Harvesting and Storing Corn Silage Karl Hoppe Ph
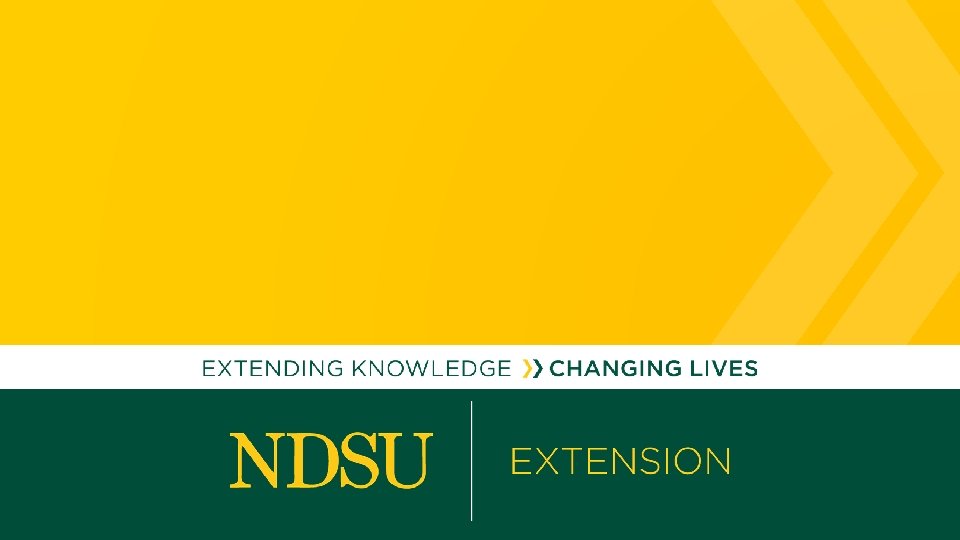
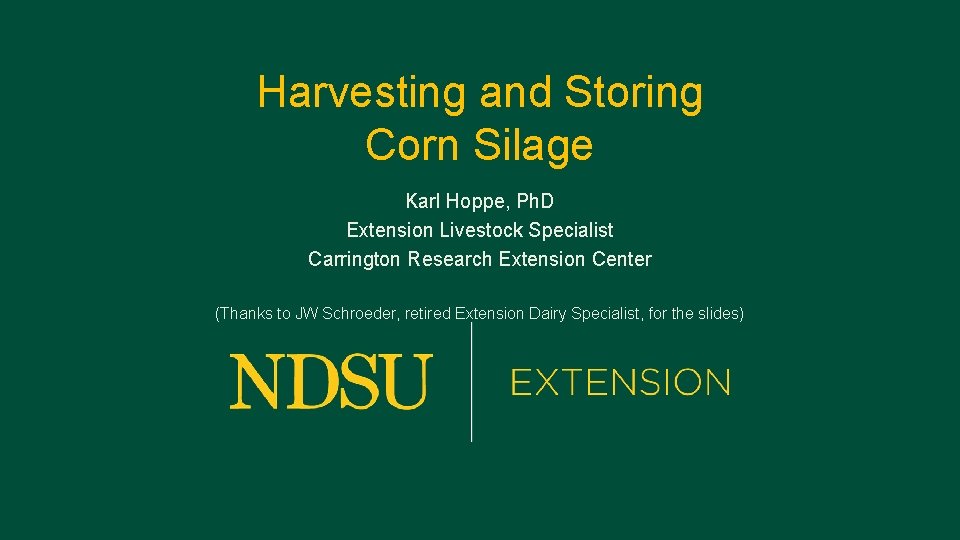
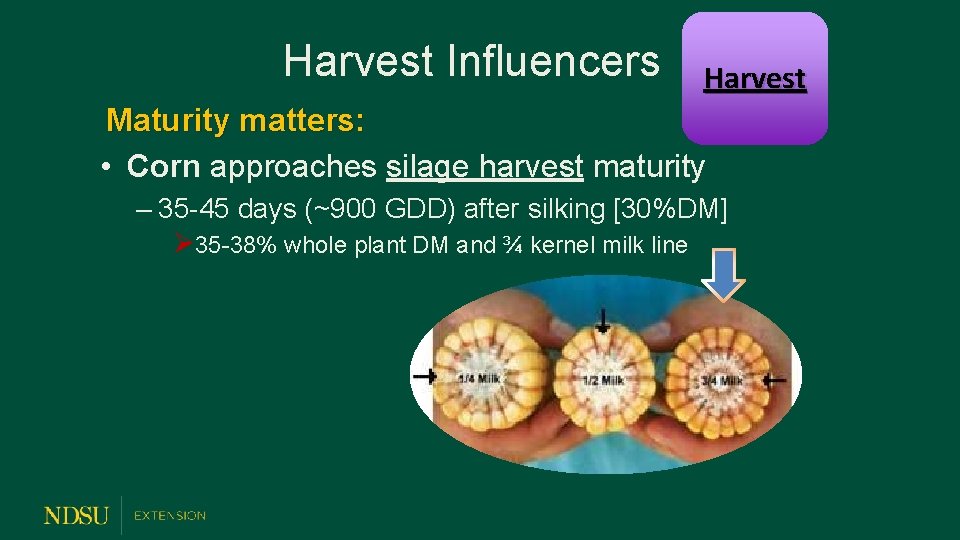
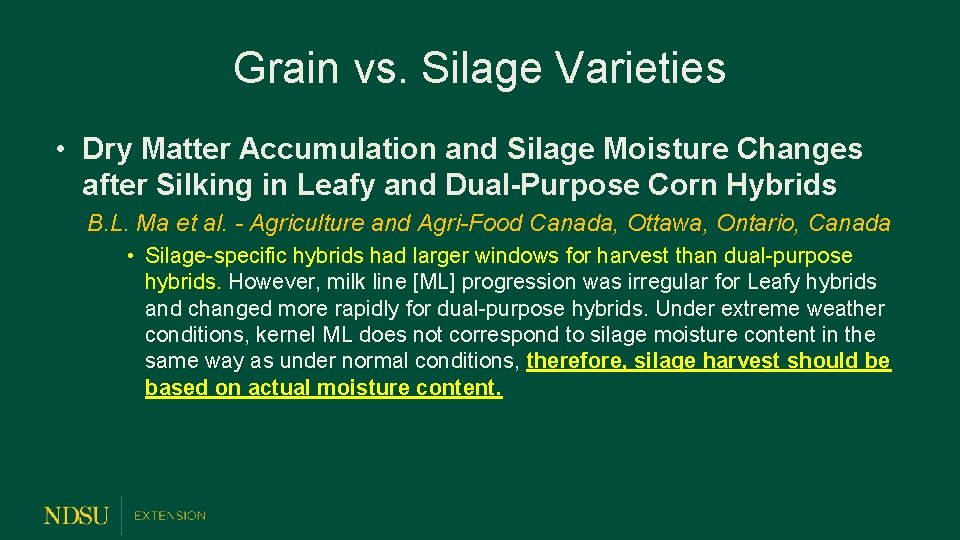
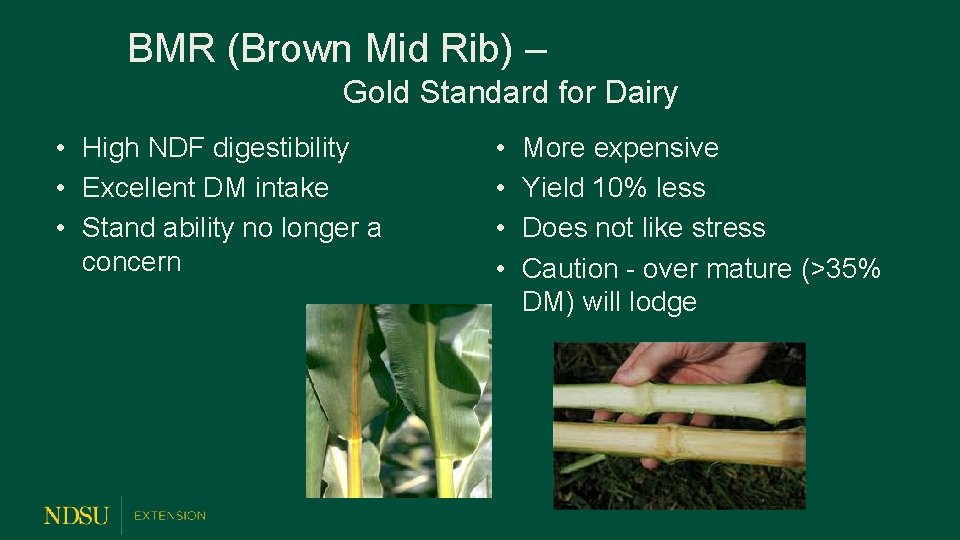
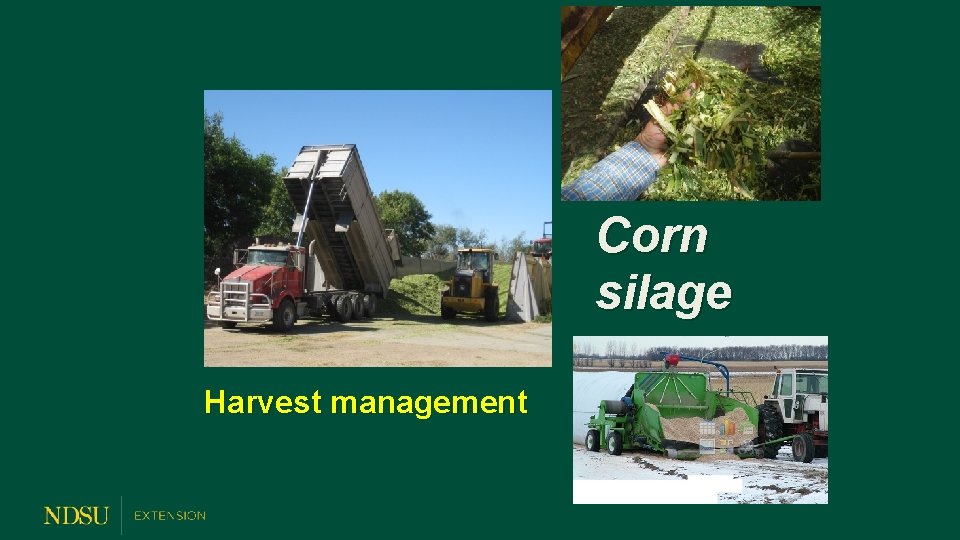
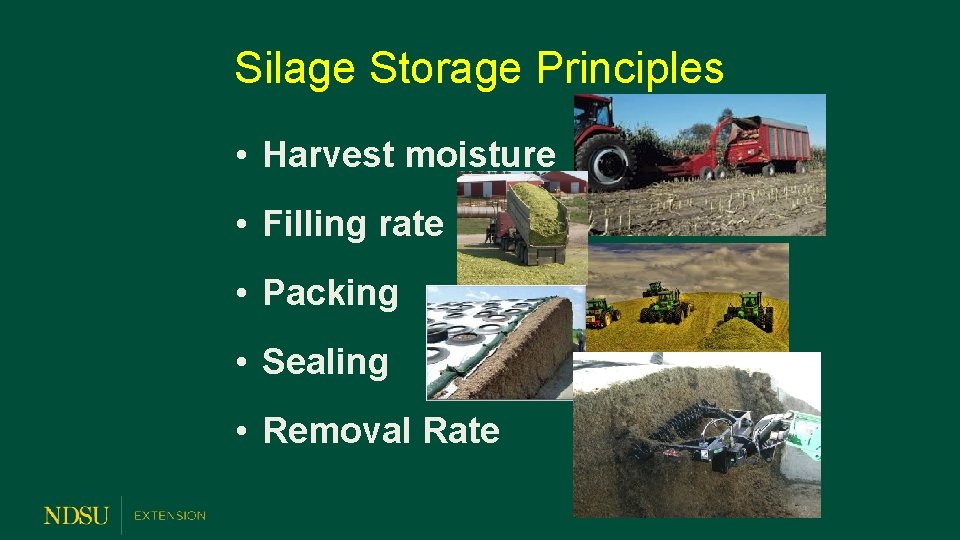
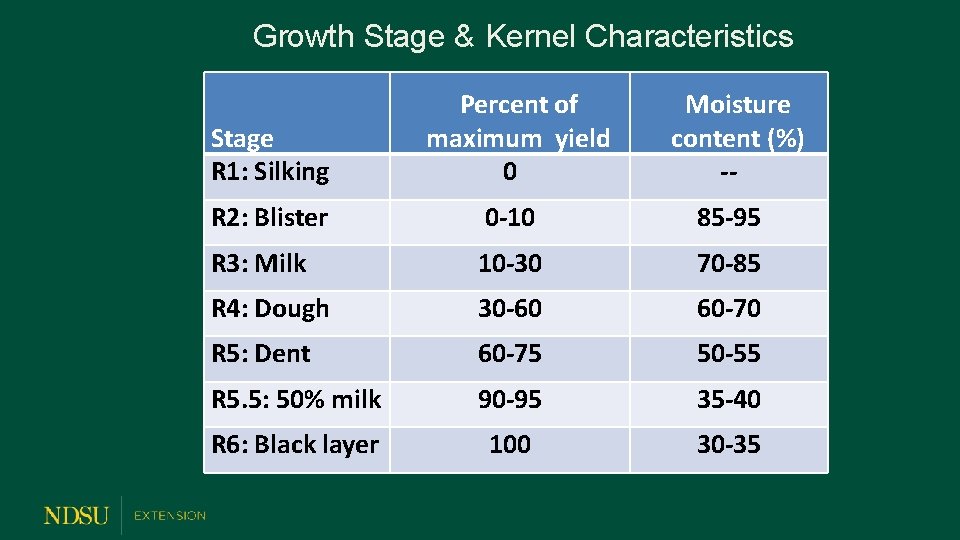
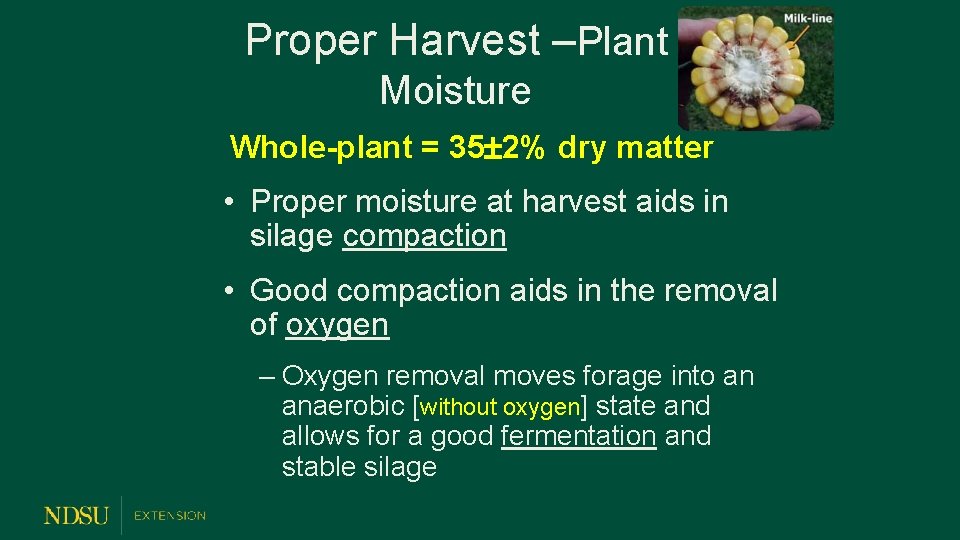

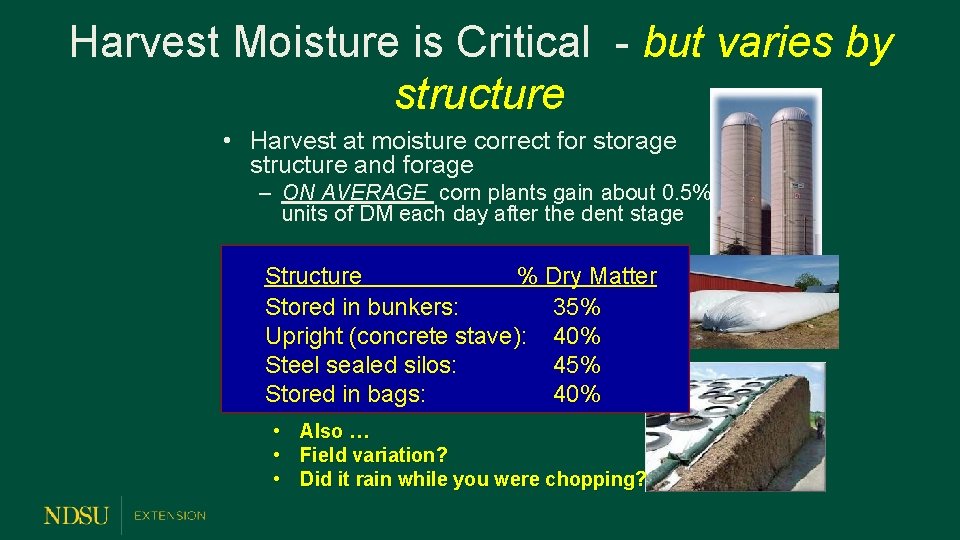
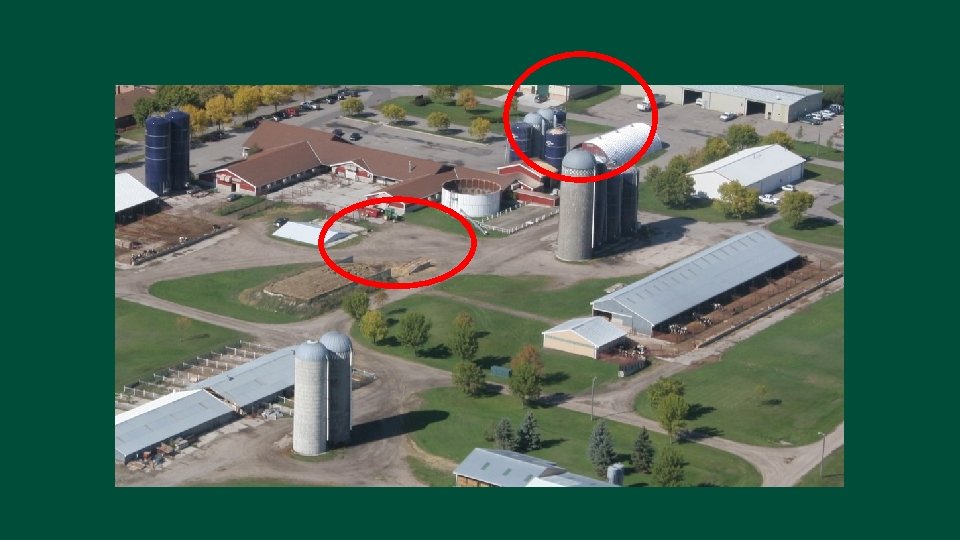
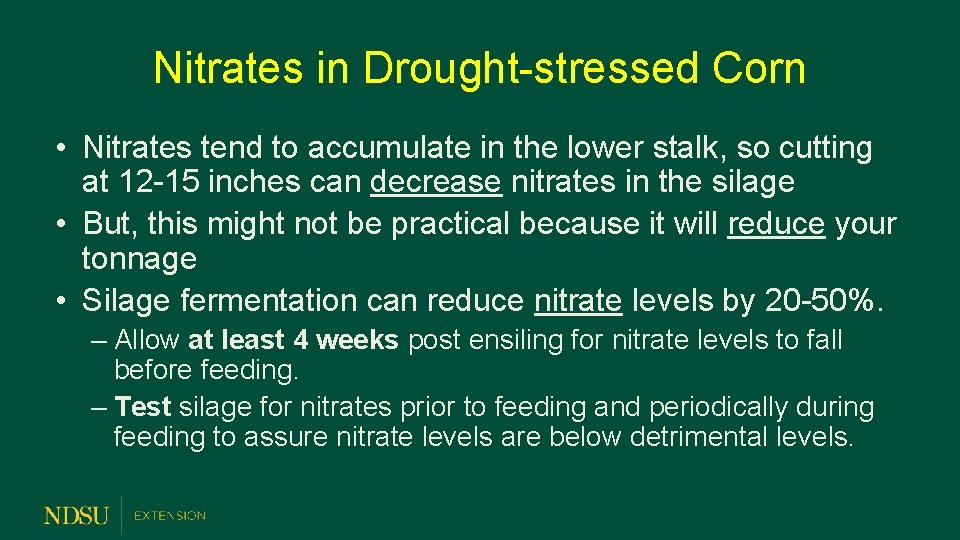
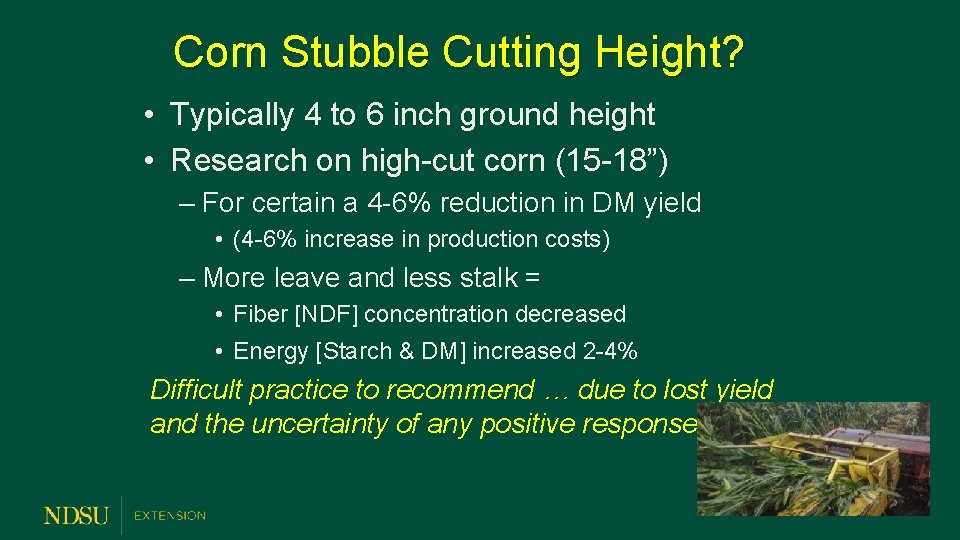
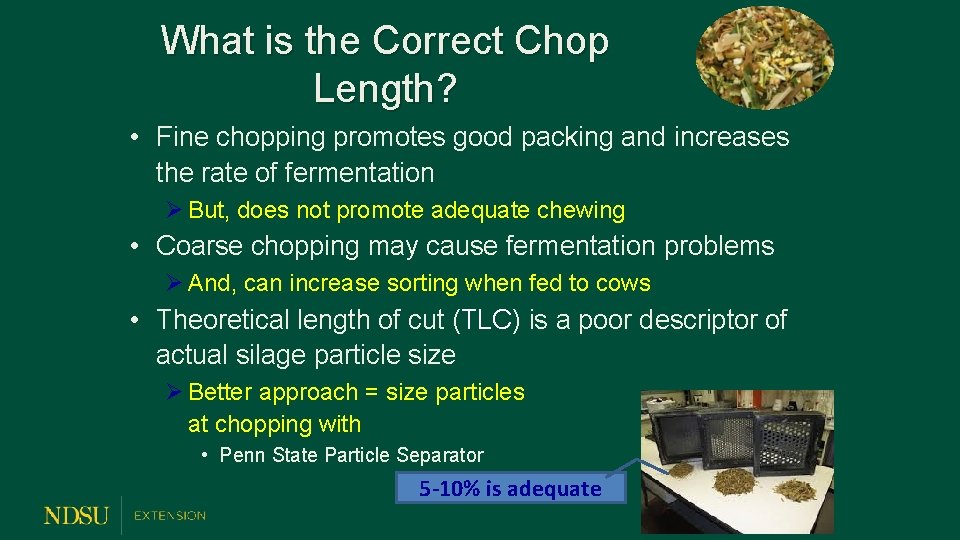
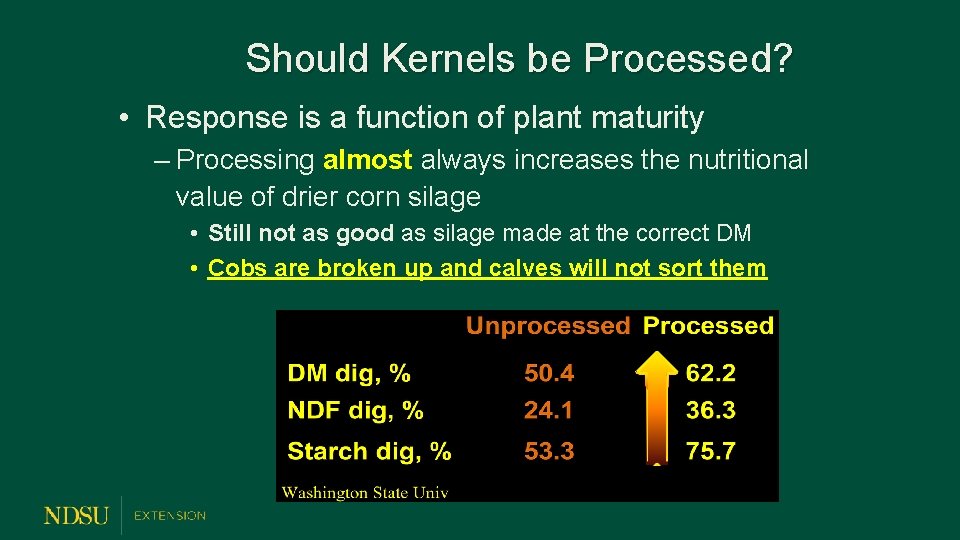
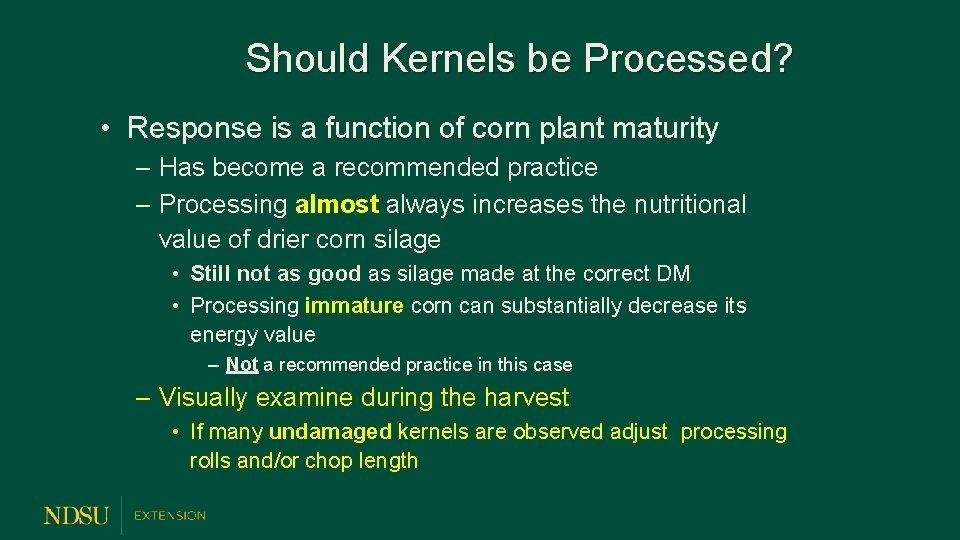
