Presentation on Applications of TIG and MIG welding
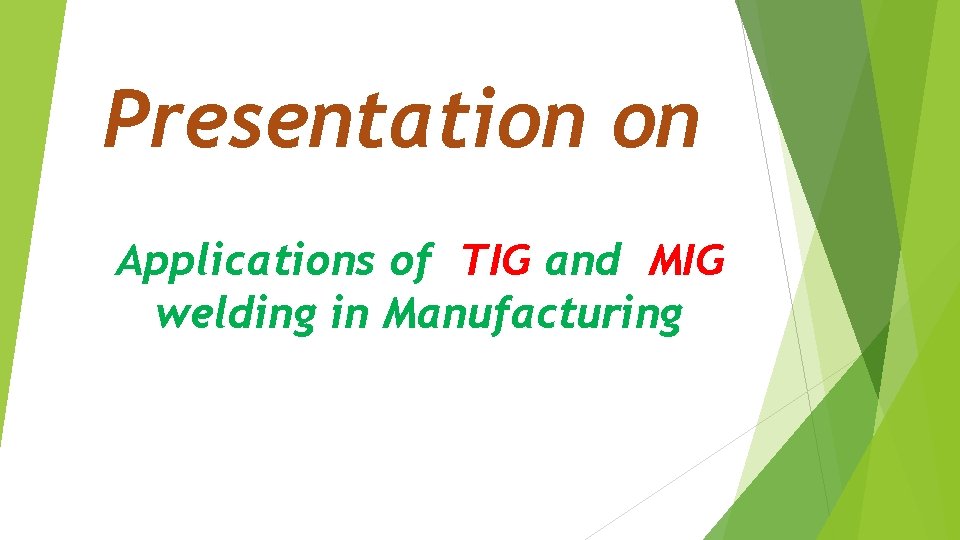
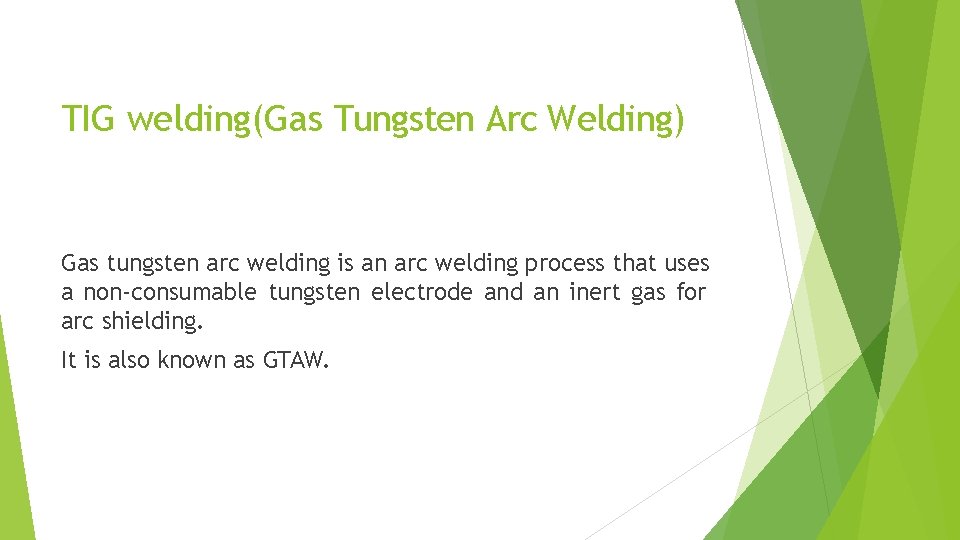
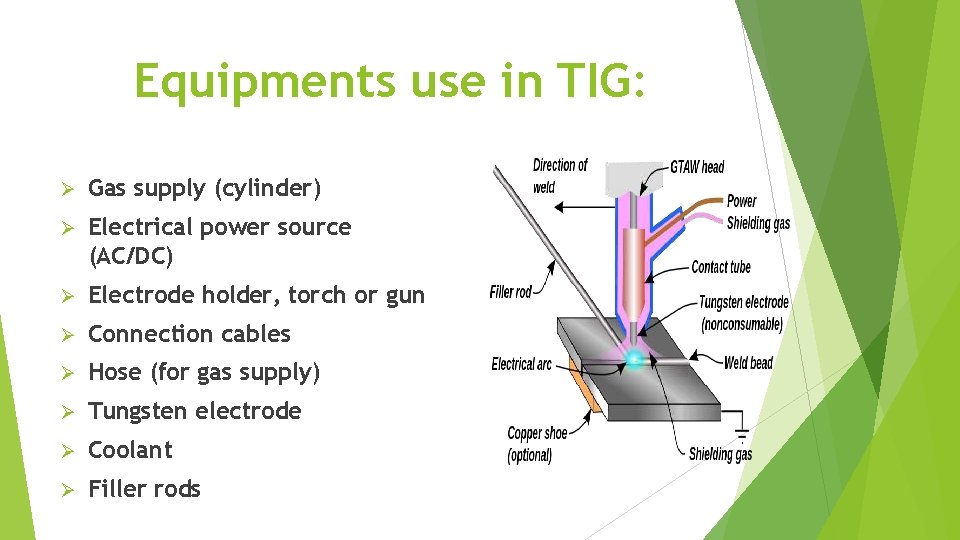
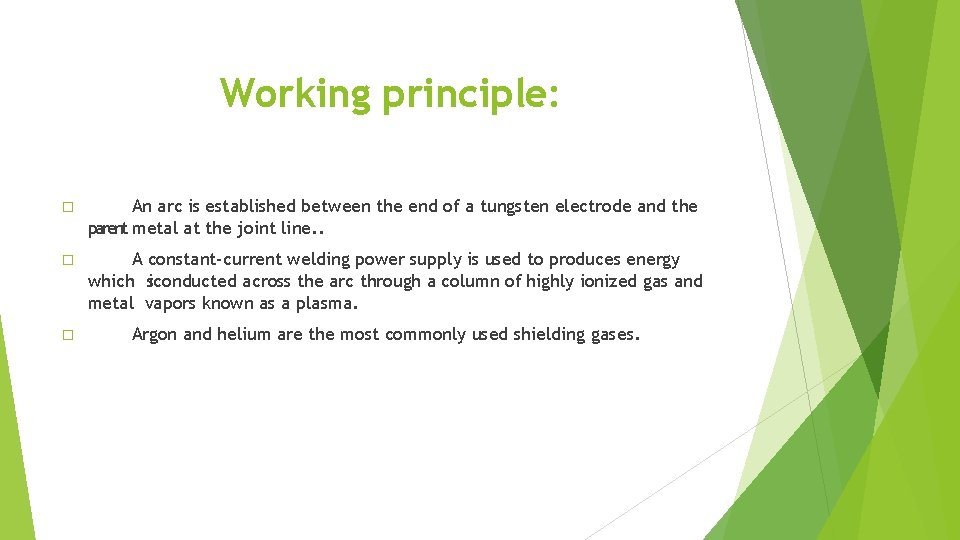
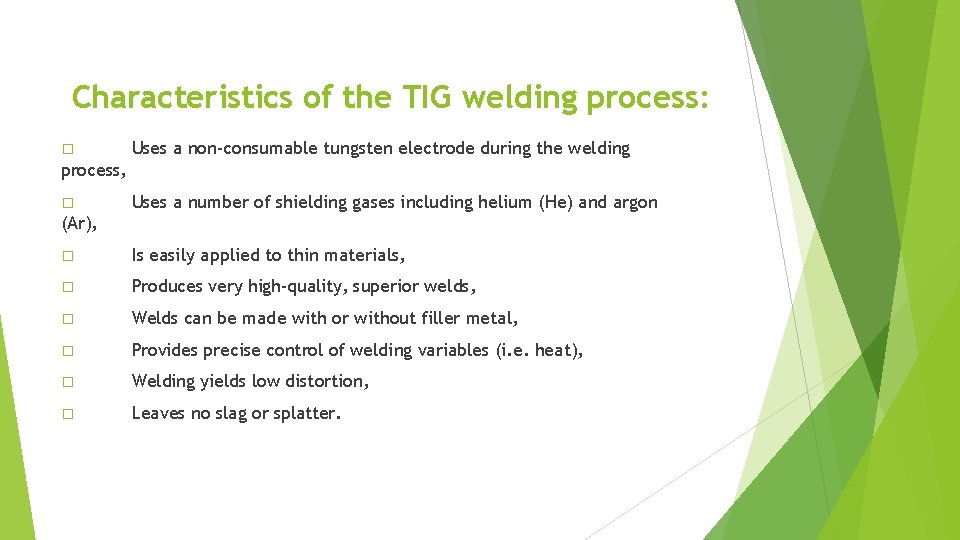
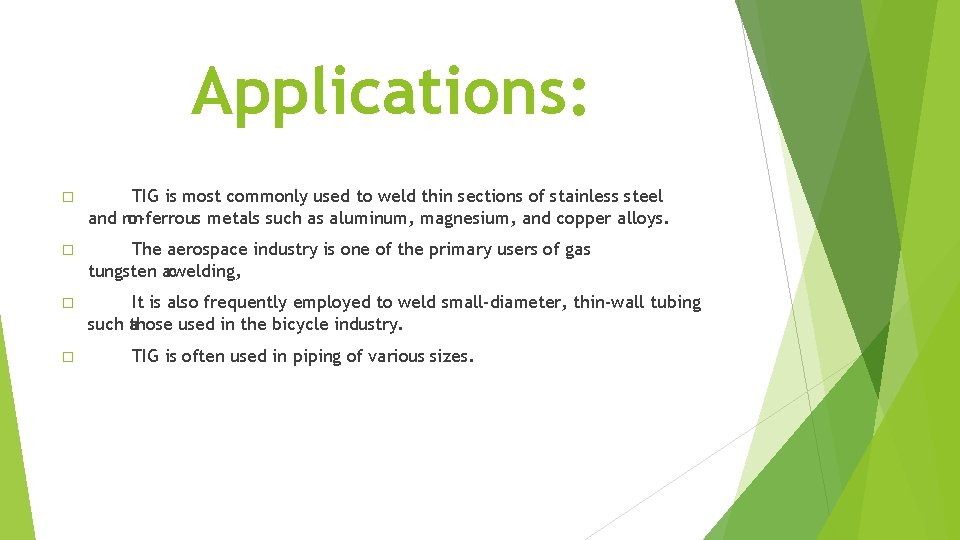
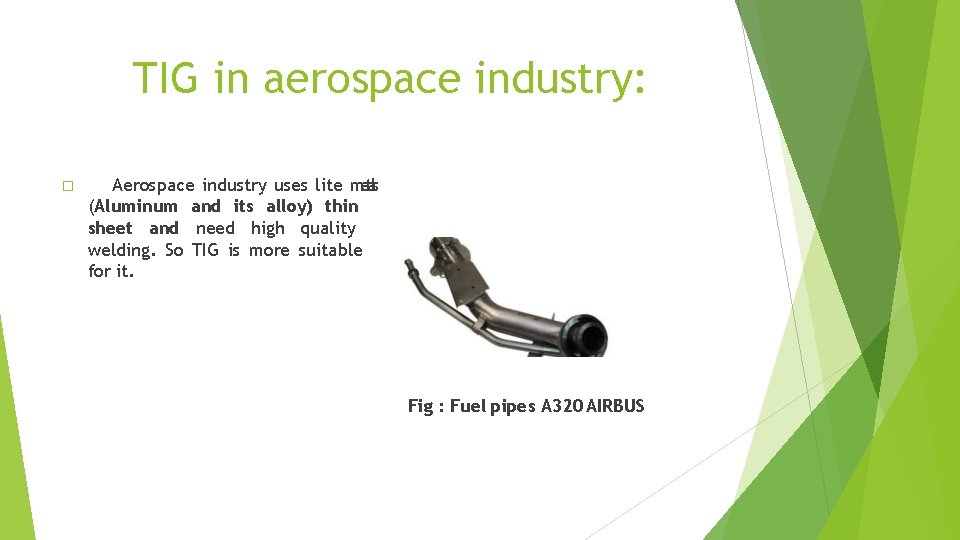
