5 credits MECE 5004 Fluid Power Systems 8
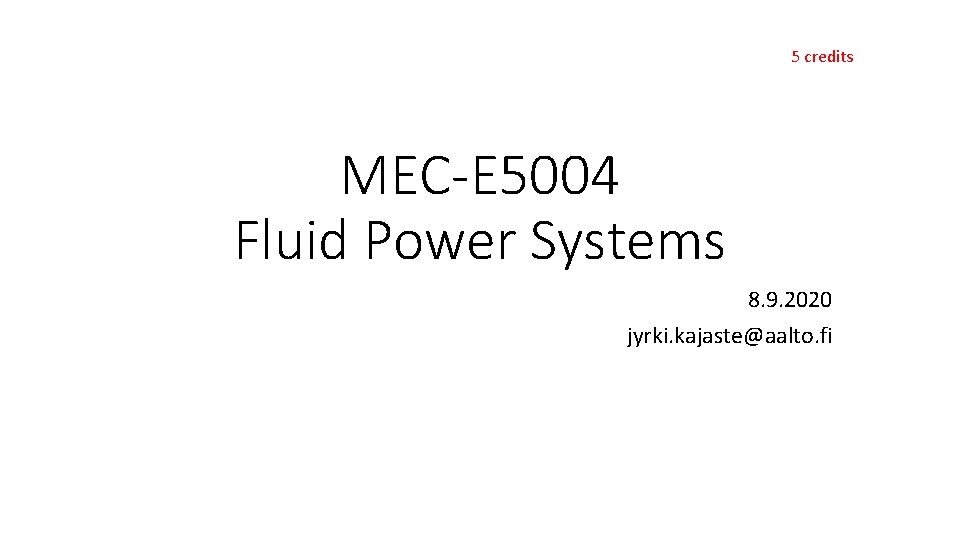

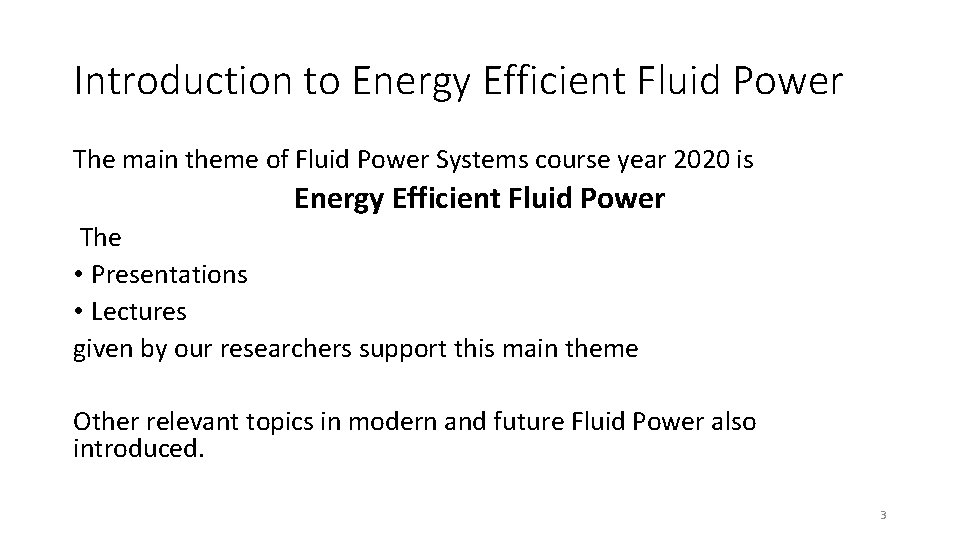
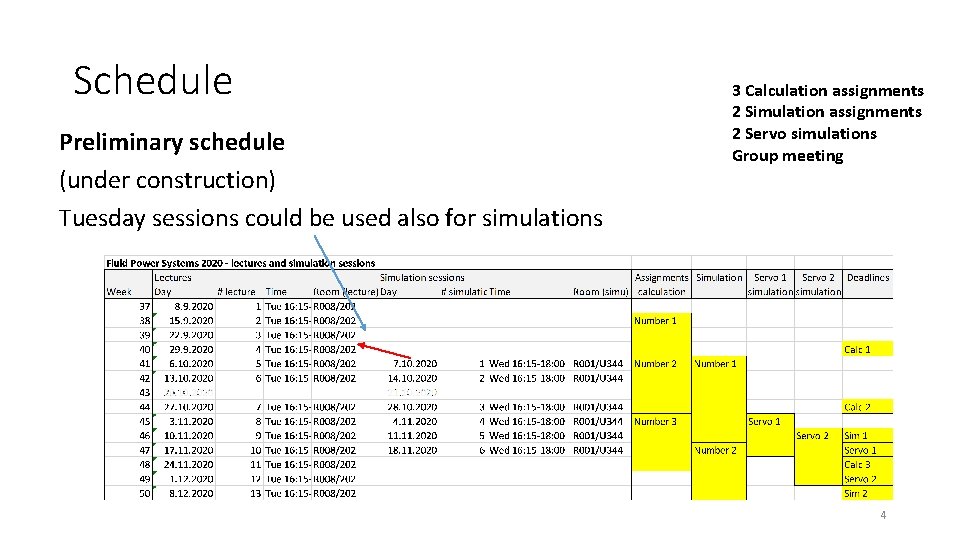
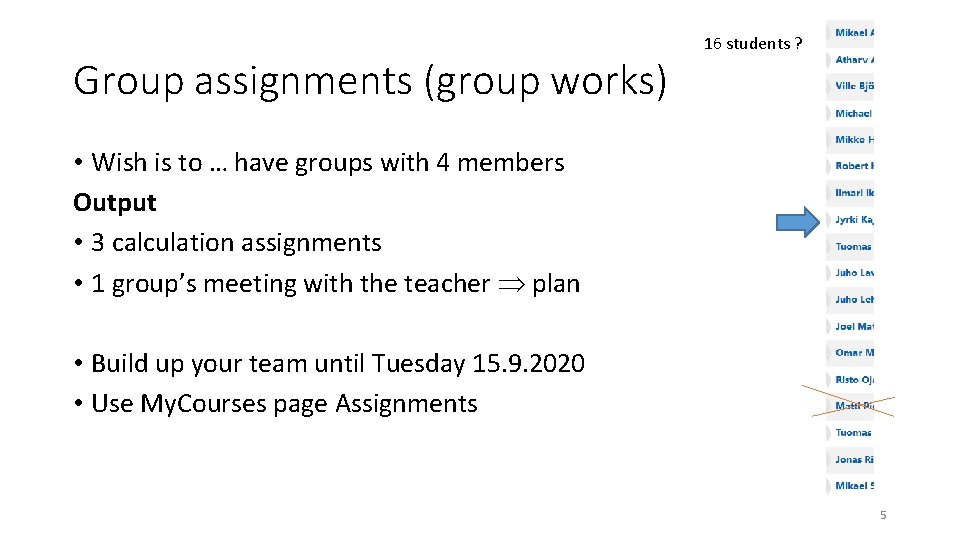
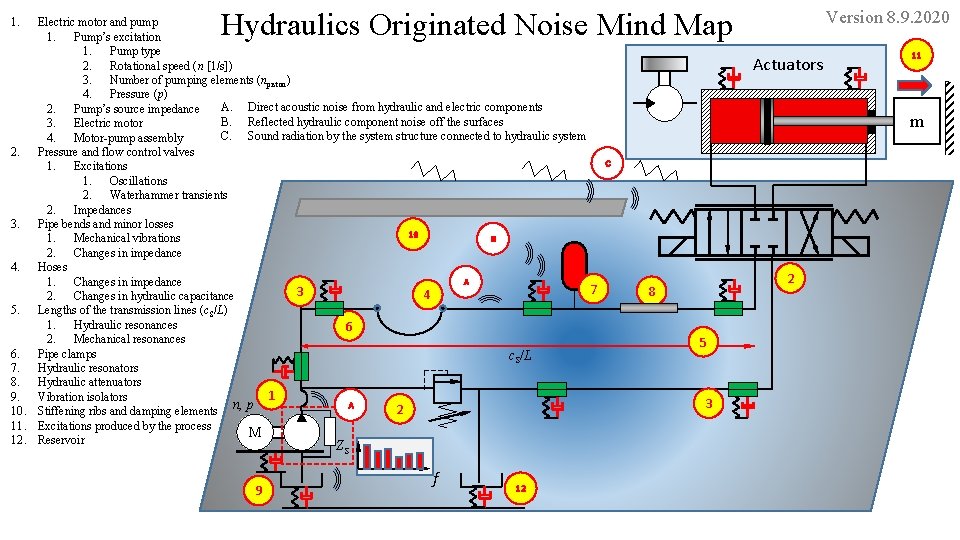
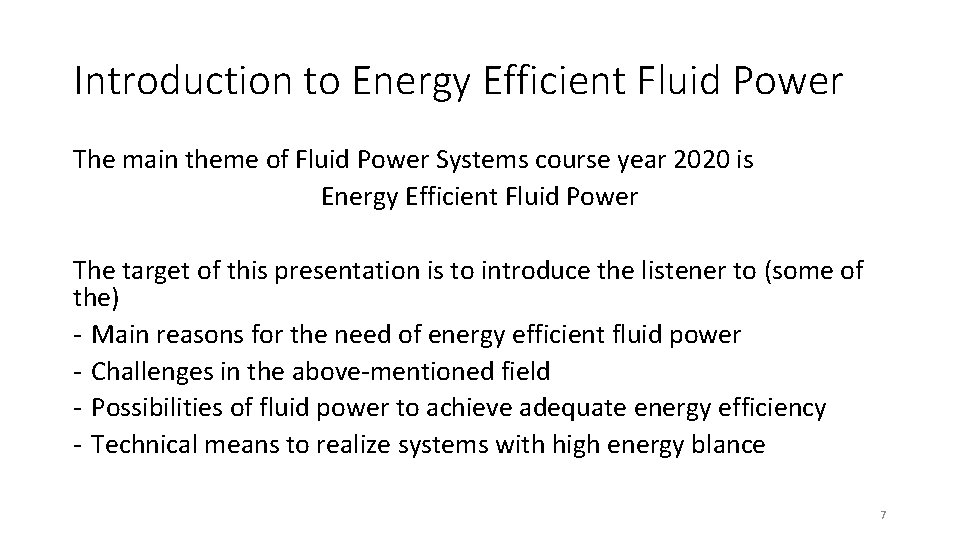
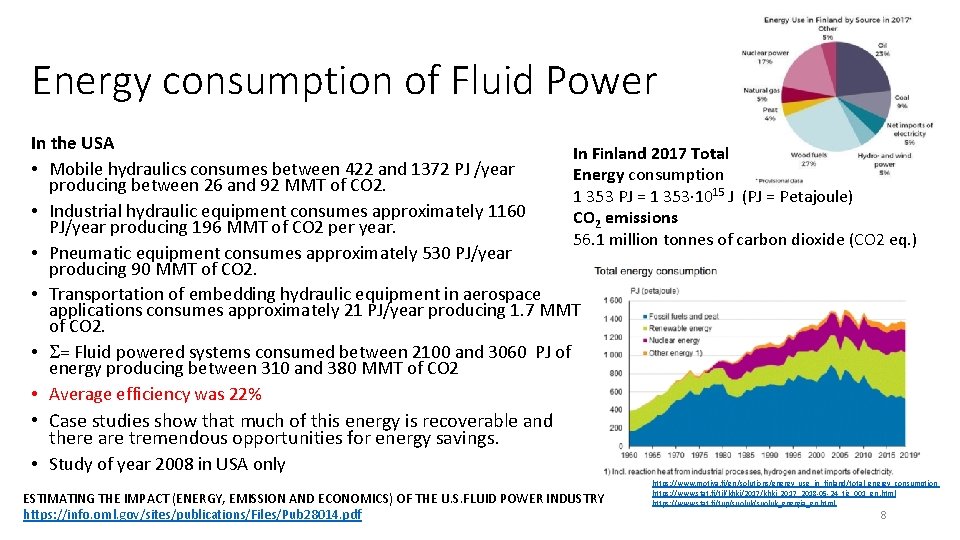
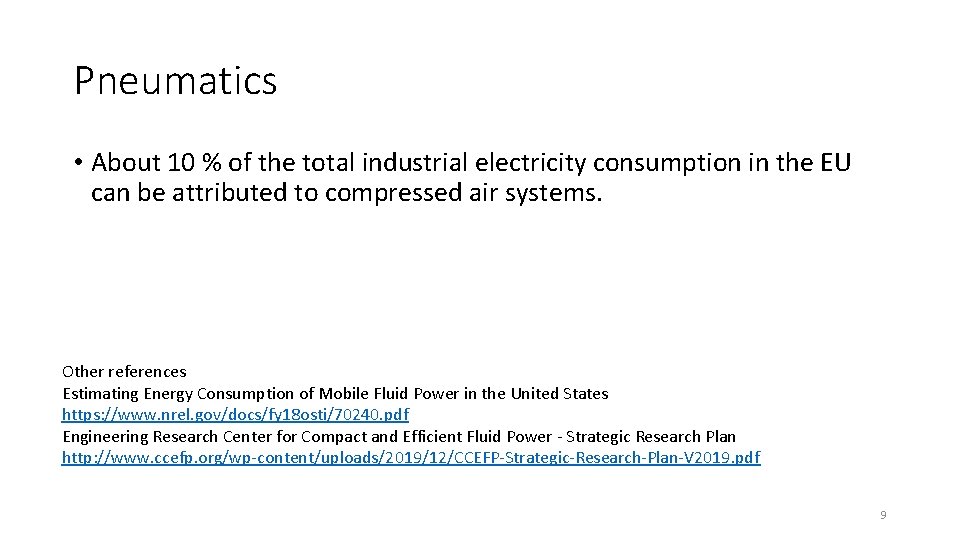
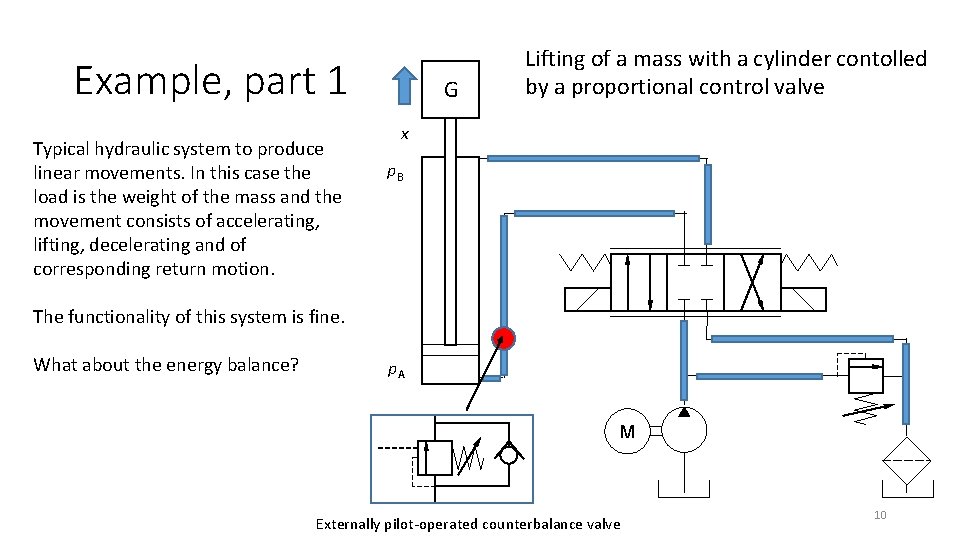
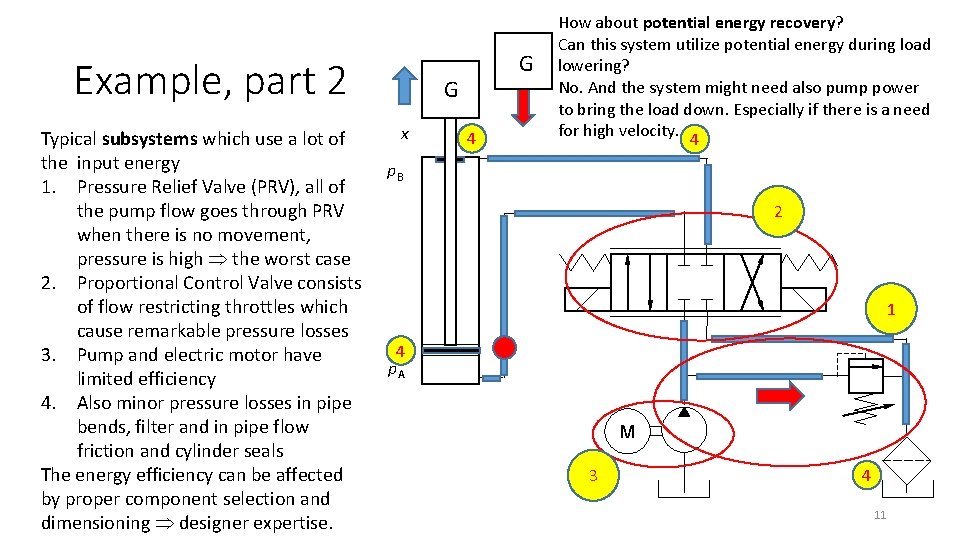
![Hydraulic power (loss) Control by throttling Flow rate qv [m 3/s] Turbulent case V Hydraulic power (loss) Control by throttling Flow rate qv [m 3/s] Turbulent case V](https://slidetodoc.com/presentation_image_h2/79bf63020bb087f7b909d6ffa7cb2d82/image-12.jpg)
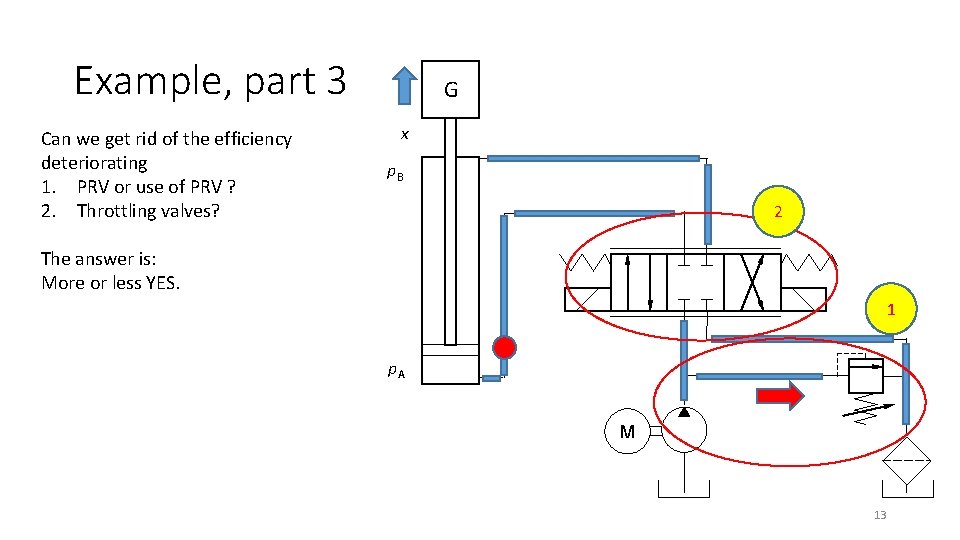
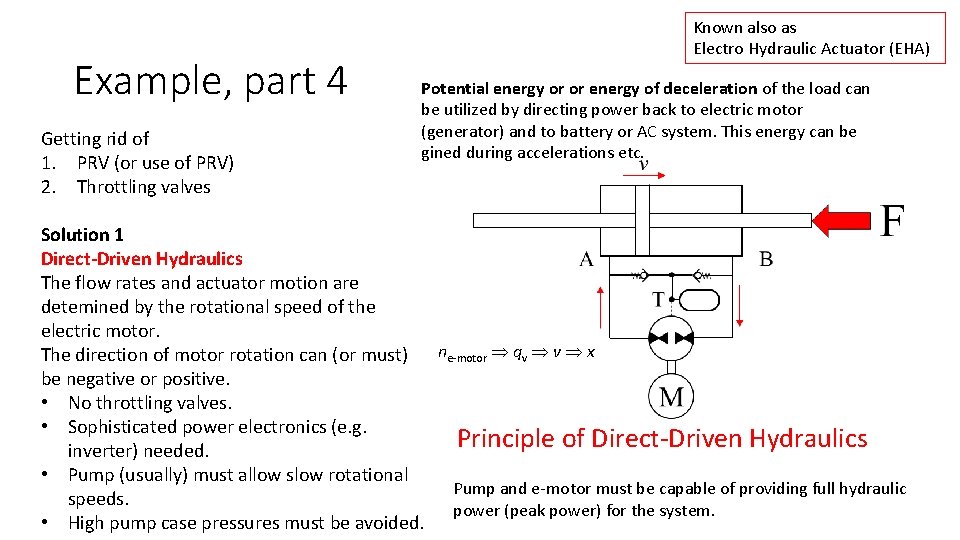
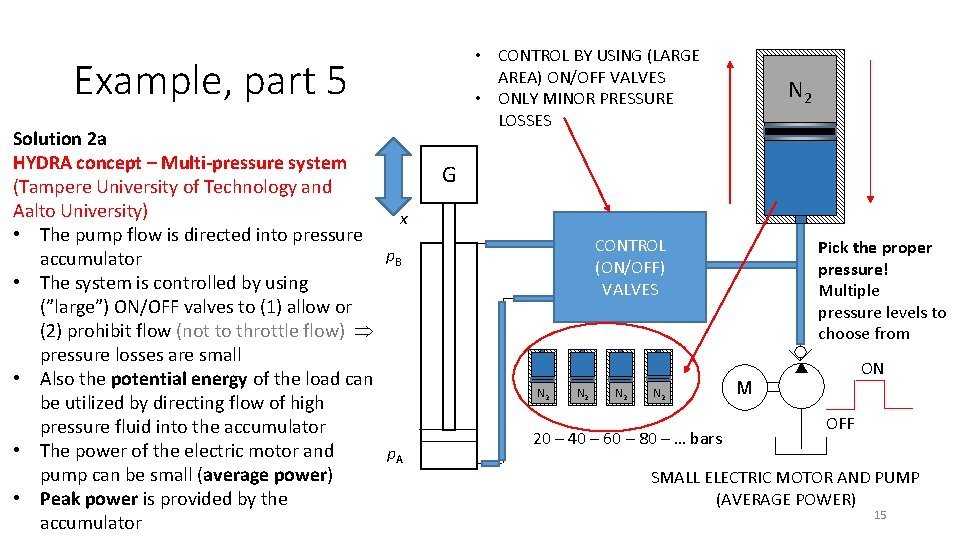
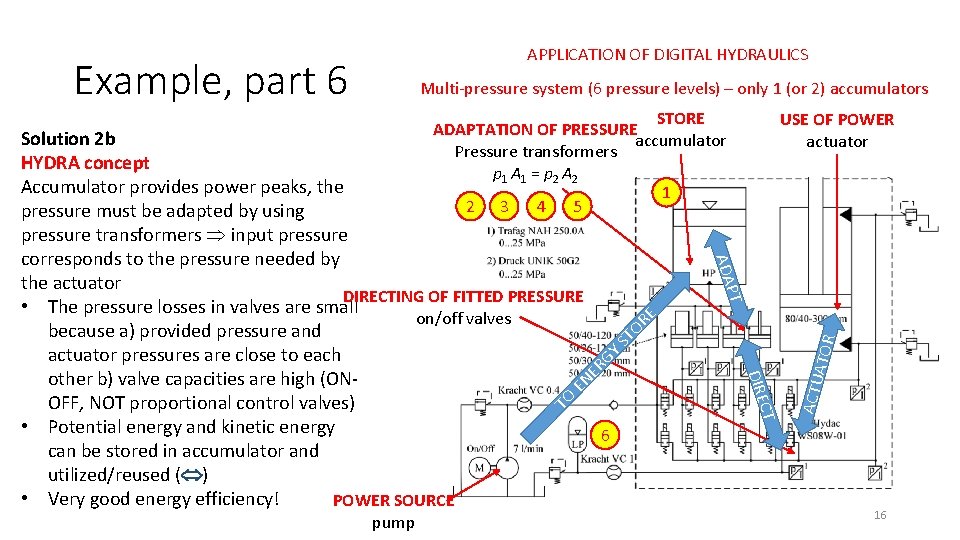
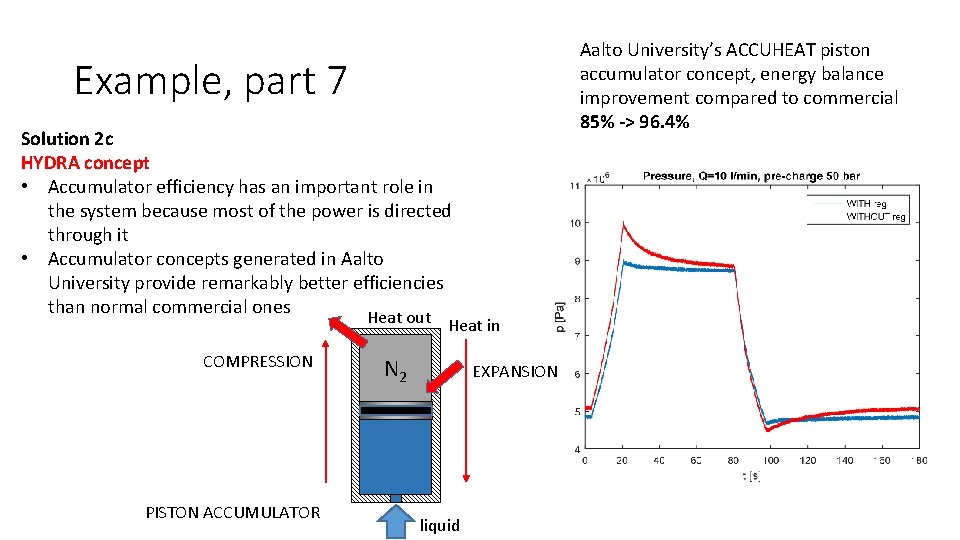
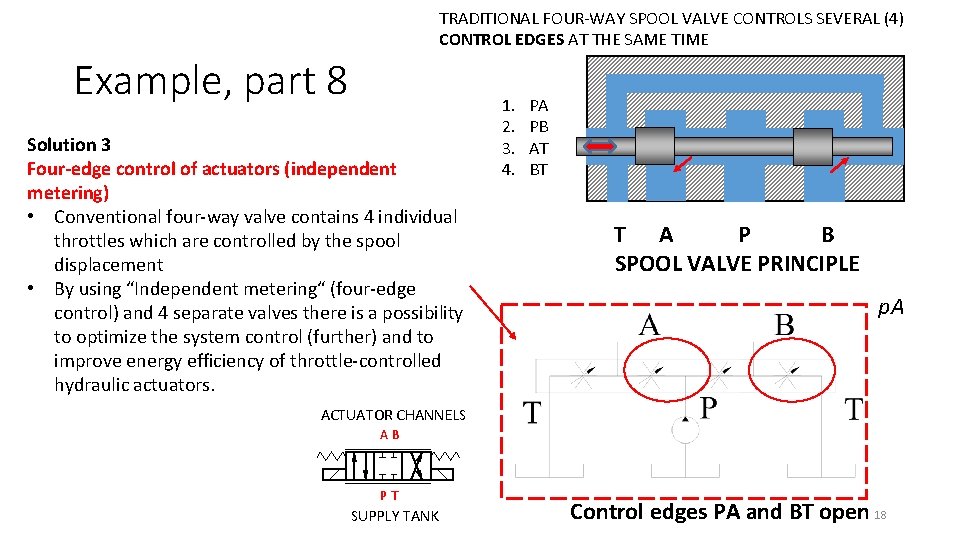
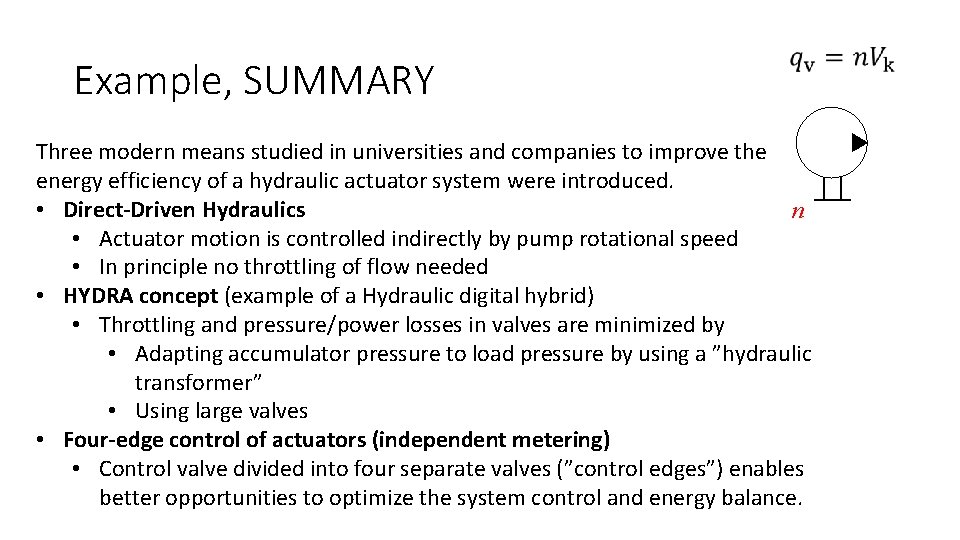
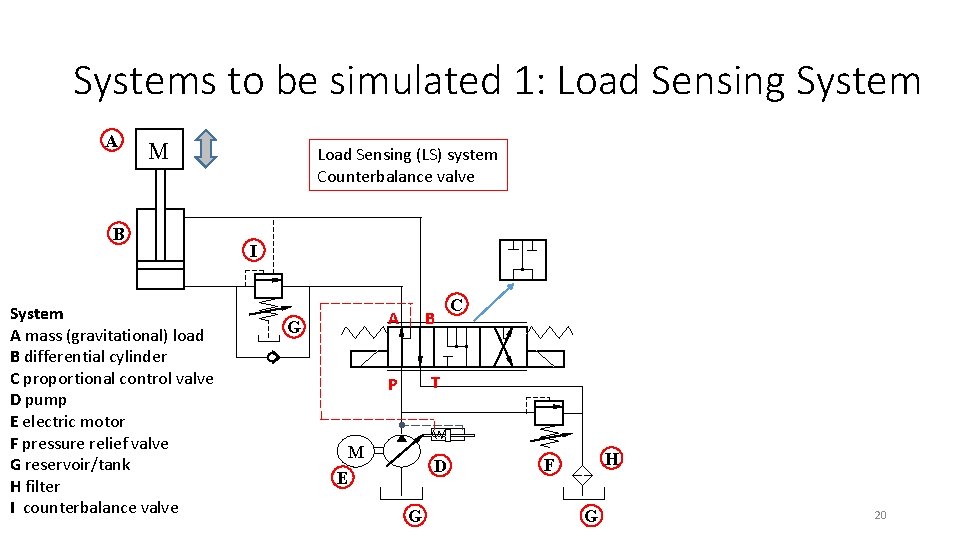
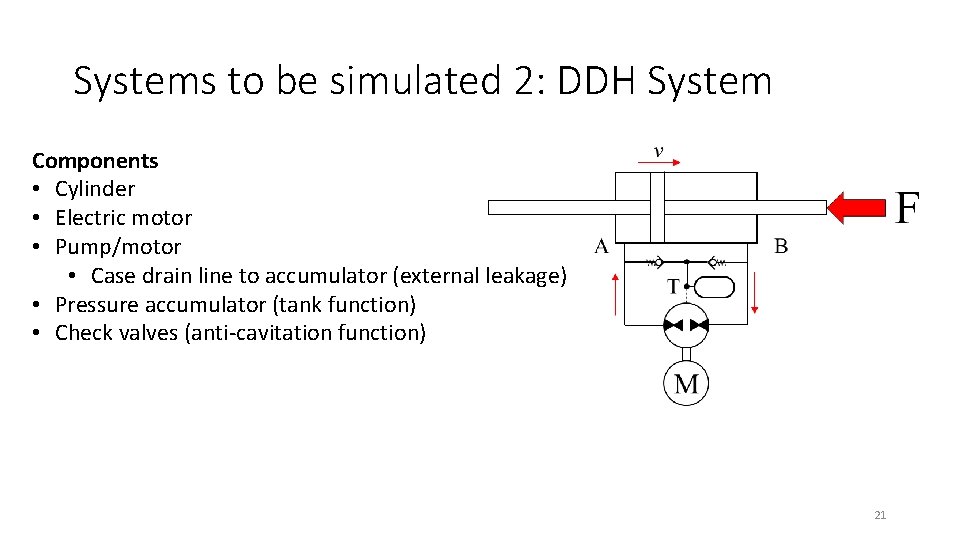
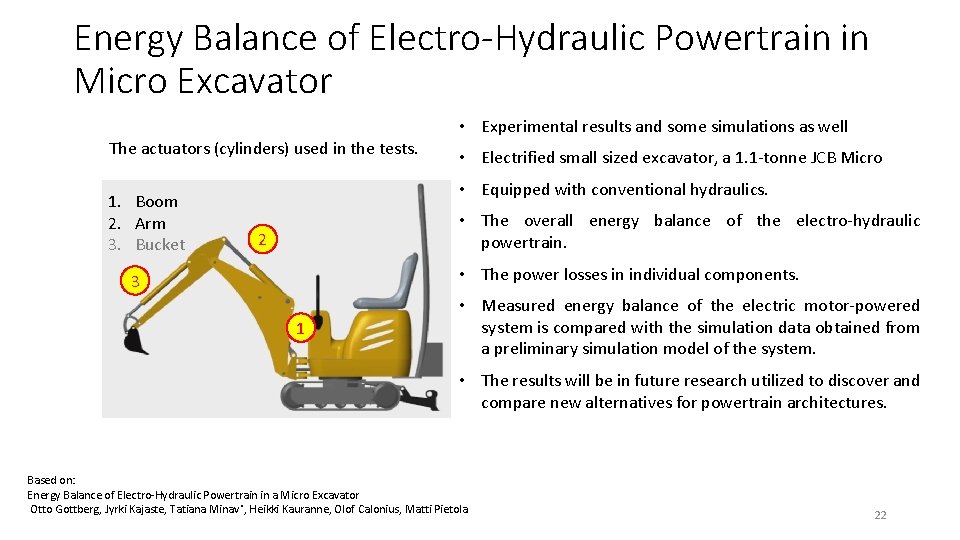
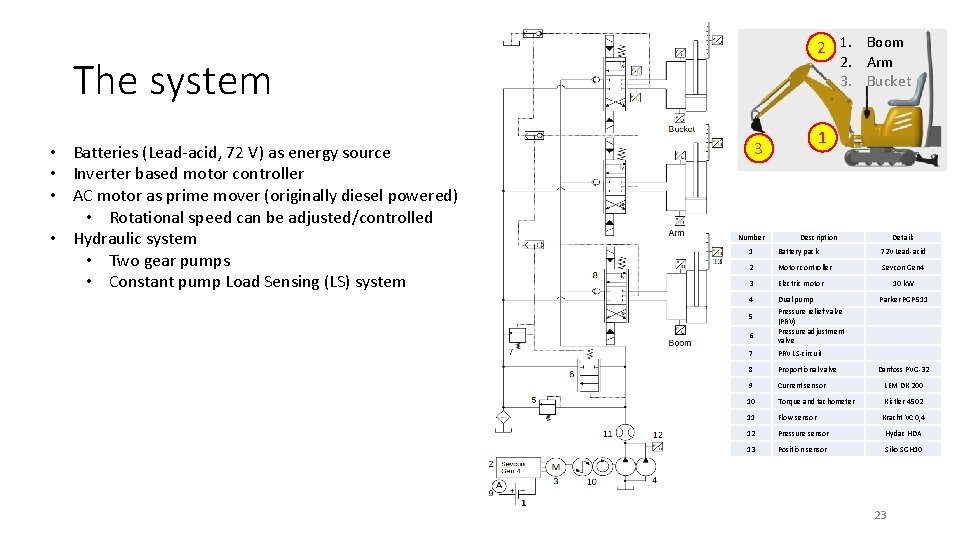
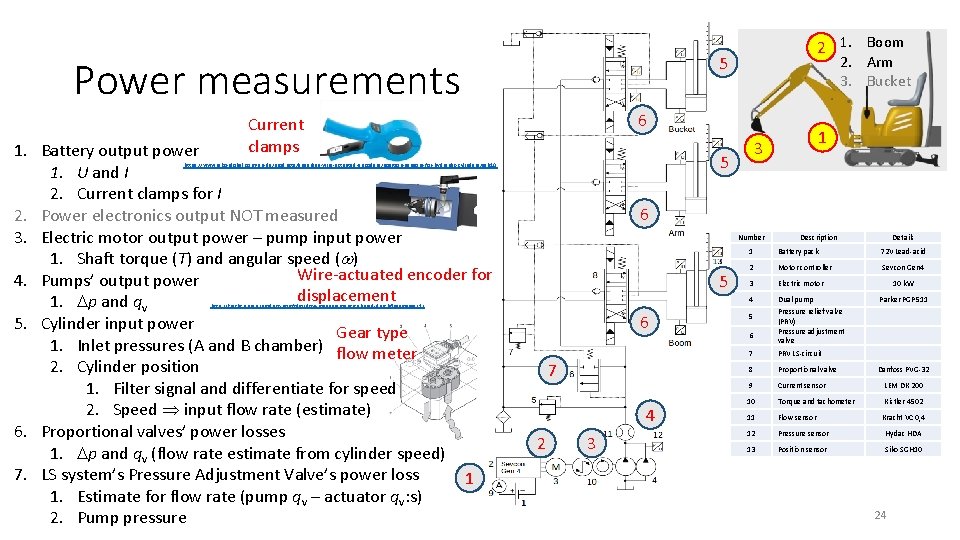
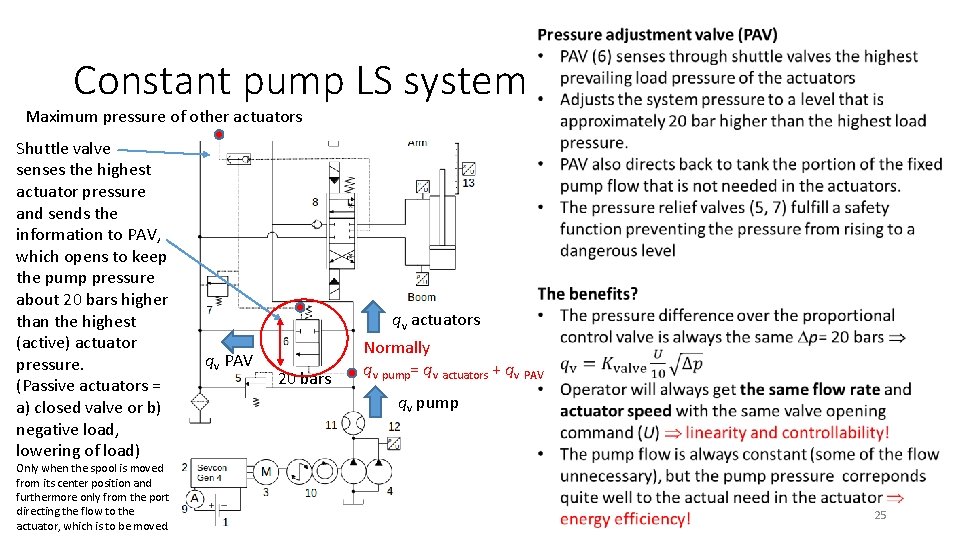
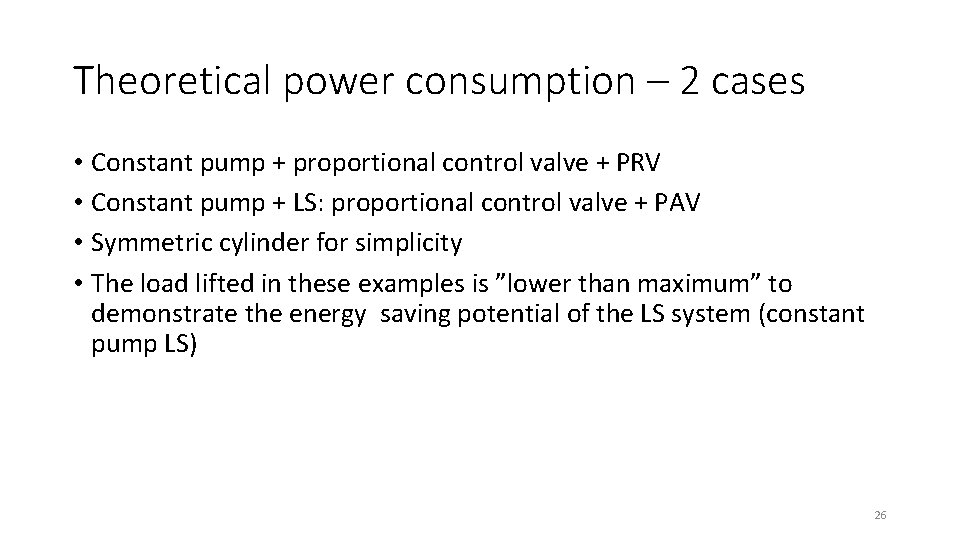
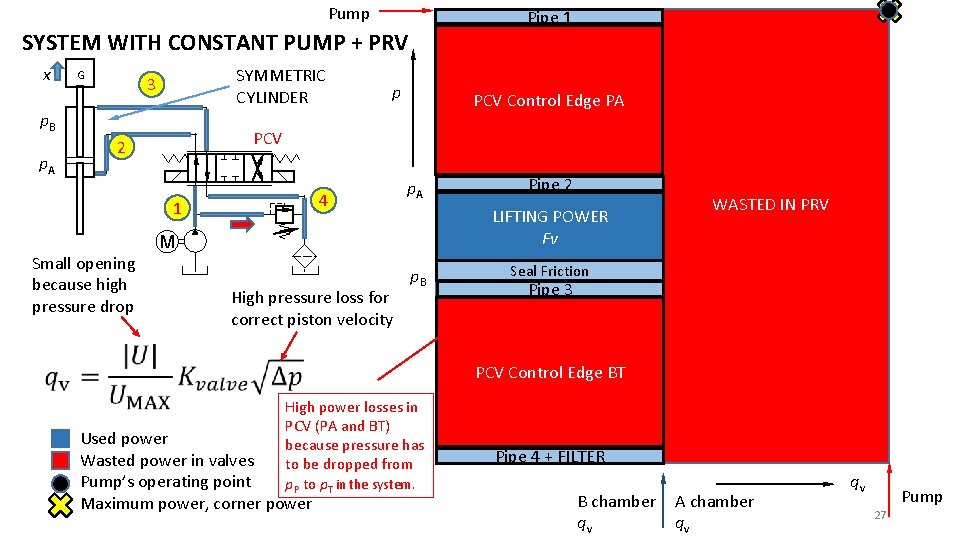
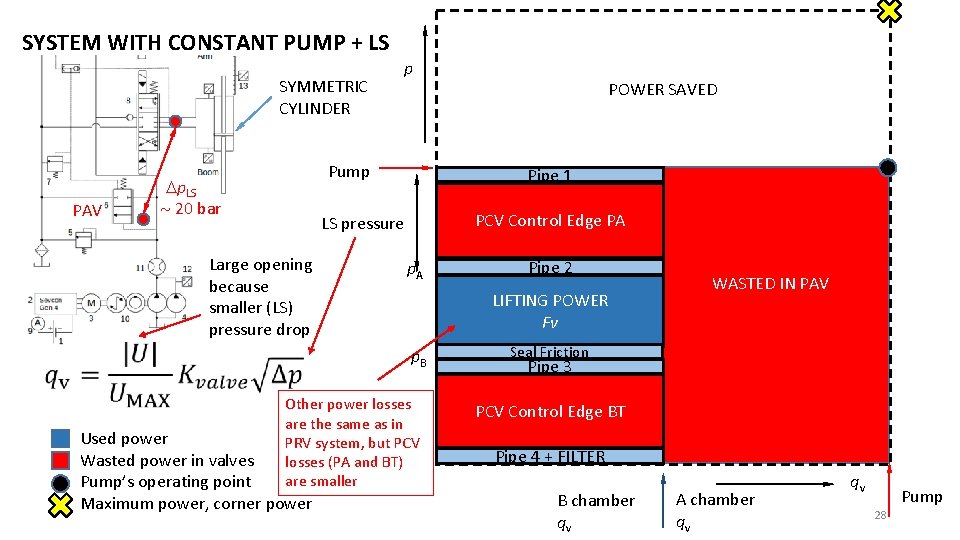
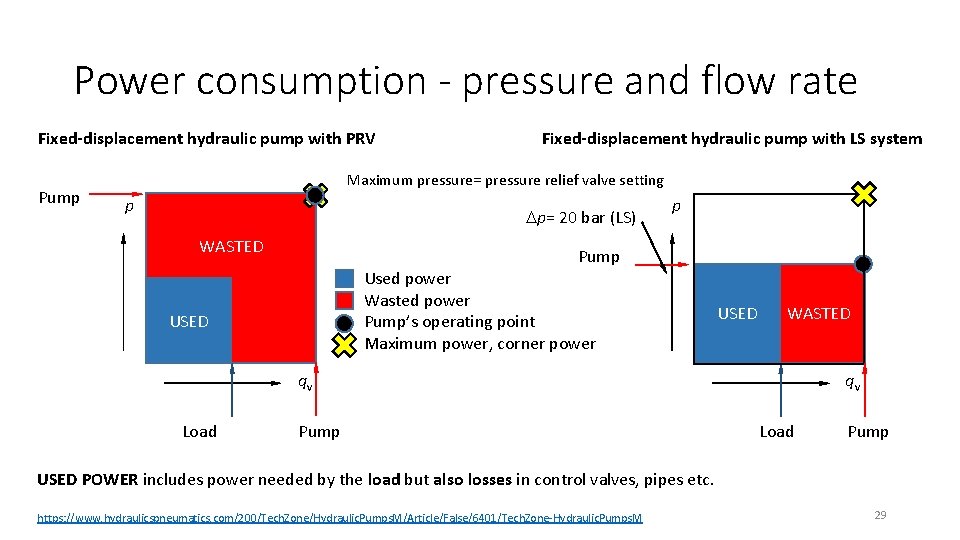
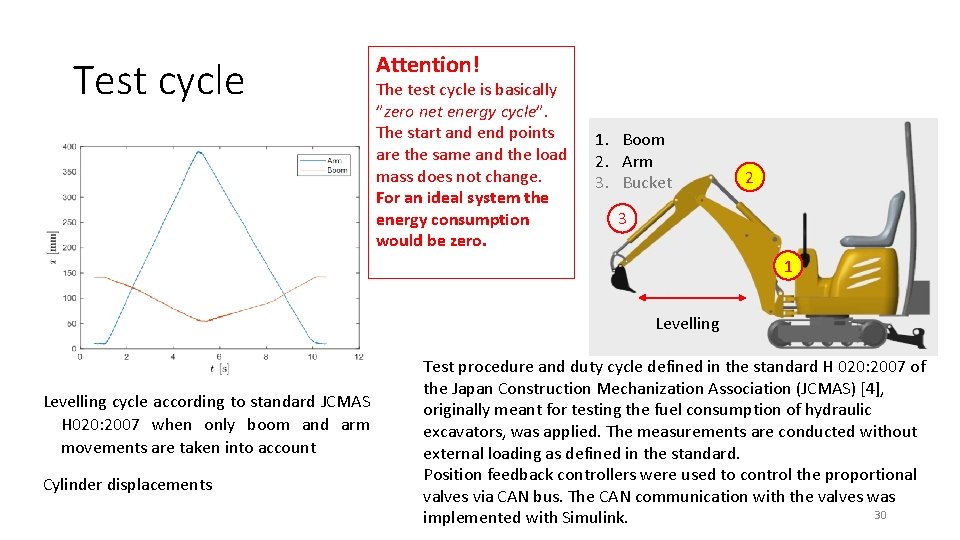
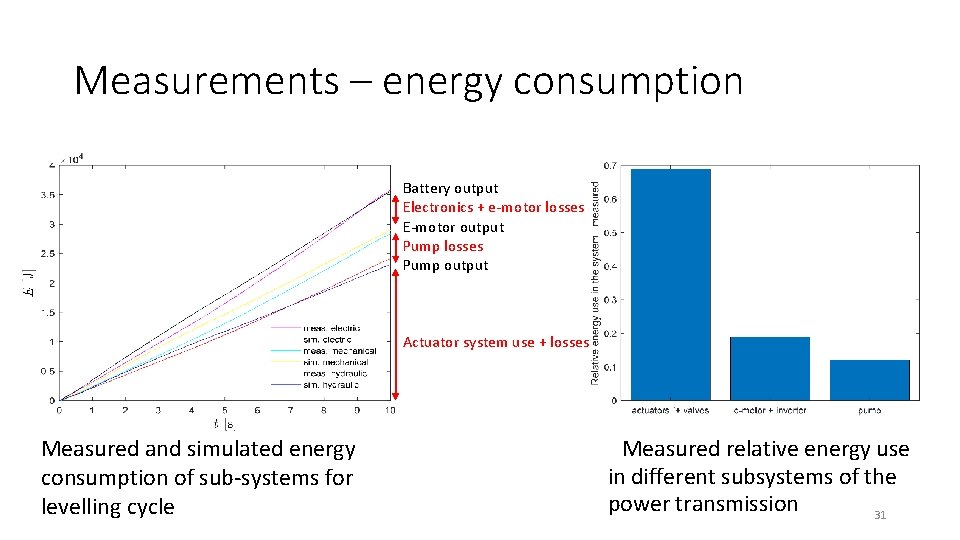
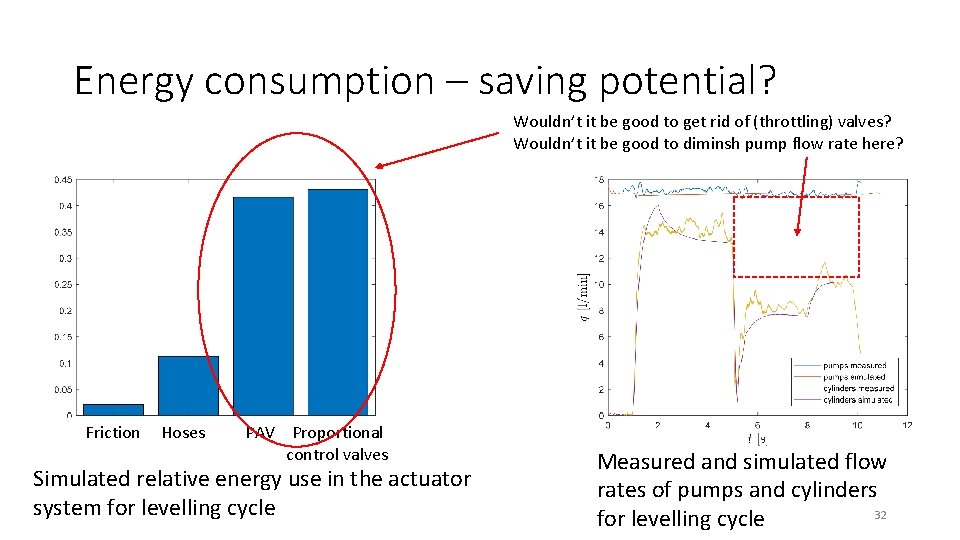
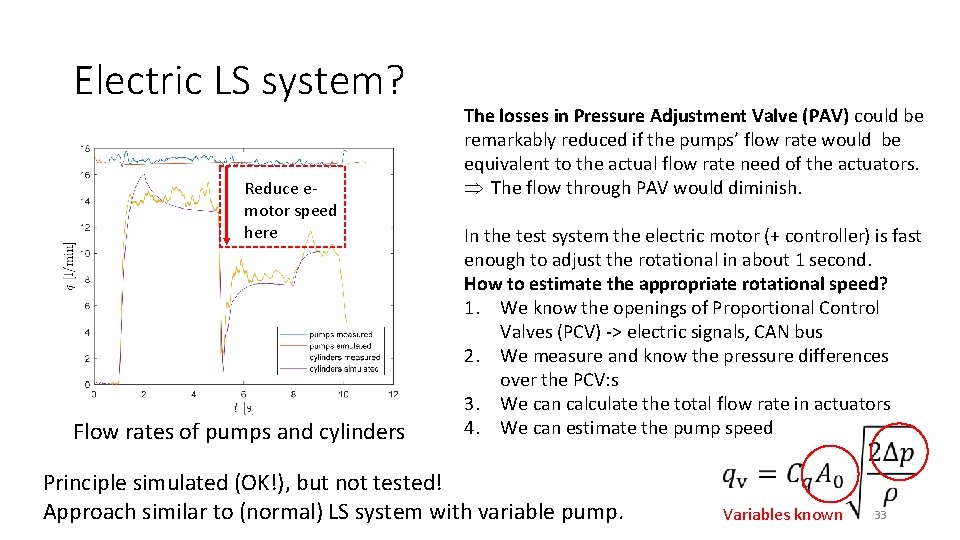
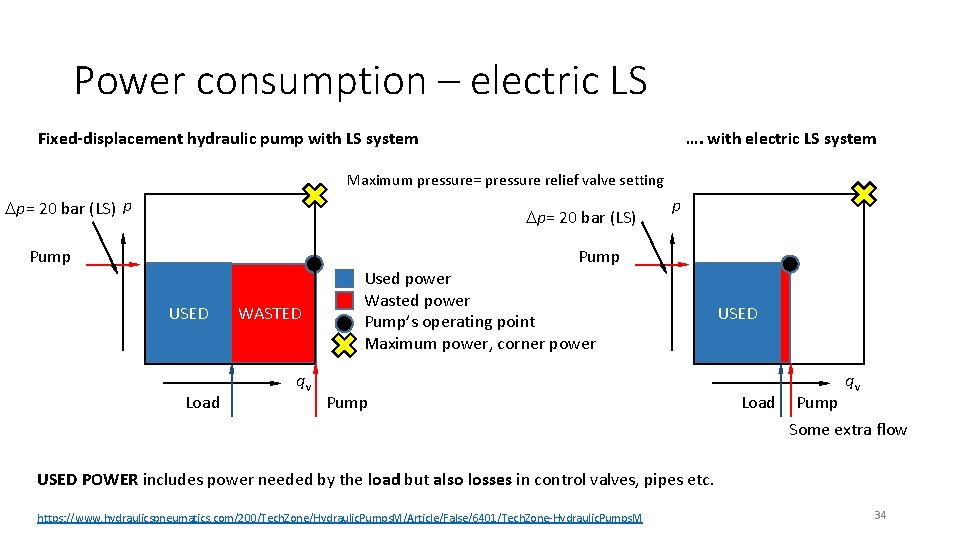
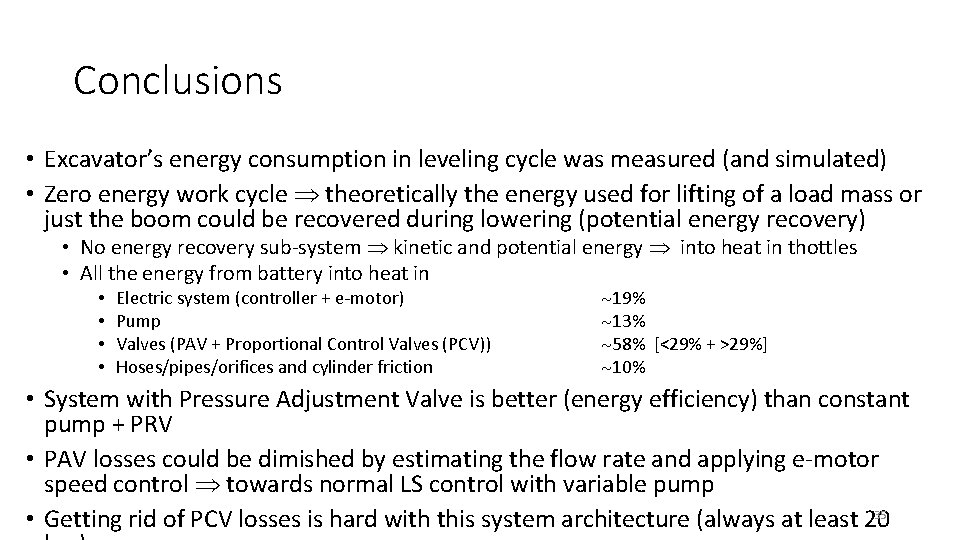
- Slides: 35
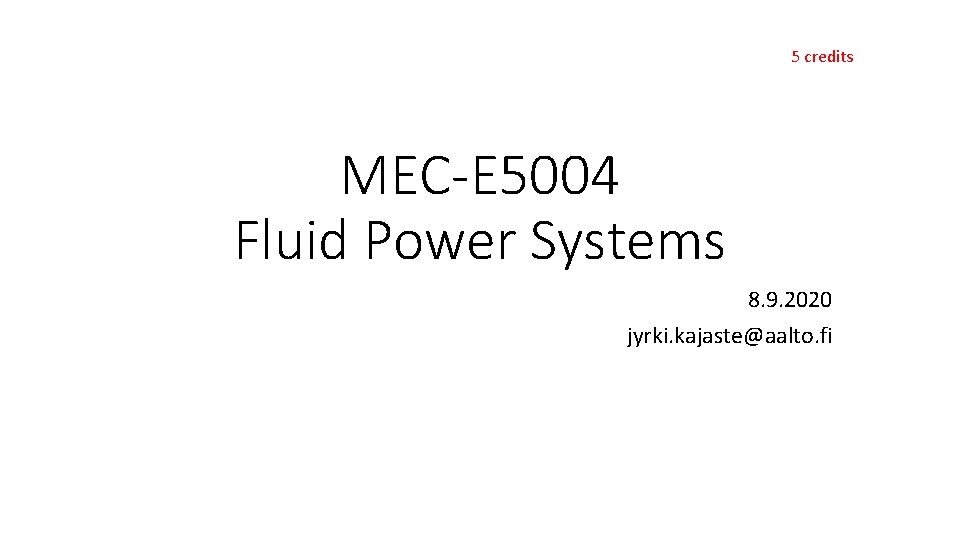
5 credits MEC-E 5004 Fluid Power Systems 8. 9. 2020 jyrki. kajaste@aalto. fi

