Speeds and Feeds Computer Integrated Manufacturing 2013 Project
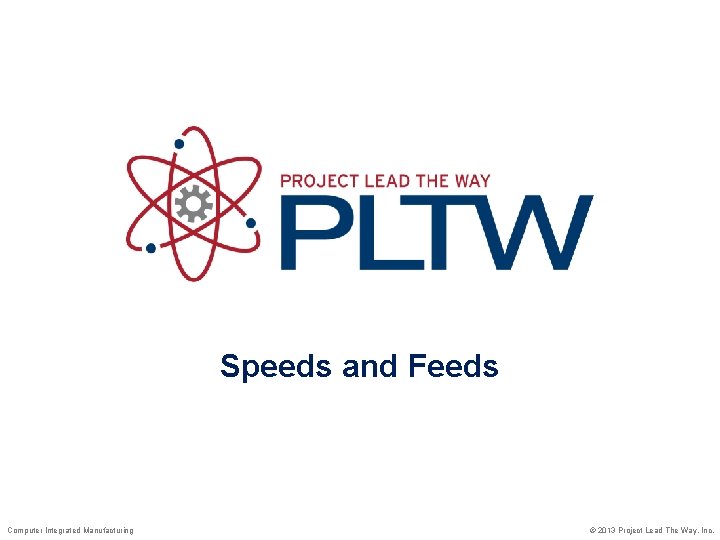
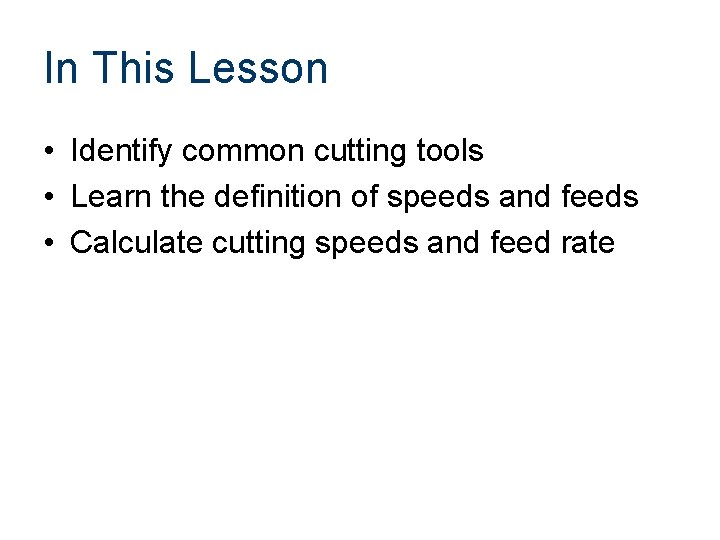
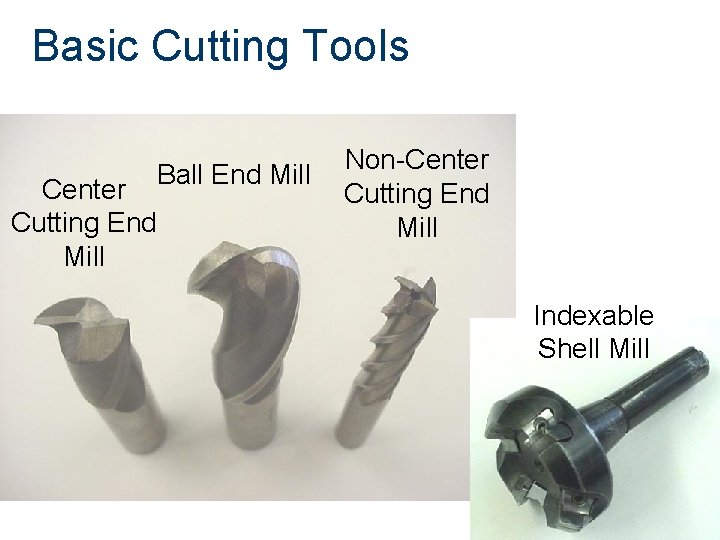
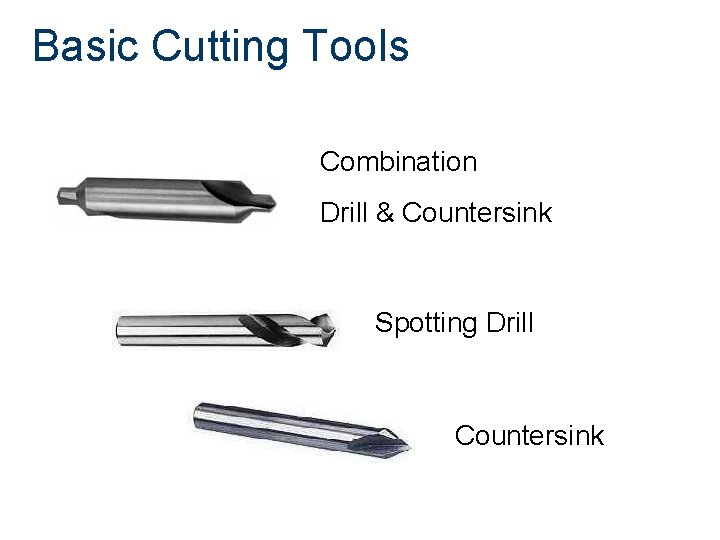
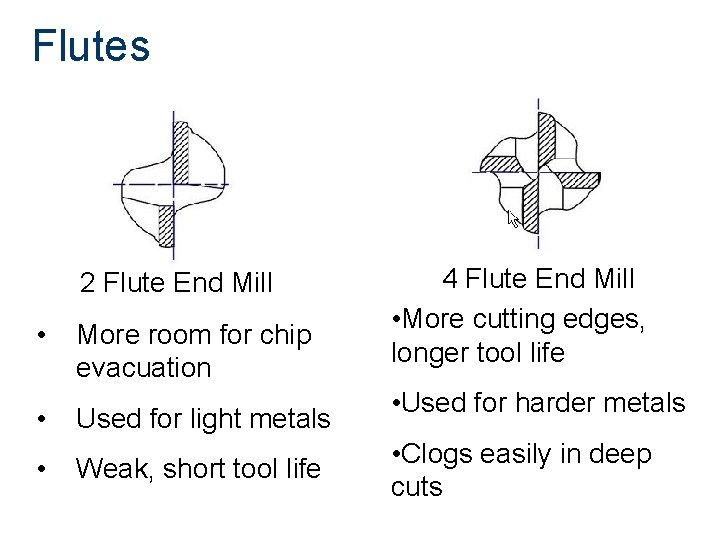
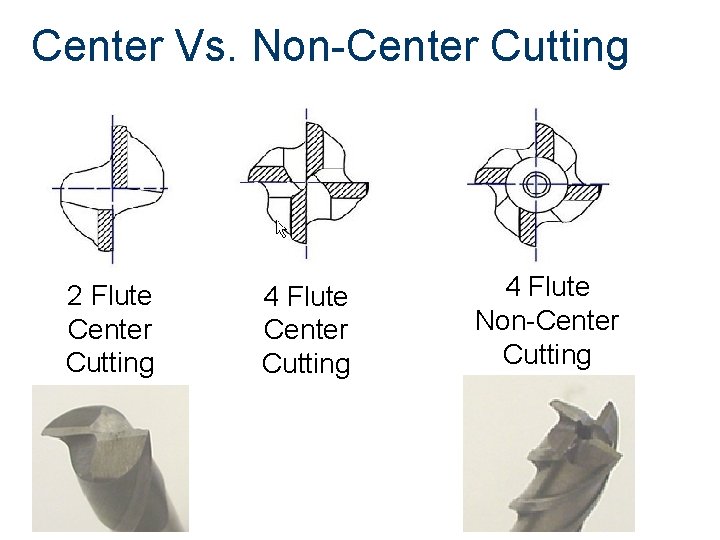
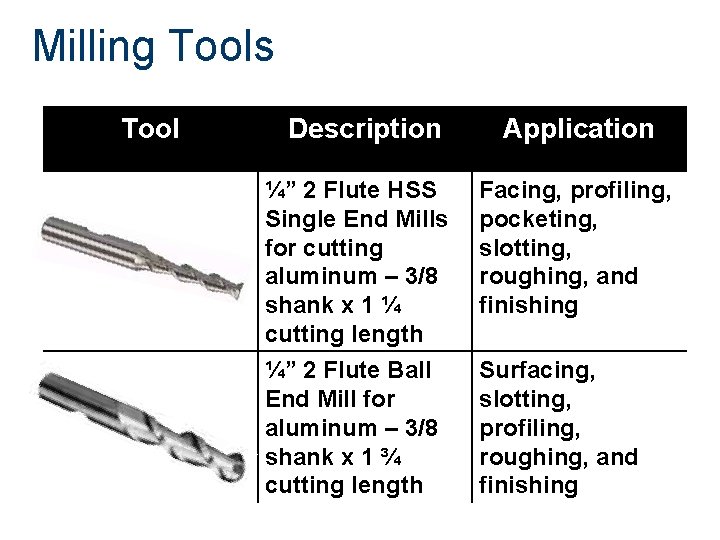
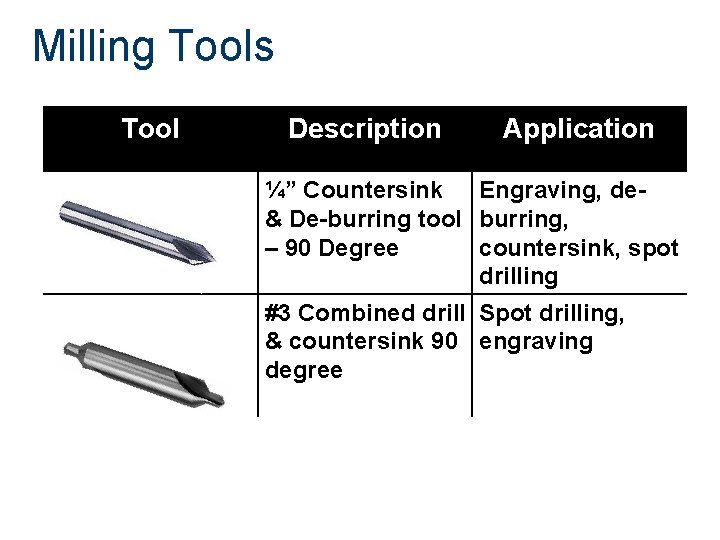
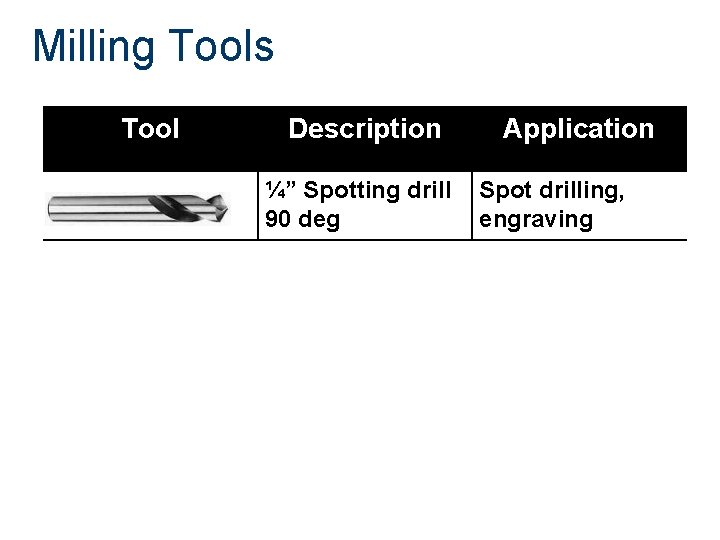

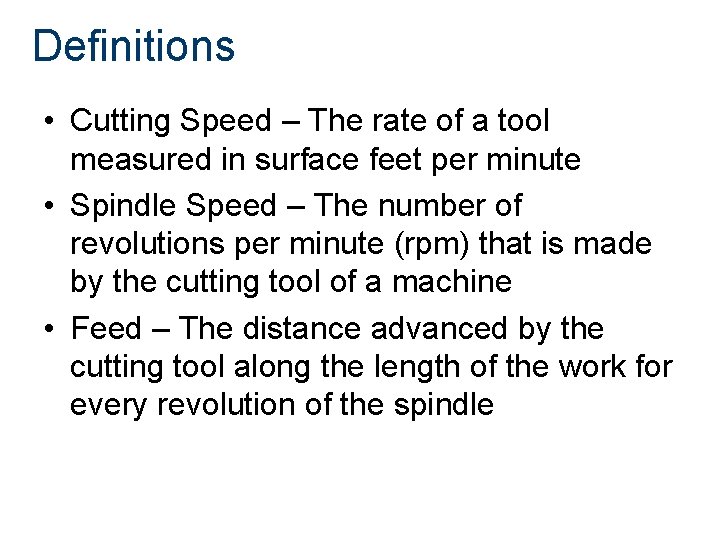
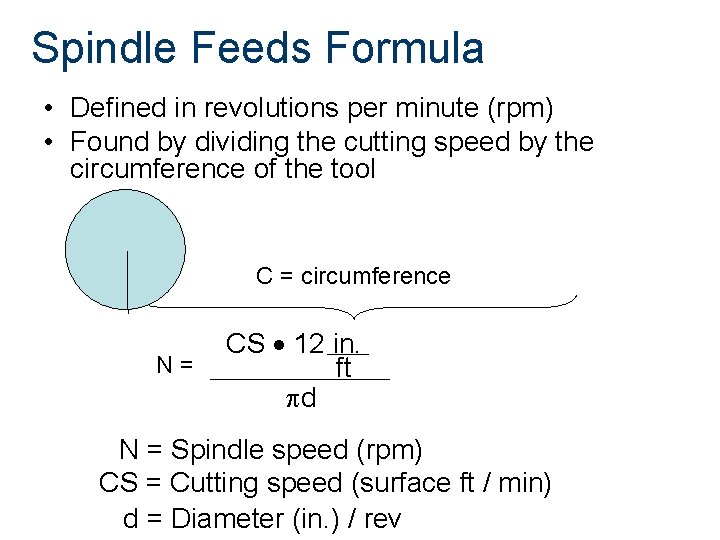
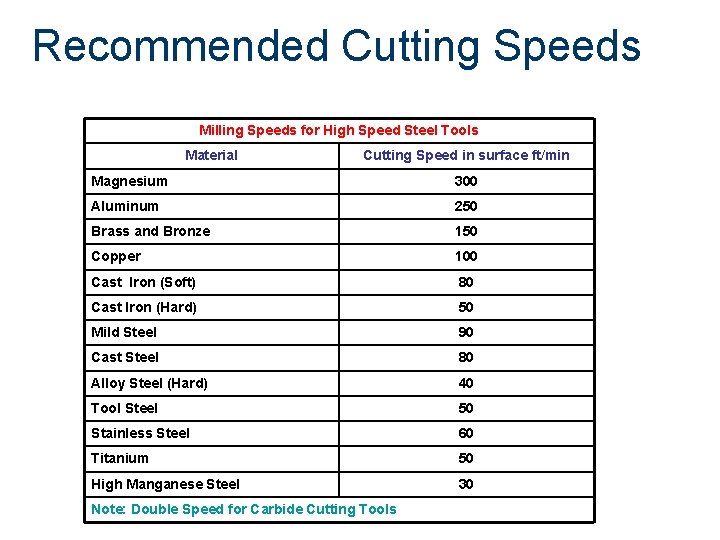
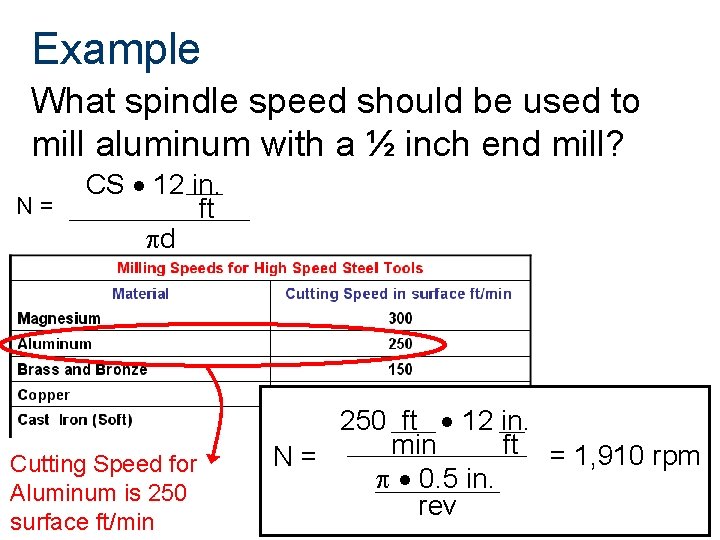
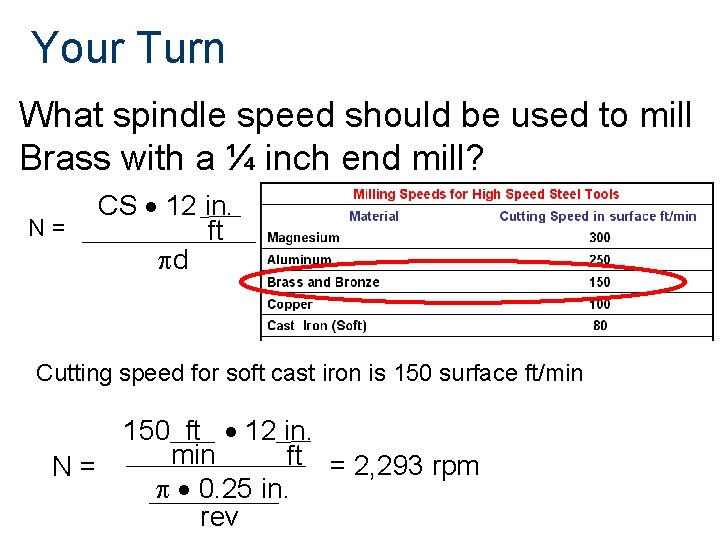
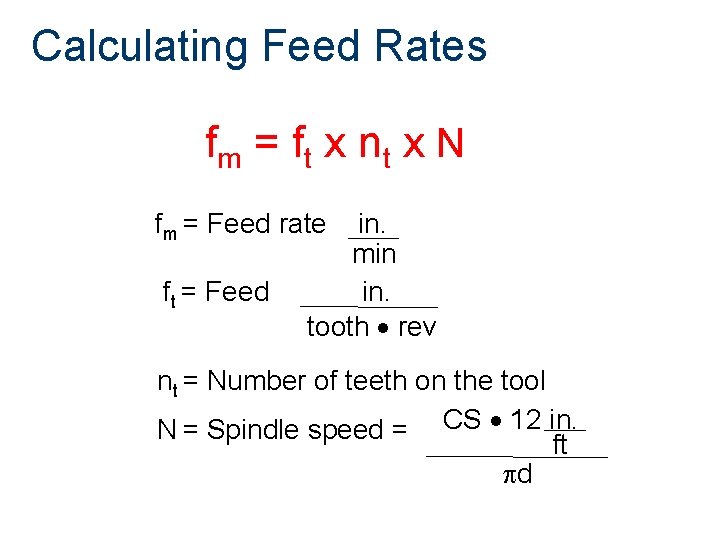
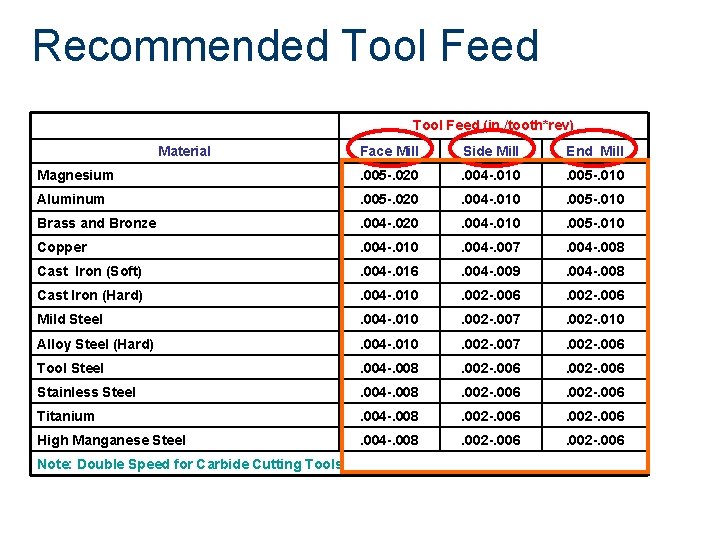
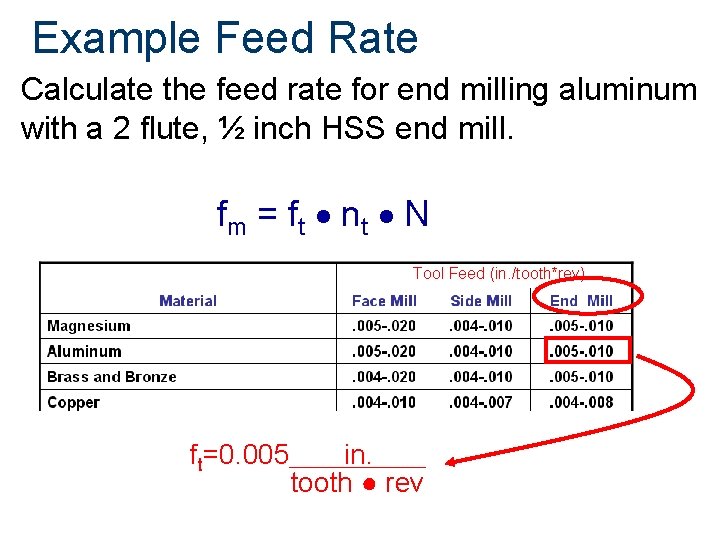
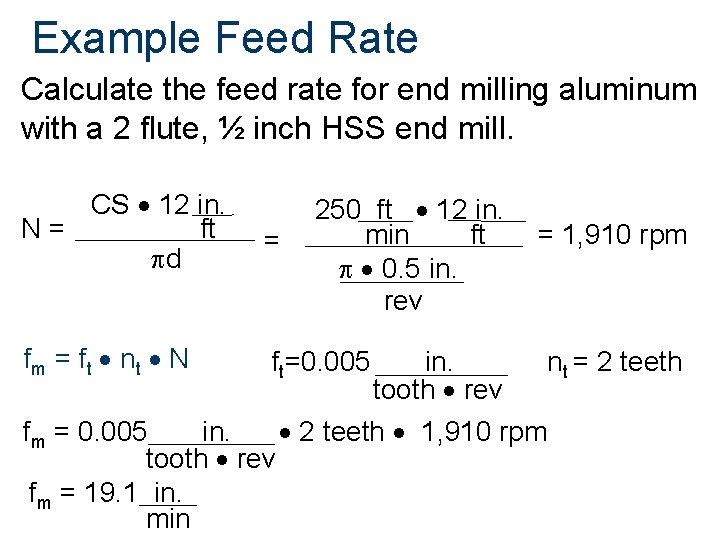
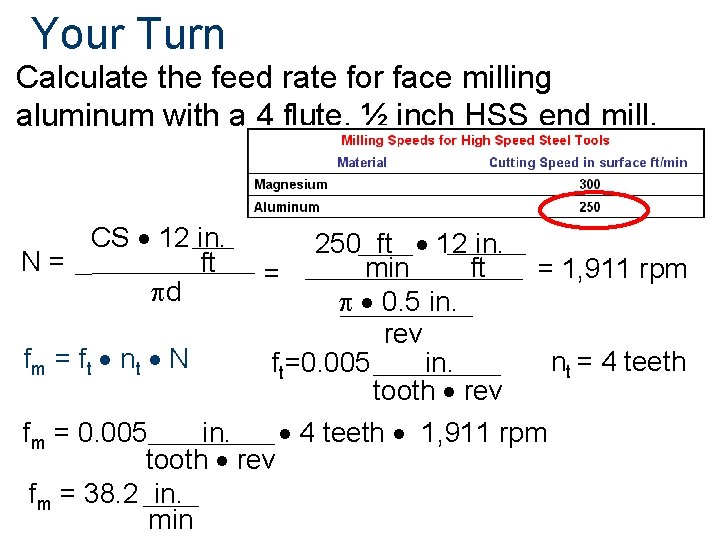
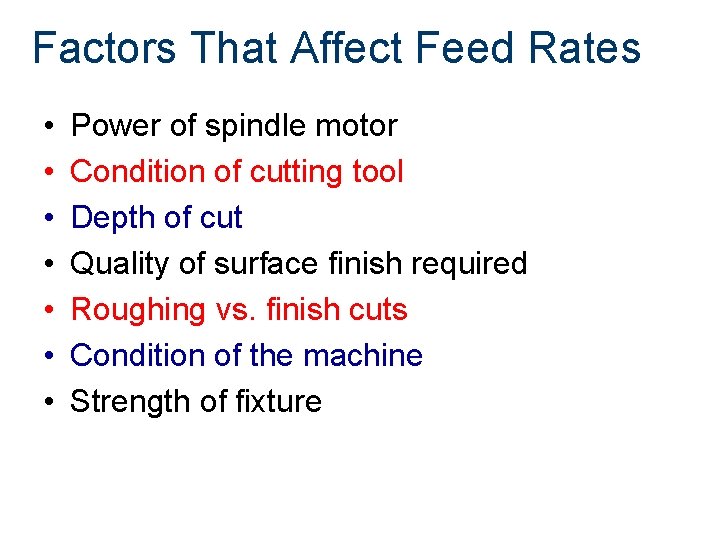
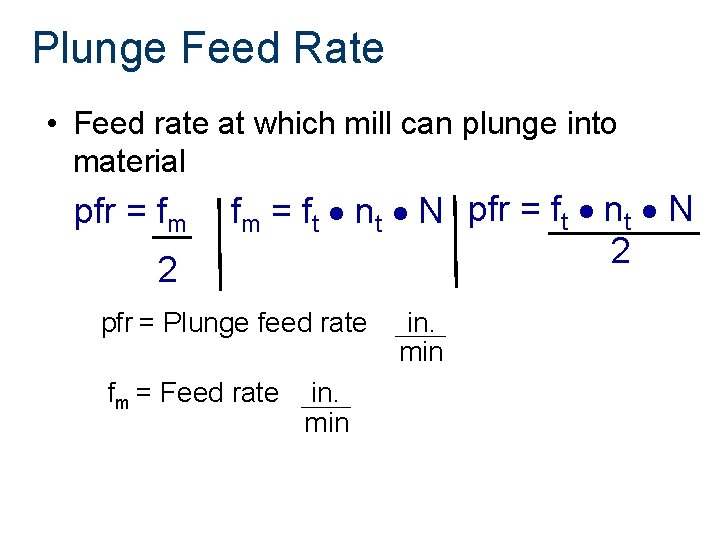
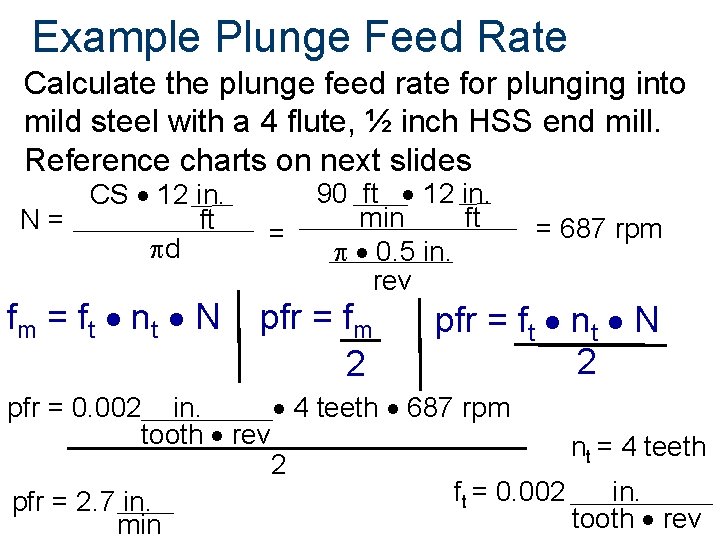
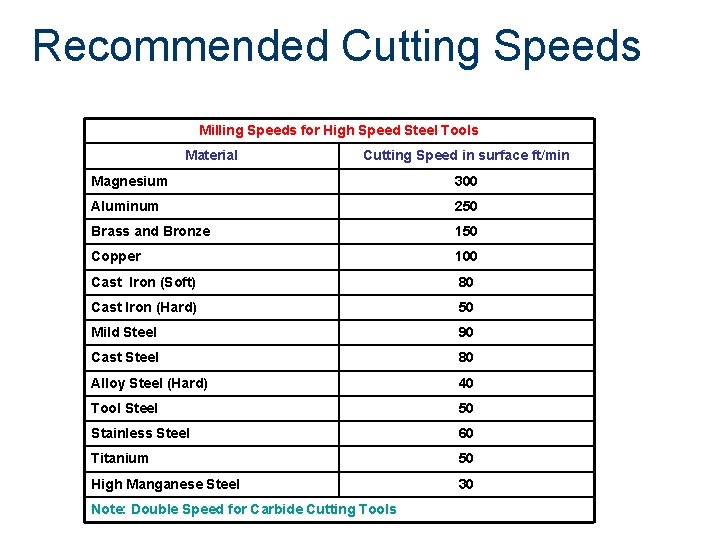
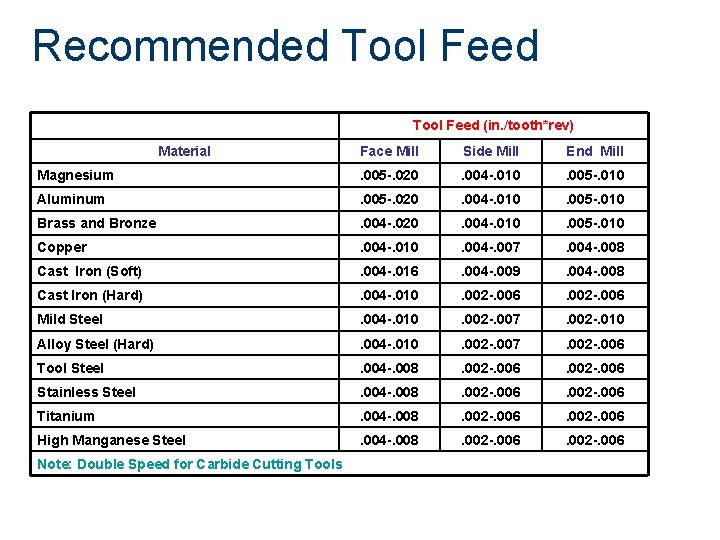
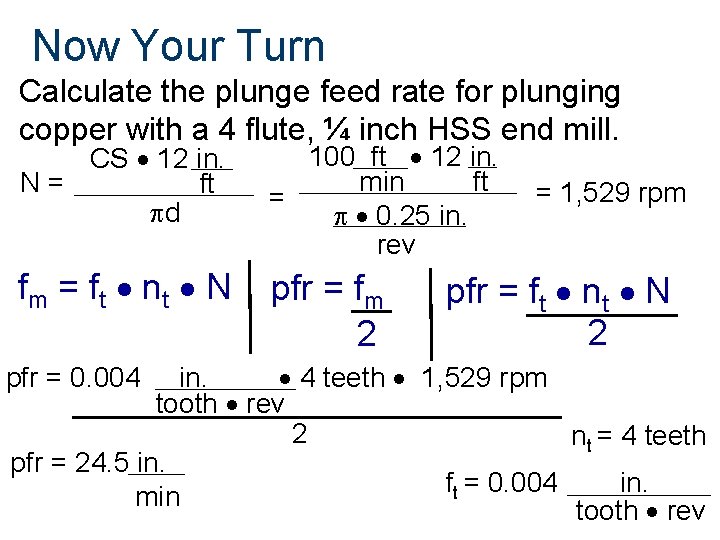
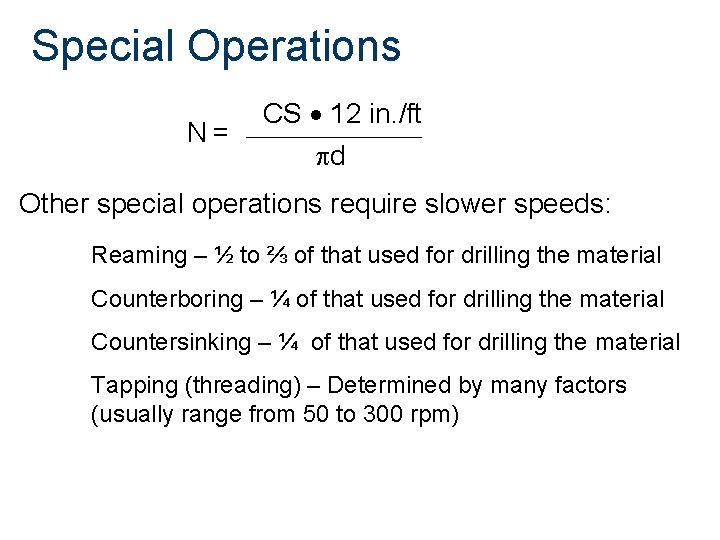
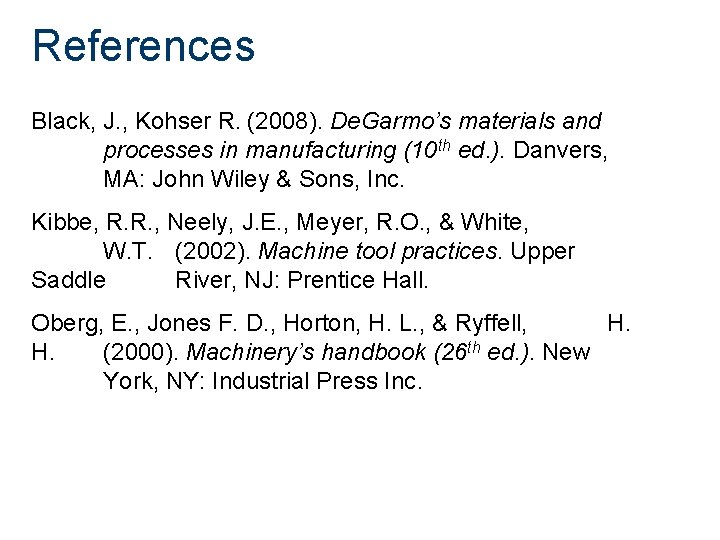
- Slides: 28
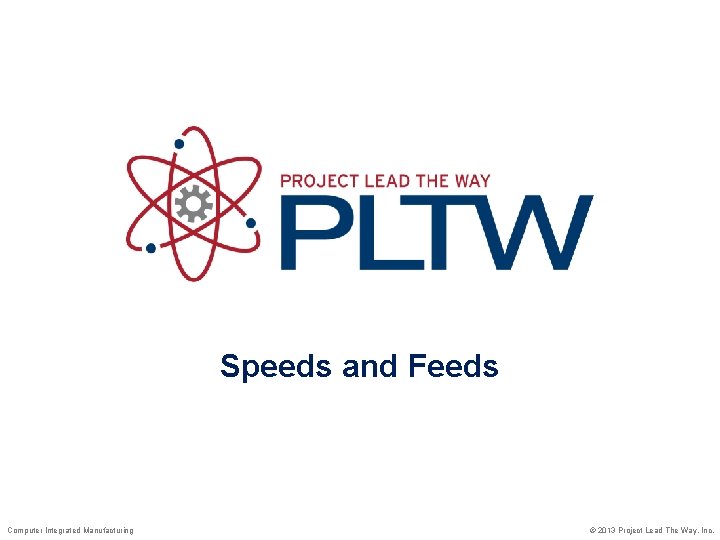
Speeds and Feeds Computer Integrated Manufacturing © 2013 Project Lead The Way, Inc.
