Occupational Health and Safety Management Systems OHSMS ANSI
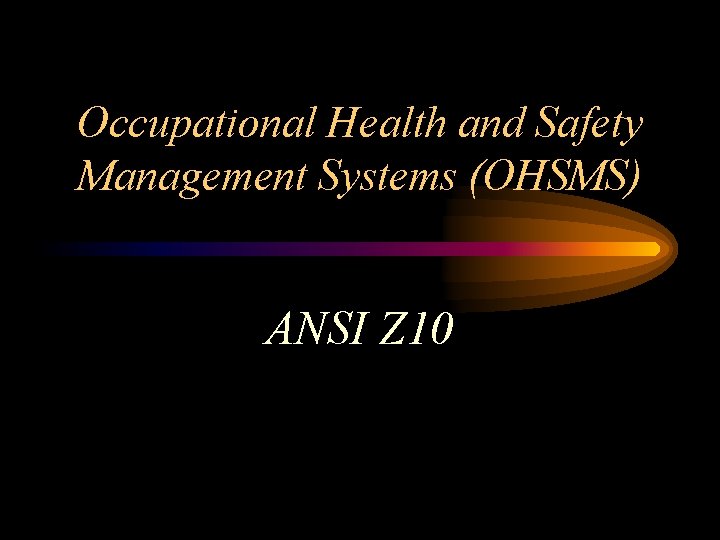
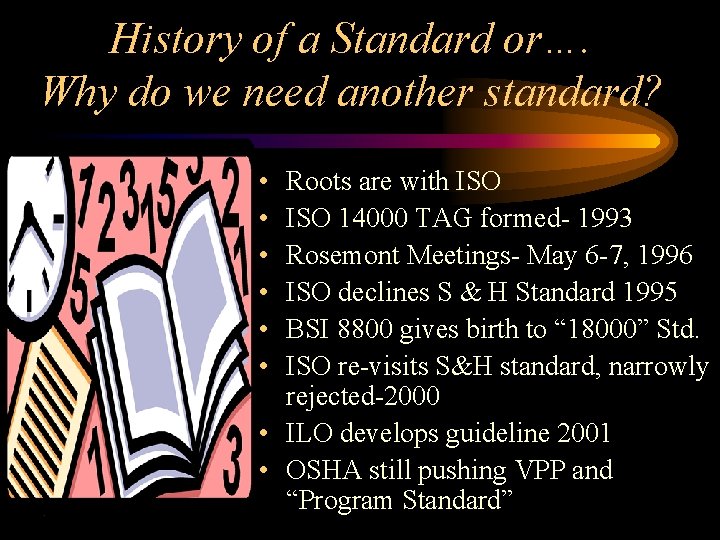
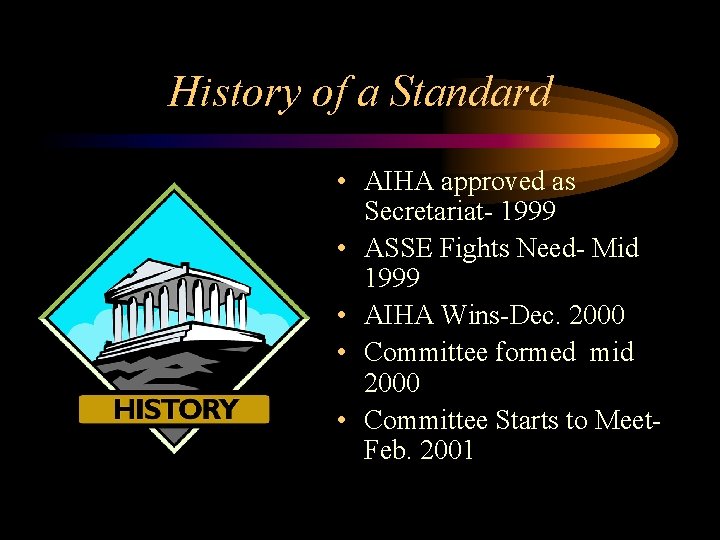
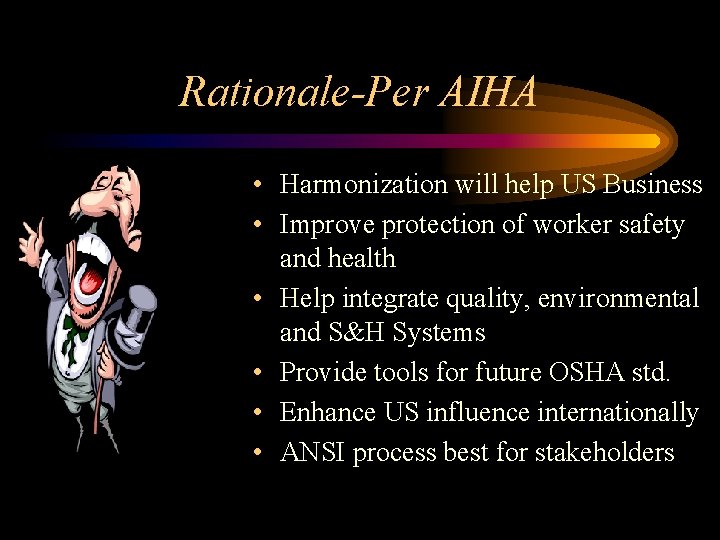
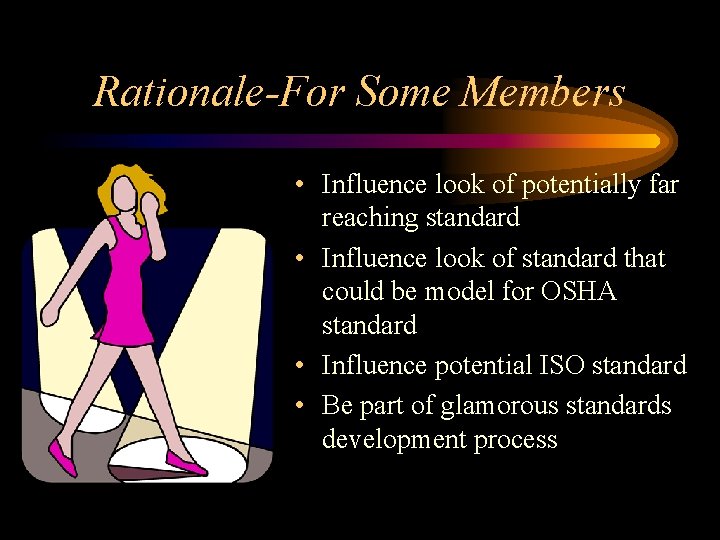
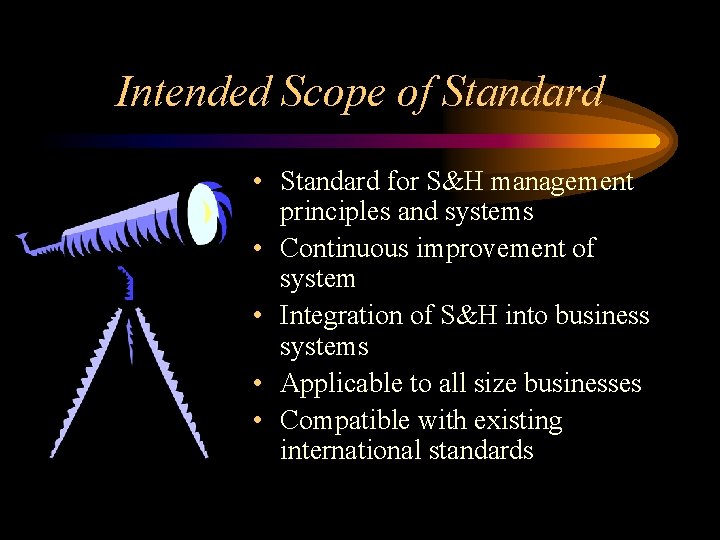
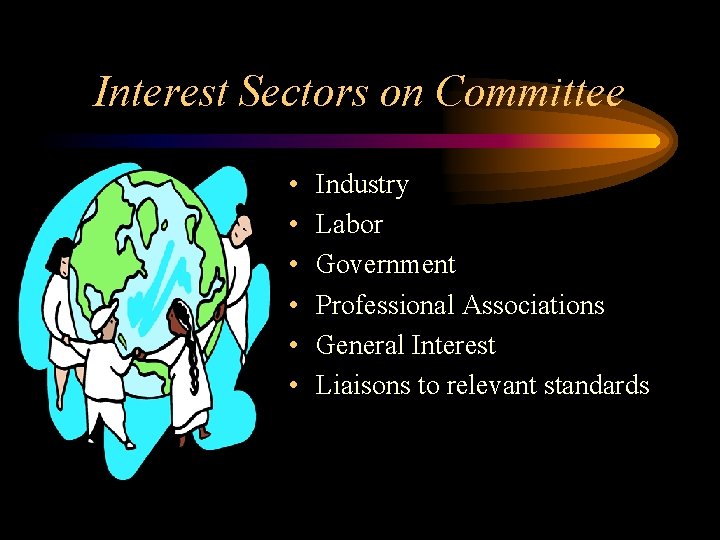
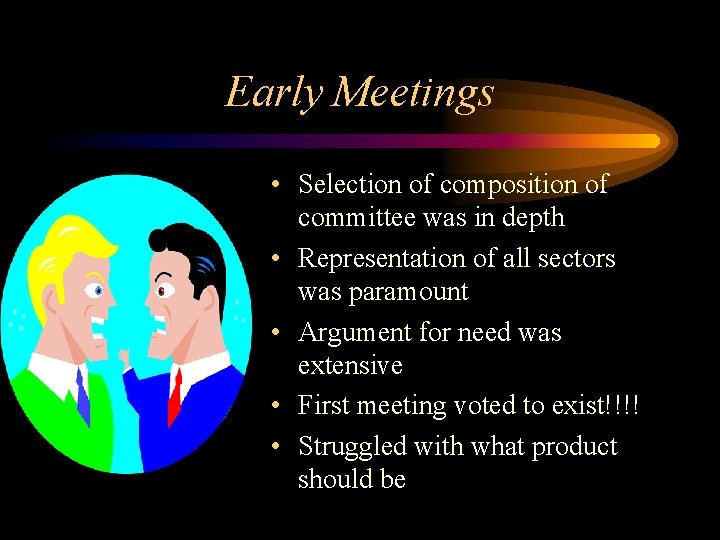
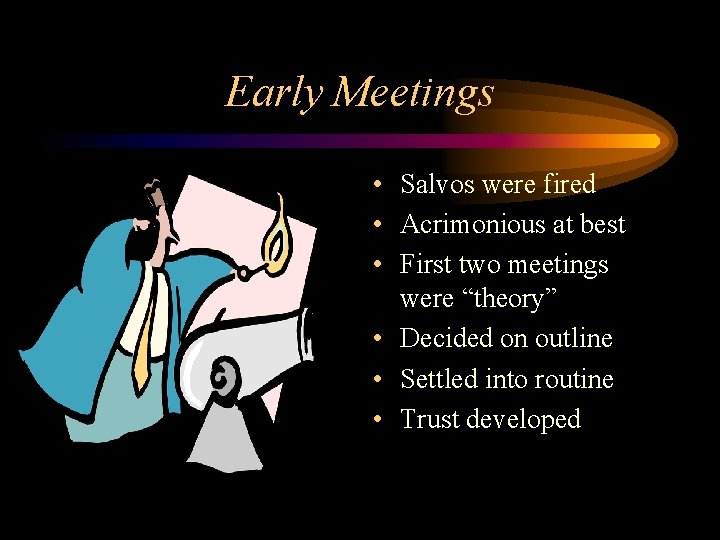
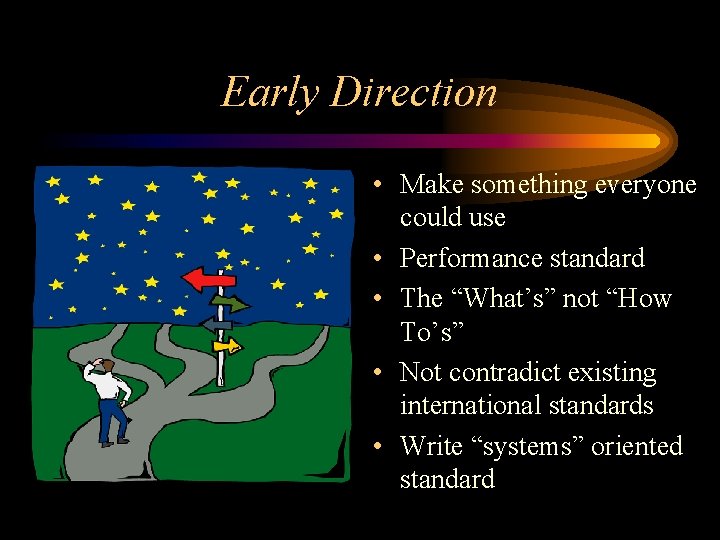
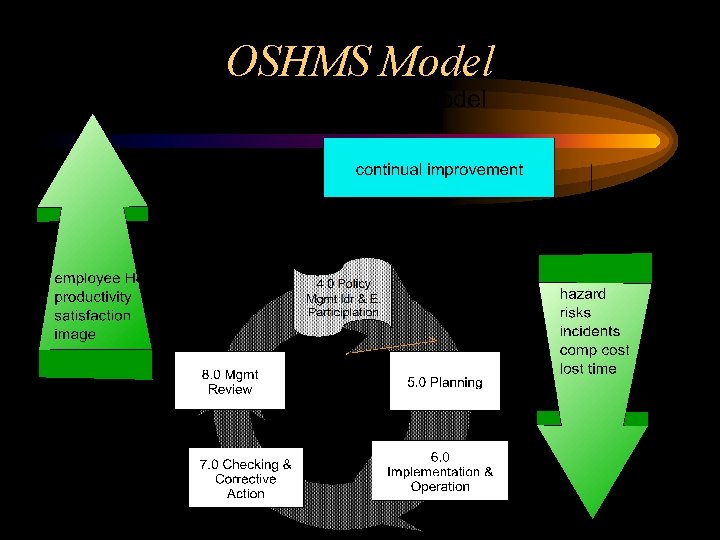
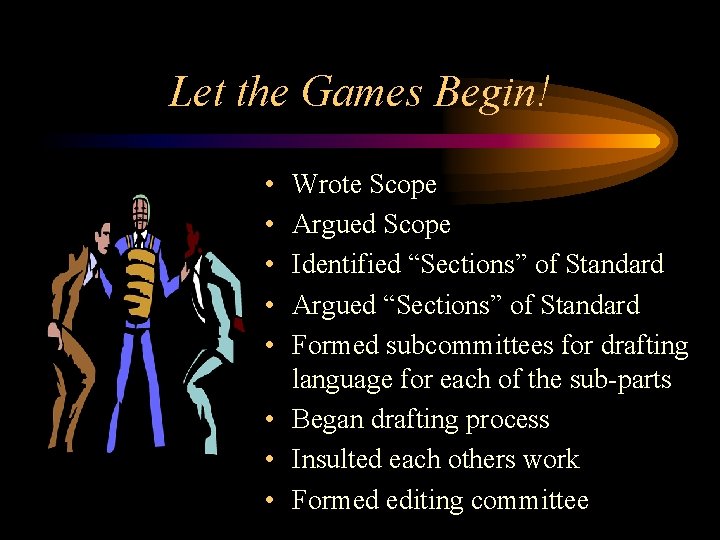
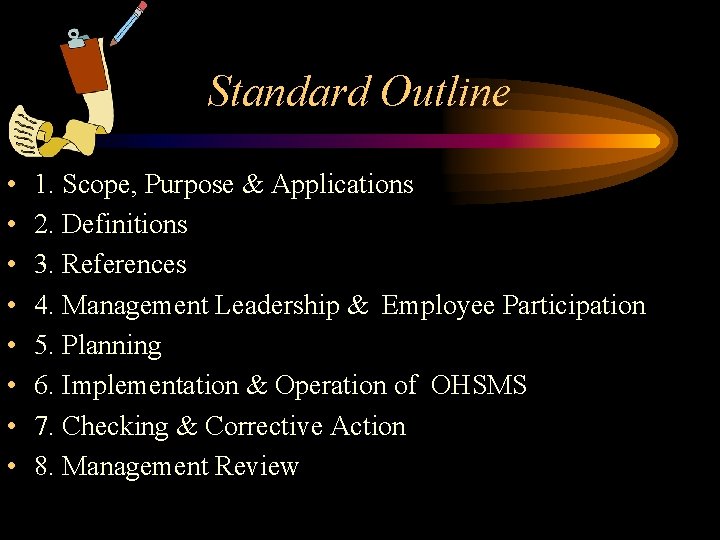
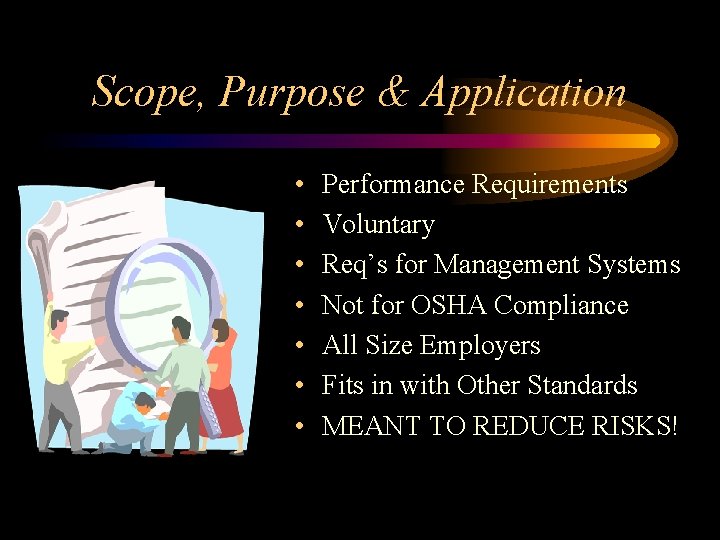
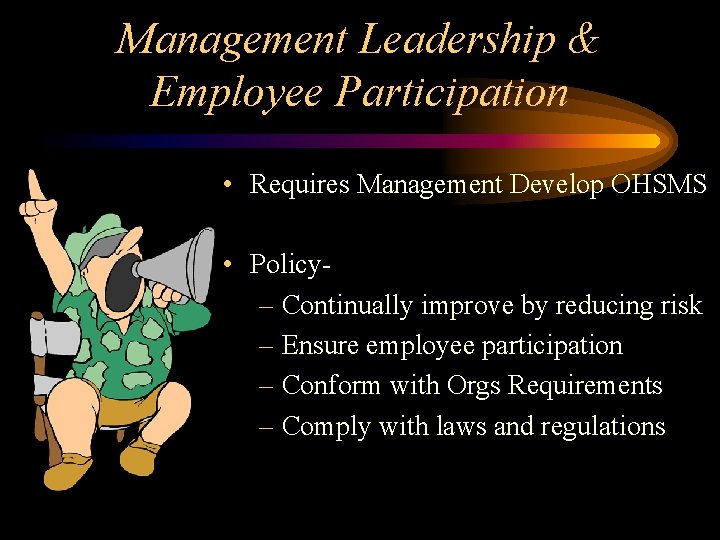
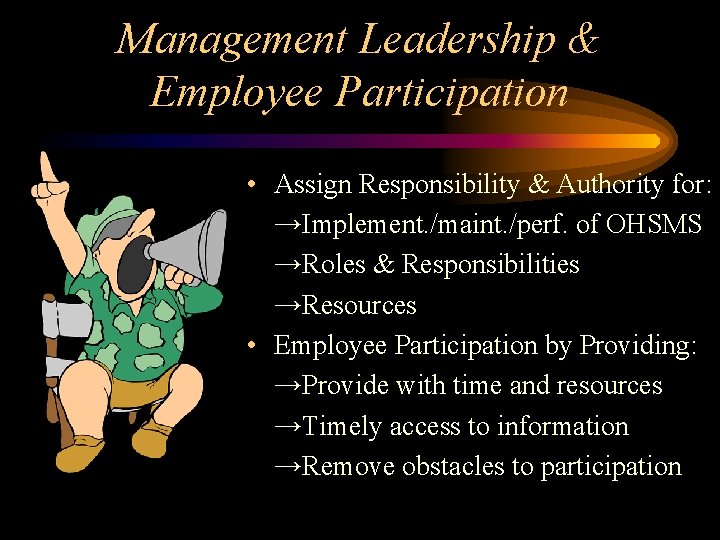
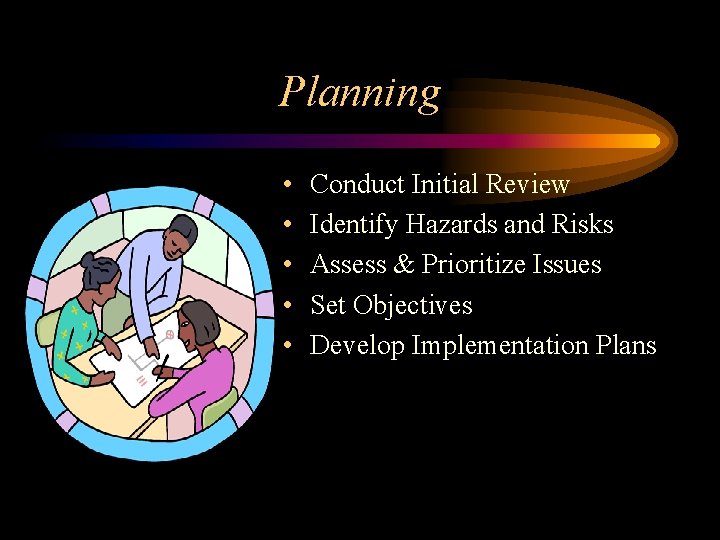
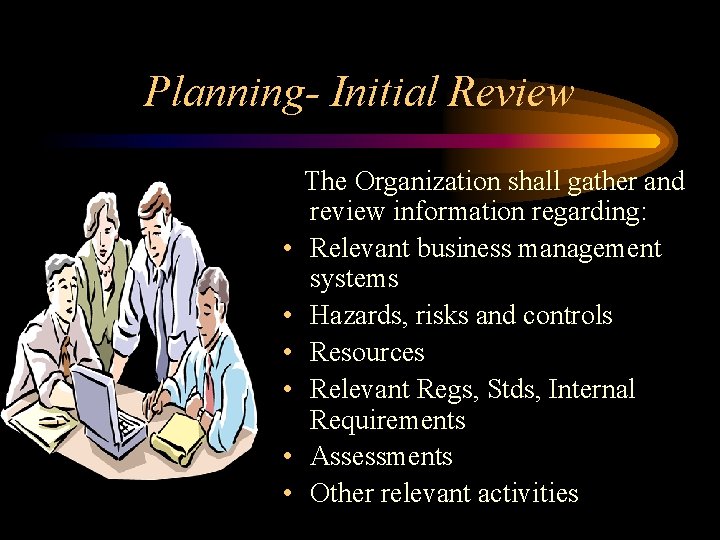
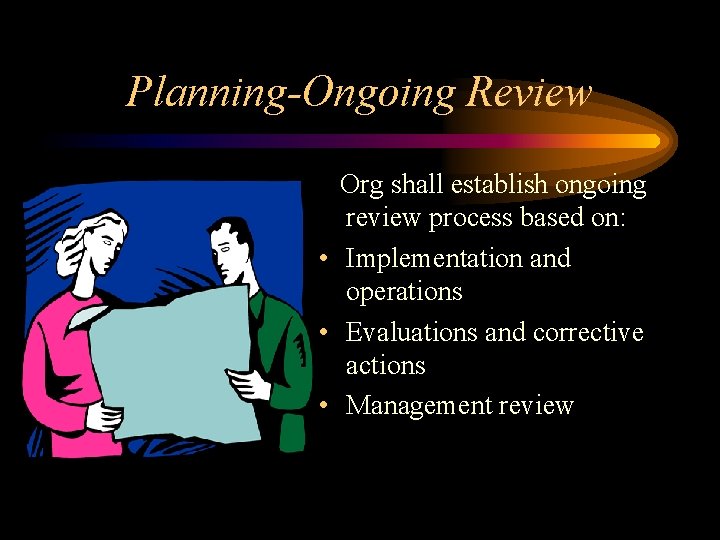
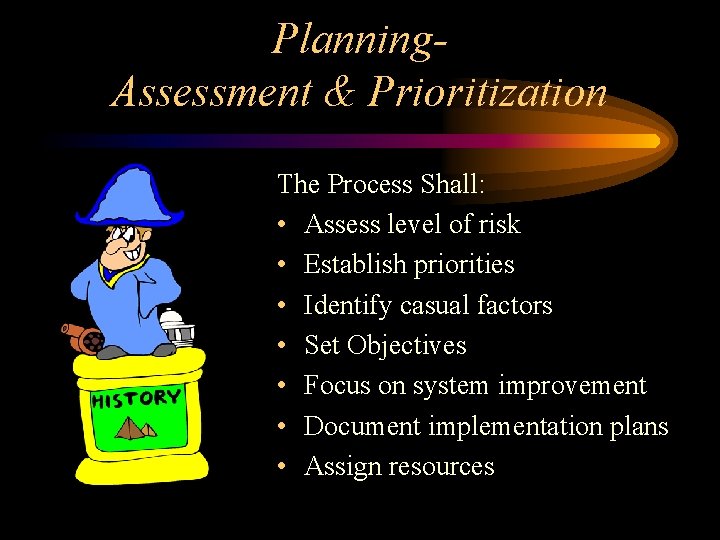
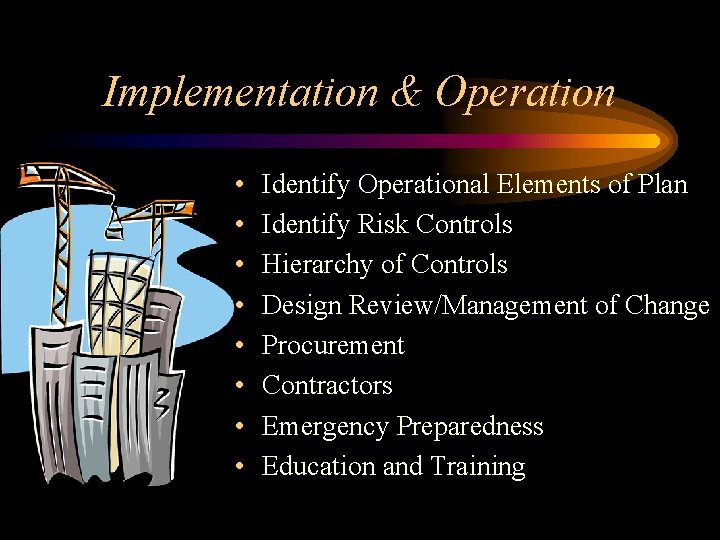
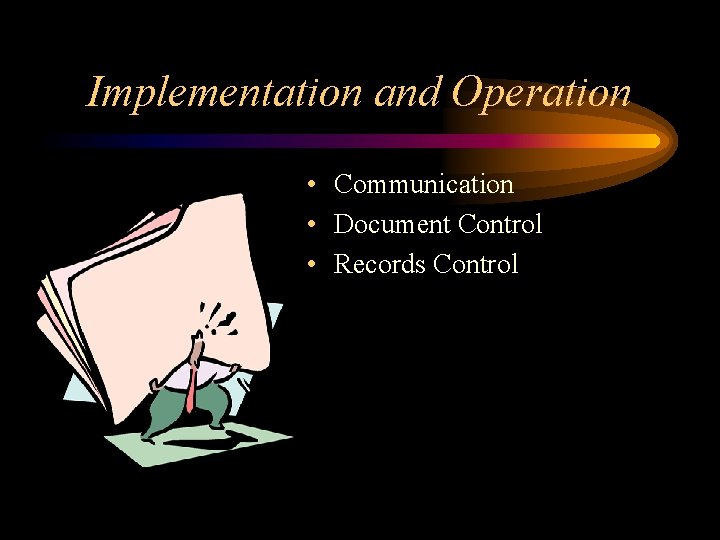
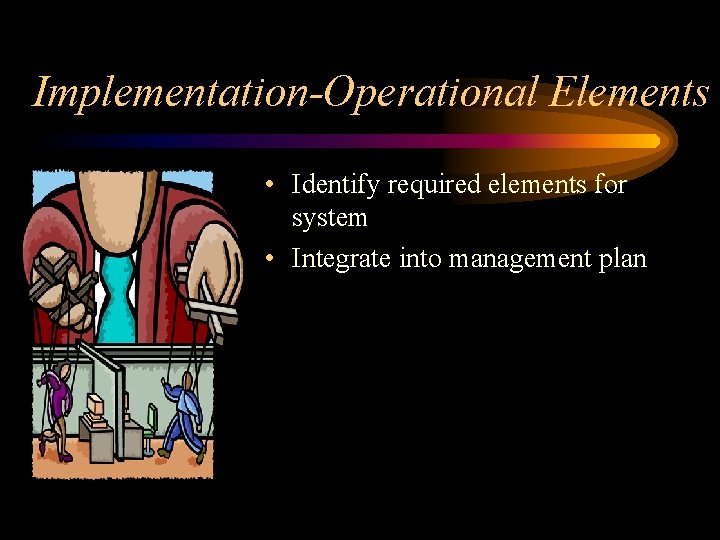
