SIX SIGMA HISTORY Six Sigma is the hottest
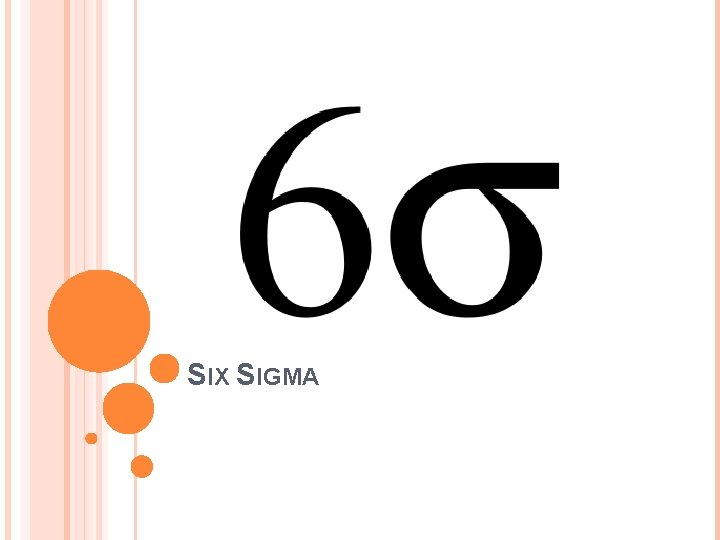
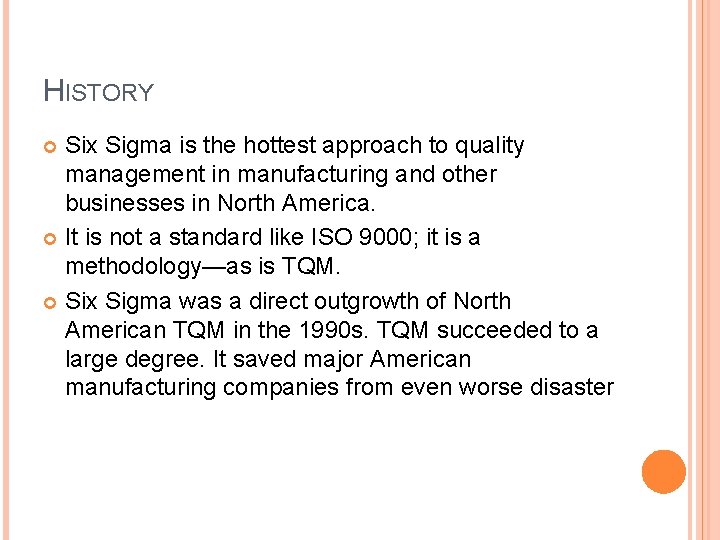
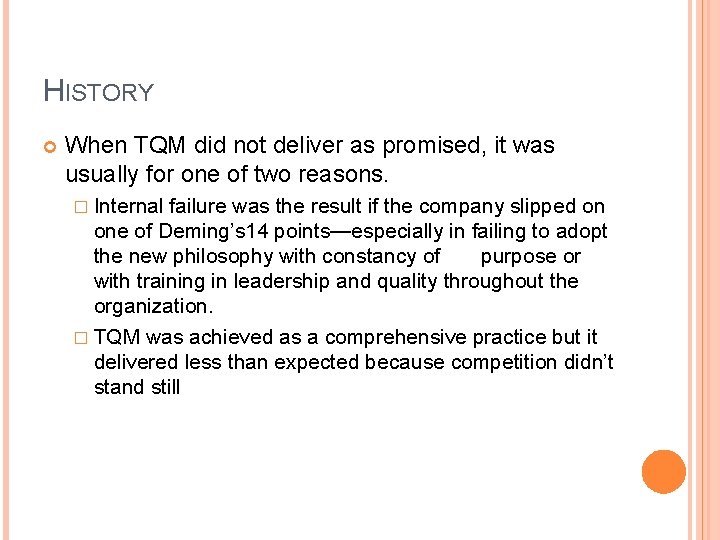
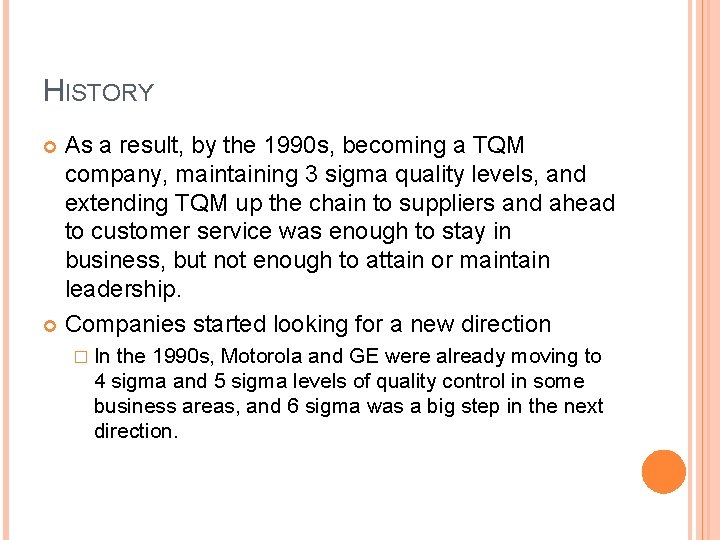
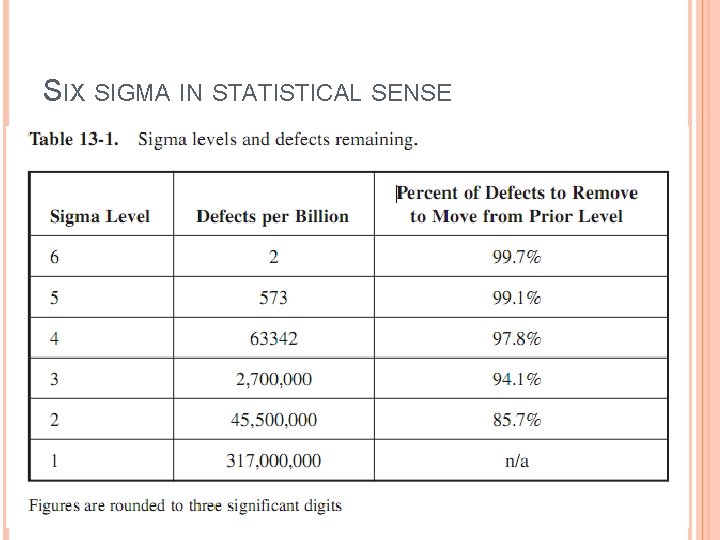
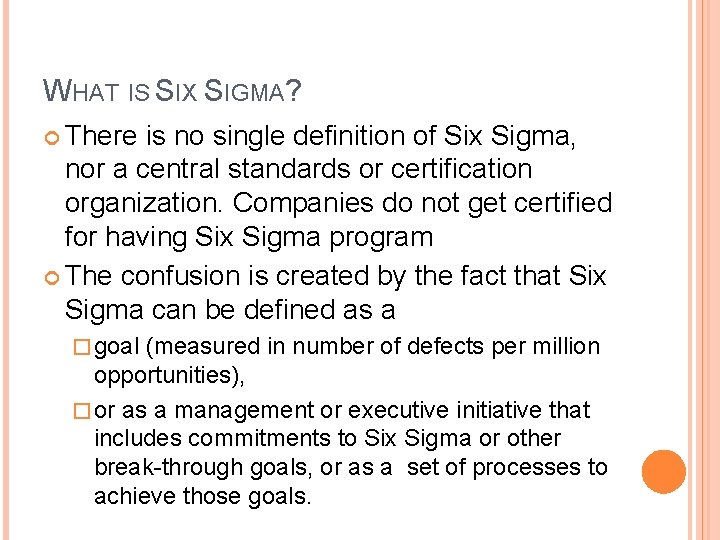
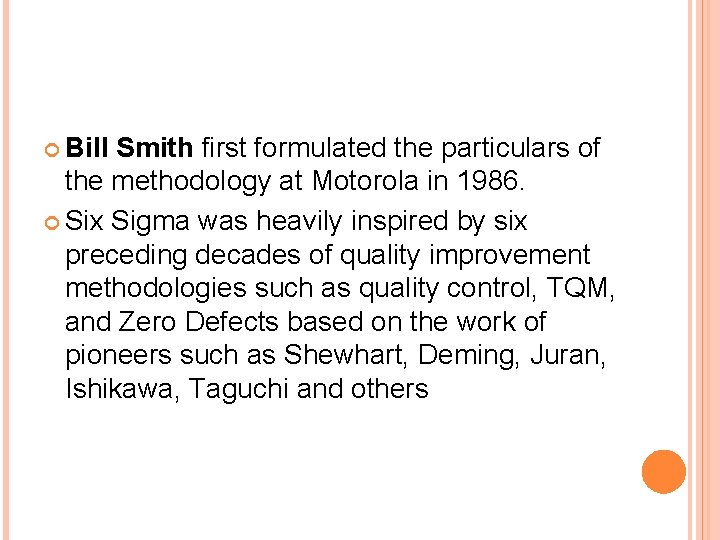
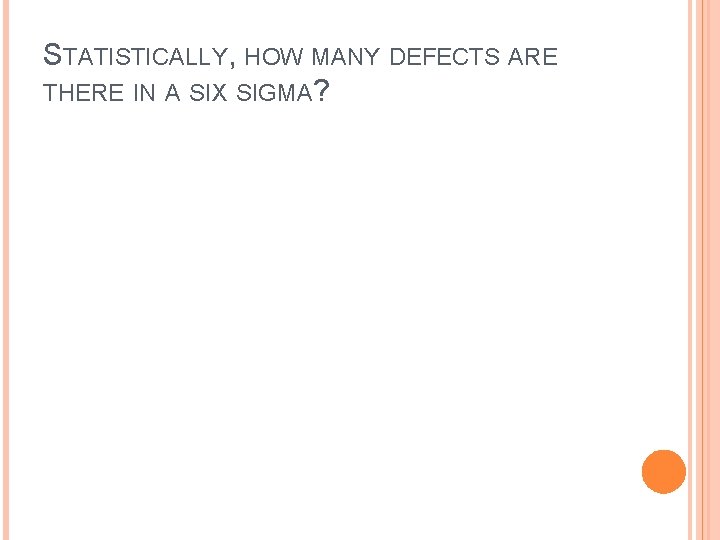
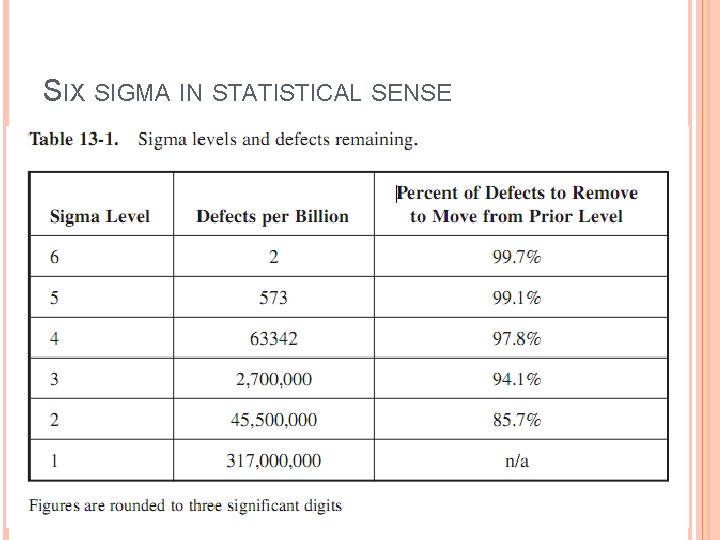
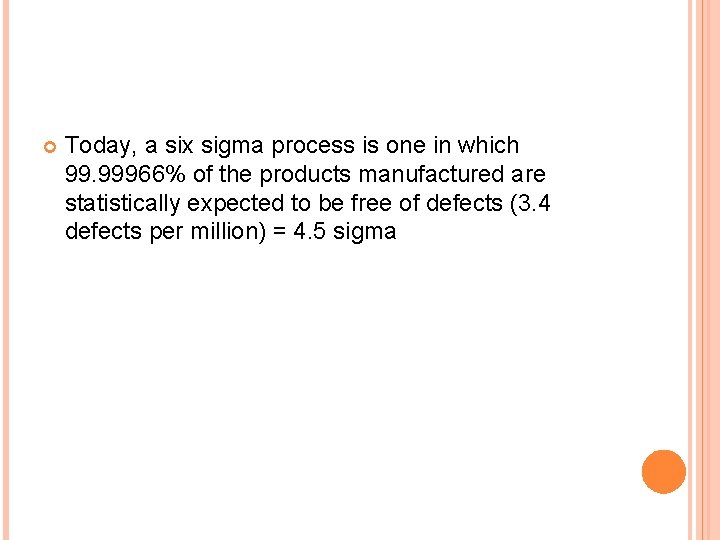
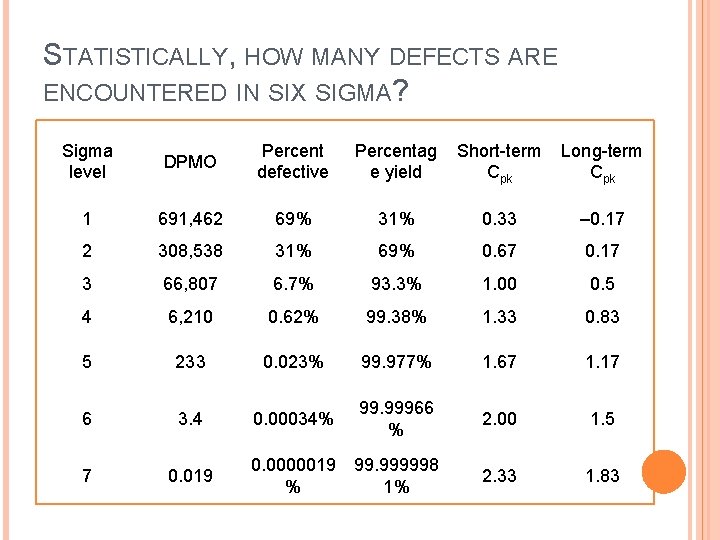
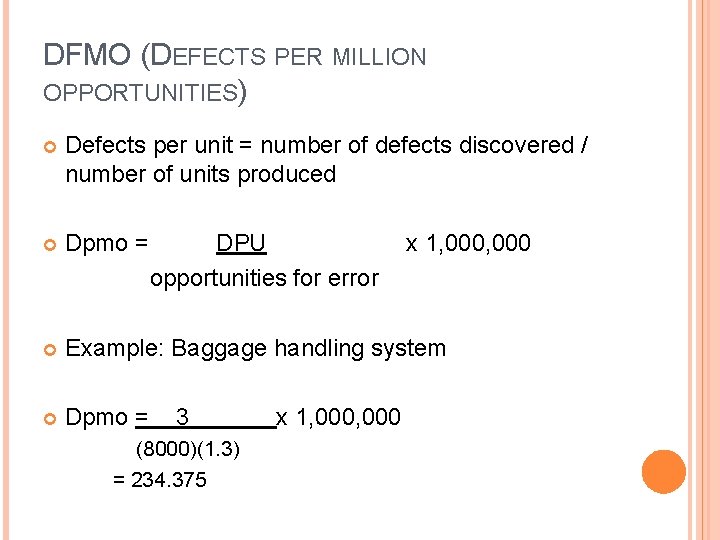
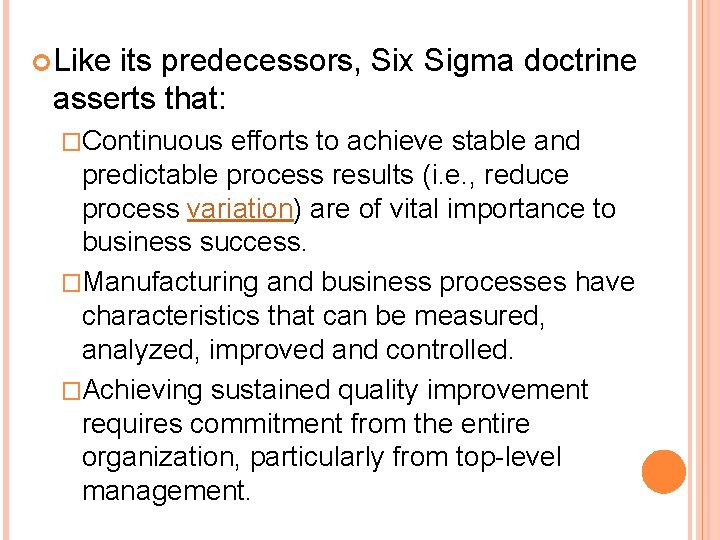