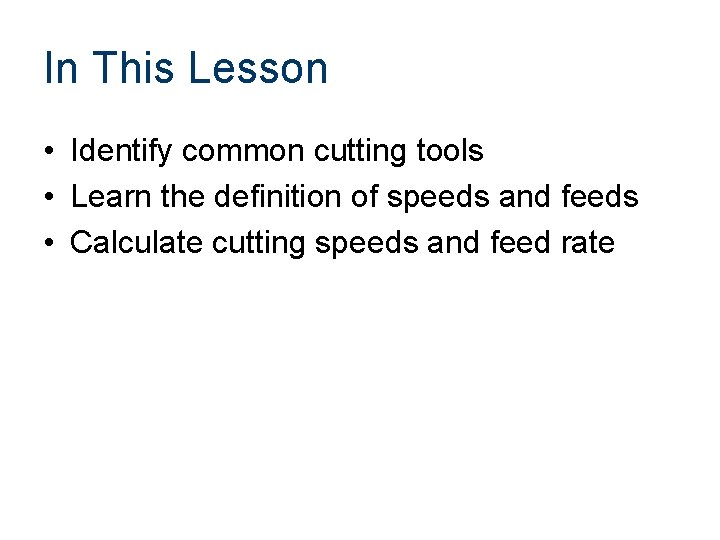
In This Lesson • Identify common cutting tools • Learn the definition of speeds and feeds • Calculate cutting speeds and feed rate
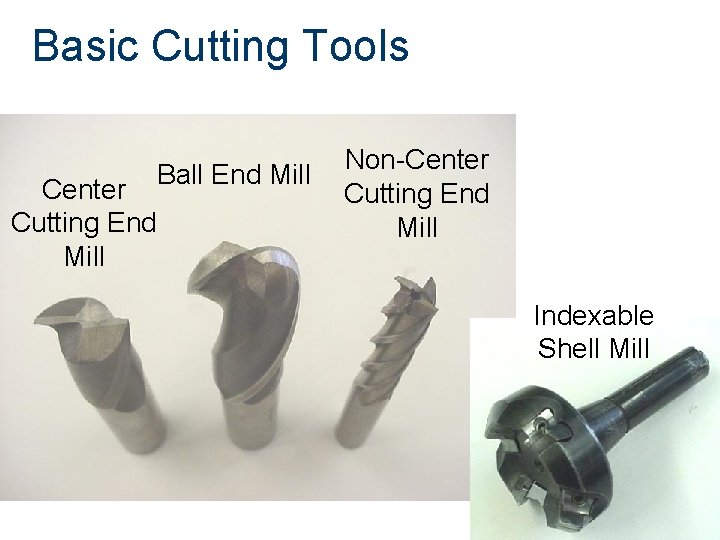
Basic Cutting Tools Ball End Mill Center Cutting End Mill Non-Center Cutting End Mill Indexable Shell Mill
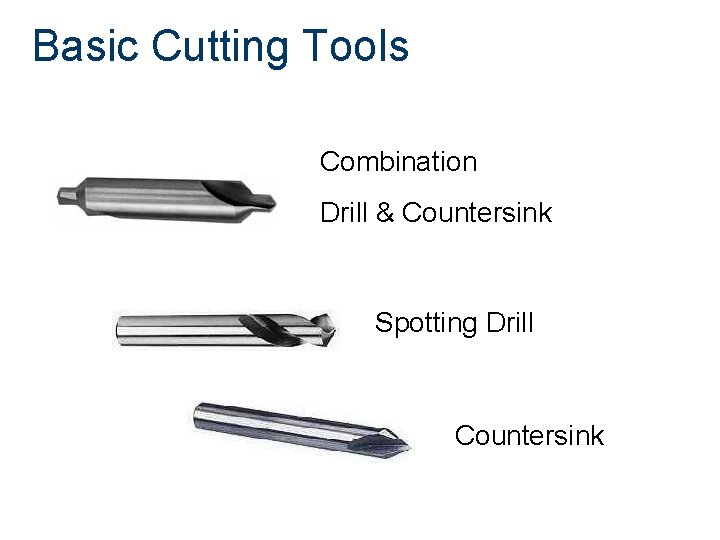
Basic Cutting Tools Combination Drill & Countersink Spotting Drill Countersink
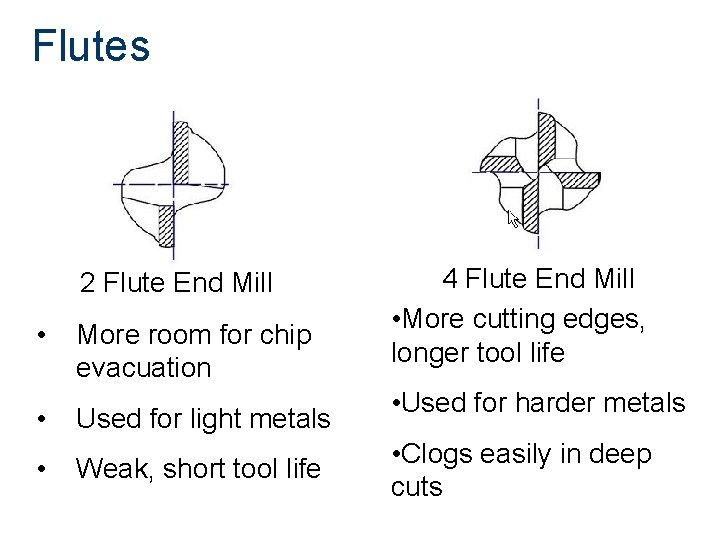
Flutes 2 Flute End Mill • More room for chip evacuation • Used for light metals • Weak, short tool life 4 Flute End Mill • More cutting edges, longer tool life • Used for harder metals • Clogs easily in deep cuts
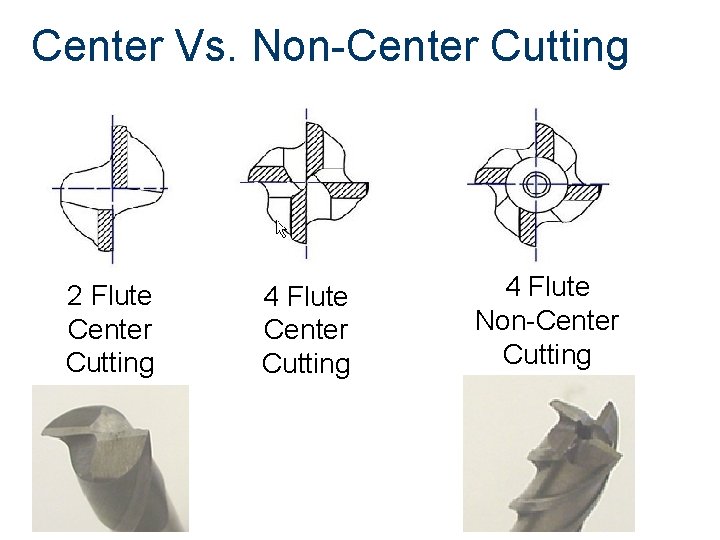
Center Vs. Non-Center Cutting 2 Flute Center Cutting 4 Flute Non-Center Cutting
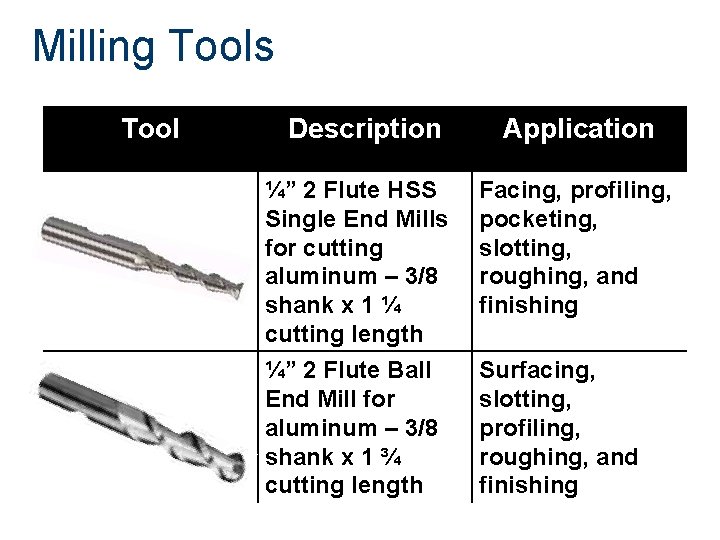
Milling Tools Tool Description Application ¼” 2 Flute HSS Single End Mills for cutting aluminum – 3/8 shank x 1 ¼ cutting length Facing, profiling, pocketing, slotting, roughing, and finishing ¼” 2 Flute Ball End Mill for aluminum – 3/8 shank x 1 ¾ cutting length Surfacing, slotting, profiling, roughing, and finishing
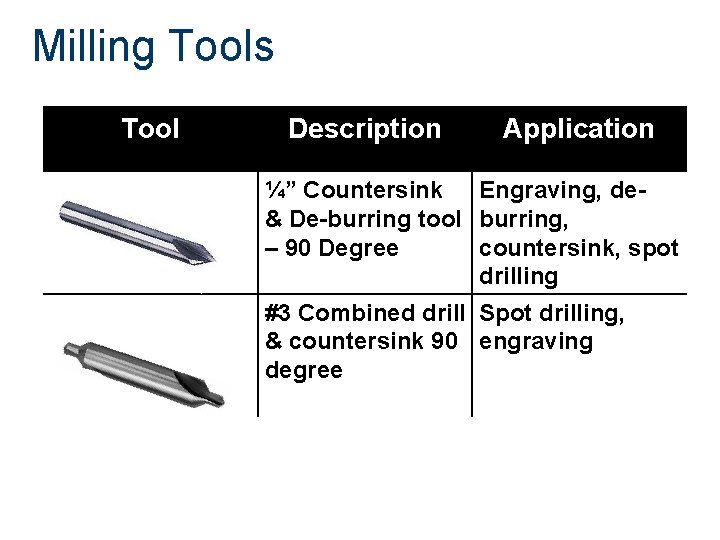
