Proto DUNE 2 Installation Steps William Miller University
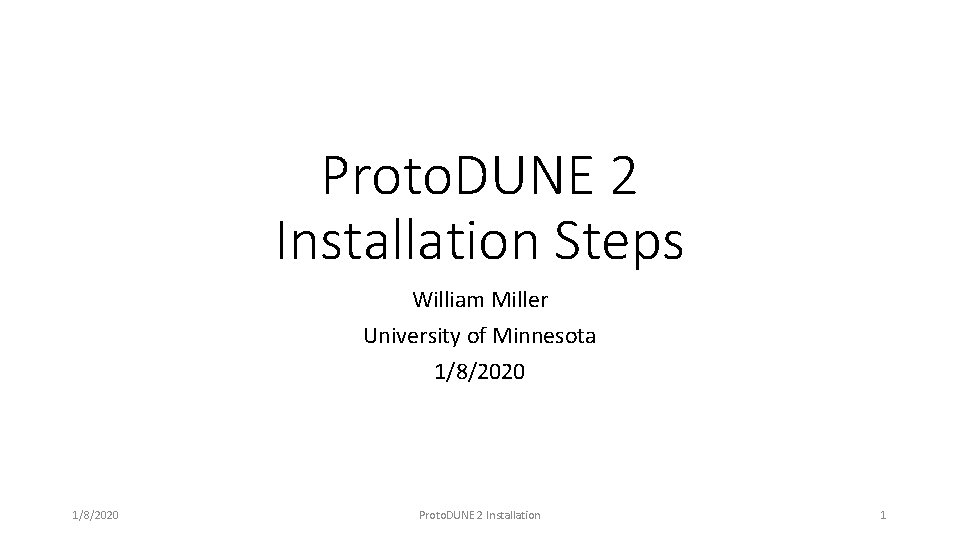
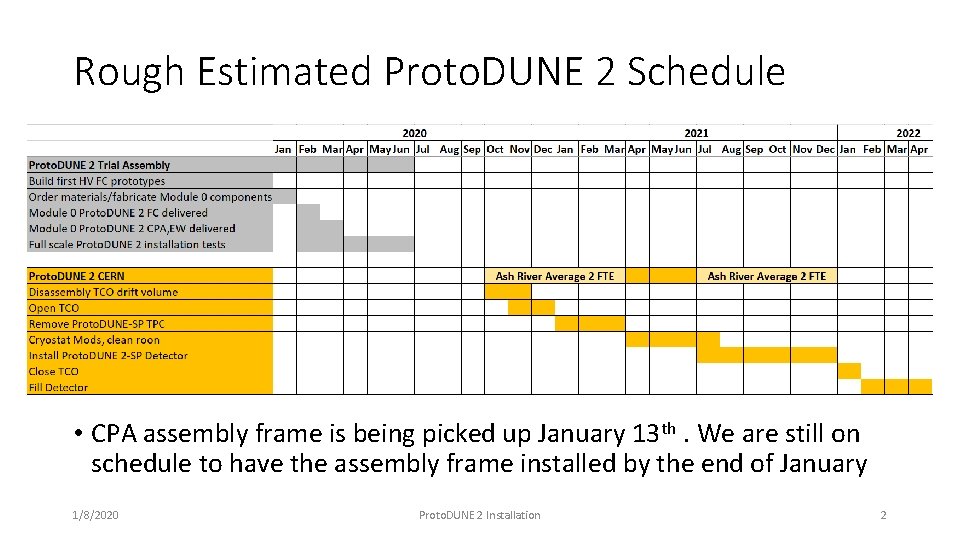
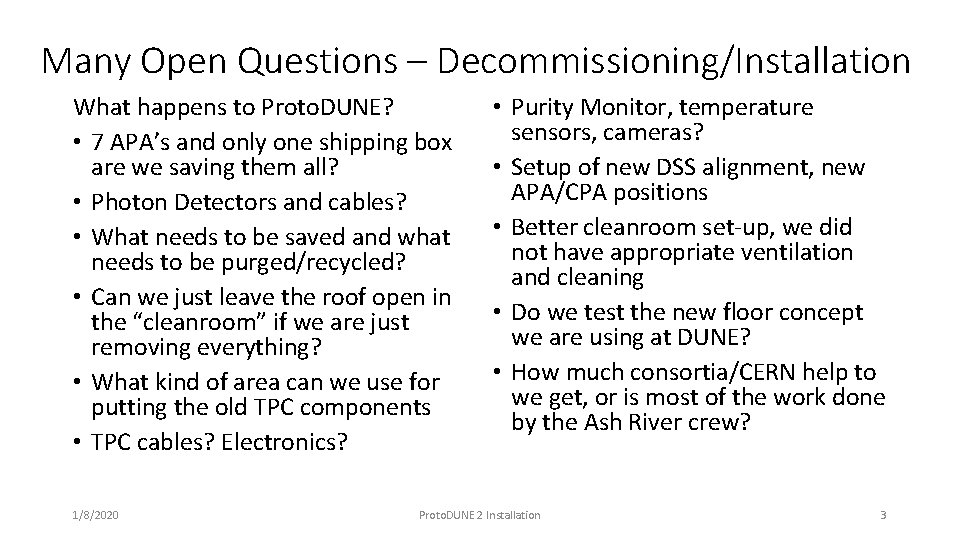
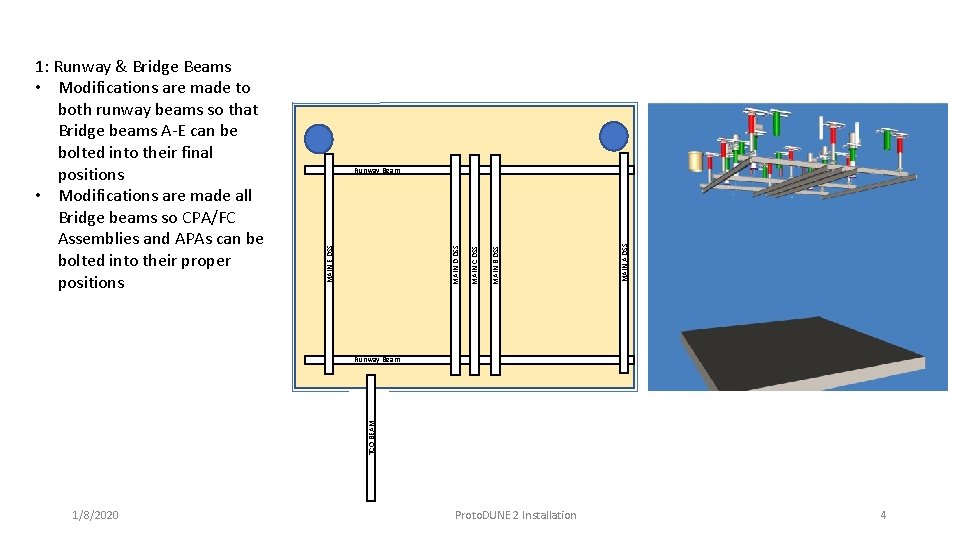
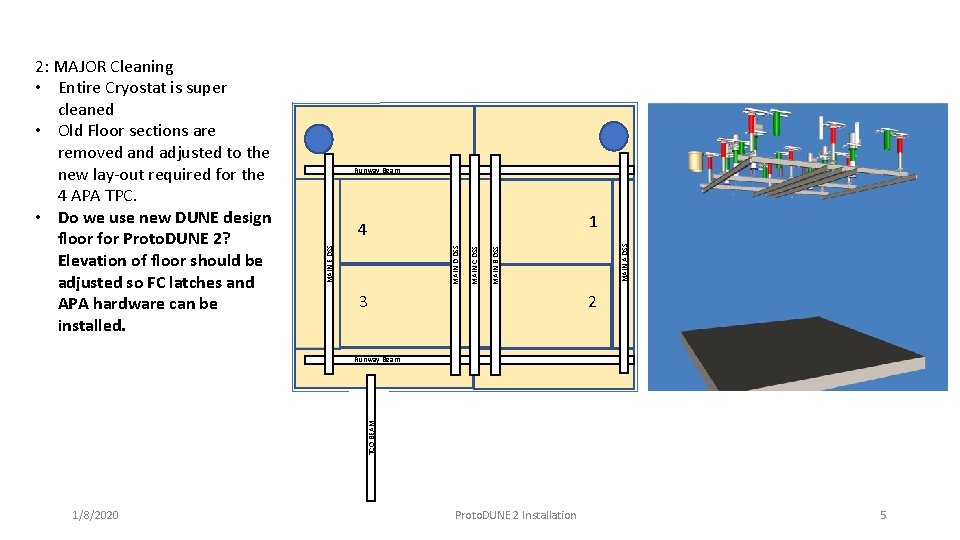
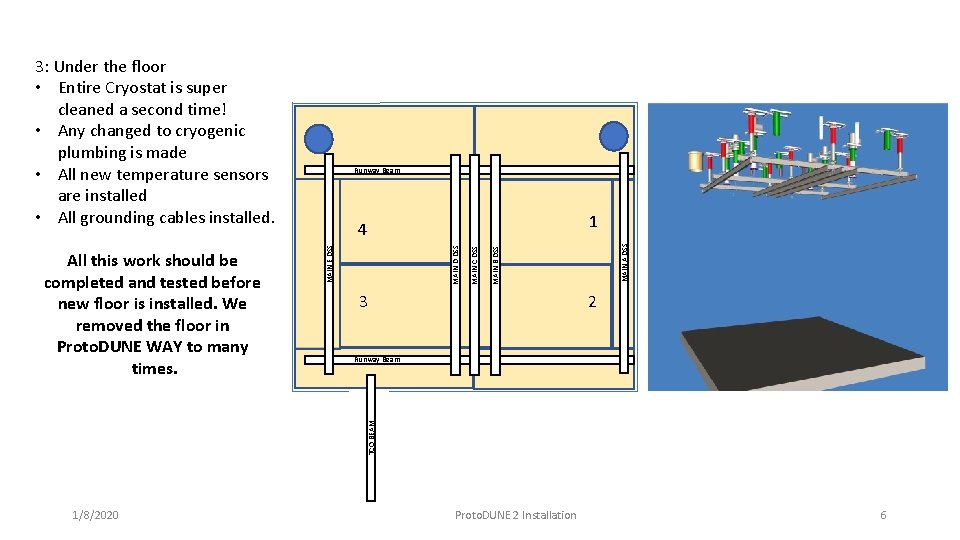
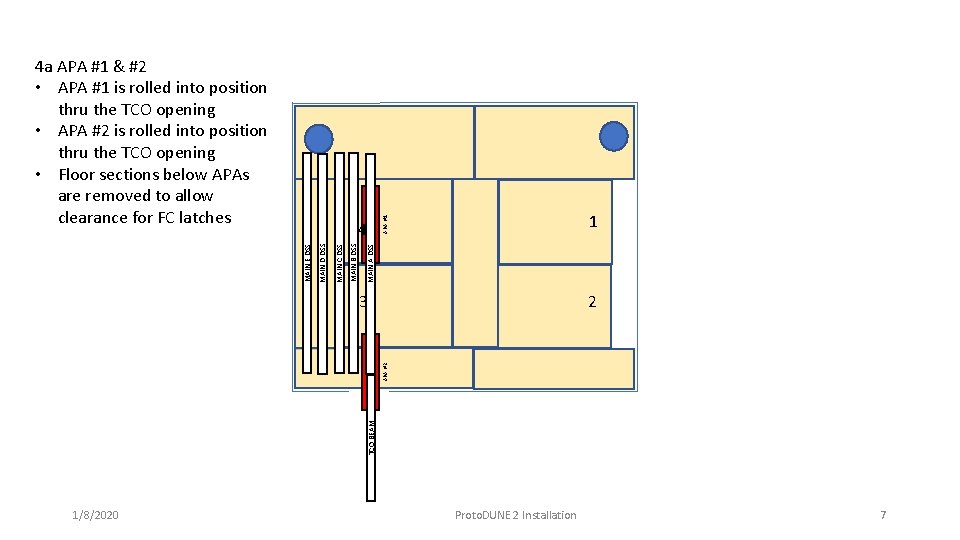
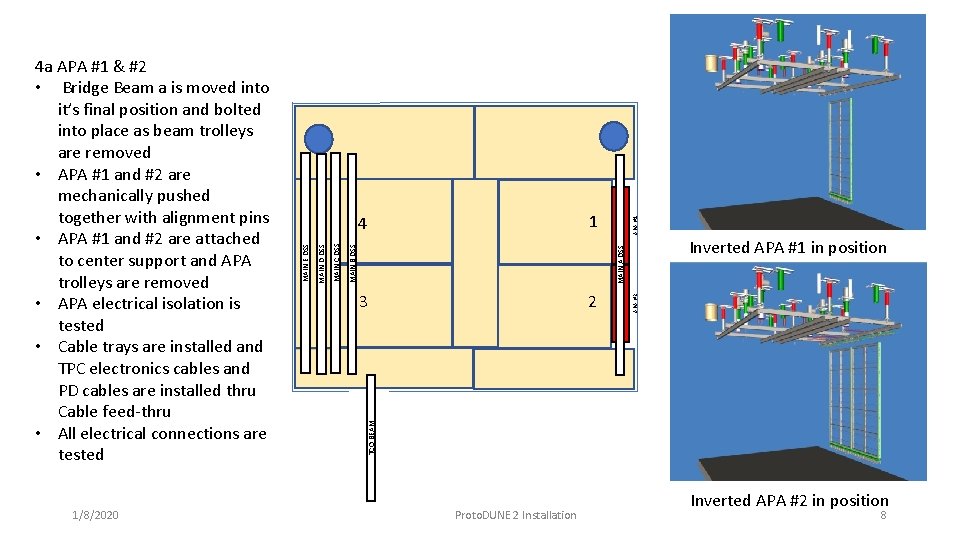
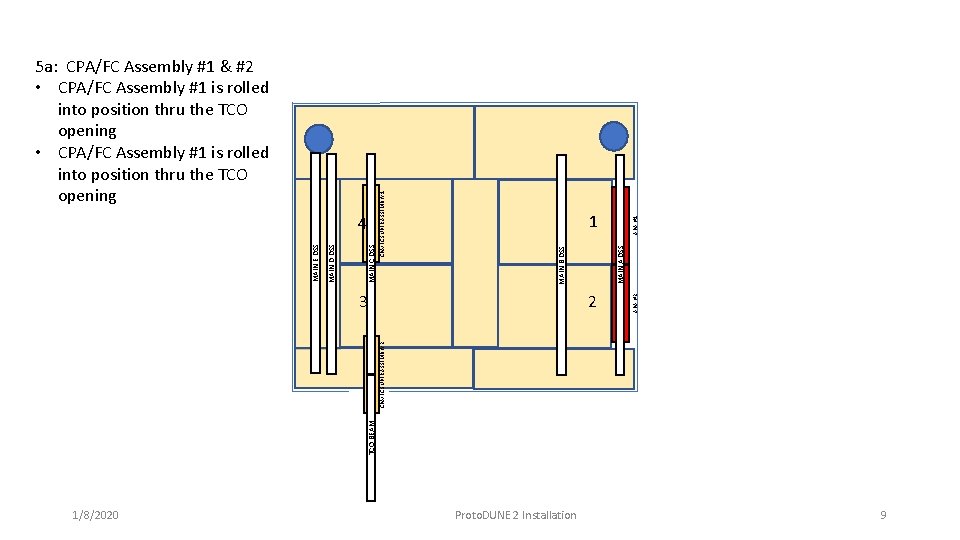
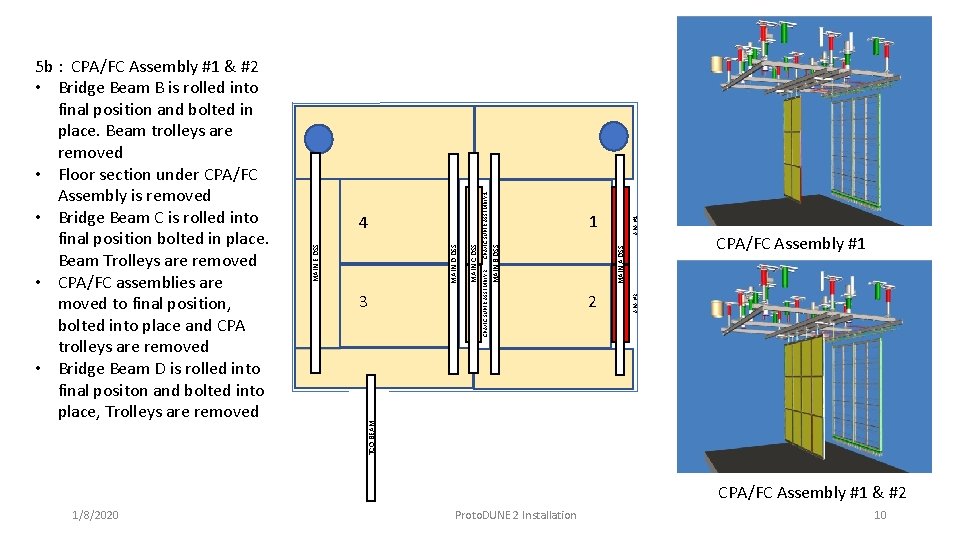
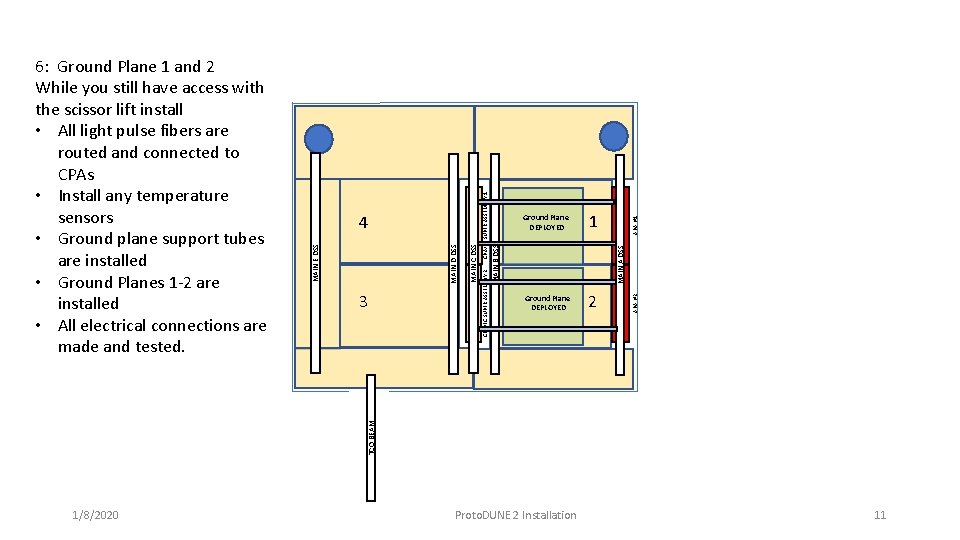
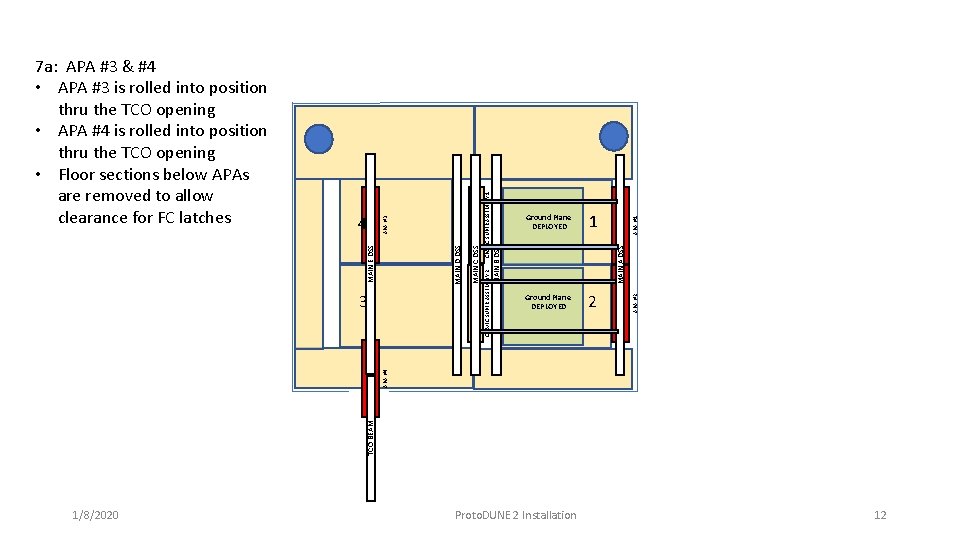
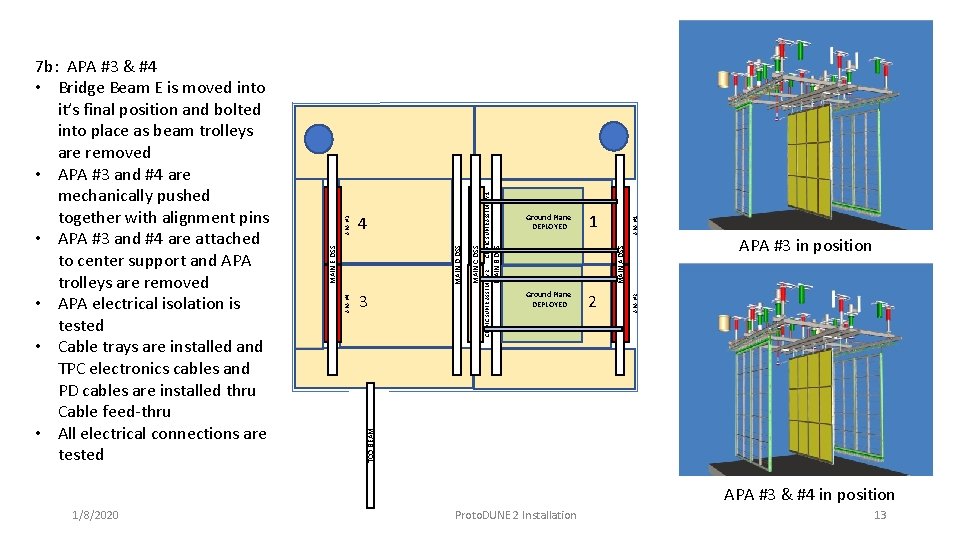
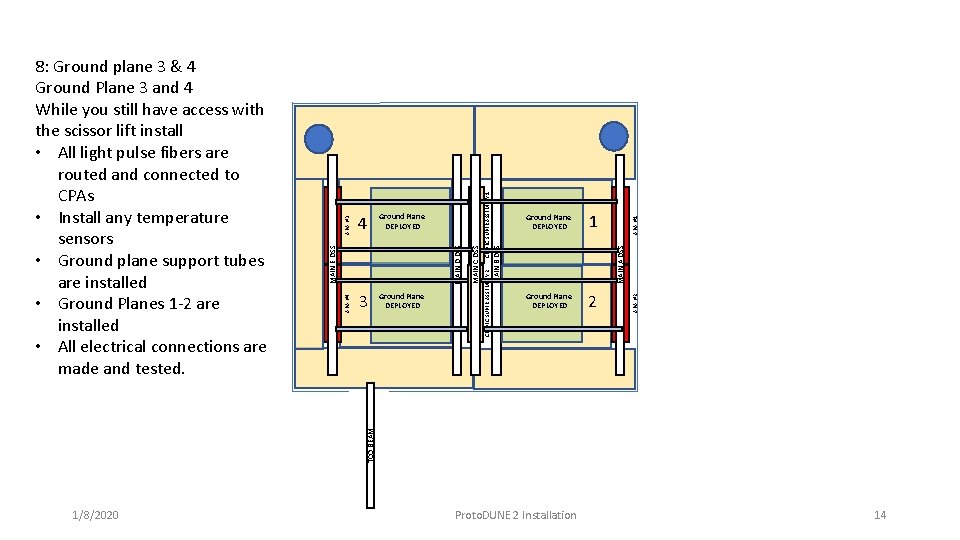
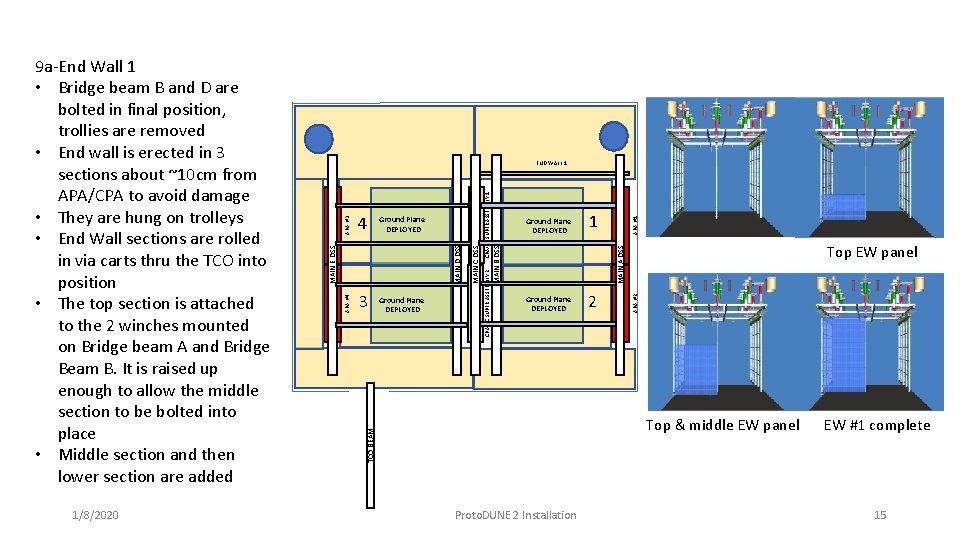
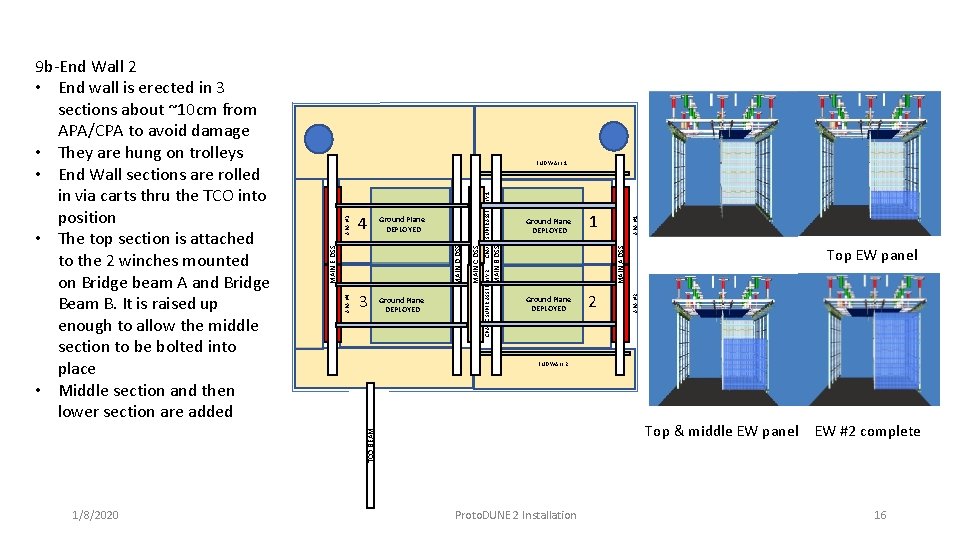
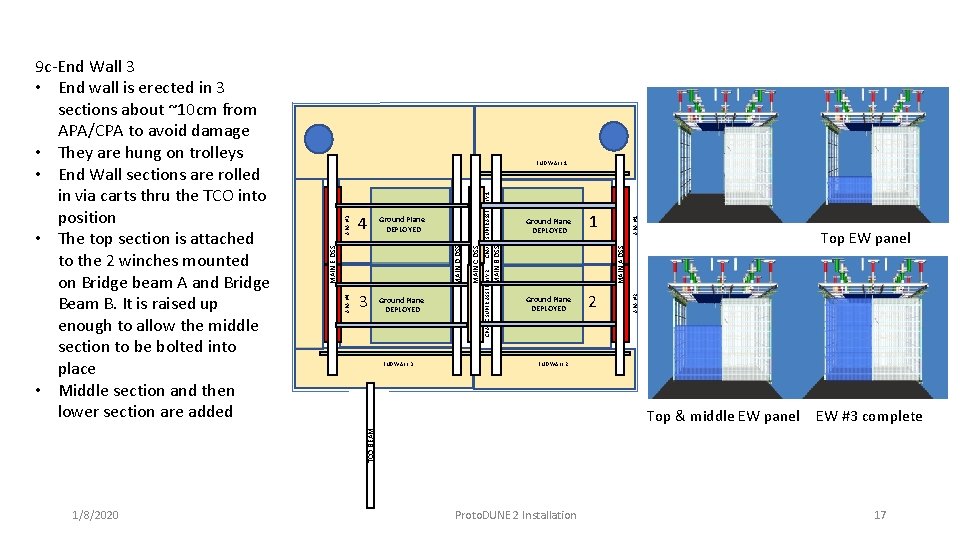
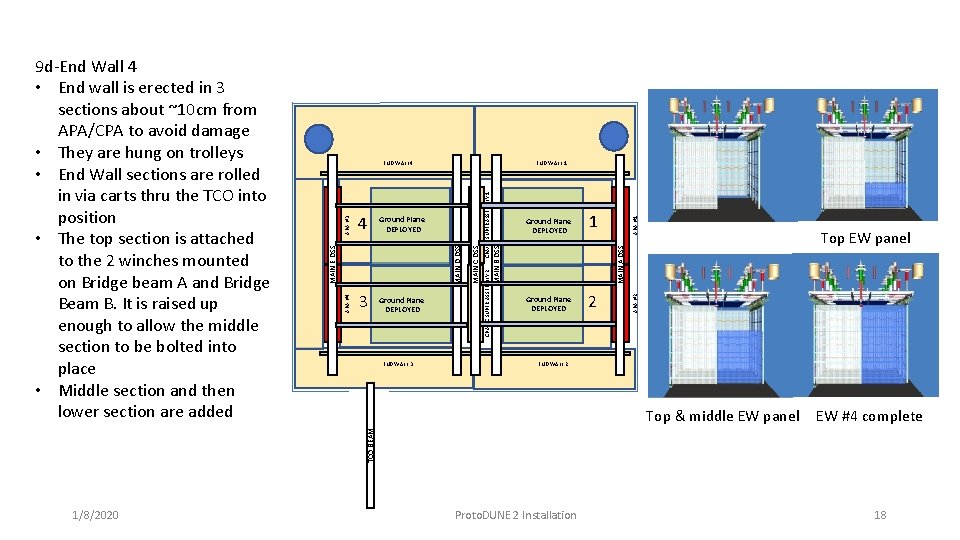
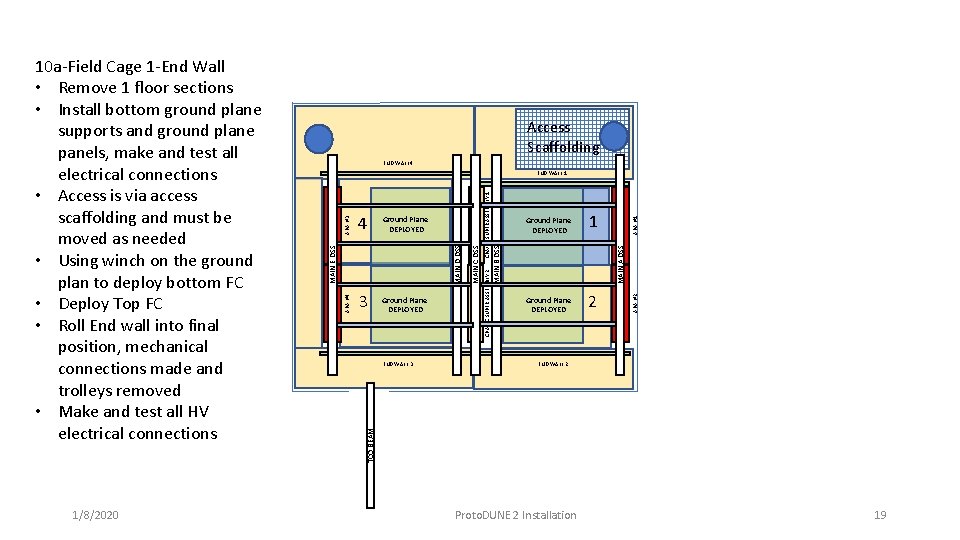
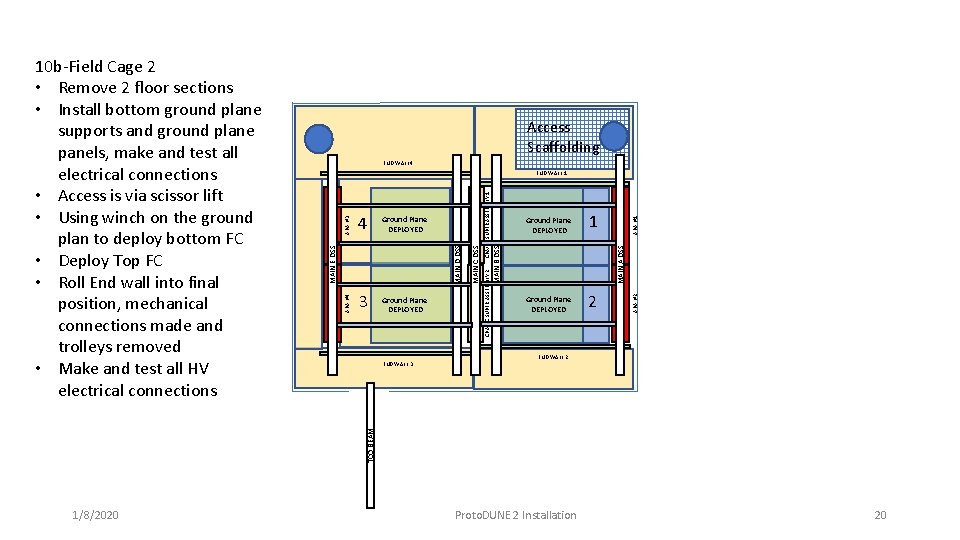
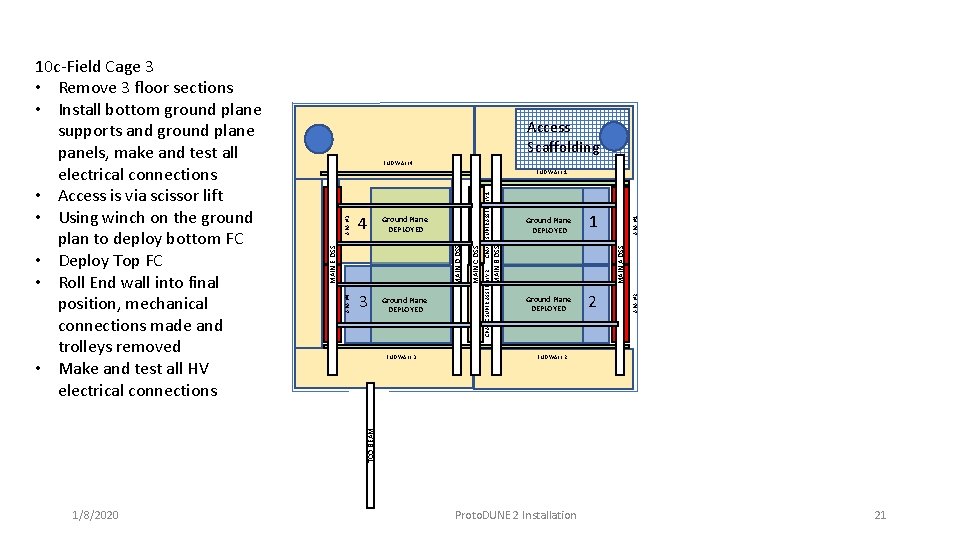
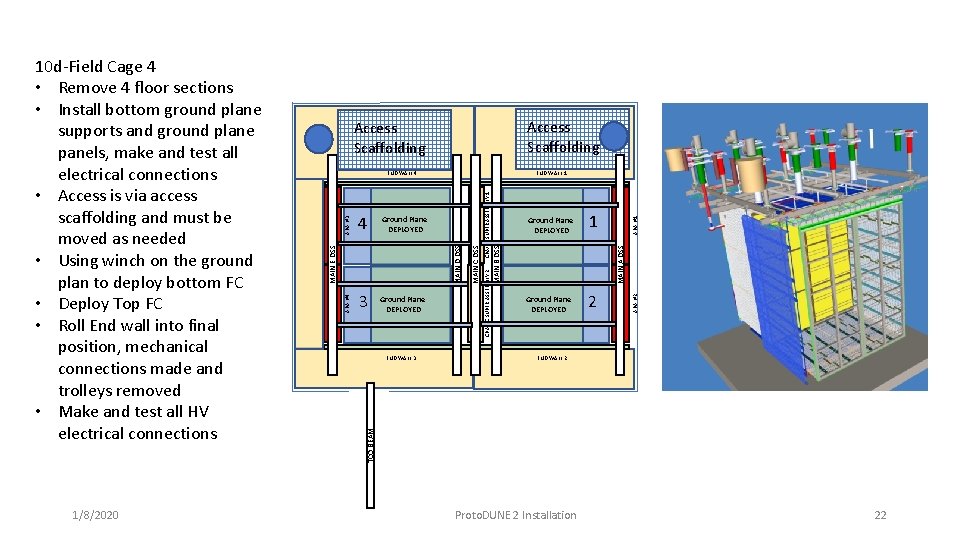
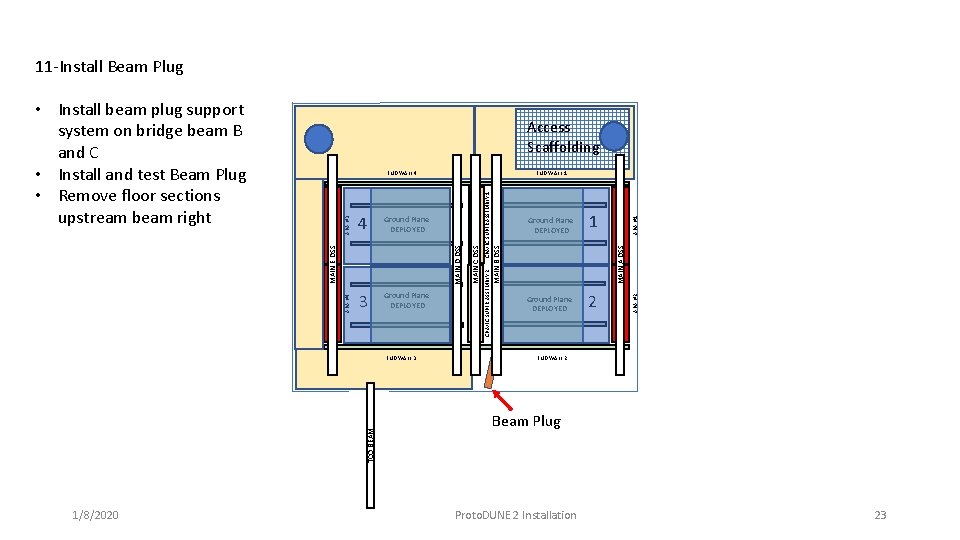
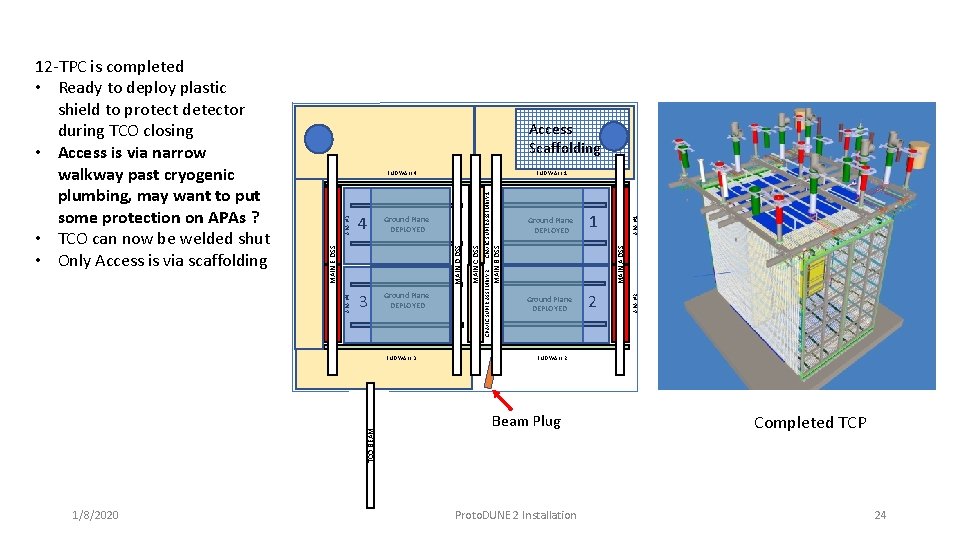
- Slides: 24
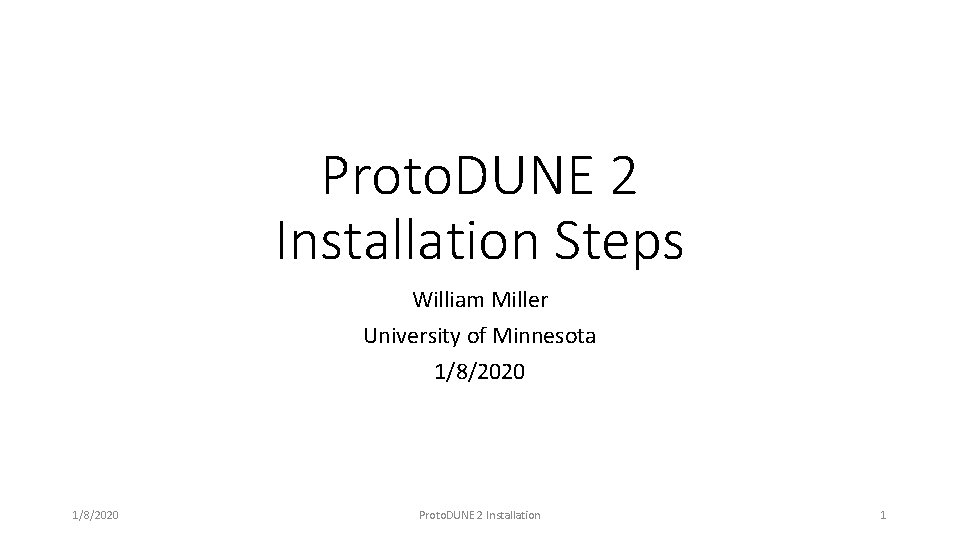
Proto. DUNE 2 Installation Steps William Miller University of Minnesota 1/8/2020 Proto. DUNE 2 Installation 1
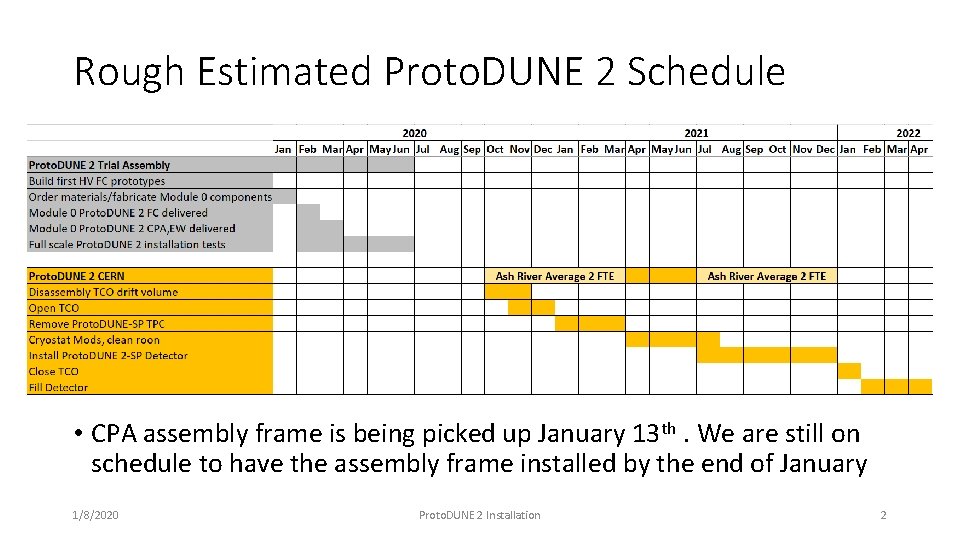
Rough Estimated Proto. DUNE 2 Schedule • CPA assembly frame is being picked up January 13 th. We are still on schedule to have the assembly frame installed by the end of January 1/8/2020 Proto. DUNE 2 Installation 2
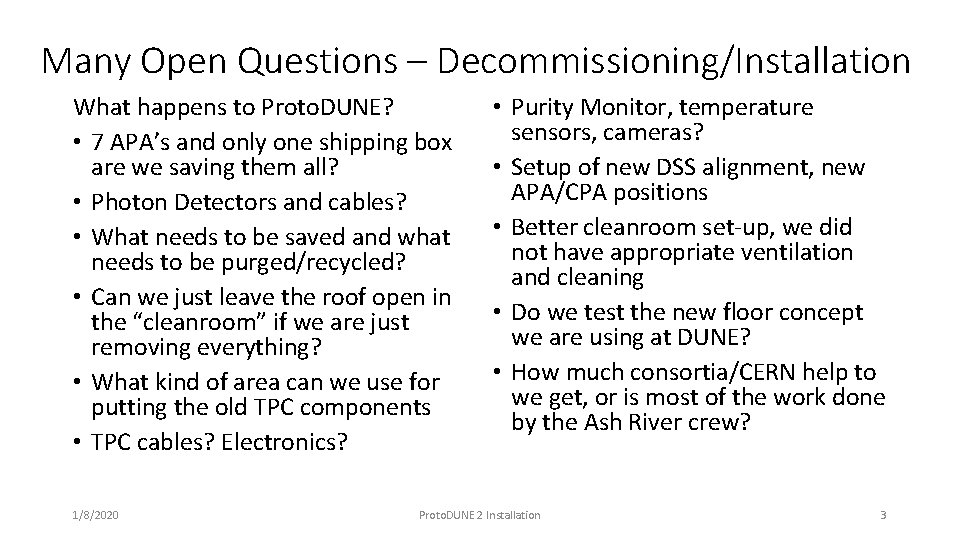
Many Open Questions – Decommissioning/Installation What happens to Proto. DUNE? • 7 APA’s and only one shipping box are we saving them all? • Photon Detectors and cables? • What needs to be saved and what needs to be purged/recycled? • Can we just leave the roof open in the “cleanroom” if we are just removing everything? • What kind of area can we use for putting the old TPC components • TPC cables? Electronics? 1/8/2020 • Purity Monitor, temperature sensors, cameras? • Setup of new DSS alignment, new APA/CPA positions • Better cleanroom set-up, we did not have appropriate ventilation and cleaning • Do we test the new floor concept we are using at DUNE? • How much consortia/CERN help to we get, or is most of the work done by the Ash River crew? Proto. DUNE 2 Installation 3
