Unit 3 MANUFACTURING PROCESS Prof Kiran Gore Contents
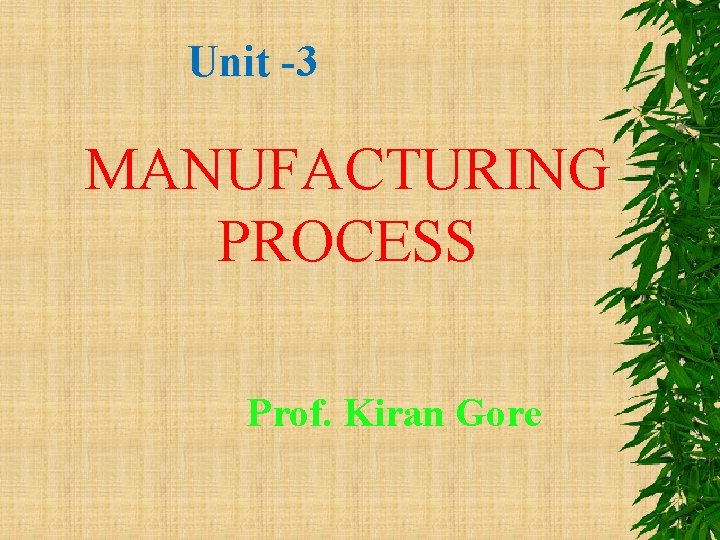
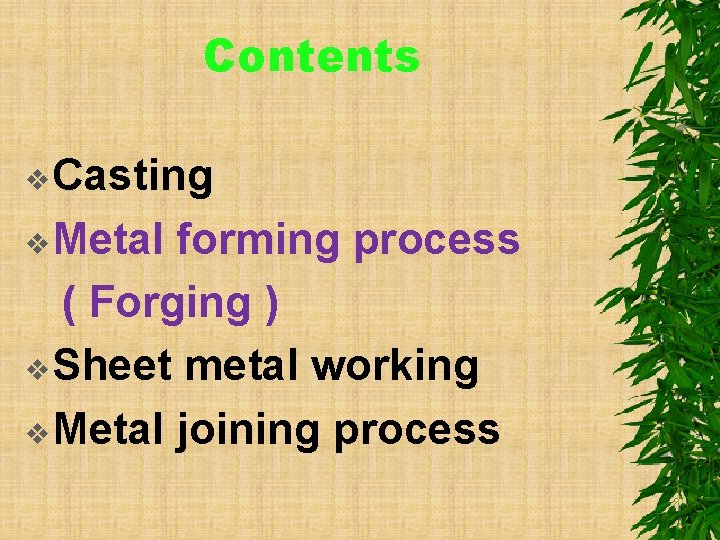
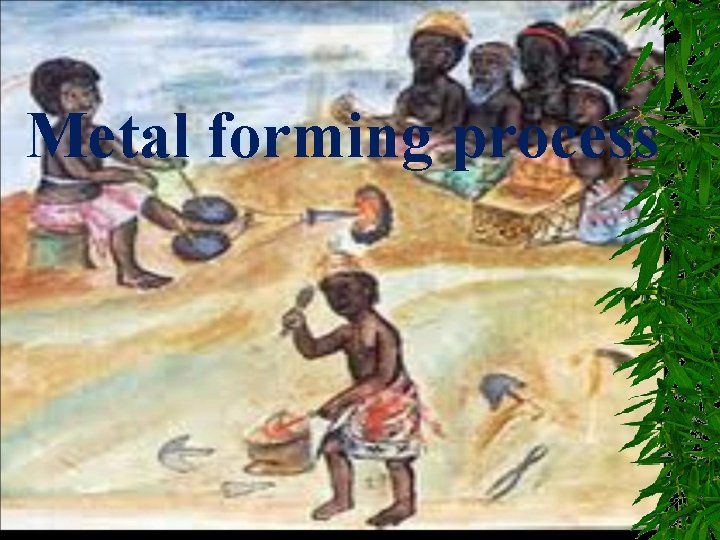
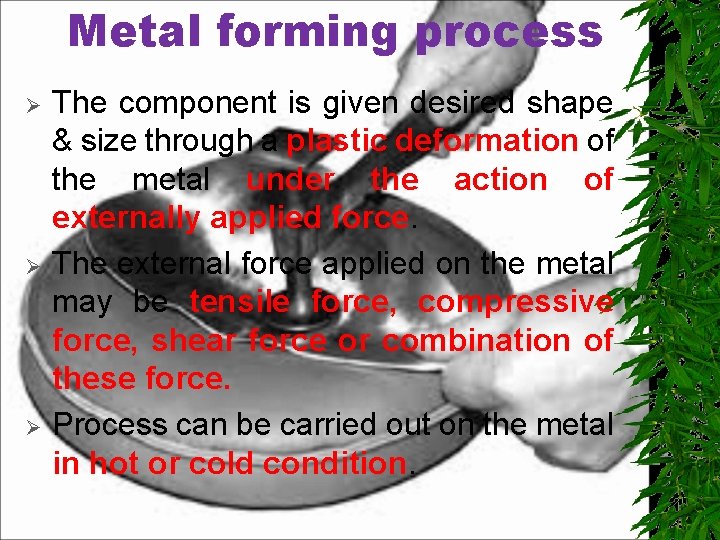
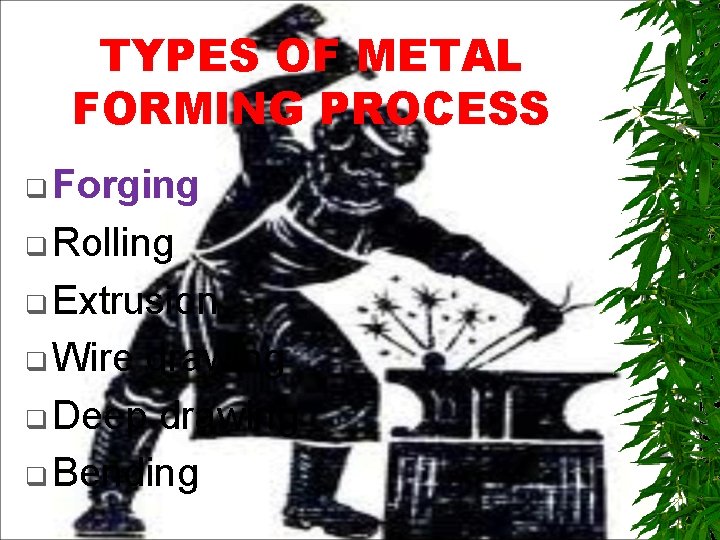
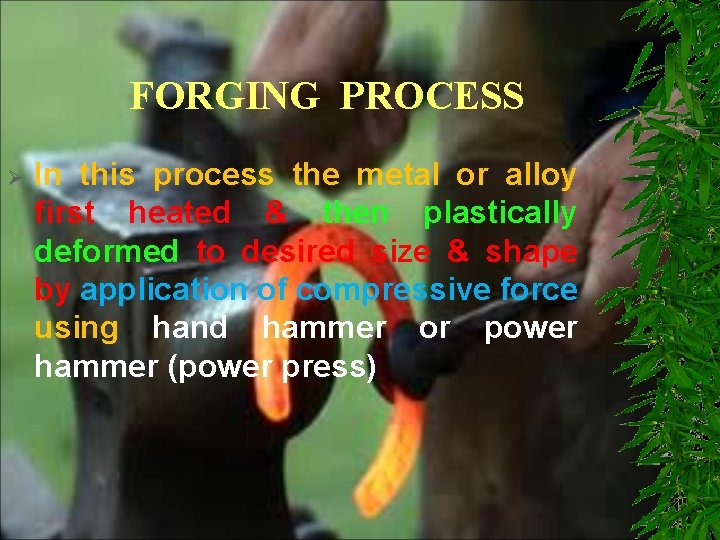
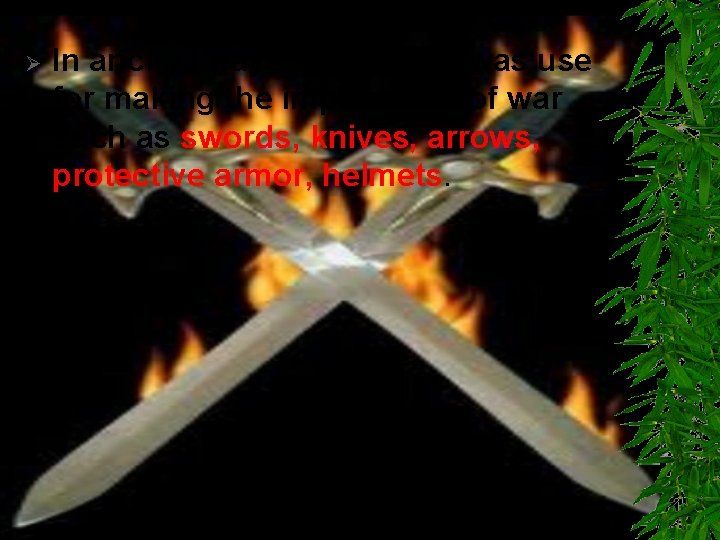
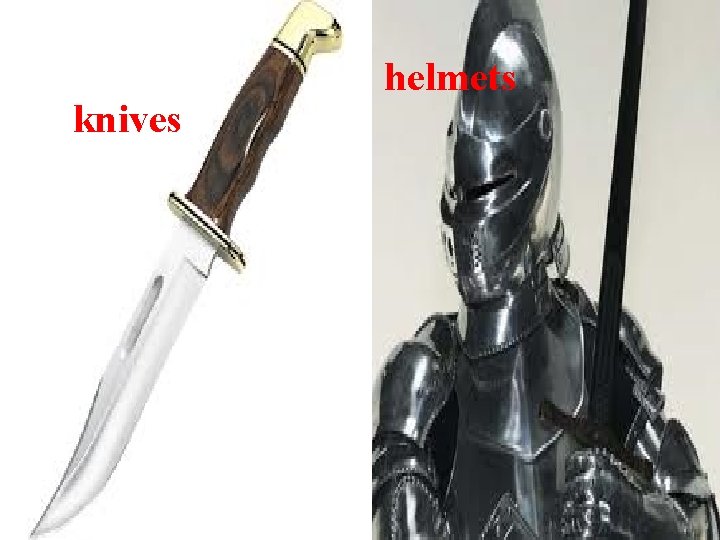
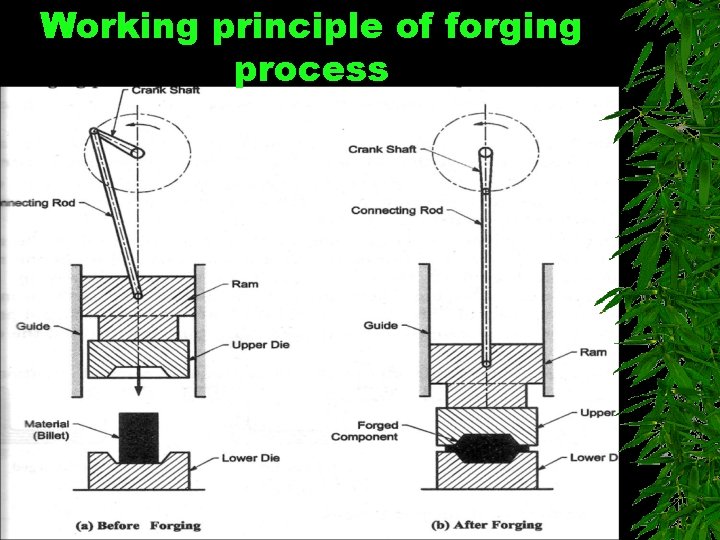
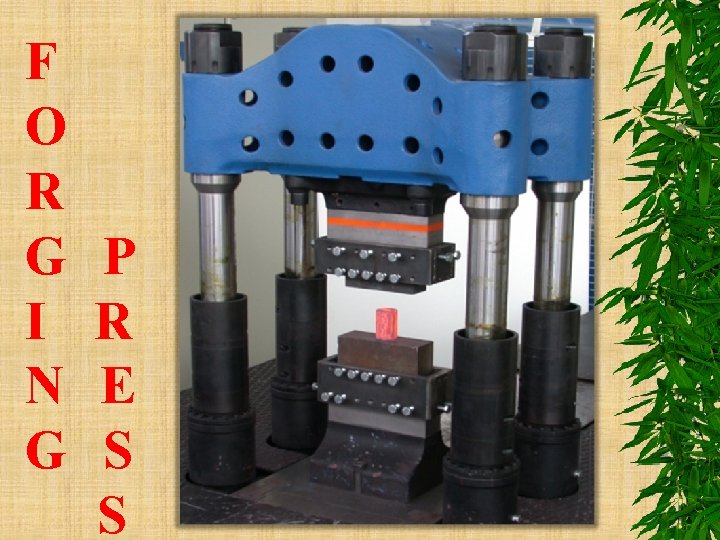
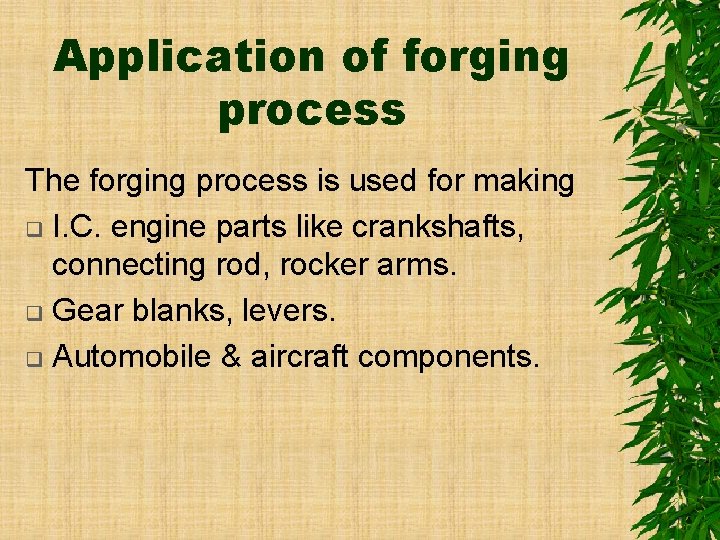
