MACH 112 Cutting Tools Measurement Reamers and Reaming
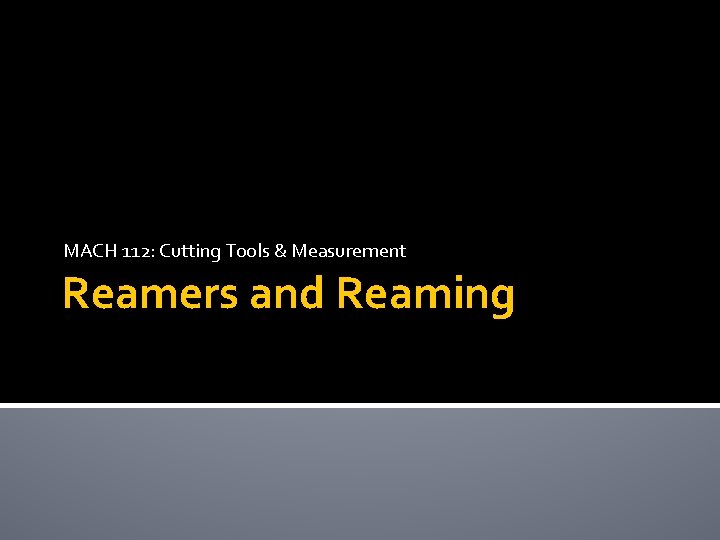
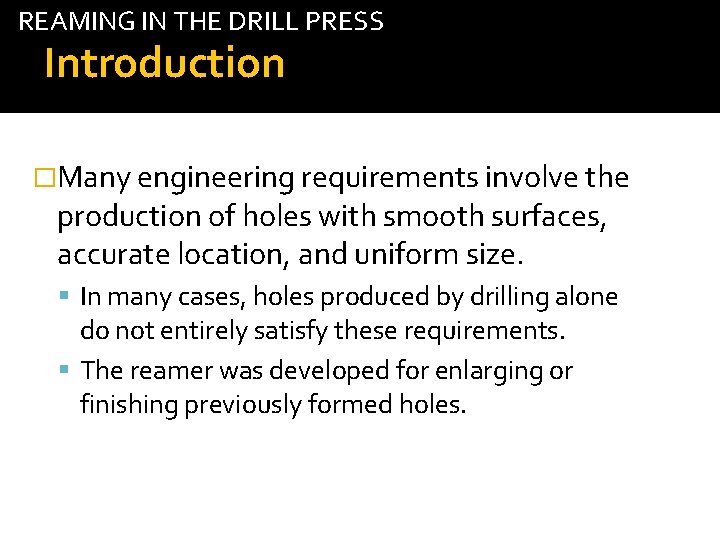
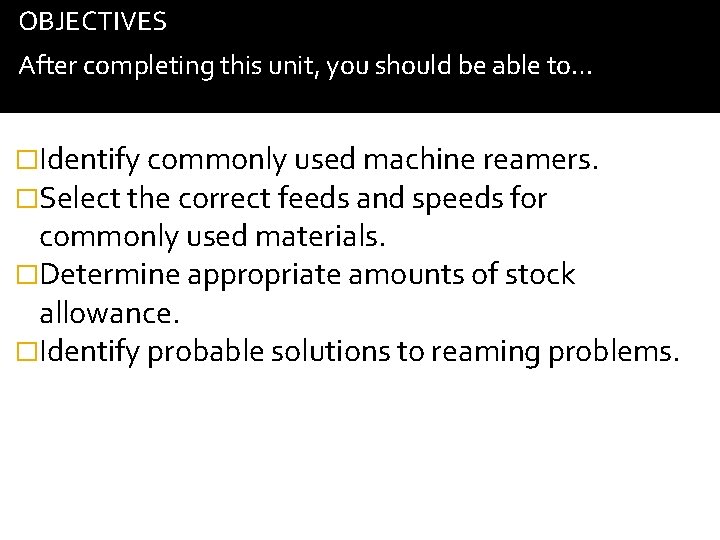
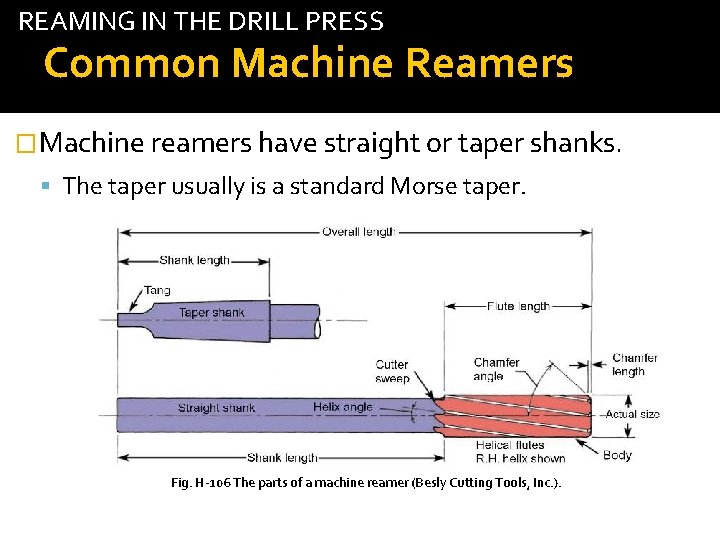
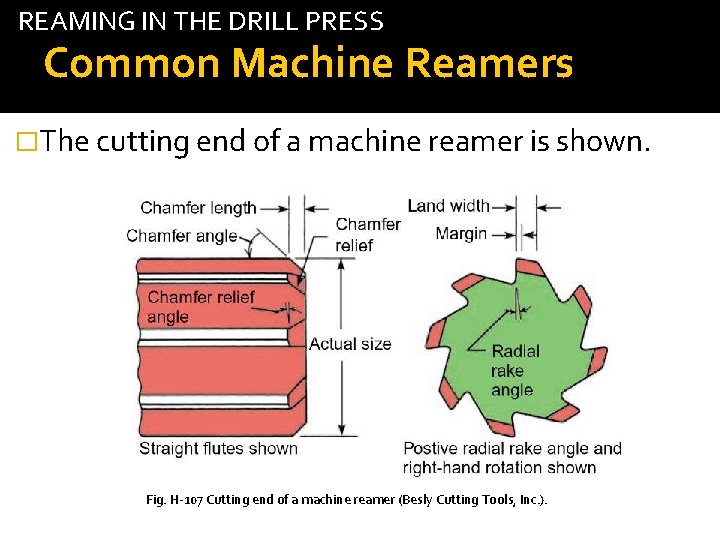
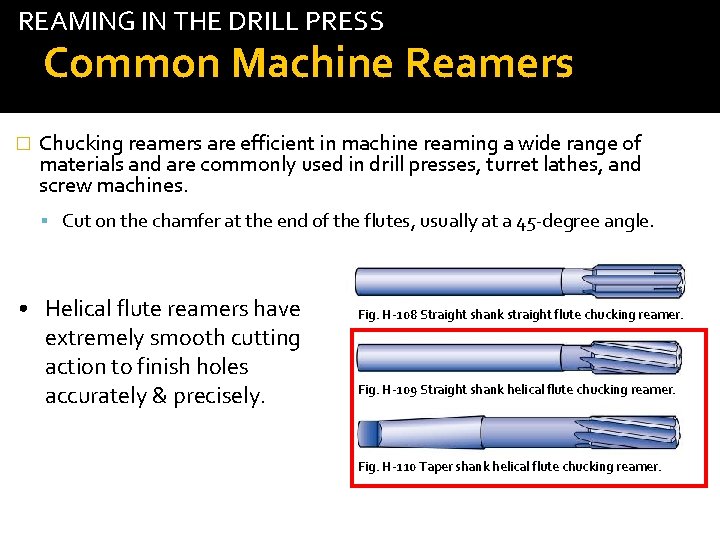

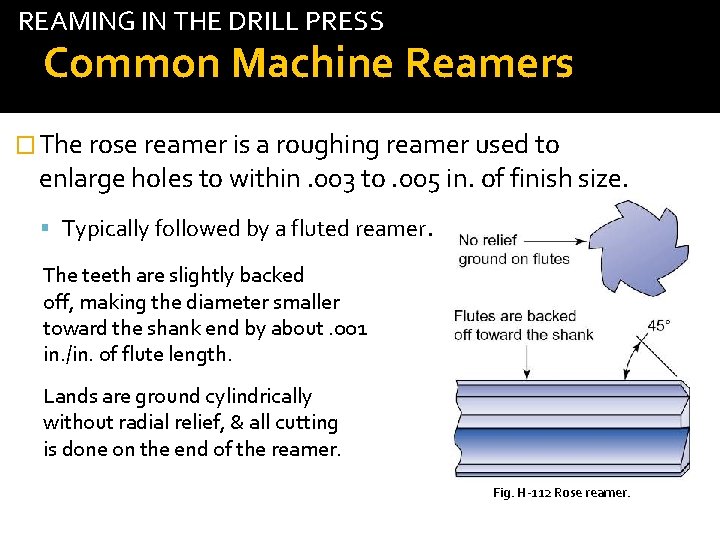
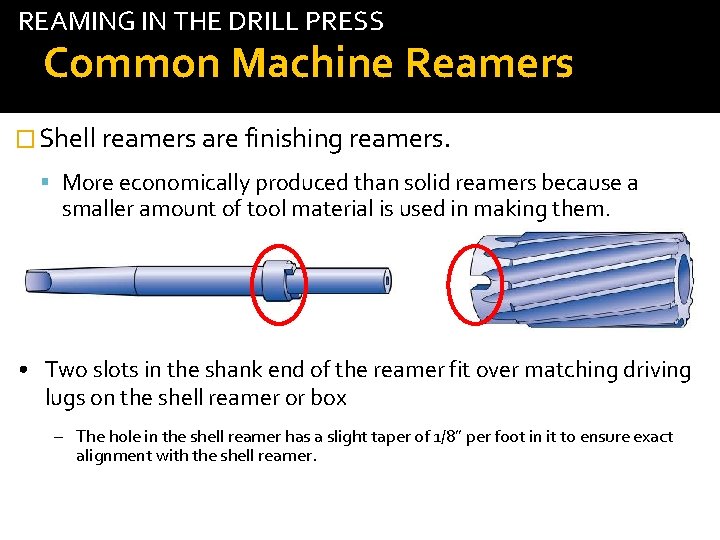
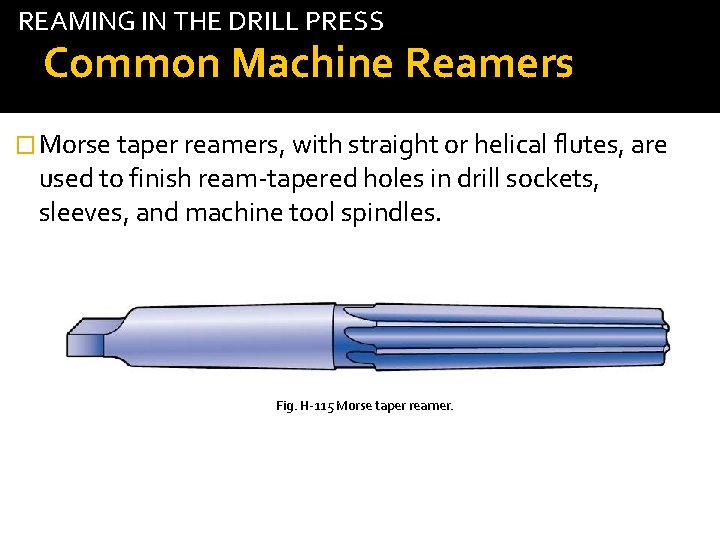