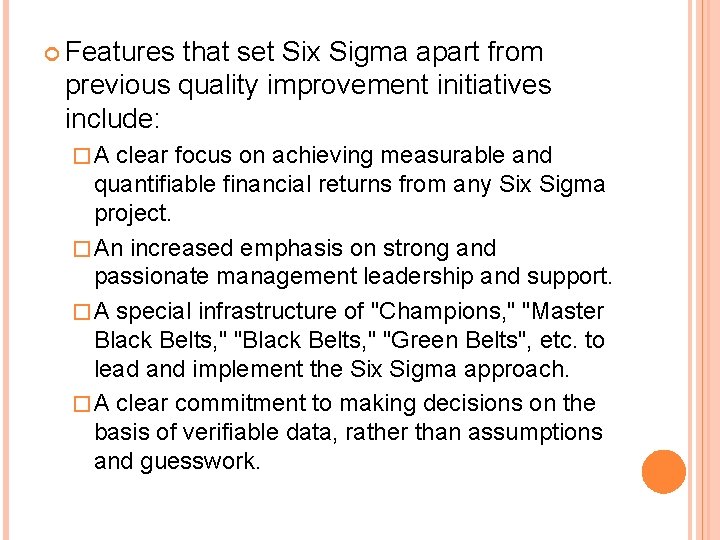
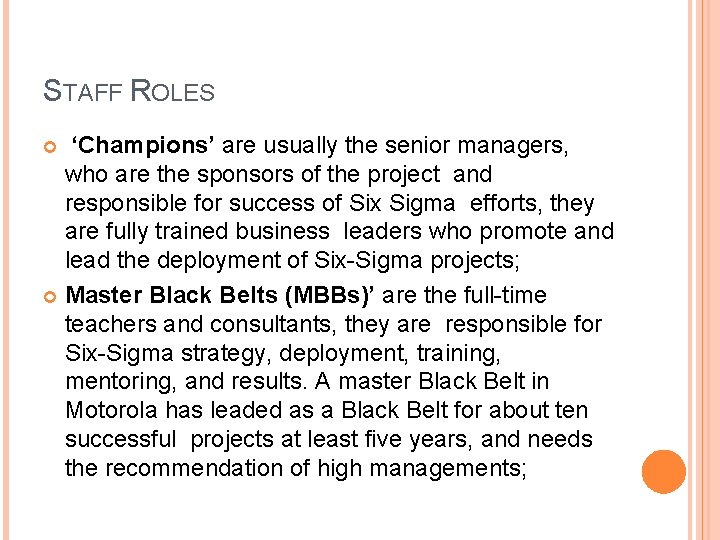
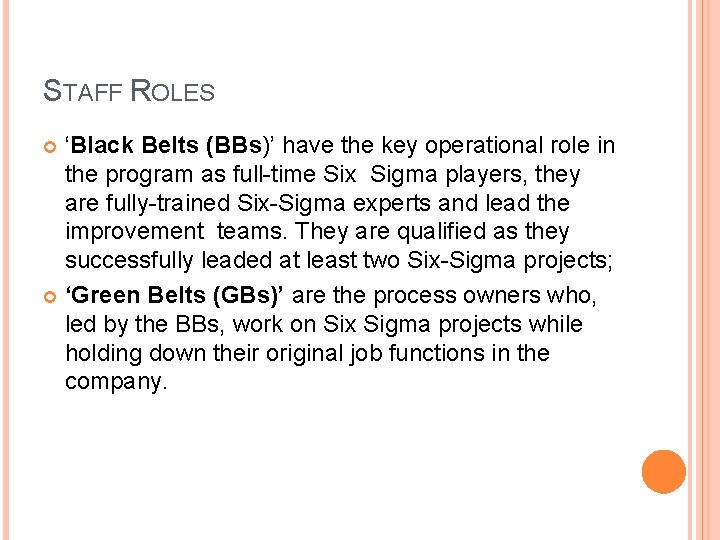
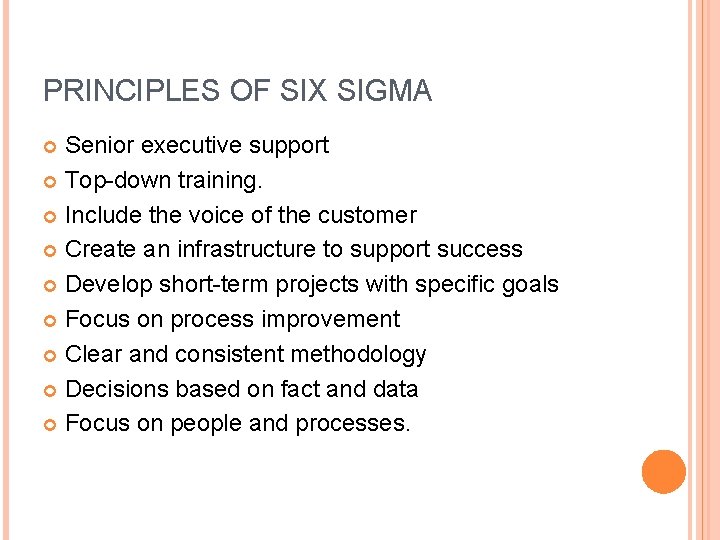
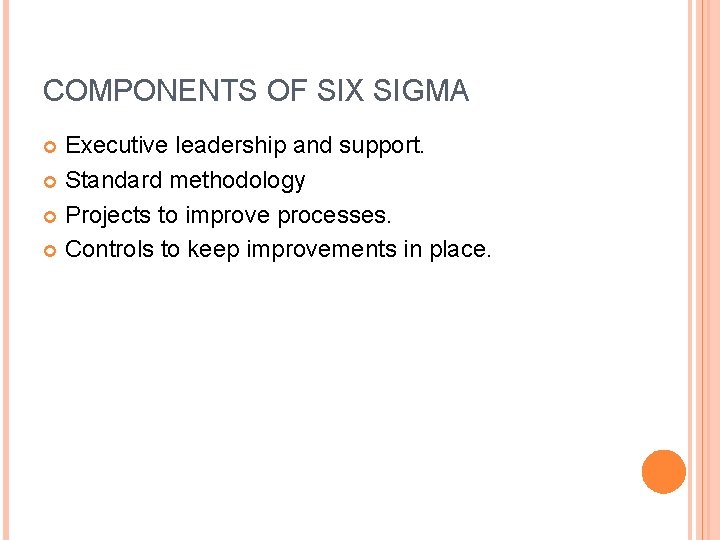
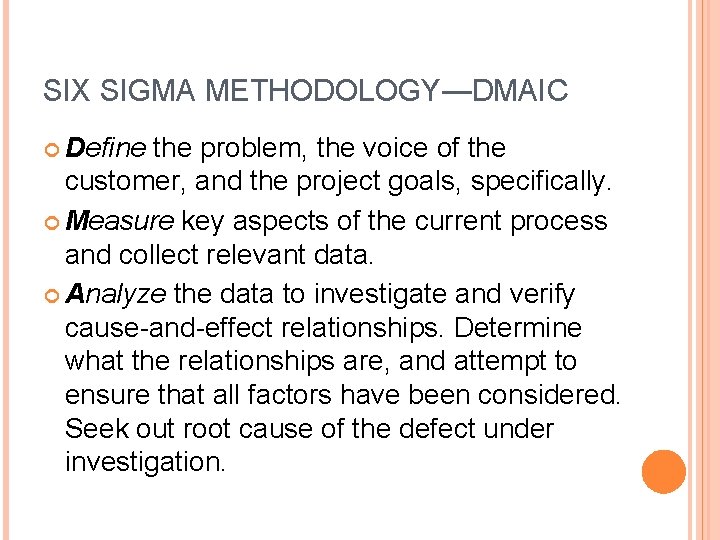
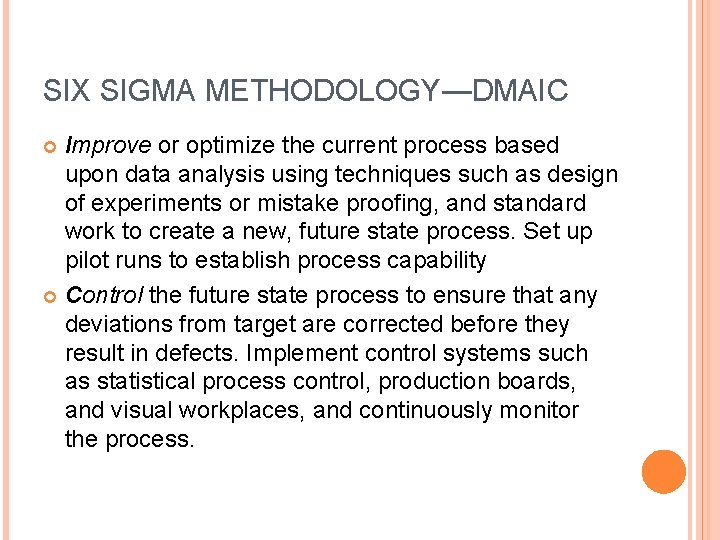
- Slides: 20
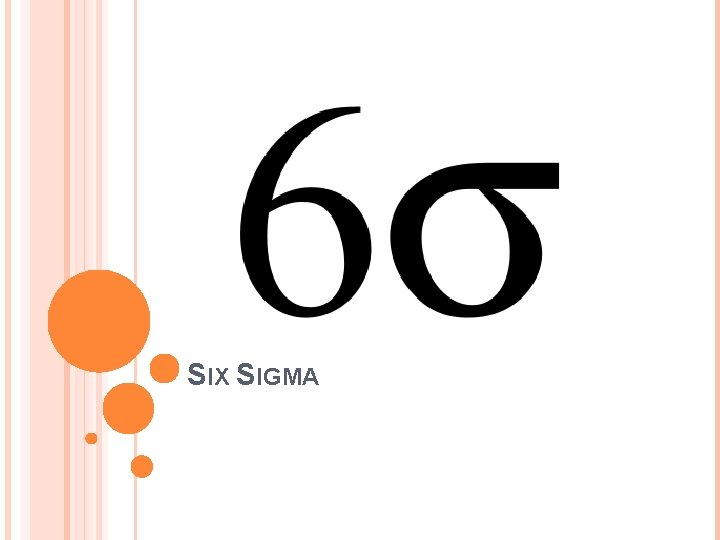
SIX SIGMA
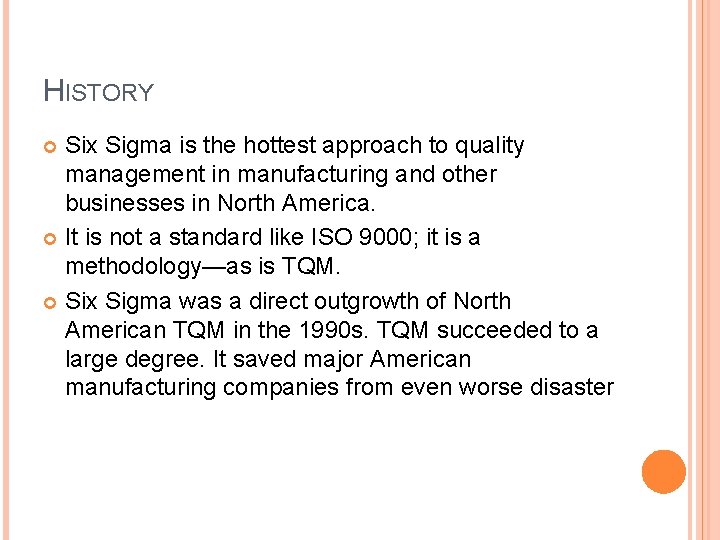
HISTORY Six Sigma is the hottest approach to quality management in manufacturing and other businesses in North America. It is not a standard like ISO 9000; it is a methodology—as is TQM. Six Sigma was