Conventional Facilities Activities SLAC April 9 2006 Acknowledgment
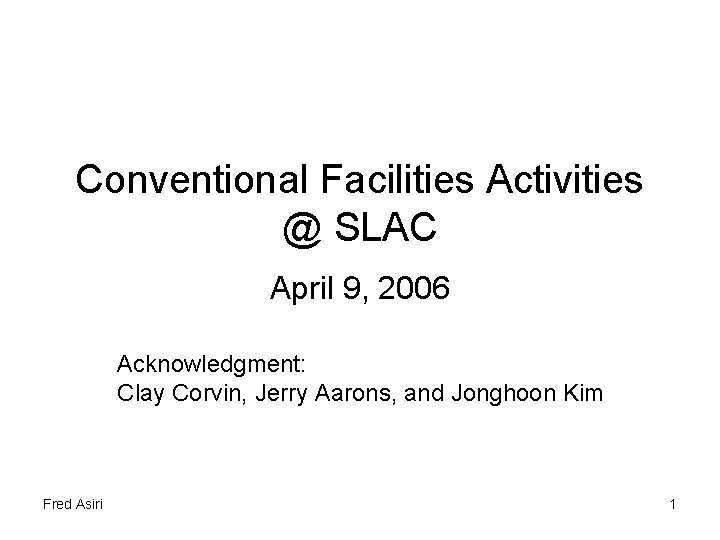
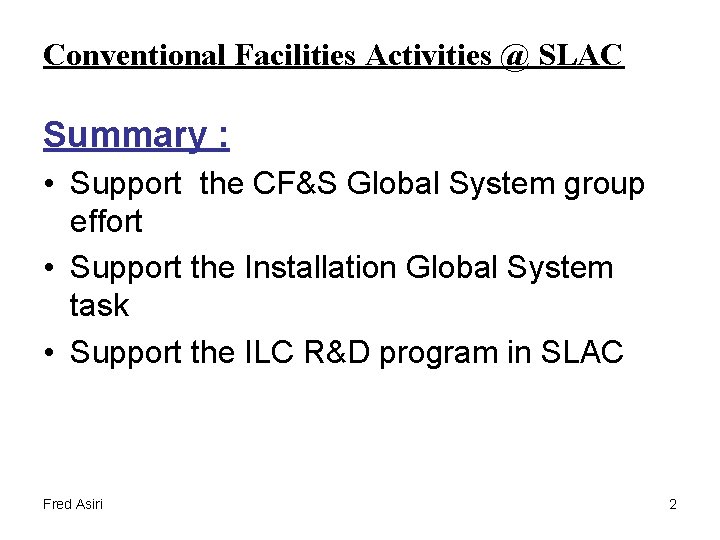
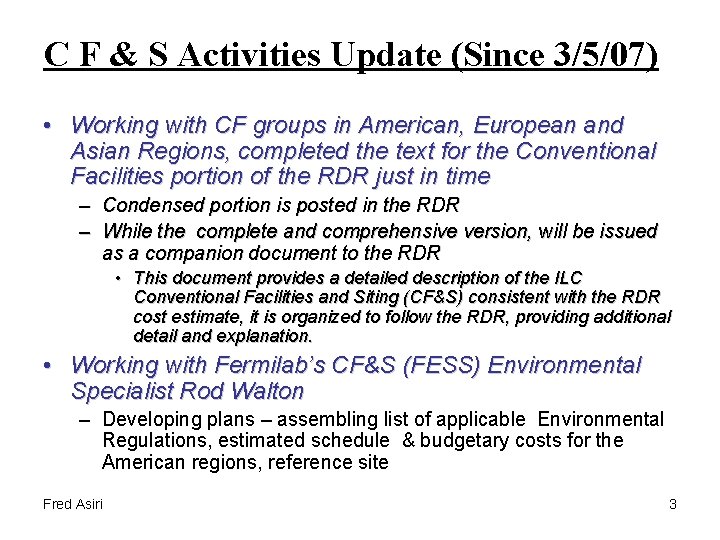
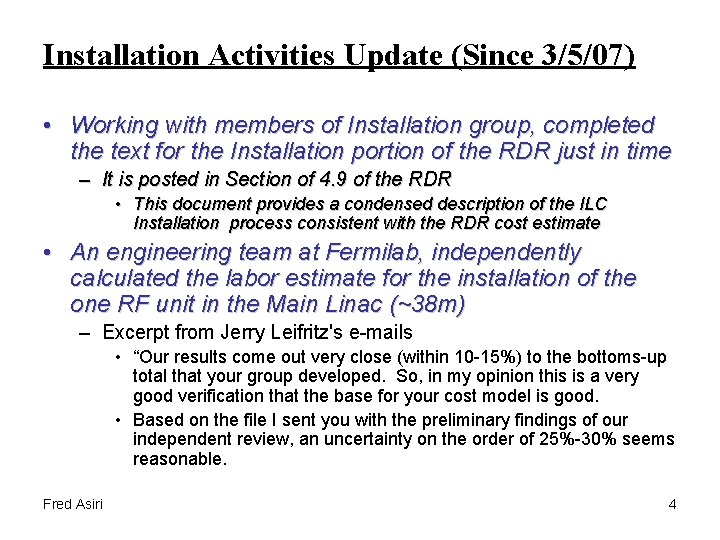
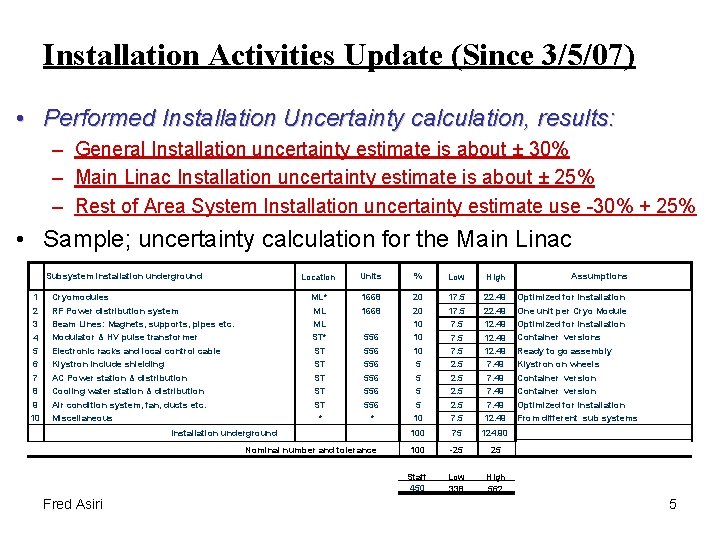
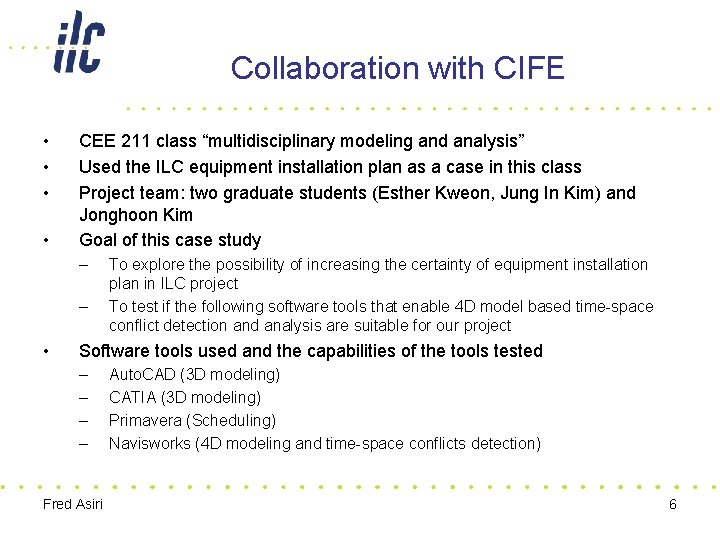
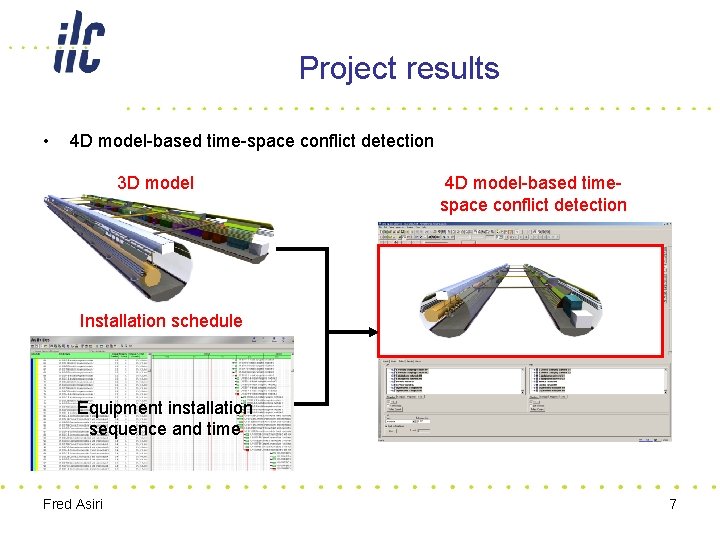
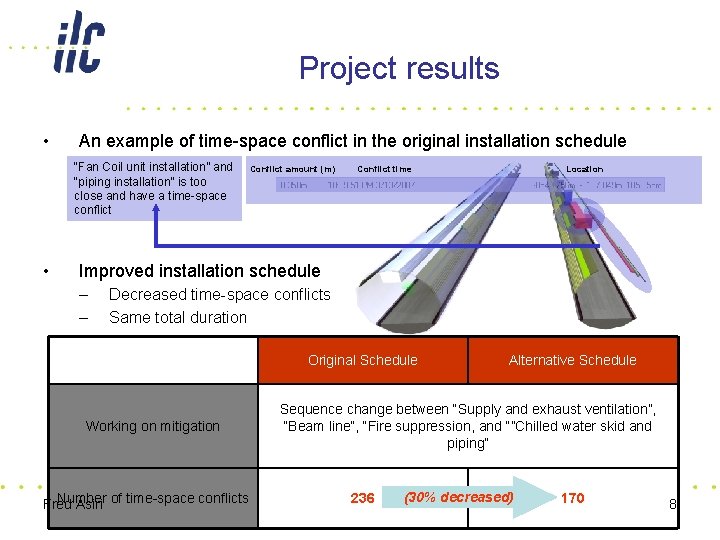
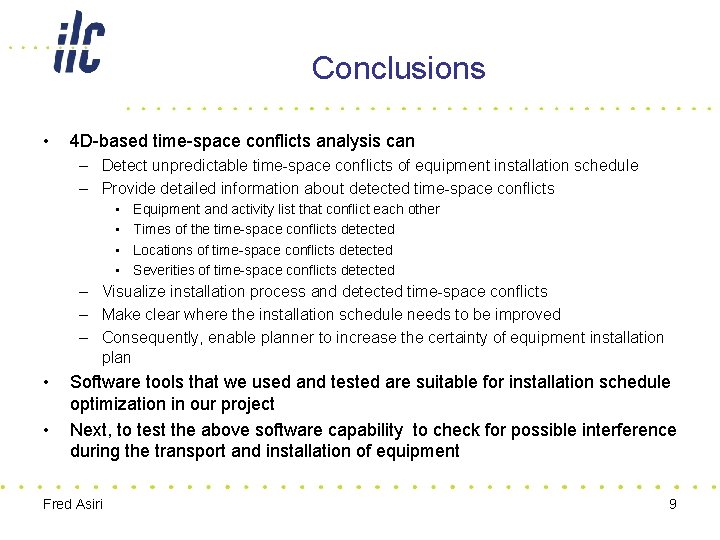
- Slides: 9
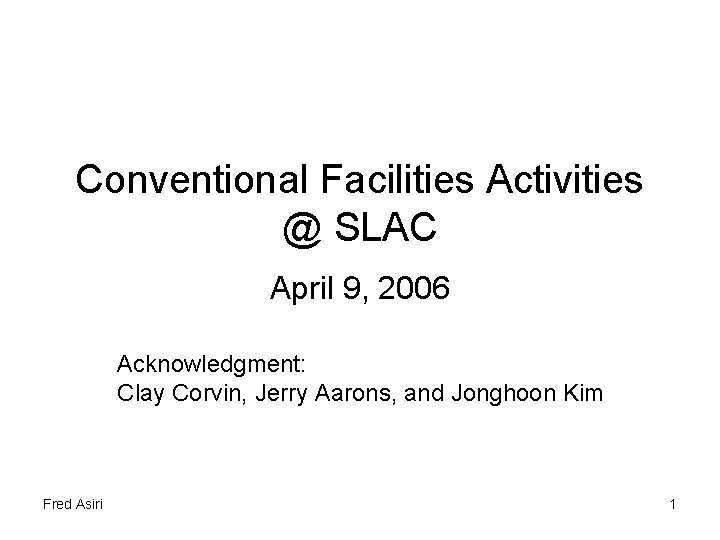
Conventional Facilities Activities @ SLAC April 9, 2006 Acknowledgment: Clay Corvin, Jerry Aarons, and Jonghoon Kim Fred Asiri 1
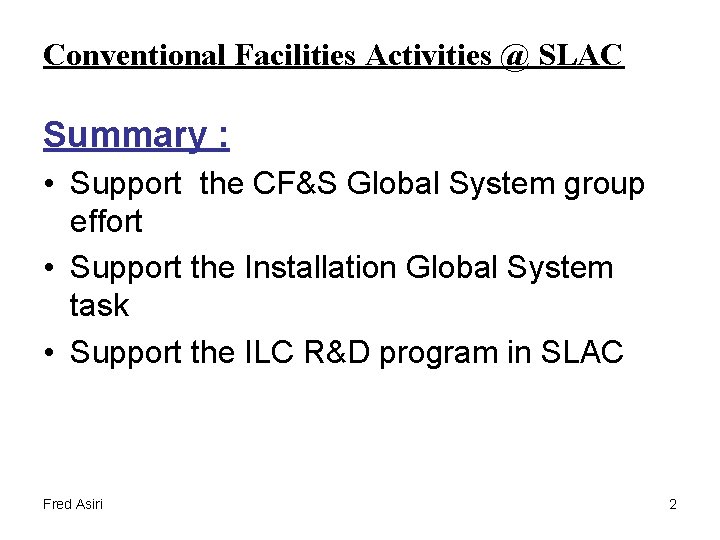
Conventional Facilities Activities @ SLAC Summary : • Support the CF&S Global System group effort • Support the Installation Global System task • Support the ILC R&D program in SLAC Fred Asiri 2
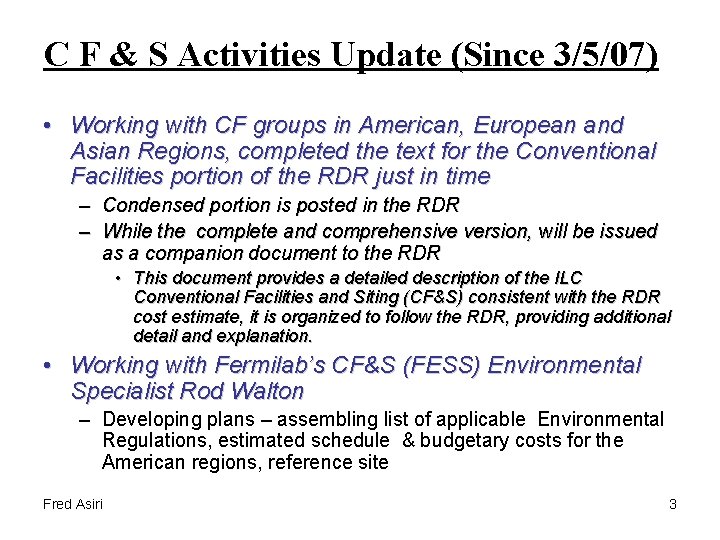