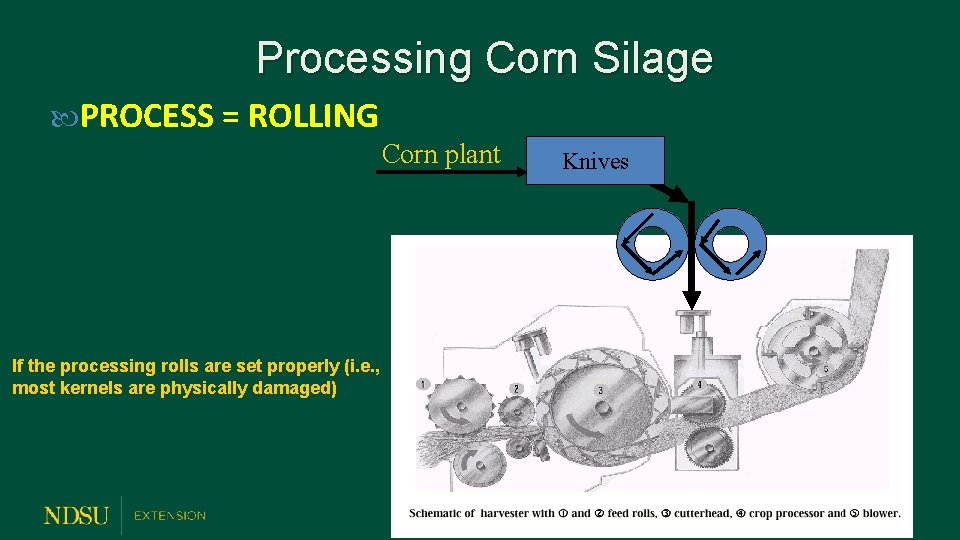
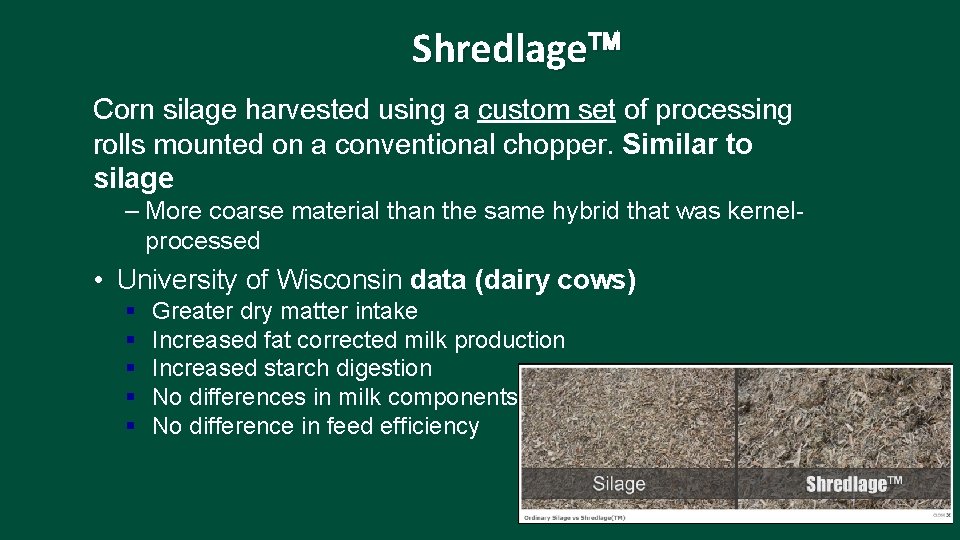
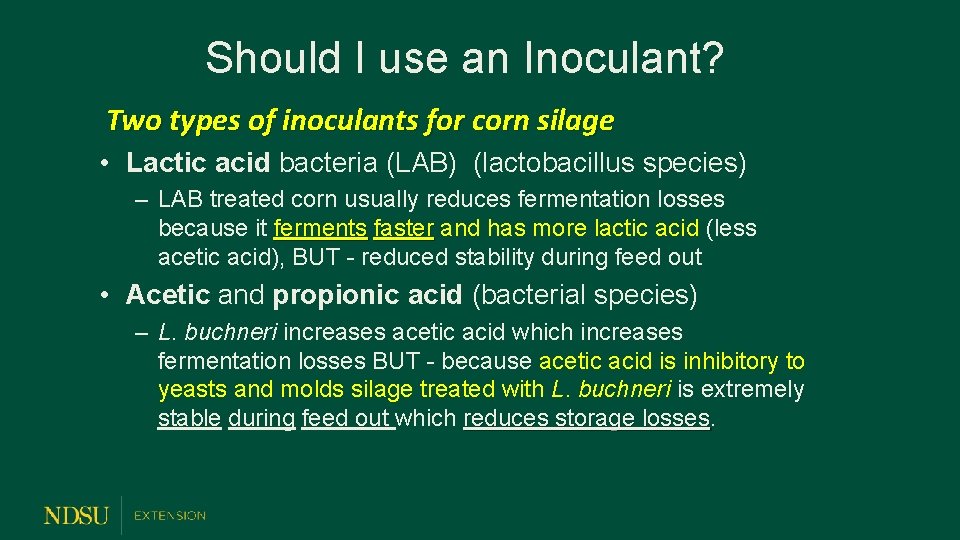
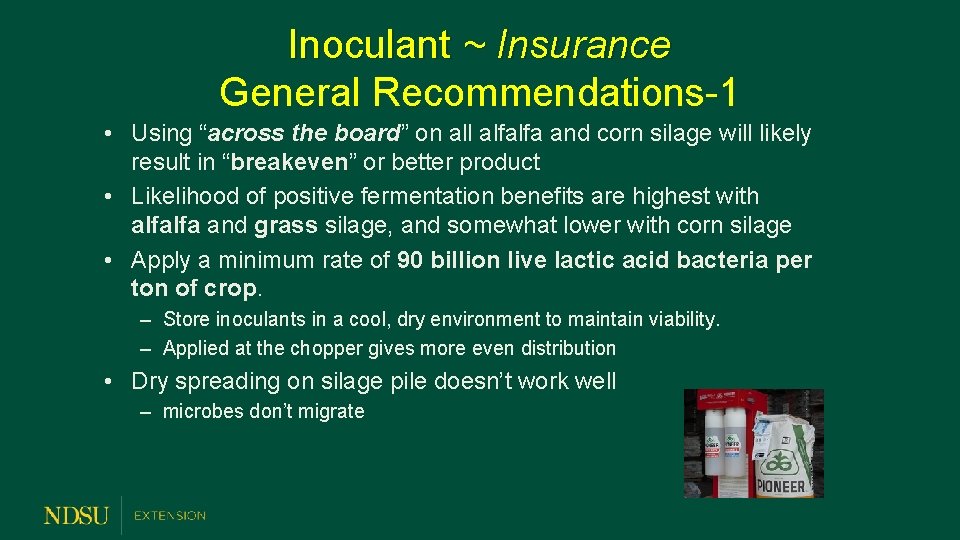
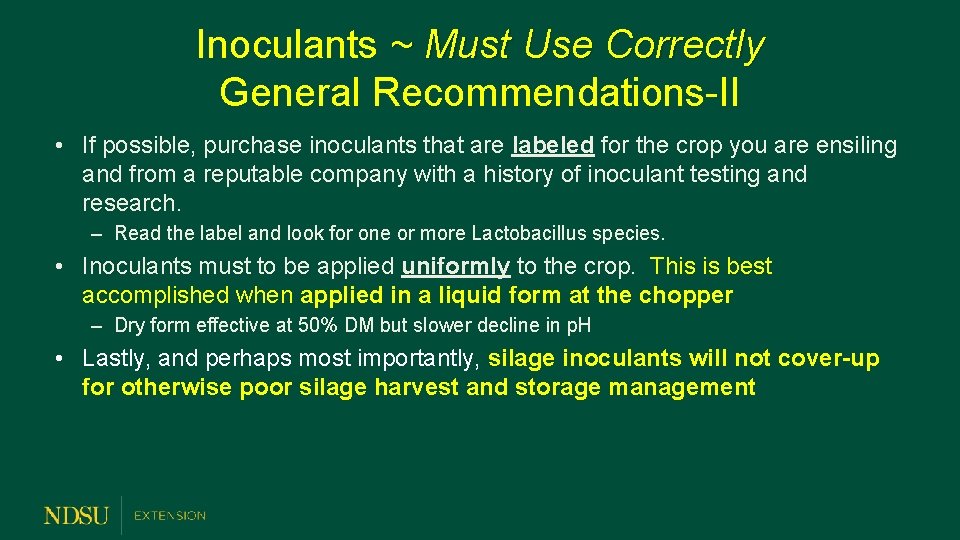
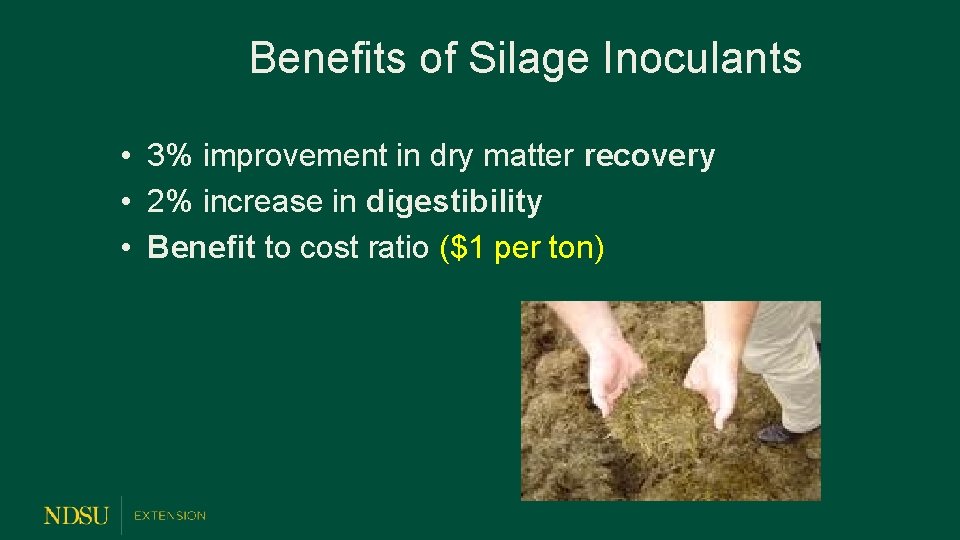
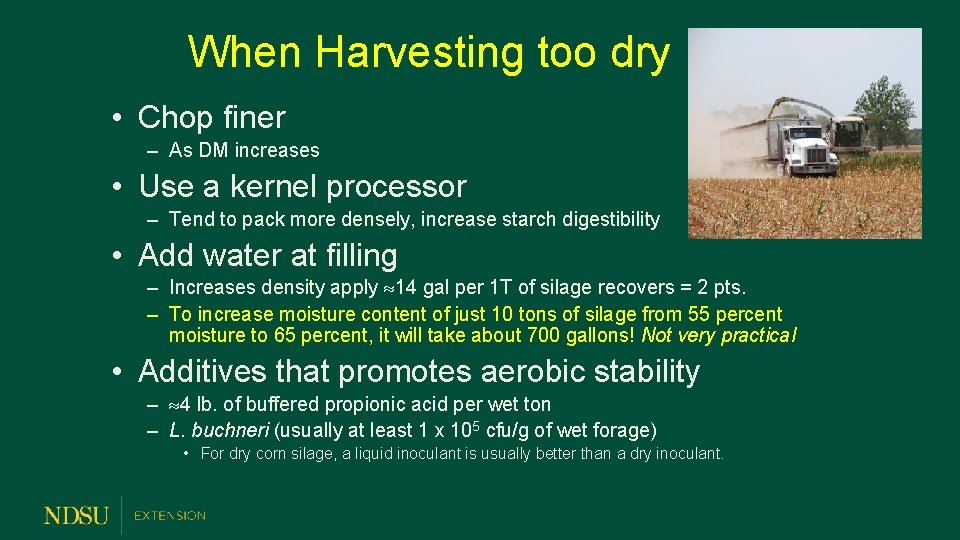
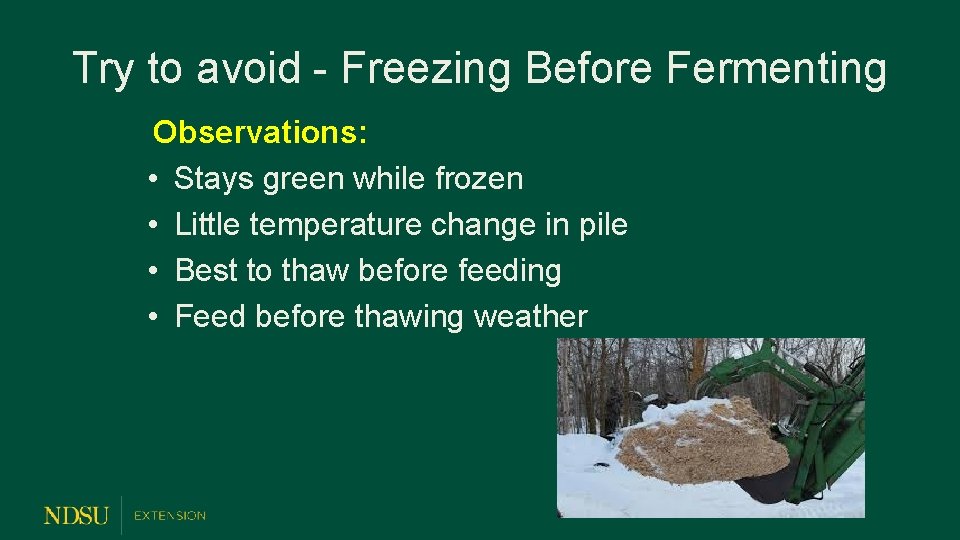
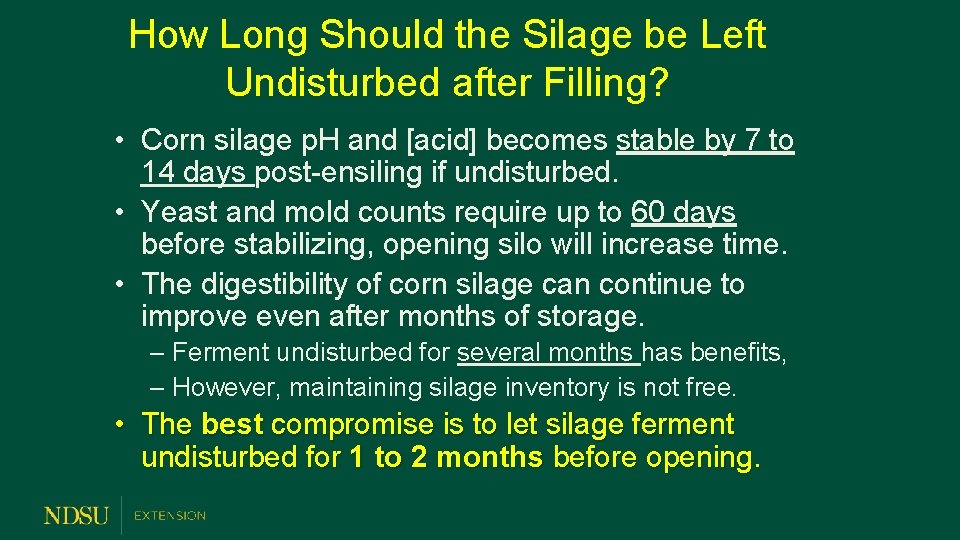
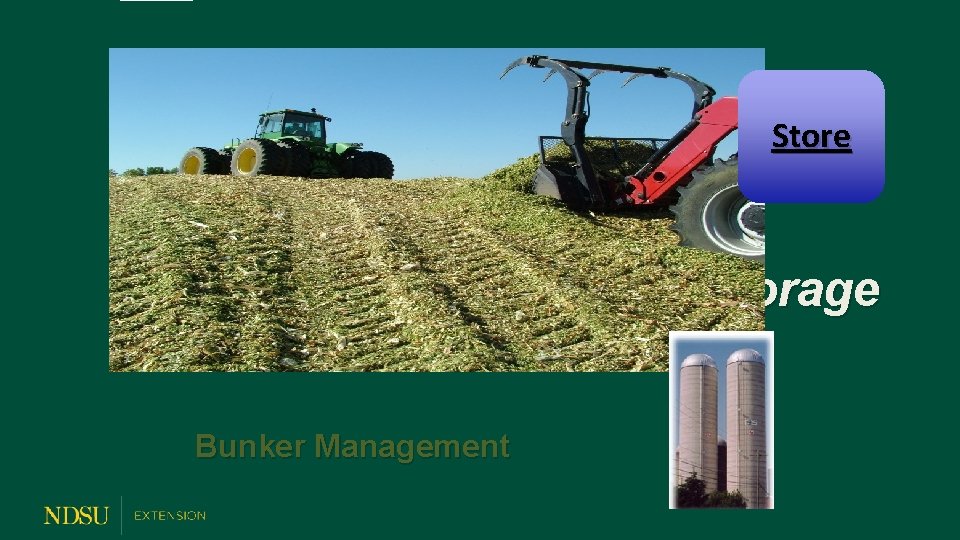
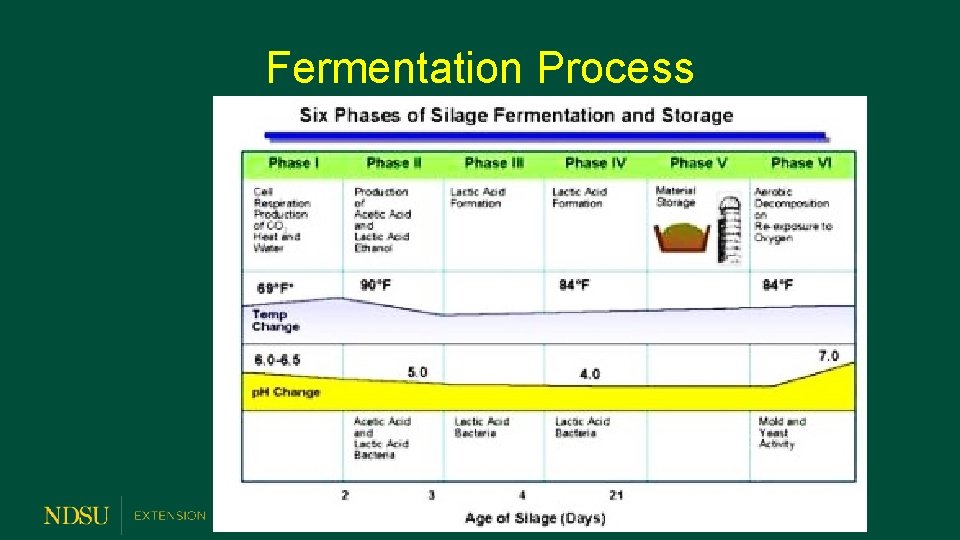
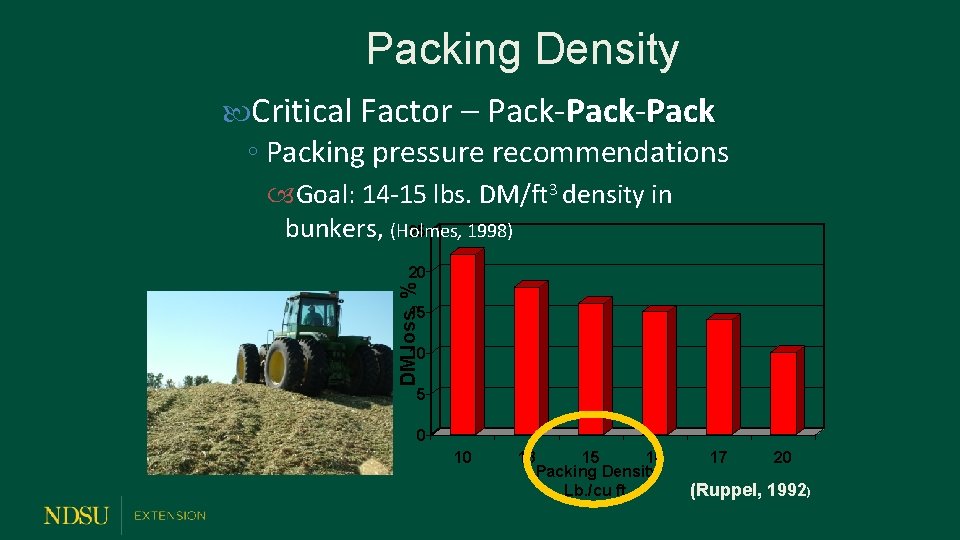
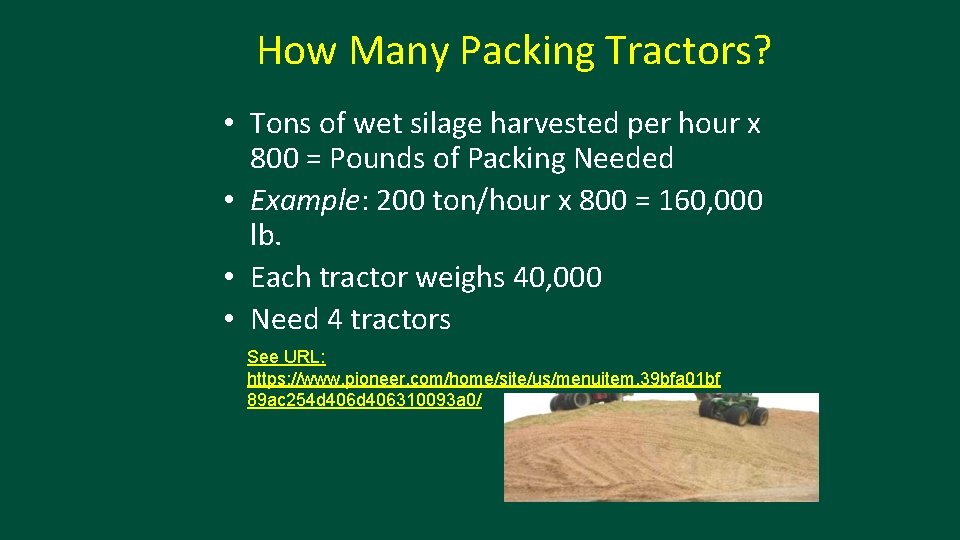
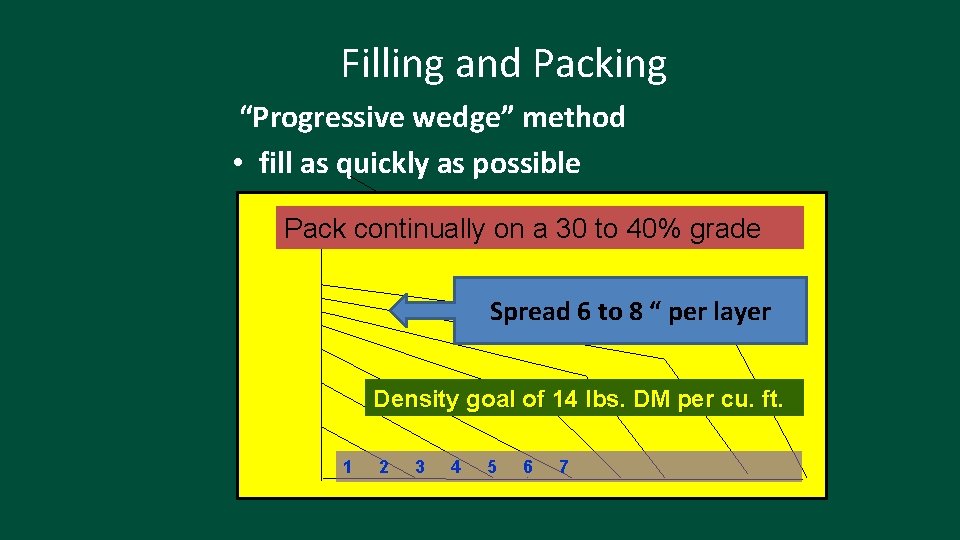
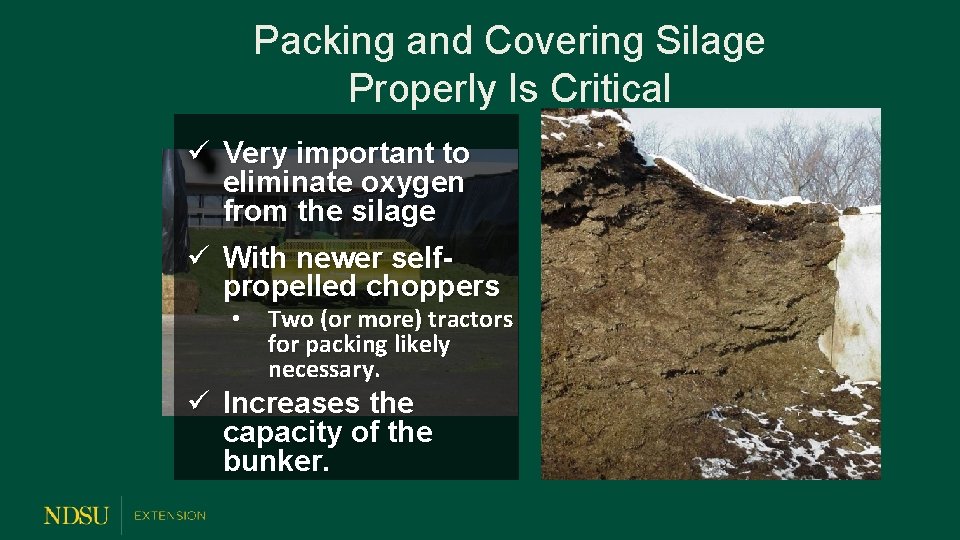
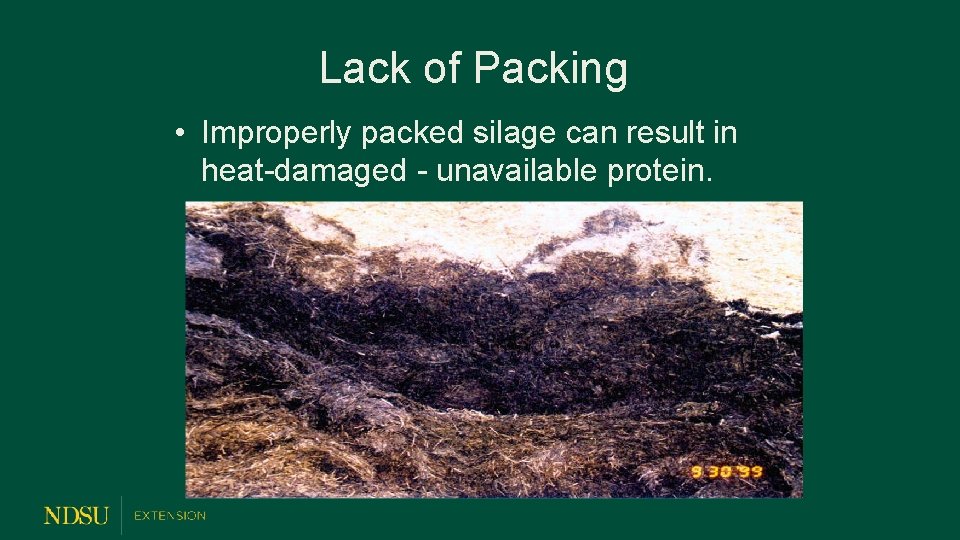
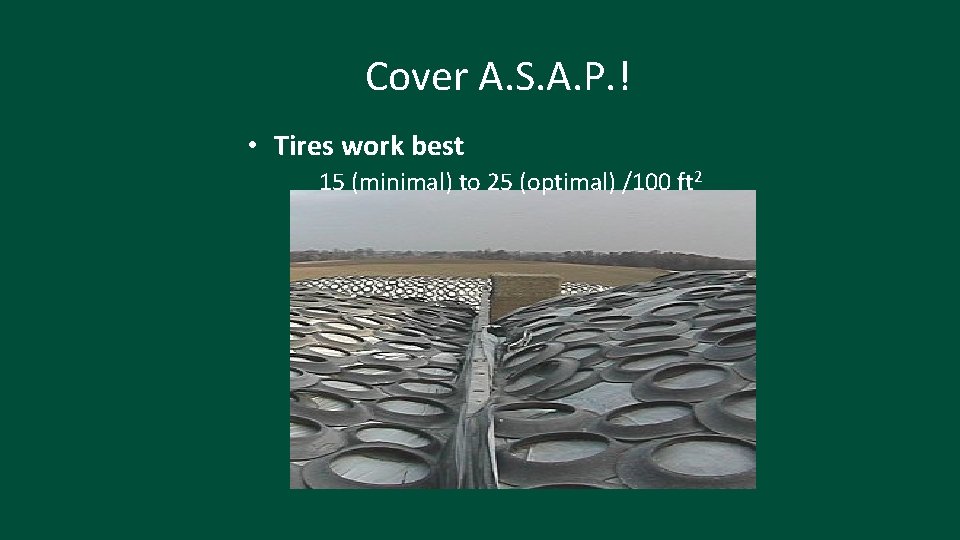