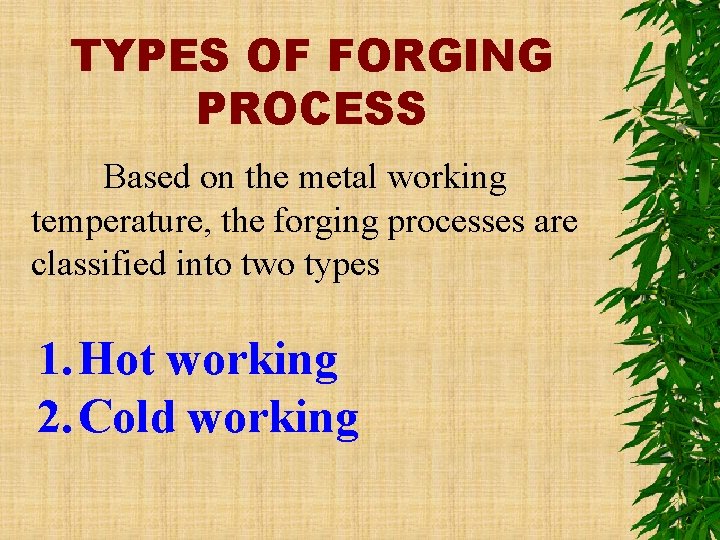
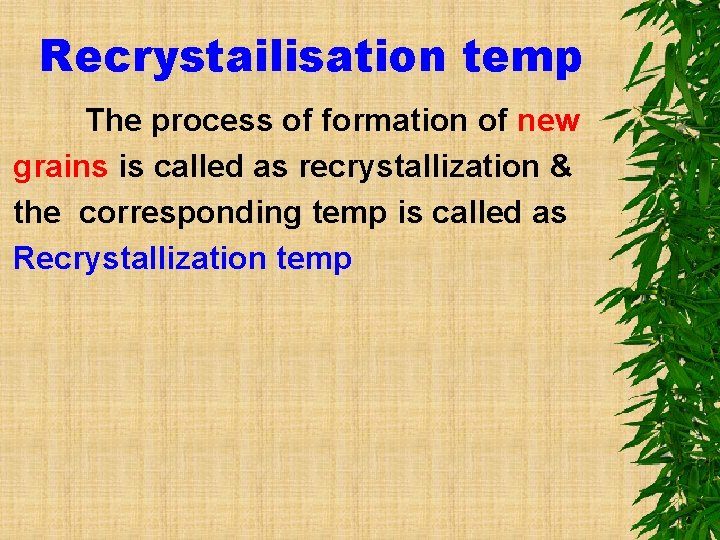
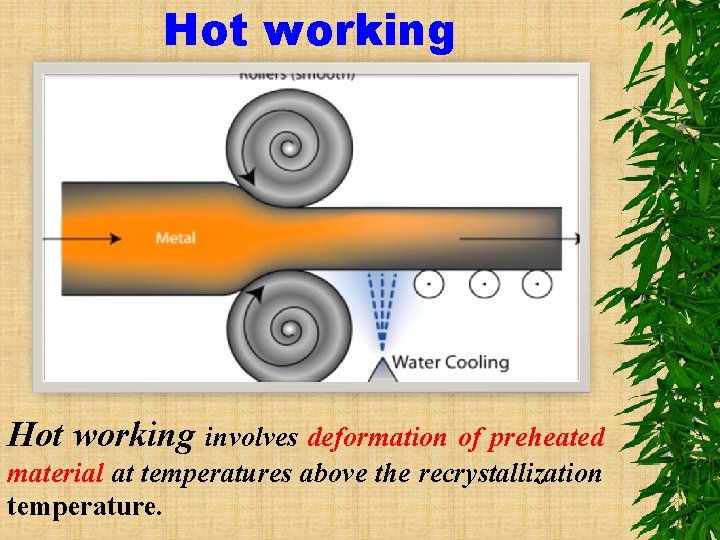

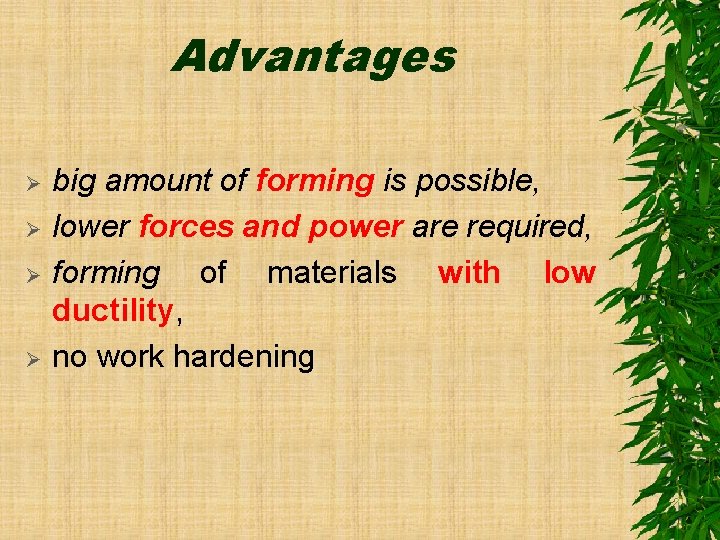
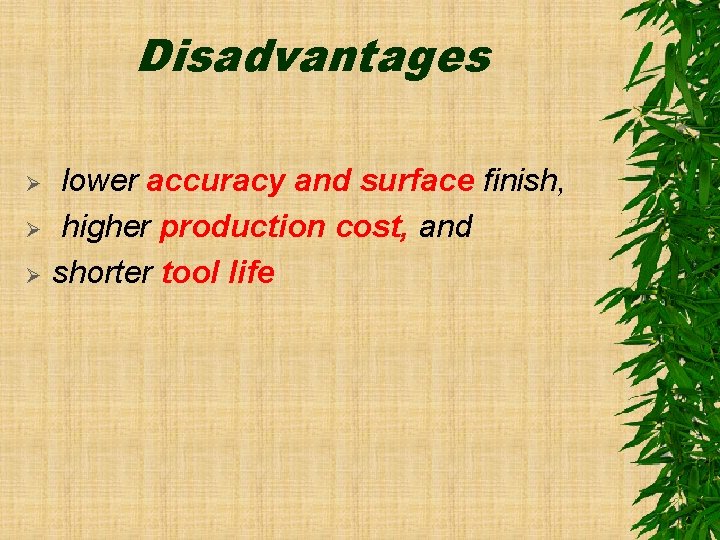
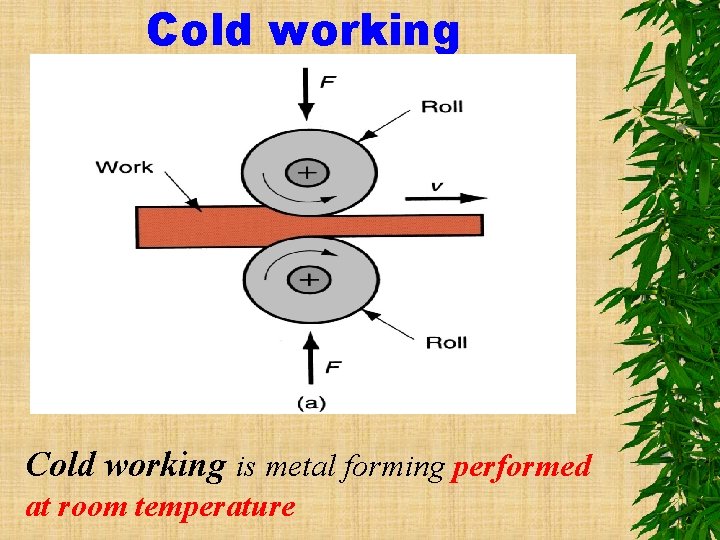
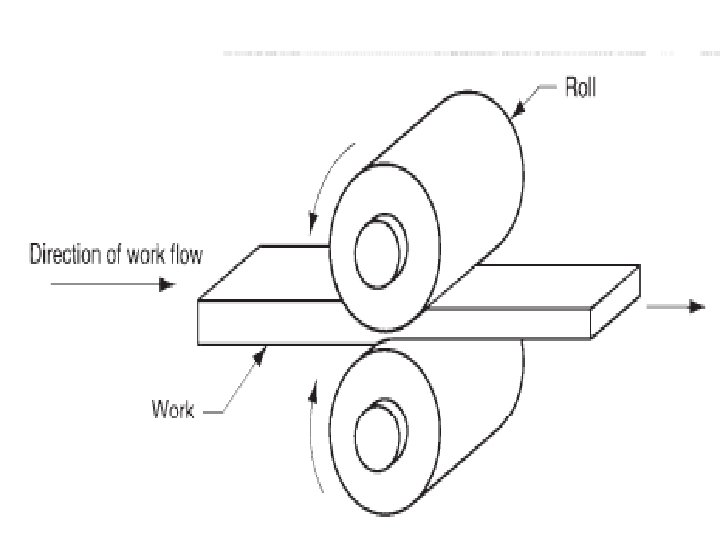
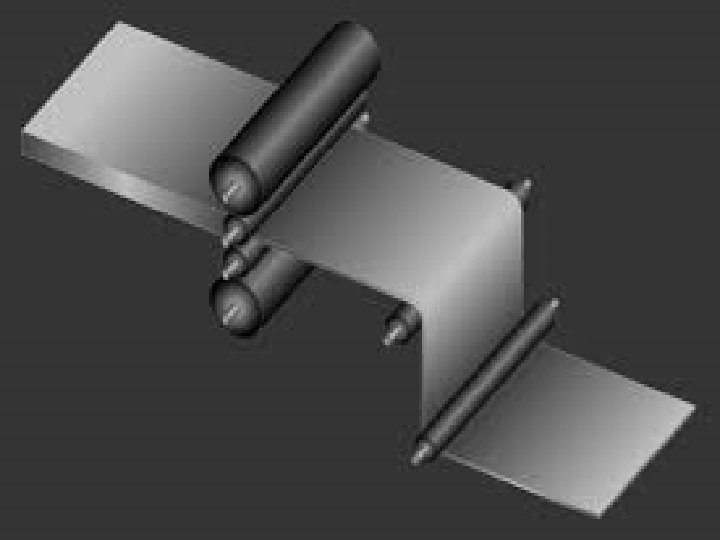
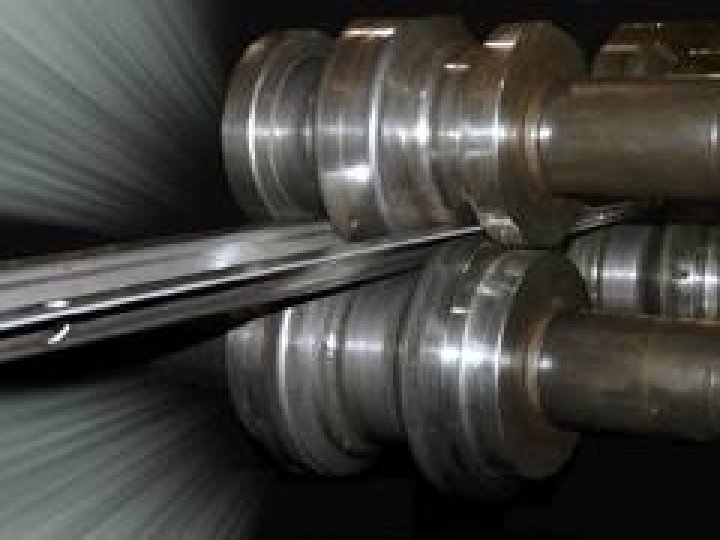
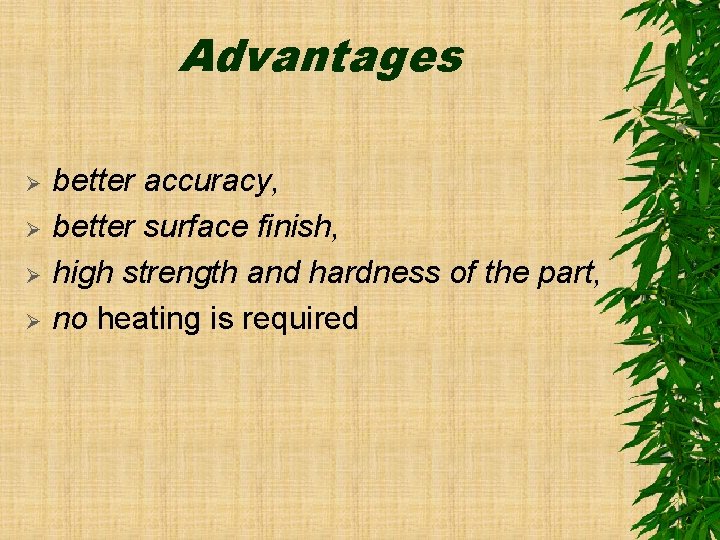
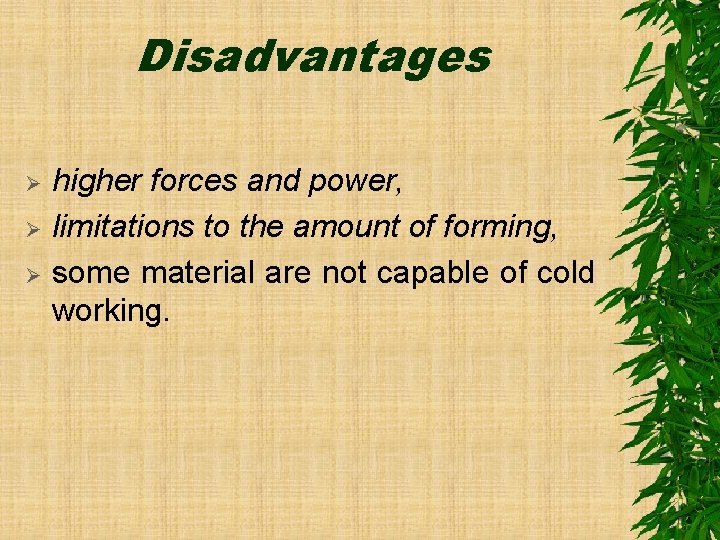
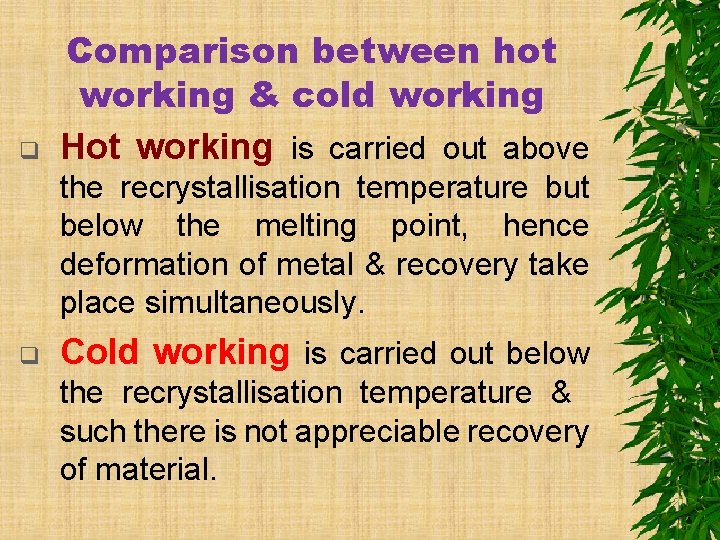
