PLANEJAMENTO E ACOMPANHAMENTO DA PRODUO CAPITULO 10 ACOMPANHAMENTO
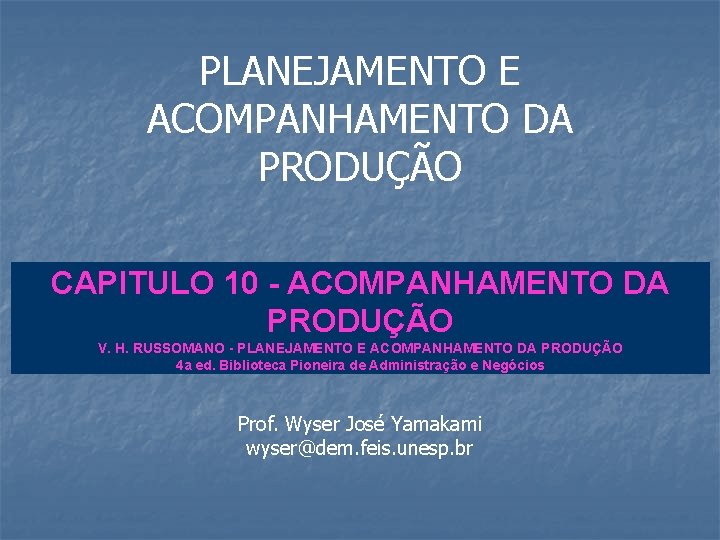
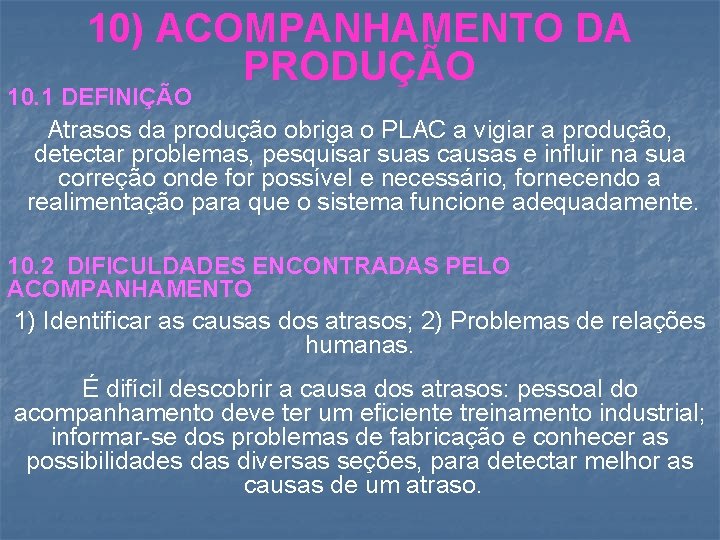
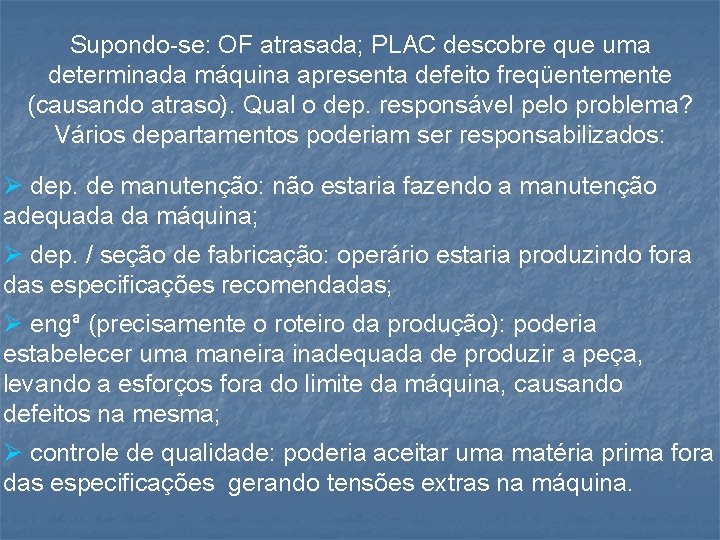
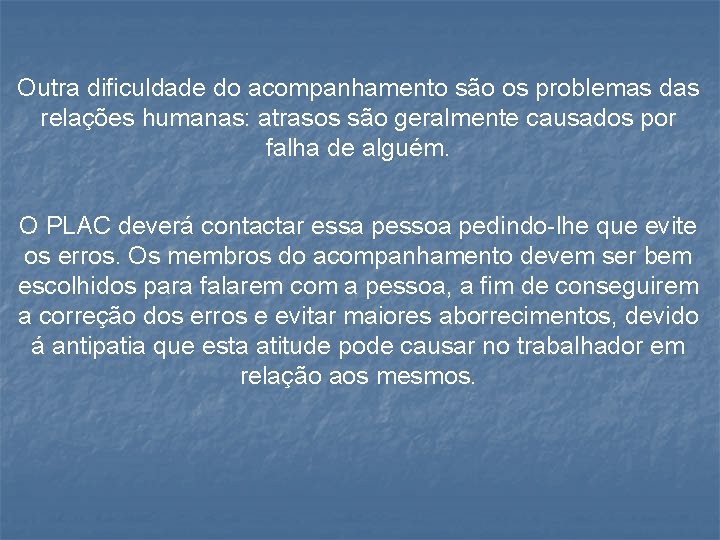
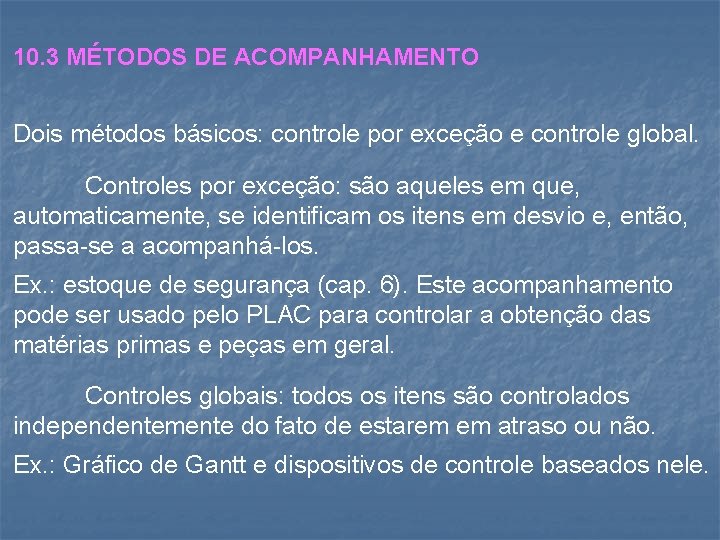
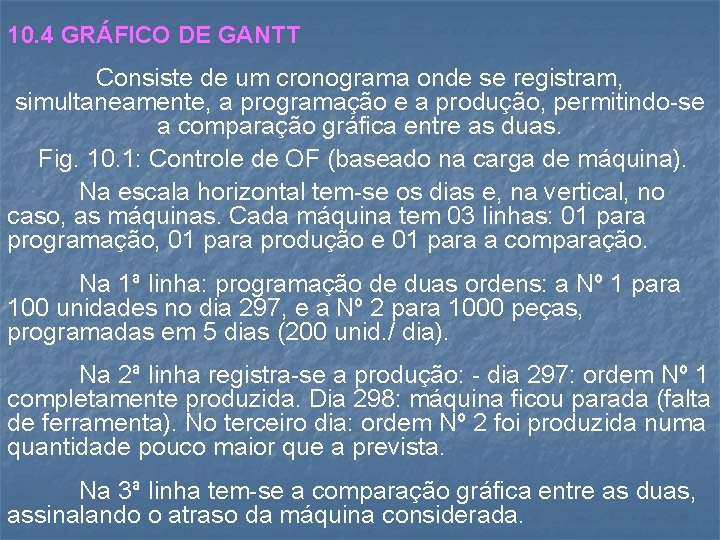
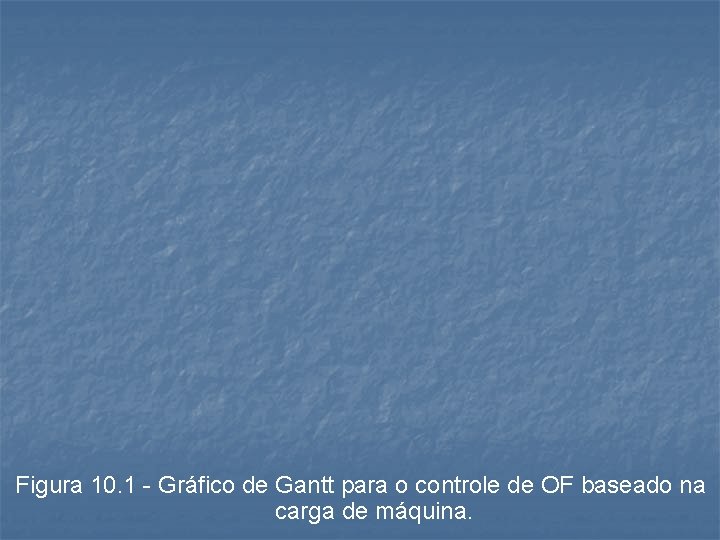
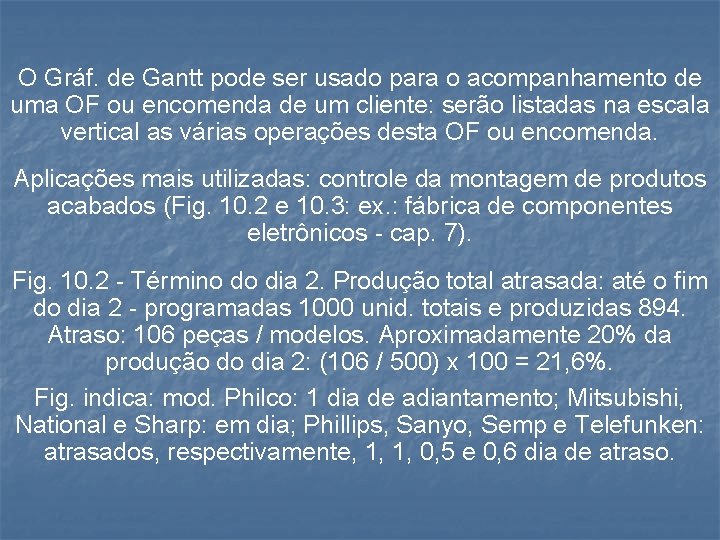
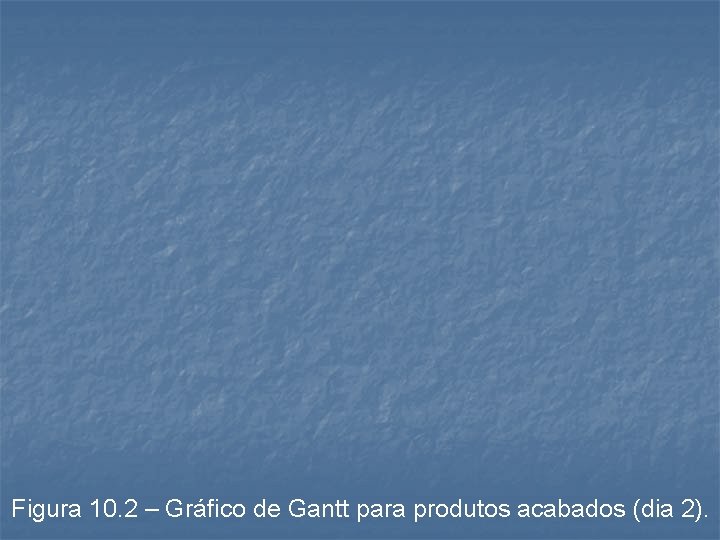
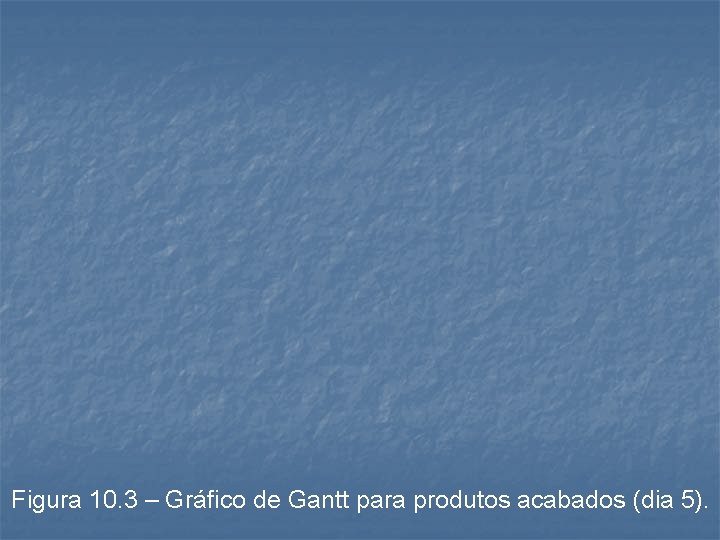

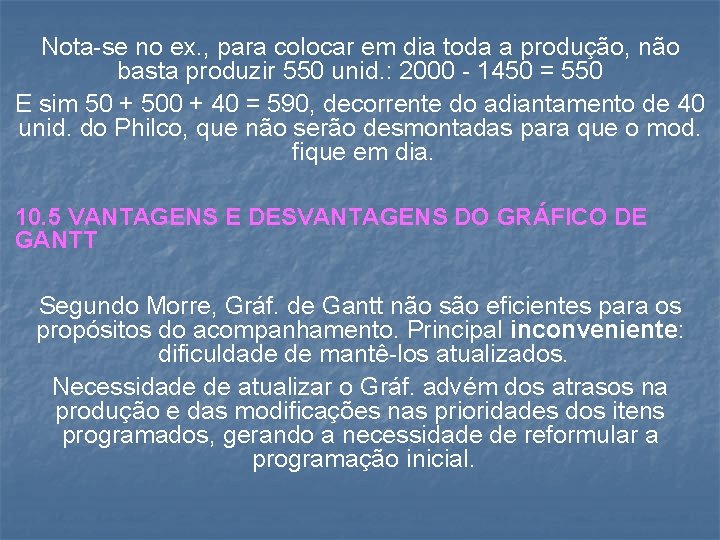
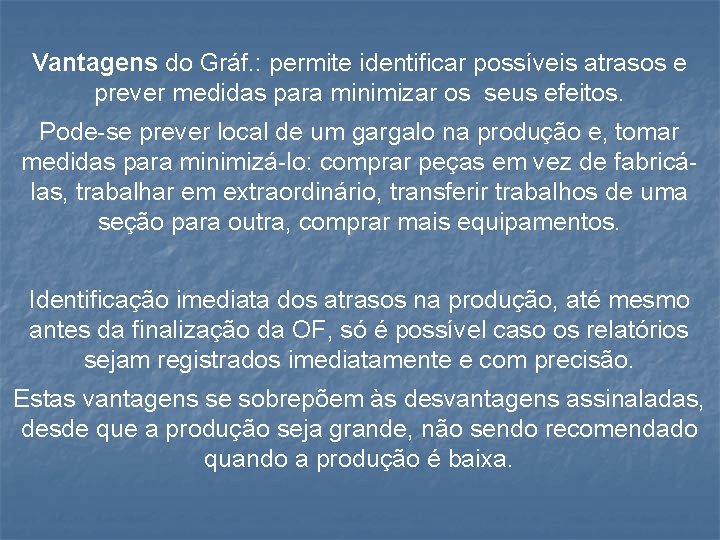
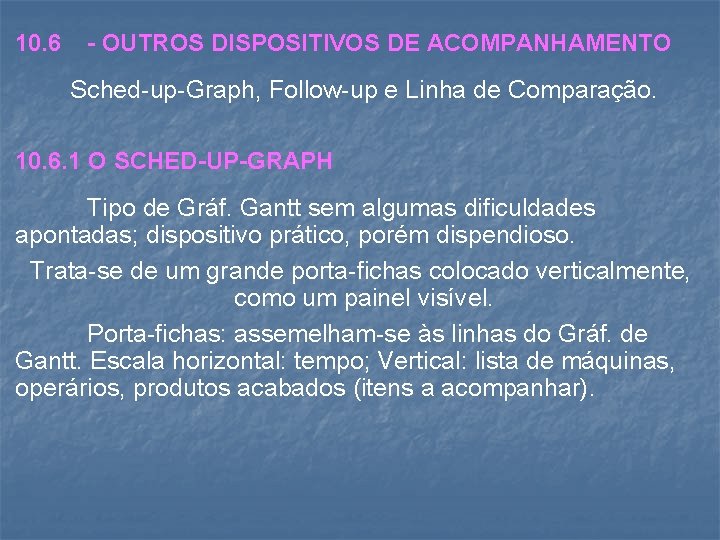
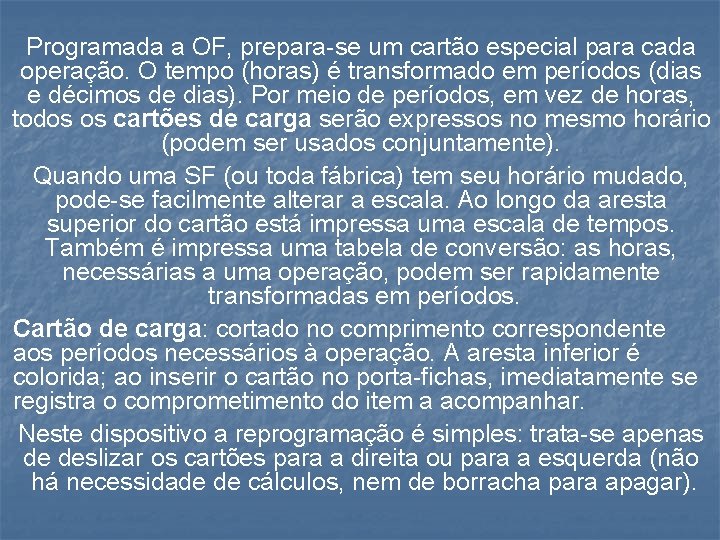
