CHAPTER 2 Pipeline Coatings 1 Effectiveness of Coatings
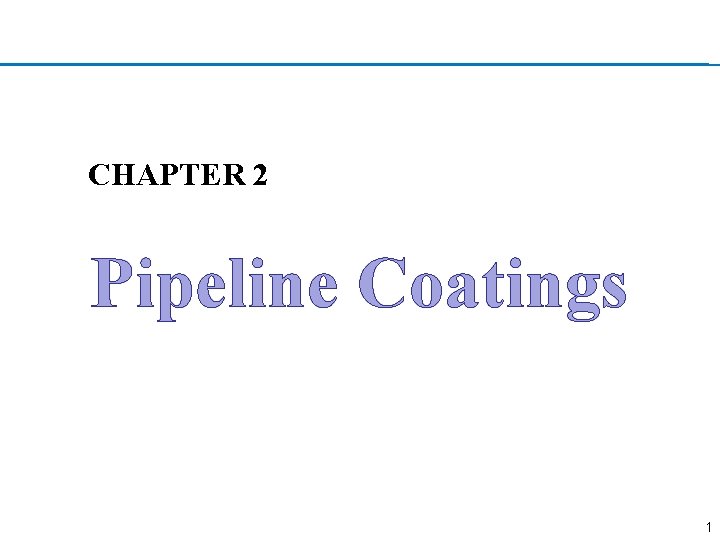
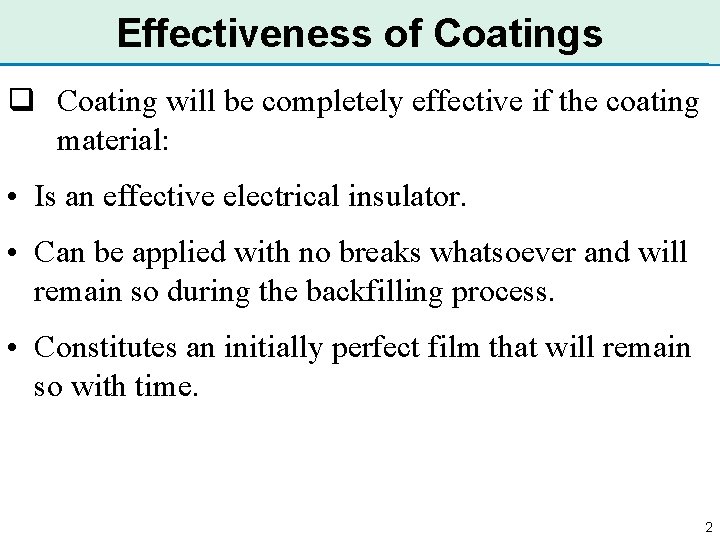
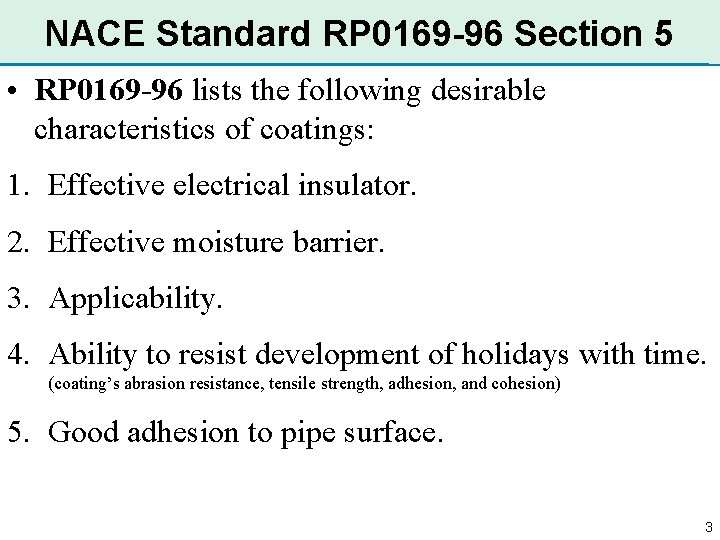
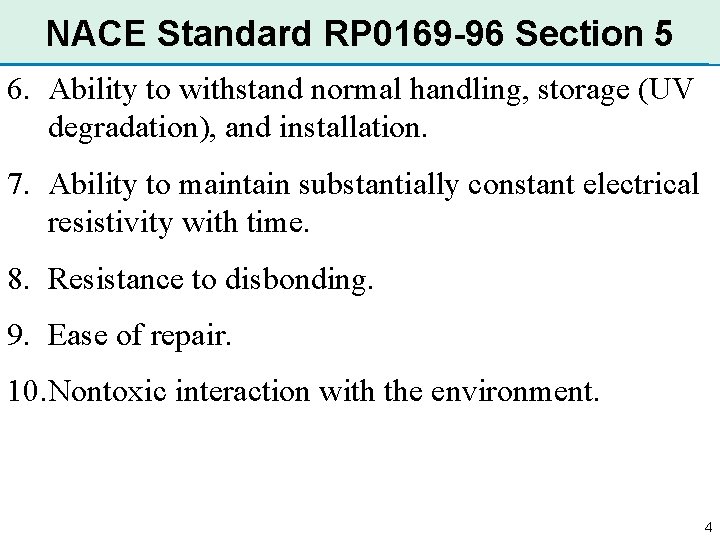
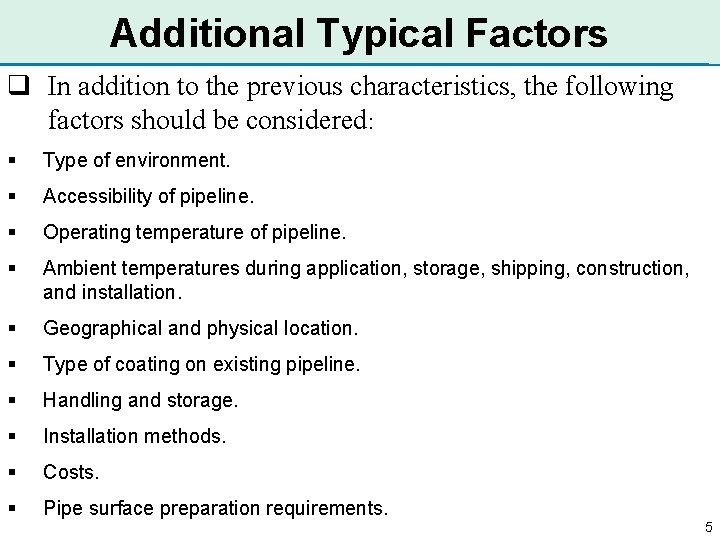
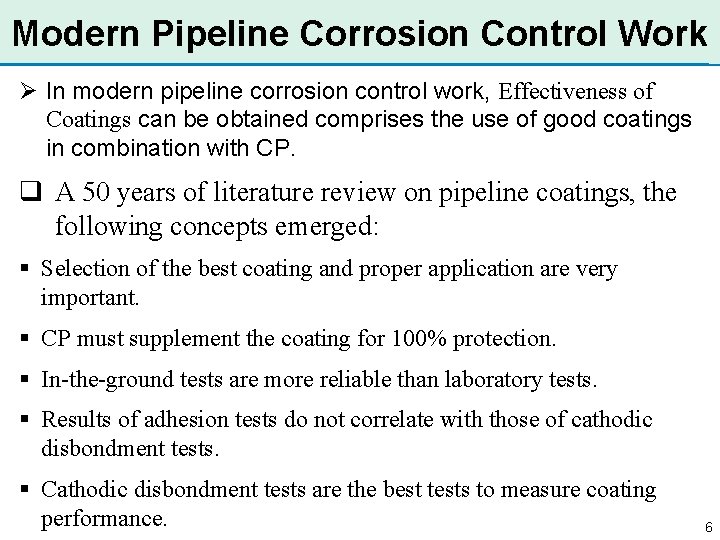
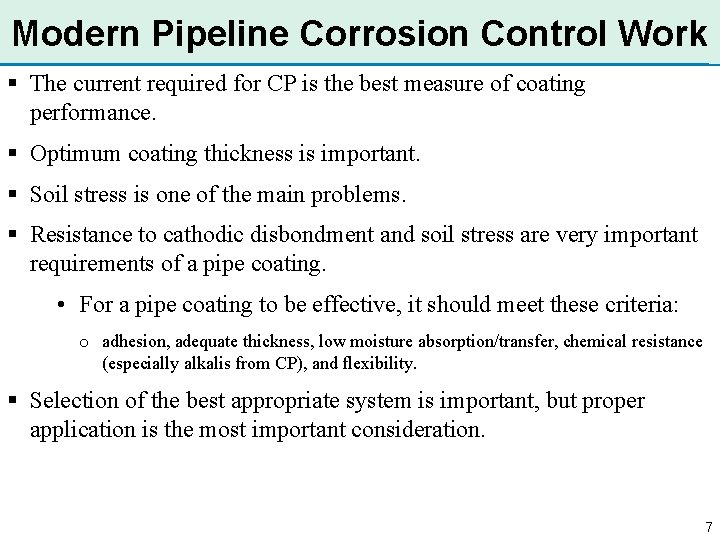
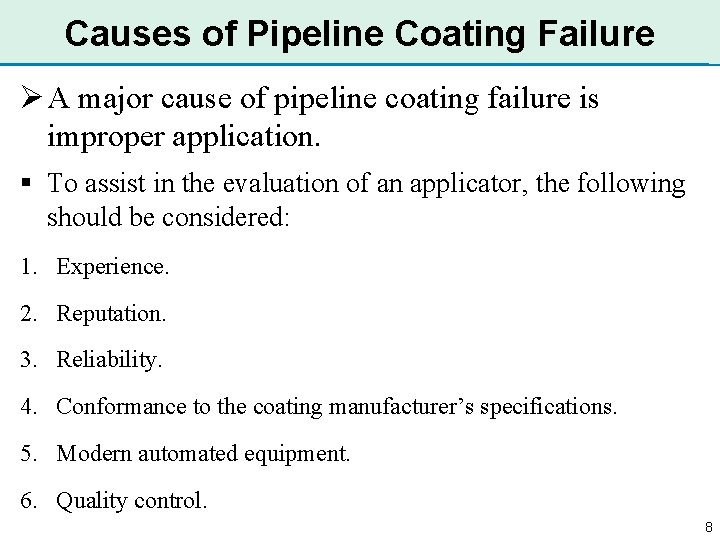
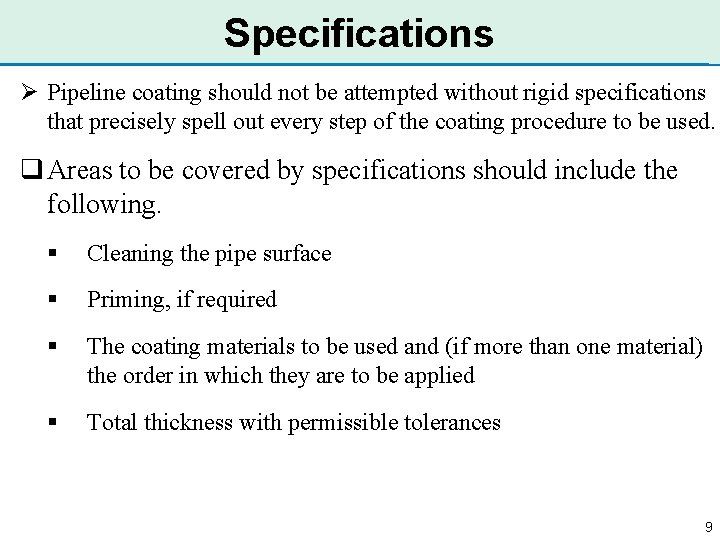
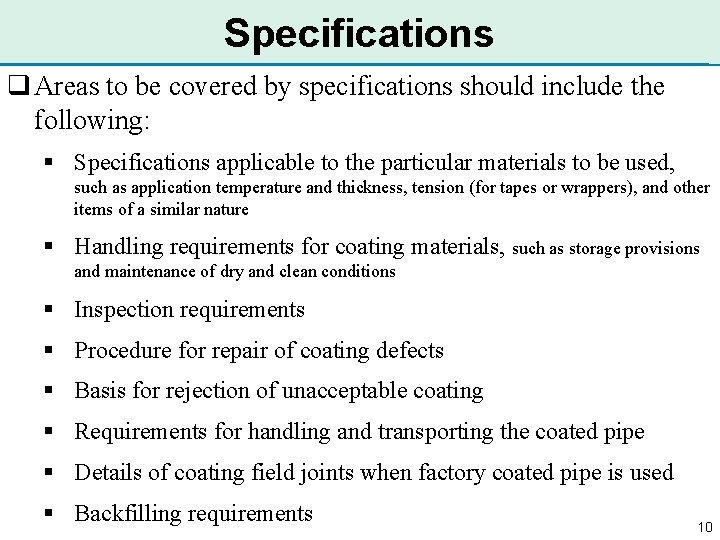
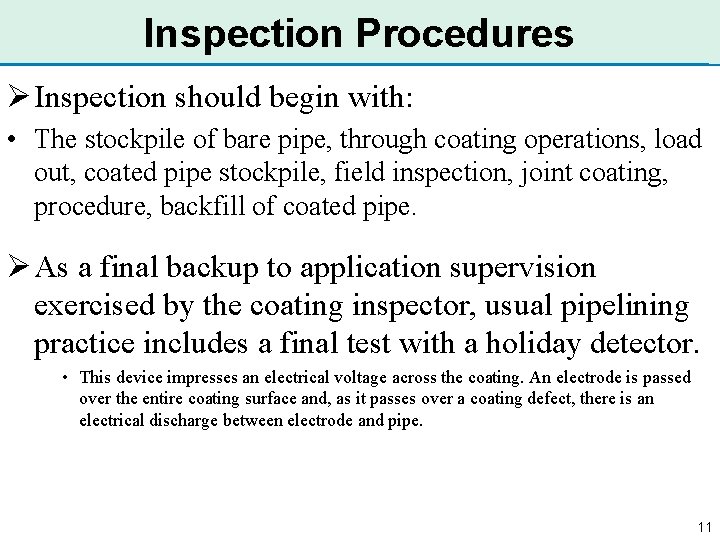
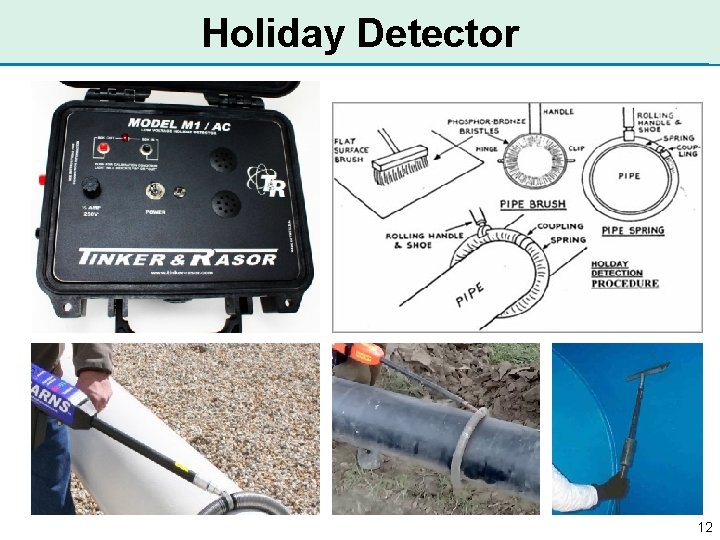
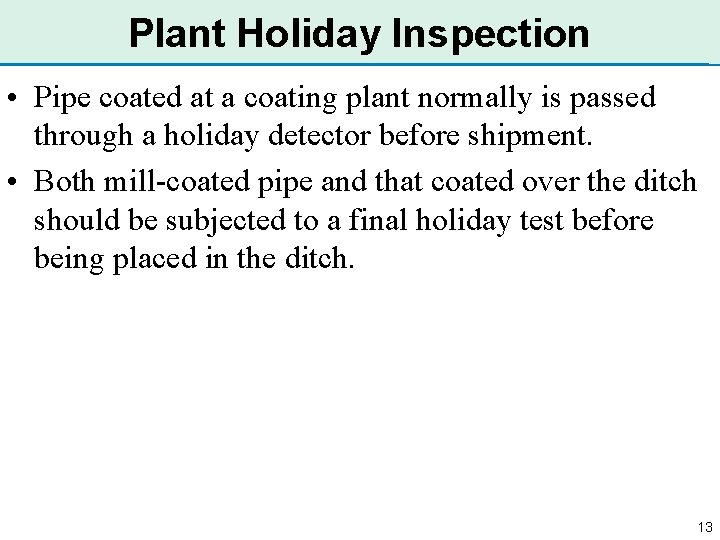
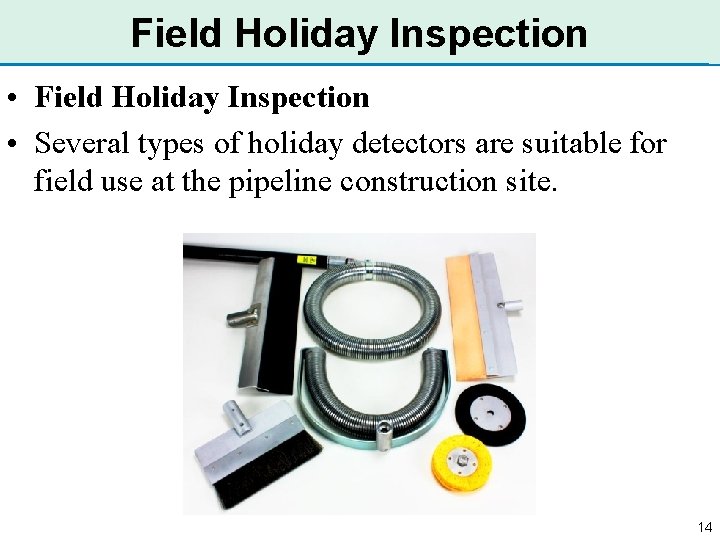
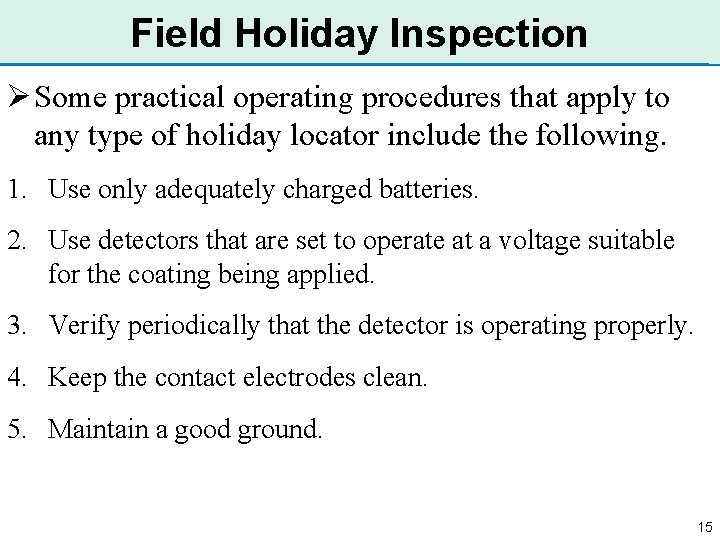
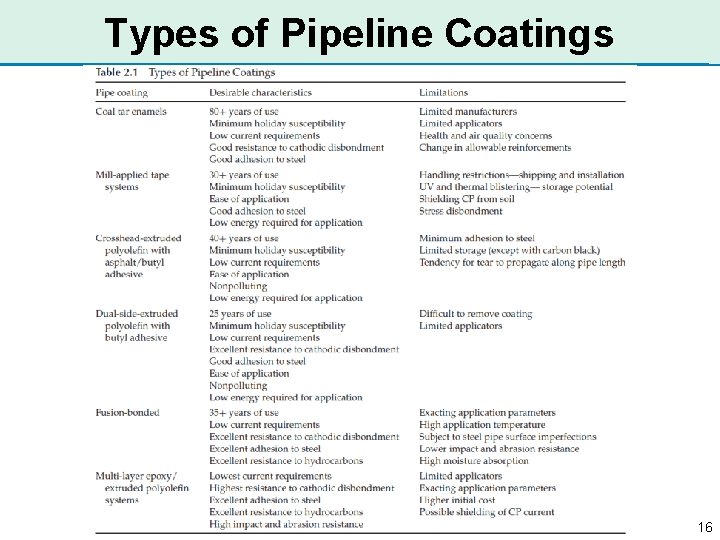
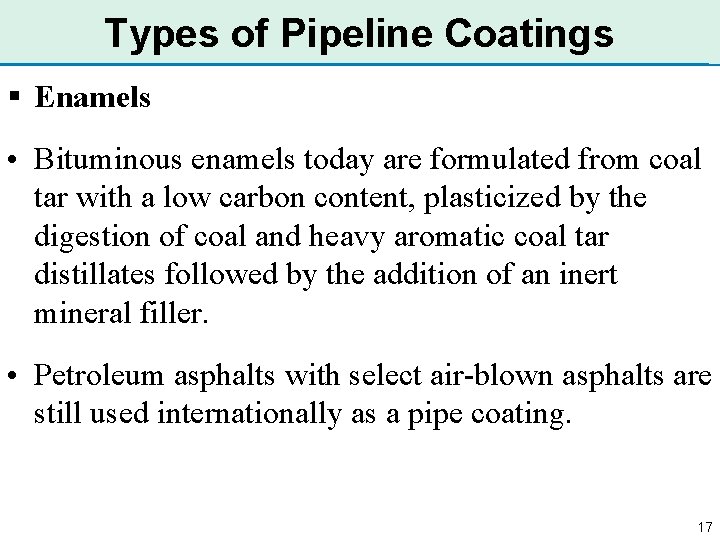
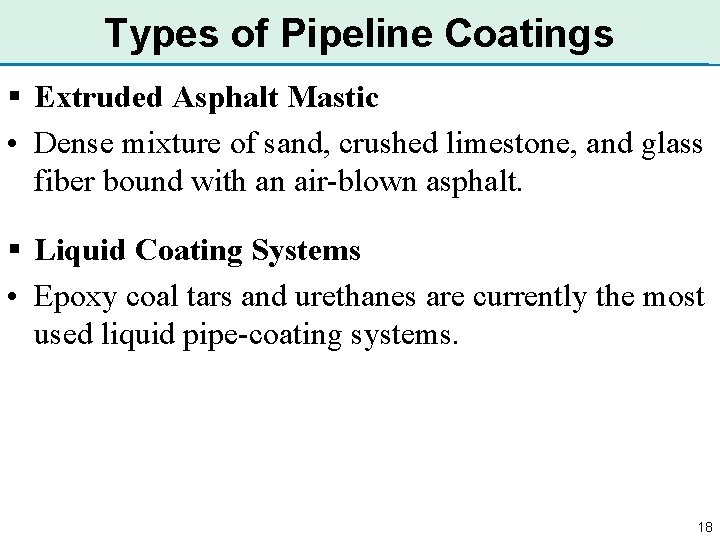
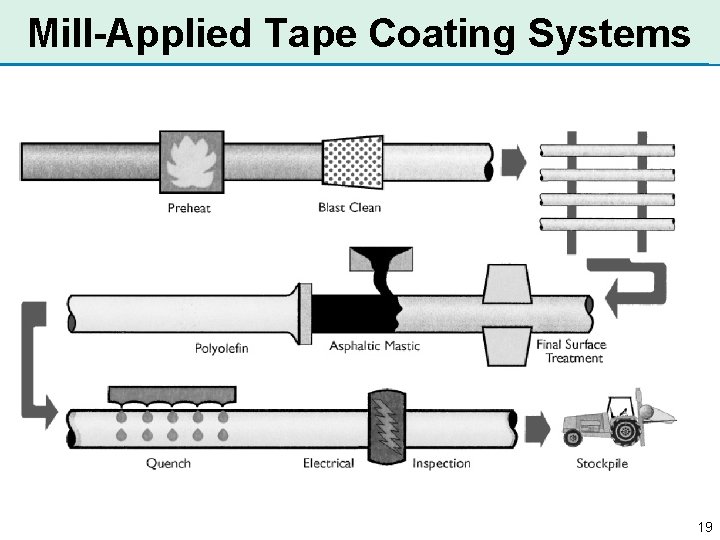
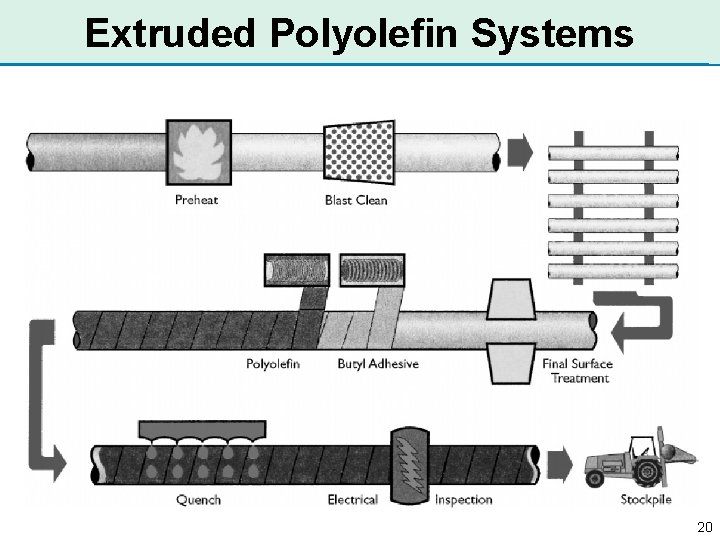
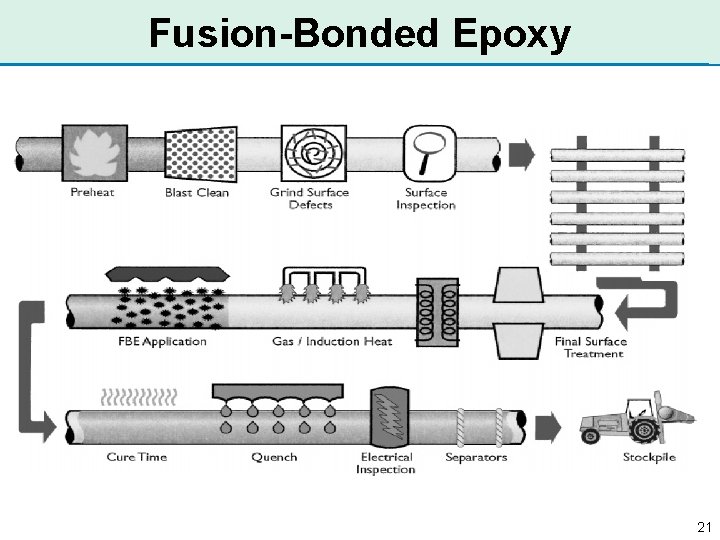
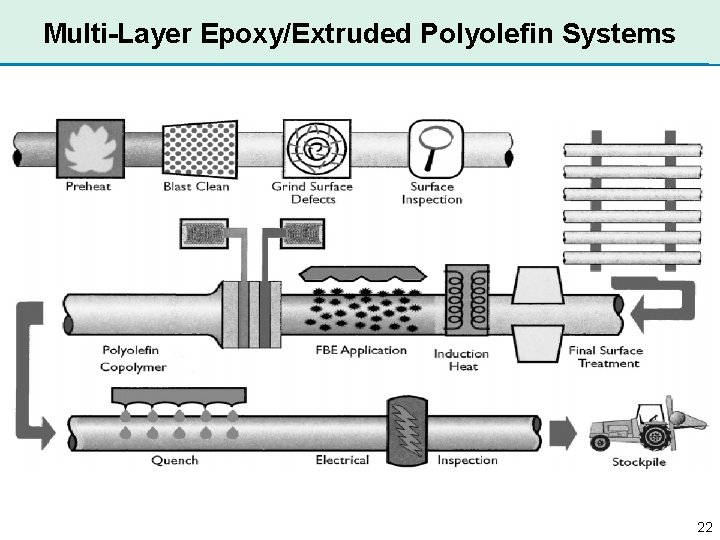
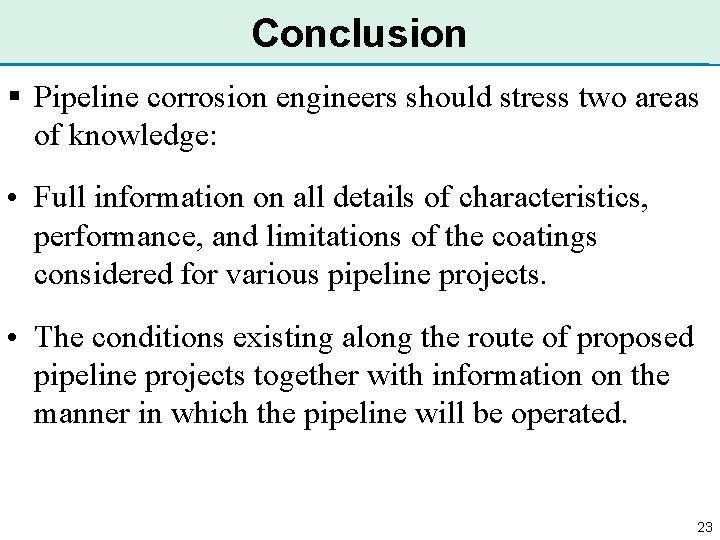
- Slides: 23
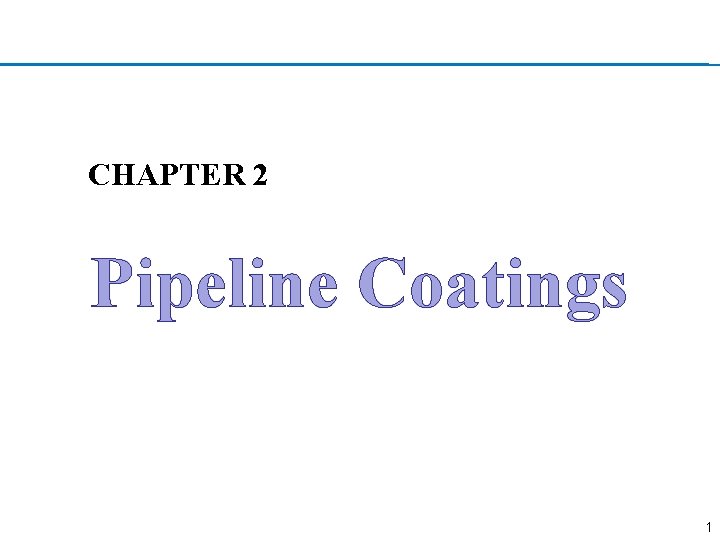
CHAPTER 2 Pipeline Coatings 1
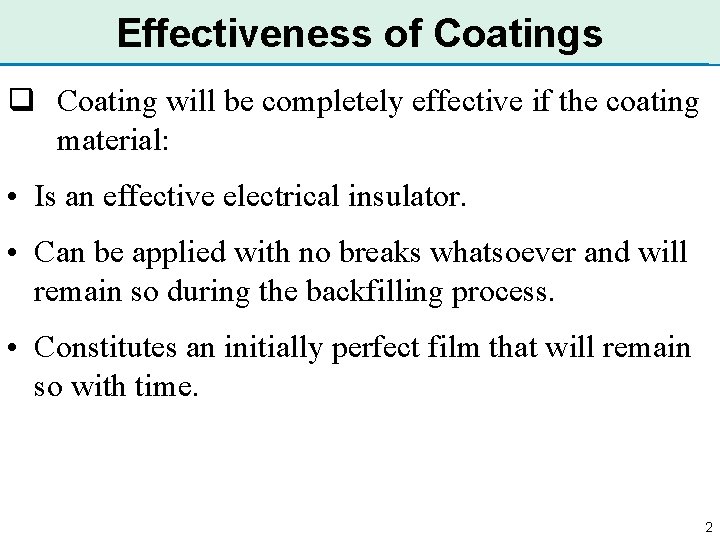