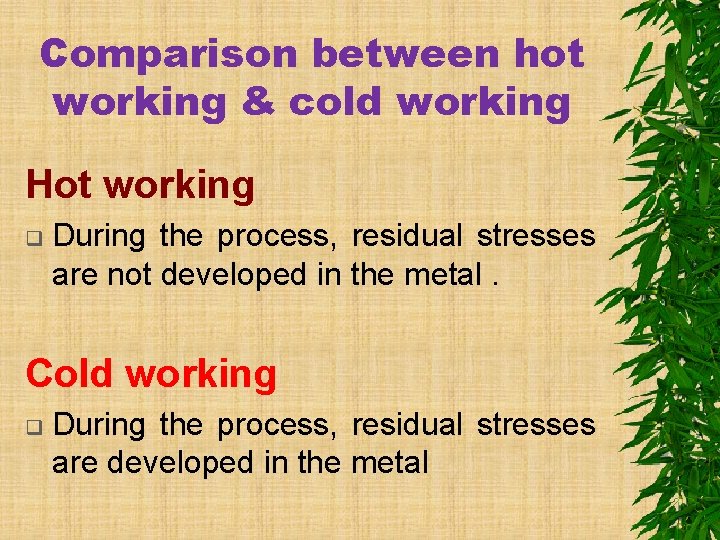
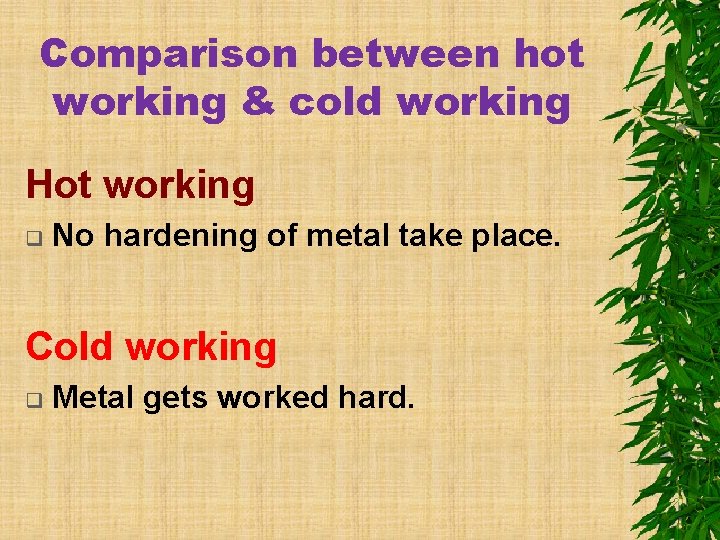
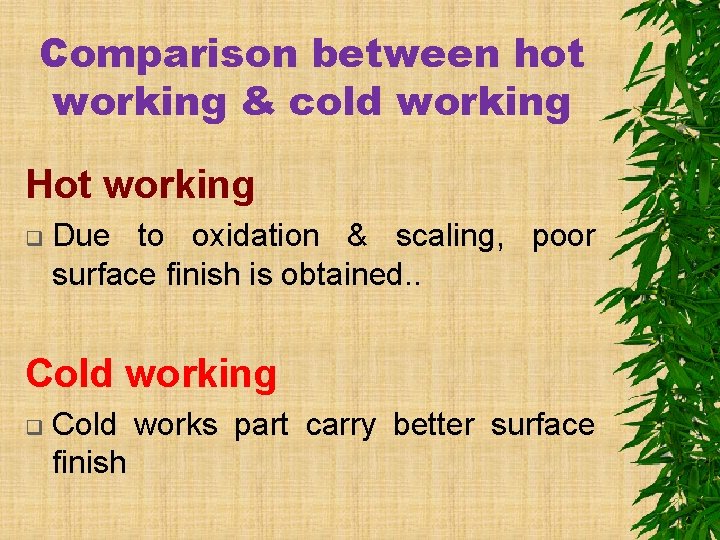
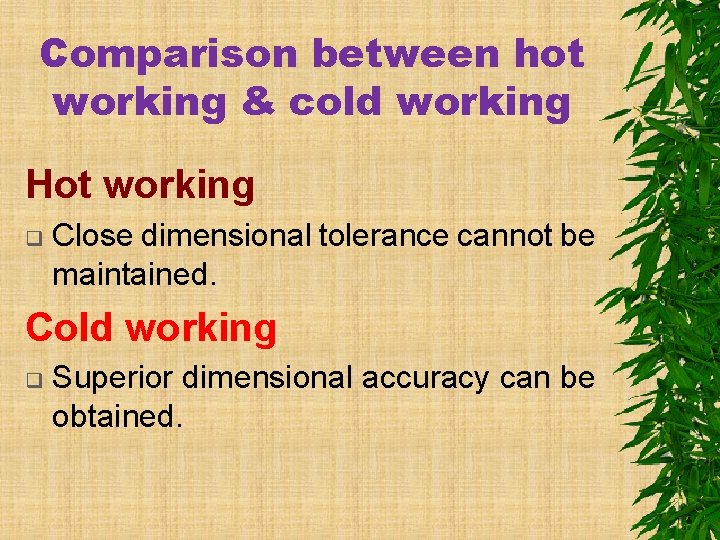
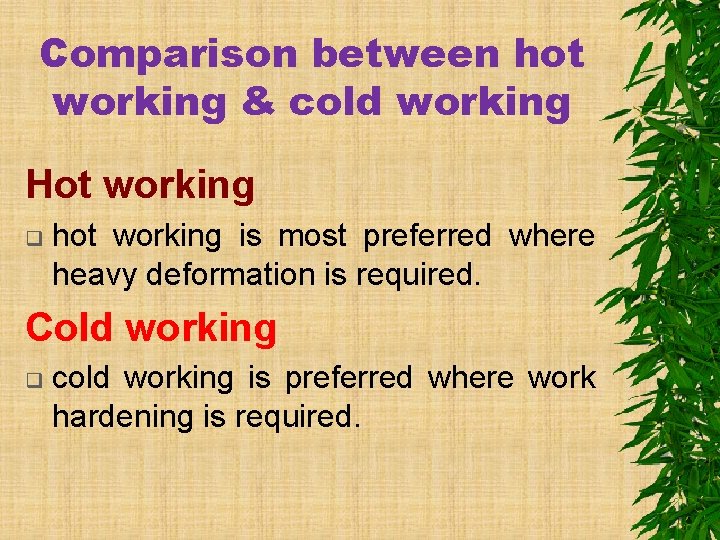
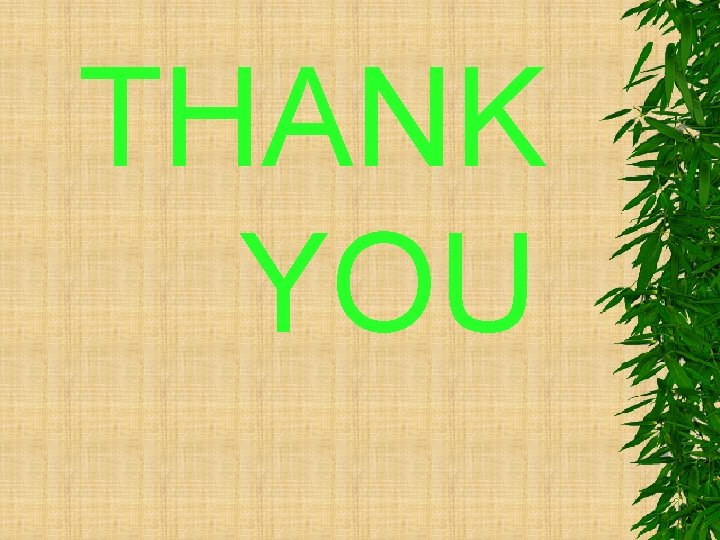
- Slides: 30
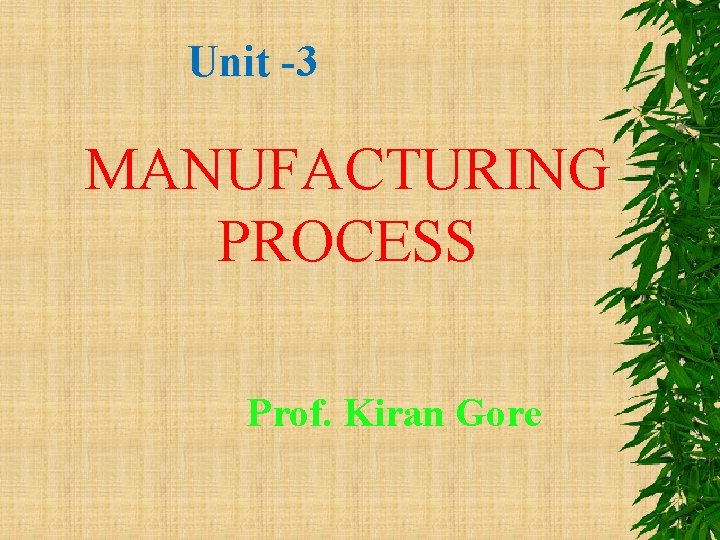
Unit -3 MANUFACTURING PROCESS Prof. Kiran Gore
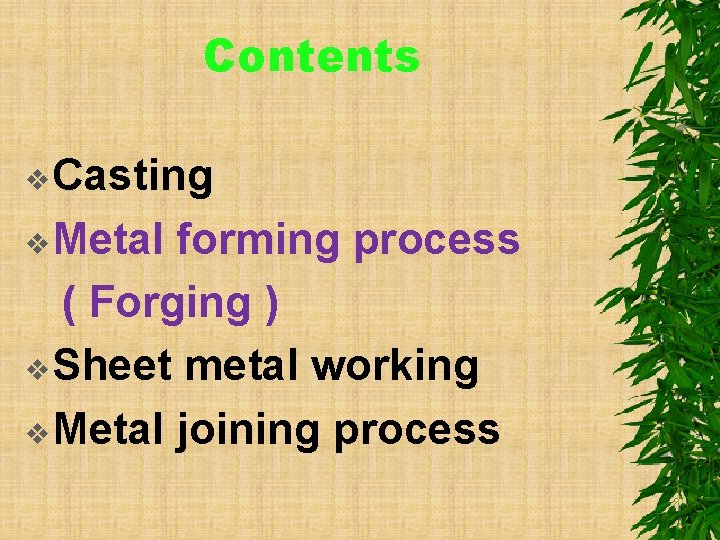
Contents v Casting v Metal forming process ( Forging ) v Sheet metal working v Metal joining process