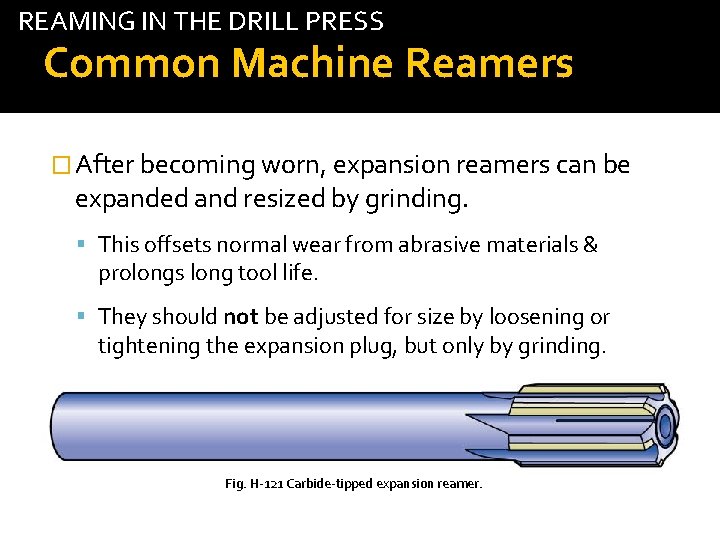
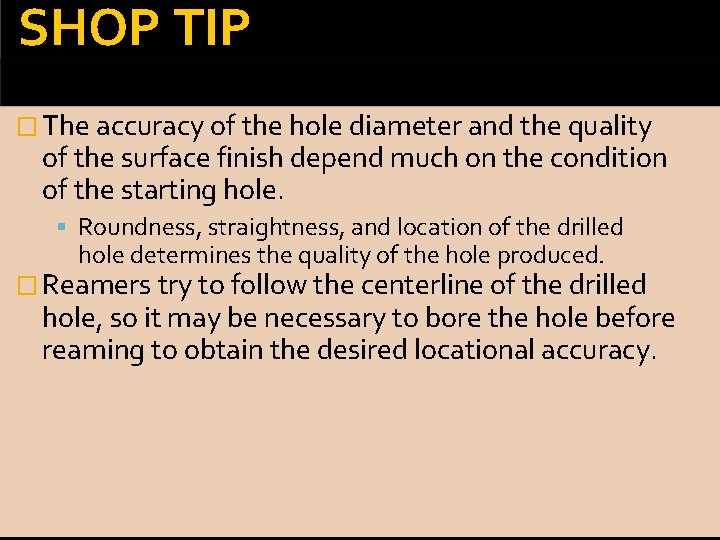
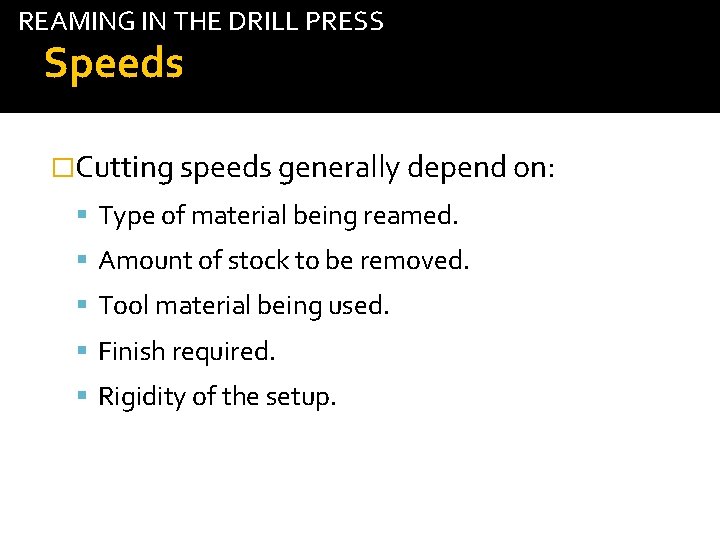
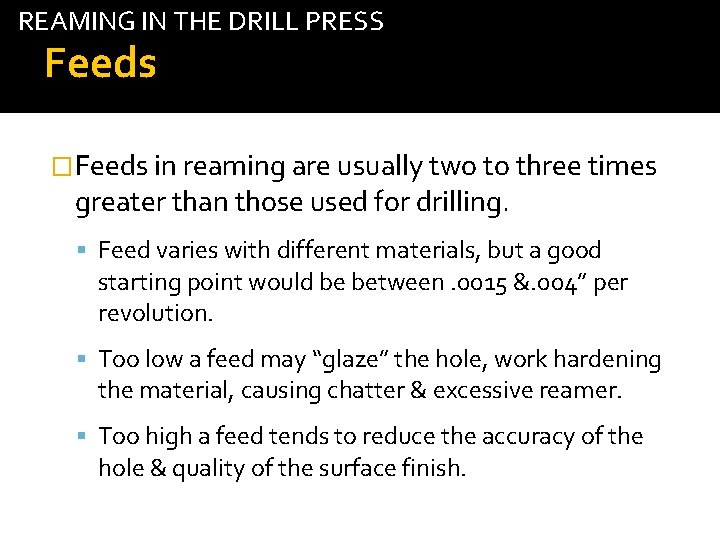
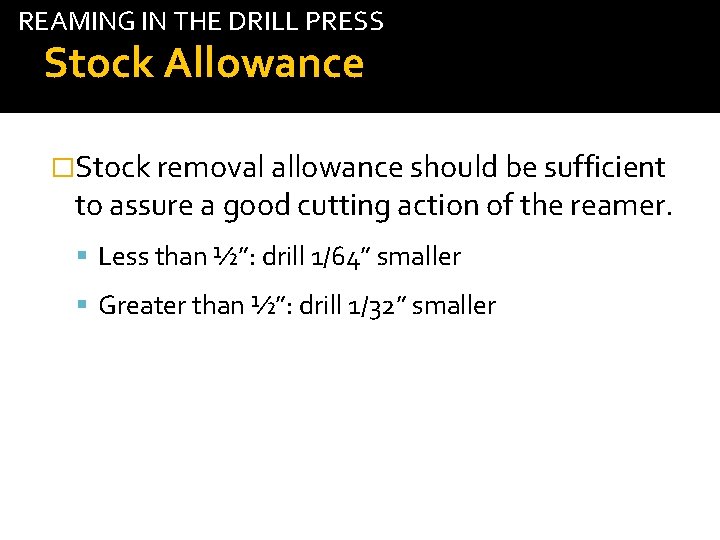
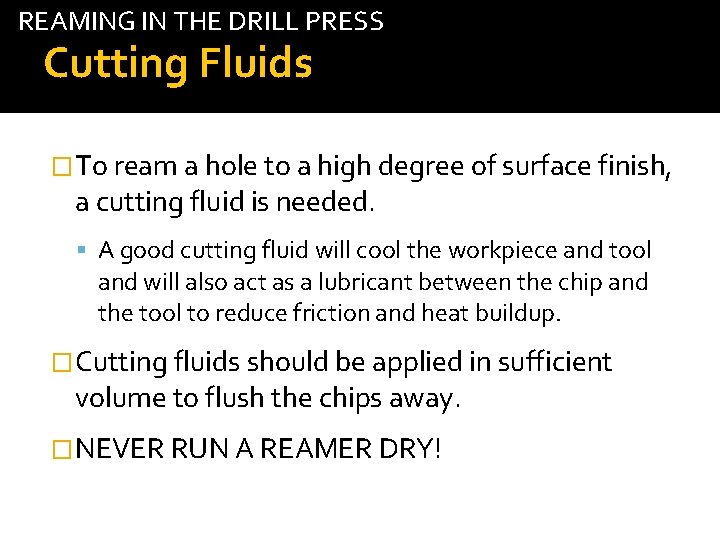
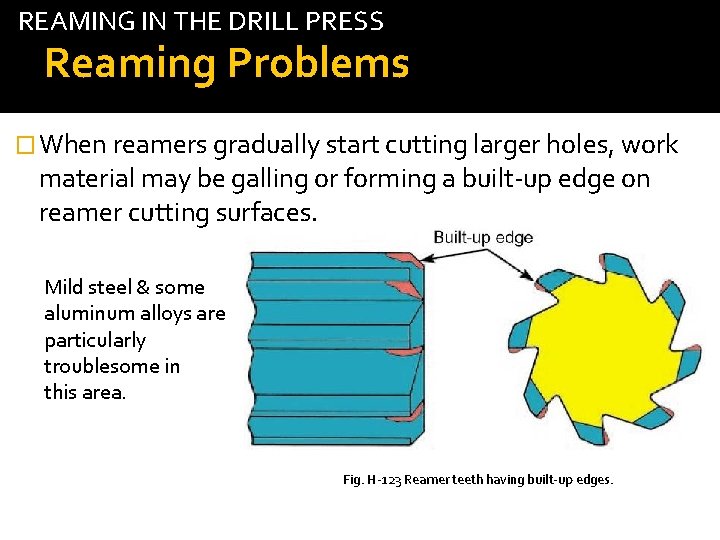
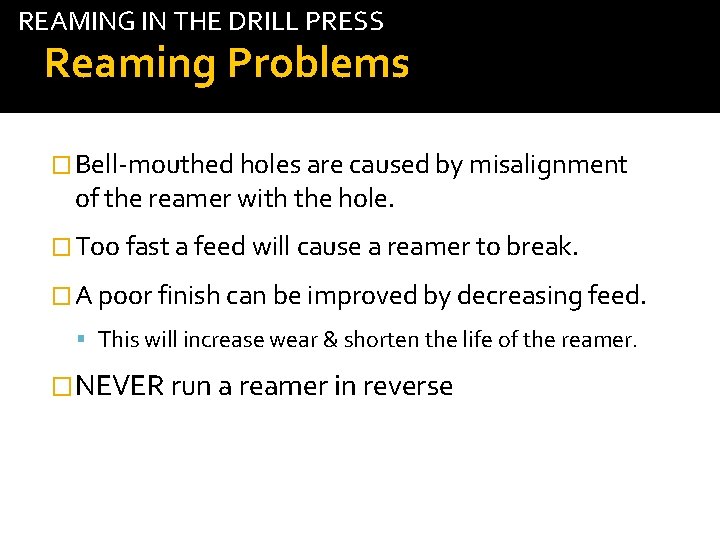
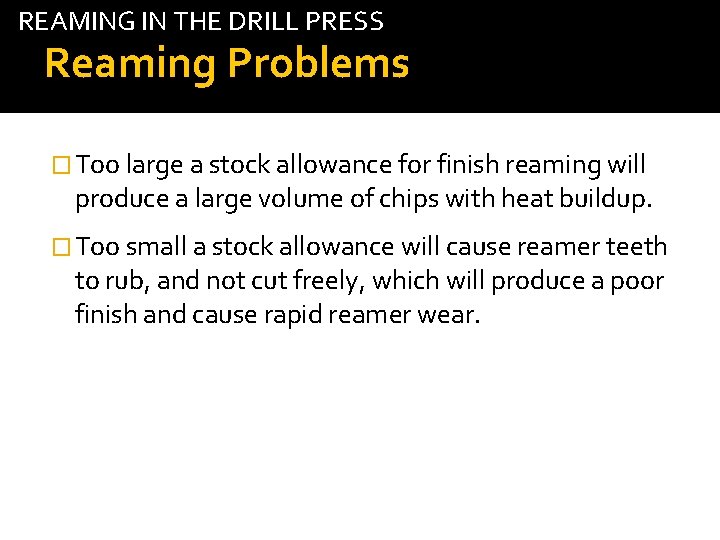
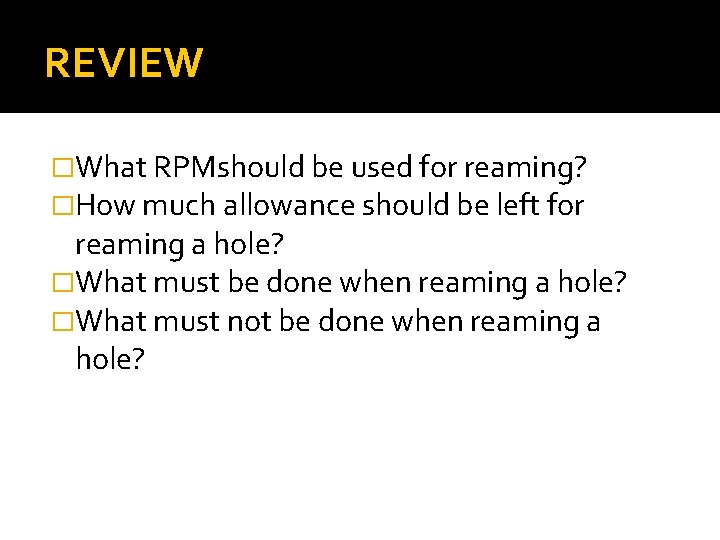
