Multidisciplinary Senior Design MSD I P 18718 Detailed
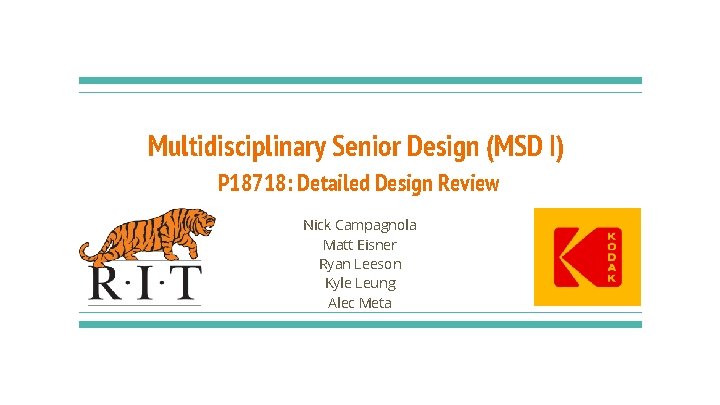
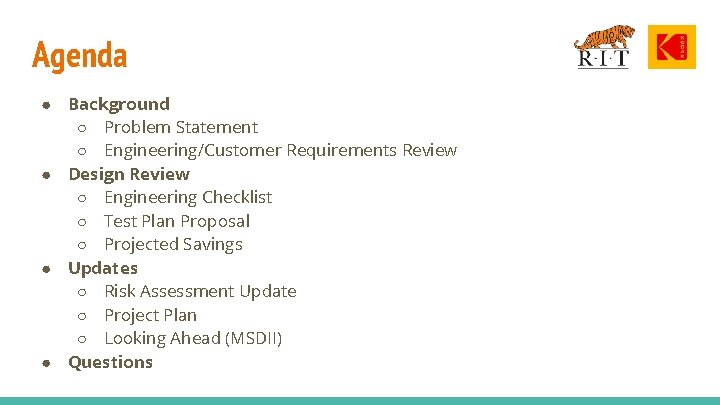
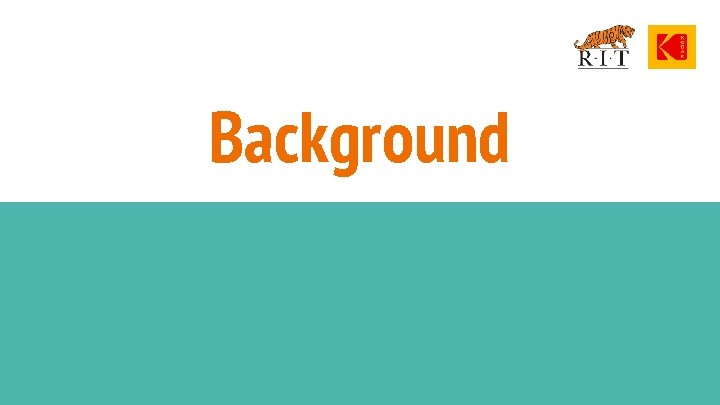
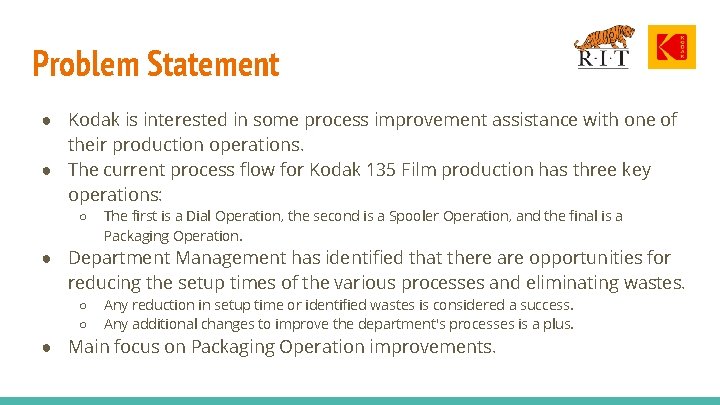
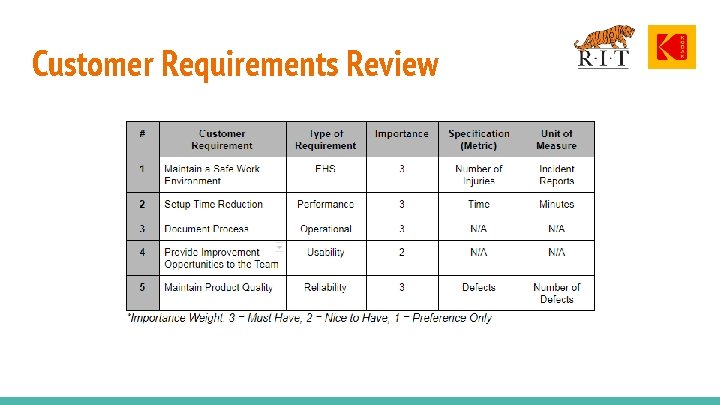
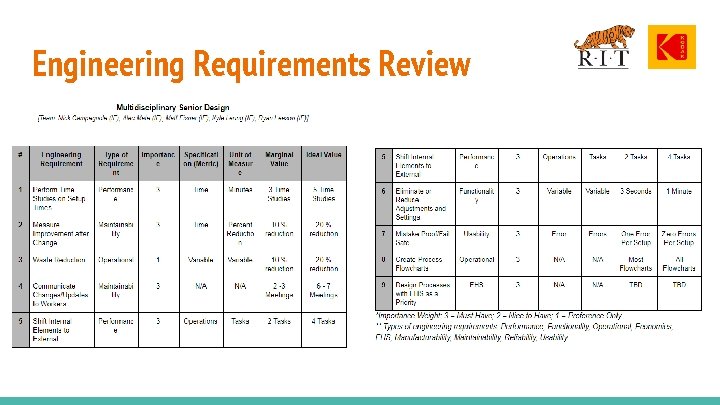
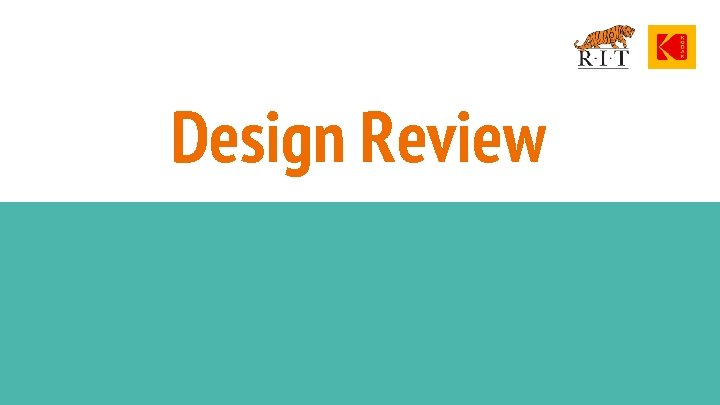
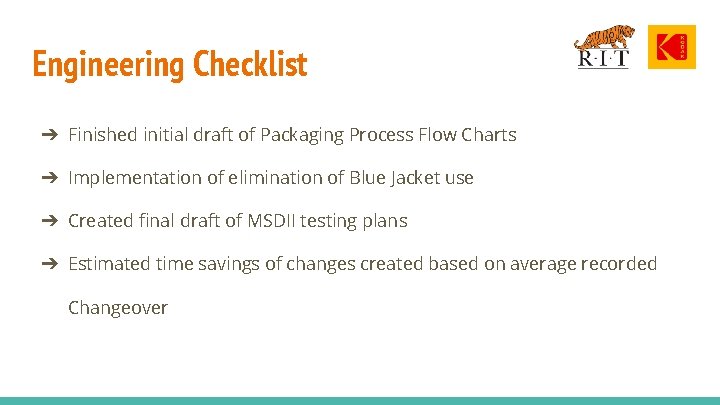
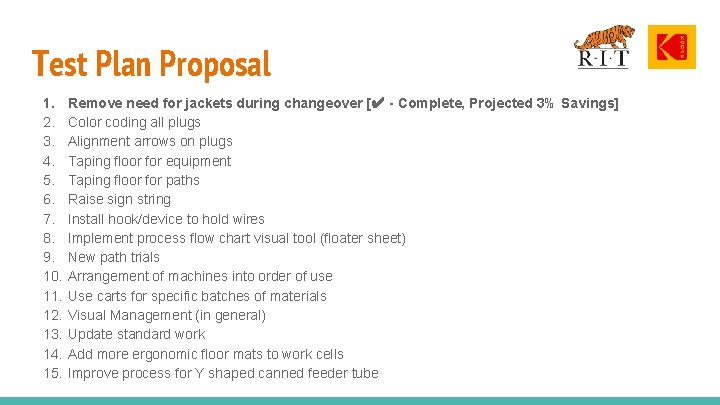
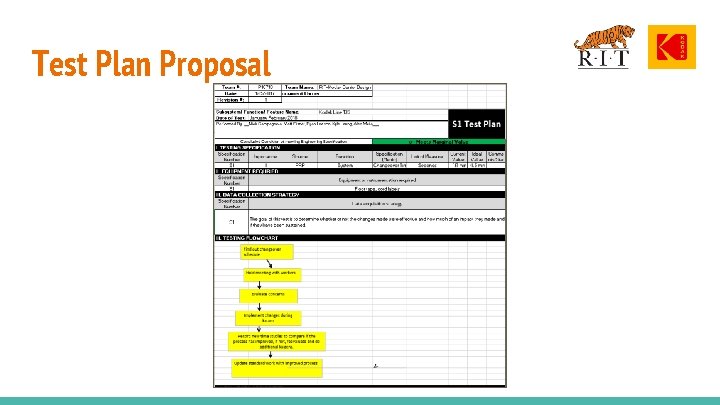
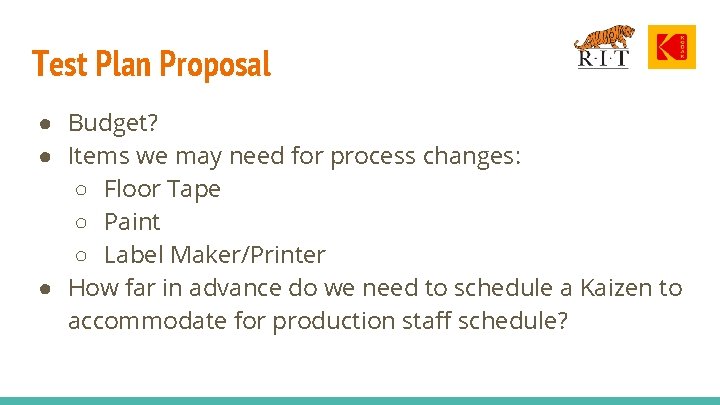

