CantedCosineTheta CCT magnets Shlomo Caspi Superconducting Magnet Group
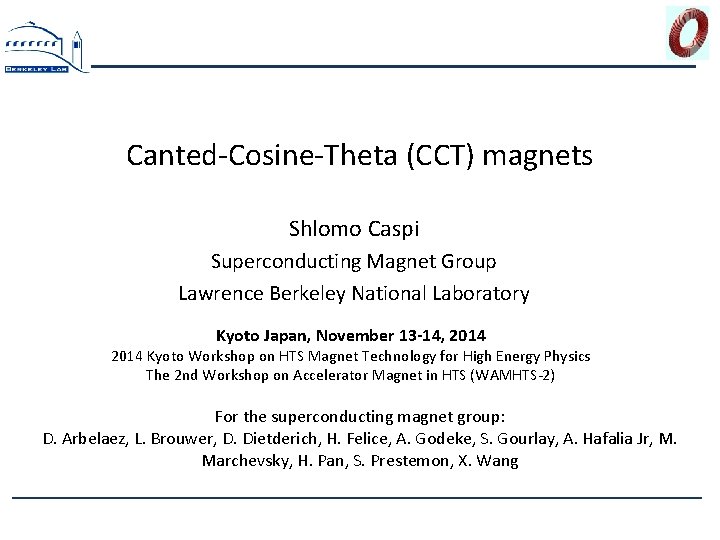
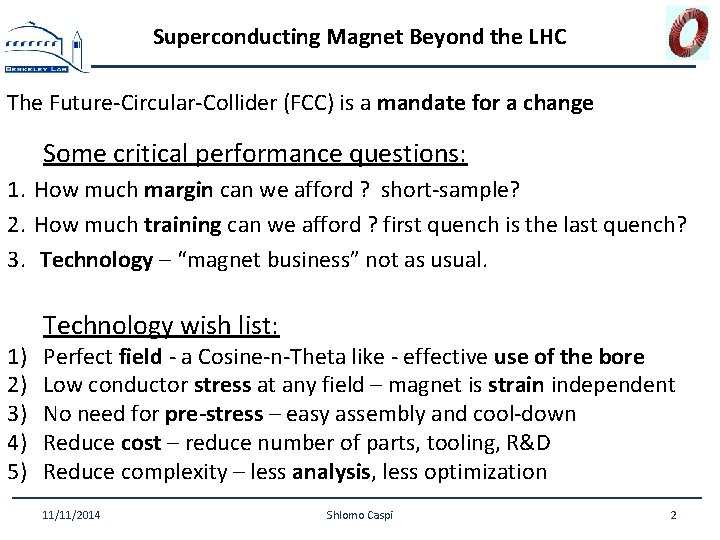
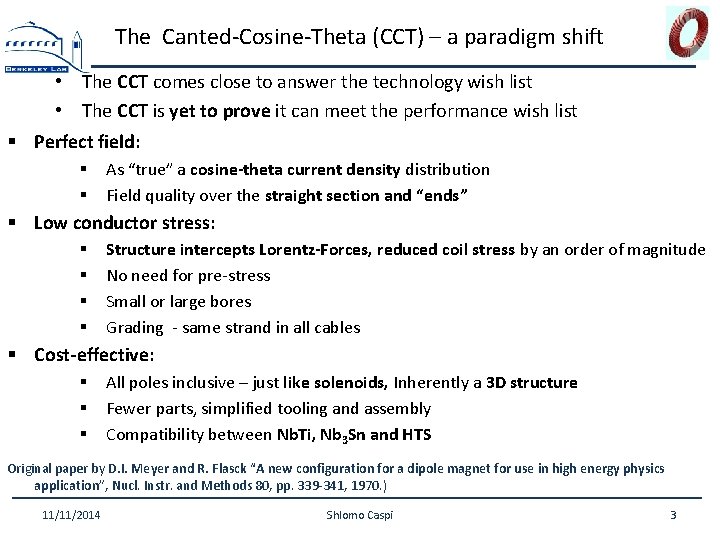
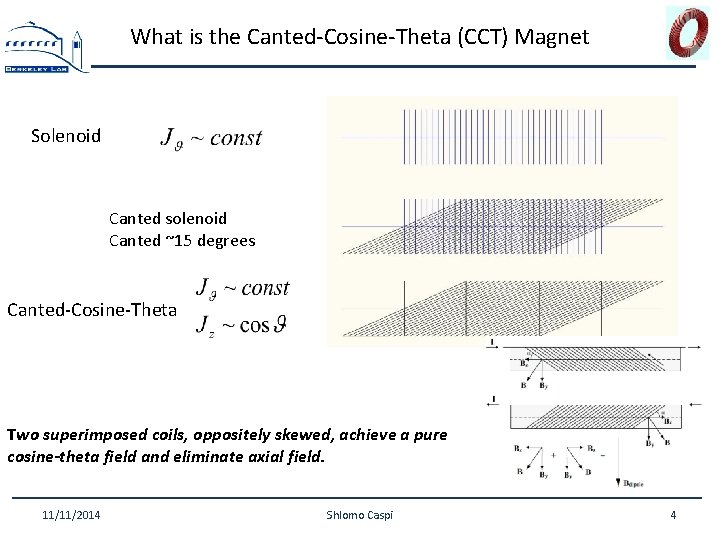
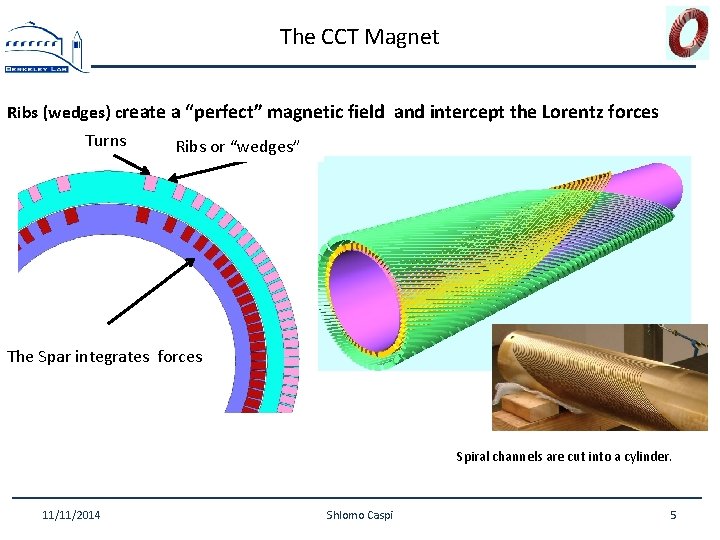
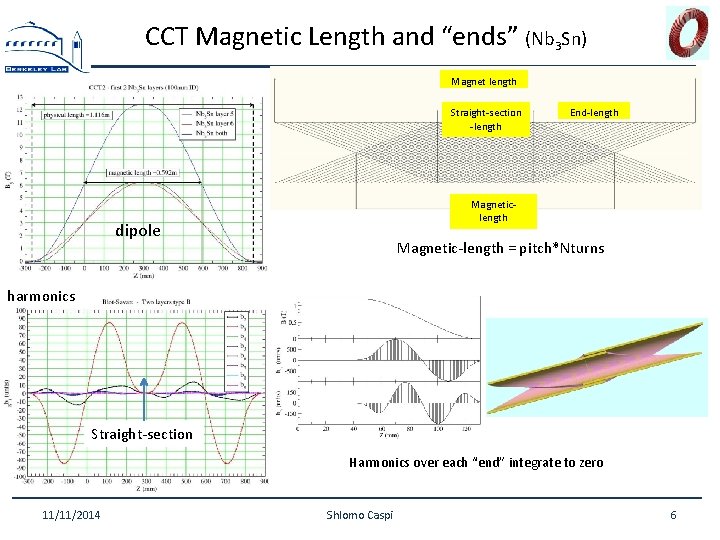
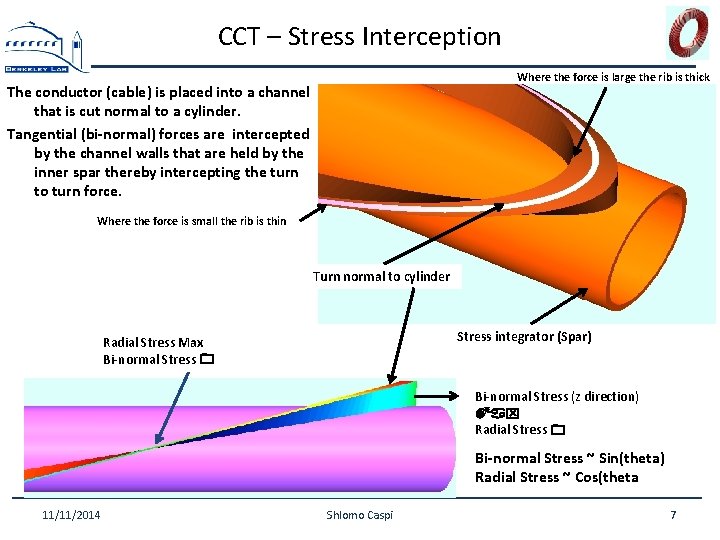
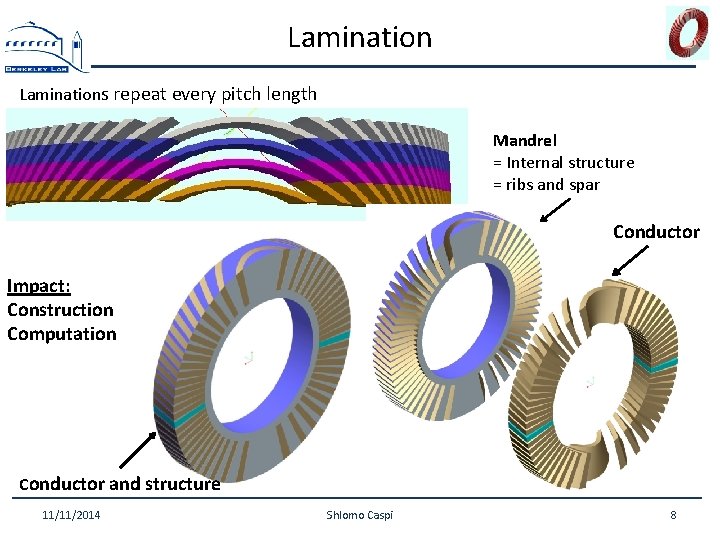
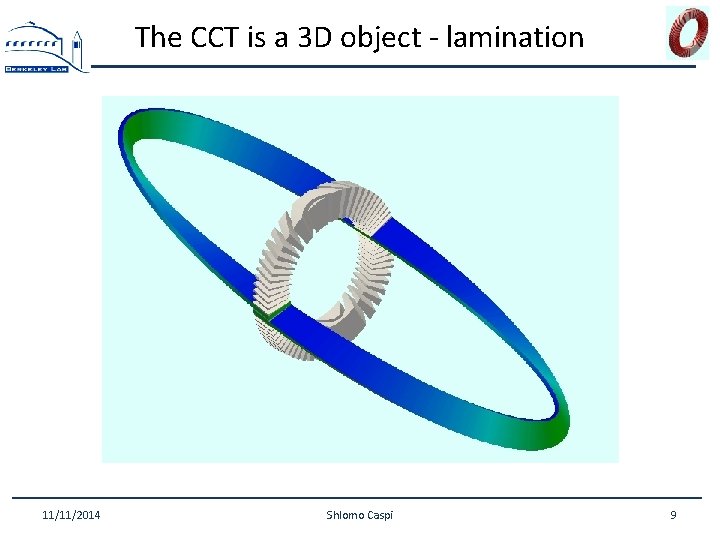
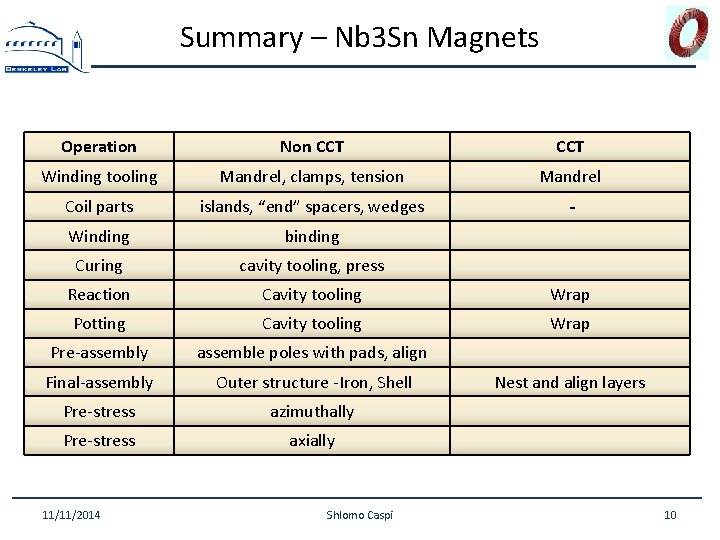
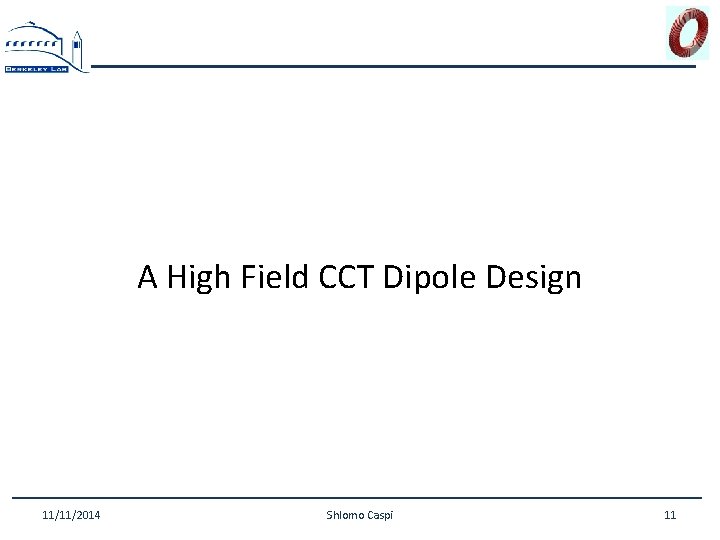
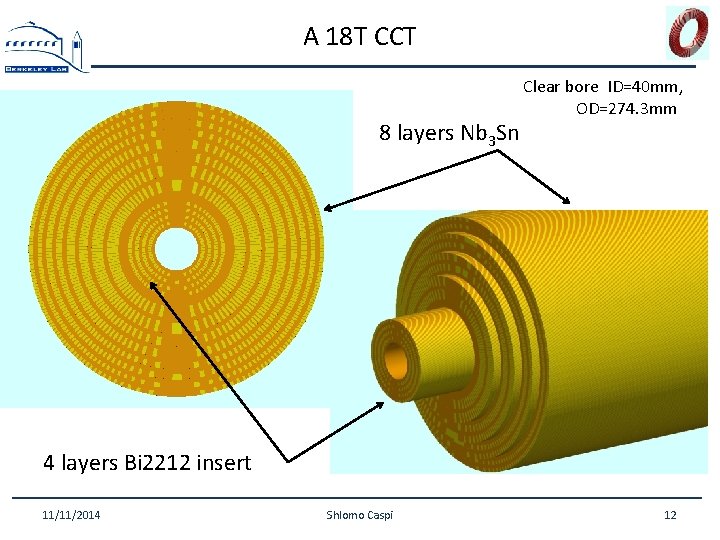
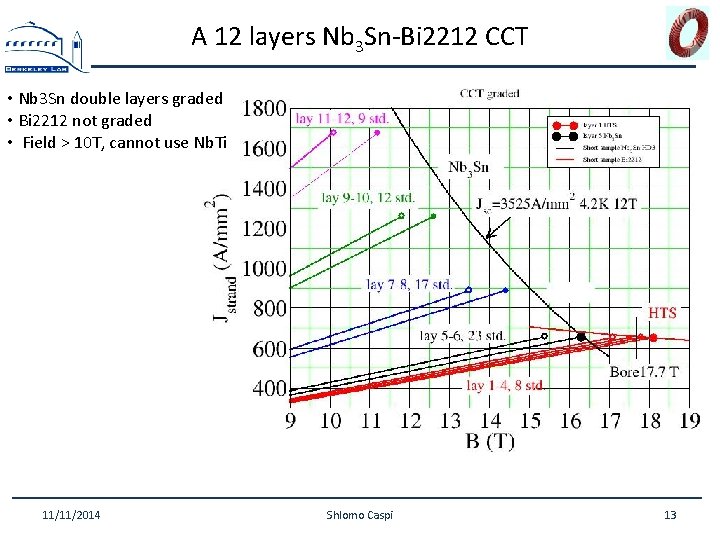
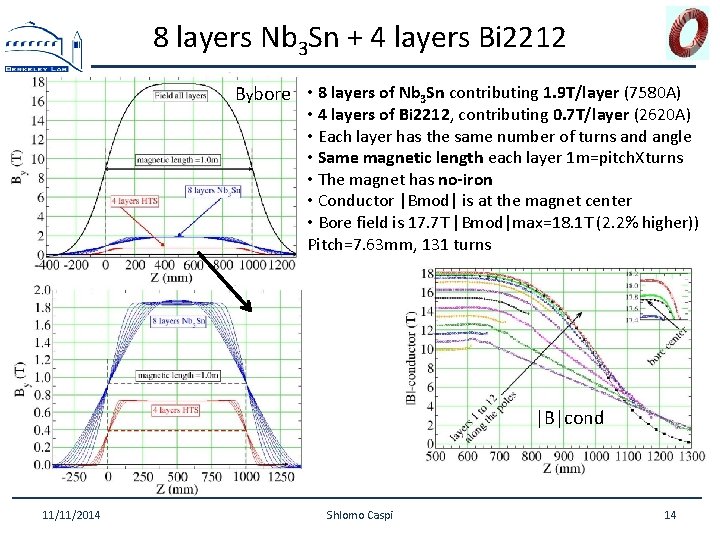
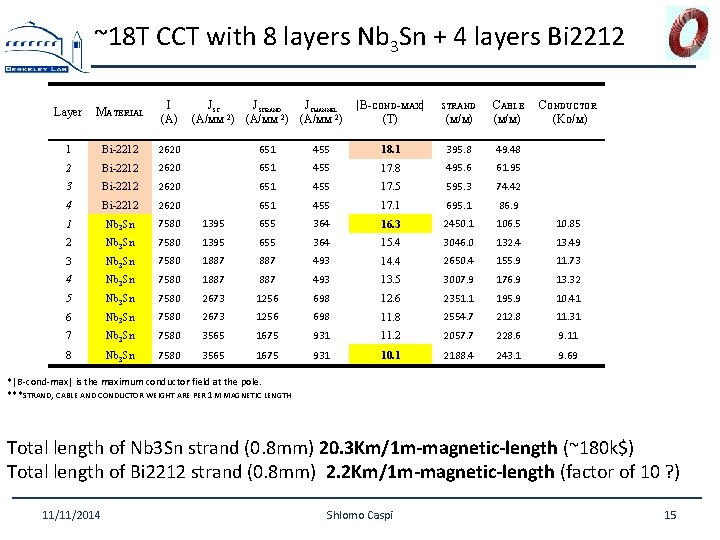
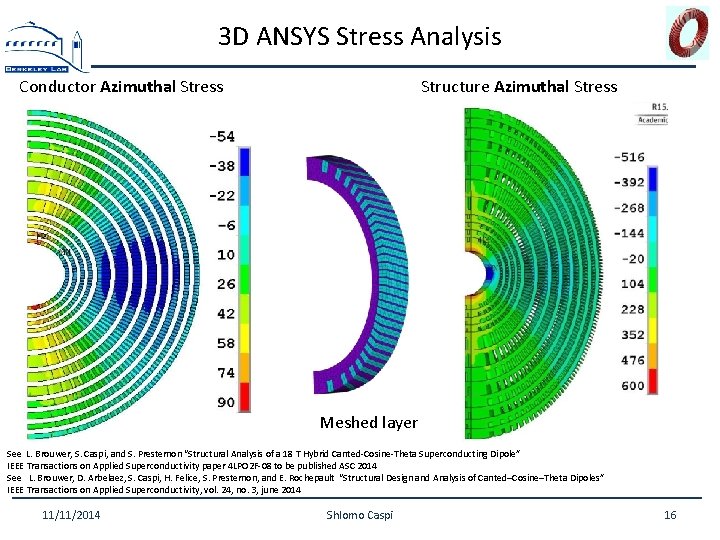
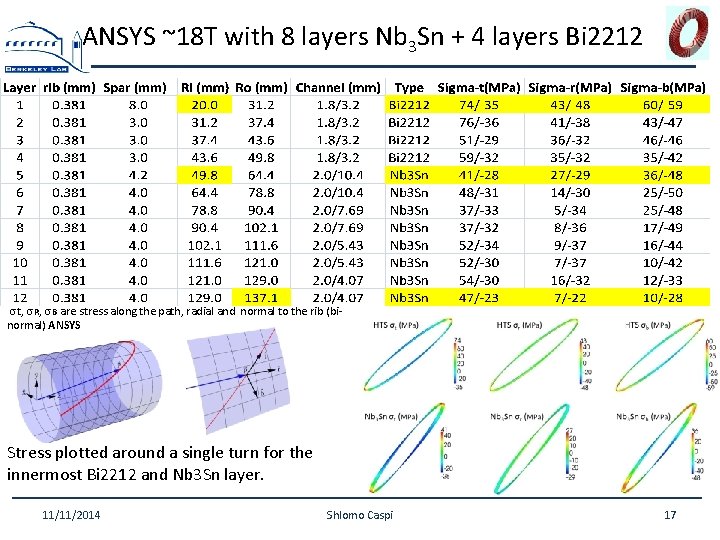
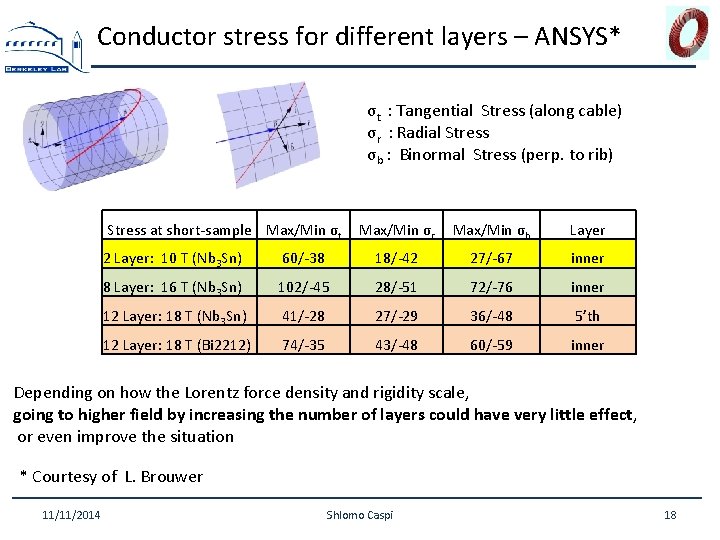
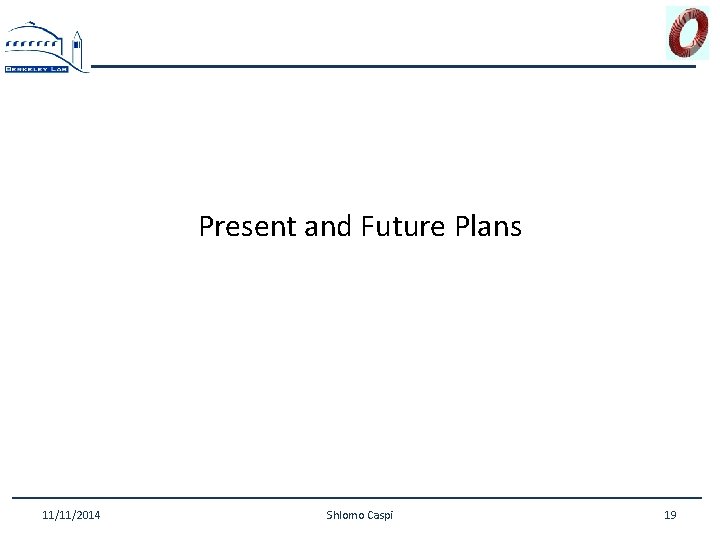
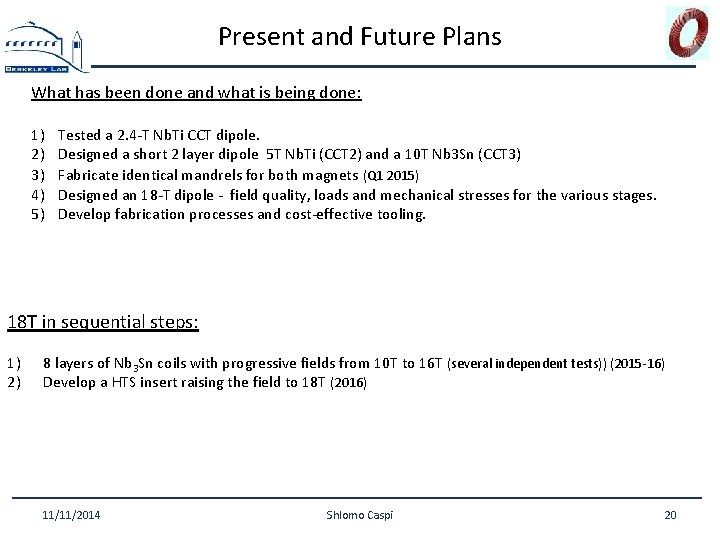
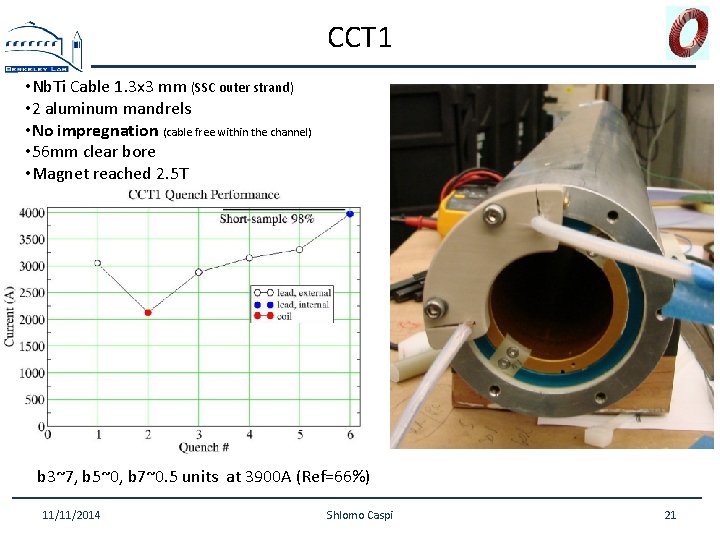

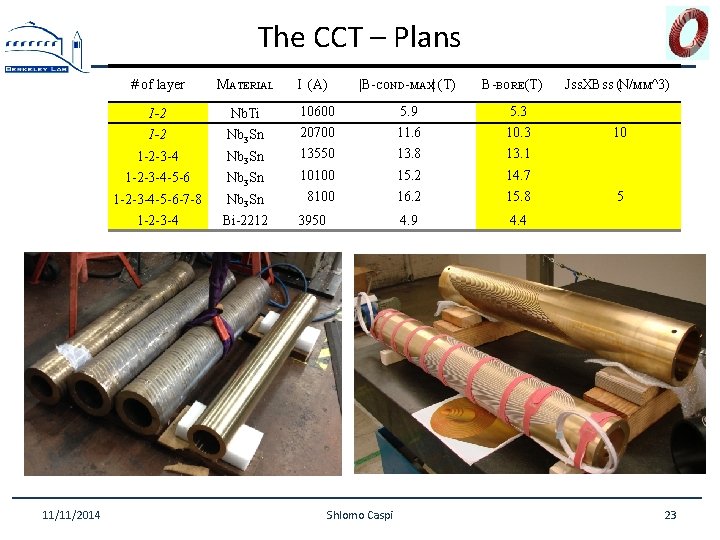
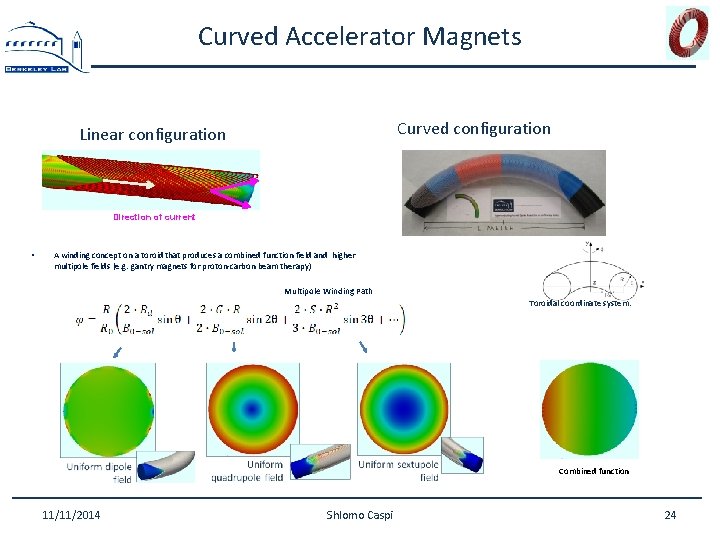
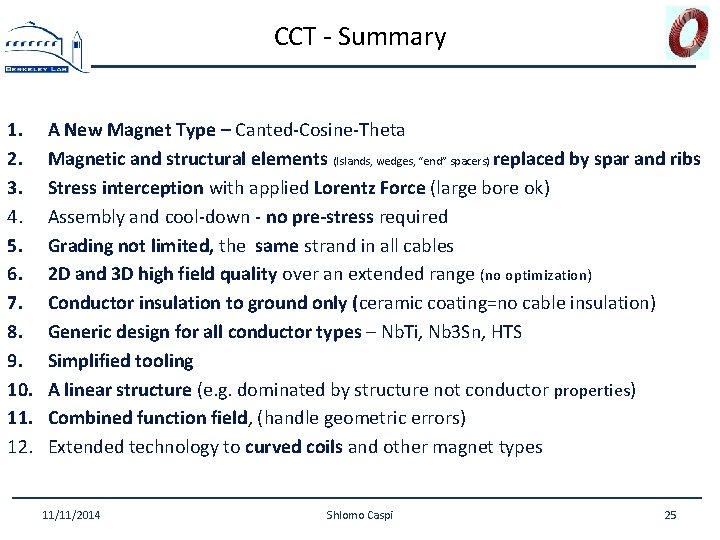
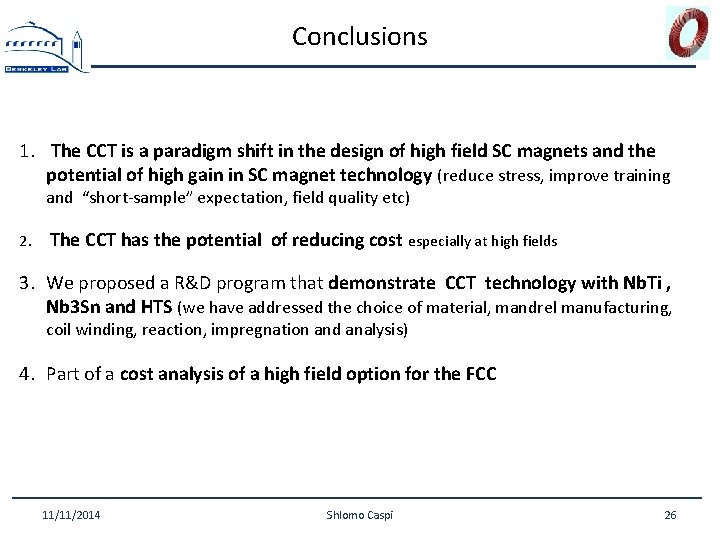
- Slides: 26
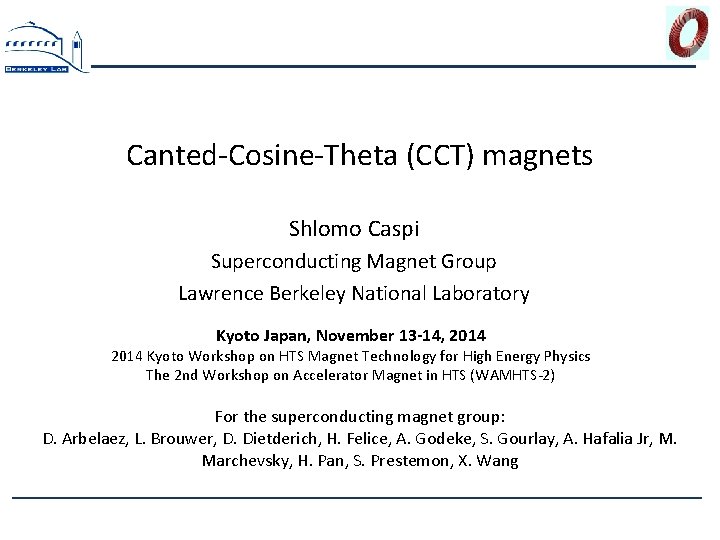
Canted-Cosine-Theta (CCT) magnets Shlomo Caspi Superconducting Magnet Group Lawrence Berkeley National Laboratory Kyoto Japan, November 13 -14, 2014 Kyoto Workshop on HTS Magnet Technology for High Energy Physics The 2 nd Workshop on Accelerator Magnet in HTS (WAMHTS-2) For the superconducting magnet group: D. Arbelaez, L. Brouwer, D. Dietderich, H. Felice, A. Godeke, S. Gourlay, A. Hafalia Jr, M. Marchevsky, H. Pan, S. Prestemon, X. Wang
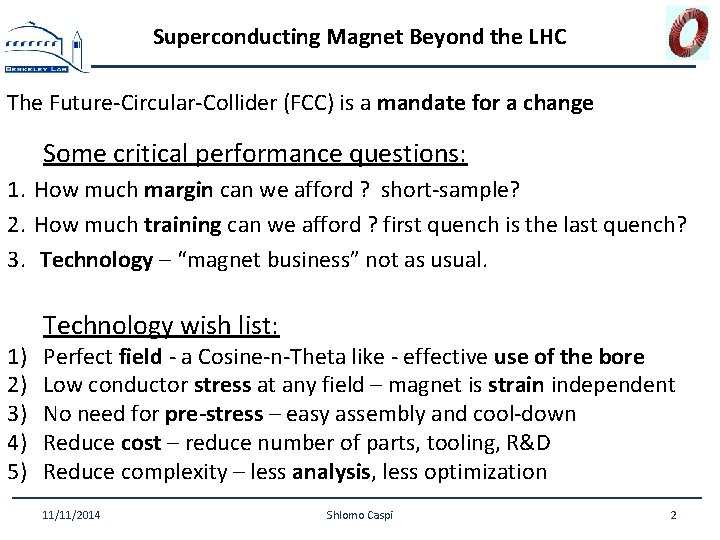
