Manufacturing processes UNIT III Sheet Metal Working 1222022
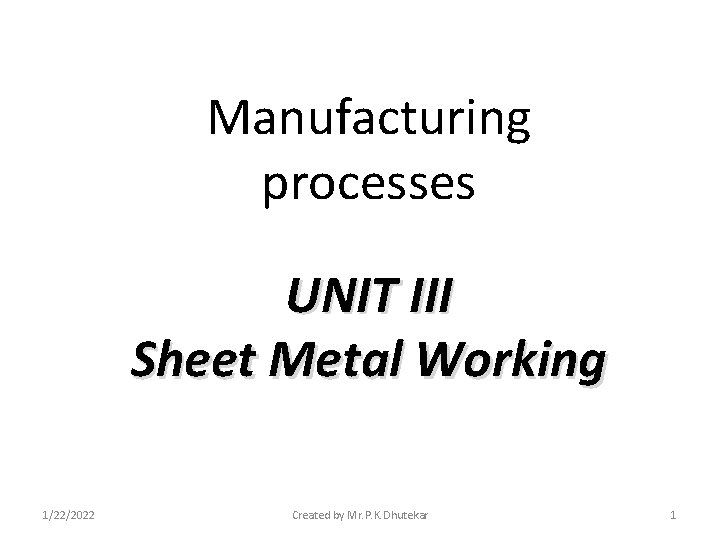
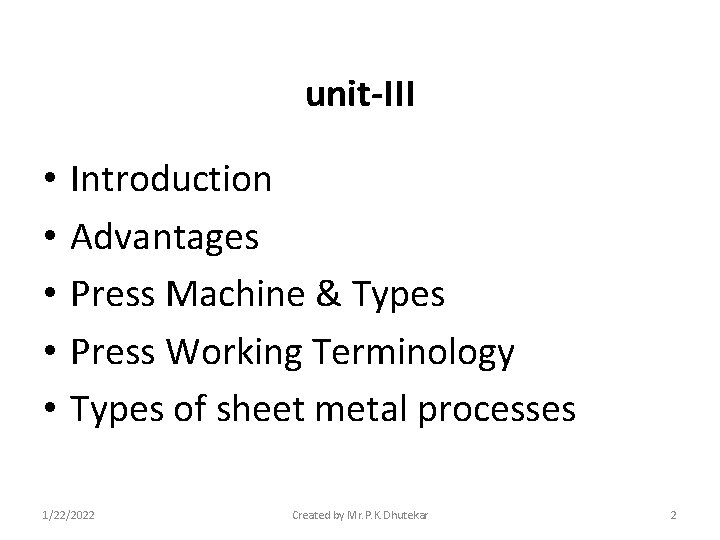
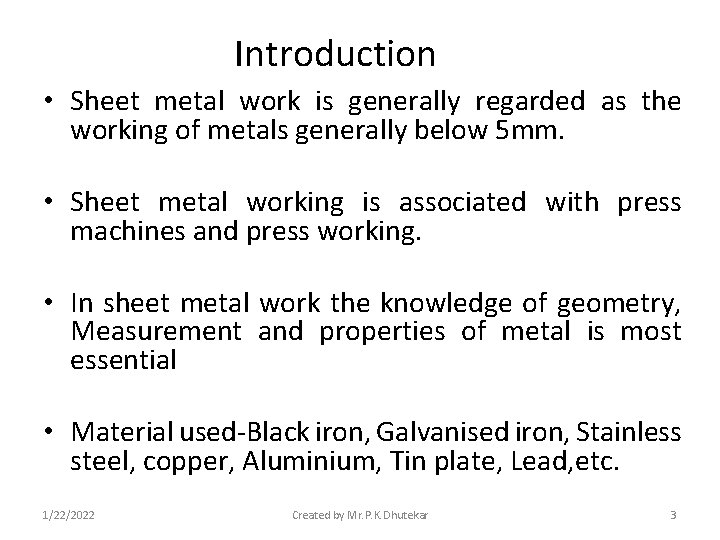
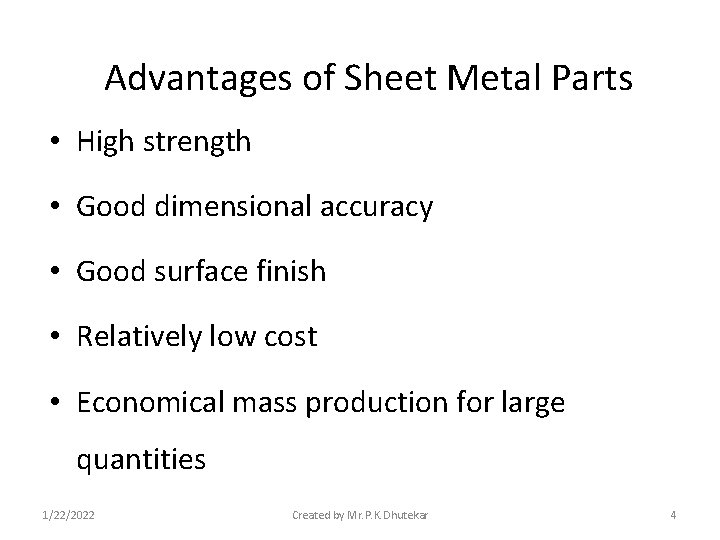
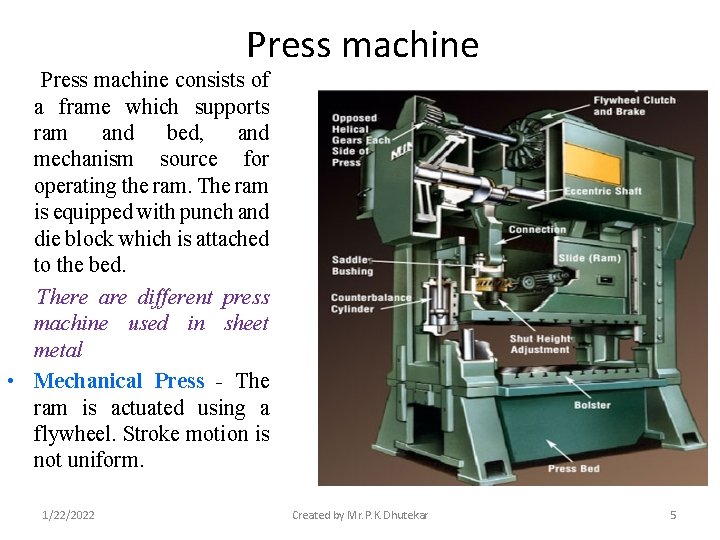
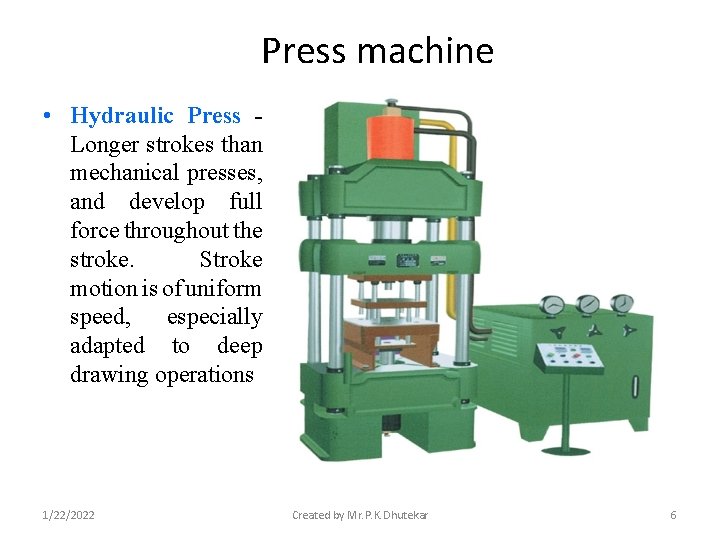
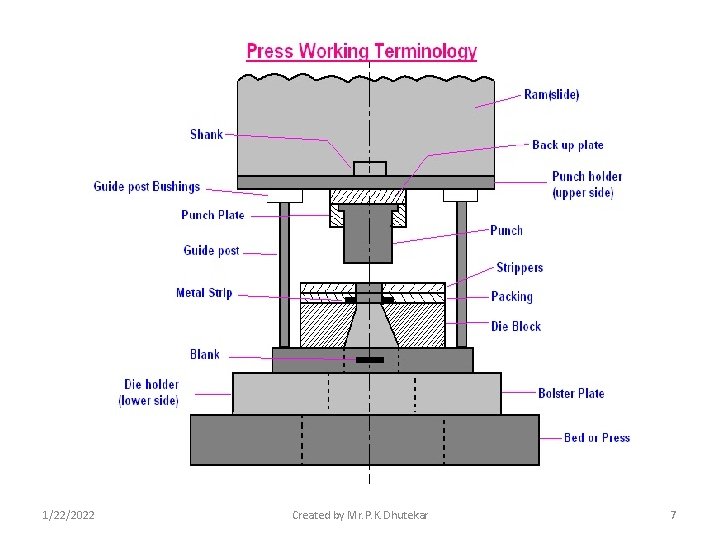
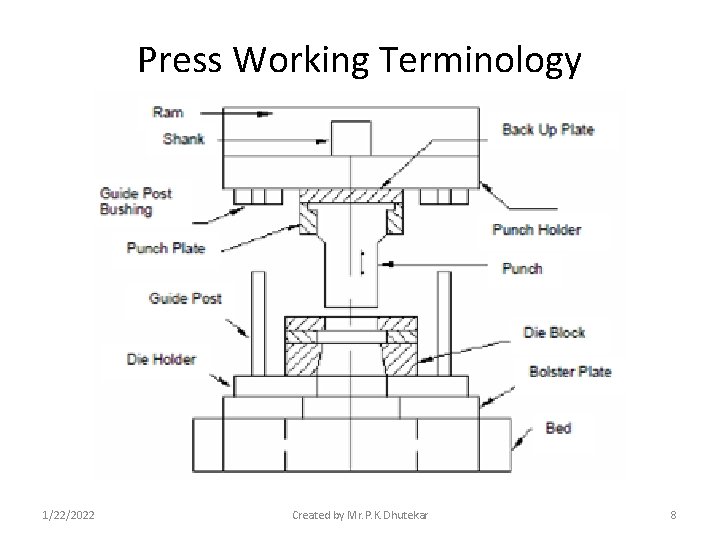
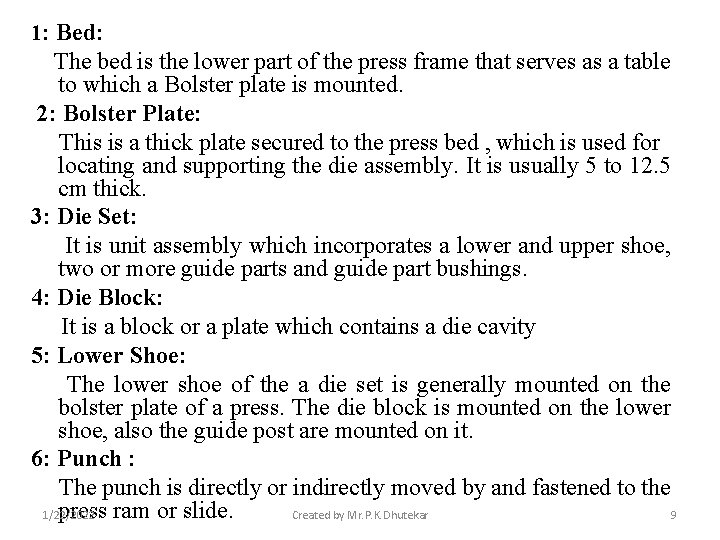
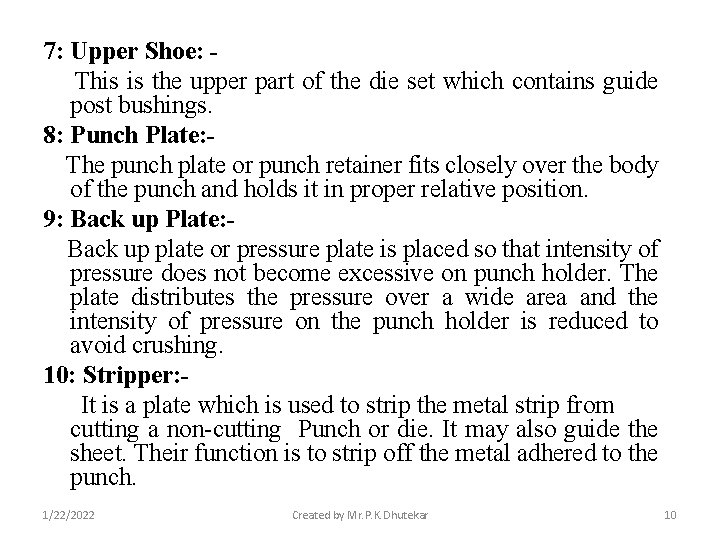
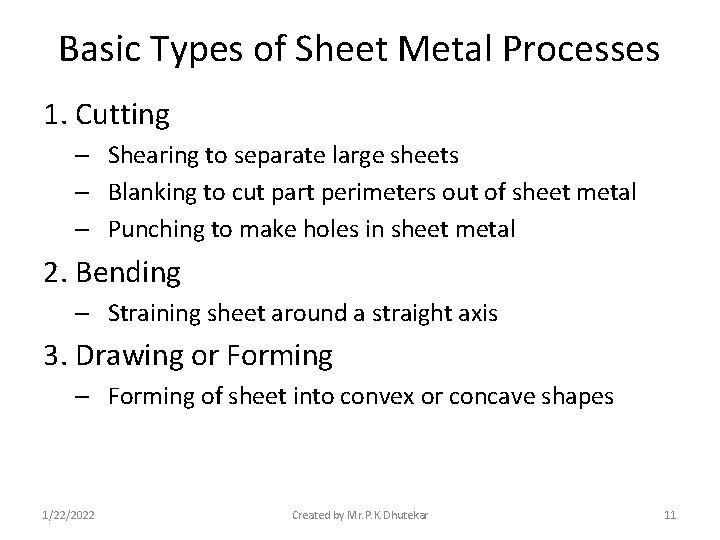
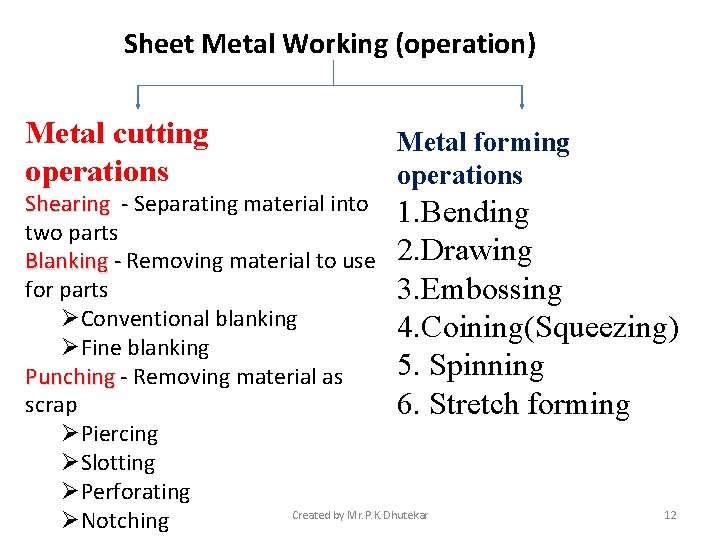
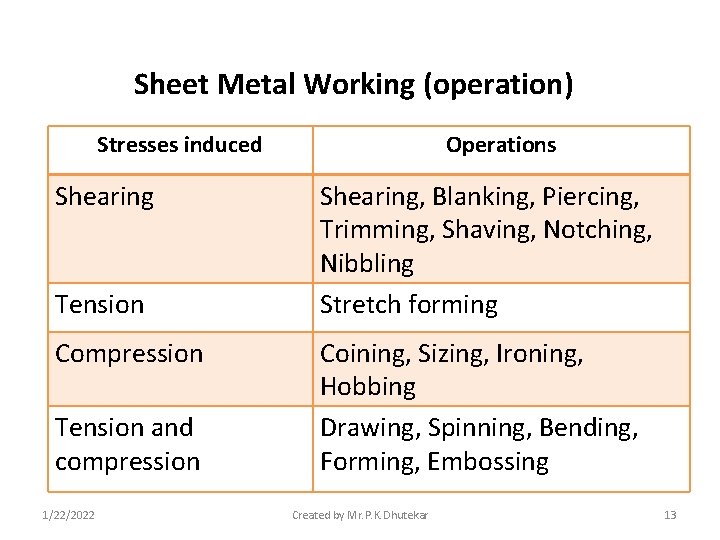
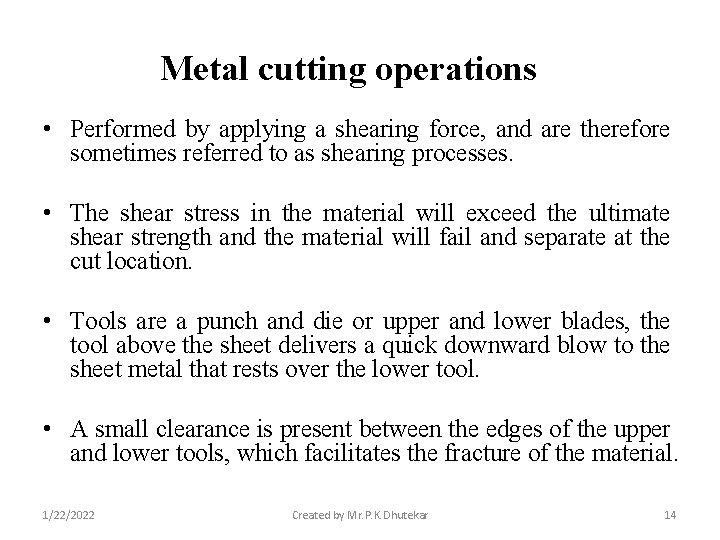
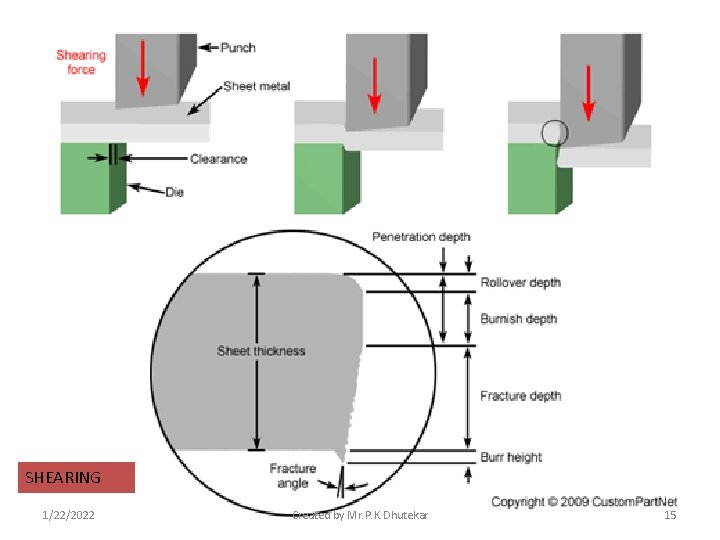
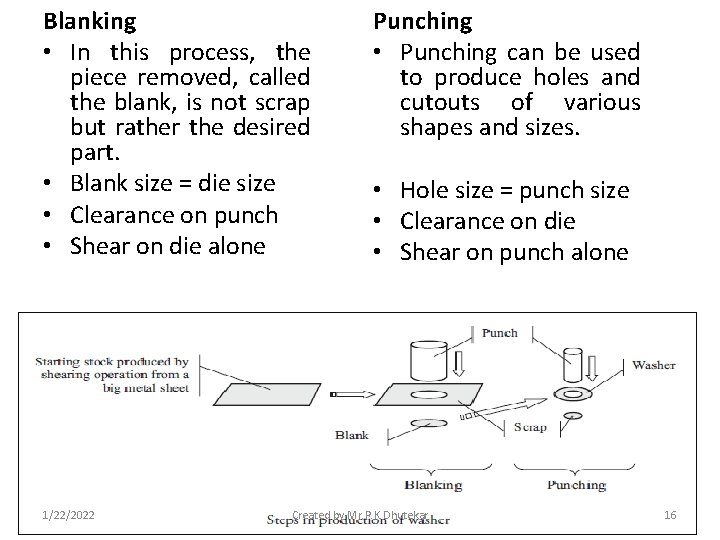
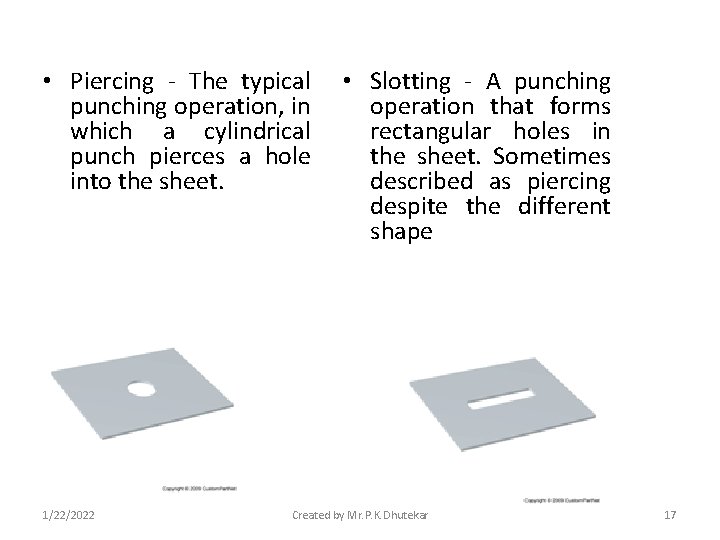
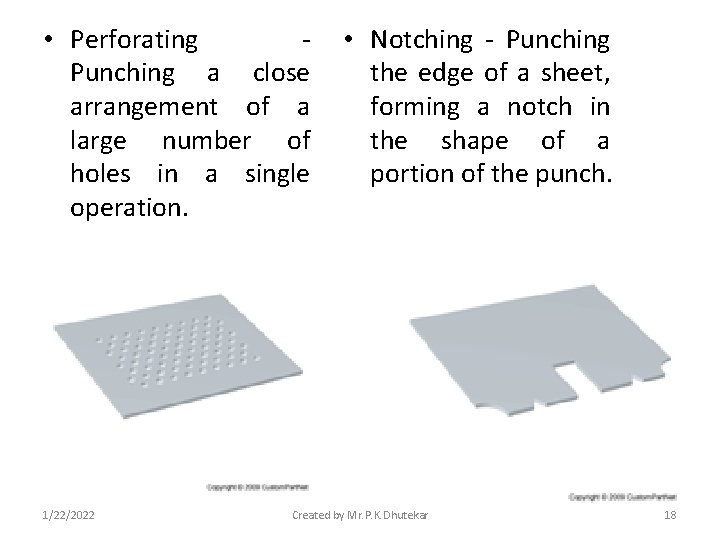
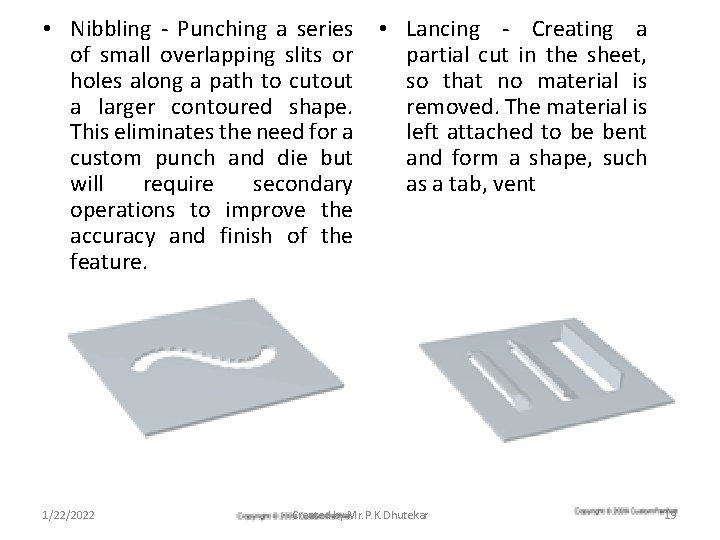


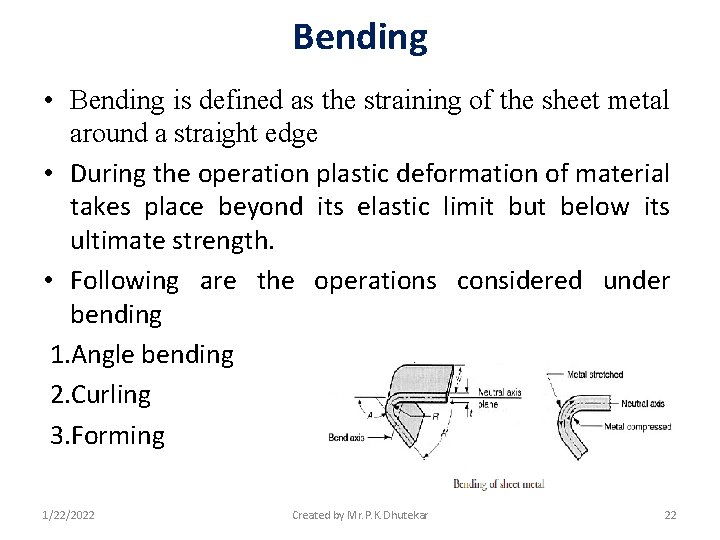
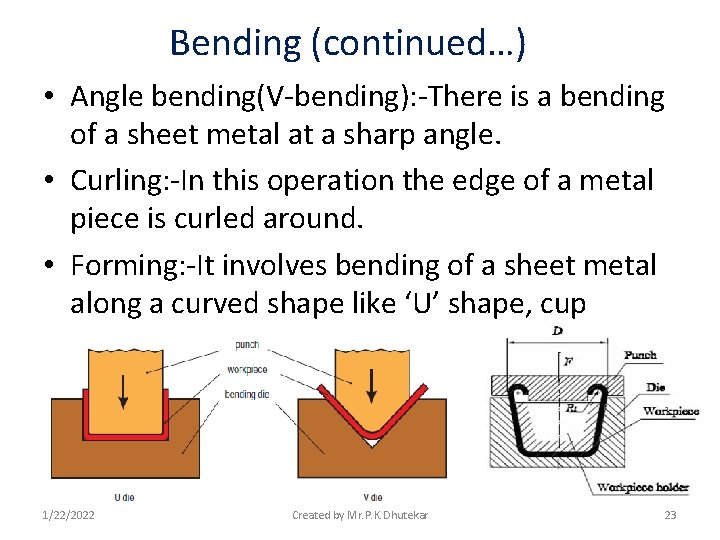
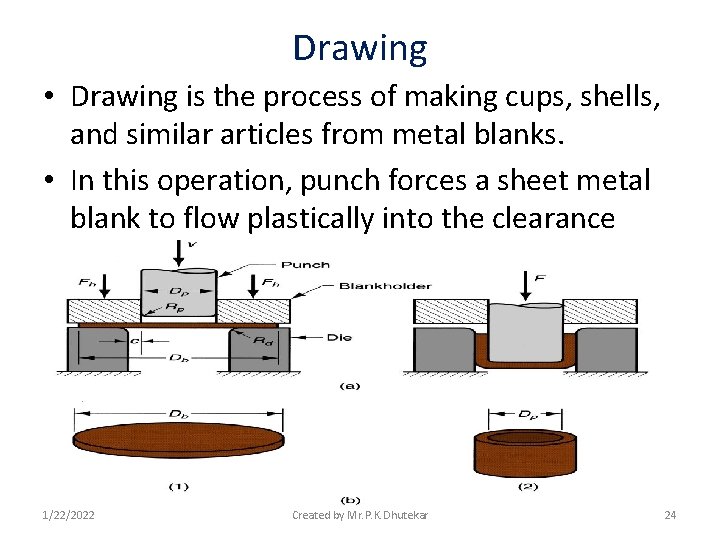
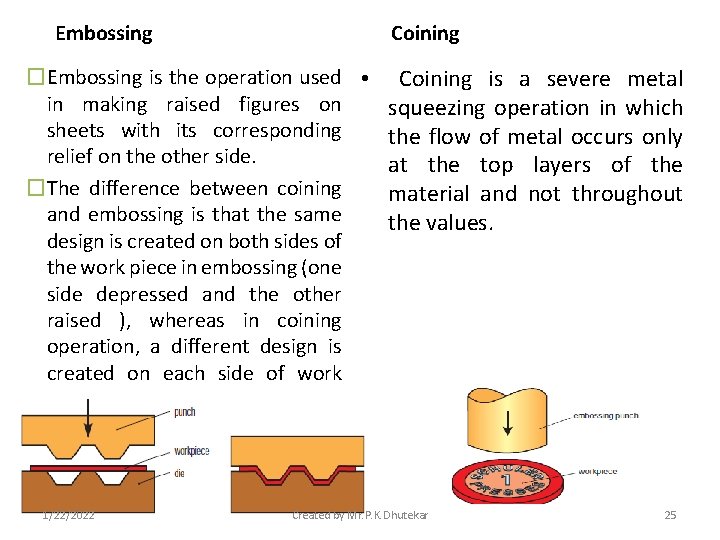
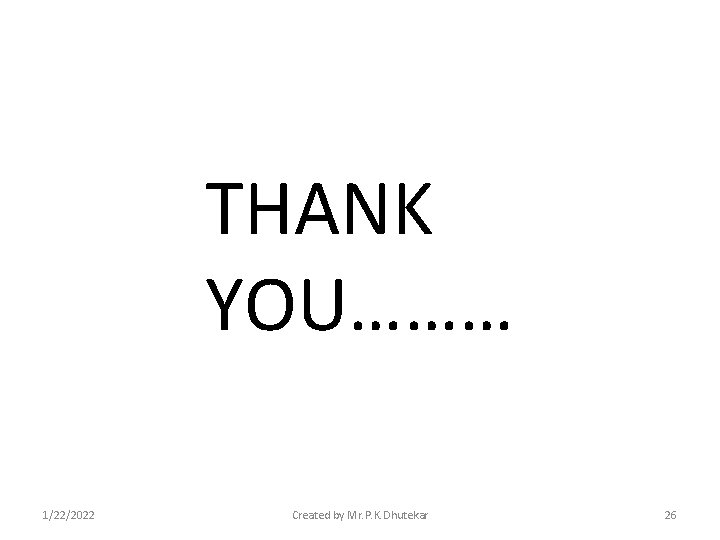
- Slides: 26
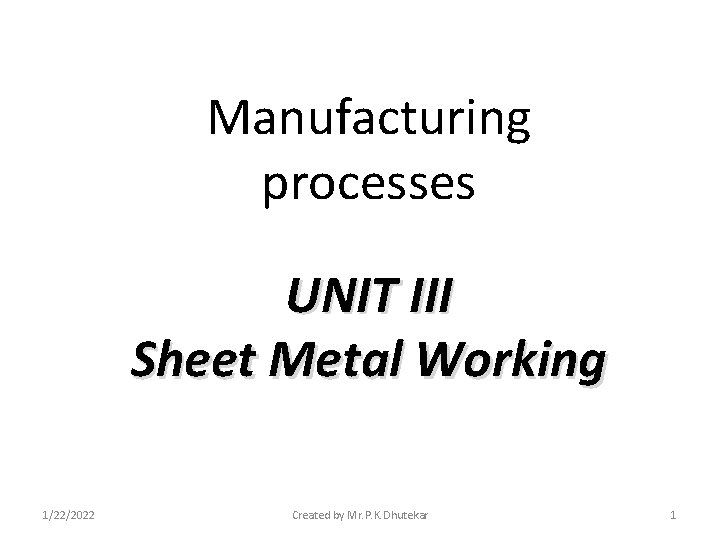
Manufacturing processes UNIT III Sheet Metal Working 1/22/2022 Created by Mr. P. K. Dhutekar 1
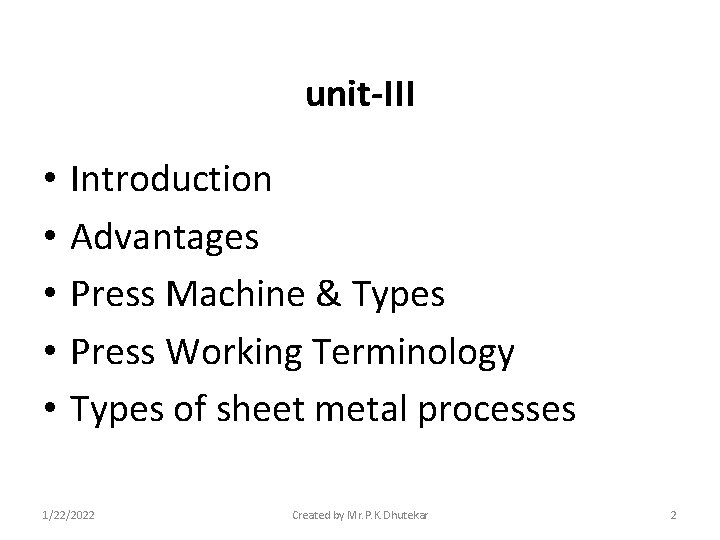
unit-III • • • Introduction Advantages Press Machine & Types Press Working Terminology Types of sheet metal processes 1/22/2022 Created by Mr. P. K. Dhutekar 2