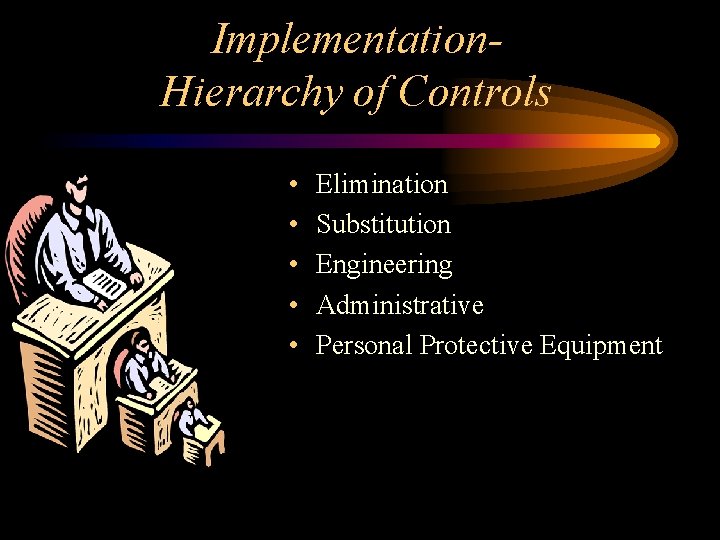
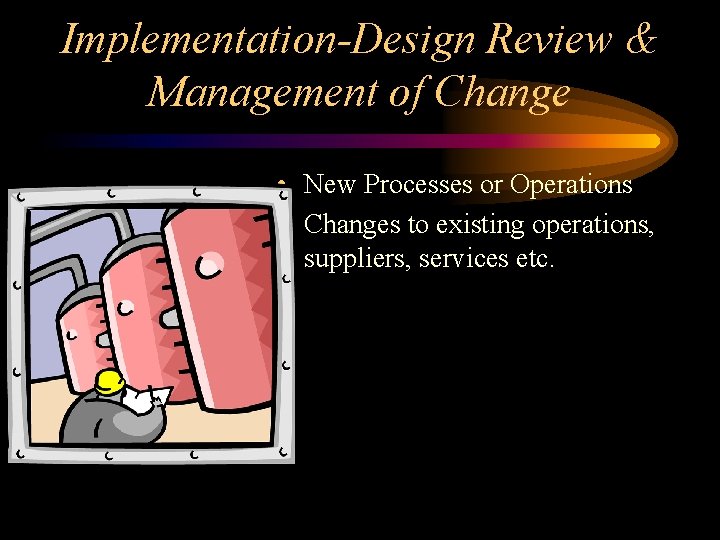
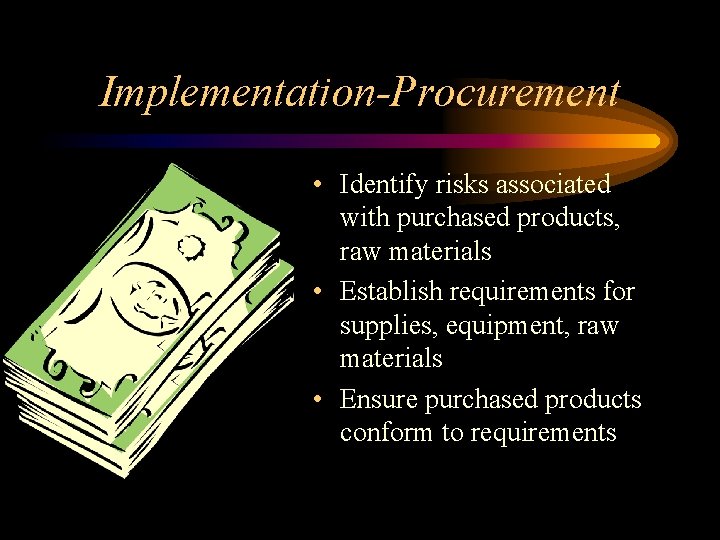
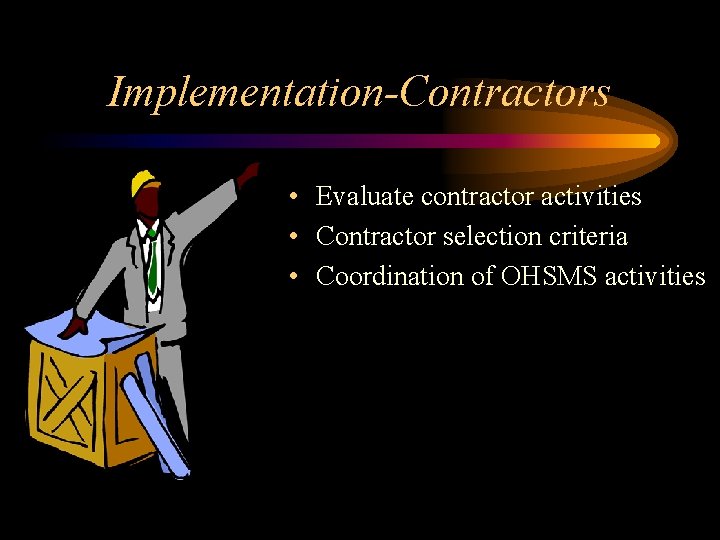
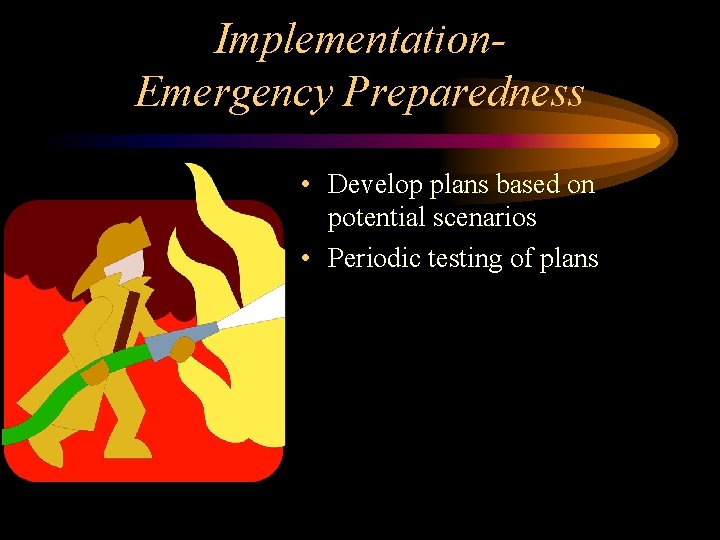
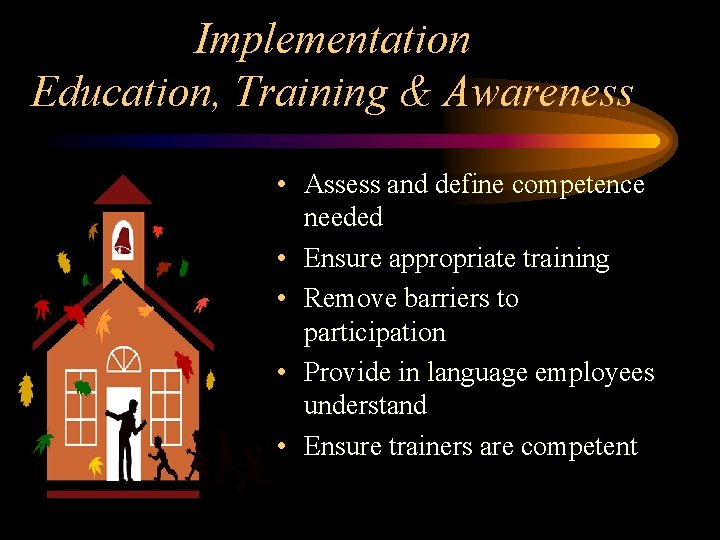
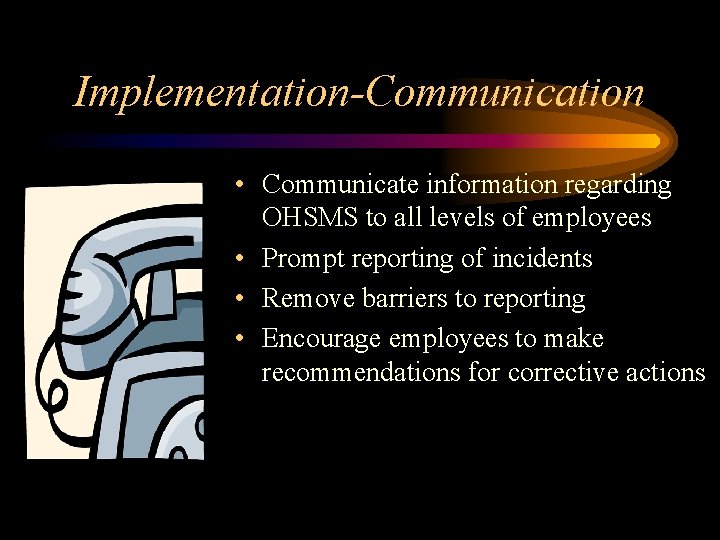
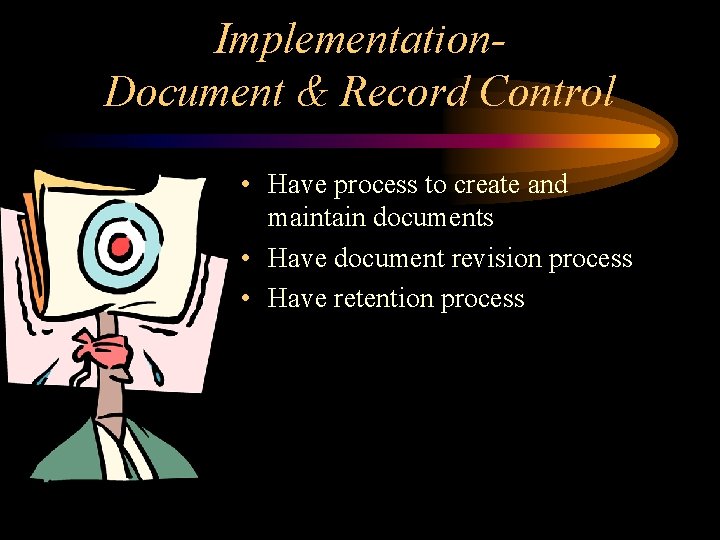
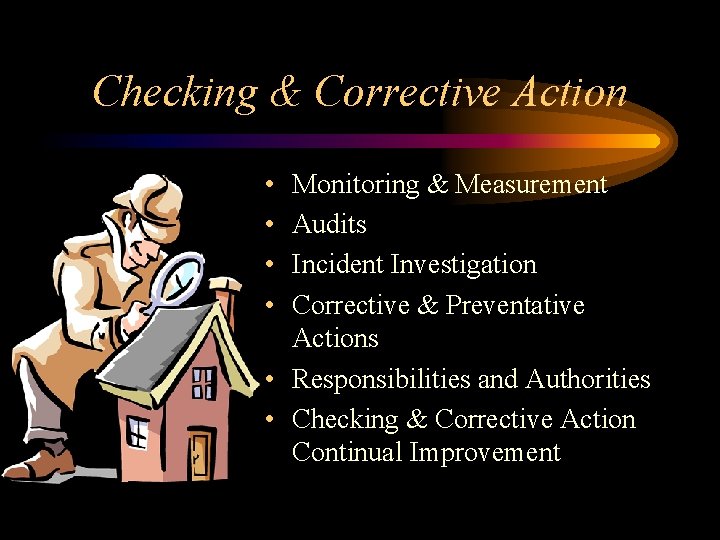
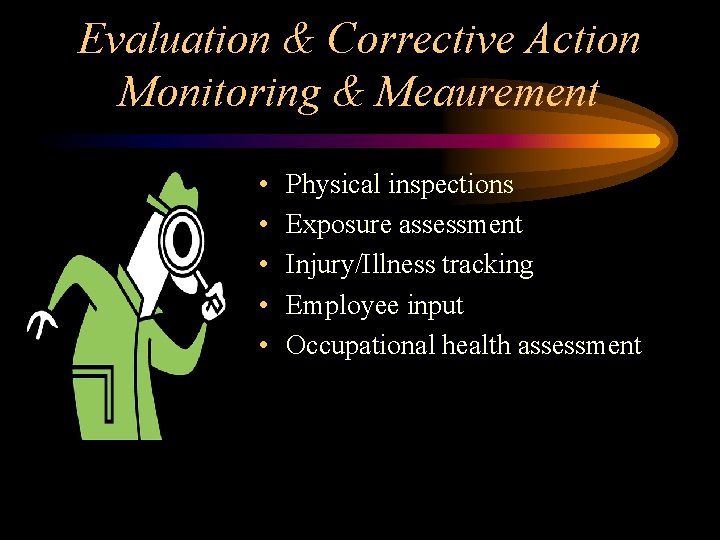
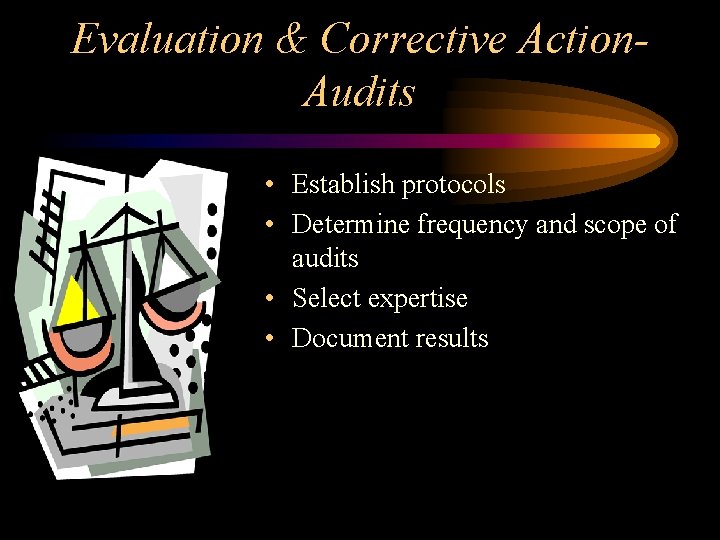
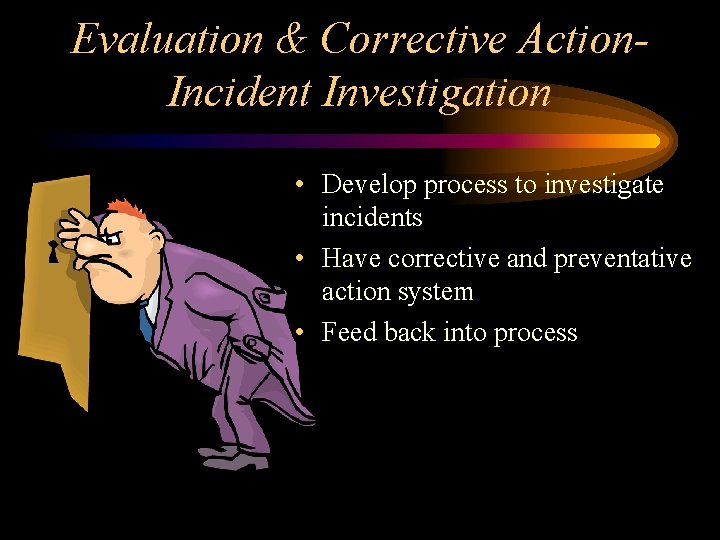
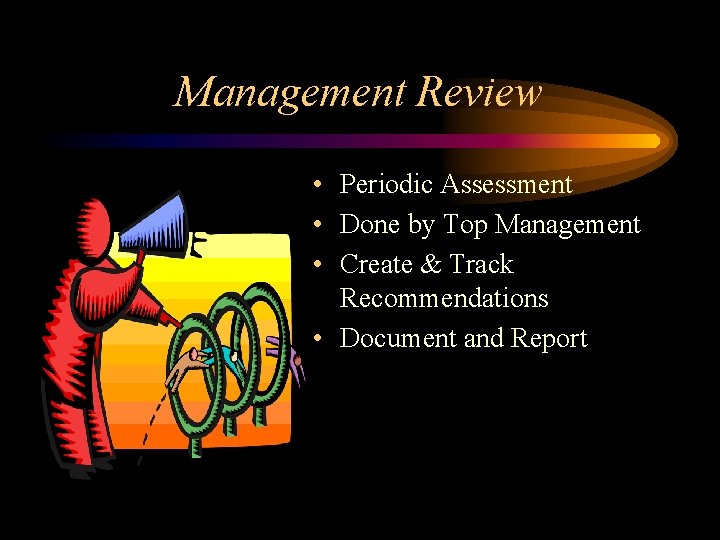
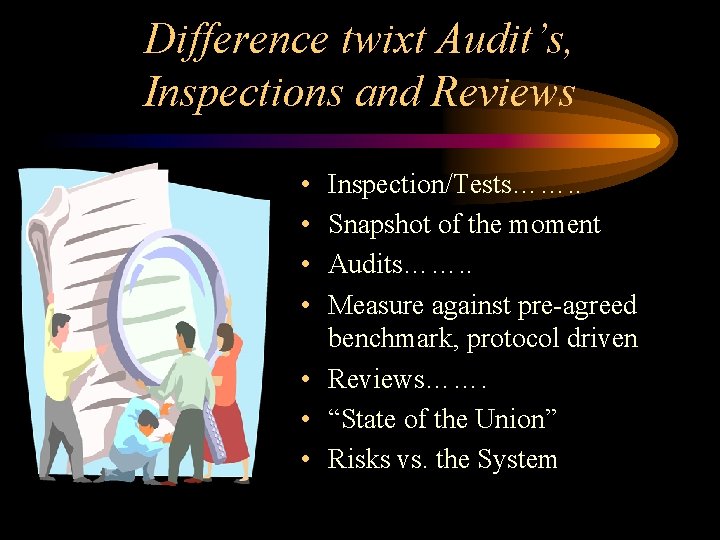
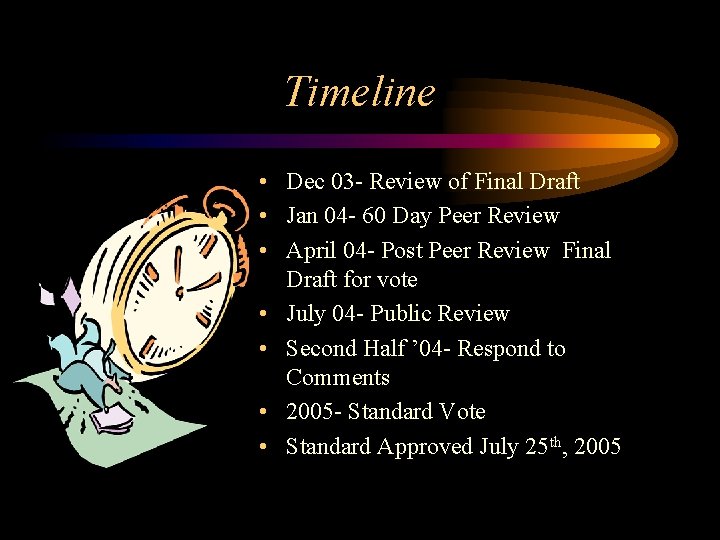
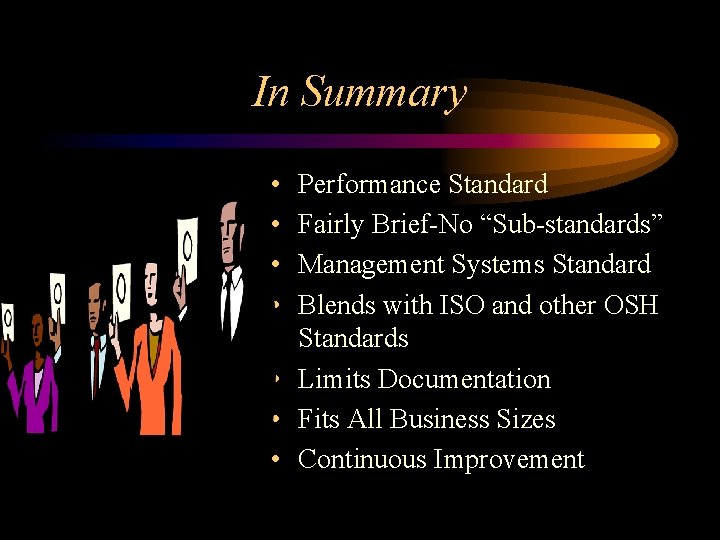
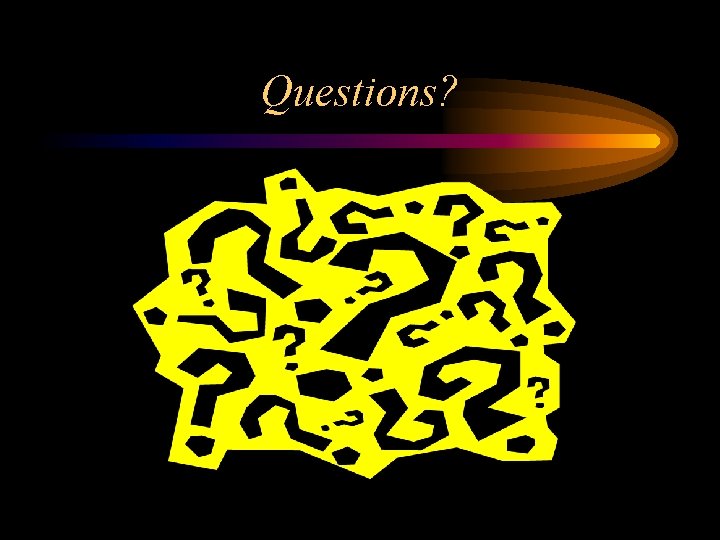
- Slides: 40
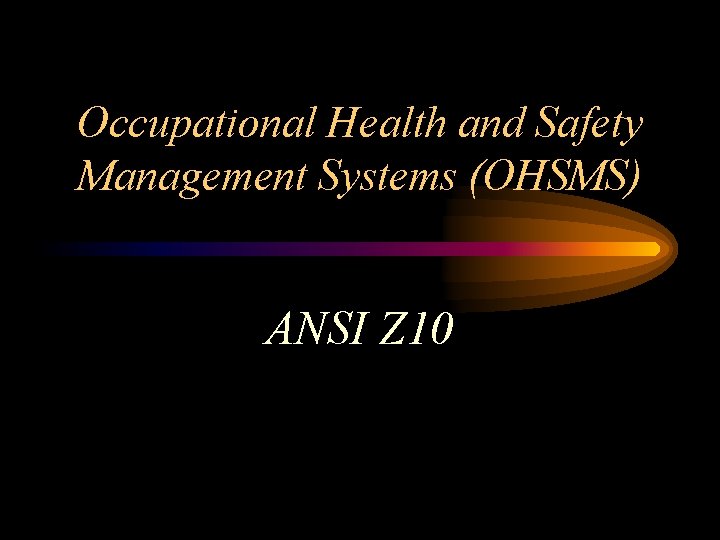
Occupational Health and Safety Management Systems (OHSMS) ANSI Z 10
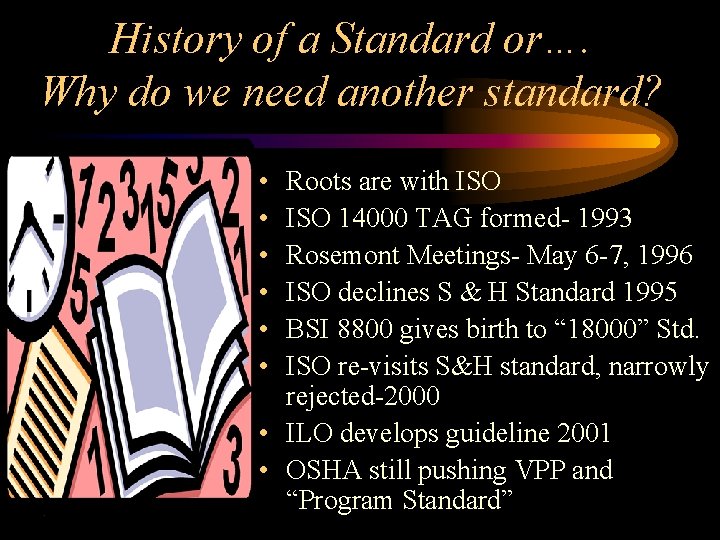
History of a Standard or…. Why do we need another standard? • • • Roots are with ISO 14000 TAG formed- 1993 Rosemont Meetings- May 6 -7, 1996 ISO declines