REFRACTORIES 152022 Source Confidential 1 What is a
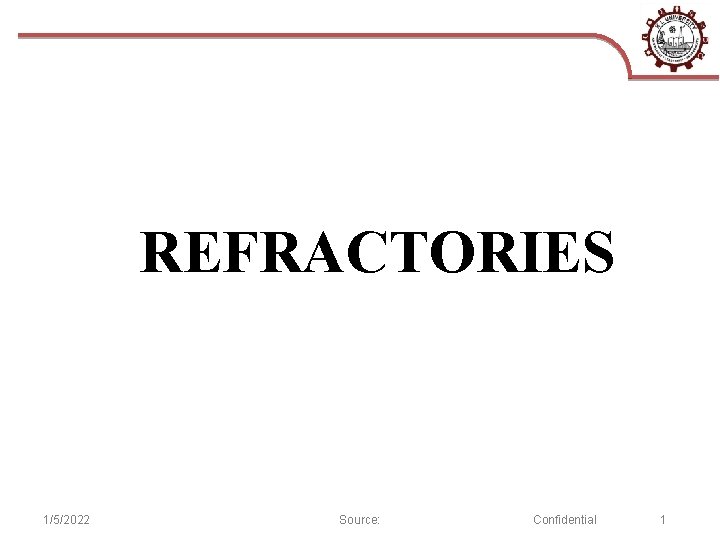
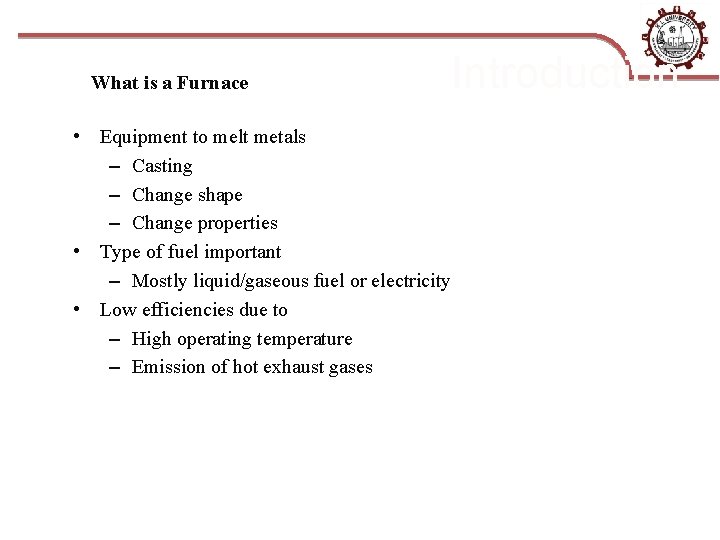
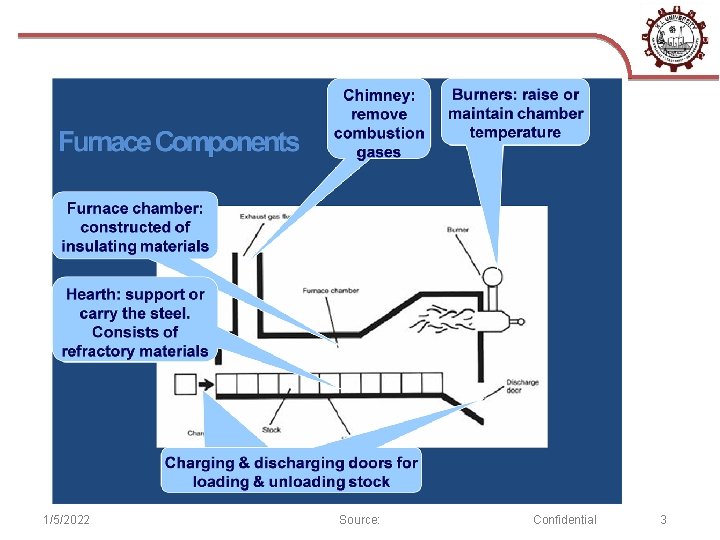
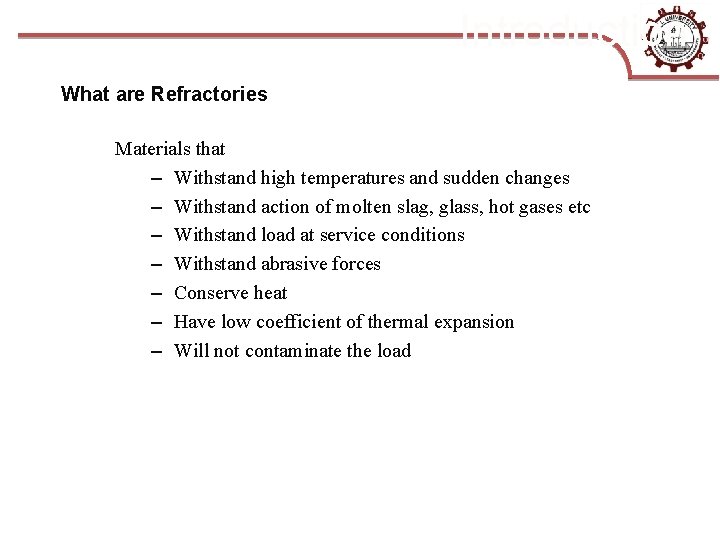
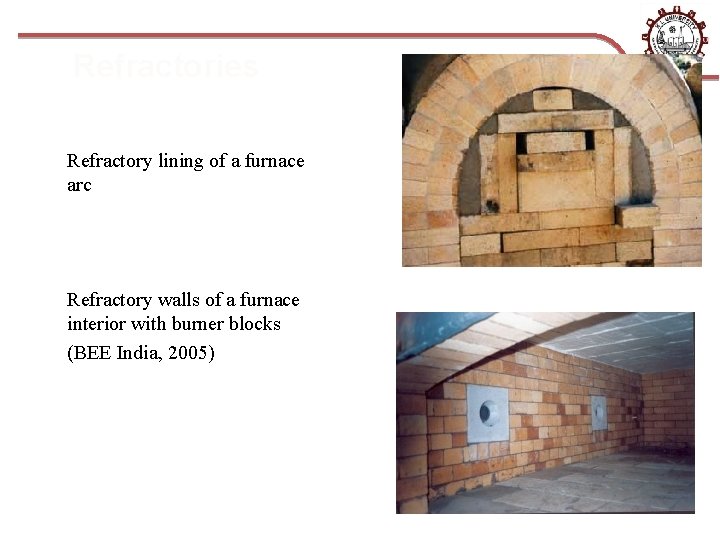
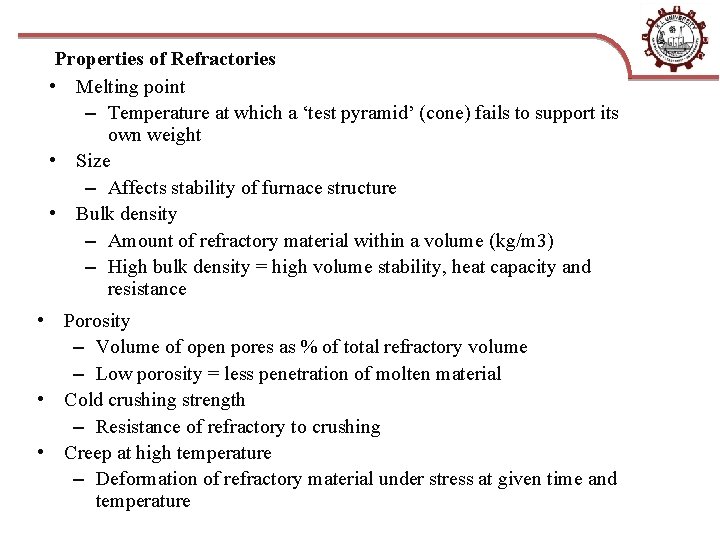
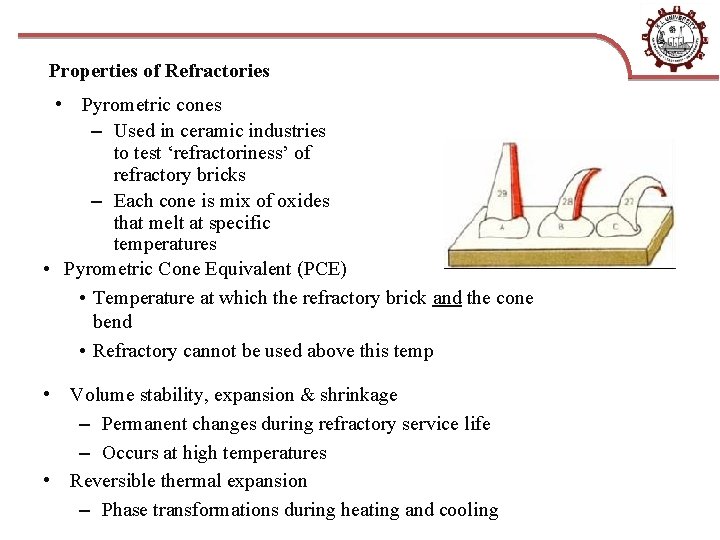
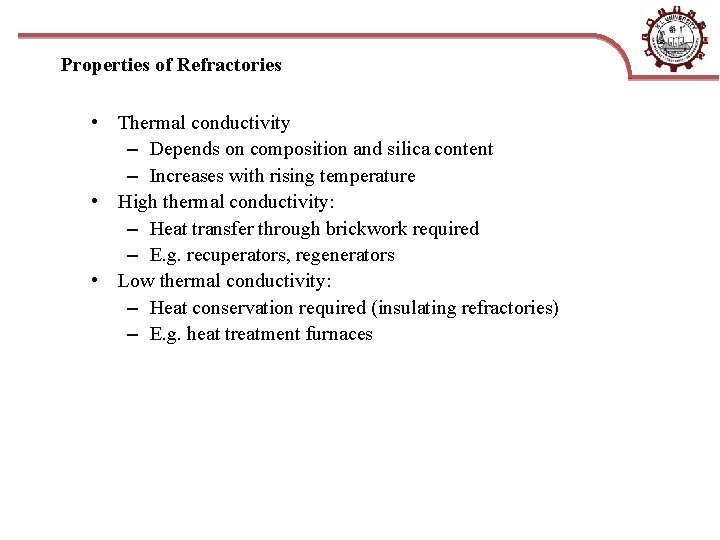
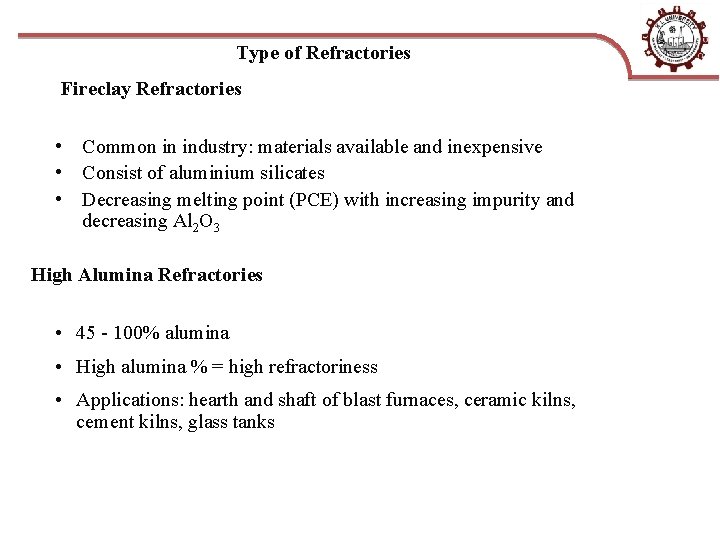
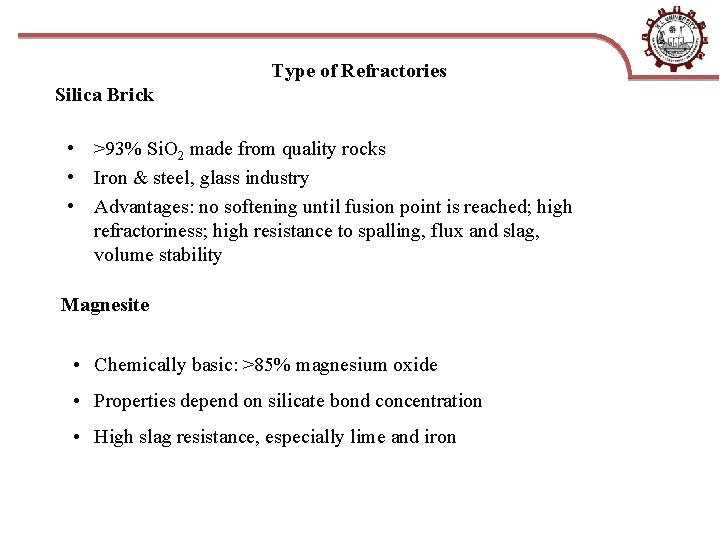
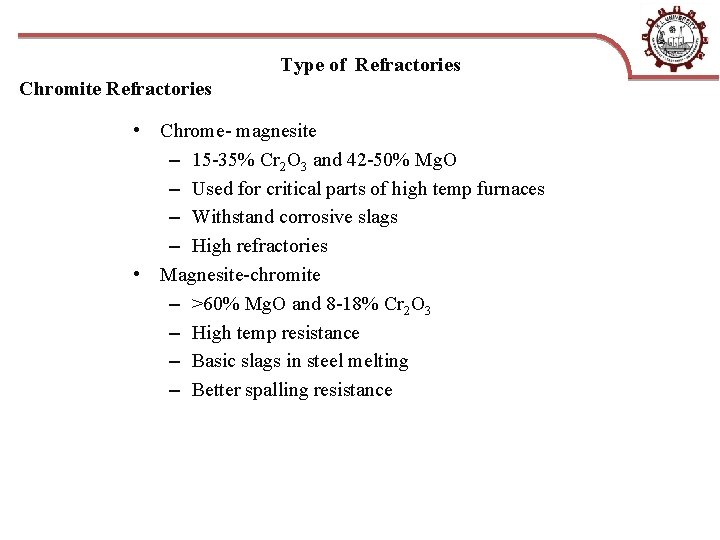
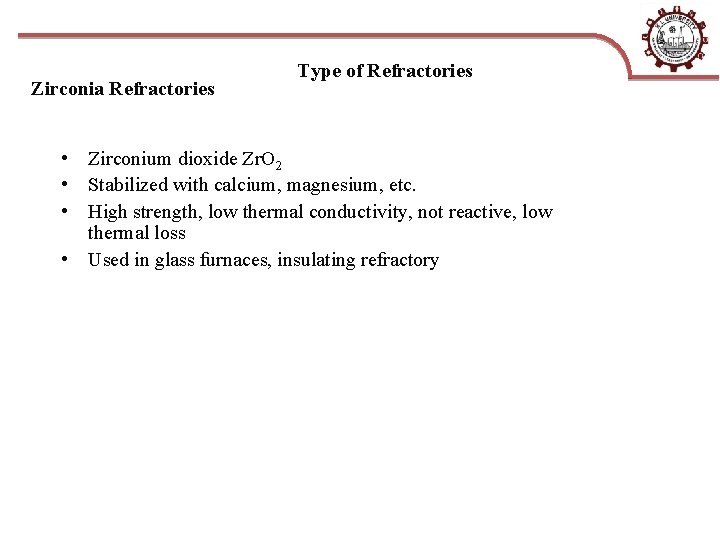
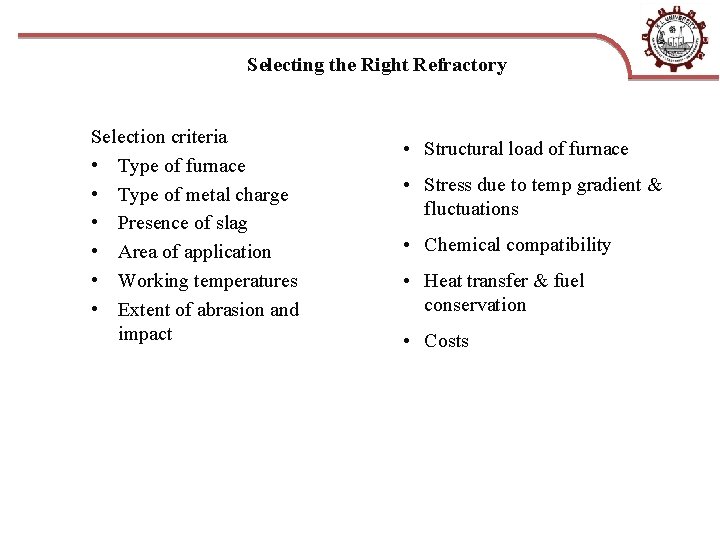
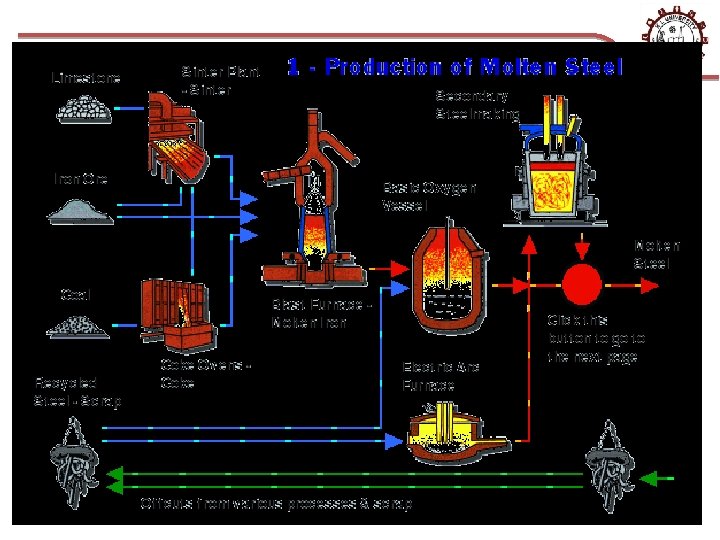
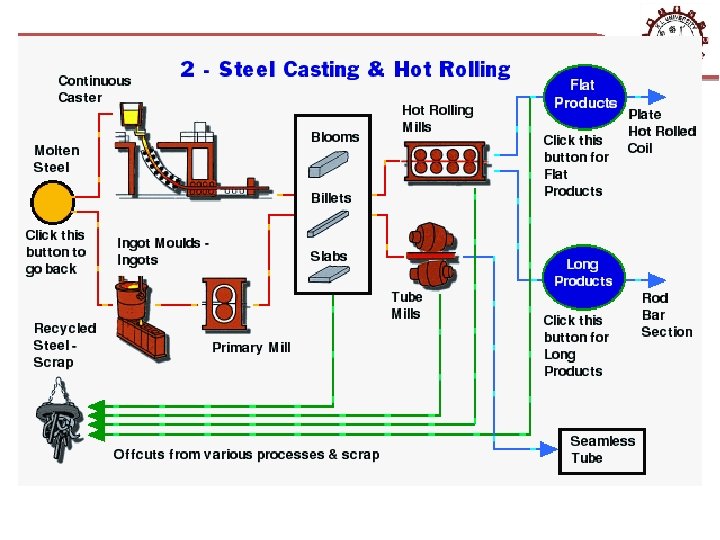
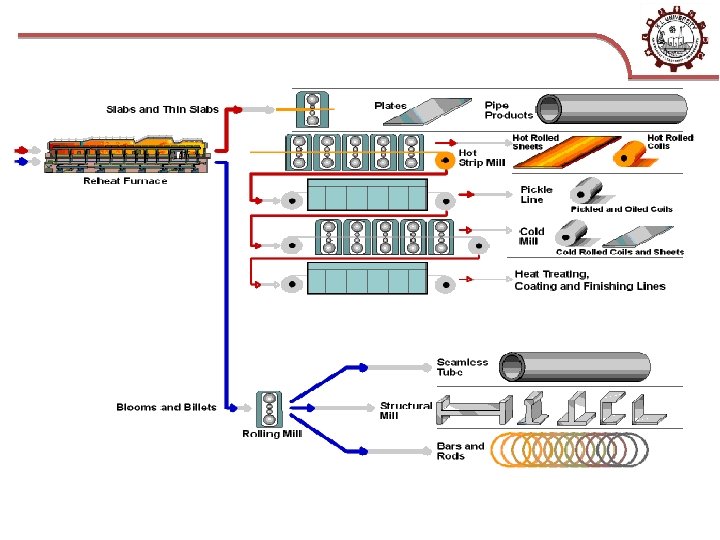
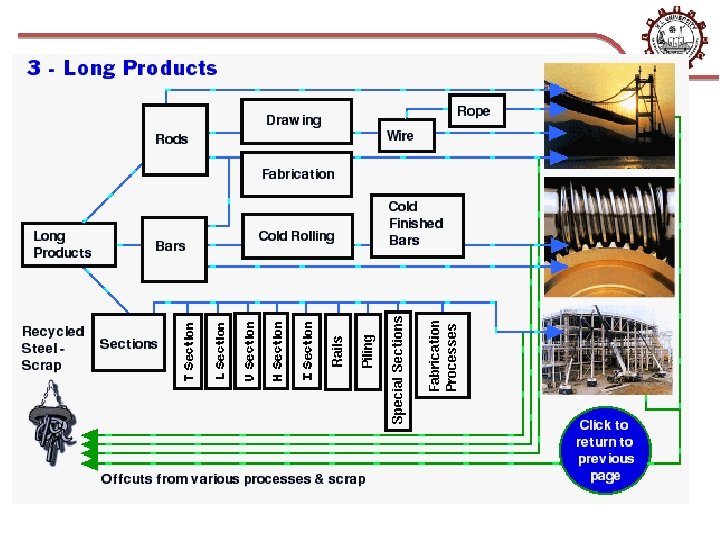
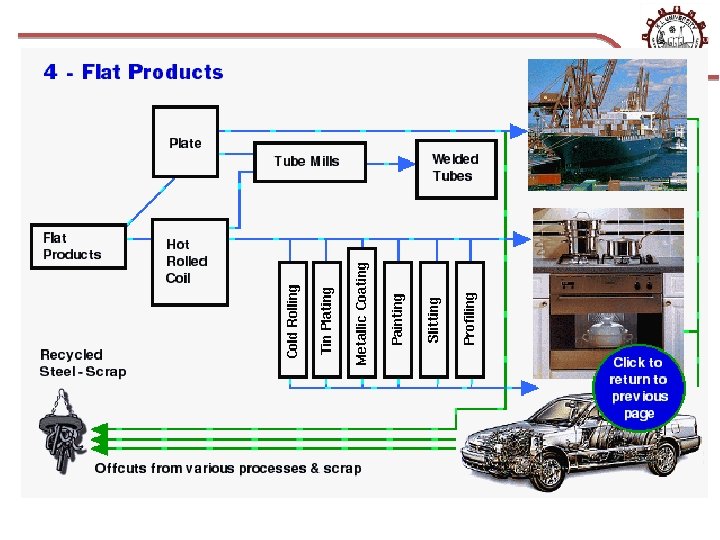
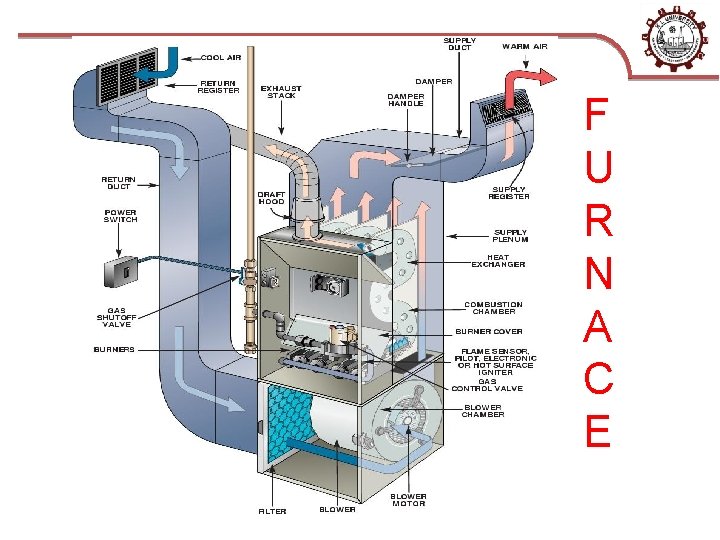
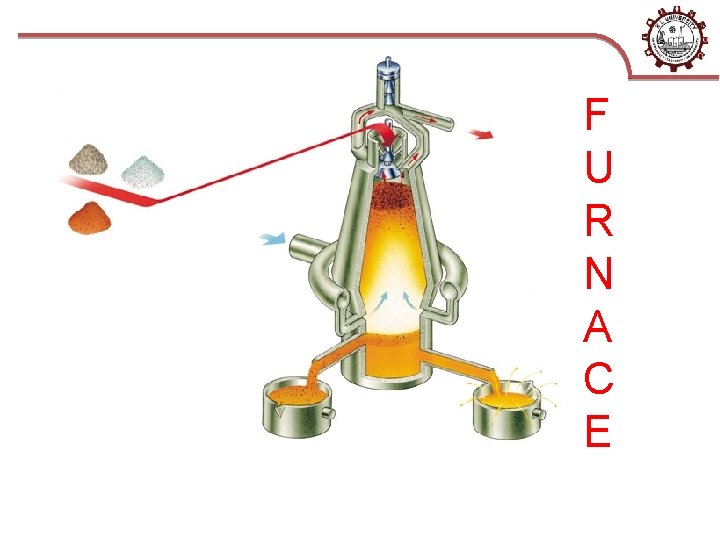
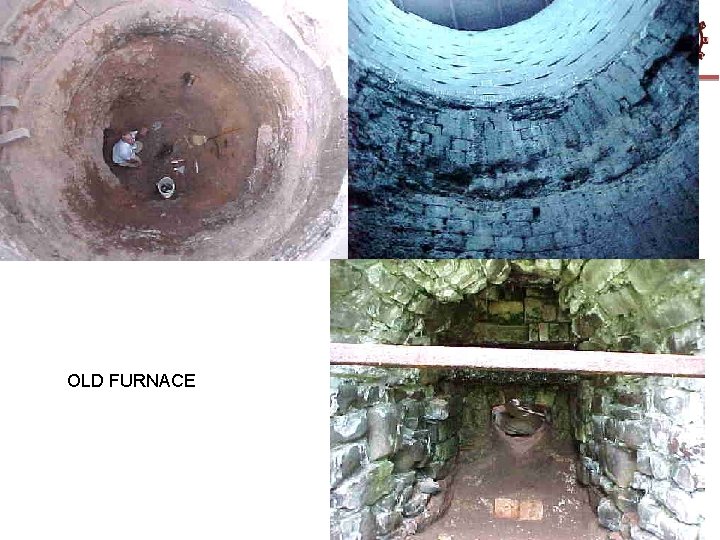
