COMPACT HEAT EXCHANGER COMPACT HEAT EXCHANGERS Plate and
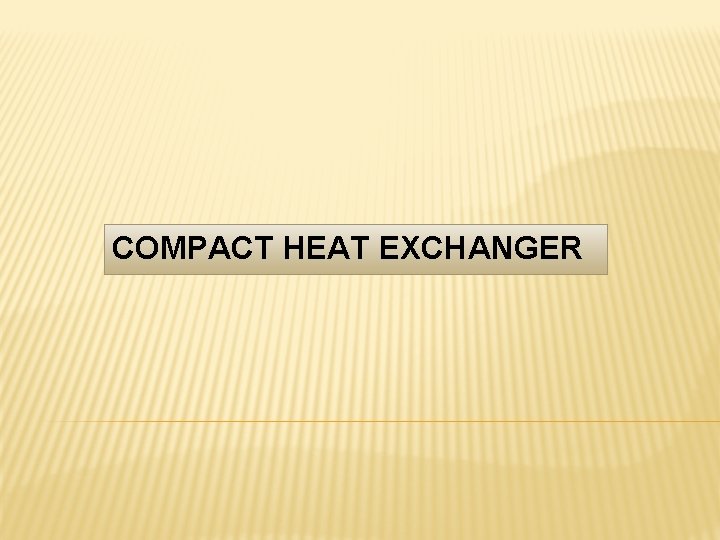
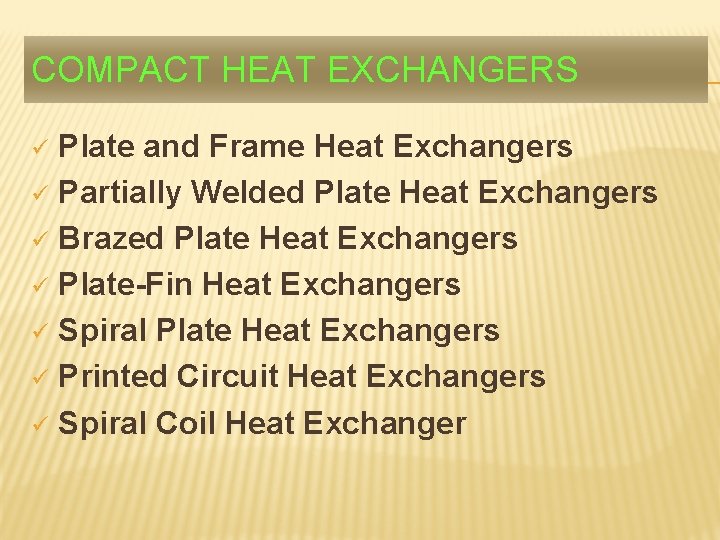
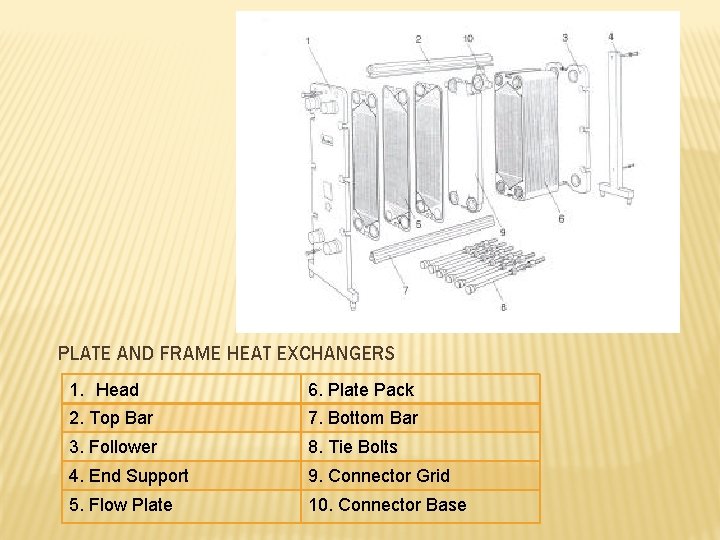
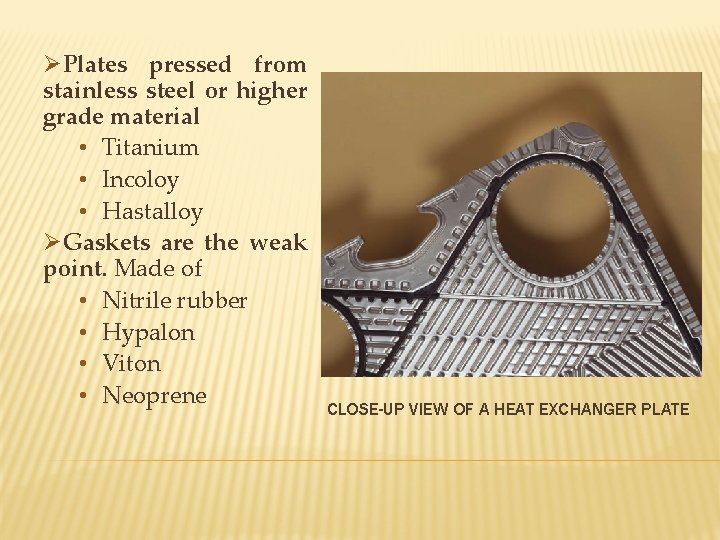
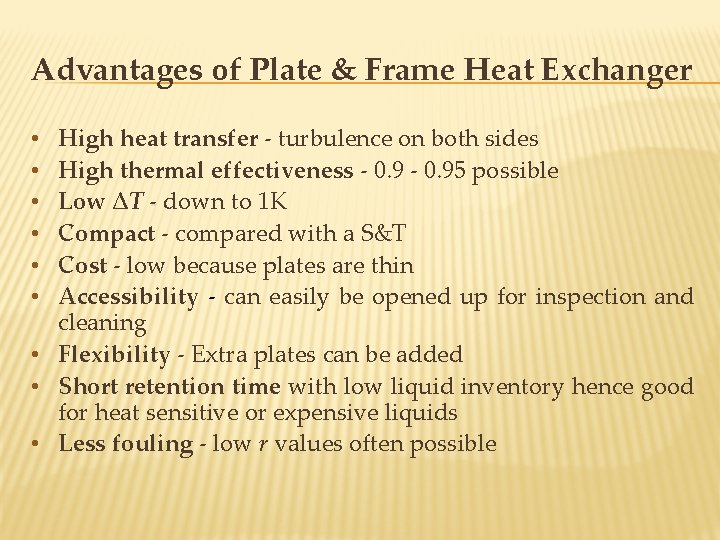
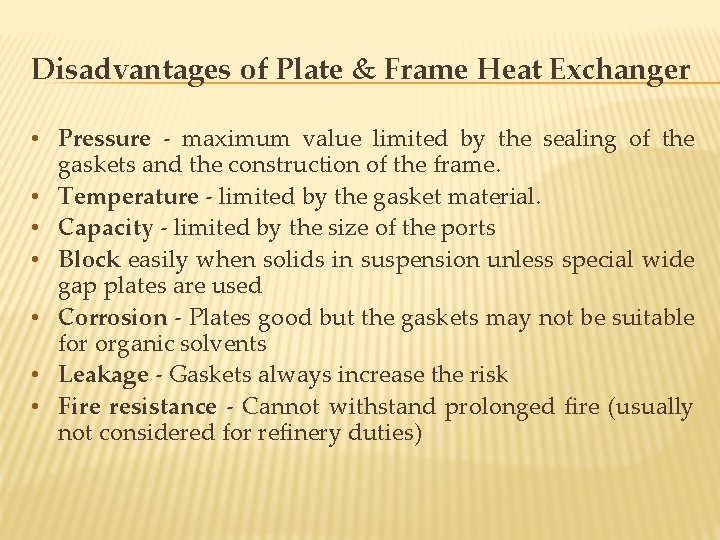
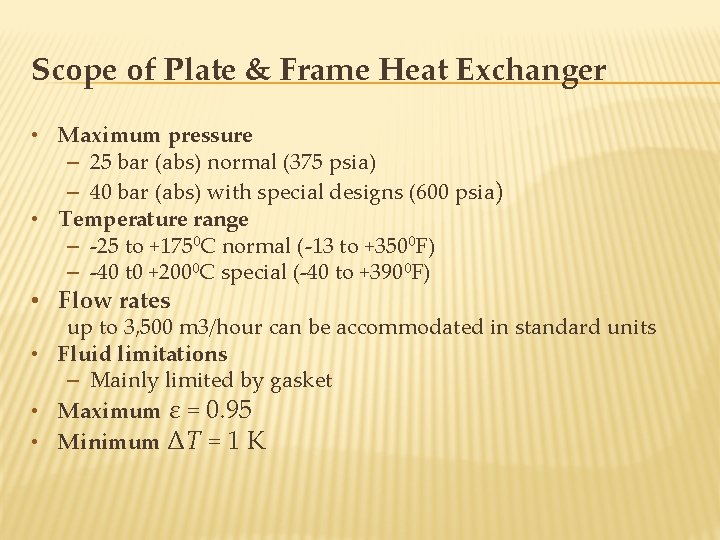
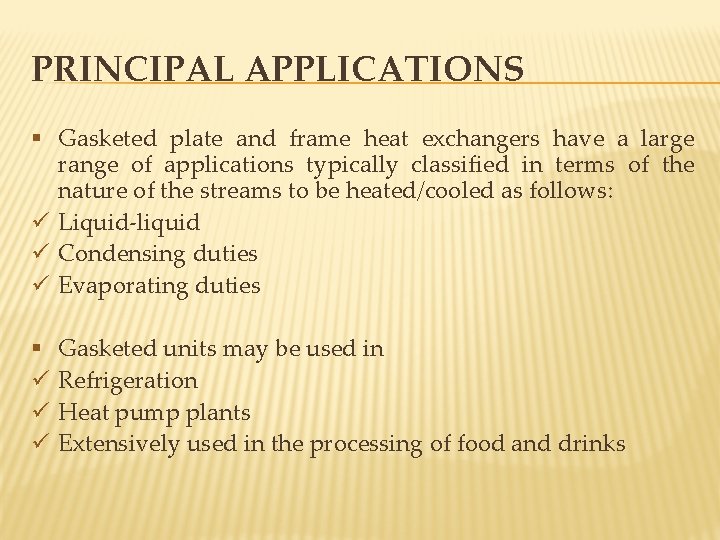
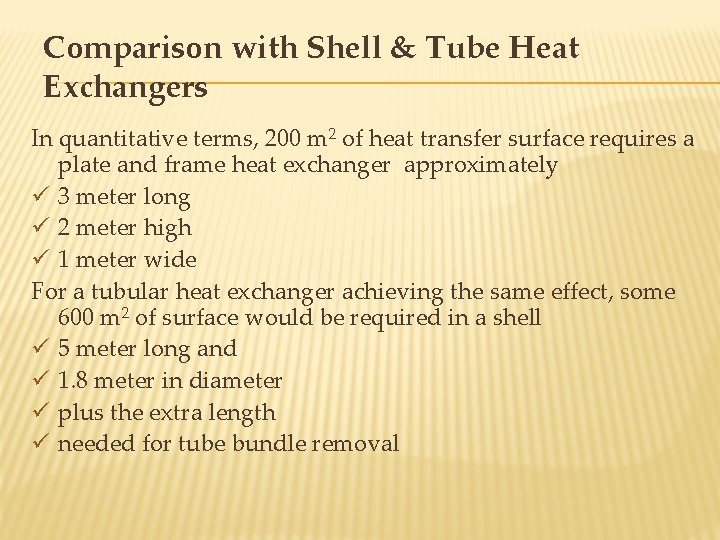
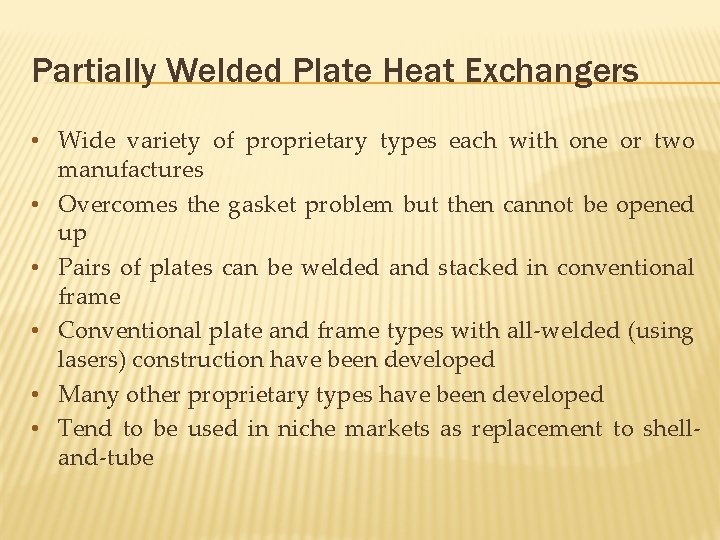
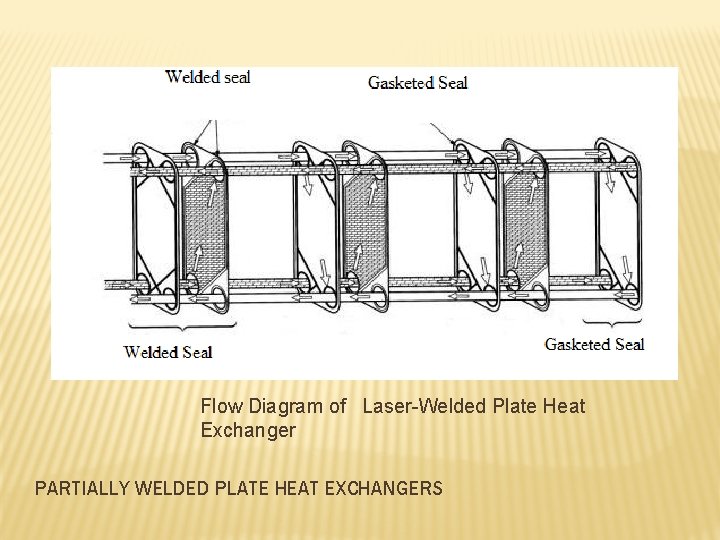
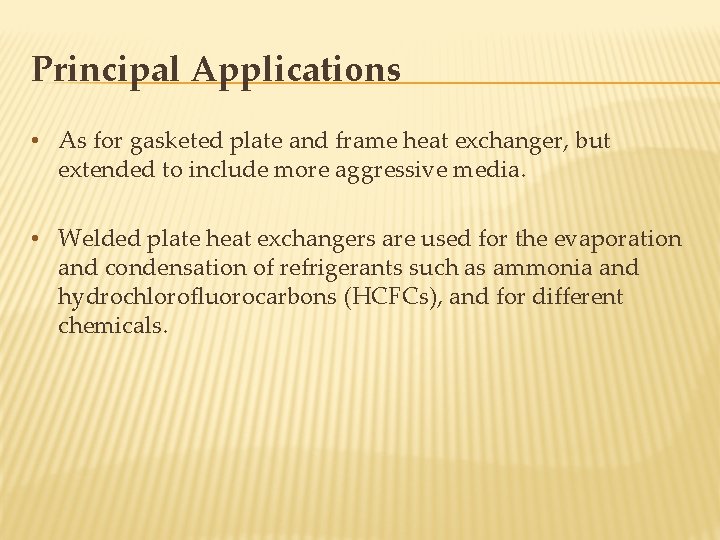
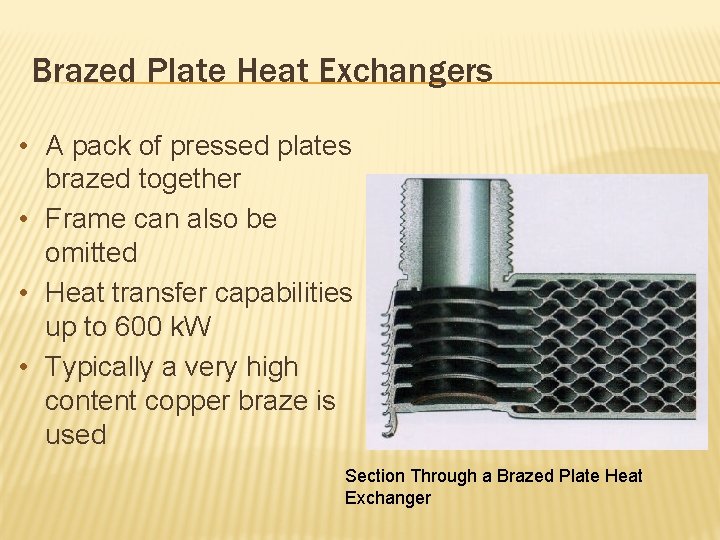
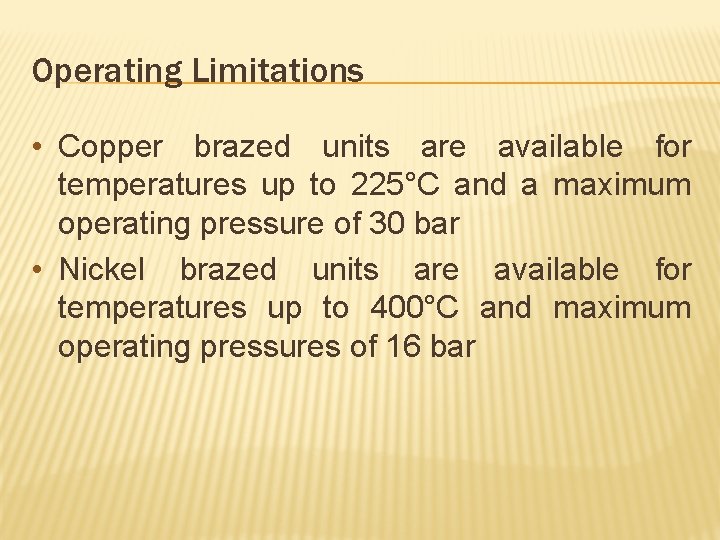
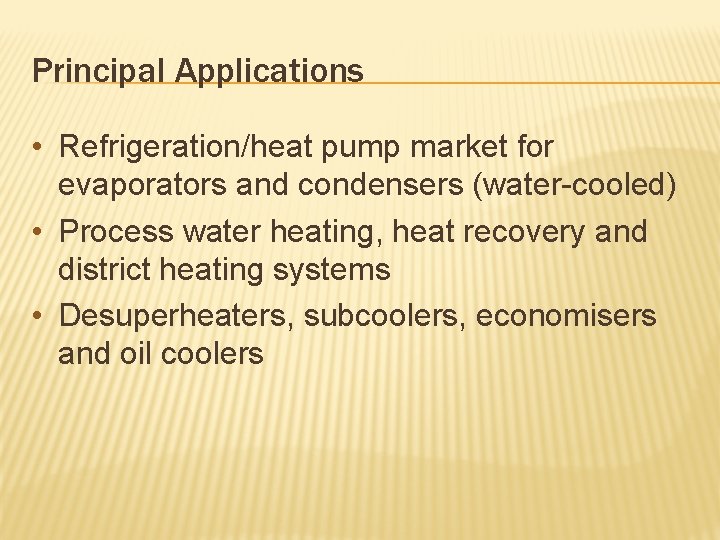
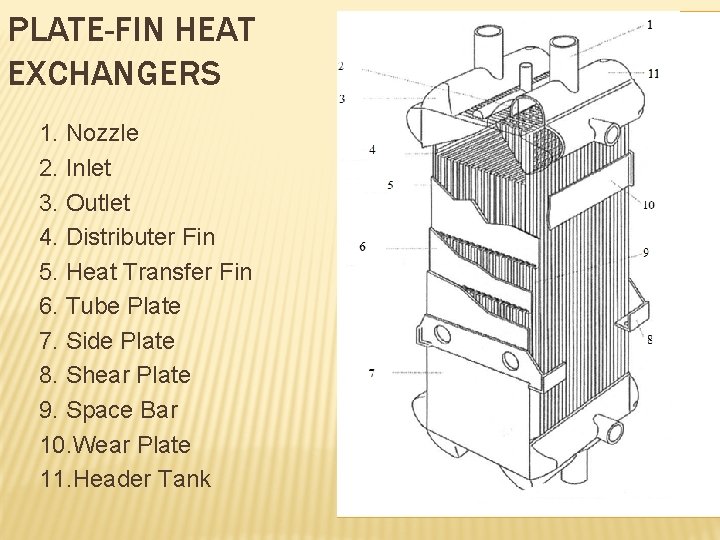
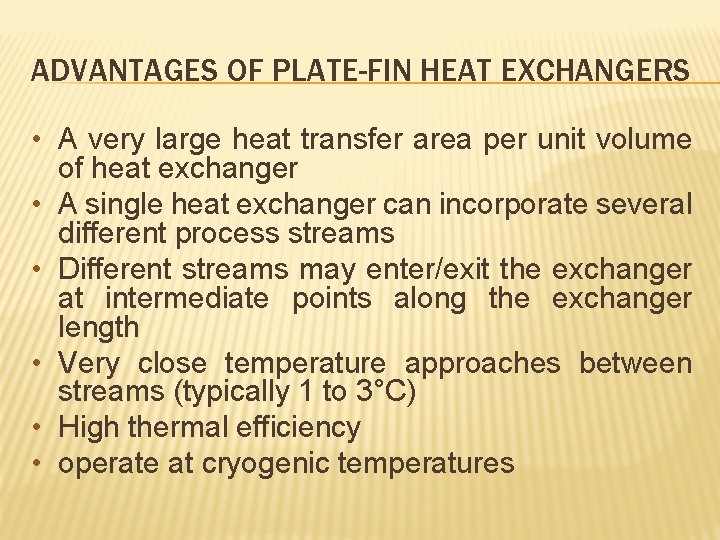
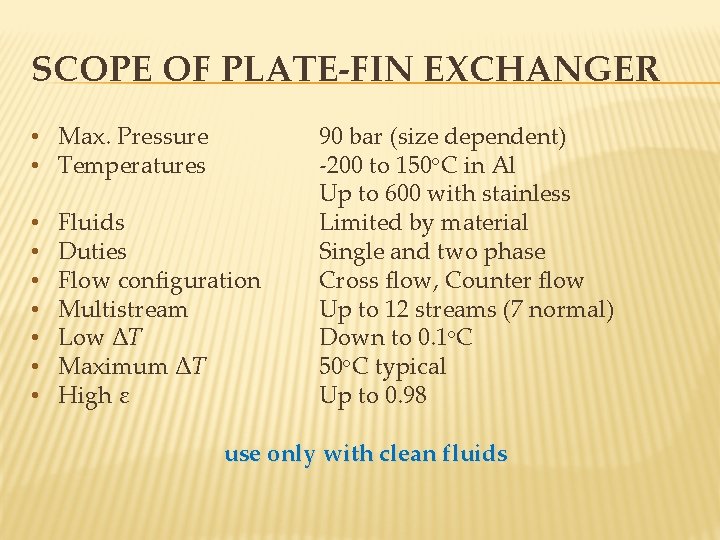
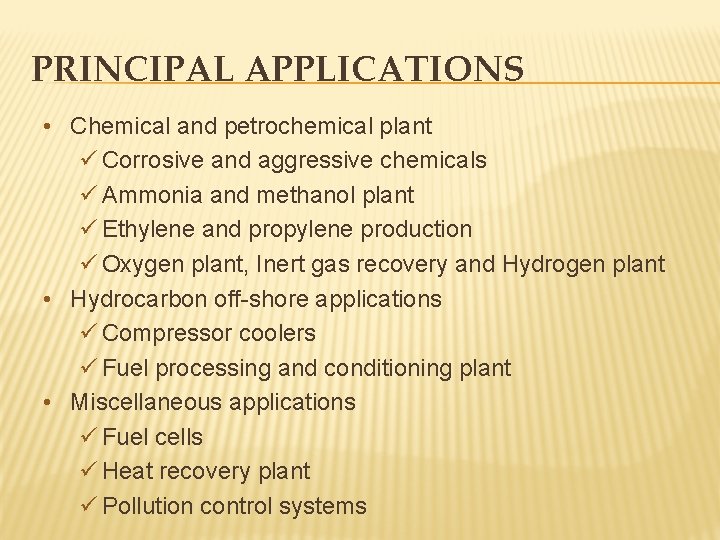
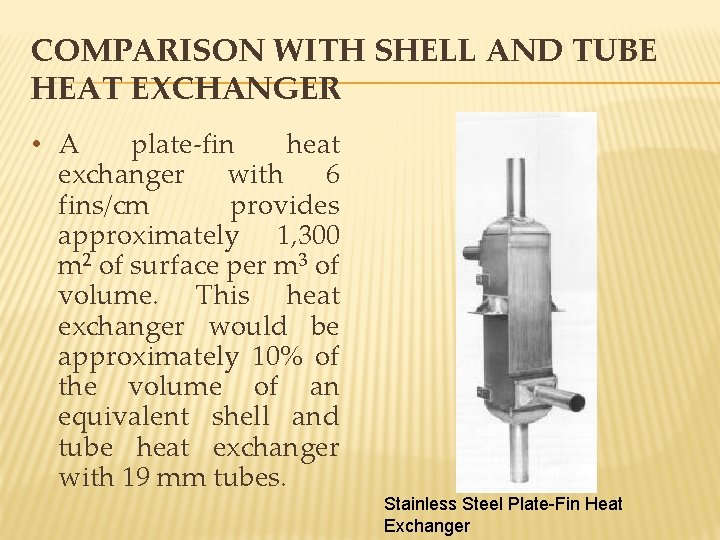
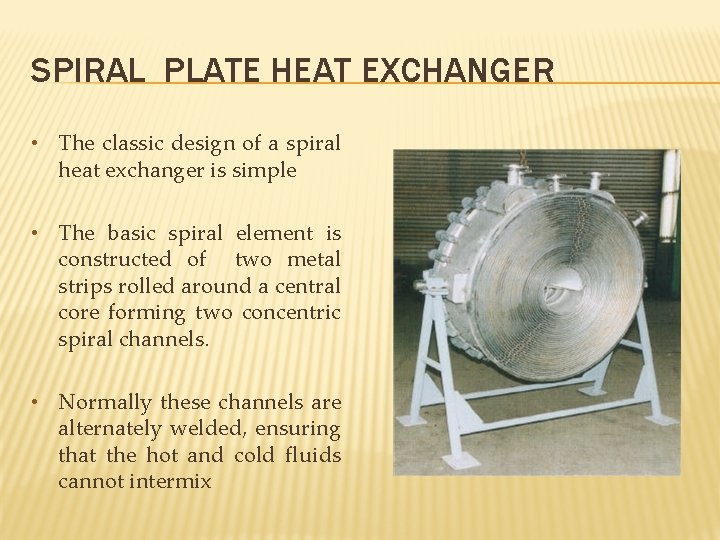
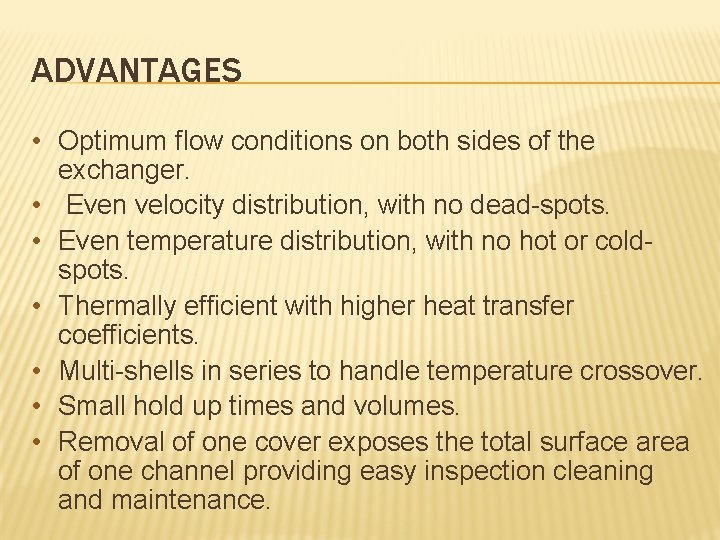
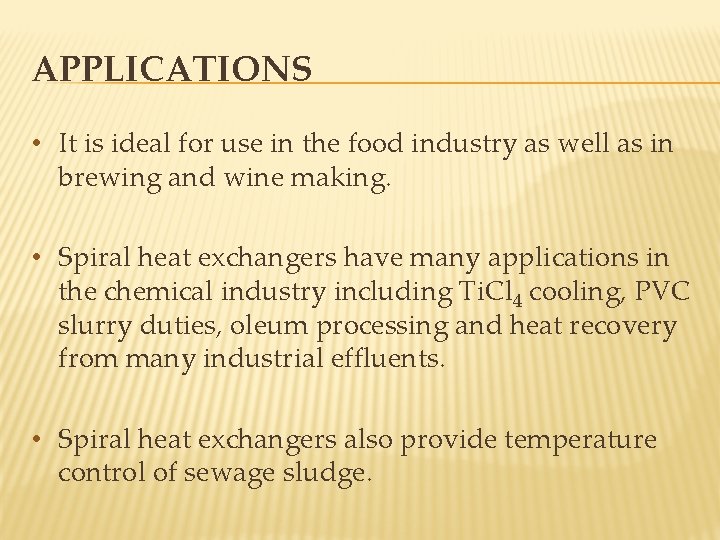
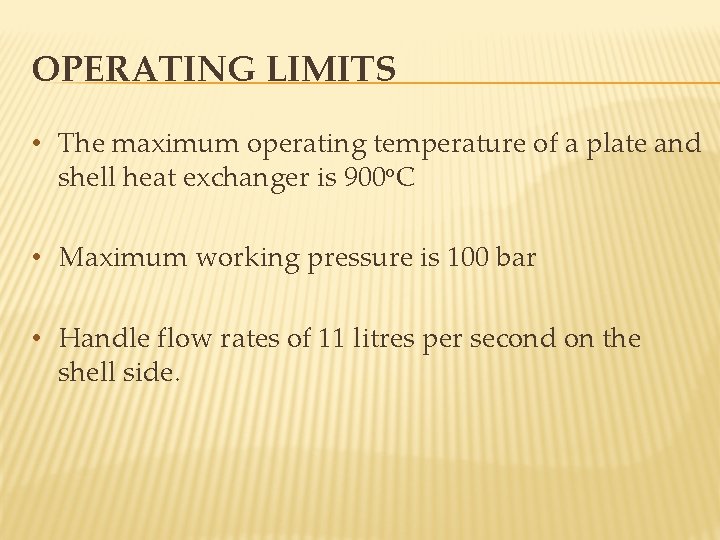
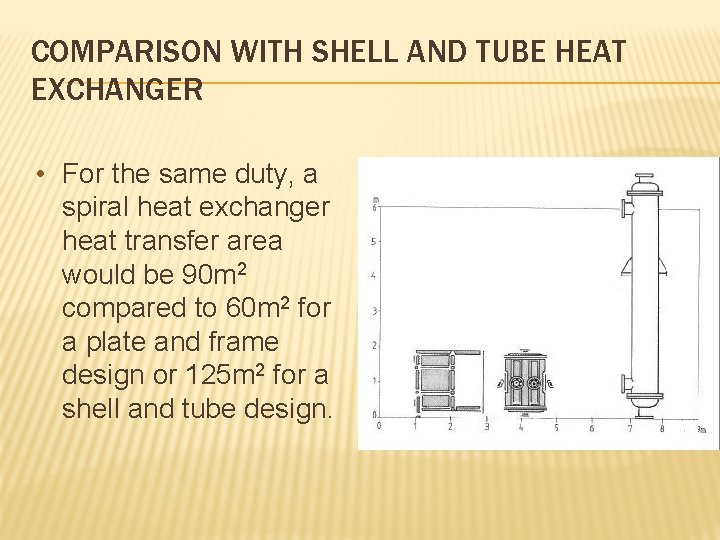
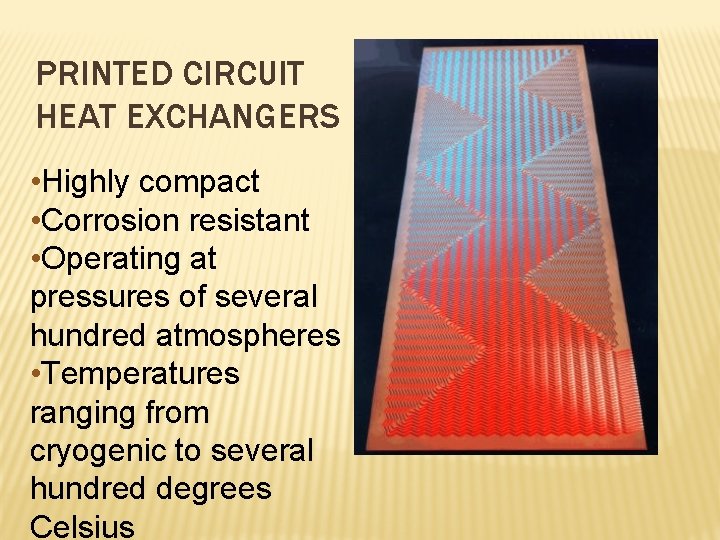
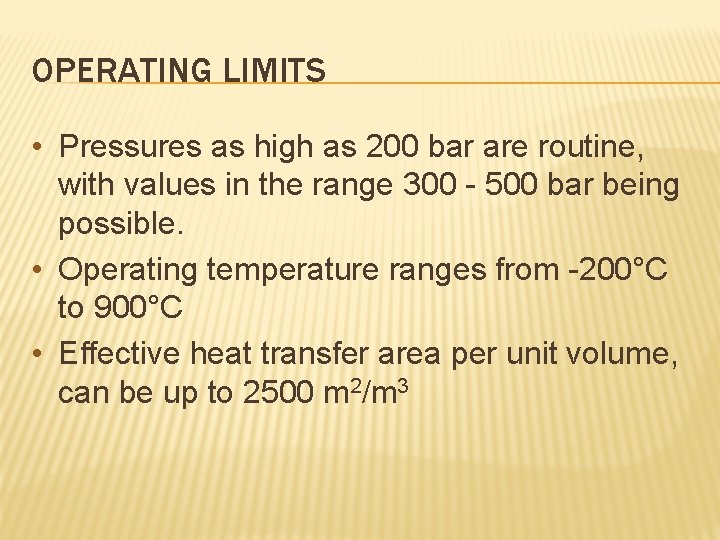
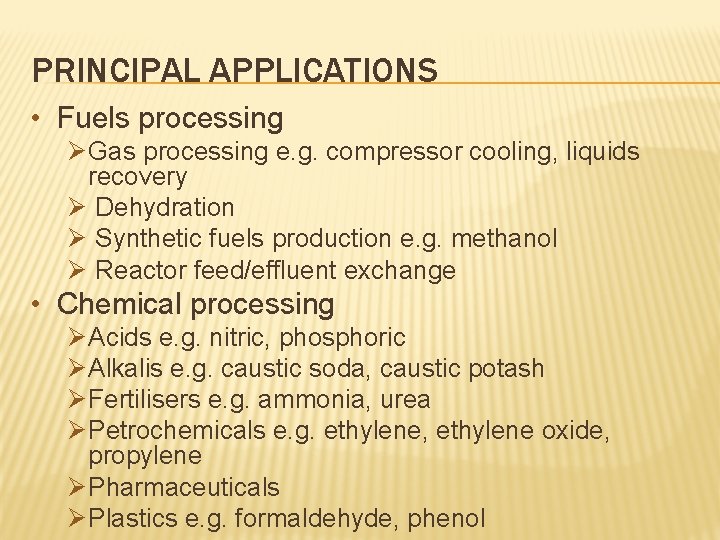
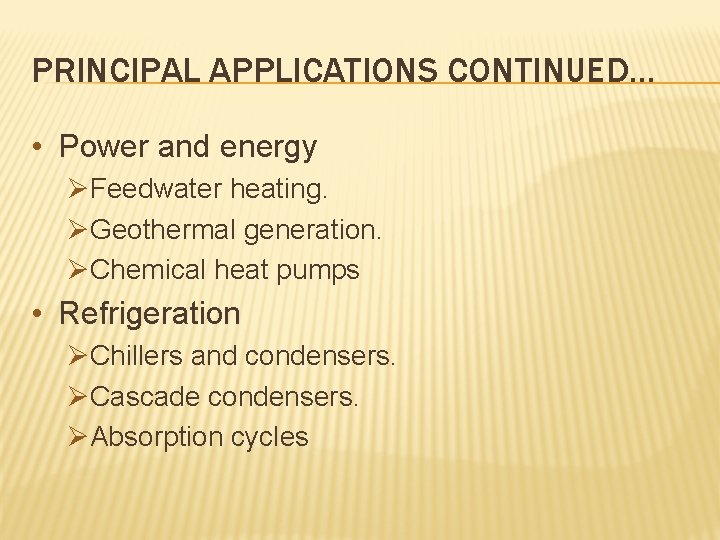
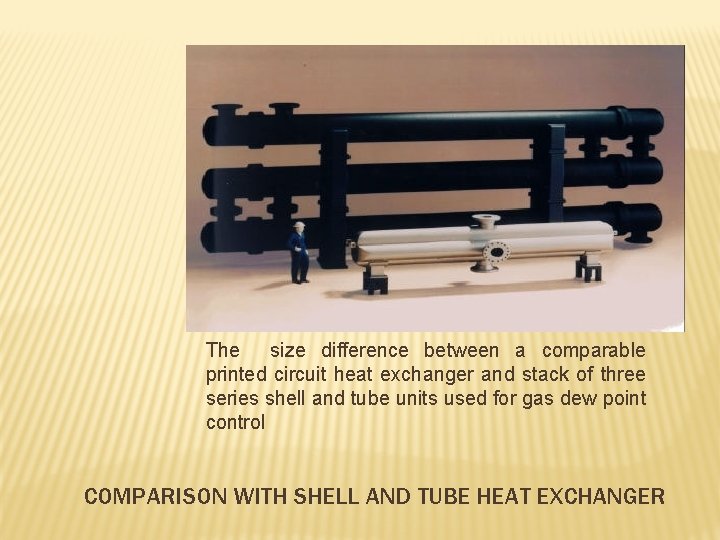
- Slides: 30
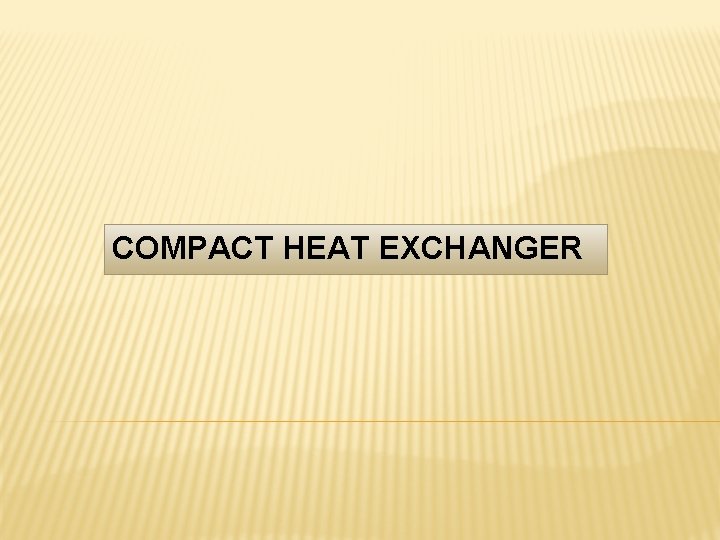
COMPACT HEAT EXCHANGER
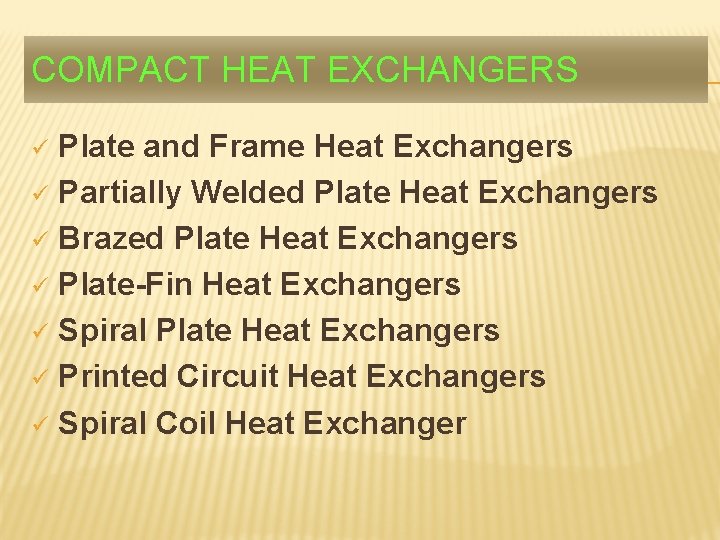