a direct outgrowth of North American TQM in the 1990 s. TQM succeeded to a large degree. It saved major American manufacturing companies from even worse disaster
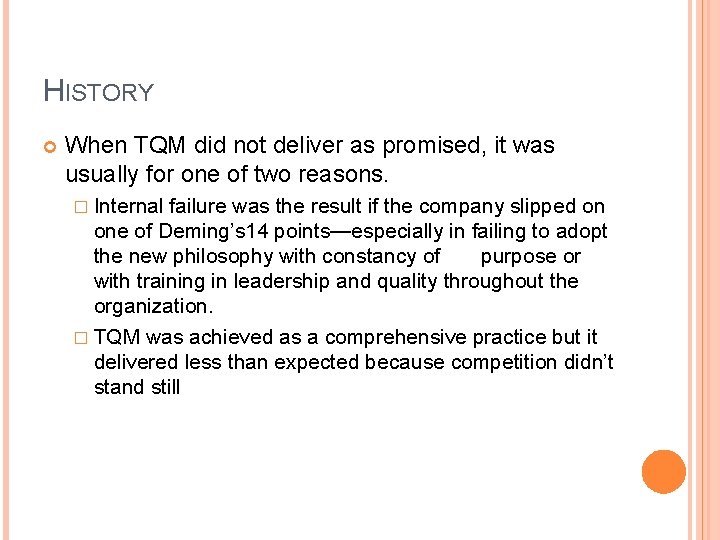
HISTORY When TQM did not deliver as promised, it was usually for one of two reasons. � Internal failure was the result if the company slipped on one of Deming’s 14 points—especially in failing to adopt the new philosophy with constancy of purpose or with training in leadership and quality throughout the organization. � TQM was achieved as a comprehensive practice but it delivered less than expected because competition didn’t stand still