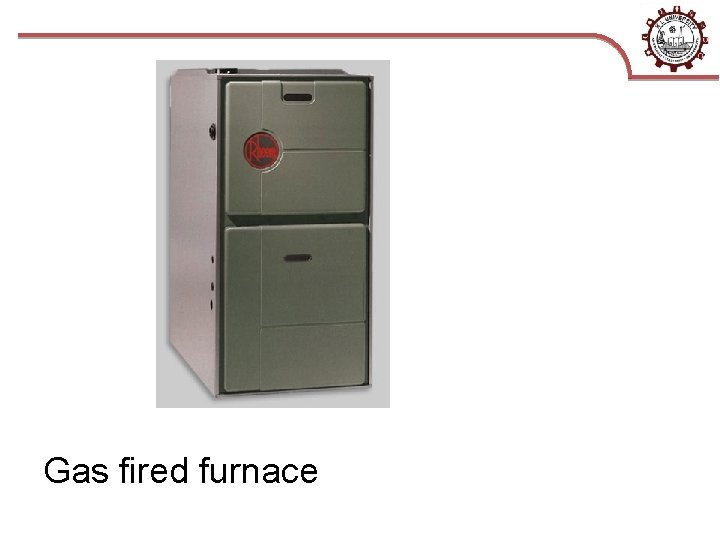
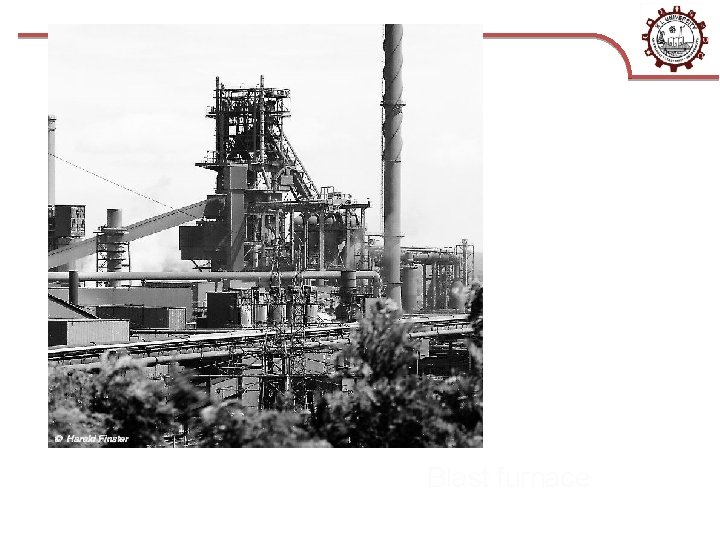
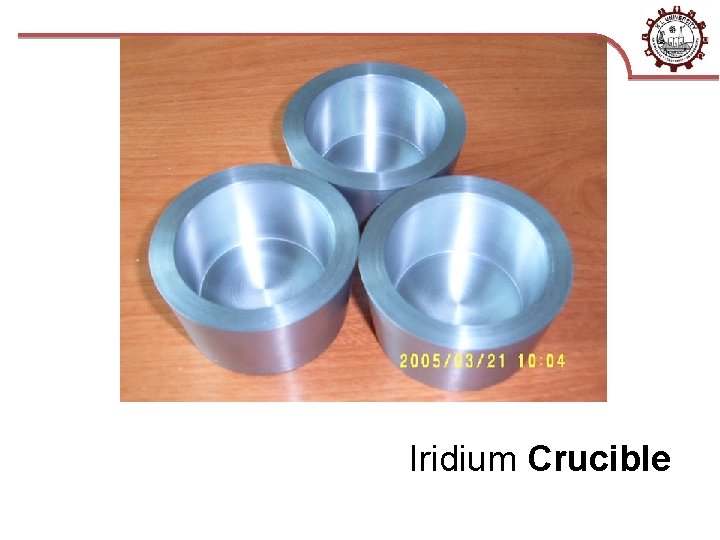
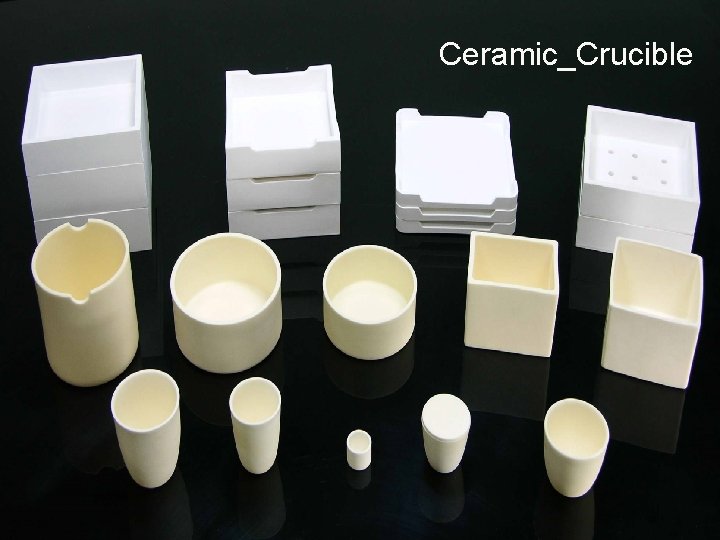
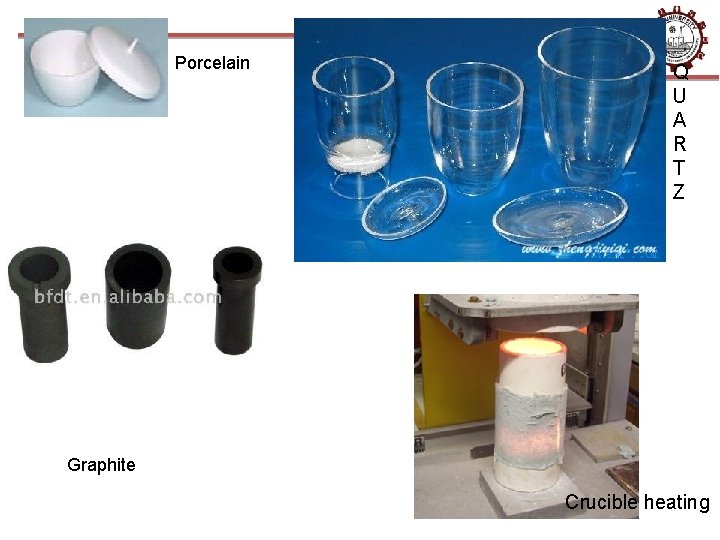
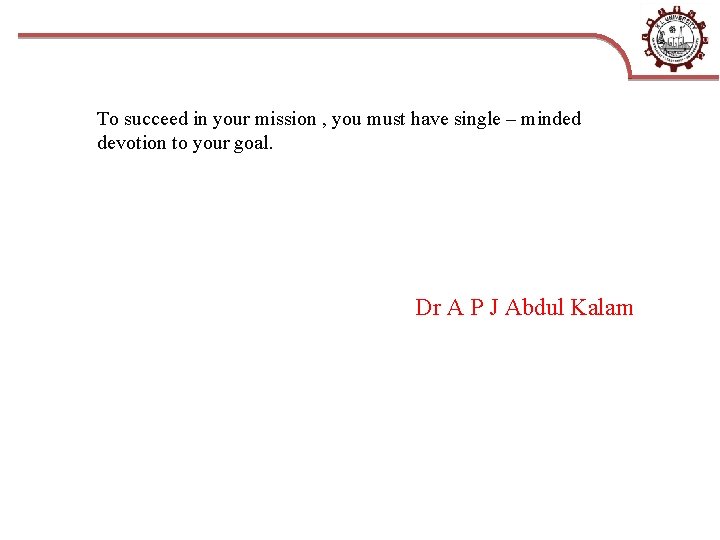
- Slides: 27
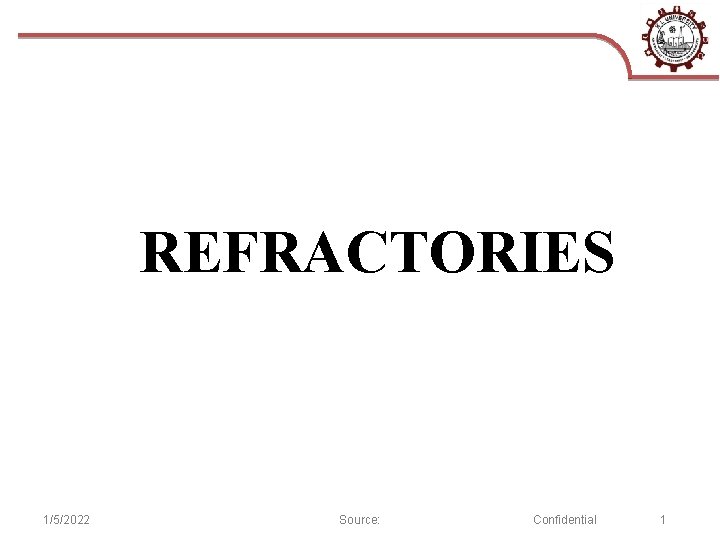
REFRACTORIES 1/5/2022 Source: Confidential 1
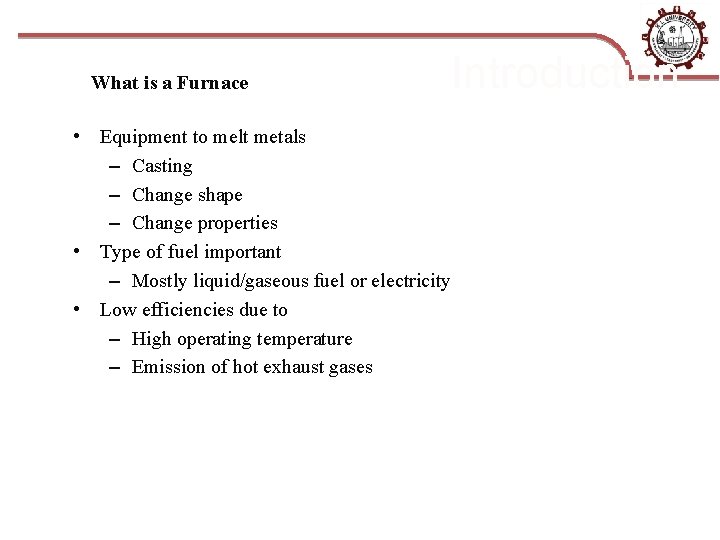
What is a Furnace Introduction • Equipment to melt metals – Casting – Change shape – Change properties • Type of fuel important – Mostly liquid/gaseous fuel or electricity • Low efficiencies due to – High operating temperature – Emission of hot exhaust gases
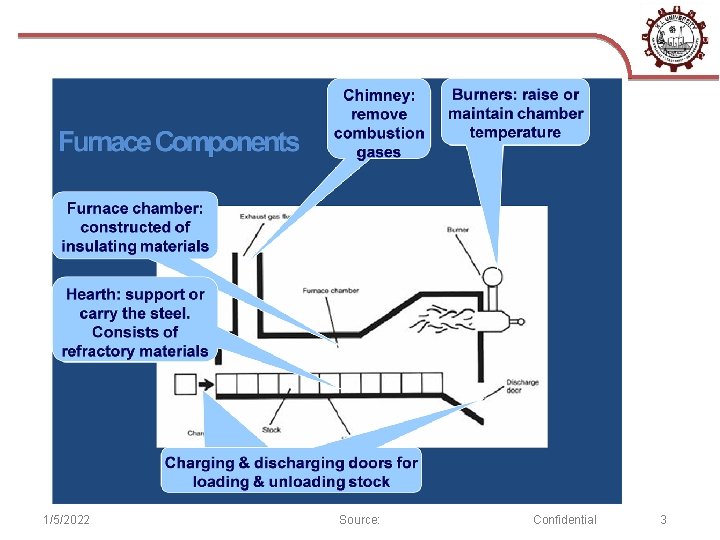
1/5/2022 Source: Confidential 3
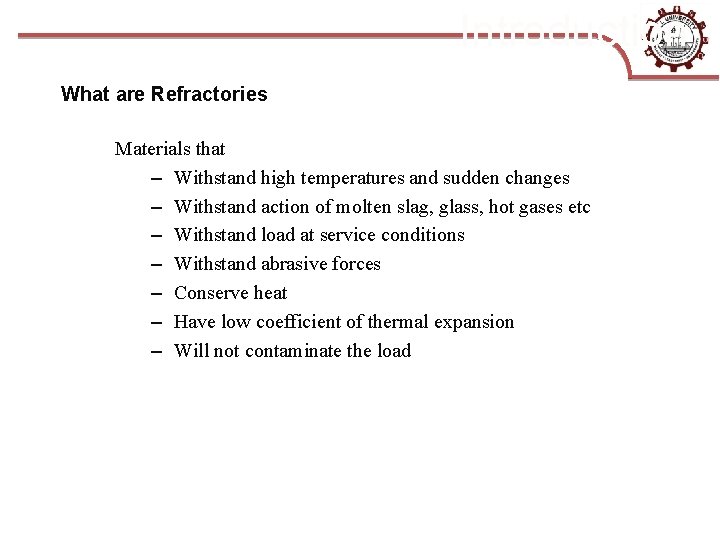
