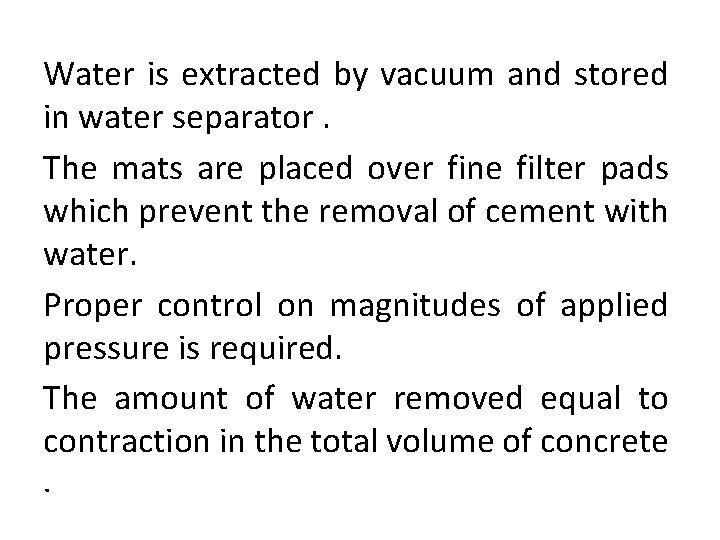
Water is extracted by vacuum and stored in water separator. The mats are placed over fine filter pads which prevent the removal of cement with water. Proper control on magnitudes of applied pressure is required. The amount of water removed equal to contraction in the total volume of concrete.
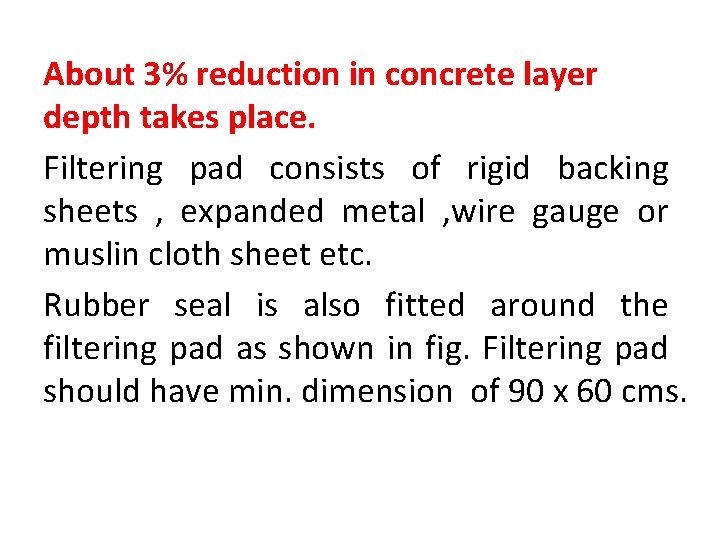
About 3% reduction in concrete layer depth takes place. Filtering pad consists of rigid backing sheets , expanded metal , wire gauge or muslin cloth sheet etc. Rubber seal is also fitted around the filtering pad as shown in fig. Filtering pad should have min. dimension of 90 x 60 cms.
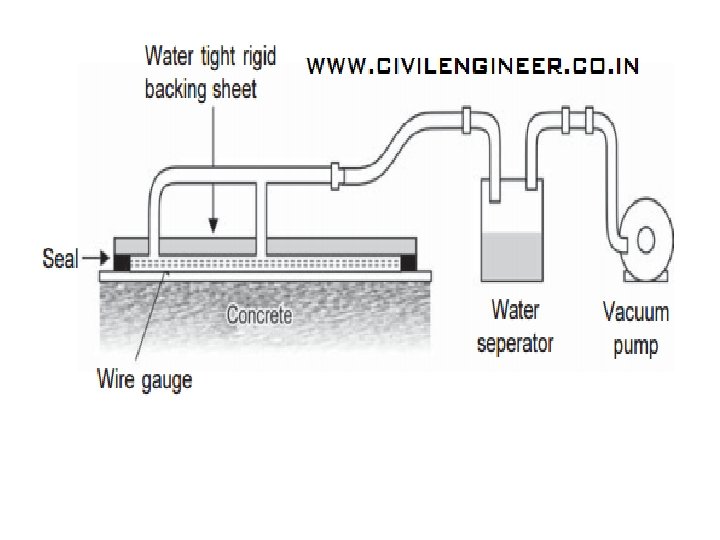
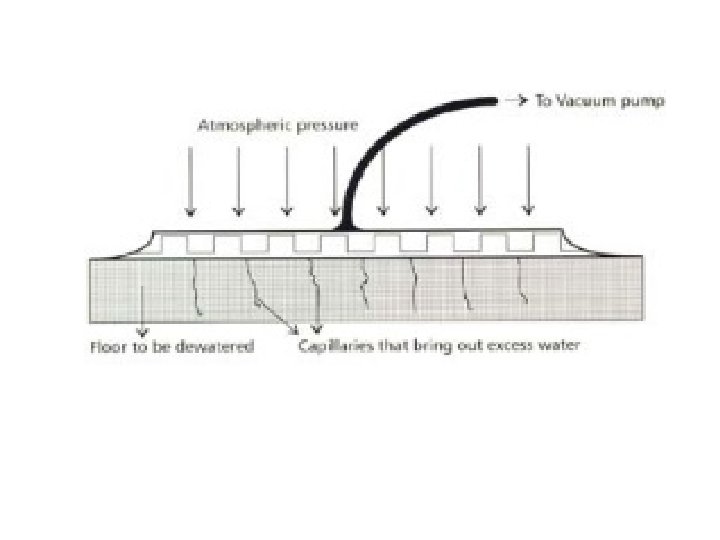
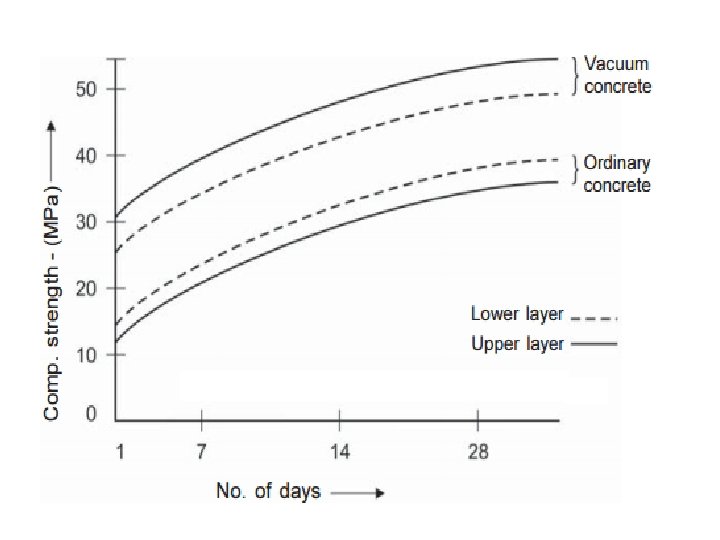
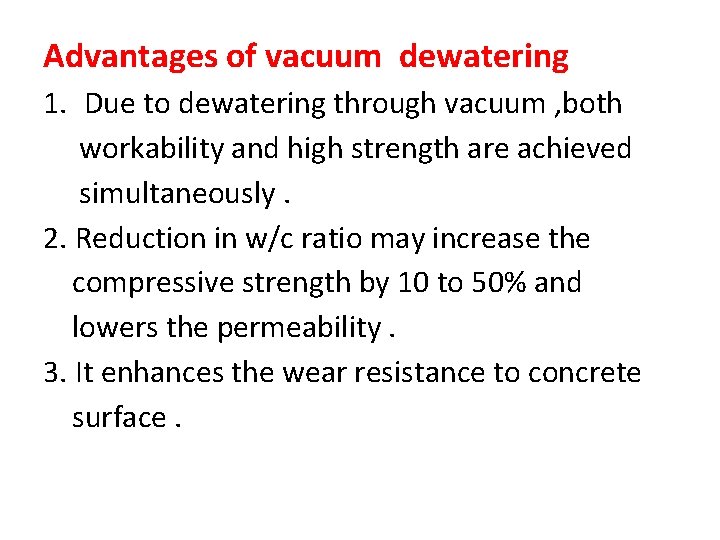
Advantages of vacuum dewatering 1. Due to dewatering through vacuum , both workability and high strength are achieved simultaneously. 2. Reduction in w/c ratio may increase the compressive strength by 10 to 50% and lowers the permeability. 3. It enhances the wear resistance to concrete surface.
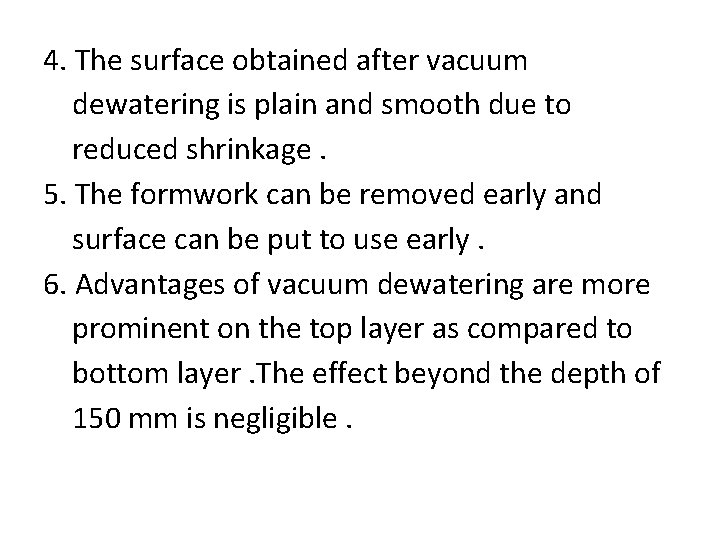
4. The surface obtained after vacuum dewatering is plain and smooth due to reduced shrinkage. 5. The formwork can be removed early and surface can be put to use early. 6. Advantages of vacuum dewatering are more prominent on the top layer as compared to bottom layer. The effect beyond the depth of 150 mm is negligible.