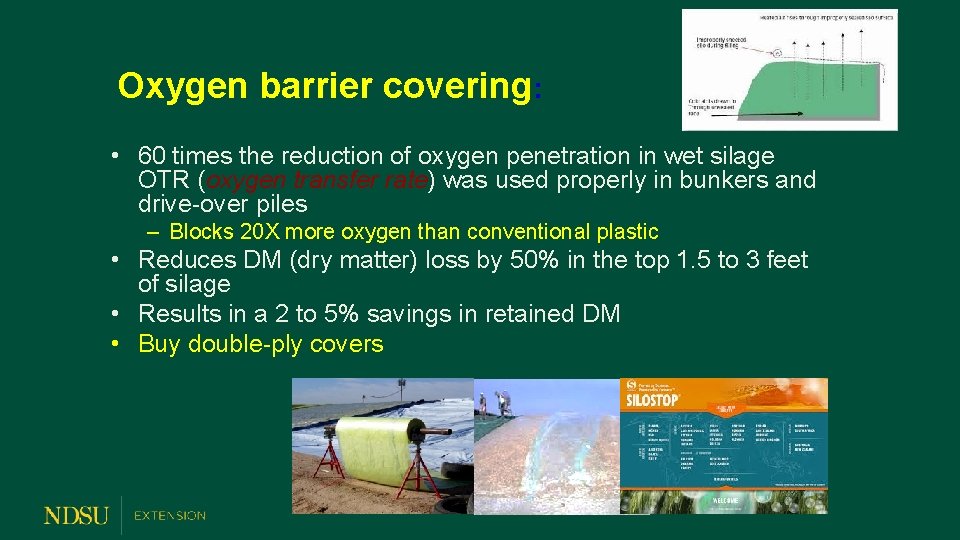
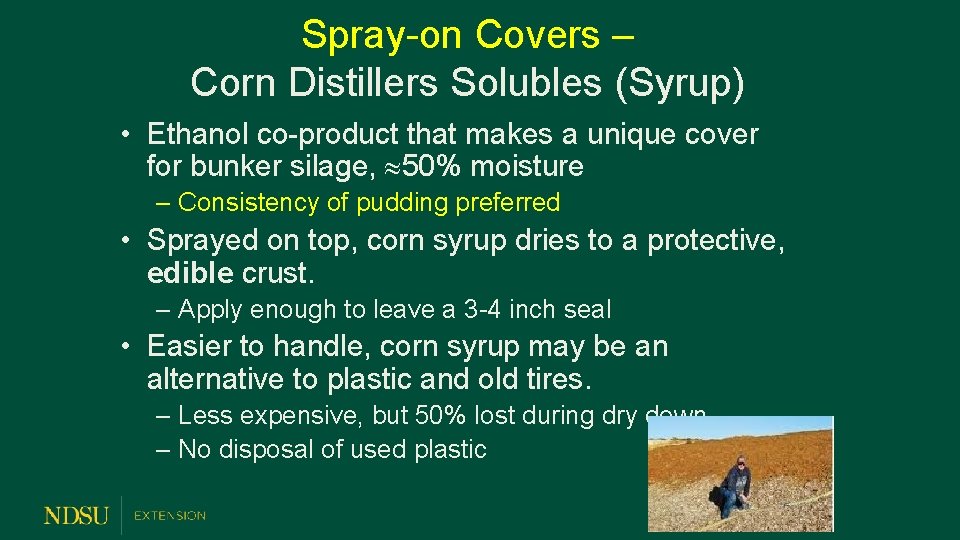
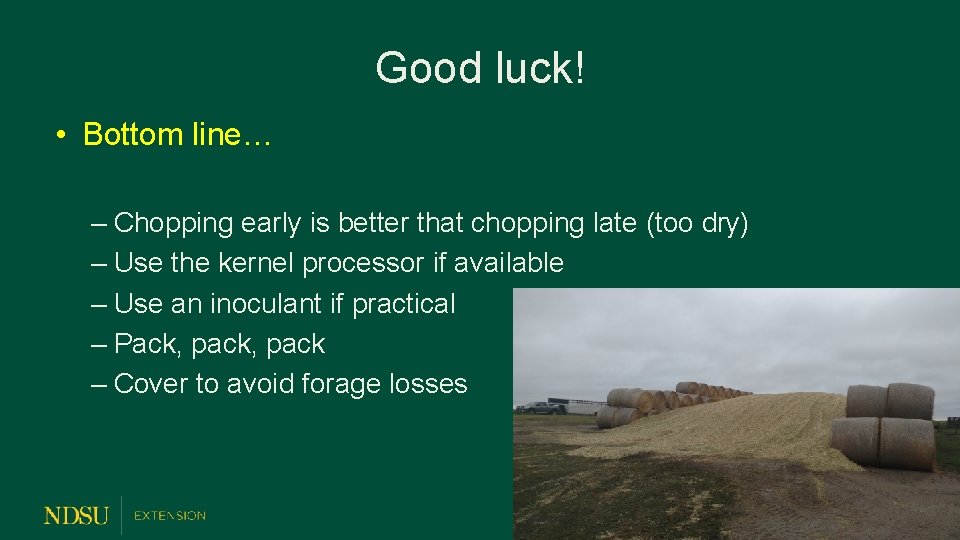
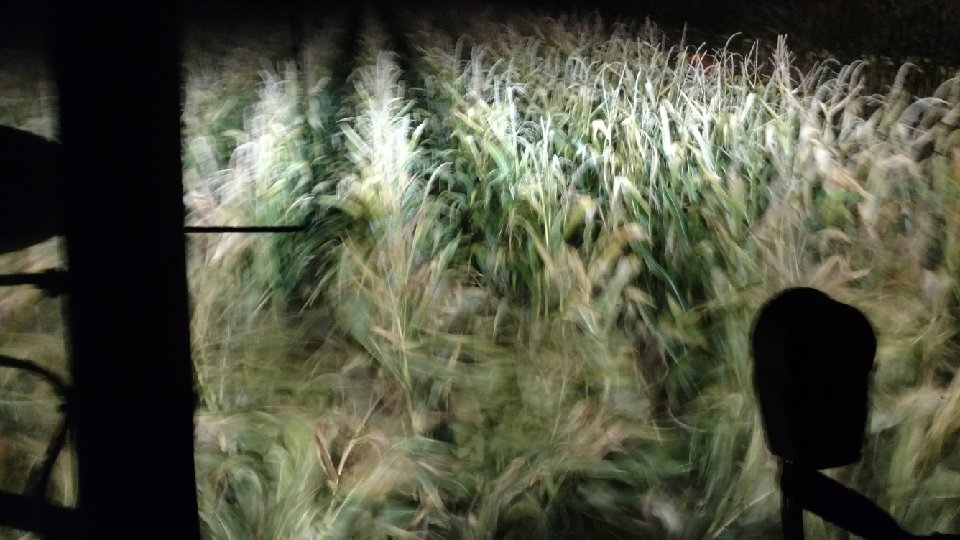
- Slides: 38
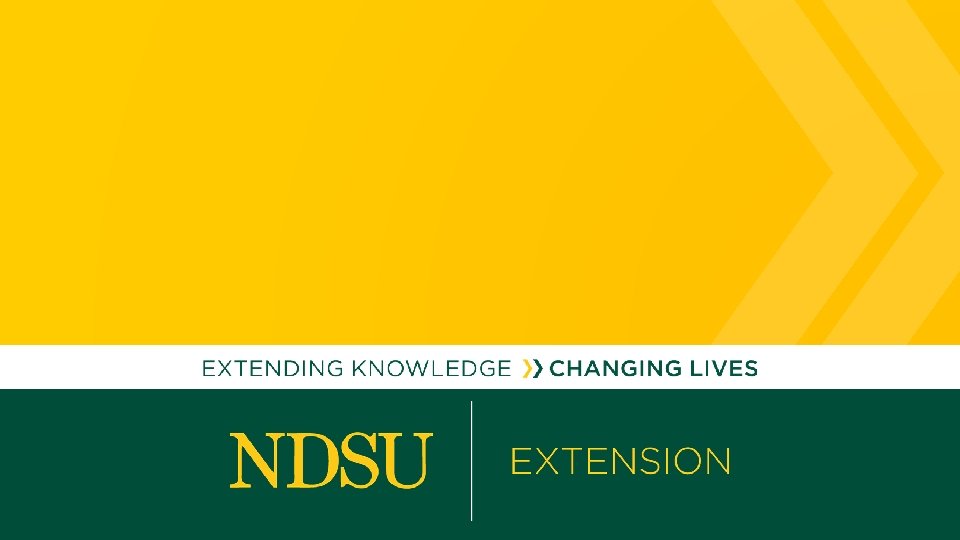
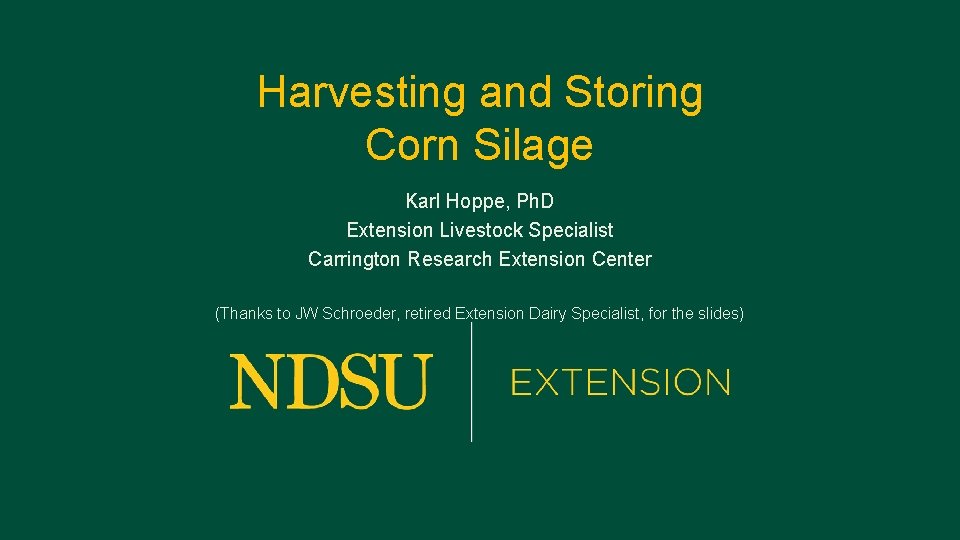
Harvesting and Storing Corn Silage Karl Hoppe, Ph. D Extension Livestock Specialist Carrington Research Extension Center (Thanks to JW Schroeder, retired Extension Dairy Specialist, for the slides)
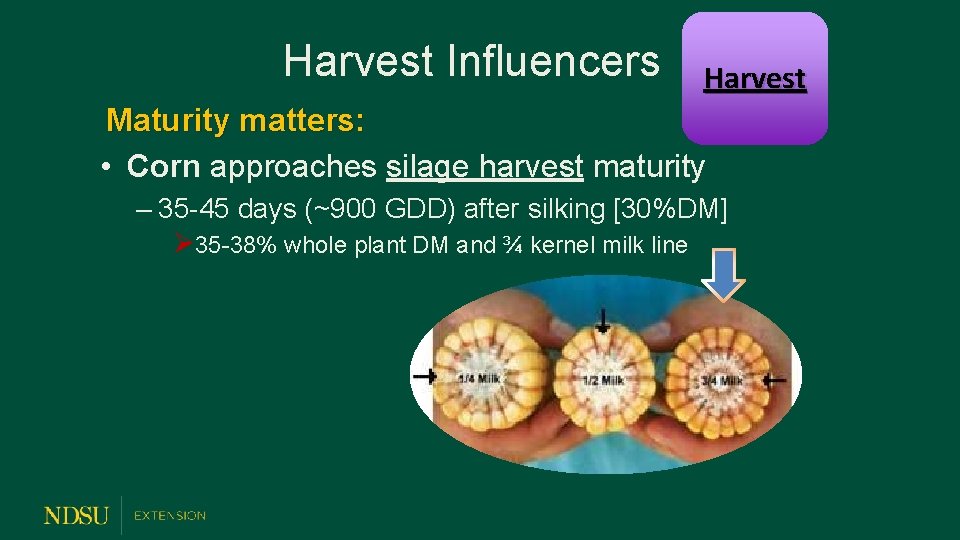
Harvest Influencers Harvest Maturity matters: • Corn approaches silage harvest maturity – 35 -45 days (~900 GDD) after silking [30%DM] Ø 35 -38% whole plant DM and ¾ kernel milk line
