Unit No 3 Manufacturing Processes Sheet Metal Working
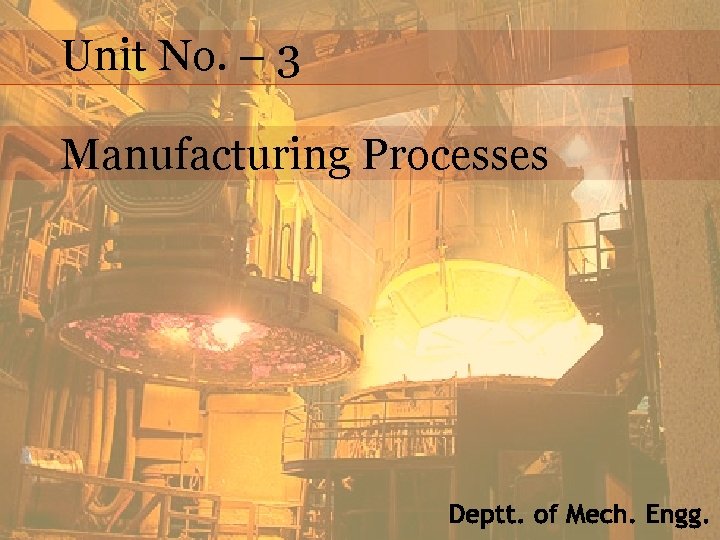

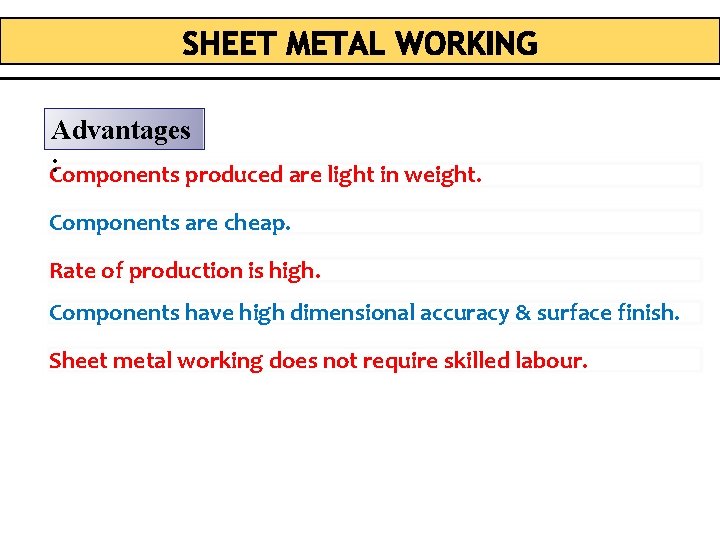
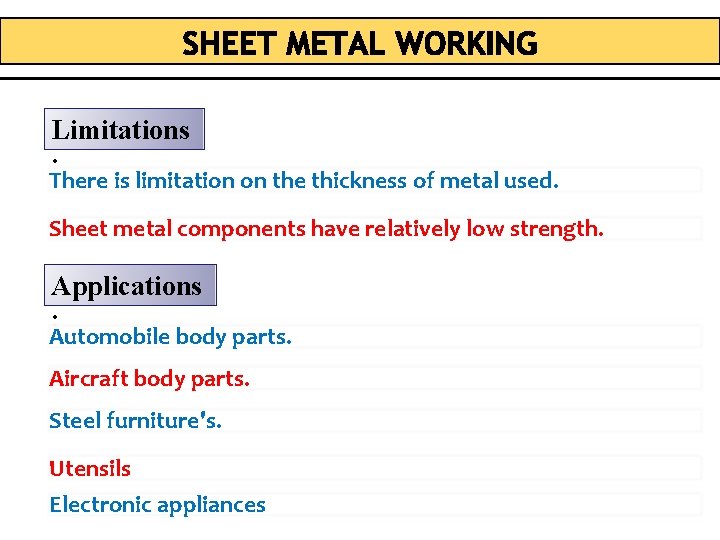
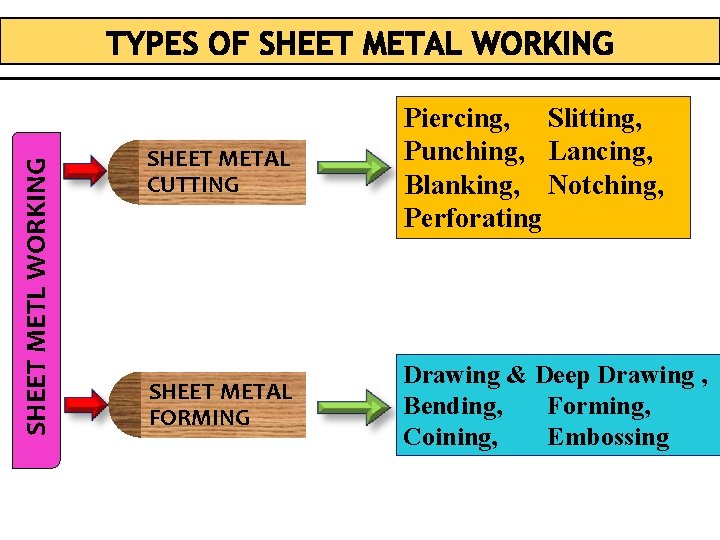
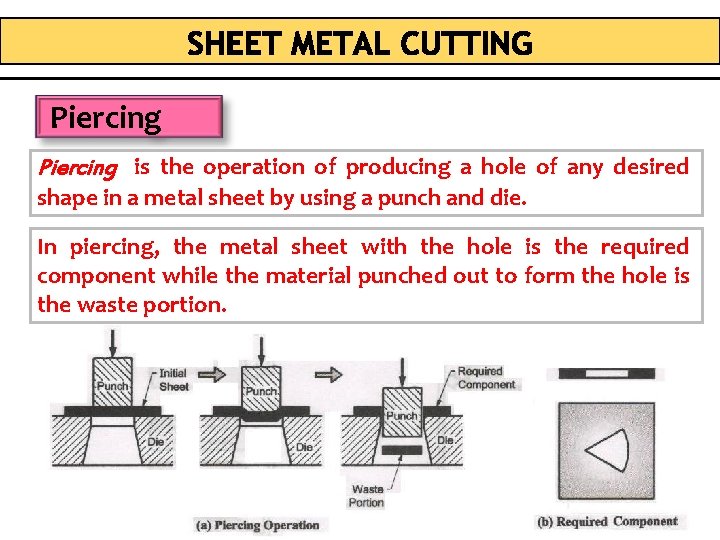
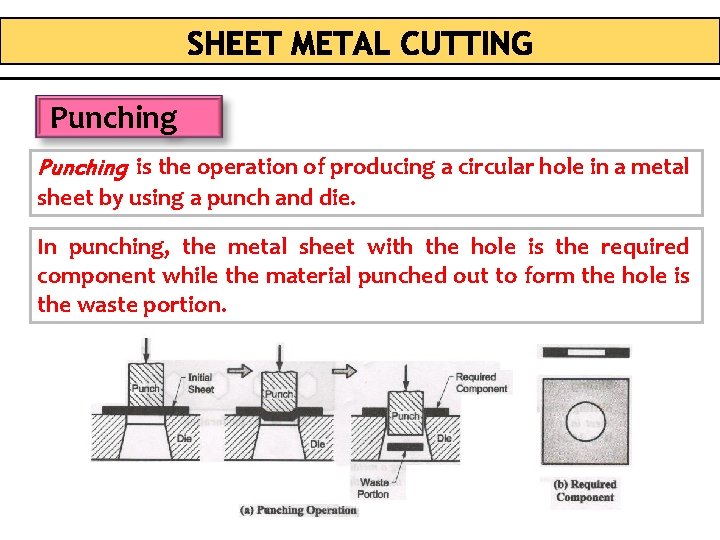
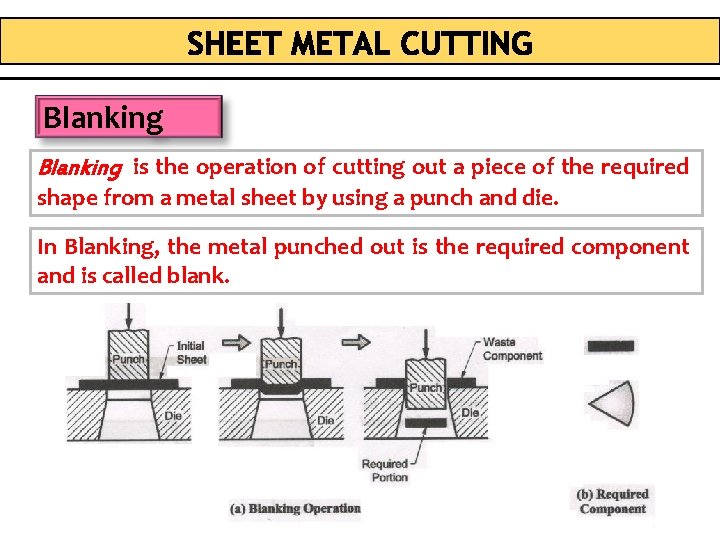