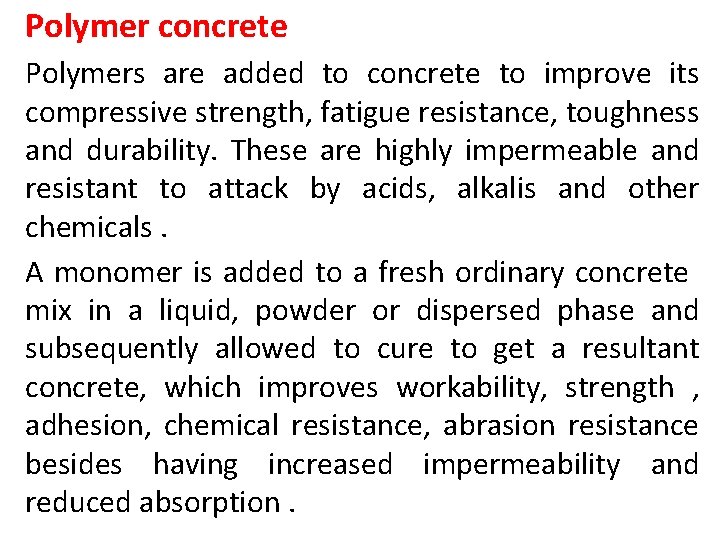
Polymer concrete Polymers are added to concrete to improve its compressive strength, fatigue resistance, toughness and durability. These are highly impermeable and resistant to attack by acids, alkalis and other chemicals. A monomer is added to a fresh ordinary concrete mix in a liquid, powder or dispersed phase and subsequently allowed to cure to get a resultant concrete, which improves workability, strength , adhesion, chemical resistance, abrasion resistance besides having increased impermeability and reduced absorption.

The polymer cement ratio is generally 6 -20%by weight. This concrete is used with advantage in overlays to bridge decks, deep patching, parking garages, industrial floors etc.
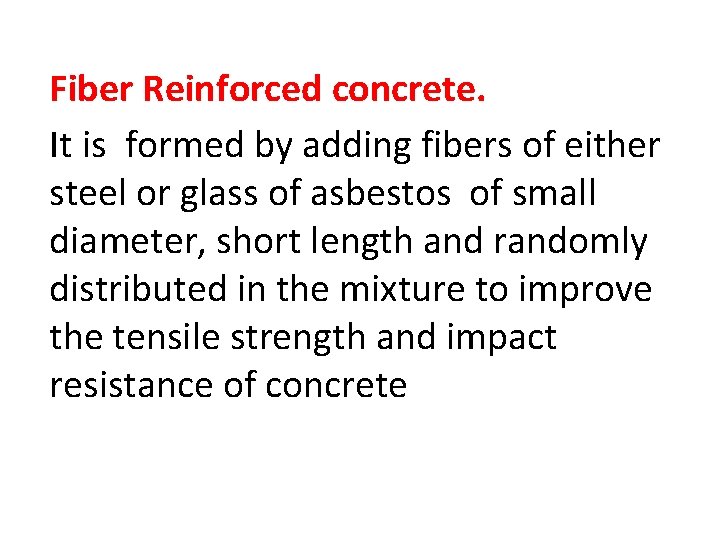
Fiber Reinforced concrete. It is formed by adding fibers of either steel or glass of asbestos of small diameter, short length and randomly distributed in the mixture to improve the tensile strength and impact resistance of concrete
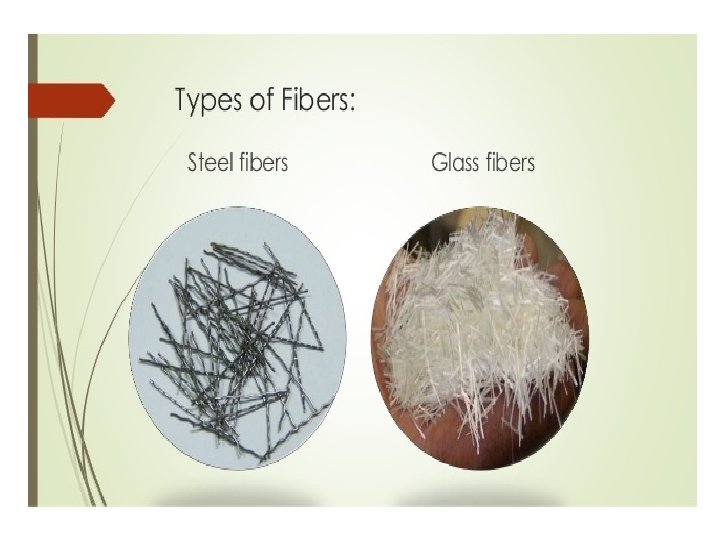
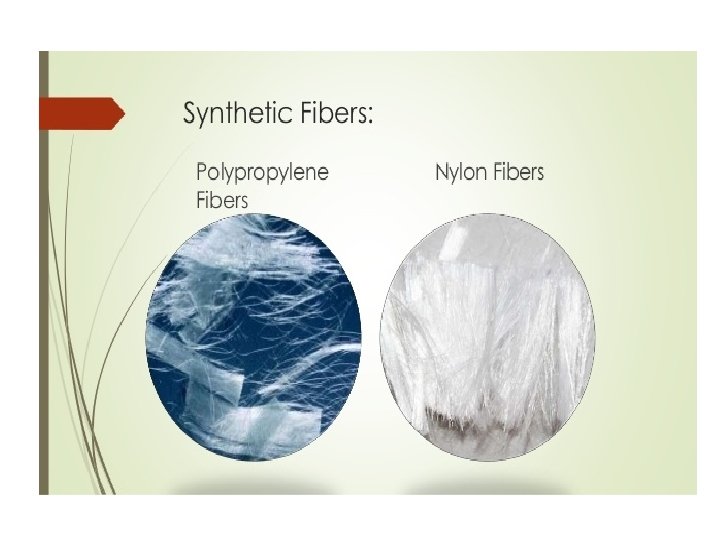
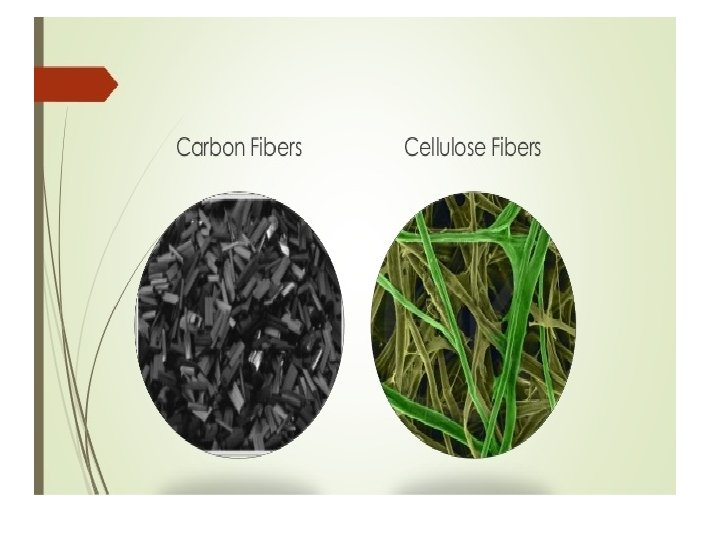
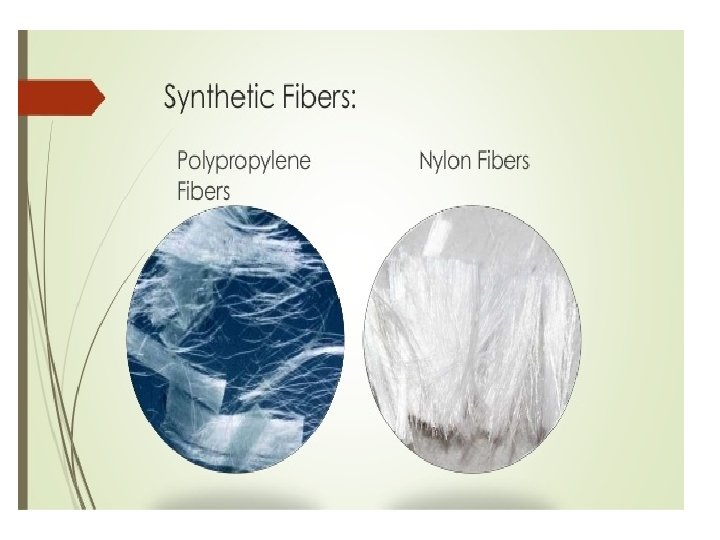
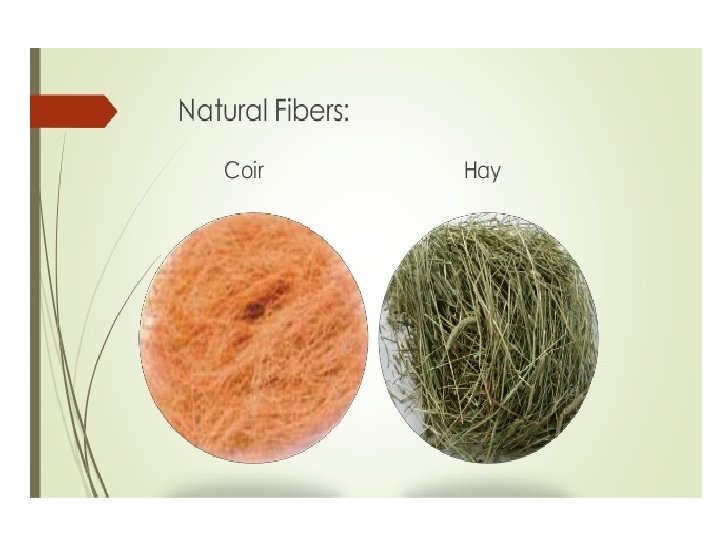
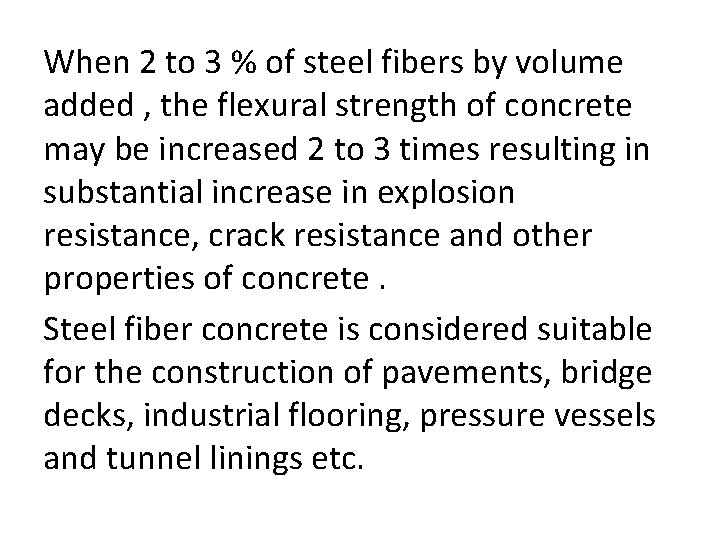
When 2 to 3 % of steel fibers by volume added , the flexural strength of concrete may be increased 2 to 3 times resulting in substantial increase in explosion resistance, crack resistance and other properties of concrete. Steel fiber concrete is considered suitable for the construction of pavements, bridge decks, industrial flooring, pressure vessels and tunnel linings etc.