Superconducting Magnet Beyond the LHC The Future-Circular-Collider (FCC) is a mandate for a change Some critical performance questions: 1. How much margin can we afford ? short-sample? 2. How much training can we afford ? first quench is the last quench? 3. Technology – “magnet business” not as usual. 1) 2) 3) 4) 5) Technology wish list: Perfect field - a Cosine-n-Theta like - effective use of the bore Low conductor stress at any field – magnet is strain independent No need for pre-stress – easy assembly and cool-down Reduce cost – reduce number of parts, tooling, R&D Reduce complexity – less analysis, less optimization 11/11/2014 Shlomo Caspi 2
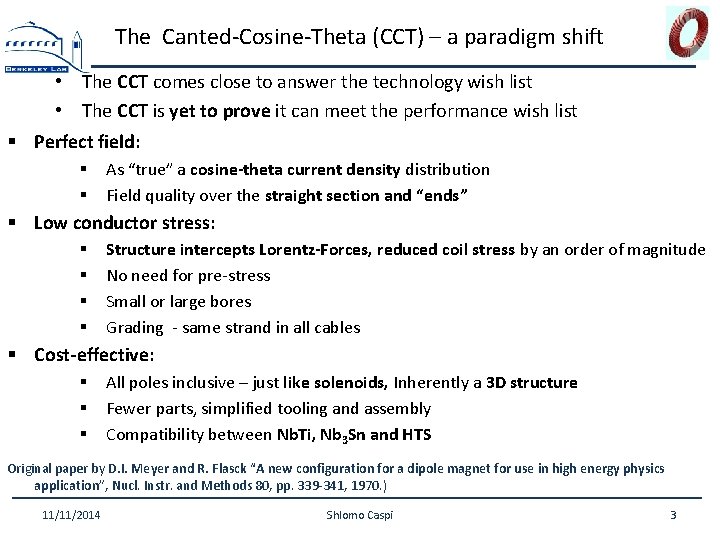
The Canted-Cosine-Theta (CCT) – a paradigm shift • The CCT comes close to answer the technology wish list • The CCT is yet to prove it can meet the performance wish list § Perfect field: § § As “true” a cosine-theta current density distribution Field quality over the straight section and “ends” § Low conductor stress: § § Structure intercepts Lorentz-Forces, reduced coil stress by an order of magnitude No need for pre-stress Small or large bores Grading - same strand in all cables § Cost-effective: § § § All poles inclusive – just like solenoids, Inherently a 3 D structure Fewer parts, simplified tooling and assembly Compatibility between Nb. Ti, Nb 3 Sn and HTS Original paper by D. I. Meyer and R. Flasck “A new configuration for a dipole magnet for use in high energy physics application”, Nucl. Instr. and Methods 80, pp. 339 -341, 1970. ) 11/11/2014 Shlomo Caspi 3
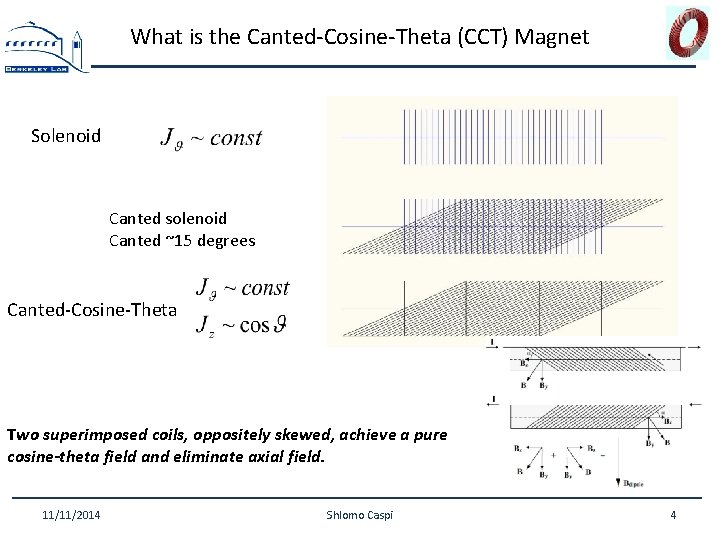
