LNG READY SOLUTION USING A MARK FIT LNG
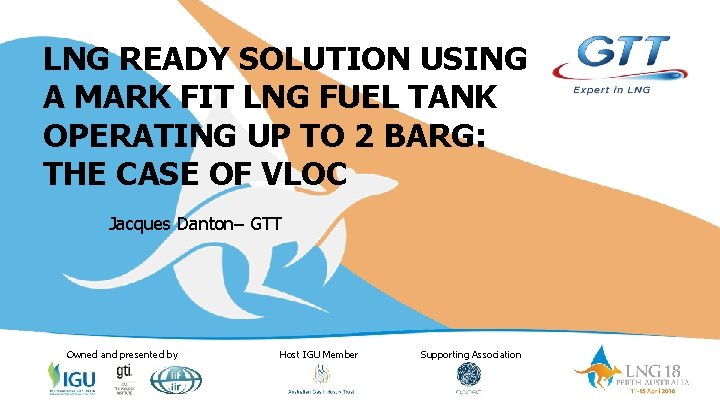
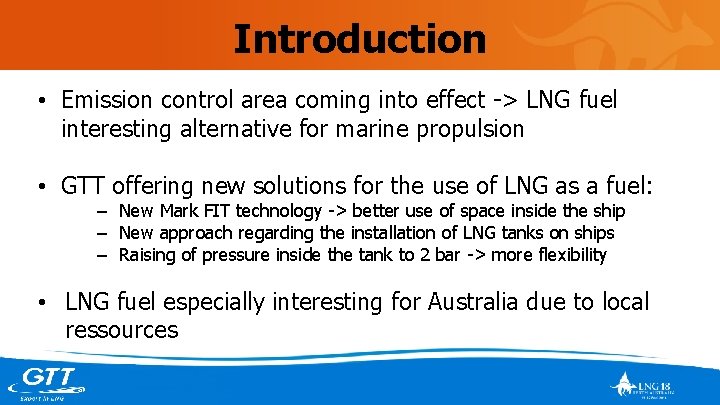
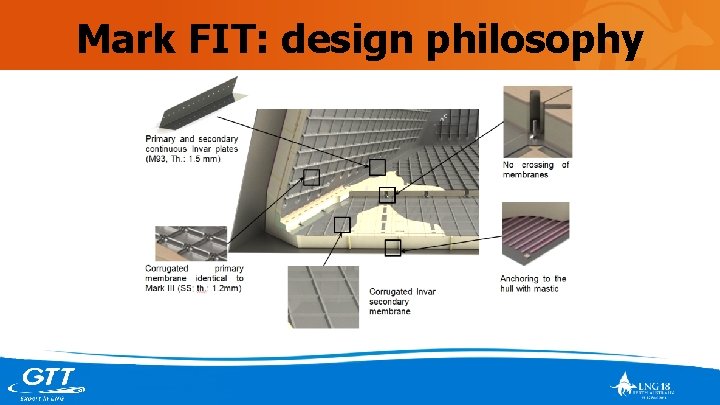
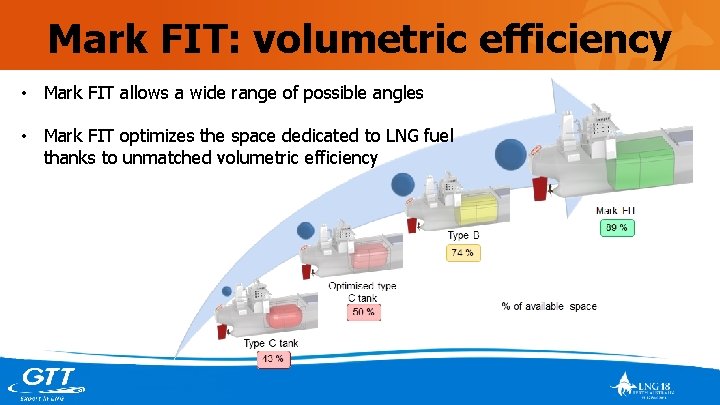
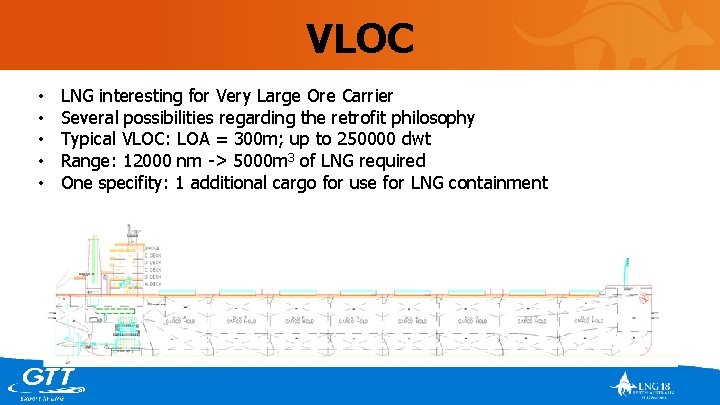
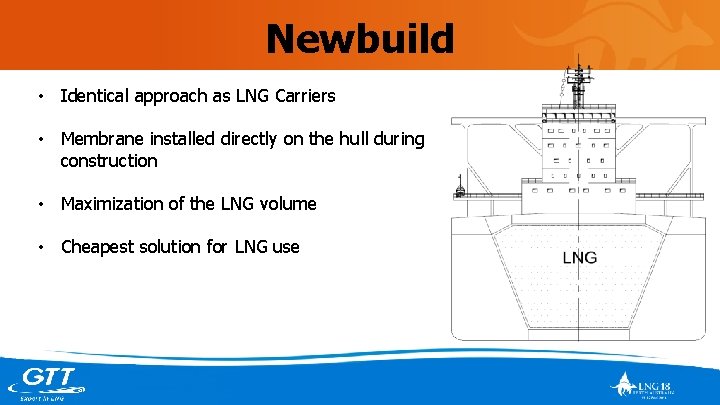
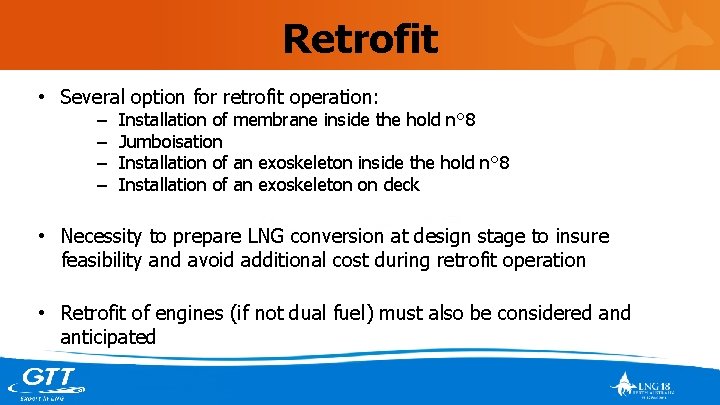
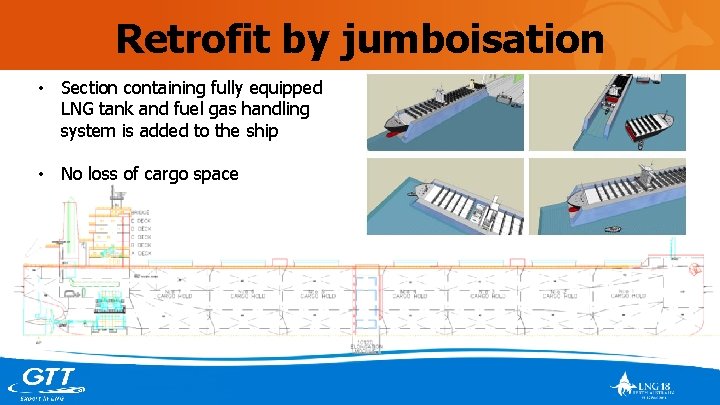
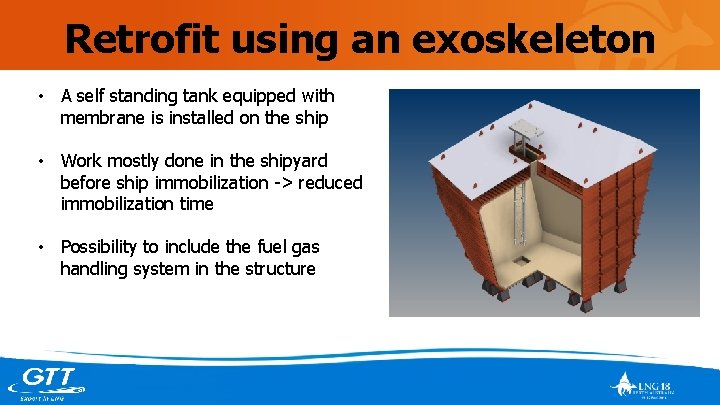
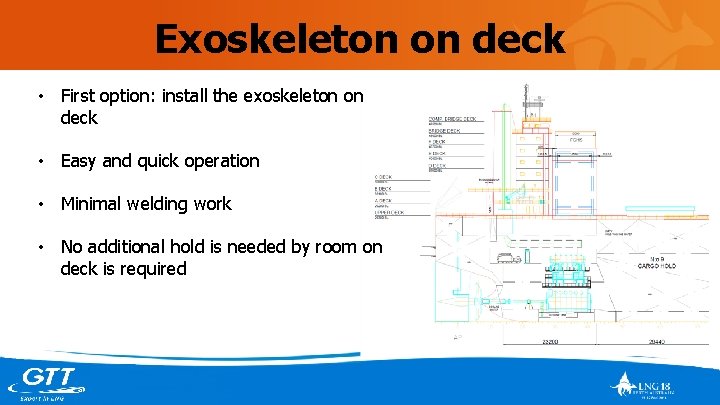
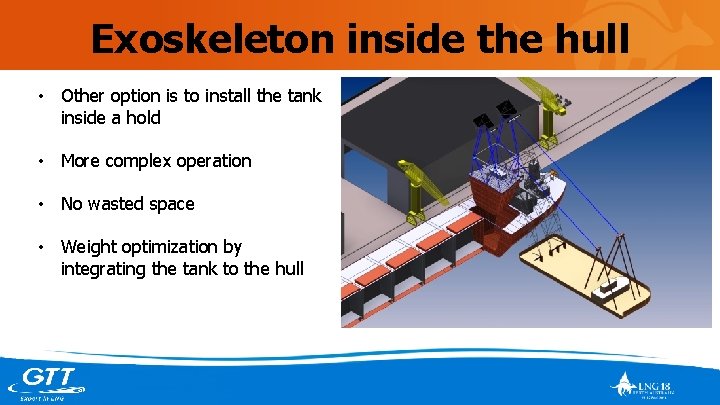
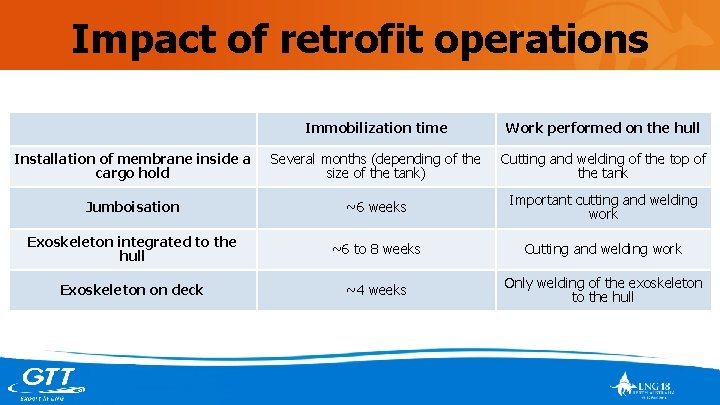
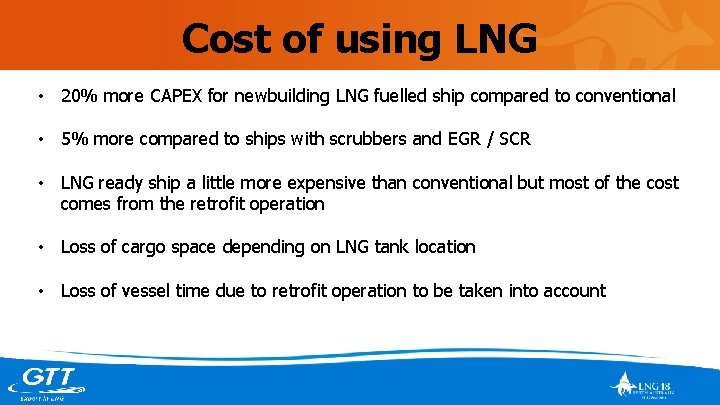
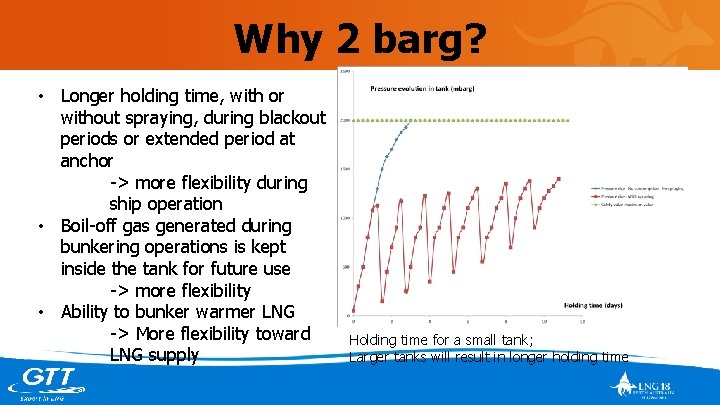
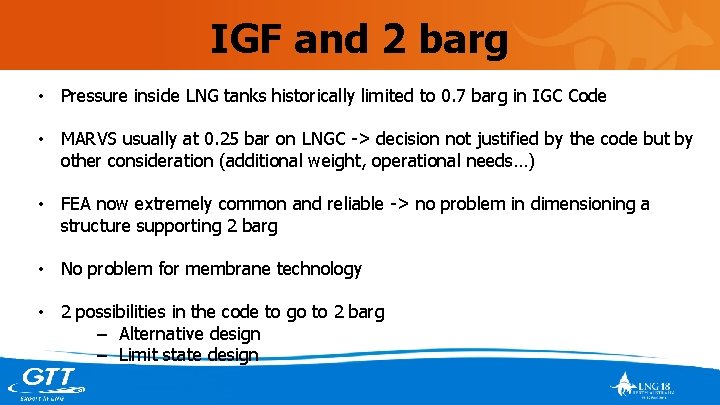
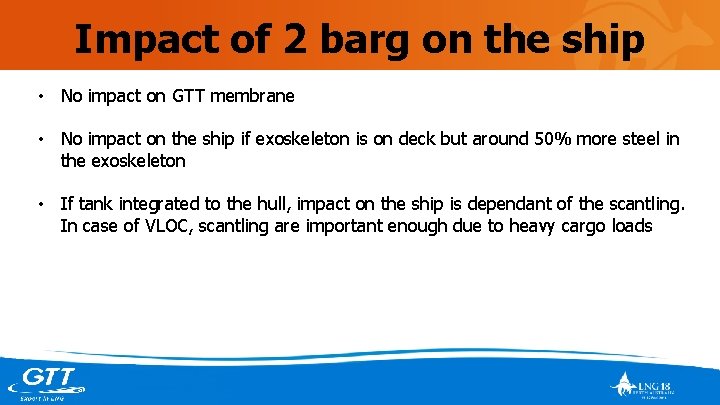
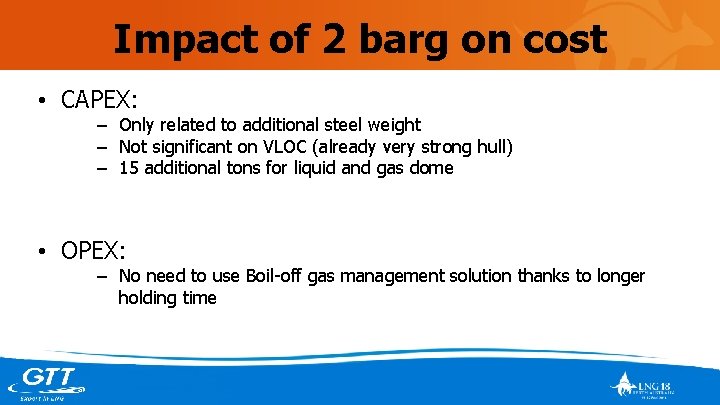
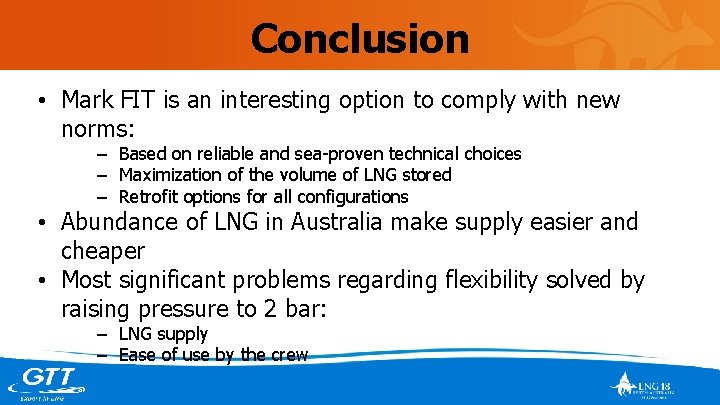
- Slides: 18
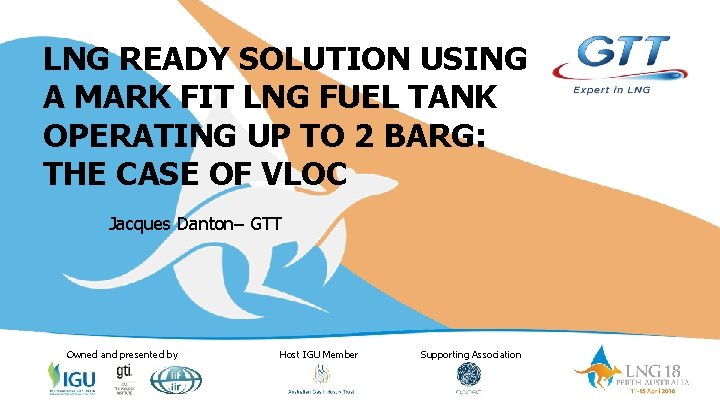
