Chapter 7 Fluid Power Systems Introduction Mechanical electromechanical
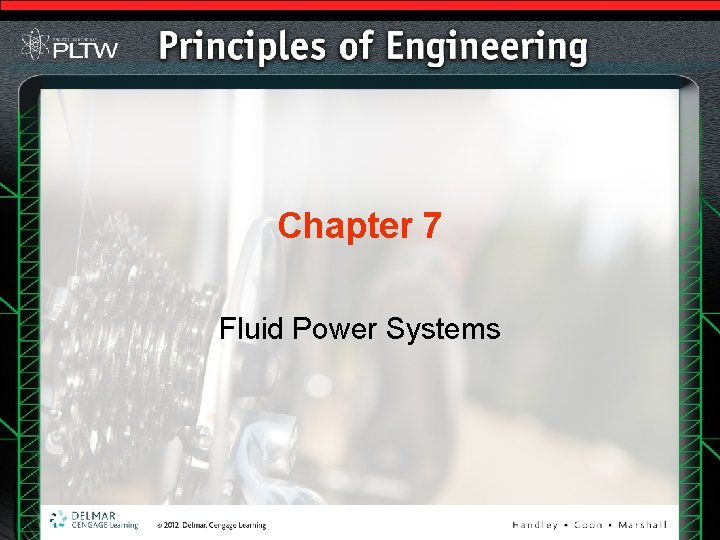
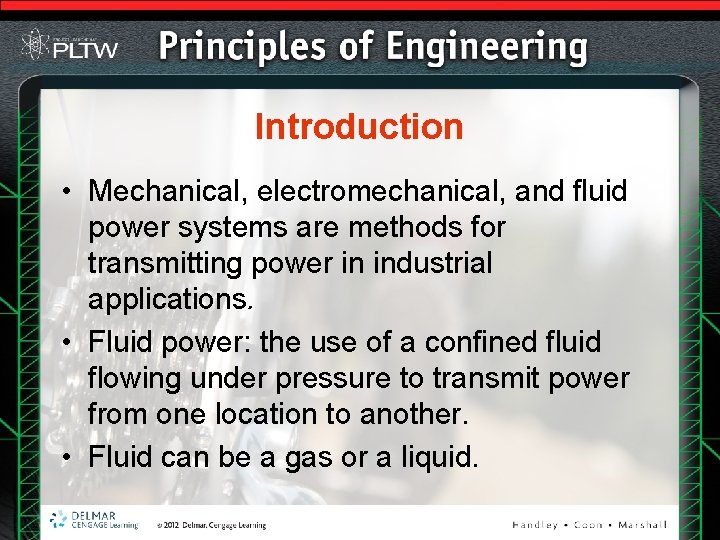

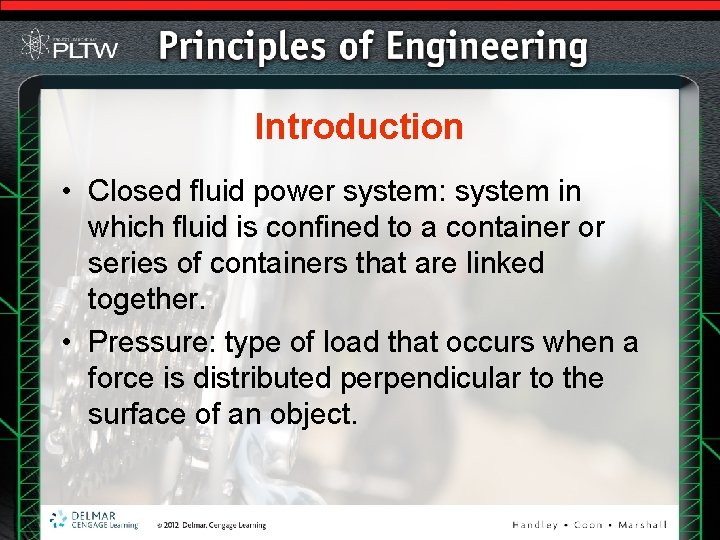
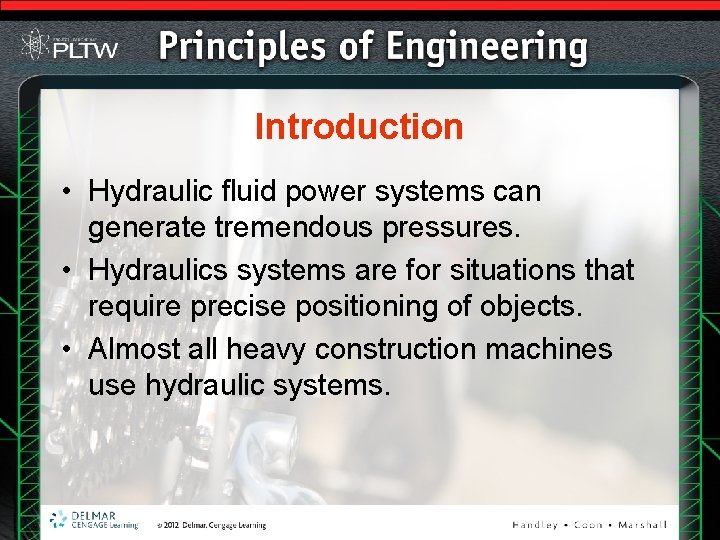
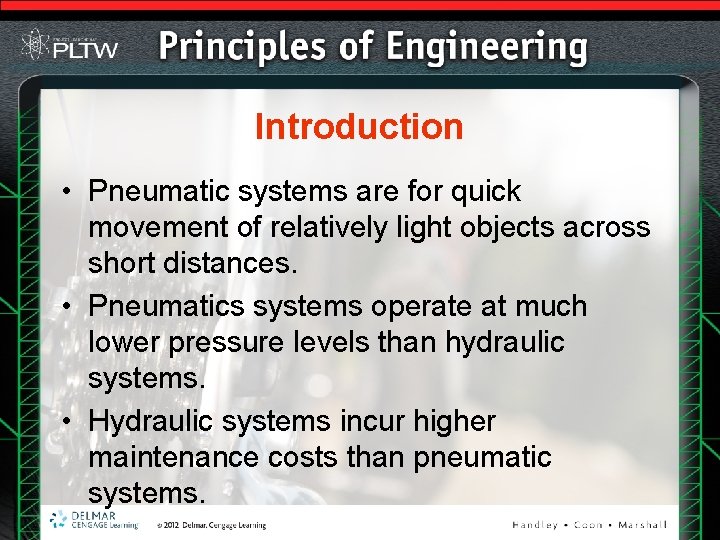
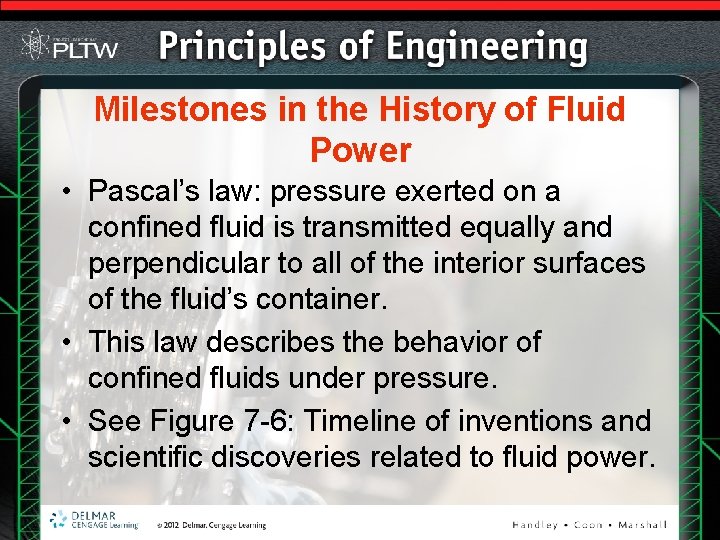
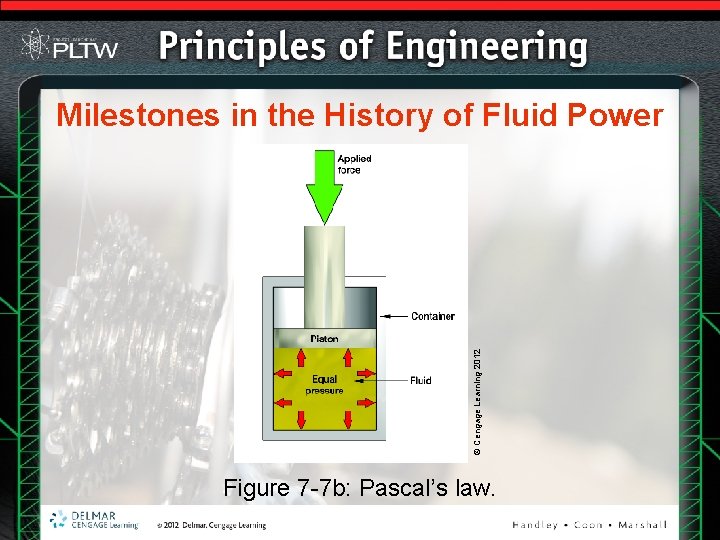
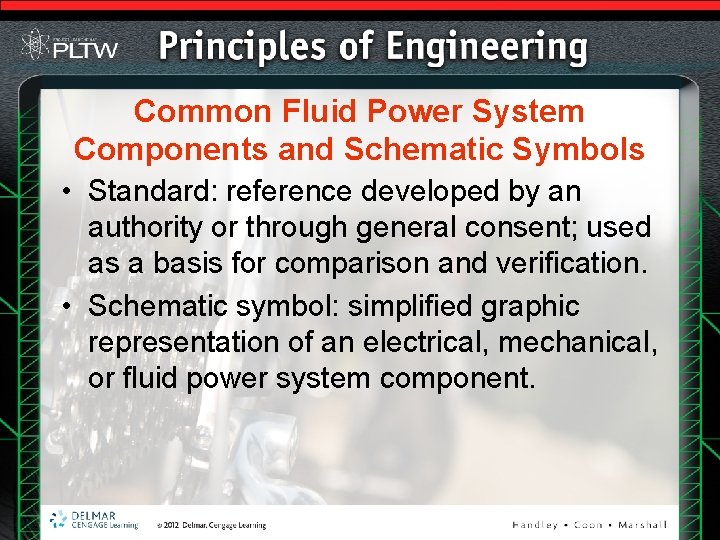
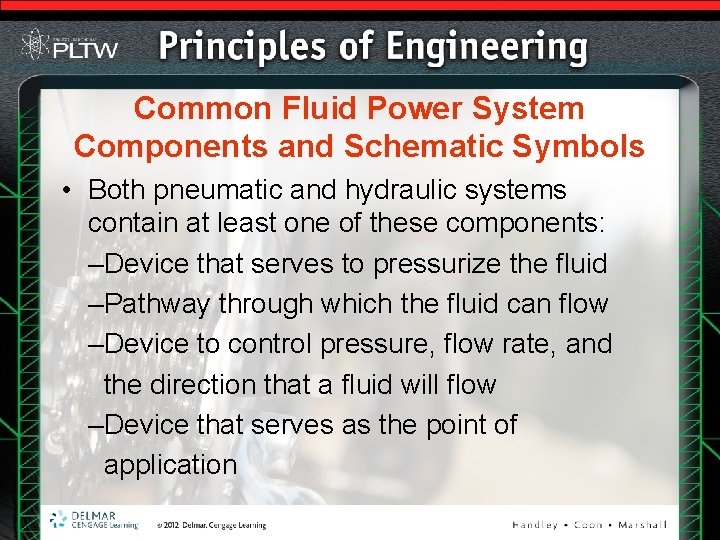
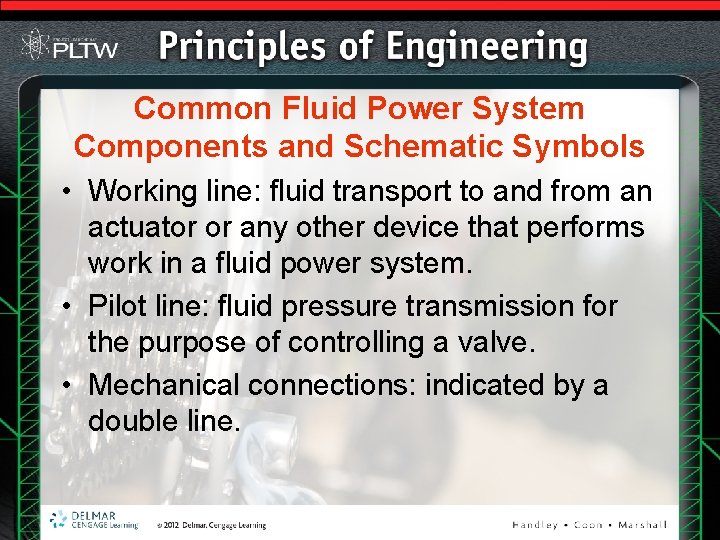
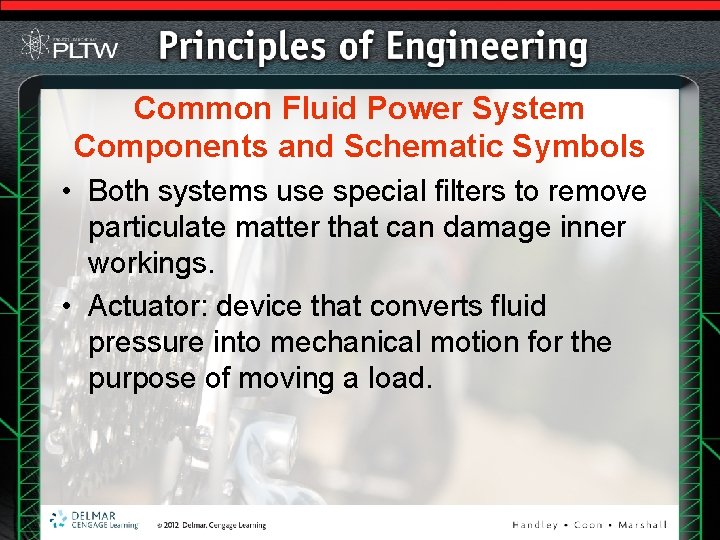

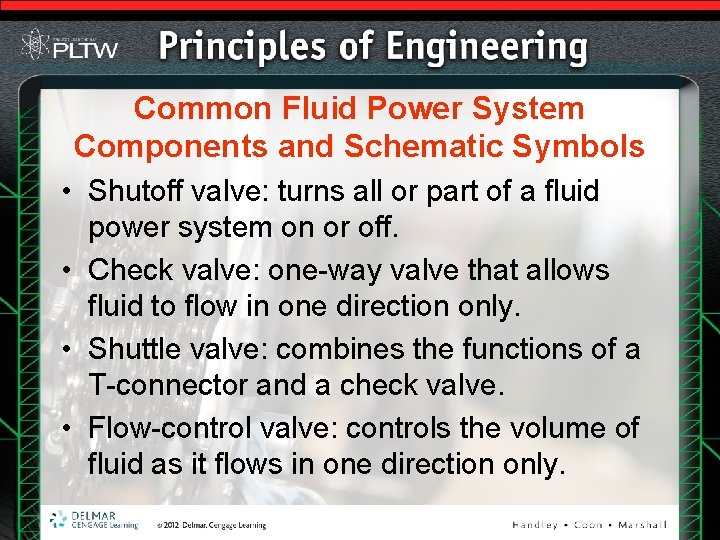
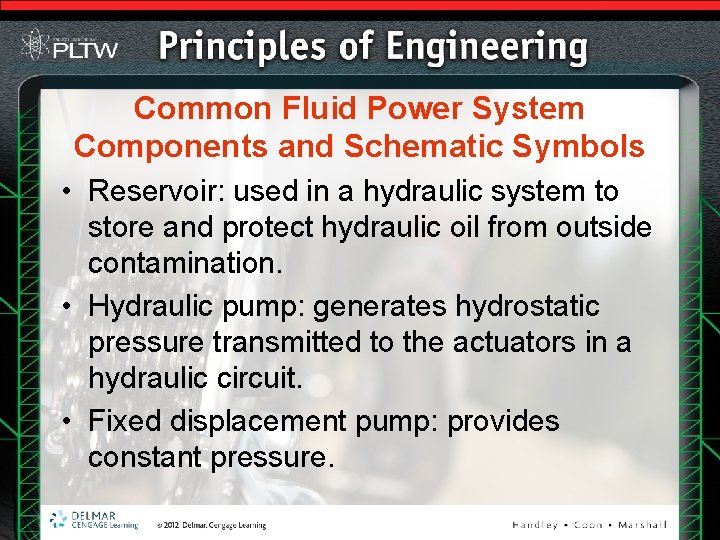
