FUNDAO PARA A CINCIA E TECNOLOGIA FCT Trainee
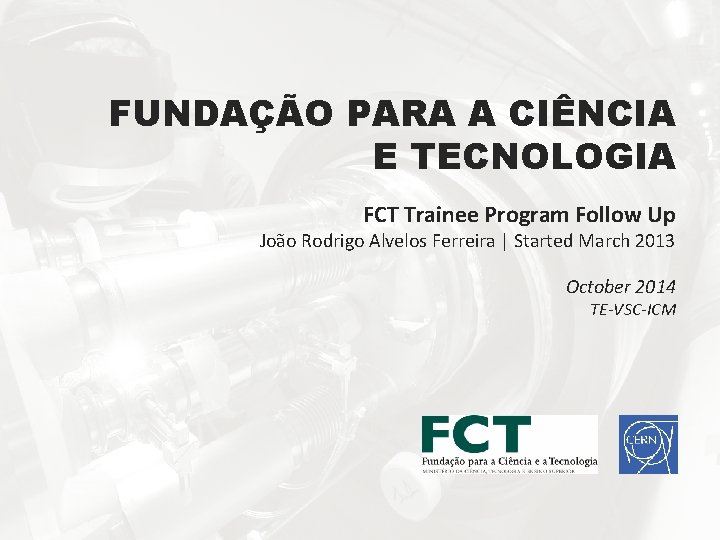
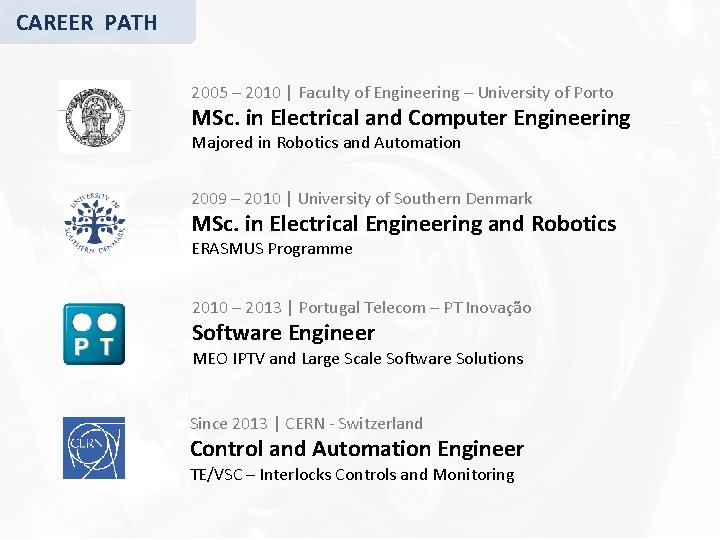
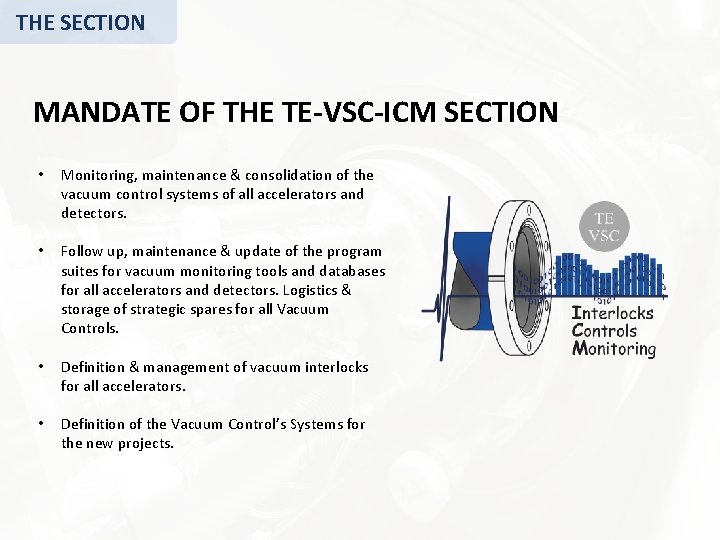
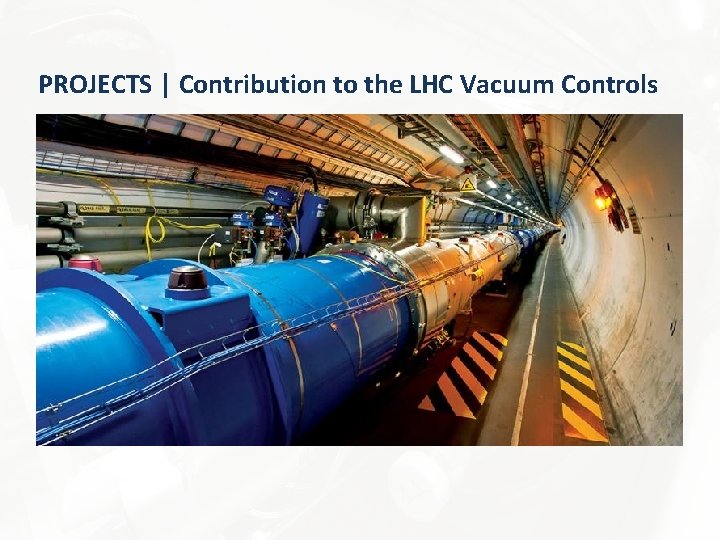
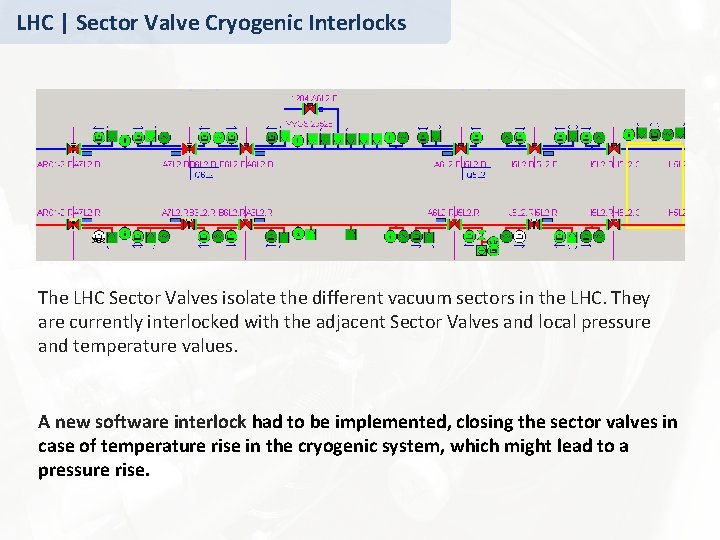
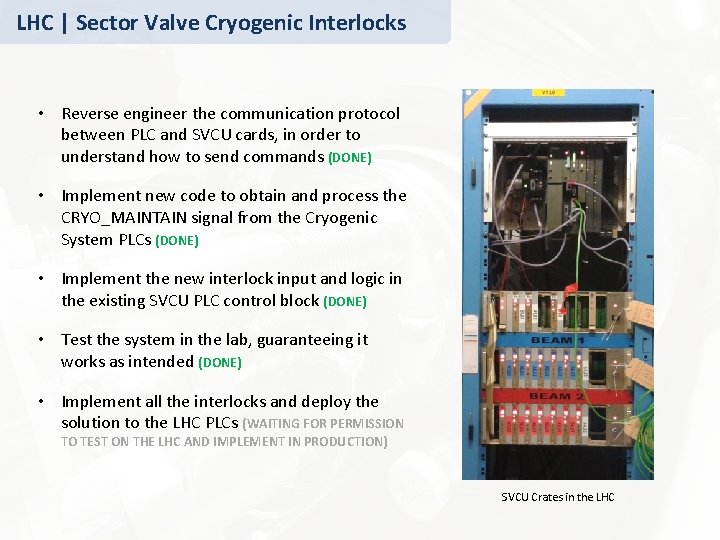
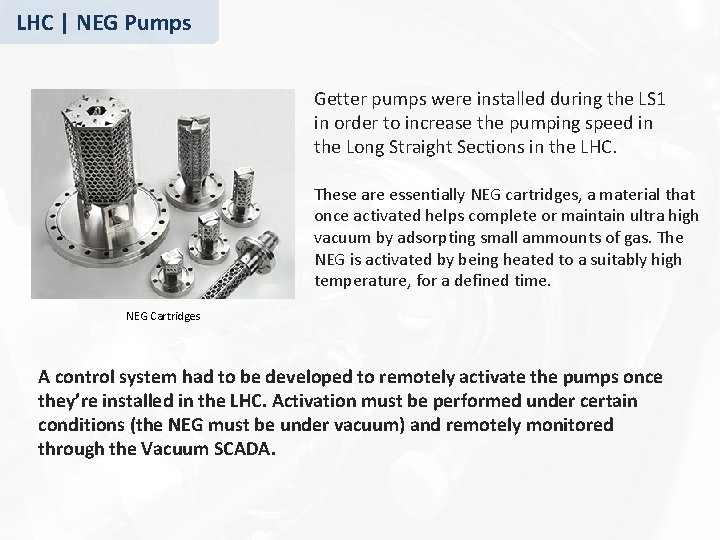
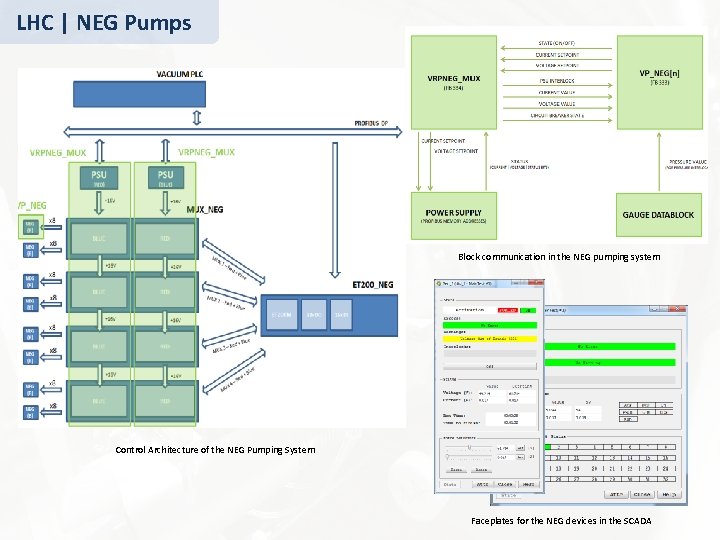
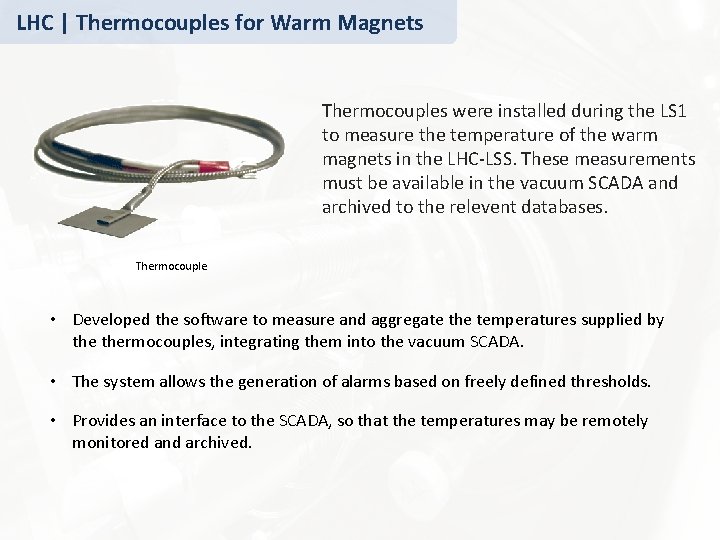
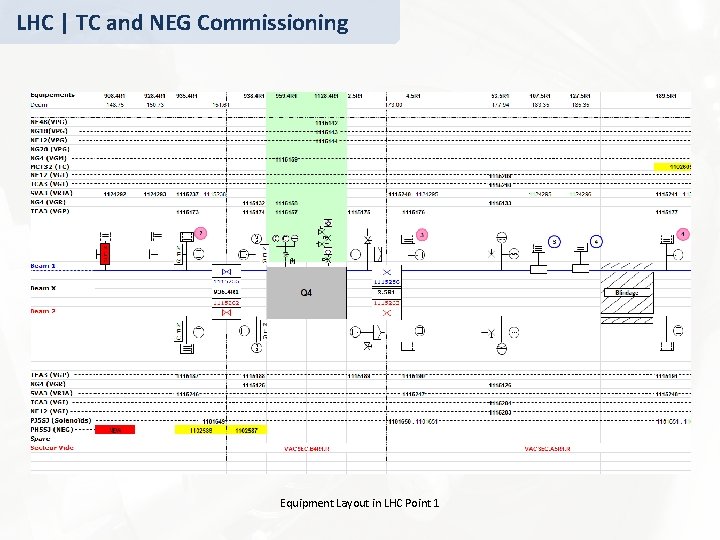
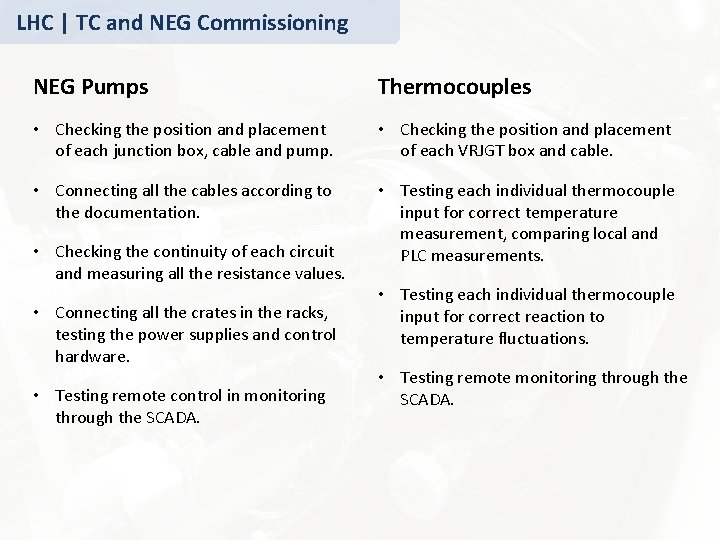
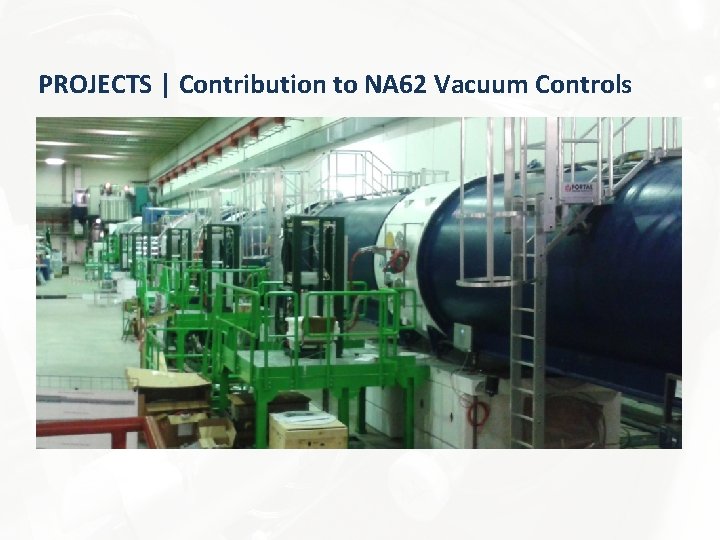
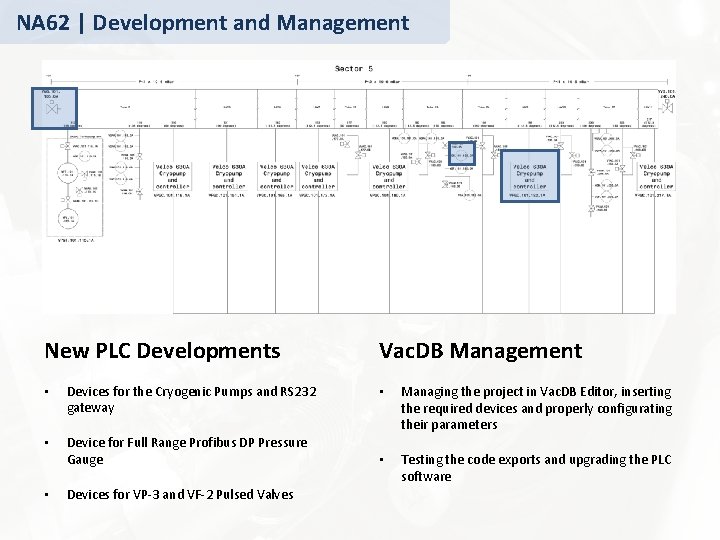
