Status on longwavelength In P waveguide heterojunction phototransistors
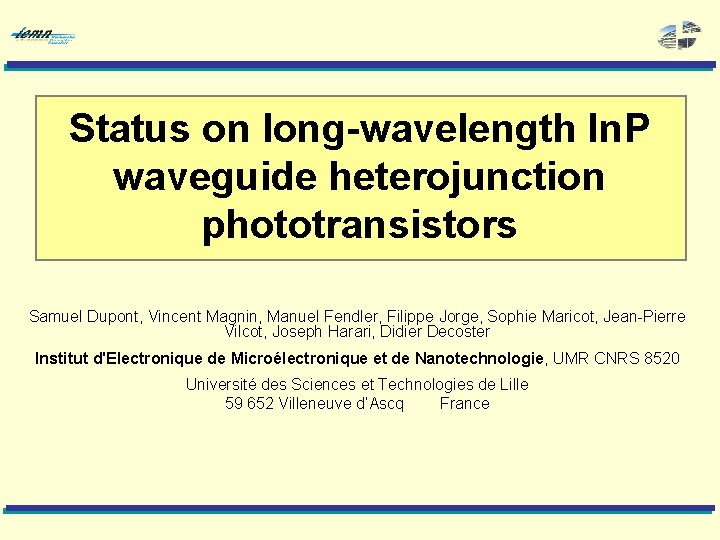
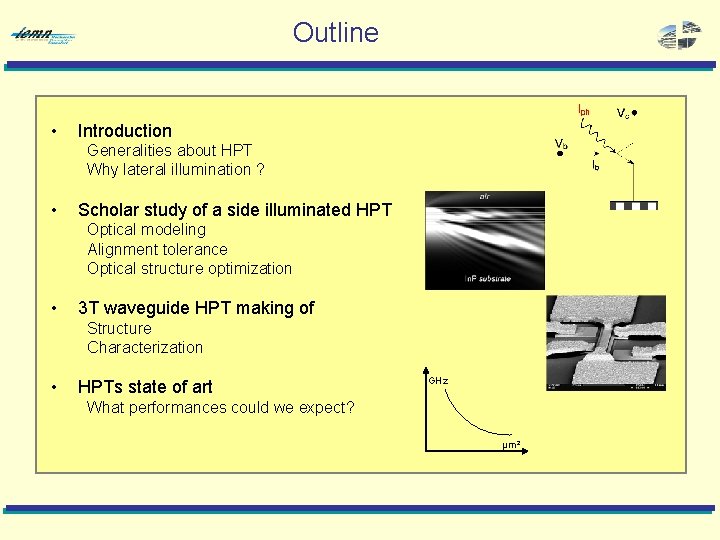
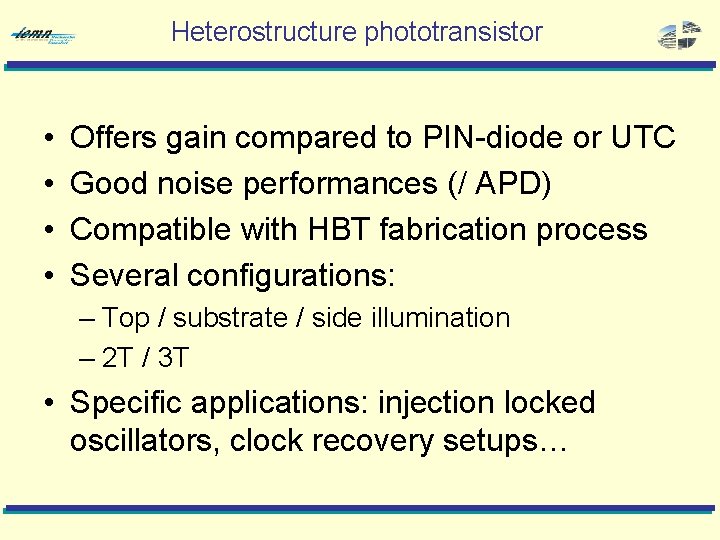
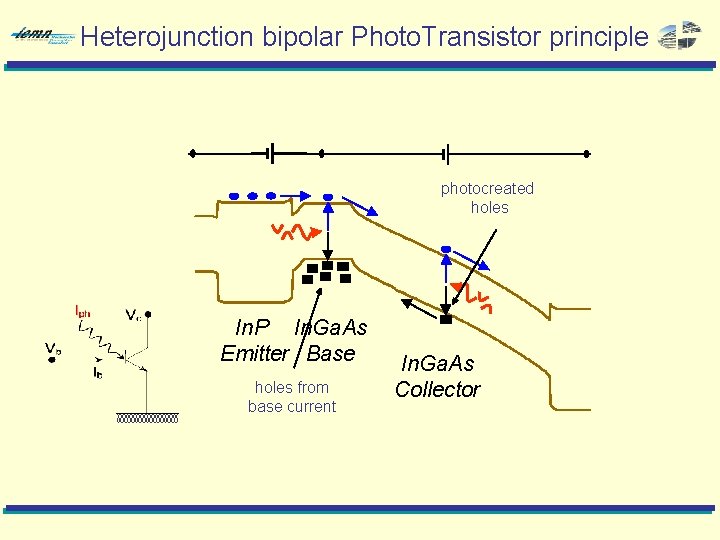
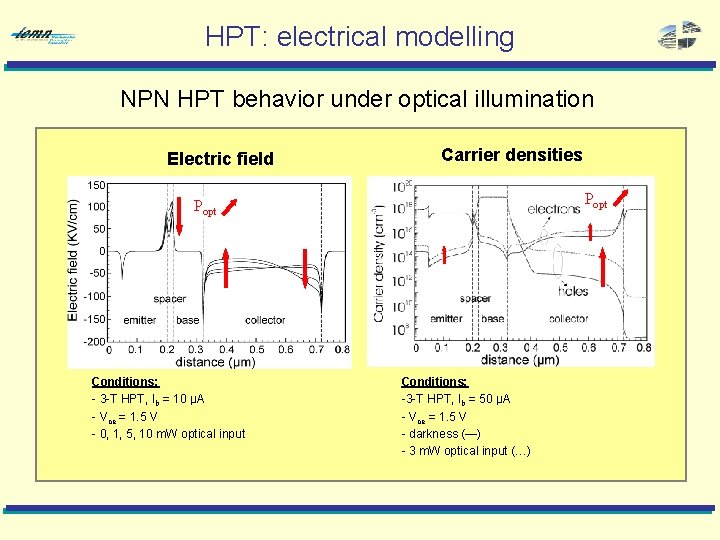
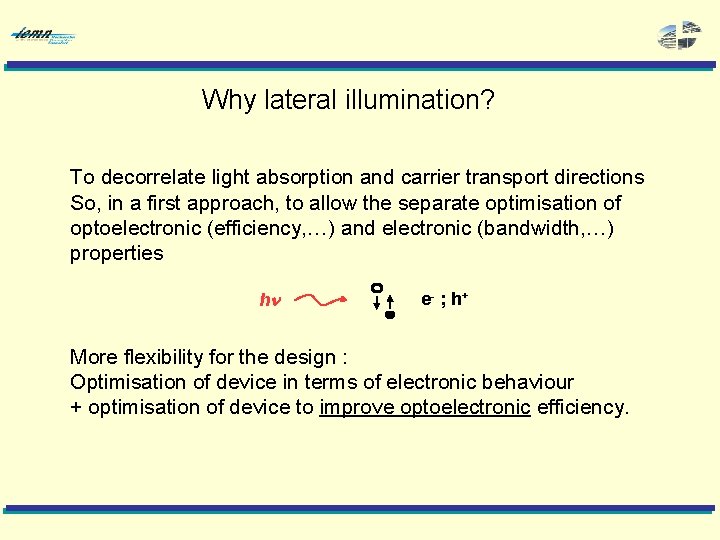
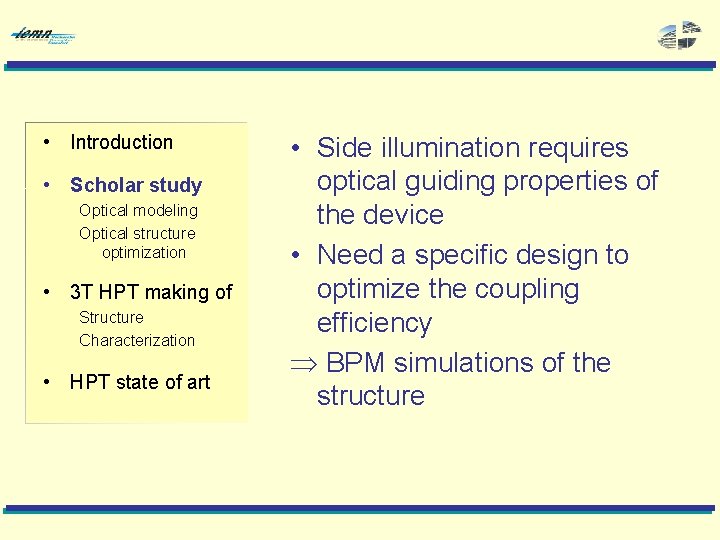
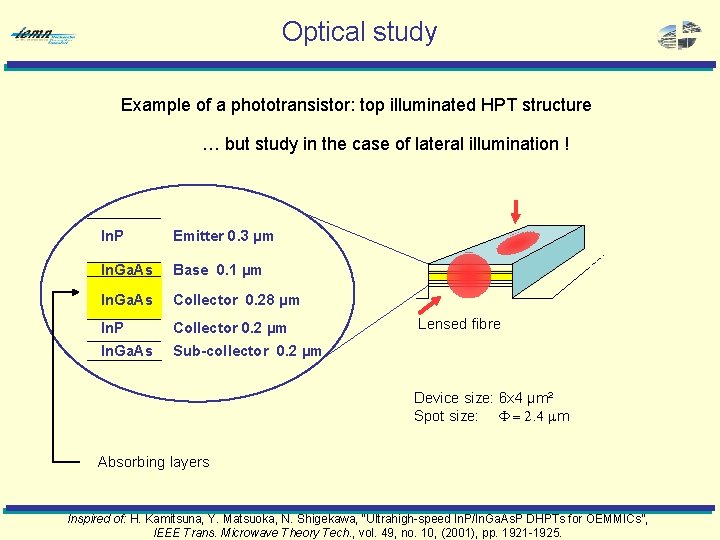
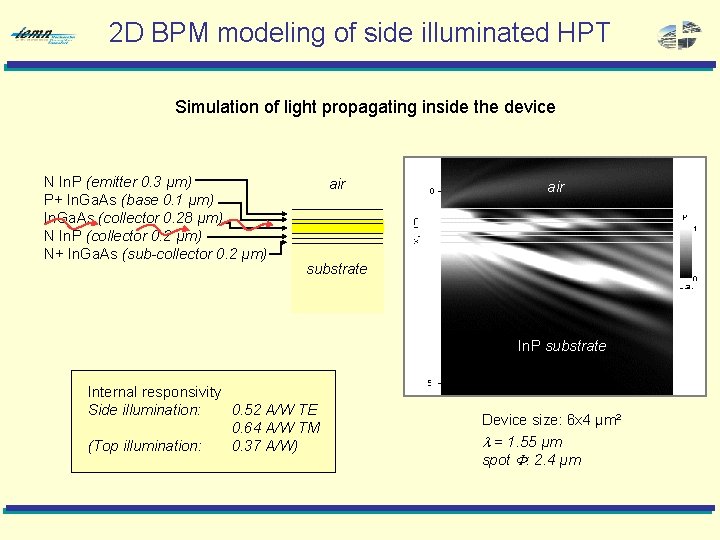
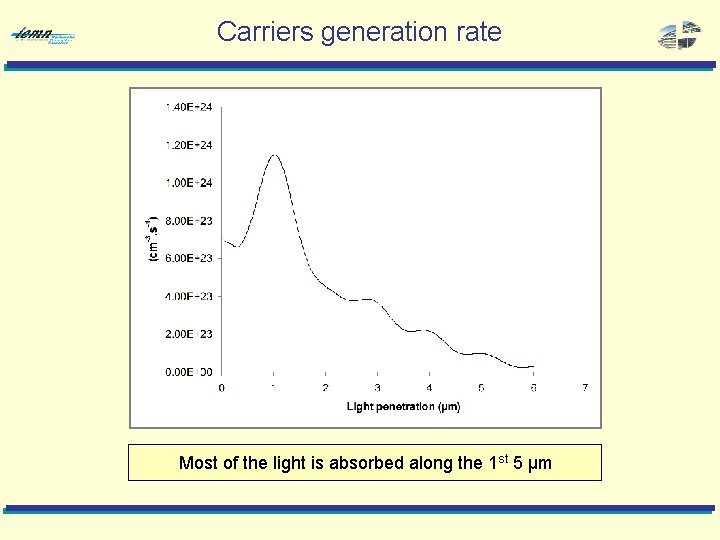
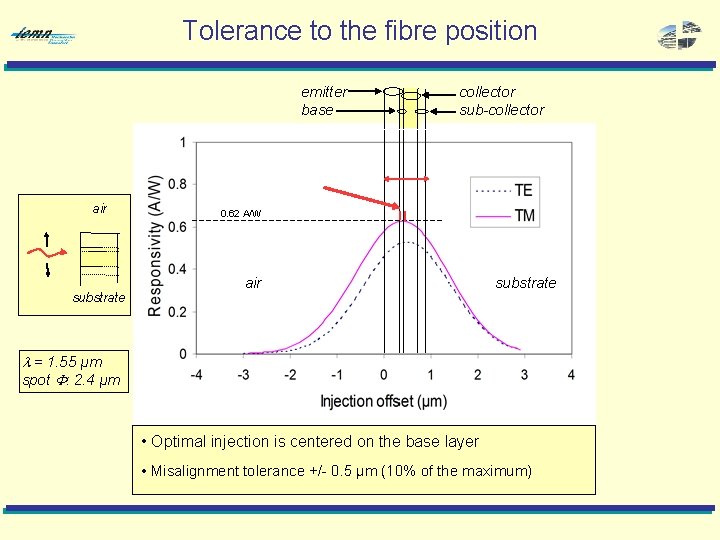
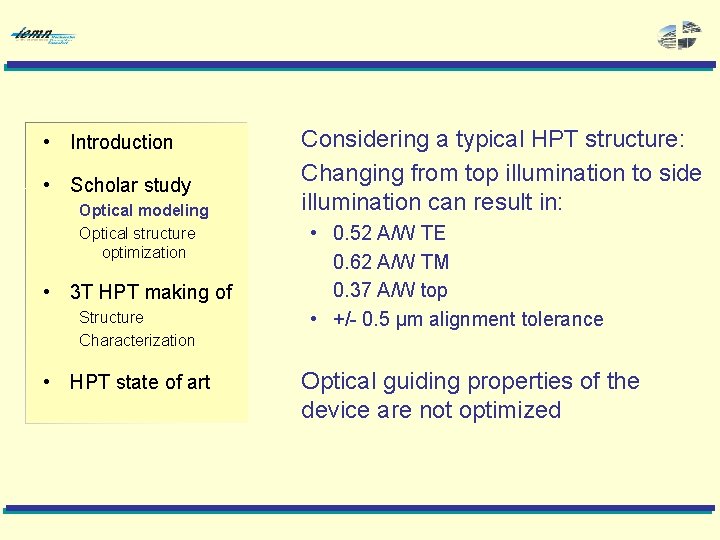
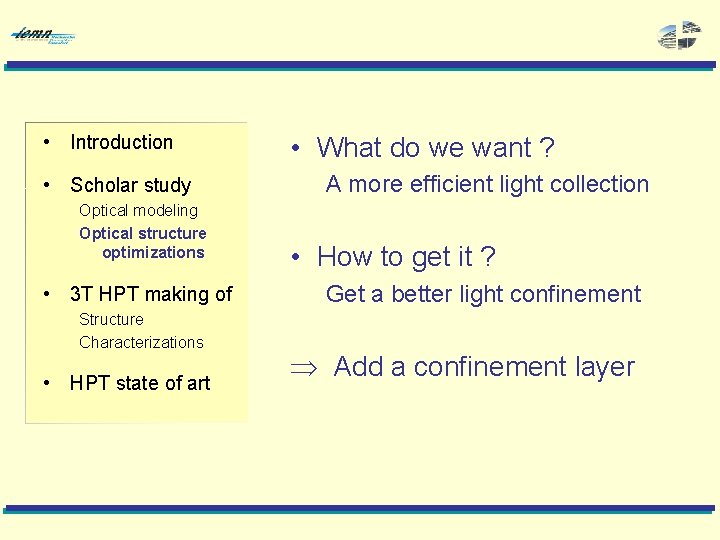
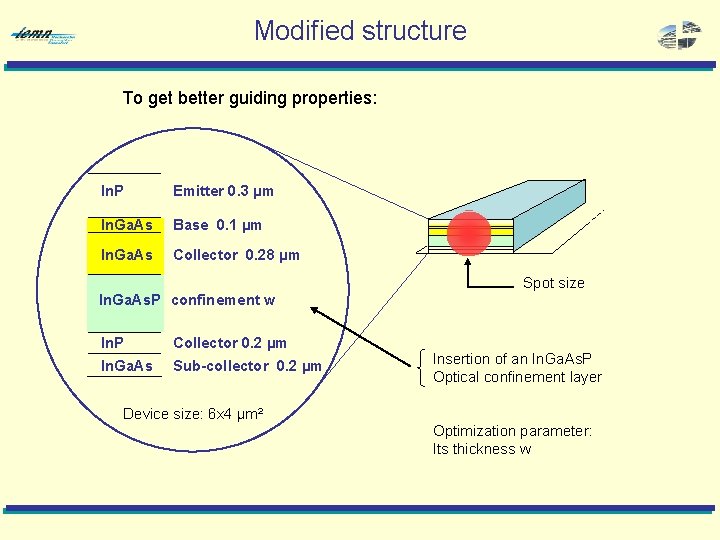
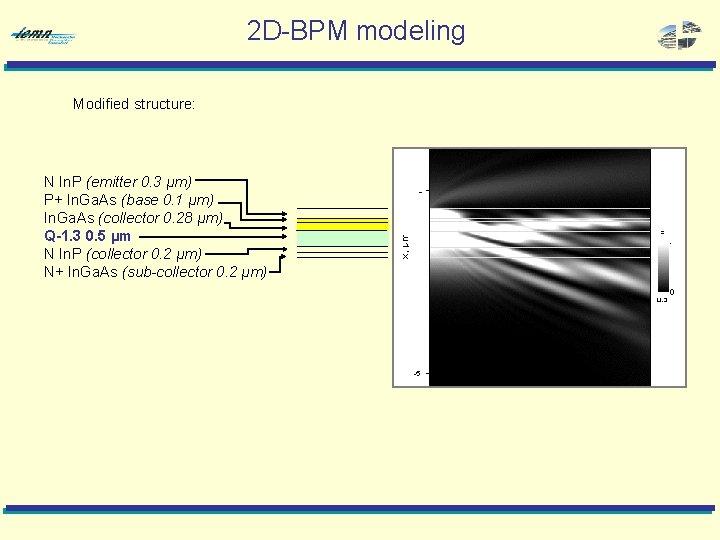
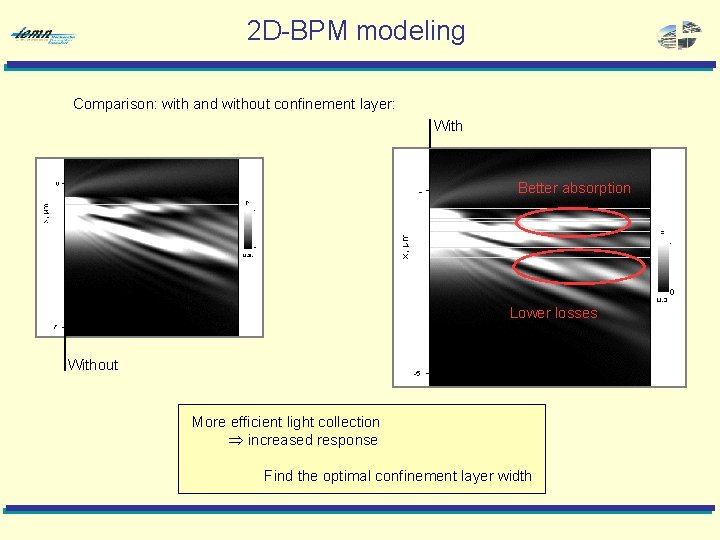
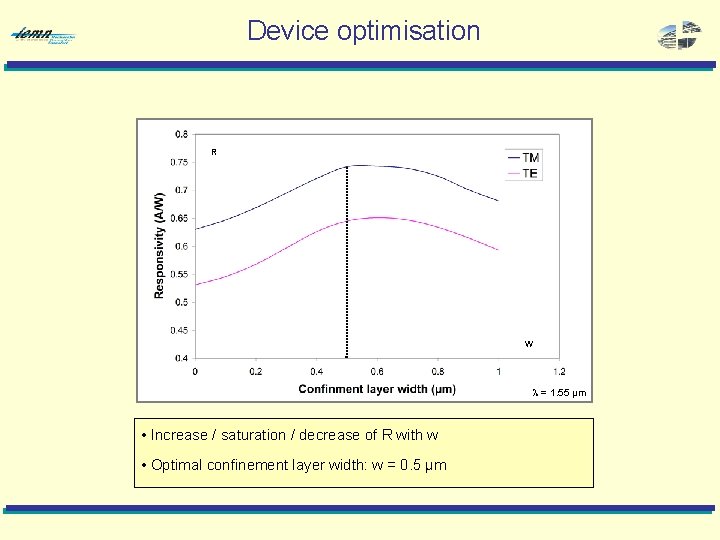
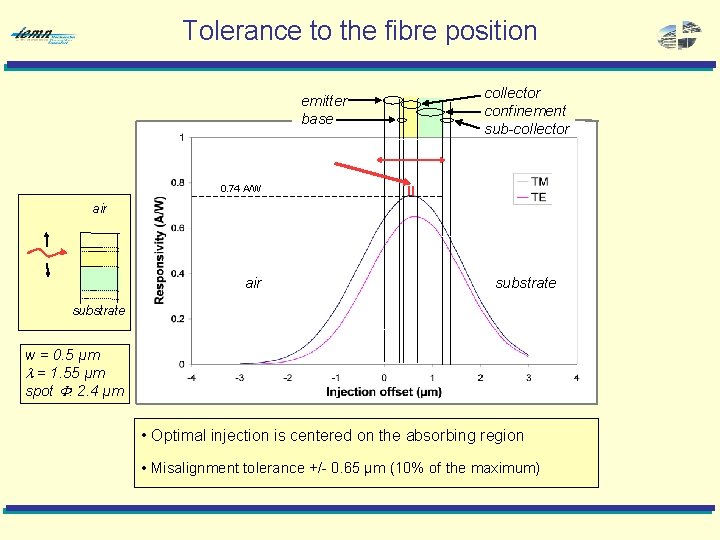
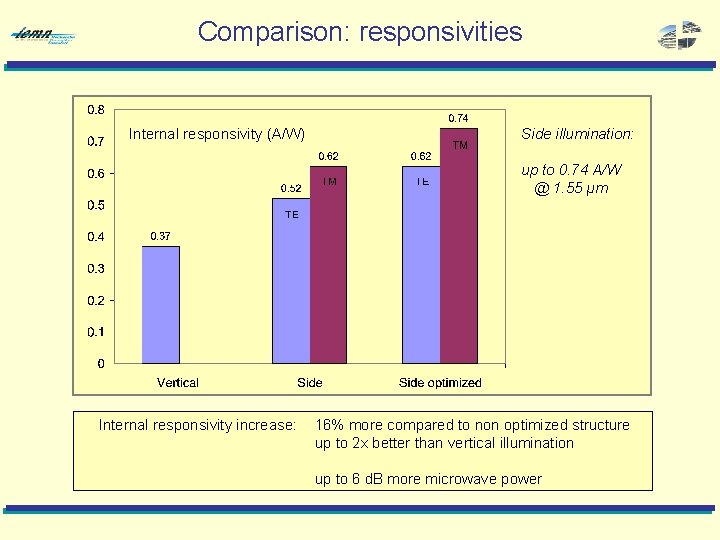
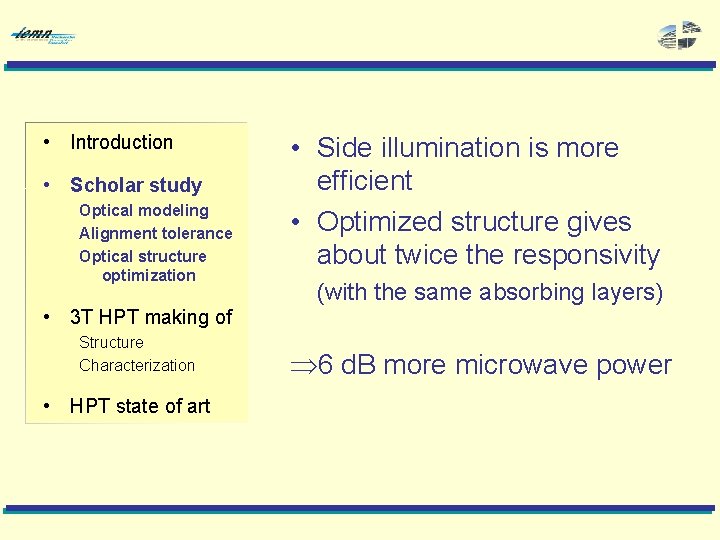
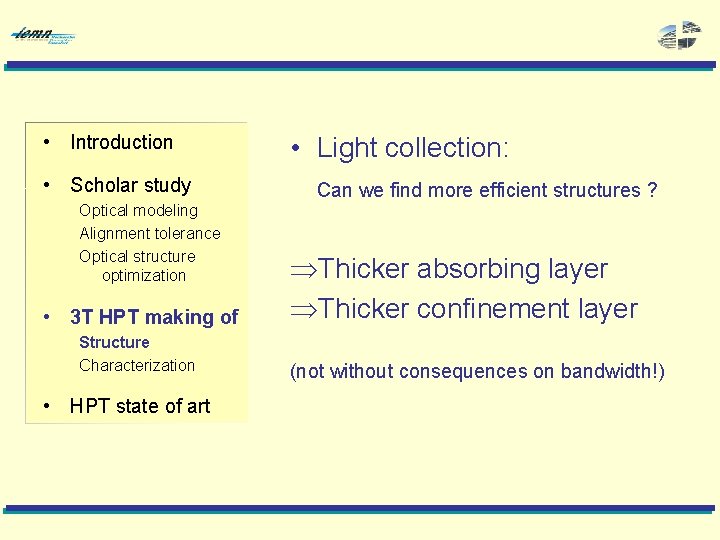
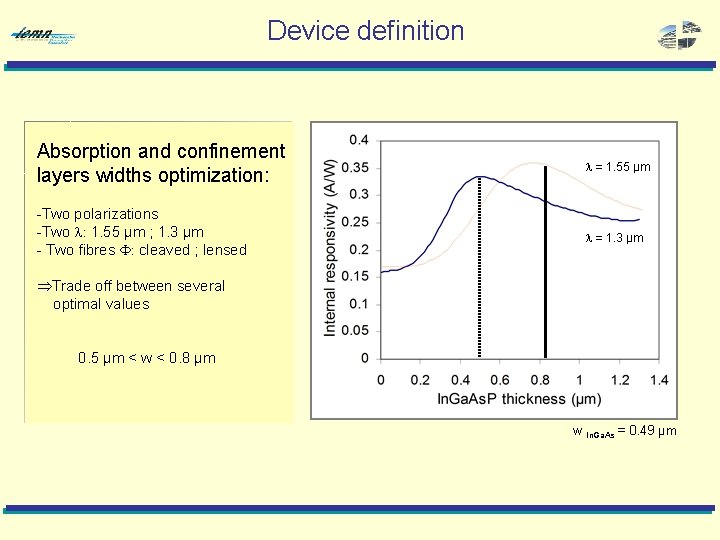
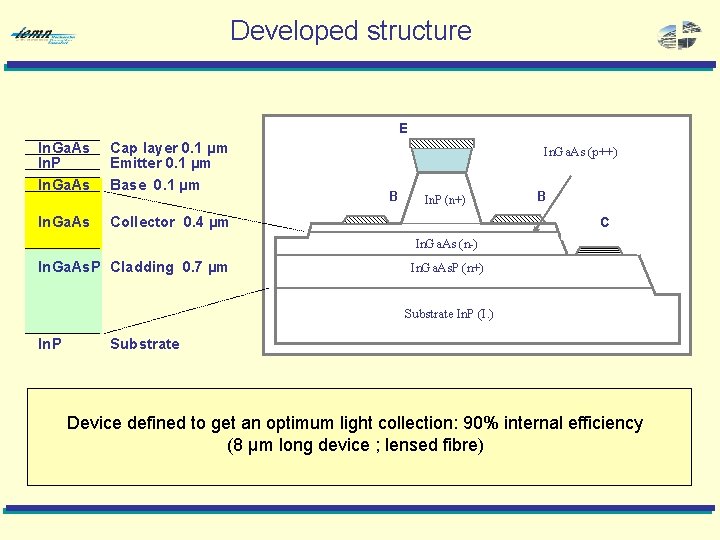
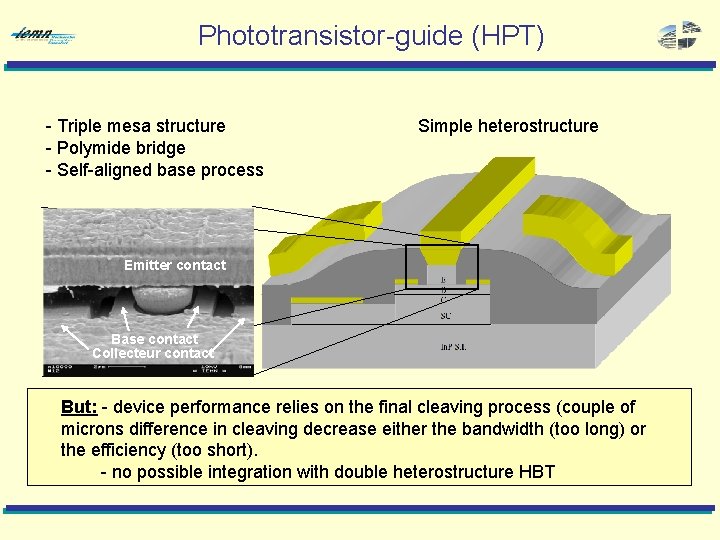
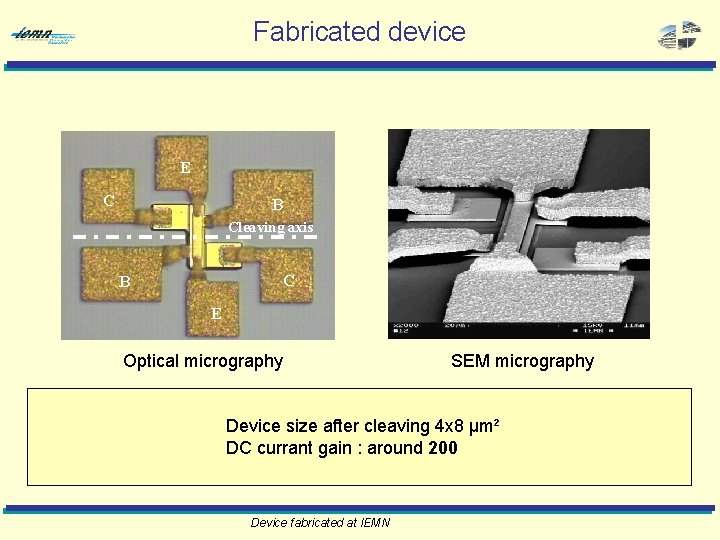
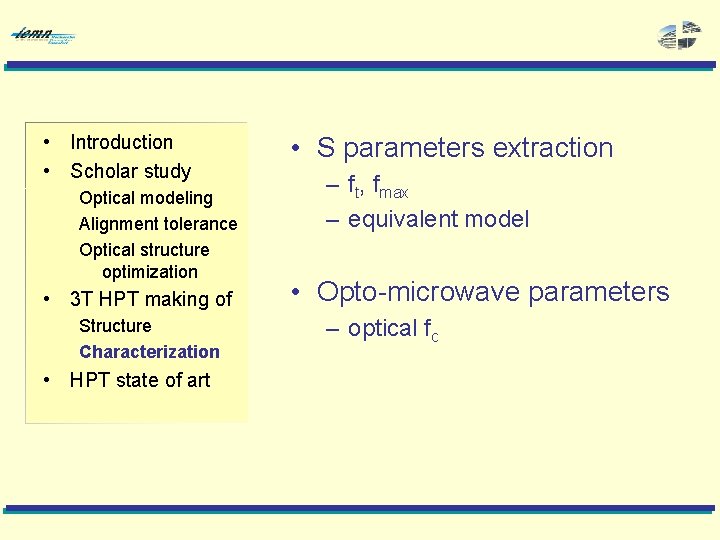
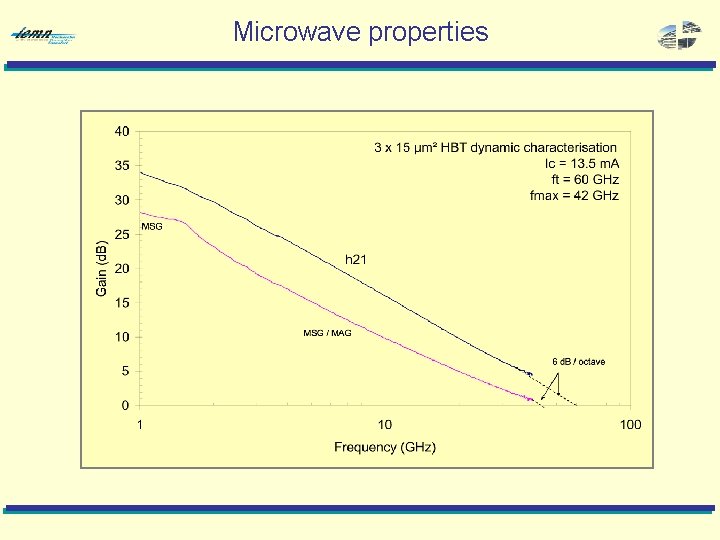
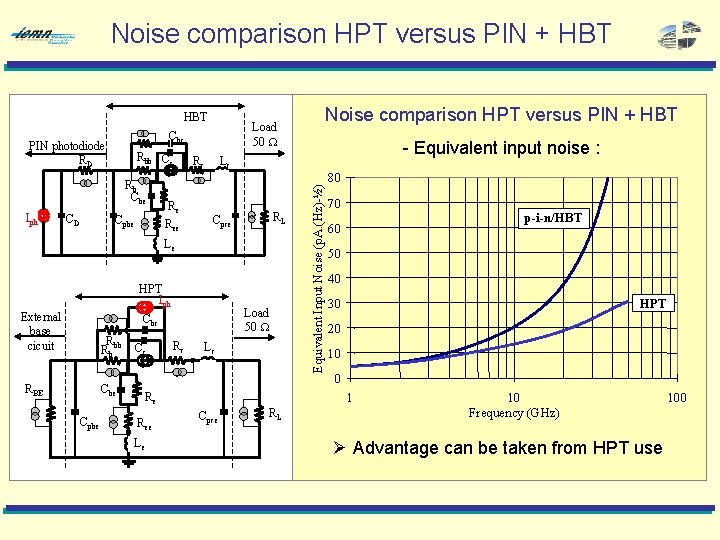
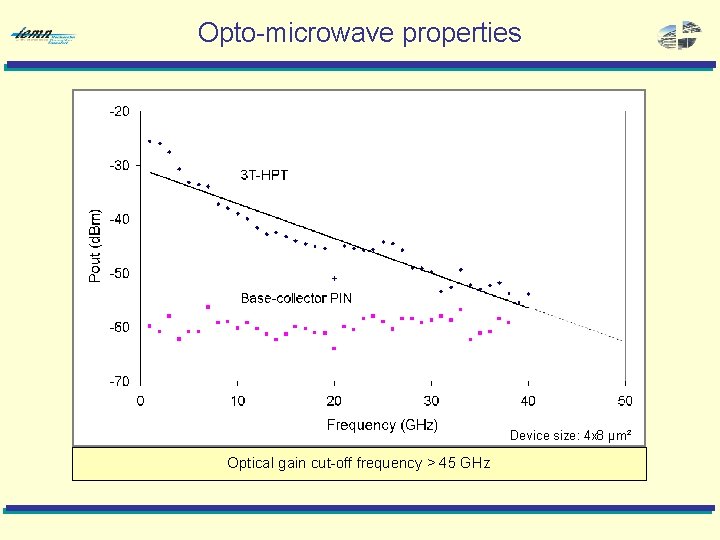
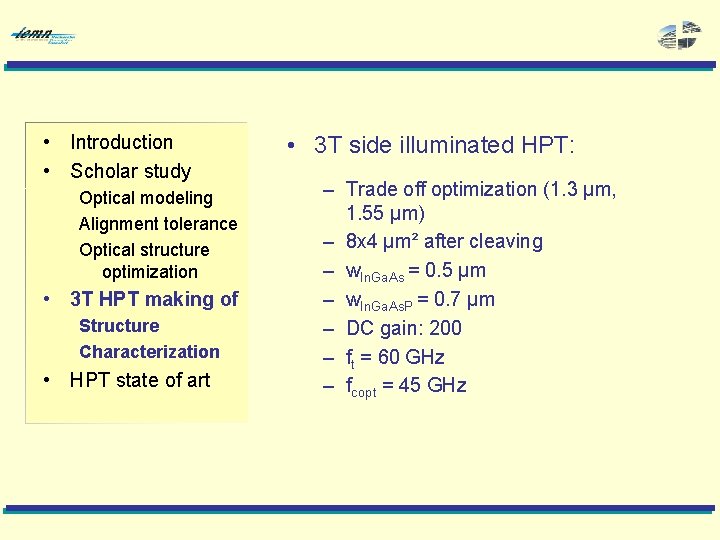
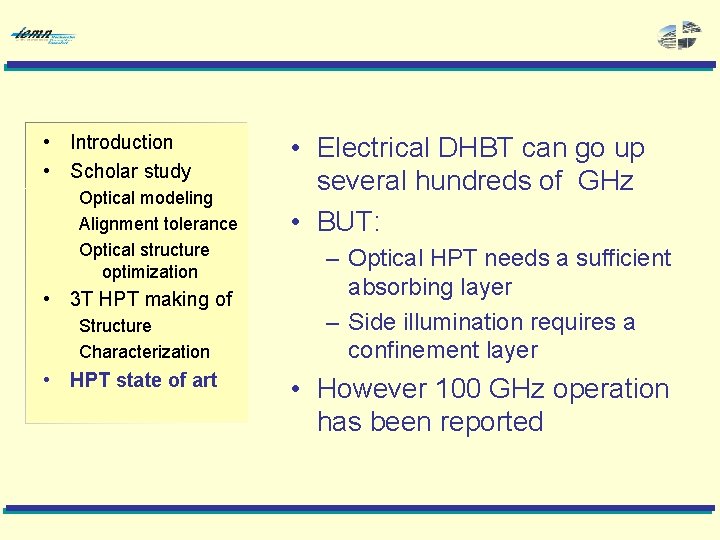
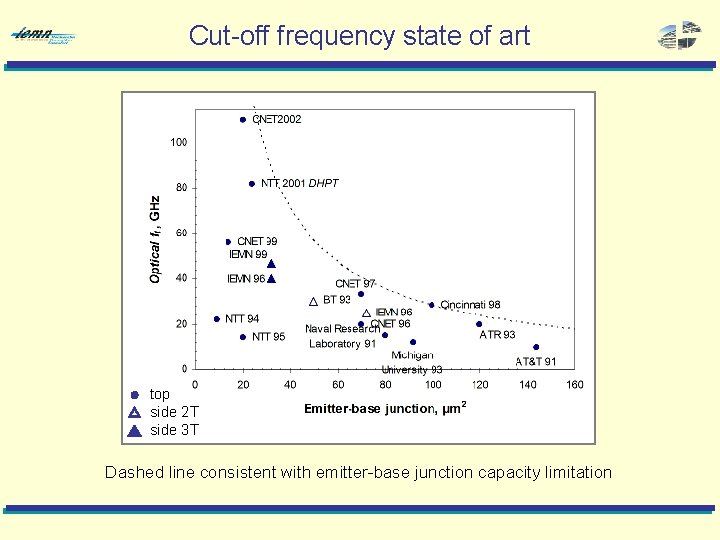