C F & S Activities Update (Since 3/5/07) • Working with CF groups in American, European and Asian Regions, completed the text for the Conventional Facilities portion of the RDR just in time – Condensed portion is posted in the RDR – While the complete and comprehensive version, will be issued as a companion document to the RDR • This document provides a detailed description of the ILC Conventional Facilities and Siting (CF&S) consistent with the RDR cost estimate, it is organized to follow the RDR, providing additional detail and explanation. • Working with Fermilab’s CF&S (FESS) Environmental Specialist Rod Walton – Developing plans – assembling list of applicable Environmental Regulations, estimated schedule & budgetary costs for the American regions, reference site Fred Asiri 3
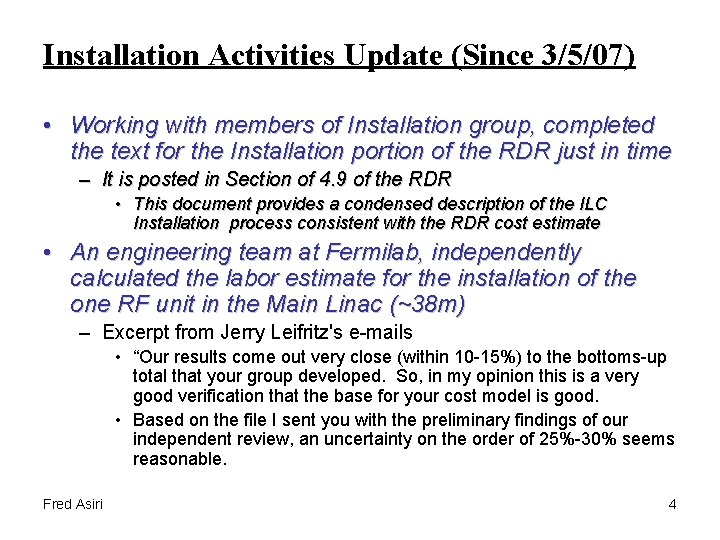