Introduction What are Refractories Materials that – Withstand high temperatures and sudden changes – Withstand action of molten slag, glass, hot gases etc – Withstand load at service conditions – Withstand abrasive forces – Conserve heat – Have low coefficient of thermal expansion – Will not contaminate the load
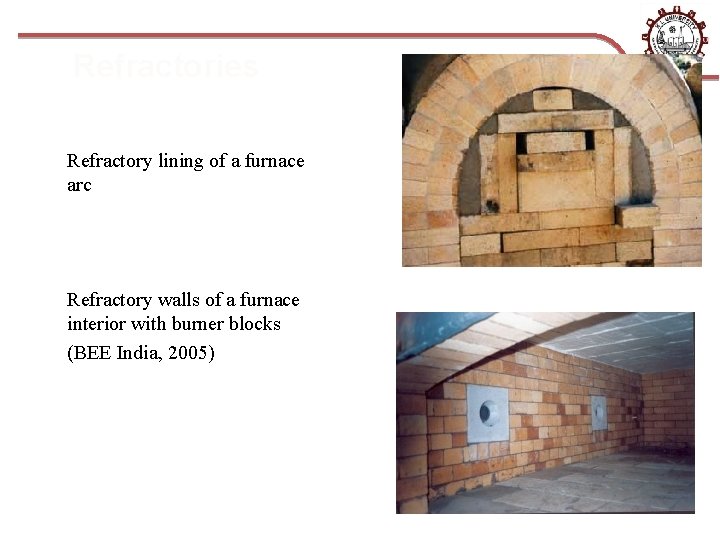
Refractories Refractory lining of a furnace arc Refractory walls of a furnace interior with burner blocks (BEE India, 2005)
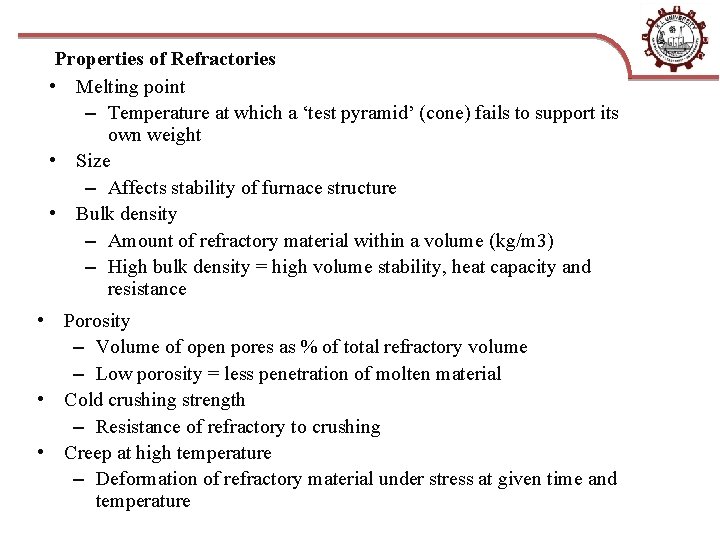
Properties of Refractories • Melting point – Temperature at which a ‘test pyramid’ (cone) fails to support its own weight • Size – Affects stability of furnace structure • Bulk density – Amount of refractory material within a volume (kg/m 3) – High bulk density = high volume stability, heat capacity and resistance • Porosity – Volume of open pores as % of total refractory volume – Low porosity = less penetration of molten material • Cold crushing strength – Resistance of refractory to crushing • Creep at high temperature – Deformation of refractory material under stress at given time and temperature
