Towards the Enhancement of Aircraft Cargo Compartment Fire
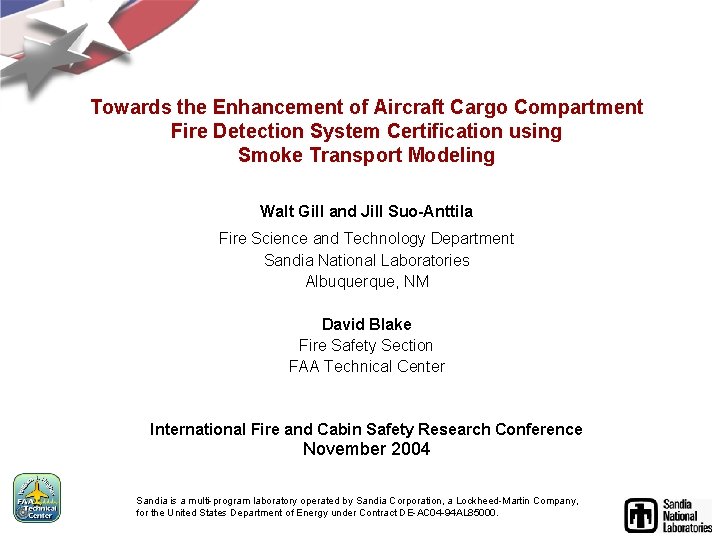
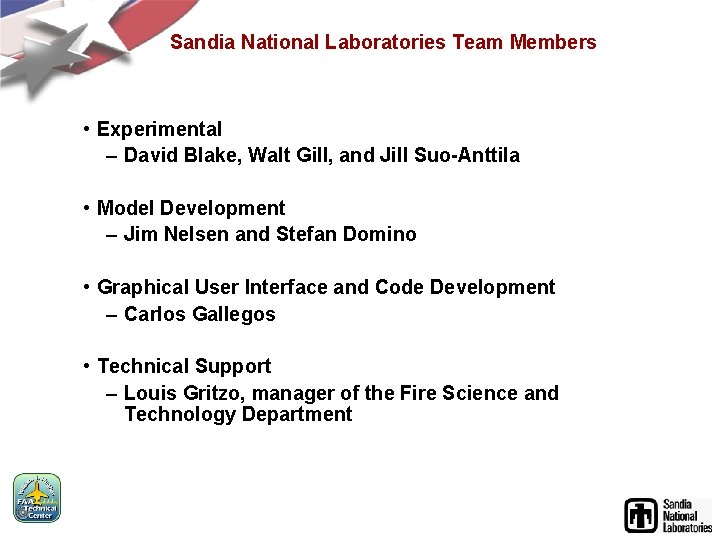
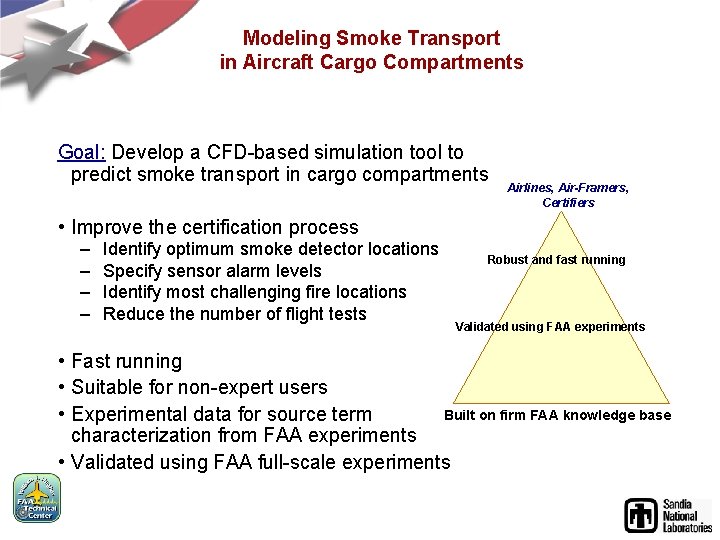
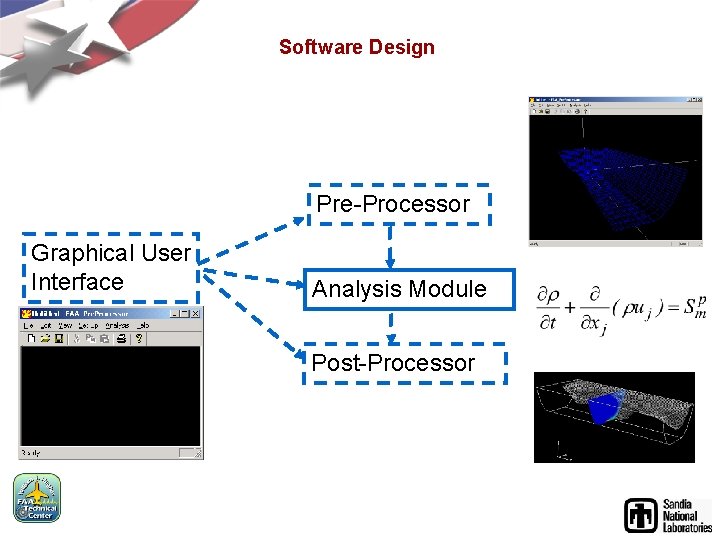
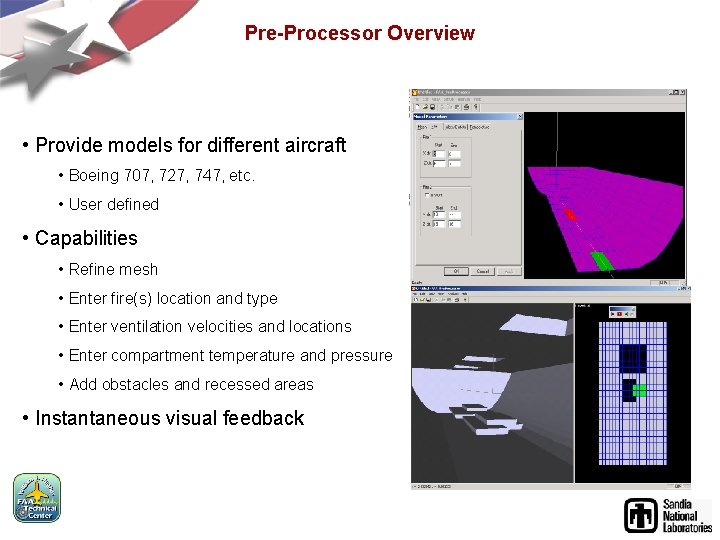
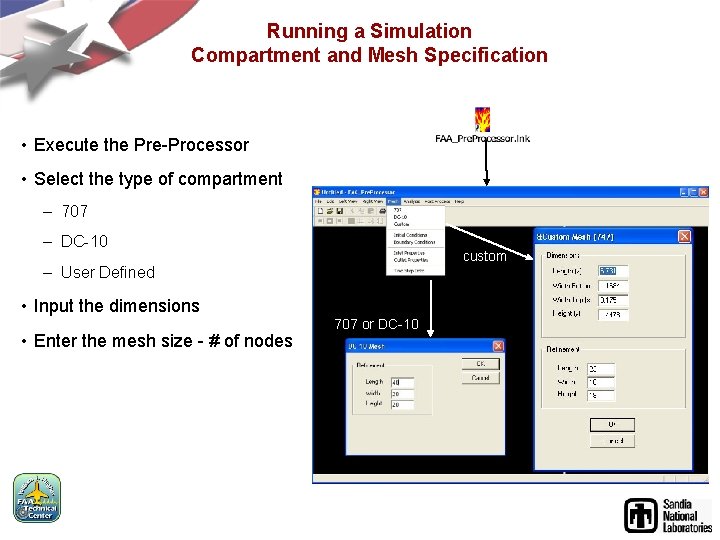
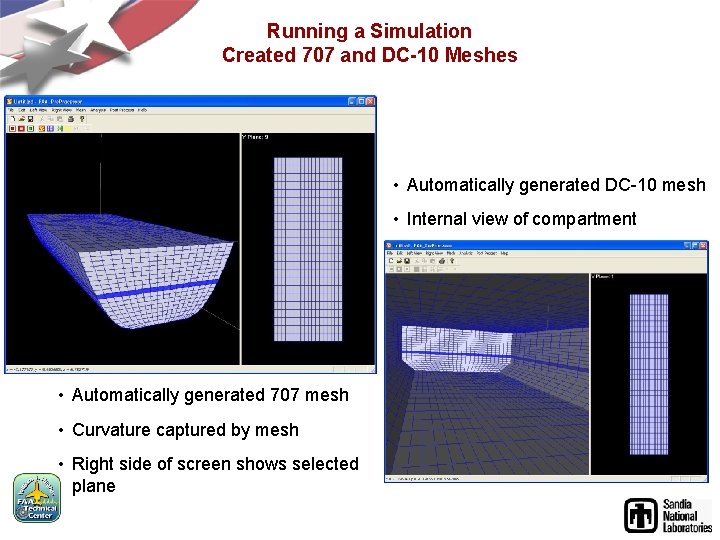
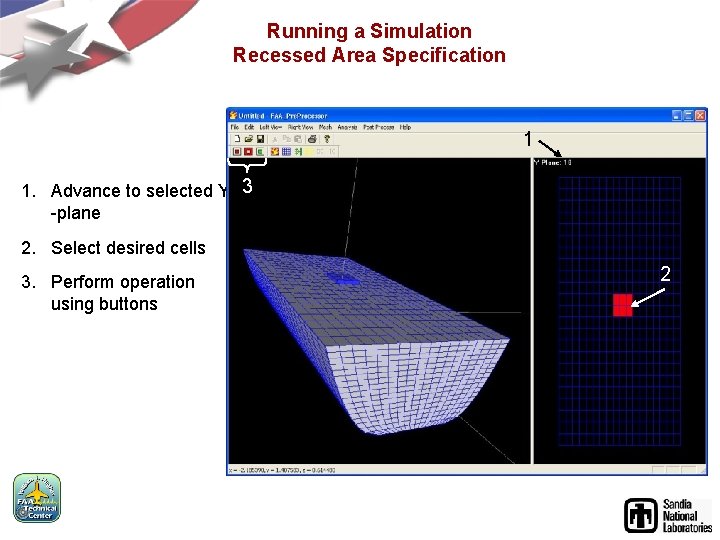