Effectiveness of Coatings q Coating will be completely effective if the coating material: • Is an effective electrical insulator. • Can be applied with no breaks whatsoever and will remain so during the backfilling process. • Constitutes an initially perfect film that will remain so with time. 2
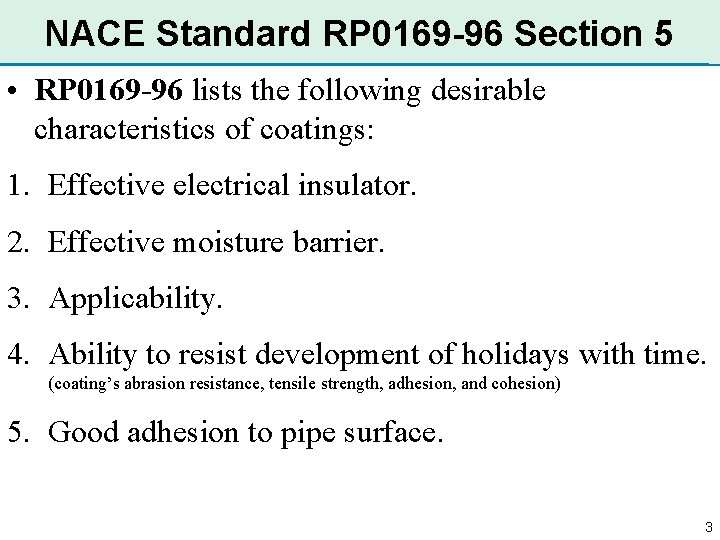
NACE Standard RP 0169 -96 Section 5 • RP 0169 -96 lists the following desirable characteristics of coatings: 1. Effective electrical insulator. 2. Effective moisture barrier. 3. Applicability. 4. Ability to resist development of holidays with time. (coating’s abrasion resistance, tensile strength, adhesion, and cohesion) 5. Good adhesion to pipe surface. 3
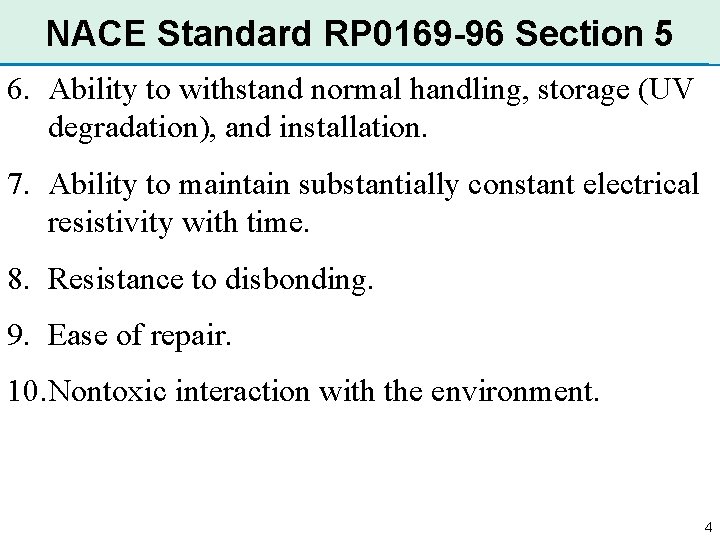
NACE Standard RP 0169 -96 Section 5 6. Ability to withstand normal handling, storage (UV degradation), and installation. 7. Ability to maintain substantially constant electrical resistivity with time. 8. Resistance to disbonding. 9. Ease of repair. 10. Nontoxic interaction with the environment. 4
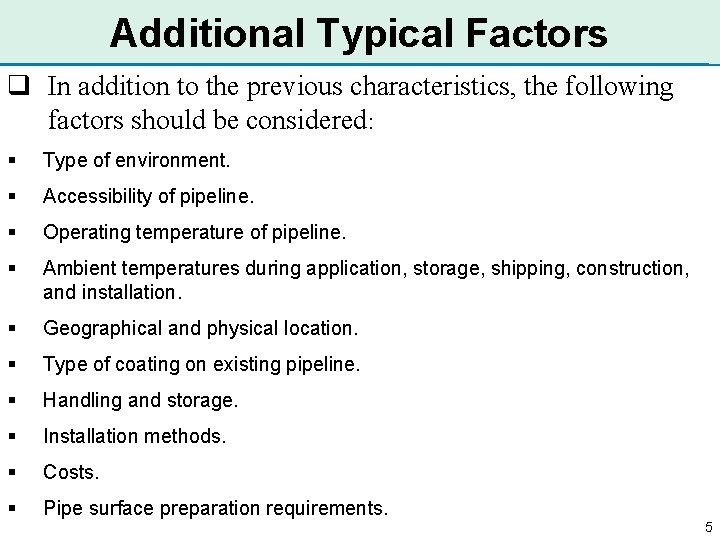