COMPACT HEAT EXCHANGERS Plate and Frame Heat Exchangers ü Partially Welded Plate Heat Exchangers ü Brazed Plate Heat Exchangers ü Plate-Fin Heat Exchangers ü Spiral Plate Heat Exchangers ü Printed Circuit Heat Exchangers ü Spiral Coil Heat Exchanger ü
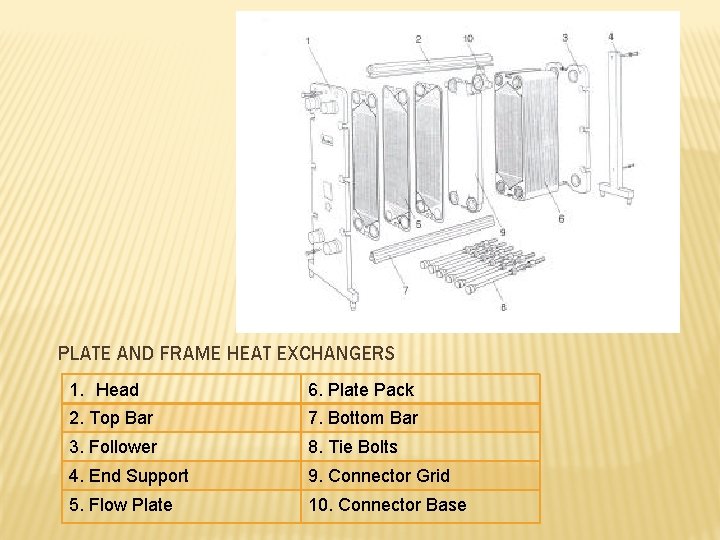
PLATE AND FRAME HEAT EXCHANGERS 1. Head 6. Plate Pack 2. Top Bar 7. Bottom Bar 3. Follower 8. Tie Bolts 4. End Support 9. Connector Grid 5. Flow Plate 10. Connector Base
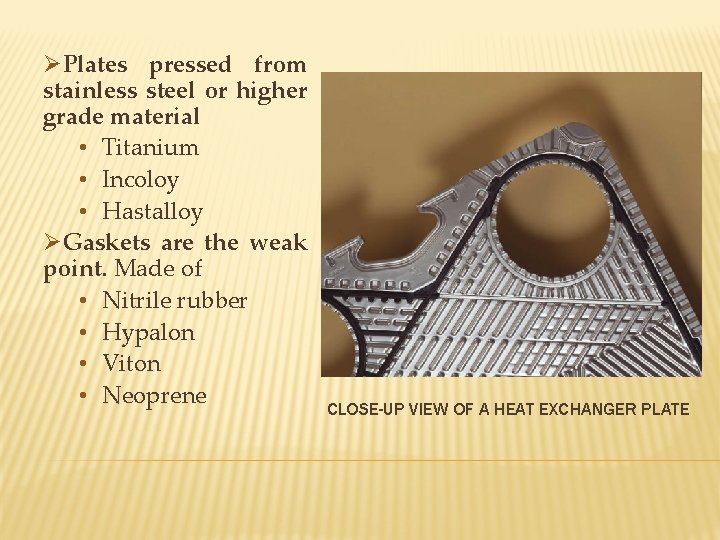
ØPlates pressed from stainless steel or higher grade material • Titanium • Incoloy • Hastalloy ØGaskets are the weak point. Made of • Nitrile rubber • Hypalon • Viton • Neoprene CLOSE-UP VIEW OF A HEAT EXCHANGER PLATE
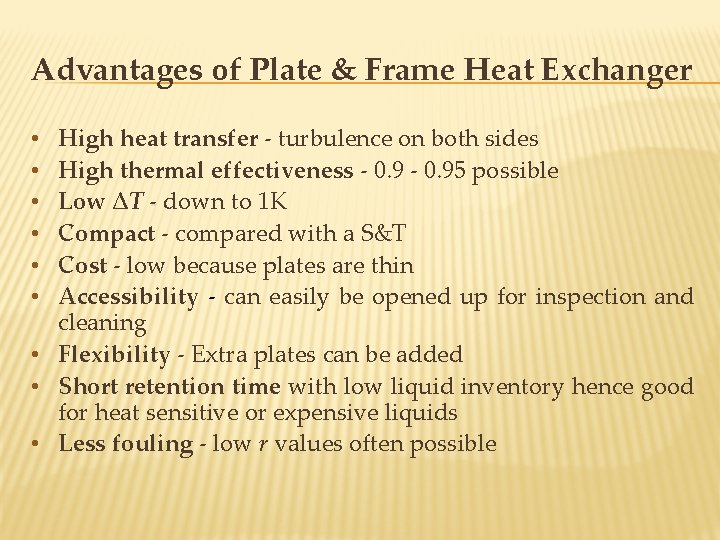
Advantages of Plate & Frame Heat Exchanger High heat transfer - turbulence on both sides High thermal effectiveness - 0. 95 possible Low ΔT - down to 1 K Compact - compared with a S&T Cost - low because plates are thin Accessibility - can easily be opened up for inspection and cleaning • Flexibility - Extra plates can be added • Short retention time with low liquid inventory hence good for heat sensitive or expensive liquids • Less fouling - low r values often possible • • •
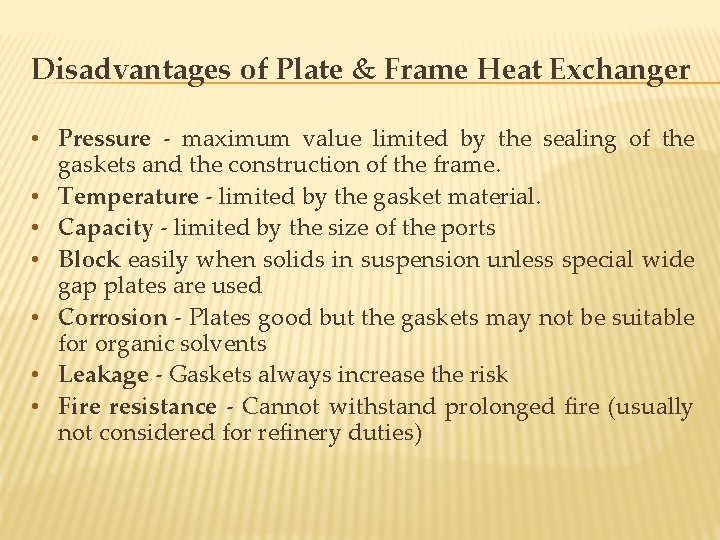