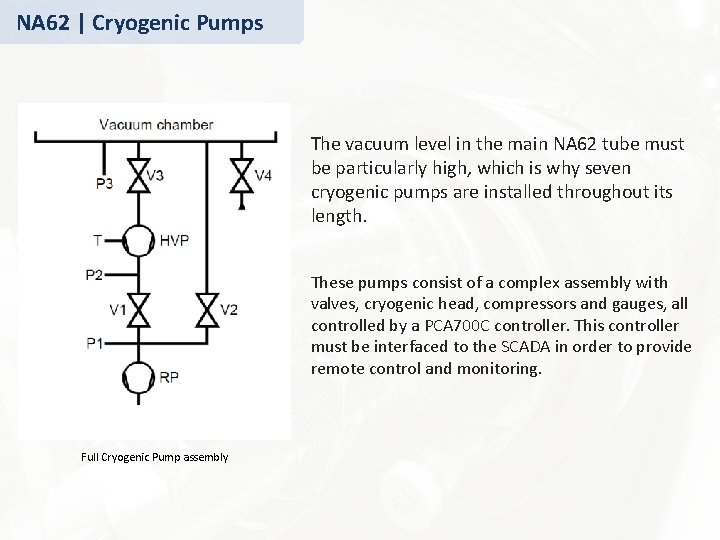
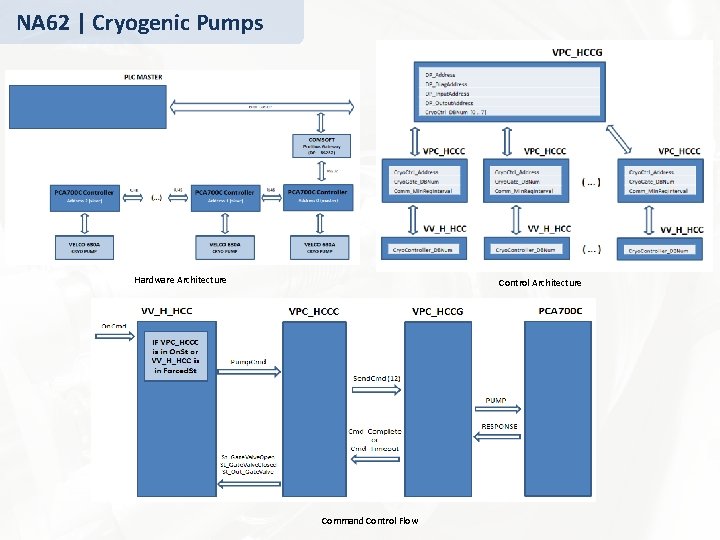
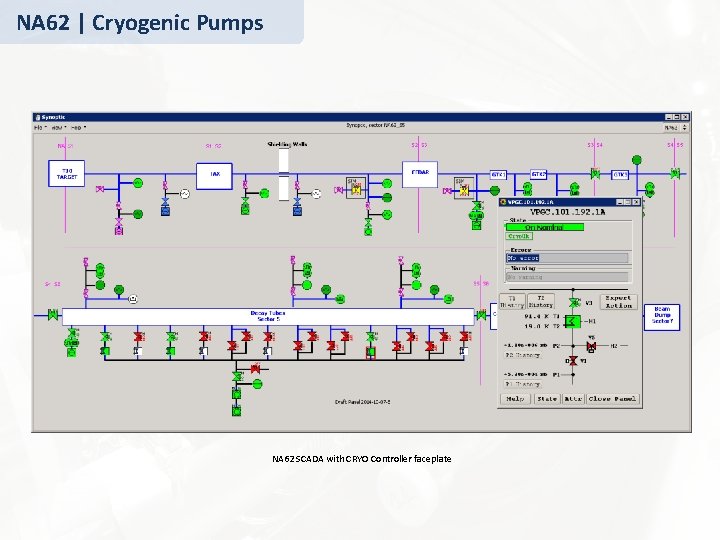
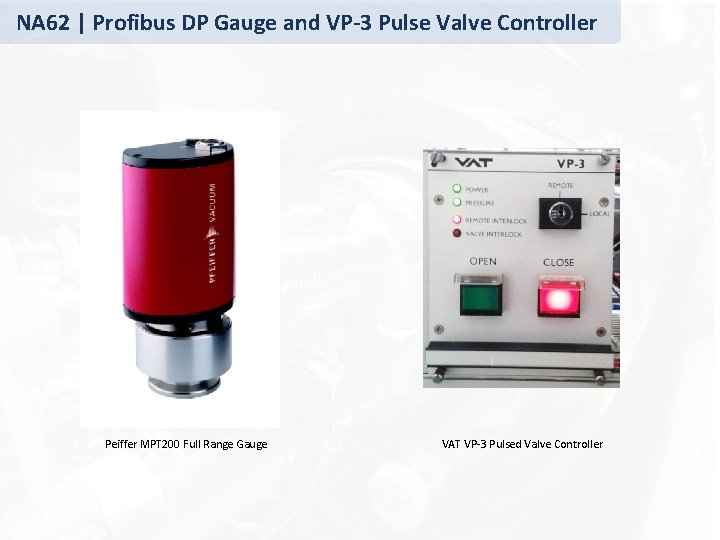
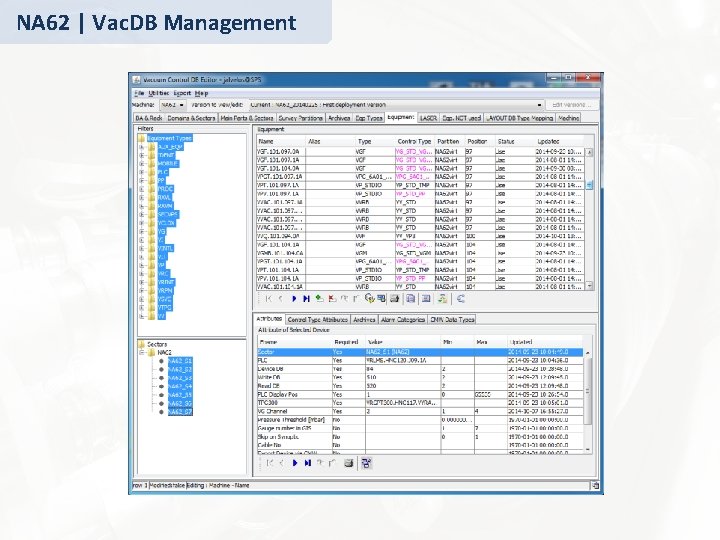
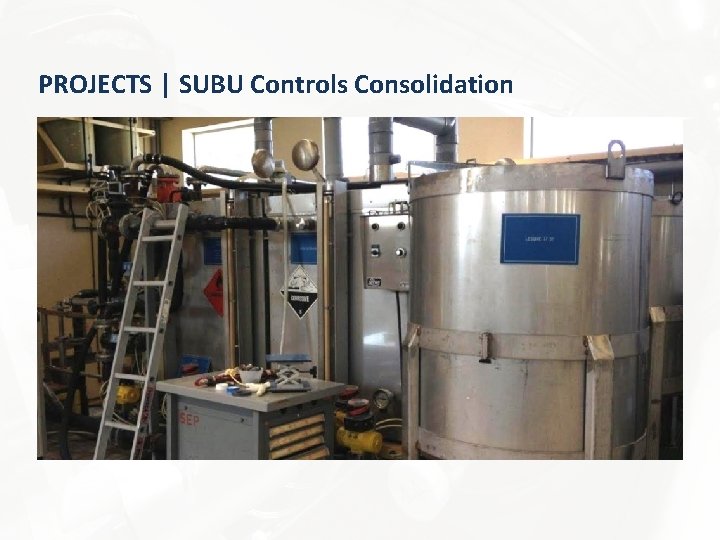
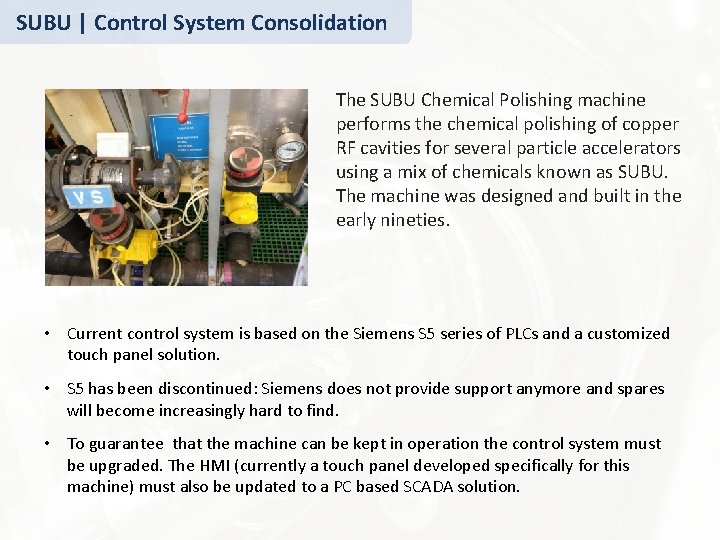
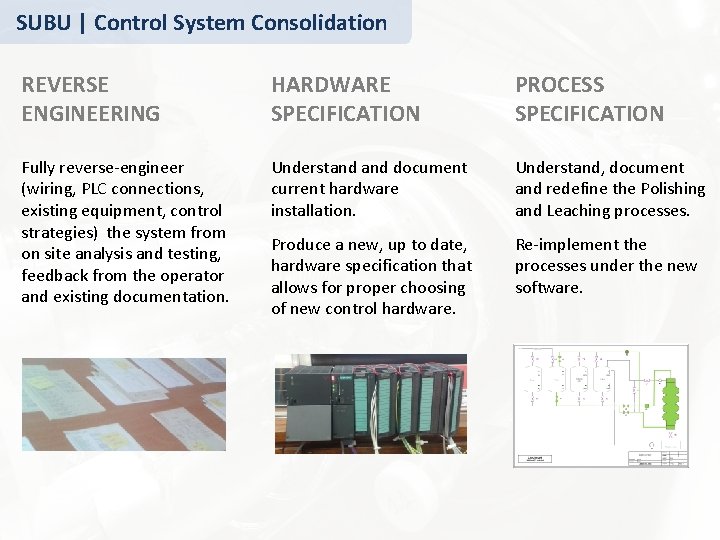
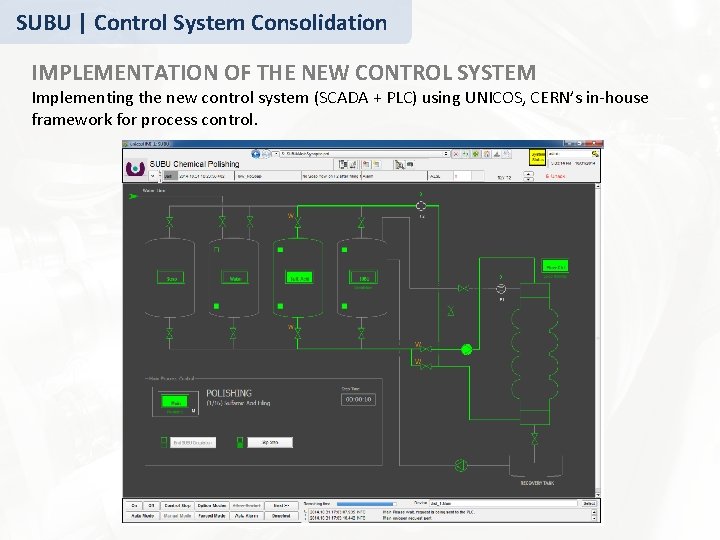
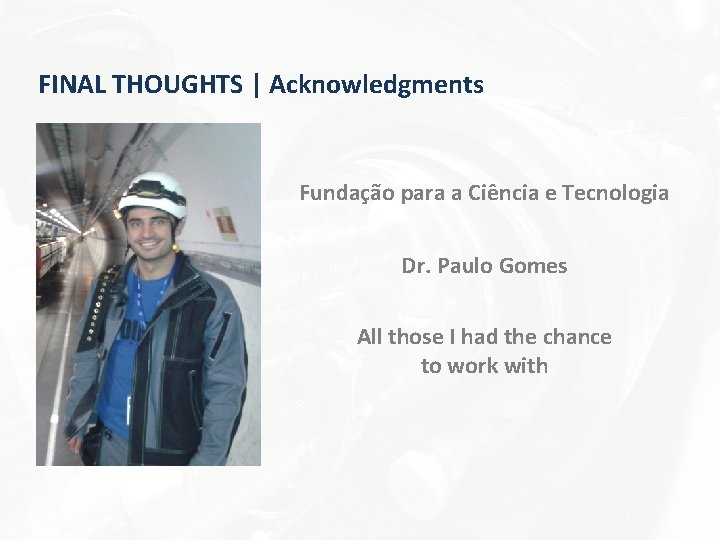
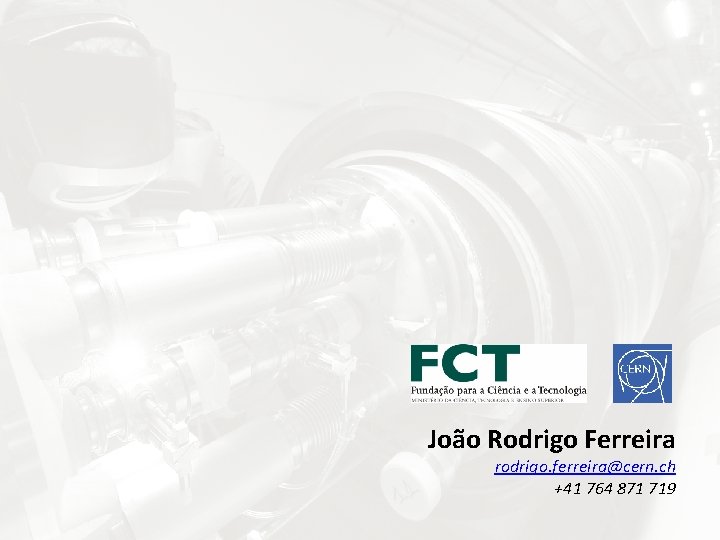
- Slides: 24
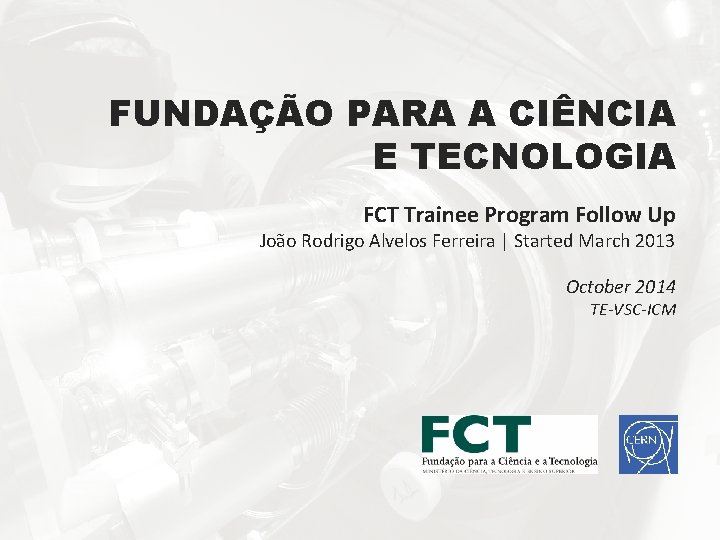
