Heat transfer and quench propagation from protection heaters
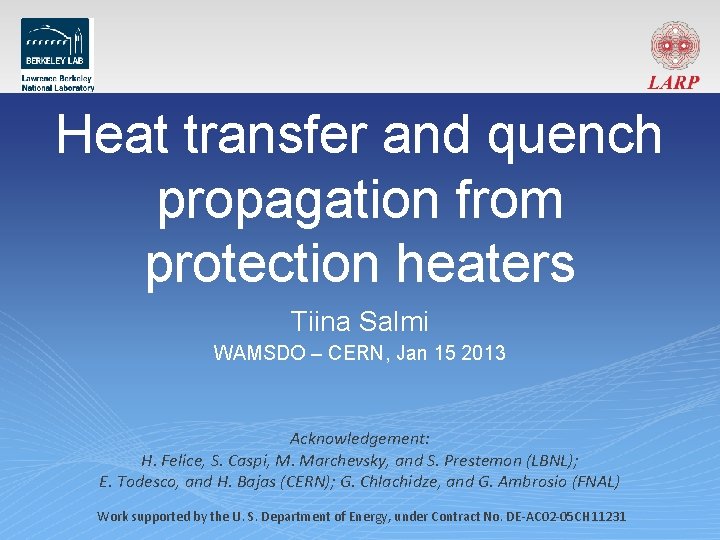
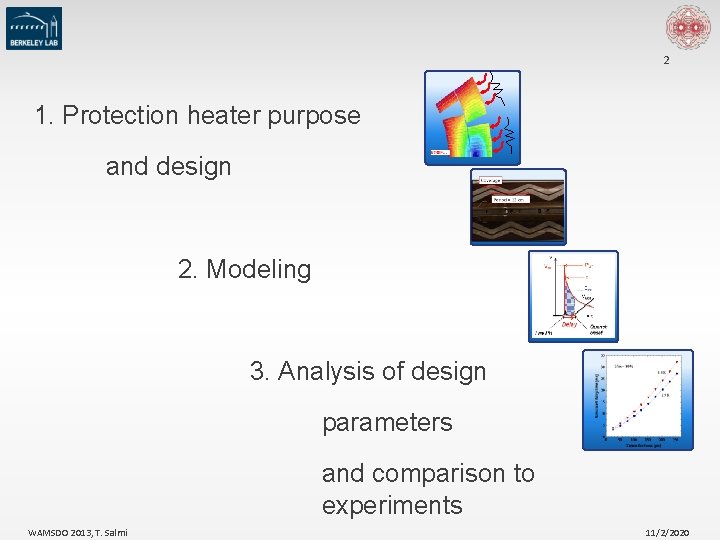
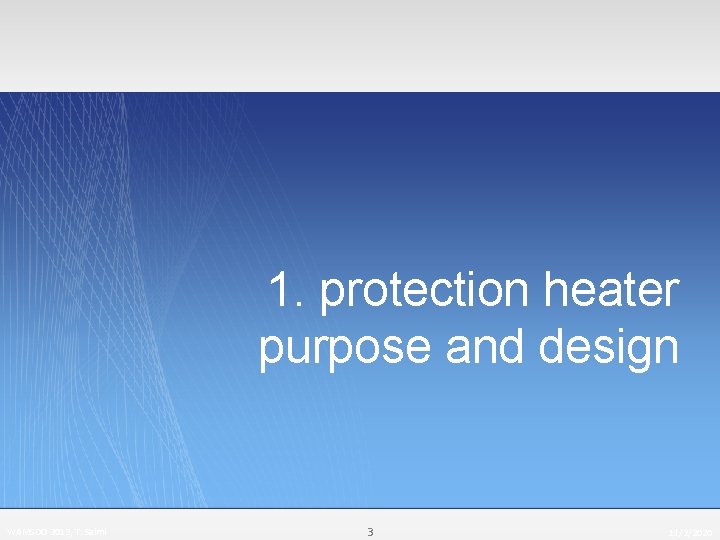
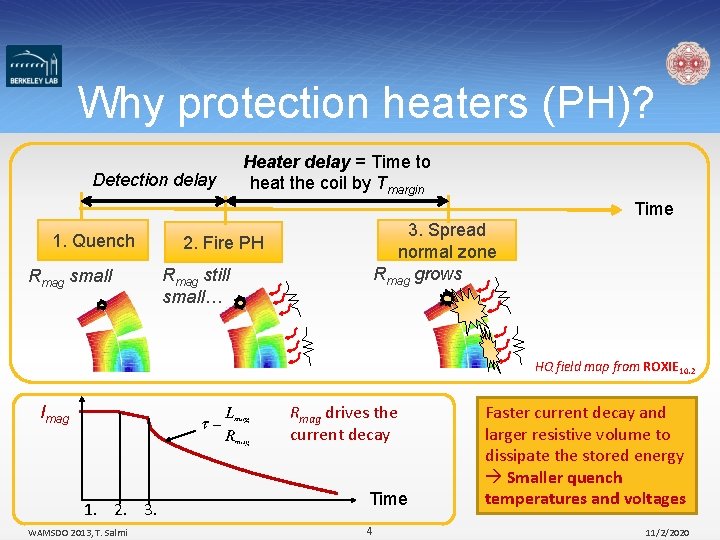
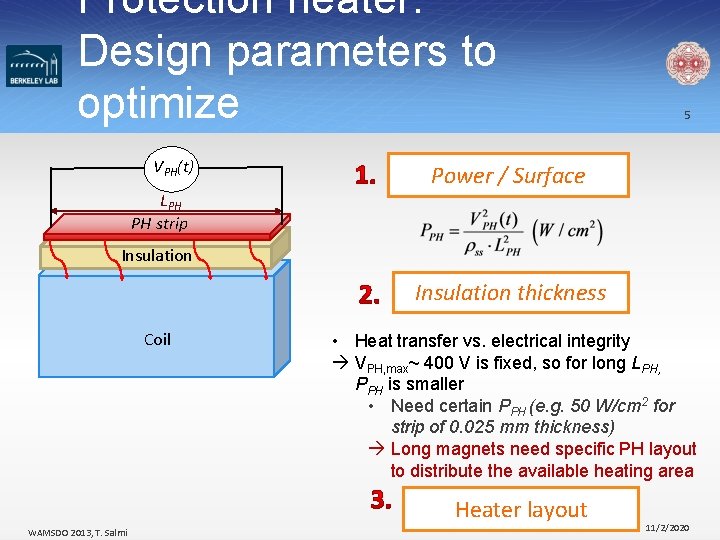
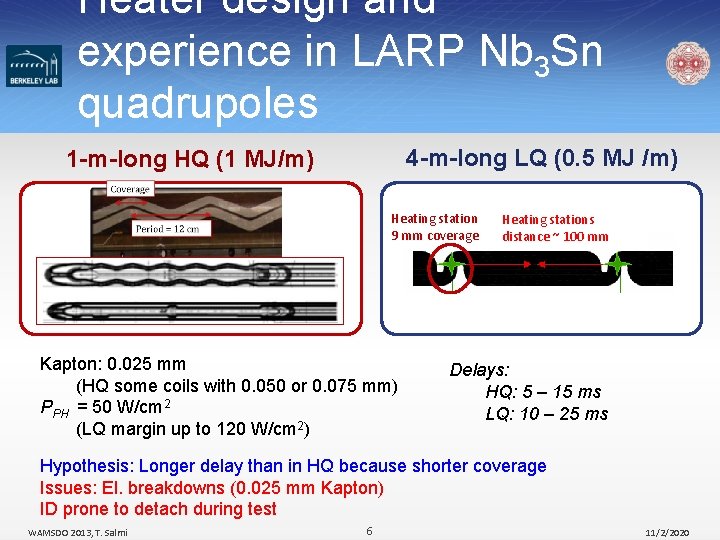
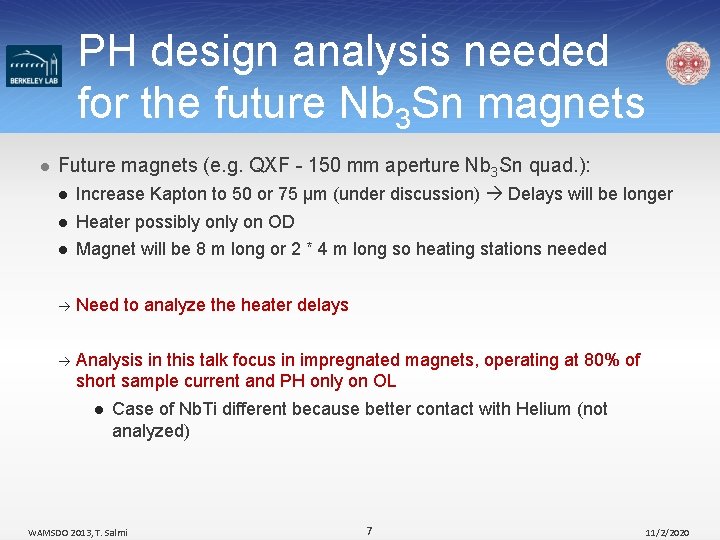
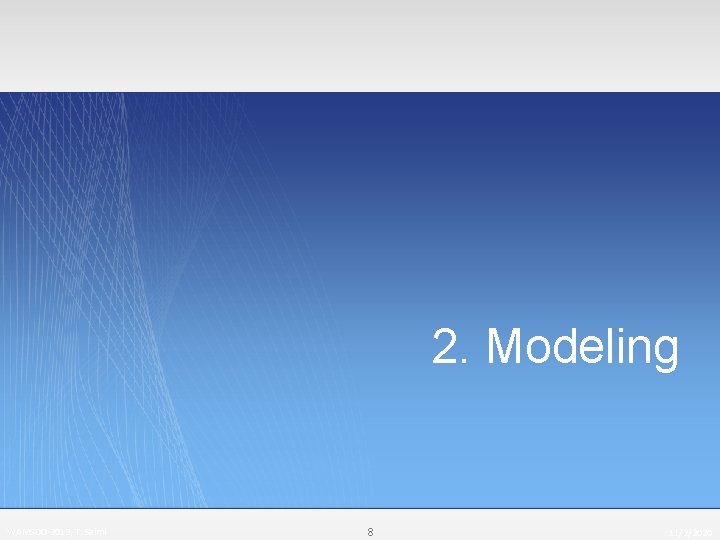
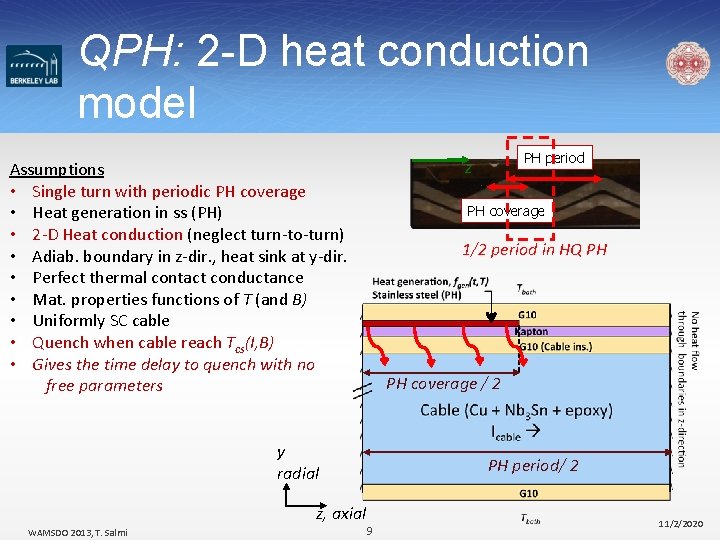
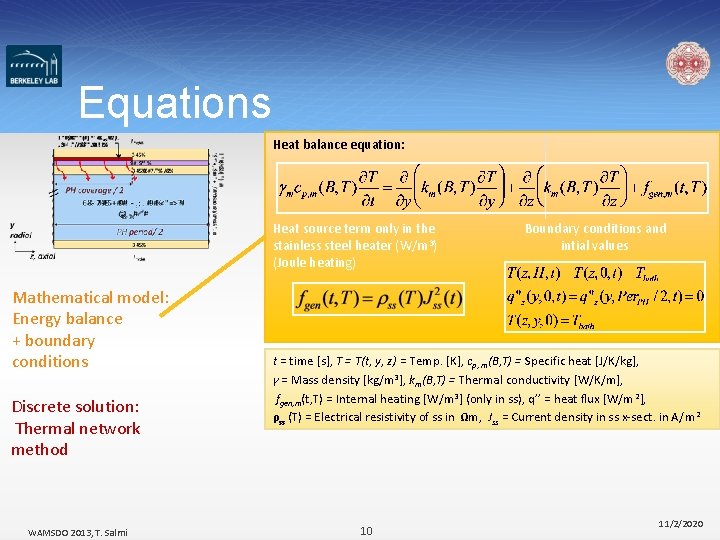
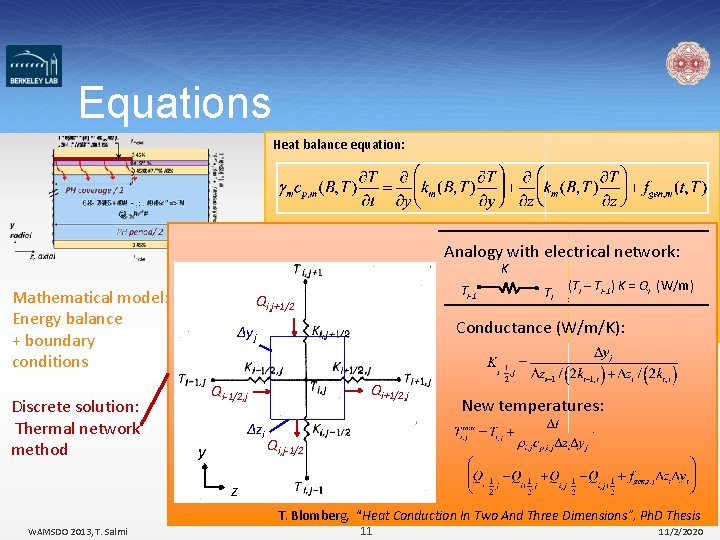
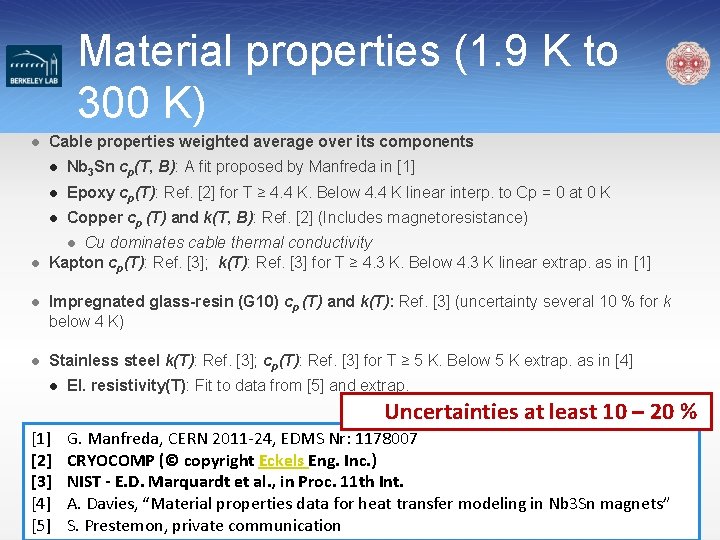
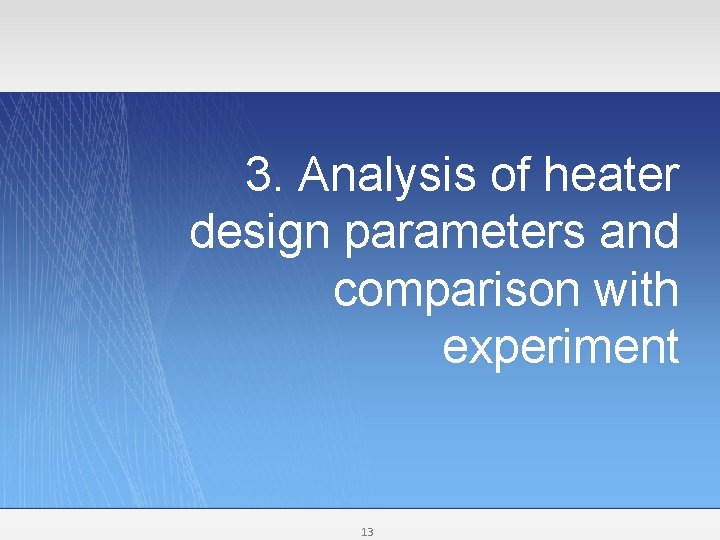
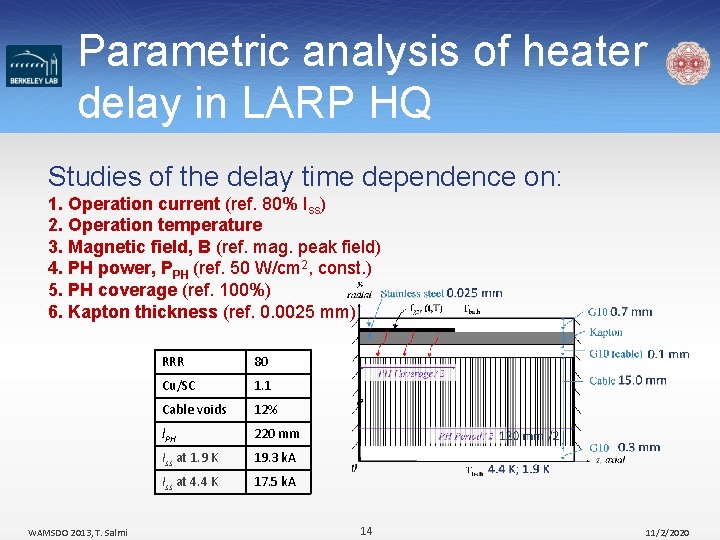
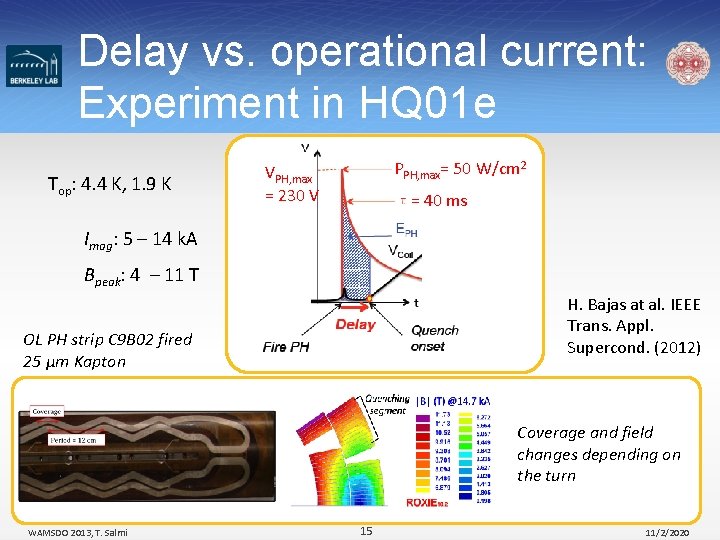
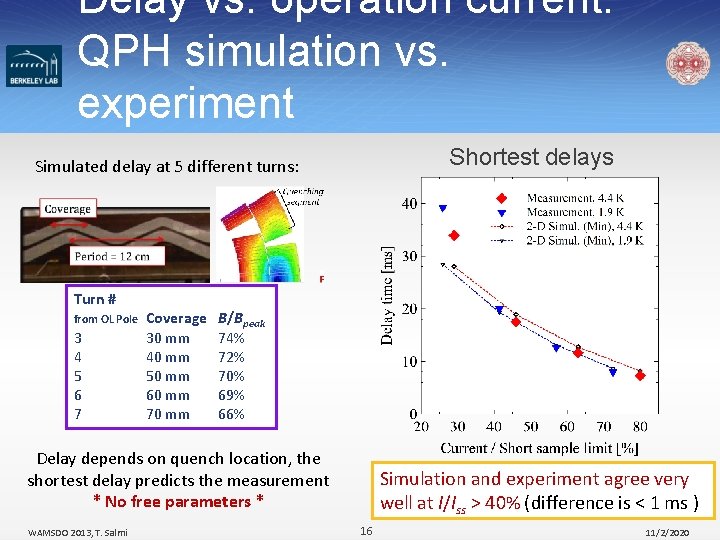
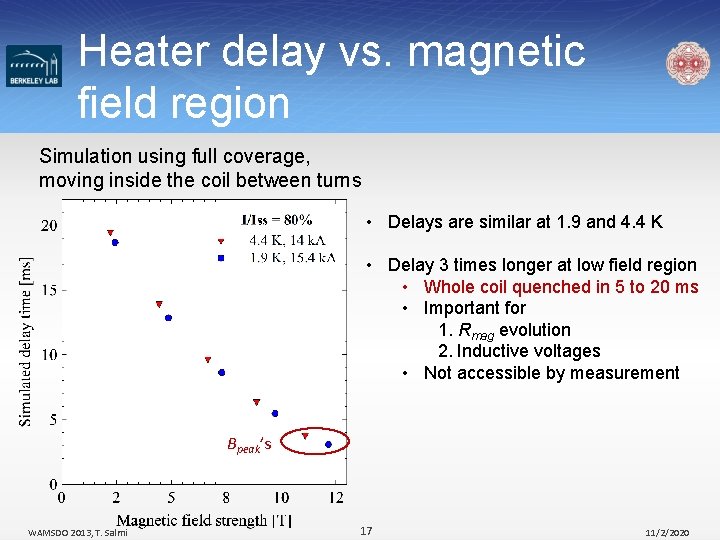
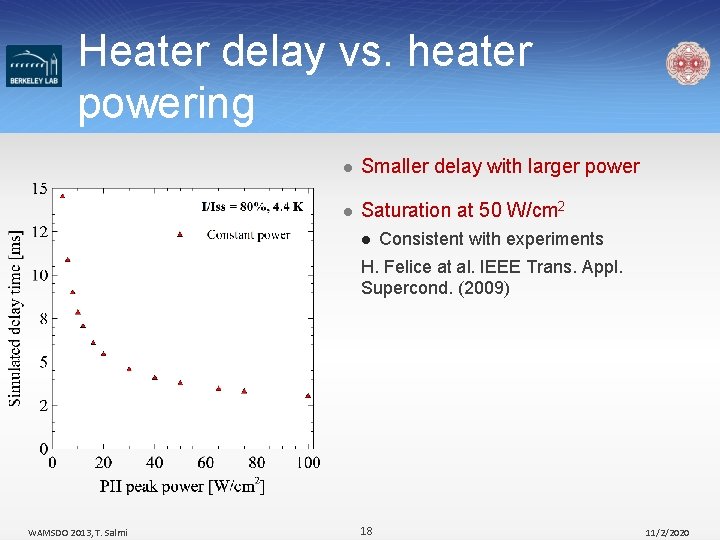
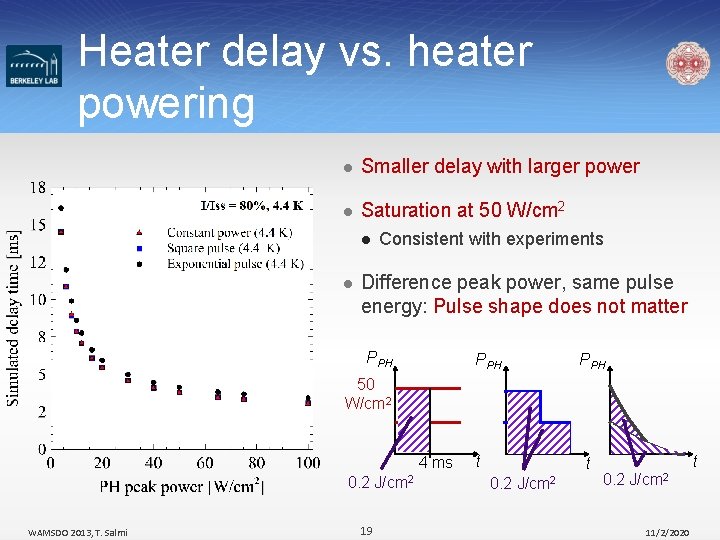
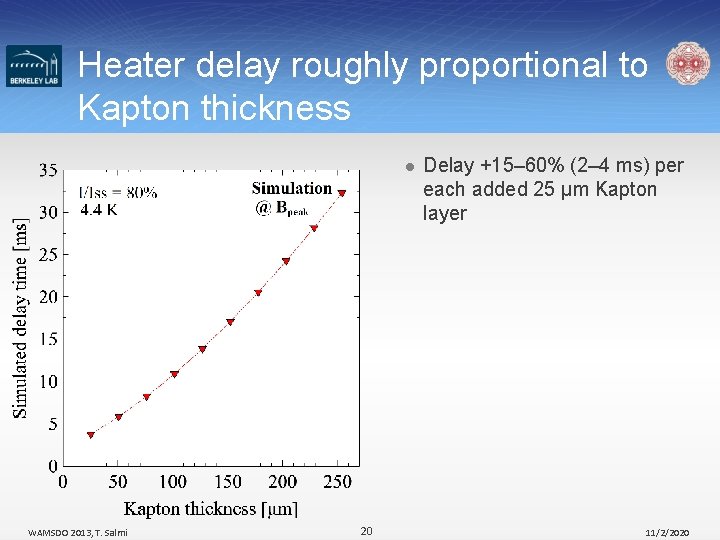
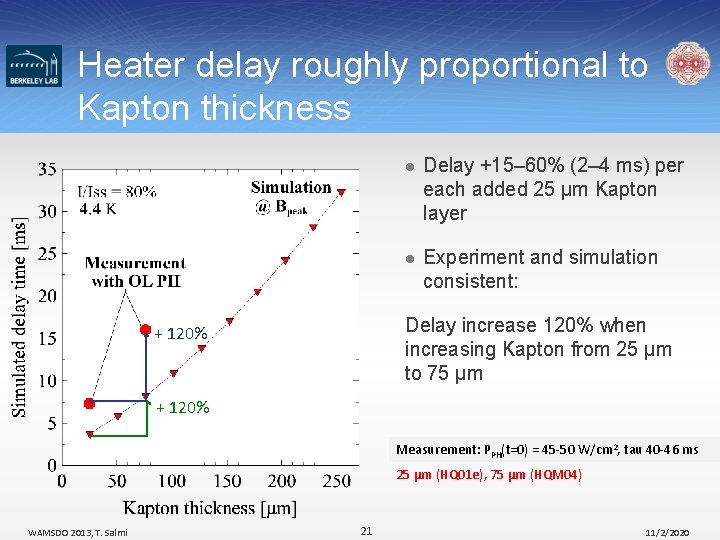
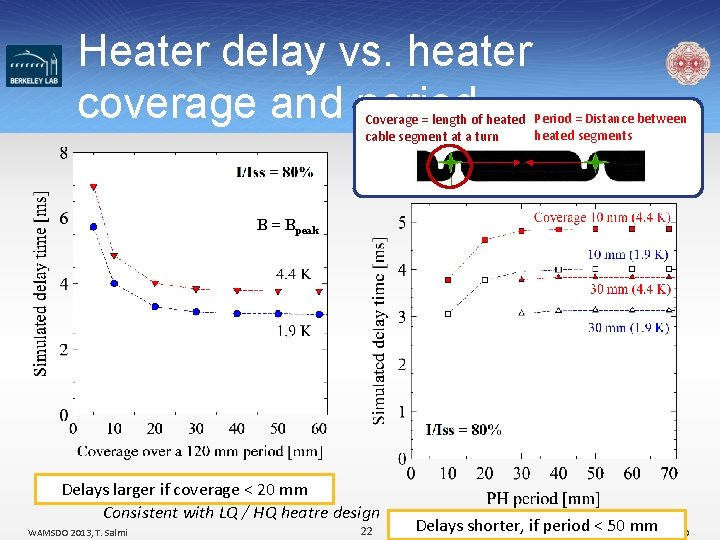
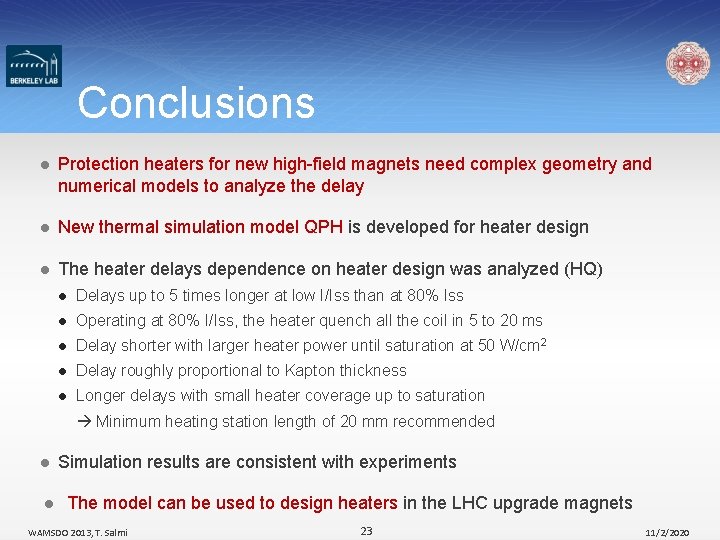
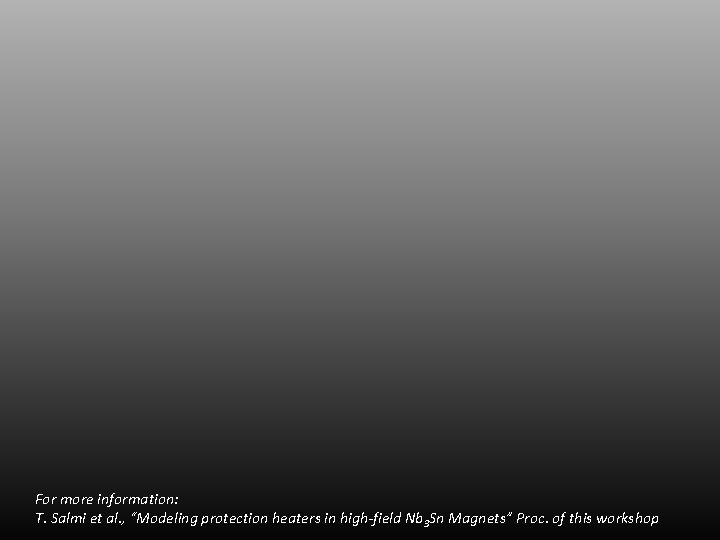
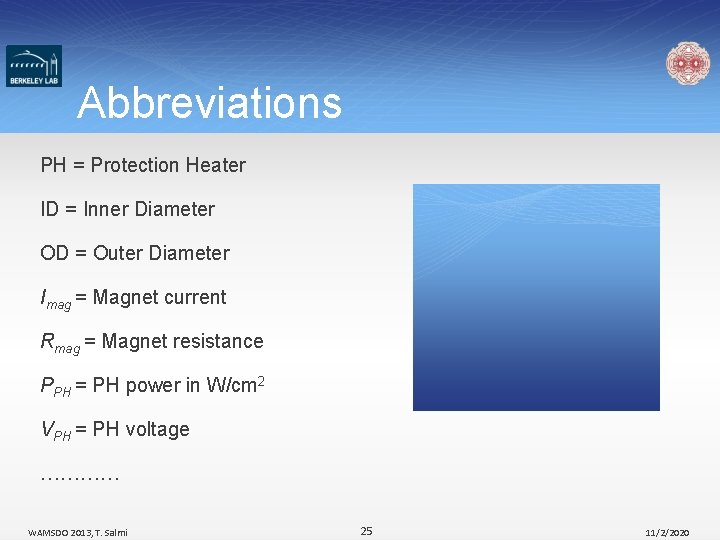
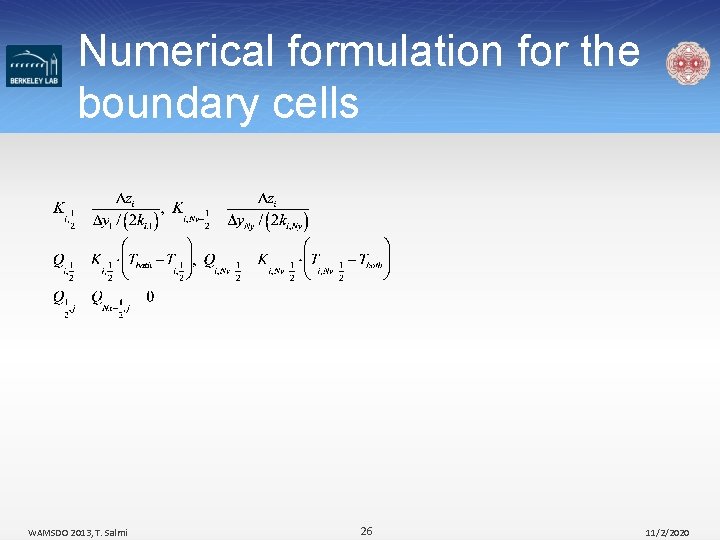
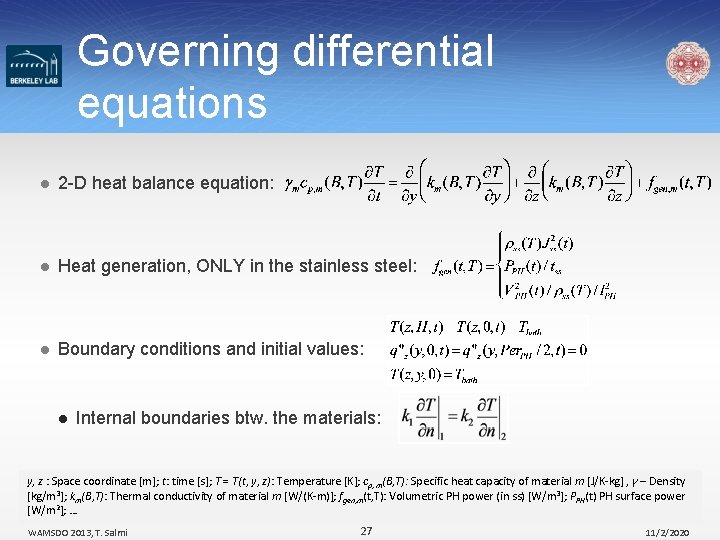
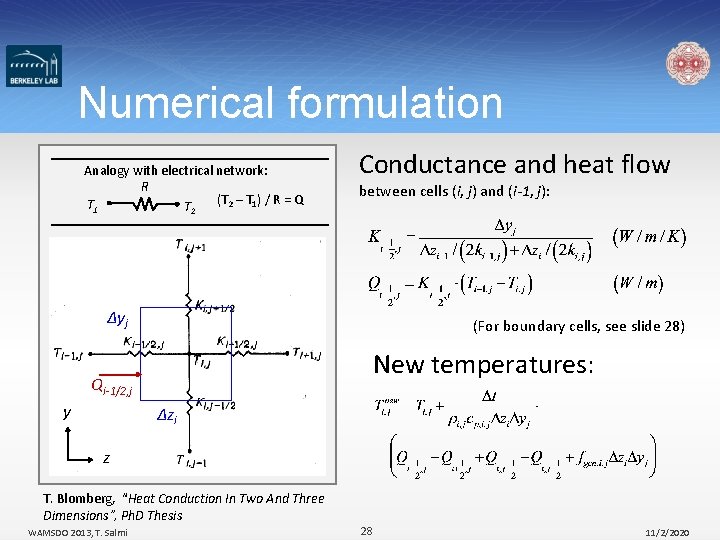
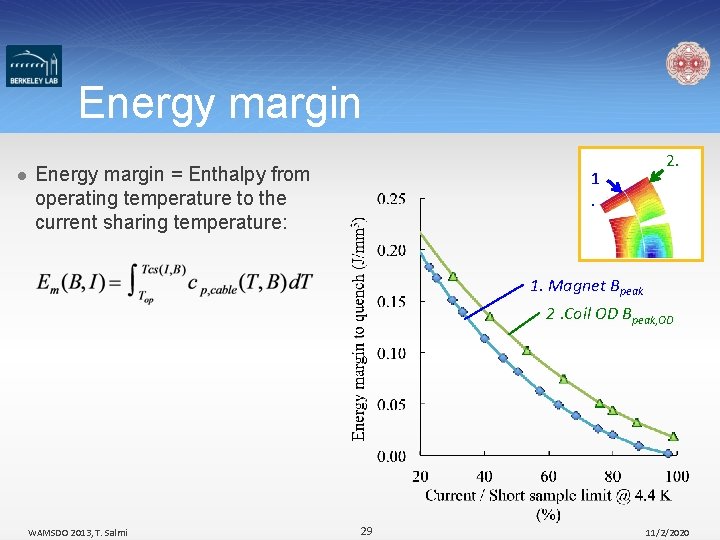
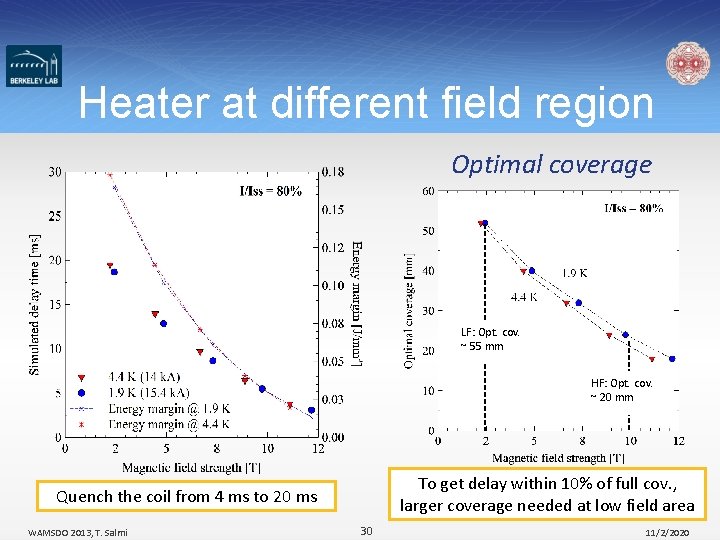
- Slides: 30
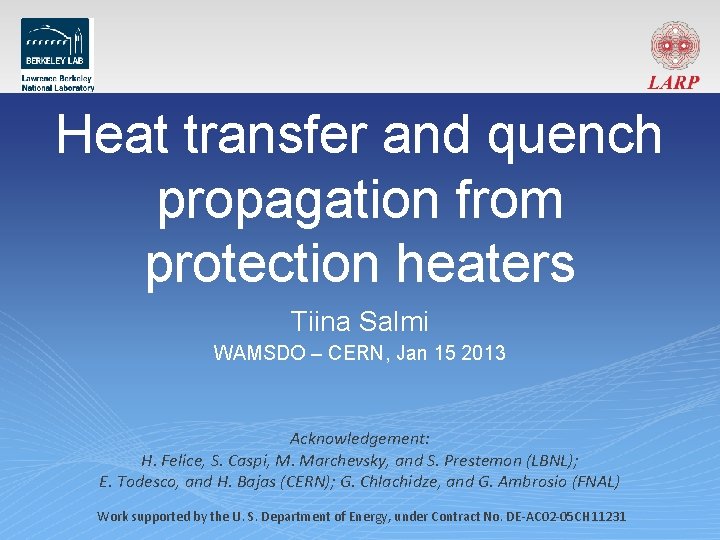
Heat transfer and quench propagation from protection heaters Tiina Salmi WAMSDO – CERN, Jan 15 2013 Acknowledgement: H. Felice, S. Caspi, M. Marchevsky, and S. Prestemon (LBNL); E. Todesco, and H. Bajas (CERN); G. Chlachidze, and G. Ambrosio (FNAL) Work supported by the U. S. Department of Energy, under Contract No. DE-AC 02 -05 CH 11231
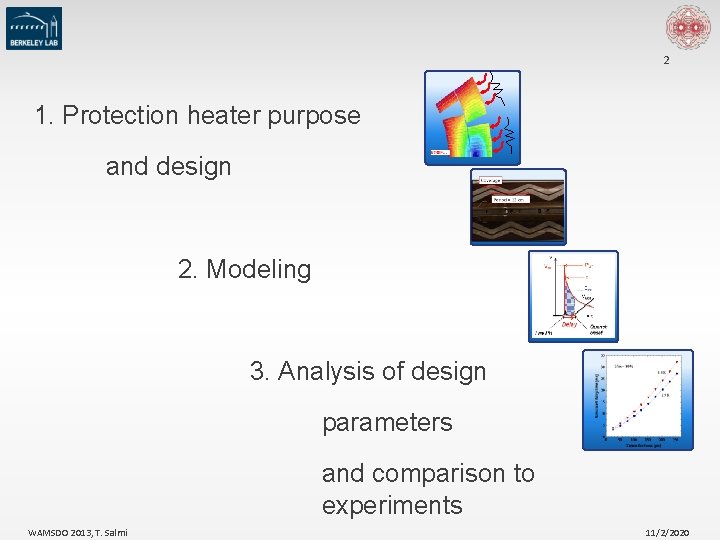