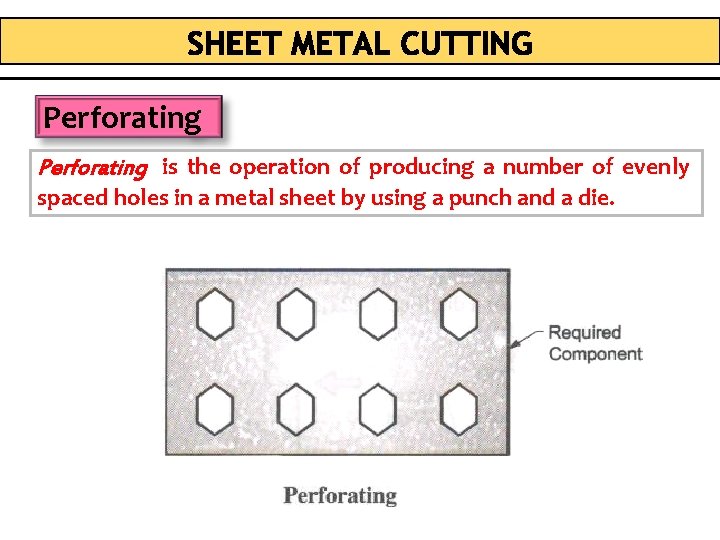
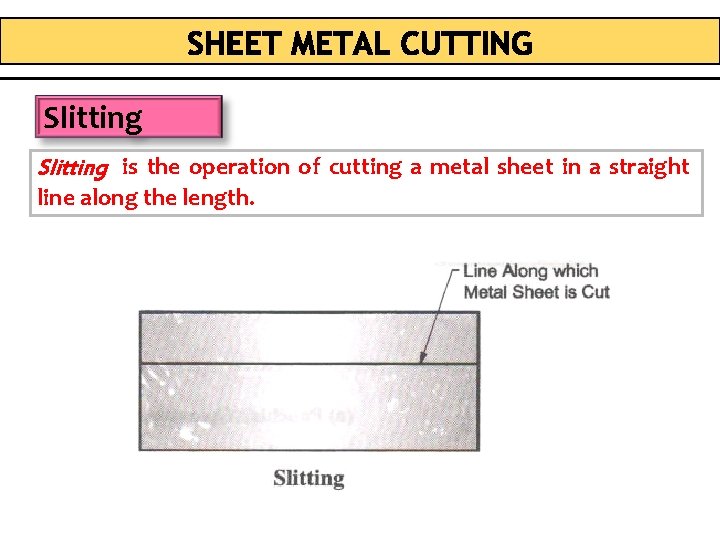
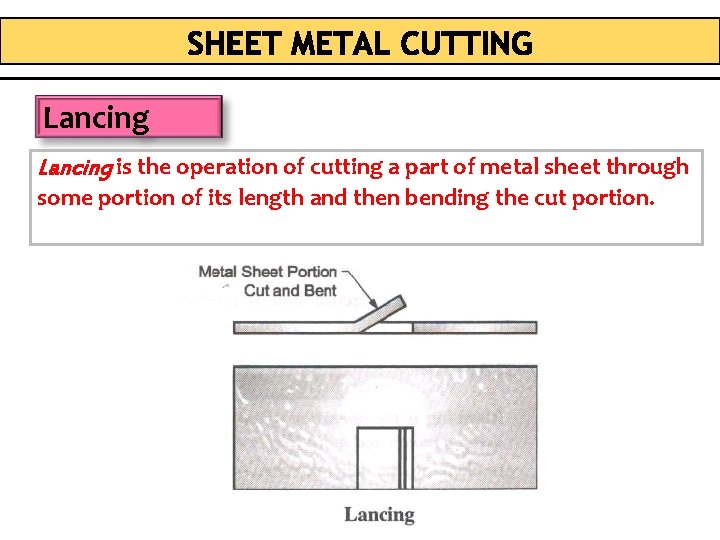
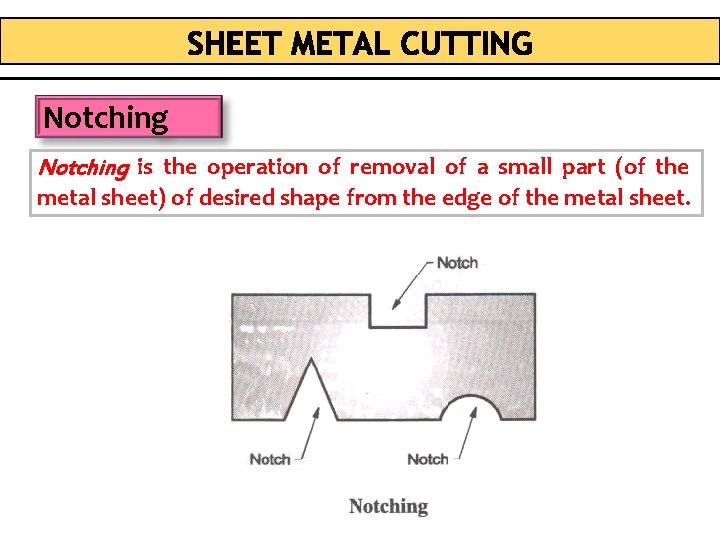
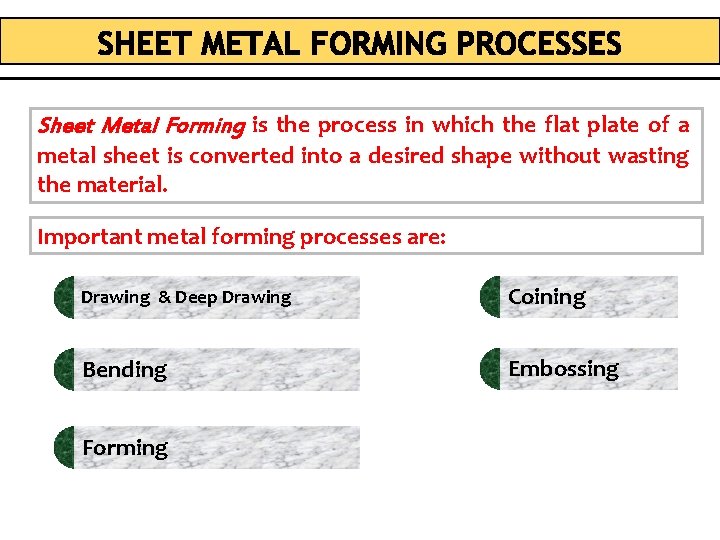
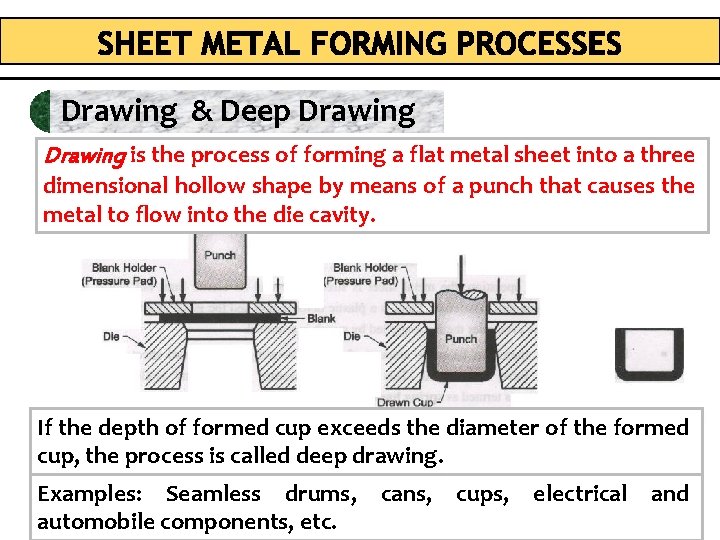
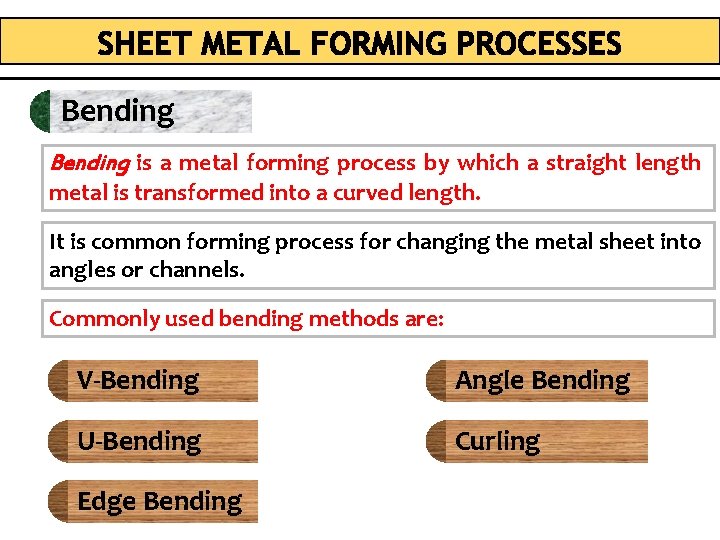
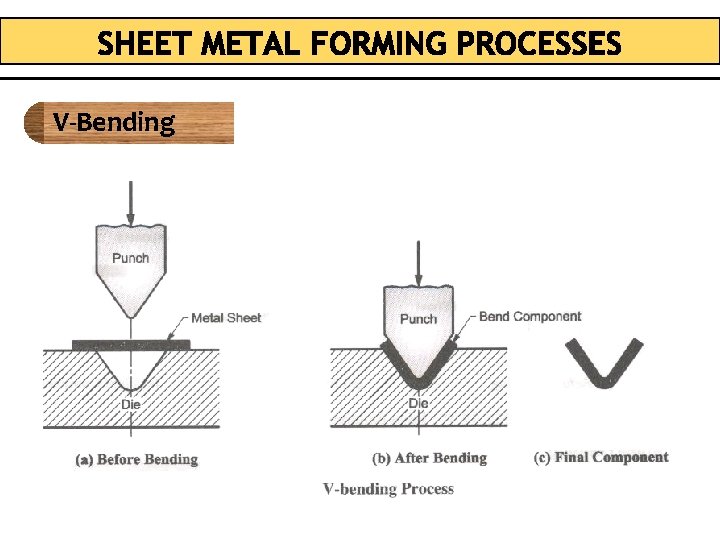