Milling Tools Tool Description Application ¼” Countersink Engraving, de& De-burring tool burring, – 90 Degree countersink, spot drilling #3 Combined drill Spot drilling, & countersink 90 engraving degree
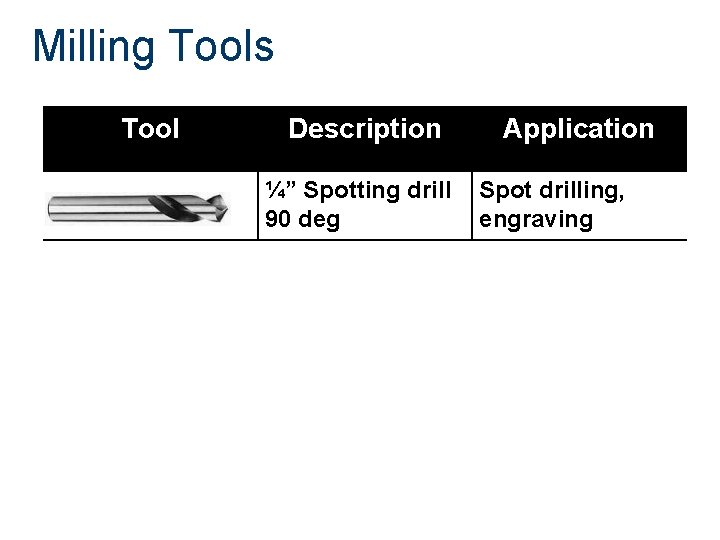
Milling Tools Tool Description ¼” Spotting drill 90 deg Application Spot drilling, engraving

Cutting Tool Material Video
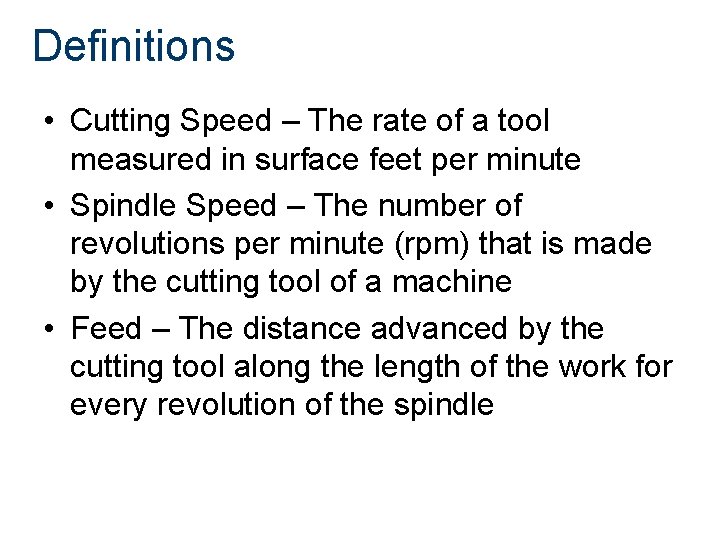
Definitions • Cutting Speed – The rate of a tool measured in surface feet per minute • Spindle Speed – The number of revolutions per minute (rpm) that is made by the cutting tool of a machine • Feed – The distance advanced by the cutting tool along the length of the work for every revolution of the spindle
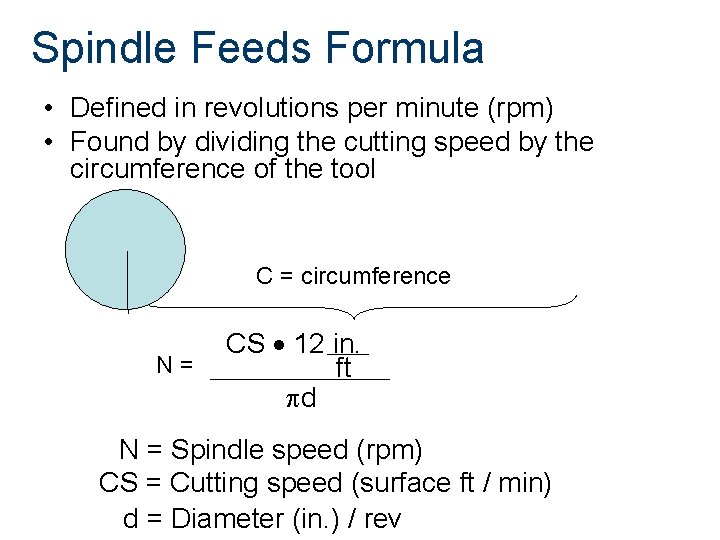
Spindle Feeds Formula • Defined in revolutions per minute (rpm) • Found by dividing the cutting speed by the circumference of the tool N= CS C N= C = circumference CS 12 in. ft d N = Spindle speed (rpm) CS = Cutting speed (surface ft / min) d = Diameter (in. ) / rev
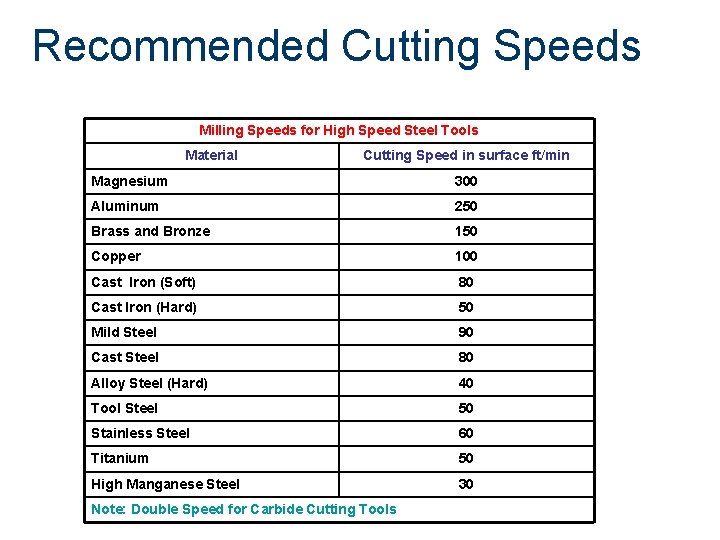
Recommended Cutting Speeds Milling Speeds for High Speed Steel Tools Material Cutting Speed in surface ft/min Magnesium 300 Aluminum 250 Brass and Bronze 150 Copper 100 Cast Iron (Soft) 80 Cast Iron (Hard) 50 Mild Steel 90 Cast Steel 80 Alloy Steel (Hard) 40 Tool Steel 50 Stainless Steel 60 Titanium 50 High Manganese Steel 30 Note: Double Speed for Carbide Cutting Tools
