New illustration is coming MINING USER CONFERENCE MAY
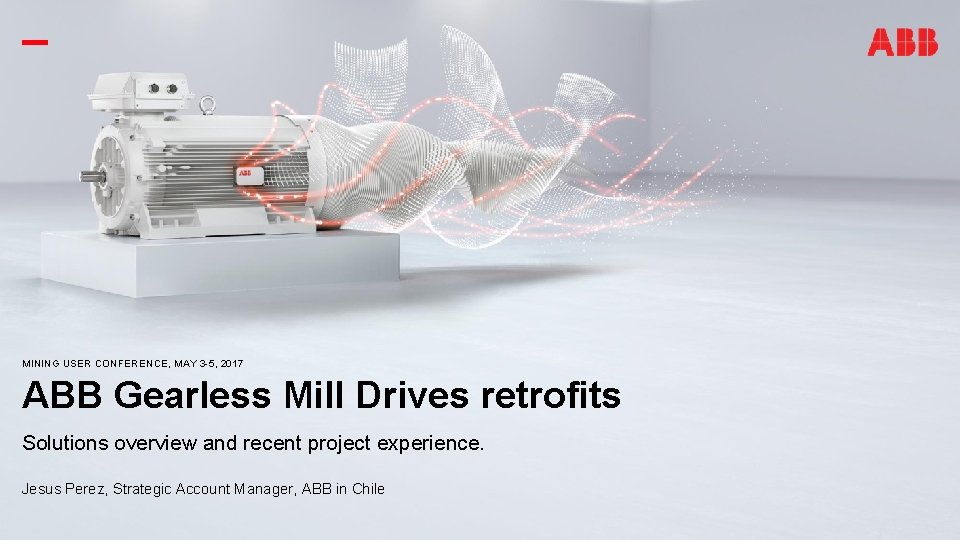
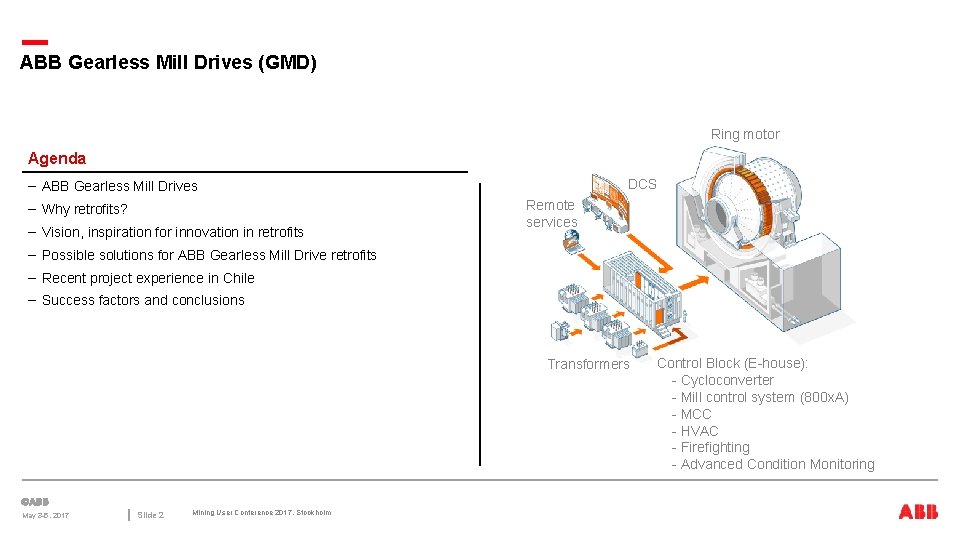
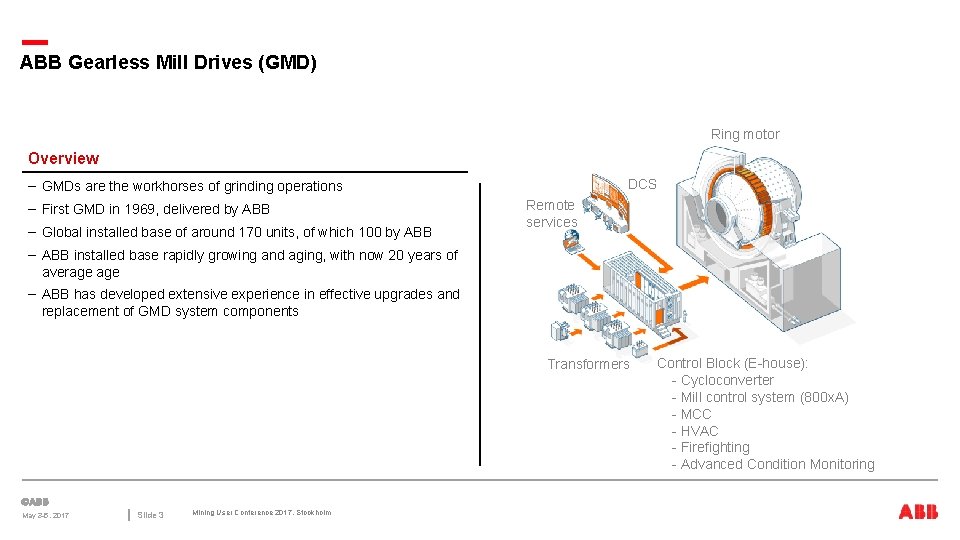
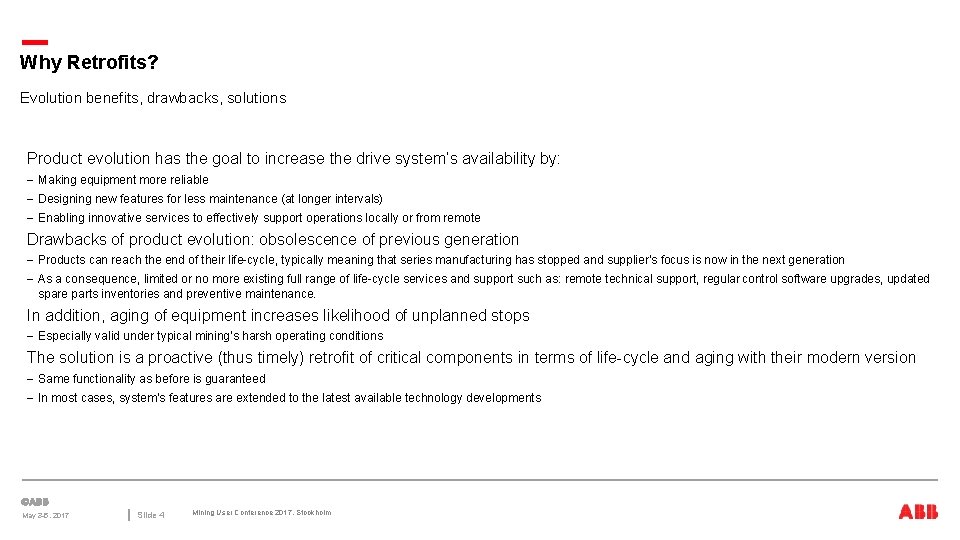
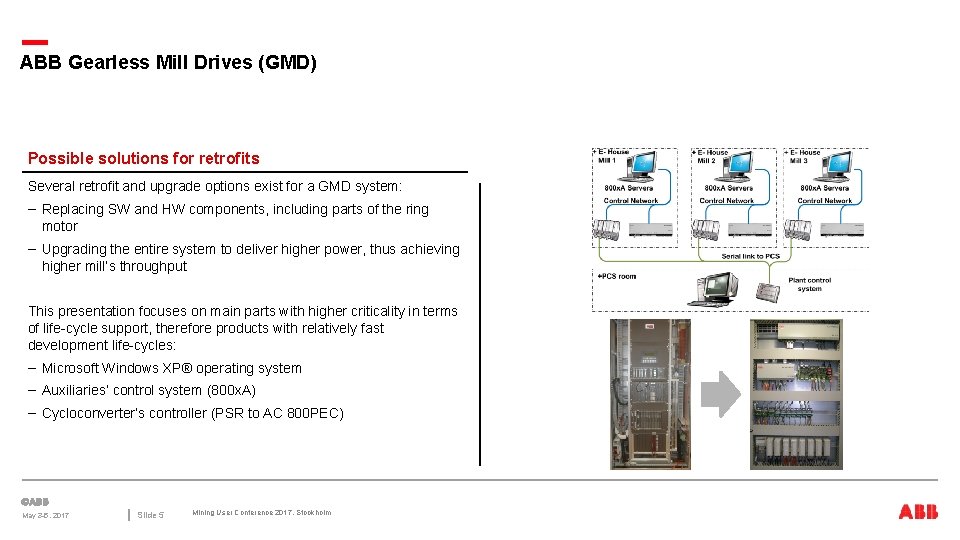
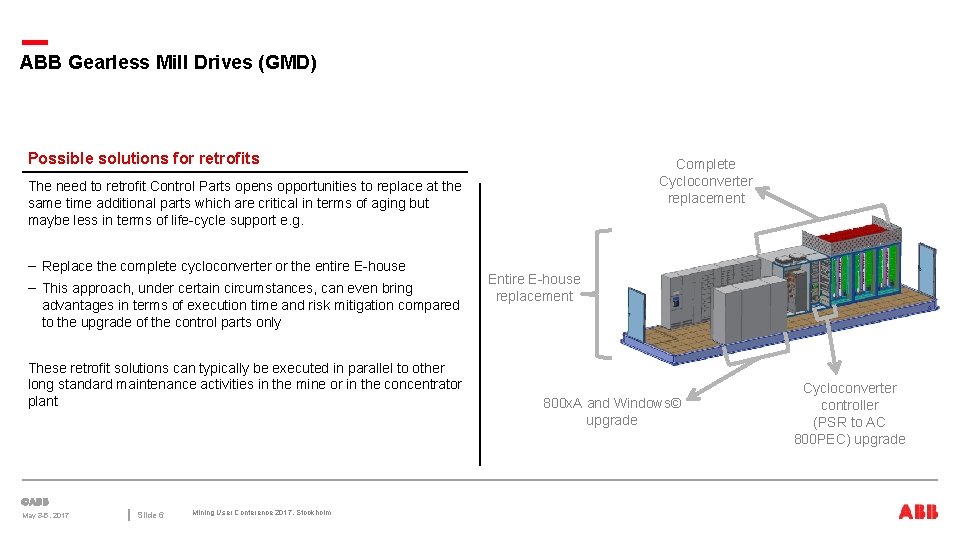
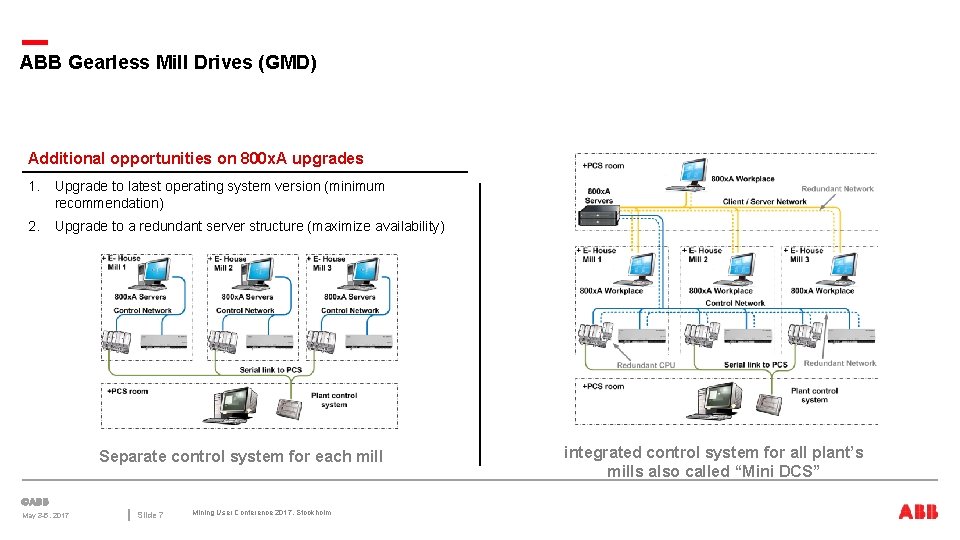
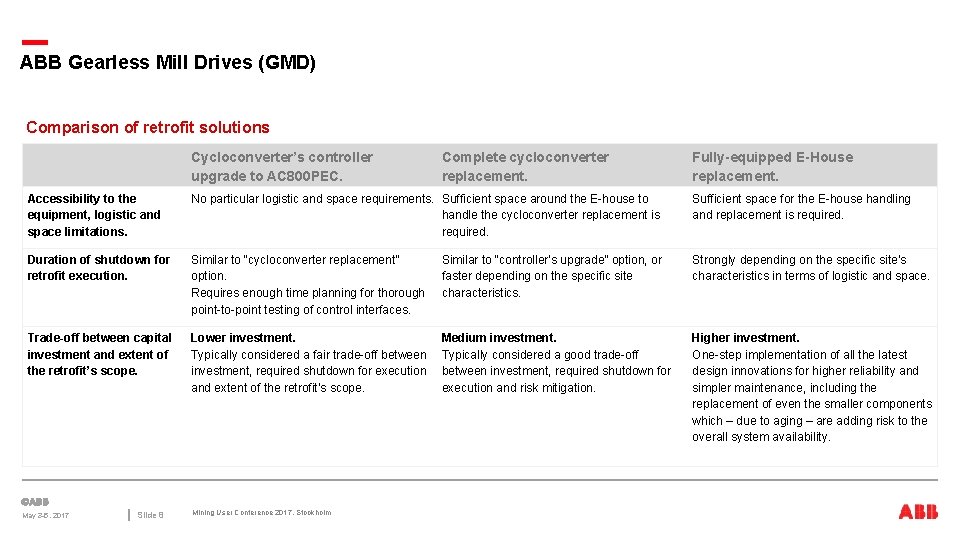
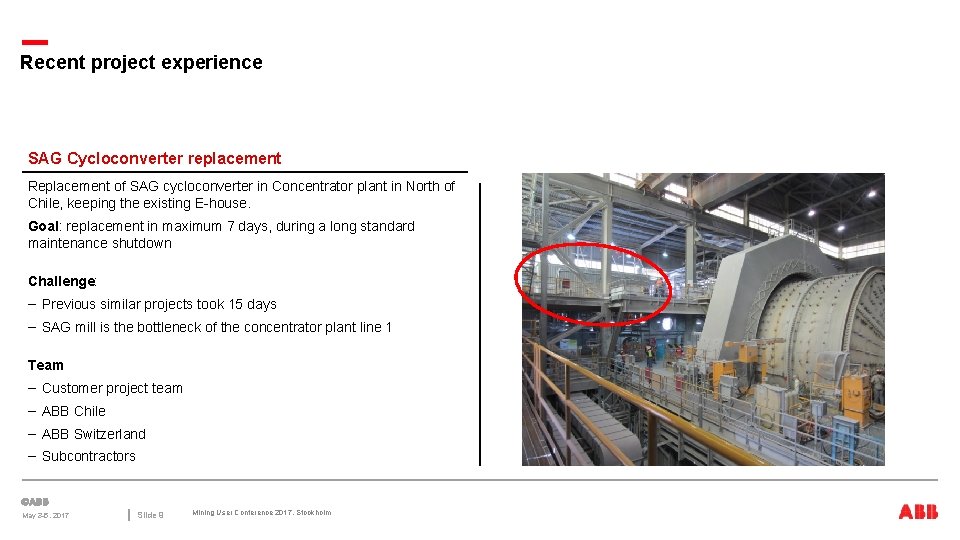
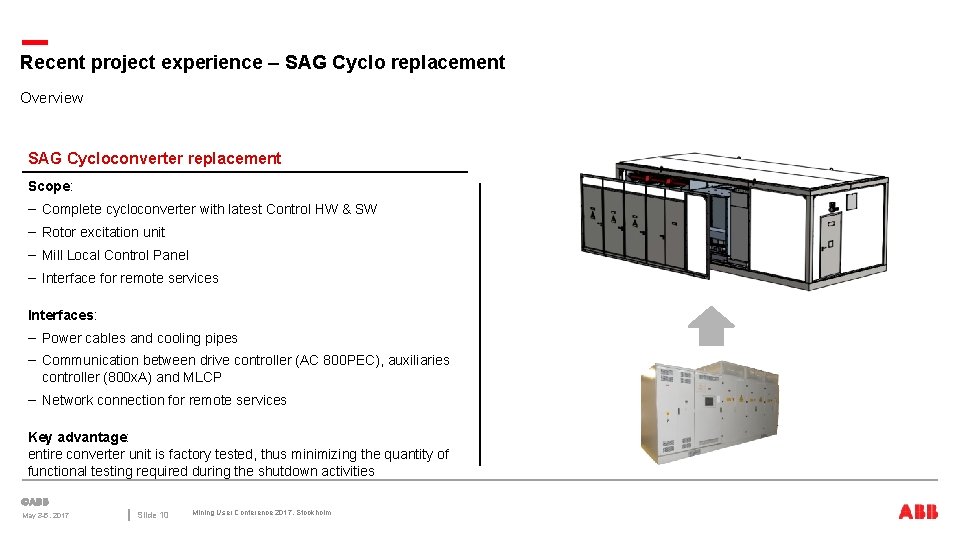
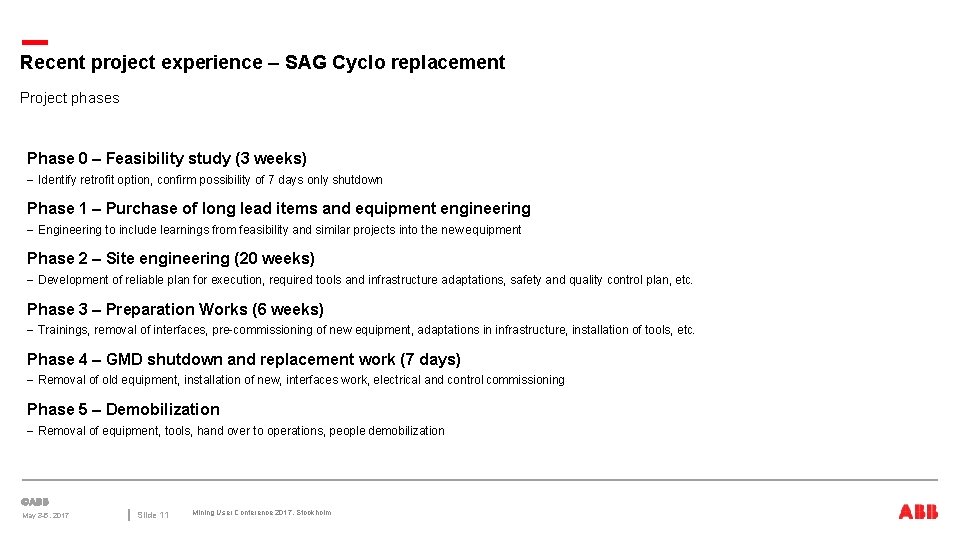
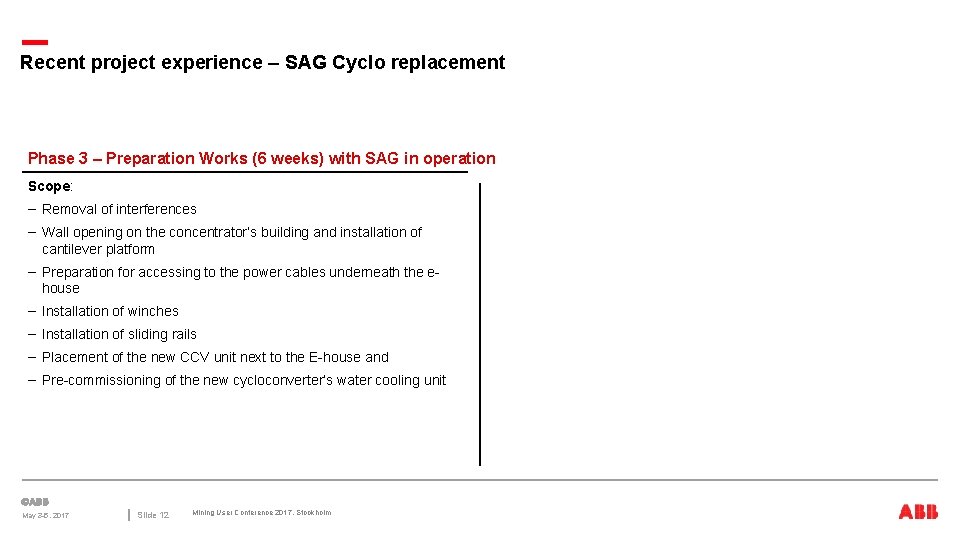
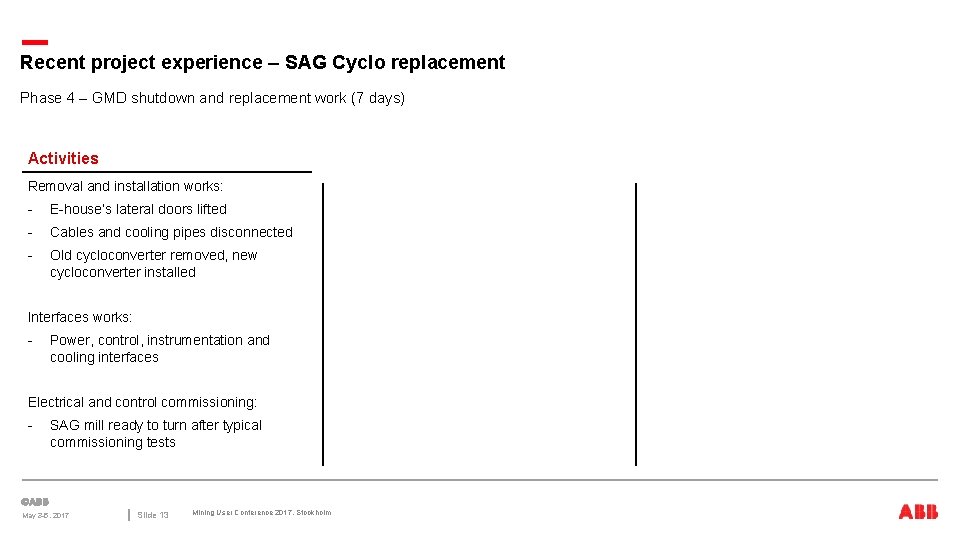
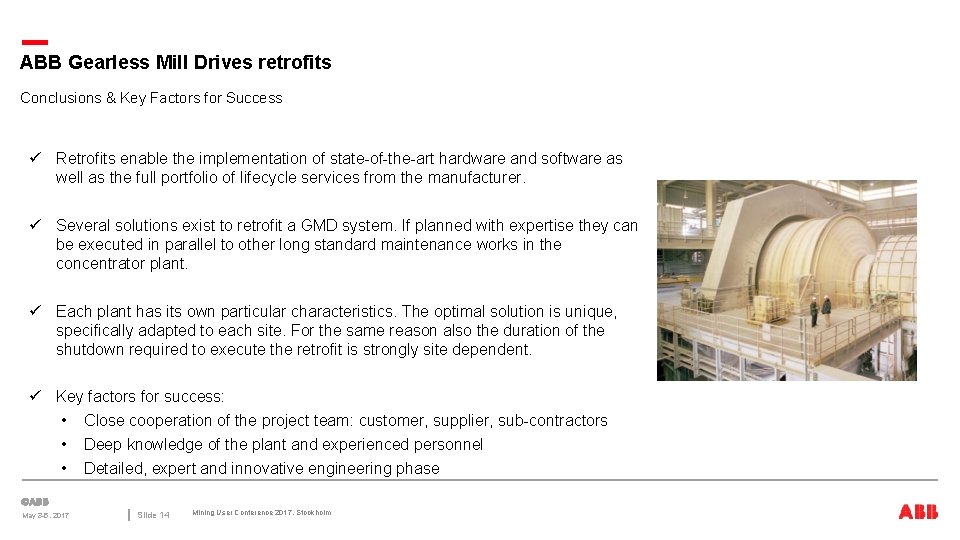
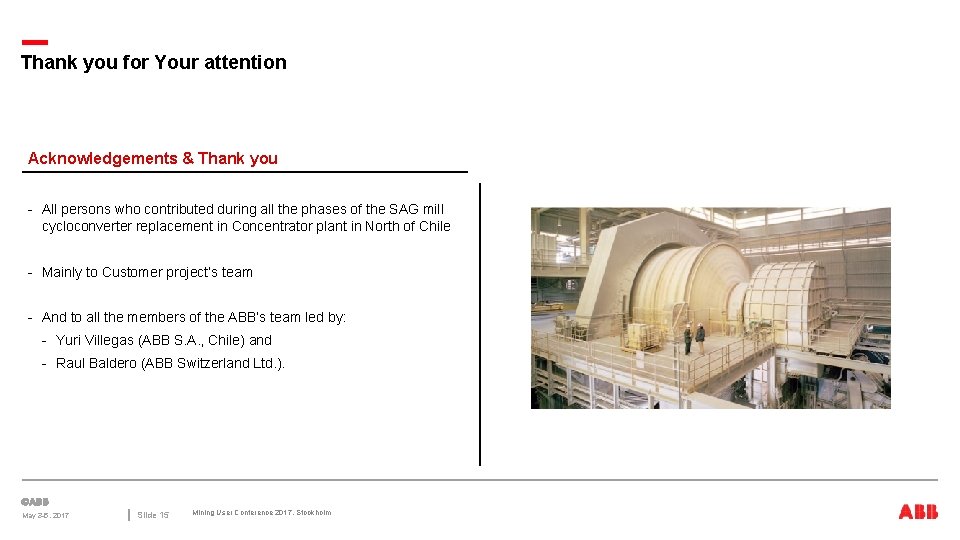
- Slides: 15
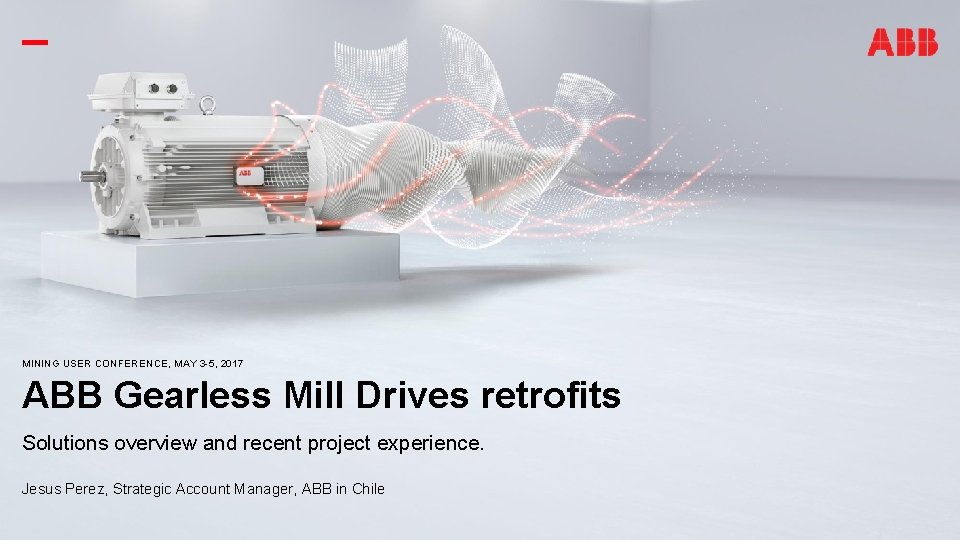
New illustration is coming MINING USER CONFERENCE, MAY 3 -5, 2017 ABB Gearless Mill Drives retrofits Solutions overview and recent project experience. Jesus Perez, Strategic Account Manager, ABB in Chile
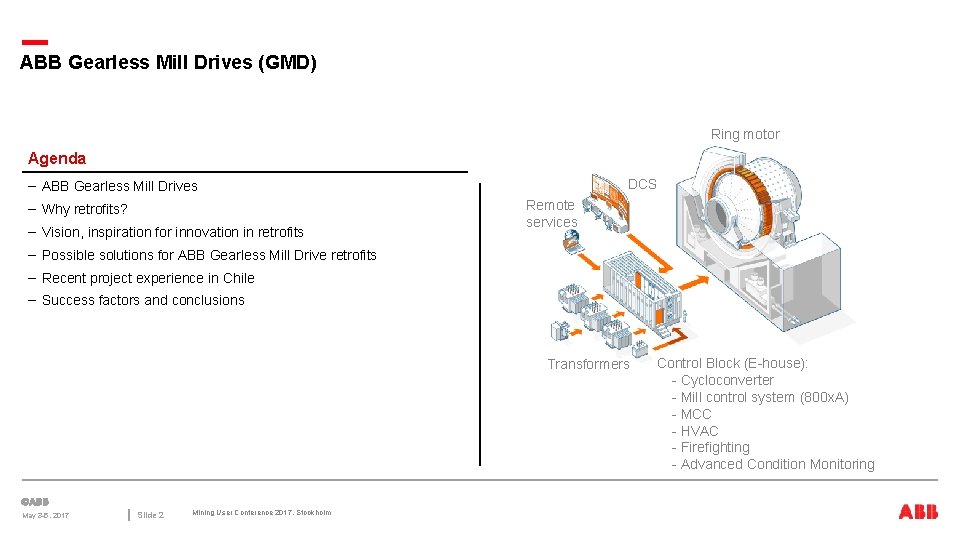
ABB Gearless Mill Drives (GMD) Ring motor Agenda DCS – ABB Gearless Mill Drives – Why retrofits? – Vision, inspiration for innovation in retrofits Remote services – Possible solutions for ABB