Electrolytic process for chlorine caustic soda production Raw
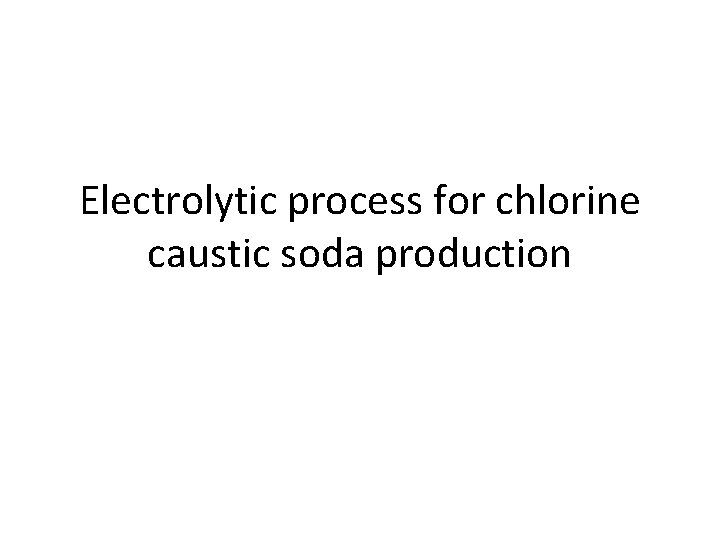
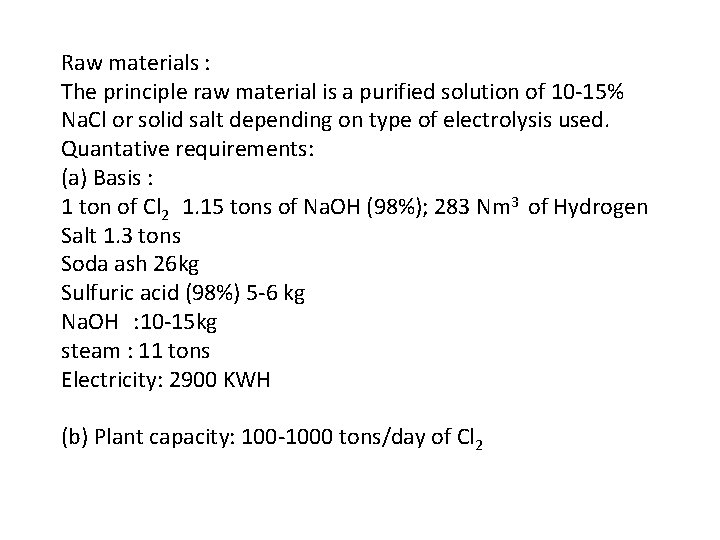
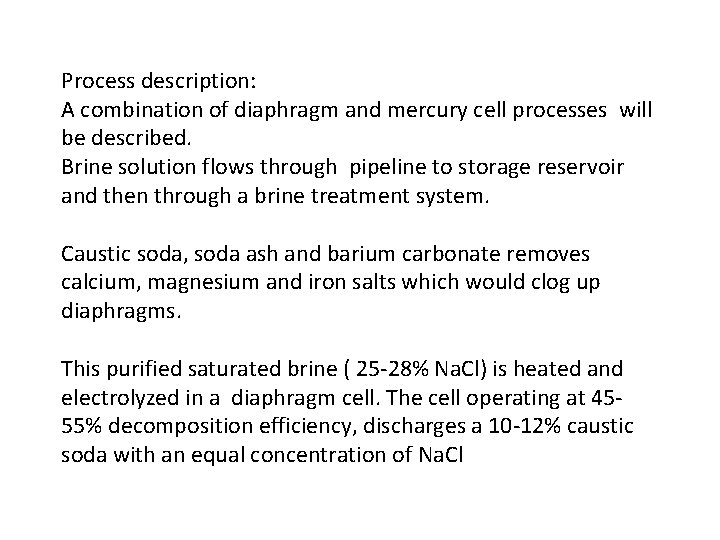
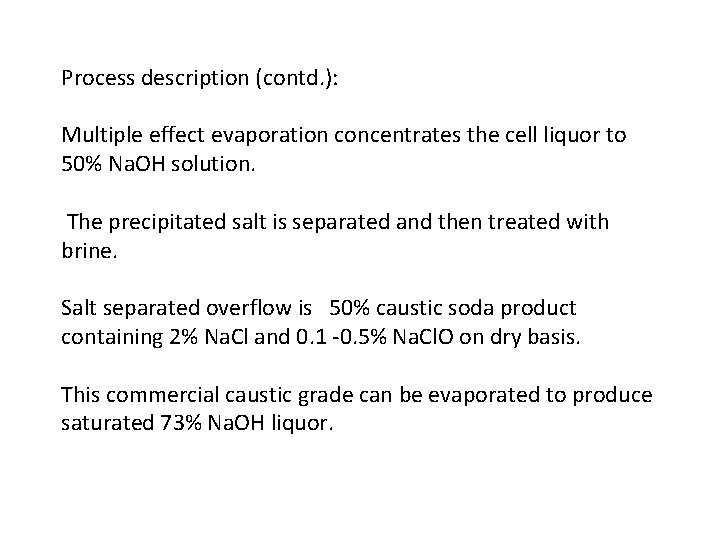
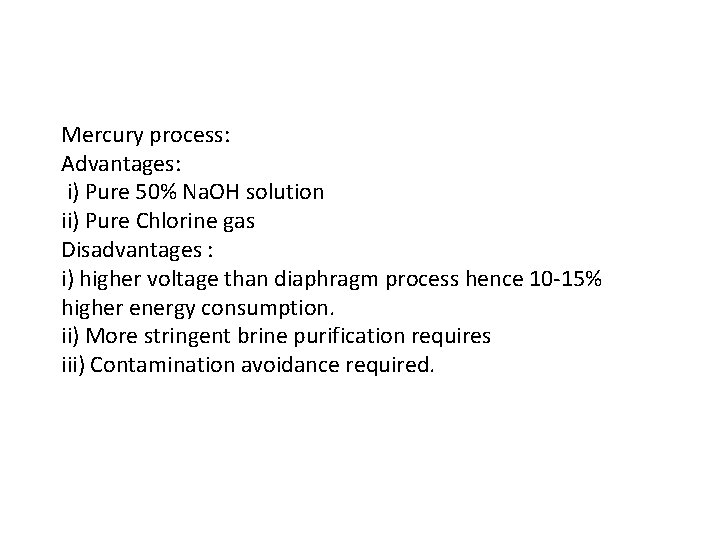
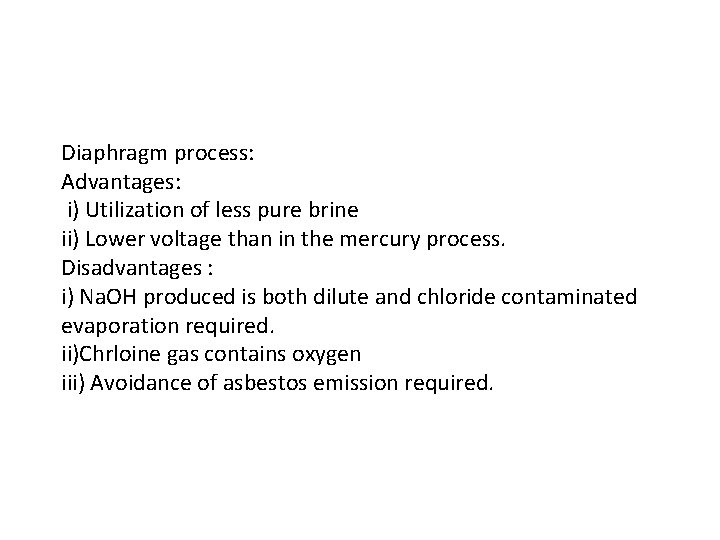

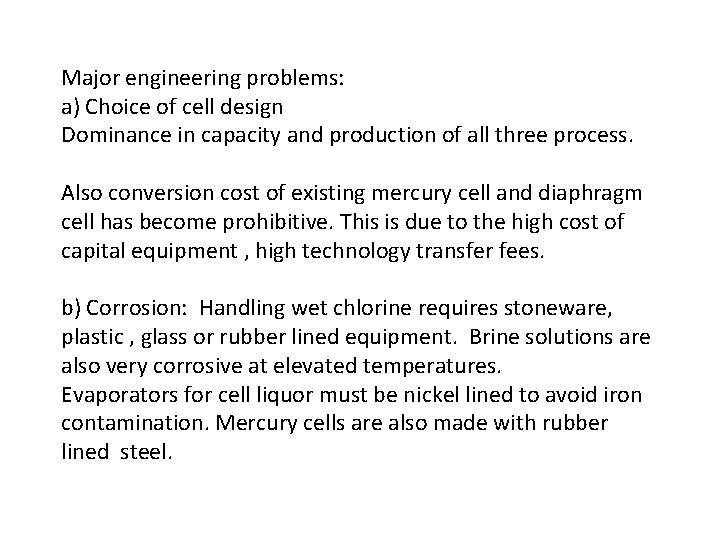
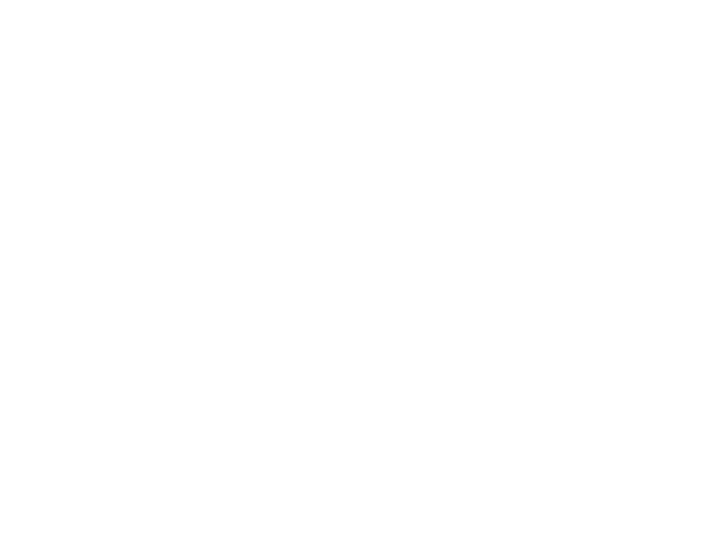
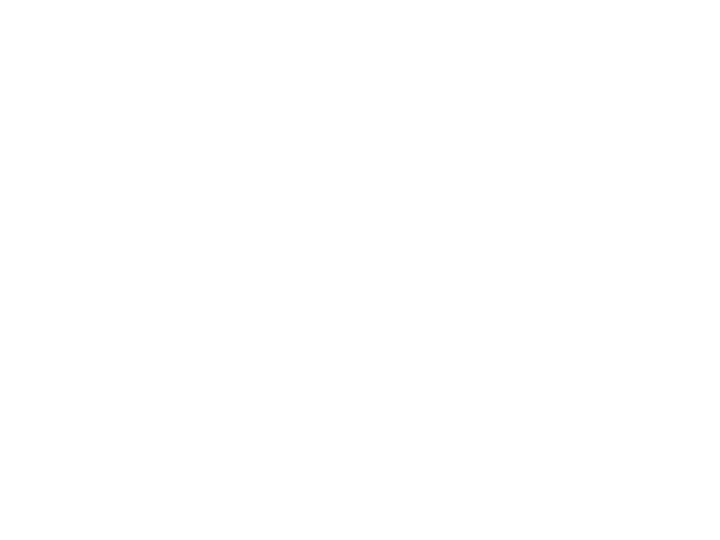
