ACARP Roadway Development Operators Workshop March 2008 Roadway
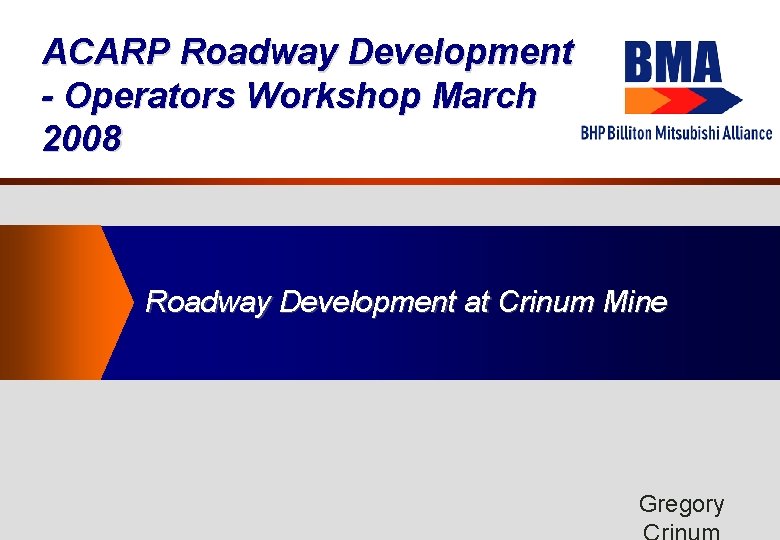
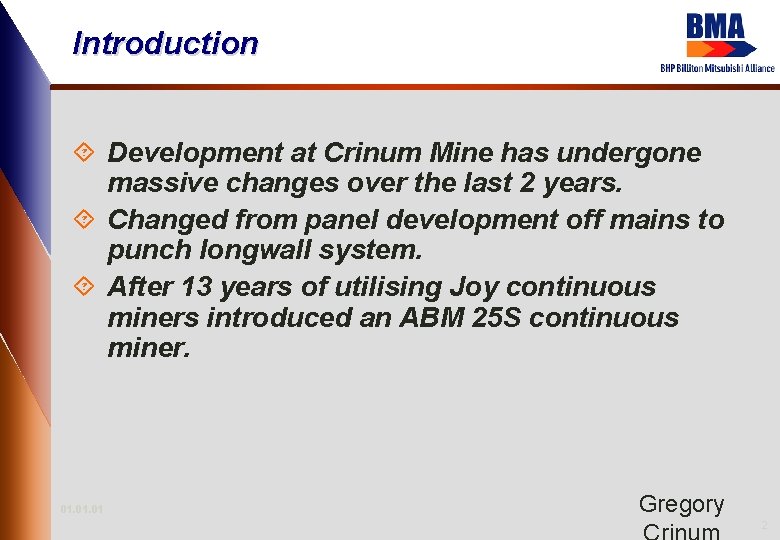
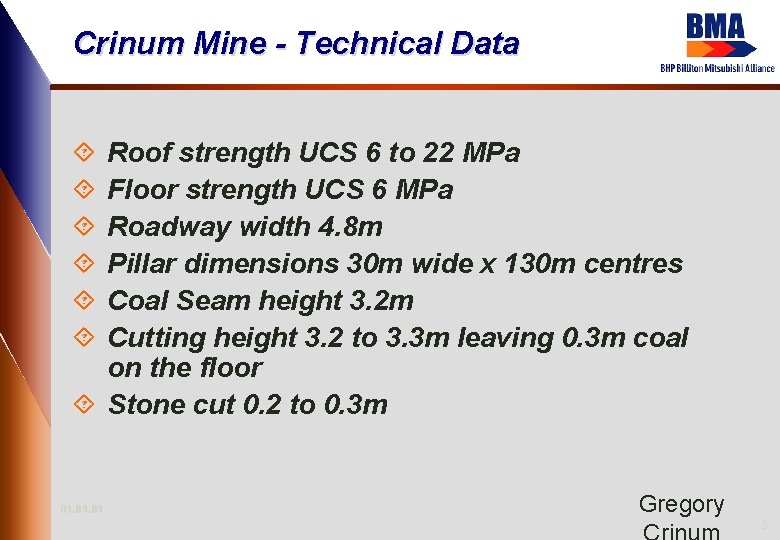
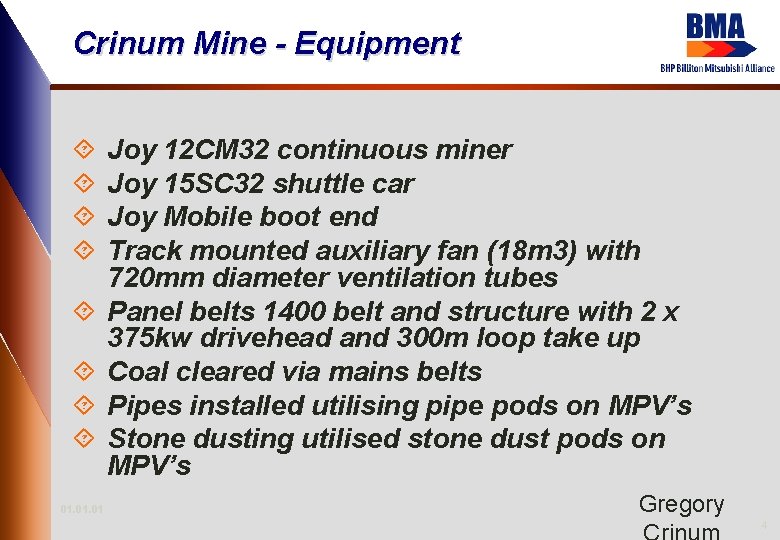
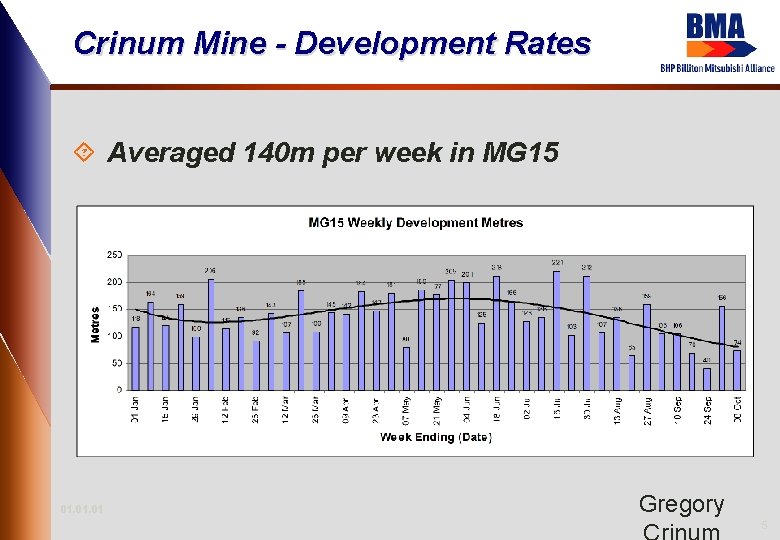
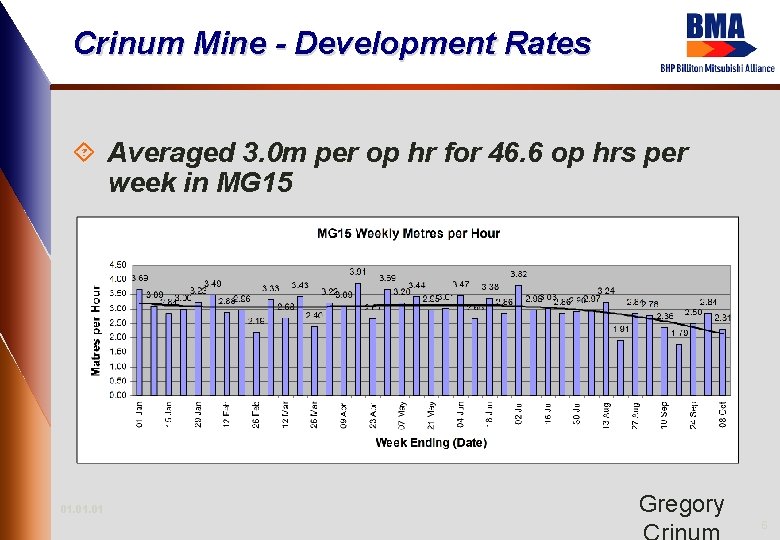
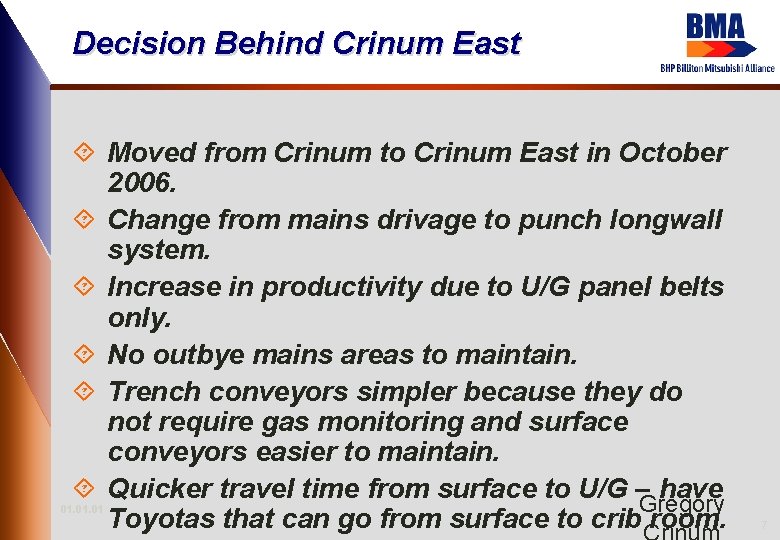
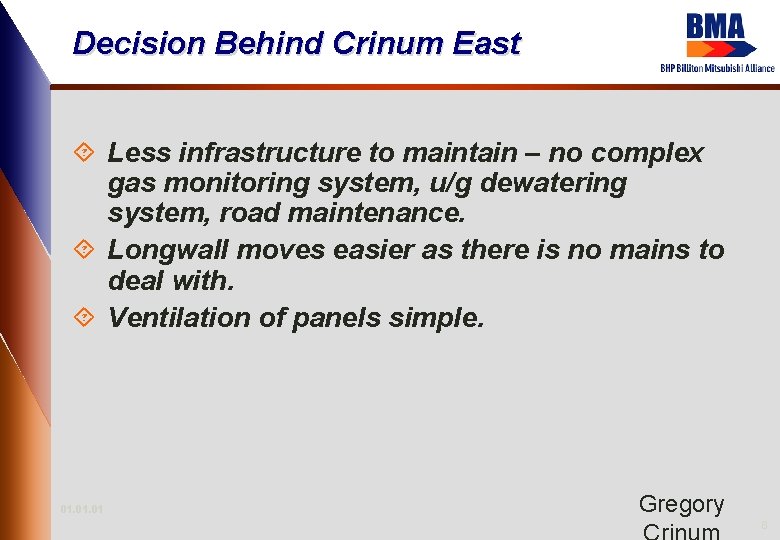
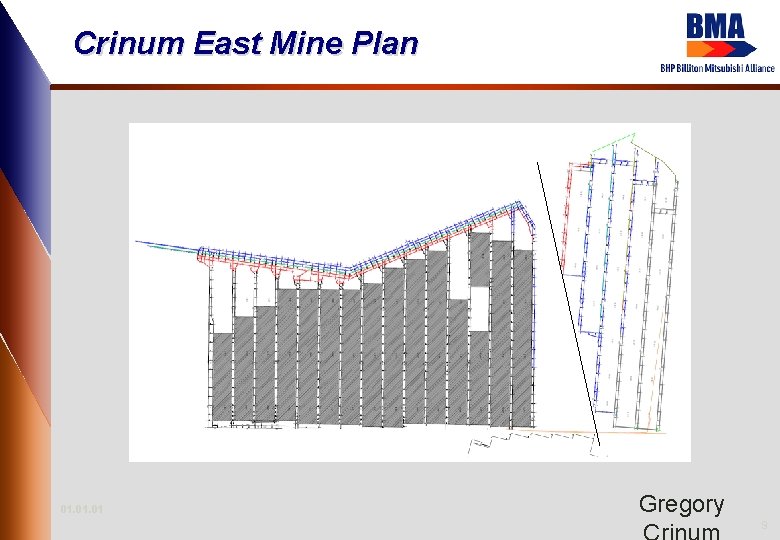
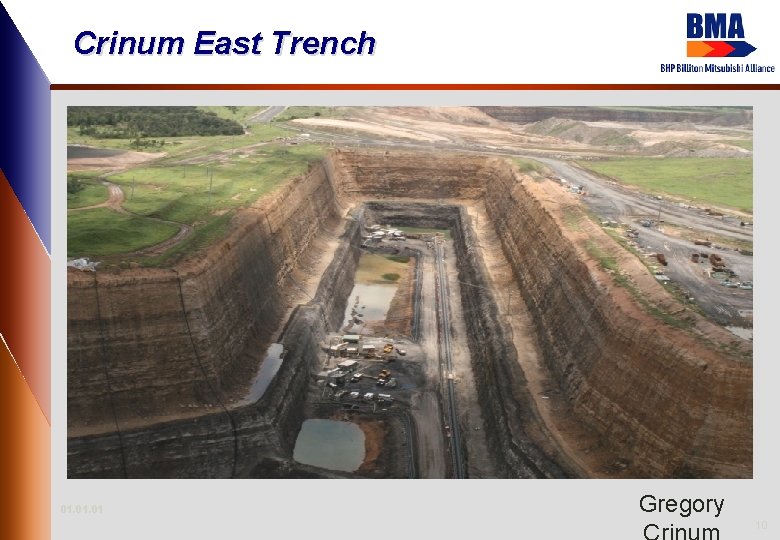
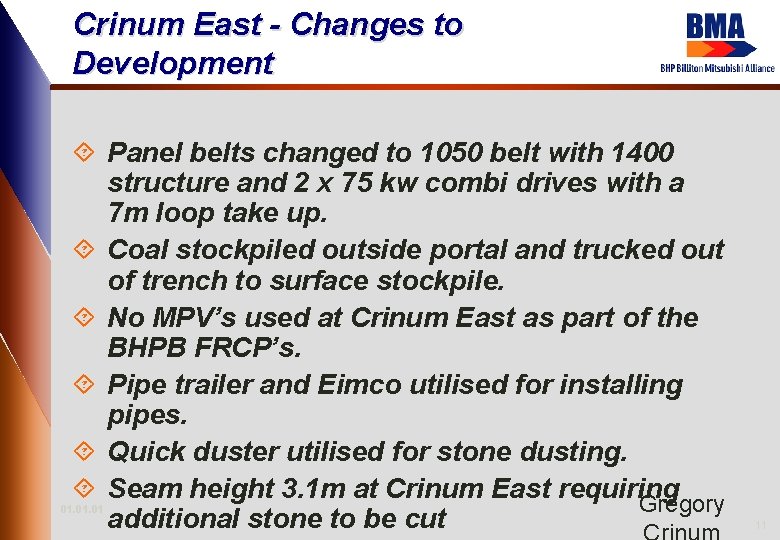
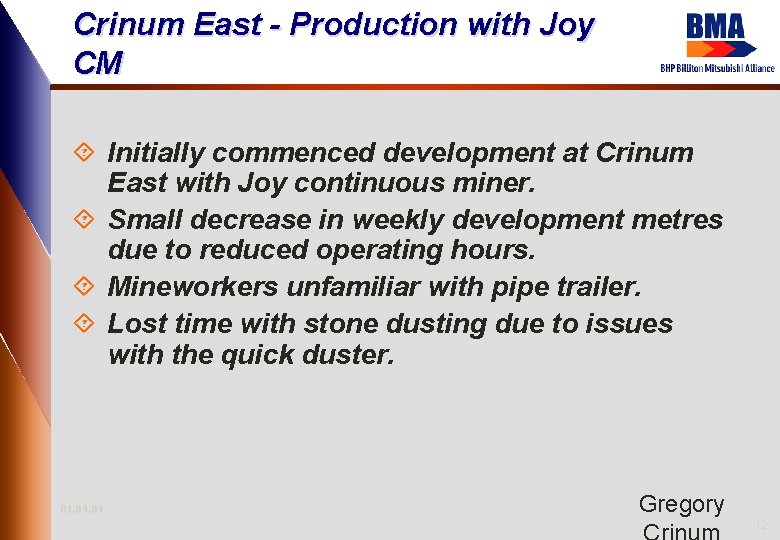
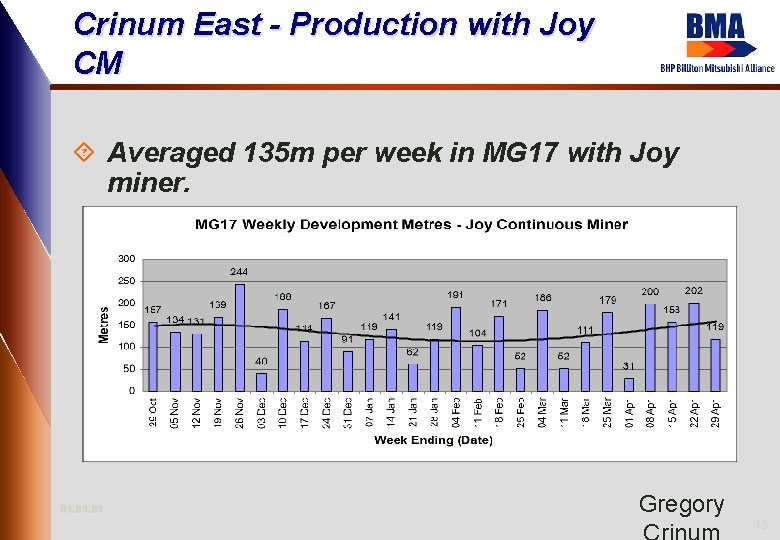
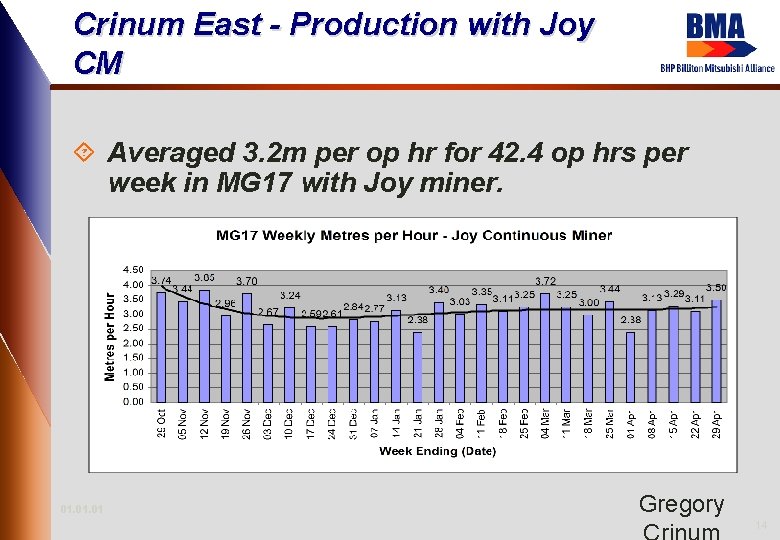
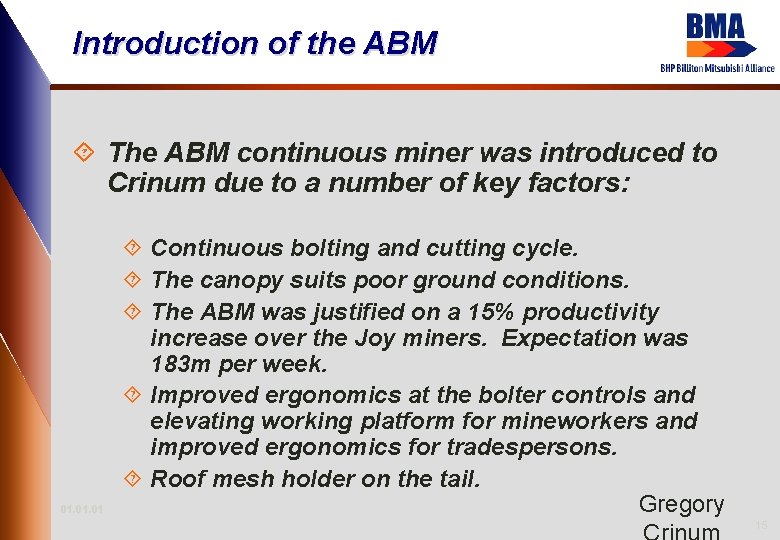

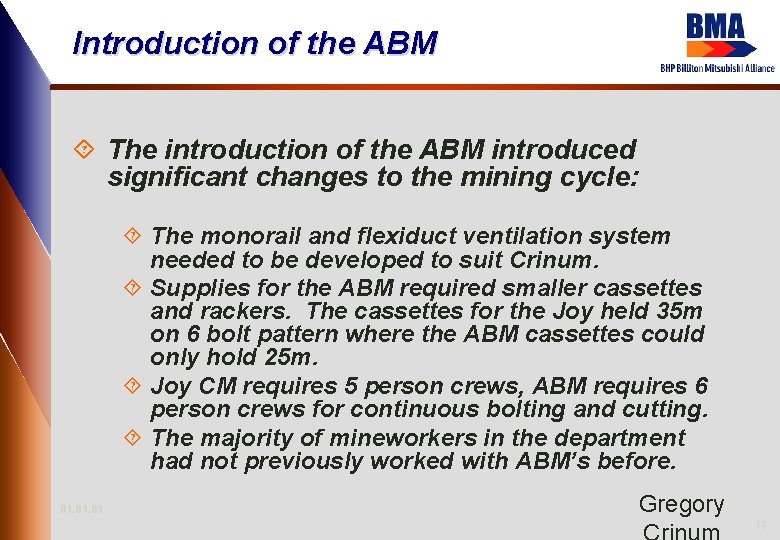
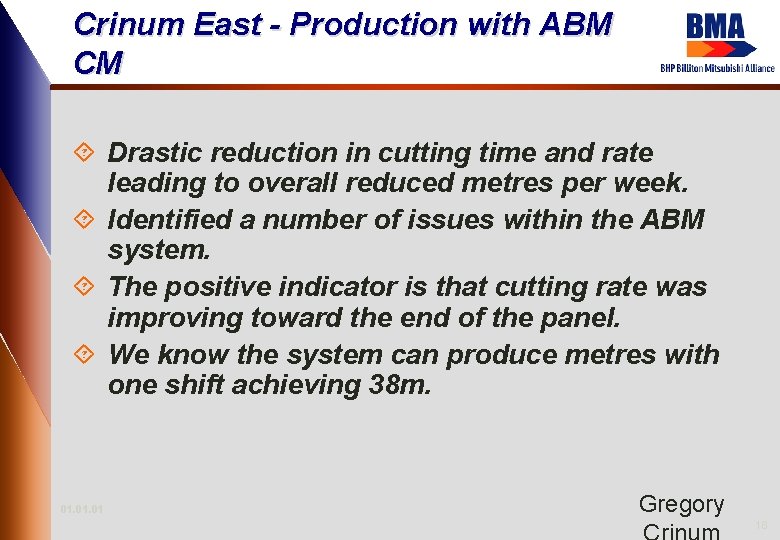
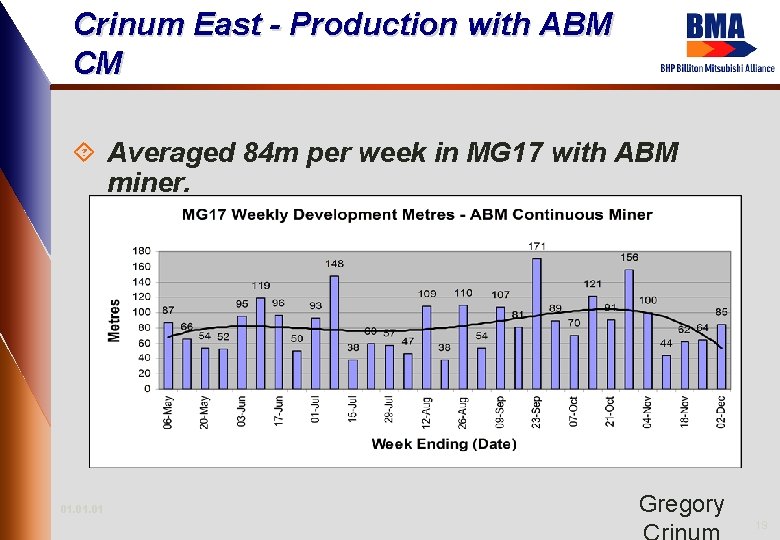
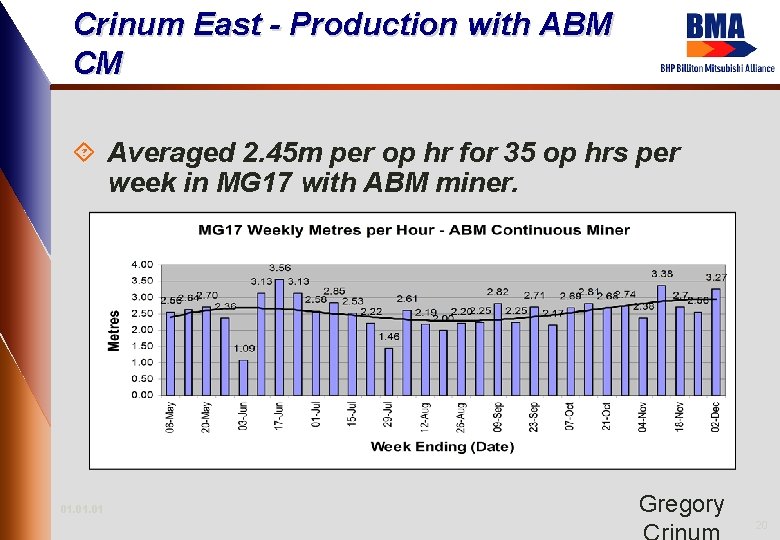
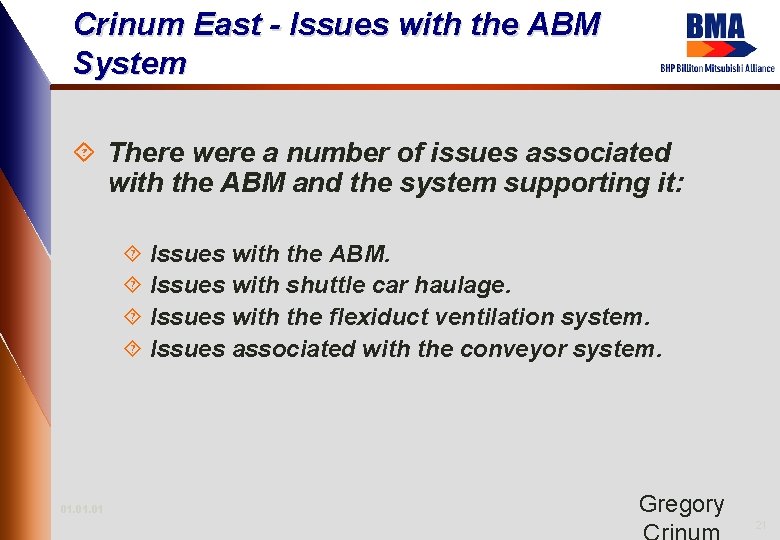
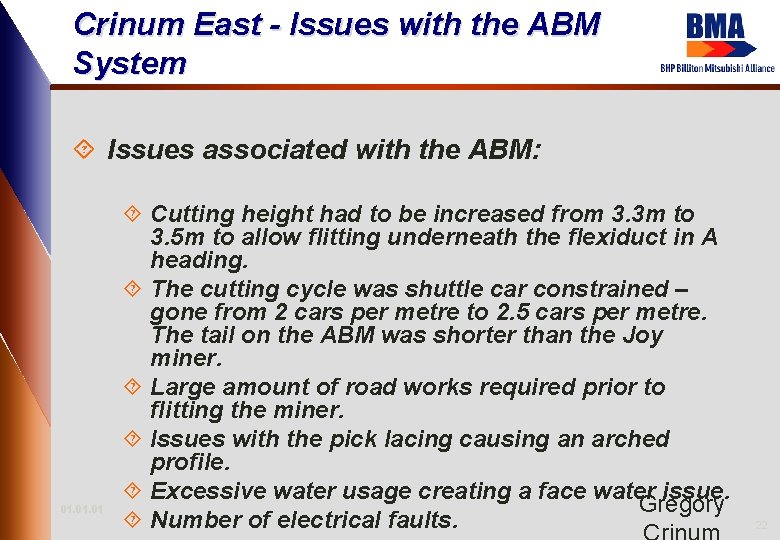
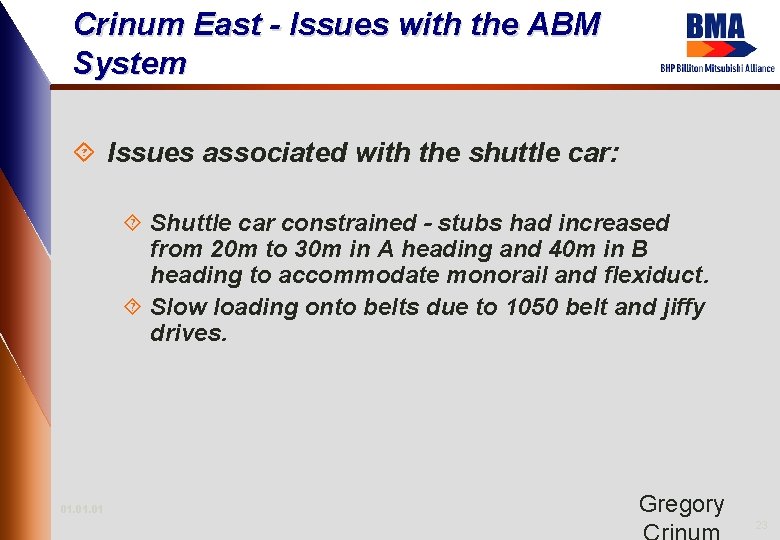
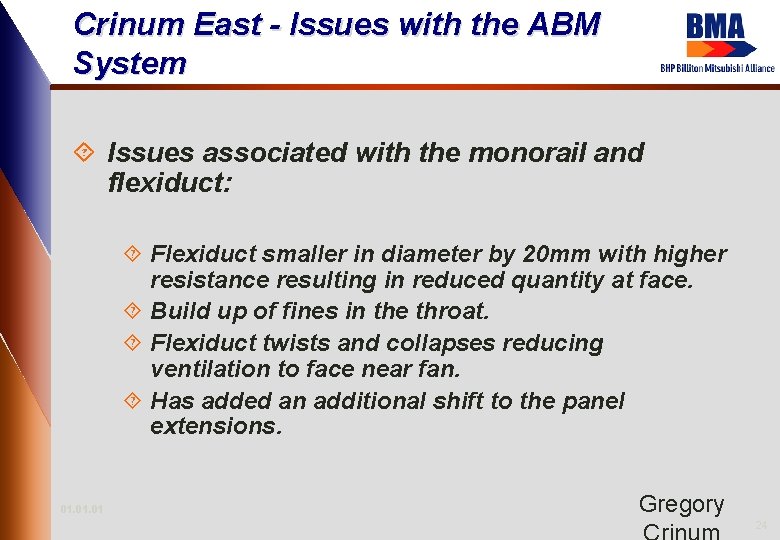
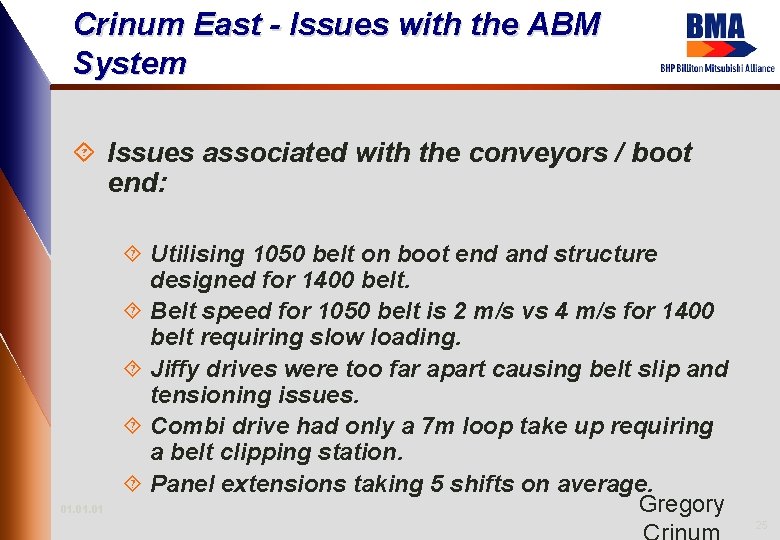
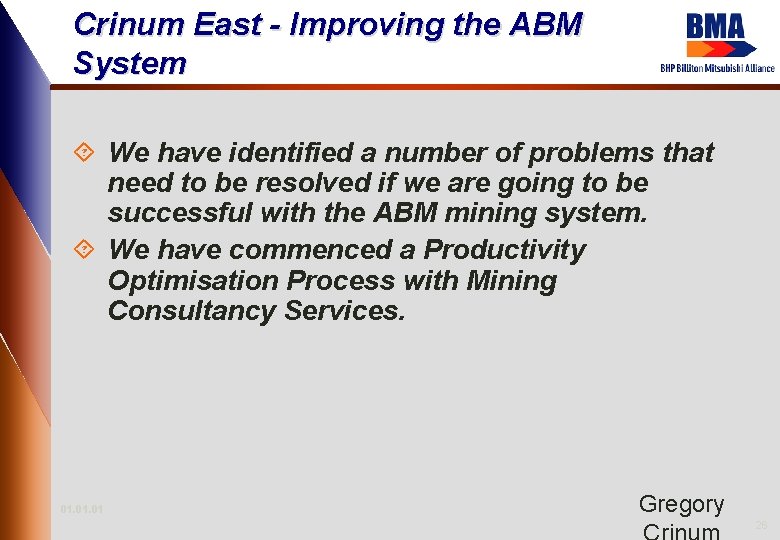
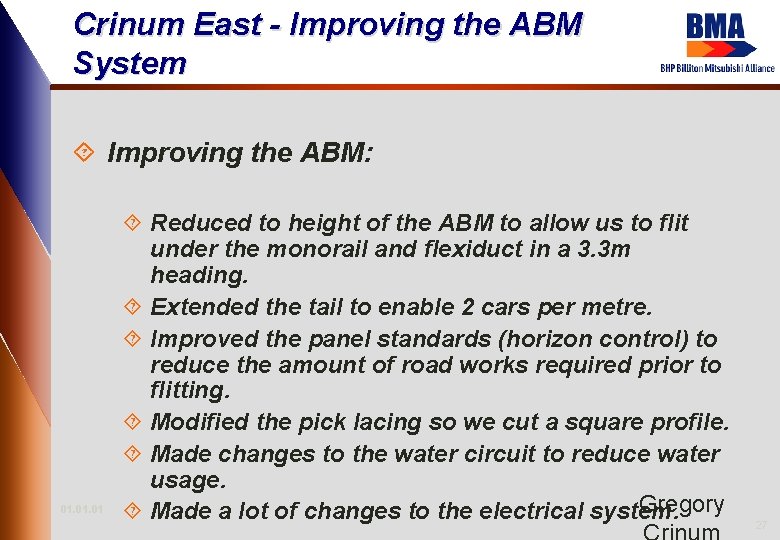
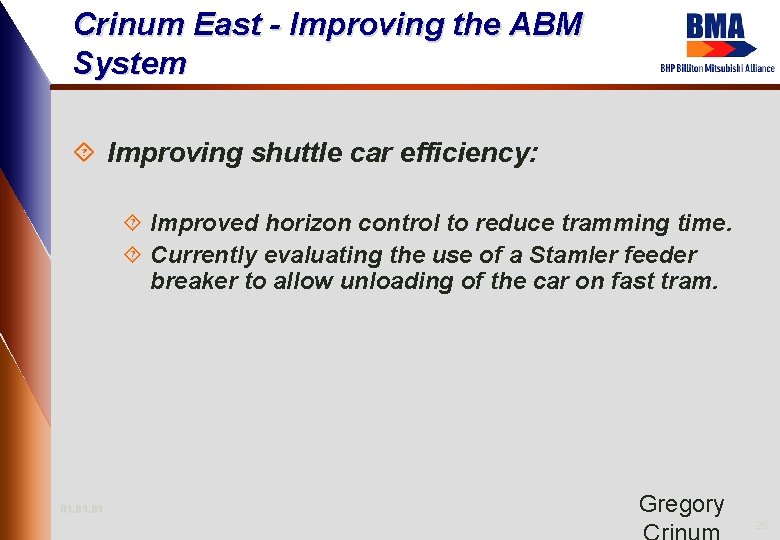
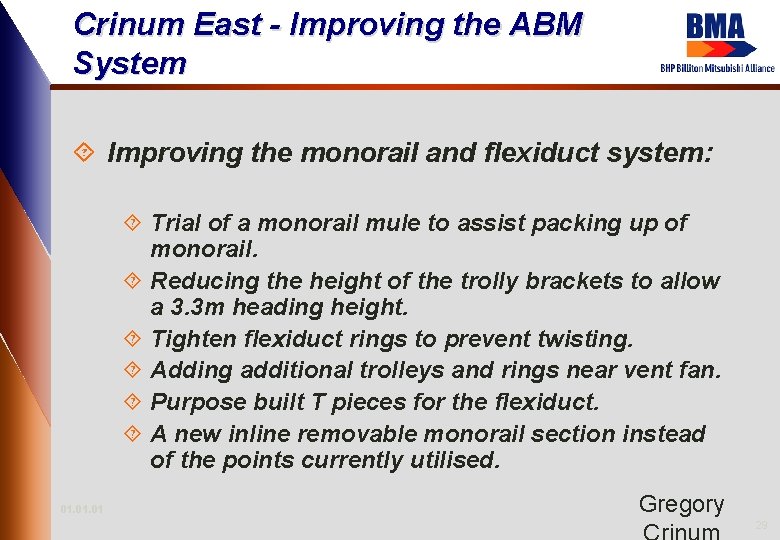
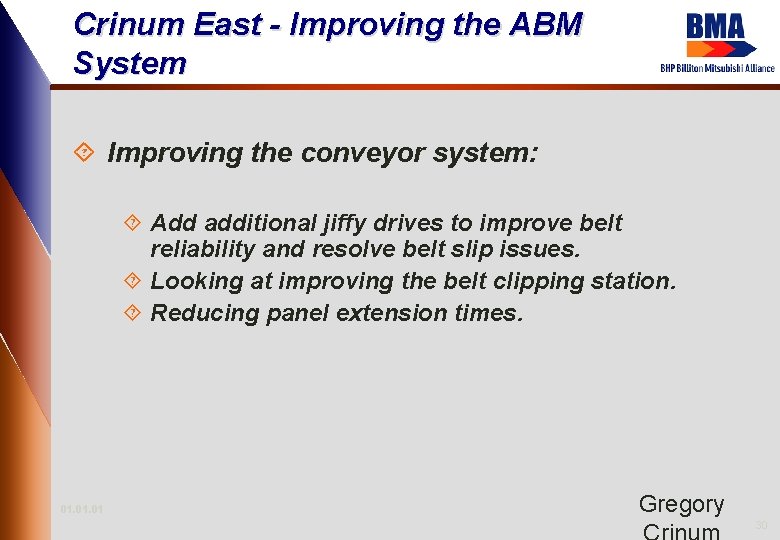
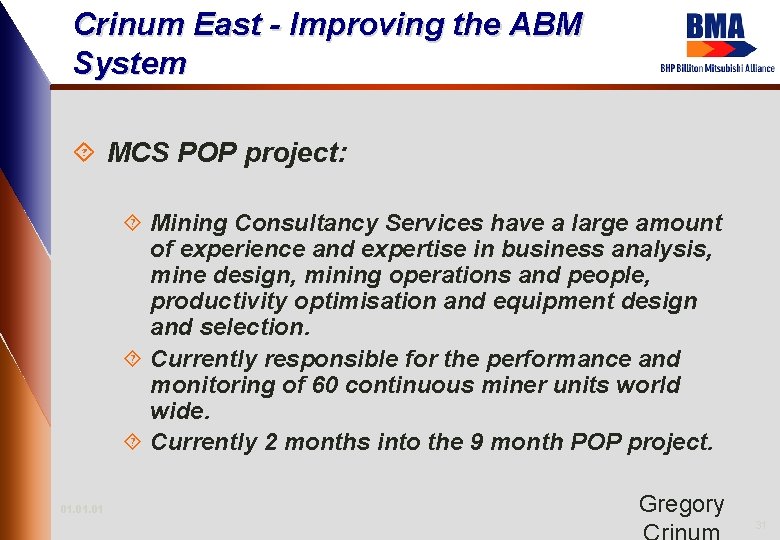
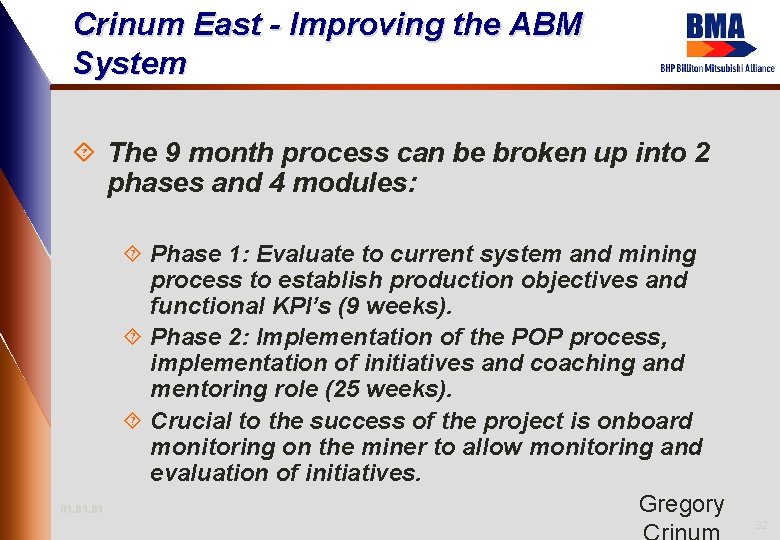
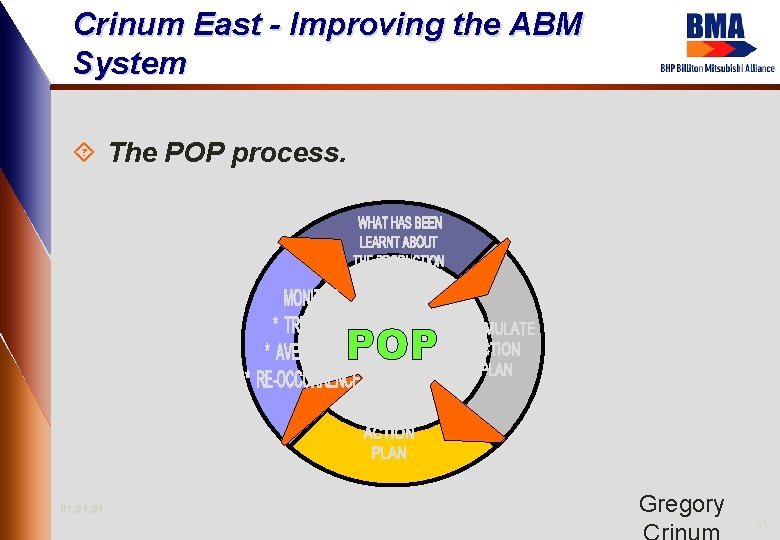
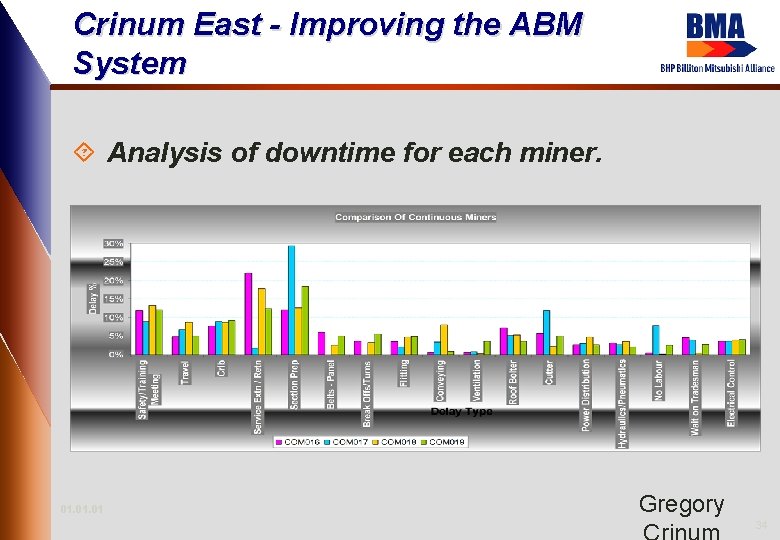
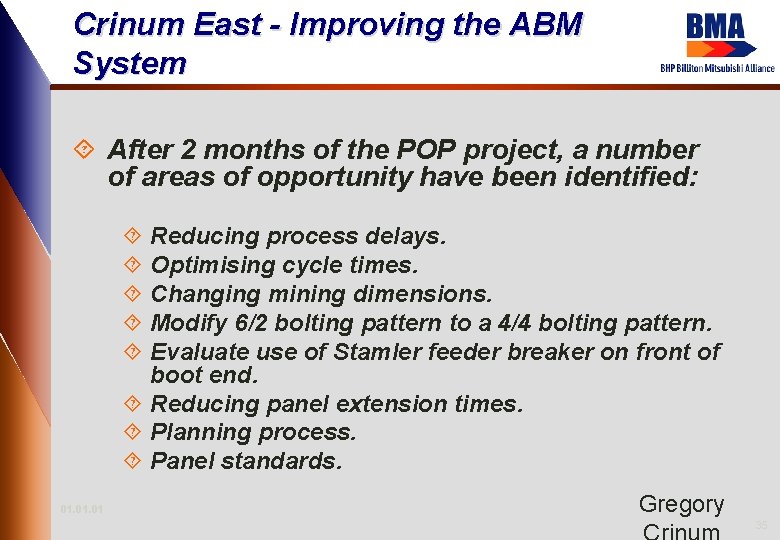
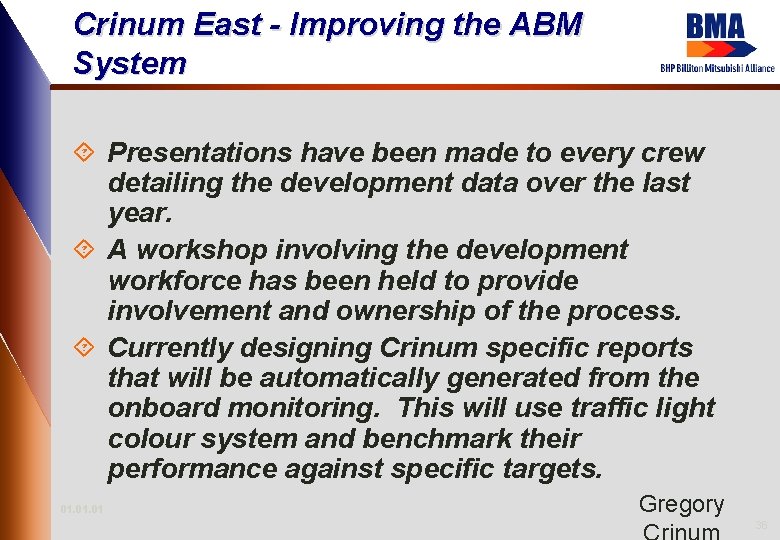
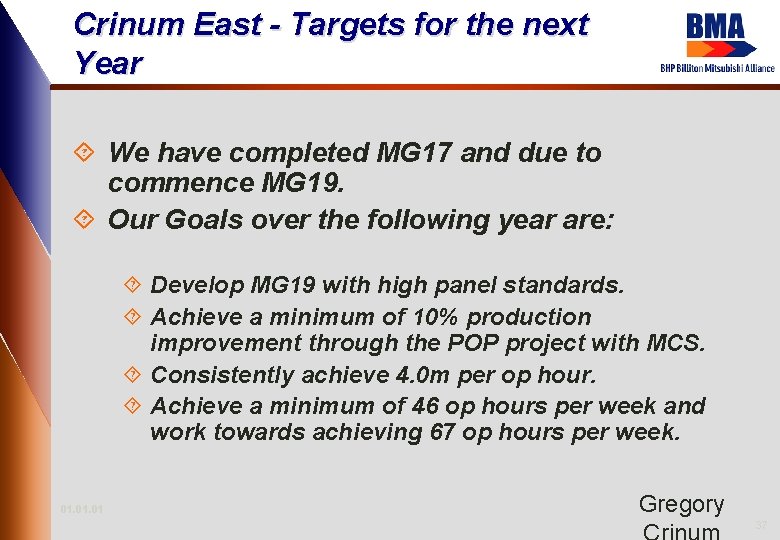
- Slides: 37
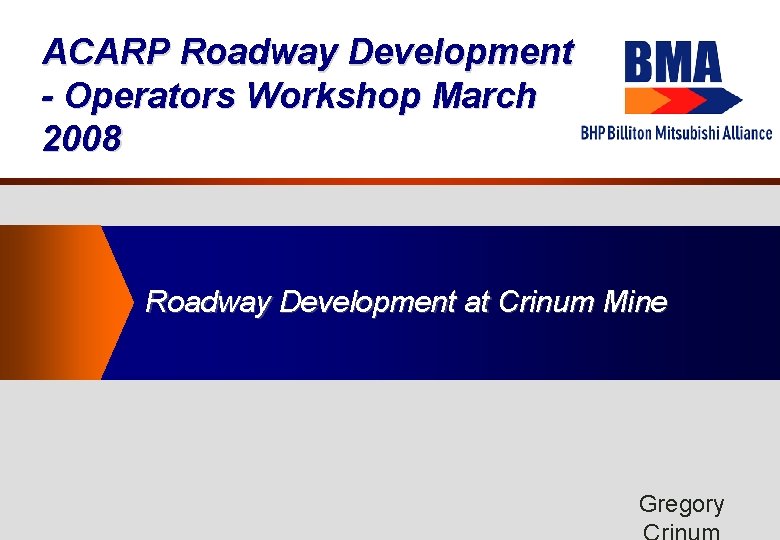
ACARP Roadway Development - Operators Workshop March 2008 Roadway Development at Crinum Mine Gregory
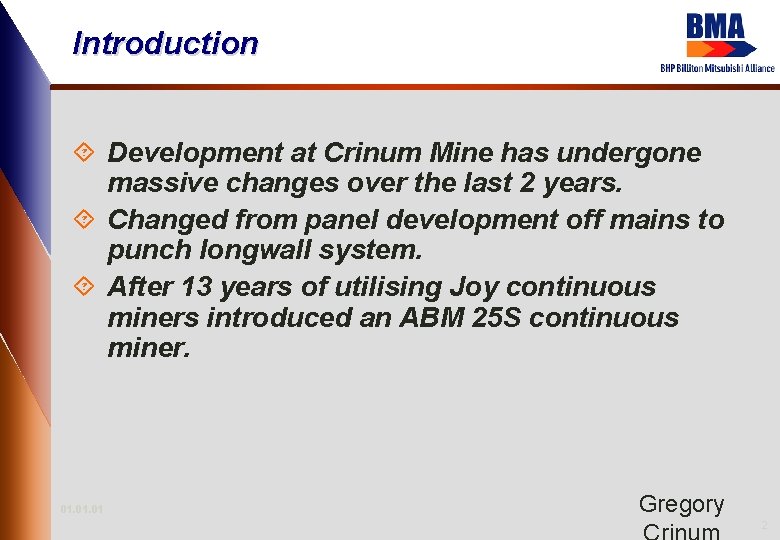
Introduction ´ Development at Crinum Mine has undergone massive changes over the last 2 years. ´ Changed from panel development off mains to punch longwall system. ´ After 13 years of utilising Joy continuous miners introduced an ABM 25 S continuous miner. 01. 01 Gregory 2