2 1. Protection heater purpose and design 2. Modeling 3. Analysis of design parameters and comparison to experiments WAMSDO 2013, T. Salmi 11/2/2020
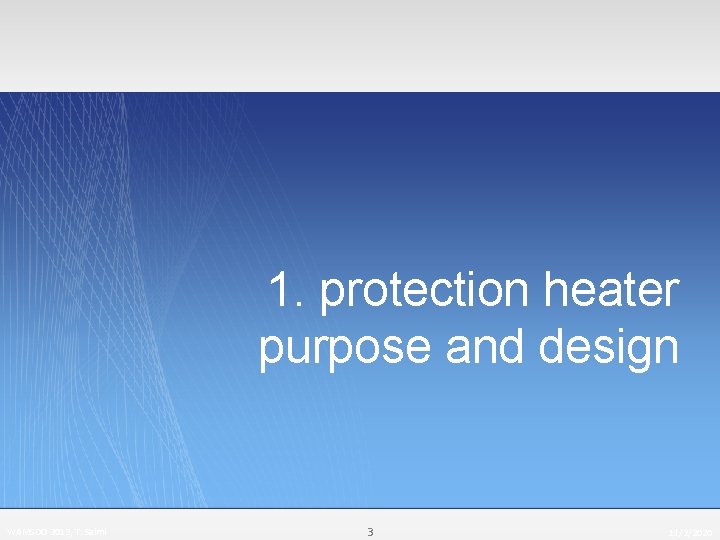
1. protection heater purpose and design WAMSDO 2013, T. Salmi 3 11/2/2020
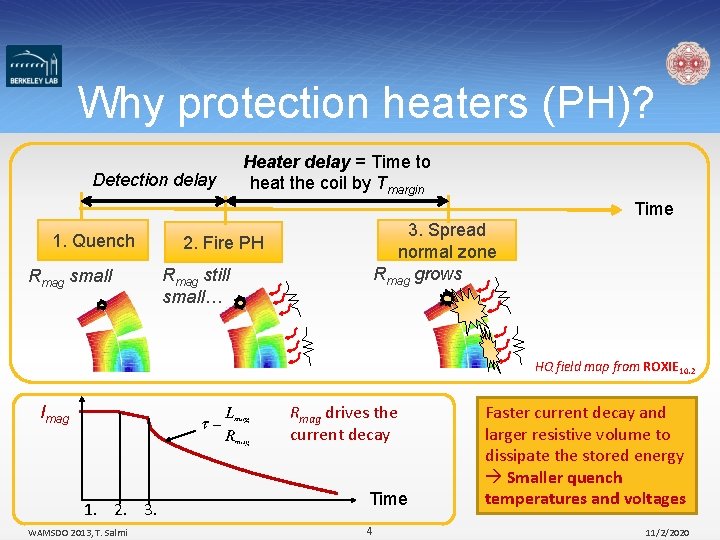
Why protection heaters (PH)? Detection delay Heater delay = Time to heat the coil by Tmargin Time 1. Quench Rmag small 2. Fire PH Rmag still small… 3. Spread normal zone Rmag grows HQ field map from ROXIE 10. 2 Rmag drives the current decay Imag 1. 2. 3. WAMSDO 2013, T. Salmi Time 4 Faster current decay and larger resistive volume to dissipate the stored energy Smaller quench temperatures and voltages 11/2/2020
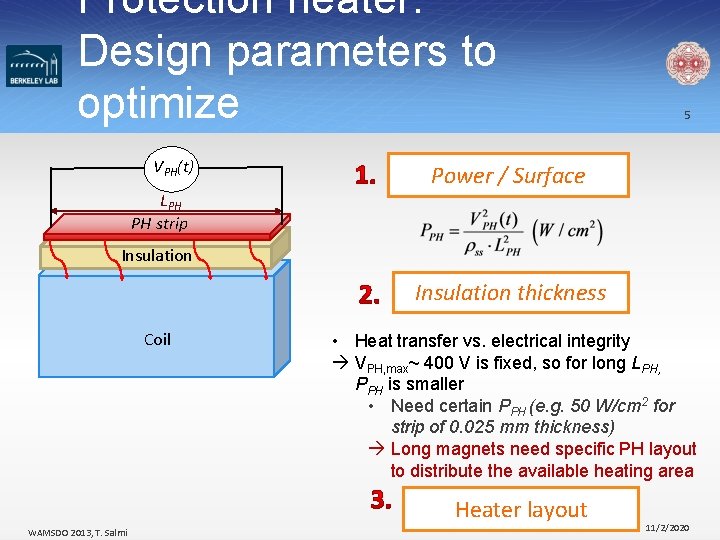
Protection heater: Design parameters to optimize VPH(t) LPH PH strip 5 Power / Surface Insulation thickness Coil • Heat transfer vs. electrical integrity VPH, max~ 400 V is fixed, so for long LPH, PPH is smaller • Need certain PPH (e. g. 50 W/cm 2 for strip of 0. 025 mm thickness) Long magnets need specific PH layout to distribute the available heating area Heater layout WAMSDO 2013, T. Salmi 11/2/2020
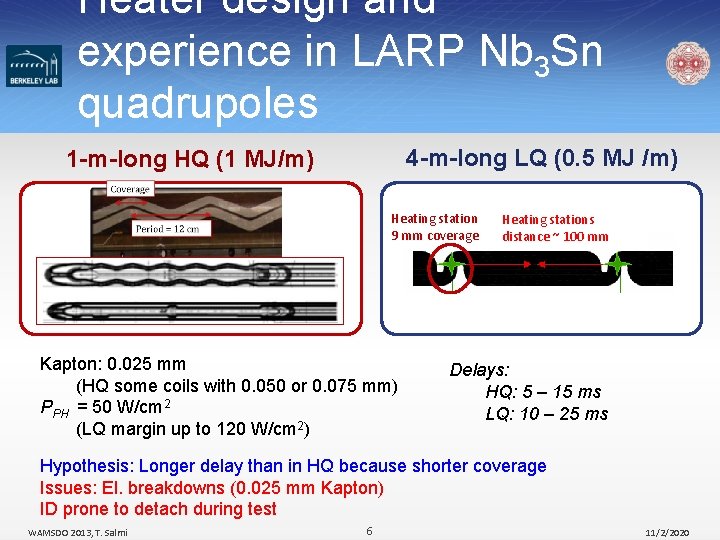
Heater design and experience in LARP Nb 3 Sn quadrupoles 4 -m-long LQ (0. 5 MJ /m) 1 -m-long HQ (1 MJ/m) Heating station 9 mm coverage Kapton: 0. 025 mm (HQ some coils with 0. 050 or 0. 075 mm) PPH = 50 W/cm 2 (LQ margin up to 120 W/cm 2) Heating stations distance ~ 100 mm Delays: HQ: 5 – 15 ms LQ: 10 – 25 ms Hypothesis: Longer delay than in HQ because shorter coverage Issues: El. breakdowns (0. 025 mm Kapton) ID prone to detach during test WAMSDO 2013, T. Salmi 6 11/2/2020
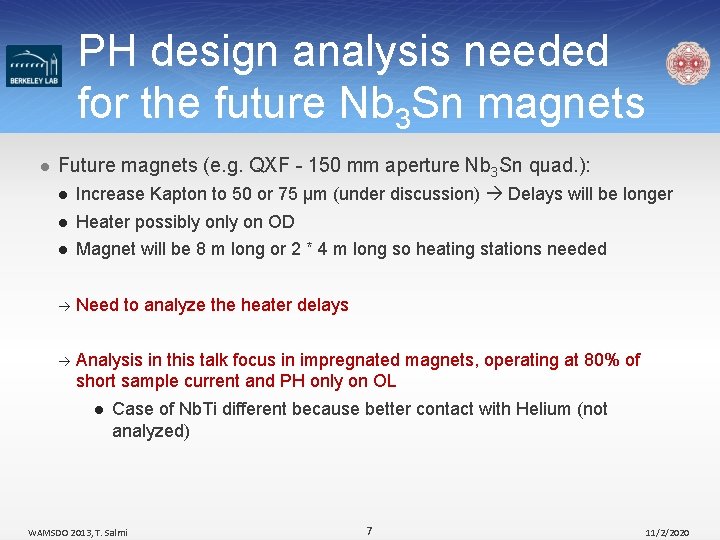
