PNEUMATICS 101 FOR FRC 2017 An Introduction Mark
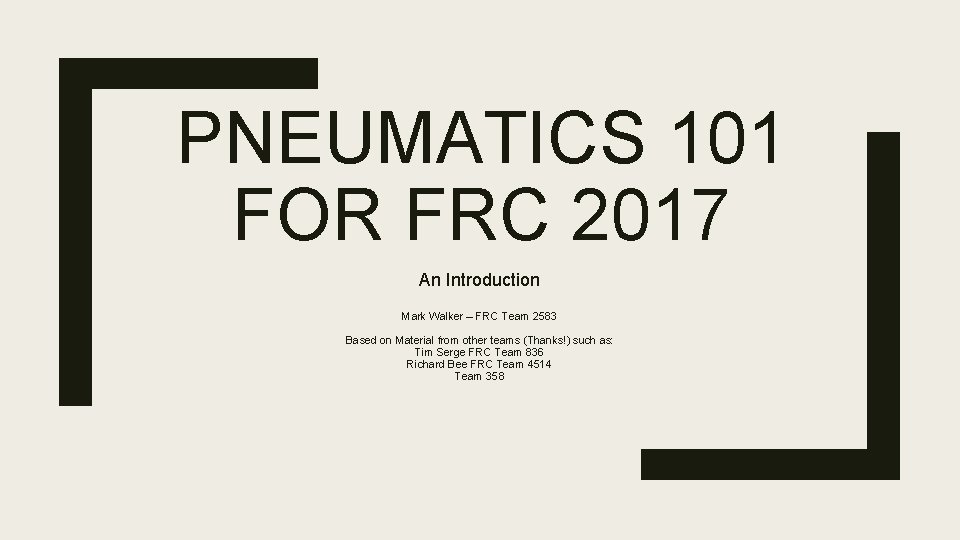
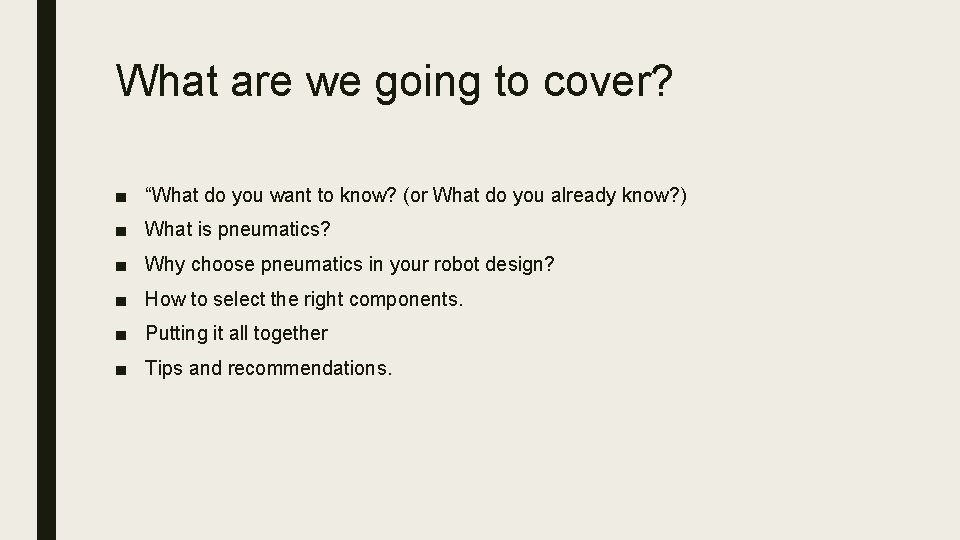
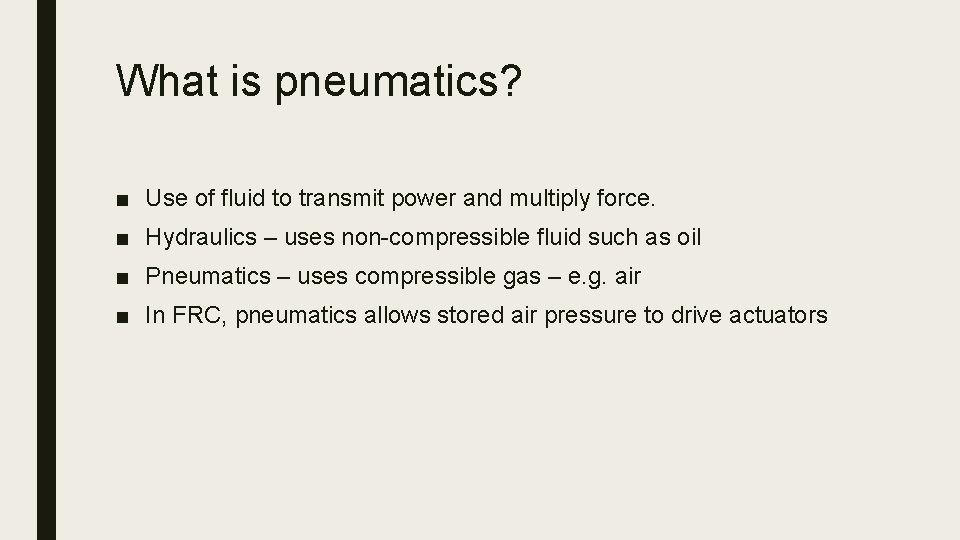
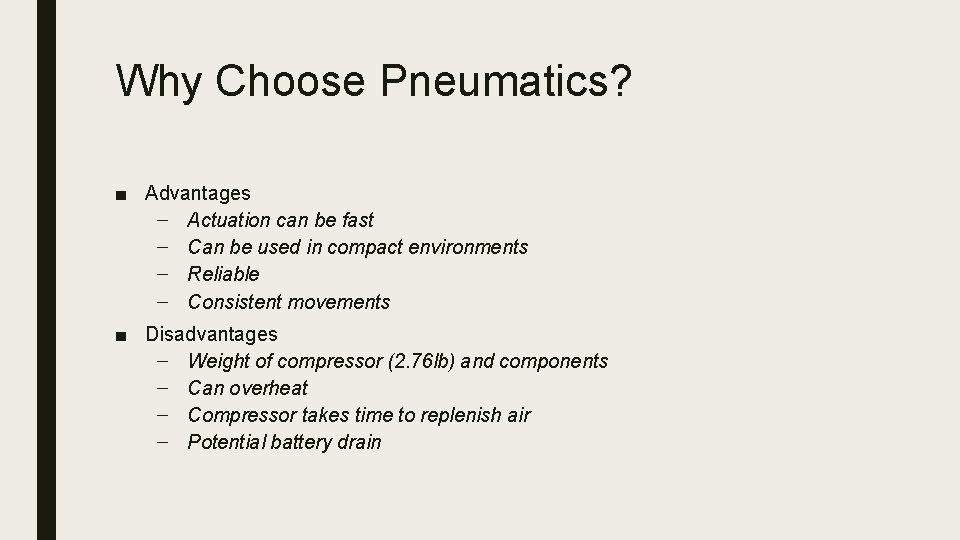
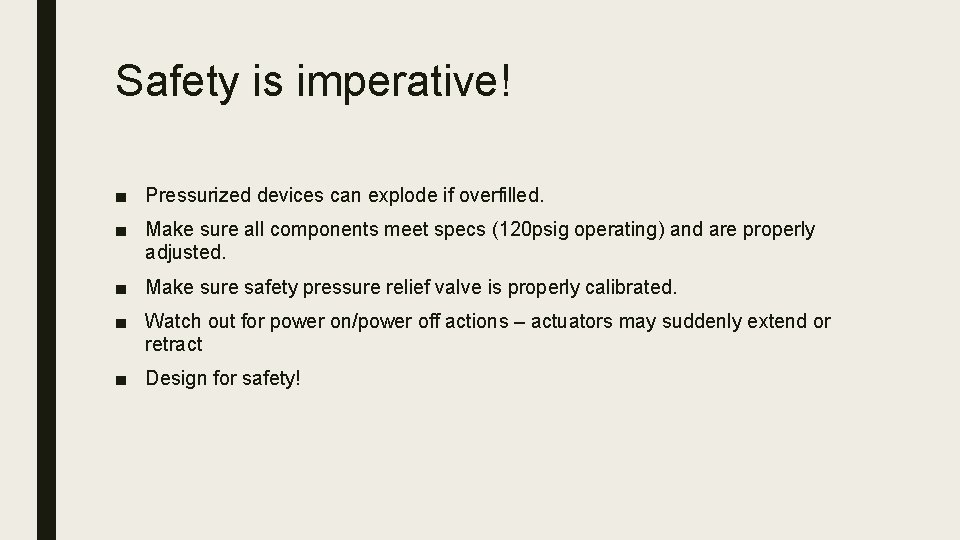
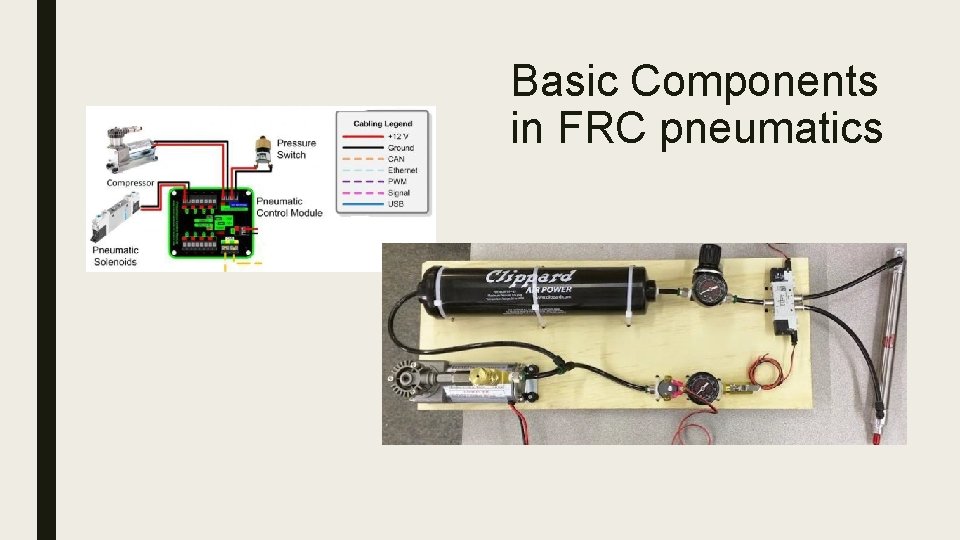
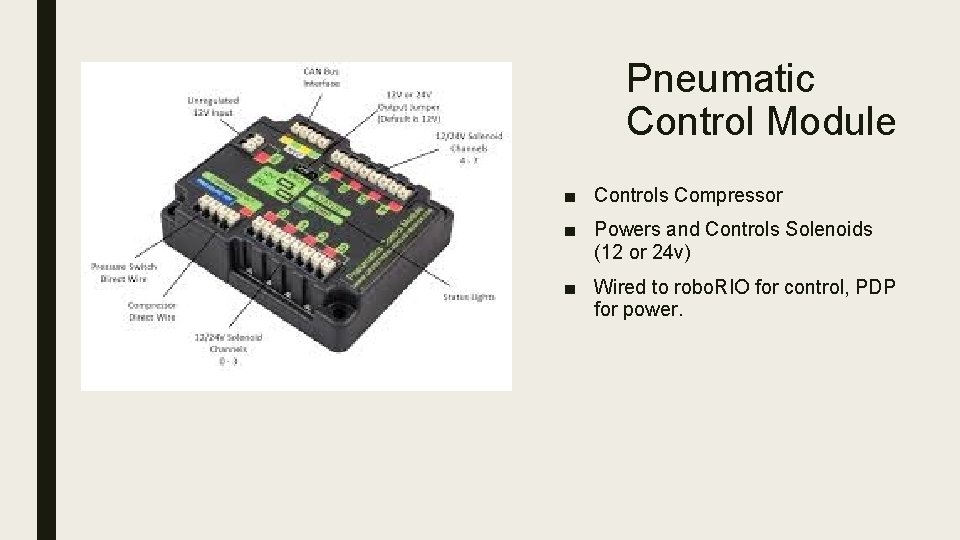
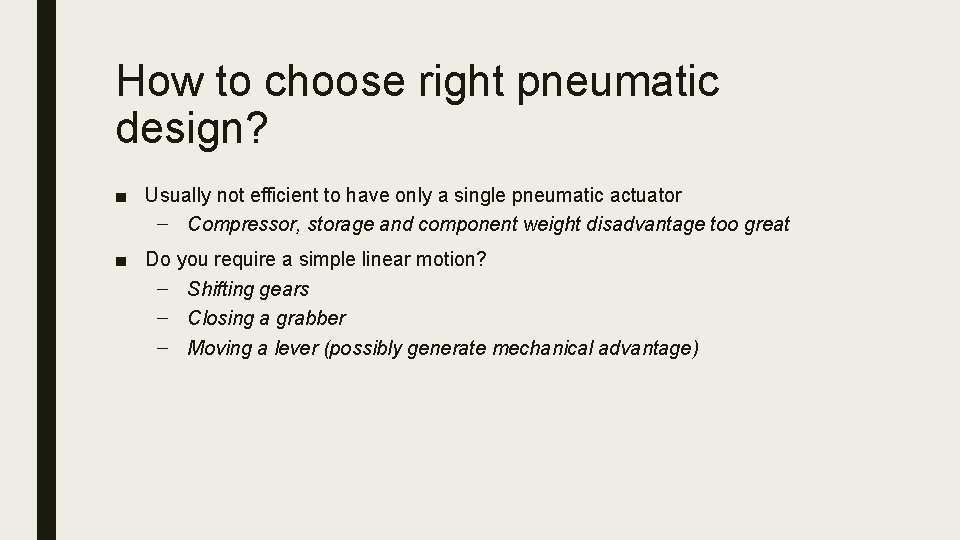
