Status of Optical Strain Measurements at ENMME Mechanical
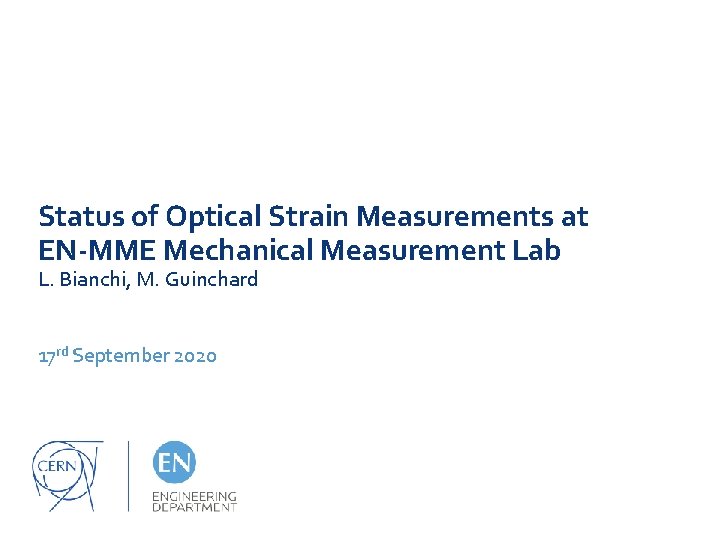
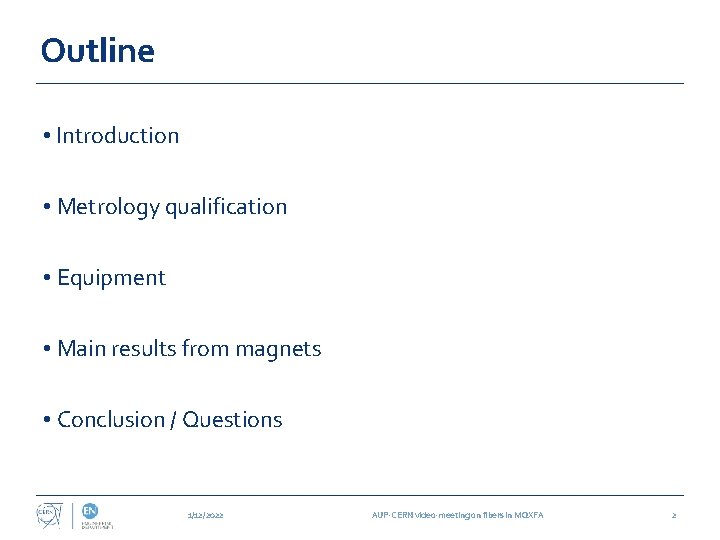
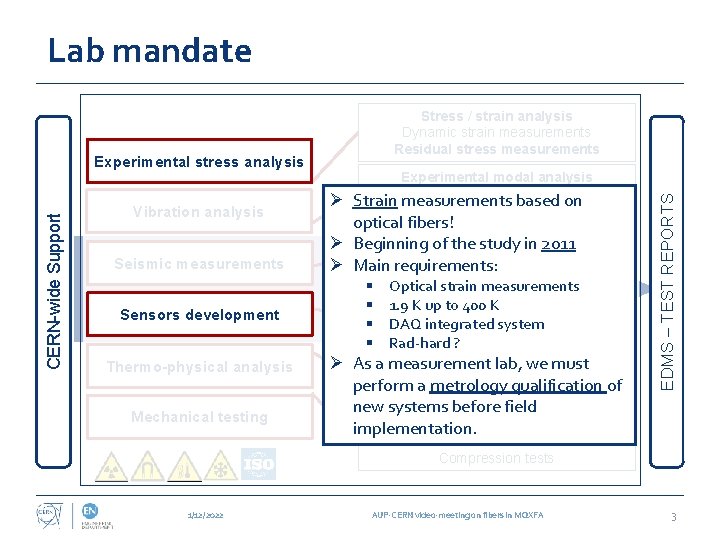
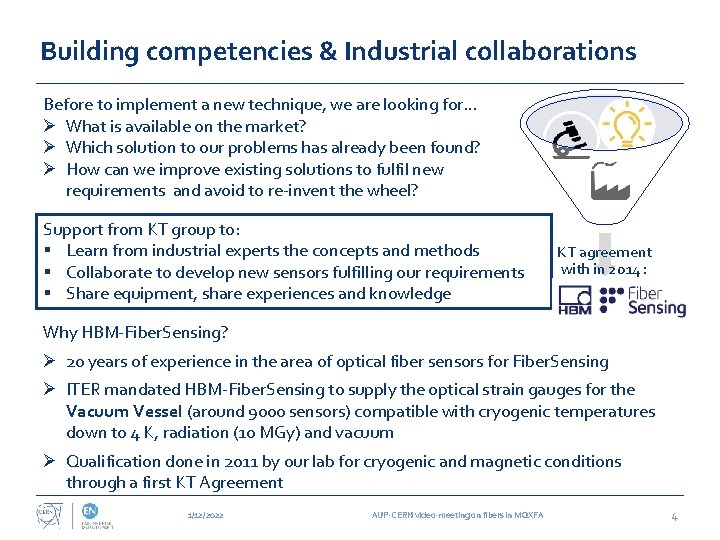
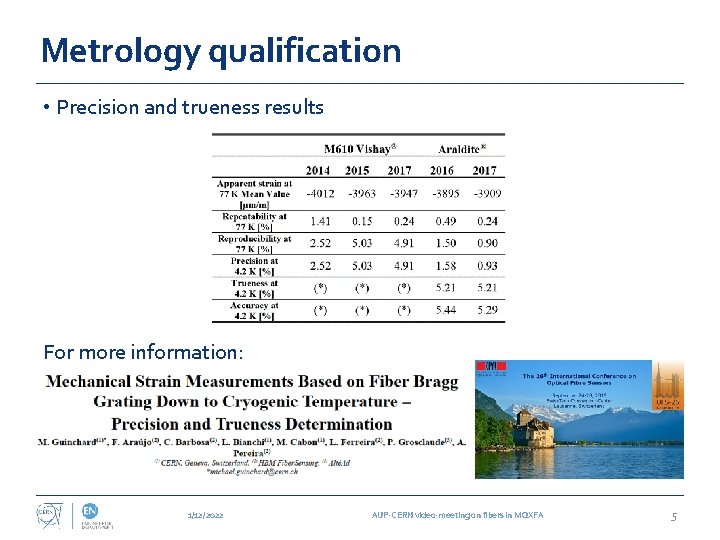
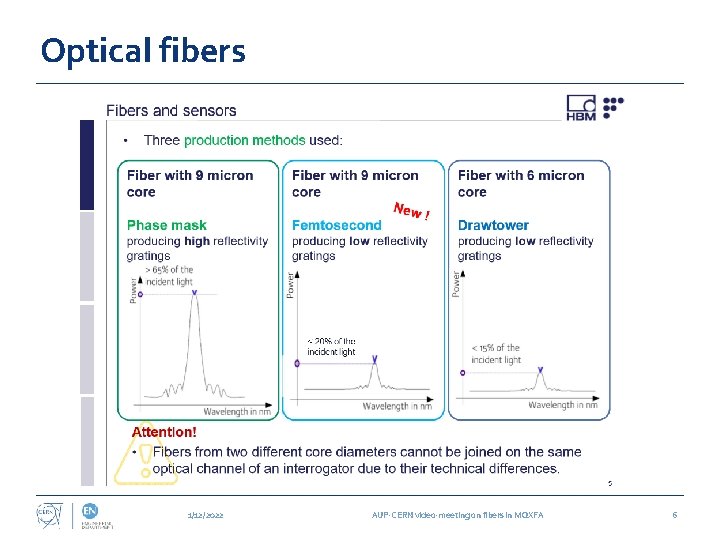
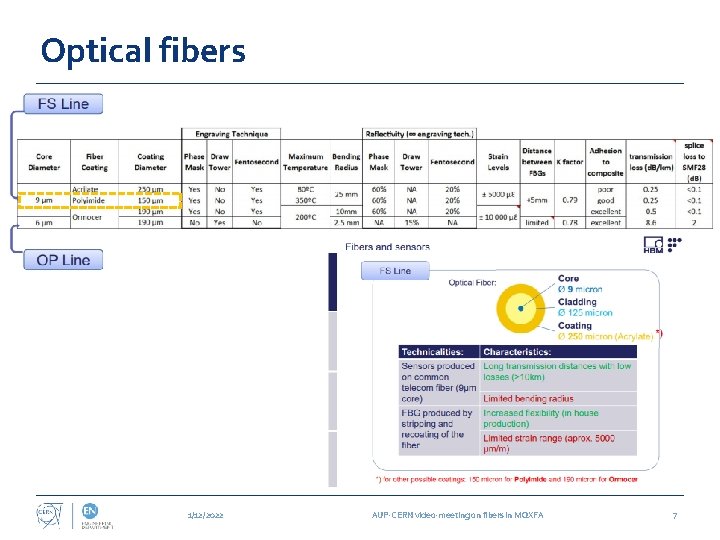
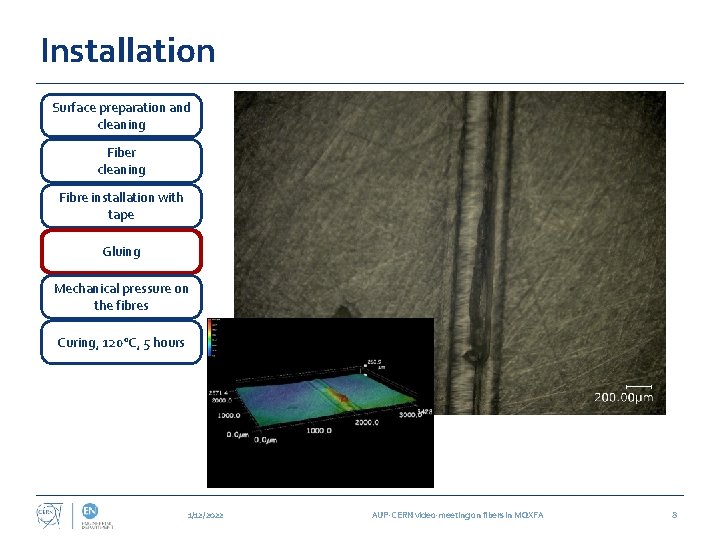
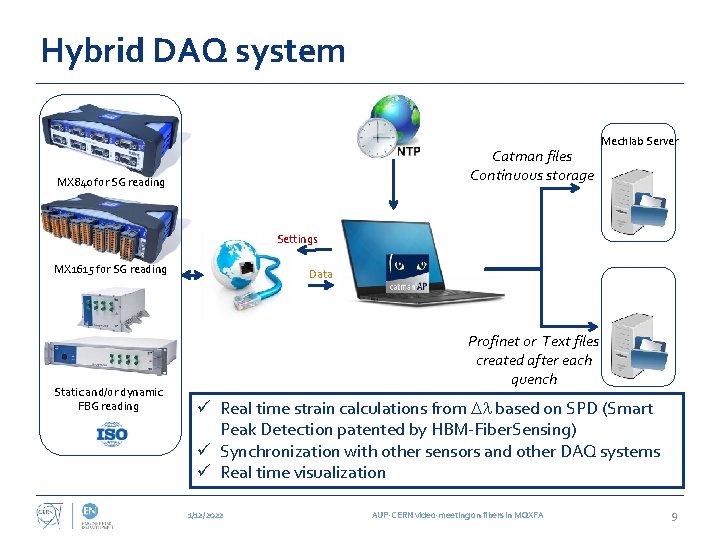
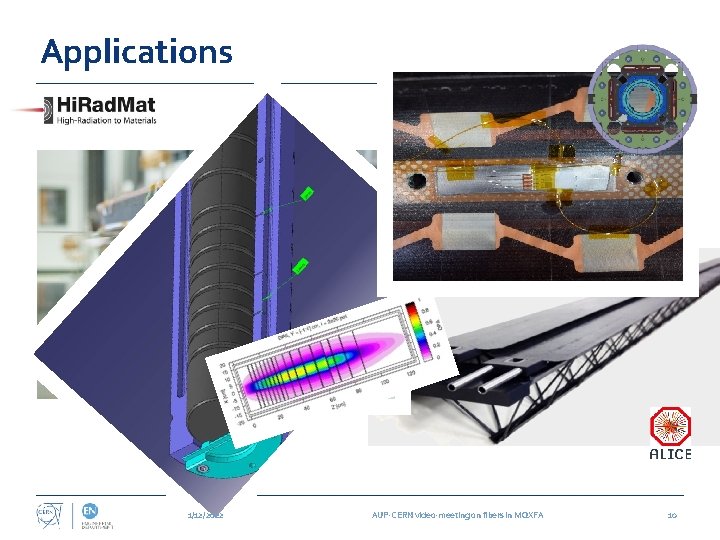
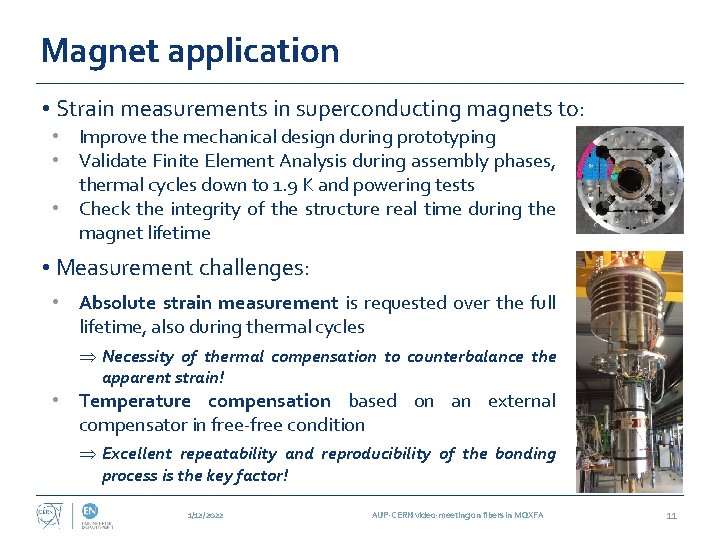
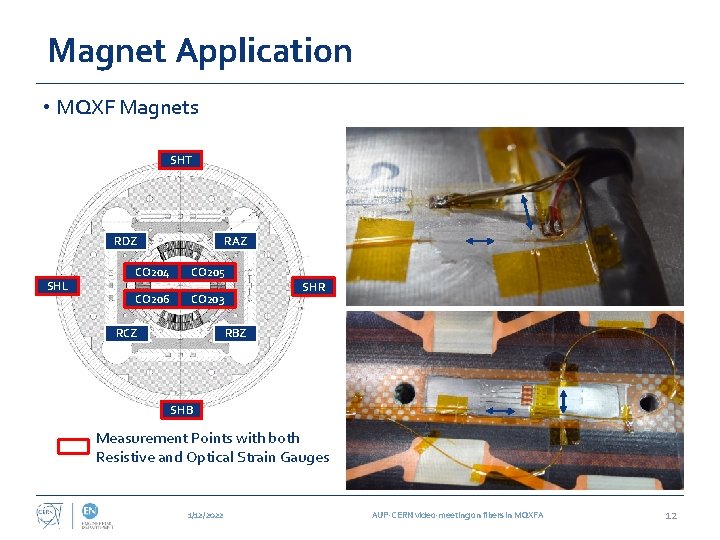
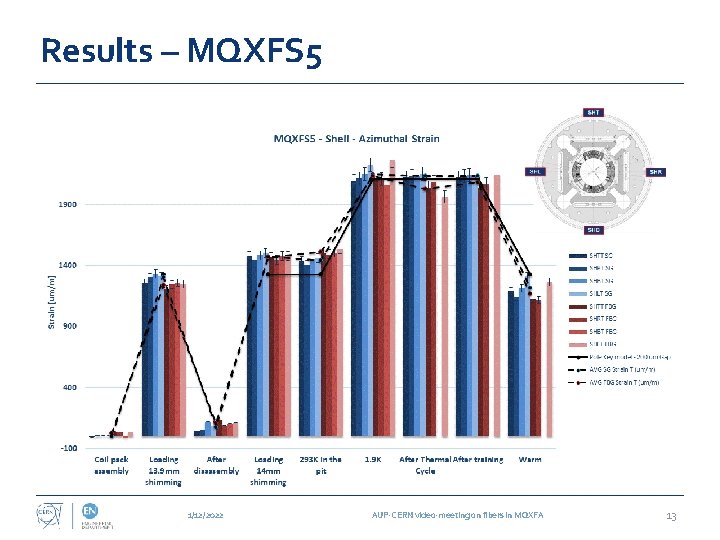
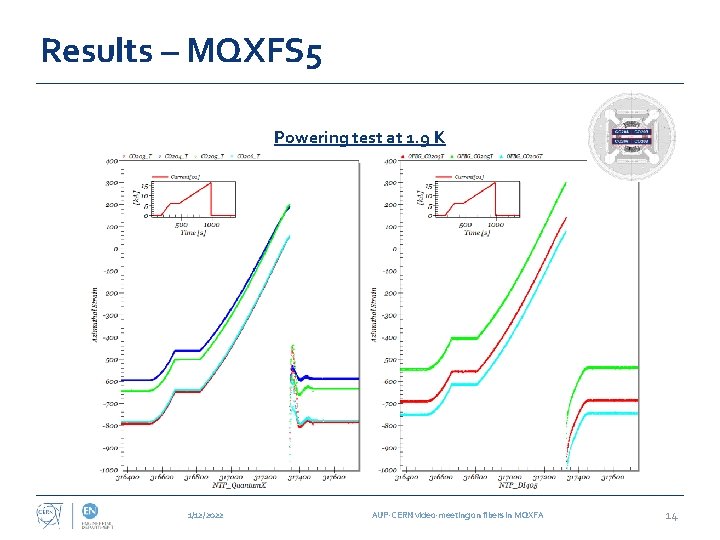
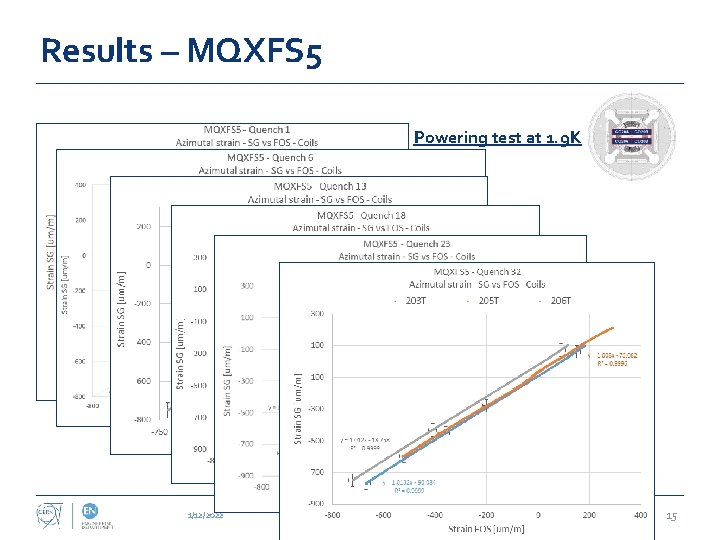
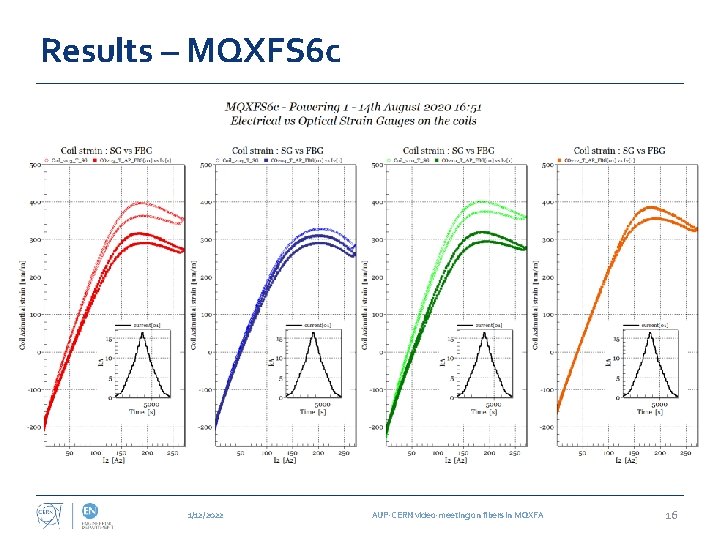
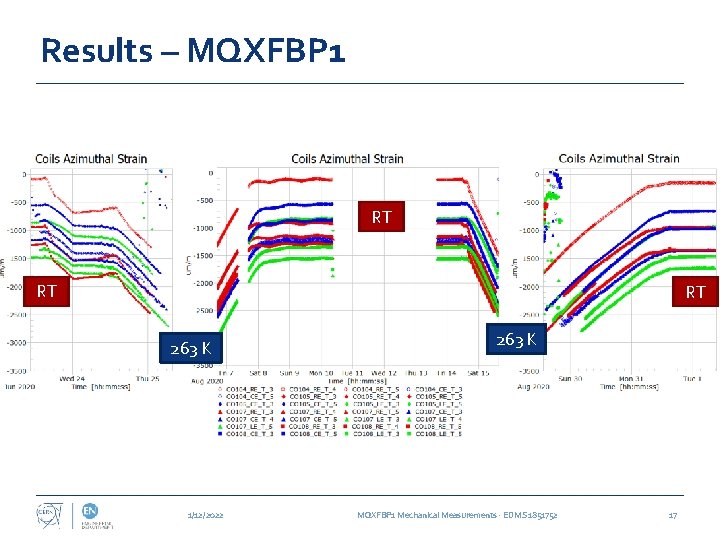
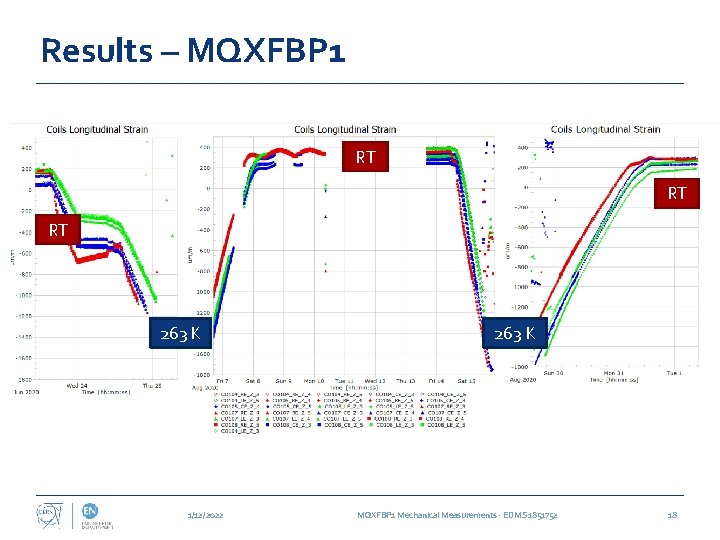
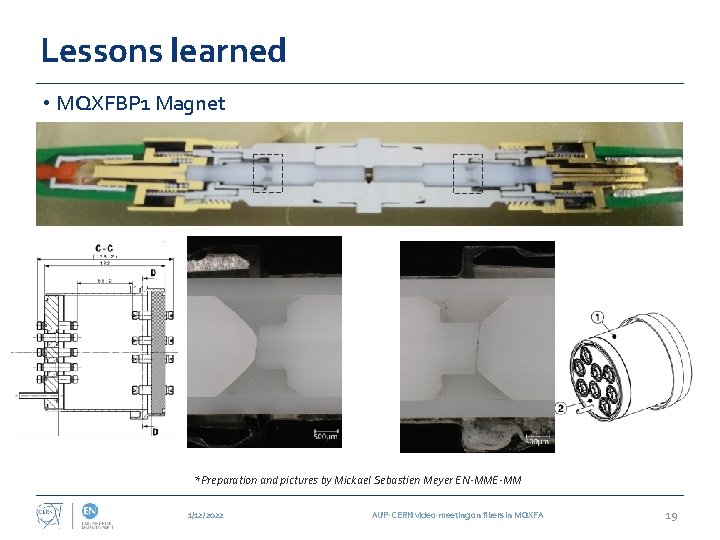
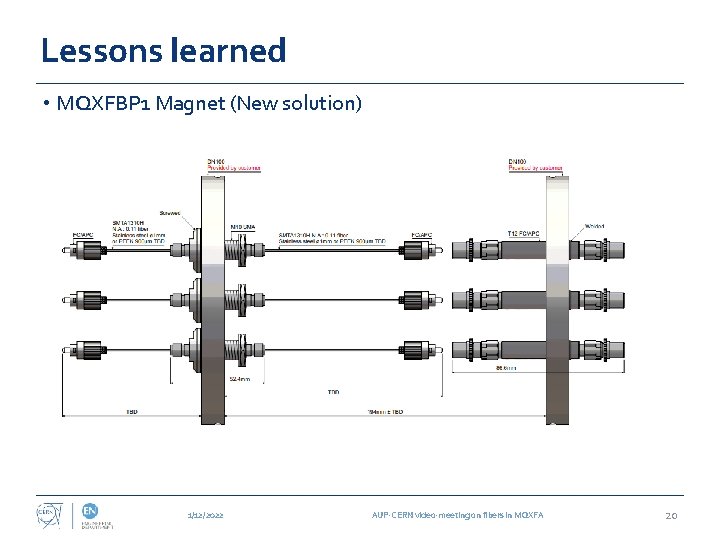
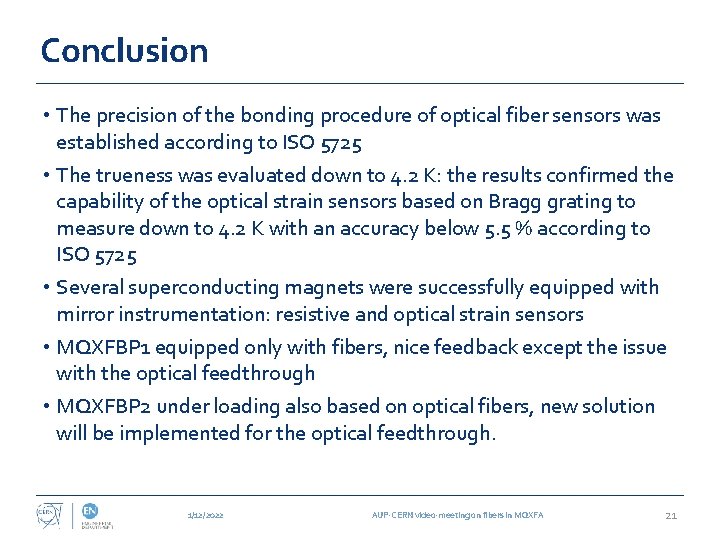
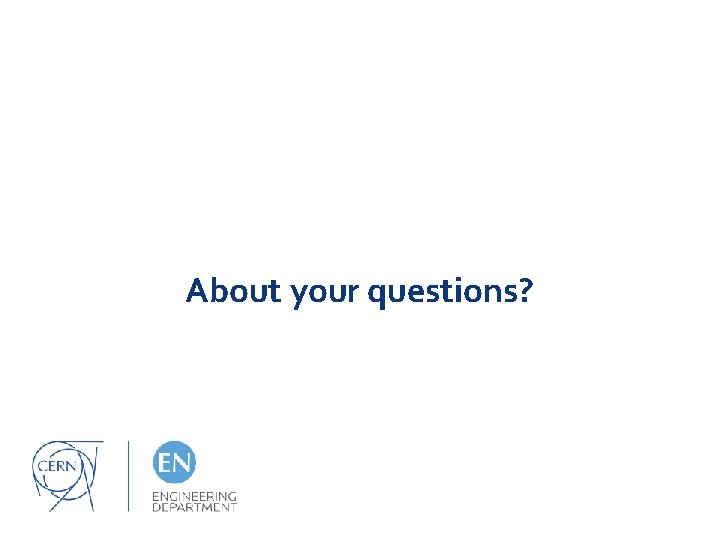
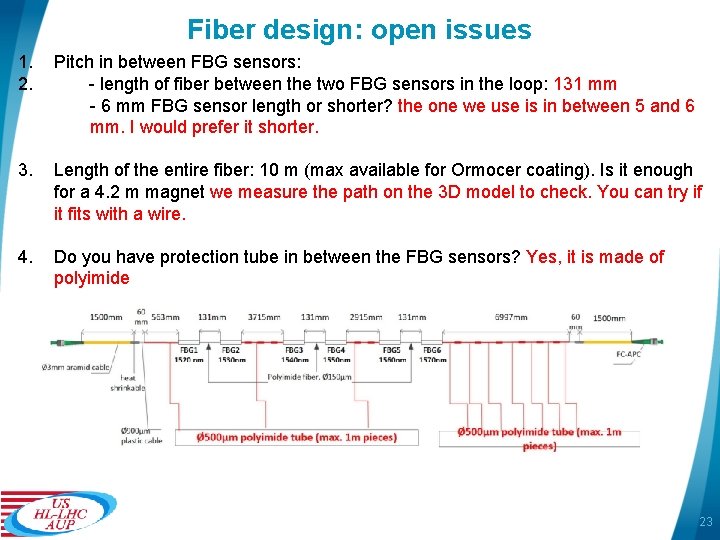
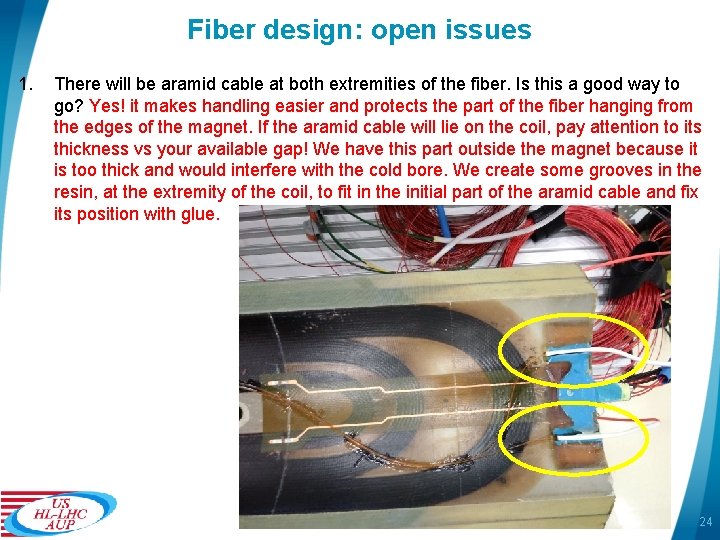
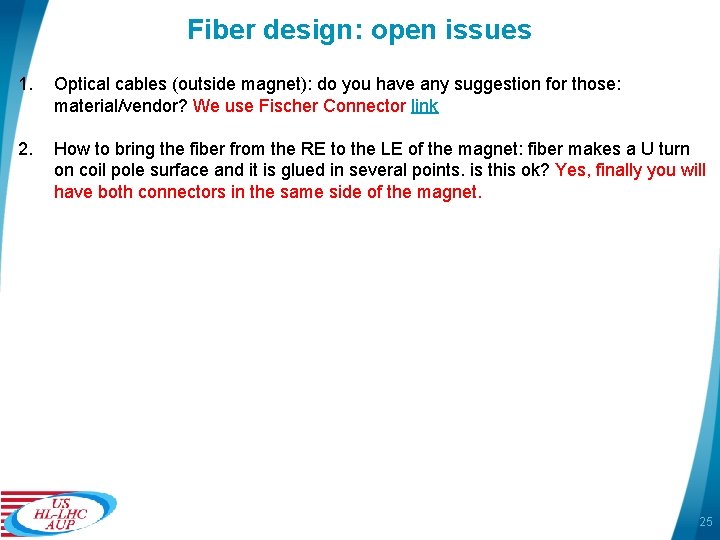
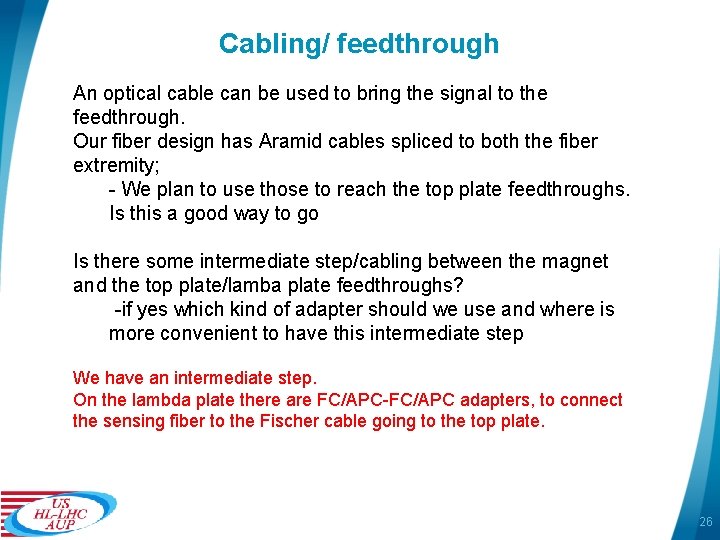
