SURFACE PREPARATION TESTING A Special Presentation on CHLOR
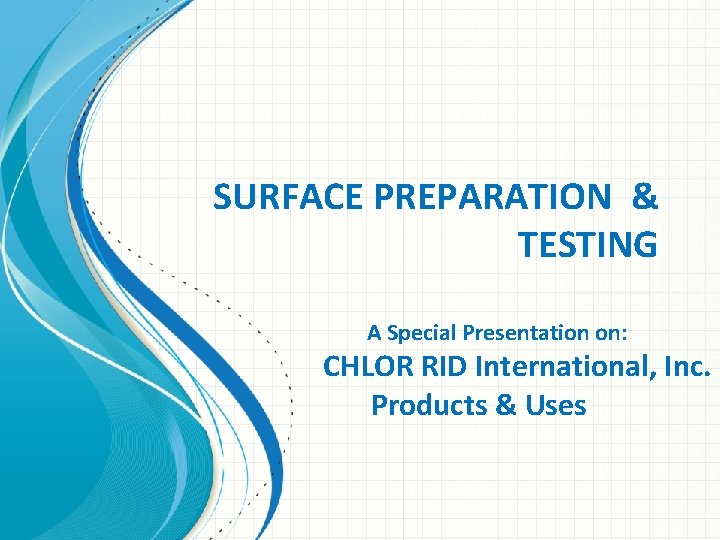
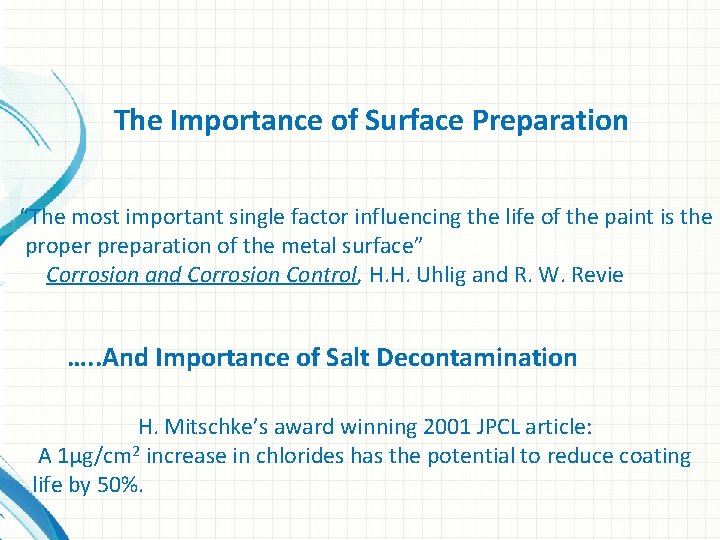
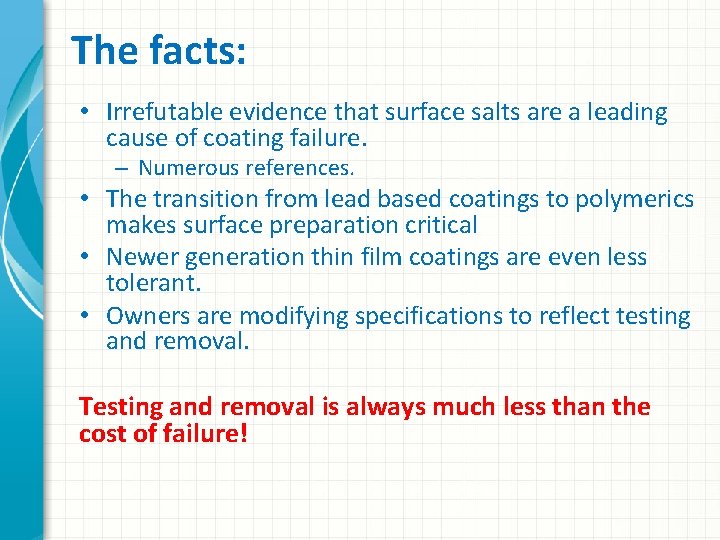
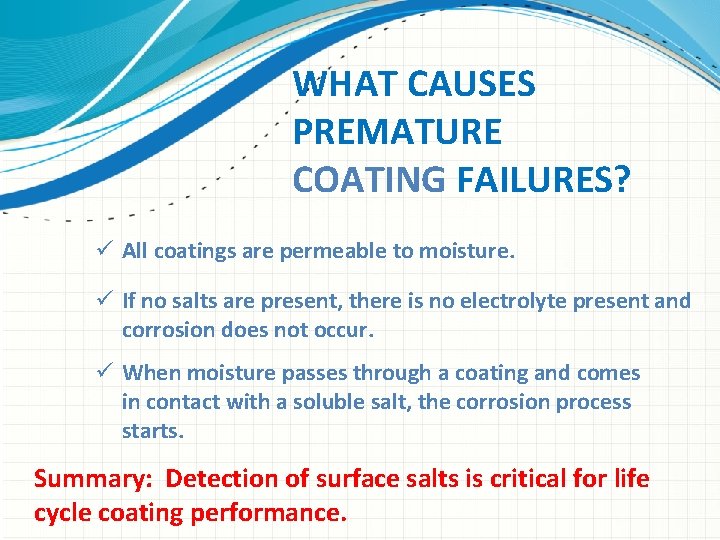
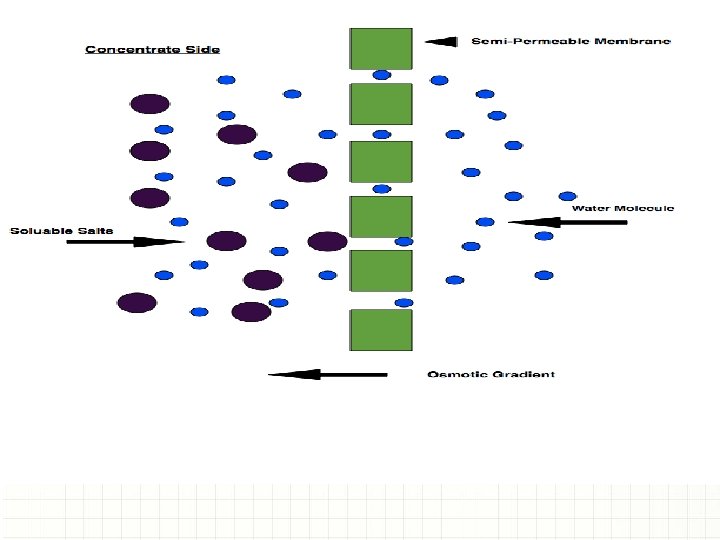
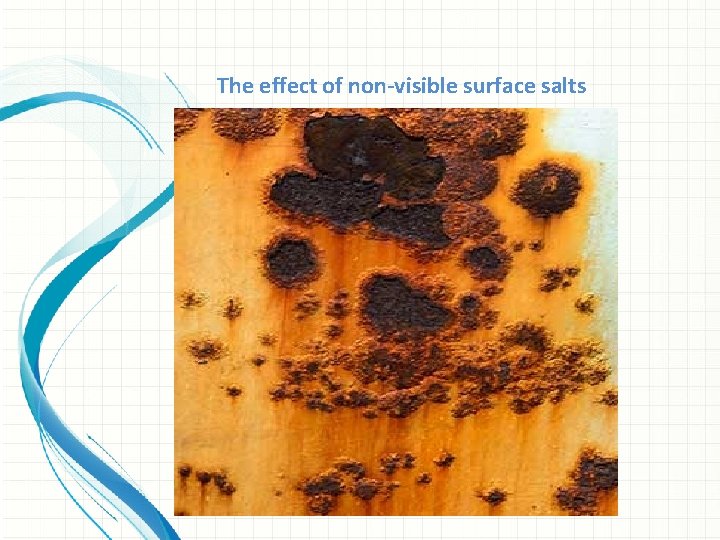
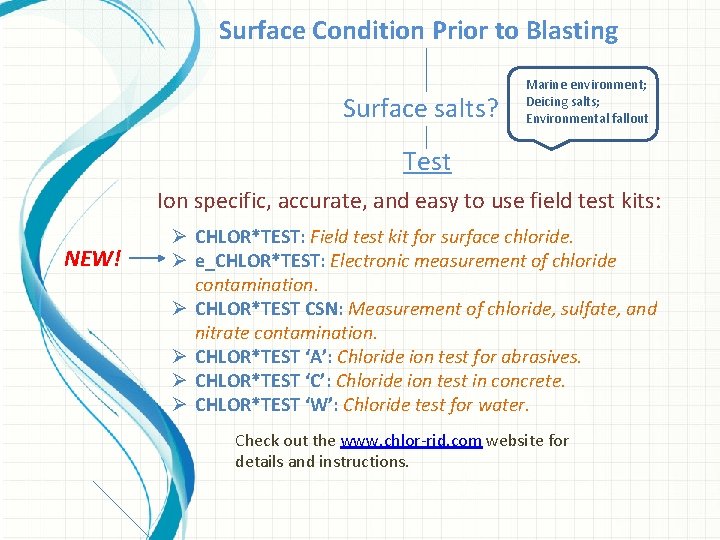
