TC Straw man layout for ATLAS ID for
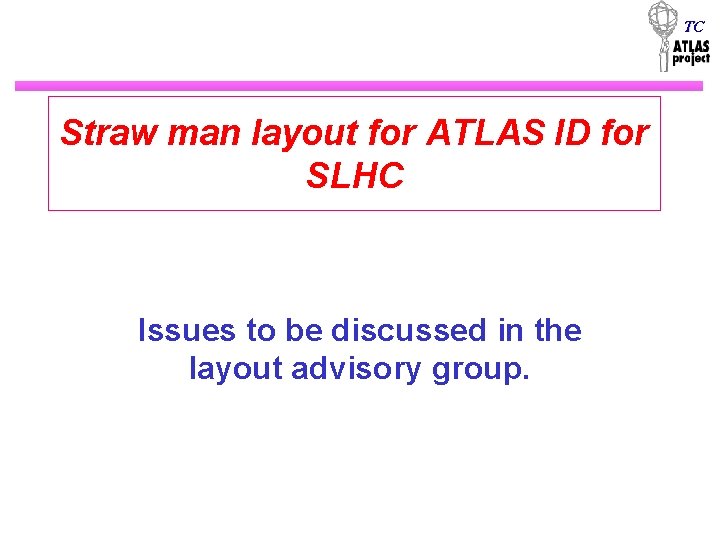
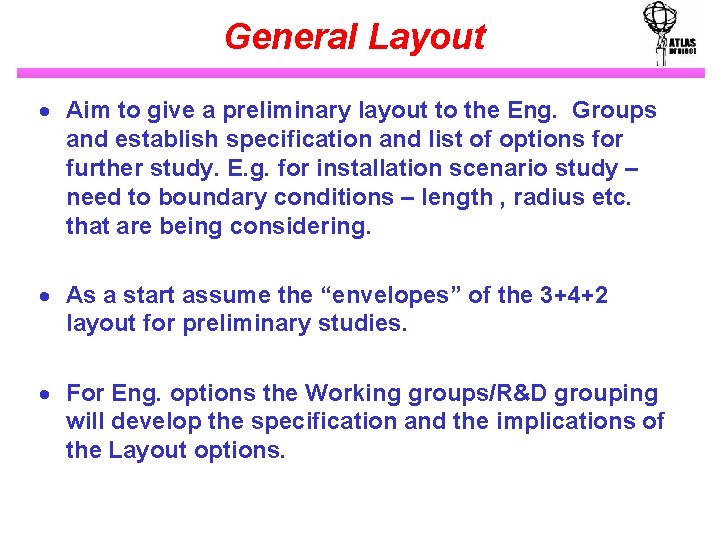
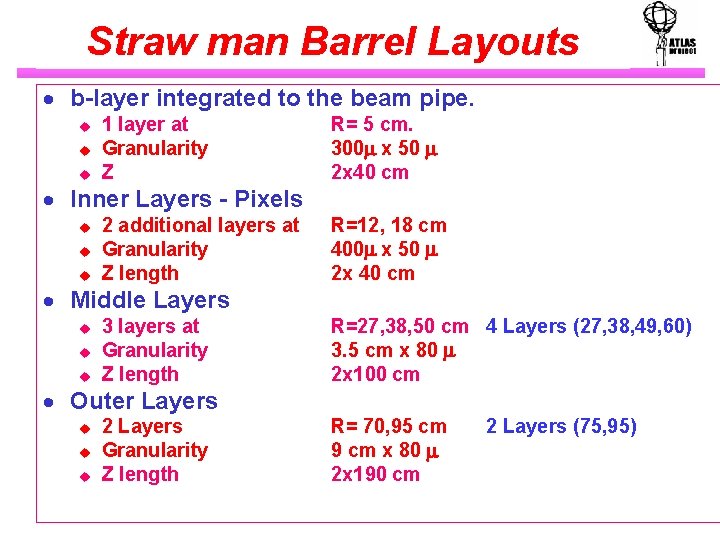
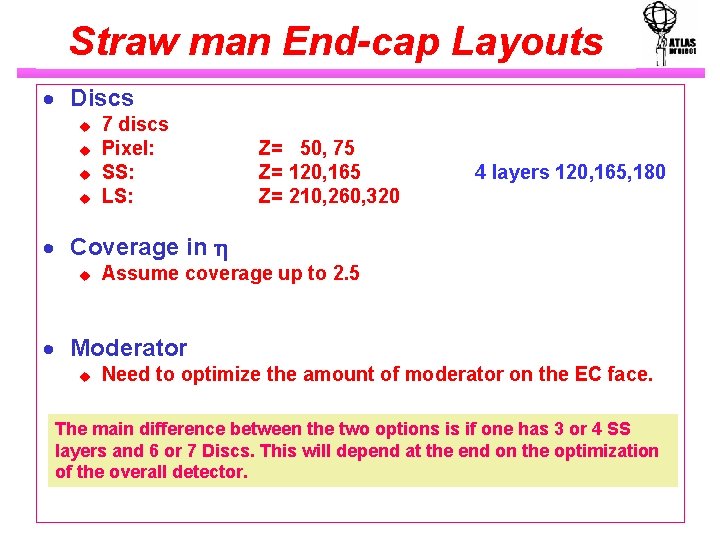
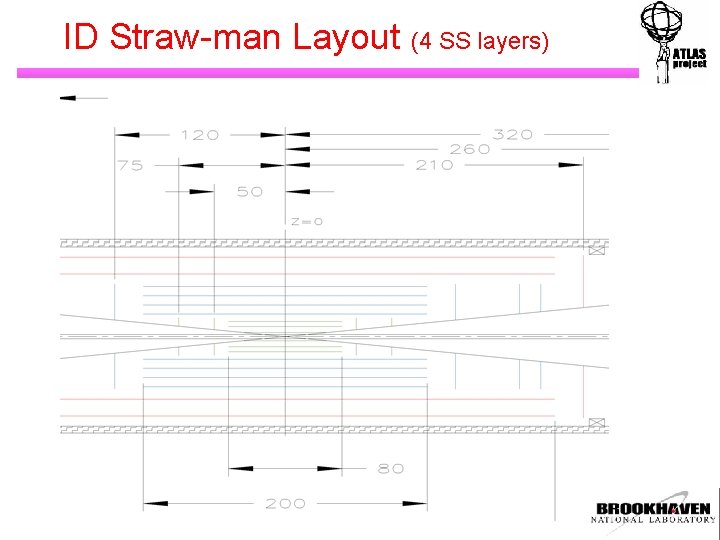
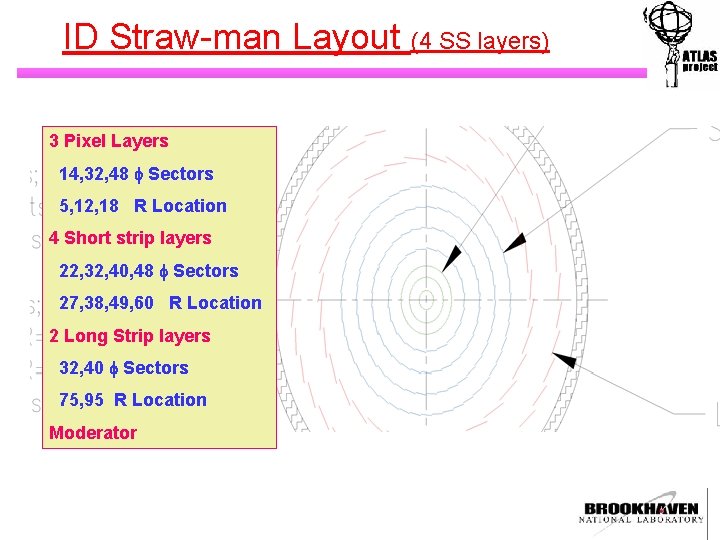

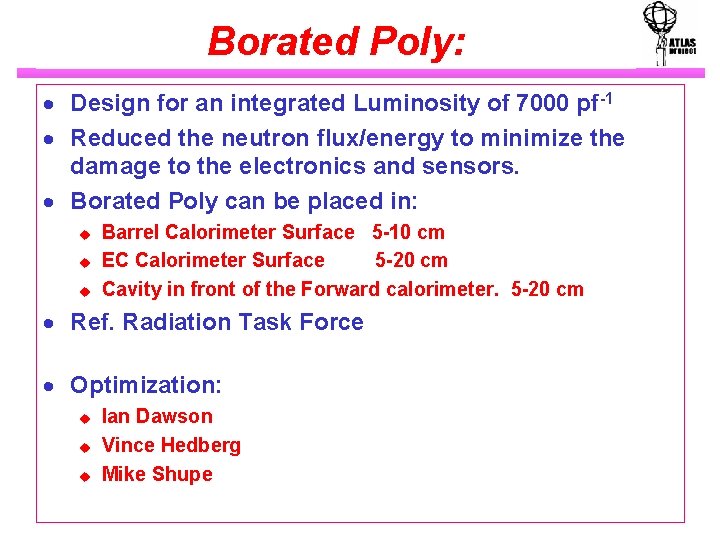
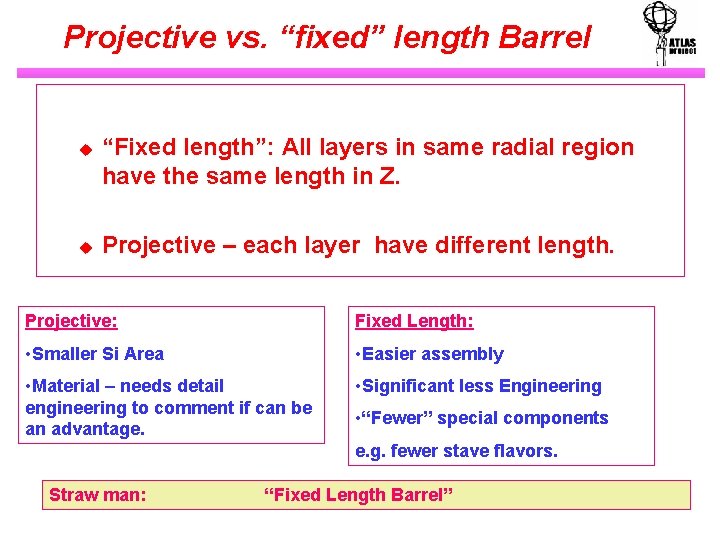
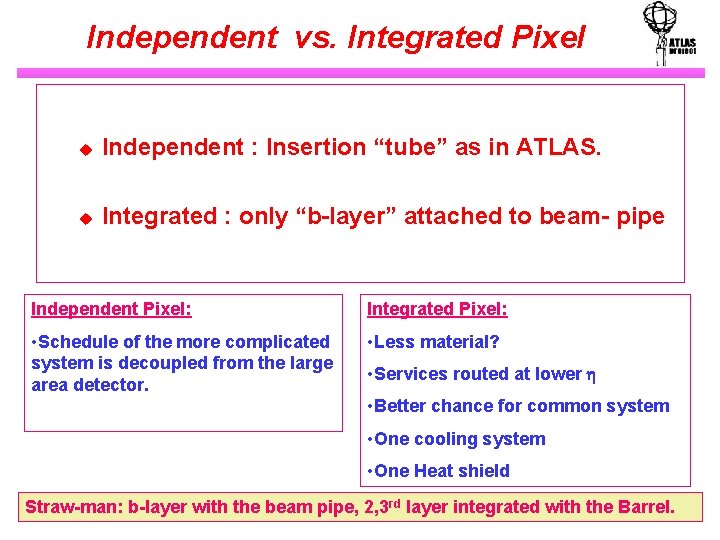
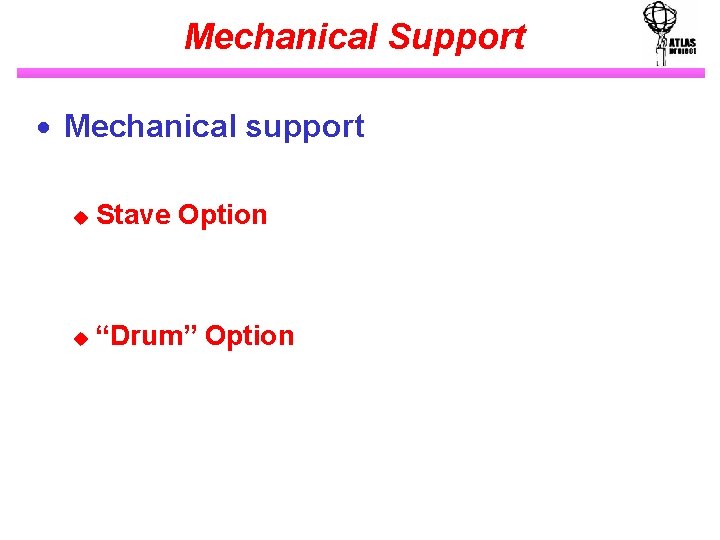
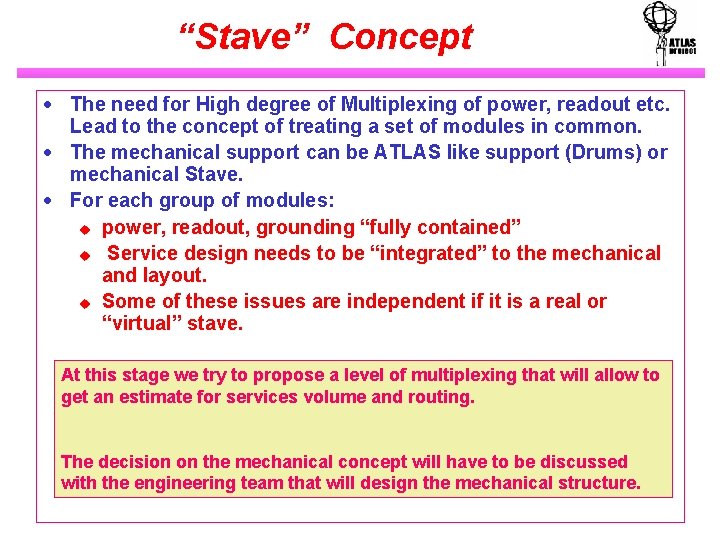