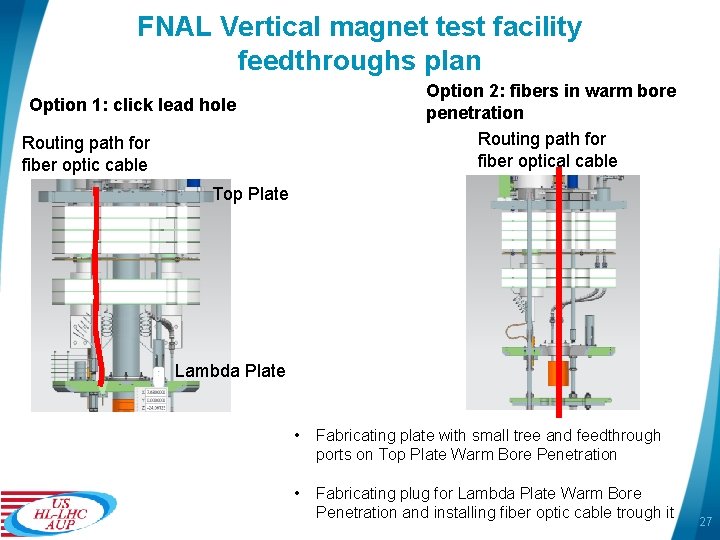
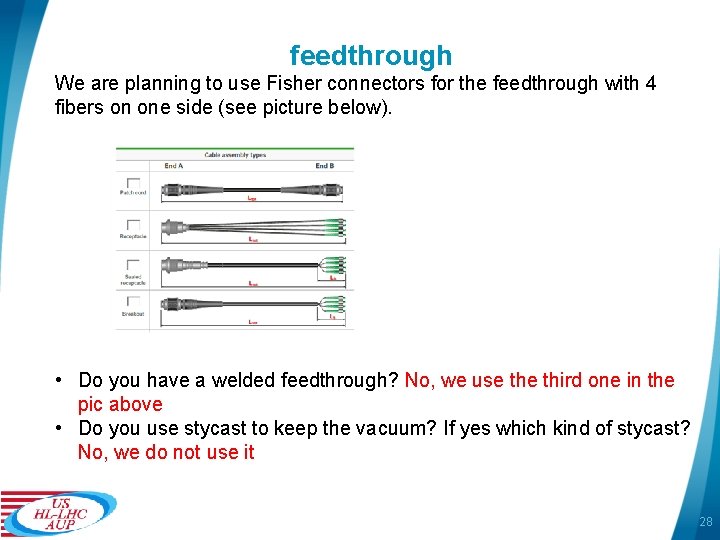
- Slides: 28
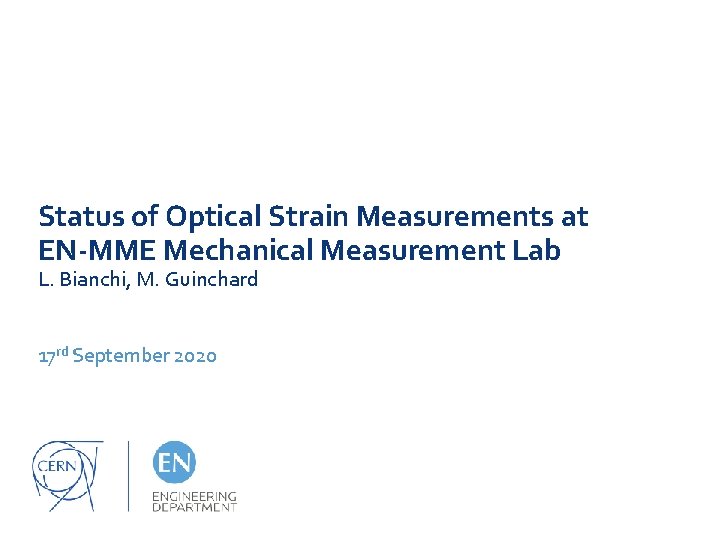
Status of Optical Strain Measurements at EN-MME Mechanical Measurement Lab L. Bianchi, M. Guinchard 17 rd September 2020
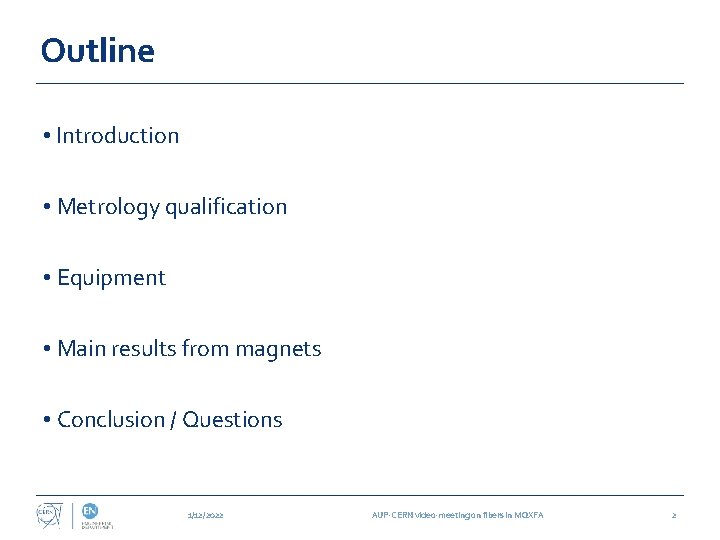
Outline • Introduction • Metrology qualification • Equipment • Main results from magnets • Conclusion / Questions 1/12/2022 AUP-CERN video-meeting on fibers in MQXFA 2
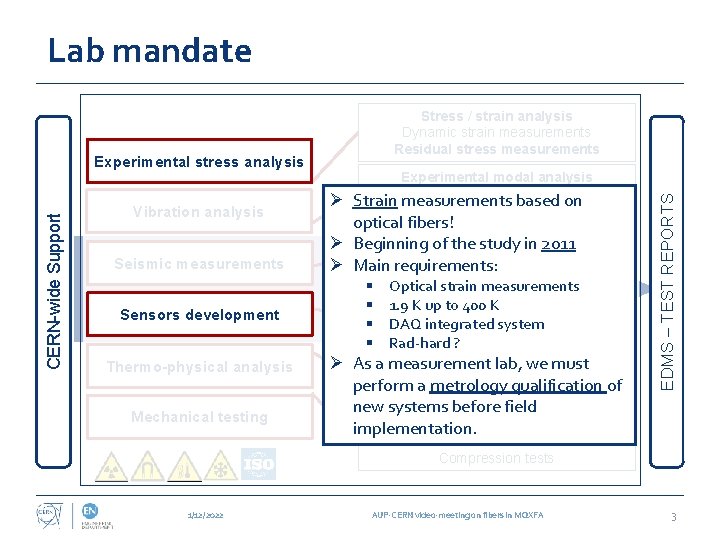
Lab mandate CERN-wide Support Experimental stress analysis Vibration analysis Seismic measurements Sensors development Thermo-physical analysis Mechanical testing Ø Experimental modal analysis Vibration monitoring Strain measurements based on Operating deflection shape optical fibers! Transfer Ø Beginning of thefunction study inanalysis 2011 Transfer path analysis Ø Main Coherence requirements: length measurements § § Optical strain measurements Load based 1. 9 K cell up to 400 Kon strain gauges Displacement sensors DAQ integrated system Capacitive gauges Rad-hard ? Conductivity Ø As a Thermal measurement lab, and we Diffusivity must