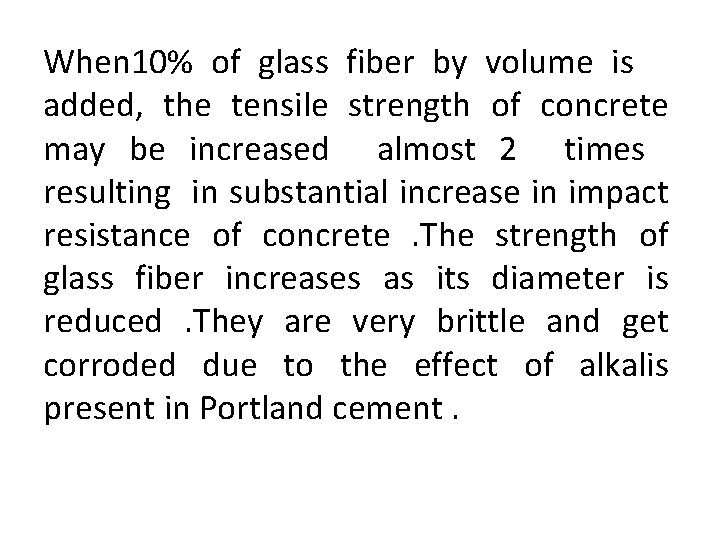
When 10% of glass fiber by volume is added, the tensile strength of concrete may be increased almost 2 times resulting in substantial increase in impact resistance of concrete. The strength of glass fiber increases as its diameter is reduced. They are very brittle and get corroded due to the effect of alkalis present in Portland cement.
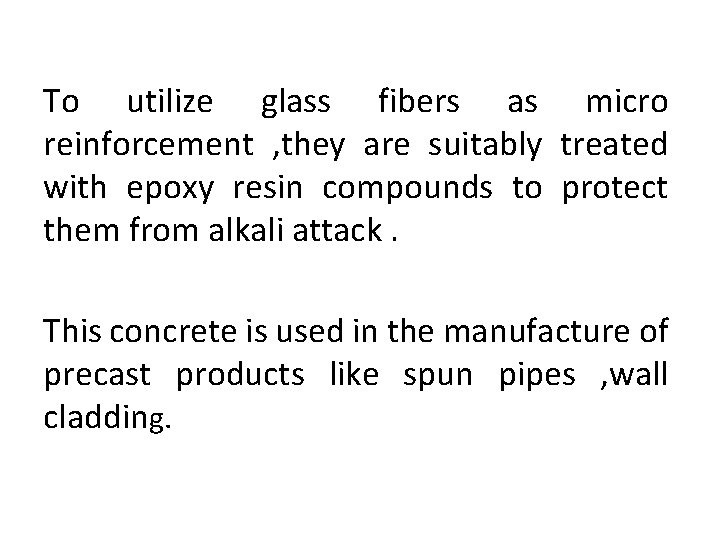
To utilize glass fibers as micro reinforcement , they are suitably treated with epoxy resin compounds to protect them from alkali attack. This concrete is used in the manufacture of precast products like spun pipes , wall cladding.
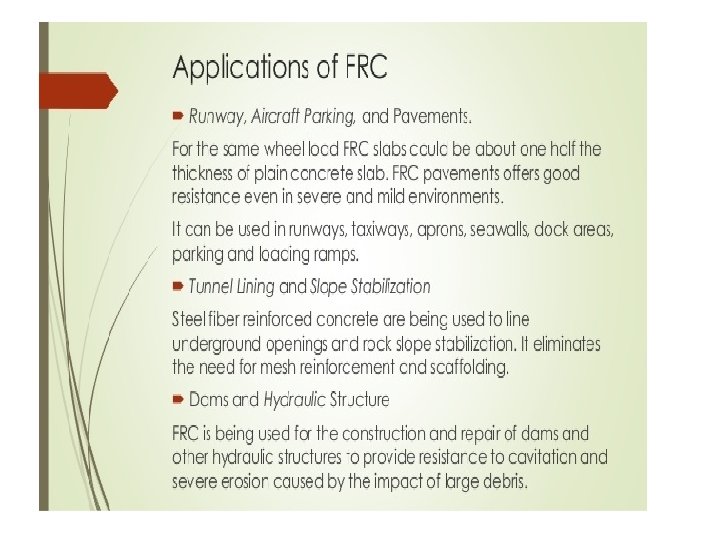
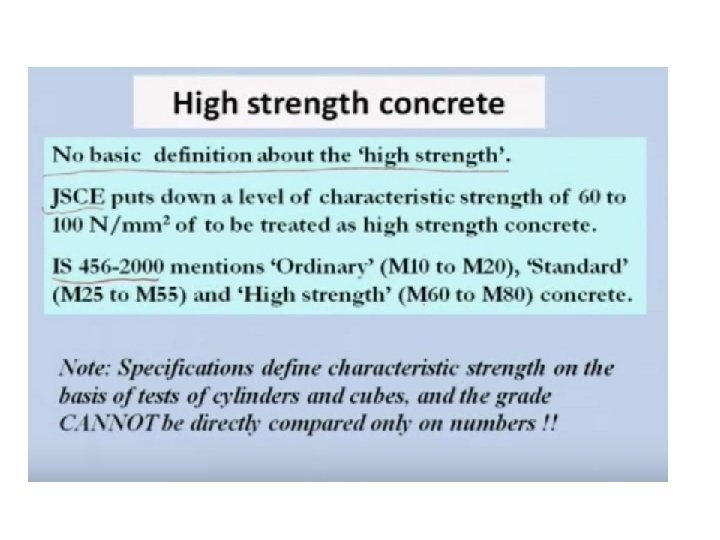
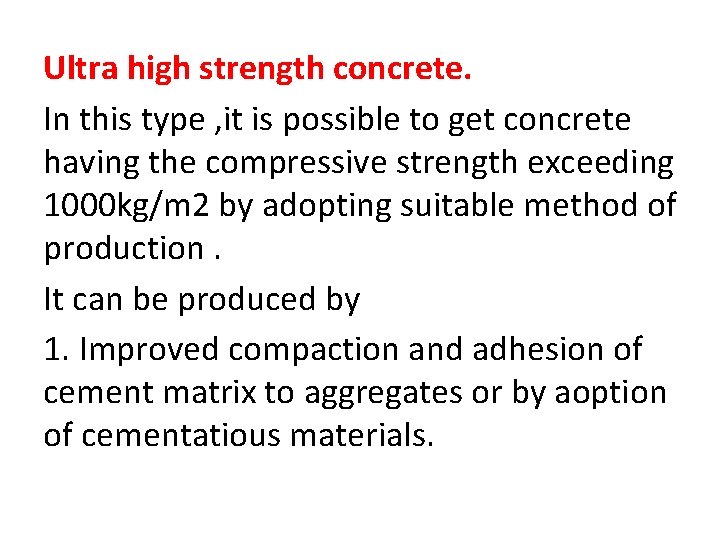
Ultra high strength concrete. In this type , it is possible to get concrete having the compressive strength exceeding 1000 kg/m 2 by adopting suitable method of production. It can be produced by 1. Improved compaction and adhesion of cement matrix to aggregates or by aoption of cementatious materials.