LNG READY SOLUTION USING A MARK FIT LNG FUEL TANK OPERATING UP TO 2 BARG: THE CASE OF VLOC Jacques Danton– GTT Owned and presented by Host IGU Member Supporting Association
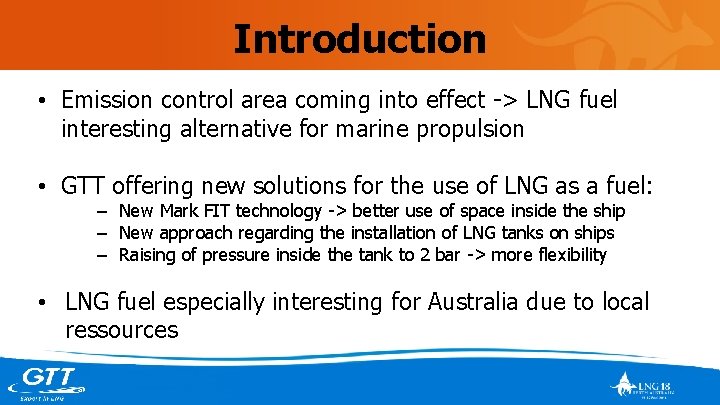
Introduction • Emission control area coming into effect -> LNG fuel interesting alternative for marine propulsion • GTT offering new solutions for the use of LNG as a fuel: – New Mark FIT technology -> better use of space inside the ship – New approach regarding the installation of LNG tanks on ships – Raising of pressure inside the tank to 2 bar -> more flexibility • LNG fuel especially interesting for Australia due to local ressources
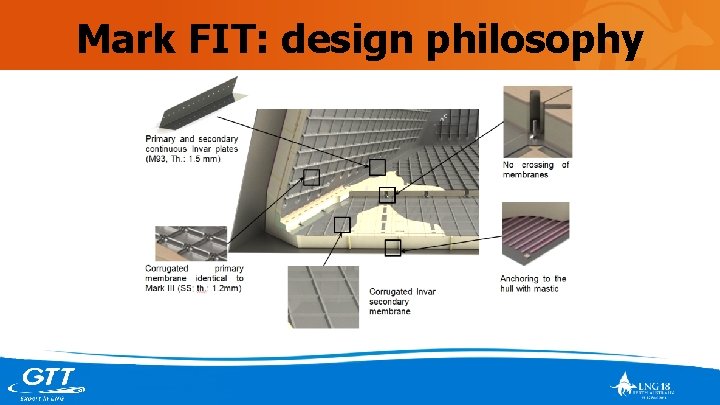
Mark FIT: design philosophy
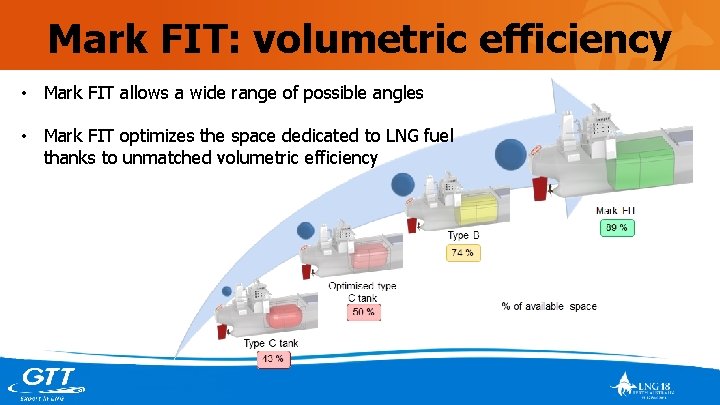
Mark FIT: volumetric efficiency • Mark FIT allows a wide range of possible angles • Mark FIT optimizes the space dedicated to LNG fuel thanks to unmatched volumetric efficiency
