DTTDRM02 Design Review Meeting Frascati 14 March 2019
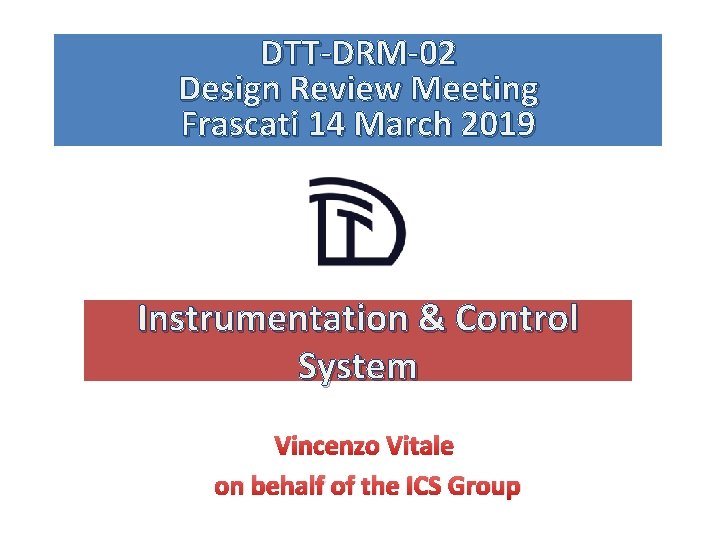
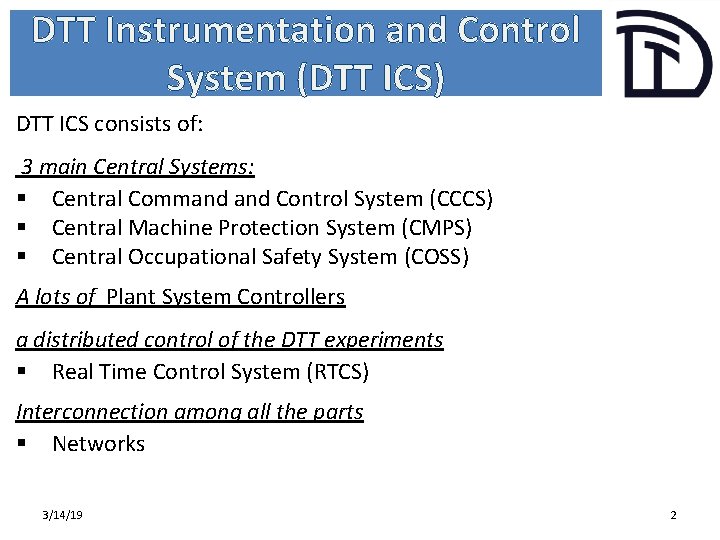
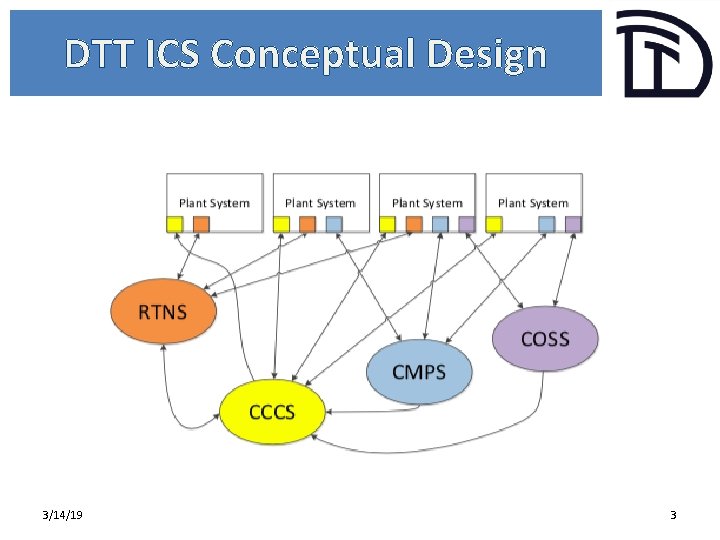
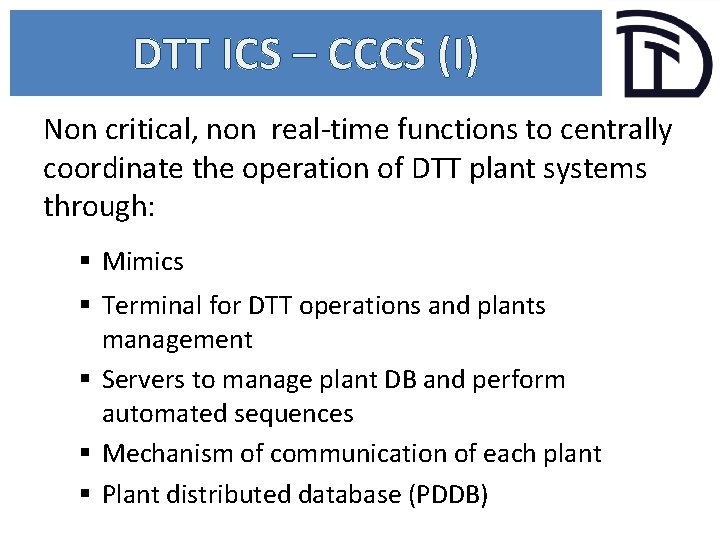
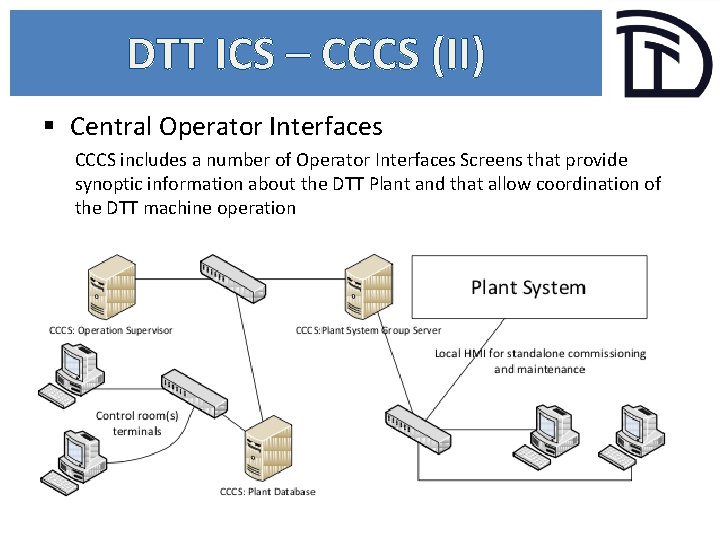
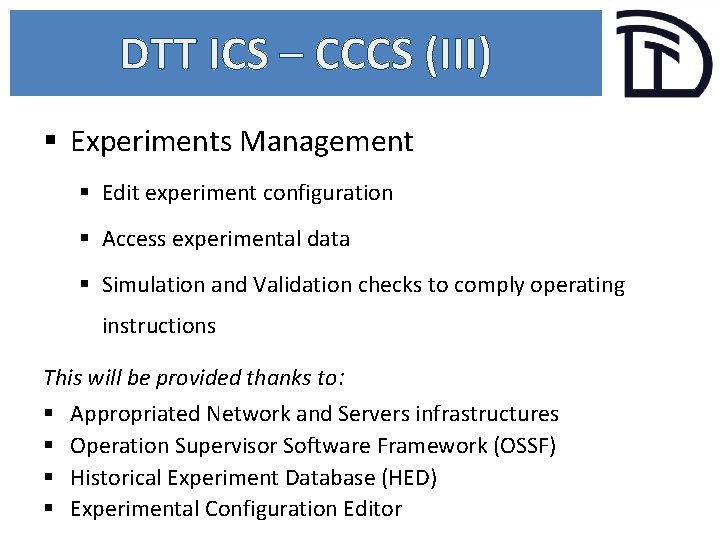
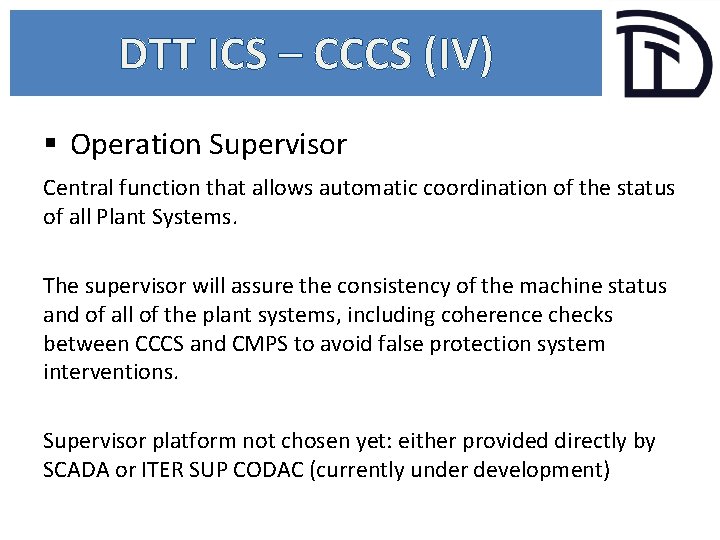
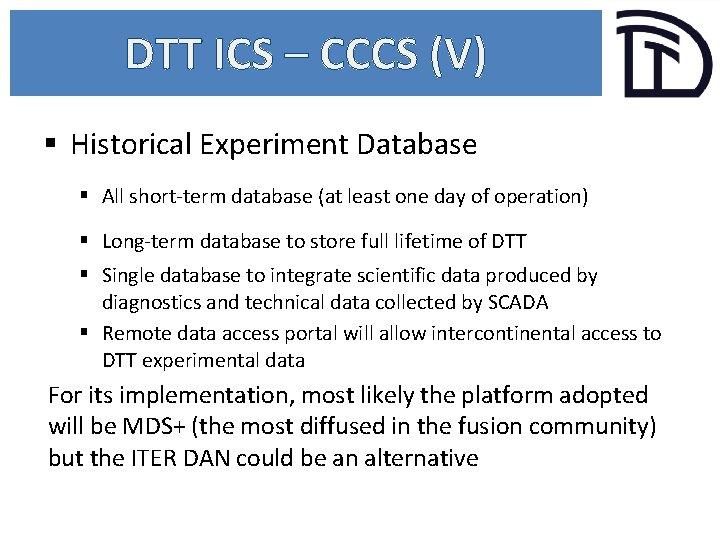
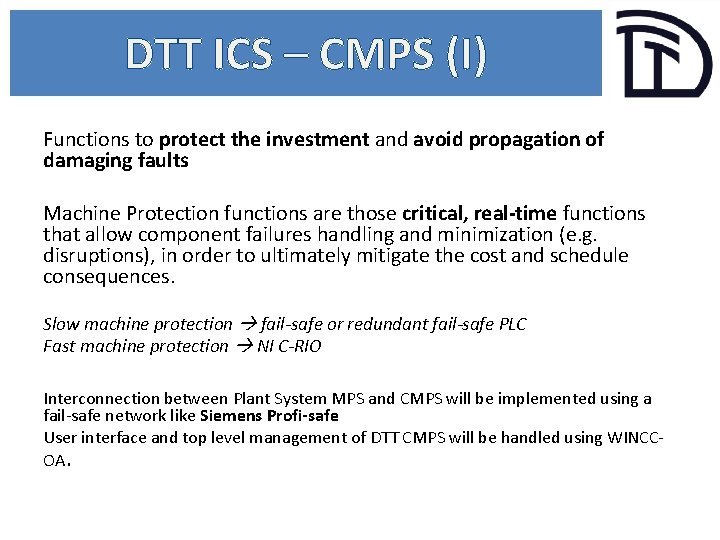
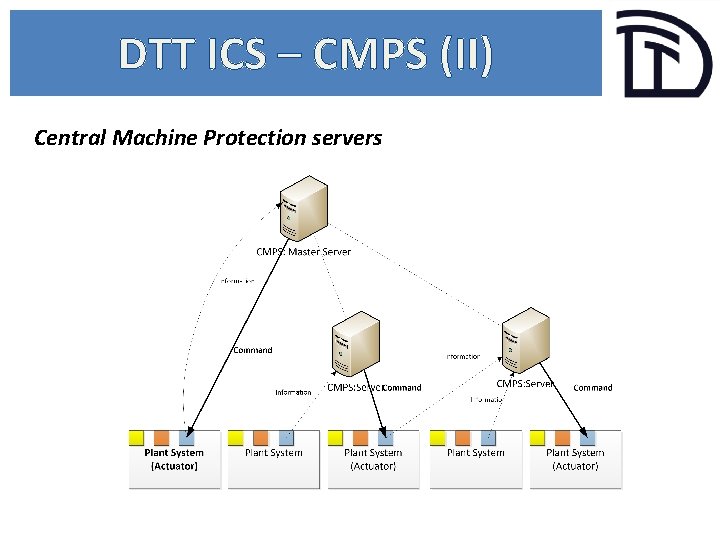
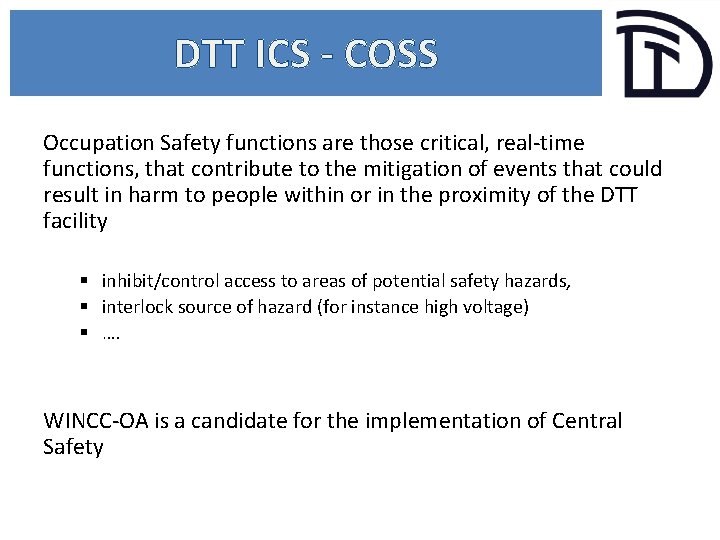

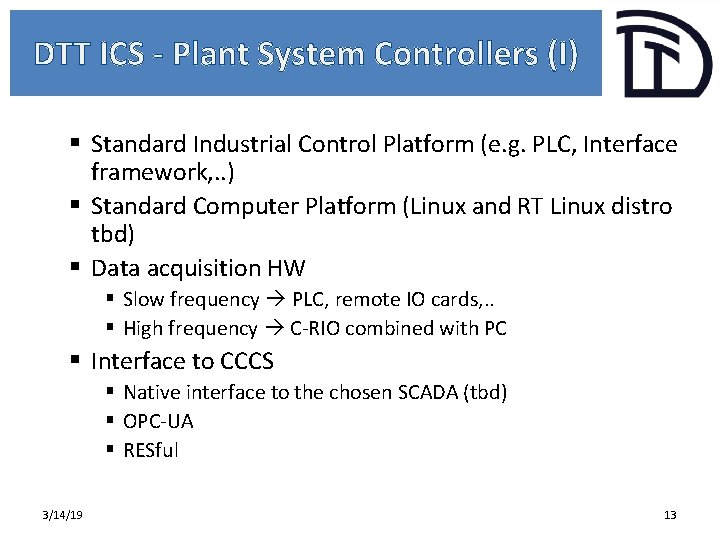
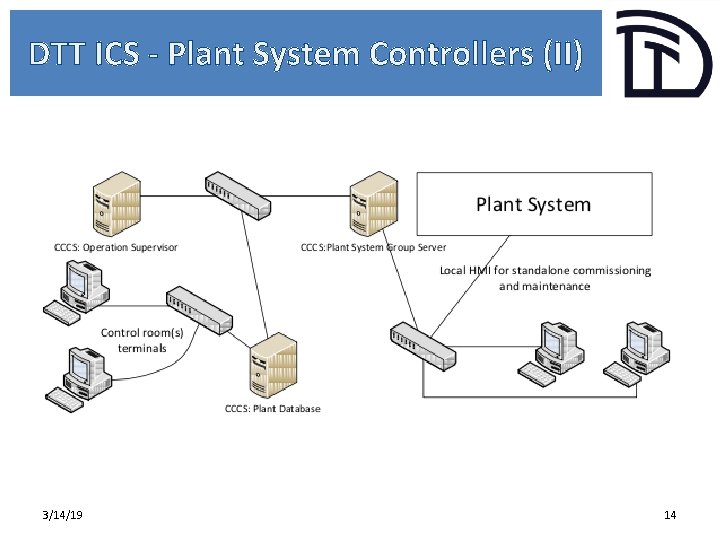
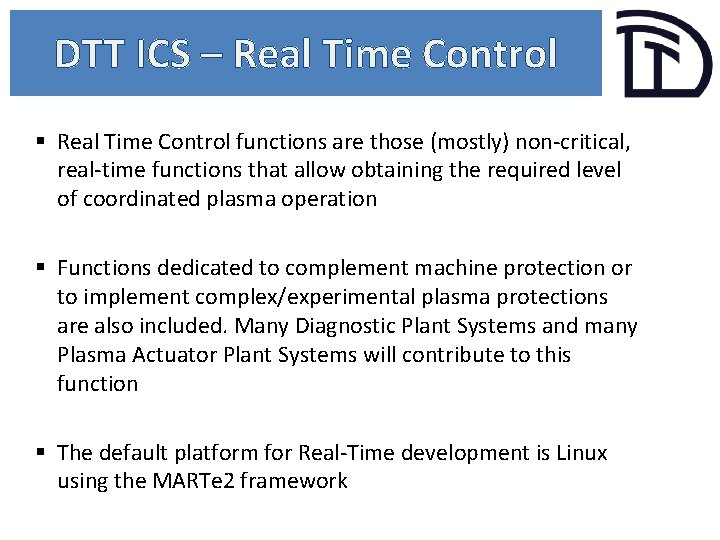
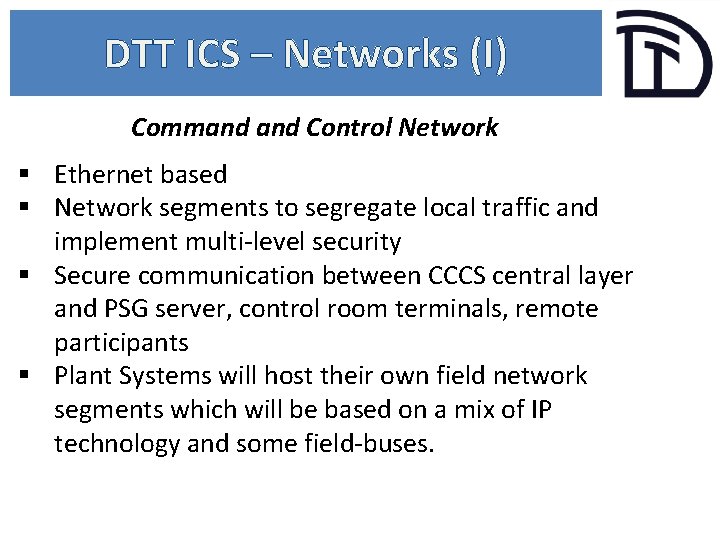
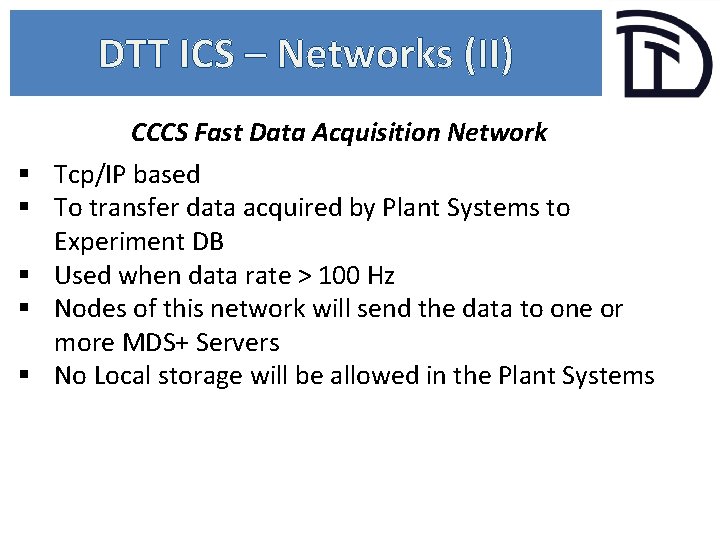

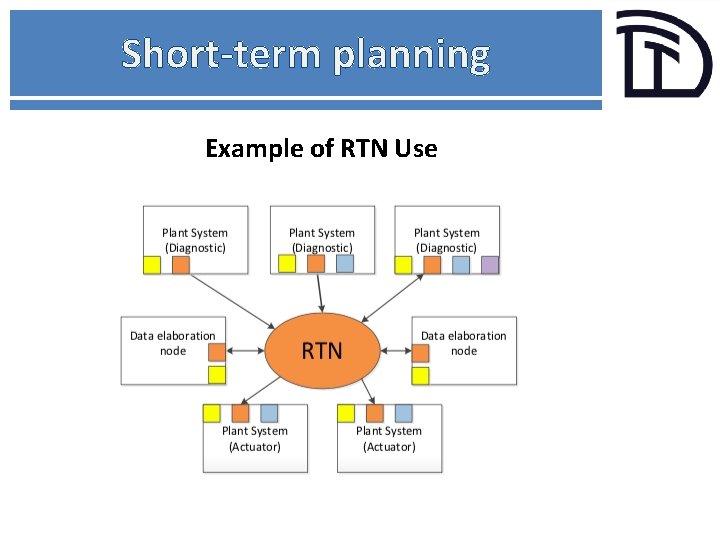
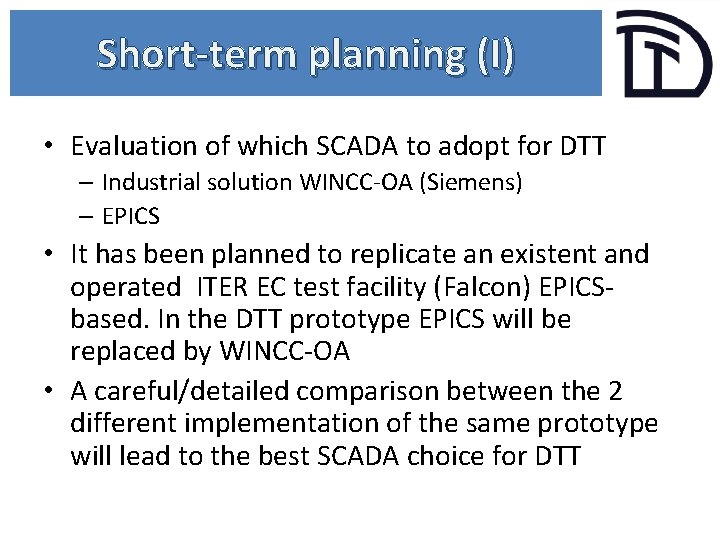
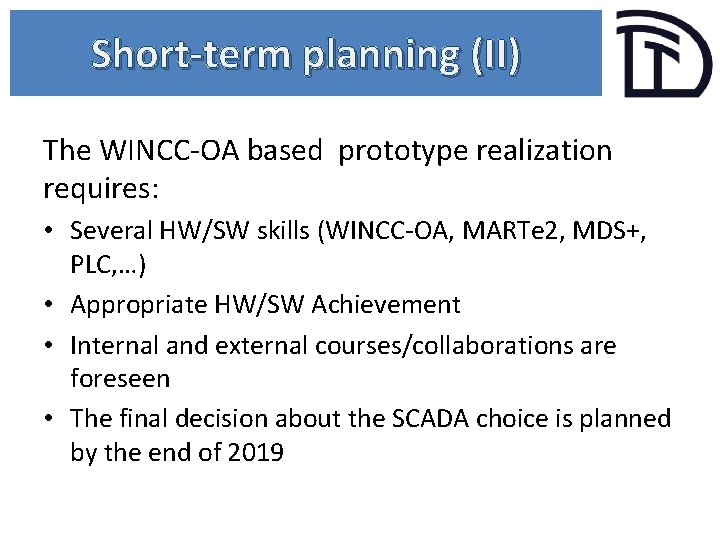
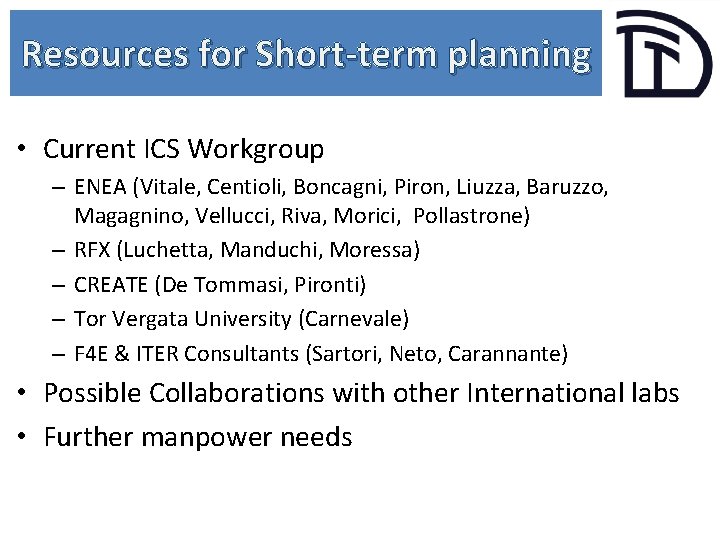
