NCSX Autoclave FDR Steve Raftopoulos 60303 Agenda Presentation
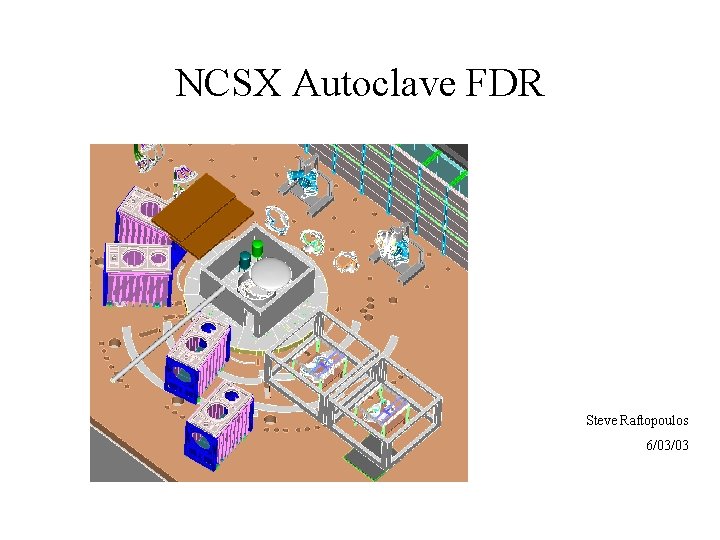
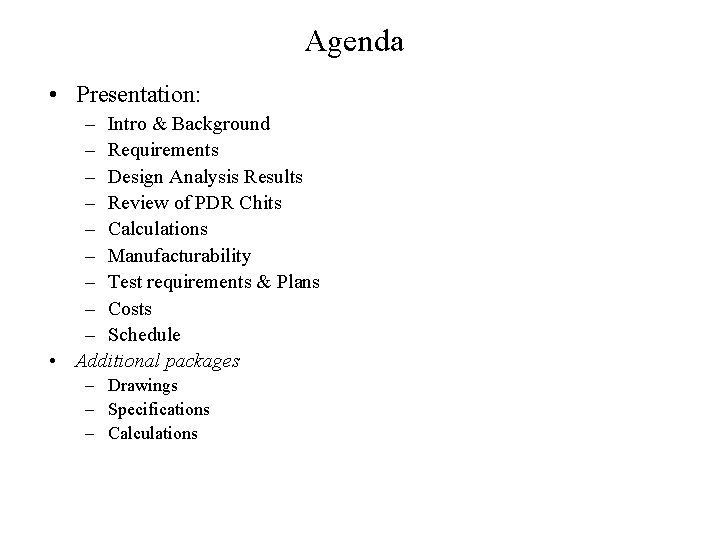
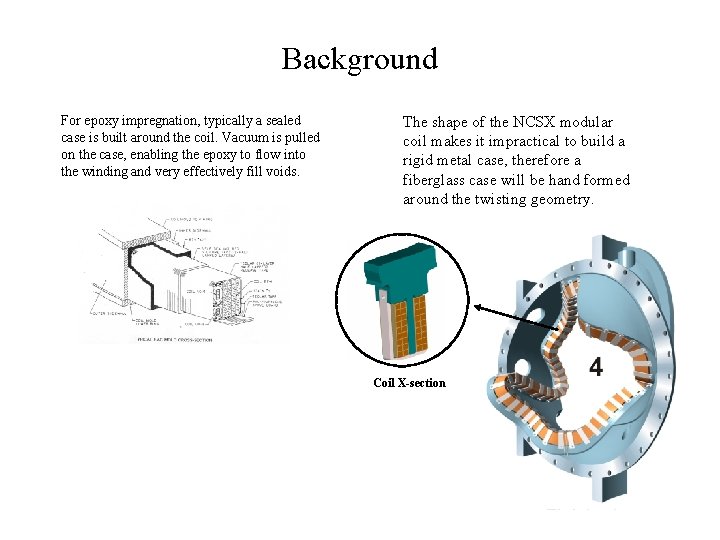
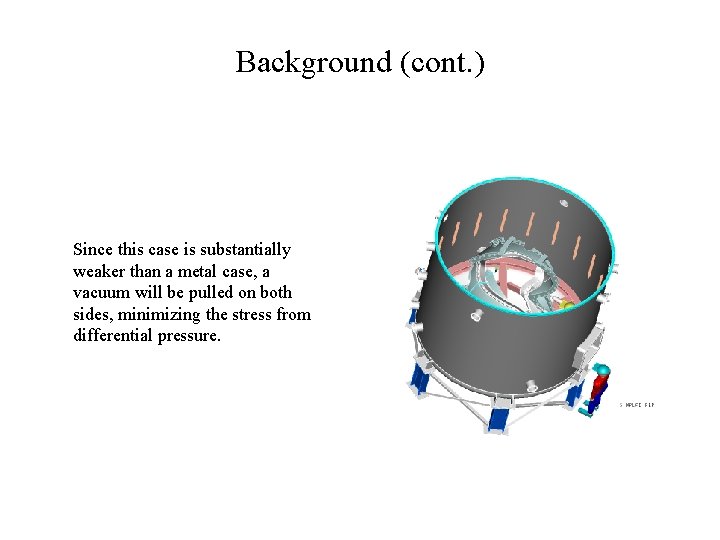
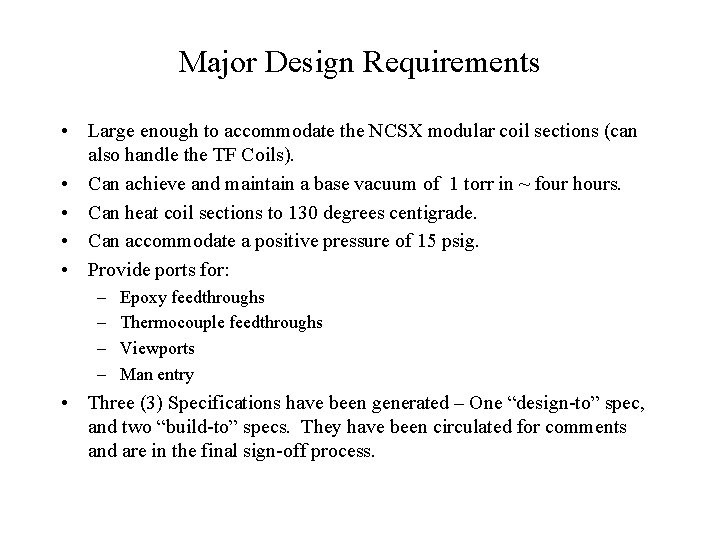
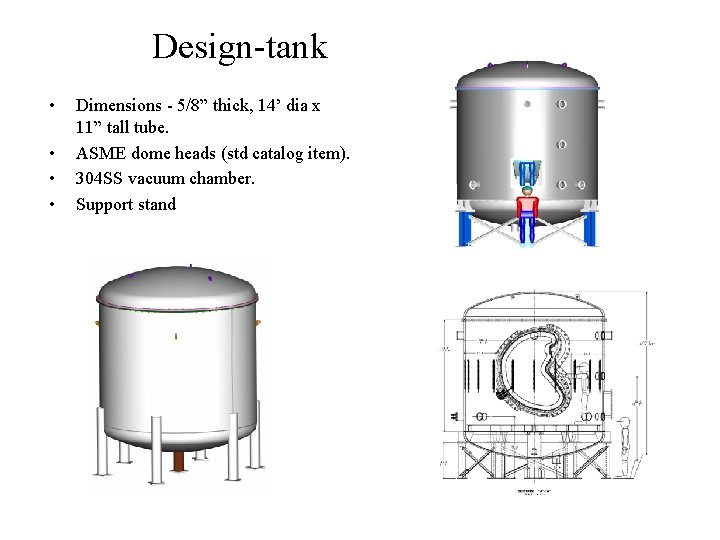
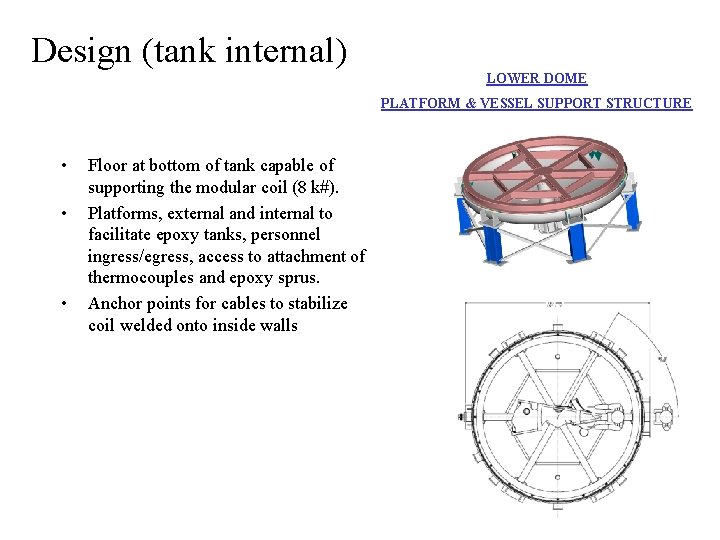
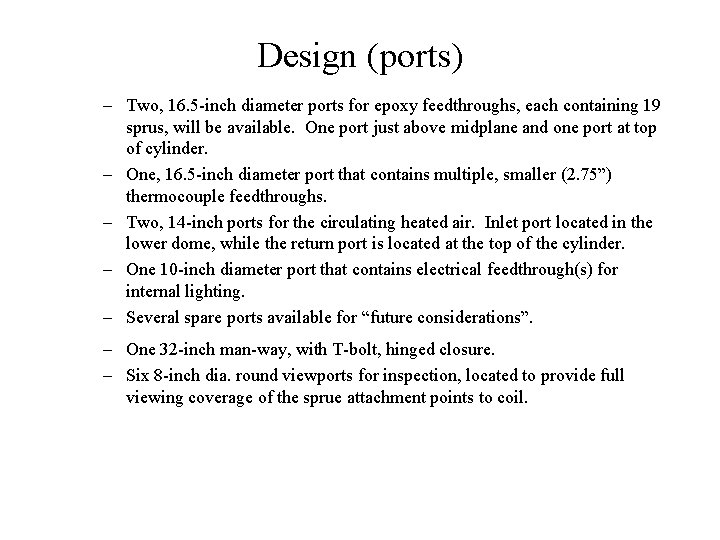
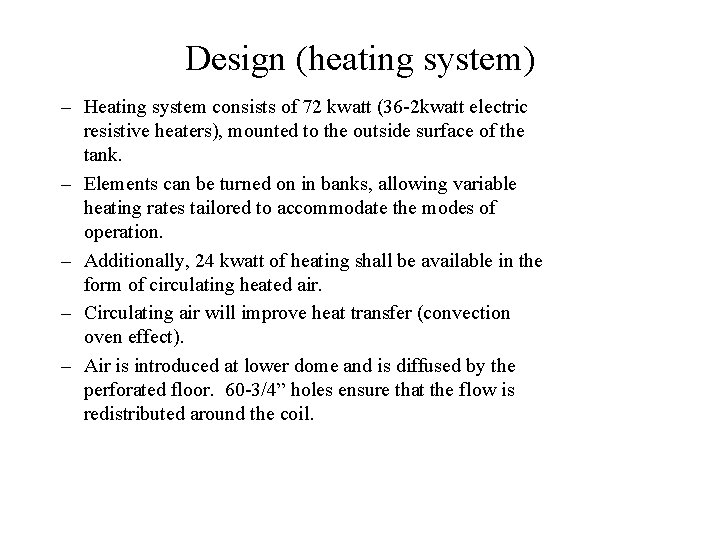
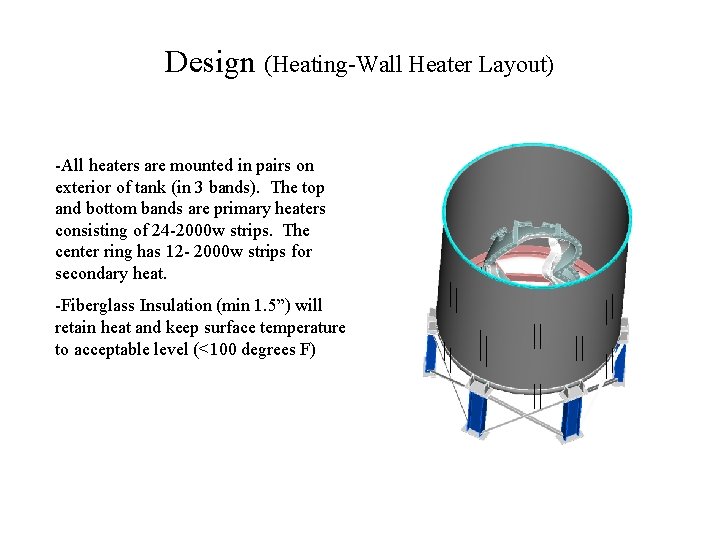
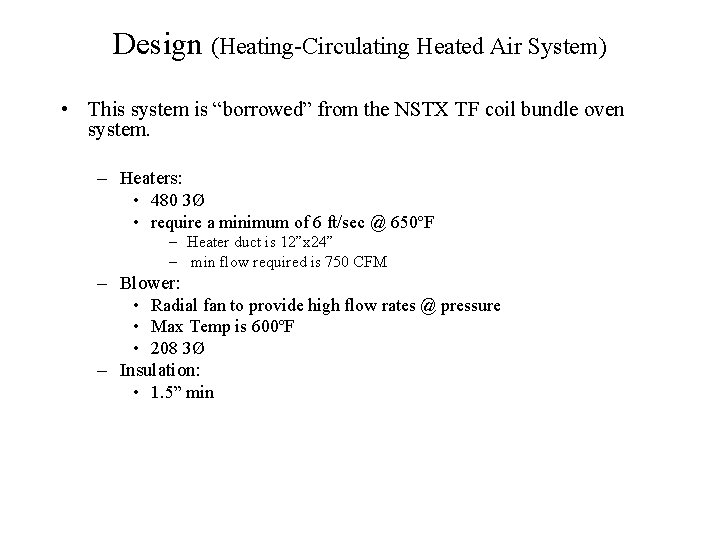
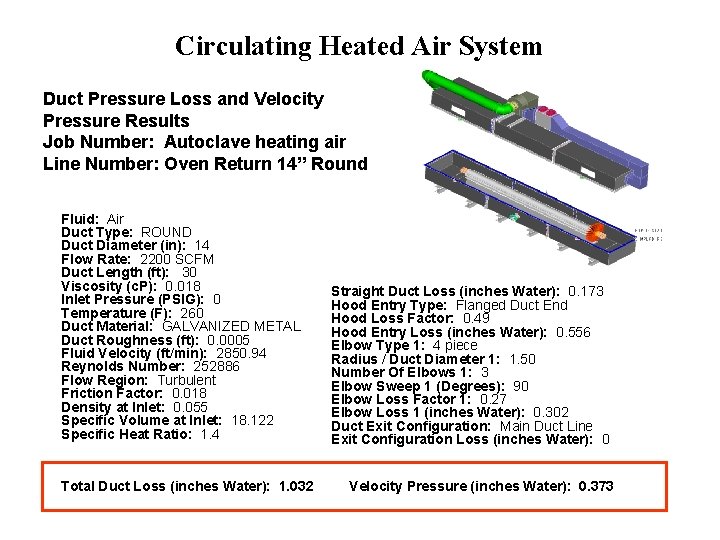