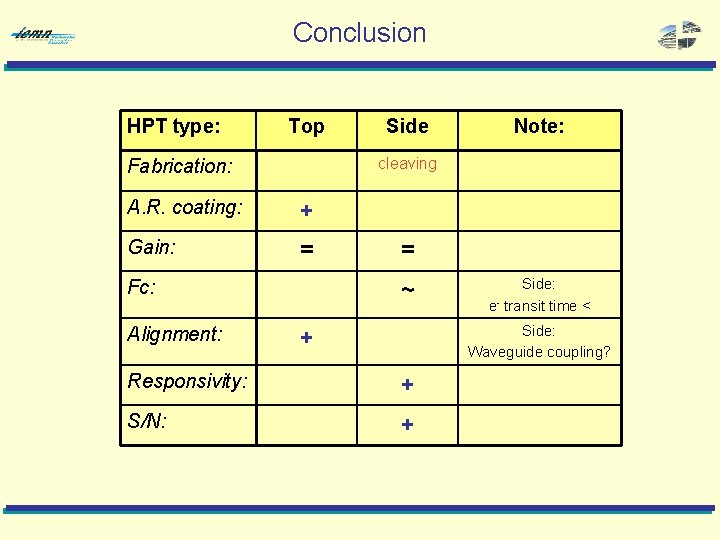
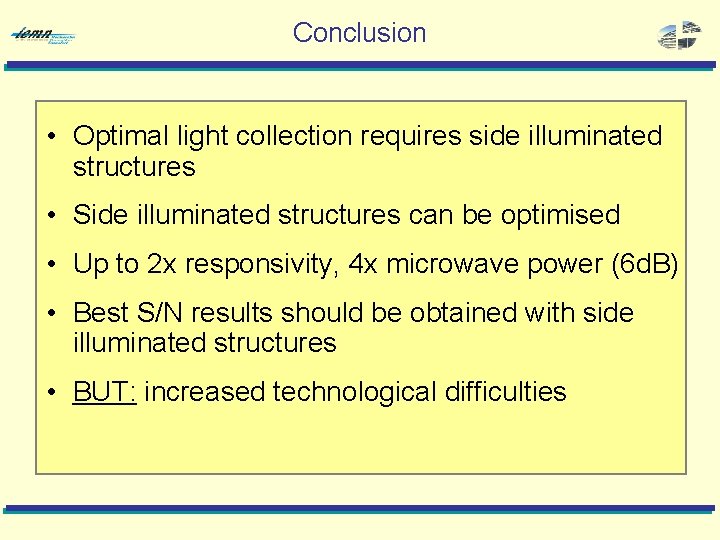
- Slides: 34
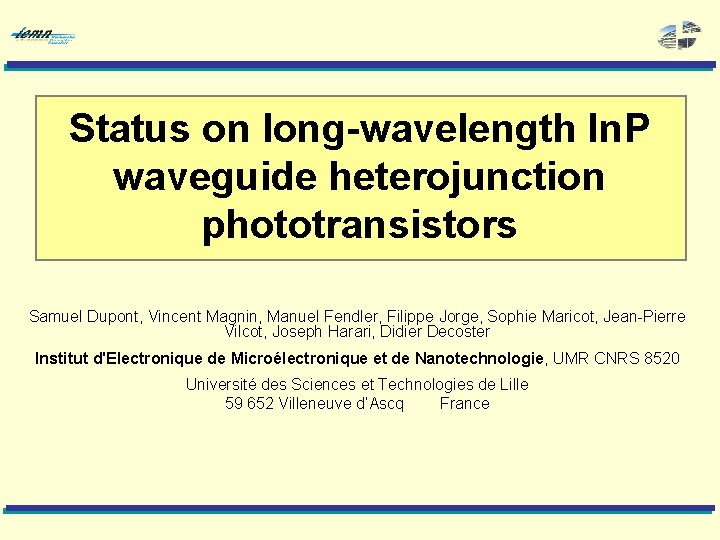
Status on long-wavelength In. P waveguide heterojunction phototransistors Samuel Dupont, Vincent Magnin, Manuel Fendler, Filippe Jorge, Sophie Maricot, Jean-Pierre Vilcot, Joseph Harari, Didier Decoster Institut d'Electronique de Microélectronique et de Nanotechnologie, UMR CNRS 8520 Université des Sciences et Technologies de Lille 59 652 Villeneuve d’Ascq France
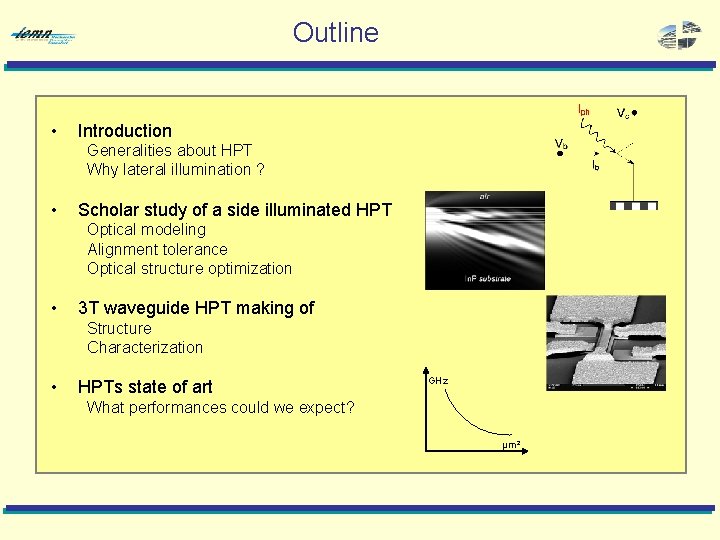
Outline • Introduction Generalities about HPT Why lateral illumination ? • Scholar study of a side illuminated HPT Optical modeling Alignment tolerance Optical structure optimization • 3 T waveguide HPT making of Structure Characterization • HPTs state of art GHz What performances could we expect? µm²
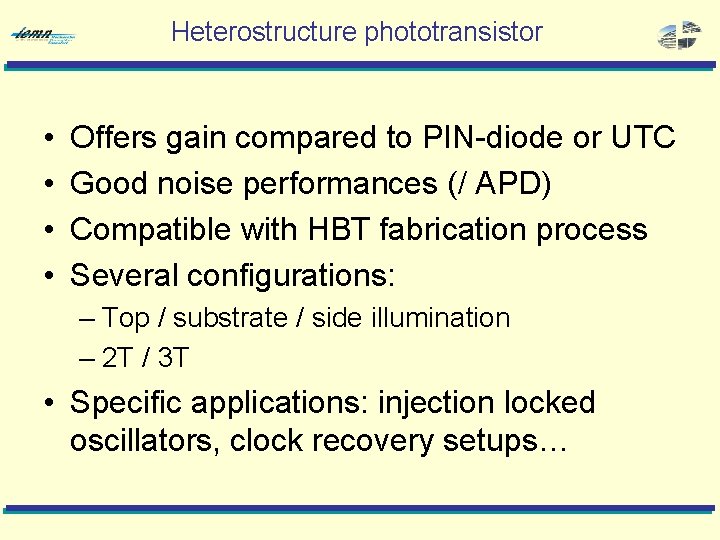
Heterostructure phototransistor • • Offers gain compared to PIN-diode or UTC Good noise performances (/ APD) Compatible with HBT fabrication process Several configurations: – Top / substrate / side illumination – 2 T / 3 T • Specific applications: injection locked oscillators, clock recovery setups…
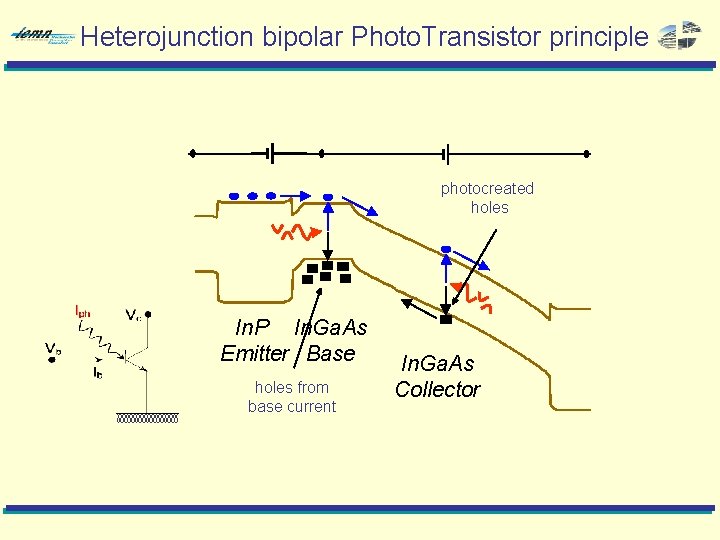
Heterojunction bipolar Photo. Transistor principle photocreated holes In. P In. Ga. As Emitter Base holes from base current In. Ga. As Collector
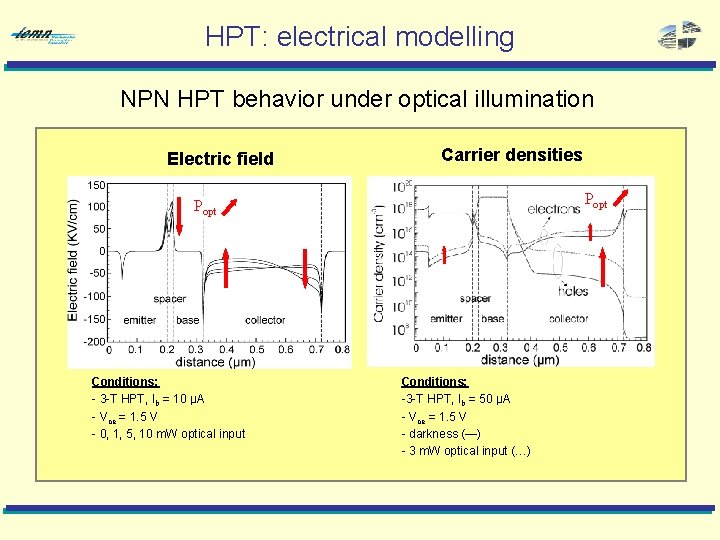