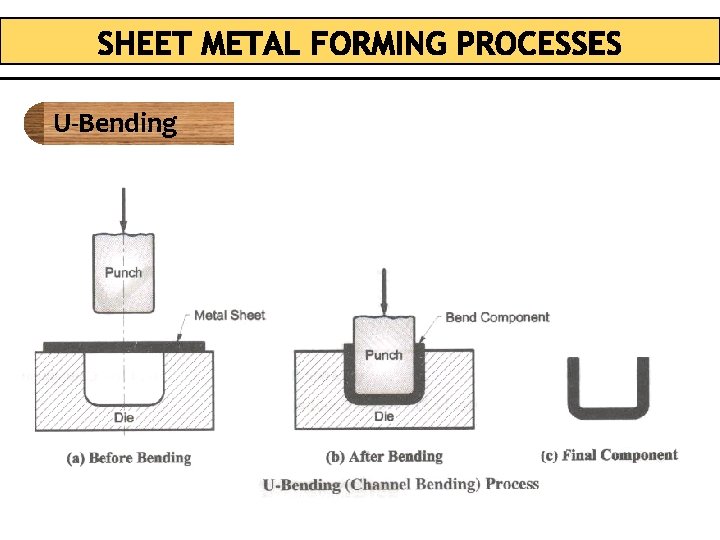
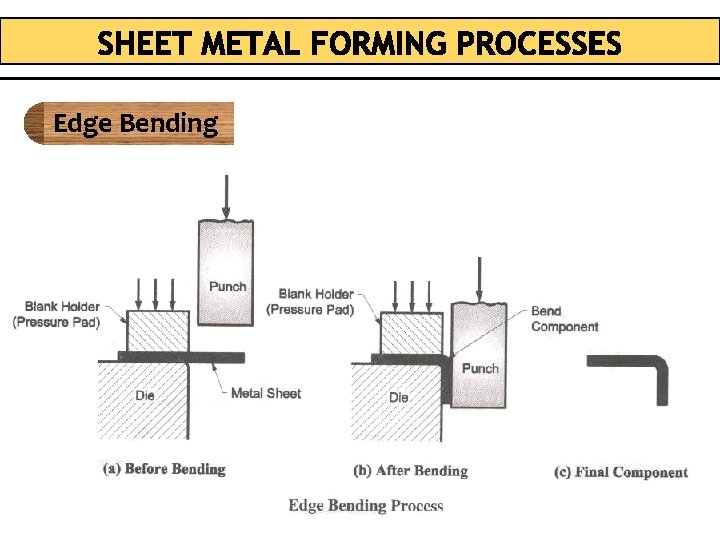
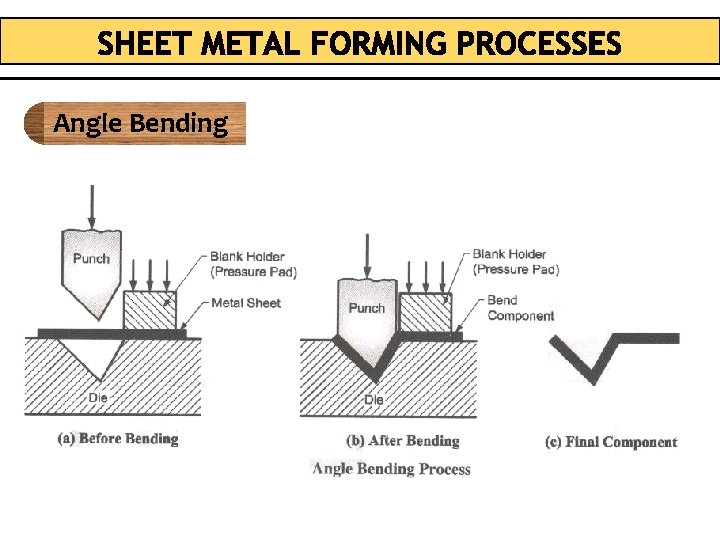
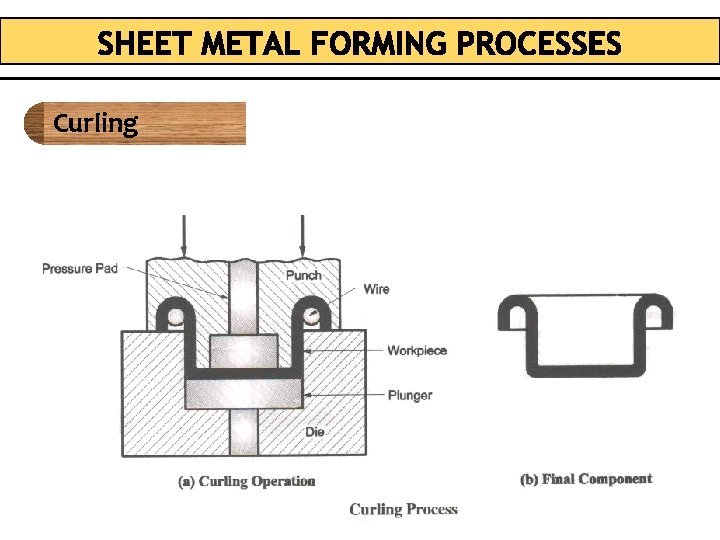
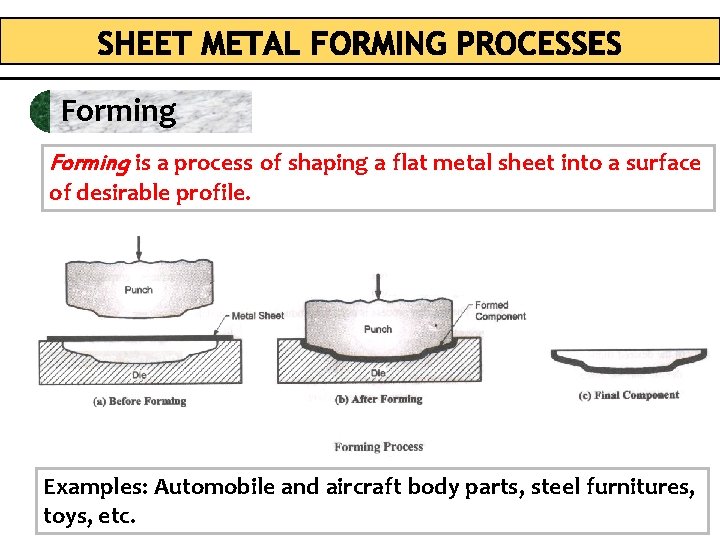
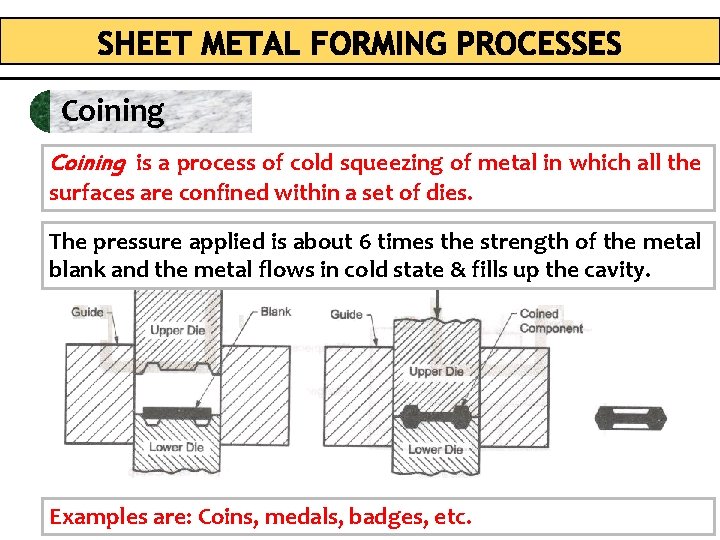
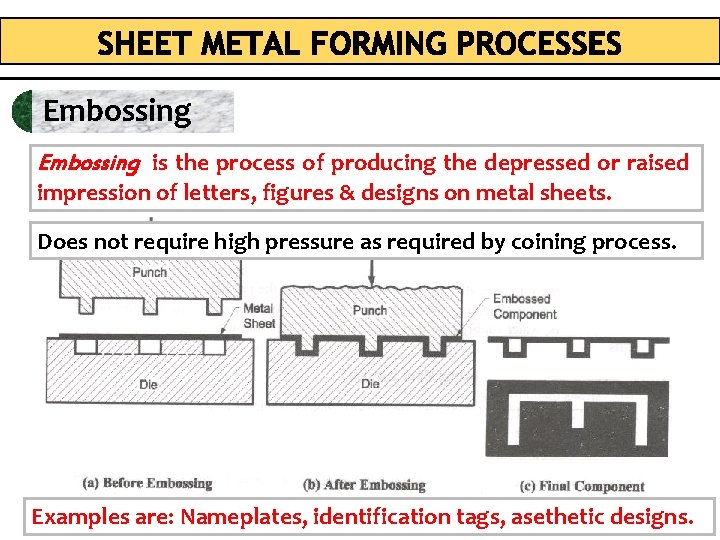
- Slides: 23
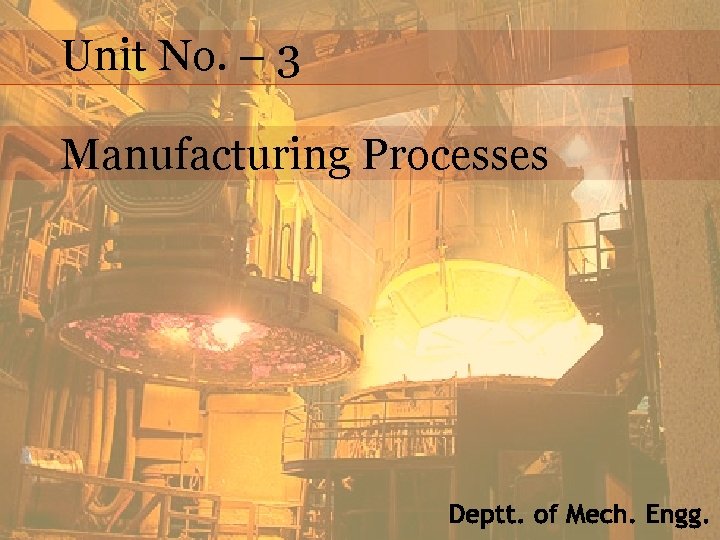
Unit No. – 3 Manufacturing Processes

Sheet Metal Working is the process of manufacturing the components or parts from the sheet-metal of thickness ranging from 0. 1 mm to about 6 to 8 mm. The sheet metal working is generally carried out with machine tools called as press. Therefore, it is also known as press working.
