Economically Attractive and Environmentally Friendly FLEXICOKING Resid Upgrading
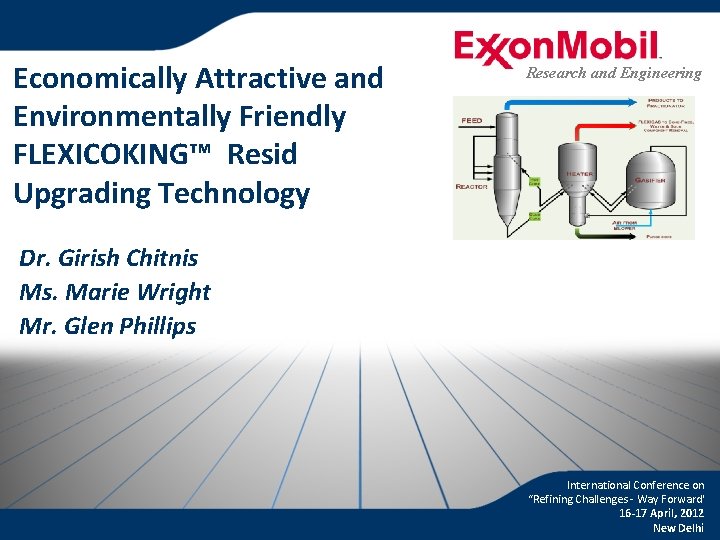
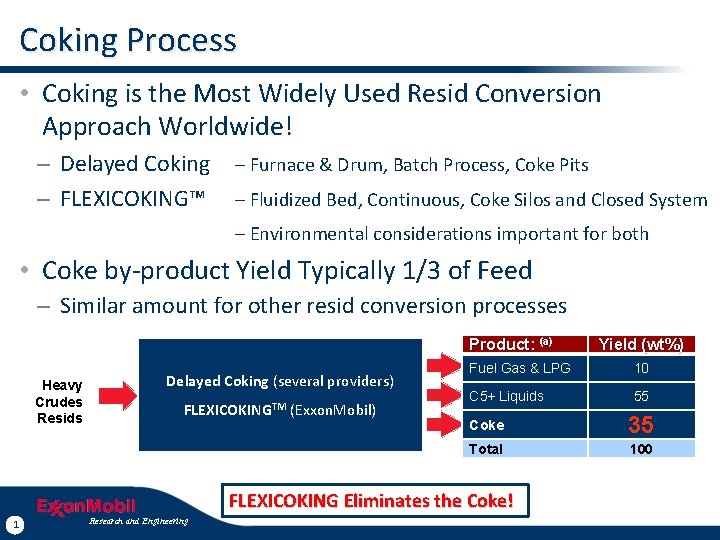
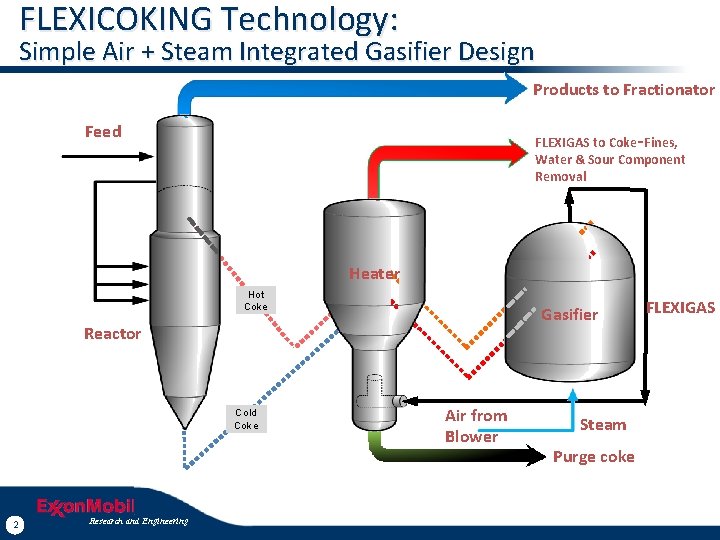
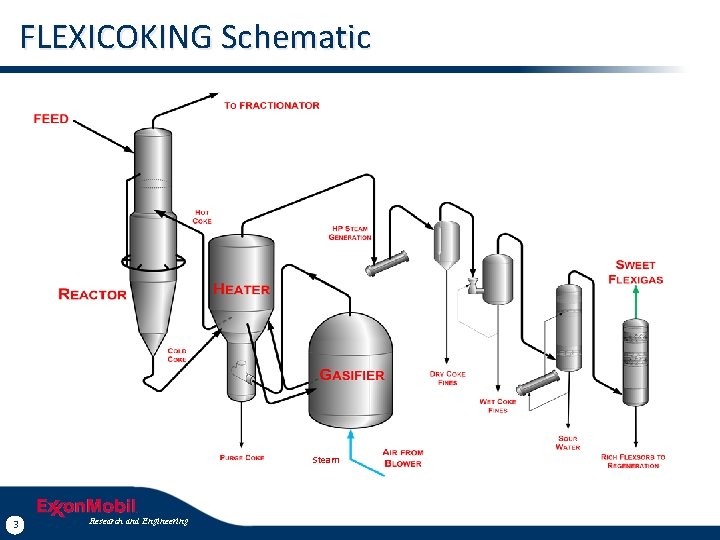
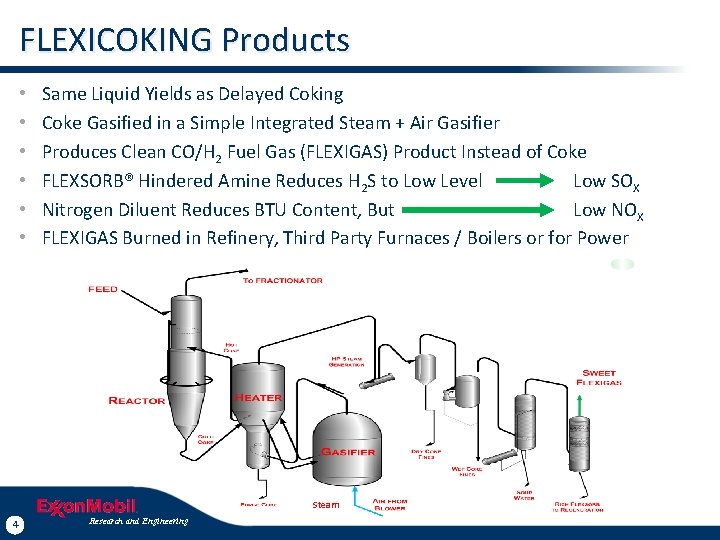
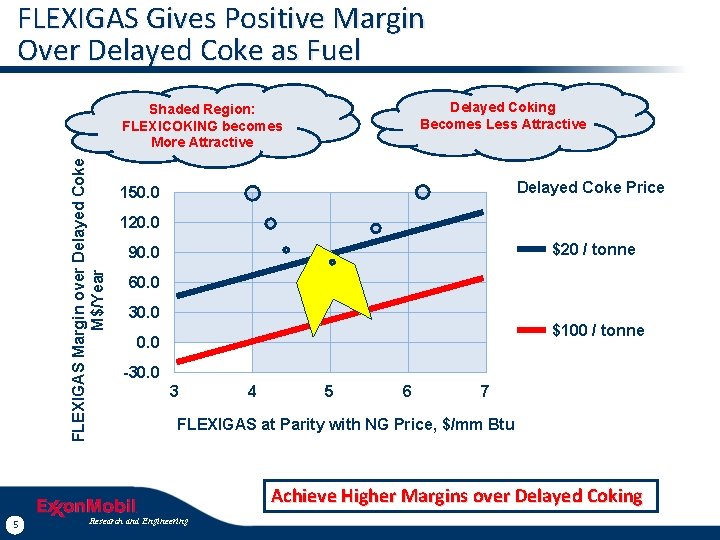
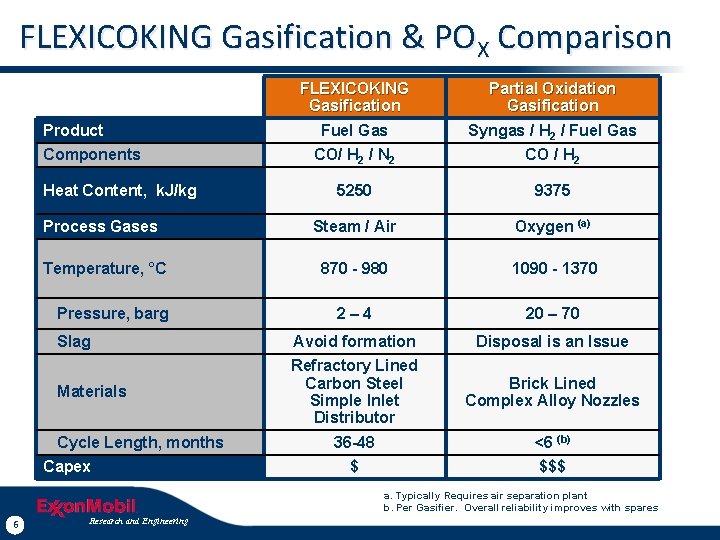
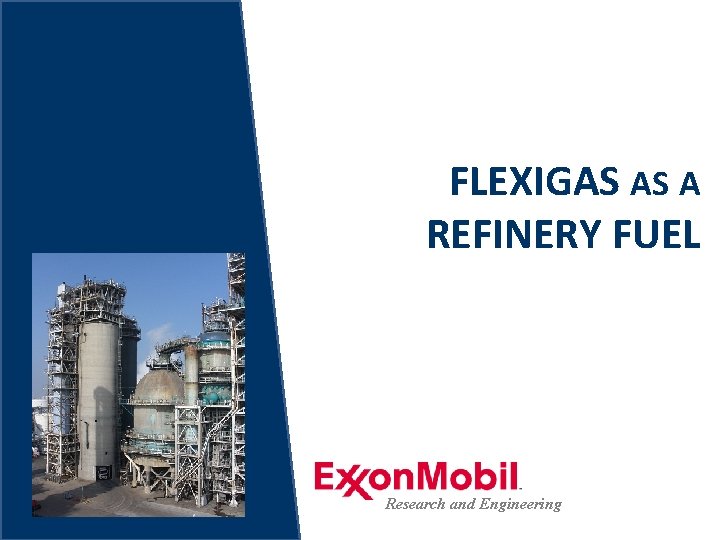
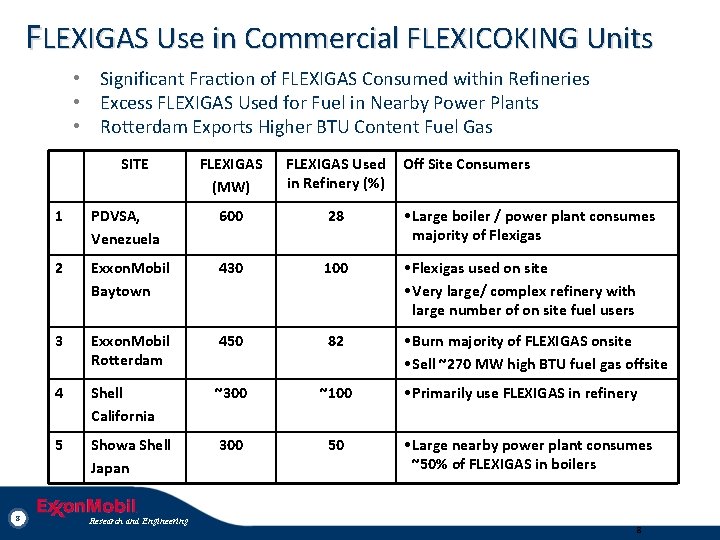
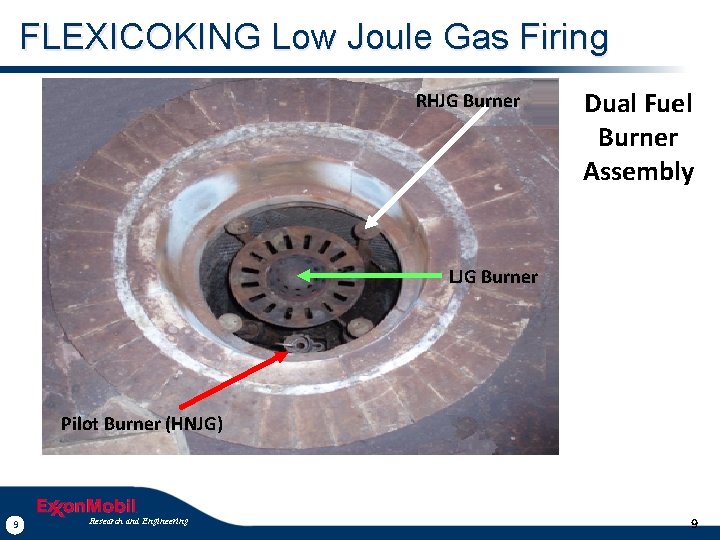
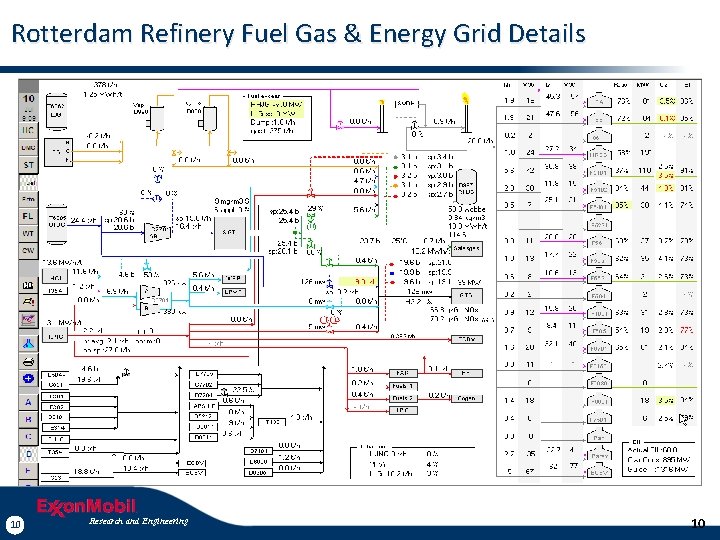
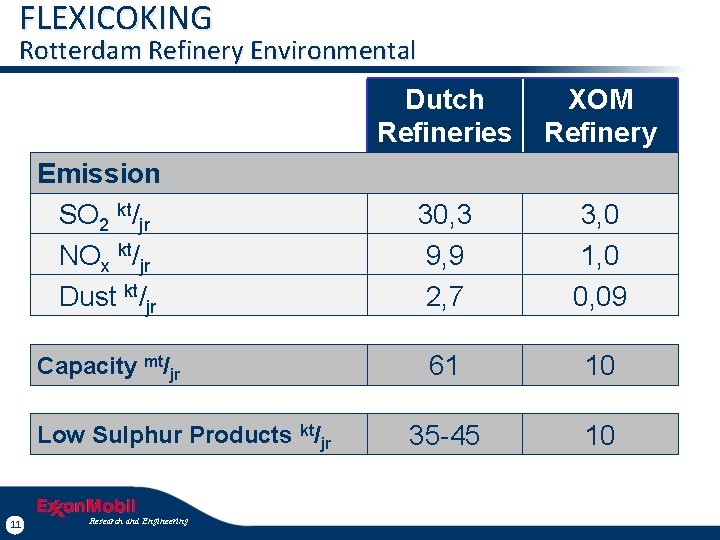
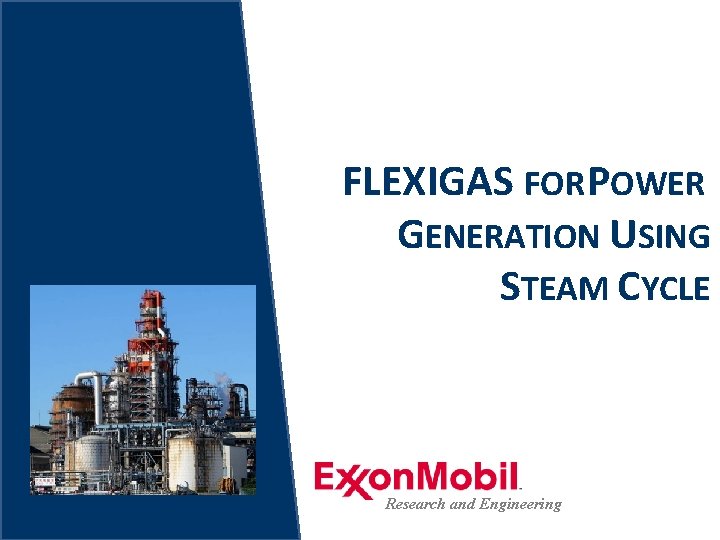
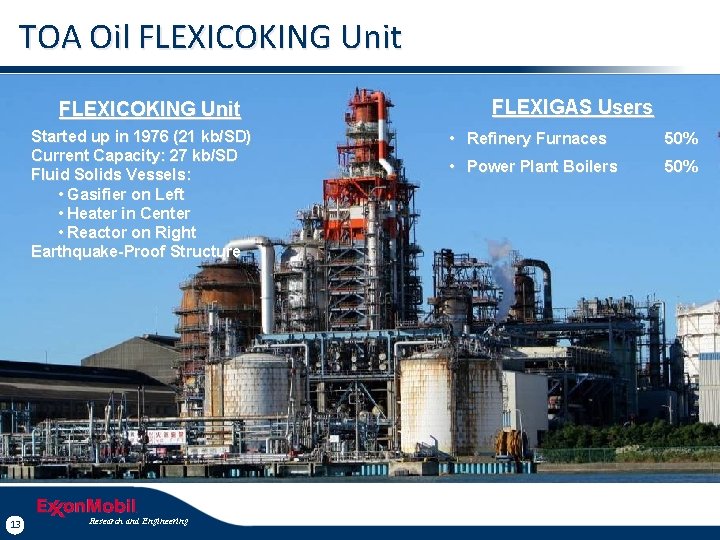
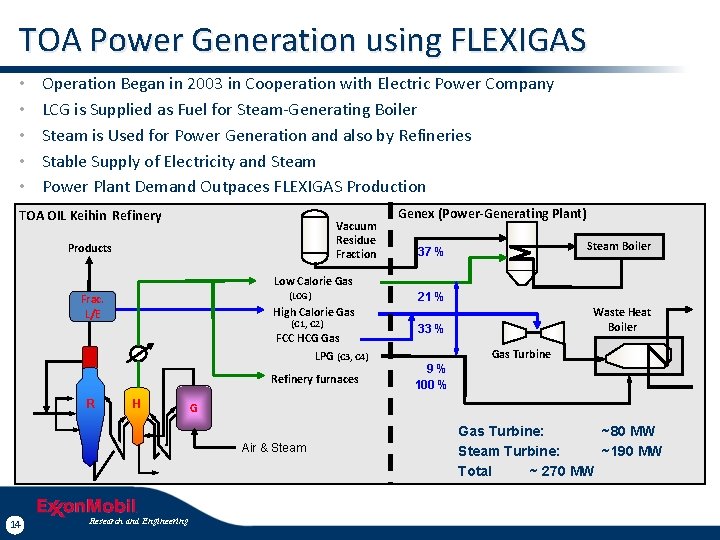
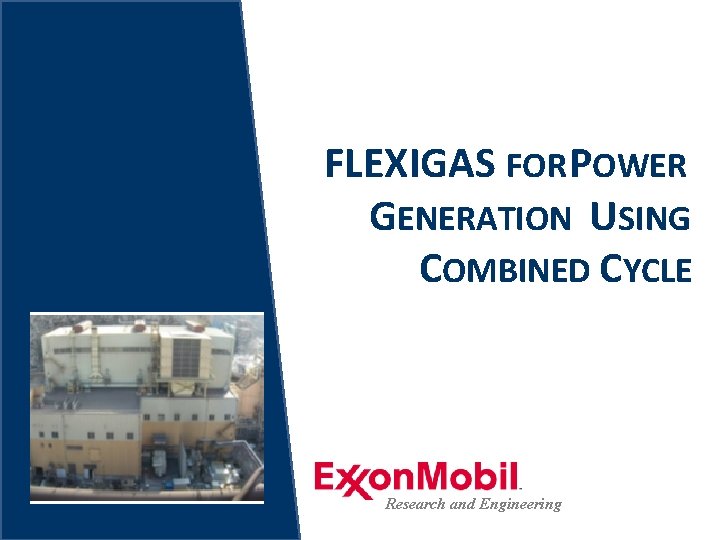
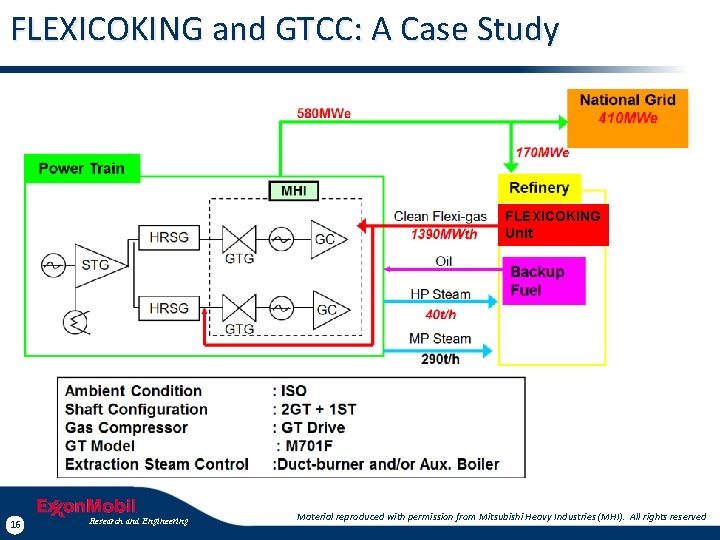
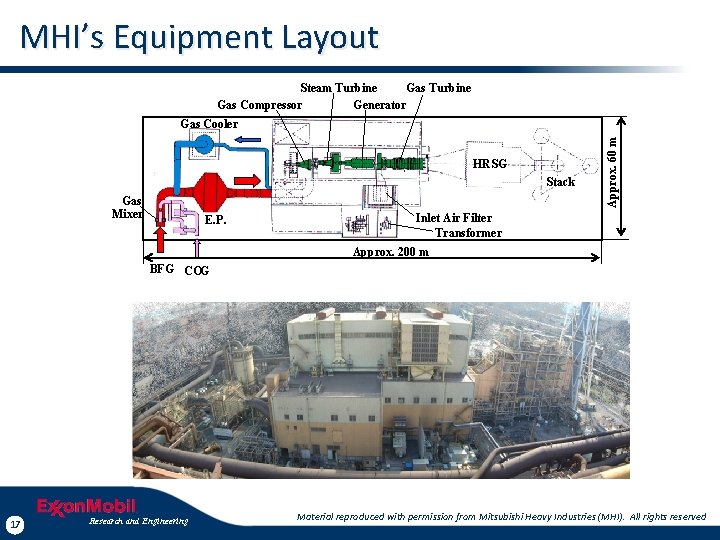
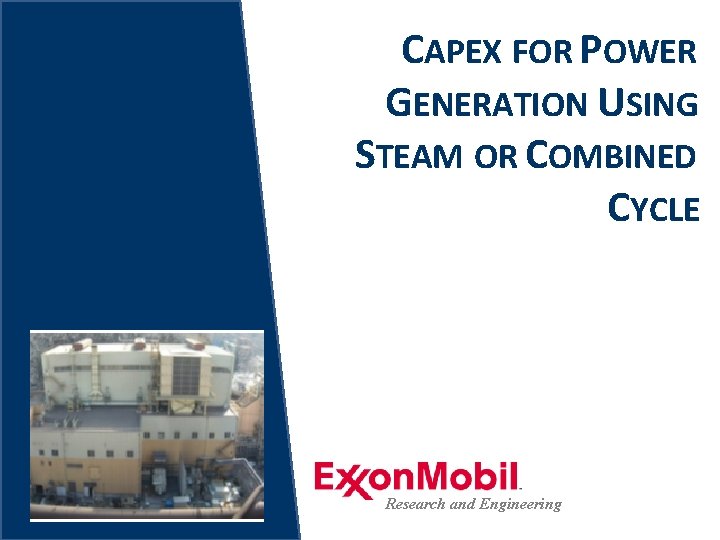
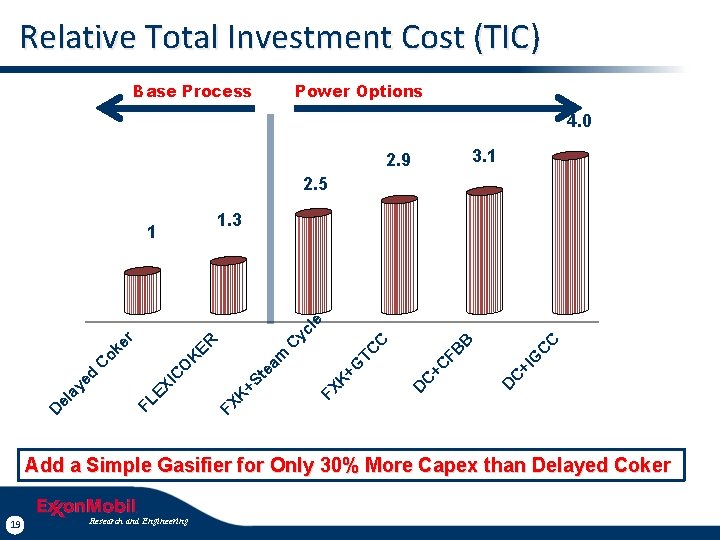
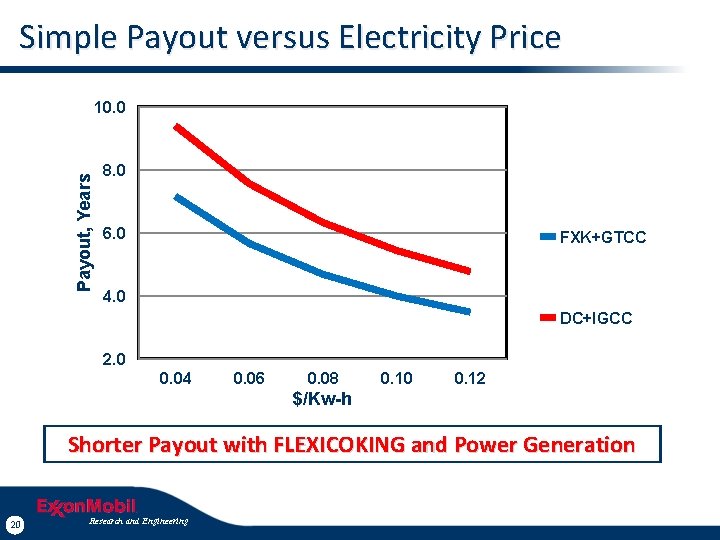
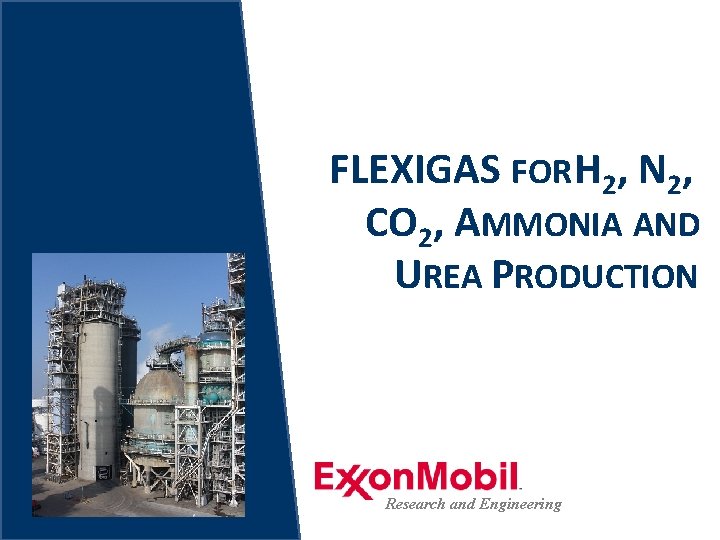
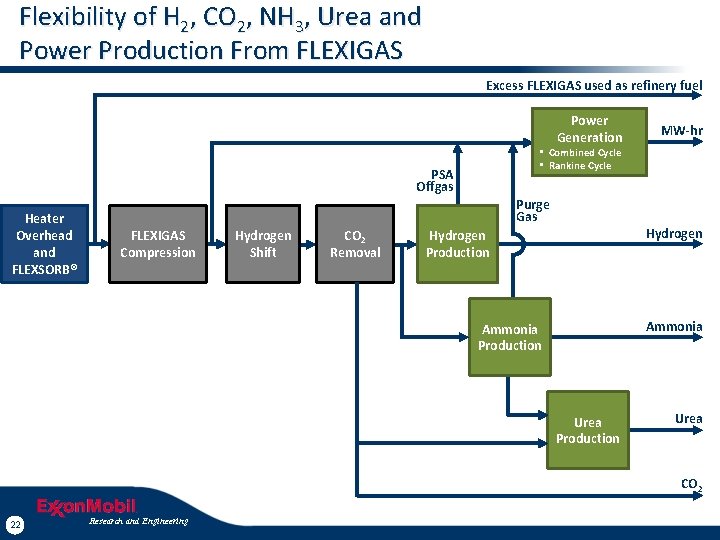
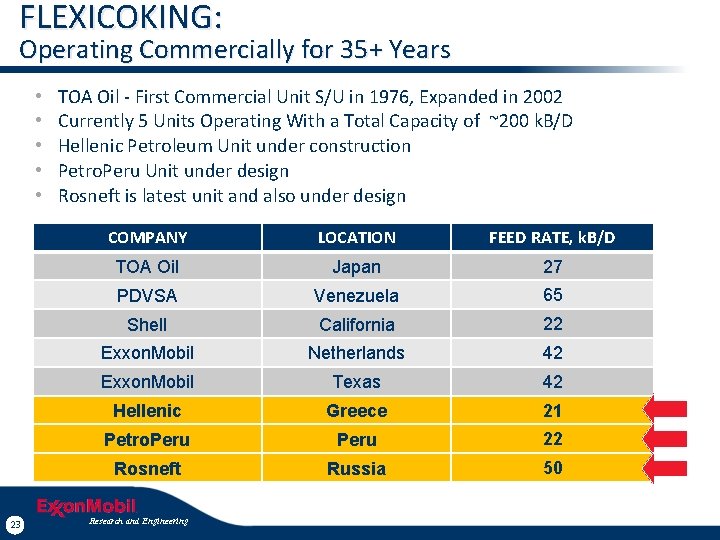
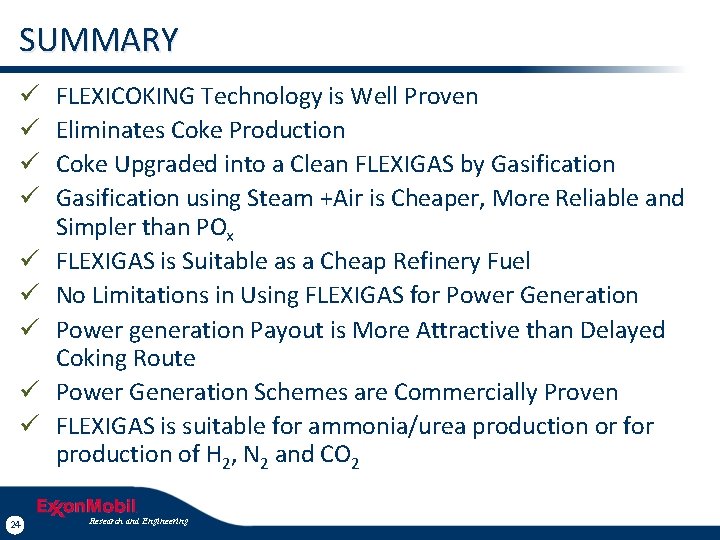
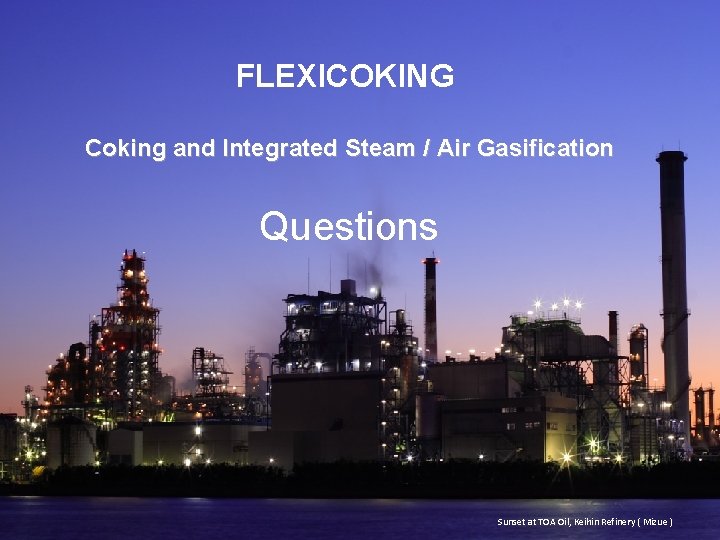
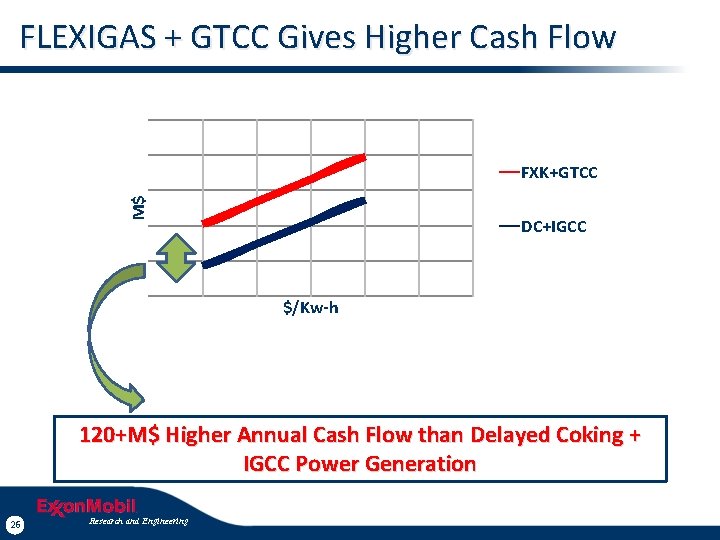
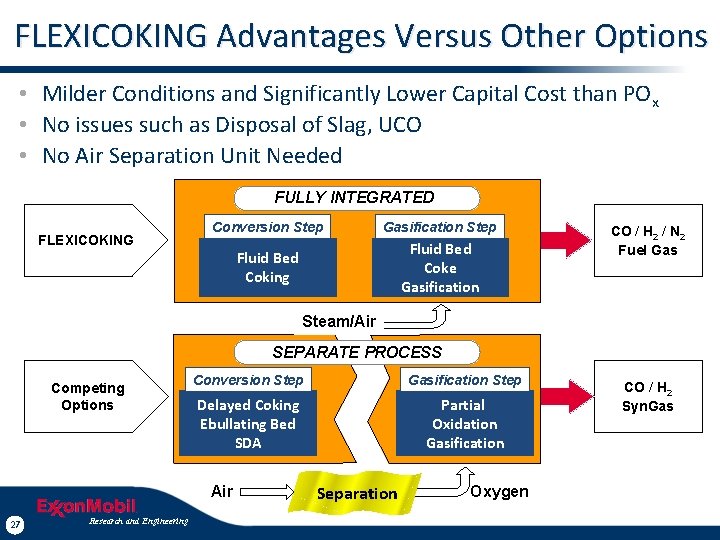
- Slides: 28
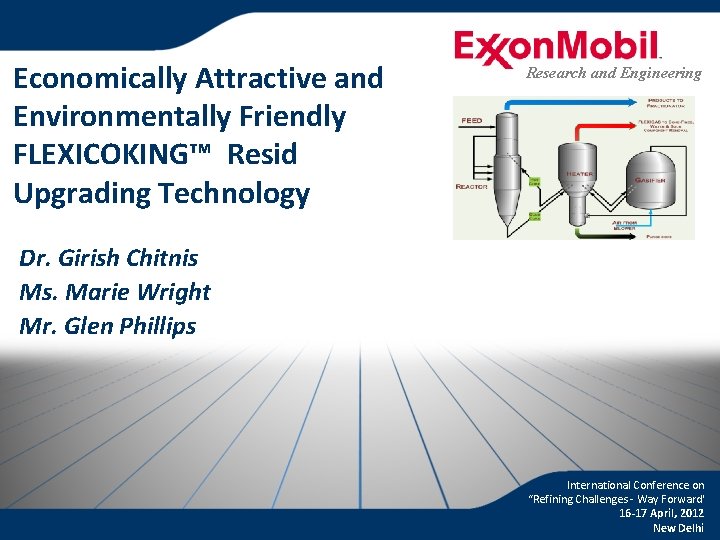
Economically Attractive and Environmentally Friendly FLEXICOKING™ Resid Upgrading Technology Research and Engineering Dr. Girish Chitnis Ms. Marie Wright Mr. Glen Phillips 0 International Conference on “Refining Challenges - Way Forward' 16 -17 April, 2012 New Delhi
