MECE 5004 Fluid Power Systems Servo simulation and
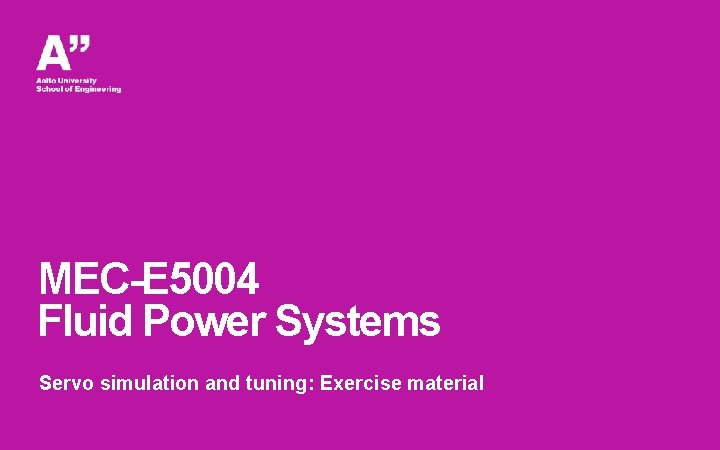
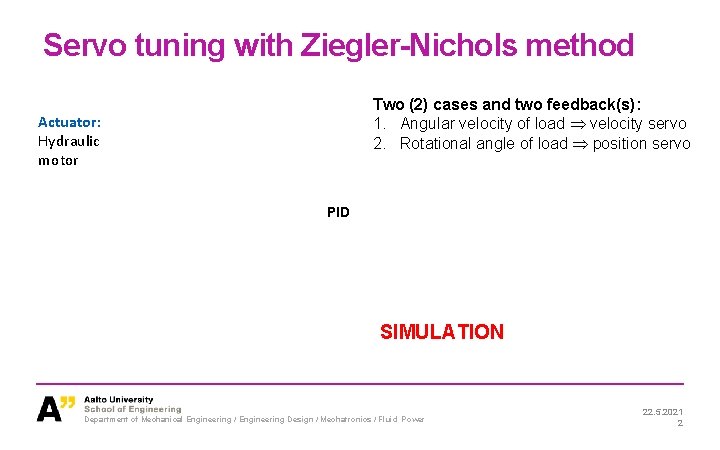
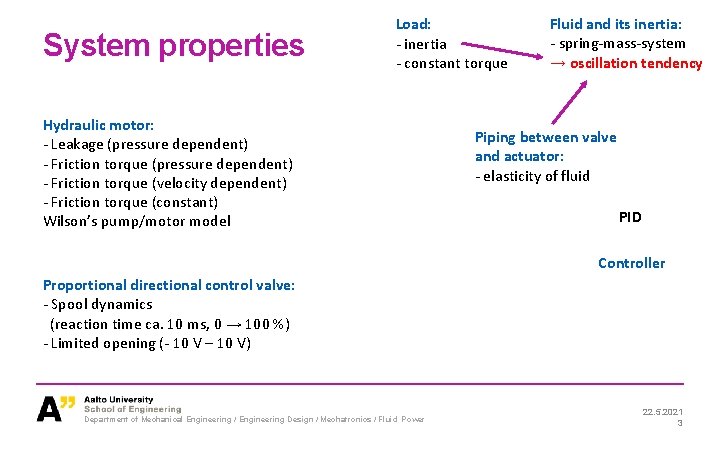
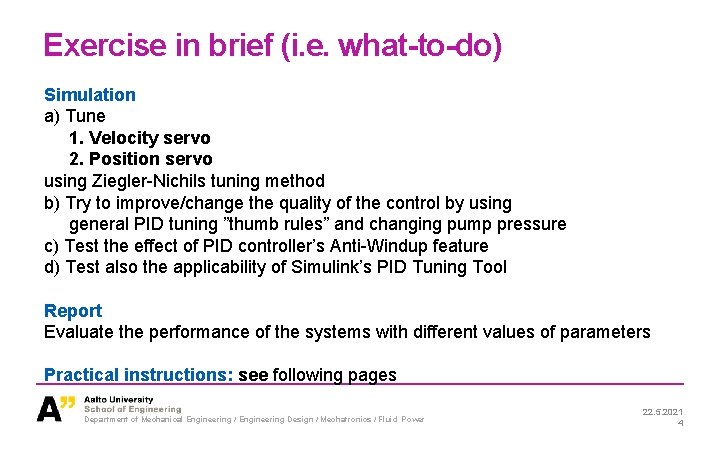
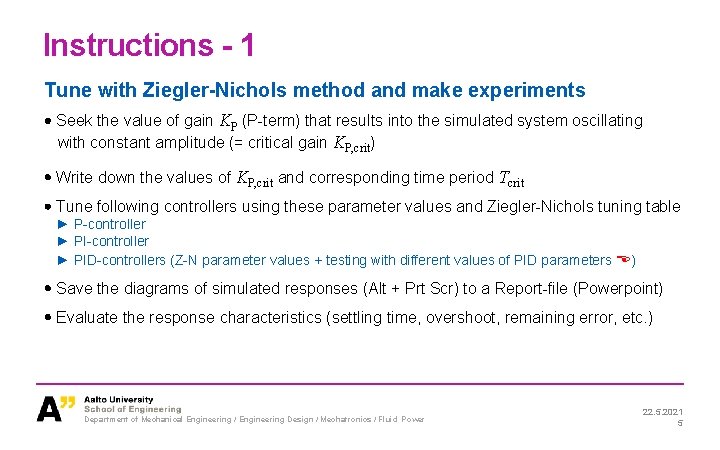
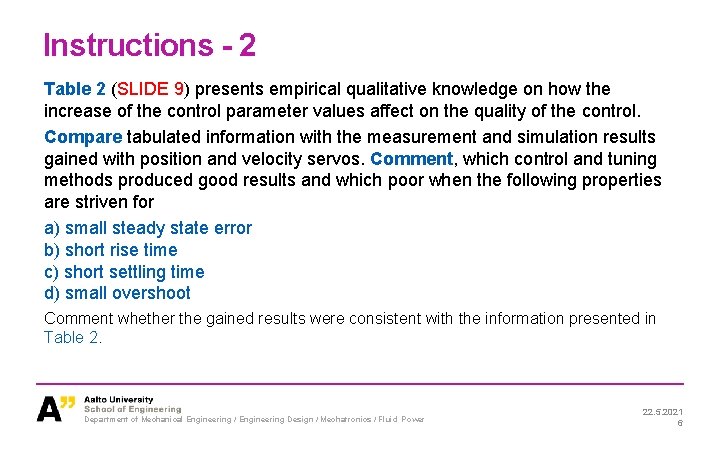
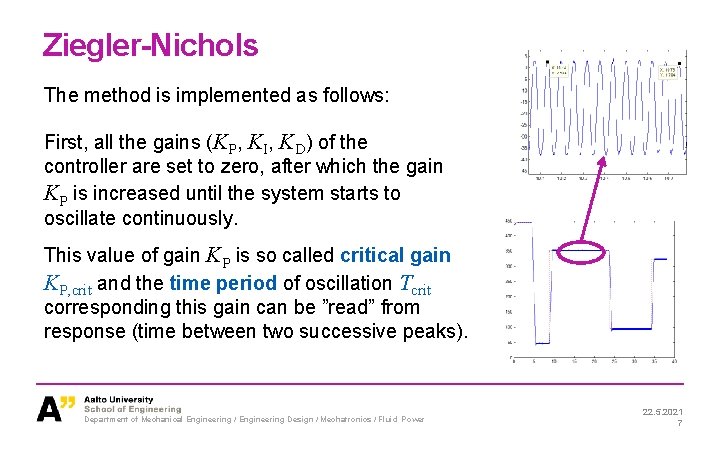
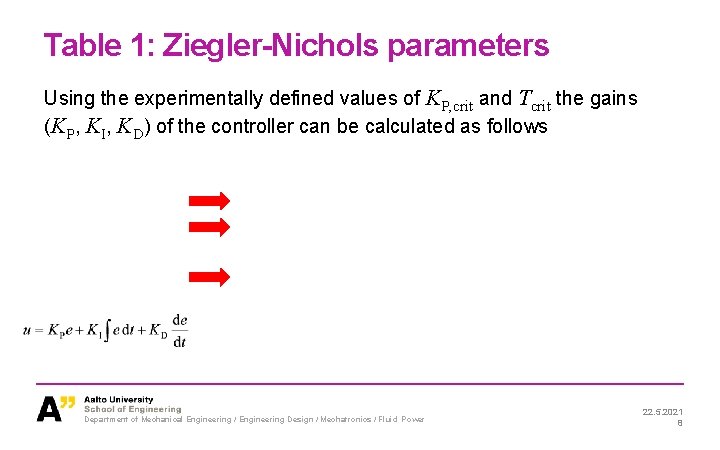
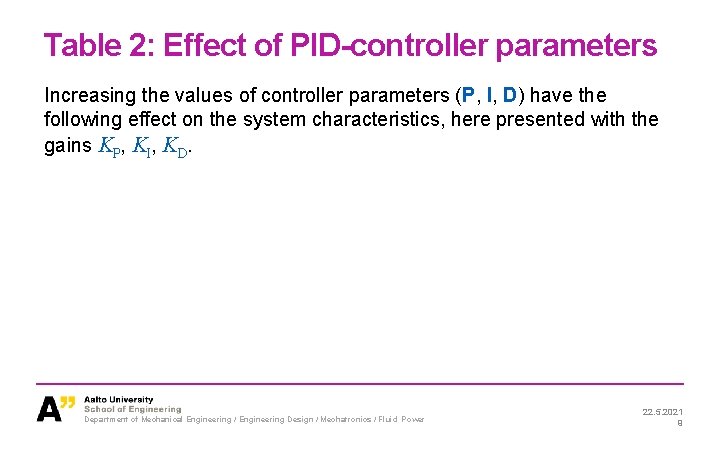
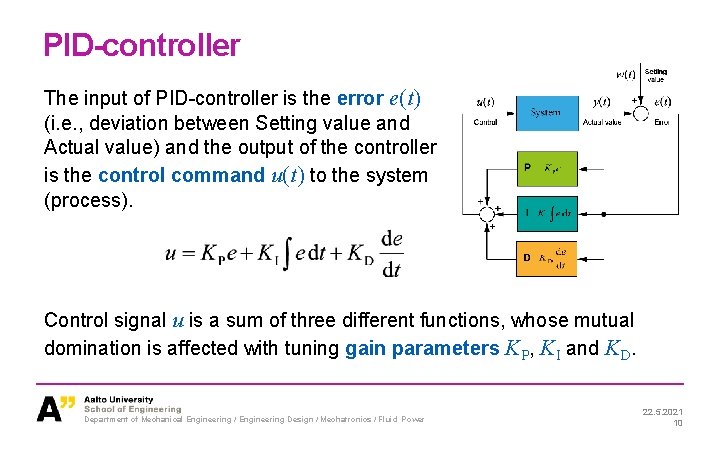
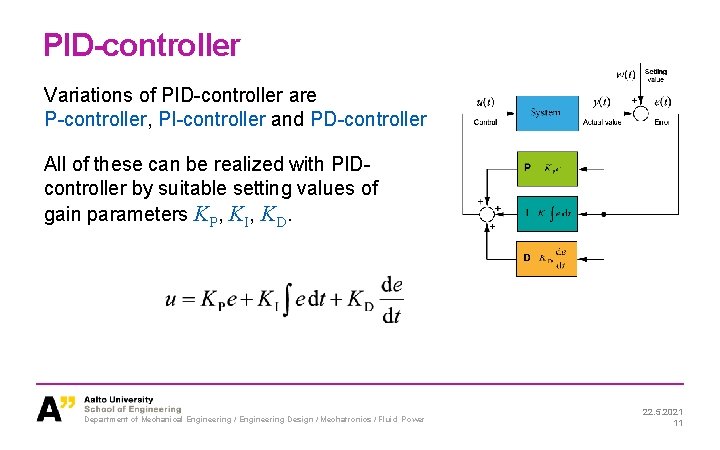
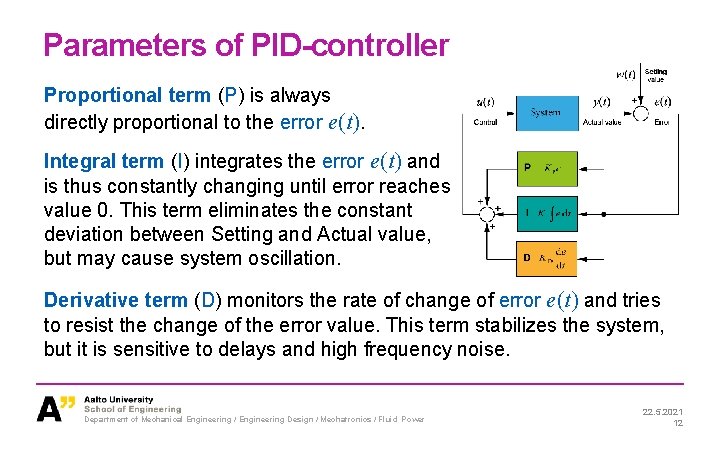
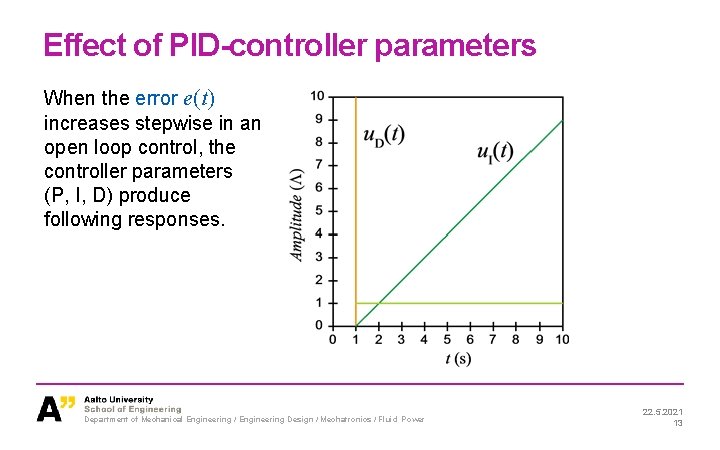
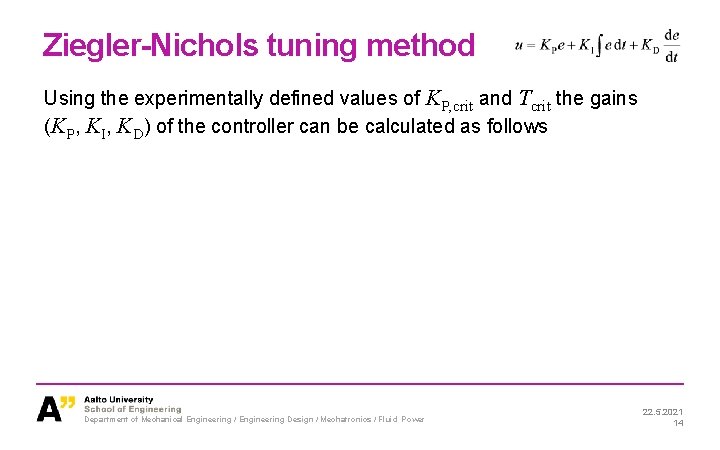
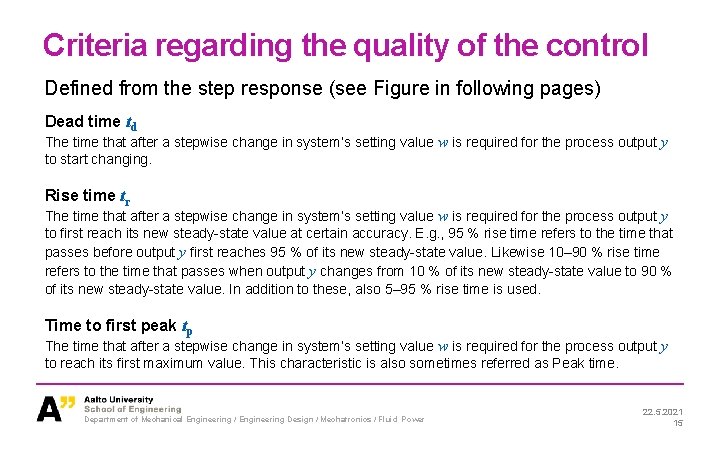
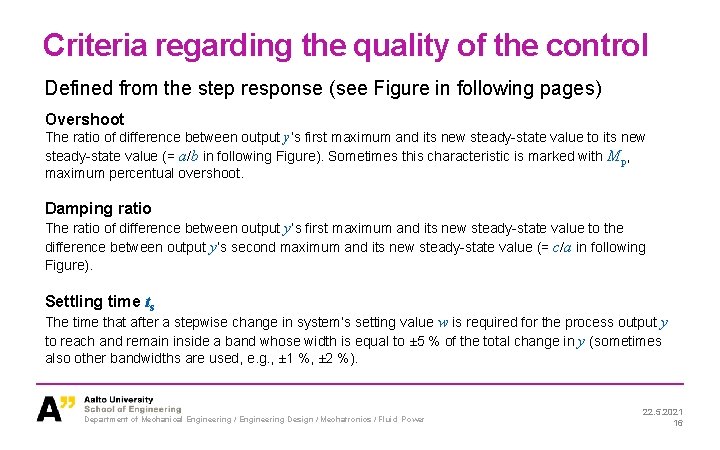
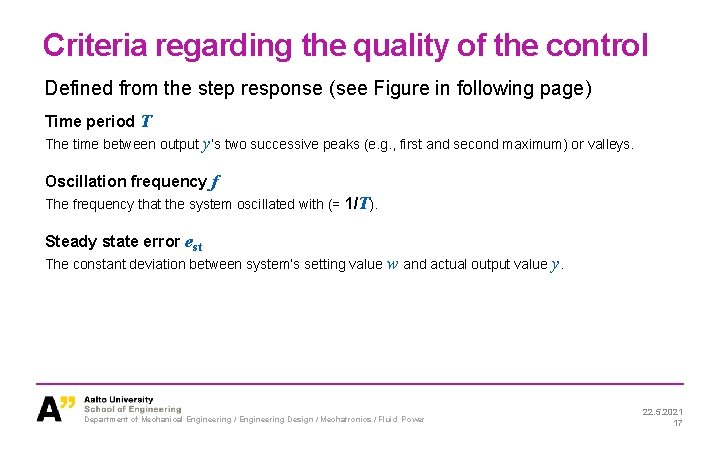
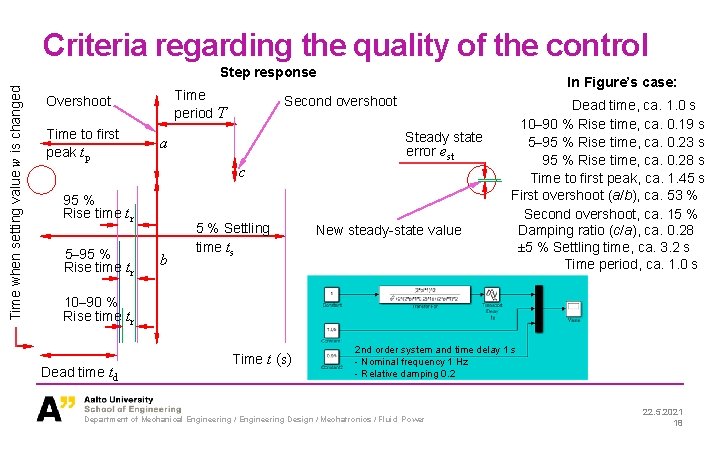
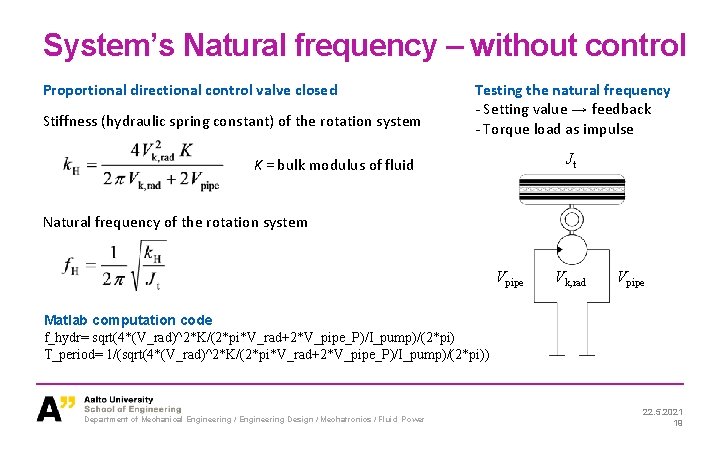
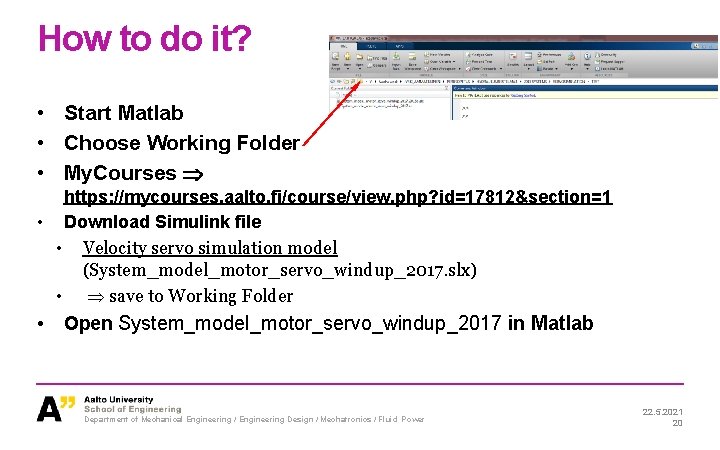
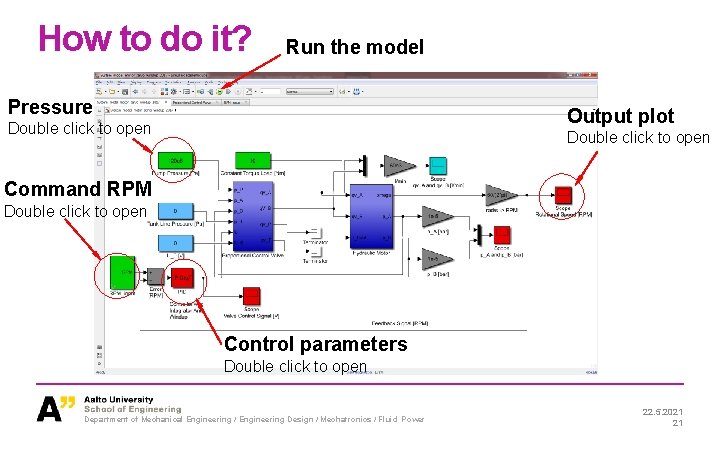
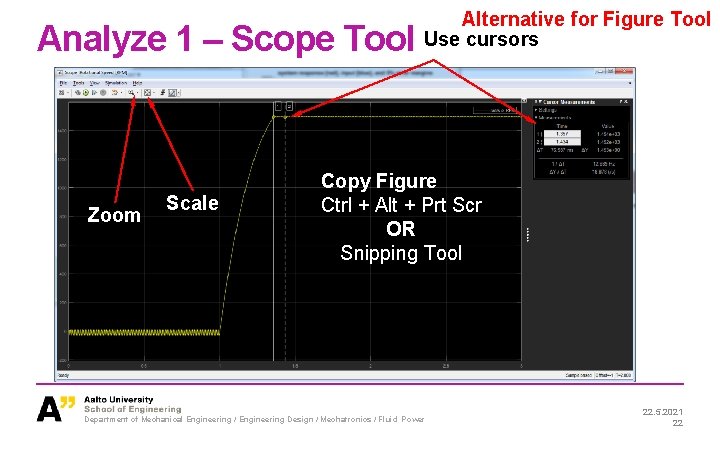
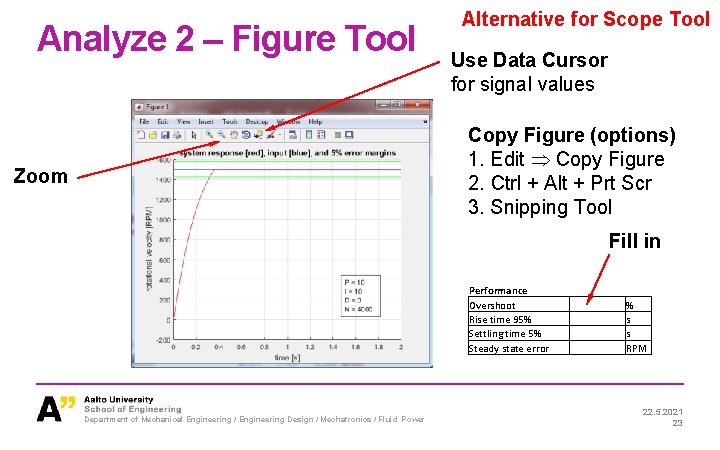
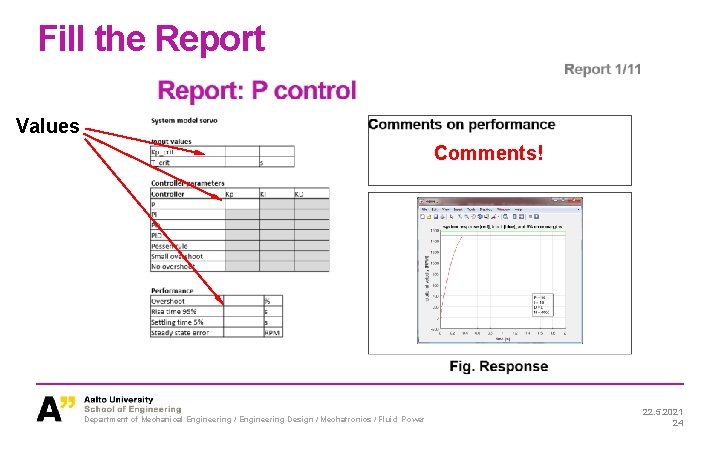
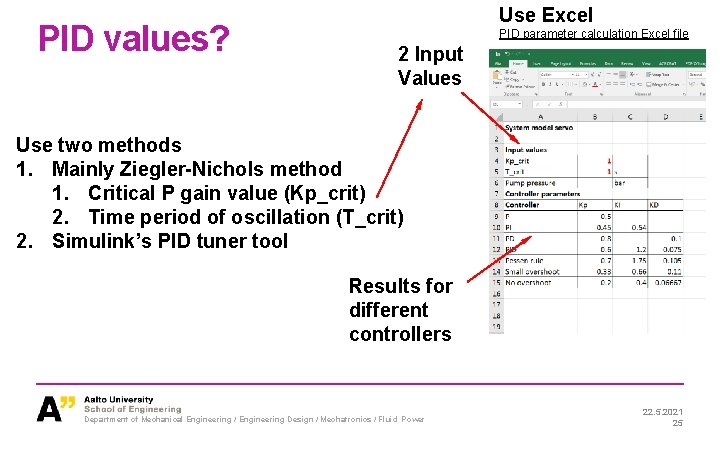
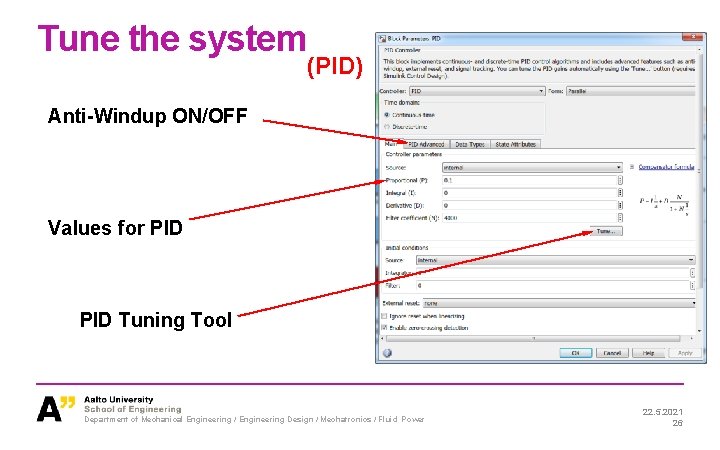
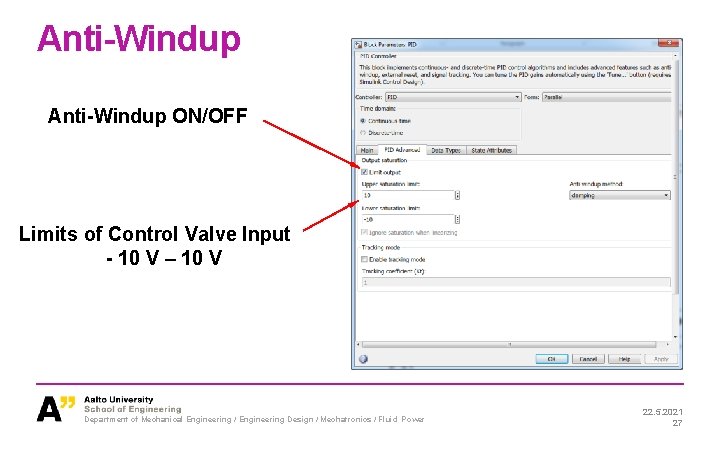
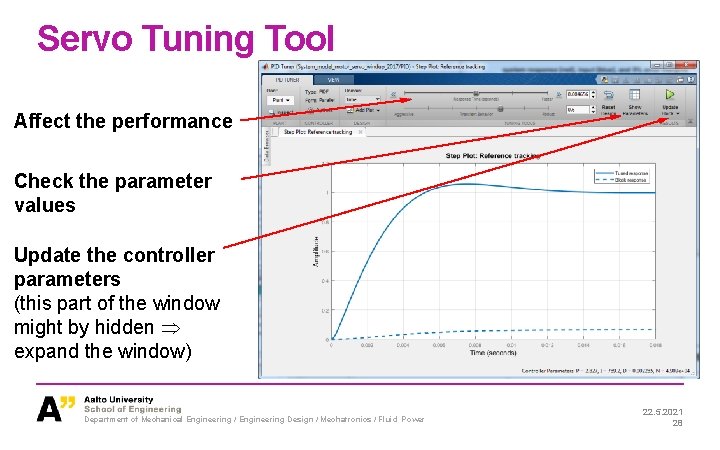
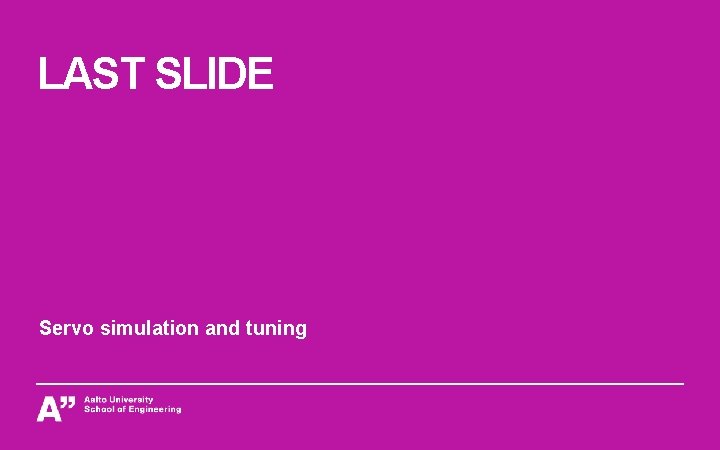
- Slides: 29
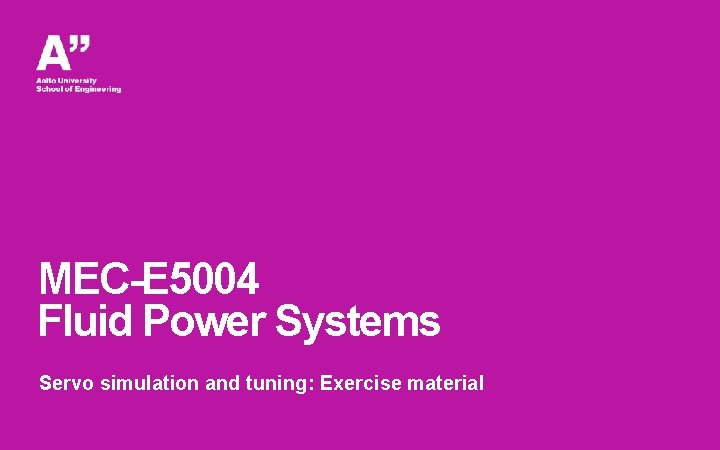
MEC-E 5004 Fluid Power Systems Servo simulation and tuning: Exercise material
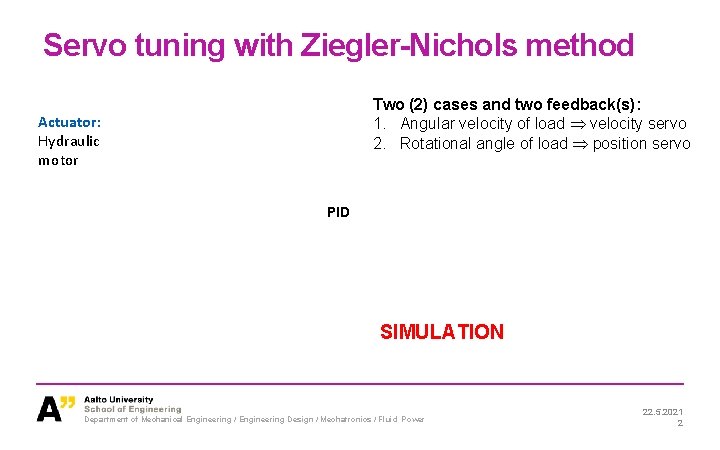
Servo tuning with Ziegler-Nichols method Two (2) cases and two feedback(s): 1. Angular velocity of load velocity servo 2. Rotational angle of load position servo Actuator: Hydraulic motor PID SIMULATION Department of Mechanical Engineering / Engineering Design / Mechatronics / Fluid Power 22. 5. 2021 2
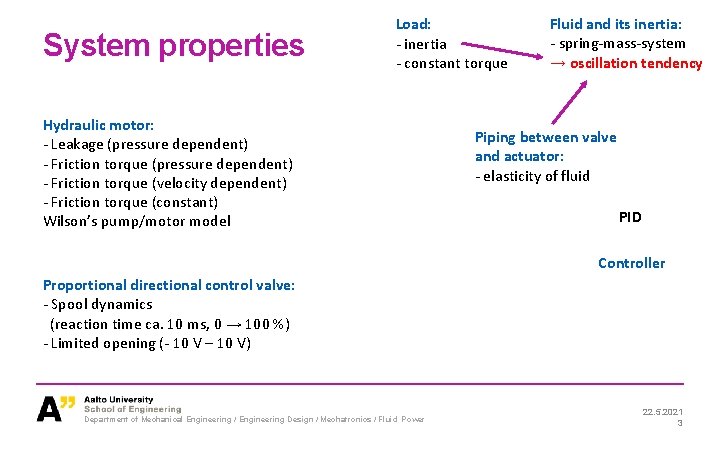