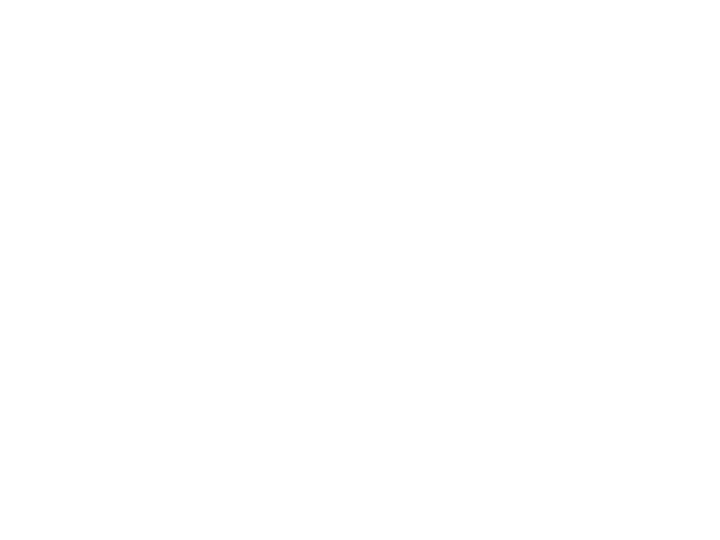
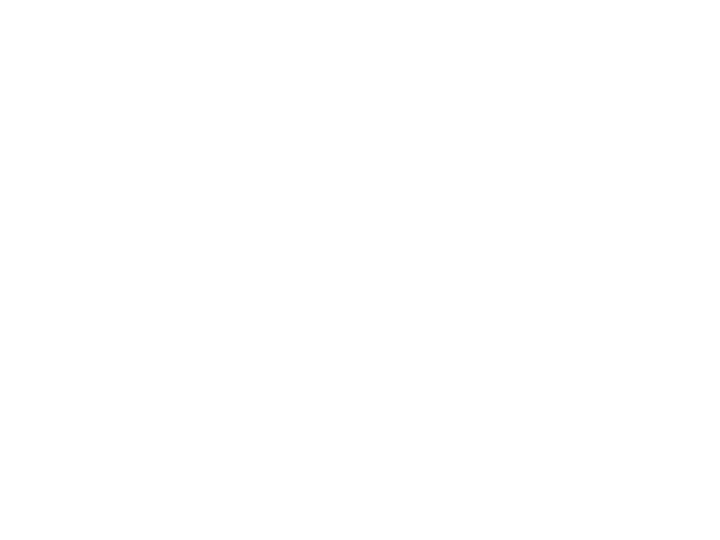
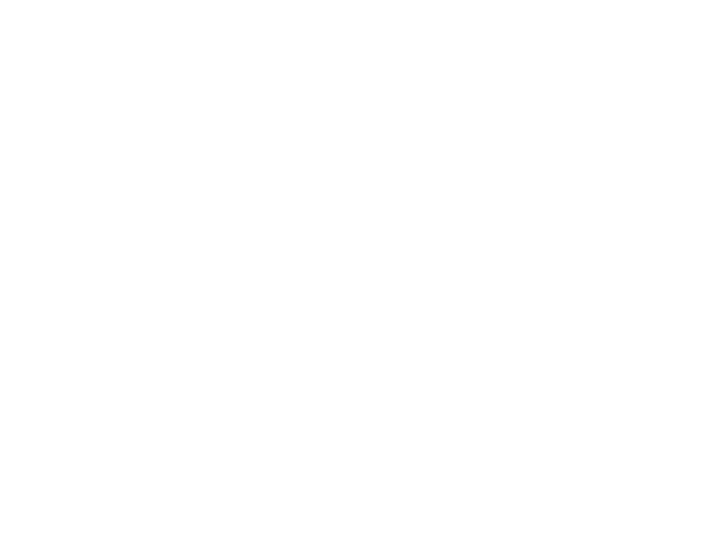
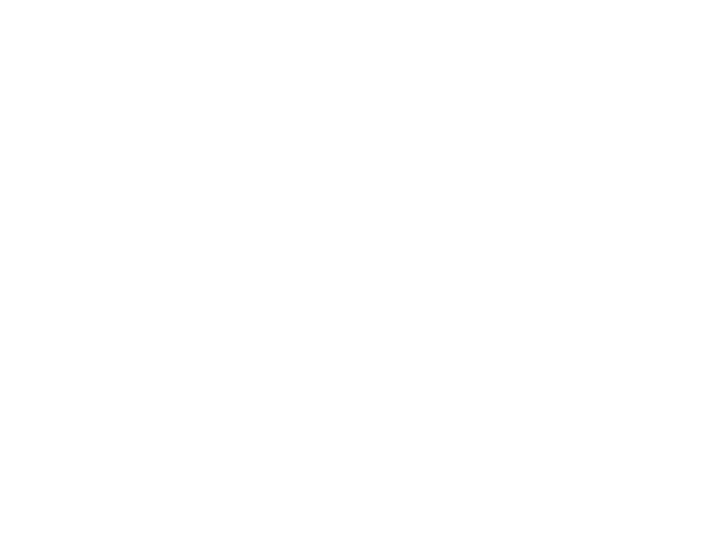
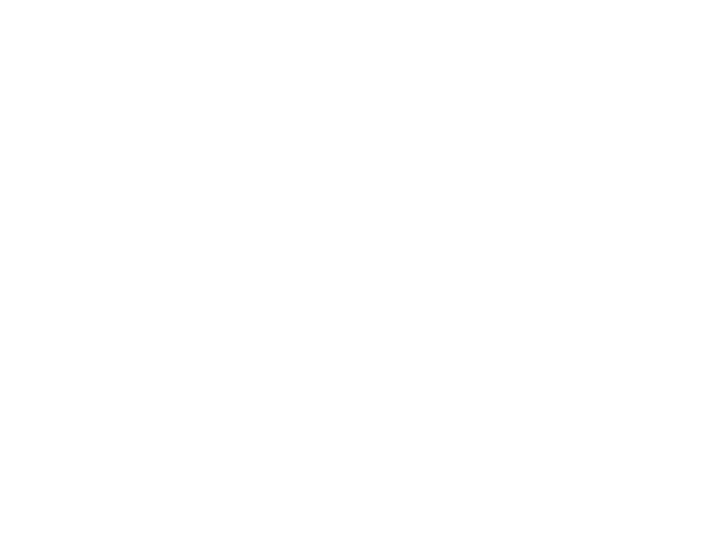
- Slides: 15
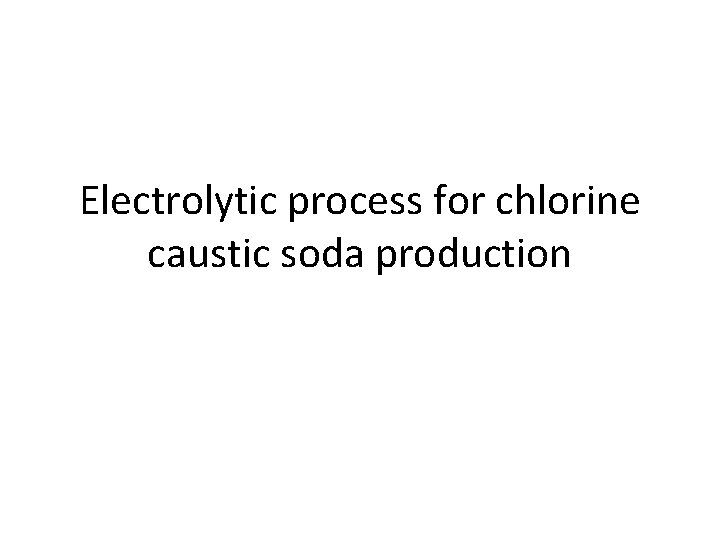
Electrolytic process for chlorine caustic soda production
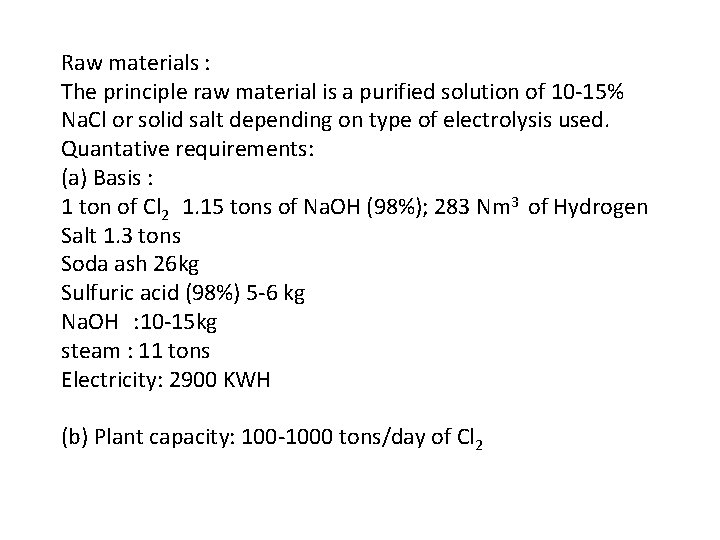
Raw materials : The principle raw material is a purified solution of 10 -15% Na. Cl