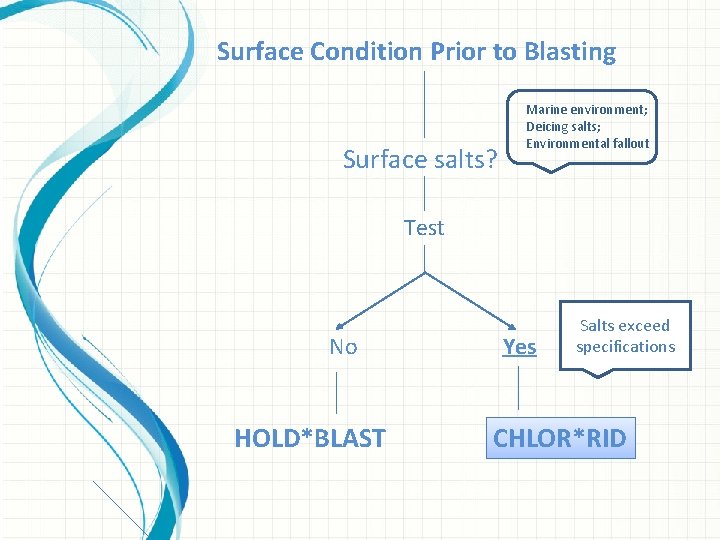
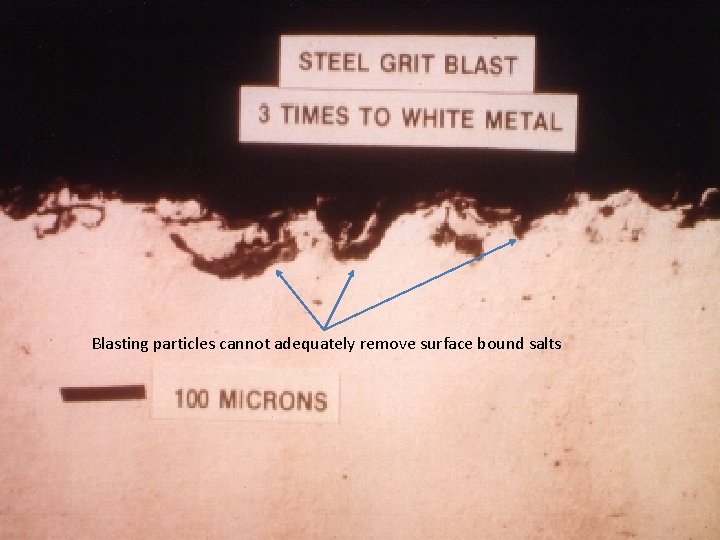
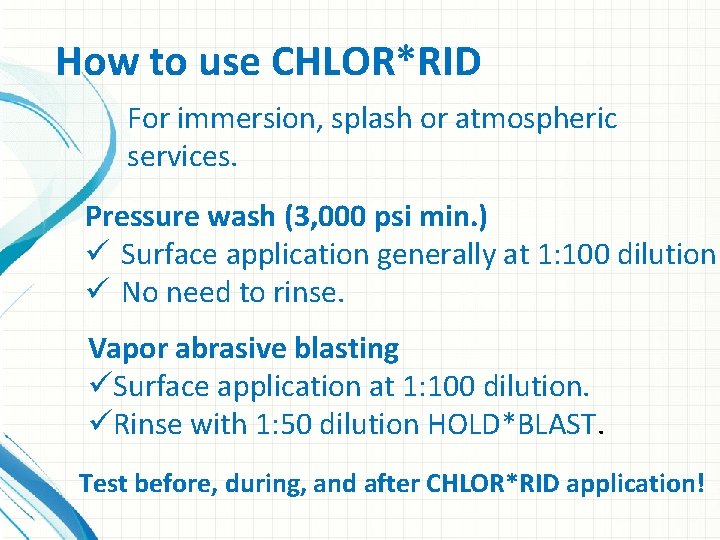
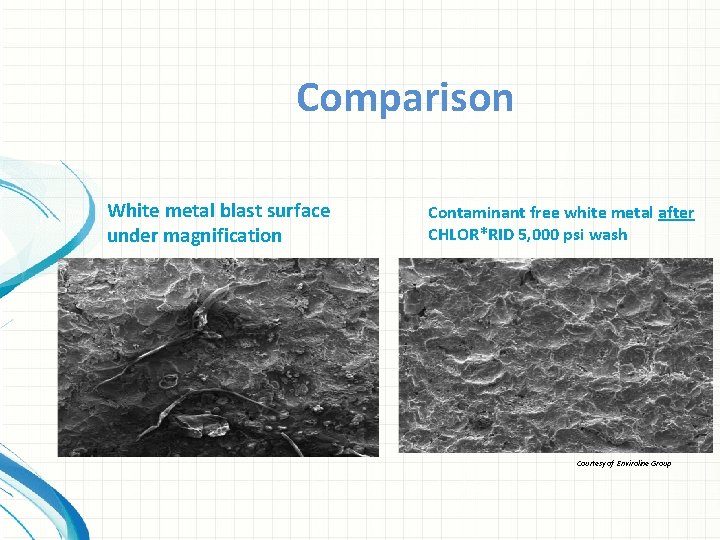
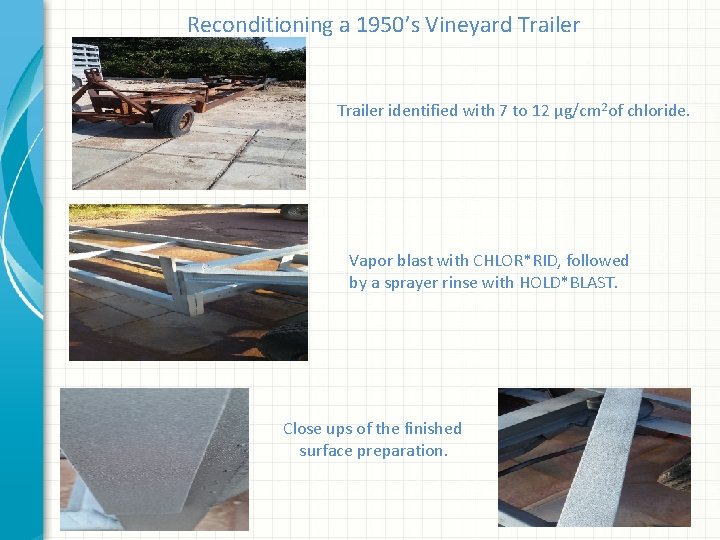
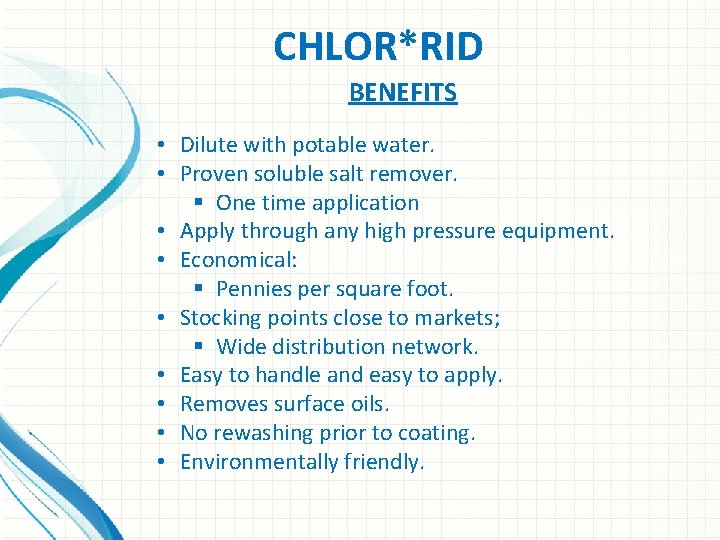
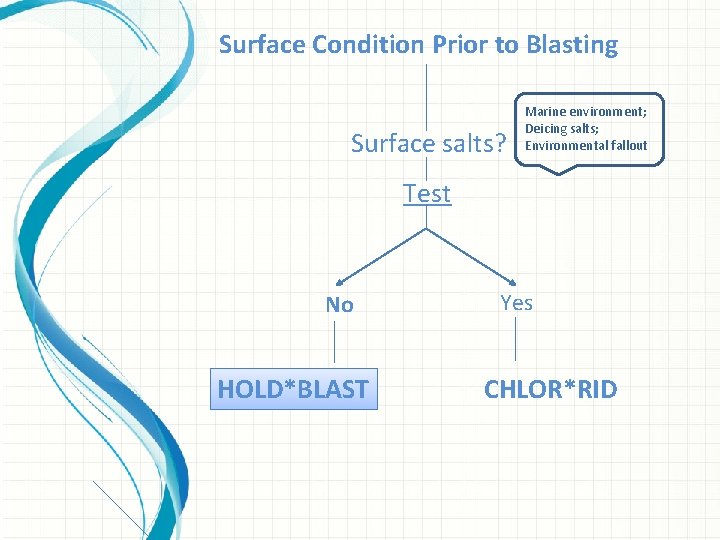
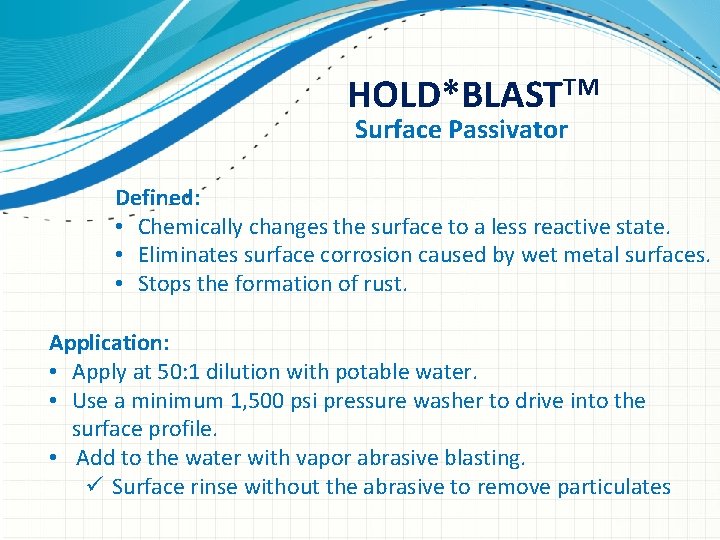
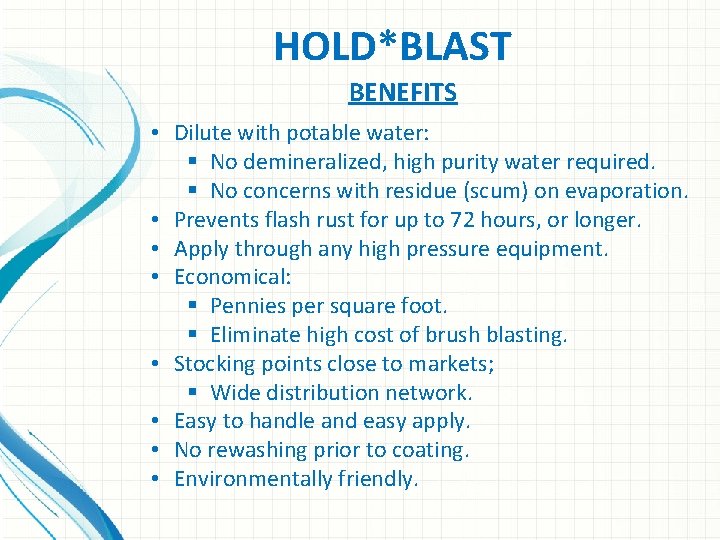