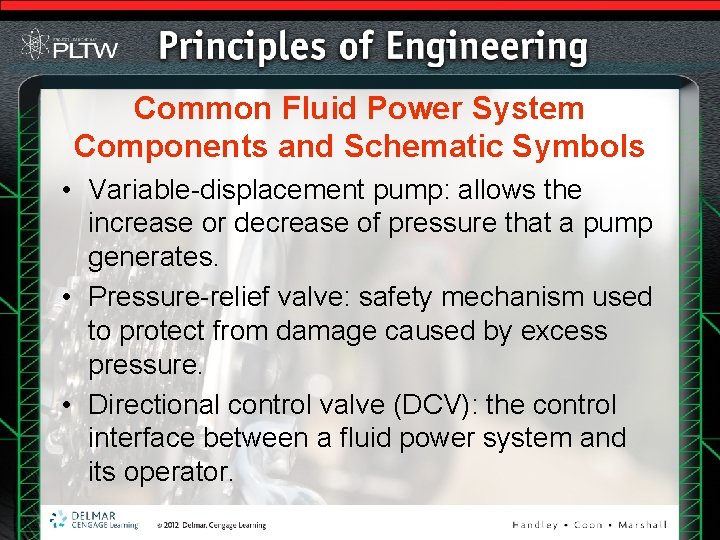
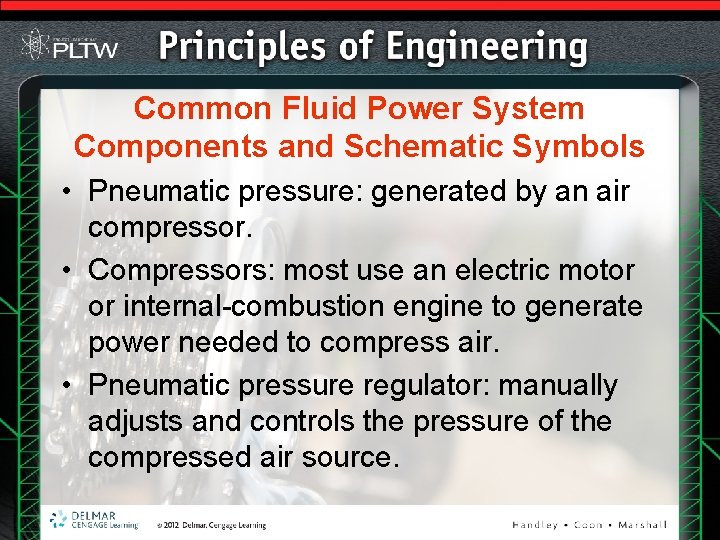
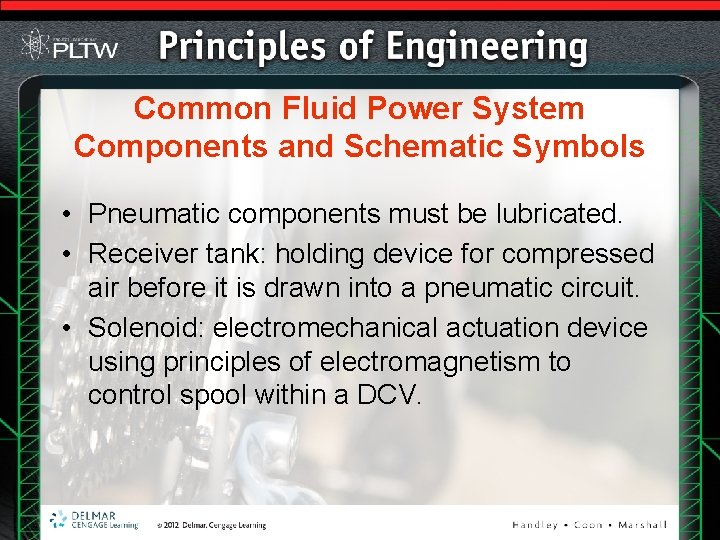
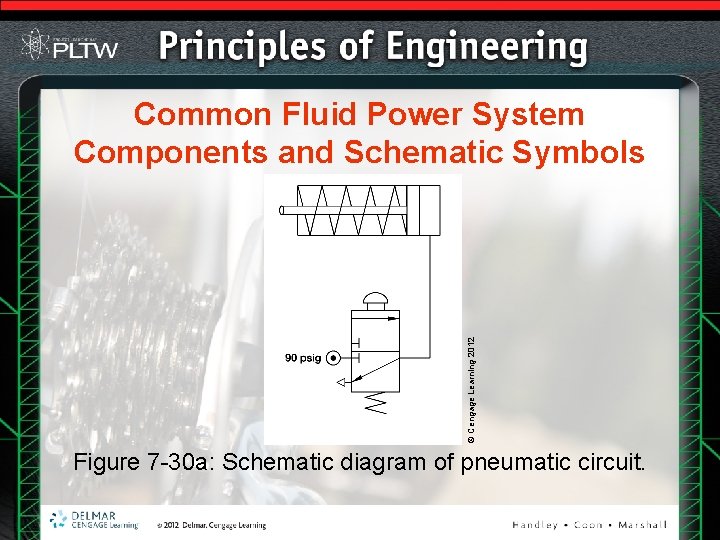
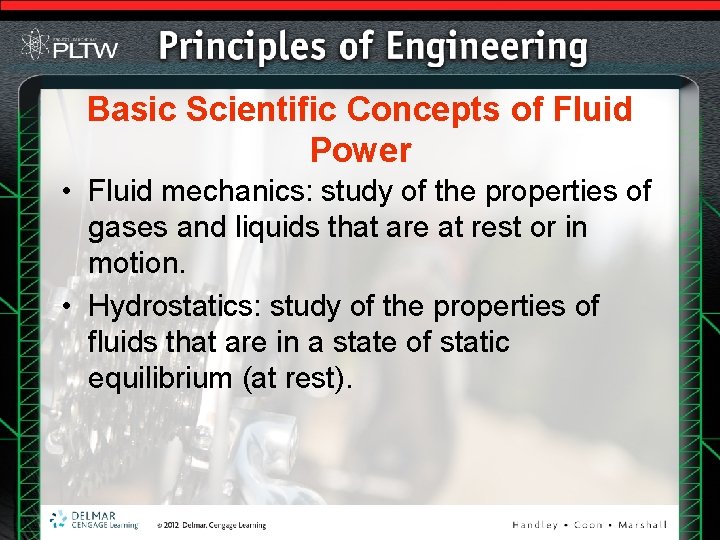
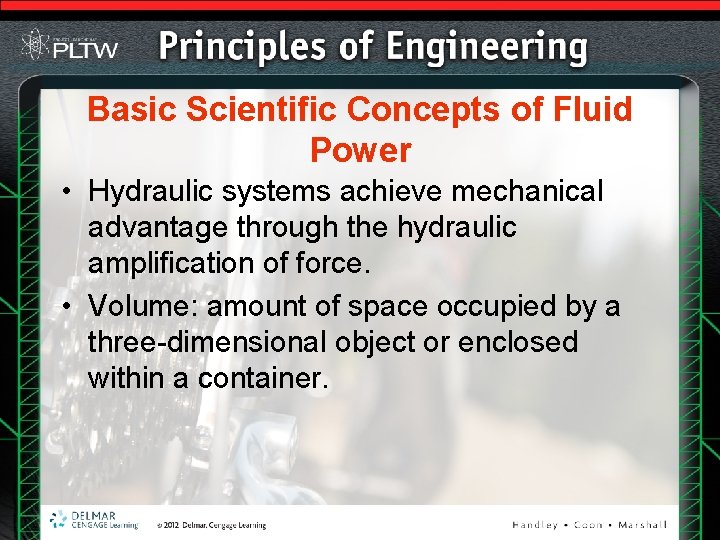
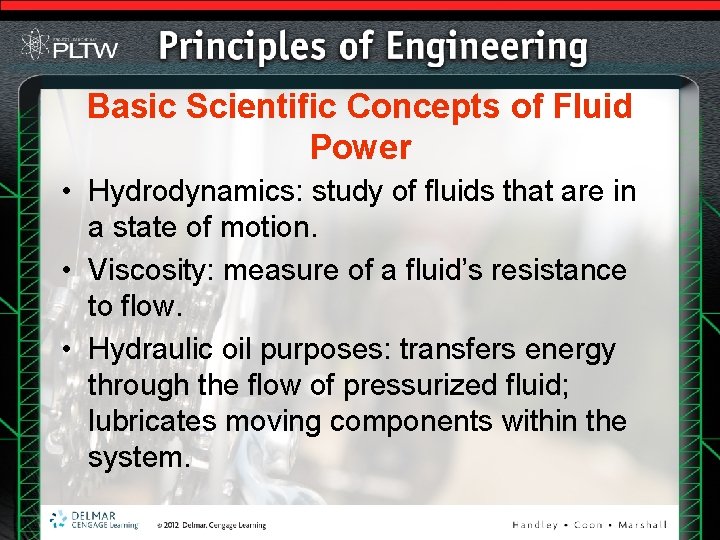
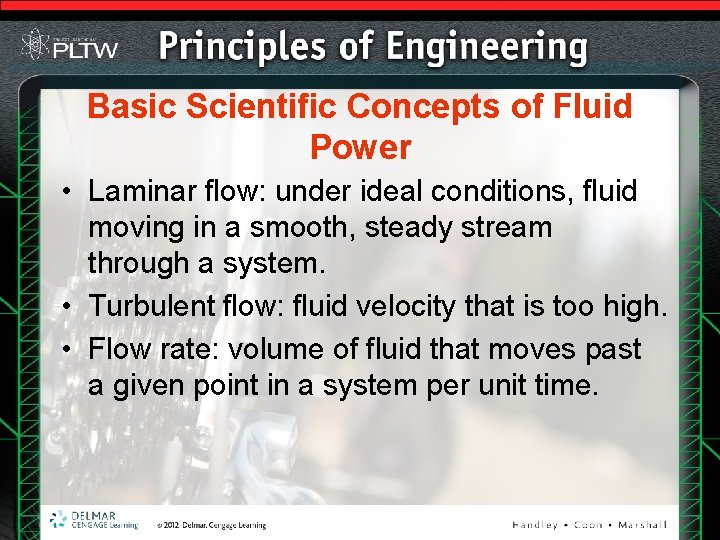
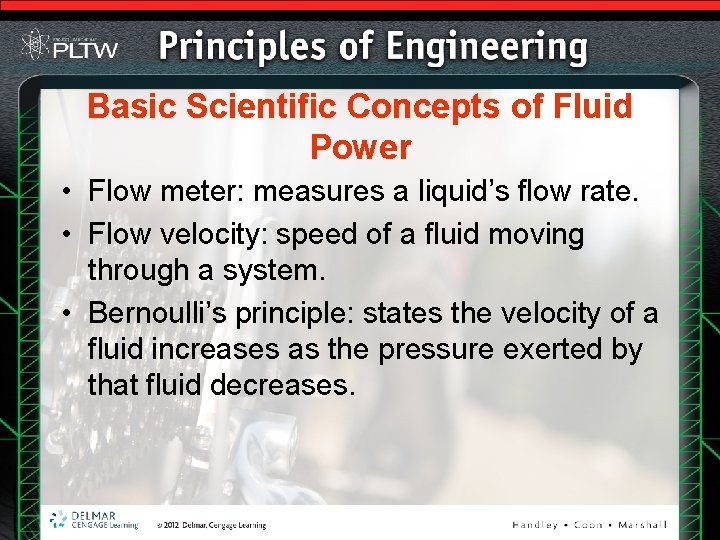
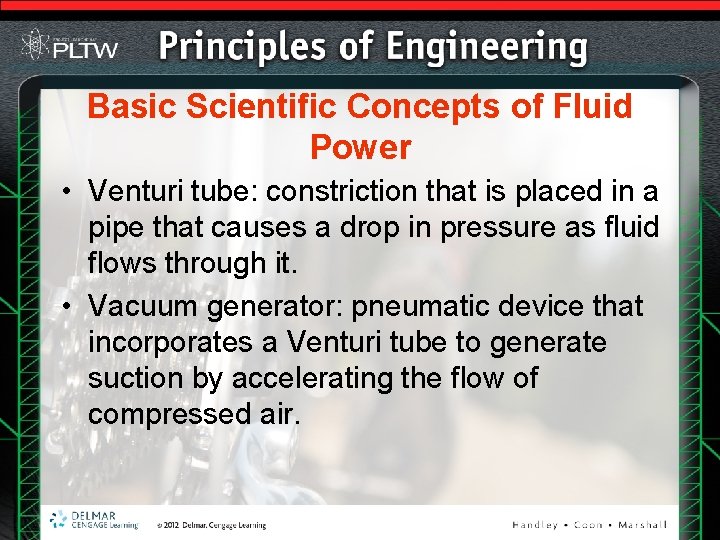
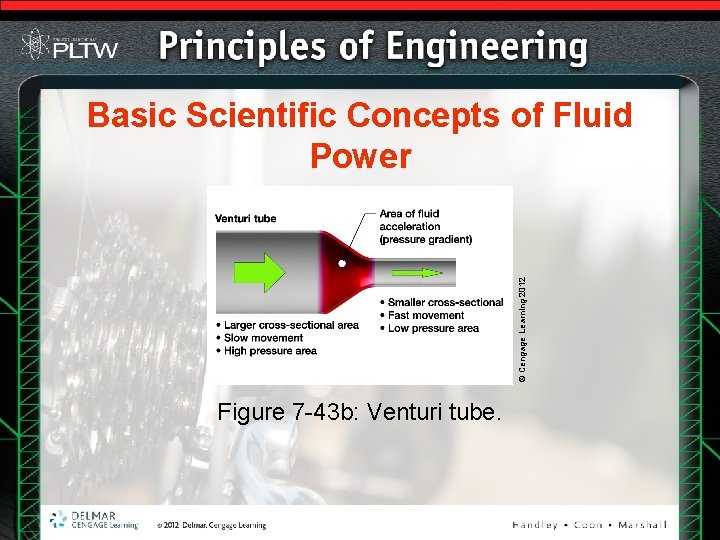
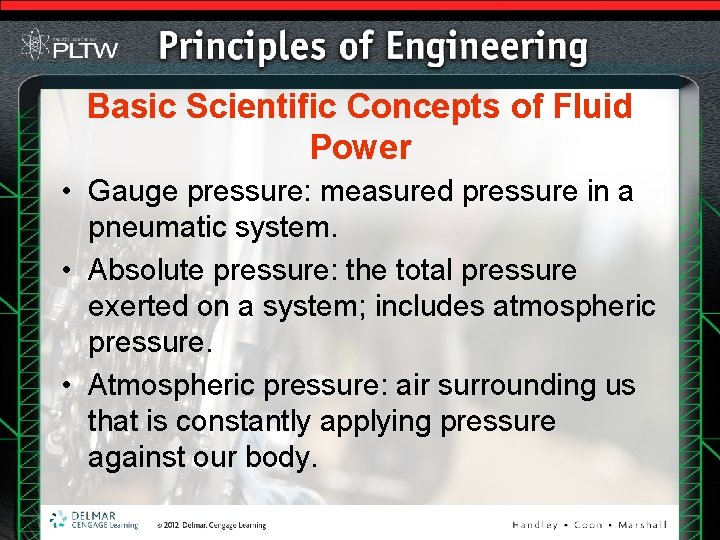
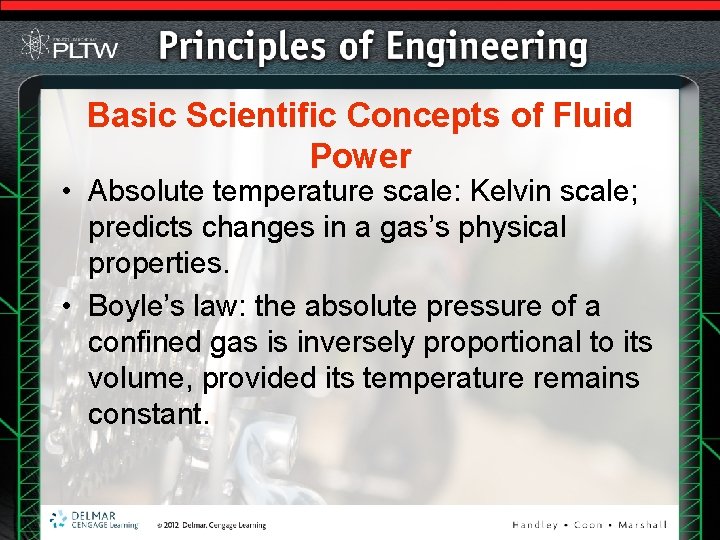
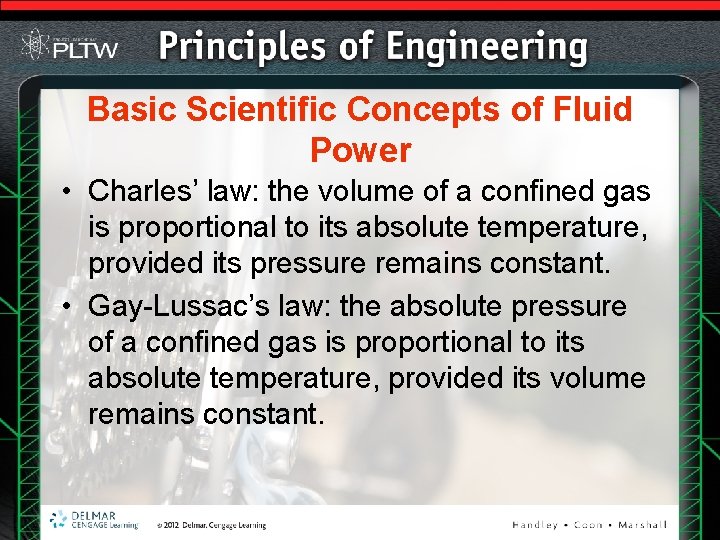
