SIX SIGMA Faculty Name S Pradeep Kumar Designation
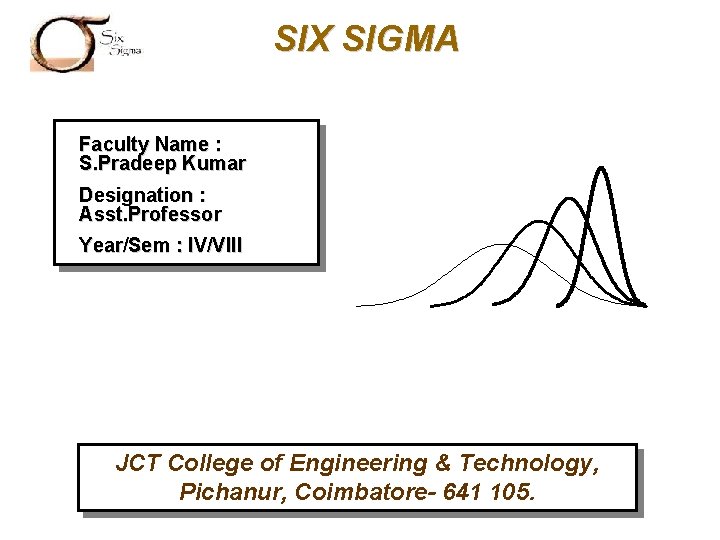
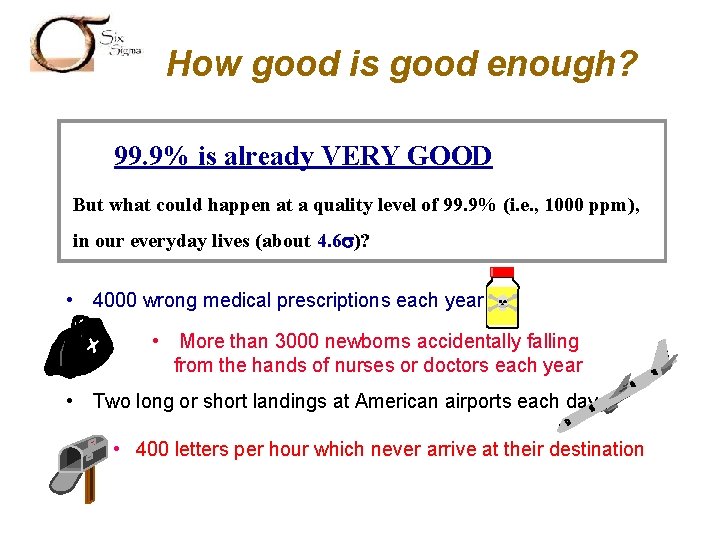
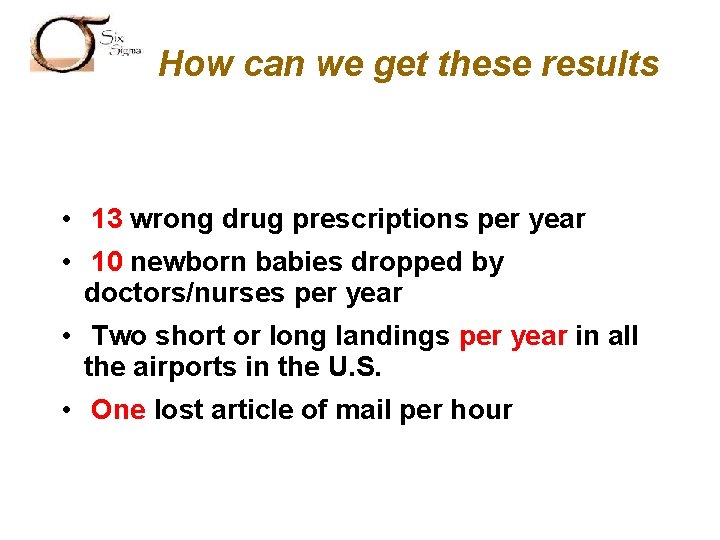

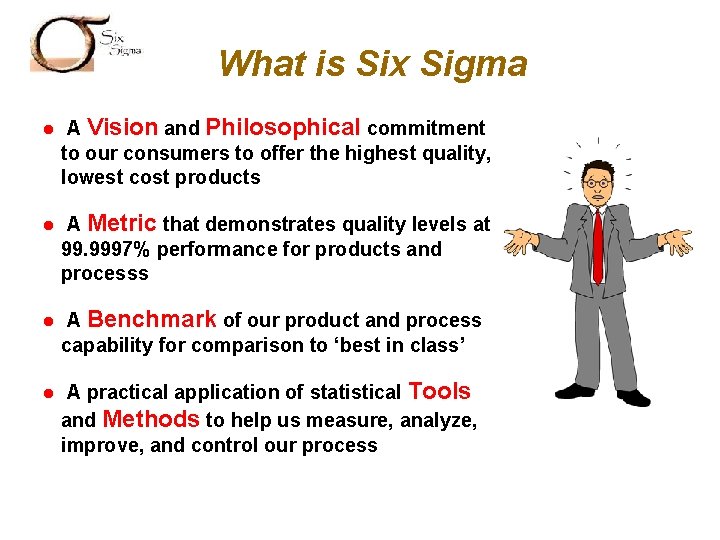
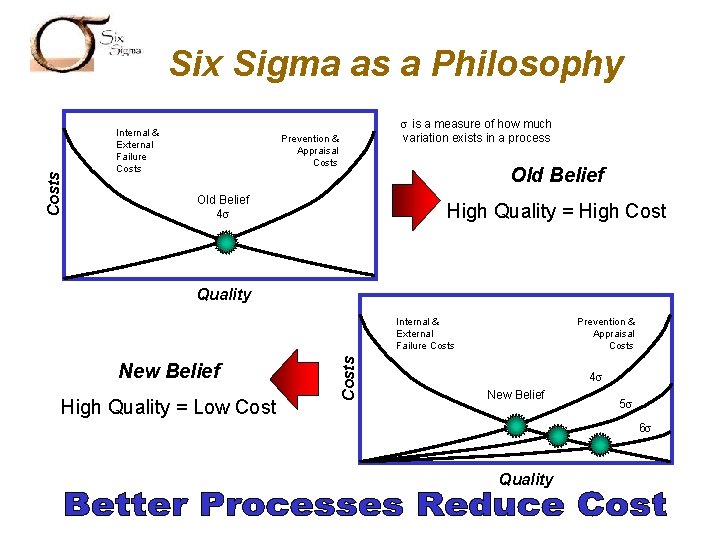