Installation Activities Update (Since 3/5/07) • Working with members of Installation group, completed the text for the Installation portion of the RDR just in time – It is posted in Section of 4. 9 of the RDR • This document provides a condensed description of the ILC Installation process consistent with the RDR cost estimate • An engineering team at Fermilab, independently calculated the labor estimate for the installation of the one RF unit in the Main Linac (~38 m) – Excerpt from Jerry Leifritz's e-mails • “Our results come out very close (within 10 -15%) to the bottoms-up total that your group developed. So, in my opinion this is a very good verification that the base for your cost model is good. • Based on the file I sent you with the preliminary findings of our independent review, an uncertainty on the order of 25%-30% seems reasonable. Fred Asiri 4
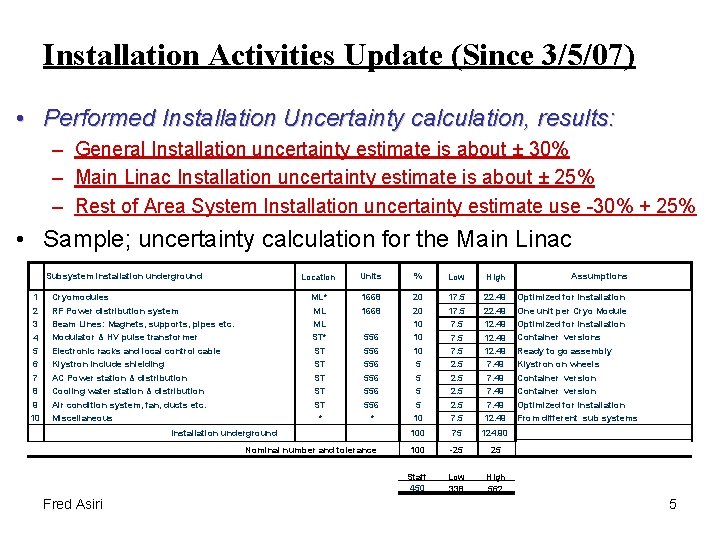