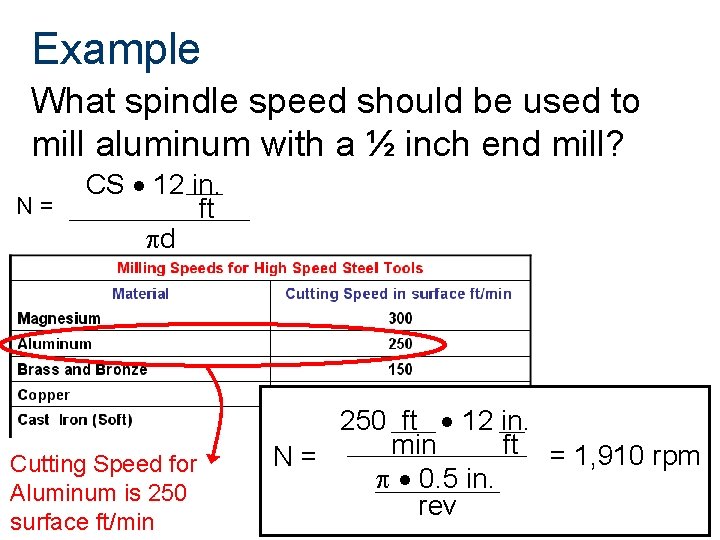
Example What spindle speed should be used to mill aluminum with a ½ inch end mill? N= CS 12 in. ft d Cutting Speed for Aluminum is 250 surface ft/min 250 ft 12 in. min ft = 1, 910 rpm N= 0. 5 in. rev
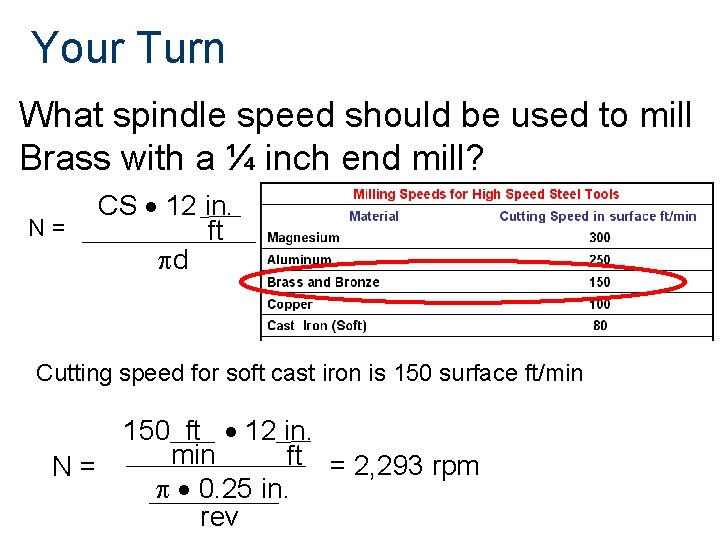
Your Turn What spindle speed should be used to mill Brass with a ¼ inch end mill? N= CS 12 in. ft d Cutting speed for soft cast iron is 150 surface ft/min 150 ft 12 in. min ft = 2, 293 rpm N= 0. 25 in. rev
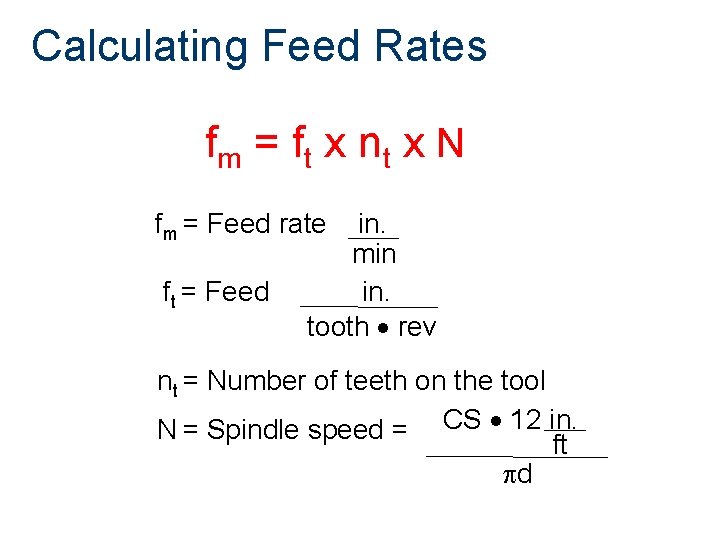
Calculating Feed Rates fm = f t x n t x N fm = Feed rate ft = Feed in. min in. tooth rev nt = Number of teeth on the tool N = Spindle speed = CS 12 in. ft d
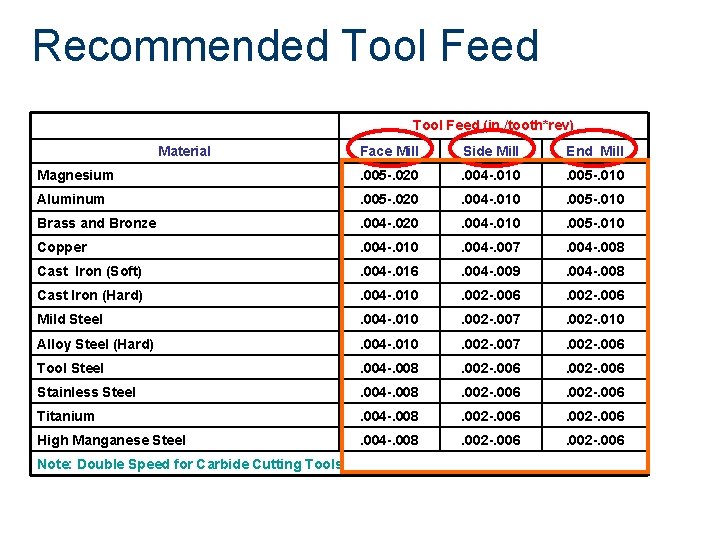
Recommended Tool Feed (in. /tooth*rev) Material Face Mill Side Mill End Mill Magnesium . 005 -. 020 . 004 -. 010 . 005 -. 010 Aluminum . 005 -. 020 . 004 -. 010 . 005 -. 010 Brass and Bronze . 004 -. 020 . 004 -. 010 . 005 -. 010 Copper . 004 -. 010 . 004 -. 007 . 004 -. 008 Cast Iron (Soft) . 004 -. 016 . 004 -. 009 . 004 -. 008 Cast Iron (Hard) . 004 -. 010 . 002 -. 006 Mild Steel . 004 -. 010 . 002 -. 007 . 002 -. 010 Alloy Steel (Hard) . 004 -. 010 . 002 -. 007 . 002 -. 