University of Huddersfield Centre for Precision Technologies HILHCUK
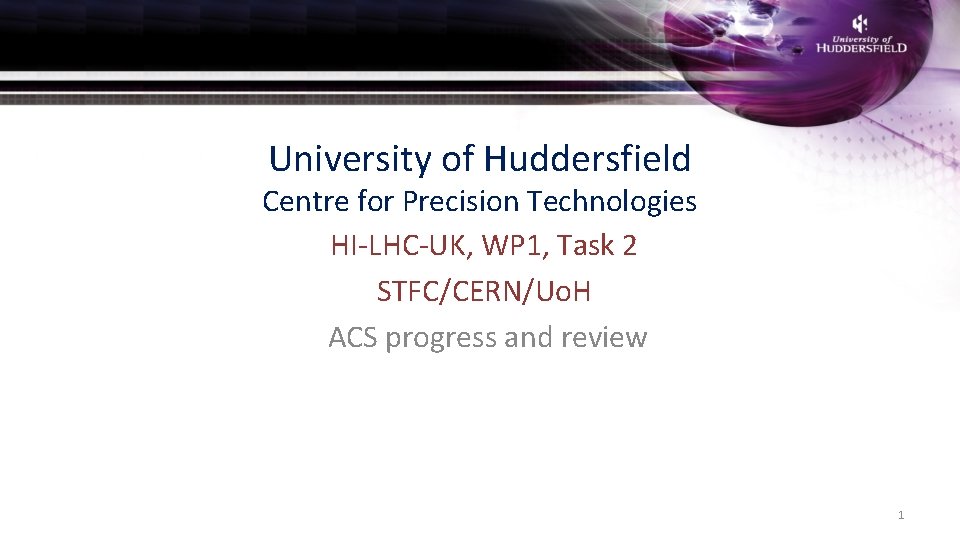
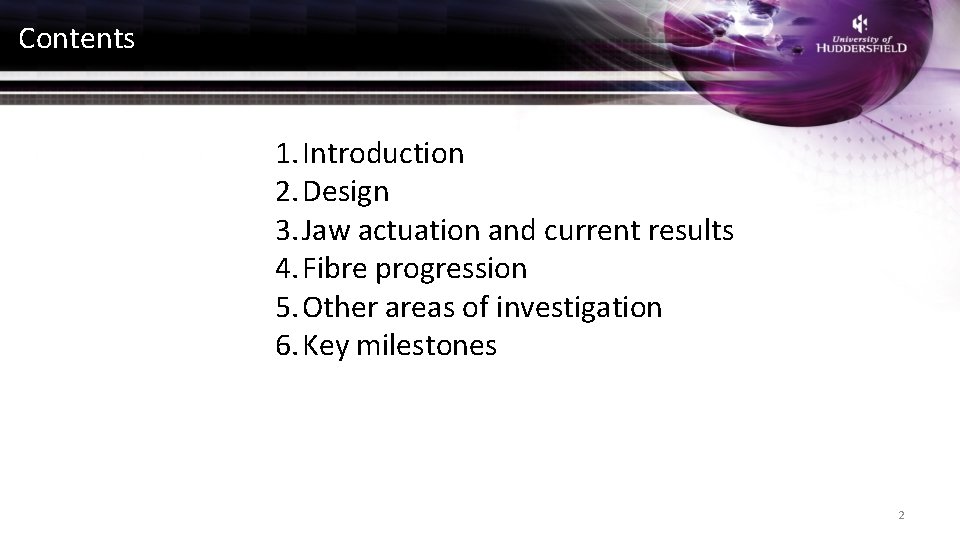
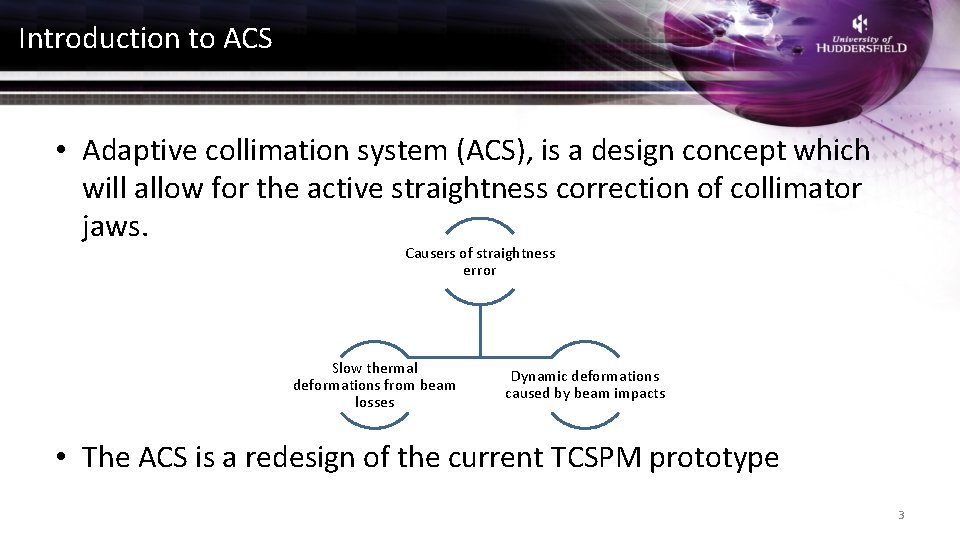
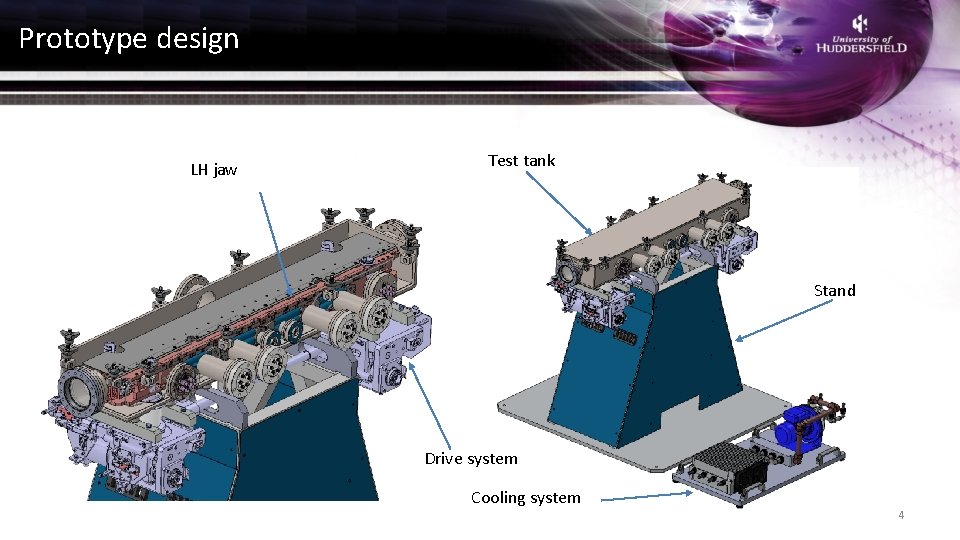
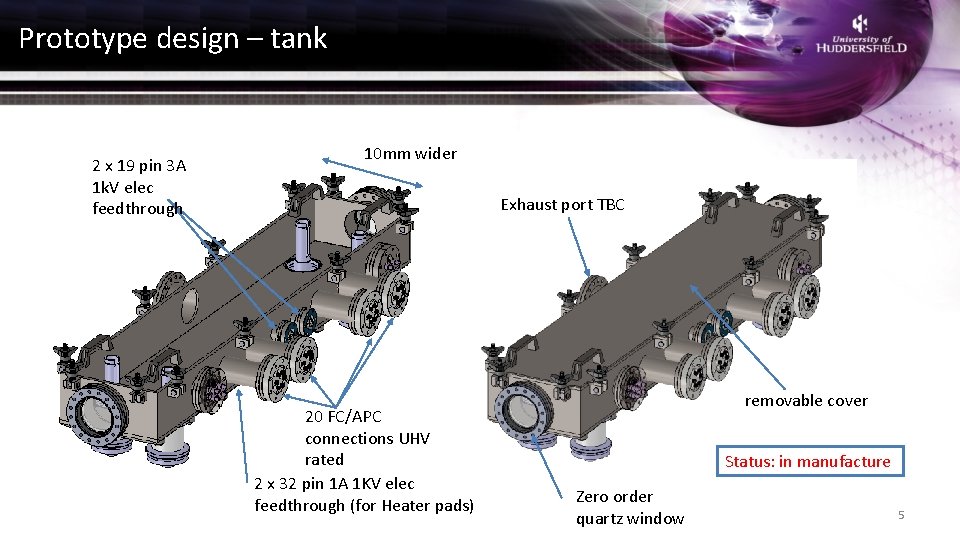
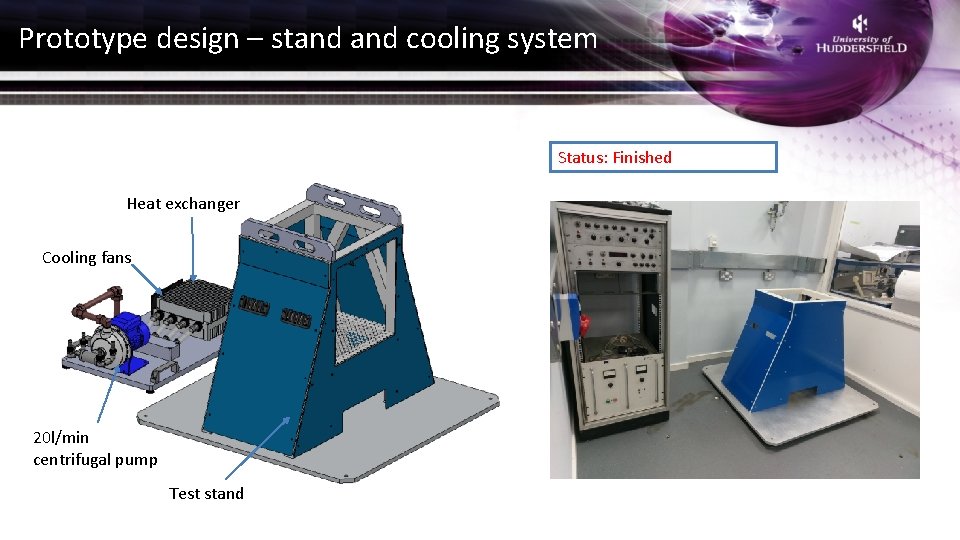
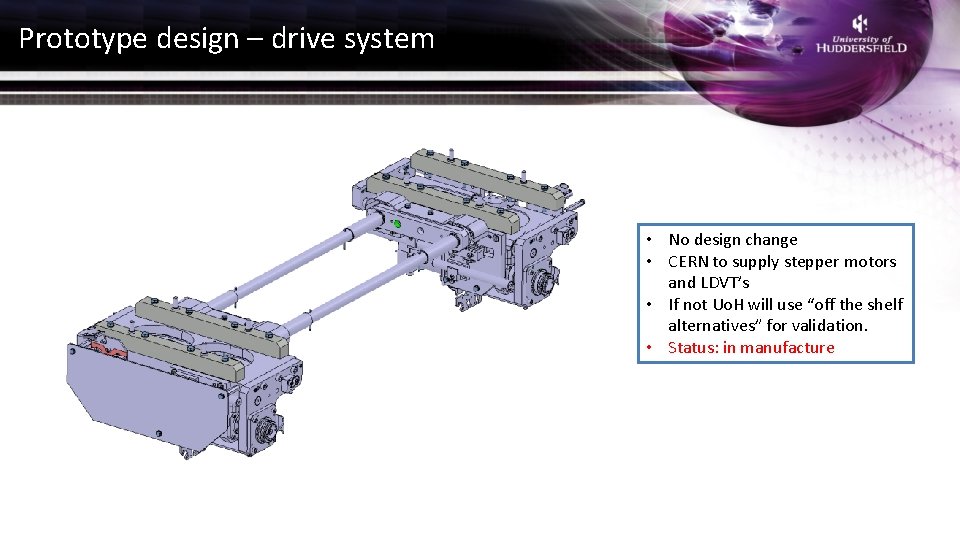
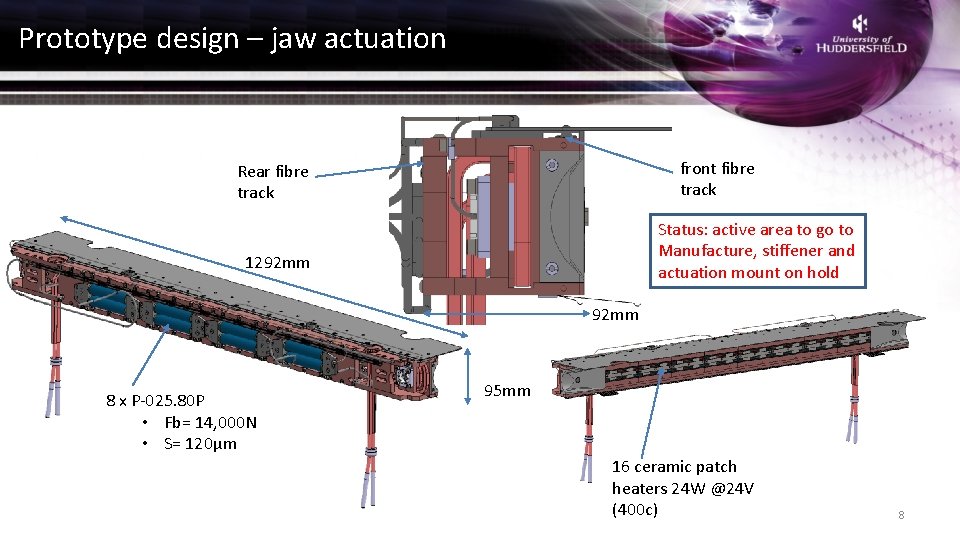
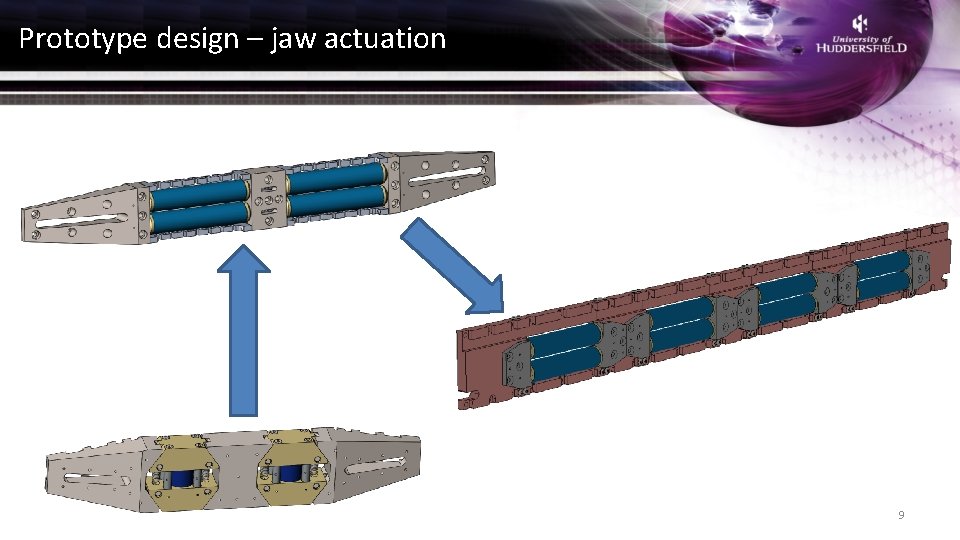
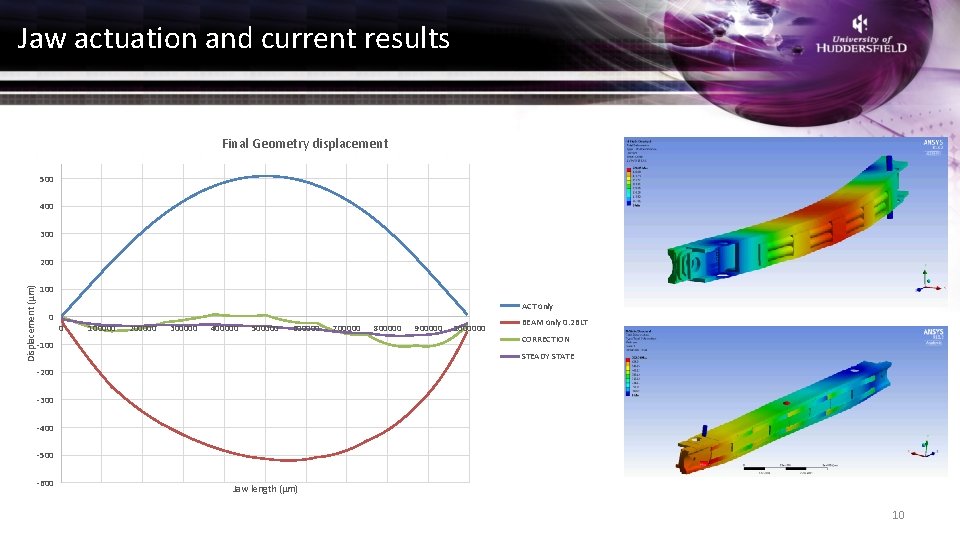
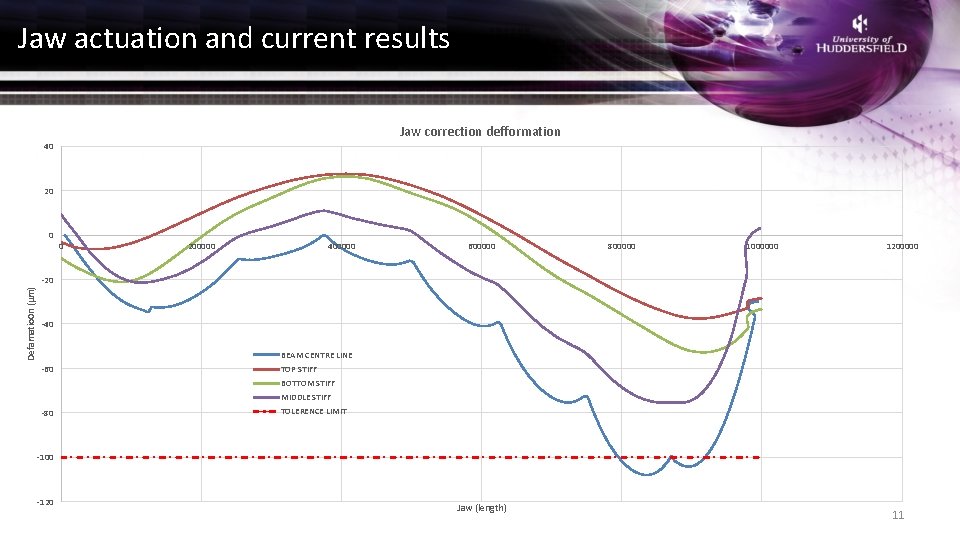
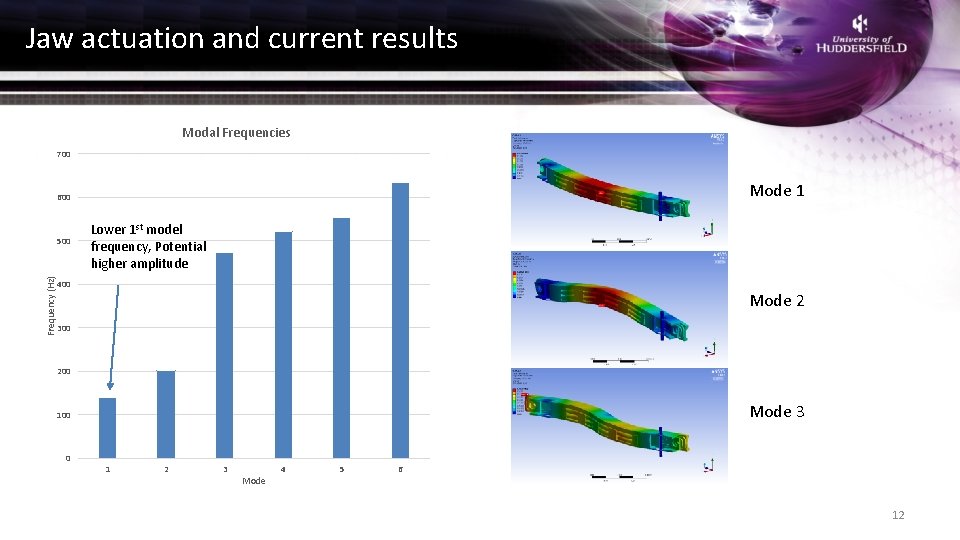
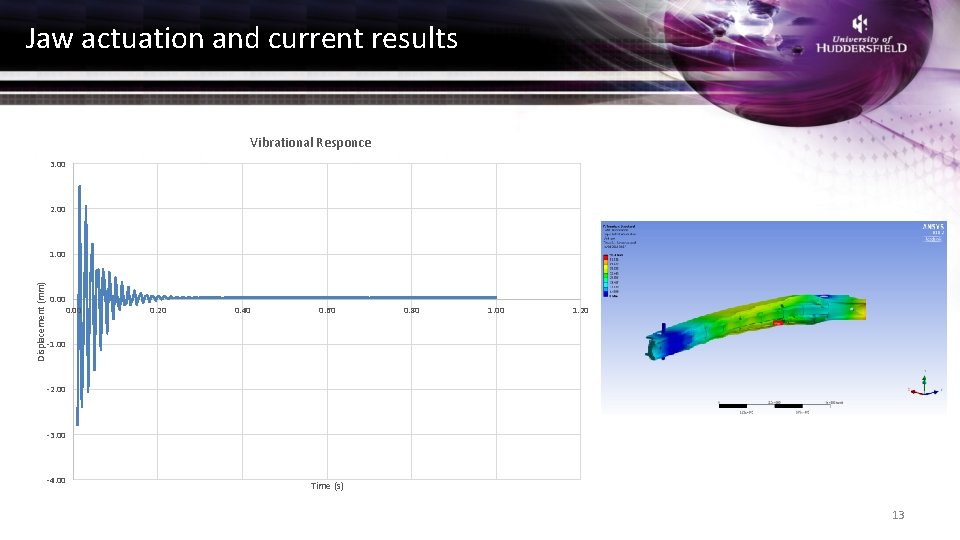
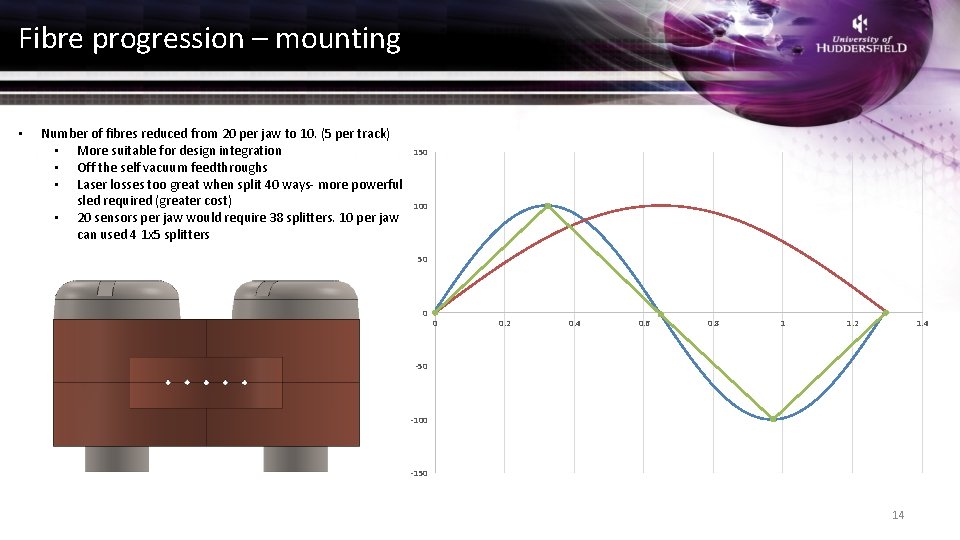
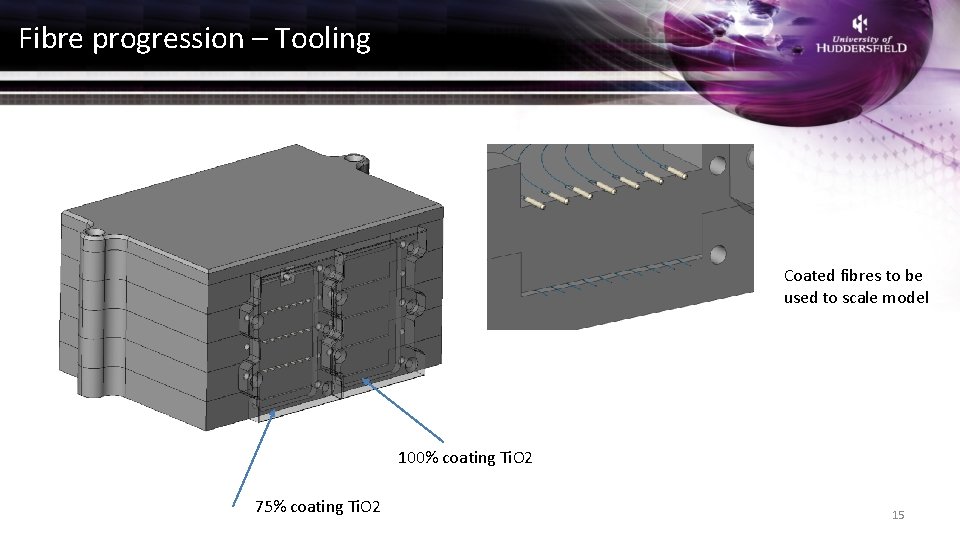
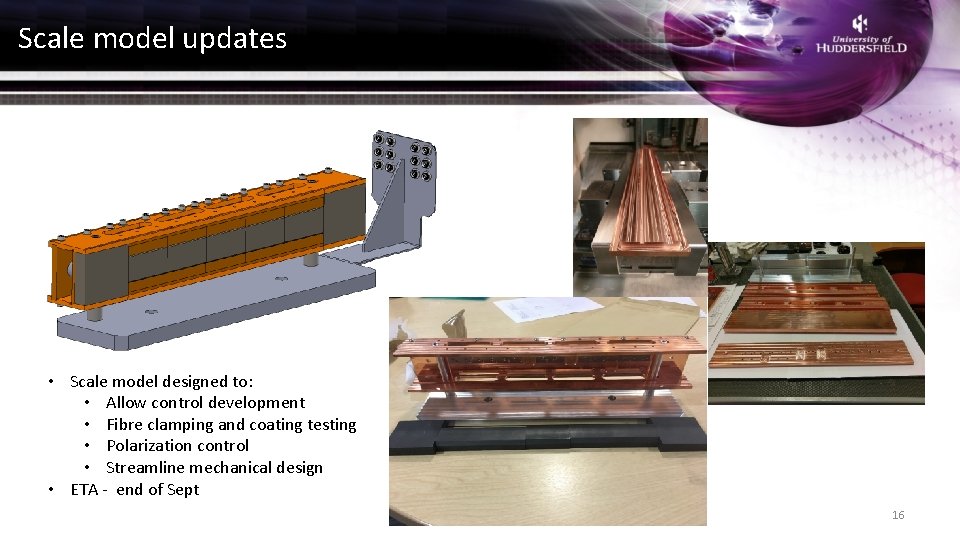
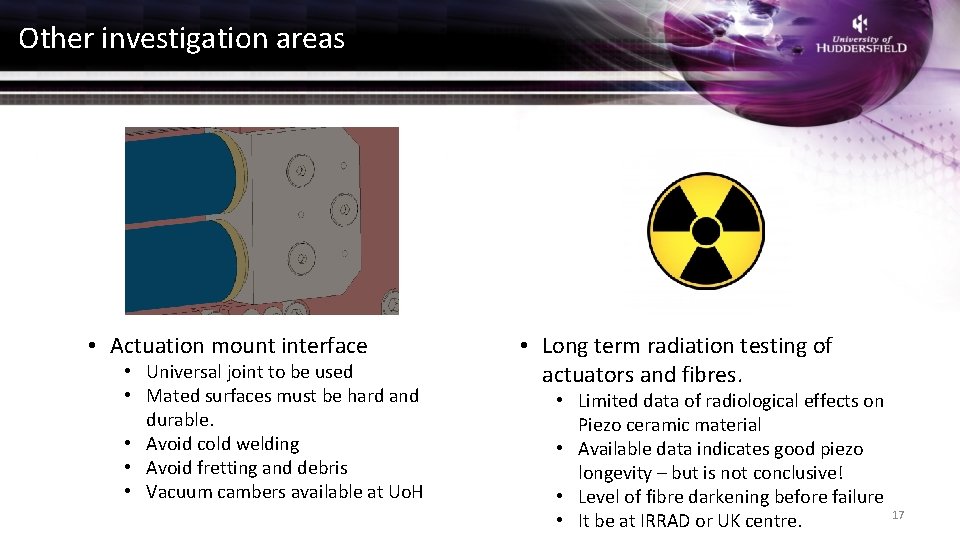
