Material Flow Cost Accounting March 2013 YoshikuniFurukawa Secretary
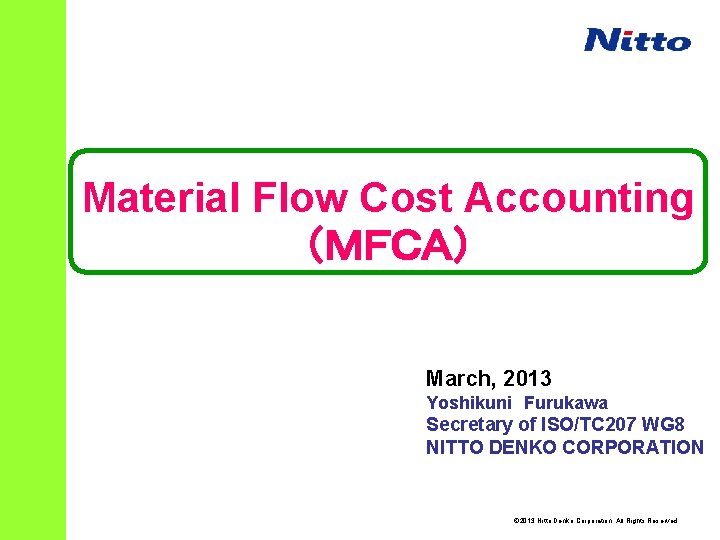
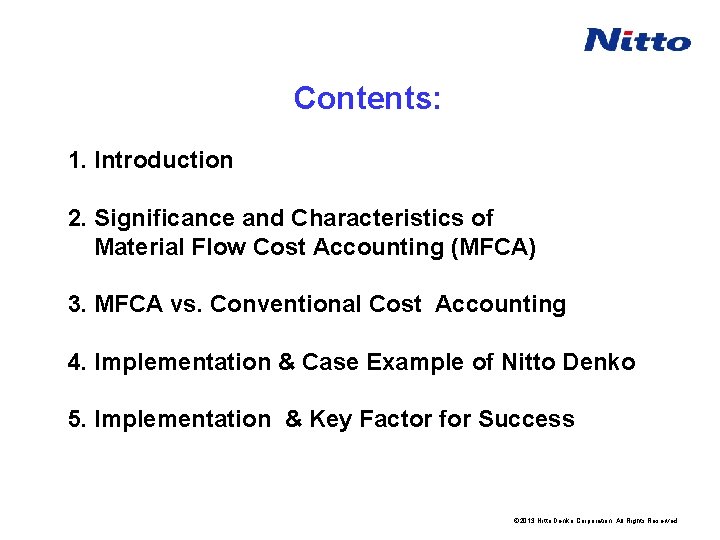
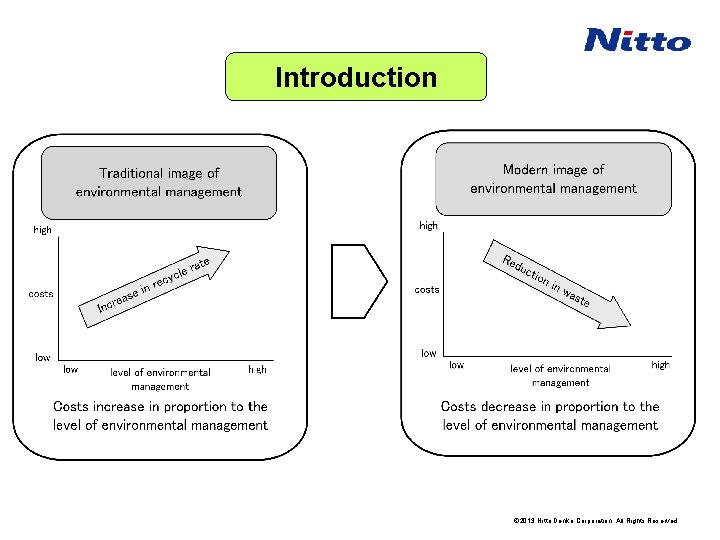
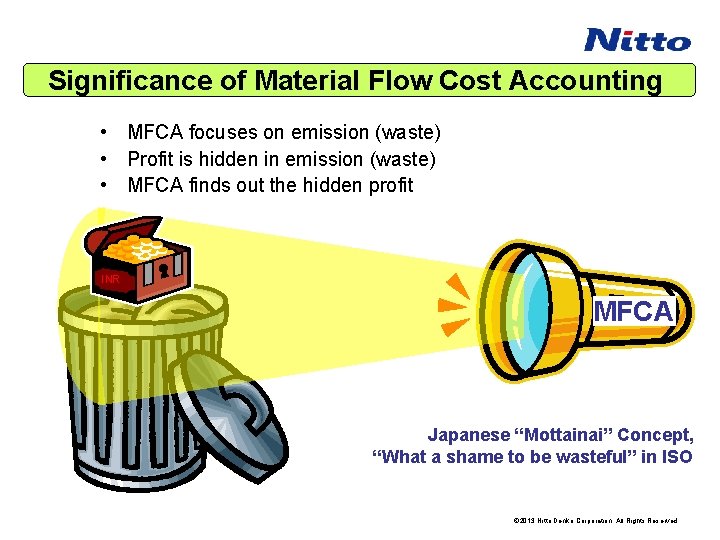

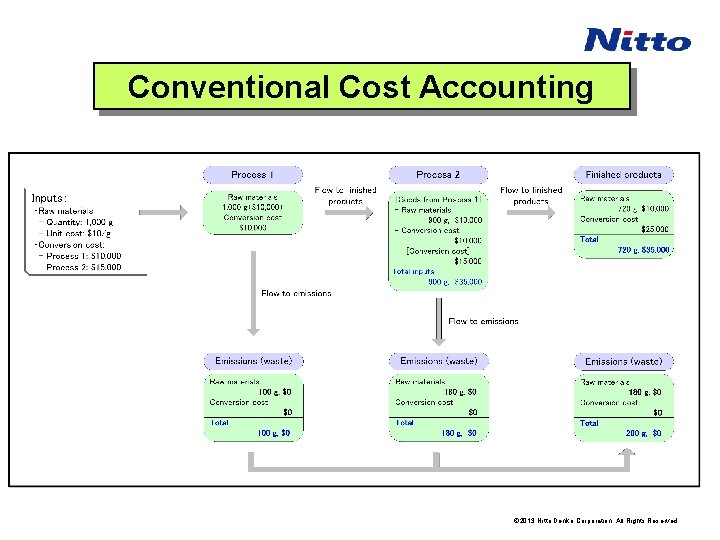
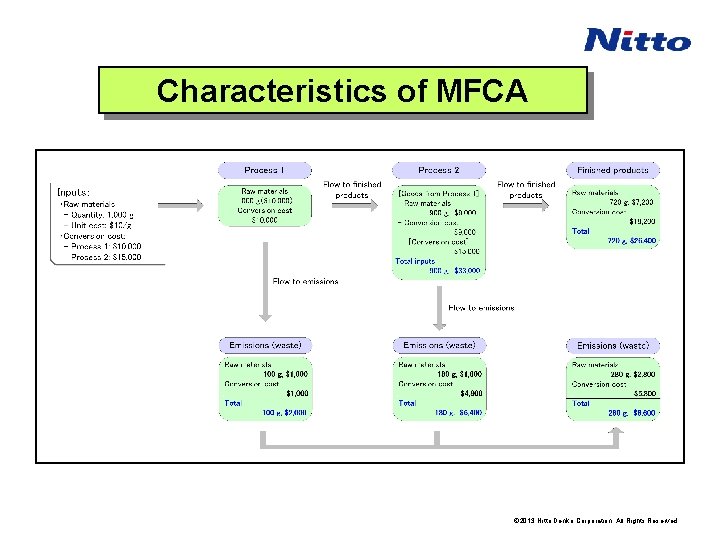
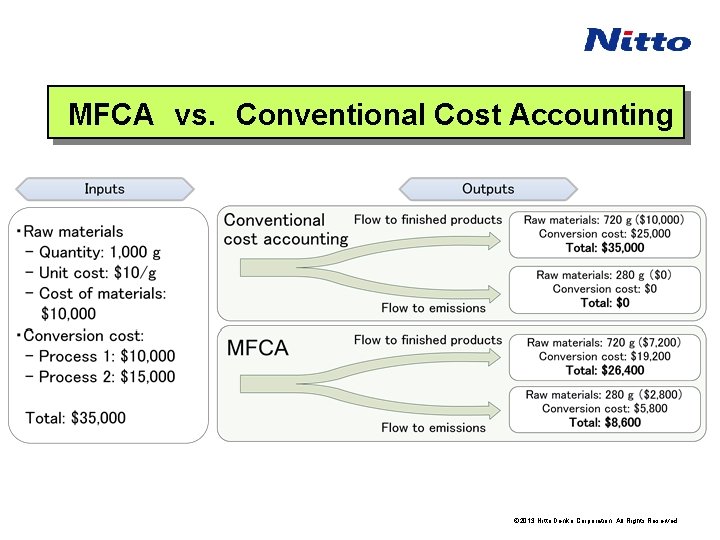
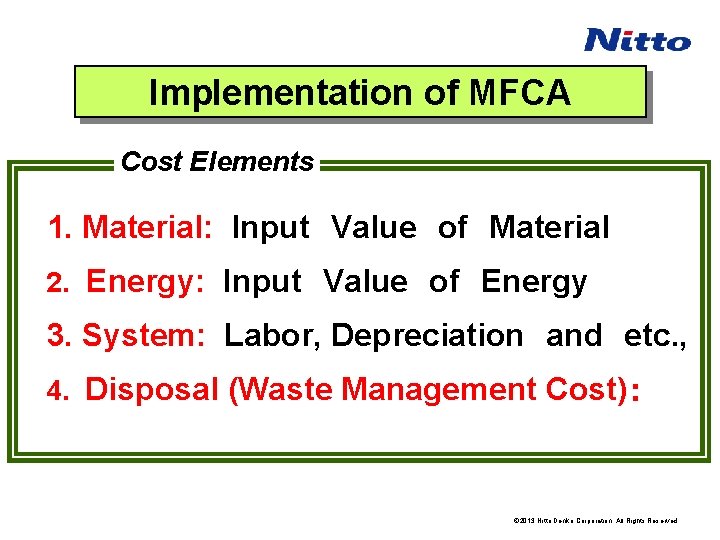
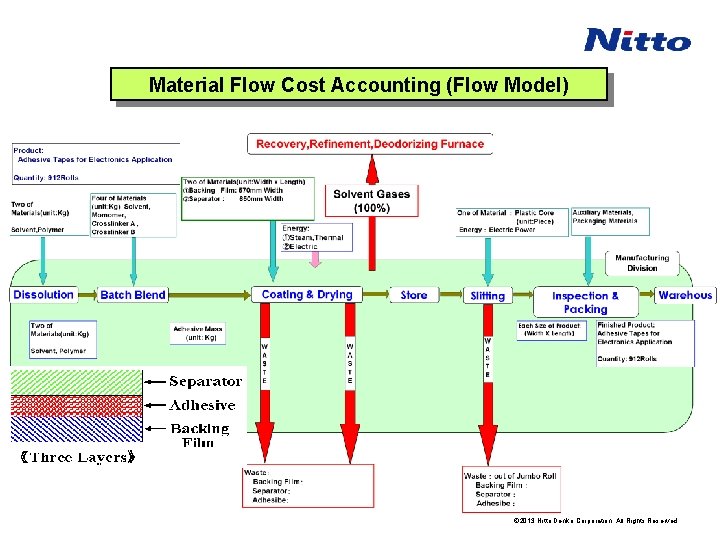
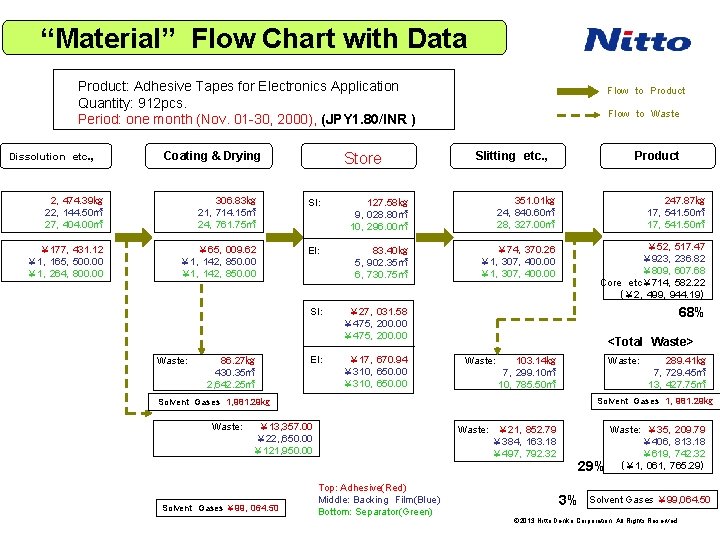
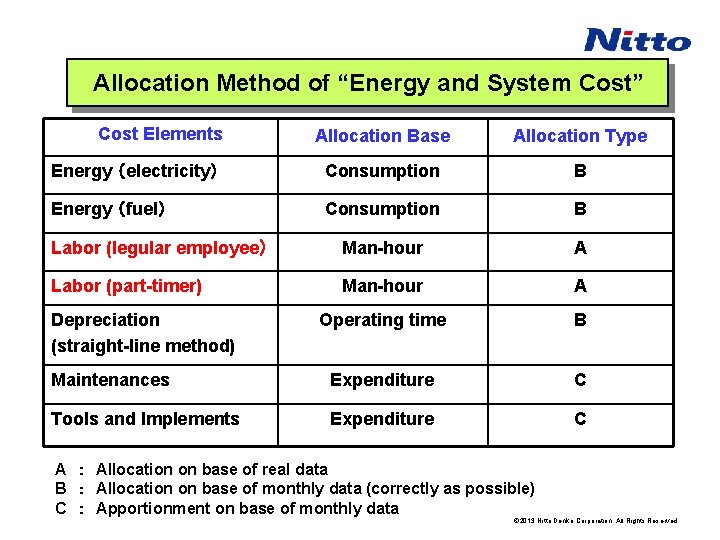
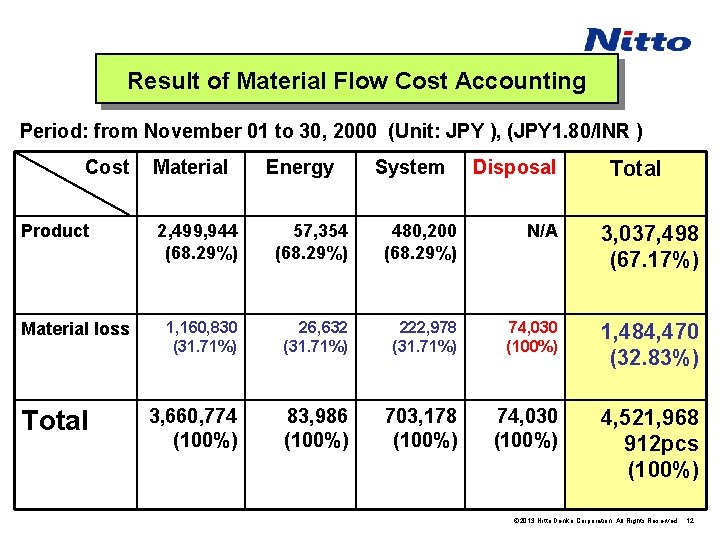
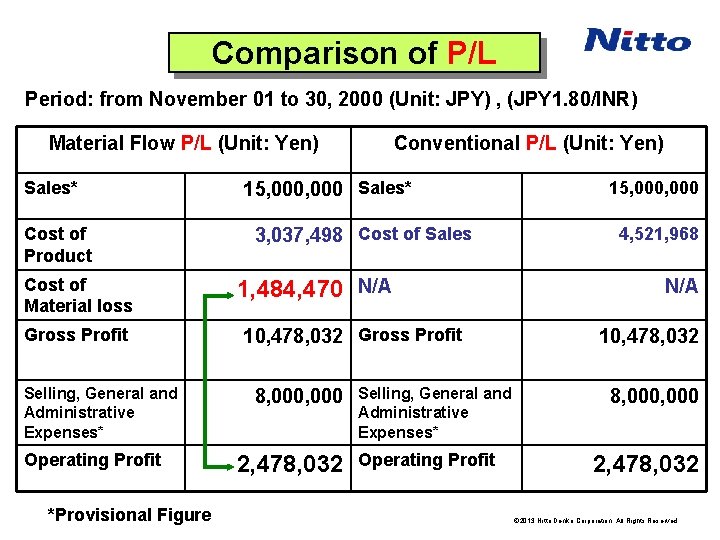