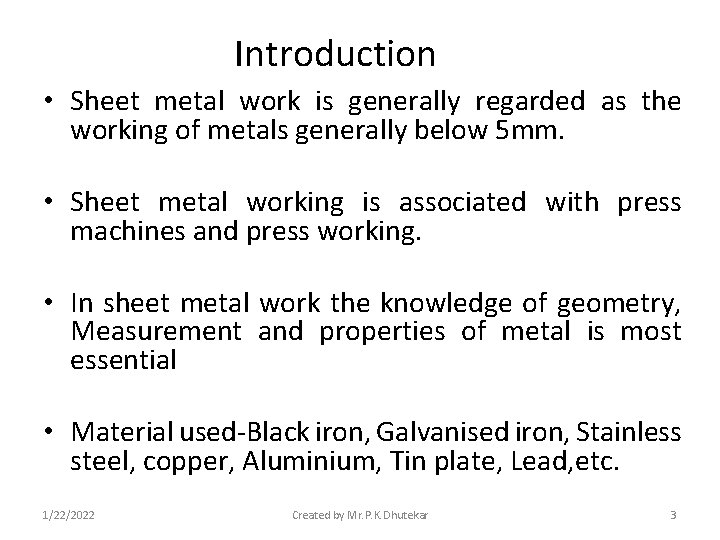
Introduction • Sheet metal work is generally regarded as the working of metals generally below 5 mm. • Sheet metal working is associated with press machines and press working. • In sheet metal work the knowledge of geometry, Measurement and properties of metal is most essential • Material used-Black iron, Galvanised iron, Stainless steel, copper, Aluminium, Tin plate, Lead, etc. 1/22/2022 Created by Mr. P. K. Dhutekar 3
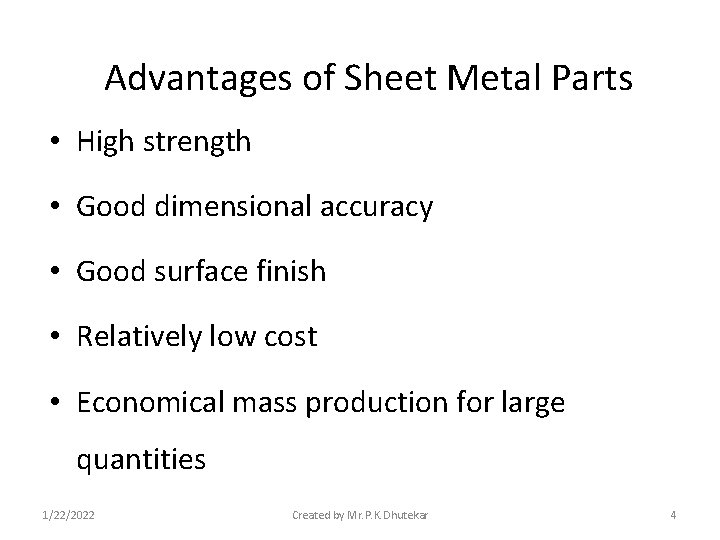
Advantages of Sheet Metal Parts • High strength • Good dimensional accuracy • Good surface finish • Relatively low cost • Economical mass production for large quantities 1/22/2022 Created by Mr. P. K. Dhutekar 4
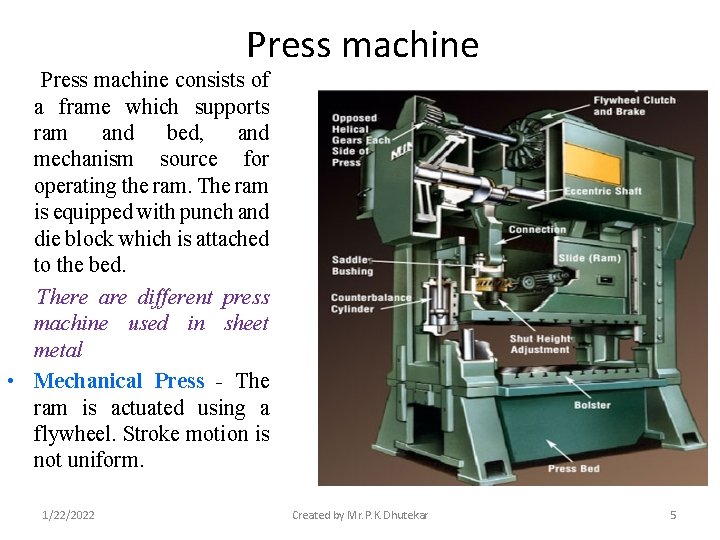
Press machine consists of a frame which supports ram and bed, and mechanism source for operating the ram. The ram is equipped with punch and die block which is attached to the bed. There are different press machine used in sheet metal • Mechanical Press - The ram is actuated using a flywheel. Stroke motion is not uniform. 1/22/2022 Created by Mr. P. K. Dhutekar 5
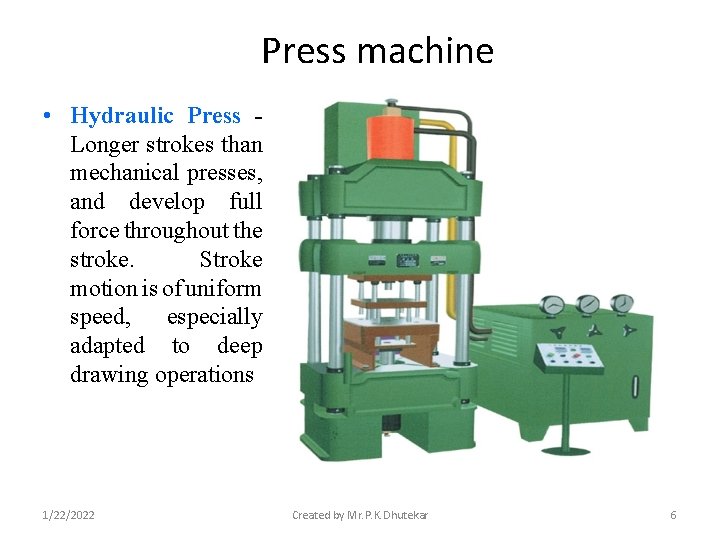
Press machine • Hydraulic Press Longer strokes than mechanical presses, and develop full force throughout the stroke. Stroke motion is of uniform speed, especially adapted to deep drawing operations 1/22/2022 Created by Mr. P. K. Dhutekar 6