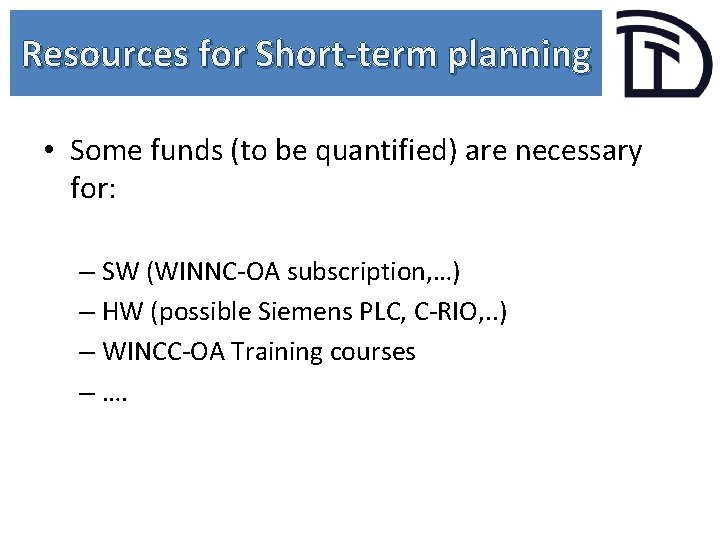
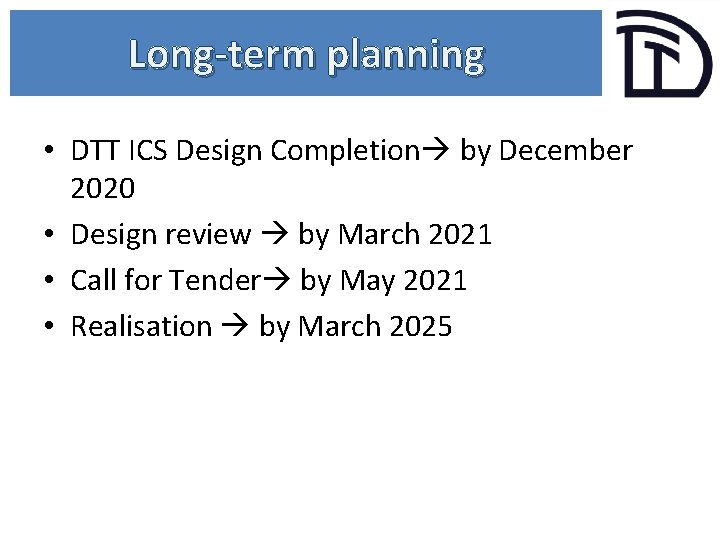
- Slides: 24
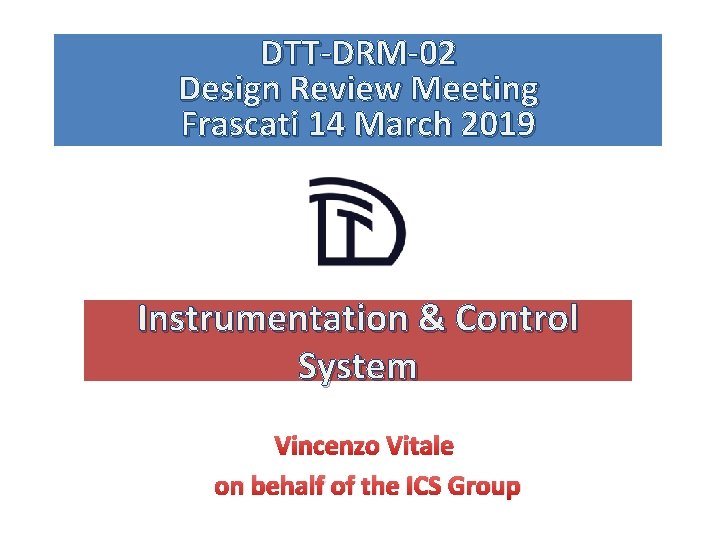
DTT-DRM-02 Design Review Meeting Frascati 14 March 2019 Instrumentation & Control System Vincenzo Vitale on behalf of the ICS Group
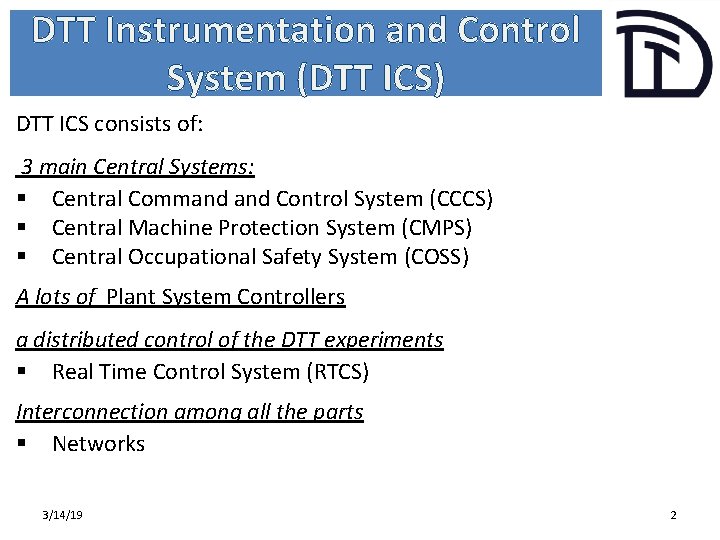
DTT Instrumentation and Control System (DTT ICS) DTT ICS consists of: 3 main Central Systems: § Central Command Control System (CCCS) § Central Machine Protection System (CMPS) § Central Occupational Safety System (COSS) A lots of Plant System Controllers a distributed control of the DTT experiments § Real Time Control System (RTCS) Interconnection among all the parts § Networks 3/14/19 2
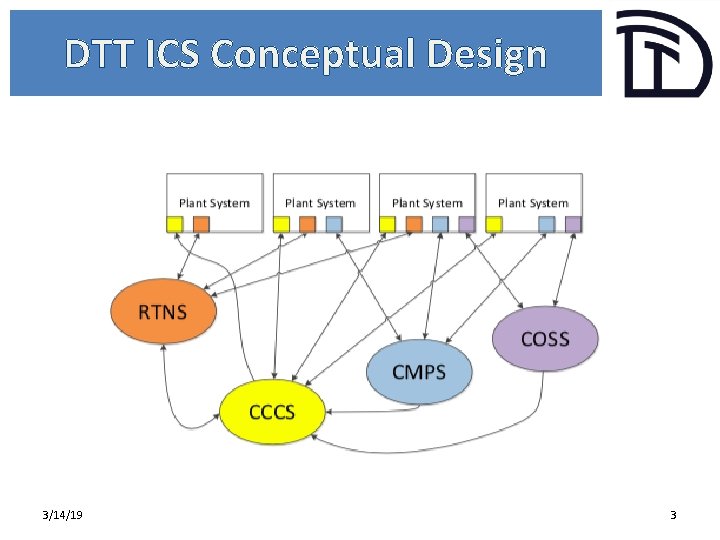
DTT ICS Conceptual Design 3/14/19 3
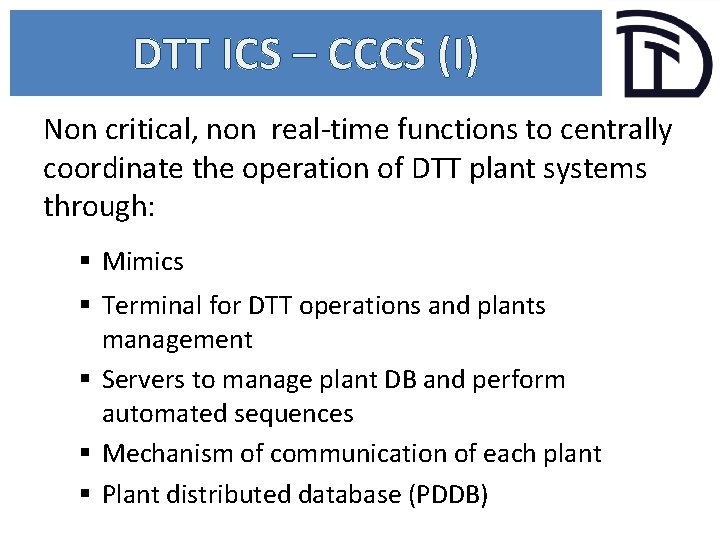