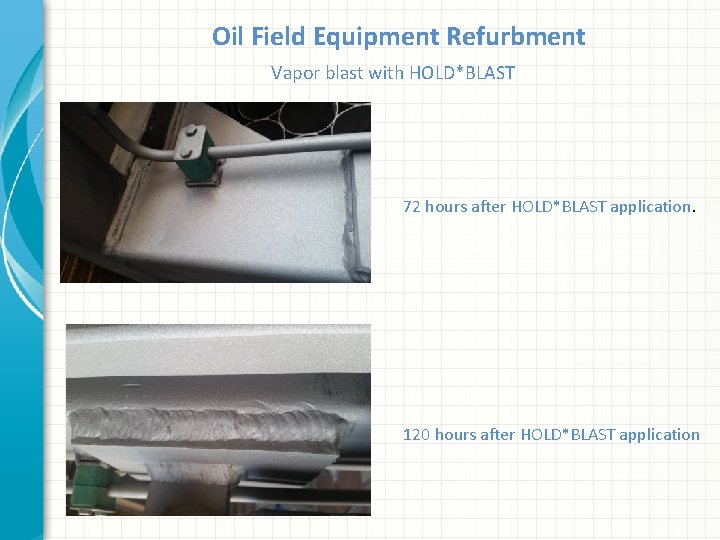
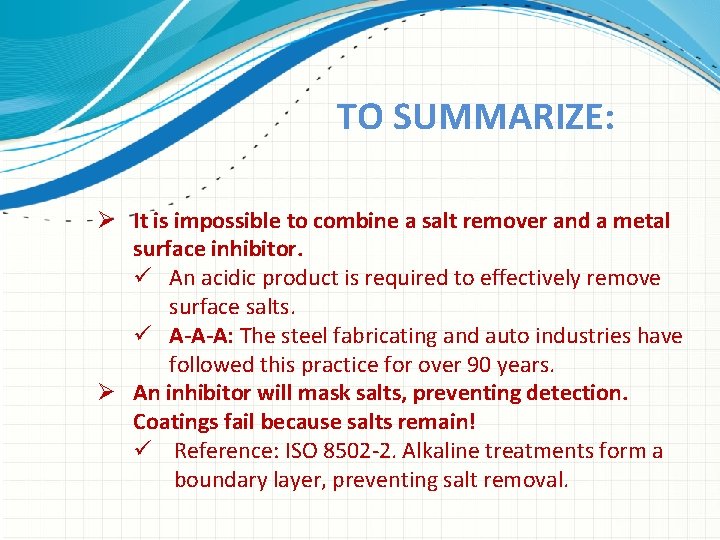
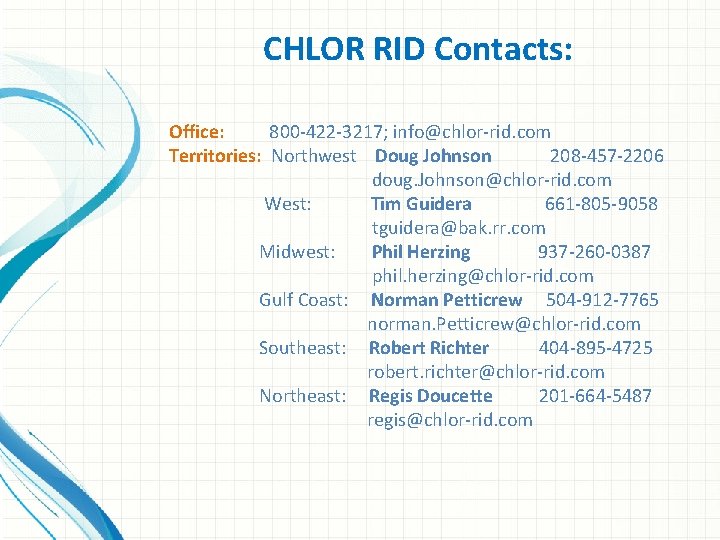
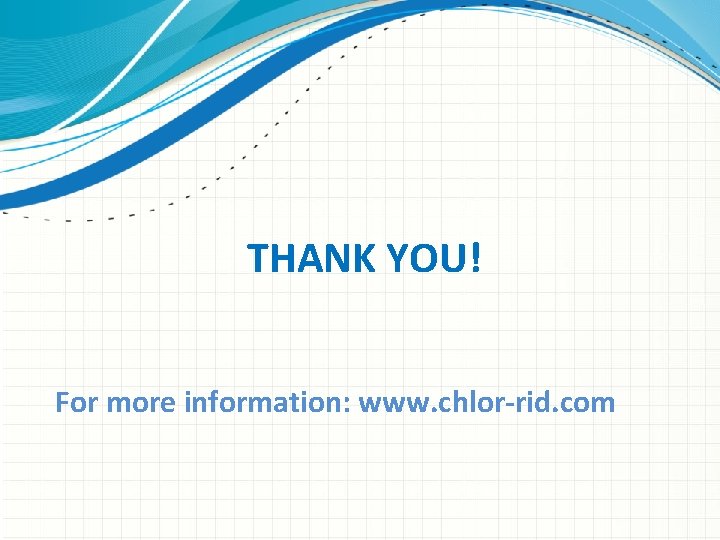
- Slides: 20
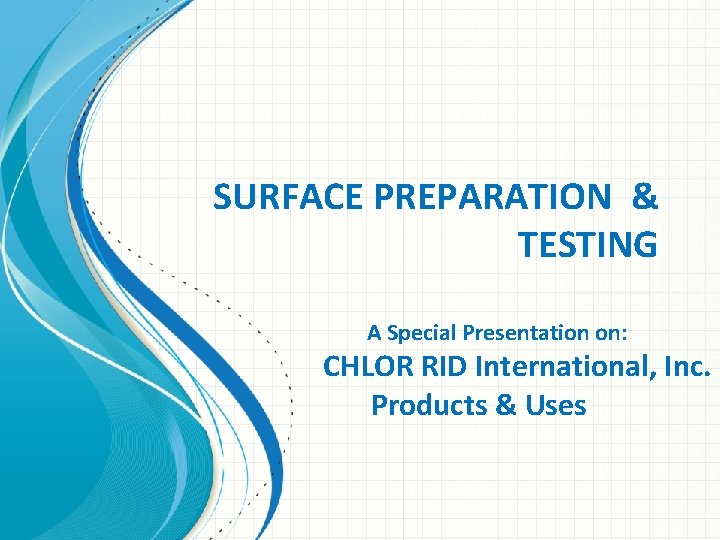
SURFACE PREPARATION & TESTING A Special Presentation on: CHLOR RID International, Inc. Products & Uses
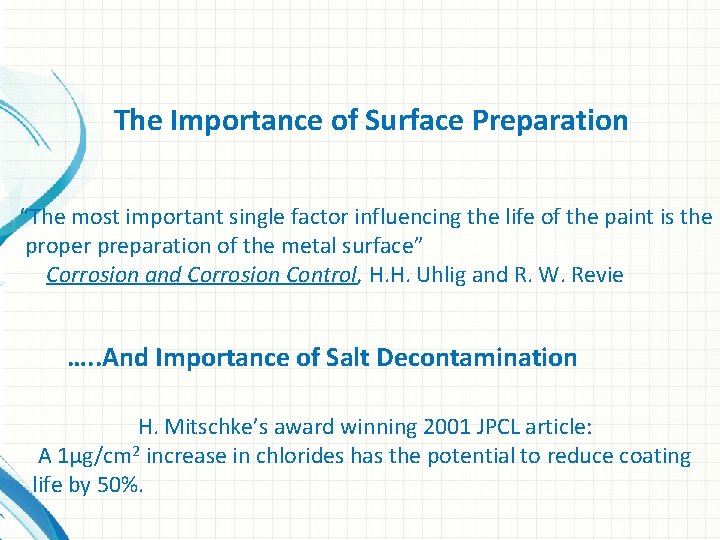
The Importance of Surface Preparation “The most important single factor influencing the life of the paint is the proper preparation of the metal surface” Corrosion and Corrosion Control, H. H. Uhlig and R. W. Revie …. . And Importance of Salt Decontamination H. Mitschke’s award winning 2001 JPCL article: A 1µg/cm 2 increase in chlorides has the potential to reduce coating life by 50%.