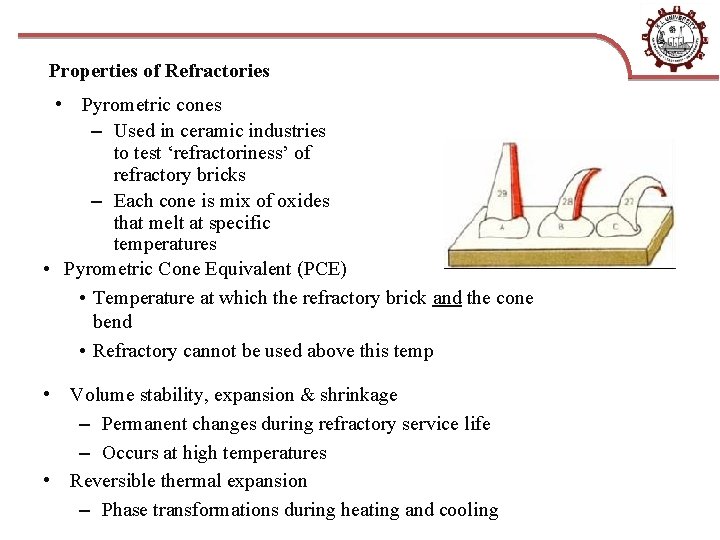
Properties of Refractories • Pyrometric cones – Used in ceramic industries to test ‘refractoriness’ of refractory bricks – Each cone is mix of oxides that melt at specific temperatures • Pyrometric Cone Equivalent (PCE) • Temperature at which the refractory brick and the cone bend • Refractory cannot be used above this temp • Volume stability, expansion & shrinkage – Permanent changes during refractory service life – Occurs at high temperatures • Reversible thermal expansion – Phase transformations during heating and cooling
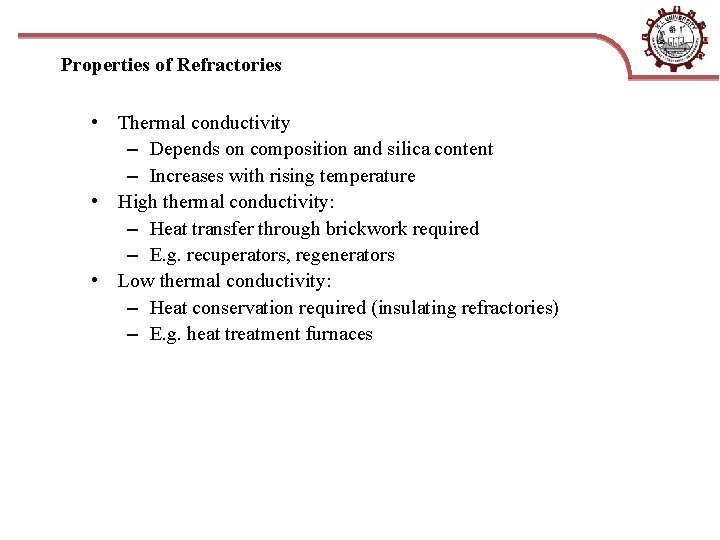
Properties of Refractories • Thermal conductivity – Depends on composition and silica content – Increases with rising temperature • High thermal conductivity: – Heat transfer through