DTT ICS – CCCS (I) Non critical, non real-time functions to centrally coordinate the operation of DTT plant systems through: § Mimics § Terminal for DTT operations and plants management § Servers to manage plant DB and perform automated sequences § Mechanism of communication of each plant § Plant distributed database (PDDB)
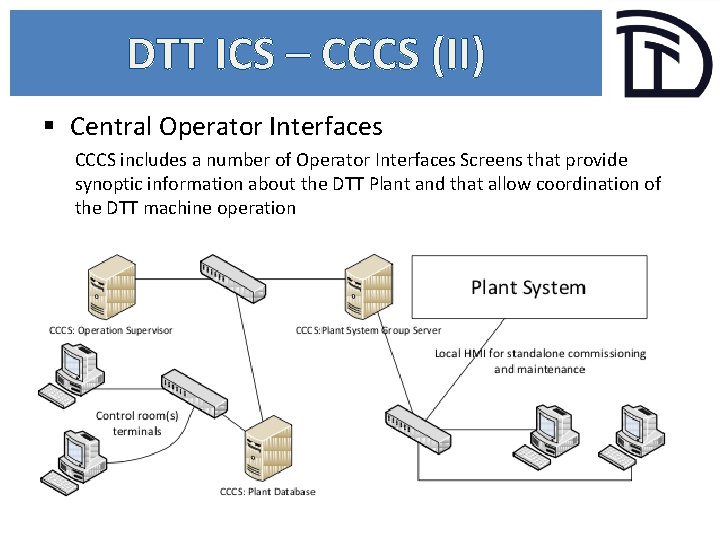
DTT ICS – CCCS (II) § Central Operator Interfaces CCCS includes a number of Operator Interfaces Screens that provide synoptic information about the DTT Plant and that allow coordination of the DTT machine operation
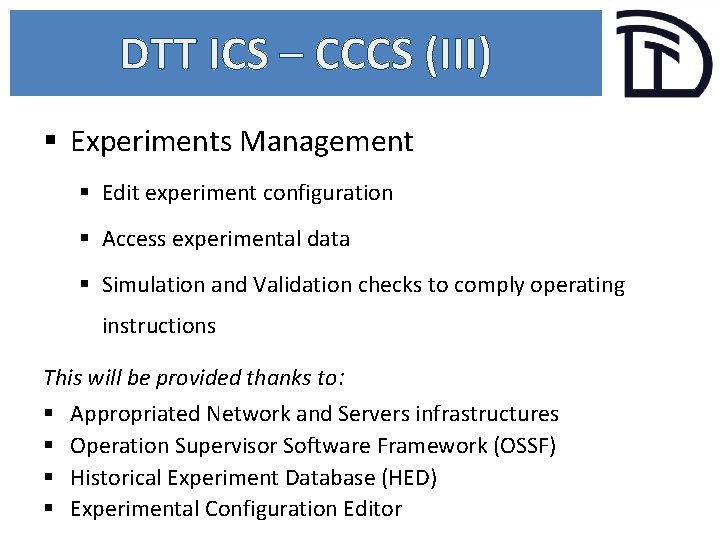
DTT ICS – CCCS (III) § Experiments Management § Edit experiment configuration § Access experimental data § Simulation and Validation checks to comply operating instructions This will be provided thanks to: § § Appropriated Network and Servers infrastructures Operation Supervisor Software Framework (OSSF) Historical Experiment Database (HED) Experimental Configuration Editor