Structure of studies and Grade components IN BRIEF • Presentations and lectures • Simulation assignments 1. Tuning a hydraulic servo 2. Building hydraulic simulation models 1. 2. Load Sensing (LS) system Direct Drive Hydraulic (DDH) system • Each student: Individual Reports • Group assignment • 3 calculation assignments • group’s discussions with the teacher Common and organized Studies (almost) every Tuesday 16. 15 -18. 00 Simulation (4) and servo simulation (2) exercises on 4 Wednesdays 16. 00 -18. 00 (see detailed schedule) Student groups arrange their own meetings and teamwork conventions 2
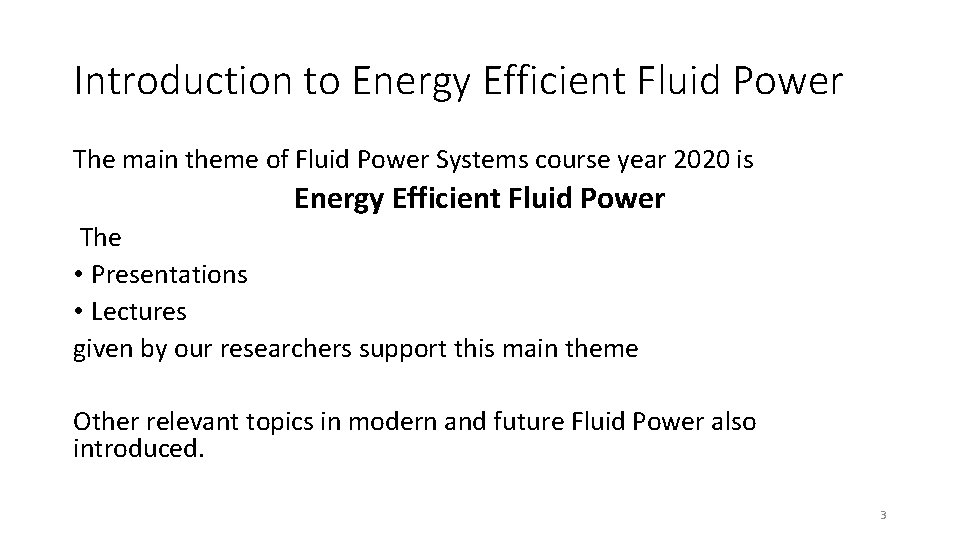
Introduction to Energy Efficient Fluid Power The main theme of Fluid Power Systems course year 2020 is Energy Efficient Fluid Power The • Presentations • Lectures given by our researchers support this main theme Other relevant topics in modern and future Fluid Power also introduced. 3
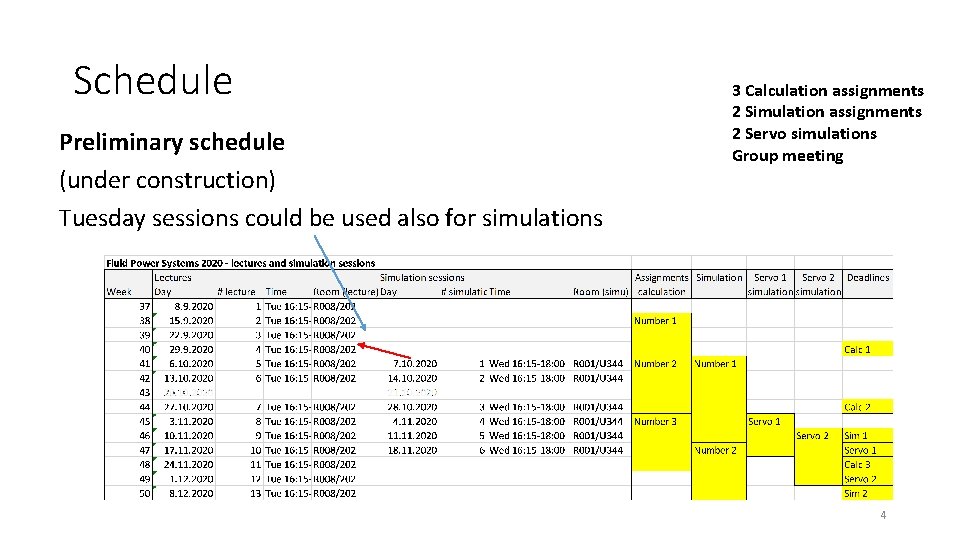
Schedule Preliminary schedule (under construction) Tuesday sessions could be used also for simulations 3 Calculation assignments 2 Simulation assignments 2 Servo simulations Group meeting 4
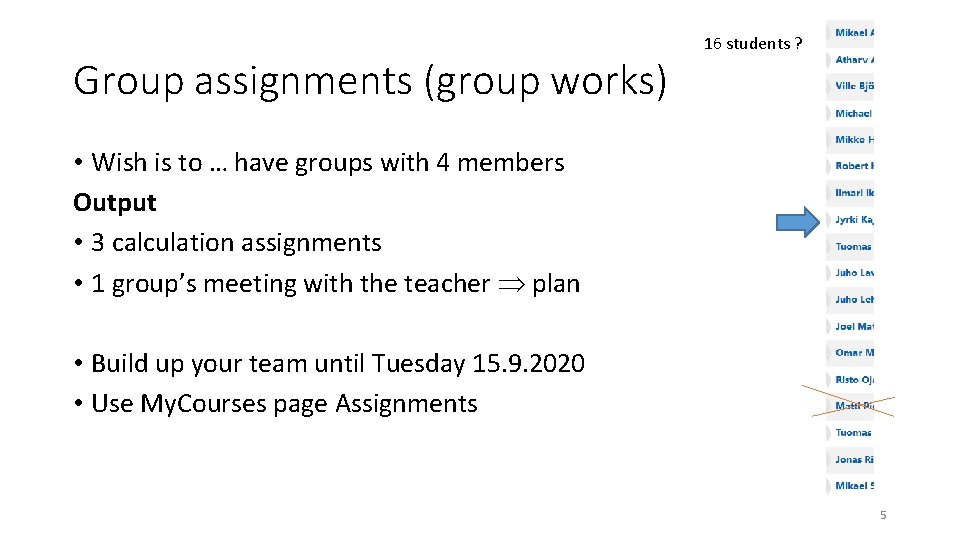
Group assignments (group works) 16 students ? • Wish is to … have groups with 4 members Output • 3 calculation assignments • 1 group’s meeting with the teacher plan • Build up your team until Tuesday 15. 9. 2020 • Use My. Courses page Assignments 5
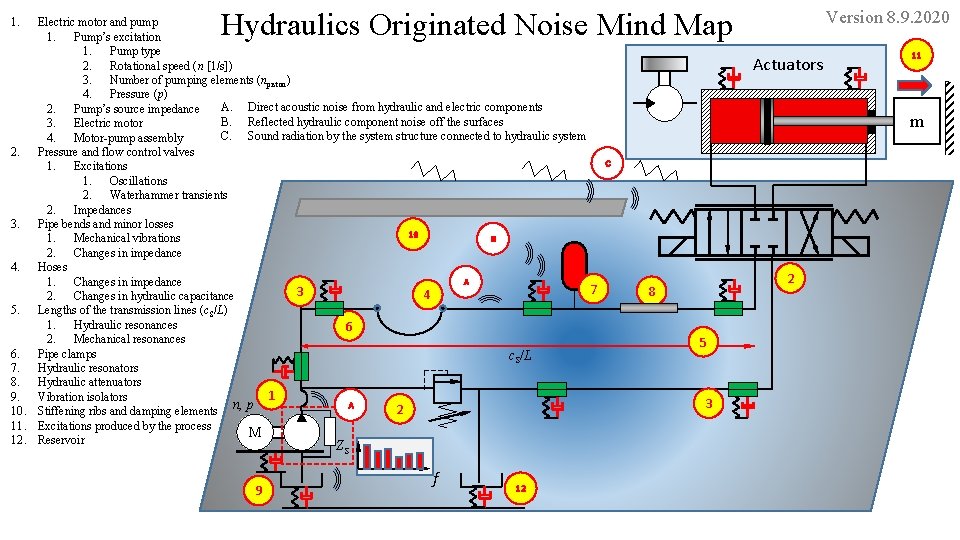
1. Hydraulics Originated Noise Mind Map Electric motor and pump 1. Pump’s excitation 1. Pump type 2. Rotational speed (n [1/s]) 3. Number of pumping elements (npiston) 4. Pressure (p) A. Direct acoustic noise from hydraulic and electric components 2. Pump’s source impedance B. Reflected hydraulic component noise off the surfaces 3. Electric motor C. Sound radiation by the system structure connected to hydraulic system 4. Motor-pump assembly 2. Pressure and flow control valves C 1. Excitations 1. Oscillations 2. Waterhammer transients 2. Impedances 3. Pipe bends and minor losses 10 B 1. Mechanical vibrations 2. Changes in impedance 4. Hoses