Chapter 6 No enterprise can stand aside and
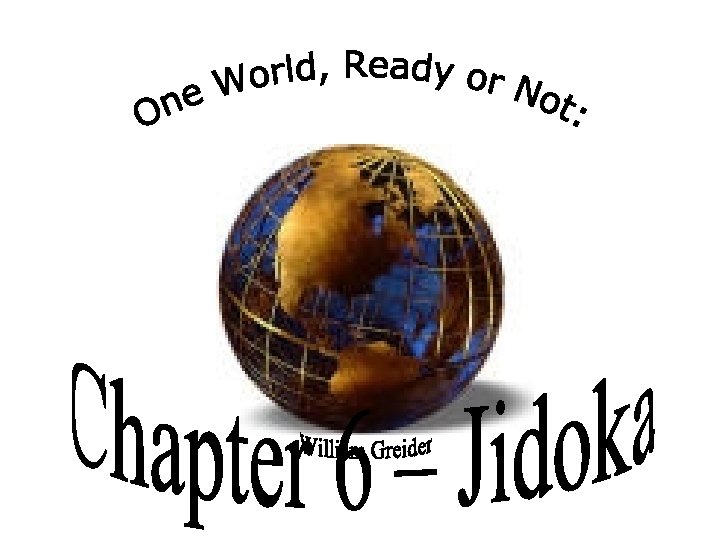
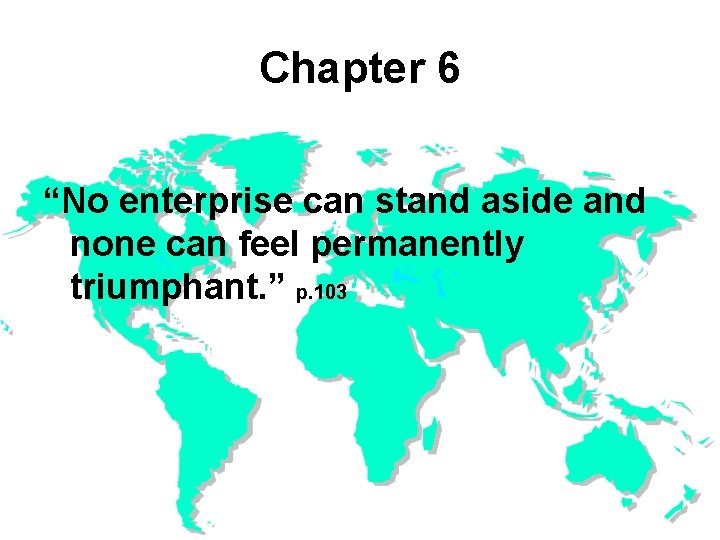
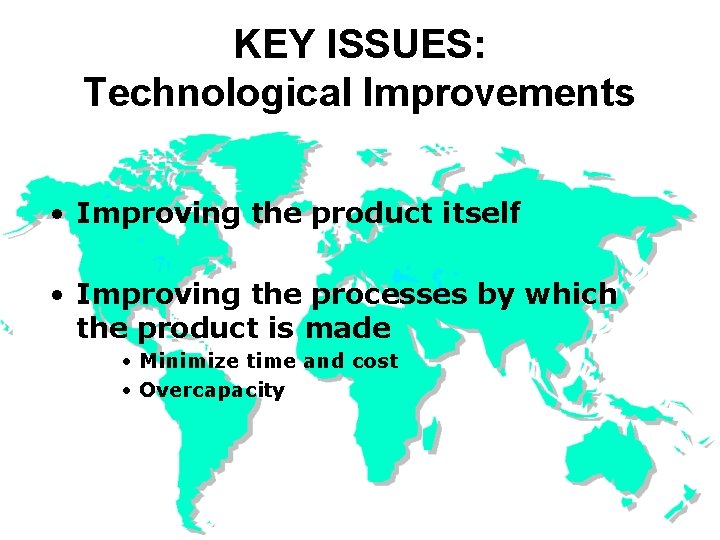
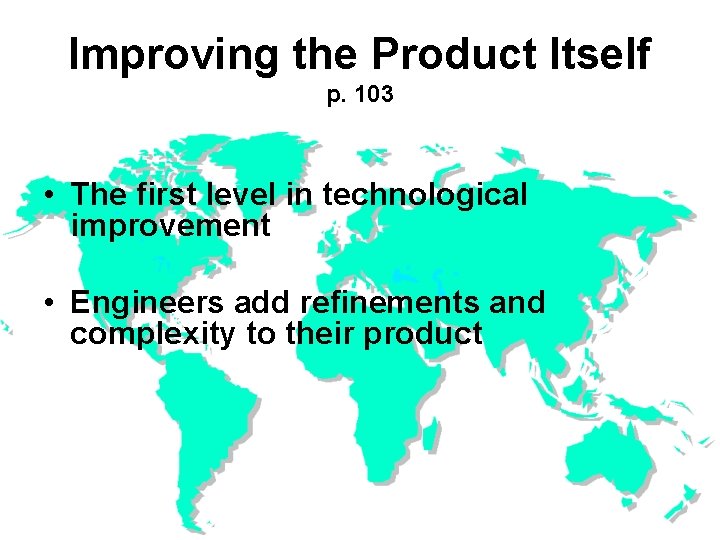
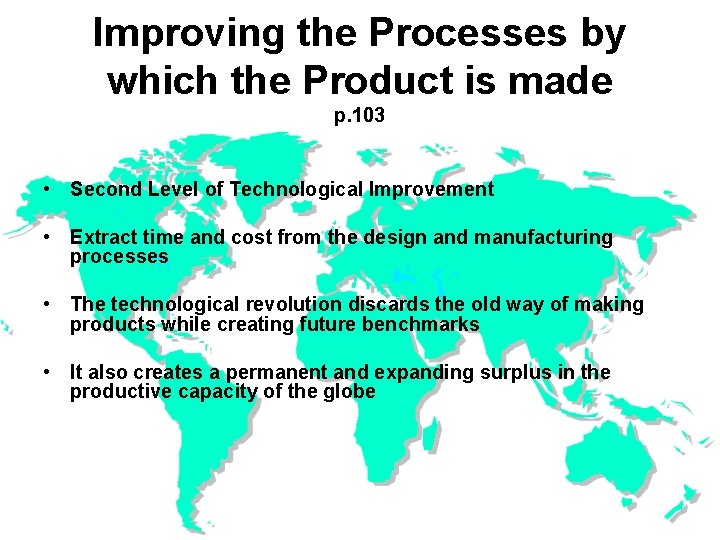
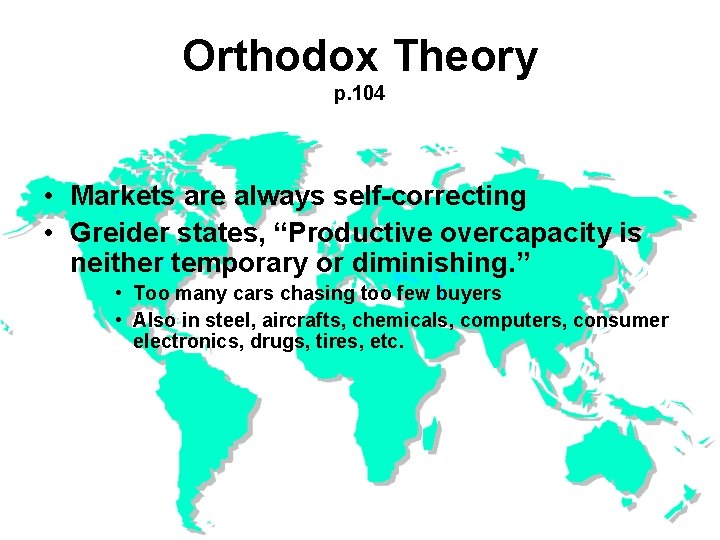
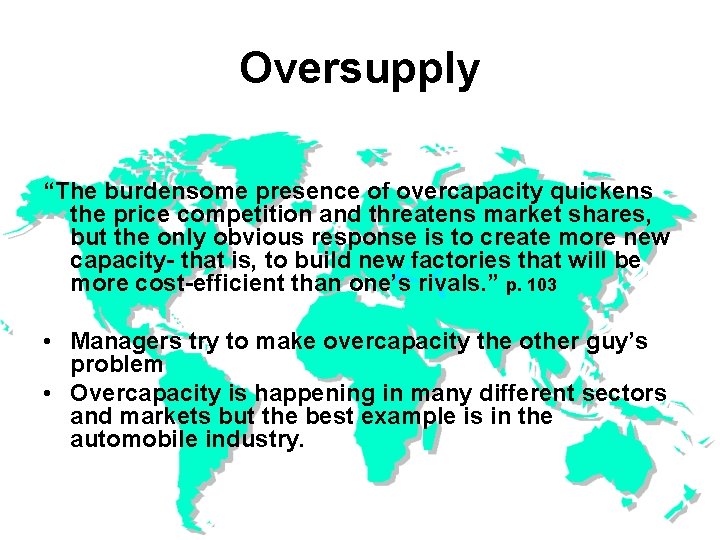
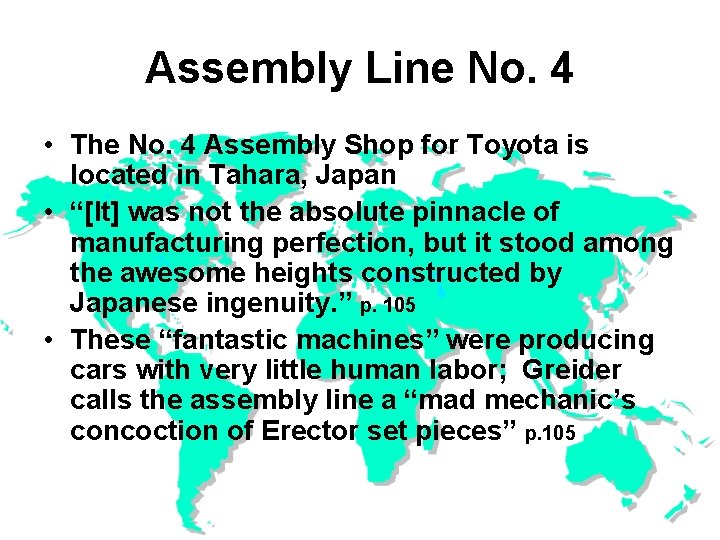
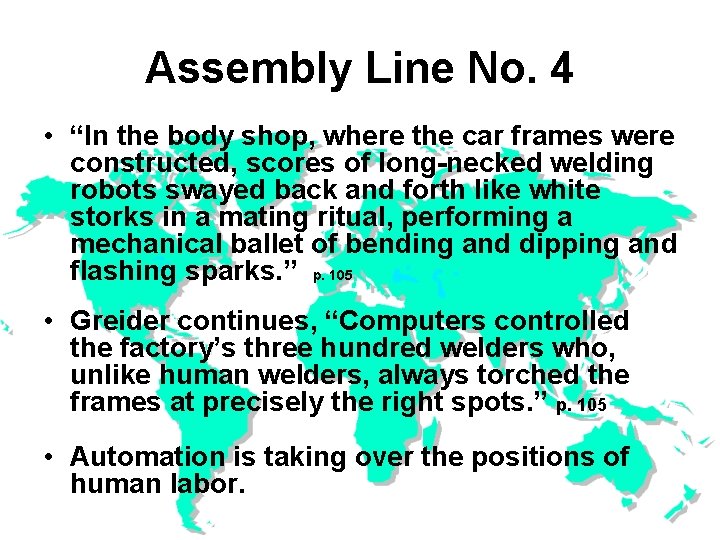
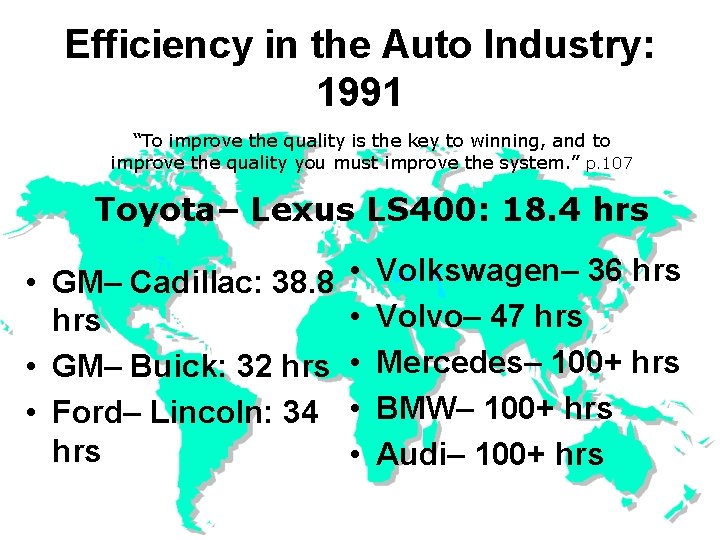
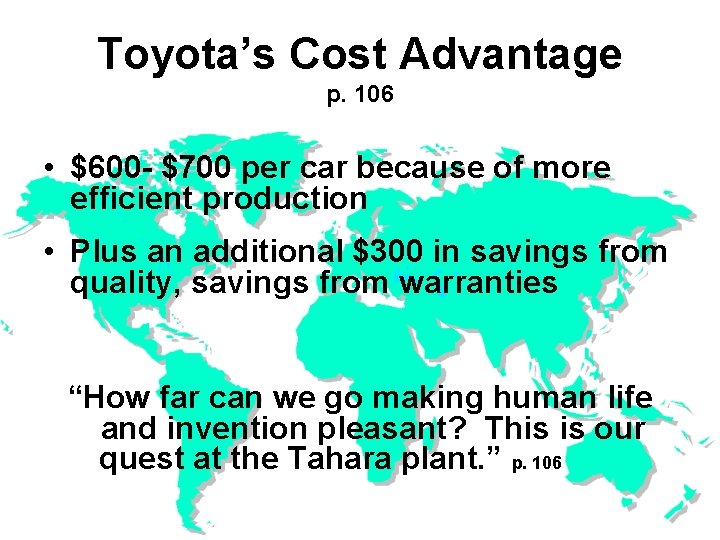
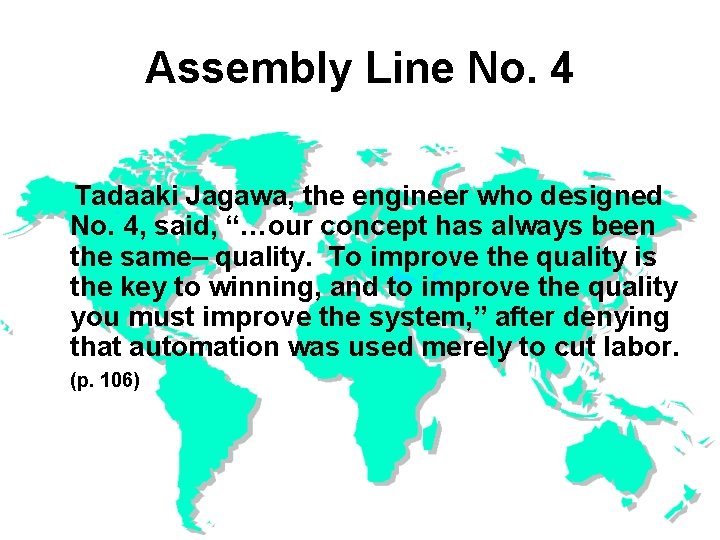