PH design analysis needed for the future Nb 3 Sn magnets l Future magnets (e. g. QXF - 150 mm aperture Nb 3 Sn quad. ): l Increase Kapton to 50 or 75 μm (under discussion) Delays will be longer l Heater possibly on OD l Magnet will be 8 m long or 2 * 4 m long so heating stations needed Need to analyze the heater delays Analysis in this talk focus in impregnated magnets, operating at 80% of short sample current and PH only on OL l Case of Nb. Ti different because better contact with Helium (not analyzed) WAMSDO 2013, T. Salmi 7 11/2/2020
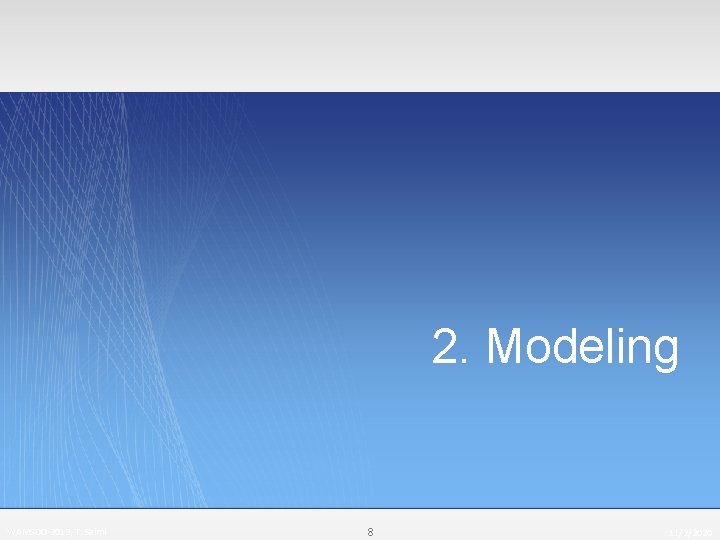
2. Modeling WAMSDO 2013, T. Salmi 8 11/2/2020
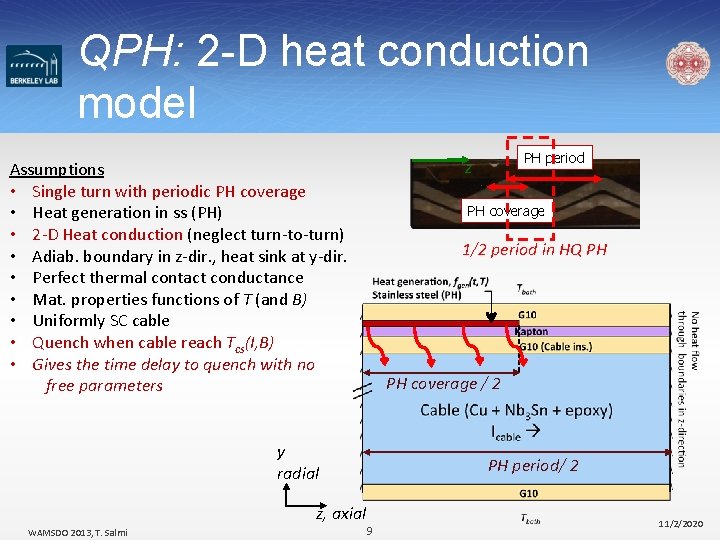
QPH: 2 -D heat conduction model PH coverage 1/2 period in HQ PH PH coverage / 2 y radial z, axial WAMSDO 2013, T. Salmi PH period z Assumptions • Single turn with periodic PH coverage • Heat generation in ss (PH) • 2 -D Heat conduction (neglect turn-to-turn) • Adiab. boundary in z-dir. , heat sink at y-dir. • Perfect thermal contact conductance • Mat. properties functions of T (and B) • Uniformly SC cable • Quench when cable reach Tcs(I, B) • Gives the time delay to quench with no free parameters PH period/ 2 9 11/2/2020
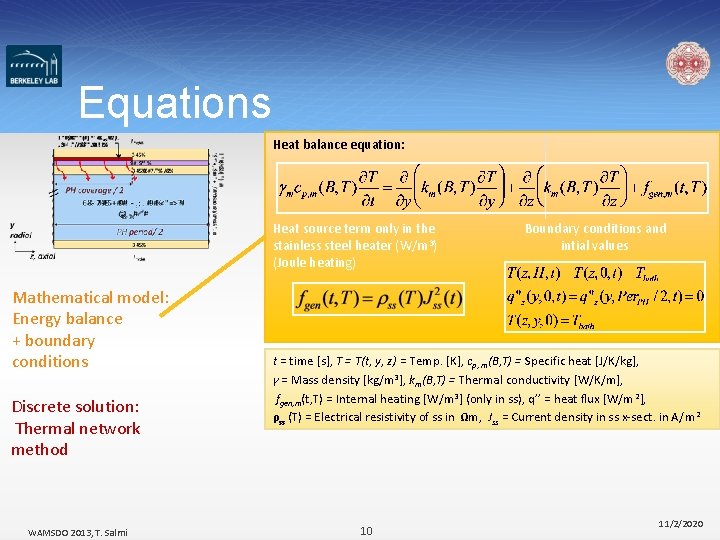
Equations Heat balance equation: Heat source term only in the stainless steel heater (W/m 3) (Joule heating) Mathematical model: Energy balance + boundary conditions Discrete solution: Thermal network method WAMSDO 2013, T. Salmi Boundary conditions and intial values t = time [s], T = T(t, y, z) = Temp. [K], cp, m(B, T) = Specific heat [J/K/kg], γ = Mass density [kg/m 3], km(B, T) = Thermal conductivity [W/K/m], fgen, m(t, T) = Internal heating [W/m 3] (only in ss), q’’ = heat flux [W/m 2], ρss (T) = Electrical resistivity of ss in Ωm, Jss = Current density in ss x-sect. in A/m 2 10 11/2/2020