Gearless Mill Drive retrofits – Recent project experience in Chile – Success factors and conclusions Transformers May 3 -5, 2017 Slide 2 Mining User Conference 2017, Stockholm Control Block (E-house): - Cycloconverter - Mill control system (800 x. A) - MCC - HVAC - Firefighting - Advanced Condition Monitoring
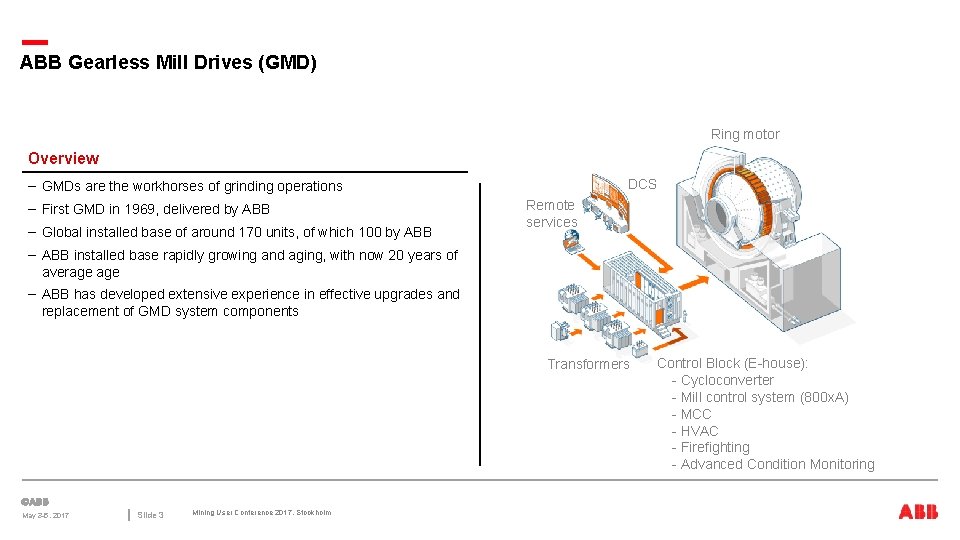
ABB Gearless Mill Drives (GMD) Ring motor Overview DCS – GMDs are the workhorses of grinding operations – First GMD in 1969, delivered by ABB – Global installed base of around 170 units, of which 100 by ABB Remote services – ABB installed base rapidly growing and aging, with now 20 years of average – ABB has developed extensive experience in effective upgrades and replacement of GMD system components Transformers May 3 -5, 2017 Slide 3 Mining User Conference 2017, Stockholm Control Block (E-house): - Cycloconverter - Mill control system (800 x. A) - MCC - HVAC - Firefighting - Advanced Condition Monitoring
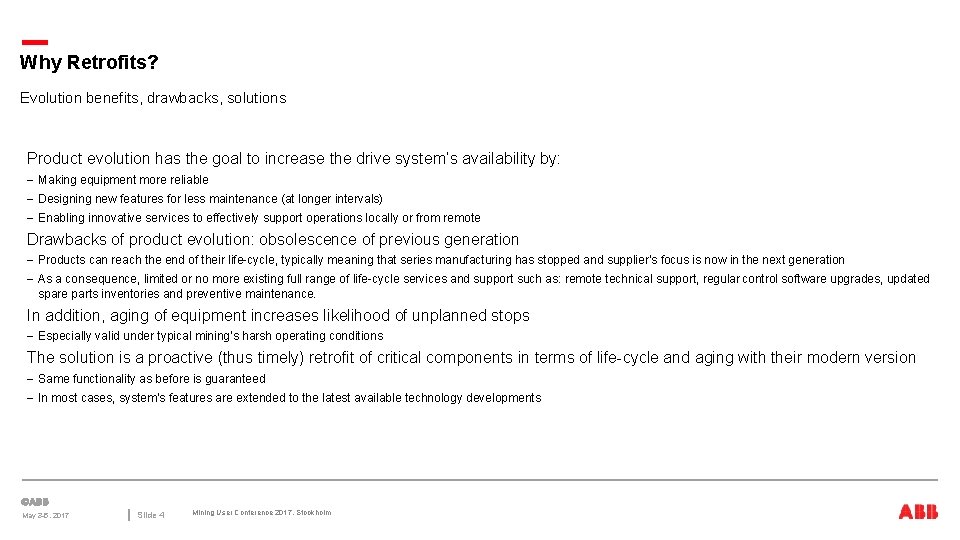