A 1. Changes in impedance 7 3 4 2. Changes in hydraulic capacitance 5. Lengths of the transmission lines (c. S/L) 1. Hydraulic resonances 6 2. Mechanical resonances 6. Pipe clamps c. S/L 7. Hydraulic resonators 8. Hydraulic attenuators 1 9. Vibration isolators A n, p 2 10. Stiffening ribs and damping elements 11. Excitations produced by the process M 12. Reservoir ZS 9 f 12 Version 8. 9. 2020 Actuators 11 m 2 8 5 3
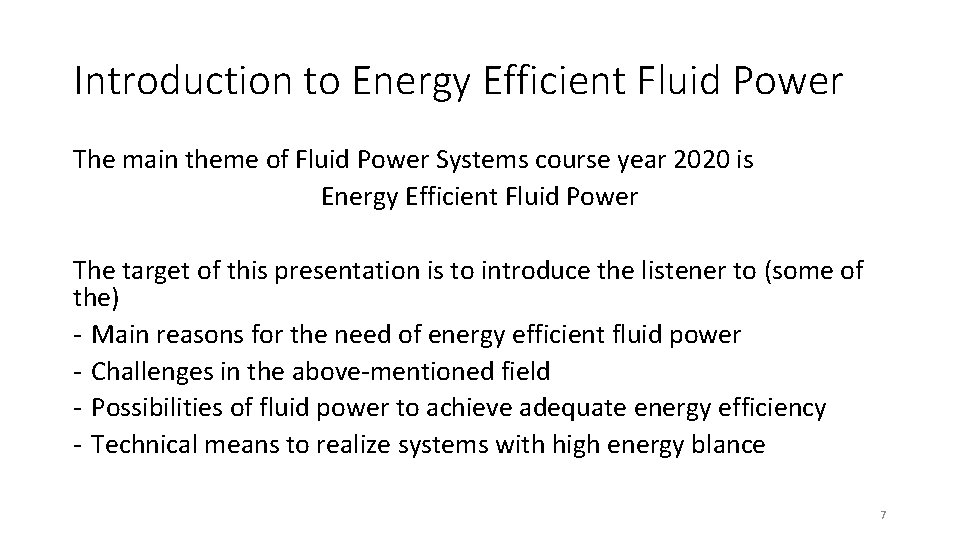
Introduction to Energy Efficient Fluid Power The main theme of Fluid Power Systems course year 2020 is Energy Efficient Fluid Power The target of this presentation is to introduce the listener to (some of the) - Main reasons for the need of energy efficient fluid power - Challenges in the above-mentioned field - Possibilities of fluid power to achieve adequate energy efficiency - Technical means to realize systems with high energy blance 7
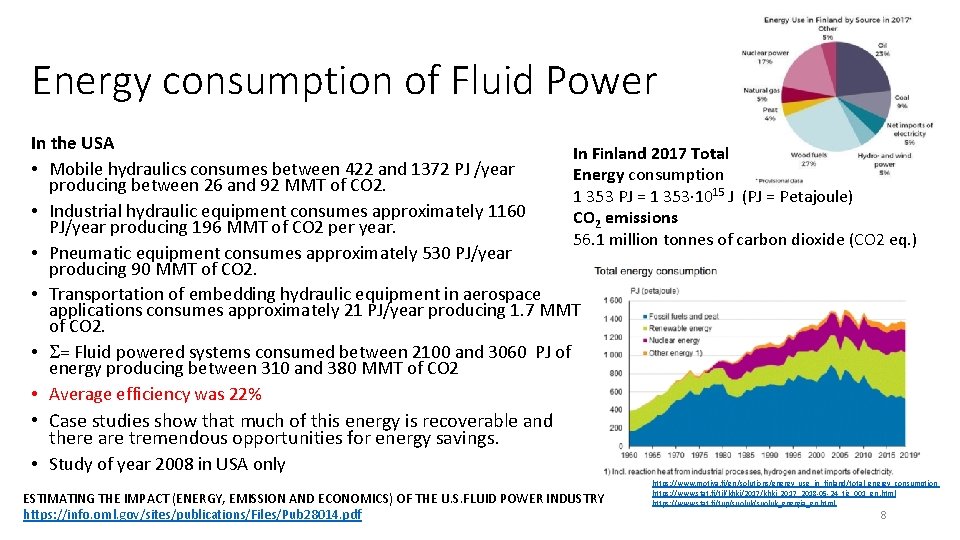
Energy consumption of Fluid Power In the USA In Finland 2017 Total • Mobile hydraulics consumes between 422 and 1372 PJ /year Energy consumption producing between 26 and 92 MMT of CO 2. 1 353 PJ = 1 353 1015 J (PJ = Petajoule) • Industrial hydraulic equipment consumes approximately 1160 CO 2 emissions PJ/year producing 196 MMT of CO 2 per year. 56. 1 million tonnes of carbon dioxide (CO 2 eq. ) • Pneumatic equipment consumes approximately 530 PJ/year producing 90 MMT of CO 2. • Transportation of embedding hydraulic equipment in aerospace applications consumes approximately 21 PJ/year producing 1. 7 MMT of CO 2. • = Fluid powered systems consumed between 2100 and 3060 PJ of energy producing between 310 and 380 MMT of CO 2 • Average efficiency was 22% • Case studies show that much of this energy is recoverable and there are tremendous opportunities for energy savings. • Study of year 2008 in USA only ESTIMATING THE IMPACT (ENERGY, EMISSION AND ECONOMICS) OF THE U. S. FLUID POWER INDUSTRY https: //info. ornl. gov/sites/publications/Files/Pub 28014. pdf https: //www. motiva. fi/en/solutions/energy_use_in_finland/total_energy_consumption https: //www. stat. fi/til/khki/2017/khki_2017_2018 -05 -24_tie_001_en. html https: //www. stat. fi/tup/suoluk_energia_en. html 8
