MATERIAL REQUIREMENTS PLANNING MRP PLANNING AND CONTROL SYSTEM
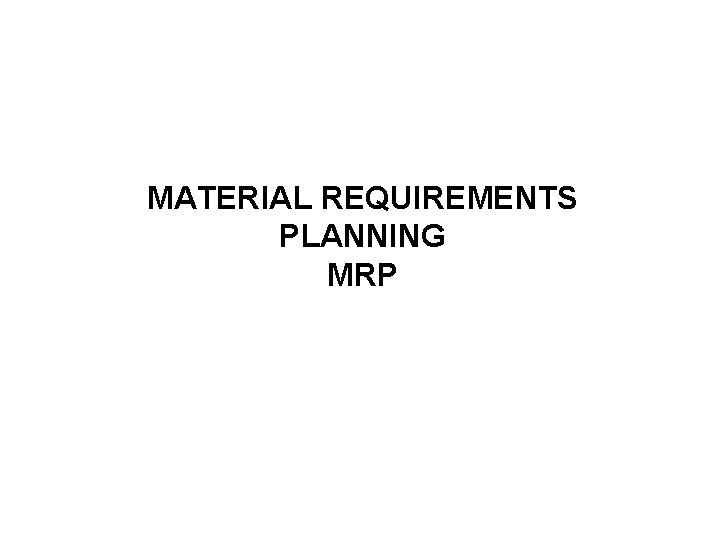
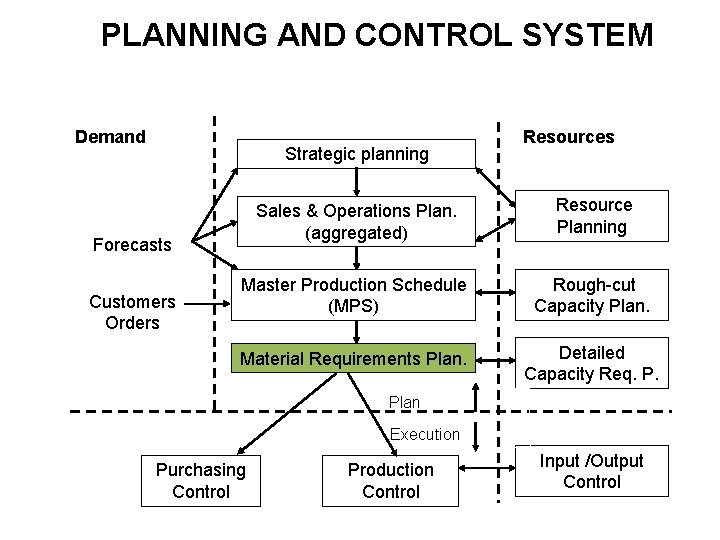
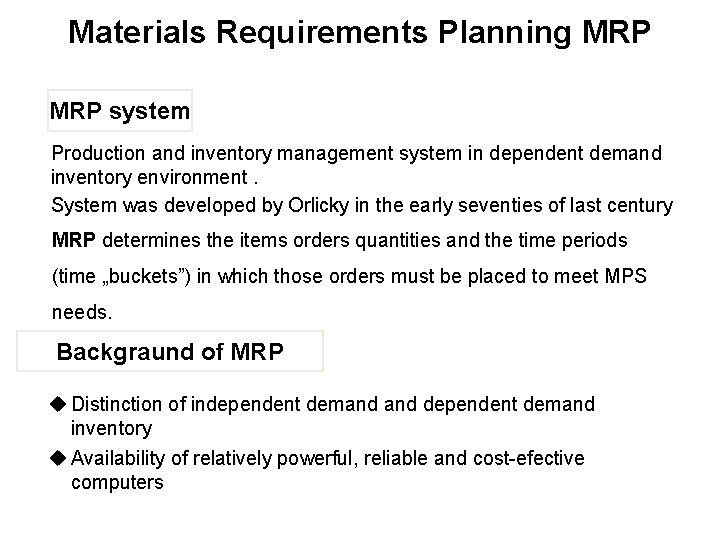
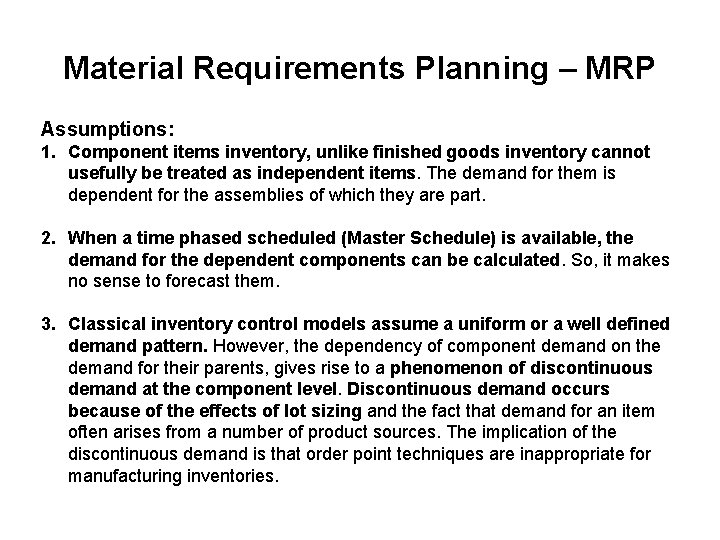
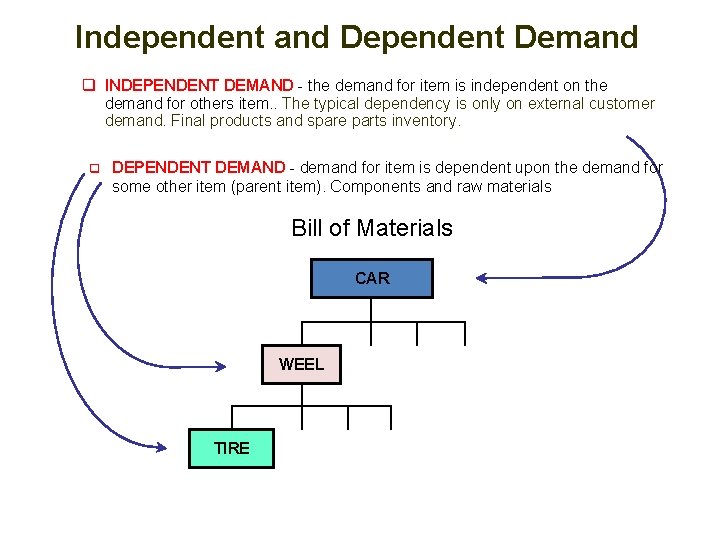
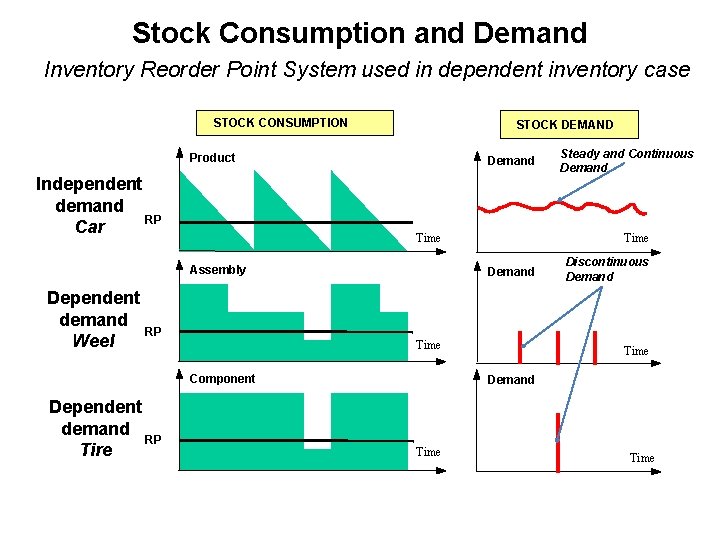
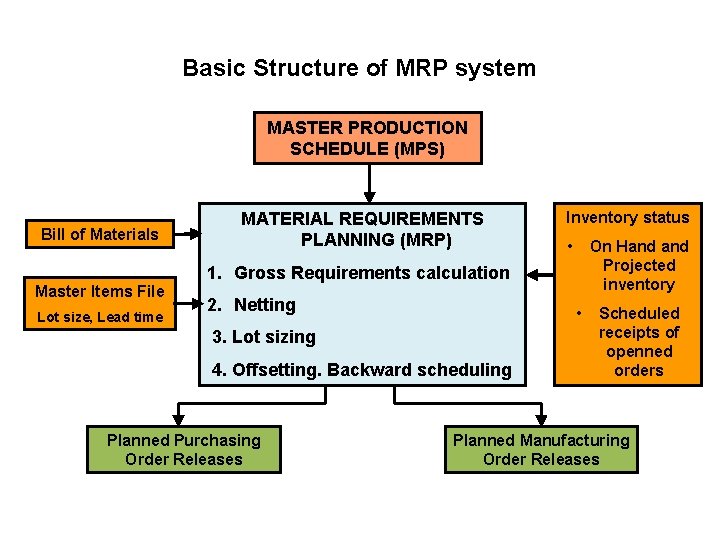
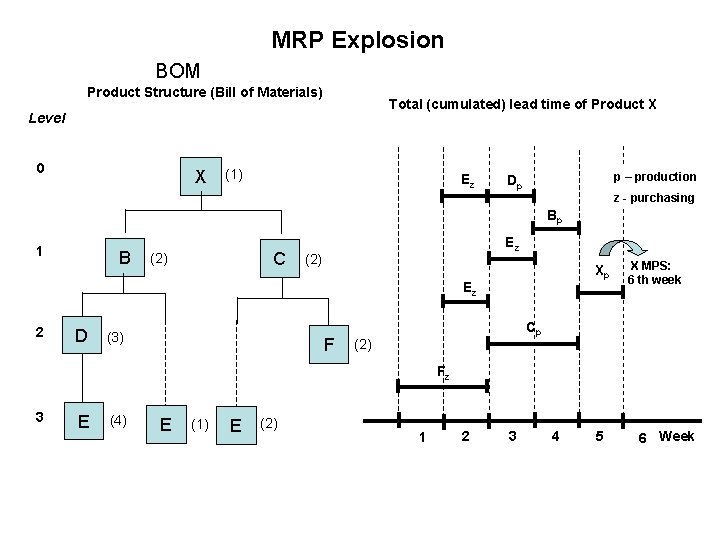
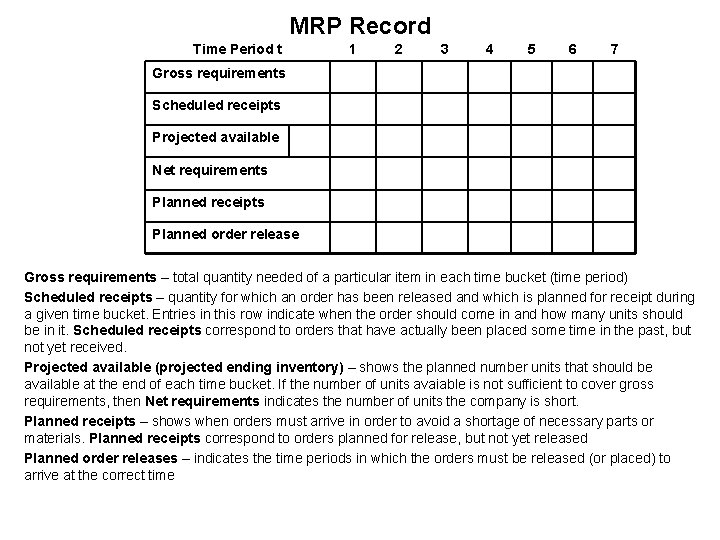
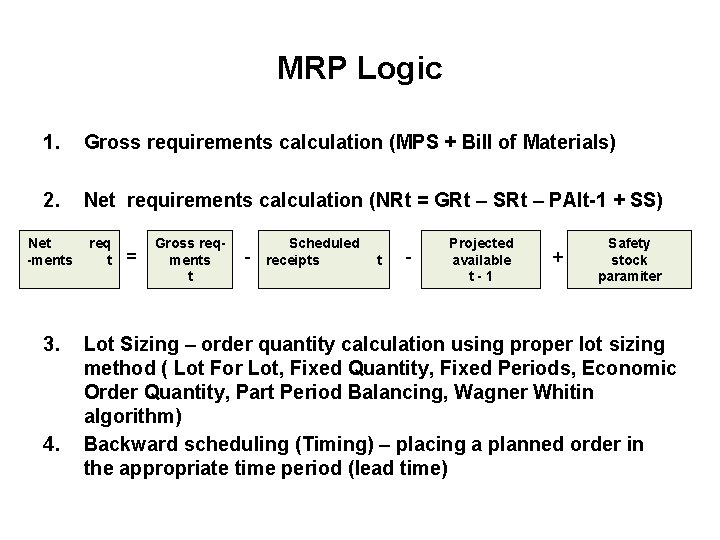
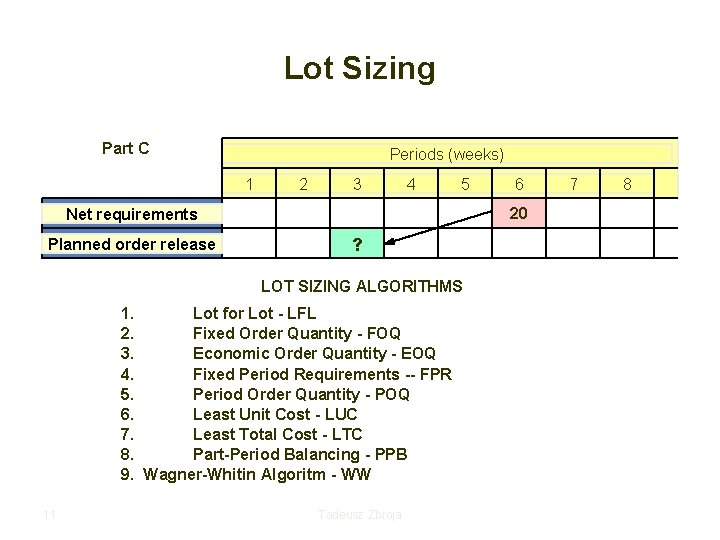
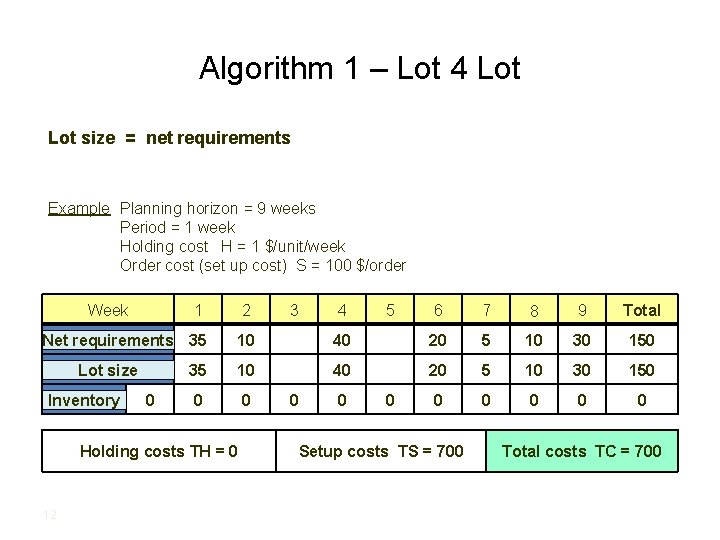
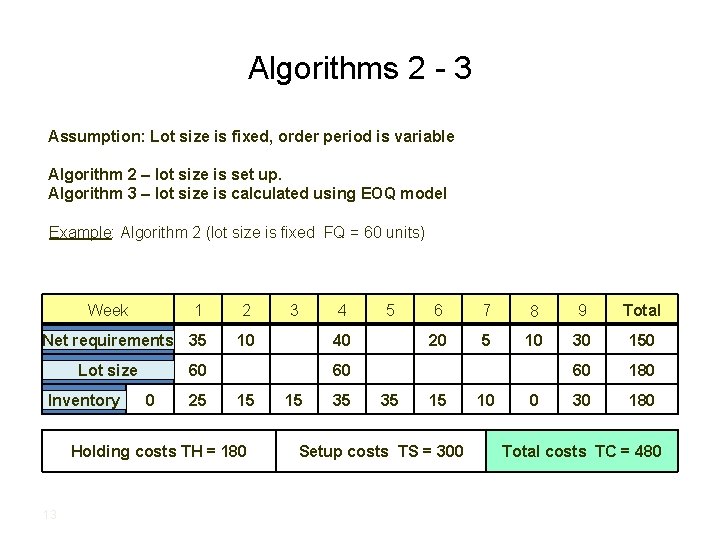
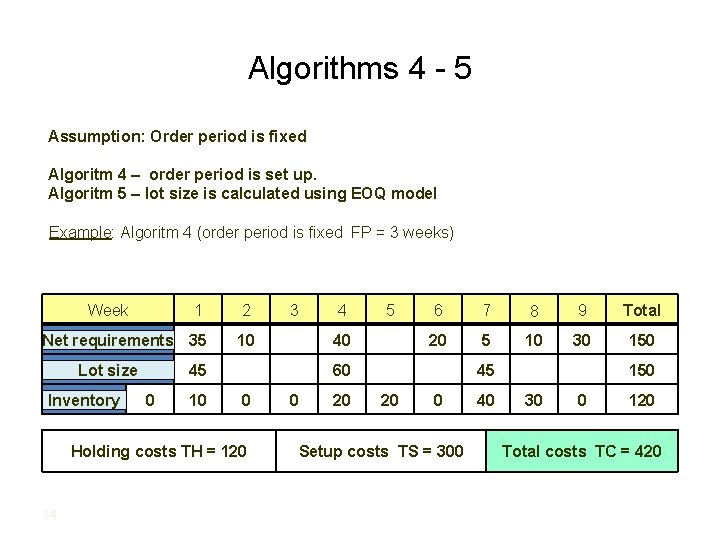
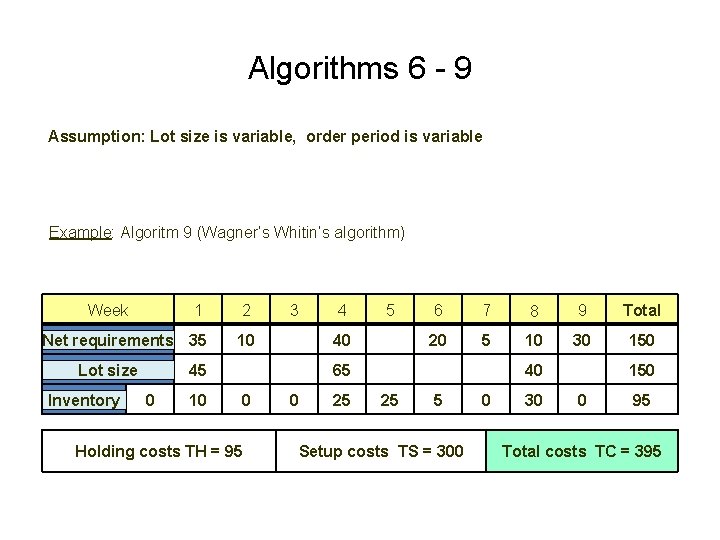
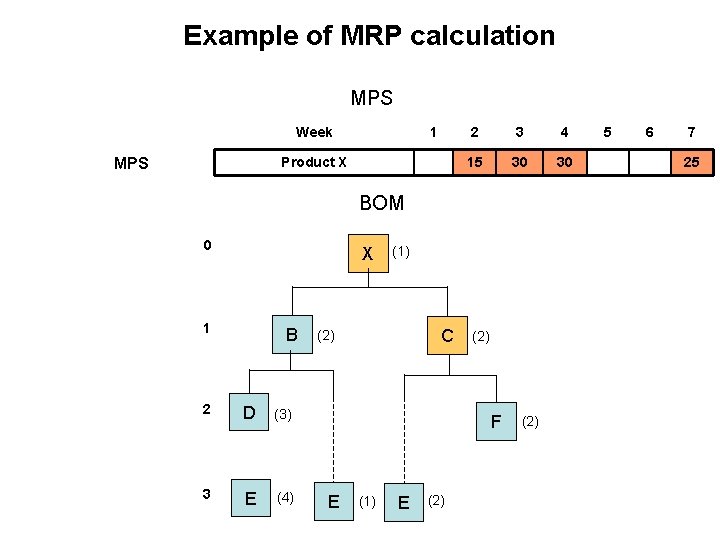