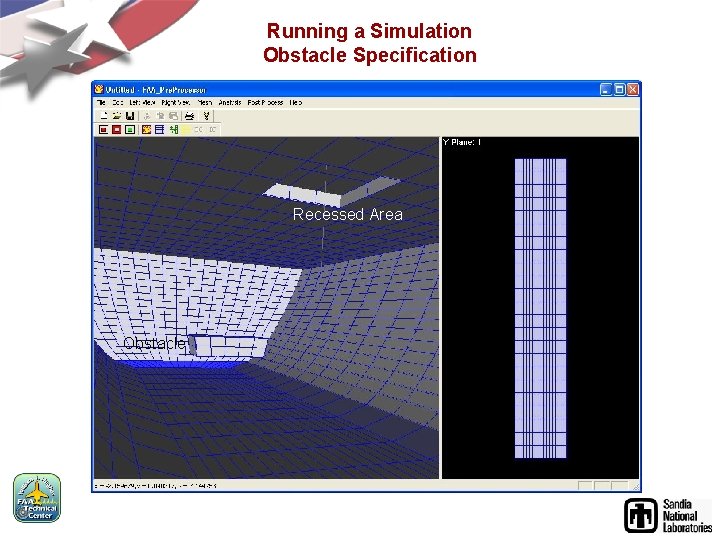
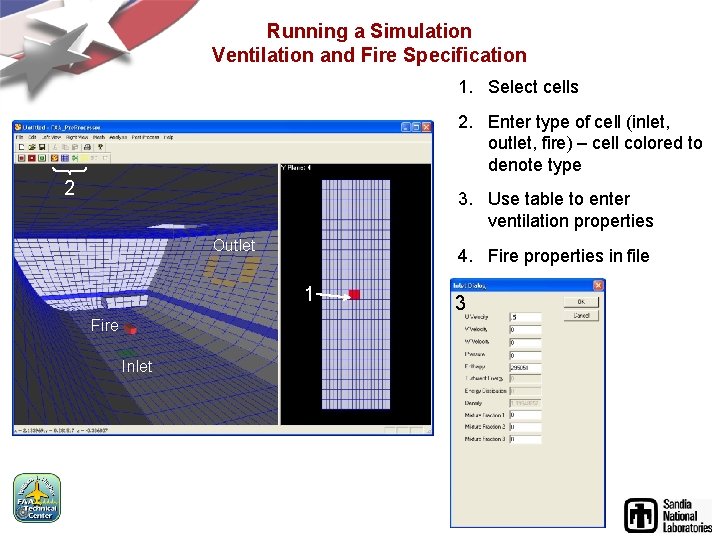
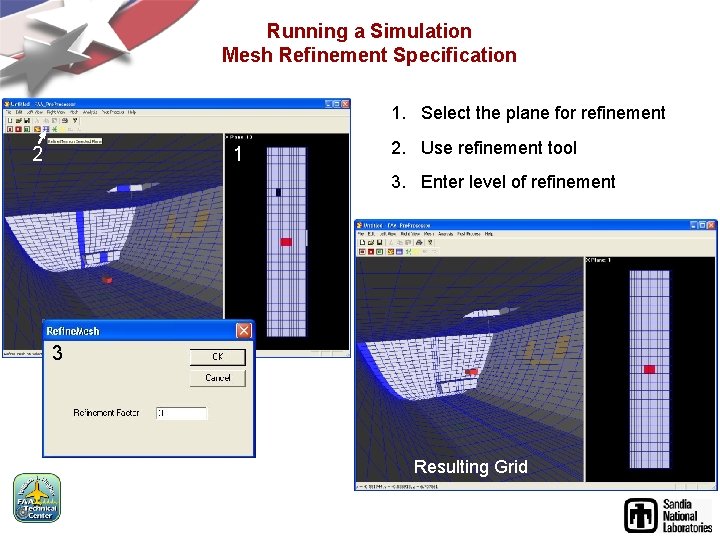
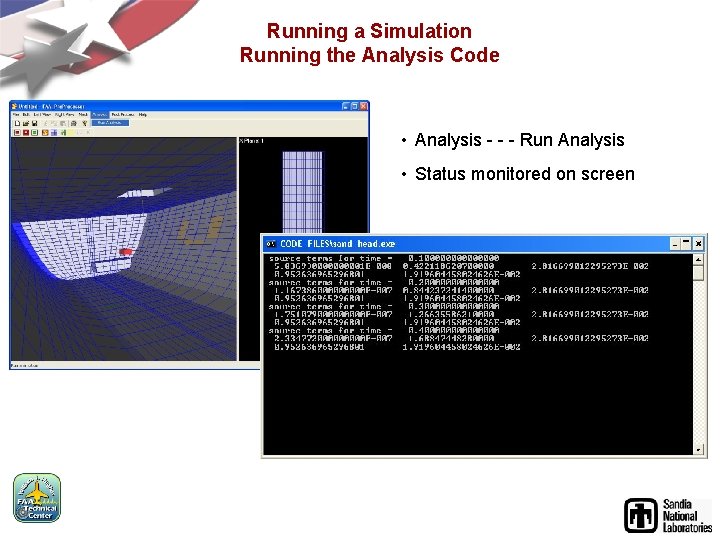
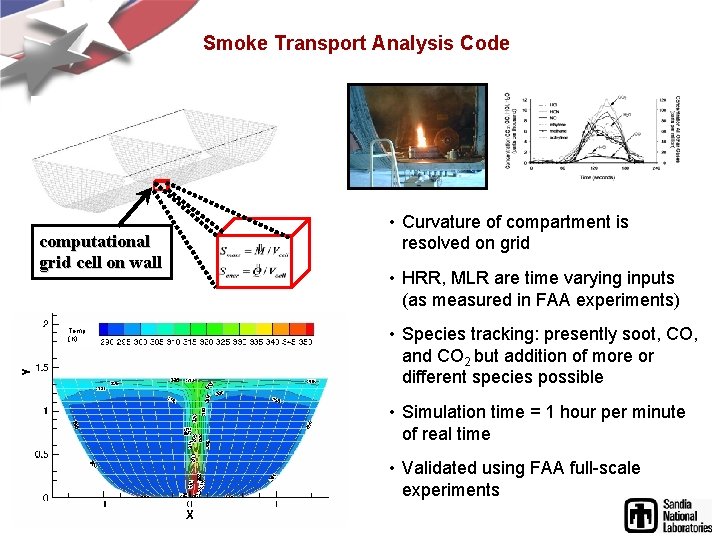
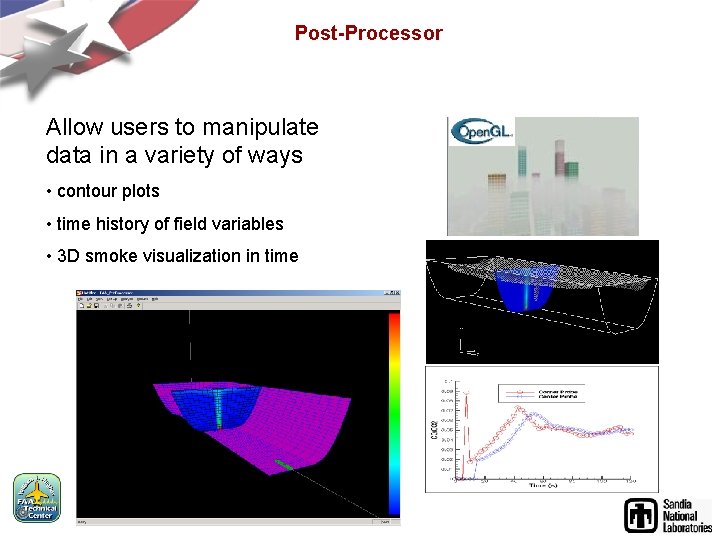
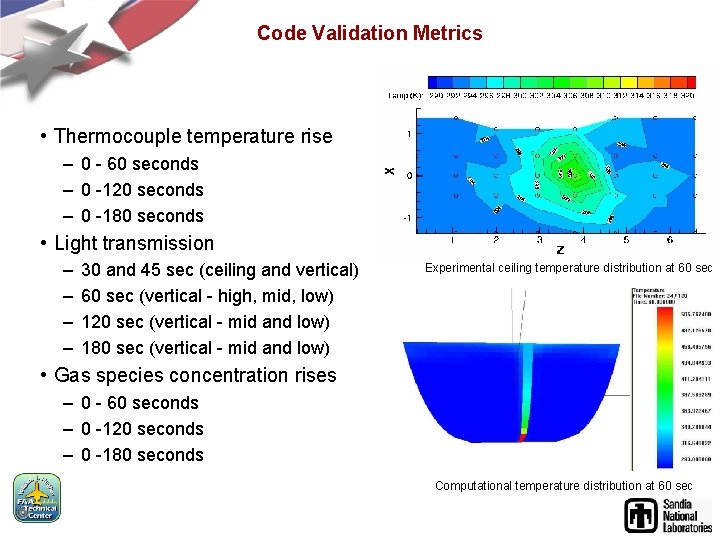
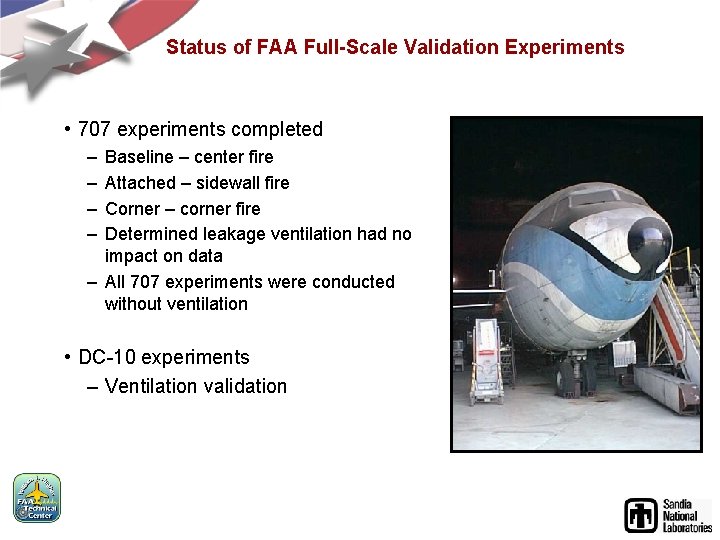