FUNDAÇÃO PARA A CIÊNCIA E TECNOLOGIA FCT Trainee Program Follow Up João Rodrigo Alvelos Ferreira | Started March 2013 October 2014 TE-VSC-ICM
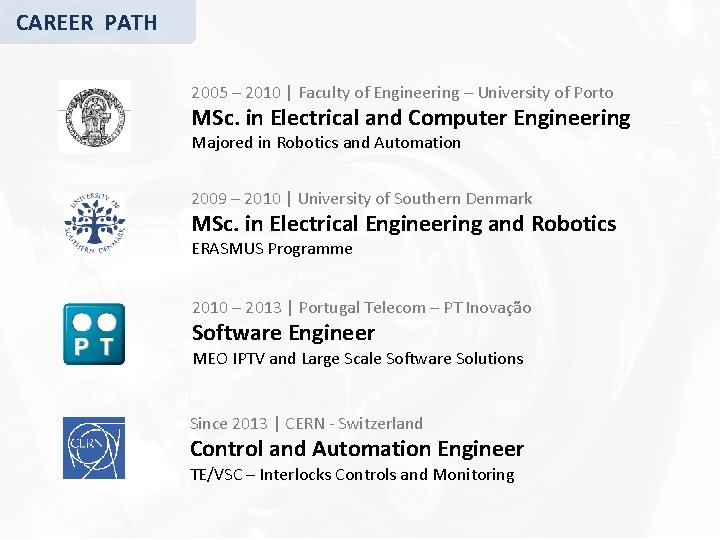
CAREER PATH 2005 – 2010 | Faculty of Engineering – University of Porto MSc. in Electrical and Computer Engineering Majored in Robotics and Automation 2009 – 2010 | University of Southern Denmark MSc. in Electrical Engineering and Robotics ERASMUS Programme 2010 – 2013 | Portugal Telecom – PT Inovação Software Engineer MEO IPTV and Large Scale Software Solutions Since 2013 | CERN - Switzerland Control and Automation Engineer TE/VSC – Interlocks Controls and Monitoring