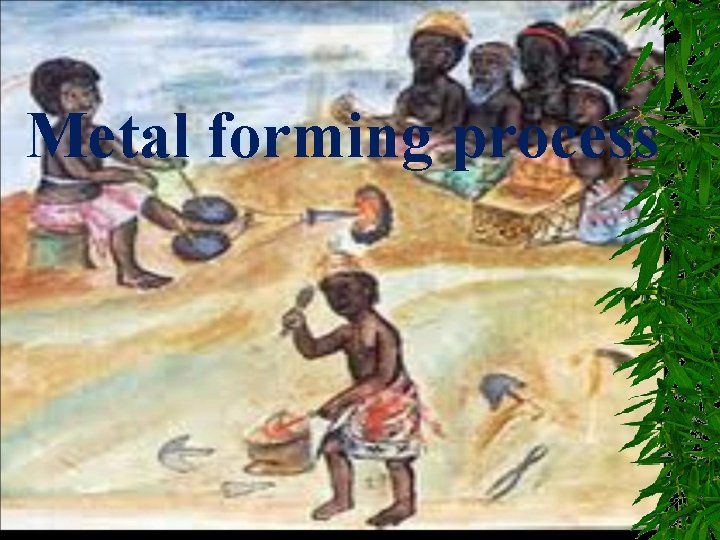
Metal forming process
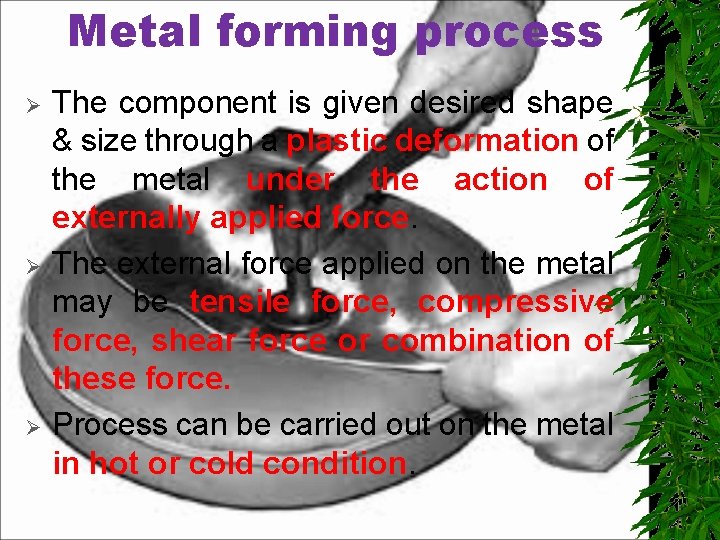
Metal forming process Ø Ø Ø The component is given desired shape & size through a plastic deformation of the metal under the action of externally applied force. The external force applied on the metal may be tensile force, compressive force, shear force or combination of these force. Process can be carried out on the metal in hot or cold condition.
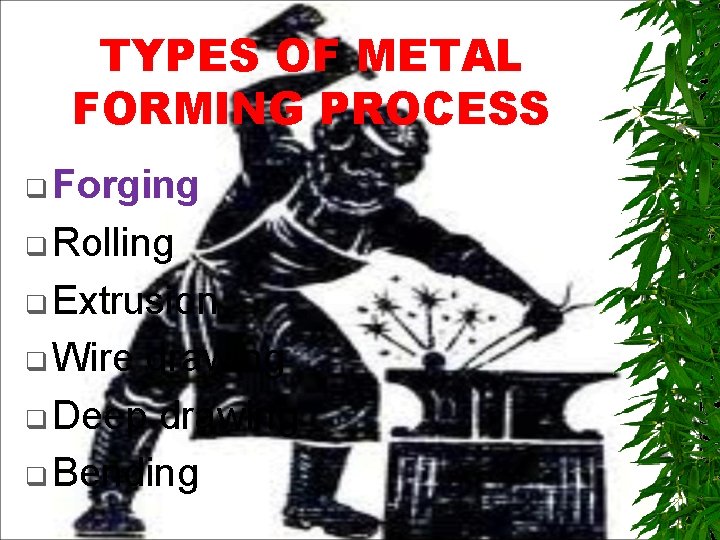