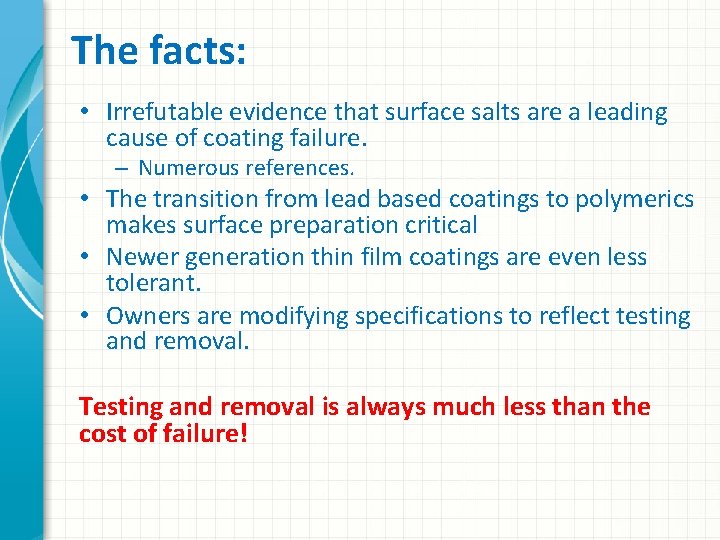
The facts: • Irrefutable evidence that surface salts are a leading cause of coating failure. – Numerous references. • The transition from lead based coatings to polymerics makes surface preparation critical • Newer generation thin film coatings are even less tolerant. • Owners are modifying specifications to reflect testing and removal. Testing and removal is always much less than the cost of failure!
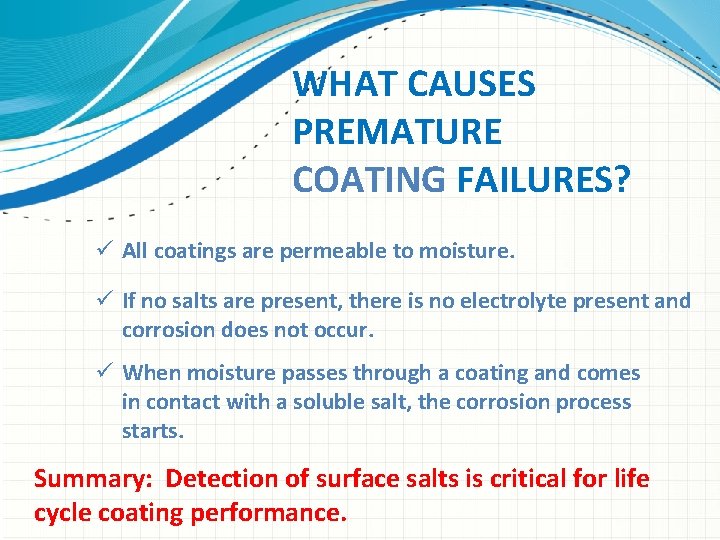
WHAT CAUSES PREMATURE COATING FAILURES? ü All coatings are permeable to moisture. ü If no salts are present, there is no electrolyte present and corrosion does not occur. ü When moisture passes through a coating and comes in contact with a soluble salt, the corrosion process starts. Summary: Detection of surface salts is critical for life cycle coating performance.
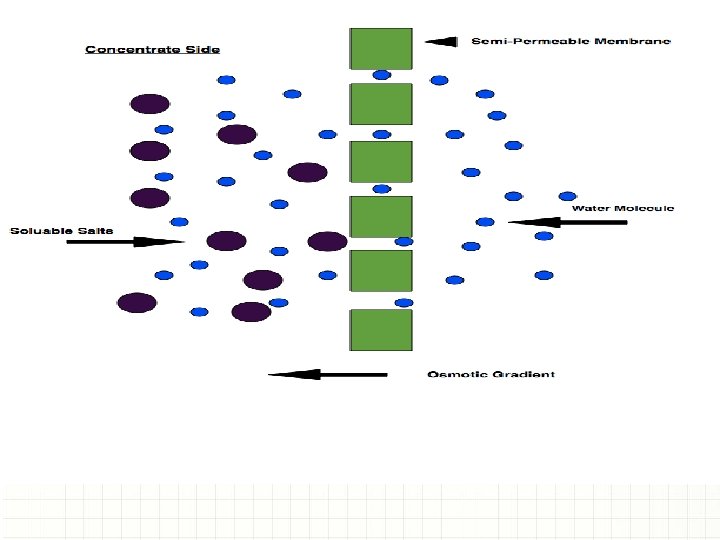
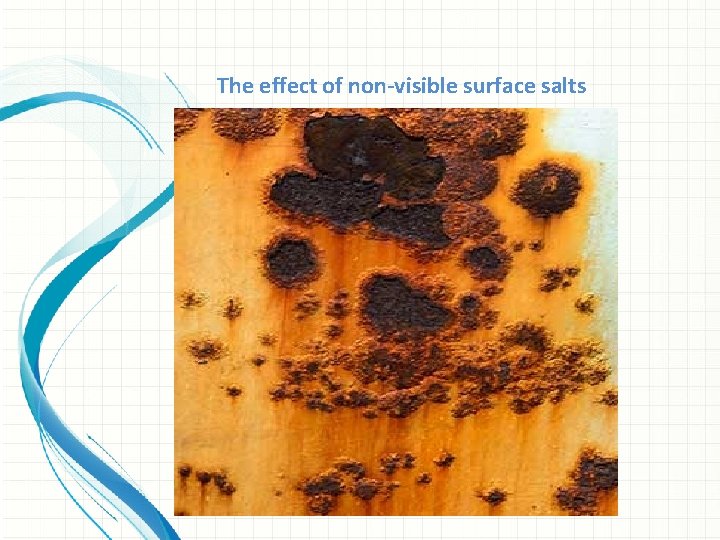
The effect of non-visible surface salts
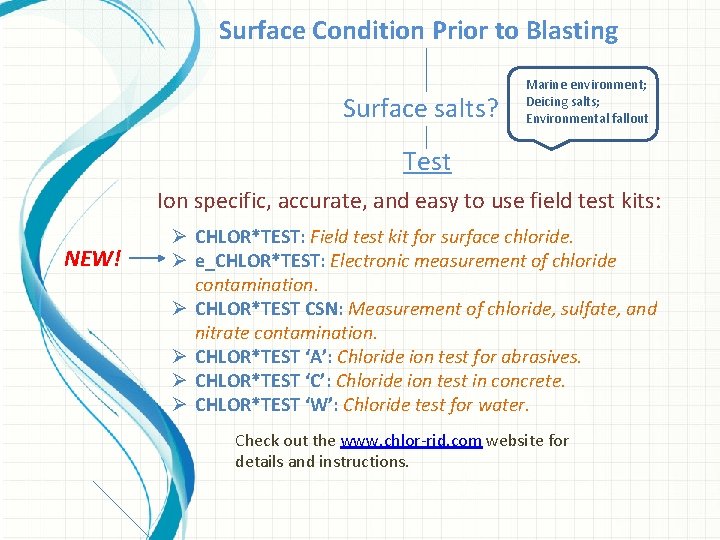
Surface Condition Prior to Blasting Surface salts? Marine environment; Deicing salts; Environmental fallout Test Ion specific, accurate, and easy to use field test kits: NEW! Ø CHLOR*TEST: Field test kit for surface chloride. Ø e_CHLOR*TEST: Electronic measurement of chloride contamination. Ø CHLOR*TEST CSN: Measurement of chloride, sulfate, and nitrate contamination. Ø CHLOR*TEST ‘A’: Chloride ion test for abrasives. Ø CHLOR*TEST ‘C’: Chloride ion test in concrete. Ø CHLOR*TEST ‘W’: Chloride test for water. Check out the www. chlor-rid. com website for details and instructions.