Additional Typical Factors q In addition to the previous characteristics, the following factors should be considered: § Type of environment. § Accessibility of pipeline. § Operating temperature of pipeline. § Ambient temperatures during application, storage, shipping, construction, and installation. § Geographical and physical location. § Type of coating on existing pipeline. § Handling and storage. § Installation methods. § Costs. § Pipe surface preparation requirements. 5
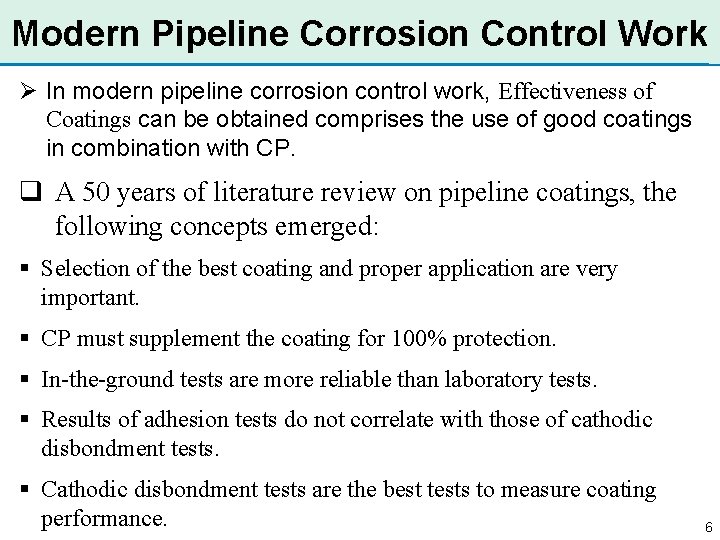
Modern Pipeline Corrosion Control Work Ø In modern pipeline corrosion control work, Effectiveness of Coatings can be obtained comprises the use of good coatings in combination with CP. q A 50 years of literature review on pipeline coatings, the following concepts emerged: § Selection of the best coating and proper application are very important. § CP must supplement the coating for 100% protection. § In-the-ground tests are more reliable than laboratory tests. § Results of adhesion tests do not correlate with those of cathodic disbondment tests. § Cathodic disbondment tests are the best tests to measure coating performance. 6
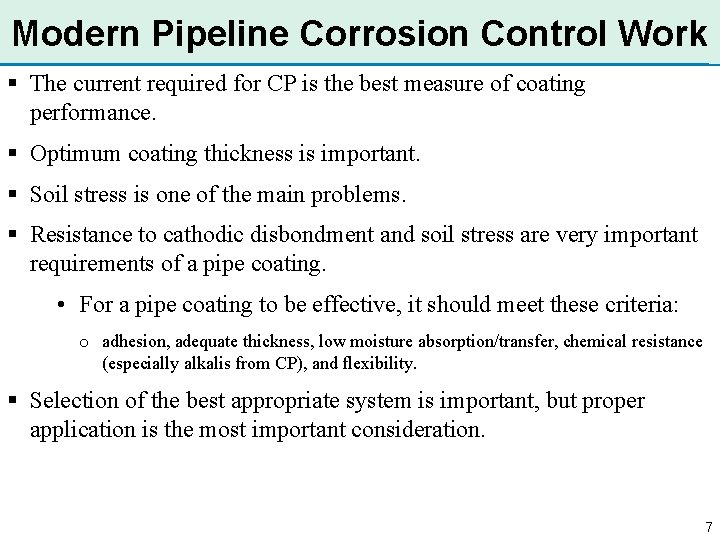