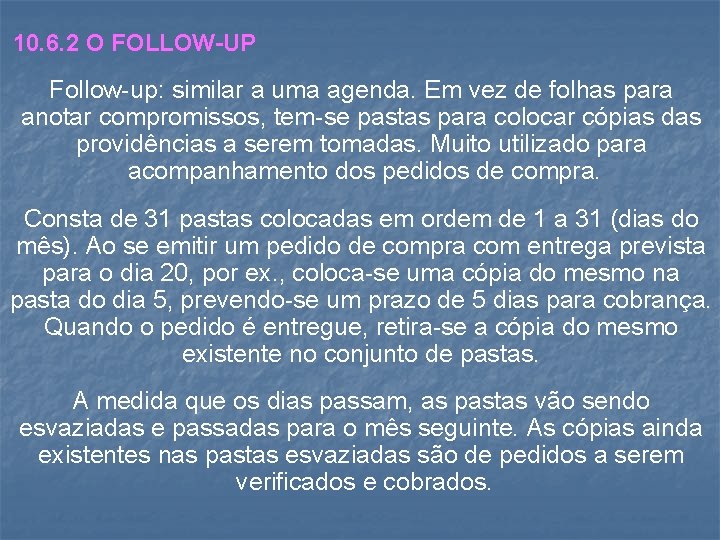
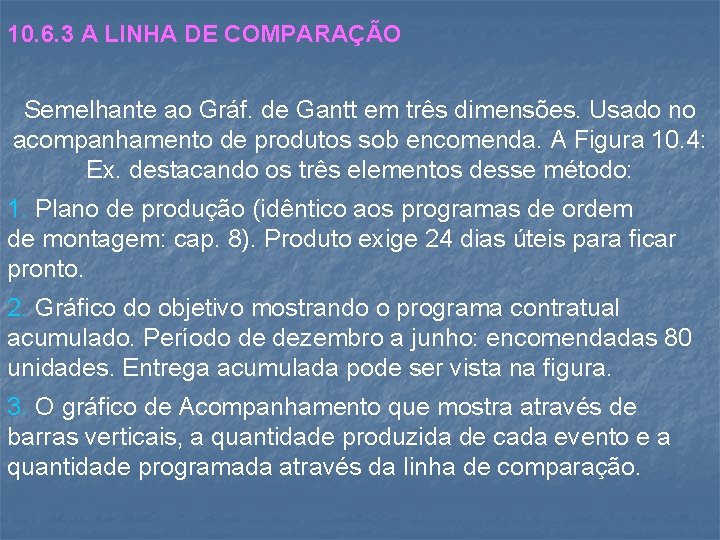
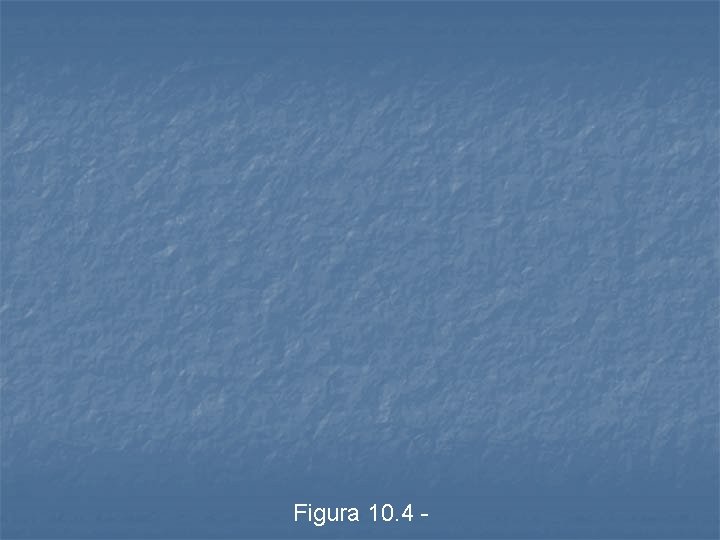
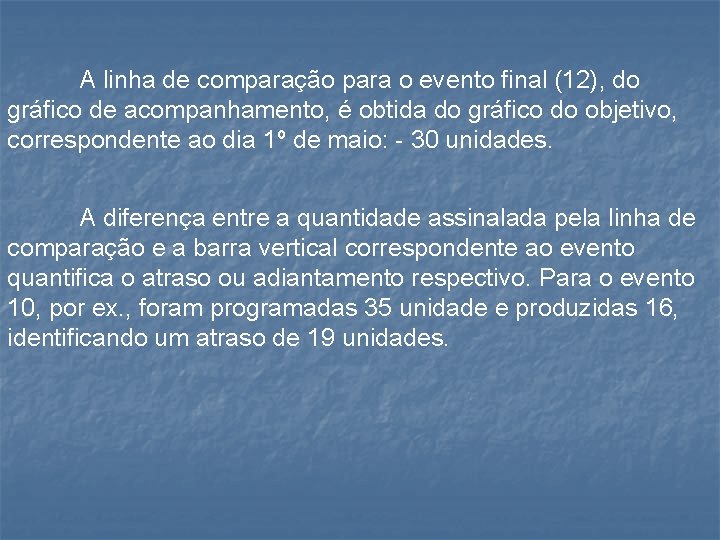
- Slides: 19
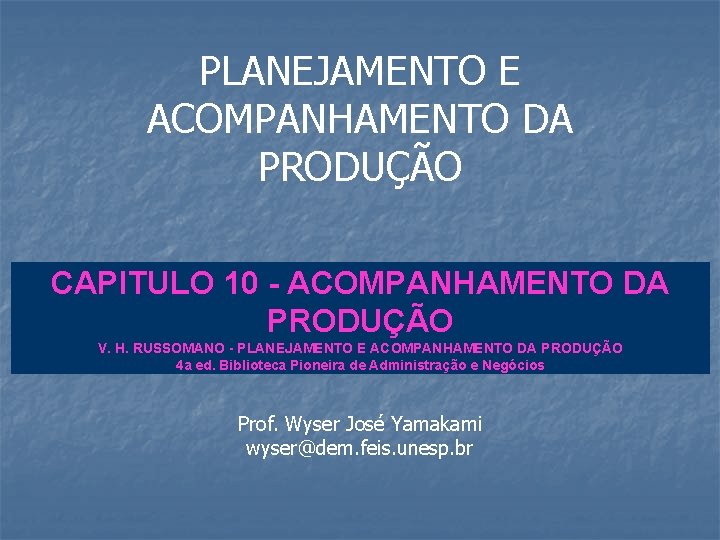
PLANEJAMENTO E ACOMPANHAMENTO DA PRODUÇÃO CAPITULO 10 - ACOMPANHAMENTO DA PRODUÇÃO V. H. RUSSOMANO - PLANEJAMENTO E ACOMPANHAMENTO DA PRODUÇÃO 4 a ed. Biblioteca Pioneira de Administração e Negócios Prof. Wyser José Yamakami wyser@dem. feis. unesp. br
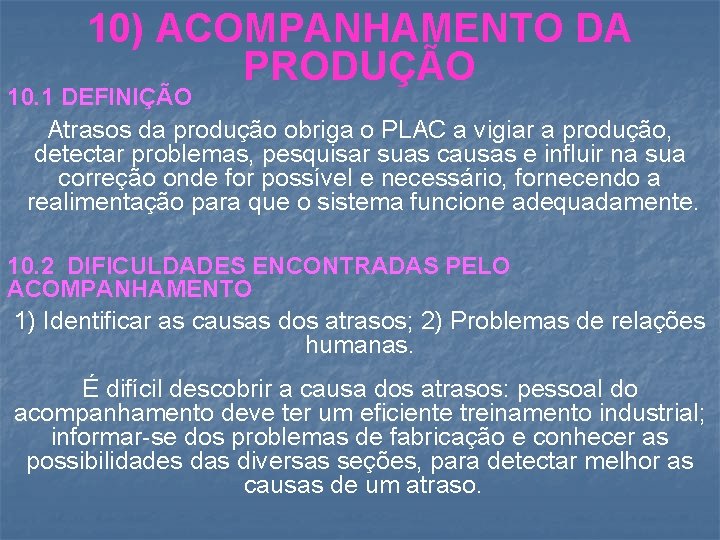
10) ACOMPANHAMENTO DA PRODUÇÃO 10. 