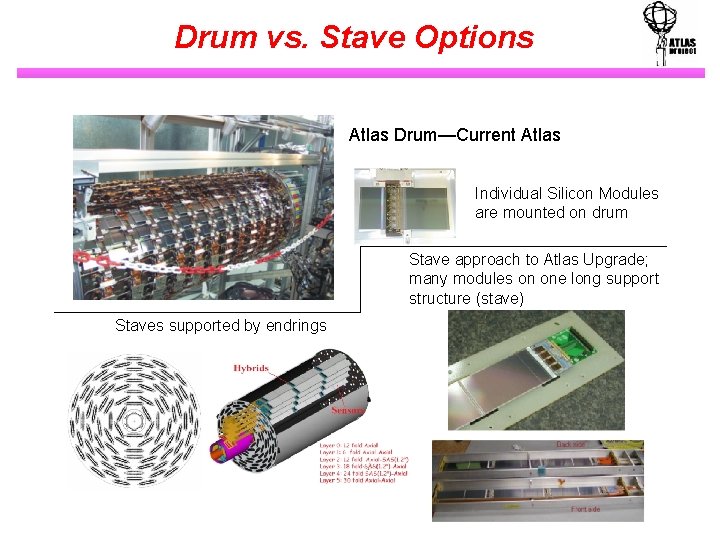
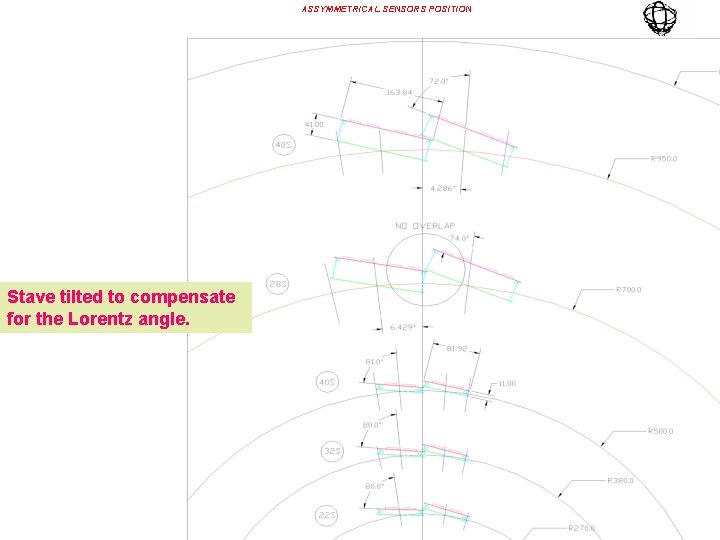
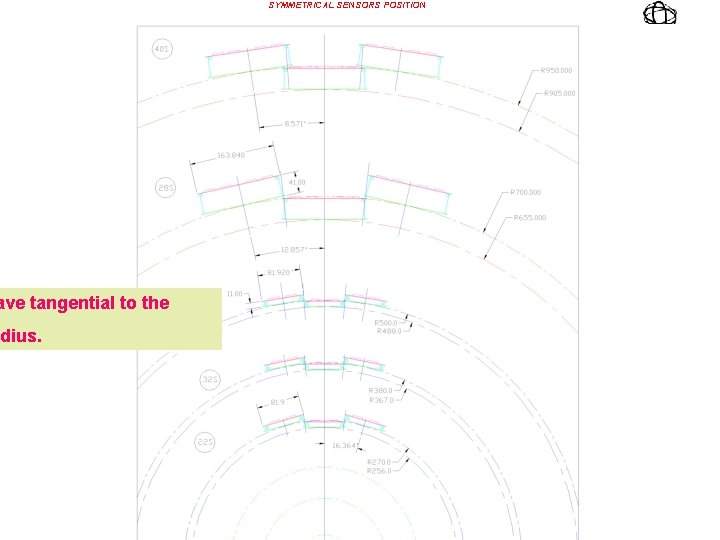
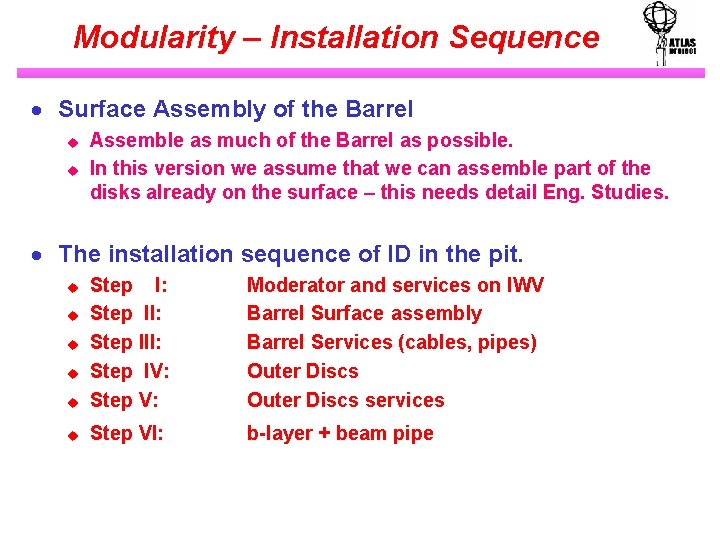
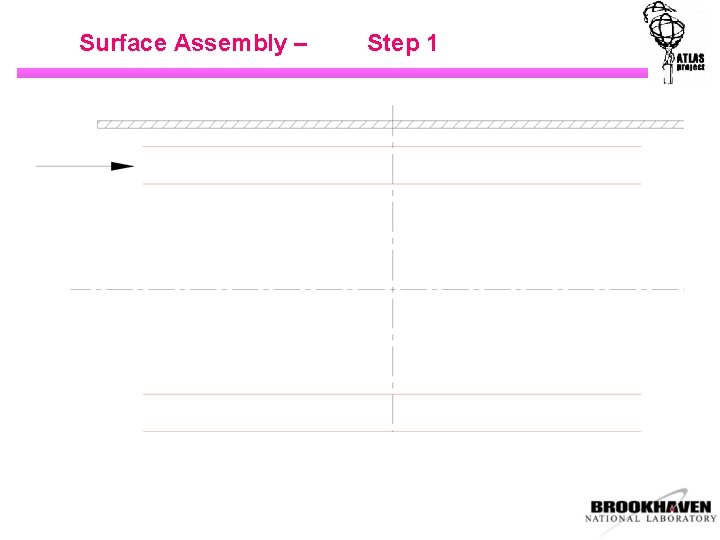
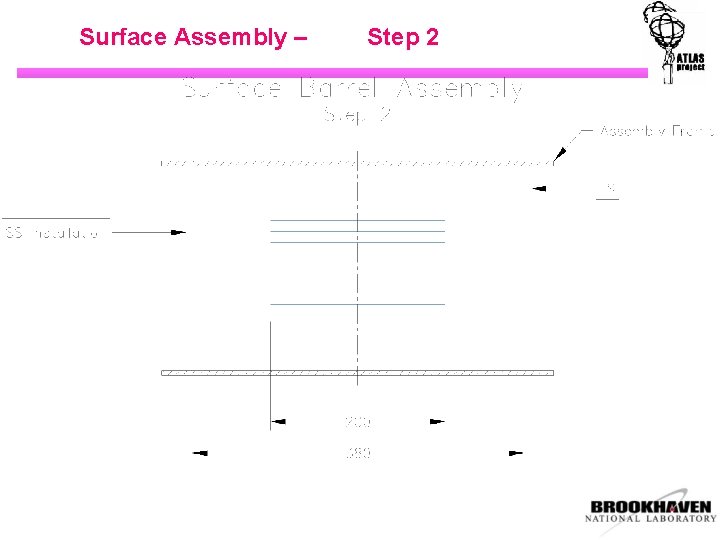
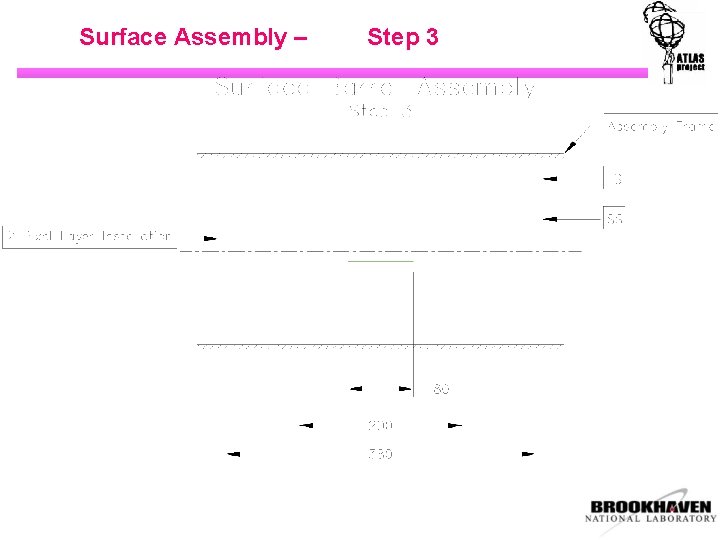
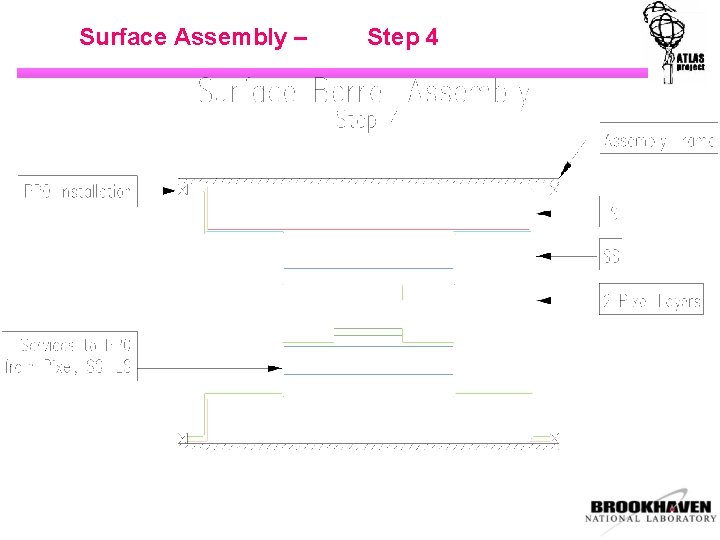
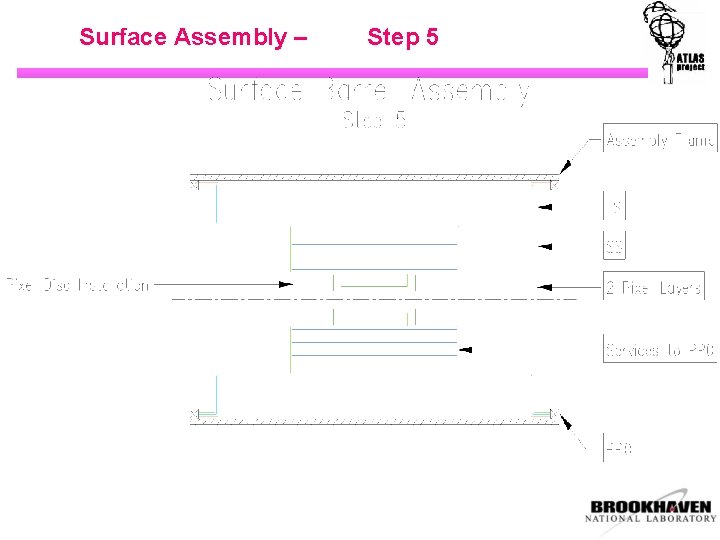
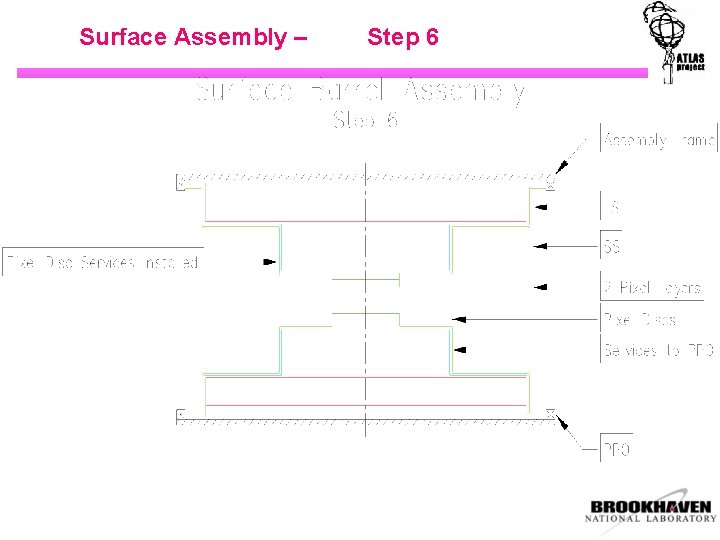
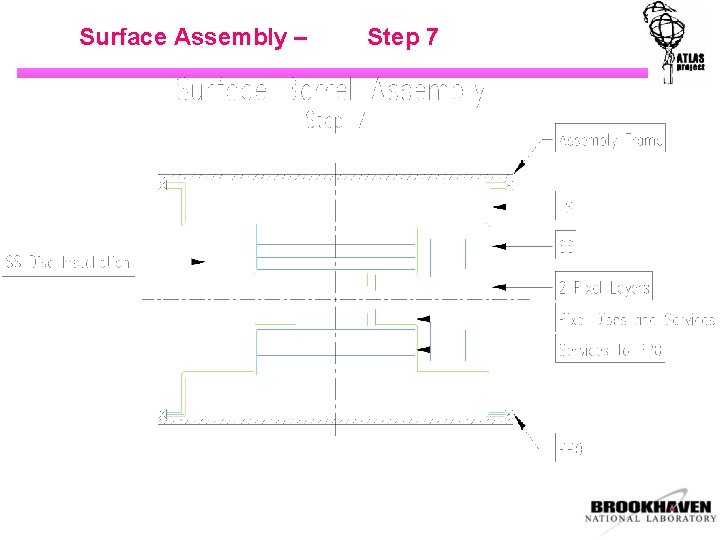