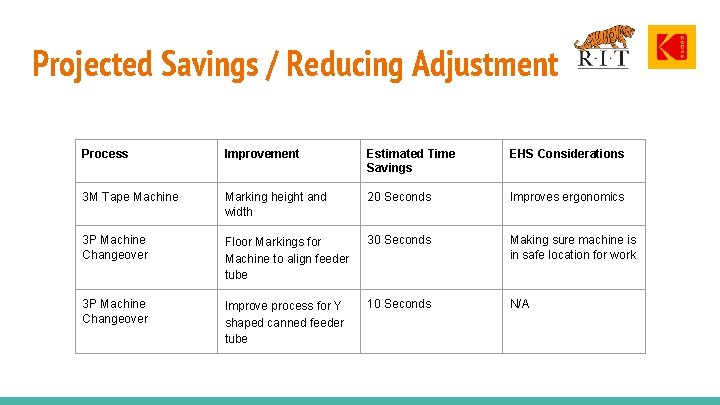
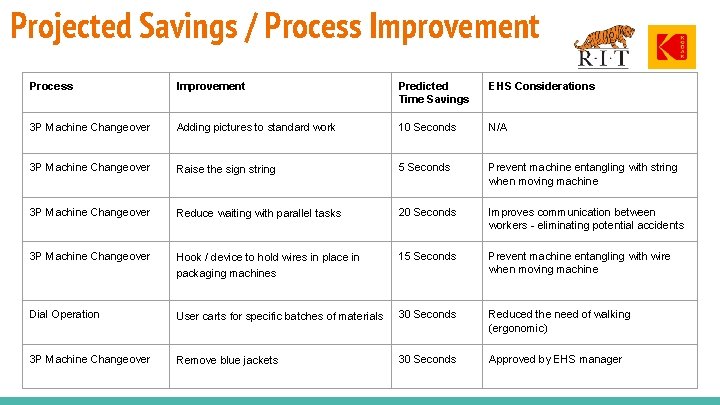
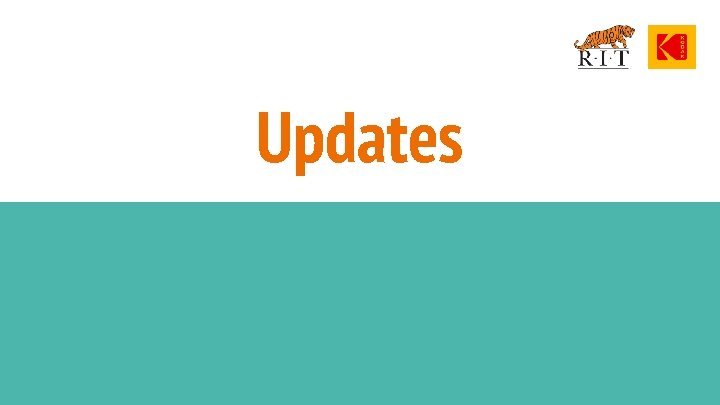
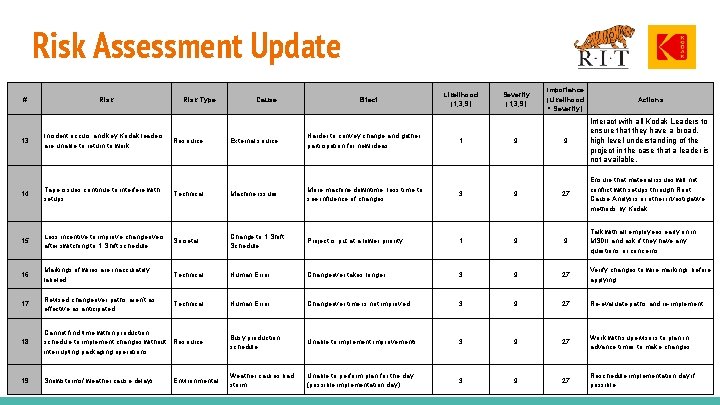
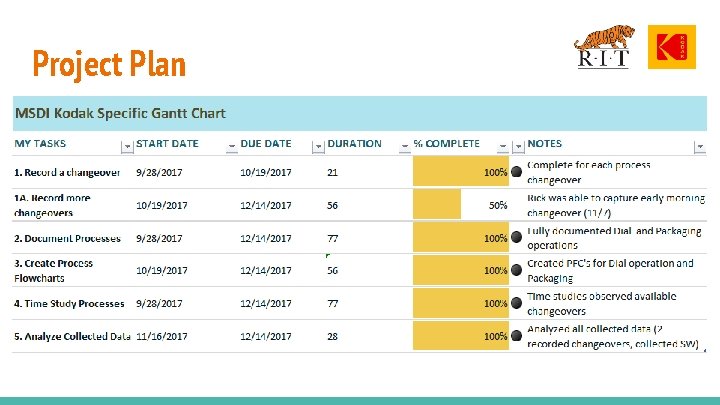
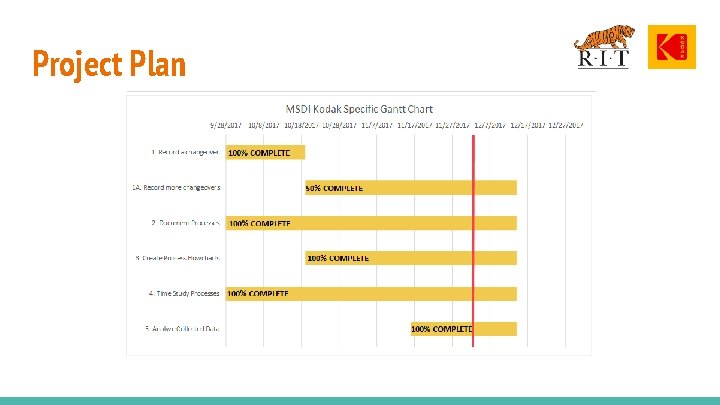
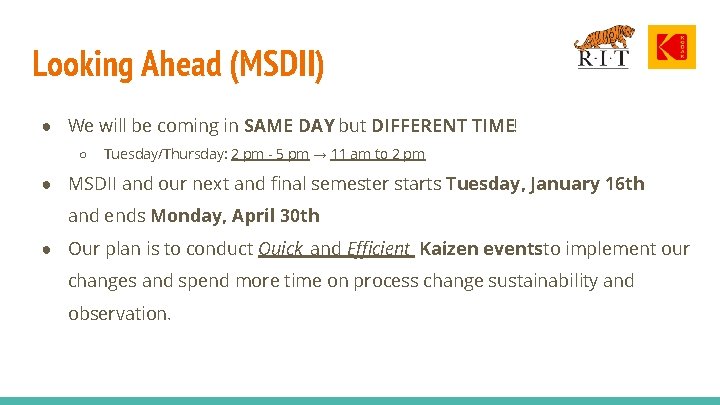
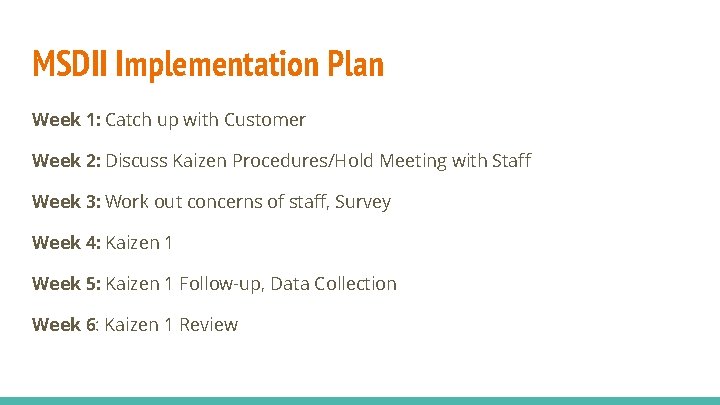
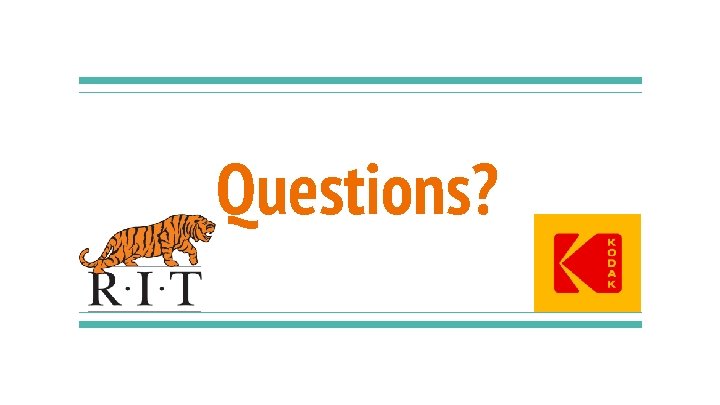
- Slides: 21
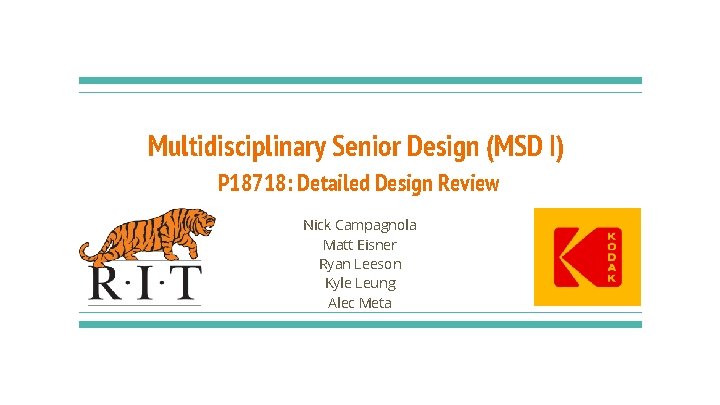
Multidisciplinary Senior Design (MSD I) P 18718: Detailed Design Review Nick Campagnola Matt Eisner Ryan Leeson Kyle Leung Alec Meta