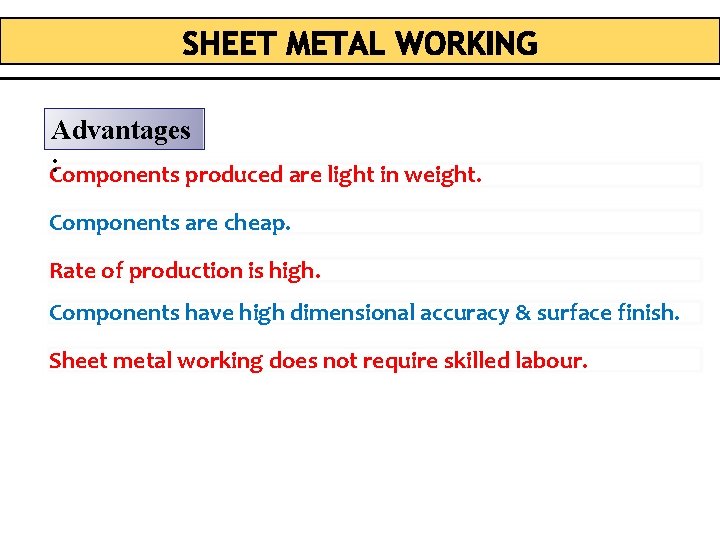
Advantages : Components produced are light in weight. Components are cheap. Rate of production is high. Components have high dimensional accuracy & surface finish. Sheet metal working does not require skilled labour.
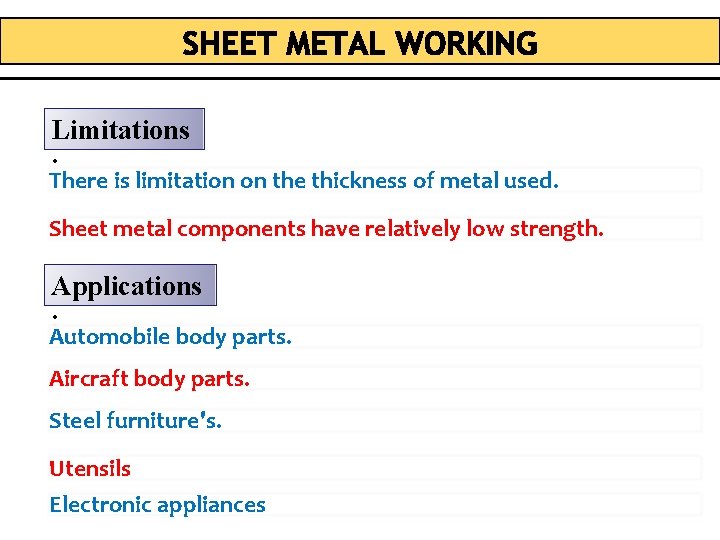
Limitations : There is limitation on the thickness of metal used. Sheet metal components have relatively low strength. Applications : Automobile body parts. Aircraft body parts. Steel furniture's. Utensils Electronic appliances
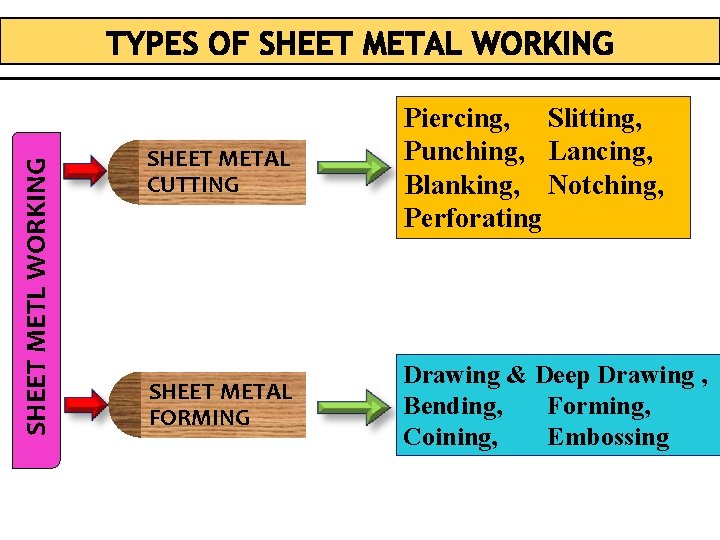
SHEET METL WORKING SHEET METAL CUTTING Piercing, Slitting, Punching, Lancing, Blanking, Notching, Perforating SHEET METAL FORMING Drawing & Deep Drawing , Bending, Forming, Coining, Embossing
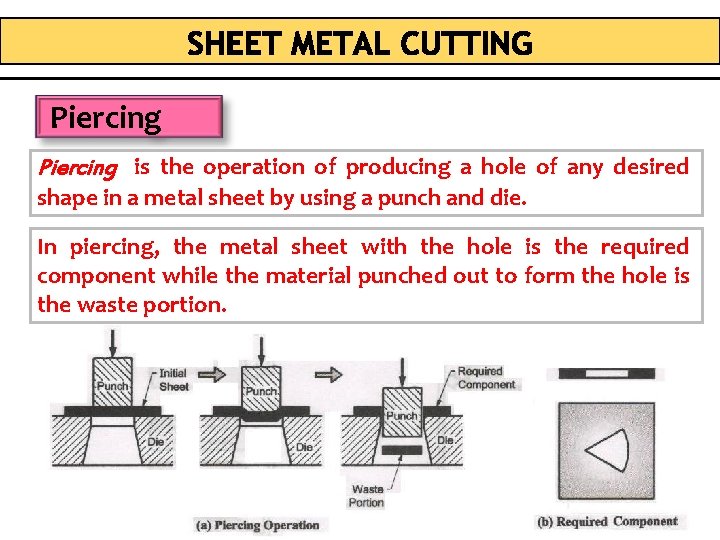
Piercing is the operation of producing a hole of any desired shape in a metal sheet by using a punch and die. In piercing, the metal sheet with the hole is the required component while the material punched out to form the hole is the waste portion.
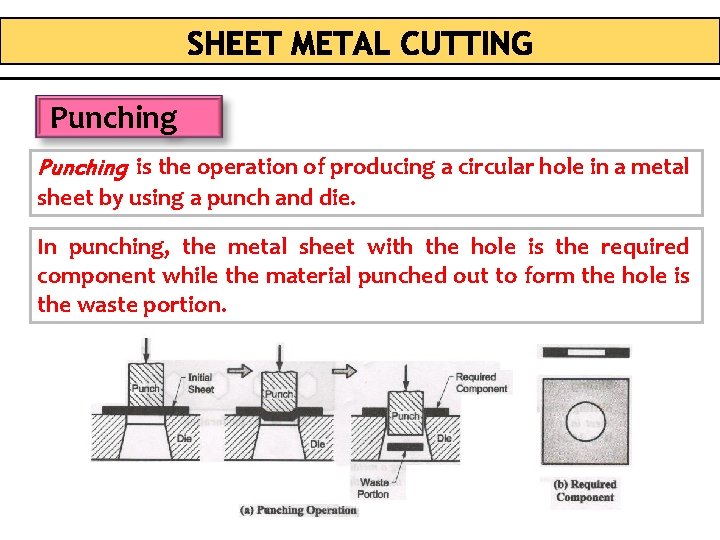
Punching is the operation of producing a circular hole in a metal sheet by using a punch and die. In punching, the metal sheet with the hole is the required component while the material punched out to form the hole is the waste portion.