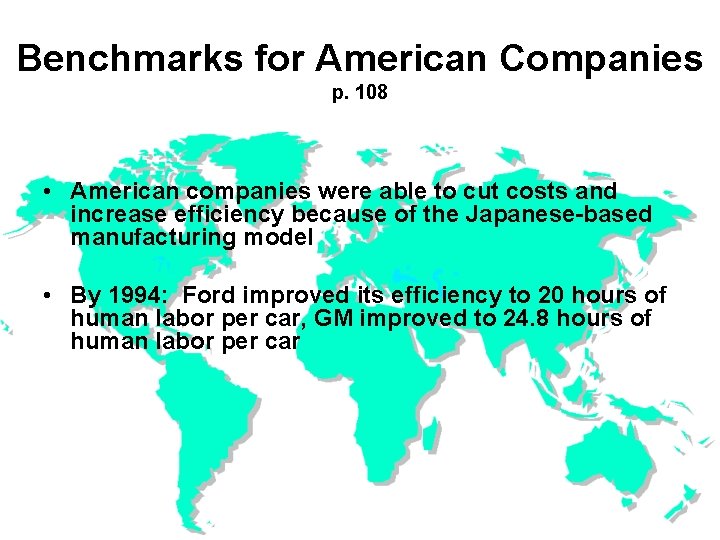
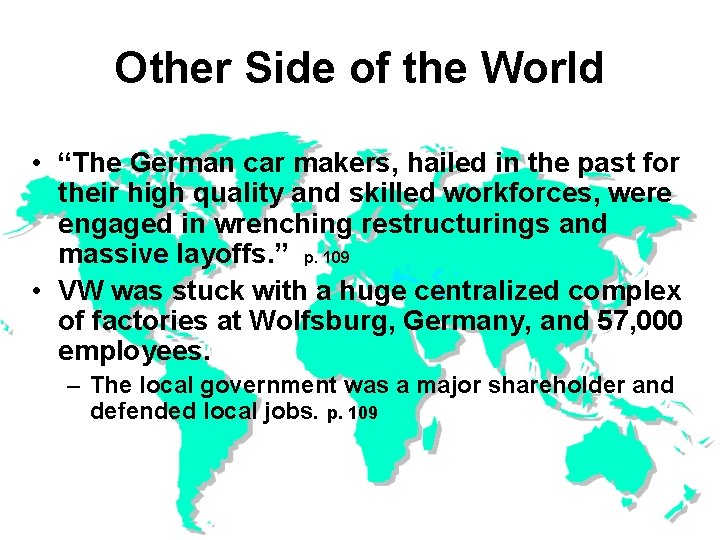

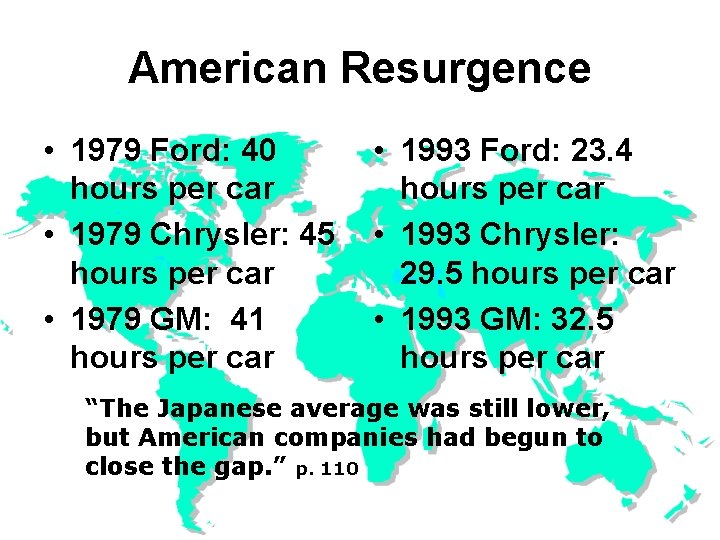
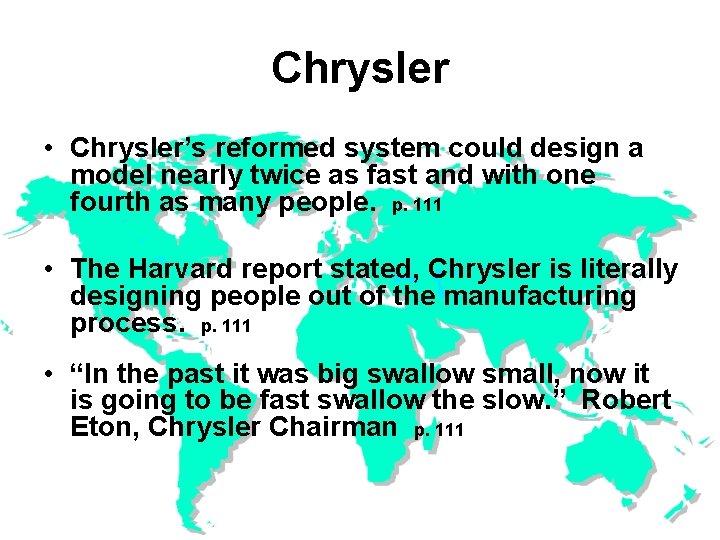
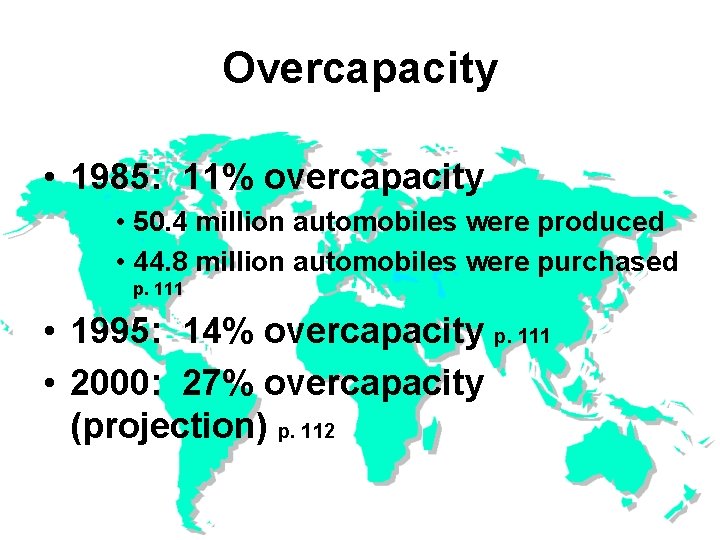
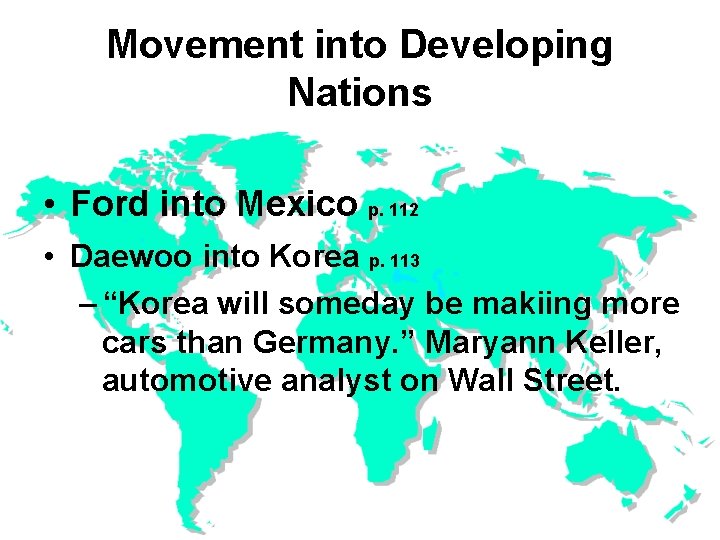
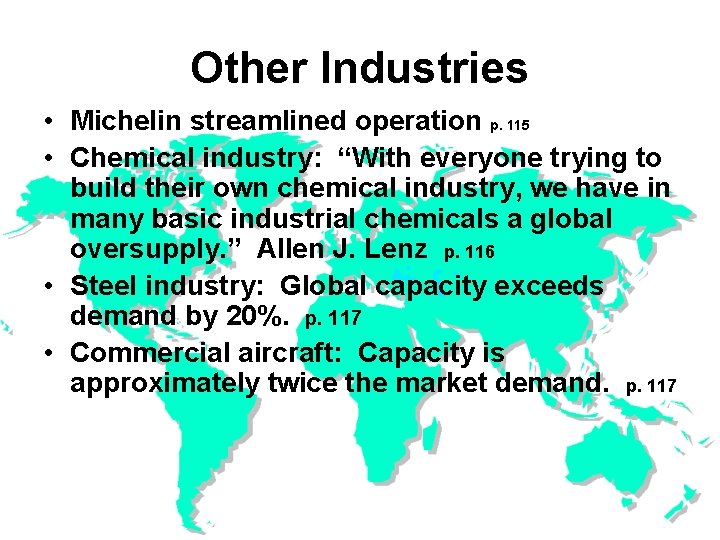
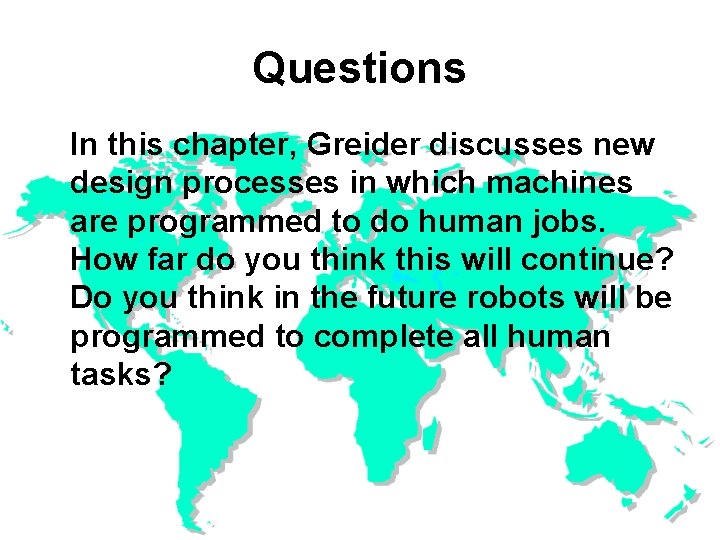
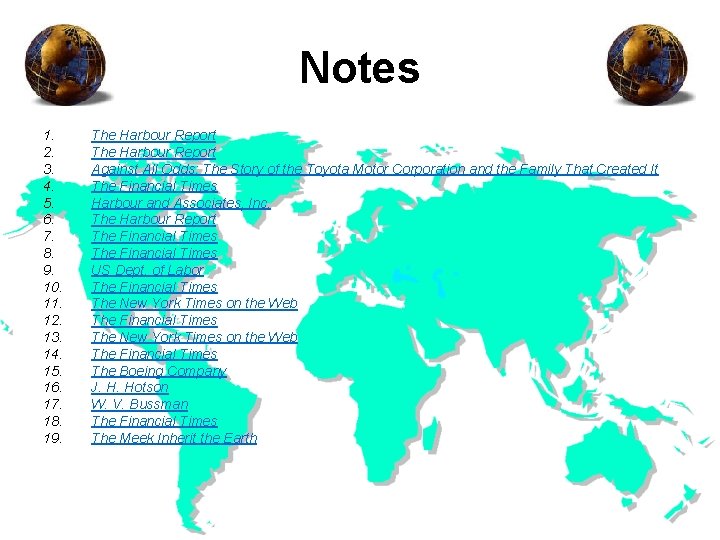
- Slides: 22
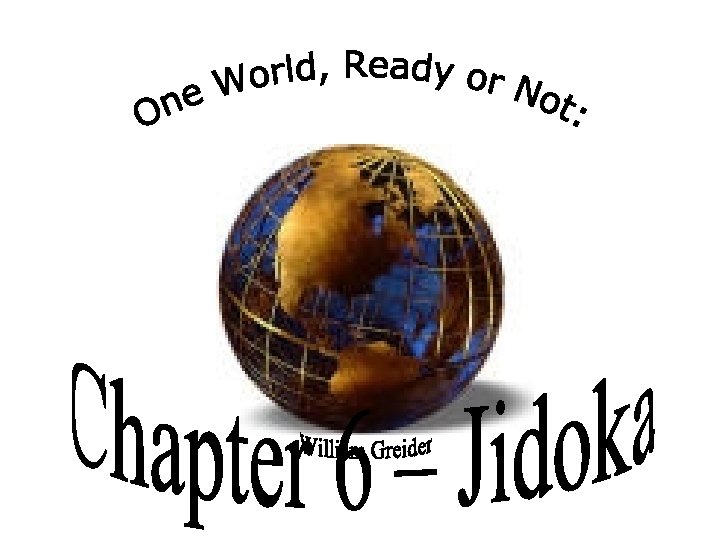
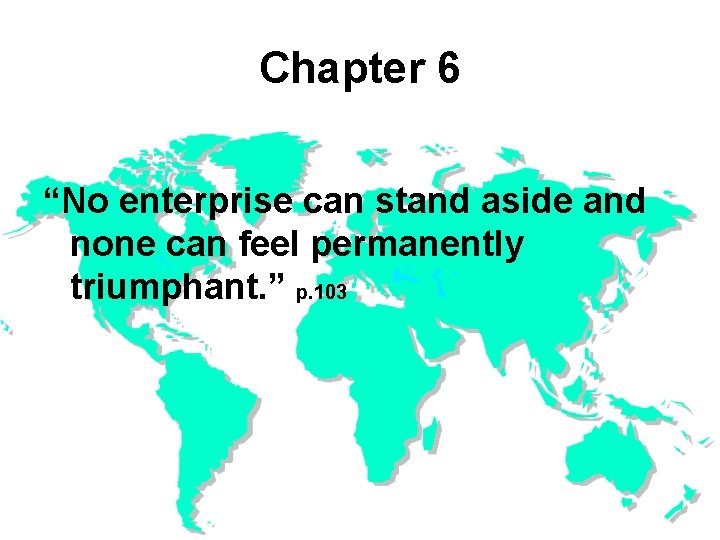
Chapter 6 “No enterprise can stand aside and none can feel permanently triumphant. ” p. 103