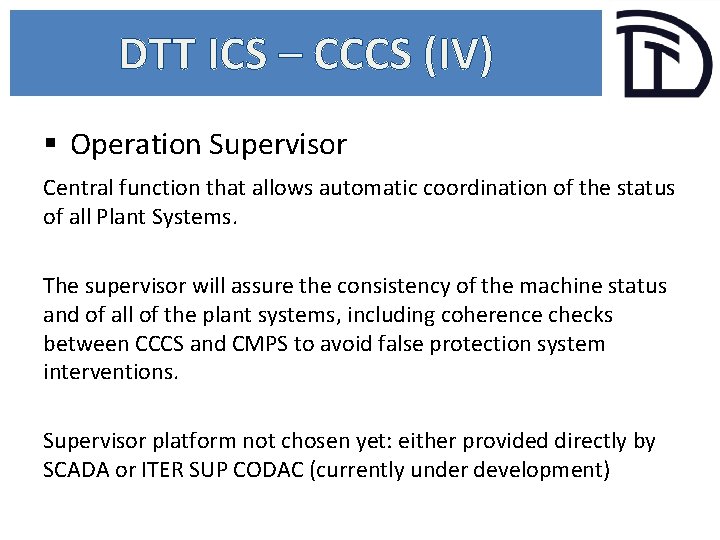
DTT ICS – CCCS (IV) § Operation Supervisor Central function that allows automatic coordination of the status of all Plant Systems. The supervisor will assure the consistency of the machine status and of all of the plant systems, including coherence checks between CCCS and CMPS to avoid false protection system interventions. Supervisor platform not chosen yet: either provided directly by SCADA or ITER SUP CODAC (currently under development)
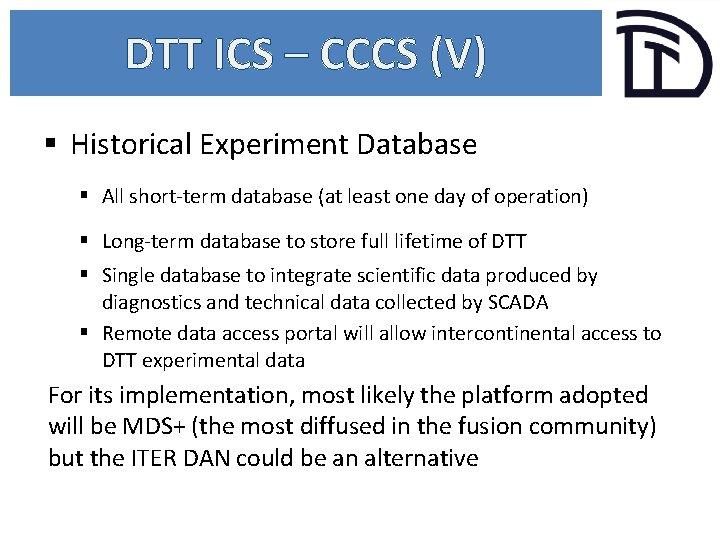
DTT ICS – CCCS (V) § Historical Experiment Database § All short-term database (at least one day of operation) § Long-term database to store full lifetime of DTT § Single database to integrate scientific data produced by diagnostics and technical data collected by SCADA § Remote data