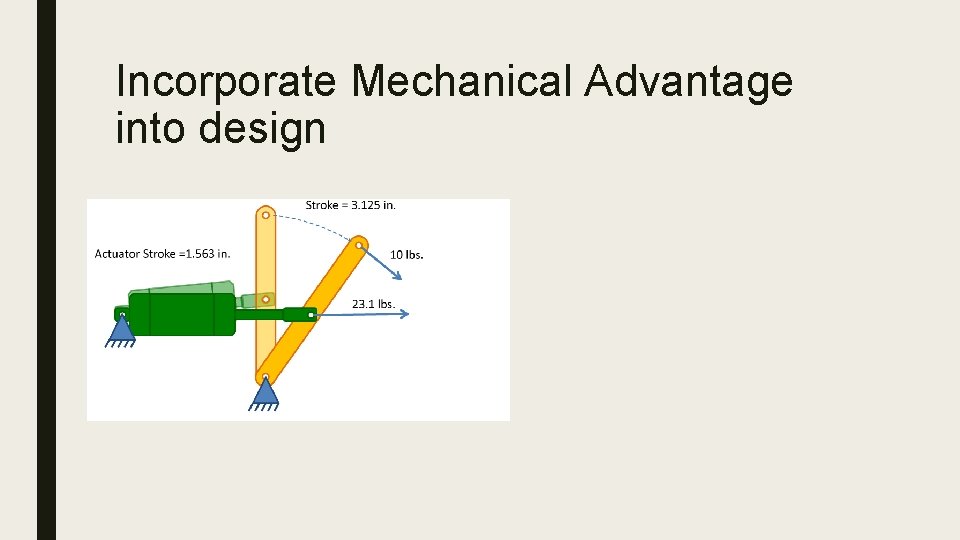
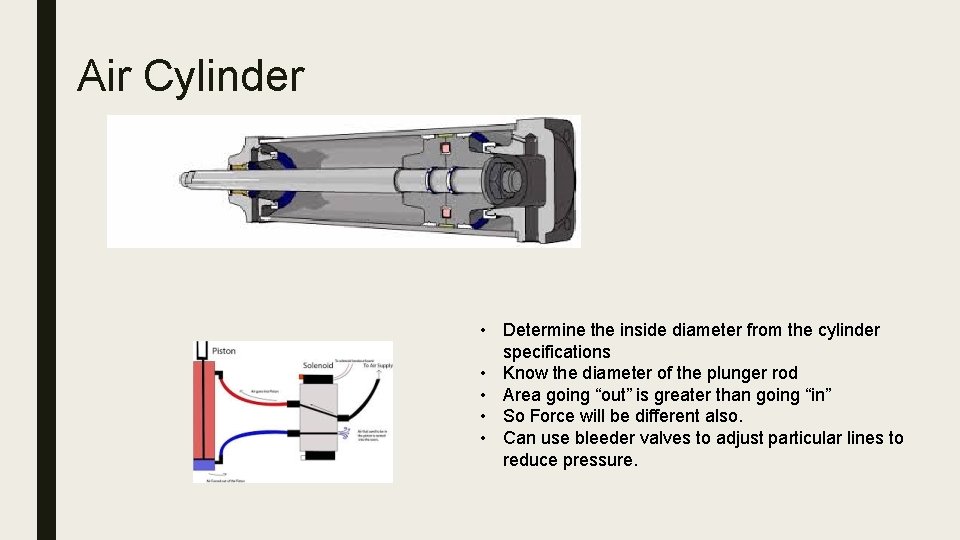
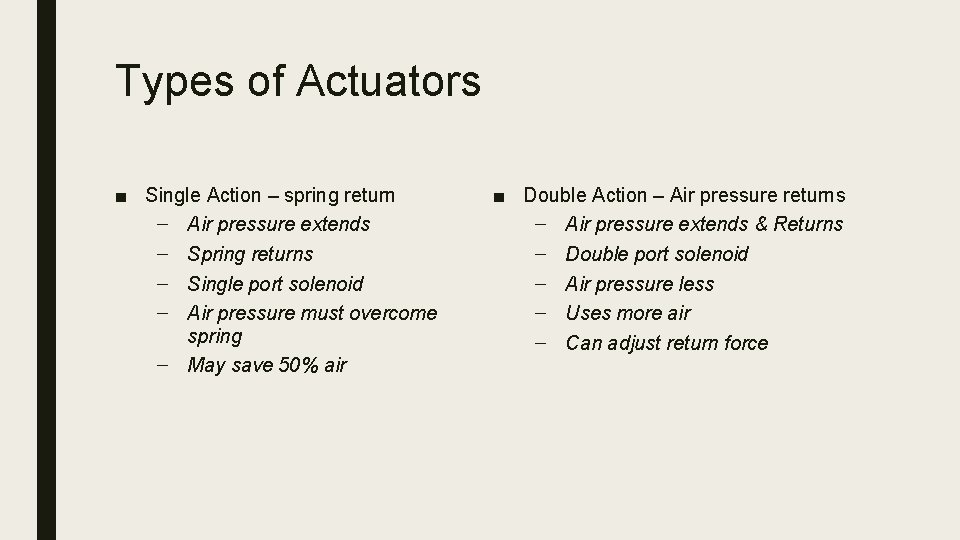
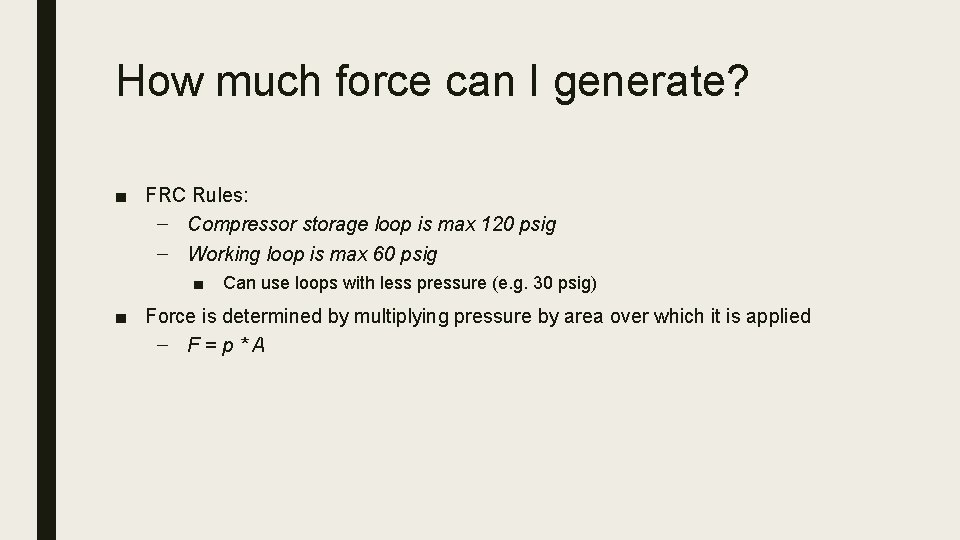
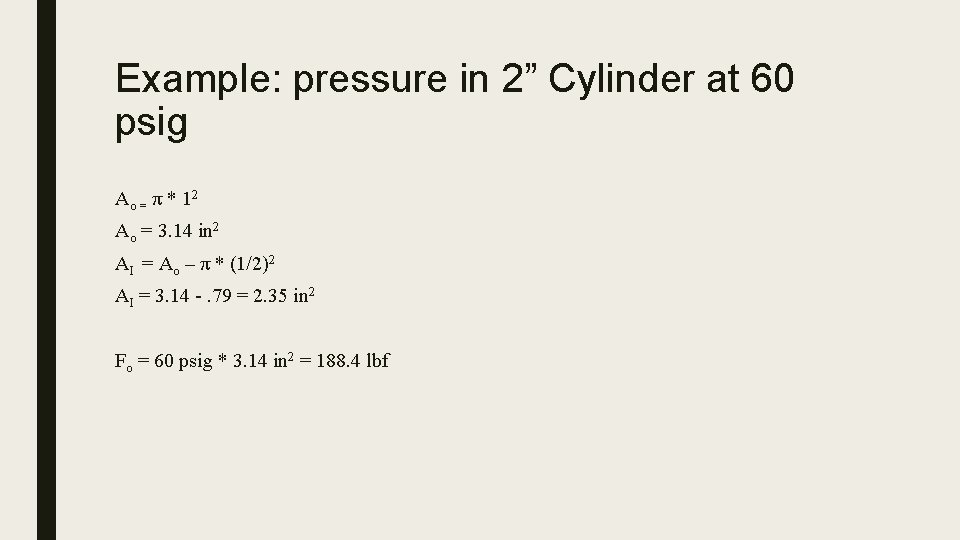
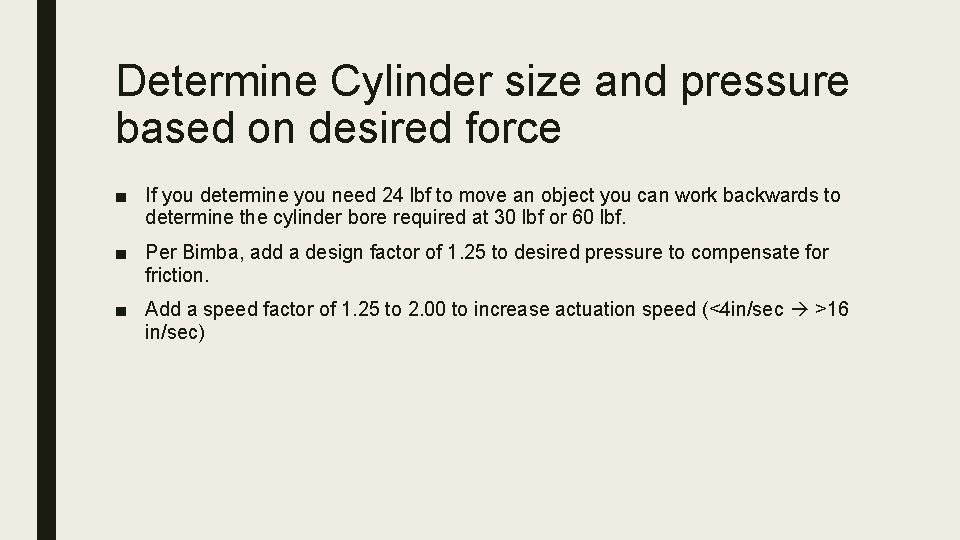
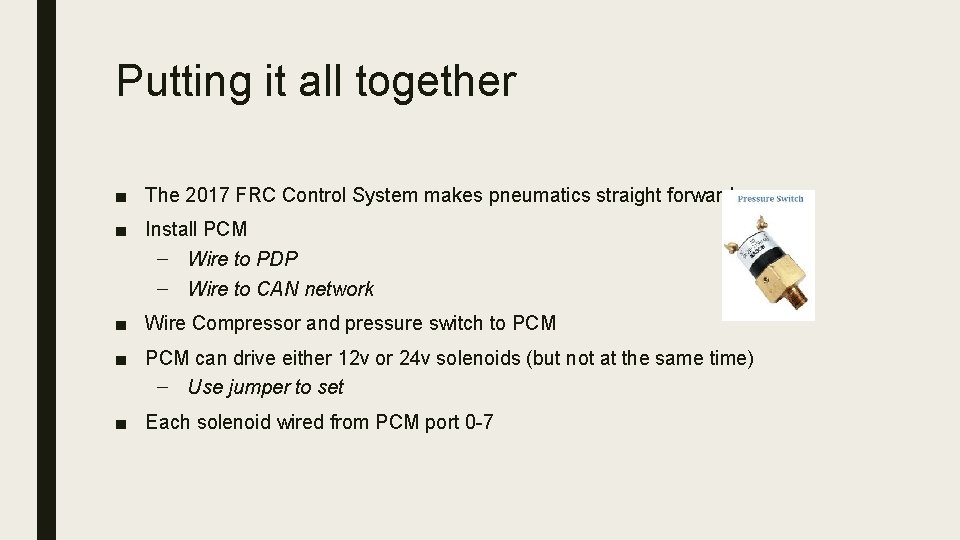
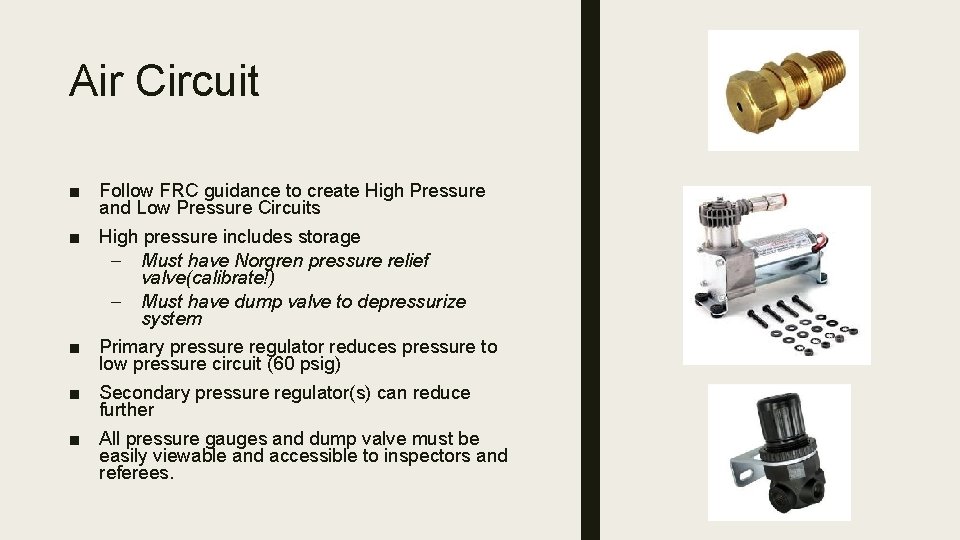
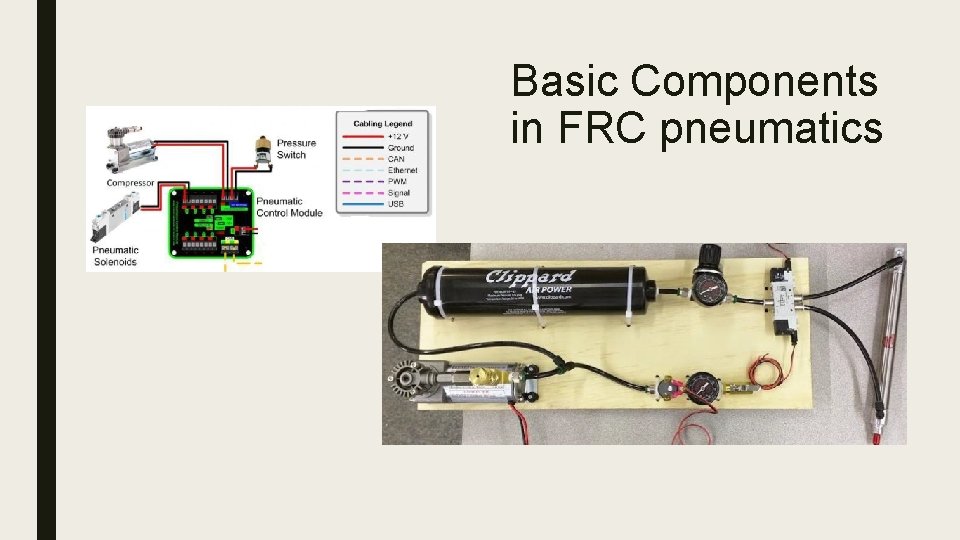