What is the Canted-Cosine-Theta (CCT) Magnet Solenoid Canted solenoid Canted ~15 degrees Canted-Cosine-Theta Two superimposed coils, oppositely skewed, achieve a pure cosine-theta field and eliminate axial field. 11/11/2014 Shlomo Caspi 4
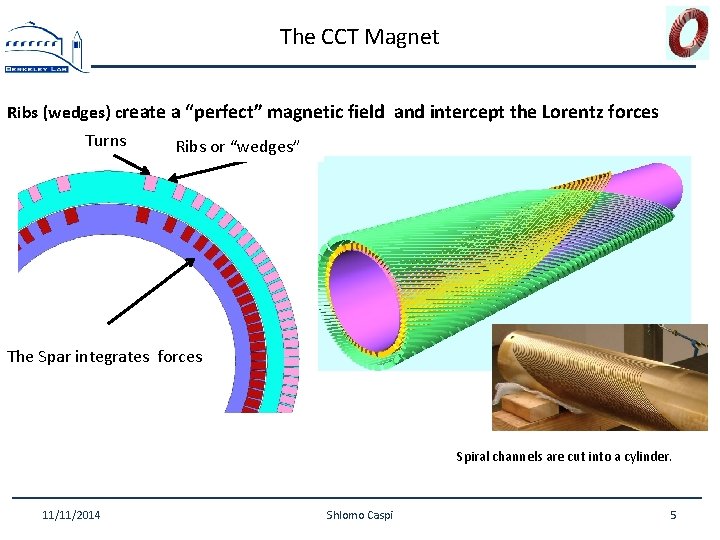
The CCT Magnet Ribs (wedges) create a “perfect” magnetic field and intercept the Lorentz forces Turns Ribs or “wedges” The Spar integrates forces Spiral channels are cut into a cylinder. 11/11/2014 Shlomo Caspi 5
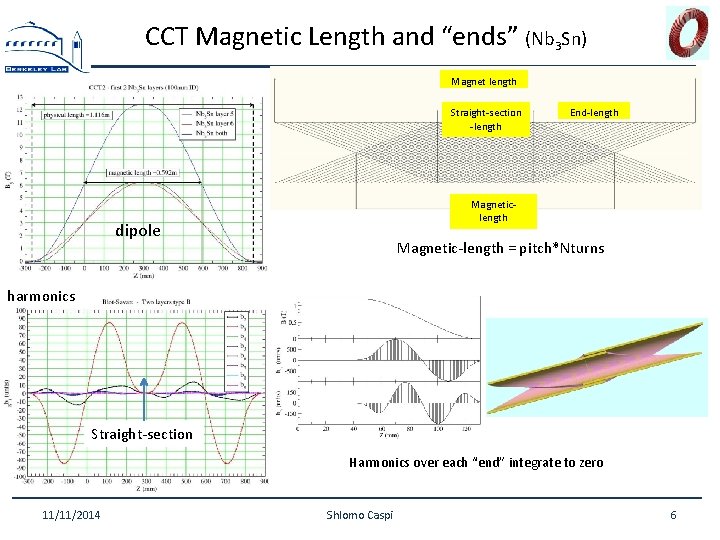
CCT Magnetic Length and “ends” (Nb 3 Sn) Magnet length Straight-section -length End-length Magneticlength dipole Magnetic-length = pitch*Nturns harmonics Straight-section Harmonics over each “end” integrate to zero 11/11/2014 Shlomo Caspi 6
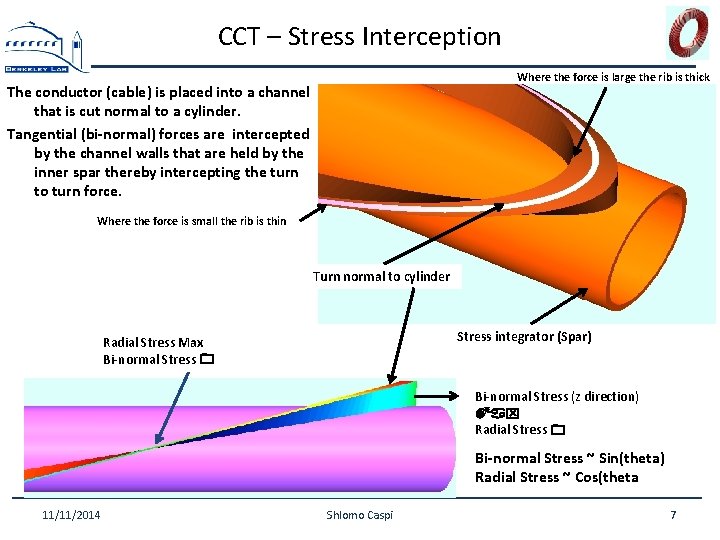
CCT – Stress Interception Where the force is large the rib is thick The conductor (cable) is placed into a channel that is cut normal to a cylinder. Tangential (bi-normal) forces are intercepted by the channel walls that are held by the inner spar thereby intercepting the turn to turn force. Where the force is small the rib is thin Turn normal to cylinder Stress integrator (Spar) Radial Stress Max Bi-normal Stress 0 Bi-normal Stress (z direction) Max Radial Stress 0 Bi-normal Stress ~ Sin(theta) Radial Stress ~ Cos(theta 11/11/2014 Shlomo Caspi 7
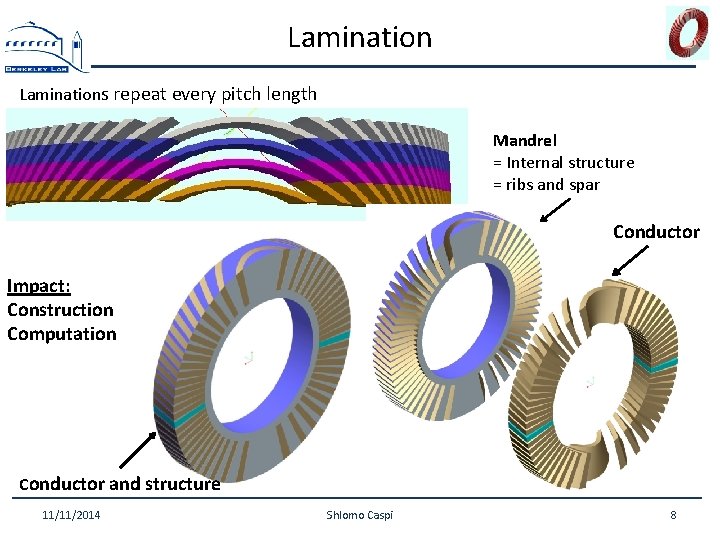
Laminations repeat every pitch length Mandrel = Internal structure = ribs and spar Conductor Impact: Construction Computation Conductor and structure 11/11/2014 Shlomo Caspi 8
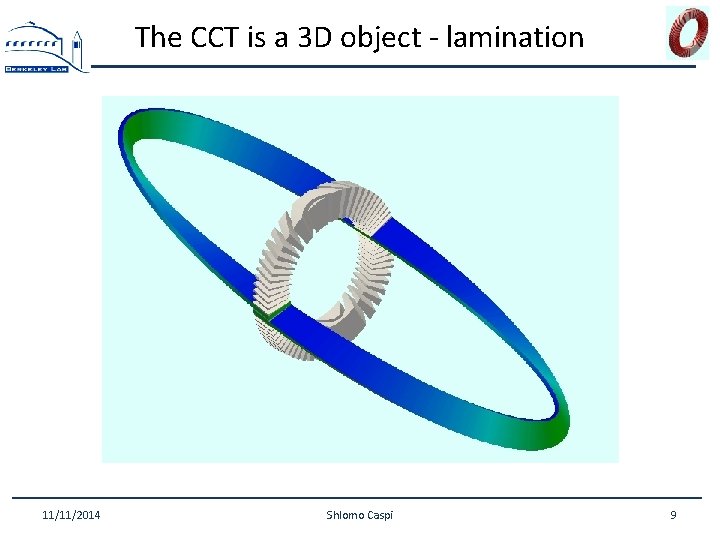
The CCT is a 3 D object - lamination 11/11/2014 Shlomo Caspi 9