Modern Pipeline Corrosion Control Work § The current required for CP is the best measure of coating performance. § Optimum coating thickness is important. § Soil stress is one of the main problems. § Resistance to cathodic disbondment and soil stress are very important requirements of a pipe coating. • For a pipe coating to be effective, it should meet these criteria: o adhesion, adequate thickness, low moisture absorption/transfer, chemical resistance (especially alkalis from CP), and flexibility. § Selection of the best appropriate system is important, but proper application is the most important consideration. 7
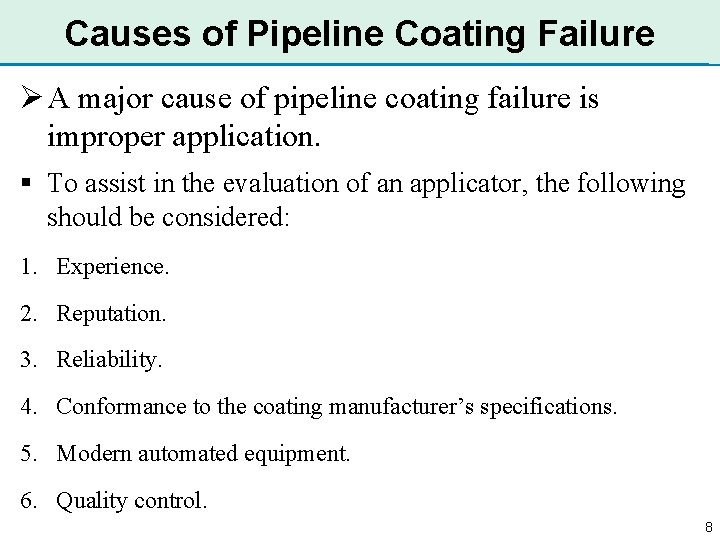
Causes of Pipeline Coating Failure Ø A major cause of pipeline coating failure is improper application. § To assist in the evaluation of an applicator, the following should be considered: 1. Experience. 2. Reputation. 3. Reliability. 4. Conformance to the coating manufacturer’s specifications. 5. Modern automated equipment. 6. Quality control. 8
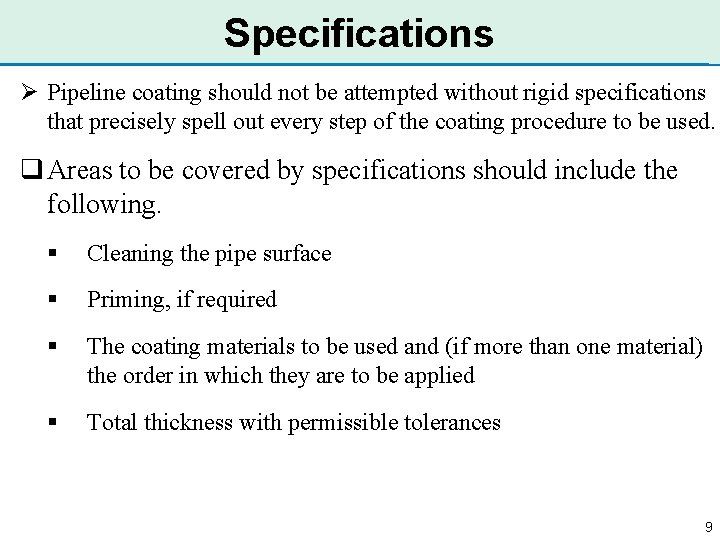
Specifications Ø Pipeline coating should not be attempted without rigid specifications that precisely spell out every step of the coating procedure to be used. q Areas to be covered by specifications should include the following. § Cleaning the pipe surface § Priming, if required § The coating materials to be used and (if more than one material) the order in which they are to be applied § Total thickness with permissible tolerances 9