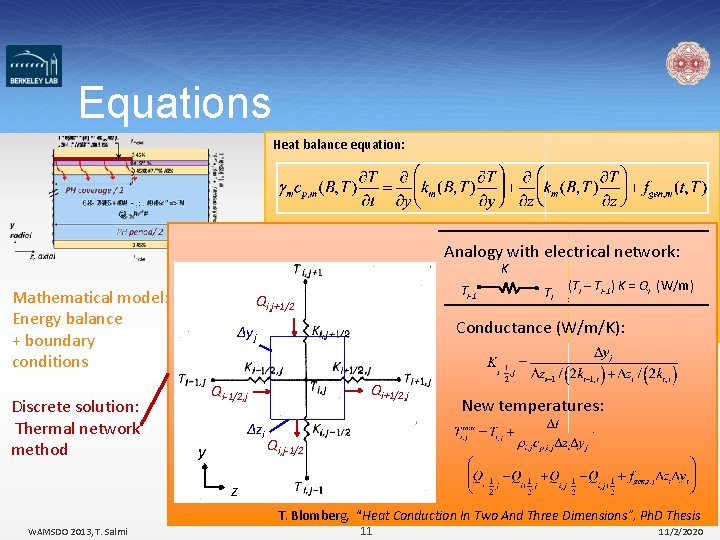
Equations Heat balance equation: Heat source term only in the Boundary conditions and stainless steel heater (Joule heating) intial values Analogy with electrical network: K Mathematical model: Energy balance + boundary conditions Discrete solution: Thermal network method Ti-1 Qi, j+1/2 Qi+1/2, j Qi-1/2, j y (Ti – Ti-1) K = Qi (W/m) Conductance (W/m/K): Δyj Δzi Ti New temperatures: Qi, j-1/2 z T. Blomberg, “Heat Conduction In Two And Three Dimensions”, Ph. D Thesis WAMSDO 2013, T. Salmi 11 11/2/2020
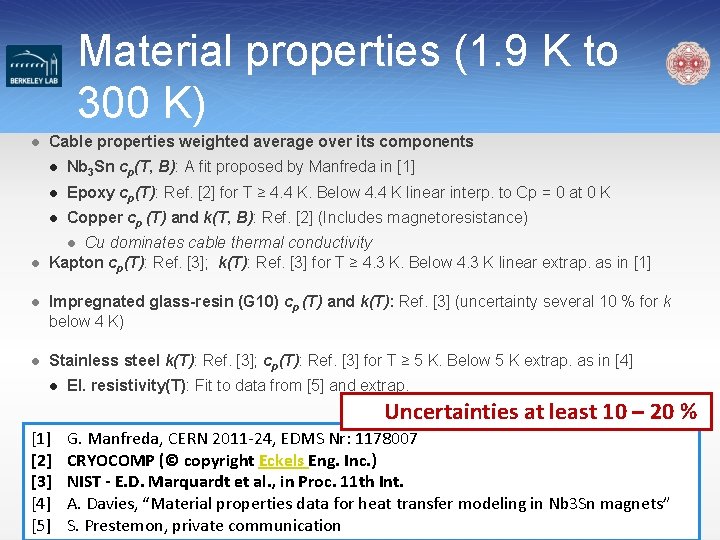
Material properties (1. 9 K to 300 K) l Cable properties weighted average over its components l Nb 3 Sn cp(T, B): A fit proposed by Manfreda in [1] l Epoxy cp(T): Ref. [2] for T ≥ 4. 4 K. Below 4. 4 K linear interp. to Cp = 0 at 0 K l Copper cp (T) and k(T, B): Ref. [2] (Includes magnetoresistance) Cu dominates cable thermal conductivity Kapton cp(T): Ref. [3]; k(T): Ref. [3] for T ≥ 4. 3 K. Below 4. 3 K linear extrap. as in [1] l l l Impregnated glass-resin (G 10) cp (T) and k(T): Ref. [3] (uncertainty several 10 % for k below 4 K) l Stainless steel k(T): Ref. [3]; cp(T): Ref. [3] for T ≥ 5 K. Below 5 K extrap. as in [4] l El. resistivity(T): Fit to data from [5] and extrap. Uncertainties at least 10 – 20 % [1] G. Manfreda, CERN 2011 -24, EDMS Nr: 1178007 [2] CRYOCOMP (© copyright Eckels Eng. Inc. ) [3] NIST - E. D. Marquardt et al. , in Proc. 11 th Int. [4] A. Davies, “Material properties data for heat transfer modeling in Nb 3 Sn magnets” [5] S. Prestemon, private communication 12 11/2/2020 WAMSDO 2013, T. Salmi
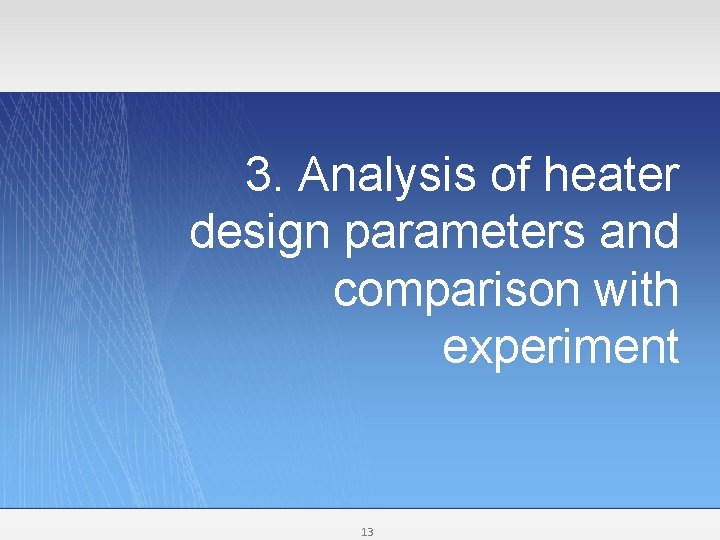
3. Analysis of heater design parameters and comparison with experiment 13