006 Tool Steel . 004 -. 008 . 002 -. 006 Stainless Steel . 004 -. 008 . 002 -. 006 Titanium . 004 -. 008 . 002 -. 006 High Manganese Steel . 004 -. 008 . 002 -. 006 Note: Double Speed for Carbide Cutting Tools
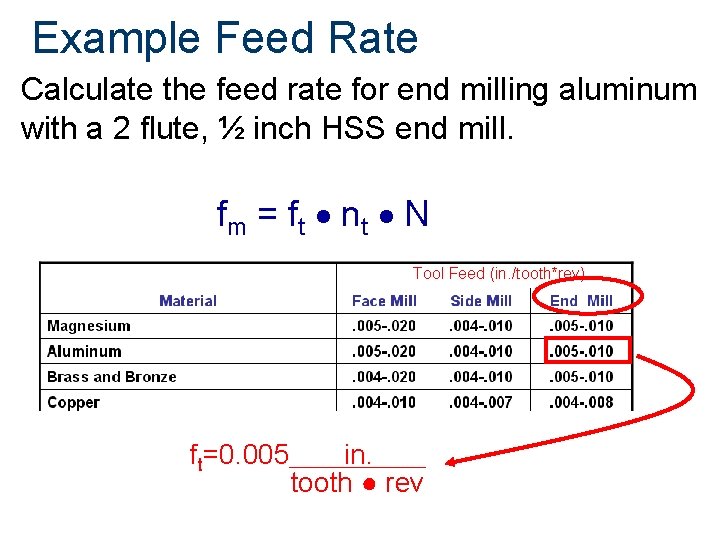
Example Feed Rate Calculate the feed rate for end milling aluminum with a 2 flute, ½ inch HSS end mill. fm = f t nt N Tool Feed (in. /tooth*rev) ft=0. 005 in. tooth ● rev
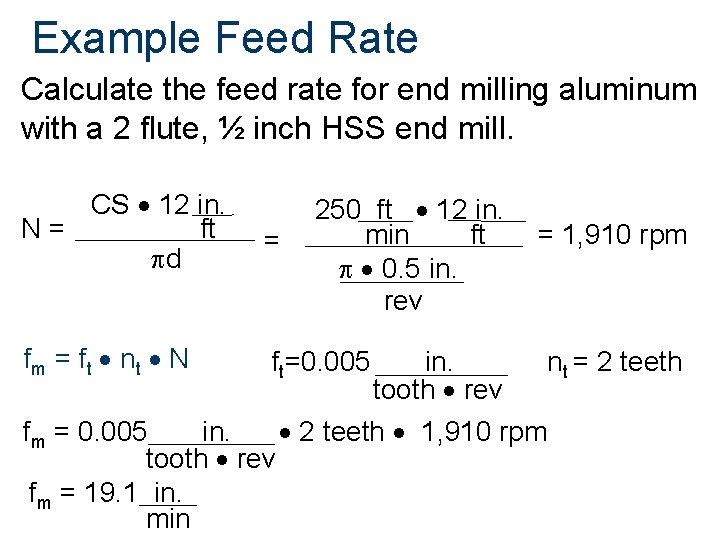
Example Feed Rate Calculate the feed rate for end milling aluminum with a 2 flute, ½ inch HSS end mill. CS 12 in. N= ft d = fm = f t nt N ft=0. 005 250 ft 12 in. min ft 0. 5 in. rev in. tooth rev = 1, 910 rpm nt = 2 teeth fm = 0. 005 in. 2 teeth 1, 910 rpm tooth rev fm = 19. 1 in. min
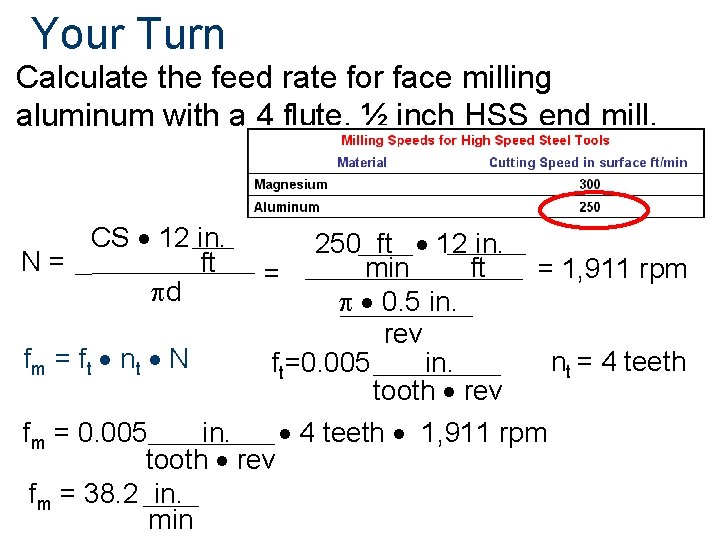
Your Turn Calculate the feed rate for face milling aluminum with a 4 flute, ½ inch HSS end mill. CS 12 in. N= ft d fm = f t nt N 250 ft 12 in. min ft = 0. 5 in. rev ft=0. 005 in. tooth rev = 1, 911 rpm fm = 0. 005 in. 4 teeth 1, 911 rpm tooth rev fm = 38. 2 in. min nt = 4 teeth
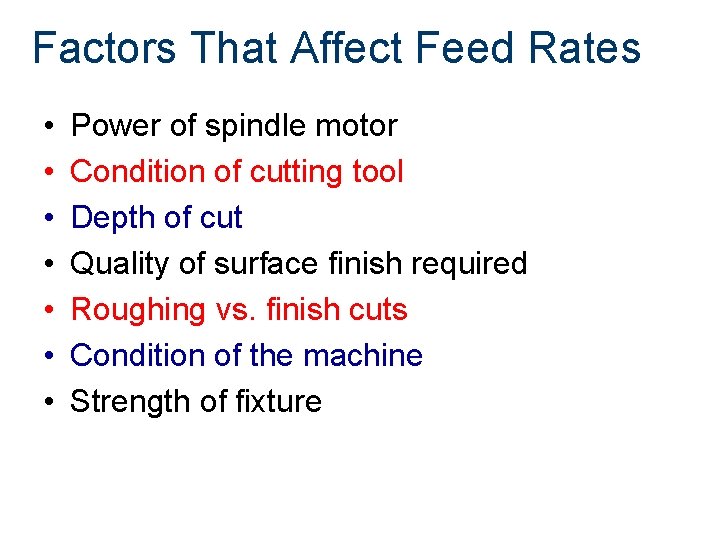
Factors That Affect Feed Rates • • Power of spindle motor Condition of cutting tool Depth of cut Quality of surface finish required Roughing vs. finish cuts Condition of the machine Strength of fixture
