Chapter 13 Applications and Processing of Ceramics ISSUES
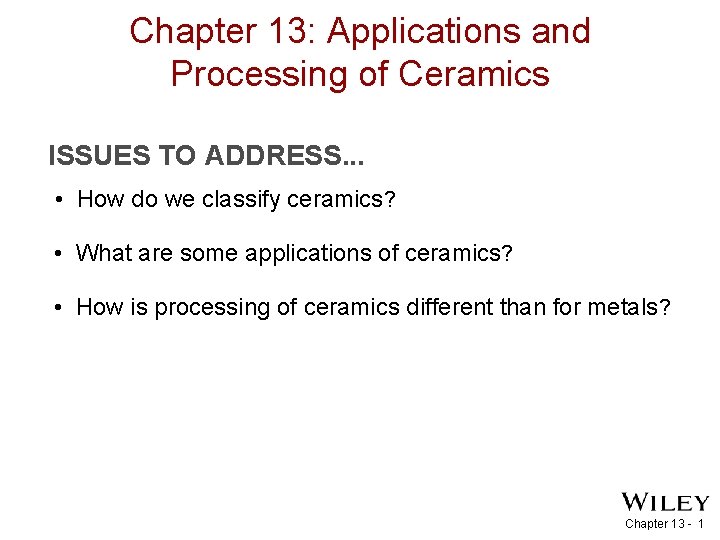
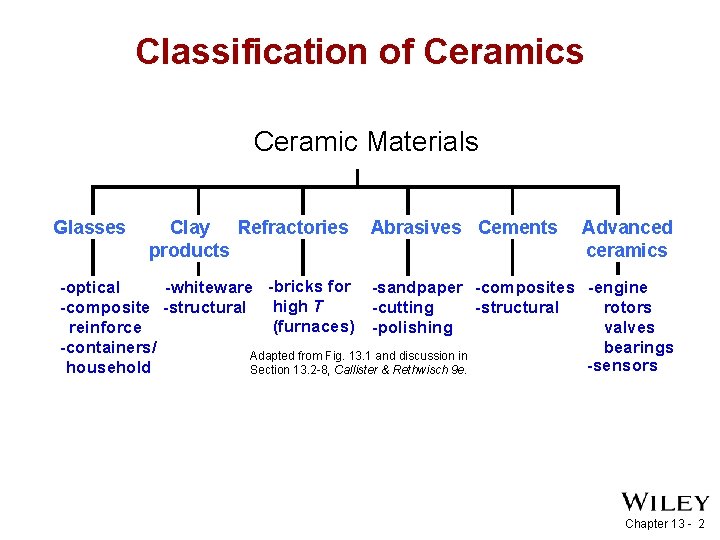
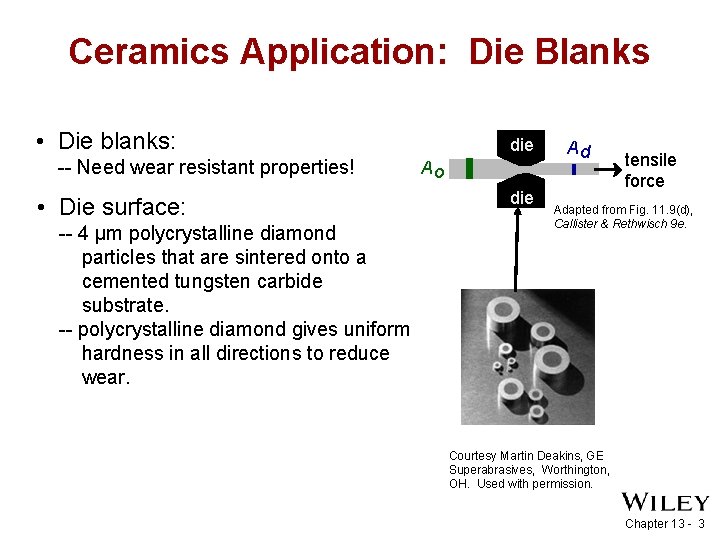
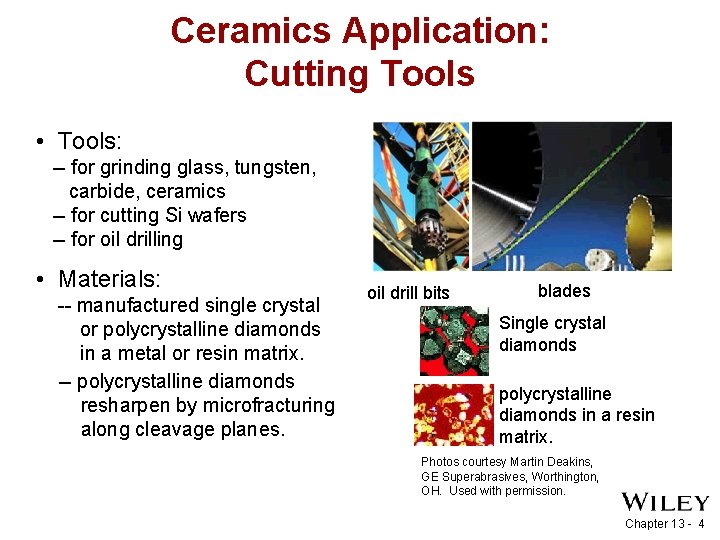
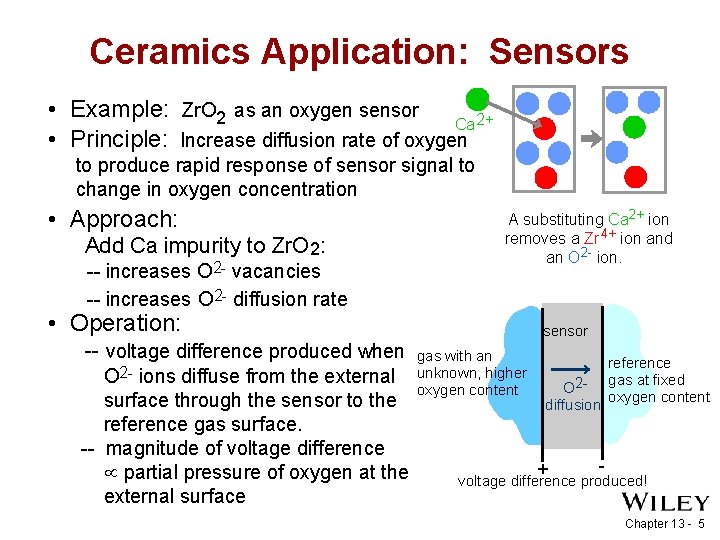
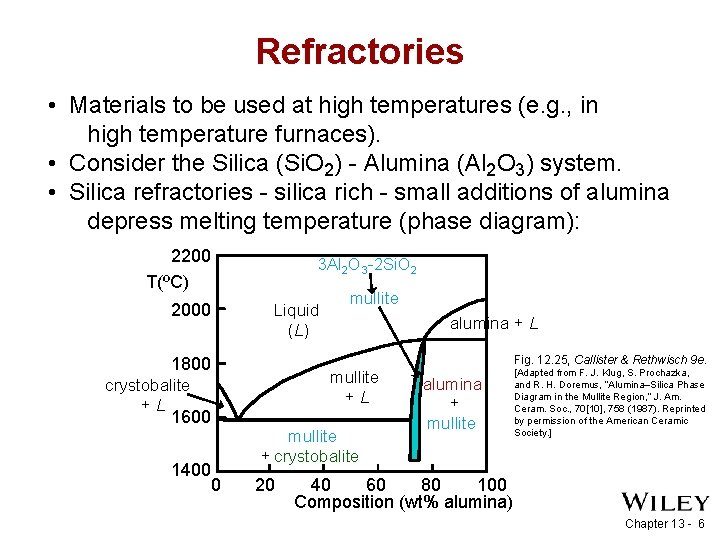
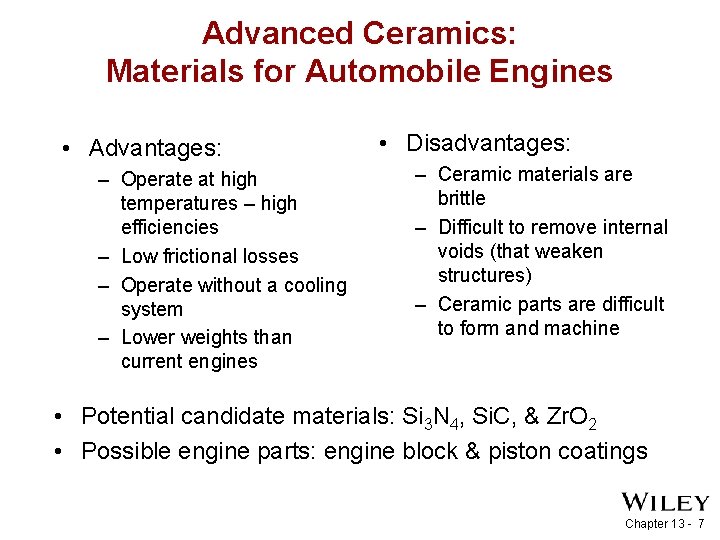
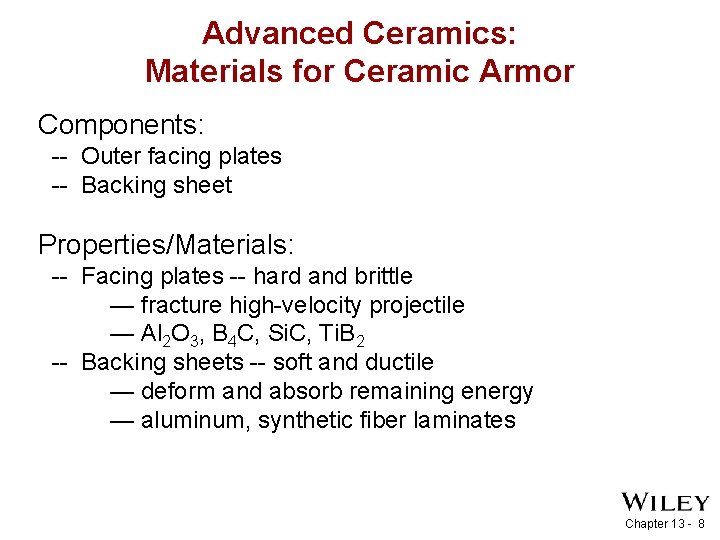
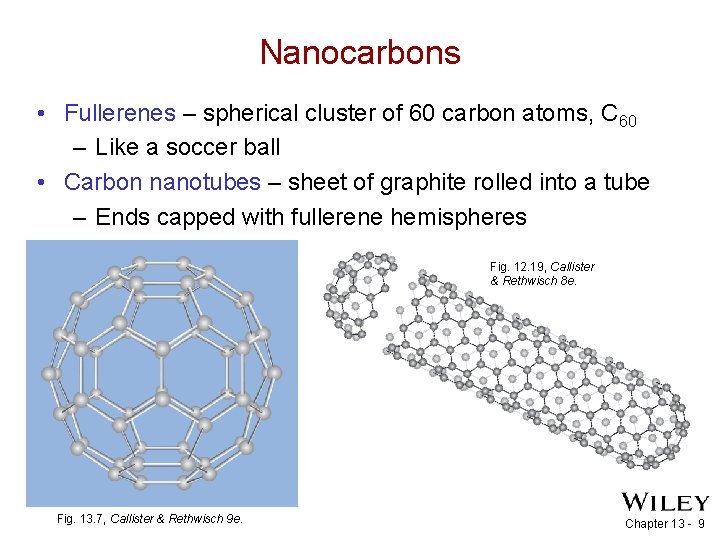
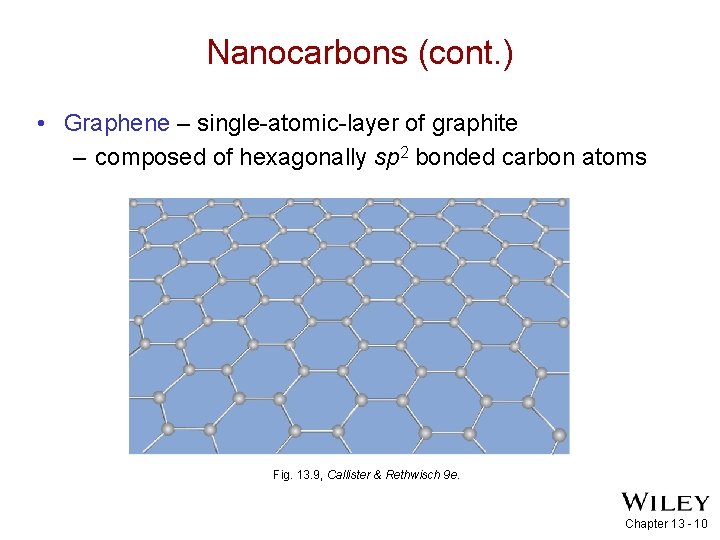
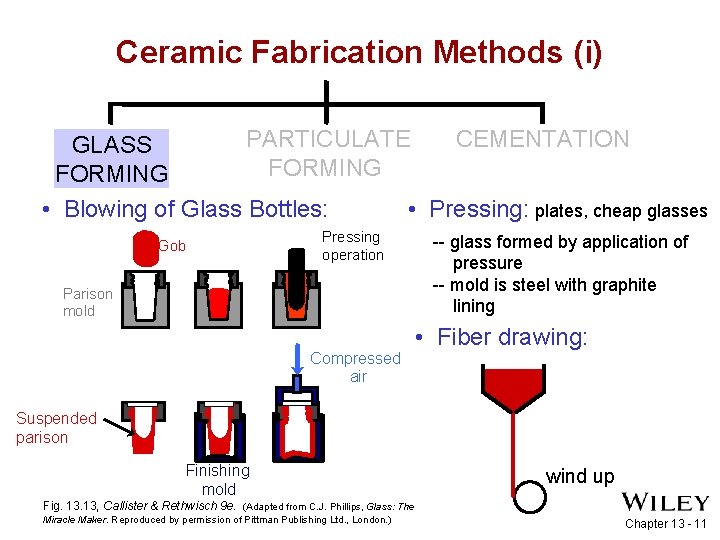
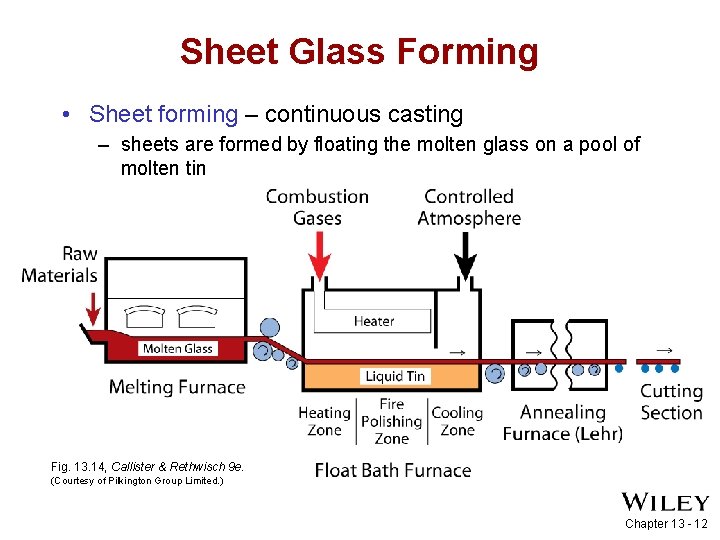
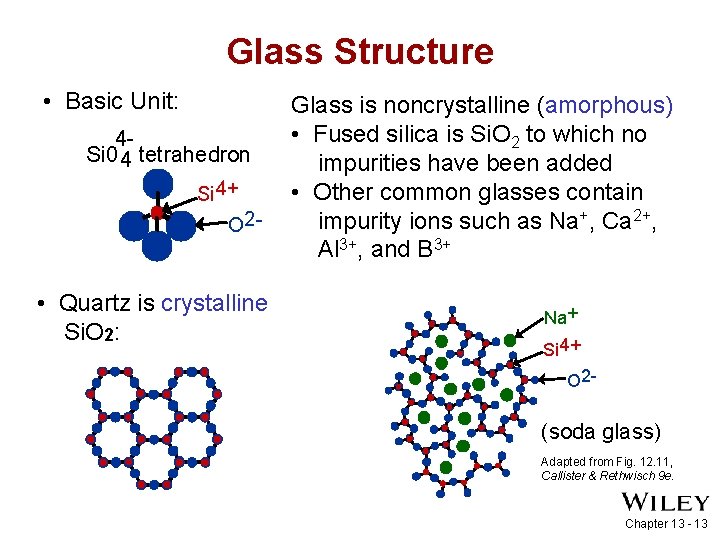
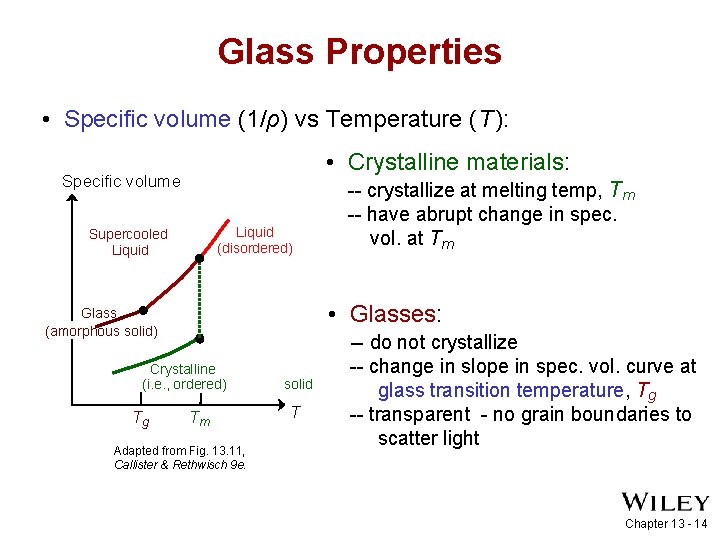
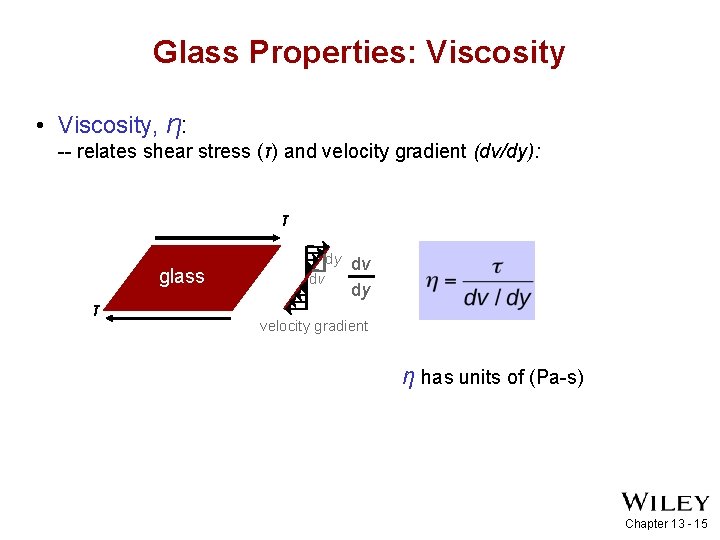
![Log Glass Viscosity vs. Temperature • Viscosity decreases with T Viscosity [Pa-s] a ilic Log Glass Viscosity vs. Temperature • Viscosity decreases with T Viscosity [Pa-s] a ilic](https://slidetodoc.com/presentation_image_h2/0b38c874d1b08ab7550d966bf802b51c/image-16.jpg)
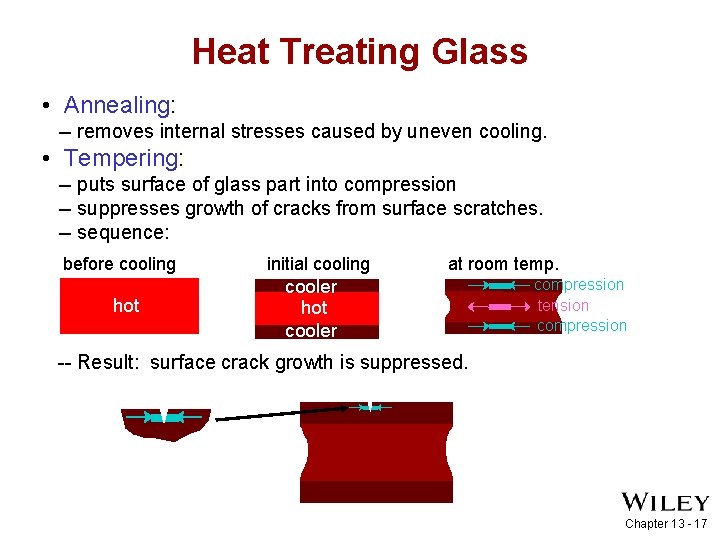
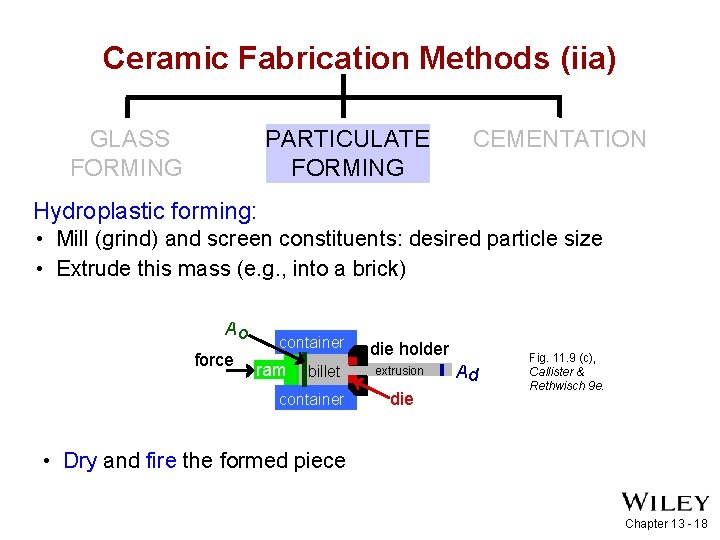
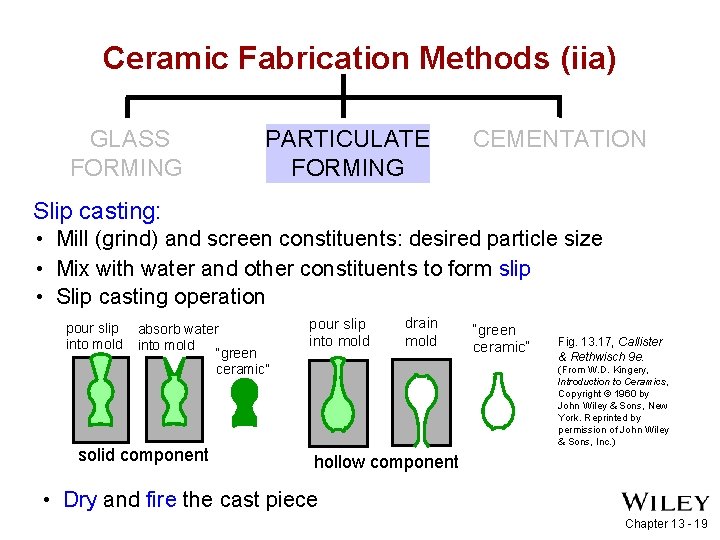
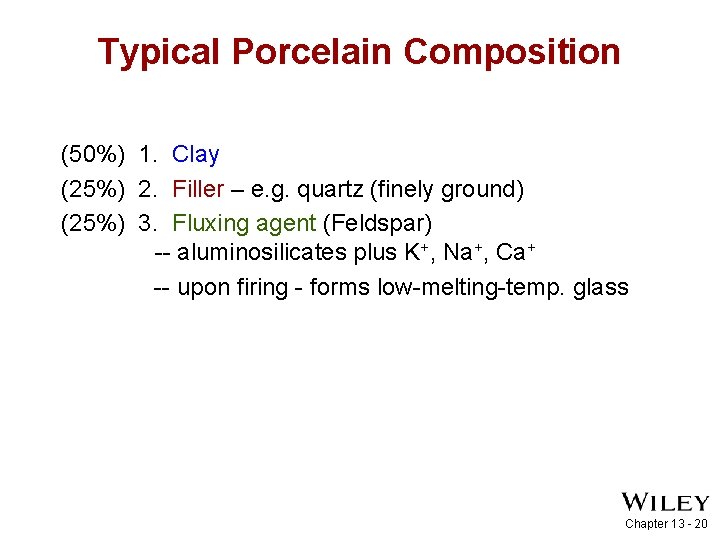
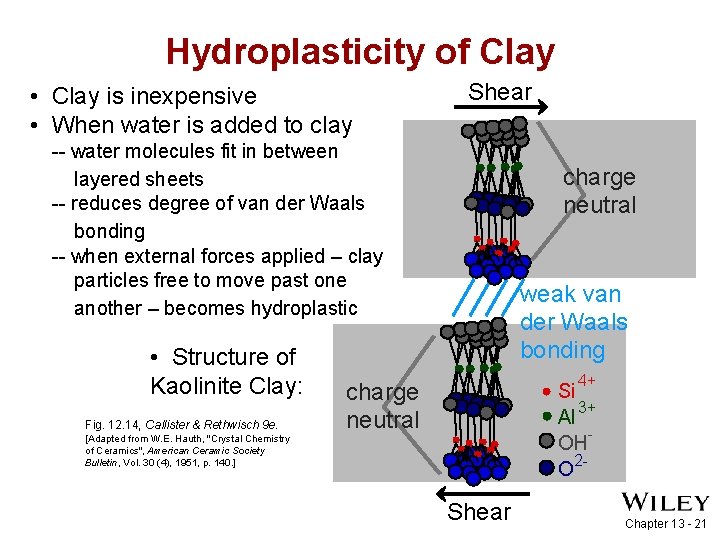
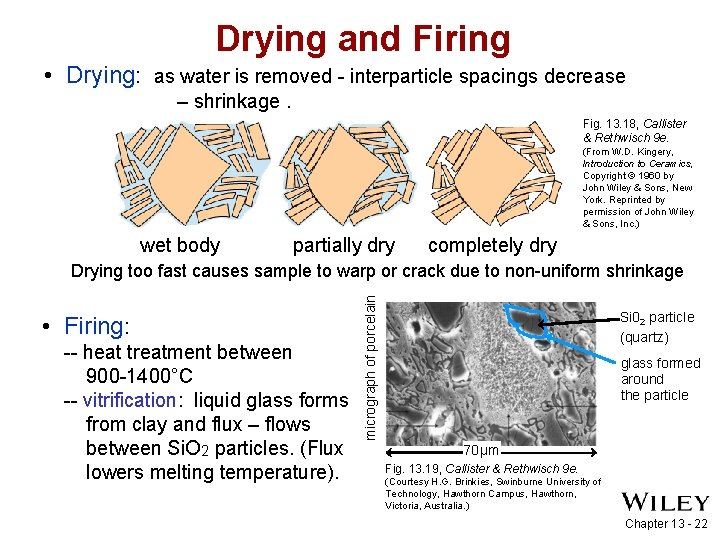
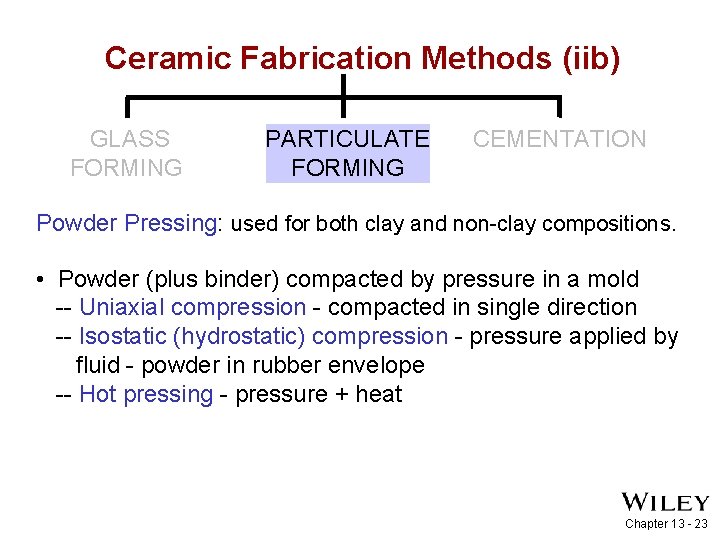
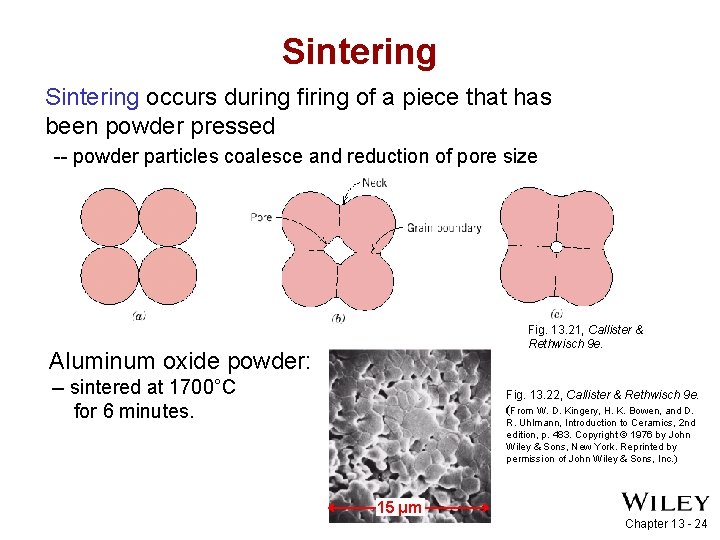
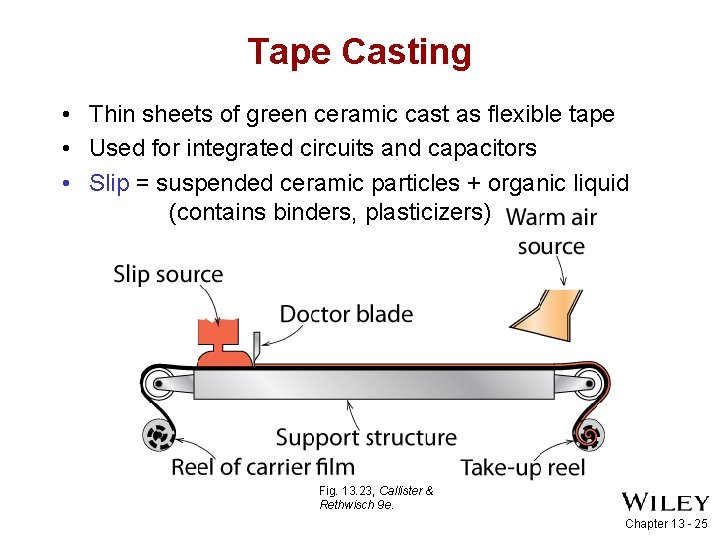
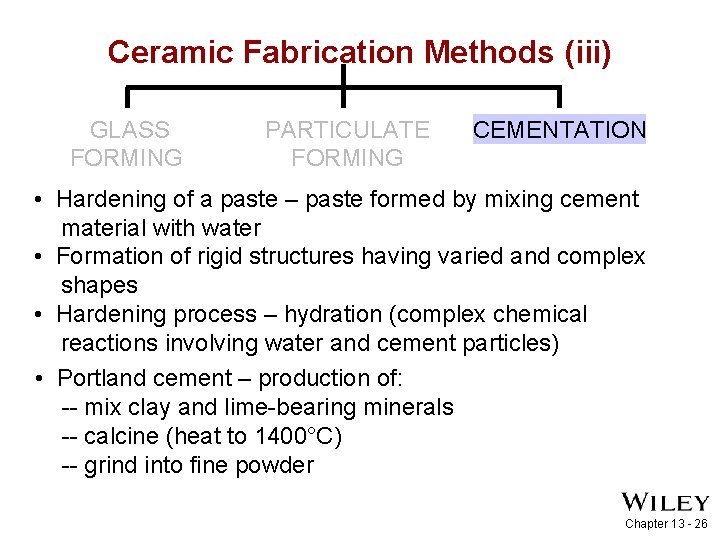

- Slides: 27
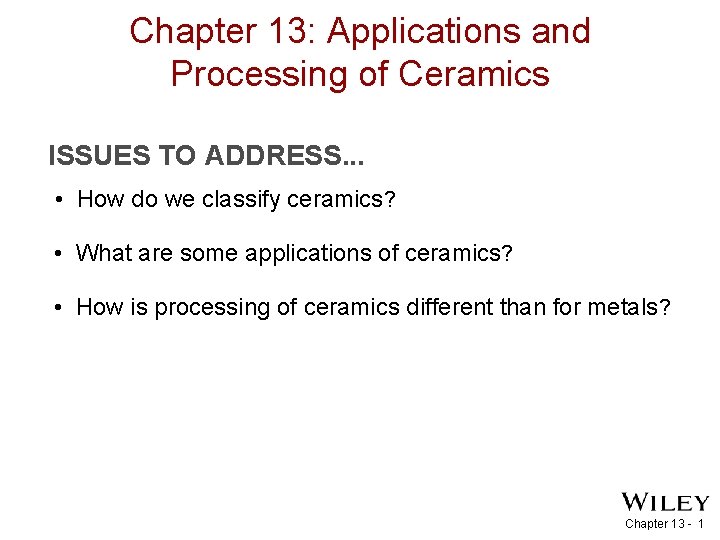
Chapter 13: Applications and Processing of Ceramics ISSUES TO ADDRESS. . . • How do we classify ceramics? • What are some applications of ceramics? • How is processing of ceramics different than for metals? Chapter 13 - 1
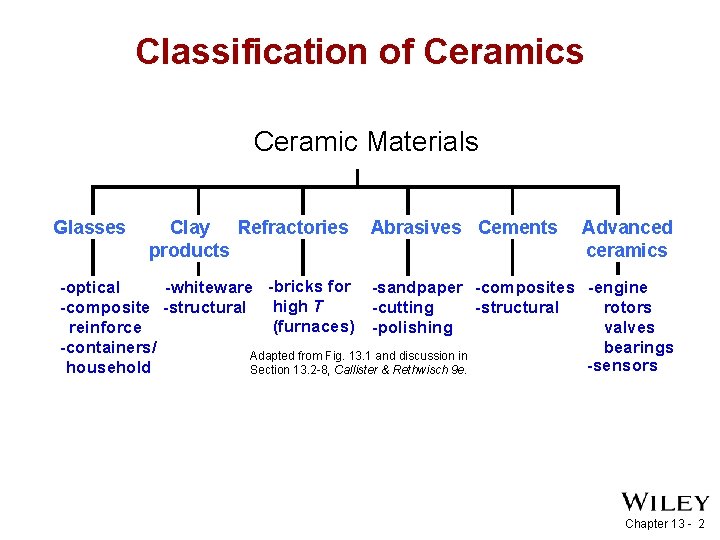
Classification of Ceramics Ceramic Materials Glasses Clay Refractories products Abrasives Cements Advanced ceramics -optical -whiteware -bricks for -sandpaper -composites -engine -composite -structural high T -cutting -structural rotors (furnaces) -polishing reinforce valves -containers/ bearings Adapted from Fig. 13. 1 and discussion in -sensors household Section 13. 2 -8, Callister & Rethwisch 9 e. Chapter 13 - 2