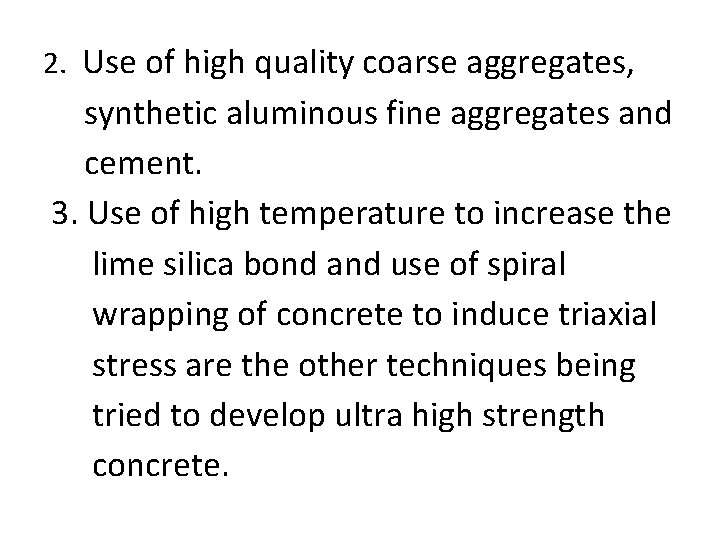
2. Use of high quality coarse aggregates, synthetic aluminous fine aggregates and cement. 3. Use of high temperature to increase the lime silica bond and use of spiral wrapping of concrete to induce triaxial stress are the other techniques being tried to develop ultra high strength concrete.
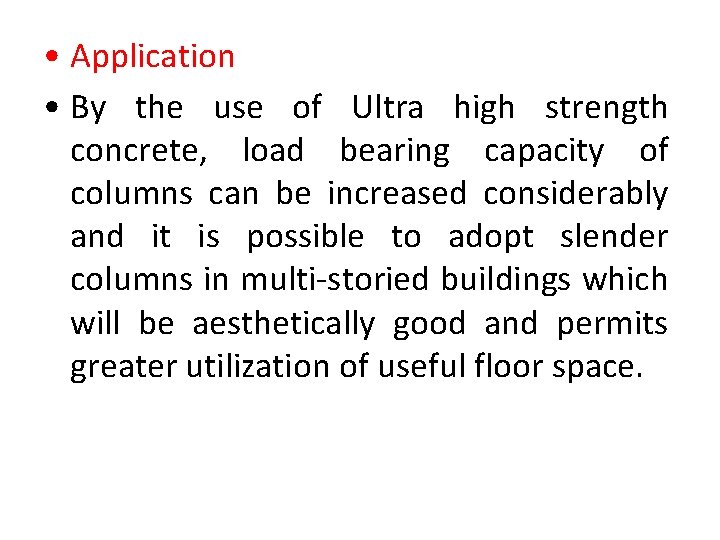
• Application • By the use of Ultra high strength concrete, load bearing capacity of columns can be increased considerably and it is possible to adopt slender columns in multi-storied buildings which will be aesthetically good and permits greater utilization of useful floor space.
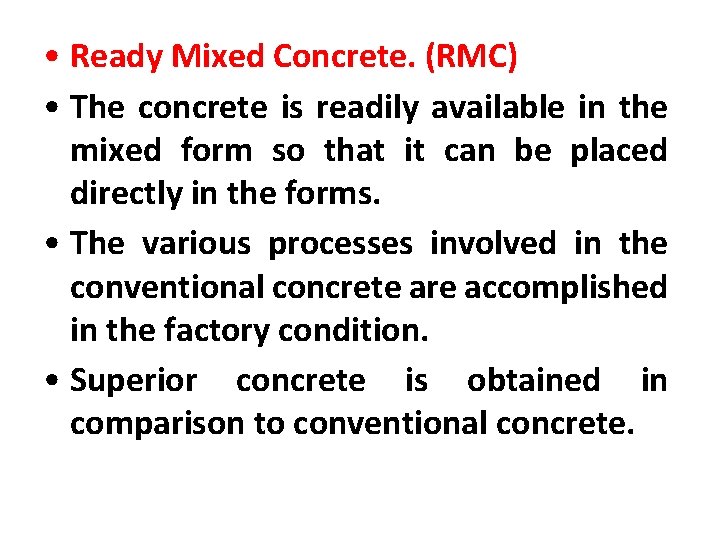
• Ready Mixed Concrete. (RMC) • The concrete is readily available in the mixed form so that it can be placed directly in the forms. • The various processes involved in the conventional concrete are accomplished in the factory condition. • Superior concrete is obtained in comparison to conventional concrete.
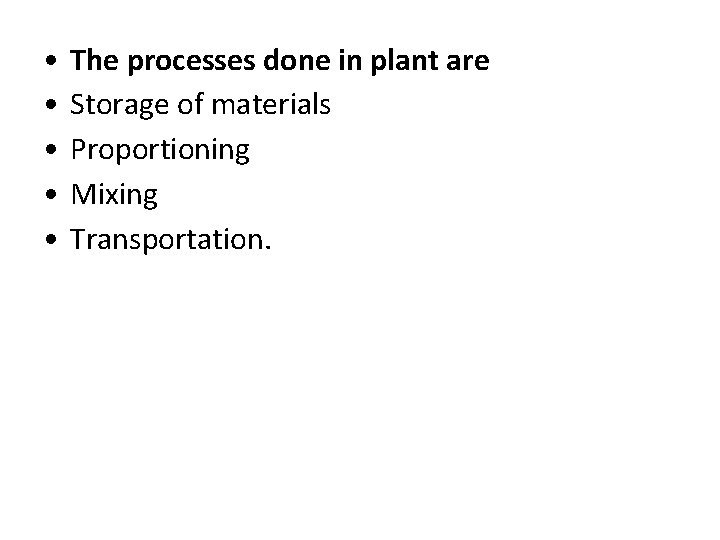
• • • The processes done in plant are Storage of materials Proportioning Mixing Transportation.
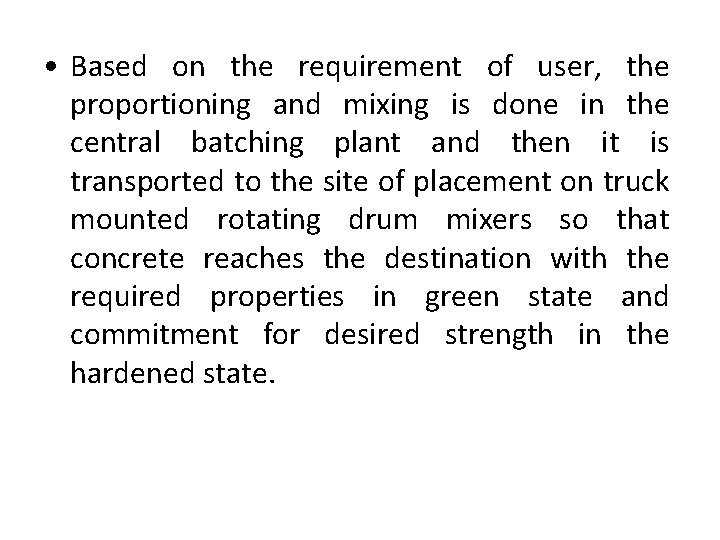
• Based on the requirement of user, the proportioning and mixing is done in the central batching plant and then it is transported to the site of placement on truck mounted rotating drum mixers so that concrete reaches the destination with the required properties in green state and commitment for desired strength in the hardened state.
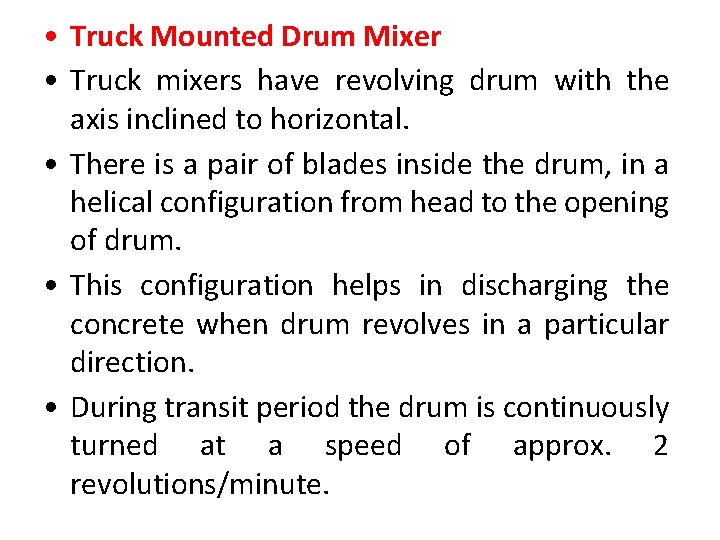
• Truck Mounted Drum Mixer • Truck mixers have revolving drum with the axis inclined to horizontal. • There is a pair of blades inside the drum, in a helical configuration from head to the opening of drum. • This configuration helps in discharging the concrete when drum revolves in a particular direction. • During transit period the drum is continuously turned at a speed of approx. 2 revolutions/minute.