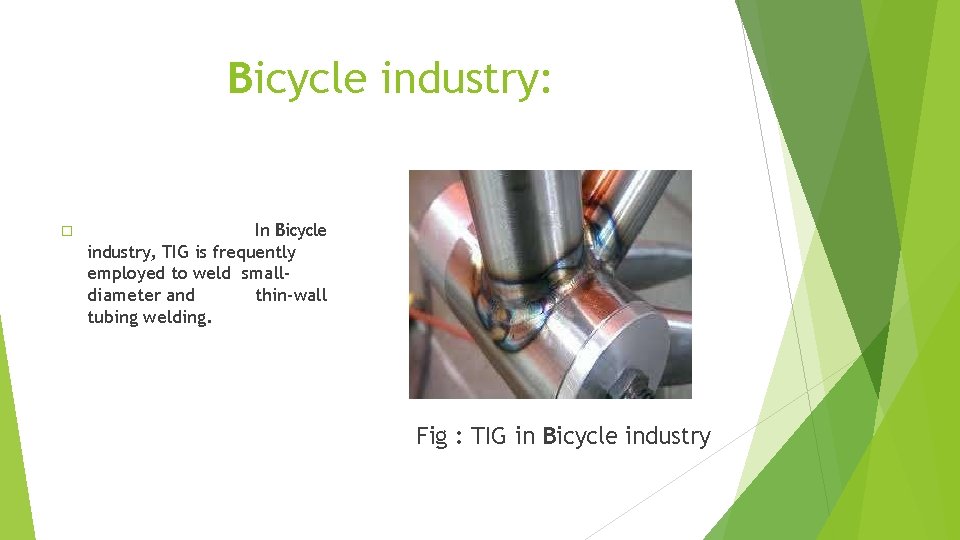
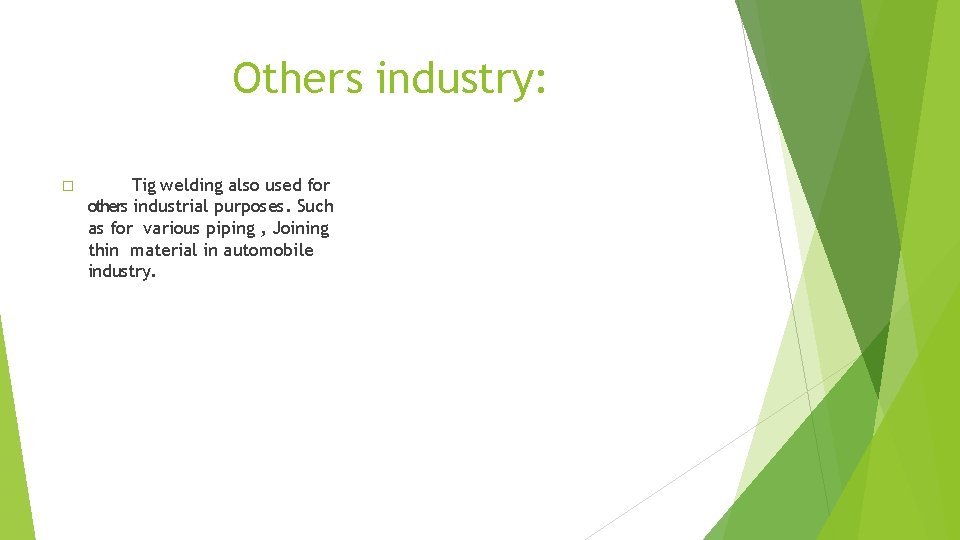
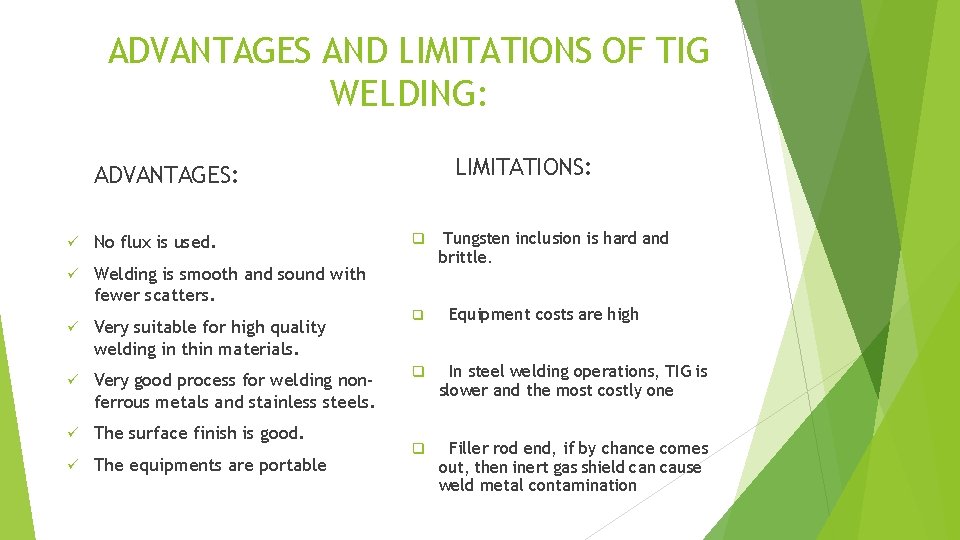
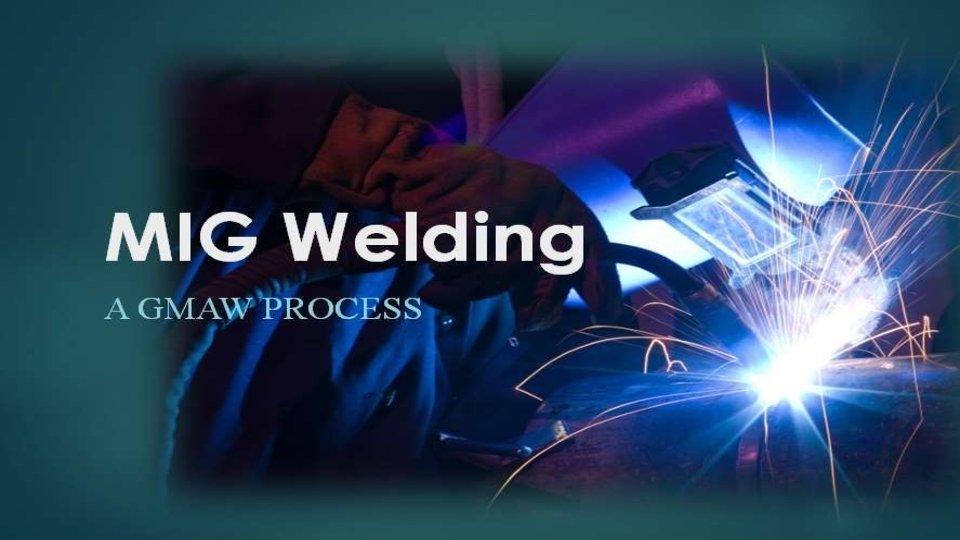
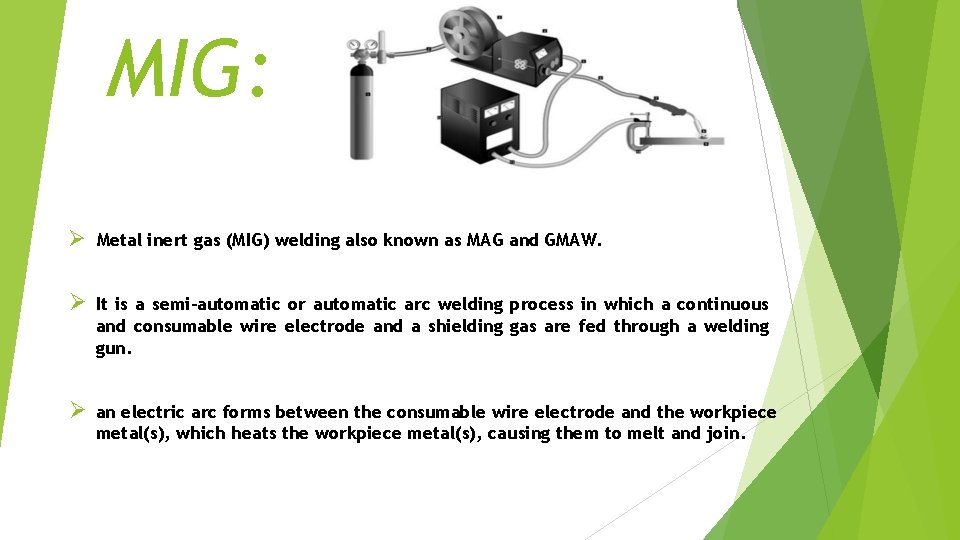
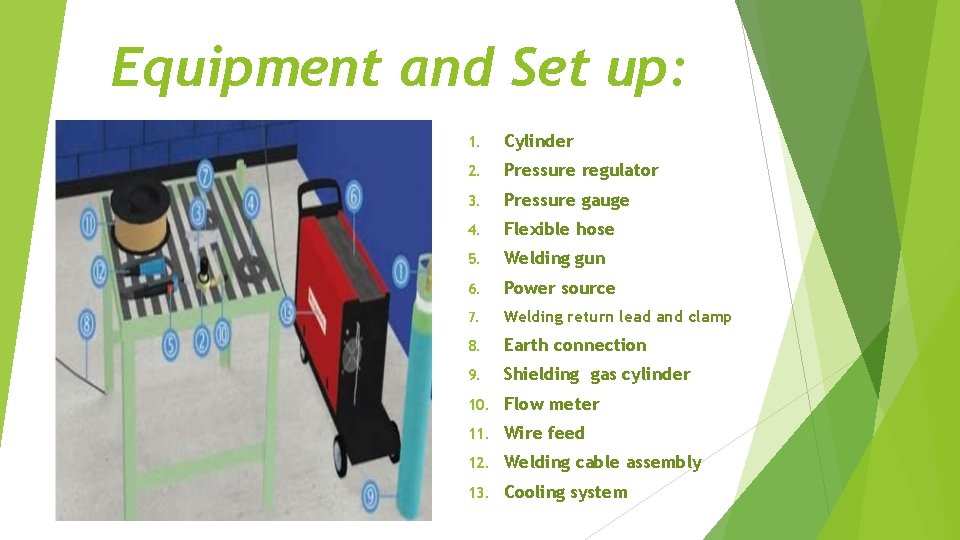
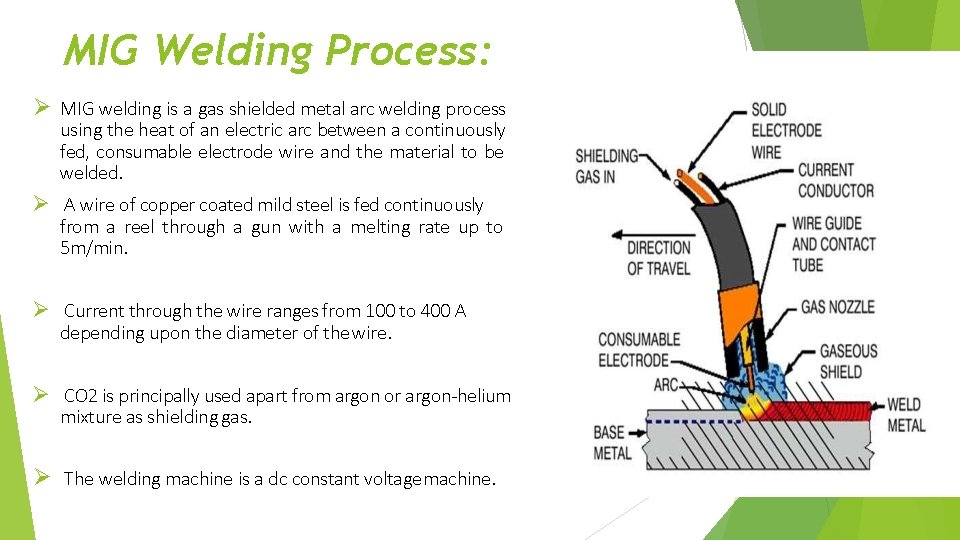
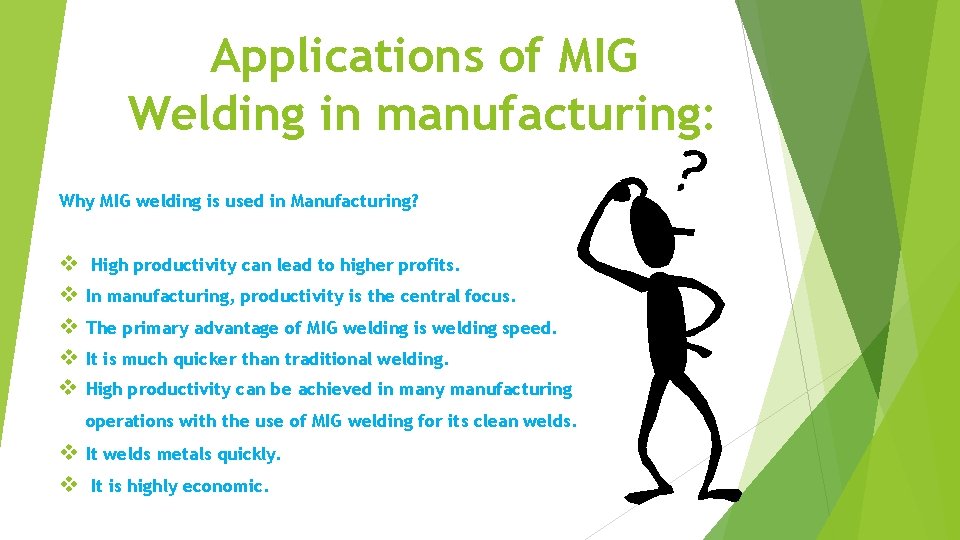