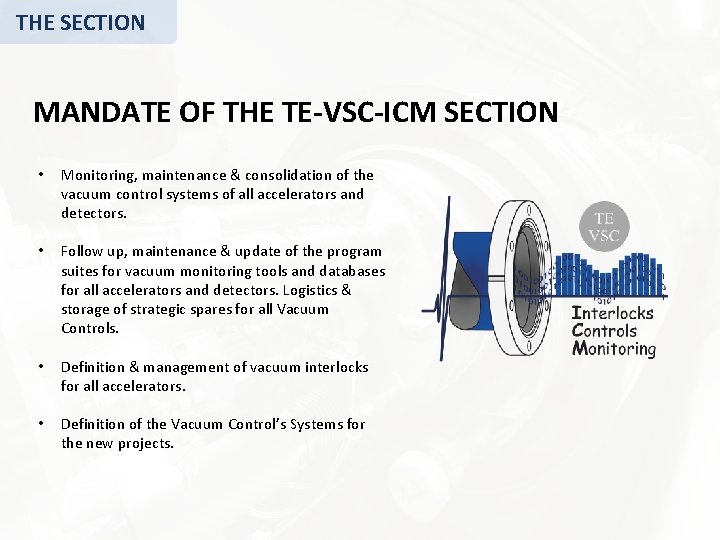
THE SECTION MANDATE OF THE TE-VSC-ICM SECTION • Monitoring, maintenance & consolidation of the vacuum control systems of all accelerators and detectors. • Follow up, maintenance & update of the program suites for vacuum monitoring tools and databases for all accelerators and detectors. Logistics & storage of strategic spares for all Vacuum Controls. • Definition & management of vacuum interlocks for all accelerators. • Definition of the Vacuum Control’s Systems for the new projects.