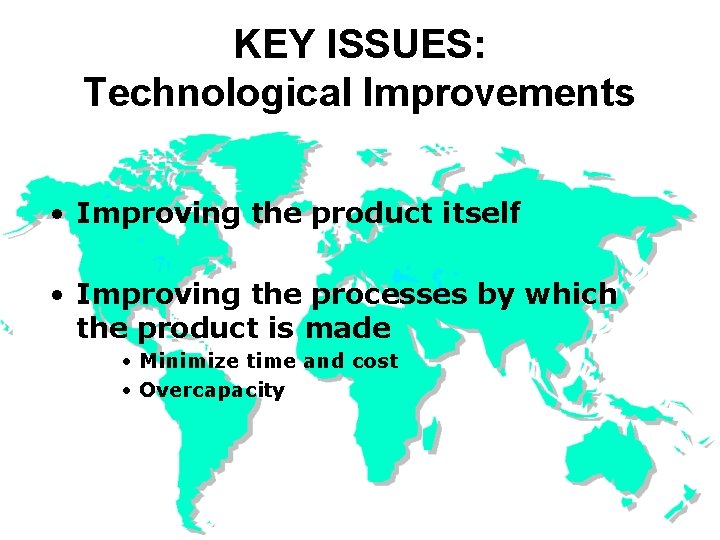
KEY ISSUES: Technological Improvements • Improving the product itself • Improving the processes by which the product is made • Minimize time and cost • Overcapacity
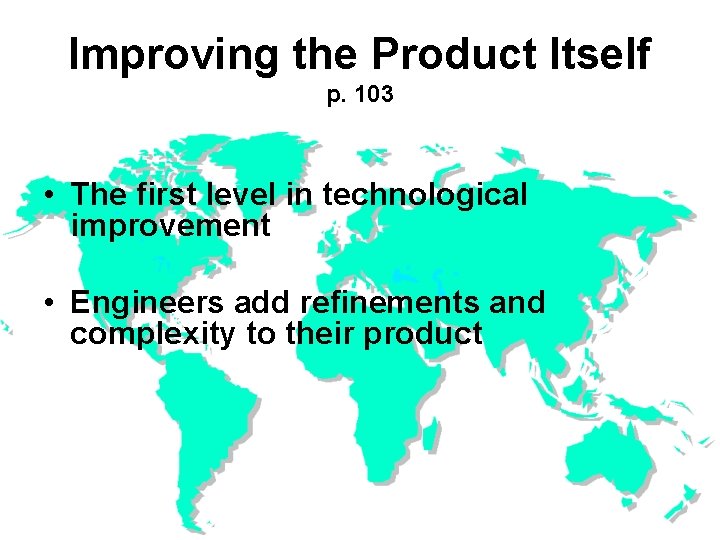
Improving the Product Itself p. 103 • The first level in technological improvement • Engineers add refinements and complexity to their product
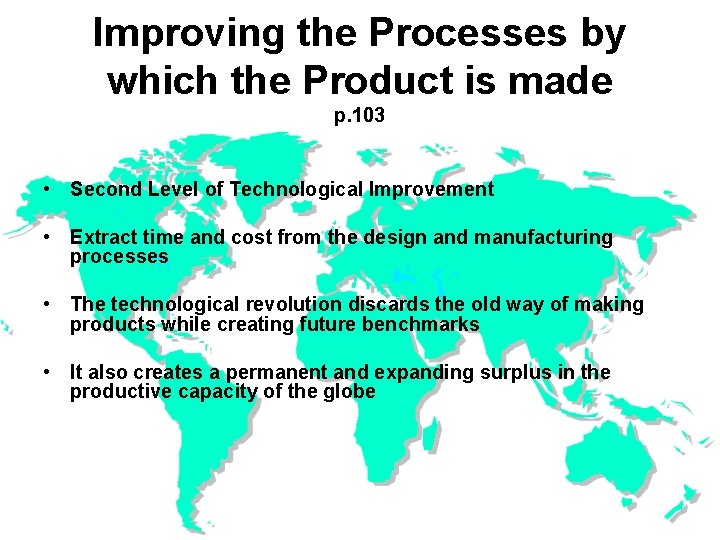
Improving the Processes by which the Product is made p. 103 • Second Level of Technological