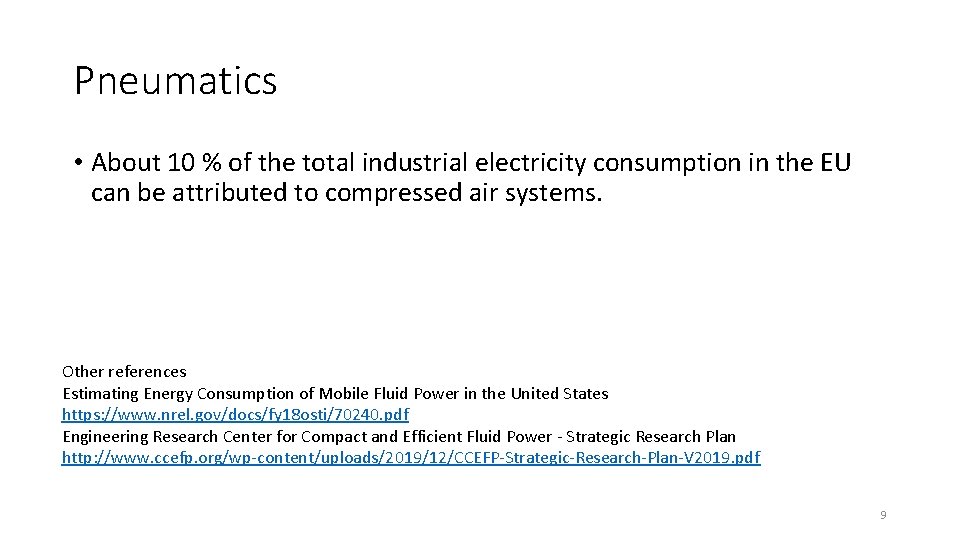
Pneumatics • About 10 % of the total industrial electricity consumption in the EU can be attributed to compressed air systems. Other references Estimating Energy Consumption of Mobile Fluid Power in the United States https: //www. nrel. gov/docs/fy 18 osti/70240. pdf Engineering Research Center for Compact and Efficient Fluid Power - Strategic Research Plan http: //www. ccefp. org/wp-content/uploads/2019/12/CCEFP-Strategic-Research-Plan-V 2019. pdf 9
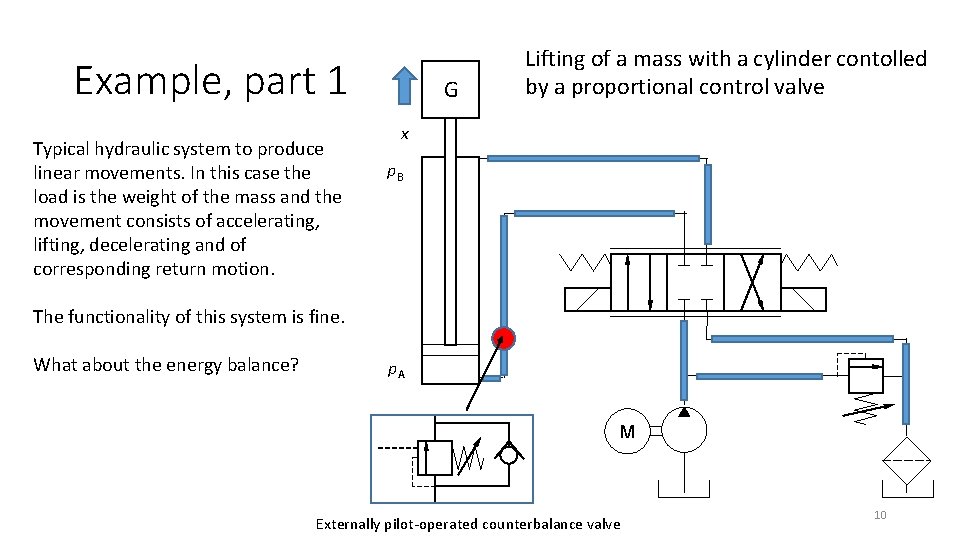
Example, part 1 Typical hydraulic system to produce linear movements. In this case the load is the weight of the mass and the movement consists of accelerating, lifting, decelerating and of corresponding return motion. G Lifting of a mass with a cylinder contolled by a proportional control valve x p. B The functionality of this system is fine. What about the energy balance? p. A M Externally pilot-operated counterbalance valve 10
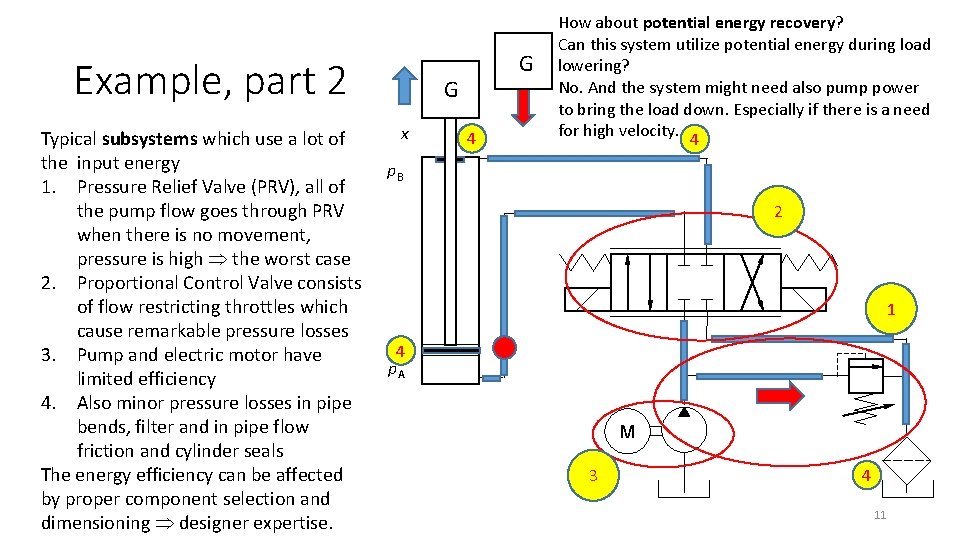
Example, part 2 Typical subsystems which use a lot of the input energy 1. Pressure Relief Valve (PRV), all of the pump flow goes through PRV when there is no movement, pressure is high the worst case 2. Proportional Control Valve consists of flow restricting throttles which cause remarkable pressure losses 3. Pump and electric motor have limited efficiency 4. Also minor pressure losses in pipe bends, filter and in pipe flow friction and cylinder seals The energy efficiency can be affected by proper component selection and dimensioning designer expertise. G G x 4 How about potential energy recovery? Can this system utilize potential energy during load lowering? No. And the system might need also pump power to bring the load down. Especially if there is a need for high velocity. 4 p. B 2 1 4 p. A M 3 4 11