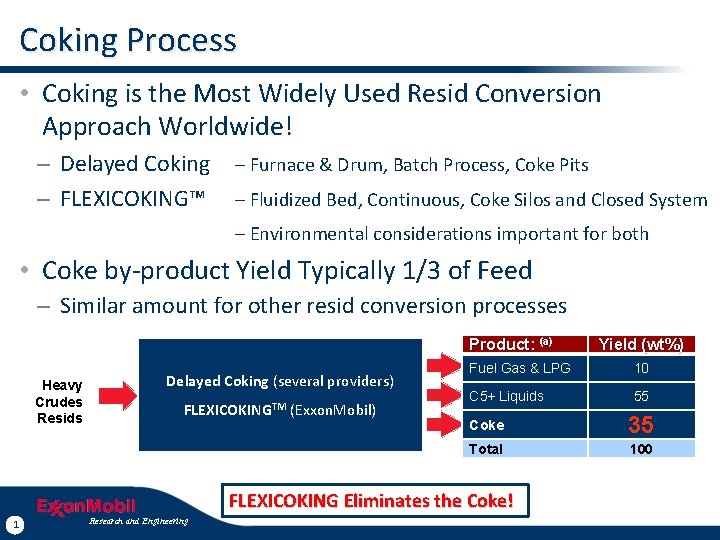
Coking Process • Coking is the Most Widely Used Resid Conversion Approach Worldwide! – Delayed Coking – FLEXICOKING™ – Furnace & Drum, Batch Process, Coke Pits – Fluidized Bed, Continuous, Coke Silos and Closed System – Environmental considerations important for both • Coke by-product Yield Typically 1/3 of Feed – Similar amount for other resid conversion processes Product: (a) Heavy Crudes Resids Delayed Coking (several providers) FLEXICOKINGTM (Exxon. Mobil) Fuel Gas & LPG 10 C 5+ Liquids 55 Coke 35 Total 100 FLEXICOKING Eliminates the Coke! 1 Research and Engineering Yield (wt%)
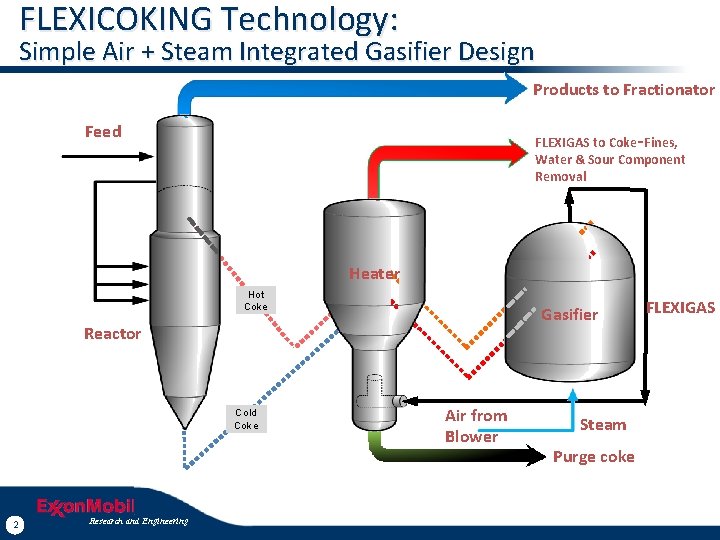
FLEXICOKING Technology: Simple Air + Steam Integrated Gasifier Design Products to Fractionator Feed FLEXIGAS to Coke‑Fines, Water & Sour Component Removal Heater Hot Coke Gasifier Reactor Cold Coke 2 Research and Engineering Air from Blower Steam Purge coke FLEXIGAS
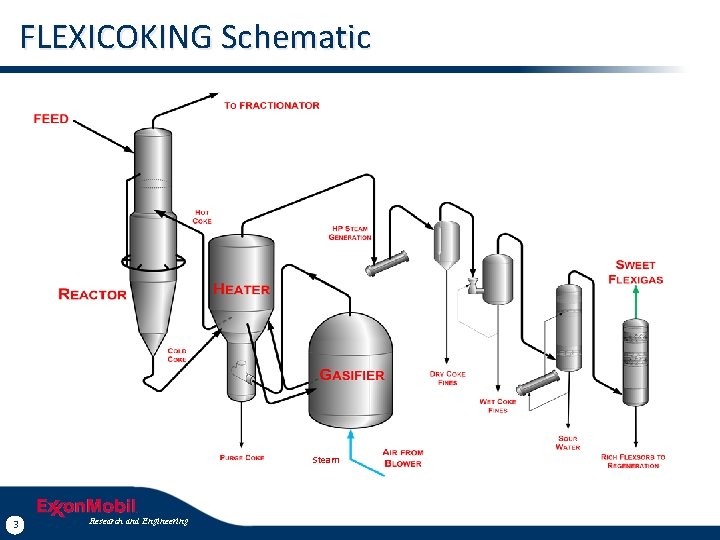
FLEXICOKING Schematic Steam 3 Research and Engineering
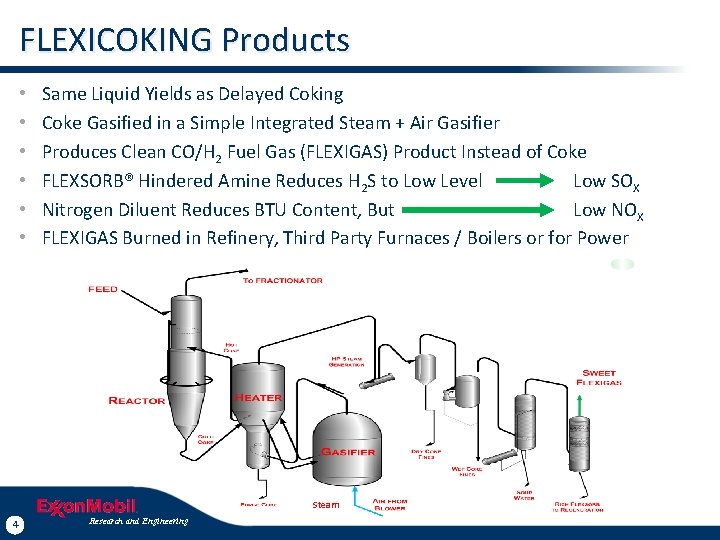
FLEXICOKING Products • • • Same Liquid Yields as Delayed Coking Coke Gasified in a Simple Integrated Steam + Air Gasifier Produces Clean CO/H 2 Fuel Gas (FLEXIGAS) Product Instead of Coke FLEXSORB® Hindered Amine Reduces H 2 S to Low Level Low SOX Nitrogen Diluent Reduces BTU Content, But Low NOX FLEXIGAS Burned in Refinery, Third Party Furnaces / Boilers or for Power Steam 4 Research and Engineering