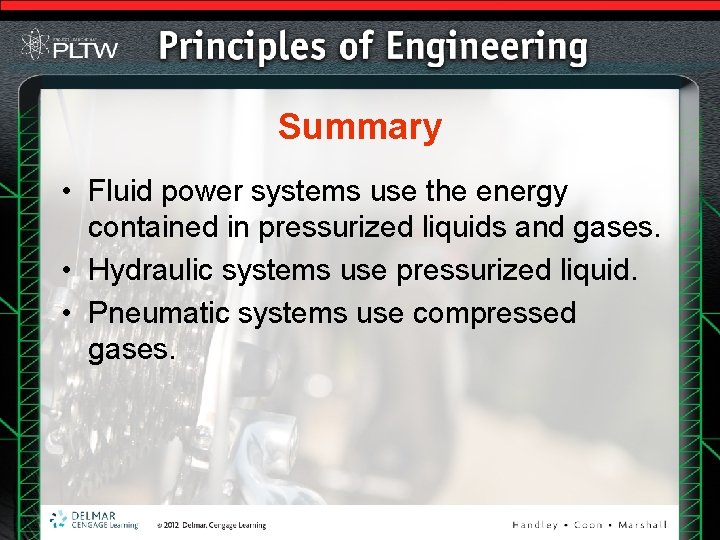
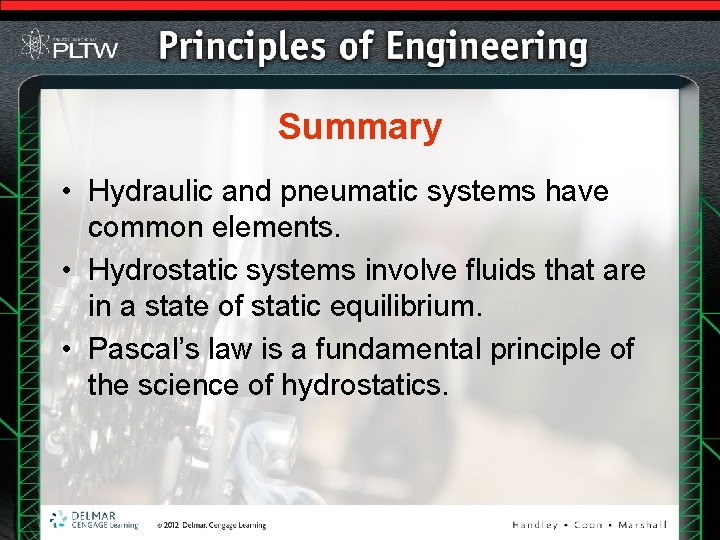
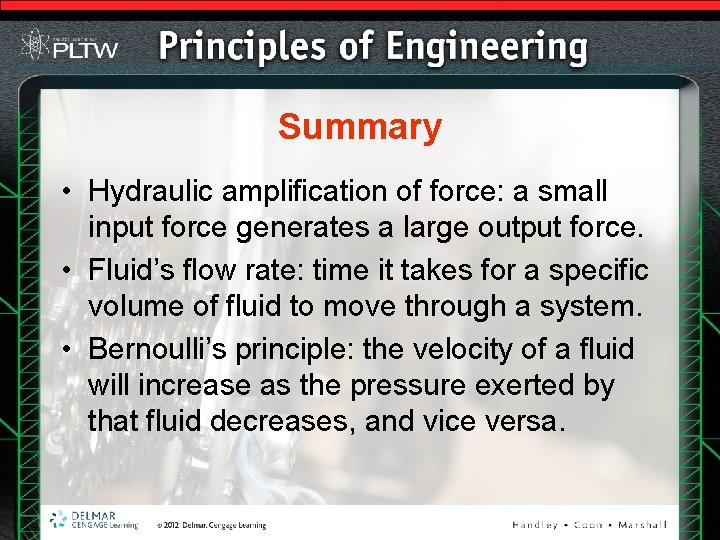
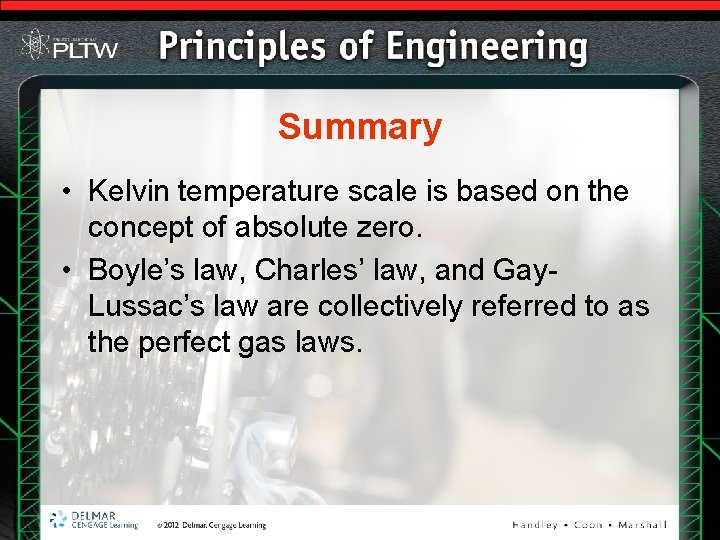
- Slides: 33
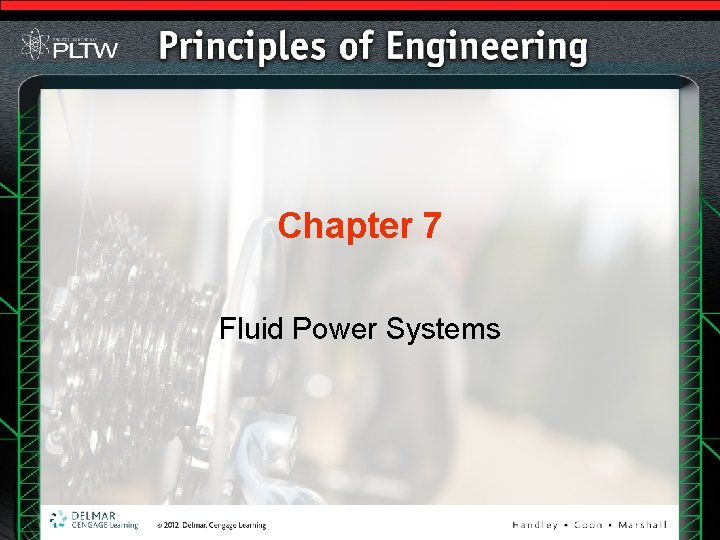
Chapter 7 Fluid Power Systems
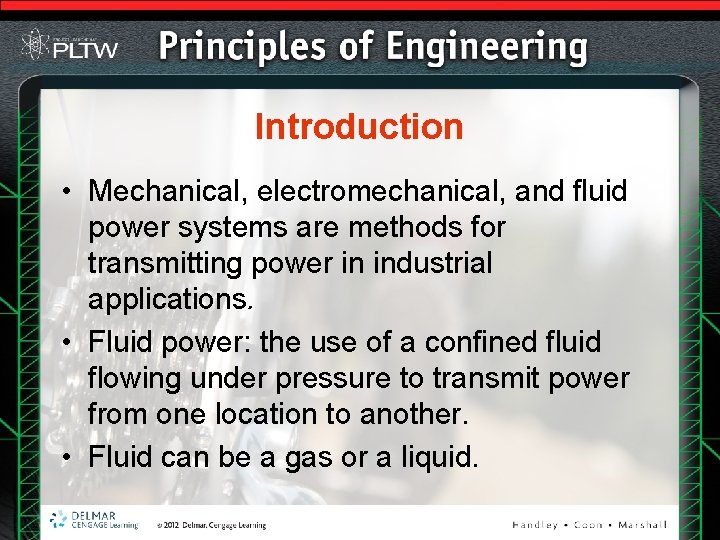
Introduction • Mechanical, electromechanical, and fluid power systems are methods for transmitting power in industrial applications. • Fluid power: the use of a confined fluid flowing under pressure to transmit power from one location to another. • Fluid can be a gas or a liquid.