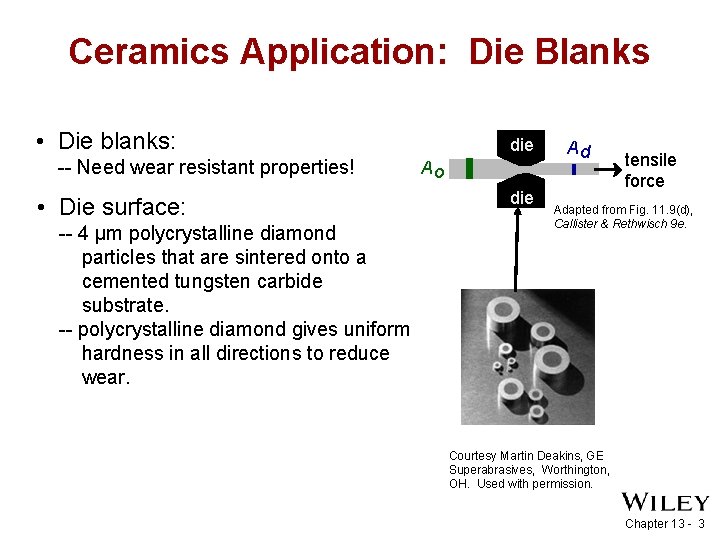
Ceramics Application: Die Blanks • Die blanks: -- Need wear resistant properties! • Die surface: -- 4 μm polycrystalline diamond particles that are sintered onto a cemented tungsten carbide substrate. -- polycrystalline diamond gives uniform hardness in all directions to reduce wear. die Ao die Ad tensile force Adapted from Fig. 11. 9(d), Callister & Rethwisch 9 e. Courtesy Martin Deakins, GE Superabrasives, Worthington, OH. Used with permission. Chapter 13 - 3
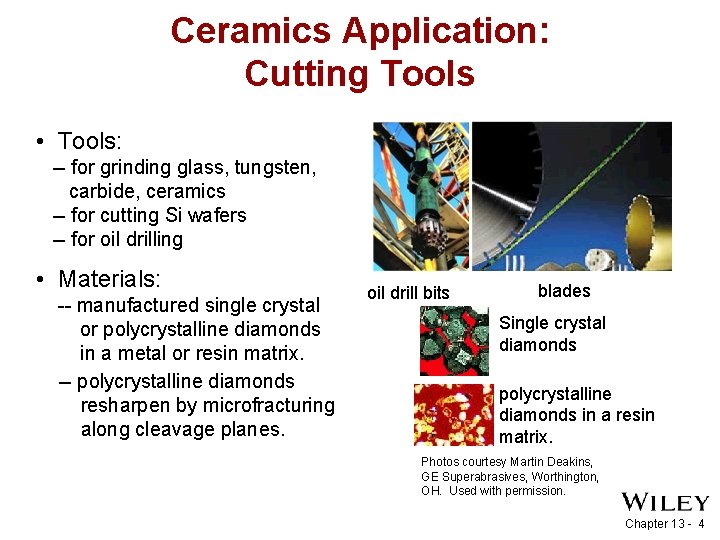
Ceramics Application: Cutting Tools • Tools: -- for grinding glass, tungsten, carbide, ceramics -- for cutting Si wafers -- for oil drilling • Materials: -- manufactured single crystal or polycrystalline diamonds in a metal or resin matrix. -- polycrystalline diamonds resharpen by microfracturing along cleavage planes. oil drill bits blades Single crystal diamonds polycrystalline diamonds in a resin matrix. Photos courtesy Martin Deakins, GE Superabrasives, Worthington, OH. Used with permission. Chapter 13 - 4
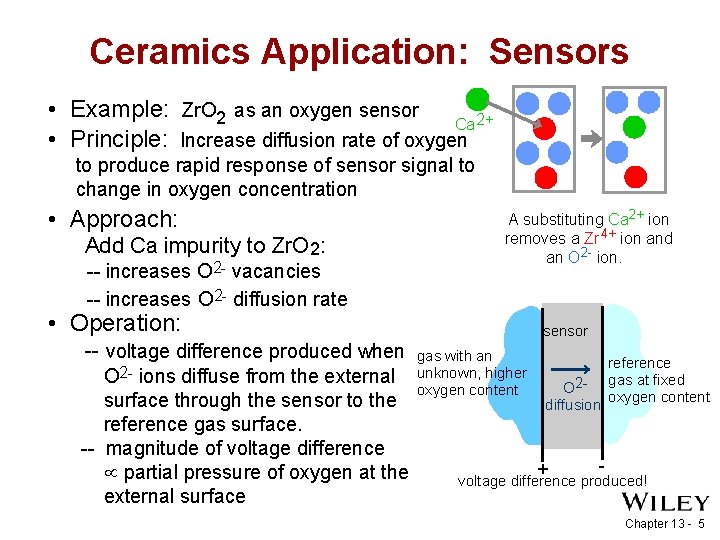
Ceramics Application: Sensors • Example: Zr. O 2 as an oxygen sensor Ca 2+ • Principle: Increase diffusion rate of oxygen to produce rapid response of sensor signal to change in oxygen concentration • Approach: Add Ca impurity to Zr. O 2: -- increases O 2 - vacancies -- increases O 2 - diffusion rate A substituting Ca 2+ ion removes a Zr 4+ ion and an O 2 - ion. • Operation: -- voltage difference produced when O 2 - ions diffuse from the external surface through the sensor to the reference gas surface. -- magnitude of voltage difference partial pressure of oxygen at the external surface sensor gas with an unknown, higher oxygen content O 2 diffusion + reference gas at fixed oxygen content - voltage difference produced! Chapter 13 - 5