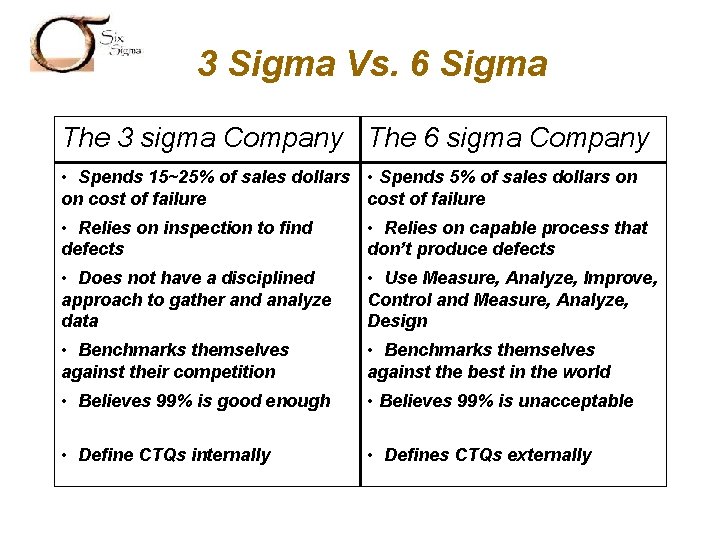
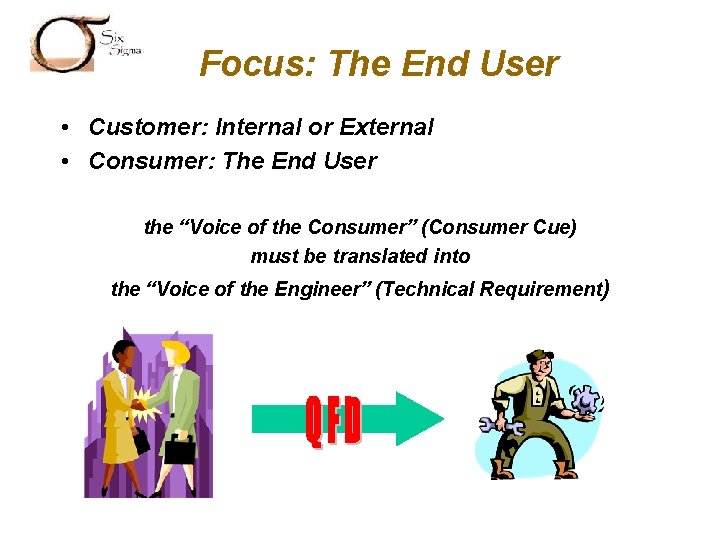

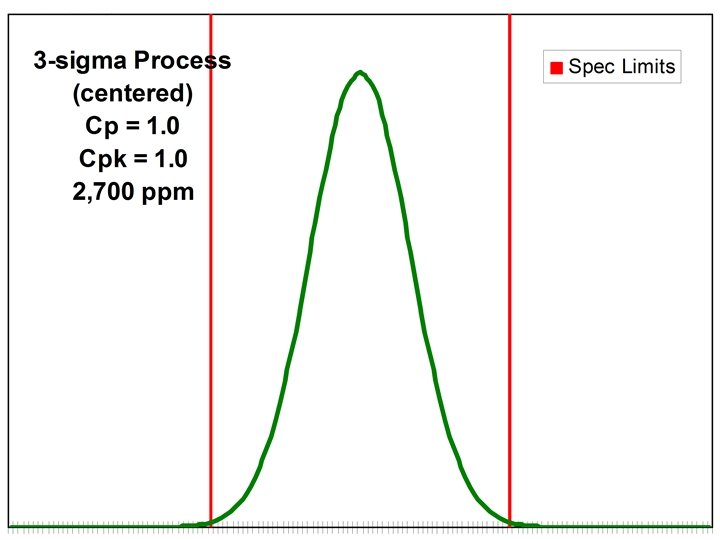
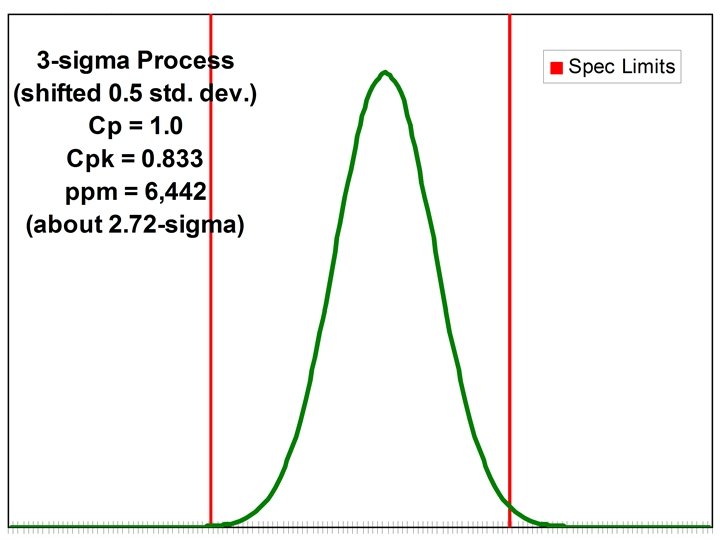

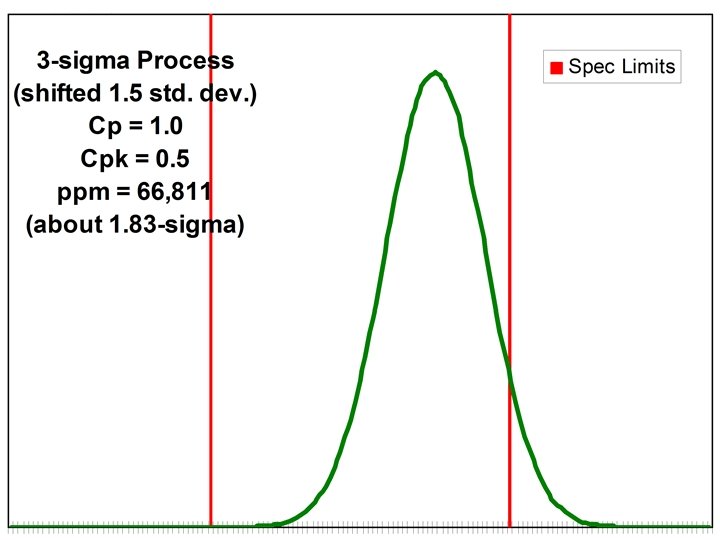