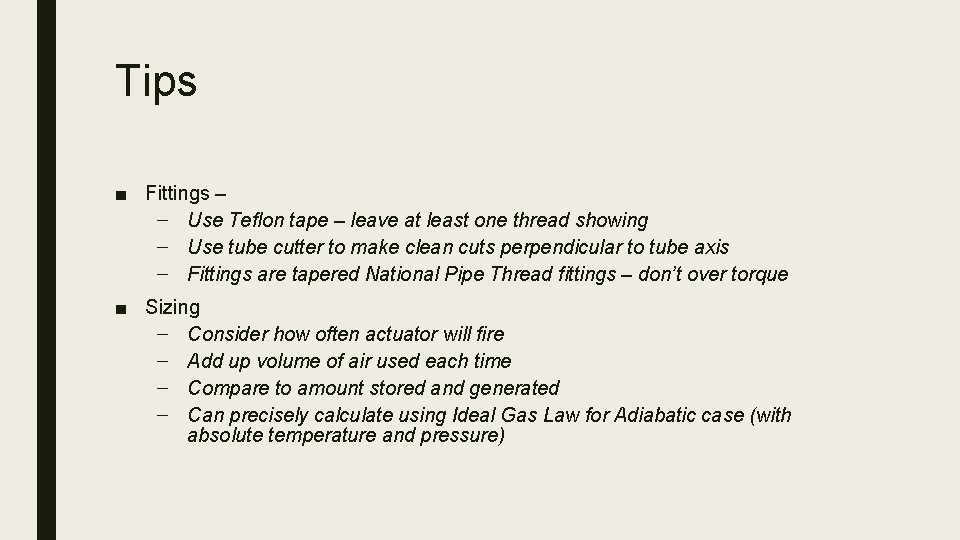
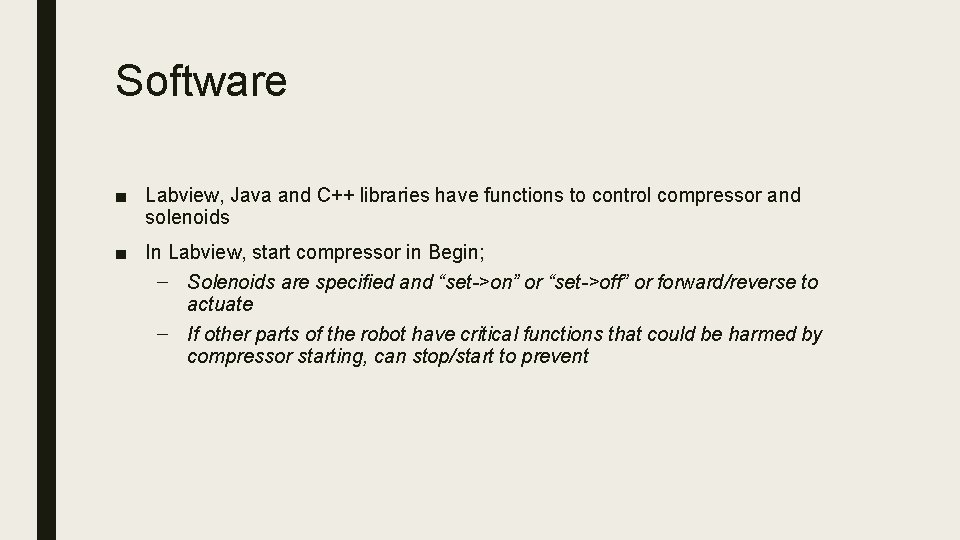
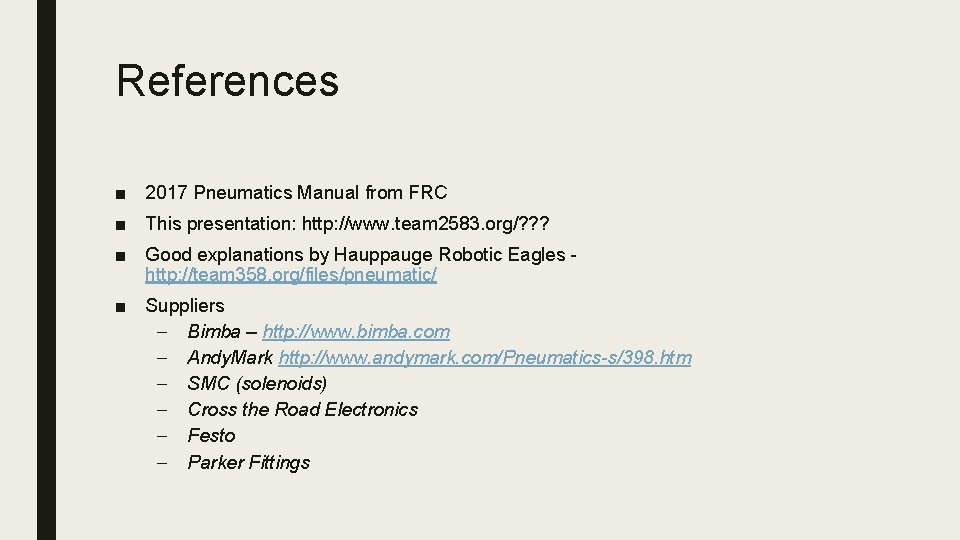
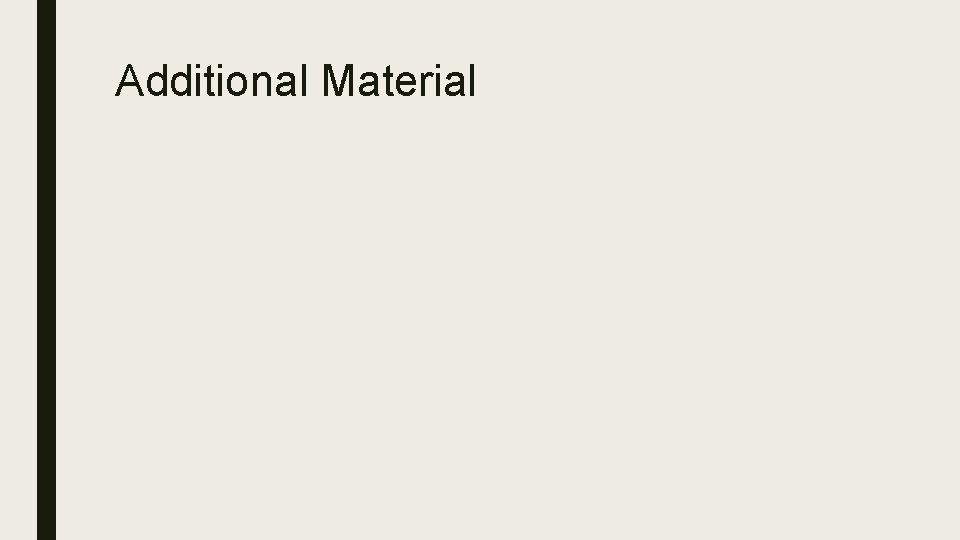
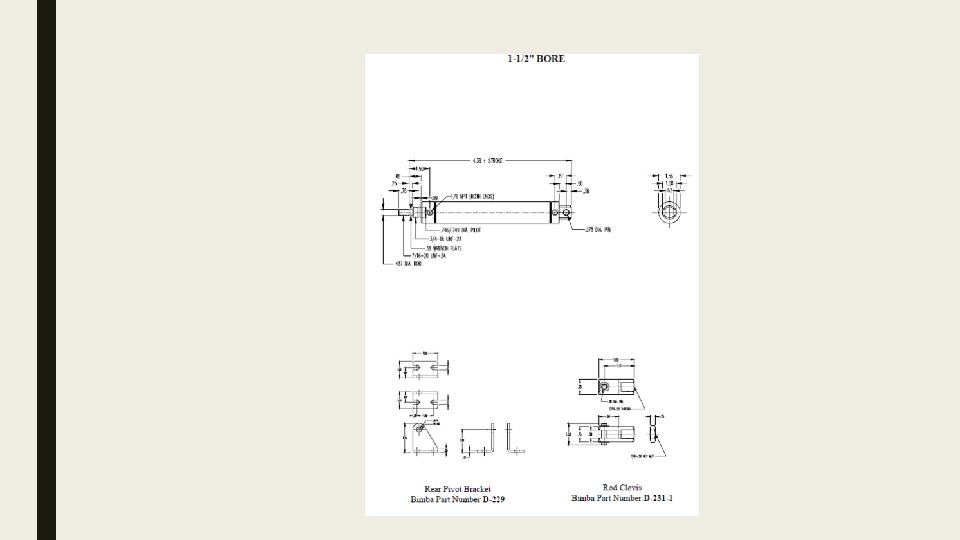
- Slides: 22
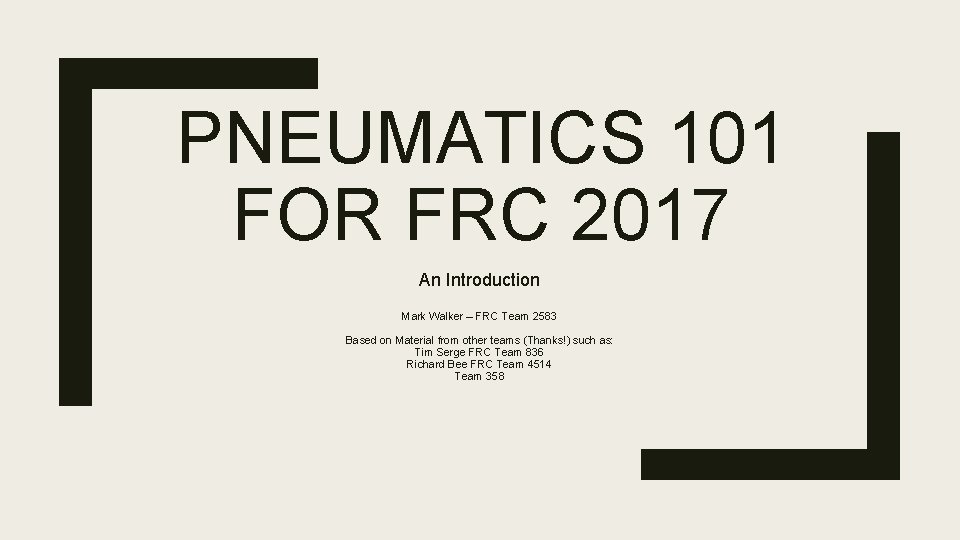
PNEUMATICS 101 FOR FRC 2017 An Introduction Mark Walker – FRC Team 2583 Based on Material from other teams (Thanks!) such as: Tim Serge FRC Team 836 Richard Bee FRC Team 4514 Team 358
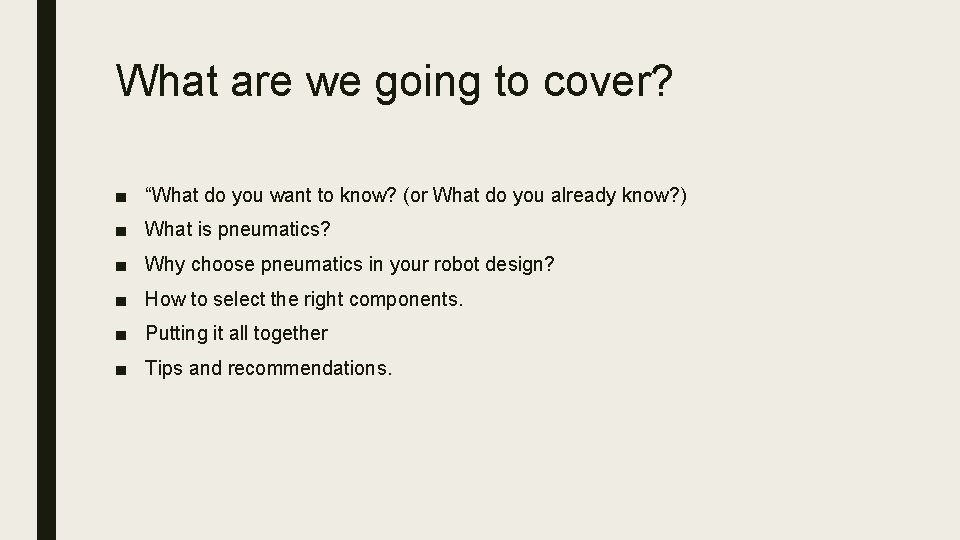
What are we going to cover? ■ “What do you want to know? (or What do you already know? ) ■ What is pneumatics? ■ Why choose pneumatics in your robot design? ■ How to select the right components. ■ Putting it all together ■ Tips and recommendations.