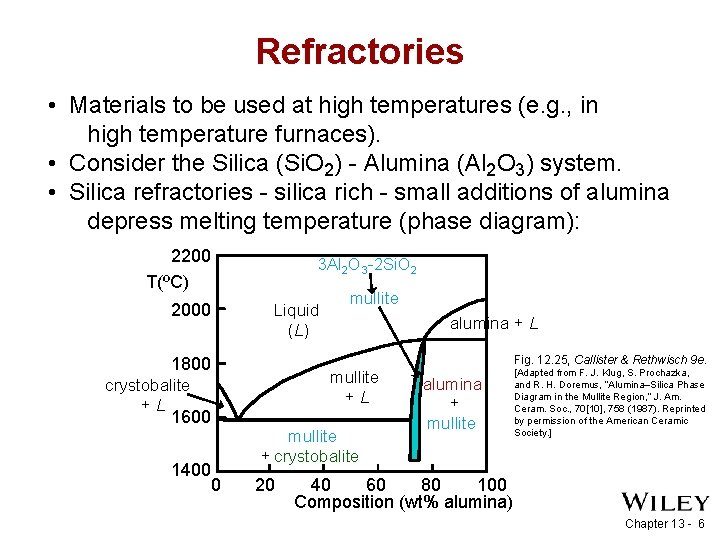
Refractories • Materials to be used at high temperatures (e. g. , in high temperature furnaces). • Consider the Silica (Si. O 2) - Alumina (Al 2 O 3) system. • Silica refractories - silica rich - small additions of alumina depress melting temperature (phase diagram): 2200 T(ºC) 2000 3 Al 2 O 3 -2 Si. O 2 Liquid (L) mullite alumina + L Fig. 12. 25, Callister & Rethwisch 9 e. 1800 mullite +L crystobalite +L 1600 1400 0 mullite + crystobalite 20 alumina + mullite [Adapted from F. J. Klug, S. Prochazka, and R. H. Doremus, “Alumina–Silica Phase Diagram in the Mullite Region, ” J. Am. Ceram. Soc. , 70[10], 758 (1987). Reprinted by permission of the American Ceramic Society. ] 40 60 80 100 Composition (wt% alumina) Chapter 13 - 6
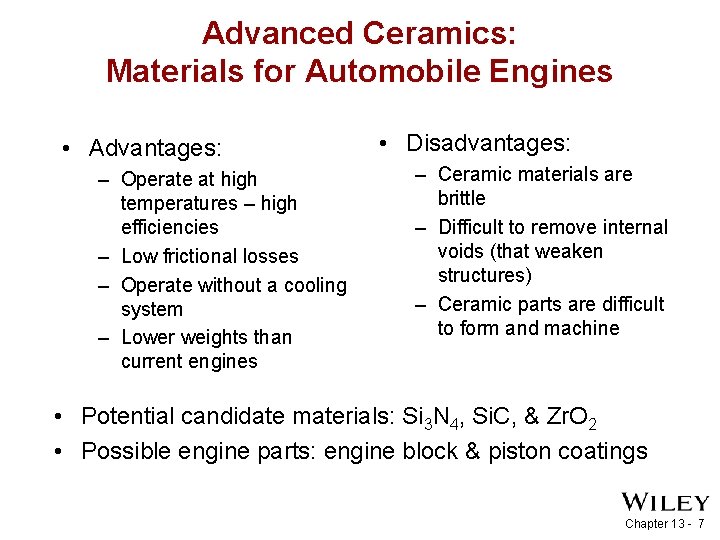
Advanced Ceramics: Materials for Automobile Engines • Advantages: – Operate at high temperatures – high efficiencies – Low frictional losses – Operate without a cooling system – Lower weights than current engines • Disadvantages: – Ceramic materials are brittle – Difficult to remove internal voids (that weaken structures) – Ceramic parts are difficult to form and machine • Potential candidate materials: Si 3 N 4, Si. C, & Zr. O 2 • Possible engine parts: engine block & piston coatings Chapter 13 - 7
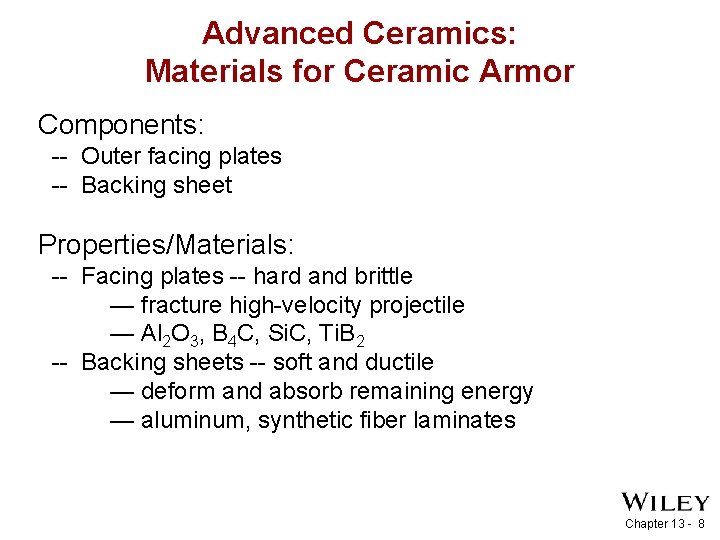
Advanced Ceramics: Materials for Ceramic Armor Components: -- Outer facing plates -- Backing sheet Properties/Materials: -- Facing plates -- hard and brittle — fracture high-velocity projectile — Al 2 O 3, B 4 C, Si. C, Ti. B 2 -- Backing sheets -- soft and ductile — deform and absorb remaining energy — aluminum, synthetic fiber laminates Chapter 13 - 8
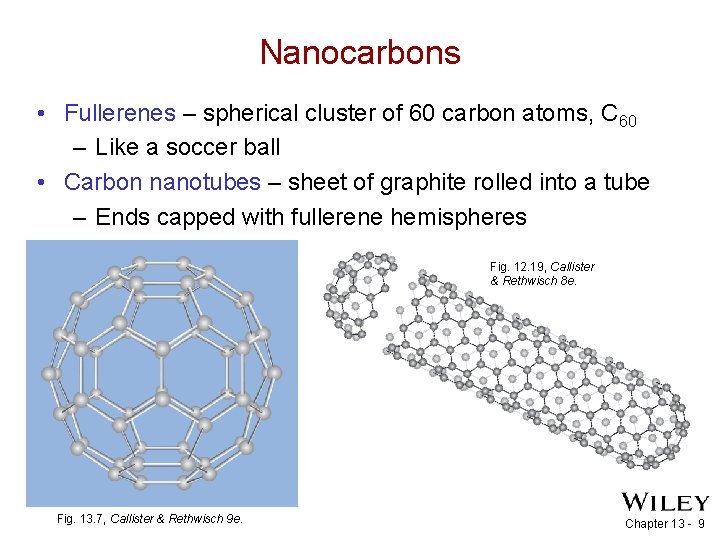