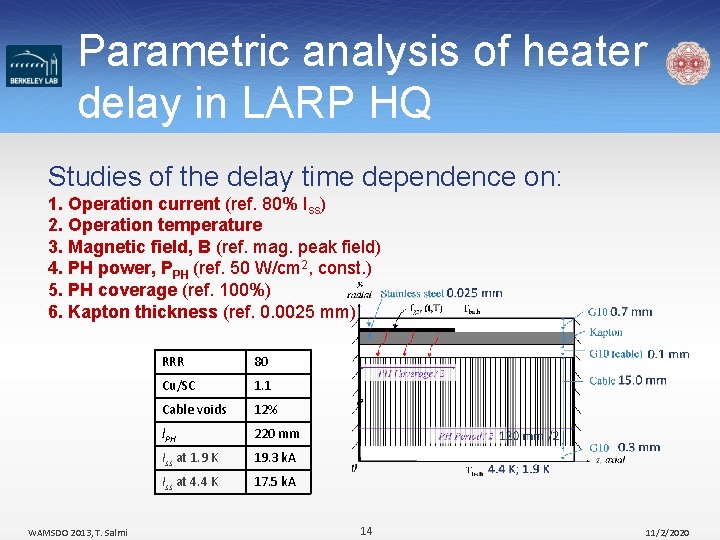
Parametric analysis of heater delay in LARP HQ Studies of the delay time dependence on: 1. Operation current (ref. 80% Iss) 2. Operation temperature 3. Magnetic field, B (ref. mag. peak field) 4. PH power, PPH (ref. 50 W/cm 2, const. ) 5. PH coverage (ref. 100%) 6. Kapton thickness (ref. 0. 0025 mm) WAMSDO 2013, T. Salmi RRR 80 Cu/SC 1. 1 Cable voids 12% l. PH 220 mm Iss at 1. 9 K 19. 3 k. A Iss at 4. 4 K 17. 5 k. A 14 11/2/2020
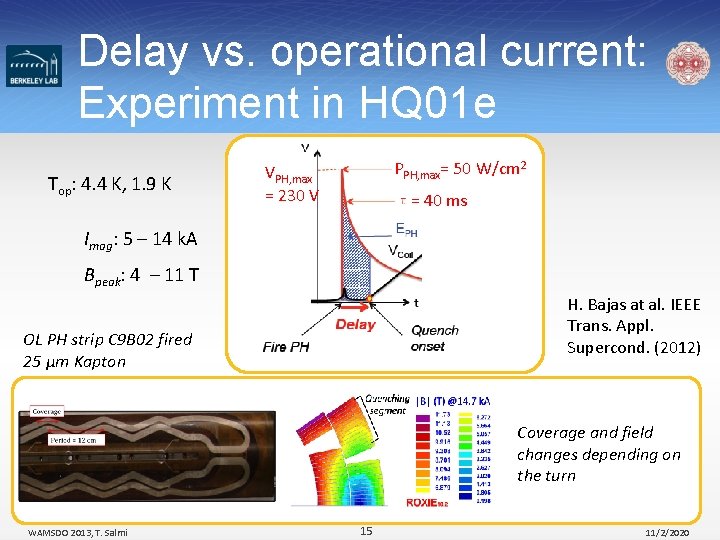
Delay vs. operational current: Experiment in HQ 01 e Top: 4. 4 K, 1. 9 K PPH, max= 50 W/cm 2 VPH, max = 230 V = 40 ms Imag: 5 – 14 k. A Bpeak: 4 – 11 T H. Bajas at al. IEEE Trans. Appl. Supercond. (2012) OL PH strip C 9 B 02 fired 25 μm Kapton Coverage and field changes depending on the turn WAMSDO 2013, T. Salmi 15 11/2/2020
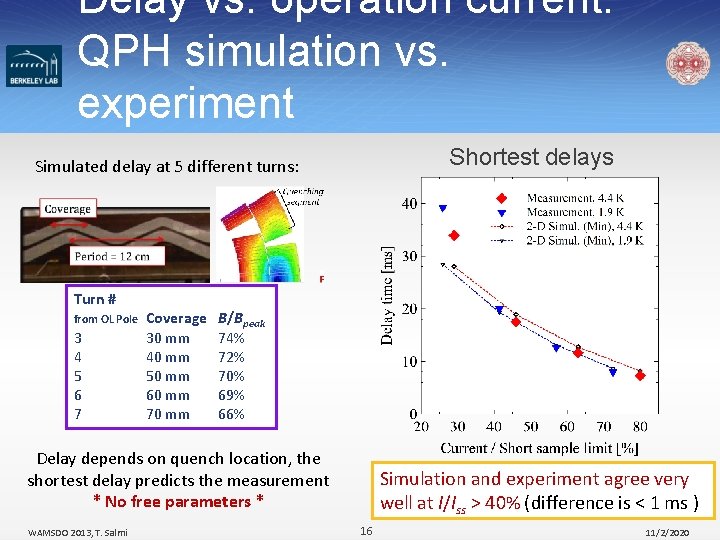
Delay vs. operation current: QPH simulation vs. experiment Shortest delays Simulated delay at 5 different turns: Turn # from OL Pole 3 4 5 6 7 Coverage B/Bpeak 30 mm 74% 40 mm 72% 50 mm 70% 60 mm 69% 70 mm 66% Delay depends on quench location, the shortest delay predicts the measurement * No free parameters * WAMSDO 2013, T. Salmi Simulation and experiment agree very well at I/Iss > 40% (difference is < 1 ms ) 16 11/2/2020
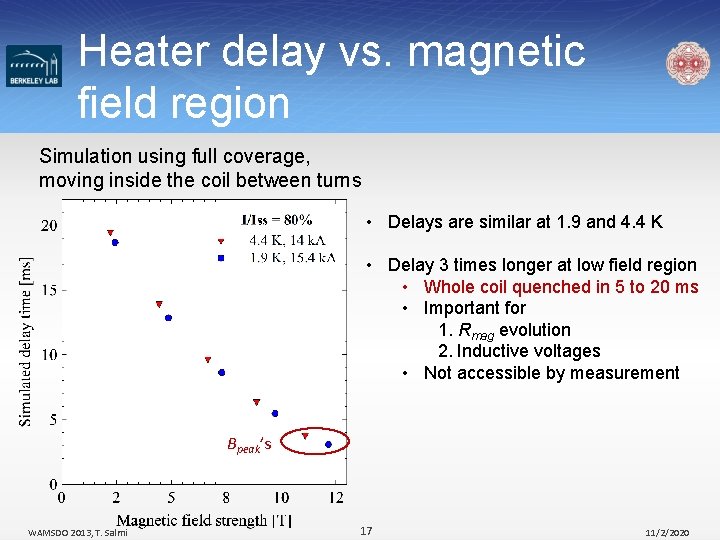
Heater delay vs. magnetic field region Simulation using full coverage, moving inside the coil between turns • Delays are similar at 1. 9 and 4. 4 K • Delay 3 times longer at low field region • Whole coil quenched in 5 to 20 ms • Important for 1. Rmag evolution 2. Inductive voltages • Not accessible by measurement Bpeak’s WAMSDO 2013, T. Salmi 17 11/2/2020