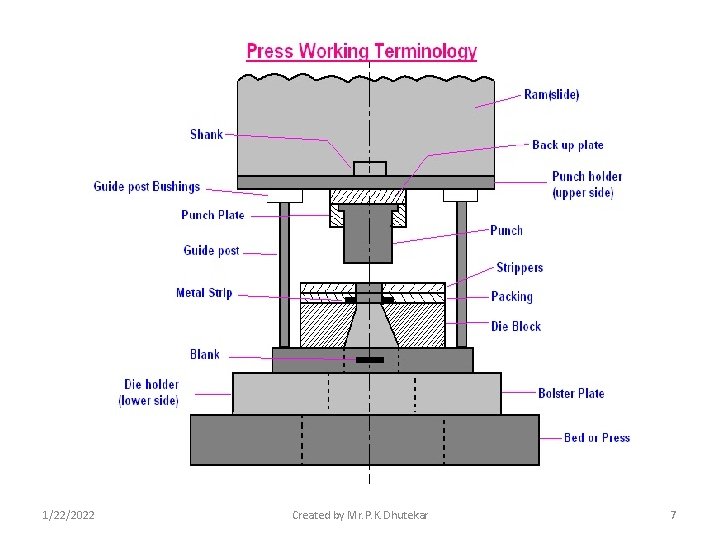
1/22/2022 Created by Mr. P. K. Dhutekar 7
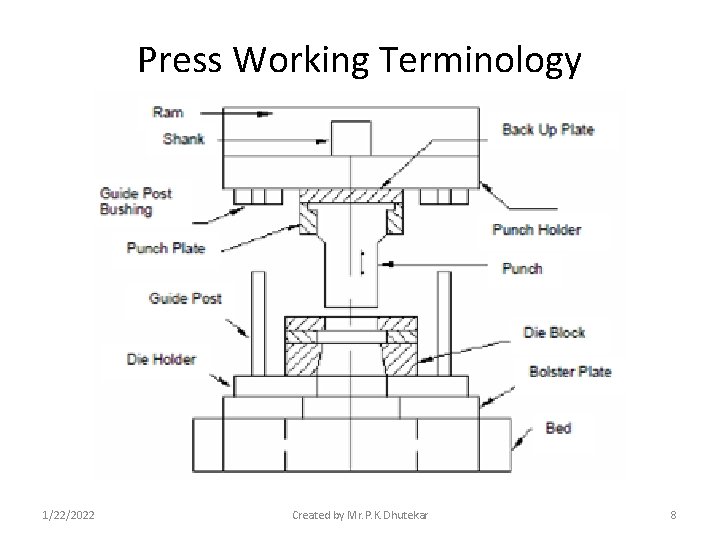
Press Working Terminology 1/22/2022 Created by Mr. P. K. Dhutekar 8
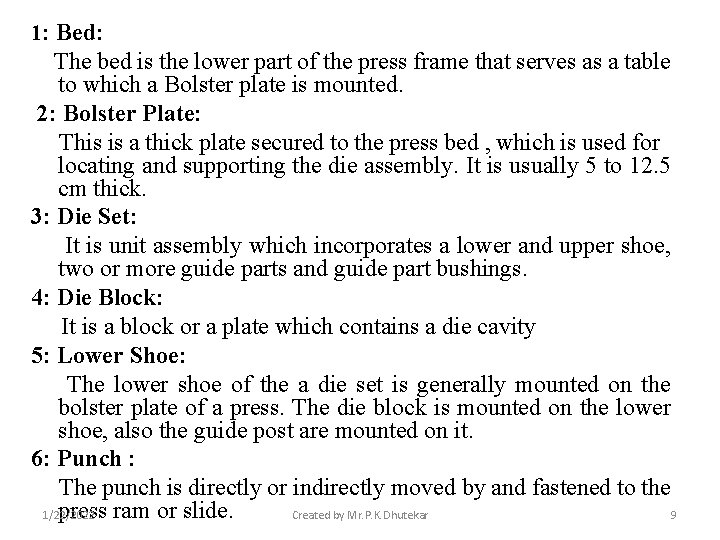
1: Bed: The bed is the lower part of the press frame that serves as a table to which a Bolster plate is mounted. 2: Bolster Plate: This is a thick plate secured to the press bed , which is used for locating and supporting the die assembly. It is usually 5 to 12. 5 cm thick. 3: Die Set: It is unit assembly which incorporates a lower and upper shoe, two or more guide parts and guide part bushings. 4: Die Block: It is a block or a plate which contains a die cavity 5: Lower Shoe: The lower shoe of the a die set is generally mounted on the bolster plate of a press. The die block is mounted on the lower shoe, also the guide post are mounted on it. 6: Punch : The punch is directly or indirectly moved by and fastened to the press ram or slide. 1/22/2022 Created by Mr. P. K. Dhutekar 9
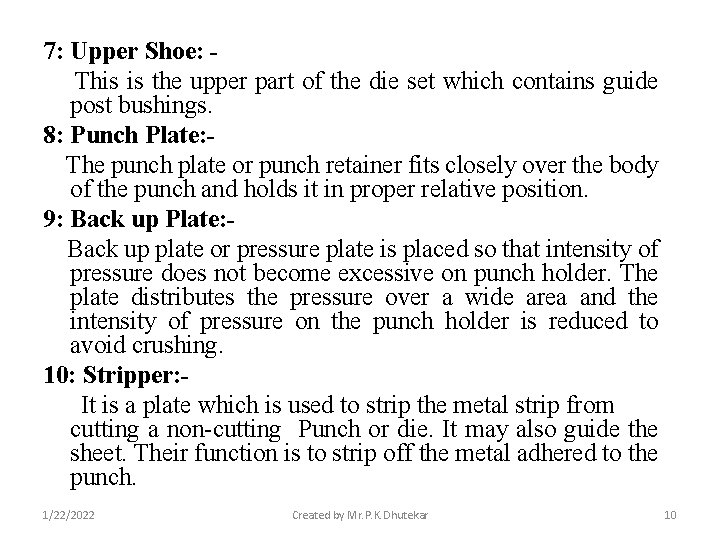
7: Upper Shoe: This is the upper part of the die set which contains guide post bushings. 8: Punch Plate: The punch plate or punch retainer fits closely over the body of the punch and holds it in proper relative position. 