Disadvantages of Plate & Frame Heat Exchanger • Pressure - maximum value limited by the sealing of the gaskets and the construction of the frame. • Temperature - limited by the gasket material. • Capacity - limited by the size of the ports • Block easily when solids in suspension unless special wide gap plates are used • Corrosion - Plates good but the gaskets may not be suitable for organic solvents • Leakage - Gaskets always increase the risk • Fire resistance - Cannot withstand prolonged fire (usually not considered for refinery duties)
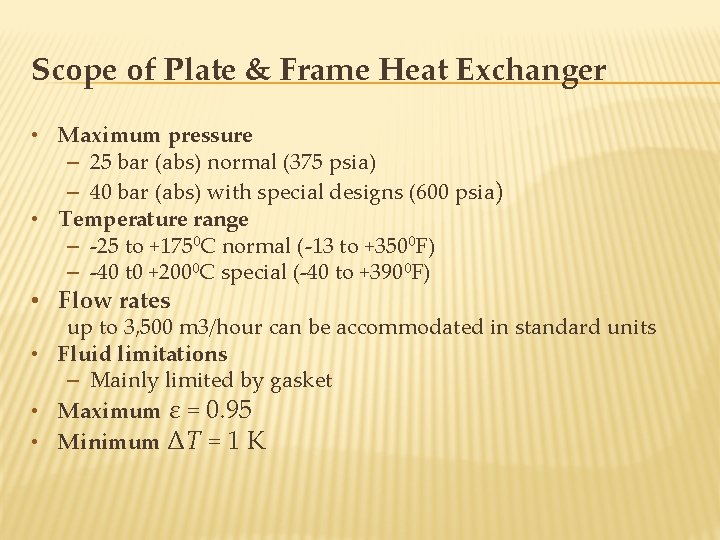
Scope of Plate & Frame Heat Exchanger • Maximum pressure – 25 bar (abs) normal (375 psia) – 40 bar (abs) with special designs (600 psia) • Temperature range – -25 to +1750 C normal (-13 to +3500 F) – -40 t 0 +2000 C special (-40 to +3900 F) • Flow rates up to 3, 500 m 3/hour can be accommodated in standard units • Fluid limitations – Mainly limited by gasket • Maximum ε = 0. 95 • Minimum ΔT = 1 K
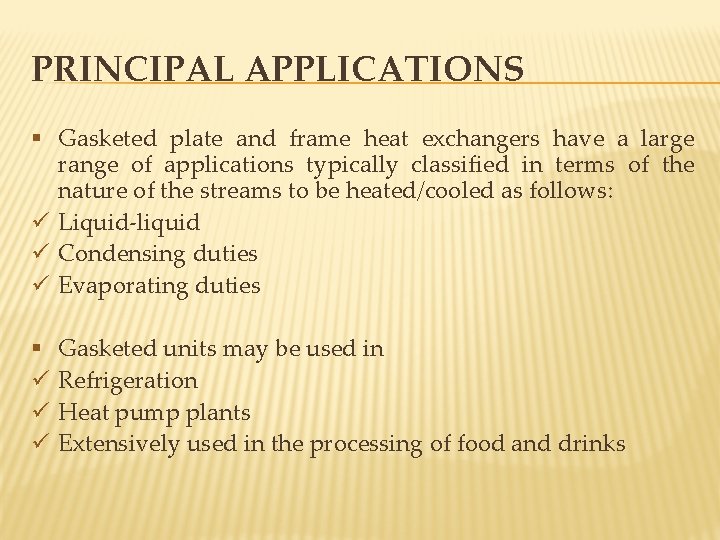
PRINCIPAL APPLICATIONS § Gasketed plate and frame heat exchangers have a large range of applications typically classified in terms of the nature of the streams to be heated/cooled as follows: ü Liquid-liquid ü Condensing duties ü Evaporating duties § ü ü ü Gasketed units may be used in Refrigeration Heat pump plants Extensively used in the processing of food and drinks
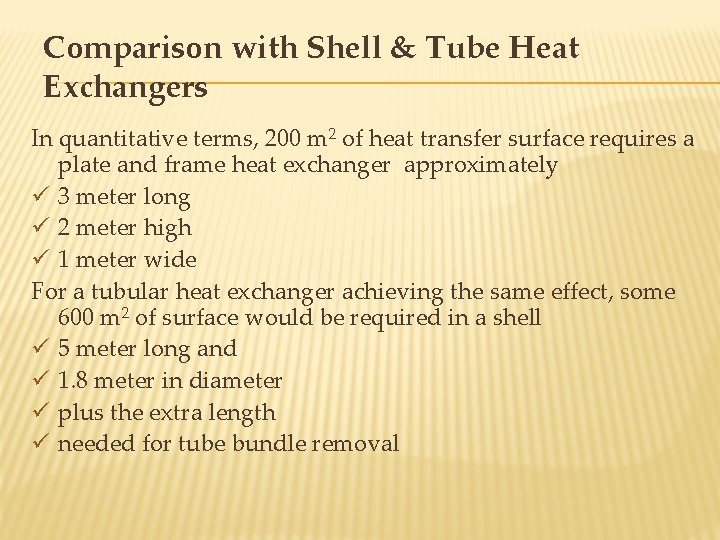