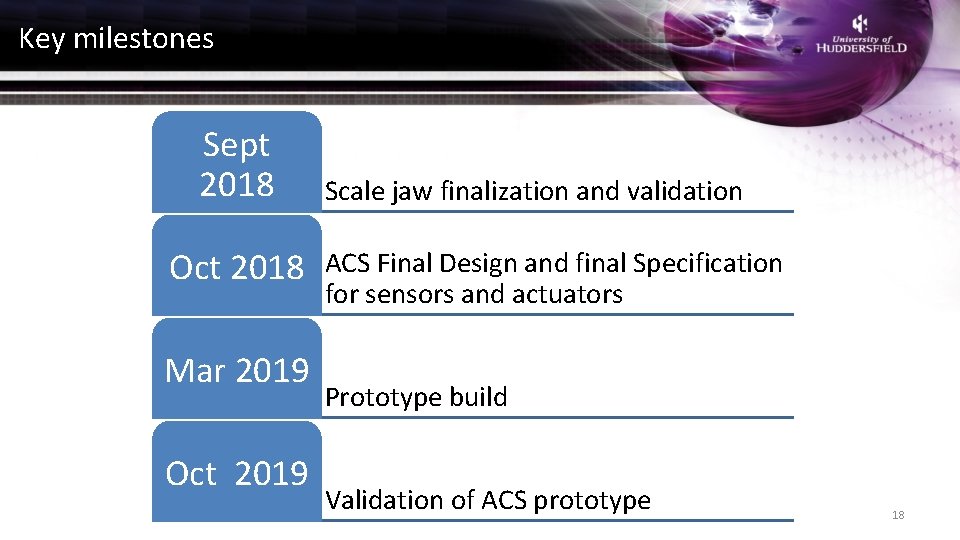
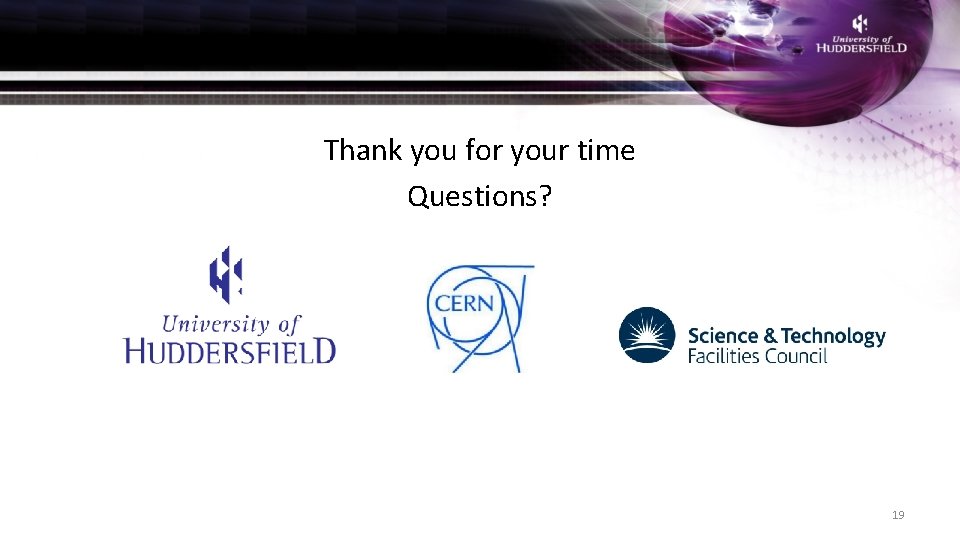
- Slides: 19
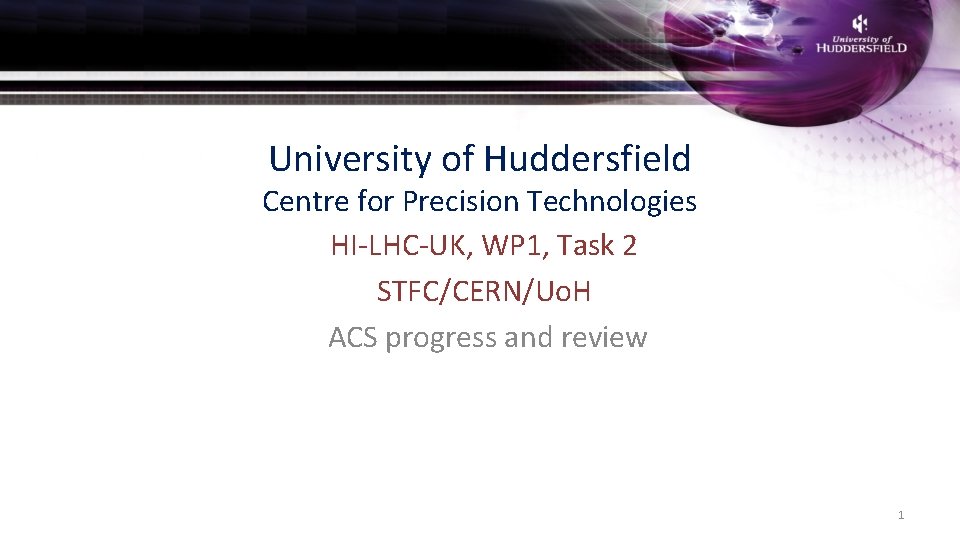
University of Huddersfield Centre for Precision Technologies HI-LHC-UK, WP 1, Task 2 STFC/CERN/Uo. H ACS progress and review 1
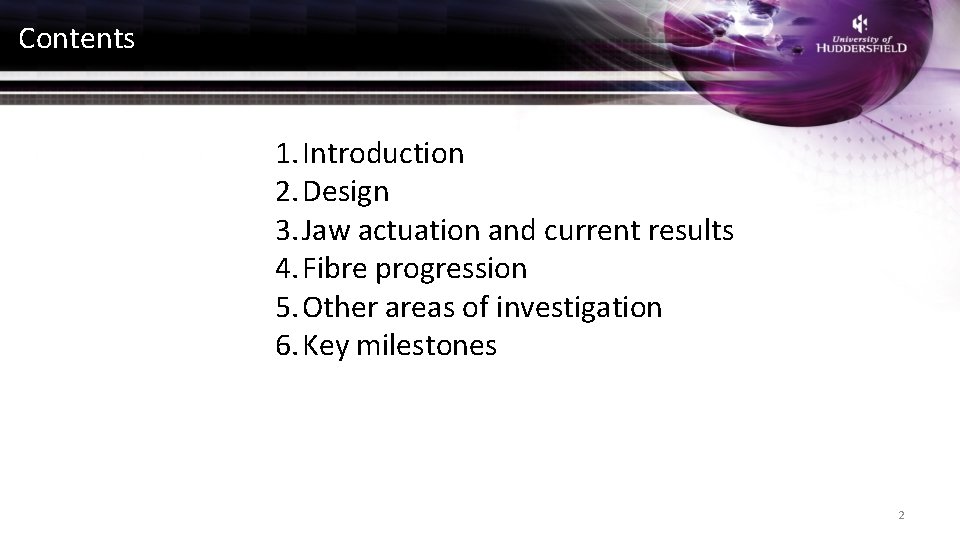
Contents 1. Introduction 2. Design 3. Jaw actuation and current results 4. Fibre progression 5. Other areas of investigation 6. Key milestones 2
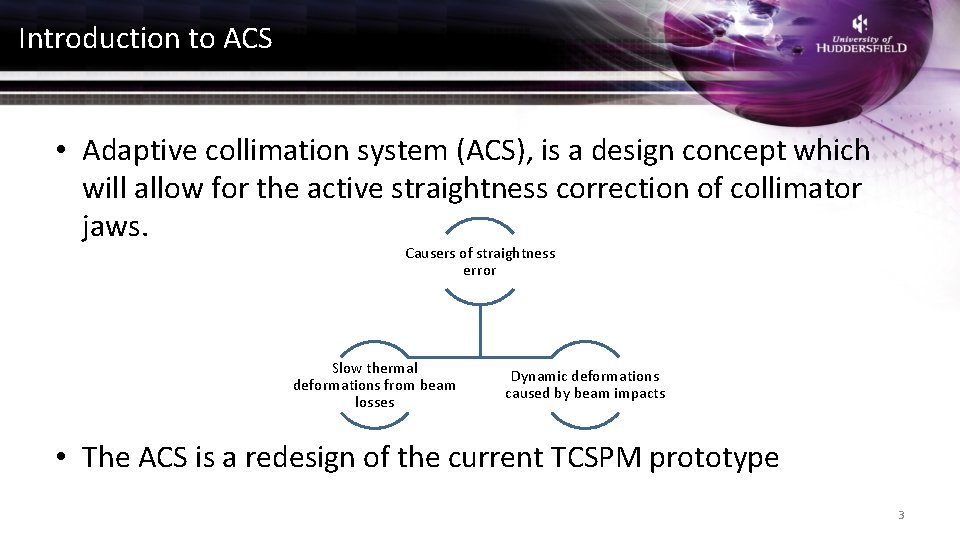
Introduction to ACS • Adaptive collimation system (ACS), is a design concept which will allow for the active straightness correction of collimator jaws. Causers of straightness error Slow thermal deformations from beam losses Dynamic deformations caused by beam impacts • The ACS is a redesign of the current TCSPM prototype 3