System properties Load: - inertia - constant torque Hydraulic motor: - Leakage (pressure dependent) - Friction torque (velocity dependent) - Friction torque (constant) Wilson’s pump/motor model Fluid and its inertia: - spring-mass-system → oscillation tendency Piping between valve and actuator: - elasticity of fluid PID Controller Proportional directional control valve: - Spool dynamics (reaction time ca. 10 ms, 0 → 100 %) - Limited opening (- 10 V – 10 V) Department of Mechanical Engineering / Engineering Design / Mechatronics / Fluid Power 22. 5. 2021 3
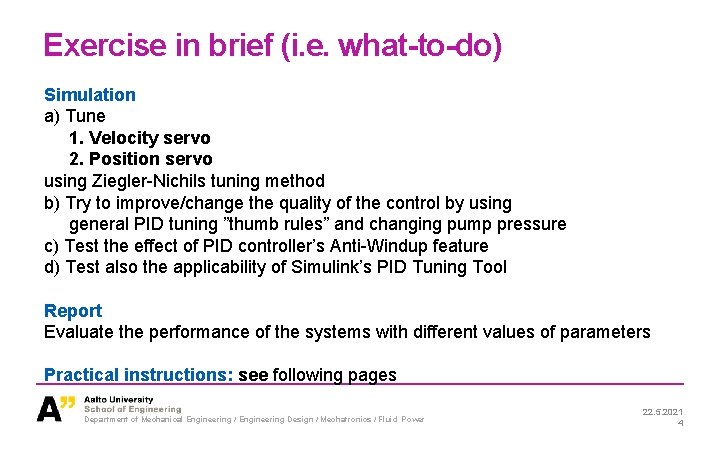
Exercise in brief (i. e. what-to-do) Simulation a) Tune 1. Velocity servo 2. Position servo using Ziegler-Nichils tuning method b) Try to improve/change the quality of the control by using general PID tuning ”thumb rules” and changing pump pressure c) Test the effect of PID controller’s Anti-Windup feature d) Test also the applicability of Simulink’s PID Tuning Tool Report Evaluate the performance of the systems with different values of parameters Practical instructions: see following pages Department of Mechanical Engineering / Engineering Design / Mechatronics / Fluid Power 22. 5. 2021 4
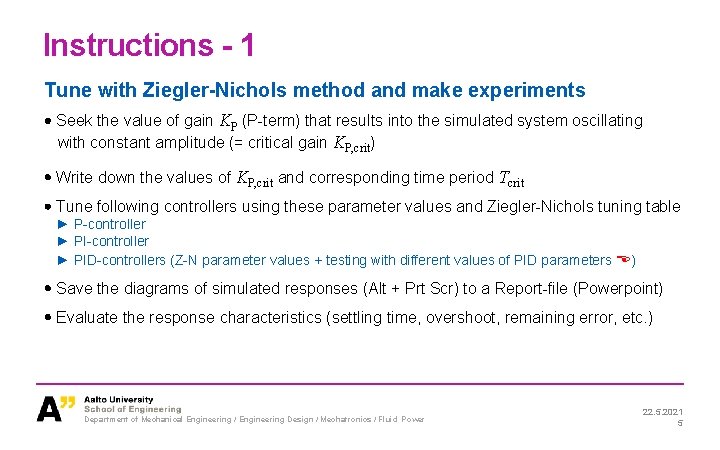
Instructions - 1 Tune with Ziegler-Nichols method and make experiments Seek the value of gain KP (P-term) that results into the simulated system oscillating with constant amplitude (= critical gain KP, crit) Write down the values of KP, crit and corresponding time period Tcrit Tune following controllers using these parameter values and Ziegler-Nichols tuning table ► P-controller ► PID-controllers (Z-N parameter values + testing with different values of PID parameters ) Save the diagrams of simulated responses (Alt + Prt Scr) to a Report-file (Powerpoint) Evaluate the response characteristics (settling time, overshoot, remaining error, etc. ) Department of Mechanical Engineering / Engineering Design / Mechatronics / Fluid Power 22. 5. 2021 5
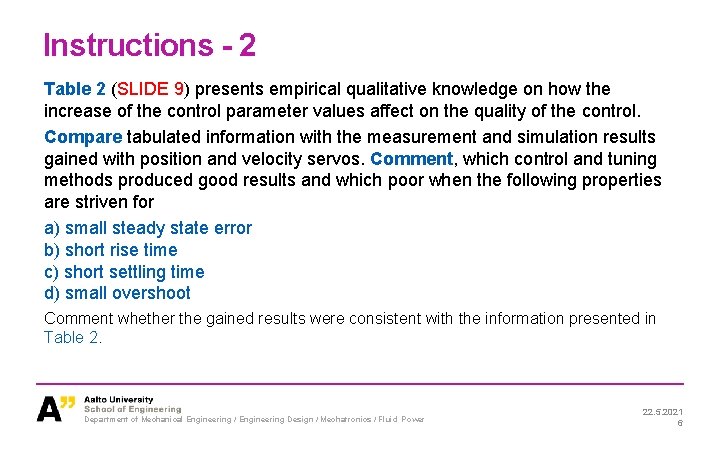