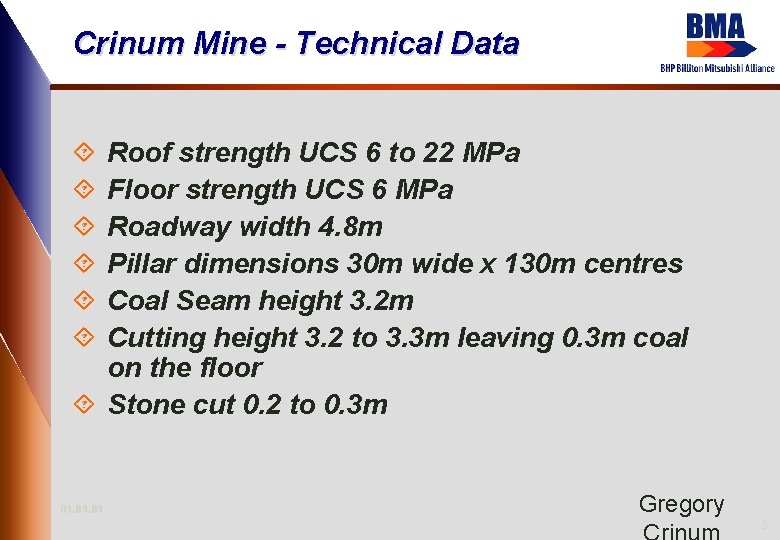
Crinum Mine - Technical Data ´ ´ ´ Roof strength UCS 6 to 22 MPa Floor strength UCS 6 MPa Roadway width 4. 8 m Pillar dimensions 30 m wide x 130 m centres Coal Seam height 3. 2 m Cutting height 3. 2 to 3. 3 m leaving 0. 3 m coal on the floor ´ Stone cut 0. 2 to 0. 3 m 01. 01 Gregory 3
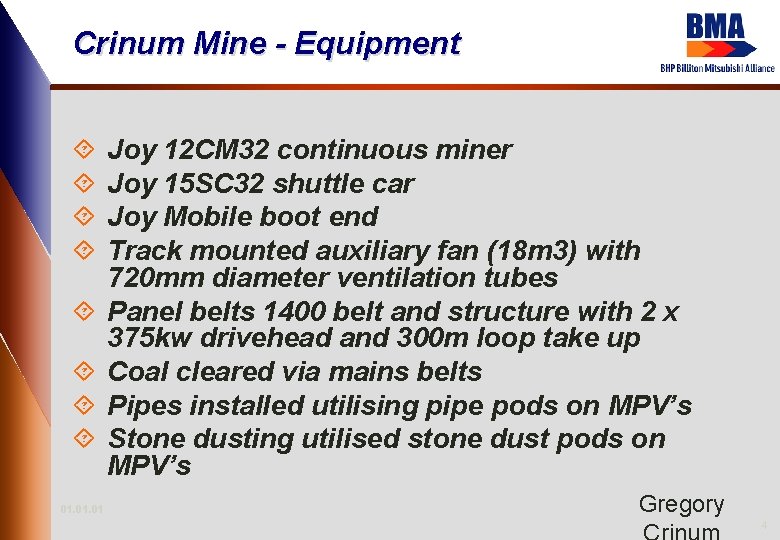
Crinum Mine - Equipment ´ ´ ´ ´ 01. 01 Joy 12 CM 32 continuous miner Joy 15 SC 32 shuttle car Joy Mobile boot end Track mounted auxiliary fan (18 m 3) with 720 mm diameter ventilation tubes Panel belts 1400 belt and structure with 2 x 375 kw drivehead and 300 m loop take up Coal cleared via mains belts Pipes installed utilising pipe pods on MPV’s Stone dusting utilised stone dust pods on MPV’s Gregory 4
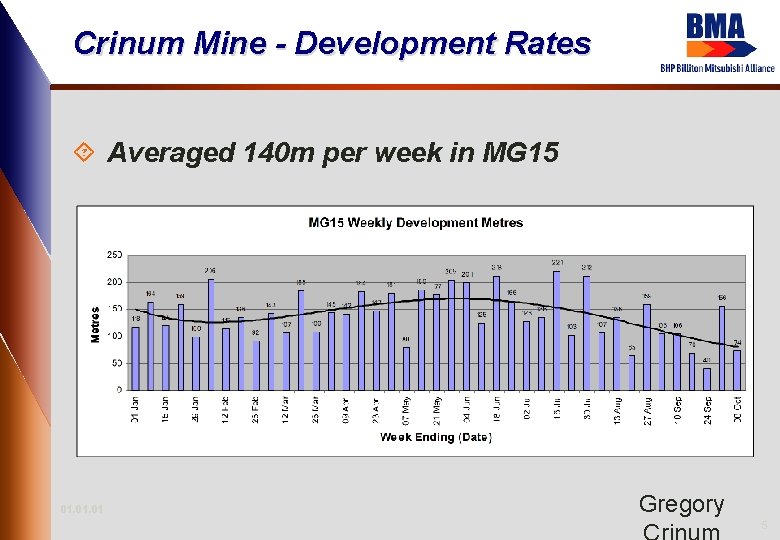
Crinum Mine - Development Rates ´ Averaged 140 m per week in MG 15 01. 01 Gregory 5
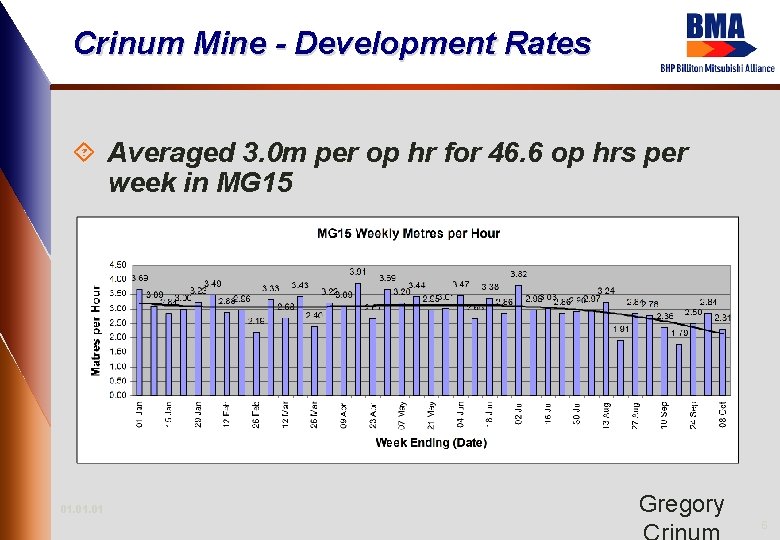
Crinum Mine - Development Rates ´ Averaged 3. 0 m per op hr for 46. 6 op hrs per week in MG 15 01. 01 Gregory 6
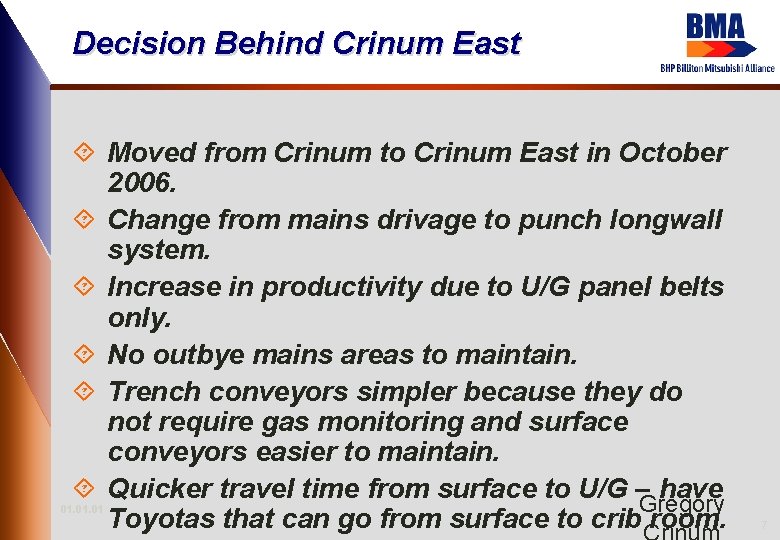
Decision Behind Crinum East ´ Moved from Crinum to Crinum East in October 2006. ´ Change from mains drivage to punch longwall system. ´ Increase in productivity due to U/G panel belts only. ´ No outbye mains areas to maintain. ´ Trench conveyors simpler because they do not require gas monitoring and surface conveyors easier to maintain. ´ Quicker travel time from surface to U/G – have Gregory Toyotas that can go from surface to crib room. 01. 01 7
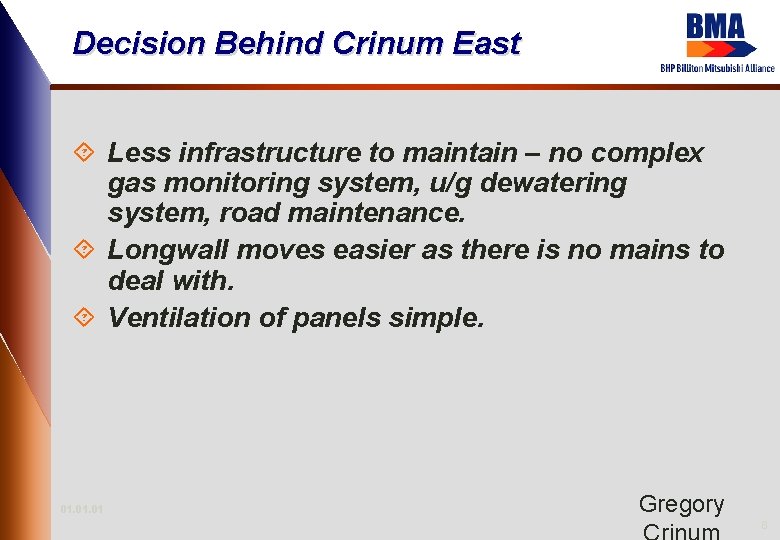
Decision Behind Crinum East ´ Less infrastructure to maintain – no complex gas monitoring system, u/g dewatering system, road maintenance. ´ Longwall moves easier as there is no mains to deal with. ´ Ventilation of panels simple. 01. 01 Gregory 8