Specific Heat perform a metrology qualification of Density and CTE new systems before field Impact testing method implementation. EDMS – TEST REPORTS Stress / strain analysis Dynamic strain measurements Residual stress measurements Tensile and Flexural tests Compression tests 1/12/2022 AUP-CERN video-meeting on fibers in MQXFA 3
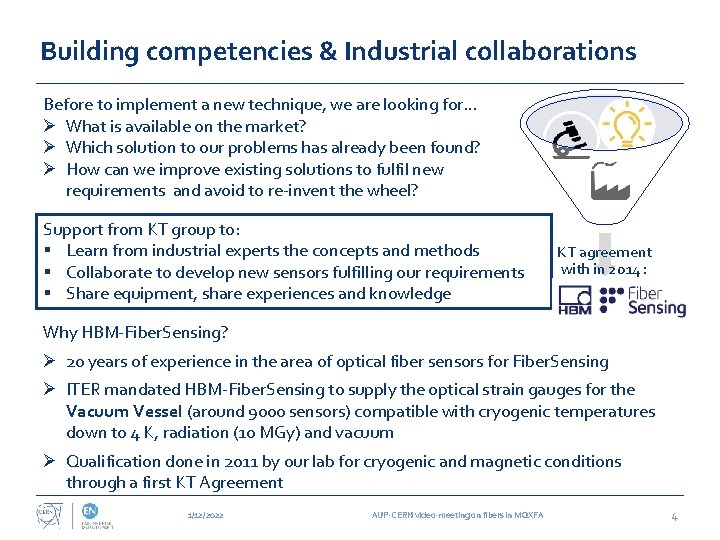
Building competencies & Industrial collaborations Before to implement a new technique, we are looking for… Ø What is available on the market? Ø Which solution to our problems has already been found? Ø How can we improve existing solutions to fulfil new requirements and avoid to re-invent the wheel? Support from KT group to: § Learn from industrial experts the concepts and methods § Collaborate to develop new sensors fulfilling our requirements § Share equipment, share experiences and knowledge KT agreement with in 2014 : Why HBM-Fiber. Sensing? Ø 20 years of experience in the area of optical fiber sensors for Fiber. Sensing Ø ITER mandated HBM-Fiber. Sensing to supply the optical strain gauges for the Vacuum Vessel (around 9000 sensors) compatible with