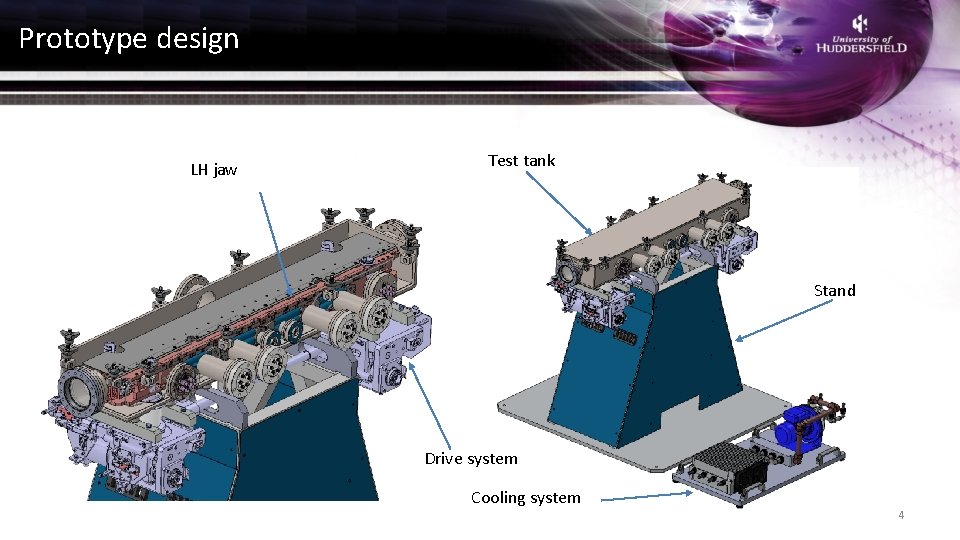
Prototype design LH jaw Test tank Stand Drive system Cooling system 4
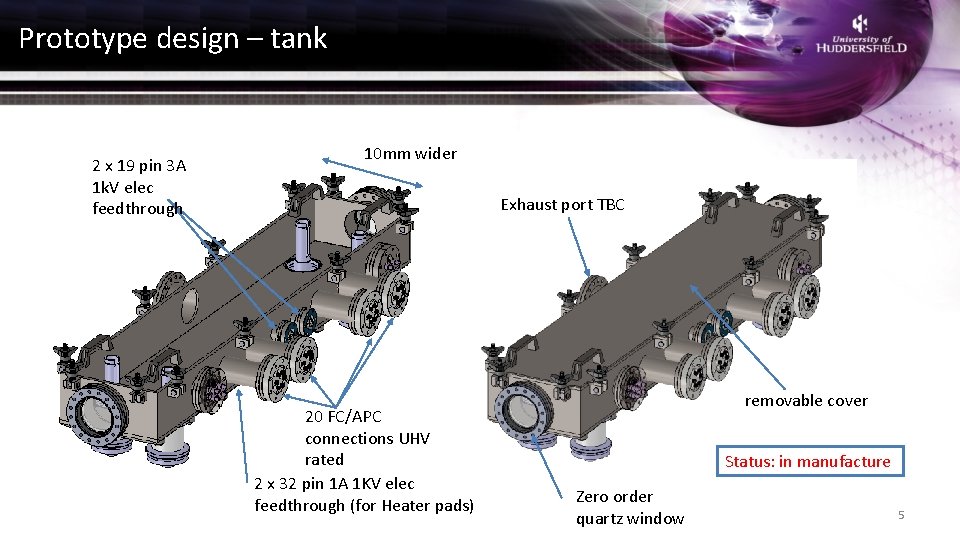
Prototype design – tank 2 x 19 pin 3 A 1 k. V elec feedthrough 10 mm wider Exhaust port TBC 20 FC/APC connections UHV rated 2 x 32 pin 1 A 1 KV elec feedthrough (for Heater pads) removable cover Status: in manufacture Zero order quartz window 5
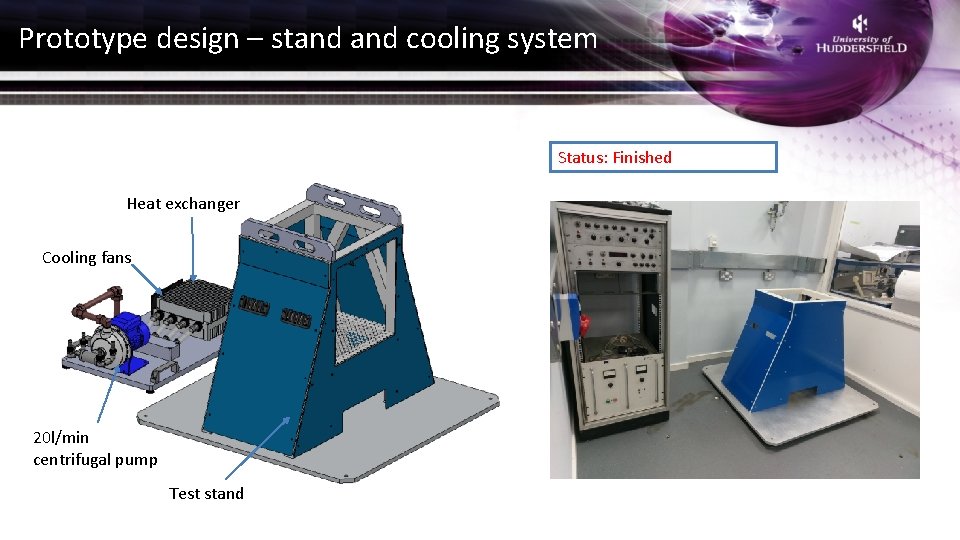
Prototype design – stand cooling system Status: Finished Heat exchanger Cooling fans 20 l/min centrifugal pump Test stand
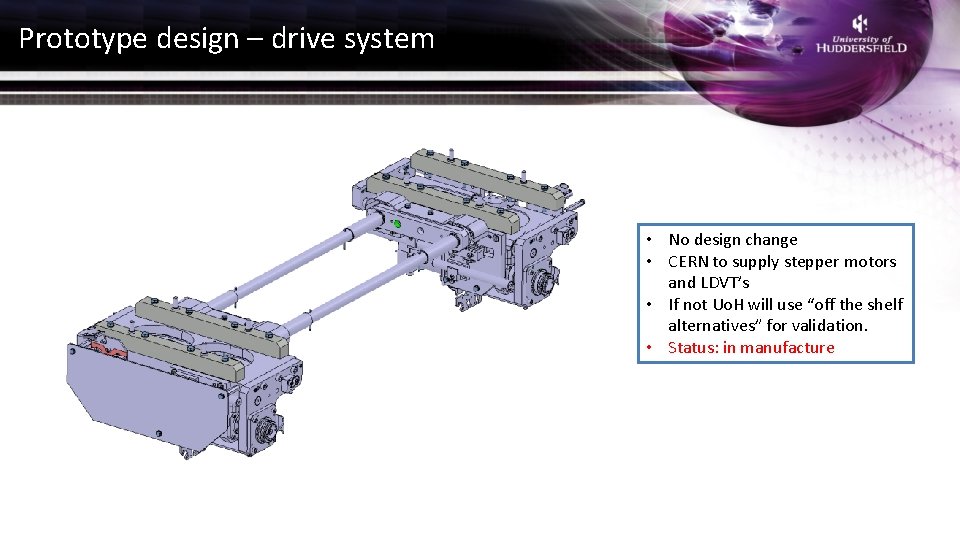
