ERT 4224 Piping and instrumentation diagram Pid MISS
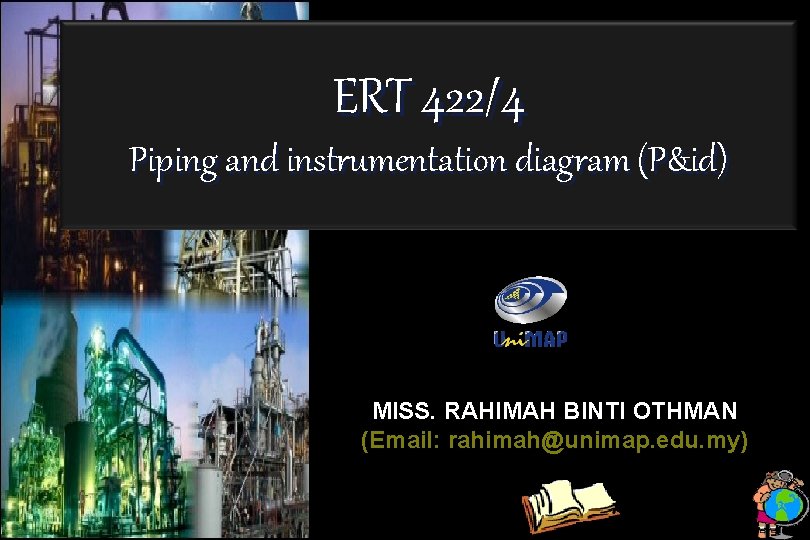
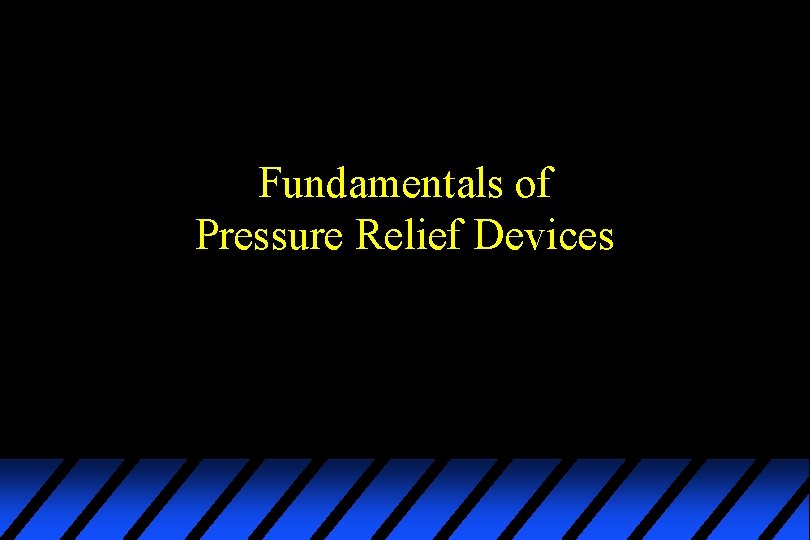
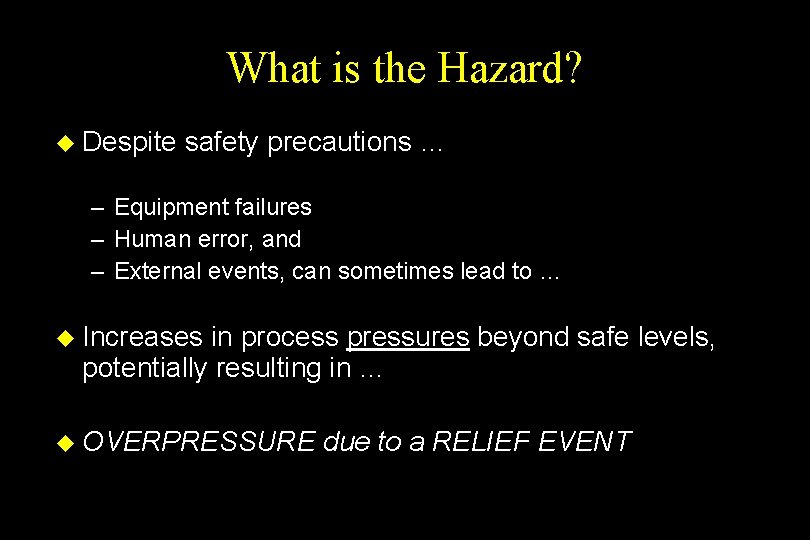
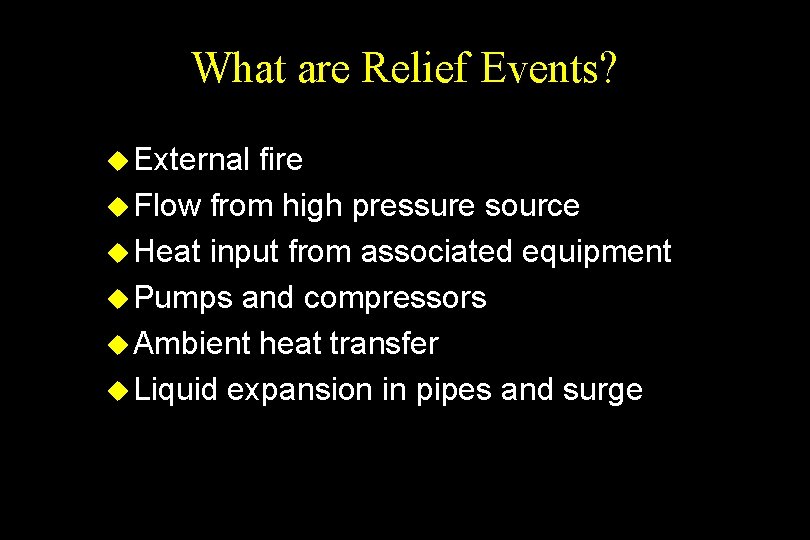
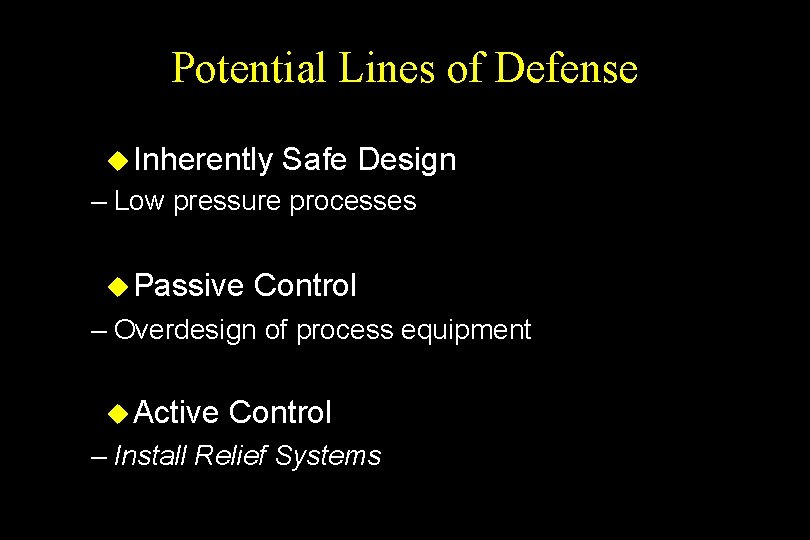
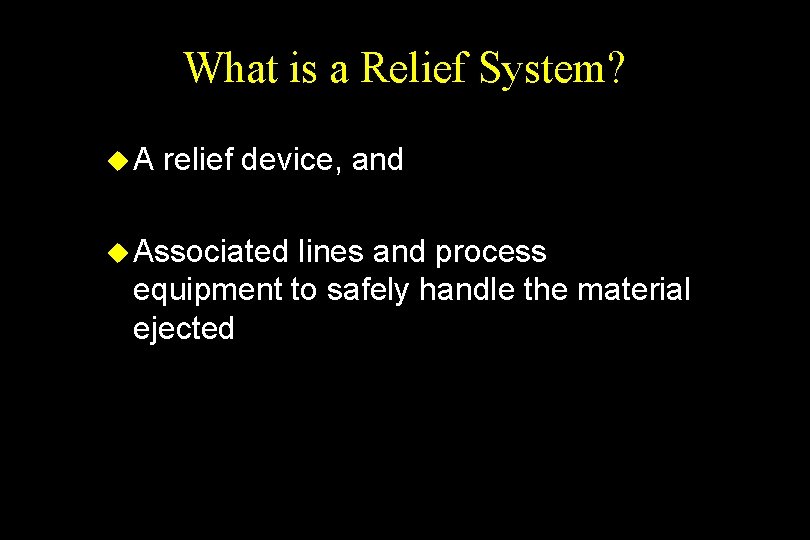
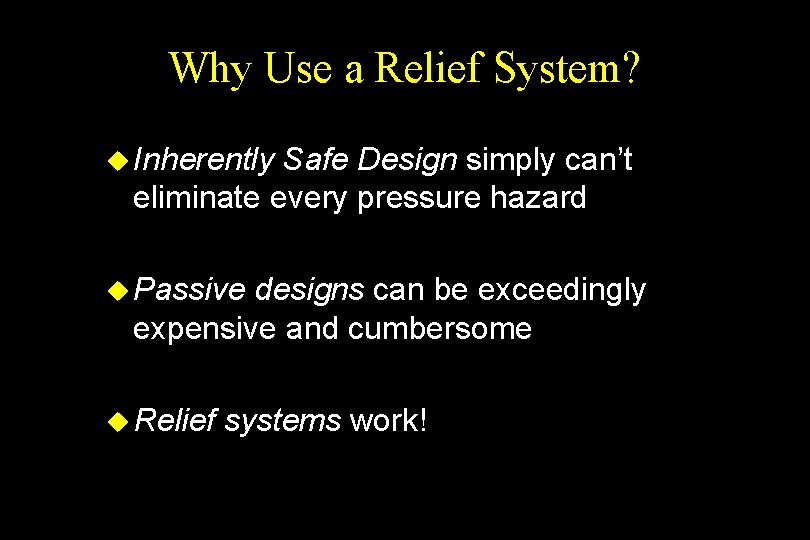
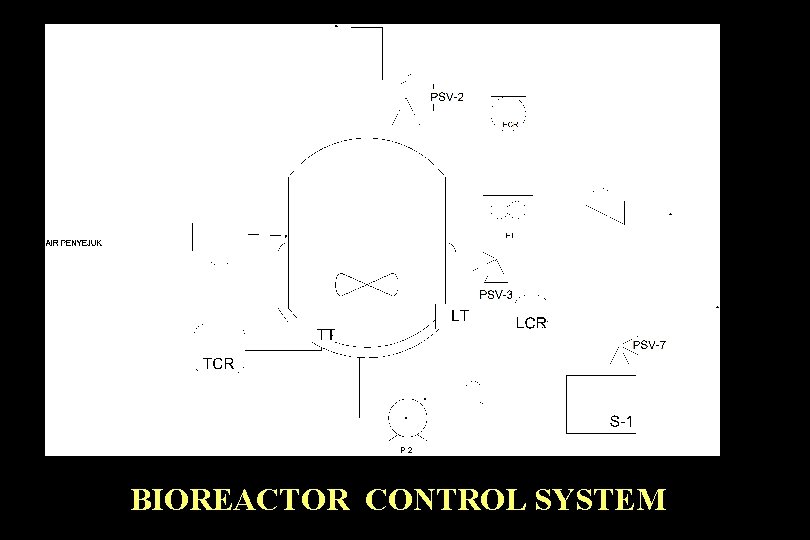
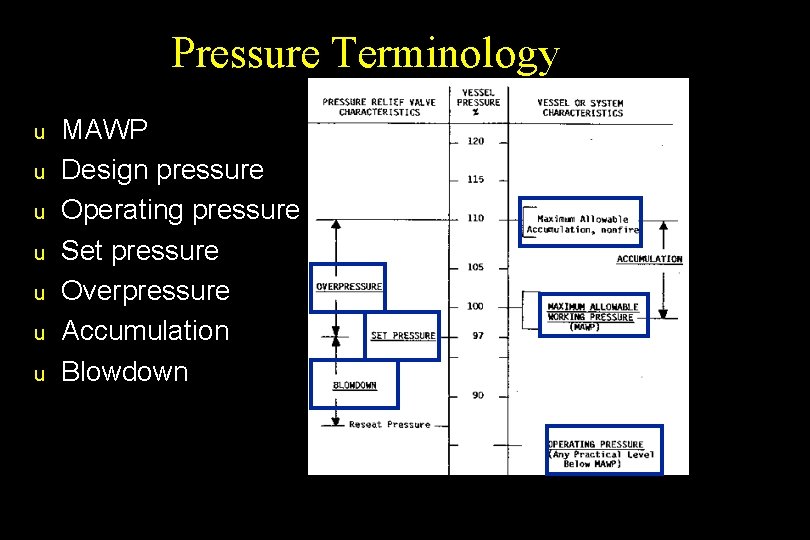
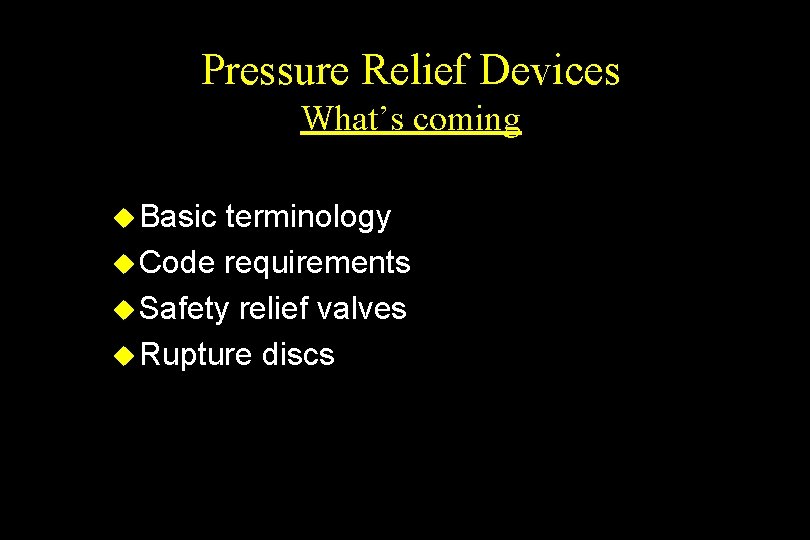
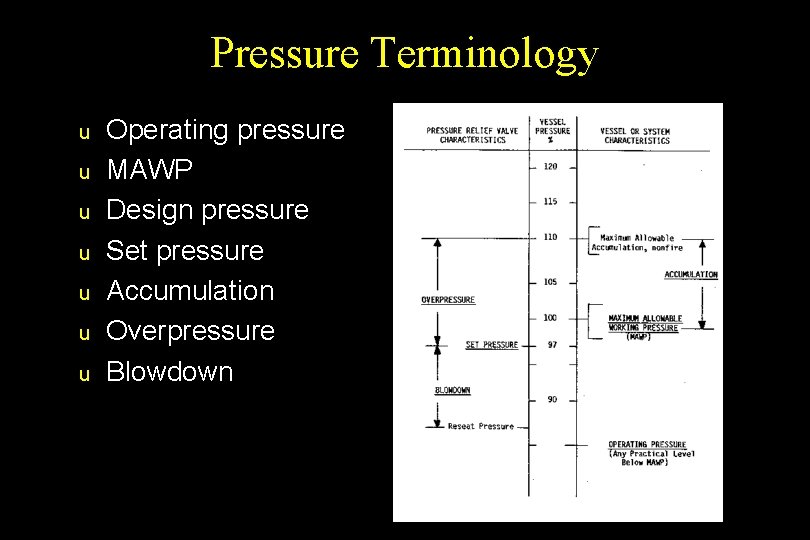
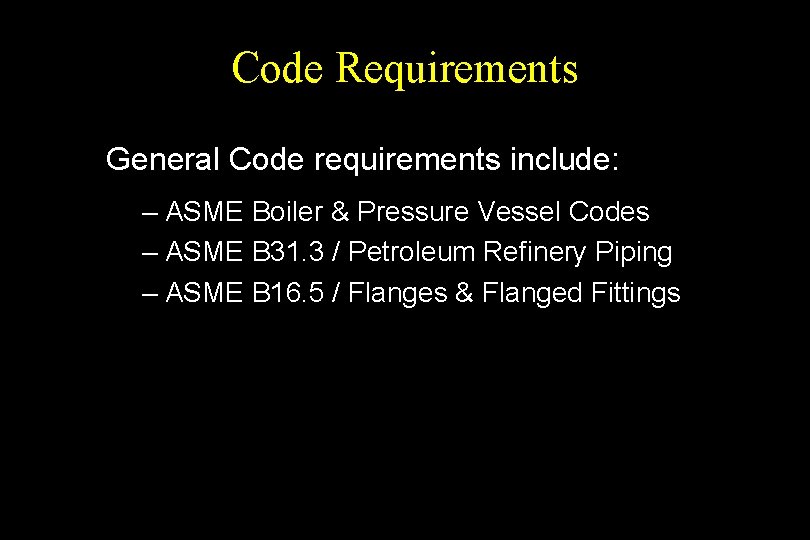
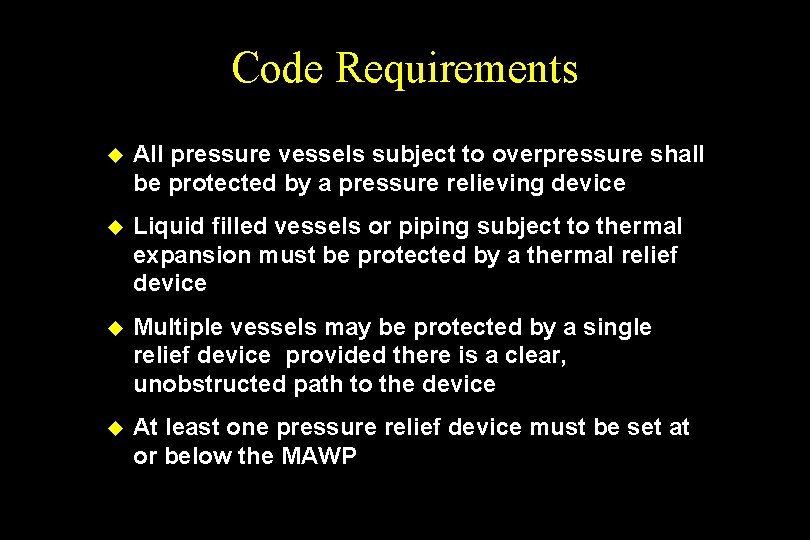
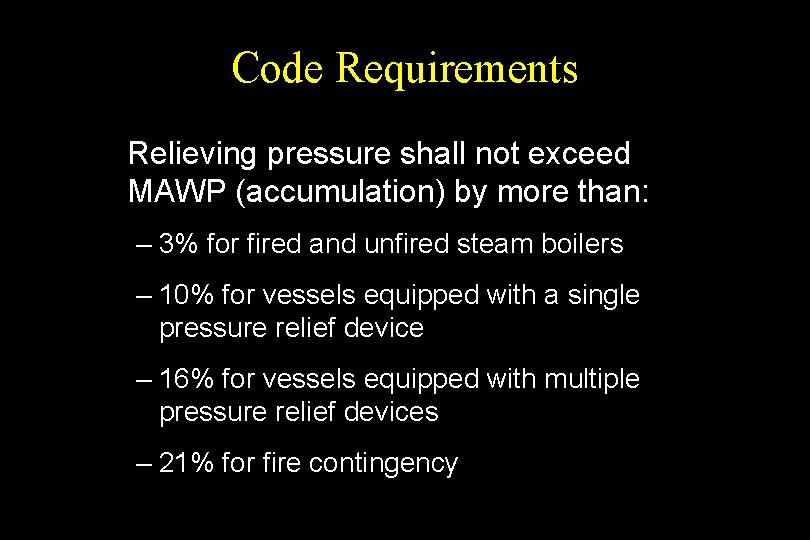
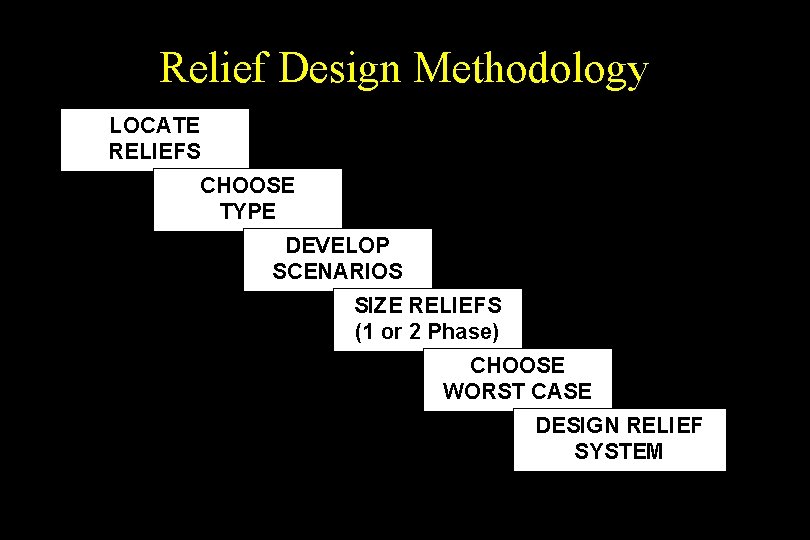

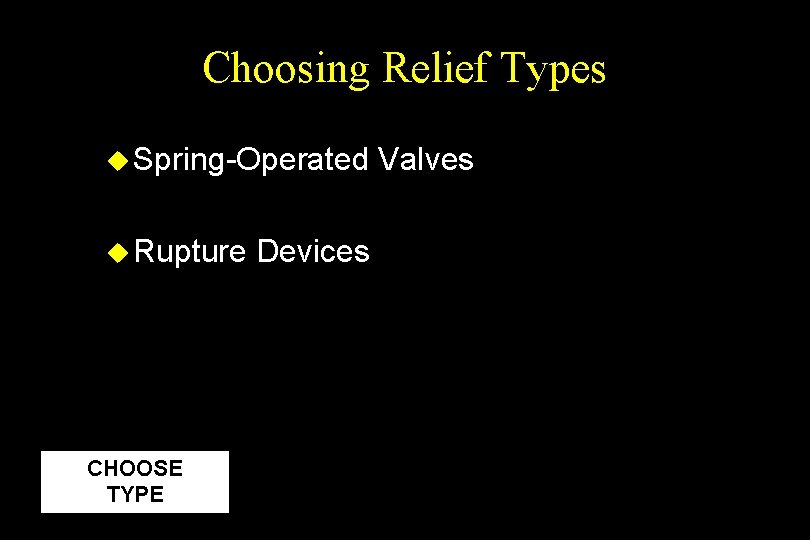
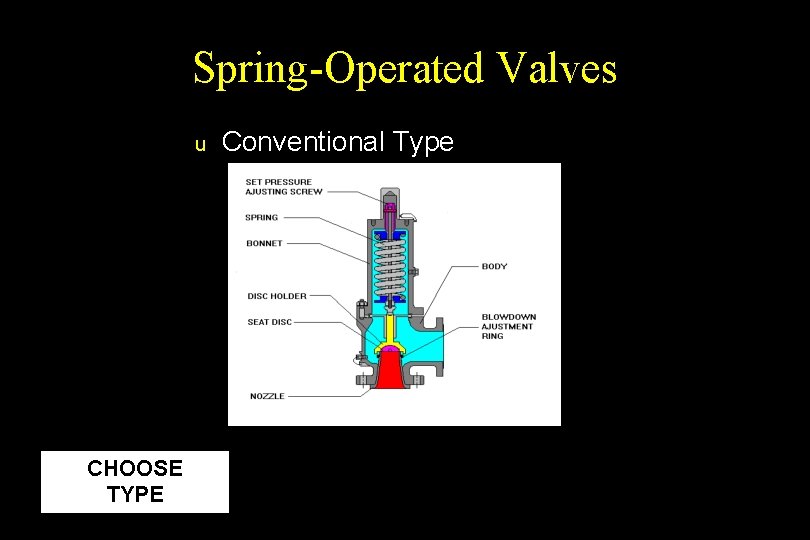
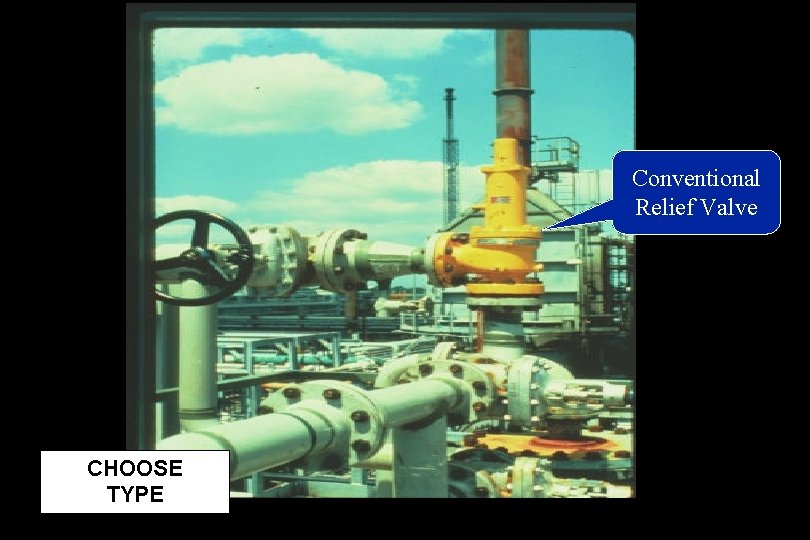
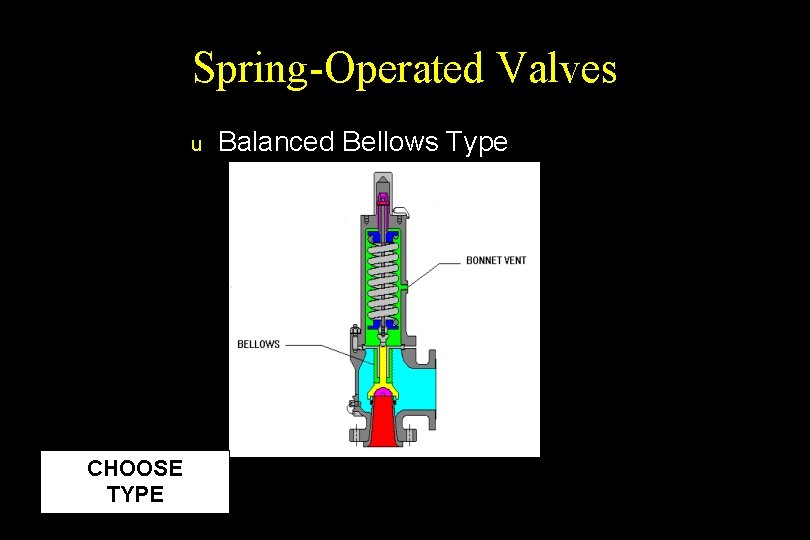
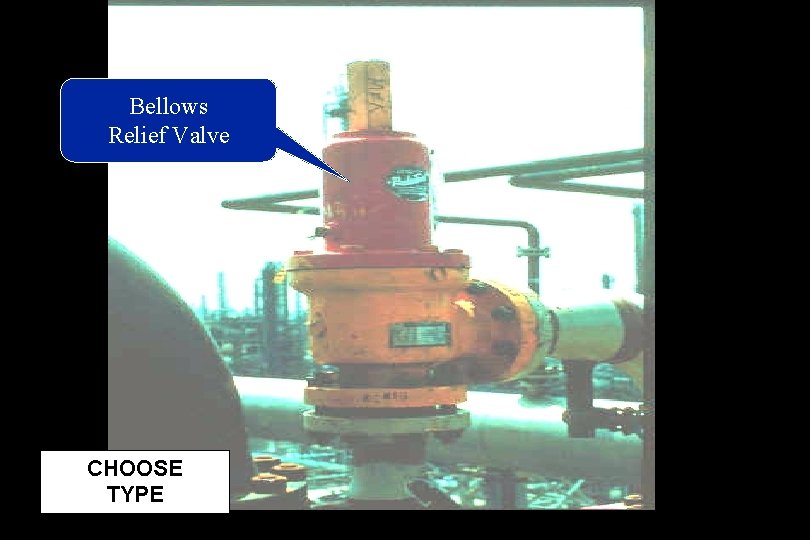
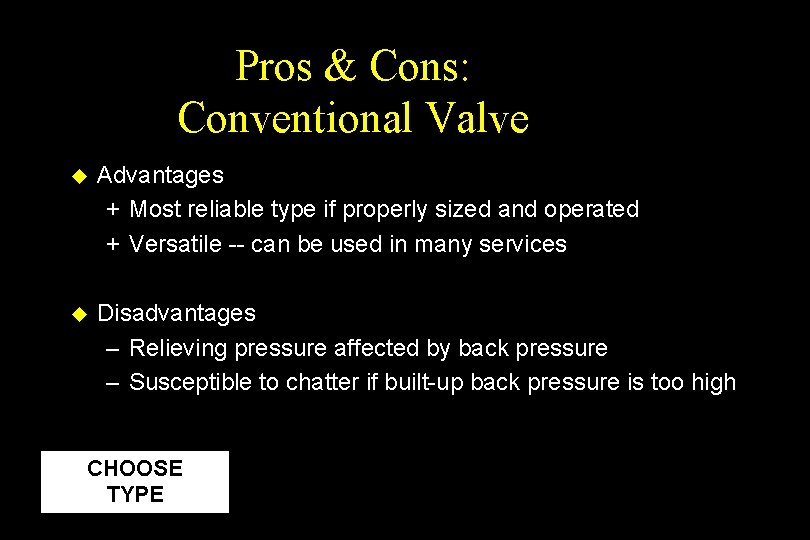
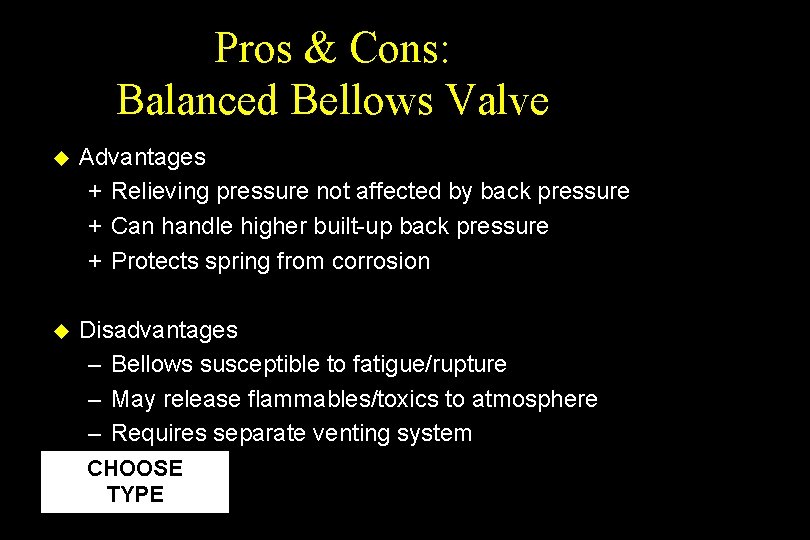
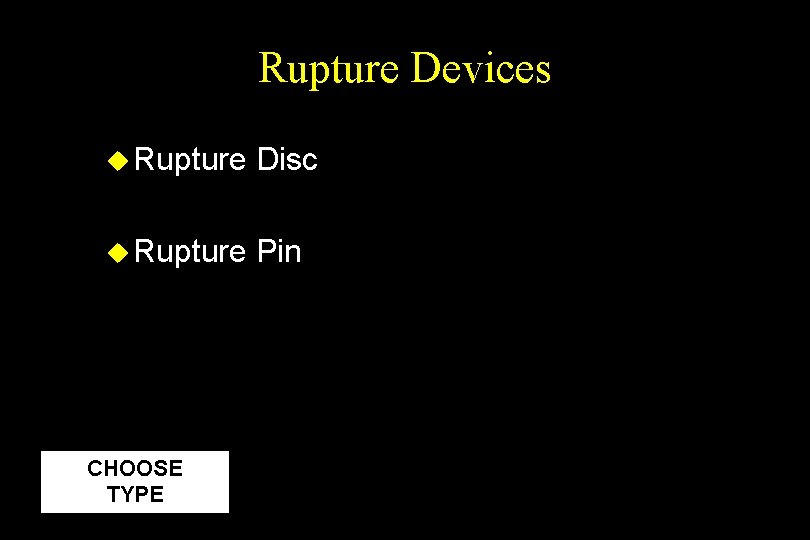
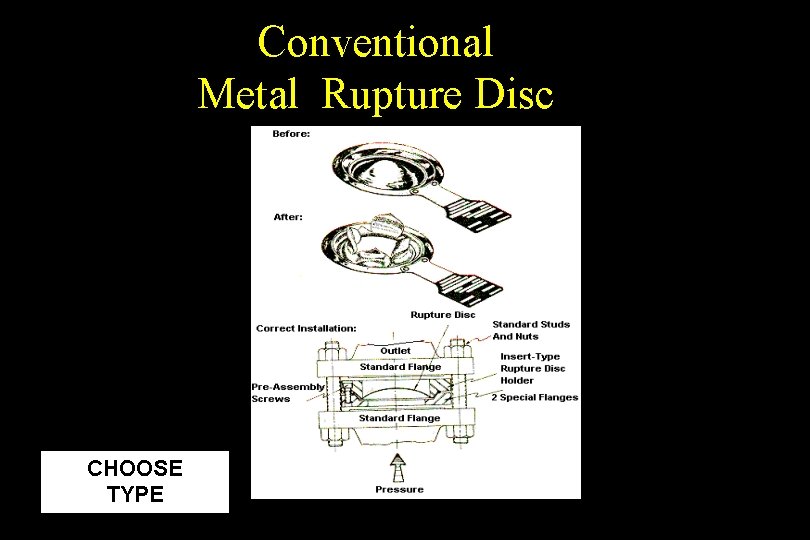