![Hydraulic power loss Control by throttling Flow rate qv m 3s Turbulent case V Hydraulic power (loss) Control by throttling Flow rate qv [m 3/s] Turbulent case V](https://slidetodoc.com/presentation_image_h2/79bf63020bb087f7b909d6ffa7cb2d82/image-12.jpg)
Hydraulic power (loss) Control by throttling Flow rate qv [m 3/s] Turbulent case V 1 q 12 IN - Flow coefficient Cq Flow area A 0 Pressure diference p Fluid density The other way to look at the (”constant”) relation p 1 OUT p 2 OUT -q 12 IN Power loss qv p heat generated V 2 Control valve: Flow rate is affected by Flow coefficient - Changing flow area • Pressure loss is generated Non-linear, power of two (2)! • Power loss is generated More flow much more pressure loss! 12
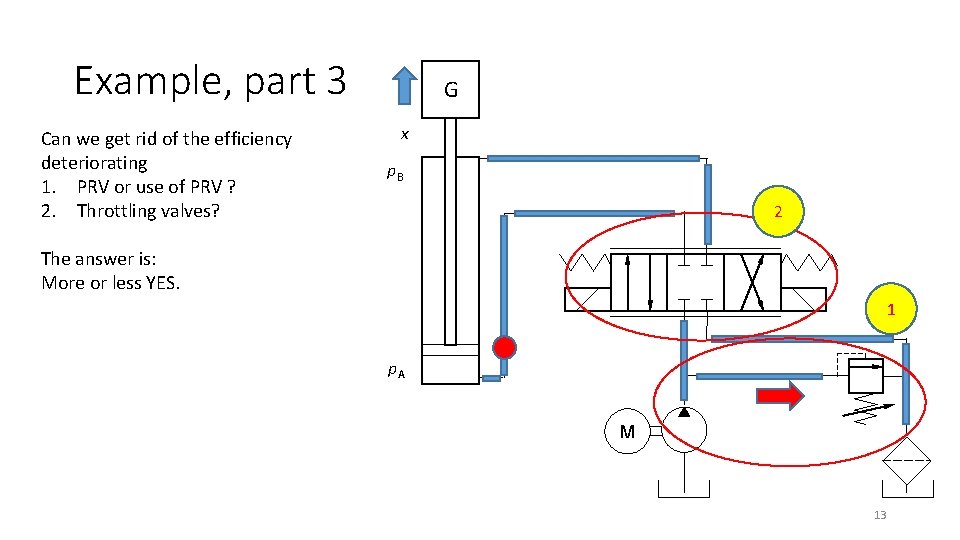
Example, part 3 Can we get rid of the efficiency deteriorating 1. PRV or use of PRV ? 2. Throttling valves? G x p. B 2 The answer is: More or less YES. 1 p. A M 13
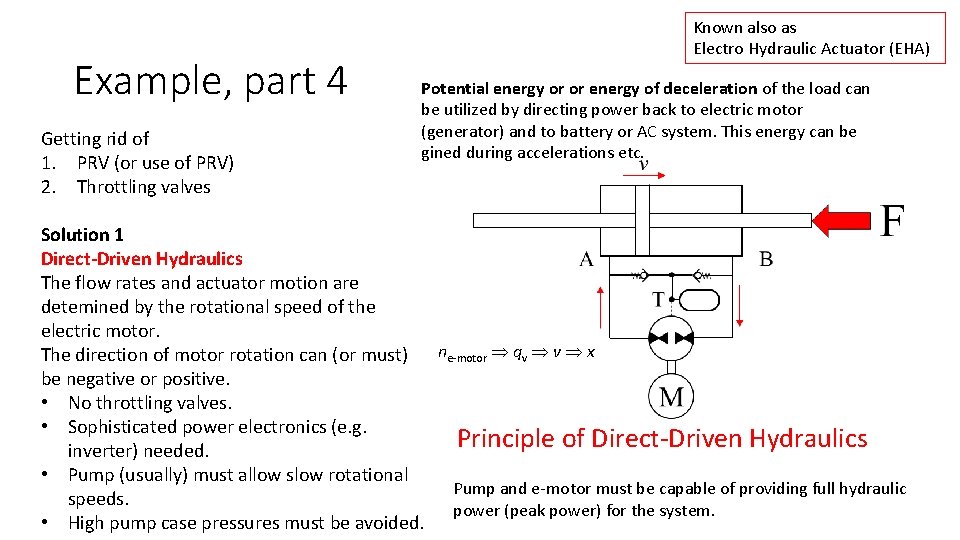
Example, part 4 Getting rid of 1. PRV (or use of PRV) 2. Throttling valves Known also as Electro Hydraulic Actuator (EHA) Potential energy or or energy of deceleration of the load can be utilized by directing power back to electric motor (generator) and to battery or AC system. This energy can be gined during accelerations etc. Solution 1 Direct-Driven Hydraulics The flow rates and actuator motion are detemined by the rotational speed of the electric motor. ne-motor qv v x The direction of motor rotation can (or must) be negative or positive. • No throttling valves. • Sophisticated power electronics (e. g. Principle of Direct-Driven Hydraulics inverter) needed. • Pump (usually) must allow slow rotational Pump and e-motor must be capable of providing full hydraulic speeds. power (peak power) for the system. • High pump case pressures must be avoided.