Prototype design – drive system • No design change • CERN to supply stepper motors and LDVT’s • If not Uo. H will use “off the shelf alternatives” for validation. • Status: in manufacture
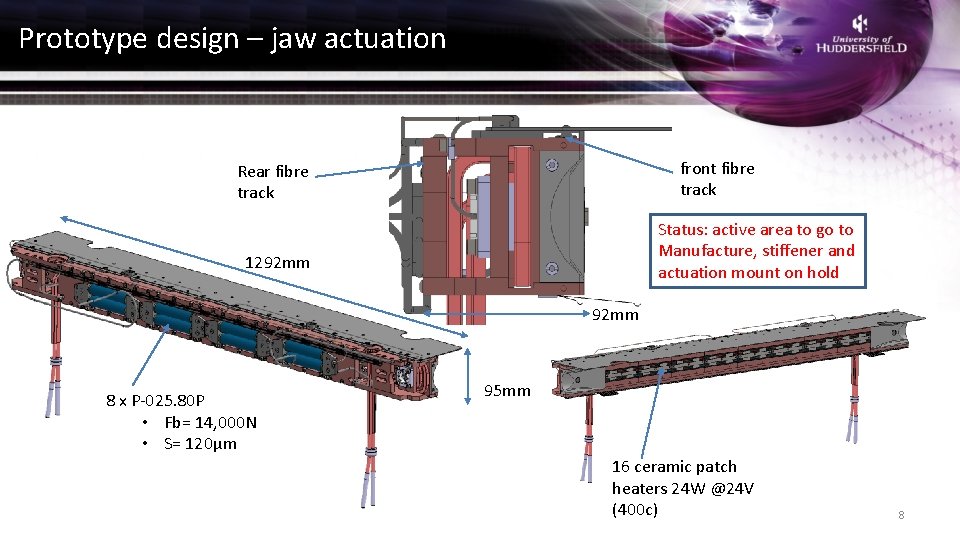
Prototype design – jaw actuation front fibre track Rear fibre track Status: active area to go to Manufacture, stiffener and actuation mount on hold 1292 mm 8 x P-025. 80 P • Fb= 14, 000 N • S= 120µm 95 mm 16 ceramic patch heaters 24 W @24 V (400 c) 8
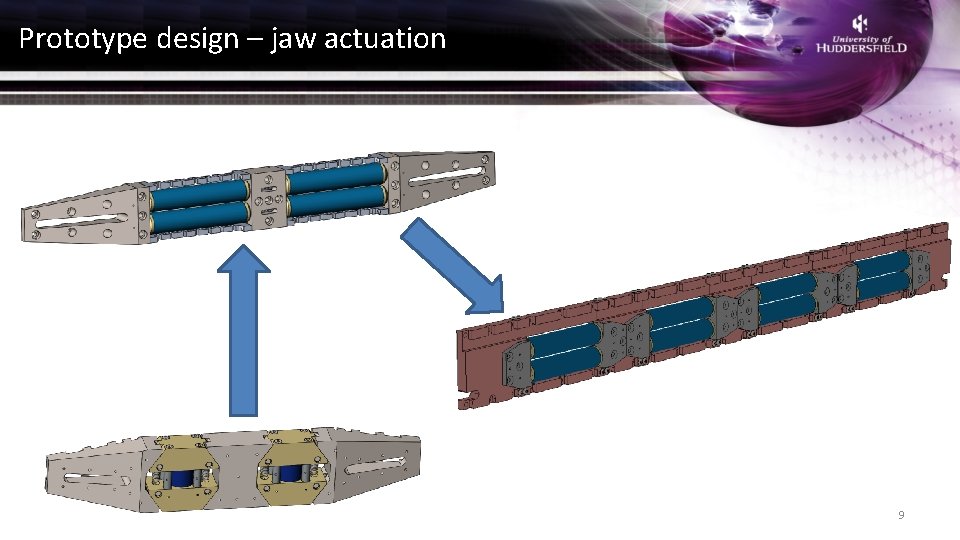
Prototype design – jaw actuation 9
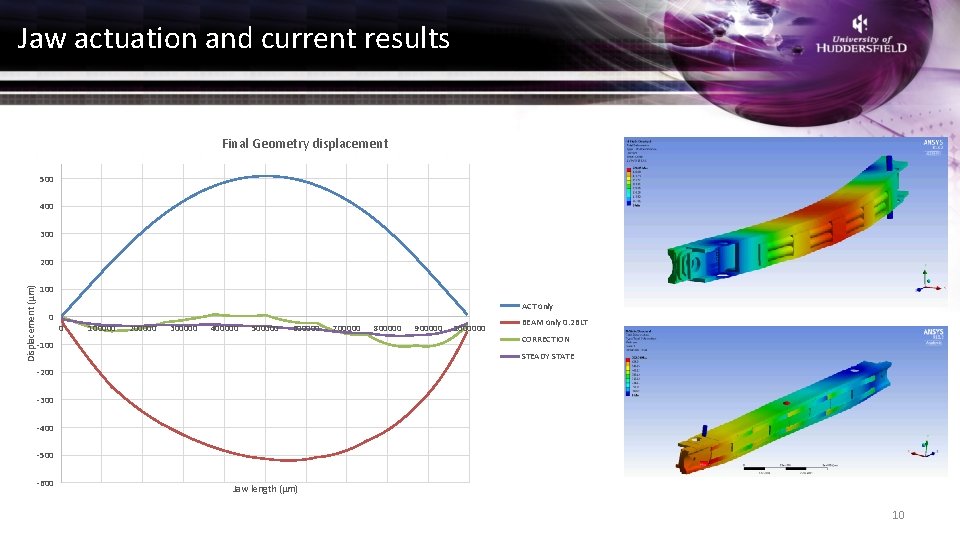
Jaw actuation and current results Final Geometry displacement 500 400 300 Displacement (µm) 200 100 ACT only 0 0 100000 200000 300000 400000 500000 600000 700000 800000 900000 1000000 BEAM only 0. 2 BLT CORRECTION -100 STEADY STATE -200 -300 -400 -500 -600 Jaw length (µm) 10