HPT: electrical modelling NPN HPT behavior under optical illumination Electric field Carrier densities Popt Conditions: - 3 -T HPT, Ib = 10 µA - Vce = 1. 5 V - 0, 1, 5, 10 m. W optical input Conditions: -3 -T HPT, Ib = 50 µA - Vce = 1. 5 V - darkness (—) - 3 m. W optical input ( )
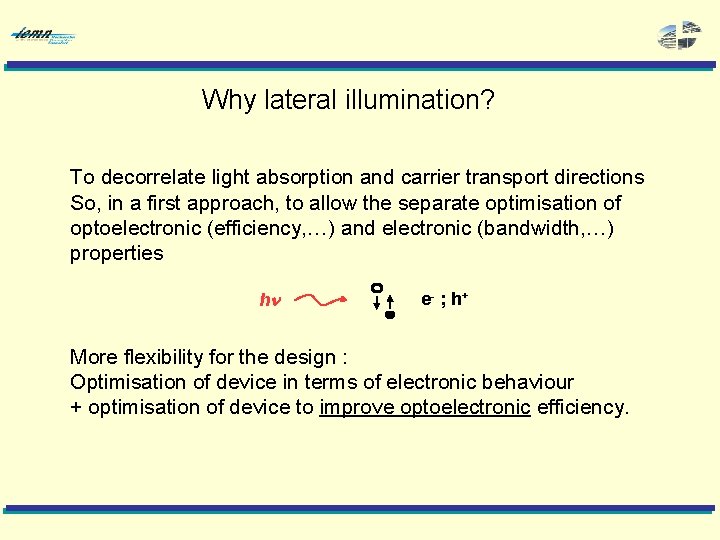
Why lateral illumination? To decorrelate light absorption and carrier transport directions So, in a first approach, to allow the separate optimisation of optoelectronic (efficiency, …) and electronic (bandwidth, …) properties hn e- ; h + More flexibility for the design : Optimisation of device in terms of electronic behaviour + optimisation of device to improve optoelectronic efficiency.
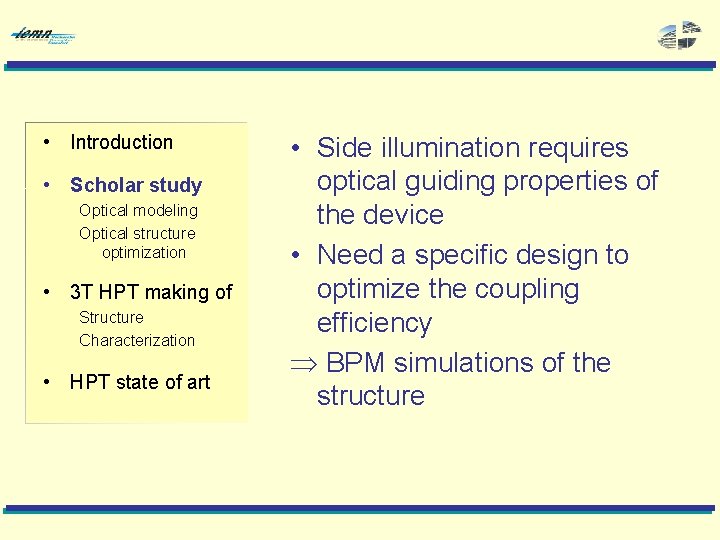
• Introduction • Scholar study Optical modeling Optical structure optimization • 3 T HPT making of Structure Characterization • HPT state of art • Side illumination requires optical guiding properties of the device • Need a specific design to optimize the coupling efficiency Þ BPM simulations of the structure
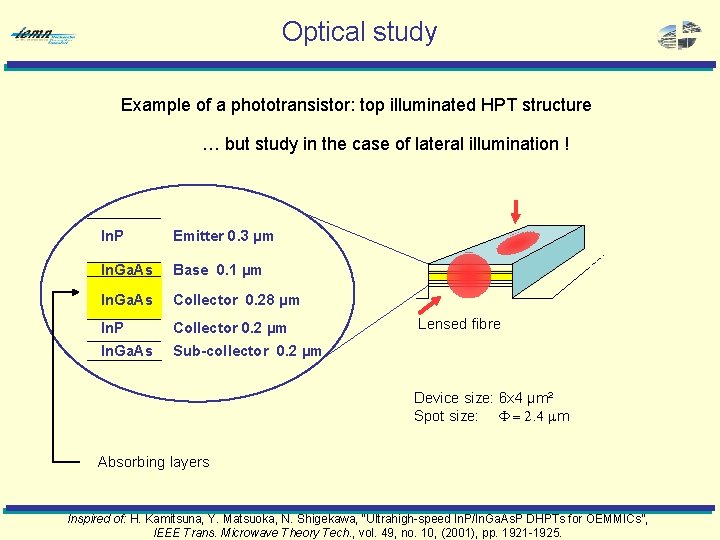
Optical study Example of a phototransistor: top illuminated HPT structure … but study in the case of lateral illumination ! In. P Emitter 0. 3 µm In. Ga. As Base 0. 1 µm In. Ga. As Collector 0. 28 µm In. P Collector 0. 2 µm In. Ga. As Sub-collector 0. 2 µm Lensed fibre Device size: 6 x 4 µm² Spot size: F = 2. 