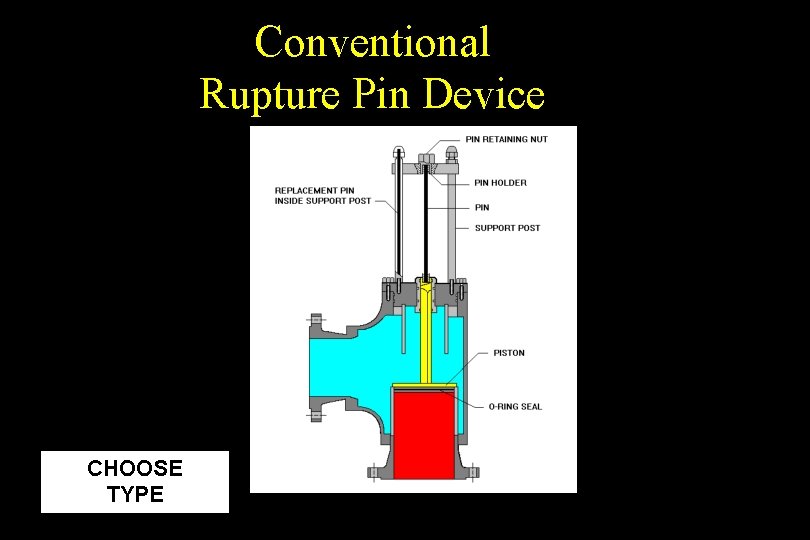
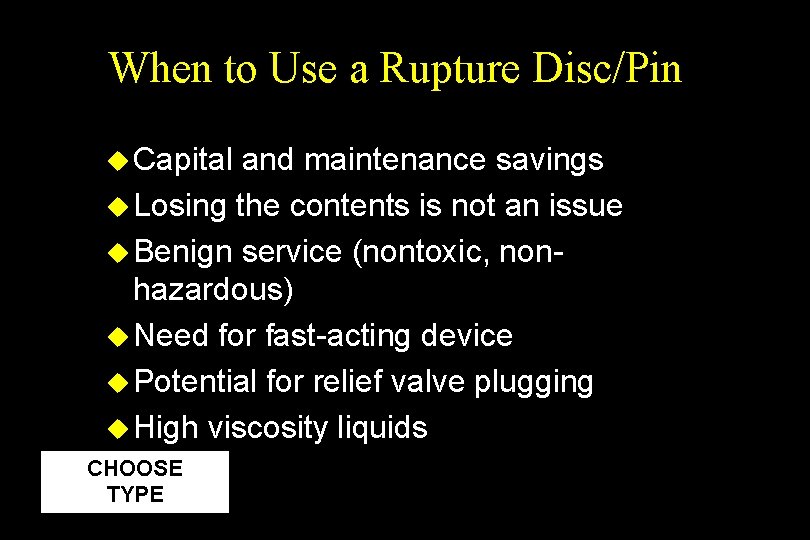
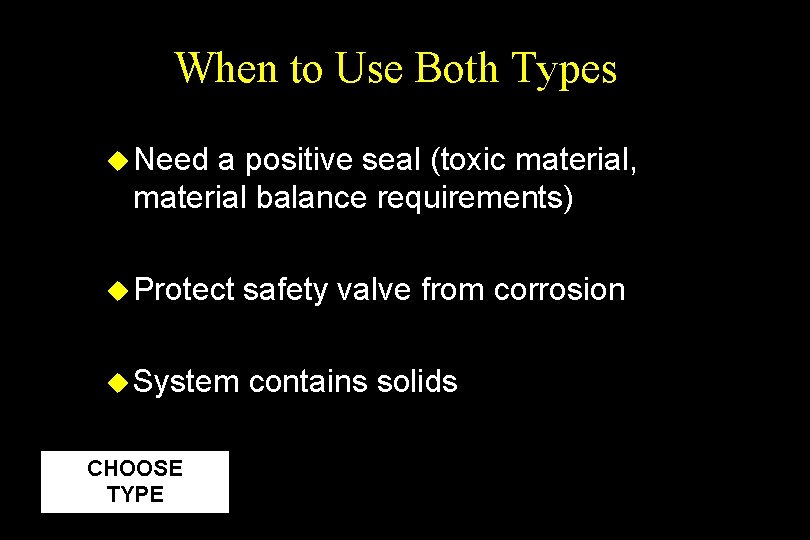
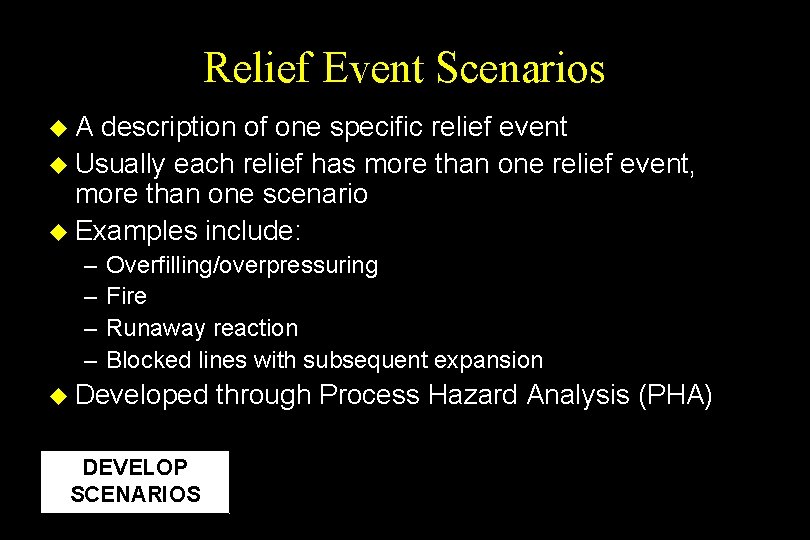
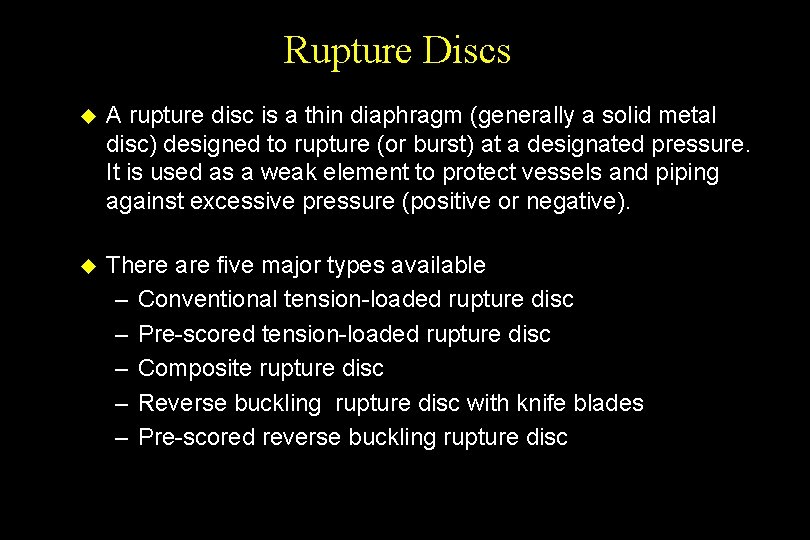
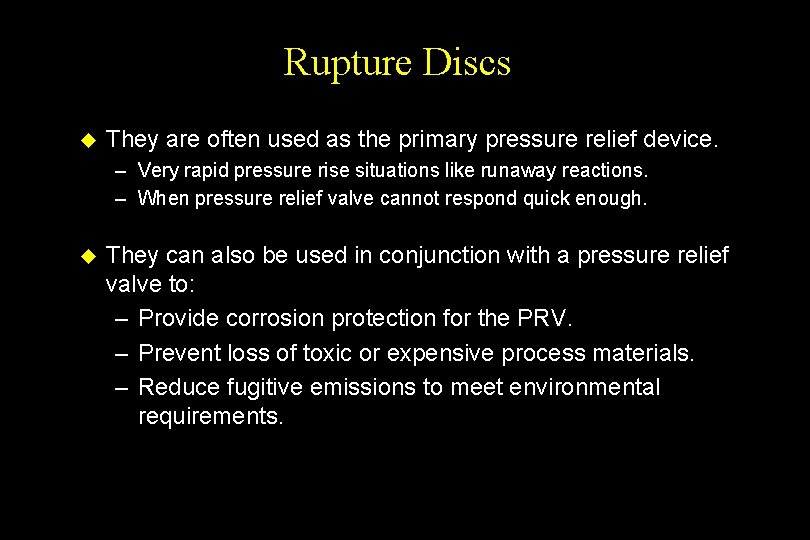
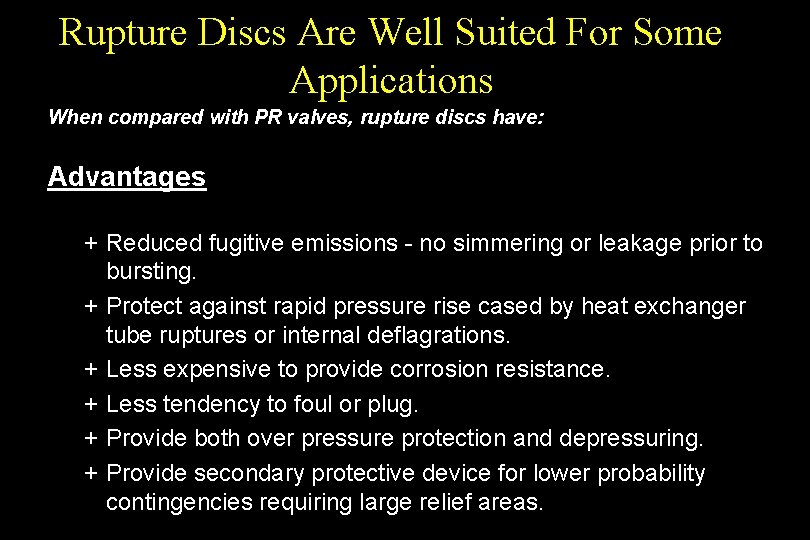
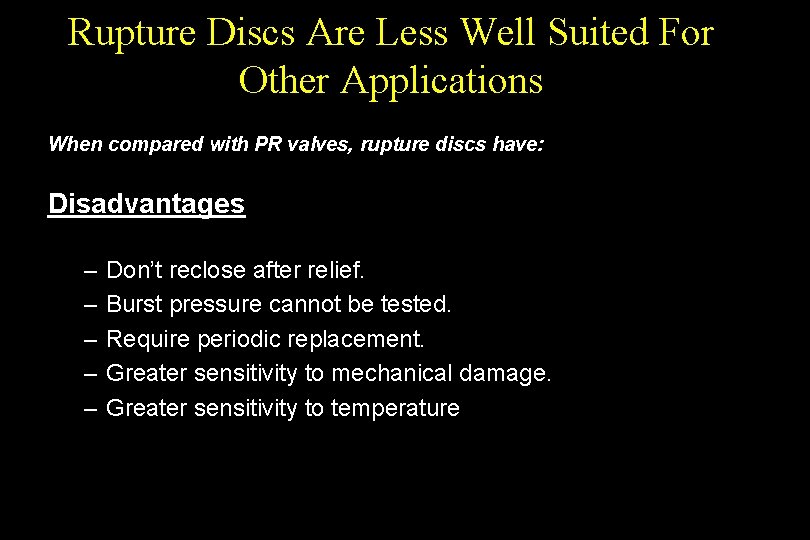
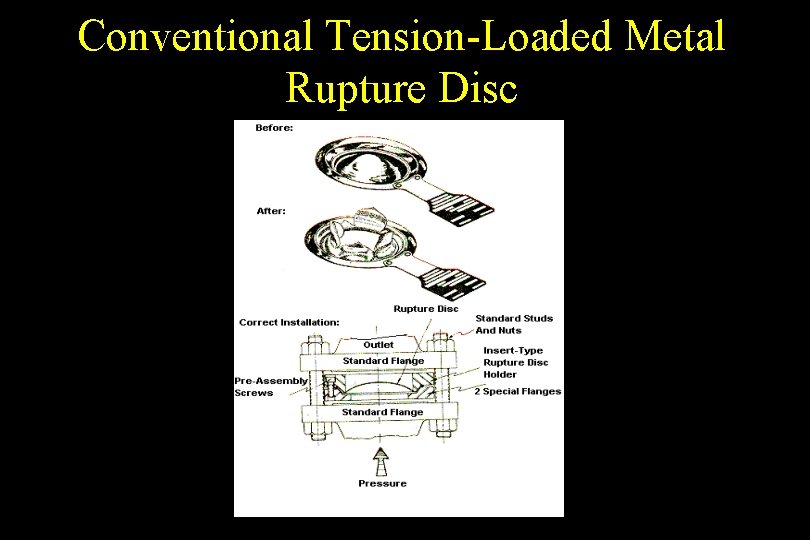
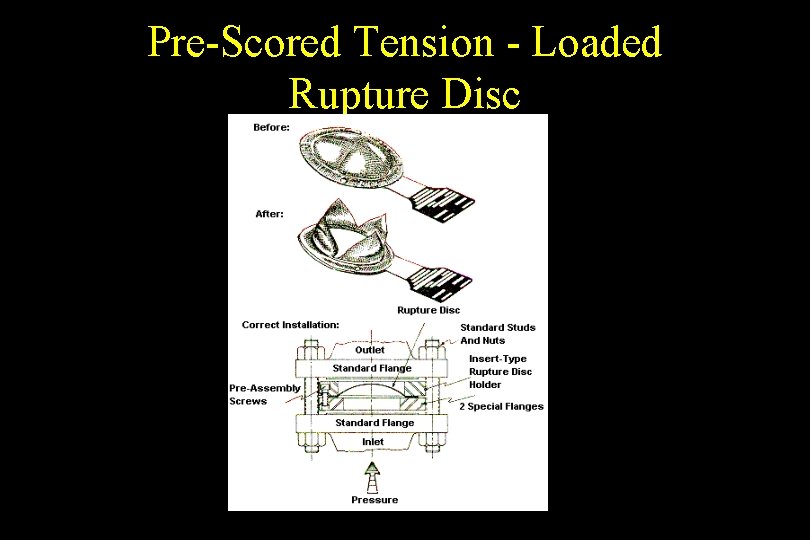
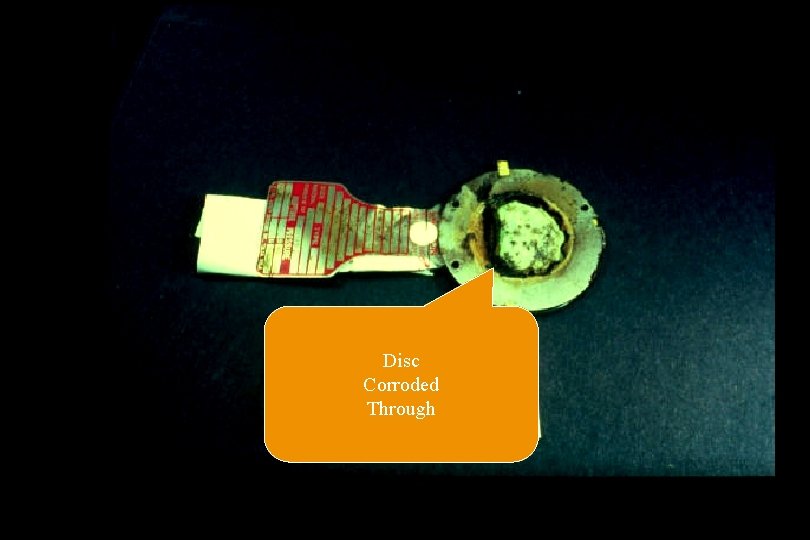
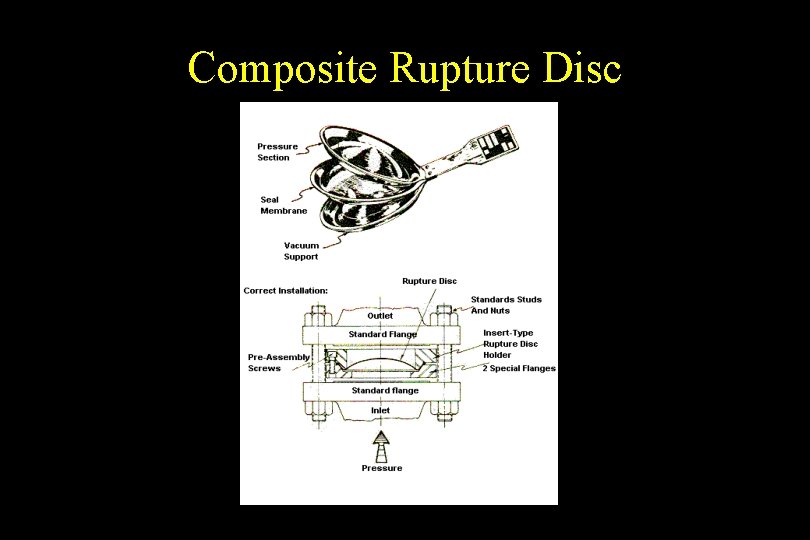
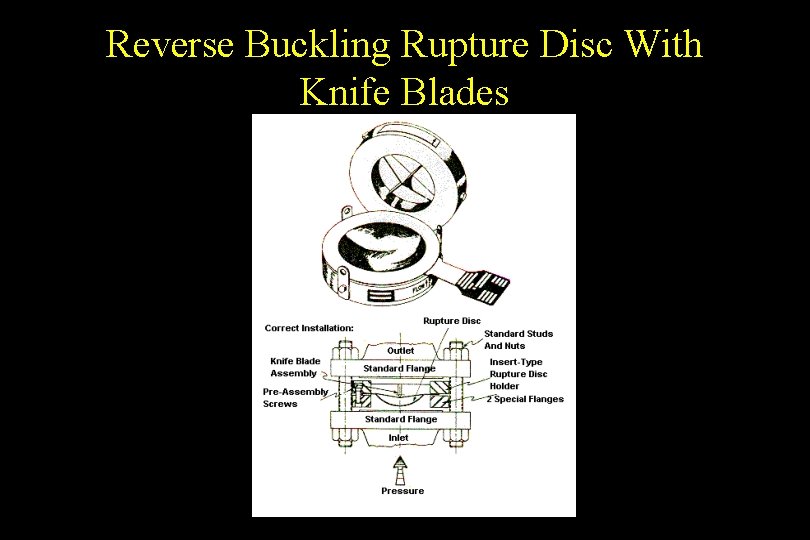
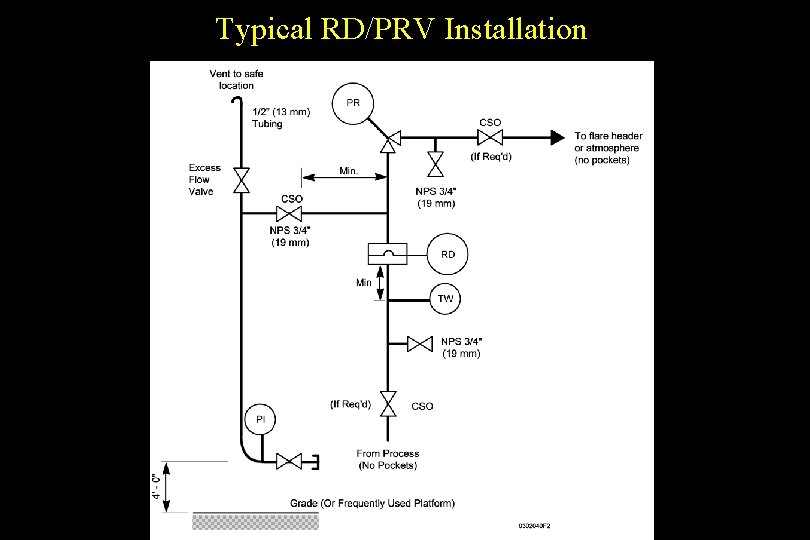
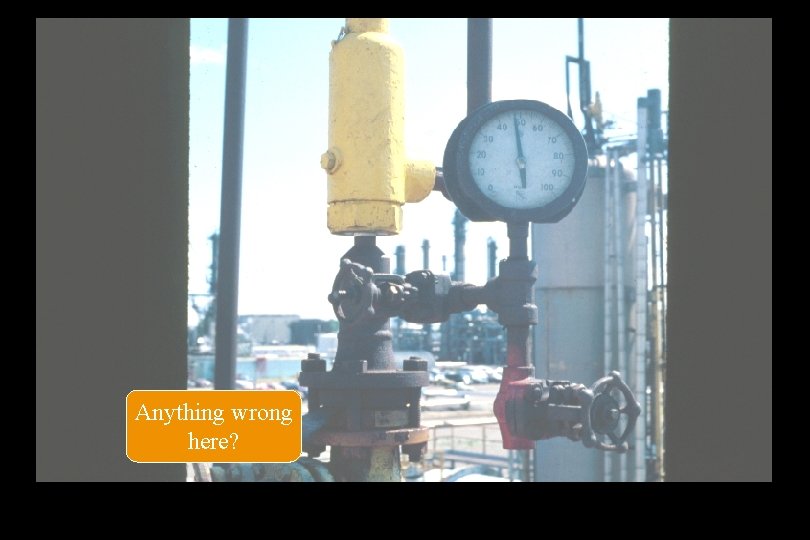
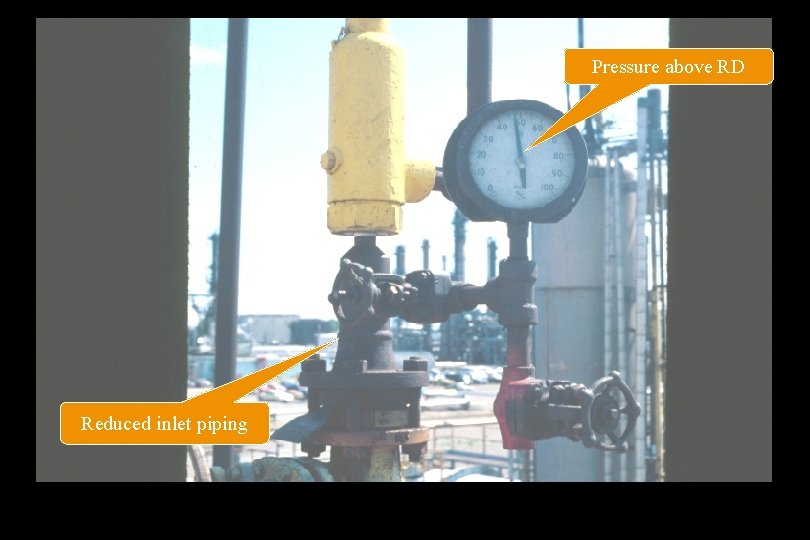
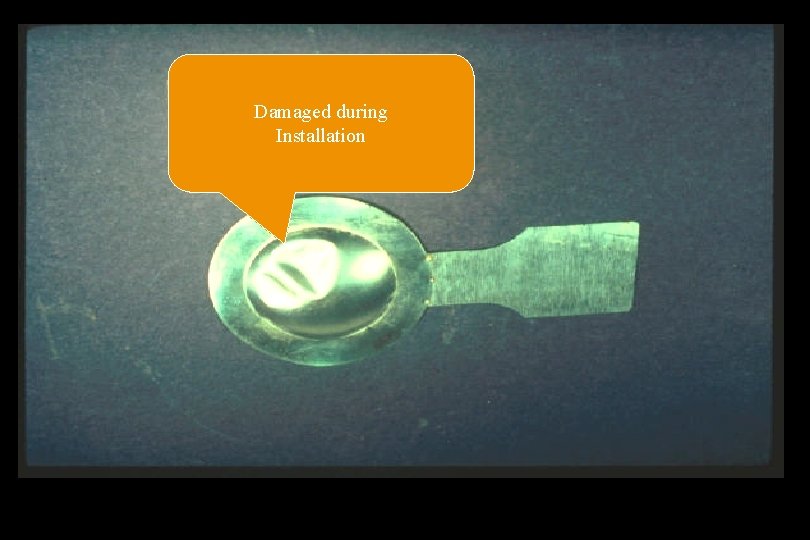
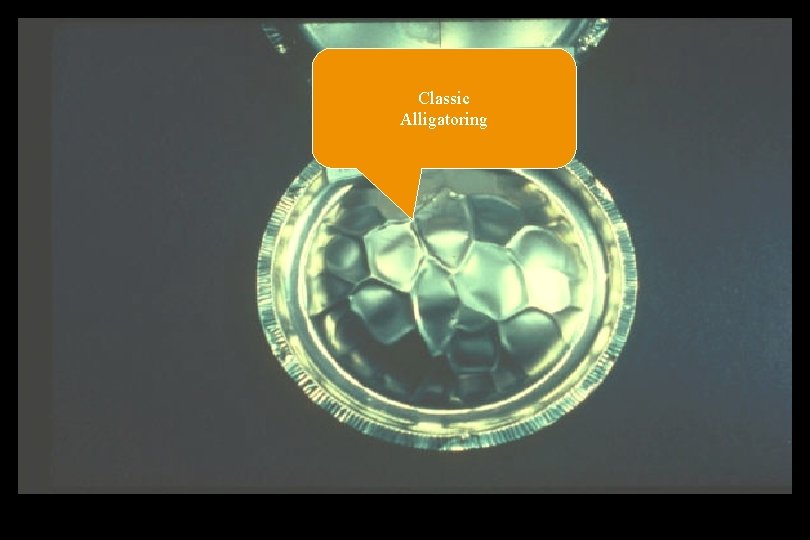
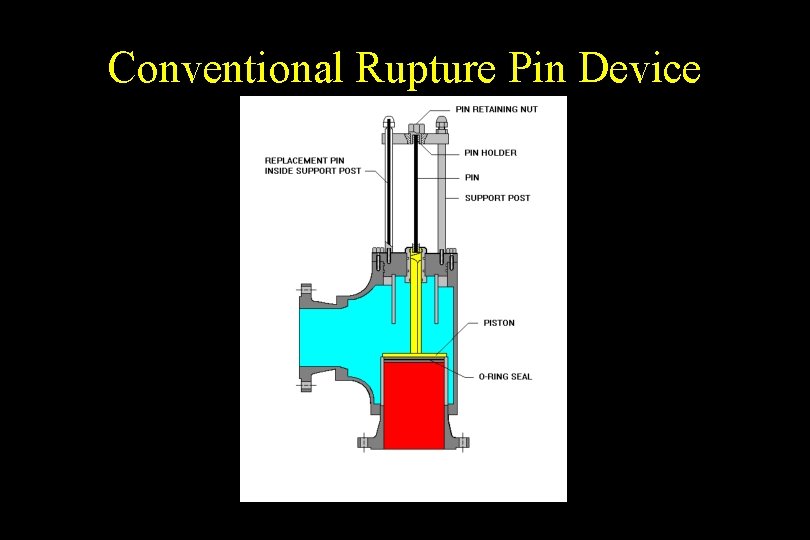
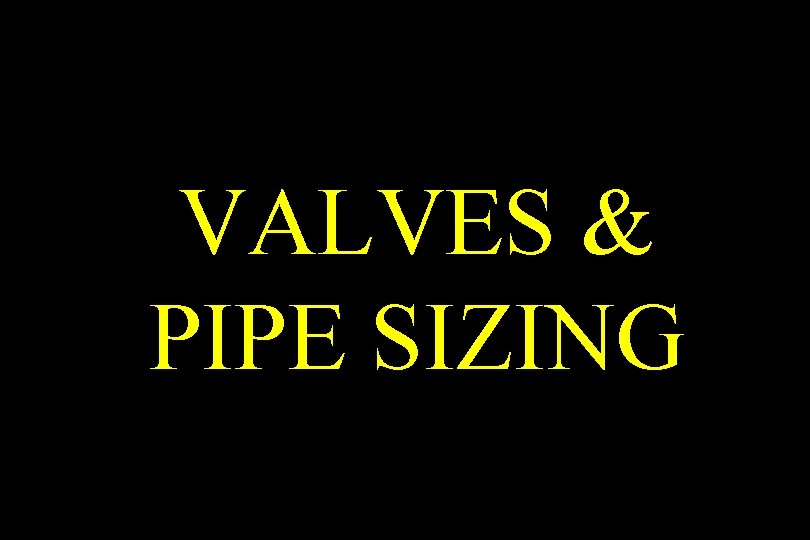
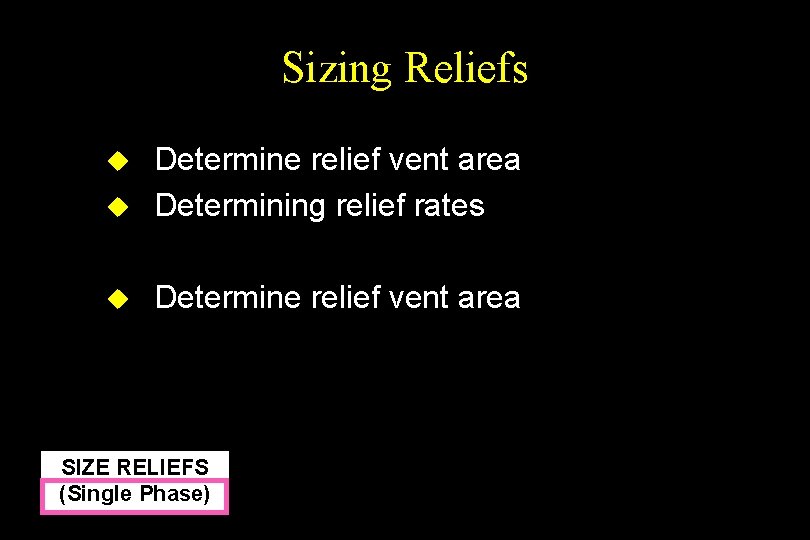
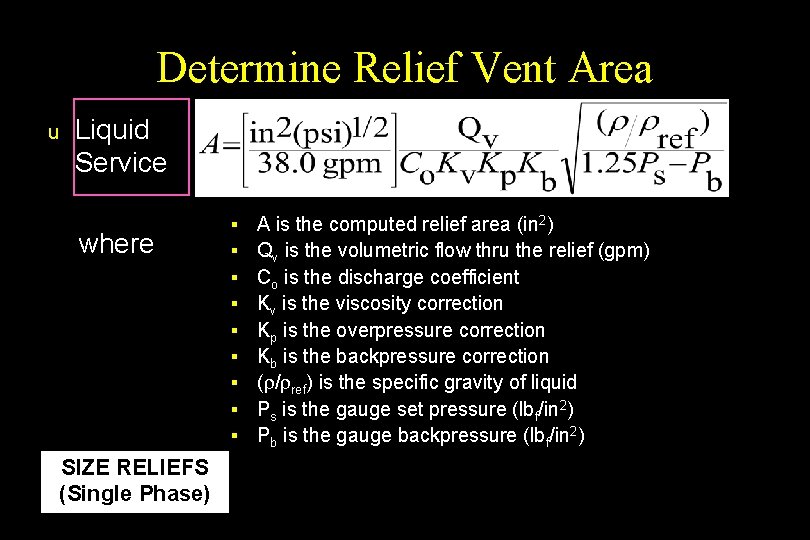
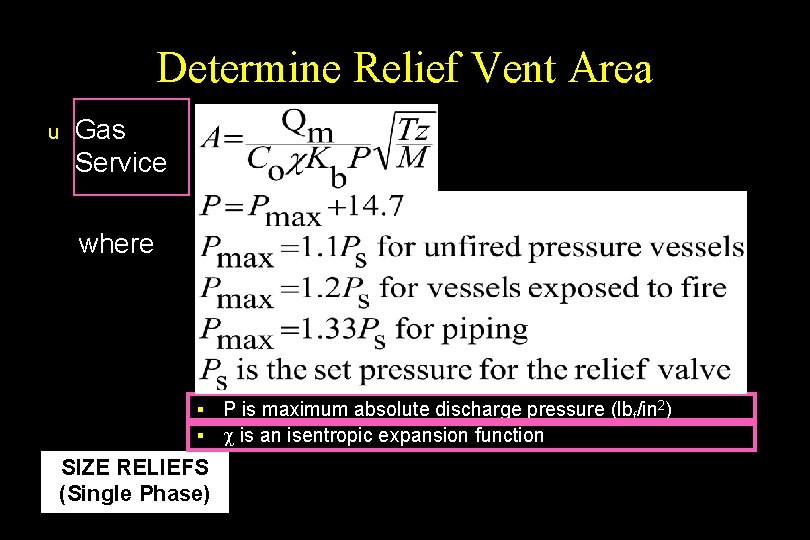
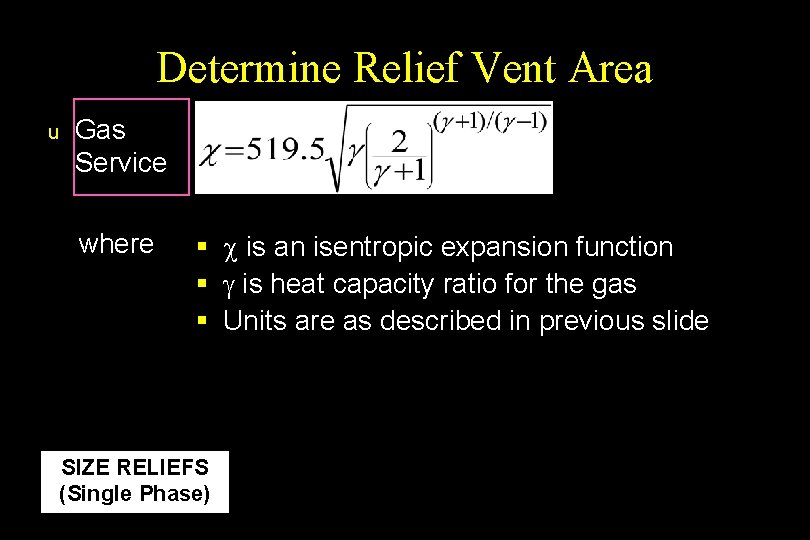
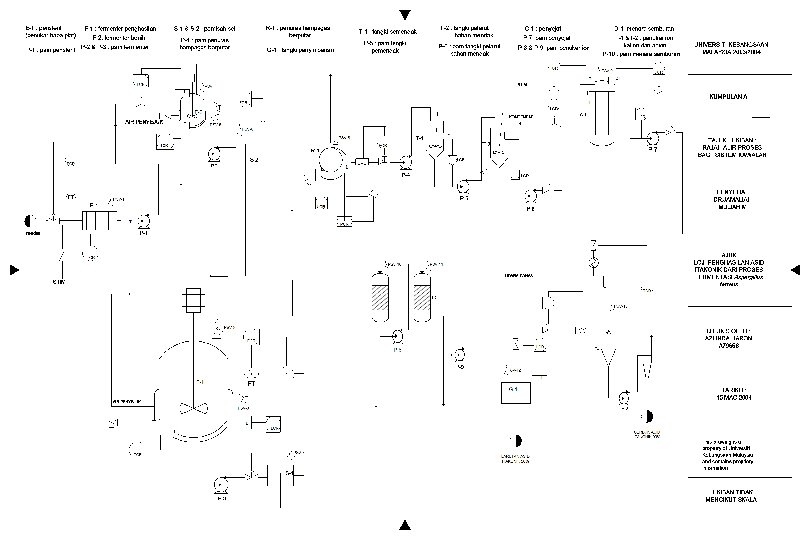