- Slides: 20
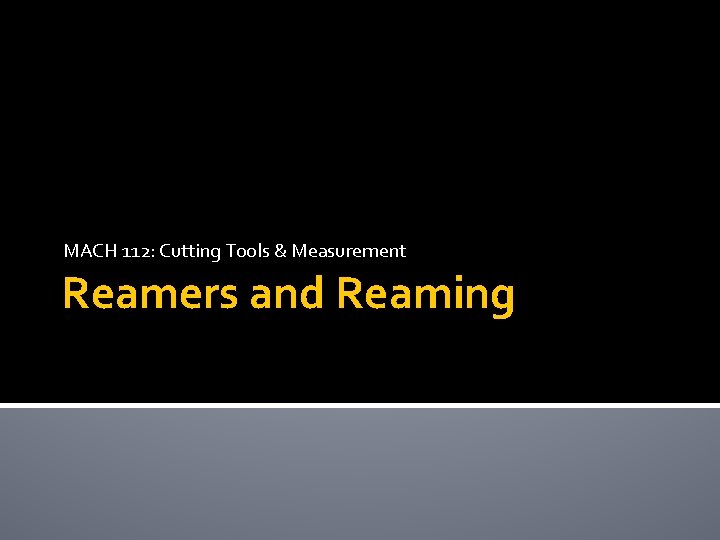
MACH 112: Cutting Tools & Measurement Reamers and Reaming
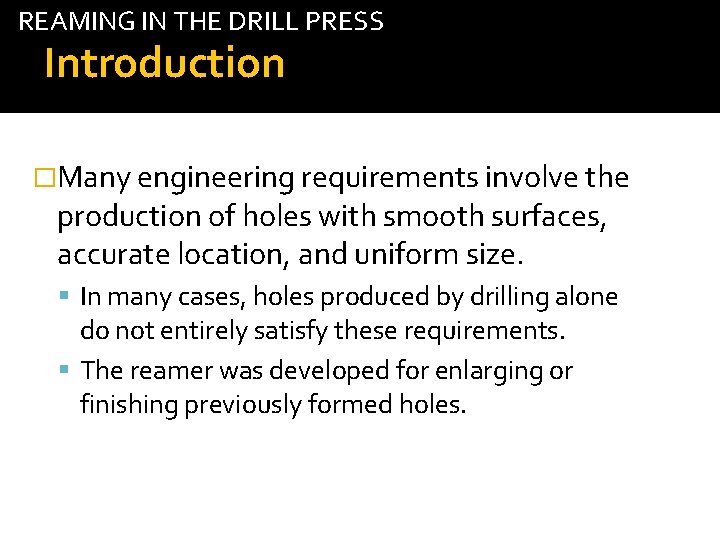
REAMING IN THE DRILL PRESS Introduction �Many engineering requirements involve the production of holes with smooth surfaces, accurate location, and uniform size. In many cases, holes produced by drilling alone do not entirely satisfy these