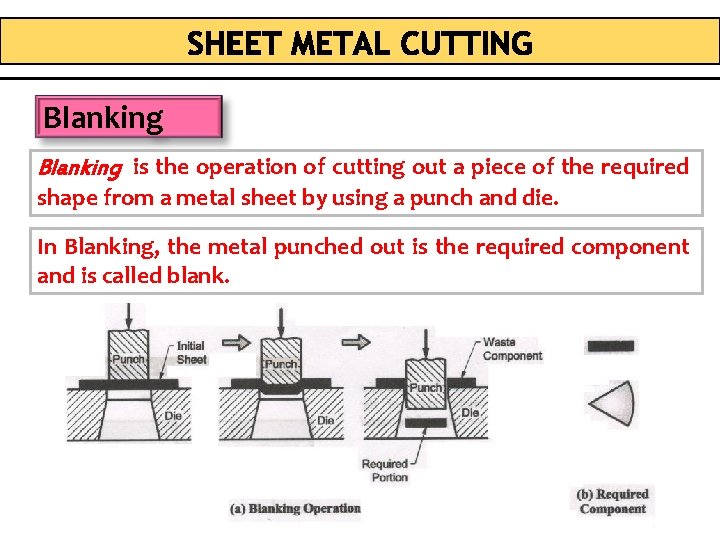
Blanking is the operation of cutting out a piece of the required shape from a metal sheet by using a punch and die. In Blanking, the metal punched out is the required component and is called blank.
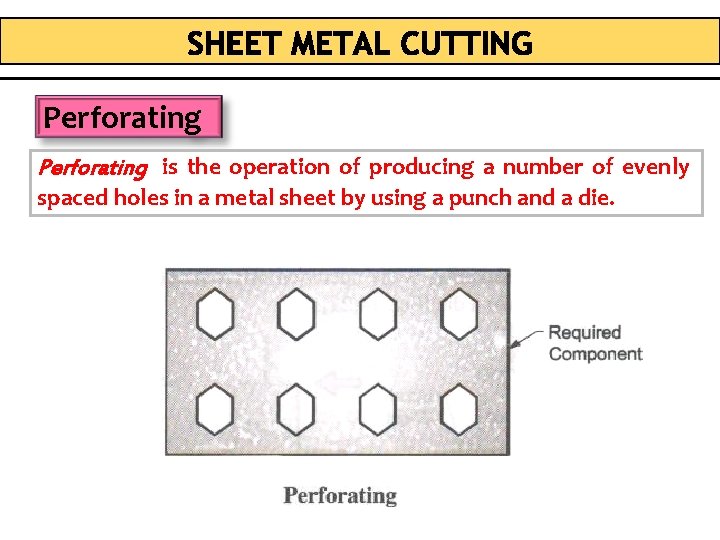
Perforating is the operation of producing a number of evenly spaced holes in a metal sheet by using a punch and a die.
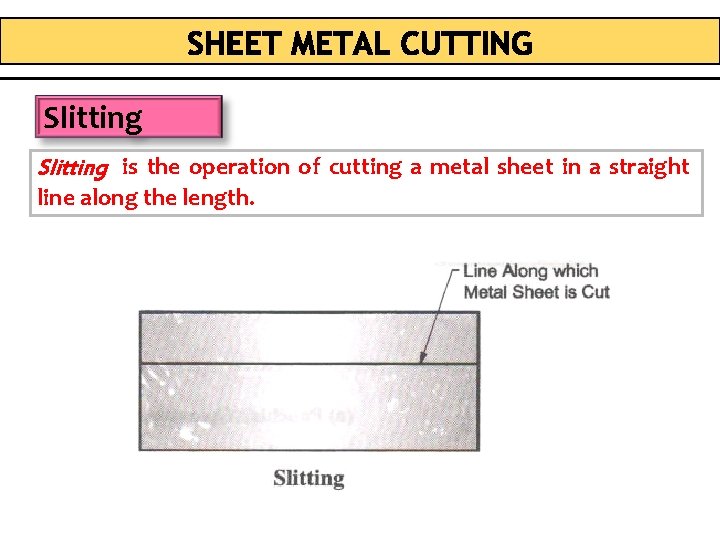
Slitting is the operation of cutting a metal sheet in a straight line along the length.
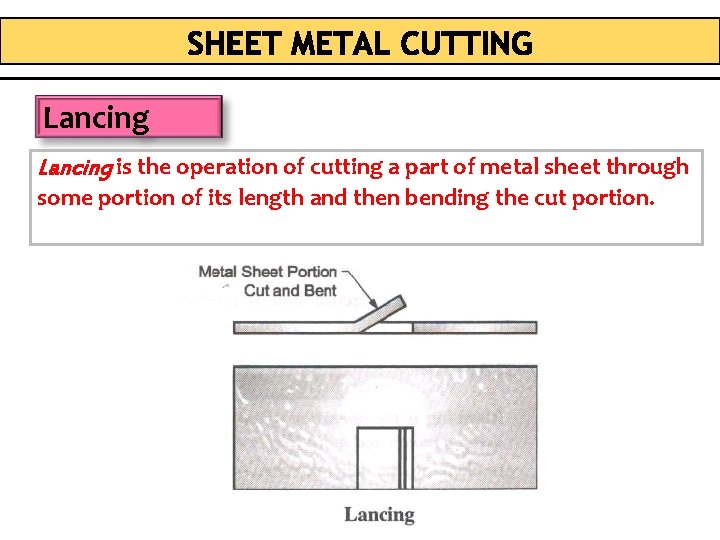
Lancing is the operation of cutting a part of metal sheet through some portion of its length and then bending the cut portion.
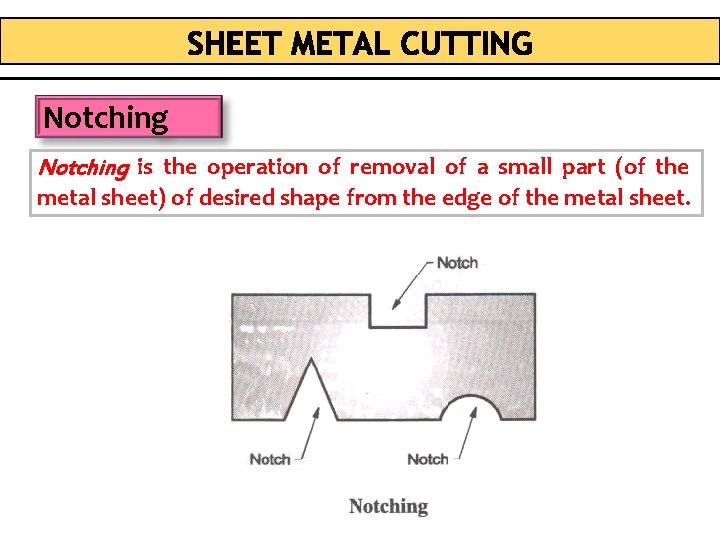
Notching is the operation of removal of a small part (of the metal sheet) of desired shape from the edge of the metal sheet.
