Mu 2 e Protection Collimator PC Andy Stefanik

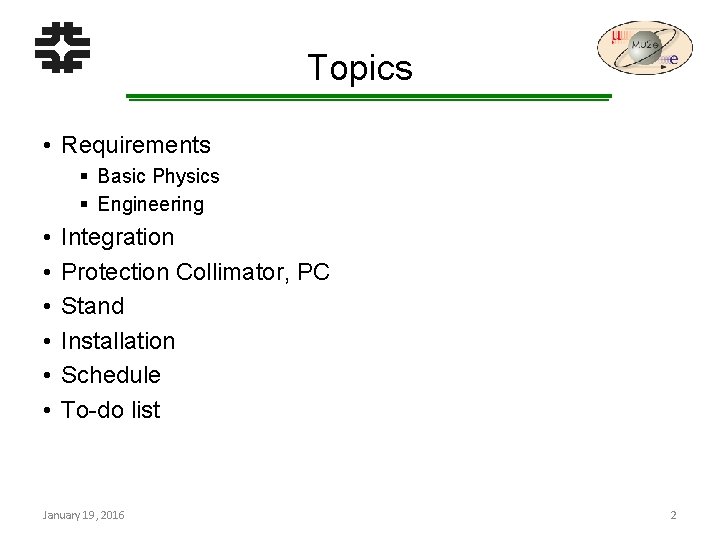
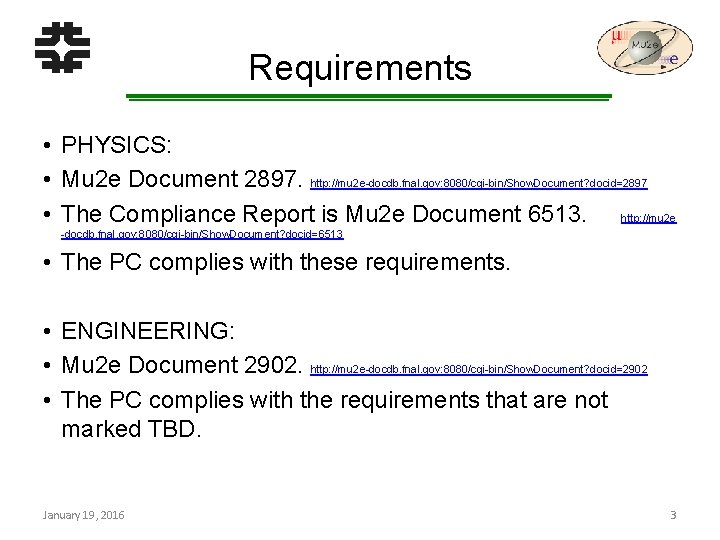
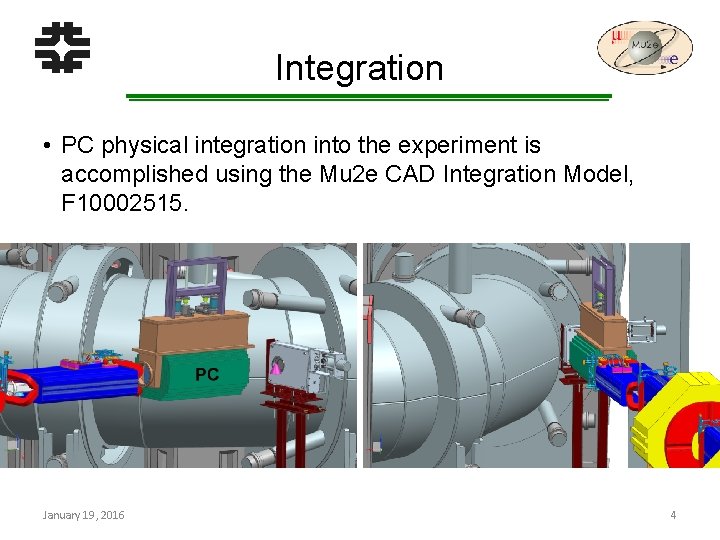
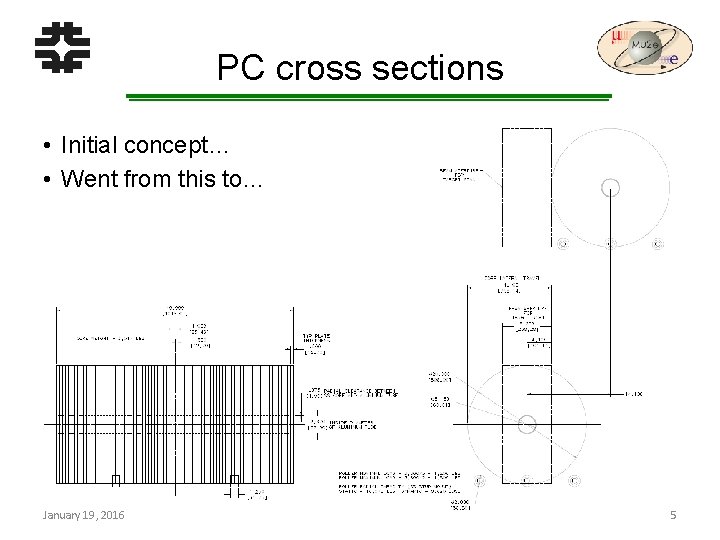
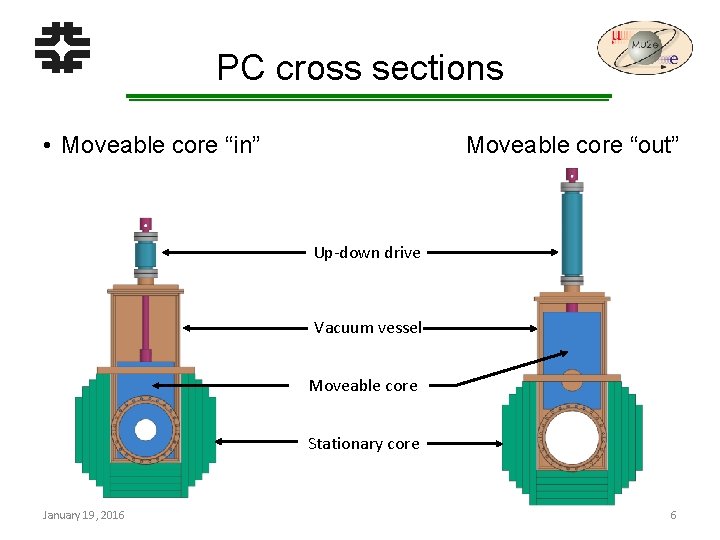
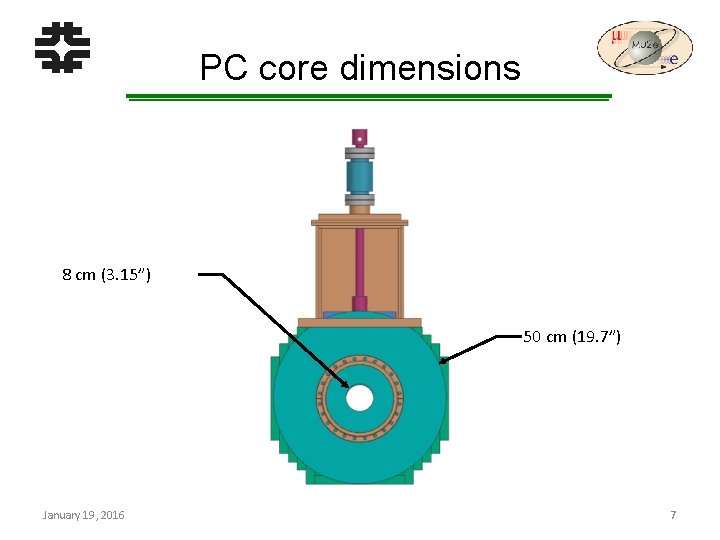
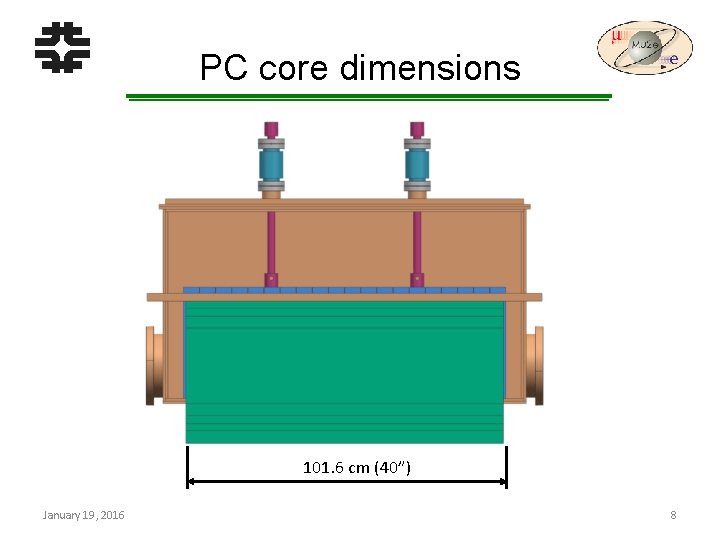
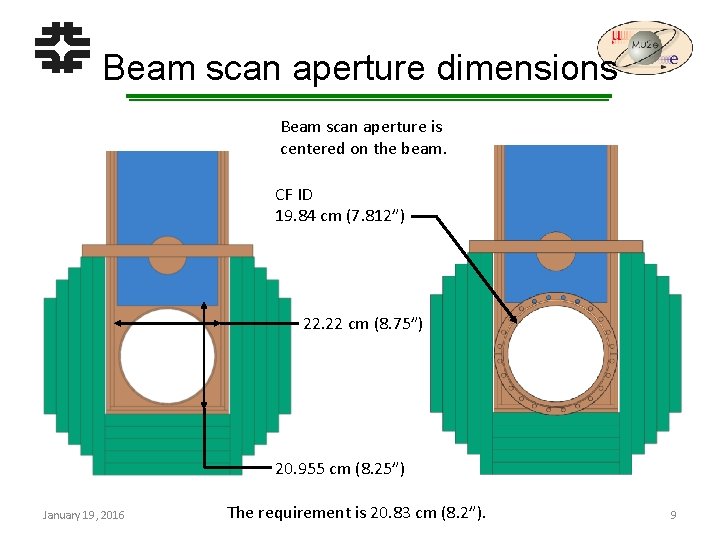
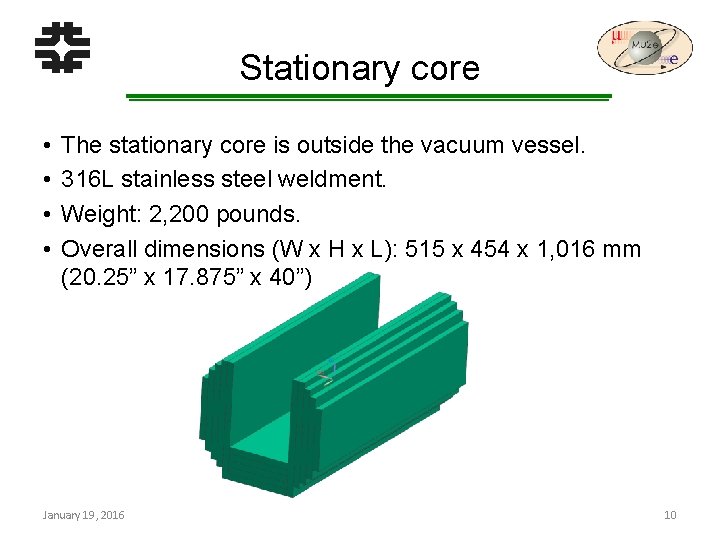
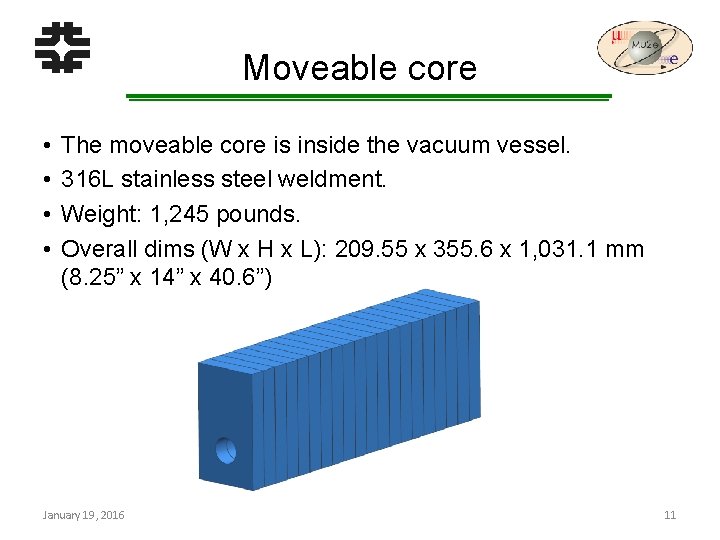
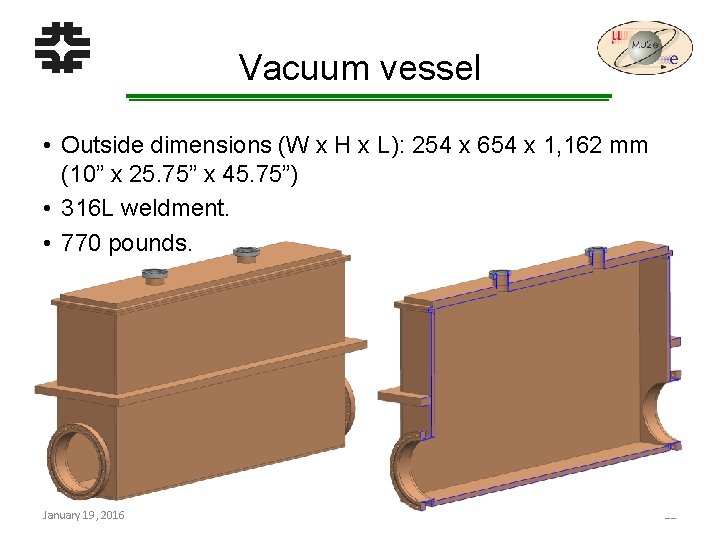
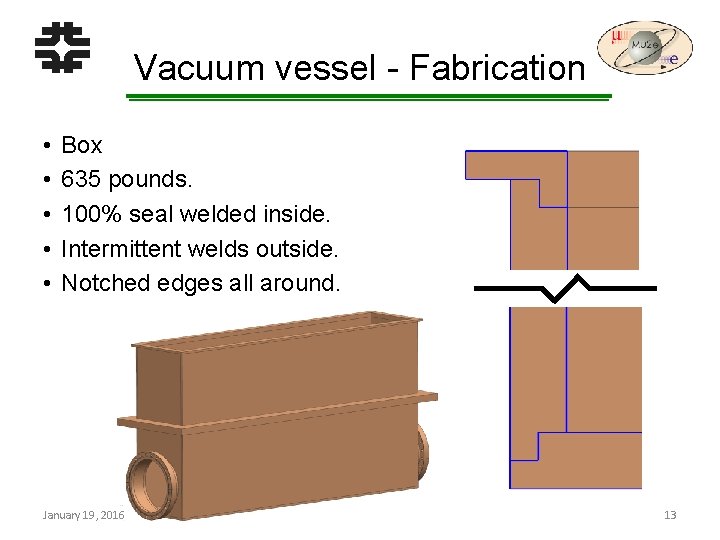
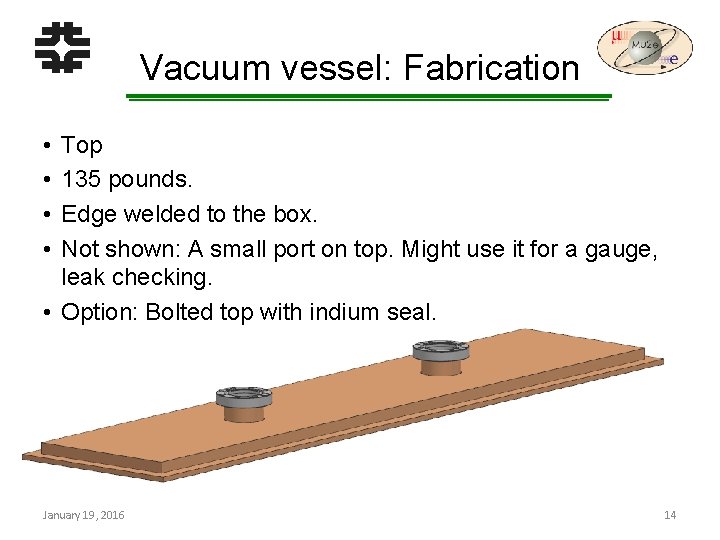
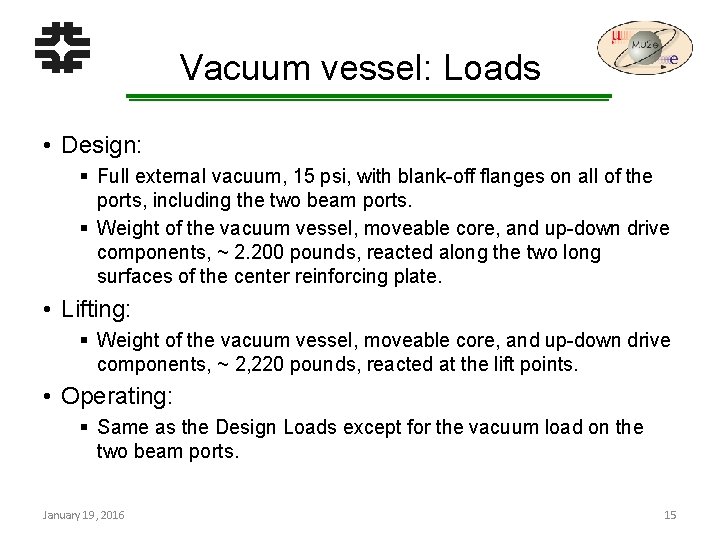
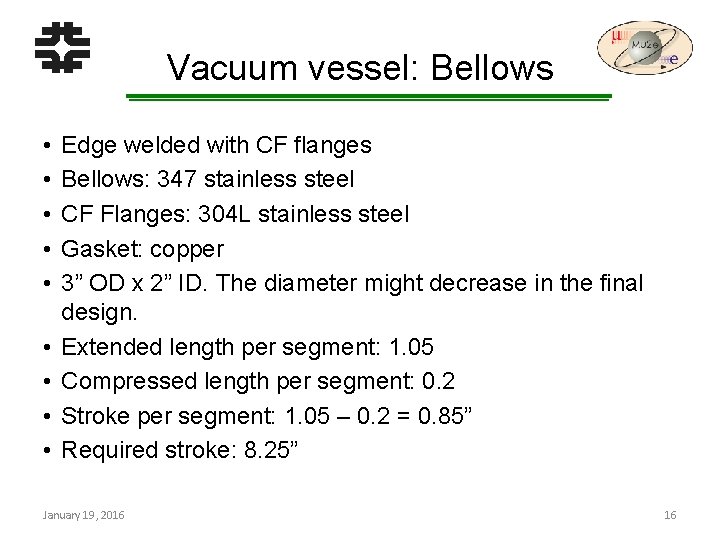
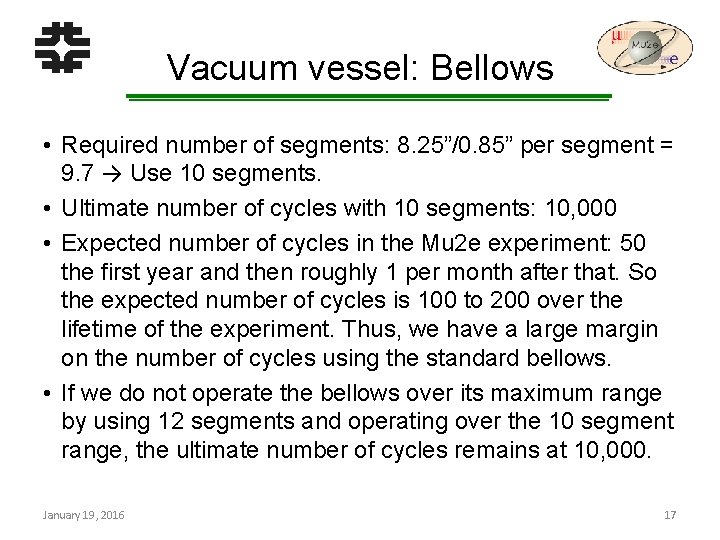
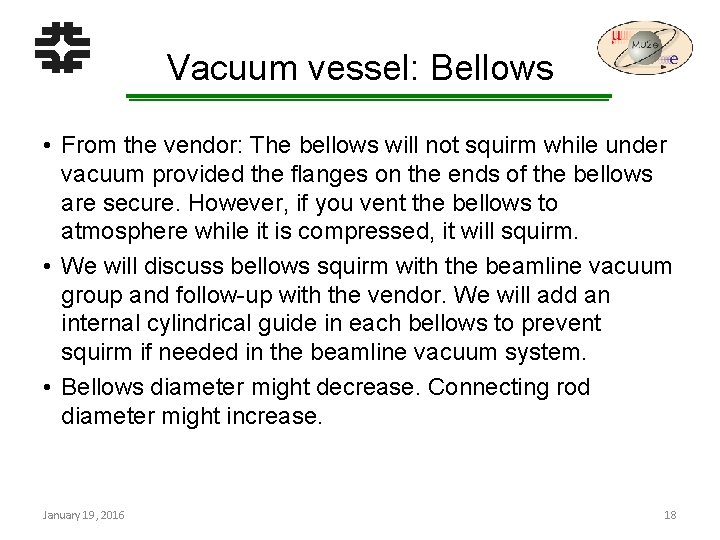
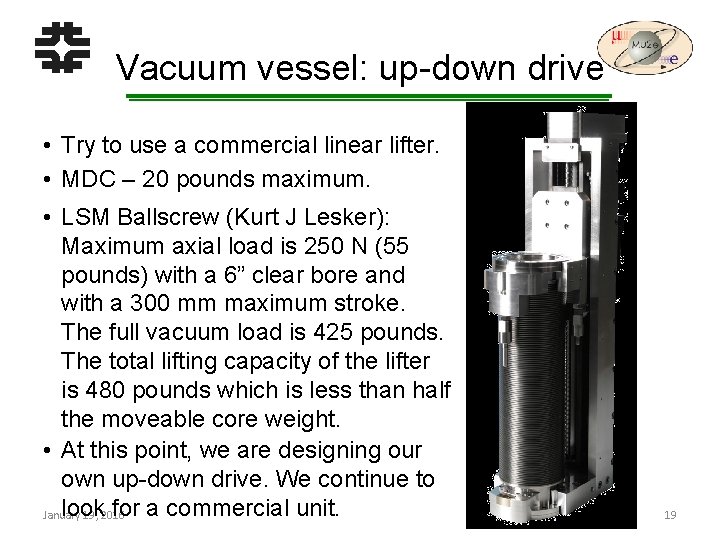
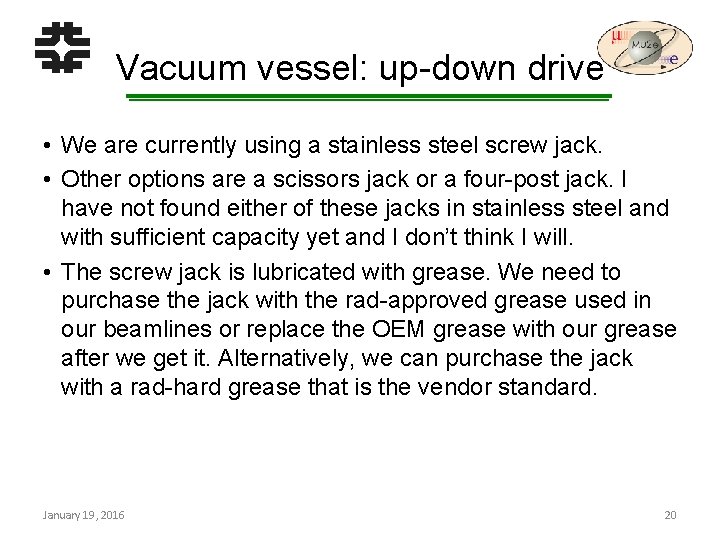
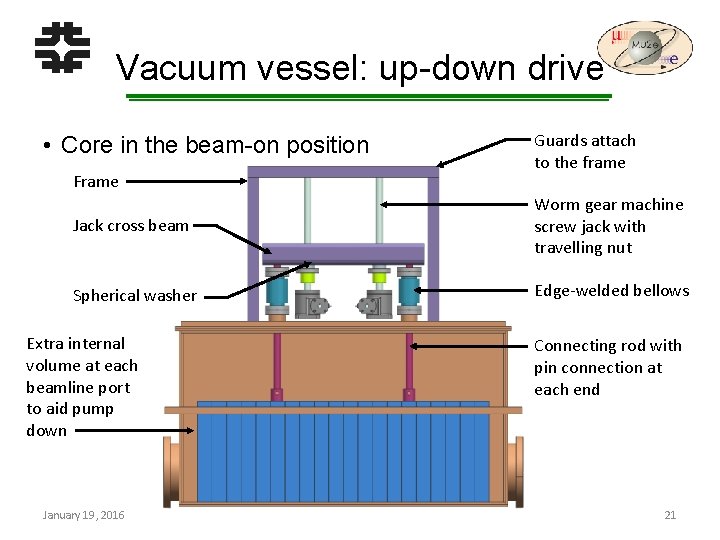
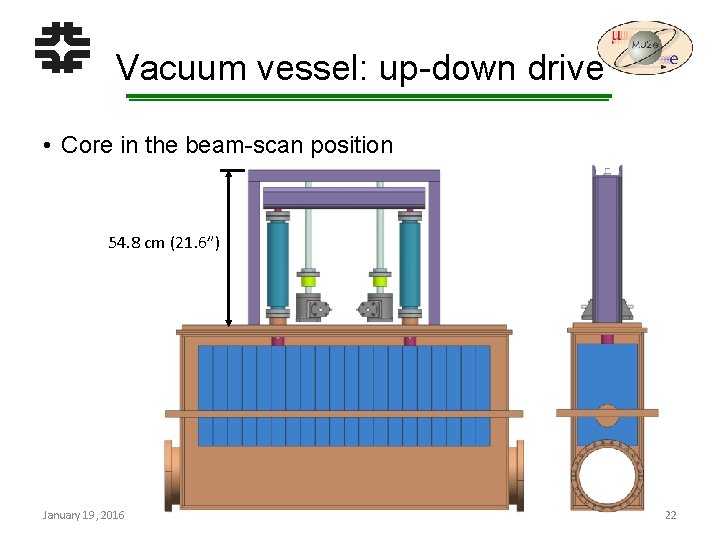
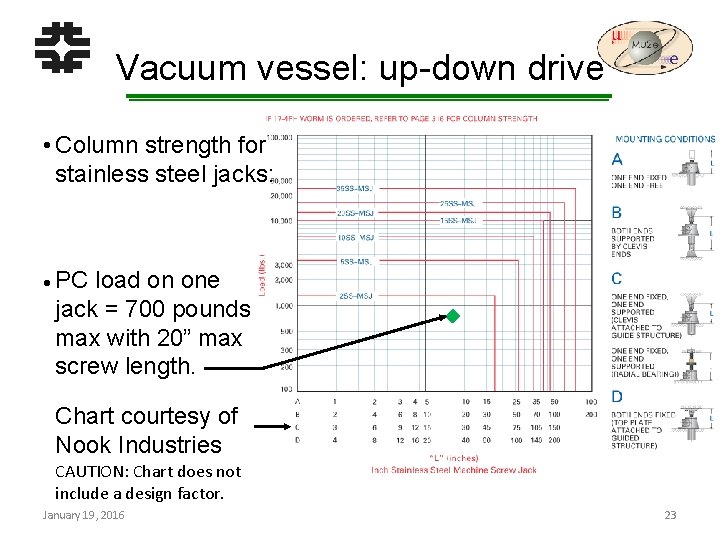
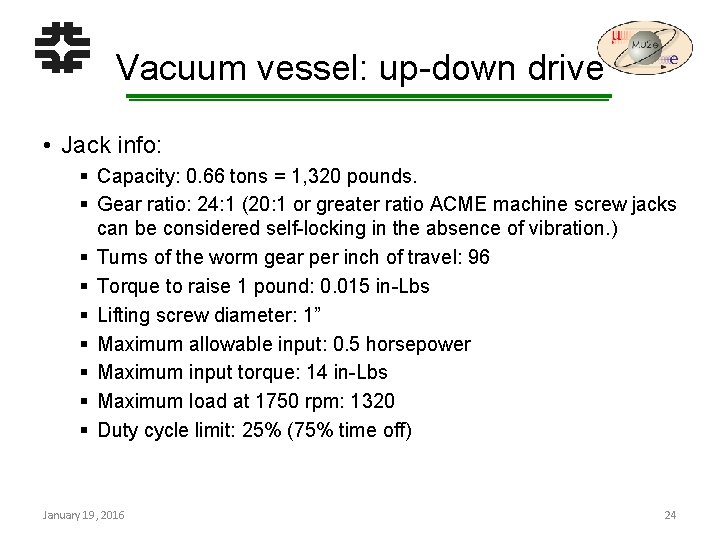
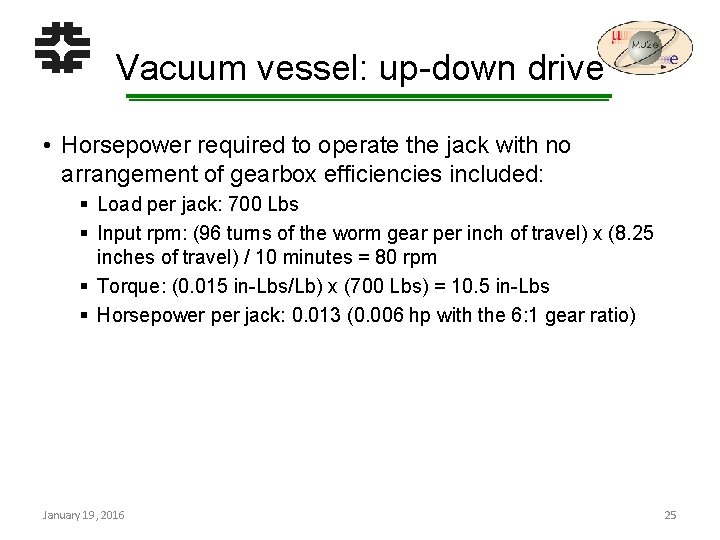
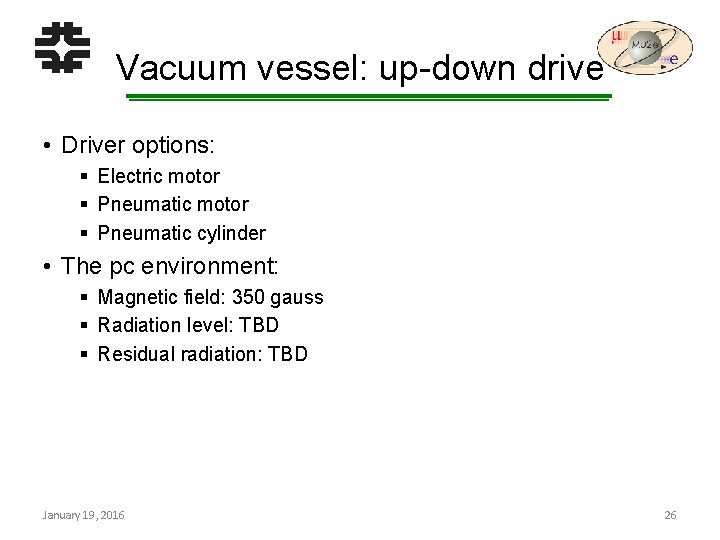
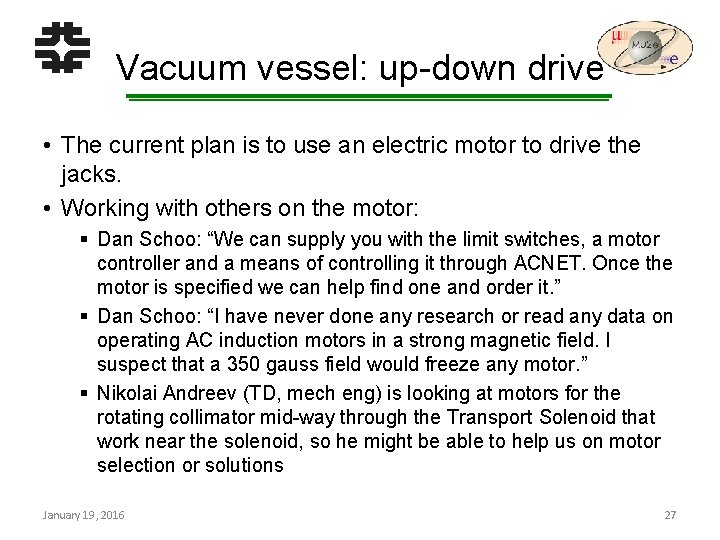
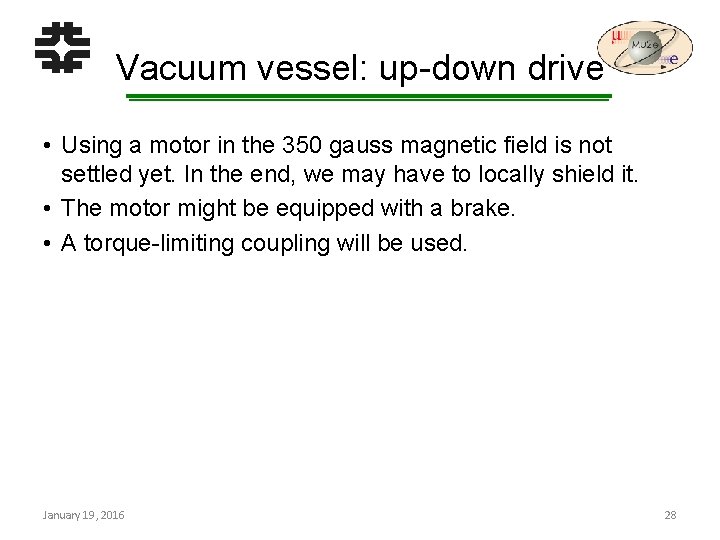
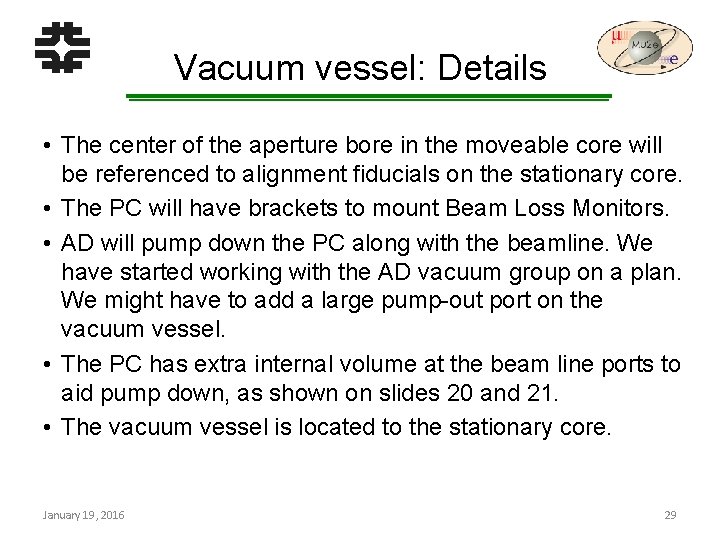
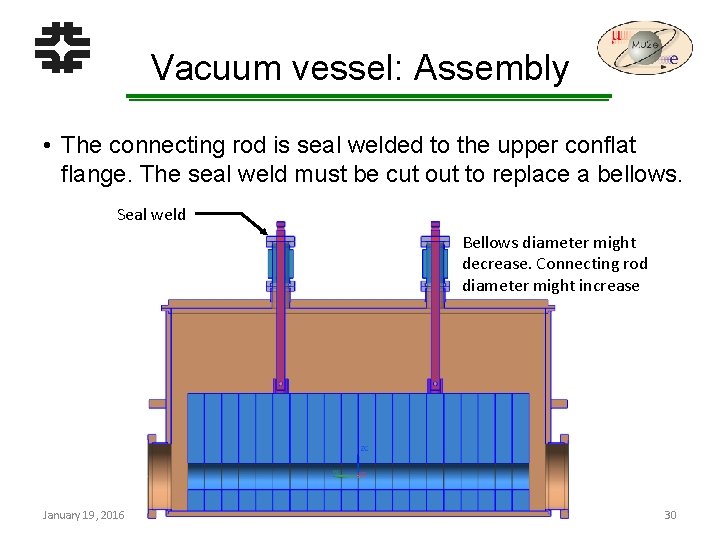
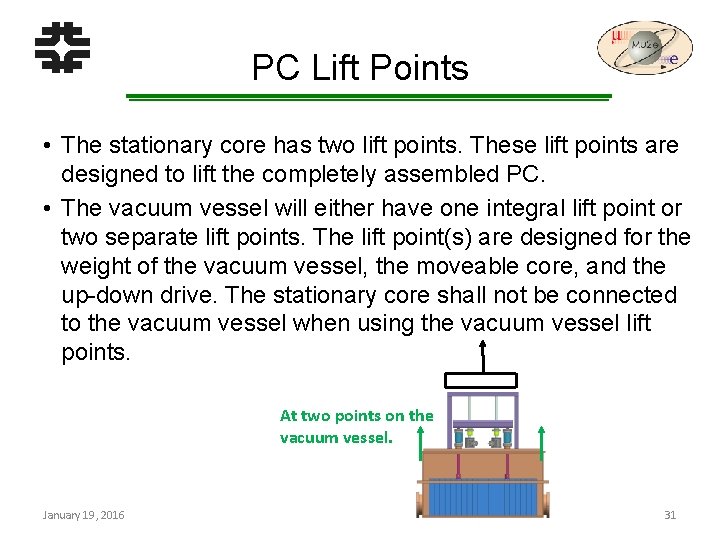
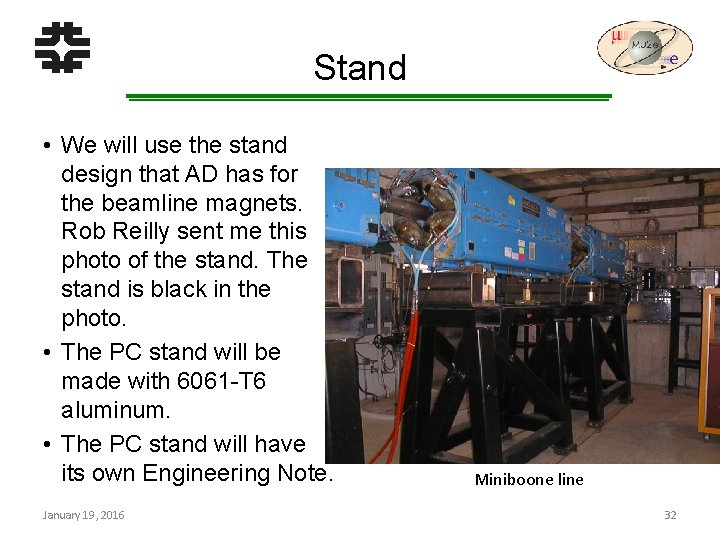
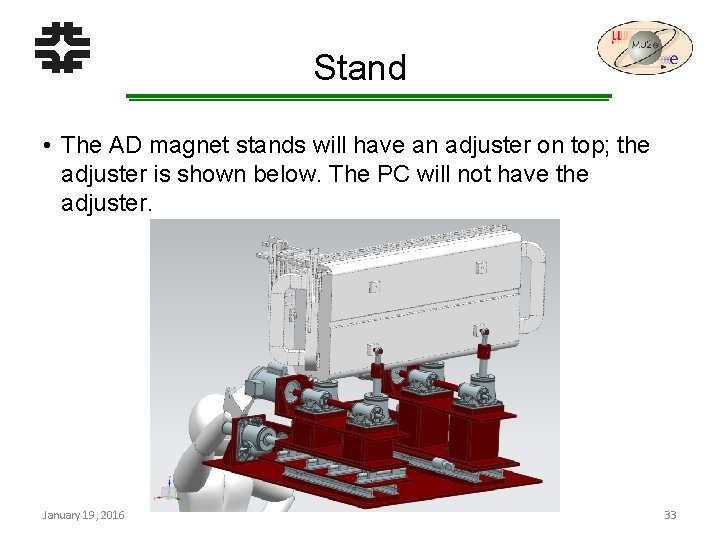
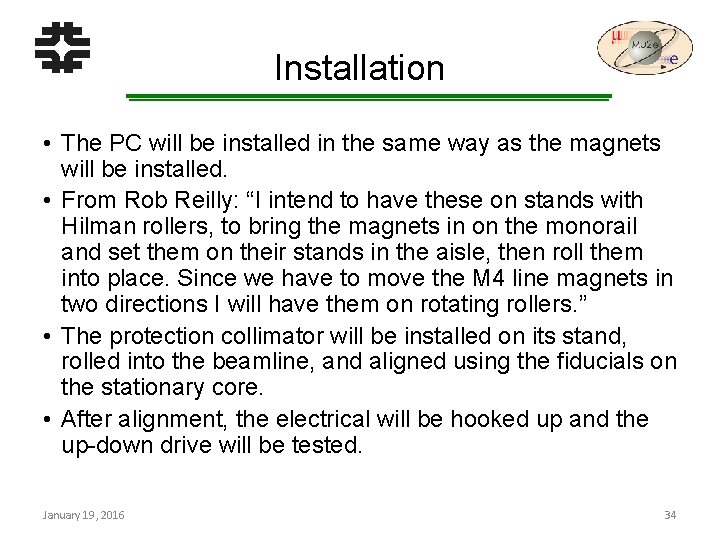
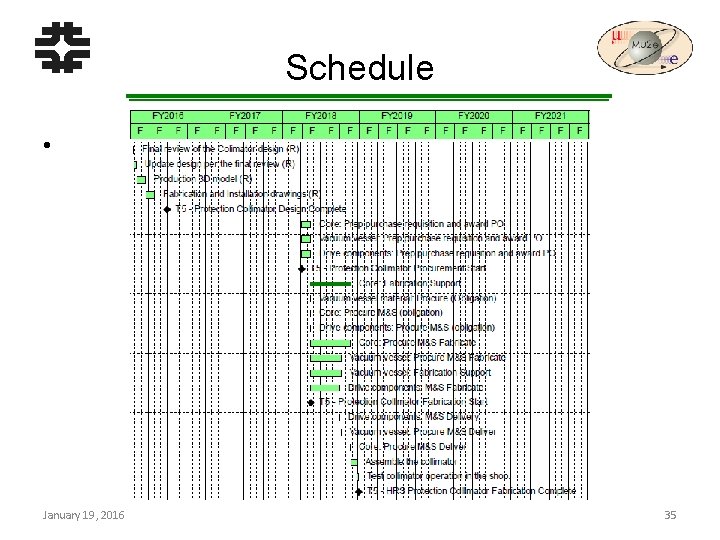

- Slides: 36

Mu 2 e Protection Collimator, PC Andy Stefanik January 19, 2016
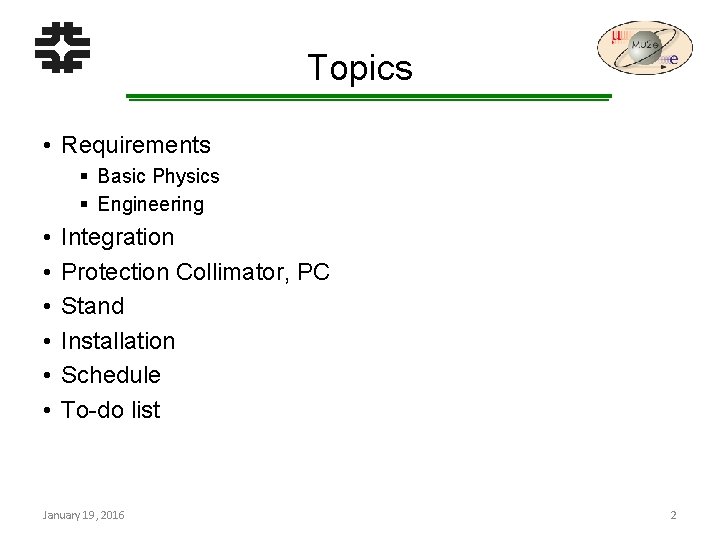
Topics • Requirements § Basic Physics § Engineering • • • Integration Protection Collimator, PC Stand Installation Schedule To-do list January 19, 2016 2
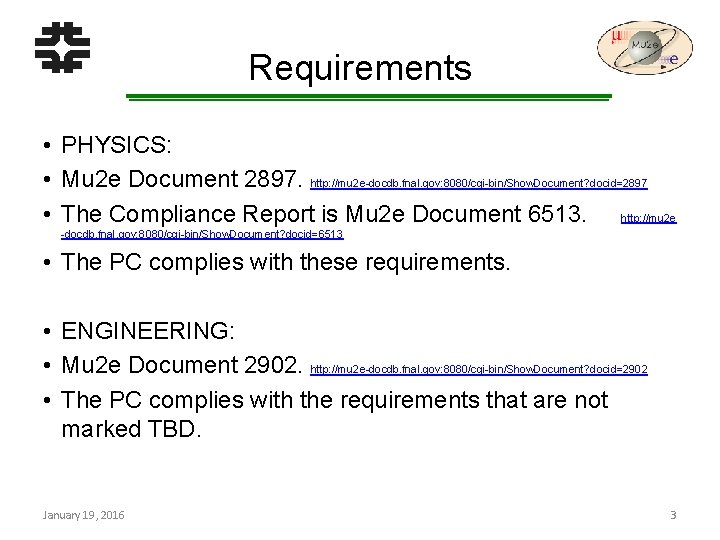