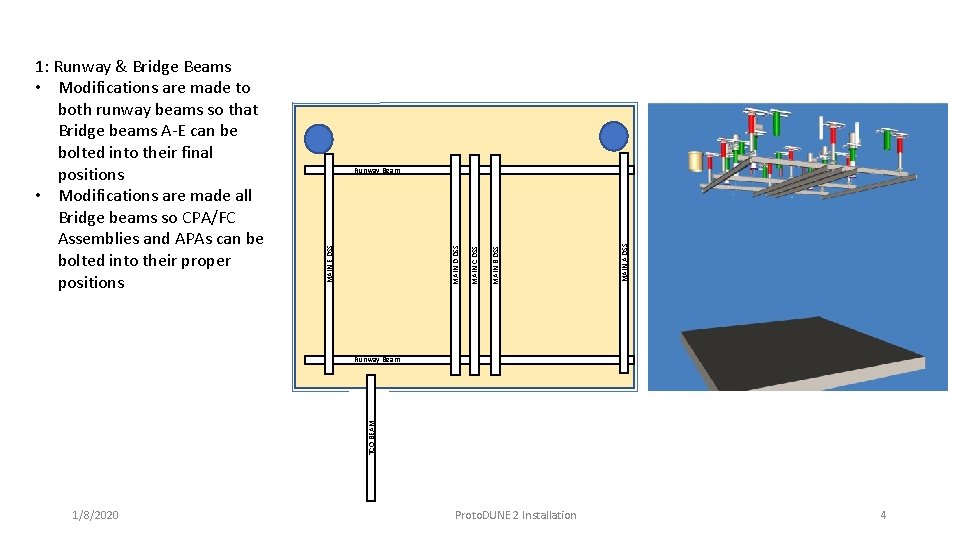
MAIN A DSS MAIN B DSS MAIN D DSS MAIN C DSS Runway Beam MAIN E DSS 1: Runway & Bridge Beams • Modifications are made to both runway beams so that Bridge beams A-E can be bolted into their final positions • Modifications are made all Bridge beams so CPA/FC Assemblies and APAs can be bolted into their proper positions TCO BEAM Runway Beam 1/8/2020 Proto. DUNE 2 Installation 4
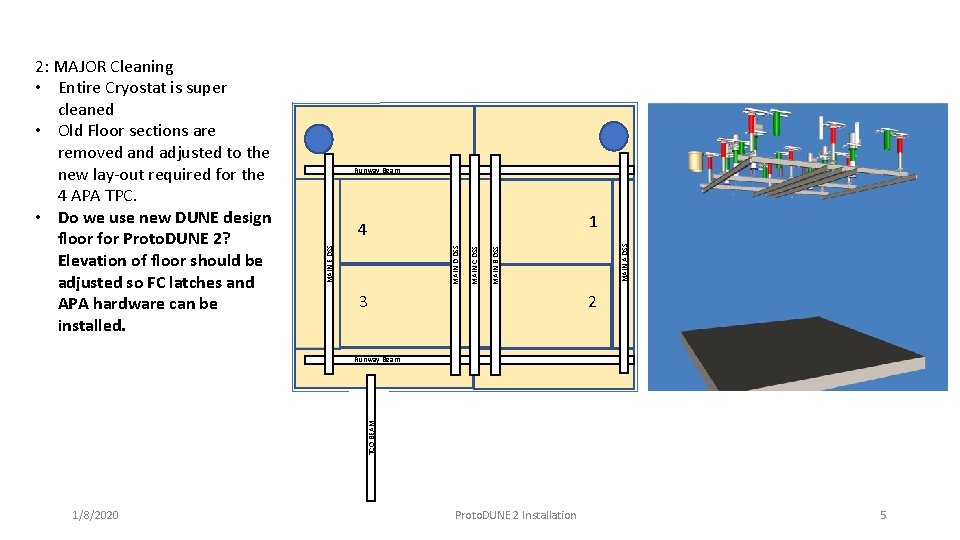
Runway Beam MAIN B DSS MAIN C DSS MAIN D DSS MAIN A DSS 1 4 MAIN E DSS 2: MAJOR Cleaning • Entire Cryostat is super cleaned • Old Floor sections are removed and adjusted to the new lay-out required for the 4 APA TPC. • Do we use new DUNE design floor for Proto. DUNE 2? Elevation of floor should be adjusted so FC latches and APA hardware can be installed. 2 3 TCO BEAM Runway Beam 1/8/2020 Proto. DUNE 2 Installation 5
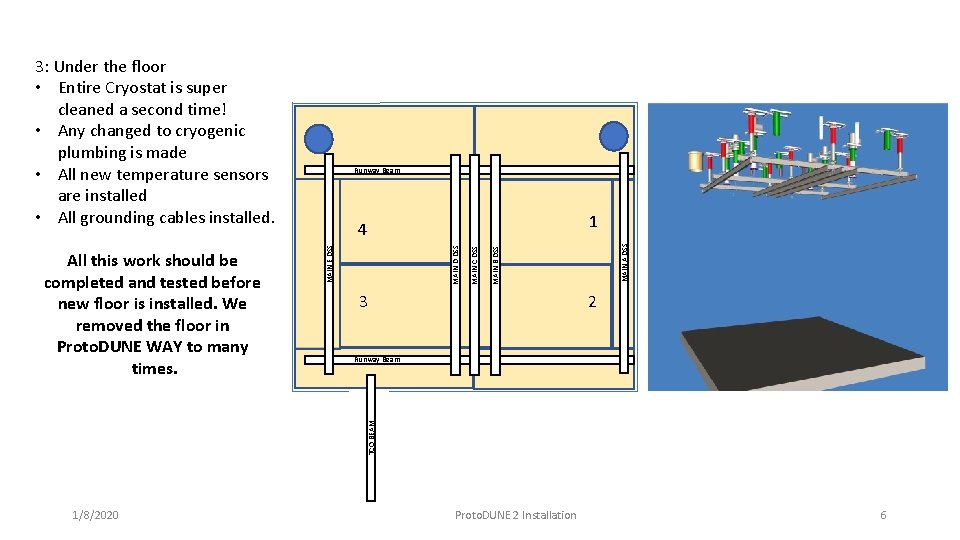
3: Under the floor • Entire Cryostat is super cleaned a second time! • Any changed to cryogenic plumbing is made • All new temperature sensors are installed • All grounding cables installed. MAIN B DSS MAIN C DSS MAIN D DSS MAIN A DSS 1 4 MAIN E DSS 2 3 Runway Beam TCO BEAM All this work should be completed and tested before new floor is installed. We removed the floor in Proto. DUNE WAY to many times. Runway Beam 1/8/2020 Proto. DUNE 2 Installation 6
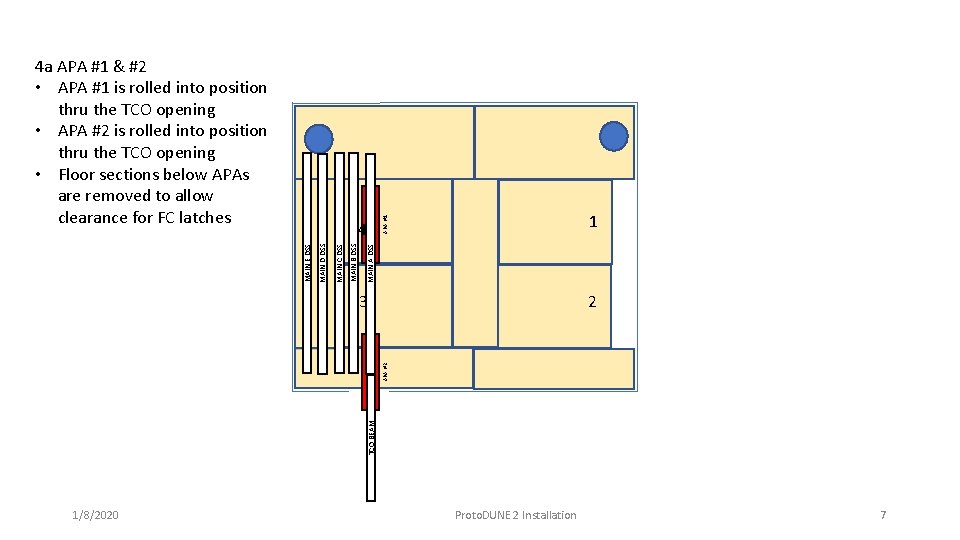
1 MAIN A DSS MAIN B DSS MAIN C DSS MAIN D DSS MAIN E DSS 4 APA #1 4 a APA #1 & #2 • APA #1 is rolled into position thru the TCO opening • APA #2 is rolled into position thru the TCO opening • Floor sections below APAs are removed to allow clearance for FC latches 2 TCO BEAM APA #2 3 1/8/2020 Proto. DUNE 2 Installation 7