Comparison with Shell & Tube Heat Exchangers In quantitative terms, 200 m 2 of heat transfer surface requires a plate and frame heat exchanger approximately ü 3 meter long ü 2 meter high ü 1 meter wide For a tubular heat exchanger achieving the same effect, some 600 m 2 of surface would be required in a shell ü 5 meter long and ü 1. 8 meter in diameter ü plus the extra length ü needed for tube bundle removal
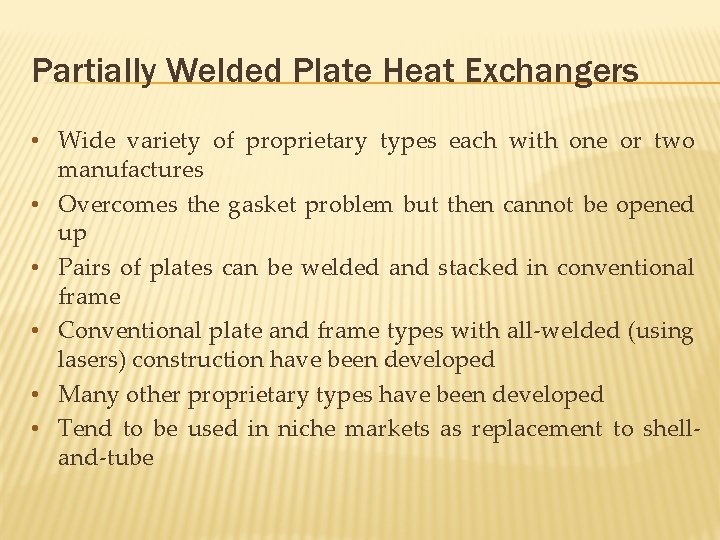
Partially Welded Plate Heat Exchangers • Wide variety of proprietary types each with one or two manufactures • Overcomes the gasket problem but then cannot be opened up • Pairs of plates can be welded and stacked in conventional frame • Conventional plate and frame types with all-welded (using lasers) construction have been developed • Many other proprietary types have been developed • Tend to be used in niche markets as replacement to shelland-tube
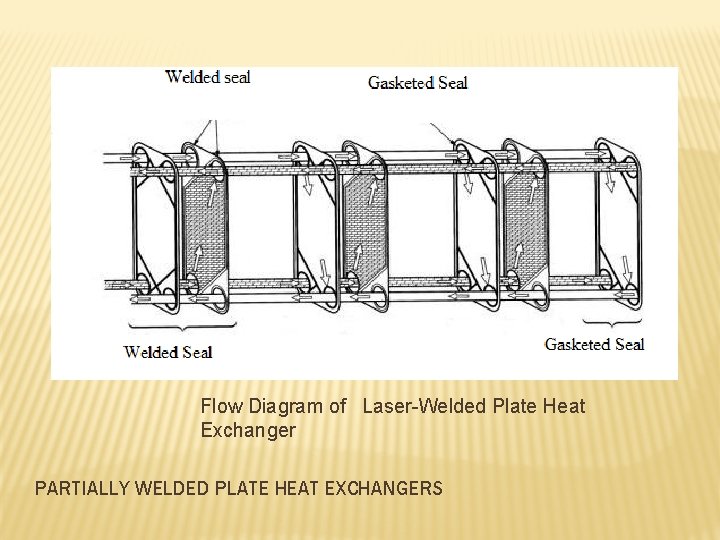
Flow Diagram of Laser-Welded Plate Heat Exchanger PARTIALLY WELDED PLATE HEAT EXCHANGERS
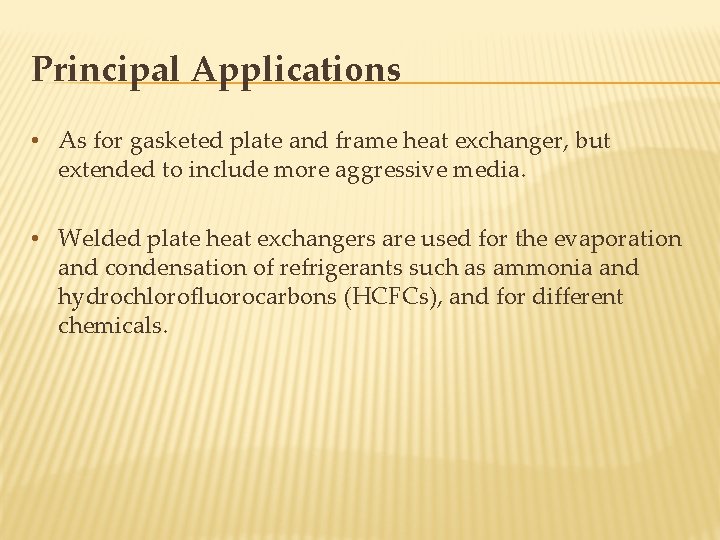
Principal Applications • As for gasketed plate and frame heat exchanger, but extended to include more aggressive media. • Welded plate heat exchangers are used for the evaporation and condensation of refrigerants such as ammonia and hydrochlorofluorocarbons (HCFCs), and for different chemicals.
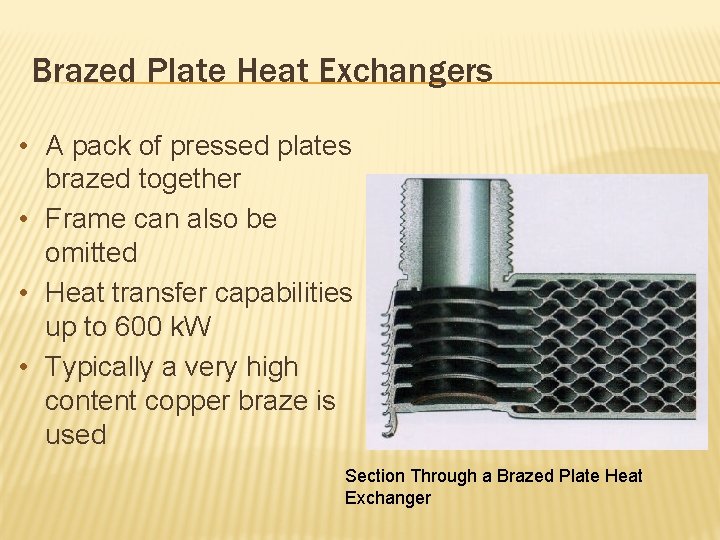