TYPES OF METAL FORMING PROCESS q Forging q Rolling q Extrusion q Wire drawing q Deep drawing q Bending
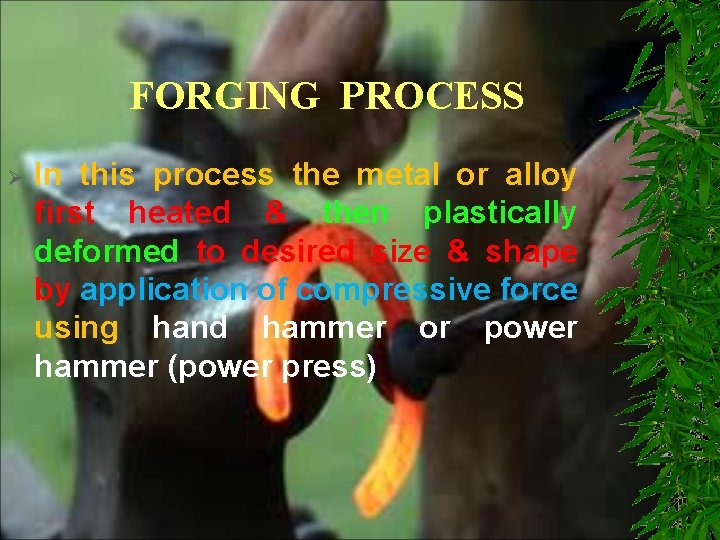
FORGING PROCESS Ø In this process the metal or alloy first heated & then plastically deformed to desired size & shape by application of compressive force using hand hammer or power hammer (power press)
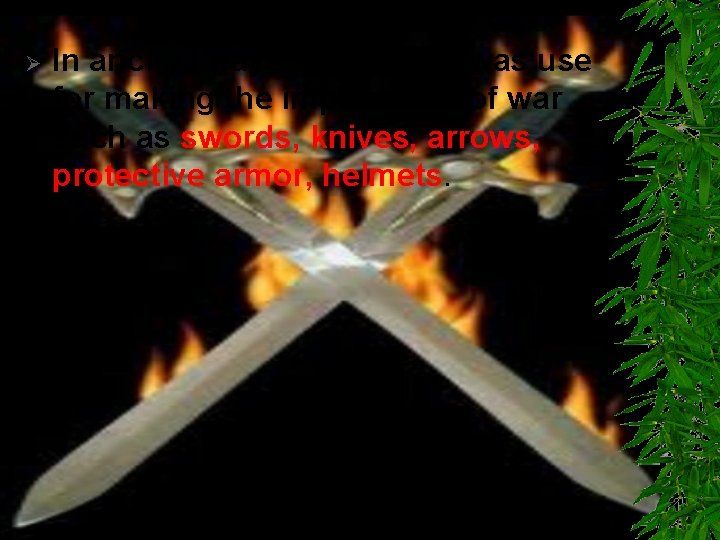
Ø In ancient days the forging was use for making the implements of war such as swords, knives, arrows, protective armor, helmets.