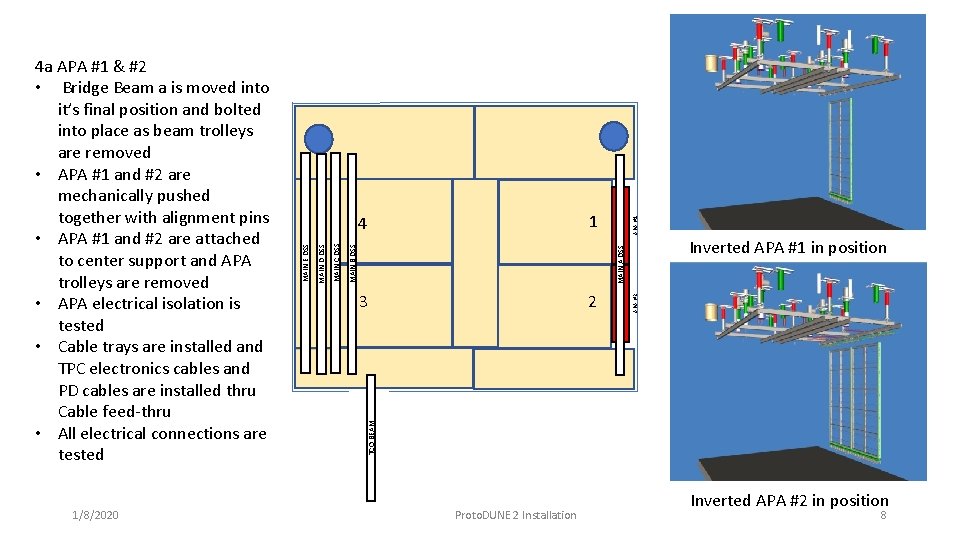
1/8/2020 Inverted APA #1 in position 2 TCO BEAM 3 APA #2 MAIN A DSS MAIN B DSS MAIN C DSS MAIN D DSS APA #1 1 4 MAIN E DSS 4 a APA #1 & #2 • Bridge Beam a is moved into it’s final position and bolted into place as beam trolleys are removed • APA #1 and #2 are mechanically pushed together with alignment pins • APA #1 and #2 are attached to center support and APA trolleys are removed • APA electrical isolation is tested • Cable trays are installed and TPC electronics cables and PD cables are installed thru Cable feed-thru • All electrical connections are tested Proto. DUNE 2 Installation Inverted APA #2 in position 8
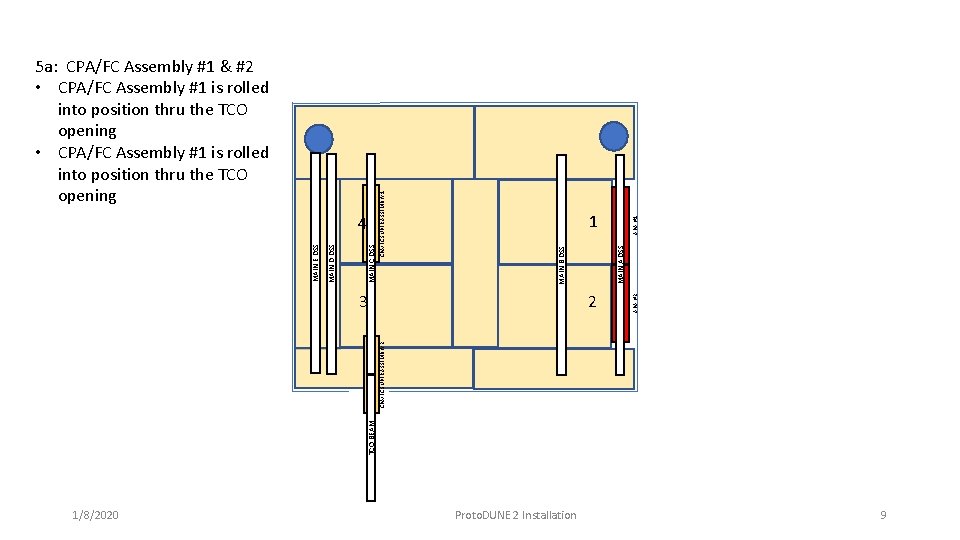
TCO BEAM CPA/FC SUPER ASSEMBLY 2 APA #2 MAIN A DSS 2 3 APA #1 1 MAIN B DSS MAIN C DSS MAIN D DSS MAIN E DSS 4 CPA/FC SUPER ASSEMBLY 1 5 a: CPA/FC Assembly #1 & #2 • CPA/FC Assembly #1 is rolled into position thru the TCO opening 1/8/2020 Proto. DUNE 2 Installation 9
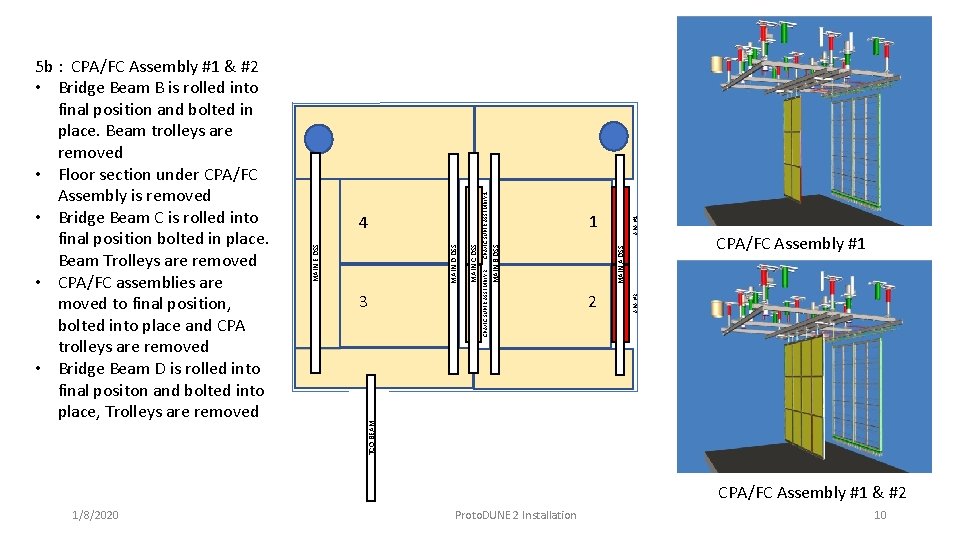
2 APA #1 CPA/FC Assembly #1 APA #2 MAIN A DSS CPA/FC SUPER ASSEMBLY 1 MAIN B DSS MAIN C DSS MAIN D DSS 1 TCO BEAM 3 CPA/FC SUPER ASSEMBLY 2 4 MAIN E DSS 5 b : CPA/FC Assembly #1 & #2 • Bridge Beam B is rolled into final position and bolted in place. Beam trolleys are removed • Floor section under CPA/FC Assembly is removed • Bridge Beam C is rolled into final position bolted in place. Beam Trolleys are removed • CPA/FC assemblies are moved to final position, bolted into place and CPA trolleys are removed • Bridge Beam D is rolled into final positon and bolted into place, Trolleys are removed CPA/FC Assembly #1 & #2 1/8/2020 Proto. DUNE 2 Installation 10
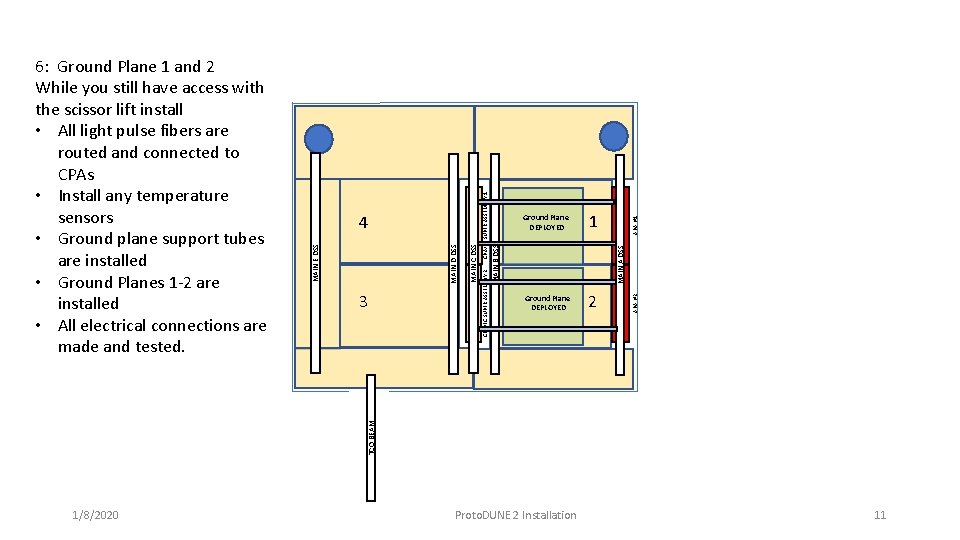
2 APA #1 Ground Plane DEPLOYED APA #2 MAIN A DSS CPA/FC SUPER ASSEMBLY 1 1 MAIN B DSS MAIN C DSS MAIN D DSS Ground Plane DEPLOYED TCO BEAM 3 CPA/FC SUPER ASSEMBLY 2 4 MAIN E DSS 6: Ground Plane 1 and 2 While you still have access with the scissor lift install • All light pulse fibers are routed and connected to CPAs • Install any temperature sensors • Ground plane support tubes are installed • Ground Planes 1 -2 are installed • All electrical connections are made and tested. 1/8/2020 Proto. DUNE 2 Installation 11