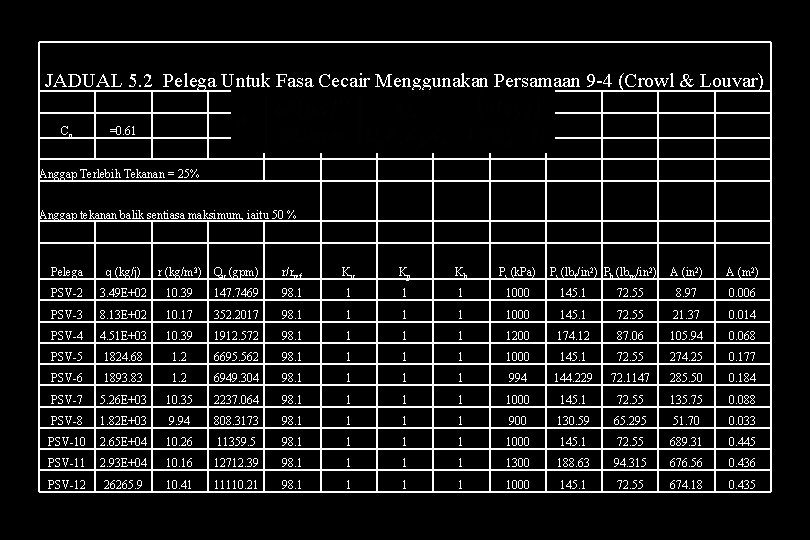
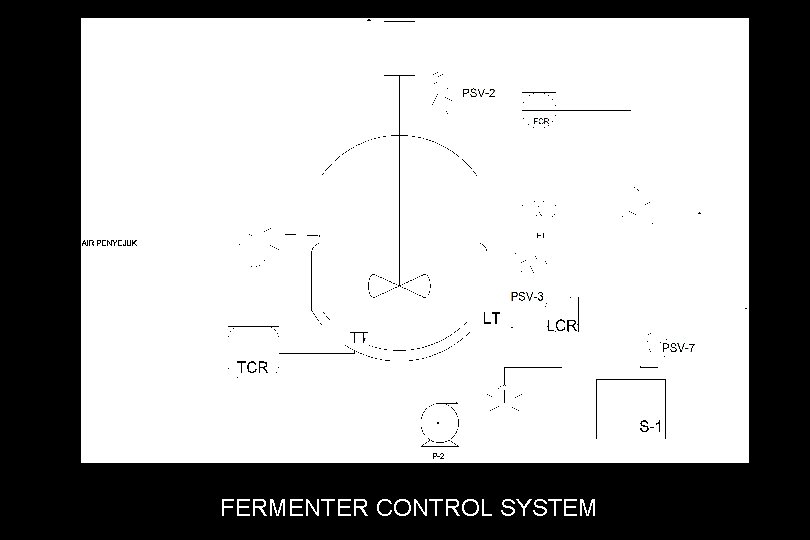
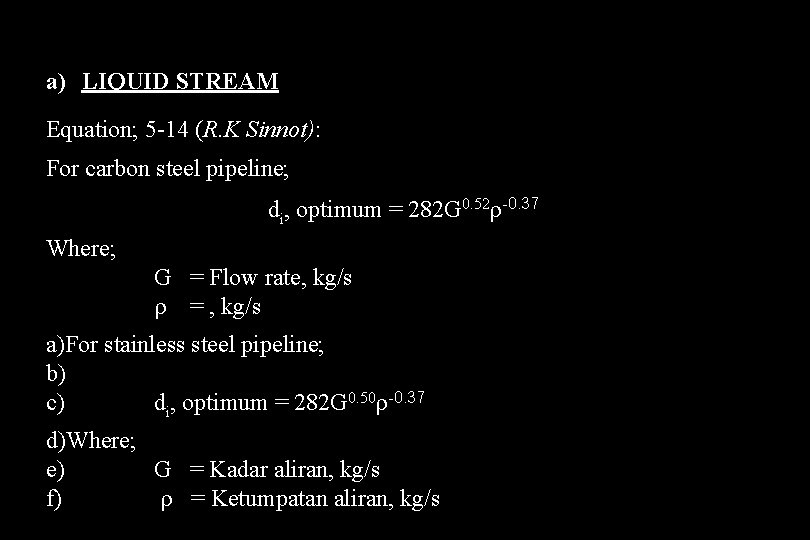
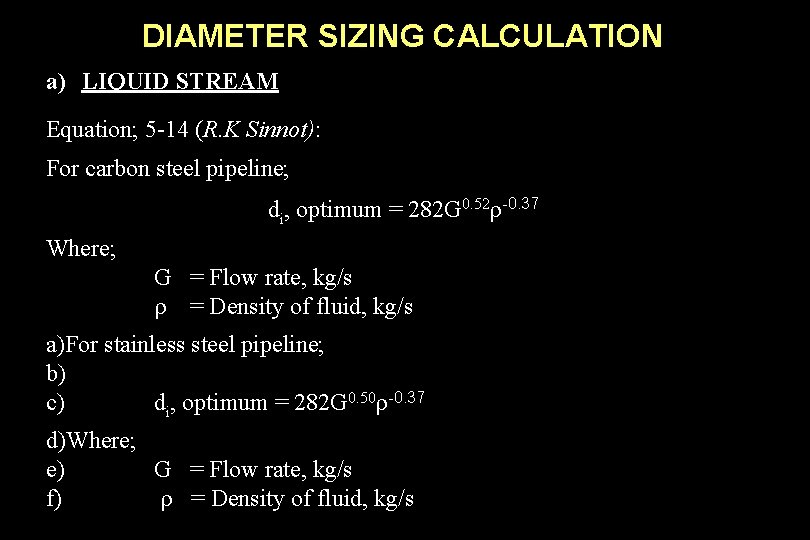
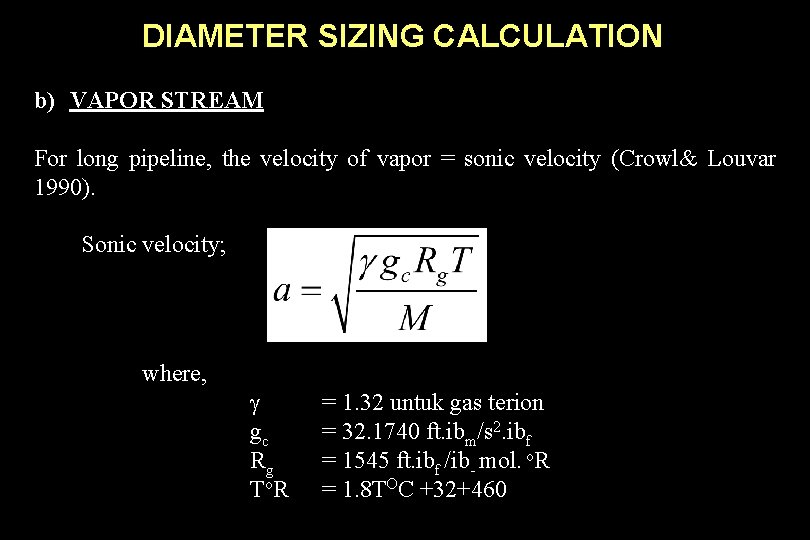
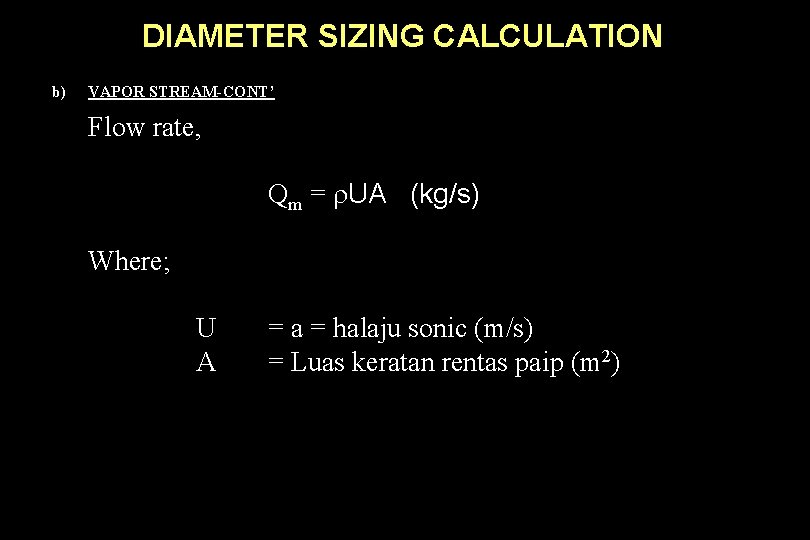
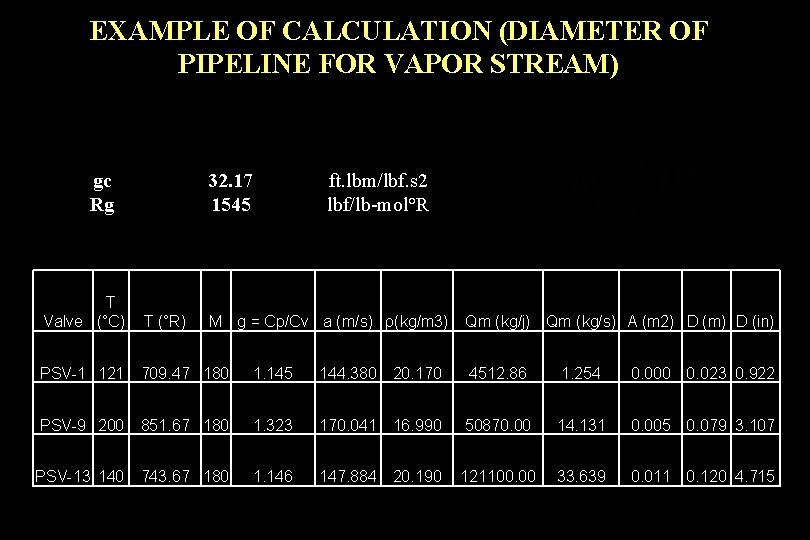
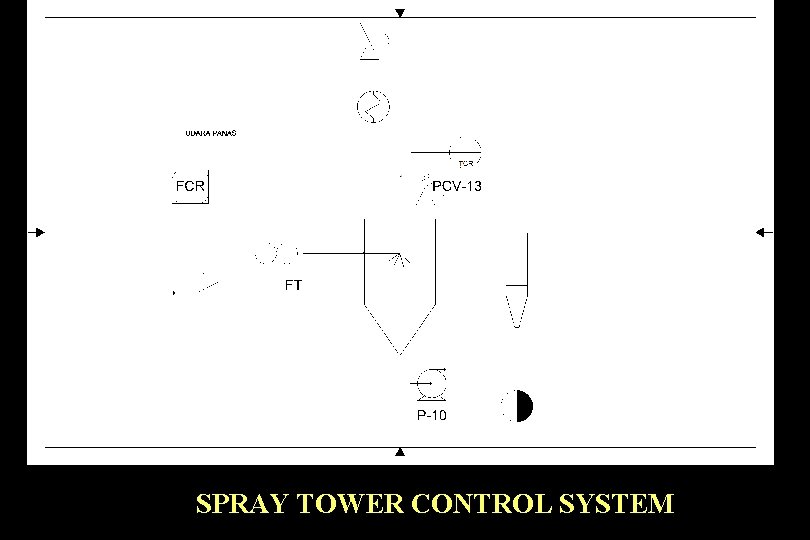
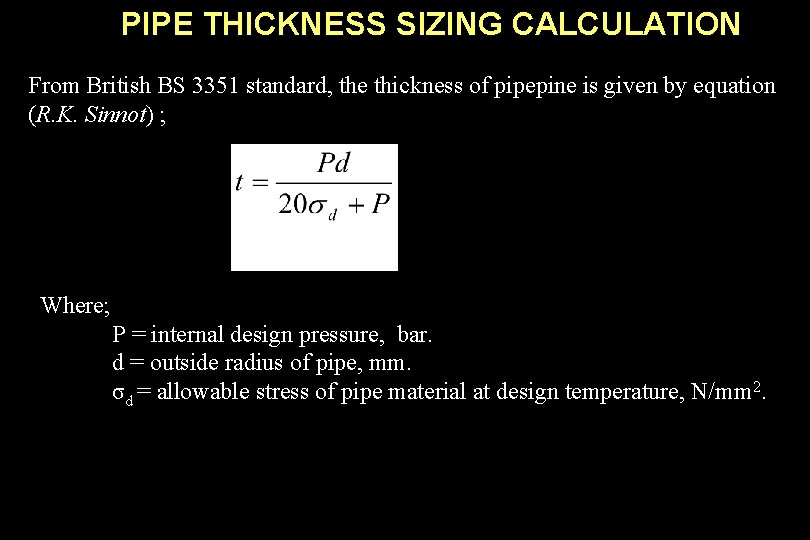
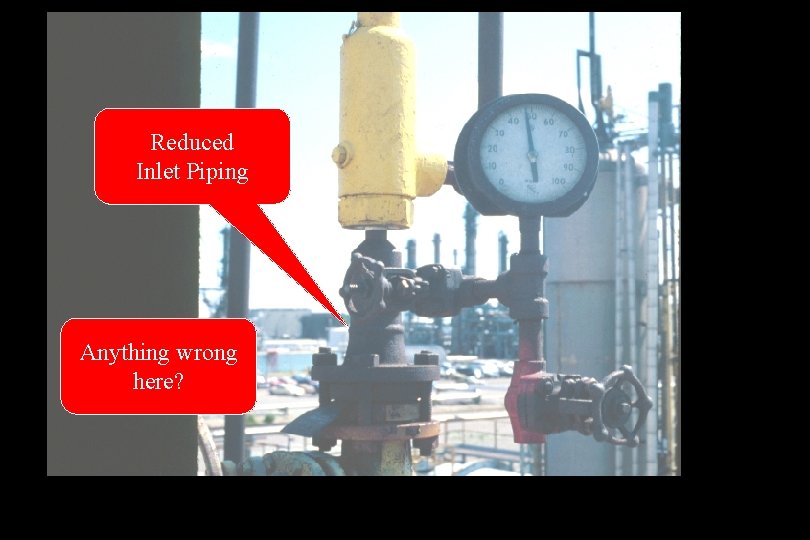
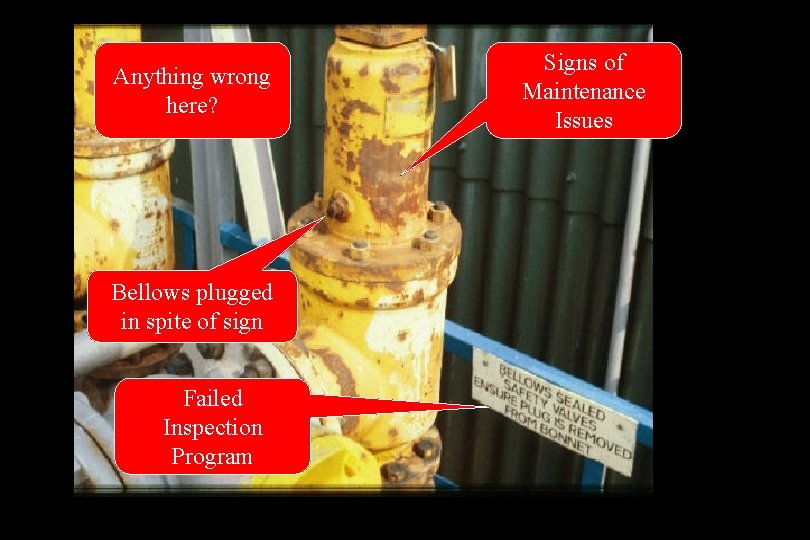
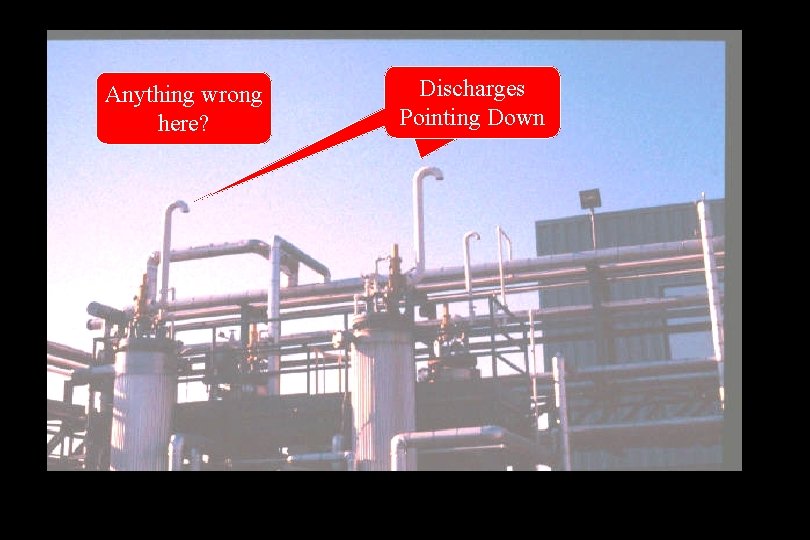
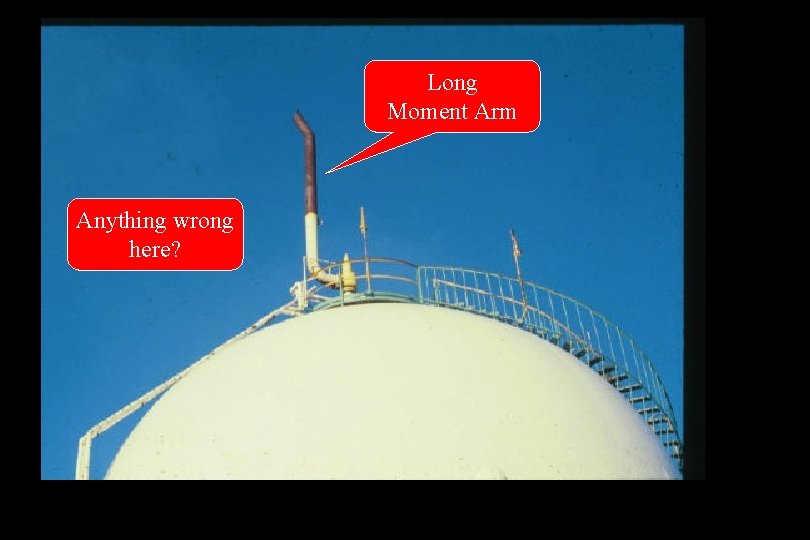
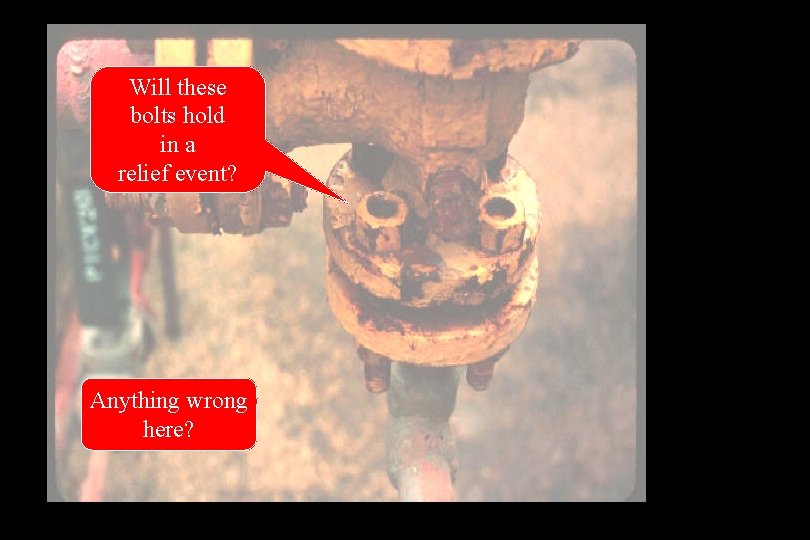
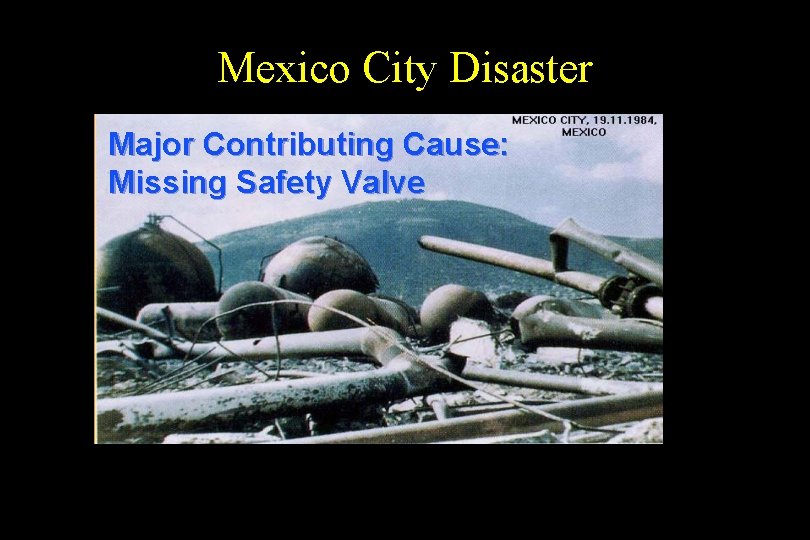
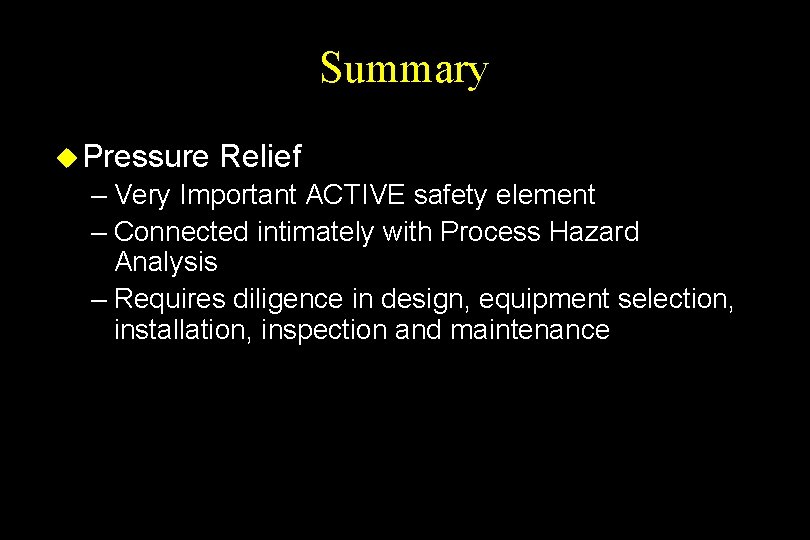
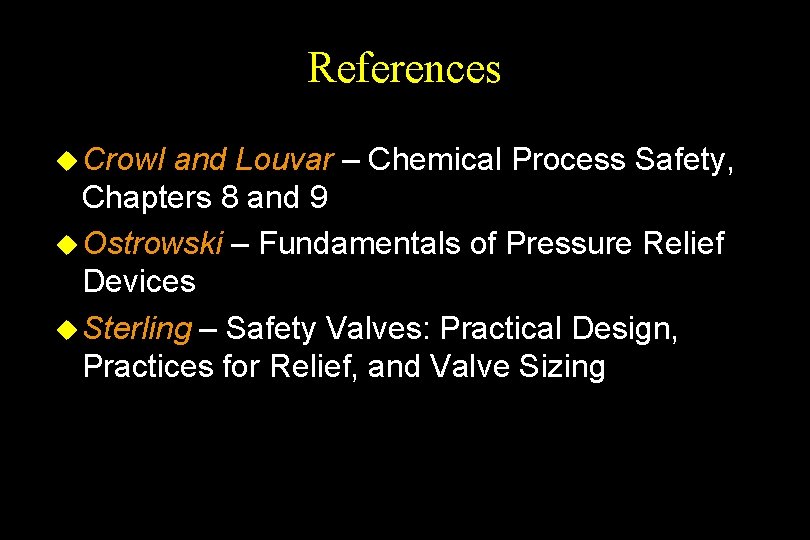
- Slides: 67
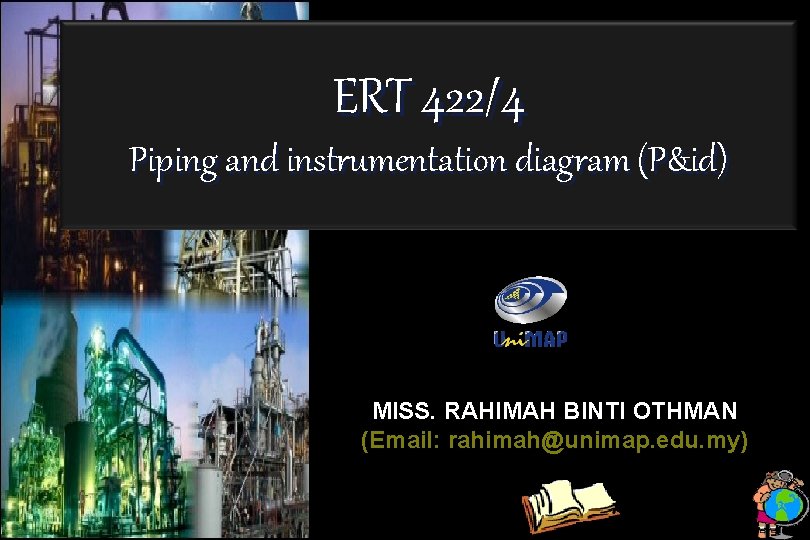
ERT 422/4 Piping and instrumentation diagram (P&id) MISS. RAHIMAH BINTI OTHMAN (Email: rahimah@unimap. edu. my)
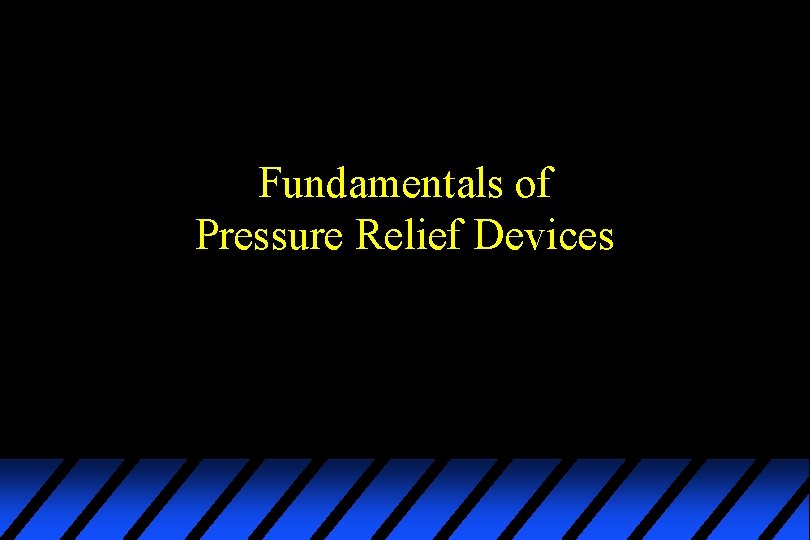
Fundamentals of Pressure Relief Devices
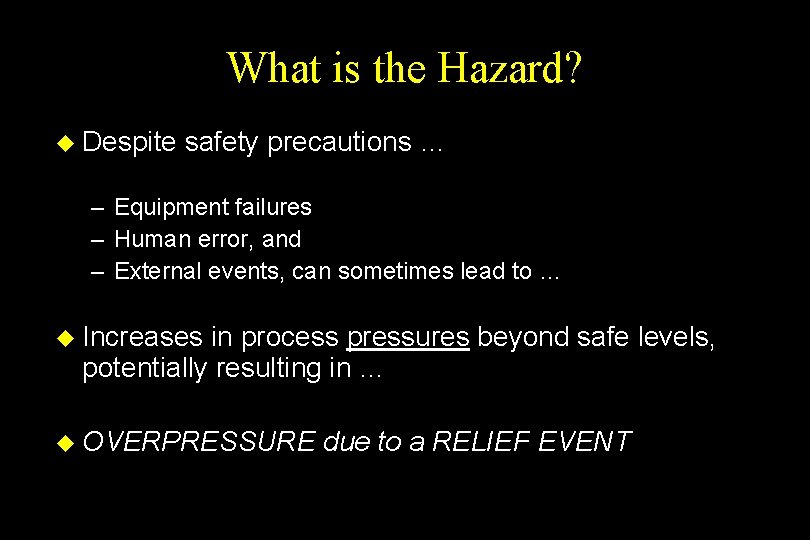