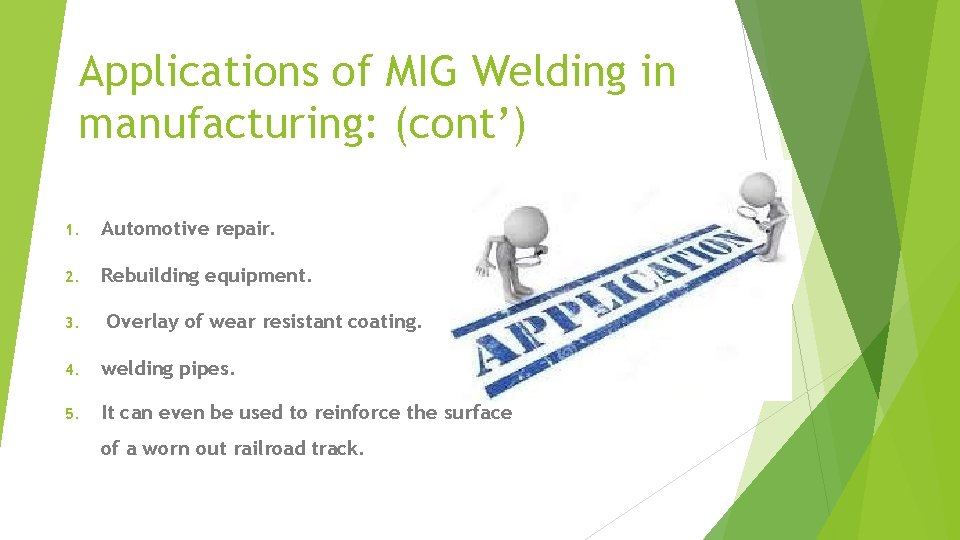
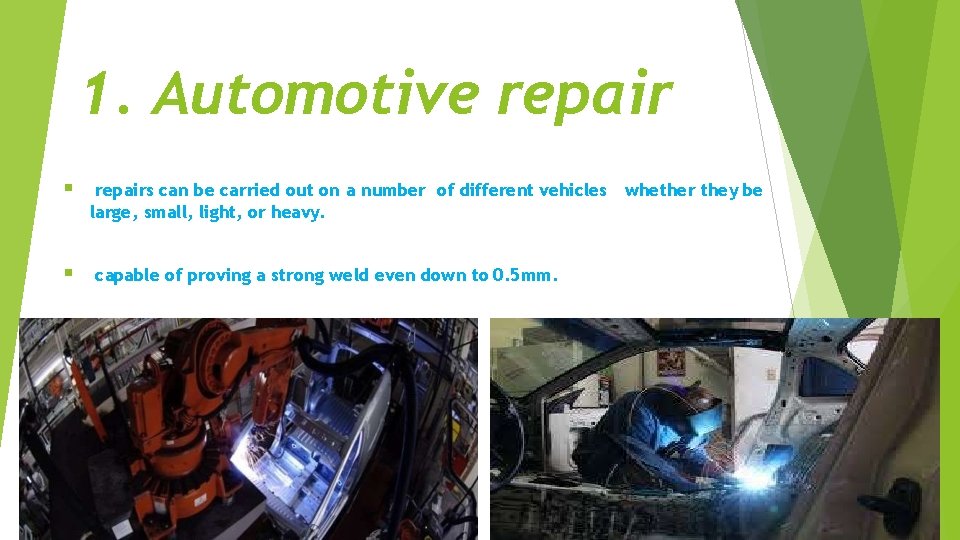
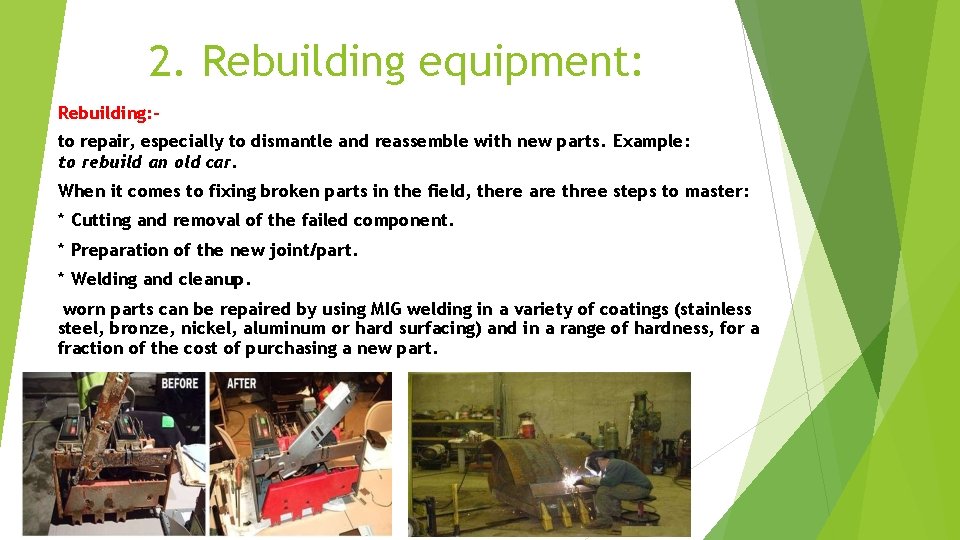
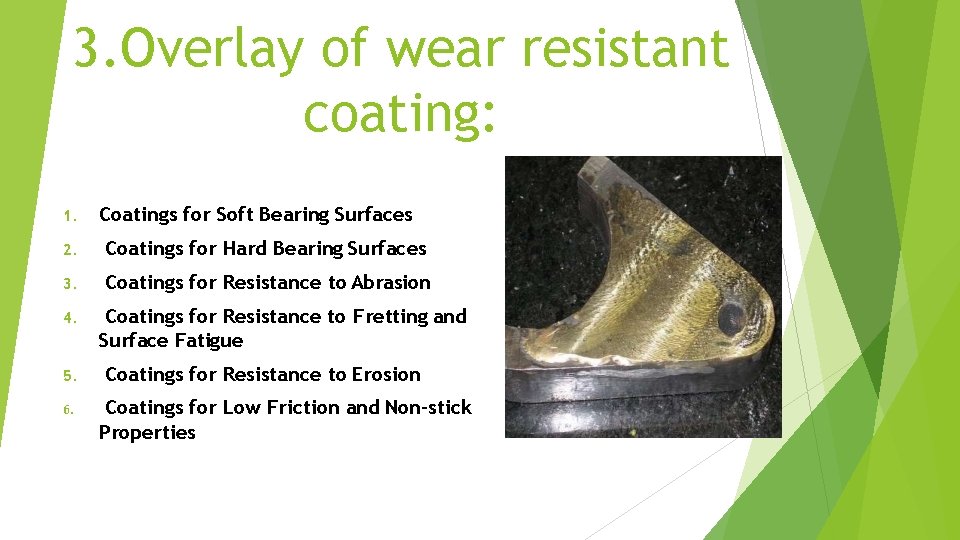
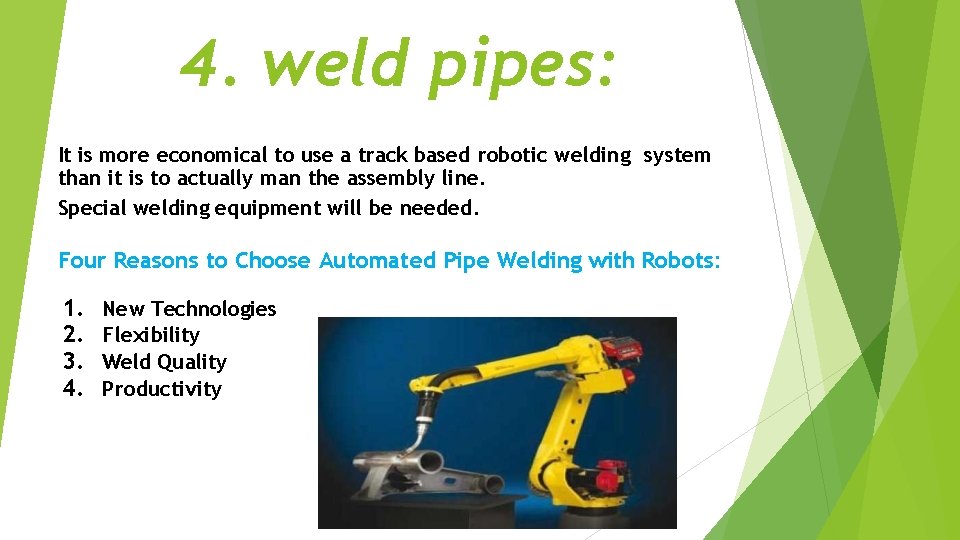
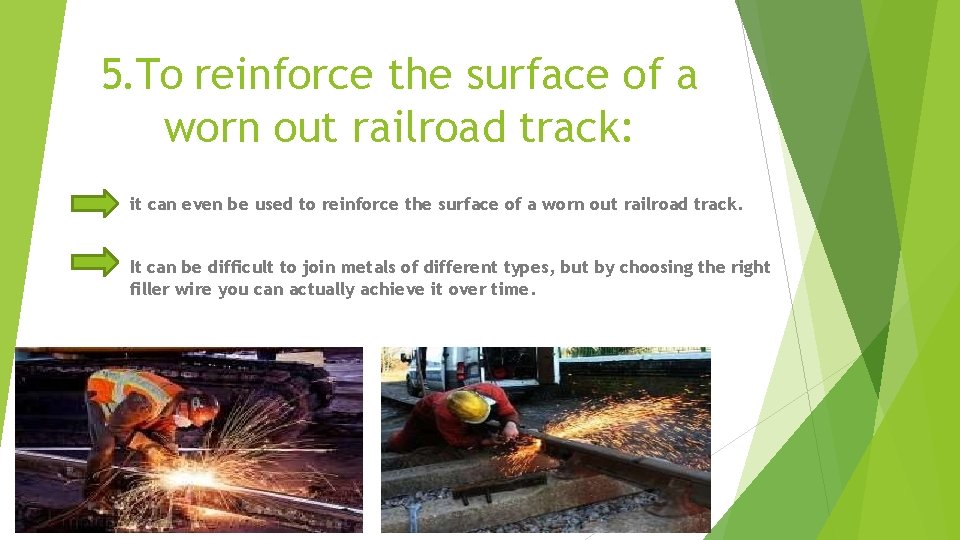
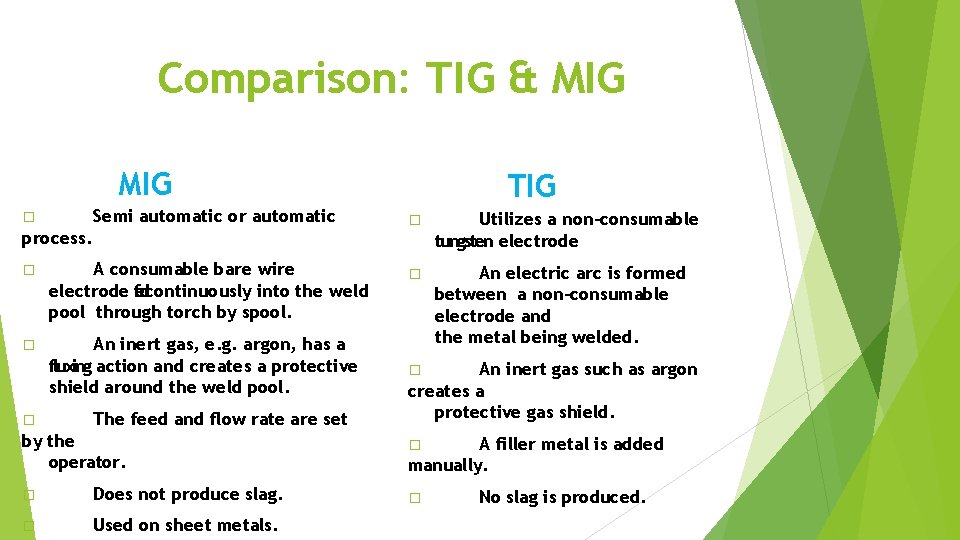
- Slides: 22