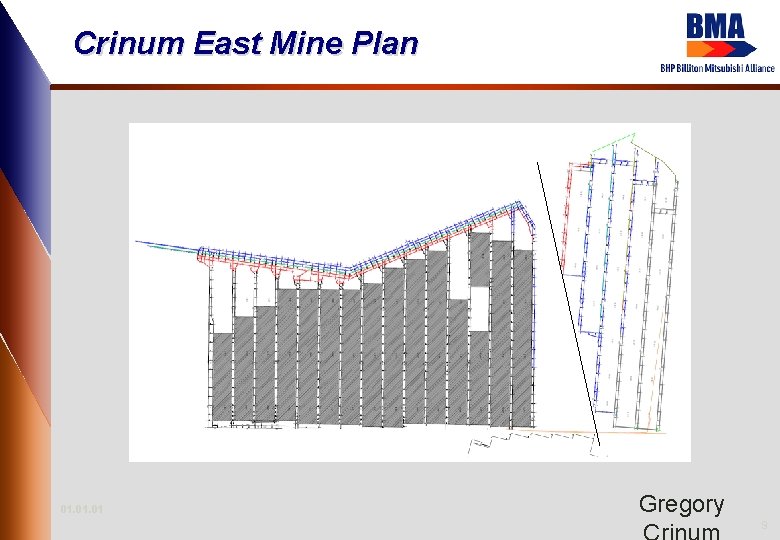
Crinum East Mine Plan 01. 01 Gregory 9
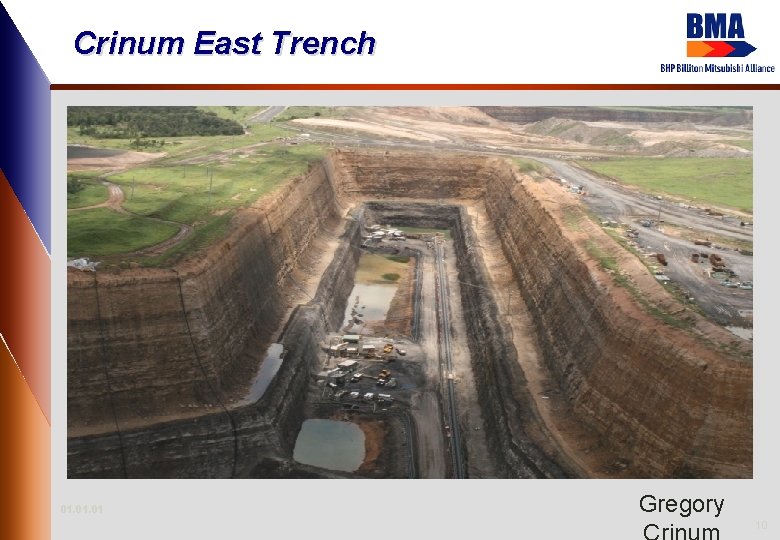
Crinum East Trench 01. 01 Gregory 10
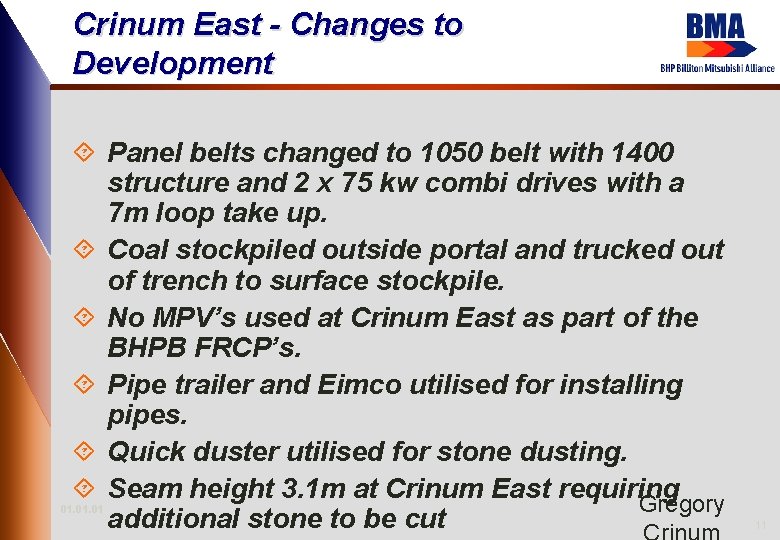
Crinum East - Changes to Development ´ Panel belts changed to 1050 belt with 1400 structure and 2 x 75 kw combi drives with a 7 m loop take up. ´ Coal stockpiled outside portal and trucked out of trench to surface stockpile. ´ No MPV’s used at Crinum East as part of the BHPB FRCP’s. ´ Pipe trailer and Eimco utilised for installing pipes. ´ Quick duster utilised for stone dusting. ´ Seam height 3. 1 m at Crinum East requiring Gregory additional stone to be cut 01. 01 11
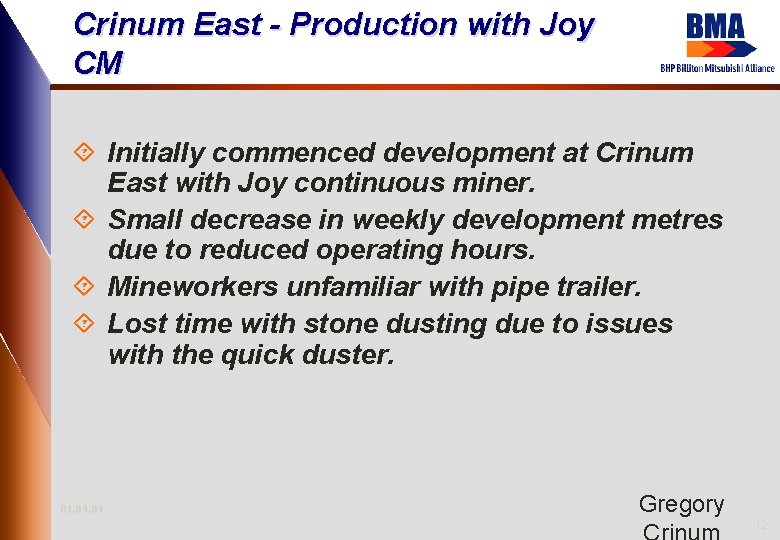
Crinum East - Production with Joy CM ´ Initially commenced development at Crinum East with Joy continuous miner. ´ Small decrease in weekly development metres due to reduced operating hours. ´ Mineworkers unfamiliar with pipe trailer. ´ Lost time with stone dusting due to issues with the quick duster. 01. 01 Gregory 12
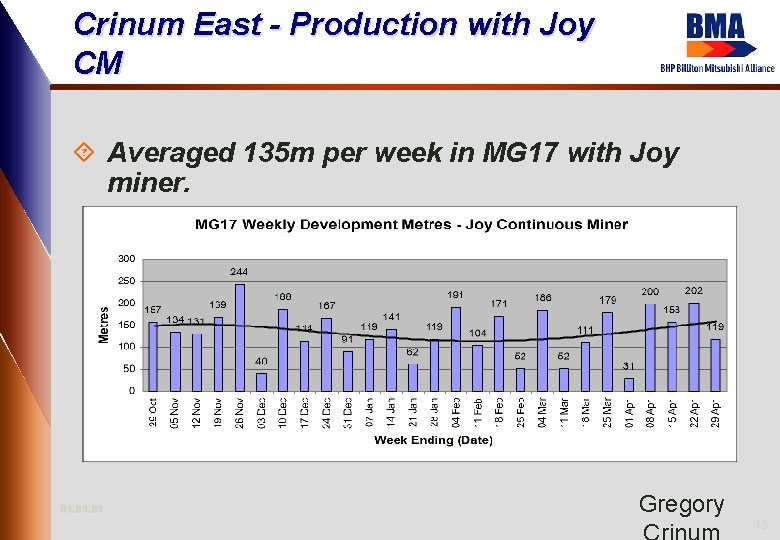
Crinum East - Production with Joy CM ´ Averaged 135 m per week in MG 17 with Joy miner. 01. 01 Gregory 13
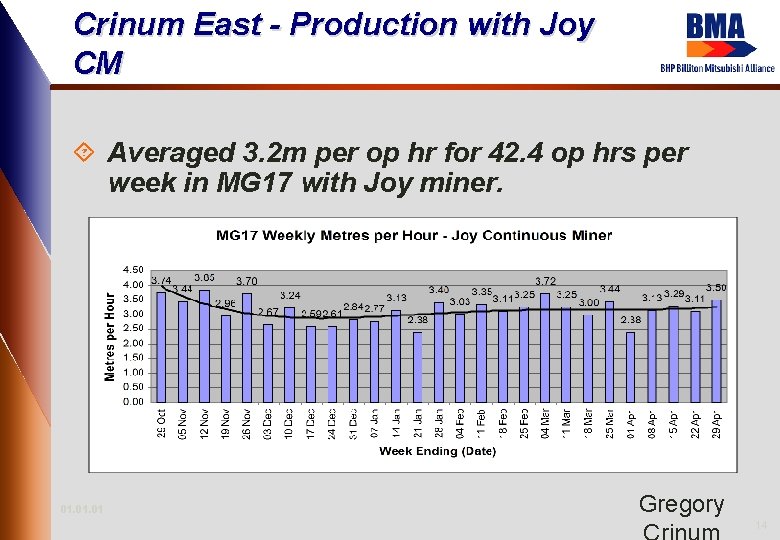
Crinum East - Production with Joy CM ´ Averaged 3. 2 m per op hr for 42. 4 op hrs per week in MG 17 with Joy miner. 01. 01 Gregory 14
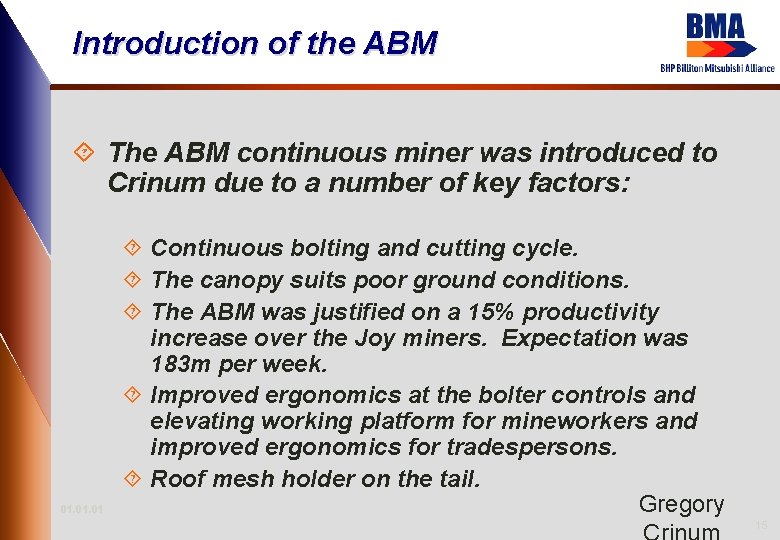
Introduction of the ABM ´ The ABM continuous miner was introduced to Crinum due to a number of key factors: 01. 01 ´ Continuous bolting and cutting cycle. ´ The canopy suits poor ground conditions. ´ The ABM was justified on a 15% productivity increase over the Joy miners. Expectation was 183 m per week. ´ Improved ergonomics at the bolter controls and elevating working platform for mineworkers and improved ergonomics for tradespersons. ´ Roof mesh holder on the tail. Gregory 15