Nanocarbons • Fullerenes – spherical cluster of 60 carbon atoms, C 60 – Like a soccer ball • Carbon nanotubes – sheet of graphite rolled into a tube – Ends capped with fullerene hemispheres Fig. 12. 19, Callister & Rethwisch 8 e. Fig. 13. 7, Callister & Rethwisch 9 e. Chapter 13 - 9
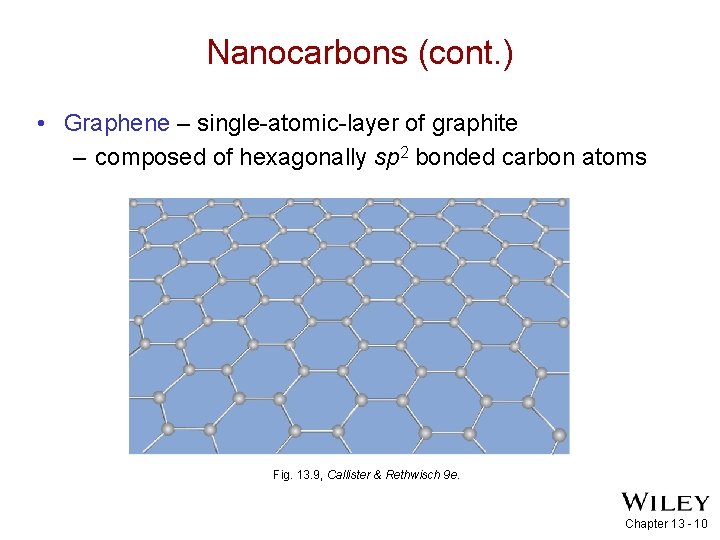
Nanocarbons (cont. ) • Graphene – single-atomic-layer of graphite – composed of hexagonally sp 2 bonded carbon atoms Fig. 13. 9, Callister & Rethwisch 9 e. Chapter 13 - 10
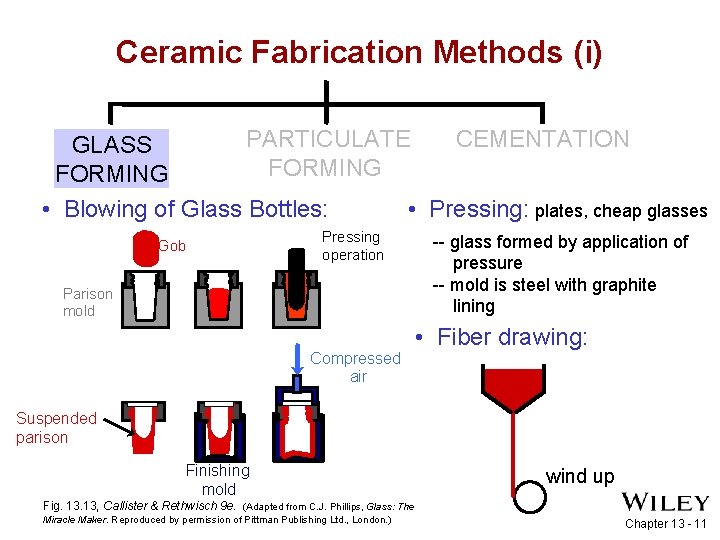
Ceramic Fabrication Methods (i) PARTICULATE CEMENTATION GLASS FORMING • Blowing of Glass Bottles: • Pressing: plates, cheap glasses Gob Pressing operation Parison mold Compressed air -- glass formed by application of pressure -- mold is steel with graphite lining • Fiber drawing: Suspended parison Finishing mold wind up Fig. 13, Callister & Rethwisch 9 e. (Adapted from C. J. Phillips, Glass: The Miracle Maker. Reproduced by permission of Pittman Publishing Ltd. , London. ) Chapter 13 - 11
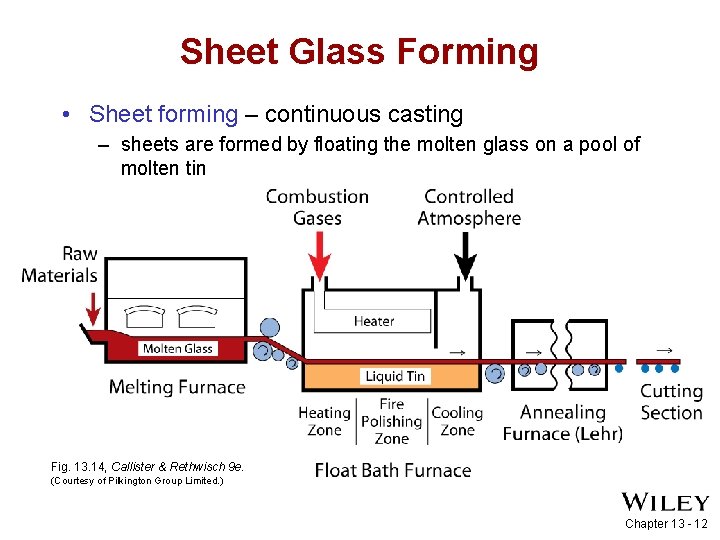
Sheet Glass Forming • Sheet forming – continuous casting – sheets are formed by floating the molten glass on a pool of molten tin Fig. 13. 14, Callister & Rethwisch 9 e. (Courtesy of Pilkington Group Limited. ) Chapter 13 - 12
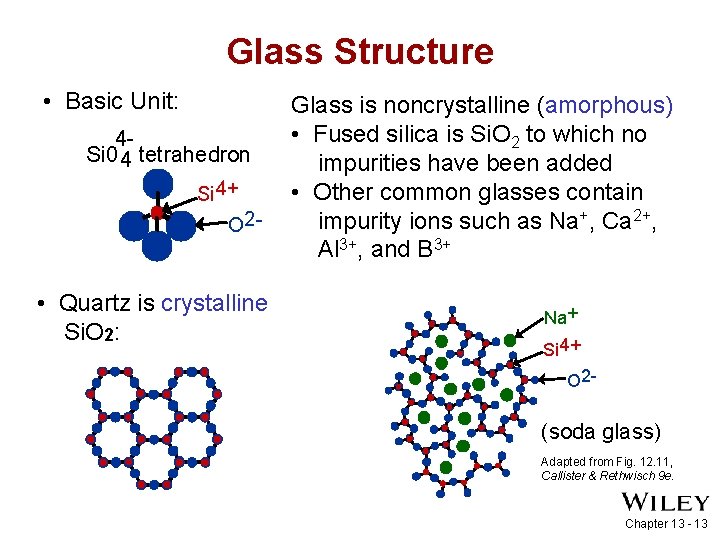
Glass Structure • Basic Unit: 4 Si 0 4 tetrahedron Si 4+ O 2 - • Quartz is crystalline Si. O 2: Glass is noncrystalline (amorphous) • Fused silica is Si. O 2 to which no impurities have been added • Other common glasses contain impurity ions such as Na+, Ca 2+, Al 3+, and B 3+ Na + Si 4+ O 2 - (soda glass) Adapted from Fig. 12. 11, Callister & Rethwisch 9 e. Chapter 13 - 13
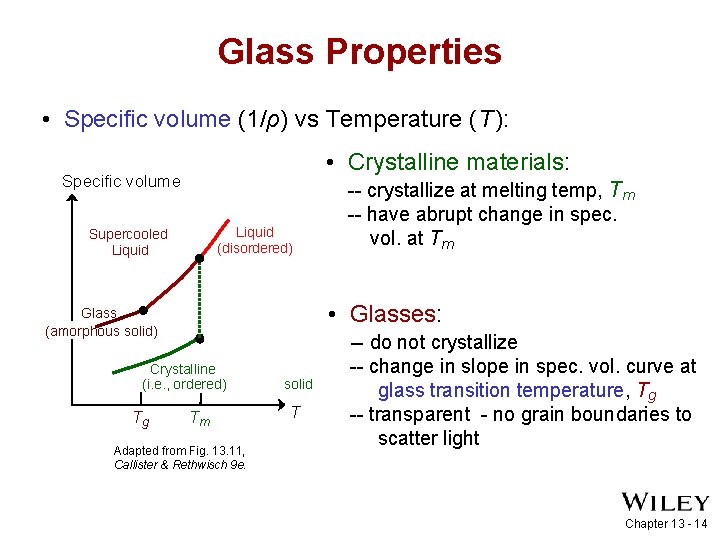
Glass Properties • Specific volume (1/ρ) vs Temperature (T ): • Crystalline materials: Specific volume Liquid (disordered) Supercooled Liquid • Glasses: Glass (amorphous solid) Crystalline (i. e. , ordered) Tg -- crystallize at melting temp, Tm -- have abrupt change in spec. vol. at Tm Tm Adapted from Fig. 13. 11, Callister & Rethwisch 9 e. solid T -- do not crystallize -- change in slope in spec. vol. curve at glass transition temperature, Tg -- transparent - no grain boundaries to scatter light Chapter 13 - 14