Instructions - 2 Table 2 (SLIDE 9) presents empirical qualitative knowledge on how the increase of the control parameter values affect on the quality of the control. Compare tabulated information with the measurement and simulation results gained with position and velocity servos. Comment, which control and tuning methods produced good results and which poor when the following properties are striven for a) small steady state error b) short rise time c) short settling time d) small overshoot Comment whether the gained results were consistent with the information presented in Table 2. Department of Mechanical Engineering / Engineering Design / Mechatronics / Fluid Power 22. 5. 2021 6
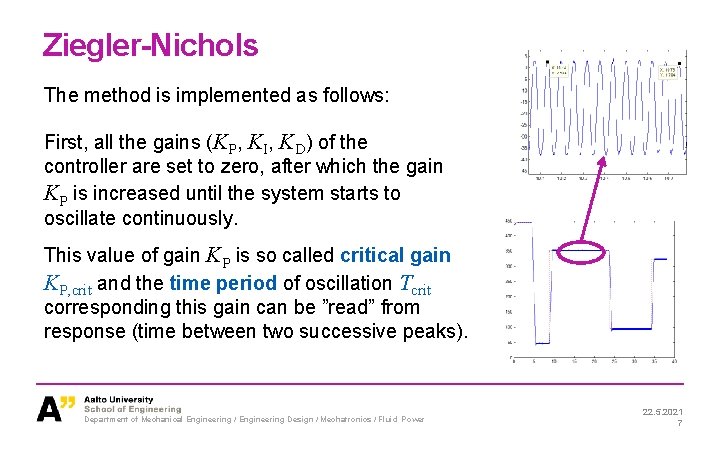
Ziegler-Nichols The method is implemented as follows: First, all the gains (KP, KI, KD) of the controller are set to zero, after which the gain KP is increased until the system starts to oscillate continuously. This value of gain KP is so called critical gain KP, crit and the time period of oscillation Tcrit corresponding this gain can be ”read” from response (time between two successive peaks). Department of Mechanical Engineering / Engineering Design / Mechatronics / Fluid Power 22. 5. 2021 7
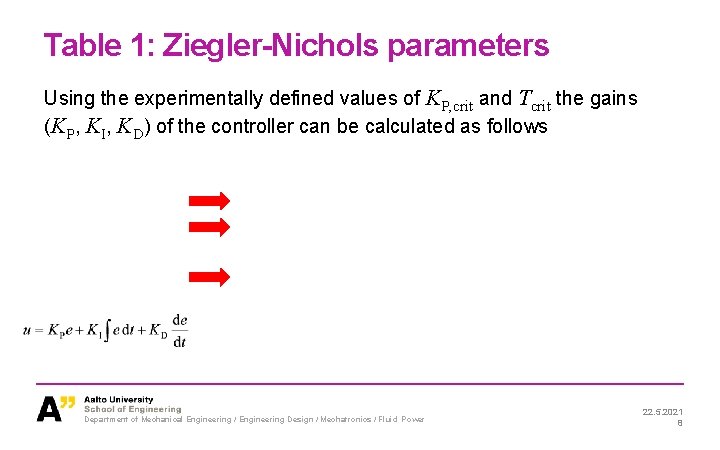
Table 1: Ziegler-Nichols parameters Using the experimentally defined values of KP, crit and Tcrit the gains (KP, KI, KD) of the controller can be calculated as follows Department of Mechanical Engineering / Engineering Design / Mechatronics / Fluid Power 22. 5. 2021 8
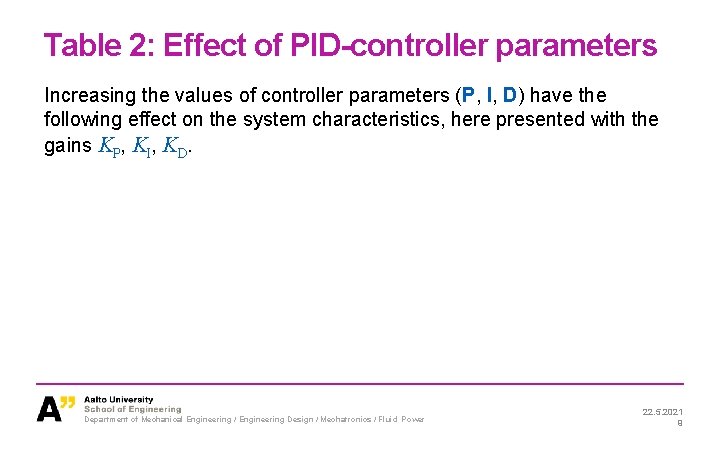
Table 2: Effect of PID-controller parameters Increasing the values of controller parameters (P, I, D) have the following effect on the system characteristics, here presented with the gains KP, KI, KD. Department of Mechanical Engineering / Engineering Design / Mechatronics / Fluid Power 22. 5. 2021 9
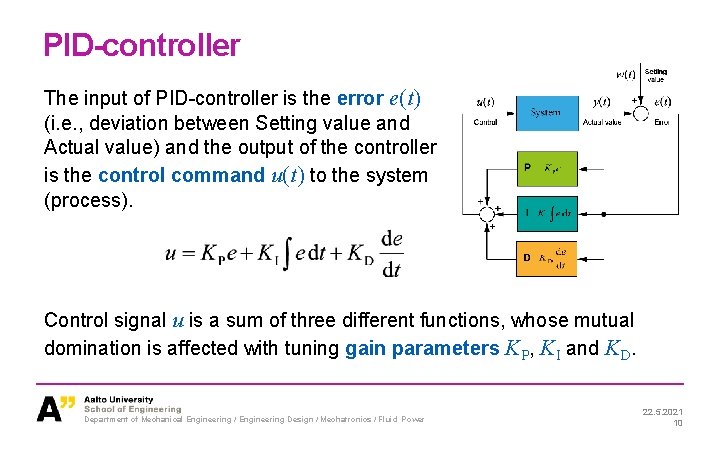