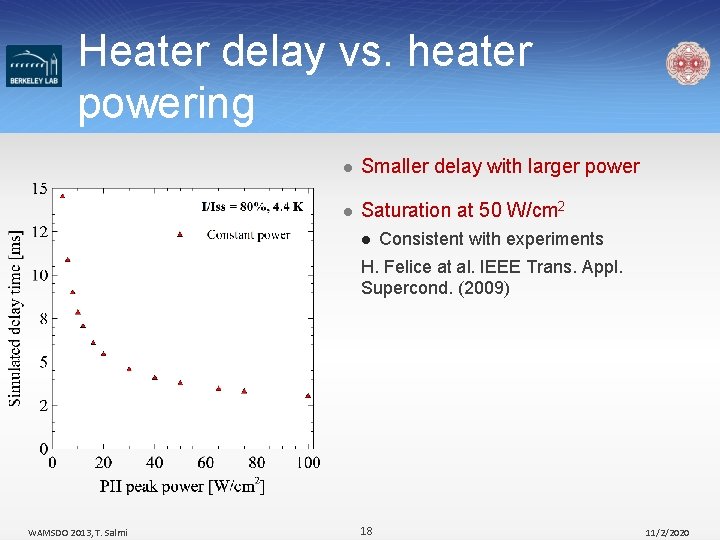
Heater delay vs. heater powering l Smaller delay with larger power l Saturation at 50 W/cm 2 l Consistent with experiments H. Felice at al. IEEE Trans. Appl. Supercond. (2009) WAMSDO 2013, T. Salmi 18 11/2/2020
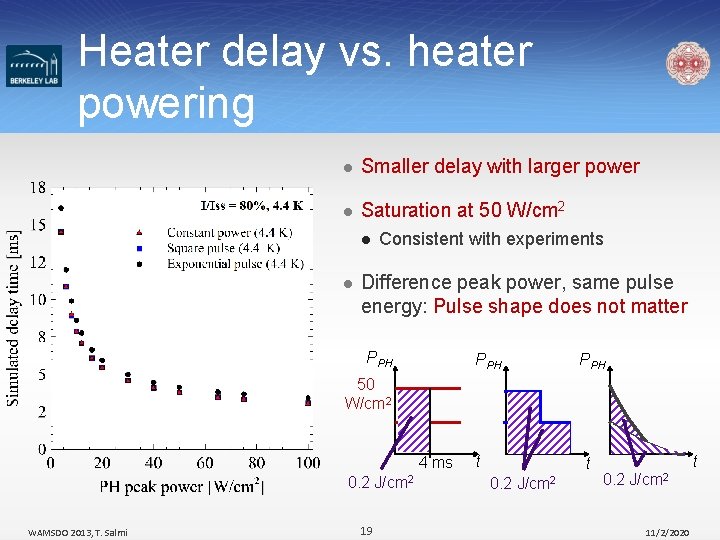
Heater delay vs. heater powering l Smaller delay with larger power l Saturation at 50 W/cm 2 l l Consistent with experiments Difference peak power, same pulse energy: Pulse shape does not matter PPH PPH 50 W/cm 2 4 ms 0. 2 J/cm 2 WAMSDO 2013, T. Salmi 19 t t 0. 2 J/cm 2 11/2/2020
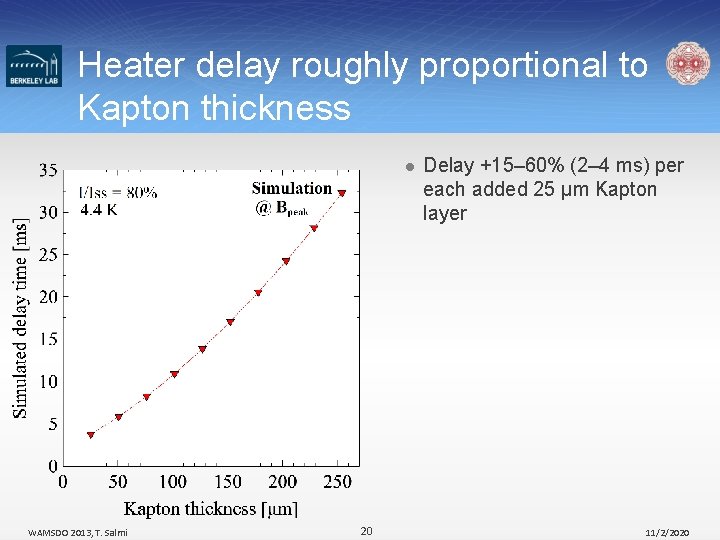
Heater delay roughly proportional to Kapton thickness l WAMSDO 2013, T. Salmi 20 Delay +15– 60% (2– 4 ms) per each added 25 μm Kapton layer 11/2/2020
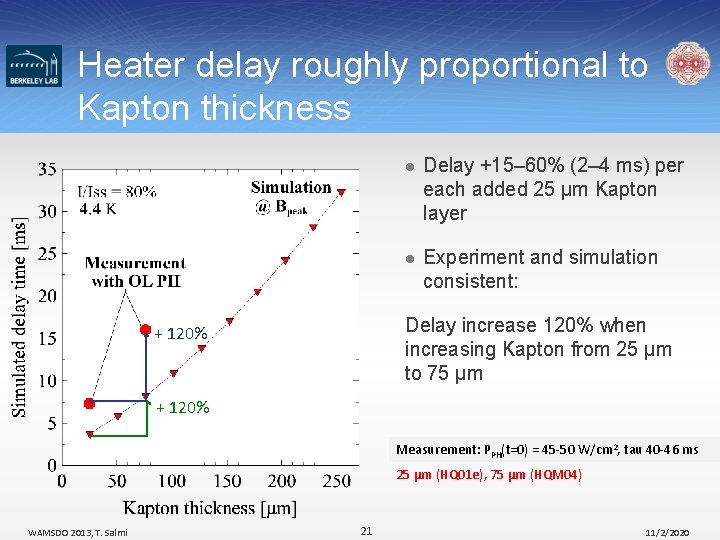
Heater delay roughly proportional to Kapton thickness l Delay +15– 60% (2– 4 ms) per each added 25 μm Kapton layer l Experiment and simulation consistent: Delay increase 120% when increasing Kapton from 25 μm to 75 μm + 120% Measurement: PPH(t=0) = 45 -50 W/cm 2, tau 40 -46 ms 25 μm (HQ 01 e), 75 μm (HQM 04) WAMSDO 2013, T. Salmi 21 11/2/2020
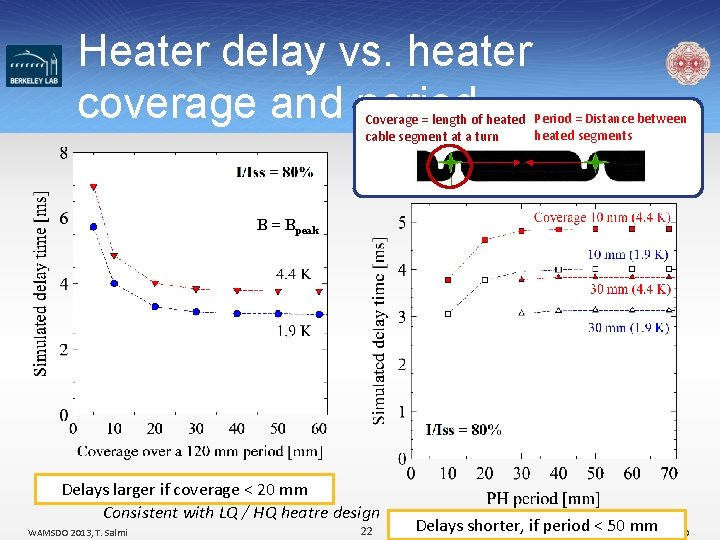
Heater delay vs. heater coverage and period Coverage = length of heated Period = Distance between heated segments cable segment at a turn B = Bpeak Delays larger if coverage < 20 mm Consistent with LQ / HQ heatre design WAMSDO 2013, T. Salmi 22 Delays shorter, if period < 50 mm 11/2/2020
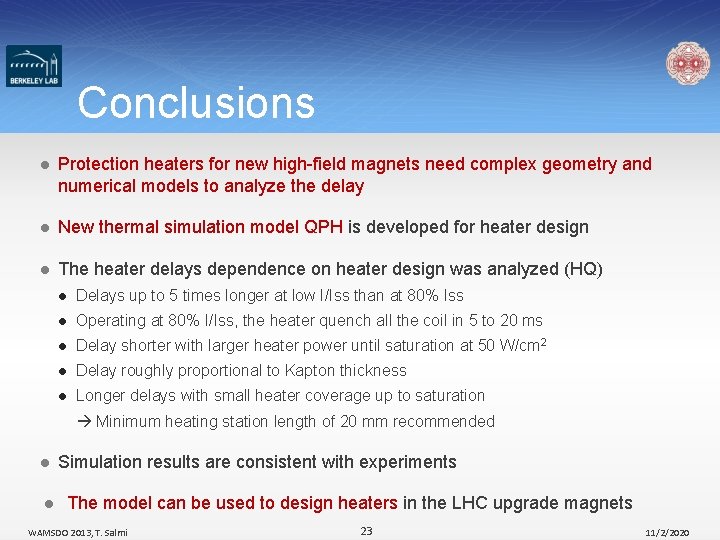