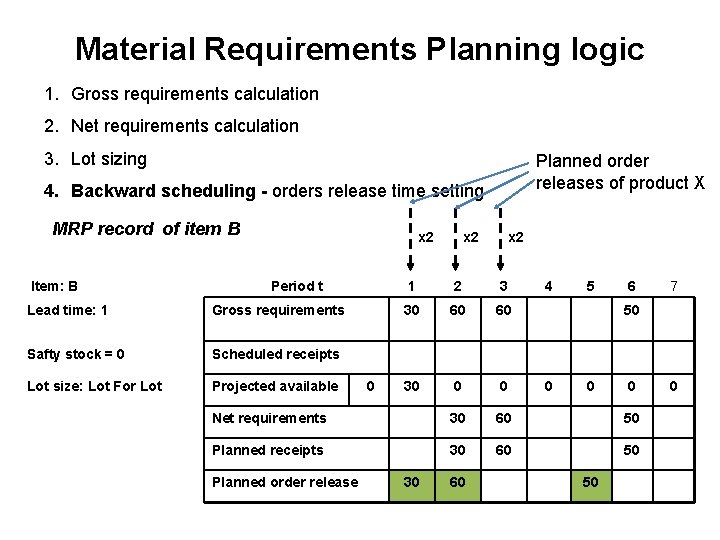
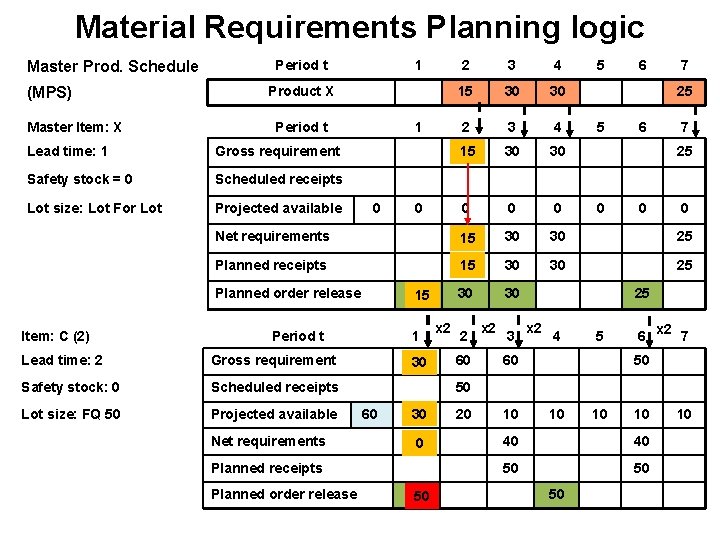
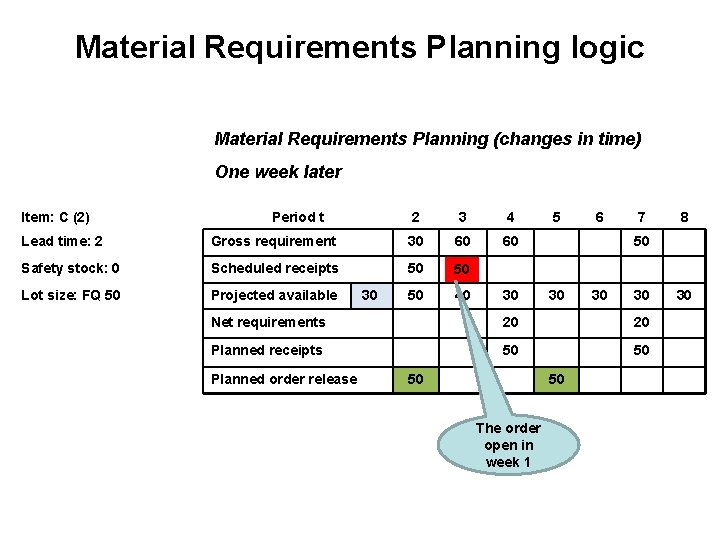
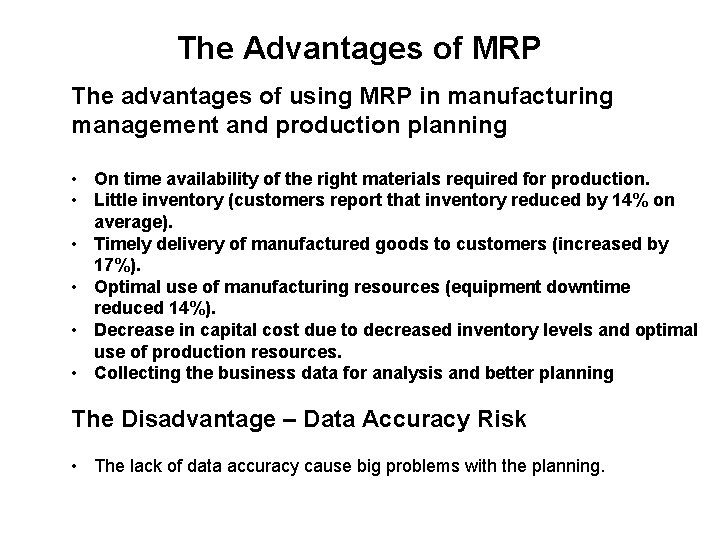
- Slides: 20
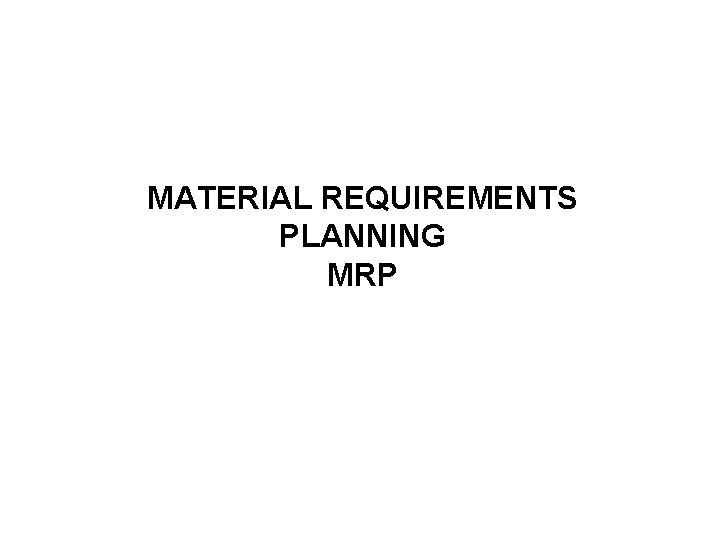
MATERIAL REQUIREMENTS PLANNING MRP
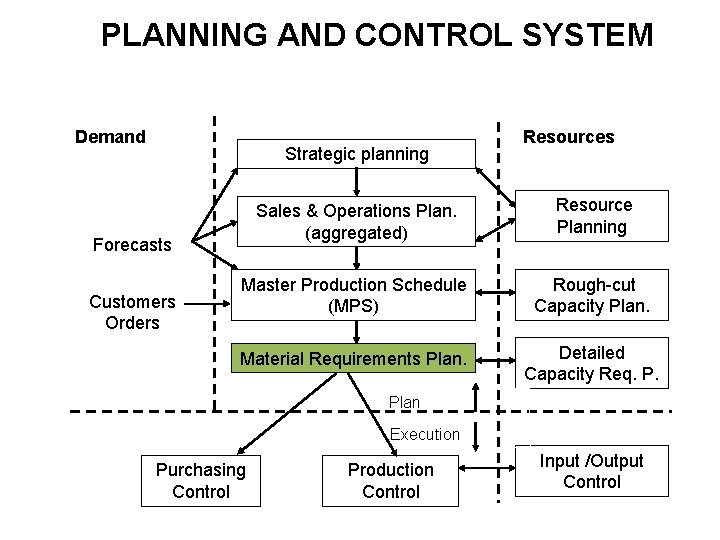
PLANNING AND CONTROL SYSTEM Demand Strategic planning Sales & Operations Plan. (aggregated) Resource Planning Master Production Schedule (MPS) Rough-cut Capacity Plan. Material Requirements Plan. Detailed Capacity Req. P. Forecasts Customers Orders Resources Plan Execution Purchasing Control Production Control Input /Output Control
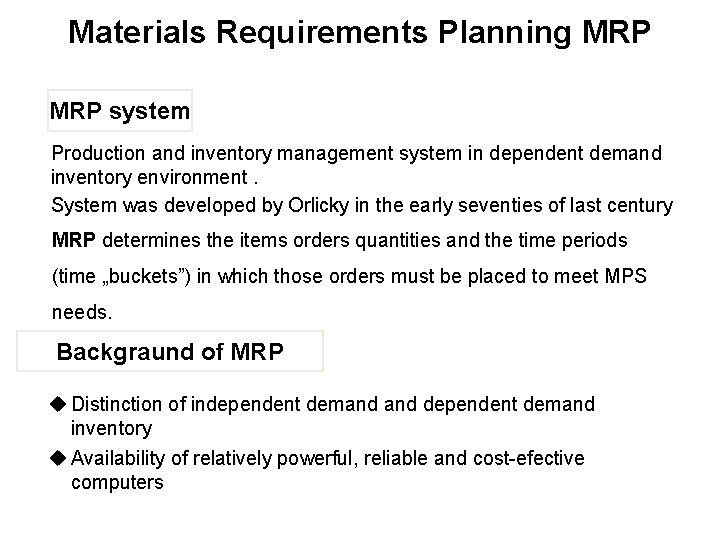