Introduction • Fluid power systems: pneumatics (gases); hydraulics (liquids). • Hydraulics: physical science and technologies associated with liquids that are at rest or flowing under pressure. • Pneumatics: physical science and technologies associated with mechanics of pressurized gases. • Power density: power per unit volume.
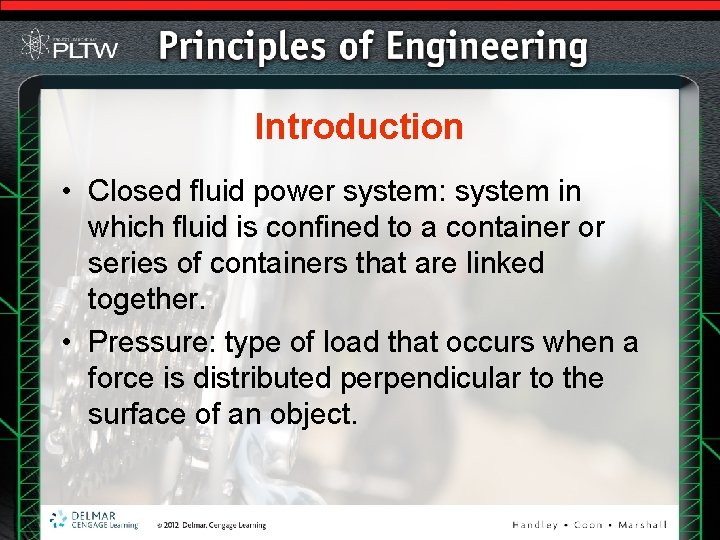
Introduction • Closed fluid power system: system in which fluid is confined to a container or series of containers that are linked together. • Pressure: type of load that occurs when a force is distributed perpendicular to the surface of an object.