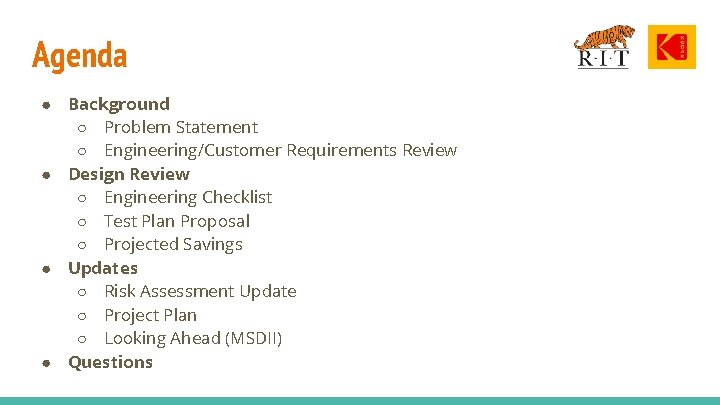
Agenda ● Background ○ Problem Statement ○ Engineering/Customer Requirements Review ● Design Review ○ Engineering Checklist ○ Test Plan Proposal ○ Projected Savings ● Updates ○ Risk Assessment Update ○ Project Plan ○ Looking Ahead (MSDII) ● Questions
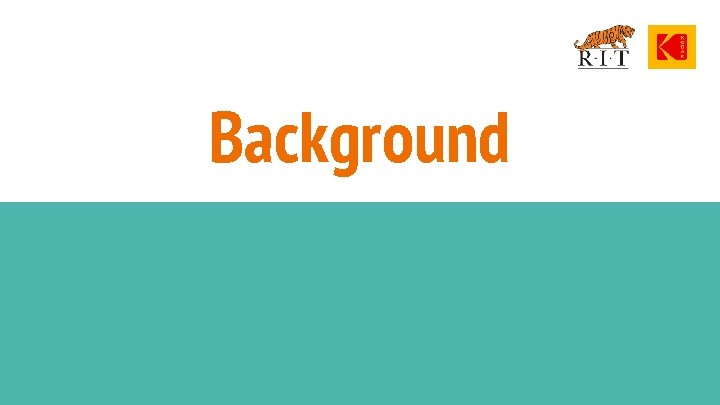
Background
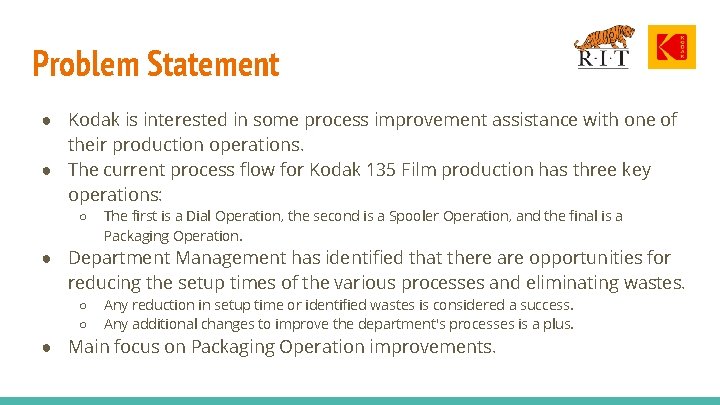
Problem Statement ● Kodak is interested in some process improvement assistance with one of their production operations. ● The current process flow for Kodak 135 Film production has three key operations: ○ The first is a Dial Operation, the second is a Spooler Operation, and the final is a Packaging Operation. ● Department Management has identified that there are opportunities for reducing the setup times of the various processes and eliminating wastes. ○ ○ Any reduction in setup time or identified wastes is considered a success. Any additional changes to improve the department's processes is a plus. ● Main focus on Packaging Operation improvements.