PID-controller The input of PID-controller is the error e(t) (i. e. , deviation between Setting value and Actual value) and the output of the controller is the control command u(t) to the system (process). Control signal u is a sum of three different functions, whose mutual domination is affected with tuning gain parameters KP, KI and KD. Department of Mechanical Engineering / Engineering Design / Mechatronics / Fluid Power 22. 5. 2021 10
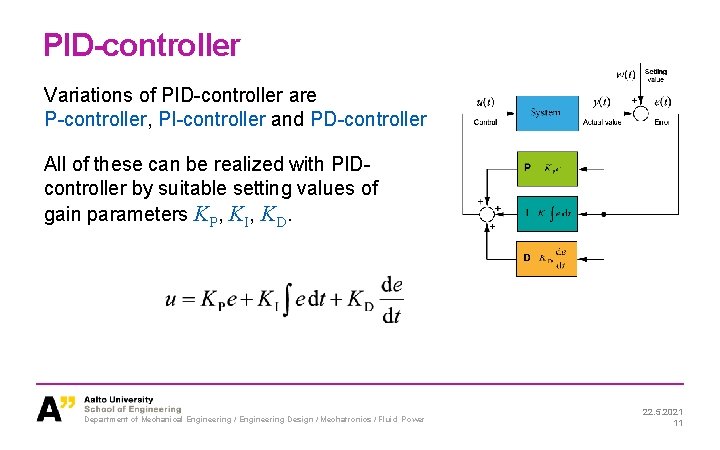
PID-controller Variations of PID-controller are P-controller, PI-controller and PD-controller All of these can be realized with PIDcontroller by suitable setting values of gain parameters KP, KI, KD. Department of Mechanical Engineering / Engineering Design / Mechatronics / Fluid Power 22. 5. 2021 11
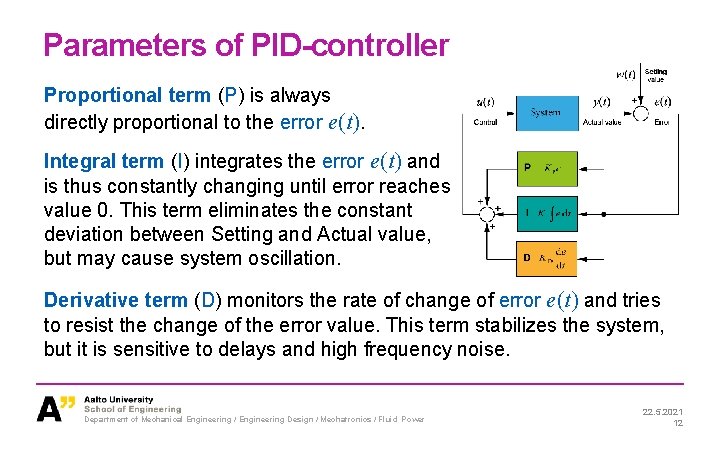
Parameters of PID-controller Proportional term (P) is always directly proportional to the error e(t). Integral term (I) integrates the error e(t) and is thus constantly changing until error reaches value 0. This term eliminates the constant deviation between Setting and Actual value, but may cause system oscillation. Derivative term (D) monitors the rate of change of error e(t) and tries to resist the change of the error value. This term stabilizes the system, but it is sensitive to delays and high frequency noise. Department of Mechanical Engineering / Engineering Design / Mechatronics / Fluid Power 22. 5. 2021 12
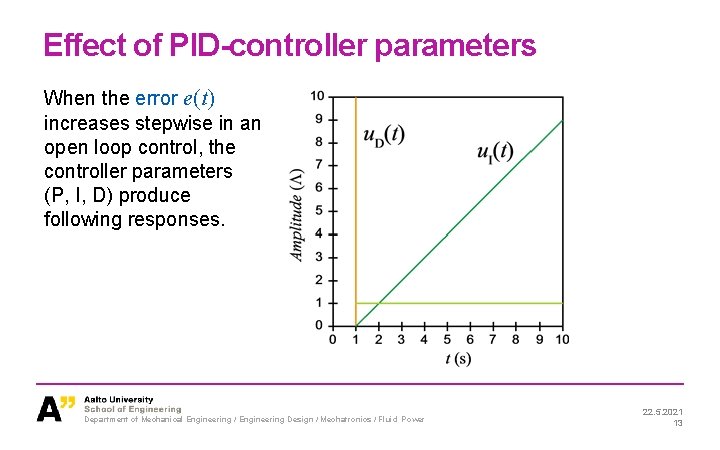
Effect of PID-controller parameters When the error e(t) increases stepwise in an open loop control, the controller parameters (P, I, D) produce following responses. Department of Mechanical Engineering / Engineering Design / Mechatronics / Fluid Power 22. 5. 2021 13
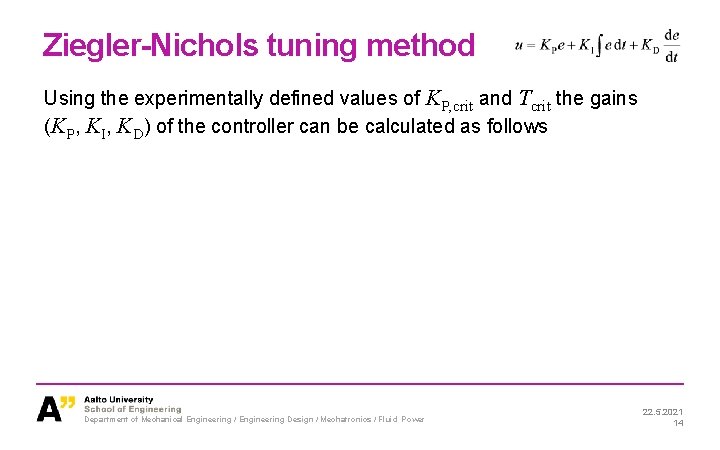
Ziegler-Nichols tuning method Using the experimentally defined values of KP, crit and Tcrit the gains (KP, KI, KD) of the controller can be calculated as follows Department of Mechanical Engineering / Engineering Design / Mechatronics / Fluid Power 22. 5. 2021 14