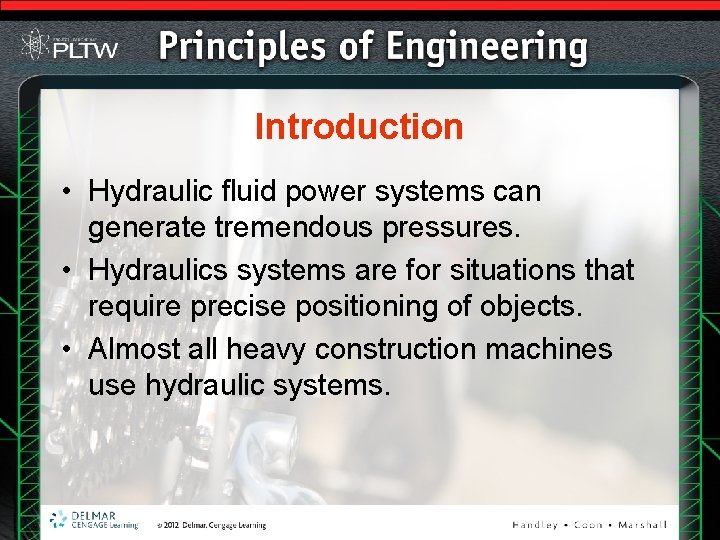
Introduction • Hydraulic fluid power systems can generate tremendous pressures. • Hydraulics systems are for situations that require precise positioning of objects. • Almost all heavy construction machines use hydraulic systems.
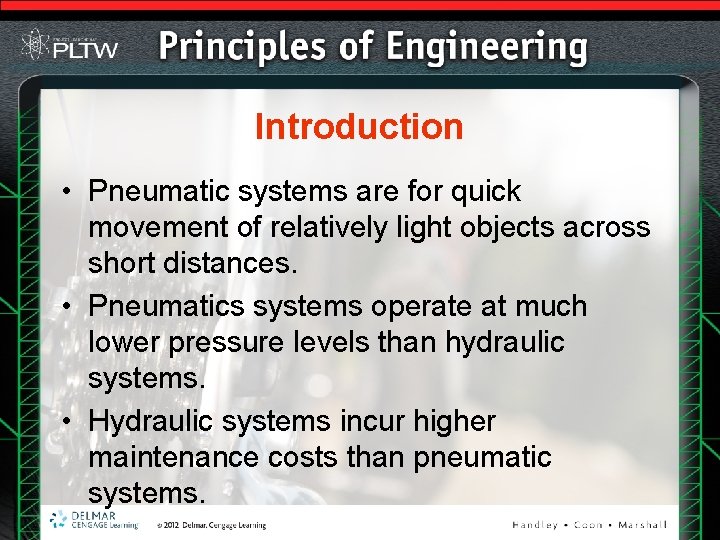
Introduction • Pneumatic systems are for quick movement of relatively light objects across short distances. • Pneumatics systems operate at much lower pressure levels than hydraulic systems. • Hydraulic systems incur higher maintenance costs than pneumatic systems.
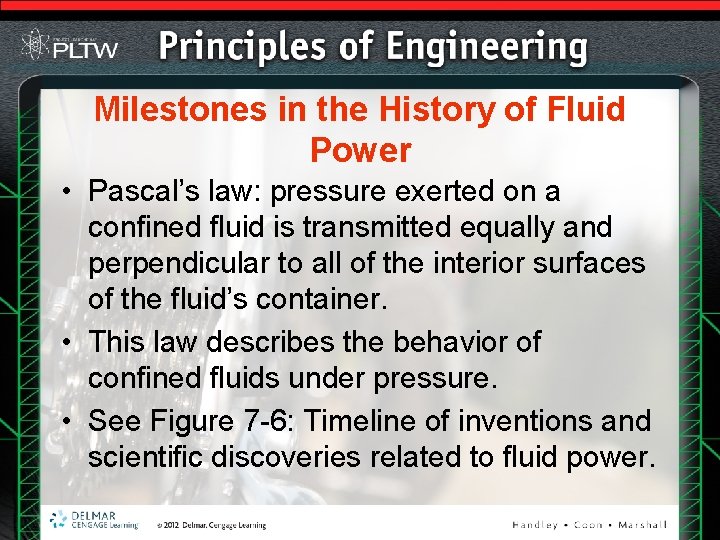
Milestones in the History of Fluid Power • Pascal’s law: pressure exerted on a confined fluid is transmitted equally and perpendicular to all of the interior surfaces of the fluid’s container. • This law describes the behavior of confined fluids under pressure. • See Figure 7 -6: Timeline of inventions and scientific discoveries related to fluid power.
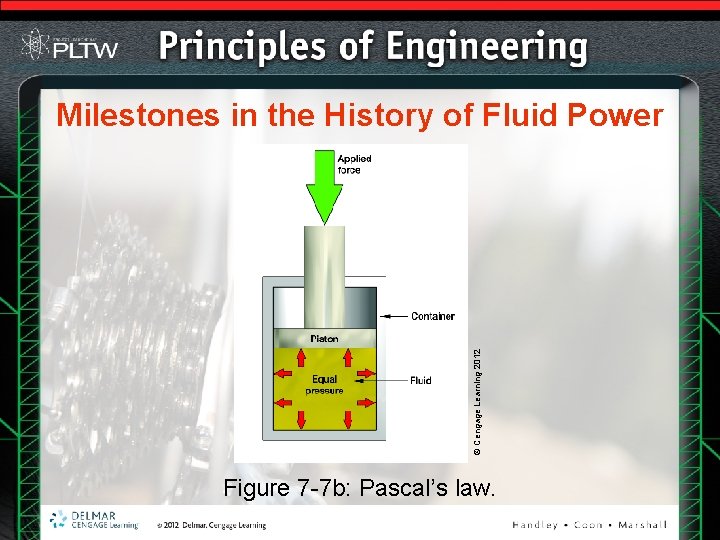
© Cengage Learning 2012 Milestones in the History of Fluid Power Figure 7 -7 b: Pascal’s law.
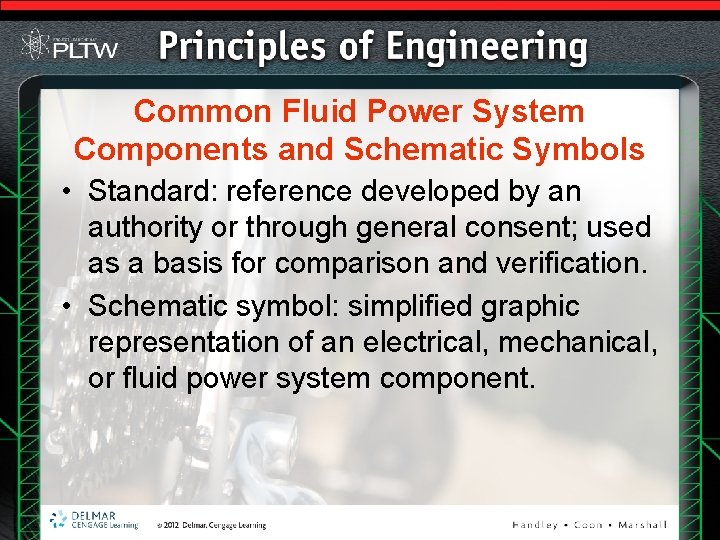
Common Fluid Power System Components and Schematic Symbols • Standard: reference developed by an authority or through general consent; used as a basis for comparison and verification. • Schematic symbol: simplified graphic representation of an electrical, mechanical, or fluid power system component.
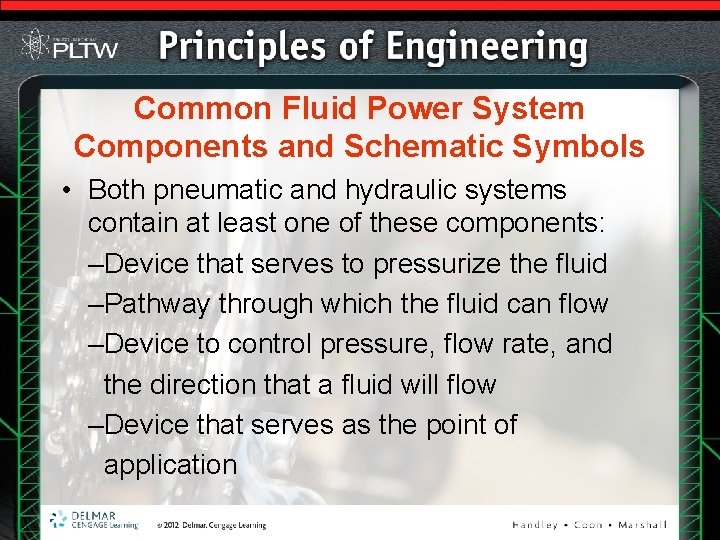
Common Fluid Power System Components and Schematic Symbols • Both pneumatic and hydraulic systems contain at least one of these components: –Device that serves to pressurize the fluid –Pathway through which the fluid can flow –Device to control pressure, flow rate, and the direction that a fluid will flow –Device that serves as the point of application
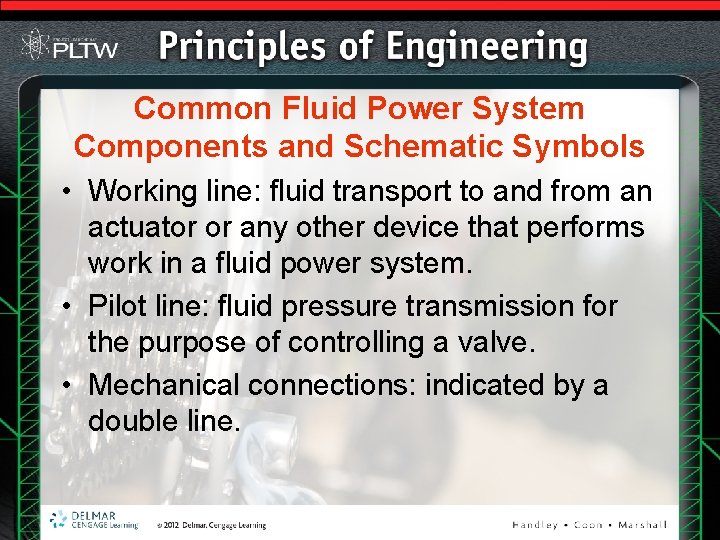
Common Fluid Power System Components and Schematic Symbols • Working line: fluid transport to and from an actuator or any other device that performs work in a fluid power system. • Pilot line: fluid pressure transmission for the purpose of controlling a valve. • Mechanical connections: indicated by a double line.