Improvement • Extract time and cost from the design and manufacturing processes • The technological revolution discards the old way of making products while creating future benchmarks • It also creates a permanent and expanding surplus in the productive capacity of the globe
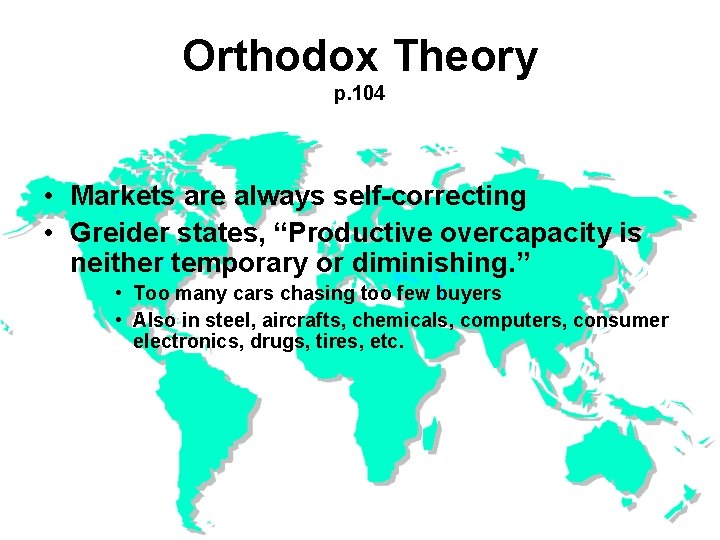
Orthodox Theory p. 104 • Markets are always self-correcting • Greider states, “Productive overcapacity is neither temporary or diminishing. ” • Too many cars chasing too few buyers • Also in steel, aircrafts, chemicals, computers, consumer electronics, drugs, tires, etc.