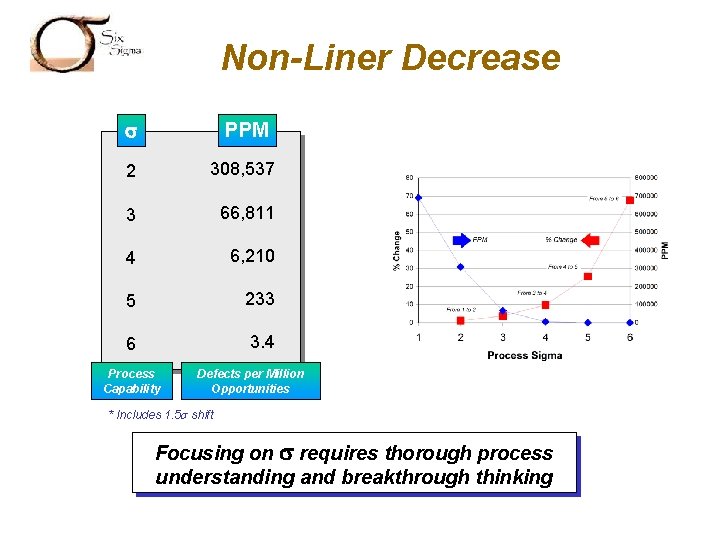
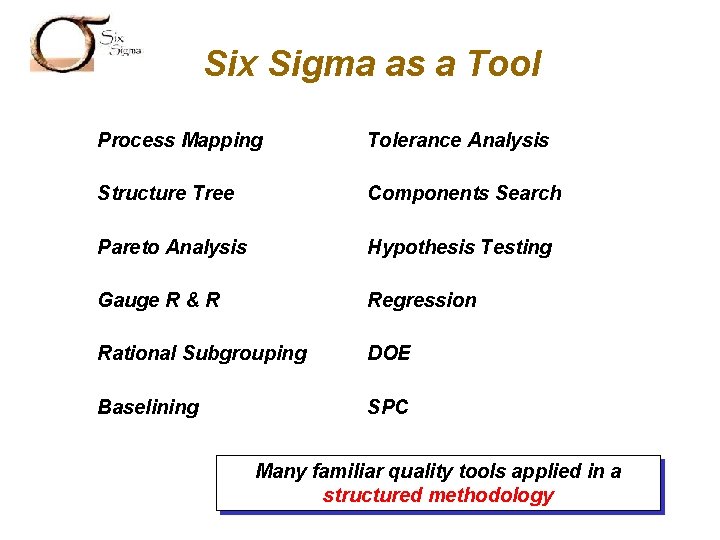
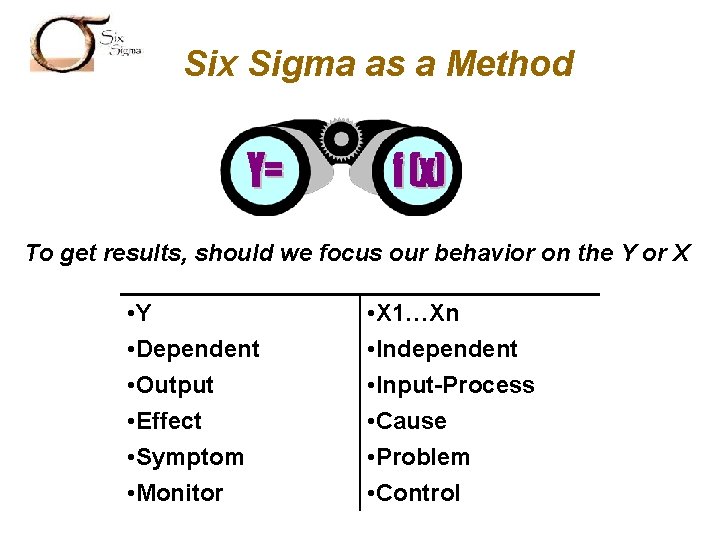
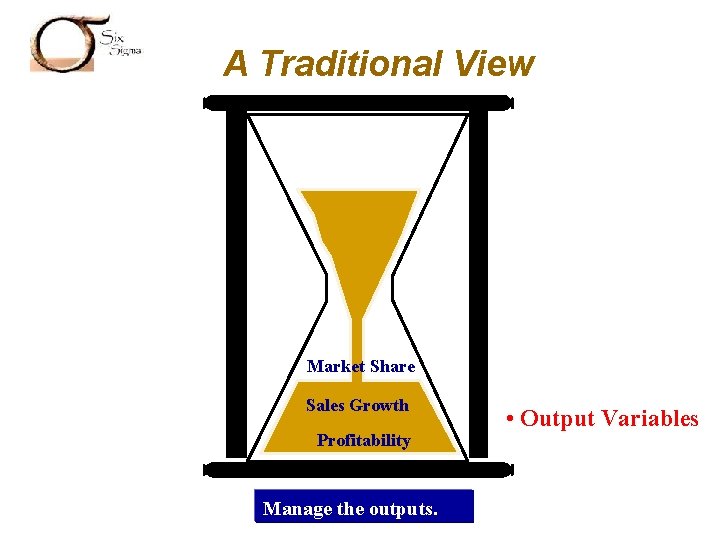
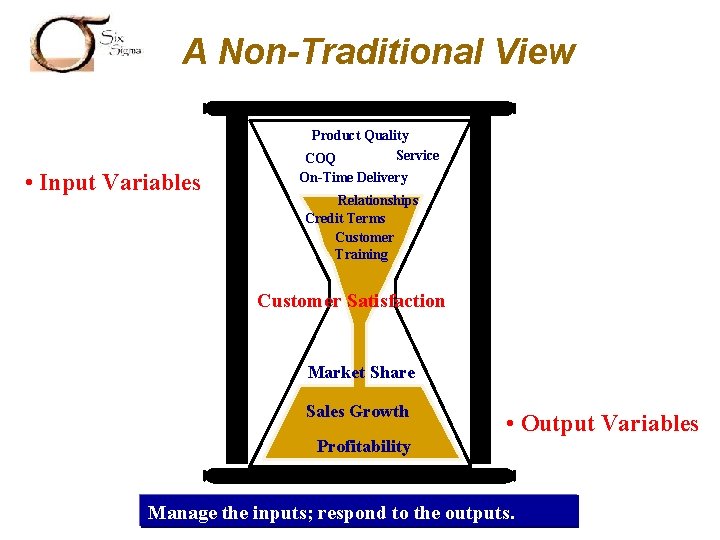
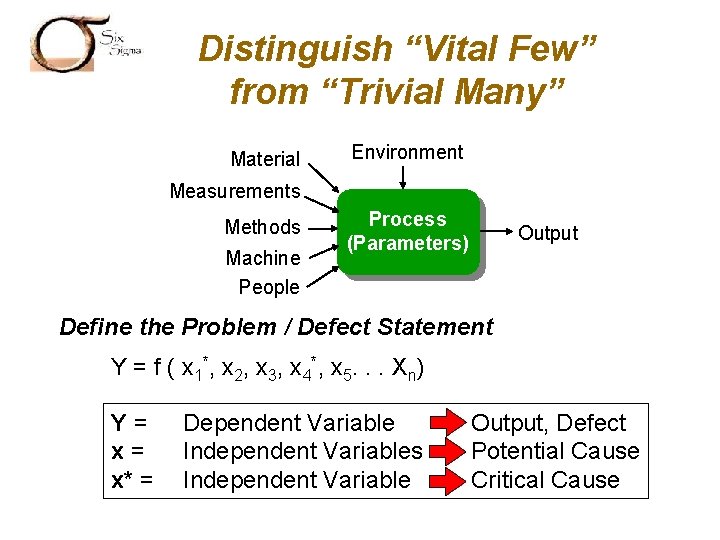