1 DEFINIÇÃO Atrasos da produção obriga o PLAC a vigiar a produção, detectar problemas, pesquisar suas causas e influir na sua correção onde for possível e necessário, fornecendo a realimentação para que o sistema funcione adequadamente. 10. 2 DIFICULDADES ENCONTRADAS PELO ACOMPANHAMENTO 1) Identificar as causas dos atrasos; 2) Problemas de relações humanas. É difícil descobrir a causa dos atrasos: pessoal do acompanhamento deve ter um eficiente treinamento industrial; informar-se dos problemas de fabricação e conhecer as possibilidades das diversas seções, para detectar melhor as causas de um atraso.
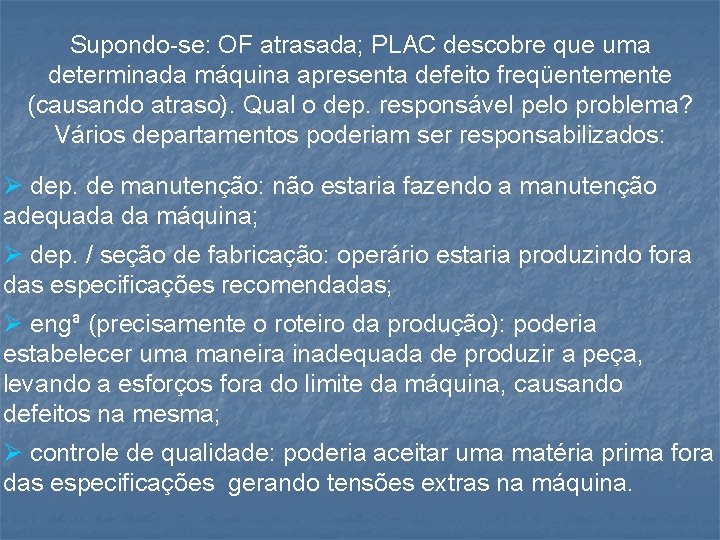
Supondo-se: OF atrasada; PLAC descobre que uma determinada máquina apresenta defeito freqüentemente (causando atraso). Qual o dep. responsável pelo problema? Vários departamentos poderiam ser responsabilizados: Ø dep. de manutenção: não estaria fazendo a manutenção adequada da máquina; Ø dep. / seção de fabricação: operário estaria produzindo fora das especificações recomendadas; Ø engª (precisamente o roteiro da produção): poderia estabelecer uma maneira inadequada de produzir a peça, levando a esforços fora do limite da máquina, causando defeitos na mesma; Ø controle de qualidade: poderia aceitar uma matéria prima fora das especificações gerando tensões extras na máquina.