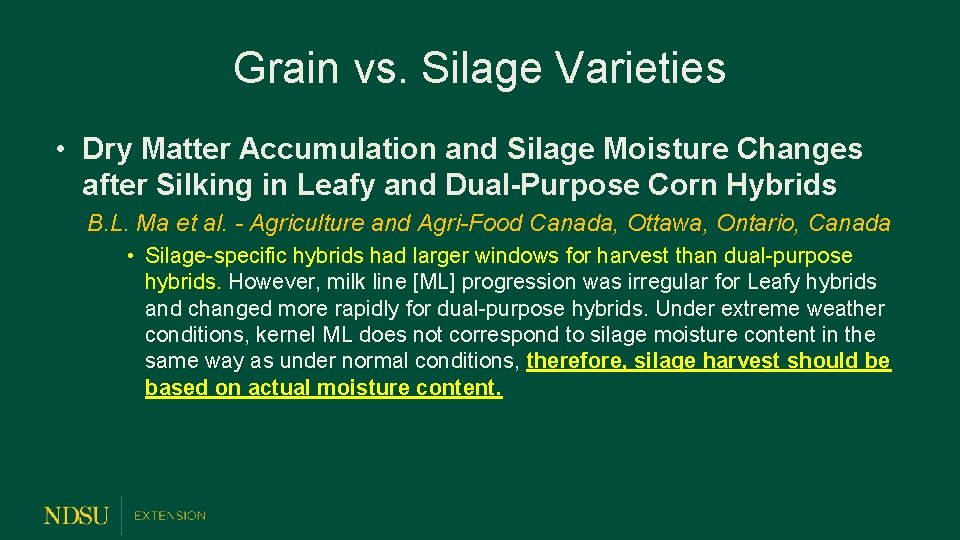
Grain vs. Silage Varieties • Dry Matter Accumulation and Silage Moisture Changes after Silking in Leafy and Dual-Purpose Corn Hybrids B. L. Ma et al. - Agriculture and Agri-Food Canada, Ottawa, Ontario, Canada • Silage-specific hybrids had larger windows for harvest than dual-purpose hybrids. However, milk line [ML] progression was irregular for Leafy hybrids and changed more rapidly for dual-purpose hybrids. Under extreme weather conditions, kernel ML does not correspond to silage moisture content in the same way as under normal conditions, therefore, silage harvest should be same way as under normal conditions based on actual moisture content.