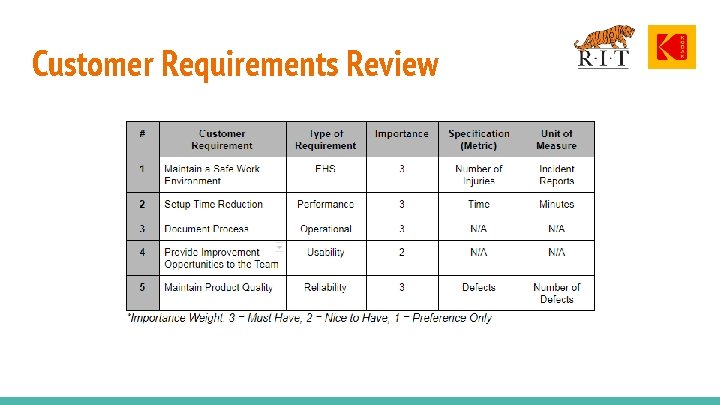
Customer Requirements Review
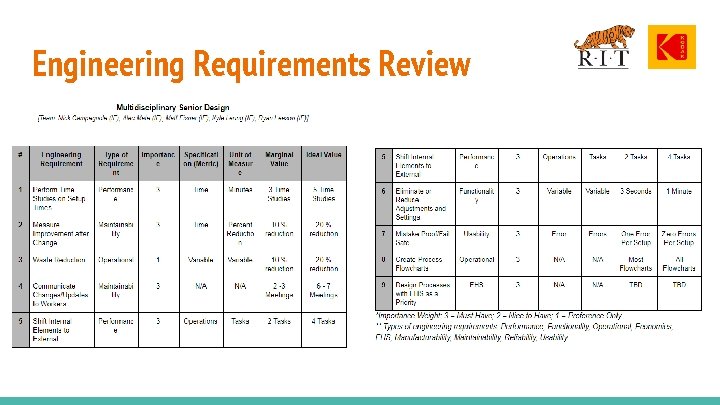
Engineering Requirements Review
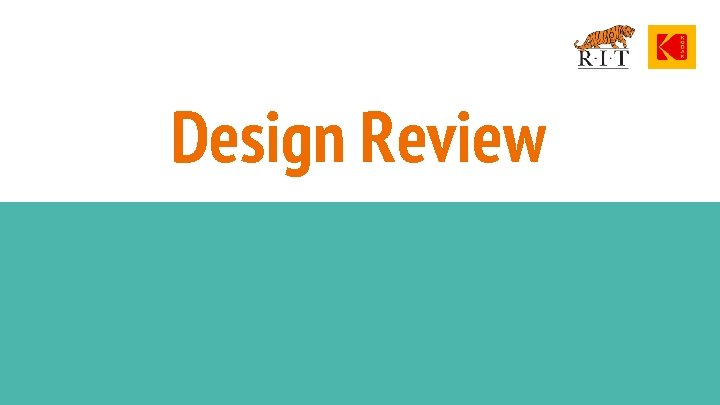
Design Review
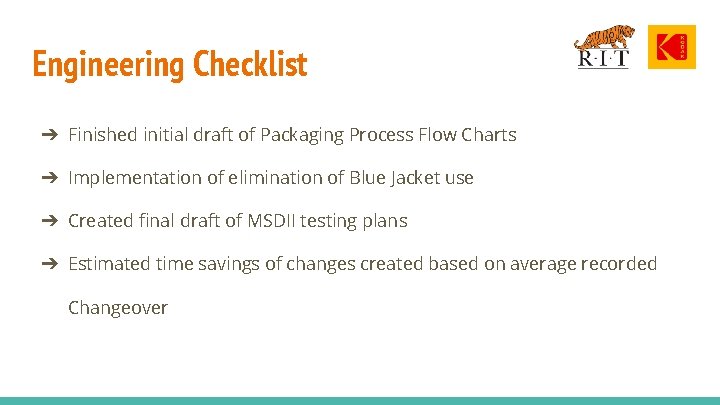
Engineering Checklist ➔ Finished initial draft of Packaging Process Flow Charts ➔ Implementation of elimination of Blue Jacket use ➔ Created final draft of MSDII testing plans ➔ Estimated time savings of changes created based on average recorded Changeover
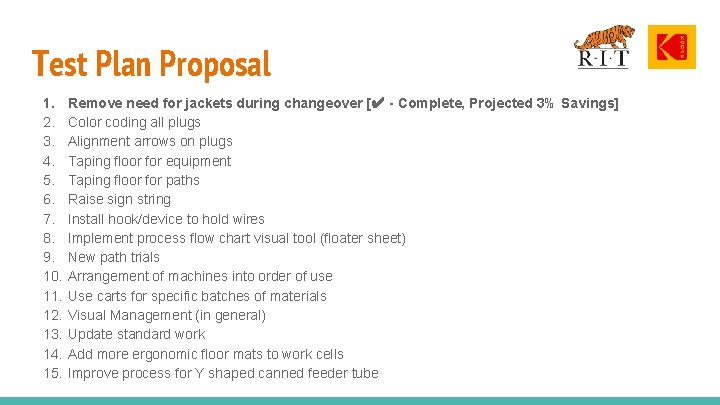
Test Plan Proposal 1. 2. 3. 4. 5. 6. 7. 8. 9. 10. 11. 12. 13. 14. 15. Remove need for jackets during changeover [✔ - Complete, Projected 3% Savings] Color coding all plugs Alignment arrows on plugs Taping floor for equipment Taping floor for paths Raise sign string Install hook/device to hold wires Implement process flow chart visual tool (floater sheet) New path trials Arrangement of machines into order of use Use carts for specific batches of materials Visual Management (in general) Update standard work Add more ergonomic floor mats to work cells Improve process for Y shaped canned feeder tube
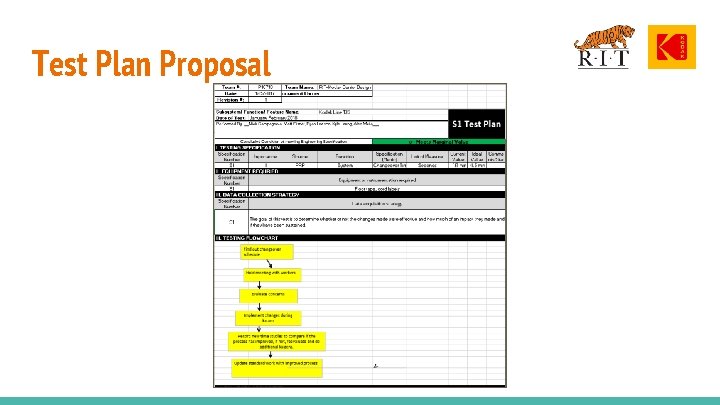
Test Plan Proposal
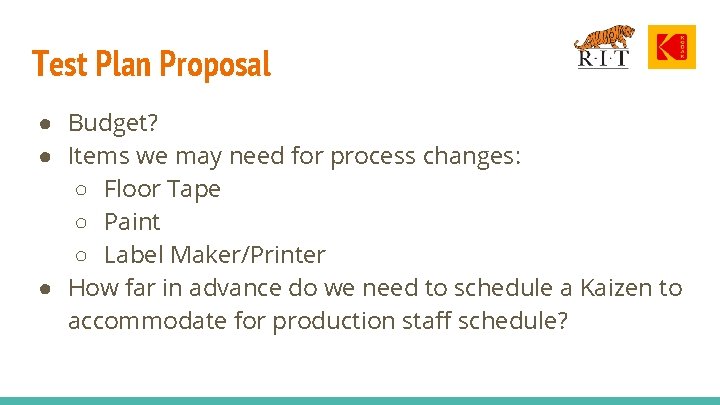
Test Plan Proposal ● Budget? ● Items we may need for process changes: ○ Floor Tape ○ Paint ○ Label Maker/Printer ● How far in advance do we need to schedule a Kaizen to accommodate for production staff schedule?