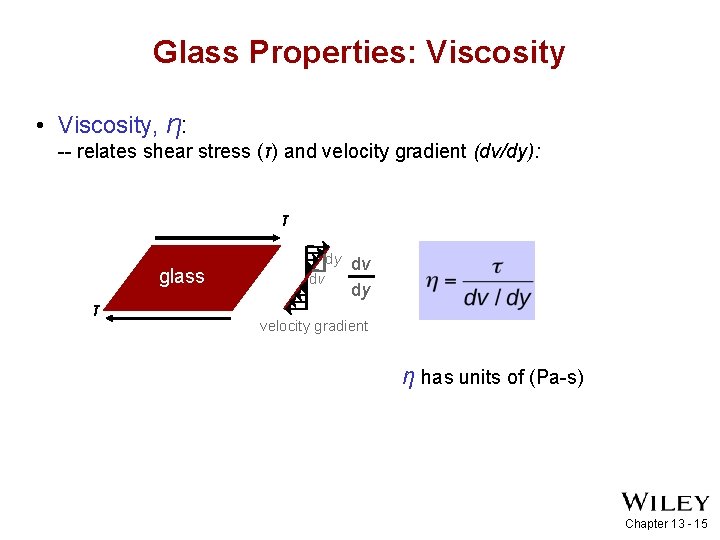
Glass Properties: Viscosity • Viscosity, η: -- relates shear stress (τ) and velocity gradient (dv/dy): τ glass τ dy dv dv dy velocity gradient η has units of (Pa-s) Chapter 13 - 15
![Log Glass Viscosity vs Temperature Viscosity decreases with T Viscosity Pas a ilic Log Glass Viscosity vs. Temperature • Viscosity decreases with T Viscosity [Pa-s] a ilic](https://slidetodoc.com/presentation_image_h2/0b38c874d1b08ab7550d966bf802b51c/image-16.jpg)
Log Glass Viscosity vs. Temperature • Viscosity decreases with T Viscosity [Pa-s] a ilic ds a se ilic s fu x % 96 yre e P -lim da so ss gla 10 14 10 10 10 6 10 2 1 200 • soda-lime glass: 70% Si. O 2 balance Na 2 O (soda) & Ca. O (lime) • borosilicate (Pyrex): 13% B 2 O 3, 3. 5% Na 2 O, 2. 5% Al 2 O 3 • Vycor: 96% Si. O 2, 4% B 2 O 3 • fused silica: > 99. 5 wt% Si. O 2 strain point annealing point Working range: glass-forming carried out Tmelt 600 1000 1400 1800 T(ºC) Fig. 13. 12, Callister & Rethwisch 9 e. (From E. B. Shand, Engineering Glass, Modern Materials, Vol. 6, Academic Press, New York, 1968, p. 262. ) Chapter 13 - 16
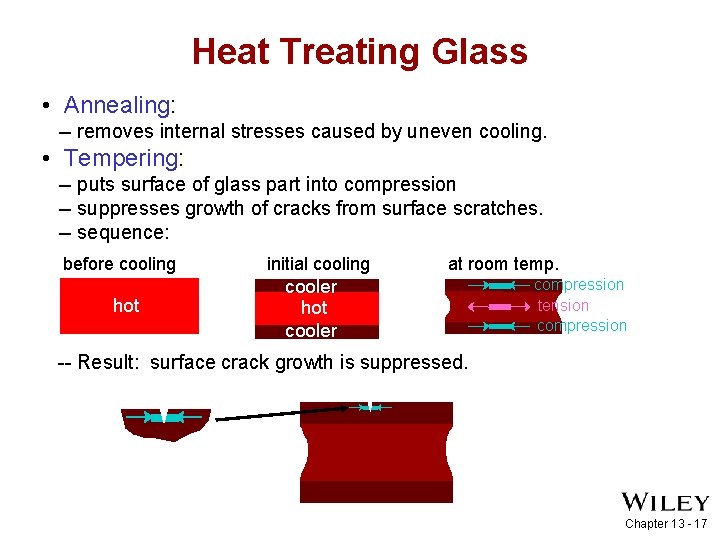
Heat Treating Glass • Annealing: -- removes internal stresses caused by uneven cooling. • Tempering: -- puts surface of glass part into compression -- suppresses growth of cracks from surface scratches. -- sequence: before cooling hot initial cooling at room temp. cooler hot cooler compression tension compression -- Result: surface crack growth is suppressed. Chapter 13 - 17
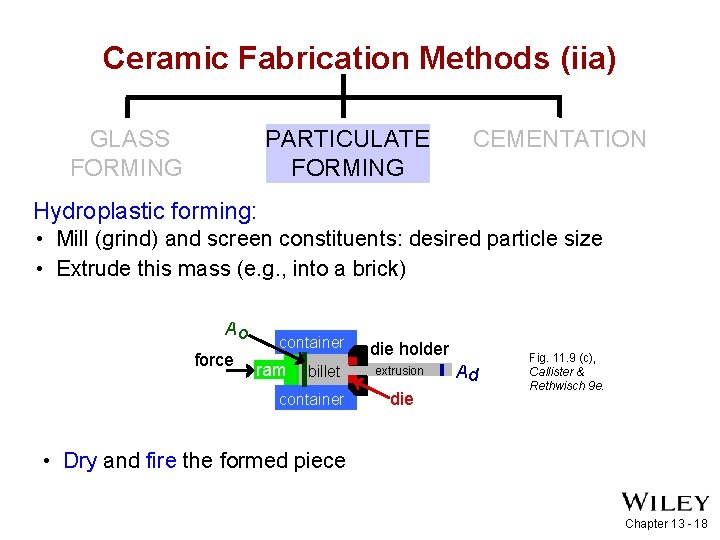