Brazed Plate Heat Exchangers • A pack of pressed plates brazed together • Frame can also be omitted • Heat transfer capabilities up to 600 k. W • Typically a very high content copper braze is used Section Through a Brazed Plate Heat Exchanger
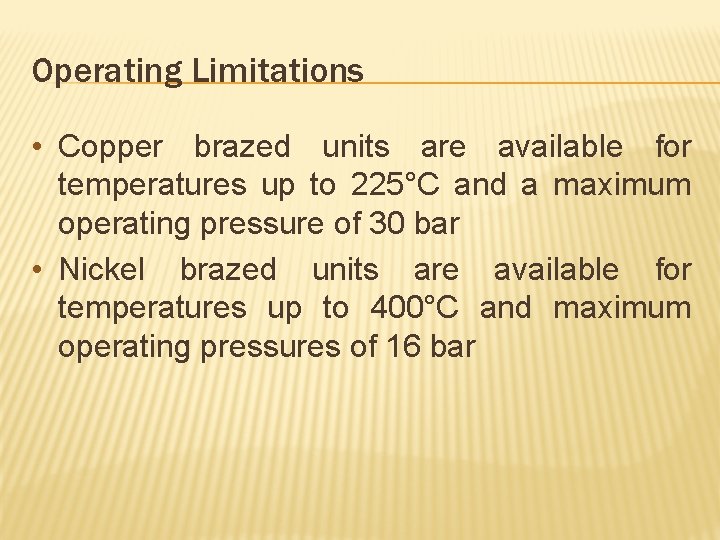
Operating Limitations • Copper brazed units are available for temperatures up to 225°C and a maximum operating pressure of 30 bar • Nickel brazed units are available for temperatures up to 400°C and maximum operating pressures of 16 bar
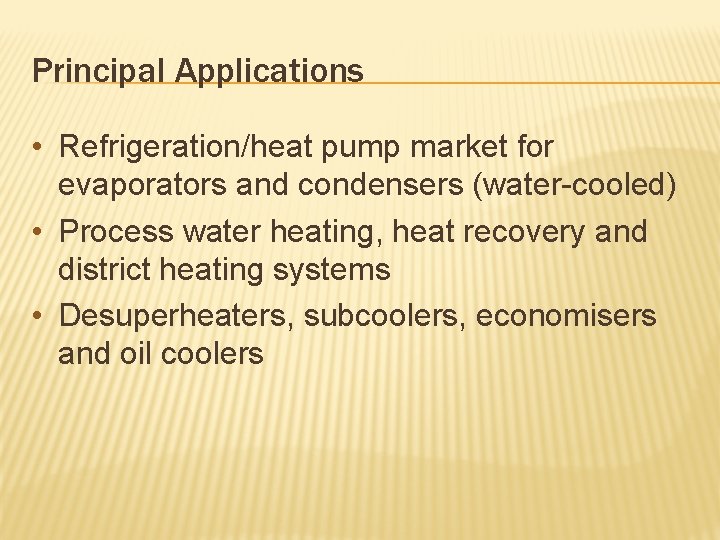
Principal Applications • Refrigeration/heat pump market for evaporators and condensers (water-cooled) • Process water heating, heat recovery and district heating systems • Desuperheaters, subcoolers, economisers and oil coolers
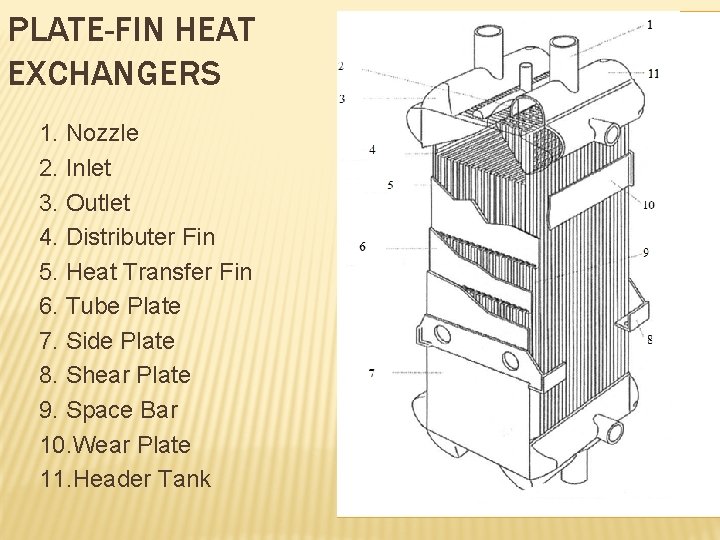
PLATE-FIN HEAT EXCHANGERS 1. Nozzle 2. Inlet 3. Outlet 4. Distributer Fin 5. Heat Transfer Fin 6. Tube Plate 7. Side Plate 8. Shear Plate 9. Space Bar 10. Wear Plate 11. Header Tank
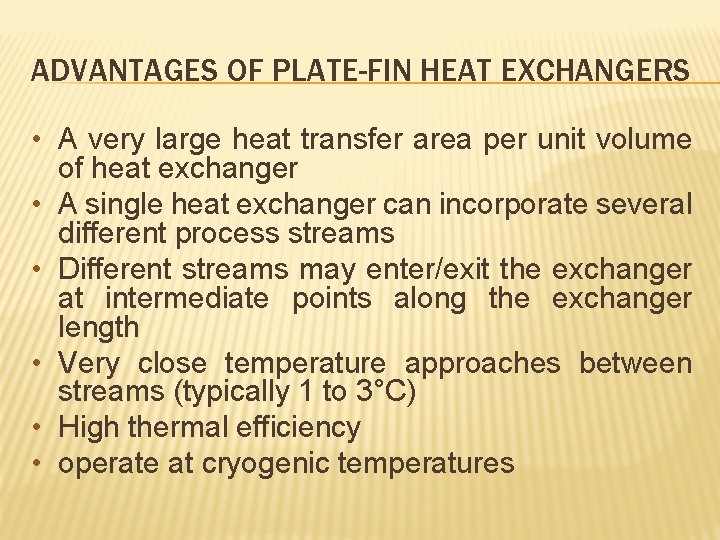
ADVANTAGES OF PLATE-FIN HEAT EXCHANGERS • A very large heat transfer area per unit volume of heat exchanger • A single heat exchanger can incorporate several different process streams • Different streams may enter/exit the exchanger at intermediate points along the exchanger length • Very close temperature approaches between streams (typically 1 to 3°C) • High thermal efficiency • operate at cryogenic temperatures