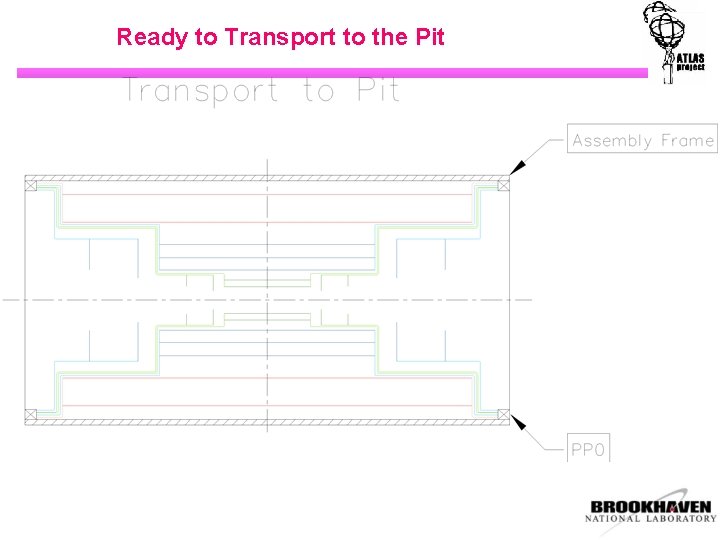
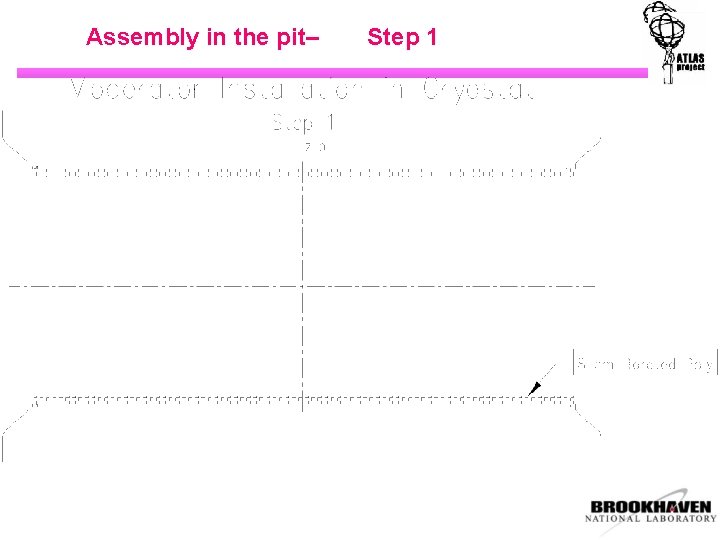
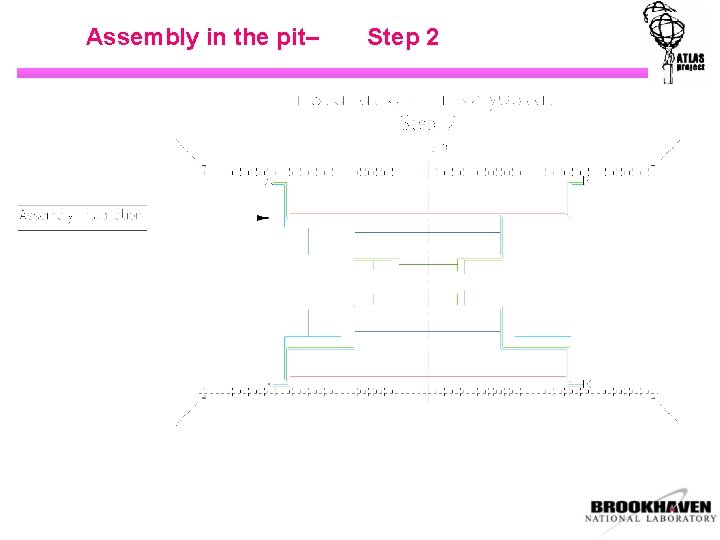
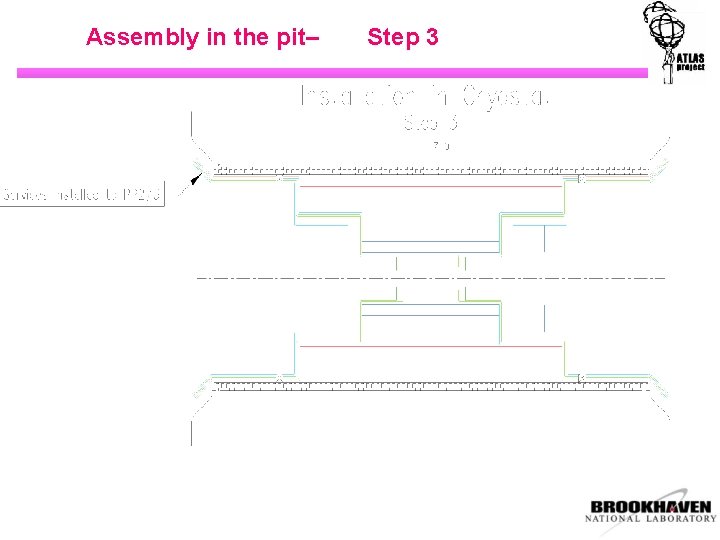
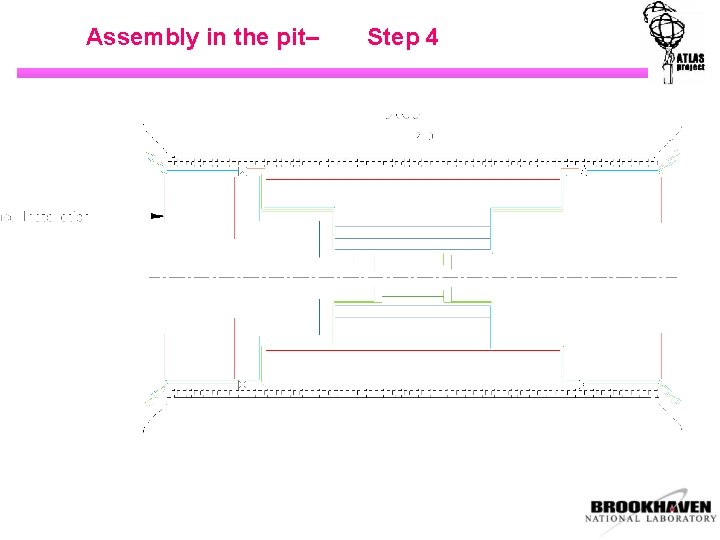
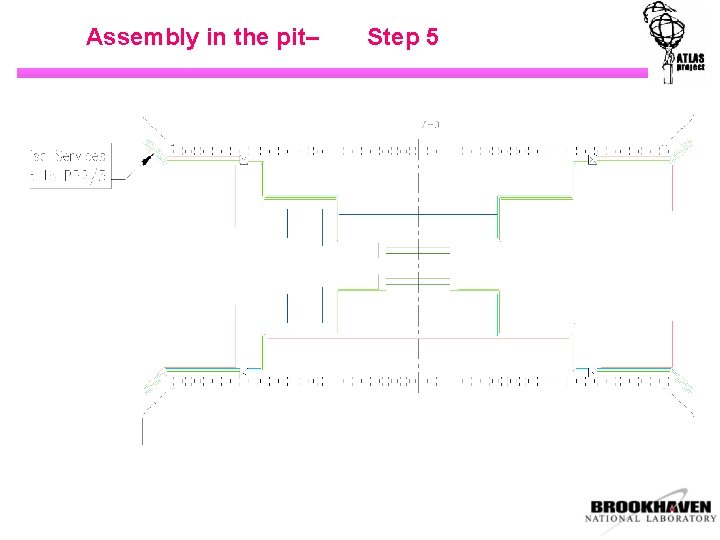
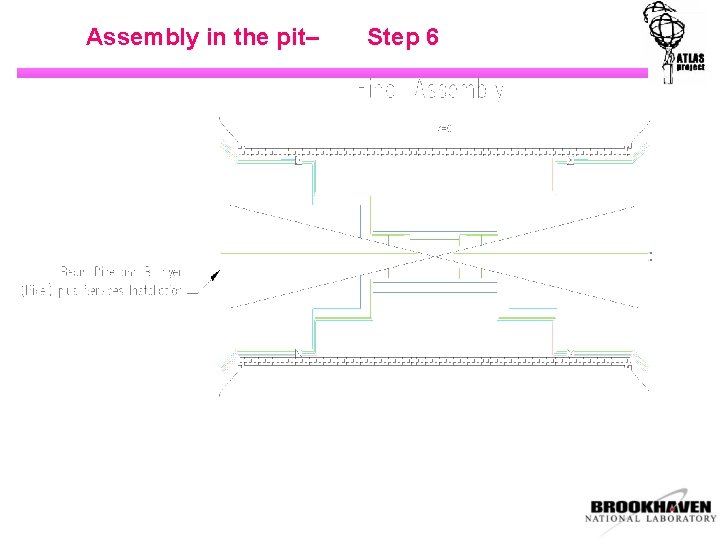
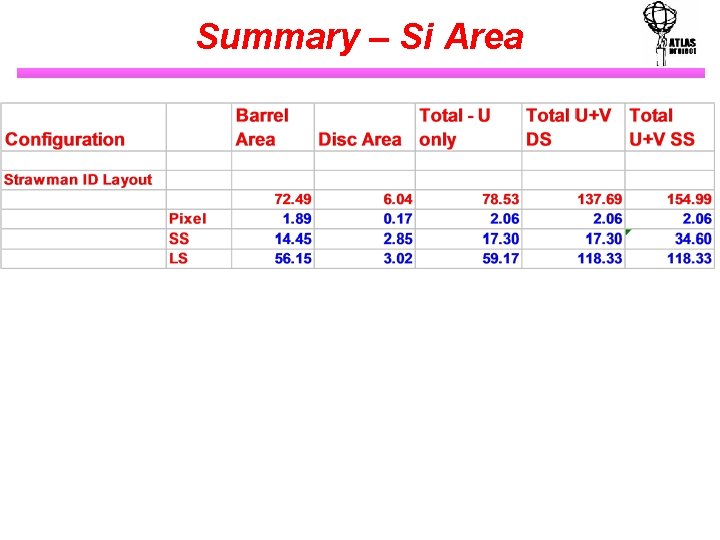
- Slides: 32
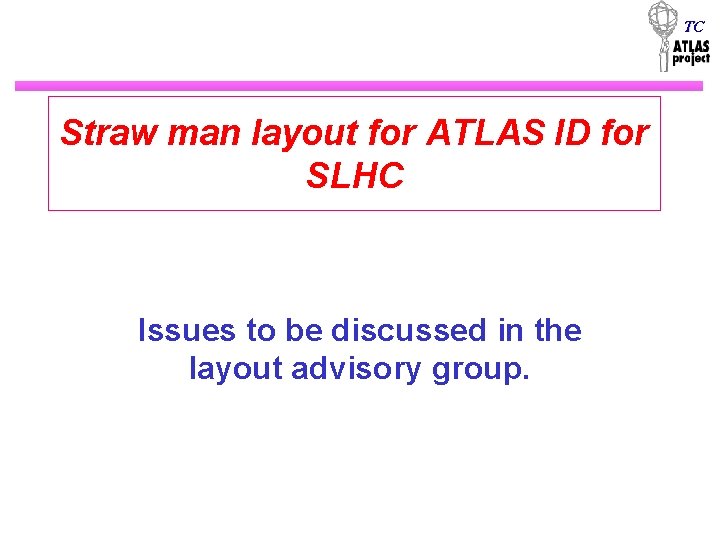
TC Straw man layout for ATLAS ID for SLHC Issues to be discussed in the layout advisory group.
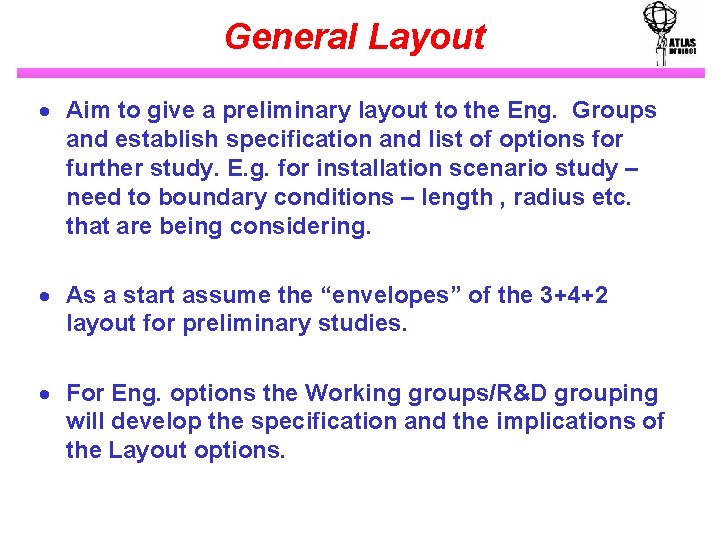
General Layout · Aim to give a preliminary layout to the Eng. Groups and establish specification and list of options for further study. E. g. for installation scenario study – need to boundary conditions – length , radius etc. that are being considering. · As a start assume the “envelopes” of the 3+4+2 layout for preliminary studies. · For Eng. options the Working groups/R&D grouping will develop the specification and the implications of the Layout options.