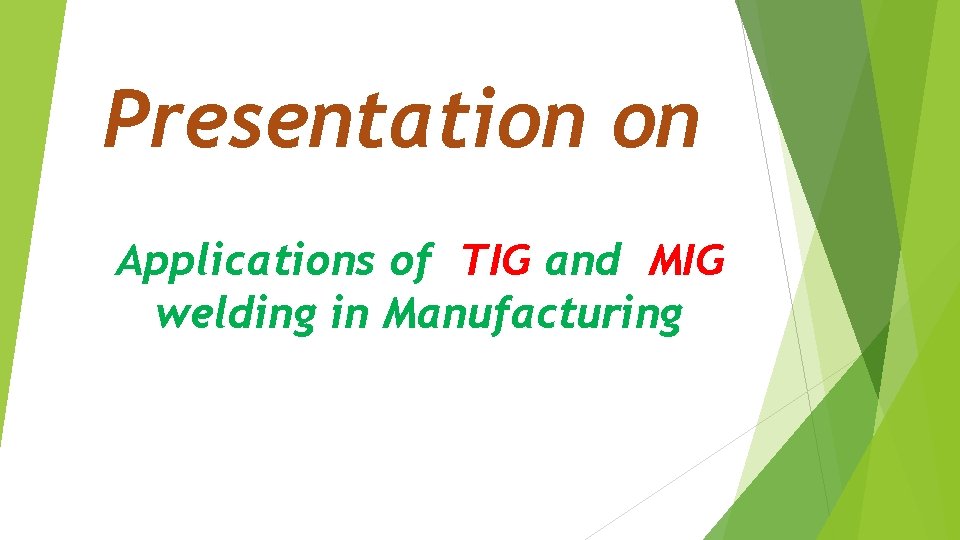
Presentation on Applications of TIG and MIG welding in Manufacturing
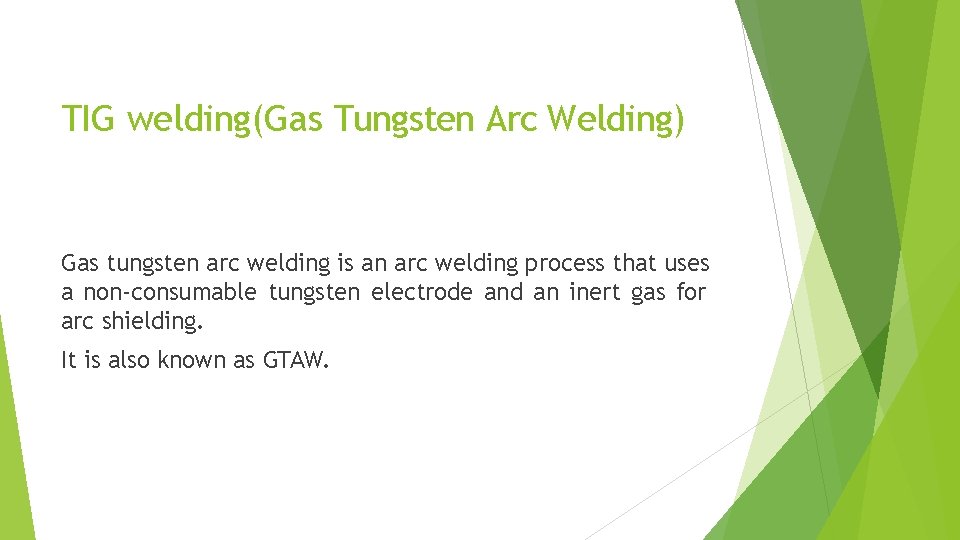
TIG welding(Gas Tungsten Arc Welding) Gas tungsten arc welding is an arc welding process that uses a non-consumable tungsten electrode and an inert gas for arc shielding. It is also known as GTAW.