requirements. The reamer was developed for enlarging or finishing previously formed holes. tab
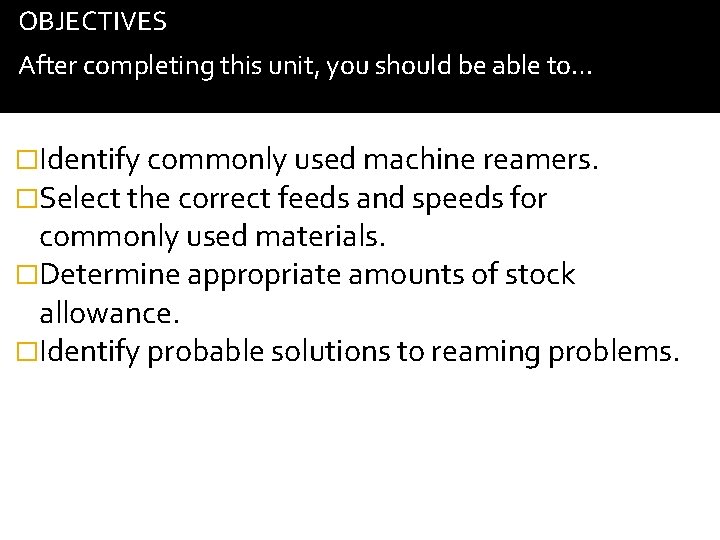
OBJECTIVES After completing this unit, you should be able to… �Identify commonly used machine reamers. �Select the correct feeds and speeds for commonly used materials. �Determine appropriate amounts of stock allowance. �Identify probable solutions to reaming problems.