Requirements • PHYSICS: • Mu 2 e Document 2897. http: //mu 2 e-docdb. fnal. gov: 8080/cgi-bin/Show. Document? docid=2897 • The Compliance Report is Mu 2 e Document 6513. http: //mu 2 e -docdb. fnal. gov: 8080/cgi-bin/Show. Document? docid=6513 • The PC complies with these requirements. • ENGINEERING: • Mu 2 e Document 2902. http: //mu 2 e-docdb. fnal. gov: 8080/cgi-bin/Show. Document? docid=2902 • The PC complies with the requirements that are not marked TBD. January 19, 2016 3
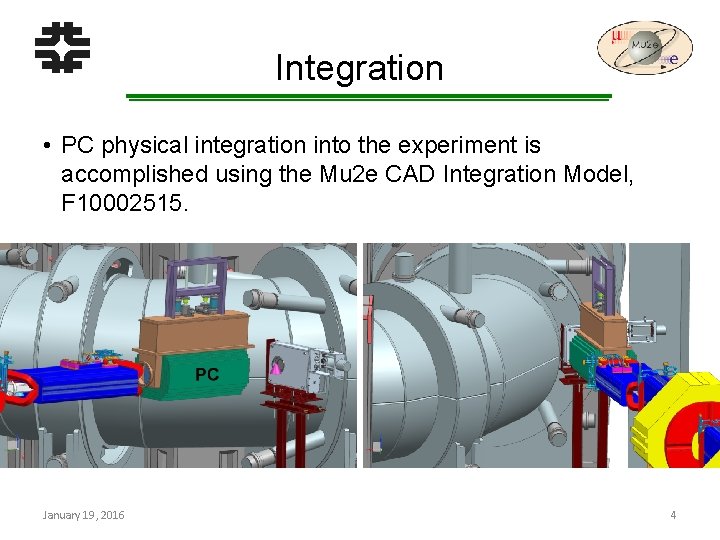
Integration • PC physical integration into the experiment is accomplished using the Mu 2 e CAD Integration Model, F 10002515. January 19, 2016 4
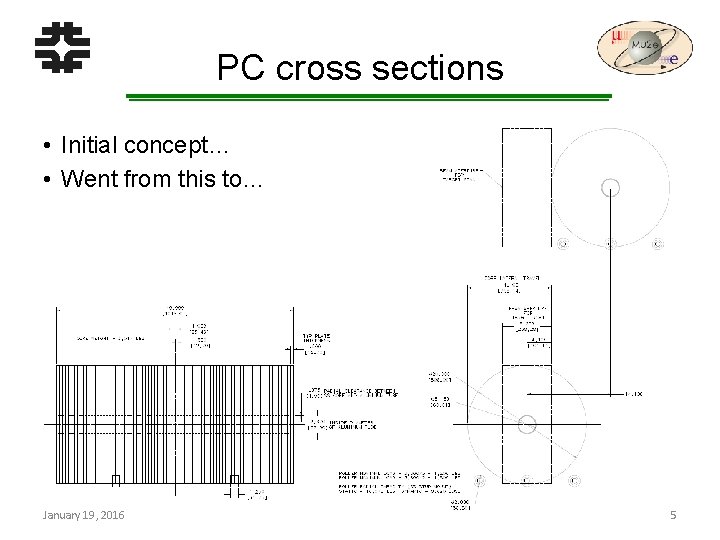
PC cross sections • Initial concept… • Went from this to… January 19, 2016 5
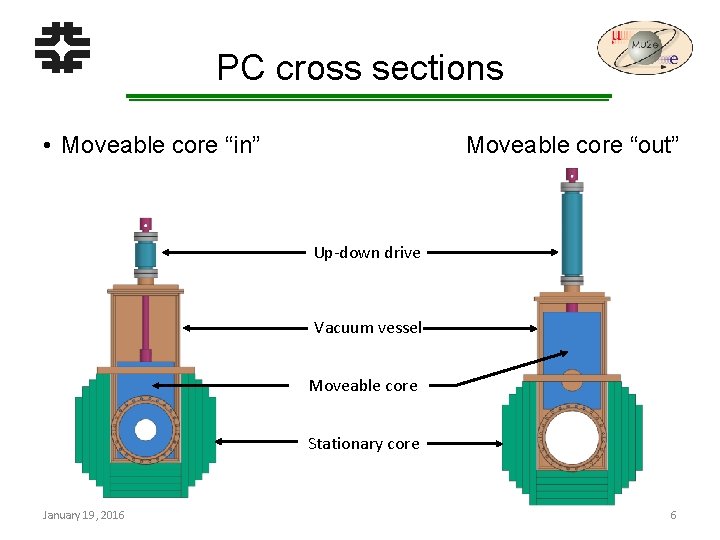
PC cross sections • Moveable core “in” Moveable core “out” Up-down drive Vacuum vessel Moveable core Stationary core January 19, 2016 6
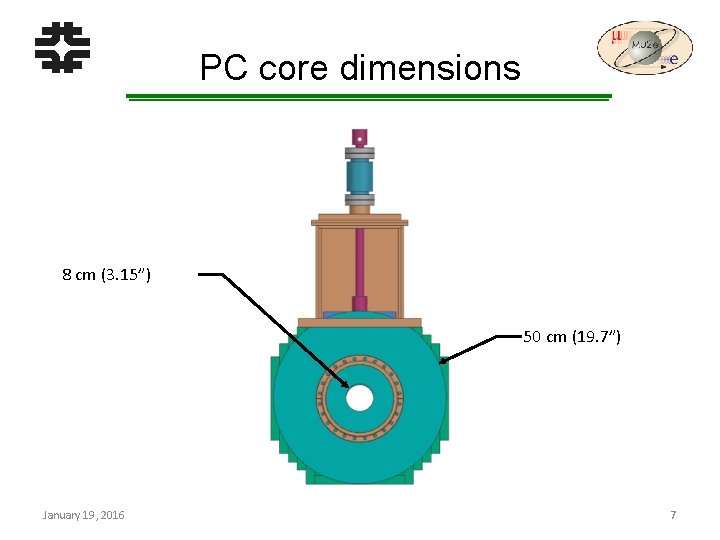
PC core dimensions 8 cm (3. 15”) 50 cm (19. 7”) January 19, 2016 7
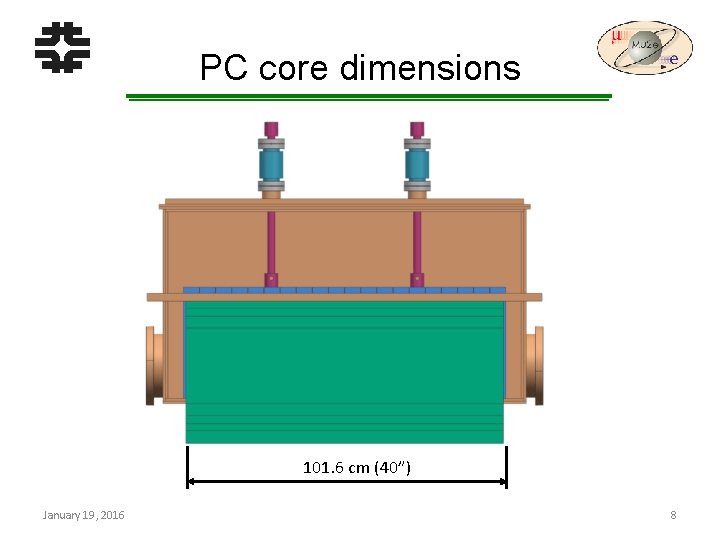
PC core dimensions 101. 6 cm (40”) January 19, 2016 8
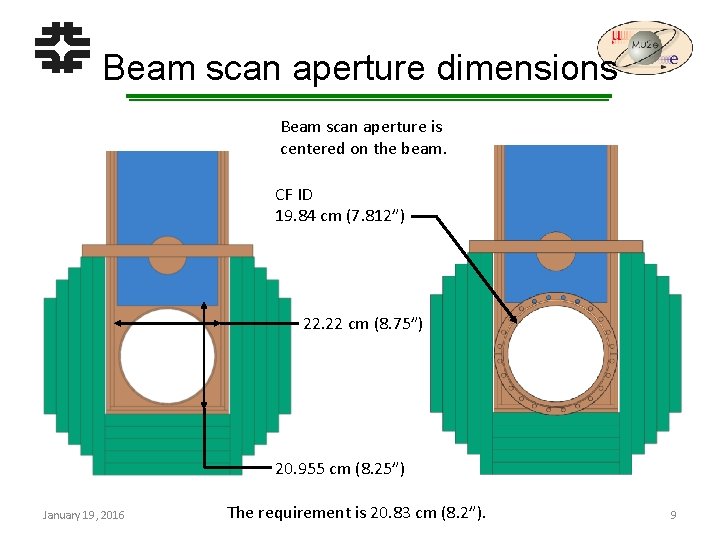
Beam scan aperture dimensions Beam scan aperture is centered on the beam. CF ID 19. 84 cm (7. 812”) 22. 22 cm (8. 75”) 20. 955 cm (8. 25”) January 19, 2016 The requirement is 20. 83 cm (8. 2”). 9
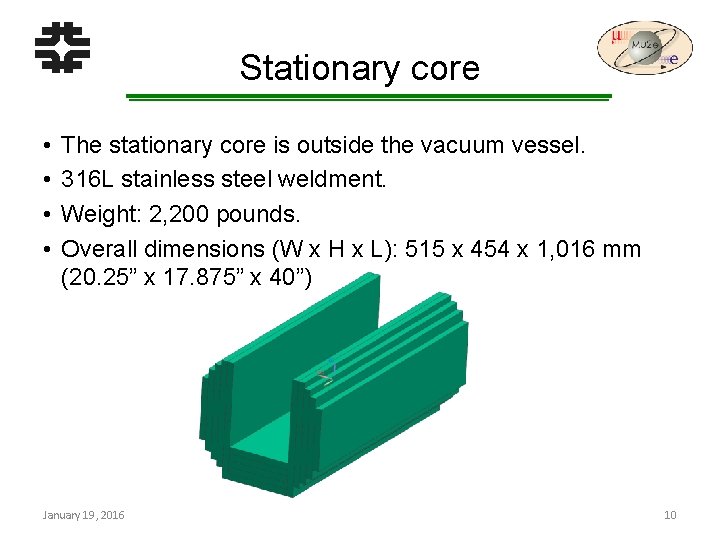
Stationary core • • The stationary core is outside the vacuum vessel. 316 L stainless steel weldment. Weight: 2, 200 pounds. Overall dimensions (W x H x L): 515 x 454 x 1, 016 mm (20. 25” x 17. 875” x 40”) January 19, 2016 10
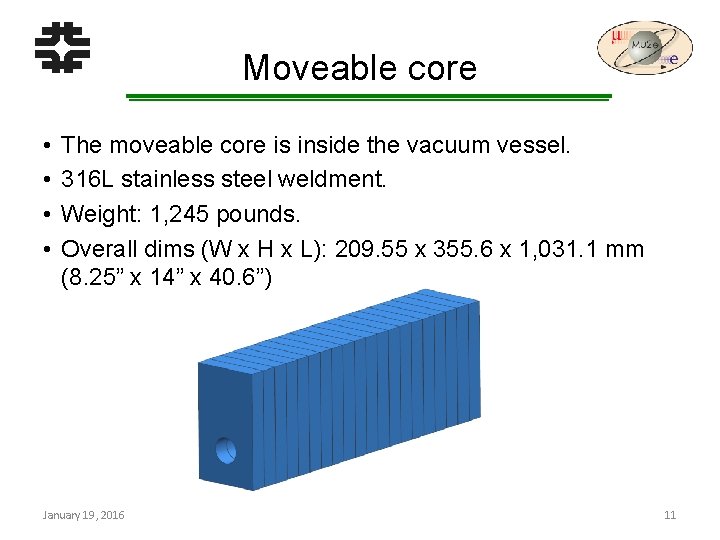
Moveable core • • The moveable core is inside the vacuum vessel. 316 L stainless steel weldment. Weight: 1, 245 pounds. Overall dims (W x H x L): 209. 55 x 355. 6 x 1, 031. 1 mm (8. 25” x 14” x 40. 6”) January 19, 2016 11