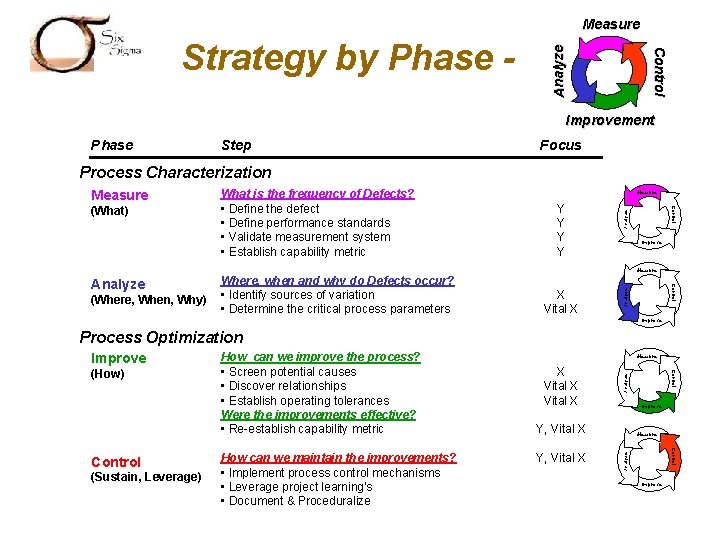
- Slides: 20
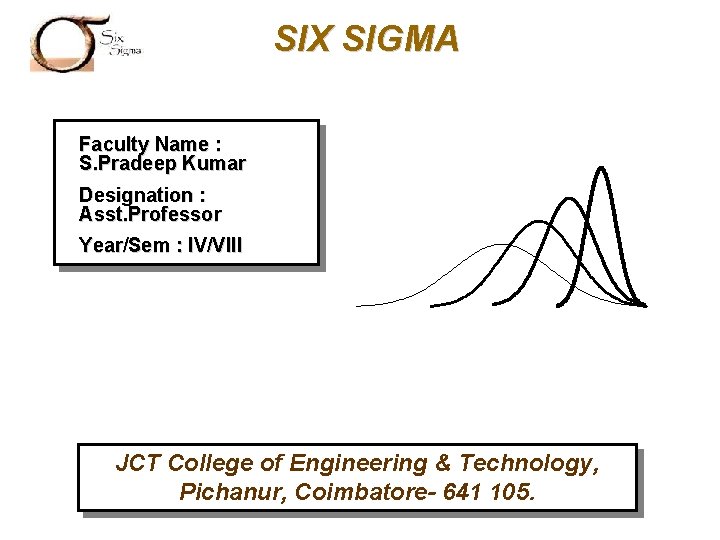
SIX SIGMA Faculty Name : S. Pradeep Kumar Designation : Asst. Professor Year/Sem : IV/VIII JCT College of Engineering & Technology, Pichanur, Coimbatore- 641 105.