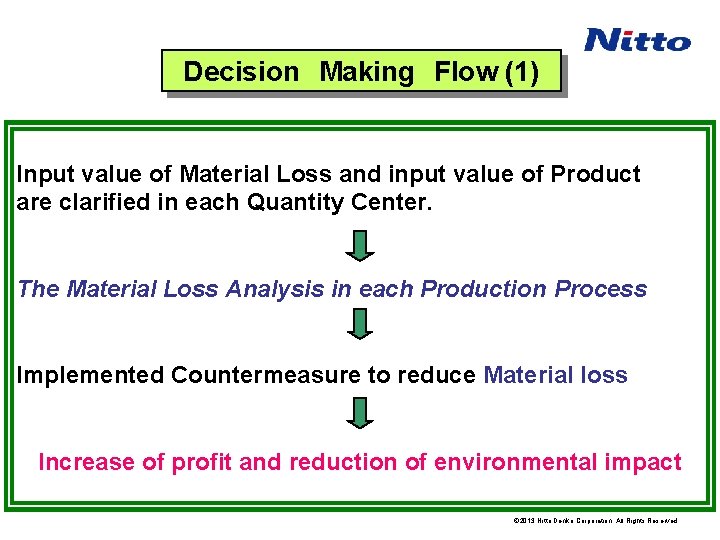
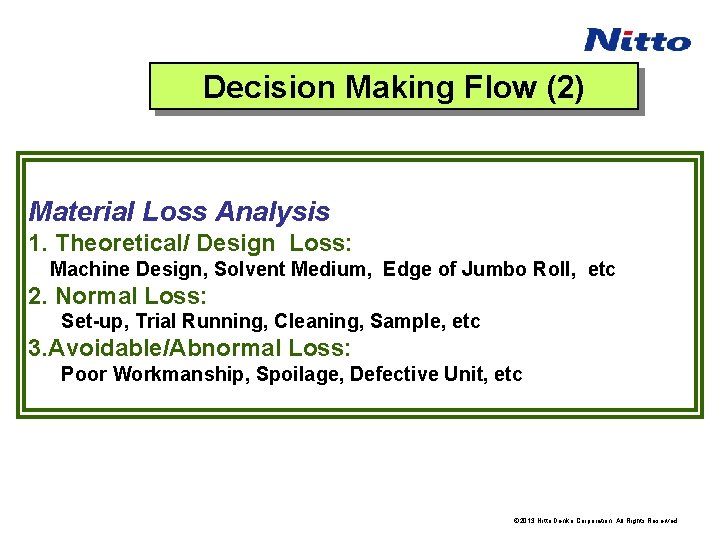
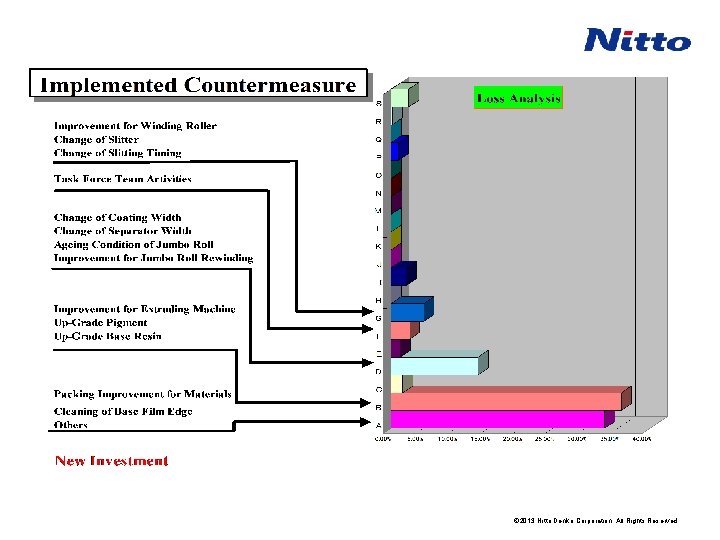
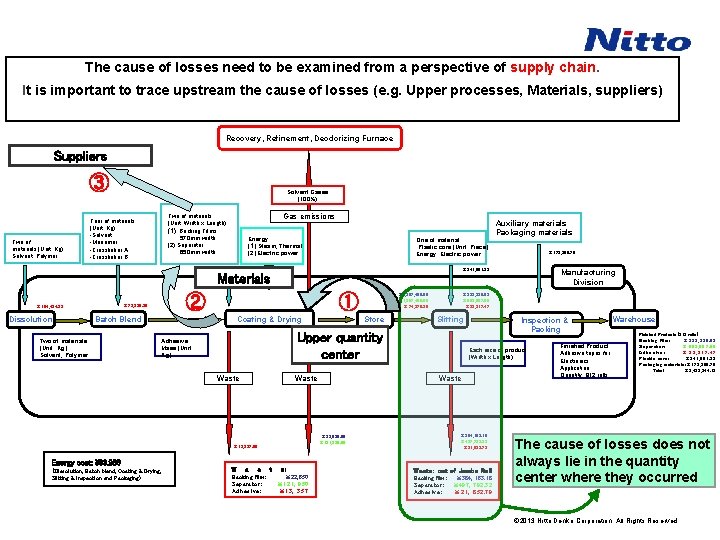
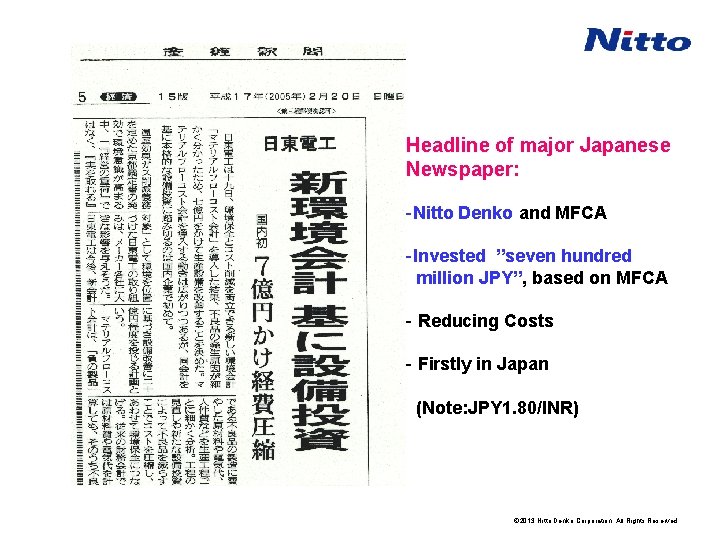
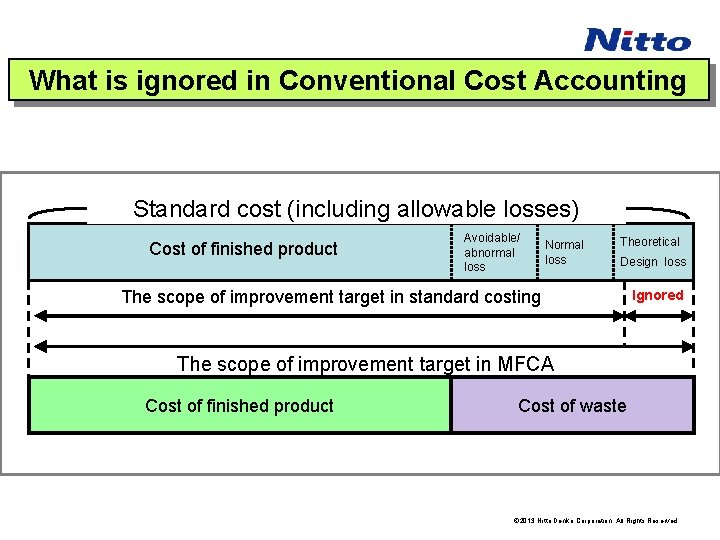
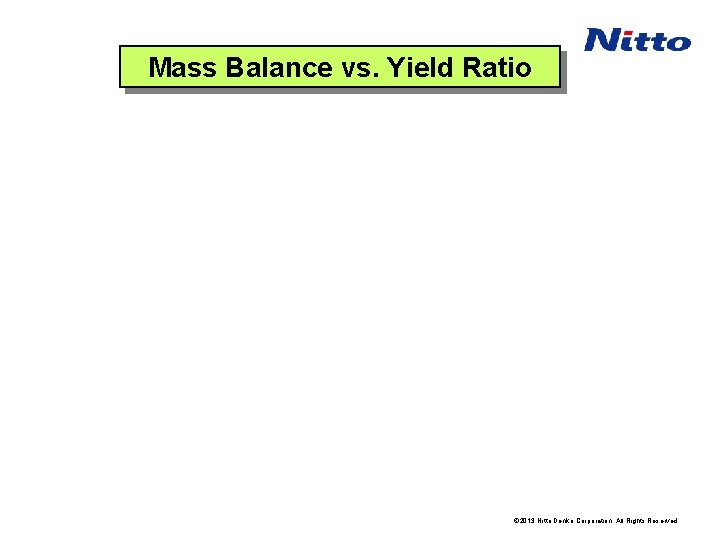
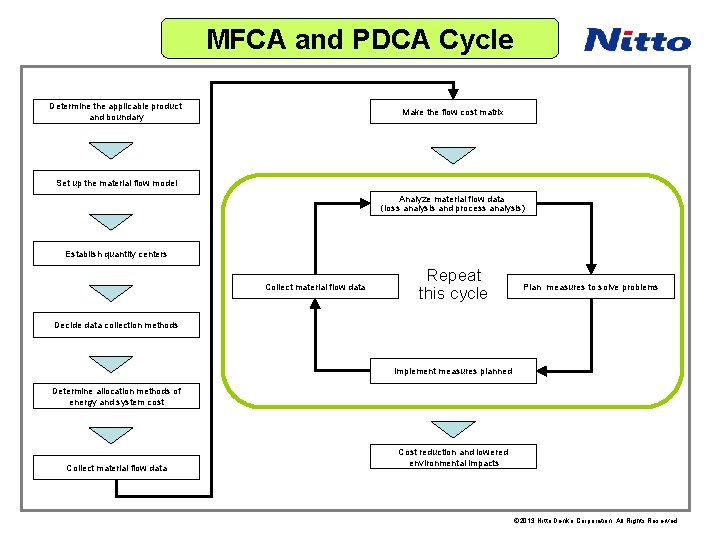
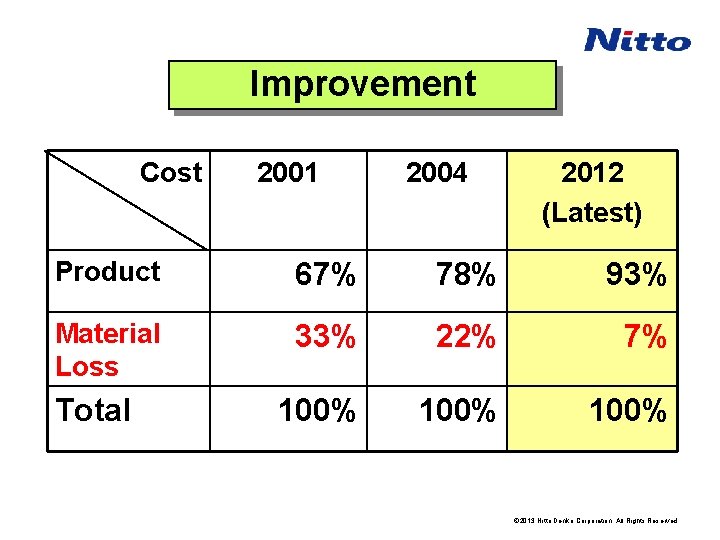
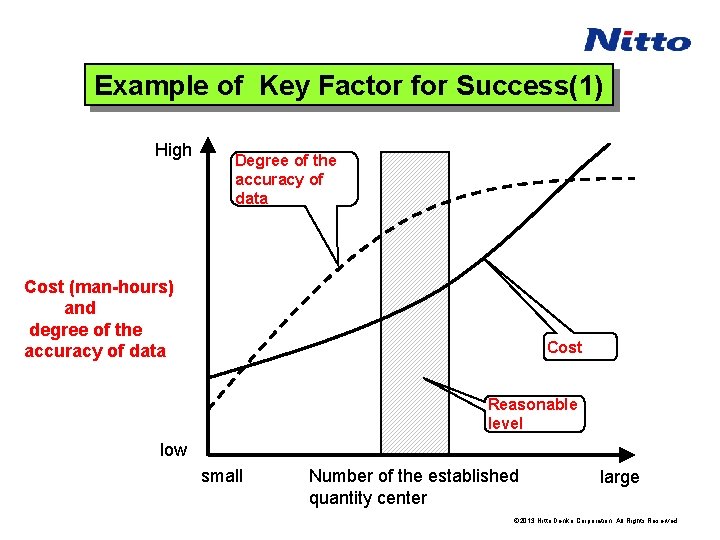
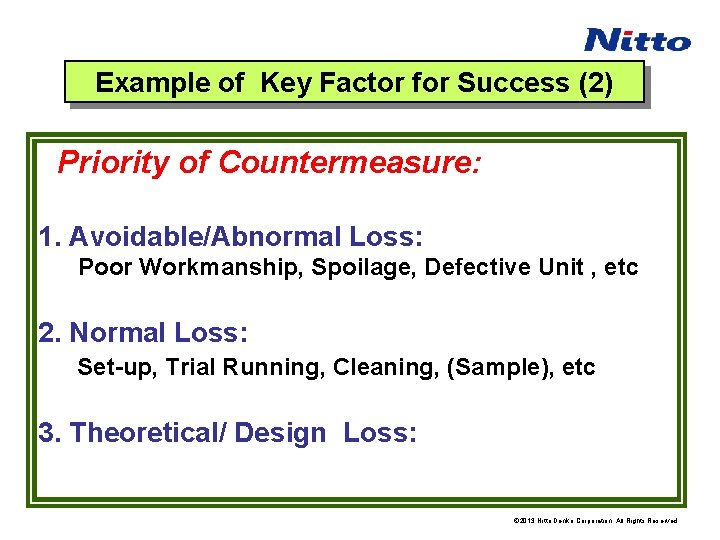
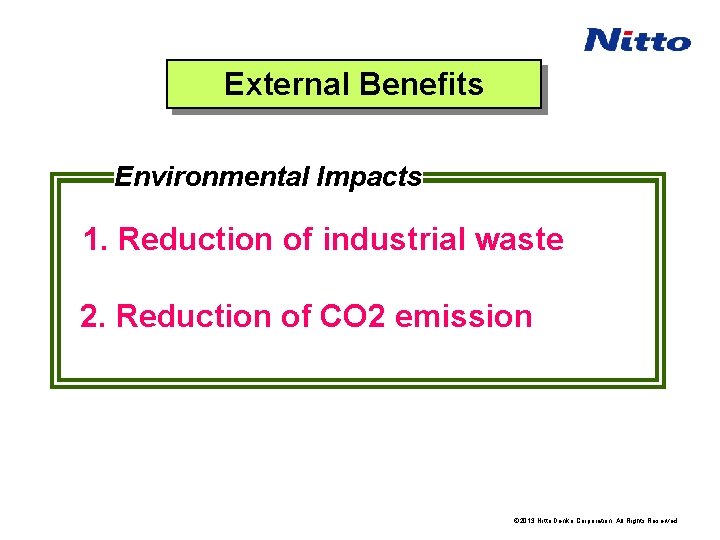
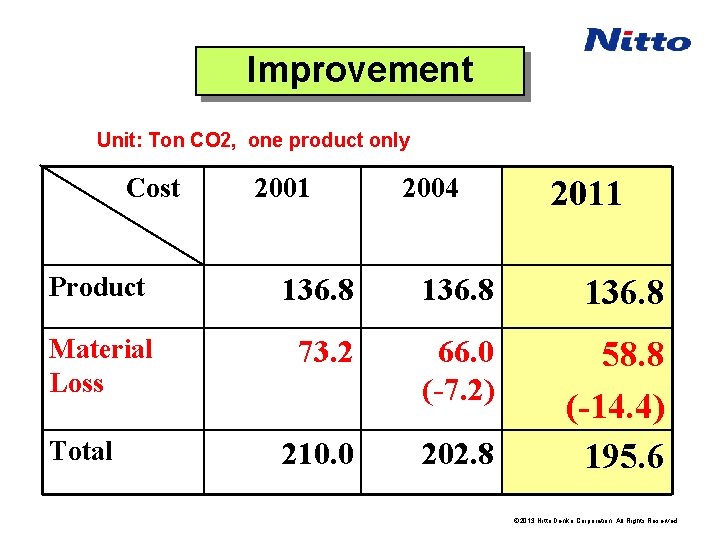
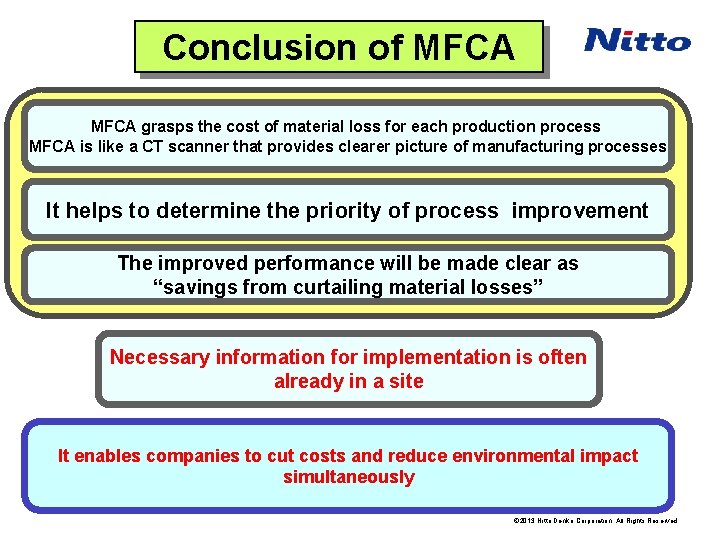
- Slides: 28