9: Back up Plate: Back up plate or pressure plate is placed so that intensity of pressure does not become excessive on punch holder. The plate distributes the pressure over a wide area and the intensity of pressure on the punch holder is reduced to avoid crushing. 10: Stripper: It is a plate which is used to strip the metal strip from cutting a non-cutting Punch or die. It may also guide the sheet. Their function is to strip off the metal adhered to the punch. 1/22/2022 Created by Mr. P. K. Dhutekar 10
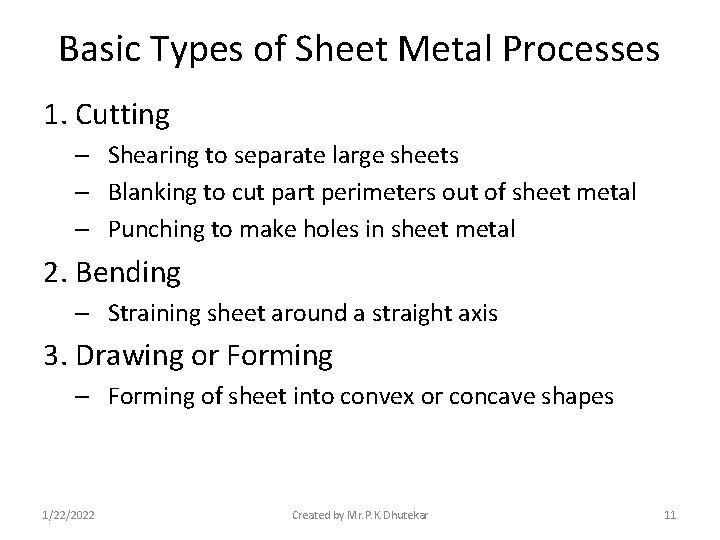
Basic Types of Sheet Metal Processes 1. Cutting – Shearing to separate large sheets – Blanking to cut part perimeters out of sheet metal – Punching to make holes in sheet metal 2. Bending – Straining sheet around a straight axis 3. Drawing or Forming – Forming of sheet into convex or concave shapes 1/22/2022 Created by Mr. P. K. Dhutekar 11
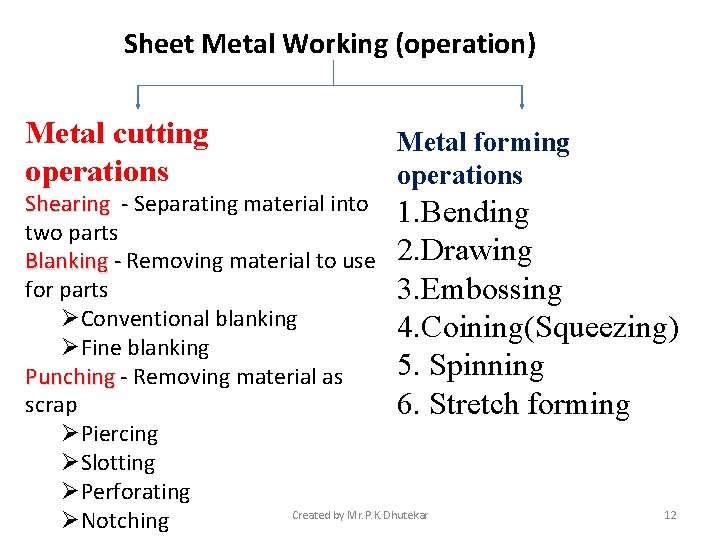
Sheet Metal Working (operation) Metal cutting operations Metal forming operations Shearing - Separating material into 1. Bending two parts Blanking - Removing material to use 2. Drawing for parts 3. Embossing ØConventional blanking 4. Coining(Squeezing) ØFine blanking 5. Spinning Punching - Removing material as scrap 6. Stretch forming ØPiercing ØSlotting ØPerforating Created by Mr. P. K. Dhutekar 12 ØNotching
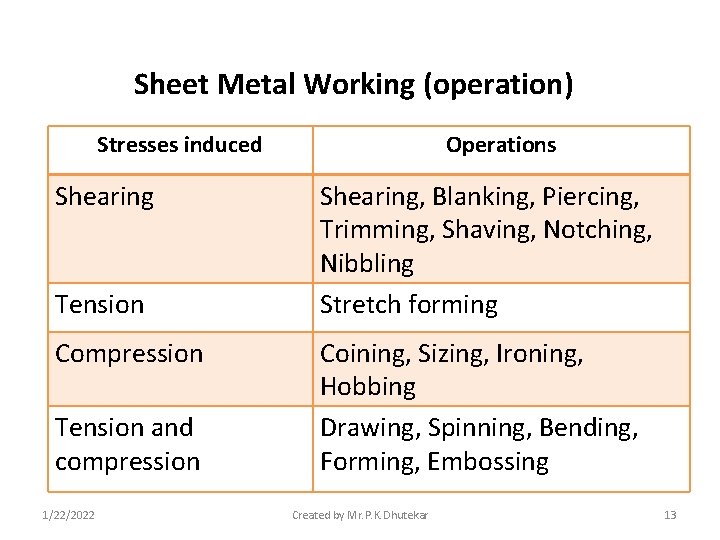