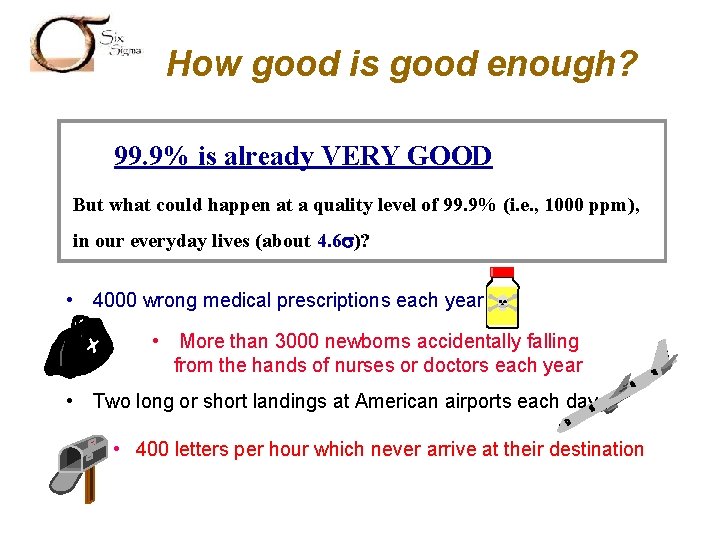
SIX SIGMA How good is good enough? 99. 9% is already VERY GOOD But what could happen at a quality level of 99. 9% (i. e. , 1000 ppm), in our everyday lives (about 4. 6 )? • 4000 wrong medical prescriptions each year • More than 3000 newborns accidentally falling from the hands of nurses or doctors each year • Two long or short landings at American airports each day • 400 letters per hour which never arrive at their destination
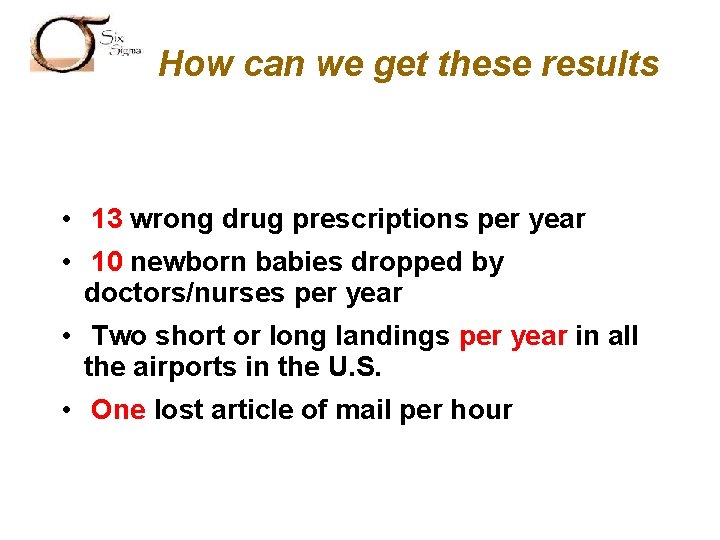
SIX SIGMA How can we get these results • 13 wrong drug prescriptions per year • 10 newborn babies dropped by doctors/nurses per year • Two short or long landings per year in all the airports in the U. S. • One lost article of mail per hour

SIX SIGMA The answer is: Six Sigma
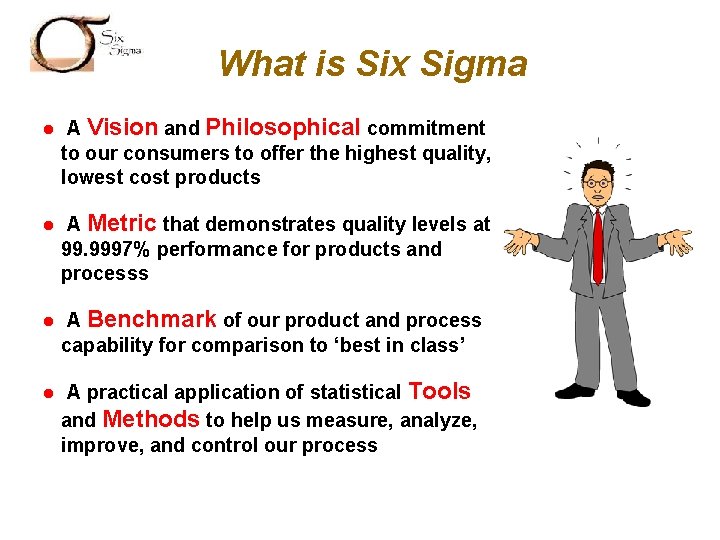
SIX SIGMA What is Six Sigma l l A Vision and Philosophical commitment to our consumers to offer the highest quality, lowest cost products A Metric that demonstrates quality levels at 99. 9997% performance for products and processs A Benchmark of our product and process capability for comparison to ‘best in class’ A practical application of statistical Tools and Methods to help us measure, analyze, improve, and control our process
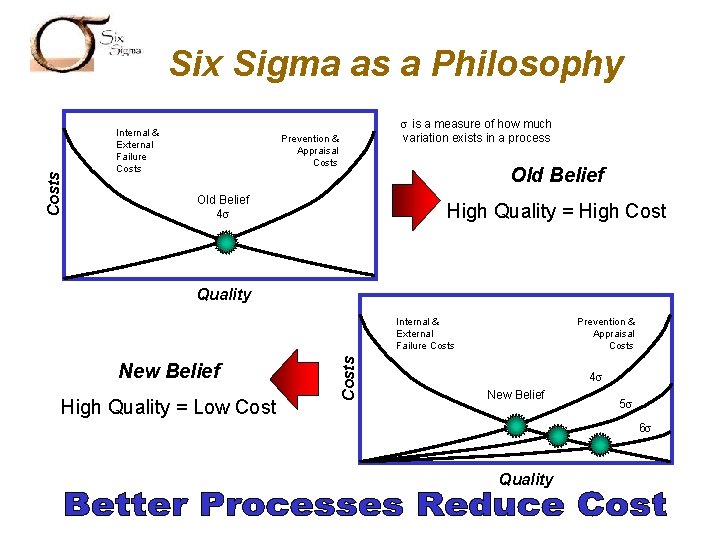
Costs SIX SIGMA Six Sigma as a Philosophy Internal & External Failure Costs s is a measure of how much variation exists in a process Prevention & Appraisal Costs Old Belief 4 s High Quality = High Cost Quality New Belief High Quality = Low Costs Internal & External Failure Costs Prevention & Appraisal Costs 4 s New Belief 5 s 6 s Quality