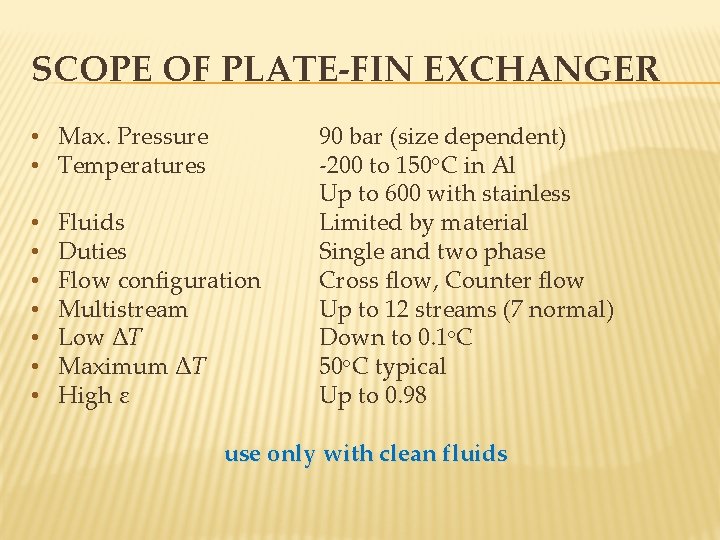
SCOPE OF PLATE-FIN EXCHANGER • Max. Pressure • Temperatures • • Fluids Duties Flow configuration Multistream Low ΔT Maximum ΔT High ε 90 bar (size dependent) -200 to 150 o. C in Al Up to 600 with stainless Limited by material Single and two phase Cross flow, Counter flow Up to 12 streams (7 normal) Down to 0. 1 o. C 50 o. C typical Up to 0. 98 use only with clean fluids
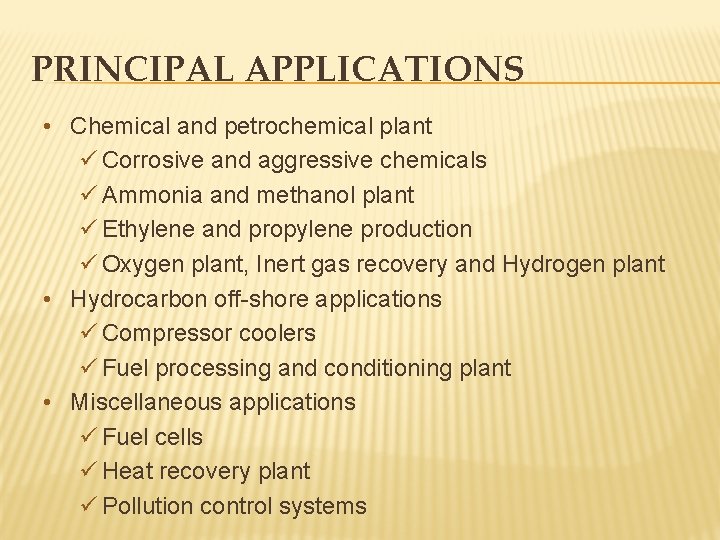
PRINCIPAL APPLICATIONS • Chemical and petrochemical plant ü Corrosive and aggressive chemicals ü Ammonia and methanol plant ü Ethylene and propylene production ü Oxygen plant, Inert gas recovery and Hydrogen plant • Hydrocarbon off-shore applications ü Compressor coolers ü Fuel processing and conditioning plant • Miscellaneous applications ü Fuel cells ü Heat recovery plant ü Pollution control systems
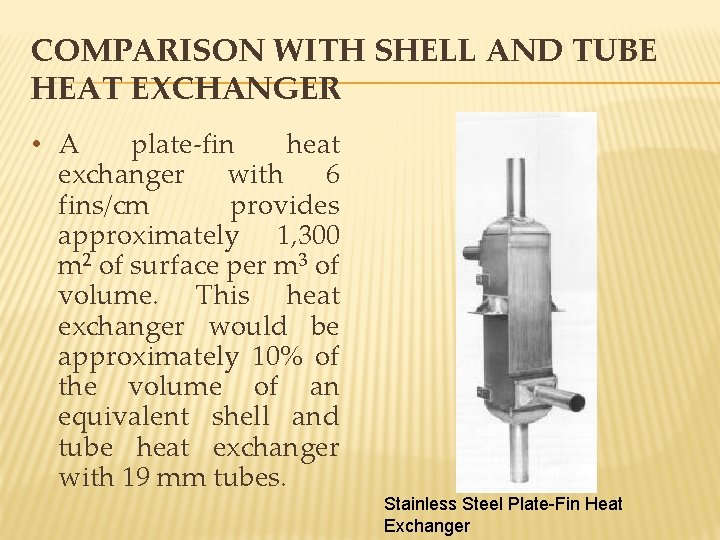
COMPARISON WITH SHELL AND TUBE HEAT EXCHANGER • A plate-fin heat exchanger with 6 fins/cm provides approximately 1, 300 m 2 of surface per m 3 of volume. This heat exchanger would be approximately 10% of the volume of an equivalent shell and tube heat exchanger with 19 mm tubes. Stainless Steel Plate-Fin Heat Exchanger
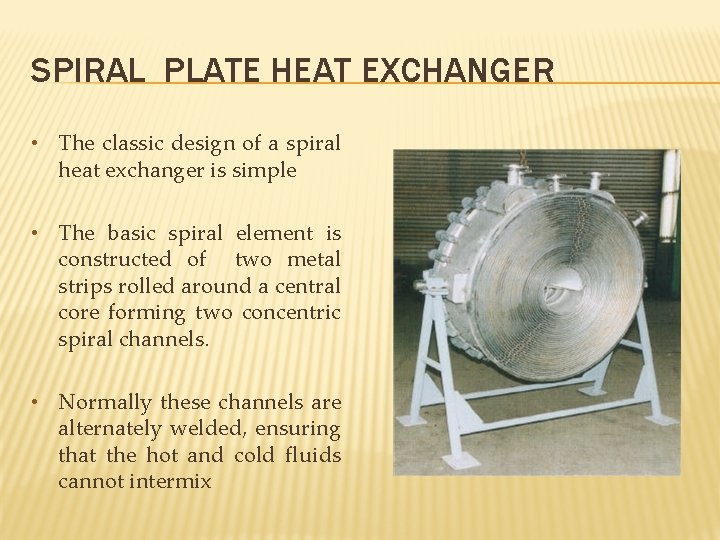