4 mm Absorbing layers Inspired of: H. Kamitsuna, Y. Matsuoka, N. Shigekawa, “Ultrahigh-speed In. P/In. Ga. As. P DHPTs for OEMMICs”, IEEE Trans. Microwave Theory Tech. , vol. 49, no. 10, (2001), pp. 1921 -1925.
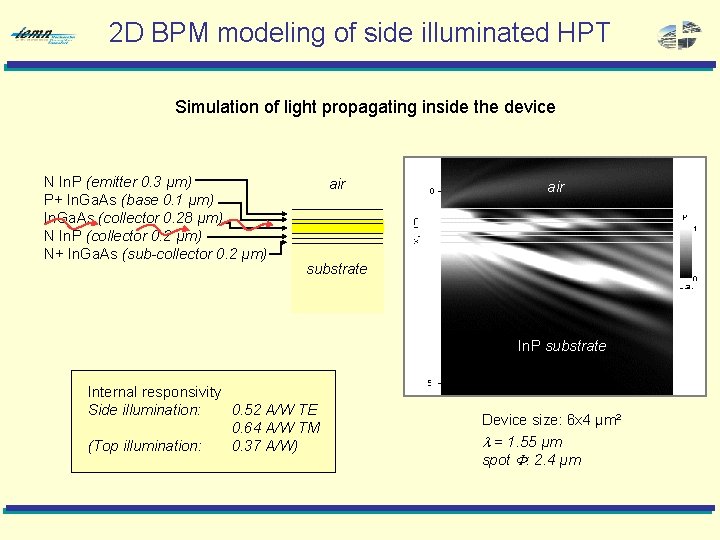
2 D BPM modeling of side illuminated HPT Simulation of light propagating inside the device N In. P (emitter 0. 3 µm) P+ In. Ga. As (base 0. 1 µm) In. Ga. As (collector 0. 28 µm) N In. P (collector 0. 2 µm) N+ In. Ga. As (sub-collector 0. 2 µm) air substrate In. P substrate Internal responsivity Side illumination: 0. 52 A/W TE 0. 64 A/W TM (Top illumination: 0. 37 A/W) Device size: 6 x 4 µm² l = 1. 55 µm spot F: 2. 4 µm
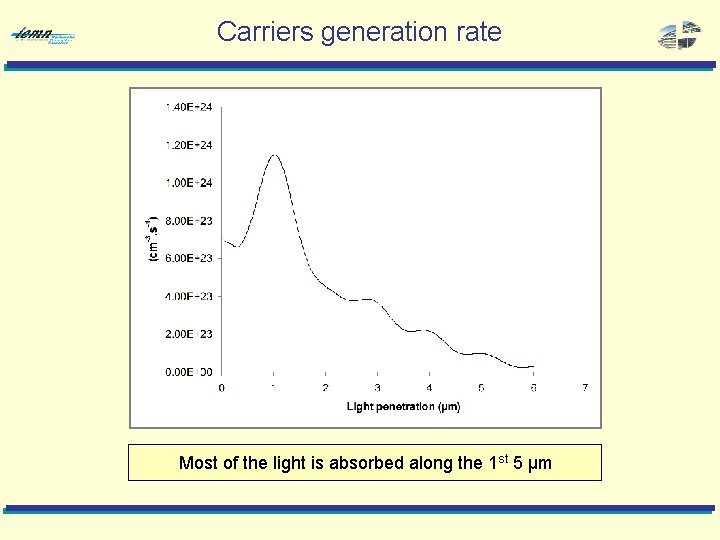
Carriers generation rate Most of the light is absorbed along the 1 st 5 µm
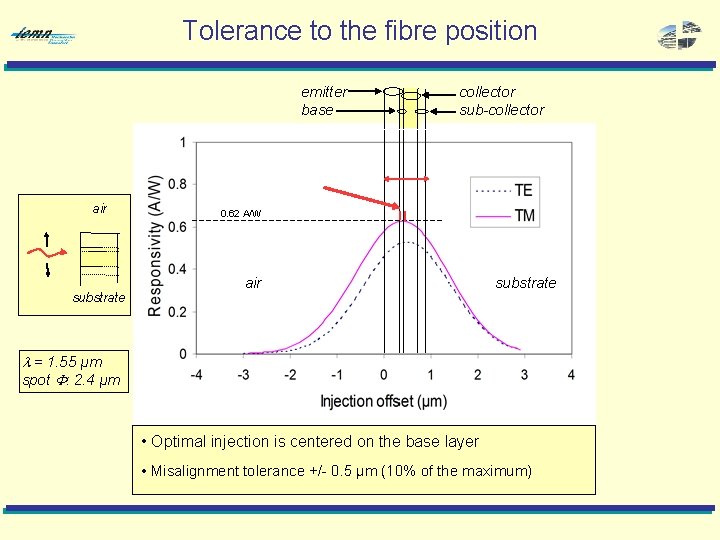
Tolerance to the fibre position emitter base air substrate collector sub-collector 0. 62 A/W air substrate l = 1. 55 µm spot F: 2. 4 µm • Optimal injection is centered on the base layer • Misalignment tolerance +/- 0. 5 µm (10% of the maximum)
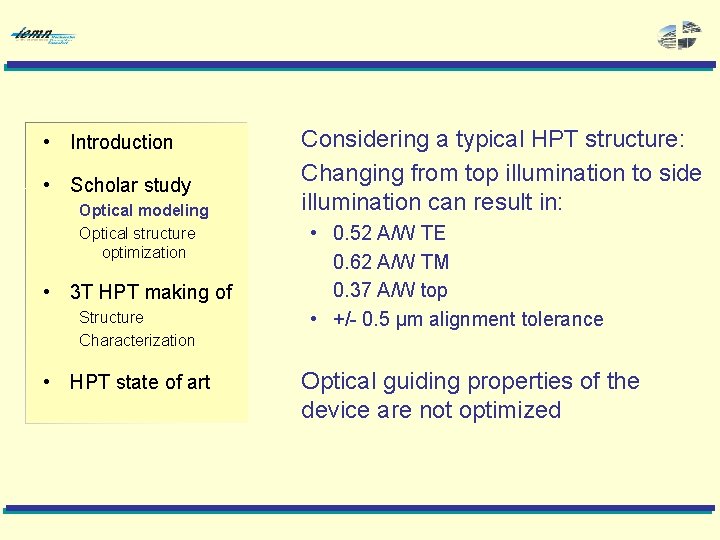
• Introduction • Scholar study Optical modeling Optical structure optimization • 3 T HPT making of Structure Characterization • HPT state of art Considering a typical HPT structure: Changing from top illumination to side illumination can result in: • 0. 52 A/W TE 0. 62 A/W TM 0. 37 A/W top • +/- 0. 5 µm alignment tolerance Optical guiding properties of the device are not optimized