Installation Activities Update (Since 3/5/07) • Performed Installation Uncertainty calculation, results: – General Installation uncertainty estimate is about ± 30% – Main Linac Installation uncertainty estimate is about ± 25% – Rest of Area System Installation uncertainty estimate use -30% + 25% • Sample; uncertainty calculation for the Main Linac Subsystem installation underground Location Units % Low High Assumptions 1668 20 20 17. 5 22. 49 Optimized for installation One unit per Cryo Module 7. 5 12. 49 Optimized for installation Container versions Ready to go assembly 1 2 Cryomodules RF Power distribution system ML* ML 3 4 Beam Lines: Magnets, supports, pipes etc. Modulator & HV pulse transformer Electronic racks and local control cable ML ST* ST 556 10 10 10 Klystron include shielding AC Power station & distribution ST ST 556 5 5 7. 5 2. 5 12. 49 7. 49 Cooling water station & distribution Air condition system, fan, ducts etc. ST ST 556 5 5 2. 5 7. 49 * * 10 7. 5 12. 49 100 75 124. 90 100 -25 25 Staff 450 Low 338 High 562 5 6 7 8 9 10 Miscellaneous Installation underground Nominal number and tolerance Fred Asiri Klystron on wheels Container version Optimized for installation From different sub systems 5
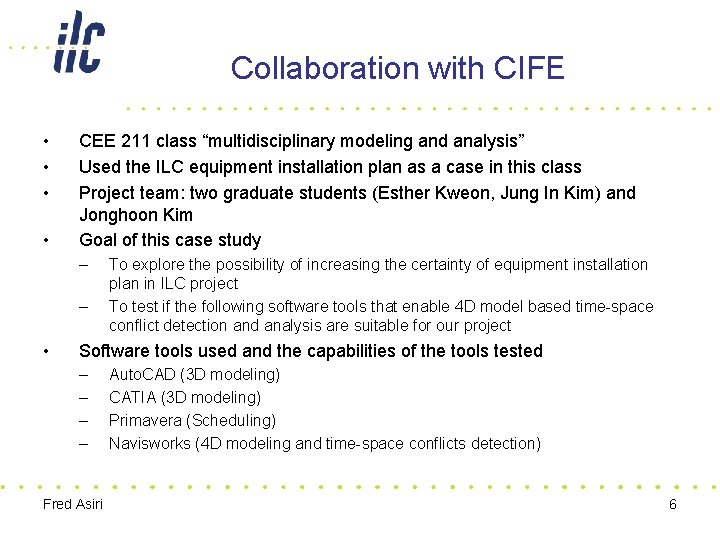
Collaboration with CIFE • • CEE 211 class “multidisciplinary modeling and analysis” Used the ILC equipment installation plan as a case in this class Project team: two graduate students (Esther Kweon, Jung In Kim) and Jonghoon Kim Goal of this case study – – • To explore the possibility of increasing the certainty of equipment installation plan in ILC project To test if the following software tools that enable 4 D model based time-space conflict detection and analysis are suitable for our project Software tools used and the capabilities of the tools tested – – Fred Asiri Auto. CAD (3 D modeling) CATIA (3 D modeling) Primavera (Scheduling) Navisworks (4 D modeling and time-space conflicts detection) 6