What is the Hazard? u Despite safety precautions … – Equipment failures – Human error, and – External events, can sometimes lead to … u Increases in process pressures beyond safe levels, potentially resulting in … u OVERPRESSURE due to a RELIEF EVENT
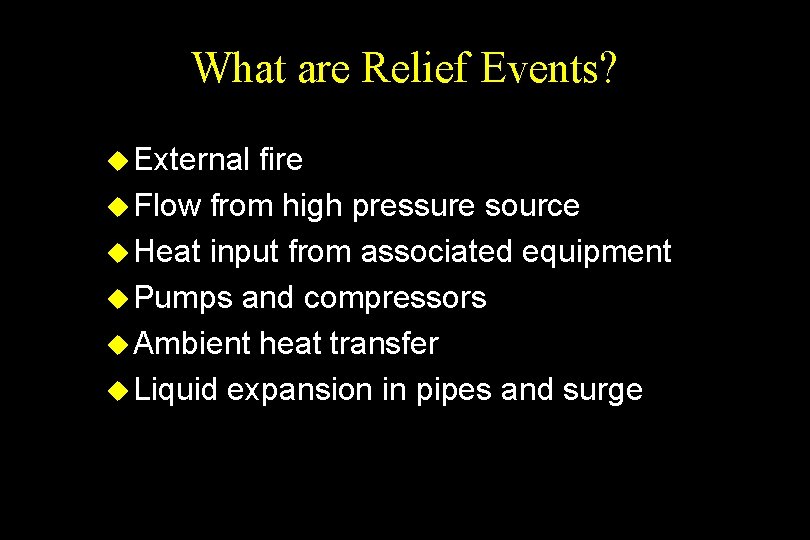
What are Relief Events? u External fire u Flow from high pressure source u Heat input from associated equipment u Pumps and compressors u Ambient heat transfer u Liquid expansion in pipes and surge
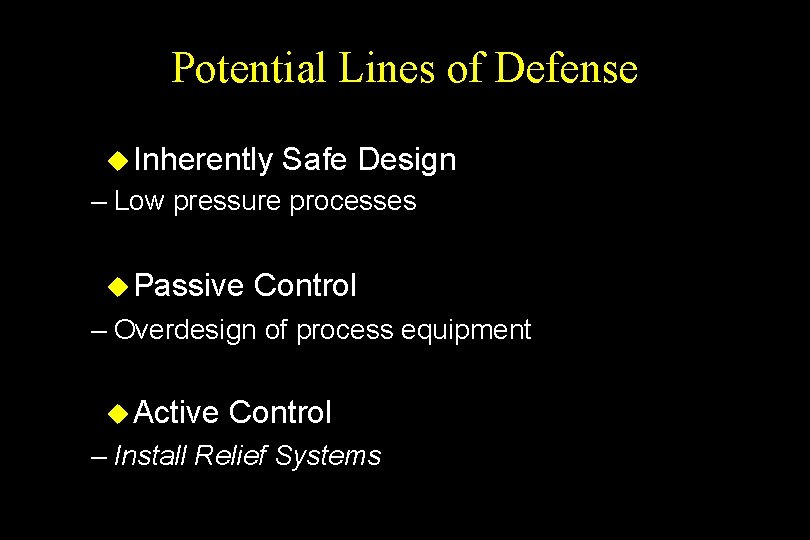
Potential Lines of Defense u Inherently Safe Design – Low pressure processes u Passive Control – Overdesign of process equipment u Active Control – Install Relief Systems
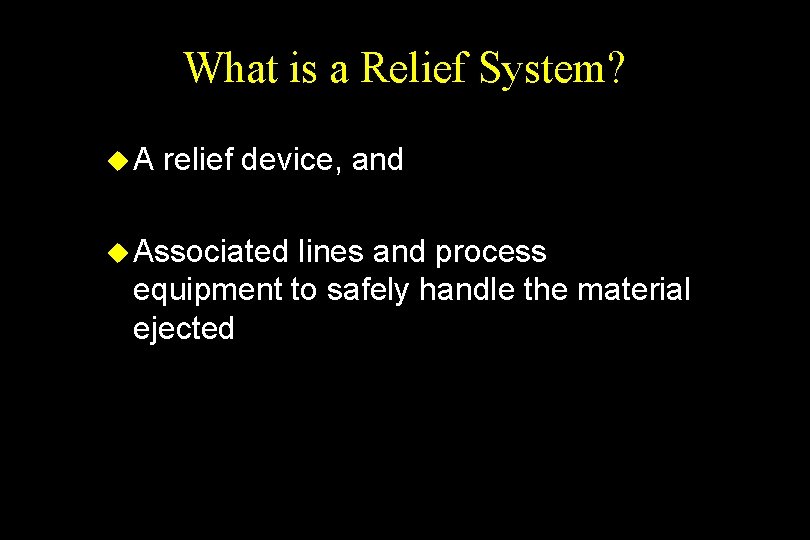
What is a Relief System? u. A relief device, and u Associated lines and process equipment to safely handle the material ejected
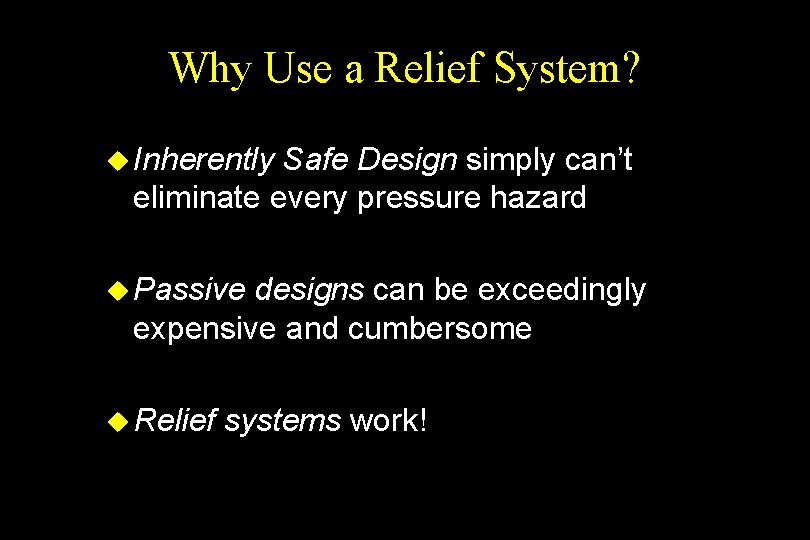
Why Use a Relief System? u Inherently Safe Design simply can’t eliminate every pressure hazard u Passive designs can be exceedingly expensive and cumbersome u Relief systems work!