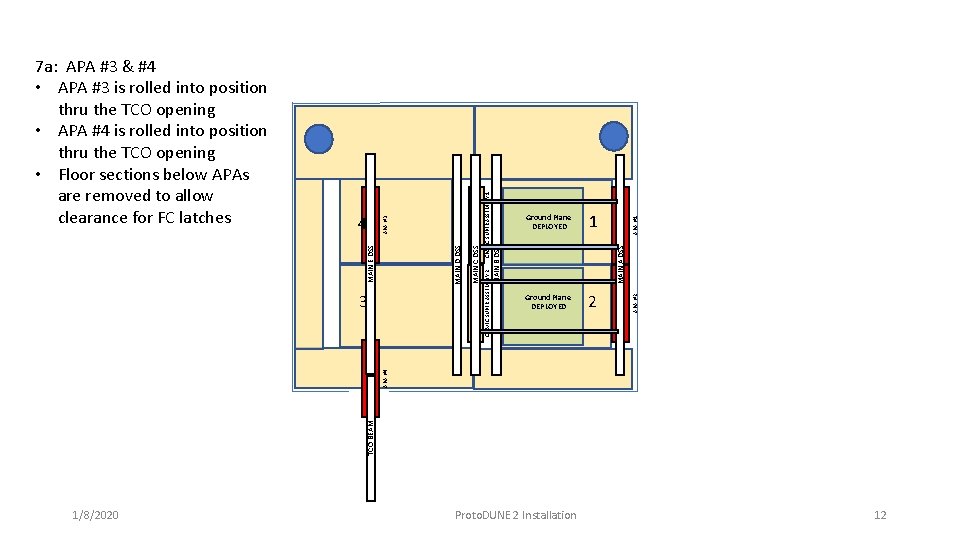
2 APA #1 Ground Plane DEPLOYED APA #2 MAIN A DSS CPA/FC SUPER ASSEMBLY 1 1 MAIN B DSS MAIN C DSS MAIN D DSS Ground Plane DEPLOYED TCO BEAM APA #4 3 CPA/FC SUPER ASSEMBLY 2 APA #3 4 MAIN E DSS 7 a: APA #3 & #4 • APA #3 is rolled into position thru the TCO opening • APA #4 is rolled into position thru the TCO opening • Floor sections below APAs are removed to allow clearance for FC latches 1/8/2020 Proto. DUNE 2 Installation 12
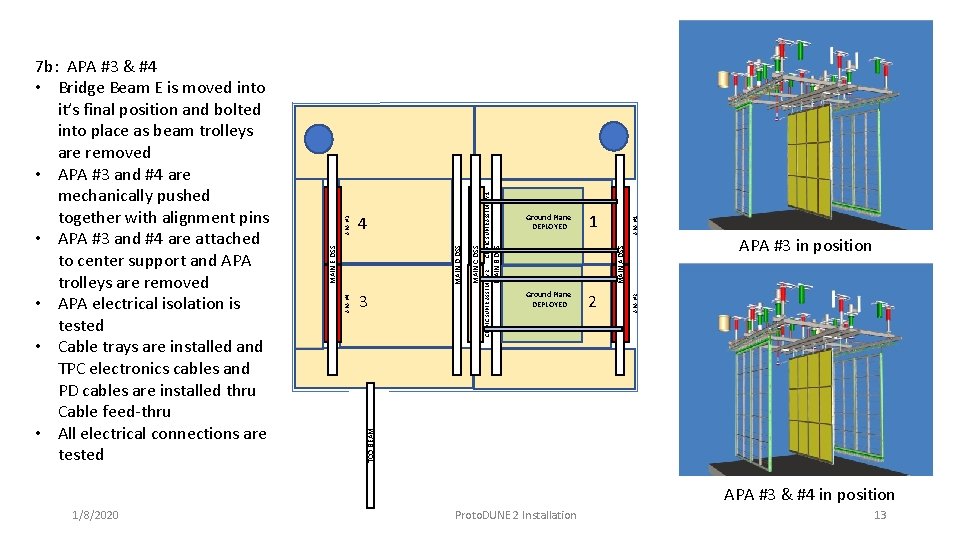
Ground Plane DEPLOYED 2 APA #1 APA #3 in position APA #2 MAIN A DSS CPA/FC SUPER ASSEMBLY 1 1 MAIN B DSS MAIN C DSS Ground Plane DEPLOYED TCO BEAM CPA/FC SUPER ASSEMBLY 2 APA #4 3 MAIN D DSS APA #3 4 MAIN E DSS 7 b: APA #3 & #4 • Bridge Beam E is moved into it’s final position and bolted into place as beam trolleys are removed • APA #3 and #4 are mechanically pushed together with alignment pins • APA #3 and #4 are attached to center support and APA trolleys are removed • APA electrical isolation is tested • Cable trays are installed and TPC electronics cables and PD cables are installed thru Cable feed-thru • All electrical connections are tested APA #3 & #4 in position 1/8/2020 Proto. DUNE 2 Installation 13
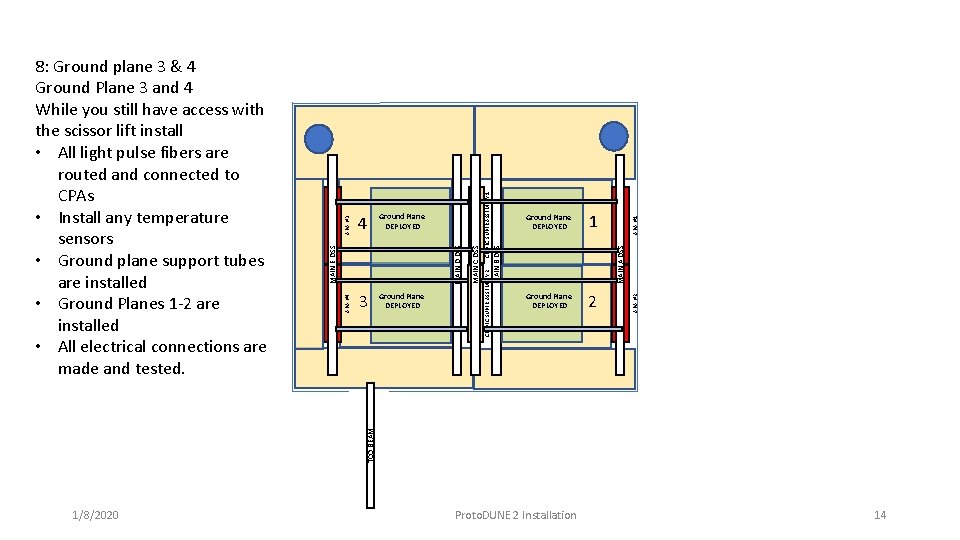
Ground Plane DEPLOYED 2 APA #1 1 TCO BEAM APA #2 MAIN A DSS CPA/FC SUPER ASSEMBLY 1 Ground Plane DEPLOYED MAIN B DSS Ground Plane DEPLOYED MAIN C DSS APA #4 3 CPA/FC SUPER ASSEMBLY 2 Ground Plane DEPLOYED MAIN D DSS APA #3 4 MAIN E DSS 8: Ground plane 3 & 4 Ground Plane 3 and 4 While you still have access with the scissor lift install • All light pulse fibers are routed and connected to CPAs • Install any temperature sensors • Ground plane support tubes are installed • Ground Planes 1 -2 are installed • All electrical connections are made and tested. 1/8/2020 Proto. DUNE 2 Installation 14