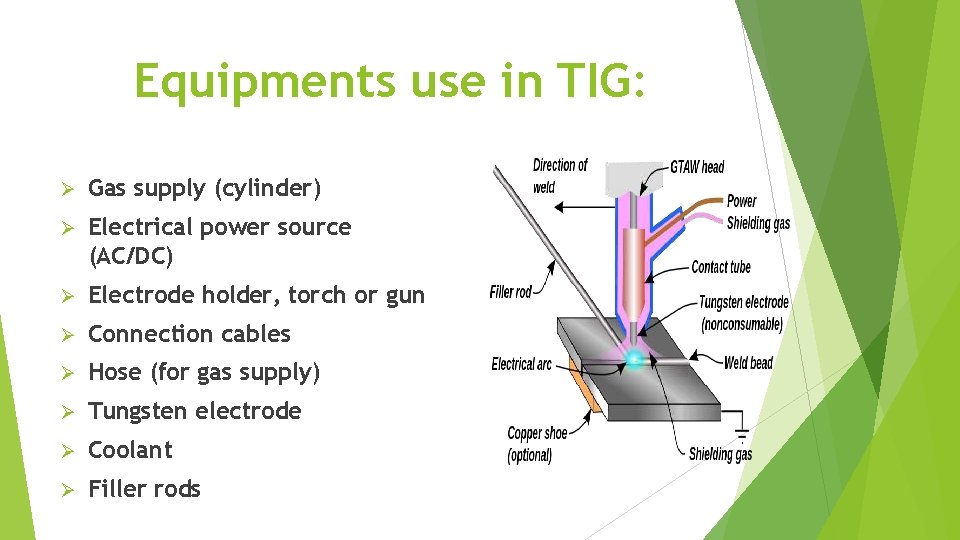
Equipments use in TIG: Gas supply (cylinder) Electrical power source (AC/DC) Electrode holder, torch or gun Connection cables Hose (for gas supply) Tungsten electrode Coolant Filler rods
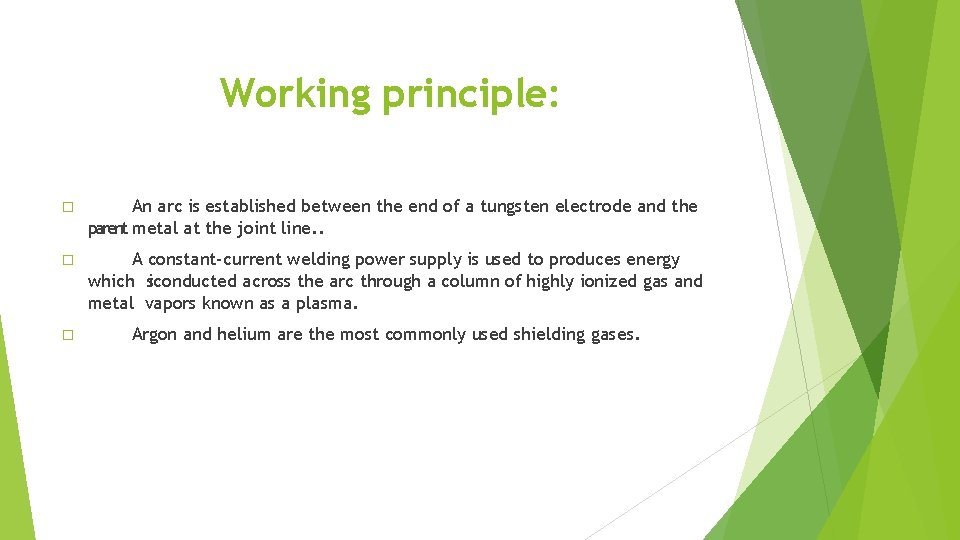
Working principle: � An arc is established between the end of a tungsten electrode and the parent metal at the joint line. . � A constant-current welding power supply is used to produces energy which siconducted across the arc through a column of highly ionized gas and metal vapors known as a plasma. � Argon and helium are the most commonly used shielding gases.
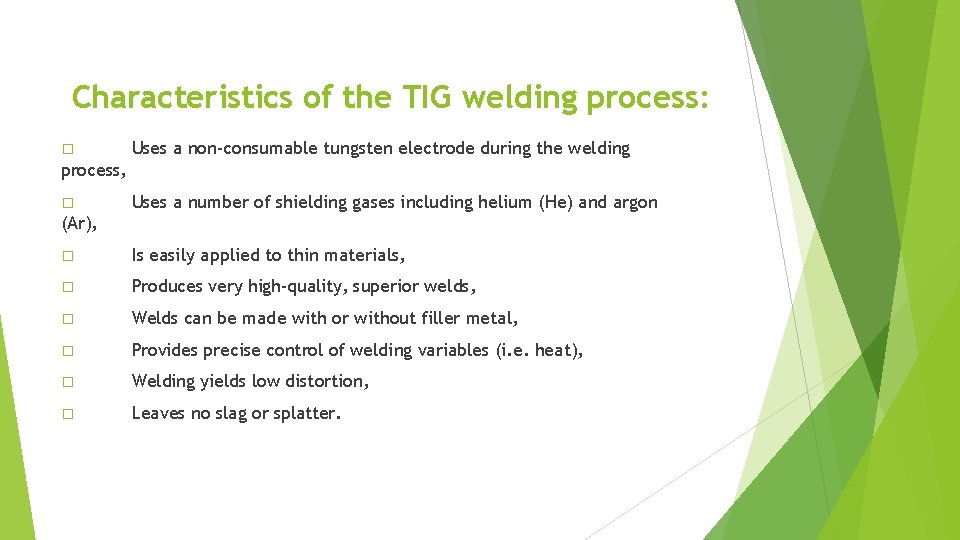
Characteristics of the TIG welding process: � Uses a non-consumable tungsten electrode during the welding process, � Uses a number of shielding gases including helium (He) and argon (Ar), � Is easily applied to thin materials, � Produces very high-quality, superior welds, � Welds can be made with or without filler metal, � Provides precise control of welding variables (i. e. heat), � Welding yields low distortion, � Leaves no slag or splatter.
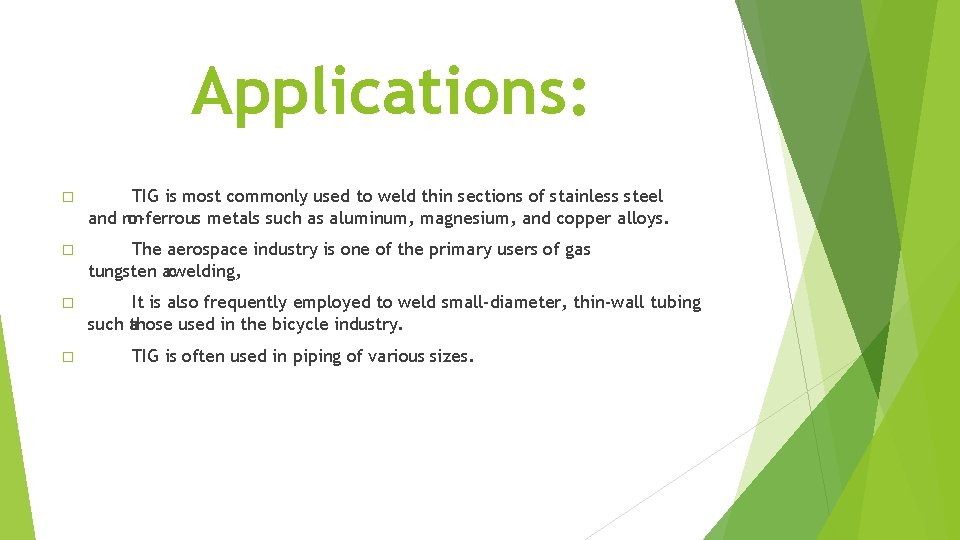
Applications: � TIG is most commonly used to weld thin sections of stainless steel and non-ferrous metals such as aluminum, magnesium, and copper alloys. � The aerospace industry is one of the primary users of gas tungsten arcwelding, � It is also frequently employed to weld small-diameter, thin-wall tubing such a those s used in the bicycle industry. � TIG is often used in piping of various sizes.