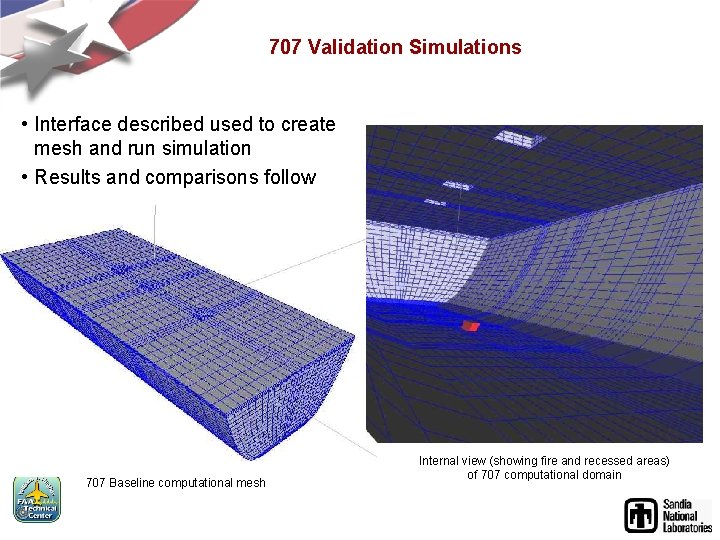
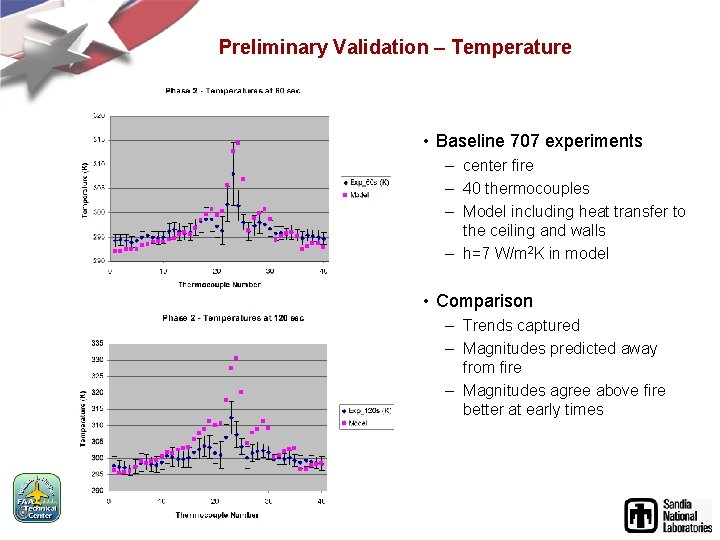
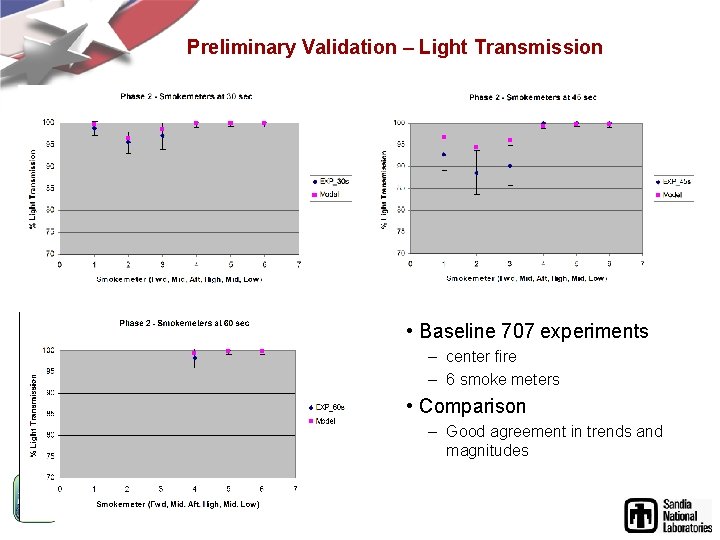
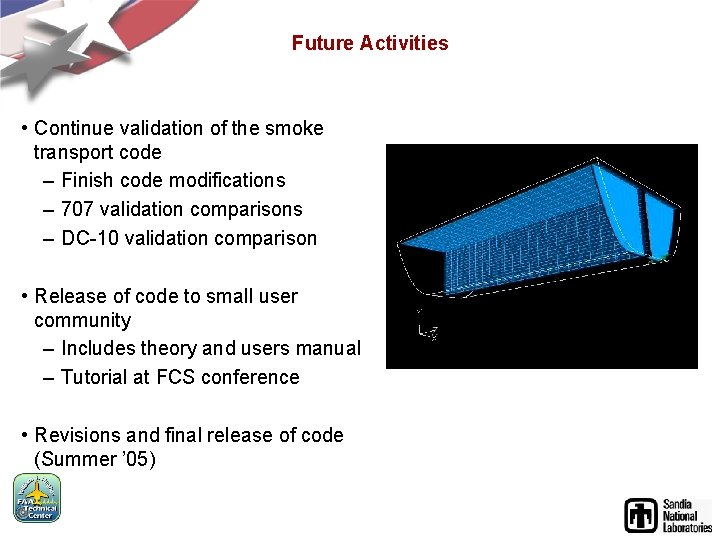

- Slides: 21
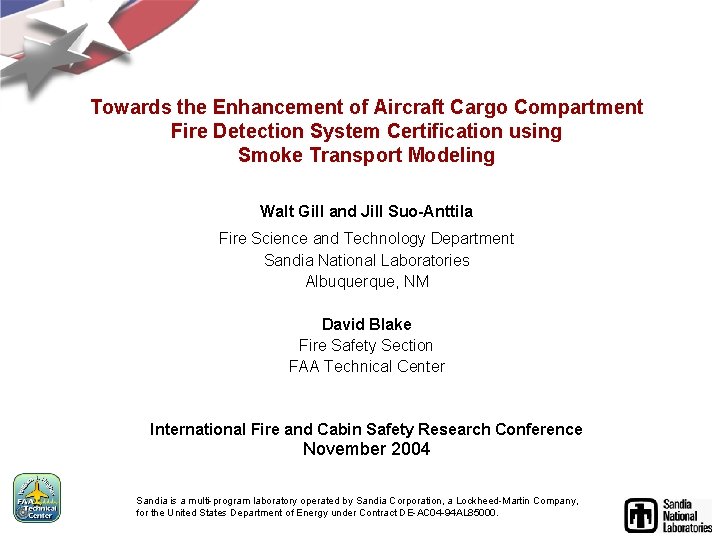
Towards the Enhancement of Aircraft Cargo Compartment Fire Detection System Certification using Smoke Transport Modeling Walt Gill and Jill Suo-Anttila Fire Science and Technology Department Sandia National Laboratories Albuquerque, NM David Blake Fire Safety Section FAA Technical Center International Fire and Cabin Safety Research Conference November 2004 Sandia is a multi-program laboratory operated by Sandia Corporation, a Lockheed-Martin Company, for the United States Department of Energy under Contract DE-AC 04 -94 AL 85000.