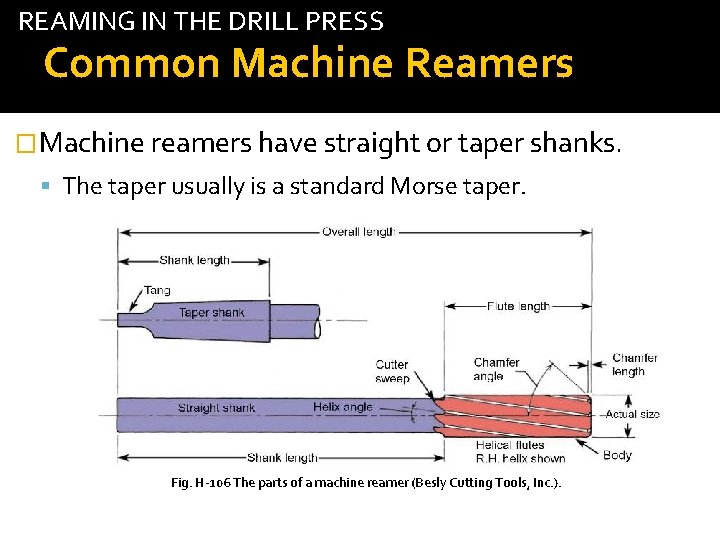
REAMING IN THE DRILL PRESS Common Machine Reamers �Machine reamers have straight or taper shanks. The taper usually is a standard Morse taper. Fig. H-106 The parts of a machine reamer (Besly Cutting Tools, Inc. ). tab
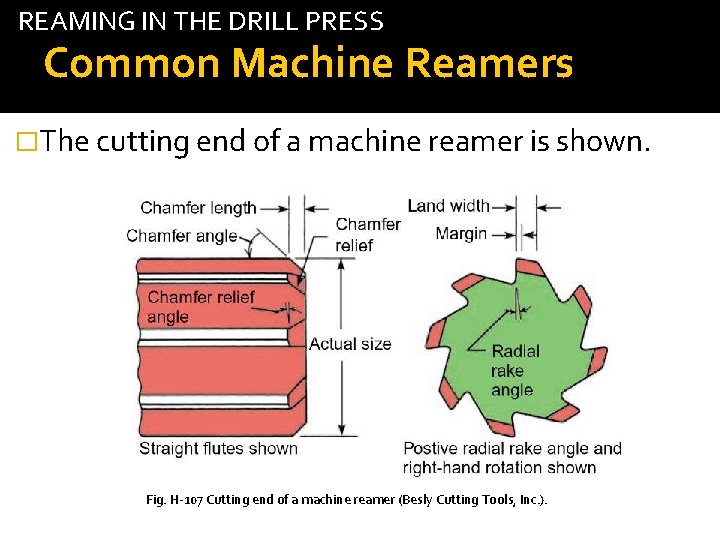
REAMING IN THE DRILL PRESS Common Machine Reamers �The cutting end of a machine reamer is shown. Fig. H-107 Cutting end of a machine reamer (Besly Cutting Tools, Inc. ). tab
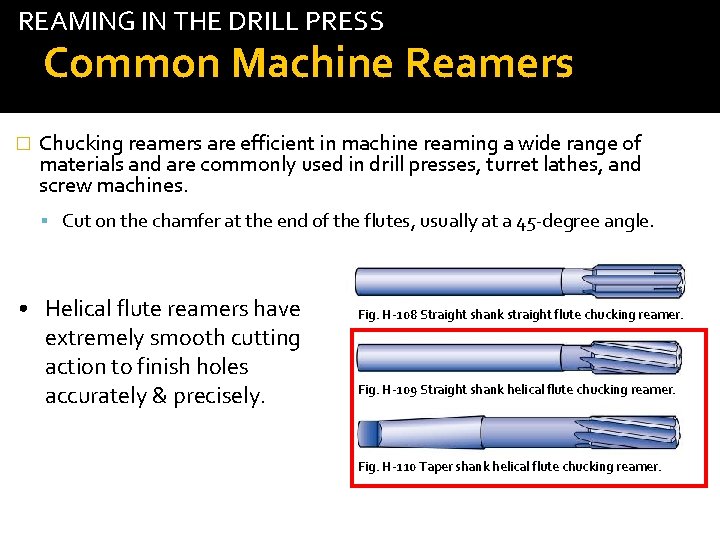
REAMING IN THE DRILL PRESS tab Common Machine Reamers � Chucking reamers are efficient in machine reaming a wide range of materials and are commonly used in drill presses, turret lathes, and screw machines. Cut on the chamfer at the end of the flutes, usually at a 45 -degree angle. • Helical flute reamers have extremely smooth cutting action to finish holes accurately & precisely. Fig. H-108 Straight shank straight flute chucking reamer. Fig. H-109 Straight shank helical flute chucking reamer. Fig. H-110 Taper shank helical flute chucking reamer.

REAMING IN THE DRILL PRESS tab Common Machine Reamers �Jobber’s reamers are used where a longer flute length than that of chucking reamers is needed. Additional flute length gives added guide to the reamer, especially when reaming deep holes. Fig. H-111 Taper shank straight flute jobber’s reamer.