Why Retrofits? Evolution benefits, drawbacks, solutions Product evolution has the goal to increase the drive system’s availability by: – Making equipment more reliable – Designing new features for less maintenance (at longer intervals) – Enabling innovative services to effectively support operations locally or from remote Drawbacks of product evolution: obsolescence of previous generation – Products can reach the end of their life-cycle, typically meaning that series manufacturing has stopped and supplier’s focus is now in the next generation – As a consequence, limited or no more existing full range of life-cycle services and support such as: remote technical support, regular control software upgrades, updated spare parts inventories and preventive maintenance. In addition, aging of equipment increases likelihood of unplanned stops – Especially valid under typical mining’s harsh operating conditions The solution is a proactive (thus timely) retrofit of critical components in terms of life-cycle and aging with their modern version – Same functionality as before is guaranteed – In most cases, system’s features are extended to the latest available technology developments May 3 -5, 2017 Slide 4 Mining User Conference 2017, Stockholm
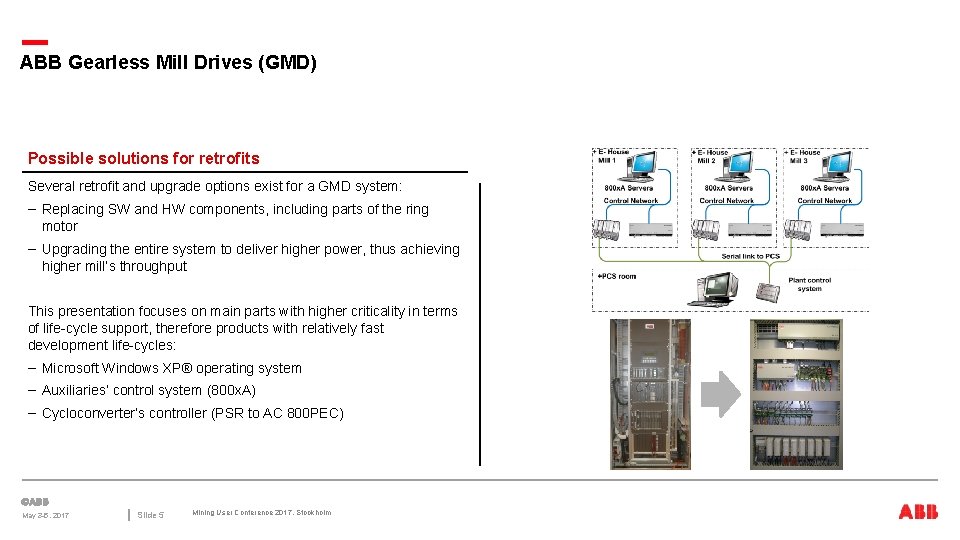