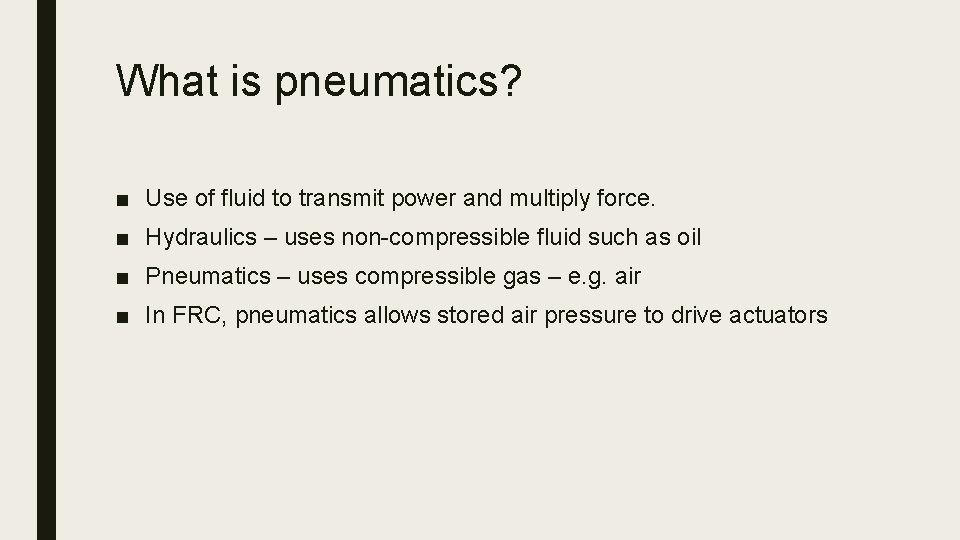
What is pneumatics? ■ Use of fluid to transmit power and multiply force. ■ Hydraulics – uses non-compressible fluid such as oil ■ Pneumatics – uses compressible gas – e. g. air ■ In FRC, pneumatics allows stored air pressure to drive actuators
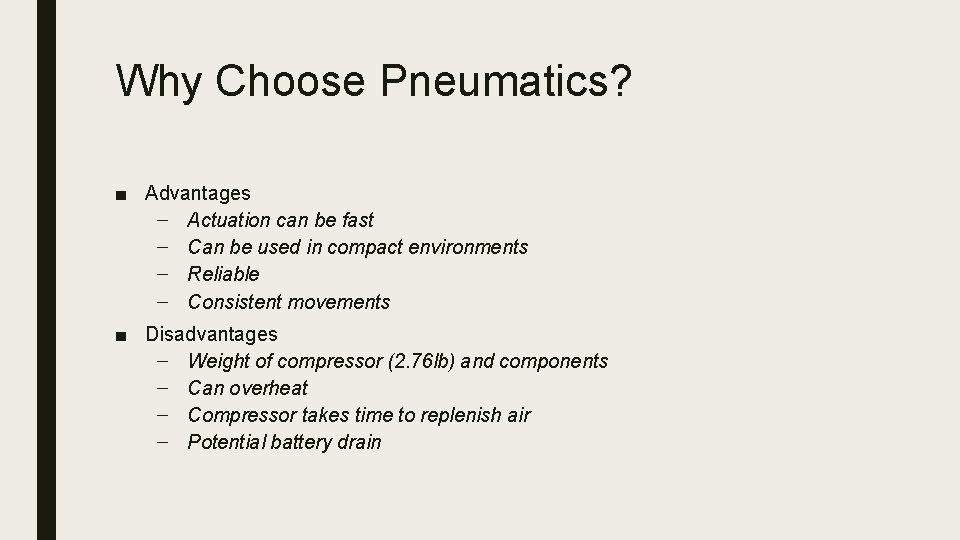
Why Choose Pneumatics? ■ Advantages – Actuation can be fast – Can be used in compact environments – Reliable – Consistent movements ■ Disadvantages – Weight of compressor (2. 76 lb) and components – Can overheat – Compressor takes time to replenish air – Potential battery drain
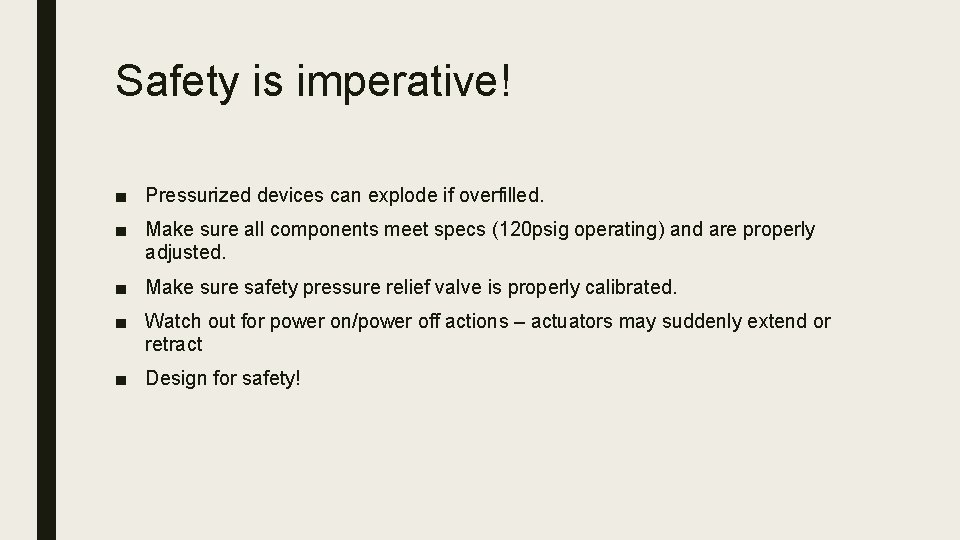
Safety is imperative! ■ Pressurized devices can explode if overfilled. ■ Make sure all components meet specs (120 psig operating) and are properly adjusted. ■ Make sure safety pressure relief valve is properly calibrated. ■ Watch out for power on/power off actions – actuators may suddenly extend or retract ■ Design for safety!
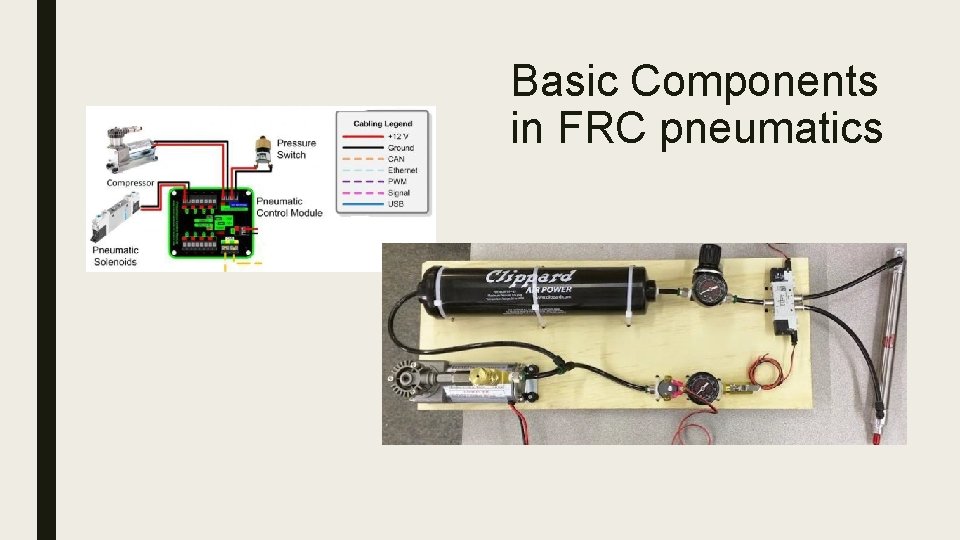
Basic Components in FRC pneumatics
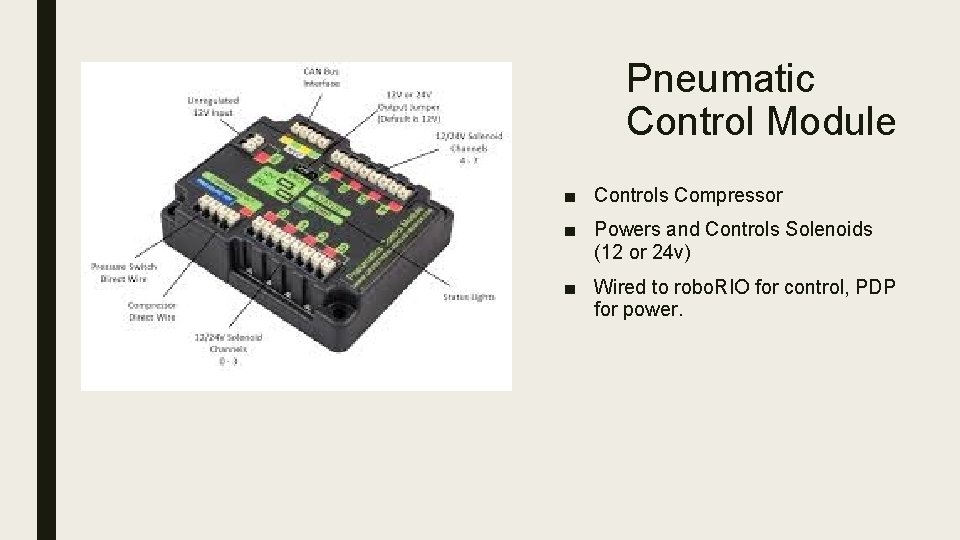
Pneumatic Control Module ■ Controls Compressor ■ Powers and Controls Solenoids (12 or 24 v) ■ Wired to robo. RIO for control, PDP for power.