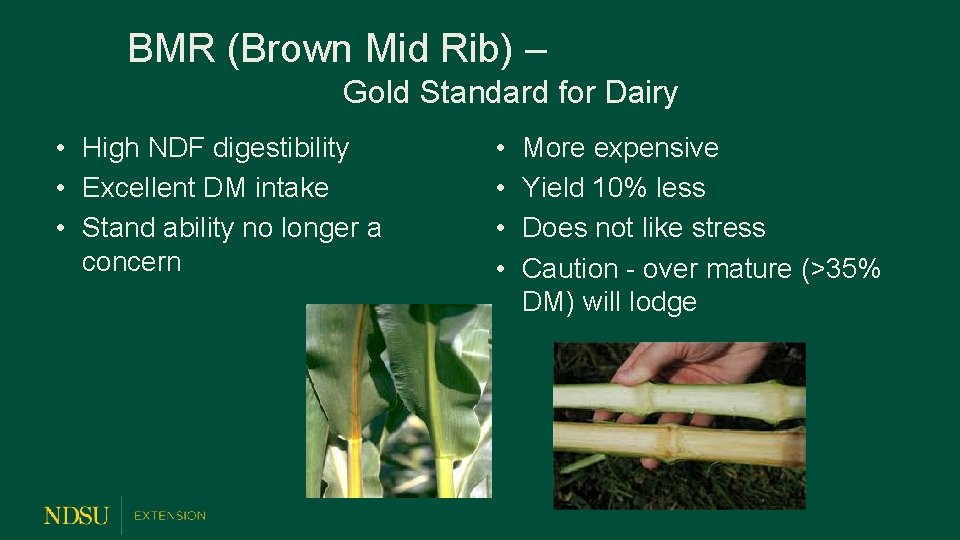
BMR (Brown Mid Rib) – Gold Standard for Dairy • High NDF digestibility • Excellent DM intake • Stand ability no longer a concern • • More expensive Yield 10% less Does not like stress Caution - over mature (>35% DM) will lodge
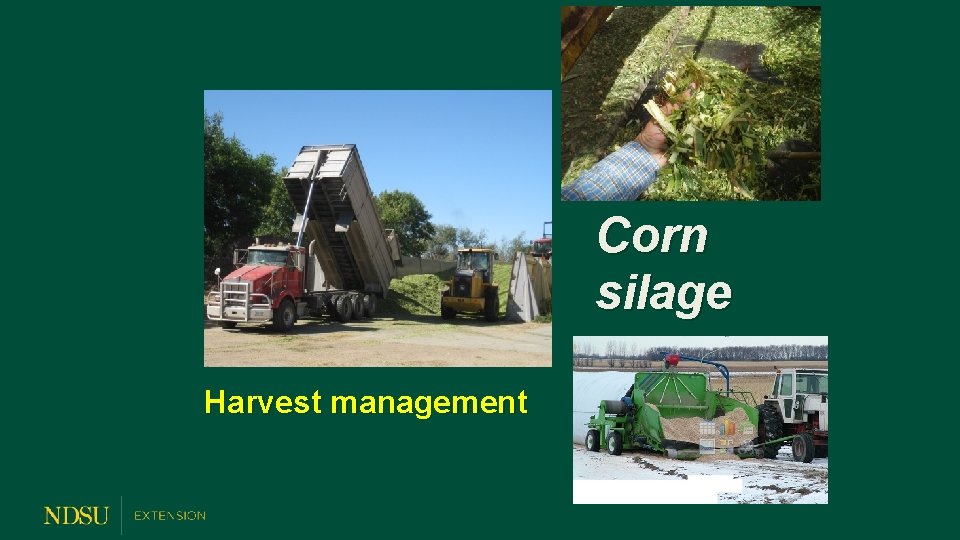
Corn silage Harvest management
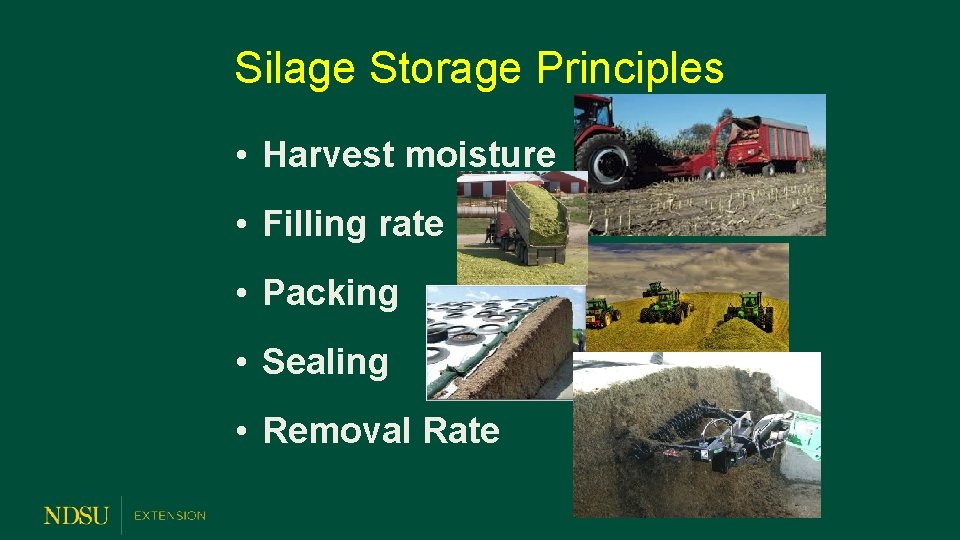
Silage Storage Principles • Harvest moisture • Filling rate • Packing • Sealing • Removal Rate
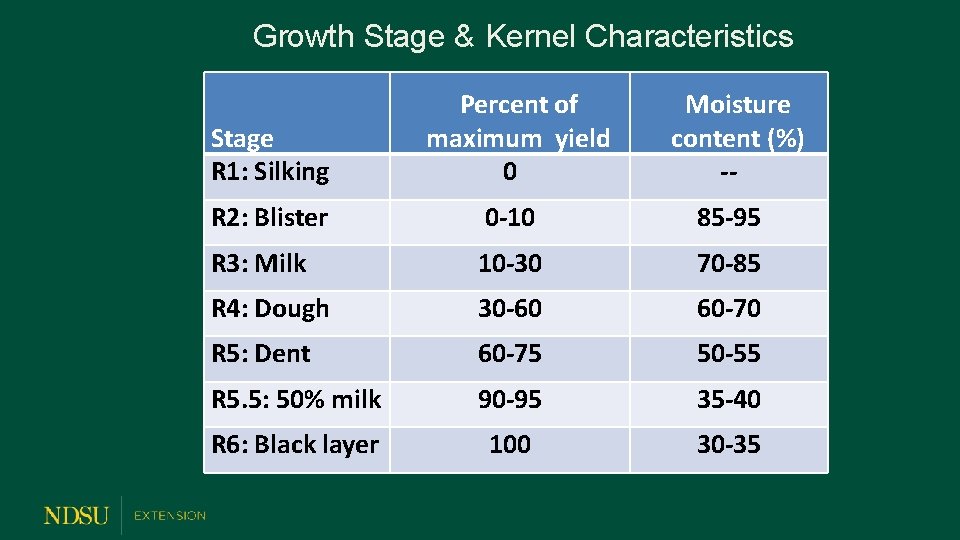
Growth Stage & Kernel Characteristics Stage R 1: Silking Percent of maximum yield 0 Moisture content (%) -- R 2: Blister 0 -10 85 -95 R 3: Milk 10 -30 70 -85 R 4: Dough 30 -60 60 -70 R 5: Dent 60 -75 50 -55 R 5. 5: 50% milk 90 -95 35 -40 R 6: Black layer 100 30 -35
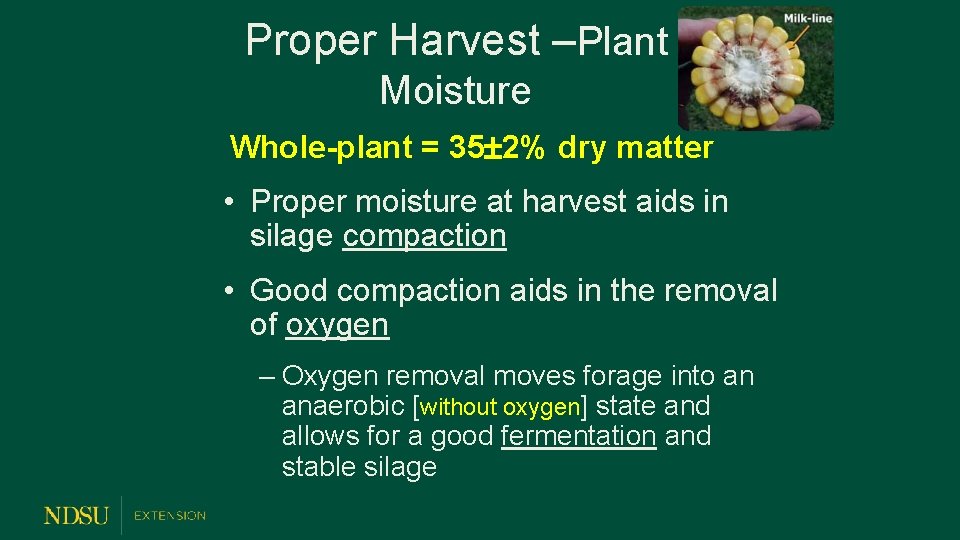
Proper Harvest –Plant Moisture Whole-plant = 35 2% dry matter • Proper moisture at harvest aids in silage compaction • Good compaction aids in the removal of oxygen – Oxygen removal moves forage into an anaerobic [without oxygen] state and allows for a good fermentation and stable silage

When Should Corn be Harvested for Silage? • Ideal DM between 30 & 38% – Depend on the storage structure • Too early (i. e. too wet) – Poor fermentation = greater losses (seepage) • Reduced intake when the silage is fed • Too late (i. e. too dry) – Limited fermentation = less stable silage • Often heats and molds at the silo face, during feed out, and in the feed bunk • Fiber and starch digestibility can be low.
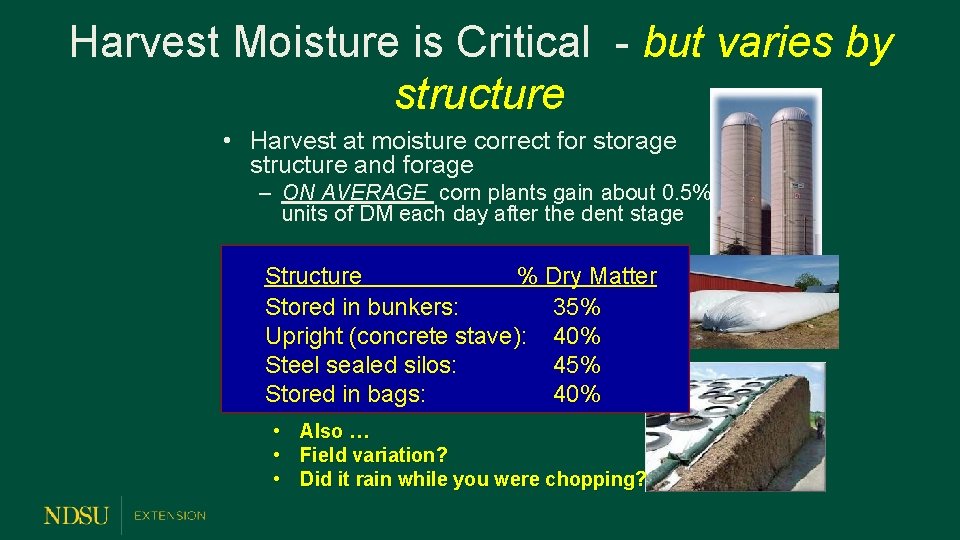
Harvest Moisture is Critical - but varies by structure • Harvest at moisture correct for storage structure and forage – ON AVERAGE corn plants gain about 0. 5% units of DM each day after the dent stage Structure % Dry Matter Stored in bunkers: 35% Upright (concrete stave): 40% Steel sealed silos: 45% Stored in bags: 40% • Also … • Field variation? • Did it rain while you were chopping?
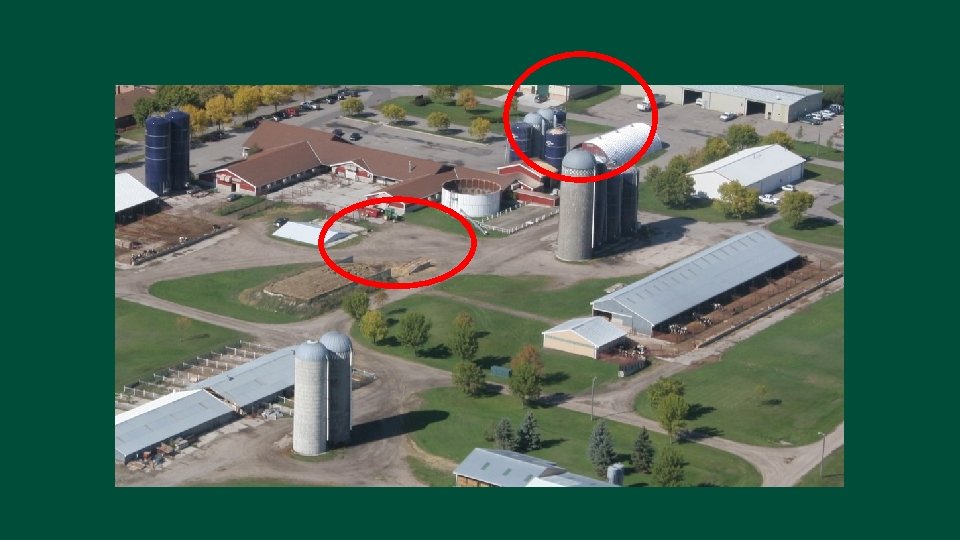
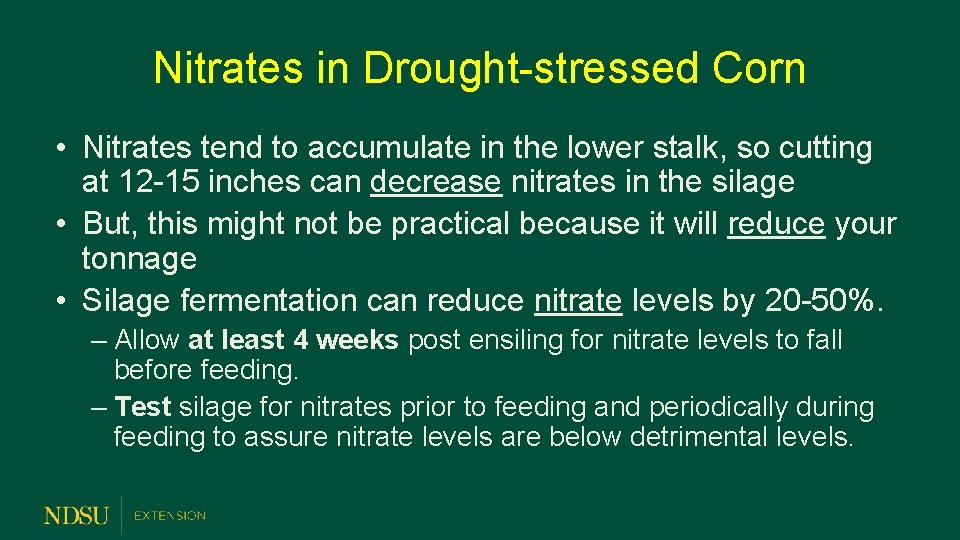
Nitrates in Drought-stressed Corn • Nitrates tend to accumulate in the lower stalk, so cutting at 12 -15 inches can decrease nitrates in the silage • But, this might not be practical because it will reduce your tonnage • Silage fermentation can reduce nitrate levels by 20 -50%. – Allow at least 4 weeks post ensiling for nitrate levels to fall before feeding. – Test silage for nitrates prior to feeding and periodically during feeding to assure nitrate levels are below detrimental levels.