or solid salt depending on type of electrolysis used. Quantative requirements: (a) Basis : 1 ton of Cl 2 1. 15 tons of Na. OH (98%); 283 Nm 3 of Hydrogen Salt 1. 3 tons Soda ash 26 kg Sulfuric acid (98%) 5 -6 kg Na. OH : 10 -15 kg steam : 11 tons Electricity: 2900 KWH (b) Plant capacity: 100 -1000 tons/day of Cl 2
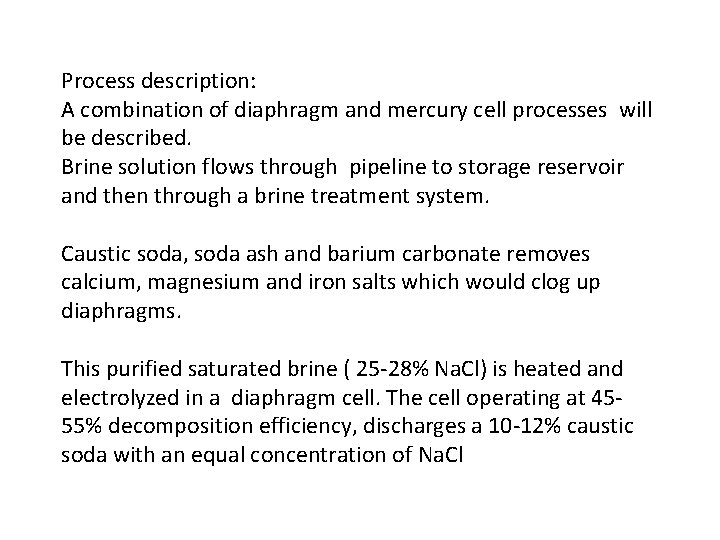
Process description: A combination of diaphragm and mercury cell processes will