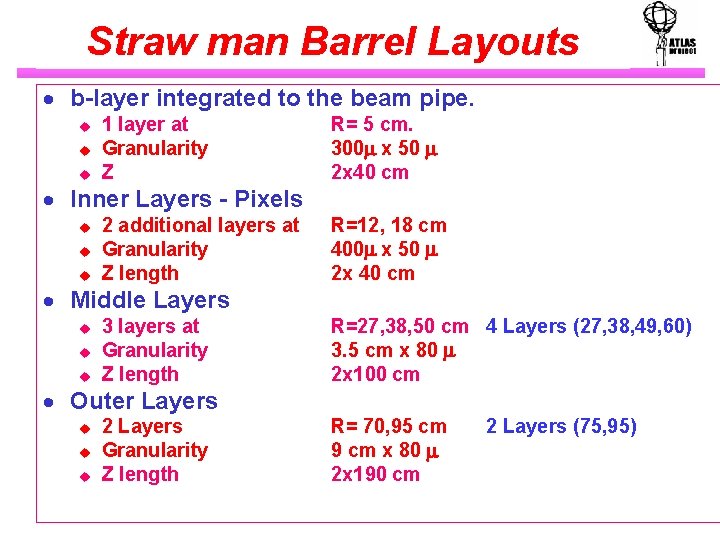
Straw man Barrel Layouts · b-layer integrated to the beam pipe. u u u 1 layer at Granularity Z R= 5 cm. 300 m x 50 m 2 x 40 cm 2 additional layers at Granularity Z length R=12, 18 cm 400 m x 50 m 2 x 40 cm 3 layers at Granularity Z length R=27, 38, 50 cm 4 Layers (27, 38, 49, 60) 3. 5 cm x 80 m 2 x 100 cm 2 Layers Granularity Z length R= 70, 95 cm 9 cm x 80 m 2 x 190 cm · Inner Layers - Pixels u u u · Middle Layers u u u · Outer Layers u u u 2 Layers (75, 95)
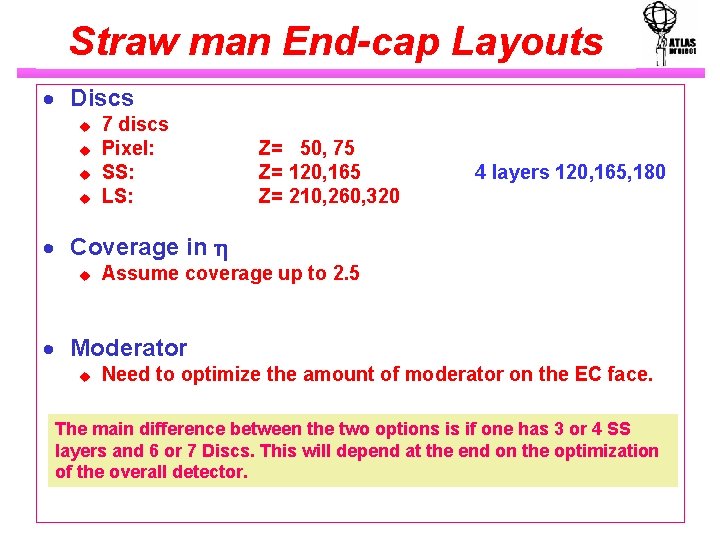
Straw man End-cap Layouts · Discs u u 7 discs Pixel: SS: LS: Z= 50, 75 Z= 120, 165 Z= 210, 260, 320 4 layers 120, 165, 180 · Coverage in h u Assume coverage up to 2. 5 · Moderator u Need to optimize the amount of moderator on the EC face. The main difference between the two options is if one has 3 or 4 SS layers and 6 or 7 Discs. This will depend at the end on the optimization of the overall detector.
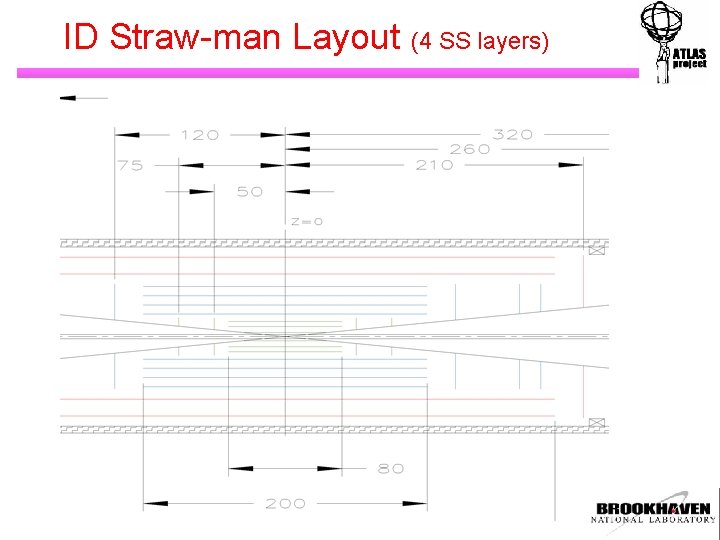
ID Straw-man Layout (4 SS layers)
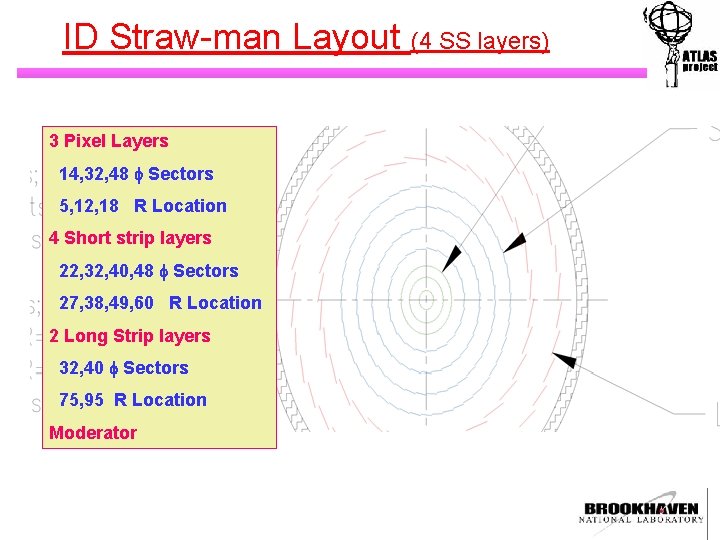
ID Straw-man Layout (4 SS layers) 3 Pixel Layers 14, 32, 48 f Sectors 5, 12, 18 R Location 4 Short strip layers 22, 32, 40, 48 f Sectors 27, 38, 49, 60 R Location 2 Long Strip layers 32, 40 f Sectors 75, 95 R Location Moderator

Straw-man Options: · Borated Poly – Locations and thickness. · Fixed Length Barrel Quasi “Projective” layout. · Integrated Pixel · Implications of sensor layout options · Mechanical Layout – options and questions u Barrel s s u Cylindrical support structure “ATLAS Like” + Discs “Staves” + Discs EC-Disc design · Cooling Options u Pressure, operating temperature
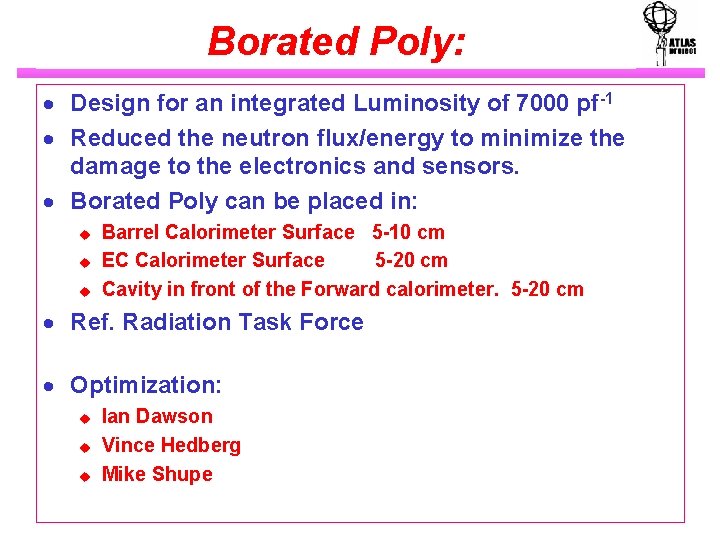
Borated Poly: · Design for an integrated Luminosity of 7000 pf-1 · Reduced the neutron flux/energy to minimize the damage to the electronics and sensors. · Borated Poly can be placed in: u u u Barrel Calorimeter Surface 5 -10 cm EC Calorimeter Surface 5 -20 cm Cavity in front of the Forward calorimeter. 5 -20 cm · Ref. Radiation Task Force · Optimization: u u u Ian Dawson Vince Hedberg Mike Shupe
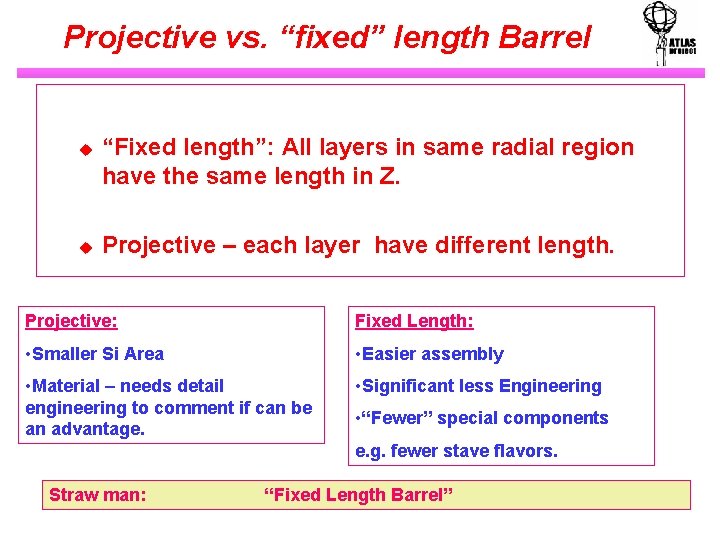
Projective vs. “fixed” length Barrel u u “Fixed length”: All layers in same radial region have the same length in Z. Projective – each layer have different length. Projective: Fixed Length: • Smaller Si Area • Easier assembly • Material – needs detail engineering to comment if can be an advantage. • Significant less Engineering • “Fewer” special components e. g. fewer stave flavors. Straw man: “Fixed Length Barrel”
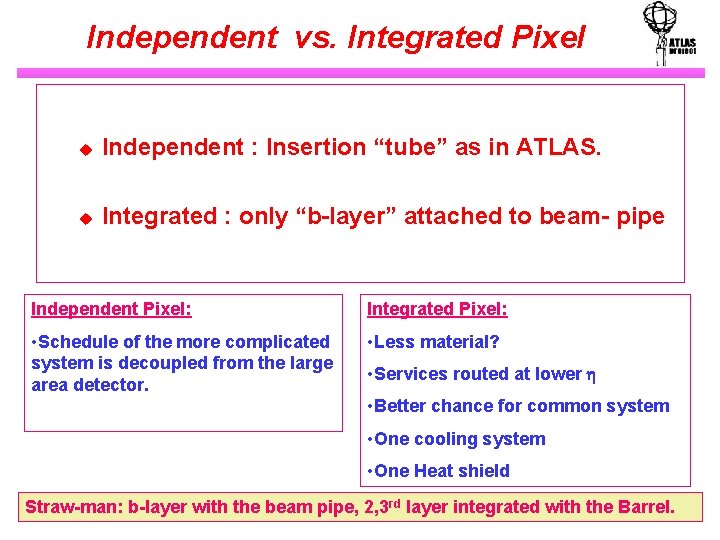
Independent vs. Integrated Pixel u Independent : Insertion “tube” as in ATLAS. u Integrated : only “b-layer” attached to beam- pipe Independent Pixel: Integrated Pixel: • Schedule of the more complicated system is decoupled from the large area detector. • Less material? • Services routed at lower h • Better chance for common system • One cooling system • One Heat shield Straw-man: b-layer with the beam pipe, 2, 3 rd layer integrated with the Barrel.