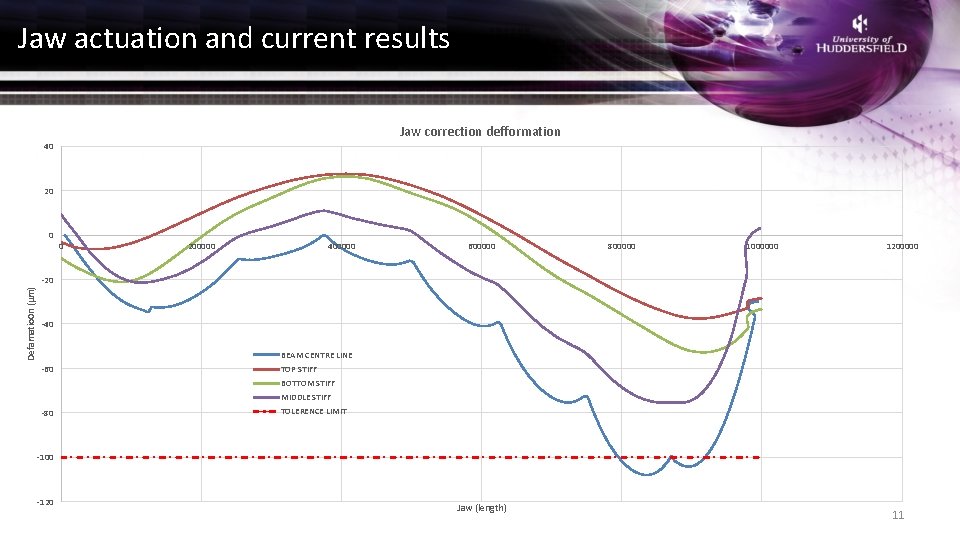
Jaw actuation and current results Jaw correction defformation 40 20 0 0 200000 400000 600000 800000 1000000 1200000 Defamatio 0 n (µm) -20 -40 BEAM CENTRE LINE -60 TOP STIFF BOTTOM STIFF MIDDLE STIFF -80 TOLERENCE LIMIT -100 -120 Jaw (length) 11
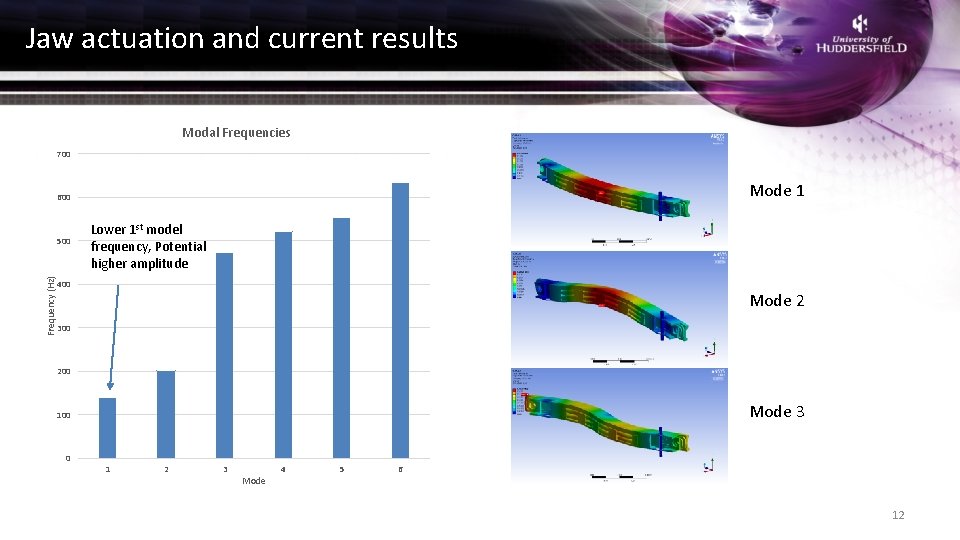
Jaw actuation and current results Modal Frequencies 700 Mode 1 600 Frequency (Hz) 500 Lower 1 st model frequency, Potential higher amplitude 400 Mode 2 300 200 Mode 3 100 0 1 2 3 Mode 4 5 6 12
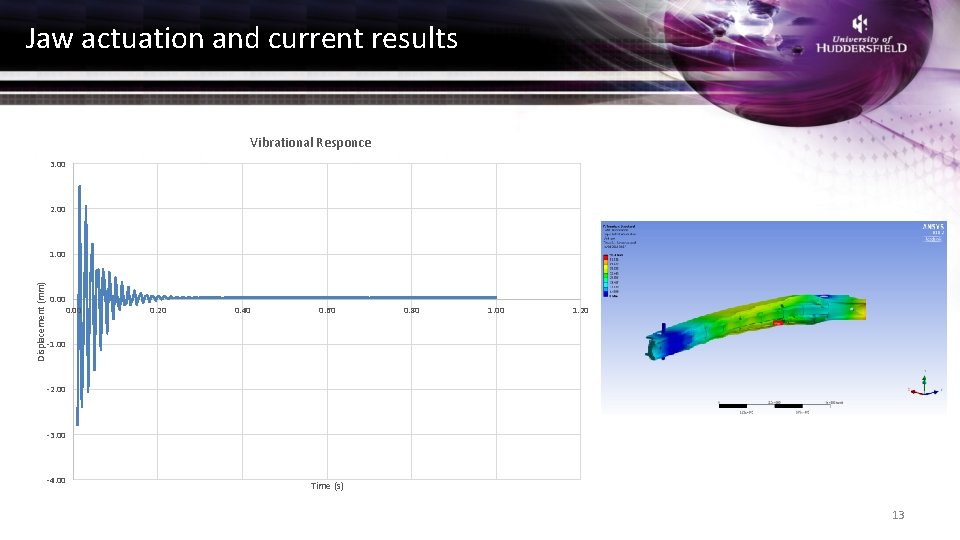
Jaw actuation and current results Vibrational Responce 3. 00 2. 00 Displacement (mm) 1. 00 0. 20 0. 40 0. 60 0. 80 1. 00 1. 20 -1. 00 -2. 00 -3. 00 -4. 00 Time (s) 13