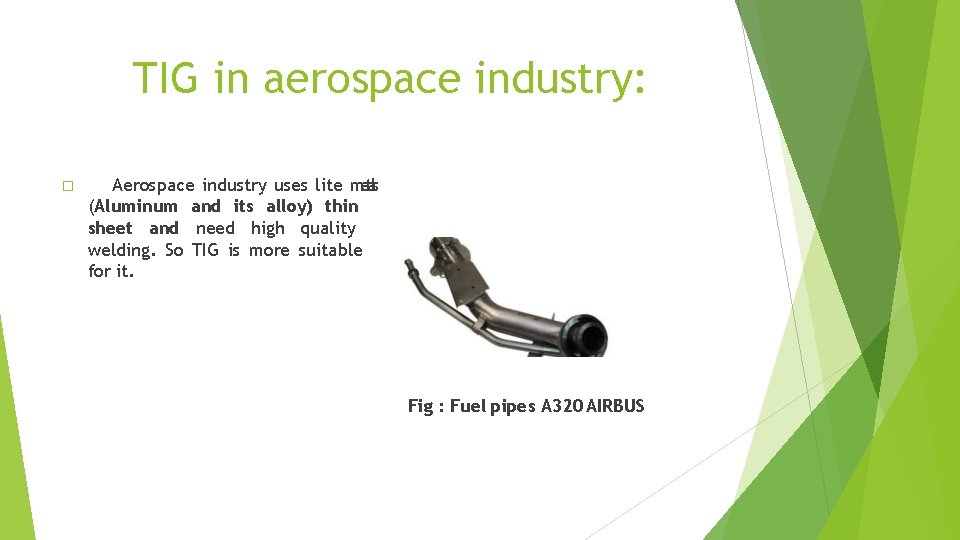
TIG in aerospace industry: � Aerospace industry uses lite metals (Aluminum and its alloy) thin sheet and need high quality welding. So TIG is more suitable for it. Fig : Fuel pipes A 320 AIRBUS
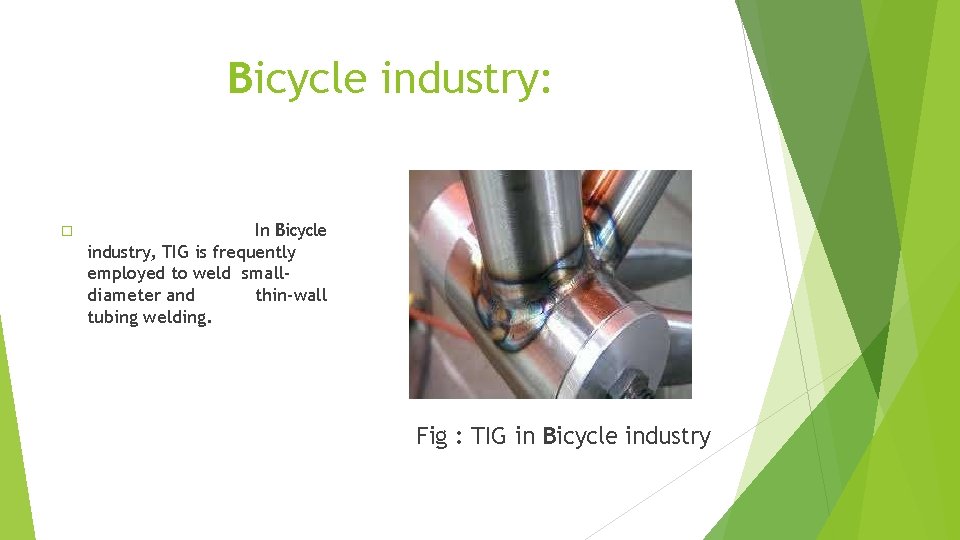
Bicycle industry: � In Bicycle industry, TIG is frequently employed to weld smalldiameter and thin-wall tubing welding. Fig : TIG in Bicycle industry
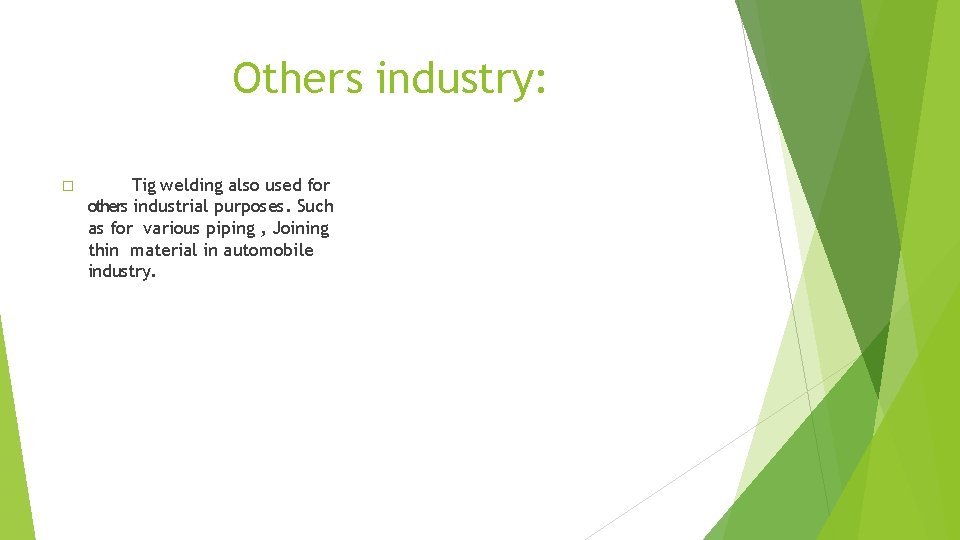
Others industry: � Tig welding also used for others industrial purposes. Such as for various piping , Joining thin material in automobile industry.
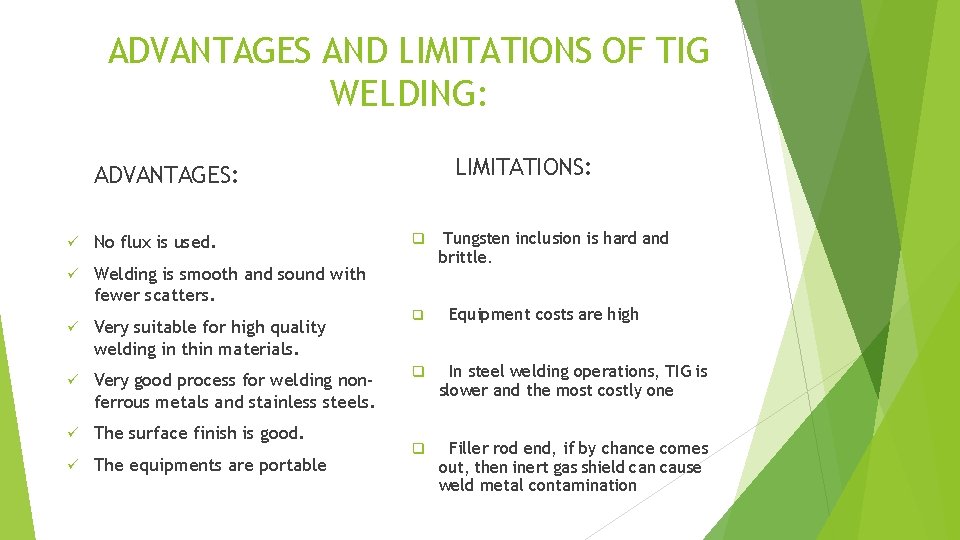
ADVANTAGES AND LIMITATIONS OF TIG WELDING: LIMITATIONS: ADVANTAGES: No flux is used. Welding is smooth and sound with fewer scatters. Very suitable for high quality welding in thin materials. Very good process for welding nonferrous metals and stainless steels. The surface finish is good. The equipments are portable Tungsten inclusion is hard and brittle. Equipment costs are high In steel welding operations, TIG is slower and the most costly one Filler rod end, if by chance comes out, then inert gas shield can cause weld metal contamination
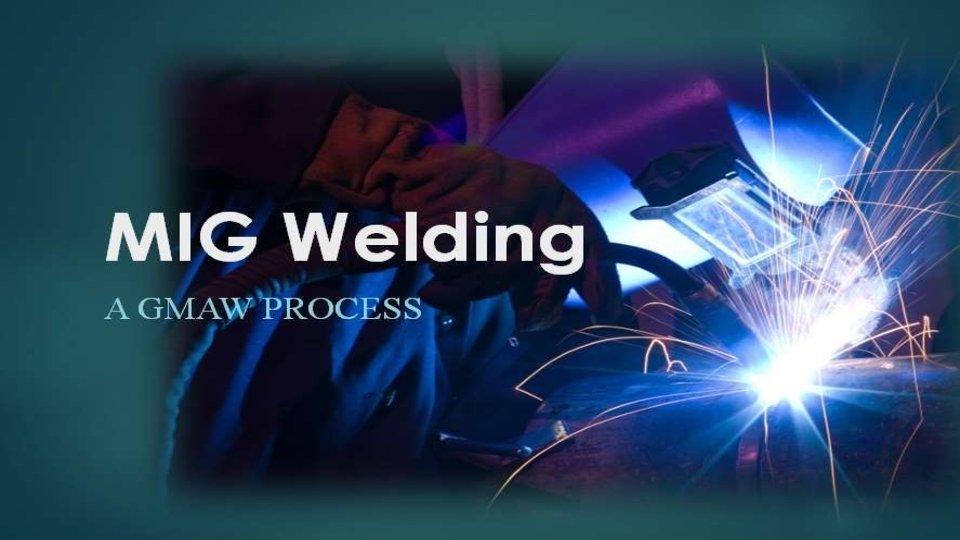
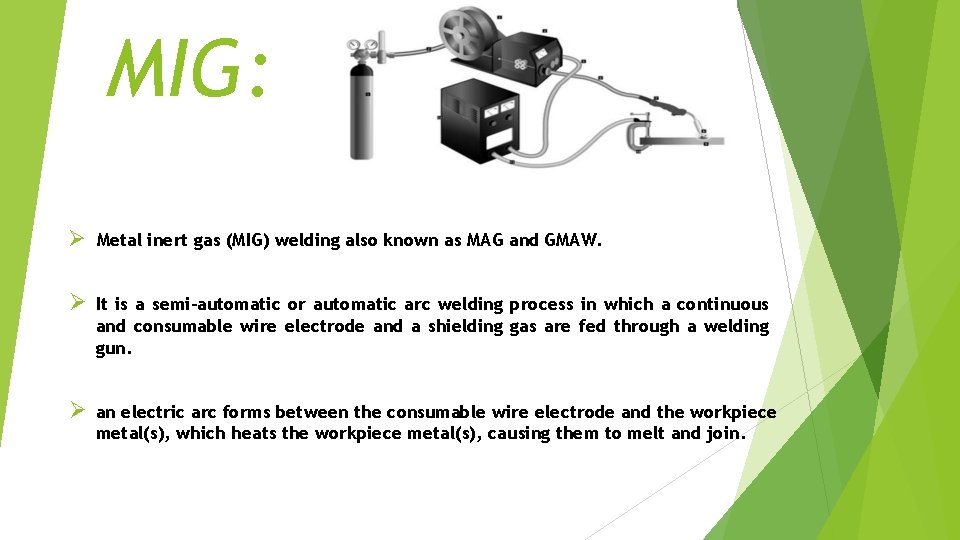
MIG: Metal inert gas (MIG) welding also known as MAG and GMAW. It is a semi-automatic or automatic arc welding process in which a continuous and consumable wire electrode and a shielding gas are fed through a welding gun. an electric arc forms between the consumable wire electrode and the workpiece metal(s), which heats the workpiece metal(s), causing them to melt and join.