Projected Savings / Visual Management Process Improvement Estimated Time Savings EHS Considerations 3 P Machine Changeover Implement process flow chart visual tool 45 Seconds N/A 3 P Machine Changeover Floor Markings for Packaging Machines 20 Seconds Setting safe location for machines 3 P Machine Changeover Color Coding Plugs 10 Seconds Prevent electrical hazards 3 P Machine Changeover Alignment Arrows on plugs 10 Seconds Prevent electrical hazards 3 P Machine Changeover Tape out path for Machine 20 Seconds Prevent machines impacting people or objects
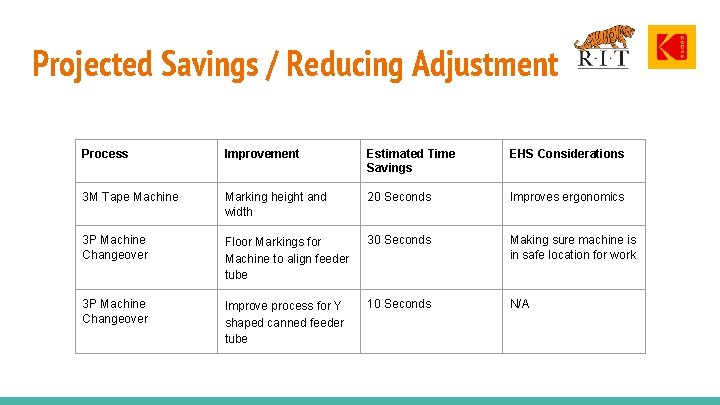
Projected Savings / Reducing Adjustment Process Improvement Estimated Time Savings EHS Considerations 3 M Tape Machine Marking height and width 20 Seconds Improves ergonomics 3 P Machine Changeover Floor Markings for Machine to align feeder tube 30 Seconds Making sure machine is in safe location for work 3 P Machine Changeover Improve process for Y shaped canned feeder tube 10 Seconds N/A
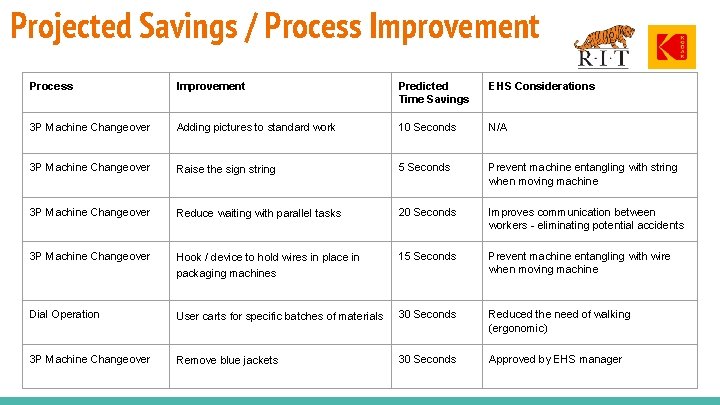
Projected Savings / Process Improvement Predicted Time Savings EHS Considerations 3 P Machine Changeover Adding pictures to standard work 10 Seconds N/A 3 P Machine Changeover Raise the sign string 5 Seconds Prevent machine entangling with string when moving machine 3 P Machine Changeover Reduce waiting with parallel tasks 20 Seconds Improves communication between workers - eliminating potential accidents 3 P Machine Changeover Hook / device to hold wires in place in packaging machines 15 Seconds Prevent machine entangling with wire when moving machine Dial Operation User carts for specific batches of materials 30 Seconds Reduced the need of walking (ergonomic) 3 P Machine Changeover Remove blue jackets 30 Seconds Approved by EHS manager