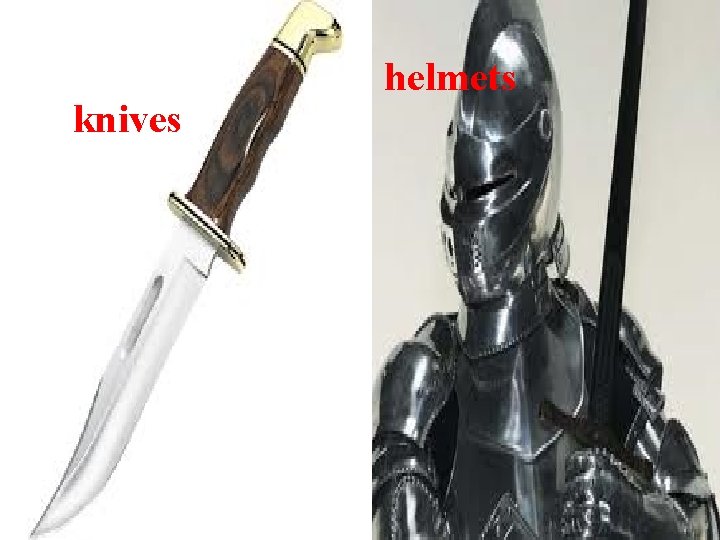
knives helmets
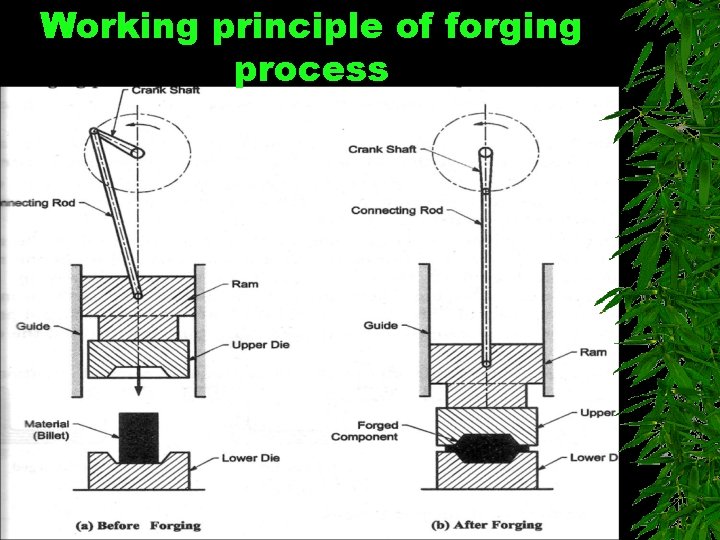
Working principle of forging process
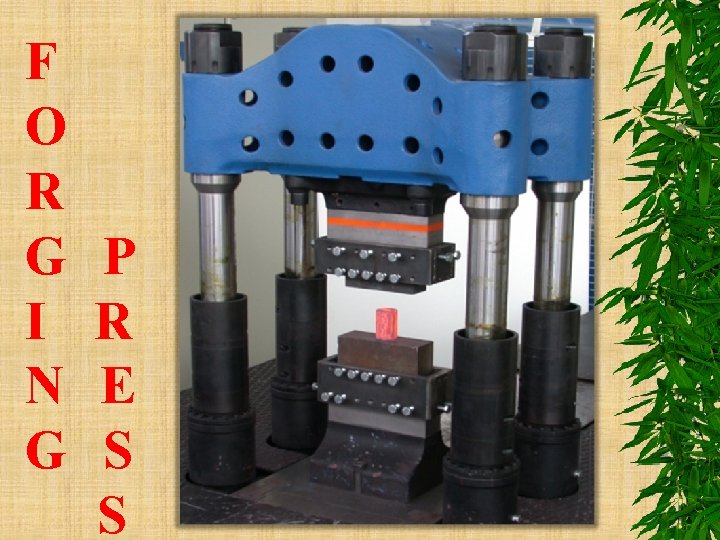
F O R G I N G P R E S S
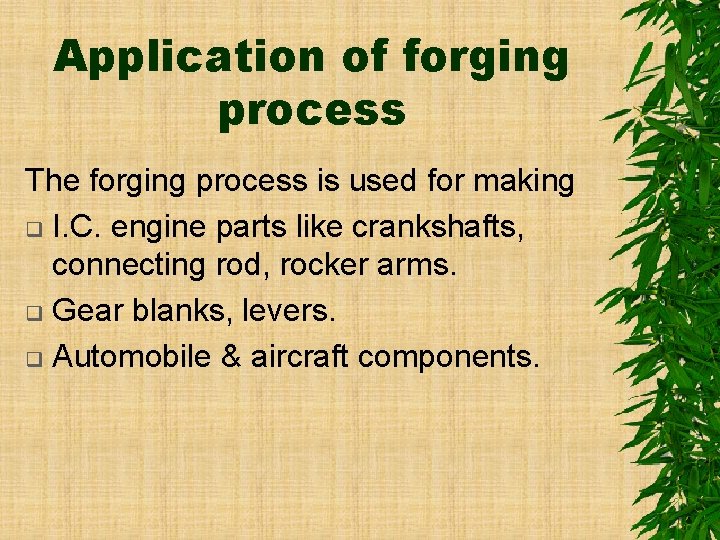
Application of forging process The forging process is used for making q I. C. engine parts like crankshafts, connecting rod, rocker arms. q Gear blanks, levers. q Automobile & aircraft components.
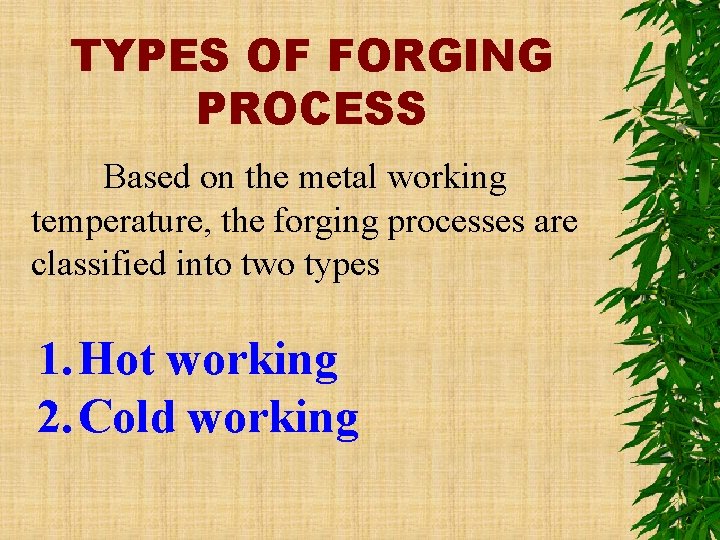
TYPES OF FORGING PROCESS Based on the metal working temperature, the forging processes are classified into two types 1. Hot working 2. Cold working
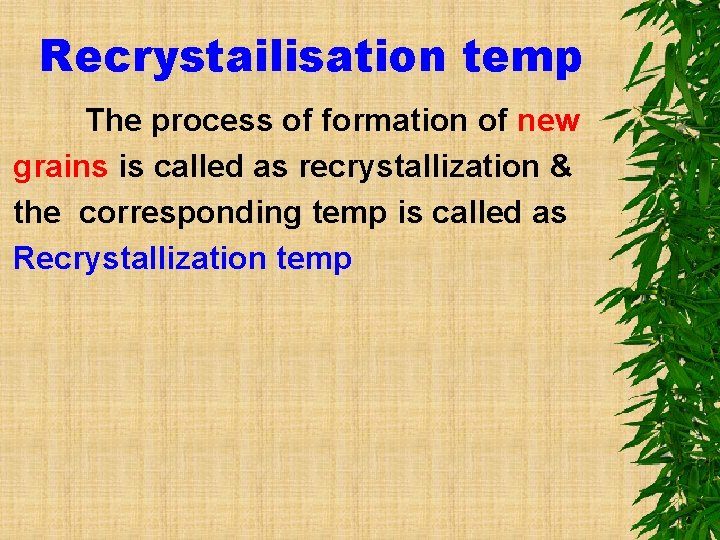
Recrystailisation temp The process of formation of new grains is called as recrystallization & the corresponding temp is called as Recrystallization temp
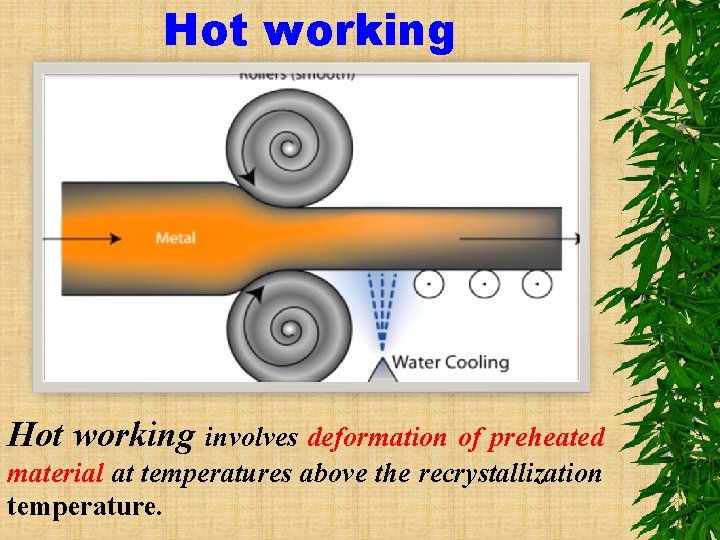
Hot working involves deformation of preheated material at temperatures above the recrystallization temperature.

Ø The average temperature necessary for hot forging of steel component is 11000 C to 12000 C. Ø The average temperature necessary for hot forging of aluminum alloy is 3500 C to 5250 C.