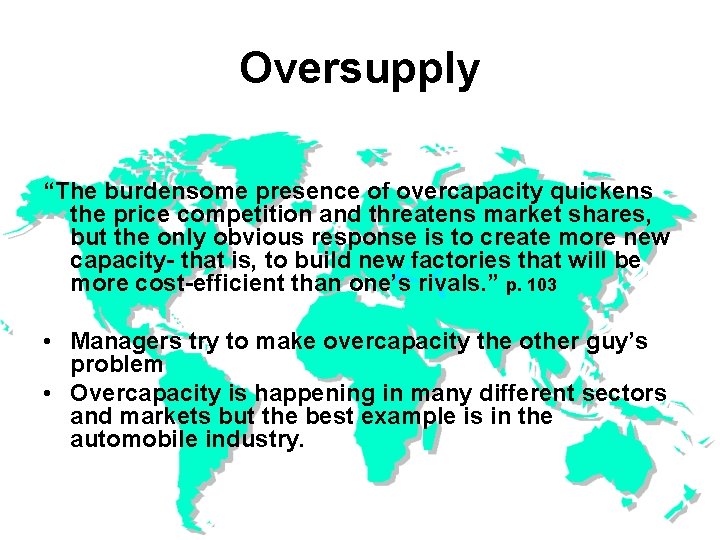
Oversupply “The burdensome presence of overcapacity quickens the price competition and threatens market shares, but the only obvious response is to create more new capacity- that is, to build new factories that will be more cost-efficient than one’s rivals. ” p. 103 • Managers try to make overcapacity the other guy’s problem • Overcapacity is happening in many different sectors and markets but the best example is in the automobile industry.