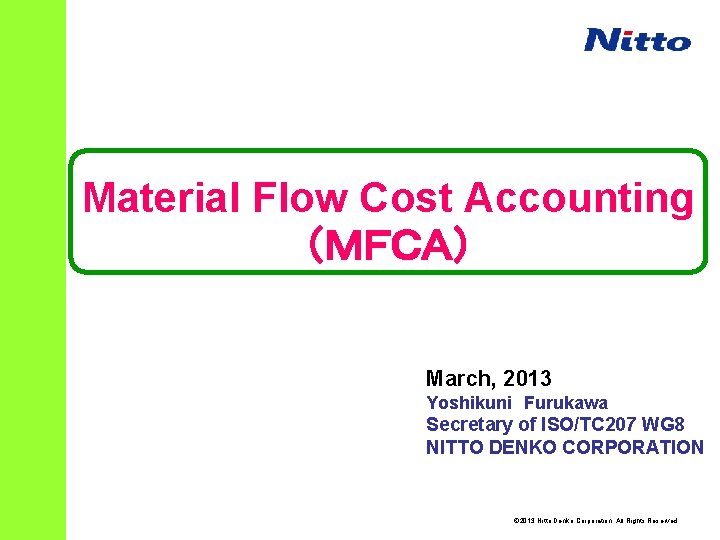
Material Flow Cost Accounting (MFCA) March, 2013 Yoshikuni Furukawa Secretary of ISO/TC 207 WG 8 NITTO DENKO CORPORATION © 2013 Nitto Denko Corporation. All Rights Reserved.
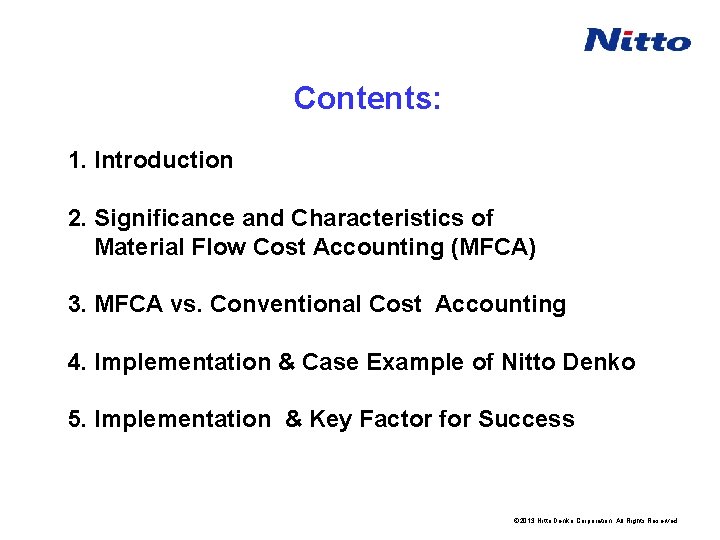
Contents: 1. Introduction 2. Significance and Characteristics of Material Flow Cost Accounting (MFCA) 3. MFCA vs. Conventional Cost Accounting 4. Implementation & Case Example of Nitto Denko 5. Implementation & Key Factor for Success © 2013 Nitto Denko Corporation. All Rights Reserved.
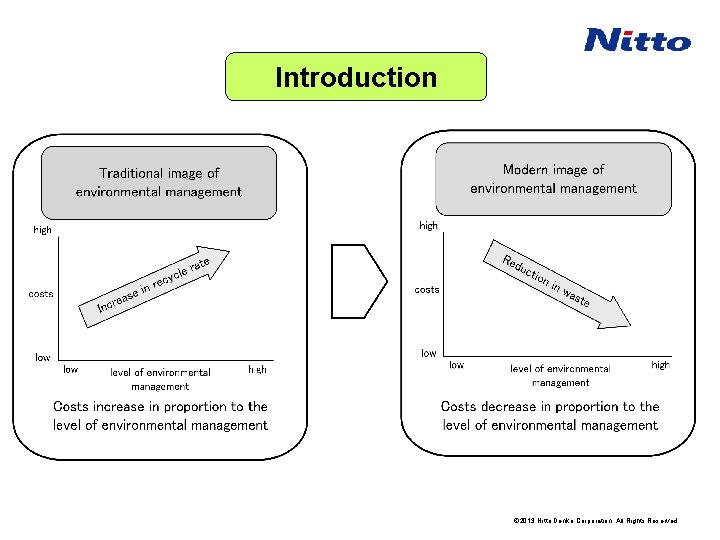