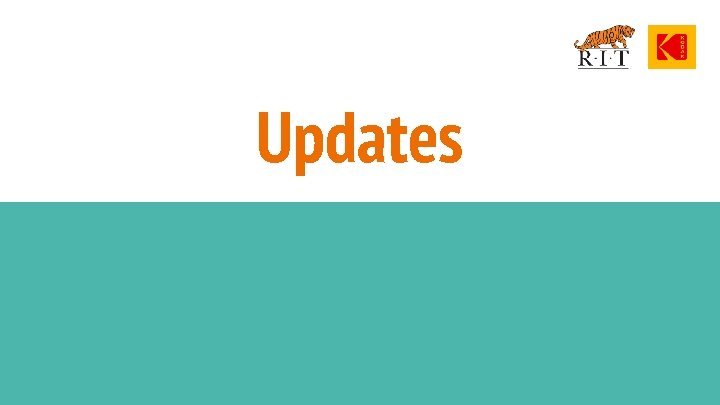
Updates
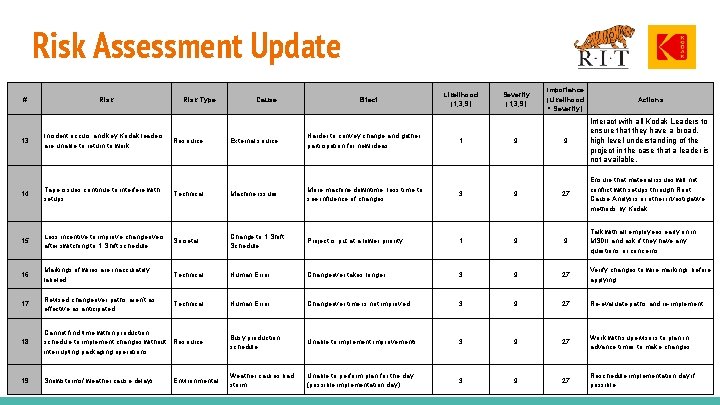
Risk Assessment Update # Risk 13 Incident occurs and key Kodak leaders are unable to return to work 14 Tape issues continue to interfere with setups 15 Risk Type Cause Effect Likelihood (1, 3, 9) Severity (1, 3, 9) Importance (Likelihood * Severity) Actions 9 Interact with all Kodak Leaders to ensure that they have a broad, high level understanding of the project in the case that a leader is not available. External source Harder to convey change and gather participation for new ideas Technical Machine issues More machine downtime, less time to see influence of changes 3 9 27 Ensure that material issues will not conflict with setups through Root Cause Analysis or other investigative methods by Kodak Less incentive to improve changeovers after switching to 1 Shift schedule Societal Change to 1 Shift Schedule Project is put at a lower priority 1 9 9 Talk with all employees early on in MSDII and ask if they have any questions or concerns. 16 Markings of wires are inaccurately labeled Technical Human Error Changeover takes longer 3 9 27 Verify changes to wire markings before applying 17 Revised changeover paths aren’t as effective as anticipated Technical Human Error Changeover time is not improved 3 9 27 Re-evaluate paths and re-implement 18 Cannot find time within production schedule to implement changes without interrupting packaging operations Resource Busy production schedule Unable to implement improvements 3 9 27 Work with supervisors to plan in advance times to make changes 19 Snowstorms/ weather cause delays Environmental Weather causes bad storm Unable to perform plan for the day (possible implementation day) 3 9 27 Reschedule implementation day if possible Resource 1 9