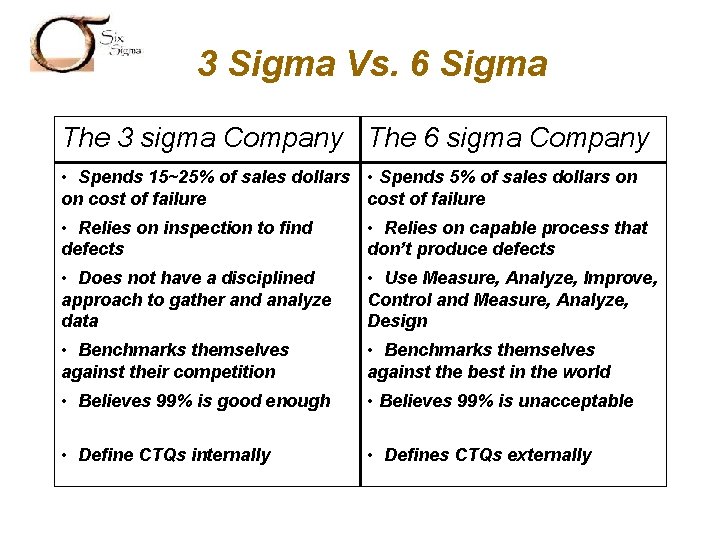
SIX SIGMA 3 Sigma Vs. 6 Sigma The 3 sigma Company The 6 sigma Company • Spends 15~25% of sales dollars • Spends 5% of sales dollars on on cost of failure • Relies on inspection to find defects • Relies on capable process that don’t produce defects • Does not have a disciplined approach to gather and analyze data • Use Measure, Analyze, Improve, Control and Measure, Analyze, Design • Benchmarks themselves against their competition • Benchmarks themselves against the best in the world • Believes 99% is good enough • Believes 99% is unacceptable • Define CTQs internally • Defines CTQs externally
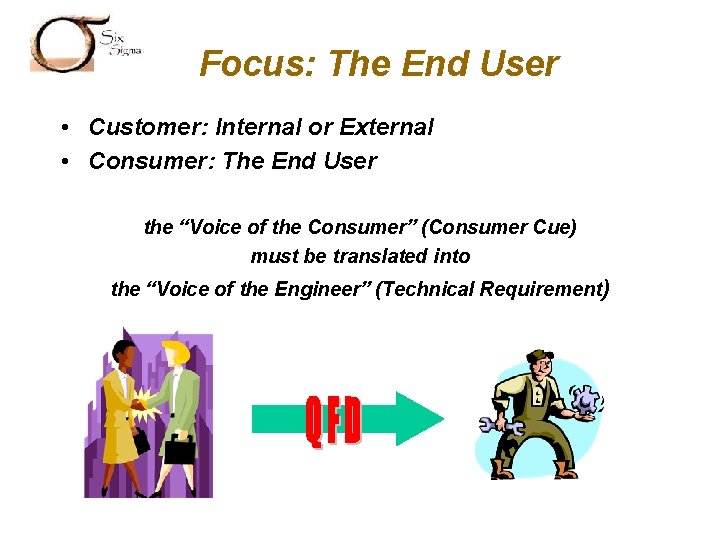
SIX SIGMA Focus: The End User • Customer: Internal or External • Consumer: The End User the “Voice of the Consumer” (Consumer Cue) must be translated into the “Voice of the Engineer” (Technical Requirement)

SO R ED SIX SIGMA Six Sigma as a Metric C Sigma = = Deviation = EN ( Square root of variance ) 7 6 5 4 3 2 1 0 -1 -2 -3 -4 -5 -6 -7 Axis graduated in Sigma between + / - 1 68. 27 % between + / - 2 95. 45 % 45500 ppm between + / - 3 99. 73 % 2700 ppm between + / - 4 99. 9937 % 63 ppm between + / - 5 99. 999943 % 0. 57 ppm between + / - 6 99. 9999998 % 0. 002 ppm result: 317300 ppm outside (deviation)
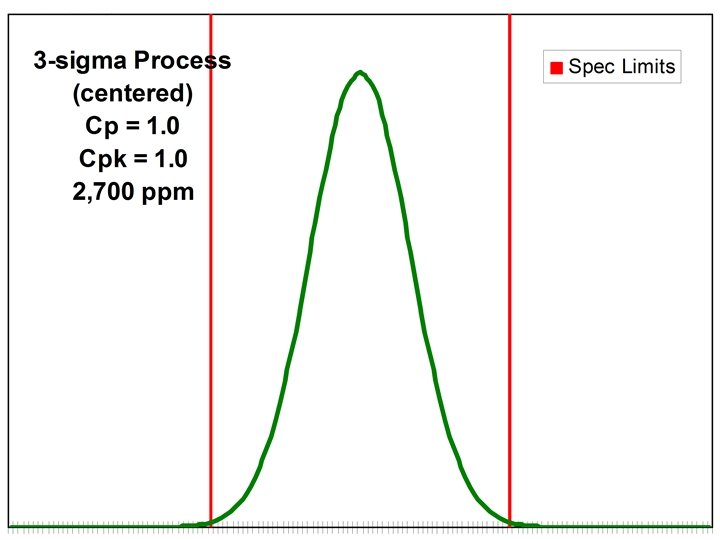
SIX SIGMA
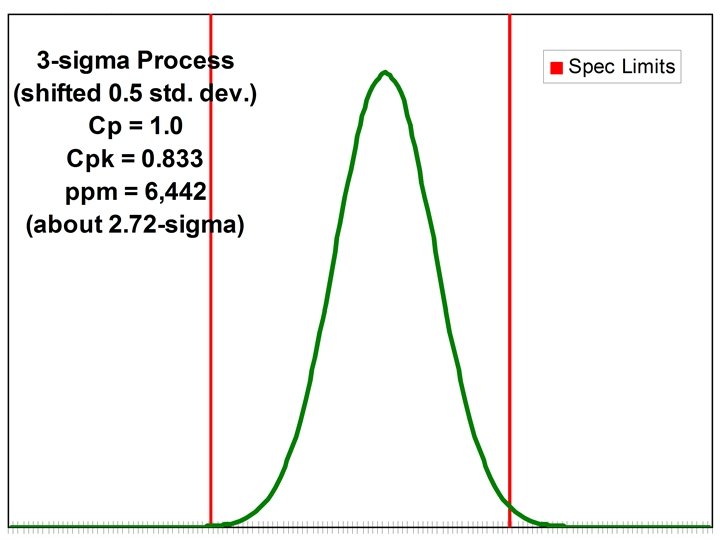
SIX SIGMA

SIX SIGMA
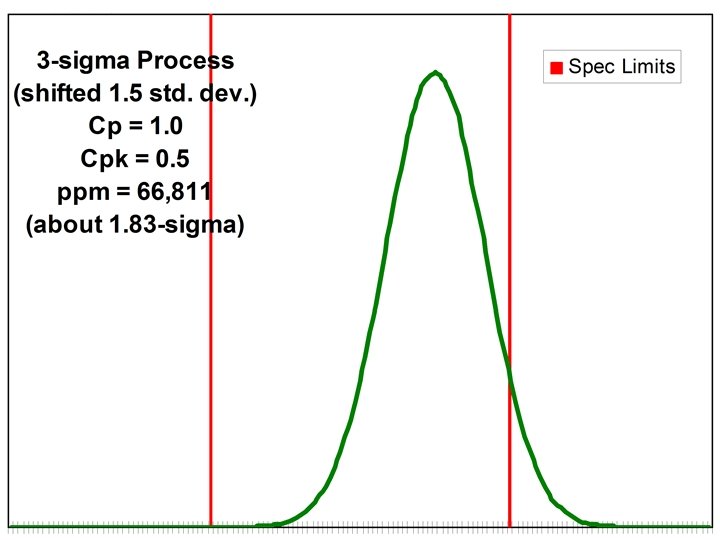
SIX SIGMA