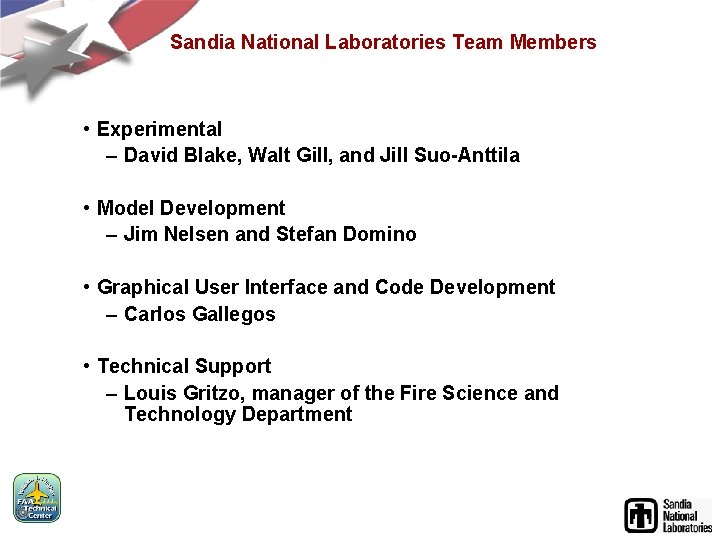
Sandia National Laboratories Team Members • Experimental – David Blake, Walt Gill, and Jill Suo-Anttila • Model Development – Jim Nelsen and Stefan Domino • Graphical User Interface and Code Development – Carlos Gallegos • Technical Support – Louis Gritzo, manager of the Fire Science and Technology Department
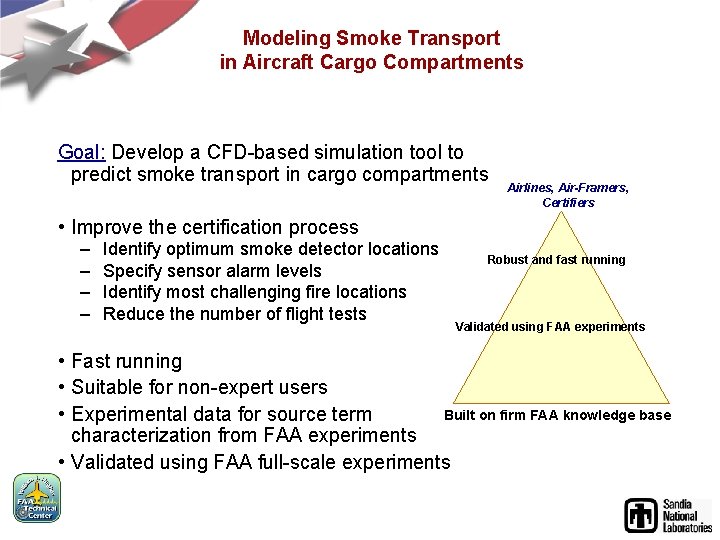
Modeling Smoke Transport in Aircraft Cargo Compartments Goal: Develop a CFD-based simulation tool to predict smoke transport in cargo compartments Airlines, Air-Framers, Certifiers • Improve the certification process – – Identify optimum smoke detector locations Specify sensor alarm levels Identify most challenging fire locations Reduce the number of flight tests Robust and fast running Validated using FAA experiments • Fast running • Suitable for non-expert users Built on firm FAA knowledge base • Experimental data for source term characterization from FAA experiments • Validated using FAA full-scale experiments
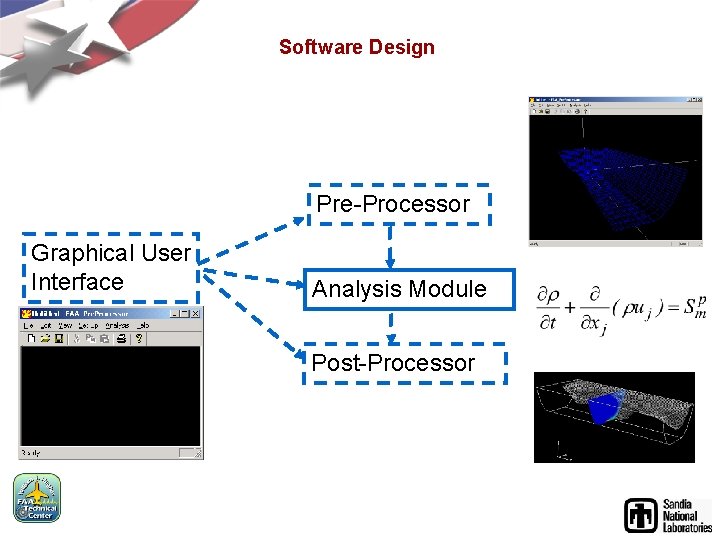
Software Design Pre-Processor Graphical User Interface Analysis Module Post-Processor
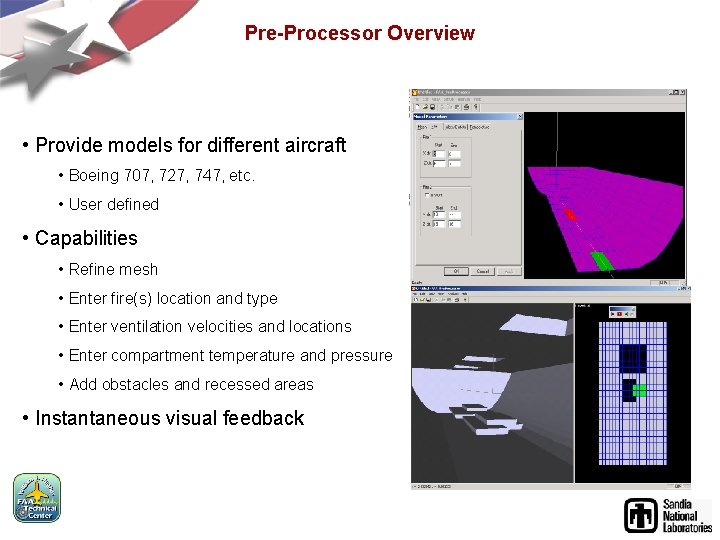
Pre-Processor Overview • Provide models for different aircraft • Boeing 707, 727, 747, etc. • User defined • Capabilities • Refine mesh • Enter fire(s) location and type • Enter ventilation velocities and locations • Enter compartment temperature and pressure • Add obstacles and recessed areas • Instantaneous visual feedback
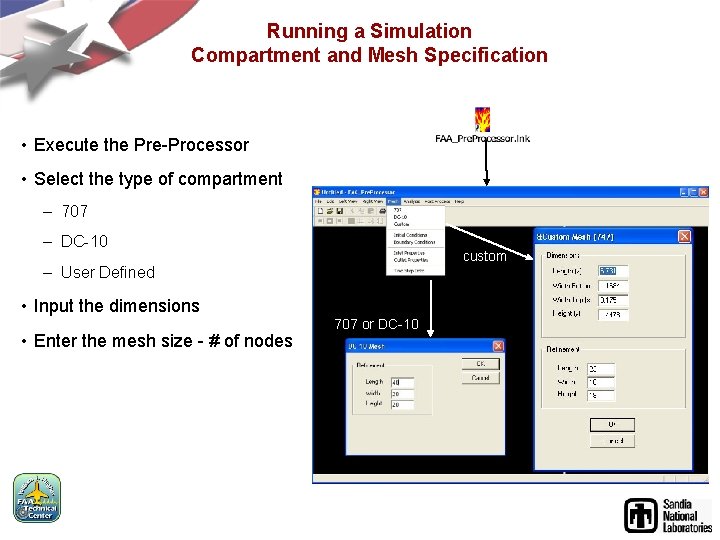