access portal will allow intercontinental access to DTT experimental data For its implementation, most likely the platform adopted will be MDS+ (the most diffused in the fusion community) but the ITER DAN could be an alternative
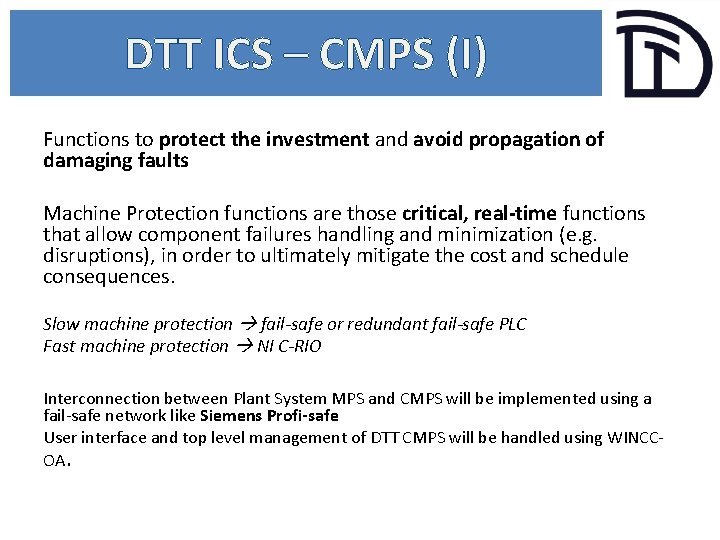
DTT ICS – CMPS (I) Functions to protect the investment and avoid propagation of damaging faults Machine Protection functions are those critical, real-time functions that allow component failures handling and minimization (e. g. disruptions), in order to ultimately mitigate the cost and schedule consequences. Slow machine protection fail-safe or redundant fail-safe PLC Fast machine protection NI C-RIO Interconnection between Plant System MPS and CMPS will be implemented using a fail-safe network like Siemens Profi-safe User interface and top level management of DTT CMPS will be handled using WINCCOA.