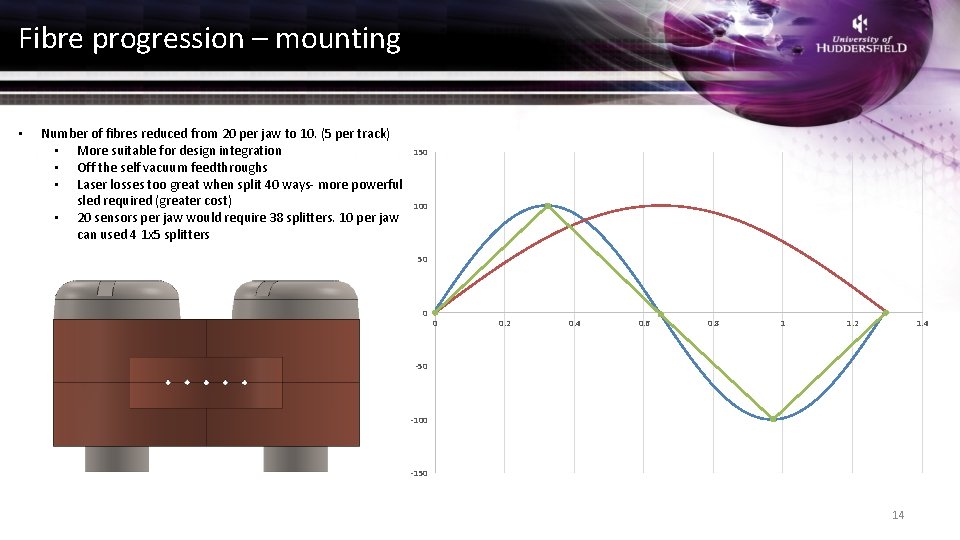
Fibre progression – mounting • Number of fibres reduced from 20 per jaw to 10. (5 per track) • More suitable for design integration • Off the self vacuum feedthroughs • Laser losses too great when split 40 ways- more powerful sled required (greater cost) • 20 sensors per jaw would require 38 splitters. 10 per jaw can used 4 1 x 5 splitters 150 100 50 0 0 0. 2 0. 4 0. 6 0. 8 1 1. 2 1. 4 -50 -100 -150 14
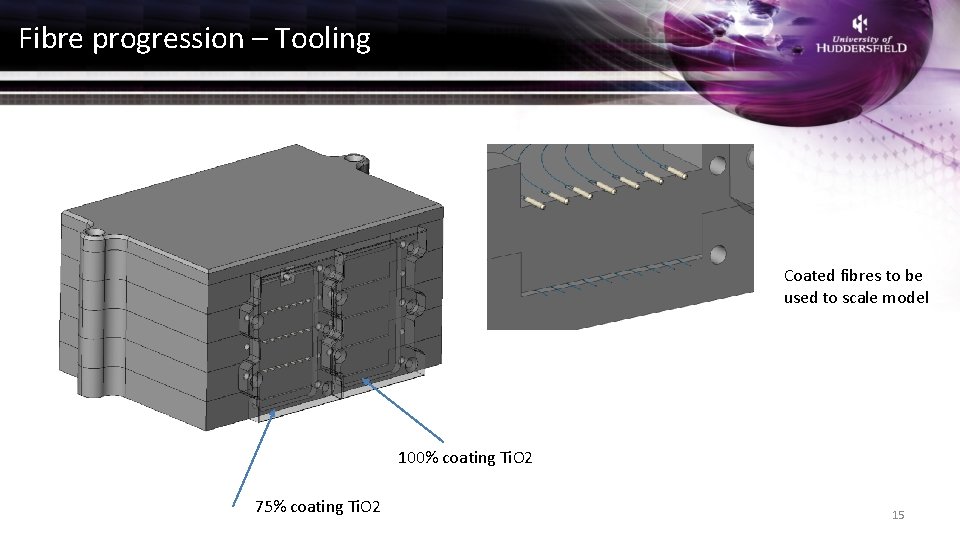
Fibre progression – Tooling Coated fibres to be used to scale model 100% coating Ti. O 2 75% coating Ti. O 2 15
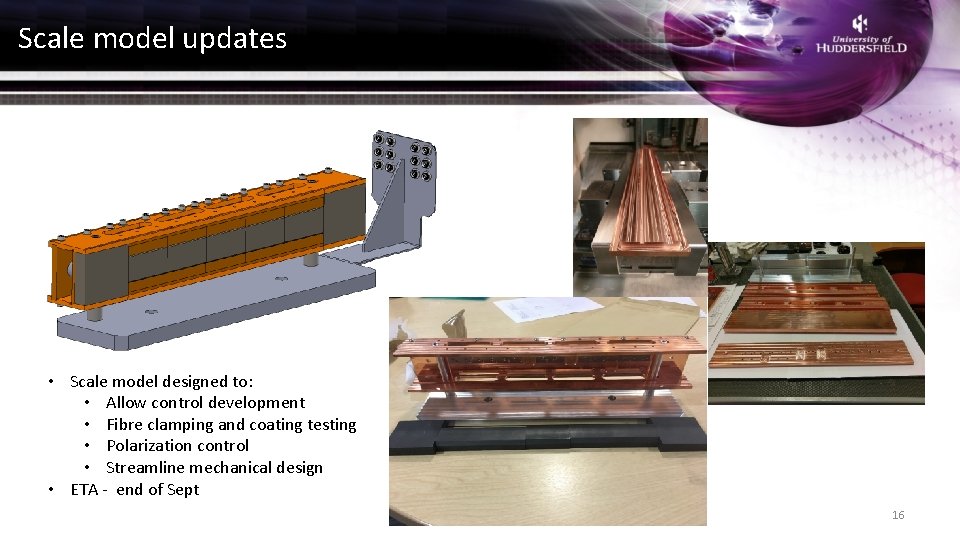