S & H Standard 1995 BSI 8800 gives birth to “ 18000” Std. ISO re-visits S&H standard, narrowly rejected-2000 • ILO develops guideline 2001 • OSHA still pushing VPP and “Program Standard”
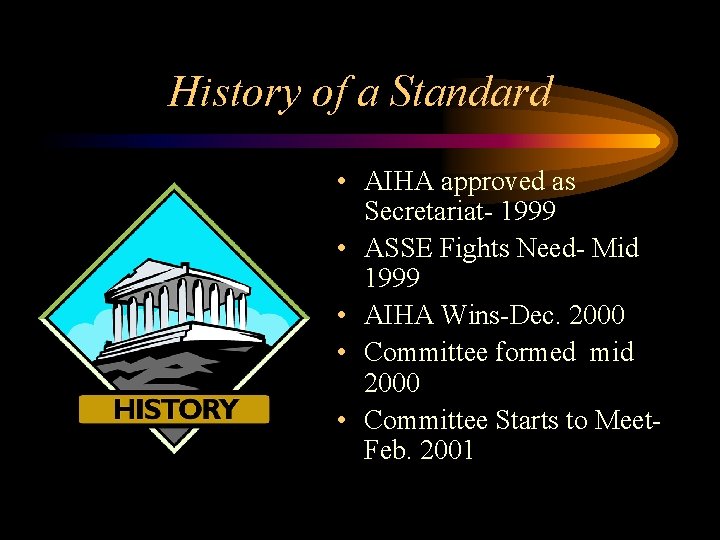
History of a Standard • AIHA approved as Secretariat- 1999 • ASSE Fights Need- Mid 1999 • AIHA Wins-Dec. 2000 • Committee formed mid 2000 • Committee Starts to Meet. Feb. 2001
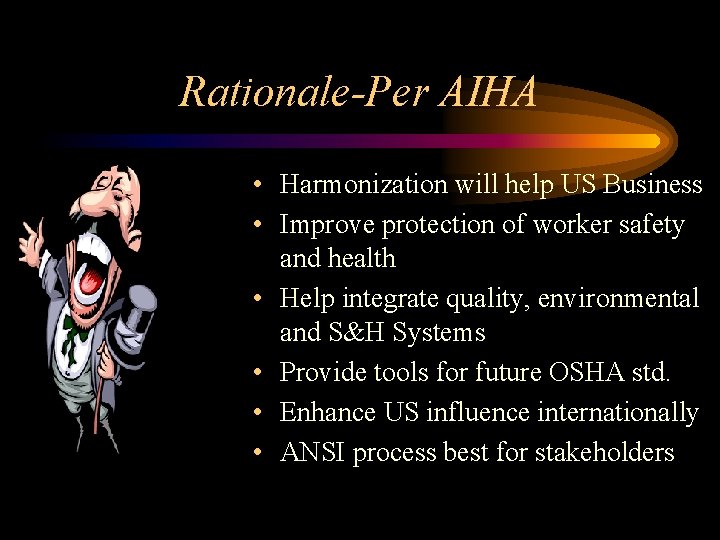
Rationale-Per AIHA • Harmonization will help US Business • Improve protection of worker safety and health • Help integrate quality, environmental and S&H Systems • Provide tools for future OSHA std. • Enhance US influence internationally • ANSI process best for stakeholders
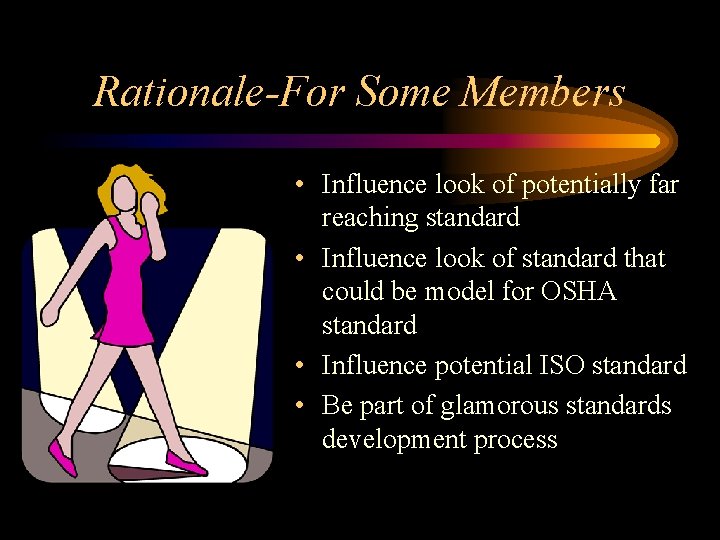
Rationale-For Some Members • Influence look of potentially far reaching standard • Influence look of standard that could be model for OSHA standard • Influence potential ISO standard • Be part of glamorous standards development process