brickwork required – E. g. recuperators, regenerators • Low thermal conductivity: – Heat conservation required (insulating refractories) – E. g. heat treatment furnaces
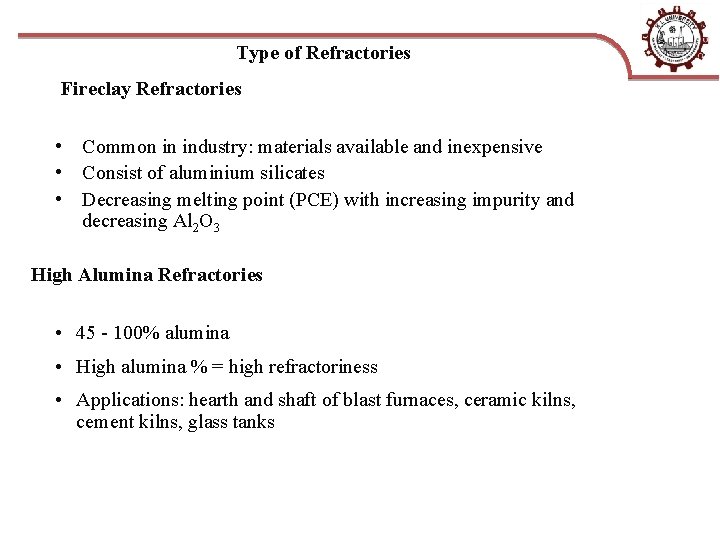
Type of Refractories Fireclay Refractories • Common in industry: materials available and inexpensive • Consist of aluminium silicates • Decreasing melting point (PCE) with increasing impurity and decreasing Al 2 O 3 High Alumina Refractories • 45 - 100% alumina • High alumina % = high refractoriness • Applications: hearth and shaft of blast furnaces, ceramic kilns, cement kilns, glass tanks
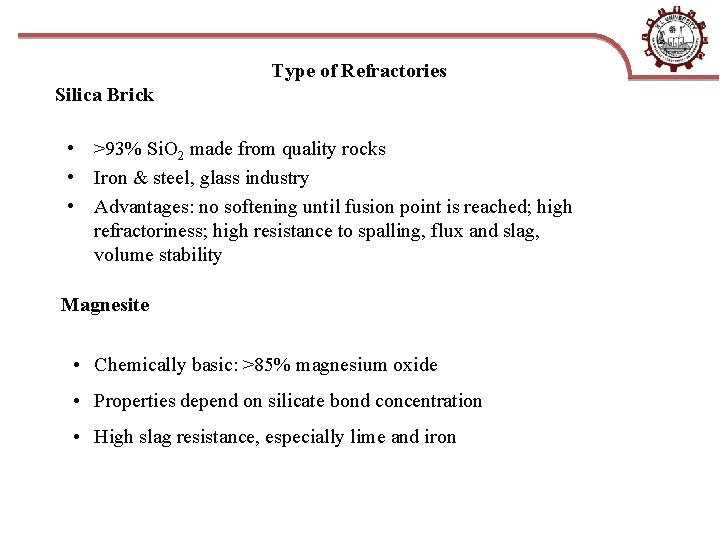
Type of Refractories Silica Brick • >93% Si. O 2 made from quality rocks • Iron & steel, glass industry • Advantages: no softening until fusion point is reached; high refractoriness; high resistance to spalling, flux and slag, volume stability Magnesite • Chemically basic: >85% magnesium oxide • Properties depend on silicate bond concentration • High slag resistance, especially lime and iron
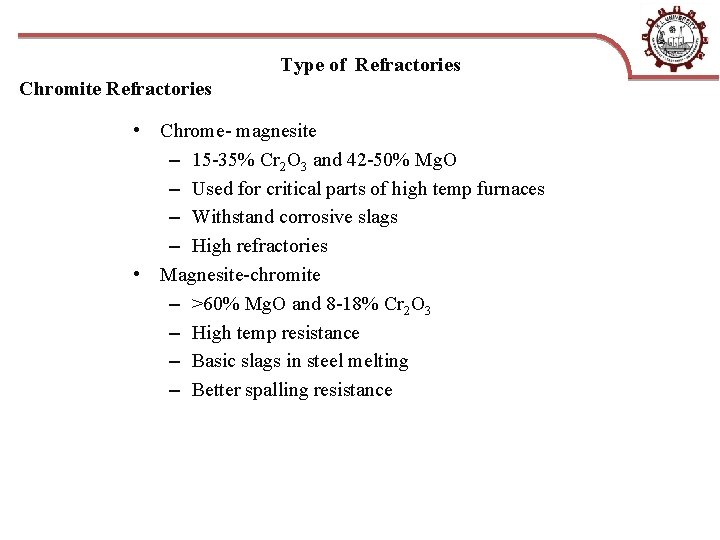
Type of Refractories Chromite Refractories • Chrome- magnesite – 15 -35% Cr 2 O 3 and 42 -50% Mg. O – Used for critical parts of high temp furnaces – Withstand corrosive slags – High refractories • Magnesite-chromite – >60% Mg. O and 8 -18% Cr 2 O 3 – High temp resistance – Basic slags in steel melting – Better spalling resistance
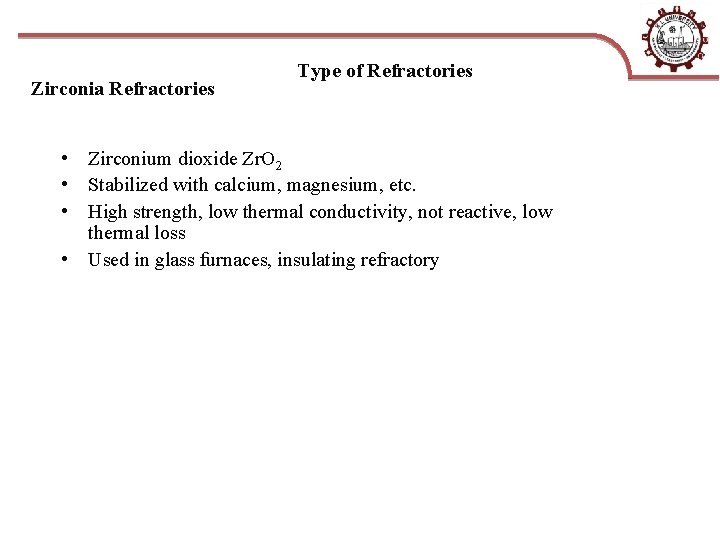
Zirconia Refractories Type of Refractories • Zirconium dioxide Zr. O 2 • Stabilized with calcium, magnesium, etc. • High strength, low thermal conductivity, not reactive, low thermal loss • Used in glass furnaces, insulating refractory
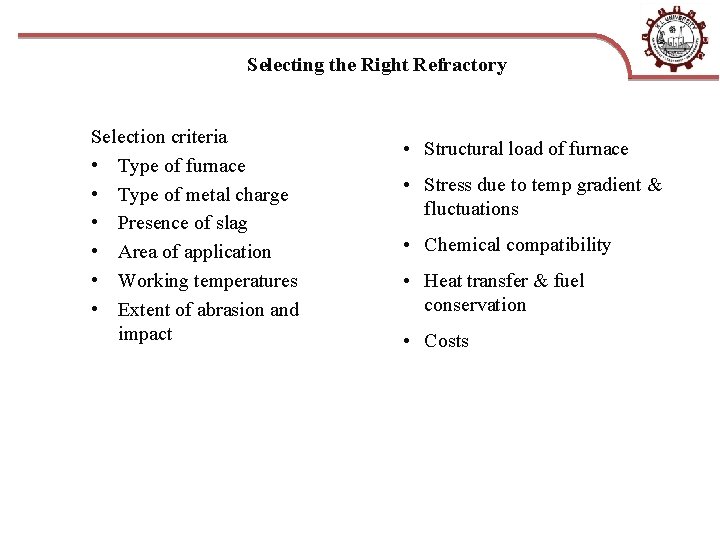