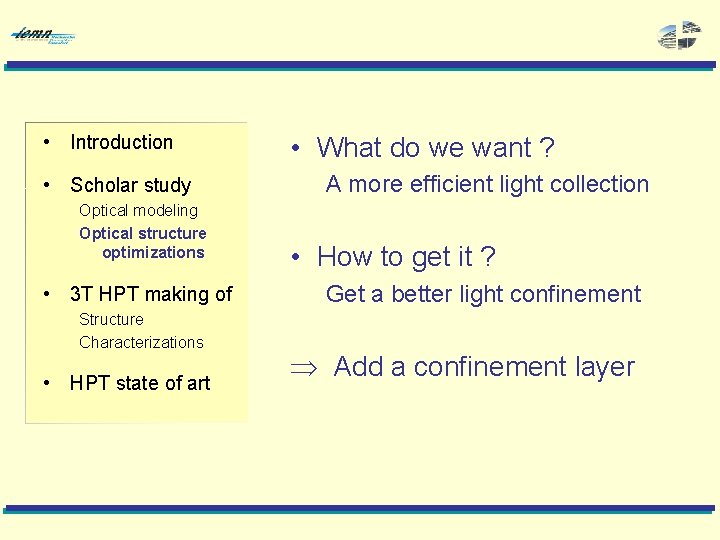
• Introduction • Scholar study Optical modeling Optical structure optimizations • 3 T HPT making of Structure Characterizations • HPT state of art • What do we want ? A more efficient light collection • How to get it ? Get a better light confinement Þ Add a confinement layer
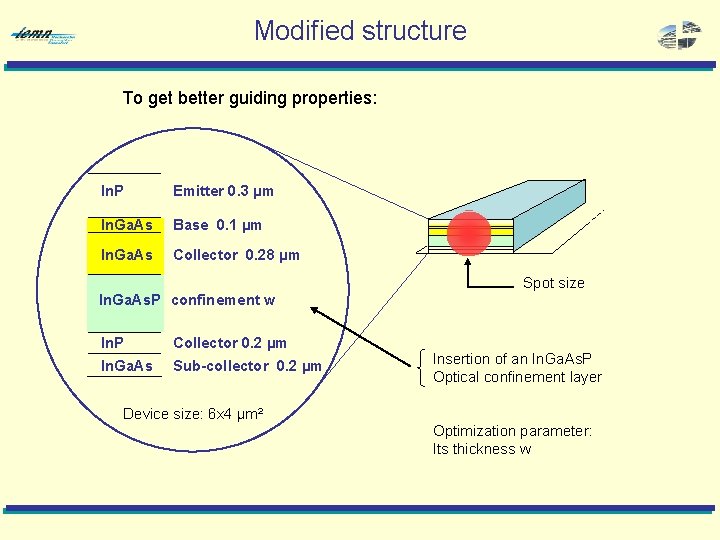
Modified structure To get better guiding properties: In. P Emitter 0. 3 µm In. Ga. As Base 0. 1 µm In. Ga. As Collector 0. 28 µm Spot size In. Ga. As. P confinement w In. P Collector 0. 2 µm In. Ga. As Sub-collector 0. 2 µm Insertion of an In. Ga. As. P Optical confinement layer Device size: 6 x 4 µm² Optimization parameter: Its thickness w
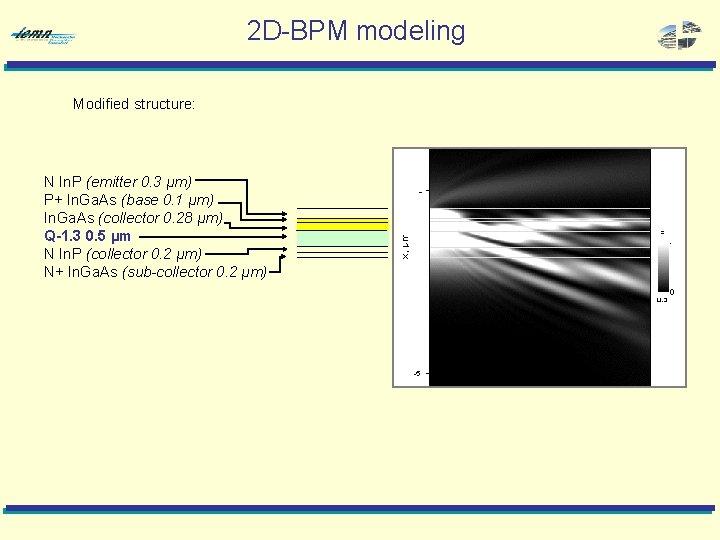
2 D-BPM modeling Modified structure: N In. P (emitter 0. 3 µm) P+ In. Ga. As (base 0. 1 µm) In. Ga. As (collector 0. 28 µm) Q-1. 3 0. 5 µm N In. P (collector 0. 2 µm) N+ In. Ga. As (sub-collector 0. 2 µm)
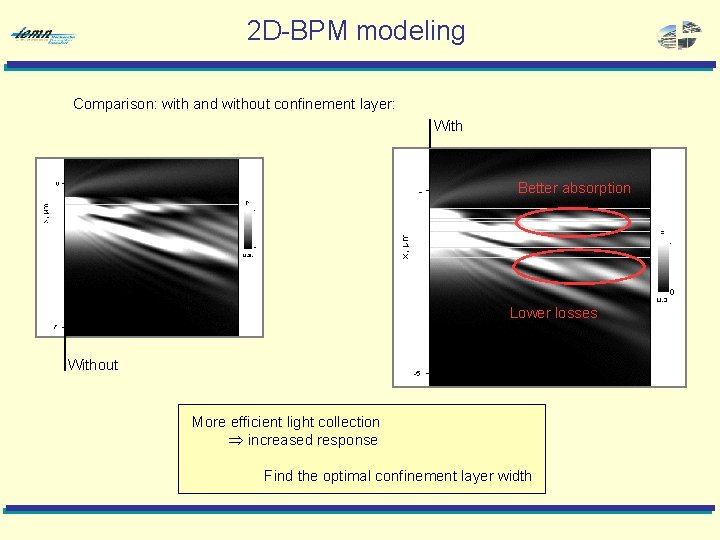
2 D-BPM modeling Comparison: with and without confinement layer: With Better absorption Lower losses Without More efficient light collection Þ increased response Find the optimal confinement layer width
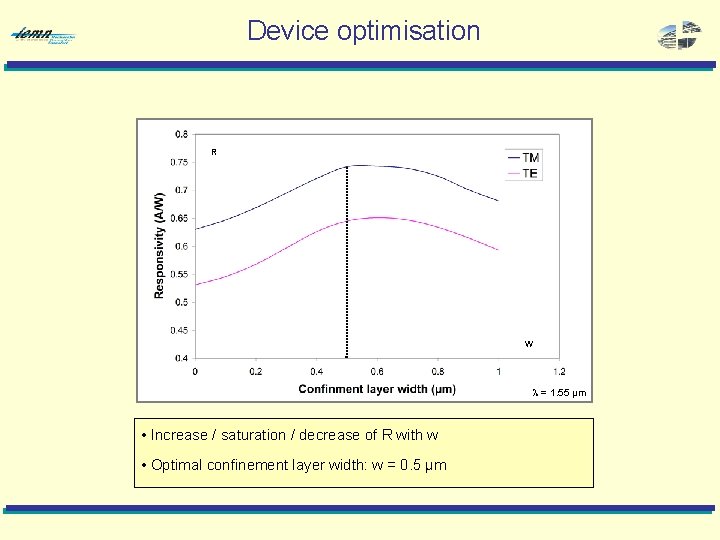