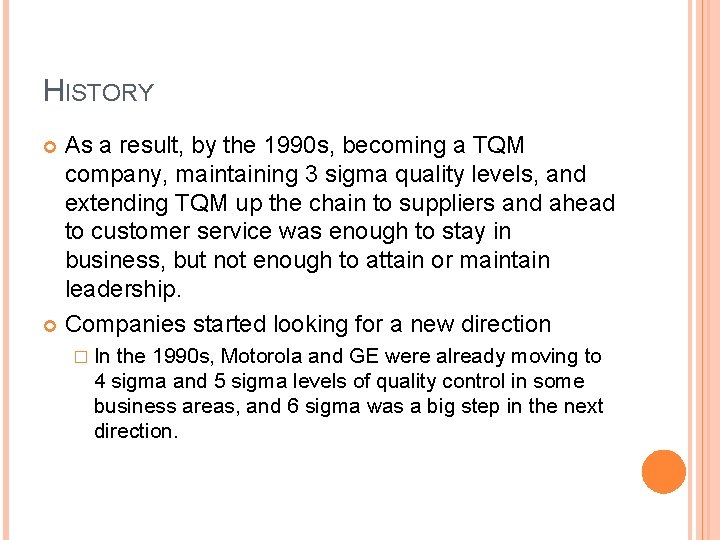
HISTORY As a result, by the 1990 s, becoming a TQM company, maintaining 3 sigma quality levels, and extending TQM up the chain to suppliers and ahead to customer service was enough to stay in business, but not enough to attain or maintain leadership. Companies started looking for a new direction � In the 1990 s, Motorola and GE were already moving to 4 sigma and 5 sigma levels of quality control in some business areas, and 6 sigma was a big step in the next direction.