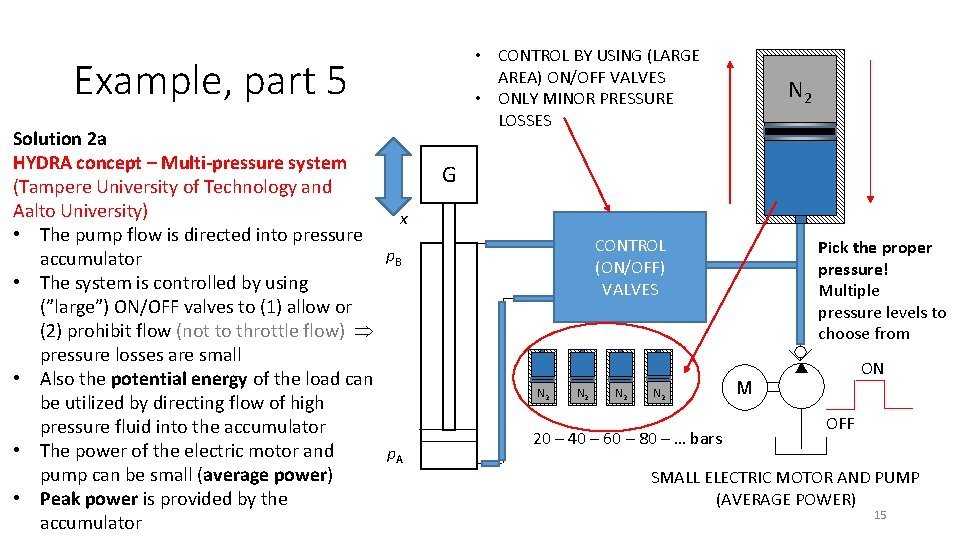
• CONTROL BY USING (LARGE AREA) ON/OFF VALVES • ONLY MINOR PRESSURE LOSSES Example, part 5 Solution 2 a HYDRA concept – Multi-pressure system (Tampere University of Technology and Aalto University) x • The pump flow is directed into pressure p. B accumulator • The system is controlled by using (”large”) ON/OFF valves to (1) allow or (2) prohibit flow (not to throttle flow) pressure losses are small • Also the potential energy of the load can be utilized by directing flow of high pressure fluid into the accumulator • The power of the electric motor and p. A pump can be small (average power) • Peak power is provided by the accumulator N 2 G CONTROL (ON/OFF) VALVES N 2 N 2 20 – 40 – 60 – 80 – … bars Pick the proper pressure! Multiple pressure levels to choose from ON M OFF SMALL ELECTRIC MOTOR AND PUMP (AVERAGE POWER) 15
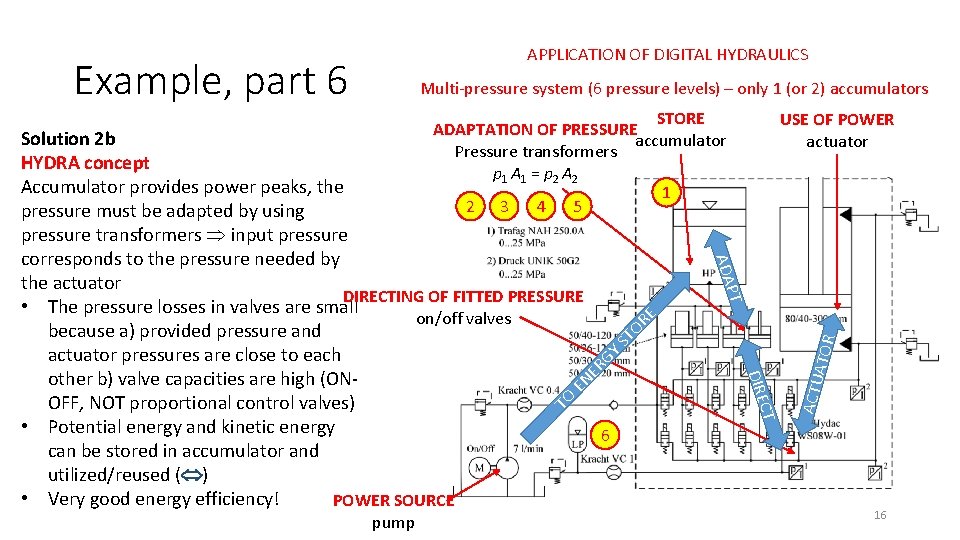
APPLICATION OF DIGITAL HYDRAULICS Example, part 6 Multi-pressure system (6 pressure levels) – only 1 (or 2) accumulators STORE ADAPTATION OF PRESSURE accumulator Pressure transformers p 1 A 1 = p 2 A 2 1 2 3 5 4 ADA ATOR ACTU EN TO pump CT DIRE ER GY ST OR E PT Solution 2 b HYDRA concept Accumulator provides power peaks, the pressure must be adapted by using pressure transformers input pressure corresponds to the pressure needed by the actuator DIRECTING OF FITTED PRESSURE • The pressure losses in valves are small on/off valves because a) provided pressure and actuator pressures are close to each other b) valve capacities are high (ONOFF, NOT proportional control valves) • Potential energy and kinetic energy 6 can be stored in accumulator and utilized/reused ( ) • Very good energy efficiency! POWER SOURCE USE OF POWER actuator 16
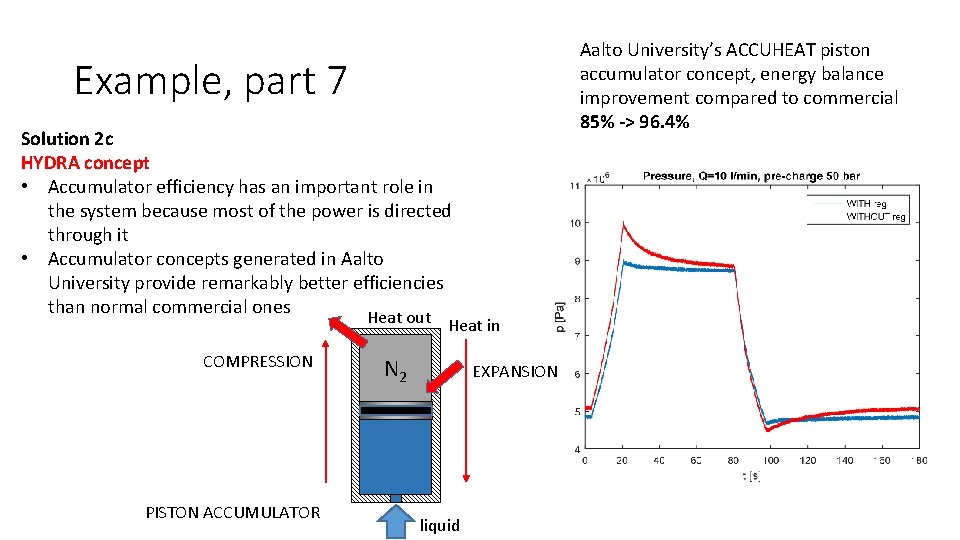
Aalto University’s ACCUHEAT piston accumulator concept, energy balance improvement compared to commercial 85% -> 96. 4% Example, part 7 Solution 2 c HYDRA concept • Accumulator efficiency has an important role in the system because most of the power is directed through it • Accumulator concepts generated in Aalto University provide remarkably better efficiencies than normal commercial ones Heat out Heat in COMPRESSION PISTON ACCUMULATOR N 2 EXPANSION liquid
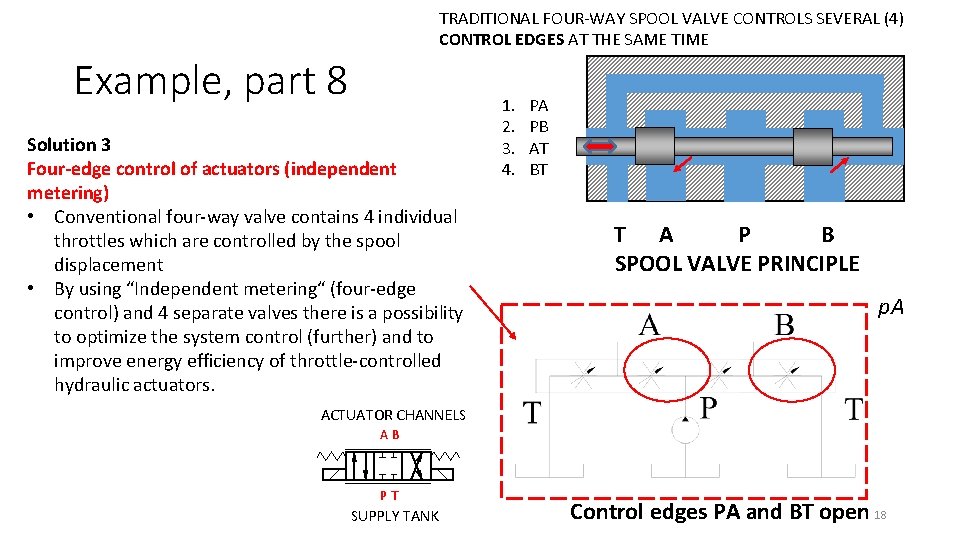
TRADITIONAL FOUR-WAY SPOOL VALVE CONTROLS SEVERAL (4) CONTROL EDGES AT THE SAME TIME Example, part 8 Solution 3 Four-edge control of actuators (independent metering) • Conventional four-way valve contains 4 individual throttles which are controlled by the spool displacement • By using “Independent metering“ (four-edge control) and 4 separate valves there is a possibility to optimize the system control (further) and to improve energy efficiency of throttle-controlled hydraulic actuators. 1. 2. 3. 4. PA PB AT BT T A P B SPOOL VALVE PRINCIPLE p. A ACTUATOR CHANNELS AB PT SUPPLY TANK Control edges PA and BT open 18
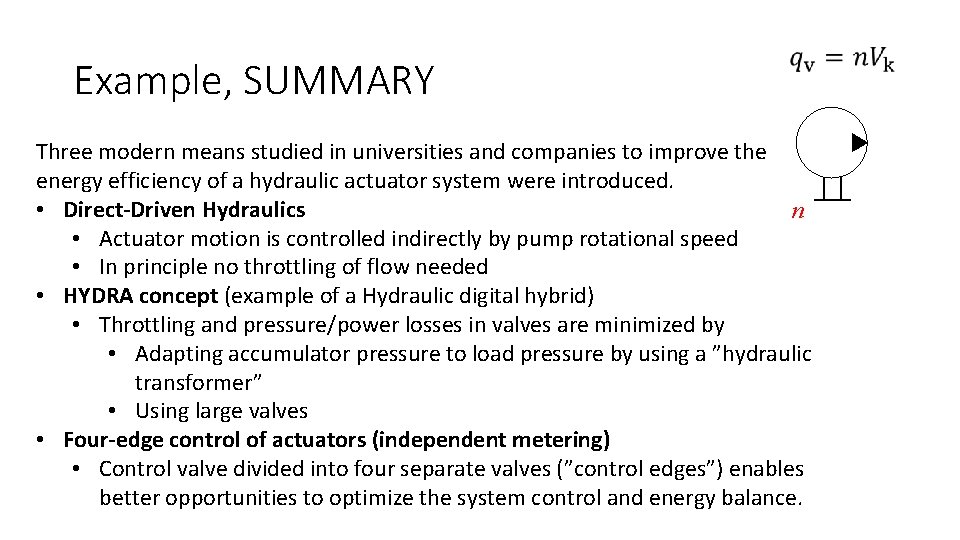
Example, SUMMARY Three modern means studied in universities and companies to improve the energy efficiency of a hydraulic actuator system were introduced. • Direct-Driven Hydraulics n • Actuator motion is controlled indirectly by pump rotational speed • In principle no throttling of flow needed • HYDRA concept (example of a Hydraulic digital hybrid) • Throttling and pressure/power losses in valves are minimized by • Adapting accumulator pressure to load pressure by using a ”hydraulic transformer” • Using large valves • Four-edge control of actuators (independent metering) • Control valve divided into four separate valves (”control edges”) enables better opportunities to optimize the system control and energy balance.