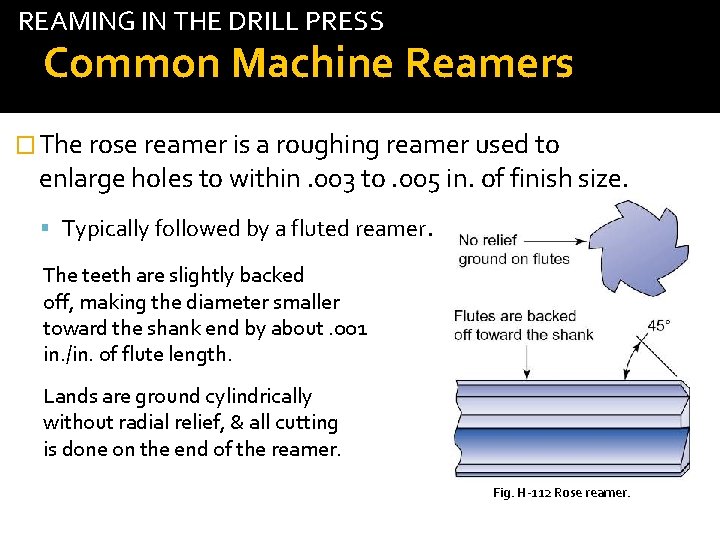
REAMING IN THE DRILL PRESS tab Common Machine Reamers � The rose reamer is a roughing reamer used to enlarge holes to within. 003 to. 005 in. of finish size. Typically followed by a fluted reamer. The teeth are slightly backed off, making the diameter smaller toward the shank end by about. 001 in. /in. of flute length. Lands are ground cylindrically without radial relief, & all cutting is done on the end of the reamer. Fig. H-112 Rose reamer.
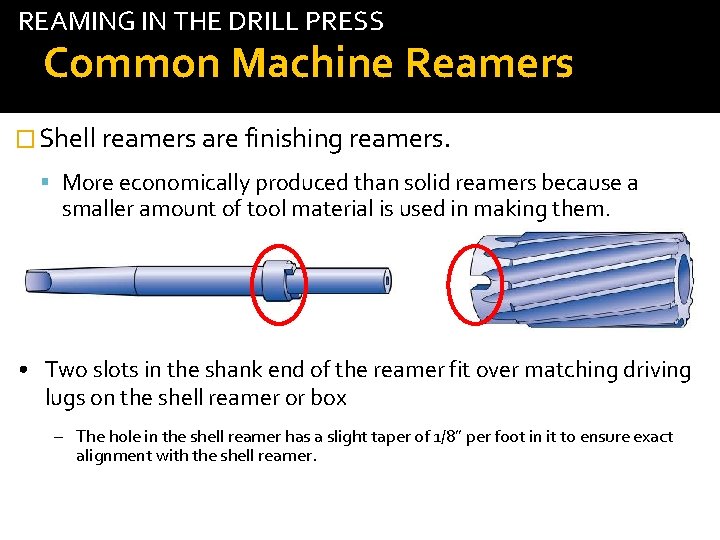
REAMING IN THE DRILL PRESS tab Common Machine Reamers � Shell reamers are finishing reamers. More economically produced than solid reamers because a smaller amount of tool material is used in making them. • Two slots in the shank end of the reamer fit over matching driving lugs on the shell reamer or box – The hole in the shell reamer has a slight taper of 1/8” per foot in it to ensure exact alignment with the shell reamer.
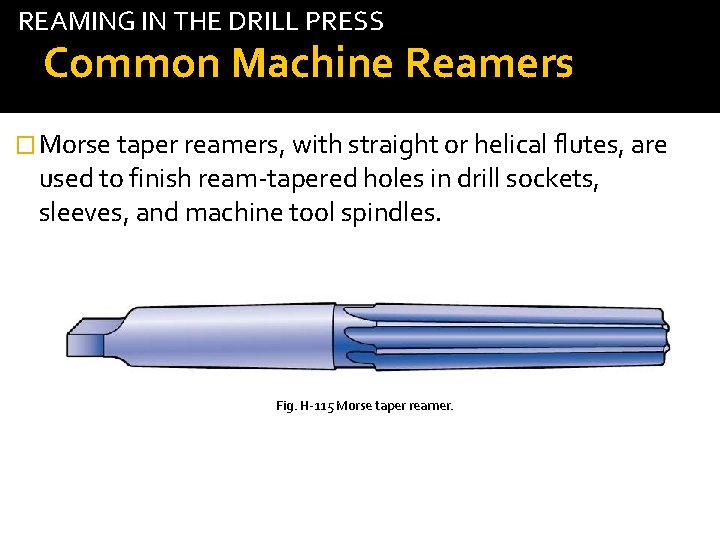
REAMING IN THE DRILL PRESS tab Common Machine Reamers � Morse taper reamers, with straight or helical flutes, are used to finish ream-tapered holes in drill sockets, sleeves, and machine tool spindles. Fig. H-115 Morse taper reamer.
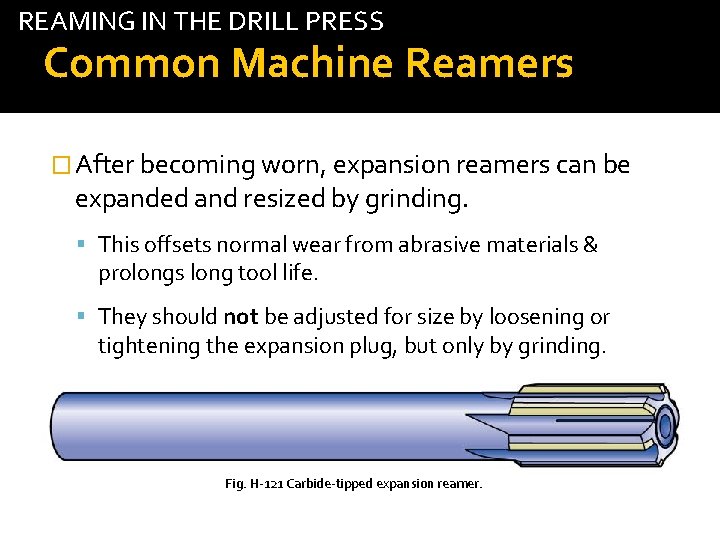
REAMING IN THE DRILL PRESS Common Machine Reamers � After becoming worn, expansion reamers can be expanded and resized by grinding. This offsets normal wear from abrasive materials & prolongs long tool life. They should not be adjusted for size by loosening or tightening the expansion plug, but only by grinding. Fig. H-121 Carbide-tipped expansion reamer. tab
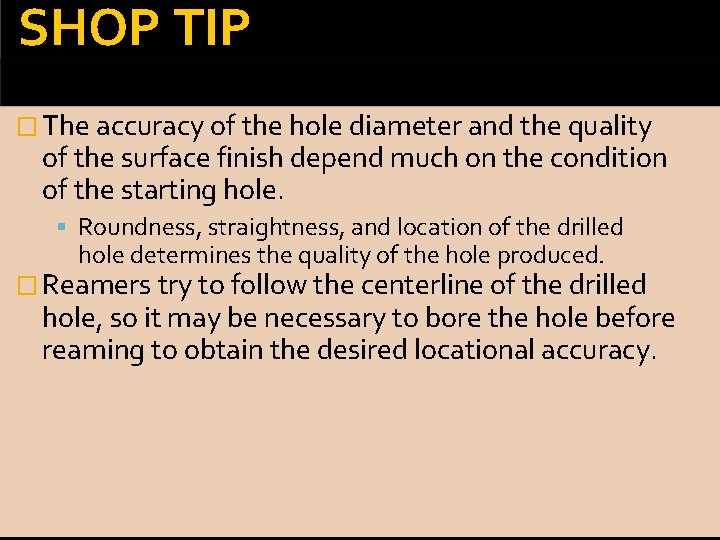
SHOP TIP tab � The accuracy of the hole diameter and the quality of the surface finish depend much on the condition of the starting hole. Roundness, straightness, and location of the drilled hole determines the quality of the hole produced. � Reamers try to follow the centerline of the drilled hole, so it may be necessary to bore the hole before reaming to obtain the desired locational accuracy.