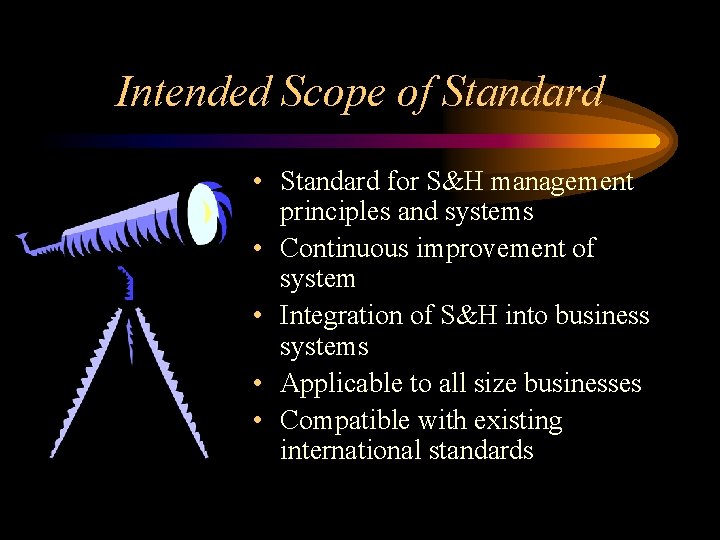
Intended Scope of Standard • Standard for S&H management principles and systems • Continuous improvement of system • Integration of S&H into business systems • Applicable to all size businesses • Compatible with existing international standards
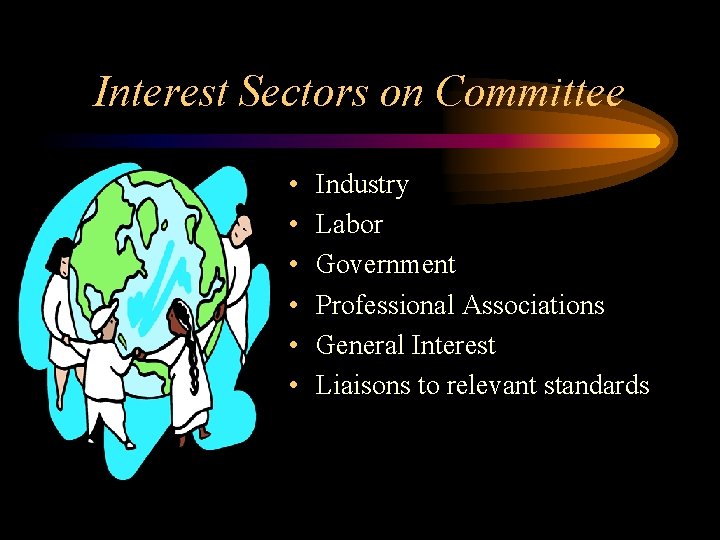
Interest Sectors on Committee • • • Industry Labor Government Professional Associations General Interest Liaisons to relevant standards
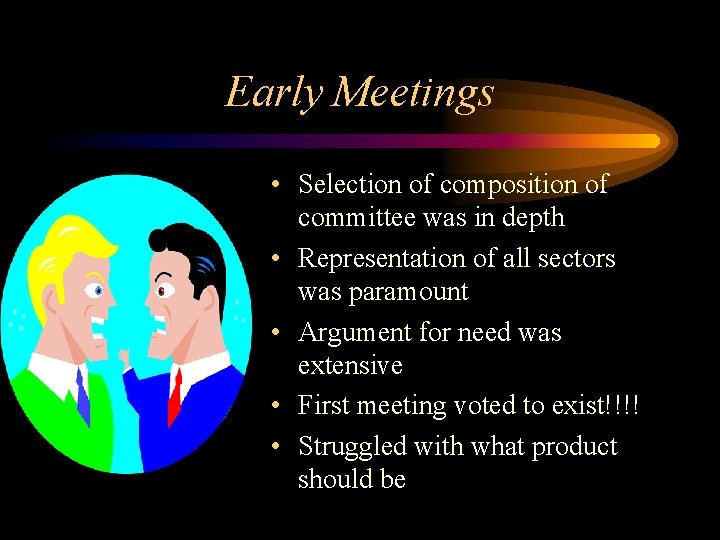
Early Meetings • Selection of composition of committee was in depth • Representation of all sectors was paramount • Argument for need was extensive • First meeting voted to exist!!!! • Struggled with what product should be
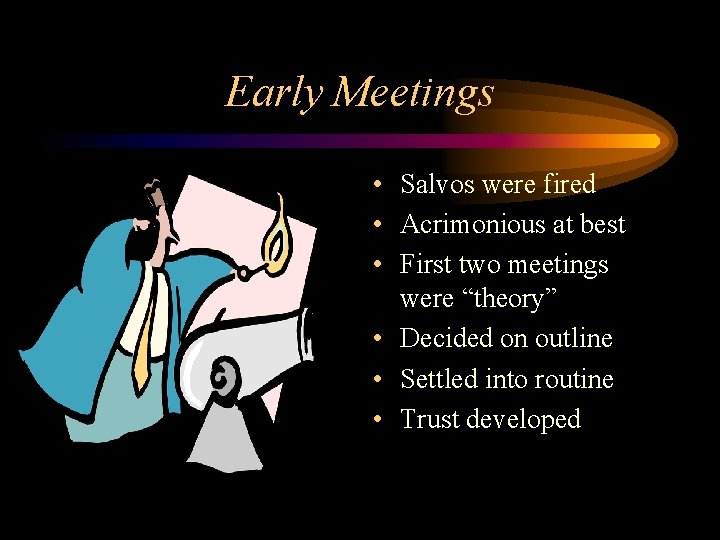
Early Meetings • Salvos were fired • Acrimonious at best • First two meetings were “theory” • Decided on outline • Settled into routine • Trust developed
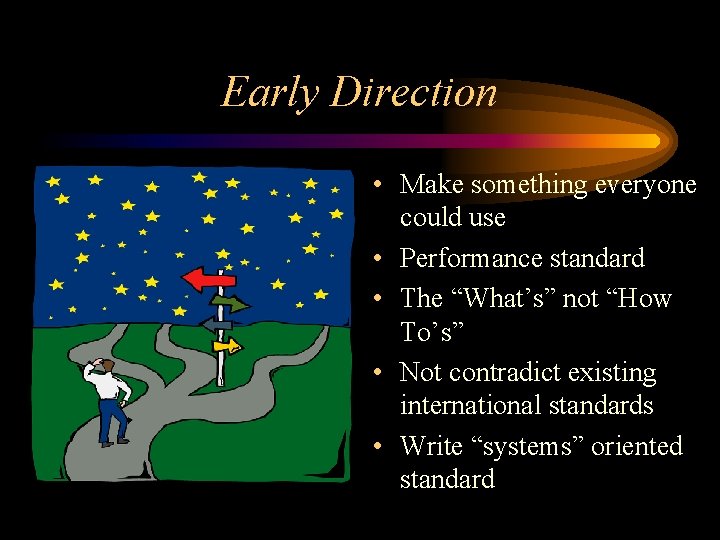