ABB Gearless Mill Drives (GMD) Possible solutions for retrofits Several retrofit and upgrade options exist for a GMD system: – Replacing SW and HW components, including parts of the ring motor – Upgrading the entire system to deliver higher power, thus achieving higher mill’s throughput This presentation focuses on main parts with higher criticality in terms of life-cycle support, therefore products with relatively fast development life-cycles: – Microsoft Windows XP® operating system – Auxiliaries’ control system (800 x. A) – Cycloconverter’s controller (PSR to AC 800 PEC) May 3 -5, 2017 Slide 5 Mining User Conference 2017, Stockholm
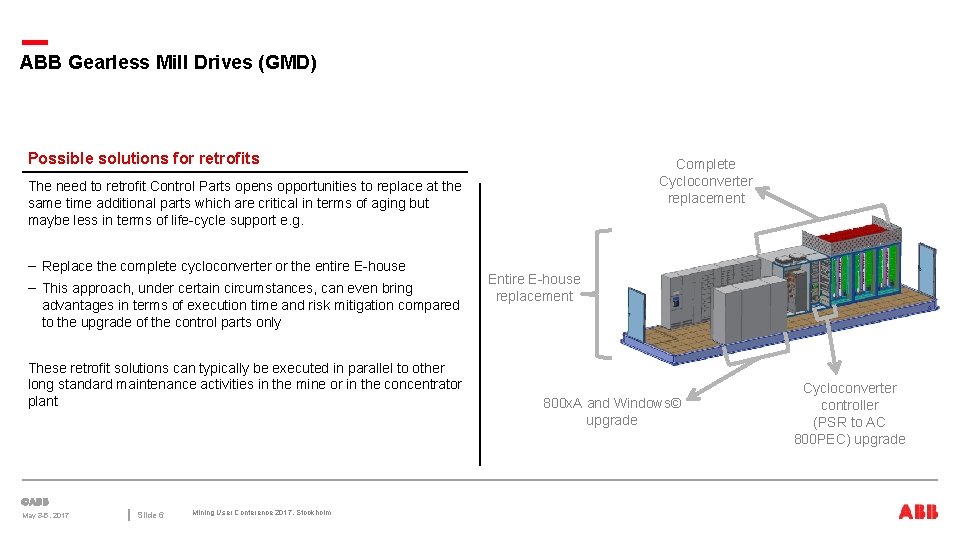
ABB Gearless Mill Drives (GMD) Possible solutions for retrofits Complete Cycloconverter replacement The need to retrofit Control Parts opens opportunities to replace at the same time additional parts which are critical in terms of aging but maybe less in terms of life-cycle support e. g. – Replace the complete cycloconverter or the entire E-house – This approach, under certain circumstances, can even bring advantages in terms of execution time and risk mitigation compared to the upgrade