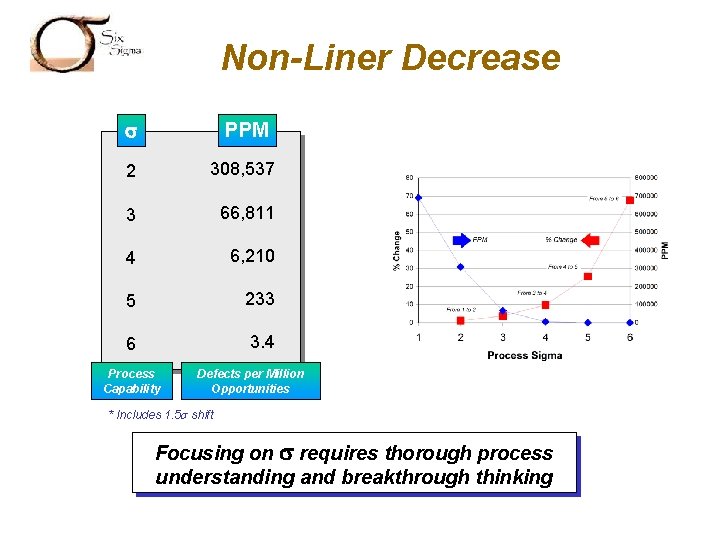
SIX SIGMA Non-Liner Decrease PPM 2 308, 537 3 66, 811 4 6, 210 5 233 6 3. 4 Process Capability Defects per Million Opportunities * Includes 1. 5 s shift Focusing on requires thorough process understanding and breakthrough thinking
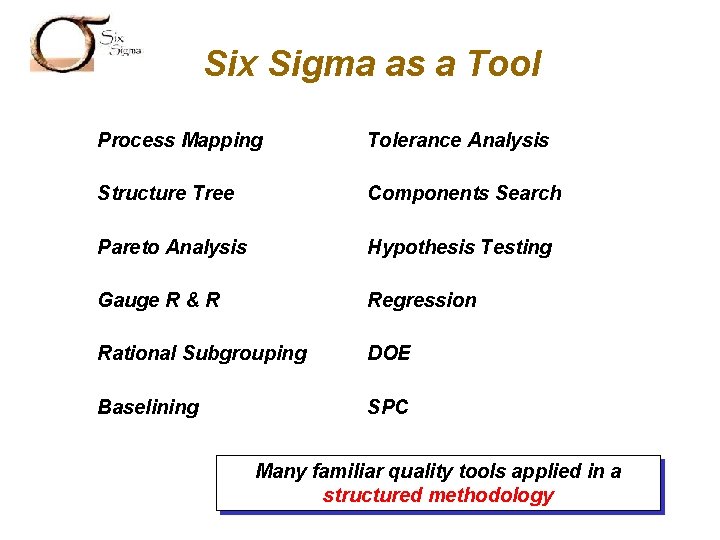
SIX SIGMA Six Sigma as a Tool Process Mapping Tolerance Analysis Structure Tree Components Search Pareto Analysis Hypothesis Testing Gauge R & R Regression Rational Subgrouping DOE Baselining SPC Many familiar quality tools applied in a structured methodology
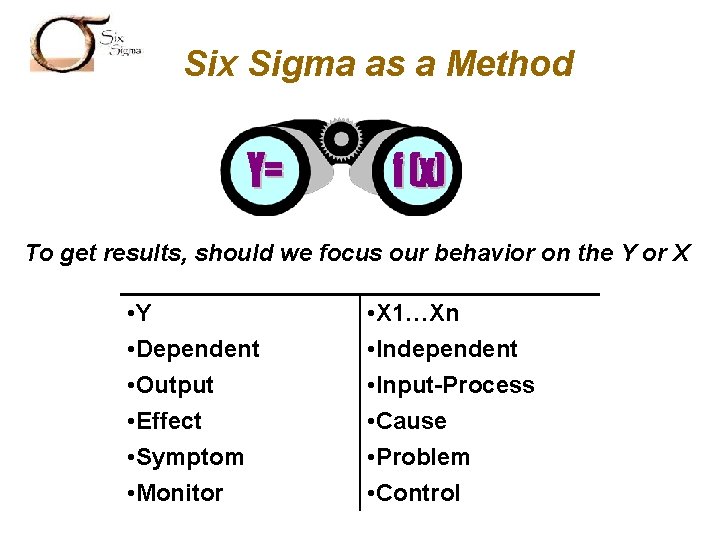
SIX SIGMA Six Sigma as a Method To get results, should we focus our behavior on the Y or X • Y • Dependent • Output • Effect • Symptom • Monitor • X 1…Xn • Independent • Input-Process • Cause • Problem • Control
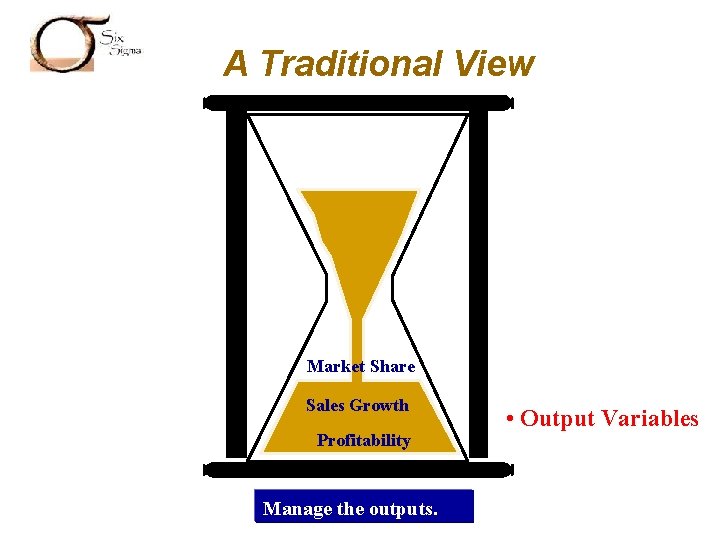
SIX SIGMA A Traditional View Market Share Sales Growth Profitability Manage the outputs. • Output Variables
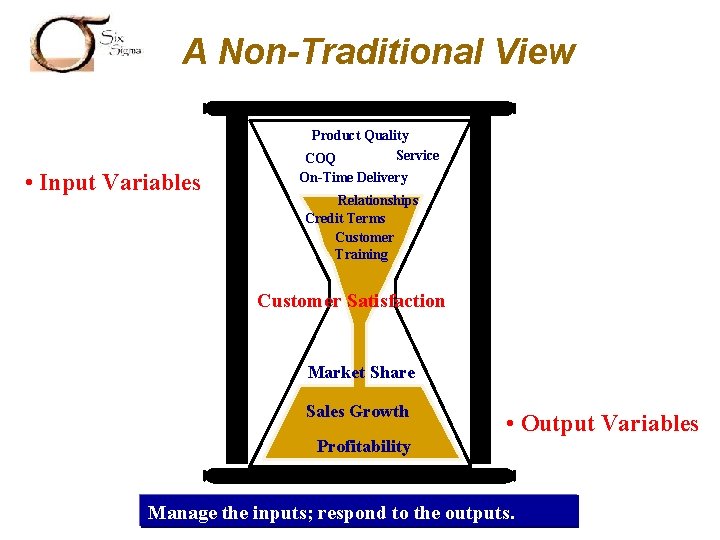
SIX SIGMA A Non-Traditional View Product Quality Service COQ • Input Variables On-Time Delivery Relationships Credit Terms Customer Training Customer Satisfaction Market Share Sales Growth Profitability • Output Variables Manage the inputs; respond to the outputs.
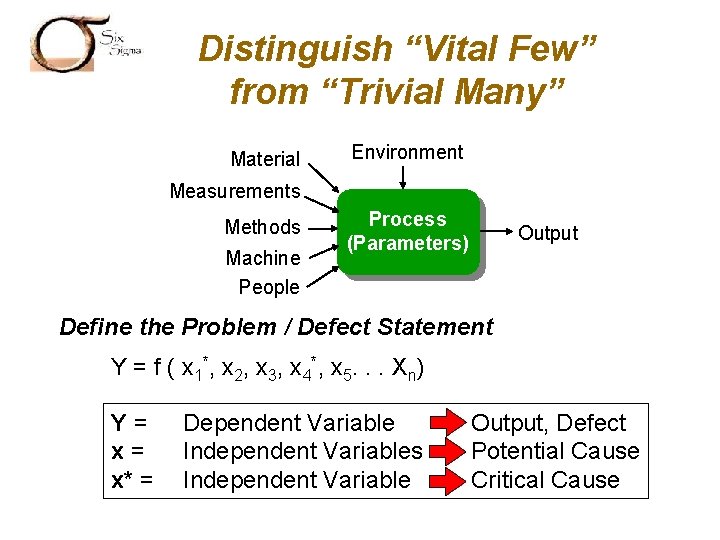
SIX SIGMA Distinguish “Vital Few” from “Trivial Many” Material Environment Measurements Methods Machine People Process (Parameters) Output Define the Problem / Defect Statement Y = f ( x 1*, x 2, x 3, x 4*, x 5. . . X n) Y= x= x* = Dependent Variable Independent Variables Independent Variable Output, Defect Potential Cause Critical Cause