Sheet Metal Working (operation) Stresses induced Shearing Tension Compression Tension and compression 1/22/2022 Operations Shearing, Blanking, Piercing, Trimming, Shaving, Notching, Nibbling Stretch forming Coining, Sizing, Ironing, Hobbing Drawing, Spinning, Bending, Forming, Embossing Created by Mr. P. K. Dhutekar 13
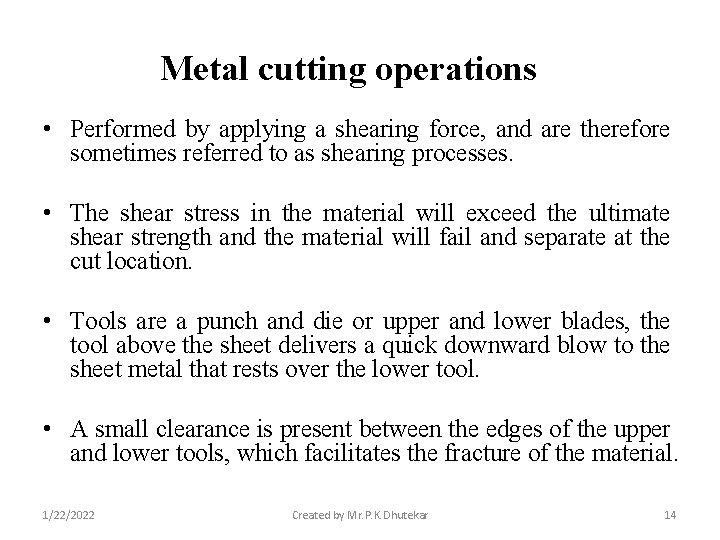
Metal cutting operations • Performed by applying a shearing force, and are therefore sometimes referred to as shearing processes. • The shear stress in the material will exceed the ultimate shear strength and the material will fail and separate at the cut location. • Tools are a punch and die or upper and lower blades, the tool above the sheet delivers a quick downward blow to the sheet metal that rests over the lower tool. • A small clearance is present between the edges of the upper and lower tools, which facilitates the fracture of the material. 1/22/2022 Created by Mr. P. K. Dhutekar 14
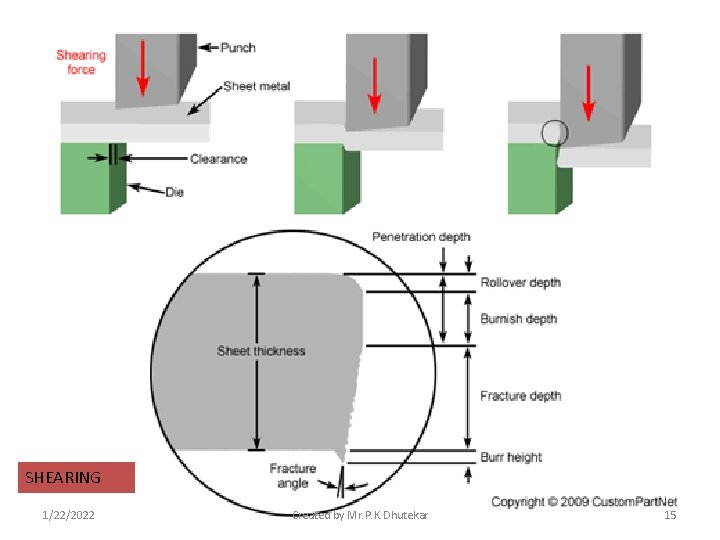
SHEARING 1/22/2022 Created by Mr. P. K. Dhutekar 15
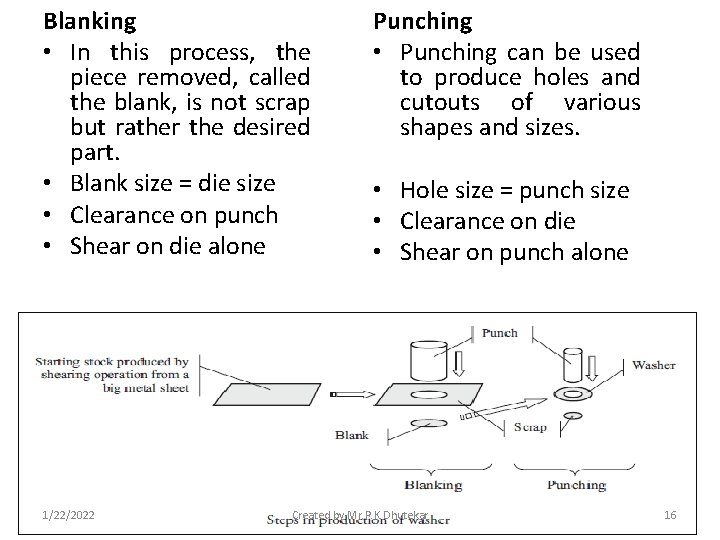
Blanking • In this process, the piece removed, called the blank, is not scrap but rather the desired part. • Blank size = die size • Clearance on punch • Shear on die alone 1/22/2022 Punching • Punching can be used to produce holes and cutouts of various shapes and sizes. • Hole size = punch size • Clearance on die • Shear on punch alone Created by Mr. P. K. Dhutekar 16
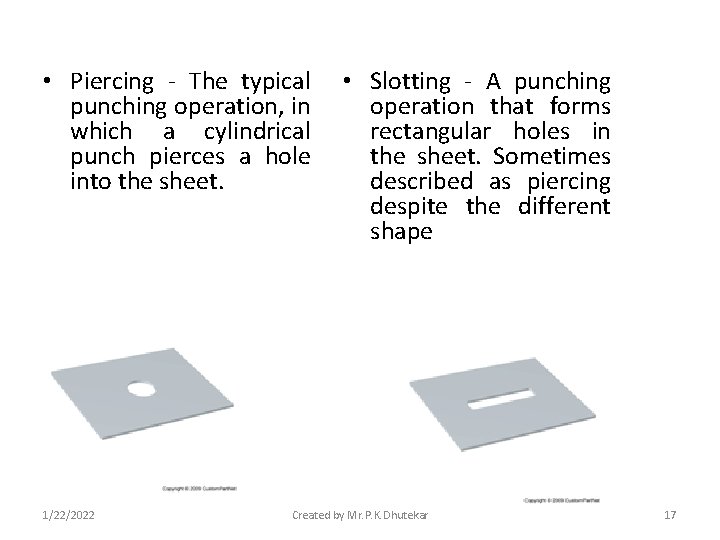