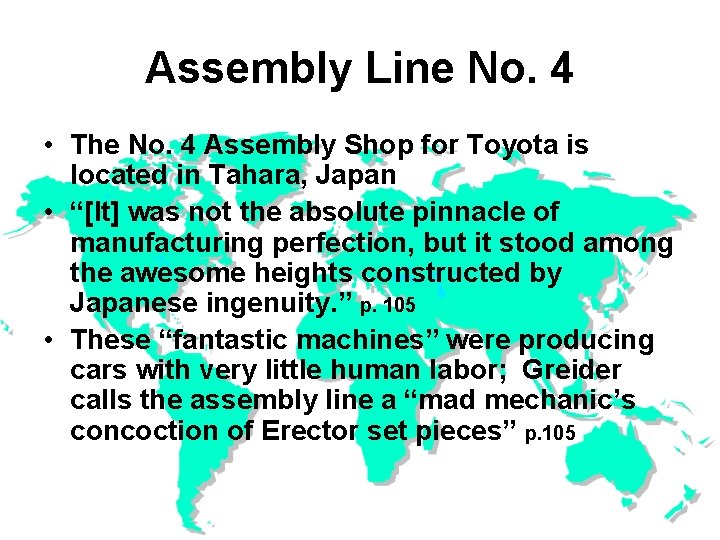
Assembly Line No. 4 • The No. 4 Assembly Shop for Toyota is located in Tahara, Japan • “[It] was not the absolute pinnacle of manufacturing perfection, but it stood among the awesome heights constructed by Japanese ingenuity. ” p. 105 • These “fantastic machines” were producing cars with very little human labor; Greider calls the assembly line a “mad mechanic’s concoction of Erector set pieces” p. 105
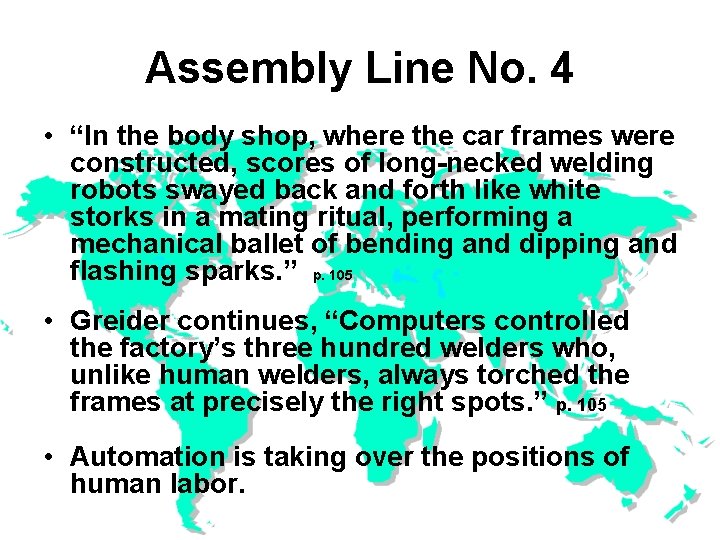
Assembly Line No. 4 • “In the body shop, where the car frames were constructed, scores of long-necked welding robots swayed back and forth like white storks in a mating ritual, performing a mechanical ballet of bending and dipping and flashing sparks. ” p. 105 • Greider continues, “Computers controlled the factory’s three hundred welders who, unlike human welders, always torched the frames at precisely the right spots. ” p. 105 • Automation is taking over the positions of human labor.
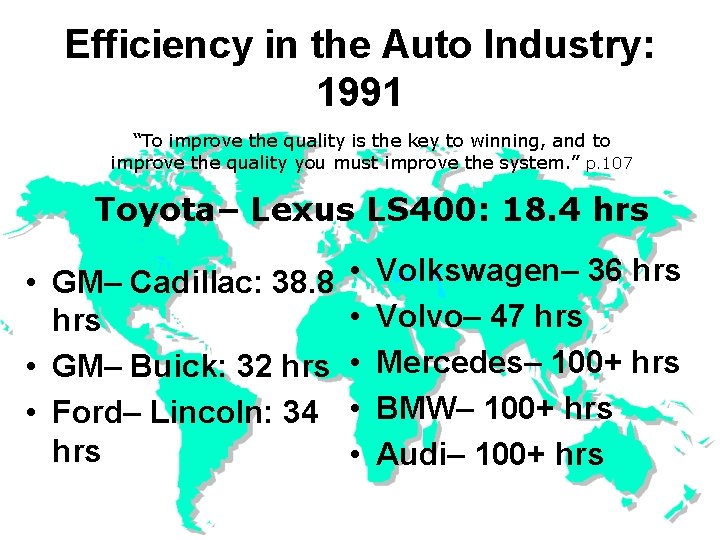
Efficiency in the Auto Industry: 1991 “To improve the quality is the key to winning, and to improve the quality you must improve the system. ” p. 107 Toyota– Lexus LS 400: 18. 4 hrs • GM– Cadillac: 38. 8 hrs • GM– Buick: 32 hrs • Ford– Lincoln: 34 hrs • • • Volkswagen– 36 hrs Volvo– 47 hrs Mercedes– 100+ hrs BMW– 100+ hrs Audi– 100+ hrs
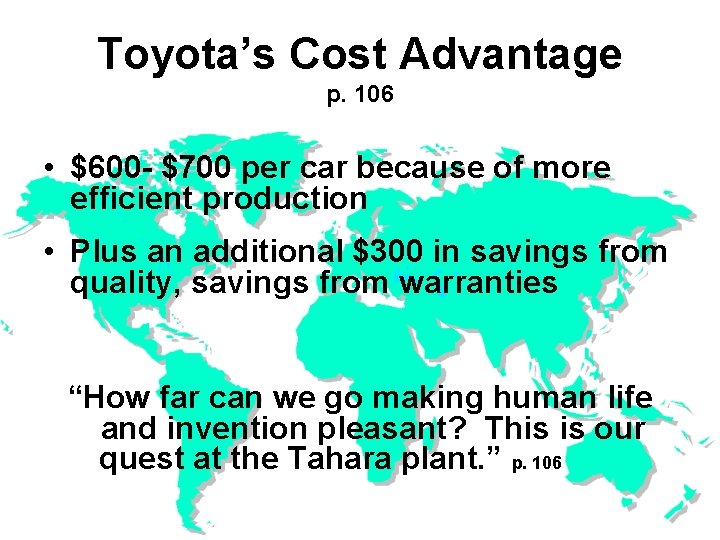
Toyota’s Cost Advantage p. 106 • $600 - $700 per car because of more efficient production • Plus an additional $300 in savings from quality, savings from warranties “How far can we go making human life and invention pleasant? This is our quest at the Tahara plant. ” p. 106
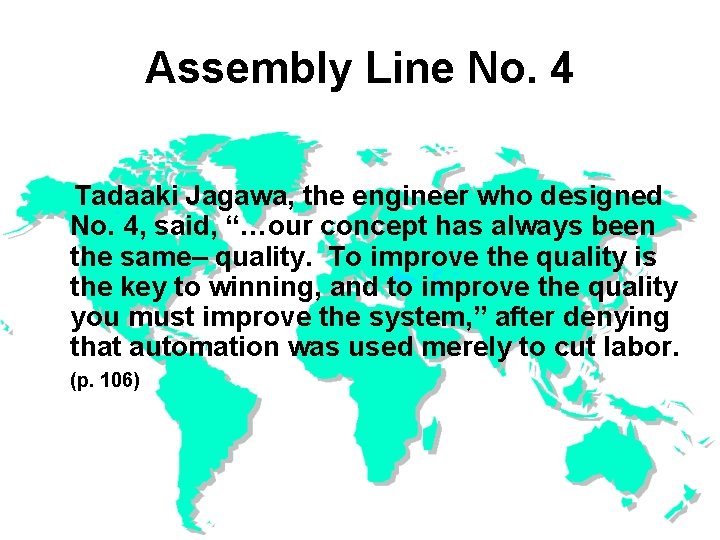
Assembly Line No. 4 Tadaaki Jagawa, the engineer who designed No. 4, said, “…our concept has always been the same– quality. To improve the quality is the key to winning, and to improve the quality you must improve the system, ” after denying that automation was used merely to cut labor. (p. 106)
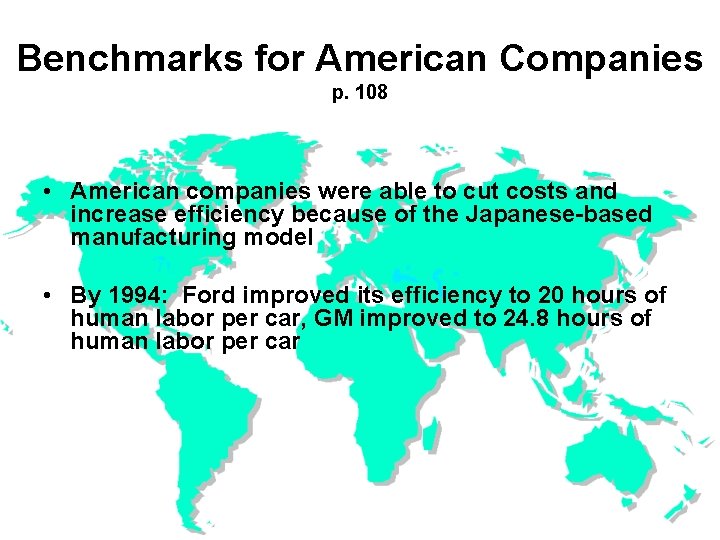