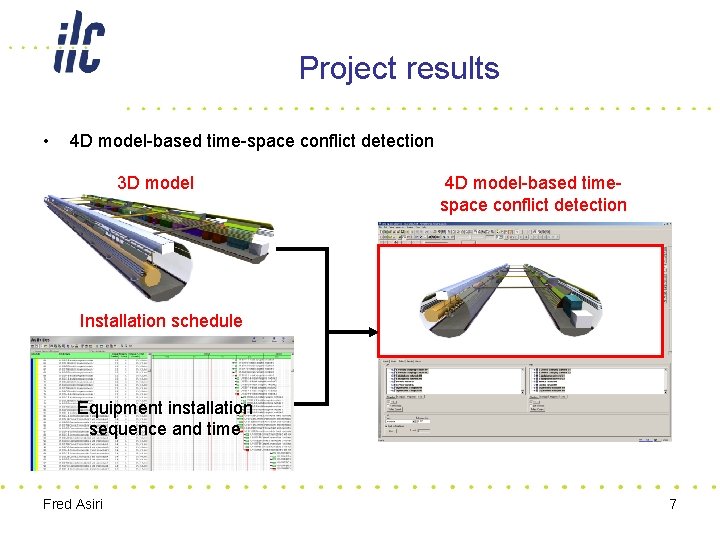
Project results • 4 D model-based time-space conflict detection 3 D model 4 D model-based timespace conflict detection Installation schedule Equipment installation sequence and time Fred Asiri 7
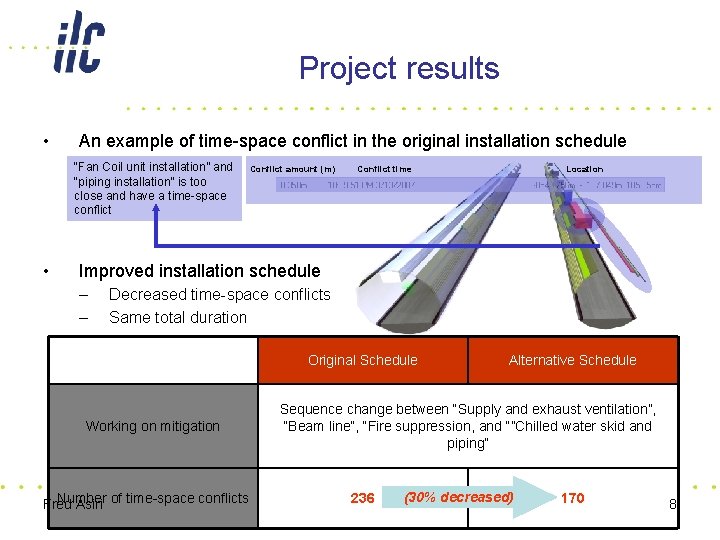
Project results • An example of time-space conflict in the original installation schedule “Fan Coil unit installation” and “piping installation” is too close and have a time-space conflict • Conflict amount (m) Conflict time Location Improved installation schedule – – Decreased time-space conflicts Same total duration Original Schedule Working on mitigation Number Fred Asiri of time-space conflicts Alternative Schedule Sequence change between “Supply and exhaust ventilation”, “Beam line”, “Fire suppression, and “”Chilled water skid and piping” 236 (30% decreased) 170 8