Ceramic Fabrication Methods (iia) GLASS FORMING PARTICULATE FORMING CEMENTATION Hydroplastic forming: • Mill (grind) and screen constituents: desired particle size • Extrude this mass (e. g. , into a brick) Ao force container ram billet container die holder extrusion die Ad Fig. 11. 9 (c), Callister & Rethwisch 9 e. • Dry and fire the formed piece Chapter 13 - 18
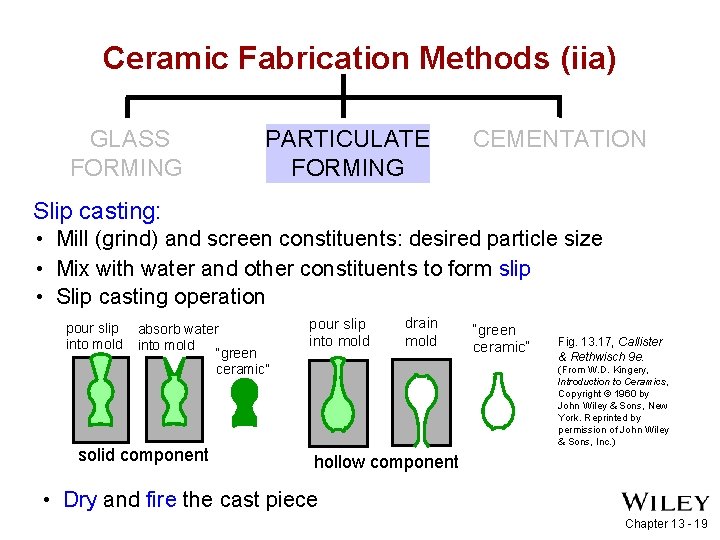
Ceramic Fabrication Methods (iia) GLASS FORMING PARTICULATE FORMING CEMENTATION Slip casting: • Mill (grind) and screen constituents: desired particle size • Mix with water and other constituents to form slip • Slip casting operation pour slip into mold absorb water into mold “green ceramic” solid component pour slip into mold drain mold “green ceramic” Fig. 13. 17, Callister & Rethwisch 9 e. (From W. D. Kingery, Introduction to Ceramics, Copyright © 1960 by John Wiley & Sons, New York. Reprinted by permission of John Wiley & Sons, Inc. ) hollow component • Dry and fire the cast piece Chapter 13 - 19
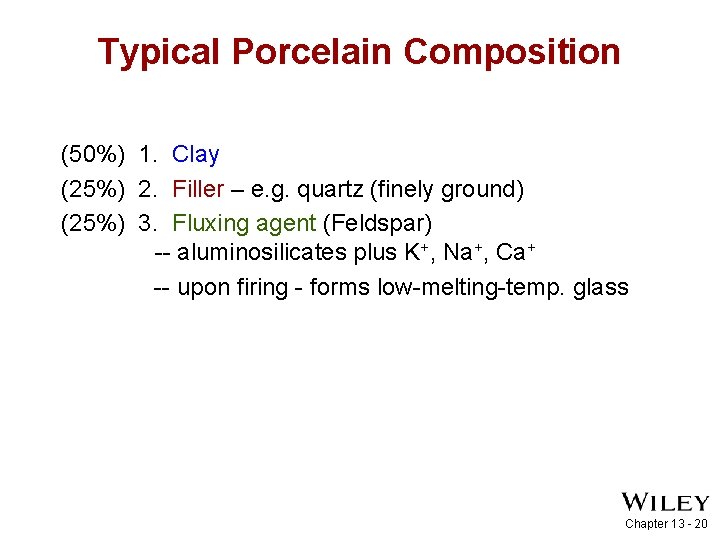
Typical Porcelain Composition (50%) 1. Clay (25%) 2. Filler – e. g. quartz (finely ground) (25%) 3. Fluxing agent (Feldspar) -- aluminosilicates plus K+, Na+, Ca+ -- upon firing - forms low-melting-temp. glass Chapter 13 - 20
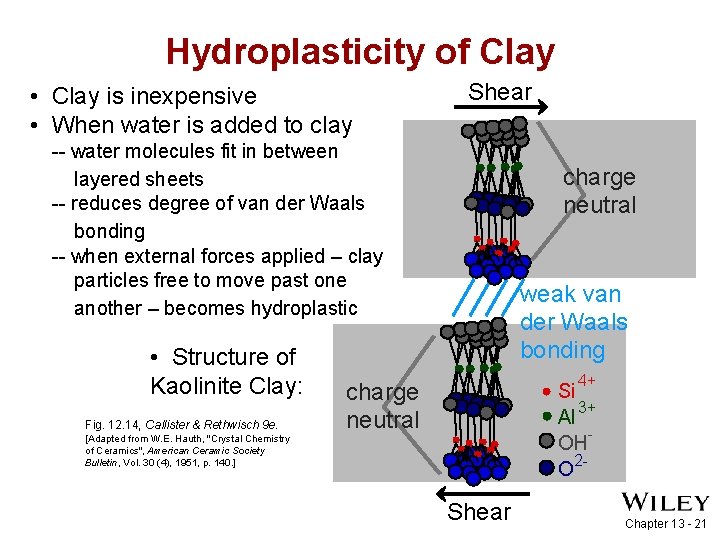
Hydroplasticity of Clay • Clay is inexpensive • When water is added to clay Shear -- water molecules fit in between layered sheets -- reduces degree of van der Waals bonding -- when external forces applied – clay particles free to move past one another – becomes hydroplastic • Structure of Kaolinite Clay: Fig. 12. 14, Callister & Rethwisch 9 e. [Adapted from W. E. Hauth, "Crystal Chemistry of Ceramics", American Ceramic Society Bulletin, Vol. 30 (4), 1951, p. 140. ] charge neutral weak van der Waals bonding 4+ charge neutral Si 3+ Al OH 2 O Shear Chapter 13 - 21
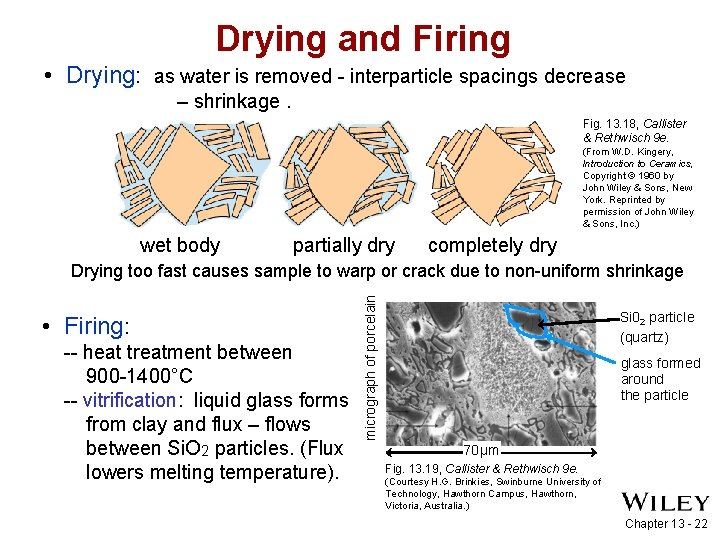