Running a Simulation Compartment and Mesh Specification • Execute the Pre-Processor • Select the type of compartment – 707 – DC-10 custom – User Defined • Input the dimensions • Enter the mesh size - # of nodes 707 or DC-10
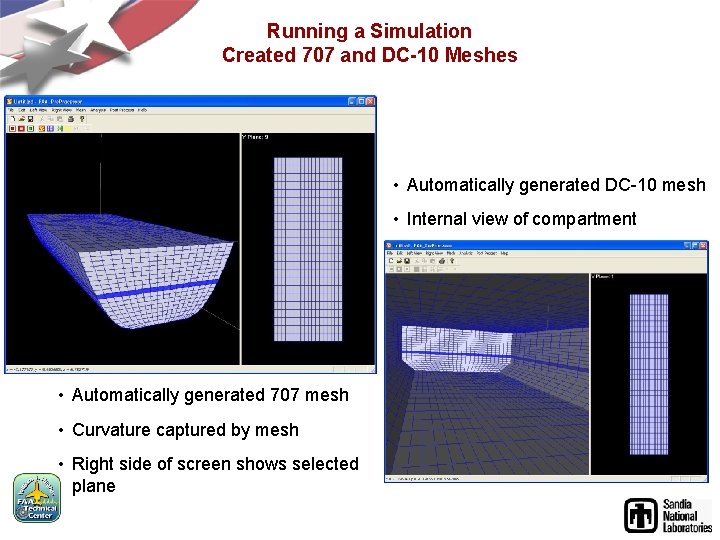
Running a Simulation Created 707 and DC-10 Meshes • Automatically generated DC-10 mesh • Internal view of compartment • Automatically generated 707 mesh • Curvature captured by mesh • Right side of screen shows selected plane
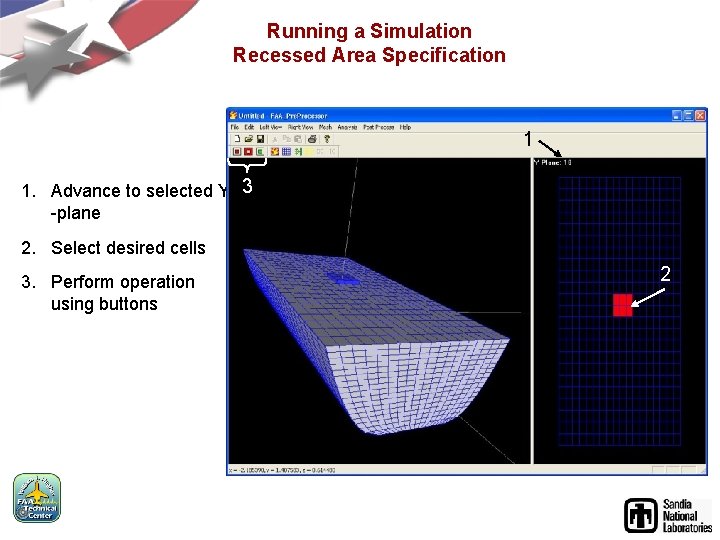
Running a Simulation Recessed Area Specification 1 1. Advance to selected Y 3 -plane 2. Select desired cells 3. Perform operation using buttons 2
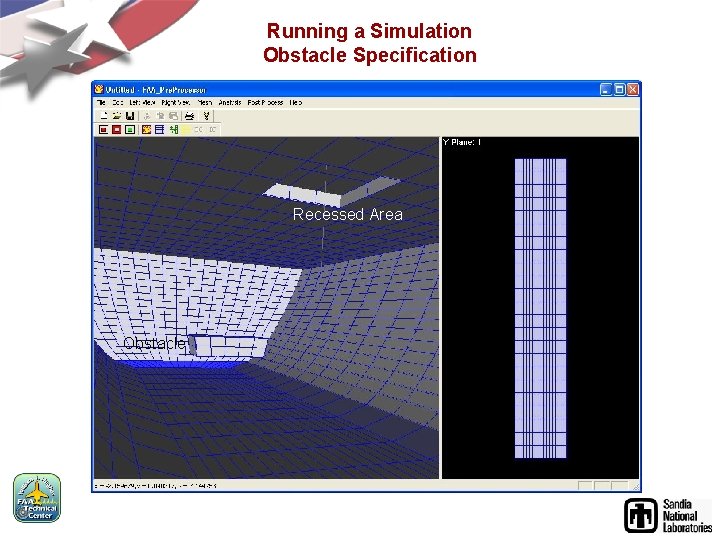
Running a Simulation Obstacle Specification Recessed Area Obstacle
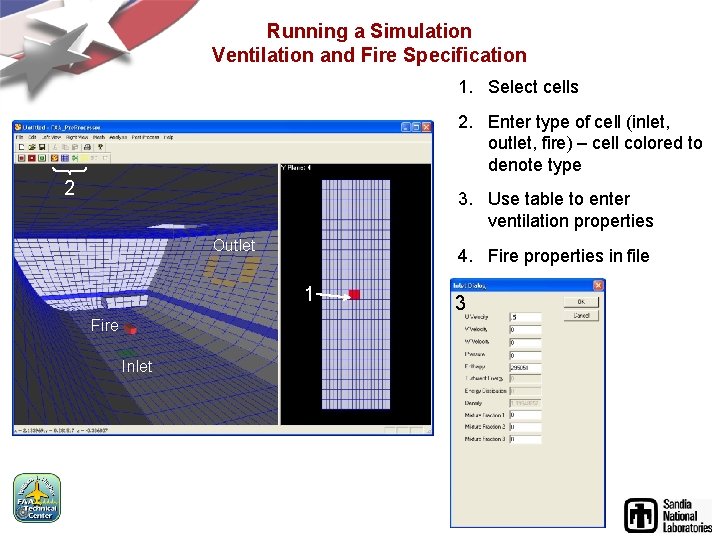
Running a Simulation Ventilation and Fire Specification 1. Select cells 2. Enter type of cell (inlet, outlet, fire) – cell colored to denote type 2 3. Use table to enter ventilation properties Outlet 4. Fire properties in file 1 Fire Inlet 3
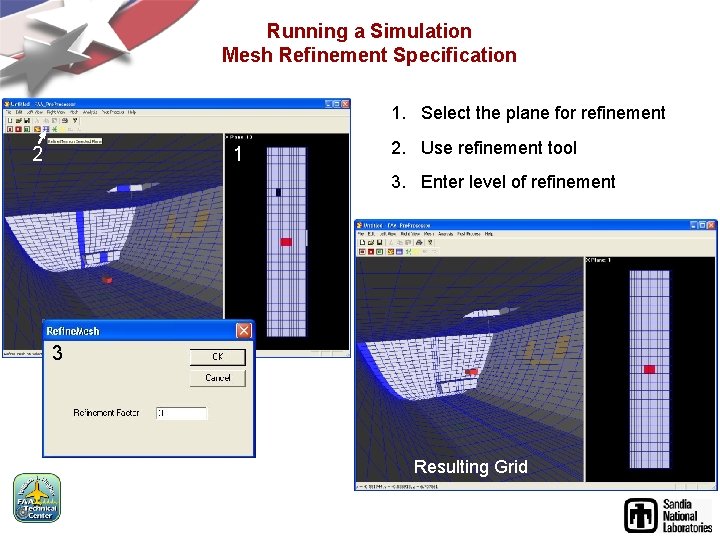
Running a Simulation Mesh Refinement Specification 1. Select the plane for refinement 2 1 2. Use refinement tool 3. Enter level of refinement 3 Resulting Grid
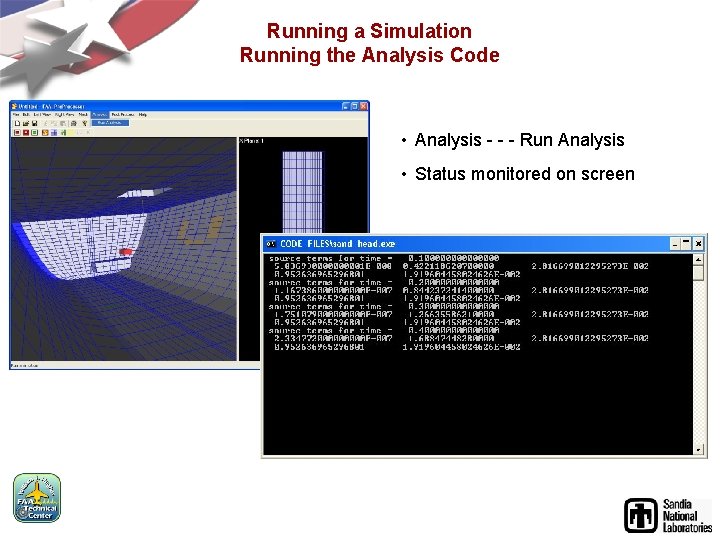
Running a Simulation Running the Analysis Code • Analysis - - - Run Analysis • Status monitored on screen
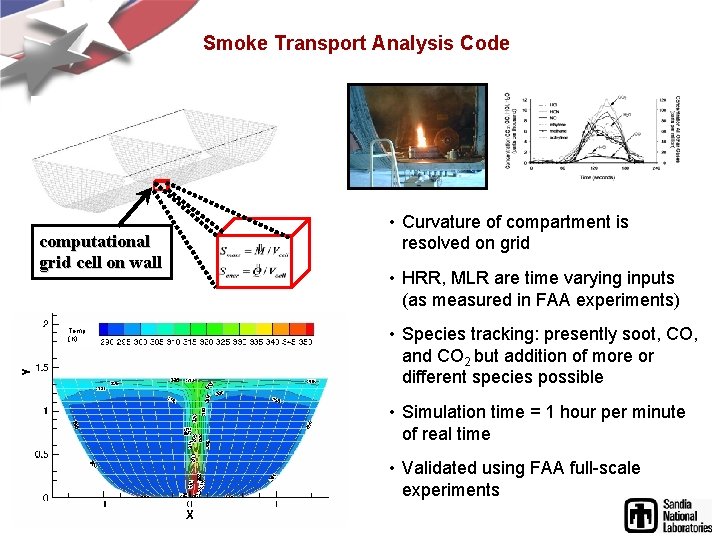
Smoke Transport Analysis Code computational grid cell on wall Temp (K) • Curvature of compartment is resolved on grid • HRR, MLR are time varying inputs (as measured in FAA experiments) • Species tracking: presently soot, CO, and CO 2 but addition of more or different species possible • Simulation time = 1 hour per minute of real time • Validated using FAA full-scale experiments