cryogenic temperatures down to 4 K, radiation (10 MGy) and vacuum Ø Qualification done in 2011 by our lab for cryogenic and magnetic conditions through a first KT Agreement 1/12/2022 AUP-CERN video-meeting on fibers in MQXFA 4
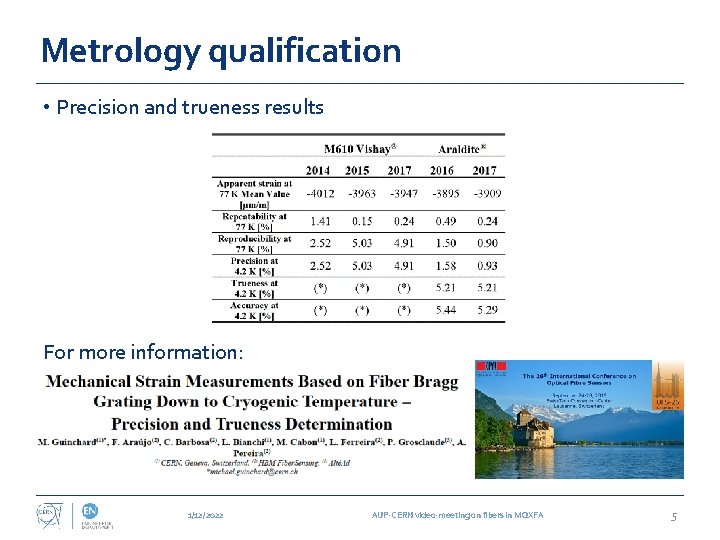
Metrology qualification • Precision and trueness results For more information: 1/12/2022 AUP-CERN video-meeting on fibers in MQXFA 5
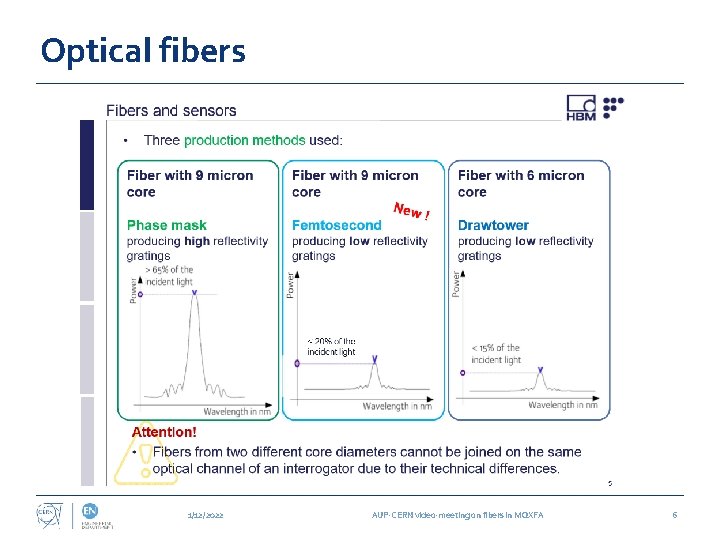
Optical fibers 1/12/2022 AUP-CERN video-meeting on fibers in MQXFA 6
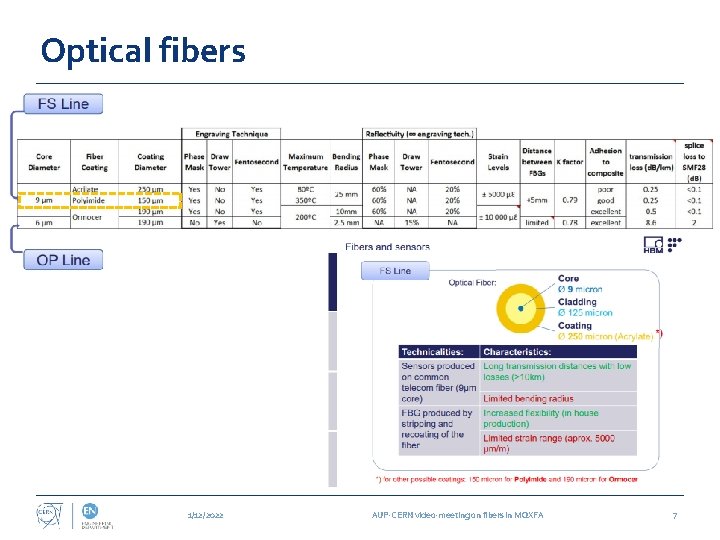
Optical fibers 1/12/2022 AUP-CERN video-meeting on fibers in MQXFA 7
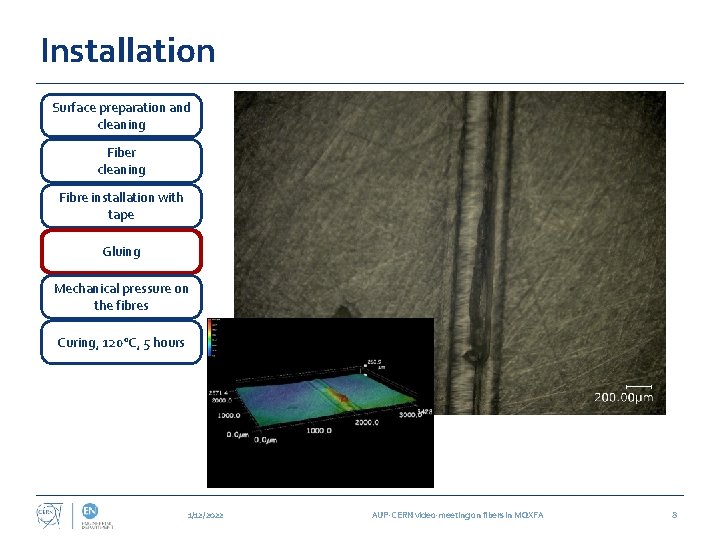
Installation Surface preparation and cleaning Groove printing Gluing Fiber cleaning Fibre installation with tape Gluing Mechanical pressure on the fibres Curing, 120°C, 5 hours Cleaning with RMS 1 Spray from HBM 1/12/2022 AUP-CERN video-meeting on fibers in MQXFA Mechanical pressure 8
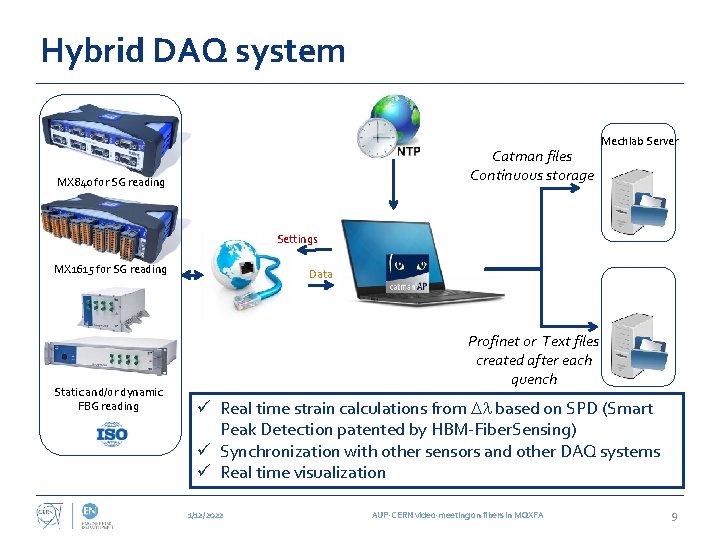