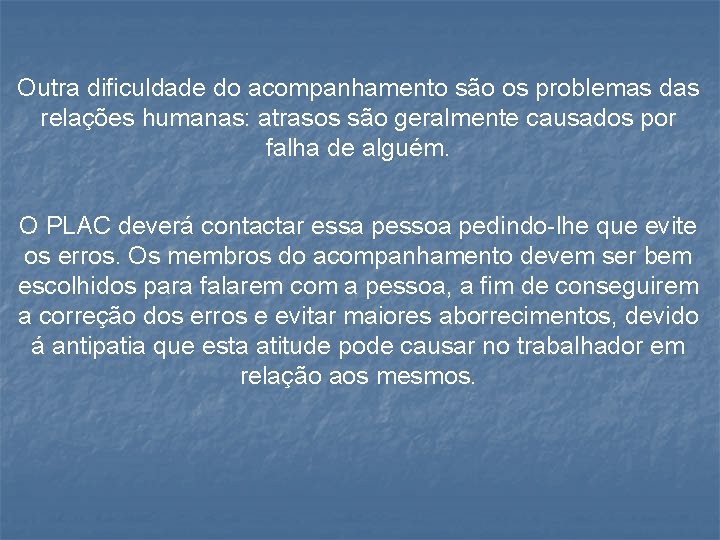
Outra dificuldade do acompanhamento são os problemas das relações humanas: atrasos são geralmente causados por falha de alguém. O PLAC deverá contactar essa pessoa pedindo-lhe que evite os erros. Os membros do acompanhamento devem ser bem escolhidos para falarem com a pessoa, a fim de conseguirem a correção dos erros e evitar maiores aborrecimentos, devido á antipatia que esta atitude pode causar no trabalhador em relação aos mesmos.
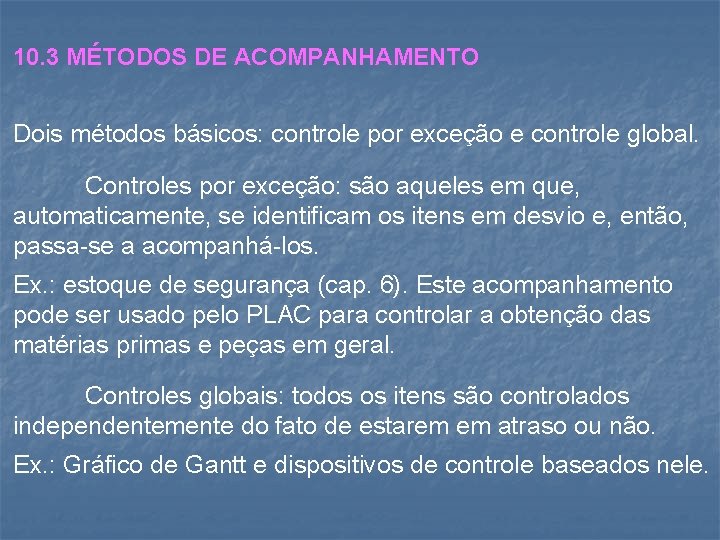
10. 3 MÉTODOS DE ACOMPANHAMENTO Dois métodos básicos: controle por exceção e controle global. Controles por exceção: são aqueles em que, automaticamente, se identificam os itens em desvio e, então, passa-se a acompanhá-los. Ex. : estoque de segurança (cap. 6). Este acompanhamento pode ser usado pelo PLAC para controlar a obtenção das matérias primas e peças em geral. Controles globais: todos os itens são controlados independentemente do fato de estarem em atraso ou não. Ex. : Gráfico de Gantt e dispositivos de controle baseados nele.
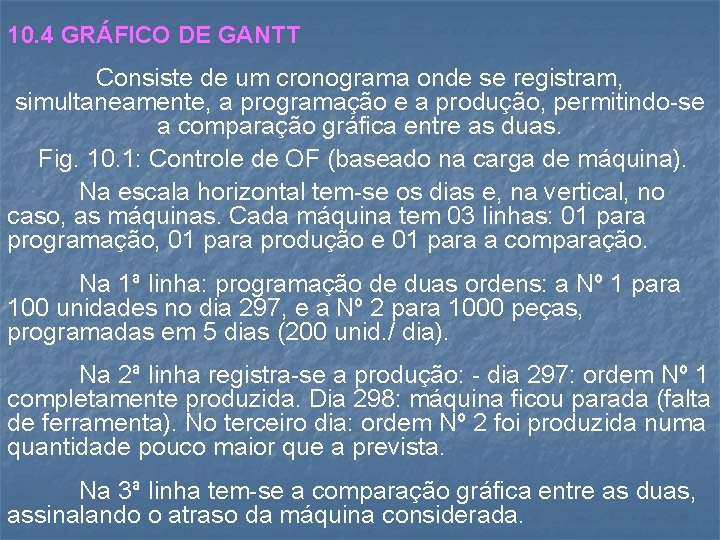
10. 4 GRÁFICO DE GANTT Consiste de um cronograma onde se registram, simultaneamente, a programação e a produção, permitindo-se a comparação gráfica entre as duas. Fig. 10. 1: Controle de OF (baseado na carga de máquina). Na escala horizontal tem-se os dias e, na vertical, no caso, as máquinas. Cada máquina tem 03 linhas: 01 para programação, 01 para produção e 01 para a comparação. Na 1ª linha: programação de duas ordens: a Nº 1 para 100 unidades no dia 297, e a Nº 2 para 1000 peças, programadas em 5 dias (200 unid. / dia). Na 2ª linha registra-se a produção: - dia 297: ordem Nº 1 completamente produzida. Dia 298: máquina ficou parada (falta de ferramenta). No terceiro dia: ordem Nº 2 foi produzida numa quantidade pouco maior que a prevista. Na 3ª linha tem-se a comparação gráfica entre as duas, assinalando o atraso da máquina considerada.
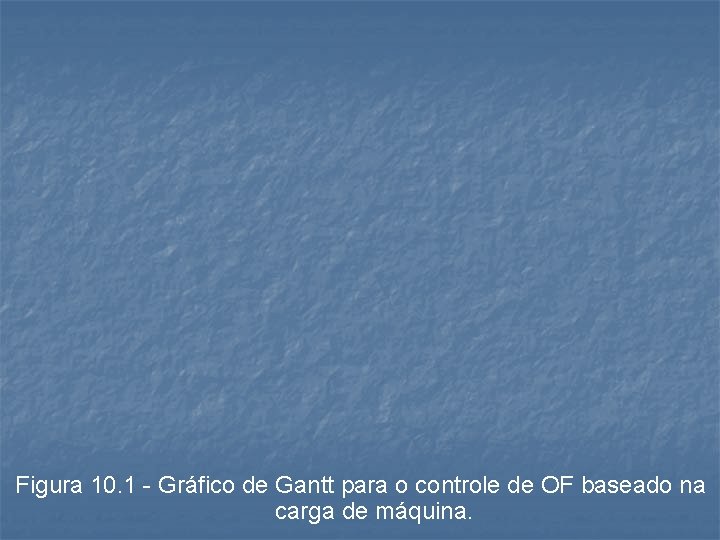
Figura 10. 1 - Gráfico de Gantt para o controle de OF baseado na carga de máquina.