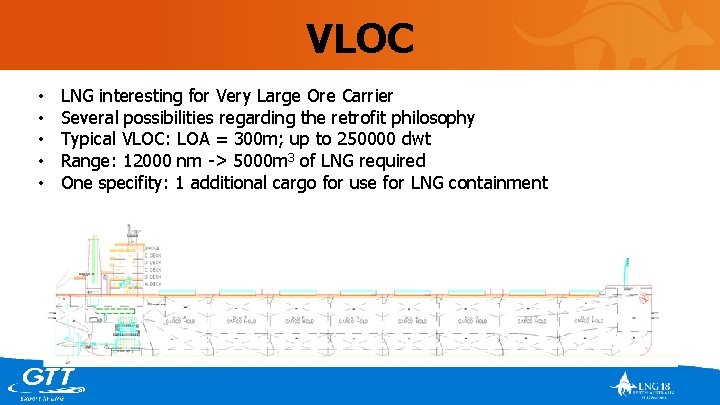
VLOC • • • LNG interesting for Very Large Ore Carrier Several possibilities regarding the retrofit philosophy Typical VLOC: LOA = 300 m; up to 250000 dwt Range: 12000 nm -> 5000 m 3 of LNG required One specifity: 1 additional cargo for use for LNG containment
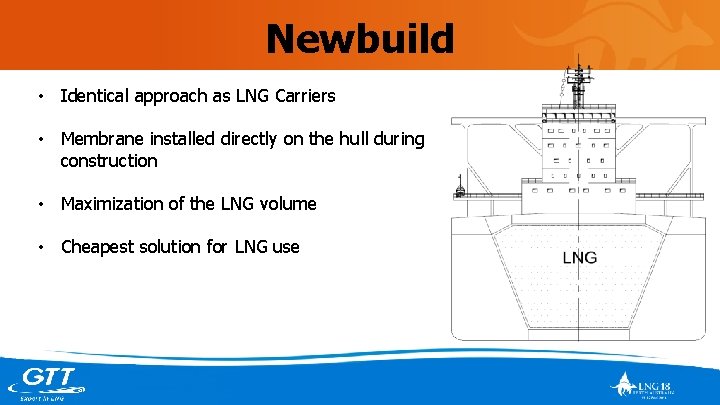
Newbuild • Identical approach as LNG Carriers • Membrane installed directly on the hull during construction • Maximization of the LNG volume • Cheapest solution for LNG use
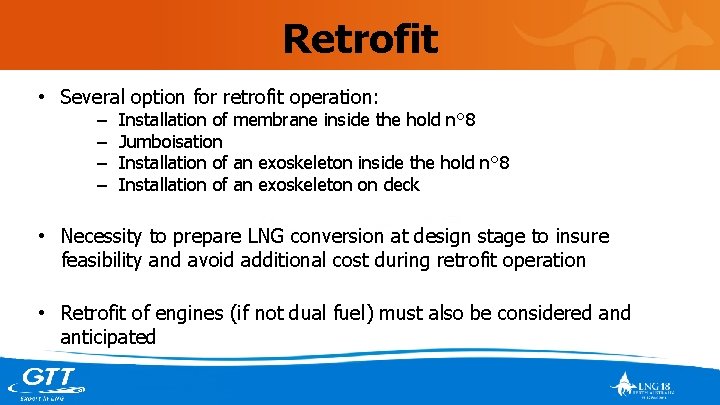
Retrofit • Several option for retrofit operation: – – Installation of membrane inside the hold n° 8 Jumboisation Installation of an exoskeleton inside the hold n° 8 Installation of an exoskeleton on deck • Necessity to prepare LNG conversion at design stage to insure feasibility and avoid additional cost during retrofit operation • Retrofit of engines (if not dual fuel) must also be considered anticipated