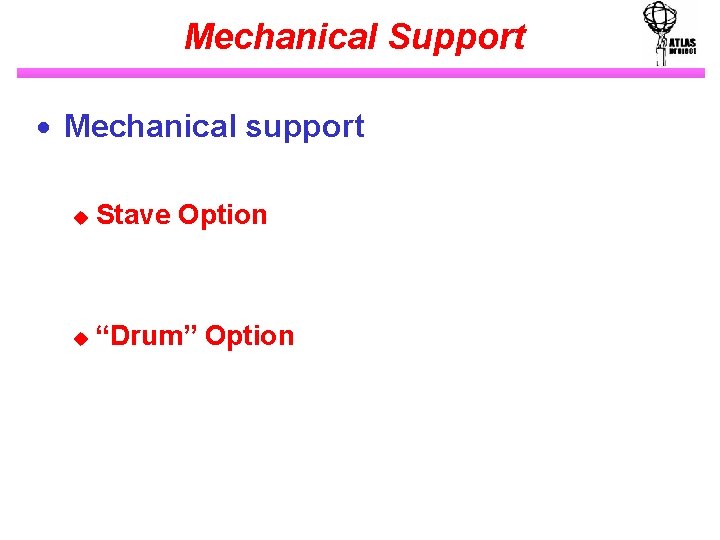
Mechanical Support · Mechanical support u Stave Option u “Drum” Option
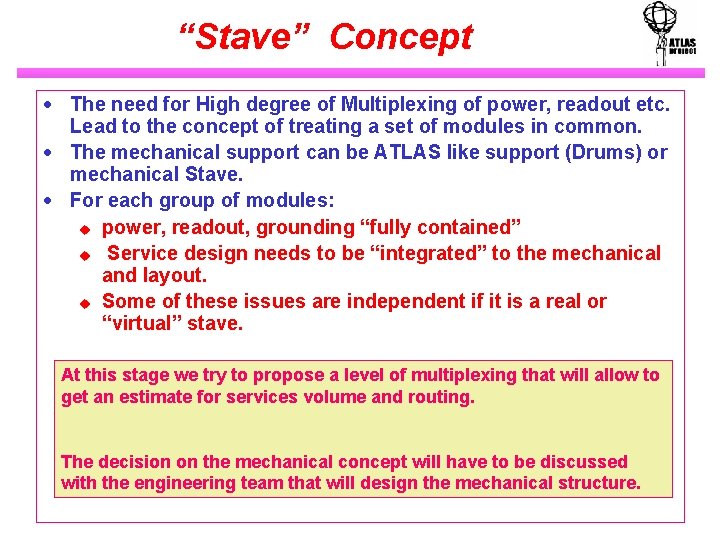
“Stave” Concept · The need for High degree of Multiplexing of power, readout etc. Lead to the concept of treating a set of modules in common. · The mechanical support can be ATLAS like support (Drums) or mechanical Stave. · For each group of modules: u power, readout, grounding “fully contained” u Service design needs to be “integrated” to the mechanical and layout. u Some of these issues are independent if it is a real or “virtual” stave. At this stage we try to propose a level of multiplexing that will allow to get an estimate for services volume and routing. The decision on the mechanical concept will have to be discussed with the engineering team that will design the mechanical structure.
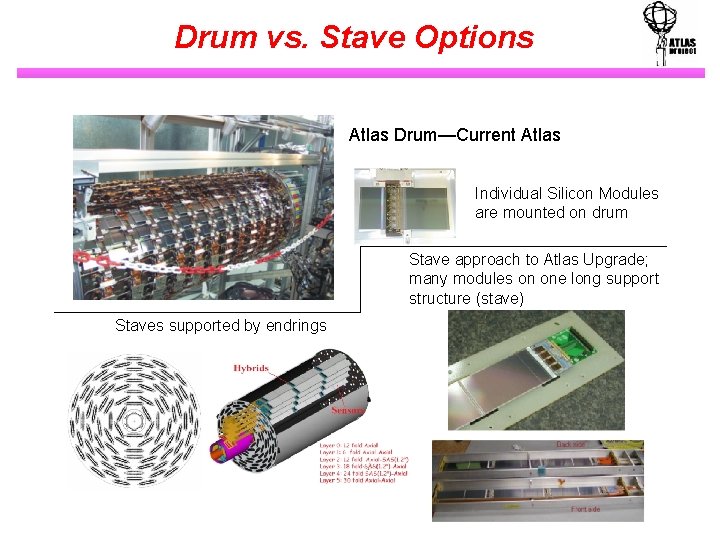
Drum vs. Stave Options Atlas Drum—Current Atlas Individual Silicon Modules are mounted on drum Stave approach to Atlas Upgrade; many modules on one long support structure (stave) Staves supported by endrings
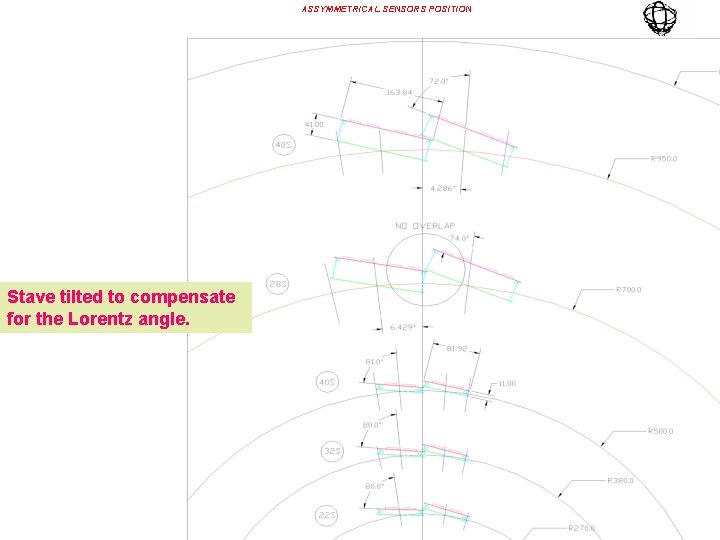
ASSYMMETRICAL SENSORS POSITION Stave tilted to compensate for the Lorentz angle.