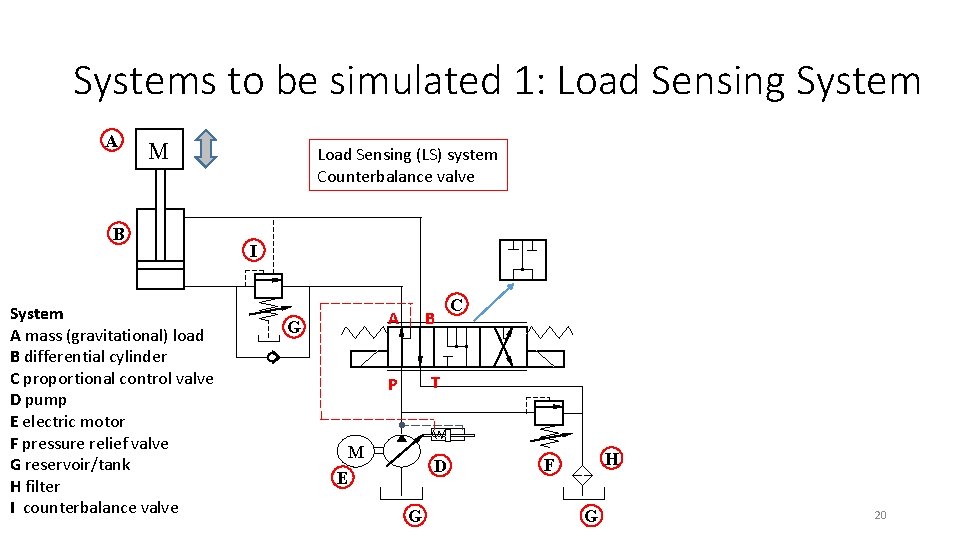
Systems to be simulated 1: Load Sensing System A M B System A mass (gravitational) load B differential cylinder C proportional control valve D pump E electric motor F pressure relief valve G reservoir/tank H filter I counterbalance valve Load Sensing (LS) system Counterbalance valve I G A B P T M E D G C H F G 20
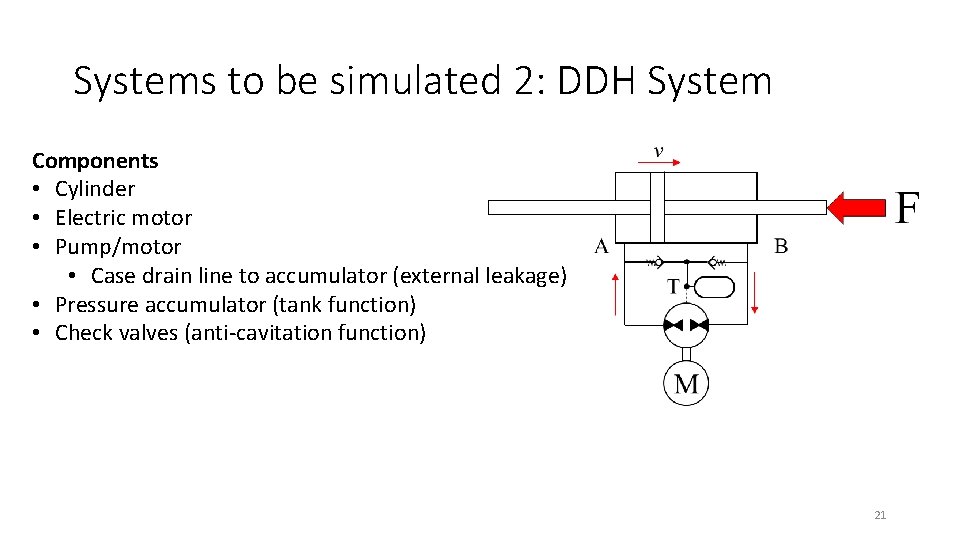
Systems to be simulated 2: DDH System Components • Cylinder • Electric motor • Pump/motor • Case drain line to accumulator (external leakage) • Pressure accumulator (tank function) • Check valves (anti-cavitation function) 21
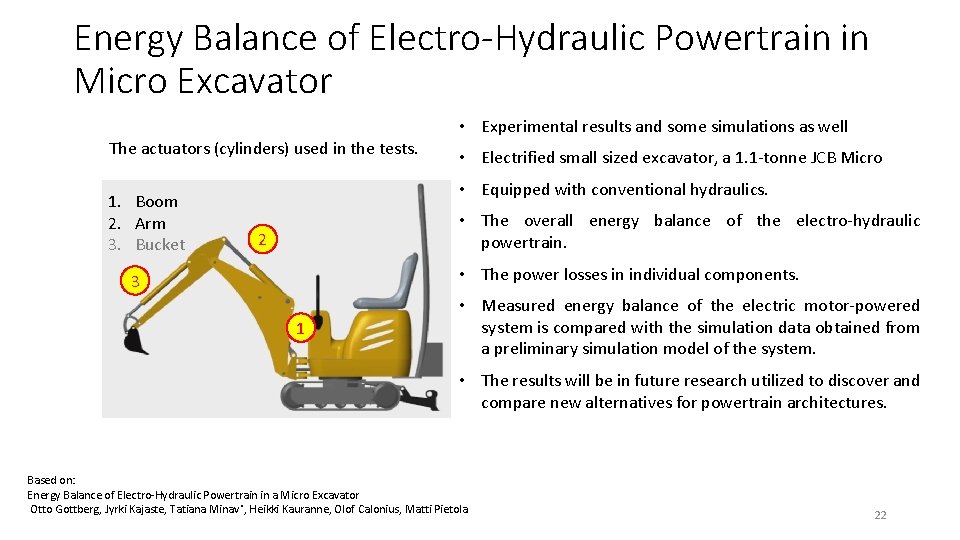
Energy Balance of Electro-Hydraulic Powertrain in Micro Excavator The actuators (cylinders) used in the tests. 1. Boom 2. Arm 3. Bucket • Experimental results and some simulations as well • Electrified small sized excavator, a 1. 1 -tonne JCB Micro • Equipped with conventional hydraulics. • The overall energy balance of the electro-hydraulic powertrain. 2 • The power losses in individual components. 3 1 • Measured energy balance of the electric motor-powered system is compared with the simulation data obtained from a preliminary simulation model of the system. • The results will be in future research utilized to discover and compare new alternatives for powertrain architectures. Based on: Energy Balance of Electro-Hydraulic Powertrain in a Micro Excavator Otto Gottberg, Jyrki Kajaste, Tatiana Minav*, Heikki Kauranne, Olof Calonius, Matti Pietola 22
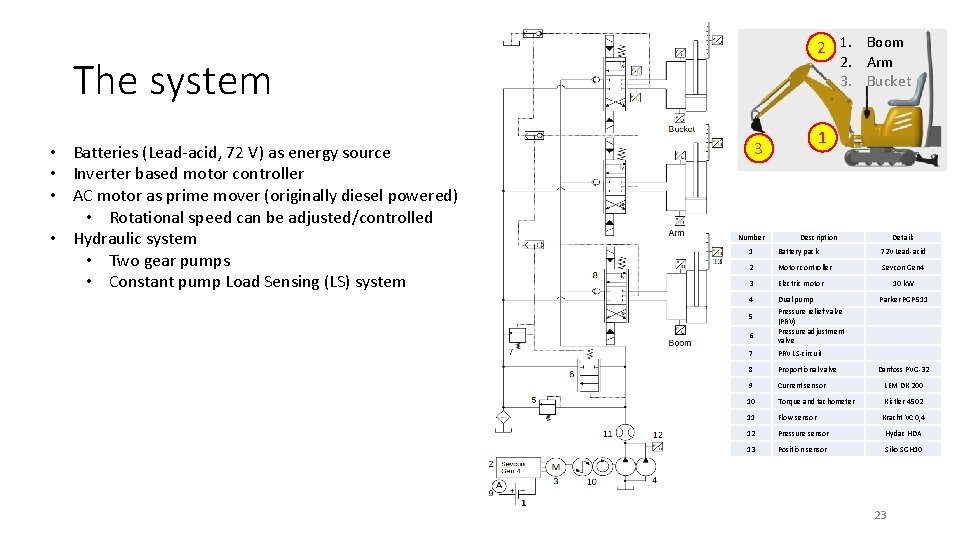
2 1. Boom 2. Arm 3. Bucket The system • Batteries (Lead-acid, 72 V) as energy source • Inverter based motor controller • AC motor as prime mover (originally diesel powered) • Rotational speed can be adjusted/controlled • Hydraulic system • Two gear pumps • Constant pump Load Sensing (LS) system 1 3 Number Description Details 1 Battery pack 72 V Lead-acid 2 Motor controller Sevcon Gen 4 3 Electric motor 4 Dual pump 5 6 10 k. W Parker PGP 511 Pressure relief valve (PRV) Pressure adjustment valve 7 PRV LS-circuit 8 Proportional valve 9 Current sensor LEM DK 200 10 Torque and tachometer Kistler 4502 11 Flow sensor 12 Pressure sensor Hydac HDA 13 Position sensor Siko SGH 10 Danfoss PVG-32 Kracht VC 0, 4 23
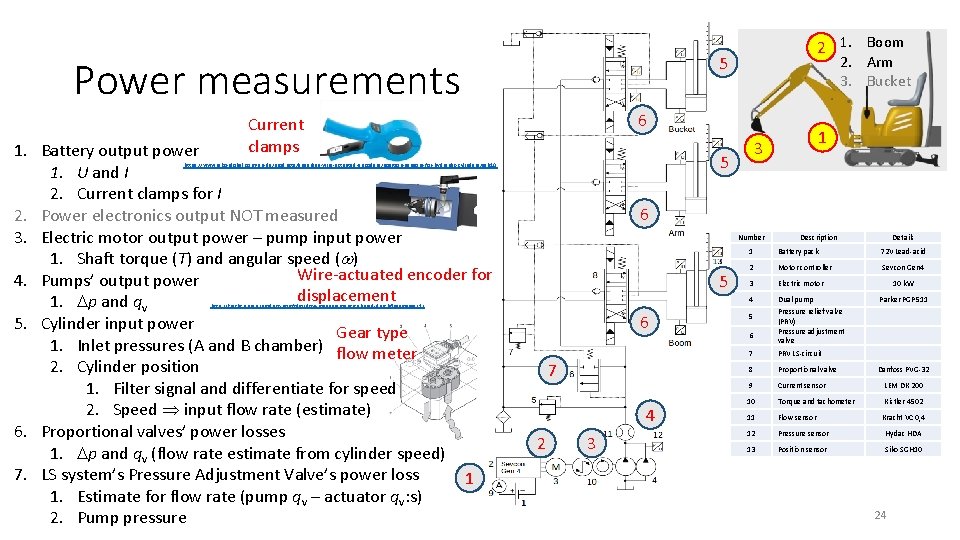
2. Arm 3. Bucket 5 Power measurements 6 Current clamps 1. Battery output power 1. U and I 2. Current clamps for I 2. Power electronics output NOT measured 3. Electric motor output power – pump input power 1. Shaft torque (T) and angular speed ( ) Wire-actuated encoder for 4. Pumps’ output power displacement 1. p and qv 5. Cylinder input power Gear type 1. Inlet pressures (A and B chamber) flow meter 2. Cylinder position 1. Filter signal and differentiate for speed 2. Speed input flow rate (estimate) 6. Proportional valves’ power losses 1. p and qv (flow rate estimate from cylinder speed) 7. LS system’s Pressure Adjustment Valve’s power loss 1 1. Estimate for flow rate (pump qv – actuator qv: s) 2. Pump pressure 2 1. Boom 5 https: //www. siko-global. com/en-de/products/linearline-wire-actuated-encoders/position-sensors-for-hydraulic-cylinders/sgh 10 1 3 6 Number 5 http: //kracht. eu/en/product-portfolio/flow-measurement/zahnrad-durchflussmesser 1/ 6 7 4 2 3 Description Details 1 Battery pack 72 V Lead-acid 2 Motor controller Sevcon Gen 4 3 Electric motor 4 Dual pump 5 6 10 k. W Parker PGP 511 Pressure relief valve (PRV) Pressure adjustment valve 7 PRV LS-circuit 8 Proportional valve 9 Current sensor LEM DK 200 10 Torque and tachometer Kistler 4502 11 Flow sensor 12 Pressure sensor Hydac HDA 13 Position sensor Siko SGH 10 Danfoss PVG-32 Kracht VC 0, 4 24
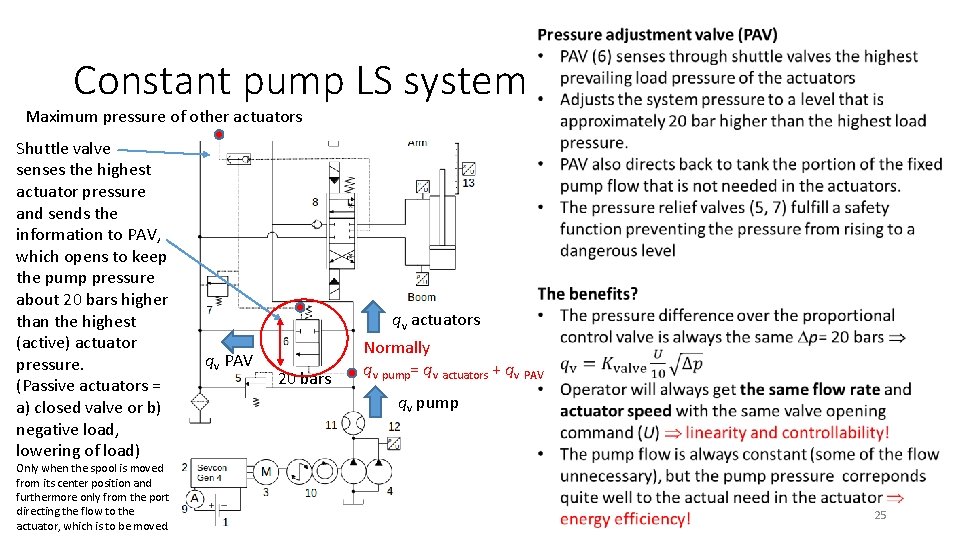
Constant pump LS system Maximum pressure of other actuators Shuttle valve senses the highest actuator pressure and sends the information to PAV, which opens to keep the pump pressure about 20 bars higher than the highest (active) actuator pressure. (Passive actuators = a) closed valve or b) negative load, lowering of load) Only when the spool is moved from its center position and furthermore only from the port directing the flow to the actuator, which is to be moved. qv actuators qv PAV 20 bars Normally qv pump= qv actuators + qv PAV qv pump 25
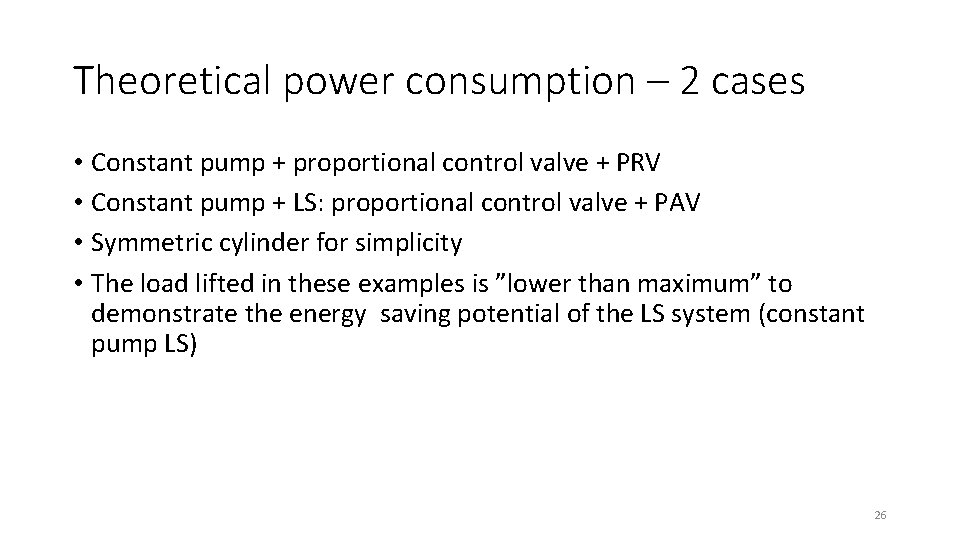
Theoretical power consumption – 2 cases • Constant pump + proportional control valve + PRV • Constant pump + LS: proportional control valve + PAV • Symmetric cylinder for simplicity • The load lifted in these examples is ”lower than maximum” to demonstrate the energy saving potential of the LS system (constant pump LS) 26
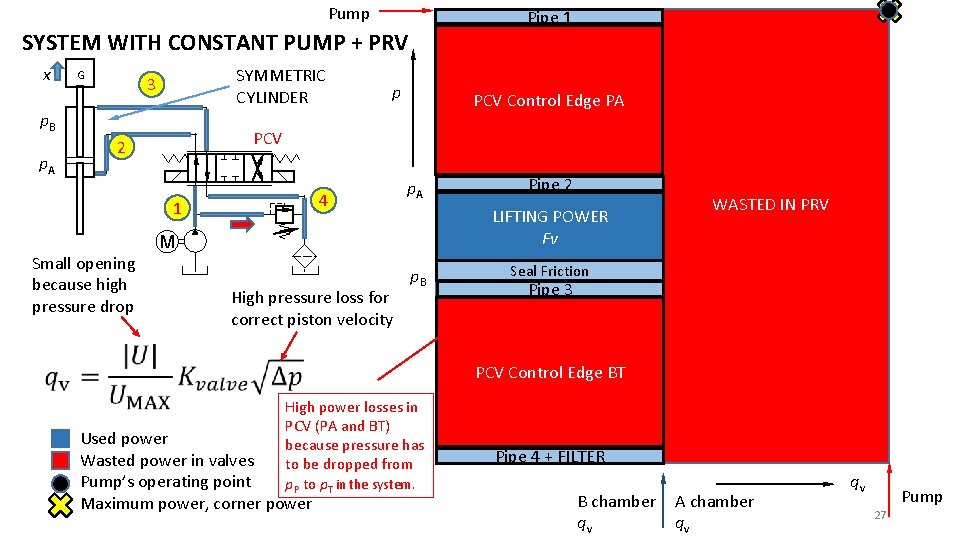
Pump Pipe 1 SYSTEM WITH CONSTANT PUMP + PRV x G SYMMETRIC CYLINDER 3 p. B p. A PCV Control Edge PA PCV 2 4 1 Small opening because high pressure drop p p. A LIFTING POWER Fv M High pressure loss for correct piston velocity Pipe 2 p. B WASTED IN PRV Seal Friction Pipe 3 PCV Control Edge BT High power losses in PCV (PA and BT) because pressure has to be dropped from p. P to p. T in the system. Used power Wasted power in valves Pump’s operating point Maximum power, corner power Pipe 4 + FILTER B chamber qv A chamber qv qv Pump 27
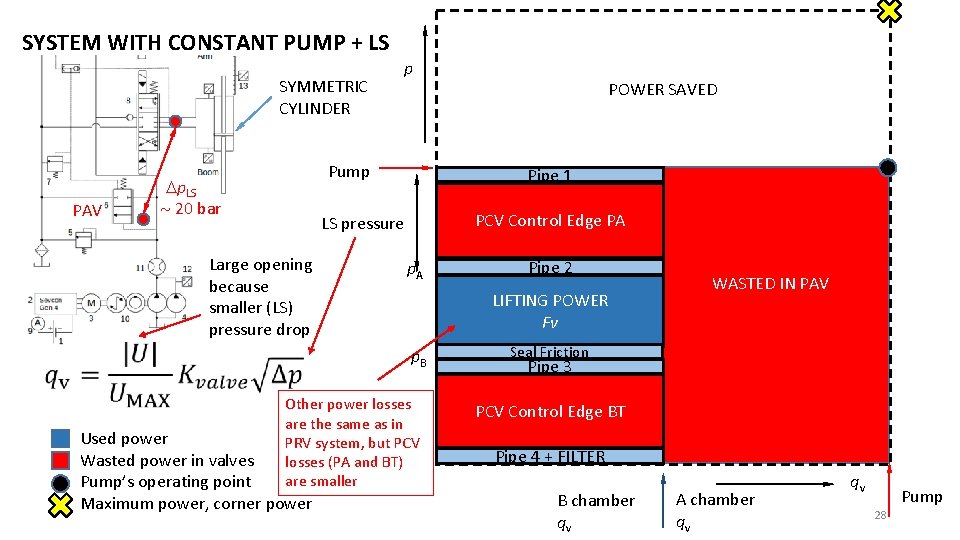
SYSTEM WITH CONSTANT PUMP + LS SYMMETRIC CYLINDER PAV p Pump p. LS 20 bar Pipe 1 PCV Control Edge PA LS pressure Large opening because smaller (LS) pressure drop p. A Pipe 2 LIFTING POWER Fv p. B Other power losses are the same as in PRV system, but PCV losses (PA and BT) are smaller Used power Wasted power in valves Pump’s operating point Maximum power, corner power POWER SAVED WASTED IN PAV Seal Friction Pipe 3 PCV Control Edge BT Pipe 4 + FILTER B chamber qv A chamber qv qv Pump 28
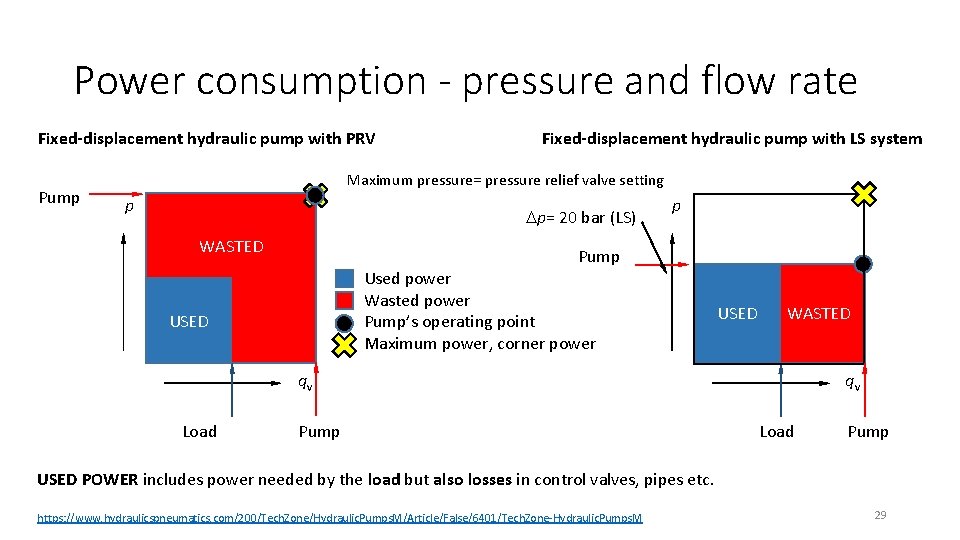
Power consumption - pressure and flow rate Fixed-displacement hydraulic pump with PRV Pump Fixed-displacement hydraulic pump with LS system Maximum pressure= pressure relief valve setting p p= 20 bar (LS) WASTED p Pump Used power Wasted power Pump’s operating point Maximum power, corner power USED WASTED qv Load Pump USED POWER includes power needed by the load but also losses in control valves, pipes etc. https: //www. hydraulicspneumatics. com/200/Tech. Zone/Hydraulic. Pumps. M/Article/False/6401/Tech. Zone-Hydraulic. Pumps. M 29
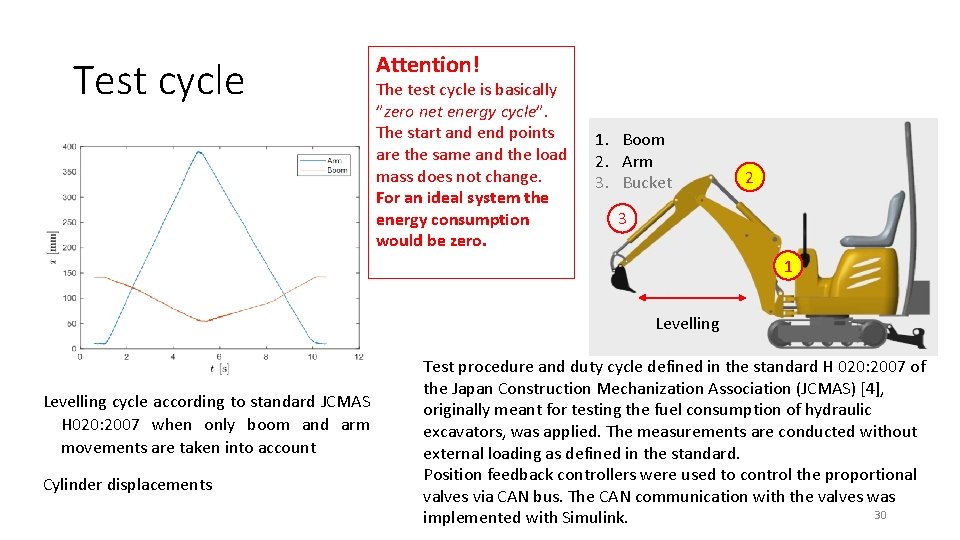
Test cycle Attention! The test cycle is basically ”zero net energy cycle”. The start and end points are the same and the load mass does not change. For an ideal system the energy consumption would be zero. 1. Boom 2. Arm 3. Bucket 2 3 1 Levelling cycle according to standard JCMAS H 020: 2007 when only boom and arm movements are taken into account Cylinder displacements Test procedure and duty cycle defined in the standard H 020: 2007 of the Japan Construction Mechanization Association (JCMAS) [4], originally meant for testing the fuel consumption of hydraulic excavators, was applied. The measurements are conducted without external loading as defined in the standard. Position feedback controllers were used to control the proportional valves via CAN bus. The CAN communication with the valves was 30 implemented with Simulink.