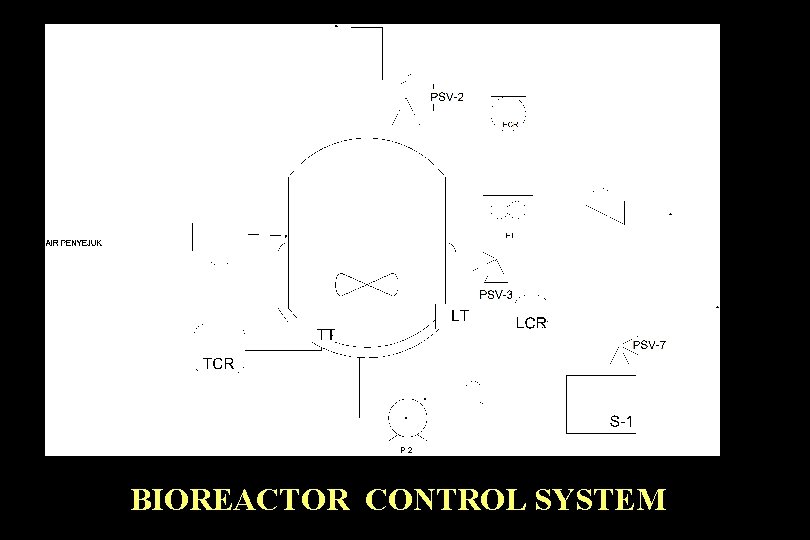
BIOREACTOR CONTROL SYSTEM
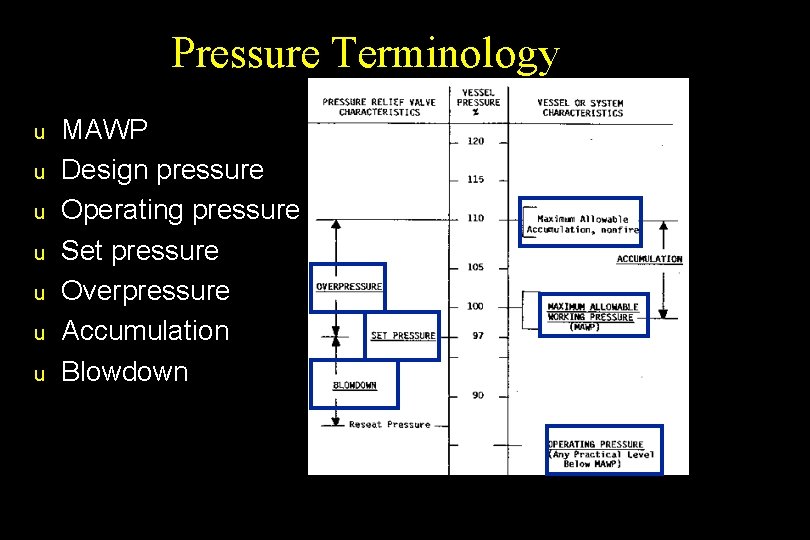
Pressure Terminology u u u u MAWP Design pressure Operating pressure Set pressure Overpressure Accumulation Blowdown
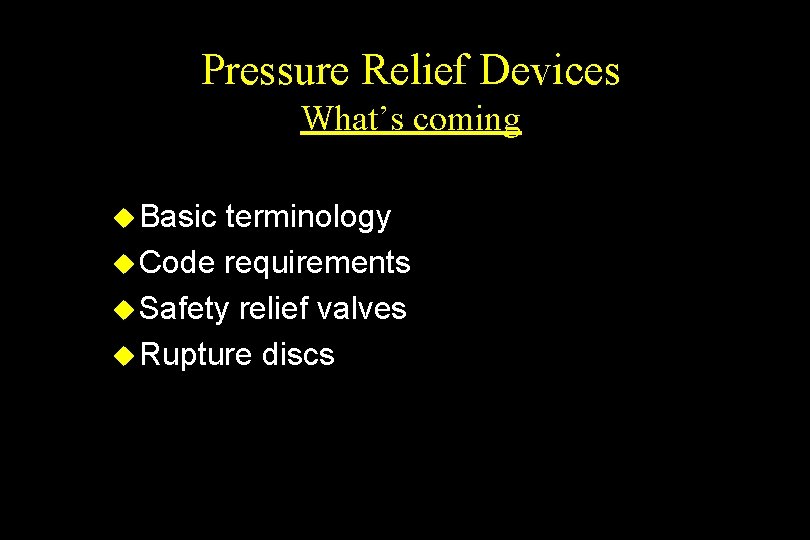
Pressure Relief Devices What’s coming u Basic terminology u Code requirements u Safety relief valves u Rupture discs
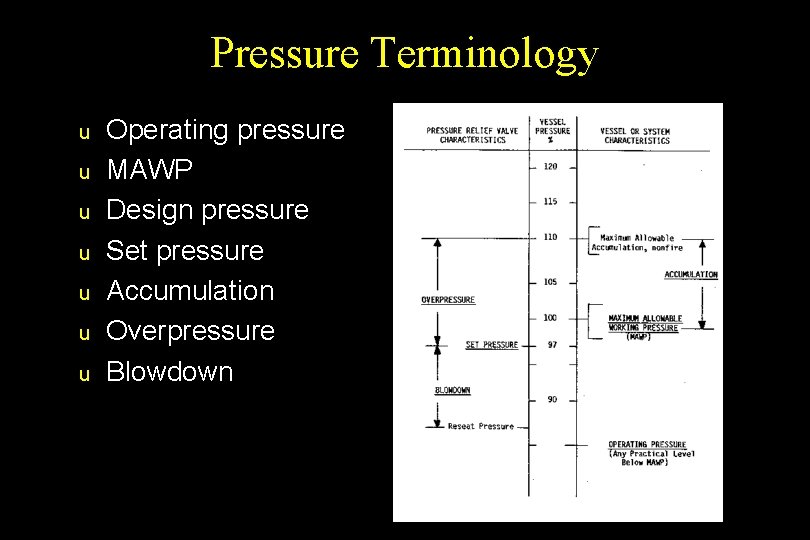
Pressure Terminology u u u u Operating pressure MAWP Design pressure Set pressure Accumulation Overpressure Blowdown
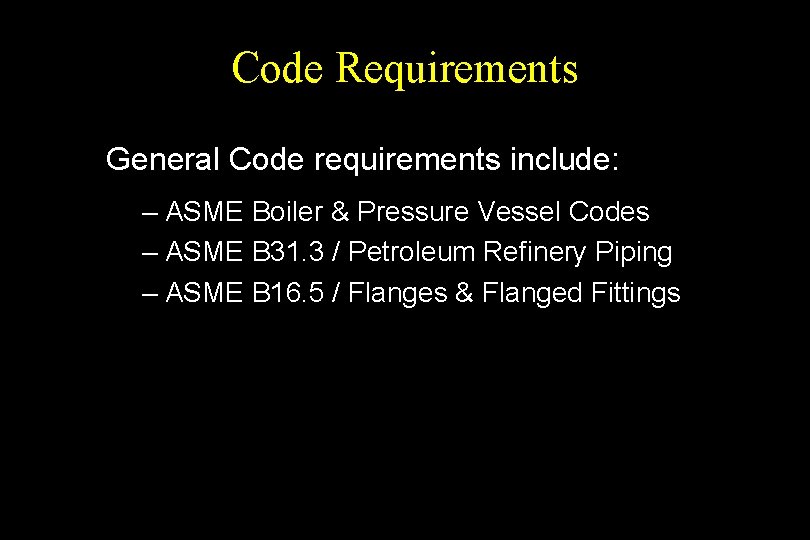
Code Requirements General Code requirements include: – ASME Boiler & Pressure Vessel Codes – ASME B 31. 3 / Petroleum Refinery Piping – ASME B 16. 5 / Flanges & Flanged Fittings
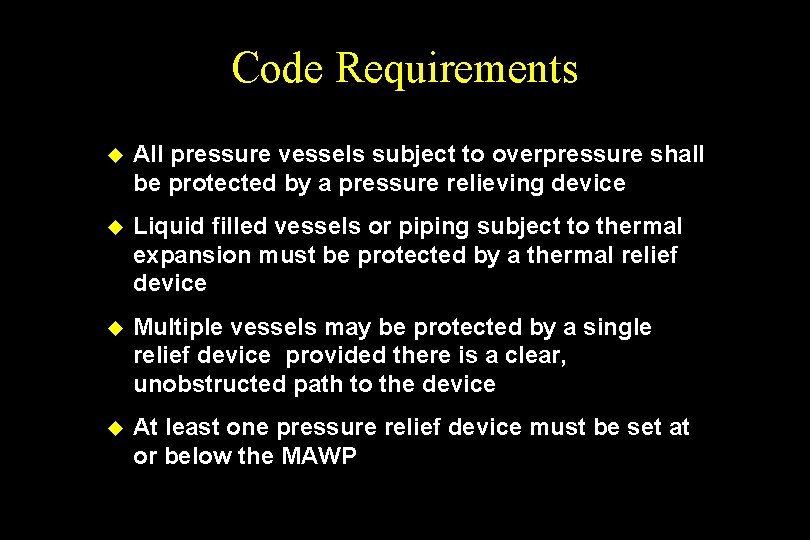
Code Requirements u All pressure vessels subject to overpressure shall be protected by a pressure relieving device u Liquid filled vessels or piping subject to thermal expansion must be protected by a thermal relief device u Multiple vessels may be protected by a single relief device provided there is a clear, unobstructed path to the device u At least one pressure relief device must be set at or below the MAWP
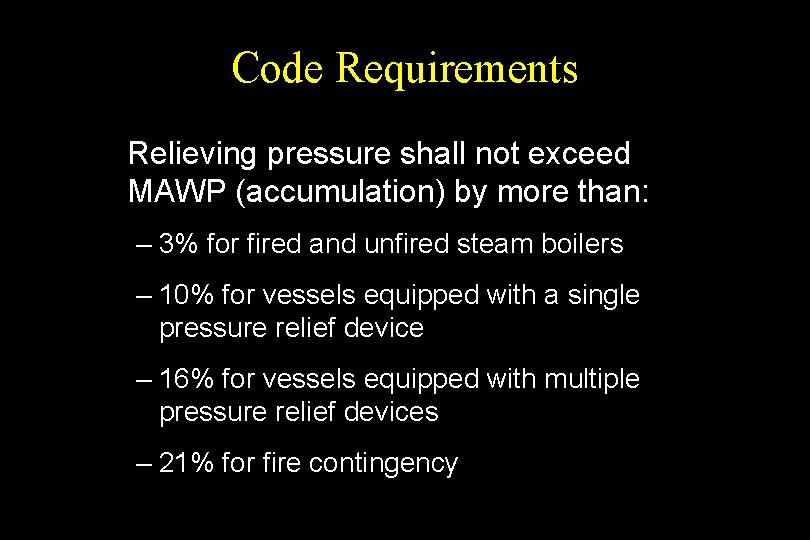
Code Requirements Relieving pressure shall not exceed MAWP (accumulation) by more than: – 3% for fired and unfired steam boilers – 10% for vessels equipped with a single pressure relief device – 16% for vessels equipped with multiple pressure relief devices – 21% for fire contingency
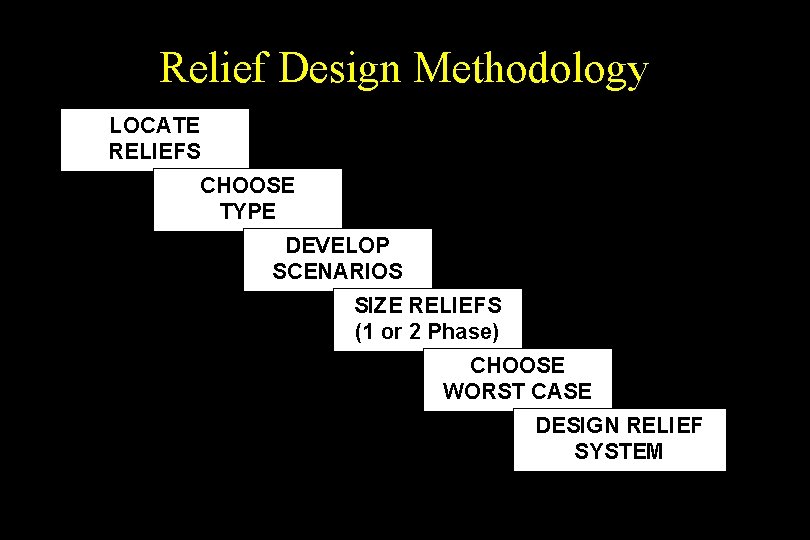
Relief Design Methodology LOCATE RELIEFS CHOOSE TYPE DEVELOP SCENARIOS SIZE RELIEFS (1 or 2 Phase) CHOOSE WORST CASE DESIGN RELIEF SYSTEM

Locating Reliefs – Where? u All vessels u Blocked in sections of cool liquid lines that are exposed to heat u Discharge sides of positive displacement pumps, compressors, and turbines u Vessel steam jackets u Where PHA indicates the need LOCATE RELIEFS
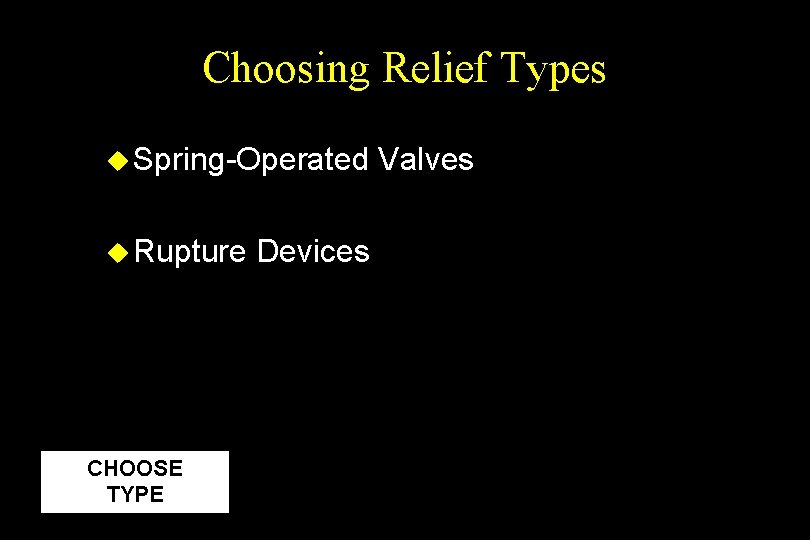
Choosing Relief Types u Spring-Operated u Rupture CHOOSE TYPE Devices Valves
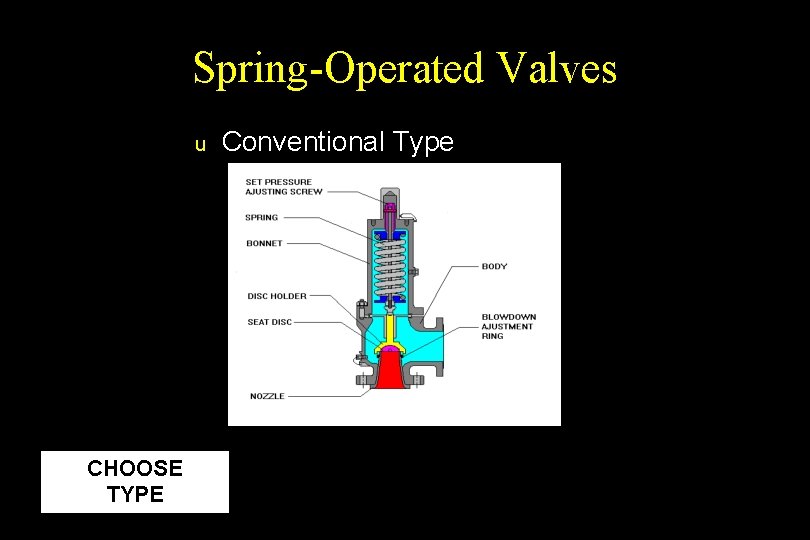
Spring-Operated Valves u CHOOSE TYPE Conventional Type
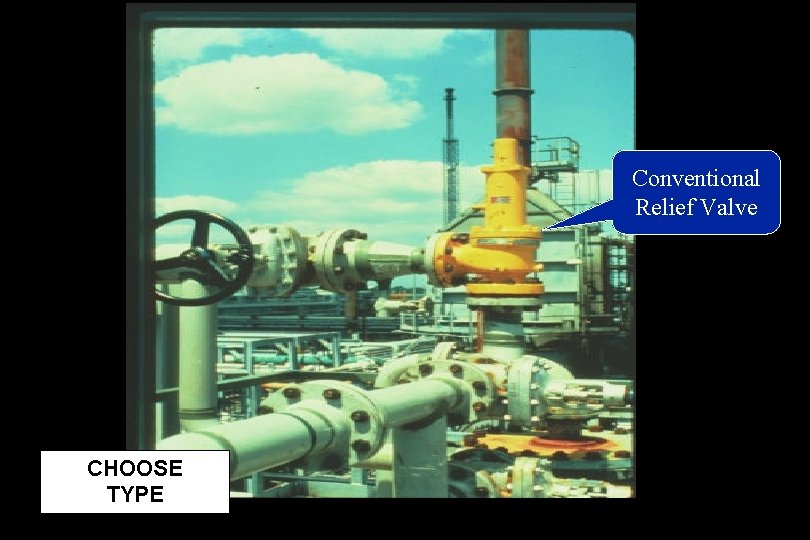
Picture: Conventional Relief Valve CHOOSE TYPE
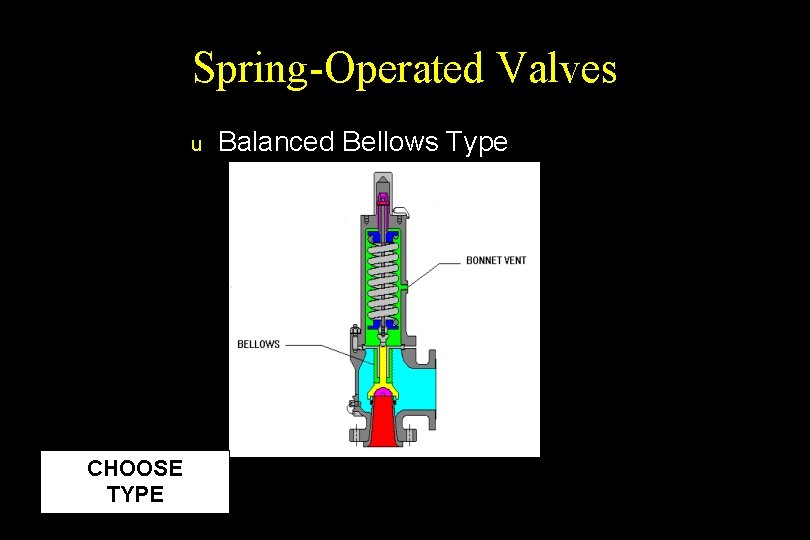
Spring-Operated Valves u CHOOSE TYPE Balanced Bellows Type
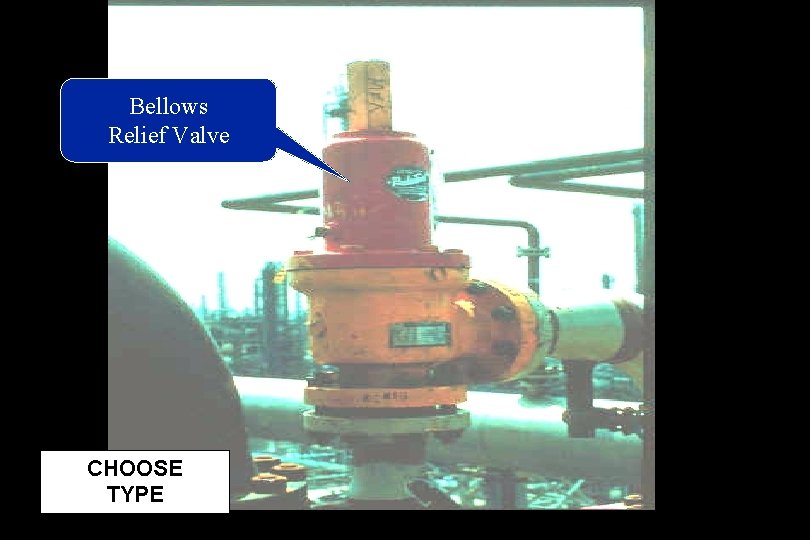
Picture: Bellows Relief Valve CHOOSE TYPE
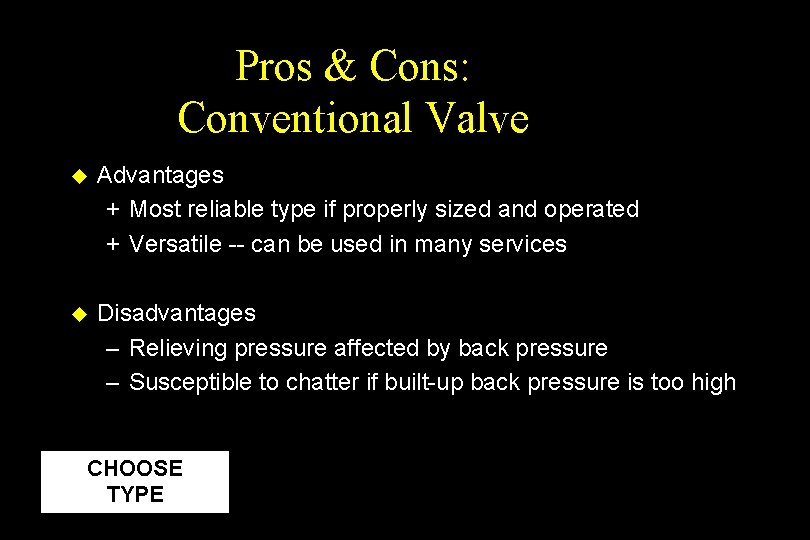
Pros & Cons: Conventional Valve u Advantages + Most reliable type if properly sized and operated + Versatile -- can be used in many services u Disadvantages – Relieving pressure affected by back pressure – Susceptible to chatter if built-up back pressure is too high CHOOSE TYPE
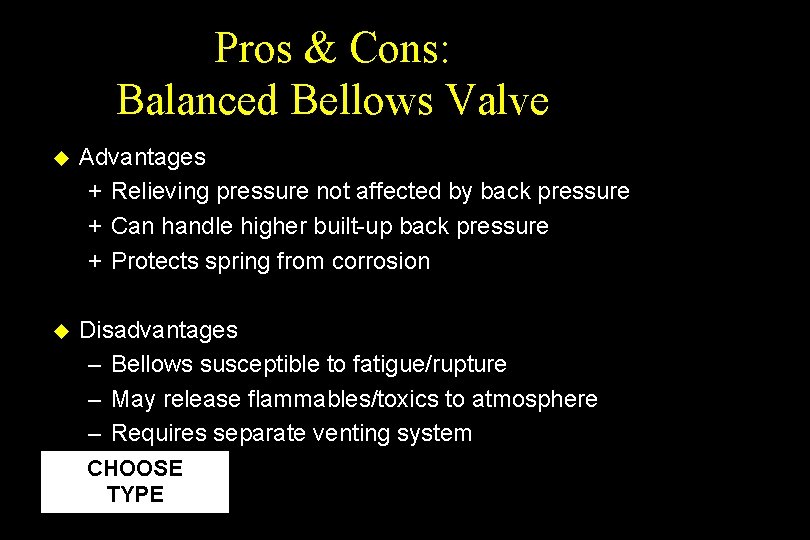
Pros & Cons: Balanced Bellows Valve u Advantages + Relieving pressure not affected by back pressure + Can handle higher built-up back pressure + Protects spring from corrosion u Disadvantages – Bellows susceptible to fatigue/rupture – May release flammables/toxics to atmosphere – Requires separate venting system CHOOSE TYPE
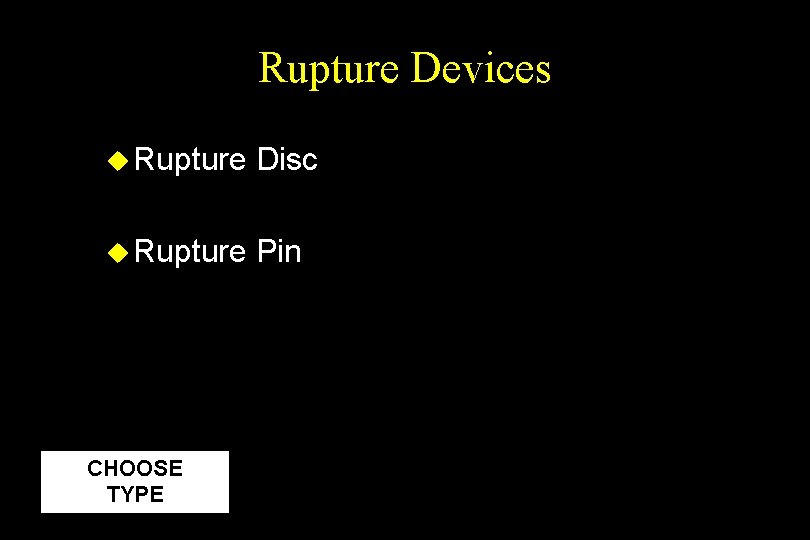
Rupture Devices u Rupture Disc u Rupture Pin CHOOSE TYPE
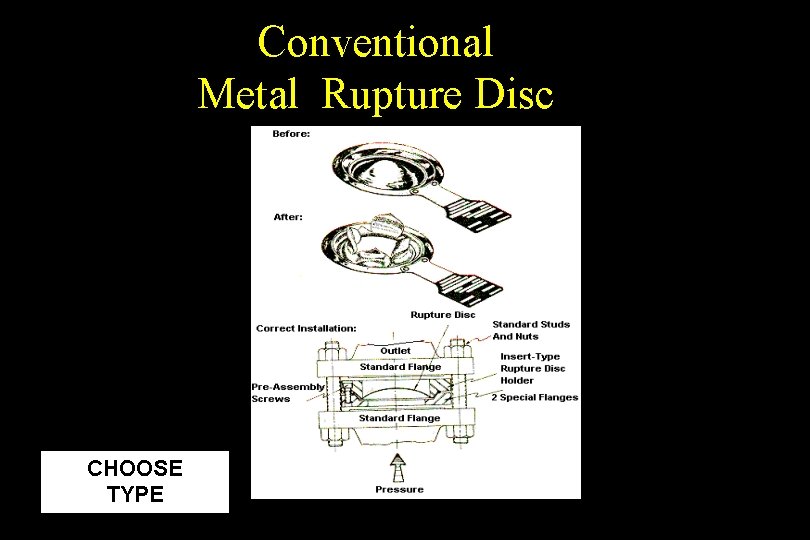
Conventional Metal Rupture Disc CHOOSE TYPE
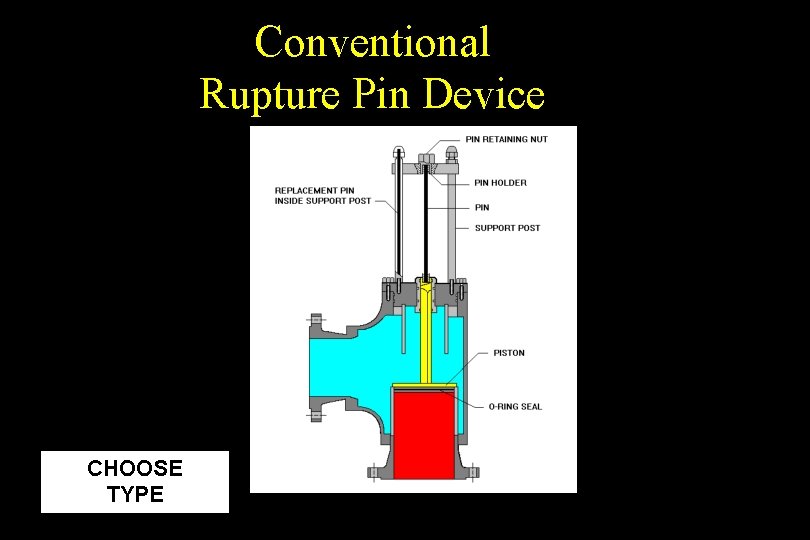