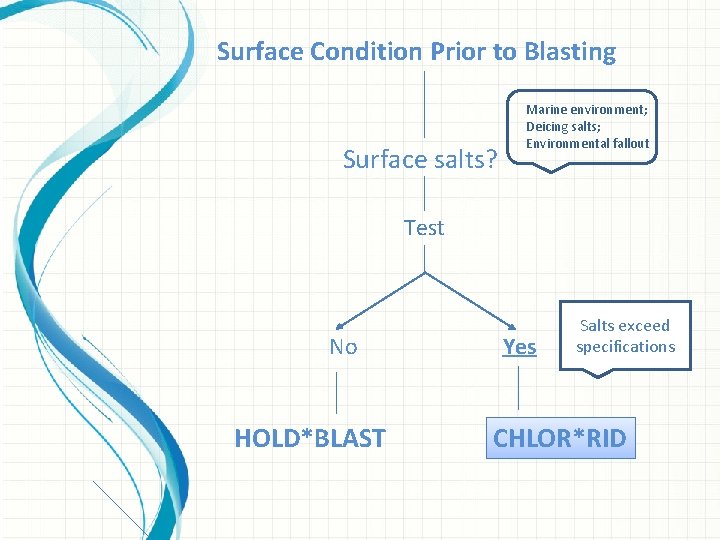
Surface Condition Prior to Blasting Surface salts? Marine environment; Deicing salts; Environmental fallout Test No HOLD*BLAST Yes Salts exceed specifications CHLOR*RID
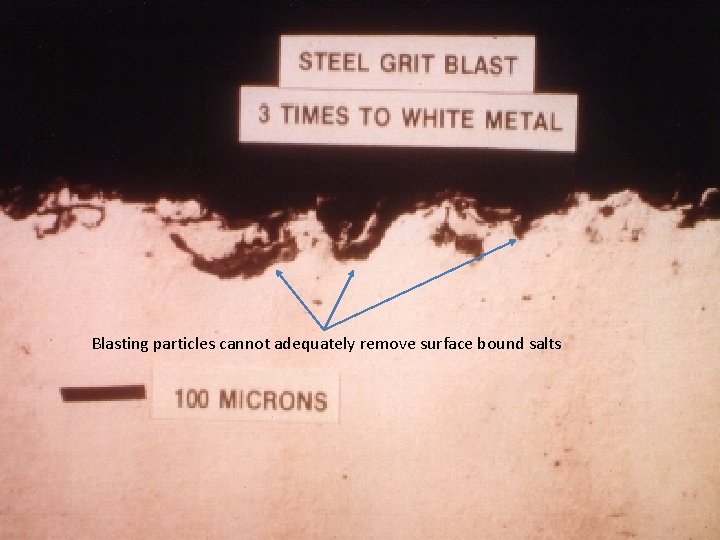
Blasting particles cannot adequately remove surface bound salts
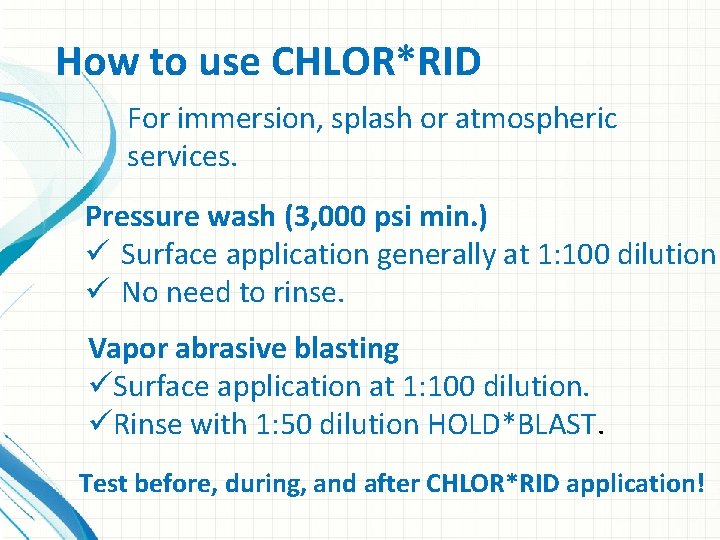
How to use CHLOR*RID For immersion, splash or atmospheric services. Pressure wash (3, 000 psi min. ) ü Surface application generally at 1: 100 dilution ü No need to rinse. Vapor abrasive blasting üSurface application at 1: 100 dilution. üRinse with 1: 50 dilution HOLD*BLAST. Test before, during, and after CHLOR*RID application!
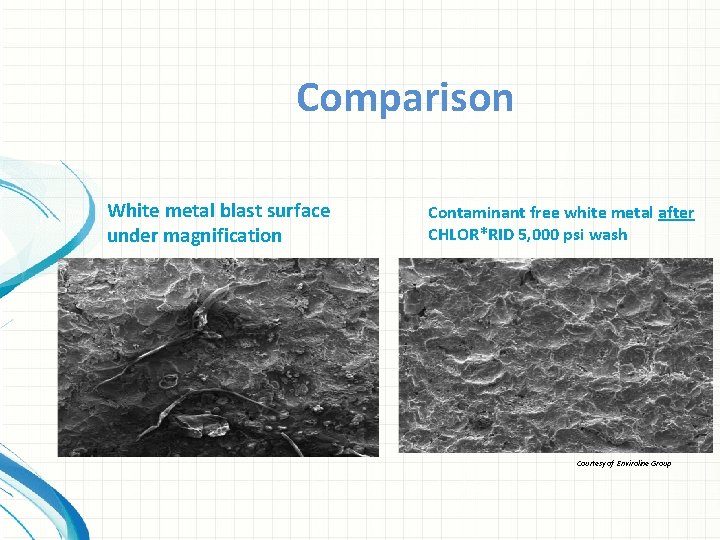
Comparison White metal blast surface under magnification Contaminant free white metal after CHLOR*RID 5, 000 psi wash Courtesy of Enviroline Group
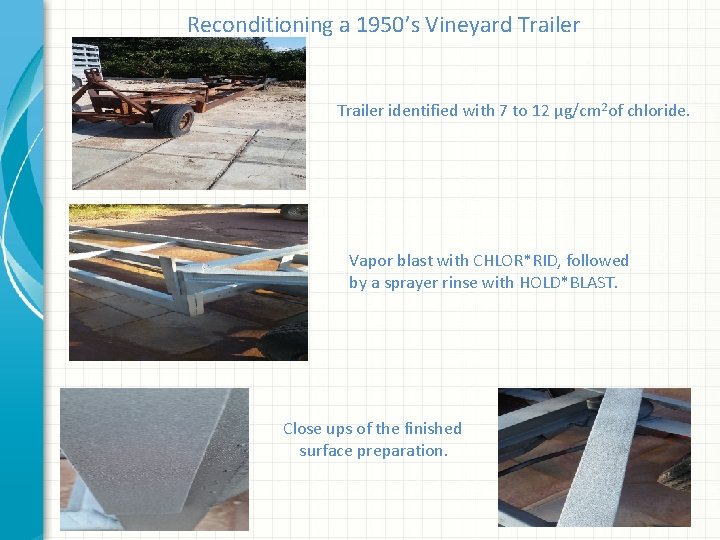
Reconditioning a 1950’s Vineyard Trailer identified with 7 to 12 µg/cm 2 of chloride. Vapor blast with CHLOR*RID, followed by a sprayer rinse with HOLD*BLAST. Close ups of the finished surface preparation.