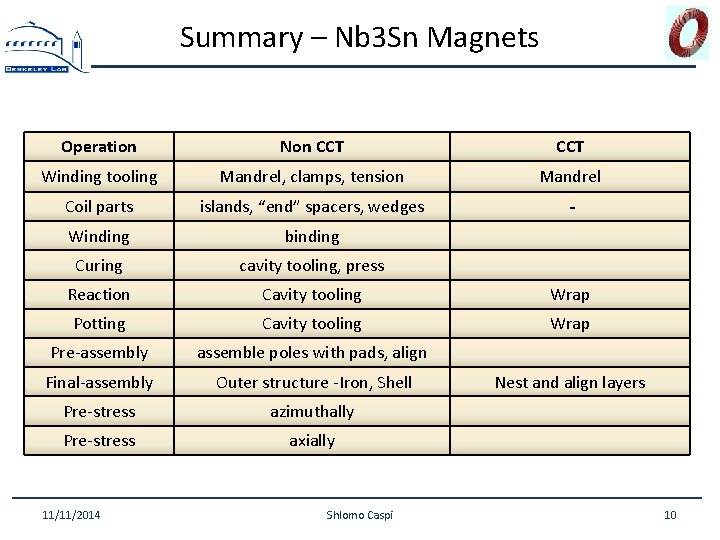
Summary – Nb 3 Sn Magnets Operation Non CCT Winding tooling Mandrel, clamps, tension Mandrel Coil parts islands, “end” spacers, wedges Winding binding Curing cavity tooling, press Reaction Cavity tooling Wrap Potting Cavity tooling Wrap Pre-assembly assemble poles with pads, align Final-assembly Outer structure -Iron, Shell Pre-stress azimuthally Pre-stress axially 11/11/2014 Shlomo Caspi Nest and align layers 10
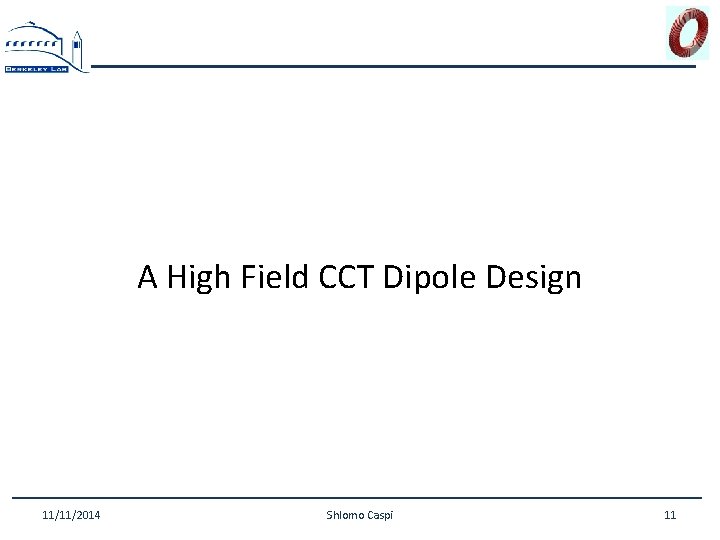
A High Field CCT Dipole Design 11/11/2014 Shlomo Caspi 11
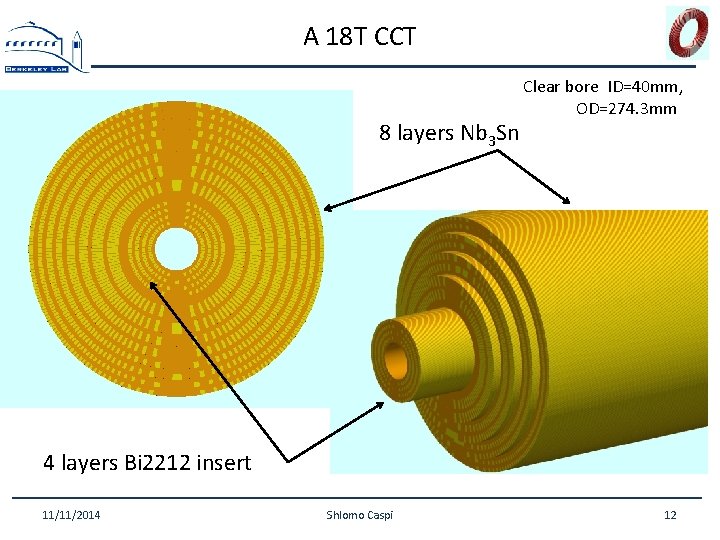
A 18 T CCT 8 layers Nb 3 Sn Clear bore ID=40 mm, OD=274. 3 mm 4 layers Bi 2212 insert 11/11/2014 Shlomo Caspi 12
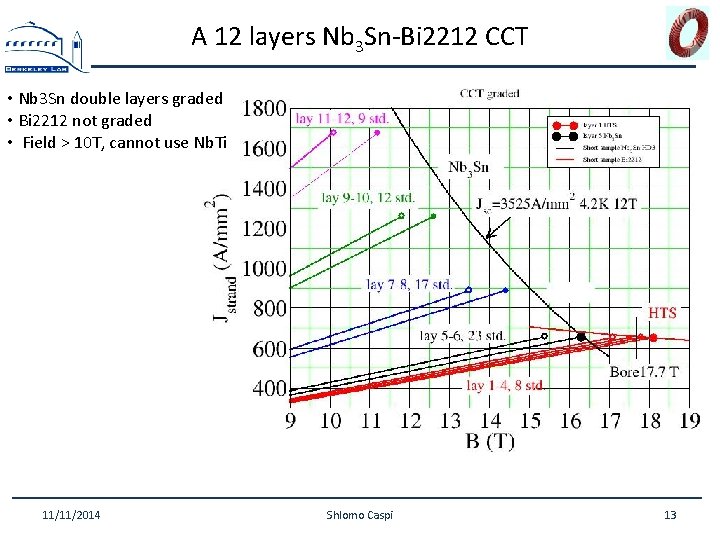
A 12 layers Nb 3 Sn-Bi 2212 CCT • Nb 3 Sn double layers graded • Bi 2212 not graded • Field > 10 T, cannot use Nb. Ti 11/11/2014 Shlomo Caspi 13
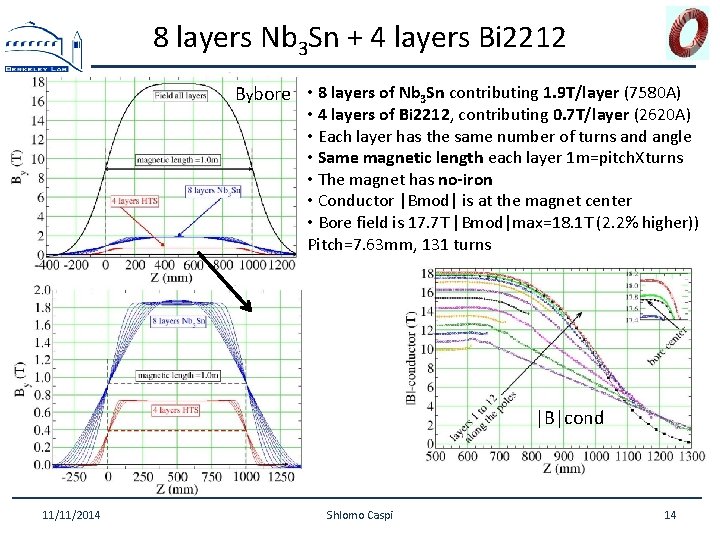
8 layers Nb 3 Sn + 4 layers Bi 2212 Bybore • 8 layers of Nb 3 Sn contributing 1. 9 T/layer (7580 A) • 4 layers of Bi 2212, contributing 0. 7 T/layer (2620 A) • Each layer has the same number of turns and angle • Same magnetic length each layer 1 m=pitch. Xturns • The magnet has no-iron • Conductor |Bmod| is at the magnet center • Bore field is 17. 7 T |Bmod|max=18. 1 T (2. 2% higher)) Pitch=7. 63 mm, 131 turns |B|cond 11/11/2014 Shlomo Caspi 14
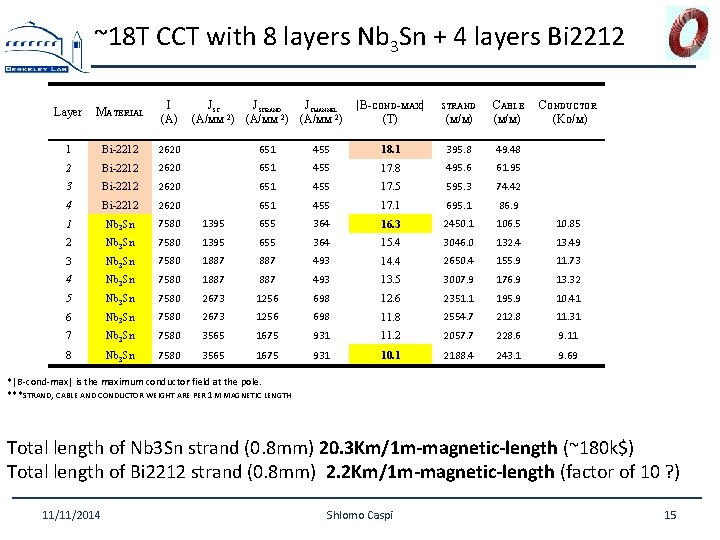