Introduction © 2013 Nitto Denko Corporation. All Rights Reserved.
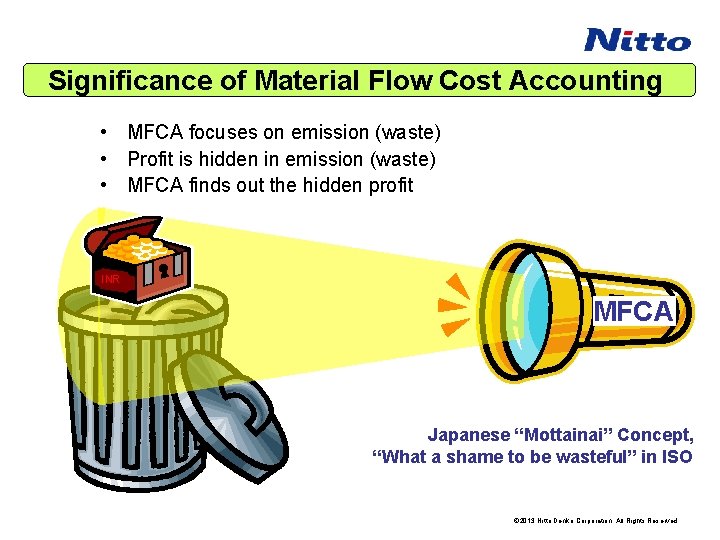
Significance of Material Flow Cost Accounting • MFCA focuses on emission (waste) • Profit is hidden in emission (waste) • MFCA finds out the hidden profit INR MFCA Japanese “Mottainai” Concept, “What a shame to be wasteful” in ISO © 2013 Nitto Denko Corporation. All Rights Reserved.

Benefits of MFCA Internal benefits l Increasing profit l Improving productivity External benefits l Reducing environmental impacts Contributing to sustainable development © 2013 Nitto Denko Corporation. All Rights Reserved.