SPIRAL PLATE HEAT EXCHANGER • The classic design of a spiral heat exchanger is simple • The basic spiral element is constructed of two metal strips rolled around a central core forming two concentric spiral channels. • Normally these channels are alternately welded, ensuring that the hot and cold fluids cannot intermix
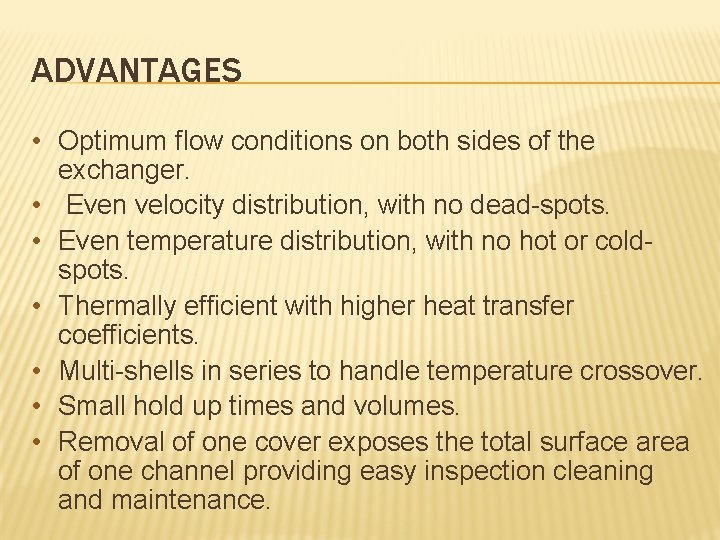
ADVANTAGES • Optimum flow conditions on both sides of the exchanger. • Even velocity distribution, with no dead-spots. • Even temperature distribution, with no hot or coldspots. • Thermally efficient with higher heat transfer coefficients. • Multi-shells in series to handle temperature crossover. • Small hold up times and volumes. • Removal of one cover exposes the total surface area of one channel providing easy inspection cleaning and maintenance.
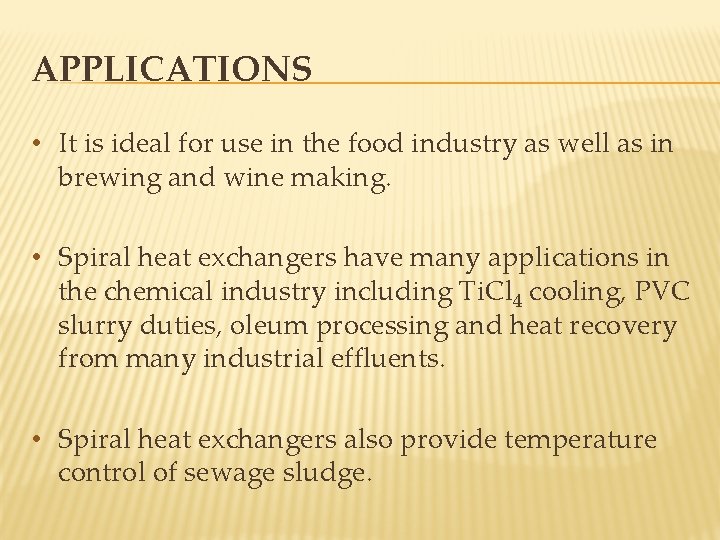
APPLICATIONS • It is ideal for use in the food industry as well as in brewing and wine making. • Spiral heat exchangers have many applications in the chemical industry including Ti. Cl 4 cooling, PVC slurry duties, oleum processing and heat recovery from many industrial effluents. • Spiral heat exchangers also provide temperature control of sewage sludge.
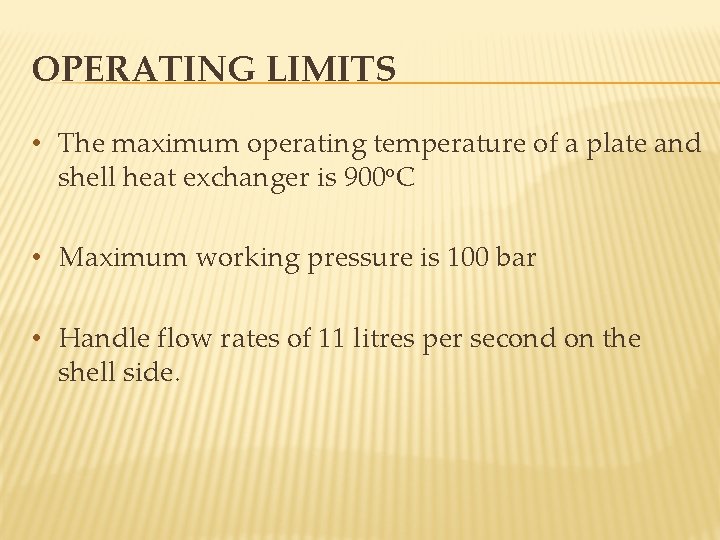
OPERATING LIMITS • The maximum operating temperature of a plate and shell heat exchanger is 900 o. C • Maximum working pressure is 100 bar • Handle flow rates of 11 litres per second on the shell side.