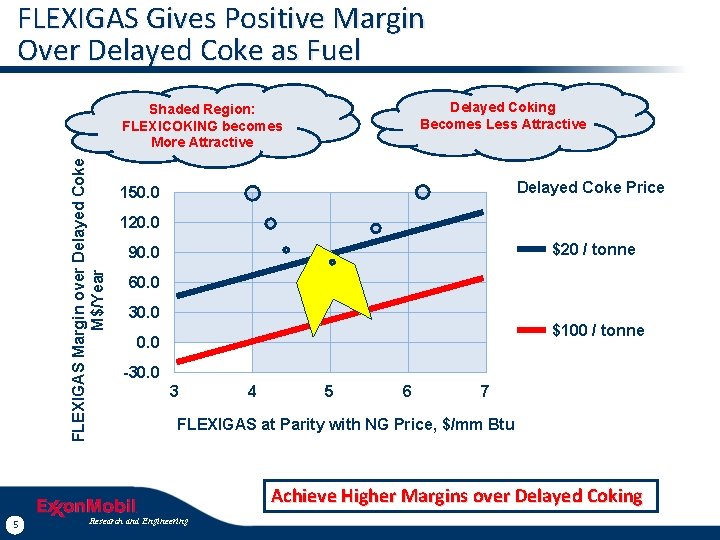
FLEXIGAS Gives Positive Margin Over Delayed Coke as Fuel Delayed Coking Becomes Less Attractive FLEXIGAS Margin over Delayed Coke M$/Year Shaded Region: FLEXICOKING becomes More Attractive Delayed Coke Price 150. 0 120. 0 $20 / tonne 90. 0 60. 0 30. 0 $100 / tonne 0. 0 -30. 0 3 4 5 6 7 FLEXIGAS at Parity with NG Price, $/mm Btu Achieve Higher Margins over Delayed Coking 5 Research and Engineering
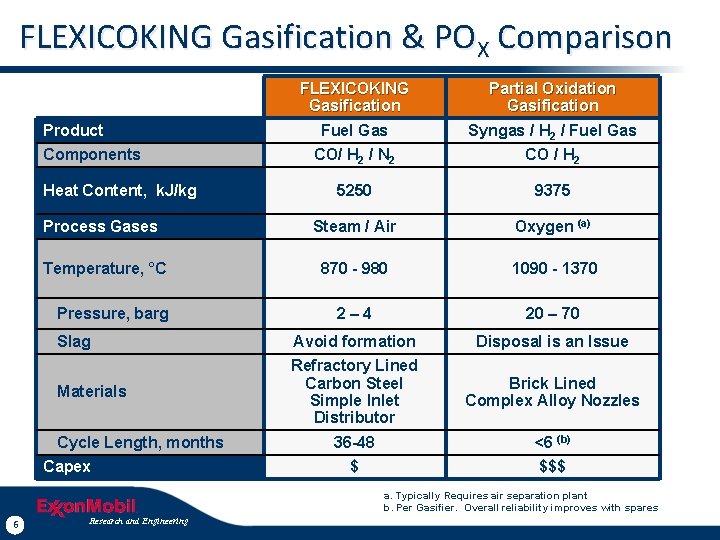
FLEXICOKING Gasification & POX Comparison FLEXICOKING Gasification Fuel Gas Partial Oxidation Gasification Syngas / H 2 / Fuel Gas CO/ H 2 / N 2 CO / H 2 5250 9375 Process Gases Steam / Air Oxygen (a) Temperature, °C 870 - 980 1090 - 1370 2– 4 20 – 70 Slag Avoid formation Disposal is an Issue Materials Refractory Lined Carbon Steel Simple Inlet Distributor Brick Lined Complex Alloy Nozzles 36 -48 <6 (b) $ $$$ Product Components Heat Content, k. J/kg Pressure, barg Cycle Length, months Capex a. Typically Requires air separation plant b. Per Gasifier. Overall reliability improves with spares 6 Research and Engineering
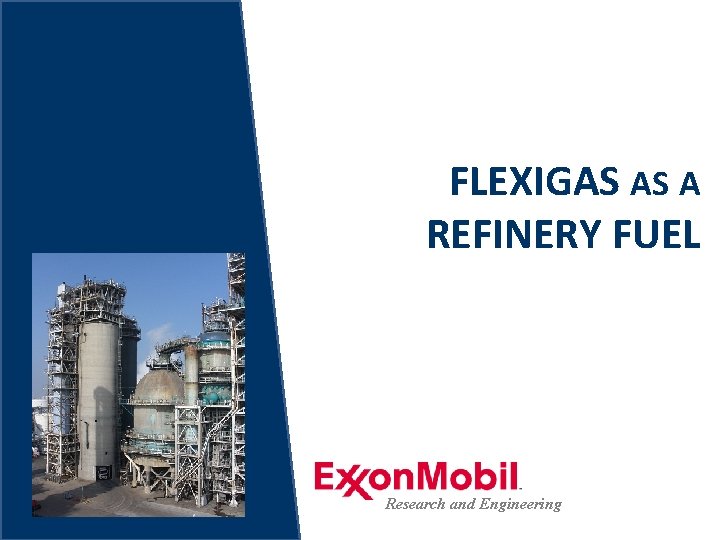
FLEXIGAS AS A REFINERY FUEL Research and Engineering 7
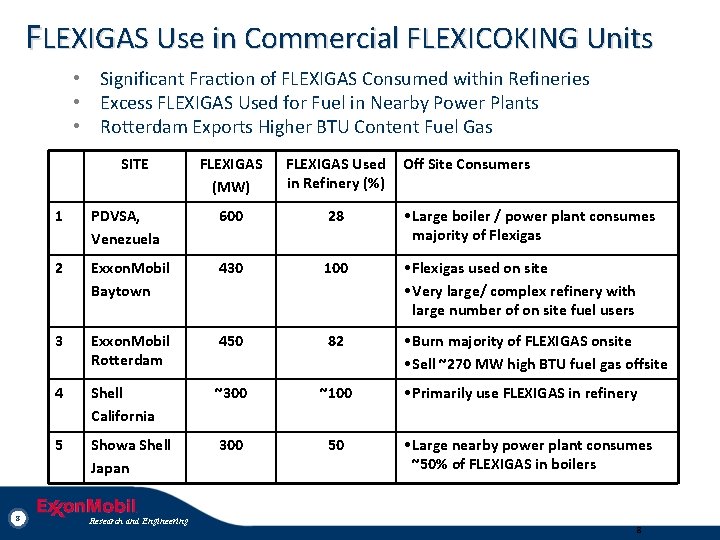