Conventional Rupture Pin Device CHOOSE TYPE
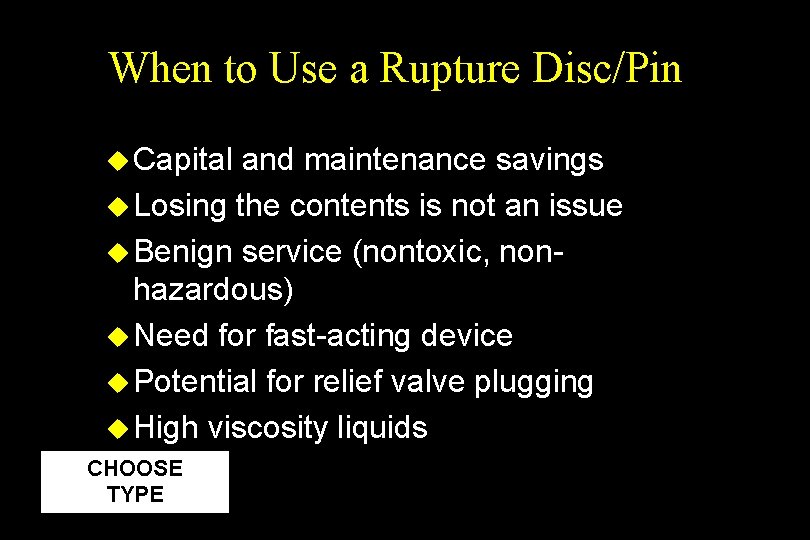
When to Use a Rupture Disc/Pin u Capital and maintenance savings u Losing the contents is not an issue u Benign service (nontoxic, nonhazardous) u Need for fast-acting device u Potential for relief valve plugging u High viscosity liquids CHOOSE TYPE
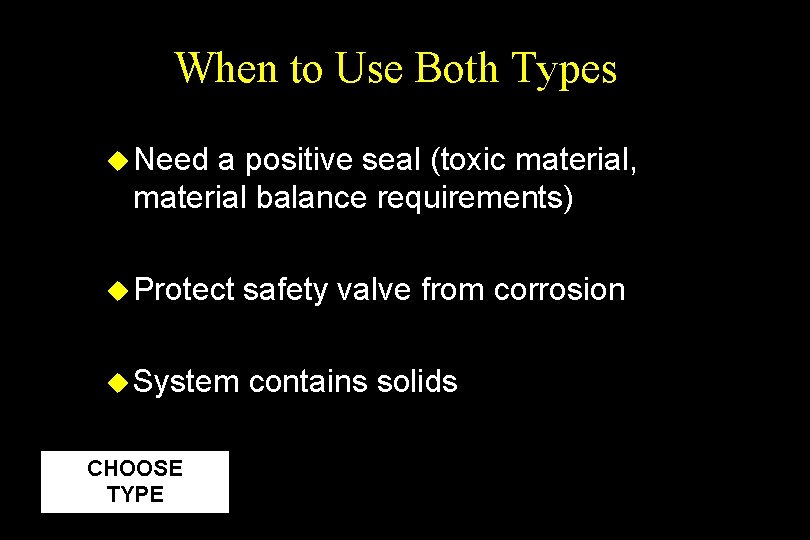
When to Use Both Types u Need a positive seal (toxic material, material balance requirements) u Protect safety valve from corrosion u System contains solids CHOOSE TYPE
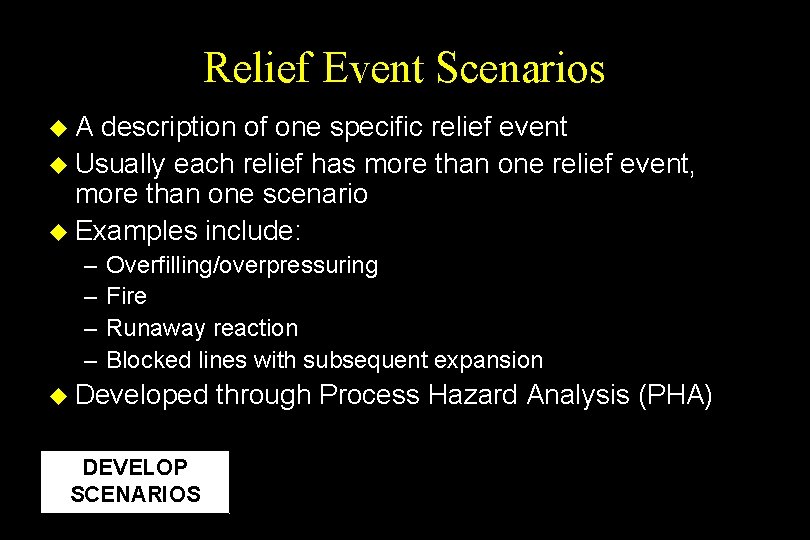
Relief Event Scenarios u. A description of one specific relief event u Usually each relief has more than one relief event, more than one scenario u Examples include: – – Overfilling/overpressuring Fire Runaway reaction Blocked lines with subsequent expansion u Developed DEVELOP SCENARIOS through Process Hazard Analysis (PHA)
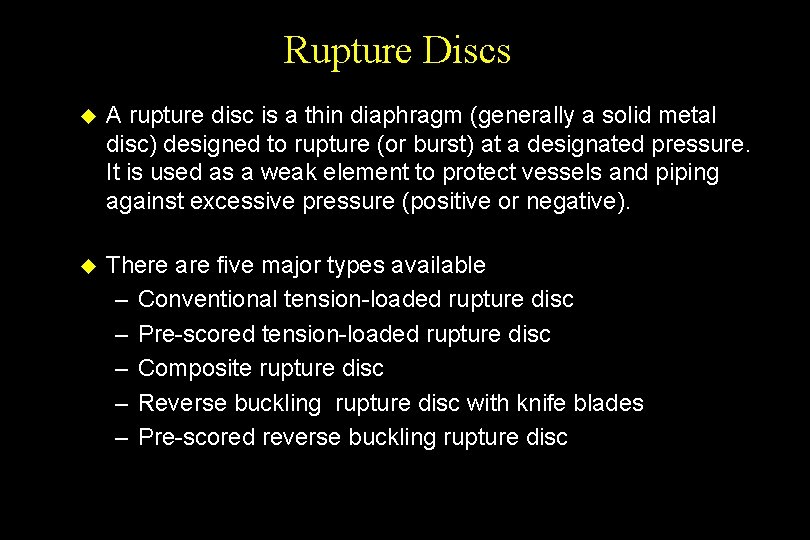
Rupture Discs u A rupture disc is a thin diaphragm (generally a solid metal disc) designed to rupture (or burst) at a designated pressure. It is used as a weak element to protect vessels and piping against excessive pressure (positive or negative). u There are five major types available – Conventional tension-loaded rupture disc – Pre-scored tension-loaded rupture disc – Composite rupture disc – Reverse buckling rupture disc with knife blades – Pre-scored reverse buckling rupture disc
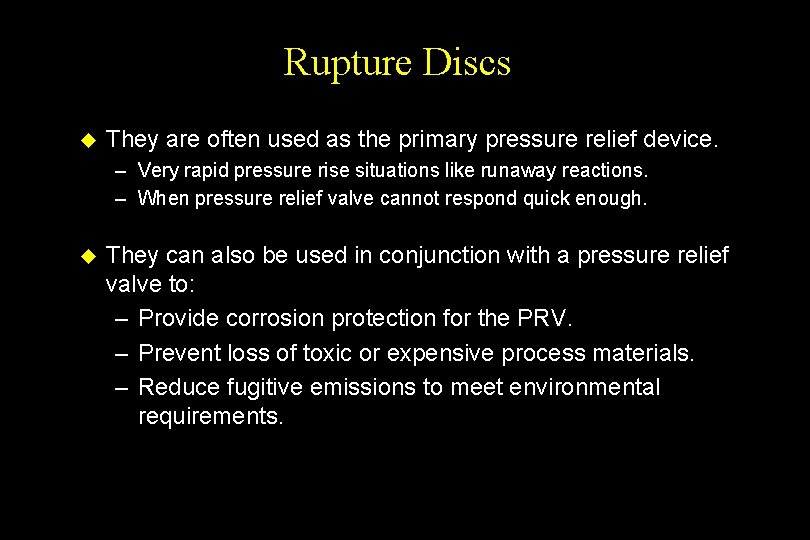
Rupture Discs u They are often used as the primary pressure relief device. – Very rapid pressure rise situations like runaway reactions. – When pressure relief valve cannot respond quick enough. u They can also be used in conjunction with a pressure relief valve to: – Provide corrosion protection for the PRV. – Prevent loss of toxic or expensive process materials. – Reduce fugitive emissions to meet environmental requirements.
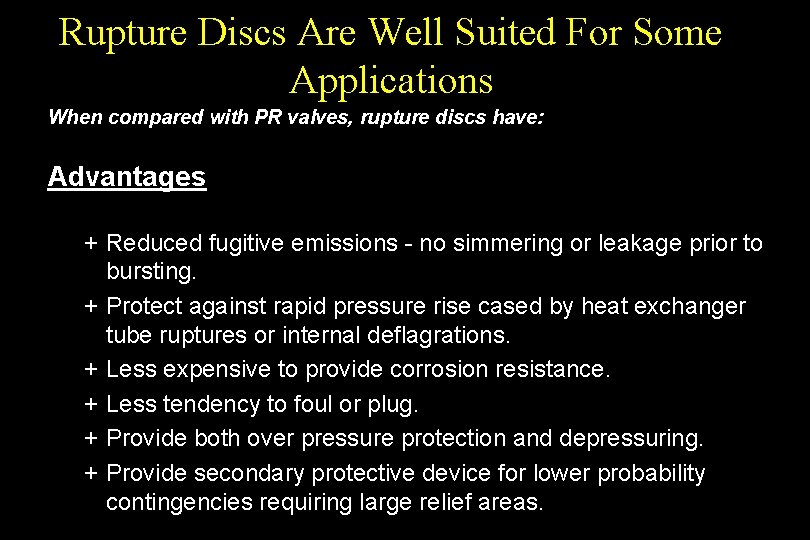
Rupture Discs Are Well Suited For Some Applications When compared with PR valves, rupture discs have: Advantages + Reduced fugitive emissions - no simmering or leakage prior to bursting. + Protect against rapid pressure rise cased by heat exchanger tube ruptures or internal deflagrations. + Less expensive to provide corrosion resistance. + Less tendency to foul or plug. + Provide both over pressure protection and depressuring. + Provide secondary protective device for lower probability contingencies requiring large relief areas.
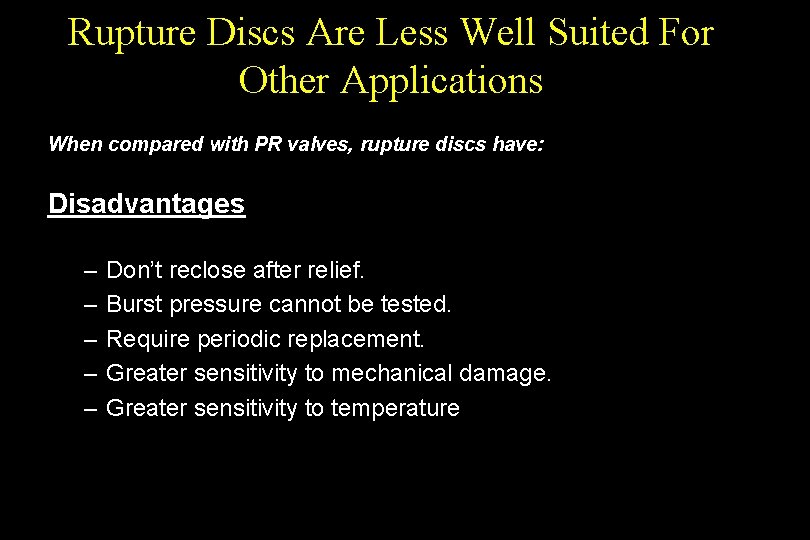
Rupture Discs Are Less Well Suited For Other Applications When compared with PR valves, rupture discs have: Disadvantages – – – Don’t reclose after relief. Burst pressure cannot be tested. Require periodic replacement. Greater sensitivity to mechanical damage. Greater sensitivity to temperature
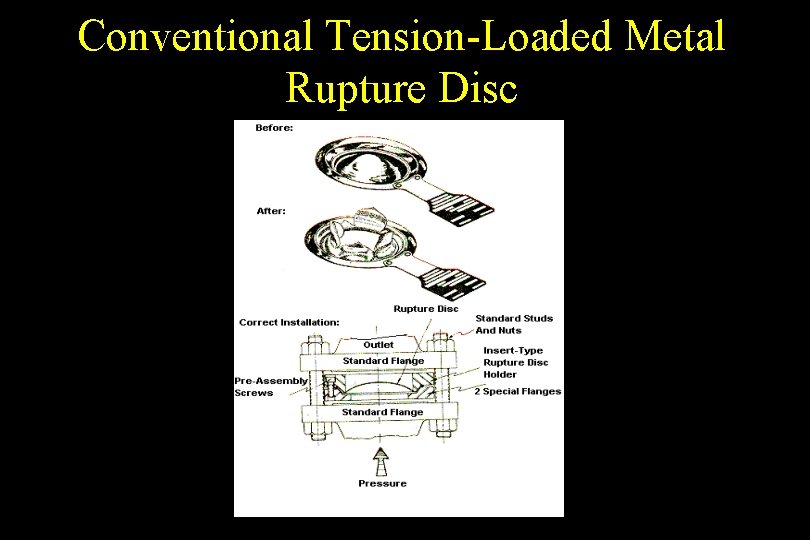
Conventional Tension-Loaded Metal Rupture Disc
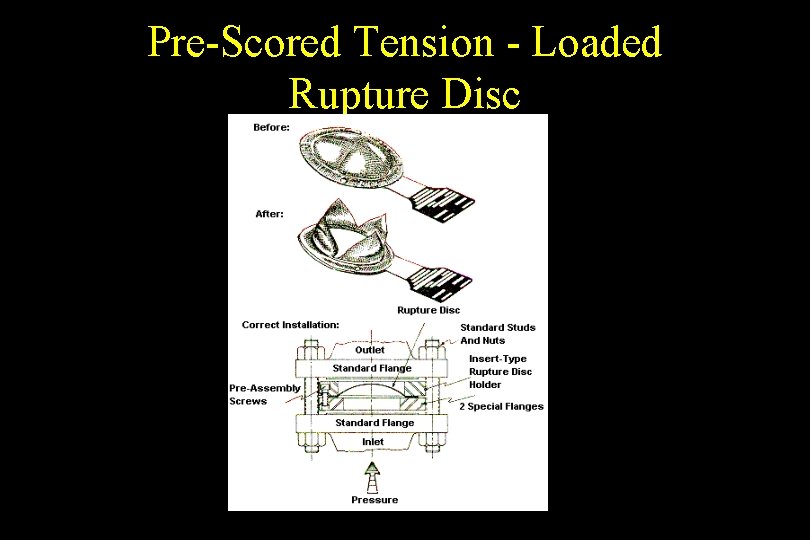
Pre-Scored Tension - Loaded Rupture Disc
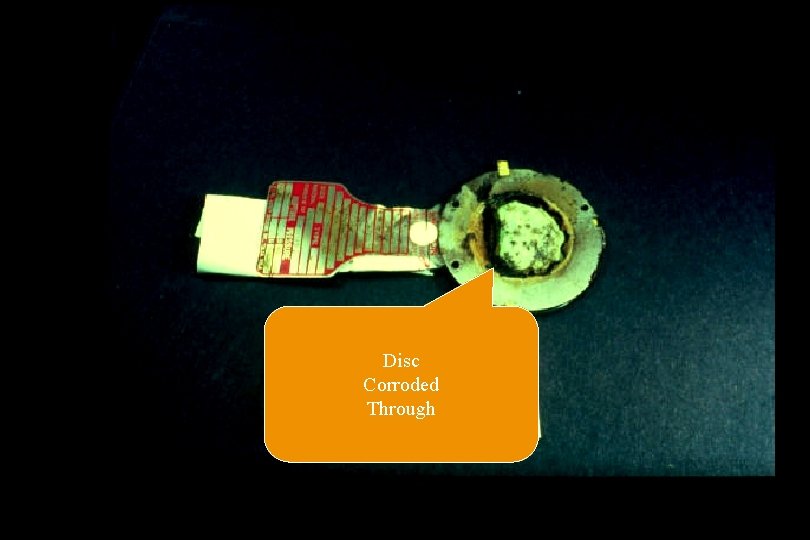
Disc Corroded Through
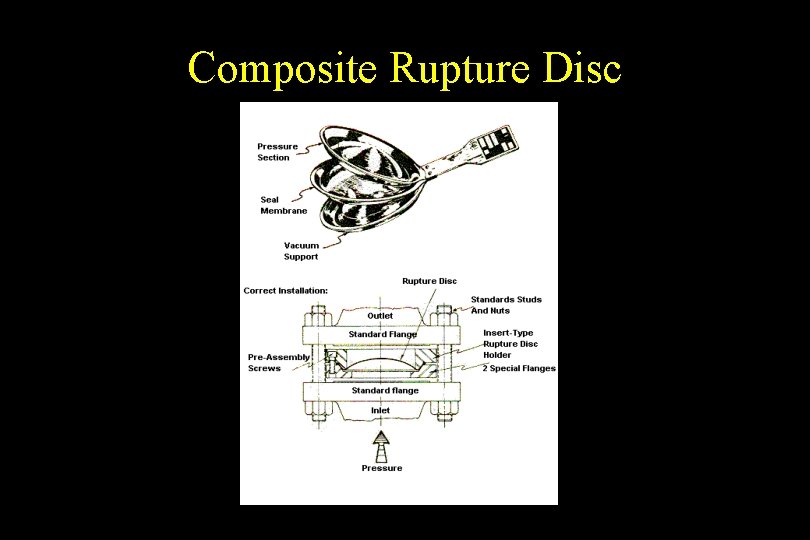
Composite Rupture Disc
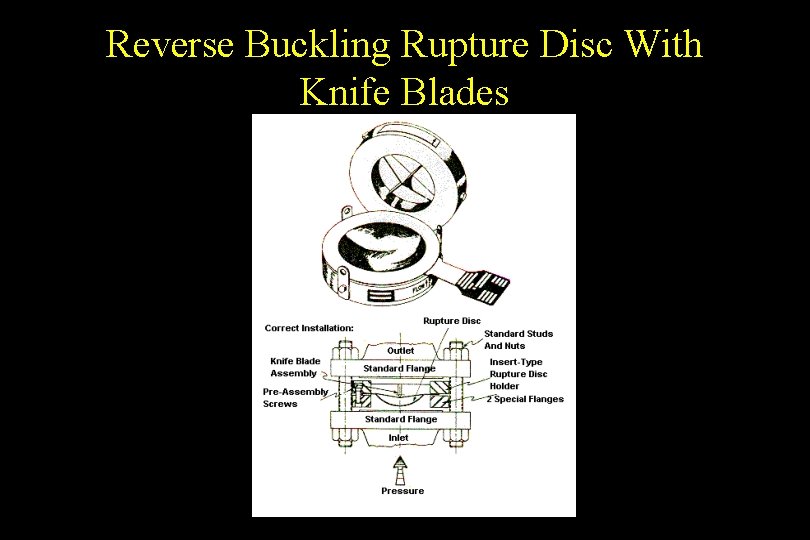
Reverse Buckling Rupture Disc With Knife Blades
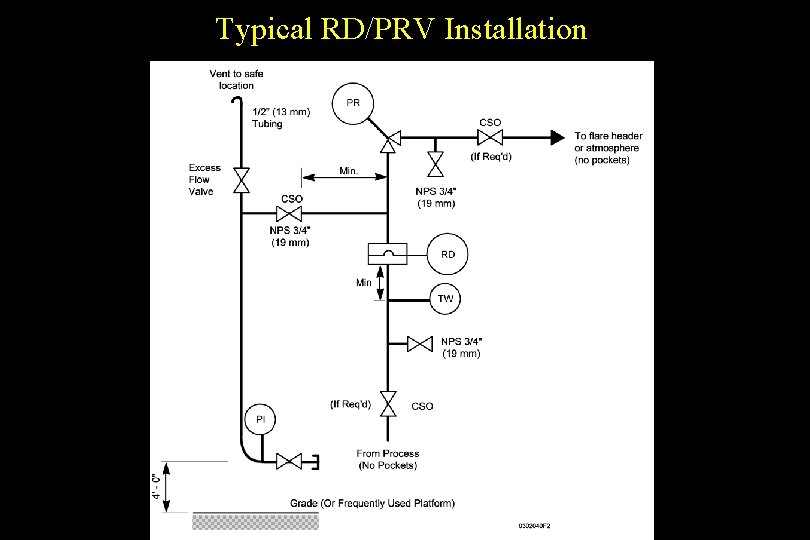
Typical RD/PRV Installation
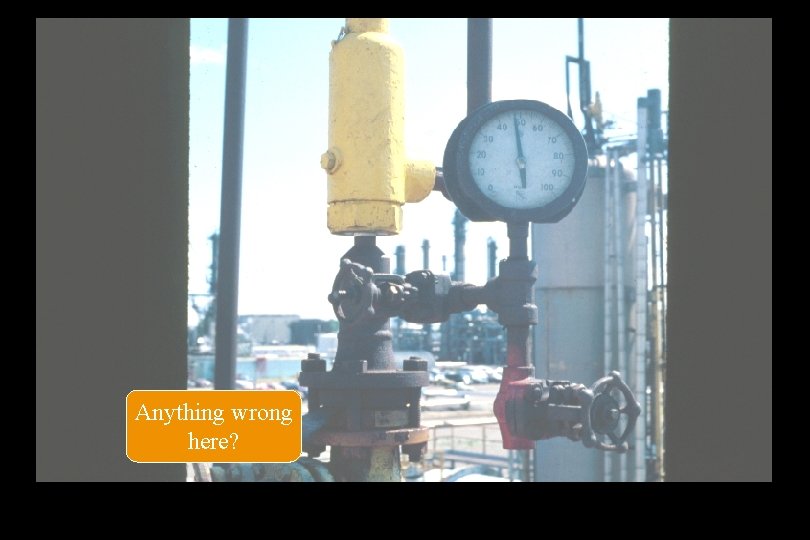
Anything wrong here?