Conclusions l Protection heaters for new high-field magnets need complex geometry and numerical models to analyze the delay l New thermal simulation model QPH is developed for heater design l The heater delays dependence on heater design was analyzed (HQ) l Delays up to 5 times longer at low I/Iss than at 80% Iss l Operating at 80% I/Iss, the heater quench all the coil in 5 to 20 ms l Delay shorter with larger heater power until saturation at 50 W/cm 2 l Delay roughly proportional to Kapton thickness l Longer delays with small heater coverage up to saturation Minimum heating station length of 20 mm recommended l l Simulation results are consistent with experiments The model can be used to design heaters in the LHC upgrade magnets WAMSDO 2013, T. Salmi 23 11/2/2020
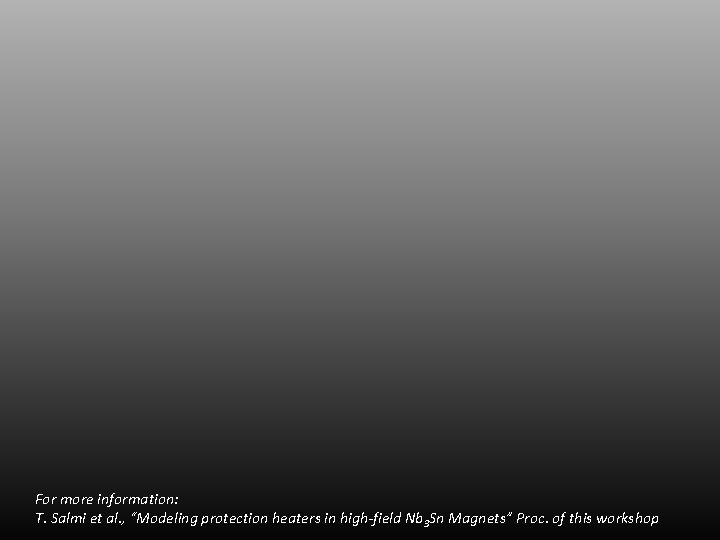
For more information: T. Salmi et al. , “Modeling protection heaters in high-field Nb 3 Sn Magnets” Proc. of this workshop WAMSDO 2013, T. Salmi 24 11/2/2020
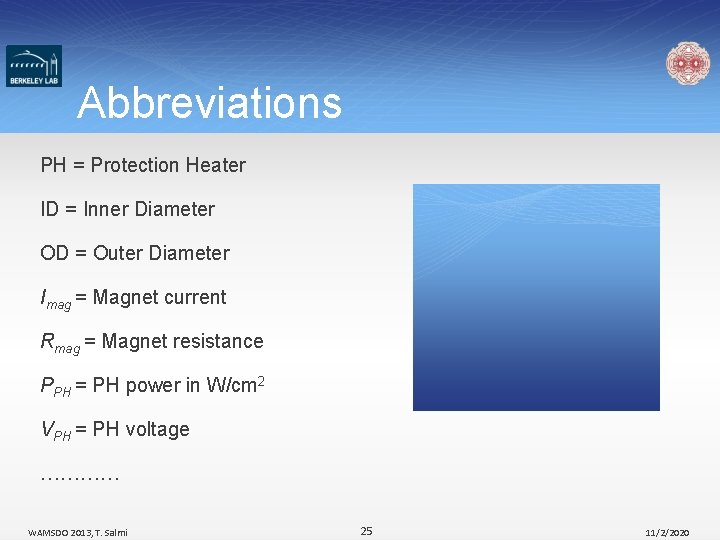
Abbreviations PH = Protection Heater ID = Inner Diameter OD = Outer Diameter Imag = Magnet current Rmag = Magnet resistance PPH = PH power in W/cm 2 VPH = PH voltage ………… WAMSDO 2013, T. Salmi 25 11/2/2020
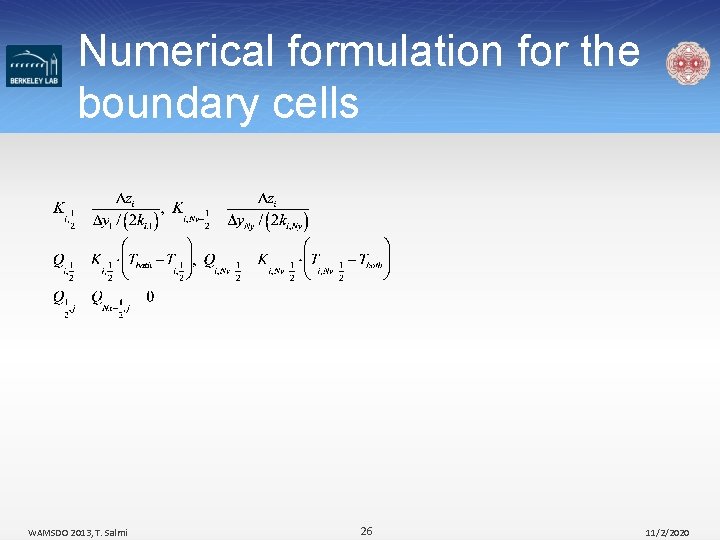
Numerical formulation for the boundary cells WAMSDO 2013, T. Salmi 26 11/2/2020
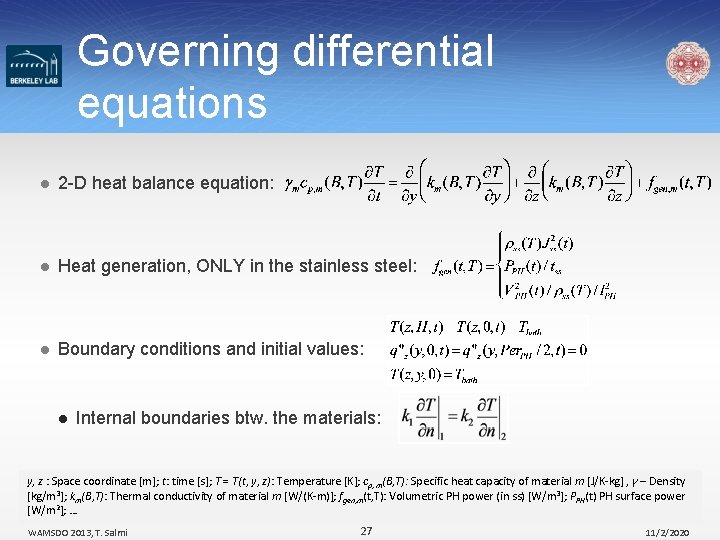
Governing differential equations l 2 -D heat balance equation: l Heat generation, ONLY in the stainless steel: l Boundary conditions and initial values: l Internal boundaries btw. the materials: y, z : Space coordinate [m]; t: time [s]; T = T(t, y, z): Temperature [K]; cp, m(B, T): Specific heat capacity of material m [J/K-kg] , γ – Density [kg/m 3]; km(B, T): Thermal conductivity of material m [W/(K-m)]; fgen, m(t, T): Volumetric PH power (in ss) [W/m 3]; PPH(t) PH surface power [W/m 2]; … WAMSDO 2013, T. Salmi 27 11/2/2020
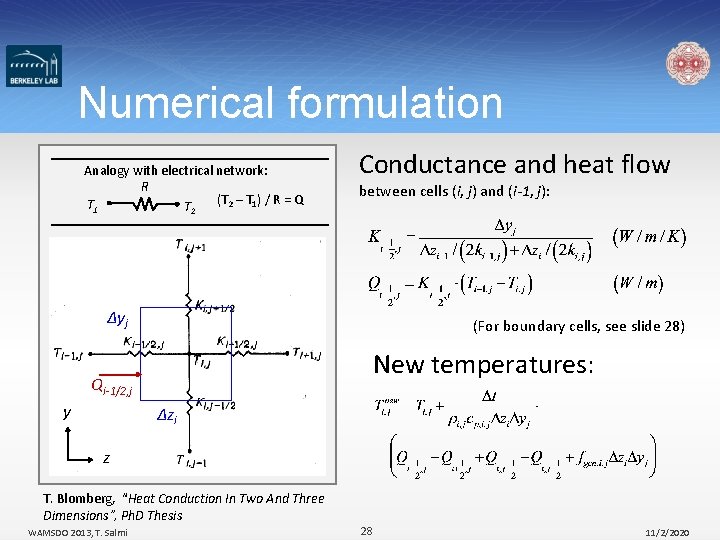