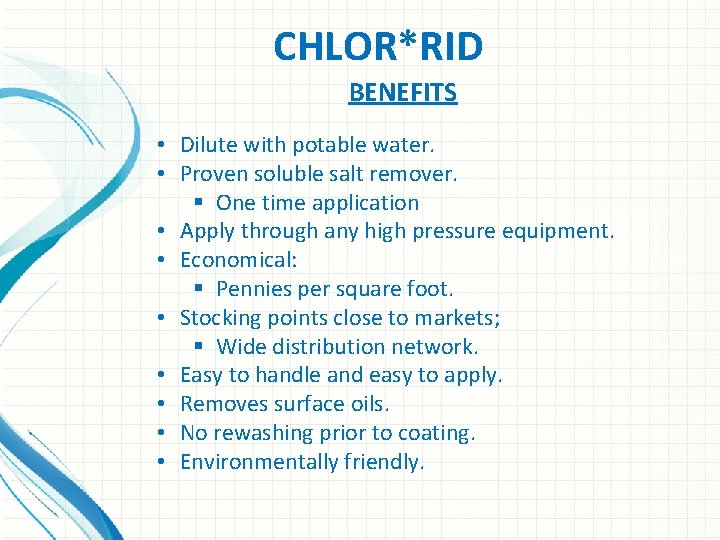
CHLOR*RID BENEFITS • Dilute with potable water. • Proven soluble salt remover. § One time application • Apply through any high pressure equipment. • Economical: § Pennies per square foot. • Stocking points close to markets; § Wide distribution network. • Easy to handle and easy to apply. • Removes surface oils. • No rewashing prior to coating. • Environmentally friendly.
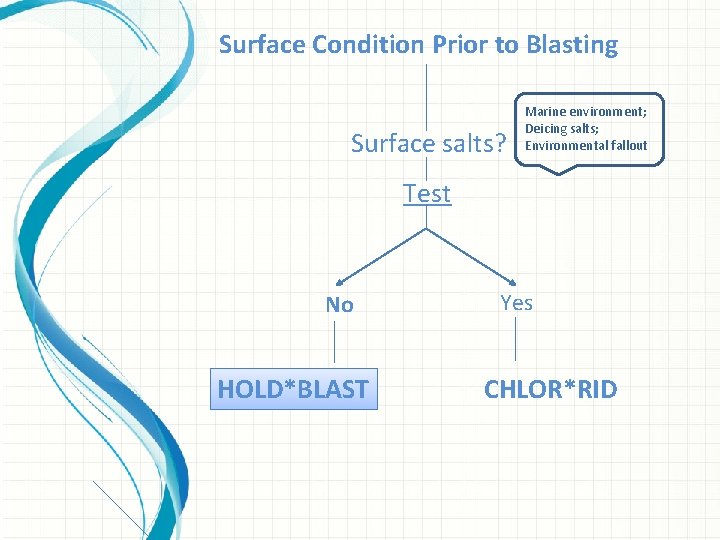
Surface Condition Prior to Blasting Surface salts? Marine environment; Deicing salts; Environmental fallout Test No HOLD*BLAST Yes CHLOR*RID
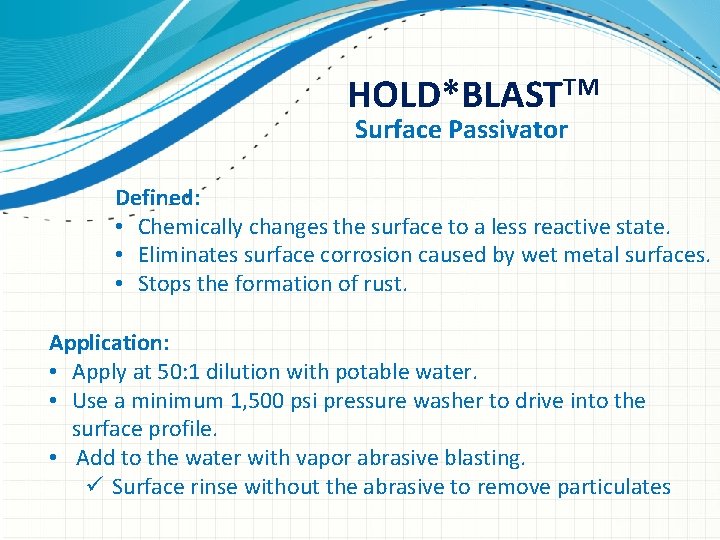
HOLD*BLASTTM Surface Passivator Defined: • Chemically changes the surface to a less reactive state. • Eliminates surface corrosion caused by wet metal surfaces. • Stops the formation of rust. Application: • Apply at 50: 1 dilution with potable water. • Use a minimum 1, 500 psi pressure washer to drive into the surface profile. • Add to the water with vapor abrasive blasting. ü Surface rinse without the abrasive to remove particulates
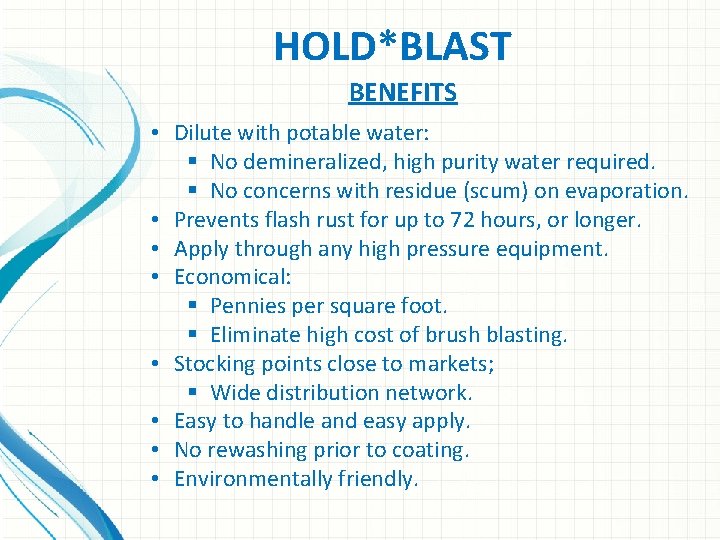
HOLD*BLAST BENEFITS • Dilute with potable water: § No demineralized, high purity water required. § No concerns with residue (scum) on evaporation. • Prevents flash rust for up to 72 hours, or longer. • Apply through any high pressure equipment. • Economical: § Pennies per square foot. § Eliminate high cost of brush blasting. • Stocking points close to markets; § Wide distribution network. • Easy to handle and easy apply. • No rewashing prior to coating. • Environmentally friendly.