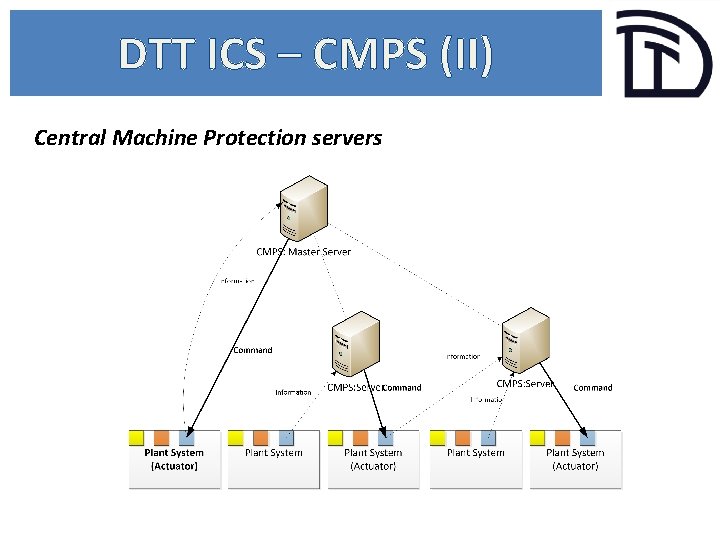
DTT ICS – CMPS (II) Central Machine Protection servers
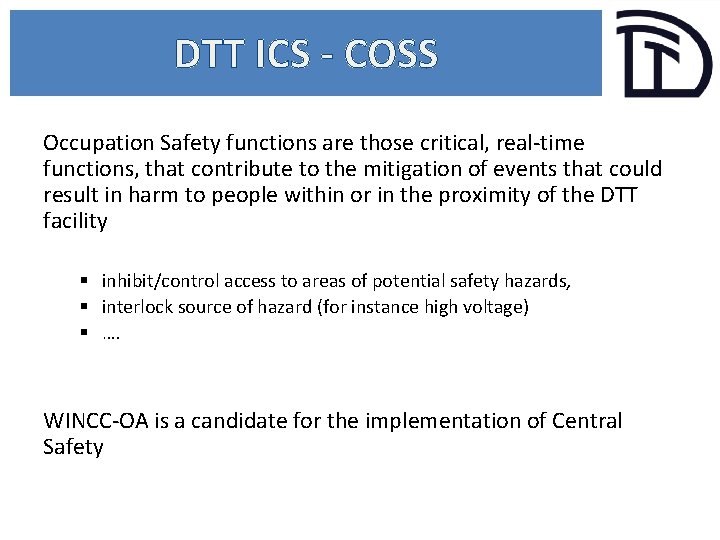
DTT ICS - COSS Occupation Safety functions are those critical, real-time functions, that contribute to the mitigation of events that could result in harm to people within or in the proximity of the DTT facility § inhibit/control access to areas of potential safety hazards, § interlock source of hazard (for instance high voltage) § …. WINCC-OA is a candidate for the implementation of Central Safety

DTT ICS – CCCS, CMPS and CCOS Interrelations • CCCS CMPS and COSS are not isolated systems. CCCS can trigger protection functions in CMPS. COSS will notify CMPS of initiating safety actions. Similarly CMPS will notify CCCS of having started a machine protection action. • COSS is owner of the Long Term Operation State of DTT and will make the information available to all central Systems. CMPS is owner of Pulse Operation State and will communicate it to the CCCS fromto CCCS CMPS Provides Pulse state notifies protection actions COSS Provides Long Term Op state CMPS COSS can trigger NC NC Provides Long Term Op state notifies protection actions
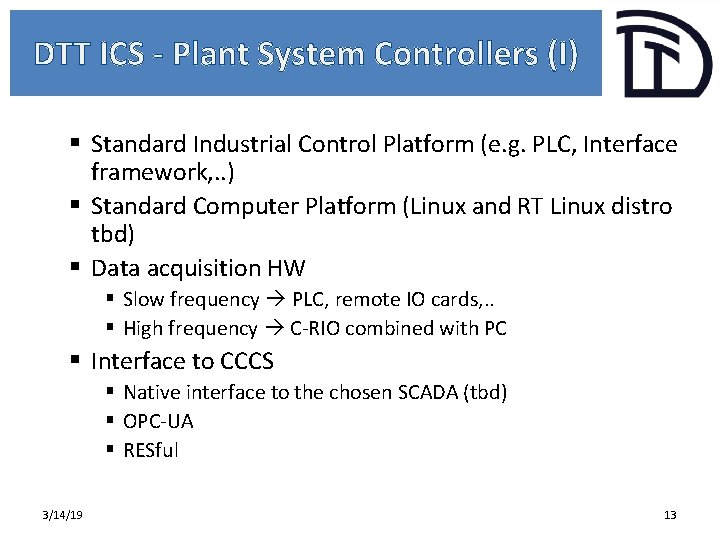
DTT ICS - Plant System Controllers (I) § Standard Industrial Control Platform (e. g. PLC, Interface framework, . . ) § Standard Computer Platform (Linux and RT Linux distro tbd) § Data acquisition HW § Slow frequency PLC, remote IO cards, . . § High frequency C-RIO combined with PC § Interface to CCCS § Native interface to the chosen SCADA (tbd) § OPC-UA § RESful 3/14/19 13
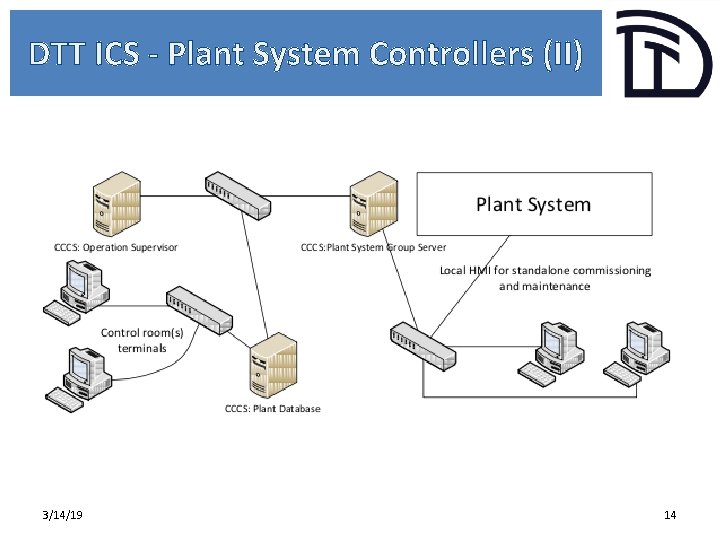
DTT ICS - Plant System Controllers (II) 3/14/19 14
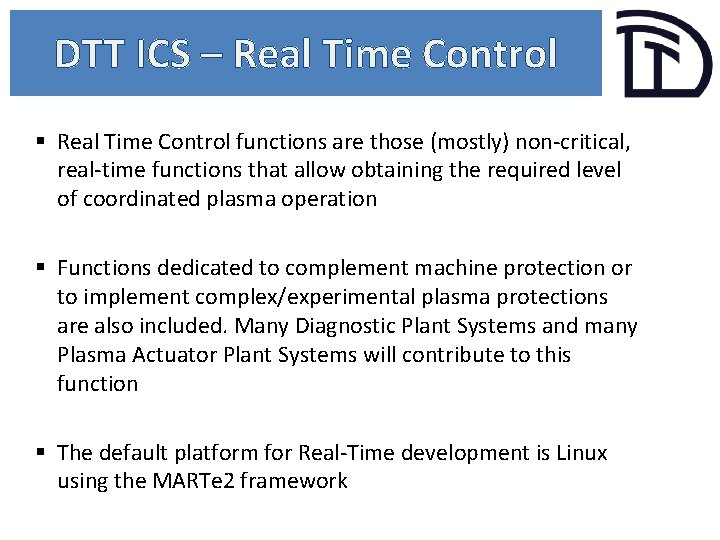