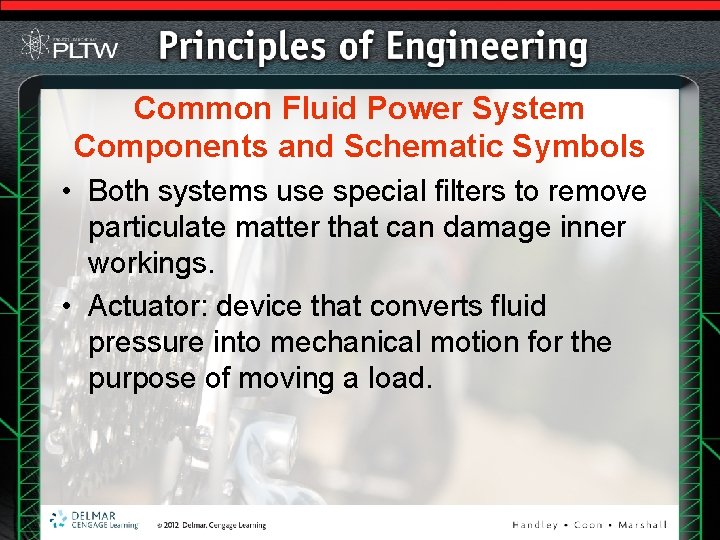
Common Fluid Power System Components and Schematic Symbols • Both systems use special filters to remove particulate matter that can damage inner workings. • Actuator: device that converts fluid pressure into mechanical motion for the purpose of moving a load.

© Cengage Learning 2012 Common Fluid Power System Components and Schematic Symbols Figure 7 -18 a: Hydraulic circuit powers a linear actuator on backhoe.
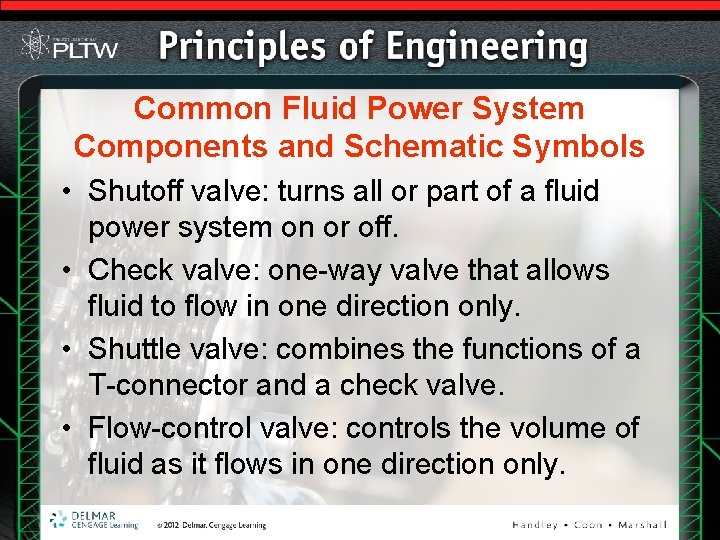
Common Fluid Power System Components and Schematic Symbols • Shutoff valve: turns all or part of a fluid power system on or off. • Check valve: one-way valve that allows fluid to flow in one direction only. • Shuttle valve: combines the functions of a T-connector and a check valve. • Flow-control valve: controls the volume of fluid as it flows in one direction only.
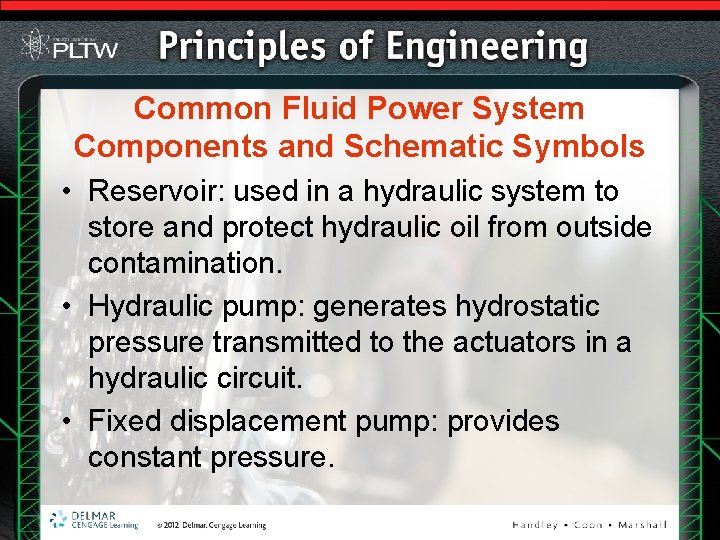
Common Fluid Power System Components and Schematic Symbols • Reservoir: used in a hydraulic system to store and protect hydraulic oil from outside contamination. • Hydraulic pump: generates hydrostatic pressure transmitted to the actuators in a hydraulic circuit. • Fixed displacement pump: provides constant pressure.
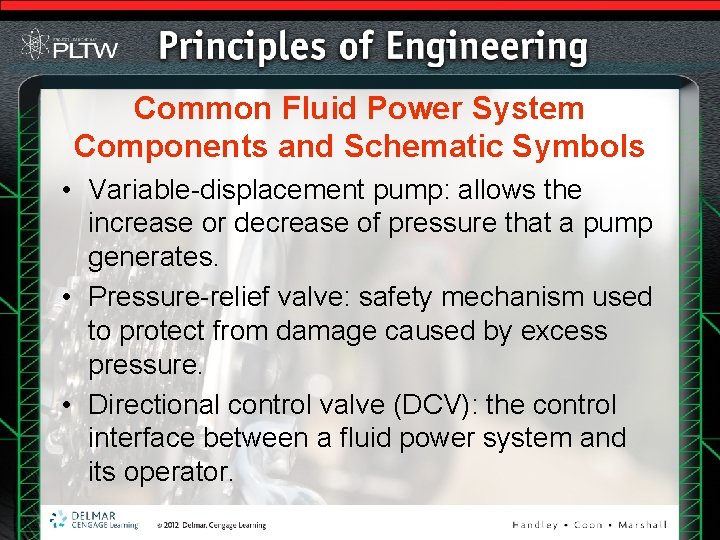
Common Fluid Power System Components and Schematic Symbols • Variable-displacement pump: allows the increase or decrease of pressure that a pump generates. • Pressure-relief valve: safety mechanism used to protect from damage caused by excess pressure. • Directional control valve (DCV): the control interface between a fluid power system and its operator.
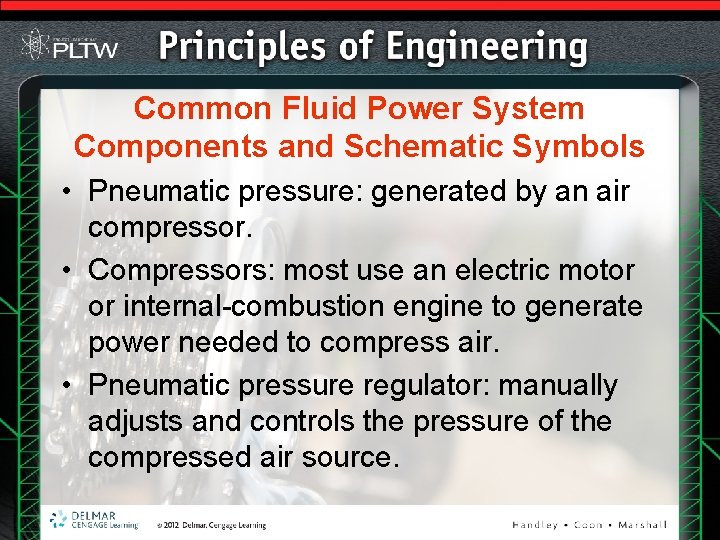
Common Fluid Power System Components and Schematic Symbols • Pneumatic pressure: generated by an air compressor. • Compressors: most use an electric motor or internal-combustion engine to generate power needed to compress air. • Pneumatic pressure regulator: manually adjusts and controls the pressure of the compressed air source.
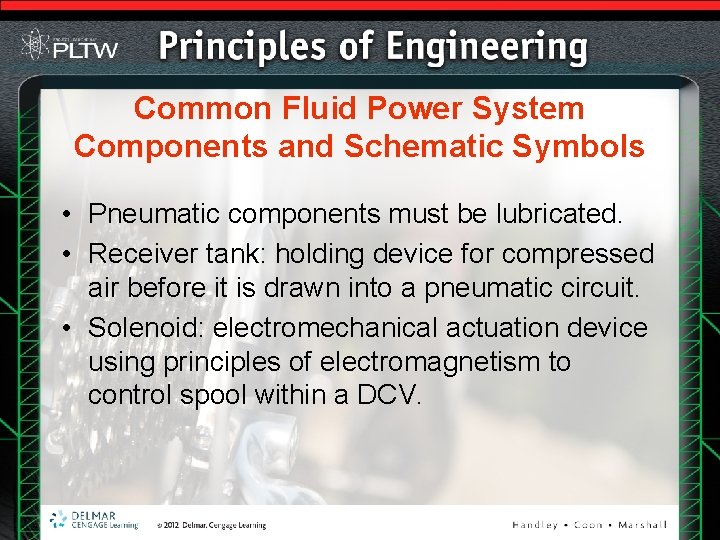
Common Fluid Power System Components and Schematic Symbols • Pneumatic components must be lubricated. • Receiver tank: holding device for compressed air before it is drawn into a pneumatic circuit. • Solenoid: electromechanical actuation device using principles of electromagnetism to control spool within a DCV.
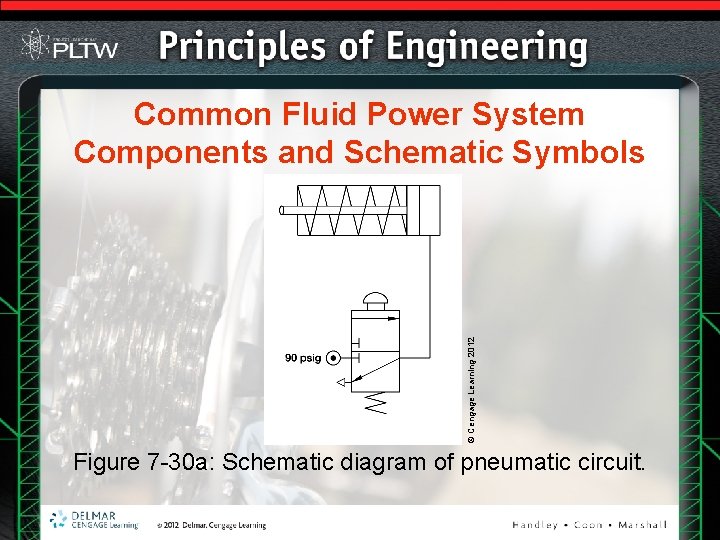
© Cengage Learning 2012 Common Fluid Power System Components and Schematic Symbols Figure 7 -30 a: Schematic diagram of pneumatic circuit.