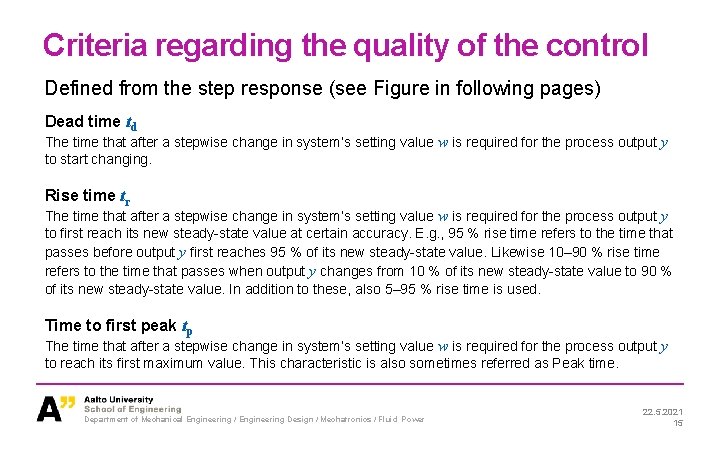
Criteria regarding the quality of the control Defined from the step response (see Figure in following pages) Dead time td The time that after a stepwise change in system’s setting value w is required for the process output y to start changing. Rise time tr The time that after a stepwise change in system’s setting value w is required for the process output y to first reach its new steady-state value at certain accuracy. E. g. , 95 % rise time refers to the time that passes before output y first reaches 95 % of its new steady-state value. Likewise 10– 90 % rise time refers to the time that passes when output y changes from 10 % of its new steady-state value to 90 % of its new steady-state value. In addition to these, also 5– 95 % rise time is used. Time to first peak tp The time that after a stepwise change in system’s setting value w is required for the process output y to reach its first maximum value. This characteristic is also sometimes referred as Peak time. Department of Mechanical Engineering / Engineering Design / Mechatronics / Fluid Power 22. 5. 2021 15
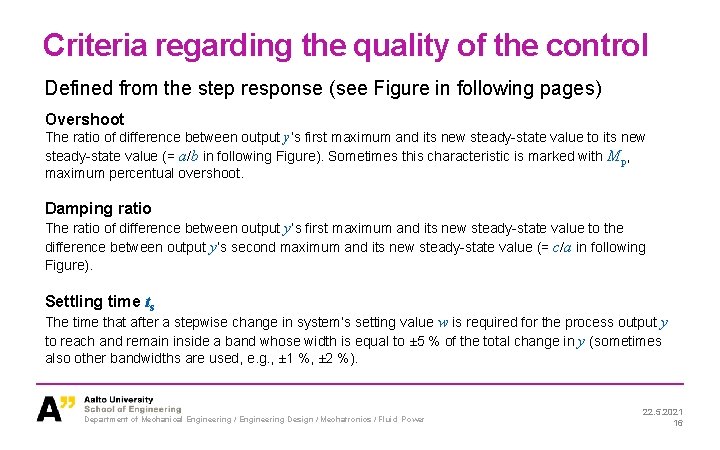
Criteria regarding the quality of the control Defined from the step response (see Figure in following pages) Overshoot The ratio of difference between output y’s first maximum and its new steady-state value to its new steady-state value (= a/b in following Figure). Sometimes this characteristic is marked with Mp, maximum percentual overshoot. Damping ratio The ratio of difference between output y’s first maximum and its new steady-state value to the difference between output y’s second maximum and its new steady-state value (= c/a in following Figure). Settling time ts The time that after a stepwise change in system’s setting value w is required for the process output y to reach and remain inside a band whose width is equal to ± 5 % of the total change in y (sometimes also other bandwidths are used, e. g. , ± 1 %, ± 2 %). Department of Mechanical Engineering / Engineering Design / Mechatronics / Fluid Power 22. 5. 2021 16