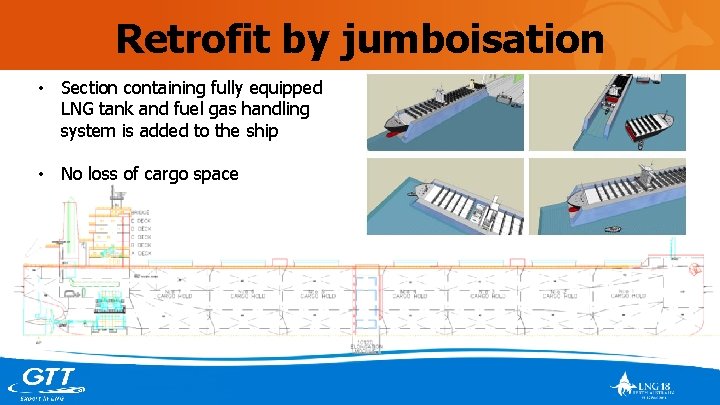
Retrofit by jumboisation • Section containing fully equipped LNG tank and fuel gas handling system is added to the ship • No loss of cargo space
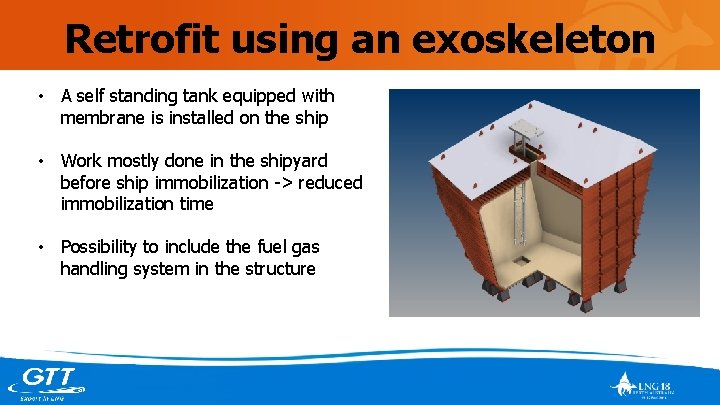
Retrofit using an exoskeleton • A self standing tank equipped with membrane is installed on the ship • Work mostly done in the shipyard before ship immobilization -> reduced immobilization time • Possibility to include the fuel gas handling system in the structure
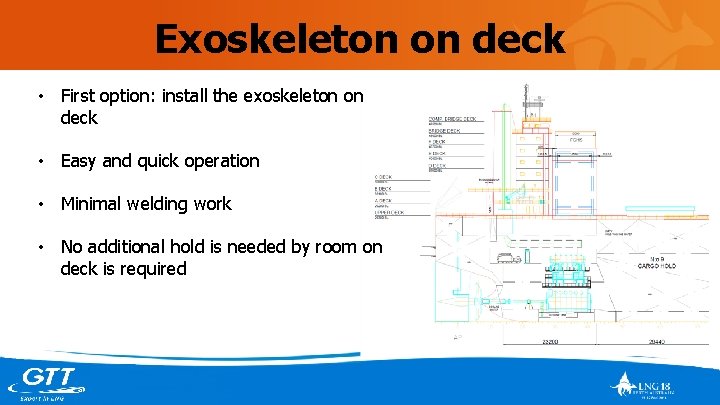
Exoskeleton on deck • First option: install the exoskeleton on deck • Easy and quick operation • Minimal welding work • No additional hold is needed by room on deck is required
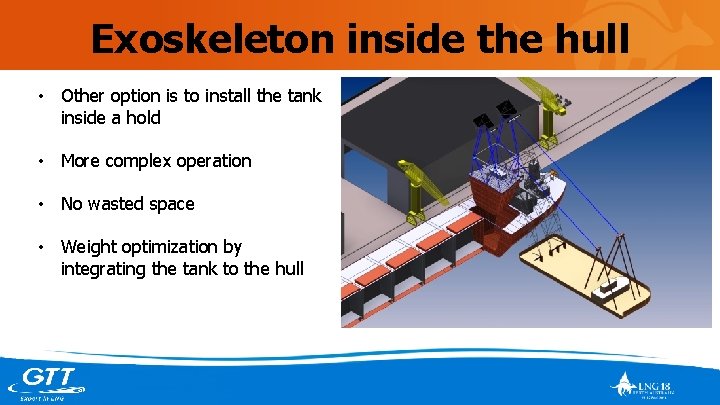