DTT ICS – Real Time Control § Real Time Control functions are those (mostly) non-critical, real-time functions that allow obtaining the required level of coordinated plasma operation § Functions dedicated to complement machine protection or to implement complex/experimental plasma protections are also included. Many Diagnostic Plant Systems and many Plasma Actuator Plant Systems will contribute to this function § The default platform for Real-Time development is Linux using the MARTe 2 framework
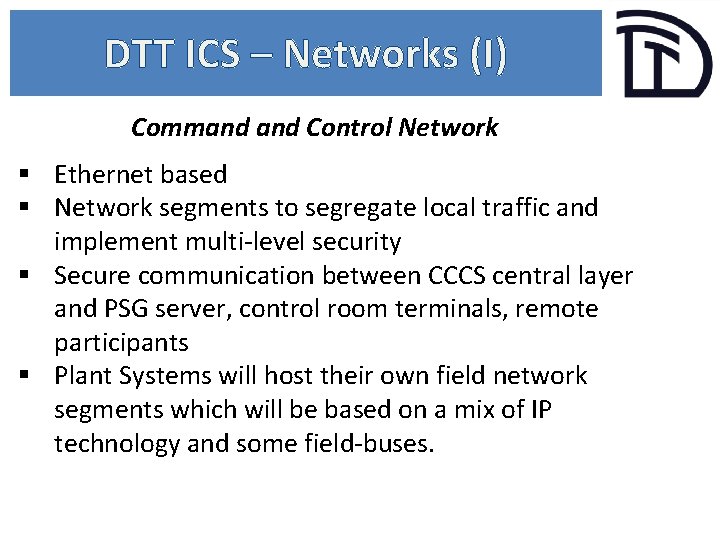
DTT ICS – Networks (I) Command Control Network § Ethernet based § Network segments to segregate local traffic and implement multi-level security § Secure communication between CCCS central layer and PSG server, control room terminals, remote participants § Plant Systems will host their own field network segments which will be based on a mix of IP technology and some field-buses.
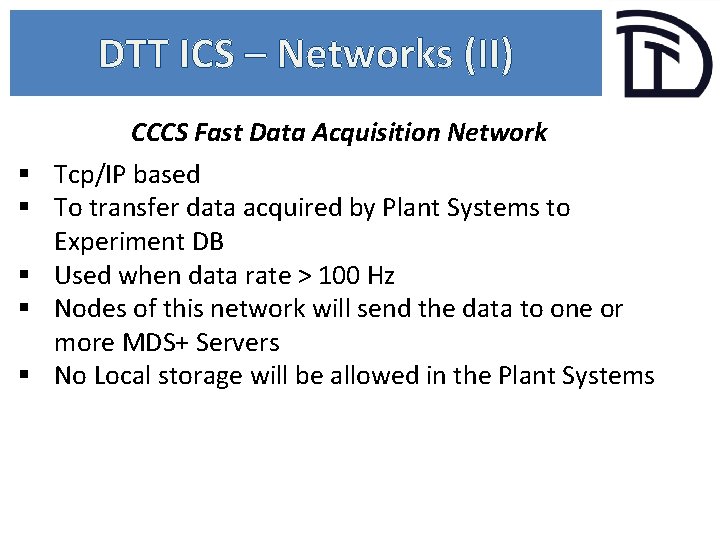
DTT ICS – Networks (II) § § § CCCS Fast Data Acquisition Network Tcp/IP based To transfer data acquired by Plant Systems to Experiment DB Used when data rate > 100 Hz Nodes of this network will send the data to one or more MDS+ Servers No Local storage will be allowed in the Plant Systems

DTT ICS – Networks (III) § § Real Time Network Communication mechanism among real-time systems Based on Gb. E and on point to multipoint (MULTICAST) User Datagram Protocol (UDP) mechanism communication Is implemented using a managed switched multi-star network topology Nodes No particular technical hardware or software platforms imposed on the Plant System
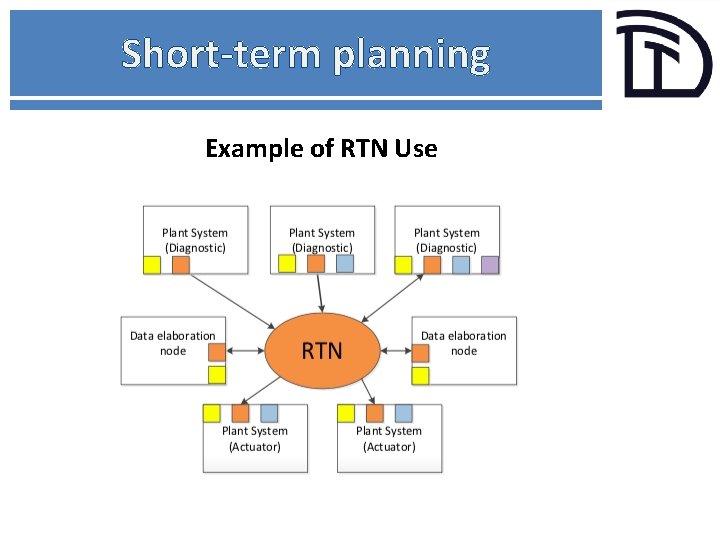
Short-term planning DTT ICS – Networks (IV) Example of RTN Use
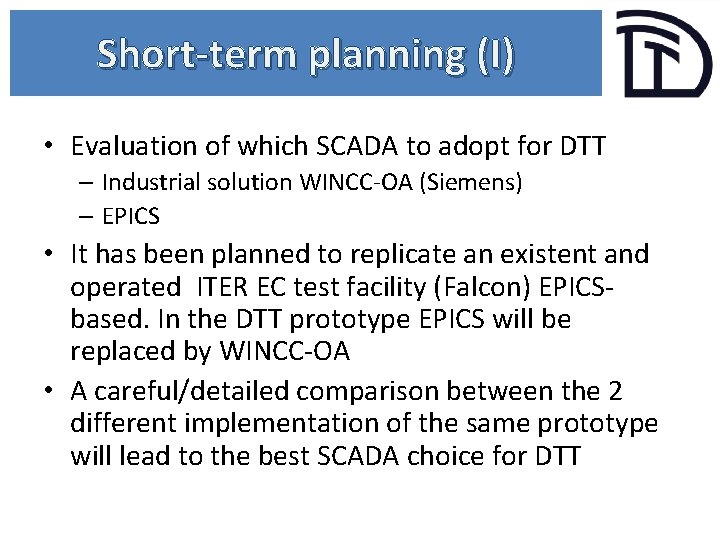
Short-term planning (I) • Evaluation of which SCADA to adopt for DTT – Industrial solution WINCC-OA (Siemens) – EPICS • It has been planned to replicate an existent and operated ITER EC test facility (Falcon) EPICSbased. In the DTT prototype EPICS will be replaced by WINCC-OA • A careful/detailed comparison between the 2 different implementation of the same prototype will lead to the best SCADA choice for DTT