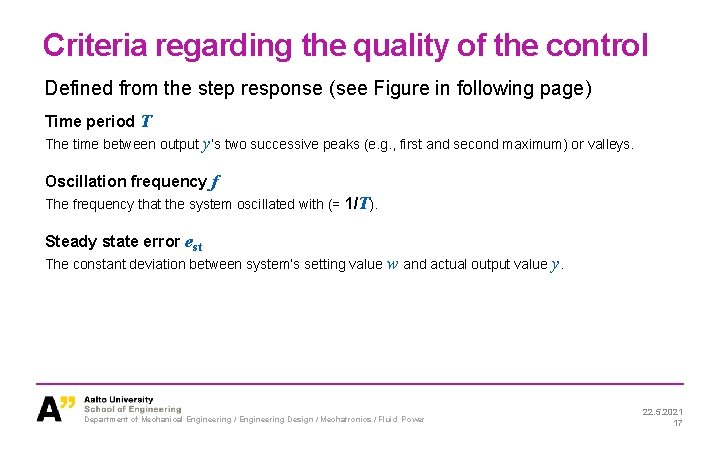
Criteria regarding the quality of the control Defined from the step response (see Figure in following page) Time period T The time between output y’s two successive peaks (e. g. , first and second maximum) or valleys. Oscillation frequency f The frequency that the system oscillated with (= 1/T). Steady state error est The constant deviation between system’s setting value w and actual output value y. Department of Mechanical Engineering / Engineering Design / Mechatronics / Fluid Power 22. 5. 2021 17
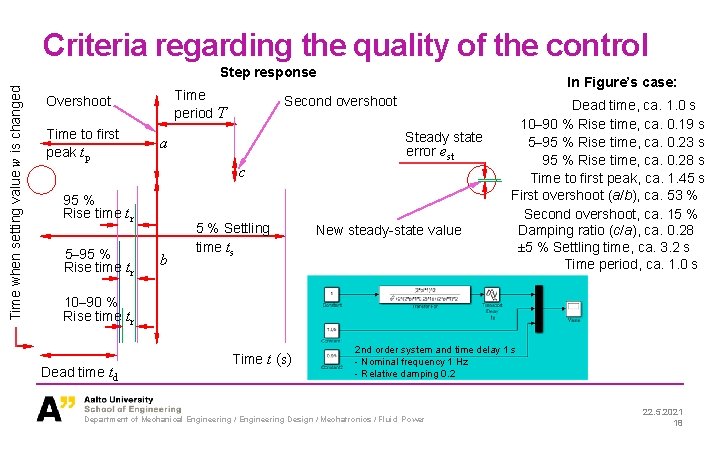
Criteria regarding the quality of the control Time when setting value w is changed Step response Time period T Overshoot Time to first peak tp Second overshoot Steady state error est a c 95 % Rise time tr 5– 95 % Rise time tr In Figure’s case: b 5 % Settling time ts New steady-state value Dead time, ca. 1. 0 s 10– 90 % Rise time, ca. 0. 19 s 5– 95 % Rise time, ca. 0. 23 s 95 % Rise time, ca. 0. 28 s Time to first peak, ca. 1. 45 s First overshoot (a/b), ca. 53 % Second overshoot, ca. 15 % Damping ratio (c/a), ca. 0. 28 ± 5 % Settling time, ca. 3. 2 s Time period, ca. 1. 0 s 10– 90 % Rise time tr Dead time td Time t (s) 2 nd order system and time delay 1 s - Nominal frequency 1 Hz - Relative damping 0. 2 Department of Mechanical Engineering / Engineering Design / Mechatronics / Fluid Power 22. 5. 2021 18
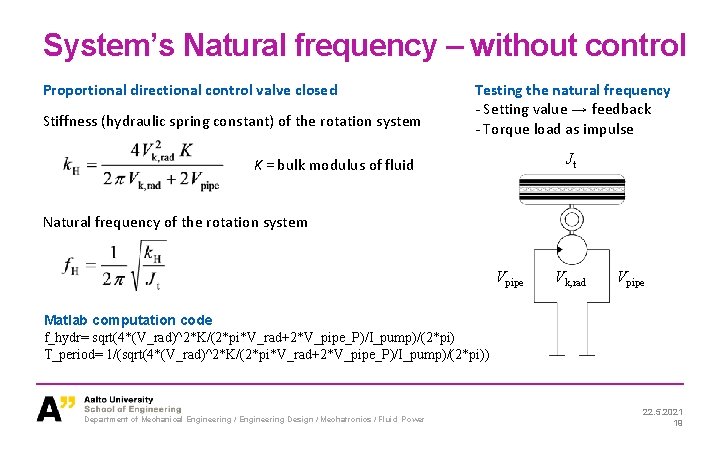
System’s Natural frequency – without control Proportional directional control valve closed Stiffness (hydraulic spring constant) of the rotation system Testing the natural frequency - Setting value → feedback - Torque load as impulse Jt K = bulk modulus of fluid Natural frequency of the rotation system Vpipe Vk, rad Vpipe Matlab computation code f_hydr= sqrt(4*(V_rad)^2*K/(2*pi*V_rad+2*V_pipe_P)/I_pump)/(2*pi) T_period= 1/(sqrt(4*(V_rad)^2*K/(2*pi*V_rad+2*V_pipe_P)/I_pump)/(2*pi)) Department of Mechanical Engineering / Engineering Design / Mechatronics / Fluid Power 22. 