Hybrid DAQ system Catman files Continuous storage MX 840 for SG reading Mechlab Server Settings MX 1615 for SG reading Static and/or dynamic FBG reading Data Profinet or Text files created after each quench ü Real time strain calculations from based on SPD (Smart Peak Detection patented by HBM-Fiber. Sensing) ü Synchronization with other sensors and other DAQ systems ü Real time visualization 1/12/2022 AUP-CERN video-meeting on fibers in MQXFA 9
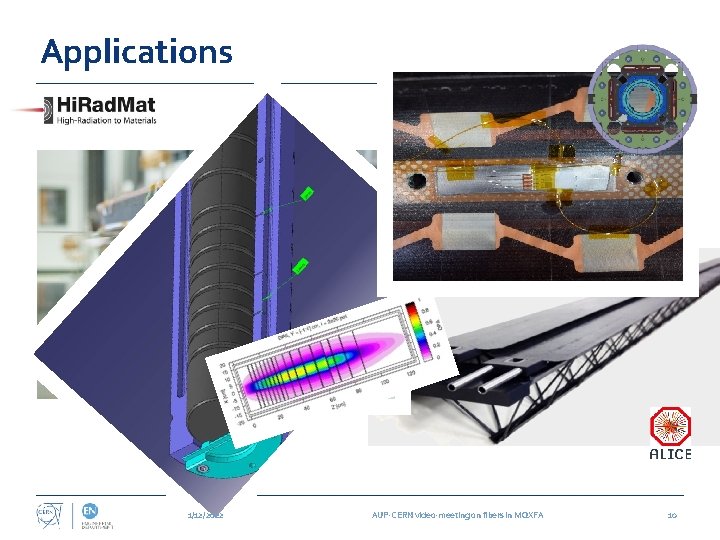
Applications 1/12/2022 AUP-CERN video-meeting on fibers in MQXFA 10
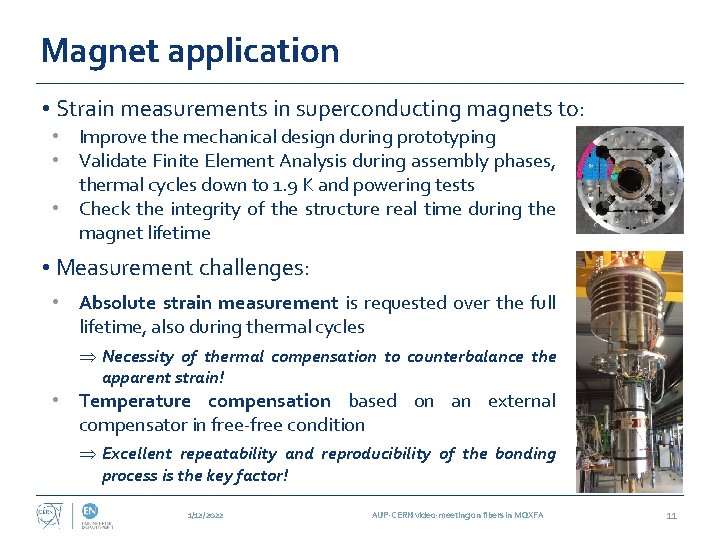
Magnet application • Strain measurements in superconducting magnets to: • Improve the mechanical design during prototyping • Validate Finite Element Analysis during assembly phases, thermal cycles down to 1. 9 K and powering tests • Check the integrity of the structure real time during the magnet lifetime • Measurement challenges: • Absolute strain measurement is requested over the full lifetime, also during thermal cycles Þ Necessity of thermal compensation to counterbalance the apparent strain! • Temperature compensation based on an external compensator in free-free condition Þ Excellent repeatability and reproducibility of the bonding process is the key factor! 1/12/2022 AUP-CERN video-meeting on fibers in MQXFA 11