of the control parts only These retrofit solutions can typically be executed in parallel to other long standard maintenance activities in the mine or in the concentrator plant May 3 -5, 2017 Slide 6 Mining User Conference 2017, Stockholm Entire E-house replacement 800 x. A and Windows© upgrade Cycloconverter controller (PSR to AC 800 PEC) upgrade
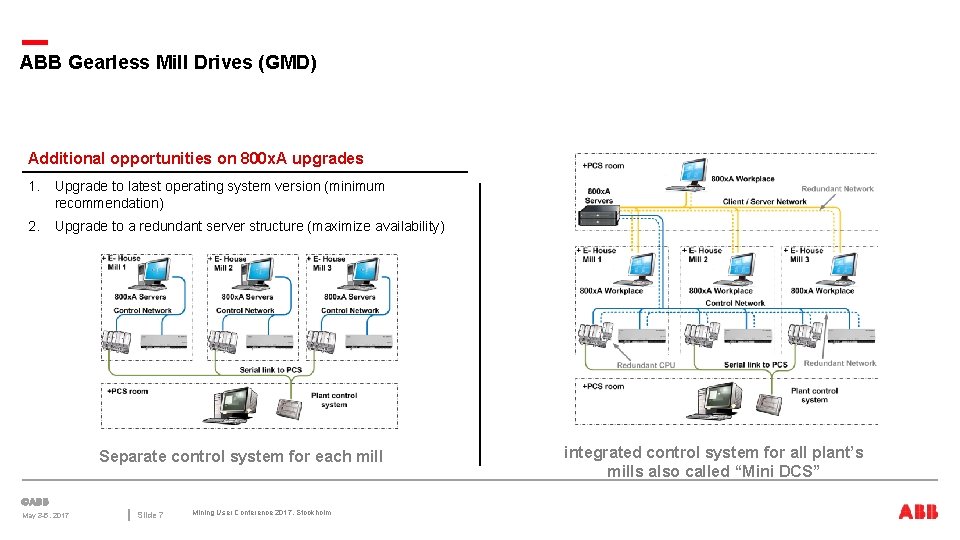
ABB Gearless Mill Drives (GMD) Additional opportunities on 800 x. A upgrades 1. Upgrade to latest operating system version (minimum recommendation) 2. Upgrade to a redundant server structure (maximize availability) Separate control system for each mill May 3 -5, 2017 Slide 7 Mining User Conference 2017, Stockholm integrated control system for all plant’s mills also called “Mini DCS”
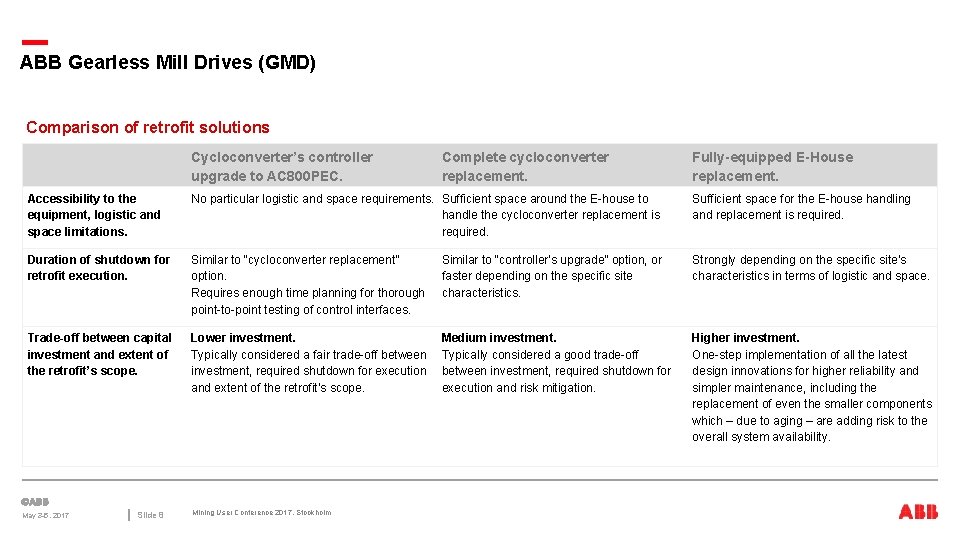
ABB Gearless Mill Drives (GMD) Comparison of retrofit solutions Cycloconverter’s controller upgrade to AC 800 PEC. Accessibility to the equipment, logistic and space limitations. No particular logistic and space requirements. Sufficient space around the E-house to handle the cycloconverter replacement is required. Sufficient space for the E-house handling and replacement is required. Duration of shutdown for retrofit execution. Similar to “cycloconverter replacement” option. Requires enough time planning for thorough point-to-point testing of control interfaces. Similar to “controller’s upgrade” option, or faster depending on the specific site characteristics. Strongly depending on the specific site’s characteristics in terms of logistic and space. Trade-off between capital investment and extent of the retrofit’s scope. Lower investment. Typically considered a fair trade-off between investment, required shutdown for execution and extent of the retrofit’s scope. Medium investment. Typically considered a good trade-off between investment, required shutdown for execution and risk mitigation. Higher investment. One-step implementation of all the latest design innovations for higher reliability and simpler maintenance, including the replacement of even the smaller components which – due to aging – are adding risk to the overall system availability. May 3 -5, 2017 Slide 8 Mining User Conference 2017, Stockholm Complete cycloconverter replacement. Fully-equipped E-House replacement.