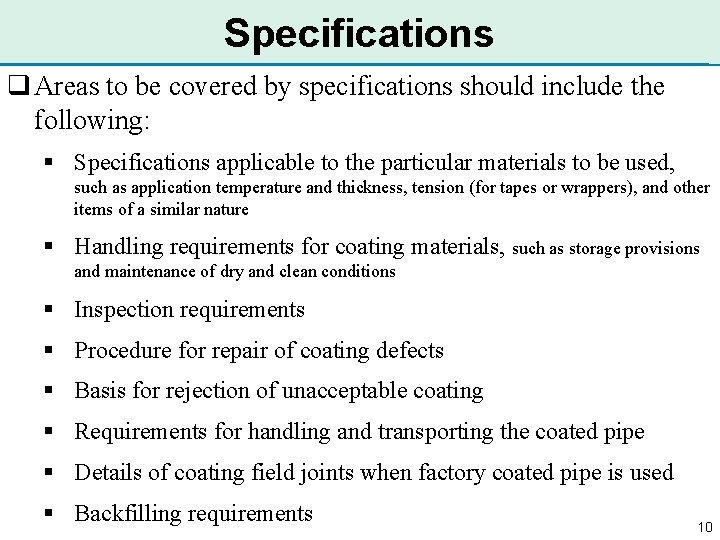
Specifications q Areas to be covered by specifications should include the following: § Specifications applicable to the particular materials to be used, such as application temperature and thickness, tension (for tapes or wrappers), and other items of a similar nature § Handling requirements for coating materials, such as storage provisions and maintenance of dry and clean conditions § Inspection requirements § Procedure for repair of coating defects § Basis for rejection of unacceptable coating § Requirements for handling and transporting the coated pipe § Details of coating field joints when factory coated pipe is used § Backfilling requirements 10
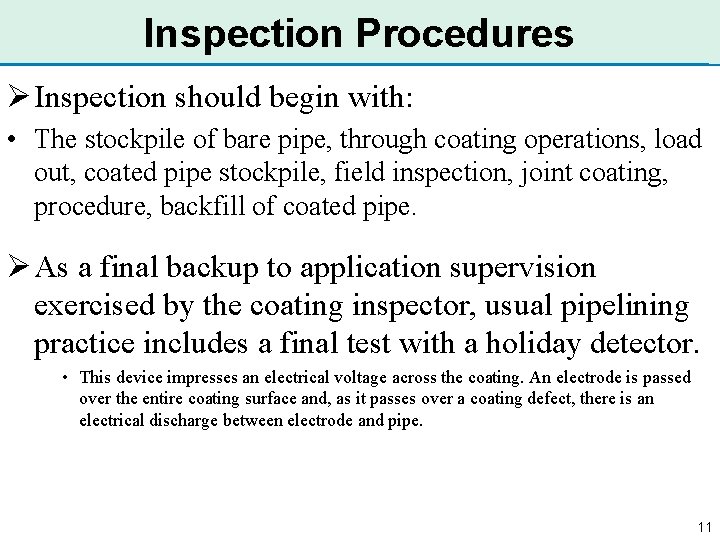
Inspection Procedures Ø Inspection should begin with: • The stockpile of bare pipe, through coating operations, load out, coated pipe stockpile, field inspection, joint coating, procedure, backfill of coated pipe. Ø As a final backup to application supervision exercised by the