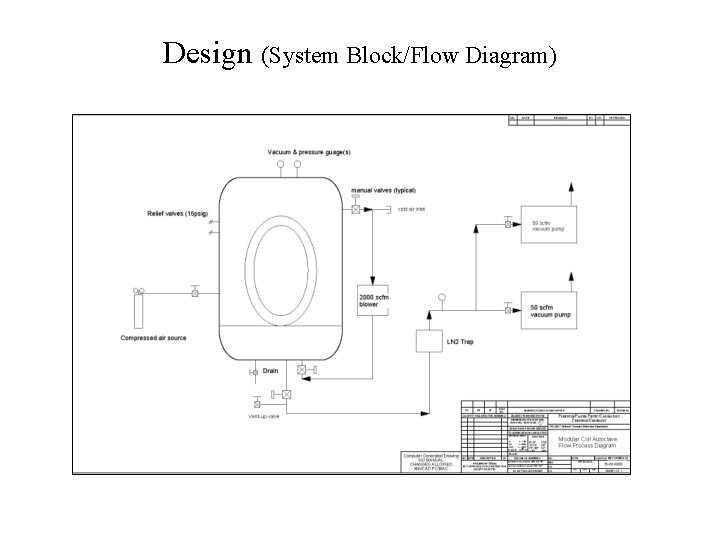
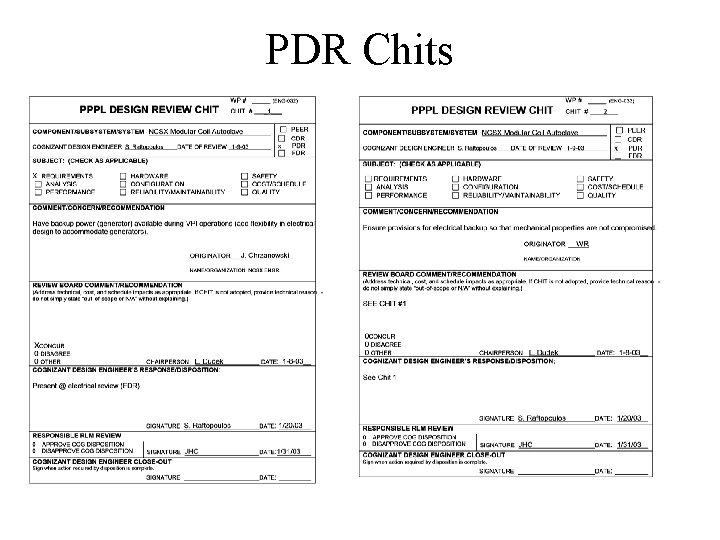
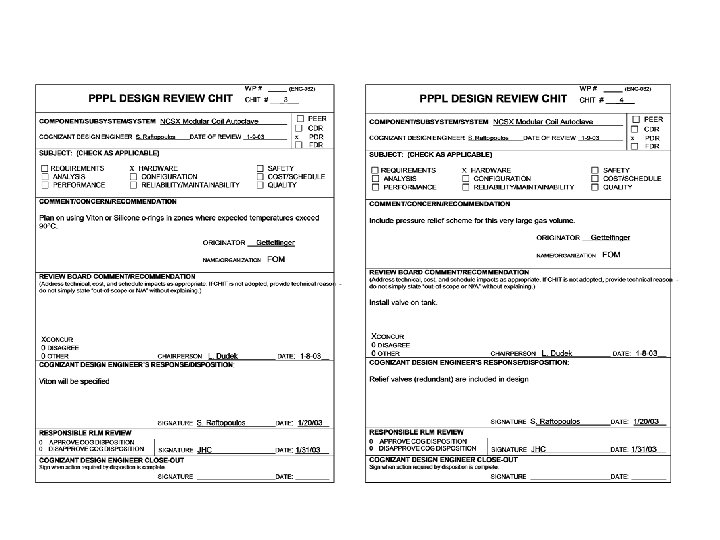
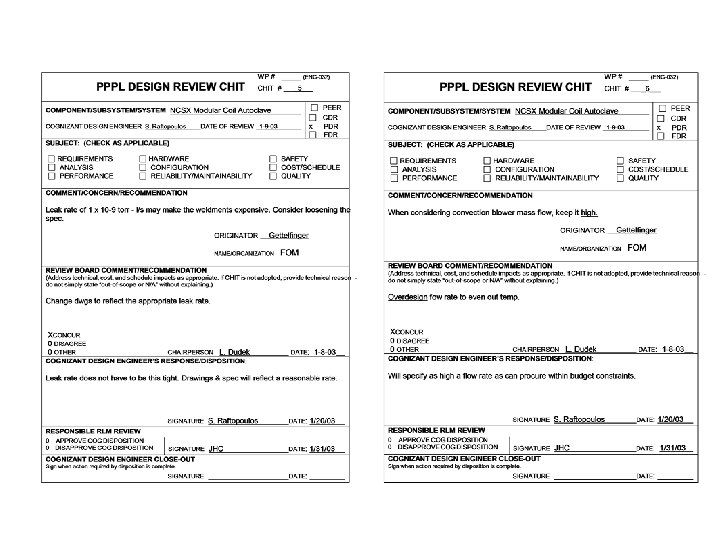
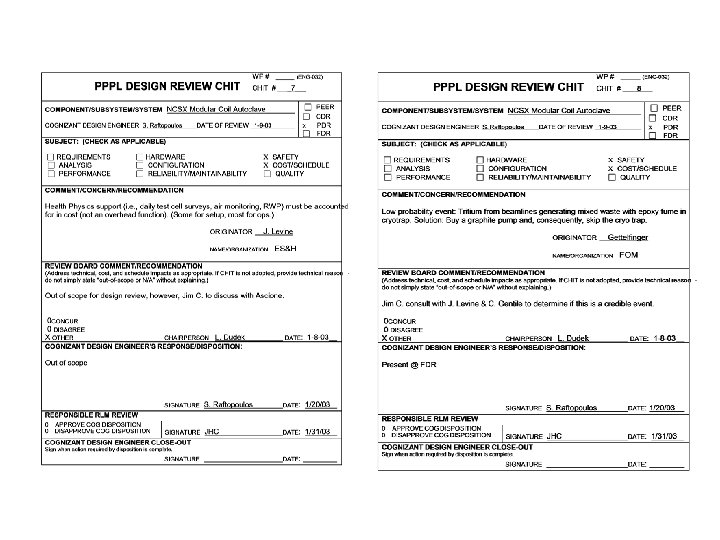
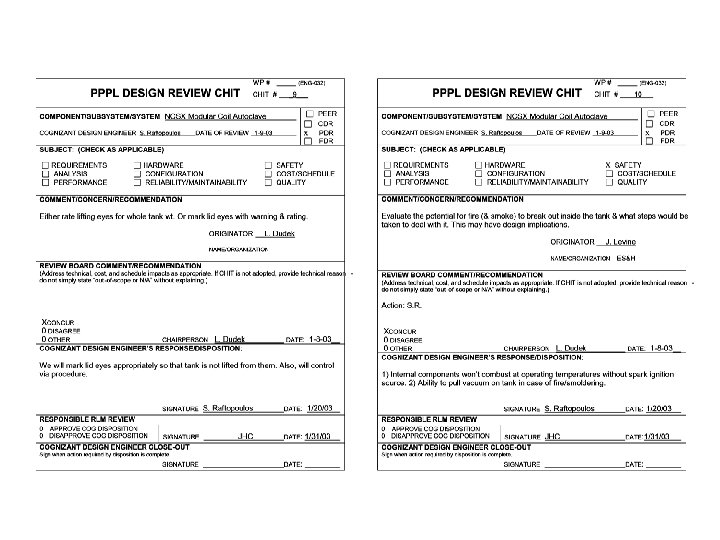
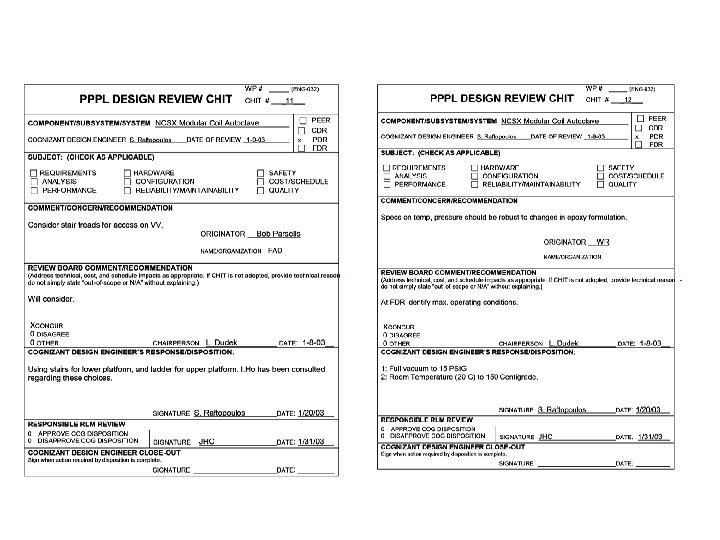
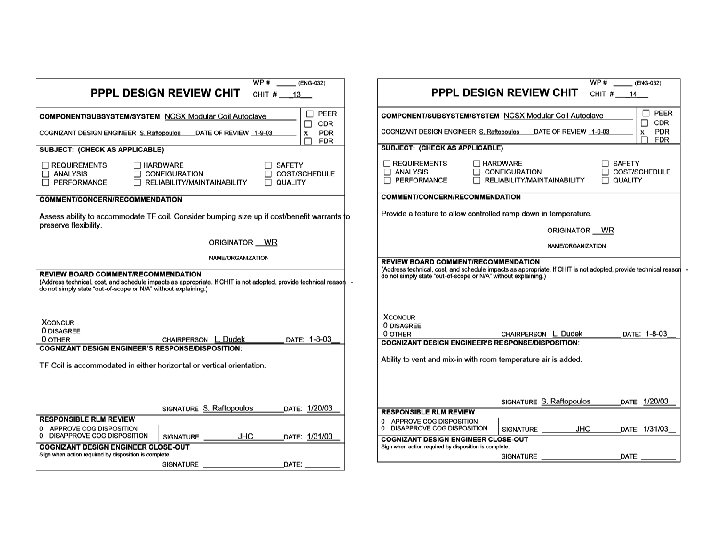
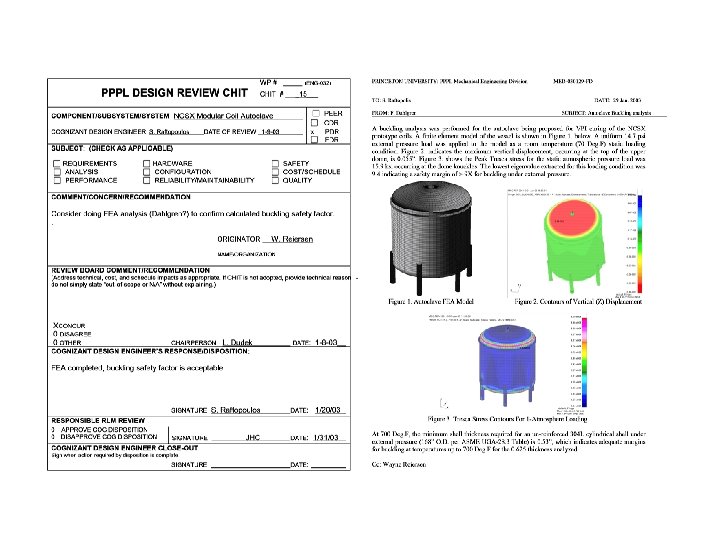
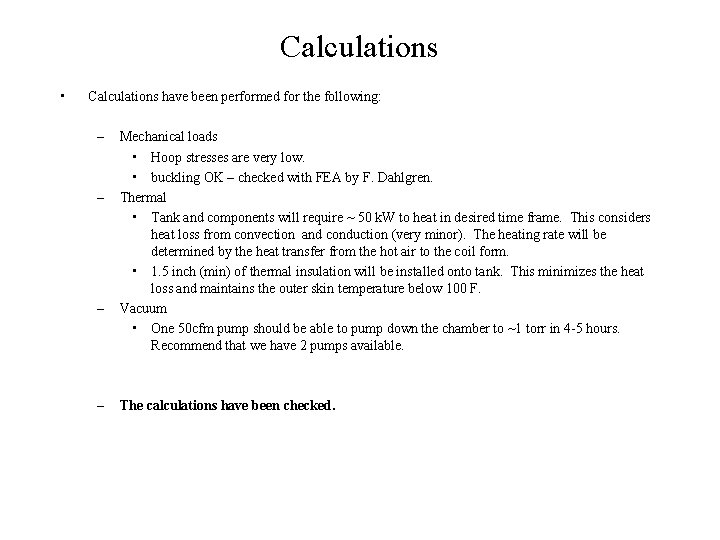
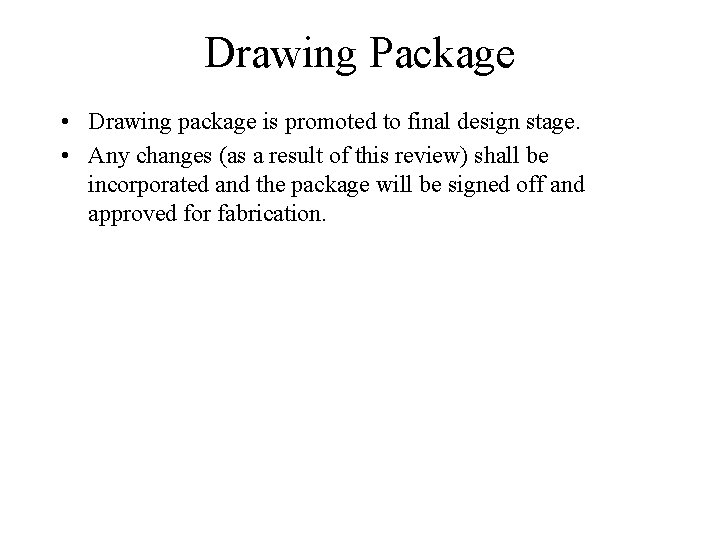
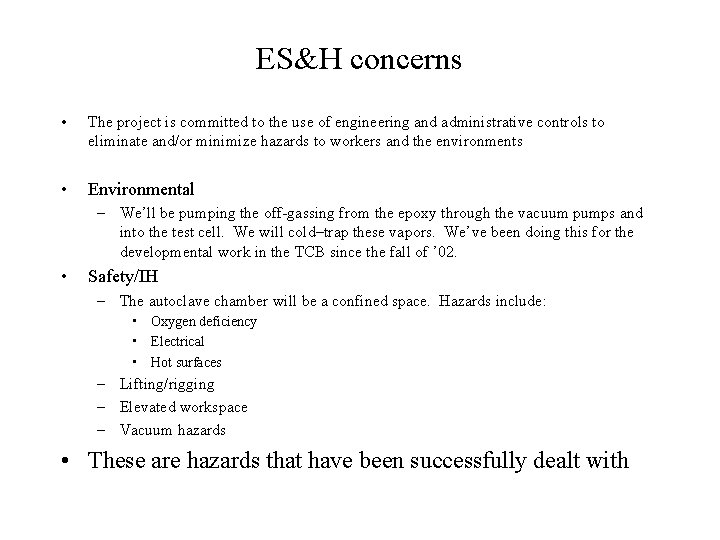
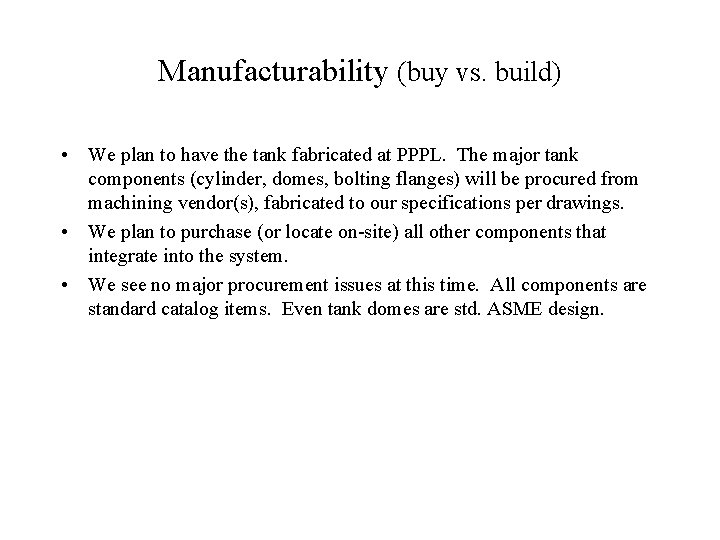
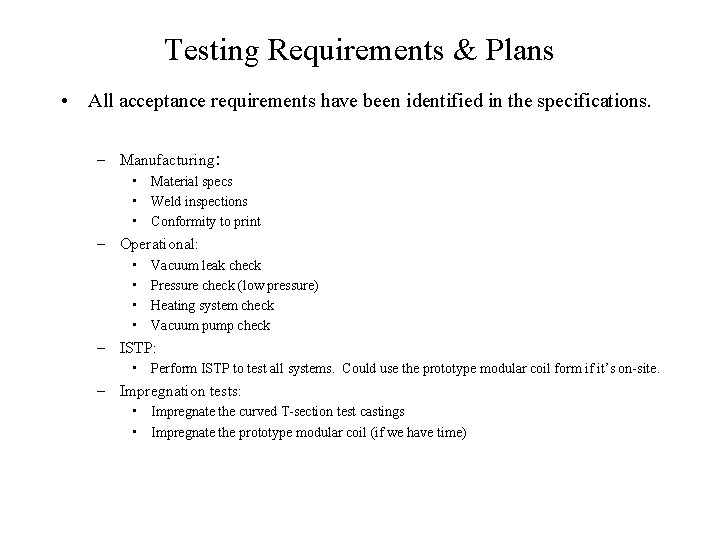
