OXYACETYLENE WELDING Course Information Packet Meridian Ag Department
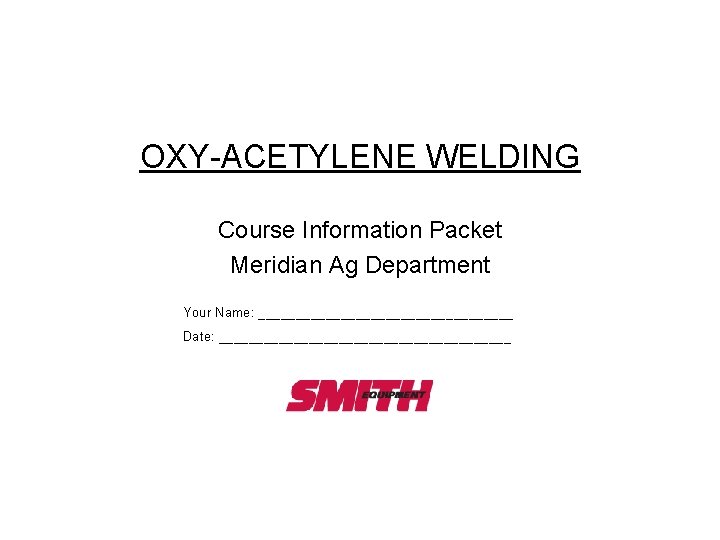
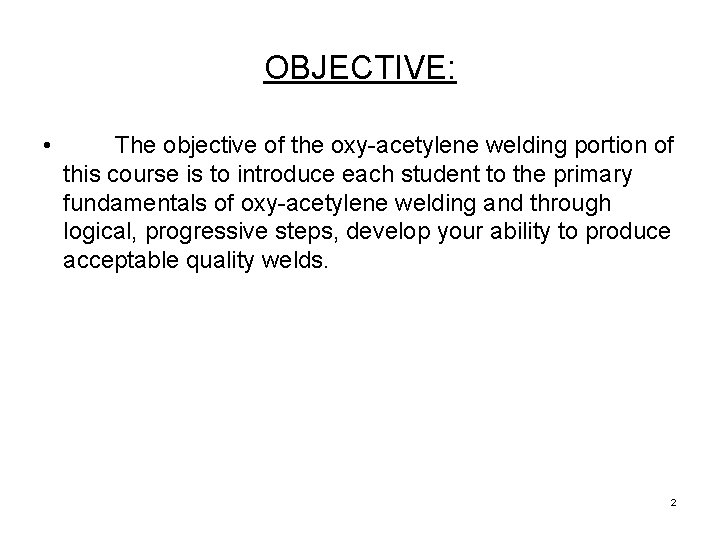
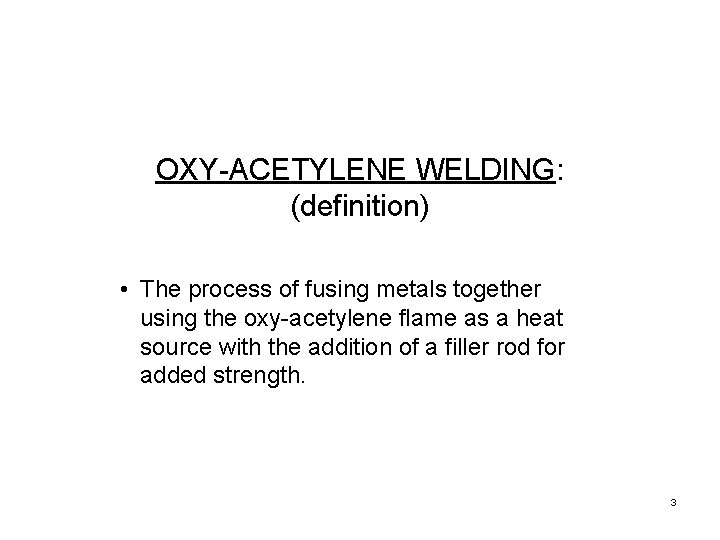
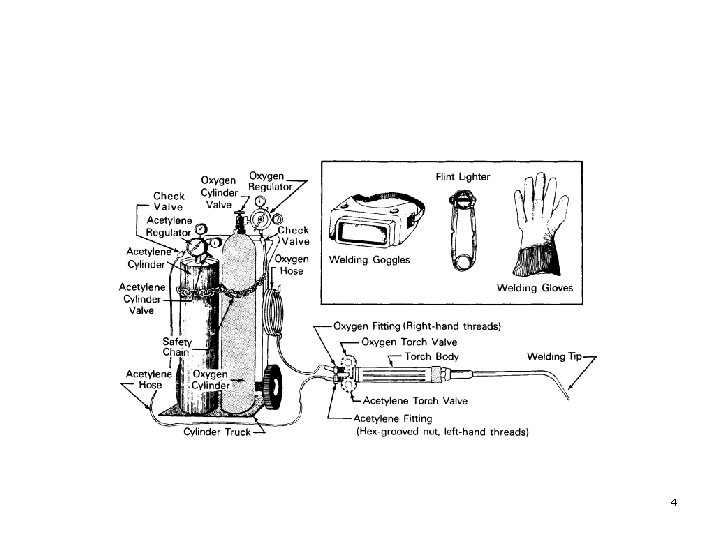
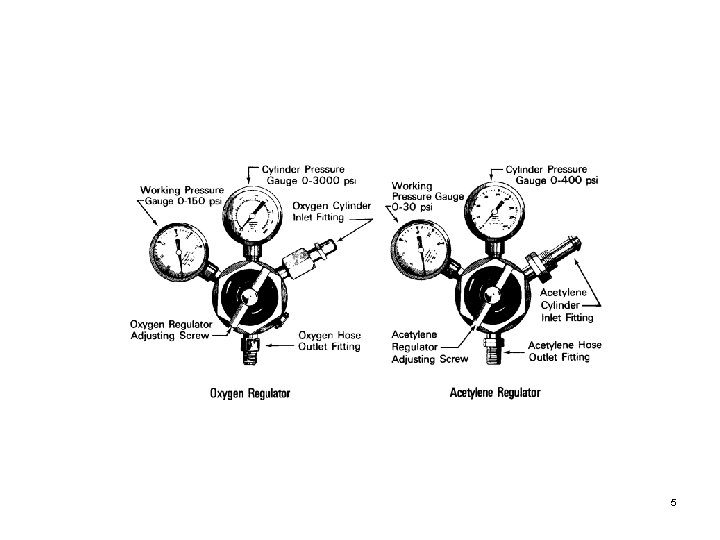
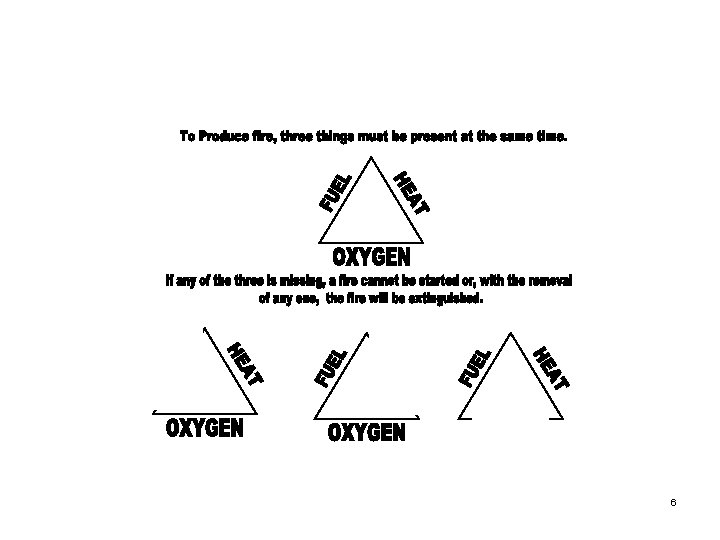
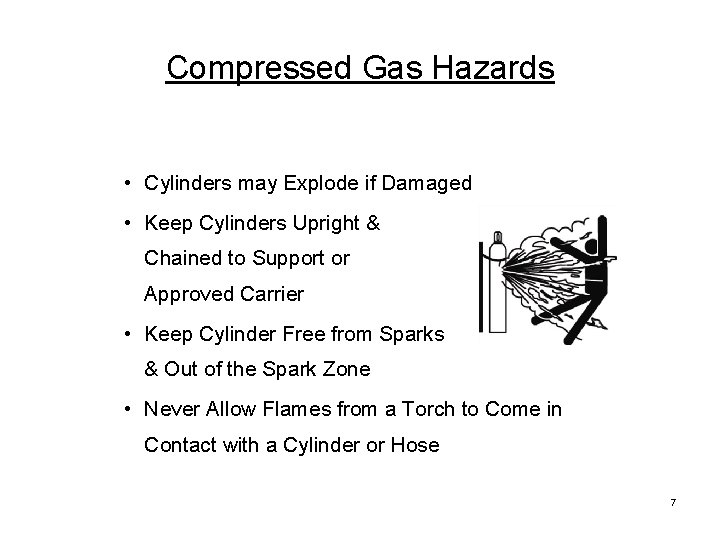
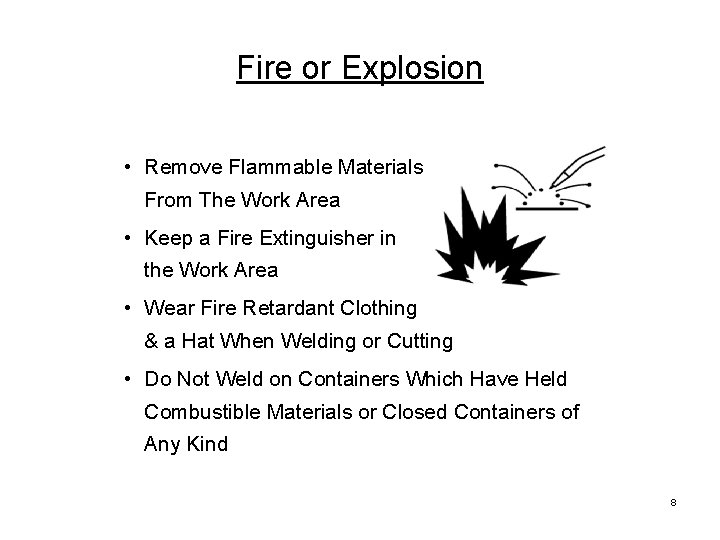
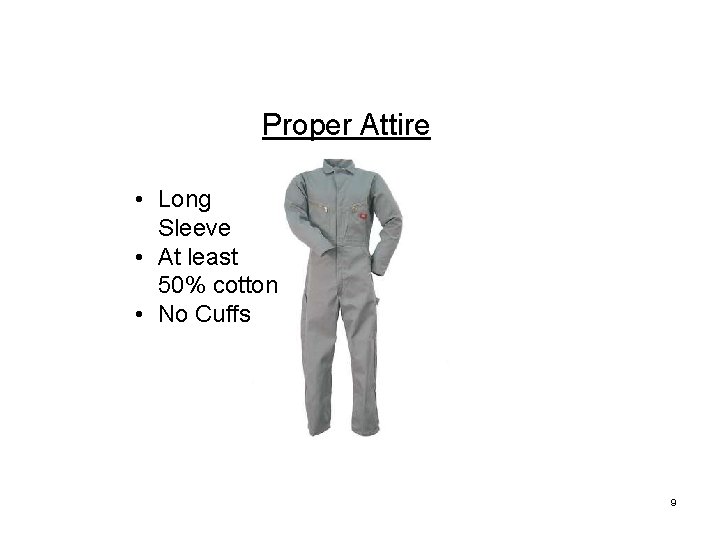
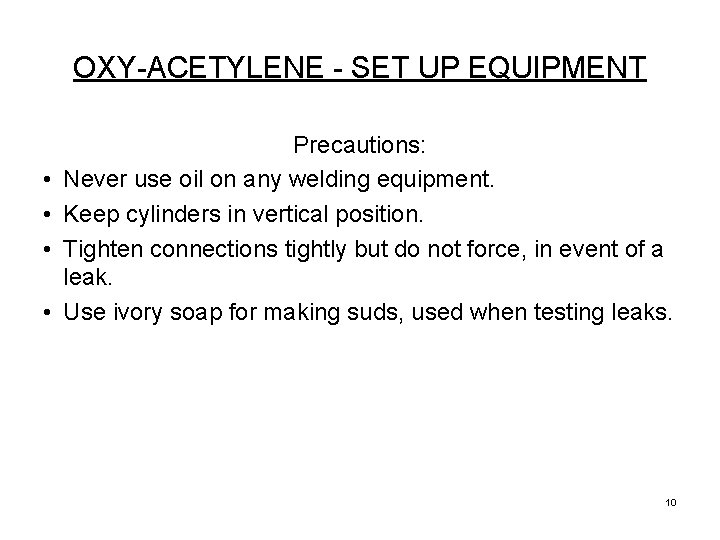
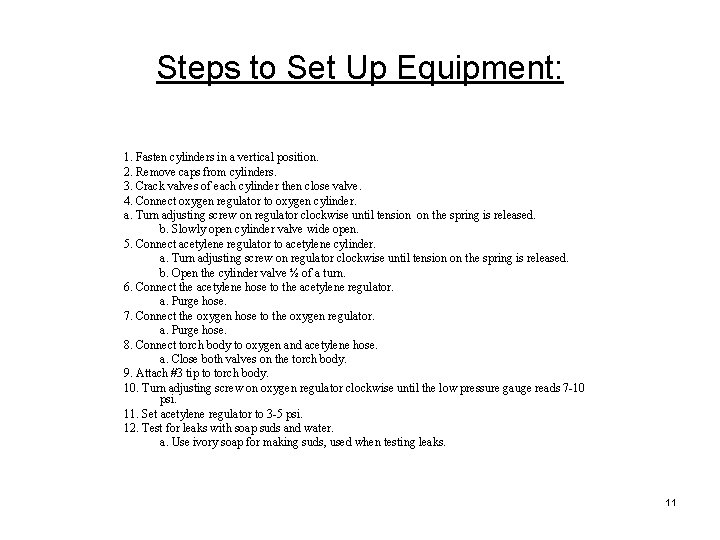
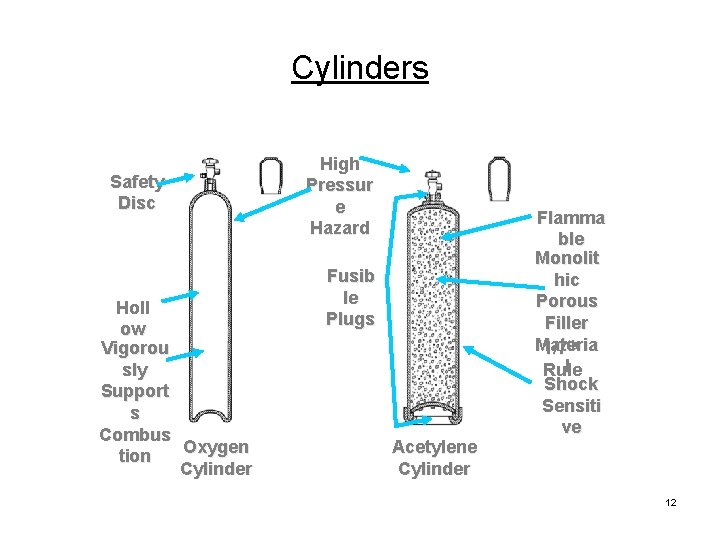
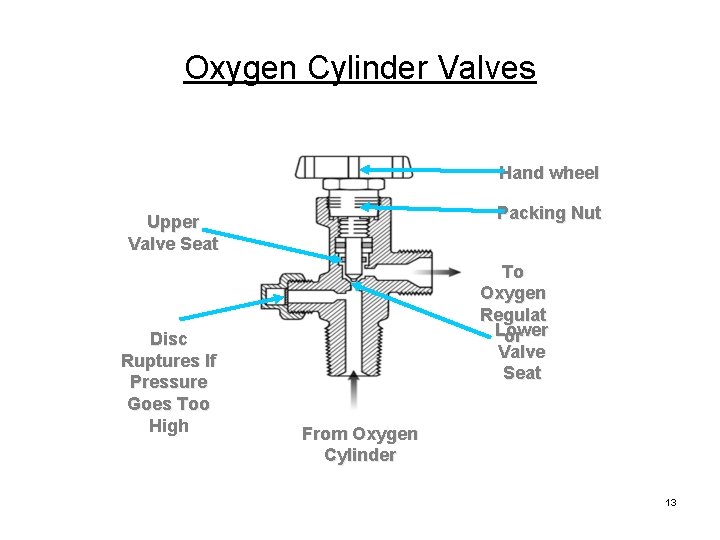
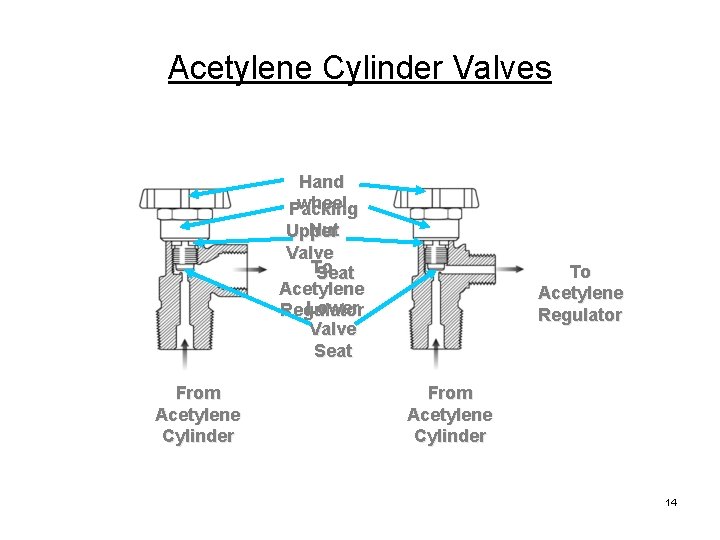
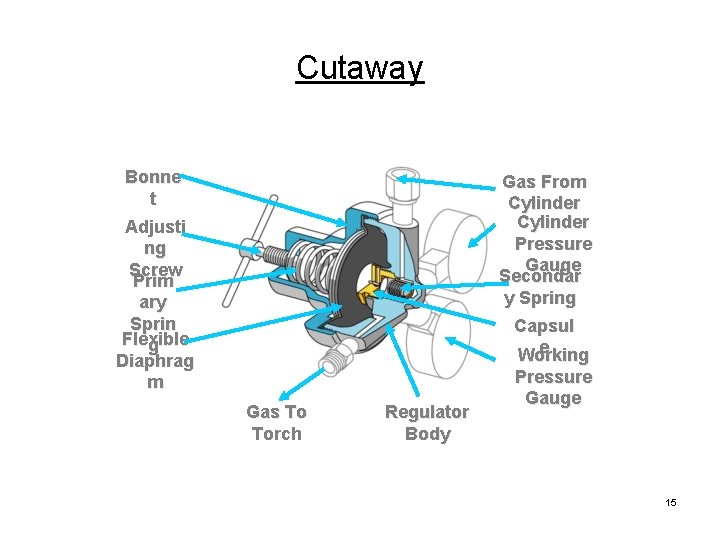
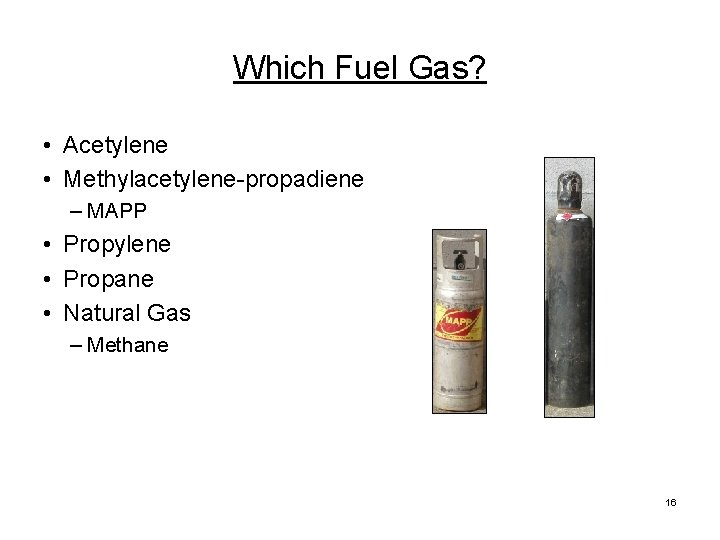
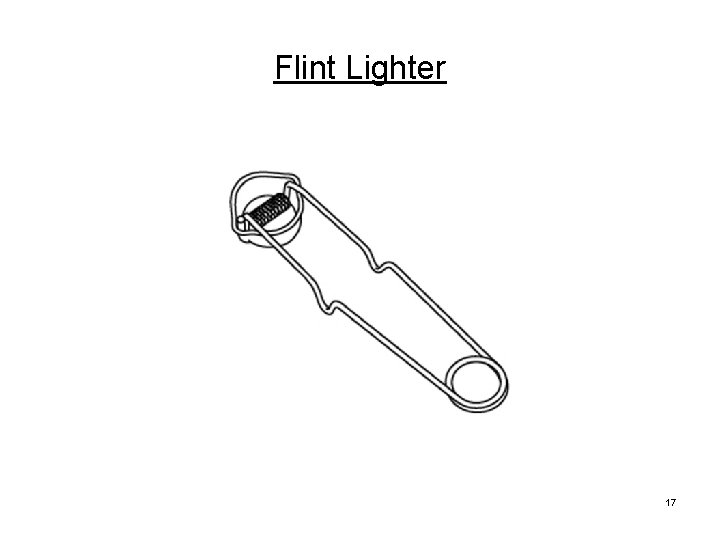
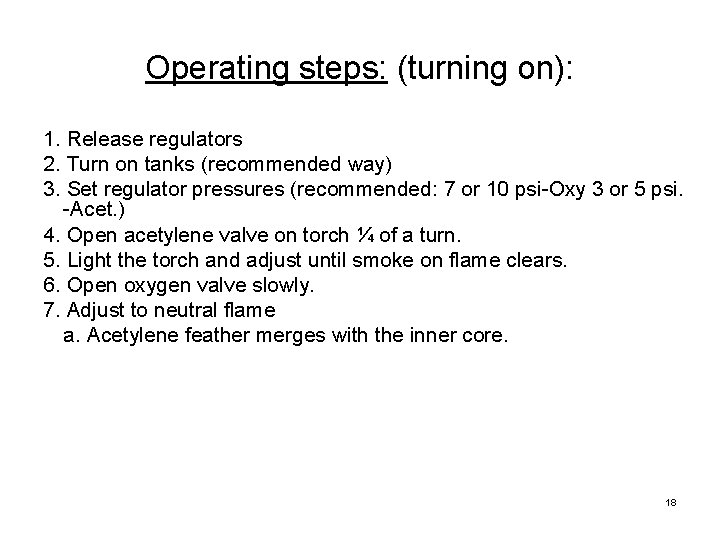
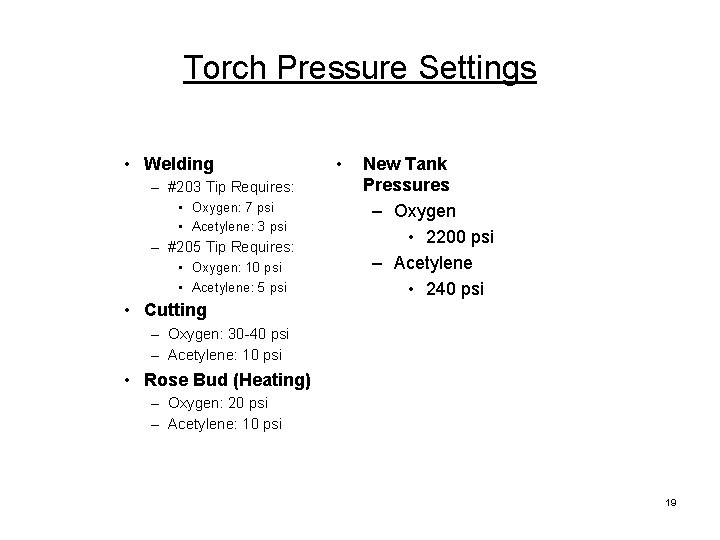
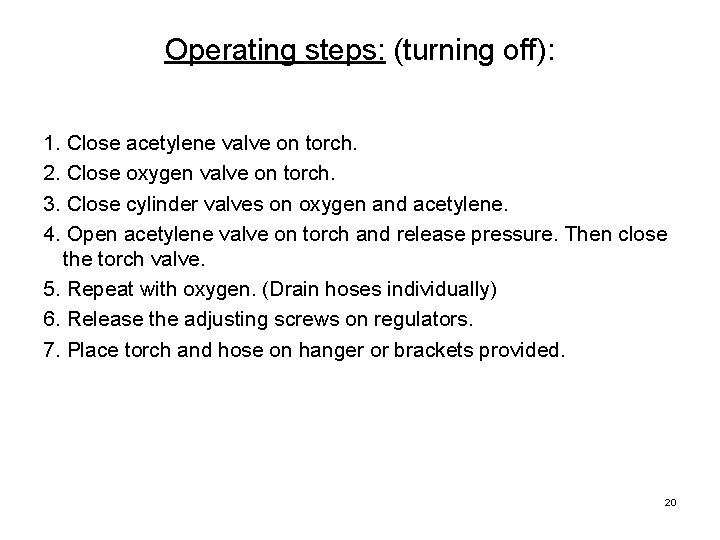
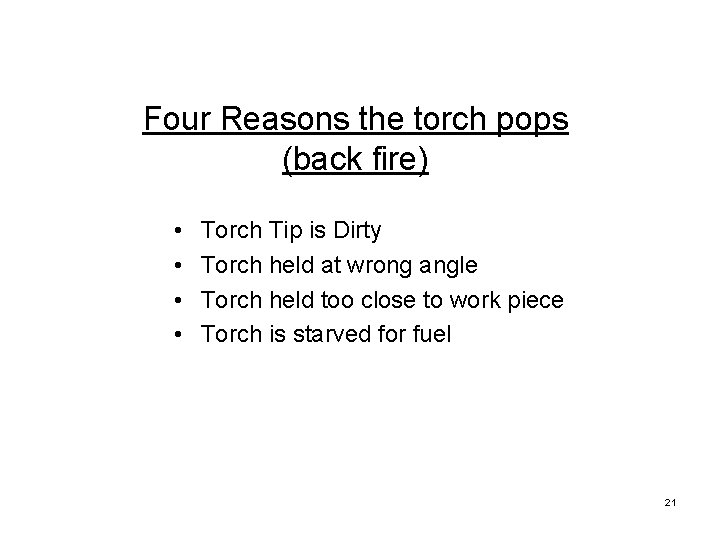
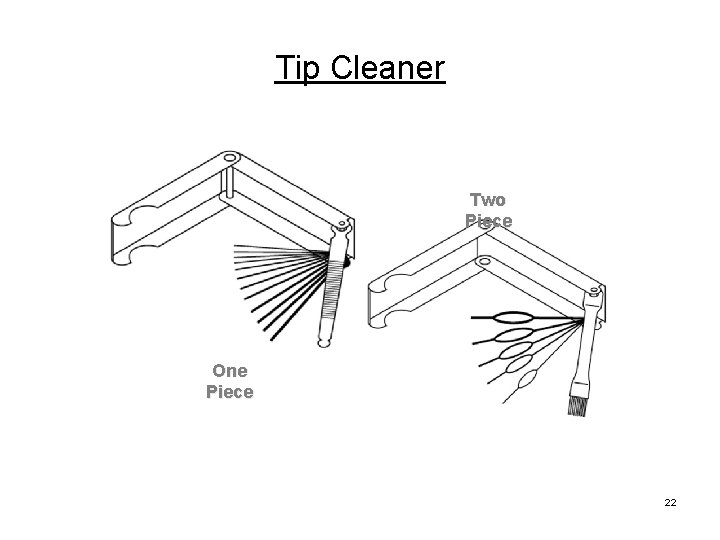
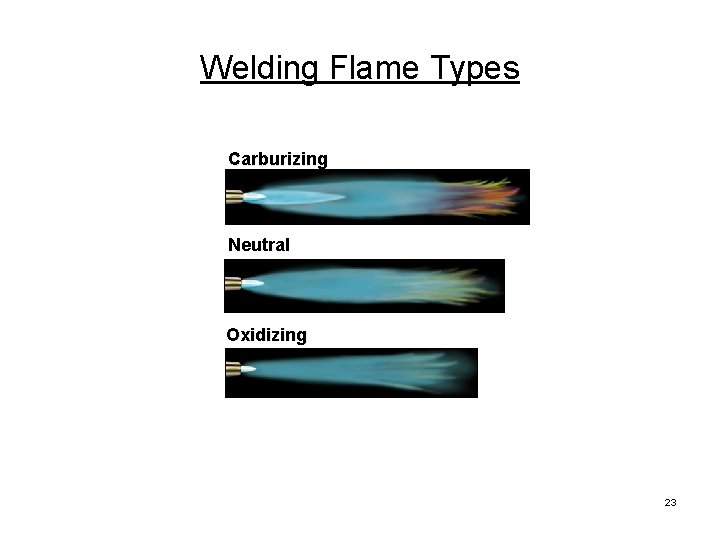
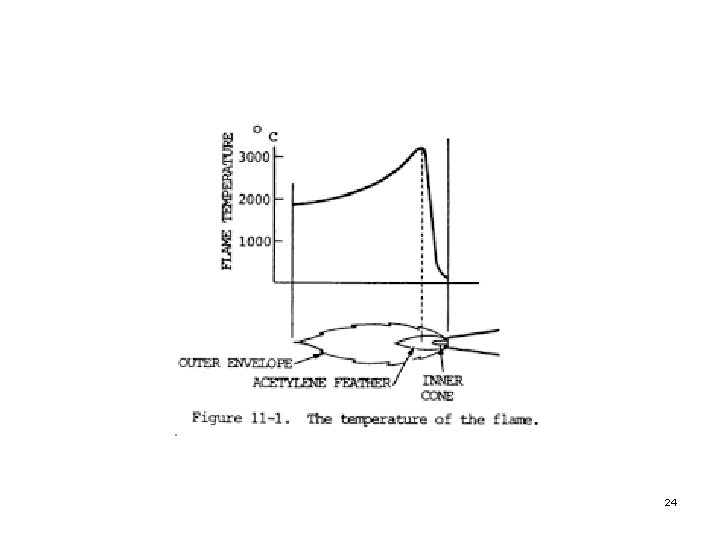
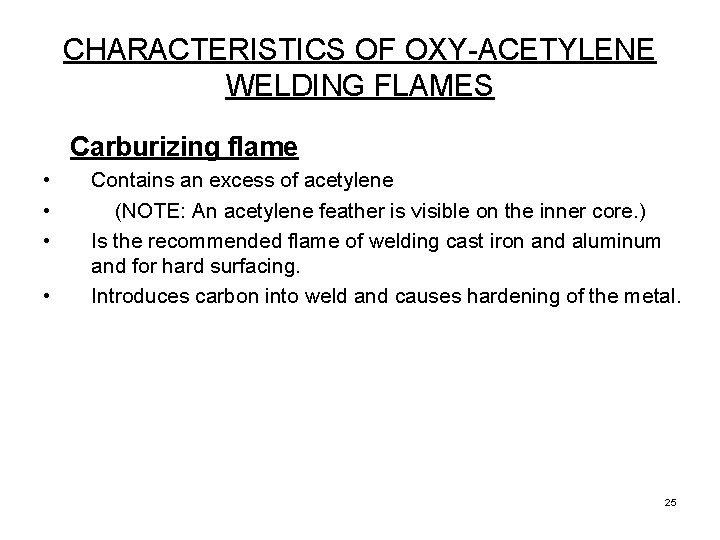
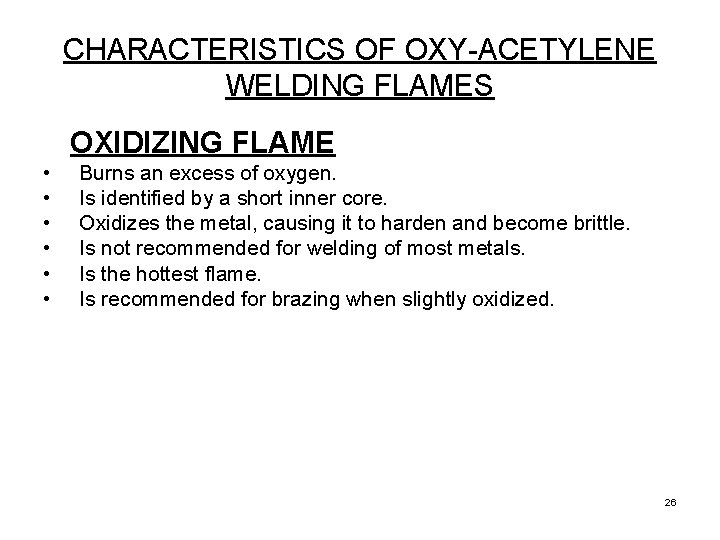
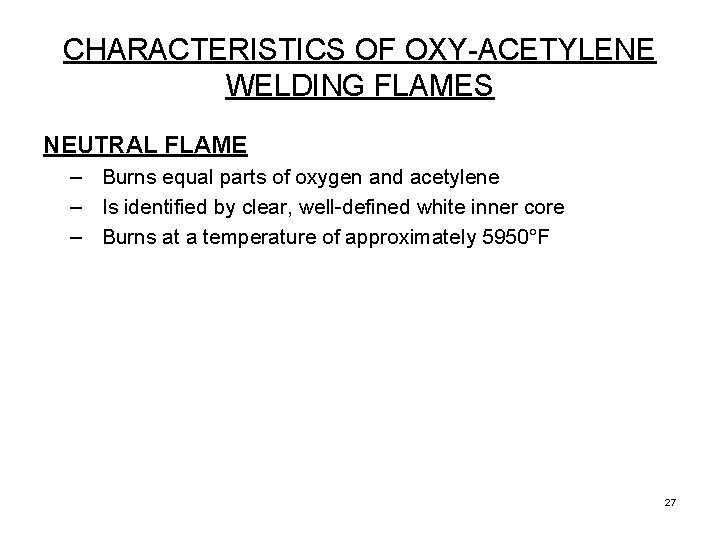
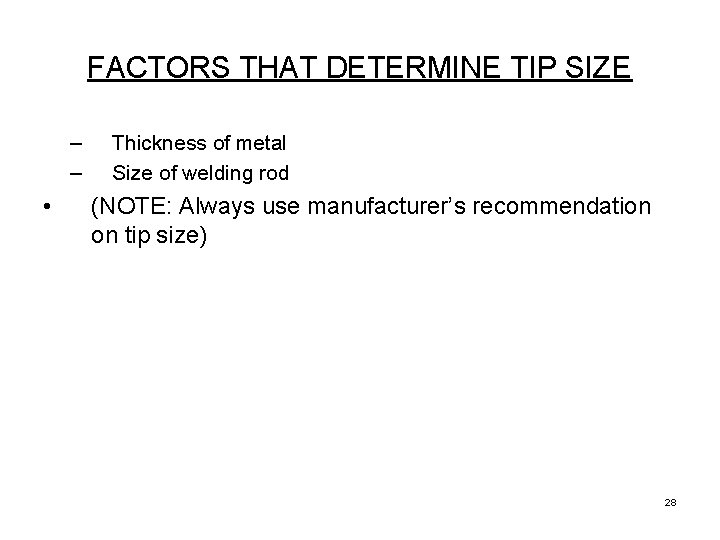
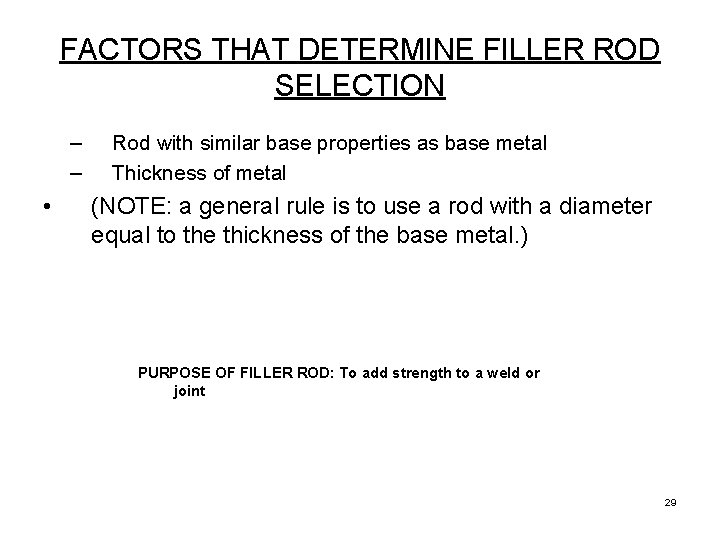
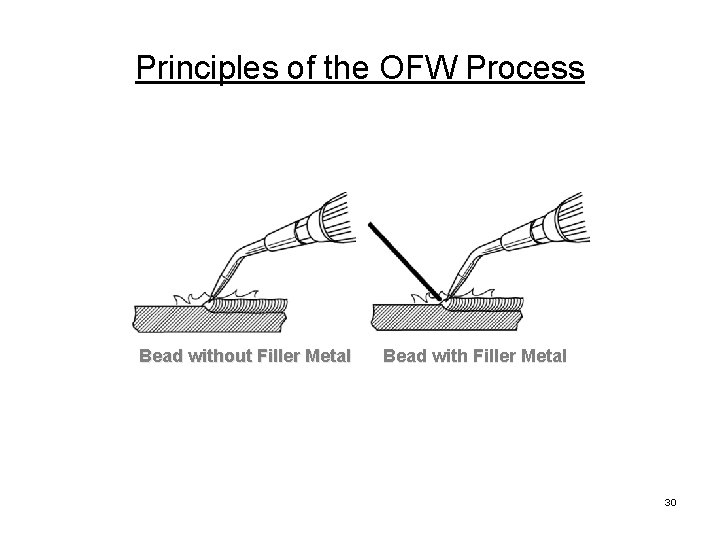
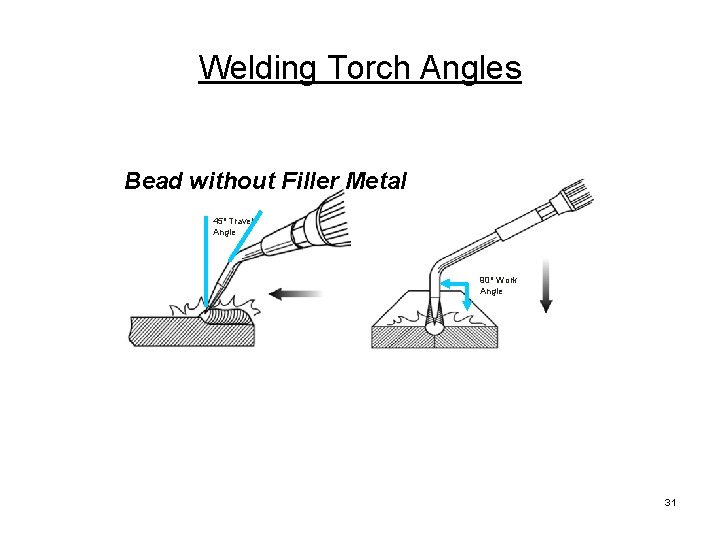

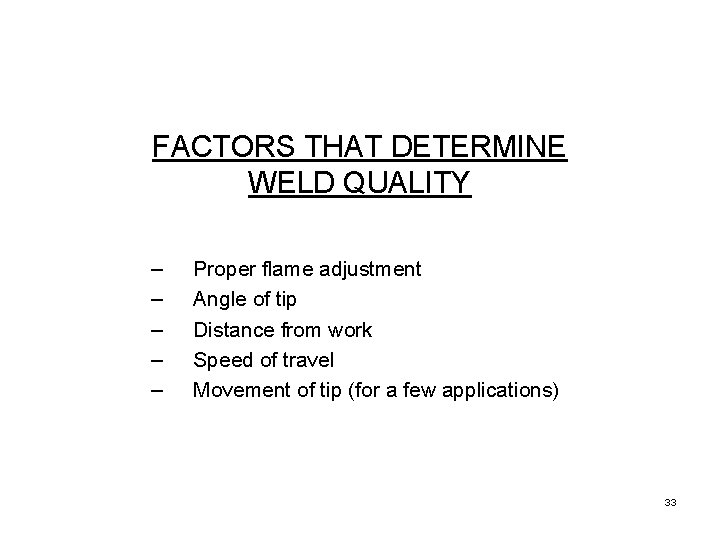
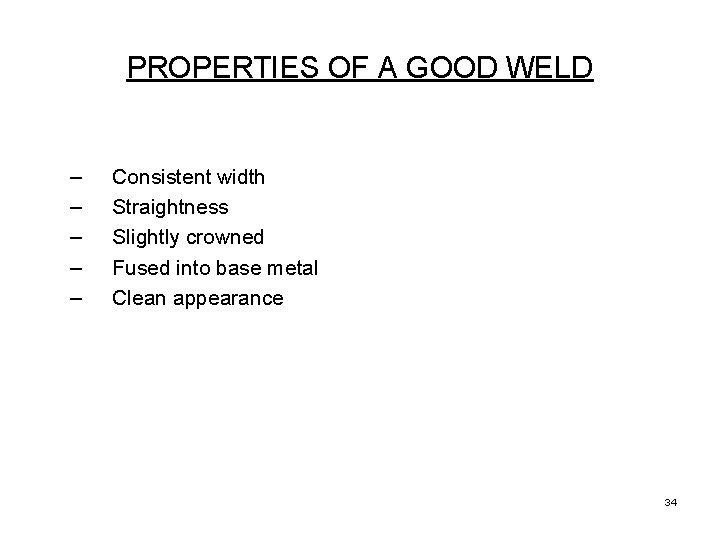
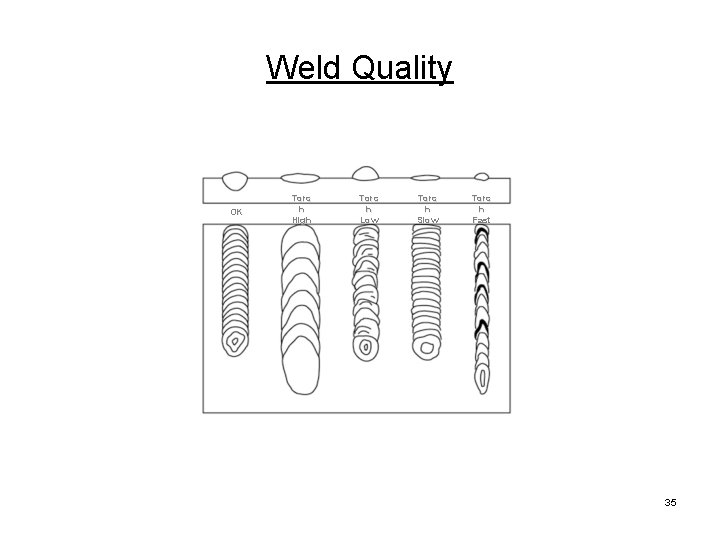
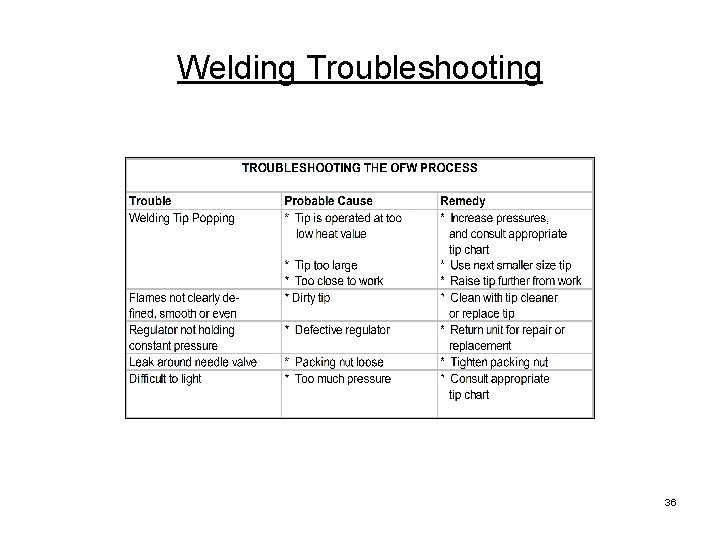
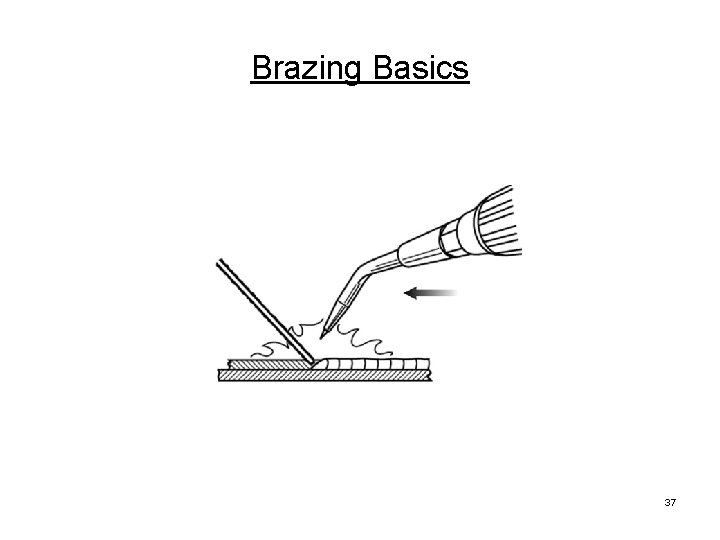
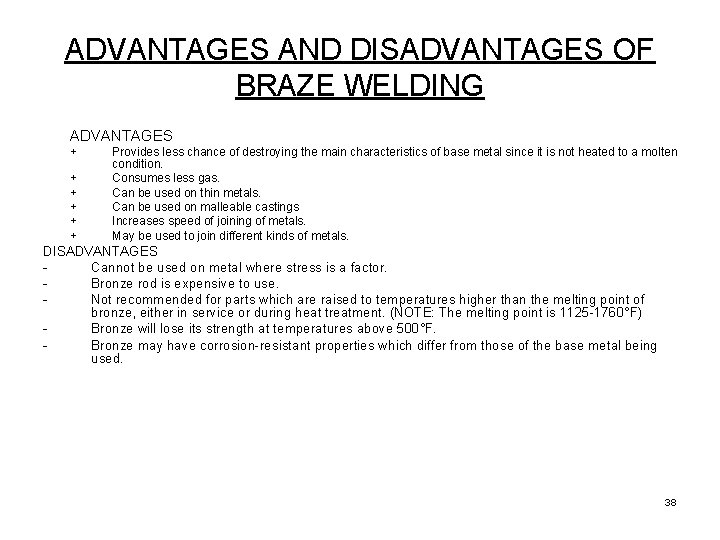
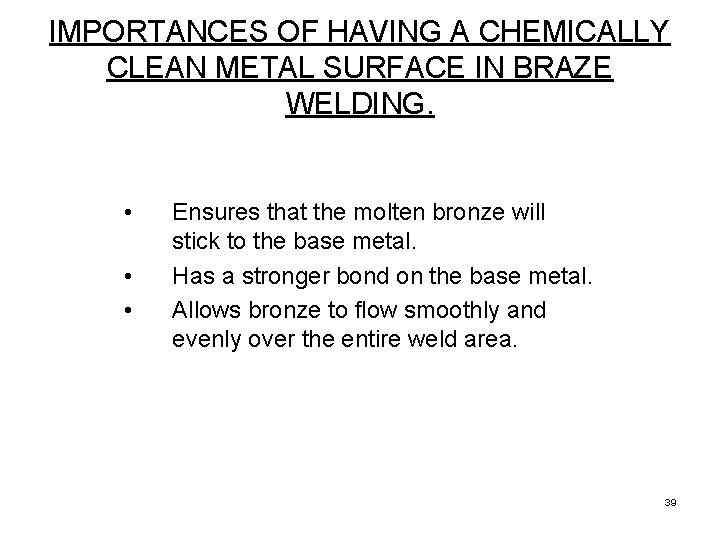
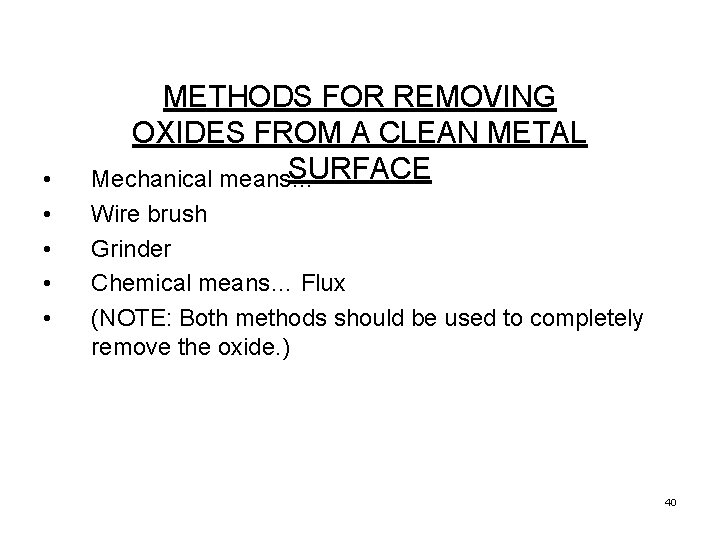
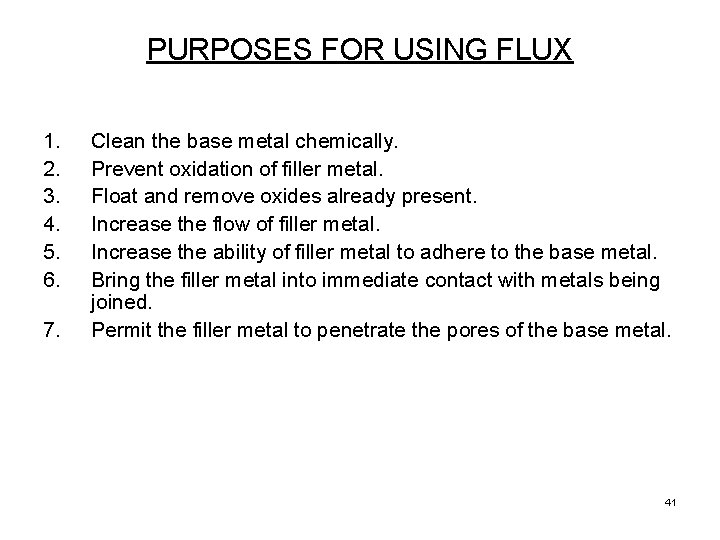
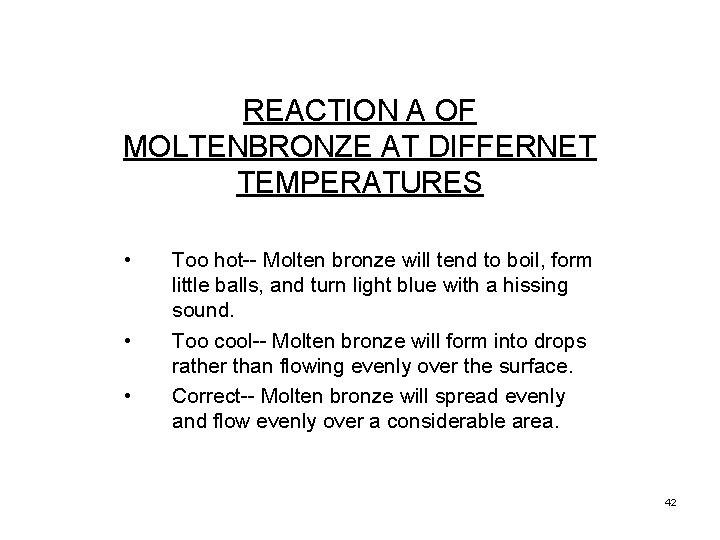
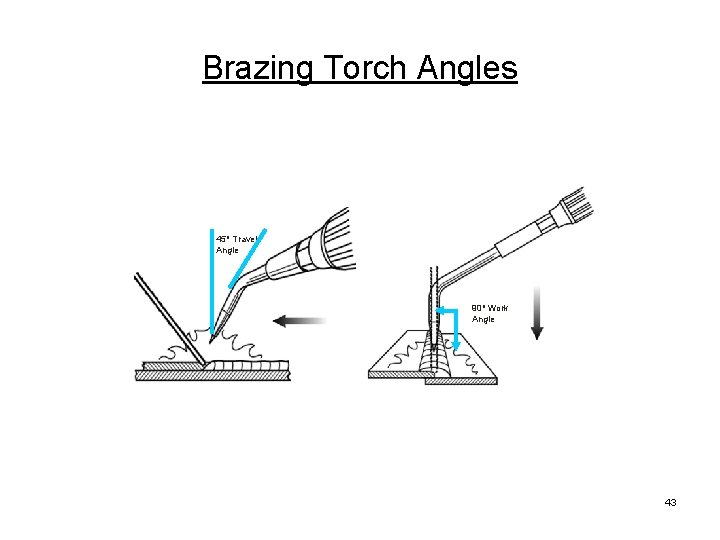
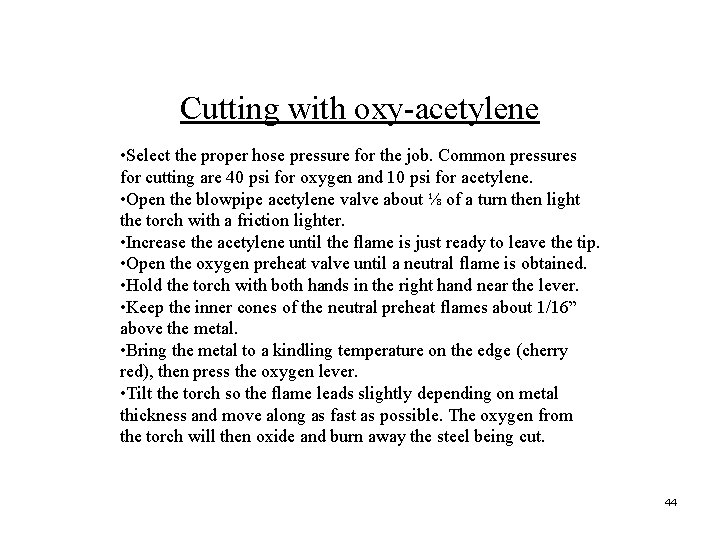
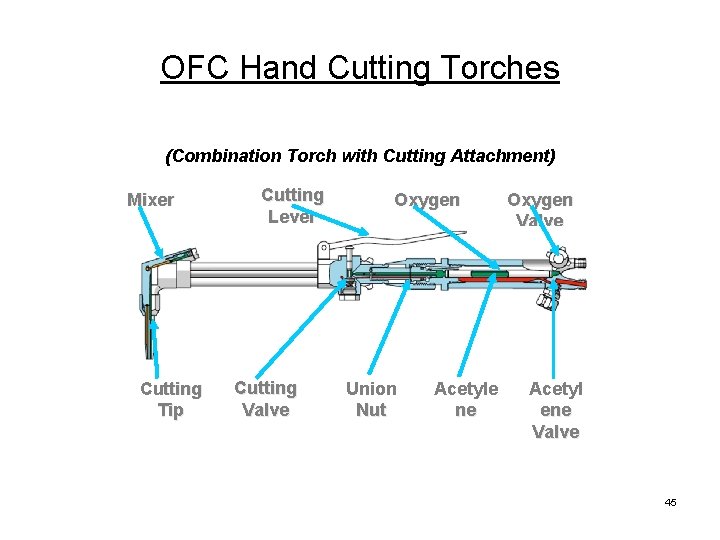
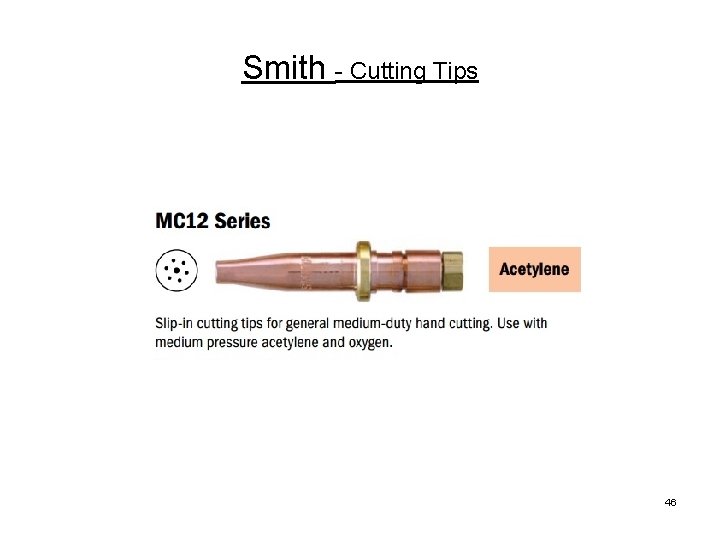
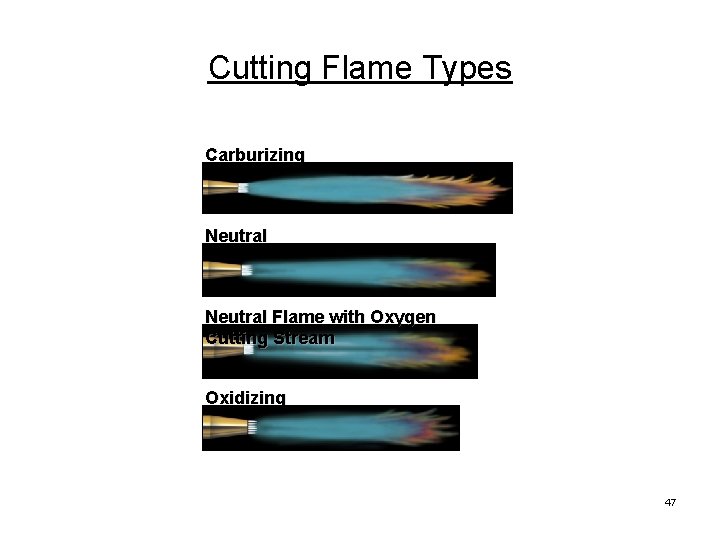
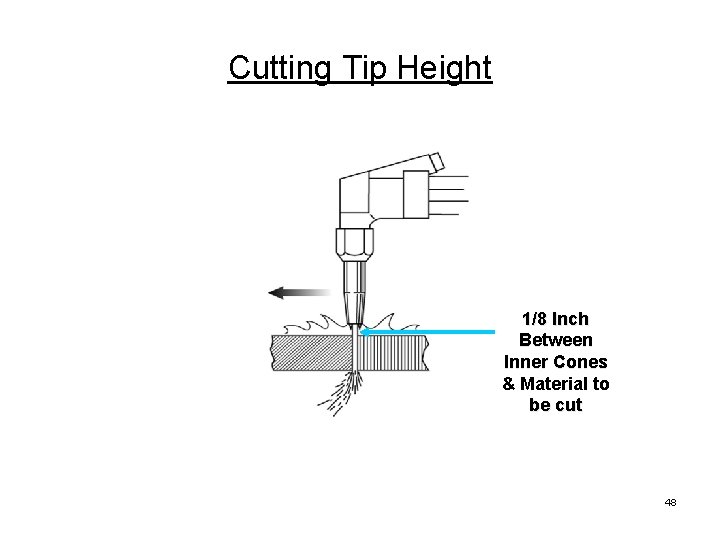
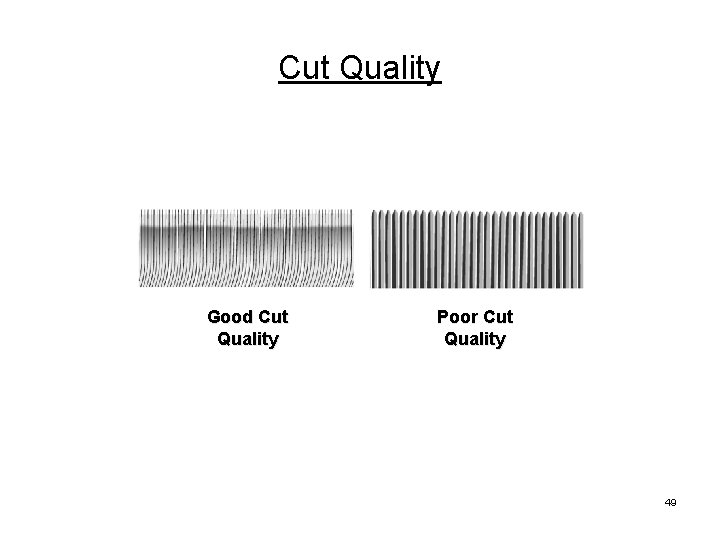
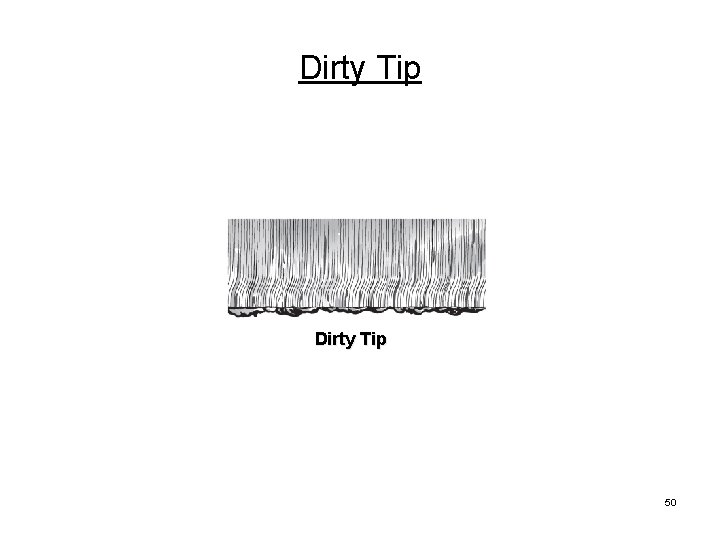

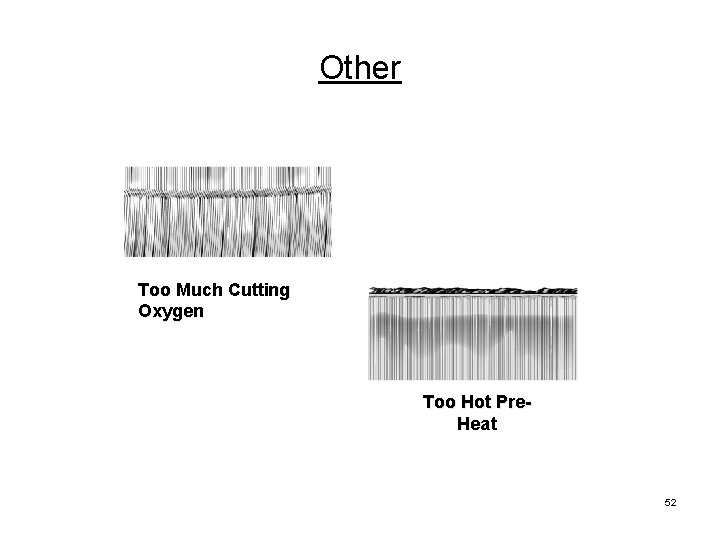
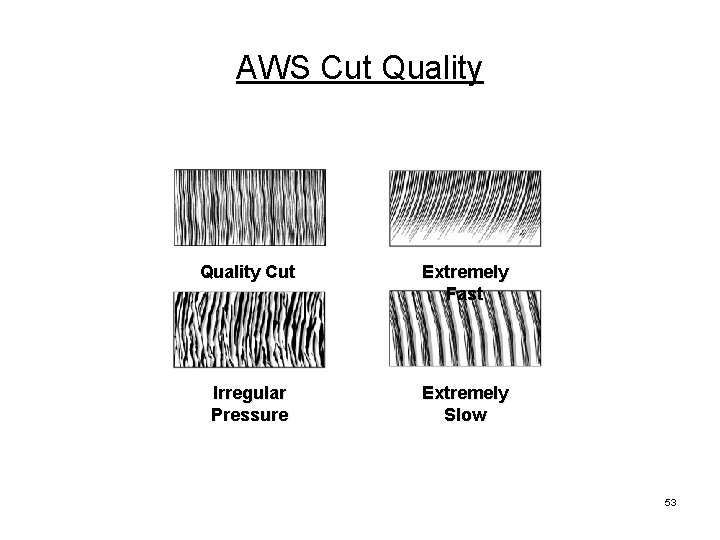
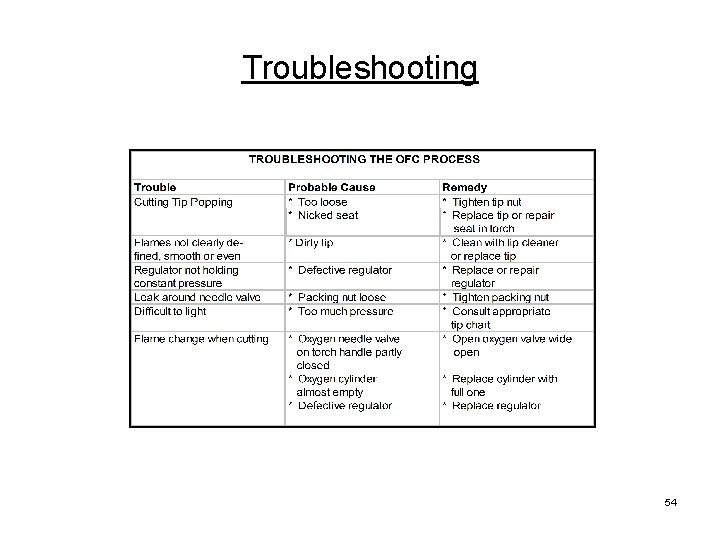
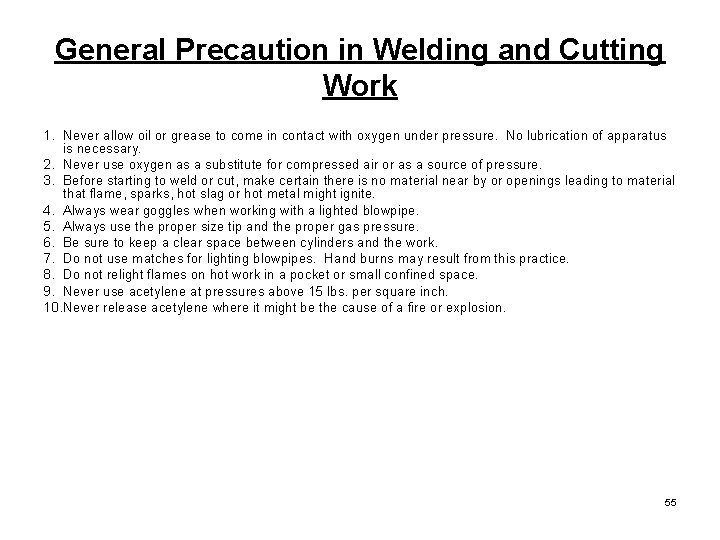
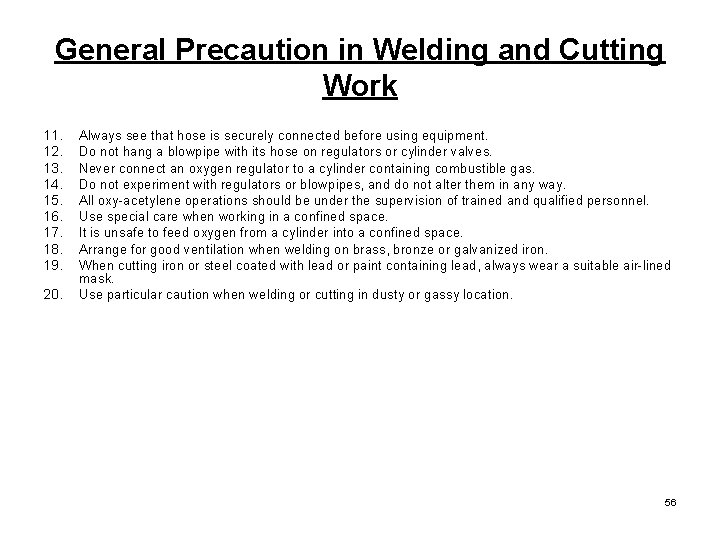
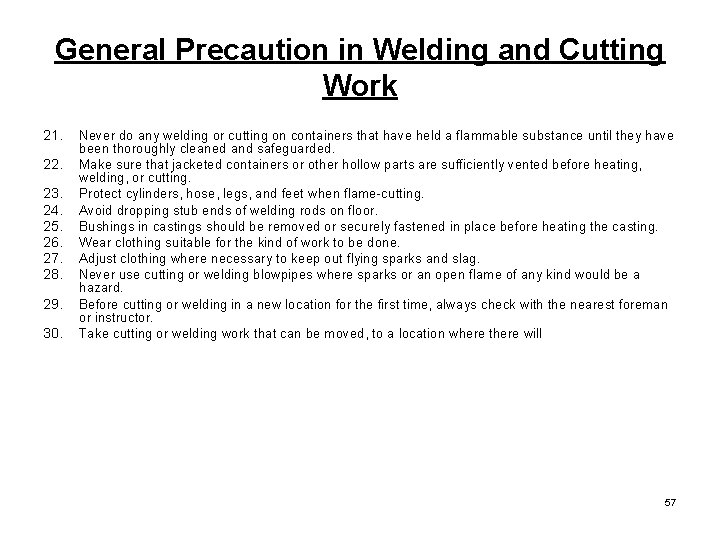
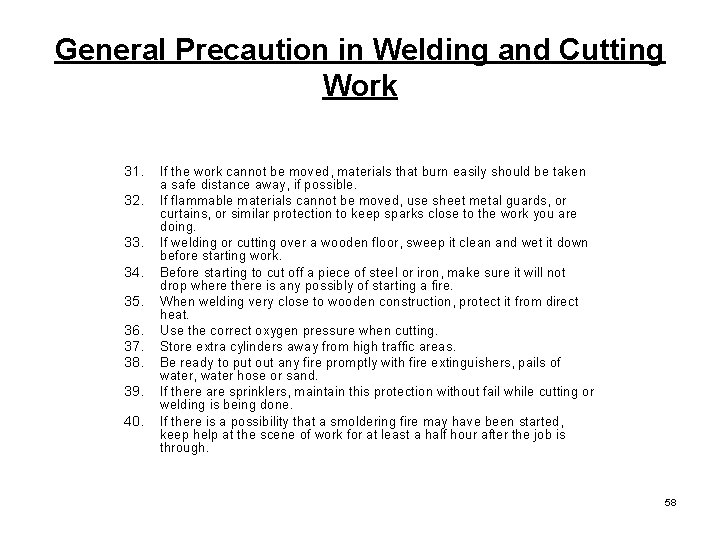
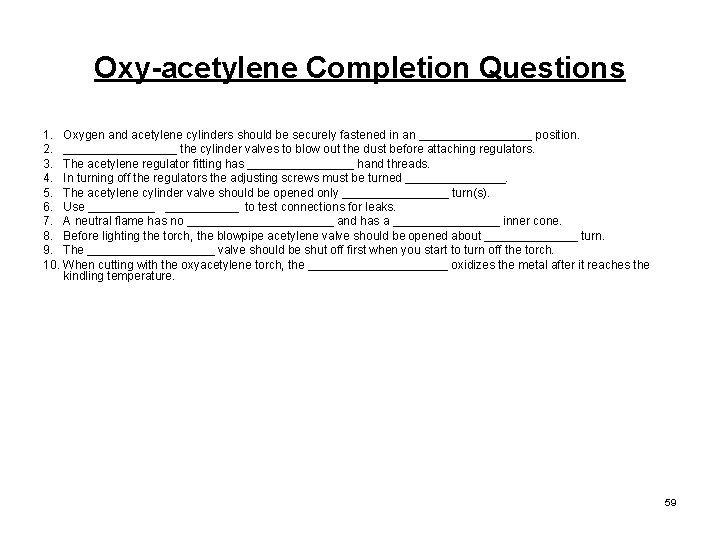
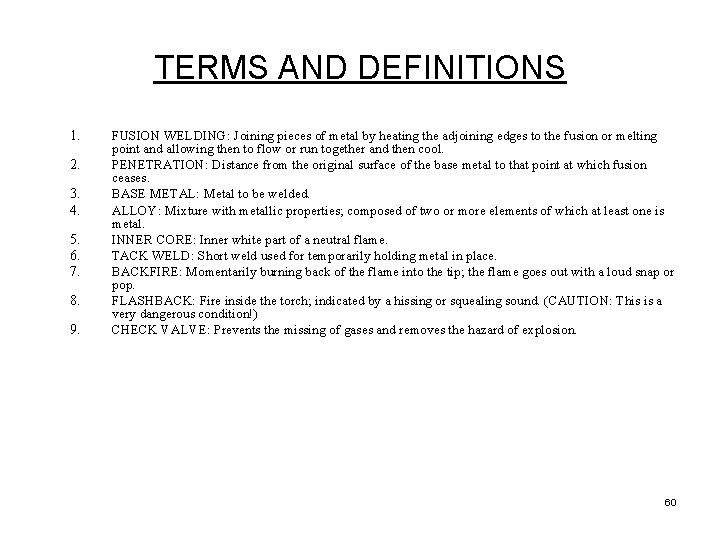
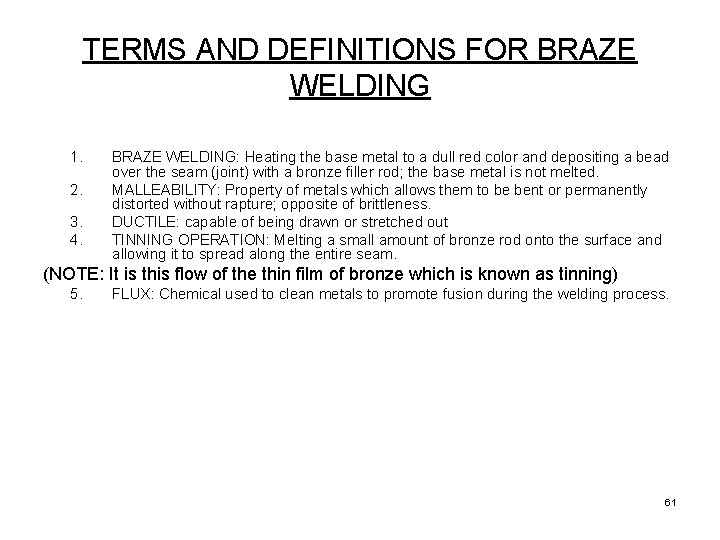
- Slides: 61
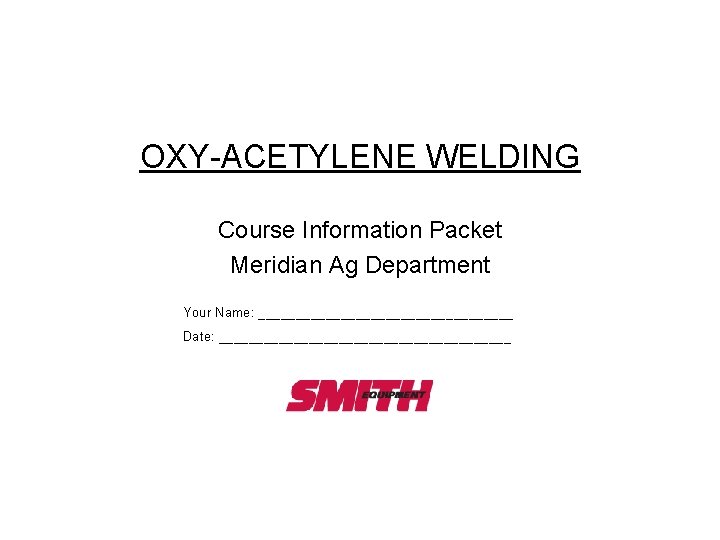
OXY-ACETYLENE WELDING Course Information Packet Meridian Ag Department Your Name: _________________ Date: ____________________