Materials Requirements Planning MRP system Production and inventory management system in dependent demand inventory environment. System was developed by Orlicky in the early seventies of last century MRP determines the items orders quantities and the time periods (time „buckets”) in which those orders must be placed to meet MPS needs. Backgraund of MRP u Distinction of independent demand inventory u Availability of relatively powerful, reliable and cost-efective computers
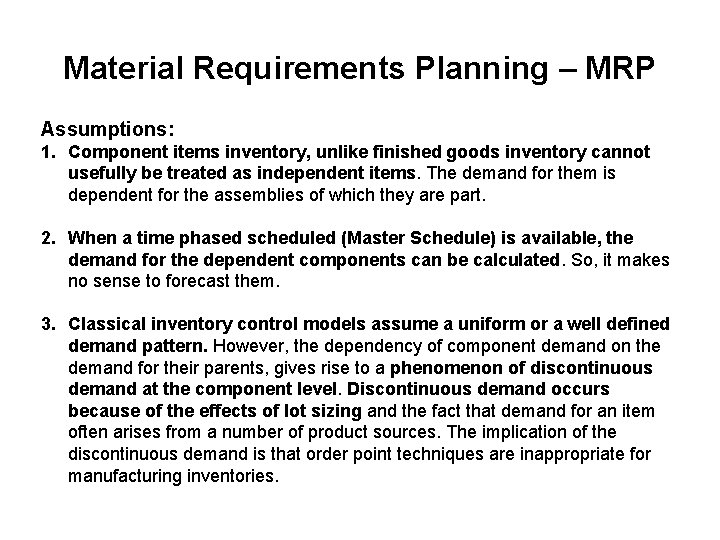
Material Requirements Planning – MRP Assumptions: 1. Component items inventory, unlike finished goods inventory cannot usefully be treated as independent items. The demand for them is dependent for the assemblies of which they are part. 2. When a time phased scheduled (Master Schedule) is available, the demand for the dependent components can be calculated. So, it makes no sense to forecast them. 3. Classical inventory control models assume a uniform or a well defined demand pattern. However, the dependency of component demand on the demand for their parents, gives rise to a phenomenon of discontinuous demand at the component level. Discontinuous demand occurs because of the effects of lot sizing and the fact that demand for an item often arises from a number of product sources. The implication of the discontinuous demand is that order point techniques are inappropriate for manufacturing inventories.