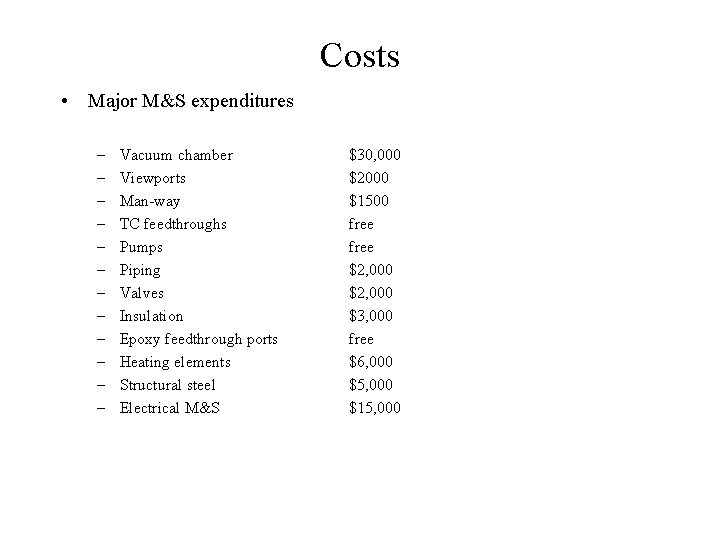
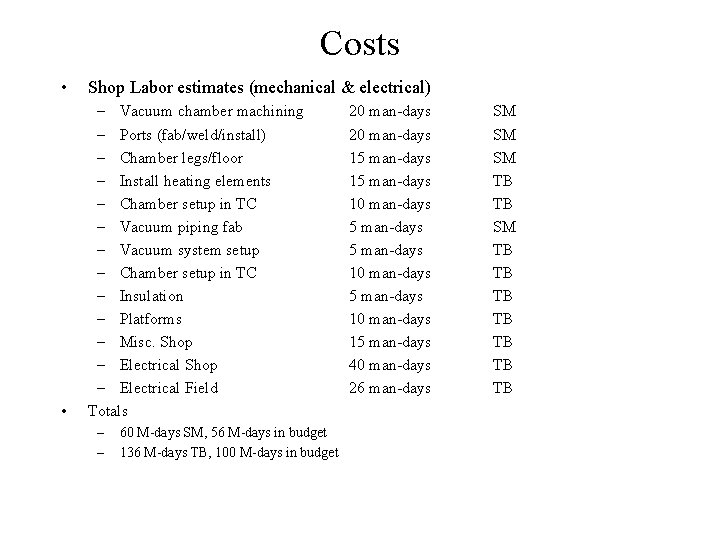
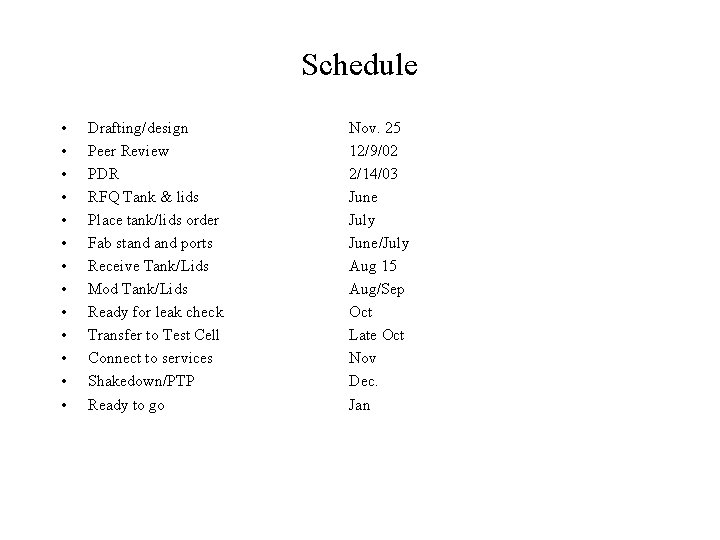
- Slides: 29
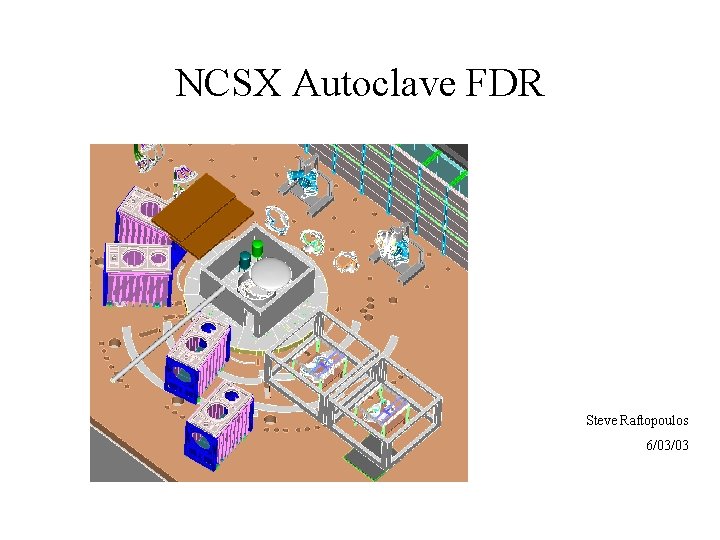
NCSX Autoclave FDR Steve Raftopoulos 6/03/03
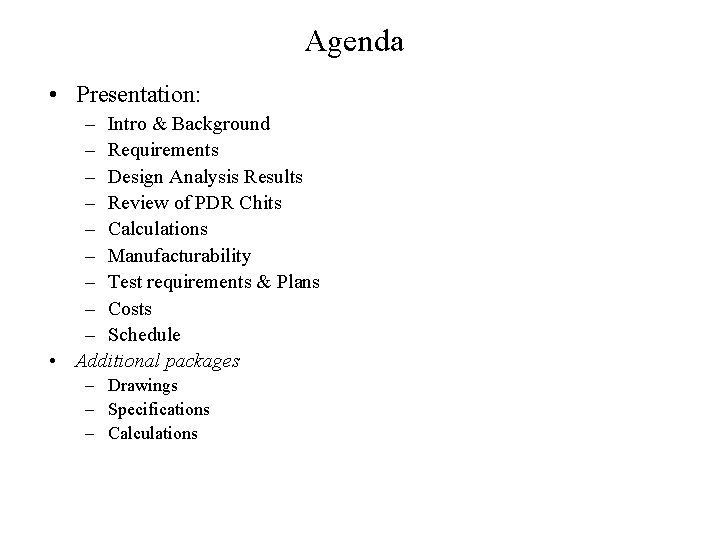
Agenda • Presentation: – Intro & Background – Requirements – Design Analysis Results – Review of PDR Chits – Calculations – Manufacturability – Test requirements & Plans – Costs – Schedule • Additional packages – Drawings – Specifications – Calculations
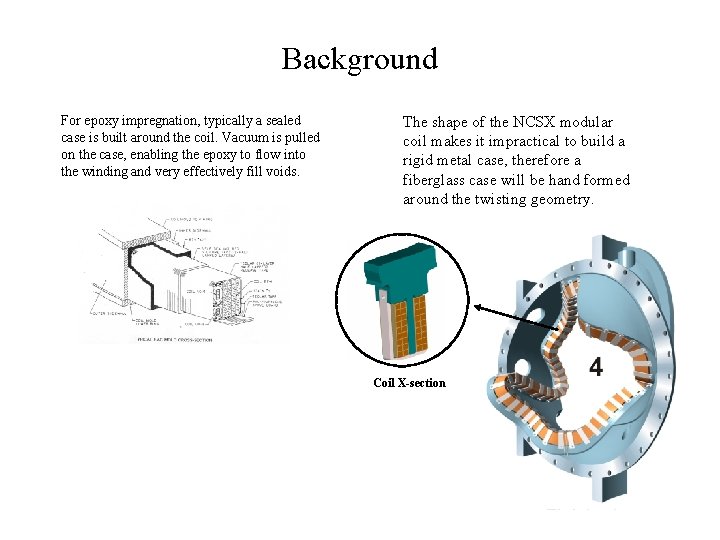