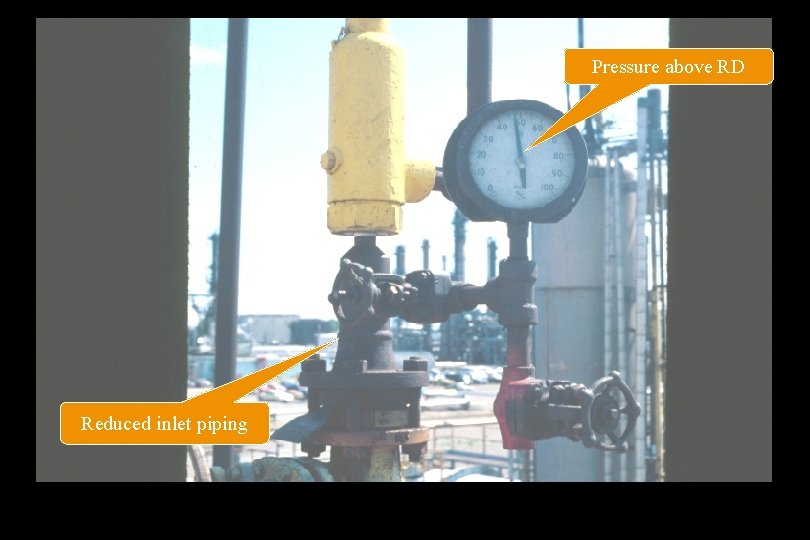
Pressure above RD Reduced inlet piping
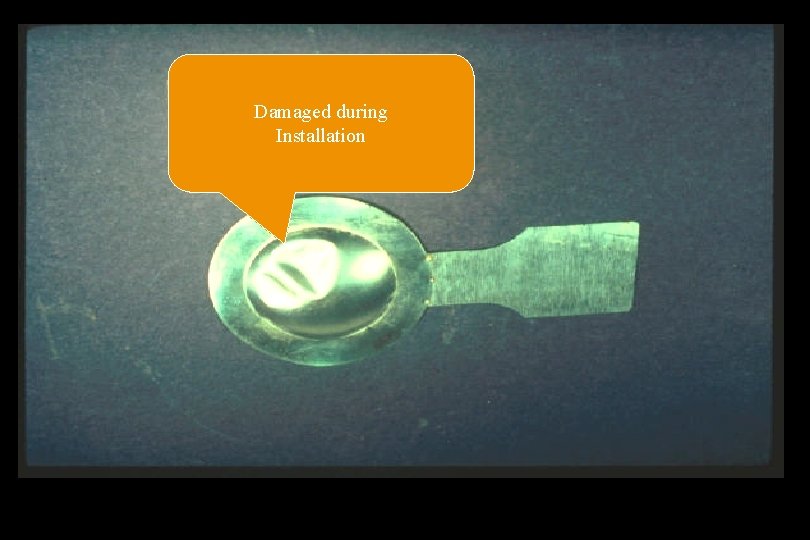
Damaged during Installation
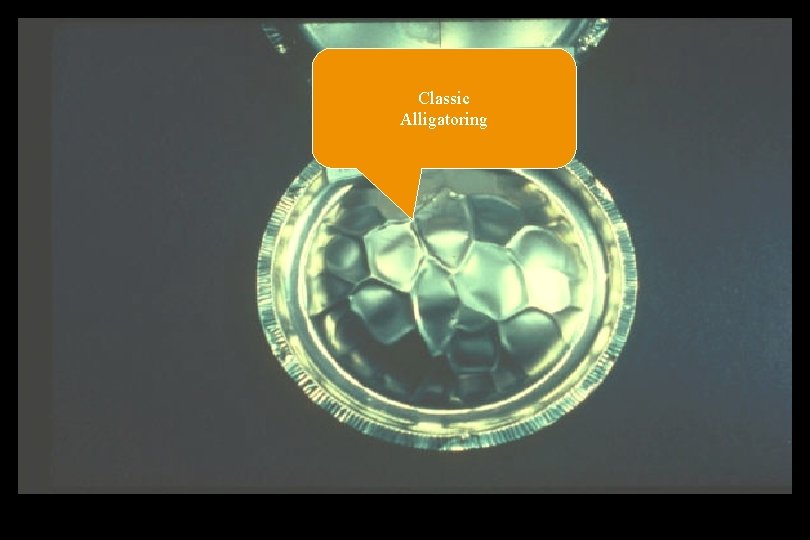
Classic Alligatoring
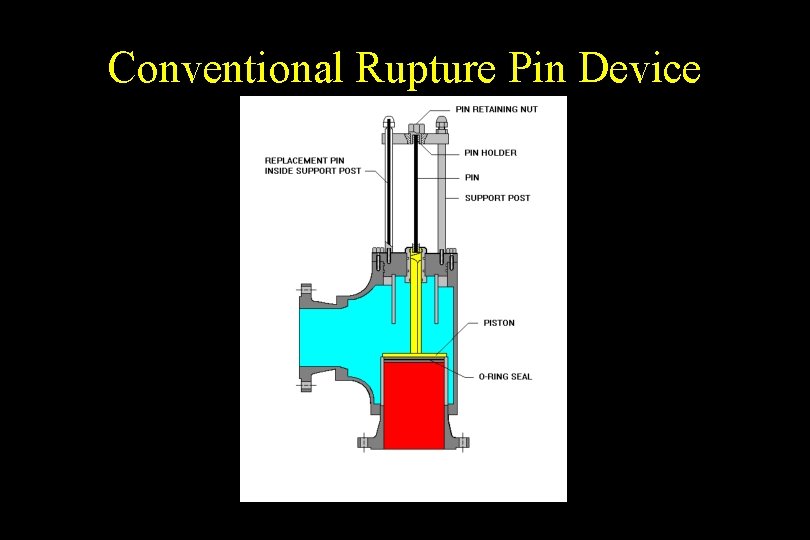
Conventional Rupture Pin Device
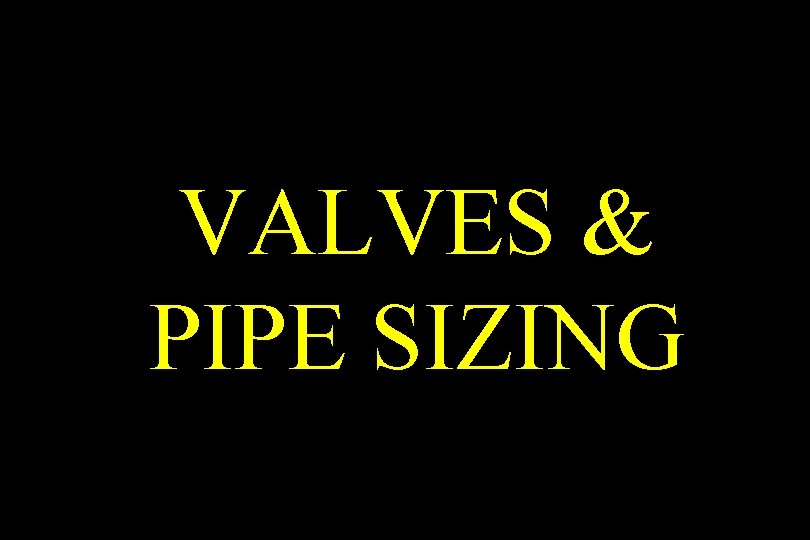
VALVES & PIPE SIZING
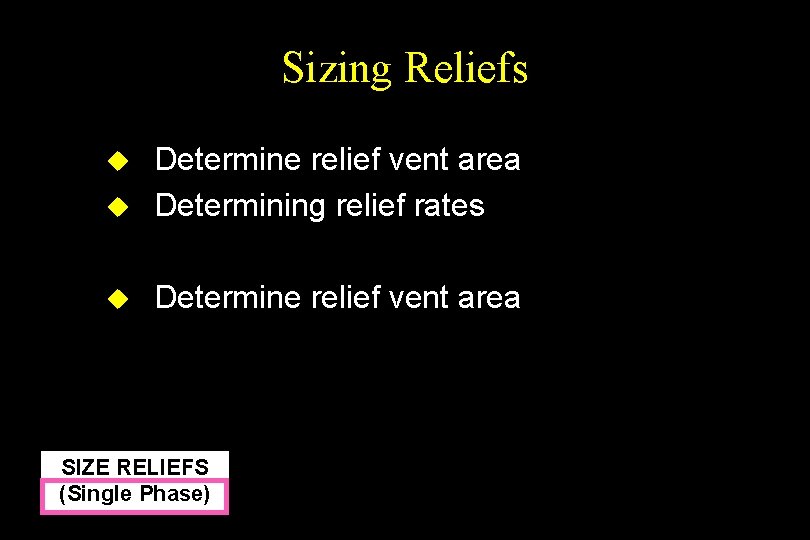
Sizing Reliefs u Determine relief vent area Determining relief rates u Determine relief vent area u SIZE RELIEFS (Single Phase)
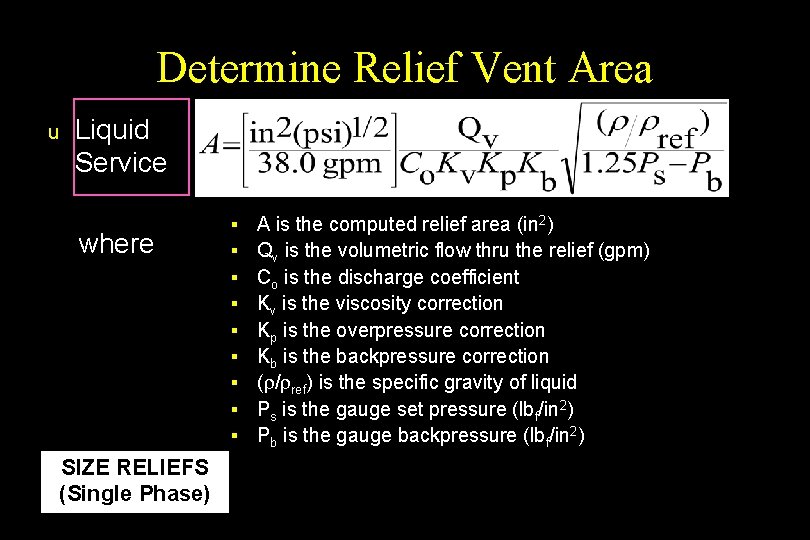
Determine Relief Vent Area u Liquid Service where SIZE RELIEFS (Single Phase) § § § § § A is the computed relief area (in 2) Qv is the volumetric flow thru the relief (gpm) Co is the discharge coefficient Kv is the viscosity correction Kp is the overpressure correction Kb is the backpressure correction ( / ref) is the specific gravity of liquid Ps is the gauge set pressure (lbf/in 2) Pb is the gauge backpressure (lbf/in 2)
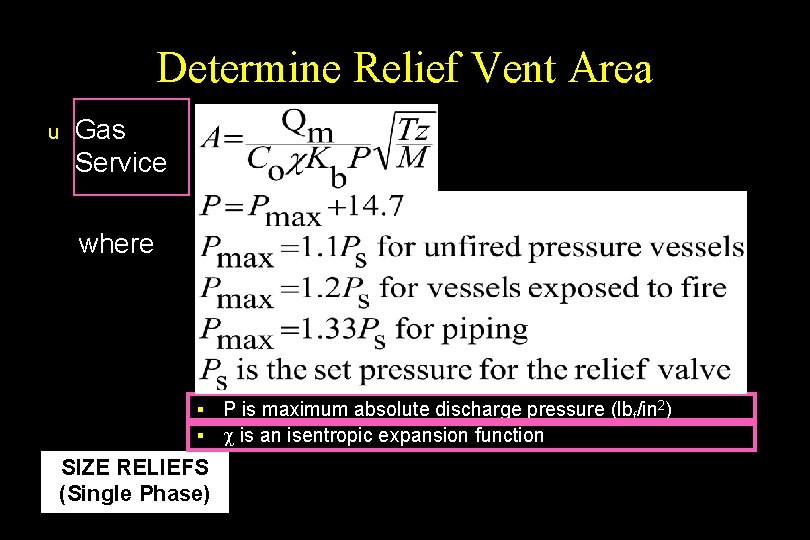
Determine Relief Vent Area u Gas Service where § § § § § SIZE RELIEFS (Single Phase) A is the computed relief area (in 2) Qm is the discharge flow thru the relief (lbm/hr) Co is the discharge coefficient Kb is the backpressure correction T is the absolute temperature of the discharge (°R) z is the compressibility factor M is average molecular weight of gas (lbm/lb-mol) P is maximum absolute discharge pressure (lbf/in 2) c is an isentropic expansion function
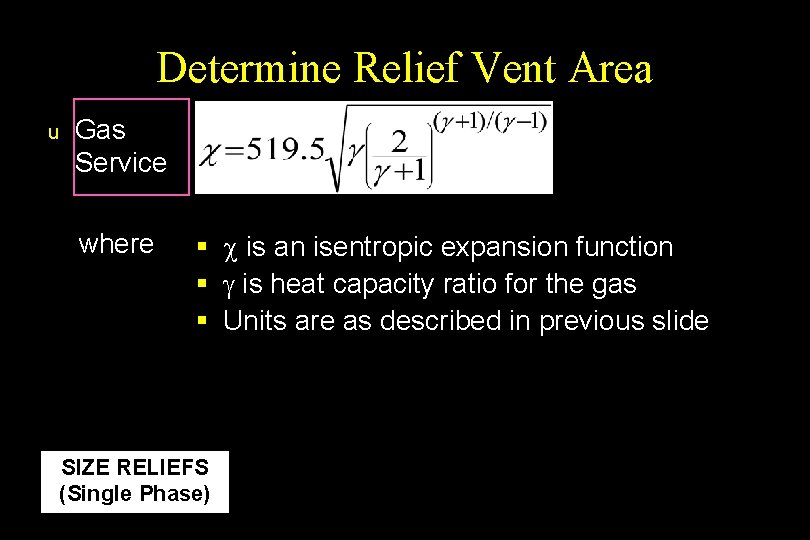
Determine Relief Vent Area u Gas Service where § c is an isentropic expansion function § is heat capacity ratio for the gas § Units are as described in previous slide SIZE RELIEFS (Single Phase)
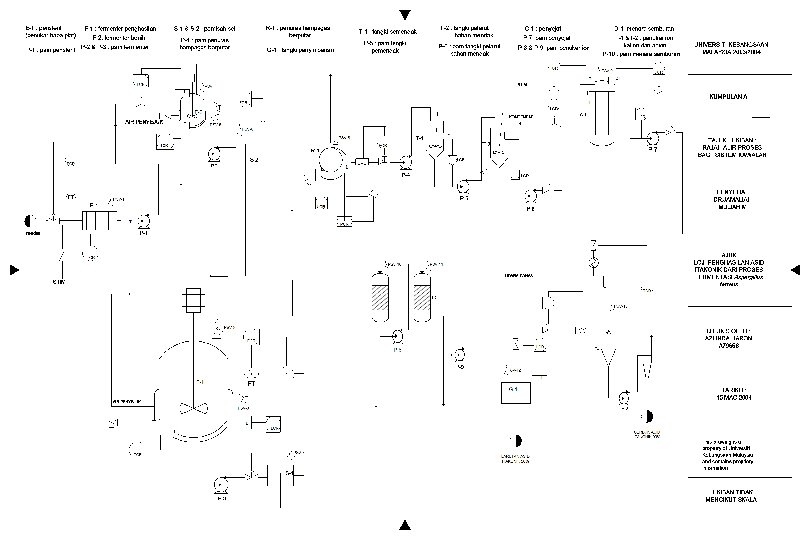
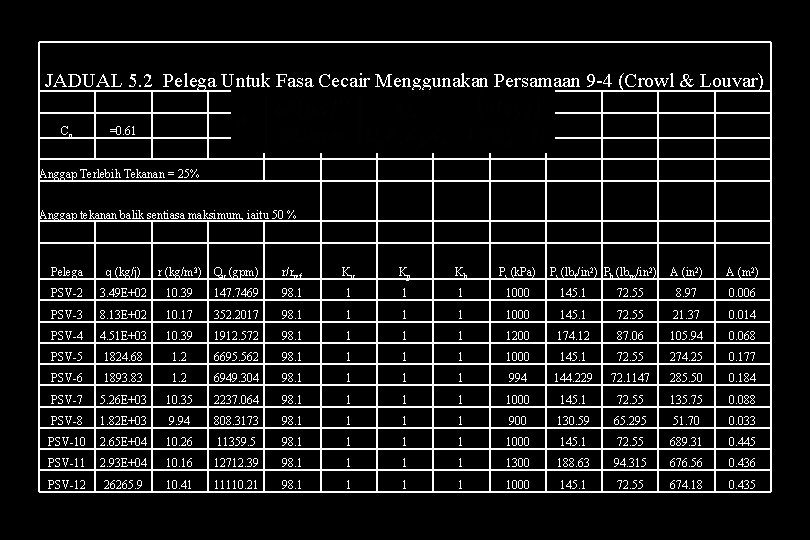
JADUAL 5. 2 Pelega Untuk Fasa Cecair Menggunakan Persamaan 9 -4 (Crowl & Louvar) Co =0. 61 Anggap Terlebih Tekanan = 25% Anggap tekanan balik sentiasa maksimum, iaitu 50 % Pelega q (kg/j) r (kg/m 3) Qv (gpm) r/rref Kv Kp Kb Ps (k. Pa) PSV-2 3. 49 E+02 10. 39 PSV-3 8. 13 E+02 PSV-4 Ps (lbf/in 2) Pb (lbm/in 2) A (m 2) 147. 7469 98. 1 1 1000 145. 1 72. 55 8. 97 0. 006 10. 17 352. 2017 98. 1 1 1000 145. 1 72. 55 21. 37 0. 014 4. 51 E+03 10. 39 1912. 572 98. 1 1 1200 174. 12 87. 06 105. 94 0. 068 PSV-5 1824. 68 1. 2 6695. 562 98. 1 1 1000 145. 1 72. 55 274. 25 0. 177 PSV-6 1893. 83 1. 2 6949. 304 98. 1 1 994 144. 229 72. 1147 285. 50 0. 184 PSV-7 5. 26 E+03 10. 35 2237. 064 98. 1 1 1000 145. 1 72. 55 135. 75 0. 088 PSV-8 1. 82 E+03 9. 94 808. 3173 98. 1 1 900 130. 59 65. 295 51. 70 0. 033 PSV-10 2. 65 E+04 10. 26 11359. 5 98. 1 1 1000 145. 1 72. 55 689. 31 0. 445 PSV-11 2. 93 E+04 10. 16 12712. 39 98. 1 1 1300 188. 63 94. 315 676. 56 0. 436 PSV-12 26265. 9 10. 41 11110. 21 98. 1 1 1000 145. 1 72. 55 674. 18 0. 435
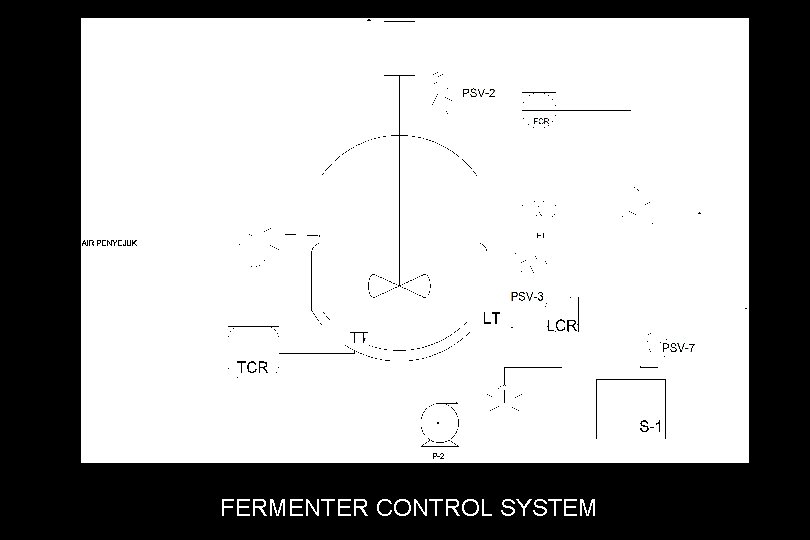
FERMENTER CONTROL SYSTEM
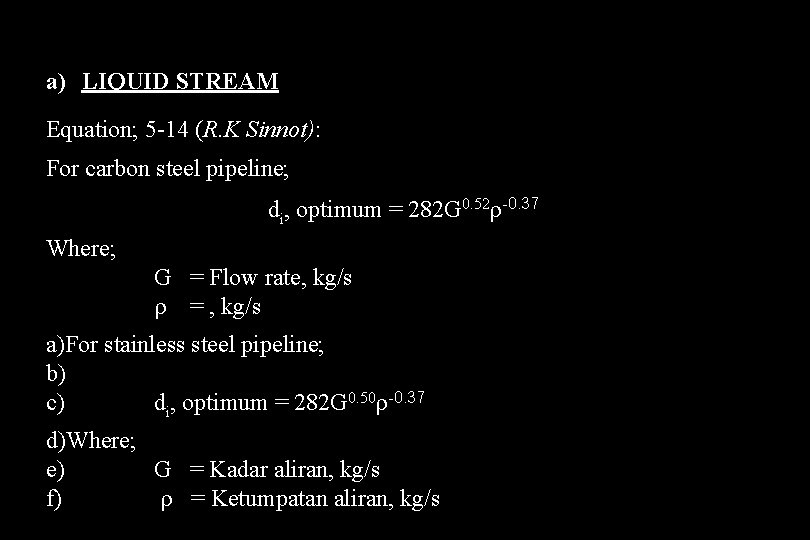
a) LIQUID STREAM Equation; 5 -14 (R. K Sinnot): For carbon steel pipeline; di, optimum = 282 G 0. 52 -0. 37 Where; G = Flow rate, kg/s = , kg/s a)For stainless steel pipeline; b) c) di, optimum = 282 G 0. 50 -0. 37 d)Where; e) G = Kadar aliran, kg/s f) = Ketumpatan aliran, kg/s
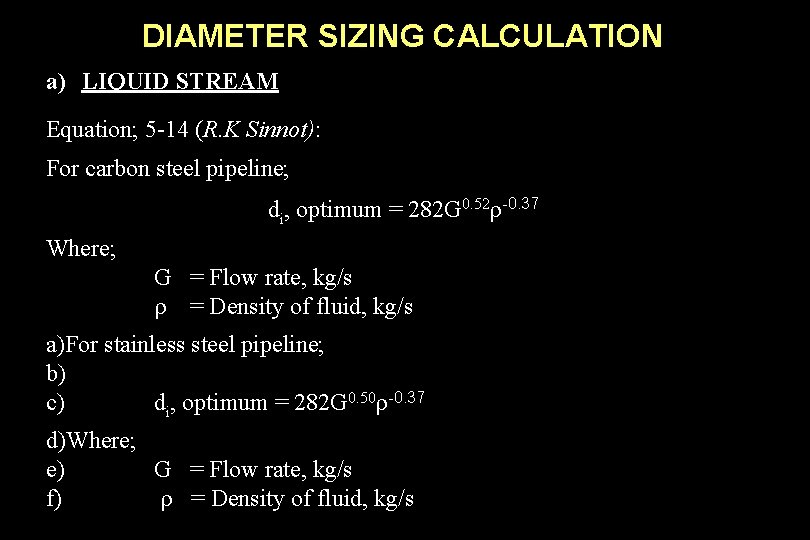
DIAMETER SIZING CALCULATION a) LIQUID STREAM Equation; 5 -14 (R. K Sinnot): For carbon steel pipeline; di, optimum = 282 G 0. 52 -0. 37 Where; G = Flow rate, kg/s = Density of fluid, kg/s a)For stainless steel pipeline; b) c) di, optimum = 282 G 0. 50 -0. 37 d)Where; e) G = Flow rate, kg/s f) = Density of fluid, kg/s
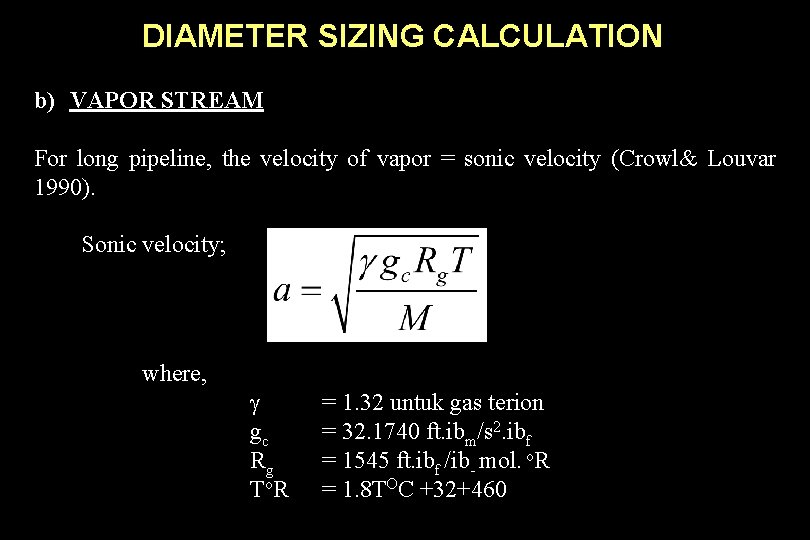
DIAMETER SIZING CALCULATION b) VAPOR STREAM For long pipeline, the velocity of vapor = sonic velocity (Crowl& Louvar 1990). Sonic velocity; where, gc Rg To. R = 1. 32 untuk gas terion = 32. 1740 ft. ibm/s 2. ibf = 1545 ft. ibf /ib- mol. o. R = 1. 8 TOC +32+460