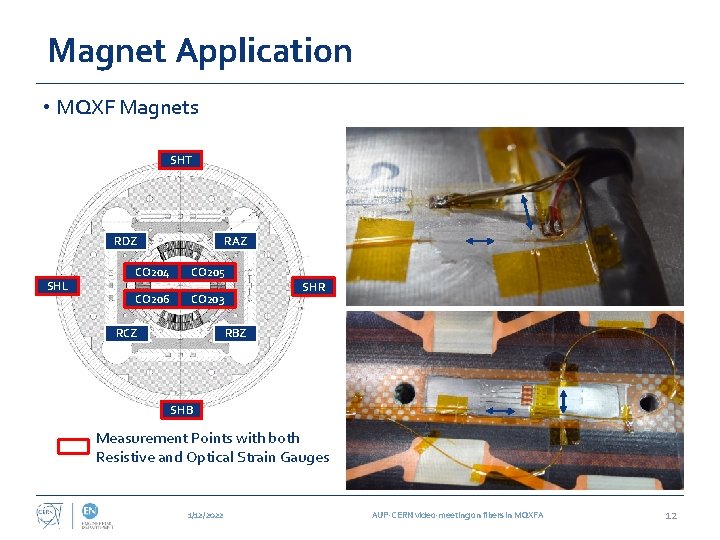
Magnet Application • MQXF Magnets SHT RDZ SHL RAZ CO 204 CO 205 CO 206 CO 203 RCZ SHR RBZ SHB Measurement Points with both Resistive and Optical Strain Gauges 1/12/2022 AUP-CERN video-meeting on fibers in MQXFA 12
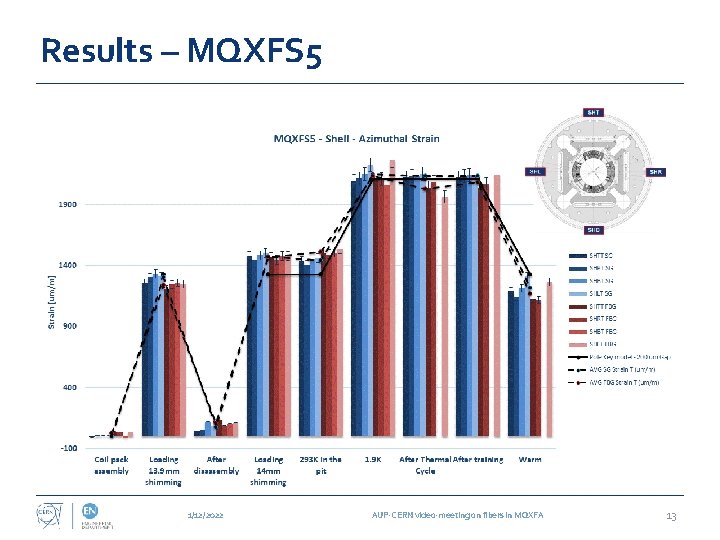
Results – MQXFS 5 1/12/2022 AUP-CERN video-meeting on fibers in MQXFA 13
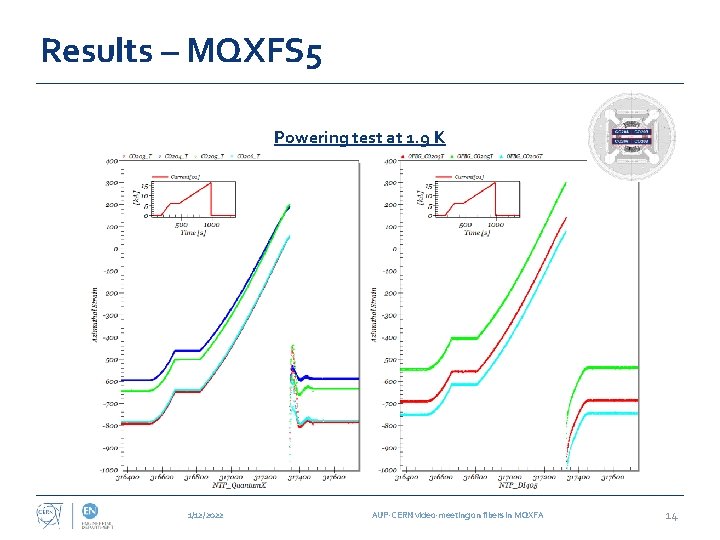
Results – MQXFS 5 Powering test at 1. 9 K 1/12/2022 AUP-CERN video-meeting on fibers in MQXFA 14
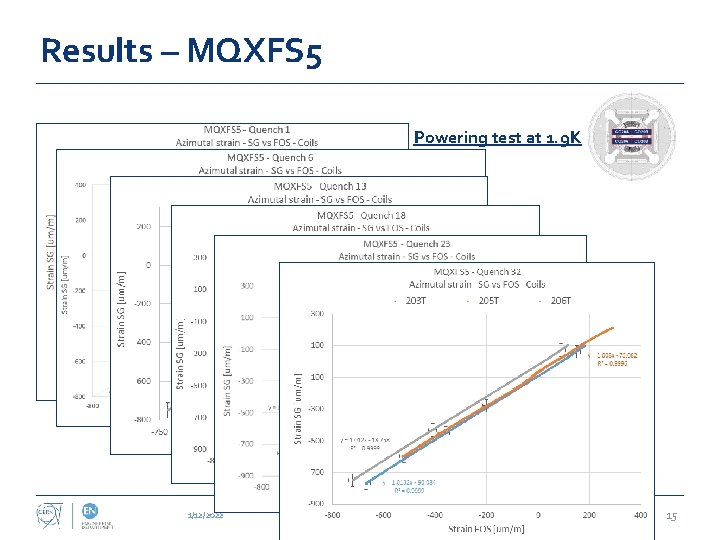
Results – MQXFS 5 Powering test at 1. 9 K 1/12/2022 AUP-CERN video-meeting on fibers in MQXFA 15
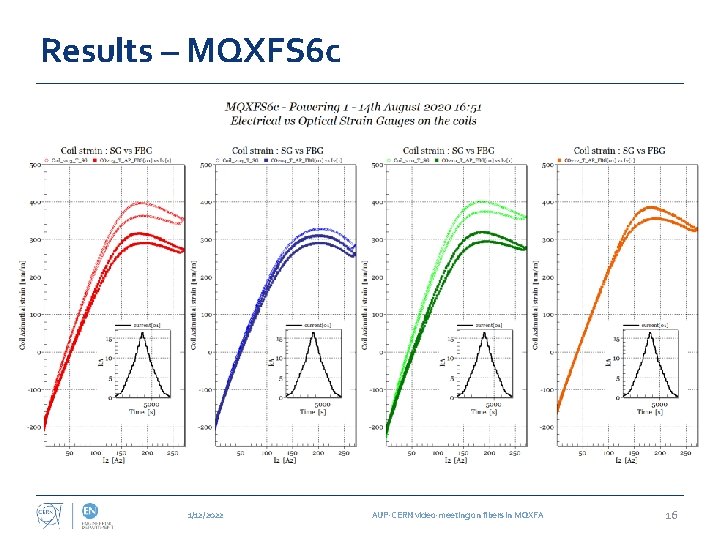
Results – MQXFS 6 c • MQXFS 6 c Magnet 1/12/2022 AUP-CERN video-meeting on fibers in MQXFA 16
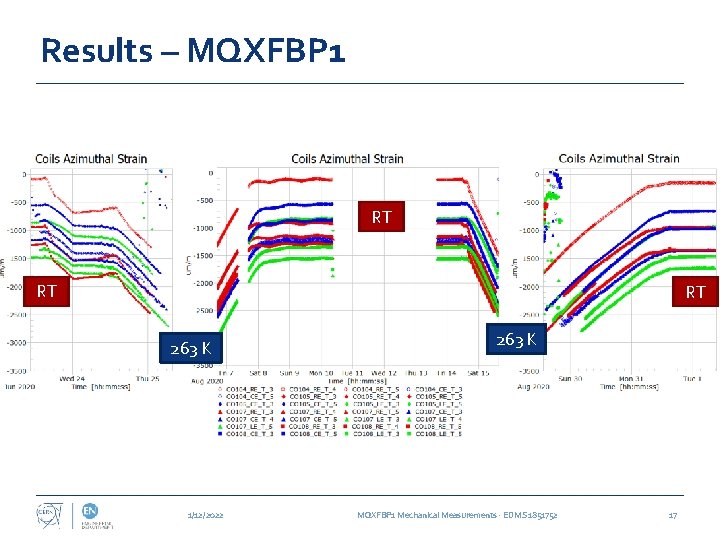
Results – MQXFBP 1 RT RT RT 263 K 1/12/2022 263 K MQXFBP 1 Mechanical Measurements - EDMS 1851752 17
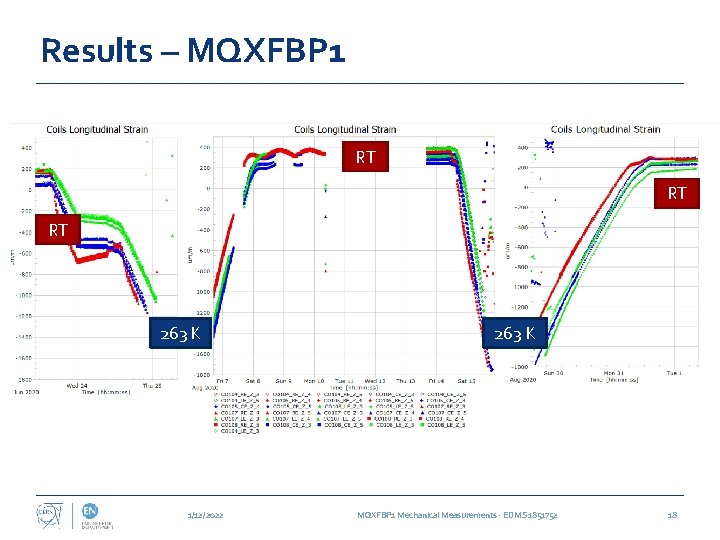
Results – MQXFBP 1 RT RT RT 263 K 1/12/2022 263 K MQXFBP 1 Mechanical Measurements - EDMS 1851752 18
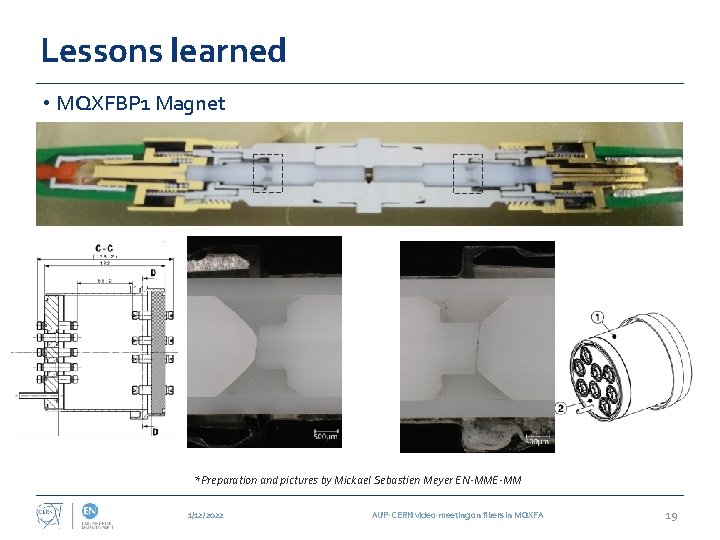