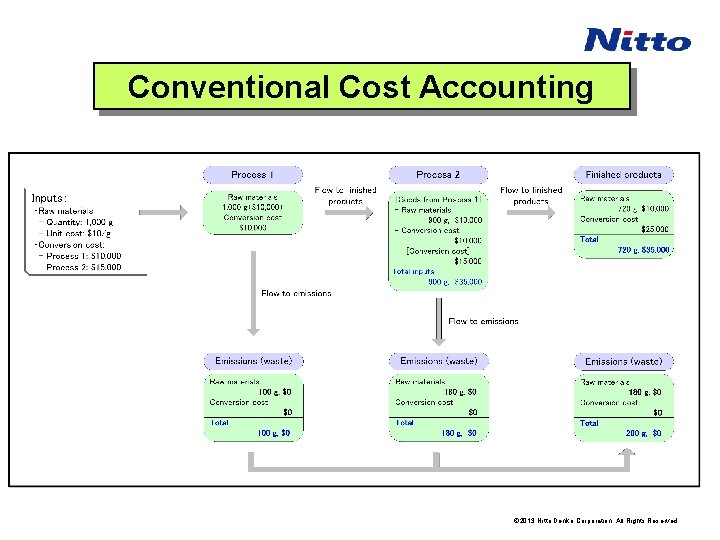
Conventional Cost Accounting © 2013 Nitto Denko Corporation. All Rights Reserved.
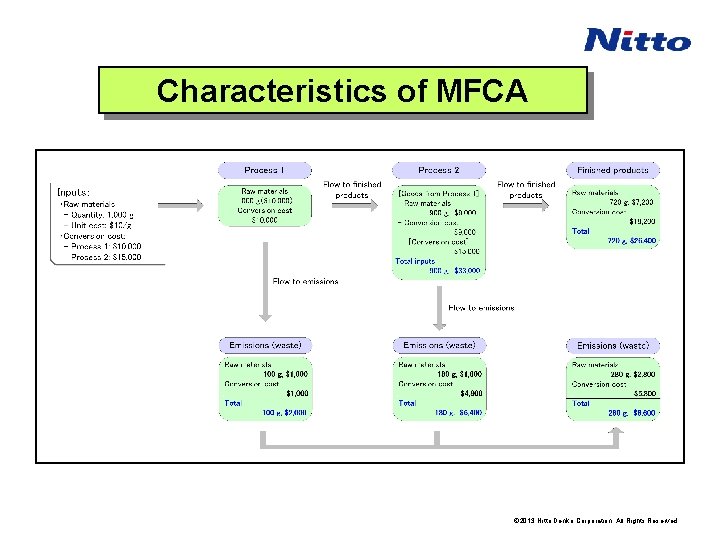
Characteristics of MFCA © 2013 Nitto Denko Corporation. All Rights Reserved.
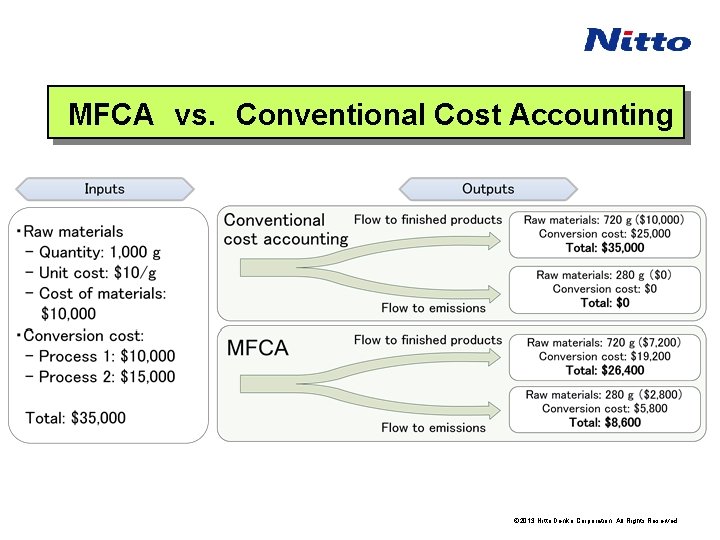
MFCA vs. Conventional Cost Accounting © 2013 Nitto Denko Corporation. All Rights Reserved.
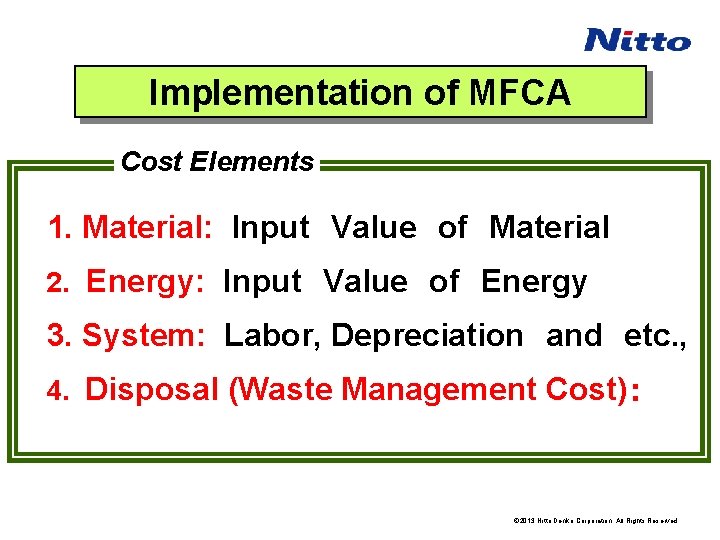
Implementation of MFCA Cost Elements 1. Material: Input Value of Material 2. Energy: Input Value of Energy 3. System: Labor, Depreciation and etc. , 4. Disposal (Waste Management Cost): © 2013 Nitto Denko Corporation. All Rights Reserved.
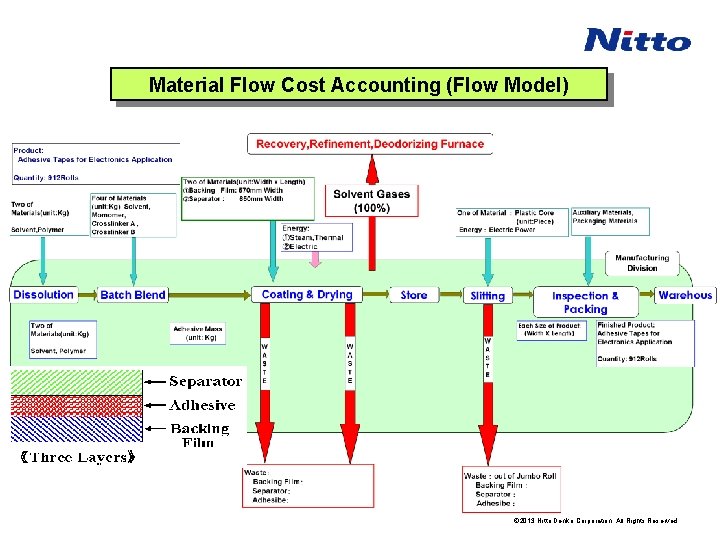
Material Flow Cost Accounting (Flow Model) © 2013 Nitto Denko Corporation. All Rights Reserved.
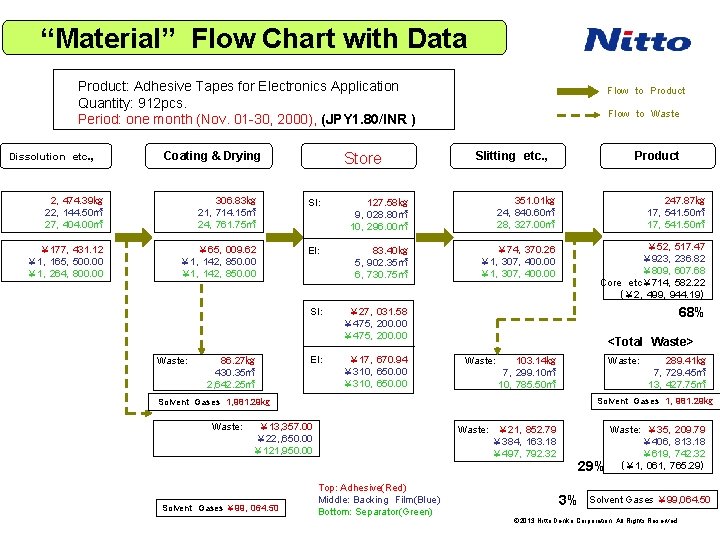
“Material” Flow Chart with Data Product: Adhesive Tapes for Electronics Application Quantity: 912 pcs. Period: one month (Nov. 01 -30, 2000), (JPY 1. 80/INR ) Dissolution etc. , 2,474. 39㎏ 22,144. 50㎡ 27,404. 00㎡ Coating & Drying Flow to Product Flow to Waste Store Product Slitting etc. , 306. 83㎏ 21,714. 15㎡ 24,761. 75㎡ SI: 127. 58㎏ 9,028. 80㎡ 10,296. 00㎡ 351. 01㎏ 24,840. 60㎡ 28,327. 00㎡ 247. 87㎏ 17,541. 50㎡ ¥ 177,431. 12 ¥ 65,009. 62 ¥ 1,165,500. 00 ¥ 1,142,850. 00 ¥ 1,264,800. 00 ¥ 1,142,850. 00 EI: 83. 40㎏ 5,902. 35㎡ 6,730. 75㎡ ¥ 74,370. 26 ¥ 1,307,400. 00 ¥ 52,517. 47 ¥ 923,236. 82 ¥ 809,607. 68 Core etc¥ 714,582. 22 (¥ 2,499,944. 19) 68% SI: ¥ 27,031. 58 ¥ 475,200. 00 Waste: 86. 27㎏ 430. 35㎡ 2, 642. 25㎡ EI: ¥ 17,670. 94 ¥ 310,650. 00 <Total Waste> Waste: 103. 14㎏ 7,299. 10㎡ 10,785. 50㎡ Waste: 289. 41㎏ 7,729. 45㎡ 13,427. 75㎡ Solvent Gases 1,981. 29㎏ Solvent Gases 1, 981. 29㎏ Waste: ¥ 13, 357. 00 ¥ 22, , 650. 00 ¥ 121, 950. 00 Waste: ¥ 21,852. 79 ¥ 384,163. 18 ¥ 497,792. 32 29% Solvent Gases ¥ 99,064. 50 Top: Adhesive(Red) Middle: Backing Film(Blue) Bottom: Separator(Green) Waste: ¥ 35,209. 79 ¥ 406,813. 18 ¥ 619,742. 32 (¥ 1,061,765. 29) 3% Solvent Gases ¥ 99, 064. 50 © 2013 Nitto Denko Corporation. All Rights Reserved.