Device optimisation R W l = 1. 55 µm • Increase / saturation / decrease of R with w • Optimal confinement layer width: w = 0. 5 µm
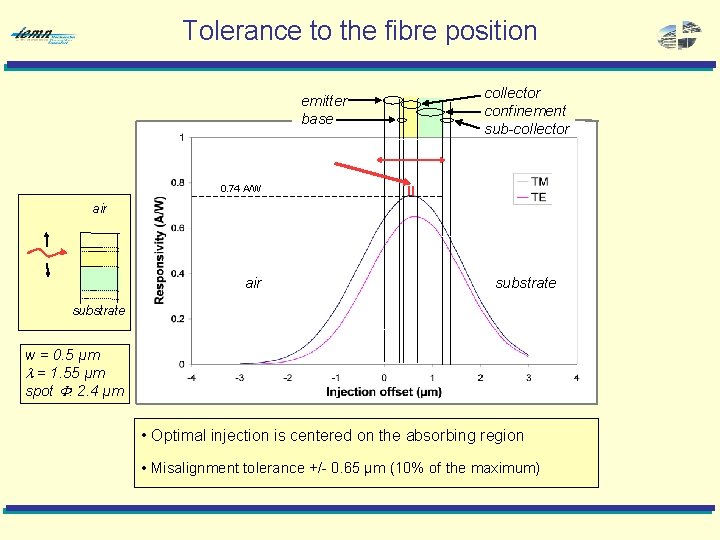
Tolerance to the fibre position emitter base collector confinement sub-collector 0. 74 A/W air substrate w = 0. 5 µm l = 1. 55 µm spot F: 2. 4 µm • Optimal injection is centered on the absorbing region • Misalignment tolerance +/- 0. 65 µm (10% of the maximum)
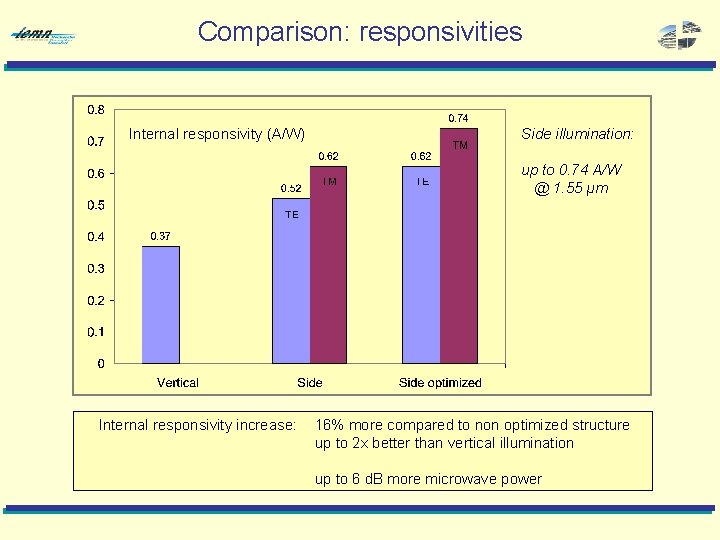
Comparison: responsivities Internal responsivity (A/W) Side illumination: up to 0. 74 A/W @ 1. 55 µm Internal responsivity increase: 16% more compared to non optimized structure up to 2 x better than vertical illumination up to 6 d. B more microwave power
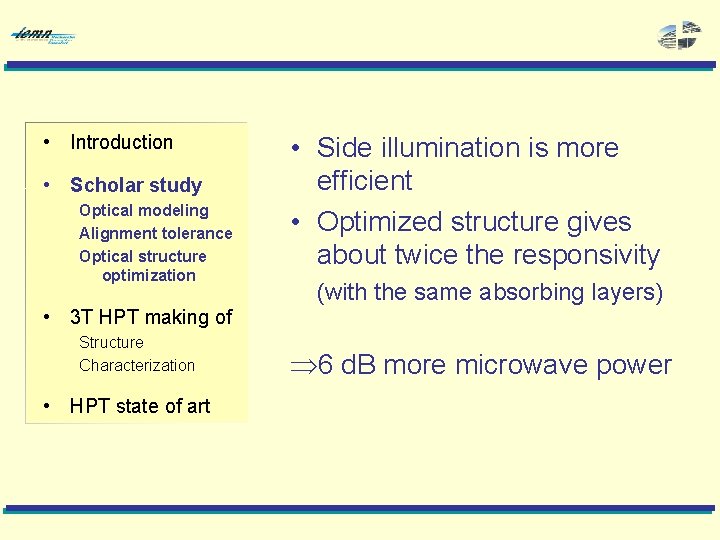
• Introduction • Scholar study Optical modeling Alignment tolerance Optical structure optimization • Side illumination is more efficient • Optimized structure gives about twice the responsivity (with the same absorbing layers) • 3 T HPT making of Structure Characterization • HPT state of art Þ 6 d. B more microwave power
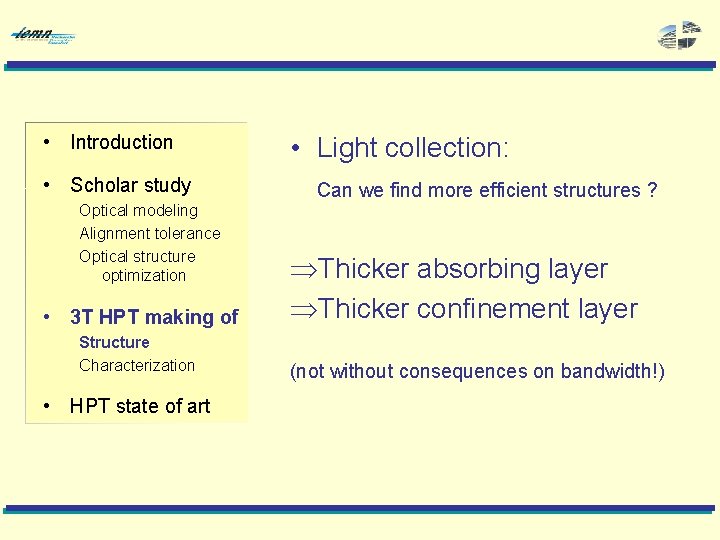
• Introduction • Scholar study Optical modeling Alignment tolerance Optical structure optimization • 3 T HPT making of Structure Characterization • HPT state of art • Light collection: Can we find more efficient structures ? ÞThicker absorbing layer ÞThicker confinement layer (not without consequences on bandwidth!)