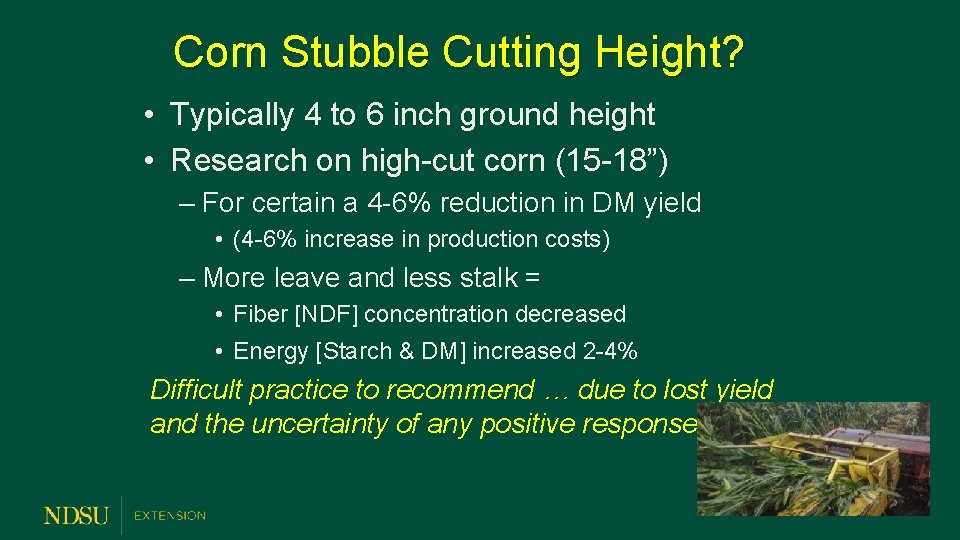
Corn Stubble Cutting Height? • Typically 4 to 6 inch ground height • Research on high-cut corn (15 -18”) – For certain a 4 -6% reduction in DM yield • (4 -6% increase in production costs) – More leave and less stalk = • Fiber [NDF] concentration decreased • Energy [Starch & DM] increased 2 -4% Difficult practice to recommend … due to lost yield and the uncertainty of any positive response.
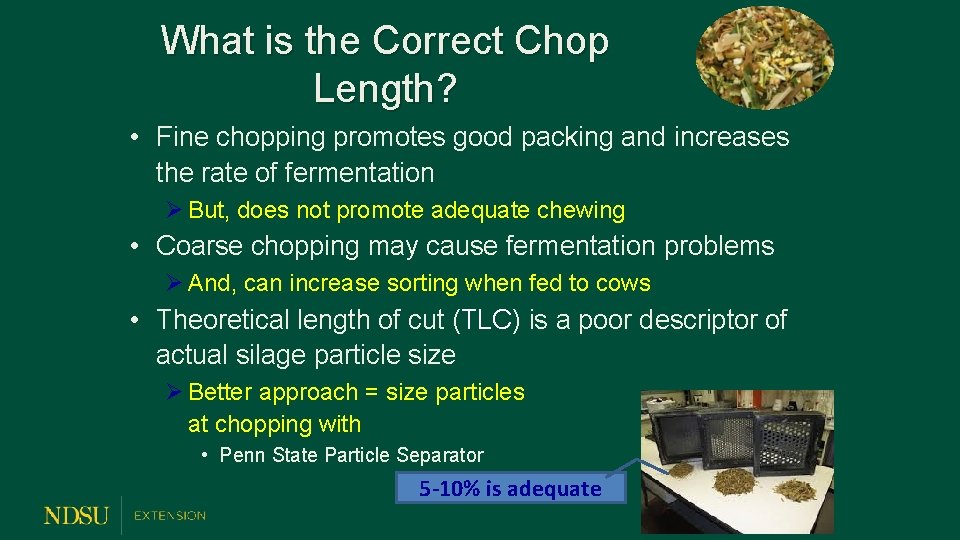
What is the Correct Chop Length? • Fine chopping promotes good packing and increases the rate of fermentation Ø But, does not promote adequate chewing • Coarse chopping may cause fermentation problems Ø And, can increase sorting when fed to cows • Theoretical length of cut (TLC) is a poor descriptor of actual silage particle size Ø Better approach = size particles at chopping with • Penn State Particle Separator 5 -10% is adequate
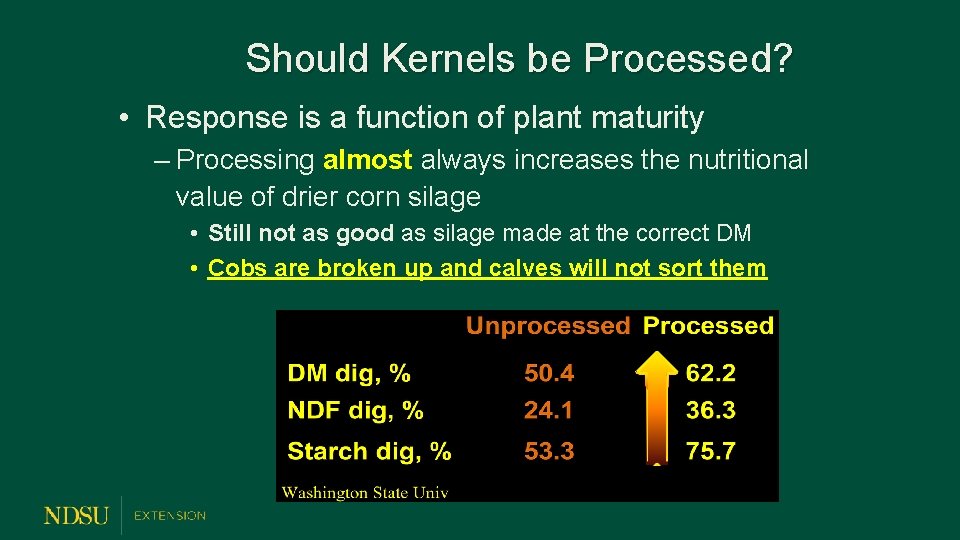
Should Kernels be Processed? • Response is a function of plant maturity – Processing almost always increases the nutritional value of drier corn silage • Still not as good as silage made at the correct DM • Cobs are broken up and calves will not sort them
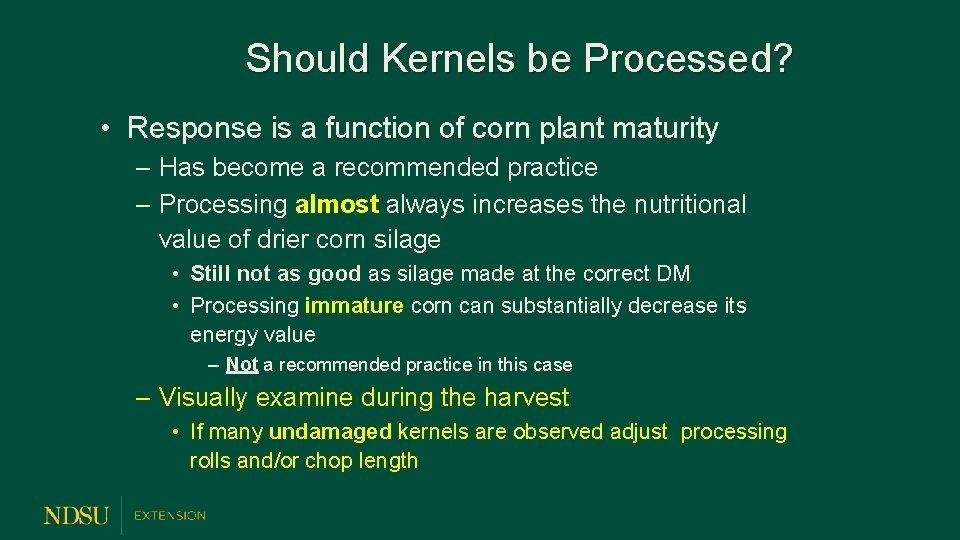
Should Kernels be Processed? • Response is a function of corn plant maturity – Has become a recommended practice – Processing almost always increases the nutritional value of drier corn silage • Still not as good as silage made at the correct DM • Processing immature corn can substantially decrease its energy value – Not a recommended practice in this case – Visually examine during the harvest • If many undamaged kernels are observed adjust processing rolls and/or chop length
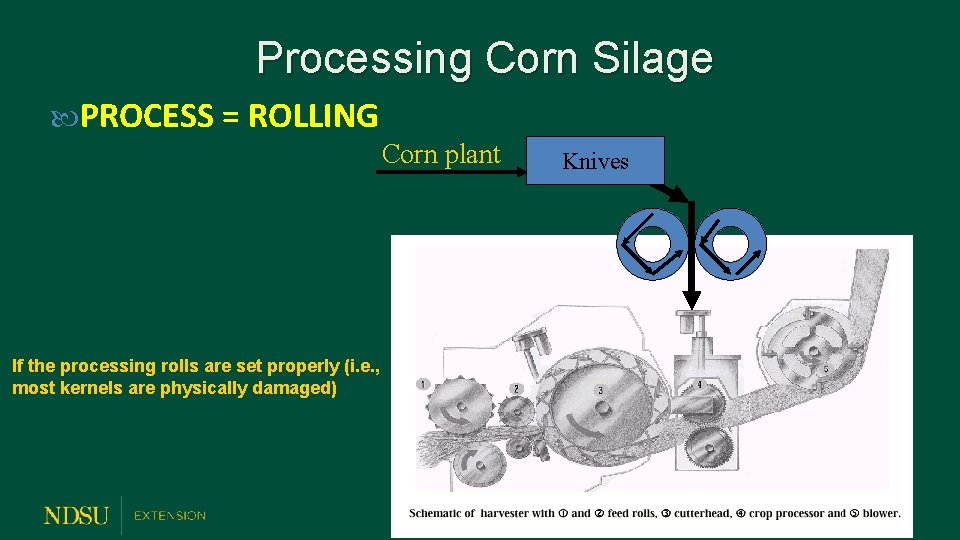
Processing Corn Silage PROCESS = ROLLING Corn plant If the processing rolls are set properly (i. e. , most kernels are physically damaged) Knives
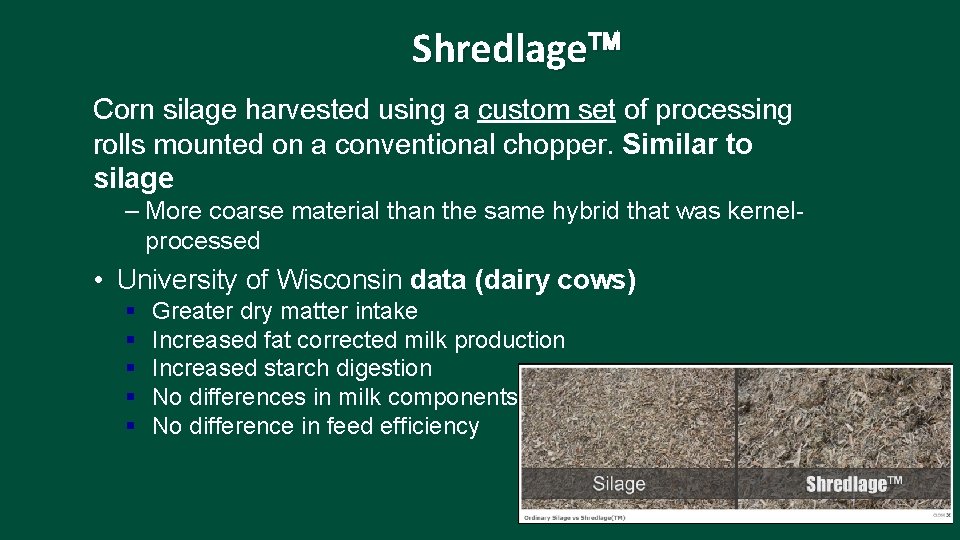
Shredlage Corn silage harvested using a custom set of processing rolls mounted on a conventional chopper. Similar to silage – More coarse material than the same hybrid that was kernelprocessed • University of Wisconsin data (dairy cows) § § § Greater dry matter intake Increased fat corrected milk production Increased starch digestion No differences in milk components No difference in feed efficiency
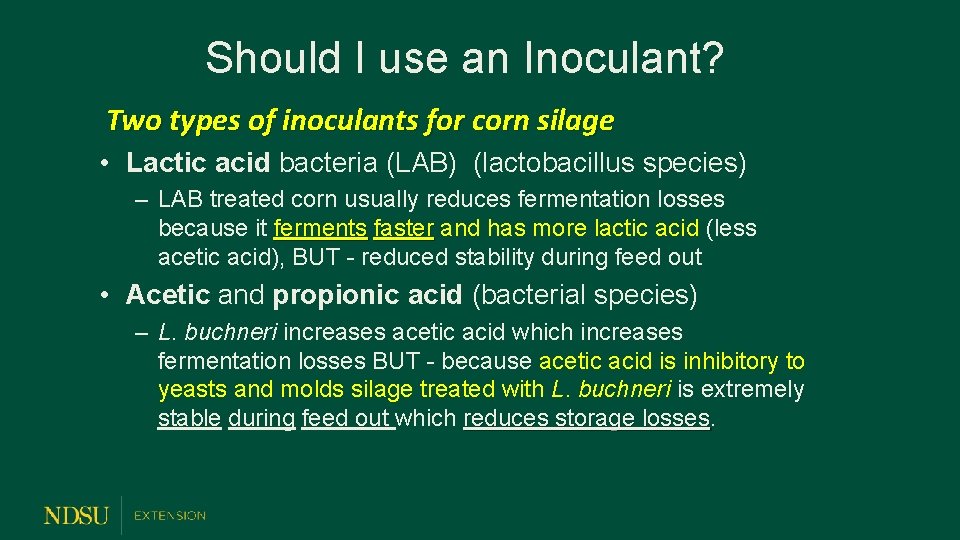
Should I use an Inoculant? Two types of inoculants for corn silage • Lactic acid bacteria (LAB) (lactobacillus species) – LAB treated corn usually reduces fermentation losses because it ferments faster and has more lactic acid (less acetic acid), BUT - reduced stability during feed out • Acetic and propionic acid (bacterial species) – L. buchneri increases acetic acid which increases fermentation losses BUT - because acetic acid is inhibitory to yeasts and molds silage treated with L. buchneri is extremely stable during feed out which reduces storage losses
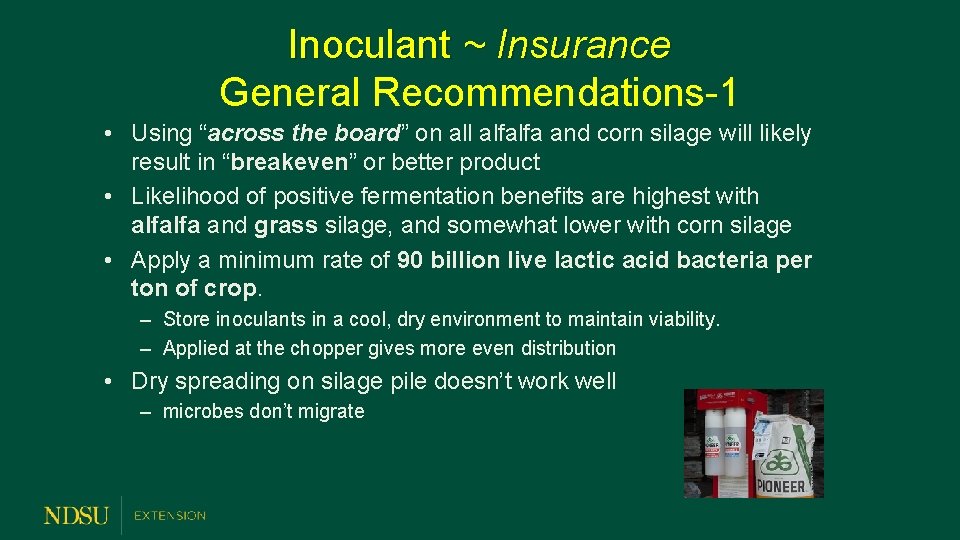
Inoculant ~ Insurance General Recommendations-1 • Using “across the board” on all alfalfa and corn silage will likely result in “breakeven” or better product • Likelihood of positive fermentation benefits are highest with alfalfa and grass silage, and somewhat lower with corn silage • Apply a minimum rate of 90 billion live lactic acid bacteria per ton of crop. – Store inoculants in a cool, dry environment to maintain viability. – Applied at the chopper gives more even distribution • Dry spreading on silage pile doesn’t work well – microbes don’t migrate