be described. Brine solution flows through pipeline to storage reservoir and then through a brine treatment system. Caustic soda, soda ash and barium carbonate removes calcium, magnesium and iron salts which would clog up diaphragms. This purified saturated brine ( 25 -28% Na. Cl) is heated and electrolyzed in a diaphragm cell. The cell operating at 4555% decomposition efficiency, discharges a 10 -12% caustic soda with an equal concentration of Na. Cl
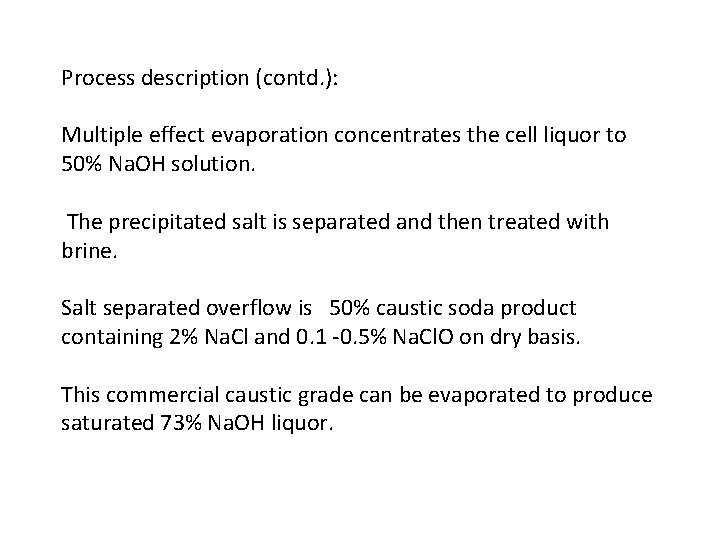
Process description (contd. ): Multiple effect evaporation concentrates the cell liquor to 50% Na. OH solution. The precipitated salt is separated and then treated with brine. Salt separated overflow is 50% caustic soda product containing 2% Na. Cl and 0. 1 -0. 5% Na. Cl. O on dry basis. This commercial caustic grade can be evaporated to produce saturated 73% Na. OH liquor.