Introduction of the ABM ´ Monorail and flexiduct ventilation system to improve cutting rate and reduce manual handling of ventilation tubes. 01. 01 Gregory 16
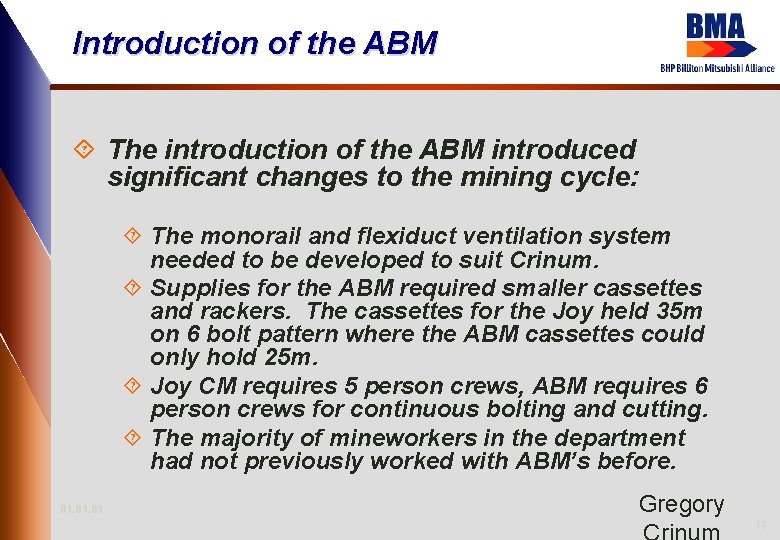
Introduction of the ABM ´ The introduction of the ABM introduced significant changes to the mining cycle: ´ The monorail and flexiduct ventilation system needed to be developed to suit Crinum. ´ Supplies for the ABM required smaller cassettes and rackers. The cassettes for the Joy held 35 m on 6 bolt pattern where the ABM cassettes could only hold 25 m. ´ Joy CM requires 5 person crews, ABM requires 6 person crews for continuous bolting and cutting. ´ The majority of mineworkers in the department had not previously worked with ABM’s before. 01. 01 Gregory 17
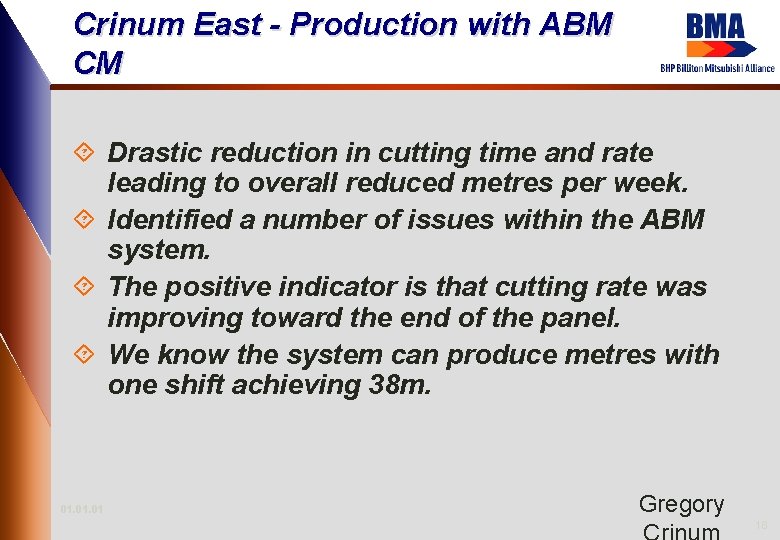
Crinum East - Production with ABM CM ´ Drastic reduction in cutting time and rate leading to overall reduced metres per week. ´ Identified a number of issues within the ABM system. ´ The positive indicator is that cutting rate was improving toward the end of the panel. ´ We know the system can produce metres with one shift achieving 38 m. 01. 01 Gregory 18
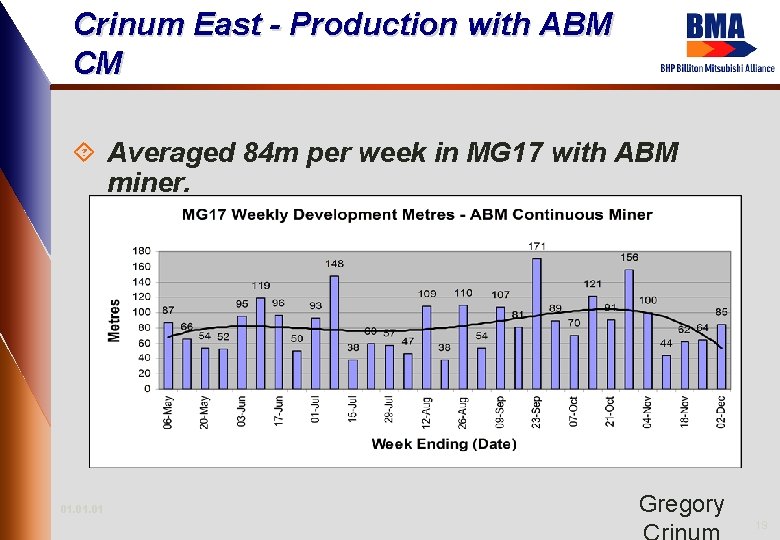
Crinum East - Production with ABM CM ´ Averaged 84 m per week in MG 17 with ABM miner. 01. 01 Gregory 19
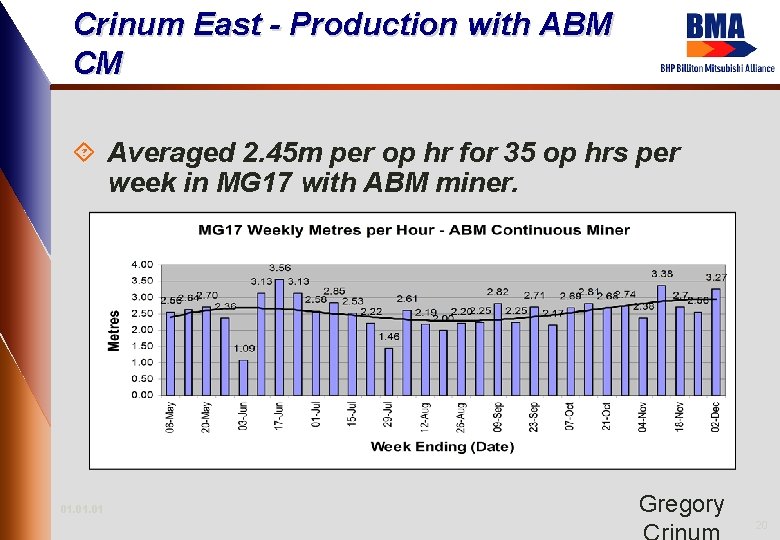
Crinum East - Production with ABM CM ´ Averaged 2. 45 m per op hr for 35 op hrs per week in MG 17 with ABM miner. 01. 01 Gregory 20
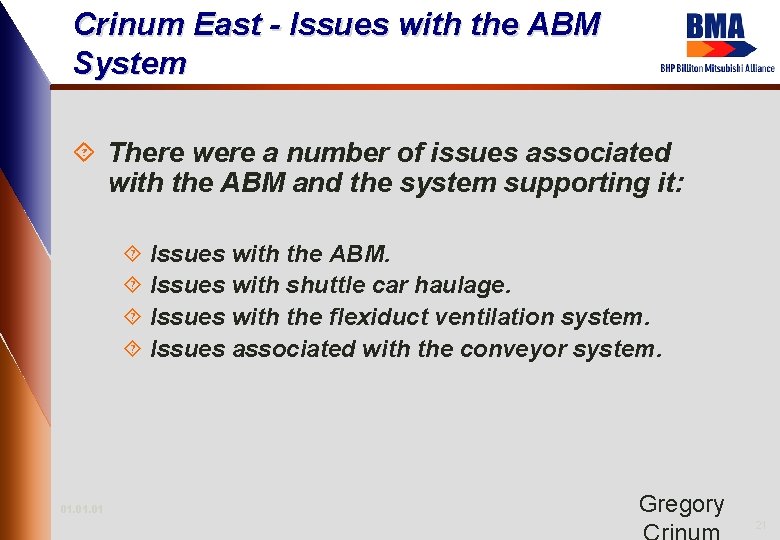
Crinum East - Issues with the ABM System ´ There were a number of issues associated with the ABM and the system supporting it: ´ Issues with the ABM. ´ Issues with shuttle car haulage. ´ Issues with the flexiduct ventilation system. ´ Issues associated with the conveyor system. 01. 01 Gregory 21