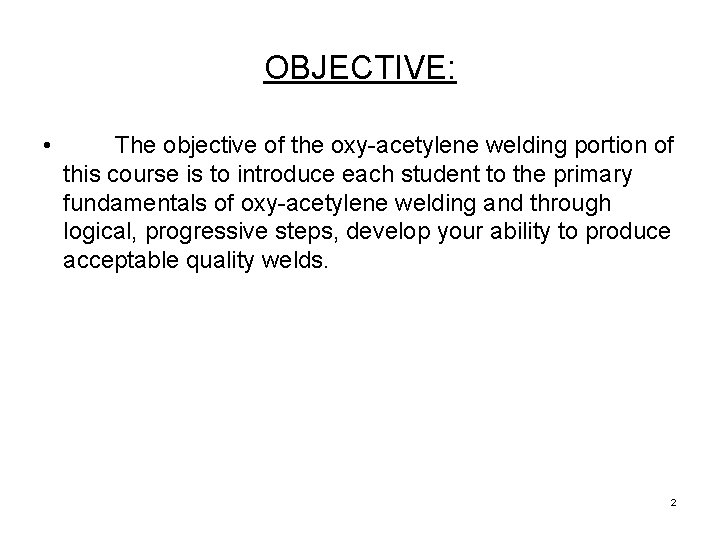
OBJECTIVE: • The objective of the oxy-acetylene welding portion of this course is to introduce each student to the primary fundamentals of oxy-acetylene welding and through logical, progressive steps, develop your ability to produce acceptable quality welds. 2
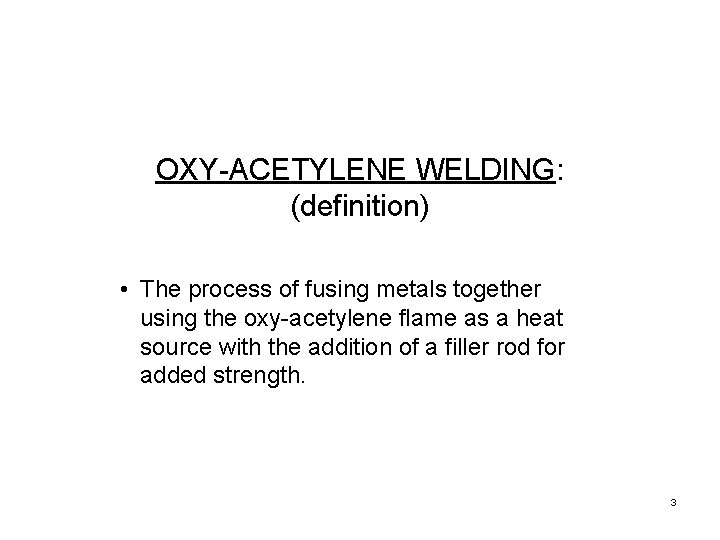
OXY-ACETYLENE WELDING: (definition) • The process of fusing metals together using the oxy-acetylene flame as a heat source with the addition of a filler rod for added strength. 3
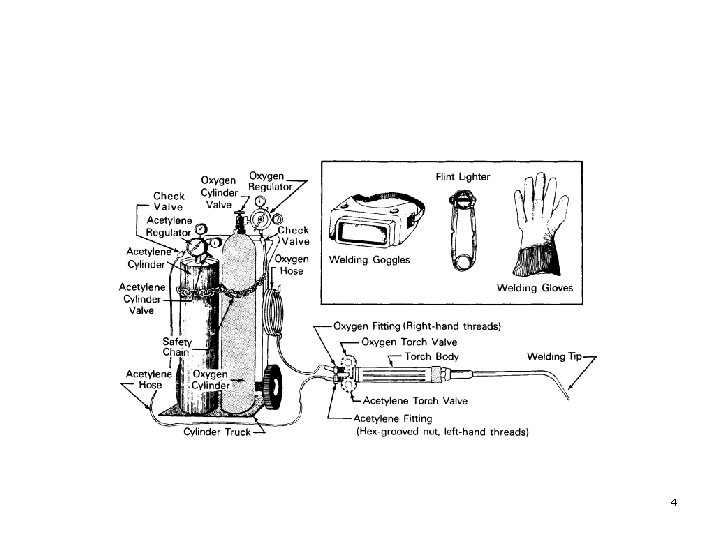
4
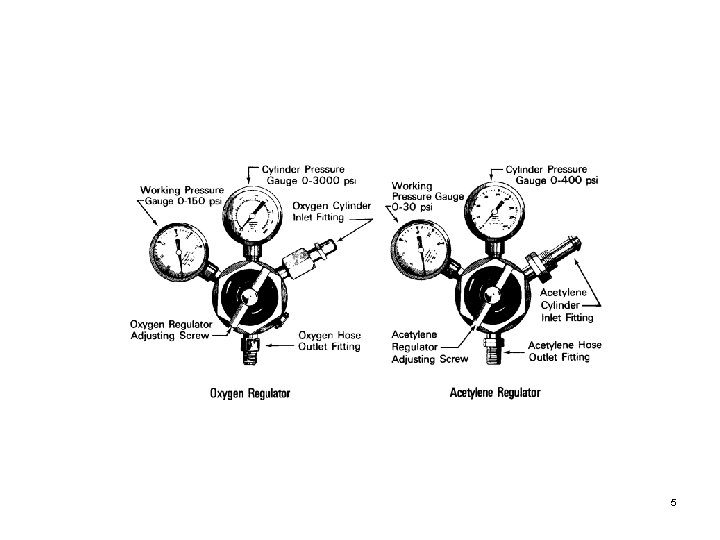
5
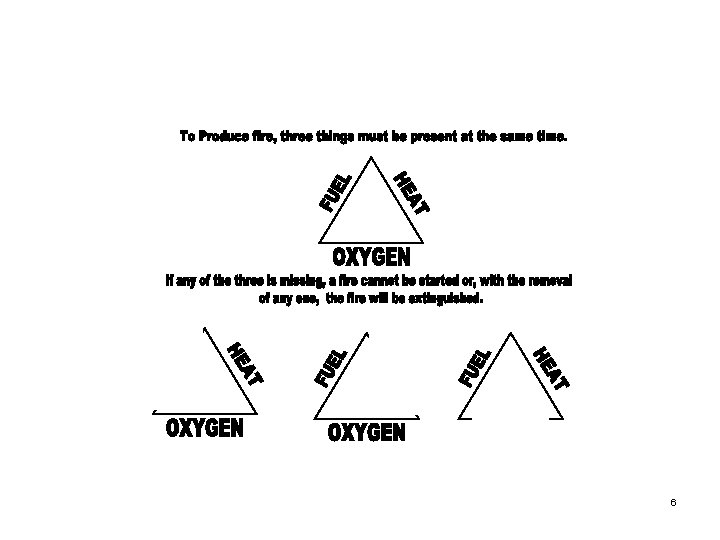
6
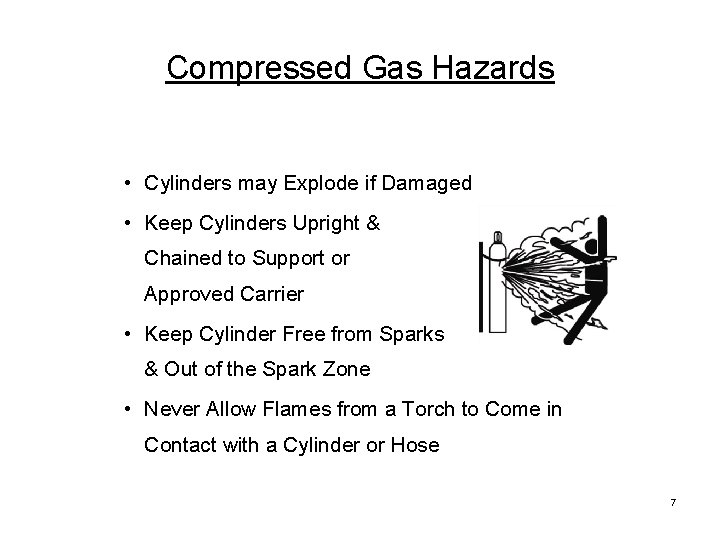
Compressed Gas Hazards • Cylinders may Explode if Damaged • Keep Cylinders Upright & Chained to Support or Approved Carrier • Keep Cylinder Free from Sparks & Out of the Spark Zone • Never Allow Flames from a Torch to Come in Contact with a Cylinder or Hose 7
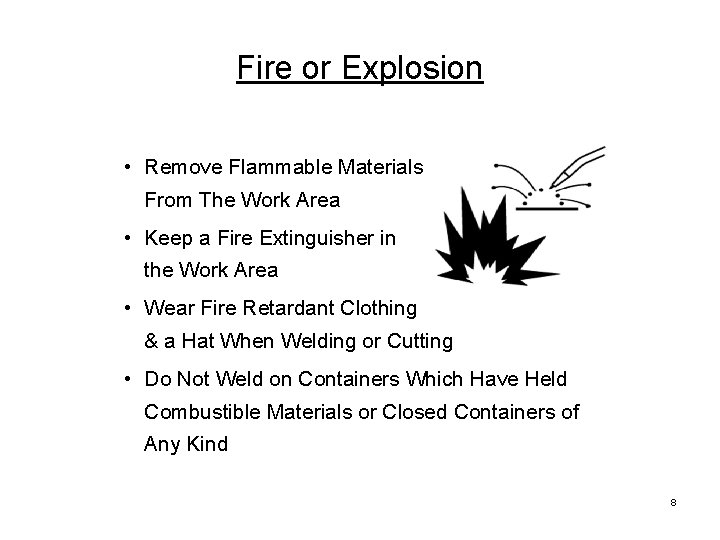
Fire or Explosion • Remove Flammable Materials From The Work Area • Keep a Fire Extinguisher in the Work Area • Wear Fire Retardant Clothing & a Hat When Welding or Cutting • Do Not Weld on Containers Which Have Held Combustible Materials or Closed Containers of Any Kind 8
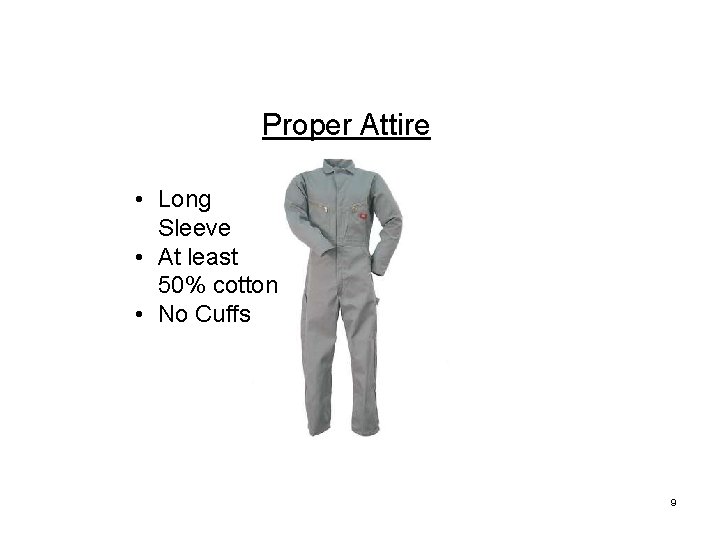
Proper Attire • Long Sleeve • At least 50% cotton • No Cuffs 9
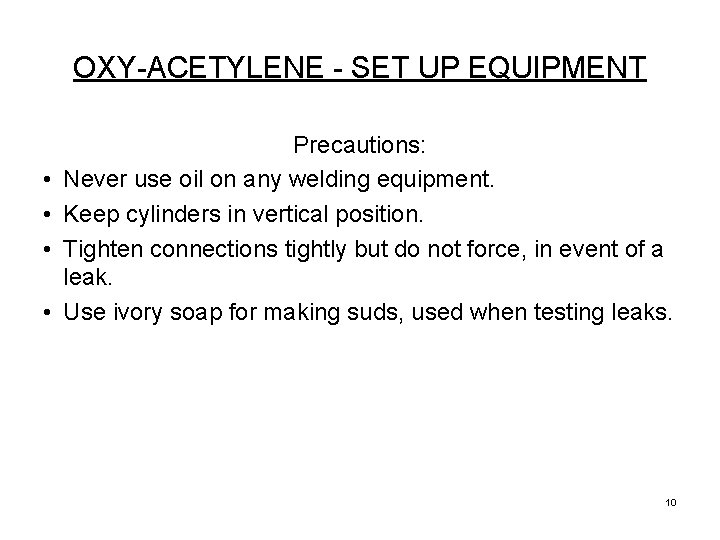
OXY-ACETYLENE - SET UP EQUIPMENT • • Precautions: Never use oil on any welding equipment. Keep cylinders in vertical position. Tighten connections tightly but do not force, in event of a leak. Use ivory soap for making suds, used when testing leaks. 10
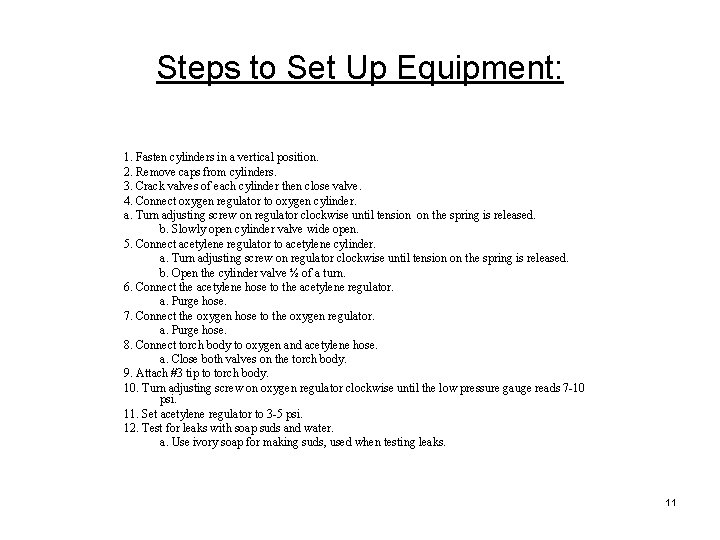
Steps to Set Up Equipment: 1. Fasten cylinders in a vertical position. 2. Remove caps from cylinders. 3. Crack valves of each cylinder then close valve. 4. Connect oxygen regulator to oxygen cylinder. a. Turn adjusting screw on regulator clockwise until tension on the spring is released. b. Slowly open cylinder valve wide open. 5. Connect acetylene regulator to acetylene cylinder. a. Turn adjusting screw on regulator clockwise until tension on the spring is released. b. Open the cylinder valve ½ of a turn. 6. Connect the acetylene hose to the acetylene regulator. a. Purge hose. 7. Connect the oxygen hose to the oxygen regulator. a. Purge hose. 8. Connect torch body to oxygen and acetylene hose. a. Close both valves on the torch body. 9. Attach #3 tip to torch body. 10. Turn adjusting screw on oxygen regulator clockwise until the low pressure gauge reads 7 -10 psi. 11. Set acetylene regulator to 3 -5 psi. 12. Test for leaks with soap suds and water. a. Use ivory soap for making suds, used when testing leaks. 11