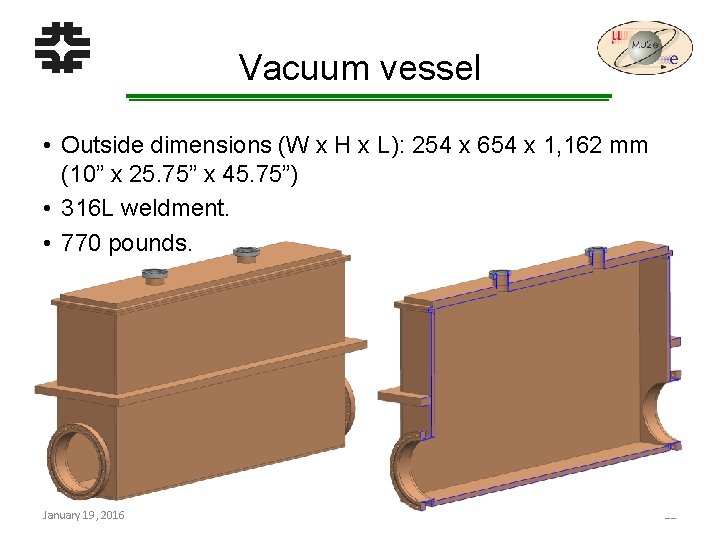
Vacuum vessel • Outside dimensions (W x H x L): 254 x 654 x 1, 162 mm (10” x 25. 75” x 45. 75”) • 316 L weldment. • 770 pounds. January 19, 2016 12
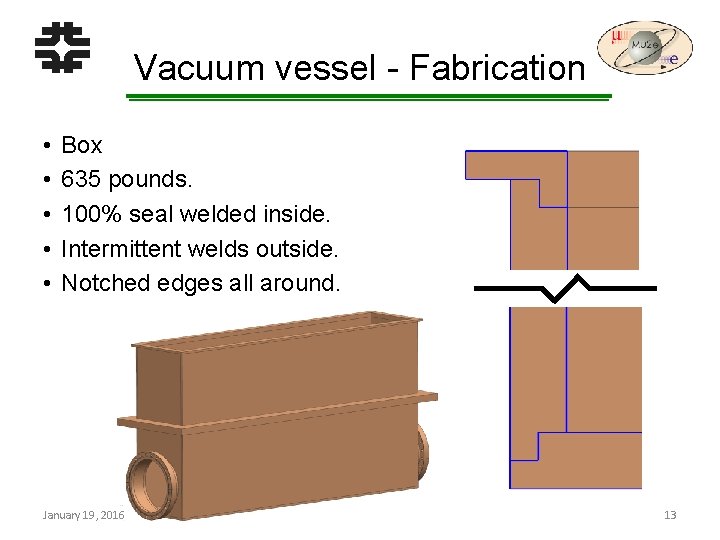
Vacuum vessel - Fabrication • • • Box 635 pounds. 100% seal welded inside. Intermittent welds outside. Notched edges all around. January 19, 2016 13
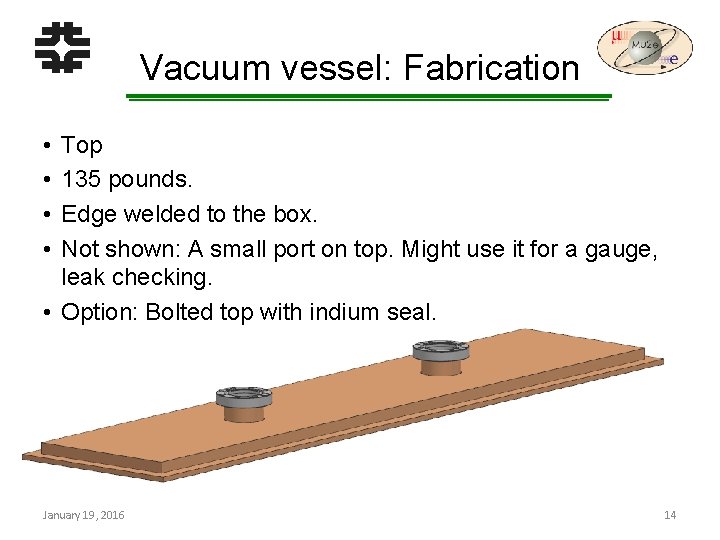
Vacuum vessel: Fabrication • • Top 135 pounds. Edge welded to the box. Not shown: A small port on top. Might use it for a gauge, leak checking. • Option: Bolted top with indium seal. January 19, 2016 14
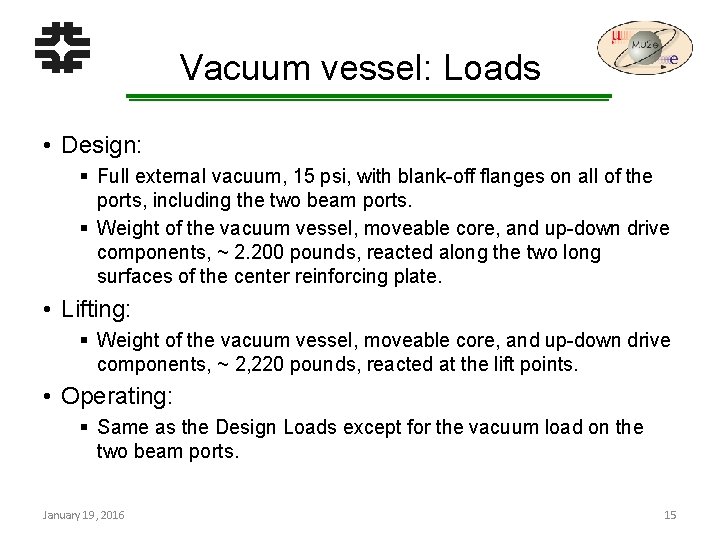
Vacuum vessel: Loads • Design: § Full external vacuum, 15 psi, with blank-off flanges on all of the ports, including the two beam ports. § Weight of the vacuum vessel, moveable core, and up-down drive components, ~ 2. 200 pounds, reacted along the two long surfaces of the center reinforcing plate. • Lifting: § Weight of the vacuum vessel, moveable core, and up-down drive components, ~ 2, 220 pounds, reacted at the lift points. • Operating: § Same as the Design Loads except for the vacuum load on the two beam ports. January 19, 2016 15
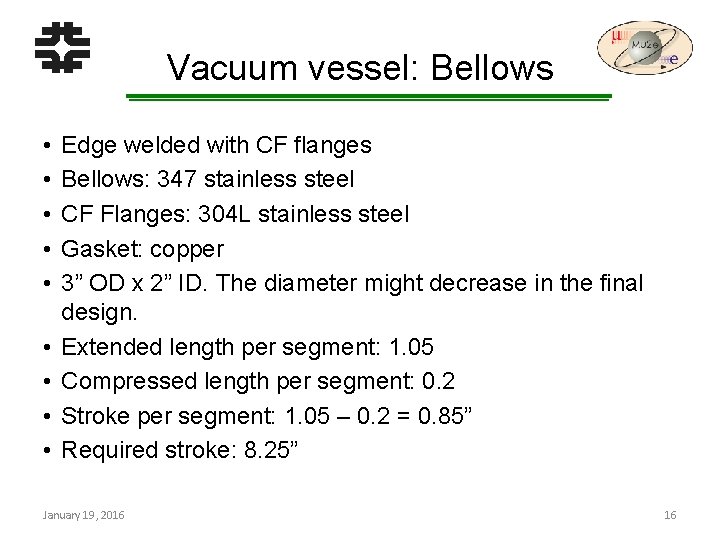
Vacuum vessel: Bellows • • • Edge welded with CF flanges Bellows: 347 stainless steel CF Flanges: 304 L stainless steel Gasket: copper 3” OD x 2” ID. The diameter might decrease in the final design. Extended length per segment: 1. 05 Compressed length per segment: 0. 2 Stroke per segment: 1. 05 – 0. 2 = 0. 85” Required stroke: 8. 25” January 19, 2016 16
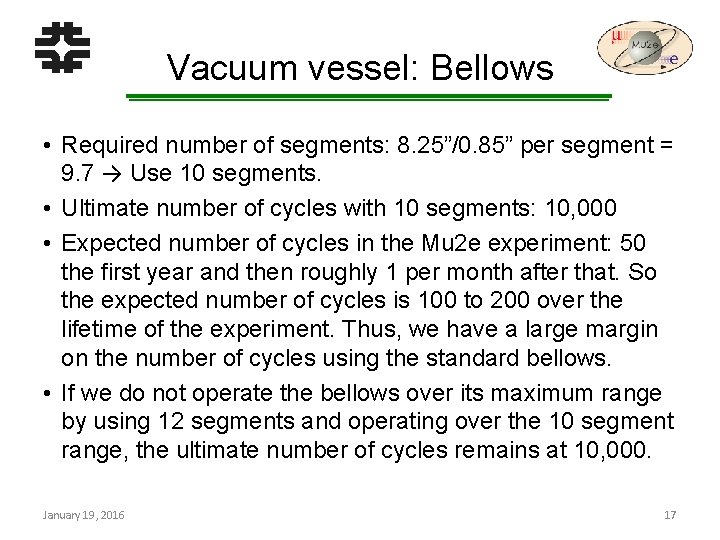