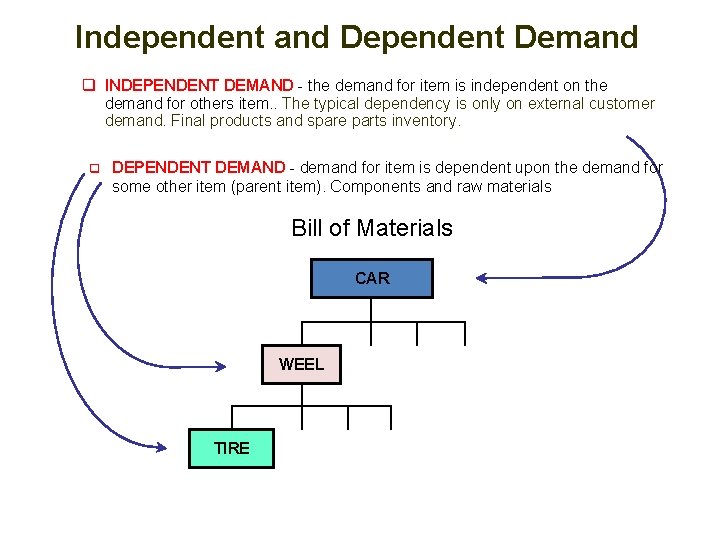
Independent and Dependent Demand q INDEPENDENT DEMAND - the demand for item is independent on the demand for others item. . The typical dependency is only on external customer demand. Final products and spare parts inventory. q DEPENDENT DEMAND - demand for item is dependent upon the demand for some other item (parent item). Components and raw materials Bill of Materials CAR WEEL TIRE
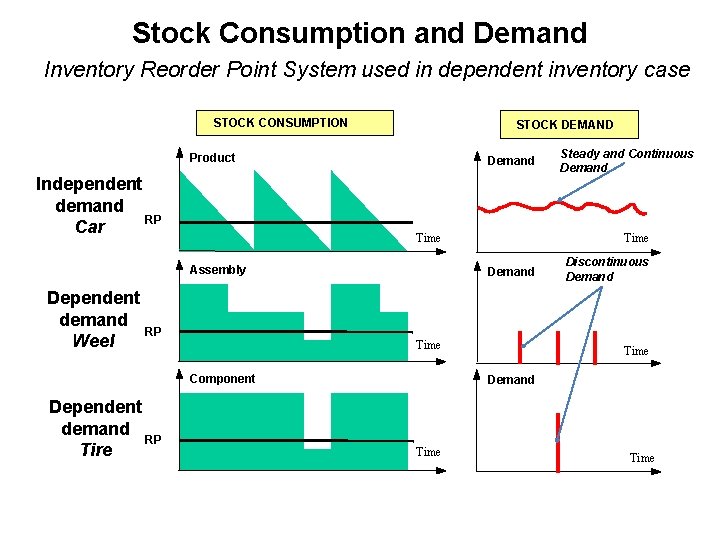
Stock Consumption and Demand Inventory Reorder Point System used in dependent inventory case STOCK CONSUMPTION STOCK DEMAND Product Independent demand RP Car Demand Time Assembly Dependent demand RP Weel Dependent demand RP Tire Time Demand Time Component Steady and Continuous Demand Discontinuous Demand Time
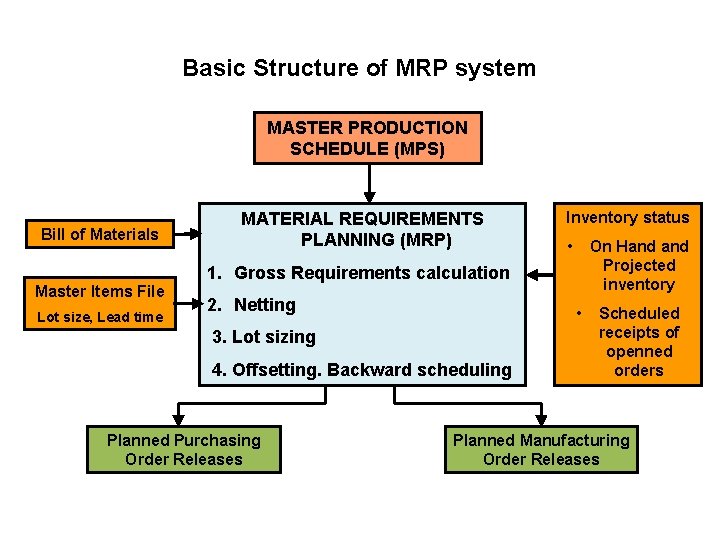
Basic Structure of MRP system MASTER PRODUCTION SCHEDULE (MPS) Bill of Materials Master Items File Lot size, Lead time MATERIAL REQUIREMENTS PLANNING (MRP) Inventory status • On Hand Projected inventory 1. Gross Requirements calculation 2. Netting • 3. Lot sizing 4. Offsetting. Backward scheduling Planned Purchasing Order Releases Scheduled receipts of openned orders Planned Manufacturing Order Releases
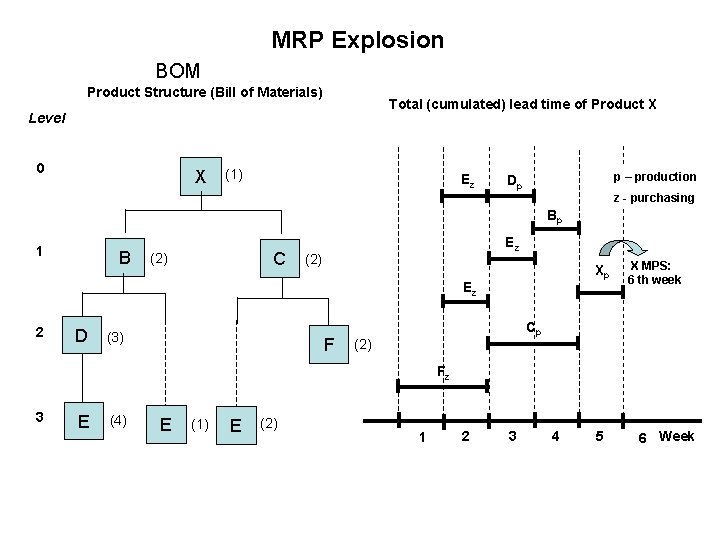
MRP Explosion BOM Product Structure (Bill of Materials) Total (cumulated) lead time of Product X Level 0 X (1) Ez p – production Dp z - purchasing Bp 1 B C (2) Ez (2) Xp Ez 2 D (3) F X MPS: 6 th week Cp (2) Fz 3 E (4) E (1) E (2) 1 2 3 4 5 6 Week
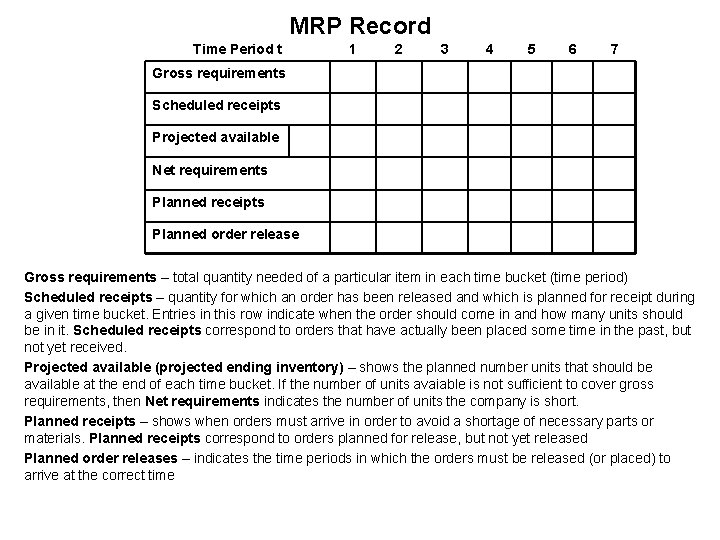
MRP Record Time Period t 1 2 3 4 5 6 7 Gross requirements Scheduled receipts Projected available Net requirements Planned receipts Planned order release Gross requirements – total quantity needed of a particular item in each time bucket (time period) Scheduled receipts – quantity for which an order has been released and which is planned for receipt during a given time bucket. Entries in this row indicate when the order should come in and how many units should be in it. Scheduled receipts correspond to orders that have actually been