coating inspector, usual pipelining practice includes a final test with a holiday detector. • This device impresses an electrical voltage across the coating. An electrode is passed over the entire coating surface and, as it passes over a coating defect, there is an electrical discharge between electrode and pipe. 11
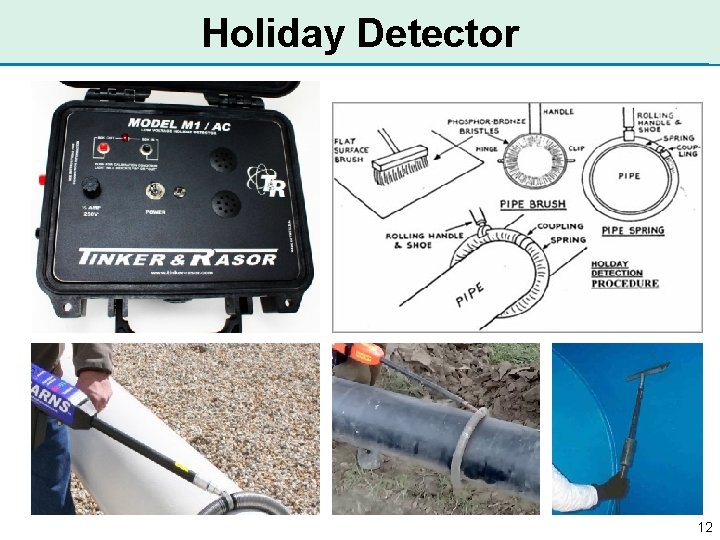
Holiday Detector 12
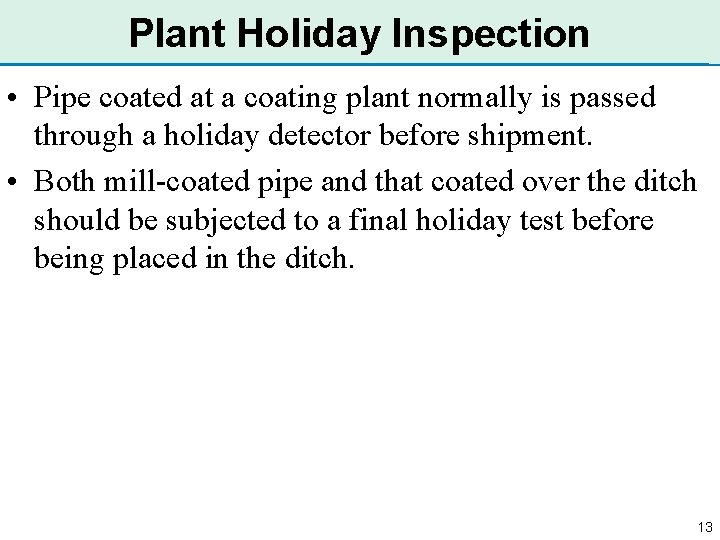
Plant Holiday Inspection • Pipe coated at a coating plant normally is passed through a holiday detector before shipment. • Both mill-coated pipe and that coated over the ditch should be subjected to a final holiday test before being placed in the ditch. 13
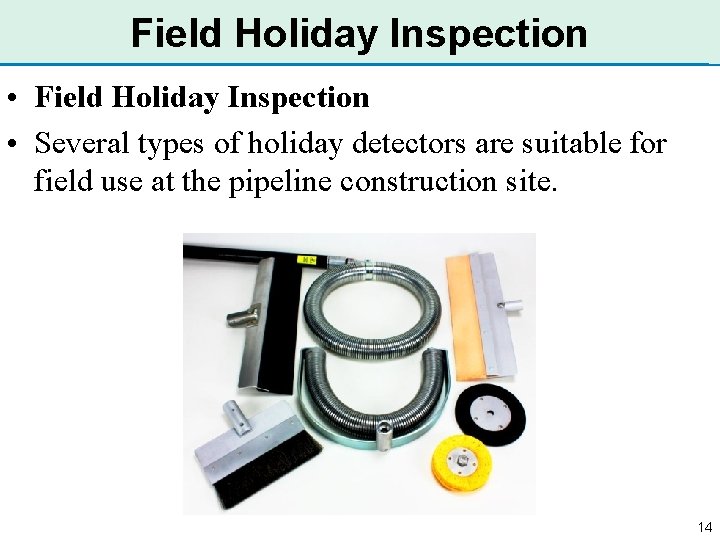
Field Holiday Inspection • Several types of holiday detectors are suitable for field use at the pipeline construction site. 14
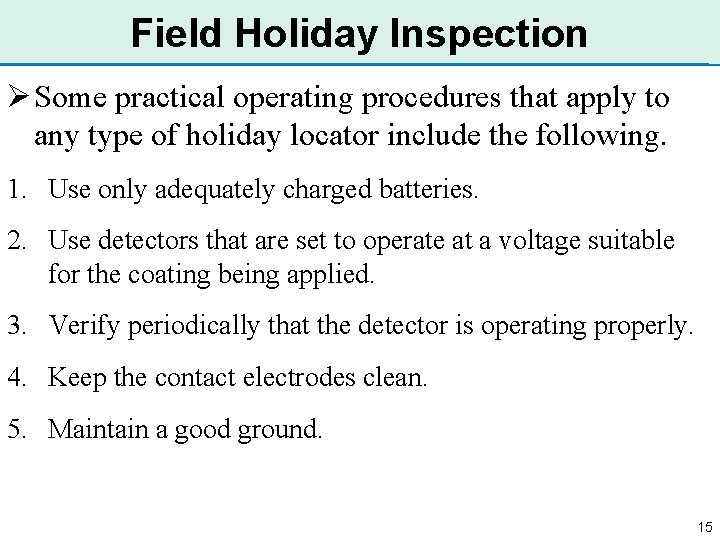
Field Holiday Inspection Ø Some practical operating procedures that apply to any type of holiday locator include the following. 1. Use only adequately charged batteries. 2. Use detectors that are set to operate at a voltage suitable for the coating being applied. 3. Verify periodically that the detector is operating properly. 4. Keep the contact electrodes clean. 5. Maintain a good ground. 15