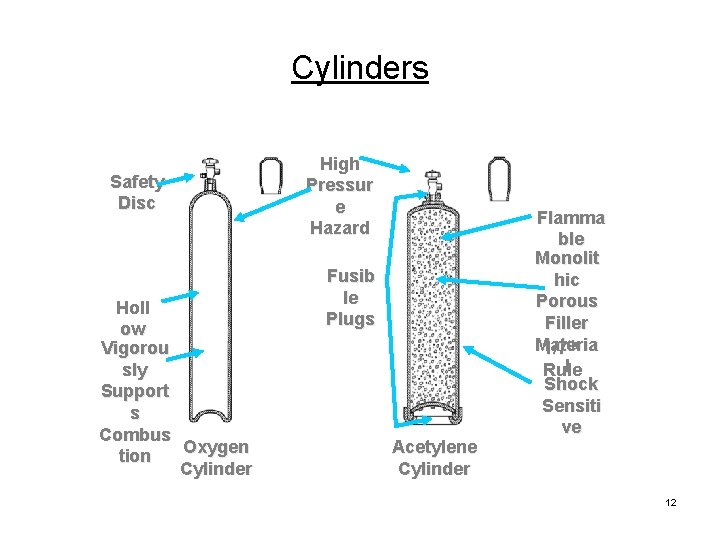
Cylinders Safety Disc Holl ow Vigorou sly Support s Combus Oxygen tion Cylinder High Pressur e Hazard Fusib le Plugs Acetylene Cylinder Flamma ble Monolit hic Porous Filler Materia 1/7 th l Rule Shock Sensiti ve 12
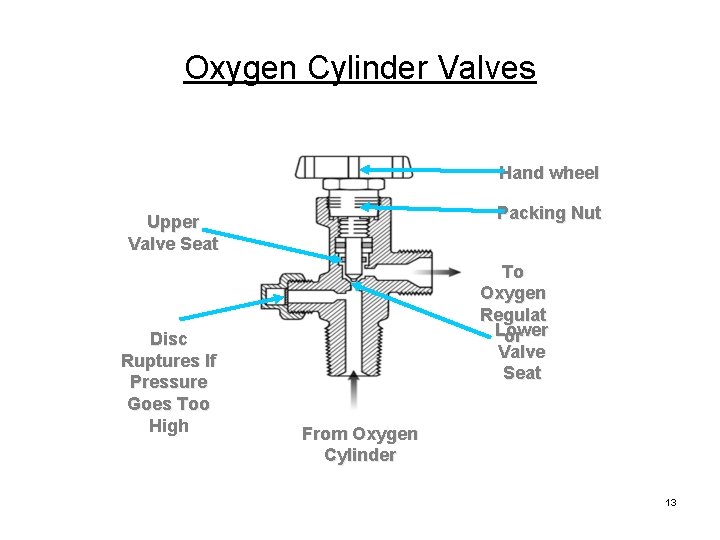
Oxygen Cylinder Valves Hand wheel Packing Nut Upper Valve Seat Disc Ruptures If Pressure Goes Too High To Oxygen Regulat Lower or Valve Seat From Oxygen Cylinder 13
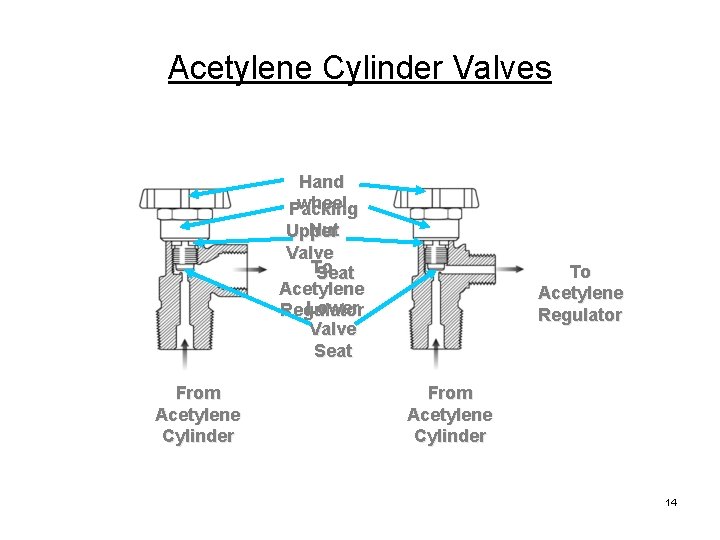
Acetylene Cylinder Valves Hand wheel Packing Nut Upper Valve To Seat Acetylene Lower Regulator Valve Seat From Acetylene Cylinder To Acetylene Regulator From Acetylene Cylinder 14
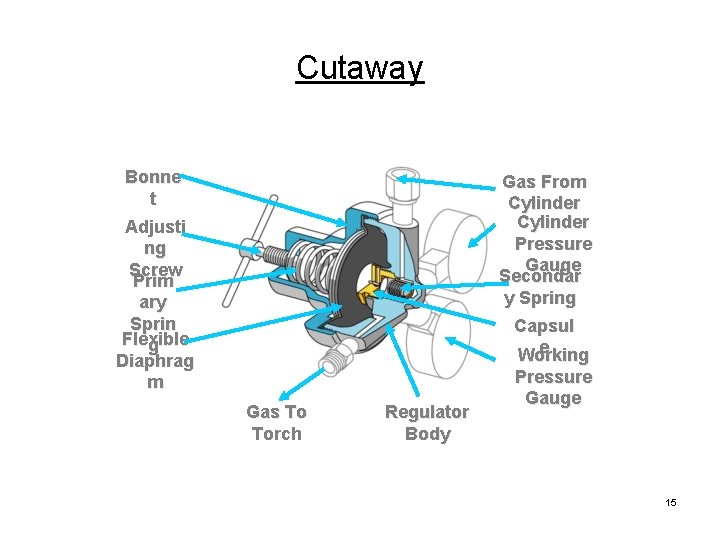
Cutaway Bonne t Gas From Cylinder Pressure Gauge Secondar y Spring Adjusti ng Screw Prim ary Sprin Flexible g Diaphrag m Capsul e Working Gas To Torch Regulator Body Pressure Gauge 15
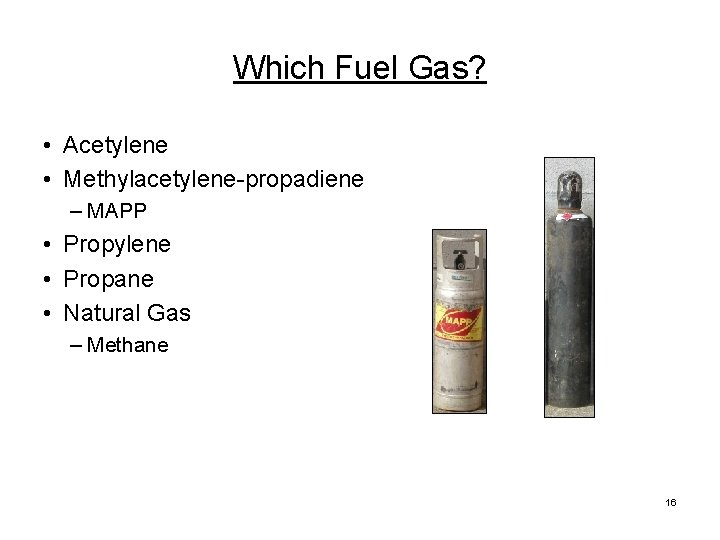
Which Fuel Gas? • Acetylene • Methylacetylene-propadiene – MAPP • Propylene • Propane • Natural Gas – Methane 16
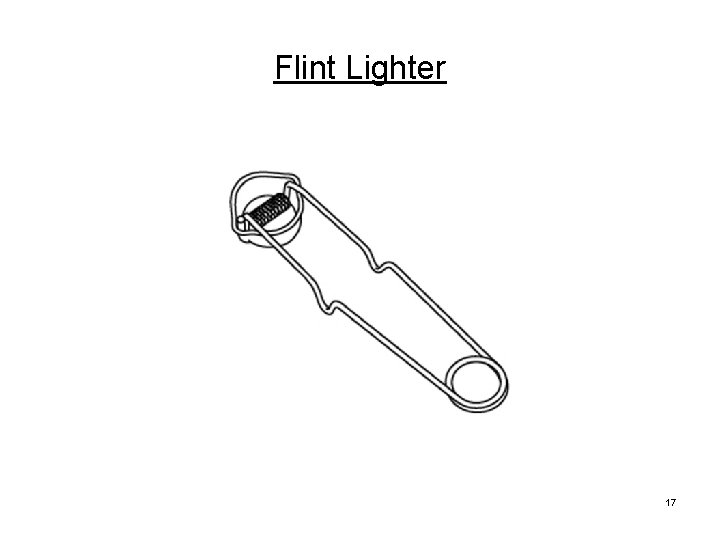
Flint Lighter 17
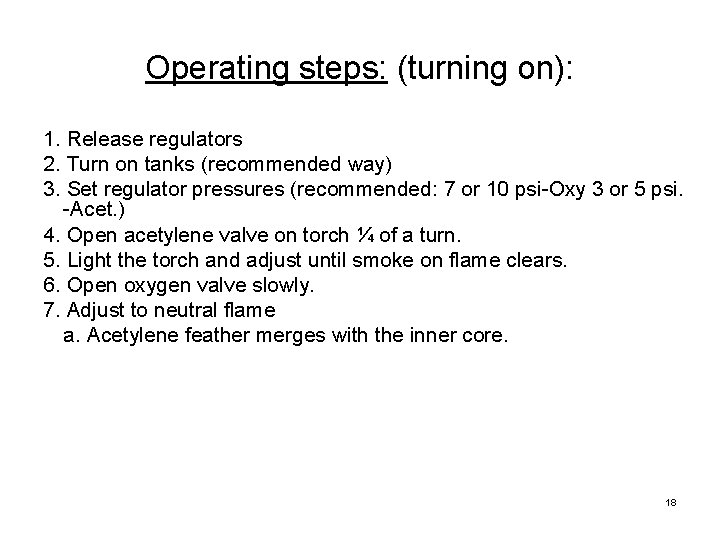
Operating steps: (turning on): 1. Release regulators 2. Turn on tanks (recommended way) 3. Set regulator pressures (recommended: 7 or 10 psi-Oxy 3 or 5 psi. -Acet. ) 4. Open acetylene valve on torch ¼ of a turn. 5. Light the torch and adjust until smoke on flame clears. 6. Open oxygen valve slowly. 7. Adjust to neutral flame a. Acetylene feather merges with the inner core. 18
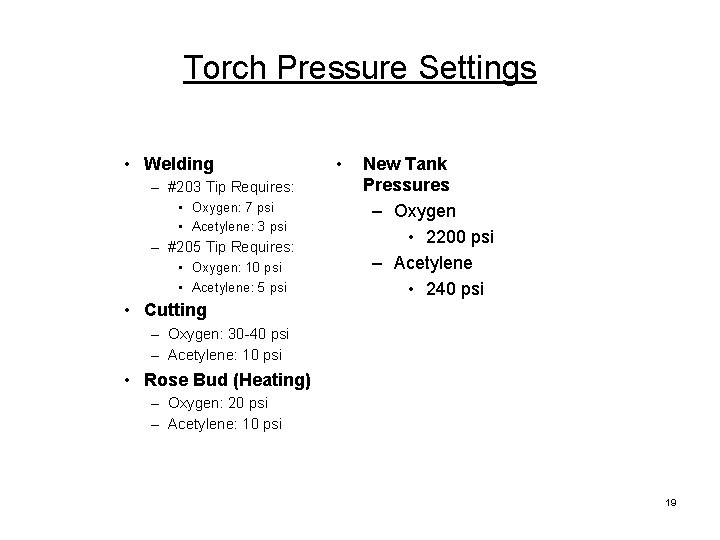
Torch Pressure Settings • Welding – #203 Tip Requires: • Oxygen: 7 psi • Acetylene: 3 psi – #205 Tip Requires: • Oxygen: 10 psi • Acetylene: 5 psi • New Tank Pressures – Oxygen • 2200 psi – Acetylene • 240 psi • Cutting – Oxygen: 30 -40 psi – Acetylene: 10 psi • Rose Bud (Heating) – Oxygen: 20 psi – Acetylene: 10 psi 19
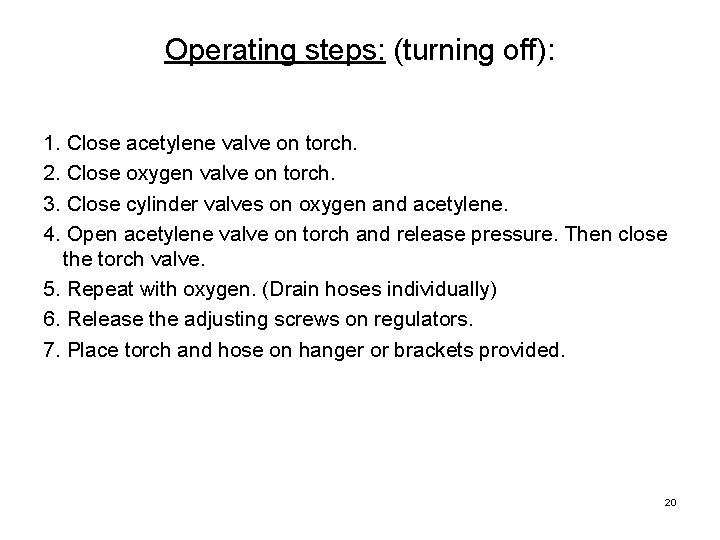
Operating steps: (turning off): 1. Close acetylene valve on torch. 2. Close oxygen valve on torch. 3. Close cylinder valves on oxygen and acetylene. 4. Open acetylene valve on torch and release pressure. Then close the torch valve. 5. Repeat with oxygen. (Drain hoses individually) 6. Release the adjusting screws on regulators. 7. Place torch and hose on hanger or brackets provided. 20
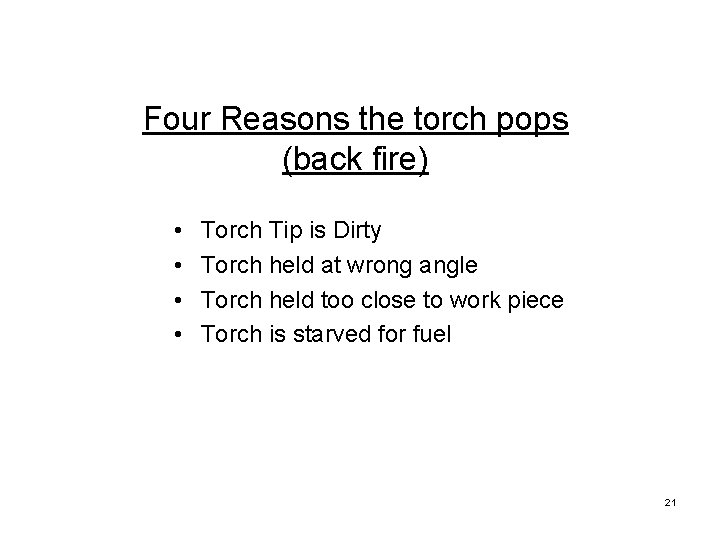
Four Reasons the torch pops (back fire) • • Torch Tip is Dirty Torch held at wrong angle Torch held too close to work piece Torch is starved for fuel 21
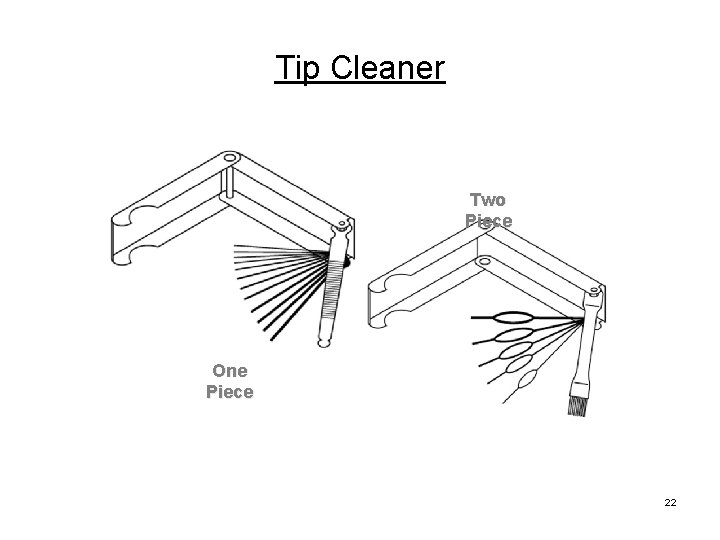