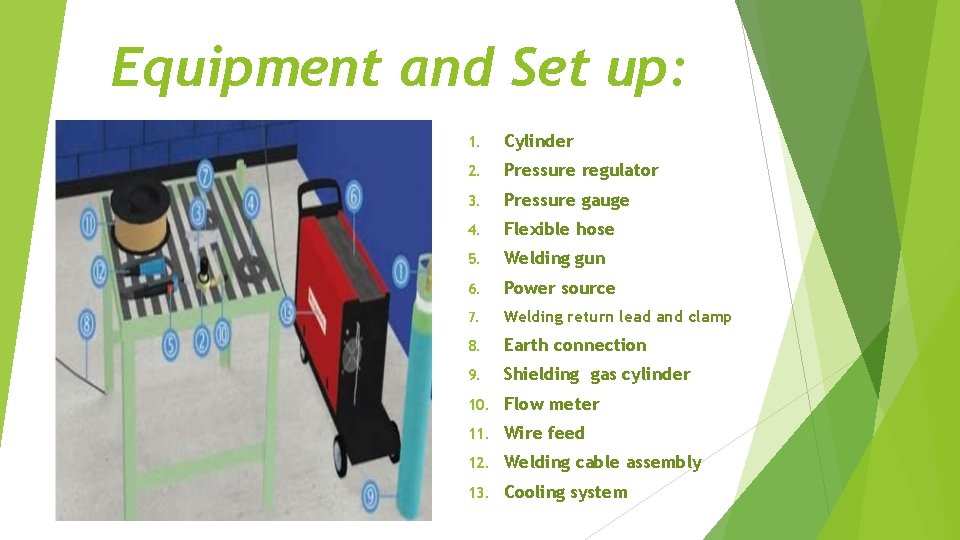
Equipment and Set up: 1. Cylinder 2. Pressure regulator 3. Pressure gauge 4. Flexible hose 5. Welding gun 6. Power source 7. Welding return lead and clamp 8. Earth connection 9. Shielding gas cylinder 10. Flow meter 11. Wire feed 12. Welding cable assembly 13. Cooling system
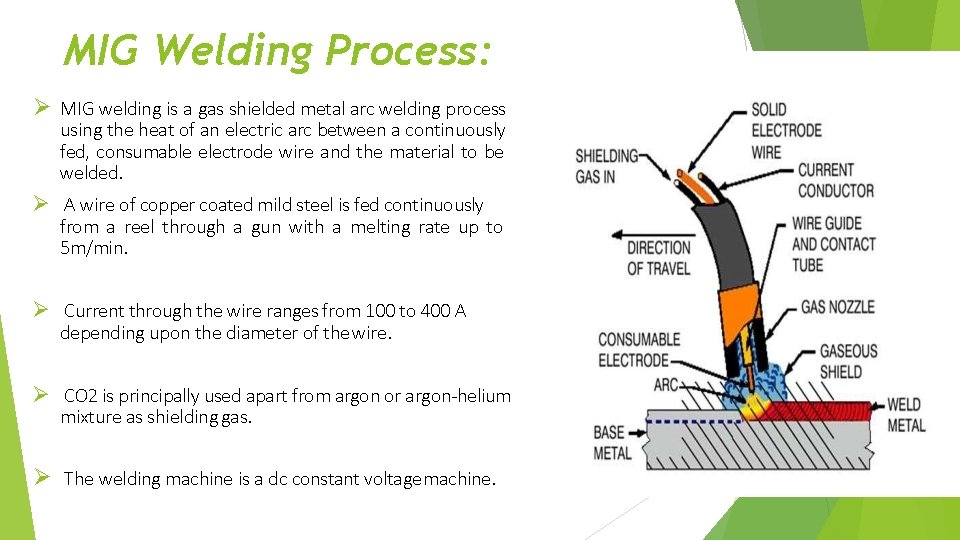
MIG Welding Process: MIG welding is a gas shielded metal arc welding process using the heat of an electric arc between a continuously fed, consumable electrode wire and the material to be welded. A wire of copper coated mild steel is fed continuously from a reel through a gun with a melting rate up to 5 m/min. Current through the wire ranges from 100 to 400 A depending upon the diameter of the wire. CO 2 is principally used apart from argon or argon-helium mixture as shielding gas. The welding machine is a dc constant voltage machine.
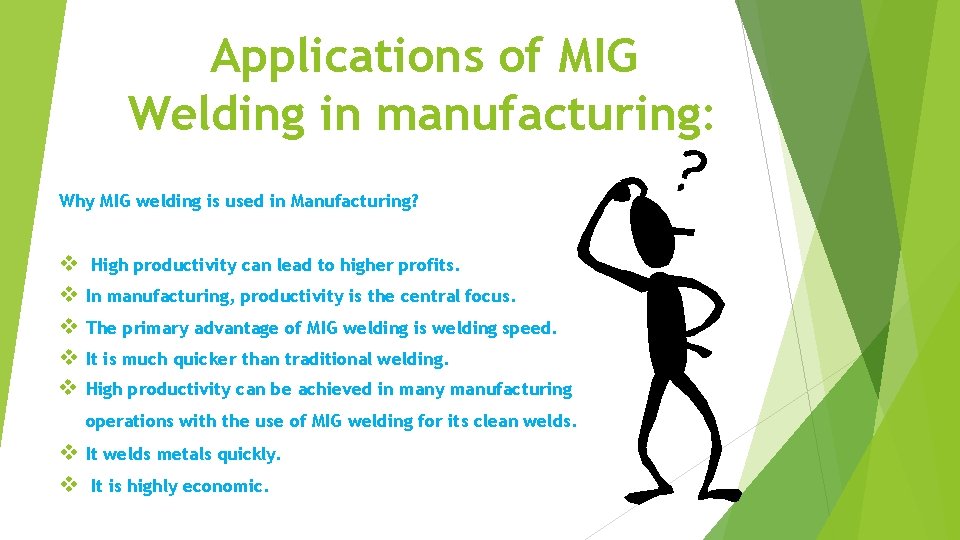
Applications of MIG Welding in manufacturing: Why MIG welding is used in Manufacturing? High productivity can lead to higher profits. In manufacturing, productivity is the central focus. The primary advantage of MIG welding is welding speed. It is much quicker than traditional welding. High productivity can be achieved in many manufacturing operations with the use of MIG welding for its clean welds. It welds metals quickly. It is highly economic.
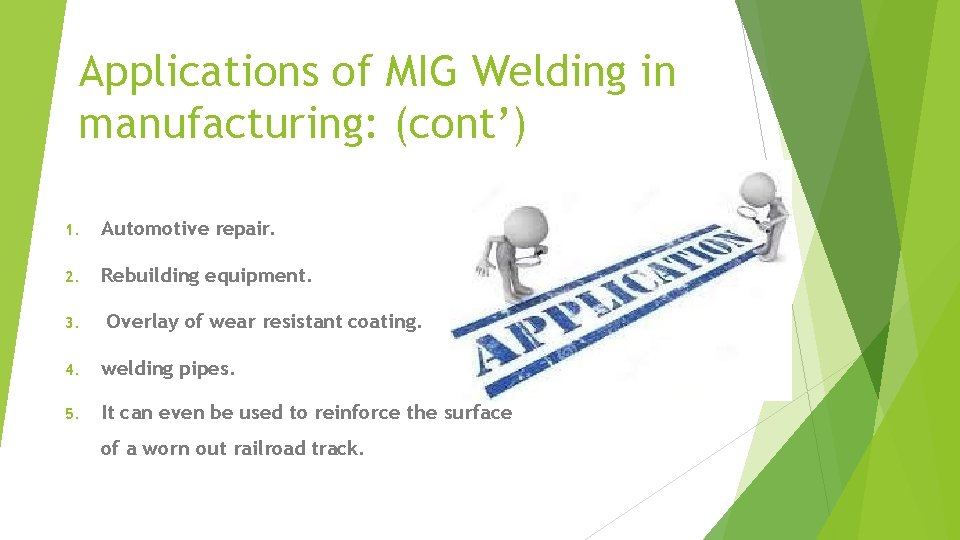
Applications of MIG Welding in manufacturing: (cont’) 1. Automotive repair. 2. Rebuilding equipment. 3. Overlay of wear resistant coating. 4. welding pipes. 5. It can even be used to reinforce the surface of a worn out railroad track.
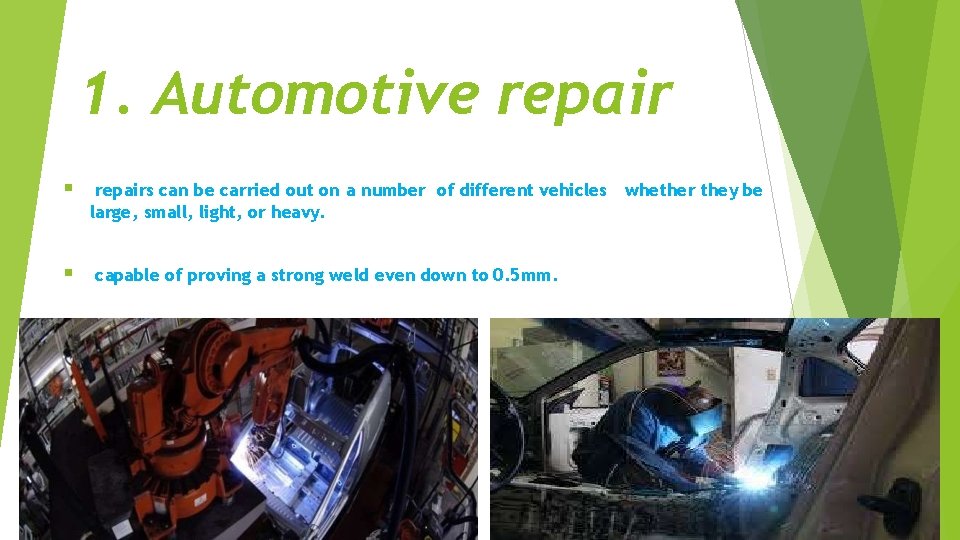
1. Automotive repairs can be carried out on a number of different vehicles whether they be large, small, light, or heavy. capable of proving a strong weld even down to 0. 5 mm.