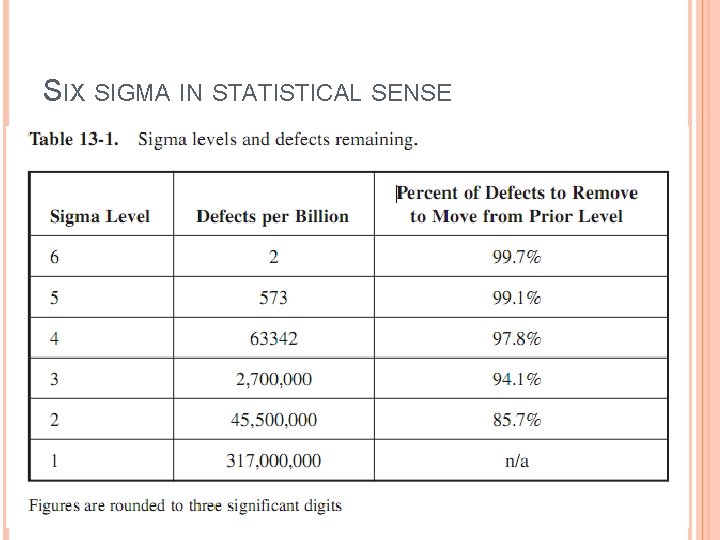
SIX SIGMA IN STATISTICAL SENSE
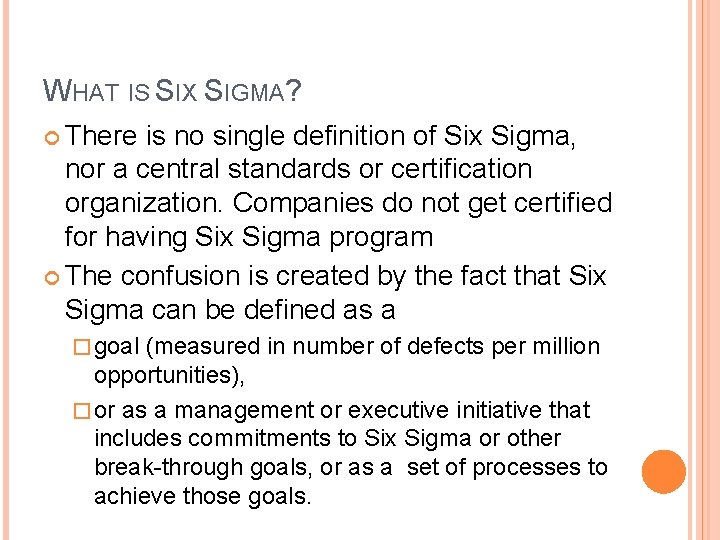
WHAT IS SIX SIGMA? There is no single definition of Six Sigma, nor a central standards or certification organization. Companies do not get certified for having Six Sigma program The confusion is created by the fact that Six Sigma can be defined as a � goal (measured in number of defects per million opportunities), � or as a management or executive initiative that includes commitments to Six Sigma or other break-through goals, or as a set of processes to achieve those goals.