placed some time in the past, but not yet received. Projected available (projected ending inventory) – shows the planned number units that should be available at the end of each time bucket. If the number of units avaiable is not sufficient to cover gross requirements, then Net requirements indicates the number of units the company is short. Planned receipts – shows when orders must arrive in order to avoid a shortage of necessary parts or materials. Planned receipts correspond to orders planned for release, but not yet released Planned order releases – indicates the time periods in which the orders must be released (or placed) to arrive at the correct time
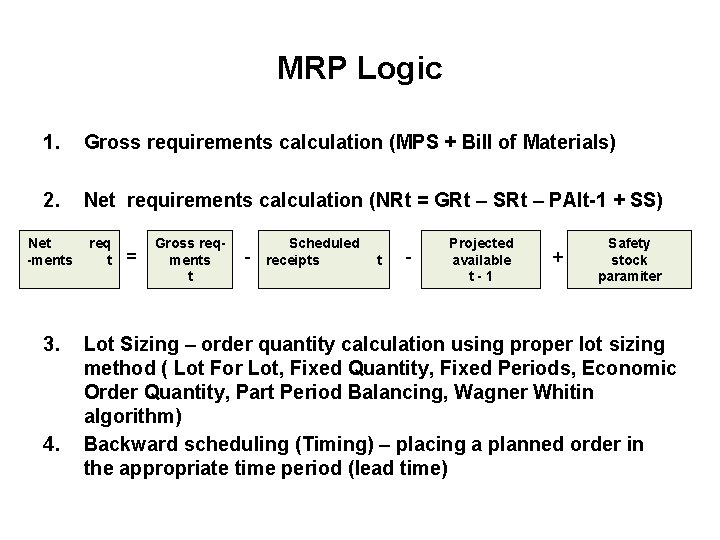
MRP Logic 1. Gross requirements calculation (MPS + Bill of Materials) 2. Net requirements calculation (NRt = GRt – SRt – PAIt-1 + SS) Net -ments 3. 4. req t = Gross reqments t - Scheduled receipts t - Projected available t-1 + Safety stock paramiter Lot Sizing – order quantity calculation using proper lot sizing method ( Lot For Lot, Fixed Quantity, Fixed Periods, Economic Order Quantity, Part Period Balancing, Wagner Whitin algorithm) Backward scheduling (Timing) – placing a planned order in the appropriate time period (lead time)
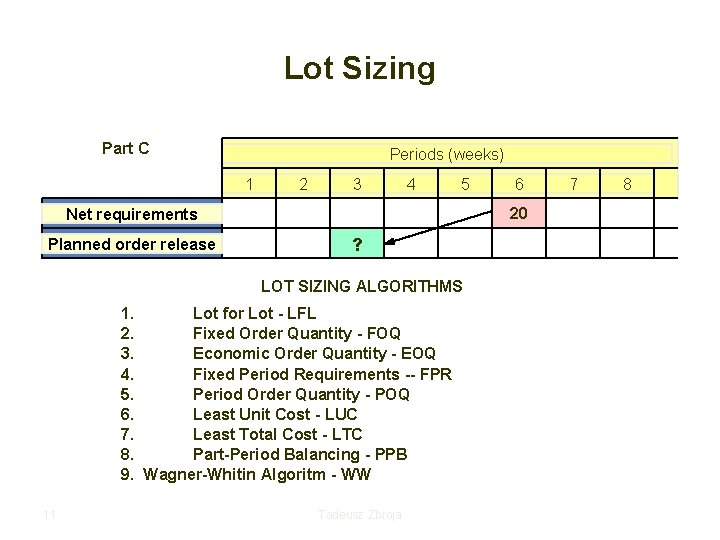
Lot Sizing Part C Periods (weeks) 1 2 3 4 5 20 Net requirements Planned order release ? LOT SIZING ALGORITHMS 1. Lot for Lot - LFL 2. Fixed Order Quantity - FOQ 3. Economic Order Quantity - EOQ 4. Fixed Period Requirements -- FPR 5. Period Order Quantity - POQ 6. Least Unit Cost - LUC 7. Least Total Cost - LTC 8. Part-Period Balancing - PPB 9. Wagner-Whitin Algoritm - WW 11 6 Tadeusz Zbroja 7 8
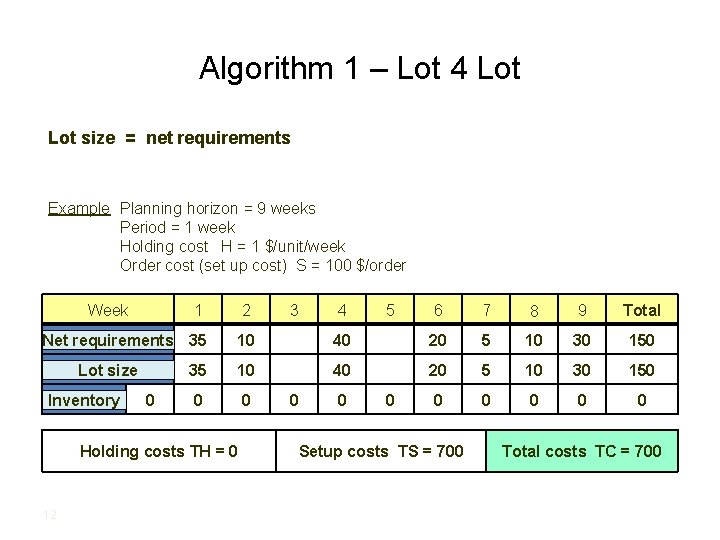
Algorithm 1 – Lot 4 Lot size = net requirements Example Planning horizon = 9 weeks Period = 1 week Holding cost H = 1 $/unit/week Order cost (set up cost) S = 100 $/order Week 1 2 Net requirements 35 10 0 0 Lot size Inventory 0 Holding costs TH = 0 12 3 0 4 6 7 8 9 Total 40 20 5 10 30 150 0 0 0 5 0 Setup costs TS = 700 Total costs TC = 700
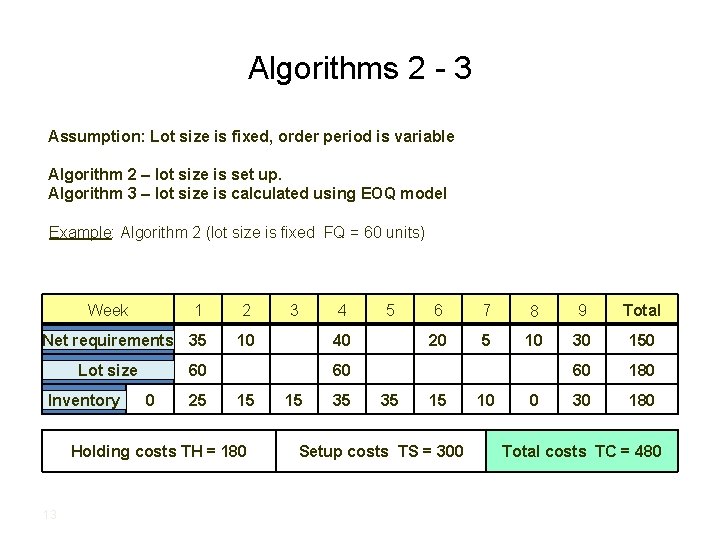