Vacuum vessel: Bellows • Required number of segments: 8. 25”/0. 85” per segment = 9. 7 → Use 10 segments. • Ultimate number of cycles with 10 segments: 10, 000 • Expected number of cycles in the Mu 2 e experiment: 50 the first year and then roughly 1 per month after that. So the expected number of cycles is 100 to 200 over the lifetime of the experiment. Thus, we have a large margin on the number of cycles using the standard bellows. • If we do not operate the bellows over its maximum range by using 12 segments and operating over the 10 segment range, the ultimate number of cycles remains at 10, 000. January 19, 2016 17
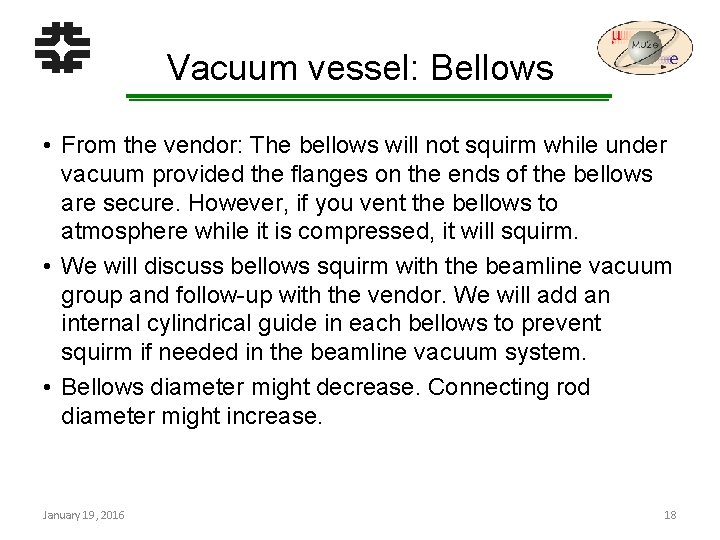
Vacuum vessel: Bellows • From the vendor: The bellows will not squirm while under vacuum provided the flanges on the ends of the bellows are secure. However, if you vent the bellows to atmosphere while it is compressed, it will squirm. • We will discuss bellows squirm with the beamline vacuum group and follow-up with the vendor. We will add an internal cylindrical guide in each bellows to prevent squirm if needed in the beamline vacuum system. • Bellows diameter might decrease. Connecting rod diameter might increase. January 19, 2016 18
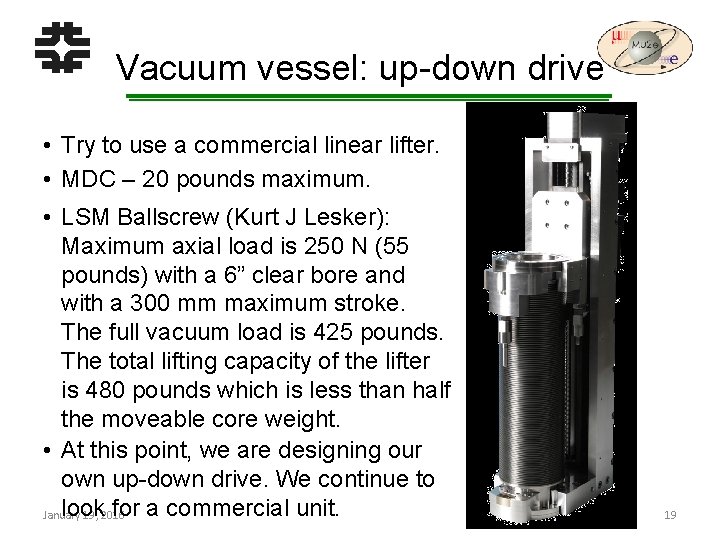
Vacuum vessel: up-down drive • Try to use a commercial linear lifter. • MDC – 20 pounds maximum. • LSM Ballscrew (Kurt J Lesker): Maximum axial load is 250 N (55 pounds) with a 6” clear bore and with a 300 mm maximum stroke. The full vacuum load is 425 pounds. The total lifting capacity of the lifter is 480 pounds which is less than half the moveable core weight. • At this point, we are designing our own up-down drive. We continue to look for a commercial unit. January 19, 2016 19
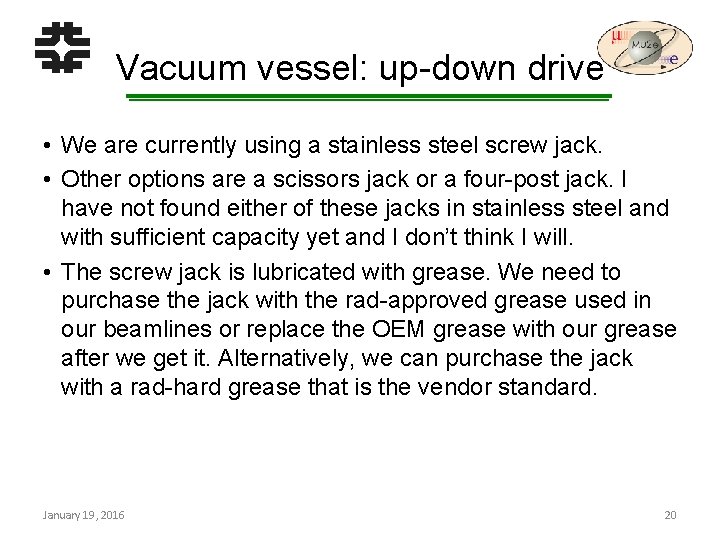