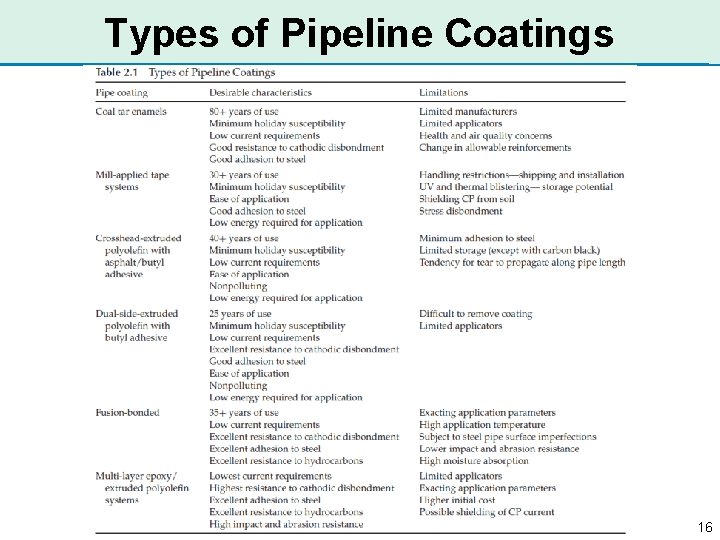
Types of Pipeline Coatings 16
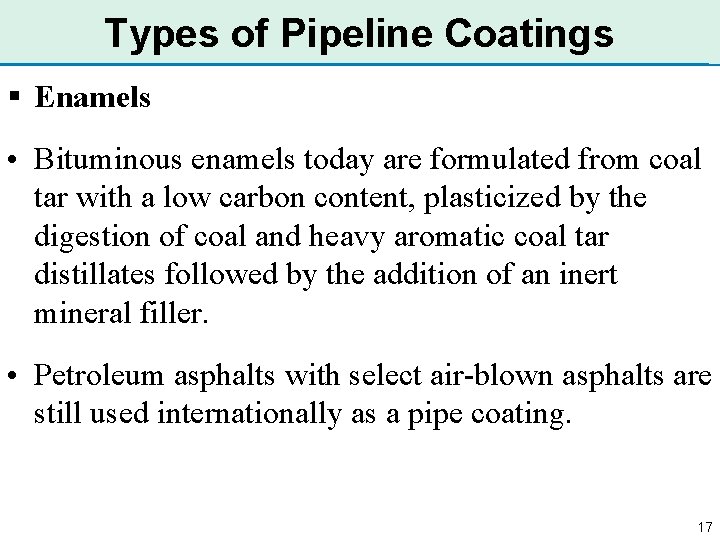
Types of Pipeline Coatings § Enamels • Bituminous enamels today are formulated from coal tar with a low carbon content, plasticized by the digestion of coal and heavy aromatic coal tar distillates followed by the addition of an inert mineral filler. • Petroleum asphalts with select air-blown asphalts are still used internationally as a pipe coating. 17
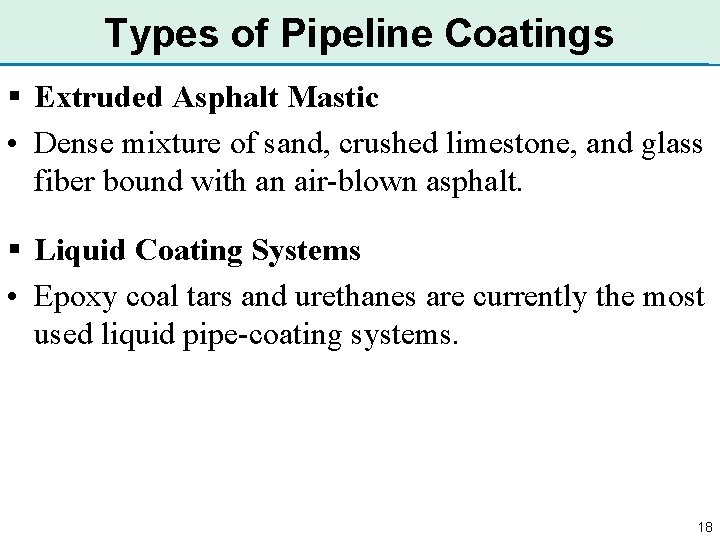
Types of Pipeline Coatings § Extruded Asphalt Mastic • Dense mixture of sand, crushed limestone, and glass fiber bound with an air-blown asphalt. § Liquid Coating Systems • Epoxy coal tars and urethanes are currently the most used liquid pipe-coating systems. 18
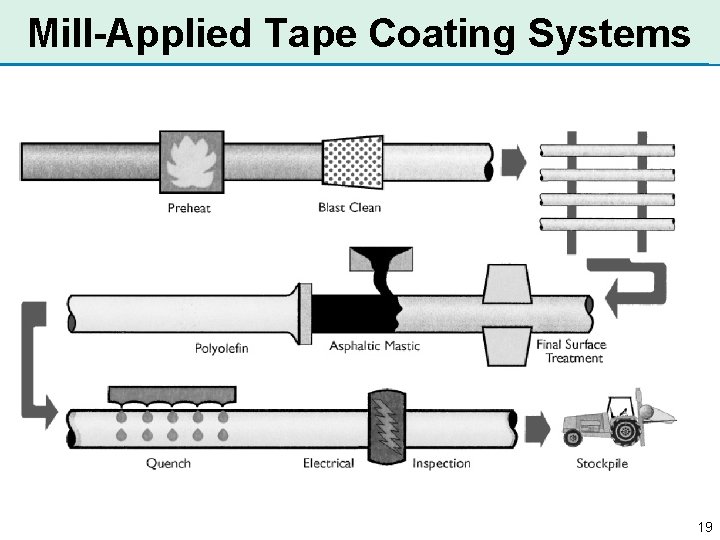
Mill-Applied Tape Coating Systems 19
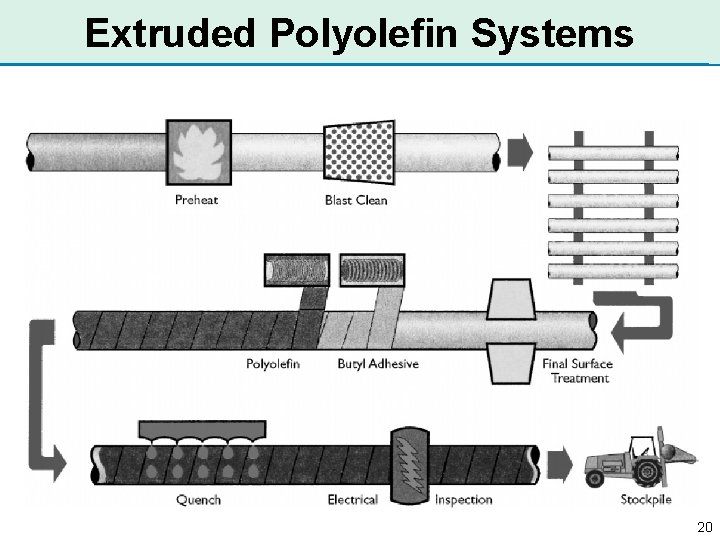
Extruded Polyolefin Systems 20
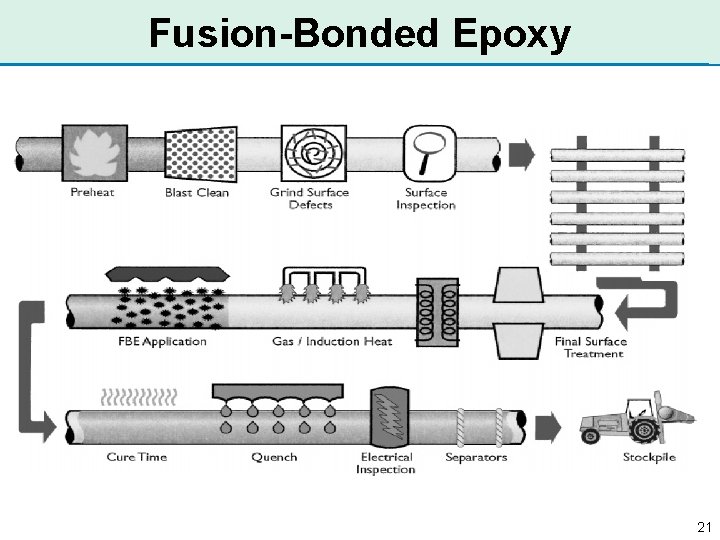
Fusion-Bonded Epoxy 21
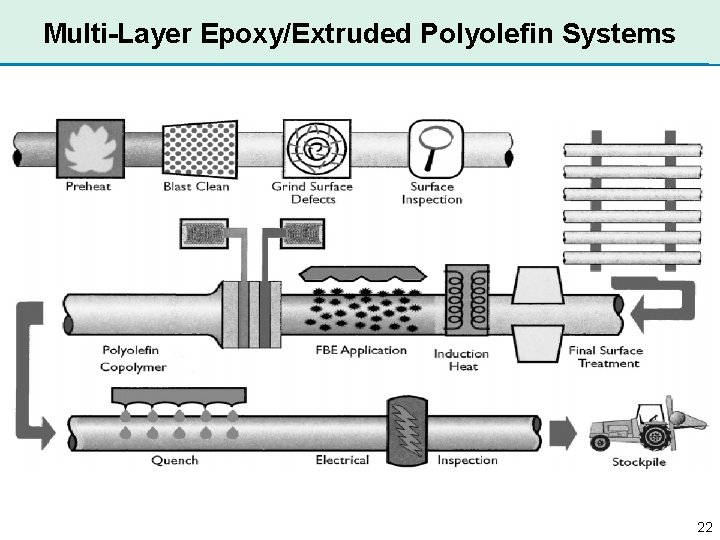
Multi-Layer Epoxy/Extruded Polyolefin Systems 22