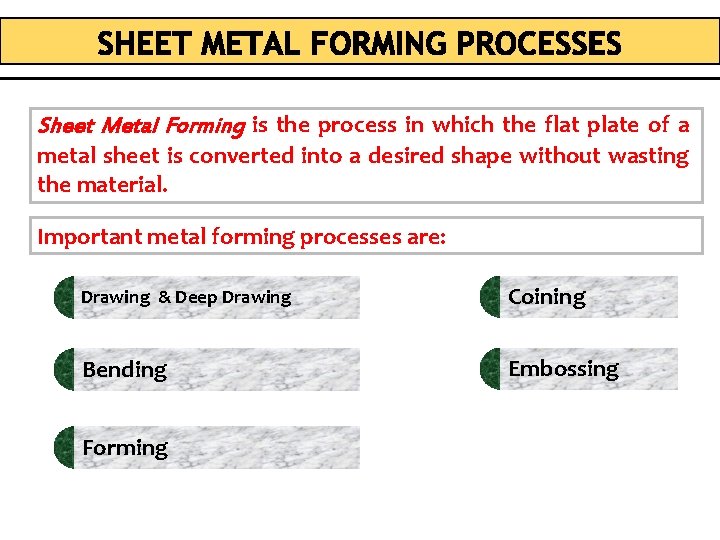
Sheet Metal Forming is the process in which the flat plate of a metal sheet is converted into a desired shape without wasting the material. Important metal forming processes are: Drawing & Deep Drawing Coining Bending Embossing Forming
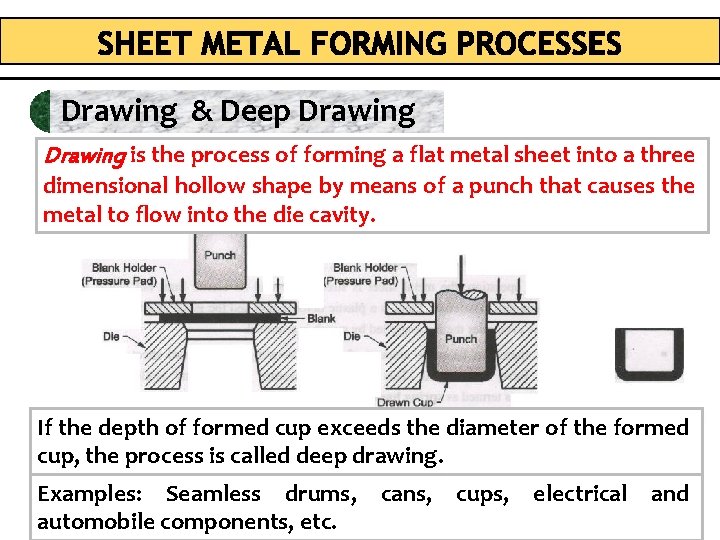
Drawing & Deep Drawing is the process of forming a flat metal sheet into a three dimensional hollow shape by means of a punch that causes the metal to flow into the die cavity. If the depth of formed cup exceeds the diameter of the formed cup, the process is called deep drawing. Examples: Seamless drums, cans, automobile components, etc. cups, electrical and
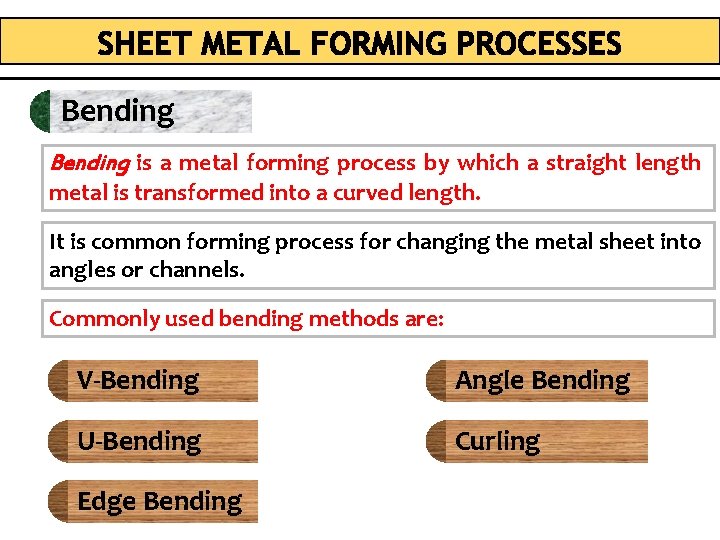
Bending is a metal forming process by which a straight length metal is transformed into a curved length. It is common forming process for changing the metal sheet into angles or channels. Commonly used bending methods are: V-Bending Angle Bending U-Bending Curling Edge Bending
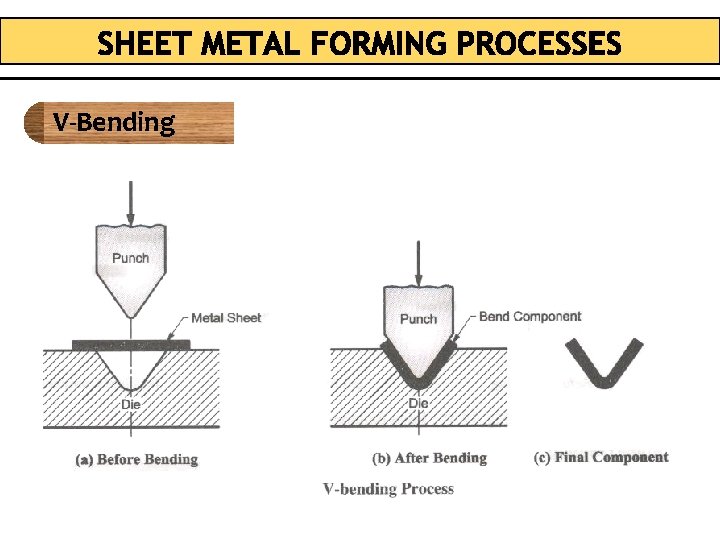
V-Bending
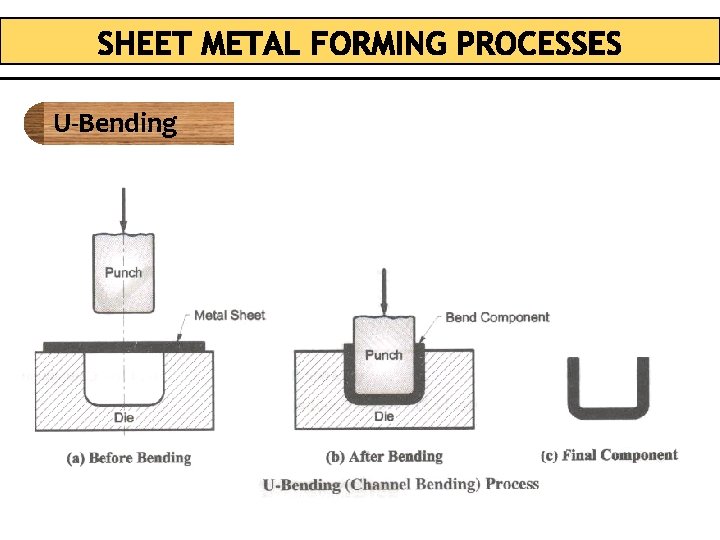
U-Bending
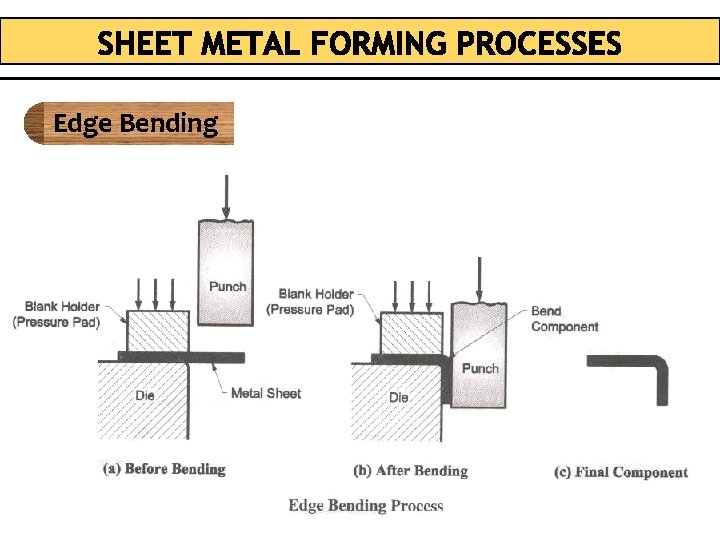
Edge Bending
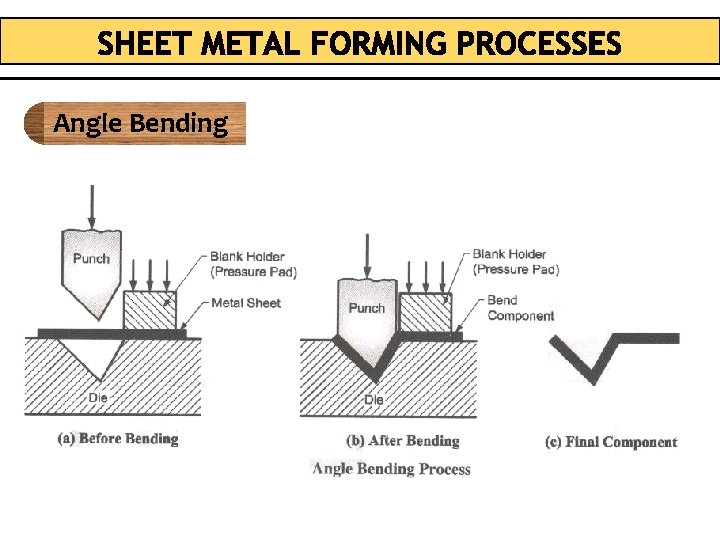
Angle Bending
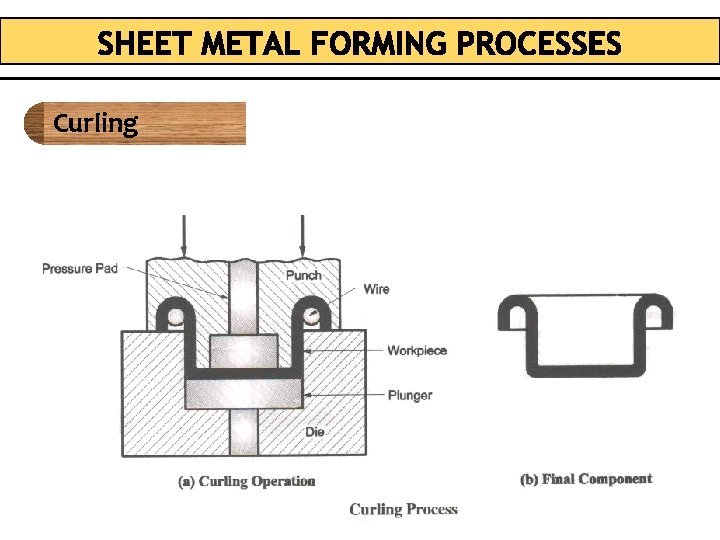
Curling
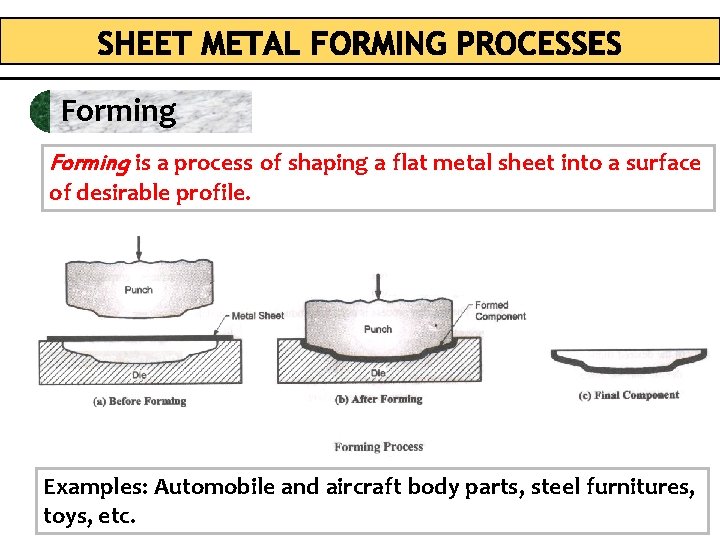
Forming is a process of shaping a flat metal sheet into a surface of desirable profile. Examples: Automobile and aircraft body parts, steel furnitures, toys, etc.