Vacuum vessel: up-down drive • We are currently using a stainless steel screw jack. • Other options are a scissors jack or a four-post jack. I have not found either of these jacks in stainless steel and with sufficient capacity yet and I don’t think I will. • The screw jack is lubricated with grease. We need to purchase the jack with the rad-approved grease used in our beamlines or replace the OEM grease with our grease after we get it. Alternatively, we can purchase the jack with a rad-hard grease that is the vendor standard. January 19, 2016 20
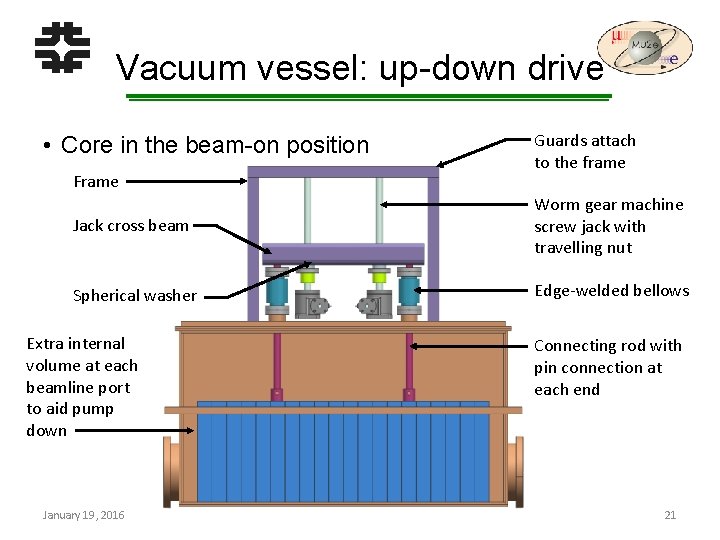
Vacuum vessel: up-down drive • Core in the beam-on position Frame Guards attach to the frame Jack cross beam Worm gear machine screw jack with travelling nut Spherical washer Edge-welded bellows Extra internal volume at each beamline port to aid pump down January 19, 2016 Connecting rod with pin connection at each end 21
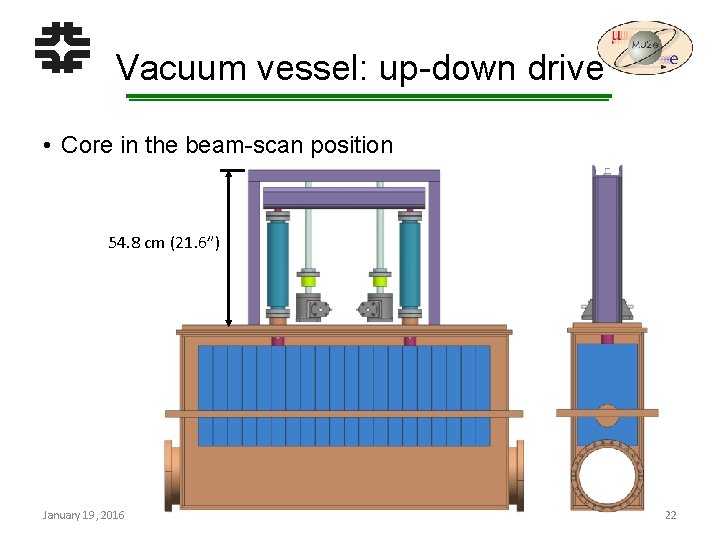
Vacuum vessel: up-down drive • Core in the beam-scan position 54. 8 cm (21. 6”) January 19, 2016 22
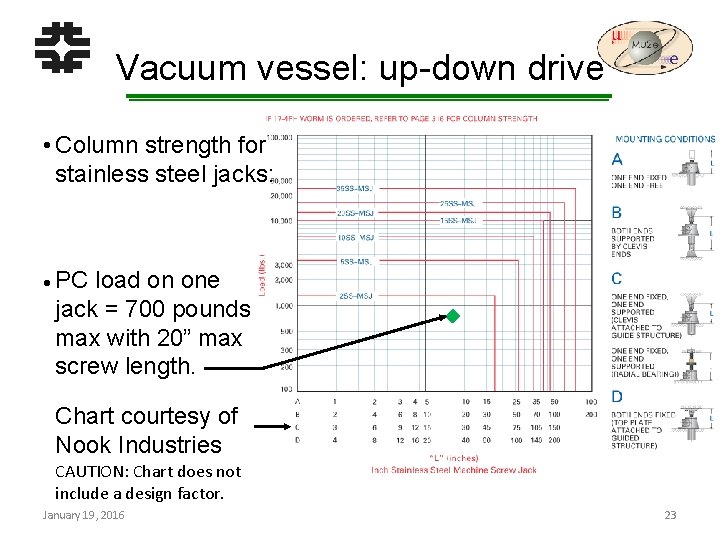
Vacuum vessel: up-down drive • Column strength for stainless steel jacks: • PC load on one jack = 700 pounds max with 20” max screw length. Chart courtesy of Nook Industries CAUTION: Chart does not include a design factor. January 19, 2016 23
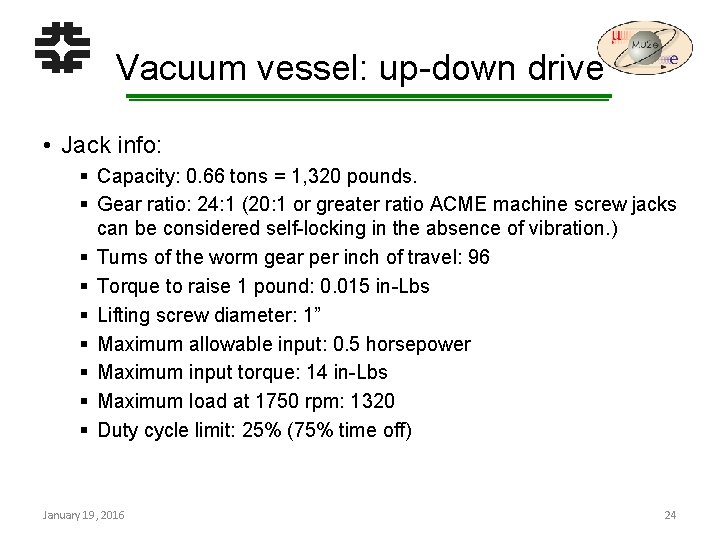
Vacuum vessel: up-down drive • Jack info: § Capacity: 0. 66 tons = 1, 320 pounds. § Gear ratio: 24: 1 (20: 1 or greater ratio ACME machine screw jacks can be considered self-locking in the absence of vibration. ) § Turns of the worm gear per inch of travel: 96 § Torque to raise 1 pound: 0. 015 in-Lbs § Lifting screw diameter: 1” § Maximum allowable input: 0. 5 horsepower § Maximum input torque: 14 in-Lbs § Maximum load at 1750 rpm: 1320 § Duty cycle limit: 25% (75% time off) January 19, 2016 24
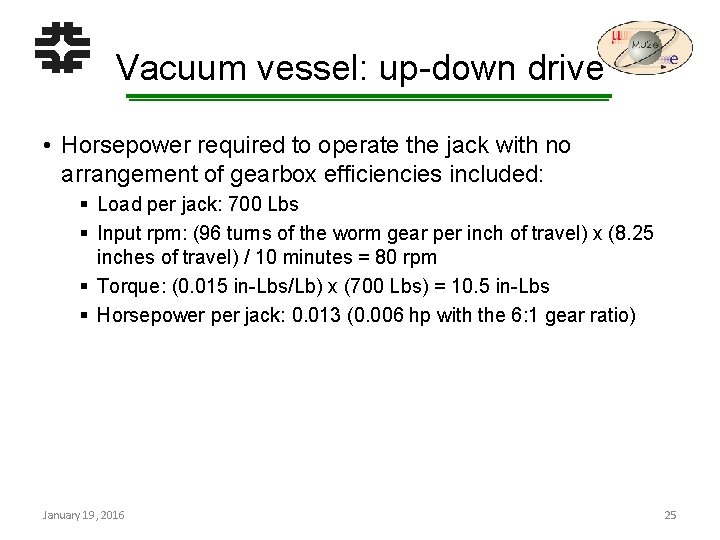