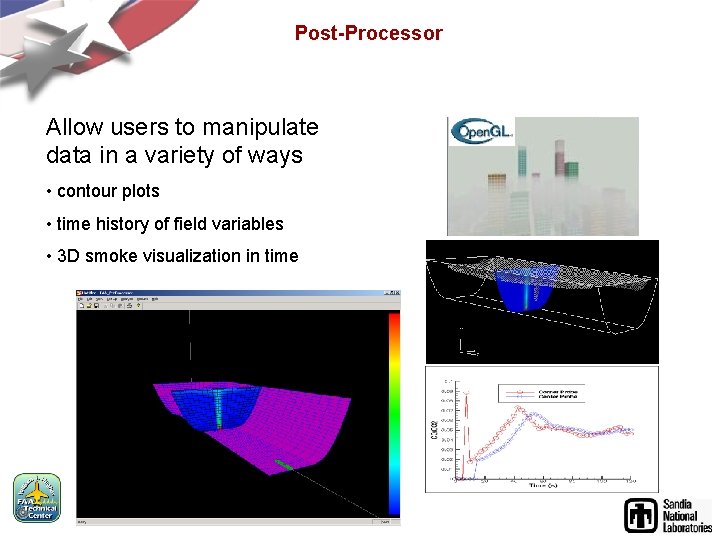
Post-Processor Allow users to manipulate data in a variety of ways • contour plots • time history of field variables • 3 D smoke visualization in time
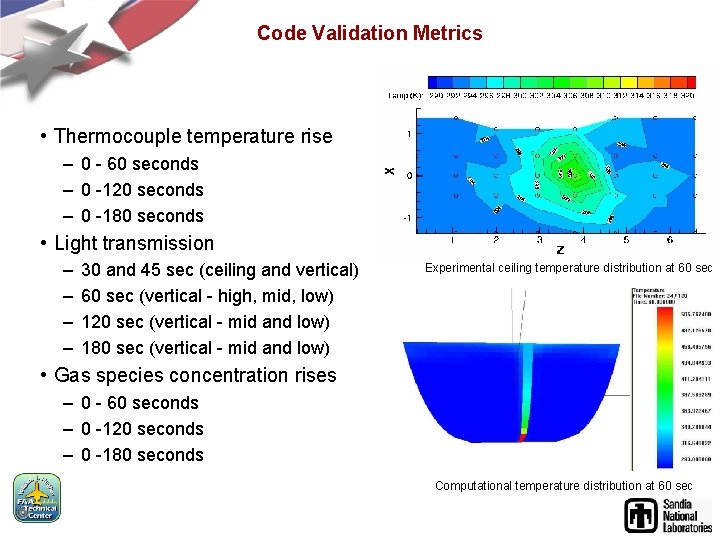
Code Validation Metrics • Thermocouple temperature rise – 0 - 60 seconds – 0 -120 seconds – 0 -180 seconds • Light transmission – 30 and 45 sec (ceiling and vertical) – 60 sec (vertical - high, mid, low) Insert most recent of temperature distribution – 120 sec movie (vertical - mid and low) – 180 sec (vertical - mid and low) Experimental ceiling temperature distribution at 60 sec • Gas species concentration rises – 0 - 60 seconds – 0 -120 seconds – 0 -180 seconds Computational temperature distribution at 60 sec
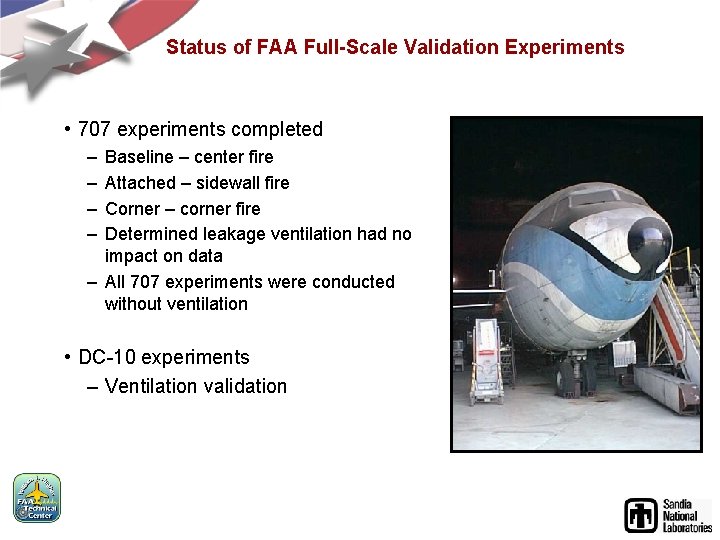
Status of FAA Full-Scale Validation Experiments • 707 experiments completed – – Baseline – center fire Attached – sidewall fire Corner – corner fire Determined leakage ventilation had no impact on data – All 707 experiments were conducted without ventilation Insert most recent movie of temperature distribution • DC-10 experiments – Ventilation validation
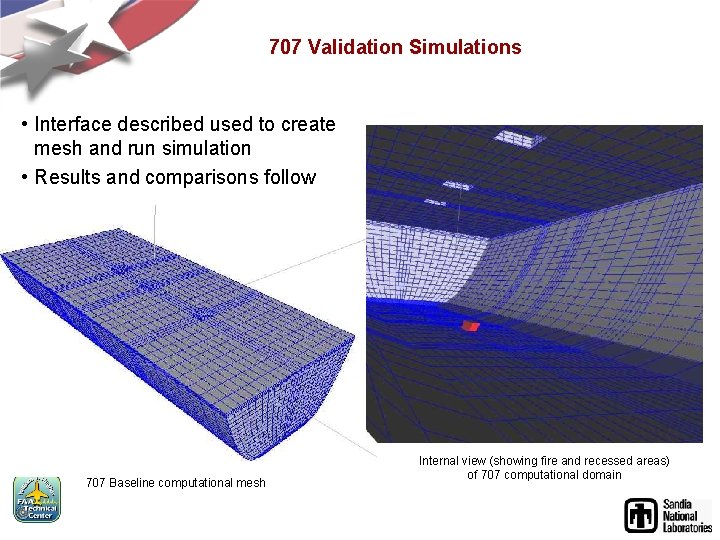
707 Validation Simulations • Interface described used to create mesh and run simulation • Results and comparisons follow Insert most recent movie of temperature distribution 707 Baseline computational mesh Internal view (showing fire and recessed areas) of 707 computational domain
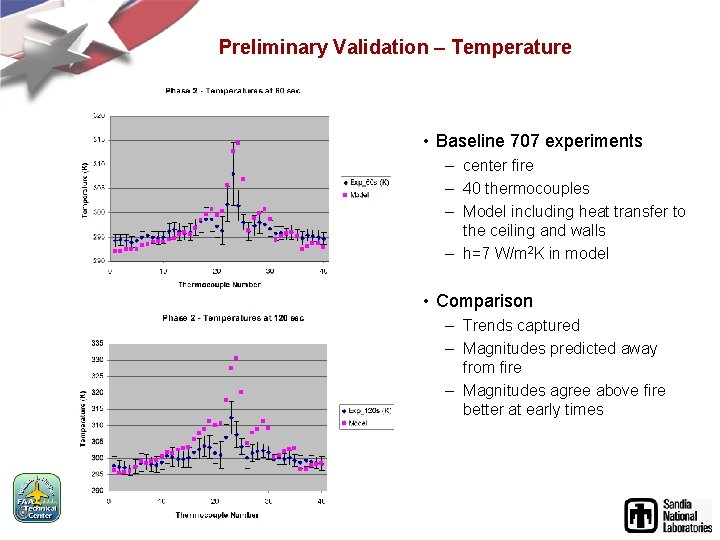