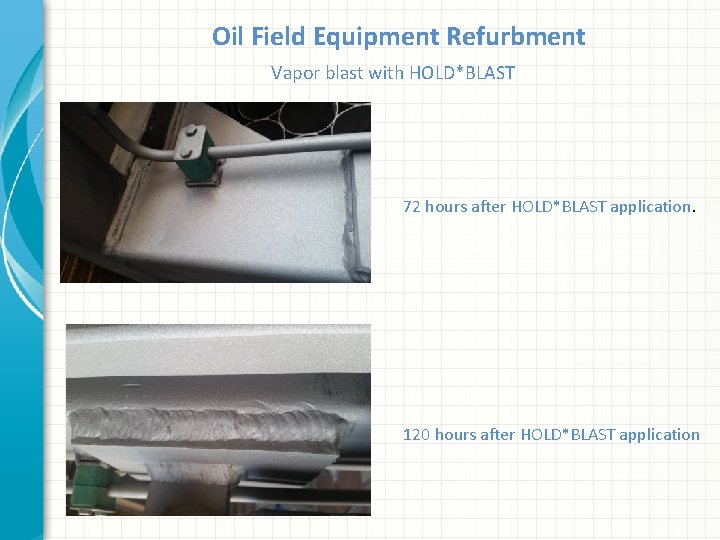
Oil Field Equipment Refurbment Vapor blast with HOLD*BLAST 72 hours after HOLD*BLAST application. 120 hours after HOLD*BLAST application
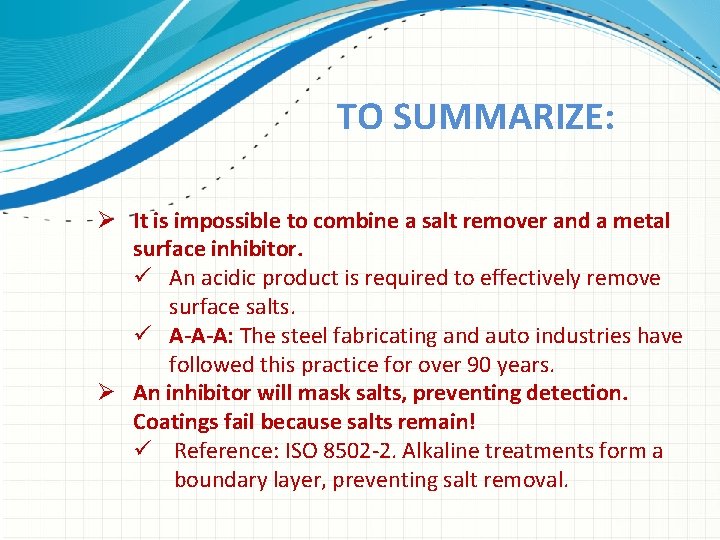
TO SUMMARIZE: Ø It is impossible to combine a salt remover and a metal surface inhibitor. ü An acidic product is required to effectively remove surface salts. ü A-A-A: The steel fabricating and auto industries have followed this practice for over 90 years. Ø An inhibitor will mask salts, preventing detection. Coatings fail because salts remain! ü Reference: ISO 8502 -2. Alkaline treatments form a boundary layer, preventing salt removal.
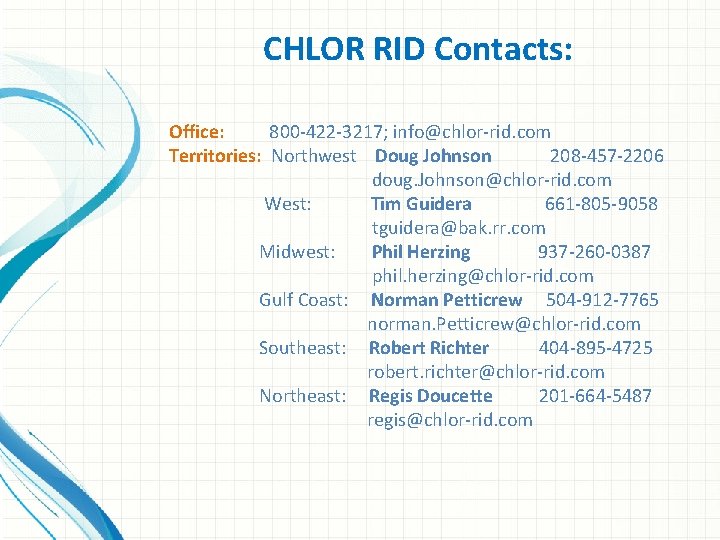
CHLOR RID Contacts: Office: 800 -422 -3217; info@chlor-rid. com Territories: Northwest Doug Johnson 208 -457 -2206 doug. Johnson@chlor-rid. com West: Tim Guidera 661 -805 -9058 tguidera@bak. rr. com Midwest: Phil Herzing 937 -260 -0387 phil. herzing@chlor-rid. com Gulf Coast: Norman Petticrew 504 -912 -7765 norman. Petticrew@chlor-rid. com Southeast: Robert Richter 404 -895 -4725 robert. richter@chlor-rid. com Northeast: Regis Doucette 201 -664 -5487 regis@chlor-rid. com
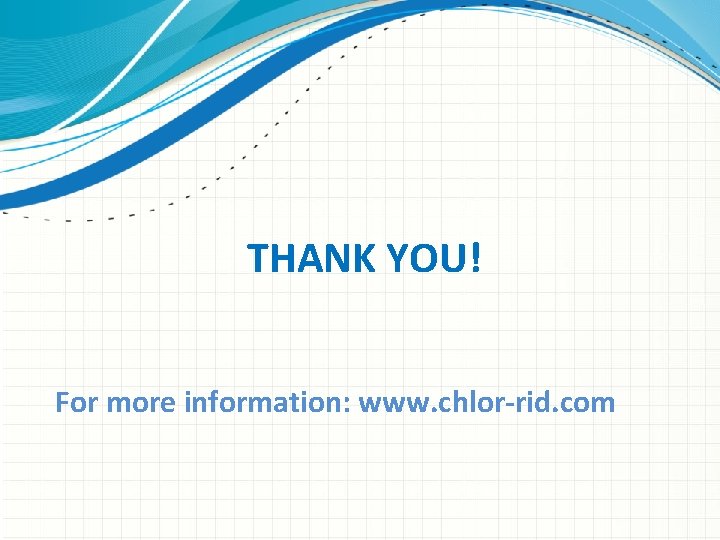
THANK YOU! For more information: www. chlor-rid. com
Promocja elektronowa
Brom skupenství
Eigenschaften der halogene
Chlor test csn salts
Reaktionen der alkane
Chlor trimeton walmart
Chlor využití
Report preparation and presentation
Report preparation and presentation in marketing research
Robust boundary value testing
Manth
Special value testing
Domain test means
Logic based testing in software testing
Du path testing
Positive negative testing
Static testing and dynamic testing
Globalization testing example
Neighborhood integration testing
Cause effect graphing technique
Control structure testing in software engineering