Vacuum vessel: up-down drive • Horsepower required to operate the jack with no arrangement of gearbox efficiencies included: § Load per jack: 700 Lbs § Input rpm: (96 turns of the worm gear per inch of travel) x (8. 25 inches of travel) / 10 minutes = 80 rpm § Torque: (0. 015 in-Lbs/Lb) x (700 Lbs) = 10. 5 in-Lbs § Horsepower per jack: 0. 013 (0. 006 hp with the 6: 1 gear ratio) January 19, 2016 25
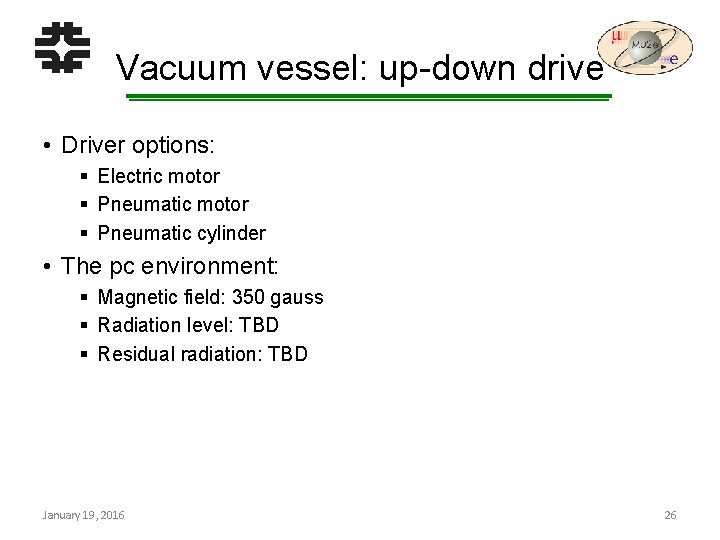
Vacuum vessel: up-down drive • Driver options: § Electric motor § Pneumatic cylinder • The pc environment: § Magnetic field: 350 gauss § Radiation level: TBD § Residual radiation: TBD January 19, 2016 26
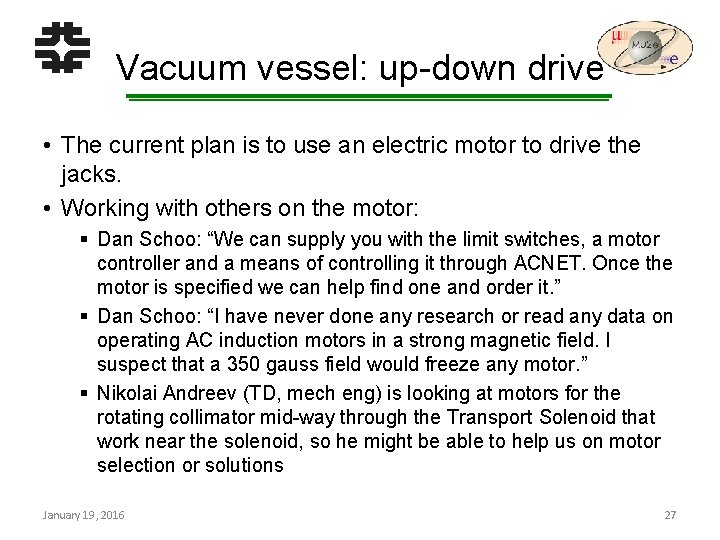
Vacuum vessel: up-down drive • The current plan is to use an electric motor to drive the jacks. • Working with others on the motor: § Dan Schoo: “We can supply you with the limit switches, a motor controller and a means of controlling it through ACNET. Once the motor is specified we can help find one and order it. ” § Dan Schoo: “I have never done any research or read any data on operating AC induction motors in a strong magnetic field. I suspect that a 350 gauss field would freeze any motor. ” § Nikolai Andreev (TD, mech eng) is looking at motors for the rotating collimator mid-way through the Transport Solenoid that work near the solenoid, so he might be able to help us on motor selection or solutions January 19, 2016 27
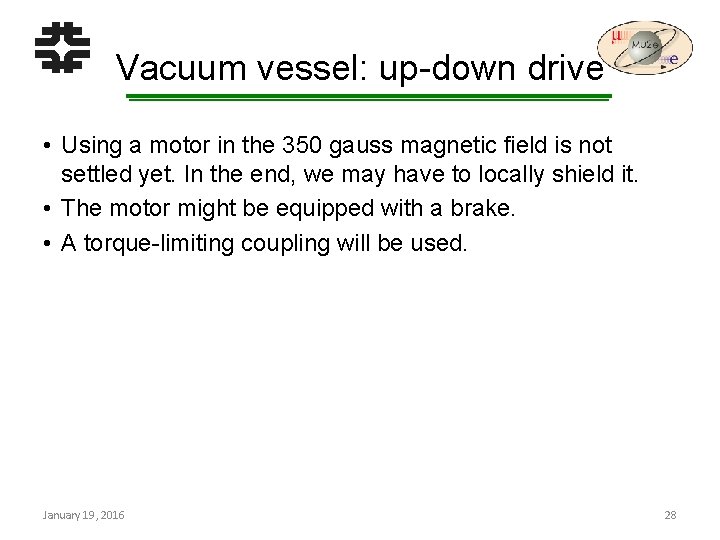
Vacuum vessel: up-down drive • Using a motor in the 350 gauss magnetic field is not settled yet. In the end, we may have to locally shield it. • The motor might be equipped with a brake. • A torque-limiting coupling will be used. January 19, 2016 28
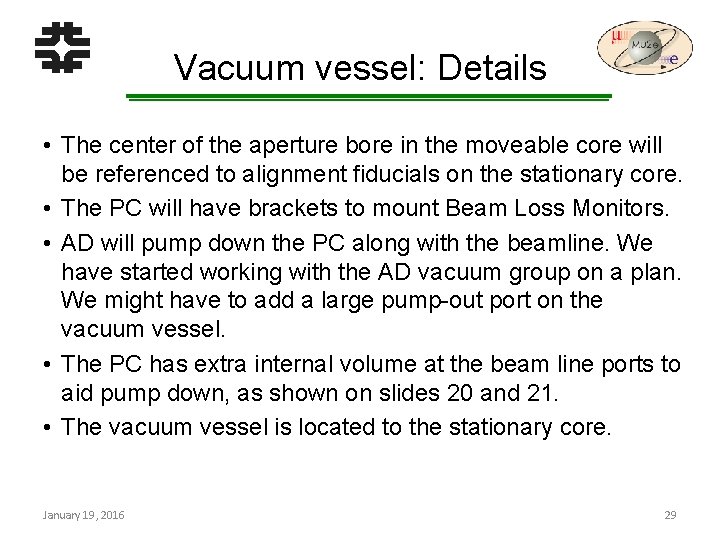