~18 T CCT with 8 layers Nb 3 Sn + 4 layers Bi 2212 Layer MATERIAL I (A) JSC JSTRAND JCHANNEL (A/MM 2) |B-COND-MAX| (T) STRAND ( M/ M) CABLE (M / M ) CONDUCTOR (KG/M) 1 Bi-2212 2620 651 455 18. 1 395. 8 49. 48 2 Bi-2212 2620 651 455 17. 8 495. 6 61. 95 3 Bi-2212 2620 651 455 17. 5 595. 3 74. 42 4 Bi-2212 2620 651 455 17. 1 695. 1 86. 9 1 Nb 3 Sn 7580 1395 655 364 16. 3 2450. 1 106. 5 10. 85 2 Nb 3 Sn 7580 1395 655 364 15. 4 3046. 0 132. 4 13. 49 3 Nb 3 Sn 7580 1887 493 14. 4 2650. 4 155. 9 11. 73 4 Nb 3 Sn 7580 1887 493 13. 5 3007. 9 176. 9 13. 32 5 Nb 3 Sn 7580 2673 1256 698 12. 6 2351. 1 195. 9 10. 41 6 Nb 3 Sn 7580 2673 1256 698 11. 8 2554. 7 212. 8 11. 31 7 Nb 3 Sn 7580 3565 1675 931 11. 2 2057. 7 228. 6 9. 11 8 Nb 3 Sn 7580 3565 1675 931 10. 1 2188. 4 243. 1 9. 69 *|B-cond-max| is the maximum conductor field at the pole. ***STRAND, CABLE AND CONDUCTOR WEIGHT ARE PER 1 M MAGNETIC LENGTH Total length of Nb 3 Sn strand (0. 8 mm) 20. 3 Km/1 m-magnetic-length (~180 k$) Total length of Bi 2212 strand (0. 8 mm) 2. 2 Km/1 m-magnetic-length (factor of 10 ? ) 11/11/2014 Shlomo Caspi 15
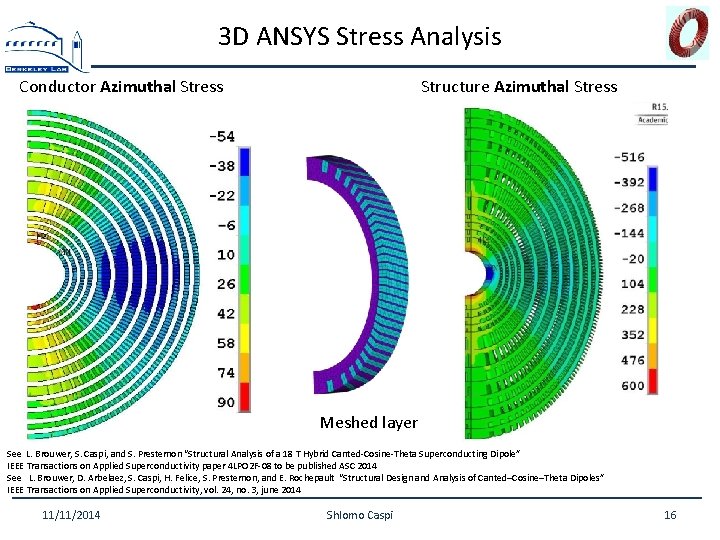
3 D ANSYS Stress Analysis Conductor Azimuthal Stress Structure Azimuthal Stress Meshed layer See L. Brouwer, S. Caspi, and S. Prestemon “Structural Analysis of a 18 T Hybrid Canted-Cosine-Theta Superconducting Dipole” IEEE Transactions on Applied Superconductivity paper 4 LPO 2 F-08 to be published ASC 2014 See L. Brouwer, D. Arbelaez, S. Caspi, H. Felice, S. Prestemon, and E. Rochepault “Structural Design and Analysis of Canted–Cosine–Theta Dipoles” IEEE Transactions on Applied Superconductivity, vol. 24, no. 3, june 2014 11/11/2014 Shlomo Caspi 16
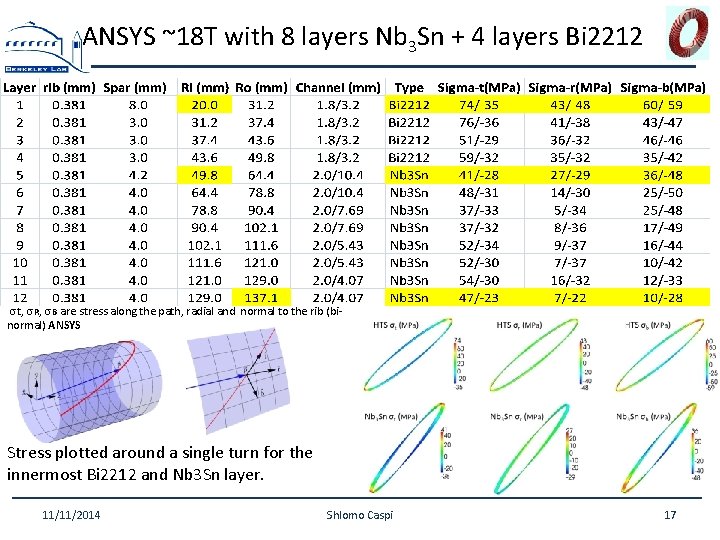
ANSYS ~18 T with 8 layers Nb 3 Sn + 4 layers Bi 2212 t, R, B are stress along the path, radial and normal to the rib (binormal) ANSYS Stress plotted around a single turn for the innermost Bi 2212 and Nb 3 Sn layer. 11/11/2014 Shlomo Caspi 17