Early Direction • Make something everyone could use • Performance standard • The “What’s” not “How To’s” • Not contradict existing international standards • Write “systems” oriented standard
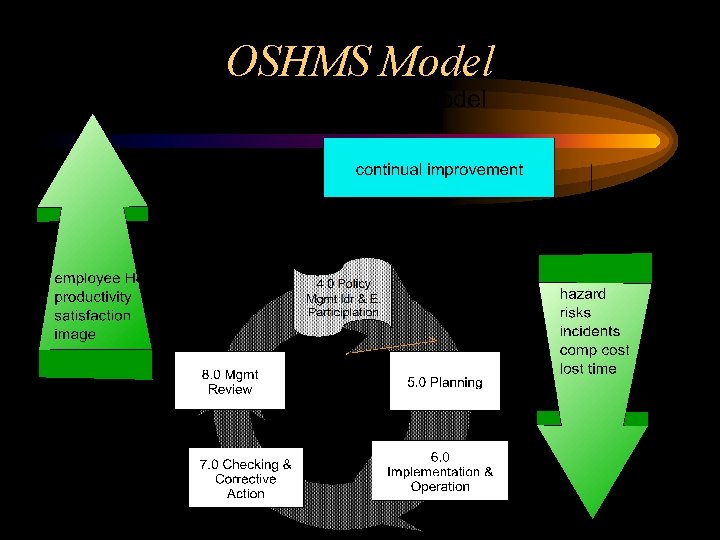
OSHMS Model
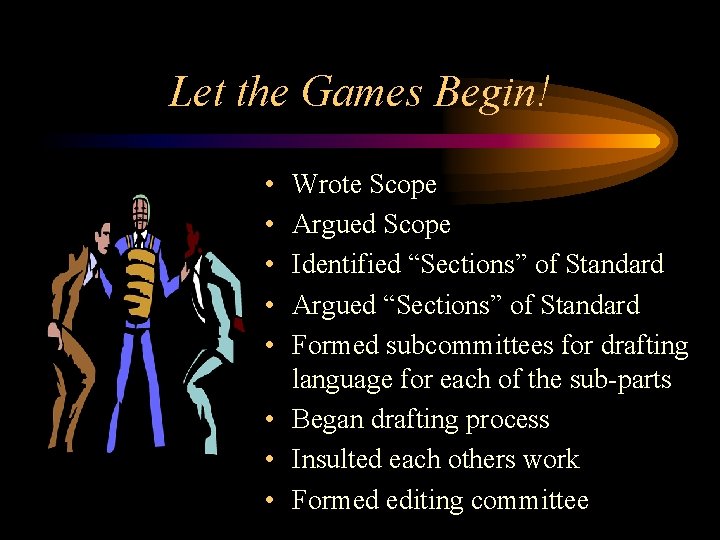
Let the Games Begin! • • • Wrote Scope Argued Scope Identified “Sections” of Standard Argued “Sections” of Standard Formed subcommittees for drafting language for each of the sub-parts • Began drafting process • Insulted each others work • Formed editing committee
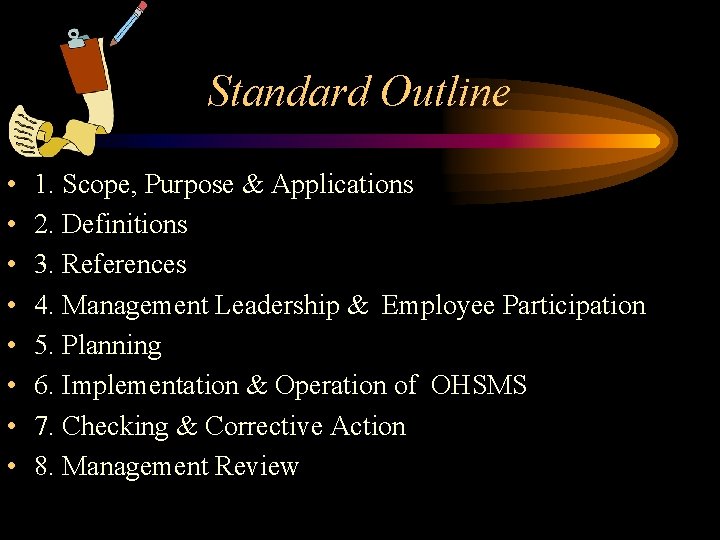
Standard Outline • • 1. Scope, Purpose & Applications 2. Definitions 3. References 4. Management Leadership & Employee Participation 5. Planning 6. Implementation & Operation of OHSMS 7. Checking & Corrective Action 8. Management Review
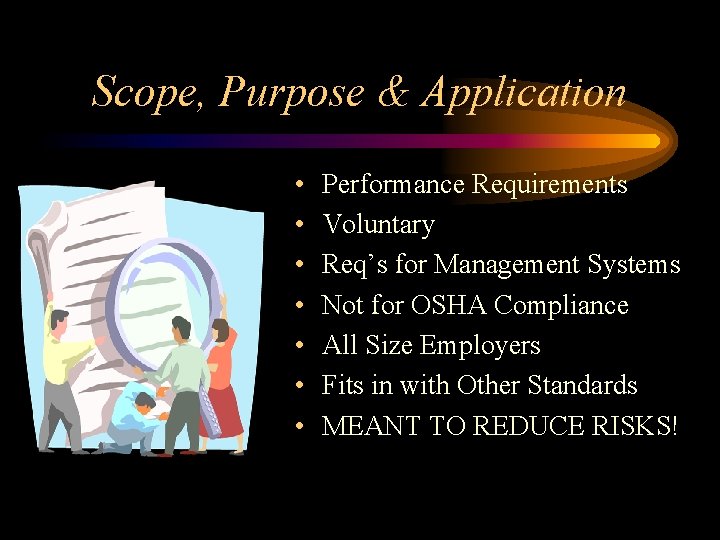
Scope, Purpose & Application • • Performance Requirements Voluntary Req’s for Management Systems Not for OSHA Compliance All Size Employers Fits in with Other Standards MEANT TO REDUCE RISKS!