FLEXIGAS Use in Commercial FLEXICOKING Units • Significant Fraction of FLEXIGAS Consumed within Refineries • Excess FLEXIGAS Used for Fuel in Nearby Power Plants • Rotterdam Exports Higher BTU Content Fuel Gas SITE 8 8 FLEXIGAS (MW) FLEXIGAS Used in Refinery (%) Off Site Consumers 1 PDVSA, Venezuela 600 28 • Large boiler / power plant consumes majority of Flexigas 2 Exxon. Mobil Baytown 430 100 • Flexigas used on site • Very large/ complex refinery with large number of on site fuel users 3 Exxon. Mobil Rotterdam 450 82 • Burn majority of FLEXIGAS onsite • Sell ~270 MW high BTU fuel gas offsite 4 Shell California ~300 ~100 5 Showa Shell Japan 300 50 Research and Engineering • Primarily use FLEXIGAS in refinery • Large nearby power plant consumes ~50% of FLEXIGAS in boilers 8
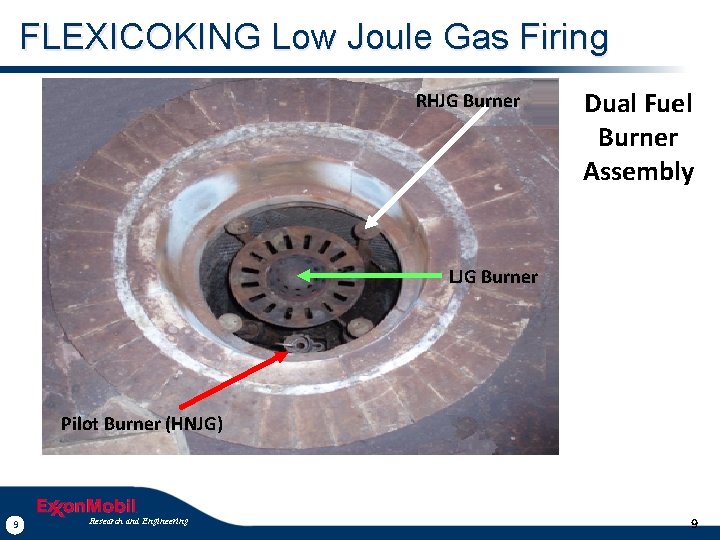
FLEXICOKING Low Joule Gas Firing RHJG Burner Dual Fuel Burner Assembly LJG Burner Pilot Burner (HNJG) 9 Research and Engineering 9
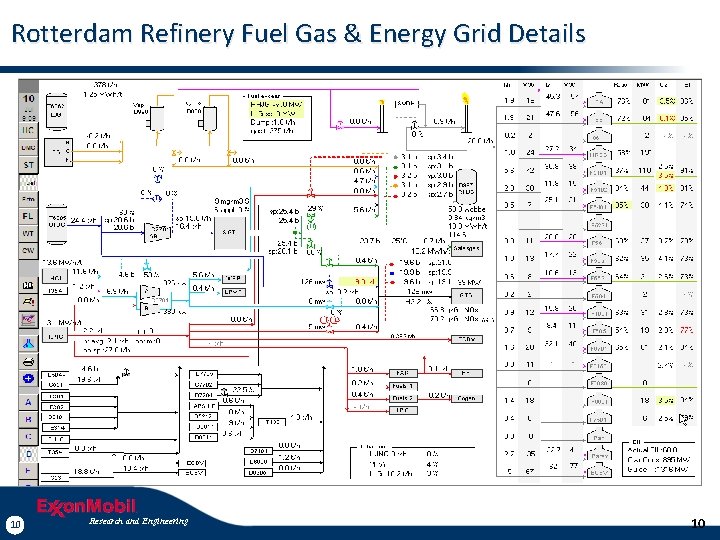
Rotterdam Refinery Fuel Gas & Energy Grid Details 10 Research and Engineering 10
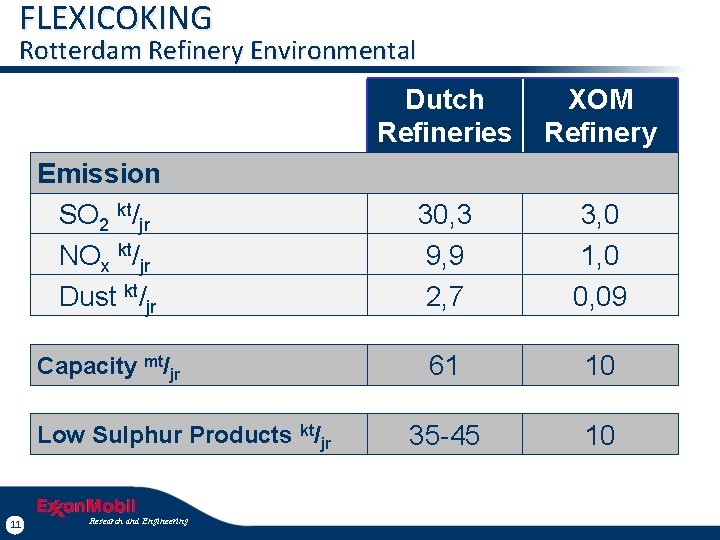
FLEXICOKING Rotterdam Refinery Environmental Emission SO 2 kt/jr NOx kt/jr Dust kt/jr Capacity mt/jr Low Sulphur Products kt/jr 11 Research and Engineering Dutch Refineries XOM Refinery 30, 3 9, 9 2, 7 3, 0 1, 0 0, 09 61 10 35 -45 10
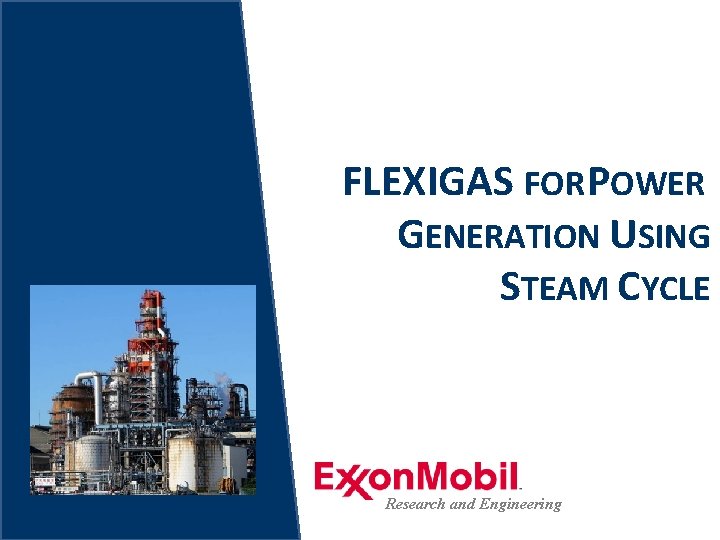
FLEXIGAS FOR POWER GENERATION USING STEAM CYCLE Research and Engineering 12
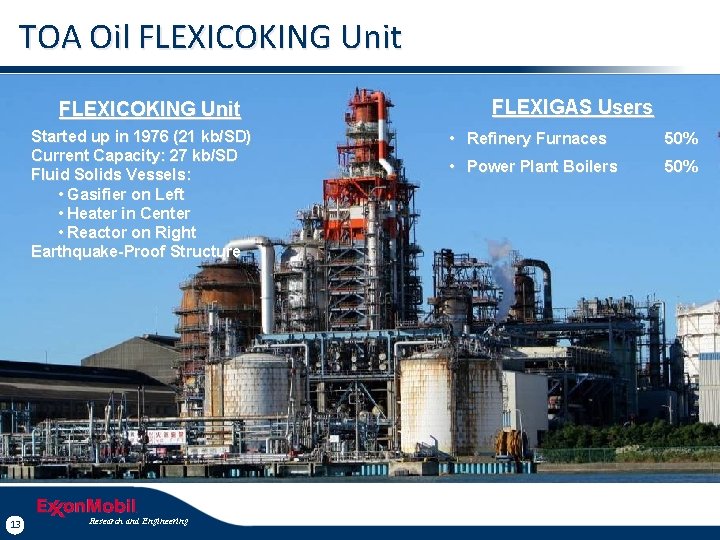