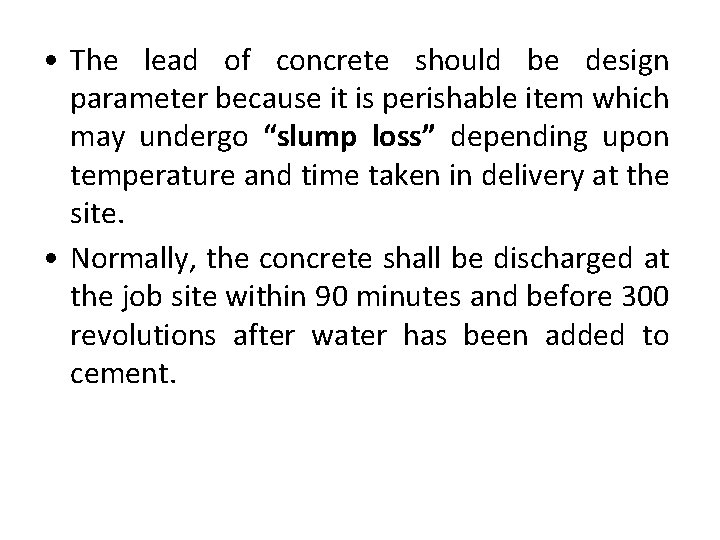
• The lead of concrete should be design parameter because it is perishable item which may undergo “slump loss” depending upon temperature and time taken in delivery at the site. • Normally, the concrete shall be discharged at the job site within 90 minutes and before 300 revolutions after water has been added to cement.
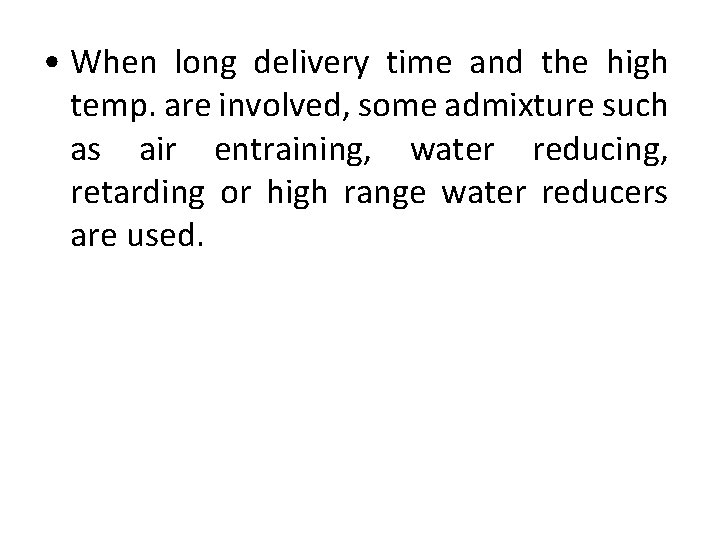
• When long delivery time and the high temp. are involved, some admixture such as air entraining, water reducing, retarding or high range water reducers are used.
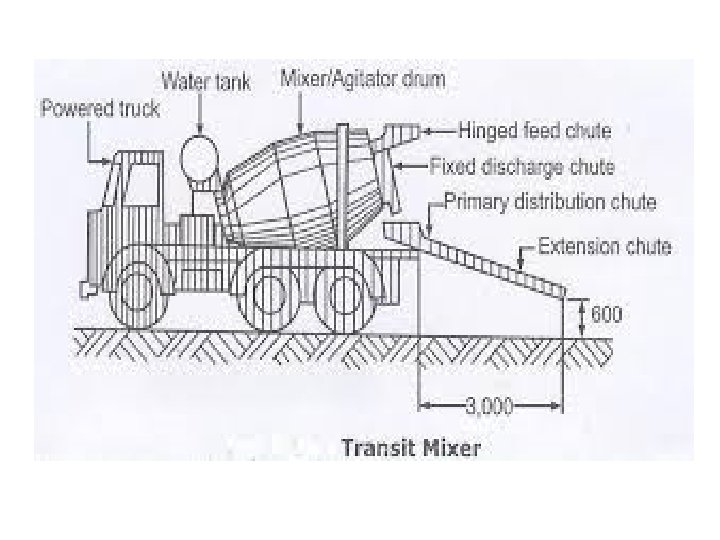
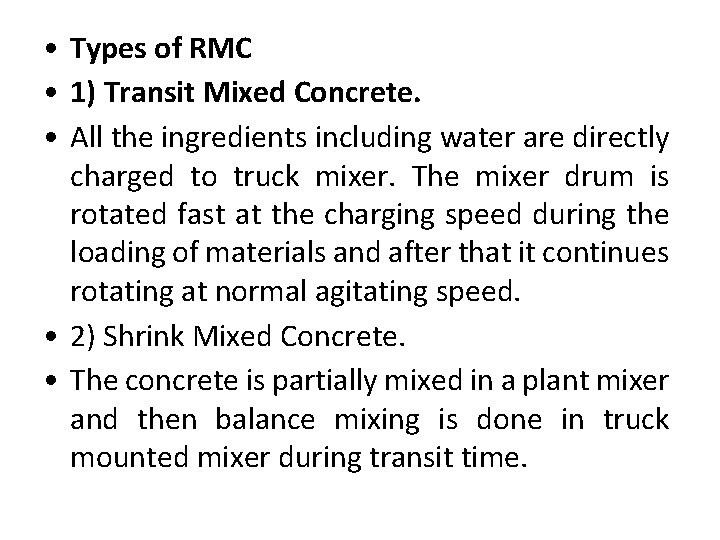
• Types of RMC • 1) Transit Mixed Concrete. • All the ingredients including water are directly charged to truck mixer. The mixer drum is rotated fast at the charging speed during the loading of materials and after that it continues rotating at normal agitating speed. • 2) Shrink Mixed Concrete. • The concrete is partially mixed in a plant mixer and then balance mixing is done in truck mounted mixer during transit time.
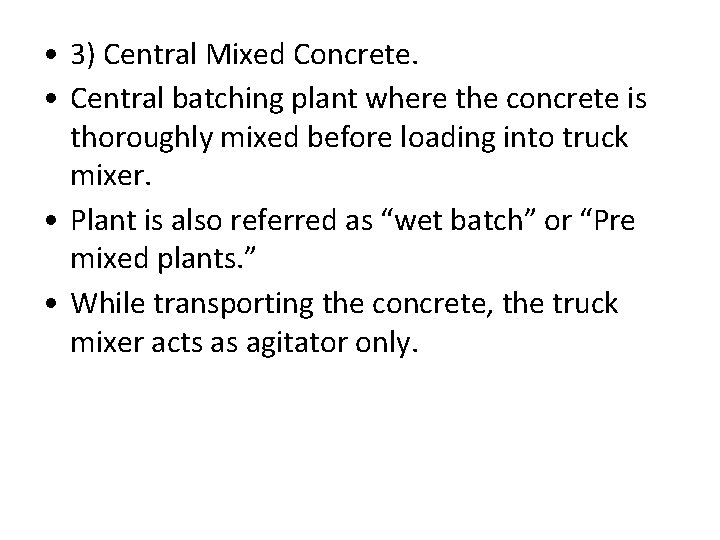
• 3) Central Mixed Concrete. • Central batching plant where the concrete is thoroughly mixed before loading into truck mixer. • Plant is also referred as “wet batch” or “Pre mixed plants. ” • While transporting the concrete, the truck mixer acts as agitator only.
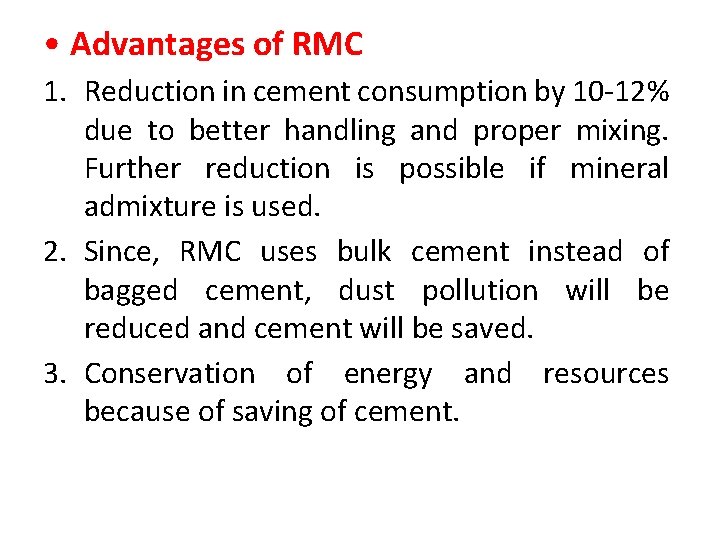
• Advantages of RMC 1. Reduction in cement consumption by 10 -12% due to better handling and proper mixing. Further reduction is possible if mineral admixture is used. 2. Since, RMC uses bulk cement instead of bagged cement, dust pollution will be reduced and cement will be saved. 3. Conservation of energy and resources because of saving of cement.