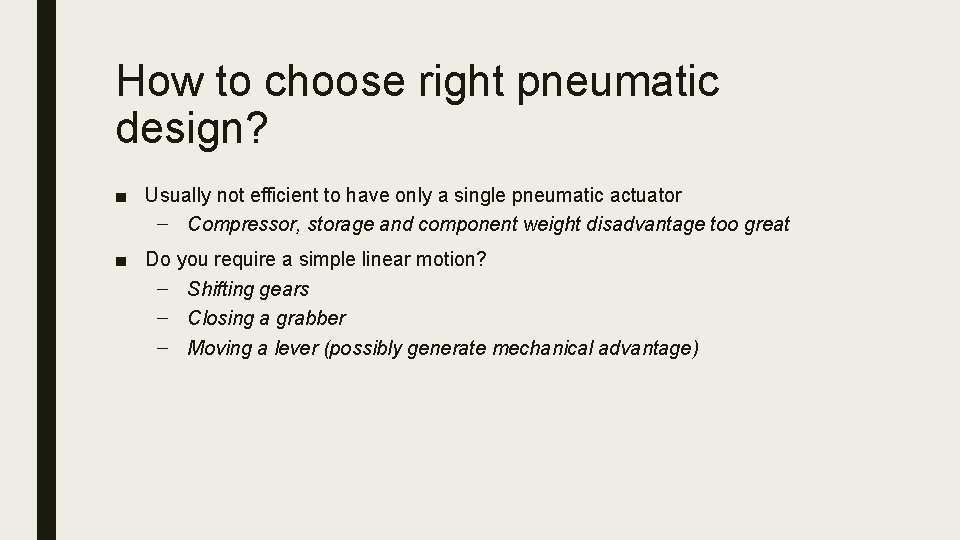
How to choose right pneumatic design? ■ Usually not efficient to have only a single pneumatic actuator – Compressor, storage and component weight disadvantage too great ■ Do you require a simple linear motion? – Shifting gears – Closing a grabber – Moving a lever (possibly generate mechanical advantage)
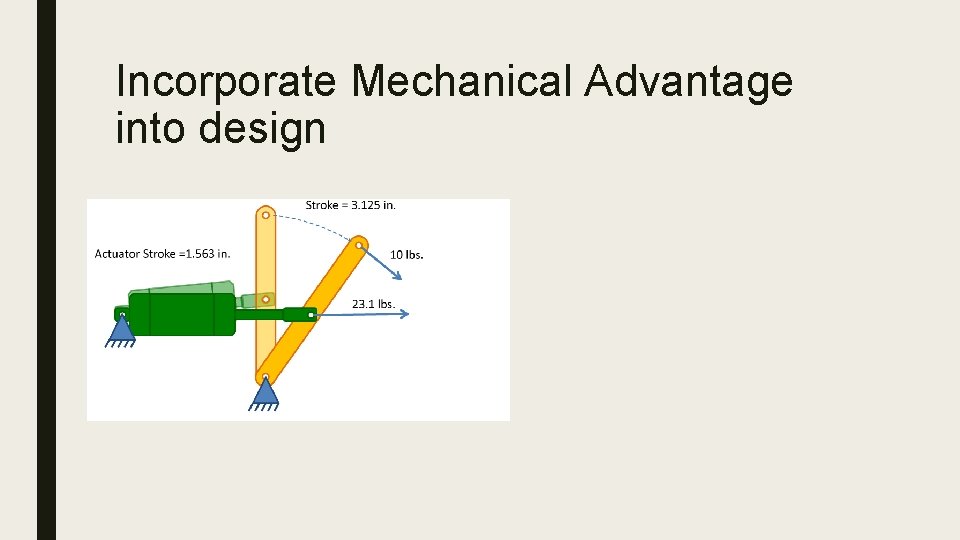
Incorporate Mechanical Advantage into design
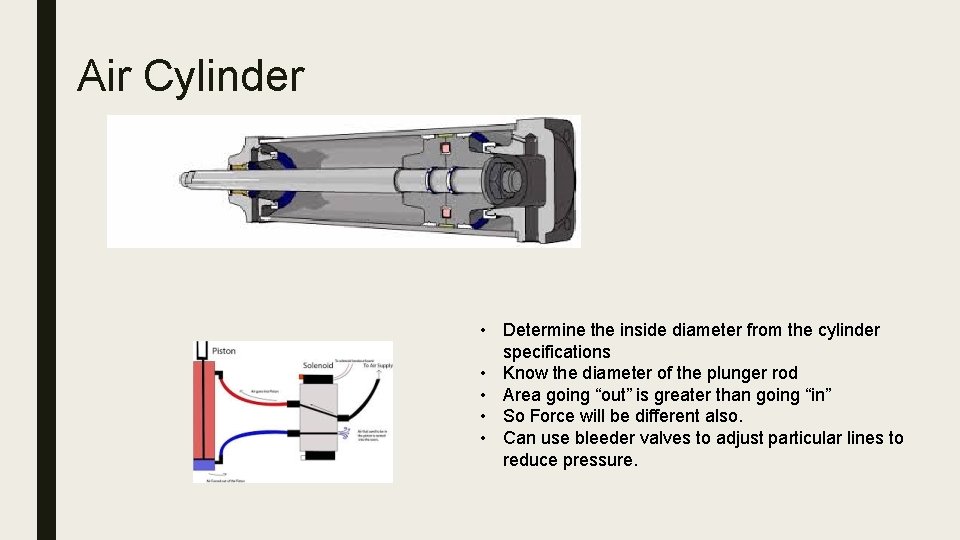
Air Cylinder • Determine the inside diameter from the cylinder specifications • Know the diameter of the plunger rod • Area going “out” is greater than going “in” • So Force will be different also. • Can use bleeder valves to adjust particular lines to reduce pressure.
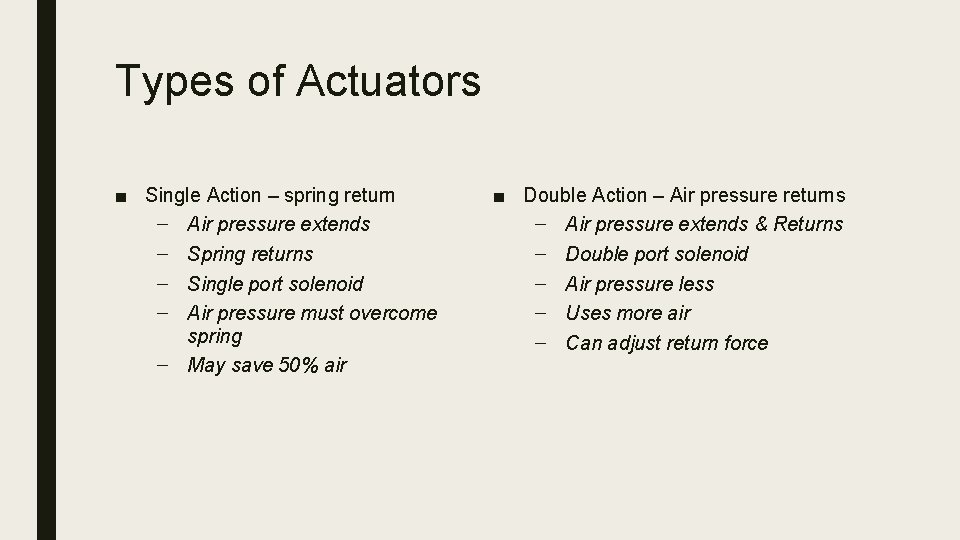
Types of Actuators ■ Single Action – spring return – Air pressure extends – Spring returns – Single port solenoid – Air pressure must overcome spring – May save 50% air ■ Double Action – Air pressure returns – Air pressure extends & Returns – Double port solenoid – Air pressure less – Uses more air – Can adjust return force
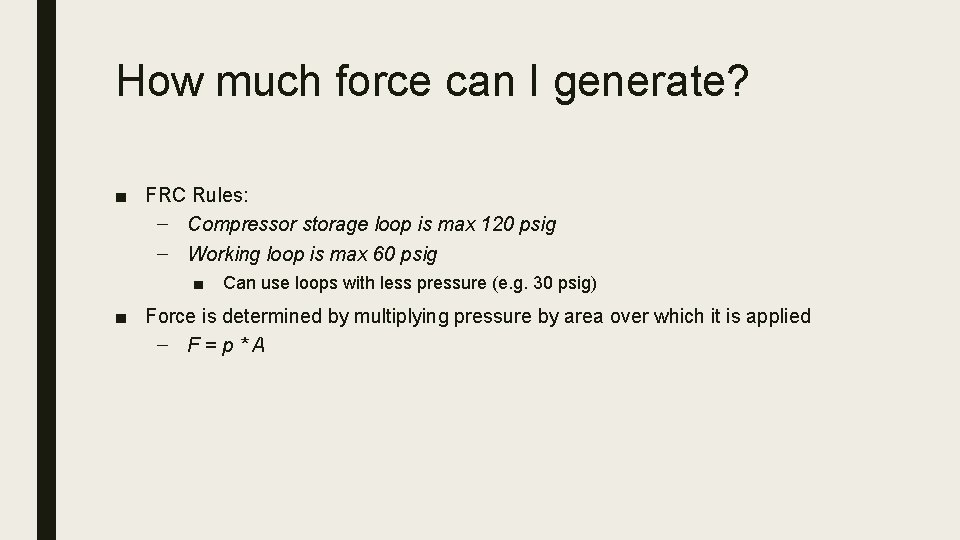
How much force can I generate? ■ FRC Rules: – Compressor storage loop is max 120 psig – Working loop is max 60 psig ■ Can use loops with less pressure (e. g. 30 psig) ■ Force is determined by multiplying pressure by area over which it is applied – F=p*A
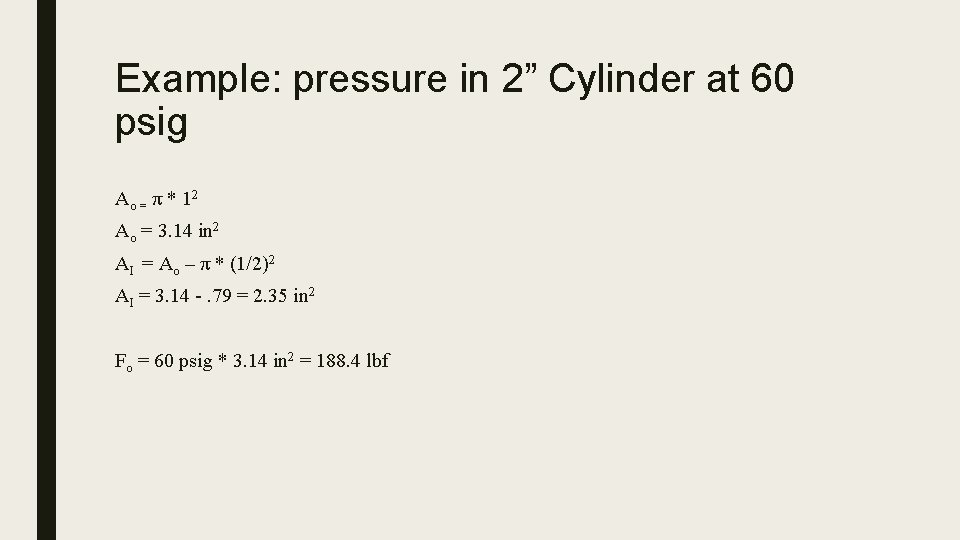