Drying and Firing • Drying: as water is removed - interparticle spacings decrease – shrinkage. Fig. 13. 18, Callister & Rethwisch 9 e. (From W. D. Kingery, Introduction to Ceramics, Copyright © 1960 by John Wiley & Sons, New York. Reprinted by permission of John Wiley & Sons, Inc. ) wet body partially dry completely dry • Firing: -- heat treatment between 900 -1400°C -- vitrification: liquid glass forms from clay and flux – flows between Si. O 2 particles. (Flux lowers melting temperature). micrograph of porcelain Drying too fast causes sample to warp or crack due to non-uniform shrinkage Si 02 particle (quartz) glass formed around the particle 70 μm Fig. 13. 19, Callister & Rethwisch 9 e. (Courtesy H. G. Brinkies, Swinburne University of Technology, Hawthorn Campus, Hawthorn, Victoria, Australia. ) Chapter 13 - 22
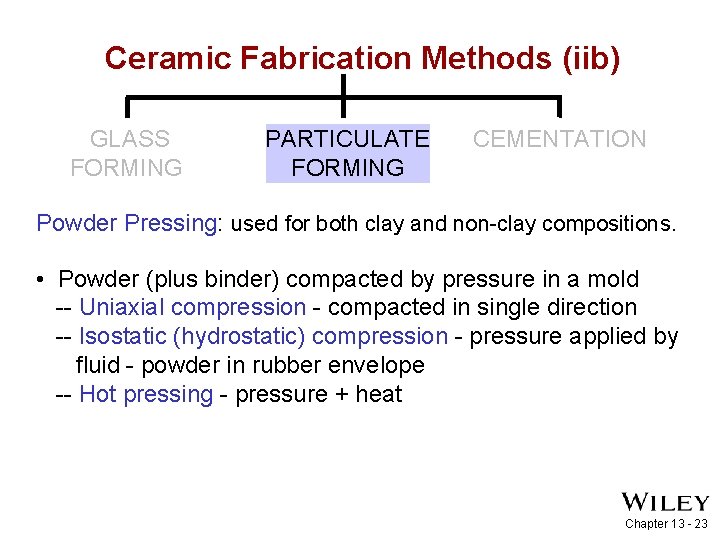
Ceramic Fabrication Methods (iib) GLASS FORMING PARTICULATE FORMING CEMENTATION Powder Pressing: used for both clay and non-clay compositions. • Powder (plus binder) compacted by pressure in a mold -- Uniaxial compression - compacted in single direction -- Isostatic (hydrostatic) compression - pressure applied by fluid - powder in rubber envelope -- Hot pressing - pressure + heat Chapter 13 - 23
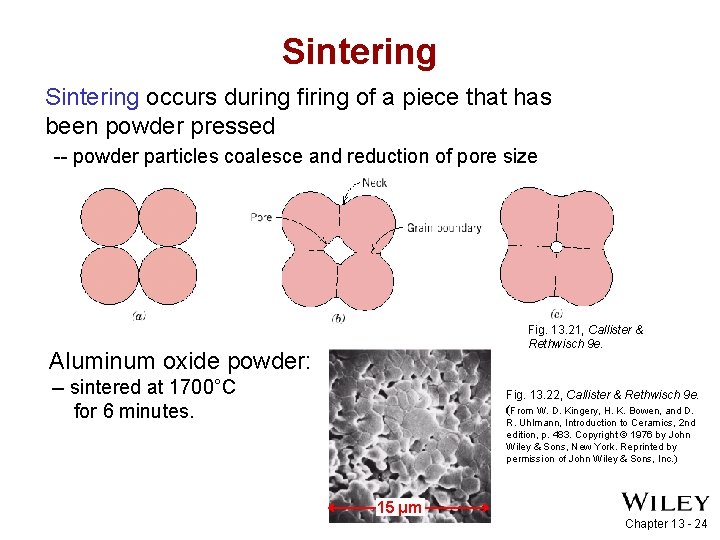
Sintering occurs during firing of a piece that has been powder pressed -- powder particles coalesce and reduction of pore size Fig. 13. 21, Callister & Rethwisch 9 e. Aluminum oxide powder: -- sintered at 1700°C for 6 minutes. Fig. 13. 22, Callister & Rethwisch 9 e. (From W. D. Kingery, H. K. Bowen, and D. R. Uhlmann, Introduction to Ceramics, 2 nd edition, p. 483. Copyright © 1976 by John Wiley & Sons, New York. Reprinted by permission of John Wiley & Sons, Inc. ) 15 μm Chapter 13 - 24
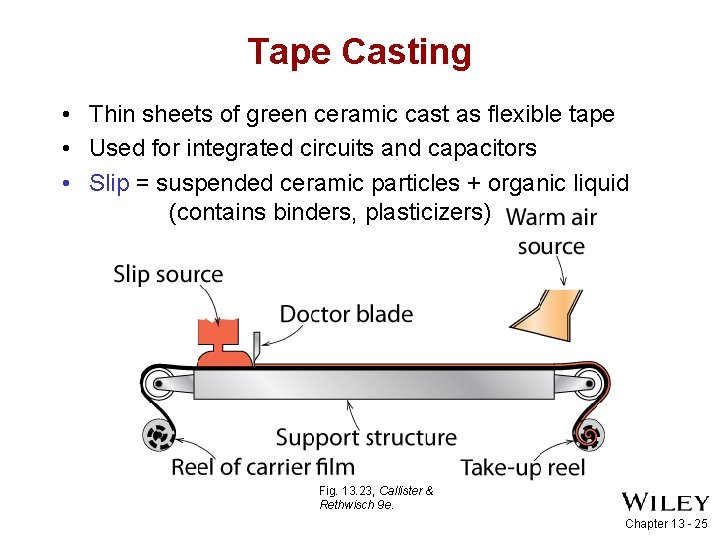
Tape Casting • Thin sheets of green ceramic cast as flexible tape • Used for integrated circuits and capacitors • Slip = suspended ceramic particles + organic liquid (contains binders, plasticizers) Fig. 13. 23, Callister & Rethwisch 9 e. Chapter 13 - 25