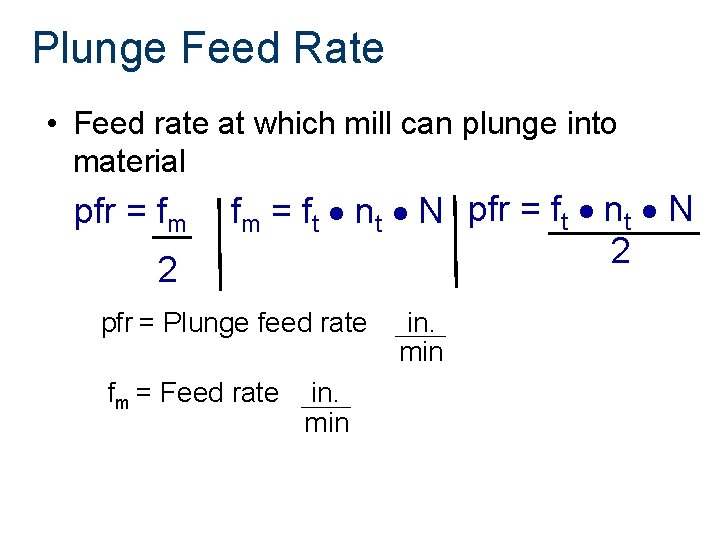
Plunge Feed Rate • Feed rate at which mill can plunge into material pfr = fm 2 fm = ft nt N pfr = ft nt N 2 pfr = Plunge feed rate fm = Feed rate in. min
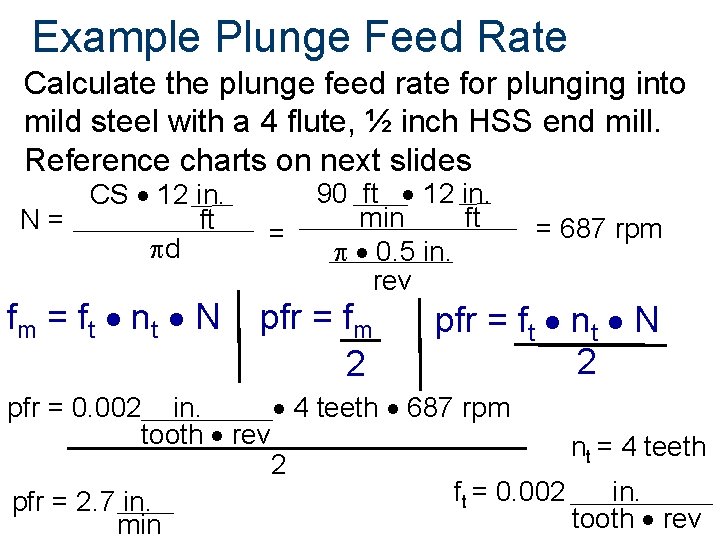
Example Plunge Feed Rate Calculate the plunge feed rate for plunging into mild steel with a 4 flute, ½ inch HSS end mill. Reference charts on next slides CS 12 in. N= ft d fm = f t nt N = 90 ft 12 in. min ft 0. 5 in. rev pfr = fm 2 = 687 rpm pfr = ft nt N 2 pfr = 0. 002 in. 4 teeth 687 rpm tooth rev nt = 4 teeth 2 ft = 0. 002 in. pfr = 2. 7 in. tooth rev min
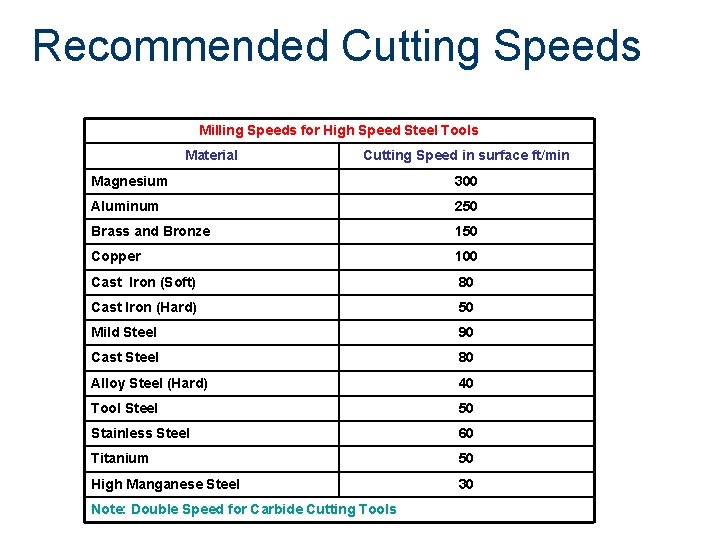
Recommended Cutting Speeds Milling Speeds for High Speed Steel Tools Material Cutting Speed in surface ft/min Magnesium 300 Aluminum 250 Brass and Bronze 150 Copper 100 Cast Iron (Soft) 80 Cast Iron (Hard) 50 Mild Steel 90 Cast Steel 80 Alloy Steel (Hard) 40 Tool Steel 50 Stainless Steel 60 Titanium 50 High Manganese Steel 30 Note: Double Speed for Carbide Cutting Tools
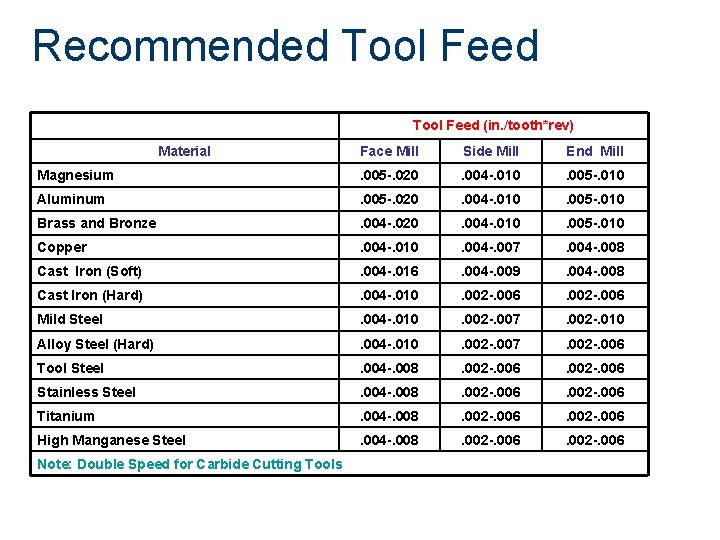
Recommended Tool Feed (in. /tooth*rev) Material Face Mill Side Mill End Mill Magnesium . 005 -. 020 . 004 -. 010 . 005 -. 010 Aluminum . 005 -. 020 . 004 -. 010 . 005 -. 010 Brass and Bronze . 004 -. 020 . 004 -. 010 . 