Exoskeleton inside the hull • Other option is to install the tank inside a hold • More complex operation • No wasted space • Weight optimization by integrating the tank to the hull
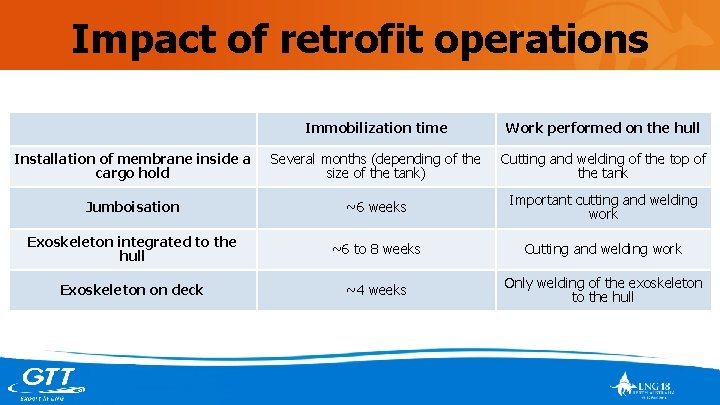
Impact of retrofit operations Immobilization time Work performed on the hull Installation of membrane inside a cargo hold Several months (depending of the size of the tank) Cutting and welding of the top of the tank Jumboisation ~6 weeks Important cutting and welding work Exoskeleton integrated to the hull ~6 to 8 weeks Cutting and welding work Exoskeleton on deck ~4 weeks Only welding of the exoskeleton to the hull
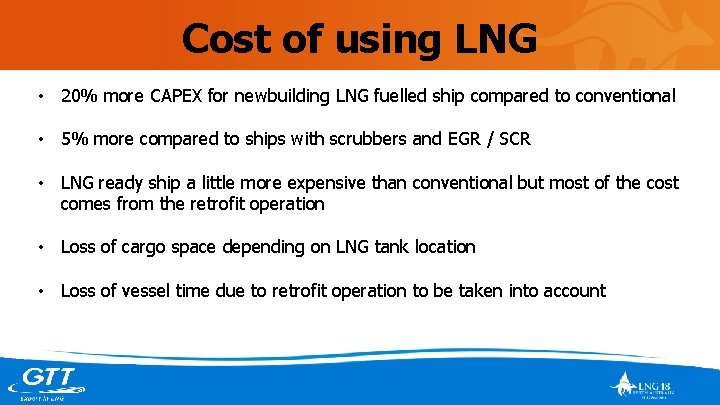
Cost of using LNG • 20% more CAPEX for newbuilding LNG fuelled ship compared to conventional • 5% more compared to ships with scrubbers and EGR / SCR • LNG ready ship a little more expensive than conventional