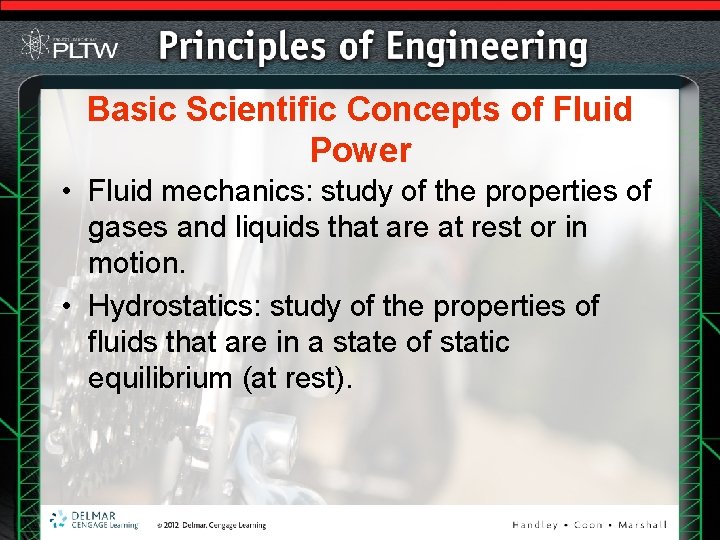
Basic Scientific Concepts of Fluid Power • Fluid mechanics: study of the properties of gases and liquids that are at rest or in motion. • Hydrostatics: study of the properties of fluids that are in a state of static equilibrium (at rest).
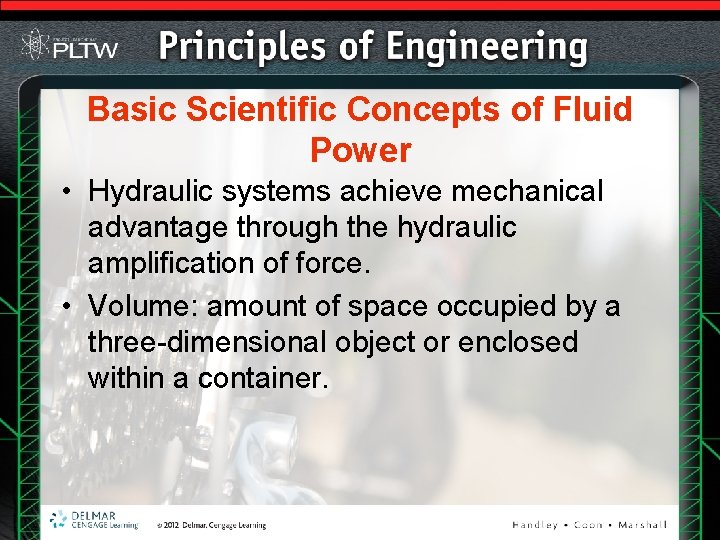
Basic Scientific Concepts of Fluid Power • Hydraulic systems achieve mechanical advantage through the hydraulic amplification of force. • Volume: amount of space occupied by a three-dimensional object or enclosed within a container.
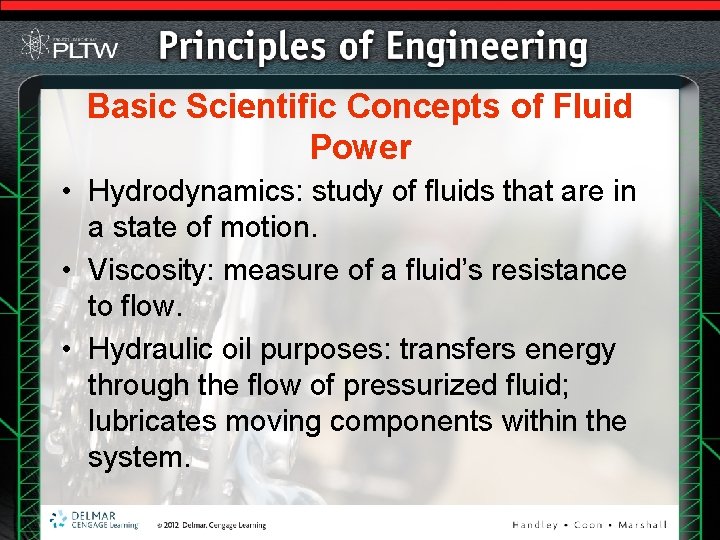
Basic Scientific Concepts of Fluid Power • Hydrodynamics: study of fluids that are in a state of motion. • Viscosity: measure of a fluid’s resistance to flow. • Hydraulic oil purposes: transfers energy through the flow of pressurized fluid; lubricates moving components within the system.
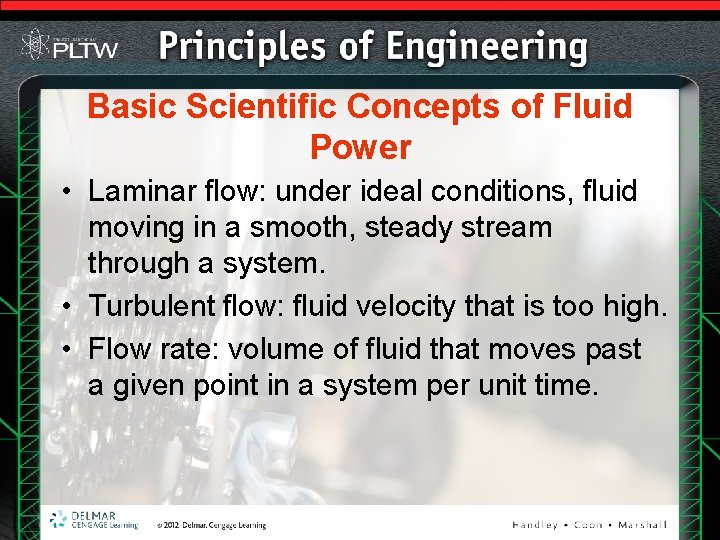
Basic Scientific Concepts of Fluid Power • Laminar flow: under ideal conditions, fluid moving in a smooth, steady stream through a system. • Turbulent flow: fluid velocity that is too high. • Flow rate: volume of fluid that moves past a given point in a system per unit time.
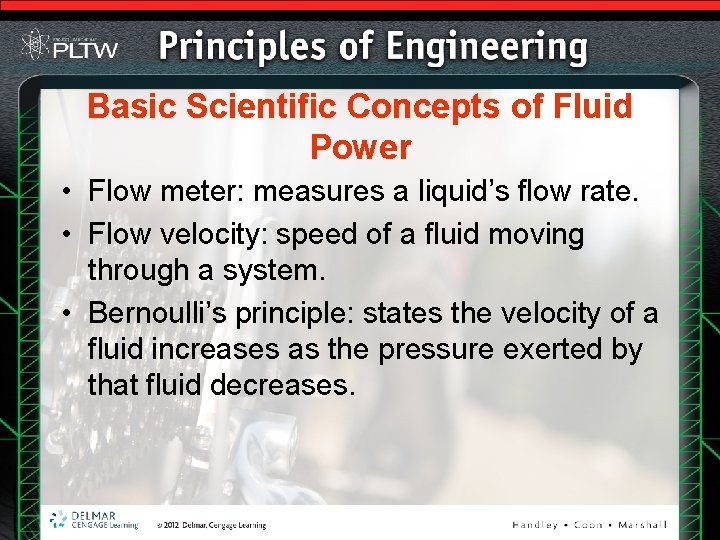
Basic Scientific Concepts of Fluid Power • Flow meter: measures a liquid’s flow rate. • Flow velocity: speed of a fluid moving through a system. • Bernoulli’s principle: states the velocity of a fluid increases as the pressure exerted by that fluid decreases.
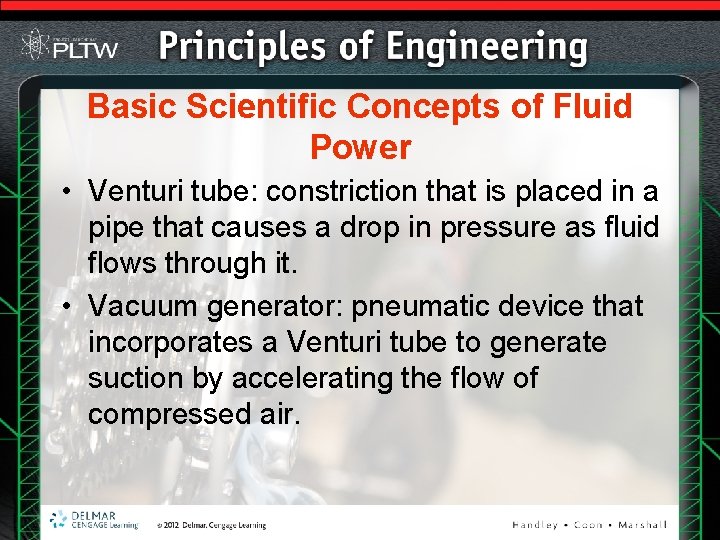
Basic Scientific Concepts of Fluid Power • Venturi tube: constriction that is placed in a pipe that causes a drop in pressure as fluid flows through it. • Vacuum generator: pneumatic device that incorporates a Venturi tube to generate suction by accelerating the flow of compressed air.
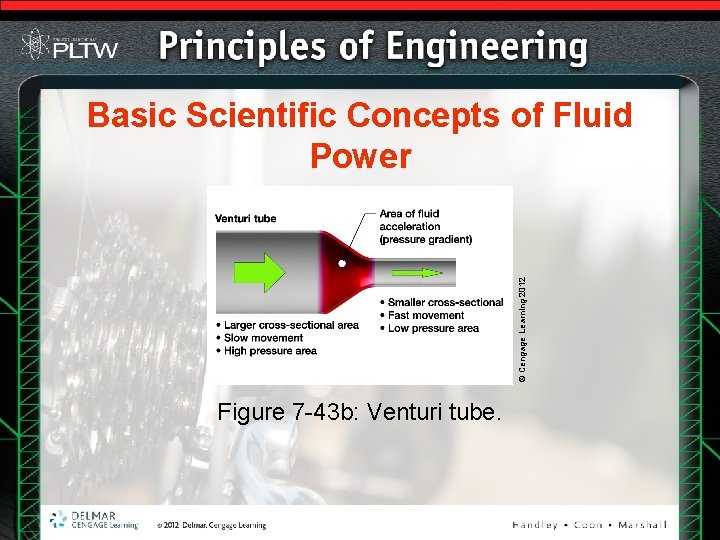
© Cengage Learning 2012 Basic Scientific Concepts of Fluid Power Figure 7 -43 b: Venturi tube.