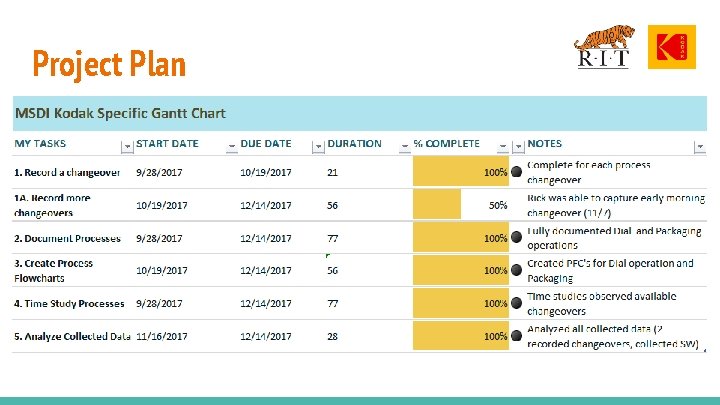
Project Plan
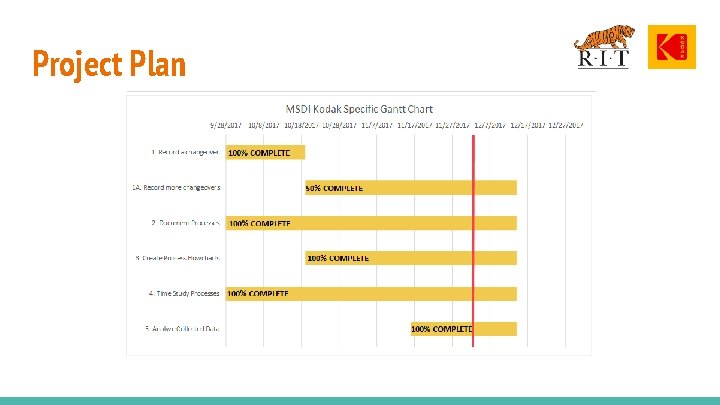
Project Plan
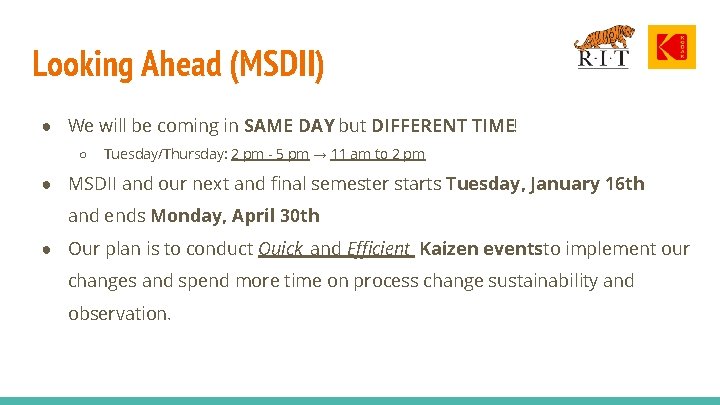
Looking Ahead (MSDII) ● We will be coming in SAME DAY but DIFFERENT TIME! ○ Tuesday/Thursday: 2 pm - 5 pm → 11 am to 2 pm ● MSDII and our next and final semester starts Tuesday, January 16 th and ends Monday, April 30 th. ● Our plan is to conduct Quick and Efficient Kaizen eventsto implement our changes and spend more time on process change sustainability and observation.
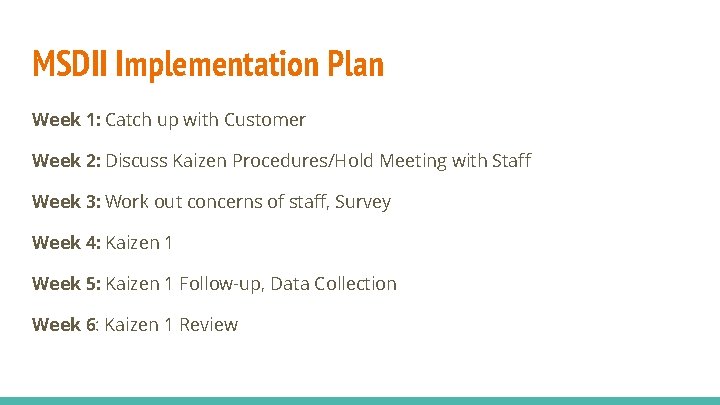
MSDII Implementation Plan Week 1: Catch up with Customer Week 2: Discuss Kaizen Procedures/Hold Meeting with Staff Week 3: Work out concerns of staff, Survey Week 4: Kaizen 1 Week 5: Kaizen 1 Follow-up, Data Collection Week 6: Kaizen 1 Review
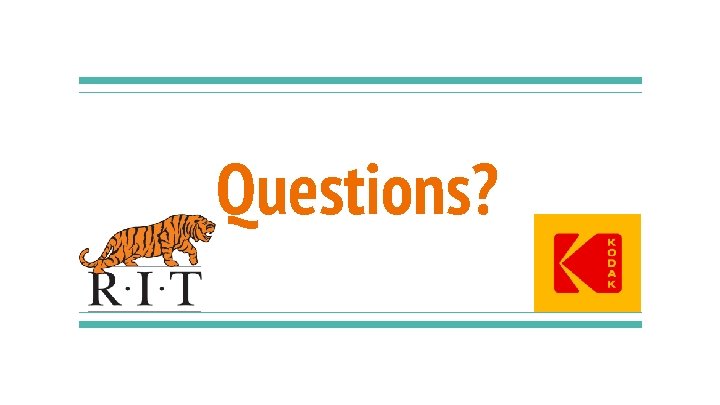
Questions?
Detailed design in software engineering
Detailed design software
Msd project clear
Msd bullying
Msd basics review
Msd mean square displacement
Msd
Msd menu
Odac
Cp heat exchanger
Gambar hamil 6 minggu
Msd i
Msd propecia 1mg
Msd suisse
Tim pennock
Scope of multidisciplinary nature of environmental studies
Multidisciplinary team pros and cons
Temasek laboratories
Multidisciplinary vs interdisciplinary
Interdisciplinary design curriculum
Multidisciplinary nature of environmental studies ppt
Multidisciplinary engineering definition