005 -. 010 Copper . 004 -. 010 . 004 -. 007 . 004 -. 008 Cast Iron (Soft) . 004 -. 016 . 004 -. 009 . 004 -. 008 Cast Iron (Hard) . 004 -. 010 . 002 -. 006 Mild Steel . 004 -. 010 . 002 -. 007 . 002 -. 010 Alloy Steel (Hard) . 004 -. 010 . 002 -. 007 . 002 -. 006 Tool Steel . 004 -. 008 . 002 -. 006 Stainless Steel . 004 -. 008 . 002 -. 006 Titanium . 004 -. 008 . 002 -. 006 High Manganese Steel . 004 -. 008 . 002 -. 006 Note: Double Speed for Carbide Cutting Tools
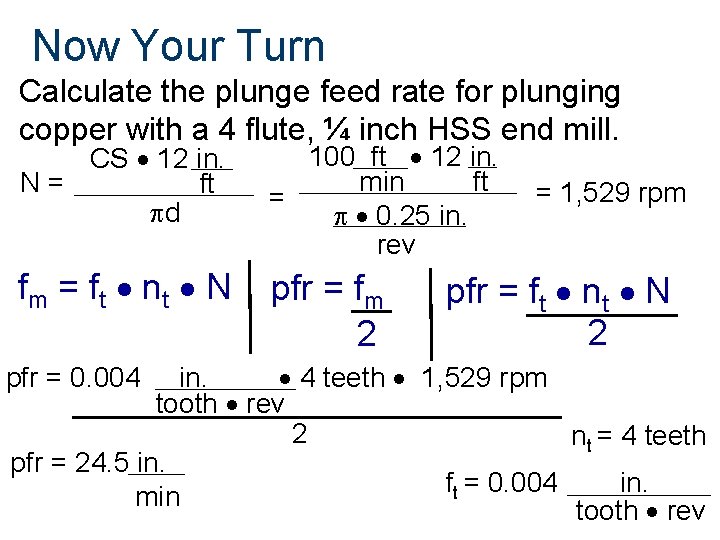
Now Your Turn Calculate the plunge feed rate for plunging copper with a 4 flute, ¼ inch HSS end mill. CS 12 in. N= ft d 100 ft 12 in. min ft = 0. 25 in. rev fm = f t nt N pfr = fm 2 = 1, 529 rpm pfr = ft nt N 2 in. 4 teeth 1, 529 rpm tooth rev 2 nt = 4 teeth pfr = 24. 5 in. ft = 0. 004 in. min tooth rev pfr = 0. 004
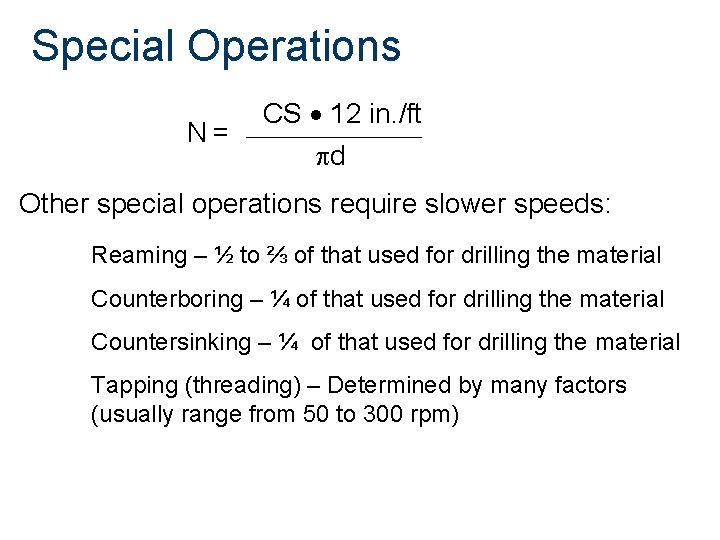
Special Operations N= CS 12 in. /ft d Other special operations require slower speeds: Reaming – ½ to ⅔ of that used for drilling the material Counterboring – ¼ of that used for drilling the material Countersinking – ¼ of that used for drilling the material Tapping (threading) – Determined by many factors (usually range from 50 to 300 rpm)
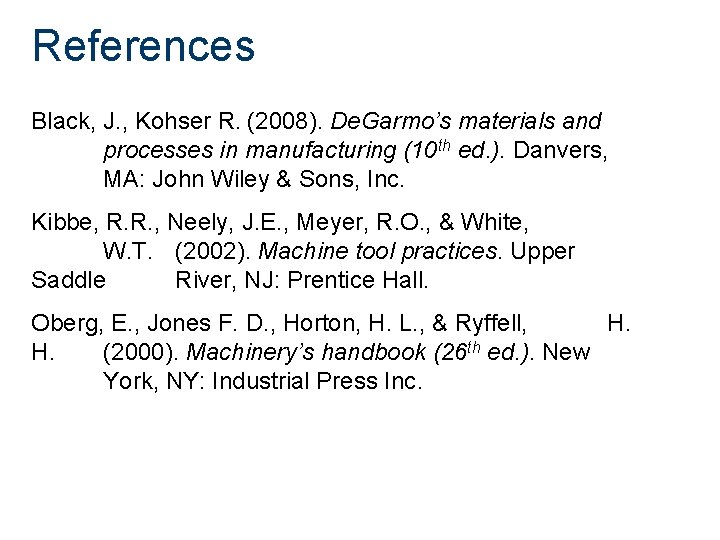