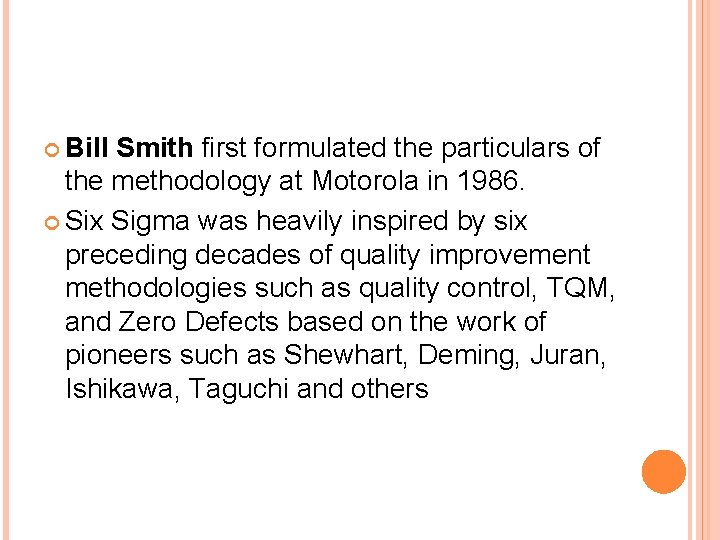
Bill Smith first formulated the particulars of the methodology at Motorola in 1986. Six Sigma was heavily inspired by six preceding decades of quality improvement methodologies such as quality control, TQM, and Zero Defects based on the work of pioneers such as Shewhart, Deming, Juran, Ishikawa, Taguchi and others
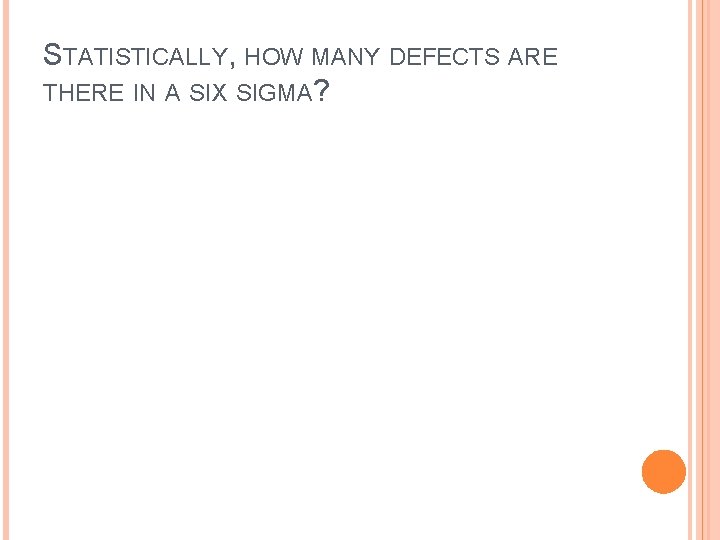
STATISTICALLY, HOW MANY DEFECTS ARE THERE IN A SIX SIGMA?
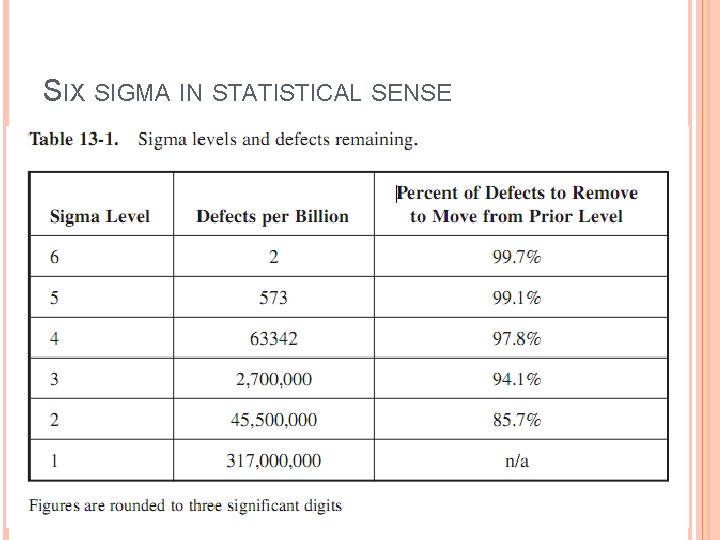
SIX SIGMA IN STATISTICAL SENSE
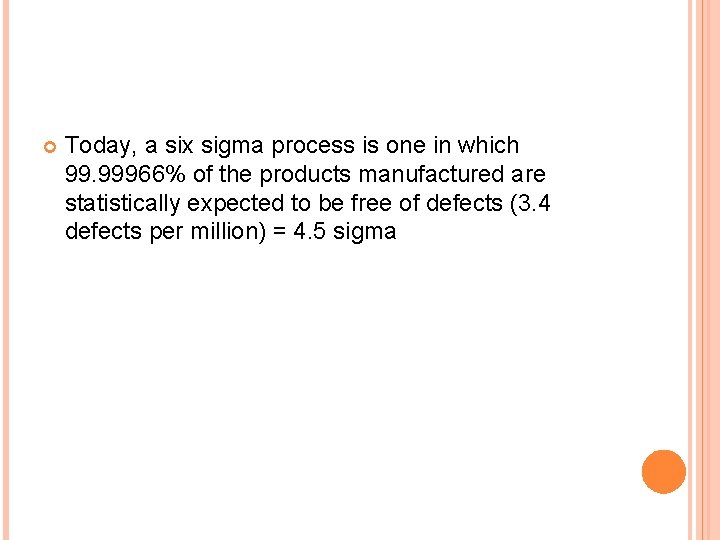
Today, a six sigma process is one in which 99. 99966% of the products manufactured are statistically expected to be free of defects (3. 4 defects per million) = 4. 5 sigma
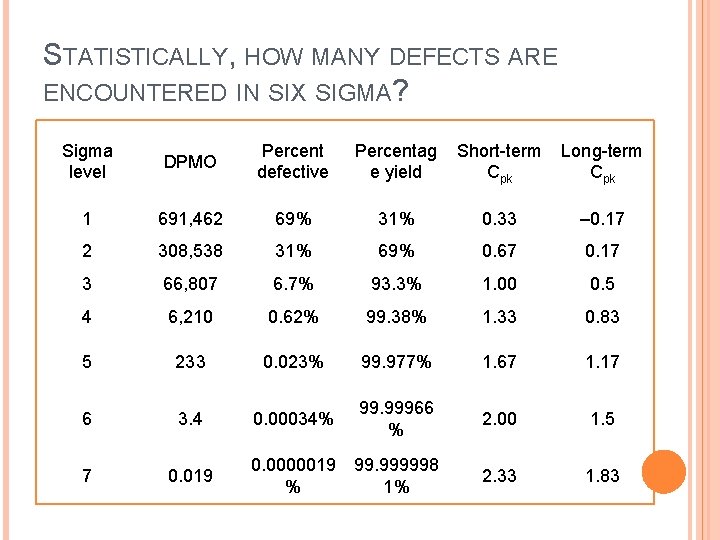
STATISTICALLY, HOW MANY DEFECTS ARE ENCOUNTERED IN SIX SIGMA? Sigma level DPMO Percent defective Percentag e yield Short-term Cpk Long-term Cpk 1 691, 462 69% 31% 0. 33 – 0. 17 2 308, 538 31% 69% 0. 67 0. 17 3 66, 807 6. 7% 93. 3% 1. 00 0. 5 4 6, 210 0. 62% 99. 38% 1. 33 0. 83 5 233 0. 023% 99. 977% 1. 67 1. 17 6 3. 4 0. 00034% 99. 99966 % 2. 00 1. 5 7 0. 019 0. 0000019 99. 999998 % 1% 2. 33 1. 83
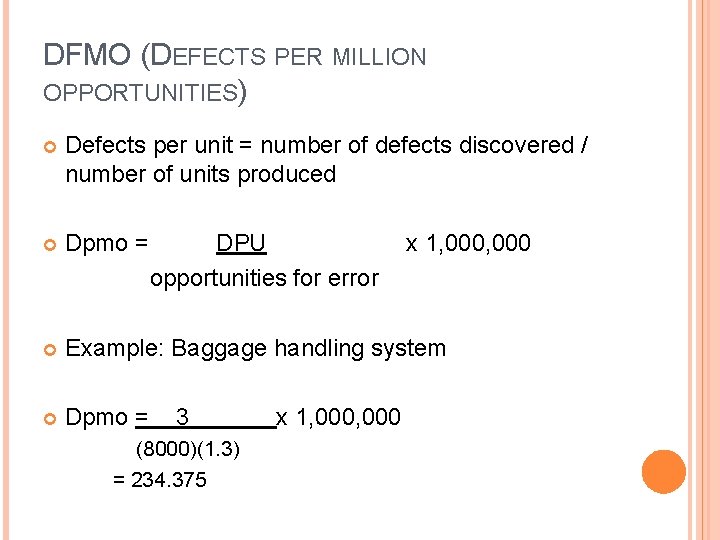
DFMO (DEFECTS PER MILLION OPPORTUNITIES) Defects per unit = number of defects discovered / number of units produced Dpmo = Example: Baggage handling system Dpmo = DPU opportunities for error 3 (8000)(1. 3) = 234. 375 x 1, 000, 000
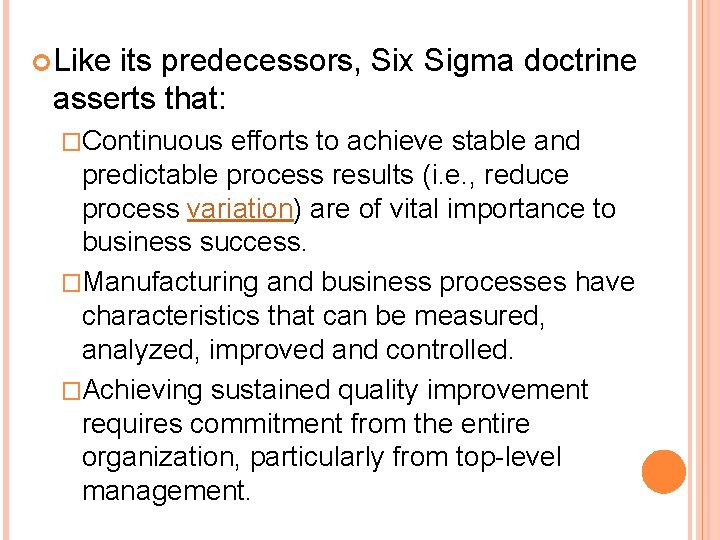
Like its predecessors, Six Sigma doctrine asserts that: �Continuous efforts to achieve stable and predictable process results (i. e. , reduce process variation) are of vital importance to business success. �Manufacturing and business processes have characteristics that can be measured, analyzed, improved and controlled. �Achieving sustained quality improvement requires commitment from the entire organization, particularly from top-level management.