Preliminary Validation – Temperature • Baseline 707 experiments – center fire – 40 thermocouples – Model including heat transfer to the ceiling and walls – h=7 W/m 2 K in model • Comparison Insert most recent movie of temperature distribution – Trends captured – Magnitudes predicted away from fire – Magnitudes agree above fire better at early times
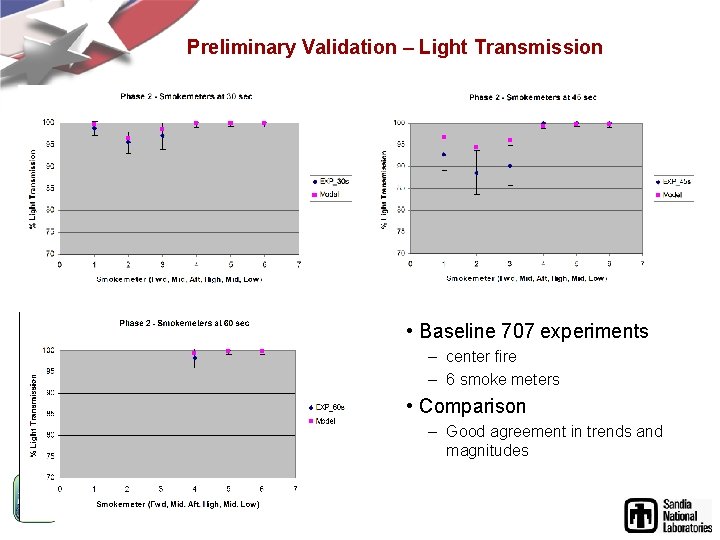
Preliminary Validation – Light Transmission Insert most recent movie of temperature distribution • Baseline 707 experiments – center fire – 6 smoke meters • Comparison – Good agreement in trends and magnitudes
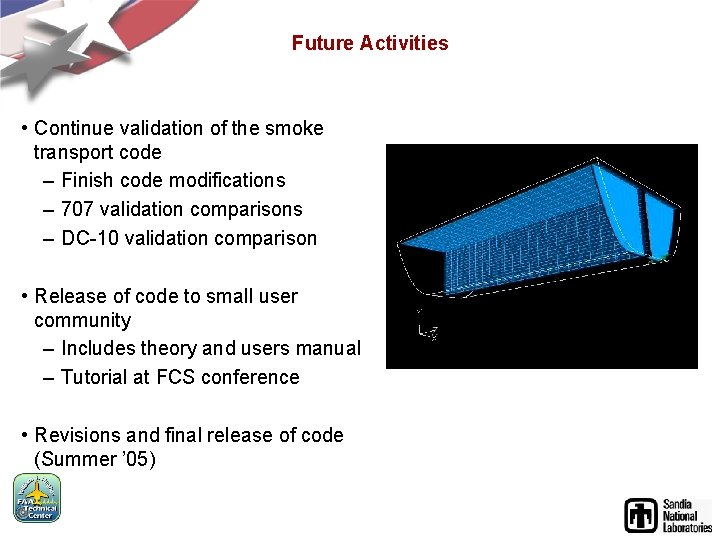
Future Activities • Continue validation of the smoke transport code – Finish code modifications – 707 validation comparisons – DC-10 validation comparison • Release of code to small user community – Includes theory and users manual – Tutorial at FCS conference • Revisions and final release of code (Summer ’ 05)

The Fourth Triennial International Aircraft Fire and Cabin Safety Research Conference
Class e cargo compartment
Class e cargo compartment
Compartment fire behavior training
Compartment fire
Compartment fire behavior training
His wrath towards you burns like fire figurative language
His wrath towards you burns like fire figurative language
Aircraft materials fire test handbook
A-e rwi
Reichstag fire who was the fire starter
Race fire
Fire damper access
Fire hose reel signage standards
Michelson water reclamation plant
Compartment syndrome 7p
Supinator muscle nerve supply
What is the definition of sanitizing servsafe
Peroneus tertius compartment
Scalene fissure
Muscles of mastication nerve supply
Renata pecova
Muscle compartment of thigh