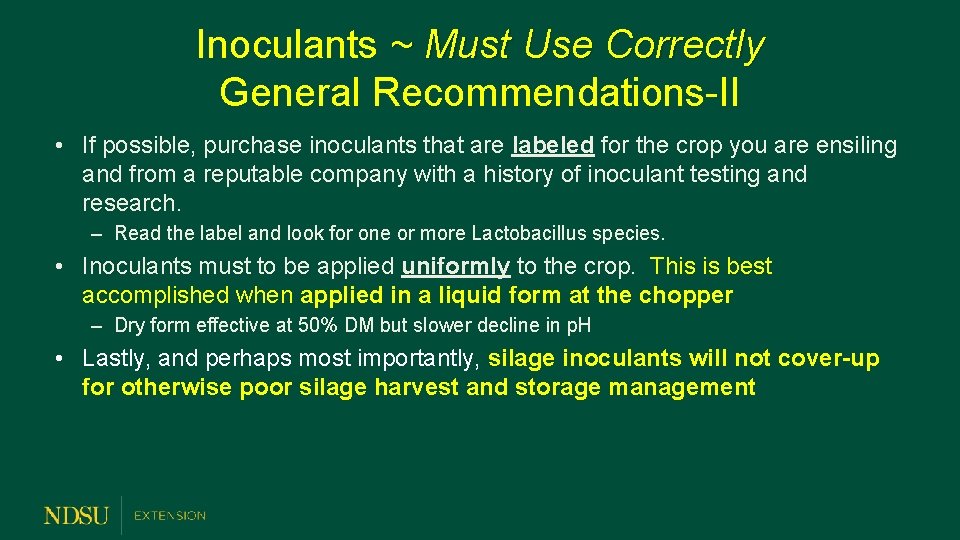
Inoculants ~ Must Use Correctly General Recommendations-II • If possible, purchase inoculants that are labeled for the crop you are ensiling and from a reputable company with a history of inoculant testing and research. – Read the label and look for one or more Lactobacillus species. • Inoculants must to be applied uniformly to the crop. This is best accomplished when applied in a liquid form at the chopper – Dry form effective at 50% DM but slower decline in p. H • Lastly, and perhaps most importantly, silage inoculants will not cover-up for otherwise poor silage harvest and storage management
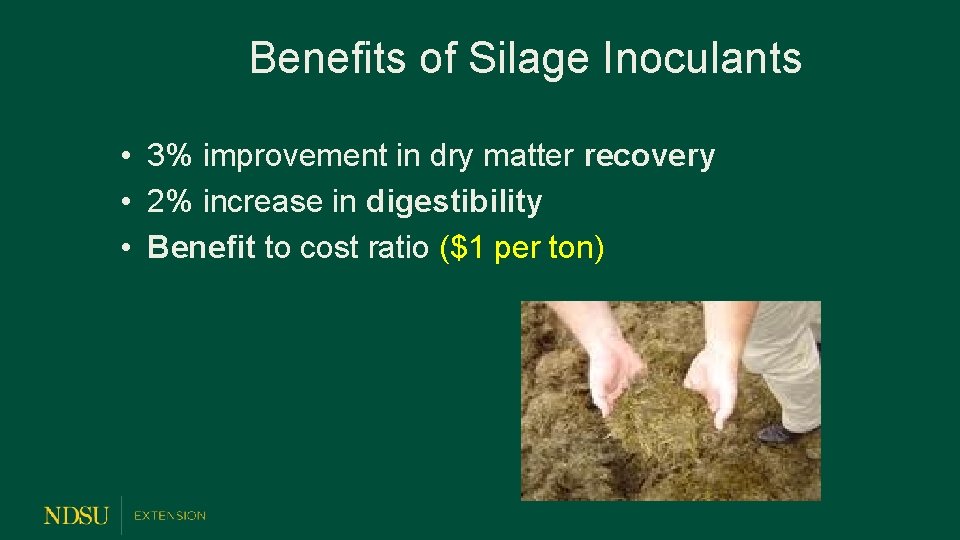
Benefits of Silage Inoculants • 3% improvement in dry matter recovery • 2% increase in digestibility • Benefit to cost ratio ($1 per ton)
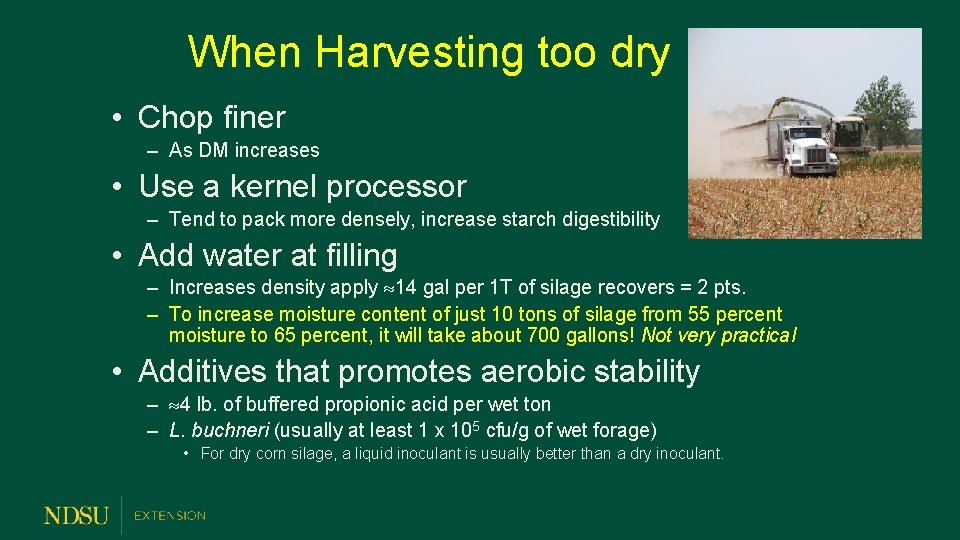
When Harvesting too dry • Chop finer – As DM increases • Use a kernel processor – Tend to pack more densely, increase starch digestibility • Add water at filling – Increases density apply 14 gal per 1 T of silage recovers = 2 pts. – To increase moisture content of just 10 tons of silage from 55 percent moisture to 65 percent, it will take about 700 gallons! Not very practical • Additives that promotes aerobic stability – 4 lb. of buffered propionic acid per wet ton – L. buchneri (usually at least 1 x 105 cfu/g of wet forage) • For dry corn silage, a liquid inoculant is usually better than a dry inoculant.
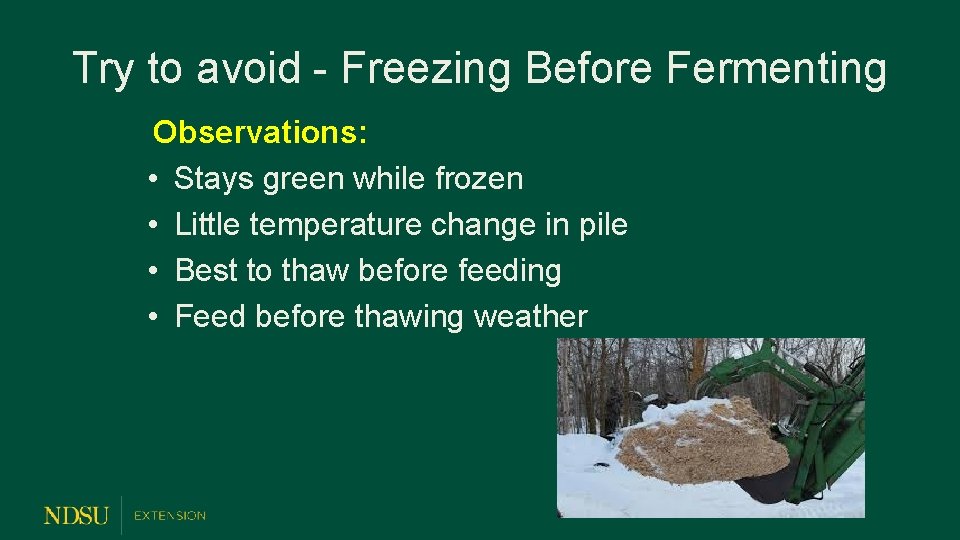
Try to avoid - Freezing Before Fermenting Observations: • Stays green while frozen • Little temperature change in pile • Best to thaw before feeding • Feed before thawing weather
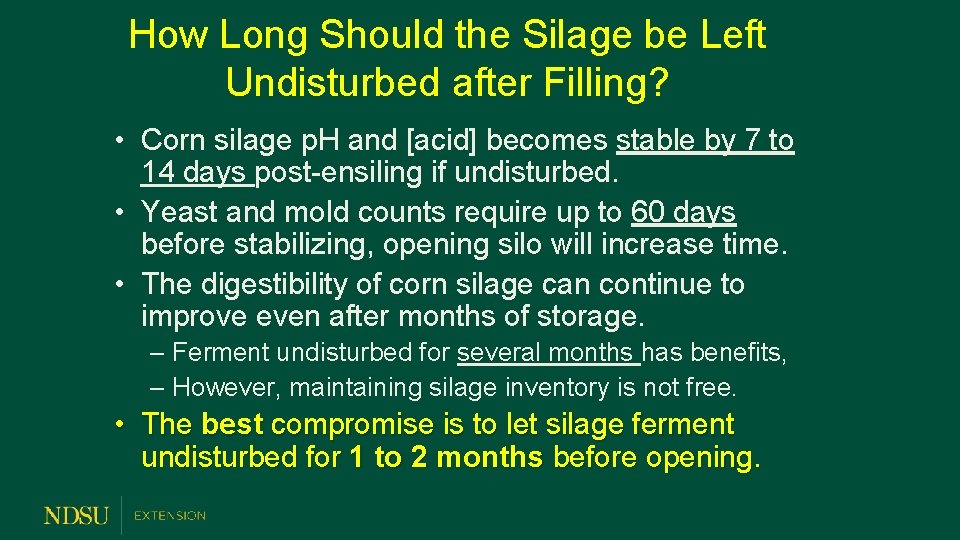
How Long Should the Silage be Left Undisturbed after Filling? • Corn silage p. H and [acid] becomes stable by 7 to 14 days post-ensiling if undisturbed. • Yeast and mold counts require up to 60 days before stabilizing, opening silo will increase time. • The digestibility of corn silage can continue to improve even after months of storage. – Ferment undisturbed for several months has benefits, – However, maintaining silage inventory is not free. • The best compromise is to let silage ferment undisturbed for 1 to 2 months before opening.
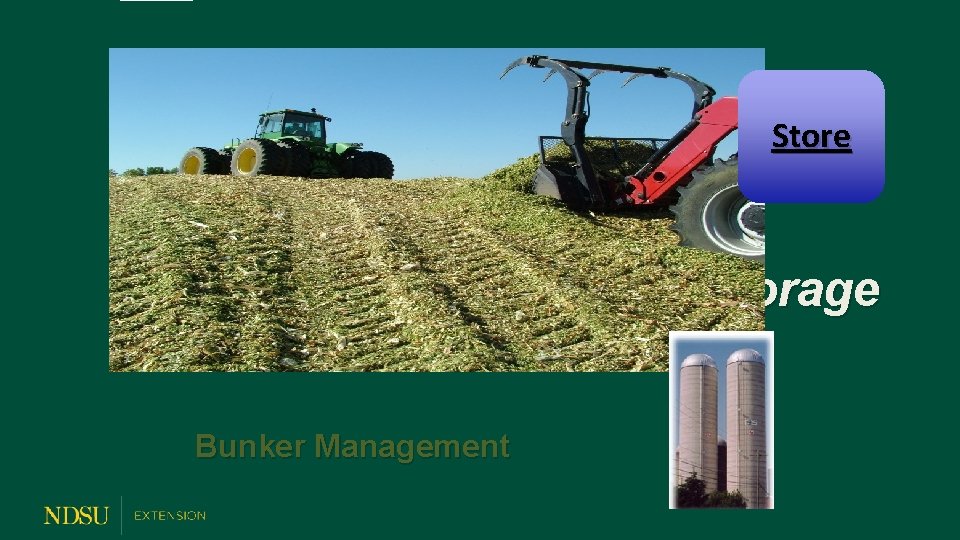
Store Storage Bunker Management
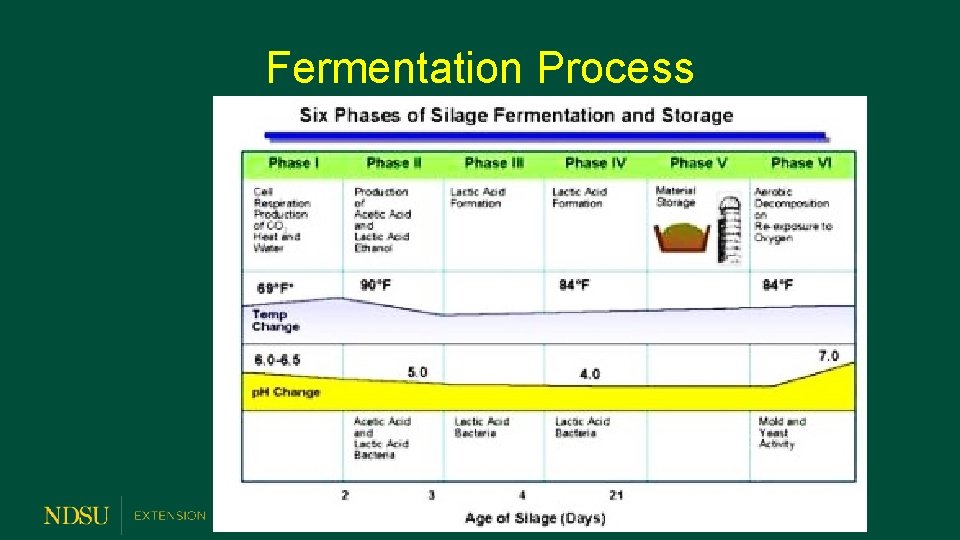
Fermentation Process
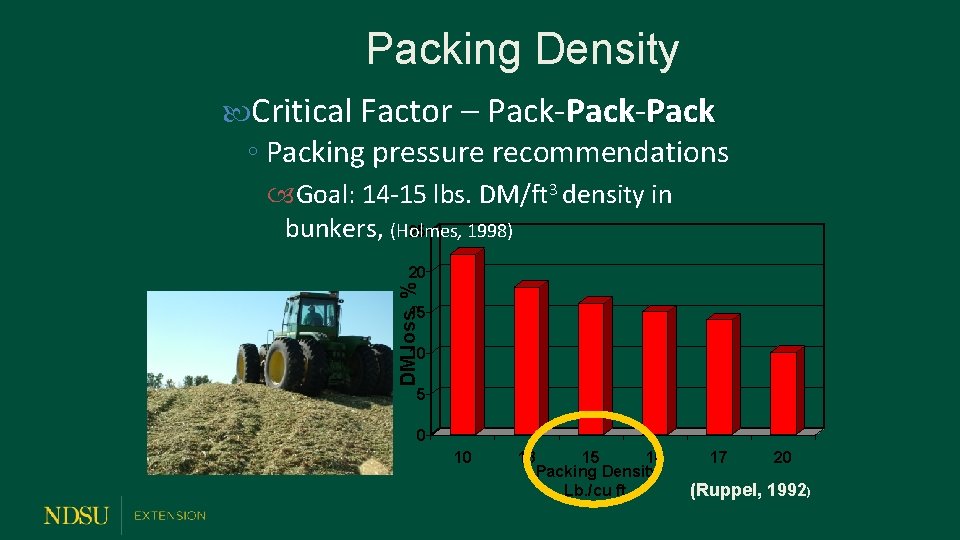
Packing Density Critical Factor – Pack-Pack ◦ Packing pressure recommendations Goal: 14 -15 lbs. DM/ft 3 density in bunkers, (Holmes, 1998) 25 DM loss, % 20 15 10 5 0 10 13 15 16 Packing Density Lb. /cu ft. 17 20 (Ruppel, 1992)
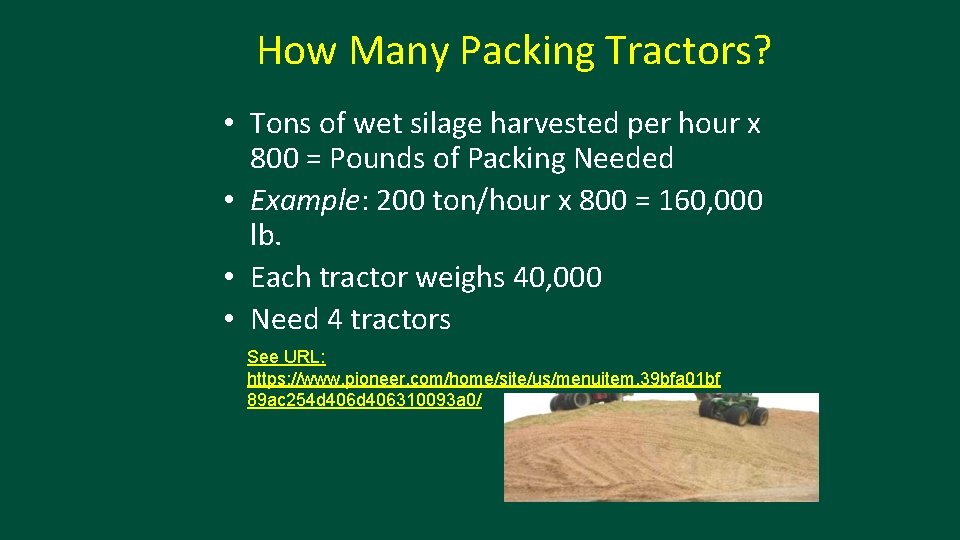
How Many Packing Tractors? • Tons of wet silage harvested per hour x 800 = Pounds of Packing Needed • Example: 200 ton/hour x 800 = 160, 000 lb. • Each tractor weighs 40, 000 • Need 4 tractors See URL: https: //www. pioneer. com/home/site/us/menuitem. 39 bfa 01 bf 89 ac 254 d 406310093 a 0/
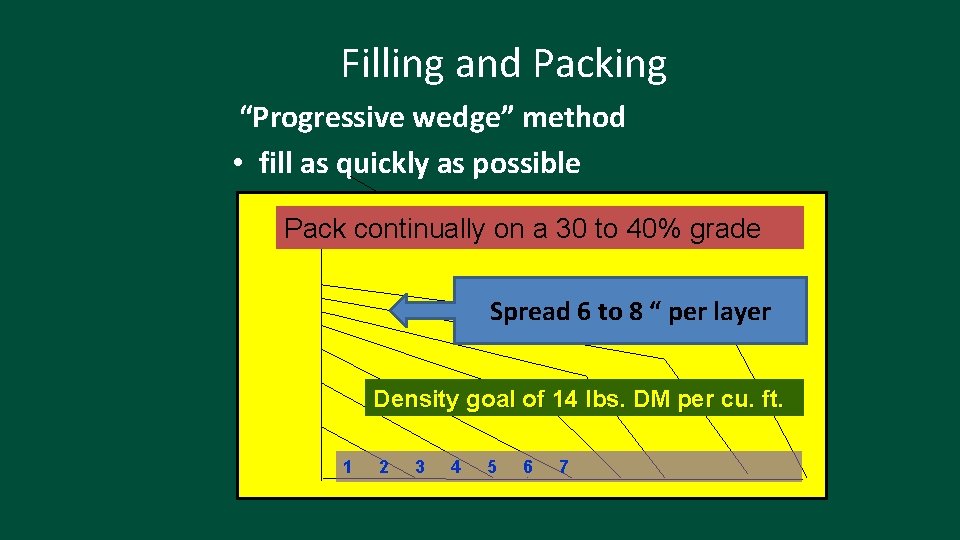
Filling and Packing “Progressive wedge” method • fill as quickly as possible Pack continually on a 30 to 40% grade Spread 6 to 8 “ per layer Density goal of 14 lbs. DM per cu. ft. 1 2 3 4 5 6 7
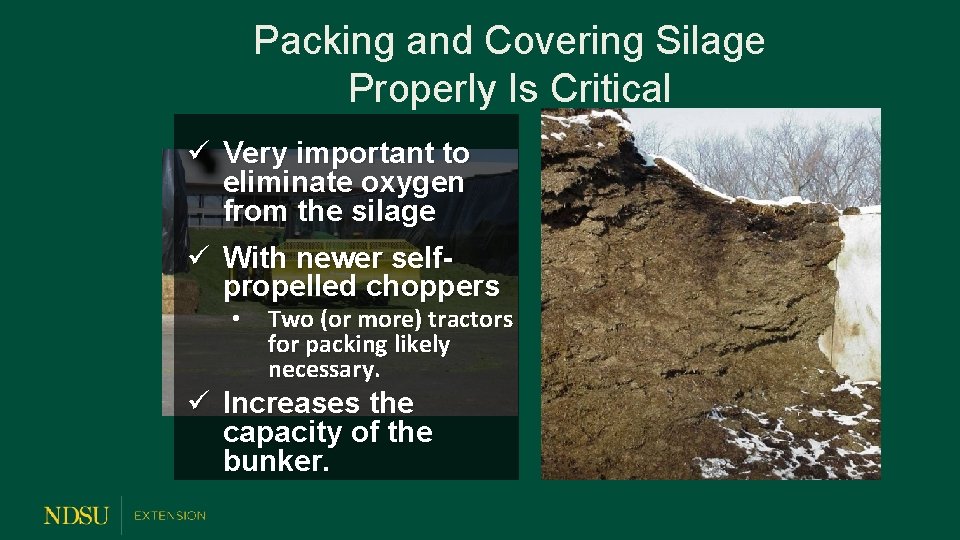
Packing and Covering Silage Properly Is Critical ü Very important to eliminate oxygen from the silage ü With newer selfpropelled choppers • Two (or more) tractors for packing likely necessary. ü Increases the capacity of the bunker.