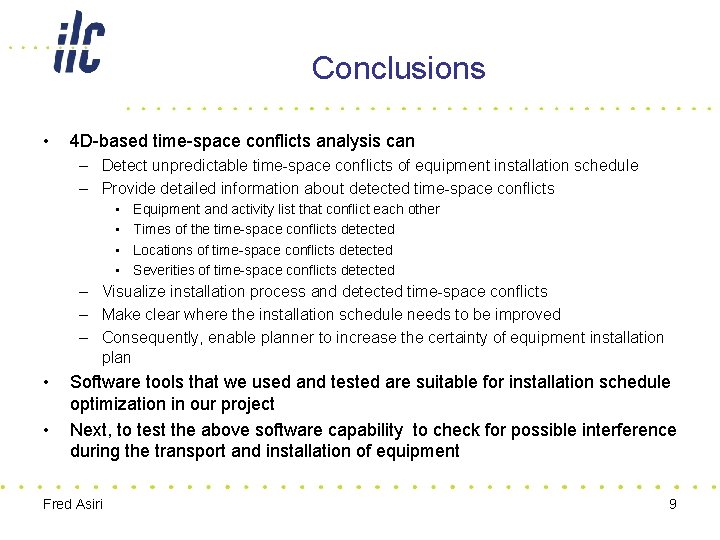
Conclusions • 4 D-based time-space conflicts analysis can – Detect unpredictable time-space conflicts of equipment installation schedule – Provide detailed information about detected time-space conflicts • • Equipment and activity list that conflict each other Times of the time-space conflicts detected Locations of time-space conflicts detected Severities of time-space conflicts detected – Visualize installation process and detected time-space conflicts – Make clear where the installation schedule needs to be improved – Consequently, enable planner to increase the certainty of equipment installation plan • • Software tools that we used and tested are suitable for installation schedule optimization in our project Next, to test the above software capability to check for possible interference during the transport and installation of equipment Fred Asiri 9