Tip Cleaner Two Piece One Piece 22
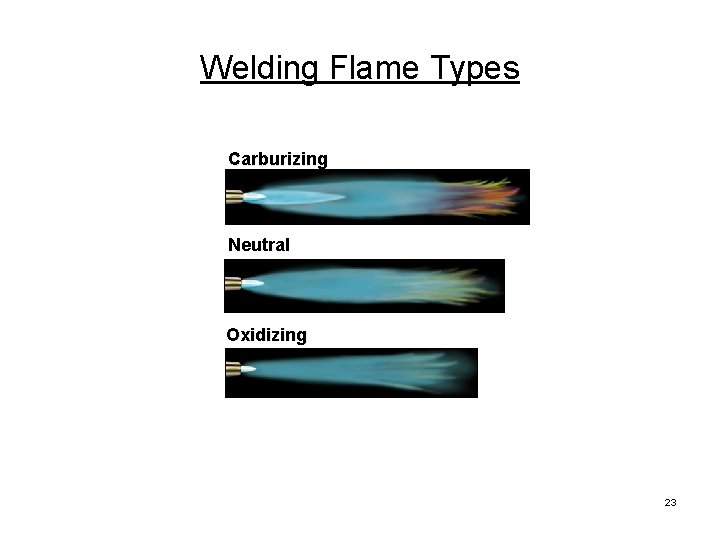
Welding Flame Types Carburizing Flame Neutral Flame Oxidizing Flame 23
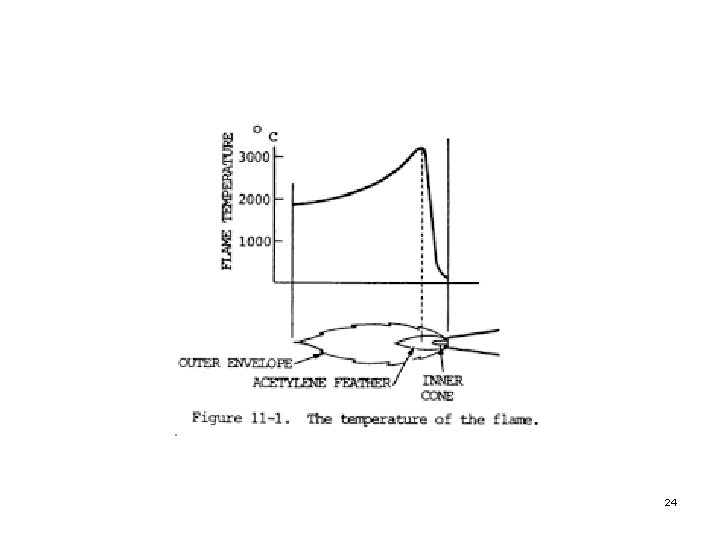
24
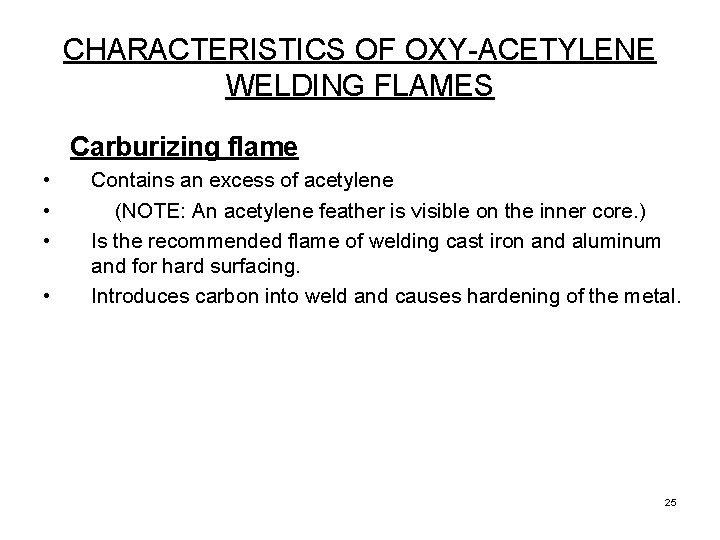
CHARACTERISTICS OF OXY-ACETYLENE WELDING FLAMES Carburizing flame • • Contains an excess of acetylene (NOTE: An acetylene feather is visible on the inner core. ) Is the recommended flame of welding cast iron and aluminum and for hard surfacing. Introduces carbon into weld and causes hardening of the metal. 25
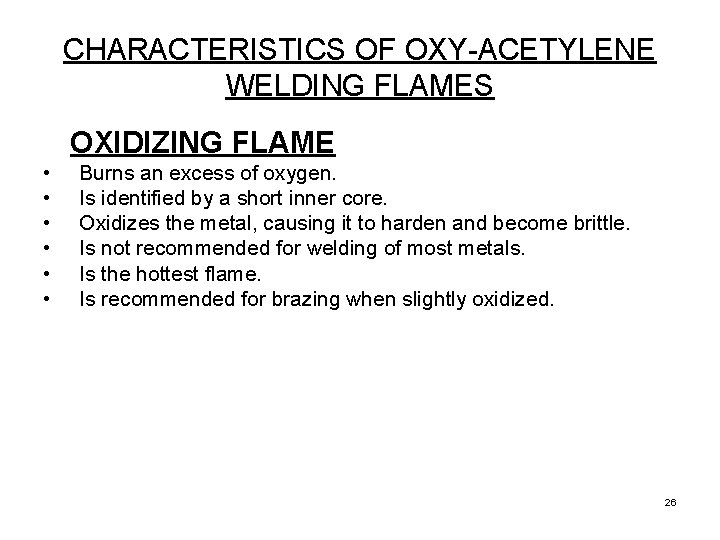
CHARACTERISTICS OF OXY-ACETYLENE WELDING FLAMES OXIDIZING FLAME • • • Burns an excess of oxygen. Is identified by a short inner core. Oxidizes the metal, causing it to harden and become brittle. Is not recommended for welding of most metals. Is the hottest flame. Is recommended for brazing when slightly oxidized. 26
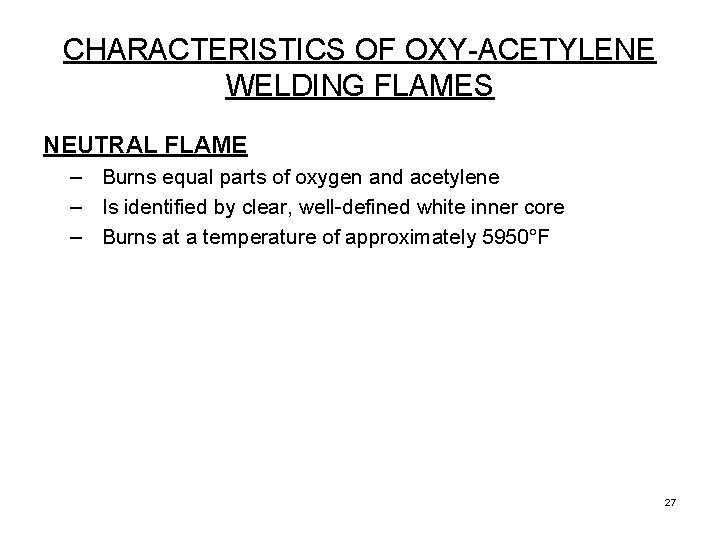
CHARACTERISTICS OF OXY-ACETYLENE WELDING FLAMES NEUTRAL FLAME – Burns equal parts of oxygen and acetylene – Is identified by clear, well-defined white inner core – Burns at a temperature of approximately 5950°F 27
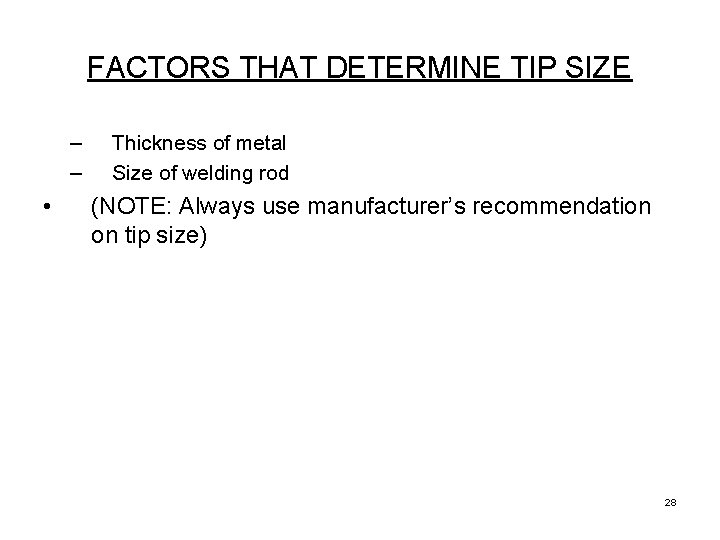
FACTORS THAT DETERMINE TIP SIZE – – • Thickness of metal Size of welding rod (NOTE: Always use manufacturer’s recommendation on tip size) 28
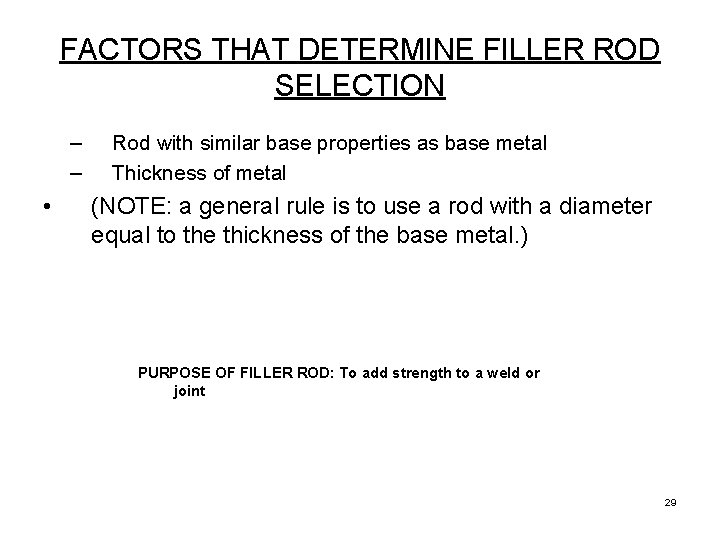
FACTORS THAT DETERMINE FILLER ROD SELECTION – – • Rod with similar base properties as base metal Thickness of metal (NOTE: a general rule is to use a rod with a diameter equal to the thickness of the base metal. ) PURPOSE OF FILLER ROD: To add strength to a weld or joint 29
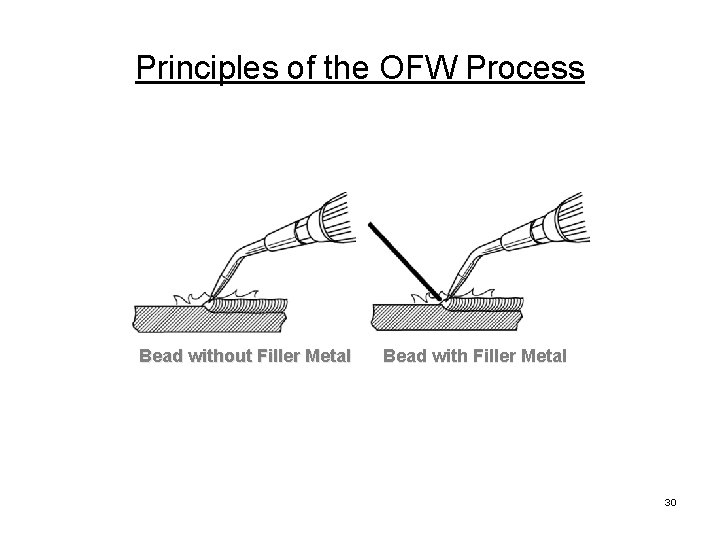
Principles of the OFW Process Bead without Filler Metal Bead with Filler Metal 30
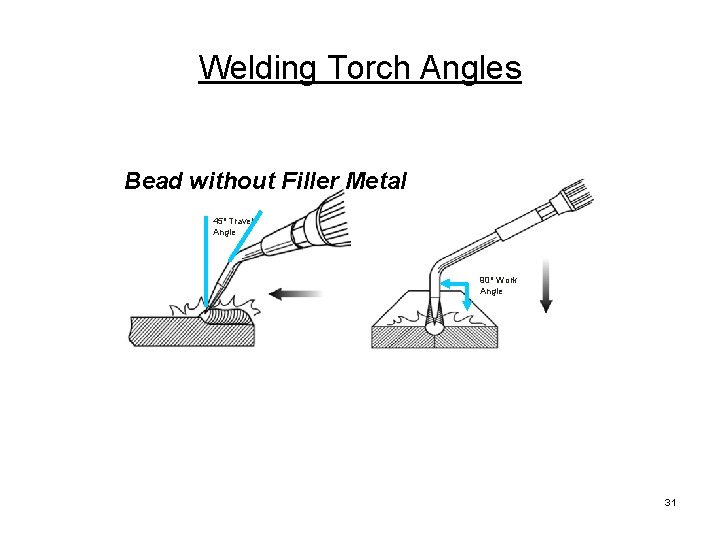
Welding Torch Angles Bead without Filler Metal 45 o Travel Angle 90 o Work Angle 31

Welding Torch Angles Bead with Filler Metal 45 o Travel Angle 90 o Work Angle 32
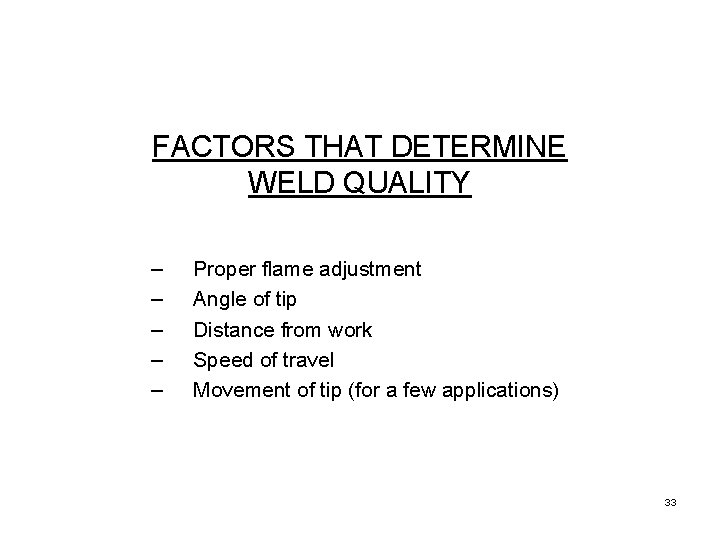
FACTORS THAT DETERMINE WELD QUALITY – – – Proper flame adjustment Angle of tip Distance from work Speed of travel Movement of tip (for a few applications) 33
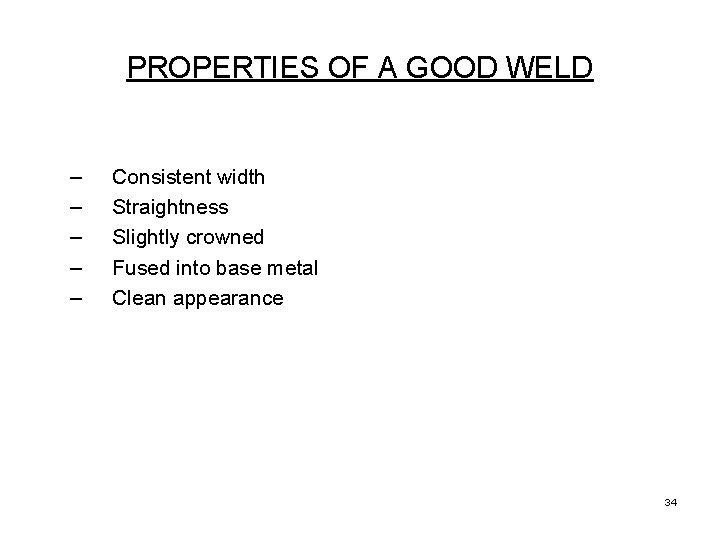
PROPERTIES OF A GOOD WELD – – – Consistent width Straightness Slightly crowned Fused into base metal Clean appearance 34
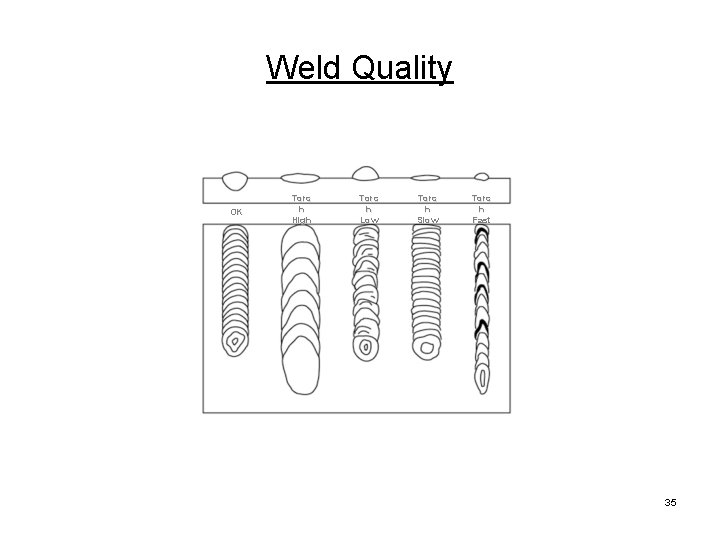
Weld Quality OK Torc h High Torc h Low Torc h Slow Torc h Fast 35
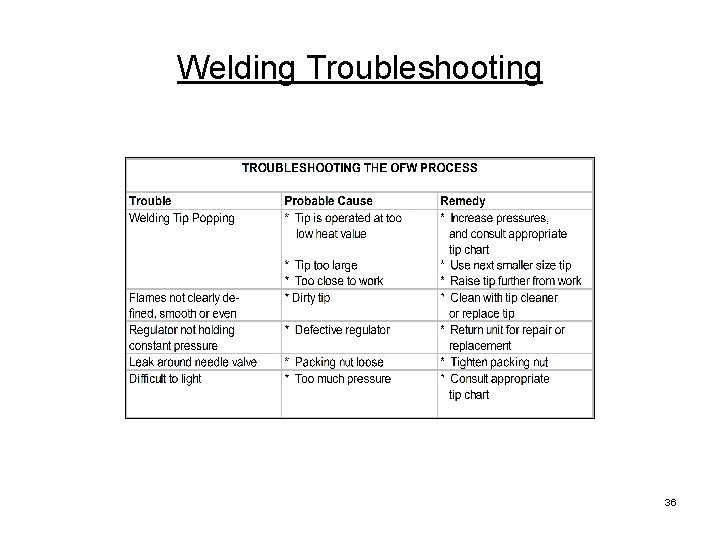
Welding Troubleshooting 36
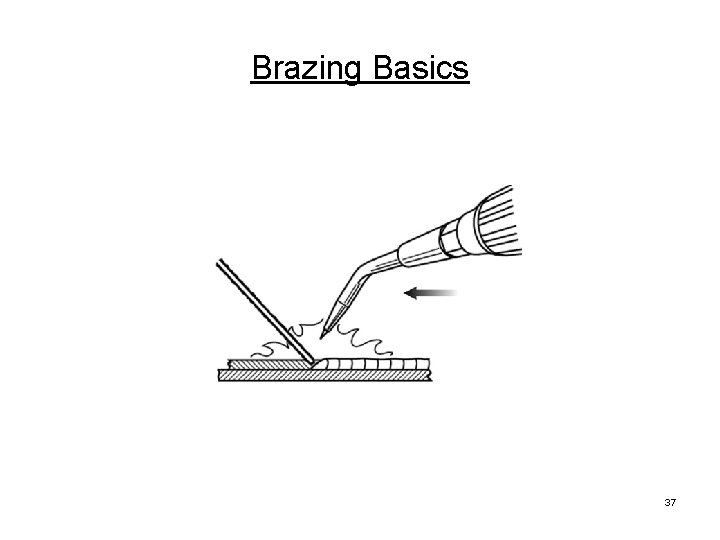
Brazing Basics 37
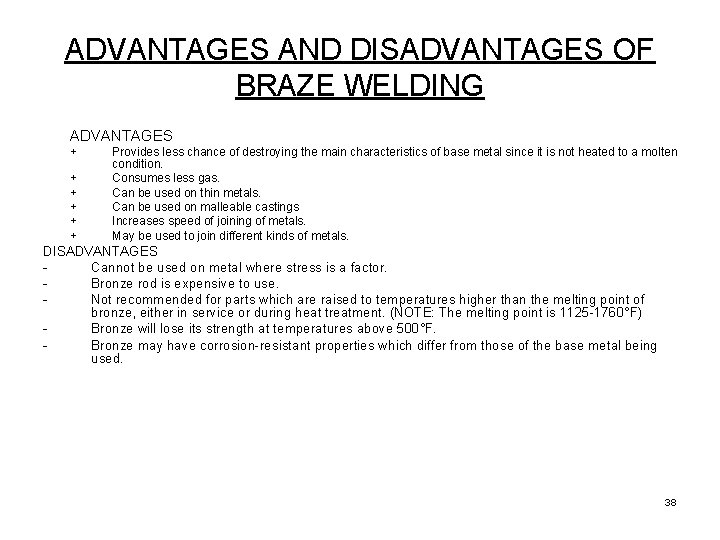