TOA Oil FLEXICOKING Unit Started up in 1976 (21 kb/SD) Current Capacity: 27 kb/SD Fluid Solids Vessels: • Gasifier on Left • Heater in Center • Reactor on Right Earthquake-Proof Structure 13 Research and Engineering FLEXIGAS Users • Refinery Furnaces 50% • Power Plant Boilers 50%
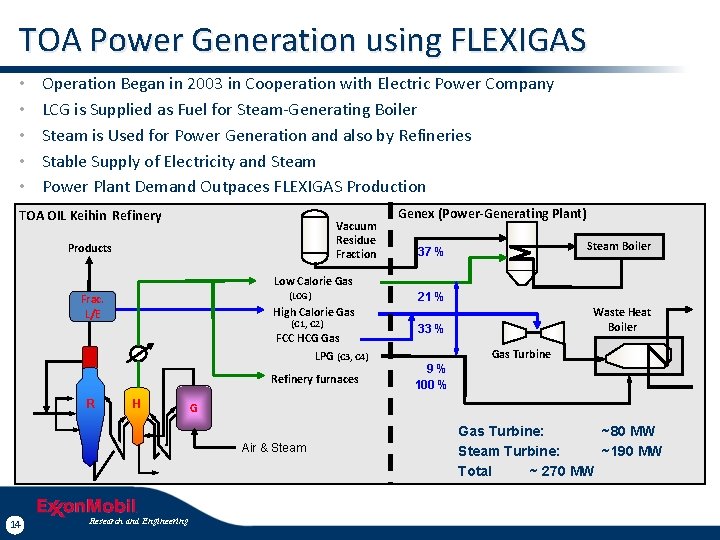
TOA Power Generation using FLEXIGAS • • • Operation Began in 2003 in Cooperation with Electric Power Company LCG is Supplied as Fuel for Steam-Generating Boiler Steam is Used for Power Generation and also by Refineries Stable Supply of Electricity and Steam Power Plant Demand Outpaces FLEXIGAS Production TOA OIL Keihin Refinery Vacuum Residue Fraction Products Genex (Power-Generating Plant) Steam Boiler 37 % Low Calorie Gas (LCG) Frac. L/E (C 1, C 2) FCC HCG Gas LPG (C 3, C 4) Refinery furnaces R H Research and Engineering Waste Heat Boiler 33 % Gas Turbine 9% 100 % G Air & Steam 14 21 % High Calorie Gas Turbine: ~80 MW Steam Turbine: ~190 MW Total ~ 270 MW
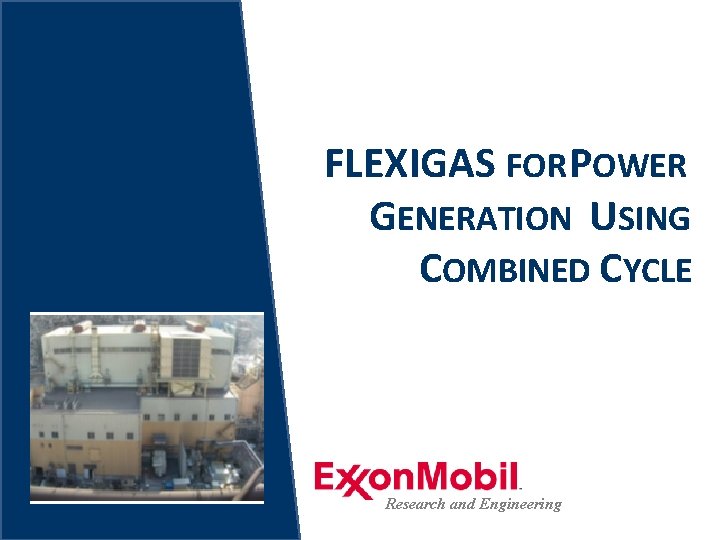
FLEXIGAS FOR POWER GENERATION USING COMBINED CYCLE Research and Engineering 15
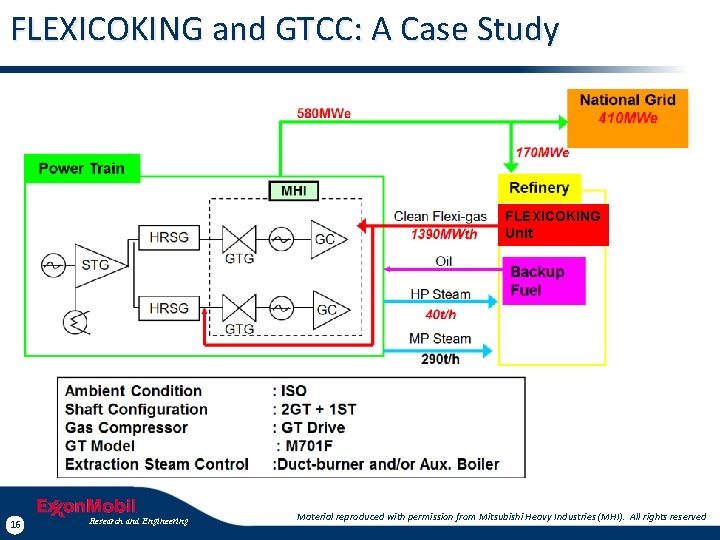
FLEXICOKING and GTCC: A Case Study FLEXICOKING Unit 16 Research and Engineering Material reproduced with permission from Mitsubishi Heavy Industries (MHI). All rights reserved
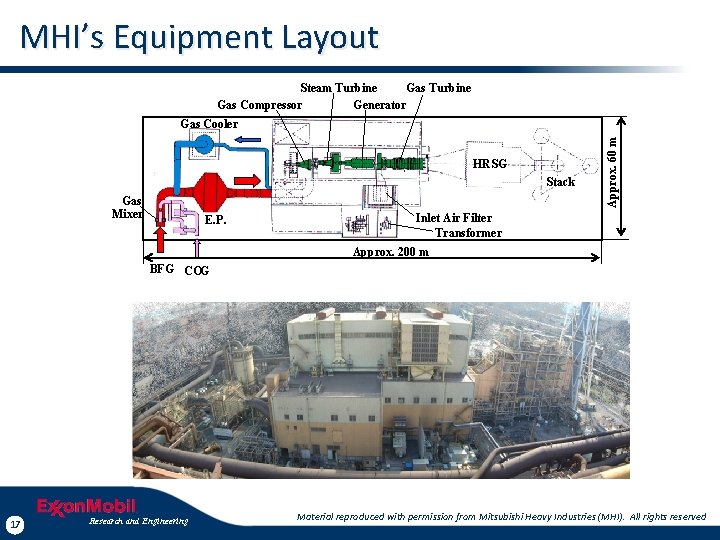