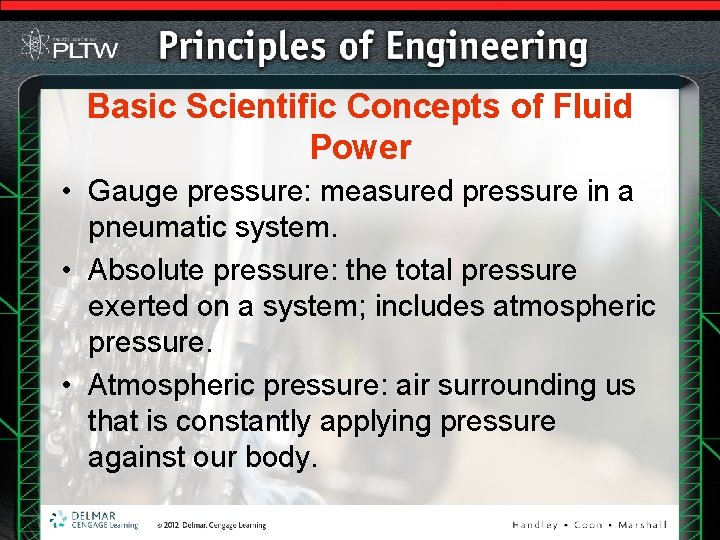
Basic Scientific Concepts of Fluid Power • Gauge pressure: measured pressure in a pneumatic system. • Absolute pressure: the total pressure exerted on a system; includes atmospheric pressure. • Atmospheric pressure: air surrounding us that is constantly applying pressure against our body.
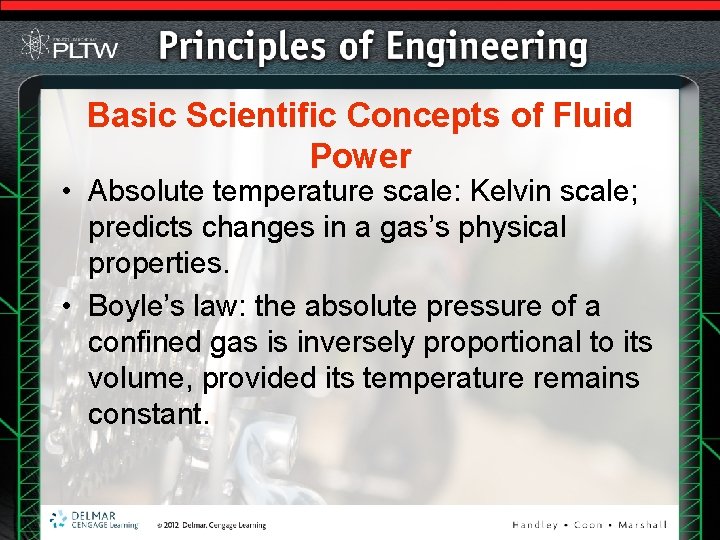
Basic Scientific Concepts of Fluid Power • Absolute temperature scale: Kelvin scale; predicts changes in a gas’s physical properties. • Boyle’s law: the absolute pressure of a confined gas is inversely proportional to its volume, provided its temperature remains constant.
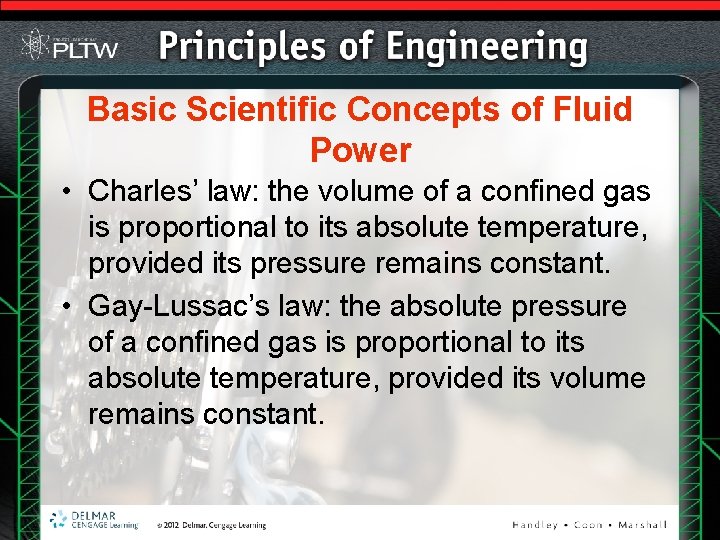
Basic Scientific Concepts of Fluid Power • Charles’ law: the volume of a confined gas is proportional to its absolute temperature, provided its pressure remains constant. • Gay-Lussac’s law: the absolute pressure of a confined gas is proportional to its absolute temperature, provided its volume remains constant.
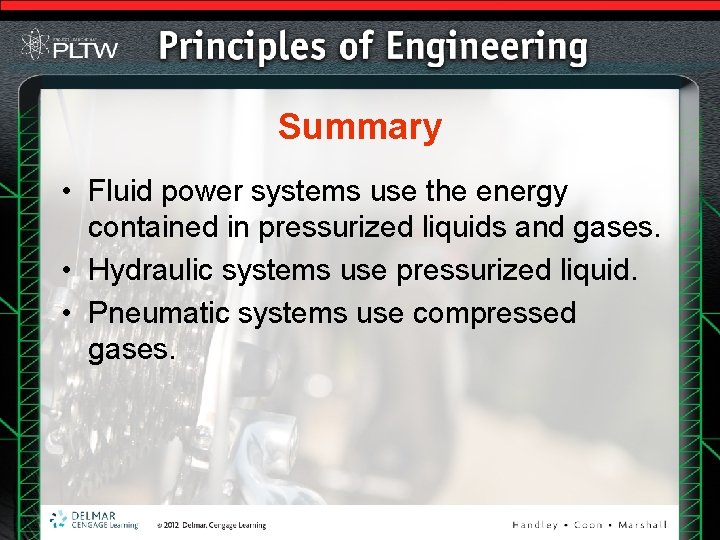
Summary • Fluid power systems use the energy contained in pressurized liquids and gases. • Hydraulic systems use pressurized liquid. • Pneumatic systems use compressed gases.
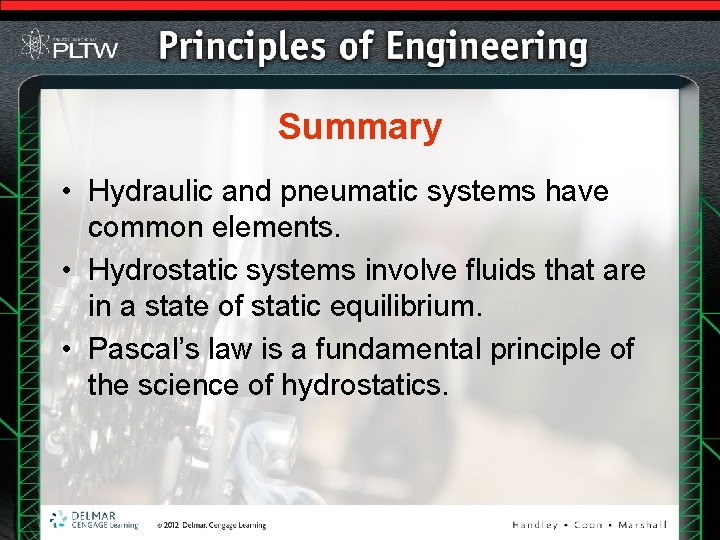
Summary • Hydraulic and pneumatic systems have common elements. • Hydrostatic systems involve fluids that are in a state of static equilibrium. • Pascal’s law is a fundamental principle of the science of hydrostatics.
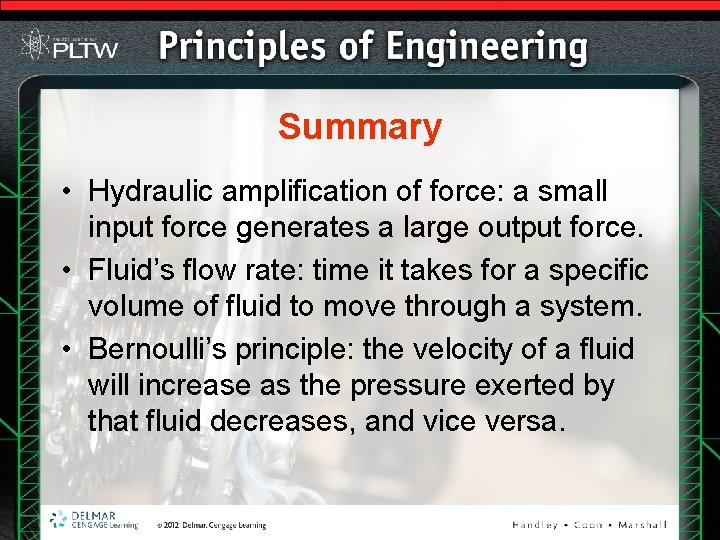
Summary • Hydraulic amplification of force: a small input force generates a large output force. • Fluid’s flow rate: time it takes for a specific volume of fluid to move through a system. • Bernoulli’s principle: the velocity of a fluid will increase as the pressure exerted by that fluid decreases, and vice versa.
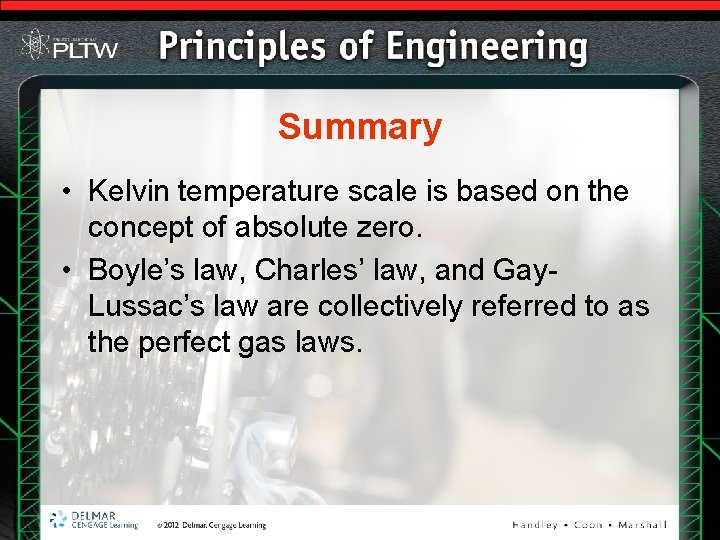
Summary • Kelvin temperature scale is based on the concept of absolute zero. • Boyle’s law, Charles’ law, and Gay. Lussac’s law are collectively referred to as the perfect gas laws.
Sin changwon
Electromechanical association
Treeing and tracking breakdown
Basic period of computer
Electromechanical games
Voltage regulator purpose
Electromechanical component
Synovial membrane
Fluid statics deals with fluid at rest
Fluid statics deals with
Total body water
How does water go through your body
Interstitial fluid vs extracellular fluid
Fluid mechanics chapter 4
Movement of body fluids
Fluid thrill ascites volume
The real lesson 21
Fluid mechanics
Introduction to electrical power systems
Actual mechanical advantage vs ideal mechanical advantage
Natural fluid systems
Marine fluid systems
Powerflow fluid systems
Berendsen fluid power bundaberg
Unidirectional hydraulic motor symbol
Fluid power system ppt
Fluid power system ppt
Bidirectional variable displacement pump symbol
Fluid power system
Pump exercise
Pneumatic system
Fluid power technology
Fluid power control
Fluid power dynamics