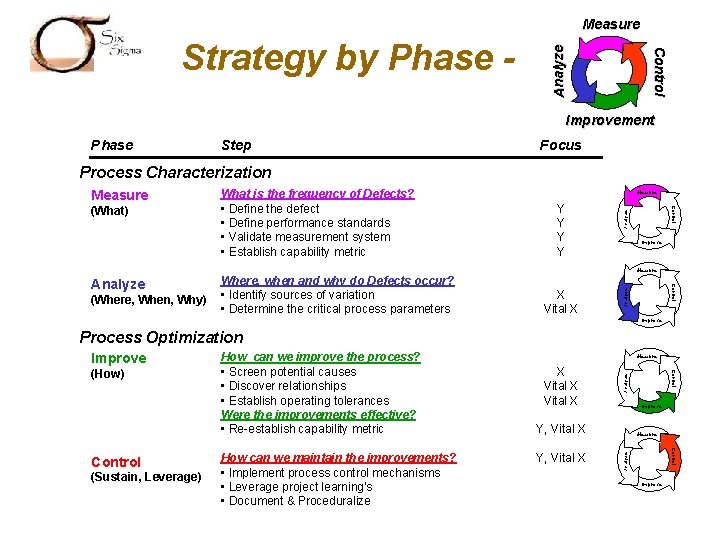
Analyze Control SIX SIGMA Strategy by Phase - Measure Improvement Phase Step Focus Process Characterization Measure Y Y Control (What) What is the frequency of Defects? • Define the defect • Define performance standards • Validate measurement system • Establish capability metric Analyze Measure Improve Measure X Vital X Analyze (Where, When, Why) Control Analyze Where, when and why do Defects occur? • Identify sources of variation • Determine the critical process parameters Improve Process Optimization (Sustain, Leverage) How can we maintain the improvements? • Implement process control mechanisms • Leverage project learning's • Document & Proceduralize Analyze X Vital X Improve Y, Vital X Measure Control (How) How can we improve the process? • Screen potential causes • Discover relationships • Establish operating tolerances Were the improvements effective? • Re-establish capability metric Analyze Improve
Cholegogue
Pradeep kurukulasuriya
Dr pradeep tandon lakhimpur kheri
Dr chopra rhode island
Sushil dubey intel
Pradeep sharma university of houston
Vcom white coat ceremony
Sigma sigma phi vcom
Cmmi six sigma
Pilot plan template six sigma
Explain the importance of tollgates in the dmaic process
Six sigma data types
Who is this
Six sigma qualtec
Lean six sigma forum
Six sigma kpov
Mse six sigma
Lean six sigma storyboard
Six sigma belts hierarchy
Statistical symbols and meanings
Measurement system analysis