Algorithms 2 - 3 Assumption: Lot size is fixed, order period is variable Algorithm 2 – lot size is set up. Algorithm 3 – lot size is calculated using EOQ model Example: Algorithm 2 (lot size is fixed FQ = 60 units) Week 1 2 Net requirements 35 10 Lot size Inventory 4 0 25 5 40 60 6 7 8 9 Total 20 5 10 30 150 60 180 30 180 60 15 Holding costs TH = 180 13 3 15 35 35 15 Setup costs TS = 300 10 0 Total costs TC = 480
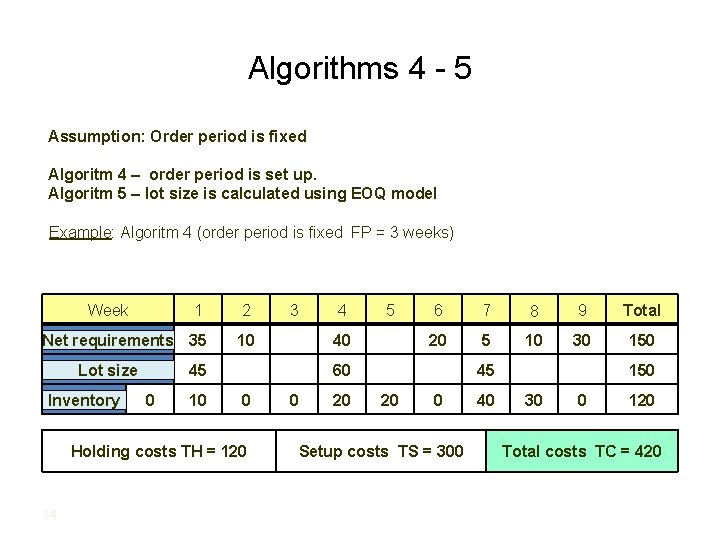
Algorithms 4 - 5 Assumption: Order period is fixed Algoritm 4 – order period is set up. Algoritm 5 – lot size is calculated using EOQ model Example: Algoritm 4 (order period is fixed FP = 3 weeks) Week 1 2 Net requirements 35 10 Lot size Inventory 0 10 4 5 40 45 6 7 8 9 Total 20 5 10 30 150 60 0 Holding costs TH = 120 14 3 0 20 45 20 0 Setup costs TS = 300 40 150 30 0 120 Total costs TC = 420
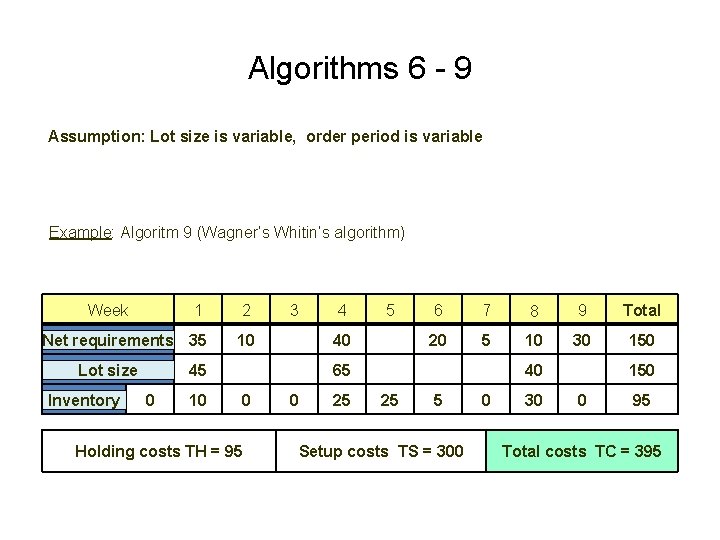
Algorithms 6 - 9 Assumption: Lot size is variable, order period is variable Example: Algoritm 9 (Wagner’s Whitin’s algorithm) Week 1 2 Net requirements 35 10 Lot size Inventory 3 10 5 40 45 0 4 6 7 8 9 Total 20 5 10 30 150 65 0 Holding costs TH = 95 0 25 40 25 5 Setup costs TS = 300 0 30 150 0 95 Total costs TC = 395
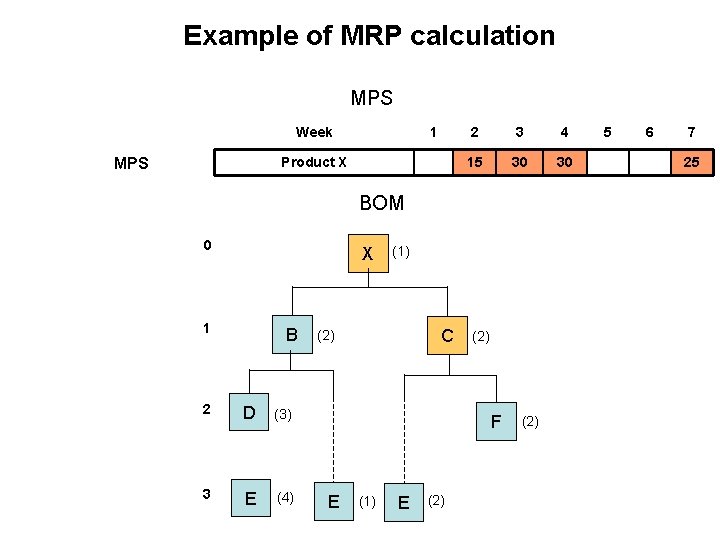
Example of MRP calculation MPS Week 1 Product X MPS 2 3 4 15 30 30 BOM 0 X 1 B 2 D (3) 3 E (4) (1) C (2) F E (1) E (2) 5 6 7 25
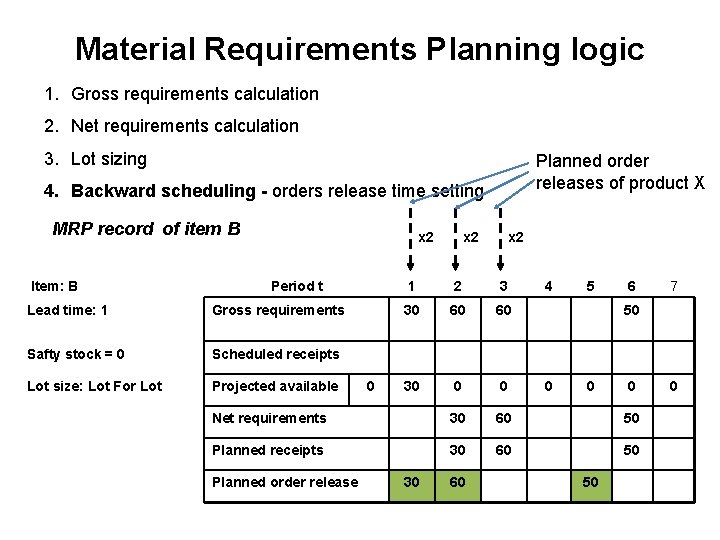
Material Requirements Planning logic 1. Gross requirements calculation 2. Net requirements calculation 3. Lot sizing Planned order releases of product X 4. Backward scheduling - orders release time setting MRP record of item B Item: B x 2 Period t x 2 1 2 3 30 60 60 30 0 0 Net requirements 30 60 50 Planned receipts 30 60 50 Lead time: 1 Gross requirements Safty stock = 0 Scheduled receipts Lot size: Lot For Lot Projected available Planned order release 0 30 60 4 5 6 7 50 0 0
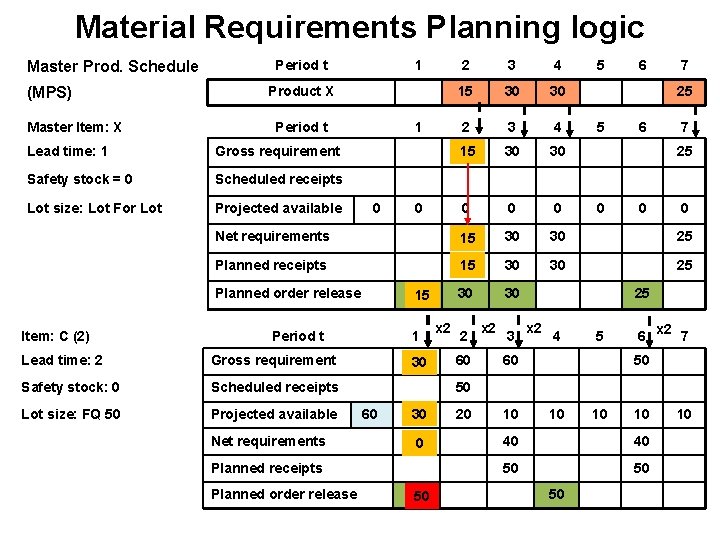