but most of the cost comes from the retrofit operation • Loss of cargo space depending on LNG tank location • Loss of vessel time due to retrofit operation to be taken into account
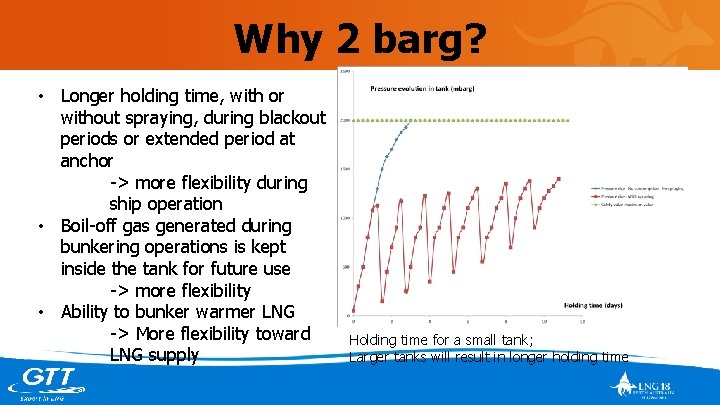
Why 2 barg? • Longer holding time, with or without spraying, during blackout periods or extended period at anchor -> more flexibility during ship operation • Boil-off gas generated during bunkering operations is kept inside the tank for future use -> more flexibility • Ability to bunker warmer LNG -> More flexibility toward LNG supply Holding time for a small tank; Larger tanks will result in longer holding time
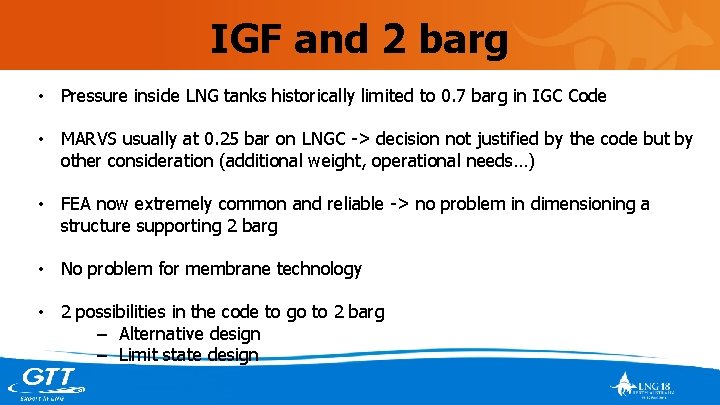
IGF and 2 barg • Pressure inside LNG tanks historically limited to 0. 7 barg in IGC Code • MARVS usually at 0. 