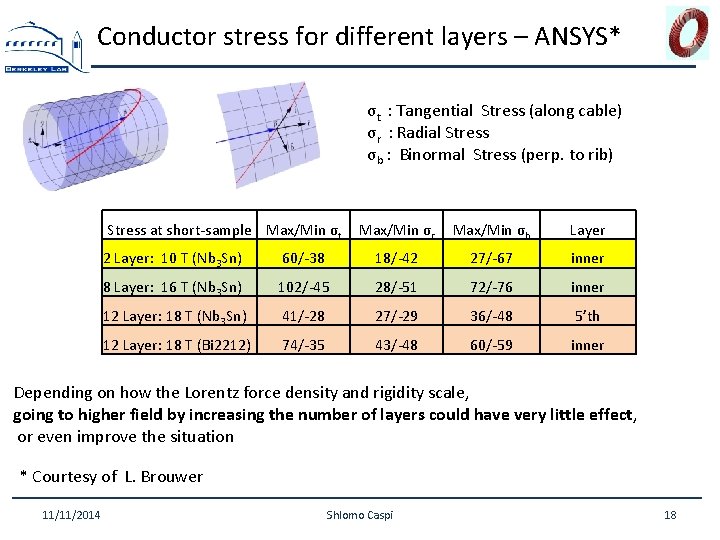
Conductor stress for different layers – ANSYS* σt : Tangential Stress (along cable) σr : Radial Stress σb : Binormal Stress (perp. to rib) Stress at short-sample Max/Min σt Max/Min σr Max/Min σb Layer 2 Layer: 10 T (Nb 3 Sn) 60/-38 18/-42 27/-67 inner 8 Layer: 16 T (Nb 3 Sn) 102/-45 28/-51 72/-76 inner 12 Layer: 18 T (Nb 3 Sn) 41/-28 27/-29 36/-48 5’th 12 Layer: 18 T (Bi 2212) 74/-35 43/-48 60/-59 inner Depending on how the Lorentz force density and rigidity scale, going to higher field by increasing the number of layers could have very little effect, or even improve the situation * Courtesy of L. Brouwer 11/11/2014 Shlomo Caspi 18
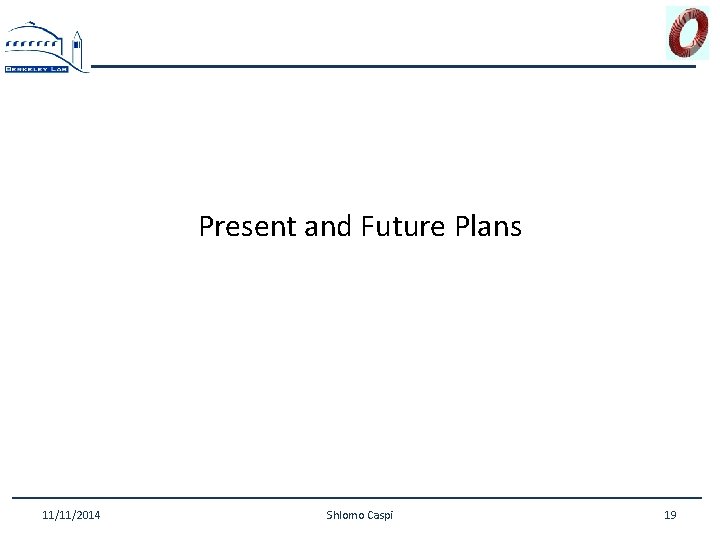
Present and Future Plans 11/11/2014 Shlomo Caspi 19
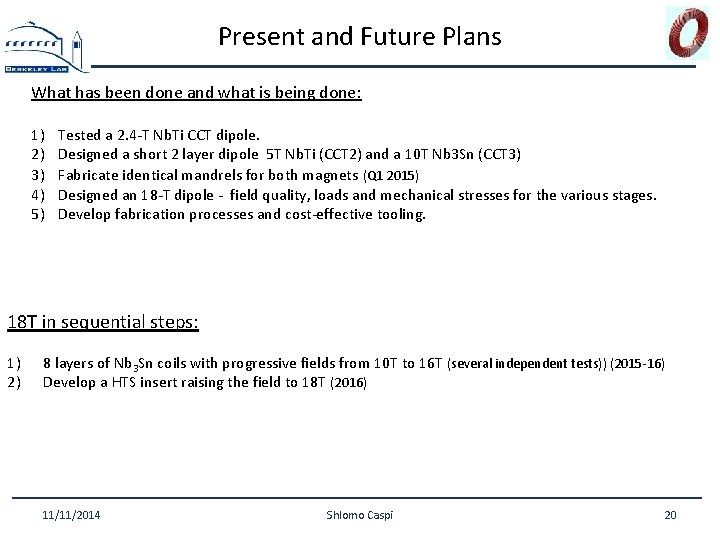
Present and Future Plans What has been done and what is being done: 1) 2) 3) 4) 5) Tested a 2. 4 -T Nb. Ti CCT dipole. Designed a short 2 layer dipole 5 T Nb. Ti (CCT 2) and a 10 T Nb 3 Sn (CCT 3) Fabricate identical mandrels for both magnets (Q 1 2015) Designed an 18 -T dipole - field quality, loads and mechanical stresses for the various stages. Develop fabrication processes and cost-effective tooling. 18 T in sequential steps: 1) 2) 8 layers of Nb 3 Sn coils with progressive fields from 10 T to 16 T (several independent tests)) (2015 -16) Develop a HTS insert raising the field to 18 T (2016) 11/11/2014 Shlomo Caspi 20
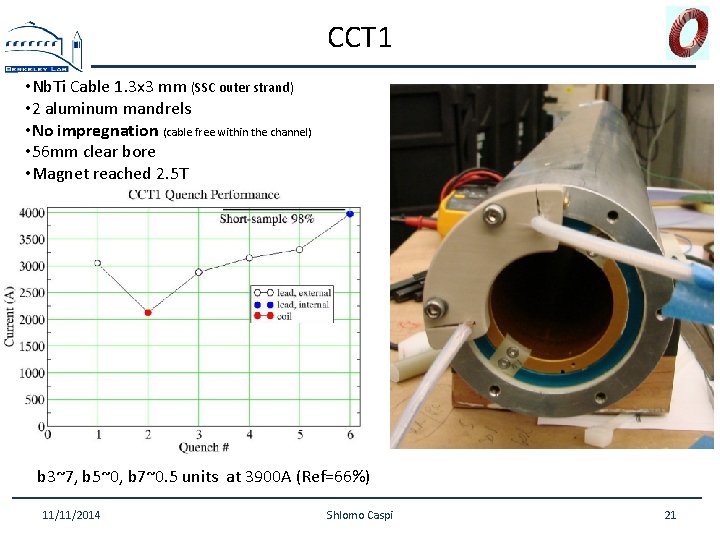