MHI’s Equipment Layout Steam Turbine Gas Compressor Generator HRSG Stack Gas Mixer E. P. Approx. 60 m Gas Cooler Inlet Air Filter Transformer Approx. 200 m BFG COG 17 Research and Engineering Material reproduced with permission from Mitsubishi Heavy Industries (MHI). All rights reserved
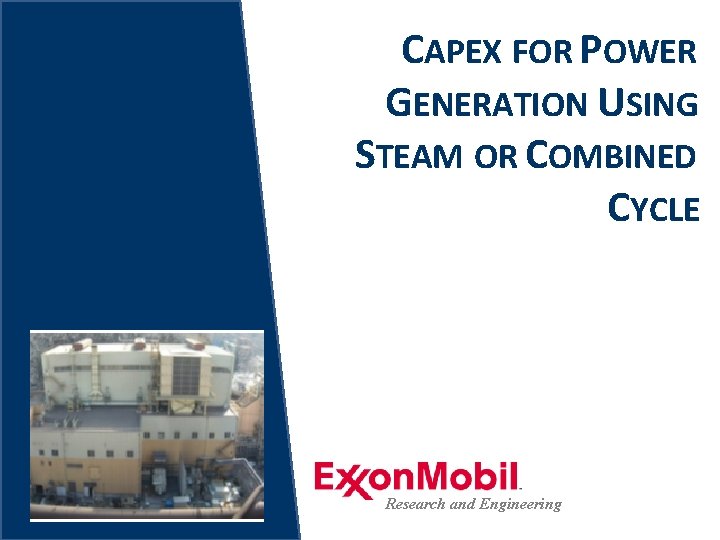
CAPEX FOR POWER GENERATION USING STEAM OR COMBINED CYCLE Research and Engineering 18
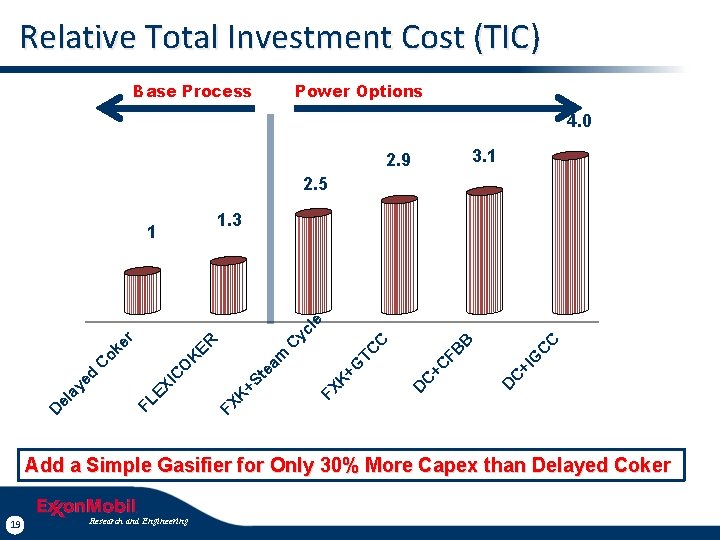
Relative Total Investment Cost (TIC) Base Process Power Options 4. 0 3. 1 2. 9 2. 5 1. 3 C B D C +I G C FB +C C D +G TC K FX te +S FX K C yc l am K FL EX IC O C el ay ed D C ER ok er e 1 Add a Simple Gasifier for Only 30% More Capex than Delayed Coker 19 Research and Engineering
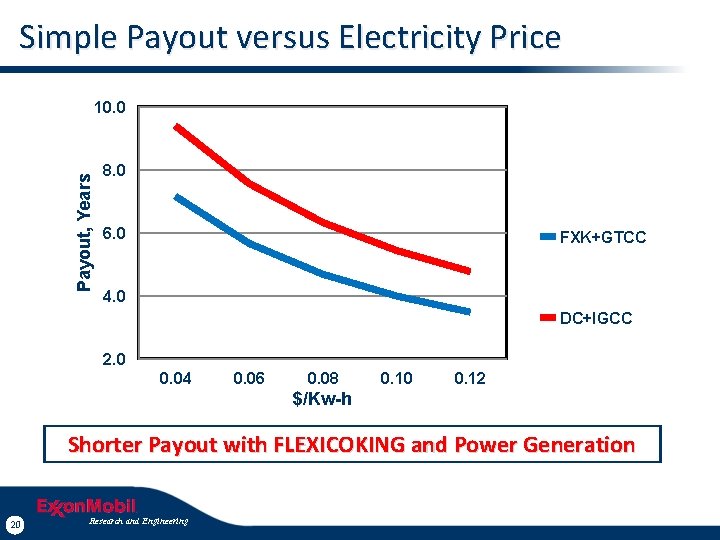
Simple Payout versus Electricity Price Payout, Years 10. 0 8. 0 6. 0 FXK+GTCC 4. 0 DC+IGCC 2. 0 0. 04 0. 06 0. 08 0. 10 0. 12 $/Kw-h Shorter Payout with FLEXICOKING and Power Generation 20 Research and Engineering
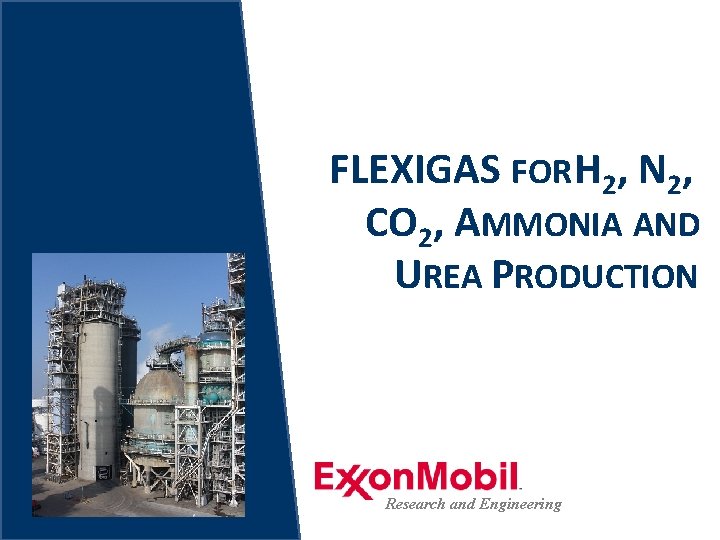
FLEXIGAS FOR H 2, N 2, CO 2, AMMONIA AND UREA PRODUCTION Research and Engineering 21
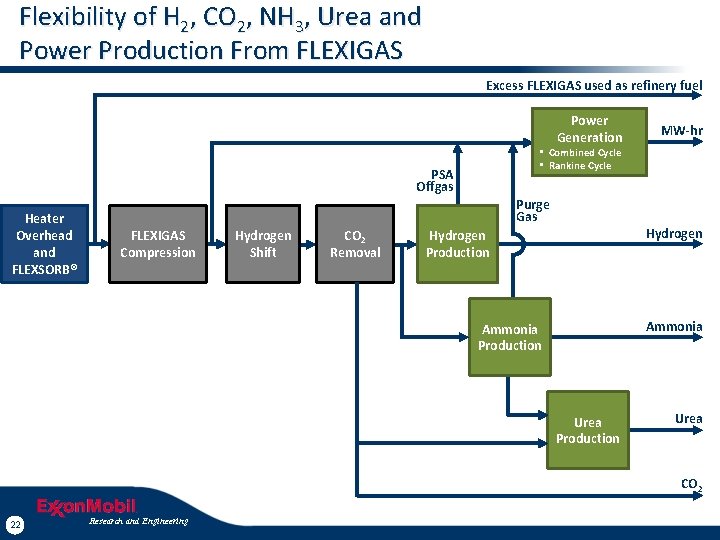
Flexibility of H 2, CO 2, NH 3, Urea and Power Production From FLEXIGAS Excess FLEXIGAS used as refinery fuel Power Generation • Combined Cycle • Rankine Cycle PSA Offgas Heater Overhead and FLEXSORB® MW-hr Purge Gas FLEXIGAS Compression Hydrogen Shift CO 2 Removal Hydrogen Production Ammonia Production Urea CO 2 22 Research and Engineering
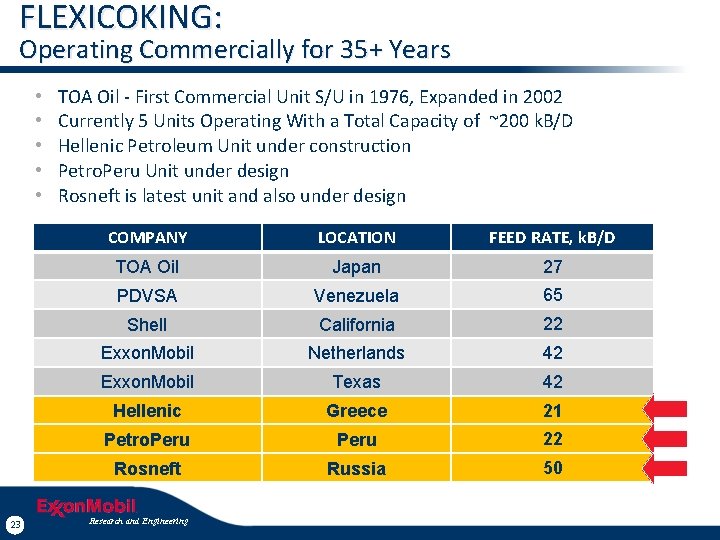