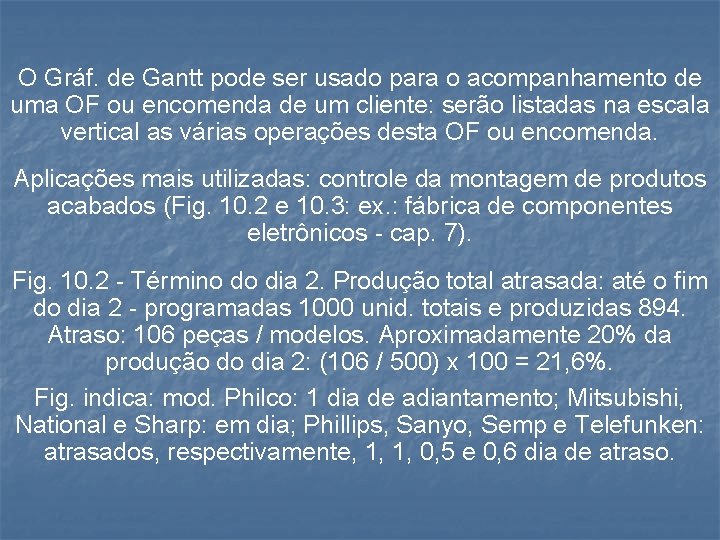
O Gráf. de Gantt pode ser usado para o acompanhamento de uma OF ou encomenda de um cliente: serão listadas na escala vertical as várias operações desta OF ou encomenda. Aplicações mais utilizadas: controle da montagem de produtos acabados (Fig. 10. 2 e 10. 3: ex. : fábrica de componentes eletrônicos - cap. 7). Fig. 10. 2 - Término do dia 2. Produção total atrasada: até o fim do dia 2 - programadas 1000 unid. totais e produzidas 894. Atraso: 106 peças / modelos. Aproximadamente 20% da produção do dia 2: (106 / 500) x 100 = 21, 6%. Fig. indica: mod. Philco: 1 dia de adiantamento; Mitsubishi, National e Sharp: em dia; Phillips, Sanyo, Semp e Telefunken: atrasados, respectivamente, 1, 1, 0, 5 e 0, 6 dia de atraso.
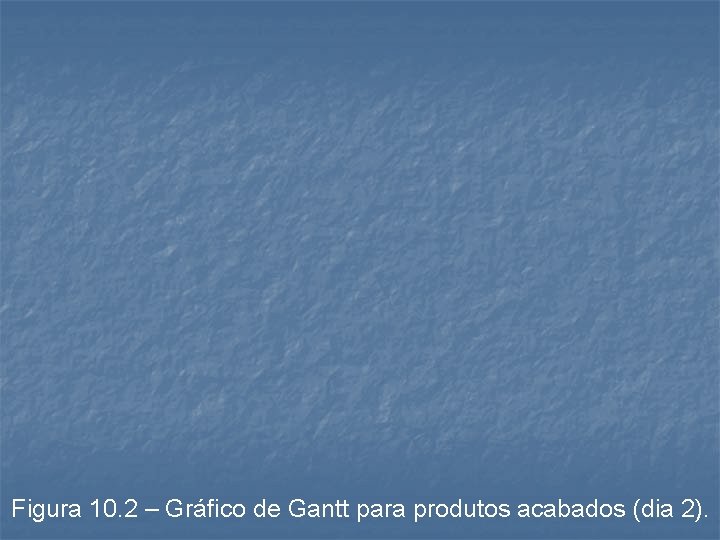
Figura 10. 2 – Gráfico de Gantt para produtos acabados (dia 2).
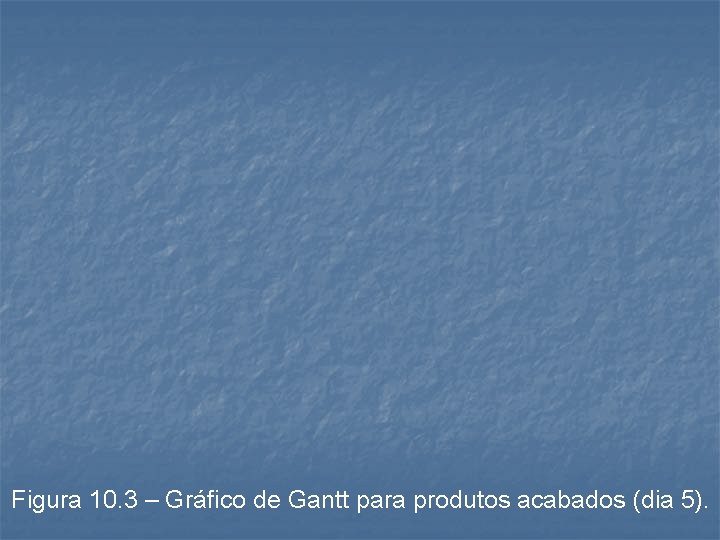
Figura 10. 3 – Gráfico de Gantt para produtos acabados (dia 5).

Supondo-se agora a seguinte produção para o dia 5: National: 10 Philco: 240 Sanyo : 130 Sharp: 100 Semp: 70 Telefunken: 6 Total: 556 Figura 10. 3: gráfico após lançada esta produção. Produção continua atrasada: 50 unidades (10% do programa para o dia 5). A Fig. indica: - Philco: em 1, 2 dias adiantada; Mitsubishi, Sharp e Semp: em dia; National, Phillips, Sanyo e Telefunken: 0, 5; 2; 0, 4 e 1 dias de atraso, respectivamente.
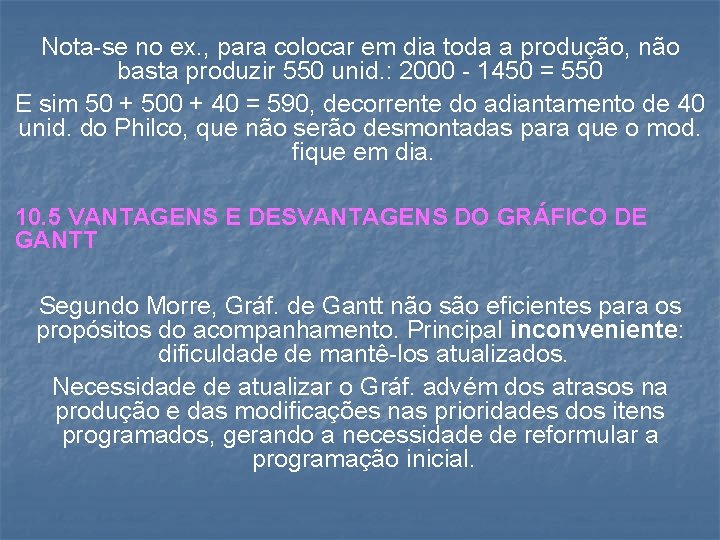
Nota-se no ex. , para colocar em dia toda a produção, não basta produzir 550 unid. : 2000 - 1450 = 550 E sim 50 + 500 + 40 = 590, decorrente do adiantamento de 40 unid. do Philco, que não serão desmontadas para que o mod. fique em dia. 10. 5 VANTAGENS E DESVANTAGENS DO GRÁFICO DE GANTT Segundo Morre, Gráf. de Gantt não são eficientes para os propósitos do acompanhamento. Principal inconveniente: dificuldade de mantê-los atualizados. Necessidade de atualizar o Gráf. advém dos atrasos na produção e das modificações nas prioridades dos itens programados, gerando a necessidade de reformular a programação inicial.