CCT 1 • Nb. Ti Cable 1. 3 x 3 mm (SSC outer strand) • 2 aluminum mandrels • No impregnation (cable free within the channel) • 56 mm clear bore • Magnet reached 2. 5 T b 3~7, b 5~0, b 7~0. 5 units at 3900 A (Ref=66%) 11/11/2014 Shlomo Caspi 21

CCT Magnet Technology – in progress Reaction tooling Winding, no tension no curing Potting tooling Wind using a deeper channel --2 x 10 mm Test reaction tooling and winding position Test potting tooling and winding position Reacted coil 11/11/2014 Shlomo Caspi 22
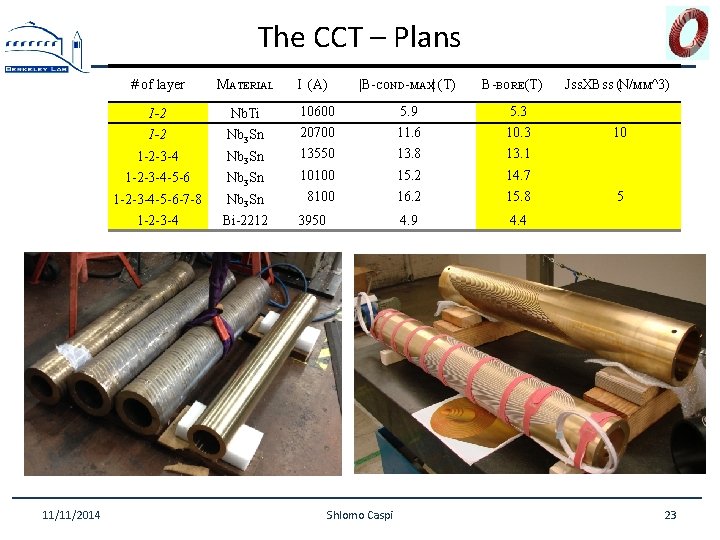
The CCT – Plans 11/11/2014 # of layer MATERIAL I (A) |B-COND-MAX| (T) 1 -2 Nb. Ti 10600 5. 9 5. 3 1 -2 Nb 3 Sn 20700 11. 6 10. 3 1 -2 -3 -4 Nb 3 Sn 13550 13. 8 13. 1 1 -2 -3 -4 -5 -6 Nb 3 Sn 10100 15. 2 14. 7 1 -2 -3 -4 -5 -6 -7 -8 Nb 3 Sn 8100 16. 2 15. 8 1 -2 -3 -4 Bi-2212 4. 9 4. 4 3950 Shlomo Caspi B-BORE (T) JSSXBSS (N/MM^3) 10 5 23
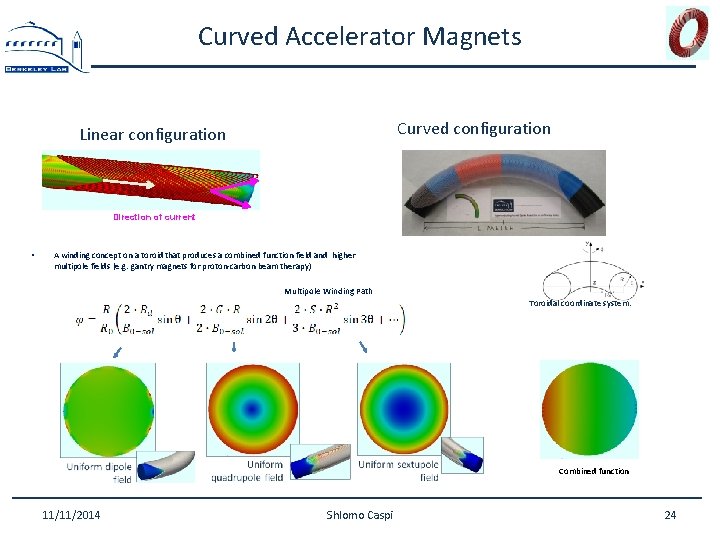
Curved Accelerator Magnets Curved configuration Linear configuration Direction of current • A winding concept on a toroid that produces a combined function field and higher multipole fields (e. g. gantry magnets for proton-carbon beam therapy) Multipole Winding Path Toroidal coordinate system. Combined function 11/11/2014 Shlomo Caspi 24
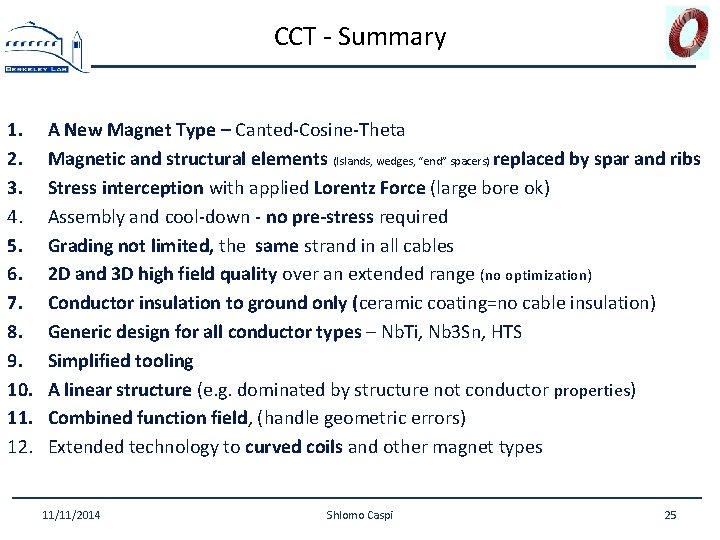
CCT - Summary 1. 2. 3. 4. 5. 6. 7. 8. 9. 10. 11. 12. A New Magnet Type – Canted-Cosine-Theta Magnetic and structural elements (Islands, wedges, “end” spacers) replaced by spar and ribs Stress interception with applied Lorentz Force (large bore ok) Assembly and cool-down - no pre-stress required Grading not limited, the same strand in all cables 2 D and 3 D high field quality over an extended range (no optimization) Conductor