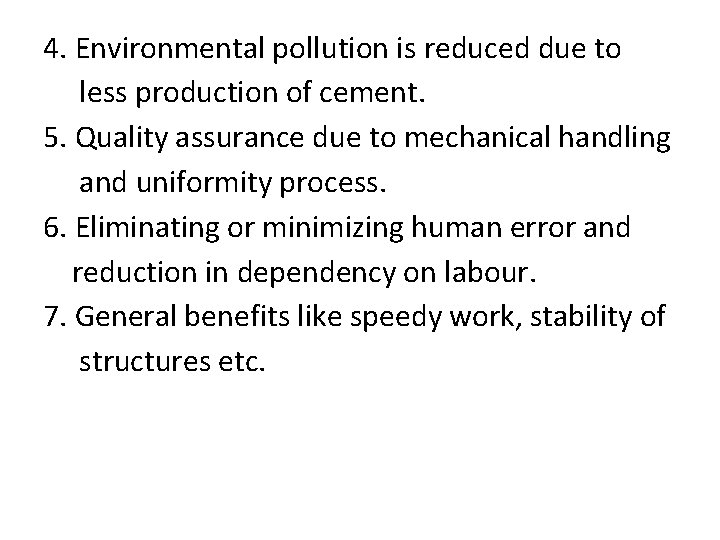
4. Environmental pollution is reduced due to less production of cement. 5. Quality assurance due to mechanical handling and uniformity process. 6. Eliminating or minimizing human error and reduction in dependency on labour. 7. General benefits like speedy work, stability of structures etc.
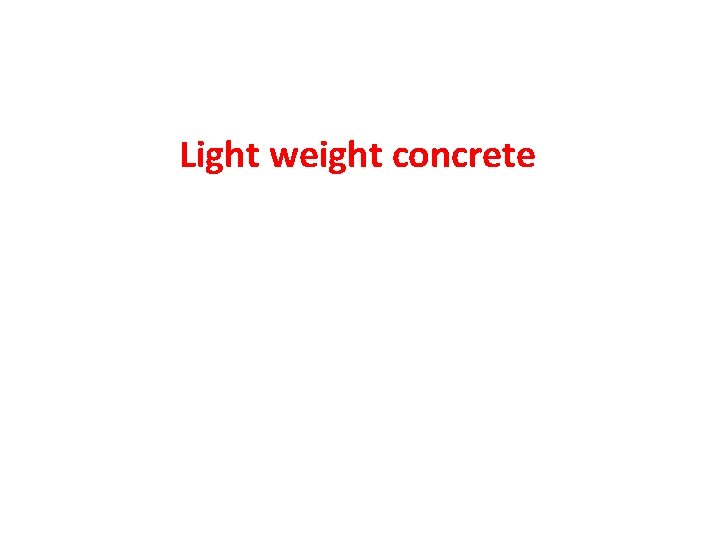
Light weight concrete
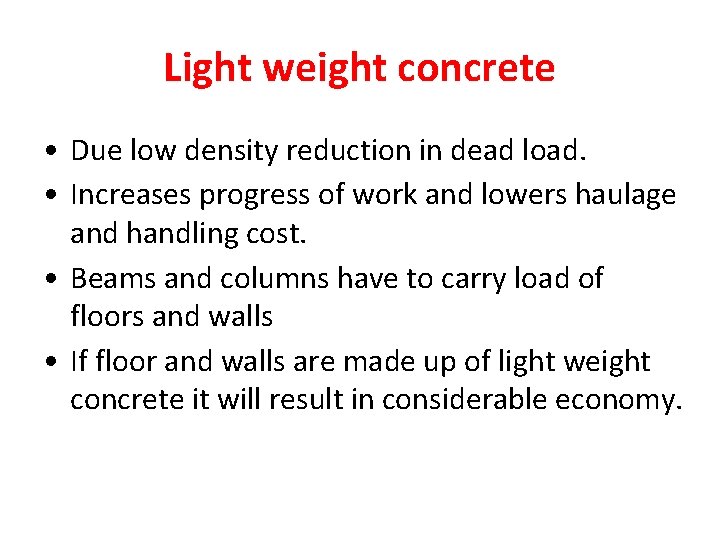
Light weight concrete • Due low density reduction in dead load. • Increases progress of work and lowers haulage and handling cost. • Beams and columns have to carry load of floors and walls • If floor and walls are made up of light weight concrete it will result in considerable economy.
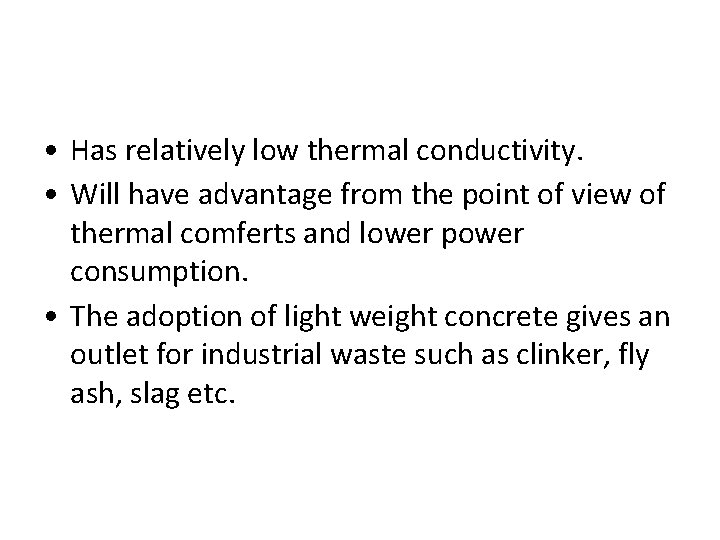
• Has relatively low thermal conductivity. • Will have advantage from the point of view of thermal comferts and lower power consumption. • The adoption of light weight concrete gives an outlet for industrial waste such as clinker, fly ash, slag etc.
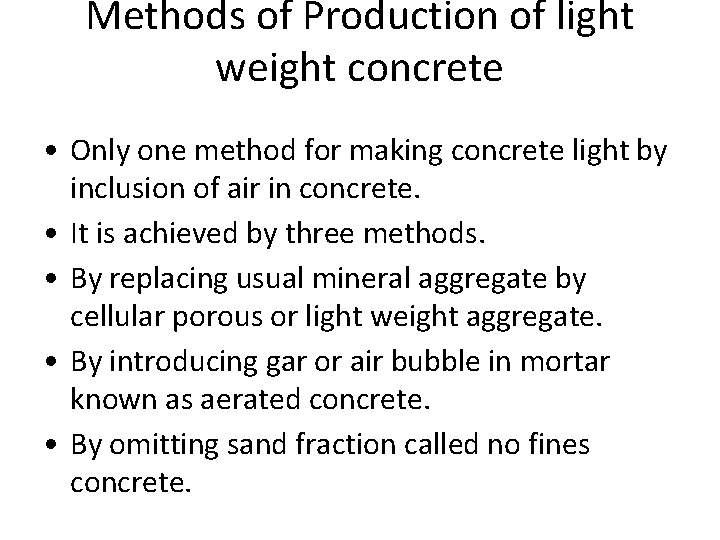
Methods of Production of light weight concrete • Only one method for making concrete light by inclusion of air in concrete. • It is achieved by three methods. • By replacing usual mineral aggregate by cellular porous or light weight aggregate. • By introducing gar or air bubble in mortar known as aerated concrete. • By omitting sand fraction called no fines concrete.