• Piercing - The typical punching operation, in which a cylindrical punch pierces a hole into the sheet. 1/22/2022 • Slotting - A punching operation that forms rectangular holes in the sheet. Sometimes described as piercing despite the different shape Created by Mr. P. K. Dhutekar 17
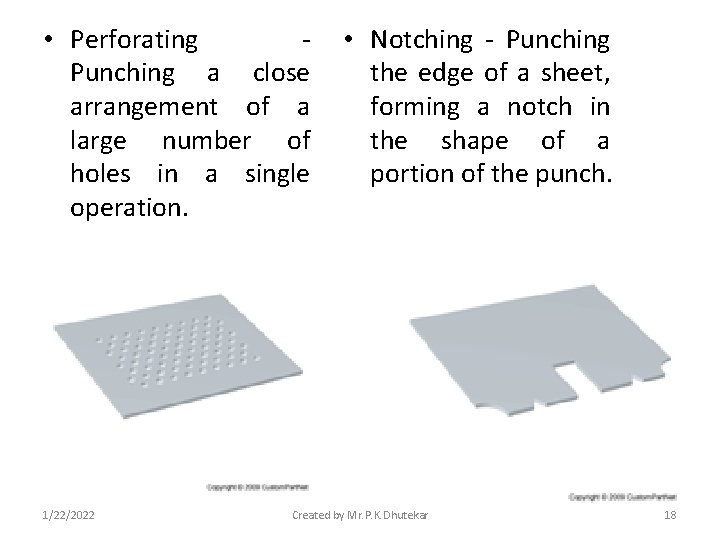
• Perforating Punching a close arrangement of a large number of holes in a single operation. 1/22/2022 • Notching - Punching the edge of a sheet, forming a notch in the shape of a portion of the punch. Created by Mr. P. K. Dhutekar 18
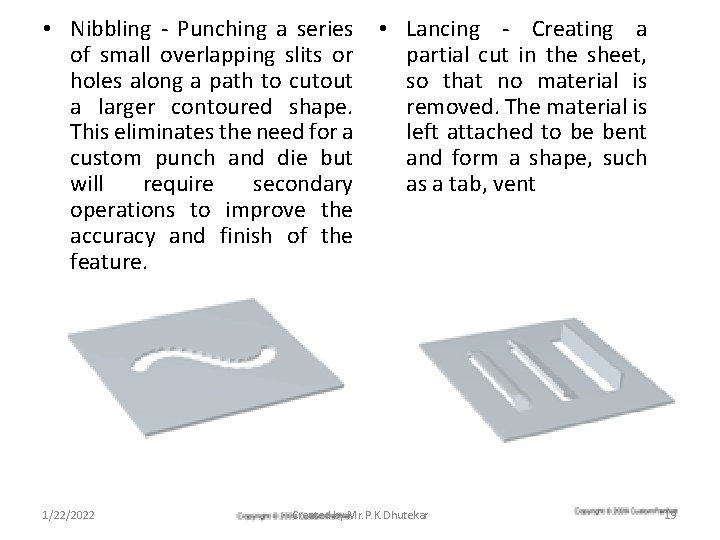
• Nibbling - Punching a series of small overlapping slits or holes along a path to cutout a larger contoured shape. This eliminates the need for a custom punch and die but will require secondary operations to improve the accuracy and finish of the feature. 1/22/2022 • Lancing - Creating a partial cut in the sheet, so that no material is removed. The material is left attached to be bent and form a shape, such as a tab, vent Created by Mr. P. K. Dhutekar 19

• Slitting - Cutting straight lines in the sheet. No scrap material is produced 1/22/2022 • Parting - Separating a part from the remaining sheet, by punching away the material between parts Created by Mr. P. K. Dhutekar 20