Lessons learned • MQXFBP 1 Magnet *Preparation and pictures by Mickael Sebastien Meyer EN-MME-MM 1/12/2022 AUP-CERN video-meeting on fibers in MQXFA 19
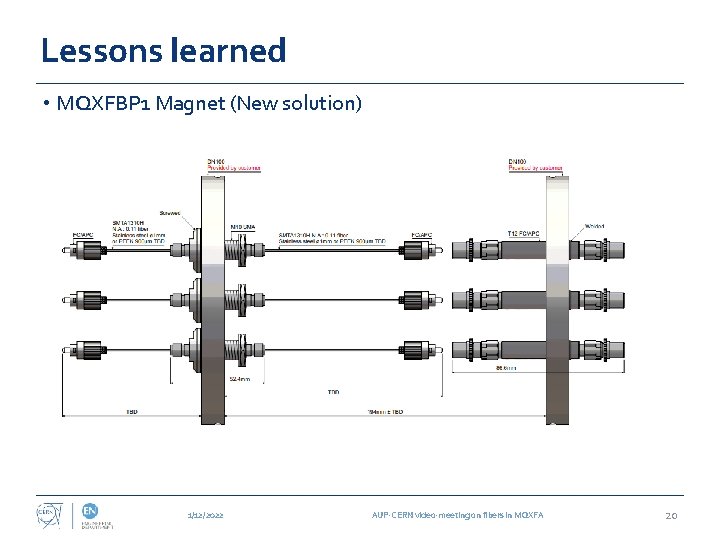
Lessons learned • MQXFBP 1 Magnet (New solution) 1/12/2022 AUP-CERN video-meeting on fibers in MQXFA 20
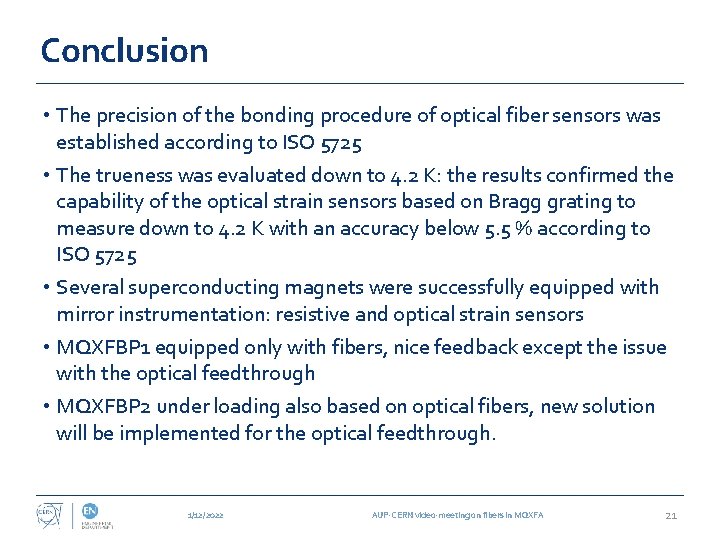
Conclusion • The precision of the bonding procedure of optical fiber sensors was established according to ISO 5725 • The trueness was evaluated down to 4. 2 K: the results confirmed the capability of the optical strain sensors based on Bragg grating to measure down to 4. 2 K with an accuracy below 5. 5 % according to ISO 5725 • Several superconducting magnets were successfully equipped with mirror instrumentation: resistive and optical strain sensors • MQXFBP 1 equipped only with fibers, nice feedback except the issue with the optical feedthrough • MQXFBP 2 under loading also based on optical fibers, new solution will be implemented for the optical feedthrough. 1/12/2022 AUP-CERN video-meeting on fibers in MQXFA 21
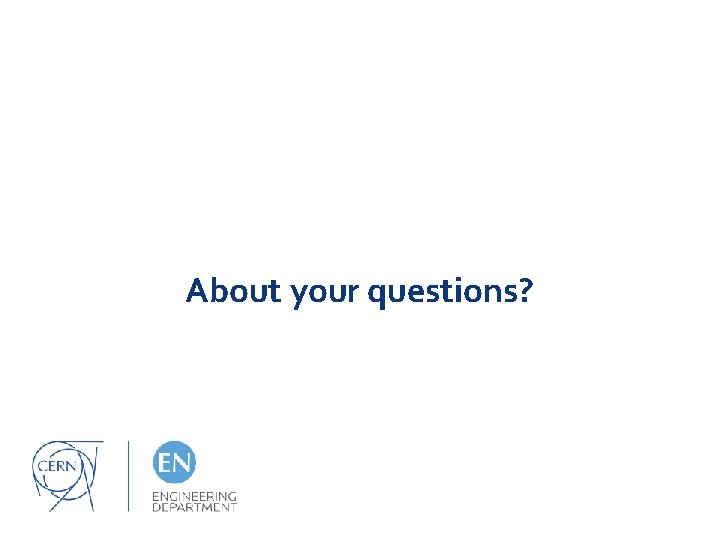
About your questions?