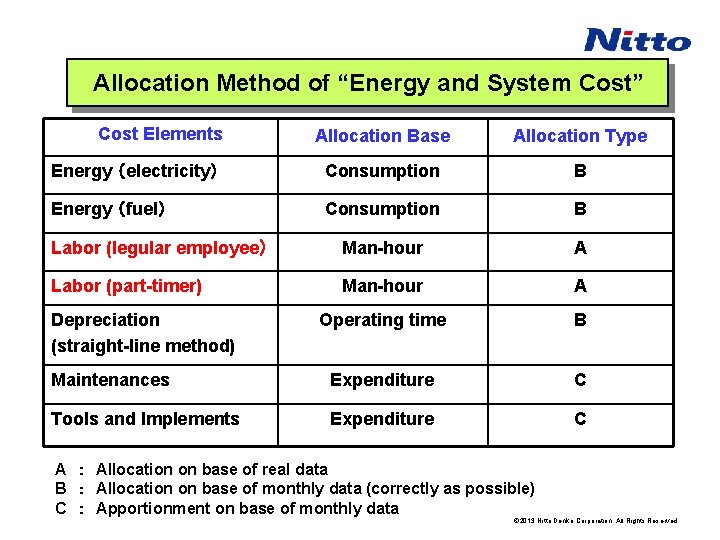
Allocation Method of “Energy and System Cost” Cost Elements Allocation Base Allocation Type Energy (electricity) Consumption B Energy (fuel) Consumption B Labor (legular employee) Man-hour A Labor (part-timer) Man-hour A Operating time B Maintenances Expenditure C Tools and Implements Expenditure C Depreciation (straight-line method) A : Allocation on base of real data B : Allocation on base of monthly data (correctly as possible) C : Apportionment on base of monthly data © 2013 Nitto Denko Corporation. All Rights Reserved.
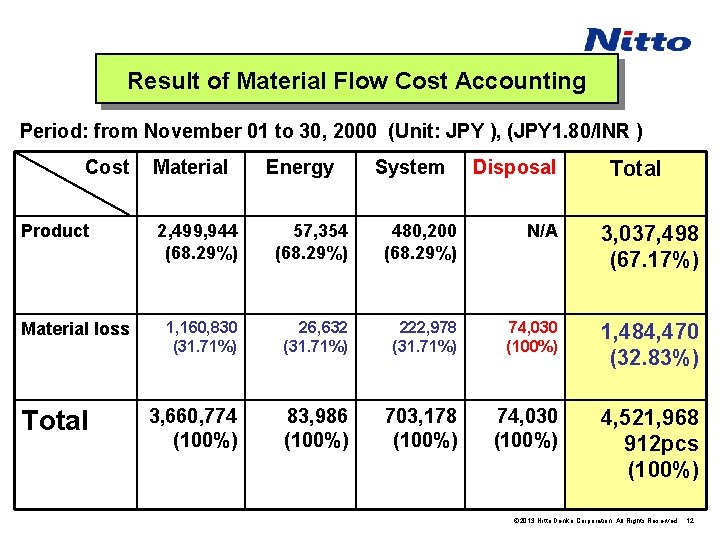
Result of Material Flow Cost Accounting Period: from November 01 to 30, 2000 (Unit: JPY ), (JPY 1. 80/INR ) Cost Product Material loss Total Material Energy System Disposal Total 2, 499, 944 (68. 29%) 57, 354 (68. 29%) 480, 200 (68. 29%) N/A 3, 037, 498 (67. 17%) 1, 160, 830 (31. 71%) 26, 632 (31. 71%) 222, 978 (31. 71%) 74, 030 (100%) 1, 484, 470 (32. 83%) 3, 660, 774 (100%) 83, 986 (100%) 703, 178 (100%) 74, 030 (100%) 4, 521, 968 912 pcs (100%) © 2013 Nitto Denko Corporation. All Rights Reserved. 12
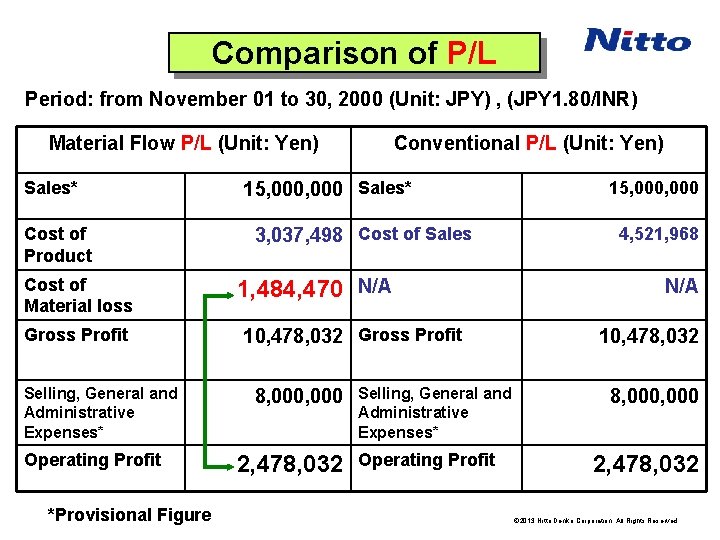
Comparison of P/L Period: from November 01 to 30, 2000 (Unit: JPY) , (JPY 1. 80/INR) Material Flow P/L (Unit: Yen) Sales* Cost of Product Cost of Material loss Gross Profit Selling, General and Administrative Expenses* Operating Profit *Provisional Figure Conventional P/L (Unit: Yen) 15, 000 Sales* 3, 037, 498 Cost of Sales 1, 484, 470 N/A 10, 478, 032 Gross Profit 8, 000 2, 478, 032 Selling, General and Administrative Expenses* Operating Profit 15, 000 4, 521, 968 N/A 10, 478, 032 8, 000 2, 478, 032 © 2013 Nitto Denko Corporation. All Rights Reserved.
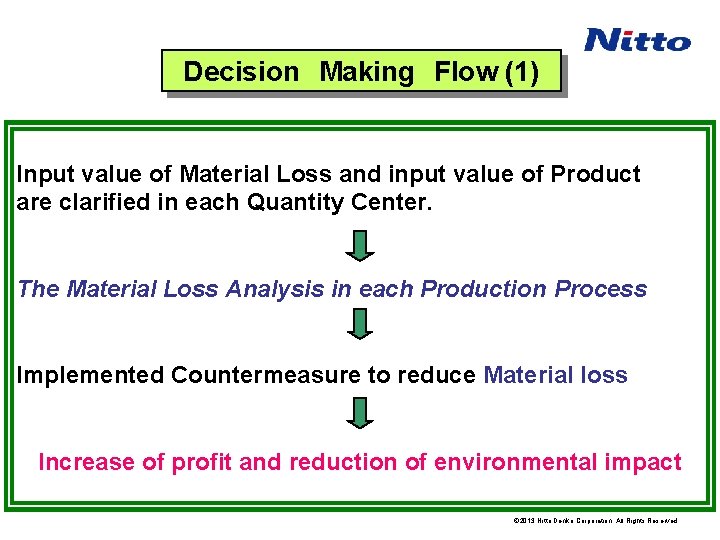
Decision Making Flow (1) Input value of Material Loss and input value of Product are clarified in each Quantity Center. The Material Loss Analysis in each Production Process Implemented Countermeasure to reduce Material loss Increase of profit and reduction of environmental impact © 2013 Nitto Denko Corporation. All Rights Reserved.
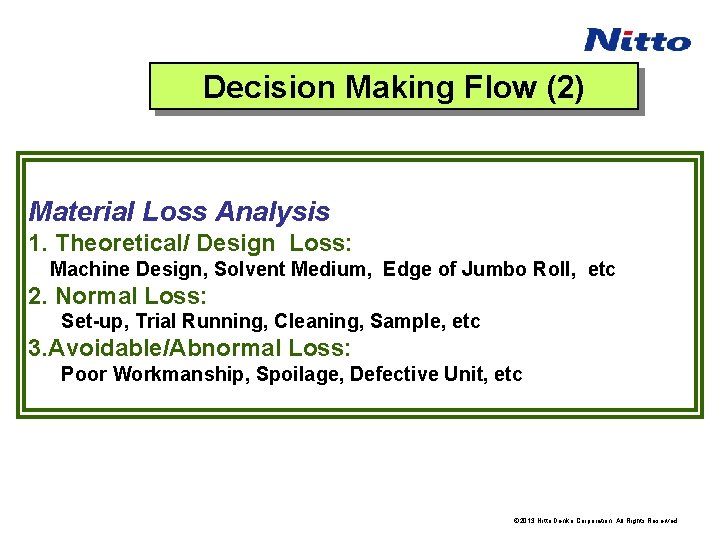
Decision Making Flow (2) Material Loss Analysis 1. Theoretical/ Design Loss: Machine Design, Solvent Medium, Edge of Jumbo Roll, etc 2. Normal Loss: Set-up, Trial Running, Cleaning, Sample, etc 3. Avoidable/Abnormal Loss: Poor Workmanship, Spoilage, Defective Unit, etc © 2013 Nitto Denko Corporation. All Rights Reserved.
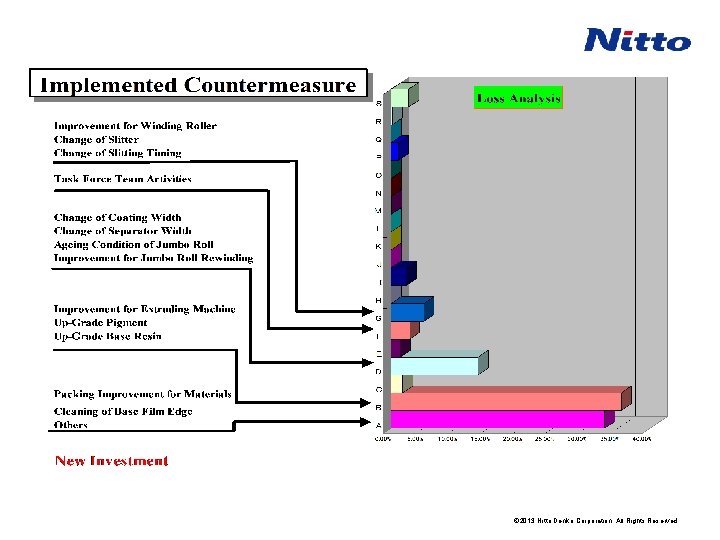
© 2013 Nitto Denko Corporation. All Rights Reserved.