Vacuum vessel: Details • The center of the aperture bore in the moveable core will be referenced to alignment fiducials on the stationary core. • The PC will have brackets to mount Beam Loss Monitors. • AD will pump down the PC along with the beamline. We have started working with the AD vacuum group on a plan. We might have to add a large pump-out port on the vacuum vessel. • The PC has extra internal volume at the beam line ports to aid pump down, as shown on slides 20 and 21. • The vacuum vessel is located to the stationary core. January 19, 2016 29
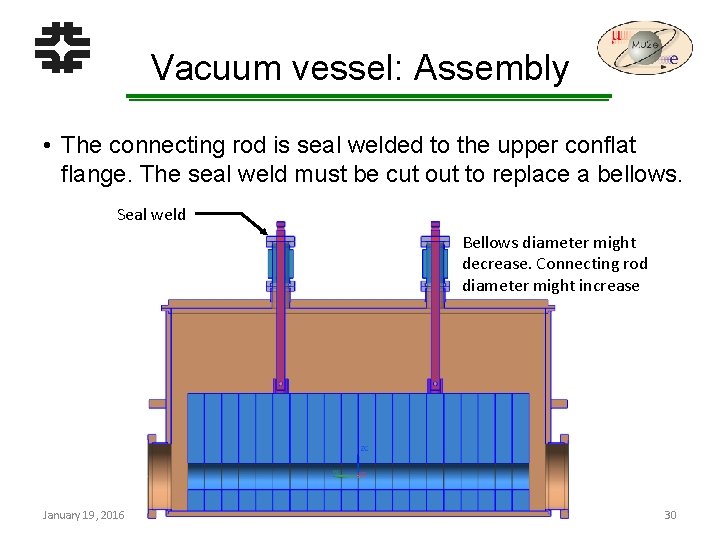
Vacuum vessel: Assembly • The connecting rod is seal welded to the upper conflat flange. The seal weld must be cut out to replace a bellows. Seal weld Bellows diameter might decrease. Connecting rod diameter might increase January 19, 2016 30
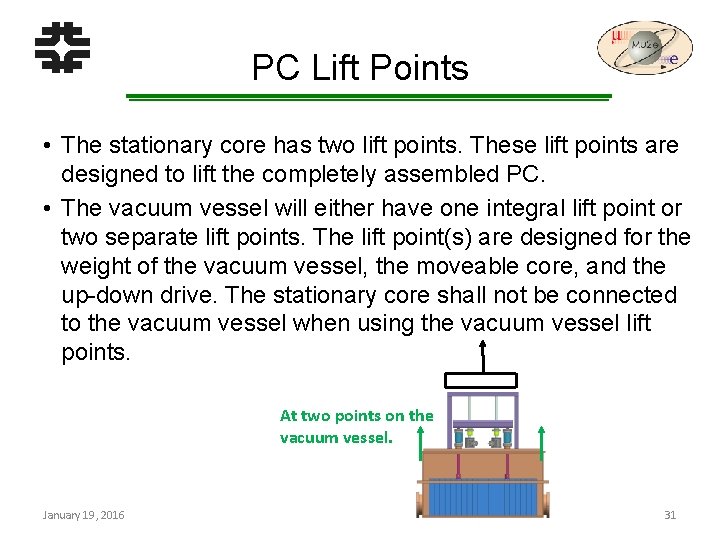
PC Lift Points • The stationary core has two lift points. These lift points are designed to lift the completely assembled PC. • The vacuum vessel will either have one integral lift point or two separate lift points. The lift point(s) are designed for the weight of the vacuum vessel, the moveable core, and the up-down drive. The stationary core shall not be connected to the vacuum vessel when using the vacuum vessel lift points. At two points on the vacuum vessel. January 19, 2016 31
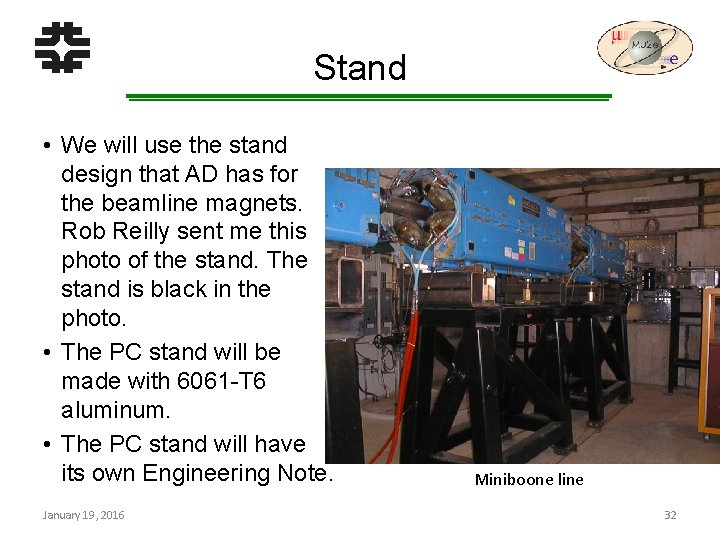
Stand • We will use the stand design that AD has for the beamline magnets. Rob Reilly sent me this photo of the stand. The stand is black in the photo. • The PC stand will be made with 6061 -T 6 aluminum. • The PC stand will have its own Engineering Note. January 19, 2016 Miniboone line 32
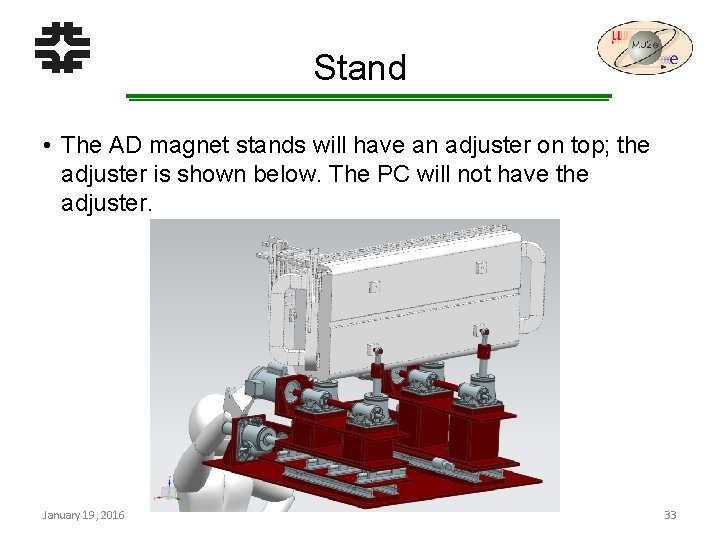
Stand • The AD magnet stands will have an adjuster on top; the adjuster is shown below. The PC will not have the adjuster. January 19, 2016 33
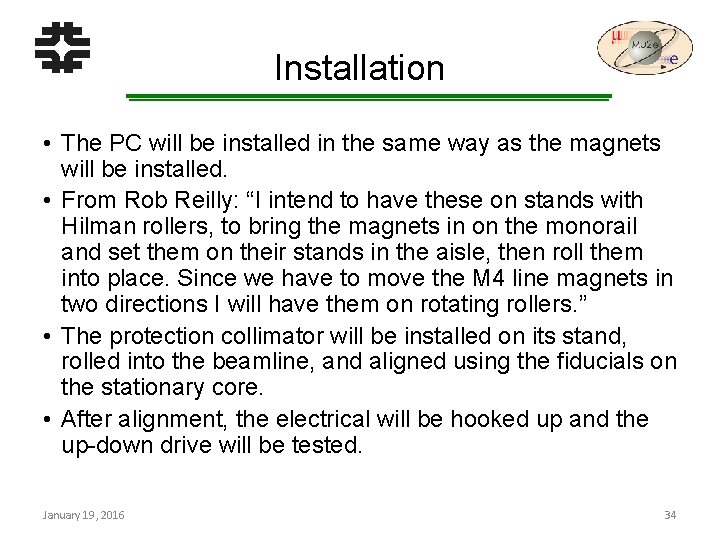