5. 2021 19
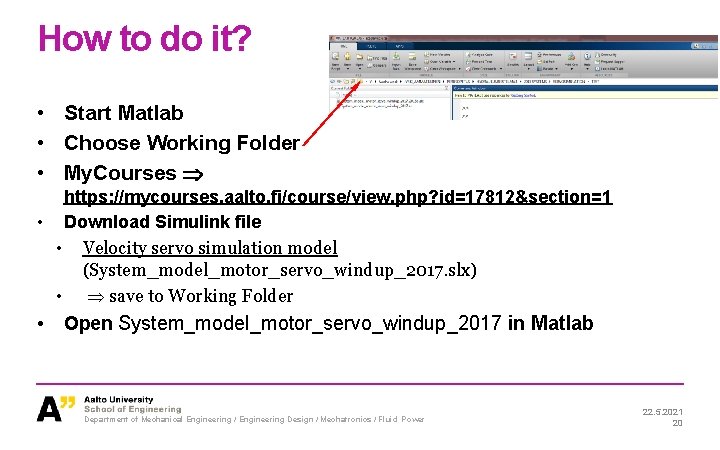
How to do it? • Start Matlab • Choose Working Folder • My. Courses https: //mycourses. aalto. fi/course/view. php? id=17812§ion=1 • Download Simulink file • Velocity servo simulation model (System_model_motor_servo_windup_2017. slx) • save to Working Folder • Open System_model_motor_servo_windup_2017 in Matlab Department of Mechanical Engineering / Engineering Design / Mechatronics / Fluid Power 22. 5. 2021 20
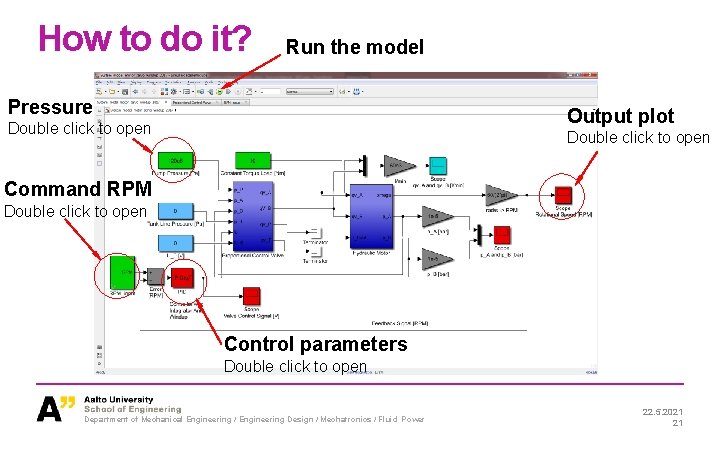
How to do it? Run the model Pressure Output plot Double click to open Command RPM Double click to open Control parameters Double click to open Department of Mechanical Engineering / Engineering Design / Mechatronics / Fluid Power 22. 5. 2021 21
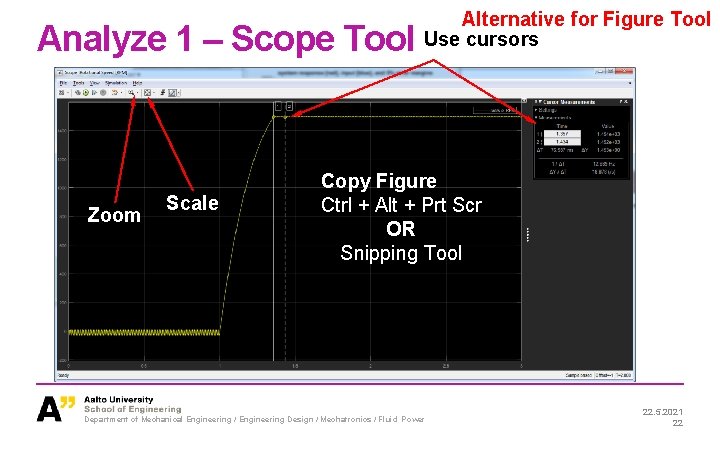
Analyze 1 – Scope Tool Zoom Scale Alternative for Figure Tool Use cursors Copy Figure Ctrl + Alt + Prt Scr OR Snipping Tool Department of Mechanical Engineering / Engineering Design / Mechatronics / Fluid Power 22. 5. 2021 22
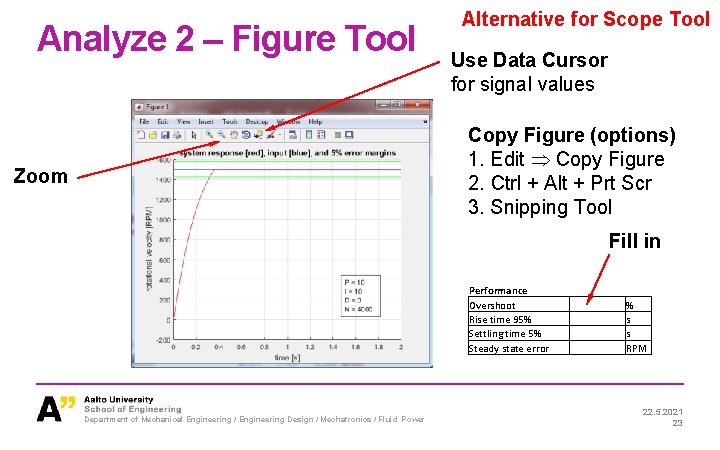
Analyze 2 – Figure Tool Alternative for Scope Tool Use Data Cursor for signal values Copy Figure (options) 1. Edit Copy Figure 2. Ctrl + Alt + Prt Scr 3. Snipping Tool Zoom Fill in Performance Overshoot Rise time 95% Settling time 5% Steady state error Department of Mechanical Engineering / Engineering Design / Mechatronics / Fluid Power % s s RPM 22. 5. 2021 23
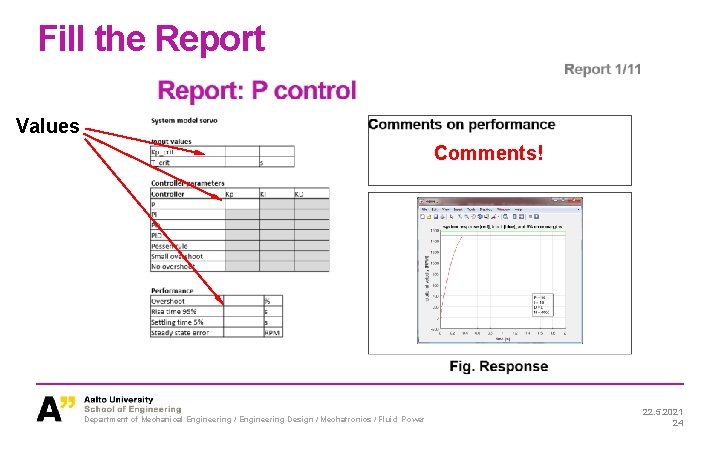
Fill the Report Values Comments! Department of Mechanical Engineering / Engineering Design / Mechatronics / Fluid Power 22. 5. 2021 24
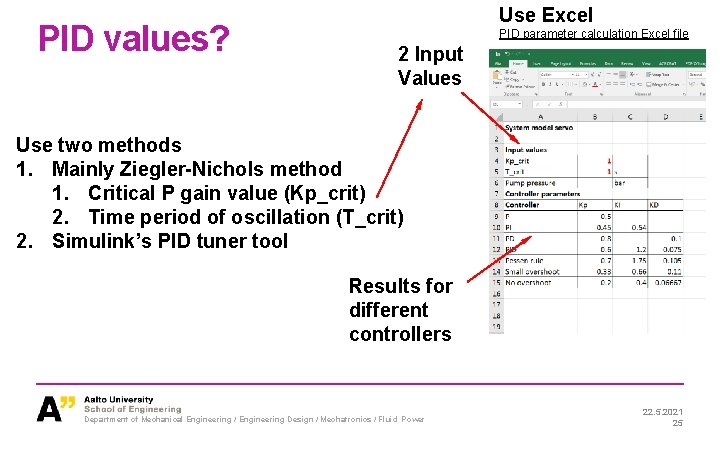