FLEXICOKING: Operating Commercially for 35+ Years • • • 23 TOA Oil - First Commercial Unit S/U in 1976, Expanded in 2002 Currently 5 Units Operating With a Total Capacity of ~200 k. B/D Hellenic Petroleum Unit under construction Petro. Peru Unit under design Rosneft is latest unit and also under design COMPANY LOCATION FEED RATE, k. B/D TOA Oil Japan 27 PDVSA Venezuela 65 Shell California 22 Exxon. Mobil Netherlands 42 Exxon. Mobil Texas 42 Hellenic Greece 21 Petro. Peru 22 Rosneft Russia 50 Research and Engineering
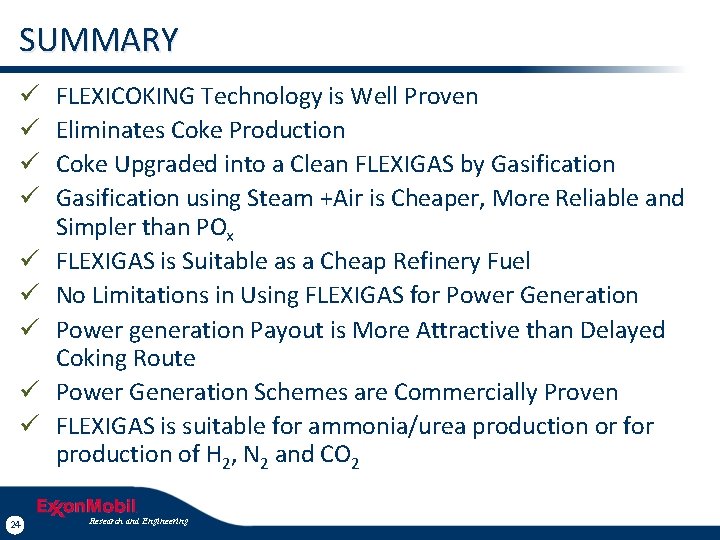
SUMMARY ü ü ü ü ü 24 FLEXICOKING Technology is Well Proven Eliminates Coke Production Coke Upgraded into a Clean FLEXIGAS by Gasification using Steam +Air is Cheaper, More Reliable and Simpler than POx FLEXIGAS is Suitable as a Cheap Refinery Fuel No Limitations in Using FLEXIGAS for Power Generation Power generation Payout is More Attractive than Delayed Coking Route Power Generation Schemes are Commercially Proven FLEXIGAS is suitable for ammonia/urea production or for production of H 2, N 2 and CO 2 Research and Engineering
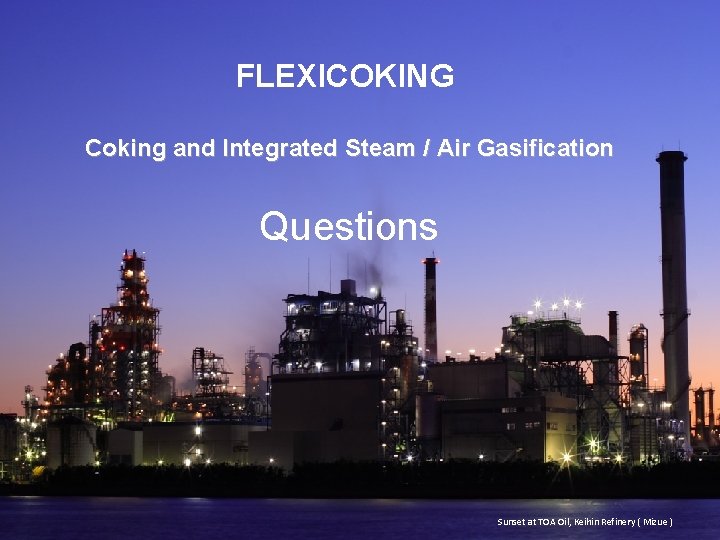
FLEXICOKING Coking and Integrated Steam / Air Gasification Questions 25 Research and Engineering Sunset at TOA Oil, Keihin Refinery ( Mizue )
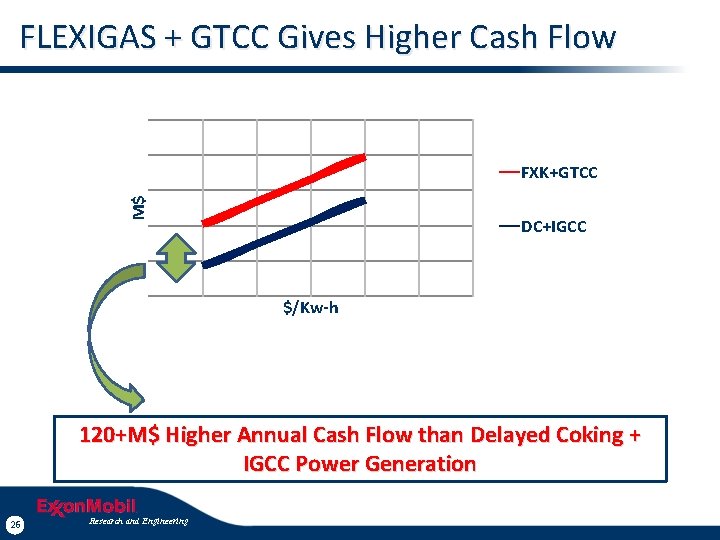
FLEXIGAS + GTCC Gives Higher Cash Flow M$ FXK+GTCC DC+IGCC $/Kw-h 120+M$ Higher Annual Cash Flow than Delayed Coking + IGCC Power Generation 26 Research and Engineering