Selecting the Right Refractory Selection criteria • Type of furnace • Type of metal charge • Presence of slag • Area of application • Working temperatures • Extent of abrasion and impact • Structural load of furnace • Stress due to temp gradient & fluctuations • Chemical compatibility • Heat transfer & fuel conservation • Costs
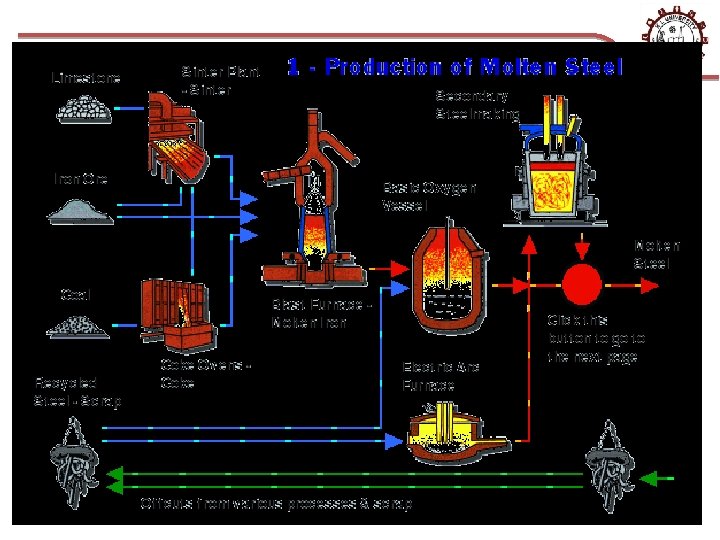
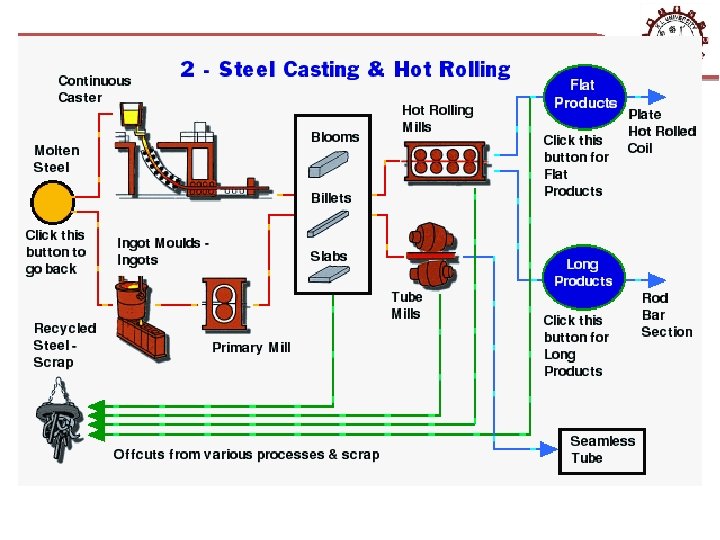
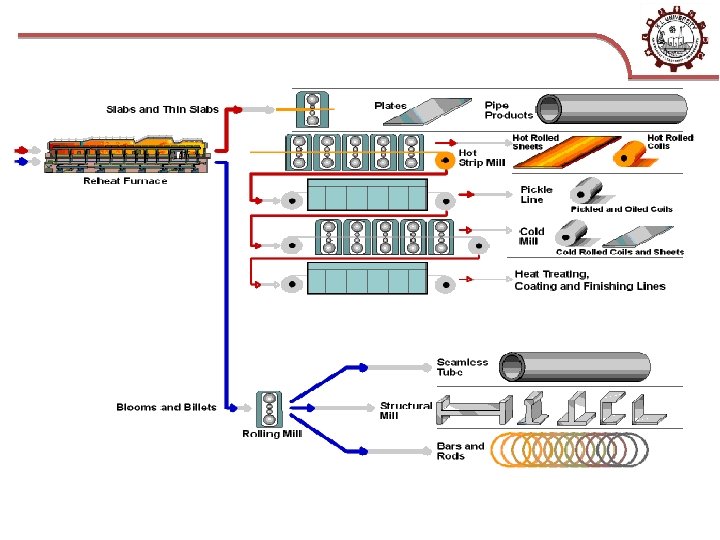
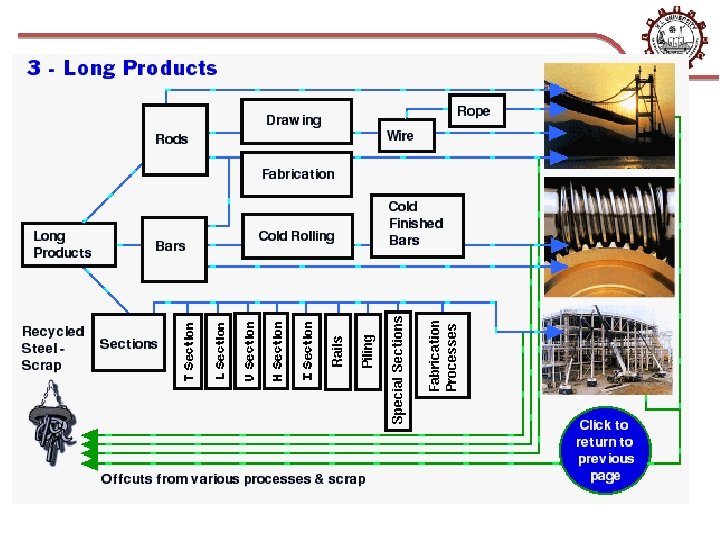
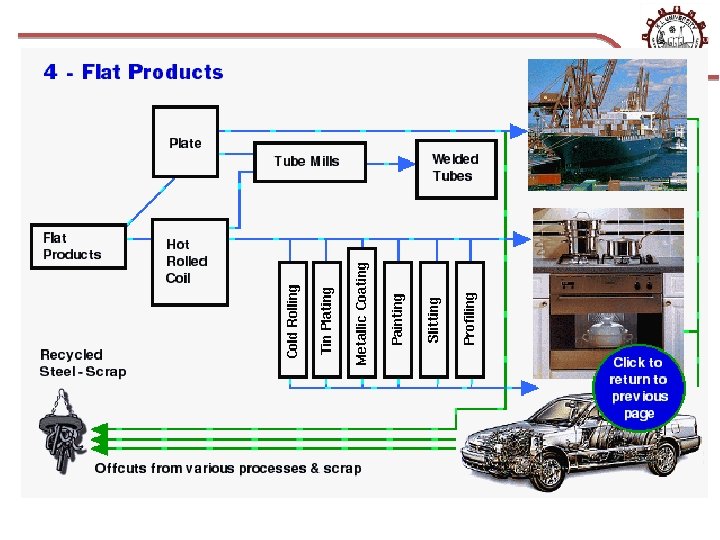
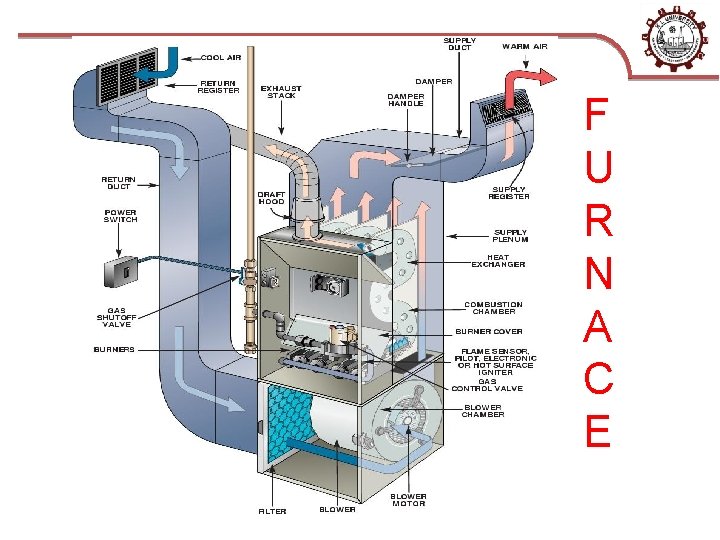
F U R N A C E
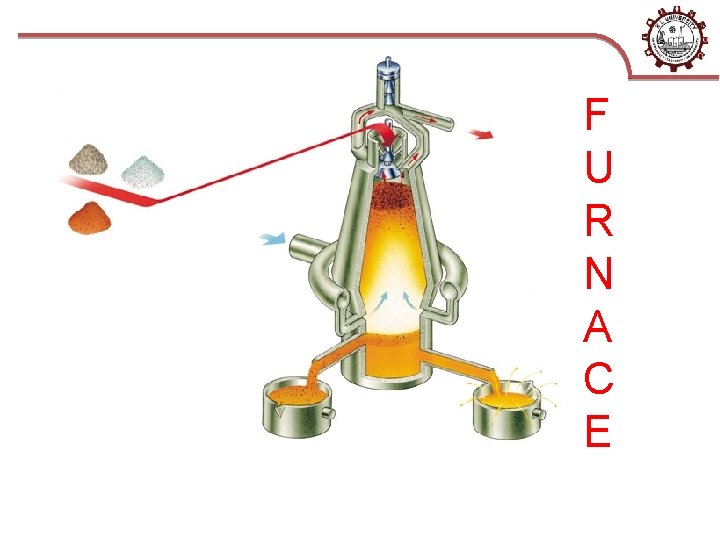
F U R N A C E
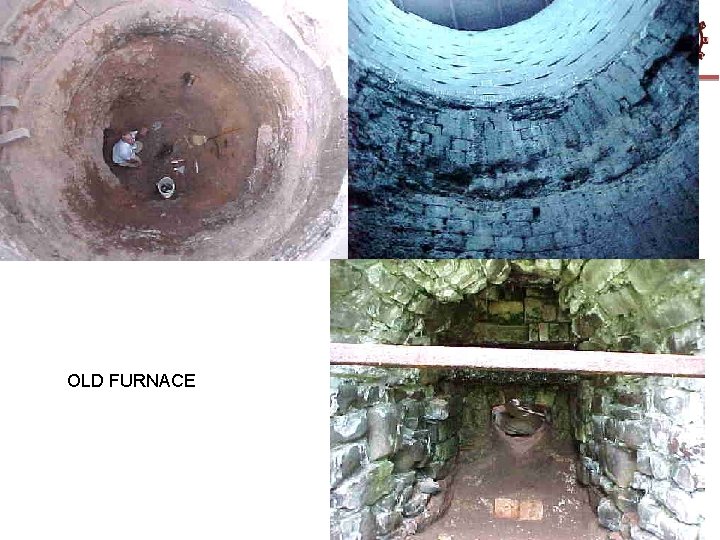
OLD FURNACE
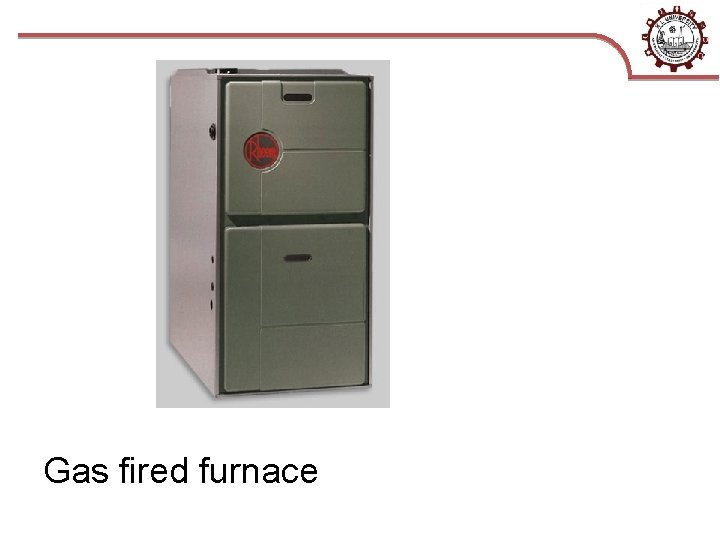
Gas fired furnace
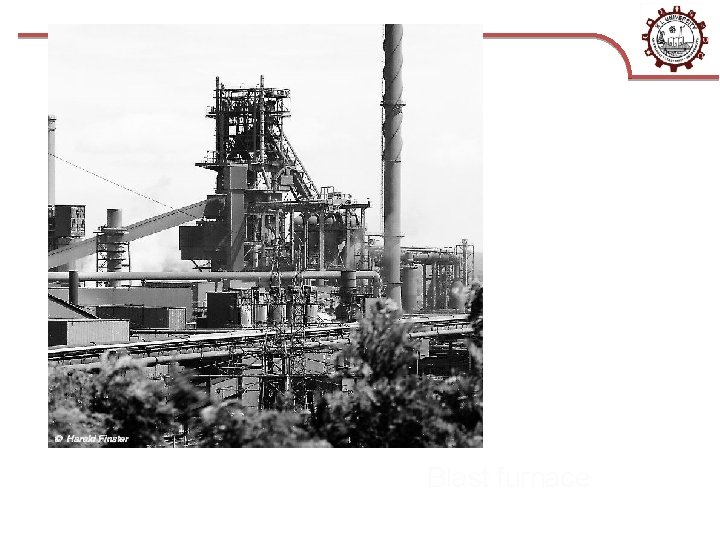
Blast furnace
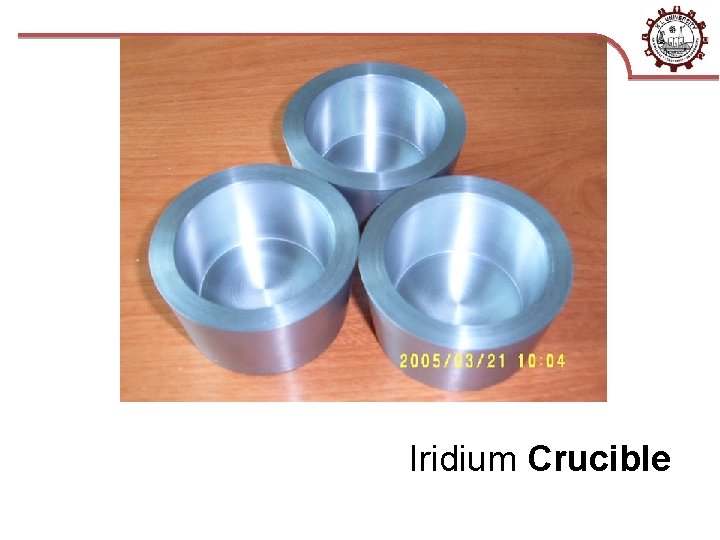
Iridium Crucible
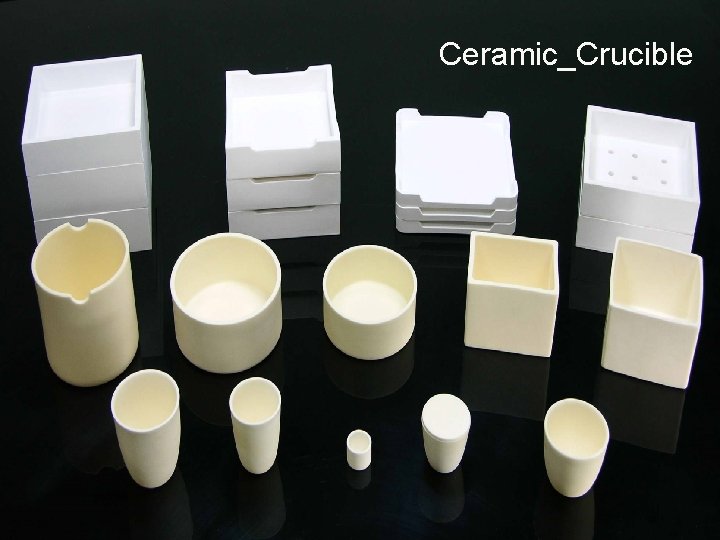
Ceramic_Crucible
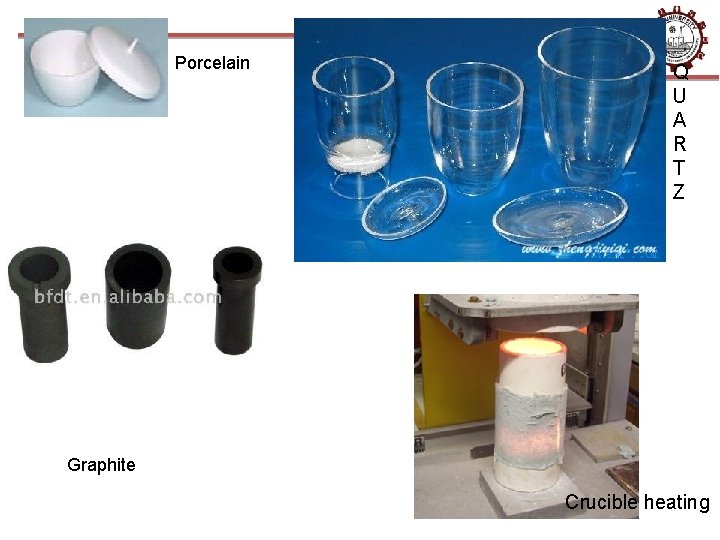