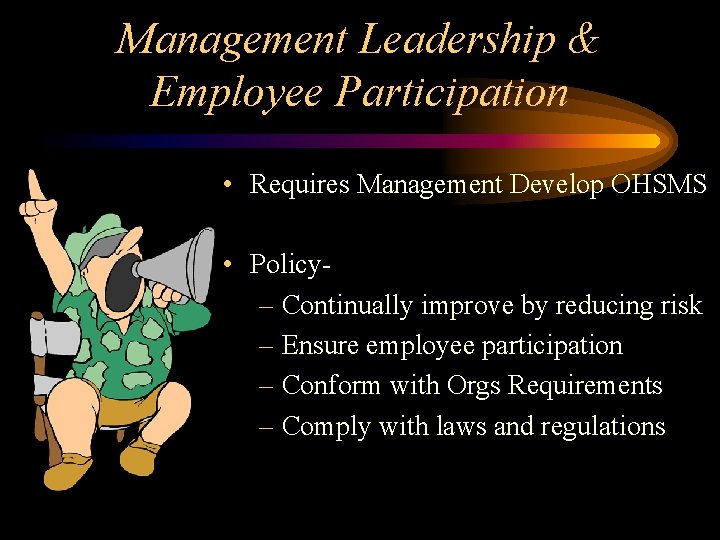
Management Leadership & Employee Participation • Requires Management Develop OHSMS • Policy– Continually improve by reducing risk – Ensure employee participation – Conform with Orgs Requirements – Comply with laws and regulations
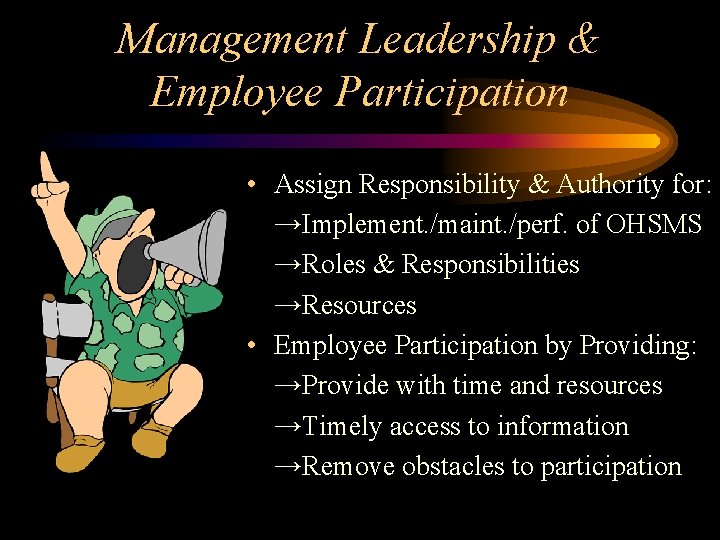
Management Leadership & Employee Participation • Assign Responsibility & Authority for: →Implement. /maint. /perf. of OHSMS →Roles & Responsibilities →Resources • Employee Participation by Providing: →Provide with time and resources →Timely access to information →Remove obstacles to participation
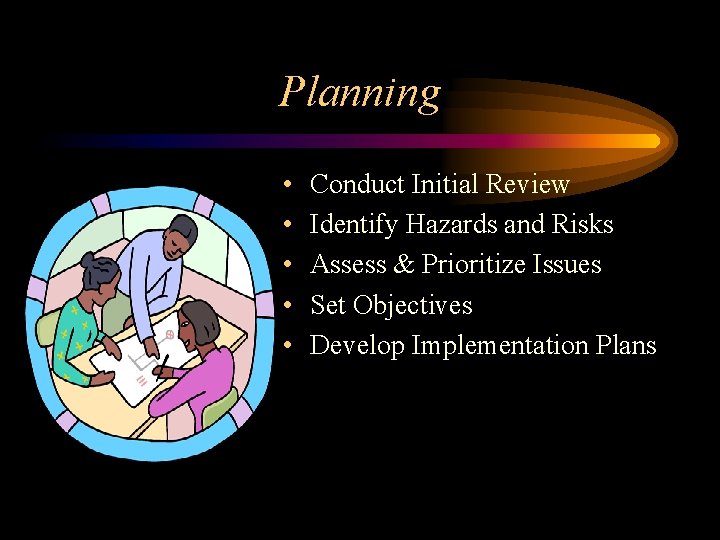
Planning • • • Conduct Initial Review Identify Hazards and Risks Assess & Prioritize Issues Set Objectives Develop Implementation Plans
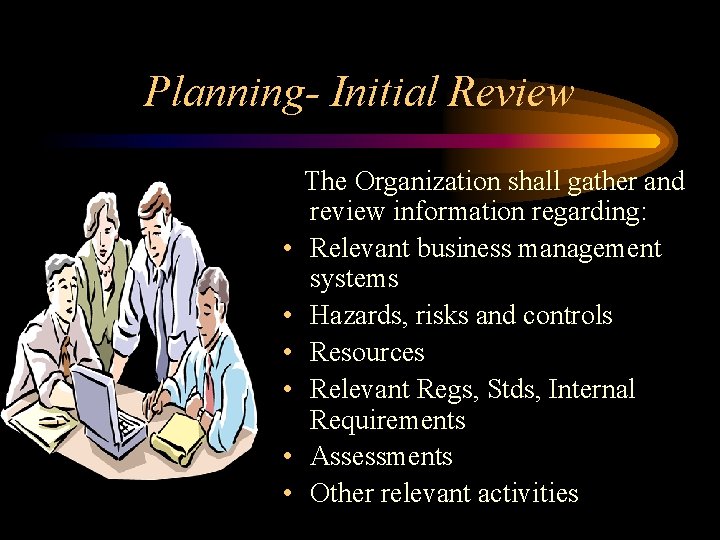
Planning- Initial Review • • • The Organization shall gather and review information regarding: Relevant business management systems Hazards, risks and controls Resources Relevant Regs, Stds, Internal Requirements Assessments Other relevant activities
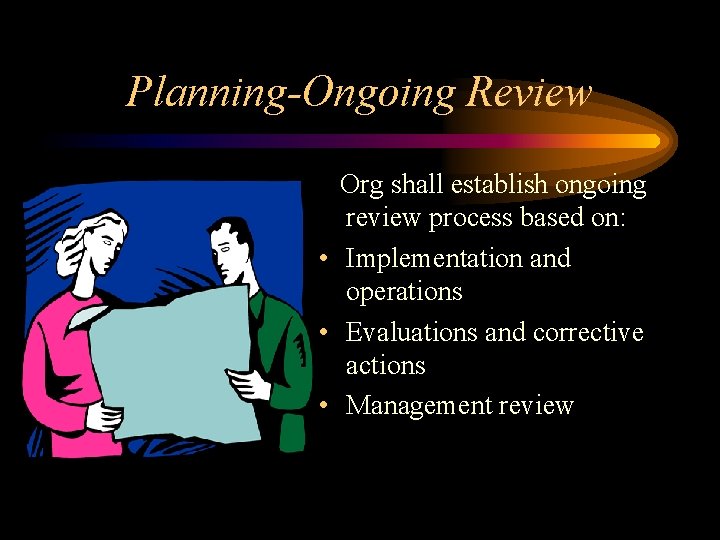
Planning-Ongoing Review Org shall establish ongoing review process based on: • Implementation and operations • Evaluations and corrective actions • Management review
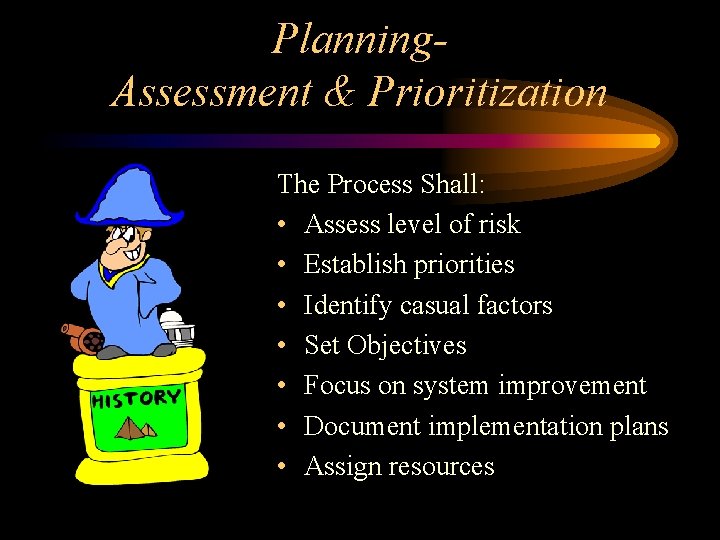
Planning. Assessment & Prioritization The Process Shall: • Assess level of risk • Establish priorities • Identify casual factors • Set Objectives • Focus on system improvement • Document implementation plans • Assign resources
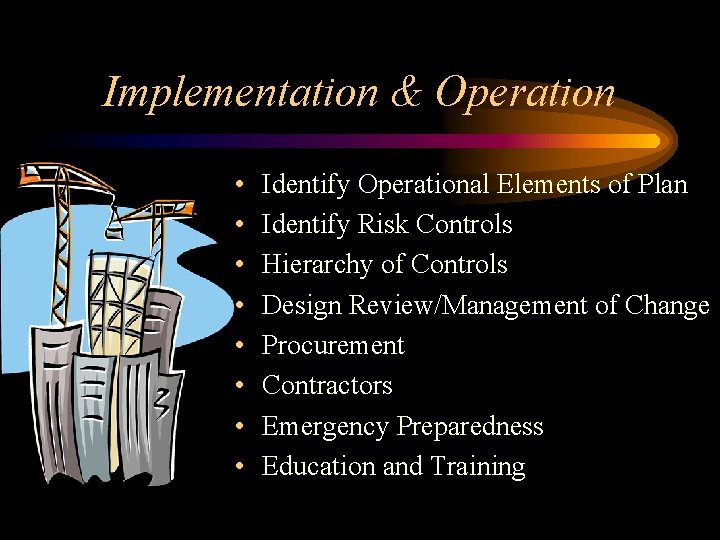
Implementation & Operation • • Identify Operational Elements of Plan Identify Risk Controls Hierarchy of Controls Design Review/Management of Change Procurement Contractors Emergency Preparedness Education and Training
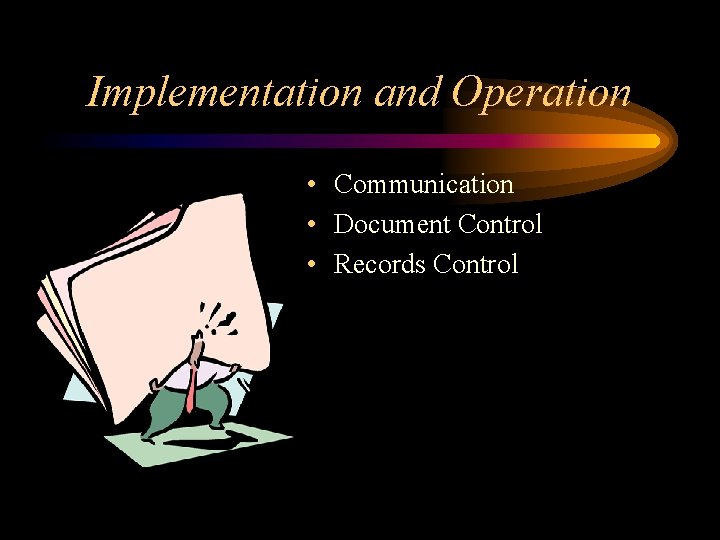
Implementation and Operation • Communication • Document Control • Records Control
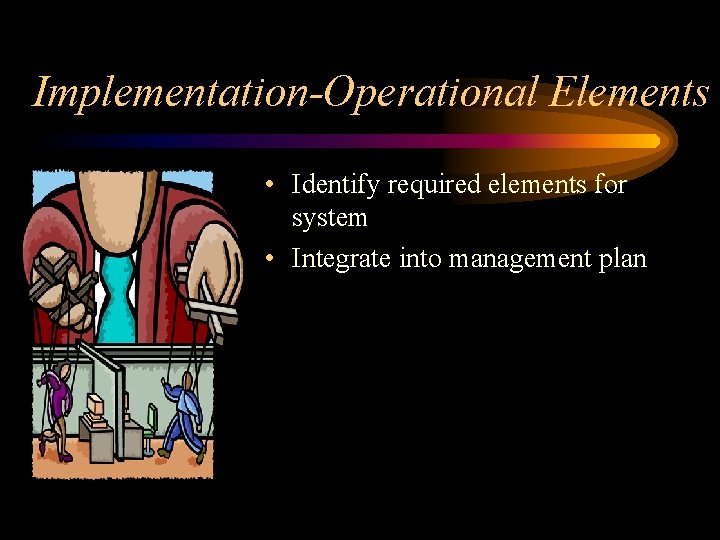
Implementation-Operational Elements • Identify required elements for system • Integrate into management plan
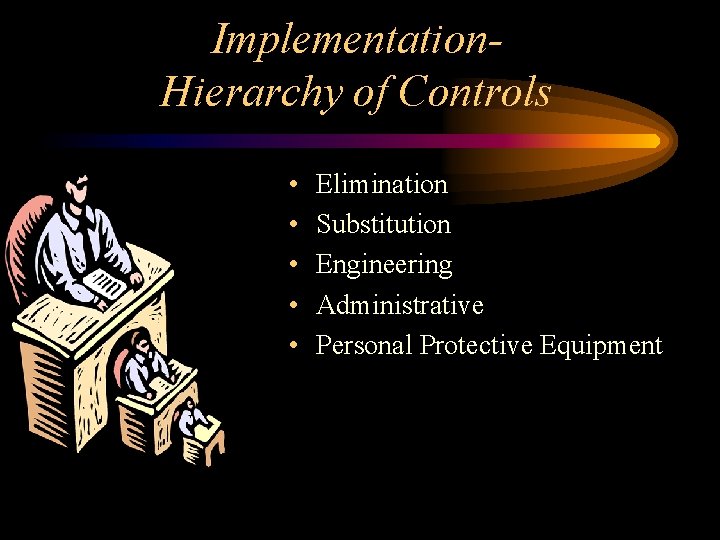
Implementation. Hierarchy of Controls • • • Elimination Substitution Engineering Administrative Personal Protective Equipment
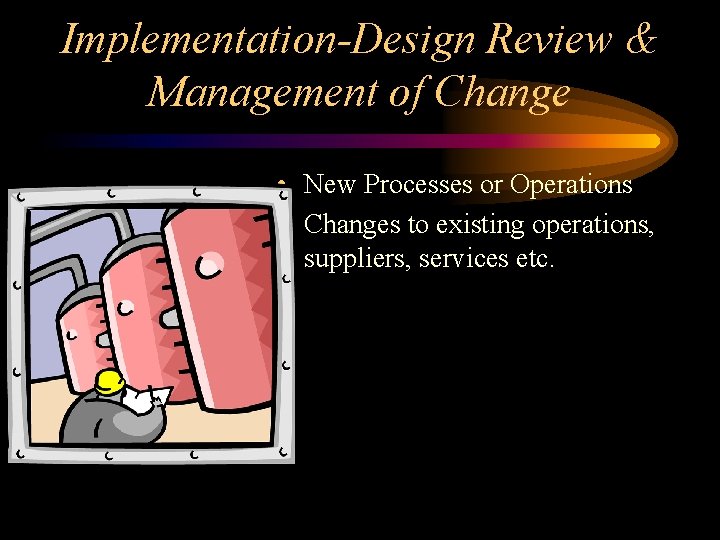