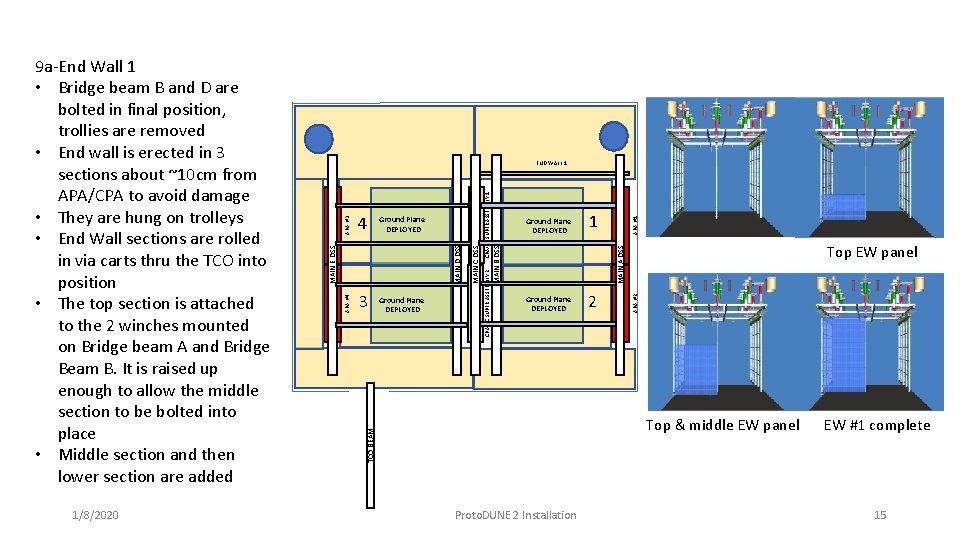
1/8/2020 APA #1 Top EW panel MAIN A DSS MAIN B DSS CPA/FC SUPER ASSEMBLY 1 1 Ground Plane DEPLOYED 2 APA #2 Ground Plane DEPLOYED Top & middle EW panel TCO BEAM APA #4 3 MAIN C DSS Ground Plane DEPLOYED CPA/FC SUPER ASSEMBLY 2 4 MAIN D DSS APA #3 END WALL 1 MAIN E DSS 9 a-End Wall 1 • Bridge beam B and D are bolted in final position, trollies are removed • End wall is erected in 3 sections about ~10 cm from APA/CPA to avoid damage • They are hung on trolleys • End Wall sections are rolled in via carts thru the TCO into position • The top section is attached to the 2 winches mounted on Bridge beam A and Bridge Beam B. It is raised up enough to allow the middle section to be bolted into place • Middle section and then lower section are added Proto. DUNE 2 Installation EW #1 complete 15
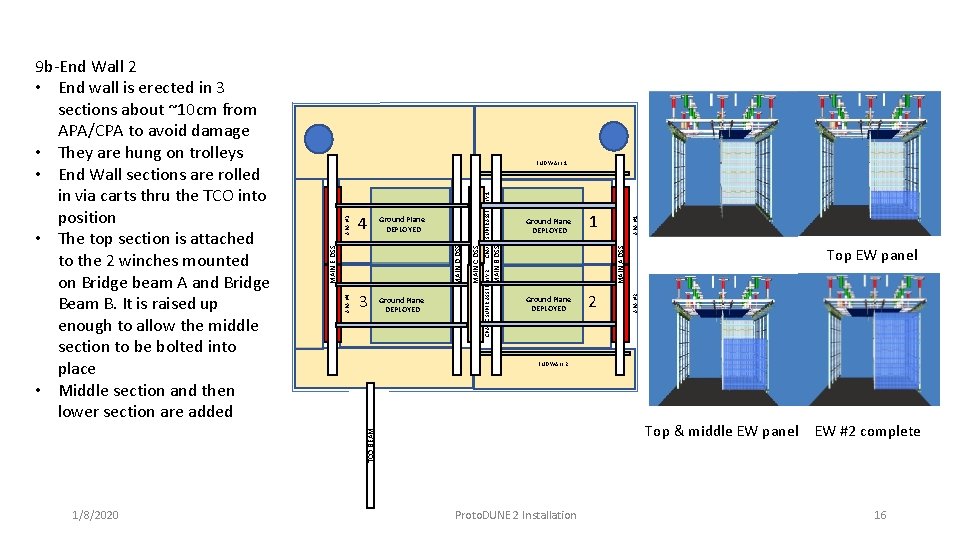
1/8/2020 APA #1 Top EW panel MAIN A DSS MAIN B DSS CPA/FC SUPER ASSEMBLY 1 1 Ground Plane DEPLOYED 2 APA #2 Ground Plane DEPLOYED END WALL 2 Top & middle EW panel TCO BEAM APA #4 3 MAIN C DSS Ground Plane DEPLOYED CPA/FC SUPER ASSEMBLY 2 4 MAIN D DSS APA #3 END WALL 1 MAIN E DSS 9 b-End Wall 2 • End wall is erected in 3 sections about ~10 cm from APA/CPA to avoid damage • They are hung on trolleys • End Wall sections are rolled in via carts thru the TCO into position • The top section is attached to the 2 winches mounted on Bridge beam A and Bridge Beam B. It is raised up enough to allow the middle section to be bolted into place • Middle section and then lower section are added Proto. DUNE 2 Installation EW #2 complete 16
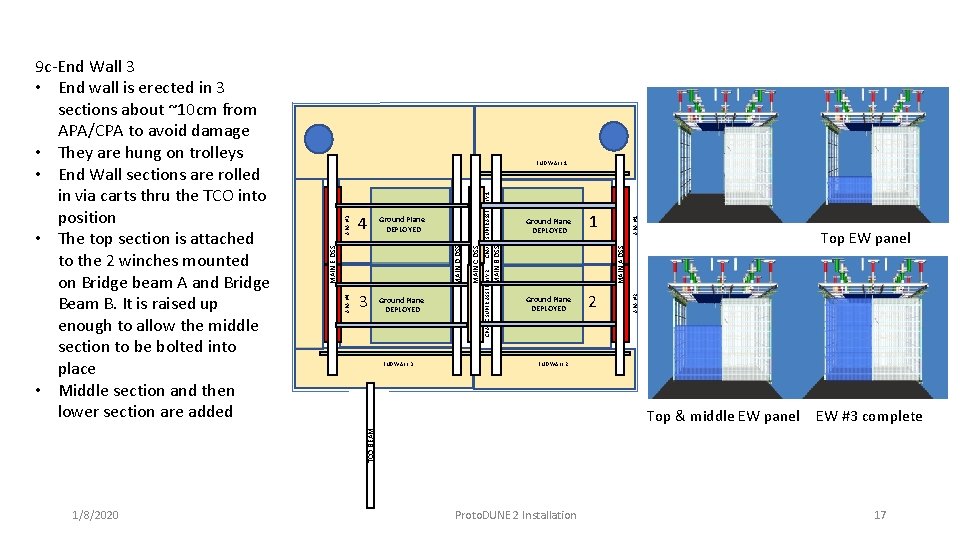