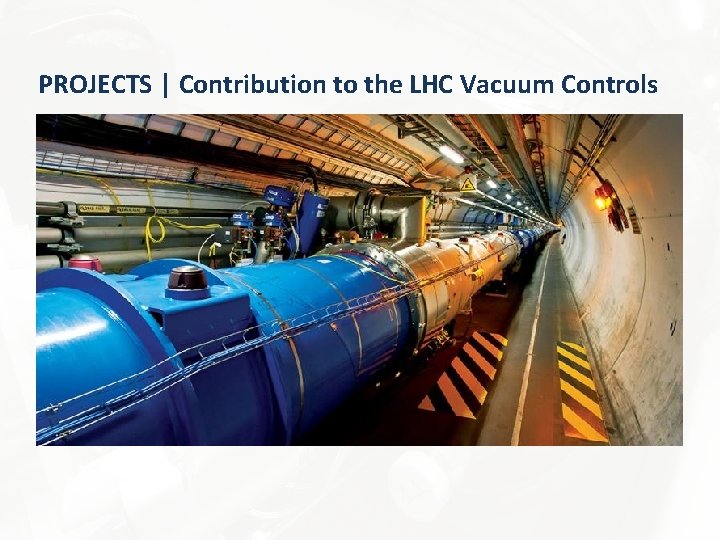
PROJECTS | Contribution to the LHC Vacuum Controls
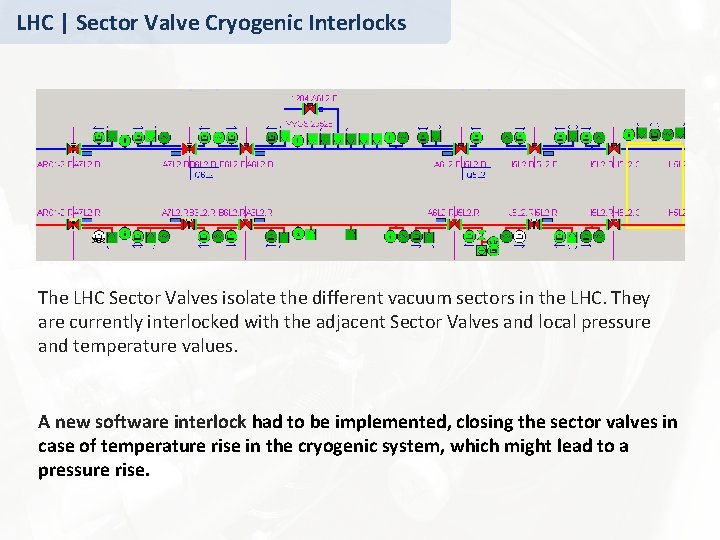
LHC | Sector Valve Cryogenic Interlocks The LHC Sector Valves isolate the different vacuum sectors in the LHC. They are currently interlocked with the adjacent Sector Valves and local pressure and temperature values. A new software interlock had to be implemented, closing the sector valves in case of temperature rise in the cryogenic system, which might lead to a pressure rise.
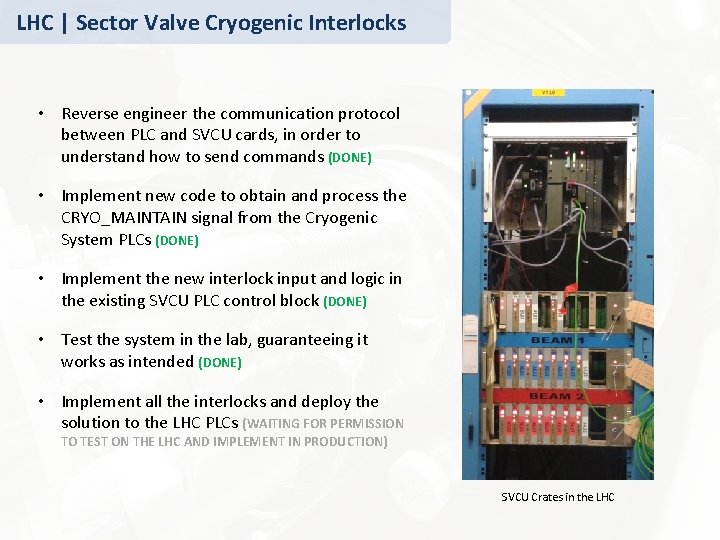
LHC | Sector Valve Cryogenic Interlocks • Reverse engineer the communication protocol between PLC and SVCU cards, in order to understand how to send commands (DONE) • Implement new code to obtain and process the CRYO_MAINTAIN signal from the Cryogenic System PLCs (DONE) • Implement the new interlock input and logic in the existing SVCU PLC control block (DONE) • Test the system in the lab, guaranteeing it works as intended (DONE) • Implement all the interlocks and deploy the solution to the LHC PLCs (WAITING FOR PERMISSION TO TEST ON THE LHC AND IMPLEMENT IN PRODUCTION) SVCU Crates in the LHC
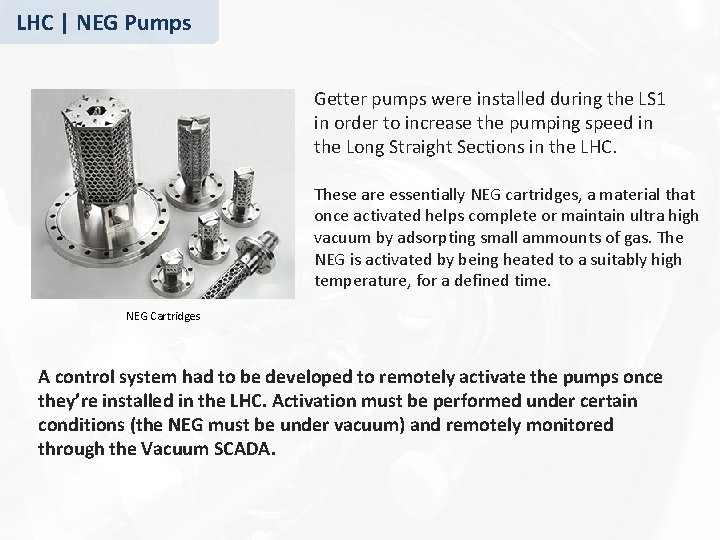
LHC | NEG Pumps Getter pumps were installed during the LS 1 in order to increase the pumping speed in the Long Straight Sections in the LHC. These are essentially NEG cartridges, a material that once activated helps complete or maintain ultra high vacuum by adsorpting small ammounts of gas. The NEG is activated by being heated to a suitably high temperature, for a defined time. NEG Cartridges A control system had to be developed to remotely activate the pumps once they’re installed in the LHC. Activation must be performed under certain conditions (the NEG must be under vacuum) and remotely monitored through the Vacuum SCADA.