• Cutoff - Separating a part from the remaining sheet, without producing any scrap. The punch will produce a cut line that may be straight, angled, or curved. 1/22/2022 • Trimming - Punching away excess material from the perimeter of a part, such as trimming the flange from a drawn cup. Created by Mr. P. K. Dhutekar 21
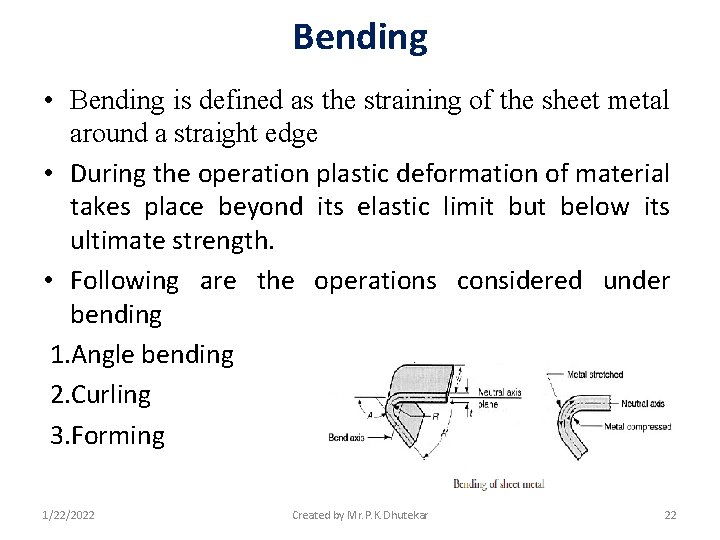
Bending • Bending is defined as the straining of the sheet metal around a straight edge • During the operation plastic deformation of material takes place beyond its elastic limit but below its ultimate strength. • Following are the operations considered under bending 1. Angle bending 2. Curling 3. Forming 1/22/2022 Created by Mr. P. K. Dhutekar 22
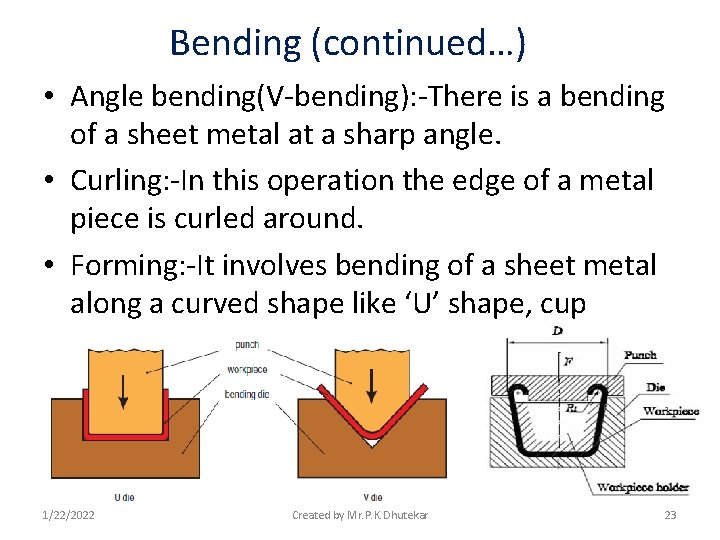
Bending (continued…) • Angle bending(V-bending): -There is a bending of a sheet metal at a sharp angle. • Curling: -In this operation the edge of a metal piece is curled around. • Forming: -It involves bending of a sheet metal along a curved shape like ‘U’ shape, cup shape. etc. 1/22/2022 Created by Mr. P. K. Dhutekar 23
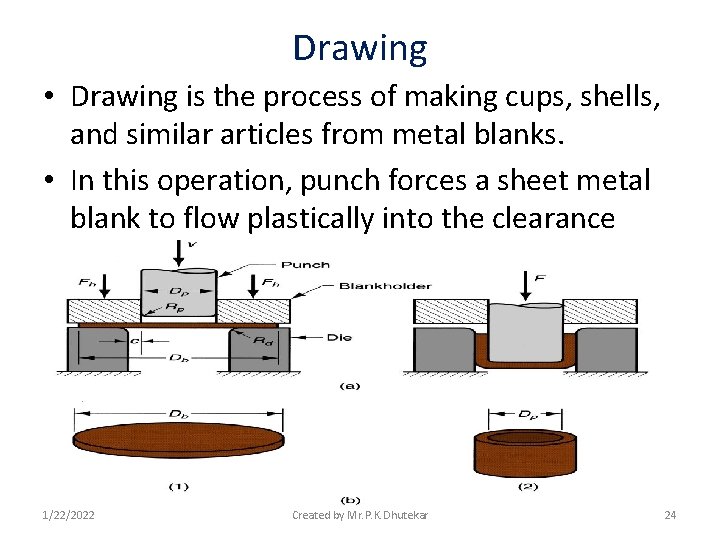
Drawing • Drawing is the process of making cups, shells, and similar articles from metal blanks. • In this operation, punch forces a sheet metal blank to flow plastically into the clearance between the punch and die. 1/22/2022 Created by Mr. P. K. Dhutekar 24
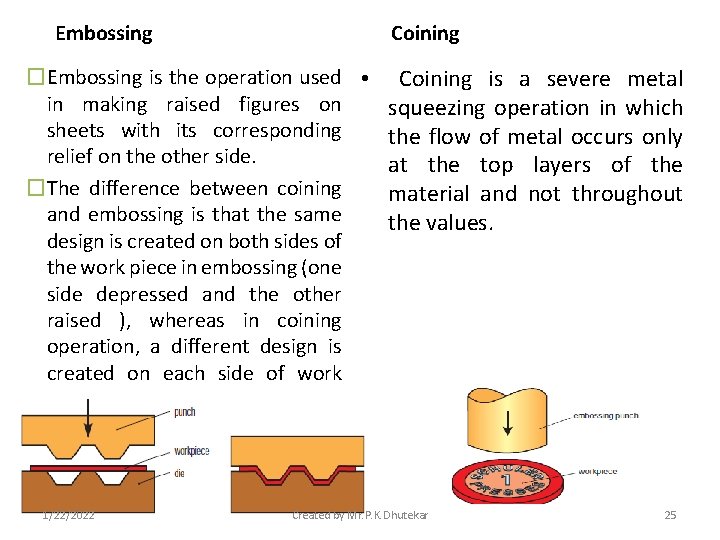