Porcelain Q U A R T Z Graphite Crucible heating
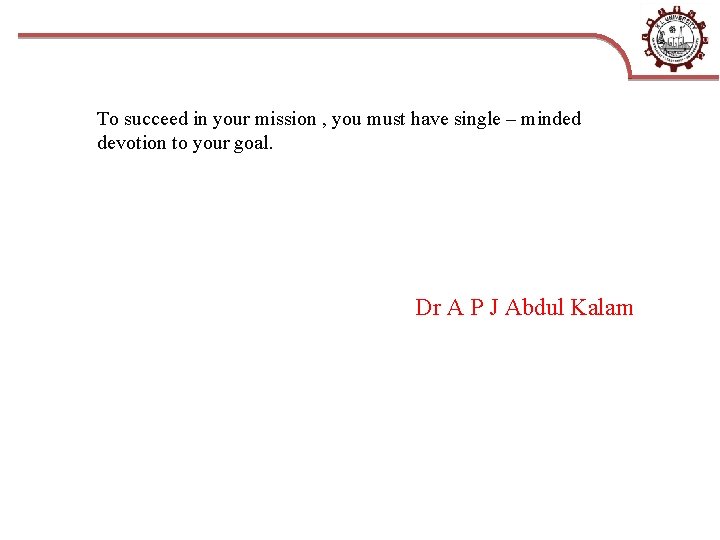
To succeed in your mission , you must have single – minded devotion to your goal. Dr A P J Abdul Kalam
Refractories for power industry
Refractory castable
Continuous casting refractories
Seger cone test
Strictly private and confidential
Strictly private and confidential
Slot rf confidential
Motion to determine confidentiality of court records
Simply confidential
Difference between antiferromagnetism and ferrimagnetism
Confidential copyright
Confidential unit exclusion
Copyright confidential
Gtb invest
Hp recruitment process
Sspos
Confidential
Confidential & proprietary
Ioss azonosító
Confidential renault
Hp confidential
Airbus deutschland gmbh
Confidential document solutions
Nadav amit
Strictly private and confidential
Ruckus wireless glassdoor
Confidential company profile
[email protected]