Material Requirements Planning logic Master Prod. Schedule (MPS) Master Item: X Period t 1 2 3 4 15 30 30 0 0 0 Net requirements 15 30 30 25 Planned receipts 15 30 30 25 30 30 Product X Period t Lead time: 1 Gross requirement Safety stock = 0 Scheduled receipts Lot size: Lot For Lot Projected available 1 0 Planned order release Item: C (2) 15 Period t Lead time: 2 Gross requirement Safety stock: 0 Scheduled receipts Lot size: FQ 50 Projected available Net requirements 0 1 30 2 60 x 2 3 6 7 25 5 6 7 25 0 0 0 25 x 2 4 5 60 6 x 2 7 50 50 60 30 0 Planned receipts Planned order release x 2 5 50 50 20 10 10 40 40 50 50 50 10
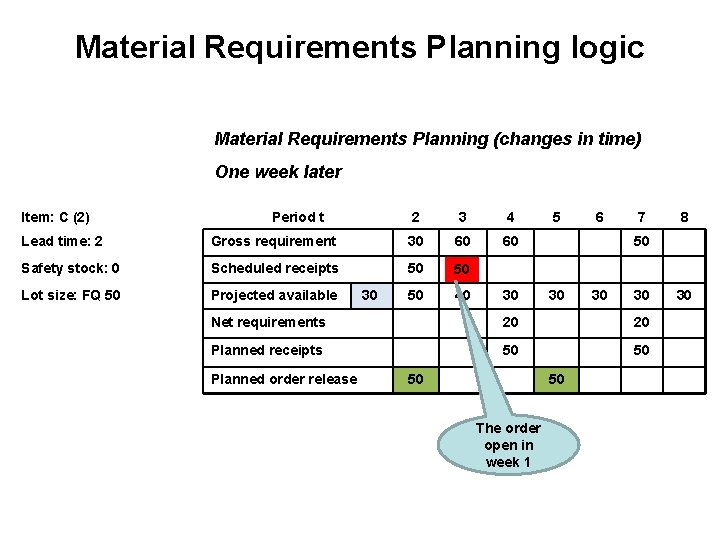
Material Requirements Planning logic Material Requirements Planning (changes in time) One week later Item: C (2) Period t 2 3 4 60 Lead time: 2 Gross requirement 30 60 Safety stock: 0 Scheduled receipts 50 50 Lot size: FQ 50 Projected available 50 40 30 30 5 6 7 50 30 30 30 Net requirements 20 20 Planned receipts 50 50 Planned order release 50 50 The order open in week 1 8 30
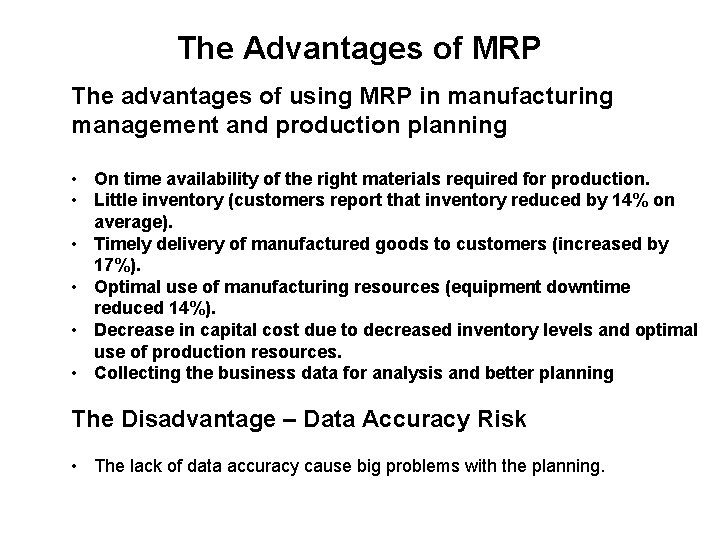
The Advantages of MRP The advantages of using MRP in manufacturing management and production planning • On time availability of the right materials required for production. • Little inventory (customers report that inventory reduced by 14% on average). • Timely delivery of manufactured goods to customers (increased by 17%). • Optimal use of manufacturing resources (equipment downtime reduced 14%). • Decrease in capital cost due to decreased inventory levels and optimal use of production resources. • Collecting the business data for analysis and better planning The Disadvantage – Data Accuracy Risk • The lack of data accuracy cause big problems with the planning.
Mrp et erp
Mrp 2
System mrp 1
Material requirements planning
Material requirements planning
Material requirements planning concepts
Mps vs mrp
Erp requirements planning
Difference between mrp and drp
Feature of size
What is cultural divergence
What is real culture
Examples of non material culture
Why are material useful
Quota sap
Mrp 2 in operations management
Auxiliary dental material
Gross material requirements plan
Material yield variance formula
Planowanie mrp
Avante erp system