END WALL 3 Ground Plane DEPLOYED 2 APA #1 1 Top EW panel APA #2 MAIN A DSS CPA/FC SUPER ASSEMBLY 1 Ground Plane DEPLOYED MAIN B DSS Ground Plane DEPLOYED MAIN C DSS 3 CPA/FC SUPER ASSEMBLY 2 Ground Plane DEPLOYED MAIN D DSS APA #3 4 APA #4 END WALL 1 MAIN E DSS END WALL 2 Top & middle EW panel EW #3 complete TCO BEAM 9 c-End Wall 3 • End wall is erected in 3 sections about ~10 cm from APA/CPA to avoid damage • They are hung on trolleys • End Wall sections are rolled in via carts thru the TCO into position • The top section is attached to the 2 winches mounted on Bridge beam A and Bridge Beam B. It is raised up enough to allow the middle section to be bolted into place • Middle section and then lower section are added 1/8/2020 Proto. DUNE 2 Installation 17
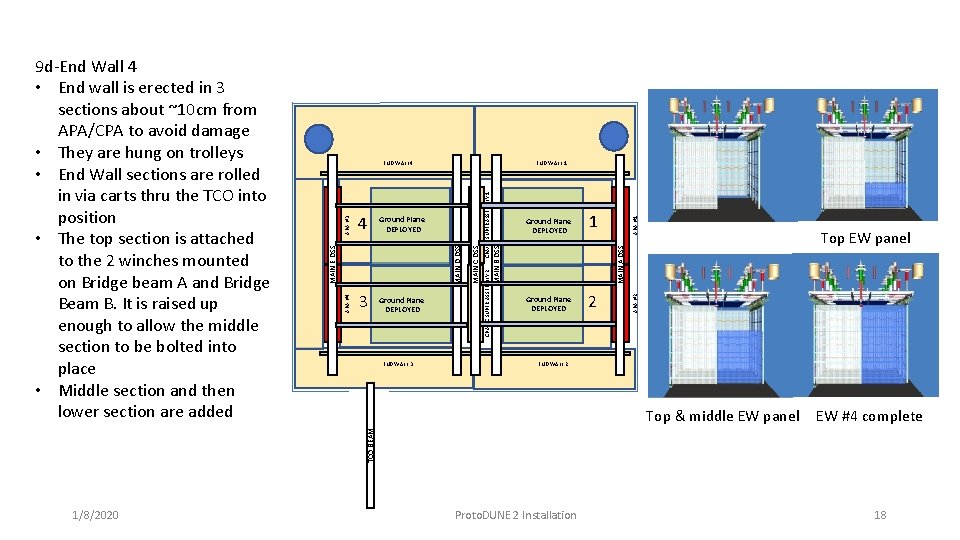
END WALL 3 1 Ground Plane DEPLOYED 2 Top EW panel APA #2 MAIN A DSS CPA/FC SUPER ASSEMBLY 1 Ground Plane DEPLOYED MAIN B DSS Ground Plane DEPLOYED MAIN C DSS APA #4 3 CPA/FC SUPER ASSEMBLY 2 Ground Plane DEPLOYED MAIN D DSS APA #3 4 APA #1 END WALL 4 MAIN E DSS END WALL 2 Top & middle EW panel EW #4 complete TCO BEAM 9 d-End Wall 4 • End wall is erected in 3 sections about ~10 cm from APA/CPA to avoid damage • They are hung on trolleys • End Wall sections are rolled in via carts thru the TCO into position • The top section is attached to the 2 winches mounted on Bridge beam A and Bridge Beam B. It is raised up enough to allow the middle section to be bolted into place • Middle section and then lower section are added 1/8/2020 Proto. DUNE 2 Installation 18
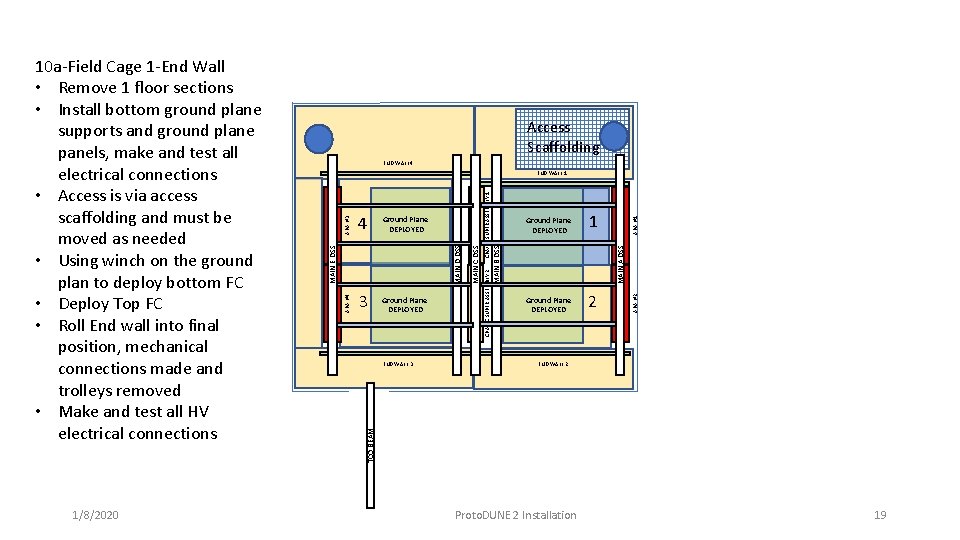
1/8/2020 Access Scaffolding END WALL 4 2 APA #1 Ground Plane DEPLOYED APA #2 MAIN A DSS CPA/FC SUPER ASSEMBLY 1 1 END WALL 2 TCO BEAM END WALL 3 Ground Plane DEPLOYED MAIN B DSS Ground Plane DEPLOYED MAIN C DSS 3 CPA/FC SUPER ASSEMBLY 2 Ground Plane DEPLOYED MAIN D DSS APA #3 4 APA #4 END WALL 1 MAIN E DSS 10 a-Field Cage 1 -End Wall • Remove 1 floor sections • Install bottom ground plane supports and ground plane panels, make and test all electrical connections • Access is via access scaffolding and must be moved as needed • Using winch on the ground plan to deploy bottom FC • Deploy Top FC • Roll End wall into final position, mechanical connections made and trolleys removed • Make and test all HV electrical connections Proto. DUNE 2 Installation 19