25 bar on LNGC -> decision not justified by the code but by other consideration (additional weight, operational needs…) • FEA now extremely common and reliable -> no problem in dimensioning a structure supporting 2 barg • No problem for membrane technology • 2 possibilities in the code to go to 2 barg – Alternative design – Limit state design
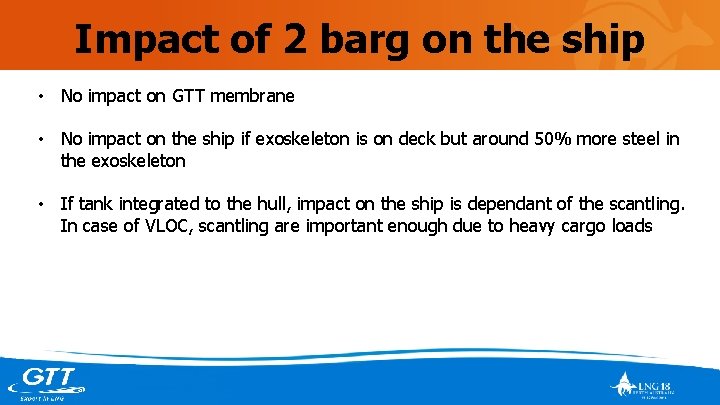
Impact of 2 barg on the ship • No impact on GTT membrane • No impact on the ship if exoskeleton is on deck but around 50% more steel in the exoskeleton • If tank integrated to the hull, impact on the ship is dependant of the scantling. In case of VLOC, scantling are important enough due to heavy cargo loads
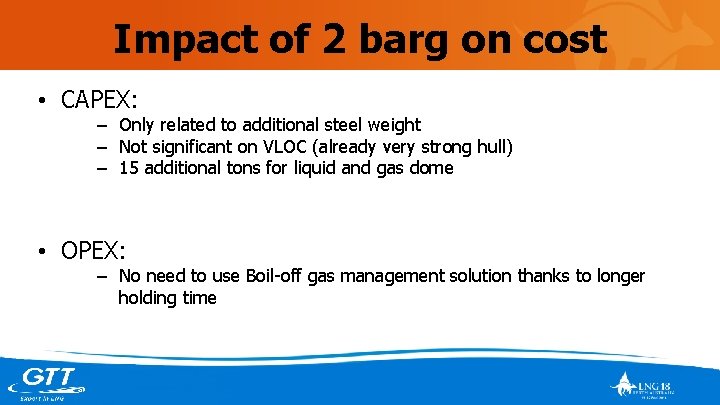
Impact of 2 barg on cost • CAPEX: – Only related to additional steel weight – Not significant on VLOC (already very strong hull) – 15 additional tons for liquid and gas dome • OPEX: – No need to use Boil-off gas management solution thanks to longer holding time