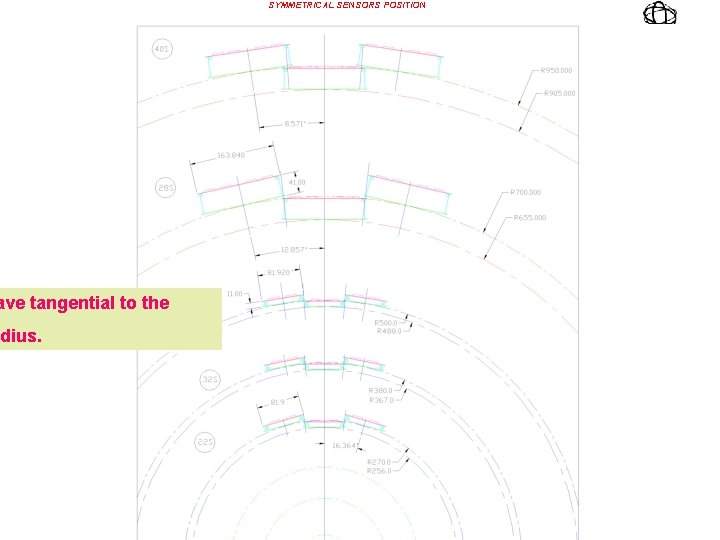
ave tangential to the adius. SYMMETRICAL SENSORS POSITION
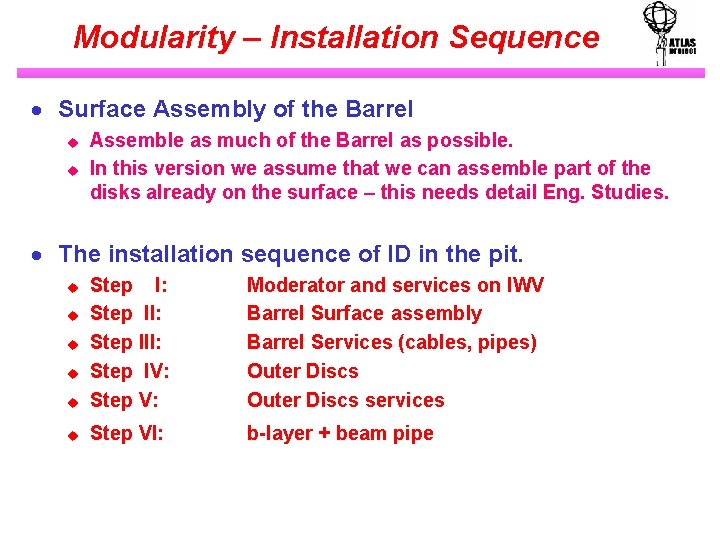
Modularity – Installation Sequence · Surface Assembly of the Barrel u u Assemble as much of the Barrel as possible. In this version we assume that we can assemble part of the disks already on the surface – this needs detail Eng. Studies. · The installation sequence of ID in the pit. u Step I: Step III: Step IV: Step V: Moderator and services on IWV Barrel Surface assembly Barrel Services (cables, pipes) Outer Discs services u Step VI: b-layer + beam pipe u u
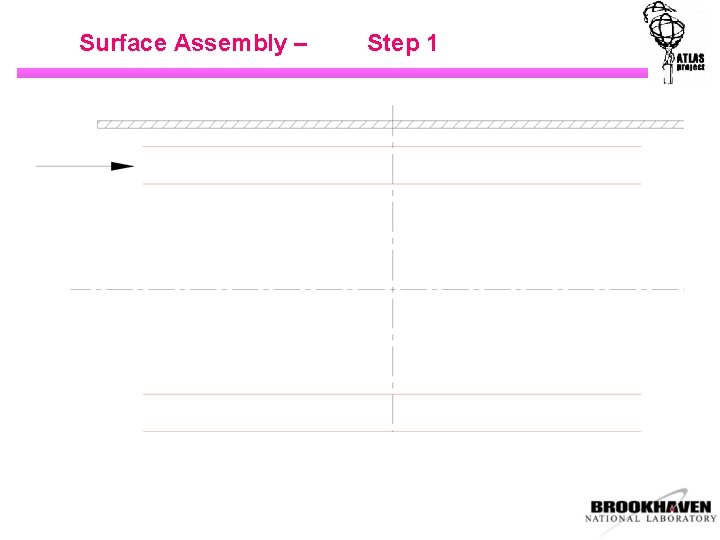
Surface Assembly – Step 1
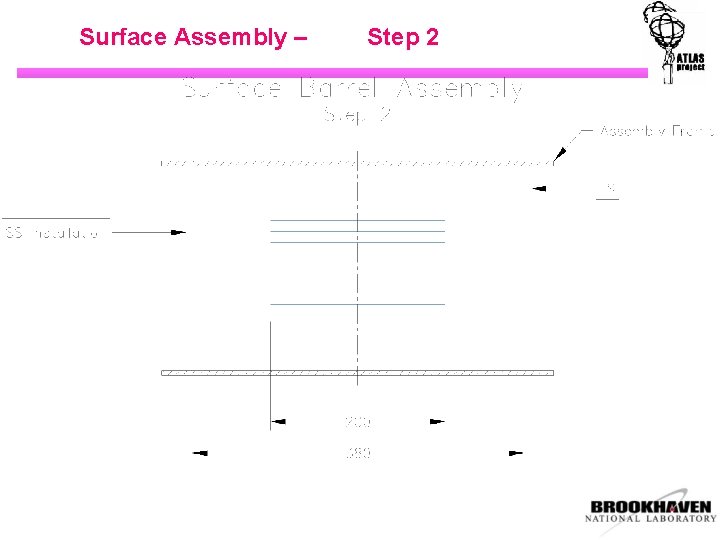
Surface Assembly – Step 2
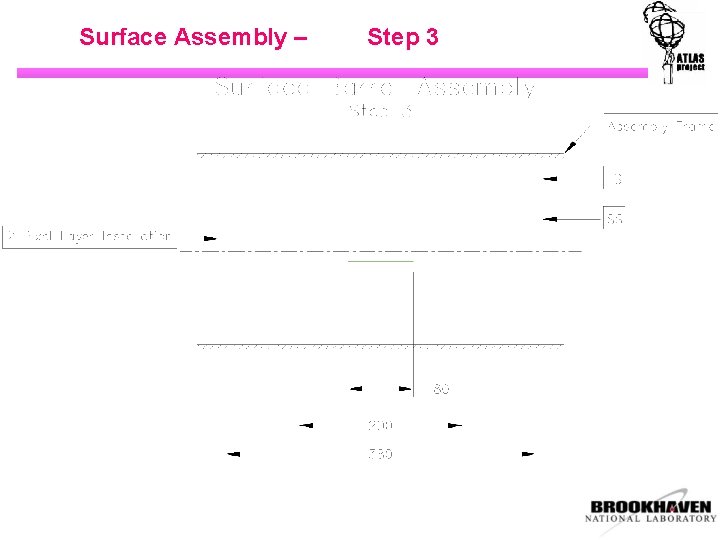
Surface Assembly – Step 3
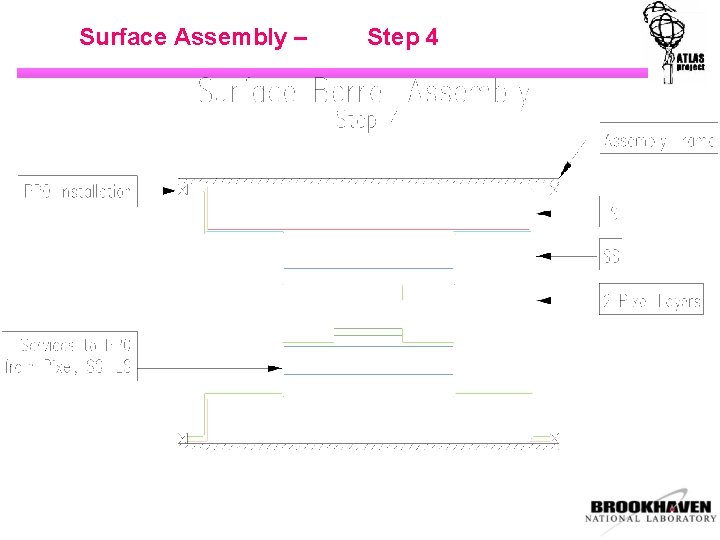
Surface Assembly – Step 4
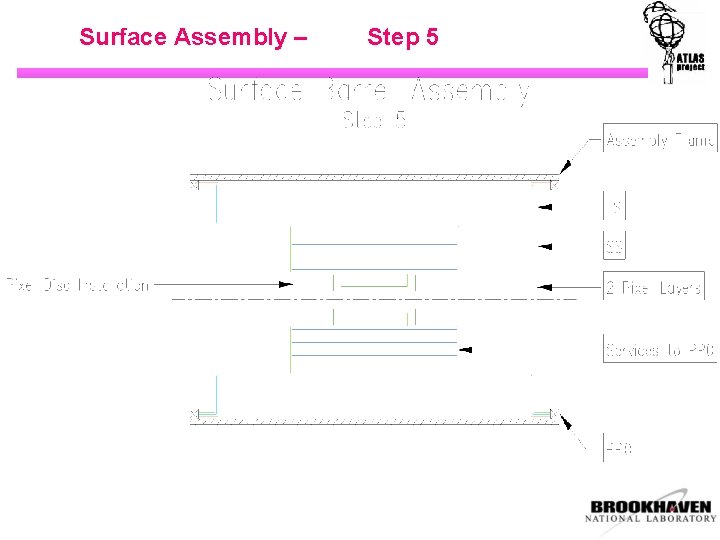
Surface Assembly – Step 5
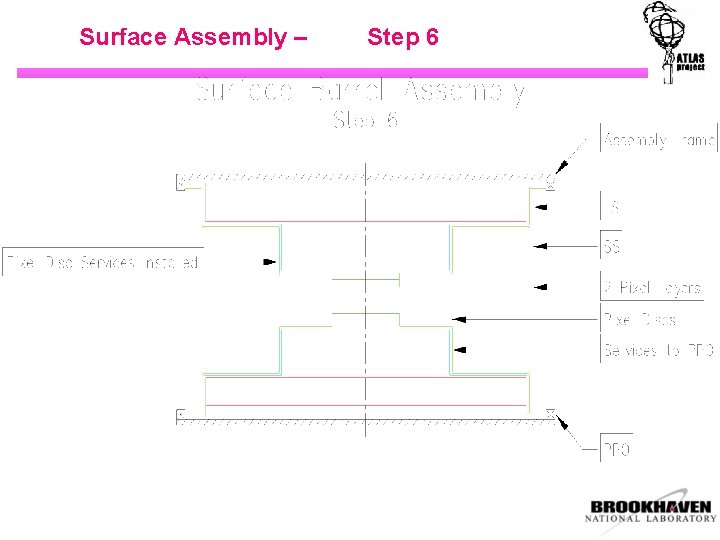
Surface Assembly – Step 6
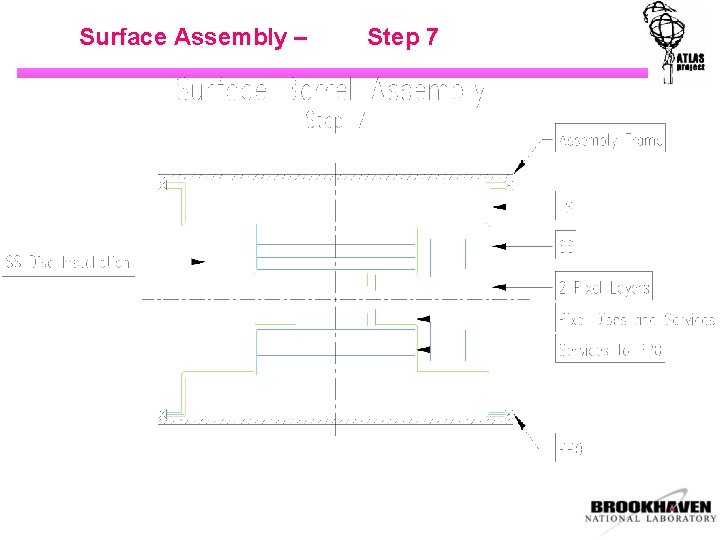
Surface Assembly – Step 7

Surface Assembly – Step 8
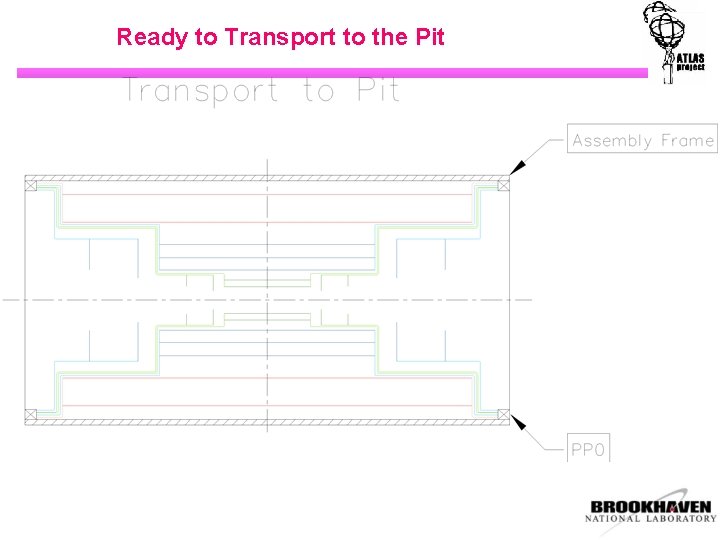
Ready to Transport to the Pit
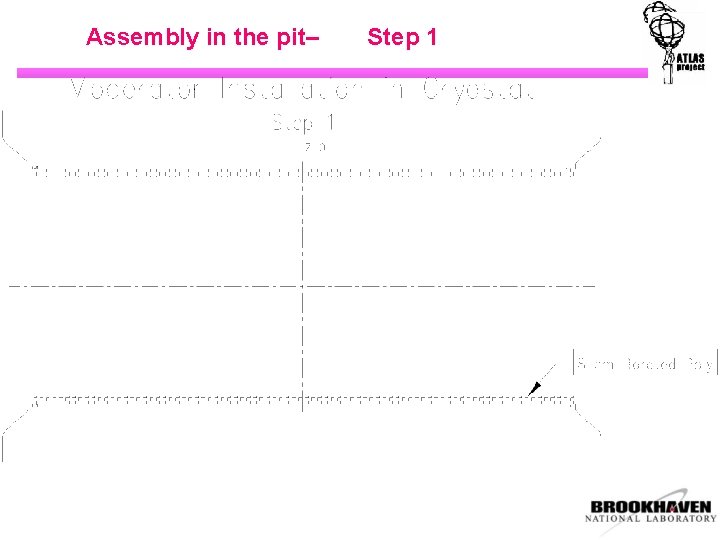