insulation to ground only (ceramic coating=no cable insulation) Generic design for all conductor types – Nb. Ti, Nb 3 Sn, HTS Simplified tooling A linear structure (e. g. dominated by structure not conductor properties) Combined function field, (handle geometric errors) Extended technology to curved coils and other magnet types 11/11/2014 Shlomo Caspi 25
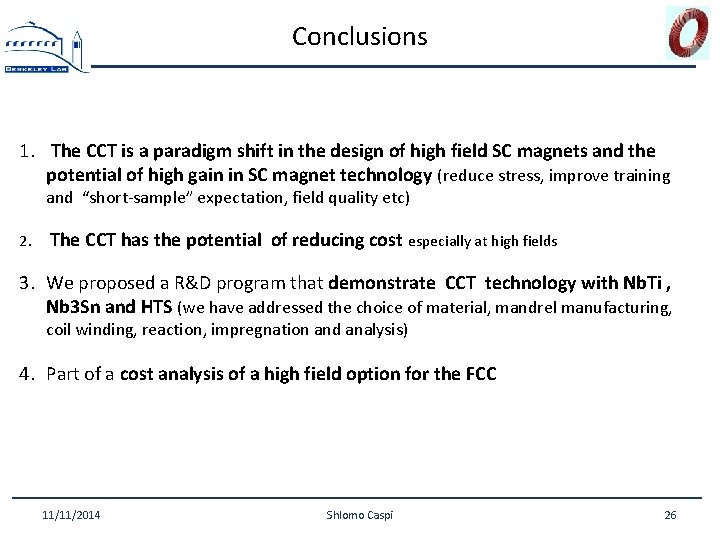
Conclusions 1. The CCT is a paradigm shift in the design of high field SC magnets and the potential of high gain in SC magnet technology (reduce stress, improve training and “short-sample” expectation, field quality etc) 2. The CCT has the potential of reducing cost especially at high fields 3. We proposed a R&D program that demonstrate CCT technology with Nb. Ti , Nb 3 Sn and HTS (we have addressed the choice of material, mandrel manufacturing, coil winding, reaction, impregnation and analysis) 4. Part of a cost analysis of a high field option for the FCC 11/11/2014 Shlomo Caspi 26
Magnets attract and repel
Shlomo hershkop
Shlomo kramer
Shlomo hershkop
Shlomo ta'asan
Temporary vs permanent magnets
Magnet berasal dari kata
What happens if you break a magnet in half
Superconducting devices in quantum optics
Stj
Western superconducting
Oxford superconducting technology
Superconducting tunnel junction
Superconducting energy gap
Youtube.com
Superconducting tunnel junction
Superconducting ring
Superconducting tunnel junction
Pascal febvre
Cct de la escuela secundaria gabriela mistral
Cct qualiroutes
Escuela secundaria carlos marx 214
Cct qualiroutes
Communication culture and technology
Certified calibration technician training
Cct 104
Cct 100