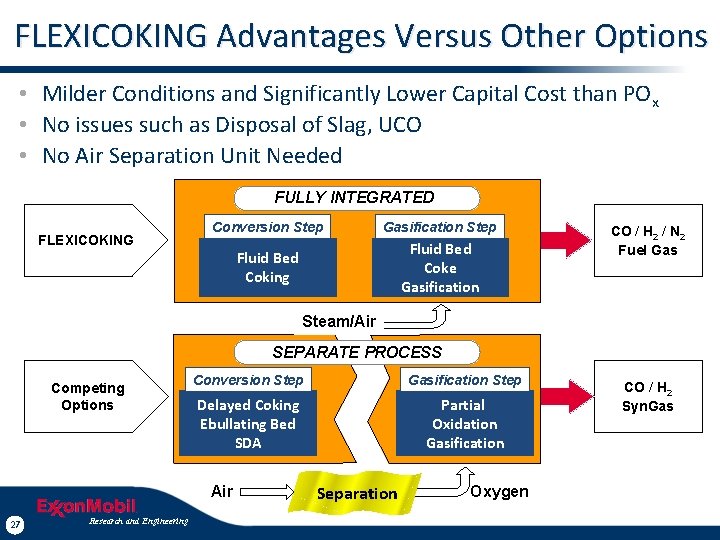
FLEXICOKING Advantages Versus Other Options • Milder Conditions and Significantly Lower Capital Cost than POx • No issues such as Disposal of Slag, UCO • No Air Separation Unit Needed FULLY INTEGRATED FLEXICOKING Conversion Step Gasification Step Fluid Bed Coking Fluid Bed Coke Gasification CO / H 2 / N 2 Fuel Gas Steam/Air SEPARATE PROCESS Competing Options Conversion Step Gasification Step Delayed Coking Ebullating Bed SDA Partial Oxidation Gasification Air 27 Research and Engineering Separation Oxygen CO / H 2 Syn. Gas
Flexicoking
Environmentally friendly pickling
Upgrading rhel 6 to 7
Economically speaking
Environmentally safe refrigerant service tips & techniques
Temperature glide
Characteristics of environmentally sustainable business
Environmentally sound drilling practices
Asean working group on environmentally sustainable cities
What is environmentally critical areas
Intermolecular forces in water
Target market attractiveness
Seven domains of attractive opportunities
Mullins seven domains model
Attractive meaning
Attractive sce
Attractive force
Good/well comparative and superlative
The seven domains of attractive opportunities
Which of the following parsers is the most powerful ?
Imfs
Attractive forces
Attractive forces
Business letter vs friendly letter
Combining normal random variables
Comparative superlative well
Clever portl
Disapprobation in to kill a mockingbird
Friendly business letter format