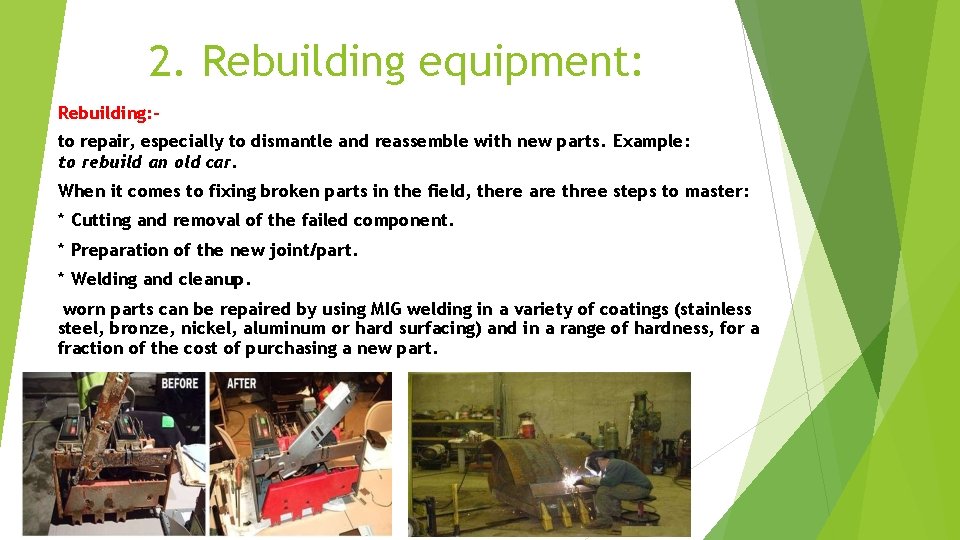
2. Rebuilding equipment: Rebuilding: to repair, especially to dismantle and reassemble with new parts. Example: to rebuild an old car. When it comes to fixing broken parts in the field, there are three steps to master: * Cutting and removal of the failed component. * Preparation of the new joint/part. * Welding and cleanup. worn parts can be repaired by using MIG welding in a variety of coatings (stainless steel, bronze, nickel, aluminum or hard surfacing) and in a range of hardness, for a fraction of the cost of purchasing a new part.
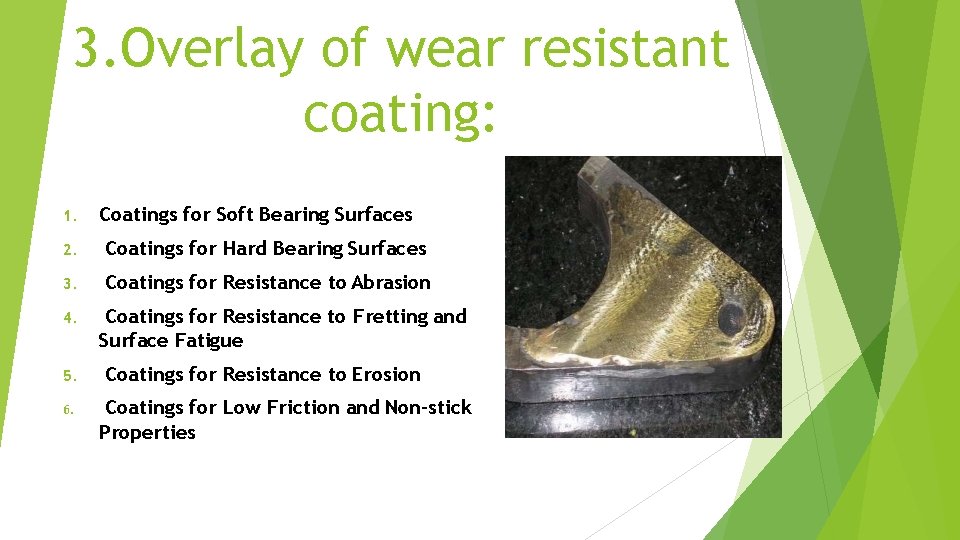
3. Overlay of wear resistant coating: 1. Coatings for Soft Bearing Surfaces 2. Coatings for Hard Bearing Surfaces 3. Coatings for Resistance to Abrasion 4. 5. 6. Coatings for Resistance to Fretting and Surface Fatigue Coatings for Resistance to Erosion Coatings for Low Friction and Non-stick Properties
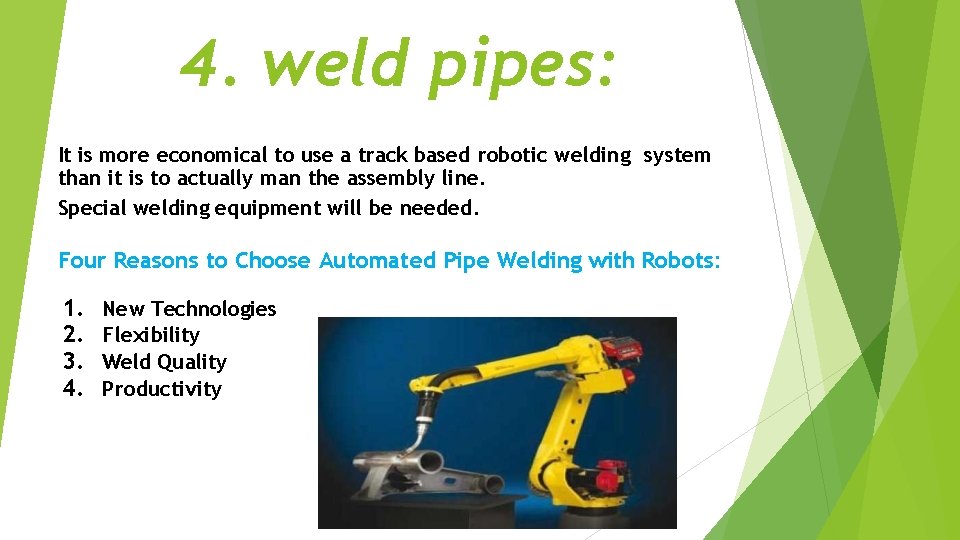
4. weld pipes: It is more economical to use a track based robotic welding system than it is to actually man the assembly line. Special welding equipment will be needed. Four Reasons to Choose Automated Pipe Welding with Robots: 1. 2. 3. 4. New Technologies Flexibility Weld Quality Productivity
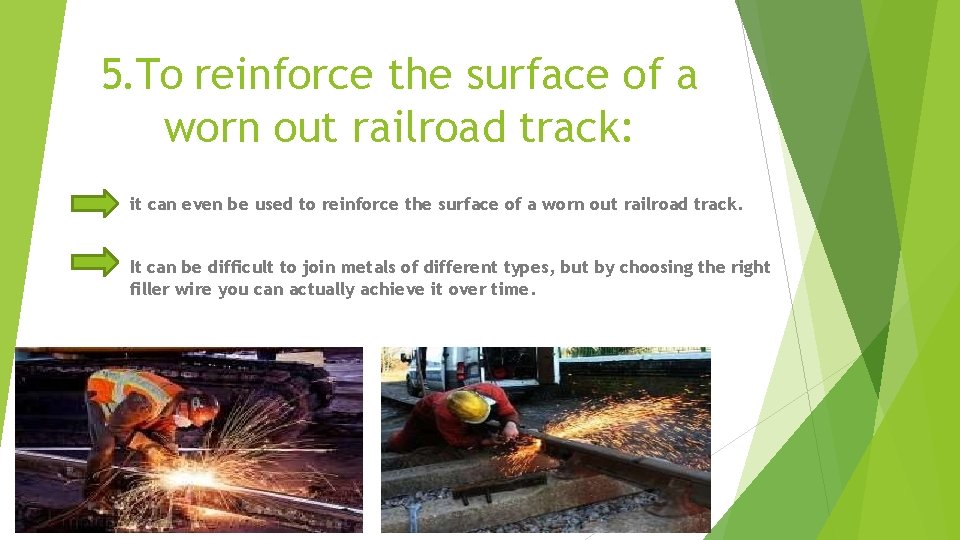
5. To reinforce the surface of a worn out railroad track: it can even be used to reinforce the surface of a worn out railroad track. It can be difficult to join metals of different types, but by choosing the right filler wire you can actually achieve it over time.
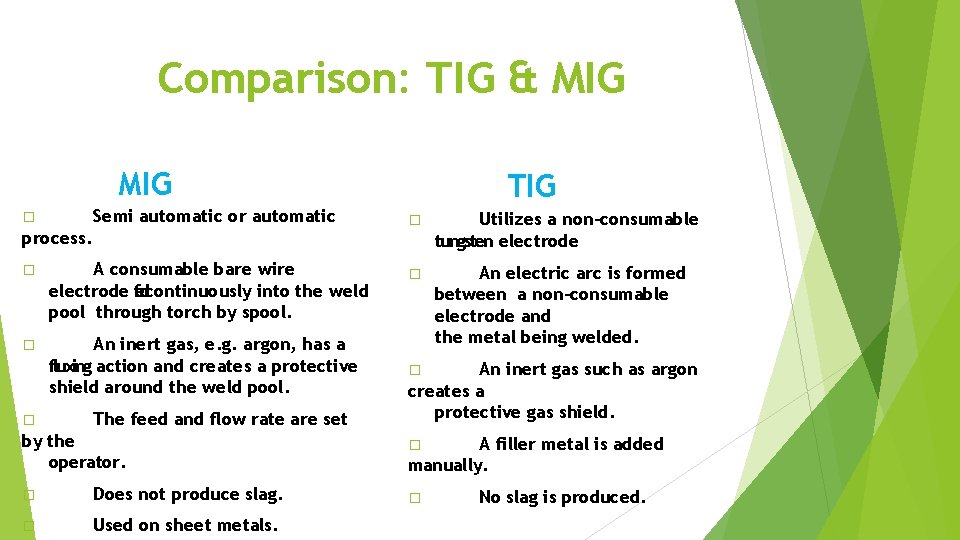
Comparison: TIG & MIG Semi automatic or automatic � process. � A consumable bare wire electrode fedcontinuously into the weld pool through torch by spool. � An inert gas, e. g. argon, has a fluxing action and creates a protective shield around the weld pool. � The feed and flow rate are set by the operator. � Does not produce slag. � Used on sheet metals. TIG � Utilizes a non-consumable tungsten electrode � An electric arc is formed between a non-consumable electrode and the metal being welded. An inert gas such as argon creates a protective gas shield. � A filler metal is added manually. � � No slag is produced.
Mig welding patterns
Tig welding advantages and disadvantages
Objective of tig welding
"tig welding techniques"
Tig welding definition
Mig welding voltage and current chart
Mig welding pics
Mig welding objective
Disadvantages of mig welding
Objective of mig welding
Gmaw components
Hidratação pediatria
Mufradot asari
Tig (tungsten inert gas)
Tig (tungsten inert gas)
Tig (tungsten inert gas)
Cinquain tula
Tabla de amperaje para soldadura mig
Joint design in welding
What is seam welding process
Percussion welding applications
Mig sport
Acetylene cylinder cutaway