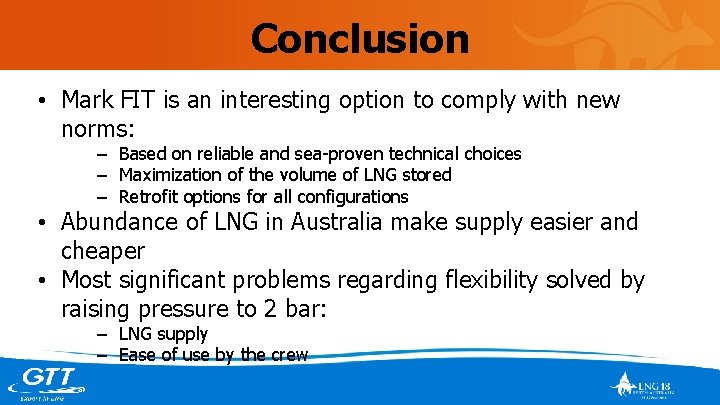
Conclusion • Mark FIT is an interesting option to comply with new norms: – Based on reliable and sea-proven technical choices – Maximization of the volume of LNG stored – Retrofit options for all configurations • Abundance of LNG in Australia make supply easier and cheaper • Most significant problems regarding flexibility solved by raising pressure to 2 bar: – LNG supply – Ease of use by the crew
First fit next fit best fit worst fit
Memory allocation policy
Stay ready to keep from getting ready
Transition fit
Person-job fit and person-organization fit
Cng vs lng
Coil wound heat exchanger
Cng vs lng
Lng
Spectrum lng
"tangguh lng"
Sn lng
Lng cng
Lng
Lng kmutt
Freeport lng train 4
Lng value chain cost structure
Perbedaan lng dan lpg
Vapour pressure composition curve for non ideal solution