Example: pressure in 2” Cylinder at 60 psig Ao = π * 12 Ao = 3. 14 in 2 AI = Ao – π * (1/2)2 AI = 3. 14 -. 79 = 2. 35 in 2 Fo = 60 psig * 3. 14 in 2 = 188. 4 lbf
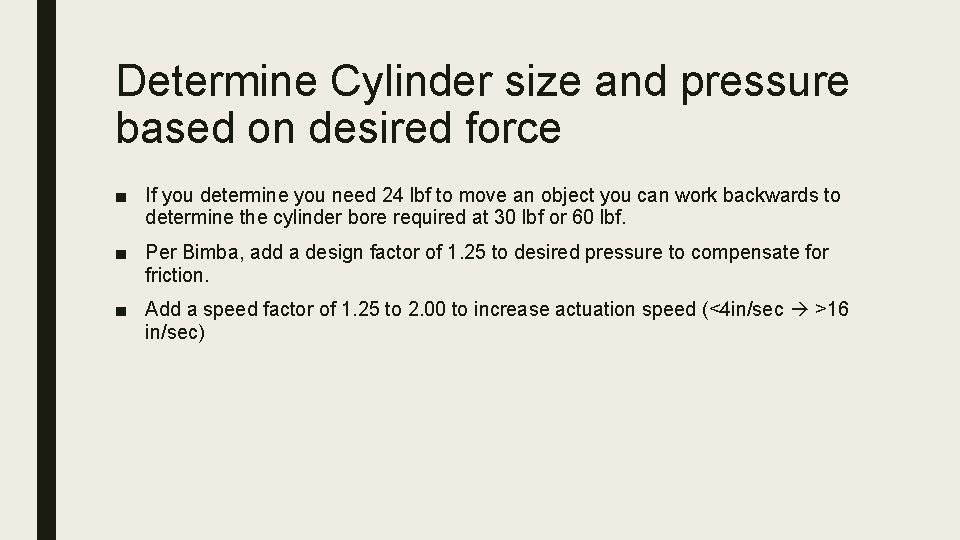
Determine Cylinder size and pressure based on desired force ■ If you determine you need 24 lbf to move an object you can work backwards to determine the cylinder bore required at 30 lbf or 60 lbf. ■ Per Bimba, add a design factor of 1. 25 to desired pressure to compensate for friction. ■ Add a speed factor of 1. 25 to 2. 00 to increase actuation speed (<4 in/sec >16 in/sec)
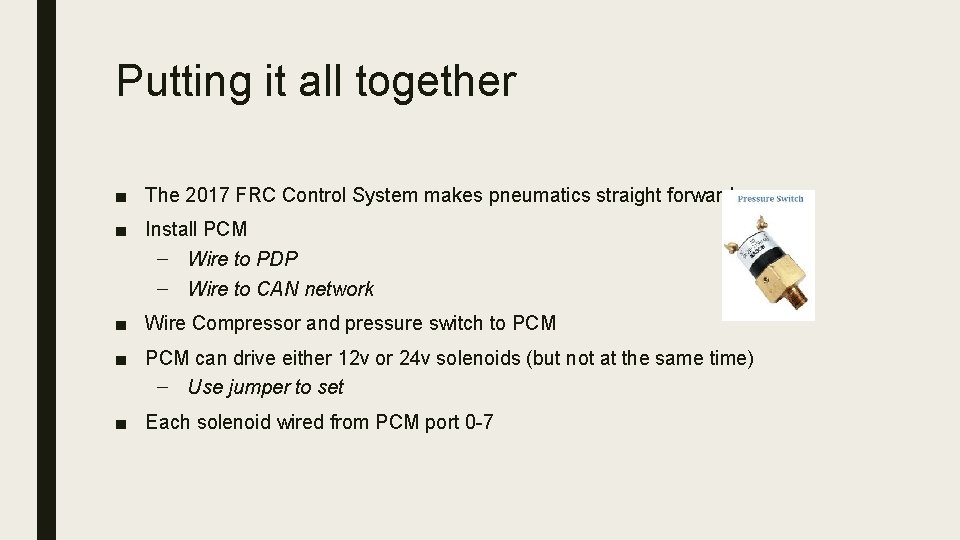
Putting it all together ■ The 2017 FRC Control System makes pneumatics straight forward. ■ Install PCM – Wire to PDP – Wire to CAN network ■ Wire Compressor and pressure switch to PCM ■ PCM can drive either 12 v or 24 v solenoids (but not at the same time) – Use jumper to set ■ Each solenoid wired from PCM port 0 -7
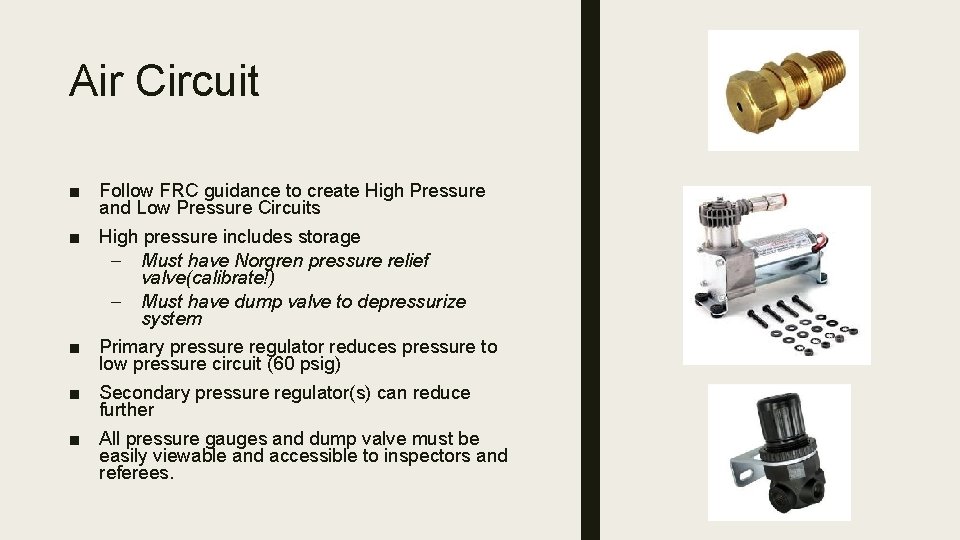
Air Circuit ■ Follow FRC guidance to create High Pressure and Low Pressure Circuits ■ High pressure includes storage – Must have Norgren pressure relief valve(calibrate!) – Must have dump valve to depressurize system ■ Primary pressure regulator reduces pressure to low pressure circuit (60 psig) ■ Secondary pressure regulator(s) can reduce further ■ All pressure gauges and dump valve must be easily viewable and accessible to inspectors and referees.