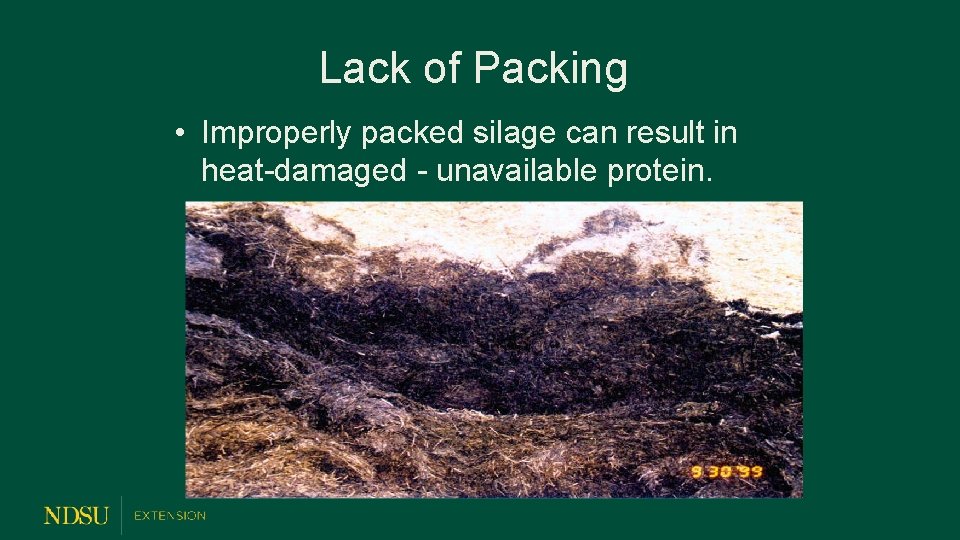
Lack of Packing • Improperly packed silage can result in heat-damaged - unavailable protein.
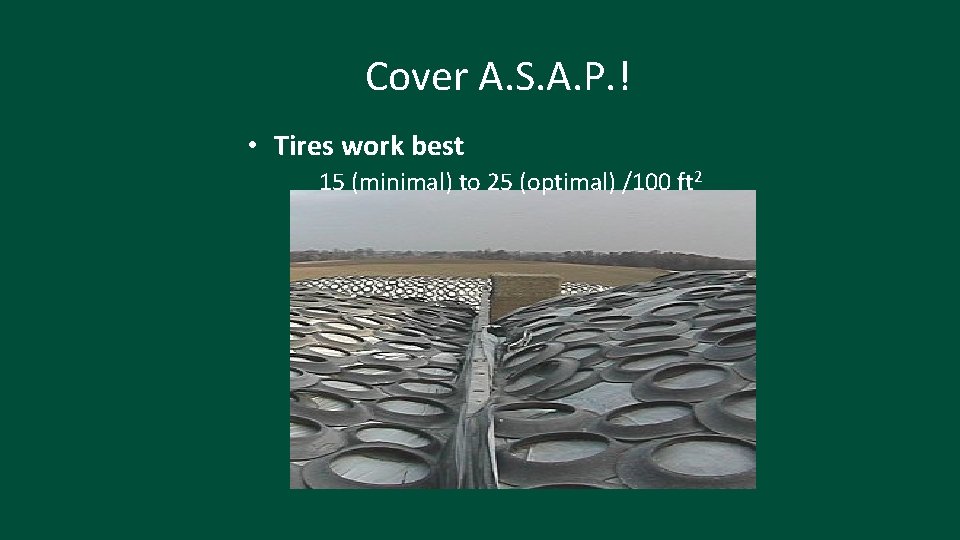
Cover A. S. A. P. ! • Tires work best 15 (minimal) to 25 (optimal) /100 ft 2
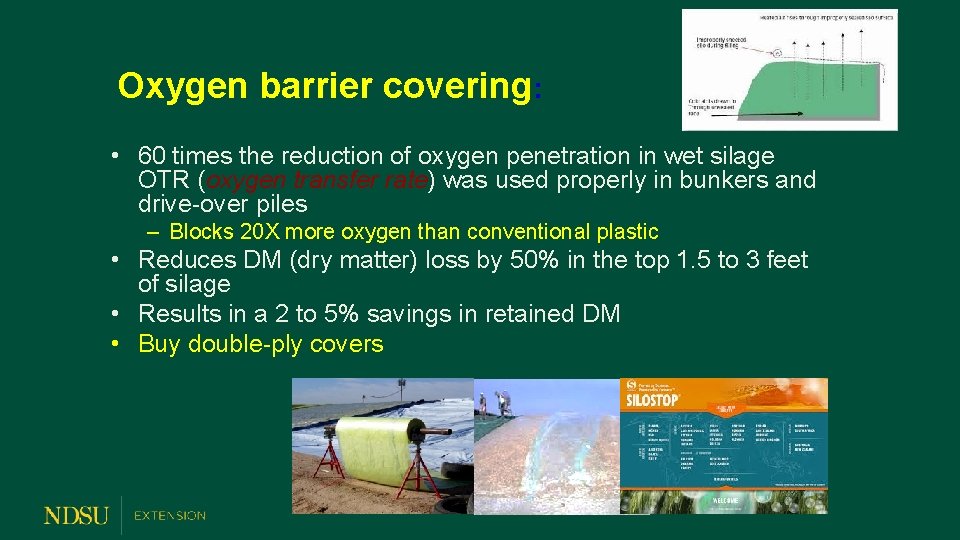
Oxygen barrier covering: • 60 times the reduction of oxygen penetration in wet silage OTR (oxygen transfer rate) was used properly in bunkers and drive-over piles – Blocks 20 X more oxygen than conventional plastic • Reduces DM (dry matter) loss by 50% in the top 1. 5 to 3 feet of silage • Results in a 2 to 5% savings in retained DM • Buy double-ply covers
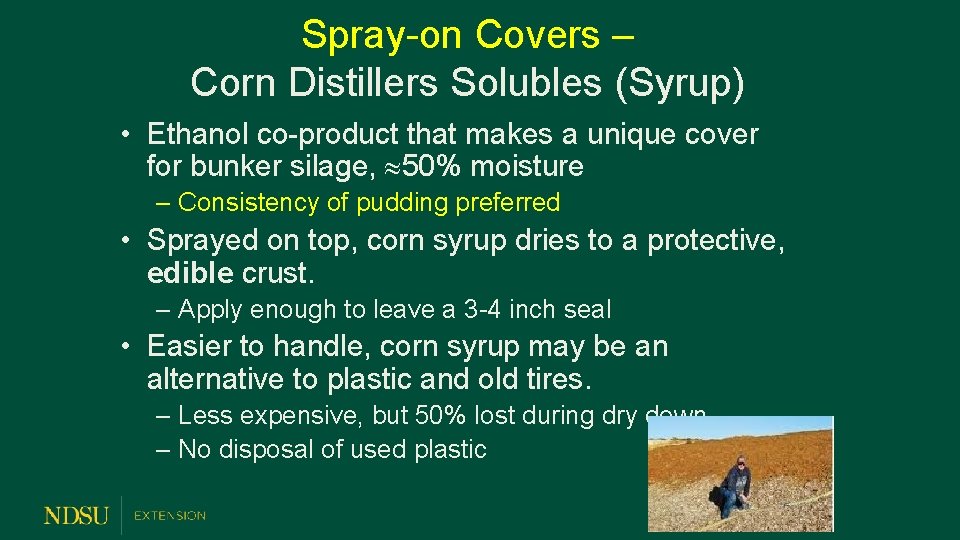
Spray-on Covers – Corn Distillers Solubles (Syrup) • Ethanol co-product that makes a unique cover for bunker silage, 50% moisture – Consistency of pudding preferred • Sprayed on top, corn syrup dries to a protective, edible crust. – Apply enough to leave a 3 -4 inch seal • Easier to handle, corn syrup may be an alternative to plastic and old tires. – Less expensive, but 50% lost during dry down – No disposal of used plastic
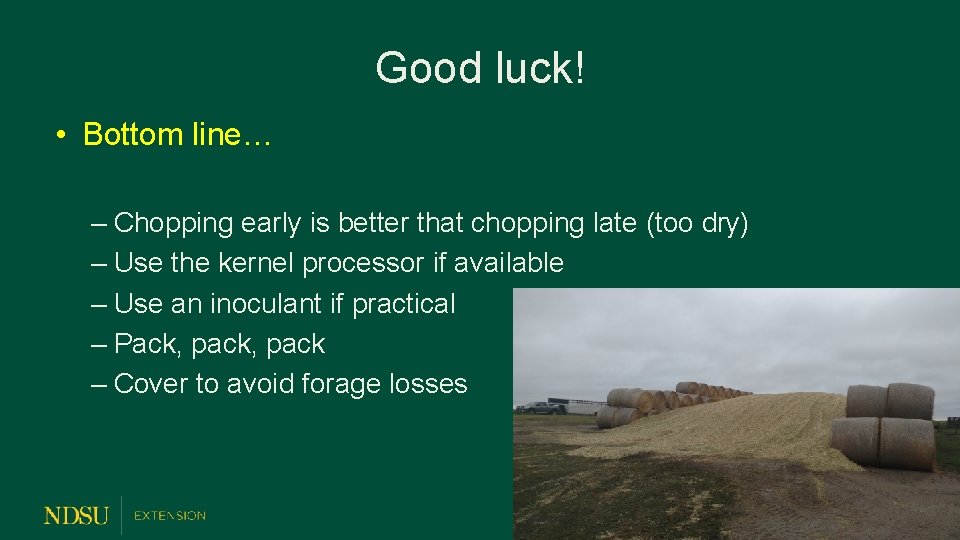
Good luck! • Bottom line… – Chopping early is better that chopping late (too dry) – Use the kernel processor if available – Use an inoculant if practical – Pack, pack – Cover to avoid forage losses
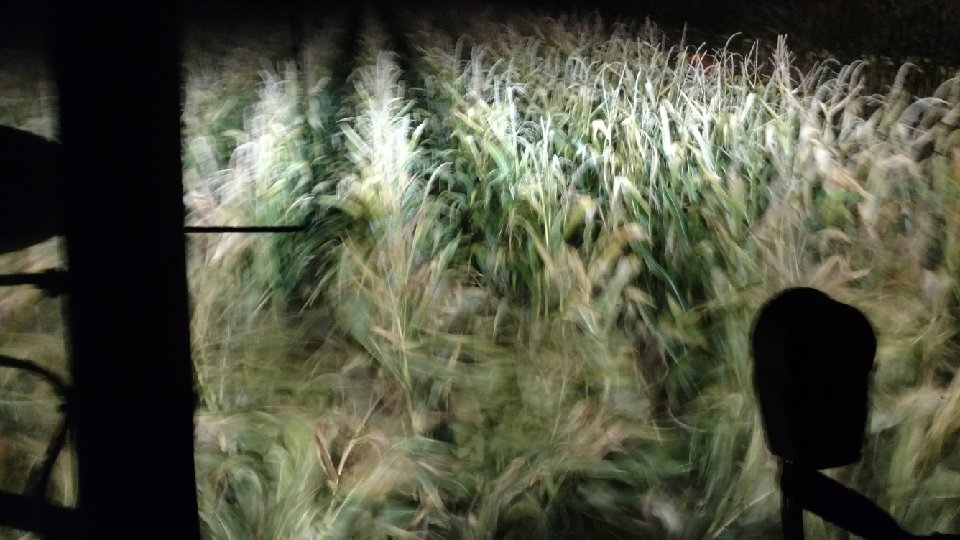
Vad gör du klockan åtta
Silage pro
Karl hoppe
Hugues hoppe
Dr david hoppe
Hugues hoppe
Hugues hoppe
Storing and issuing the product
What is havest
Harvesting and marketing of fish
Conclusion on rainwater harvesting
Prepare dessert and sweet sauces
Describing and storing data in dbms
Selection and storage of eggs
Taking in and storing information 10-1
Chapter 10 ten words in context answer key
Memory chips storing permanent data and instructions
Storing images in database pros and cons
Unpacking and storing guest luggage
Food storing and issuing control
Harvesting strategy
Future of rainwater harvesting
Autonomous data harvesting
Rainwater harvesting calgary
Rainwater harvesting ireland cost
Bibliography for rainwater harvesting
Inovasi dan inovatif adalah
Fish harvesting methods
Methods of harvesting a venture
Direct harvesting definition
Outcome harvesting training
Reference of rainwater harvesting
Function of rainwater harvesting
What is rainwater harvesting
Chapter 9 cellular respiration harvesting chemical energy
Coarse mesh in rainwater harvesting
Rainwater harvesting introduction
Sod harvesting
Corkglass