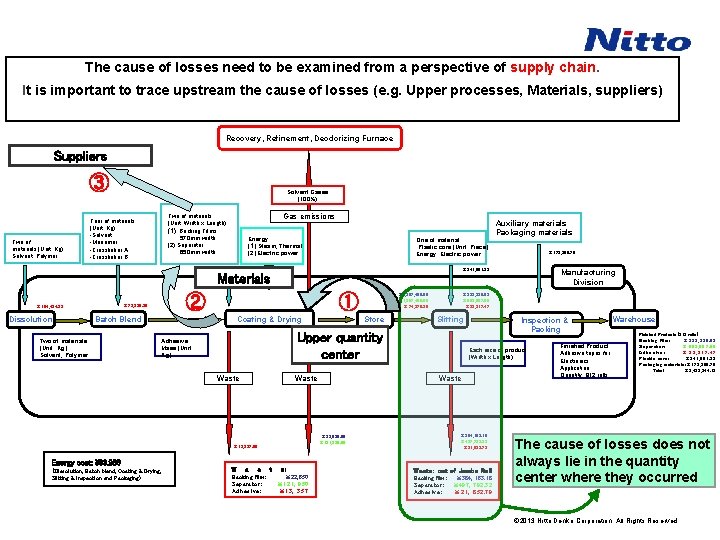
The cause of losses need to be examined from a perspective of supply chain. It is important to trace upstream the cause of losses (e. g. Upper processes, Materials, suppliers) Recovery, Refinement, Deodorizing Furnace Suppliers ③ Two of materials (Unit: Kg) Solvent, Polymer Solvent Gases (100%) Four of materials (Unit: Kg) -Solvent -Monomer -Crosslinker A -Crosslinker B Gas emissions Two of materials (Unit: Width x Length) (1) Backing Films: 570 mm width (2) Separator: 650 mm width Energy (1) Steam, Thermal (2) Electric power One of material: Plastic core (Unit: Piece) Energy: Electric power ¥ 72, 936. 90 Dissolution ② Two of materials (Unit: Kg) Solvent, Polymer ① Coating & Drying Batch Blend Store Waste Energy cost: 83, 986 (Dissolution, Batch blend, Coating & Drying, Slitting & Inspection and Packaging) Slitting W a s t e: Backing film: ¥ 22, 650 Separator: ¥ 121,950 A d h e s i v e: ¥ 1 3, 3 5 7 Inspection & Packing Each size of product (Width x Length) Waste ¥ 22, 650. 00 ¥ 13, 357. 00 ¥ 121, 950. 00 Manufacturing Division ¥ 923, 236. 82 ¥ 809, 607. 68 ¥ 52, 517. 47 ¥ 1, 307, 400. 00 ¥ 74, 370. 26 Upper quantity center Adhesive Mass (Unit: Kg) ¥ 172, 900. 70 ¥ 541, 681. 52 Materials ¥ 104, 494. 22 Auxiliary materials Packaging materials ¥ 384, 163. 18 ¥ 497, 792. 32 ¥ 21, 852. 79 W a s t e: out of Jumb o Roll Backing film: ¥ 384,163. 18 Separator: ¥ 4 9 7,792. 32 Adhesive: ¥ 2 1, 852. 79 Finished Product: Adhesive tapes for Electronics Application Quantity: 912 rolls Warehouse Finished Products(912 rolls) Backing film: ¥ 923, 236. 82 Separator: ¥ 809, 607. 68 Adhesive: ¥ 52, 517. 47 Plastic core: ¥ 541, 681. 52 Packaging materials: ¥ 172, 900. 70 Total ¥ 2, 499, 944. 19 The cause of losses does not always lie in the quantity center where they occurred © 2013 Nitto Denko Corporation. All Rights Reserved.
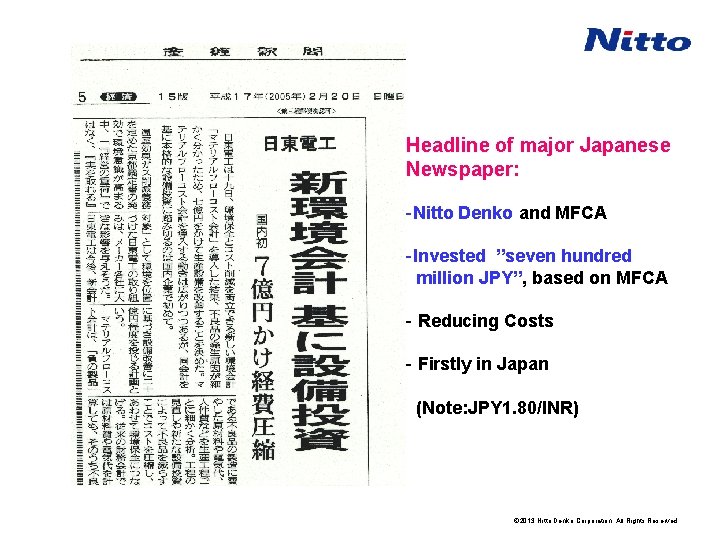
Headline of major Japanese Newspaper: -Nitto Denko and MFCA -Invested ”seven hundred million JPY”, based on MFCA - Reducing Costs - Firstly in Japan (Note: JPY 1. 80/INR) © 2013 Nitto Denko Corporation. All Rights Reserved.
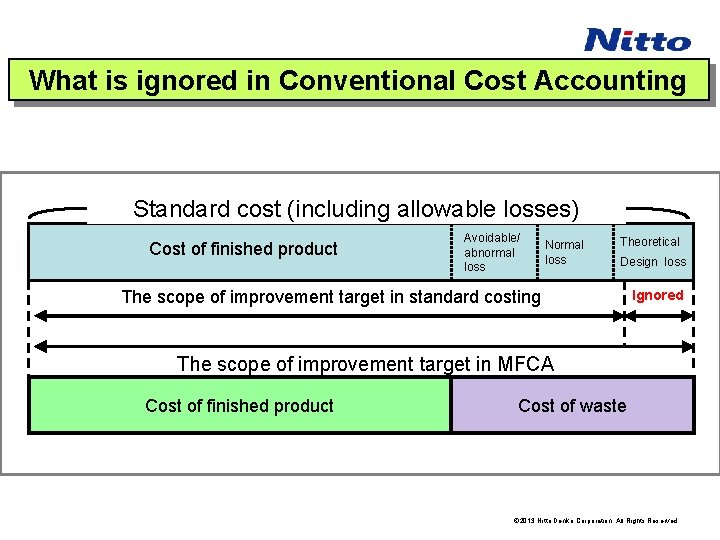
What is ignored in Conventional Cost Accounting Standard cost (including allowable losses) Cost of finished product Avoidable/ abnormal loss Normal loss Theoretical Design loss The scope of improvement target in standard costing Ignored The scope of improvement target in MFCA Cost of finished product Cost of waste © 2013 Nitto Denko Corporation. All Rights Reserved.
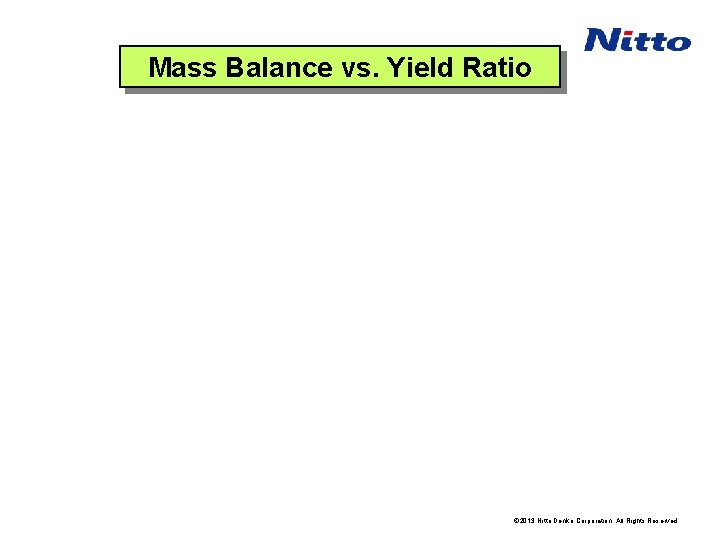
Mass Balance vs. Yield Ratio © 2013 Nitto Denko Corporation. All Rights Reserved.
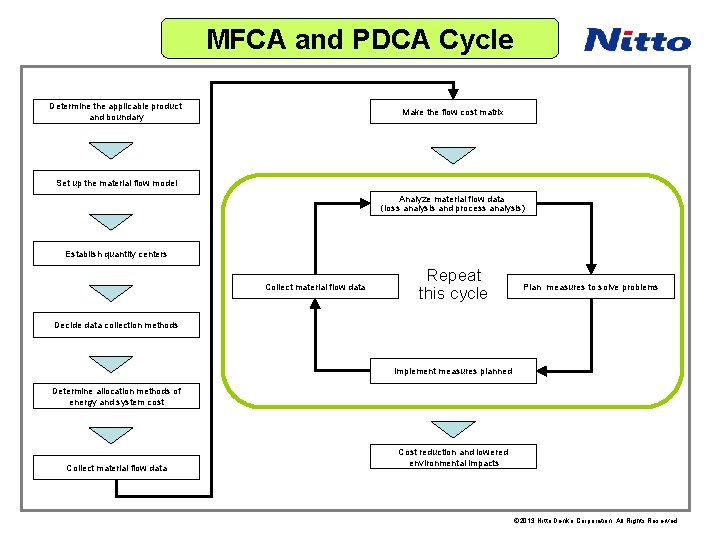
MFCA and PDCA Cycle Determine the applicable product and boundary Make the flow cost matrix Set up the material flow model Analyze material flow data (loss analysis and process analysis) Establish quantity centers Collect material flow data Repeat this cycle Plan measures to solve problems Decide data collection methods Implement measures planned Determine allocation methods of energy and system cost Collect material flow data Cost reduction and lowered environmental impacts © 2013 Nitto Denko Corporation. All Rights Reserved.