Assembly in the pit– Step 1
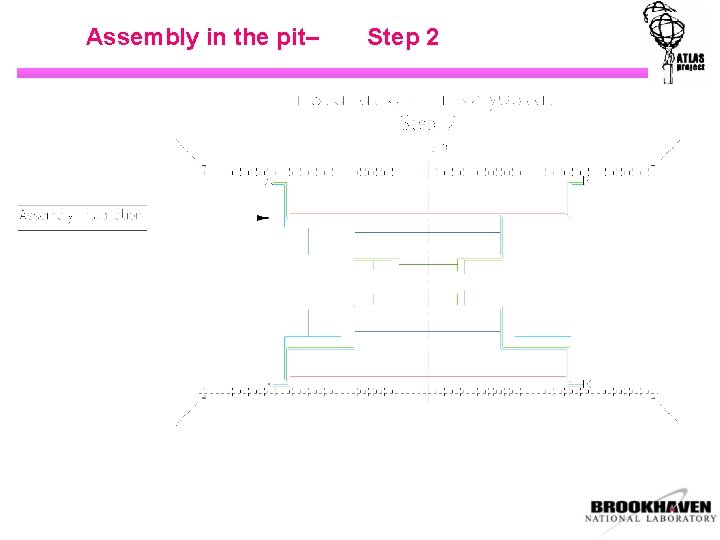
Assembly in the pit– Step 2
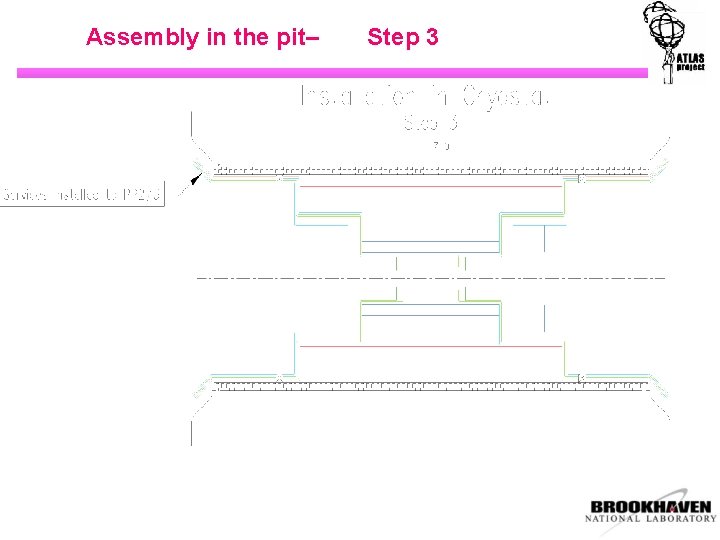
Assembly in the pit– Step 3
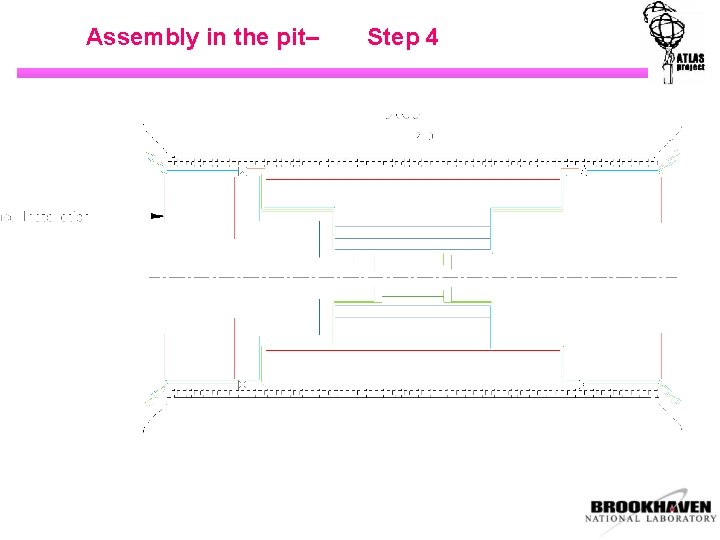
Assembly in the pit– Step 4
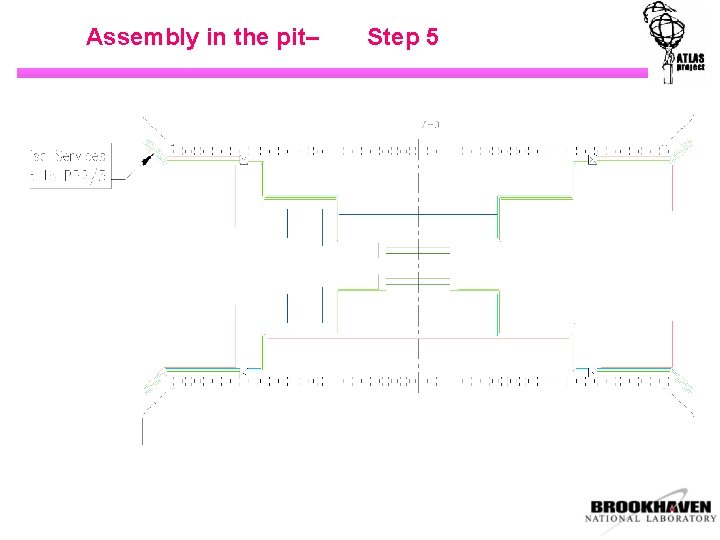
Assembly in the pit– Step 5
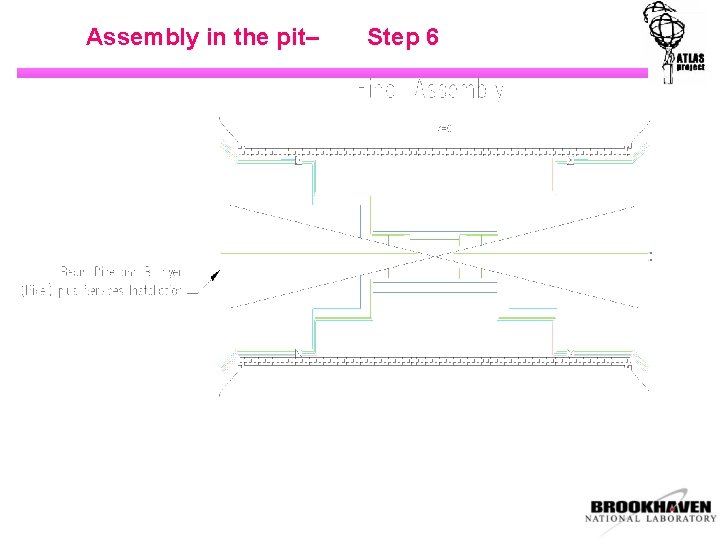
Assembly in the pit– Step 6
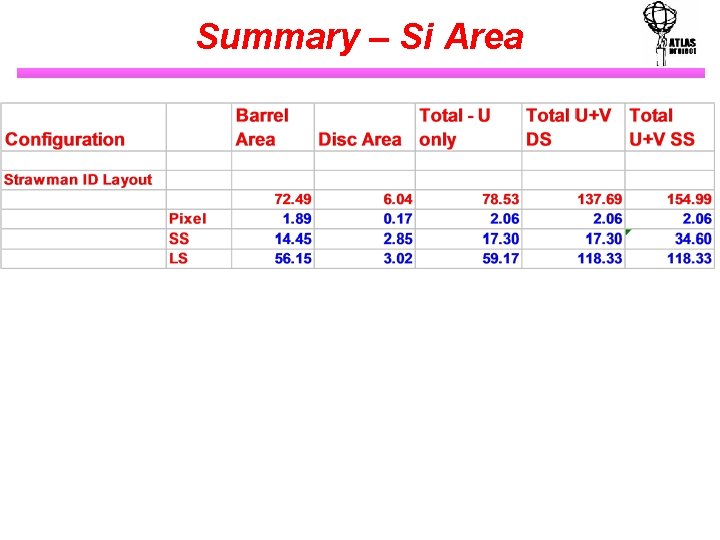
Summary – Si Area
What is man vs man
Strawman proposal
Straw man fallacy
Whats a straw man argument
Examples of straw man fallacy
Anecdotal fallacy
Straw man fallacy in the crucible
Strawman argument
The three little pigs once upon a time
Strawboard partition
Straw in asl
How to build a straw bale dog house
Straw coloured fluid
Three little pigs once upon a time
The egg drop project fairview
Froude
The passionate shepherd to his love rhyme scheme
Straw truss bridge
Underground water
That old straw sojourner
How does a straw work physics
Last straw
Straw kriterleri
Air pressure straw
Pcm512
Fixed layout website example
Numerator layout
Language
Internal conflict definition literature
The white mans burden cartoon
Forbrenner man mer når man har mensen
Carnal christian characteristics
Sträckan hastighet tid