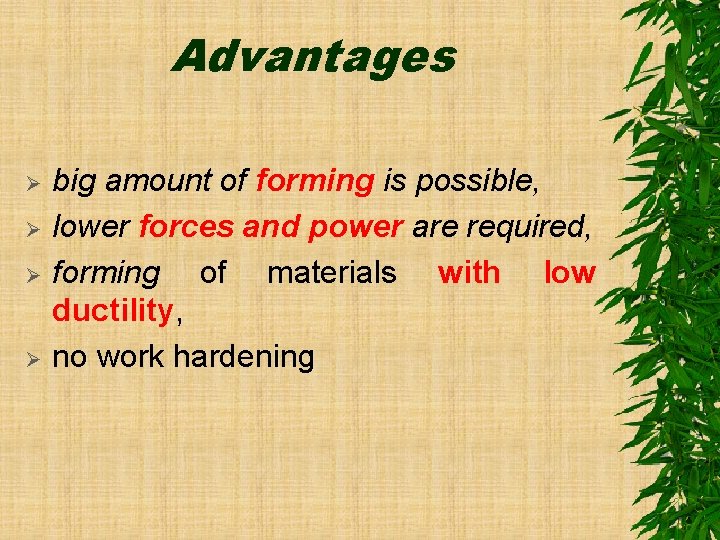
Advantages Ø Ø big amount of forming is possible, lower forces and power are required, forming of materials with low ductility, no work hardening
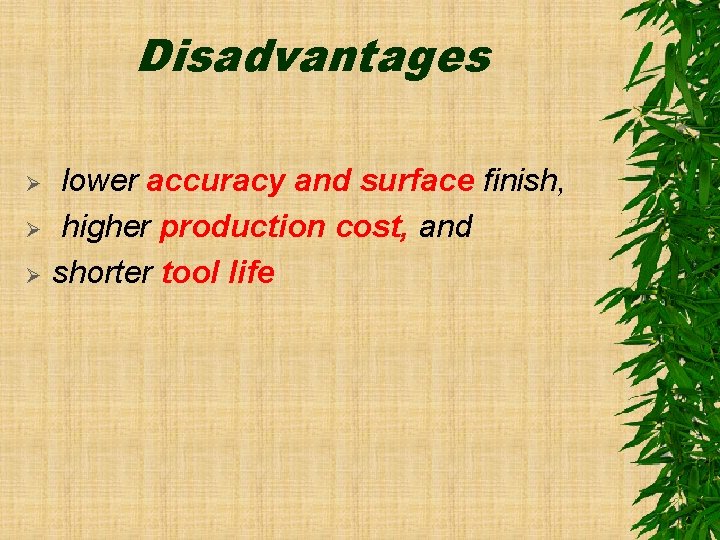
Disadvantages Ø Ø Ø lower accuracy and surface finish, higher production cost, and shorter tool life
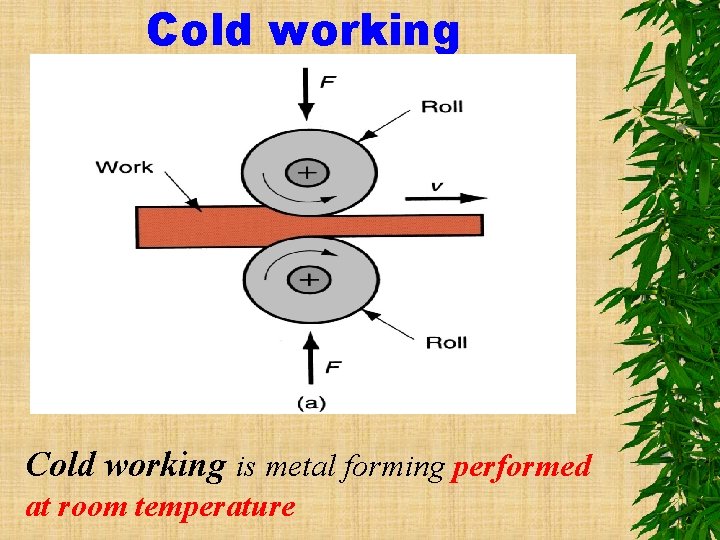
Cold working is metal forming performed at room temperature
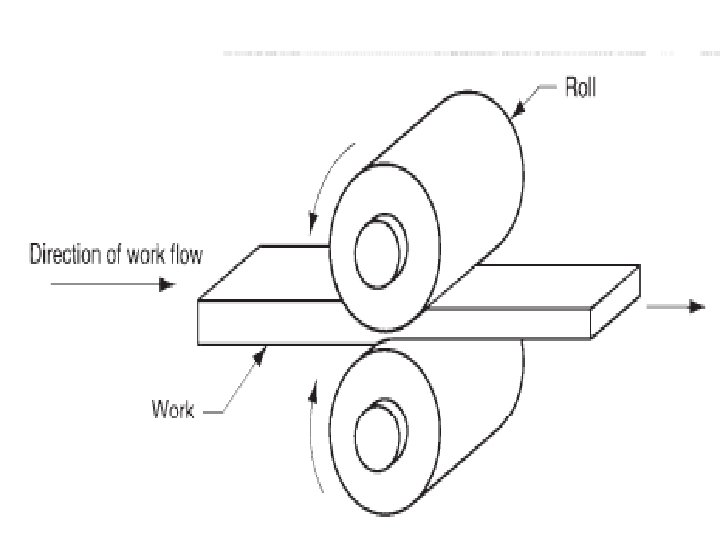
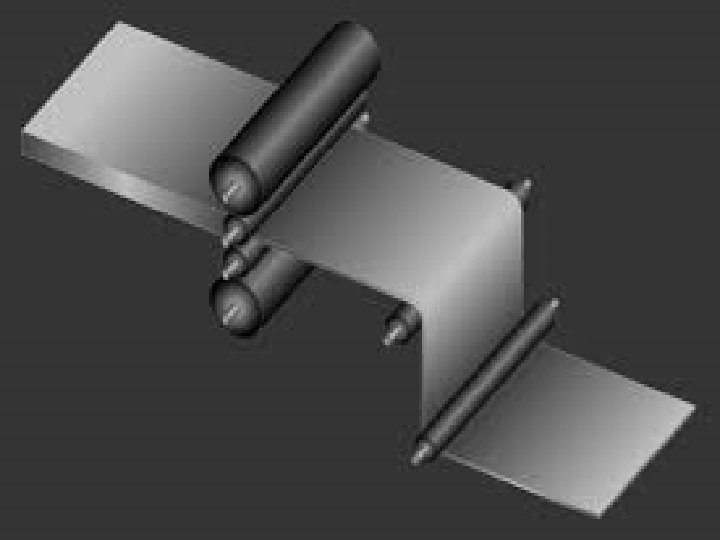
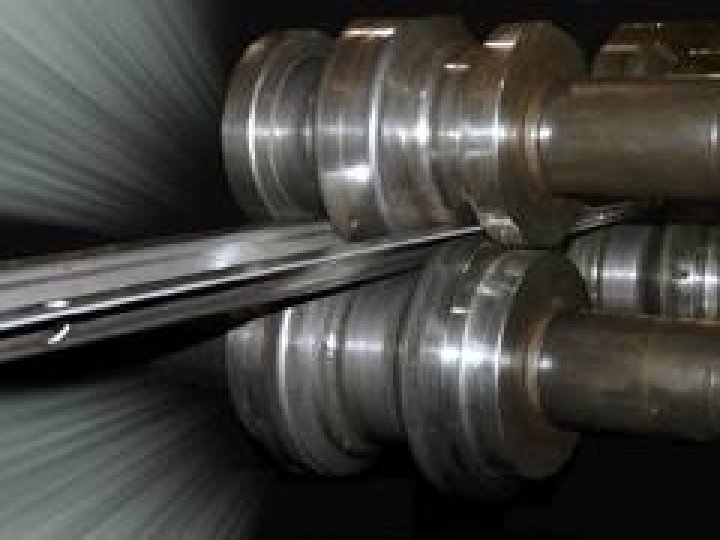
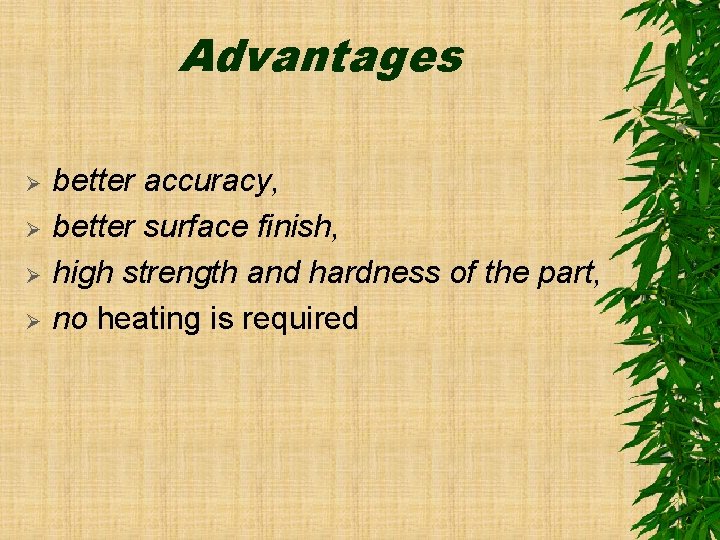
Advantages Ø Ø better accuracy, better surface finish, high strength and hardness of the part, no heating is required
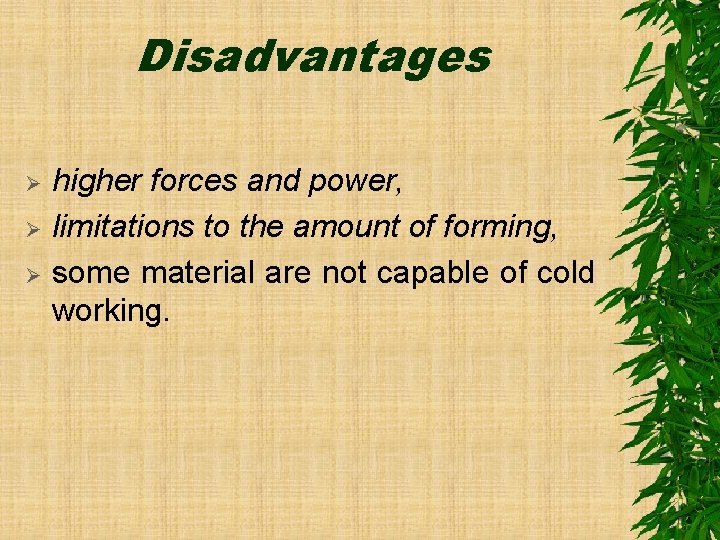
Disadvantages Ø Ø Ø higher forces and power, limitations to the amount of forming, some material are not capable of cold working.