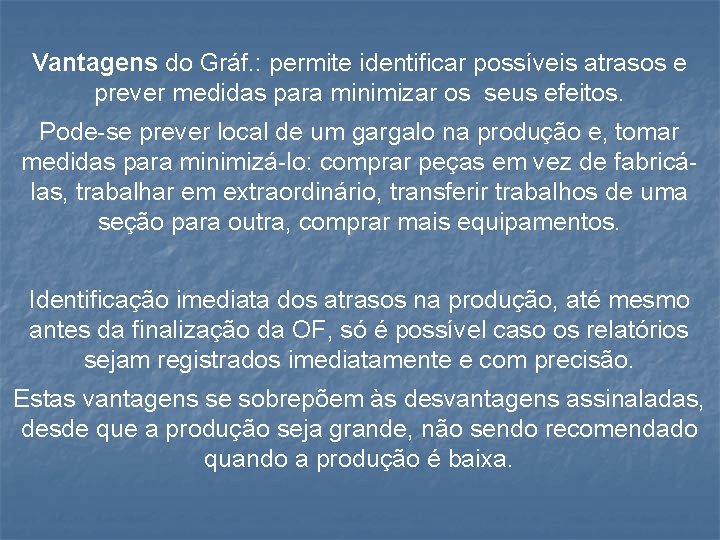
Vantagens do Gráf. : permite identificar possíveis atrasos e prever medidas para minimizar os seus efeitos. Pode-se prever local de um gargalo na produção e, tomar medidas para minimizá-lo: comprar peças em vez de fabricálas, trabalhar em extraordinário, transferir trabalhos de uma seção para outra, comprar mais equipamentos. Identificação imediata dos atrasos na produção, até mesmo antes da finalização da OF, só é possível caso os relatórios sejam registrados imediatamente e com precisão. Estas vantagens se sobrepõem às desvantagens assinaladas, desde que a produção seja grande, não sendo recomendado quando a produção é baixa.
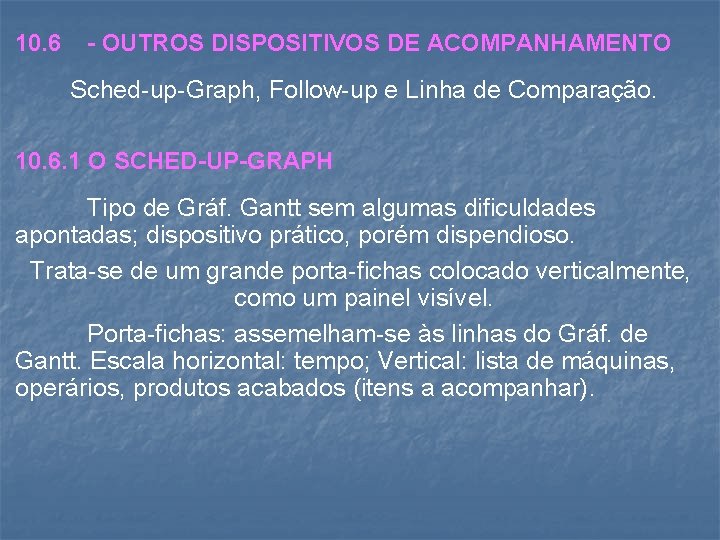
10. 6 - OUTROS DISPOSITIVOS DE ACOMPANHAMENTO Sched-up-Graph, Follow-up e Linha de Comparação. 10. 6. 1 O SCHED-UP-GRAPH Tipo de Gráf. Gantt sem algumas dificuldades apontadas; dispositivo prático, porém dispendioso. Trata-se de um grande porta-fichas colocado verticalmente, como um painel visível. Porta-fichas: assemelham-se às linhas do Gráf. de Gantt. Escala horizontal: tempo; Vertical: lista de máquinas, operários, produtos acabados (itens a acompanhar).
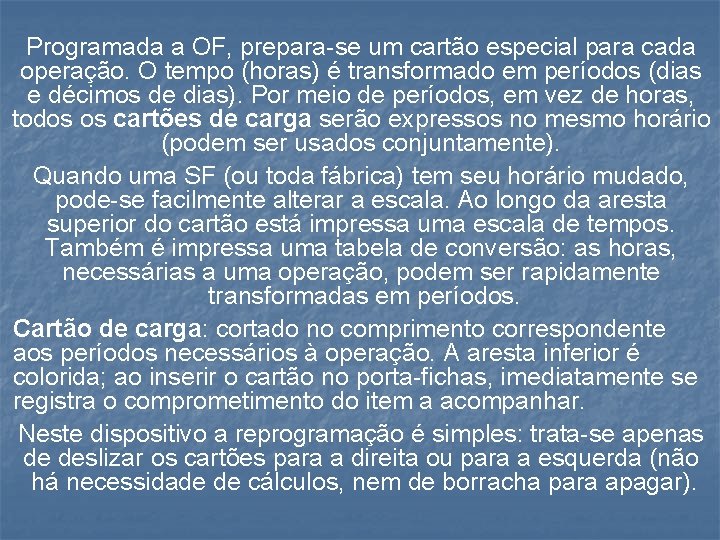
Programada a OF, prepara-se um cartão especial para cada operação. O tempo (horas) é transformado em períodos (dias e décimos de dias). Por meio de períodos, em vez de horas, todos os cartões de carga serão expressos no mesmo horário (podem ser usados conjuntamente). Quando uma SF (ou toda fábrica) tem seu horário mudado, pode-se facilmente alterar a escala. Ao longo da aresta superior do cartão está impressa uma escala de tempos. Também é impressa uma tabela de conversão: as horas, necessárias a uma operação, podem ser rapidamente transformadas em períodos. Cartão de carga: cortado no comprimento correspondente aos períodos necessários à operação. A aresta inferior é colorida; ao inserir o cartão no porta-fichas, imediatamente se registra o comprometimento do item a acompanhar. Neste dispositivo a reprogramação é simples: trata-se apenas de deslizar os cartões para a direita ou para a esquerda (não há necessidade de cálculos, nem de borracha para apagar).