Implementation-Design Review & Management of Change • New Processes or Operations • Changes to existing operations, suppliers, services etc.
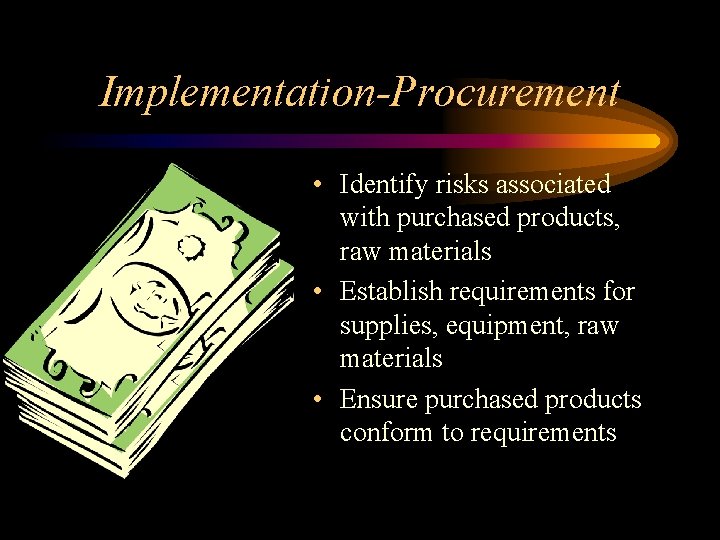
Implementation-Procurement • Identify risks associated with purchased products, raw materials • Establish requirements for supplies, equipment, raw materials • Ensure purchased products conform to requirements
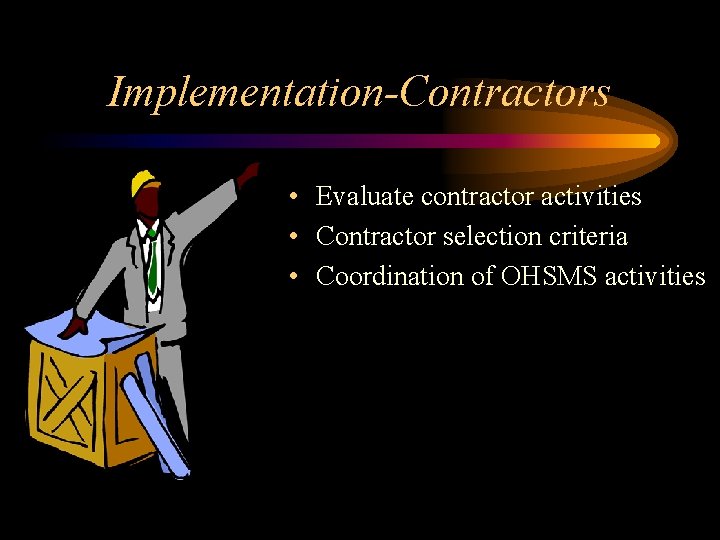
Implementation-Contractors • Evaluate contractor activities • Contractor selection criteria • Coordination of OHSMS activities
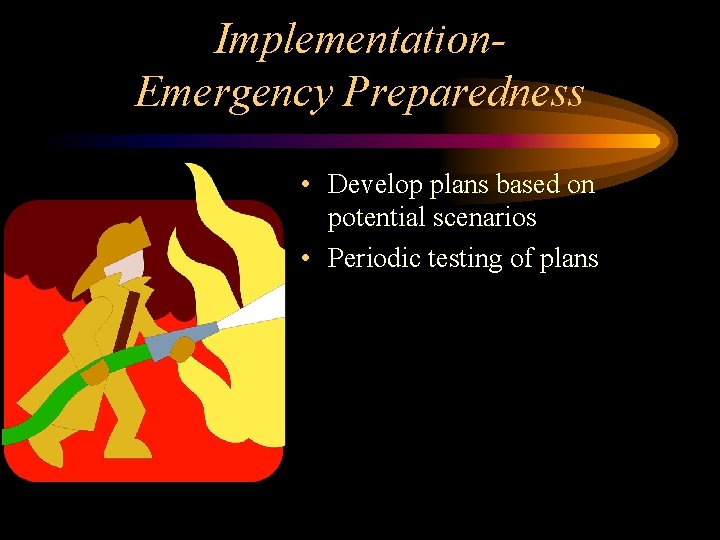
Implementation. Emergency Preparedness • Develop plans based on potential scenarios • Periodic testing of plans
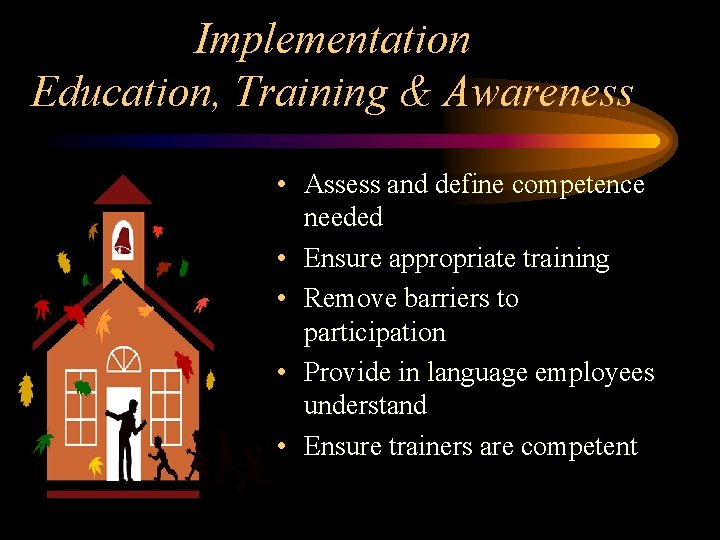
Implementation Education, Training & Awareness • Assess and define competence needed • Ensure appropriate training • Remove barriers to participation • Provide in language employees understand • Ensure trainers are competent
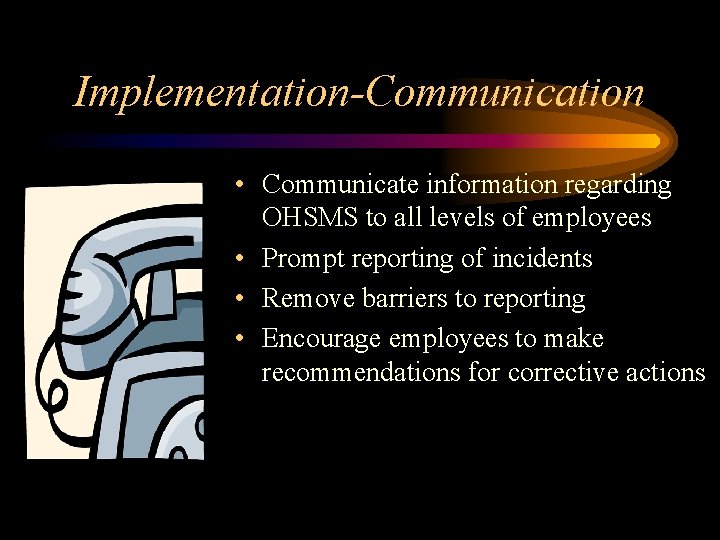
Implementation-Communication • Communicate information regarding OHSMS to all levels of employees • Prompt reporting of incidents • Remove barriers to reporting • Encourage employees to make recommendations for corrective actions
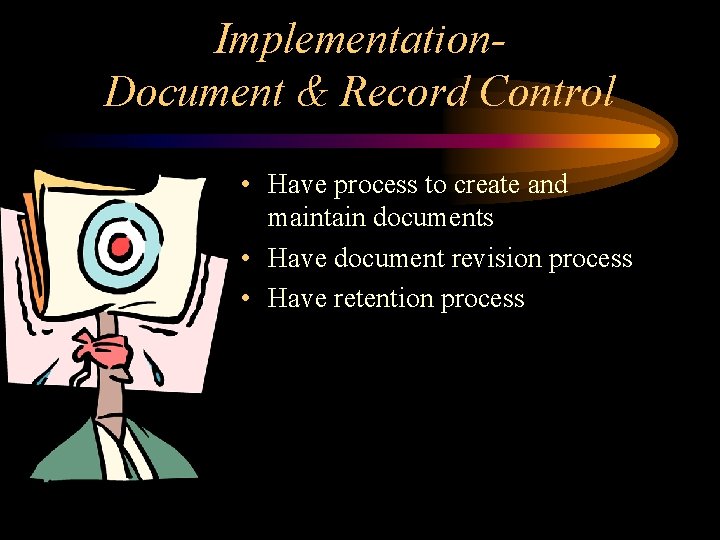
Implementation. Document & Record Control • Have process to create and maintain documents • Have document revision process • Have retention process
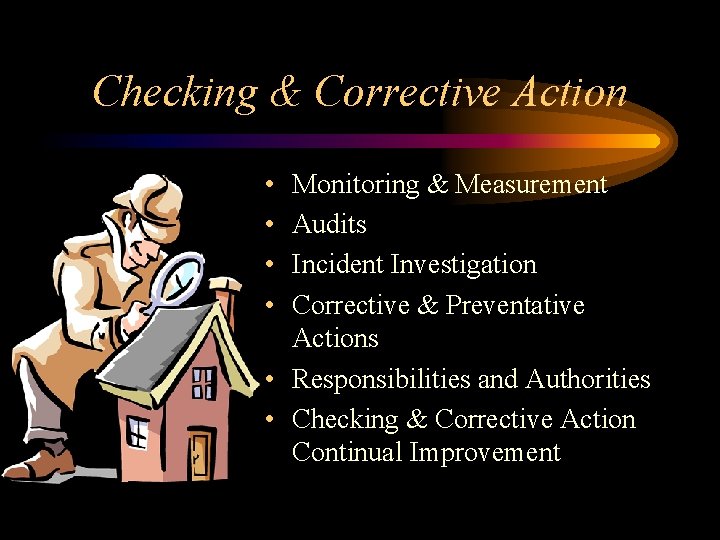
Checking & Corrective Action • • Monitoring & Measurement Audits Incident Investigation Corrective & Preventative Actions • Responsibilities and Authorities • Checking & Corrective Action Continual Improvement
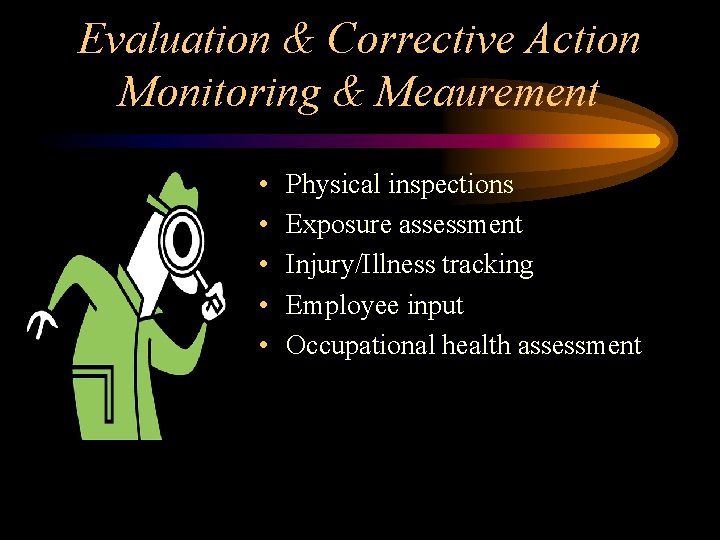
Evaluation & Corrective Action Monitoring & Meaurement • • • Physical inspections Exposure assessment Injury/Illness tracking Employee input Occupational health assessment
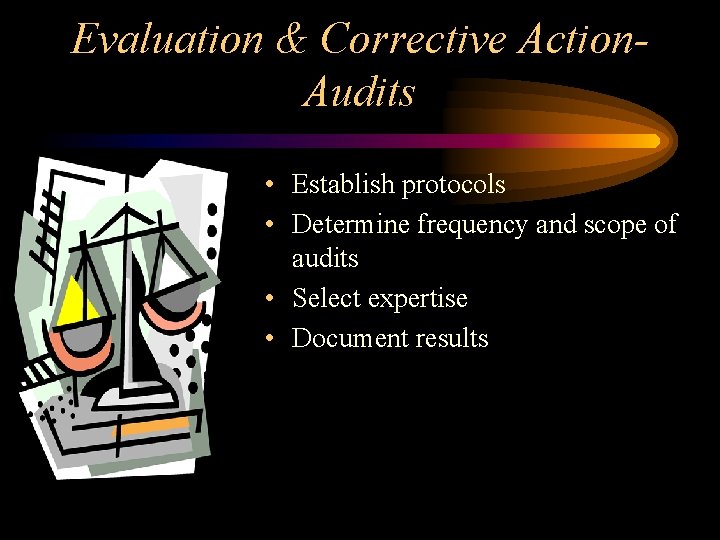
Evaluation & Corrective Action. Audits • Establish protocols • Determine frequency and scope of audits • Select expertise • Document results
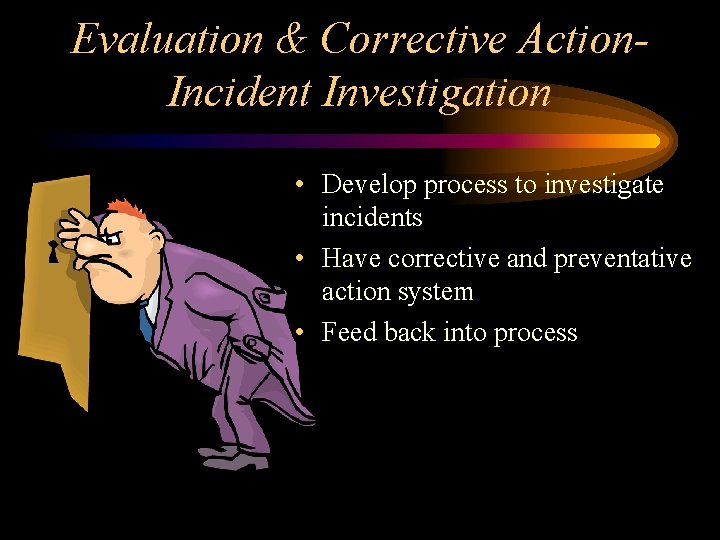
Evaluation & Corrective Action. Incident Investigation • Develop process to investigate incidents • Have corrective and preventative action system • Feed back into process
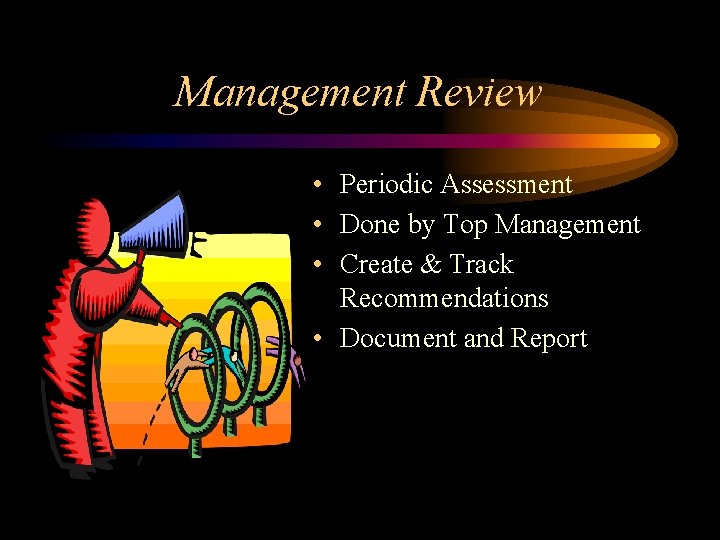
Management Review • Periodic Assessment • Done by Top Management • Create & Track Recommendations • Document and Report