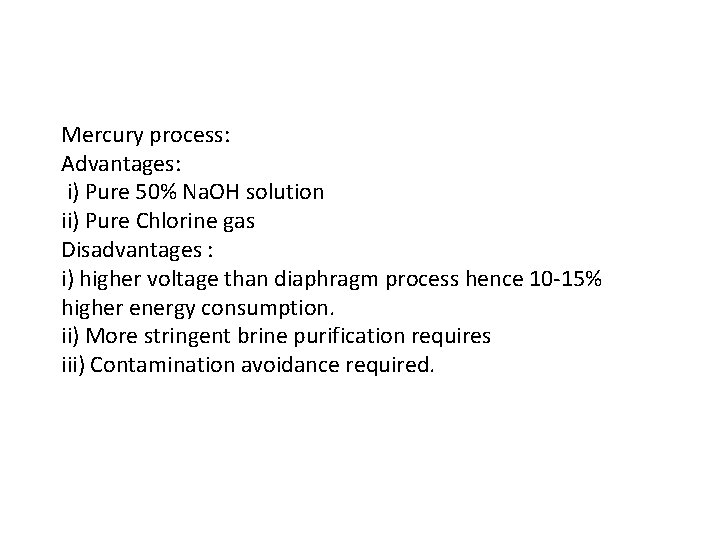
Mercury process: Advantages: i) Pure 50% Na. OH solution ii) Pure Chlorine gas Disadvantages : i) higher voltage than diaphragm process hence 10 -15% higher energy consumption. ii) More stringent brine purification requires iii) Contamination avoidance required.
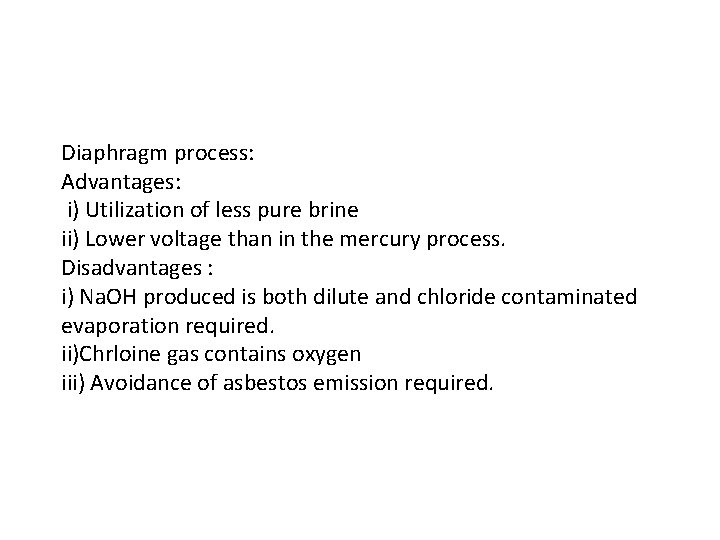
Diaphragm process: Advantages: i) Utilization of less pure brine ii) Lower voltage than in the mercury process. Disadvantages : i) Na. OH produced is both dilute and chloride contaminated evaporation required. ii)Chrloine gas contains oxygen iii) Avoidance of asbestos emission required.

Membrane process: Advantages: i) Pure Na. OH ii) Electrical energy consumption only about 77% of that mercury process iii) No mercury or asbestos required Disadvantages : i) Na. OH content only 33% by weight ii) Chlorine gas contains oxygen. iii) Very high purity brine required. iii) Present high cost and short lifetime of the membranes.
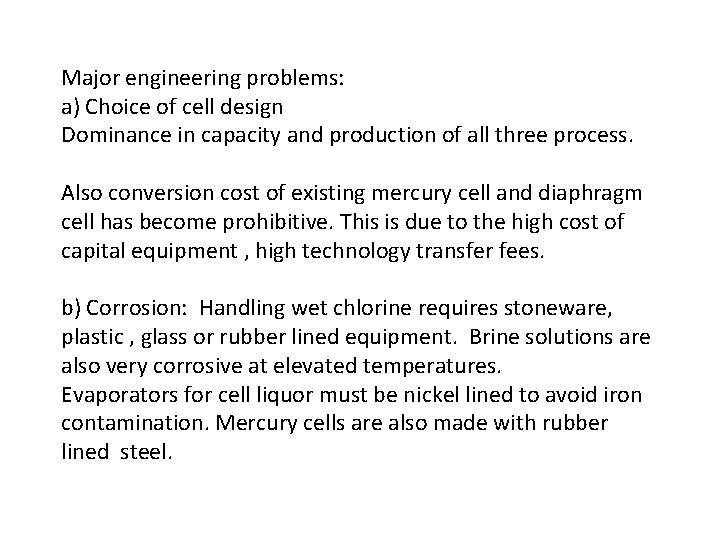
Major engineering problems: a) Choice of cell design Dominance in capacity and production of all three process. Also conversion cost of existing mercury cell and diaphragm cell has become prohibitive. This is due to the high cost of capital equipment , high technology transfer fees. b) Corrosion: Handling wet chlorine requires stoneware, plastic , glass or rubber lined equipment. Brine solutions are also very corrosive at elevated temperatures. Evaporators for cell liquor must be nickel lined to avoid iron contamination. Mercury cells are also made with rubber lined steel.