Scale model updates • Scale model designed to: • Allow control development • Fibre clamping and coating testing • Polarization control • Streamline mechanical design • ETA - end of Sept 16
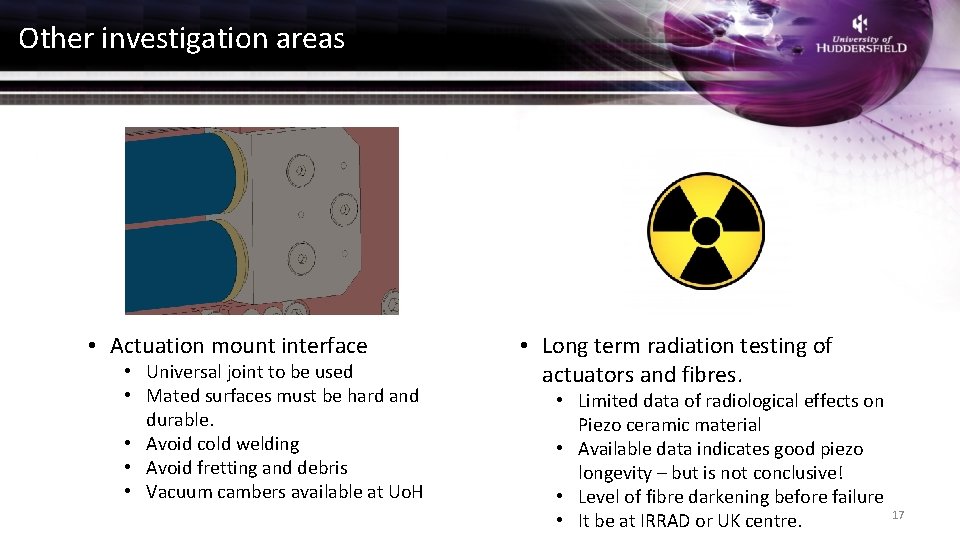
Other investigation areas • Actuation mount interface • Universal joint to be used • Mated surfaces must be hard and durable. • Avoid cold welding • Avoid fretting and debris • Vacuum cambers available at Uo. H • Long term radiation testing of actuators and fibres. • Limited data of radiological effects on Piezo ceramic material • Available data indicates good piezo longevity – but is not conclusive! • Level of fibre darkening before failure • It be at IRRAD or UK centre. 17
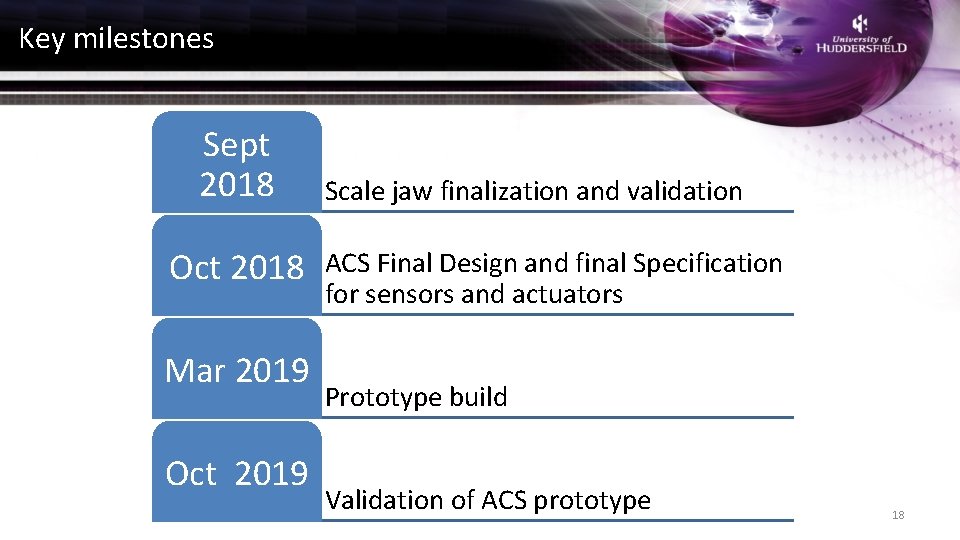