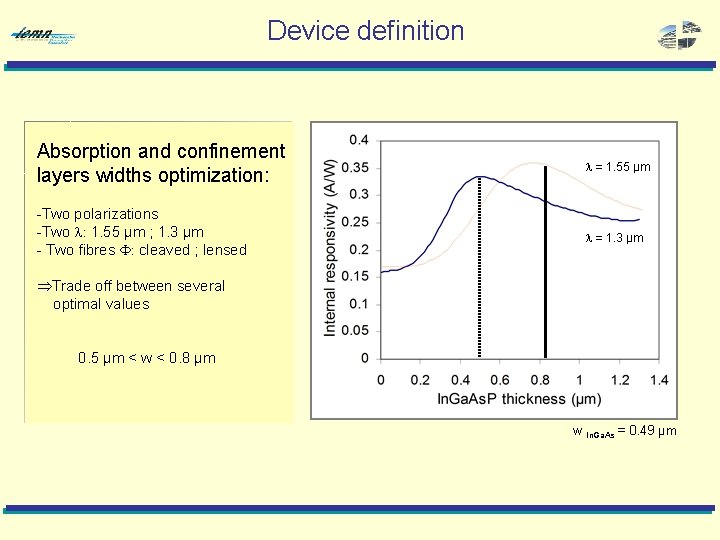
Device definition Absorption and confinement layers widths optimization: l = 1. 55 µm -Two polarizations -Two l: 1. 55 µm ; 1. 3 µm - Two fibres F: cleaved ; lensed l = 1. 3 µm ÞTrade off between several optimal values 0. 5 µm < w < 0. 8 µm w In. Ga. As = 0. 49 µm
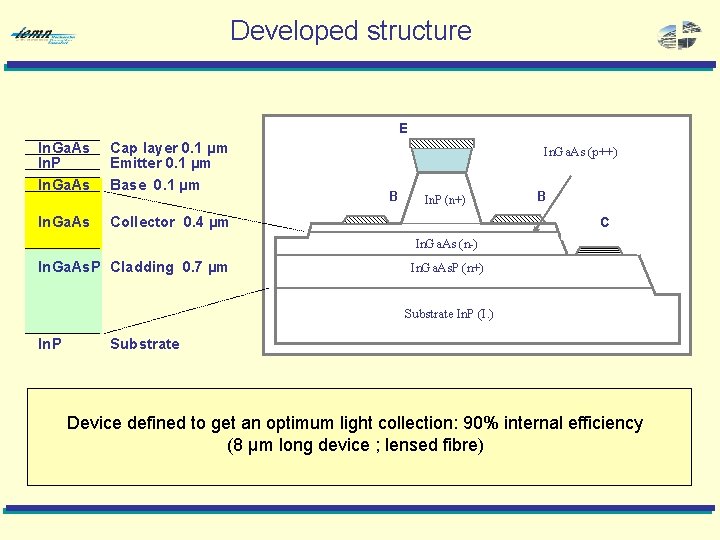
Developed structure E In. Ga. As In. P Cap layer 0. 1 µm Emitter 0. 1 µm In. Ga. As Base 0. 1 µm In. Ga. As (p++) B In. P (n+) Collector 0. 4 µm B C In. Ga. As (n-) In. Ga. As. P Cladding 0. 7 µm In. Ga. As. P (n+) Substrate In. P (I. ) In. P Substrate Device defined to get an optimum light collection: 90% internal efficiency (8 µm long device ; lensed fibre)
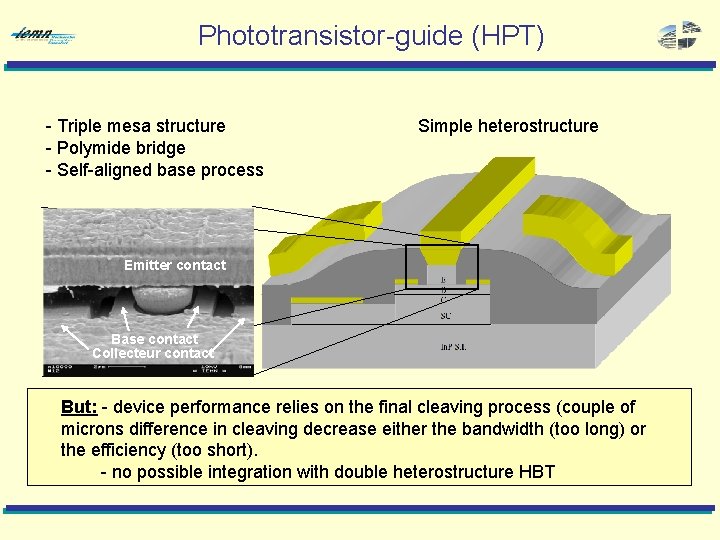
Phototransistor-guide (HPT) - Triple mesa structure - Polymide bridge - Self-aligned base process Simple heterostructure Emitter contact Base contact Collecteur contact But: - device performance relies on the final cleaving process (couple of microns difference in cleaving decrease either the bandwidth (too long) or the efficiency (too short). - no possible integration with double heterostructure HBT
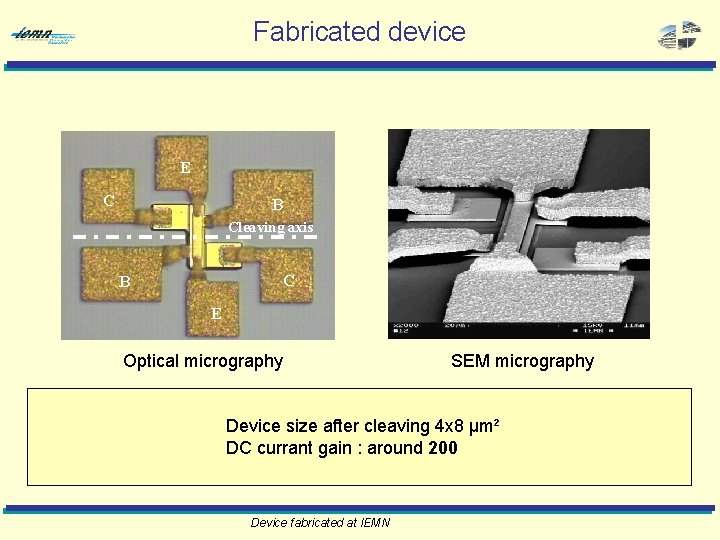
Fabricated device E C B Cleaving axis C B E Optical micrography SEM micrography Device size after cleaving 4 x 8 µm² DC currant gain : around 200 Device fabricated at IEMN
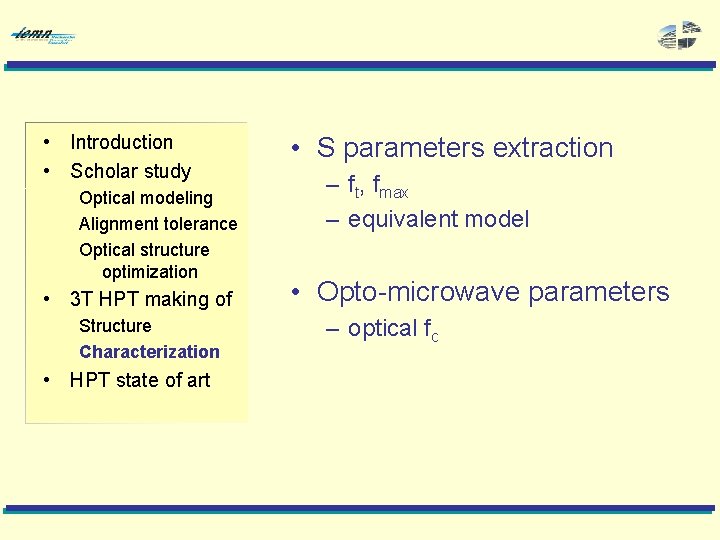
• Introduction • Scholar study Optical modeling Alignment tolerance Optical structure optimization • 3 T HPT making of Structure Characterization • HPT state of art • S parameters extraction – ft, fmax – equivalent model • Opto-microwave parameters – optical fc
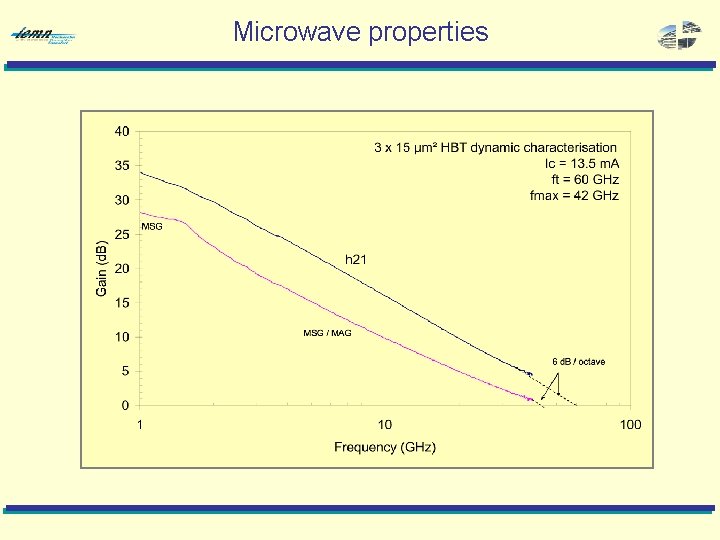
Microwave properties
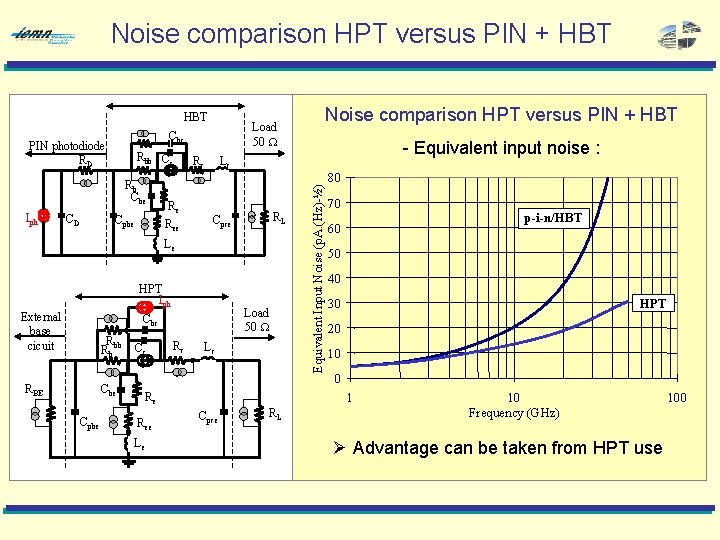
Noise comparison HPT versus PIN + HBT Cbc Rbb Cc Rb Cbe CD Cpbe Re Ree RL Cpce HPT Iph Load 50 W Cbc R Rb bb Cbe RBE Cpbe Cc Rc Lc Re Ree Le - Equivalent input noise : Lc Rc Le External base cicuit Noise comparison HPT versus PIN + HBT Equivalent Input Noise (p. A. (Hz)-½) PIN photodiode RD Iph Load 50 W 80 70 p-i-n/HBT 60 50 40 HPT 30 20 10 0 1 Cpce RL 10 Frequency (GHz) Ø Advantage can be taken from HPT use 100
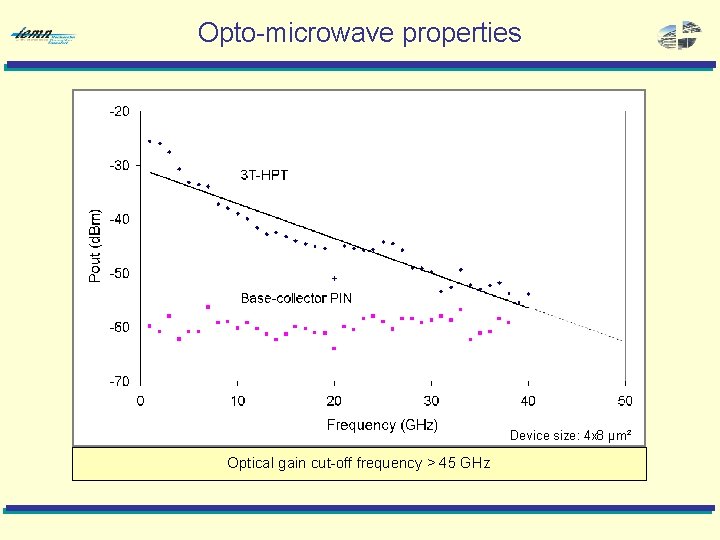
Opto-microwave properties Device size: 4 x 8 µm² Optical gain cut-off frequency > 45 GHz