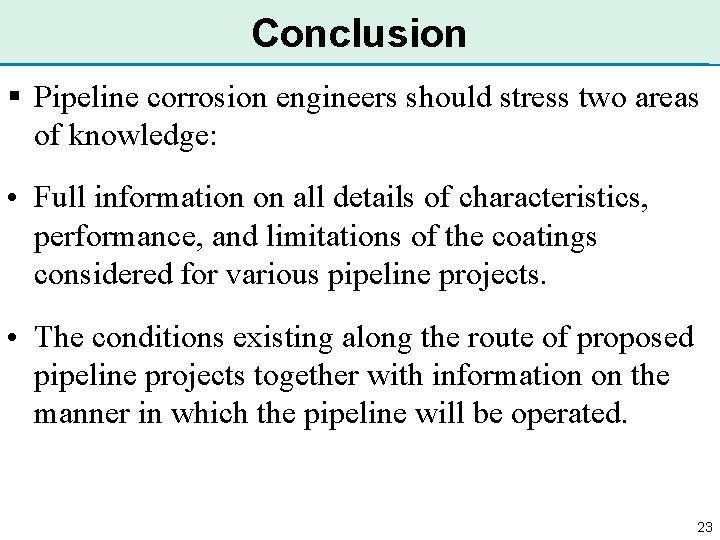
Conclusion § Pipeline corrosion engineers should stress two areas of knowledge: • Full information on all details of characteristics, performance, and limitations of the coatings considered for various pipeline projects. • The conditions existing along the route of proposed pipeline projects together with information on the manner in which the pipeline will be operated. 23
Linear pipeline in computer architecture
Scalar pipeline vs vector pipeline
Phenalkamide
Plural component spray
Hospital wall coatings
Hts coatings
Alocit
St powder coatings
Kale group of industries
St powder coatings
Sherwin williams chemical coatings store
Evaluate the effectiveness of social control inside prisons
The effectiveness of online and blended learning
What is steiners model
What are the uses of personal resources
A double pipe parallel flow heat exchanger
Effective and efficient example
Efficiency and effectiveness examples
Cath lab cost effectiveness
Liberal reforms essay higher history
Volumetric efficiency formula
What is the general range of ntu in heat exchanger design
Enhancing personal effectiveness
Slip, slop, slap campaign effectiveness