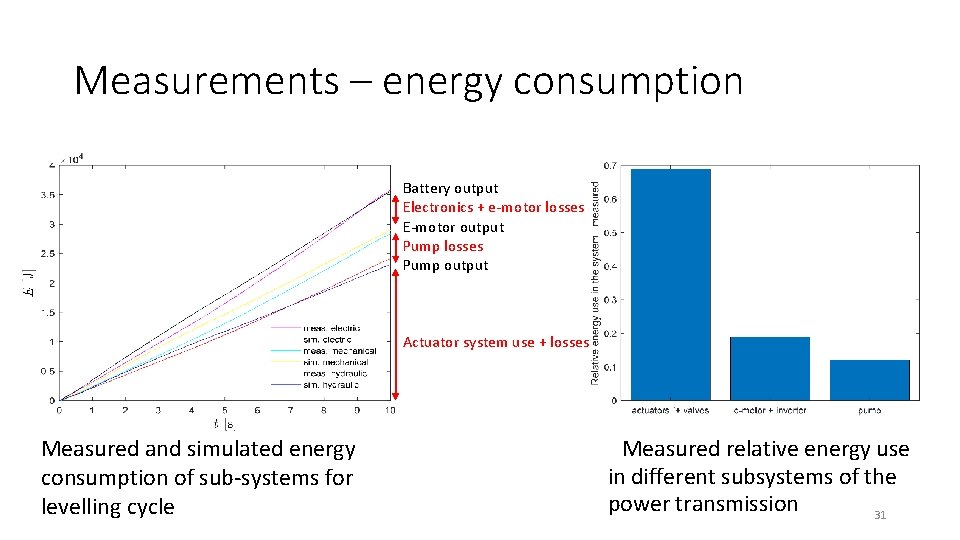
Measurements – energy consumption Battery output Electronics + e-motor losses E-motor output Pump losses Pump output Actuator system use + losses Measured and simulated energy consumption of sub-systems for levelling cycle Measured relative energy use in different subsystems of the power transmission 31
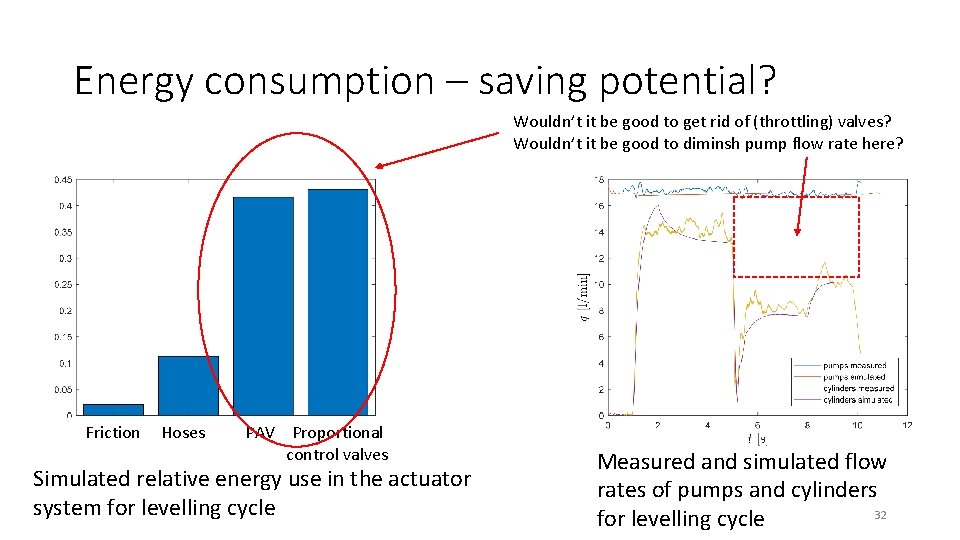
Energy consumption – saving potential? Wouldn’t it be good to get rid of (throttling) valves? Wouldn’t it be good to diminsh pump flow rate here? Friction Hoses PAV Proportional control valves Simulated relative energy use in the actuator system for levelling cycle Measured and simulated flow rates of pumps and cylinders 32 for levelling cycle
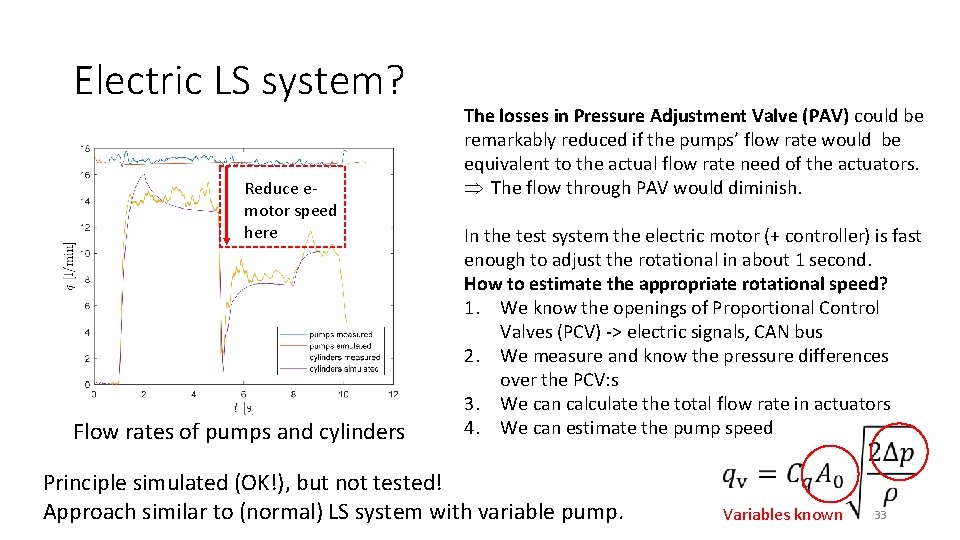
Electric LS system? Reduce emotor speed here Flow rates of pumps and cylinders The losses in Pressure Adjustment Valve (PAV) could be remarkably reduced if the pumps’ flow rate would be equivalent to the actual flow rate need of the actuators. The flow through PAV would diminish. In the test system the electric motor (+ controller) is fast enough to adjust the rotational in about 1 second. How to estimate the appropriate rotational speed? 1. We know the openings of Proportional Control Valves (PCV) -> electric signals, CAN bus 2. We measure and know the pressure differences over the PCV: s 3. We can calculate the total flow rate in actuators 4. We can estimate the pump speed Principle simulated (OK!), but not tested! Approach similar to (normal) LS system with variable pump. Variables known 33
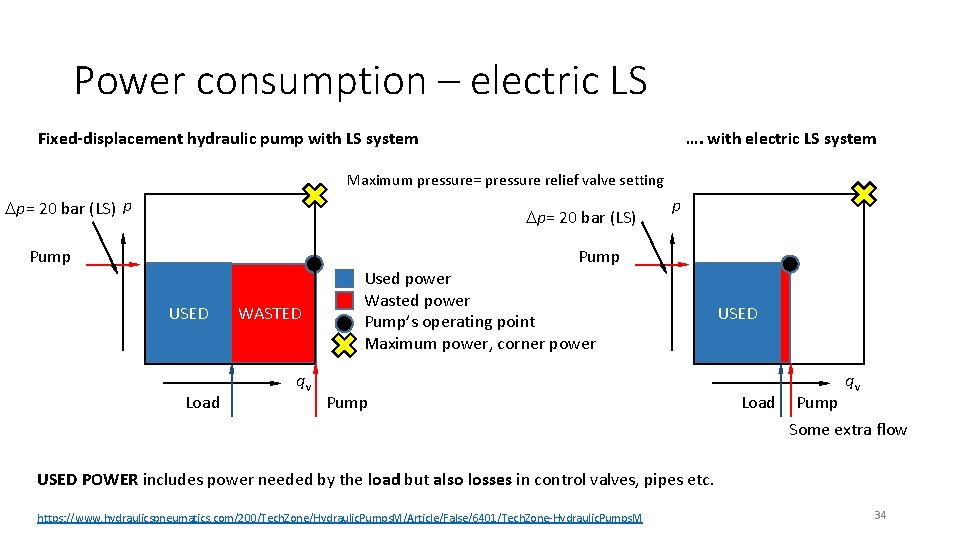
Power consumption – electric LS Fixed-displacement hydraulic pump with LS system …. with electric LS system Maximum pressure= pressure relief valve setting p= 20 bar (LS) p Pump USED Load WASTED qv Used power Wasted power Pump’s operating point Maximum power, corner power USED WASTED Pump Load Pump qv Some extra flow USED POWER includes power needed by the load but also losses in control valves, pipes etc. https: //www. hydraulicspneumatics. com/200/Tech. Zone/Hydraulic. Pumps. M/Article/False/6401/Tech. Zone-Hydraulic. Pumps. M 34
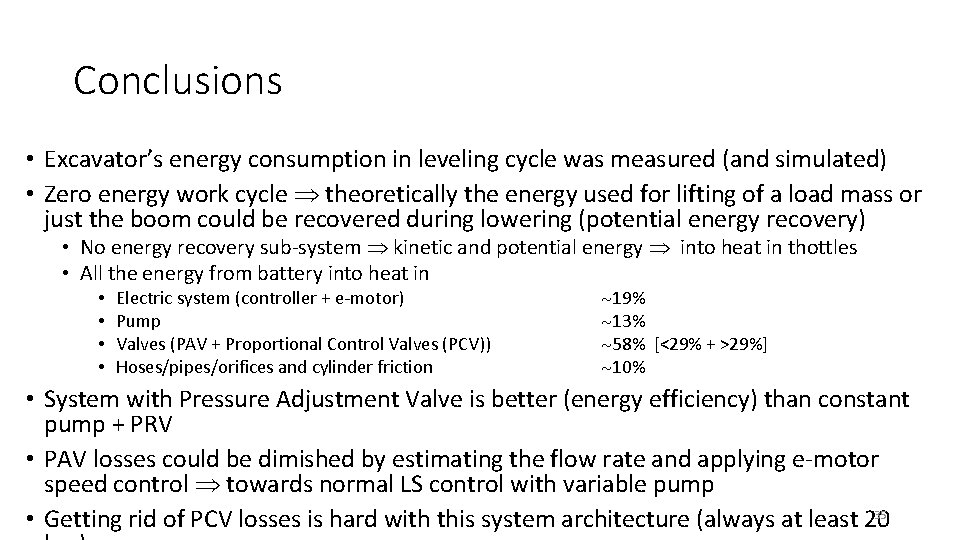
Conclusions • Excavator’s energy consumption in leveling cycle was measured (and simulated) • Zero energy work cycle theoretically the energy used for lifting of a load mass or just the boom could be recovered during lowering (potential energy recovery) • No energy recovery sub-system kinetic and potential energy into heat in thottles • All the energy from battery into heat in • • Electric system (controller + e-motor) Pump Valves (PAV + Proportional Control Valves (PCV)) Hoses/pipes/orifices and cylinder friction 19% 13% 58% [<29% + >29%] 10% • System with Pressure Adjustment Valve is better (energy efficiency) than constant pump + PRV • PAV losses could be dimished by estimating the flow rate and applying e-motor speed control towards normal LS control with variable pump 35 • Getting rid of PCV losses is hard with this system architecture (always at least 20
Thrum mat
Mece
Mece
Mece
Synovial fluid
Fluid statics deals with fluid at rest
Fluid statics deals with fluid at rest
Body fluid compartments
Bioimpedância
Interstitial vs intracellular
What is fluid kinematics
Movement of body fluids
Shifting dullness and fluid thrill
Draw power triangle
Georgijev financial group
Transfer credits vcu
Historic tax credits 101
Ects grade
Historic tax credit structure diagram
Avrupa kredi transfer sistemi
Uncc soar
Credits medical definition
New market tax credits st louis
The uniform customs and practice for documentary credits
Scu transfer credits
Epcc to utep transfer
Nsqf level chart
Episd graduation requirements
Edward scissorhands opening scene analysis
Accrued expense balance sheet
Tufts blast
Walking dead opening credits
Debits and credits cheat sheet
T-accounts debits & credits simulation
Abcclio
Imagine there is a bank account that credits you