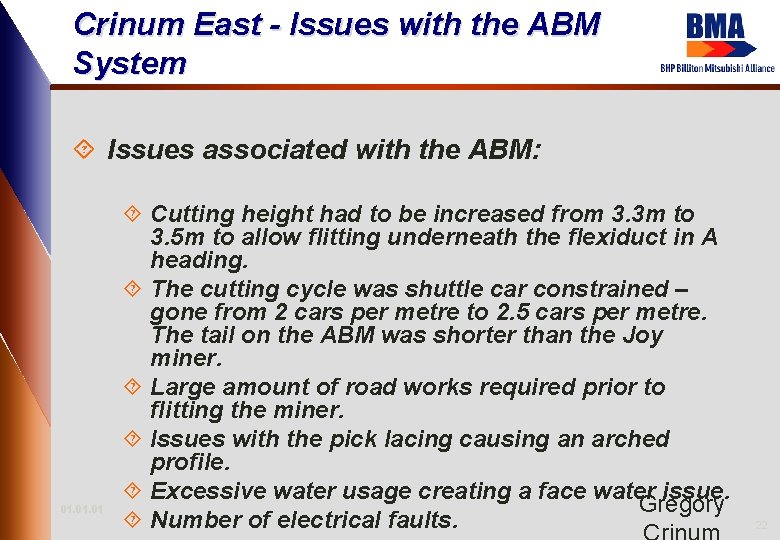
Crinum East - Issues with the ABM System ´ Issues associated with the ABM: 01. 01 ´ Cutting height had to be increased from 3. 3 m to 3. 5 m to allow flitting underneath the flexiduct in A heading. ´ The cutting cycle was shuttle car constrained – gone from 2 cars per metre to 2. 5 cars per metre. The tail on the ABM was shorter than the Joy miner. ´ Large amount of road works required prior to flitting the miner. ´ Issues with the pick lacing causing an arched profile. ´ Excessive water usage creating a face water issue. Gregory ´ Number of electrical faults. 22
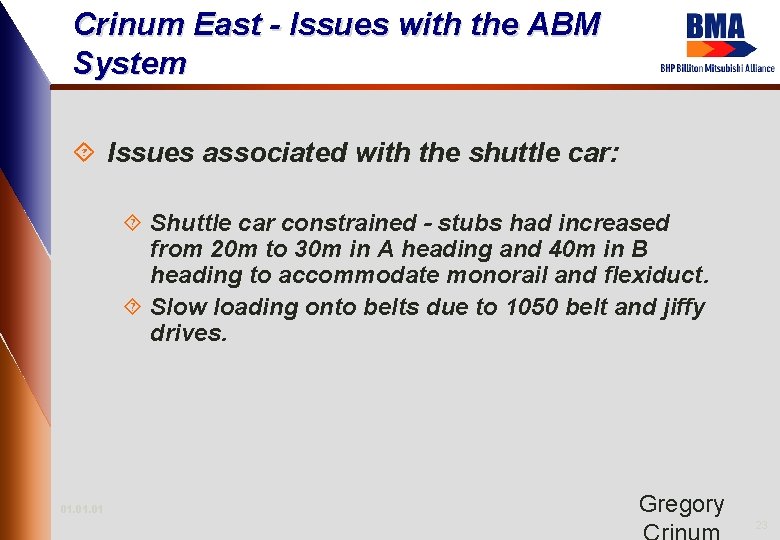
Crinum East - Issues with the ABM System ´ Issues associated with the shuttle car: ´ Shuttle car constrained - stubs had increased from 20 m to 30 m in A heading and 40 m in B heading to accommodate monorail and flexiduct. ´ Slow loading onto belts due to 1050 belt and jiffy drives. 01. 01 Gregory 23
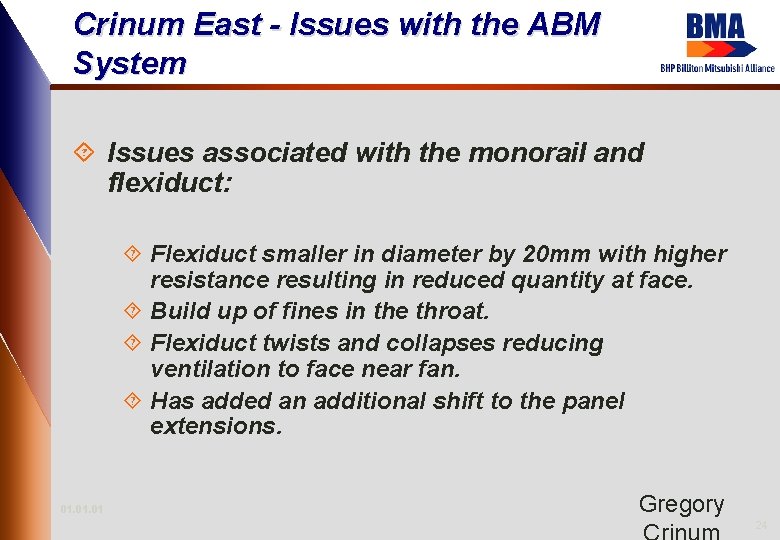
Crinum East - Issues with the ABM System ´ Issues associated with the monorail and flexiduct: ´ Flexiduct smaller in diameter by 20 mm with higher resistance resulting in reduced quantity at face. ´ Build up of fines in the throat. ´ Flexiduct twists and collapses reducing ventilation to face near fan. ´ Has added an additional shift to the panel extensions. 01. 01 Gregory 24
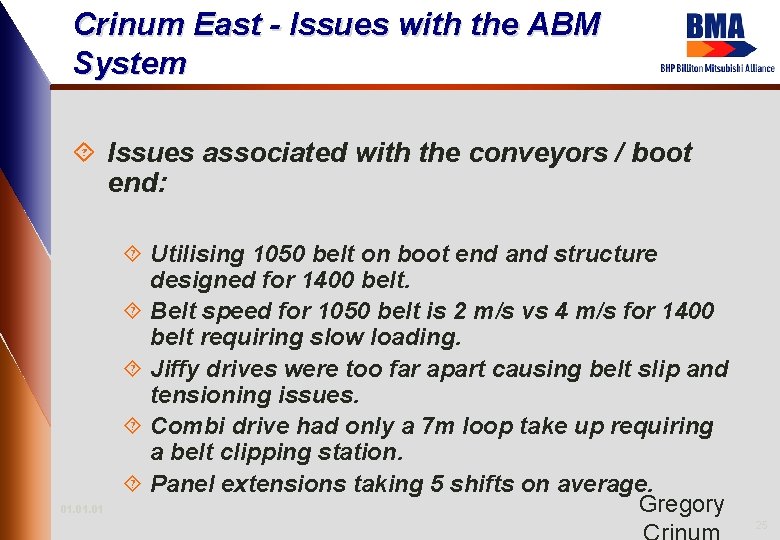
Crinum East - Issues with the ABM System ´ Issues associated with the conveyors / boot end: 01. 01 ´ Utilising 1050 belt on boot end and structure designed for 1400 belt. ´ Belt speed for 1050 belt is 2 m/s vs 4 m/s for 1400 belt requiring slow loading. ´ Jiffy drives were too far apart causing belt slip and tensioning issues. ´ Combi drive had only a 7 m loop take up requiring a belt clipping station. ´ Panel extensions taking 5 shifts on average. Gregory 25