ADVANTAGES AND DISADVANTAGES OF BRAZE WELDING ADVANTAGES + + + Provides less chance of destroying the main characteristics of base metal since it is not heated to a molten condition. Consumes less gas. Can be used on thin metals. Can be used on malleable castings Increases speed of joining of metals. May be used to join different kinds of metals. DISADVANTAGES Cannot be used on metal where stress is a factor. Bronze rod is expensive to use. Not recommended for parts which are raised to temperatures higher than the melting point of bronze, either in service or during heat treatment. (NOTE: The melting point is 1125 -1760°F) Bronze will lose its strength at temperatures above 500°F. Bronze may have corrosion-resistant properties which differ from those of the base metal being used. 38
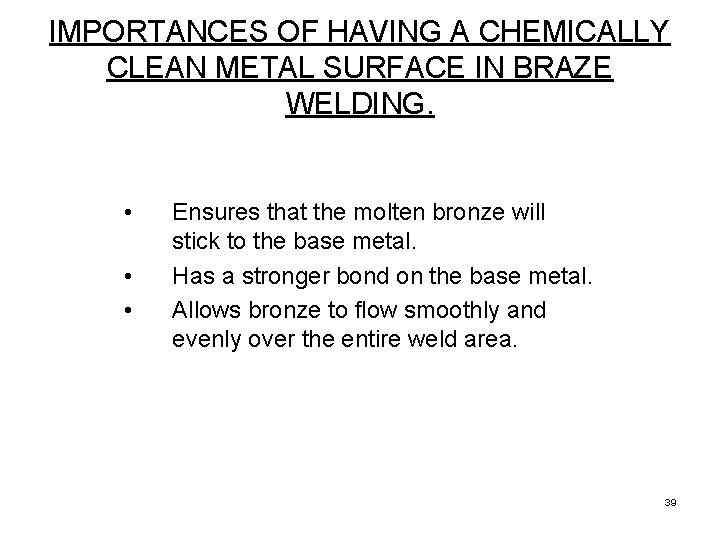
IMPORTANCES OF HAVING A CHEMICALLY CLEAN METAL SURFACE IN BRAZE WELDING. • • • Ensures that the molten bronze will stick to the base metal. Has a stronger bond on the base metal. Allows bronze to flow smoothly and evenly over the entire weld area. 39
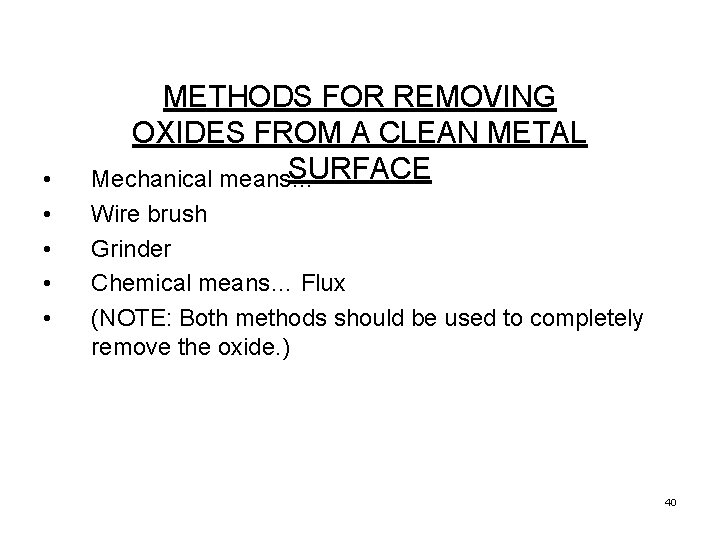
• • • METHODS FOR REMOVING OXIDES FROM A CLEAN METAL SURFACE Mechanical means… Wire brush Grinder Chemical means… Flux (NOTE: Both methods should be used to completely remove the oxide. ) 40
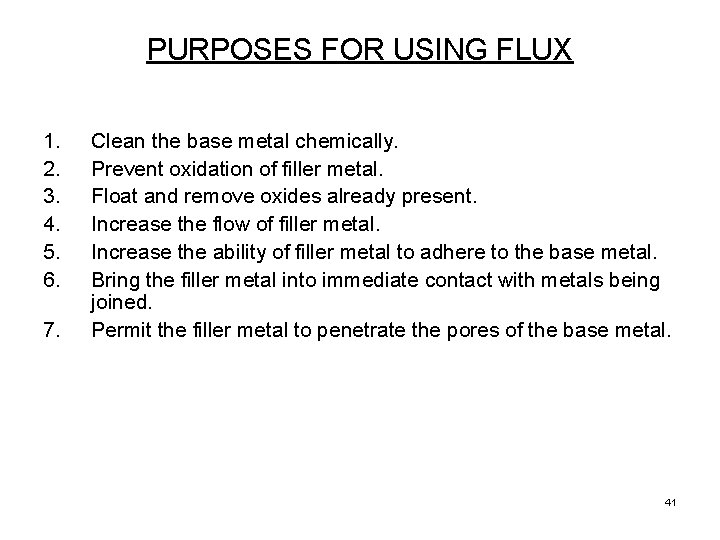
PURPOSES FOR USING FLUX 1. 2. 3. 4. 5. 6. 7. Clean the base metal chemically. Prevent oxidation of filler metal. Float and remove oxides already present. Increase the flow of filler metal. Increase the ability of filler metal to adhere to the base metal. Bring the filler metal into immediate contact with metals being joined. Permit the filler metal to penetrate the pores of the base metal. 41
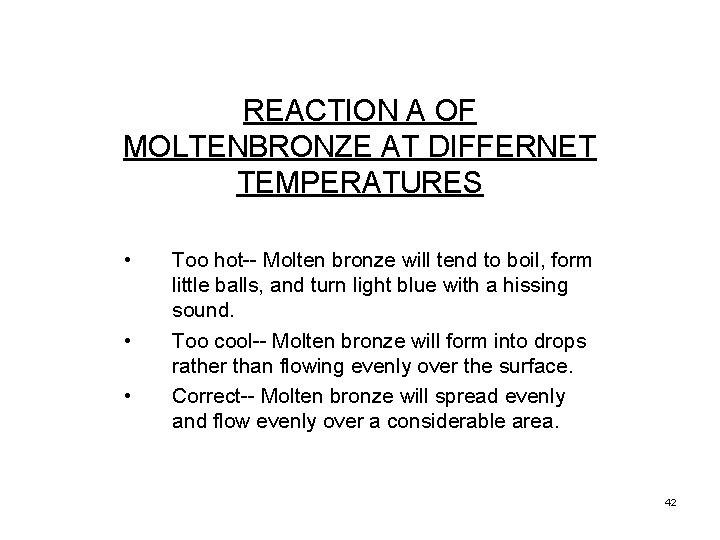
REACTION A OF MOLTENBRONZE AT DIFFERNET TEMPERATURES • • • Too hot-- Molten bronze will tend to boil, form little balls, and turn light blue with a hissing sound. Too cool-- Molten bronze will form into drops rather than flowing evenly over the surface. Correct-- Molten bronze will spread evenly and flow evenly over a considerable area. 42
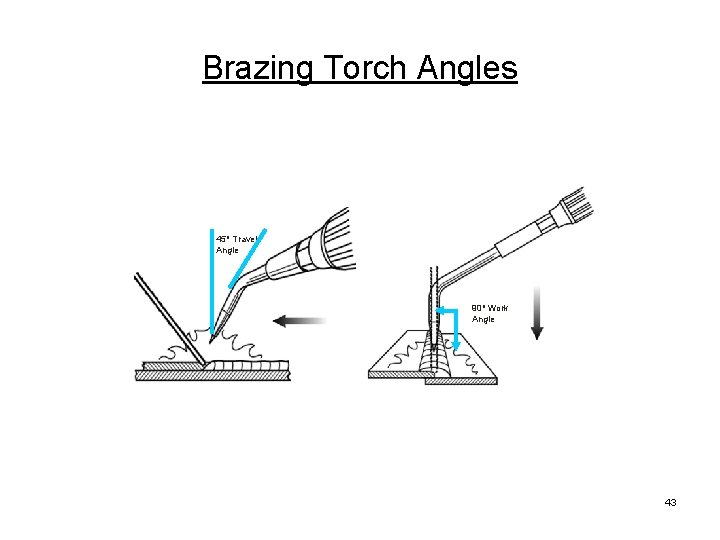
Brazing Torch Angles 45 o Travel Angle 90 o Work Angle 43
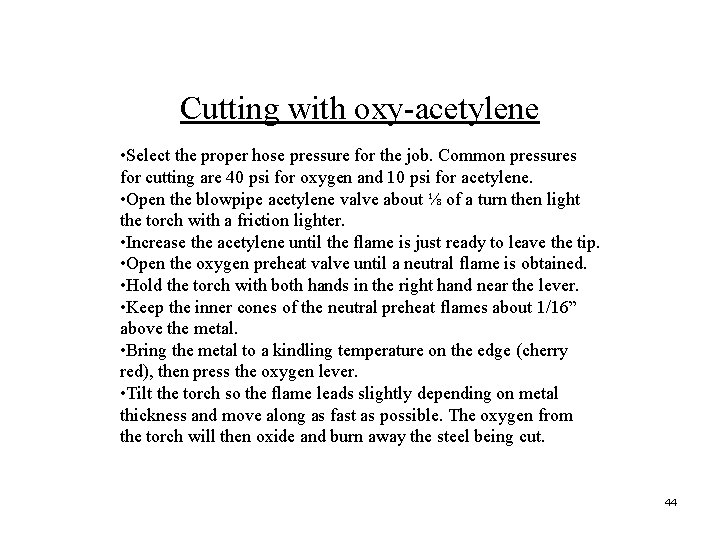
Cutting with oxy-acetylene • Select the proper hose pressure for the job. Common pressures for cutting are 40 psi for oxygen and 10 psi for acetylene. • Open the blowpipe acetylene valve about ⅛ of a turn then light the torch with a friction lighter. • Increase the acetylene until the flame is just ready to leave the tip. • Open the oxygen preheat valve until a neutral flame is obtained. • Hold the torch with