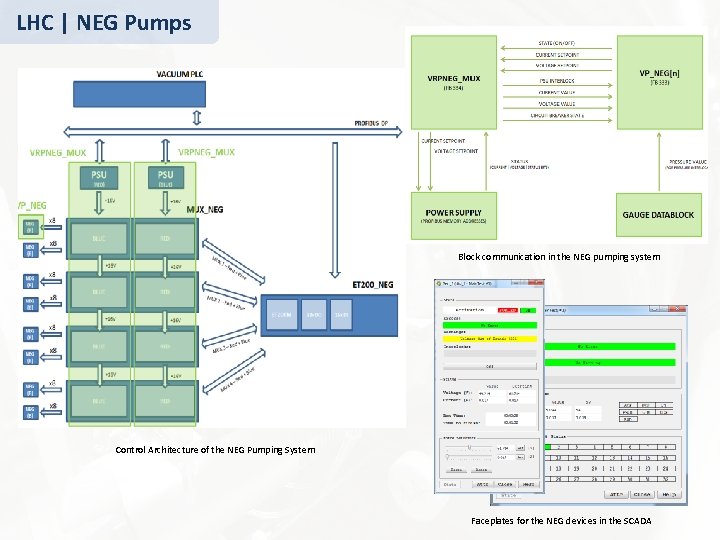
LHC | NEG Pumps Block communication in the NEG pumping system Control Architecture of the NEG Pumping System Faceplates for the NEG devices in the SCADA
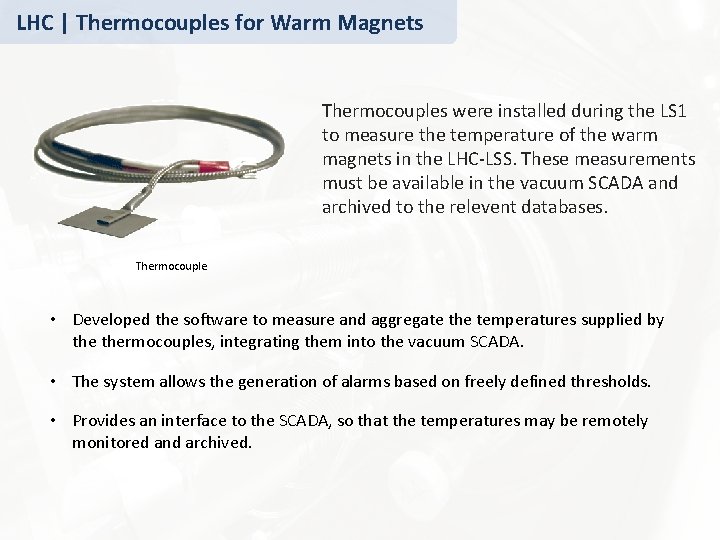
LHC | Thermocouples for Warm Magnets Thermocouples were installed during the LS 1 to measure the temperature of the warm magnets in the LHC-LSS. These measurements must be available in the vacuum SCADA and archived to the relevent databases. Thermocouple • Developed the software to measure and aggregate the temperatures supplied by thermocouples, integrating them into the vacuum SCADA. • The system allows the generation of alarms based on freely defined thresholds. • Provides an interface to the SCADA, so that the temperatures may be remotely monitored and archived.
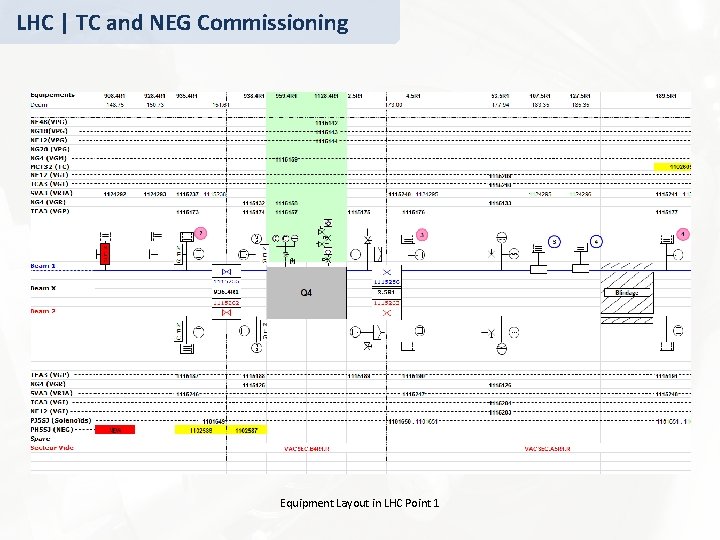
LHC | TC and NEG Commissioning Equipment Layout in LHC Point 1
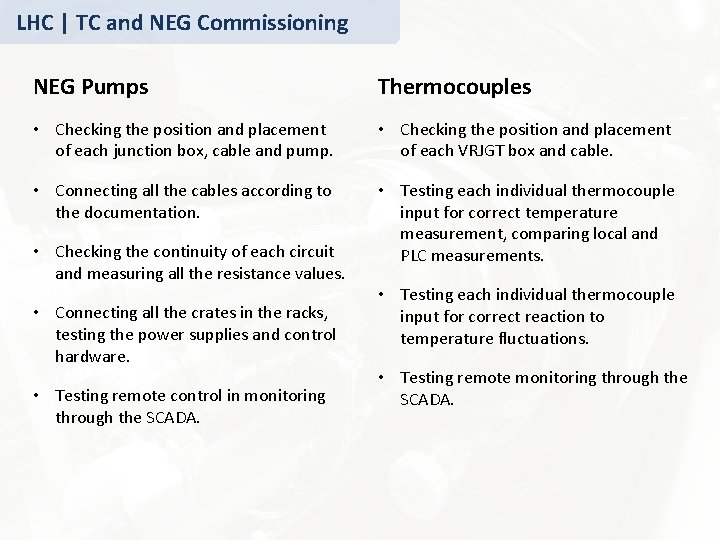
LHC | TC and NEG Commissioning NEG Pumps Thermocouples • Checking the position and placement of each junction box, cable and pump. • Checking the position and placement of each VRJGT box and cable. • Connecting all the cables according to the documentation. • Testing each individual thermocouple input for correct temperature measurement, comparing local and PLC measurements. • Checking the continuity of each circuit and measuring all the resistance values. • Connecting all the crates in the racks, testing the power supplies and control hardware. • Testing remote control in monitoring through the SCADA. • Testing each individual thermocouple input for correct reaction to temperature fluctuations. • Testing remote monitoring through the SCADA.
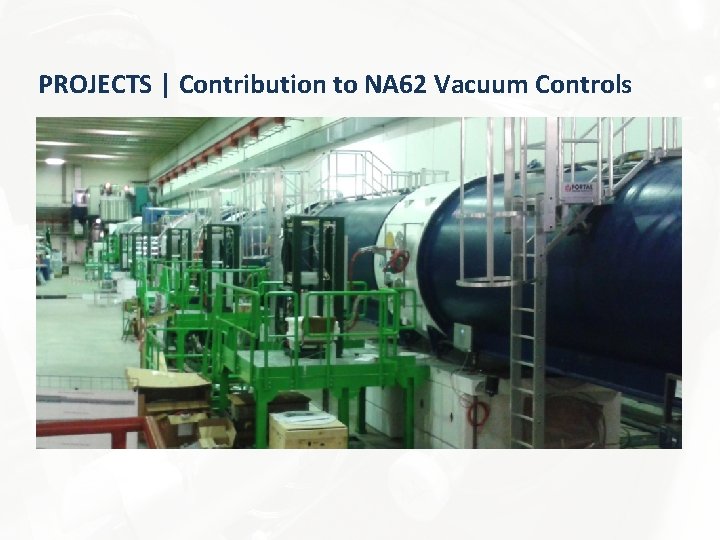
PROJECTS | Contribution to NA 62 Vacuum Controls
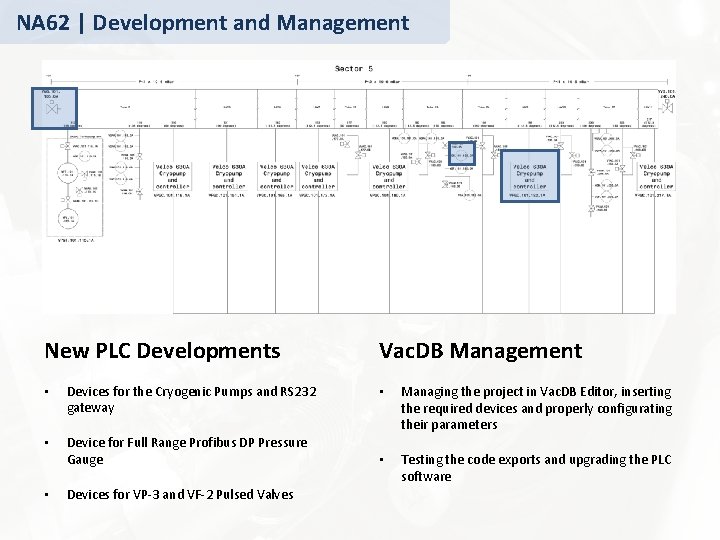