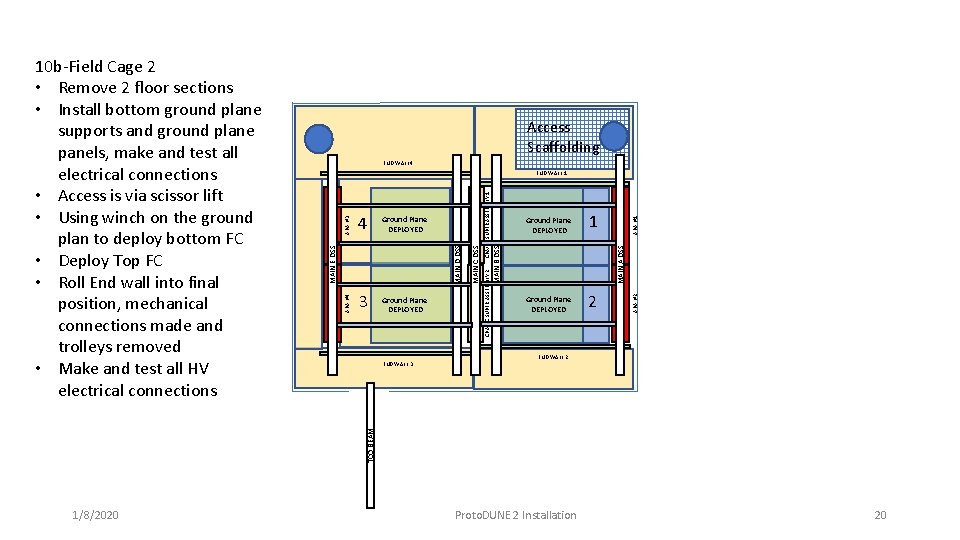
Access Scaffolding END WALL 4 2 APA #1 Ground Plane DEPLOYED APA #2 MAIN A DSS CPA/FC SUPER ASSEMBLY 1 1 END WALL 2 TCO BEAM END WALL 3 Ground Plane DEPLOYED MAIN B DSS Ground Plane DEPLOYED MAIN C DSS 3 CPA/FC SUPER ASSEMBLY 2 Ground Plane DEPLOYED MAIN D DSS APA #3 4 APA #4 END WALL 1 MAIN E DSS 10 b-Field Cage 2 • Remove 2 floor sections • Install bottom ground plane supports and ground plane panels, make and test all electrical connections • Access is via scissor lift • Using winch on the ground plan to deploy bottom FC • Deploy Top FC • Roll End wall into final position, mechanical connections made and trolleys removed • Make and test all HV electrical connections 1/8/2020 Proto. DUNE 2 Installation 20
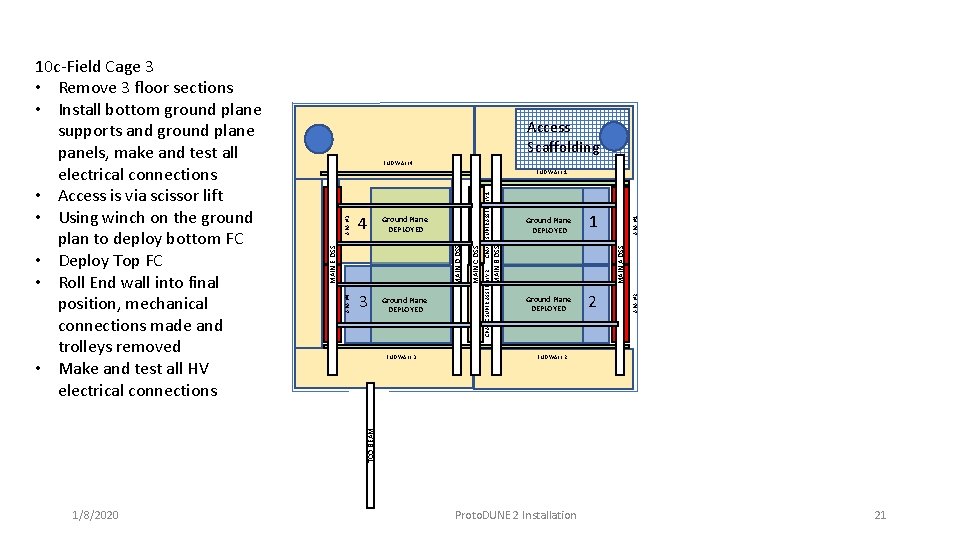
Access Scaffolding END WALL 4 2 APA #1 Ground Plane DEPLOYED APA #2 MAIN A DSS CPA/FC SUPER ASSEMBLY 1 1 END WALL 2 TCO BEAM END WALL 3 Ground Plane DEPLOYED MAIN B DSS Ground Plane DEPLOYED MAIN C DSS 3 CPA/FC SUPER ASSEMBLY 2 Ground Plane DEPLOYED MAIN D DSS APA #3 4 APA #4 END WALL 1 MAIN E DSS 10 c-Field Cage 3 • Remove 3 floor sections • Install bottom ground plane supports and ground plane panels, make and test all electrical connections • Access is via scissor lift • Using winch on the ground plan to deploy bottom FC • Deploy Top FC • Roll End wall into final position, mechanical connections made and trolleys removed • Make and test all HV electrical connections 1/8/2020 Proto. DUNE 2 Installation 21
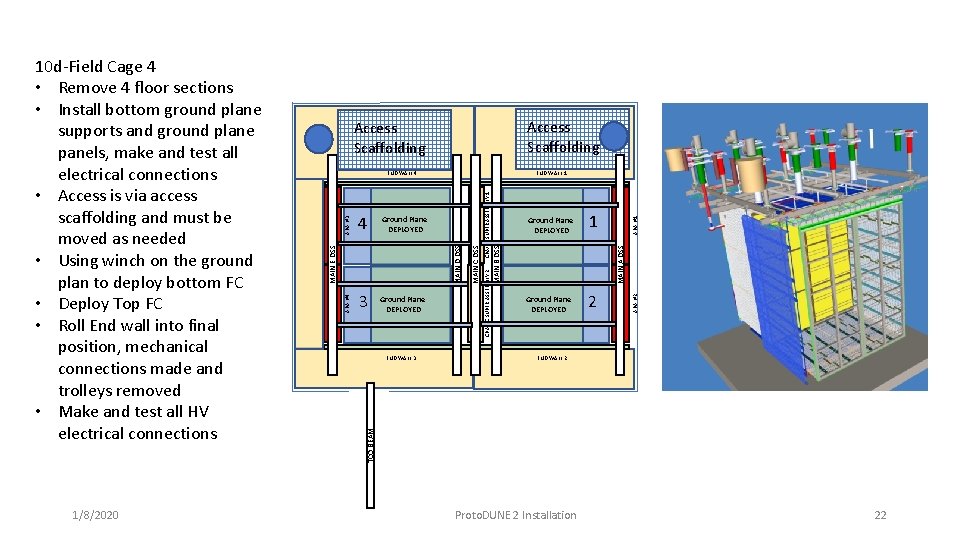
1/8/2020 Access Scaffolding 2 APA #1 Ground Plane DEPLOYED APA #2 MAIN A DSS CPA/FC SUPER ASSEMBLY 1 1 END WALL 2 TCO BEAM END WALL 3 Ground Plane DEPLOYED MAIN B DSS Ground Plane DEPLOYED MAIN C DSS 3 CPA/FC SUPER ASSEMBLY 2 Ground Plane DEPLOYED END WALL 1 MAIN D DSS APA #3 4 APA #4 END WALL 4 MAIN E DSS 10 d-Field Cage 4 • Remove 4 floor sections • Install bottom ground plane supports