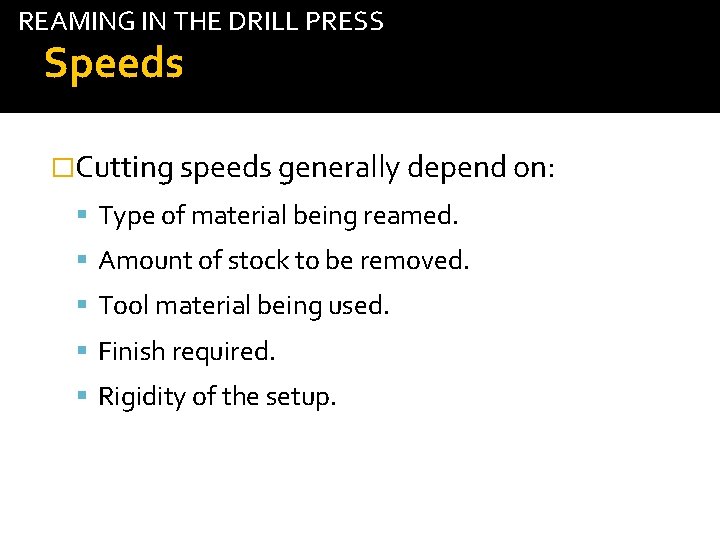
REAMING IN THE DRILL PRESS Speeds �Cutting speeds generally depend on: Type of material being reamed. Amount of stock to be removed. Tool material being used. Finish required. Rigidity of the setup. tab
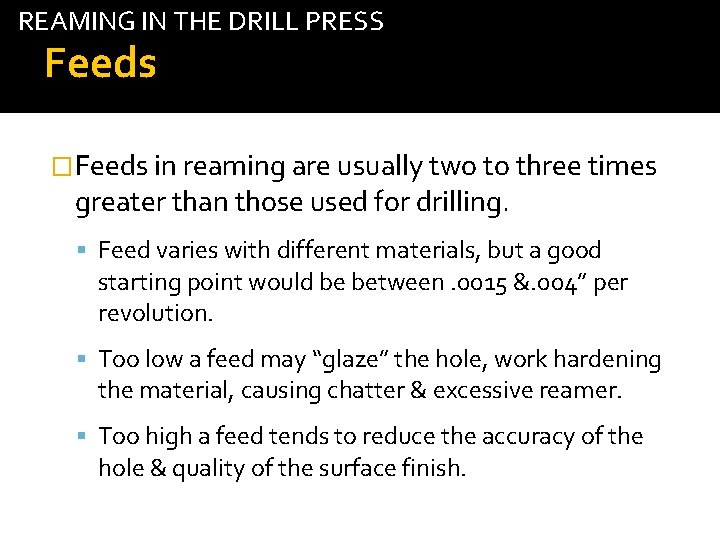
REAMING IN THE DRILL PRESS Feeds �Feeds in reaming are usually two to three times greater than those used for drilling. Feed varies with different materials, but a good starting point would be between. 0015 &. 004” per revolution. Too low a feed may “glaze” the hole, work hardening the material, causing chatter & excessive reamer. Too high a feed tends to reduce the accuracy of the hole & quality of the surface finish. tab
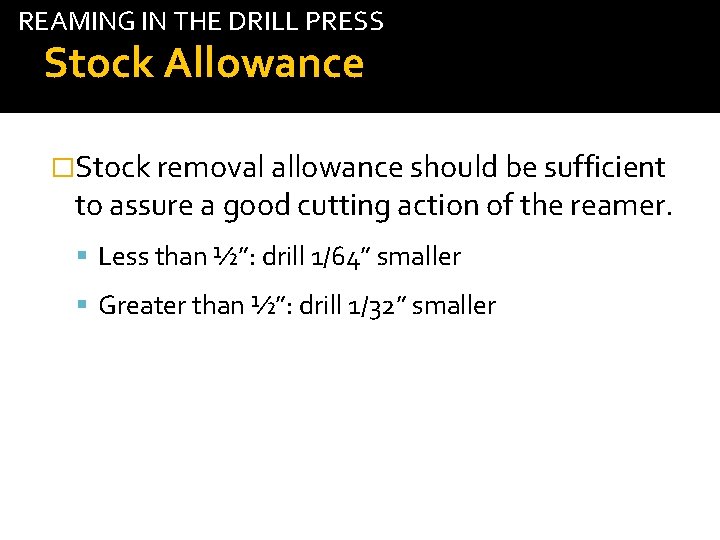
REAMING IN THE DRILL PRESS Stock Allowance �Stock removal allowance should be sufficient tab to assure a good cutting action of the reamer. Less than ½”: drill 1/64” smaller Greater than ½”: drill 1/32” smaller
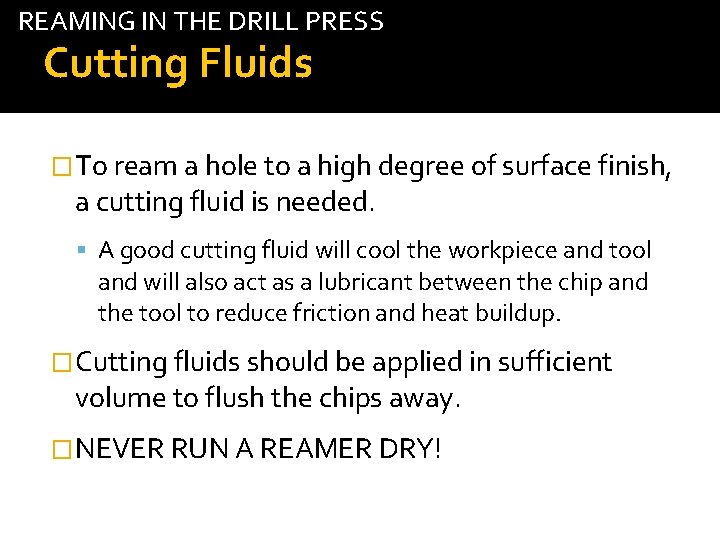
REAMING IN THE DRILL PRESS Cutting Fluids tab �To ream a hole to a high degree of surface finish, a cutting fluid is needed. A good cutting fluid will cool the workpiece and tool and will also act as a lubricant between the chip and the tool to reduce friction and heat buildup. �Cutting fluids should be applied in sufficient volume to flush the chips away. �NEVER RUN A REAMER DRY!