both hands in the right hand near the lever. • Keep the inner cones of the neutral preheat flames about 1/16” above the metal. • Bring the metal to a kindling temperature on the edge (cherry red), then press the oxygen lever. • Tilt the torch so the flame leads slightly depending on metal thickness and move along as fast as possible. The oxygen from the torch will then oxide and burn away the steel being cut. 44
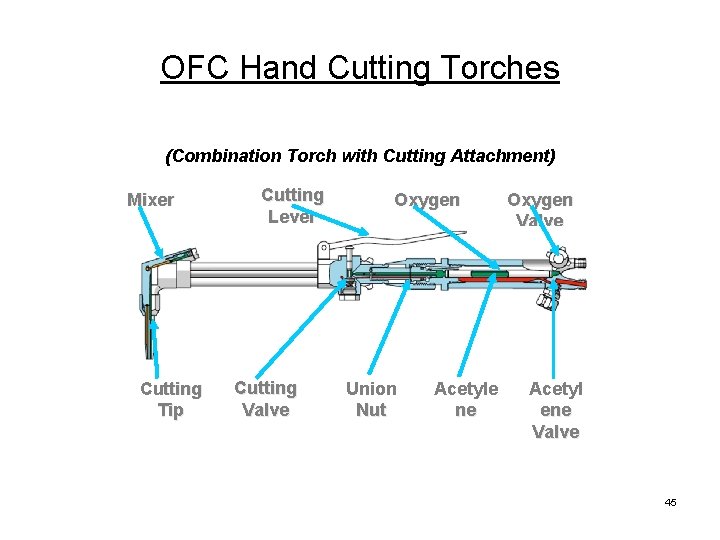
OFC Hand Cutting Torches (Combination Torch with Cutting Attachment) Mixer Cutting Tip Cutting Lever Cutting Valve Oxygen Union Nut Acetyle ne Oxygen Valve Acetyl ene Valve 45
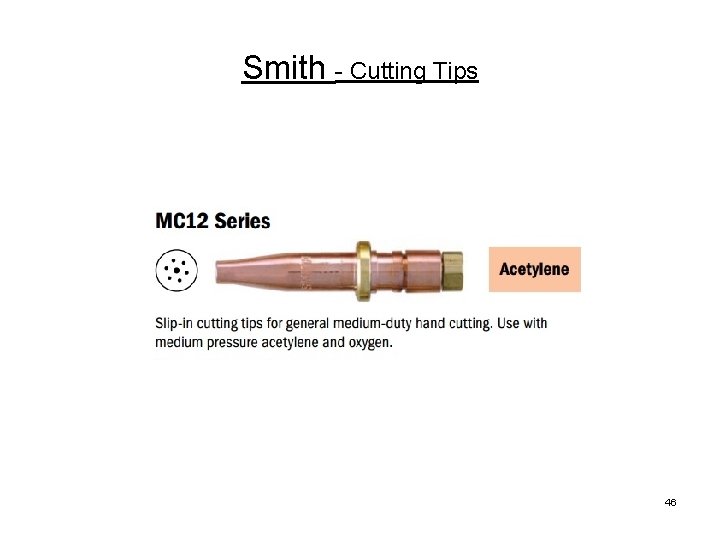
Smith - Cutting Tips 46
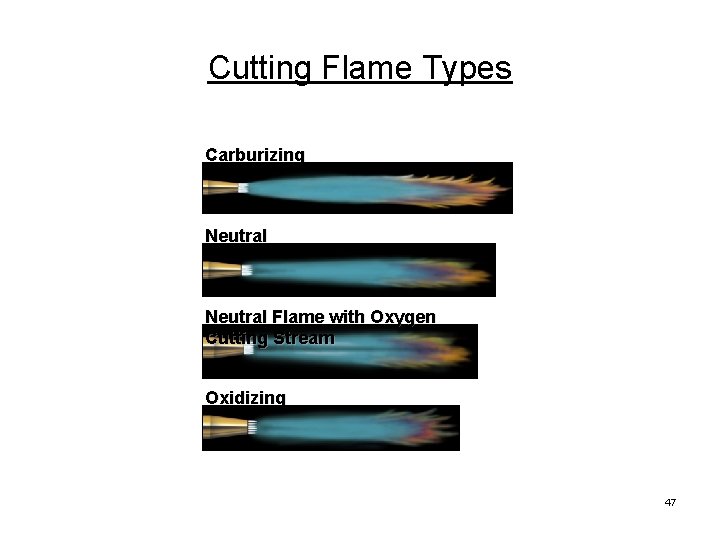
Cutting Flame Types Carburizing Flame Neutral Flame with Oxygen Cutting Stream Oxidizing Flame 47
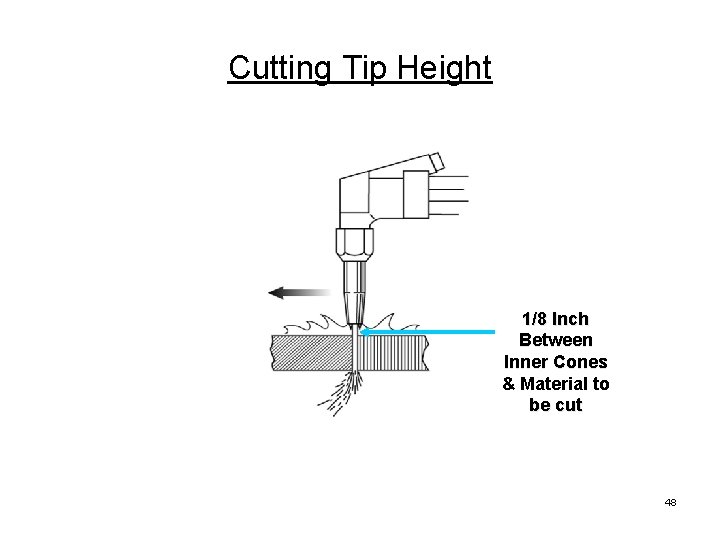
Cutting Tip Height 1/8 Inch Between Inner Cones & Material to be cut 48
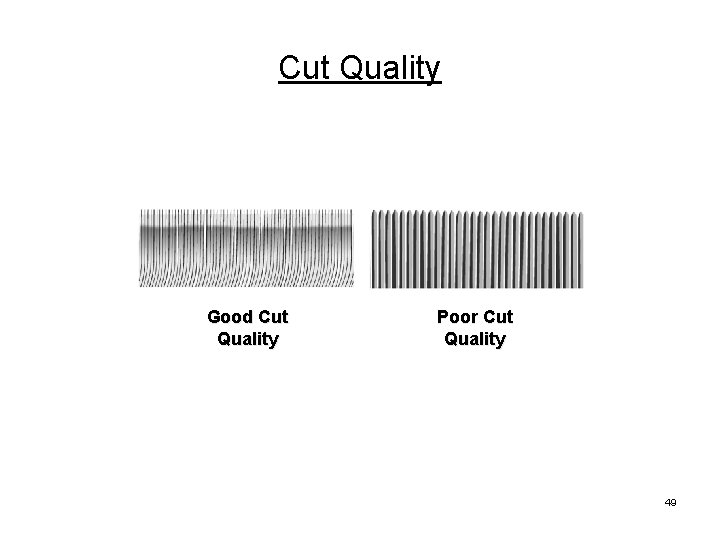
Cut Quality Good Cut Quality Poor Cut Quality 49
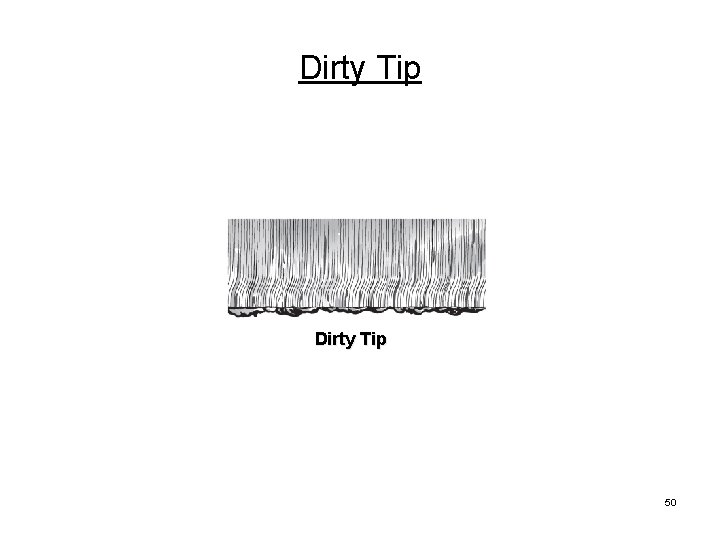
Dirty Tip 50

Speed Extremely Fast Extremely Slow Slightly Too Fast Slightly Too Slow 51
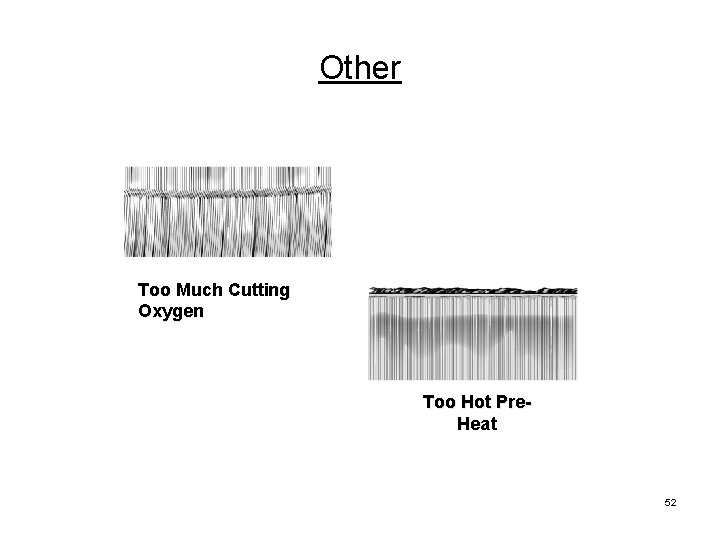
Other Too Much Cutting Oxygen Too Hot Pre. Heat 52
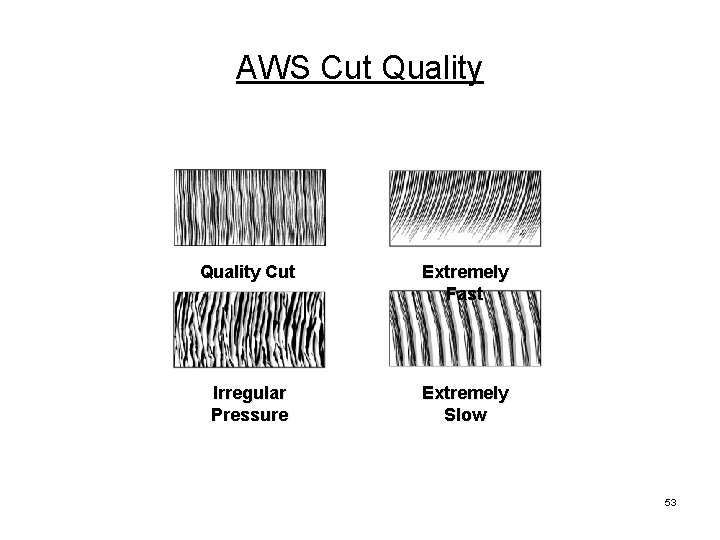
AWS Cut Quality Cut Extremely Fast Irregular Pressure Extremely Slow 53
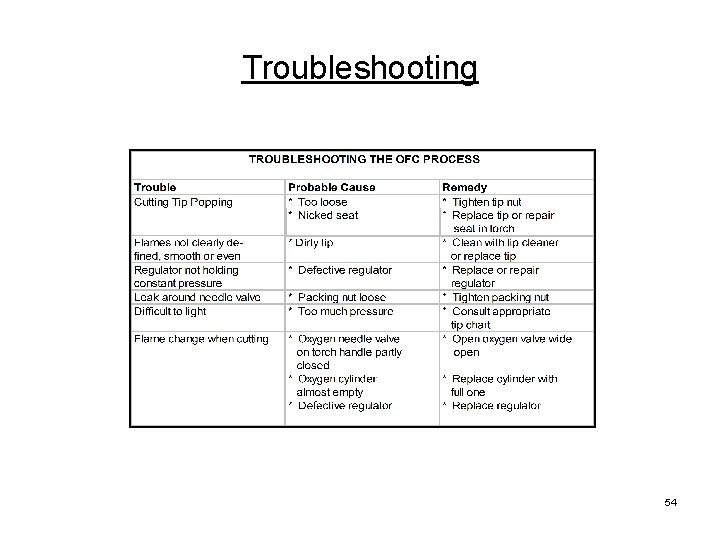
Troubleshooting 54
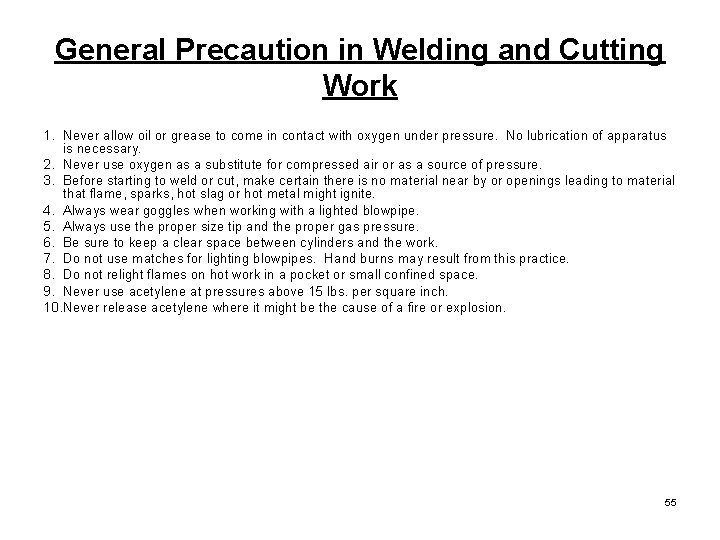
General Precaution in Welding and Cutting Work 1. Never allow oil or grease to come in contact with oxygen under pressure. No lubrication of apparatus is necessary. 2. Never use oxygen as a substitute for compressed air or as a source of pressure. 3. Before starting to weld or cut, make certain there is no material near by or openings leading to material that flame, sparks, hot slag or hot metal might ignite. 4. Always wear goggles when working with a lighted blowpipe. 5. Always use the proper size tip and the proper gas pressure. 6. Be sure to keep a clear space between cylinders and the work. 7. Do not use matches for lighting blowpipes. Hand burns may result from this practice. 8. Do not relight flames on hot work in a pocket or small confined space. 9. Never use acetylene at pressures above 15 lbs. per square inch. 10. Never release acetylene where it might be the cause of a fire or explosion. 55
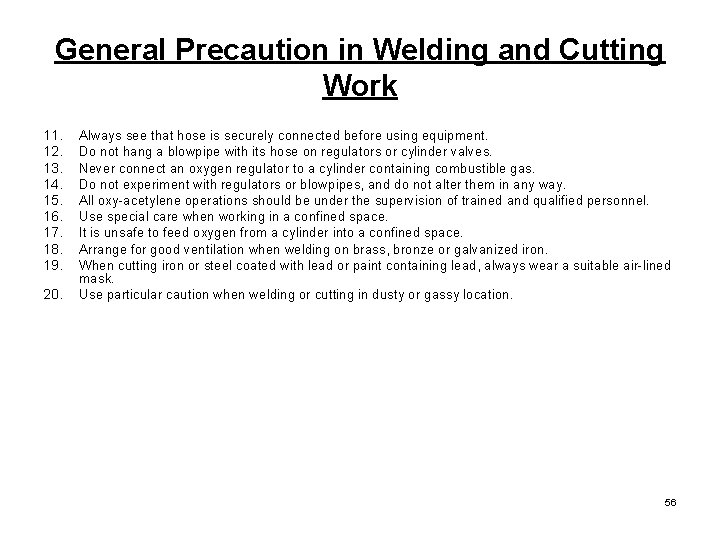