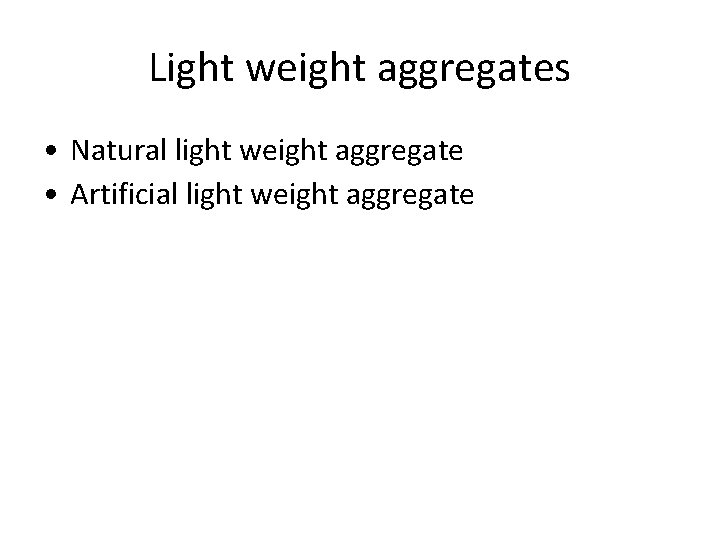
Light weight aggregates • Natural light weight aggregate • Artificial light weight aggregate
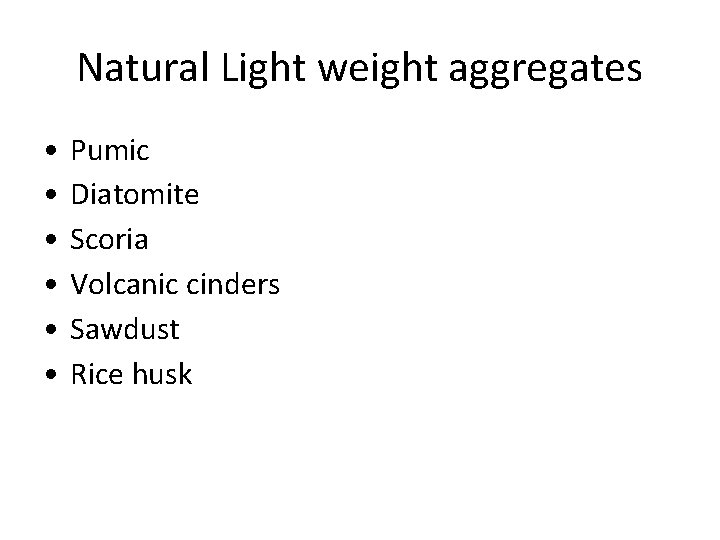
Natural Light weight aggregates • • • Pumic Diatomite Scoria Volcanic cinders Sawdust Rice husk
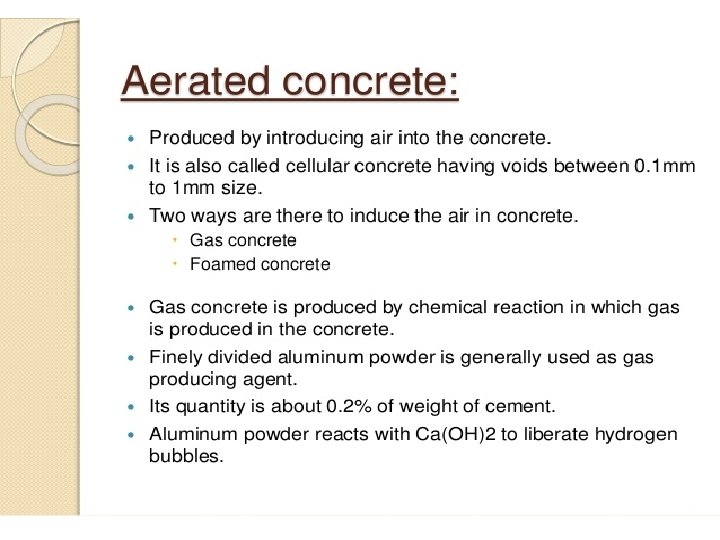
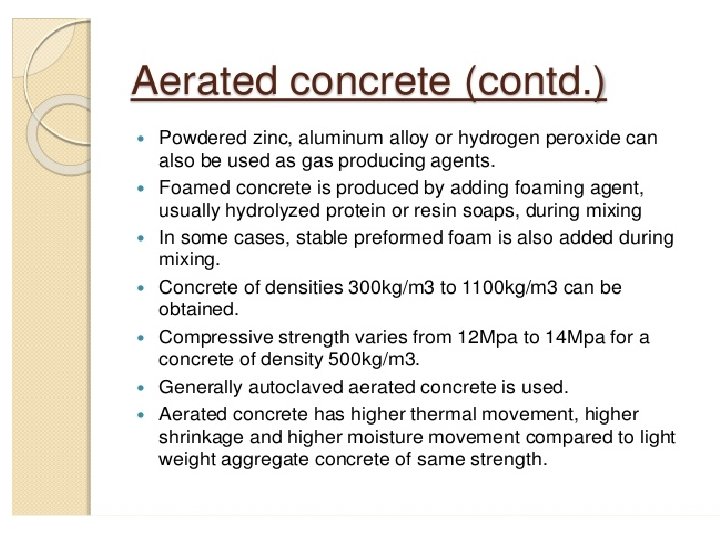
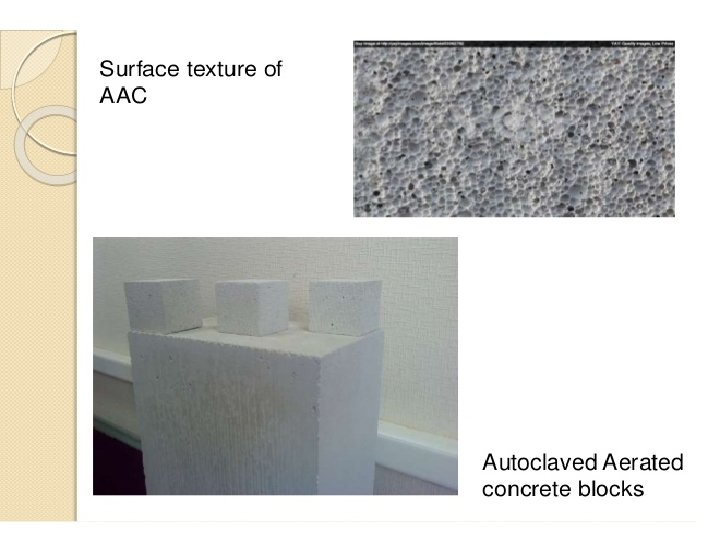

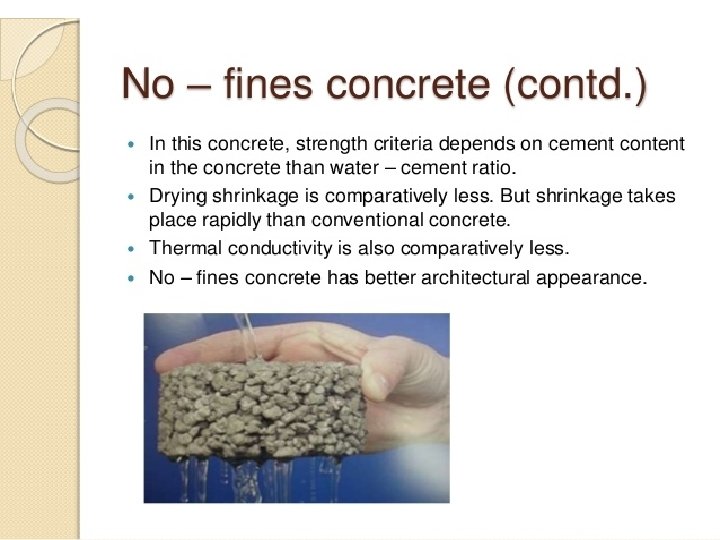
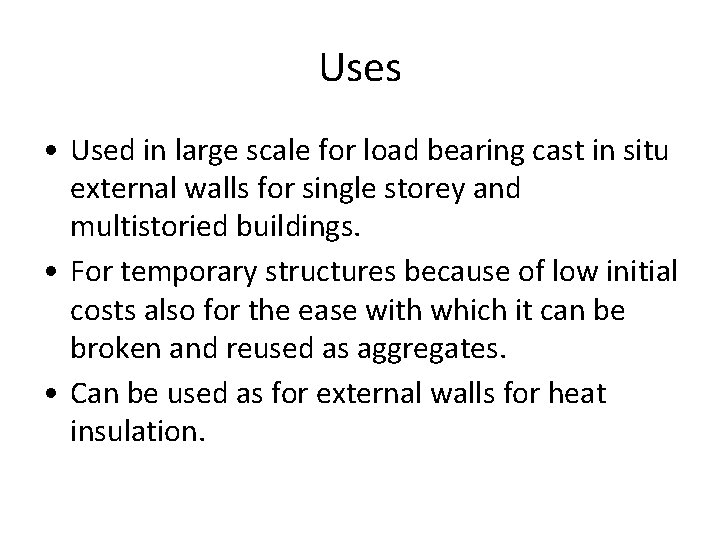
Uses • Used in large scale for load bearing cast in situ external walls for single storey and multistoried buildings. • For temporary structures because of low initial costs also for the ease with which it can be broken and reused as aggregates. • Can be used as for external walls for heat insulation.
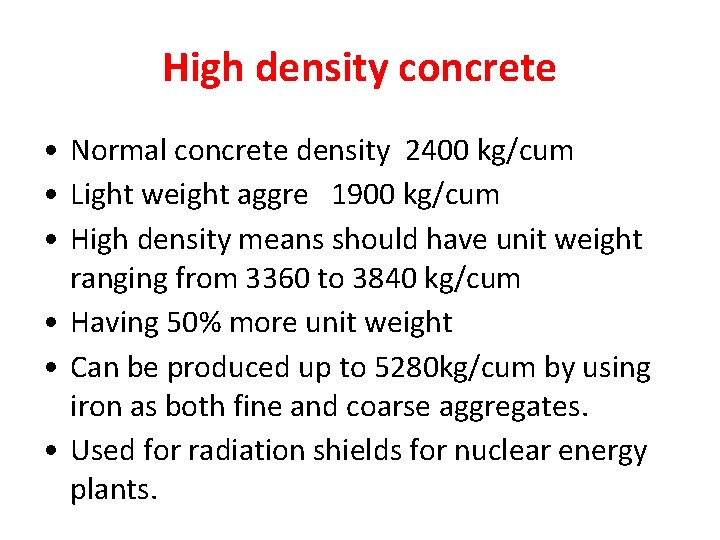
High density concrete • Normal concrete density 2400 kg/cum • Light weight aggre 1900 kg/cum • High density means should have unit weight ranging from 3360 to 3840 kg/cum • Having 50% more unit weight • Can be produced up to 5280 kg/cum by using iron as both fine and coarse aggregates. • Used for radiation shields for nuclear energy plants.