NA 62 | Development and Management New PLC Developments • Devices for the Cryogenic Pumps and RS 232 gateway • Device for Full Range Profibus DP Pressure Gauge • Devices for VP-3 and VF-2 Pulsed Valves Vac. DB Management • Managing the project in Vac. DB Editor, inserting the required devices and properly configurating their parameters • Testing the code exports and upgrading the PLC software
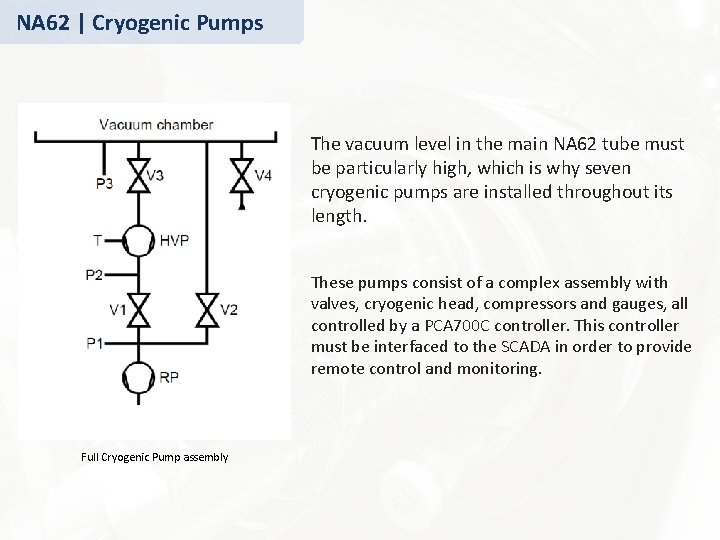
NA 62 | Cryogenic Pumps The vacuum level in the main NA 62 tube must be particularly high, which is why seven cryogenic pumps are installed throughout its length. These pumps consist of a complex assembly with valves, cryogenic head, compressors and gauges, all controlled by a PCA 700 C controller. This controller must be interfaced to the SCADA in order to provide remote control and monitoring. Full Cryogenic Pump assembly
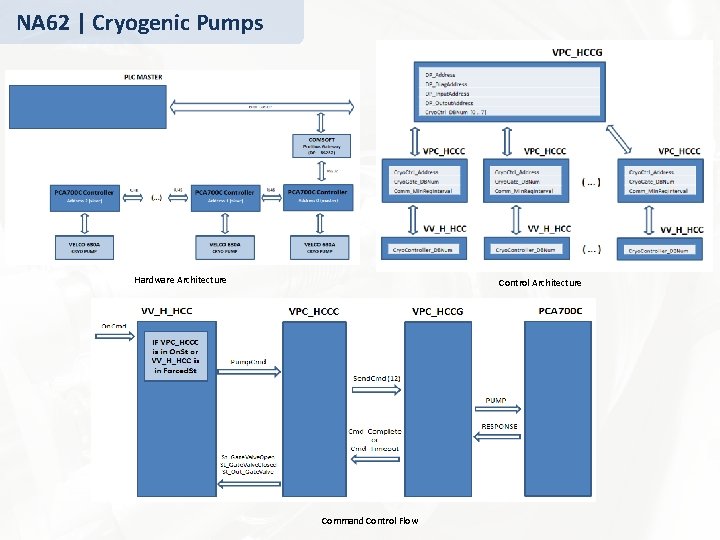
NA 62 | Cryogenic Pumps Hardware Architecture Control Architecture Command Control Flow
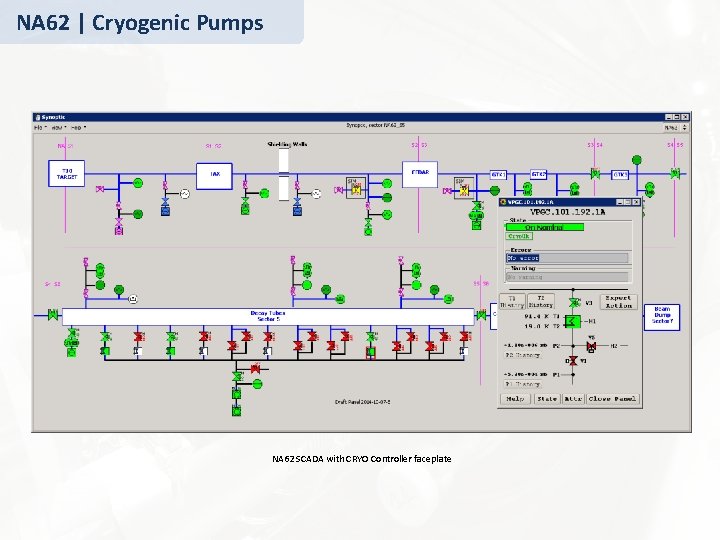
NA 62 | Cryogenic Pumps NA 62 SCADA with CRYO Controller faceplate
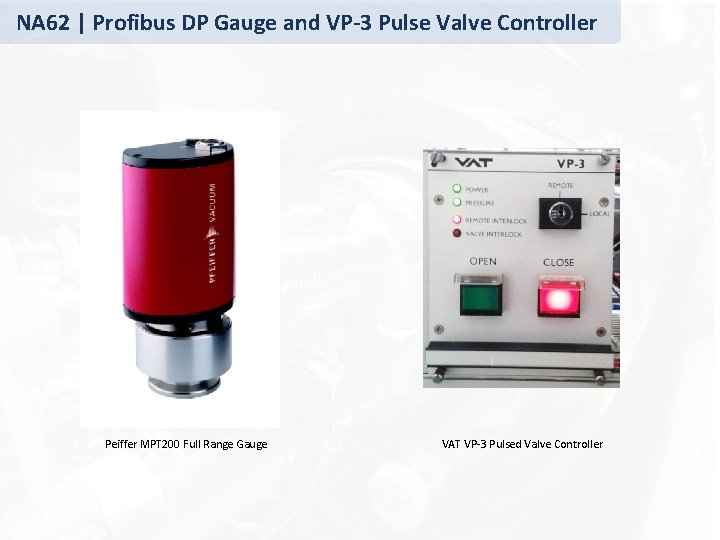
NA 62 | Profibus DP Gauge and VP-3 Pulse Valve Controller Peiffer MPT 200 Full Range Gauge VAT VP-3 Pulsed Valve Controller
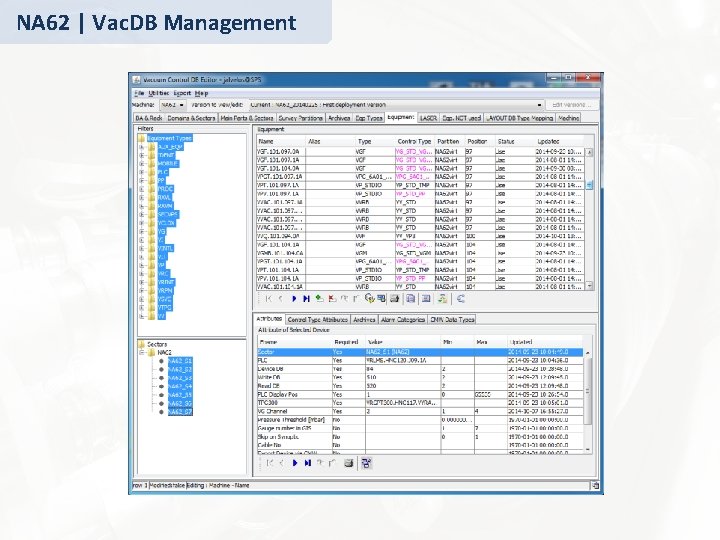
NA 62 | Vac. DB Management
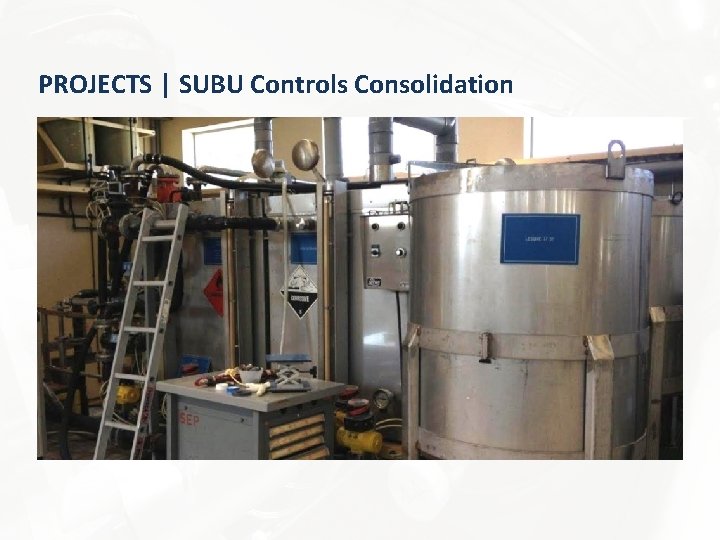
PROJECTS | SUBU Controls Consolidation
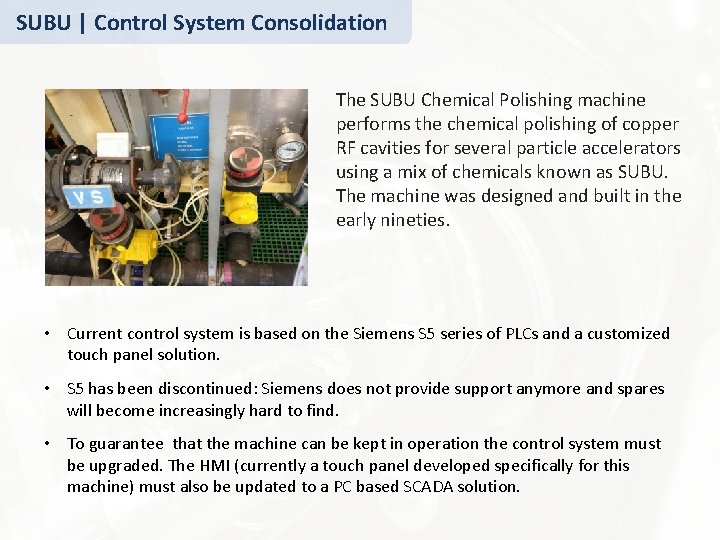
SUBU | Control System Consolidation The SUBU Chemical Polishing machine performs the chemical polishing of copper RF cavities for several particle accelerators using a mix of chemicals known as SUBU. The machine was designed and built in the early nineties. • Current control system is based on the Siemens S 5 series of PLCs and a customized touch panel solution. • S 5 has been discontinued: Siemens does not provide support anymore and spares will become increasingly hard to find. • To guarantee that the machine can be kept in operation the control system must be upgraded. The HMI (currently a touch panel developed specifically for this machine) must also be updated to a PC based SCADA solution.