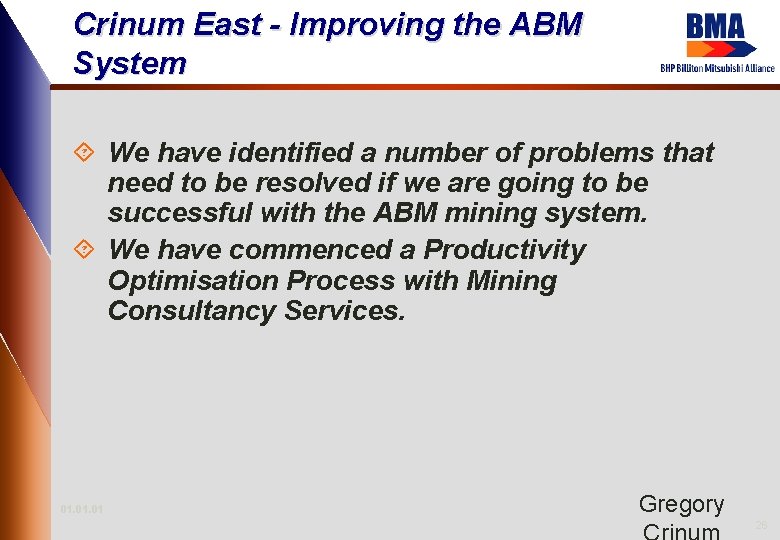
Crinum East - Improving the ABM System ´ We have identified a number of problems that need to be resolved if we are going to be successful with the ABM mining system. ´ We have commenced a Productivity Optimisation Process with Mining Consultancy Services. 01. 01 Gregory 26
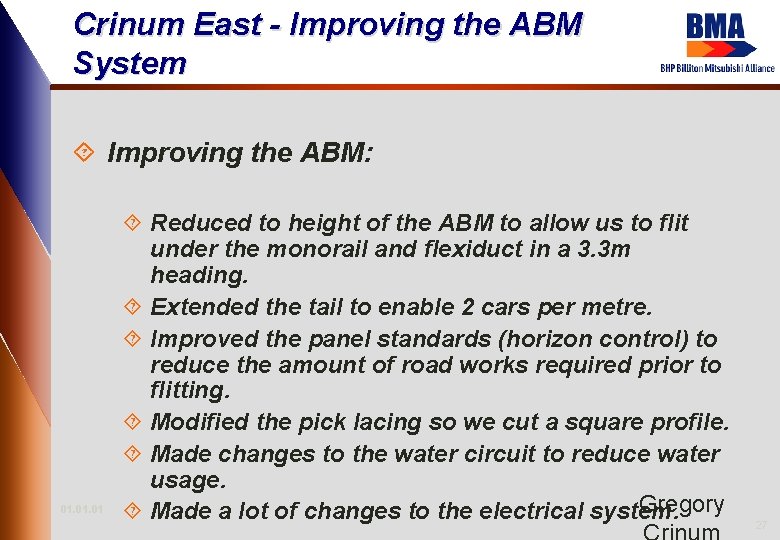
Crinum East - Improving the ABM System ´ Improving the ABM: 01. 01 ´ Reduced to height of the ABM to allow us to flit under the monorail and flexiduct in a 3. 3 m heading. ´ Extended the tail to enable 2 cars per metre. ´ Improved the panel standards (horizon control) to reduce the amount of road works required prior to flitting. ´ Modified the pick lacing so we cut a square profile. ´ Made changes to the water circuit to reduce water usage. Gregory ´ Made a lot of changes to the electrical system. 27
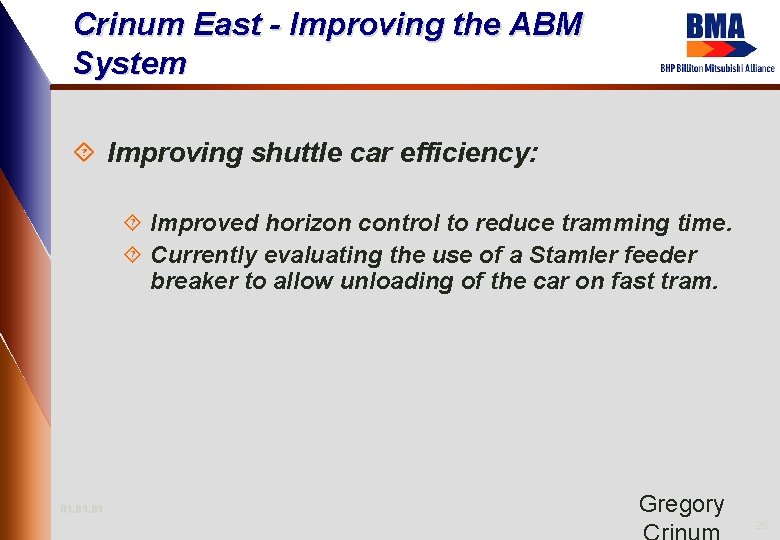
Crinum East - Improving the ABM System ´ Improving shuttle car efficiency: ´ Improved horizon control to reduce tramming time. ´ Currently evaluating the use of a Stamler feeder breaker to allow unloading of the car on fast tram. 01. 01 Gregory 28
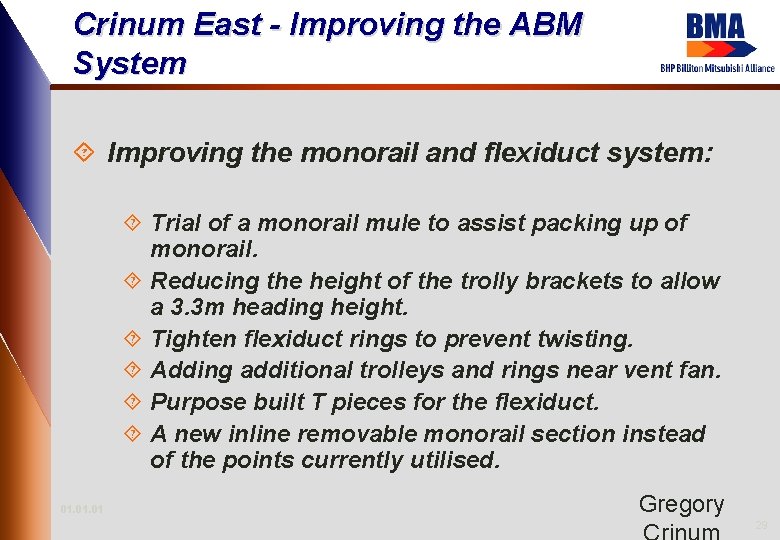
Crinum East - Improving the ABM System ´ Improving the monorail and flexiduct system: ´ Trial of a monorail mule to assist packing up of monorail. ´ Reducing the height of the trolly brackets to allow a 3. 3 m heading height. ´ Tighten flexiduct rings to prevent twisting. ´ Adding additional trolleys and rings near vent fan. ´ Purpose built T pieces for the flexiduct. ´ A new inline removable monorail section instead of the points currently utilised. 01. 01 Gregory 29
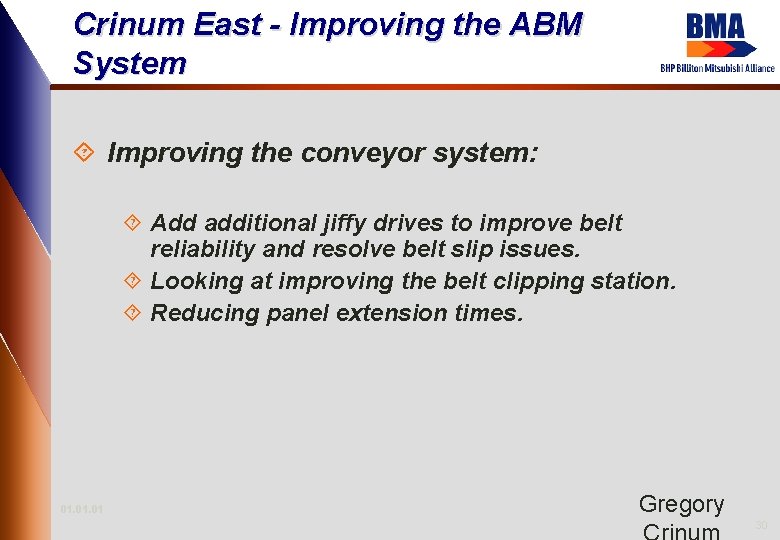
Crinum East - Improving the ABM System ´ Improving the conveyor system: ´ Add additional jiffy drives to improve belt reliability and resolve belt slip issues. ´ Looking at improving the belt clipping station. ´ Reducing panel extension times. 01. 01 Gregory 30