Background For epoxy impregnation, typically a sealed case is built around the coil. Vacuum is pulled on the case, enabling the epoxy to flow into the winding and very effectively fill voids. The shape of the NCSX modular coil makes it impractical to build a rigid metal case, therefore a fiberglass case will be hand formed around the twisting geometry. Coil X-section
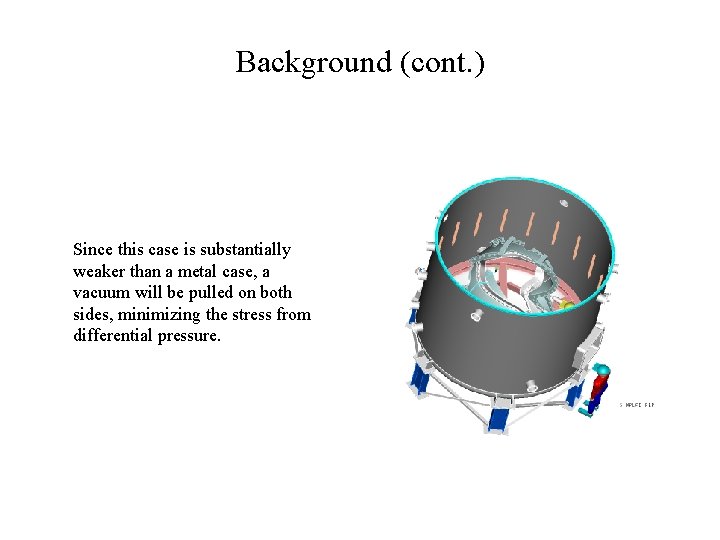
Background (cont. ) Since this case is substantially weaker than a metal case, a vacuum will be pulled on both sides, minimizing the stress from differential pressure.