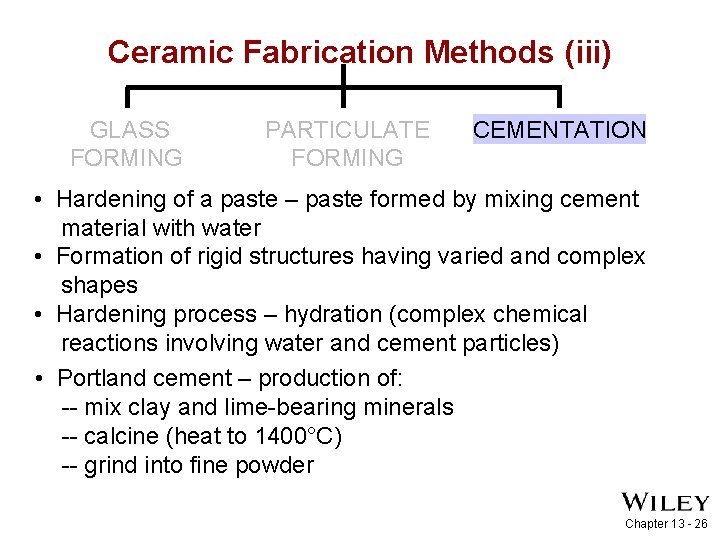
Ceramic Fabrication Methods (iii) GLASS FORMING PARTICULATE FORMING CEMENTATION • Hardening of a paste – paste formed by mixing cement material with water • Formation of rigid structures having varied and complex shapes • Hardening process – hydration (complex chemical reactions involving water and cement particles) • Portland cement – production of: -- mix clay and lime-bearing minerals -- calcine (heat to 1400°C) -- grind into fine powder Chapter 13 - 26

Summary • Categories of ceramics: -- glasses -- clay products -- refractories -- cements -- advanced ceramics • Ceramic Fabrication techniques: -- glass forming (pressing, blowing, fiber drawing). -- particulate forming (hydroplastic forming, slip casting, powder pressing, tape casting) -- cementation • Heat treating procedures -- glasses—annealing, tempering -- particulate formed pieces—drying, firing (sintering) Chapter 13 - 27
Processing of ceramics
Systems applications and products
System application and product in data processing
Applications and processing of metal alloys
Neighborhood averaging in image processing
What is primary processing of food
Batch processing and interactive processing
"hot isostatic pressing" and "punches" or "dies" -patent
Structures and properties of ceramics
Ceramic classification
Rcation/ranion
Ceramics tools vocabulary
Bottom-up processing examples
Bottom up processing vs top down processing
Top-down processing vs bottom-up processing
Point processing in image enhancement
Histogram processing in digital image processing
Parallel processing vs concurrent processing
A generalization of unsharp masking is
Point processing in image processing
Thinning and thickening in image processing example
Top-down processing example
Sgraffito ceramics
Kiln god examples
Functional ceramics application
Charlotte manser ceramics
Coiling clay definition
Particulate forming ceramics