Key milestones Sept 2018 Oct 2018 Mar 2019 Oct 2019 Scale jaw finalization and validation ACS Final Design and final Specification for sensors and actuators Prototype build Validation of ACS prototype 18
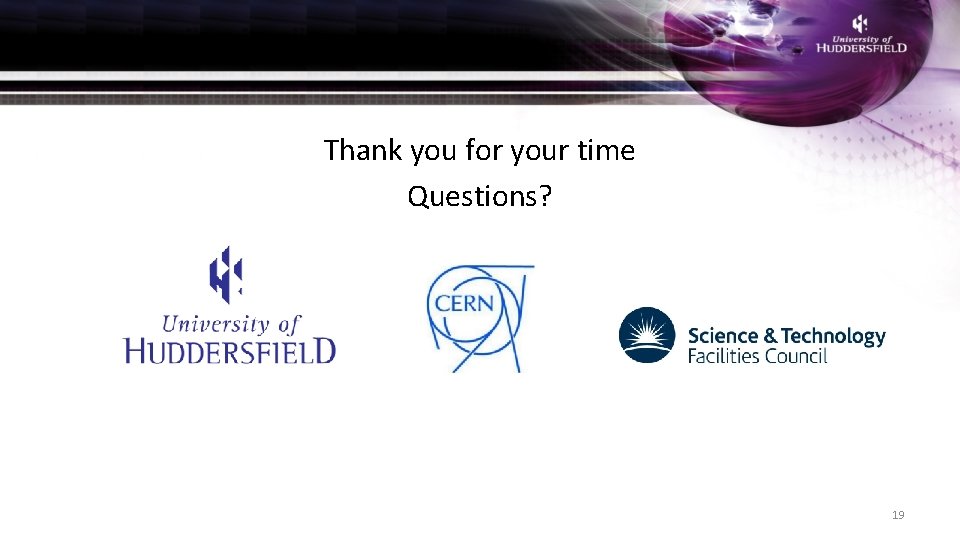
Thank you for your time Questions? 19
Example of a non-precision measuring instrument
Precision and semi precision attachments
Negatif sayıların binary gösterimi
01226 209609
Architectural design in huddersfield
Keyword research huddersfield
Apa referencing huddersfield
Castle hill school huddersfield
Handelsbanken huddersfield
Ptclms
Centroid formula
How to find centre of gravity
Tashkent university of information technologies
Msuft
Ivf maribor
Clarivites impact factor
Ontario university application center
Ljubljana university medical centre
Journey pathway
Fspos