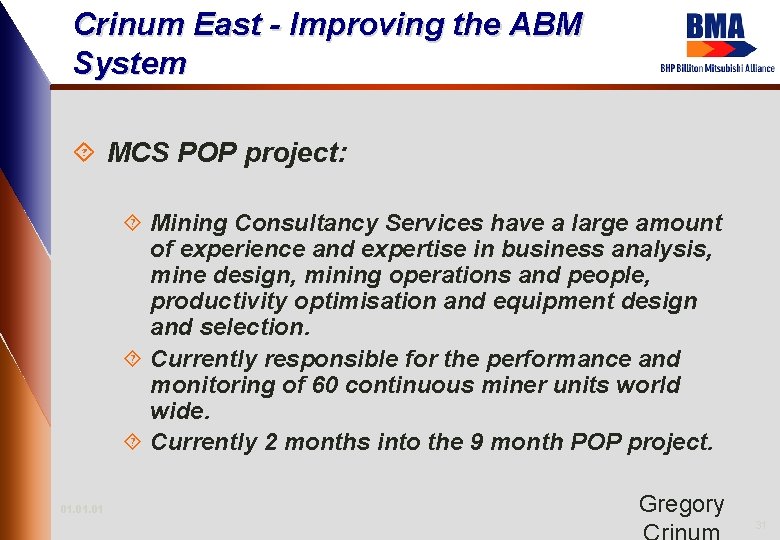
Crinum East - Improving the ABM System ´ MCS POP project: ´ Mining Consultancy Services have a large amount of experience and expertise in business analysis, mine design, mining operations and people, productivity optimisation and equipment design and selection. ´ Currently responsible for the performance and monitoring of 60 continuous miner units world wide. ´ Currently 2 months into the 9 month POP project. 01. 01 Gregory 31
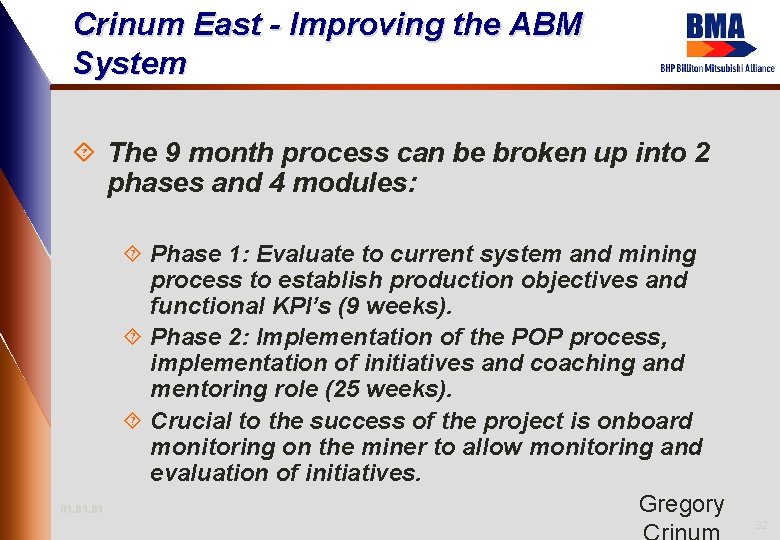
Crinum East - Improving the ABM System ´ The 9 month process can be broken up into 2 phases and 4 modules: 01. 01 ´ Phase 1: Evaluate to current system and mining process to establish production objectives and functional KPI’s (9 weeks). ´ Phase 2: Implementation of the POP process, implementation of initiatives and coaching and mentoring role (25 weeks). ´ Crucial to the success of the project is onboard monitoring on the miner to allow monitoring and evaluation of initiatives. Gregory 32
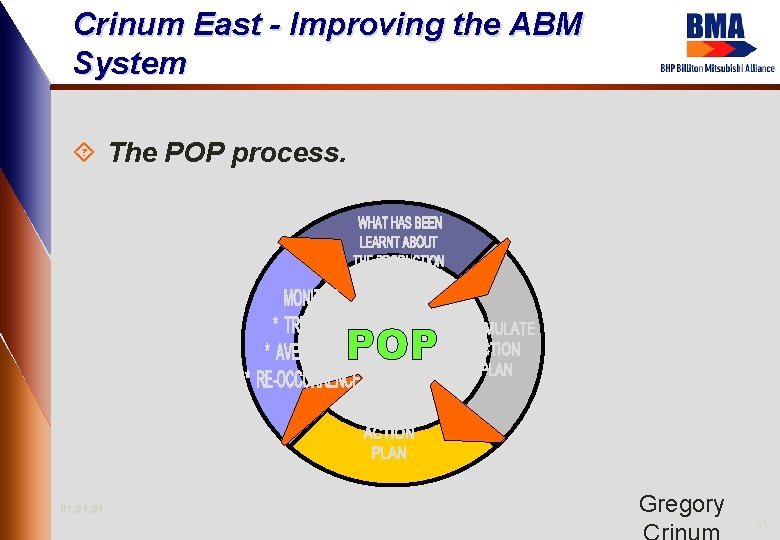
Crinum East - Improving the ABM System ´ The POP process. 01. 01 Gregory 33
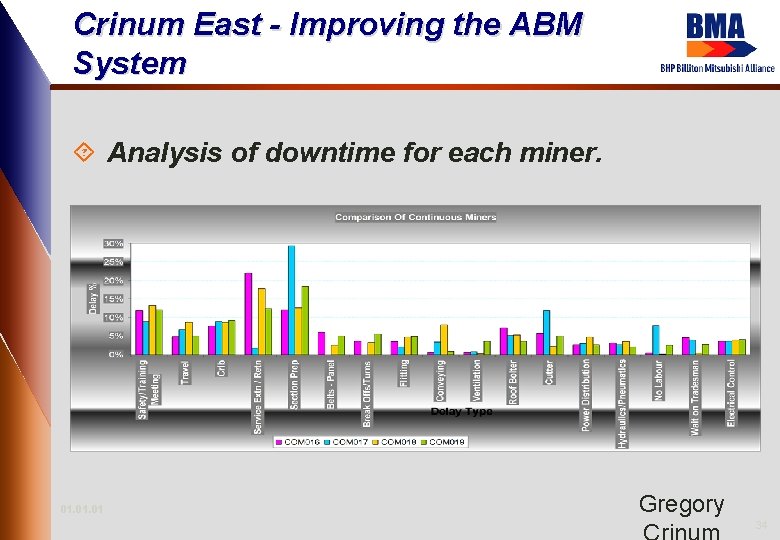
Crinum East - Improving the ABM System ´ Analysis of downtime for each miner. 01. 01 Gregory 34
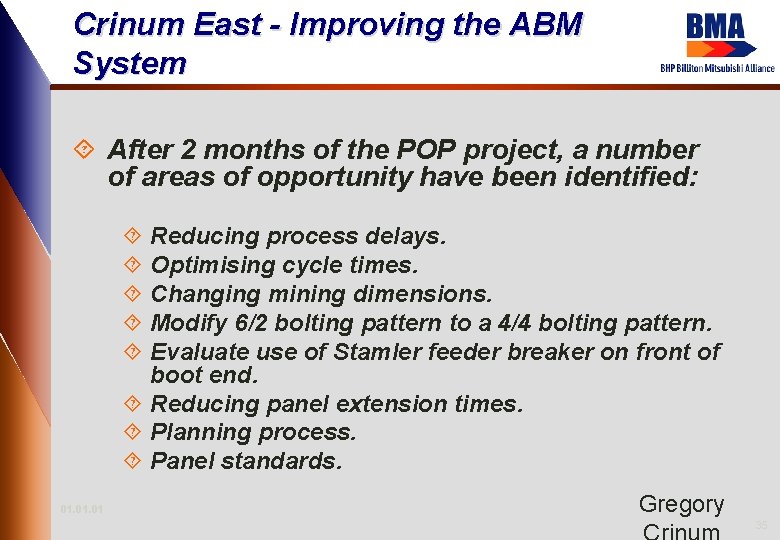
Crinum East - Improving the ABM System ´ After 2 months of the POP project, a number of areas of opportunity have been identified: ´ Reducing process delays. ´ Optimising cycle times. ´ Changing mining dimensions. ´ Modify 6/2 bolting pattern to a 4/4 bolting pattern. ´ Evaluate use of Stamler feeder breaker on front of boot end. ´ Reducing panel extension times. ´ Planning process. ´ Panel standards. 01. 01 Gregory 35
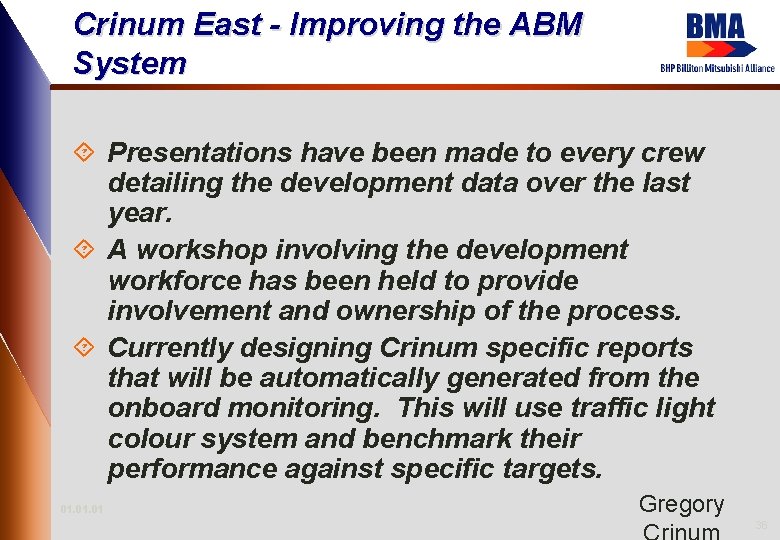