and ground plane panels, make and test all electrical connections • Access is via access scaffolding and must be moved as needed • Using winch on the ground plan to deploy bottom FC • Deploy Top FC • Roll End wall into final position, mechanical connections made and trolleys removed • Make and test all HV electrical connections Proto. DUNE 2 Installation 22
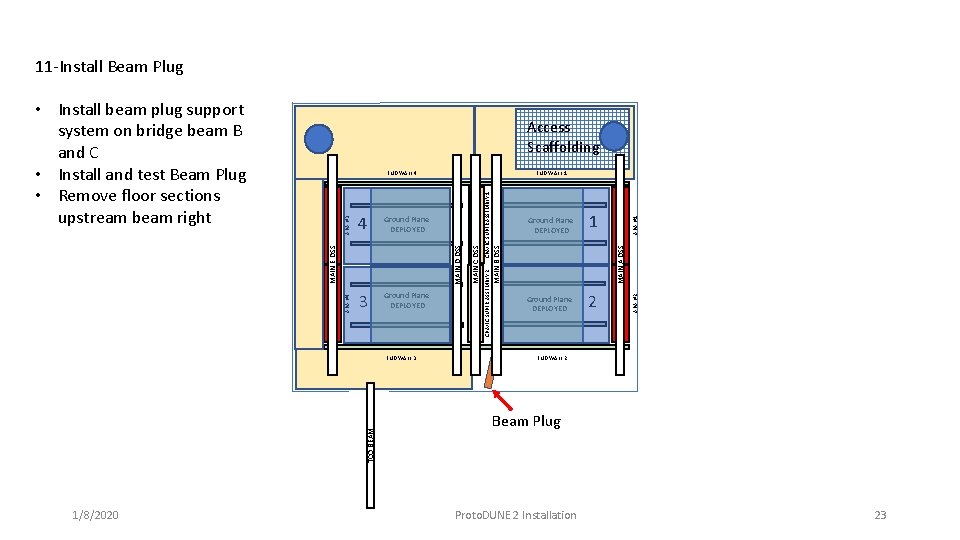
11 -Install Beam Plug • Install beam plug support system on bridge beam B and C • Install and test Beam Plug • Remove floor sections upstream beam right Access Scaffolding TCO BEAM 1/8/2020 Ground Plane DEPLOYED 2 APA #1 1 APA #2 MAIN A DSS CPA/FC SUPER ASSEMBLY 1 MAIN E DSS END WALL 3 Ground Plane DEPLOYED MAIN B DSS Ground Plane DEPLOYED MAIN C DSS 3 CPA/FC SUPER ASSEMBLY 2 Ground Plane DEPLOYED END WALL 1 MAIN D DSS APA #3 4 APA #4 END WALL 2 Beam Plug Proto. DUNE 2 Installation 23
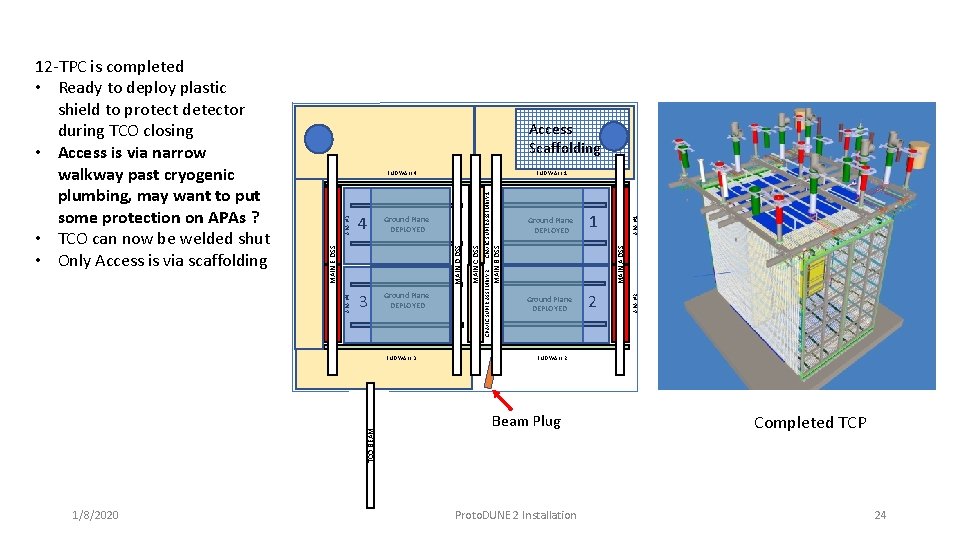
Access Scaffolding TCO BEAM END WALL 3 1/8/2020 Ground Plane DEPLOYED 2 APA #1 1 APA #2 MAIN A DSS CPA/FC SUPER ASSEMBLY 1 Ground Plane DEPLOYED MAIN B DSS Ground Plane DEPLOYED MAIN C DSS 3 CPA/FC SUPER ASSEMBLY 2 Ground Plane DEPLOYED END WALL 1 MAIN D DSS APA #3 4 APA #4 END WALL 4 MAIN E DSS 12 -TPC is completed • Ready to deploy plastic shield to protect detector during TCO closing • Access is via narrow walkway past cryogenic plumbing, may want to put some protection on APAs ? • TCO can now be welded shut • Only Access is via scaffolding END WALL 2 Beam Plug Proto. DUNE 2 Installation Completed TCP 24
How to install fusioncompute
Weiss zone law example
Dbu writing center
Medical plaza miller 131 miller street
William miller 1816
Desert pavement definition
How are sand dunes formed
Dune climax
Hyperstatisme
Dunesoftware
In the desert, ephemeral streams _____.
Dune sp
Dissertation juridique exemple
Salusa secundus
Dune rpg
La dune clib
Dune
Patron dune pyramide
Ameen rihani quotes
Plan dune
Barchan dune
Franz muheim
Dune firmware
Nida lithuania map
Tessa oliver