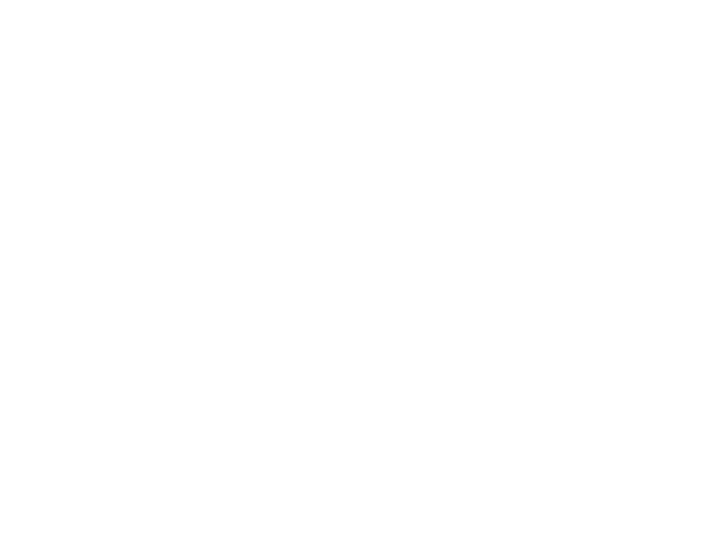
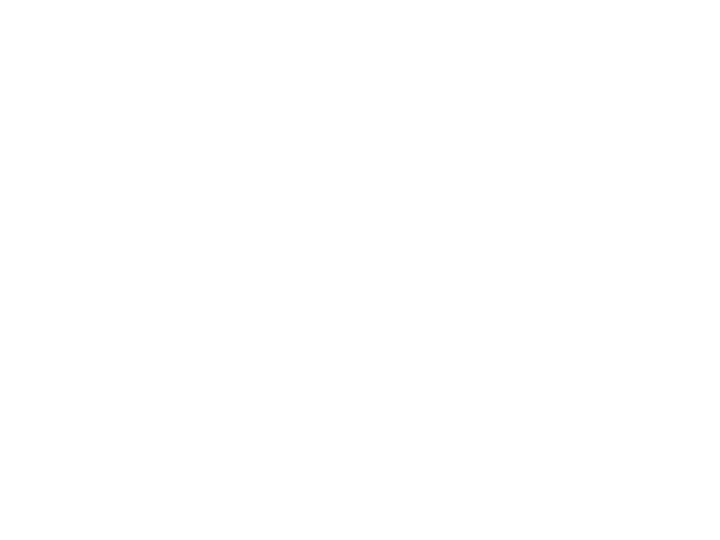
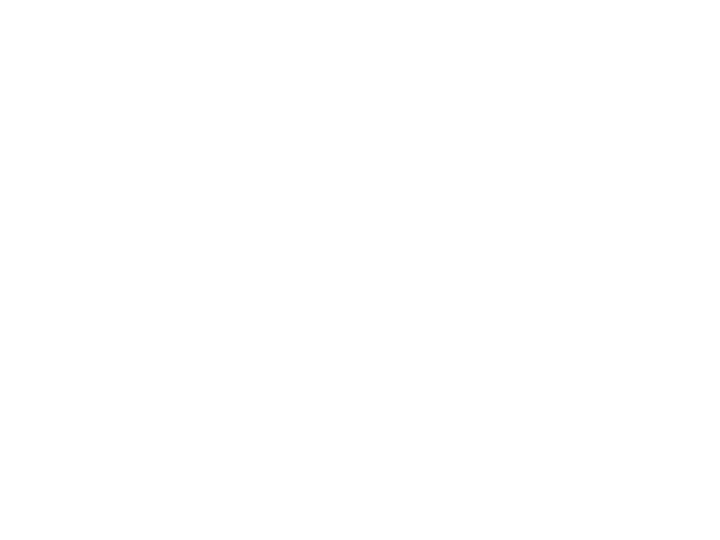
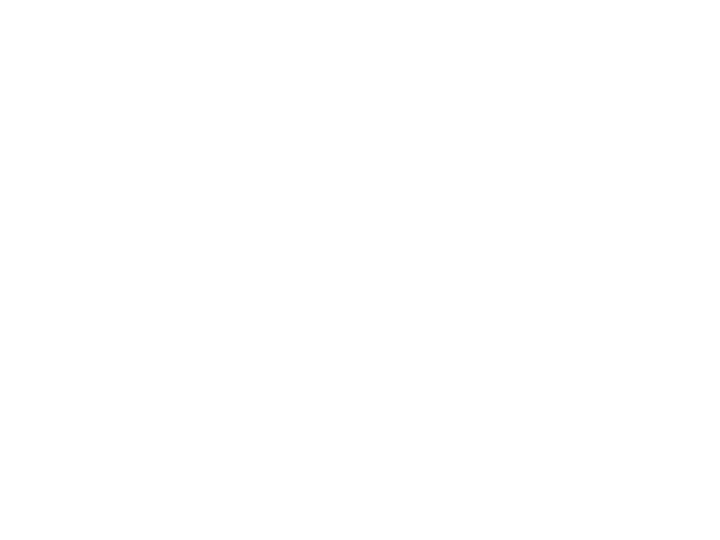
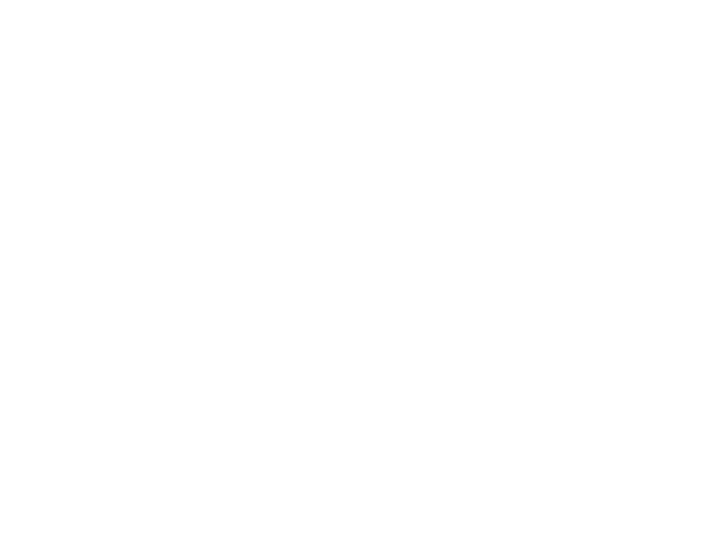
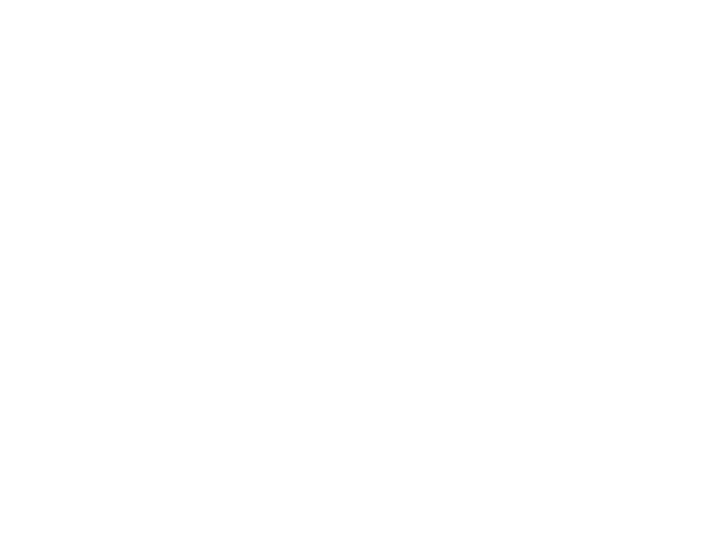
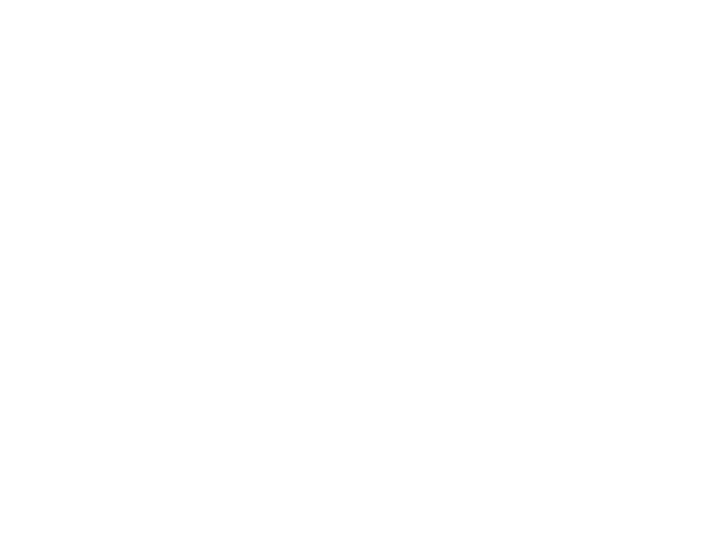
Who wrote the poem bayonet charge
Disadvantages of zeolite process in water treatment
Caustic embrittlement
Corrosion principle
Proses production
Discuss how permanent hardness of water can be removed
In lime soda process
Raw material inspection quality control
Dissociated meaning
Renocell
Electrolytic cell picture
Cell notation
Applications of electrolytic cell
Electrolytic decomposition example
Application of electrolytic cell
Electrolytic etching