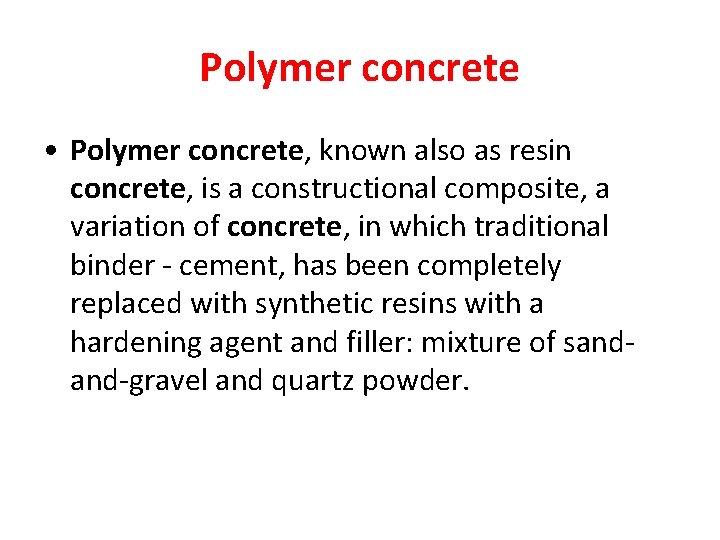
Polymer concrete • Polymer concrete, known also as resin concrete, is a constructional composite, a variation of concrete, in which traditional binder - cement, has been completely replaced with synthetic resins with a hardening agent and filler: mixture of sandand-gravel and quartz powder.
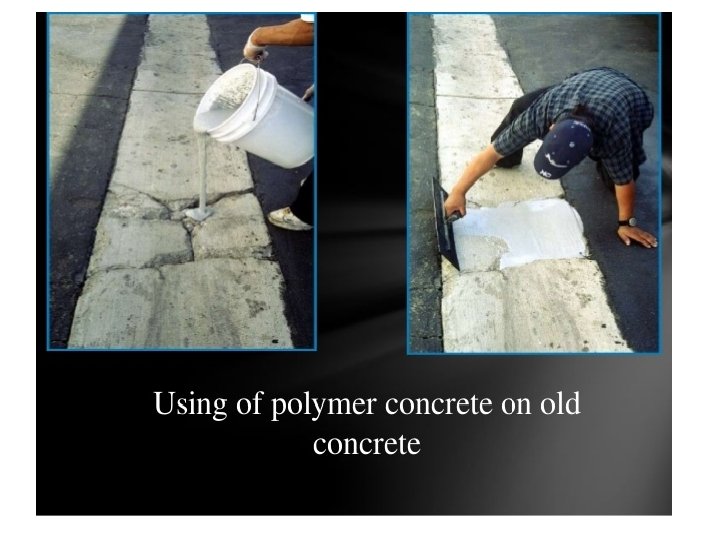
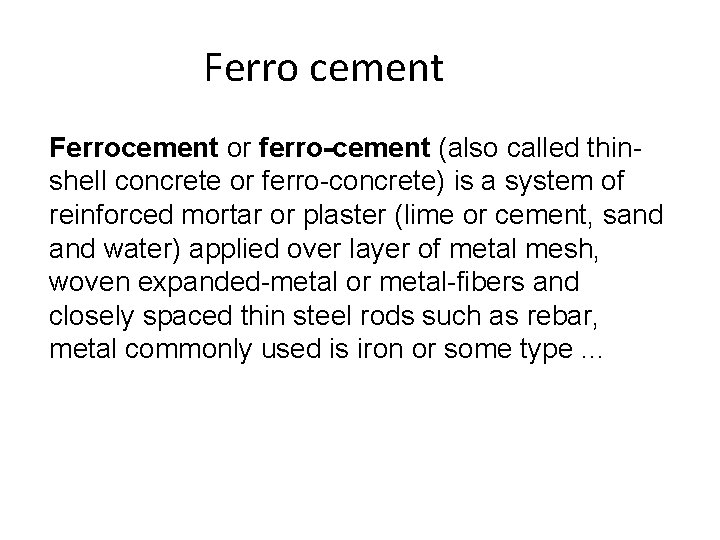
Ferro cement Ferrocement or ferro-cement (also called thinshell concrete or ferro-concrete) is a system of reinforced mortar or plaster (lime or cement, sand water) applied over layer of metal mesh, woven expanded-metal or metal-fibers and closely spaced thin steel rods such as rebar, metal commonly used is iron or some type. . .
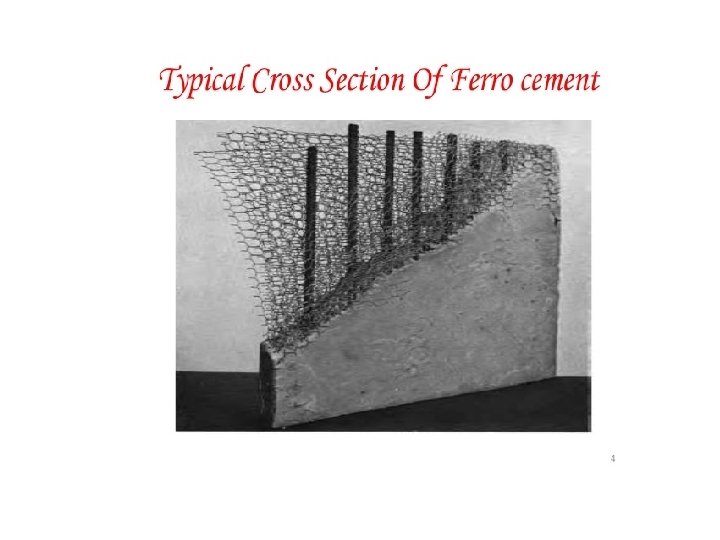
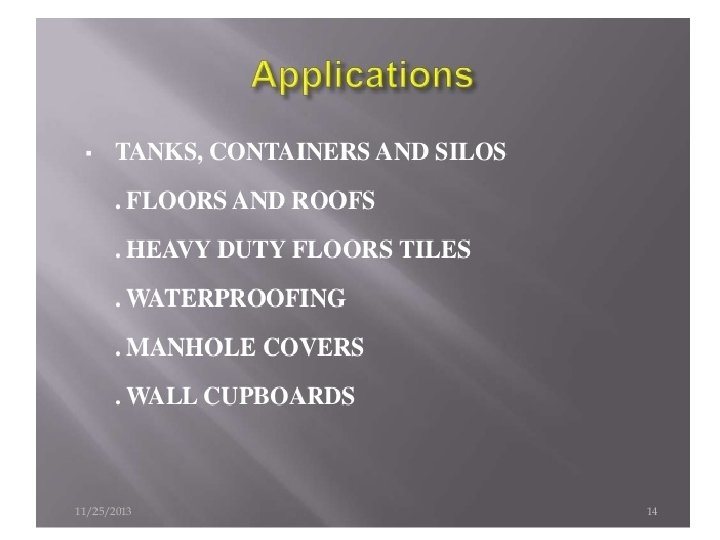
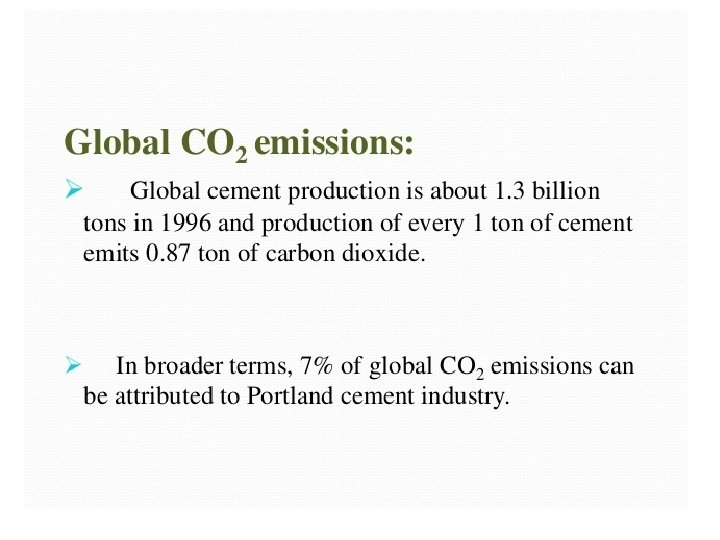
Green concrete
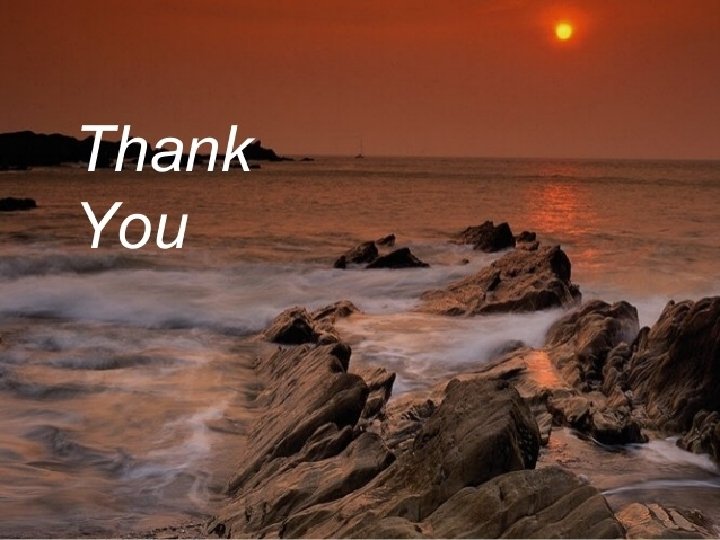