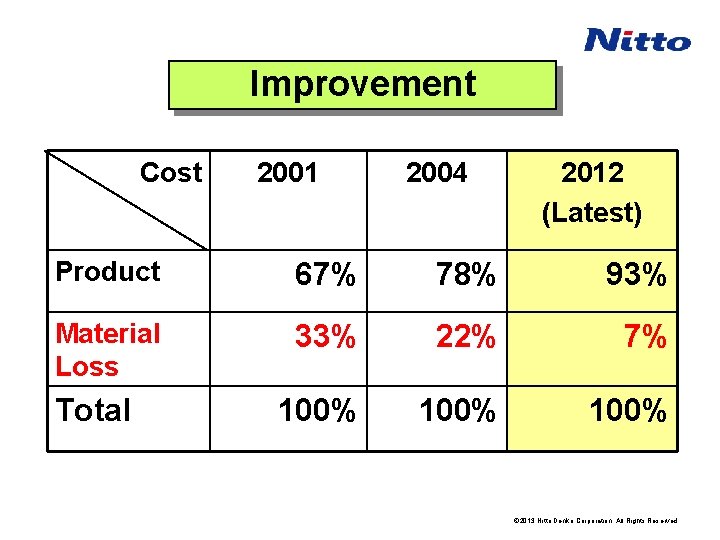
Improvement Cost 2001 2004 2012 (Latest) Product 67% 78% 93% Material Loss 33% 22% 7% 100% Total © 2013 Nitto Denko Corporation. All Rights Reserved.
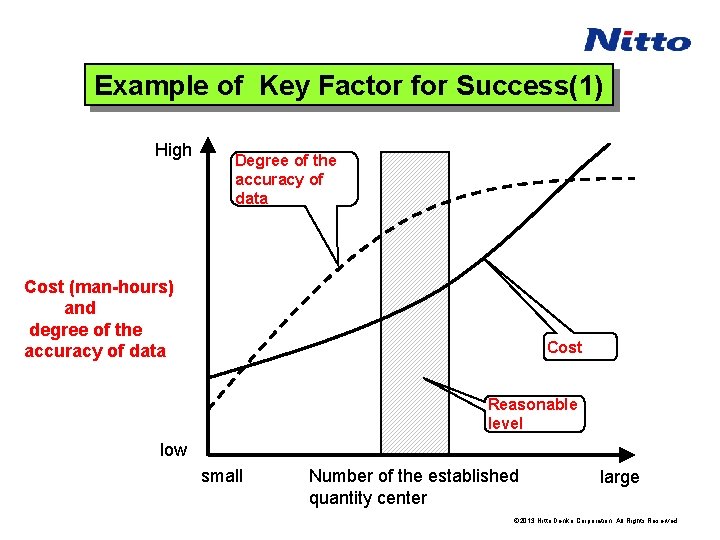
Example of Key Factor for Success(1) High Degree of the accuracy of data Cost (man-hours) and degree of the accuracy of data Cost Reasonable level low small Number of the established quantity center large © 2013 Nitto Denko Corporation. All Rights Reserved.
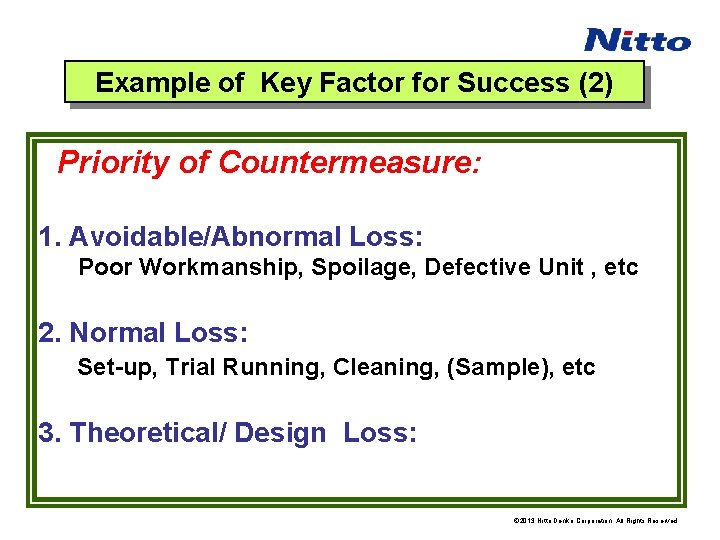
Example of Key Factor for Success (2) Priority of Countermeasure: 1. Avoidable/Abnormal Loss: Poor Workmanship, Spoilage, Defective Unit , etc 2. Normal Loss: Set-up, Trial Running, Cleaning, (Sample), etc 3. Theoretical/ Design Loss: © 2013 Nitto Denko Corporation. All Rights Reserved.
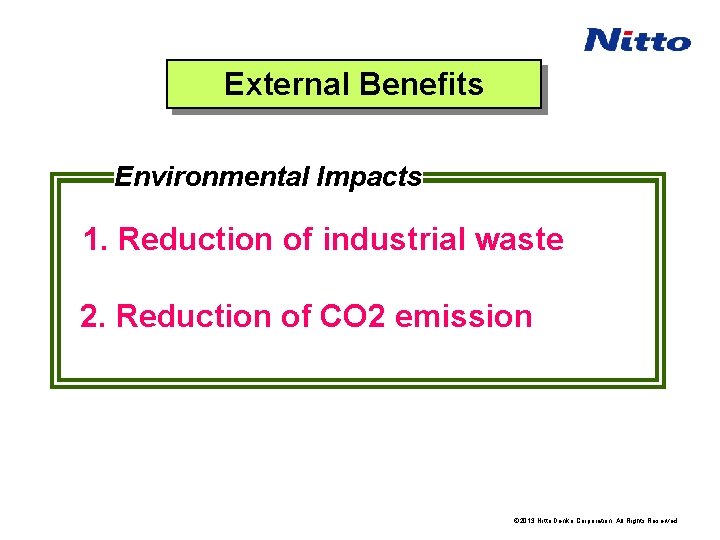
External Benefits Environmental Impacts 1. Reduction of industrial waste 2. Reduction of CO 2 emission © 2013 Nitto Denko Corporation. All Rights Reserved.
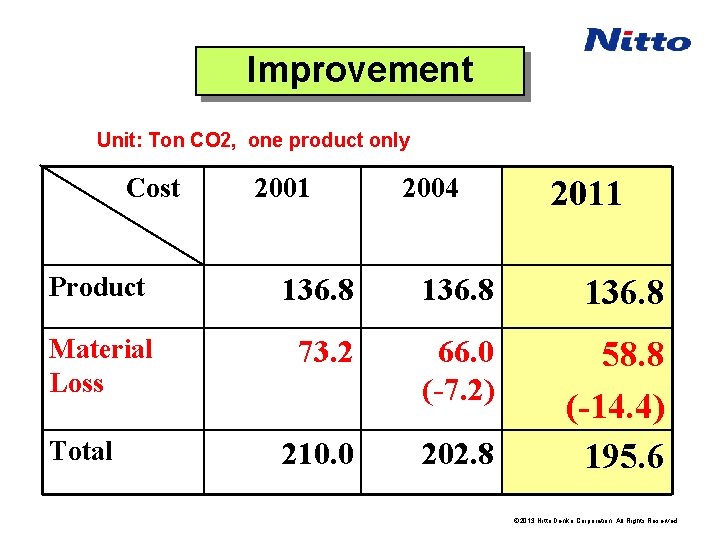
Improvement Unit: Ton CO 2, one product only Cost 2001 2004 2011 Product 136. 8 Material Loss 73. 2 66. 0 (-7. 2) 210. 0 202. 8 58. 8 (-14. 4) 195. 6 Total © 2013 Nitto Denko Corporation. All Rights Reserved.
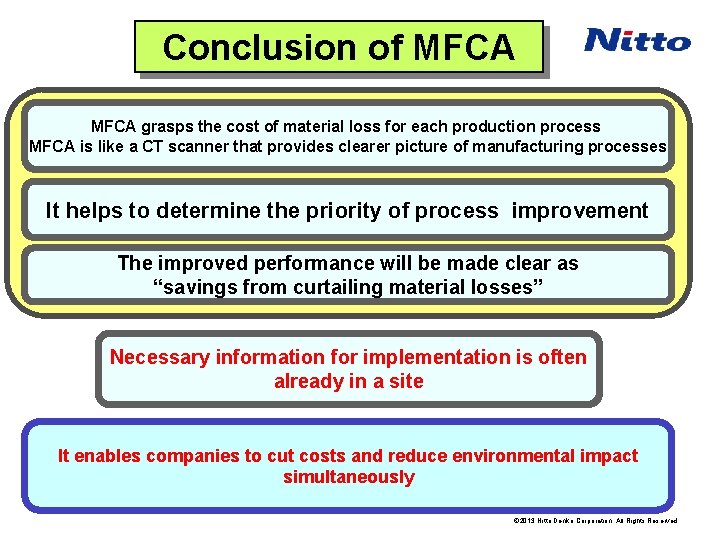
Conclusion of MFCA 製造 程単位に廃棄物原価(負の製品)を把握 MFCA grasps the cost of material loss for each production process MFCA is like a CT scanner that provides clearer picture of manufacturing processes 産廃原価はレントゲン、マテリアルフローコスト会計はCTスキャン どの製造 程の改善に人とお金を投入すべきか 優先順位が明確になる It helps to determine the priority of process improvement The improved performance will be made clear as 改善効果は「負の製品阻止額(新しい概念)」 “savings from curtailing material losses” Necessary information for implementation is often 現行の会計システムを変えるものではない already in a site It enables companies to cut costs and reduce environmental impact simultaneously © 2013 Nitto Denko Corporation. All Rights Reserved.
March march dabrowski
Writing to learn
What is ngo?
Material flow cost analysis
Flow chart in powerpoint 2013
Gd and t symbol
Rsq in standard costing
Non material culture definition
Refers to the knowledge language values customs
All groups create norms to enforce their cultural values.
Science useful and harmful materials
Company secretary meaning
Company secretary meaning
Secdef executive fellowship
Roles of a secretary after the meeting
Difference between dishonestly and fraudulently
Respiratory airway secretary
Question tag in simple present tense
Ptvi1
Role of company secretary
Esk porno
Responsibilities of a secretary
Importance of secretary
Challenges faced by company secretary during lockdown
Challenges faced by company secretary during lockdown
Board secretary training
Assistant secretary for aging
Company secretary nearby
Philosopher translator secretary architecture