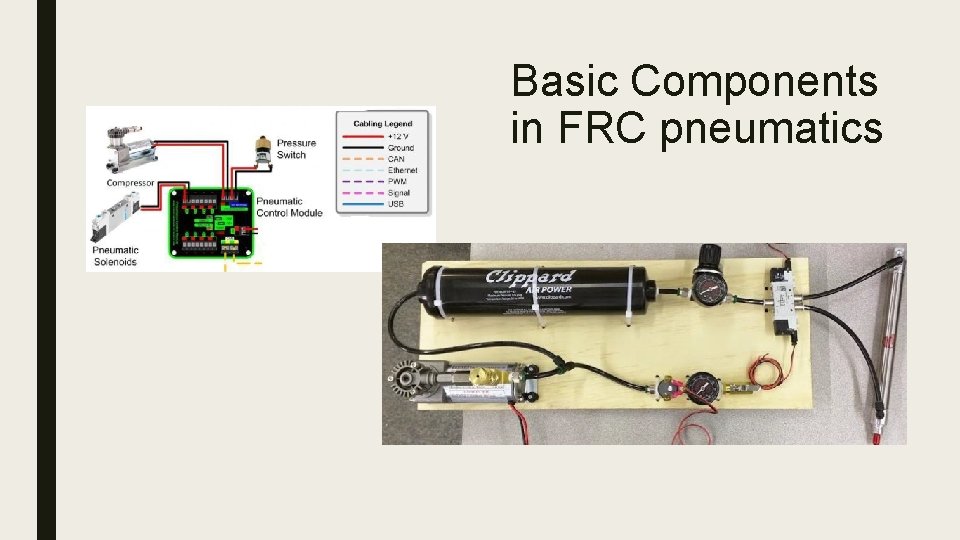
Basic Components in FRC pneumatics
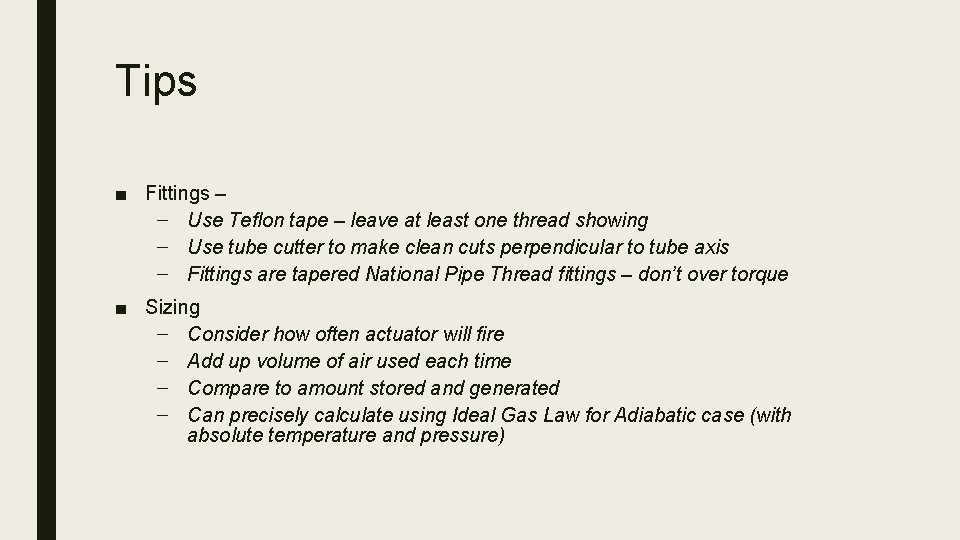
Tips ■ Fittings – – Use Teflon tape – leave at least one thread showing – Use tube cutter to make clean cuts perpendicular to tube axis – Fittings are tapered National Pipe Thread fittings – don’t over torque ■ Sizing – Consider how often actuator will fire – Add up volume of air used each time – Compare to amount stored and generated – Can precisely calculate using Ideal Gas Law for Adiabatic case (with absolute temperature and pressure)
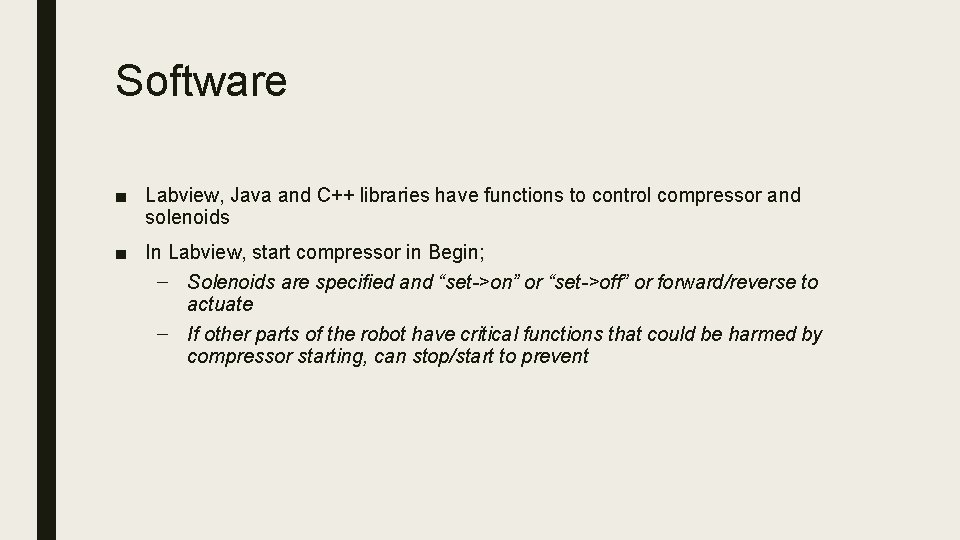
Software ■ Labview, Java and C++ libraries have functions to control compressor and solenoids ■ In Labview, start compressor in Begin; – Solenoids are specified and “set->on” or “set->off” or forward/reverse to actuate – If other parts of the robot have critical functions that could be harmed by compressor starting, can stop/start to prevent
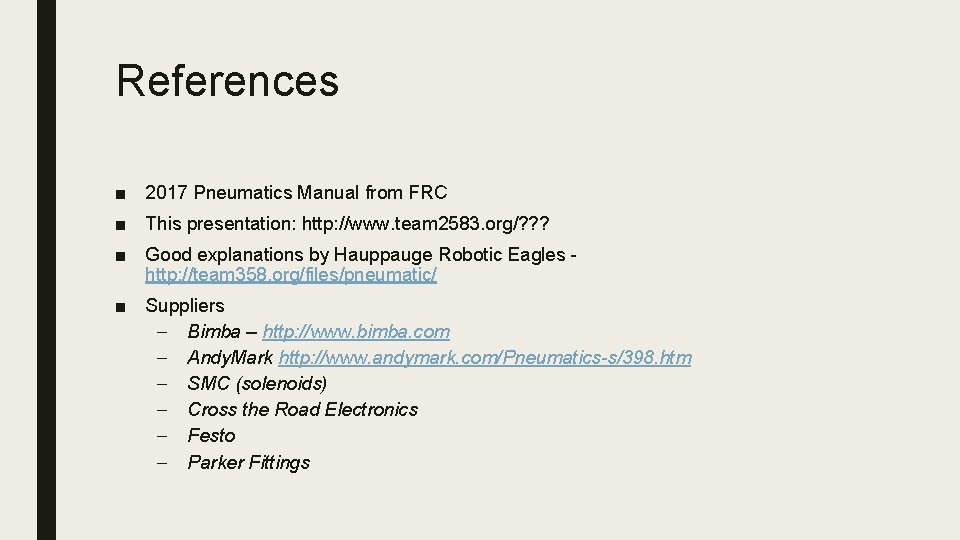
References ■ 2017 Pneumatics Manual from FRC ■ This presentation: http: //www. team 2583. org/? ? ? ■ Good explanations by Hauppauge Robotic Eagles http: //team 358. org/files/pneumatic/ ■ Suppliers – Bimba – http: //www. bimba. com – Andy. Mark http: //www. andymark. com/Pneumatics-s/398. htm – SMC (solenoids) – Cross the Road Electronics – Festo – Parker Fittings
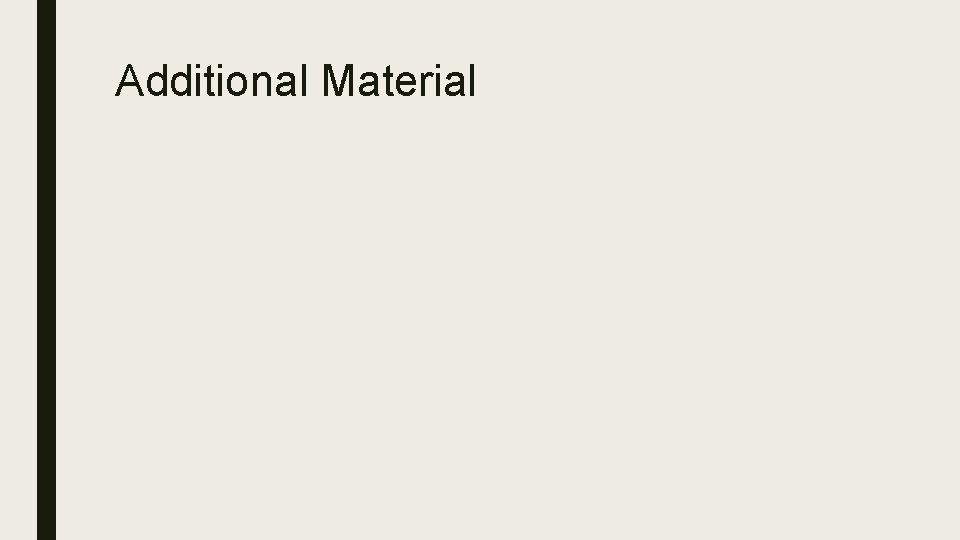
Additional Material
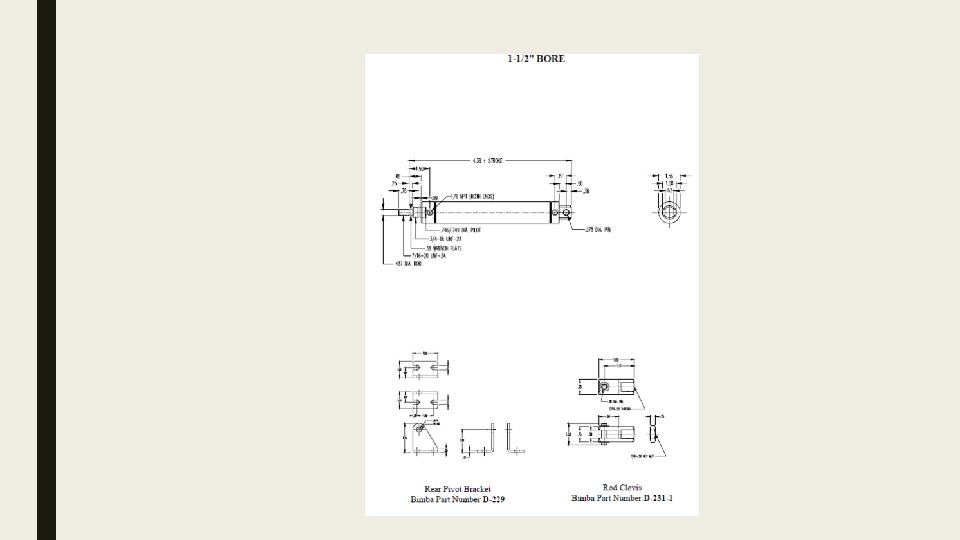
Pneumatics frc
Linear actuator frc
Introduction to hydraulics and pneumatics
Hydraulics and pneumatics
2017 sats mark scheme
Hydraulic vs pneumatic
Everyday pneumatics examples
Direct control of double acting cylinder
Dominant on
Cascade method pneumatic circuit design
Hydraulic system advantages
Slidetodoc.com
Pneumatics vs hydraulics
Basics of pneumatics
Pascal's law pneumatics
Pump exercise
Control
Pneumatics
Robo twist troubleshooting
Give the standard graphical symbols for frl unit
Pdp frc
Frc team 1717
Frc