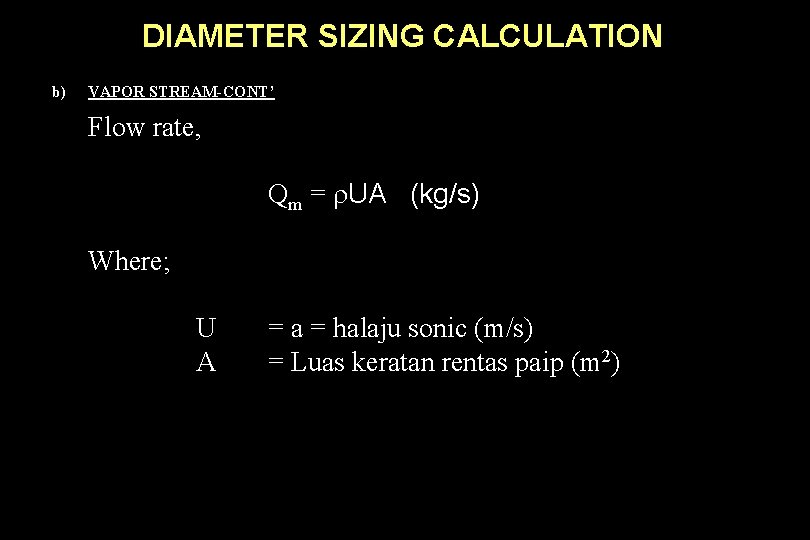
DIAMETER SIZING CALCULATION b) VAPOR STREAM-CONT’ Flow rate, Qm = UA (kg/s) Where; U A = a = halaju sonic (m/s) = Luas keratan rentas paip (m 2)
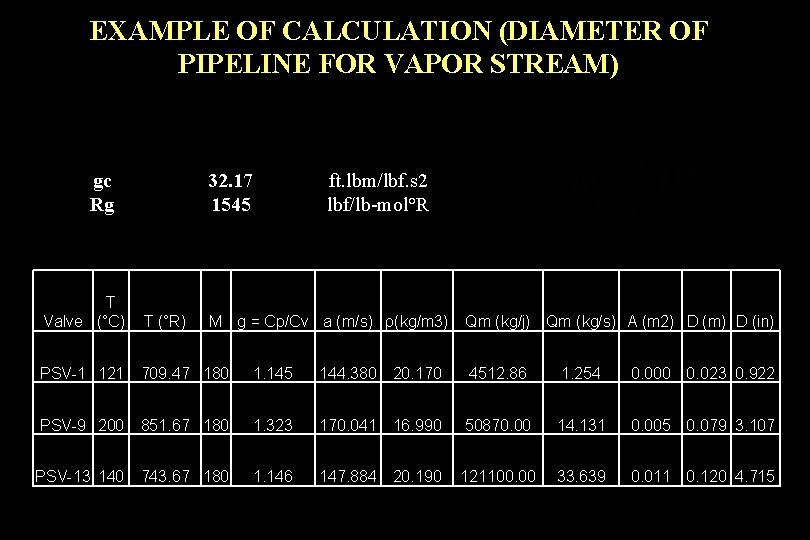
EXAMPLE OF CALCULATION (DIAMETER OF PIPELINE FOR VAPOR STREAM) gc Rg 32. 17 1545 ft. lbm/lbf. s 2 lbf/lb-mol°R T Valve (°C) T (°R) PSV-1 121 709. 47 180 1. 145 144. 380 20. 170 4512. 86 1. 254 0. 000 0. 023 0. 922 PSV-9 200 851. 67 180 1. 323 170. 041 16. 990 50870. 00 14. 131 0. 005 0. 079 3. 107 PSV-13 140 743. 67 180 1. 146 147. 884 20. 190 121100. 00 33. 639 0. 011 0. 120 4. 715 M g = Cp/Cv a (m/s) ρ(kg/m 3) Qm (kg/j) Qm (kg/s) A (m 2) D (m) D (in)
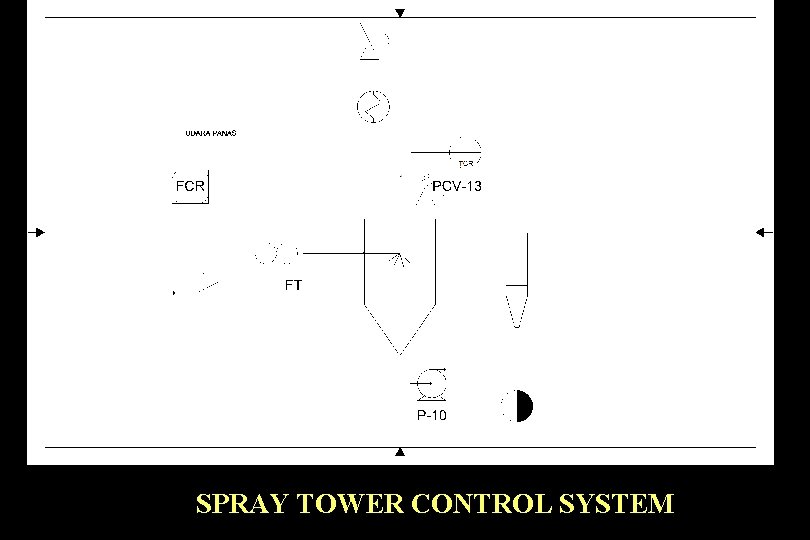
SPRAY TOWER CONTROL SYSTEM
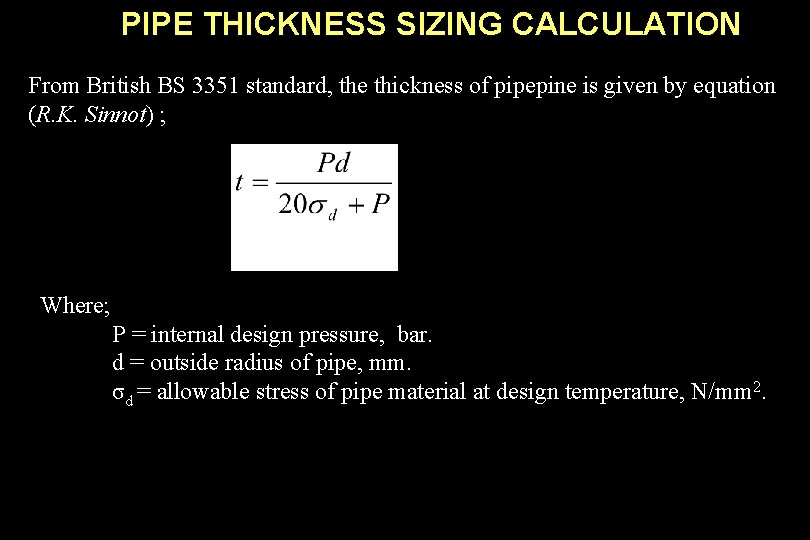
PIPE THICKNESS SIZING CALCULATION From British BS 3351 standard, the thickness of pipepine is given by equation (R. K. Sinnot) ; Where; P = internal design pressure, bar. d = outside radius of pipe, mm. σd = allowable stress of pipe material at design temperature, N/mm 2.
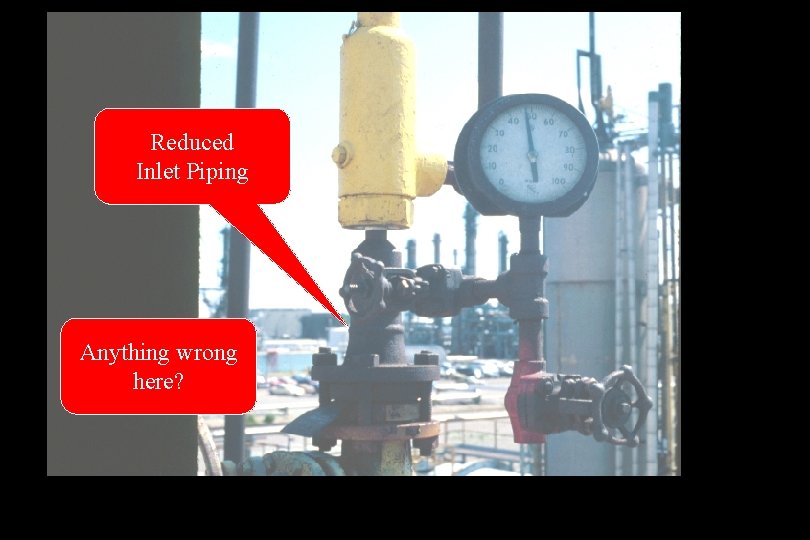
? ? Reduced Inlet Piping Anything wrong here?
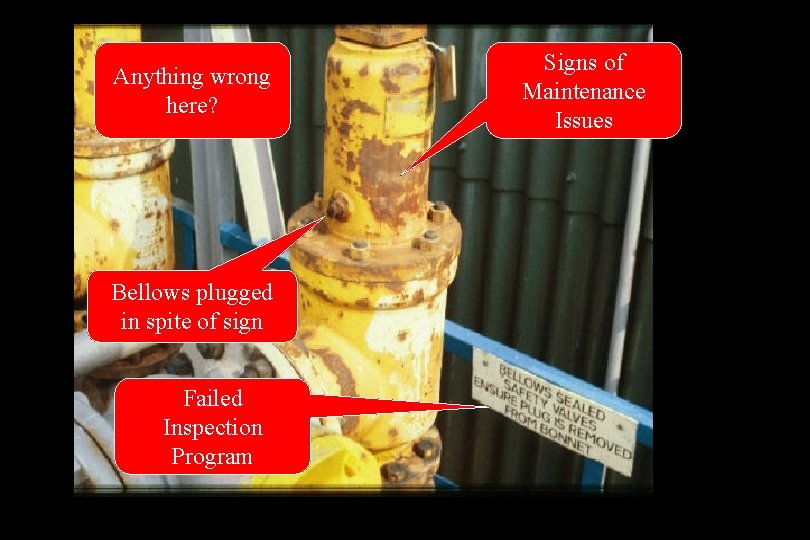
? ? Plugged Bellows, Failed Signs of Anything wrong Maintenance Inspection, Maintenance here? Issues Bellows plugged in spite of sign Failed Inspection Program
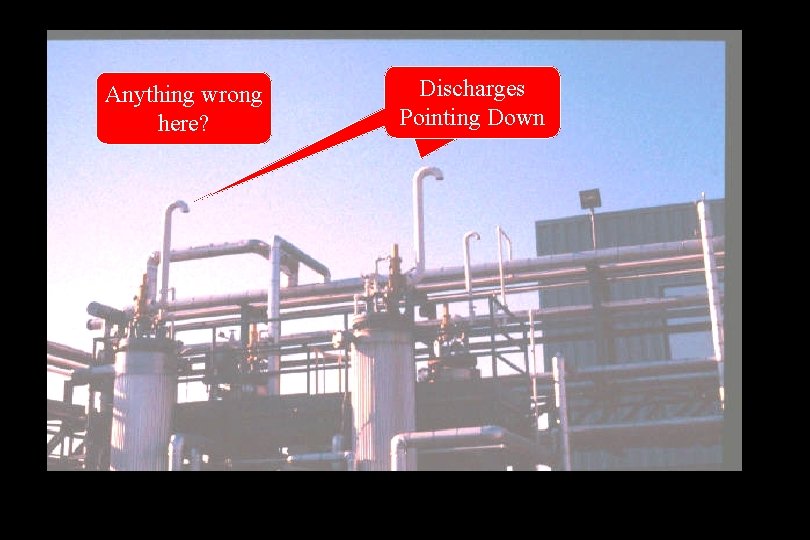
? ? Discharges Pointing Down Anything Discharges wrong Anything wrong here? Pointing here? Down
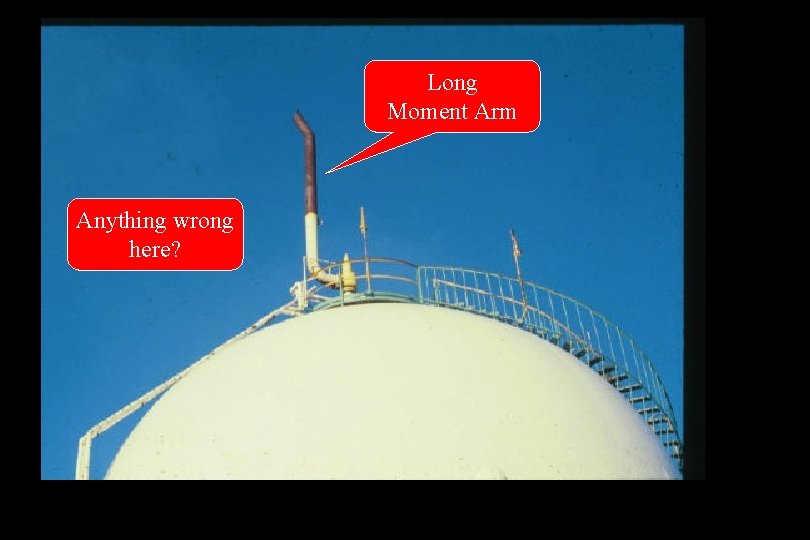
? ? Long Moment Arm Anything wrong here?
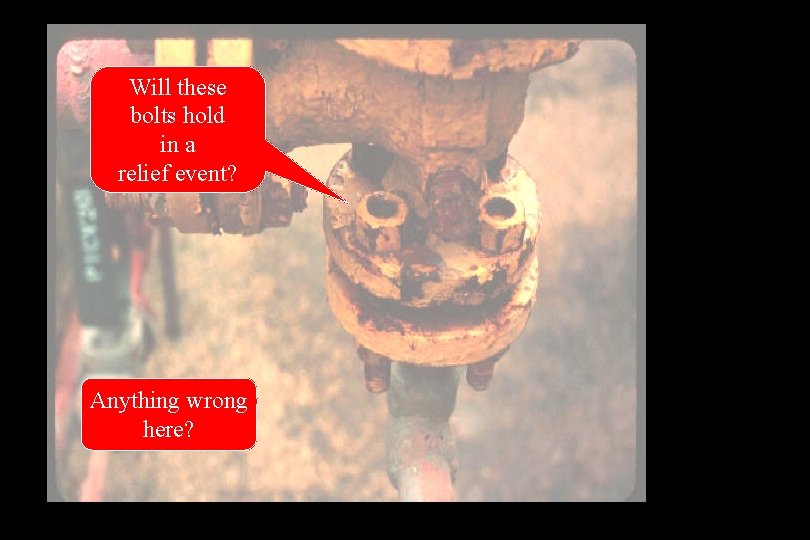
? ? Will these bolts hold in a relief Will these event bolts hold in a relief event? Anything wrong here?
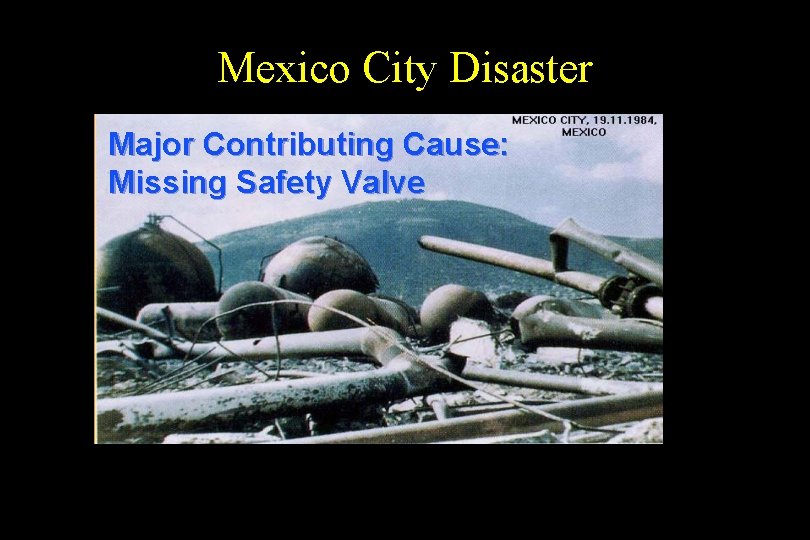
Mexico City Disaster Major Contributing Cause: Missing Safety Valve
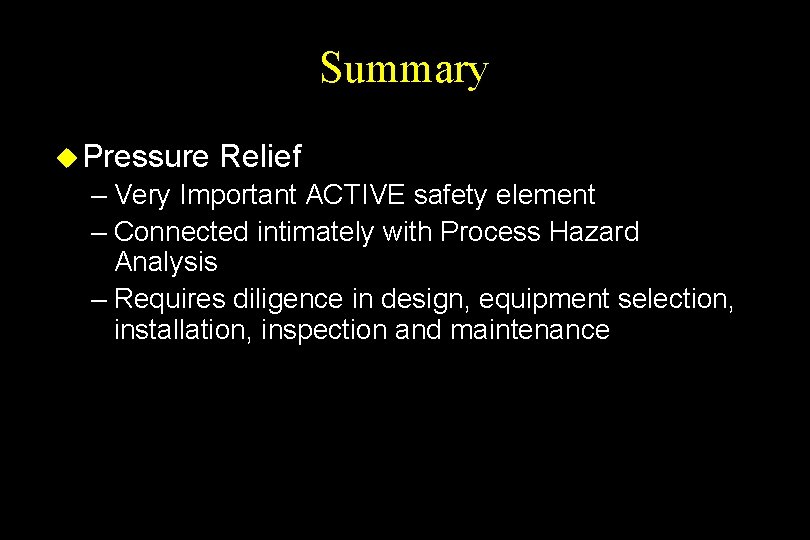
Summary u Pressure Relief – Very Important ACTIVE safety element – Connected intimately with Process Hazard Analysis – Requires diligence in design, equipment selection, installation, inspection and maintenance
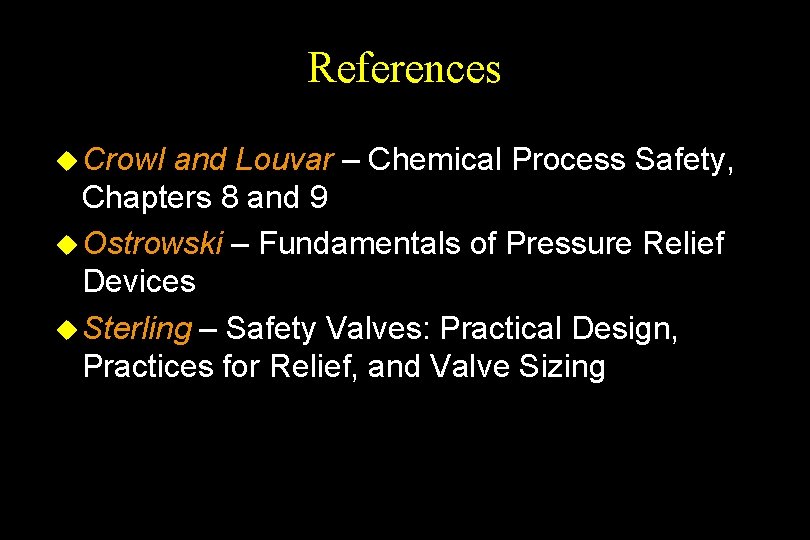
References u Crowl and Louvar – Chemical Process Safety, Chapters 8 and 9 u Ostrowski – Fundamentals of Pressure Relief Devices u Sterling – Safety Valves: Practical Design, Practices for Relief, and Valve Sizing
Piping diagram symbols
Split range control
Separator pfd symbol
Piping and instrumentation diagram (p&id)
Schéma p&id
Multi loop pid controller regolatore pid multi loop
Piping and instrumentation diagrams
Piping and instrumentation diagrams
Ert diagram
Pt = p.ert merupakan rumus dari pertumbuhan penduduk
Ert controller
Ert tool
Ert erp definition
Ert erp definition
Ert 1 programa
Ert malaysia
Wl2/8
Steam coil piping detail
Utility flow diagram
Residential plumbing layout plan
Block diagram of measuring system
Components of biomedical instrumentation system
Hplc instrumentation diagram
“control de grua” and posicionamiento
Steam tracer
Slurry pump suction piping
Seal plan 74
Me 444
Creo piping
Rsysconfig
Florida building code gas piping
Piping components
Piping
Piping engineering drawing
Process plant piping
Pipe defect in extrusion
Puma5
Piping solutions inc
Water supply requirement
Pneumatic piping system design
Piping
Mechanical seal plan
Stainless steel code number
Preposition filler
Ron had a course introduction
Piping fundamentals
Pid meting
Control procesos
Spike prime fll robot design
Pid controller tuning methods
P&id
Pid rise time
Pid identifier
Modern control
Pid lisom
Pid rise time
Control pid
Calculo pid
Classical pid control
Pid 3 step
Premenstrual syndrome discharge
Pid discharge pictures
Controle pid
Pid controller animation
Pid isa
Pid meeting
Pid xing
Pid controller introduction