Benchmarks for American Companies p. 108 • American companies were able to cut costs and increase efficiency because of the Japanese-based manufacturing model • By 1994: Ford improved its efficiency to 20 hours of human labor per car, GM improved to 24. 8 hours of human labor per car
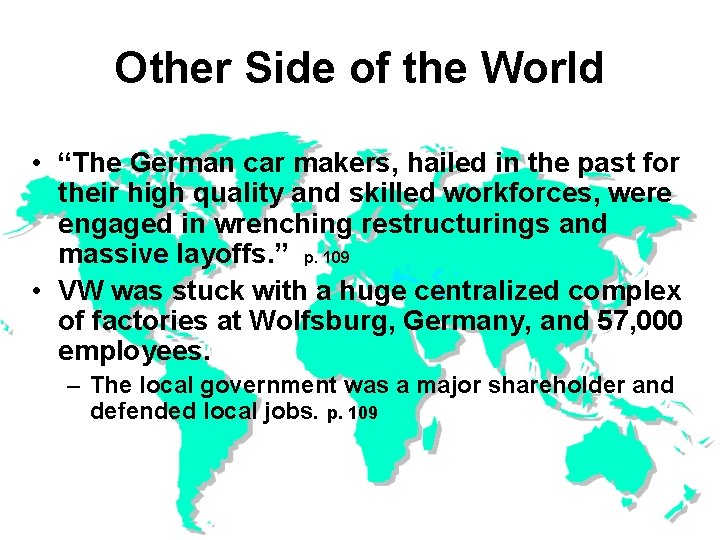
Other Side of the World • “The German car makers, hailed in the past for their high quality and skilled workforces, were engaged in wrenching restructurings and massive layoffs. ” p. 109 • VW was stuck with a huge centralized complex of factories at Wolfsburg, Germany, and 57, 000 employees. – The local government was a major shareholder and defended local jobs. p. 109

American Resurgence • “There is an inability to keep a process advantage for very long, we’re just to nimble. I’m not saying we always were but we are now. ” Oscar B. Marx III, Former Vice President of Ford p. 110
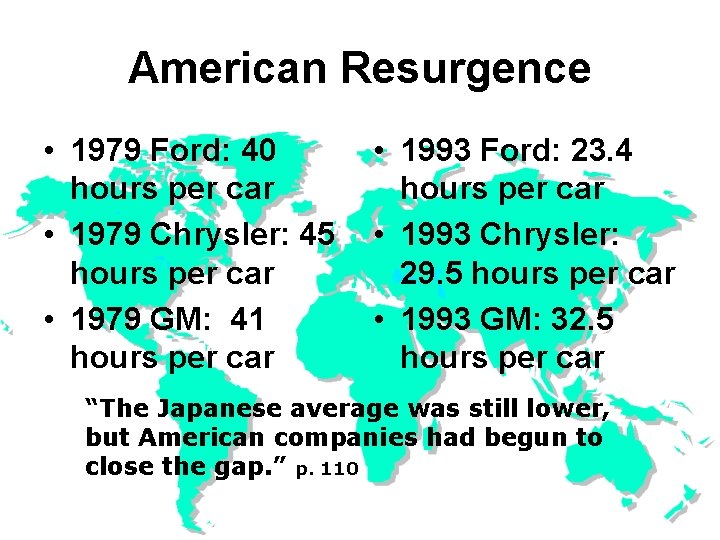
American Resurgence • 1979 Ford: 40 hours per car • 1979 Chrysler: 45 hours per car • 1979 GM: 41 hours per car • 1993 Ford: 23. 4 hours per car • 1993 Chrysler: 29. 5 hours per car • 1993 GM: 32. 5 hours per car “The Japanese average was still lower, but American companies had begun to close the gap. ” p. 110
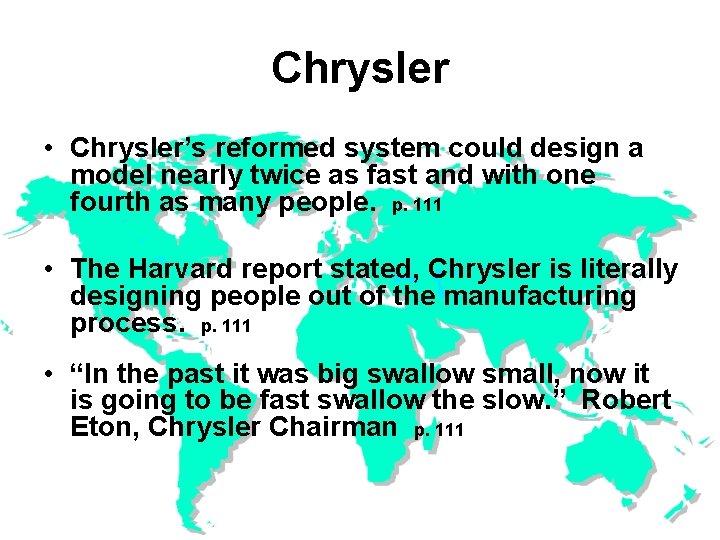
Chrysler • Chrysler’s reformed system could design a model nearly twice as fast and with one fourth as many people. p. 111 • The Harvard report stated, Chrysler is literally designing people out of the manufacturing process. p. 111 • “In the past it was big swallow small, now it is going to be fast swallow the slow. ” Robert Eton, Chrysler Chairman p. 111
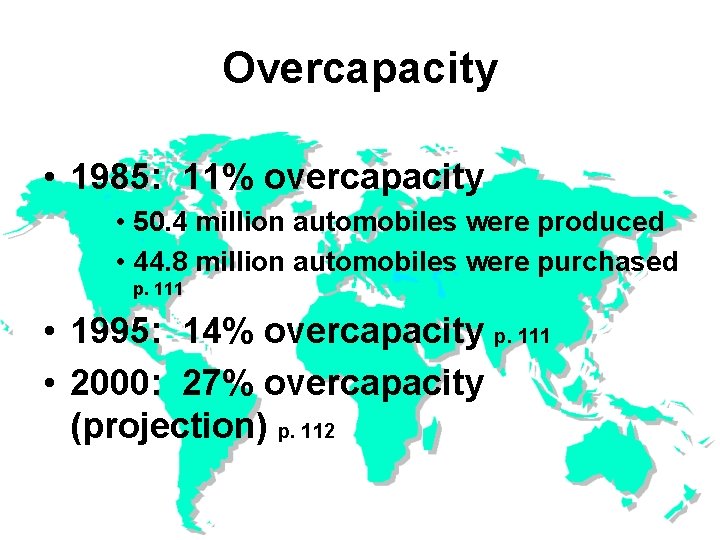
Overcapacity • 1985: 11% overcapacity • 50. 4 million automobiles were produced • 44. 8 million automobiles were purchased p. 111 • 1995: 14% overcapacity p. 111 • 2000: 27% overcapacity (projection) p. 112
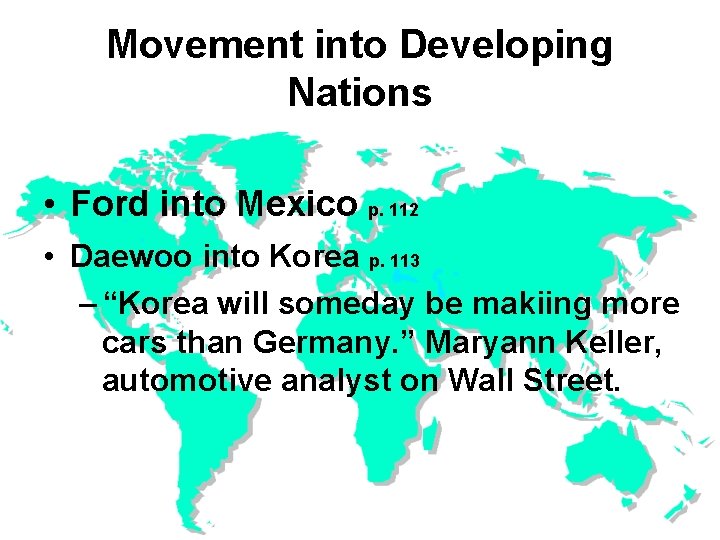
Movement into Developing Nations • Ford into Mexico p. 112 • Daewoo into Korea p. 113 – “Korea will someday be makiing more cars than Germany. ” Maryann Keller, automotive analyst on Wall Street.