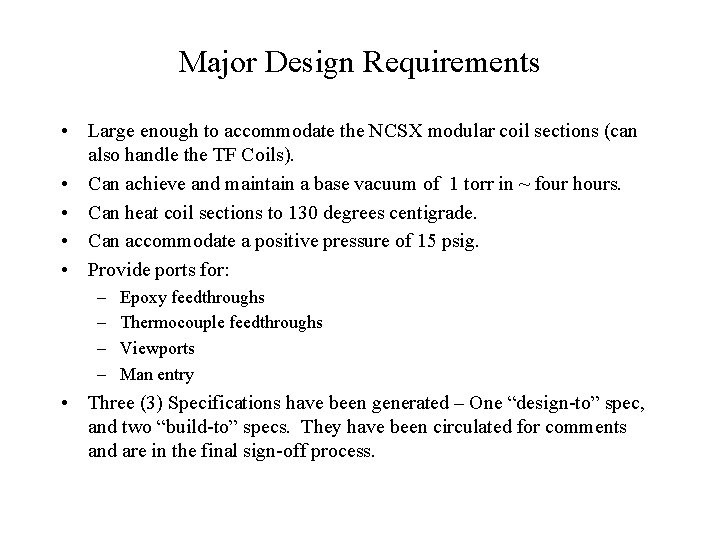
Major Design Requirements • Large enough to accommodate the NCSX modular coil sections (can also handle the TF Coils). • Can achieve and maintain a base vacuum of 1 torr in ~ four hours. • Can heat coil sections to 130 degrees centigrade. • Can accommodate a positive pressure of 15 psig. • Provide ports for: – – Epoxy feedthroughs Thermocouple feedthroughs Viewports Man entry • Three (3) Specifications have been generated – One “design-to” spec, and two “build-to” specs. They have been circulated for comments and are in the final sign-off process.
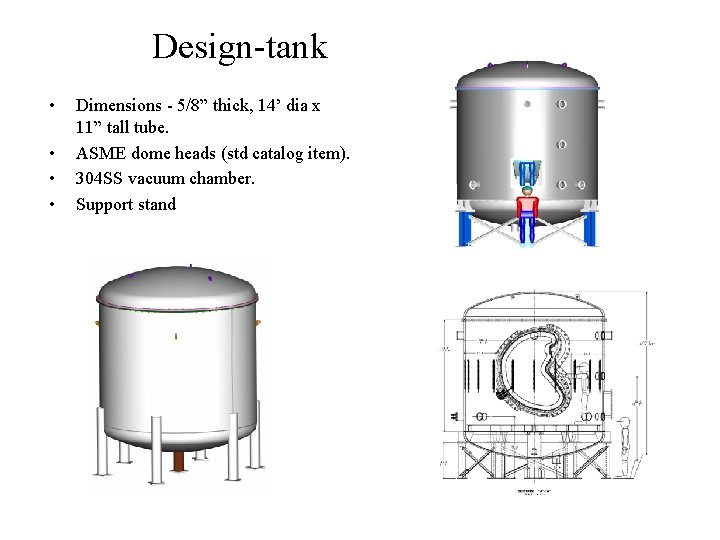
Design-tank • • Dimensions - 5/8” thick, 14’ dia x 11” tall tube. ASME dome heads (std catalog item). 304 SS vacuum chamber. Support stand
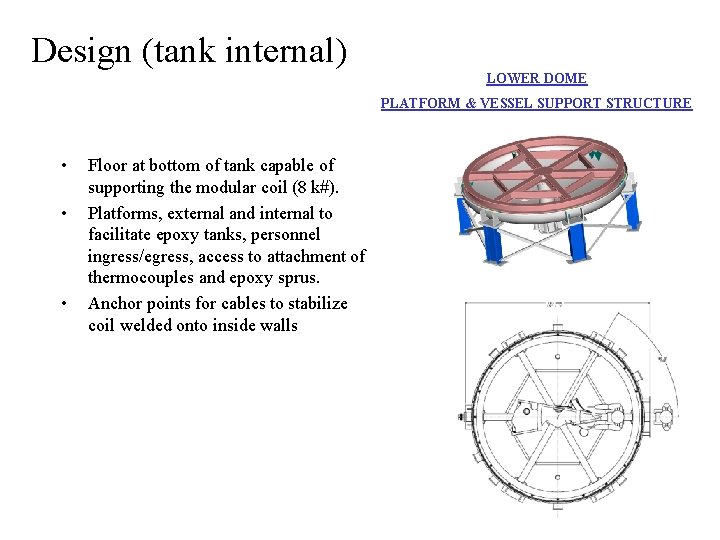
Design (tank internal) LOWER DOME PLATFORM & VESSEL SUPPORT STRUCTURE • • • Floor at bottom of tank capable of supporting the modular coil (8 k#). Platforms, external and internal to facilitate epoxy tanks, personnel ingress/egress, access to attachment of thermocouples and epoxy sprus. Anchor points for cables to stabilize coil welded onto inside walls
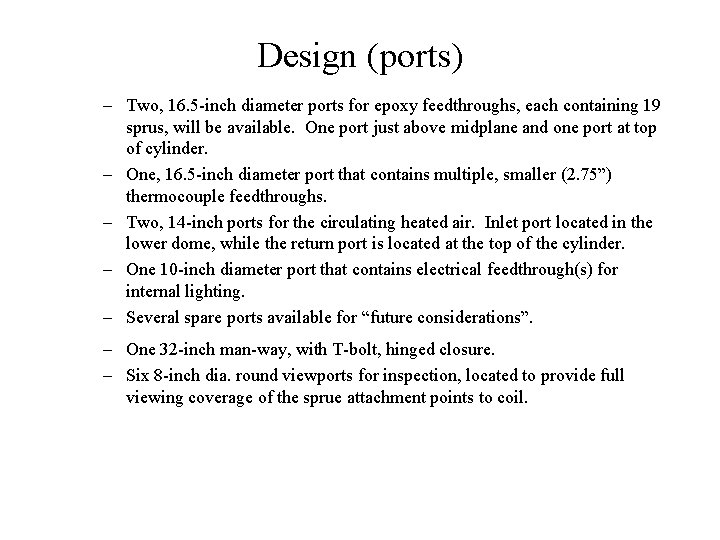
Design (ports) – Two, 16. 5 -inch diameter ports for epoxy feedthroughs, each containing 19 sprus, will be available. One port just above midplane and one port at top of cylinder. – One, 16. 5 -inch diameter port that contains multiple, smaller (2. 75”) thermocouple feedthroughs. – Two, 14 -inch ports for the circulating heated air. Inlet port located in the lower dome, while the return port is located at the top of the cylinder. – One 10 -inch diameter port that contains electrical feedthrough(s) for internal lighting. – Several spare ports available for “future considerations”. – One 32 -inch man-way, with T-bolt, hinged closure. – Six 8 -inch dia. round viewports for inspection, located to provide full viewing coverage of the sprue attachment points to coil.
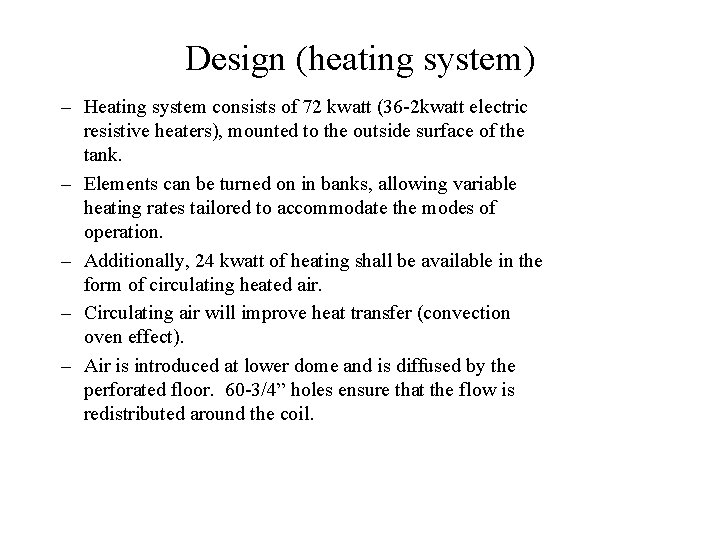
Design (heating system) – Heating system consists of 72 kwatt (36 -2 kwatt electric resistive heaters), mounted to the outside surface of the tank. – Elements can be turned on in banks, allowing variable heating rates tailored to accommodate the modes of operation. – Additionally, 24 kwatt of heating shall be available in the form of circulating heated air. – Circulating air will improve heat transfer (convection oven effect). – Air is introduced at lower dome and is diffused by the perforated floor. 60 -3/4” holes ensure that the flow is redistributed around the coil.