General Precaution in Welding and Cutting Work 11. 12. 13. 14. 15. 16. 17. 18. 19. 20. Always see that hose is securely connected before using equipment. Do not hang a blowpipe with its hose on regulators or cylinder valves. Never connect an oxygen regulator to a cylinder containing combustible gas. Do not experiment with regulators or blowpipes, and do not alter them in any way. All oxy-acetylene operations should be under the supervision of trained and qualified personnel. Use special care when working in a confined space. It is unsafe to feed oxygen from a cylinder into a confined space. Arrange for good ventilation when welding on brass, bronze or galvanized iron. When cutting iron or steel coated with lead or paint containing lead, always wear a suitable air-lined mask. Use particular caution when welding or cutting in dusty or gassy location. 56
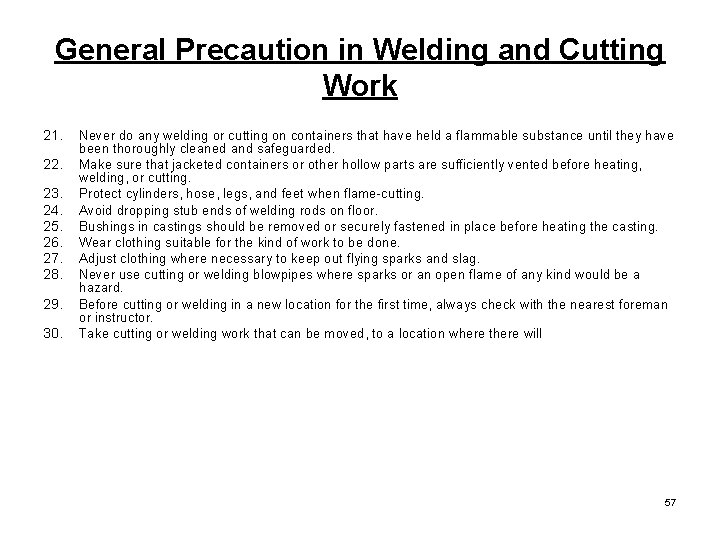
General Precaution in Welding and Cutting Work 21. 22. 23. 24. 25. 26. 27. 28. 29. 30. Never do any welding or cutting on containers that have held a flammable substance until they have been thoroughly cleaned and safeguarded. Make sure that jacketed containers or other hollow parts are sufficiently vented before heating, welding, or cutting. Protect cylinders, hose, legs, and feet when flame-cutting. Avoid dropping stub ends of welding rods on floor. Bushings in castings should be removed or securely fastened in place before heating the casting. Wear clothing suitable for the kind of work to be done. Adjust clothing where necessary to keep out flying sparks and slag. Never use cutting or welding blowpipes where sparks or an open flame of any kind would be a hazard. Before cutting or welding in a new location for the first time, always check with the nearest foreman or instructor. Take cutting or welding work that can be moved, to a location where there will 57
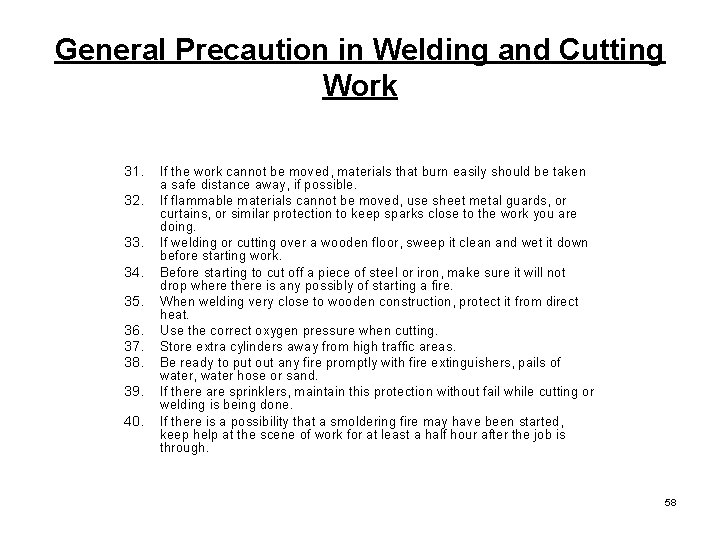
General Precaution in Welding and Cutting Work 31. 32. 33. 34. 35. 36. 37. 38. 39. 40. If the work cannot be moved, materials that burn easily should be taken a safe distance away, if possible. If flammable materials cannot be moved, use sheet metal guards, or curtains, or similar protection to keep sparks close to the work you are doing. If welding or cutting over a wooden floor, sweep it clean and wet it down before starting work. Before starting to cut off a piece of steel or iron, make sure it will not drop where there is any possibly of starting a fire. When welding very close to wooden construction, protect it from direct heat. Use the correct oxygen pressure when cutting. Store extra cylinders away from high traffic areas. Be ready to put out any fire promptly with fire extinguishers, pails of water, water hose or sand. If there are sprinklers, maintain this protection without fail while cutting or welding is being done. If there is a possibility that a smoldering fire may have been started, keep help at the scene of work for at least a half hour after the job is through. 58