References Black, J. , Kohser R. (2008). De. Garmo’s materials and processes in manufacturing (10 th ed. ). Danvers, MA: John Wiley & Sons, Inc. Kibbe, R. R. , Neely, J. E. , Meyer, R. O. , & White, W. T. (2002). Machine tool practices. Upper Saddle River, NJ: Prentice Hall. Oberg, E. , Jones F. D. , Horton, H. L. , & Ryffell, H. H. (2000). Machinery’s handbook (26 th ed. ). New York, NY: Industrial Press Inc.
Objectives of cim
Computer integrated manufacturing applications
Manufacturing cost vs non manufacturing cost
Manufacturing cost vs non manufacturing cost
Controllable expenses examples
Manufacturing cost vs non manufacturing cost
Additive manufacturing vs subtractive manufacturing
Coso internal control integrated framework 2013 pdf
Classification of feeds
A flag wags like a fishhook there in the sky
Biting the hand that feeds you figurative language
Active to passive voice
Old news figurative language
Programming rss feeds
Consonance vs alliteration
Tmg feeds
Mimaropa region
Sound will travel at different speeds in different mediums.
Sound will travel at different speeds in different mediums.
Ezyme
Sigma101
Which macromolecule speeds up chemical reactions
A movie stunt driver on a motorcycle speeds
Holding wind correction
Wave speeds
Physical features of a cheetah
Cat5e speed limit
Wave speeds
Wave train