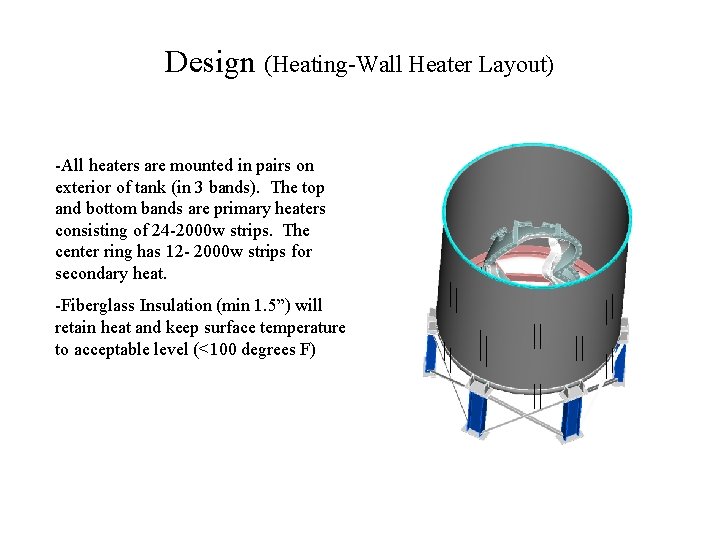
Design (Heating-Wall Heater Layout) -All heaters are mounted in pairs on exterior of tank (in 3 bands). The top and bottom bands are primary heaters consisting of 24 -2000 w strips. The center ring has 12 - 2000 w strips for secondary heat. -Fiberglass Insulation (min 1. 5”) will retain heat and keep surface temperature to acceptable level (<100 degrees F)
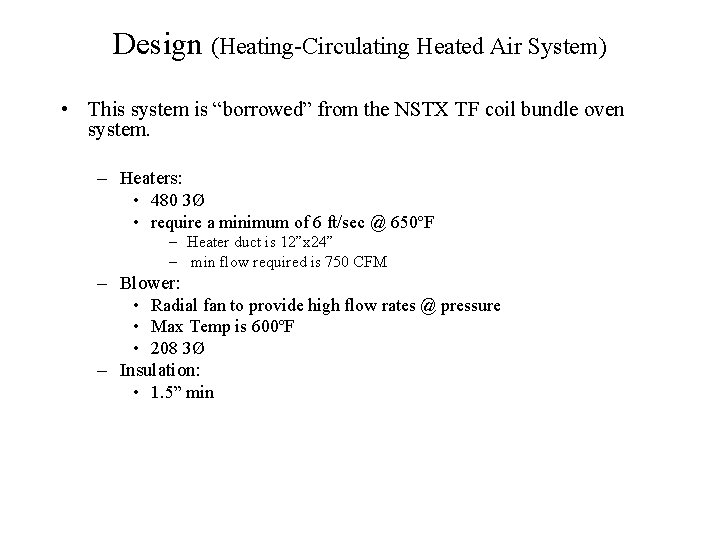
Design (Heating-Circulating Heated Air System) • This system is “borrowed” from the NSTX TF coil bundle oven system. – Heaters: • 480 3Ø • require a minimum of 6 ft/sec @ 650ºF – Heater duct is 12”x 24” – min flow required is 750 CFM – Blower: • Radial fan to provide high flow rates @ pressure • Max Temp is 600ºF • 208 3Ø – Insulation: • 1. 5” min
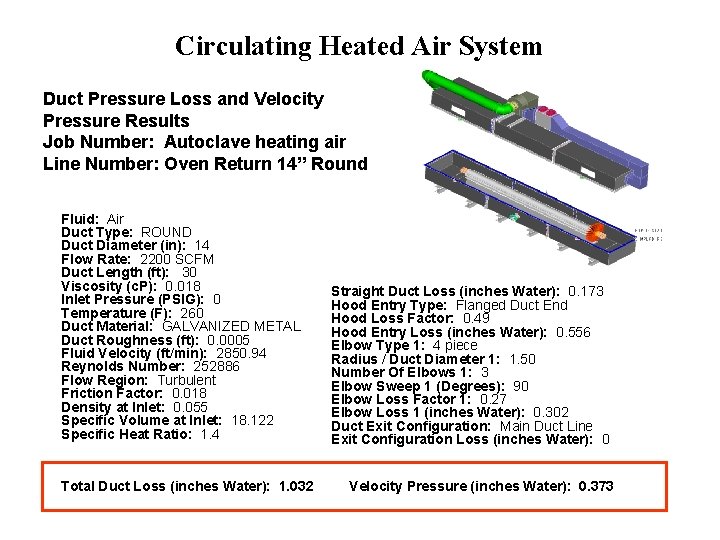
Circulating Heated Air System Duct Pressure Loss and Velocity Pressure Results Job Number: Autoclave heating air Line Number: Oven Return 14” Round Fluid: Air Duct Type: ROUND Duct Diameter (in): 14 Flow Rate: 2200 SCFM Duct Length (ft): 30 Viscosity (c. P): 0. 018 Inlet Pressure (PSIG): 0 Temperature (F): 260 Duct Material: GALVANIZED METAL Duct Roughness (ft): 0. 0005 Fluid Velocity (ft/min): 2850. 94 Reynolds Number: 252886 Flow Region: Turbulent Friction Factor: 0. 018 Density at Inlet: 0. 055 Specific Volume at Inlet: 18. 122 Specific Heat Ratio: 1. 4 Total Duct Loss (inches Water): 1. 032 Straight Duct Loss (inches Water): 0. 173 Hood Entry Type: Flanged Duct End Hood Loss Factor: 0. 49 Hood Entry Loss (inches Water): 0. 556 Elbow Type 1: 4 piece Radius / Duct Diameter 1: 1. 50 Number Of Elbows 1: 3 Elbow Sweep 1 (Degrees): 90 Elbow Loss Factor 1: 0. 27 Elbow Loss 1 (inches Water): 0. 302 Duct Exit Configuration: Main Duct Line Exit Configuration Loss (inches Water): 0 Velocity Pressure (inches Water): 0. 373