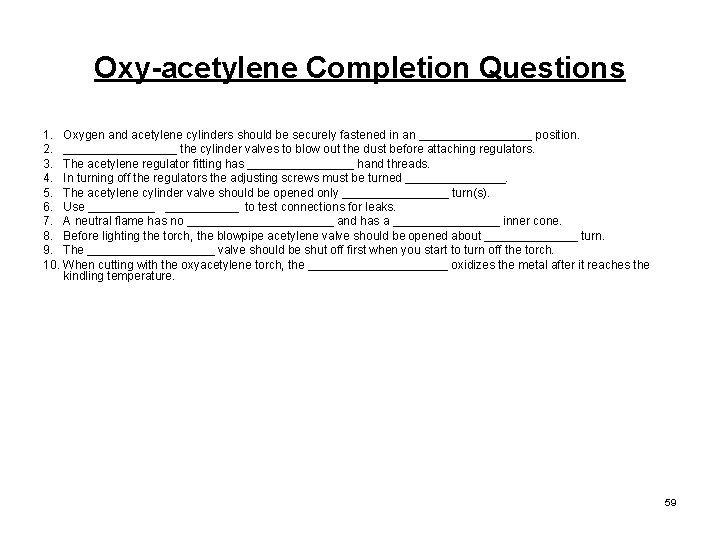
Oxy-acetylene Completion Questions 1. Oxygen and acetylene cylinders should be securely fastened in an _________ position. 2. _________ the cylinder valves to blow out the dust before attaching regulators. 3. The acetylene regulator fitting has ________ hand threads. 4. In turning off the regulators the adjusting screws must be turned ________. 5. The acetylene cylinder valve should be opened only ________ turn(s). 6. Use ______ to test connections for leaks. 7. A neutral flame has no ___________ and has a ________ inner cone. 8. Before lighting the torch, the blowpipe acetylene valve should be opened about _______ turn. 9. The __________ valve should be shut off first when you start to turn off the torch. 10. When cutting with the oxyacetylene torch, the ___________ oxidizes the metal after it reaches the kindling temperature. 59
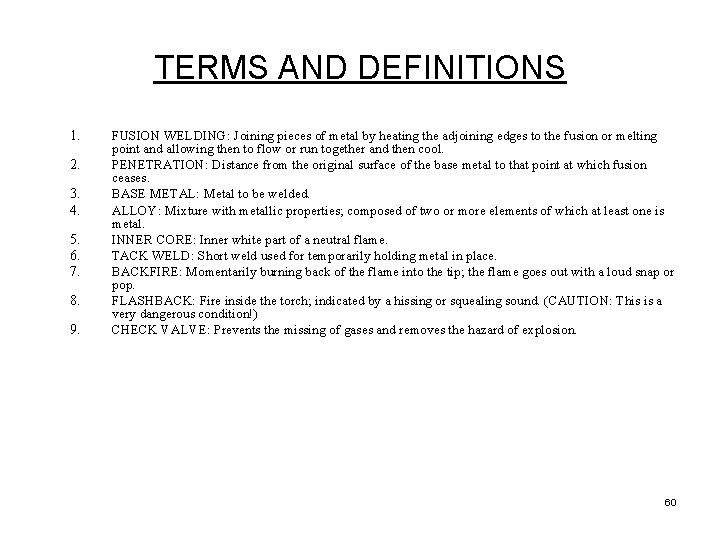
TERMS AND DEFINITIONS 1. 2. 3. 4. 5. 6. 7. 8. 9. FUSION WELDING: Joining pieces of metal by heating the adjoining edges to the fusion or melting point and allowing then to flow or run together and then cool. PENETRATION: Distance from the original surface of the base metal to that point at which fusion ceases. BASE METAL: Metal to be welded. ALLOY: Mixture with metallic properties; composed of two or more elements of which at least one is metal. INNER CORE: Inner white part of a neutral flame. TACK WELD: Short weld used for temporarily holding metal in place. BACKFIRE: Momentarily burning back of the flame into the tip; the flame goes out with a loud snap or pop. FLASHBACK: Fire inside the torch; indicated by a hissing or squealing sound. (CAUTION: This is a very dangerous condition!) CHECK VALVE: Prevents the missing of gases and removes the hazard of explosion. 60
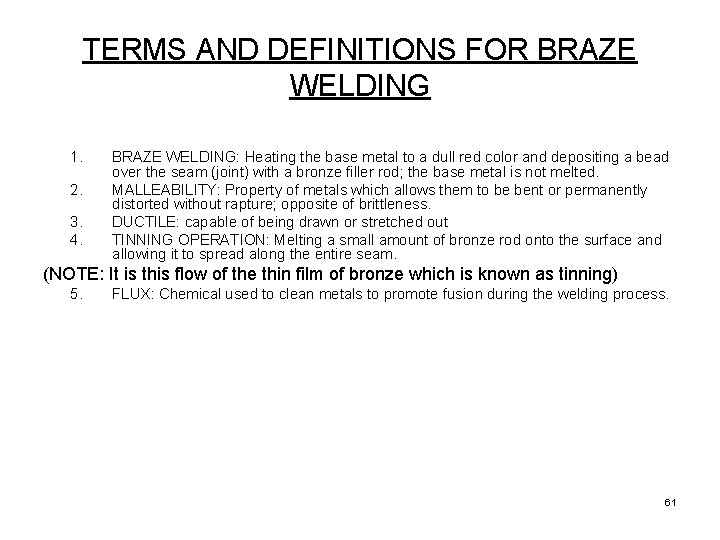
TERMS AND DEFINITIONS FOR BRAZE WELDING 1. 2. 3. 4. BRAZE WELDING: Heating the base metal to a dull red color and depositing a bead over the seam (joint) with a bronze filler rod; the base metal is not melted. MALLEABILITY: Property of metals which allows them to be bent or permanently distorted without rapture; opposite of brittleness. DUCTILE: capable of being drawn or stretched out TINNING OPERATION: Melting a small amount of bronze rod onto the surface and allowing it to spread along the entire seam. (NOTE: It is this flow of the thin film of bronze which is known as tinning) 5. FLUX: Chemical used to clean metals to promote fusion during the welding process. 61