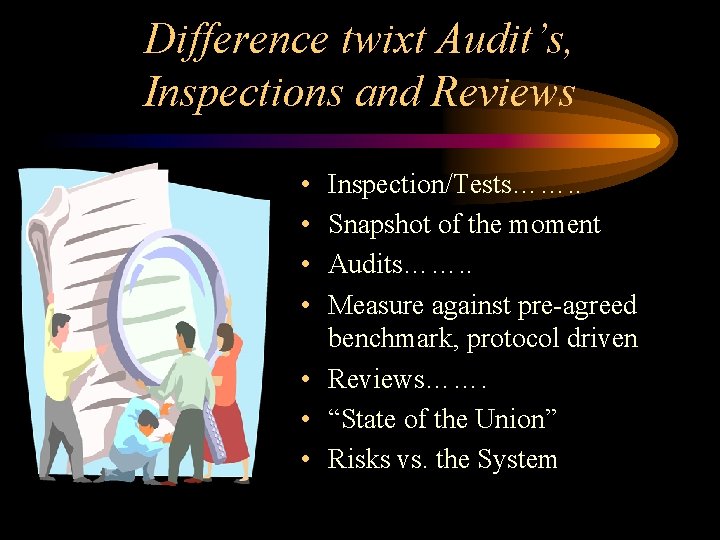
Difference twixt Audit’s, Inspections and Reviews • • Inspection/Tests……. . Snapshot of the moment Audits……. . Measure against pre-agreed benchmark, protocol driven • Reviews……. • “State of the Union” • Risks vs. the System
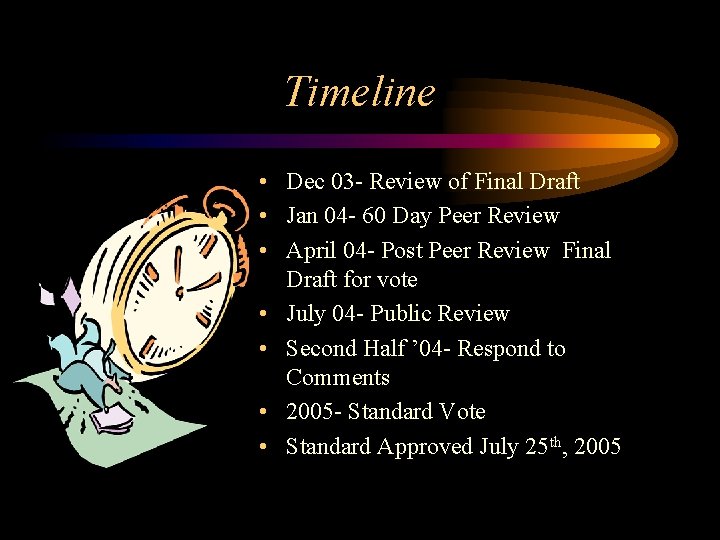
Timeline • Dec 03 - Review of Final Draft • Jan 04 - 60 Day Peer Review • April 04 - Post Peer Review Final Draft for vote • July 04 - Public Review • Second Half ’ 04 - Respond to Comments • 2005 - Standard Vote • Standard Approved July 25 th, 2005
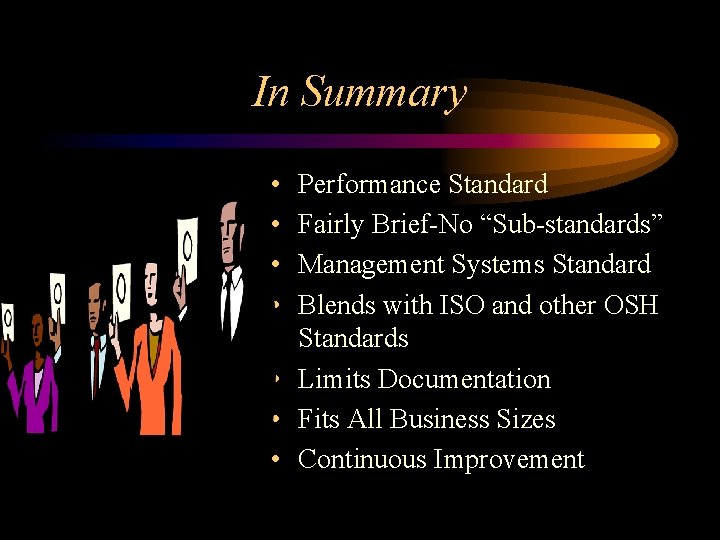
In Summary • • Performance Standard Fairly Brief-No “Sub-standards” Management Systems Standard Blends with ISO and other OSH Standards • Limits Documentation • Fits All Business Sizes • Continuous Improvement
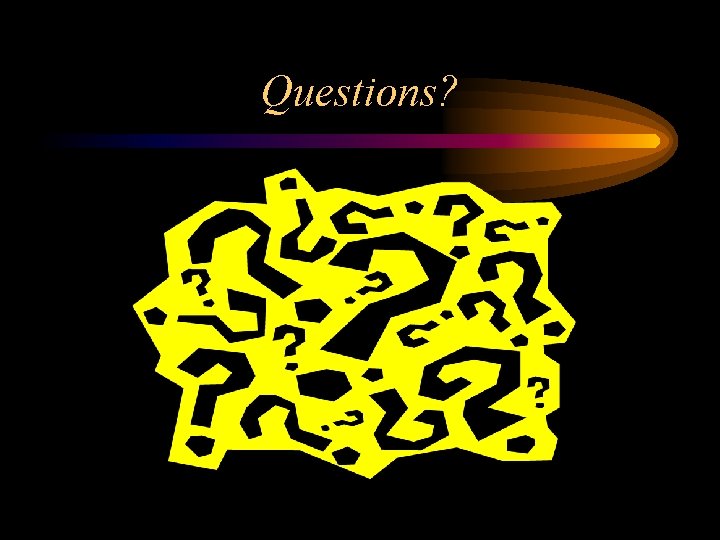
Questions?
History of osha
Occupational safety and health act 1984
Occupational health and safety presentation
Regulation 851 ontario
Ipac core competencies occupational health and safety
Global strategy on occupational safety and health
Occupational health and safety assessment series
Occupational health and safety course outline
Occupational safety and health
Occupational safety and health
Miosha respiratory protection standard
Korea occupational safety & health agency
"university of cumbria"
Korea occupational safety & health agency
Role of occupational health nurse
Ansi safety colors
Southalls safety cloud
Aims and objectives of occupational health
Occupational health cardiff university
Korea kosha
Safety management system template
Hse management standards analysis tool
Health and safety executive management standards
Chcp occupational health
Define occupational health nursing
Ecology of human performance model
Occupational health services renton
Stanford occupational health
Occupational therapy practice framework domain and process
Uhcw site map
Abu dhabi occupational health
Aota occupational profile template
Occupational health clinic for ontario workers
Mobile occupational health screening unit
Conclusion of national mental health programme
Api 1173 pipeline safety management systems
Active managerial control software
What is ansi c
Health and social care component 3
Decision support systems and intelligent systems
Four cs health and safety