Numerical formulation Analogy with electrical network: R (T 2 – T 1) / R = Q T 1 T 2 Conductance and heat flow between cells (i, j) and (i-1, j): Δyj (For boundary cells, see slide 28) New temperatures: Qi-1/2, j y Δzi z T. Blomberg, “Heat Conduction In Two And Three Dimensions”, Ph. D Thesis WAMSDO 2013, T. Salmi 28 11/2/2020
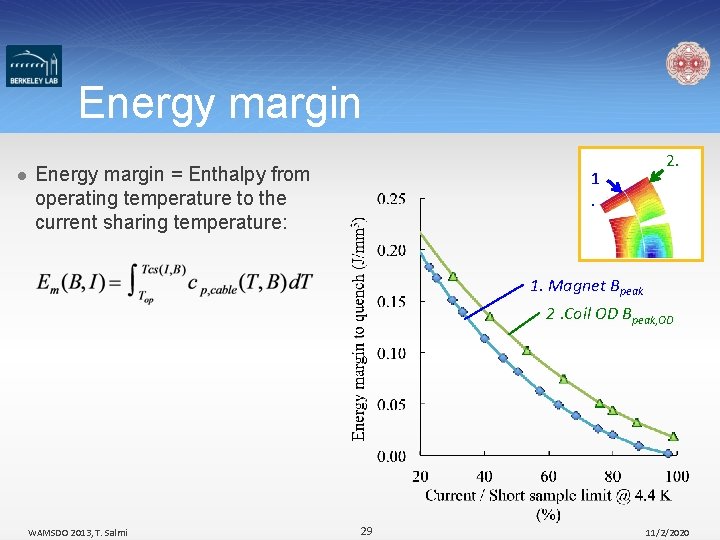
Energy margin l Energy margin = Enthalpy from operating temperature to the current sharing temperature: 1. 2. 1. Magnet Bpeak 2. Coil OD Bpeak, OD WAMSDO 2013, T. Salmi 29 11/2/2020
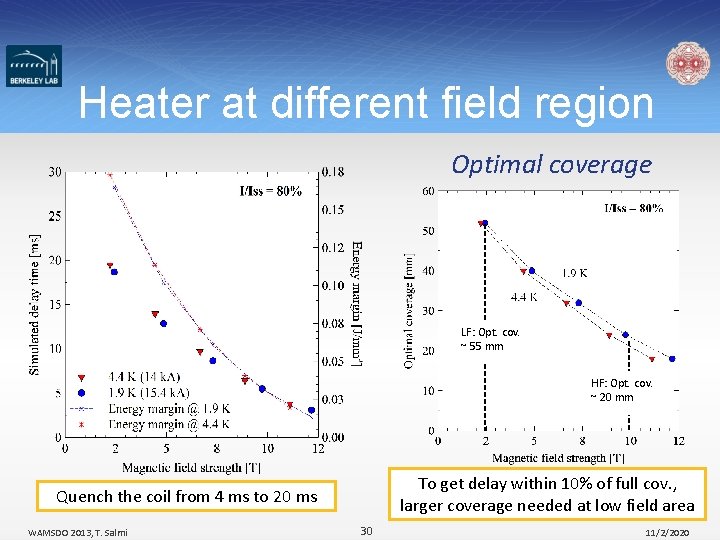
Heater at different field region Optimal coverage LF: Opt. cov. ~ 55 mm HF: Opt. cov. ~ 20 mm To get delay within 10% of full cov. , larger coverage needed at low field area Quench the coil from 4 ms to 20 ms WAMSDO 2013, T. Salmi 30 11/2/2020
Academy heaters
Rheem residential water heaters
Paul steffes
Sealed quench furnace price
Love is stronger than death poem
Mechanical seal piping plans
Lhc quench
Heat transfer
What is heat transfer conduction convection and radiation
Conduction, convection radiation examples
Q system = -q surroundings
Heat and mass transfer cengel 4th edition pdf
Heat transfer radiation
Heat and mass transfer
Heat and mass transfer
Simultaneous heat and mass transfer
Does heat radiation travel in straight lines
Heat-mass transfer and geodynamics of the lithosphere:
Chapter 7 heat transfer and change of phase
Heat transfer in hot air balloon
Fundamentals of heat and mass transfer 4th edition
Specific latent heat equation
Is a disturbance that transfers energy from place to place
Heat transfer of metals
Unit viscosity
Conduction or convection
Heat vs thermal energy
Diffusion eq
Jeopardy
Four containers were filled with warm water
Conduction vs insulation