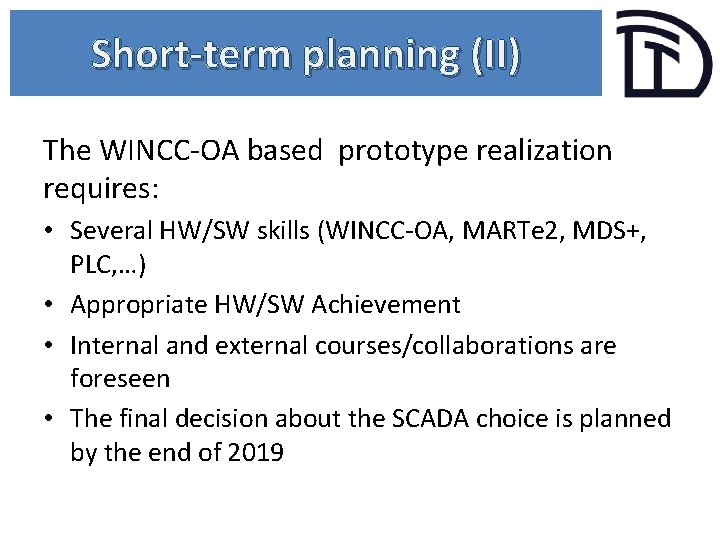
Short-term planning (II) The WINCC-OA based prototype realization requires: • Several HW/SW skills (WINCC-OA, MARTe 2, MDS+, PLC, …) • Appropriate HW/SW Achievement • Internal and external courses/collaborations are foreseen • The final decision about the SCADA choice is planned by the end of 2019
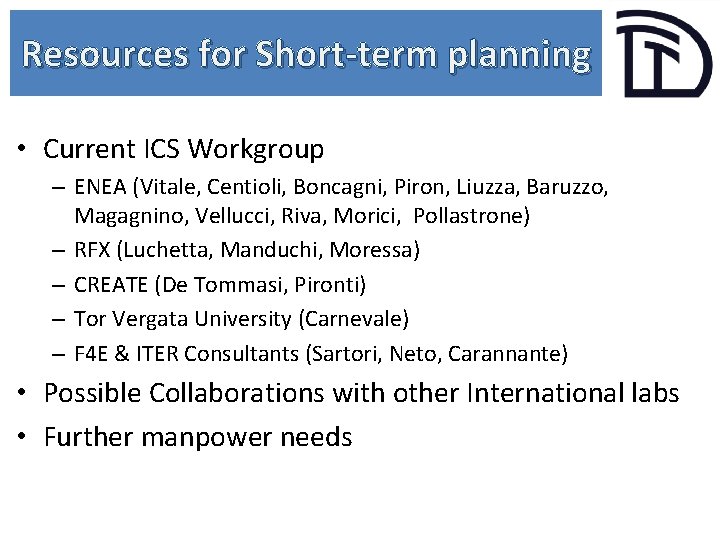
Resources for Short-term planning • Current ICS Workgroup – ENEA (Vitale, Centioli, Boncagni, Piron, Liuzza, Baruzzo, Magagnino, Vellucci, Riva, Morici, Pollastrone) – RFX (Luchetta, Manduchi, Moressa) – CREATE (De Tommasi, Pironti) – Tor Vergata University (Carnevale) – F 4 E & ITER Consultants (Sartori, Neto, Carannante) • Possible Collaborations with other International labs • Further manpower needs
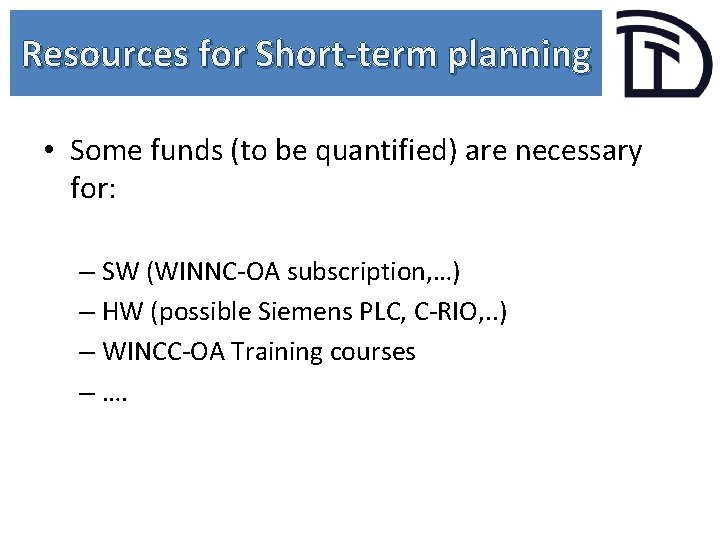
Resources for Short-term planning • Some funds (to be quantified) are necessary for: – SW (WINNC-OA subscription, …) – HW (possible Siemens PLC, C-RIO, . . ) – WINCC-OA Training courses – ….
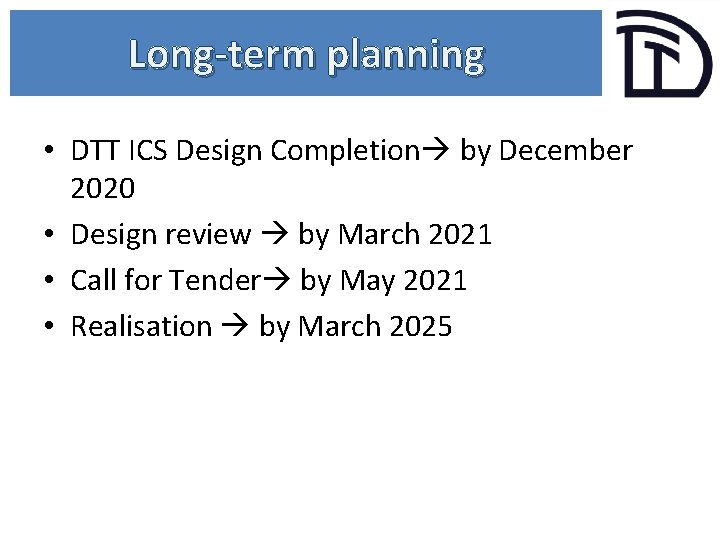
Long-term planning • DTT ICS Design Completion by December 2020 • Design review by March 2021 • Call for Tender by May 2021 • Realisation by March 2025
Poland national anthem lyrics
Grihalakshmi magazine march 2019
Game data crunch
Lnf mensa
Doc phone frascati
Silvio frascati
Bpm frascati
Sae government industry meeting 2019
Nrg oncology meeting 2016
Sae government industry meeting 2019
Nrg oncology conference
Nrg oncology meeting
For todays meeting
Proposal kickoff meeting agenda
What is meeting and types of meeting
What is meeting and types of meeting
Iso 9001 presentation
Team review meeting
Acme corporation strategic plan
Chapter review motion part a vocabulary review answer key
Ap gov review final exam review
Narrative review vs systematic review
Inclusion criteria examples
Narrative review vs systematic review
Cobit 2019 exam questions and answers pdf