Installation • The PC will be installed in the same way as the magnets will be installed. • From Rob Reilly: “I intend to have these on stands with Hilman rollers, to bring the magnets in on the monorail and set them on their stands in the aisle, then roll them into place. Since we have to move the M 4 line magnets in two directions I will have them on rotating rollers. ” • The protection collimator will be installed on its stand, rolled into the beamline, and aligned using the fiducials on the stationary core. • After alignment, the electrical will be hooked up and the up-down drive will be tested. January 19, 2016 34
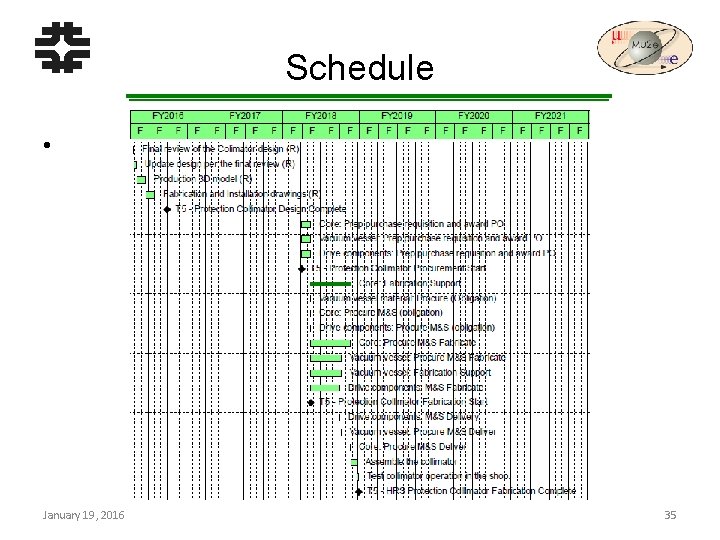
Schedule • January 19, 2016 35

To-do List • • Review all of the final requirements. Continue working with the AD Groups. Complete PC final design. Internal Project review of the PC final design. Review the schedule. Analysis and Engineering Note for the PC. Analysis and Engineering Note for the stand. Analysis and Engineering Note for the vacuum vessel spreader bar if it has two lift points. • Complete the Fermilab Engineering Manual Risk Assessment. January 19, 2016 36
Juraj štefánik
Roy stefanik
Collimator types
Collimator
Collimator of x ray tube
Collimator
Collimator of x ray tube
Andy krajewski
Shamshuritawati sharif
Put in the verbs in brackets into the gaps. use simple past
Pop art jasper johns
Dr. andy woods
Andy parker cambridge
How to put off doing a job by andy rooney
What tourist places does tamal tell andy about
Andy woods daniel
Descriptive grammar
Andy field
What is andy's opportunity cost of cleaning offices
Amd v/f
Junej
Andy garcia niece
Andy woods angelology
Andy woods soteriology
Icicle star andy goldsworthy
Andy philpott
Co teaching andy højholdt
Doble elvis andy warhol
Keely kangaroo alphafriends
Andy woods zechariah
Andy chien
Andy højholdt samarbejdsformer
Andy philippides
Andy warhol monochromatic
Andy griffith pickles
H2cor
Andy pavlo