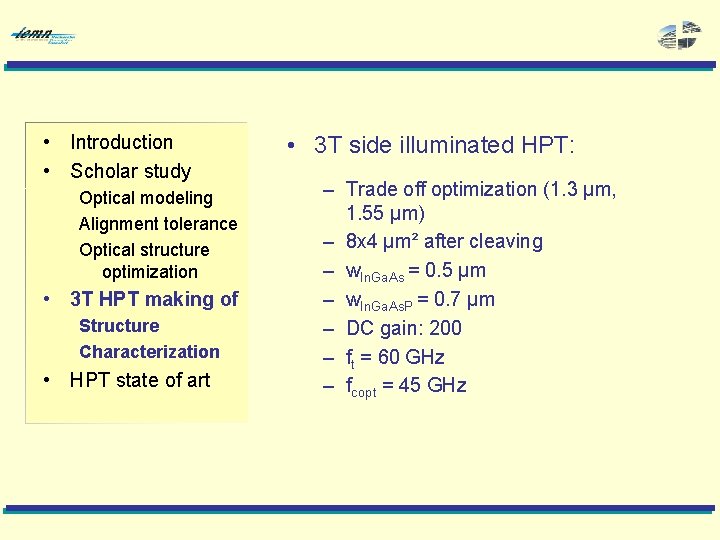
• Introduction • Scholar study Optical modeling Alignment tolerance Optical structure optimization • 3 T HPT making of Structure Characterization • HPT state of art • 3 T side illuminated HPT: – Trade off optimization (1. 3 µm, 1. 55 µm) – 8 x 4 µm² after cleaving – w. In. Ga. As = 0. 5 µm – w. In. Ga. As. P = 0. 7 µm – DC gain: 200 – ft = 60 GHz – fcopt = 45 GHz
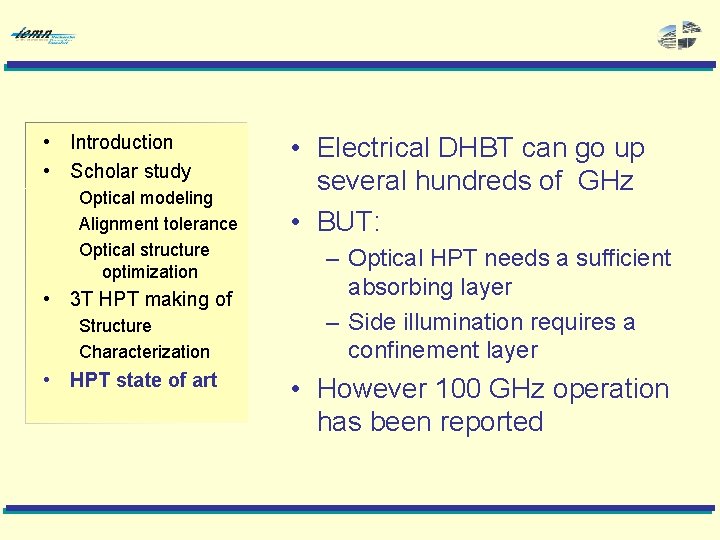
• Introduction • Scholar study Optical modeling Alignment tolerance Optical structure optimization • 3 T HPT making of Structure Characterization • HPT state of art • Electrical DHBT can go up several hundreds of GHz • BUT: – Optical HPT needs a sufficient absorbing layer – Side illumination requires a confinement layer • However 100 GHz operation has been reported
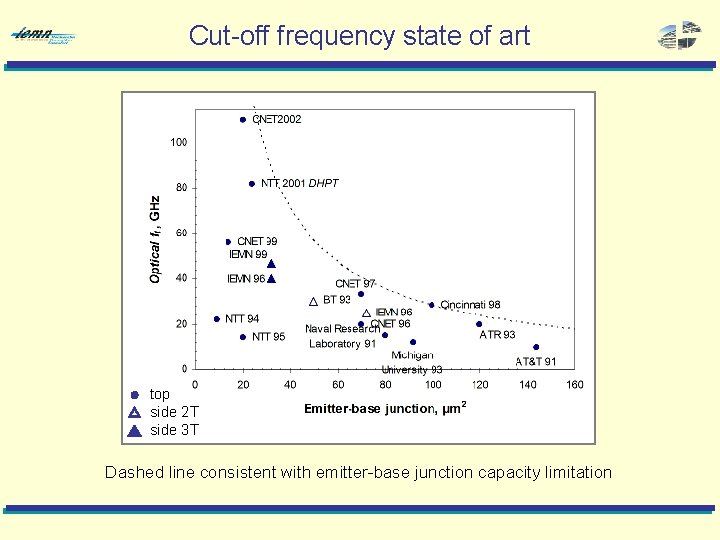
Cut-off frequency state of art top side 2 T side 3 T Dashed line consistent with emitter-base junction capacity limitation
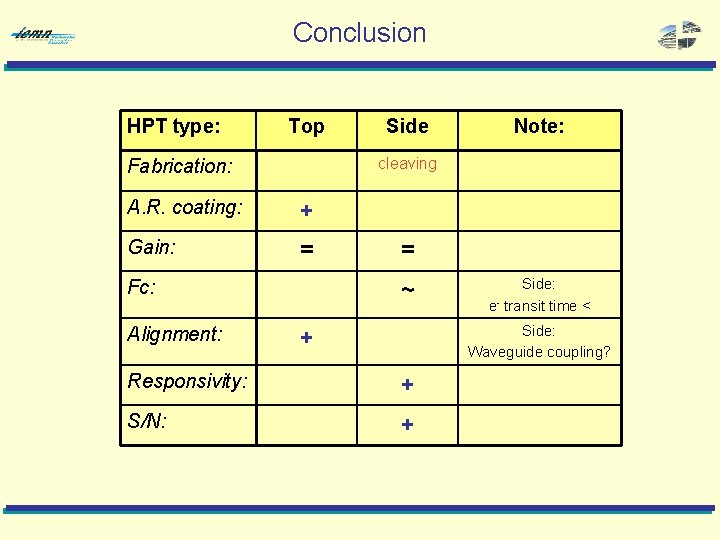
Conclusion HPT type: Top Note: cleaving Fabrication: A. R. coating: + Gain: = Fc: Alignment: Side = ~ Side: e- transit time < Side: Waveguide coupling? + Responsivity: + S/N: +
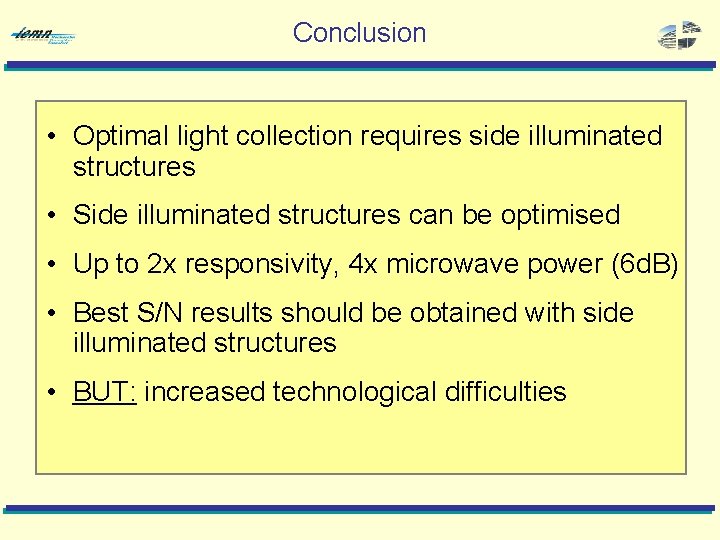
Conclusion • Optimal light collection requires side illuminated structures • Side illuminated structures can be optimised • Up to 2 x responsivity, 4 x microwave power (6 d. B) • Best S/N results should be obtained with side illuminated structures • BUT: increased technological difficulties
Wr-2100 waveguide
Rectangular waveguide mode
Diff between step index and graded index fiber
Rectangular waveguide impedance
Lumped port in hfss
Waveguide modes
Wr-2100 waveguide
Waveguide cutoff frequency
M1970v waveguide harmonic mixer
E field h field
Kaiser near me
Stages of internationalization in ihrm
Status quo analysis
You record the age marital status
Rumus status gizi anak
Cls beam status
Register is a group of
Legal status of company
Argo.status 101
Fmi status
Slac status
Status withdrawal theory was proposed by
"copyright (c) tektronix, inc." "printer status"
Process state diagram
Status quo skimming
Project status deck
Esdnl status central
Ispm 8
Wg status monitoring service
Pix status
Project status options
Neurologi status
Galileo gnss status
Harassment status
All but dissertation (abd) status