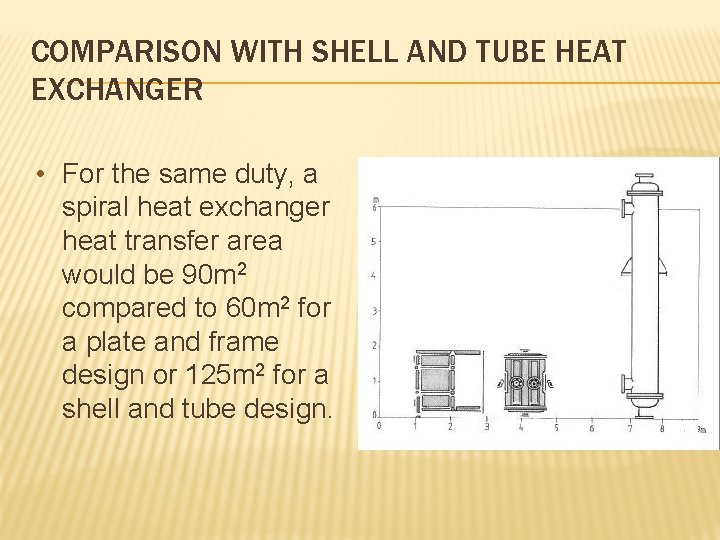
COMPARISON WITH SHELL AND TUBE HEAT EXCHANGER • For the same duty, a spiral heat exchanger heat transfer area would be 90 m 2 compared to 60 m 2 for a plate and frame design or 125 m 2 for a shell and tube design.
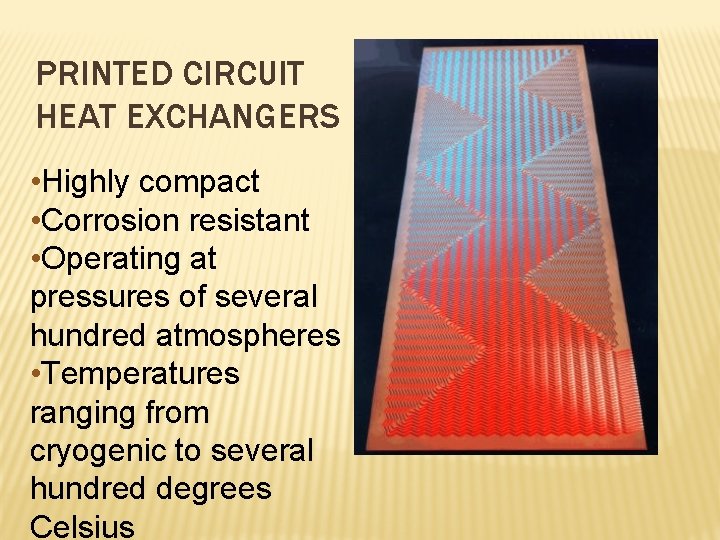
PRINTED CIRCUIT HEAT EXCHANGERS • Highly compact • Corrosion resistant • Operating at pressures of several hundred atmospheres • Temperatures ranging from cryogenic to several hundred degrees Celsius
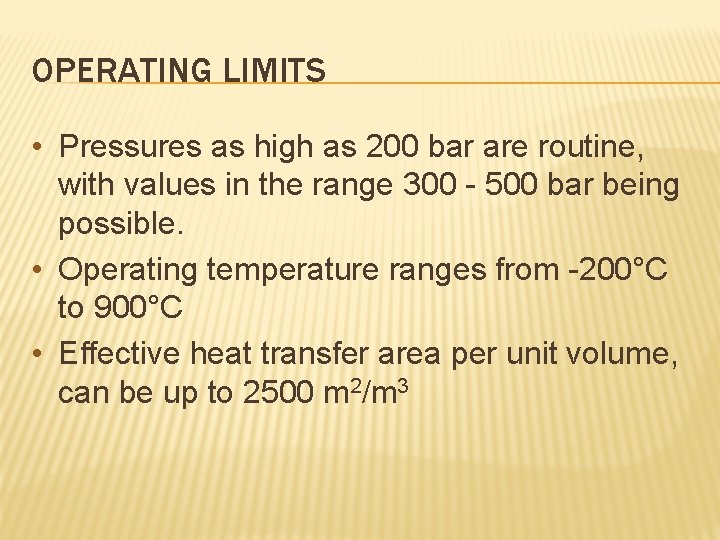
OPERATING LIMITS • Pressures as high as 200 bar are routine, with values in the range 300 - 500 bar being possible. • Operating temperature ranges from -200°C to 900°C • Effective heat transfer area per unit volume, can be up to 2500 m 2/m 3
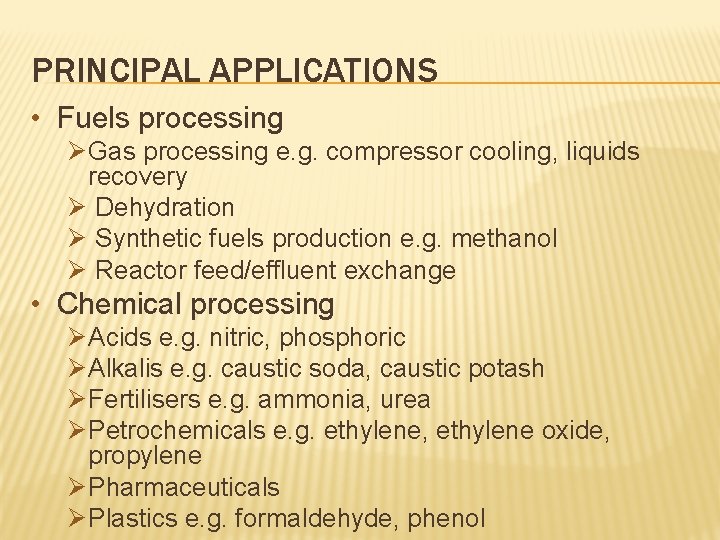
PRINCIPAL APPLICATIONS • Fuels processing Ø Gas processing e. g. compressor cooling, liquids recovery Ø Dehydration Ø Synthetic fuels production e. g. methanol Ø Reactor feed/effluent exchange • Chemical processing Ø Acids e. g. nitric, phosphoric Ø Alkalis e. g. caustic soda, caustic potash Ø Fertilisers e. g. ammonia, urea Ø Petrochemicals e. g. ethylene, ethylene oxide, propylene Ø Pharmaceuticals Ø Plastics e. g. formaldehyde, phenol
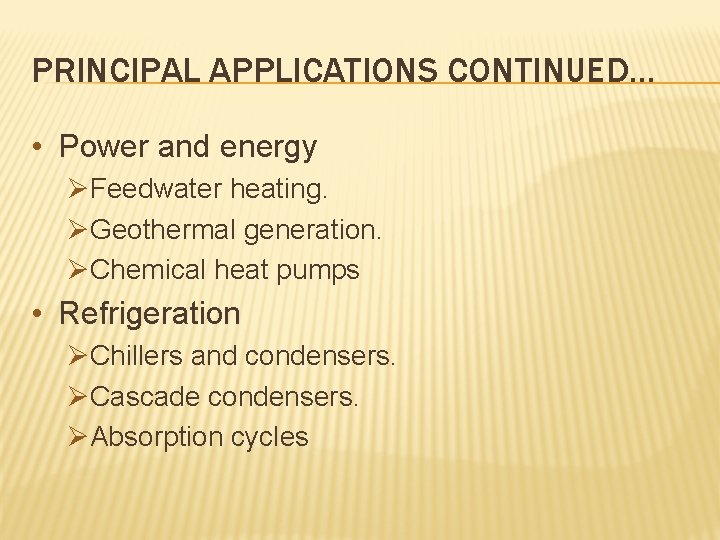
PRINCIPAL APPLICATIONS CONTINUED… • Power and energy ØFeedwater heating. ØGeothermal generation. ØChemical heat pumps • Refrigeration ØChillers and condensers. ØCascade condensers. ØAbsorption cycles
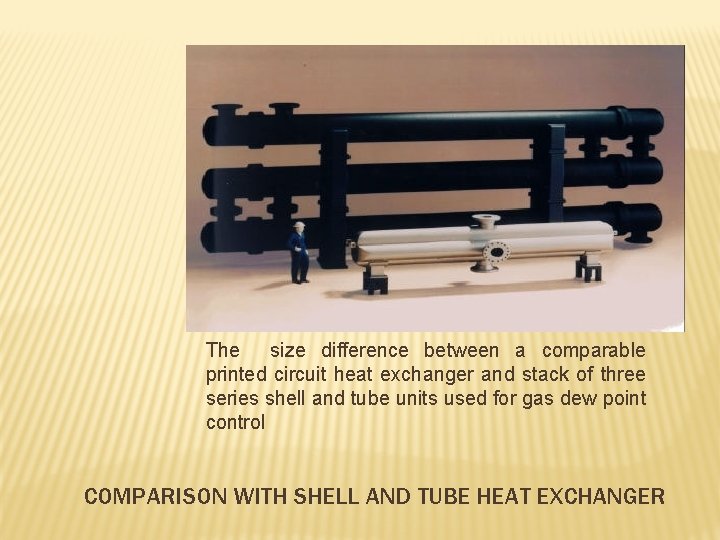
The size difference between a comparable printed circuit heat exchanger and stack of three series shell and tube units used for gas dew point control COMPARISON WITH SHELL AND TUBE HEAT EXCHANGER
Ddi heat exchangers
Tema standard for heat exchanger
Capacity of cooling tower
Scraped surface heat exchangers in food industry
Floating head heat exchanger near me
Rce heat exchangers
Ddi heat exchangers inc
Nozzle and diffuser
Plate frame heat exchanger
Recuperator heat exchanger
Standard heat exchanger
Plate type exchanger
Spiral exchanger
Plate and frame exchanger
Ntu method
Pillow plate heat exchanger
Heat exchanger
Shell and tube surface condenser
Web buckling and web crippling slideshare
Plate type exchanger
Cross flow heat exchanger
A double pipe parallel flow heat exchanger
Plate type exchanger
Air separation unit
Tema r heat exchanger
Plate type exchanger
Mass transfer in bioprocess
Nnn pmv
Plate type exchanger
Plate type exchanger
Pour plate method vs spread plate method