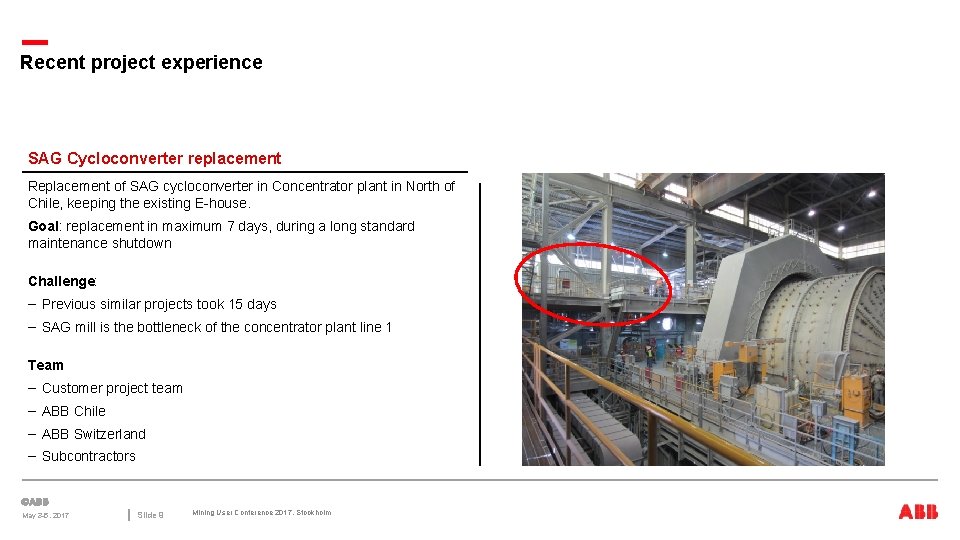
Recent project experience SAG Cycloconverter replacement Replacement of SAG cycloconverter in Concentrator plant in North of Chile, keeping the existing E-house. Goal: replacement in maximum 7 days, during a long standard maintenance shutdown Challenge: – Previous similar projects took 15 days – SAG mill is the bottleneck of the concentrator plant line 1 Team – Customer project team – ABB Chile – ABB Switzerland – Subcontractors May 3 -5, 2017 Slide 9 Mining User Conference 2017, Stockholm
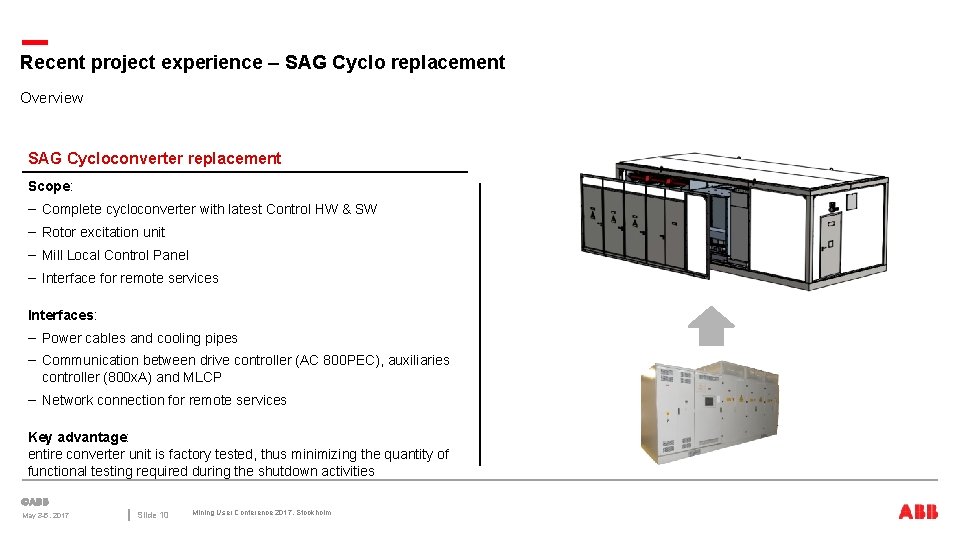
Recent project experience – SAG Cyclo replacement Overview SAG Cycloconverter replacement Scope: – Complete cycloconverter with latest Control HW & SW – Rotor excitation unit – Mill Local Control Panel – Interface for remote services Interfaces: – Power cables and cooling pipes – Communication between drive controller (AC 800 PEC), auxiliaries controller (800 x. A) and MLCP – Network connection for remote services Key advantage: entire converter unit is factory tested, thus minimizing the quantity of functional testing required during the shutdown activities May 3 -5, 2017 Slide 10 Mining User Conference 2017, Stockholm
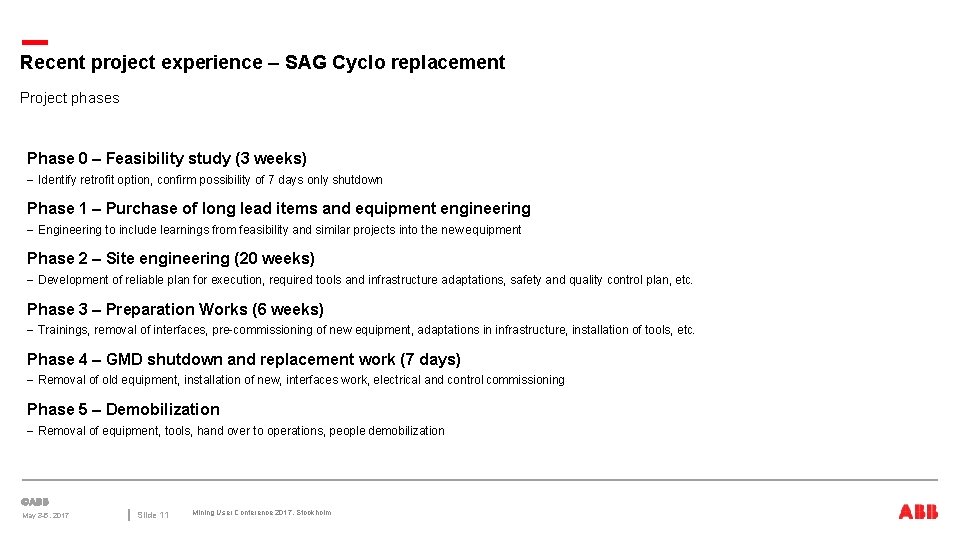
Recent project experience – SAG Cyclo replacement Project phases Phase 0 – Feasibility study (3 weeks) – Identify retrofit option, confirm possibility of 7 days only shutdown Phase 1 – Purchase of long lead items and equipment engineering – Engineering to include learnings from feasibility and similar projects into the new equipment Phase 2 – Site engineering (20 weeks) – Development of reliable plan for execution, required tools and infrastructure adaptations, safety and quality control plan, etc. Phase 3 – Preparation Works (6 weeks) – Trainings, removal of interfaces, pre-commissioning of new equipment, adaptations in infrastructure, installation of tools, etc. Phase 4 – GMD shutdown and replacement work (7 days) – Removal of old equipment, installation of new, interfaces work, electrical and control commissioning Phase 5 – Demobilization – Removal of equipment, tools, hand over to operations, people demobilization May 3 -5, 2017 Slide 11 Mining User Conference 2017, Stockholm
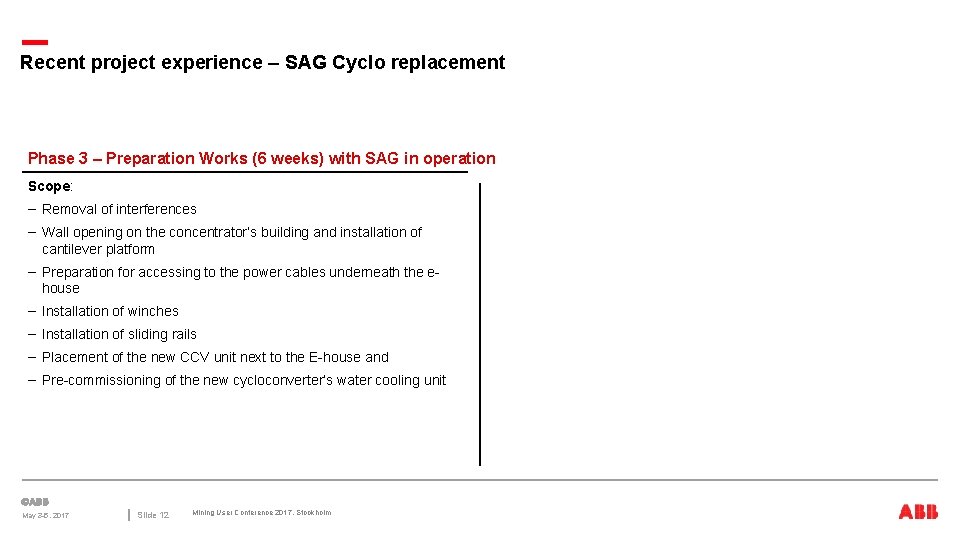
Recent project experience – SAG Cyclo replacement Phase 3 – Preparation Works (6 weeks) with SAG in operation Scope: – Removal of interferences – Wall opening on the concentrator’s building and installation of cantilever platform – Preparation for accessing to the power cables underneath the ehouse – Installation of winches – Installation of sliding rails – Placement of the new CCV unit next to the E-house and – Pre-commissioning of the new cycloconverter’s water cooling unit May 3 -5, 2017 Slide 12 Mining User Conference 2017, Stockholm