Embossing Coining �Embossing is the operation used • Coining is a severe metal in making raised figures on squeezing operation in which sheets with its corresponding the flow of metal occurs only relief on the other side. at the top layers of the �The difference between coining material and not throughout and embossing is that the same the values. design is created on both sides of the work piece in embossing (one side depressed and the other raised ), whereas in coining operation, a different design is created on each side of work piece. 1/22/2022 Created by Mr. P. K. Dhutekar 25
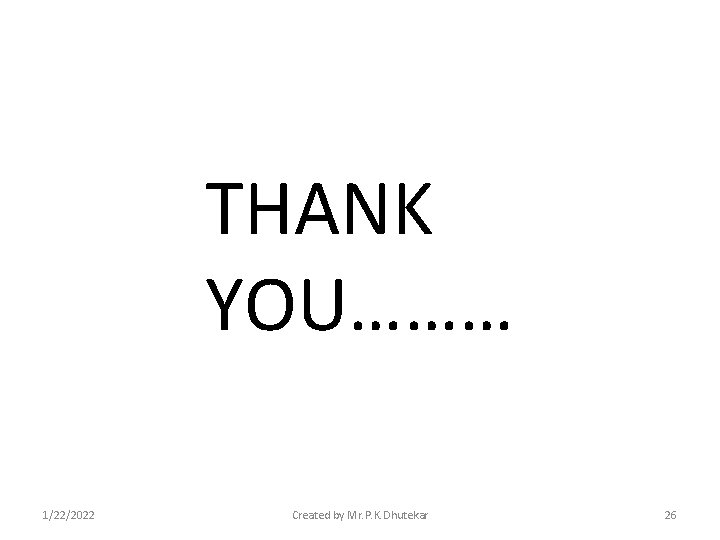
THANK YOU……… 1/22/2022 Created by Mr. P. K. Dhutekar 26
Wholesale sheet metal process
Jml sheet metal
Manufacturing cost vs non manufacturing cost
Job costing vs. process costing
Controllable costs
Manufacturing cost vs non manufacturing cost
Additively
Manufacturing processes for engineering materials 5th
Classification of production process
Introduction to manufacturing process
Composite manufacturing processes
Nontraditional manufacturing processes
Traditional manufacturing processes
The transition to new manufacturing processes
Nature of manufacturing process
Concurrent processes are processes that
Hamlet act iii scene ii
Hot working of metal is
Working hard vs working smart
Hot working and cold working difference
Machining operations
Proses pengerjaan panas
Solid and liquid venn diagram
Characteristics of metals
Acidity trends periodic table
Difference between metal oxides and non metal oxides
Nwell