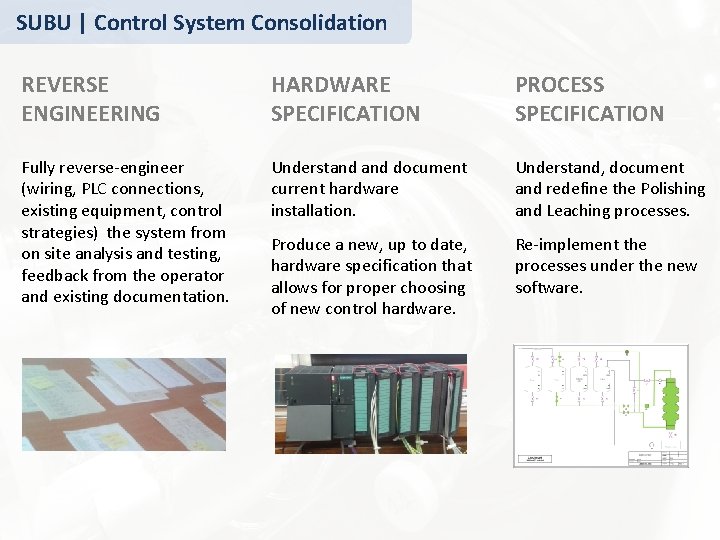
SUBU | Control System Consolidation REVERSE ENGINEERING HARDWARE SPECIFICATION PROCESS SPECIFICATION Fully reverse-engineer (wiring, PLC connections, existing equipment, control strategies) the system from on site analysis and testing, feedback from the operator and existing documentation. Understand document current hardware installation. Understand, document and redefine the Polishing and Leaching processes. Produce a new, up to date, hardware specification that allows for proper choosing of new control hardware. Re-implement the processes under the new software.
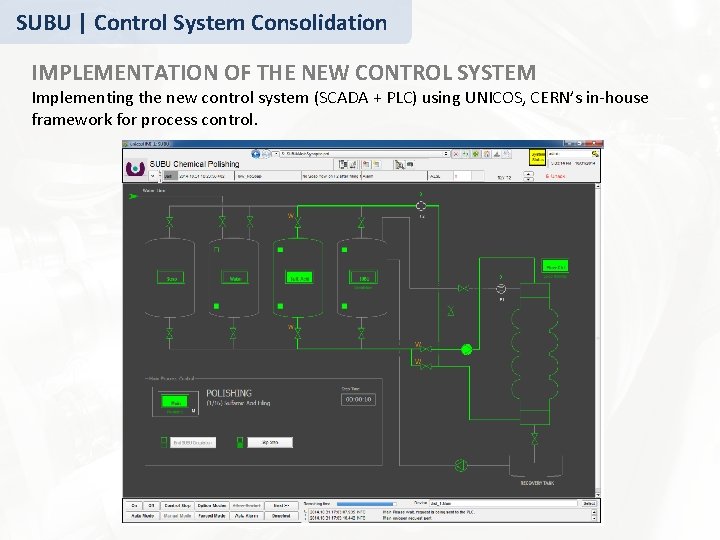
SUBU | Control System Consolidation IMPLEMENTATION OF THE NEW CONTROL SYSTEM Implementing the new control system (SCADA + PLC) using UNICOS, CERN’s in-house framework for process control.
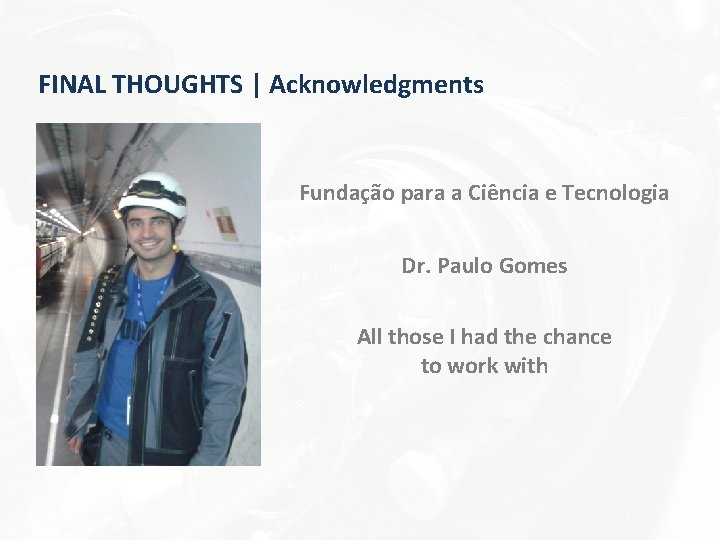
FINAL THOUGHTS | Acknowledgments Fundação para a Ciência e Tecnologia Dr. Paulo Gomes All those I had the chance to work with
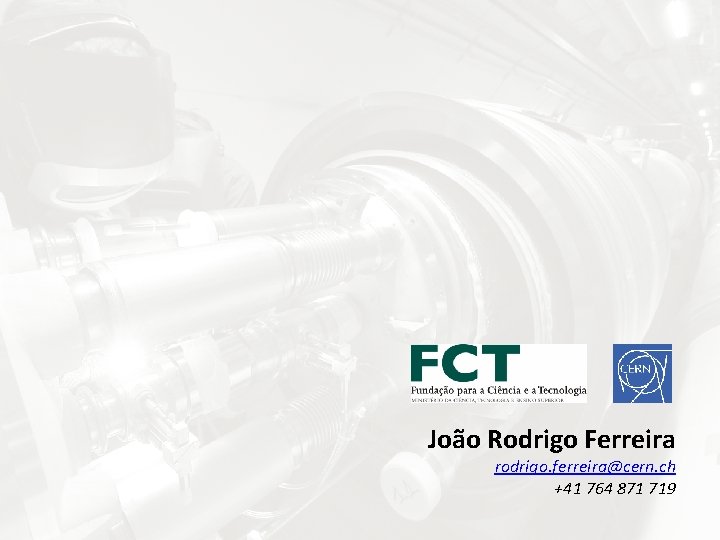
João Rodrigo Ferreira rodrigo. ferreira@cern. ch +41 764 871 719
Acincia
Campanhola fundao
Hospital oswaldo cruz ouvidoria
Fudao alfortville
Sn en 206
Babka v fct
Radyofarmasötik
Fct
Fiata sdt
Fiata fct
Fct asturias
Fct horas mínimas
Dec fct unl
Roche trainee programm
Training contract record
Sra training record template
Ogma recrutamento
Role of cbt trainee
Portance trainee
Trainee european commission
Trainee teacher reflective journal
Sf express management trainee
Indot special provisions
Government legal trainee scheme application process
Nurse hysteroscopist