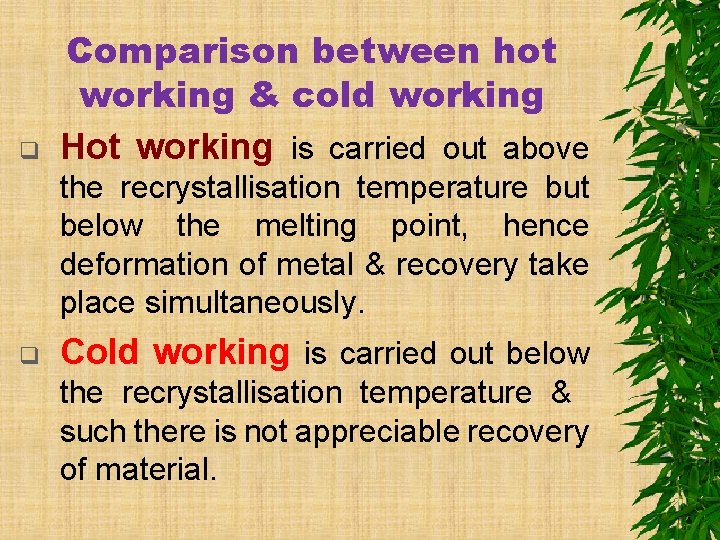
q Comparison between hot working & cold working Hot working is carried out above the recrystallisation temperature but below the melting point, hence deformation of metal & recovery take place simultaneously. q Cold working is carried out below the recrystallisation temperature & such there is not appreciable recovery of material.
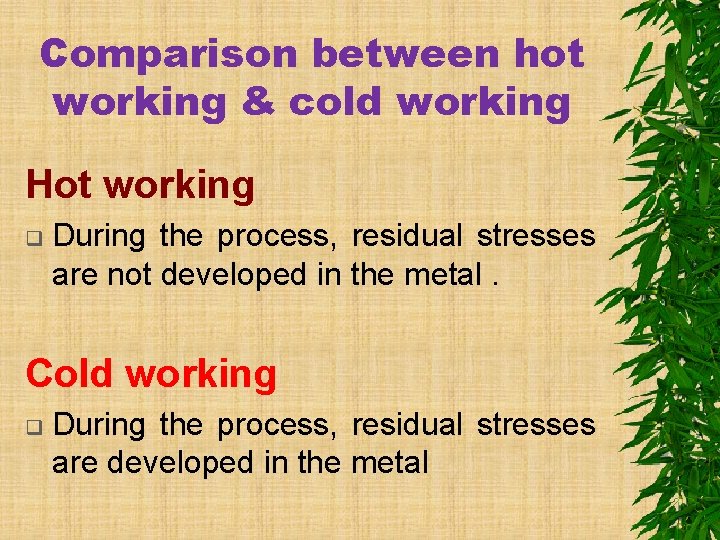
Comparison between hot working & cold working Hot working q During the process, residual stresses are not developed in the metal. Cold working q During the process, residual stresses are developed in the metal
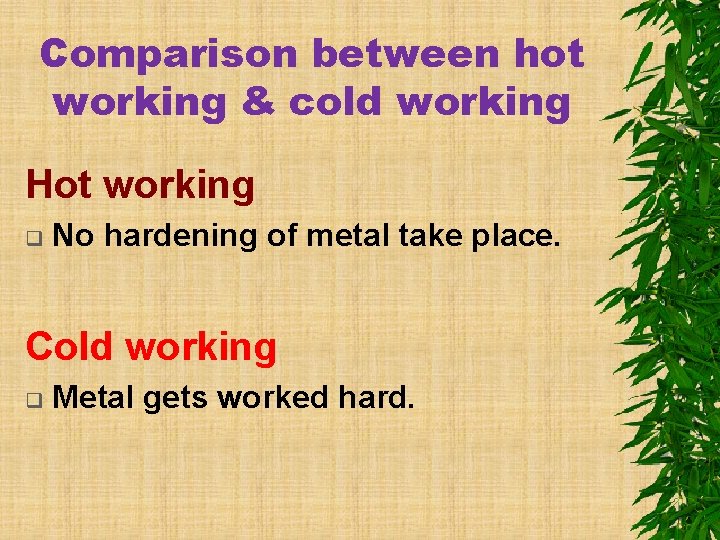
Comparison between hot working & cold working Hot working q No hardening of metal take place. Cold working q Metal gets worked hard.
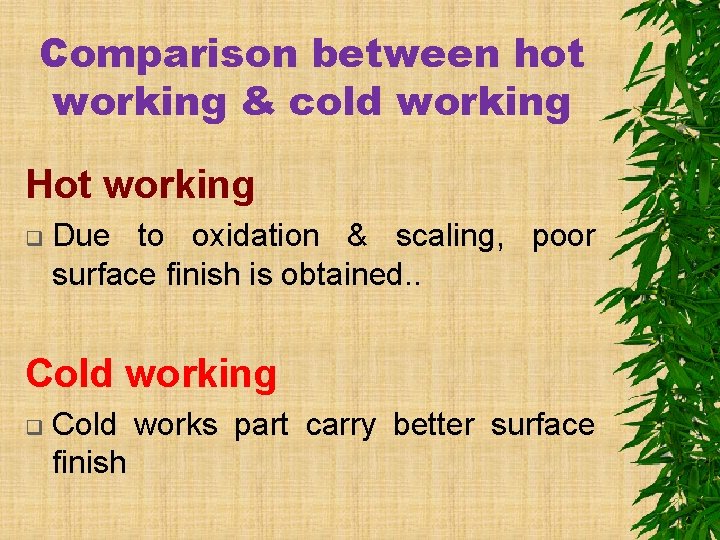
Comparison between hot working & cold working Hot working q Due to oxidation & scaling, poor surface finish is obtained. . Cold working q Cold works part carry better surface finish
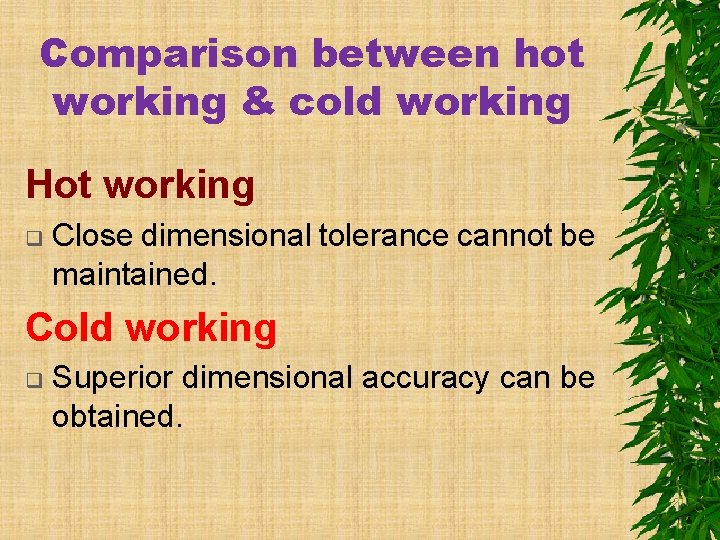
Comparison between hot working & cold working Hot working q Close dimensional tolerance cannot be maintained. Cold working q Superior dimensional accuracy can be obtained.
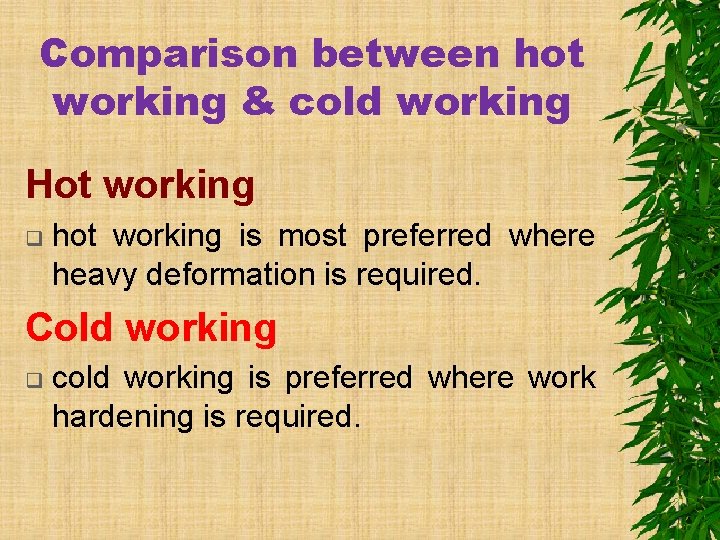
Comparison between hot working & cold working Hot working q hot working is most preferred where heavy deformation is required. Cold working q cold working is preferred where work hardening is required.
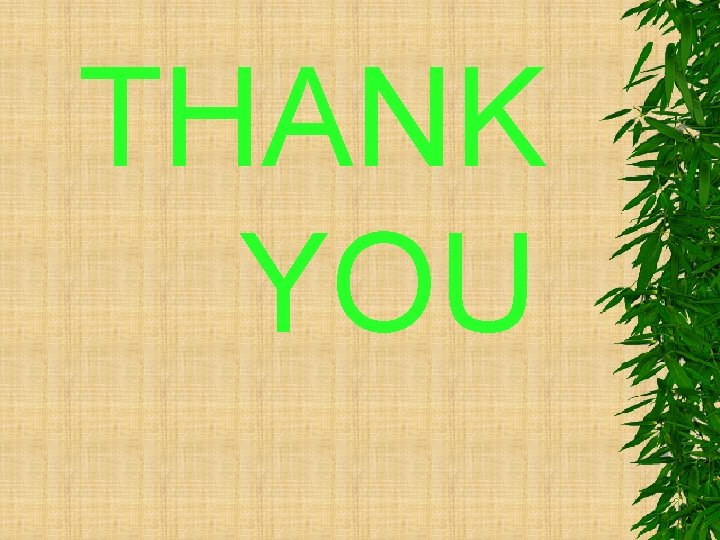
THANK YOU