PID values? Use Excel PID parameter calculation Excel file 2 Input Values Use two methods 1. Mainly Ziegler-Nichols method 1. Critical P gain value (Kp_crit) 2. Time period of oscillation (T_crit) 2. Simulink’s PID tuner tool Results for different controllers Department of Mechanical Engineering / Engineering Design / Mechatronics / Fluid Power 22. 5. 2021 25
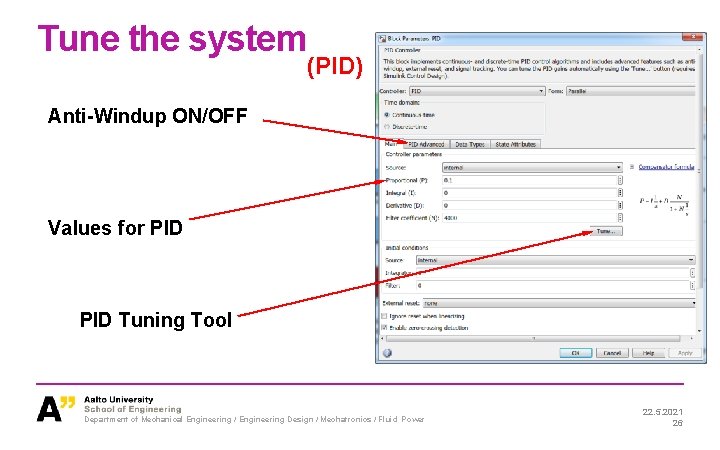
Tune the system (PID) Anti-Windup ON/OFF Values for PID Tuning Tool Department of Mechanical Engineering / Engineering Design / Mechatronics / Fluid Power 22. 5. 2021 26
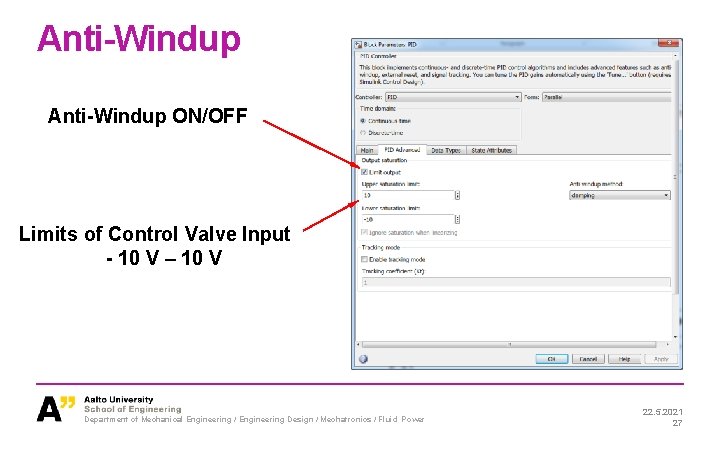
Anti-Windup ON/OFF Limits of Control Valve Input - 10 V – 10 V Department of Mechanical Engineering / Engineering Design / Mechatronics / Fluid Power 22. 5. 2021 27
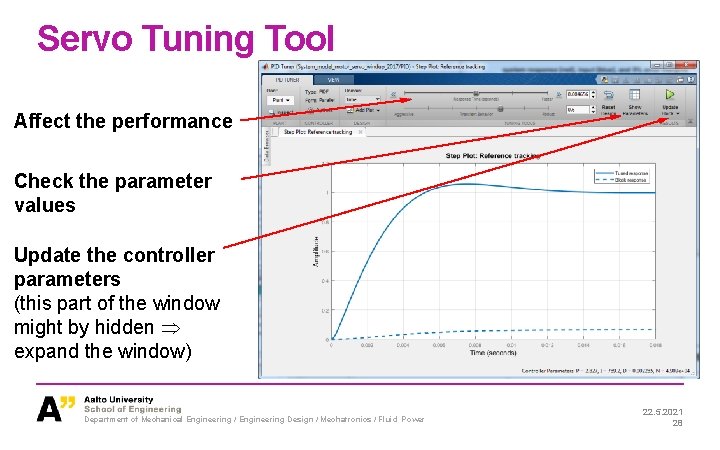
Servo Tuning Tool Affect the performance Check the parameter values Update the controller parameters (this part of the window might by hidden expand the window) Department of Mechanical Engineering / Engineering Design / Mechatronics / Fluid Power 22. 5. 2021 28
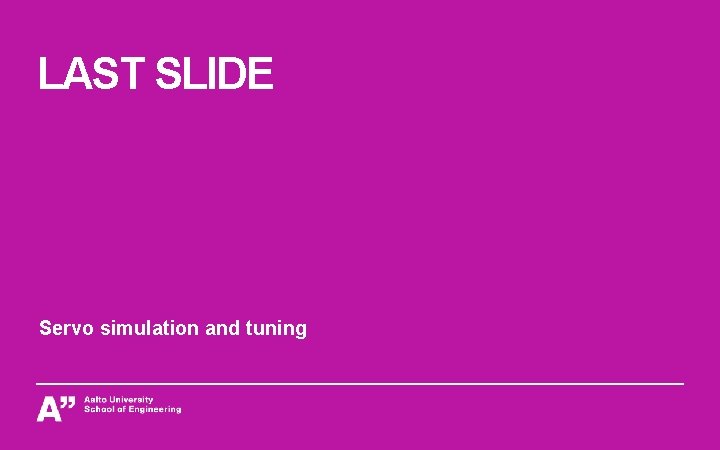
LAST SLIDE Servo simulation and tuning
Mckinsey approach to problem solving
Diffusion mechanism
Mece
Dimensionless groups in fluid mechanics
Total body water
Movement of body fluids
Matthias müller-fischer
Is synovial fluid extracellular fluid
P1-p2
Fluid statics deals with
Interstitial fluid vs extracellular fluid
Hypoosmotic
Fluid mechanics chapter 4
Shifting dullness positive
Power trianlge
Parallel and distributed simulation systems
Aerospace systems design and simulation
Fluid power hydraulics and pneumatics
Difference between proportional valve and servo valve
Arduino ultrasonic sensor
Advantages of servo motor
Natural fluid systems
Advanced fluid systems
Powerflow fluid systems
Berendsen fluid power brisbane
Symbol
Fluid power system ppt
Fluid power system ppt
Fluid power training institute
Fluid power system