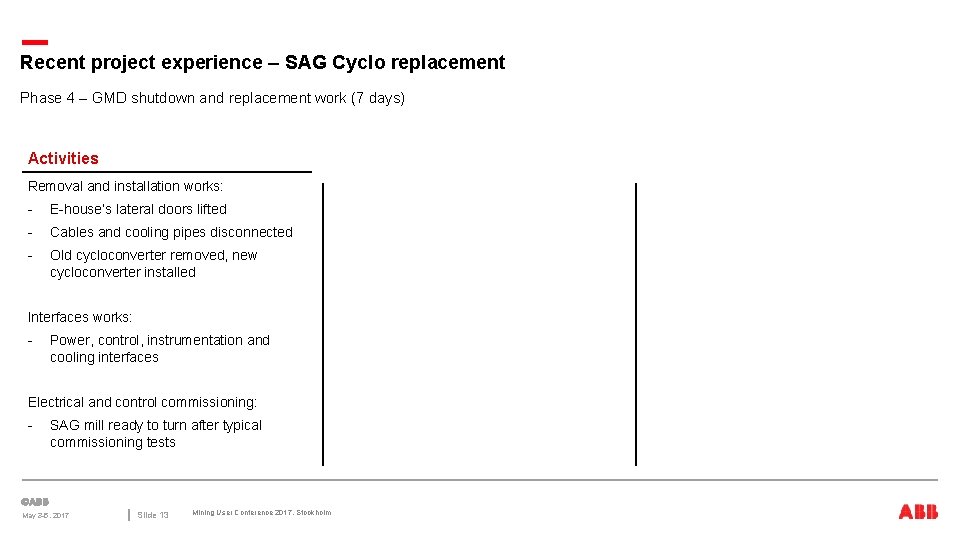
Recent project experience – SAG Cyclo replacement Phase 4 – GMD shutdown and replacement work (7 days) Activities Removal and installation works: - E-house’s lateral doors lifted - Cables and cooling pipes disconnected - Old cycloconverter removed, new cycloconverter installed Interfaces works: - Power, control, instrumentation and cooling interfaces Electrical and control commissioning: - SAG mill ready to turn after typical commissioning tests May 3 -5, 2017 Slide 13 Mining User Conference 2017, Stockholm
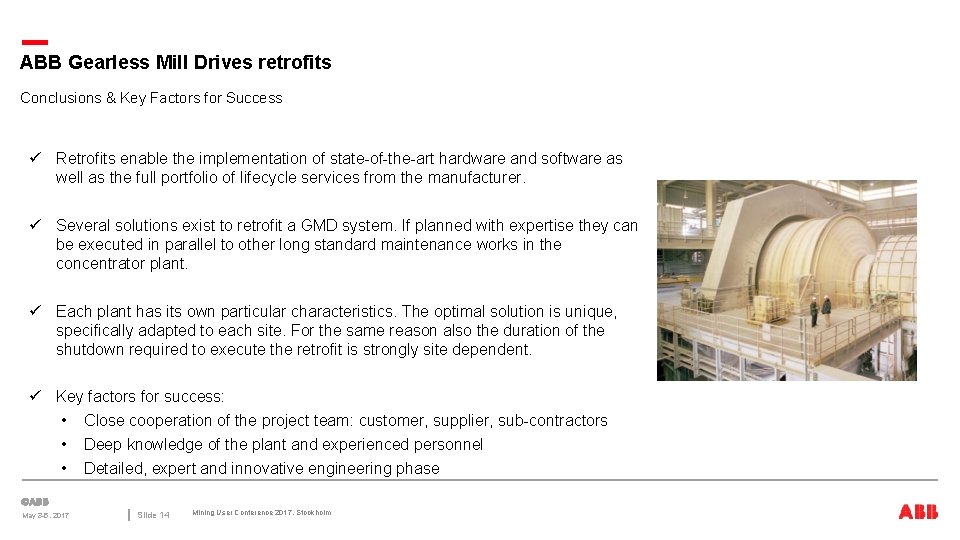
ABB Gearless Mill Drives retrofits Conclusions & Key Factors for Success ü Retrofits enable the implementation of state-of-the-art hardware and software as well as the full portfolio of lifecycle services from the manufacturer. ü Several solutions exist to retrofit a GMD system. If planned with expertise they can be executed in parallel to other long standard maintenance works in the concentrator plant. ü Each plant has its own particular characteristics. The optimal solution is unique, specifically adapted to each site. For the same reason also the duration of the shutdown required to execute the retrofit is strongly site dependent. ü Key factors for success: • Close cooperation of the project team: customer, supplier, sub-contractors • Deep knowledge of the plant and experienced personnel • Detailed, expert and innovative engineering phase May 3 -5, 2017 Slide 14 Mining User Conference 2017, Stockholm
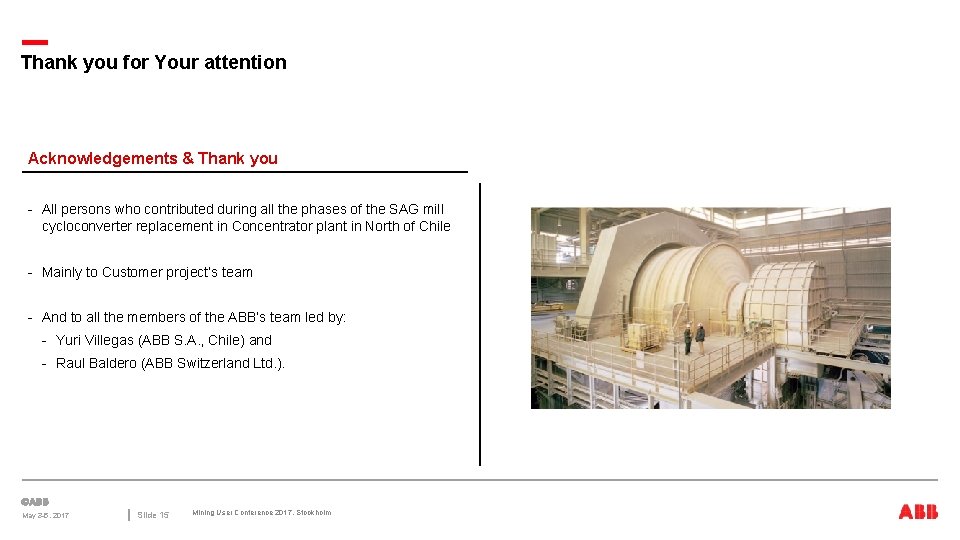
Thank you for Your attention Acknowledgements & Thank you - All persons who contributed during all the phases of the SAG mill cycloconverter replacement in Concentrator plant in North of Chile - Mainly to Customer project’s team - And to all the members of the ABB’s team led by: - Yuri Villegas (ABB S. A. , Chile) and - Raul Baldero (ABB Switzerland Ltd. ). May 3 -5, 2017 Slide 15 Mining User Conference 2017, Stockholm
Strip mining vs open pit mining
Chapter 13 mineral resources and mining worksheet answers
Difference between strip mining and open pit mining
Text and web mining
Mining multimedia databases in data mining
Mining complex types of data in data mining
Who may abide the day of his coming
Who may abide the day of his coming
Mining user similarity based on location history
Major issues in data mining are
Single user and multi user operating system
Multi user operating system
Jenkins user conference
Syteline user network conference 2017
Joint legacy viewer website
Calaters new user registration