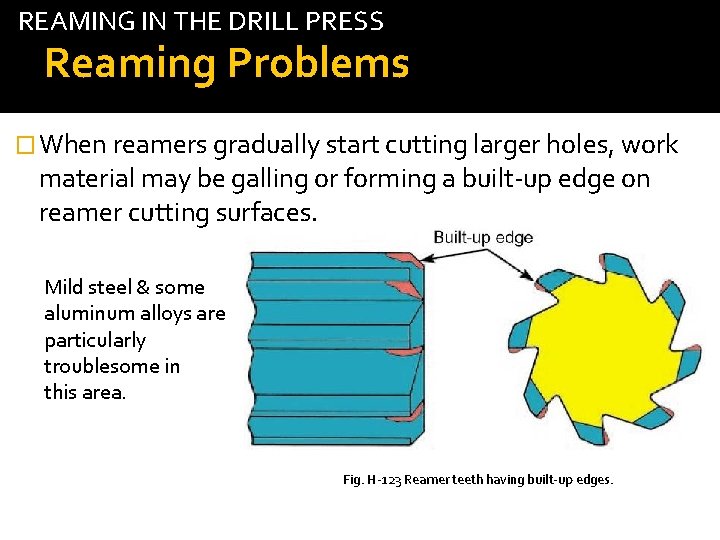
REAMING IN THE DRILL PRESS Reaming Problems tab � When reamers gradually start cutting larger holes, work material may be galling or forming a built-up edge on reamer cutting surfaces. Mild steel & some aluminum alloys are particularly troublesome in this area. Fig. H-123 Reamer teeth having built-up edges.
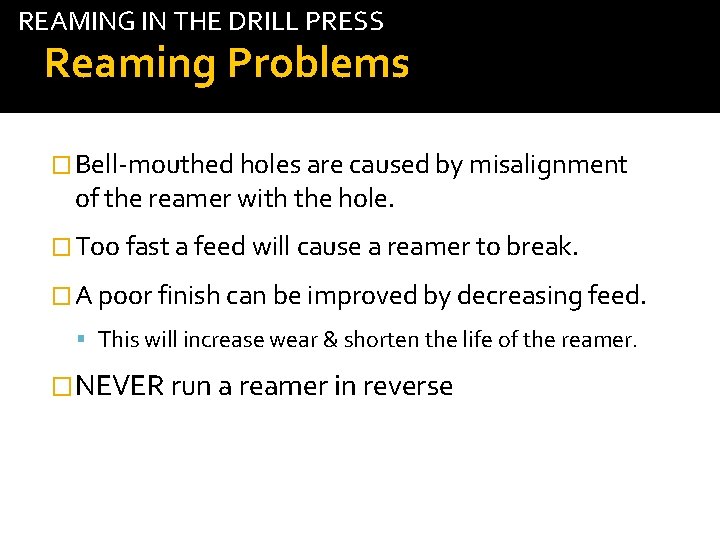
REAMING IN THE DRILL PRESS Reaming Problems � Bell-mouthed holes are caused by misalignment of the reamer with the hole. � Too fast a feed will cause a reamer to break. � A poor finish can be improved by decreasing feed. This will increase wear & shorten the life of the reamer. �NEVER run a reamer in reverse tab
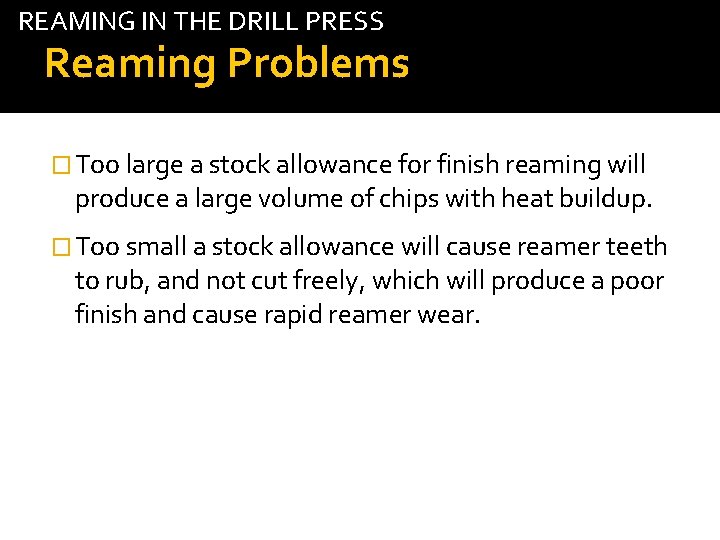
REAMING IN THE DRILL PRESS Reaming Problems tab � Too large a stock allowance for finish reaming will produce a large volume of chips with heat buildup. � Too small a stock allowance will cause reamer teeth to rub, and not cut freely, which will produce a poor finish and cause rapid reamer wear.
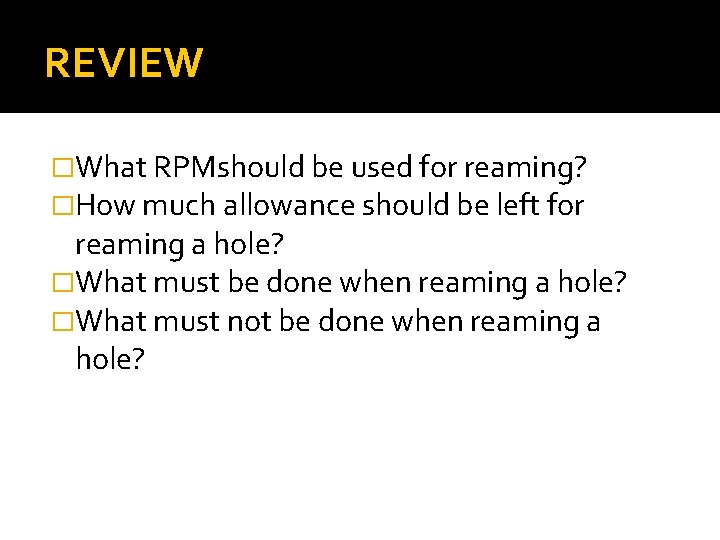
REVIEW �What RPMshould be used for reaming? �How much allowance should be left for reaming a hole? �What must be done when reaming a hole? �What must not be done when reaming a hole?
Ethical dilemma in social work
Cos 112,5
Reaming process
Drill and ream
Reaming allowance
Pipaflare
Spoon excavator history
Instrument grasps used in operative dentistry
Chapter 18 basic chairside instruments and tray systems
The appropriate cutting tool used in cutting fabrics
Lip angle of single point cutting tool
Description of holding tools
Cutting tools
Lesson 2 measurement and scientific tools answer key
Lesson 2 measurement and scientific tools answer key
Lesson 2 measurement and scientific tools answer key
Cutting tool classification
Folding knife definition floral design
Mach drills
Types of lathe tools
The tool used for making internal threads is called as