Crinum East - Improving the ABM System ´ Presentations have been made to every crew detailing the development data over the last year. ´ A workshop involving the development workforce has been held to provide involvement and ownership of the process. ´ Currently designing Crinum specific reports that will be automatically generated from the onboard monitoring. This will use traffic light colour system and benchmark their performance against specific targets. 01. 01 Gregory 36
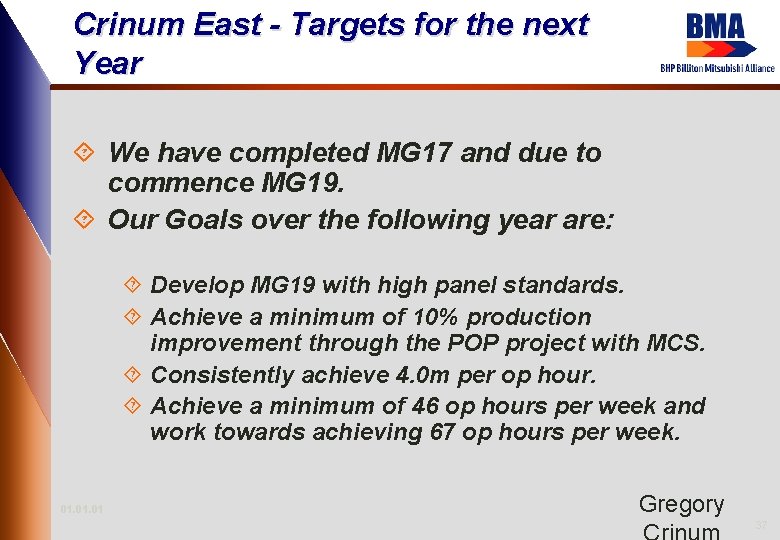
Crinum East - Targets for the next Year ´ We have completed MG 17 and due to commence MG 19. ´ Our Goals over the following year are: ´ Develop MG 19 with high panel standards. ´ Achieve a minimum of 10% production improvement through the POP project with MCS. ´ Consistently achieve 4. 0 m per op hour. ´ Achieve a minimum of 46 op hours per week and work towards achieving 67 op hours per week. 01. 01 Gregory 37
Poland national anthem lyrics
Cscape envisionrv
25 march 2008
2008 2008
Strategy development workshop
Strategy development workshop
Business development workshop
Organizational development workshop
Wavefunction
Arithmetic operators in vbscript
Verilog operators table
Short hand operator
Relational operators
Postulates of quantum mechanics
Mainstring
Relational operators matlab
Postulate of quantum mechanics
Operators in quantum mechanics
Pl/sql operators
Strips planning
Pest control operators of california
Perl assignment operators
Operator formalism in quantum mechanics
The three logic operators in java are:
Microsoft excel logical functions
Matlab bilkent
Logical operators in boolean algebra
Logical operators quiz
Rational and logical operators
Prolog arithmetic operators
Boolean algebra java
Percentage fraction table
Verilog data types and operators
Compound assignment operator
Operators in quantum mechanics
Arithmetic operators
Matlab math operators
Precedence of operators in python