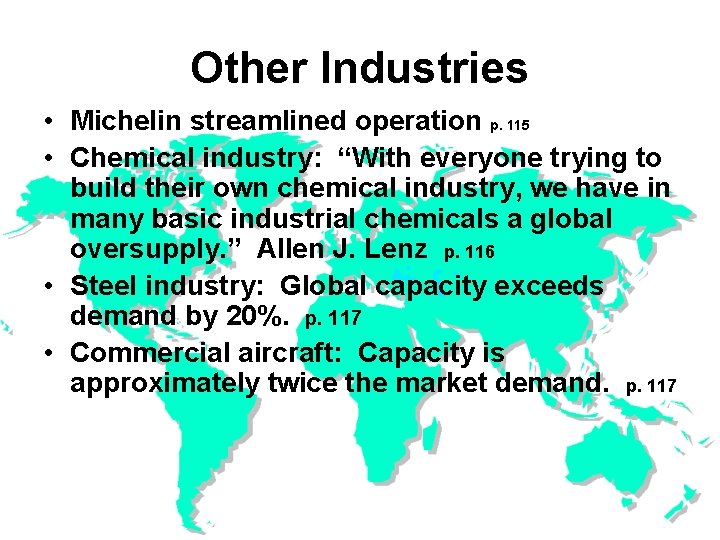
Other Industries • Michelin streamlined operation p. 115 • Chemical industry: “With everyone trying to build their own chemical industry, we have in many basic industrial chemicals a global oversupply. ” Allen J. Lenz p. 116 • Steel industry: Global capacity exceeds demand by 20%. p. 117 • Commercial aircraft: Capacity is approximately twice the market demand. p. 117
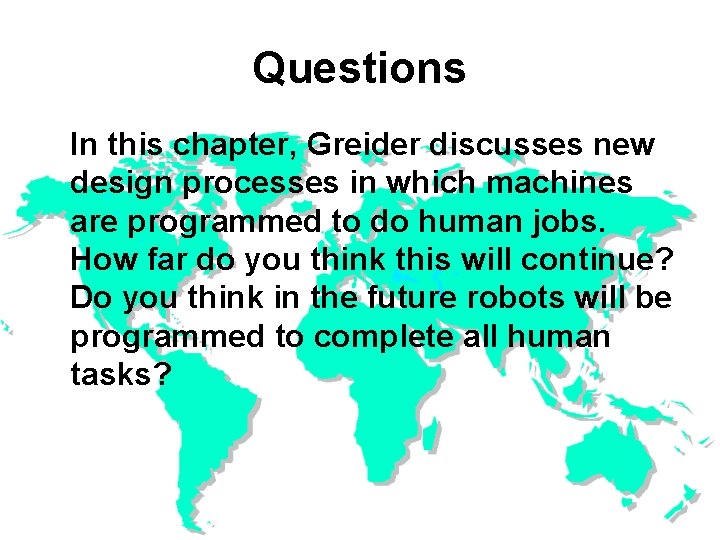
Questions In this chapter, Greider discusses new design processes in which machines are programmed to do human jobs. How far do you think this will continue? Do you think in the future robots will be programmed to complete all human tasks?
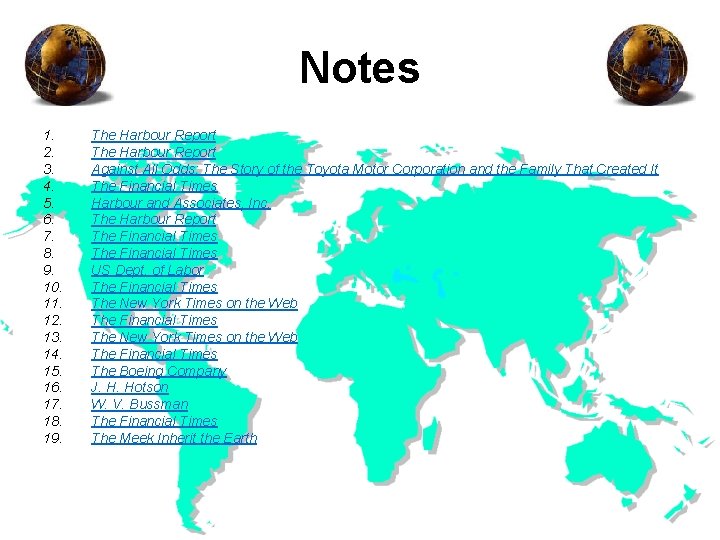
Notes 1. 2. 3. 4. 5. 6. 7. 8. 9. 10. 11. 12. 13. 14. 15. 16. 17. 18. 19. The Harbour Report Against All Odds: The Story of the Toyota Motor Corporation and the Family That Created It The Financial Times Harbour and Associates, Inc. The Harbour Report The Financial Times US Dept. of Labor The Financial Times The New York Times on the Web The Financial Times The Boeing Company J. H. Hotson W. V. Bussman The Financial Times The Meek Inherit the Earth
Stand up for jesus
Hello hello everyone i nanny shine
Putting the enterprise into the enterprise system
Enterprise
Aside example in literature
Romeo juliet
Antagonist of romeo and juliet
Soliloquy aside
Lay aside every weight example
Soliloquy and aside
Aside definition romeo and juliet
Aside definition romeo and juliet
Aside and monologue
Jesus you're my firm foundation song
What are base words
Automobile data transmission system can bus training stand
Preposition ing form
Verb patterns ing or infinitive
Forget verb pattern
What is dramatic language
Module 5 financial services
Topic vs theme
Literary definition of irony