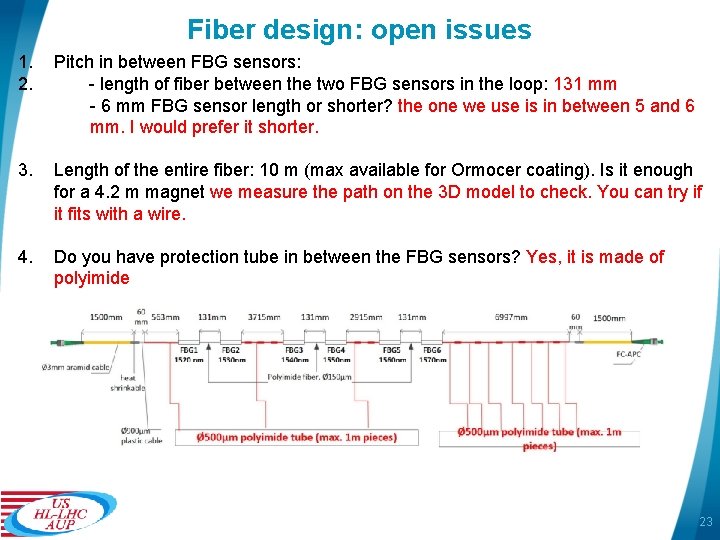
Fiber design: open issues 1. 2. Pitch in between FBG sensors: - length of fiber between the two FBG sensors in the loop: 131 mm - 6 mm FBG sensor length or shorter? the one we use is in between 5 and 6 mm. I would prefer it shorter. 3. Length of the entire fiber: 10 m (max available for Ormocer coating). Is it enough for a 4. 2 m magnet we measure the path on the 3 D model to check. You can try if it fits with a wire. 4. Do you have protection tube in between the FBG sensors? Yes, it is made of polyimide 23
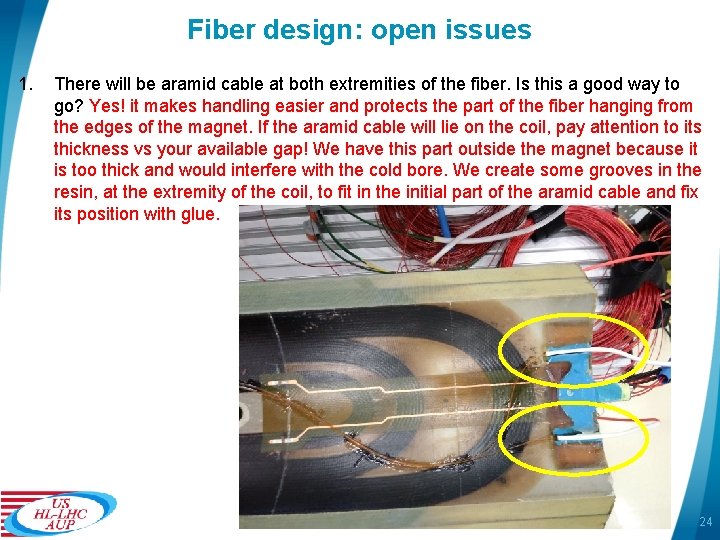
Fiber design: open issues 1. There will be aramid cable at both extremities of the fiber. Is this a good way to go? Yes! it makes handling easier and protects the part of the fiber hanging from the edges of the magnet. If the aramid cable will lie on the coil, pay attention to its thickness vs your available gap! We have this part outside the magnet because it is too thick and would interfere with the cold bore. We create some grooves in the resin, at the extremity of the coil, to fit in the initial part of the aramid cable and fix its position with glue. 24
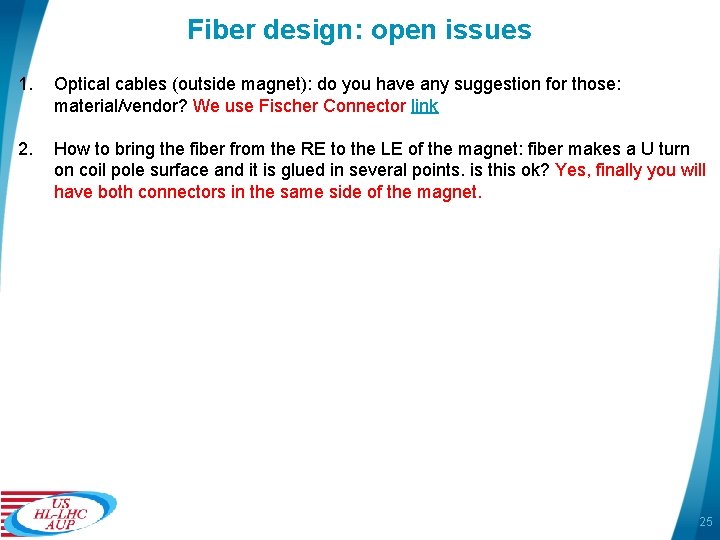
Fiber design: open issues 1. Optical cables (outside magnet): do you have any suggestion for those: material/vendor? We use Fischer Connector link 2. How to bring the fiber from the RE to the LE of the magnet: fiber makes a U turn on coil pole surface and it is glued in several points. is this ok? Yes, finally you will have both connectors in the same side of the magnet. 25
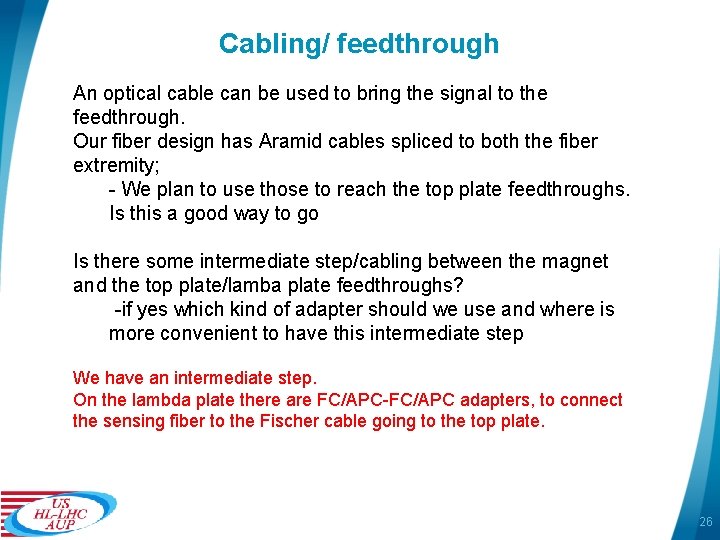
Cabling/ feedthrough An optical cable can be used to bring the signal to the feedthrough. Our fiber design has Aramid cables spliced to both the fiber extremity; - We plan to use those to reach the top plate feedthroughs. Is this a good way to go Is there some intermediate step/cabling between the magnet and the top plate/lamba plate feedthroughs? -if yes which kind of adapter should we use and where is more convenient to have this intermediate step We have an intermediate step. On the lambda plate there are FC/APC-FC/APC adapters, to connect the sensing fiber to the Fischer cable going to the top plate. 26
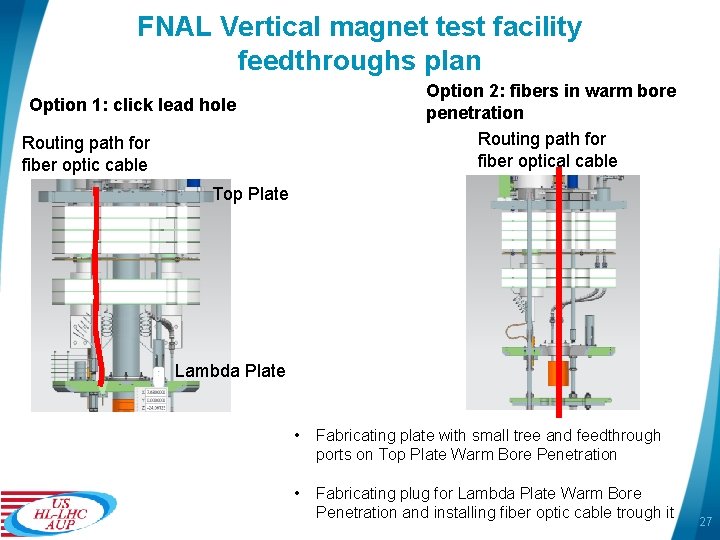
FNAL Vertical magnet test facility feedthroughs plan Option 2: fibers in warm bore penetration Routing path for fiber optical cable Option 1: click lead hole Routing path for fiber optic cable Top Plate Lambda Plate • Fabricating plate with small tree and feedthrough ports on Top Plate Warm Bore Penetration • Fabricating plug for Lambda Plate Warm Bore Penetration and installing fiber optic cable trough it 27
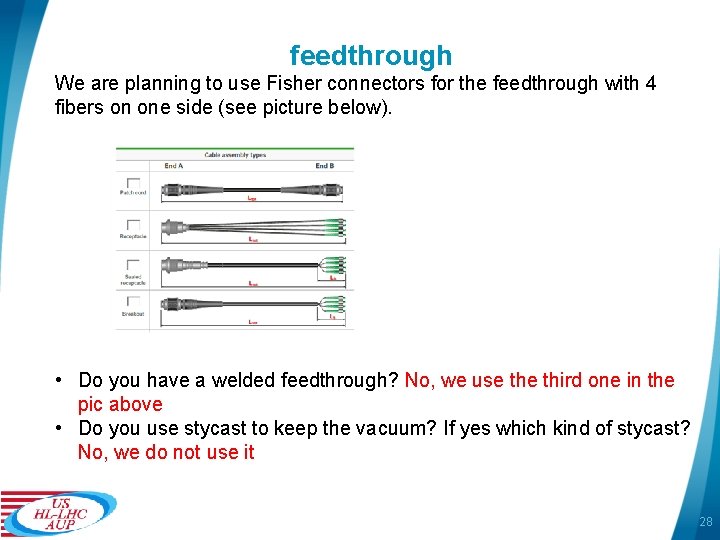
feedthrough We are planning to use Fisher connectors for the feedthrough with 4 fibers on one side (see picture below). • Do you have a welded feedthrough? No, we use third one in the pic above • Do you use stycast to keep the vacuum? If yes which kind of stycast? No, we do not use it 28
Elastic strain and plastic strain
Elasticdeformation
Enmme
Enmme
Enmme
Diego perini
Optical mechanical scanner
Actual mechanical advantage vs ideal mechanical advantage
Md solarscience
Vital signs and anthropometric measurements:
Bell measurements for teleportation
Using and expressing measurements
It consists of numbers representing counts or measurements
Chapter 12 economic indicators and measurements
Measurements in chemistry
Fitness chapter 8
Nano blackboard
Measurements system analysis
Two types of measurements
Measurement abbreviations and equivalents answer key
Liberia measurement system
Njrotc uniform
How to calculate average speed from a distance time graph
Metric and household measurements
Which civilizations were the first to record measurements?
Mathematical literacy grade 10 measurements
Temperature measurements
Cun measurements tcm
Kathleen quinlan measurements