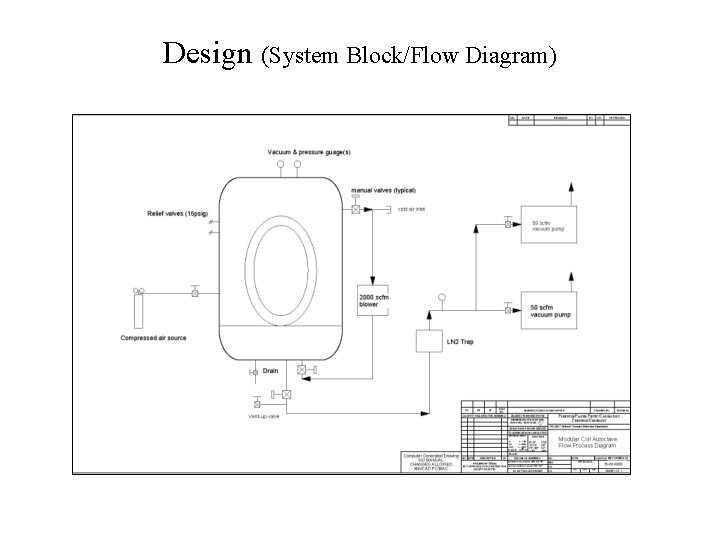
Design (System Block/Flow Diagram)
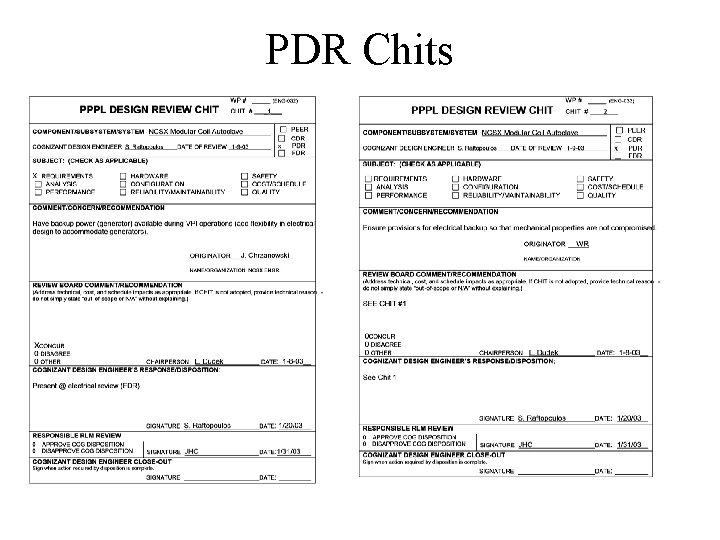
PDR Chits
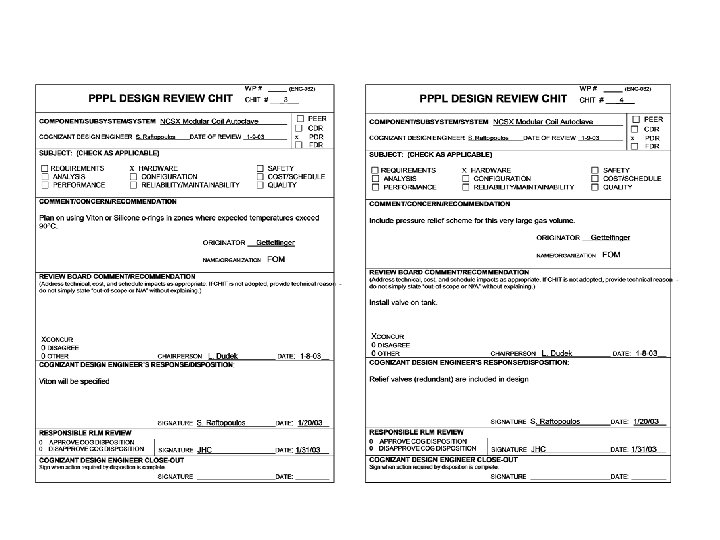
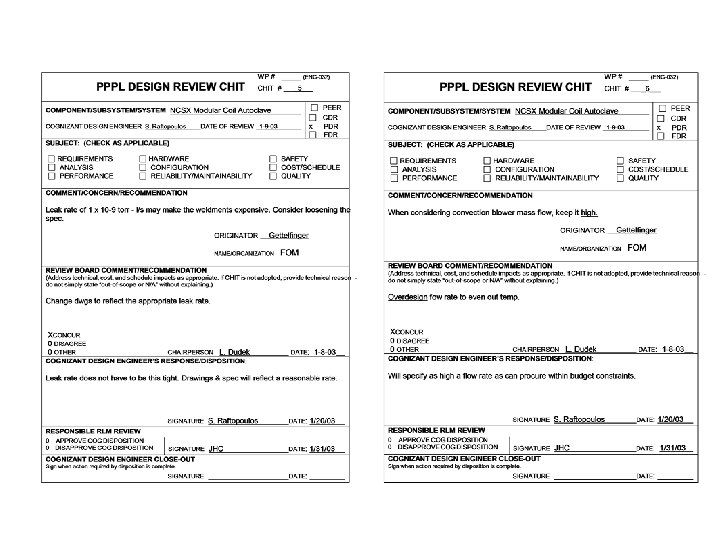
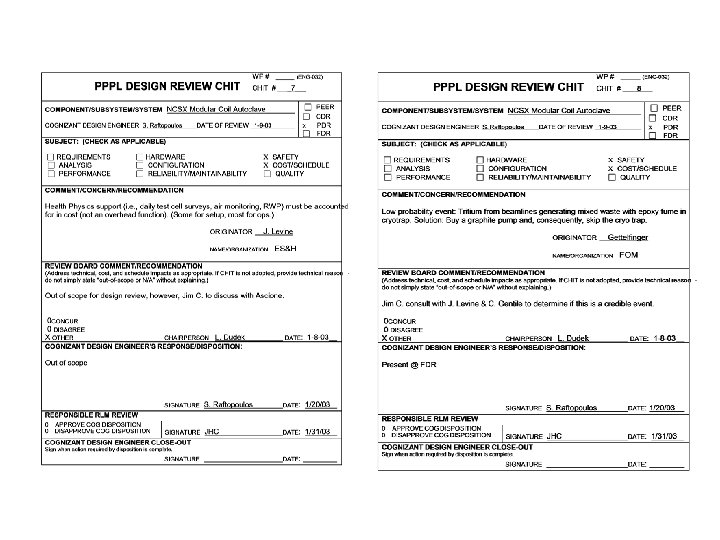
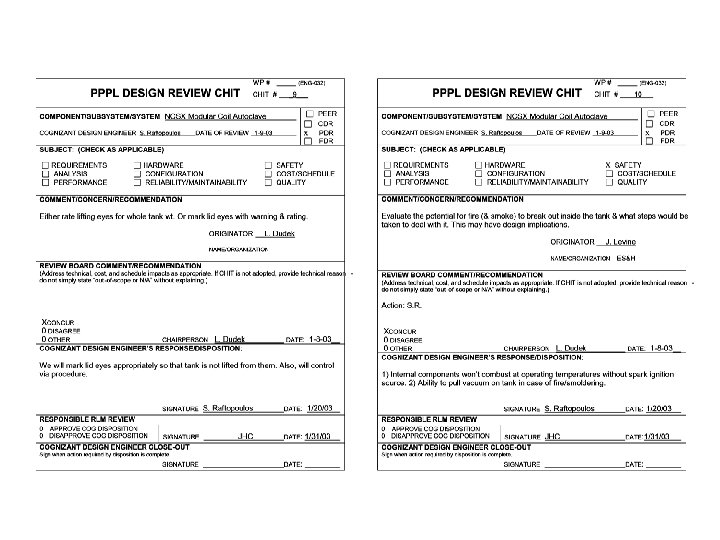
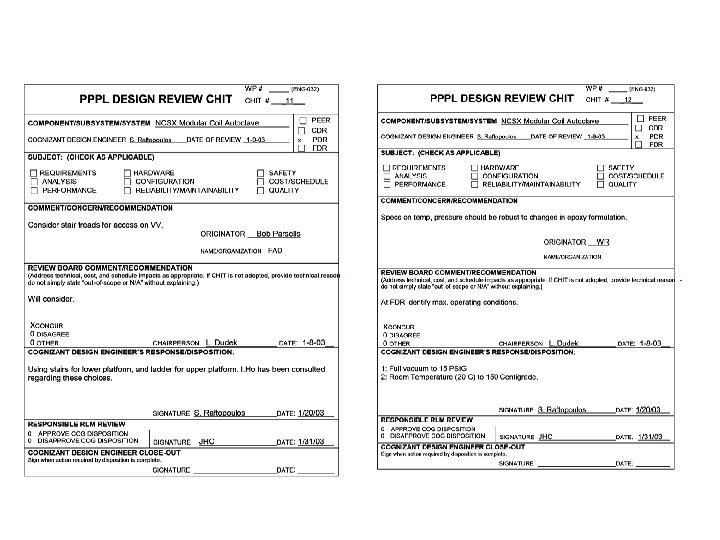
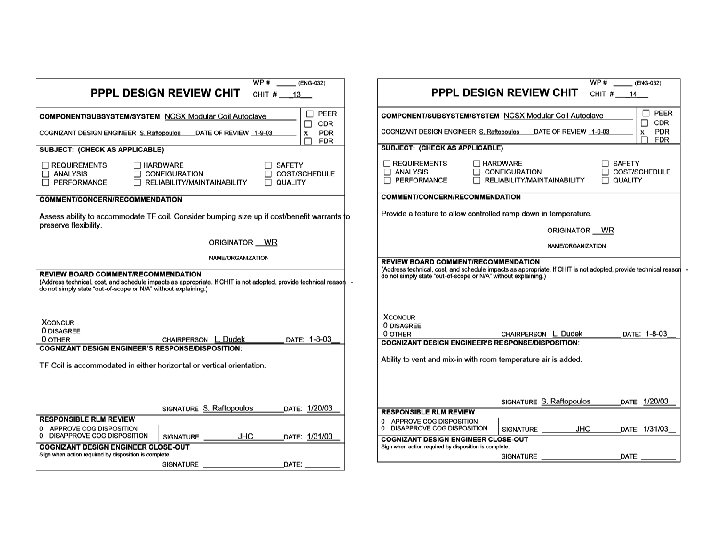
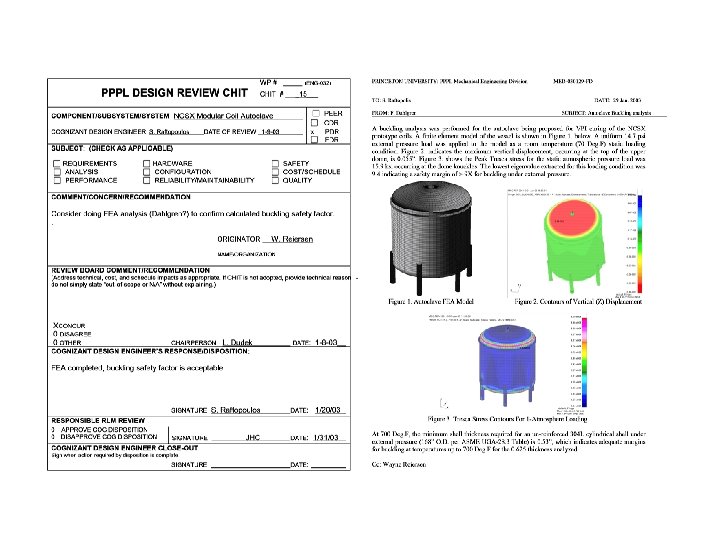
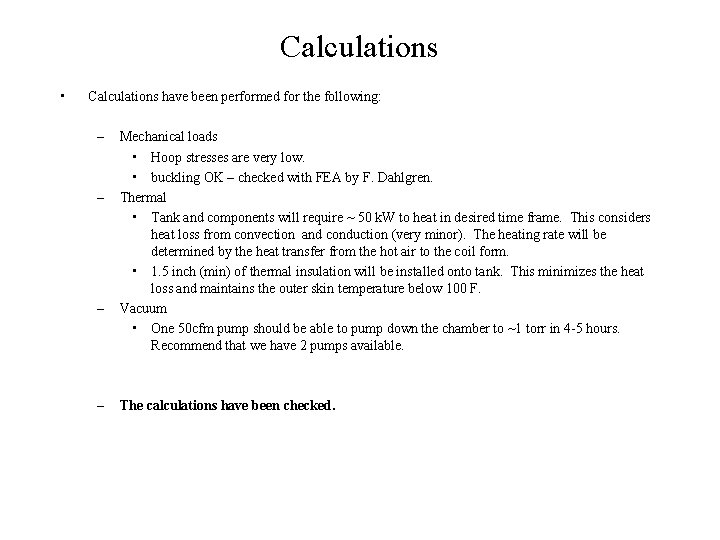
Calculations • Calculations have been performed for the following: – – Mechanical loads • Hoop stresses are very low. • buckling OK – checked with FEA by F. Dahlgren. Thermal • Tank and components will require ~ 50 k. W to heat in desired time frame. This considers heat loss from convection and conduction (very minor). The heating rate will be determined by the heat transfer from the hot air to the coil form. • 1. 5 inch (min) of thermal insulation will be installed onto tank. This minimizes the heat loss and maintains the outer skin temperature below 100 F. Vacuum • One 50 cfm pump should be able to pump down the chamber to ~1 torr in 4 -5 hours. Recommend that we have 2 pumps available. The calculations have been checked.
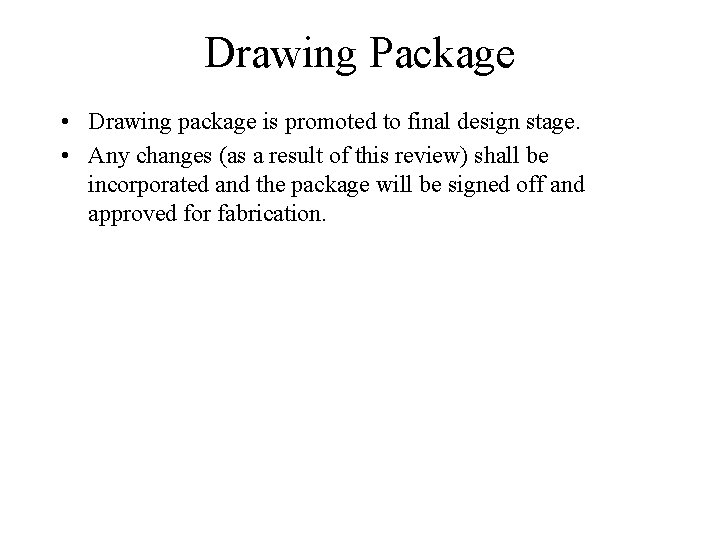
Drawing Package • Drawing package is promoted to final design stage. • Any changes (as a result of this review) shall be incorporated and the package will be signed off and approved for fabrication.