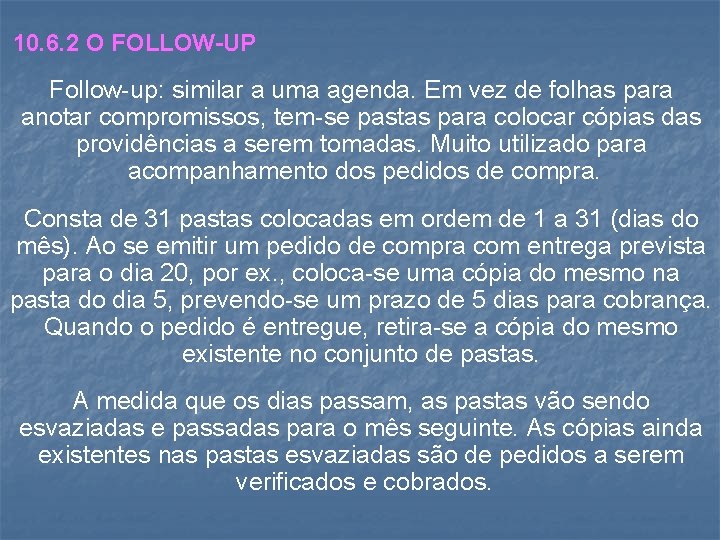
10. 6. 2 O FOLLOW-UP Follow-up: similar a uma agenda. Em vez de folhas para anotar compromissos, tem-se pastas para colocar cópias das providências a serem tomadas. Muito utilizado para acompanhamento dos pedidos de compra. Consta de 31 pastas colocadas em ordem de 1 a 31 (dias do mês). Ao se emitir um pedido de compra com entrega prevista para o dia 20, por ex. , coloca-se uma cópia do mesmo na pasta do dia 5, prevendo-se um prazo de 5 dias para cobrança. Quando o pedido é entregue, retira-se a cópia do mesmo existente no conjunto de pastas. A medida que os dias passam, as pastas vão sendo esvaziadas e passadas para o mês seguinte. As cópias ainda existentes nas pastas esvaziadas são de pedidos a serem verificados e cobrados.
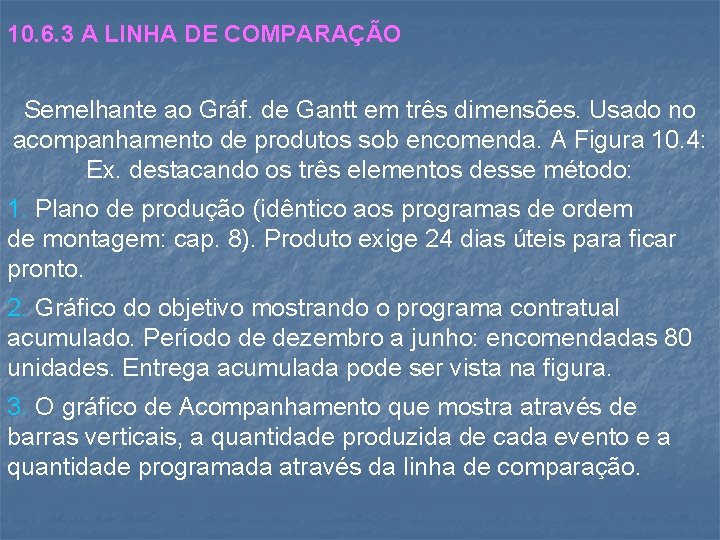
10. 6. 3 A LINHA DE COMPARAÇÃO Semelhante ao Gráf. de Gantt em três dimensões. Usado no acompanhamento de produtos sob encomenda. A Figura 10. 4: Ex. destacando os três elementos desse método: 1. Plano de produção (idêntico aos programas de ordem de montagem: cap. 8). Produto exige 24 dias úteis para ficar pronto. 2. Gráfico do objetivo mostrando o programa contratual acumulado. Período de dezembro a junho: encomendadas 80 unidades. Entrega acumulada pode ser vista na figura. 3. O gráfico de Acompanhamento que mostra através de barras verticais, a quantidade produzida de cada evento e a quantidade programada através da linha de comparação.
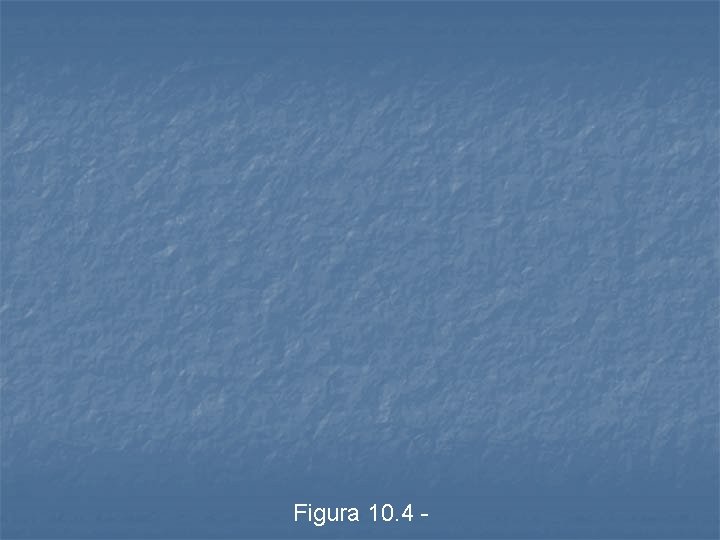
Figura 10. 4 -
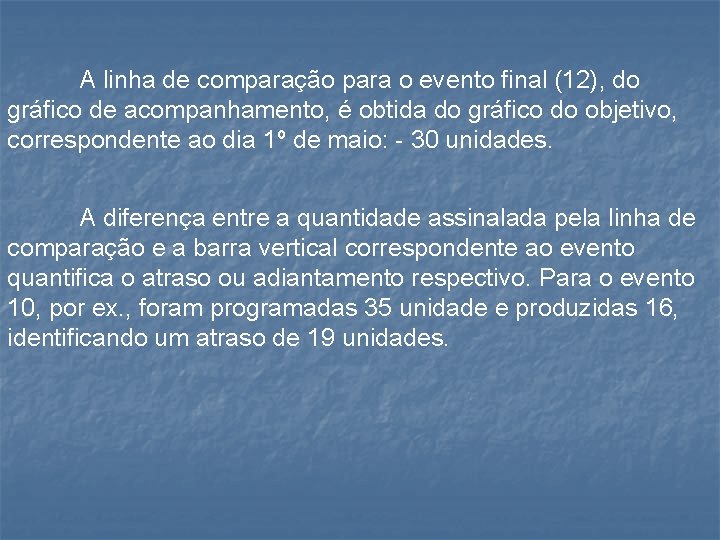
A linha de comparação para o evento final (12), do gráfico de acompanhamento, é obtida do gráfico do objetivo, correspondente ao dia 1º de maio: - 30 unidades. A diferença entre a quantidade assinalada pela linha de comparação e a barra vertical correspondente ao evento quantifica o atraso ou adiantamento respectivo. Para o evento 10, por ex. , foram programadas 35 unidade e produzidas 16, identificando um atraso de 19 unidades.
Produo pamplona
Siacof acompanhamento
N
Ouvidorsus
Redesim sp
Planejamento de experimentos
Slide planejamento familiar
Jaboatão significado
Planejamento estratégico situacional pes
Planejamento adaptativo rh
Aap2 - planejamento financeiro e orçamentário
Conceito de planejamento
Empresariamento
Processo de planejamento estratégico
Planejamento ambiental
Kanban
Planejamento de enfermagem exemplo
Qualiped
Planejamento urbano rio de janeiro
Planejamento de campanhas