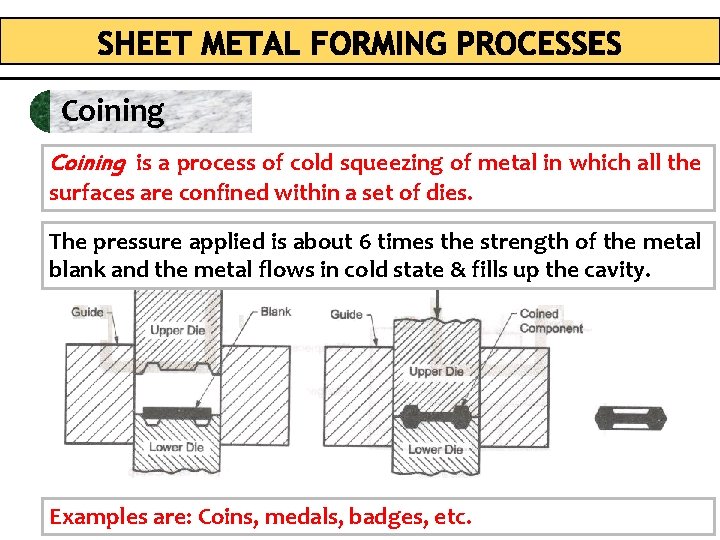
Coining is a process of cold squeezing of metal in which all the surfaces are confined within a set of dies. The pressure applied is about 6 times the strength of the metal blank and the metal flows in cold state & fills up the cavity. Examples are: Coins, medals, badges, etc.
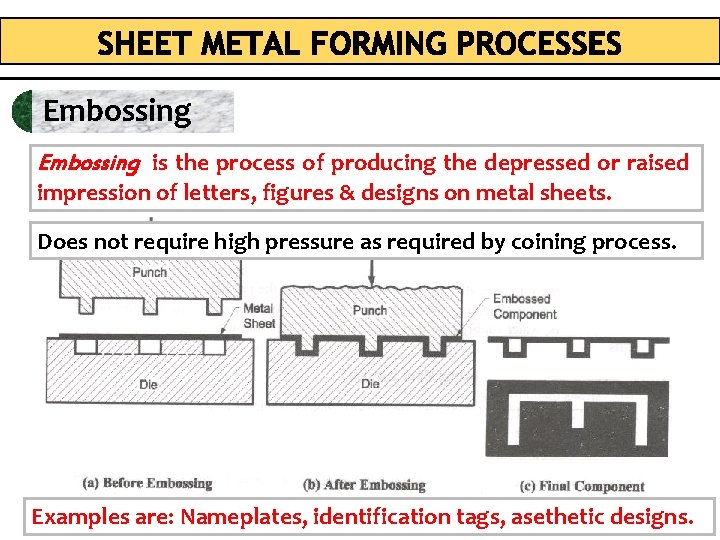
Embossing is the process of producing the depressed or raised impression of letters, figures & designs on metal sheets. Does not require high pressure as required by coining process. Examples are: Nameplates, identification tags, asethetic designs.
Flashless forging process
Sheet metal coining
Manufacturing cost vs non manufacturing cost
Job order vs process costing
Non controllable cost
Manufacturing cost vs non manufacturing cost
Additive manufacturing steps
Manufacturing process for engineering materials
Manufacturing process classification
Introduction to manufacturing process
Pultrusion advantages and disadvantages
Nontraditional manufacturing processes
Similar
Industrial revolution transition
Nature of manufacturing process
Concurrent in os
Cold working of metals
Smart work vs hard work
Hot working and cold working difference
Differentiate between hot working and cold working
Prinsip dasar proses pengerjaan panas yang benar adalah
Solid liquid and gas diagram
Characteristics of metals
Acidity trends periodic table