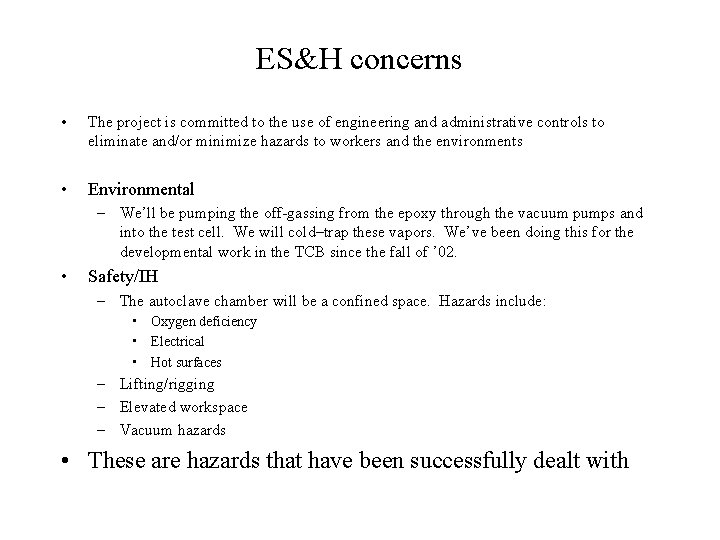
ES&H concerns • The project is committed to the use of engineering and administrative controls to eliminate and/or minimize hazards to workers and the environments • Environmental – We’ll be pumping the off-gassing from the epoxy through the vacuum pumps and into the test cell. We will cold–trap these vapors. We’ve been doing this for the developmental work in the TCB since the fall of ’ 02. • Safety/IH – The autoclave chamber will be a confined space. Hazards include: • Oxygen deficiency • Electrical • Hot surfaces – Lifting/rigging – Elevated workspace – Vacuum hazards • These are hazards that have been successfully dealt with
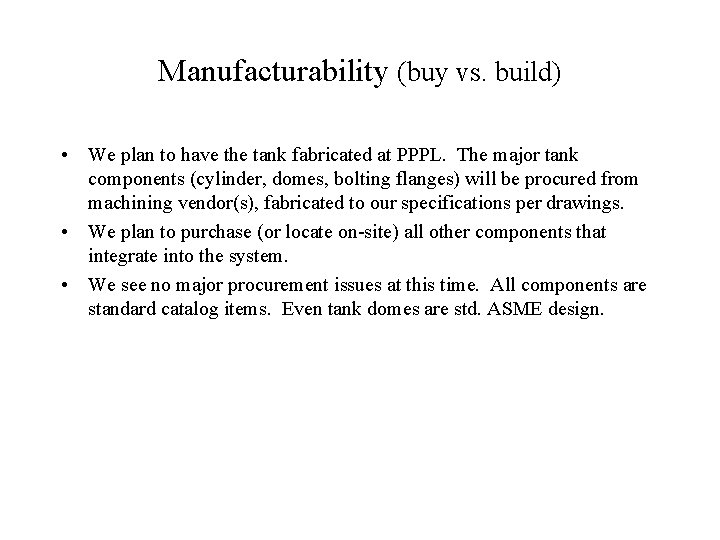
Manufacturability (buy vs. build) • We plan to have the tank fabricated at PPPL. The major tank components (cylinder, domes, bolting flanges) will be procured from machining vendor(s), fabricated to our specifications per drawings. • We plan to purchase (or locate on-site) all other components that integrate into the system. • We see no major procurement issues at this time. All components are standard catalog items. Even tank domes are std. ASME design.
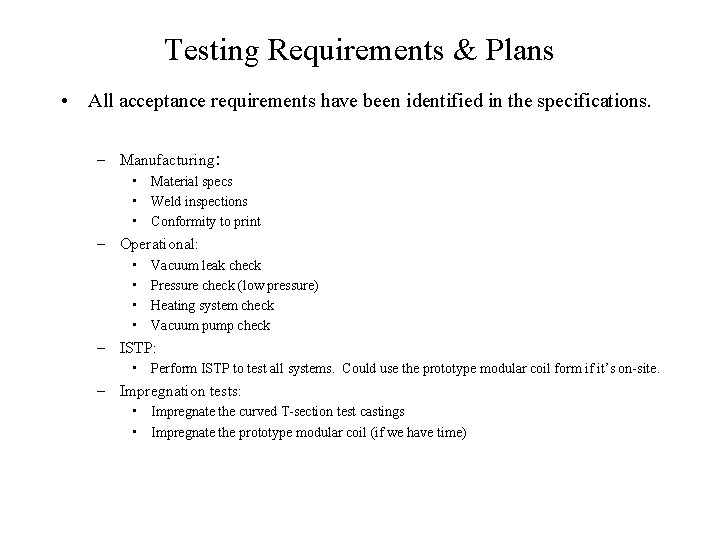
Testing Requirements & Plans • All acceptance requirements have been identified in the specifications. – Manufacturing: • Material specs • Weld inspections • Conformity to print – Operational: • • Vacuum leak check Pressure check (low pressure) Heating system check Vacuum pump check – ISTP: • Perform ISTP to test all systems. Could use the prototype modular coil form if it’s on-site. – Impregnation tests: • Impregnate the curved T-section test castings • Impregnate the prototype modular coil (if we have time)
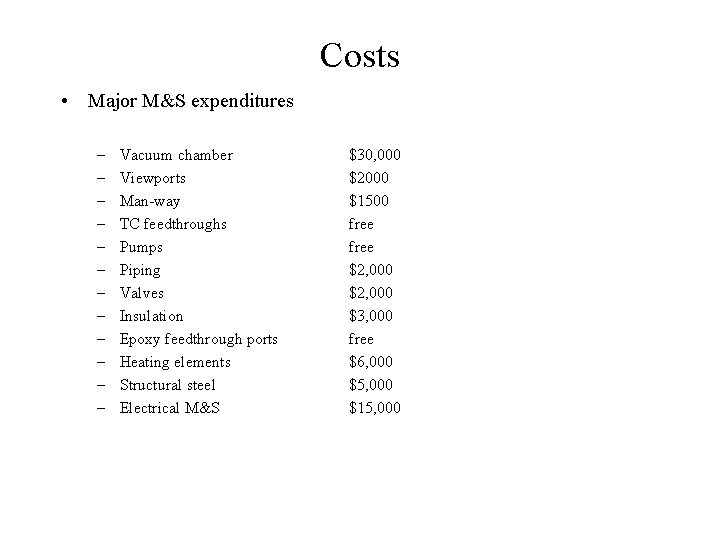
Costs • Major M&S expenditures – – – Vacuum chamber Viewports Man-way TC feedthroughs Pumps Piping Valves Insulation Epoxy feedthrough ports Heating elements Structural steel Electrical M&S $30, 000 $2000 $1500 free $2, 000 $3, 000 free $6, 000 $5, 000 $15, 000
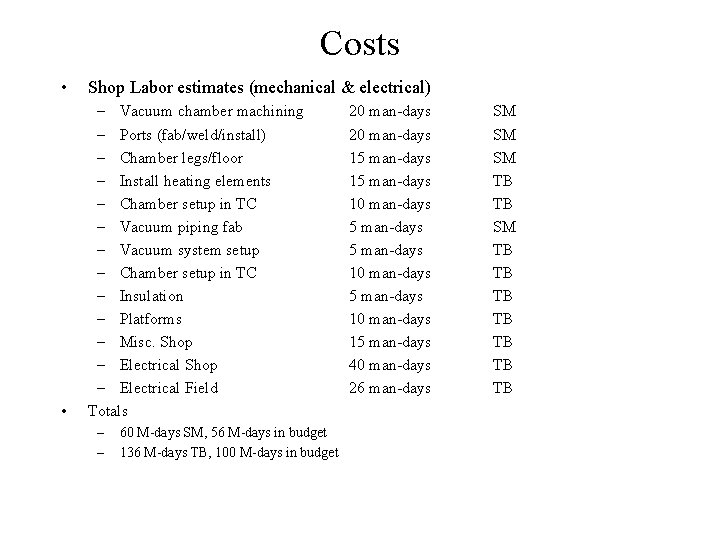
Costs • Shop Labor estimates (mechanical & electrical) • – Vacuum chamber machining – Ports (fab/weld/install) – Chamber legs/floor – Install heating elements – Chamber setup in TC – Vacuum piping fab – Vacuum system setup – Chamber setup in TC – Insulation – Platforms – Misc. Shop – Electrical Field Totals – – 60 M-days SM, 56 M-days in budget 136 M-days TB, 100 M-days in budget 20 man-days 15 man-days 10 man-days 5 man-days 10 man-days 15 man-days 40 man-days 26 man-days SM SM SM TB TB TB
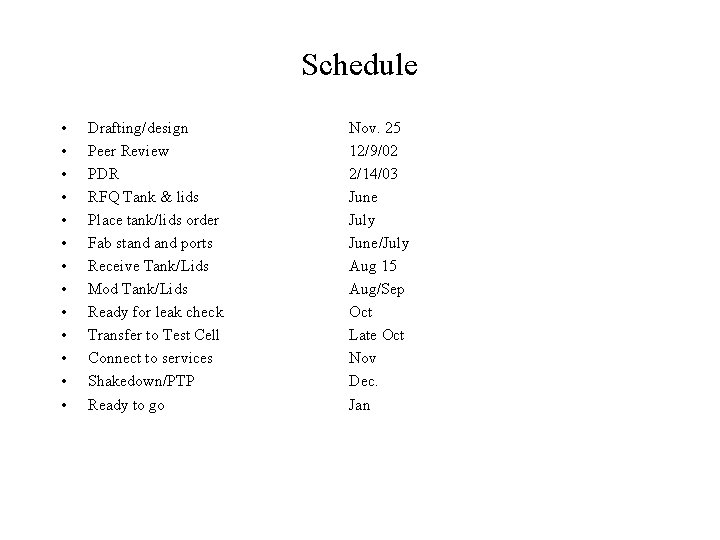
Schedule • • • • Drafting/design Peer Review PDR RFQ Tank & lids Place tank/lids order Fab stand ports Receive Tank/Lids Mod Tank/Lids Ready for leak check Transfer to Test Cell Connect to services Shakedown/PTP Ready to go Nov. 25 12/9/02 2/14/03 June July June/July Aug 15 Aug/Sep Oct Late Oct Nov Dec. Jan
Steve jobs steve wozniak and ronald wayne
Agenda sistemica y agenda institucional
Fdr q value
Fdr
Jonah 1938 political cartoon meaning
Fdr three rs
Criticism of fdr
Fdr
Grille mbti
Fdrs response to the great depression
New deal fdr
Compare and contrast hoover and fdr
Fdr political cartoons
Fdr died
Fdr
Enoxoparine
Fdr election map
Fdr dies truman becomes president
Franklin d roosevelt chief legislator
Fdr design
Fdr
Wows fdr
Fdr vps
Steve jobs presentation book
Jobs to be done template
Agenda presentation
Sales presentation agenda
Autoclave uses
Classification of autoclaves
Hpal process flow diagram