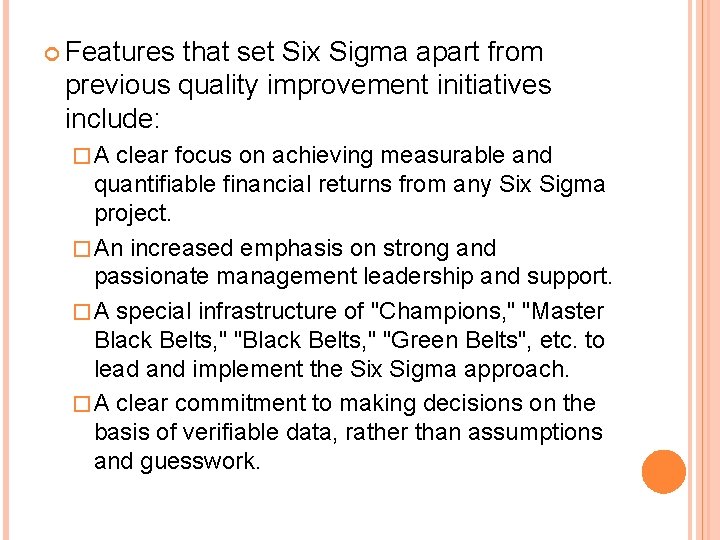
Features that set Six Sigma apart from previous quality improvement initiatives include: �A clear focus on achieving measurable and quantifiable financial returns from any Six Sigma project. � An increased emphasis on strong and passionate management leadership and support. � A special infrastructure of "Champions, " "Master Black Belts, " "Green Belts", etc. to lead and implement the Six Sigma approach. � A clear commitment to making decisions on the basis of verifiable data, rather than assumptions and guesswork.
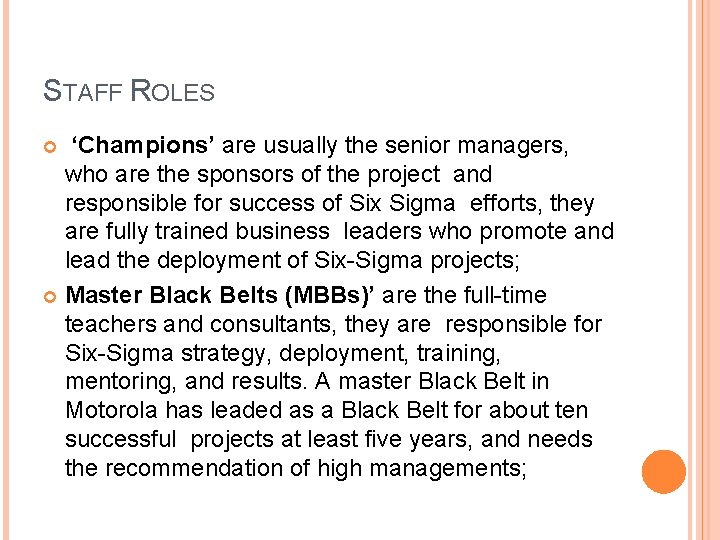
STAFF ROLES ‘Champions’ are usually the senior managers, who are the sponsors of the project and responsible for success of Six Sigma efforts, they are fully trained business leaders who promote and lead the deployment of Six-Sigma projects; Master Black Belts (MBBs)’ are the full-time teachers and consultants, they are responsible for Six-Sigma strategy, deployment, training, mentoring, and results. A master Black Belt in Motorola has leaded as a Black Belt for about ten successful projects at least five years, and needs the recommendation of high managements;
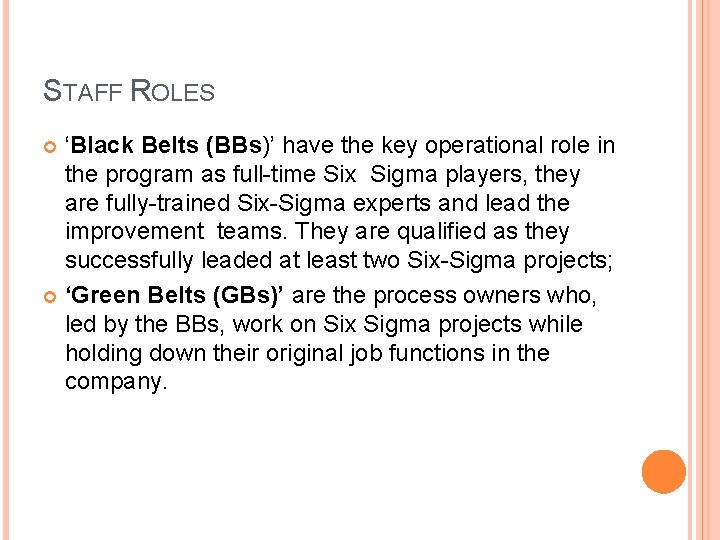
STAFF ROLES ‘Black Belts (BBs)’ have the key operational role in the program as full-time Six Sigma players, they are fully-trained Six-Sigma experts and lead the improvement teams. They are qualified as they successfully leaded at least two Six-Sigma projects; ‘Green Belts (GBs)’ are the process owners who, led by the BBs, work on Six Sigma projects while holding down their original job functions in the company.
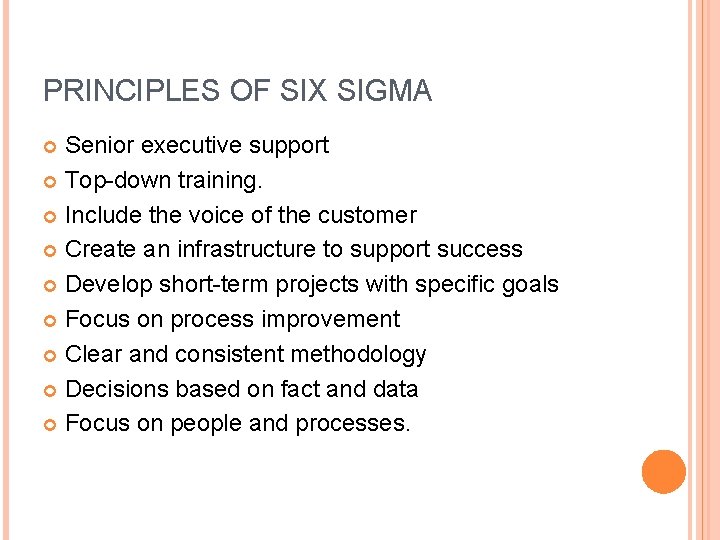
PRINCIPLES OF SIX SIGMA Senior executive support Top-down training. Include the voice of the customer Create an infrastructure to support success Develop short-term projects with specific goals Focus on process improvement Clear and consistent methodology Decisions based on fact and data Focus on people and processes.
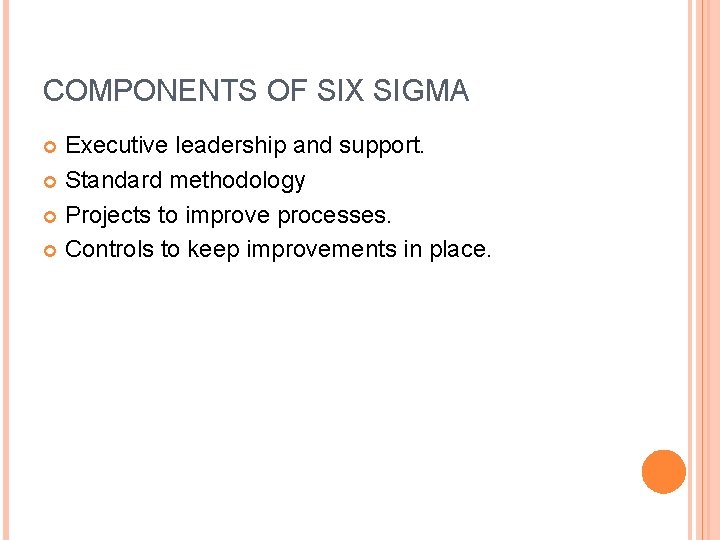
COMPONENTS OF SIX SIGMA Executive leadership and support. Standard methodology Projects to improve processes. Controls to keep improvements in place.
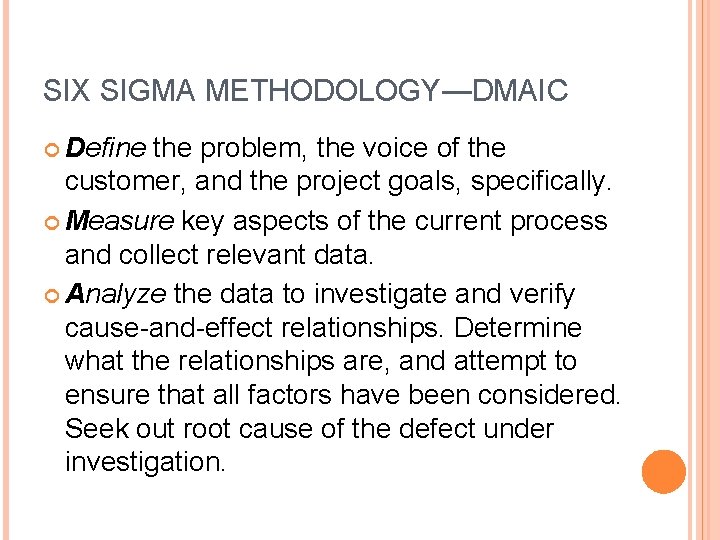
SIX SIGMA METHODOLOGY—DMAIC Define the problem, the voice of the customer, and the project goals, specifically. Measure key aspects of the current process and collect relevant data. Analyze the data to investigate and verify cause-and-effect relationships. Determine what the relationships are, and attempt to ensure that all factors have been considered. Seek out root cause of the defect under investigation.
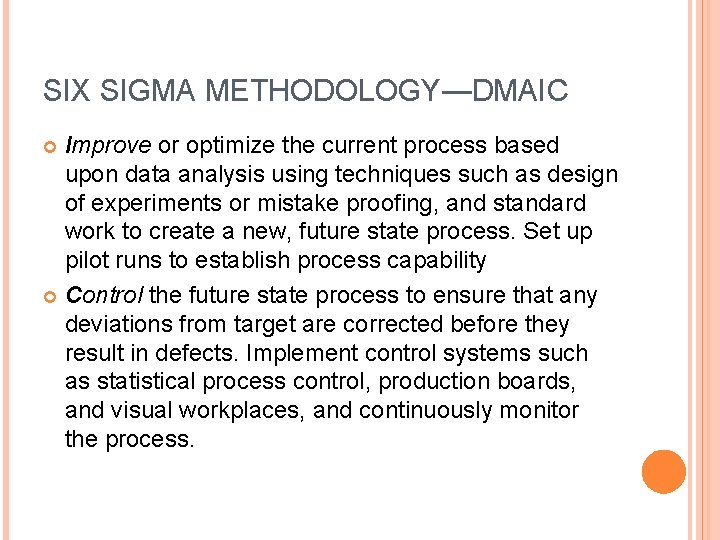
SIX SIGMA METHODOLOGY—DMAIC Improve or optimize the current process based upon data analysis using techniques such as design of experiments or mistake proofing, and standard work to create a new, future state process. Set up pilot runs to establish process capability Control the future state process to ensure that any deviations from target are corrected before they result in defects. Implement control systems such as statistical process control, production boards, and visual workplaces, and continuously monitor the process.
Troposphere characteristics
Hottest layer of atmosphere
What's the hottest planet
Star colors from coolest to hottest
Hottest coldest highest deepest read aloud
Characteristics of outer core
Oceanic crust
Hottest on the hub
Hottest topics tmo
Vcom white coat ceremony
Edward via college of osteopathic medicine - auburn campus
Cmmi six sigma
Microsoft six sigma
Voice of the customer six sigma
Statapult exercise
Who is this
Six sigma qualtec
Six sigma forum
Six sigma kpov
Mse six sigma
Dmaic storyboard template